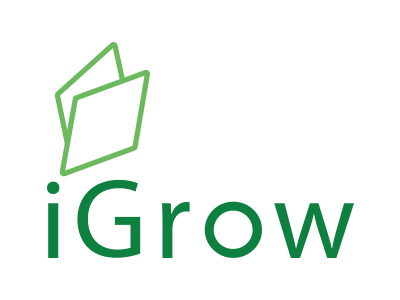
Welcome to iGrow News, Your Source for the World of Indoor Vertical Farming
Framlab Proposes Modular Vertical Farms For Brooklyn Neighbourhoods
Creative agency Framlab has proposed building modular vertical farms in Brooklyn to provide low-income neighborhoods with access to fresh produce
Creative agency Framlab has proposed building modular vertical farms in Brooklyn to provide low-income neighborhoods with access to fresh produce.
The conceptual Glasir project comprises a stack of greenhouse-like modules that could be built in various locations across the New York borough, where Framlab's research has found that 20 percent of the population are food-insecure.
A Glasir farm would be constructed on top of a stand with an area of just four square feet (0.37 square metres). It is designed to be installed in a wide variety of places, including alongside sidewalks, in backyards or public parks.
Three types of modules called Production Module, Growth Module and Occupation Module would feature in each structure. Each unit would be framed with cross-laminated timber and could be stacked in different configurations depending on the space or the area's circumstances.
The Production Modules would be where the vegetables are grown. They would be topped with a solar panel and fronted with polycarbonate and aluminum mullions.
The system would use aeroponics, a process for cultivating plants in which crops are grown in mist environments rather than soil. In addition to being water-efficient, this system would also allow faster growth and enable plants to absorb more nutrients, according to Framlab.
"These systems are extremely water-efficient — requiring less than 10 percent of the water necessitated by traditional, geoponic cultivation, while allowing the use of fertilizers and pesticides to be drastically reduced," Framlab said.
"In addition, aeroponic growth environments enable plant roots to absorb much higher levels of minerals and vitamins, which yield vegetables that pack a stronger nutritional punch."
Each unit features an aeroponic tray, water feeder line, and water trunk line. Plants would be watered through mist nozzles attached inside each Production Module.
Water would be pumped through the structure's irrigation system, a closed-loop network made up of Growth Module components that act like trunks, branches, and feeders, to the misters.
"Glasir is a project that seeks to utilize a tree's adaptable growth processes as a dynamic framework for high-yield, vertical farming," said Framlab.
"Through the elevation and distribution of production modules, the system enables high-yield, local production of greens and vegetables, while engaging with the streetscape as a distinct new urban figure."
In addition to the Production Module and the Growth Module, the Occupation Module would provide platforms and pathways for people to move through the structure.
Framlab imagines that each Glasir would be fitted with artificial intelligence (AI) sensors that would be used to monitor plant growth and environmental conditions. Eventually, the AI would be used to inform how to grow each structure.
The modules would be stacked by crane-equipped trucks but the team also has plans to implement drone transit that would eventually both build and deliver modules, when the technology is proven viable.
It also imagines that in the future drones would also be used to deliver food to local residents.
In addition to its function as a source for harvesting food, Glasir could also serve as a social space for people offering shade and shelter during the day and illuminating its surroundings at night.
Framlab was founded by Norwegian designer Andreas Tjeldflaat, and has offices in Bergen, Norway, and New York.
In 2017, the studio proposed adding clusters of honeycomb-like pods to the sides of buildings to address New York City's growing homeless population.
Other vertical farming proposals include a modular housing complex by Precht in which residents produce their own food, a multi-storey bamboo-framed structure by Rogers Stirk Harbour + Partners and a conceptual skyscraper by Pawe l Lipiński and Mateusz Frankowski envisioned for locations across sub-Saharan Africa.
Congress Funds Office of Urban & Innovative Agriculture
The Mission of the Office is to encourage and promote urban, indoor, and other emerging agricultural practices
By Brian Filipowich
The new Office of Urban Agriculture and Innovative Production created by the 2018 Farm Bill had been sitting in limbo for the past year. The USDA declined to establish it without dedicated funding from Congress.
On December 20, 2019, the President signed into law H.R. 1865, The Further Consolidated Appropriations Act of 2020. The Law includes $5 million for the Office.
The Mission of the Office is to encourage and promote urban, indoor, and other emerging agricultural practices, including:
community gardens and farms located in urban areas, suburbs, and urban clusters;
rooftop farms, outdoor vertical production, and green walls;
indoor farms, greenhouses, and high-tech vertical technology farms; and
hydroponic, aeroponic, and aquaponic farm facilities.
The Office will disburse $10 million in grants before 2023 intended to “facilitate urban agricultural production, harvesting, transportation, and marketing.”
Senator Debbie Stabenow (D-MI) was the main sponsor of the new Office and was responsible for adding it to the 2018 Farm Bill. This past Fall, Senator Stabenow introduced an amendment to appropriate the $5 million to fund it.
The next step is to establish the Advisory Committee that will guide the establishment of the Office. The Committee is to be composed of 12 individuals from various sectors of the urban and innovative ag field.
The Farm Bill directed the establishment of the advisory committee by Summer, 2019. The USDA missed the target date because of the lack of funding and the USDA’s major relocation project from Washington, DC to Kansas City, MO, which “has resulted in catastrophic attrition at USDA’s top research agencies.”
Hopefully, with the new funding, the USDA can establish the Office soon.
AEssenseGrows Adds Business Management To Cruise Control Aeroponics
The Guardian Cloud Intelligence central management system brings cloud-based data analysis and visualization of complete grow operations to AEssenseGrows’ advanced software platform for automated aeroponic plant growth
Guardian Cloud Intelligence Visualizes Complete Grow Operations with Cloud-Based Analysis, Accelerating Business Decisions
SUNNYVALE, Calif., Nov. 13, 2019 -- AEssenseGrows, an AgTech company specializing in precision automated aeroponic platforms for consistent high-yield plant production, today introduced a new set of business management features that deliver dramatically greater insight to cultivators. The Guardian Cloud Intelligence central management system brings cloud-based data analysis and visualization of complete grow operations to AEssenseGrows’ advanced software platform for automated aeroponic plant growth.
Adding to “cruise control” grow recipes, the new features help cultivators analyze the costs and revenue of various strain performance—easing the comparison of historic, current grows, and future planning—to determine the most profitable paths in the context of the latest market pricing.
“We’re really excited about the ability to run reports on our grows and cross those with our harvest yields and pricing expectations to determine the big-picture issues we can optimize over time,” said master grower Matthew Willinger, whose operation in Oakland, Calif., uses the AEssenseGrows AEtrium system. “And being able to evaluate the operational cost of a grow-- water, nutrients, labor, electricity--combined with selling prices is a great tool for analyzing the profitability of different grow rooms and strains.”
The AEssenseGrows award-winning AEtrium system delivers sensor-driven cruise-control automation to simplify aeroponics and amplify its inherent benefits. The Guardian Grow Manager central management software executes the exact grow recipe and environmental conditions set by the master cultivator. Once created, dozens of sensors in every machine report on performance and direct adjustments 24/7 and 365 days per year without hesitation, rest, or fatigue. Key variables are automatically tuned such as lighting, nutrients, HVAC, and environmental control to maintain the optimal conditions as defined in the master cultivator’s grow recipe.
Guardian Cloud Intelligence now extends the master cultivator’s knowledge with limitless cloud storage and analysis, leading to better decisions at the fingertips of the master cultivator from any convenient location at any time of day.
Key analysis and features in the Guardian Cloud Intelligence system include:
Room-level aggregated reporting for unlimited sized rooms. Sensor data can be displayed and reported per harvest by the minute, hour, day, week, quarter or year.
The availability of unlimited financial data on nutrient usage, water usage, CO2 usage, labor, maintenance, and electrical usage.
The integration of collected data with the Calendar, enabling all employees and managers to share to-do lists and action items. Users can manage labor operations for their entire facility through an easy to use calendar dashboard. Visually analyze sensor patterns over the days of the calendar. Adjust your work assignments on the fly and have those tie directly back to user assignments.
Workflow integration and dynamic form extension connect business processes, like reporting and documentation, directly to the operator’s daily activities so it is seamless and easy to follow. Every employee starts their shift with a complete list of their required activities for the day, and this is dynamically updated with changes as required. Completion of the events are all stored and integrated in the analysis in the cloud.
Market pricing and financial impact reports based on facility metrics and labor integration, produce profitability forecasts based on real-time and projected data.
AEssenseGrows Receives CE Marking For Its Automated Aeroponics Systems
The CE Marking covers both the AEssenseGrows AEtrium-2.1 and AEtrium-4 grow platforms. Last year, the company received similar certification from Underwriters Laboratories (UL), the largest not-for-profit testing laboratory in the world
The Markings Confirm That the Company’s AEtrium Grow Systems Meet
the Health, Safety and Environmental Standards Required in Europe
SUNNYVALE, Calif., Nov. 13, 2019 -- AEssenseGrows, an AgTech company specializing in precision automated aeroponic platforms for consistent high-yield plant production, announced today that its AEtrium grow systems have received Europe’s CE Marking, ensuring they meet the health, safety and environmental protection standards for products sold within the European Economic Area.
The CE Marking covers both the AEssenseGrows AEtrium-2.1 and AEtrium-4 grow platforms. Last year, the company received similar certification from Underwriters Laboratories (UL), the largest not-for-profit testing laboratory in the world. And the company’s compact high-intensity AErix LED bloom light last year received an Electrical Testing Laboratories (ETL) safety listing, exceeding or surpassing all standards for safety published by UL and other standards bodies.
The AEssenseGrows award-winning AEtrium system delivers sensor-driven cruise-control automation to simplify aeroponics and amplify its inherent benefits.
“The only thing more important to AEssenseGrows than its customers’ success is its customers’ safety,” said Phil Gibson, the company’s vice president of Marketing. “Our team has worked hard to ensure our equipment meets and exceeds all relevant regulatory standards so our customers can focus on winning in the marketplace without having to worry about safety issues”
Also today, AEssenseGrows introduced a new set of business management features that deliver dramatically greater insight to cultivators. The new Guardian Cloud Intelligence central management system brings cloud-based data analysis and visualization of complete grow operations to AEssenseGrows’ advanced software platform for automated aeroponic plant growth.
The AEtrium system hardware and software will be on display at the AEssenseGrows booth, C5308, at the MJBizCon show in Las Vegas Dec. 11-13.
More information on the products is available at www.aessensegrows.com.
About AEssenseGrows
AEssenseGrows (pronounced "essence grows"), founded in 2014, is a precision AgTech company based in Sunnyvale, Calif. A recipient of the Red Herring 2019 Top 100 North America award, AEssenseGrows provides accelerated plant growth SmartFarm platforms and software automation delivering pure, zero pesticides, year-round, enriched growth to fresh produce and medicinal plant producers globally.
With AEssenseGrows, growers can precisely control their production operations at your fingertips from anywhere in the world.
Ag Firm Signs Electric Works Lease Muncie Business Uses Fish Waste As Plant Fertilizer
This is the second tenant announcement for Electric Works featuring an agricultural technology company in two weeks. Last week, the developers announced that Sweetwater Urban Farms had signed a lease agreement. Sweetwater Urban Farms uses aeroponic technology to produce nutrient-rich greens and herbs
SHERRY SLATER | The Journal Gazette
A Muncie company that uses fish waste as plant fertilizer has signed a lease for space in Electric Works, officials announced Monday.
Balance Holdings Inc. is a commercial regenerative agriculture technology company that uses 1% of the water needed for traditional farming and less than 20% used in hydroponics, a process of growing plants without soil, officials said.
The company will grow fish and crayfish in tanks. The waste-filled water, which is full of nutrients, is channeled to plants that produce fruits and vegetables. The plants filter the water, which is then cycled back to the fish tanks, creating a closed-loop system with no waste.
Glynn Barber, the company's founder, said that “growing better food is more than just putting a better tomato into the grocery store – it's about growing a better future” for the next generation.
“We believe healthier food produces healthier people, which produce healthier communities – and we see an exciting and unique opportunity for ECSIA to make a profound impact on this community, partnering with healthcare providers and higher education institutions at Electric Works,” Barber said in a statement.
More than 300 varieties of fruits and vegetables have been grown using the company's patented system in Indiana, Texas, and Haiti.
Balance Holdings plans to sell fish, fruits, and vegetables to restaurants in the region and directly to the public at an on-site store in Electric Works.
Jeff Kingsbury, a partner in Electric Works developer RTM Ventures, said the new tenant checks a lot of boxes for the type of businesses RTM is trying to attract.
RTM Ventures, he said in a statement, is looking for “firms that are exploring new technologies and market-based solutions through strategic alliances and creative partnerships with other businesses, as well as healthcare and education institutions.”
“At the same time, (the company's) impact will be felt in the neighborhoods surrounding Electric Works – areas of the city that have struggled with access to healthy food in the past,” Kingsbury added.
This is the second tenant announcement for Electric Works featuring an agricultural technology company in two weeks. Last week, the developers announced that Sweetwater Urban Farms had signed a lease agreement.
Sweetwater Urban Farms uses aeroponic technology to produce nutrient-rich greens and herbs.
Aeroponic systems nourish plants with nothing more than nutrient-laden mist, according to the Modern Farmer website.
Electric Works is a mixed-use district of innovation, energy, and culture, developed as a public/private partnership between RTM Ventures and the city of Fort Wayne. The 39-acre campus just south of downtown is the former location of General Electric.
RTM Ventures plans to convert 1.2 million square feet in 18 historic buildings into space for office, educational, innovation, retail, residential, hotel, and entertainment uses.
Aramark Gears Up For 2019 Back-To-School Season On College Campuses
Freight Farms - East Carolina University's Freight Farm supplies the dining hall with organic produce, grown in a shipping container behind a residence hall. The shipping container provides ideal conditions for seeds to germinate, grow and be ready for harvest in eight weeks
8/28/2019
BACK TO SCHOOL: Aramark is welcoming back three million higher education students to campus, by introducing a new wave of offerings customized to the ever-changing needs of Gen Zers, including new breakfast and dessert menu items added to True Balance, Aramark's allergen solutions station.
PHILADELPHIA -- Aramark, a foodservice and facilities partner of more than 400 colleges and universities across the U.S., is ready to welcome back three million higher education students to campus by introducing a new wave of offerings customized to the ever-changing needs of Gen Zers.
"Every year, our higher education team members elevate the student experience with custom campus solutions tailored for them," said Jeff Gilliam, president of Aramark's Higher Education business.
Aramark's team of more than 450 higher education chefs develop menus using flavors and food trends from around the world, in-depth research and healthy, fresh and authentic ingredients, to satisfy and expand students' taste buds.
Some highlights of new menu items include:
Sushi Cones -- A new concept that puts a fun spin on a student favorite. Made to order, sushi cones are easy to eat and completely customizable, from the vegetables, to the protein of choice.
Kimchi Quesadilla -- Inspired by a concept that helped lead the popularity of gourmet food trucks, this quesadilla features spicy kimchi, baby spinach, queso fresco and Kogi Salsa Roja.
Beet Hummus -- Alternative hummus options have risen in popularity in the U.S. Beet hummus packs many nutrients and brightens recipes with a subtle, earthy, mildly sweet and smooth flavor.
Cooking Up Meal Kits
Aramark research found that 58% of undergraduates would be very likely or likely to use a meal kit at school, so the company is partnering with Home Chef, the second largest U.S.-based meal kit brand, to offer meal kits as a component of a meal plan this fall. Debuting on 25 campuses this September, the new plan provides meals on campus and meal kits delivered directly to students' doorstep, providing a new solution for those who enjoy or want to learn to cook.
Expanding Allergy Solutions
This academic year, students can expect breakfast and dessert menu items added to True Balance, Aramark's allergen solutions station.
Aramark's culinary team developed six new recipes utilizing products from Enjoy Life Foods, which are entirely gluten free and exclude nuts, dairy and soy. All Enjoy Life foods are free from 14 allergens and are made with 100%, all natural, non-GMO ingredients. Featured recipes include various types of muffins, banana pancakes, chocolate brownies and chocolate chip cookies.
Growing Campus Gardens
Campus gardens are sprouting up across the country, giving students the chance to eat local and see how produce is grown, first-hand. Through innovative technologies, Aramark is helping students embrace a plant-forward lifestyle.
Aeroponic Gardens - At the University of California, Irvine, 30 aeroponic towers grow over 1,320 bunches of vegetables. Harvested every three weeks, the bundles of produce go directly into the dining hall, where they are incorporated into the menu and enjoyed by UCI students. The towers also supply vegetables and herbs for the on-campus food pantry and resource center.
The University of Florida uses two aeroponic tower gardens to grow leafy greens and herbs that are donated to the on-campus food pantry that assists food insecure UF staff, faculty and students who utilize the pantry.
By utilizing aeroponic gardens, campuses are using less water, growing more product and eliminating the use of pesticides.
Freight Farms - East Carolina University's Freight Farm supplies the dining hall with organic produce, grown in a shipping container behind a residence hall. The shipping container provides ideal conditions for seeds to germinate, grow and be ready for harvest in eight weeks.
Use Of Artificial Intelligence
Aramark has expanded its use of artificial intelligence (AI) to college campuses through a partnership with Mashgin, a Palo-Alto, CA-based technology company, that creates express self-checkout kiosks that use computer vision to scan multiple items at once without barcodes.
This technology provides a frictionless customer experience with faster checkout times and shorter lines for the convenience time-pressed students and staff want. Students also can purchase grab-and-go choices without sacrificing a fulfilling meal.
Rolling Food Delivery Onto Campus
Aramark recently acquired Good Uncle , an innovative, app-based on-demand food delivery service that brings freshly prepared, restaurant quality meals to conveniently located pick-up points around college campuses. The addition of this concierge service to the Aramark portfolio furthers the company's commitment to advancing innovation through culinary-and technology-driven solutions that better serve customers and clients.
Good Uncle, launched in 2016, utilizes centralized production and a fleet of specially equipped vehicles to deliver meals to the most popular spots on and off campus. Its world-class culinary team, led by a Michelin-rated chef, crafts a diverse menu of healthy and indulgent items that rotates frequently to keep the experience enticing.
UK Tech Pioneer Conjures New Future For Farming Out of Thin Air
Change is in the air for agriculture and indoor farms developer LettUs Grow is breaking new ground with a system that produces more plants more quickly by growing their roots only in a nutrient-rich mis
Change is in the air for agriculture and indoor farms developer LettUs Grow is breaking new ground with a system that produces more plants more quickly by growing their roots only in a nutrient-rich mist. A pioneer within the field known as aeroponics, this air-based method uses 95 percent less water than conventional farming.
By MAISHA FROST
August 12, 2019
LettUs Grow Director Aims to ‘Inspire’ Food Production Generation
It can also involve lower carbon emissions compared to other soil-free systems such as hydroponics where plants are dipped enriched water. LettUs’s patent-pending technology introduces more simplicity and consistency to aeroponics while maintaining yields, explains managing director Charlie Guy. “We have developed a very efficient way of growing plants, from leafy vegetables to soft fruits, in completely controlled environments.
“Our aeroponic systems are easier to use than others on the market where water is pushed through nozzles to create an aerosol that can get clogged.
“Ours just needs a wipe down and is modular so can work with operations of all sizes, from a single layer to an entire controlled environment farm unit.
“Ostara, our software management can automate, control and collect data from the operation. That integrated licensed approach makes aeroponics accessible to anyone enabling farmers around the world to benefit from this game-changing technology.”
The clock is ticking and on LettUs’s side – by 2050 it is estimated the world must increase food production by 70 per cent to feed more than nine billion people.
Managing director Charlie Guy (Image: Jack Wiseall)
The Bristol-based firm was founded in 2015 by Guy, and fellow graduates of the city’s university Ben Crowther and Jack Farmer.
Their mission to tackle food waste and supply chain inefficiency “has always been to reduce the environmental impact of fresh produce by allowing anyone to grow food near its point of consumption,” says Guy.
“The past decade has been defined by the environmental crisis, but now food can be grown in the most unstable of climates. Any building can be converted and millions of transport miles saved.”
Two big tech changes paved the way for LettUs: cheaper, more efficient LED lighting and cloud computing enabling the harvesting of big data.
The company’s technology can match lighting to roots to optimise growth and precise delivery of the nutrients tailored to plant variety and stage of life.
The plants don't need as much water (Image: Picasa)
Systems are assembled in Bristol and pay back for growers estimated to be under five years. Overseas interest from the Middle East, Europe, Africa and US is accelerating.
More than £1million of funding, both in grants from government-backed Innovate UK and private investment, has gone into LettUs which sees potential further applications for its technology contributing to the likes of reforestation programmes.
The Royal Academy of Engineering Enterprise Hub, geared to maximise the potential of next-generation entrepreneurs, also played a crucial role in helping LettUs commercialise its innovation.
Crowther took its SME Leaders Programme, a grant-aided, coaching and mentoring support scheme for early stage engineering and technology firms with high growth potential and “that has been invaluable in accelerating our development”, says Guy.
After starting with laboratory projects such as research into plant-based proteins and pharmaceuticals, LettUs’s sales are increasing to growers and the business has plans to raise more investment this year.
The team, now 15, “is very plant-focused but diverse,” says Guy. “Not just engineers but ex-farmers and plant scientists. All our kit is made by growers for growers.”
LettUs Grow is breaking new ground with a system that produces more plants (Image: Jack Wiseal Photography)
Russia: City Farming In Tomsk
The Orlov family started an unusual business two years ago. Despite Siberian frosts, they successfully grow strawberries year-round with the help of their own engineering inventions
Growing Strawberries In The Basement of a Block of flats
The Orlov family started an unusual business two years ago. Despite Siberian frosts, they successfully grow strawberries year-round with the help of their own engineering inventions.
In the basement of a regular 5-storeyed block of flats, the city farmers grow their berries, without a single ray of sunshine and natural warmth.
“The agricultural method is based on hydroponics and aeroponics”, explains Alexander Orlov, demonstrating the small farming facility. “These are important factors, but lighting is even more vital. The technology was worked out by my son; it is his know-how that formed the basis of our business”.
The family have various technical devices, but the main factor is lighting, due to which the berries get all the needed warmth and light for growth, aroma and color.
The inventive son, Kirill Orlov, is a professional engineer, who specialized in applied mathematics in Tomsk University. His lamps allow for reduced energy consumption and stabilize the temperature regime. One lamp lasts 7.5 days, if used 18 hours a day. With these lamps, strawberries grow and ripen faster, productivity increases up to four times.
“I had already retired when one day my son came and suggested growing strawberries. He experimented with light before and grew greenery like onions, parsley and spinach quite successfully. The volume wasn’t big and nobody had thought he was going to start big production”, shares the father, Alexander Orlov.
The local government supported the idea; they liked the systematic approach and the idea of growing and selecting strawberries in Tomsk all year round. The first grant that was received for the complex creation came from the local government. Currently the growers have three rooms, two of which are occupied with beds for 3000 berry bushes and various systems, and the third one contains the enterprise management system: water conditioning, fertigation and irrigation unit and other equipment.
“We get a lot of positive feedback from customers on our Instagram page, both private persons and restaurant business representatives. Parents write that they are happy that our strawberries cause no allergic reaction with children”, shares Mrs. Alla Orlova.
“Our dream is to create the best greenhouse not only in Siberia but also in the world”, shares Kirill. “We have an opportunity to pick a suitable land plot for the construction and we want to show that Siberia can boast the most advanced agricultural technologies and contemporary profitable greenhouses. Any plant can be grown with our technology, not only strawberries but also greenery and tulips that we purchase in huge amounts form the Netherlands. I feel we can do it with the support of the family. Further development will be related to expansion of our interest and gradual fulfillment of the plans”.
The vegetation period in Orlov’s greenhouse lasts 45 days, after which harvesting is done every day all year round. 40 thousand bushes can produce 40-60 tons of berries per year.
Source: rg.ru
Publication date: 5/15/2019
Micro Farm, Macro Impact
March 25, 2019
Brooke Bilyj | Photography by Erin Elliott, except where noted
Micro Farms in Nappanee, Indiana, Hopes to Revolutionize Food Production With its Patented Hydroponic System.
From left to right: Nick Graber, Steve Kiefer and Dion Graber
Nestled in the heartland of northern Indiana’s Amish country sits a shimmering glass greenhouse where fresh produce is grown, 365 days a year, without any pesticides or herbicides. Although the facility occupies a mere quarter of an acre, the owners of Micro Farms hope to revolutionize global food production with their innovations.
“Our big-picture goal for Micro Farms is to develop technology and growing systems to provide wholesome food to people globally,” says Loren Graber, who established the hydroponic greenhouse about five years ago.
“There are too many people who go to bed hungry,” adds Dion Graber, Loren’s son and head grower. “With all the technology and resources available, we should be able to feed them.”
Building on a long farming history, the Graber family has been producing food on this property for generations. Back in the ’80s, before Dion was born, Loren ran the family’s corn, soybean and dairy farm in Nappanee, Indiana. One day, he jokingly mentioned to the farm’s agronomist, Steve Kiefer, that he would start a greenhouse operation someday.
But then, soon after Dion was born, milk prices plummeted — forcing Loren to find work in another field. At the time, he didn’t realize that his new job in vinyl fencing would inspire the innovation to bring his greenhouse to life.
“Since he was in the vinyl business and he has PVC connections, vertical farming was right up his alley,” Dion says. “He’s always been an inventor at heart, and he has multiple patents. He just loves thinking outside the box and trying to come up with new things that are more efficient.”
Leveraging his inventive curiosity, his knowledge of vinyl and his drive to make traditional agriculture more efficient, Loren designed and patented his own vertical hydroponic/aeroponic tubes. He asked Kiefer to team up with him again, and they established Micro Farms in late 2013 with the dream of farming differently. Dion jumped onboard as head grower, and several years later, his younger brother Nick joined the family business to execute their father’s dream.
Lettuce growing at Micro Farms
“Vertical” integration
Loren considered using traditional, single-layer hydroponic systems that used floating rafts — deep water culture (DWC) — or the nutrient film technique (NFT), where nutrient-rich water circulates past the bare roots of plants in enclosed channels. But these horizontal layouts required too much space — pointing him toward vertical farming instead.
“You get so much more product per square foot when you grow vertically,” Dion says. “We have 320 tubes in a 4,000-square-foot area, and we can fit 46,823 plants in that 4,000 square feet. That’s roughly 10 plants per square foot.”
Micro Farms’ “Verti Tubes” are 12 feet tall and eight inches in diameter. Loren’s patented design features removable growing cups and trays that pop out of the tube for cleaner, easier harvesting. Prongs in each cup hold a foam cube in place to support the plant’s roots, and a small groove in the bottom of each cup channels water down as it trickles through the tube.
“The biggest thing that separates us when it comes to our Verti Tubes is the removable cup,” Dion says. “Most of them are molded in and you can’t take them out, so our design is better for cleaning purposes. It’s easier to harvest your plants, because if the roots are too long, they’ll get caught when you try to pull them out.”
The foam cubes can be removed with the roots still intact, allowing Micro Farms to harvest and sell living lettuce with a shelf-life of at least two weeks — leaving minimal cleanup behind.
Micro Farms’ Verti Tube Home Growing System
Finding the right mix
The Grabers broke ground in fall 2012, and then a team of builders from Rough Brothers constructed the Venlo greenhouse in 2013. The glass structure contains a 3,000-square-foot head house for seed-starting, a 4,000-square-foot space filled with Verti Tubes, and another 4,000-square-foot space for vertical vine crops.
Dion didn’t have any experience with hydroponics, so he and Kiefer attended the Controlled Environment Agriculture Center at the University of Arizona for a “quick crash course” that packed “six months’ worth of college courses into five days, and then another four months in two days,” he says. “That’s where my knowledge started, but at least 80 percent of my growing knowledge is just hands-on.”
When Dion started growing, he experimented with 23 varieties of leafy greens that he seeded weekly. Through trials, he whittled that collection down to 10 varieties, based on what grew and sold best.
The front half of the greenhouse is dedicated to leafy greens like butterhead and oakleaf lettuce, kale and pak choi grown in Graber’s hydroponic/aeroponic Verti Tubes. In the back half, vine crops like tomatoes, red bell peppers and snacker cucumbers are strung up toward the ceiling from hydroponic Bato buckets below — which are filled with recycled glass Growstone that can be rinsed and reused.
Dion and Nick continue to explore new varieties together — switching up greens in the summer to include basil and other heat-loving plants. They’re even trying strawberries in the Verti Tubes.
“We’re constantly experimenting,” Dion says.
Micro Farms grows tomatoes in addition to its Verti Tube-grown lettuce.Photo: Brooke Bilyj
Watering the natural way
In addition to Loren’s innovation, the design of the greenhouse also drives efficiency at Micro Farms.
For example, each peak of the Venlo greenhouse roof has a vent on each side. “Whichever way the wind blows, the opposite side opens, so you don’t have a dramatic change in temperature,” Dion explains. “And then every valley has a gutter where we collect rainwater, which is stored in a 25,000-gallon tank under the floor of the headhouse.”
The roof of the warehouse next door also collects rainwater to supplement the operation. They have access to well water, if needed, but they rarely need to tap into that supply.
“The plants just respond better to rainwater,” says Dion, who also uses an O2 Grow system to “supercharge” the water with dissolved oxygen. “We’re trying to imitate exactly what a plant would get out in the ground, but with no soil.”
To that end, Kiefer formulated a mix of granular fertilizers mined from the ground — including Epsom salt, potash, potassium nitrate, monopotassium phosphate and calcium nitrate — that’s added to the water.
Building on a long farming history, the Graber family has been producing food in Indiana for generations.Photo: Brooke Bilyj
Bugging out for pest control
To keep greenhouse insects in check, Dion and Kiefer rely on beneficial bugs to provide biological pest control at Micro Farms.
“We try to keep our population up, so when pests come, we’re ready for them,” Dion says. “Pests seem to multiply quicker than your beneficial bugs, so we’re constantly ordering them.”
Dion regularly releases parasitic wasps to control pesky aphids. Meanwhile, small sachets of swirski mites hang from the plants, inviting the tiny predators to go after the eggs of thrips that can threaten crops. Beneficial insects are released once or twice a month, negating the need for sprays.
“One thing that separates us is that we do not spray any pesticides or herbicides on our plants,” Dion says. “We don’t even have to rinse our produce after harvesting, because nothing was sprayed on it.”
Ronda Kuhns, greenhouse worker at Micro Farms, harvests lettuce from its Verti Tubes.
Harvesting fresh for market
Using scissor lifts to access crops all along the 12-foot-tall tubes, Micro Farms employees harvest produce daily. While some is sold fresh to local restaurants and retail customers, Micro Farms also sells produce through an online farmers market called Market Wagon.
Founded by a fellow former dairy farmer, the online platform allows customers throughout the state to order locally grown or handmade products from various vendors, who get to set their prices and availability weekly. Then, orders are either delivered directly to consumers’ doorsteps or to local pickup points.
There are too many people who go to bed hungry. With all the technology and resources available, we should be able to feed them. — Dion Graber
Every Thursday morning, Dion drives a truckload of produce to the Market Wagon hub in Indianapolis, two hours south of Micro Farms. On the way home, he swings by another hub in LaPorte, an hour west. At each hub, he distributes orders into customers’ bags, which are delivered after every vendor drops off their goods.
Market Wagon extends Micro Farms’ reach across the northern half of Indiana. But word travels fast in the small, rural town of Nappanee — and local consumers started asking how they could get fresh hydroponic produce, too. So last November, Micro Farms began selling to the public on Saturday mornings from 9 a.m. to noon.
“At 9, you’ll see half a dozen buggies and a dozen cars in the parking lot,” Dion says. “Local people have responded very well to our products.”
Photo: Brooke Bilyj
Looking to the future
The Graber family is eager to share their hydroponic innovations with other growers. The first phase of this long-term plan is their home growing unit, which is slated to hit the retail market later this year.
A smaller version of their greenhouse Verti Tubes, the home hydroponic units, are mounted on a rolling cart that can be wheeled outside. Or, the unit can sit in a kitchen, using an optional LED strip and rotating function to provide sufficient light inside. The home unit features Loren’s patented removable cups and trays, allowing consumers to hydroponically grow 24 plants with minimal mess or maintenance.
Looking even further into the future, the Grabers’ dream of improving food production around the world by providing greenhouse supplies, resources and knowledge to communities in underserved nations like Haiti and Africa, where they’ve been involved in mission work.
“We want to teach other people how to grow. Ultimately, our big goal is to feed the hungry by educating them and setting them up for success,” Dion says. “Because our tubes maximize product per square foot, we think it could definitely make a difference.”
Brooke is a freelance writer based in Cleveland.
Vertical farms Irrigation Hydroponics Aeroponics Cucumber Lettuce
Kale Bok choy Basil Pepper
Vertical Farming For Cannabis Gets Trial Run in Langley
Leo Benne, chief growing officer of Zenabis, with the converted shipping container that will become a testbed for a vertical cannabis farm. (Matthew Claxton/Langley Advance Times)
Grower Zenabis Will Start With Industrial Hemp And May Move to
Commercial Marijuana
Jun. 6, 2019
Zenabis, which merged with longtime Langley greenhouse firm Bevo last year, has received a hemp cultivation license from Health Canada, with growing to take place in Langley, Pitt Meadows, and Aldergrove facilities.
“We expect the seed to come in this week,” said Leo Benne, chief growing officer for Zenabis.
A small portion of that seed will be planted not in one of the greenhouses facilities, but in a converted shipping container, as a test on whether cannabis can be vertically farmed.
Bevo has already helped develop a vertical farming system through CubicFarms, a Pitt Meadows-based spin off.
Vertical farming involves growing large amounts of crops on small amounts of space, indoors, and usually without any soil.
Plants are reared in racks, stacked as high as the building or container can accommodate, and grown either hydroponically or aeroponically.
Energy efficient LED lights allow the plants to grow 24 hours, seven days a week, in any weather.
In theory, the cost of the equipment and intensive rearing is offset by the ability to grow non-stop and to place the growing site much closer to the end-consumer. Rather than trucking lettuce from California or Mexico, it could be grown just a few miles outside of Canadian cities and shipped just a few kilometres.
The hemp vertical farm is just a test at this point, said Benne. A single converted shipping crate has been hauled into one of the Zenabis greenhouses in Langley and will be ready for its test run at about the same time as 20 acres of industrial hemp is planted in the three facilities, from Langley to Pitt Meadows.
While most crops planted in vertical farms are extremely low-growing, allowing for many racks close together, cannabis is usually a tall-growing crop.
Benne said that a combination of the plants chosen and growing practices is expected to keep the plants shorter for the vertical farm project.
If the project goes well, vertical farming facilities could be used for growing commercial marijuana, said Zenabis CEO Andrew Grieve.
The industrial hemp isn’t being grown for commercial marijuana sales. Instead, the hemp will be processed into CBD oil, fibre, or other derivatives. The project is separate from Zenabis’s plans for growing commercial cannabis in Langley.
While Langley’s other large cannabis cultivator has caused controversy in Aldergrove over smell issues, Benne doesn’t believe that will be an issue for Zenabis.
“We’re doing things a lot differently,” he said. “First of all, we’re constructing a closed greenhouse facility. We’re able to keep most of the air inside the greenhouse.”
There are to be no roof vents, which should not only control odour, it helps the growers control humidity and other issues.
“Because we don’t have that exchange of air with the outside, we don’t have a lot of pest issues,” he said.
Air exhaust is to be controlled through carbon filters, and if those aren’t sufficient, biofiltration. That means basically pumping all the air exhaust through a big box full of bark and cedar chips to absorb the smell.
Russia: Novosibirsk Scientists Grow Strawberries With Aeroponics
A startup from Novosibirsk is entering the international market. Soon the technology will be sold to Arabian agronomists. Until then, the scientists continue experimenting with strawberries in the basement of the campus
A startup from Novosibirsk is entering the international market. Soon the technology will be sold to Arabian agronomists. Until then, the scientists continue experimenting with strawberries in the basement of the campus.
The experimental greenhouse is as clean as an operation room. Special sensors monitor the humidity and the temperature levels. This is where the scientists conduct their experiments with strawberries. Some of the plants are grown in traditional soil, and the rest are grown in accordance with aeroponics.
“This is what the roots look like. As there is no soil, there are no pests either. Just the clean white roots hanging in the air”, shares Mr. Ivan Lapshin, the agronomist.
An automated system delivers all the substances required for plant growth. The agronomist uses switches on the machine: strawberries have much better conditions for growing on the shelves than in the open field.
The first crops grown according to the new technology are 20% taller than the regular ones. The result is due not only to aeroponics, the climate as well as the lighting strength and the length of the artificial light day have been carefully calculated.
The innovators are planning to give access to the technology to a wide audience so that anyone could grow fresh vegetables, berries and greenery in any free room all year round. The shelves are fully automated so no agronomist is required to assist them.
“We would like that people in Magadan have fresh strawberries in winter. And that they don’t fly from Egypt or Lebanon but have a proper flavor and freshness”, noted Mr. Timofey Pavlov, agronomist.
Soon the scientists will start mass production of their vertical farms. The technology raised big interest with representatives of the United Arab Emirates, where vertical farming is most pertinent. The scientists are preparing the equipment for delivery.
Source: www.nsktv.ru
Publication date: 5/9/2019
Living Greens Farm Becomes One of the Largest Indoor Farms in the World
On Feb. 22, Living Greens Farm Will Open Their Third Grow Room In Faribault, Minn.
FARIBAULT, MINN. (PRWEB) FEBRUARY 13, 2019
With the opening of a new grow room, Living Greens Farm, a vertical, indoor aeroponic farm that provides year-round fresh salads, microgreens and herbs, is set to become the largest vertical plane aeroponic farm in the world on February 22, 2019. This brings their farming operation to 60,000 square feet – allowing Living Greens to offer produce that’s better for you and the environment. Unlike most produce, Living Greens Farm never uses pesticides, herbicides or GMOs – delivering the highest standards in food safety. Because Living Greens’ products are fresher, they contain more vitamins and nutrients than conventional produce.
While aeroponics has been around for decades, Living Greens Farm has discovered a way to successfully transition and improve this technology for commercial production. Aeroponics is the practice of suspending a plant’s roots in the air and spraying them with a nutrient-rich solution, instead of burying them in soil. Living Greens Farms’ patented vertical plane design allows one acre to produce the equivalent of hundreds of conventional acres. A high-tech computer system manages the plants growing conditions for variables such as light, temperature, humidity and CO2 to grow year-round produce. Overall, Living Greens Farms’ system uses 200 times less land and 95 percent less water than traditional growing methods. While other vertical aeroponic farms are larger in square footage, Living Greens Farms’ vertical plane design is the first of its kind and is more efficient than other aeroponic growing methods which decreases labor by up to 60 percent.
“Our patented growing technology has changed the game of aeroponics, within one year our new farm will save 24 million gallons of water and several hundred thousand miles of shipping – saving over 35,000 gallons of diesel and nearly a million pounds of CO2 emissions," said Dana Anderson, Chairman and CEO of Living Greens Farm. “With our third grow room, Living Greens Farm will nearly triple its capacity, move into major market segments and position the company for even stronger growth in 2019. The expansion places Living Greens as the world’s largest vertical plane aeroponic farm in the world.”
Living Greens Farm’s new grow room will allow an expansion of their consumer product line into new states including Minnesota, Wisconsin, Illinois, Iowa, North Dakota and South Dakota by February 2019.
ABOUT LIVING GREENS FARM
Headquartered in Minnesota, Living Greens Farm is the world’s largest vertical plane aeroponic farm. Living Greens Farm produce requires 95 water and 99 percent less land to grow year-round and all products are grown without pesticides or GMOs. Living Greens Farm has a full product line that includes salads, microgreens and herbs available throughout the Midwest. For more information, please visit http://www.livinggreensfarm.com
The Future of Farming Is Up In The Air
David Thorpe | 14 February 2019
Food that’s grown in the air instead of soil could soon appear on plates in Britain and other parts of the world.
A new investment deal worth $1.8 million to build indoor farms uses technologies developed by a company called LettUs Grow, a Bristol, UK-based startup that designs irrigation and control technology for vertical farms.
The startup will partner with ECH Engineering, which manufactures controlled environment technology, traditionally in refrigeration, and urban agriculture experts from Grow Bristol. Bristol has made a name for itself as Britain’s greenest city.
The company is one of a number of startups in the fast-expanding area of indoor growing who are supplying farm management software, crop analysis and testing services, through to full indoor farm design and build.
A glimpse of the pilot aeroponics project in Bristol showing a variety of produce being tested using the system.
Following earlier seed funding, if you’ll pardon the expression, it’s now scaling up operations to produce its aeroponic system, which suspends plants in the air and feeds the roots via a nutrient-dense mist. This technique results in faster growth rates than conventional hydroponics.
“The nutrients we use are made with mineral salts, not chemicals,” co-founder and managing director of LettUs Grow Charlie Guy told The Fifth Estate.
“They’re formulated for the vegetative stage of growth in hydroponics and aeroponic systems and precisely balanced and manufactured for great results.
“In our system we reclaim and recycle most of our water and any nutrients not absorbed by the plants. Due to this recapture and reuse, we use about 95 per cent less water than traditional field-based agriculture and 30 per cent less than typical hydroponics with our unique aeroponic technology.”
Since the plants are indoors, pest control is possible without pesticides and fungicides, making the production process organic. Previous trials have seen crop yield increases of over 70 per cent compared to conventional techniques for leafy greens, salads and herbs.
Yields and crop cycle times vary from crop to crop. The shortest is just five days for certain microgreens, to just over 30 days for head lettuce from seed.
A pilot project involving Grow Bristol involved an indoor hydroponic vertical farm that produced 100 kilograms of nutrient dense leafy greens every month without the use of pesticides and with minimal environmental impact. It tested over 50 crop varieties and sold the products to over 60 customers.
Having tested over 40 different varieties LettUs Grow’s core crops are: coriander (micro), fennel (micro), leek (micro), kale, pea shoots, sunflower shoots, radish, red cabbage, lettuce (many varieties), coriander, watercress, basil, and pak choi. “They’re our main crops, but we’re also growing rooting and fruit crops too (strawberries, spring onions and carrots, for example),” Guy says.
“We are expanding this facility in 2019 by over 10 times, to allow the testing of more and more crops and to expand our work into strawberries and root crops,” he adds.
Government funding
The $718,810 government funding is derived from the UK’s innovation agency, Innovate UK, and will be matched by $157,918 from other sources and research grants.
The grants came hot on the heels of the disruptive startup’s most recent investment round, where they raised $835,179 from ClearlySo, Europe’s leading impact investment bank, which has an extensive network of high-net-worth individual and institutional investors.
“Our investors see the value, both in terms of financial and environmental/social returns from tackling this systemic global problem. That’s why they got involved in LettUs Grow. LettUs Grow provides the technological innovation piece to the vertical smart farming movement that is currently trending rapidly in the urban context,” investment manager at ClearlySo Matias Wibowo says.
The company has ambitions to supply a rapidly growing global market for efficient and sustainable farming technology.
By 2050, humanity has to increase food production by 70 per cent to feed over 9 billion people without breaking the planet’s life-support systems, which would happen if present agricultural and food industry logistics trends continue. Aeroponics can help to address the colossal degree of waste that presently exists throughout the supply chain.
“The global agri-tech industry is very exciting right now, all stemming from the necessity to improve the economic and environmental sustainability of food production. We are fielding enquiries from all around the world from food producers and farmers who want to experience the benefits of our technology across a growing range of crops,” Charlie Guy says.
The environmental footprint
The Fifth Estate asked Charlie Guy about the environmental footprint of the technology and the energy used in a given system, compared to a soil based or hydroponic system.
He says that it depends on a number of factors, including choice of crop, choice of technology, retail route, geography, climate and season. “One of the key benefits of indoor growing, over traditional methods, is the massively reduced supply chain length. This cuts the carbon footprint of produce substantially.”
LettUs Grow are working on integrating indoor and vertical growing with renewable energy technologies to further reduce energy costs and the carbon footprint.
“Indoor, vertical growing generally acts as a substitute for imported produce,” Guy says, quoting studies claiming that CO2 reductions of up to 90 per cent are achievable by growing produce at its point of consumption using hydroponics, compared to the carbon cost of importing the same product from Europe.
He also refers to independent, academic studies into the startup’s technology that have shown that its patent-pending aeroponic technology can reduce the carbon cost of production against traditional hydroponic vertical farms by between 60 and 90 per cent.
But can the operation scale up? “Scale of operation is one of these determining factors and the vertical growing industry is still some way off the scale currently reached in glasshouse growing,” Guy says.
“The productivity increases demonstrated by LettUs Grow’s aeroponic technology represent another step-change in economic viability of farms. This enables smaller farms to deliver a return on investment up to 50 per cent faster than traditional hydroponic indoor farms.
“Energy and labour are two of the greatest operational costs of running an indoor farm and LettUs Grow are working on solutions to bring these two costs down substantially. LED lighting continues to fall in price and increase in efficiency and advanced automation processes are reducing labour costs further still.”
However, Guy says his system is “lighting agnostic”. “Anyone can use our system with any lighting. In fact, you can use our aeroponic technology without any lights, such as in glasshouses.”
To reduce costs, the company is investigating automation, not dissimilar to that found in giant Amazon warehouses. “We have designed our own automated farm management system called Ostara. It is breaking down barriers to entry for indoor farming and aeroponics. Aeroponic technology has historically been seen as complex and difficult to implement. Ostara makes aeroponics easy.”
The company plans to license its technology in the future. Watch out for indoor farms springing up near you in the not too distant future.
David Thorpe is the author of the book The One Planet Life and the forthcoming book One Planet Cities.
Tags: energy, farming, food, technology
Samson Ogbole Is A Nigerian Farmer Who Wants To Bring Aeroponics To The World
Ogbole says that there are many advantages to aeroponics, the biggest being that you can grow crops at any time of the year.
by Perry Miller
Samson Ogbole is a Nigerian farmer who is trying to solve the problem of land shortages in his native country. Nigeria’s population has now reached 190 million, but there isn’t enough land in the country to grow the food needed for the ever-growing population. So, Ogbole has found a solution — aeroponics.
This unconventional method is the process of growing plants in the air without using soil. Ogbole first got involved with soilless farming in 2014, and just two years later founded PS Nutraceuticals, a company that puts cutting-edge agricultural technologies into action to improve the efficiency of food production and to ensure food security.
“Soilless growing entails removing the soil component, bringing in substitutes, and applying fertilizer to enable the plants to grow,” Ogbole says. “With soilless farming, we have been able to push for what you call urban farming, where we now have farms in cities such that we are able to cut off the middlemen and marketers.”
Ogbole says that there are many advantages to aeroponics, the biggest being that you can grow crops at any time of the year. The method has also allowed them to eliminate pathogens that naturally exist in the soil and affect crops.
Nigeria needs an estimated 78.5 million hectares of land to produce enough food for the population. But, right now there are only 30 million hectares of farmland under cultivation, according to the International Trade Administration of the United States.
And, Ogbole says that only 46 percent of Nigerian soil is fertile to grow crops, so the country needs to take steps towards self-sustainability in food production and let technology play a more prominent role. He believes that the “war of the future will be fought through agriculture.”
“We’re bringing in technology into agriculture so that the youth can actually see this as a viable option,” explains Ogbole. “We also want to ensure that food production is no longer seasonal, and we’re also bringing in smart sensor technologies into agriculture so that you’re able to get feedback from your plants.”
The farmer added that the future of the economy depends on a few people who have bright ideas and can think outside the box. It is ideas, not money, that solves problems.
Via CNN
Images via Shutterstock
Worms, Fish Farms, Hydroponics, Aeroponics Help Fuel Oregon Hotel
Many of the celebrities that stay at The Nines have requested tours of the food lab and their private chefs that travel with them are fascinated at what the restaurant is doing.
Author: Nina Mehlhaf
November 19, 2018
PORTLAND, Ore. — Some believe that the future of food combines technology and transparency, so diners know where their food comes from, and that it shouldn't come from far away. A Portland hotel is experimenting with how to do it.
Jeff Brown, the general manager of food and beverage at The Nines Hotel, is leading the charge at his facility.
And he's doing it far from the hotel lobby, and deep underground from the restaurants and kitchens of The Nines hotel.
The Nines, a luxury hotel in downtown Portland, is growing much of its own food in hydroponic facilities in the basement of the hotel. Photos by Nina Mehlhaf, KGW 2018
"Let's go feed our fish," Brown says enthusiastically as he punches in the code to unlock the keypad to a food lab in the sub-basement of the hotel. "These are tilapia, they are about 8 months old," he says of a tank full of open-mouth fish eager for food.
They're part of the farm of the future. The goal for those who embrace food-based technology growing practices is to allow food to be produced even in outer space or catastrophic climate situations.
The fish poop provides nitrate which acts as a fertilizer and is filtered through into water for some small tomato plant and basil starts nearby. It's known as aquaponics.
And hydroponics grows plants without fish, just water, LED lights to mimic the sun and no soil. Lettuce and basil grown in the hydroponic tubs in the basement are being served on the menu at Urban Farmer restaurant, one of the hotel's two signature restaurants.
"This is what I'm most excited about," says Brown as he opens the double doors to a purple-hued lit cabinet, much taller than he is. A sophisticated setup that soon, hotel guests will get to see when it's moved up to a room near the lobby. This is the aeroponics garden.
The Nines, a luxury hotel in downtown Portland, is growing much of its own food in hydroponic facilities in the basement of the hotel. Photos by Nina Mehlhaf, KGW 2018
"So these are just misters and it's just misting the root." It's the same way Matt Damon survived on Mars in the movie "The Martian." Artificial light, mist, no soil. Brown and his chefs have beta-tested 102 types of vegetables, fruit and flowers in the past year, experimenting with which method works best.
"The chefs love that they can grow specific foods and grab it themselves and don't have to worry about foods being wilted or old and they can speak to it to customers, it's the transparency component," said Brown.
"If you think about it, it's simply, it's just seeds, light and water yet people are fascinated by it. We eliminate the carbon footprint this way. But the staff feel like they're part of something bigger. They can contribute to the guest's dining experience."
Another basement-level down, in the hotel's huge trash room, another hotel is humming along. Urban Farmer and Departure, the hotel's restaurants, compost salad scraps, coffee grounds and newspaper into a huge plastic bin for red wiggler worms. The worms eat the scraps and make a nitrate-rich soil that fertilizes the plants in the food lab. The tilapia also eat the worms.
Brown loves technology almost as much as he loves food. He has ideas for augmented reality at the restaurant dinner table as well that would get rid of the high cost and trees of printing menus every day.
"You would get your phone out and look at a marker, that's what they call it, on the table for instance. And the menu would pop up on their phone and you can move it around and learn more about things through other markers around the restaurant. What farm their steak comes from, or more about the process of how their vegetables were grown here in Oregon."
Many of the celebrities that stay at The Nines have requested tours of the food lab and their private chefs that travel with them are fascinated at what the restaurant is doing.
© 2018 KGW
Technological Supplier THORILEX Is Looking For Partners And Distributors
THORILEX launched several new products this summer including reusable THORILEX Hydroponics baskets for an automatic vertical THORILEX Hydroponics system and the company is looking for partners and distributors now.
“We can see a huge opportunity on the vertical farming market that is still moving forward with a significant growth at a CAGR of 22%. The vertical farming market is projected to grow from present 2,45 billion € to 6.54 billion € till the year 2023. We would like to find great partners and distributors to grow.” Explains Marek Hrstka from THORILEX
“I know that we have truly great products that are now placed in the THORILEX Farm in the biggest glass house complex in our country and it is possible to visit the farm to see the products in operation. Finding truly great partners or distributors is important to achieve our strategy.”
“It will take some time to find the right one. We are looking for someone who haS similar thoughts, likes, innovations and have experience in the horticulture industry. It can be a big or a small company or even an individual.
We are looking for a win-win situation where both sides are prospering from mutual cooperation.” Concludes Marek
What’s The Difference: Hydroponics Vs. Aquaponics Vs. Aeroponics
Three distinct systems – all vying for the top spot in the niche of alternative growing systems.
May 9, 2018
By Heather
Three distinct systems – all vying for the top spot in the niche of alternative growing systems.
What differentiates these three systems from one another? What makes them work? These are the areas that we will be tackling today.
Hydroponics vs. aquaponics vs. aeroponics – which one is the superior system?
Hydroponics
What Is It?
The principle of hydroponics is the oldest among the three because the use of soil-less setups has been around since the age of the Hanging Gardens of Babylon.
A hydroponics system has two main parts: the grow beds and the reservoir.
The reservoir contains the nutrient solution or the water mixed with various nutrients that plants need in order to grow successfully in the media bed. The grow beds, on the other hand, contain the media and the ‘cups’ that will hold the plants in place.
To clarify, growth media will replace soil in a hydroponics setup. There are many kinds of growth media to choose from: coconut coir, perlite, organic-polymer composites, rockwool, etc.
Among the beginning enthusiasts market, the most popular is coconut coir because it’s 100% organic, expands tremendously with water and can accommodate plants easily – with spectacular results.
Perlite, on the other hand, is hailed as a near-perfect medium for growing plants but it is particularly light, which makes it problematic for flood and drain systems as it can easily float away along with the small current of the water in the grow bed.
Organic-polymer combos/composites like Perfect Starts are becoming increasingly popular because they’re easy to use and are not deformed when germinating plants are transferred from the growth trays to the main growing beds.
And finally, we have rockwool. Rockwool is a type of reusable media as it can be sanitized with steam washing after every growing season.
Rockwool is actually melted rock spun into slabs and other shapes/sizes for the purpose of growing plants.
The main point of contention with rockwool is that it’s not very environmentally friendly and thus, it goes against the main principle of switching to a more environmentally friendly method of cultivating plants.
The type of media used in a hydroponic system is so important because it will dictate the efficiency in which plants will be able to absorb the nutrients from the solution.
One of the key problems with hydroponics is that roots sometimes succumb to low oxygen levels, which predisposes crops to premature death.
A solution that growers have found effective in dealing with poor aeration and oxygen zone issues is combining two kinds of media to get the best attributes of each one.
Our personal recommendation would be to combine 50% coconut coir with 50% perlite.
Perlite is amazing when it comes to absorbing and delivering moisture plus it also improves the overall aeration of the plant’s root area. Both are highly regarded in the hydroponics community and both are also widely available to growers everywhere.
Tip: Coconut coir can be made more effective with the addition of perlite.
Hydroponics Pros And Cons
The main advantage of hydroponics is it’s designed for long-term cultivation of almost any kind of crop.
Commercial hydroponic growers harvest hundreds of kilograms of crops easily using large rockwool slabs.
The system simply works and can be easily expanded if you want to make money off your hydroponics system.
The downside is that with the booming interest in hydroponics in recent years, the price of the chemical compounds needed to create a viable nutrient solution has been steadily rising due to the over-mining of these minerals.
Another problem with hydroponics is that it uses relatively more water because after a time the buildup of salts becomes too much for the system and water has to be replaced so as not to kill the plants.
Also, there is a need to check the electrical conductivity of the water every day to make sure that the pH of the water is just right. Fluctuations in the pH level of the water can damage plants and eventually cause a die-off.
Aquaponics
Aquaponics is a hybrid system that combines the best of aquaculture and hydroponics. System-wise, it looks like a hydroponic system, but instead of relying on a main reservoir that contains a nutrient solution, the source of nutrients will be a vat of live, swimming fish.
How does this work? When you feed fish, the fish will naturally excrete waste. The waste mixes with the water, increasing the ammonia levels.
Obviously, this waste has to be mediated and reduced, so as not to kill the fish. Normally, fish tanks are regulated by biological filters and other types of filters that neutralize ammonia and reduce the impact of feces on the fish.
In an aquaponics setup, water from the fish tank is recirculated throughout the system so that it passes through the grow beds, where crops are steadily being cultivated.
The plants absorb dissolved nutrients in the water and process ammonia, which is highly toxic to fish in increased levels.
Bacteria residing the in the roots of plants, as well as good bacteria from the gut of fish work together to establish a balanced ecosystem where both fish and plants will survive.
After about half a year, the mini-ecosystem formed by an aquaponics setup will begin to show signs of high-level, self-regulation.
This will be the time when both fish and plants will begin to truly flourish. There will be great increases in both fish yield and plant yield, and the maintenance of the system will become even easier.
Tip: Be sure to check the roots of plants for signs of rot.
Aquaponics Pros And Cons
The best thing about aquaponics is you will be essentially hitting two birds with one stone – you will be raising fish and growing crops at the same time.
Fish waste, which is something that is regulated in aquaculture, will no longer be considered a problem because it becomes a sought-after source of nutrition for the plants.
Without fish waste, plants wouldn’t have nutrients.
The plants, on the other hand, will serve as a 24/7 ammonia control center for the fish tank, reducing the ammonia load and preventing toxicity in the water.
Fish are sensitive to ammonia and even a small increase in the ammonia content in the water can cause stress, shock, and disease.
Additionally, aquaponics growers now add red worms to the grow beds to increase the efficiency of waste breakdown and subsequently, the distribution of nutrients to plants.
Red worms are first grown on soil and upon adulthood, they are then soaked/washed and then transferred to the growth bed of an aquaponics setup.
The process of breaking down physical waste into smaller particles through the digestive action of red worms is – you got it right, composting!
Yes, it is amazing to imagine that you can actually compost organic material on a grow bed, on stuff that isn’t actually soil.
But there you have it – red worms do the job quite splendidly.
In addition to helping improve the nutrient levels of the water being fed to the plants, there is another big reason why red worms are now being regularly included in aquaponics systems: e. coli.
E. coli is a common pathogen/bacteria found in fish feces. E. coli infections can bring down a full-grown, healthy adult and bring him to the hospital.
Imagine what a widespread e. coli outbreak can do to a tank full of fish, with no other place to hide from the swimming bacteria.
E. coli colonizes fish feces, so these need to be broken down more quickly to prevent an e. coli outbreak from taking over the system.
Red worms can do this perfectly because they need to eat fish feces to survive.
Is there a downside to an almost perfect system? One of the downsides of aquaponics culture is you have to be very specific with the design of the system so you won’t have to shut it down during the winter.
Obviously, you can’t move large equipment and vats indoors, unless you have a really big house (or garage) but all the same, it’s an issue since frozen water can easily kill fish and winter does the same to plants.
Another downside to the system is even if you only want to grow crops for consumption or sale, you still have to tend to your fish well enough so they don’t continually die off.
Fish care can be learned and if you are a natural hobbyist and if you don’t mind looking at another component in a system, then tending to your fish won’t be much of a problem.
Aeroponics
What is It?
Aeroponics is a variation of hydroponics, but instead of using a grow bed filled with media, the plants are instead suspended, with roots facing a sprinkler system connected to the main nutrient reservoir.
Depending on the plant and the design, aeroponics systems generally use little to no media at all.
Now, you may already be wondering – what is the point of all this?
Why not just use media like everyone else? Why do you have to install a sprinkler system that periodically sprays the roots of plants with the nutrient solution?
It all boils down to oxygen. Believe it or not, even if the roots of the plants are down there in the soil, these still need oxygenation in order to thrive.
One of the limitations of hydroponics is because the roots are also submerged in water and the media, there is often poor oxygenation, which hampers plant growth.
Aeroponics solves this problem by completely liberating the roots of the plants and allowing it to come into contact with pure air.
The results are astounding.
Crops grow two to three times their normal size and yields are simply amazing.
Root formations are also incredible. Normally, the taproot of plants only have a moderate amount of root hairs around them.
In plants grown using the aeroponics method, the roots flourish widely and the root hairs become really thick – a tangle of healthy root hairs just enjoying the exposure to oxygen.
Aeroponics Pros And Cons
As with any system, aeroponics has its own set of ups and downs. The main advantage of this system is crops grow incredibly quickly and the yields are high.
If you are after high yield and shorter growing periods, aeroponics is certainly something to think about, especially if you are already investing in equipment and space for this endeavor.
Aeroponics also uses the least amount of water over time and all excess water that isn’t used by the roots of the plants are simply drained back to the nutrient tank.
Tip: Always have backup power and an extra pump in an aeroponics setup.
The nutrient tank is checked daily, much like a conventional hydroponics system.
The pump and spray system is submerged in the water and through a simple timing mechanism, is able to deliver short mists of water to the roots of the plants.
And now for the downsides. Room air doesn’t store water, even if it’s really humid. Humidity is not enough to sustain the roots of plants at all.
Aeroponics is extremely dependent on the misting system. If something should happen to the misting system, then the plants can die easily as a result of dried up roots.
To avoid this, you have to plan ahead. The misting system needs to have backup power and you need to have a backup misting system too, in case the first one fails for some reason. This usually means having an identical pump waiting in store to replace the main once it breaks down.
The misting heads also need to be checked periodically for clogs. We recommend replacing these misting heads instead of just cleaning them to get optimum results.
Remember – your plants are at the mercy of the misting system. They’re not submerged in water and plants are like fish out of water when there’s periodic misting taking place.
Container Farms: A New Type of Agriculture
Innovators within the produce industry are breaking the boundaries of food production
August 20, 2018 6:00 AM, EDT
Innovators within the produce industry are breaking the boundaries of food production — by growing crops not in fields, but in recycled shipping containers.
This modern twist on farming is designed to bypass some of the challenges and restrictions that farmers traditionally have faced, such as extreme weather, pests and limited growing seasons.
By overcoming these limitations, farming operations are capable of producing more food and growing certain crops in regions that otherwise would have had to import them.
By growing this food locally, suppliers are able to cut out the long travel distances often necessary to transport these foods to certain markets.
According to Jeff Moore, vice president of sales at produce supplier Tom Lange Co., shorter travel distances provide numerous benefits, such as fresher product, reduced transportation costs, less waste and fewer empty shelves at markets.
The use of innovative farming methods also is being pushed in Canada. Grocery retailer Loblaw Companies Ltd. announced plans to spend $150 million more each year with Canadian farmers by 2025. As part of that effort, the company pledged to help farmers implement growing techniques that will enable them to produce fruits and vegetables in Canada that the country has traditionally imported.
Freight Farms and Tiger Corner Farms are two companies that are growing produce in shipping containers through the use of hydroponics and aeroponics — methods of growing plants without the use of soil.
Freight Farms is working with NASA to find ways to grow produce in space. (Freight Farms)
Both companies use nutrient-rich water as a substitute for soil, but beyond that, their container farms are quite different.
Tiger Corner Farms’ farming units consist of five shipping containers; four are used for farming and the fifth one is used as a working station where the plants germinate and as a post-harvest station.
Tiger Corner Farms, based out of Summerville, S.C., is a family company that began with the combined interest of Stefanie Swackhamer, the general manager, and her dad, Don Taylor.
Through Grow Food Carolina, a nonprofit organization focused on preserving farming in South Carolina, Tiger Corner Farms has partnered with two other companies: Vertical Roots and Boxcar Central. Tiger Corner Farms manufactures farming units from recycled shipping containers, Boxcar Central works on the automation of the hardware and software used for these container farms, and Vertical Roots deals with the production of the produce.
With Tiger Corner Farms’ shipping container farms, Vertical Roots can increase food production. Having 13 farms in total, Vertical Roots is able to produce about 40,000 heads of lettuce in about half the time it would take a traditional farm.
Vertical Roots sells its produce to grocery stores such as Whole Foods and Harris Teeter.
Vertical Roots says it can produce 40,000 heads of lettuce in about half the time of a traditional farm. (Tiger Corner Farms)
For Vertical Roots, founded by Andrew Hare and Matt Daniels, working with Tiger Corner Farms was a no-brainer.
“Providing cleaner, fresher, better access to food was something all four of us were wanting to do. They wanted to provide jobs and educate people on the importance of sustainable agriculture, and we wanted to do the same thing,” said Hare, Vertical Roots’ general manager. “We wanted to bring transparency and education and empowering our community in knowing where their food comes from and how important the freshness and quality is.”
Meanwhile, Boston-based Freight Farms offers a hydroponic “farm in a box,” dubbed the Leafy Green Machine, built entirely inside a single 40-foot shipping container.
The company, founded in 2010 by Brad McNamara and Jon Friedman, also offers a farming service and mobile app, Farmhand, to aid farmers in monitoring their farms.
Freight Farms’ customers range from individual farmers to universities and corporations.
One of those customers is Kim Curren of Shaggy Bear Farm in Bozeman, Mont., which provides local restaurants with leafy greens that aren’t grown in the region.
Someday, hydroponic farming might even play a role in space exploration and colonization.
Freight Farms is working with NASA and Clemson University to improve the efficiency of its farming units in the hopes of eventually using them in space.
Joshua Summers is one of the professors at Clemson that worked on the project. Professors Cameron Turner and John Wagner and students Doug Chickarello, Malena Agyemang and Amaninder Singh Gill also worked on the project.
Lettuce grows inside a climate-controlled container farm from Tiger Corner Farms. (Tiger Corner Farms)
In order to enable the farming units to work in space, the Clemson team is focusing on making it a closed-loop system by looking at thermal and electrical loads of the LED lights as well as the heating, ventilation and air conditioning unit.
While working on this project, there is one major issue that Summers said needs to be taken into consideration.
“One of the major issues in moving into space is gravity. As you move away from gravity, a lot of their growing patterns are based on plants growing in a specific way,” Summers said. “Now you don’t know exactly how they are going to grow, so it’s going to be a bit more random, so we have to change some of the geometric layout to make it more efficient in terms of volume.”
Clemson, NASA and Freight Farms are working on a new proposal to continue this project.
Through its work with individual farmers as well as organizations such as NASA, Freight Farms is taking steps toward its goal of empowering anyone to grow food anywhere.
Farm in a Box
Local agricultural technology may change the way we eat
(Clockwise from top left) A lighting system nurtures infant greens; Tiger Corner Farms general manager Stefanie Swackhamer and her dad, AmplifiedAg CEO Don Taylor; green oak lettuce, nearly ready to harvest.
For conscientious eaters, the holy trinity of organic, local, and in-season can be difficult to come by. Leafy greens, in particular, are tricky to grow in the Lowcountry, and thus tough for the likes of schools and grocers to obtain. Local start-up Tiger Corner Farms has a solution: aeroponic farms built inside shipping containers, where humidity, light, nutrients, and carbon dioxide levels can all be controlled, yielding a year-round supply.
Controlled environmental agriculture is booming nationwide, but Tiger Corner has an edge: it’s part of a parent company called AmplifiedAg founded by former Benefitfocus CTO Don Taylor. AmplifiedAg’s two other divisions are Boxcar Central, an automation software platform that lets users dial in exact specifications for any plant, and Vertical Roots, whose growers operate farms in Summerville, off Clements Ferry Road, and outside Daniel Island eatery Dockery’s (which serves the greens).
“We have a continuous feedback loop that allows us to quickly make adjustments to our product to best serve the farmers,” says Tiger Corner general manager Stefanie Swackhamer about Vertical Roots, which sells to GrowFood Carolina and retailers like Whole Foods, Harris Teeter, and Earth Fare. They also supply greens to Dorchester District Two schools, and “This school year, we’re implementing a farm at Ashley Ridge High School to allow students to get involved in the growing process,” says Swackhamer.
Head Count
How many farms—and leafy green plants—is Tiger Corner Farms producing? Take a look at the numbers:
A full, turnkey farm—including 4 pods and a “clean room”—takes about 4 weeks to build and costs $550,000.
Each pod yields 3,800 to 7,000 plants (depending on variety) per month.
Tiger Corner has built 18 pods since 2016, making its very first sale to The Citadel.
Resources:
Photographs by (4) Melissa Sommer
Living Greens Unveiling Large Aeroponic Vegetable Farm
Living Greens said that its Faribault farm will be the second-largest aeroponics operation behind that of industry leader AeroFarms.
OCTOBER 6, 2018 - NEAL ST.ANTHONY@STANTHONYSTRIB
LIVING GREENS Executives Dave Augustine, left, and Dana Anderson foresee a rapid expansion of Living Greens Farm of Faribault.
The several-year founder of a growing aeroponic farm near Faribault is ready to prove his Living Greens low-input, no-dirt operation will have a big effect on the emerging world of year-round indoor vegetable growing.
CEO Dana Anderson, 50, a former financial adviser who worked on farms as a youth near Spicer, Minn., started tinkering with aeroponics in his Prior Lake garage in 2010.
Last year, Living Greens, staked by $8 million over several years contributed by founding shareholders, started slowly by testing and eventually producing increasingly larger crops of lettuce with a high-tech, rapid-growth system rooted in nutrient-rich misting and LED lighting.
By early next year, following completion of the last stage of construction, Living Greens should amount to 60,000 square feet of stacked, mechanized growing space capable of producing up to 3 million heads of high-quality lettuce.
That’s several fast-growing crops in one year.
The business plan and initial production proved impressive enough to recently draw $12 million in an inaugural round of institutional funding from Boston-based private-equity funds NXT and Wave Equity Partners.
“We’re exiting the research-and-development stage and going to market,” Anderson said.
The $6 million Faribault factory-farm will prove Living Greens’ technology innovation and its year-round, premium-lettuce model and spur construction of a second plant within a year outside of Minnesota, backers said.
“We think we have an opportunity to be a market leader in leafy greens,” Anderson said. “There are projections nationally that up to 50 percent of leafy greens could be grown indoors within 10 years from almost nothing today.
“Our goal is to be the largest indoor [farm operation]; corporate-owned and through licensing of the technology,” Anderson said. “We’re looking at joint ventures with food-service companies around the world.”
Living Greens said that its Faribault farm — a floor footprint of about 20,000 square feet that rises to about 16 feet, thus providing its 60,000 square feet of growing space — will be the second-largest aeroponics operation behind that of industry leader AeroFarms of Newark, N.J. It operates a 70,000-square-foot indoor farm in addition to smaller installations.
Living Greens already supplies a growing list of Minnesota and Wisconsin grocers with several types of leaf lettuce, arugula and mixed greens through Robinson Fresh, a division of C.H. Robinson.
By next year, it will have installed the technology to produce around 3 million bagged packages of salad greens for retail distributions.
Typical salad bags, depending on whether they include dressing and other ingredients as part of planned “salad kits,” will retail for $2.99 to $3.99.
“We’re producing about 500,000 units a year now, and it will be a sixfold expansion by spring,” Anderson projected.
The 20-employee Living Greens operation includes chief technology officer Dave Augustine, a University of Minnesota-trained electrical engineer and veteran industrialist who joined the board several years ago.
Augustine, 55, who grew up on a farm, was a several-year board member who stepped into the executive ranks as overseer of the company’s technology integration.
Living Greens has been awarded four patents on its growing process, according to Anderson.
The firm plans to produce as much lettuce indoors as would be produced by 100 times the farmland, using 95 percent less water, no pesticides, herbicides or other chemicals.
It does so thanks to its density and computer-controlled environment that blends natural light and ultra efficient LED lighting that has dramatically dropped in price in recent years thanks to widespread business and residential embracement.
“The price has been dropping by about 20 percent a year as illumination has increased by about 50 percent,” Anderson said. “The risks of foodborne illness are extremely muted compared to the traditional food chain. We use a ‘reverse-osmosis’ process to remove all the particulates from the water.”
Then there’s the local pitch.
Living Greens plans to deliver a premium product locally, at lower cost, because it won’t have the long-haul transportation expense and up to two weeks’ time to deliver from Mexico or the California-Texas Sun Belt where most fall-winter vegetables are grown.
To be sure, Living Greens has dreams of being a big company in a fragmented but fast-developing indoor agriculture market.
They include Revol Greens, the Minnesota-based greenhouse grower that has added some water- and energy-conserving wrinkles of its own, as well as Plenty, the California-based indoor grower that has raised $200 million and also has its eyes on China.
The sector is driven by the premise that farmland is limited, and industrial-scale farming can be very expensive and uses what can be unsustainable amounts of water, chemicals and land.
The challenge for the small, indoor innovators such as Living Greens is to entice buyers with tasty produce at a competitive but profitable price that customers also will patronize for their regional and environmental pitches.
“This took us longer and cost us more than we’d hoped, but I think we have a better system and technological lead,” Anderson said. “It’s a tremendous opportunity because of the demand for fresh, year-round local produce.”
Neal St. Anthony has been a Star Tribune business columnist/reporter since 1984. His work has been recognized by the Minnesota Society of Professional Journalists and the Society of American Business Editors and Writers.
Neal.St.Anthony@startribune.com 612-673-7144 @StAnthonyStrib