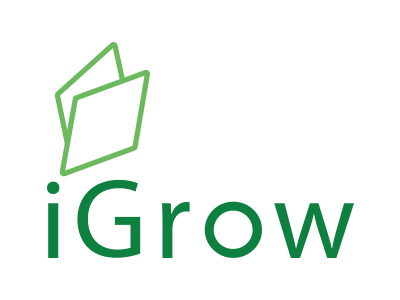
Welcome to iGrow News, Your Source for the World of Indoor Vertical Farming
Nature Fresh Farms Sales Welcomes New Team Member To Sales Staff
Zanelle Hough began her career 14 years ago in Logistics working for a South African exporter
Leamington, ON (March 31, 2020)
Nature Fresh Farms Sales expands its team, welcoming Retail Sales Account Manager, Zanelle Hough to their sales department.
Zanelle Hough began her career 14 years ago in Logistics working for a South African exporter. Wanting to gain more experience in sales, she shifted to the Walmart Global Procurement team as a Logistics and Procurement specialist sourcing South African product for the various Walmart and Sam’s Club retail stores in the USA and Asia. Two years later Zanelle fully transitioned to a sales role working for a South African exporter called Freshworld, an organization that specializes in direct retail programs throughout the world. In addition to the retail accounts, she has managed the SunkistTM Global account for various customers throughout Asia and North America.
General Manager, Frank Neufeld shared his enthusiasm for the new extension to their team: “We are very pleased to welcome Zanelle to the Nature Fresh Farms Sales team. Having many years of experience in the produce industry, she will be a great asset in supporting our rapid growth and assisting our customers in the best possible way,” said Frank. “As business continues to expand it’s essential to find key individuals who will help bring Nature Fresh Farms to even greater heights.”
As Retail Sales Account Manager, Zanelle’s responsibilities will include generating sales from new and existing accounts, raising awareness of company offerings while increasing our market share, and building strong relationships with her retail partners. With Zanelle based in Leamington, ON, she will continue to help support the rest of the sales team with her invaluable experience.
“As our company continues to expand and gain market share, we are investing in the growth of our team. Adding Zanelle to the sales team provides us with a strong individual that can continue to help propel us forward,” shared Director of Sales, Matt Quiring. “Culturally, this is a great fit as well. You can see immediately when someone fits into your company’s culture and it excites me for what the future holds!”
With further developments on the horizon, Nature Fresh Farms is thrilled with the growth of the company and the new addition to the team. As business continues to expand, the company is excited to offer new opportunities for professional development.
-30-
About Nature Fresh Farms -
Continuously expanding, Nature Fresh Farms has become one of the largest independent, vertically integrated greenhouse vegetable farms in North America. As a year-round grower with farms in Leamington, ON, Delta, OH, and Mexico, Nature Fresh Farms prides itself on consistently delivering exceptional flavor and quality to key retailers throughout North America, while continuing to innovate and introduce more viable and sustainable growing and packaging solutions.
SOURCE: Nature Fresh Farms | info@naturefresh.ca T: 519 326 1111 | www.naturefresh.ca
Here Are The ‘Dirty Dozen’ Fruit And Vegetables Laced With Legal Pesticides — Even Organics Have Traces
Nearly 70% of the fresh produce sold in the U.S. contains residues of legal though potentially harmful chemical pesticides even in small amounts, and a popular snack for children is another big offender
March 25, 2020
By Rachel Koning Beals
Raisins are surprise offenders this year with neurotoxic insecticide chlorpyrifos, which some research has shown can harm the nervous system in children
Nearly 70% of the fresh produce sold in the U.S. contains residues of legal though potentially harmful chemical pesticides even in small amounts, and a popular snack for children is another big offender.
Among the top choices to limit exposure to pesticides? Avocados, asparagus, and honeydew melon.
The analysis comes from the Environmental Working Group. Each year since 2004 it has ranked its Dirty Dozen and Clean Fifteen lists and combines them as a shopper’s guide for consumers. The “dirtiest” of all is not a fresh fruit or vegetable, but a dried one — raisins. Raisins weren’t ranked on the fresh lists but their surprising results caught the attention of EWG.
Toxicologists and other researchers at EWG compare the pesticide contamination of 47 popular conventional — meaning not farmed organically — fruits and vegetables. The review is based on the results of tests by the USDA and the Food and Drug Administration of more than 43,000 samples of produce.
Environmental Working Group
Most pesticide residues the agency finds fall within government-mandated restrictions, but advocacy groups such as EWG argue “legal does not mean safe.” Before conducting its tests, USDA washes, scrubs, and peels fruits and vegetables as consumers would.
Thomas Galligan, Ph.D., a toxicologist with EWG said researchers continue to study why raisins contained higher traces of pesticides than the grapes they’re dried from, though grapes ranked on the list this year. Read more of his analysis.
Children under the age of 15 eat a total of about 208 million pounds of raisins each year, or about half of the raisins consumed in the U.S., according to Zion Market Research. The average American consumed about 1.25 pounds of raisins in 2017, the latest year for which the USDA has information. Zion’s industry analysis shows that slightly less than two-thirds of raisins are consumed as ingredients in other foods, with the rest eaten as a stand-alone snack.
“Infants, babies and young children are exquisitely vulnerable to even low levels of pesticide exposure, so it’s important parents and caregivers take steps to safeguard children from these chemicals while also providing them diets rich in healthy fruits and vegetables,” said Dr. Philip Landrigan, a pediatrician and epidemiologist who’s director of the Program in Global Public Health and the Common Good in the Schiller Institute for Integrated Science and Society at Boston College.
“For many Americans, choosing an all-organic diet is not possible, so [pesticide guides] can help give consumers the tools to provide their families with a mix of both conventional and organic fruits and veggies without the pesticide punch,” he said.
Environmental Working Group
Producers generally use pesticides to improve crop yield, which can hold down retail prices, which is particularly important to low-income consumers. The findings also show that even produce labeled organic can show traces of pesticide.
The EWG group highlighted two chemicals in particular. One is neurotoxic insecticide chlorpyrifos, which some research has shown can harm the brain and nervous system in children at even low levels. The chemcial was detected on 5%, or 34 out of 670 samples, of conventional raisins, and 6%, or five out of 86, of organic raisin samples.
California, where the majority of the U.S. raisin supply is produced, recently banned all uses of chlorpyrifos because of the risks it poses to both children and farmworkers. That regulatory change was not carried through to the federal level, however.
The second chemical of note is neonicotinoids, which the USDA’s tests detected on almost one-fifth of fruits and vegetables. Neonics are the fastest-growing class of insecticides, “despite a decade of research making it clear that they are highly toxic to honeybees and other pollinator species,” EWG researchers said. Some studies on human health also suggest that exposure to neonics may be harmful to the developing fetus and children, they said.
Residues of at least one of three neonicotinoid pesticides banned in the European Union — imidacloprid, clothianidin, and thiamethoxam — were found on more than half the U.S. samples of potatoes, spinach and lettuce tested. At least one of these neonics was also found on more than one-fourth of the samples of U.S. cherries, watermelon, and strawberries.
The Alliance for Food and Farming, which represents both organic and conventional farmers of fruits and vegetables, argues that these annual lists overstate the amount of pesticide detection on food.
“To accurately assess consumer risks from pesticides, one needs to consider three major factors – 1) the amount of residue on the foods, 2) the amount of food consumed, and 3) the toxicity of the pesticides,” said Dr. Carl Winter, professor emeritus in toxicology at the University of California, Davis.
AFF points to an analysis and a calculator from toxicologists with the University of California’s Personal Chemical Exposure Program, which found a child could eat hundreds to thousands of servings of a fruit or vegetable in a day and still not have any health effects from residues.
Experts at EWG and the AFF stressed that maintaining fruits and vegetables in daily diets is the most important goal. Sometimes budget and availability limit shopping for organic produce.
“Although we believe consumers should be concerned about pesticide residues on the food they eat, the health benefits of a diet rich in fruits and vegetables outweigh the risks of pesticide exposure,” said Alexis Temkin, PhD, a toxicologist with EWG. “With the Shopper’s Guide, consumers don’t have to choose between pesticides and a healthy diet.”
EWG added specific guidance to its report as consumers respond to the coronavirus pandemic.
It is important to know that there is no evidence people can be exposed to the coronavirus through food, experts say. The spread pattern is quite different from foodborne pathogens like Salmonella and E.coli. That is why, even though the risks of COVID-19 are serious, consumers should continue eating plenty of healthy fruits and vegetables while in quarantine at home, the group said.
Lead photo:
Children under the age of 15 eat a total of about 208 million pounds of raisins each year or about half of the raisins consumed in the U.S. Getty Images
"With Our Concept, Everyone Can Be A City Farmer"
As Sweden is not on a lock-down yet, the virus is nevertheless having a great impact on jobs and the country’s economy
As Sweden is not on a lock-down yet, the virus is nevertheless having a great impact on jobs and the country’s economy. Crisis packages for jobs and transition are now being presented by the government. So far SweGreen has not noticed a great impact on business despite the COVID-19, rather the opposite. The absolute major part of SweGreen produce, based in Stockholm, is the distribution of their ‘Stadsbondens’ branded leafy greens and herbs to supermarkets. A particular increase in sales is visible, even though the company doesn’t do anything extra in-store to meet customers, besides deliveries.
Free greens
“We have some restaurants on our client list, and we see that they are suffering a lot now. We are actually delivering to them according to the agreement, but for free. We have chosen to not charge our restaurant partners anything during this crisis, just to show our compassion and goodwill,” Andreas Dahlin, CEO of SweGreen says.
The SweGreen salad mix
Stadsbondens
Stadsbondens, which means ‘The City Farmers’ in Swedish, is the leafy greens brand, that SweGreen uses for marketing their produce to supermarkets. As for now, the produce is sold at around ten supermarkets, located in Stockholm. SweGreen has recently set up service together with an online distributor which enables them to sell their fresh produce online and home-delivery of the greens. Dahlin notes: “It gives us the possibility to reach more people. Next to that customers don’t have to get out of the house, and our brand lovers can order the fresh produce no matter where they are located in Stockholm.”
Farming as a Service
SweGreen has developed its own farming service, which is a closed environment and automated in-store solution that gives customers within grocery and restaurants the possibility to be their own providers of fresh, nutritional, locally-produced greens harvested directly off the shelf.
A vertical basil wall
“Farming as a Service, as we like to call it, is the service we offer. We provide a whole system, containing both software and hardware, such as monitoring and steering. So basically with our concept, everyone can be a City Farmer as it automates the whole growing process”, Andreas Dahlin says. In Stockholm, the SweGreen city farm has been fully developed for automation. “We control everything that goes in and comes out. With a fully closed system, we also can digitally control every unit or crop that we provide to our client. One of the most important keys for Urban Farming is absolutely being able to get valid data from growing processes and having the ability to convert the data to value-shaping intelligence. We focus a lot on this now. In this way, we can improve the systems constantly together with our clients.”
A vertical fresh produce wall
Future aspect“
Our objective now is to further develop the Farming Service. Our customers really appreciate this service model and I think the circumstances right now prove the importance of factors such as sustainability, resilience and hyper-local production for the food industry."
Andreas Dahlin, CEO at SweGreen
"We have just closed our second seeding round with investors and we are planning on expanding internationally. Not only with the focus on supermarkets, because we also get a lot of interest from restaurants too. Restaurants and chefs are early adopters when it comes to the sustainable production of food”, Dahlin adds.
For more information:
SweGreenAndreas Dahlin, CEO, and partner
andreas.dahlin@swegreen.se
www.swegreen.com
Publication date: Fri 3 Apr 2020
Author: Rebekka Boekhout
© HortiDaily.com
Freight Farms Expands Leadership Team with New CEO and Head of Engineering as Business Scales to Meet Growing Global Interest in Decentralized Food Production
Freight Farms, the global innovation leader of containerized vertical farming with the world’s largest network of IoT-connected farms, announces today that it has hired veteran consumer brand executive Rick Vanzura as CEO who will also join the company’s Board of Directors, while cofounder Brad McNamara will remain as Freight Farms’ President
Freight Farms Produce March 27, 2020
BOSTON — Freight Farms, the global innovation leader of containerized vertical farming with the world’s largest network of IoT-connected farms, announces today that it has hired veteran consumer brand executive Rick Vanzura as CEO who will also join the company’s Board of Directors, while cofounder Brad McNamara will remain as Freight Farms’ President. The company also welcomes automation and robotics specialist Jake Felser as Head of Engineering.
The need to simplify supply chains and ensure reliable access to healthy, traceable food at a local level has become more crucial for communities worldwide. Expansion of Freight Farms’ team follows a year of strong momentum for the company as forward-thinking organizations, particularly at the institutional level, recognize the benefits of a secure, distributed, and transparent food supply. As the company scales for growing demand at speed, expansion of Freight Farms’ leadership is positioned to quicken new extensions of its technology platform and deepen market reach.
“What excites me about Freight Farms is the ability to join a passionate, mission-driven business that is already perfectly positioned to address the growing critical need for sustainable, hyper-local food production,” says Vanzura. “Freight Farms has an incredible technology platform as the originator of container farming, as well as a global footprint driving numerous sources of value. Beyond providing a meaningful solution across industries, Freight Farms’ innovation addresses issues like urban land scarcity, traceability and the need for hyper-local solutions with speed to market. The current environment demonstrates more than ever the value of Freight Farms’ offerings.”
Vanzura has driven value for companies from start-up to Fortune 5 across technology, restaurant, retail, and entertainment sectors. With a focus on leveraging innovation and developing new market channels, he led strategy for Panera, General Motors Information Services and GameStop, and as the original CEO of Wahlburgers, he built the company from a single unit into one of America’s fastest-growing restaurant brands. Vanzura’s 20 years in President and C-level roles include a decade in food service working with markets central to Freight Farms’ business. He also brings significant international experience to his role, having run Borders Group’s nearly $1 billion International business.
“As cofounders, Jon Friedman and I have taken Freight Farms from an idea to help decentralize the food system to being the leader in containerized vertical farming that’s truly putting the power of hyper-local food production into people’s hands,” said McNamara. “Rick has amplified growth across interconnected industries, and his international experience lends itself to our ongoing global expansion. His personal alignment with Freight Farms’ mission was crucial for us as well—he’s a welcomed addition to the team as we scale.”
“The potential is extraordinary,” Vanzura added, “I’m excited to be working with Brad, Jon and the team on the spectacular opportunities ahead, all while doing our part to help build a better, more sustainable food system for all.”
Jake Felser, former VP of Engineering for eatsa (now Brightloom), has also joined the Freight Farms team as Head of Engineering. With teams across hardware and software, Felser led robotics R&D and the development of eatsa’s shelf-style pickup system from conception to deployment across the company’s network of partners. Prior to eatsa, Felser was Senior Engineer and Product Manager at Cooper Perkins and has worked in hydraulics, refrigeration, structural optimization, design for development, and agriculture for companies including Blue Origin, Promethean Power Systems, and AGCO. With a passion for sustainable development, Felser is focused on automation, IoT, and machine learning-based integrations for Freight Farms growing technology portfolio.
Company growth, including ten new roles across all departments in Q1, also follows Freight Farms’ recent launch of the Greenery. Nearly 100 have been adopted by customers in 9 countries to date, bringing Freight Farms’ global footprint to more than 300 container farms around the world. The innovation also spurred interest from Sodexo in a strategic national partnership to grow food onsite at educational and corporate campuses nationwide and new investment from Ospraie Ag Science.
About Freight Farms
Founded in 2010, Freight Farms debuted the first vertical hydroponic farm built inside an intermodal shipping container—the Leafy Green Machine—with the mission of democratizing and decentralizing the local production of fresh, healthy food. Now with the Greenery and integral IoT data platform, farmhand®, its technology empowers people anywhere in the world to grow more than 500 varieties of pesticide and herbicide-free produce, from leafy greens and herbs to root vegetables and vine crops, with 99.8% less water—onsite, year-round. Freight Farms’ network of IoT-connected container farms is the largest in the world, with more than 300 operating in 25 countries and 44 U.S. states. Customers range from small business farmers to the corporate, hospitality, retail, education, and nonprofit sectors.
To learn more, please visit freightfarms.com,
Five Reasons To Go Vertical
The rapidly increasing global population means you can be sure of two things: there’s a never-ending demand for food and a rapid reduction in the availability of land on which you can grow it
The rapidly increasing global population means you can be sure of two things: there’s a never-ending demand for food and a rapid reduction in the availability of land on which you can grow it.
The UN has predicted that the global population will surpass the 9 billion mark by 2050 which leaves government officials and scientists scratching their heads as to how we’ll provide for this colossal amount of mouths to feed. Enter vertical farming. Vertical farming presents itself as one of the answers to our population growth, which in short allows plants, fruit, and veg to grow upwards rather than outwards.
With a booming culinary industry gracing the bustling global hubs such as London, New York, and Tokyo, urban farms provide a controlled and automated climate to grow more delicate niche fruit and veg, as well as mass producing heavily demanded greens and herbs on that were once upon a time confined to their natural habitats.
Although, when it comes to vertical farming the question is not “what you can grow?”, it’s “what should you grow?”. Extensive R&D shows that leafy greens and herbs remain the most profitable and sustainable crops to mass-produce at present. Vertical farming will become a huge part of the agricultural sector in the very near future, but why is it taking off so quickly? Here are 5 reasons why:
Increase your crops per m²
Although it may look smaller than your average outdoor farm, a vertical system can equate to 4-6 X more growth surface than your standard glasshouse or polytunnel area. 1 acre of vertical farm on average produces 4-6 acres depending on the crop density and cycle duration.
Protection from the elements
Vertical farming allows the grower to exploit the advantages of growing in a fully controllable climate, safe from the natural elements such as wind, rain, and frost, meaning post-harvest spoiling and crop wastage becomes significantly less of a problem. Additionally, the secure environment results in zero pests and invasive bacteria, which allows the grower to provide organic pesticide-free produce.
Reduce water consumption
Vertical farming systems allow produce to grow with 70-95% less water required for normal plant cultivation. Taking lettuce as an example: open-field production requires 250L/kg of lettuce and greenhouse systems consume 20L/kg. However, vertical systems come in at a minimal 1L/kg of lettuce, with the only water extracted during the growth cycle being that of the plant’s consumption, with any leftover water being recycled back through the filtering system and reintroduced to the irrigation.
Standardized crop growth and yields
With vertical farming technology constantly improving, the ease of creating a completely controlled environment is increasing by the day. The use of bespoke LED spectrums, automated irrigation, and climate control allows the farm to standardize each growth cycle, producing the same amount, quality and size crop, which in turn results in standardized yields.
Local production
Being a controlled environment, vertical farms can settle wherever they choose, with climates and weather patterns becoming obsolete. Local production means a positive impact on local communities, resulting in an influx of jobs and contribution to smaller economies. Its local production and harvesting of crops reduce the amount of ‘food miles’, meaning a decrease in the global carbon footprint. Research has found that vertical farms lower overall CO2 emissions by 67-92% when compared with greenhouses.
Bridge Vertical Farming partners with Urban Crop Solutions to provide high-tech automated container farms, research facilities, and bespoke vertical farming solutions.
For more information:
Bridge Vertical Farming
Keynor Lane
Chalk Lane
Chichester
PO20 7LL
bridgeverticalfarming.co.uk
bridge@urbancropsolutions.co.uk
01243 641789
Publication date: Tue 31 Mar 2020
The Future Of Farming Might Already Be Here, Inside A Shipping Container
"We are completely protected from any natural disasters, rainstorms, pests, weeds even -- there's no pollution because all of the air is filtered," the CEO of Sprout Stack said
Ali Donaldson
10 News First Senior Reporter, 25 Mar 2020
On Hugh McGilligan's farm, it's a perfect summer's day, 16 hours a day, every single day of the year.
"We are completely protected from any natural disasters, rainstorms, pests, weeds even -- there's no pollution because all of the air is filtered," the CEO of Sprout Stack said.
It's the farming of the future, packed inside converted shipping containers on Sydney's Northern beaches.
Sprout Stack runs five farms at Brookvale -- in five shipping containers --producing as much as five hectares of traditional mainland agriculture. The shipping container farms run as closed circuits, using about five percent of the water.
But it takes just five seconds to walk from one end to the other.
And depending on the crop, they can harvest within a week to five weeks.
"Here we have purple radish," Hugh says brushing his hand across the top of a miniature forest of lush leafy greens. "That's our fastest growing crop and it takes about a week from planting through to harvesting."
"That compares to traditional farming where it takes 40 percent longer to achieve the same results."
And they're not just saving on the environment.
Sprout Stack's Mick Harder has pulled off some amazing farming equipment hacks.
"I made a harvester out of a hedge trimmer from Bunnings and some steel offcuts lying around that only cost us $1000 instead of the industrial machine that's around $100,000," Mick said while feeding his ingenious machine with the latest crop.
They don't even use soil.
Instead, everything is planted into coconut husks, which are mulched in a concrete mixer -- another hack that has saved them thousands of dollars in equipment.
And they've even tinkered with Mother Nature and the precious light she provides.
Plants only use red and blue light -- mixed together it forms a beautiful fuchsia -- for all the protein and nutrients they need. So that's all that's used on these farms.
It's about customizing the best of nature in a box, including cutting out a big chunk of the rainbow.
The farms can even be controlled over a mobile phone.
Nestled in between Sprout Stack's plant beds is its "nervous system".
"It's a farm management system that tracks the environmental conditions of the farm and the computer keeps the CO2, the temperature and the humidity of the farm ideal for growing plants," Hugh said.
"It's all run by a computer so we don't have to make any decisions -- the computer is providing the plants with the ideal growing conditions."
As we talked, the lights inside the container started switching off.
"I just go an alert," he laughs, peering through the dark at his phone.
"We turned off the air-conditioning and because we are in here the farm has got a little bit warmer and shut everything down, to ensure there are no deleterious effects on the plants."
Sprout Stack poses some interesting solutions to the modern plagues on our food bowls.
"We know that we need to provide an awful lot more food and we can't do that just throwing more resources at a strained system," Hugh says.
"We've got to get more efficient about the way that we produce food and use scarce resources like water, and we have got to produce our food closer to where it's consumed."
He then runs through the traditional vegetable supply chain -- or, as he says -- "the reason why the tomato you buy at the supermarket tends not to have very much flavour."
Hugh explains it's generally picked green about a week ago, transported cold chain from the country to the capital city you live in where it sits in a distribution centre for a day.
It then gets redistributed to another distribution centre that sends it out to your supermarket.
"At that point, it's often hit with ethylene to ripen -- basically it turns red -- but in ripening it's not really ripening it's just changing colour and in the meantime the nutritional quality of that product has declined."
He claims Sprout Stack's produce is fresher and tastier because they harvest closer to where it is being consumed.
"On average we take about 16 hours between our harvest to store, which compares to about a week for traditional agriculture."
Urban Crop Solutions Appoints Commercial Representative For Asian Market
Urban Crop Solutions and BAF signed a representation agreement for the East and South-East Asian markets
Urban Crop Solutions and BAF signed a representation agreement for the East and South-East Asian markets. The collaboration fits with Urban Crop Solutions' vision for global expansion and allows for local customer service in one of the fastest-growing countries in the Asia-Pacific region.
BAF is an Aggrotech company based in Singapore which has extensive experience and network in the Agri and aqua industry in Asia and beyond. The company has also built a strong network and business track record in the region and will provide as a perfect match to operate as an agent for Urban Crop Solutions in what is called the strategic gateway for Europe to the Southern parts of Asia.
NOSH visiting an Urban Crop Solutions ‘FarmPro’ container
Kenneth Tay, Chief Executive Officer at BAF, explains: “Based on my many years of experience in the aggrotech industry, I can see a great synergy between my business and the state-of-the-art solutions that Urban Crop Solutions provides. I believe that this technology will also play a critical role towards food security goals in the region.”
For a start, BAF has already procured its first customer, NOSH Produce, a high tech start-up in the indoor vertical farming industry who has put in a purchase order for an Urban Crop Solutions ‘FarmPro’ for their very first plant production site in Singapore. This will be Singapore’s first fully automated container farm that sets to grow local herbs for the high-end retail market and restaurants. The container farm will not only have a commercial purpose but will also serve as a demonstration facility for interested buyers.
NOSH & BAF and Urban Crop Solutions closing the deal
According to Brecht Stubbe, global sales director at Urban Crop Solutions: “With this opportunity to work with BAF and NOSH, we can demonstrate the economically viable model of our vertical farming solutions in the Asia-Pacific region”
The collaboration between Urban Crop Solutions, BAF & NOSH Produce came to fruition in the beginning of January 2020. The ‘FarmPro’ is set to be operational in May 2020.
For more information:
Urban Crop Solutions
Grote Heerweg 67, 8791 Beveren-Leie (Waregem), Belgium
800 Brickell Avenue 1100 Suite, Miami (FL 33131), USA
+32 56 96 03 06
info@urbancropsolutions.com
sales@urbancropsolutions.com
urbancropsolutions.com
Publication date: Thu 26 Mar 2020
Freight Farms Expands Leadership Team with New CEO and Head of Engineering
Tune in to our webinar on March 31st with Freight Farmer Dave Ridill! Hear how he is growing produce for his snowy mountain town, all year long. Register here.
March 24, 2020
Freight Farms positions for new innovation and deepened market reach; cofounder Brad McNamara remains President
March 24, 2020 -- Freight Farms is thrilled to announce that it has hired veteran consumer brand executive Rick Vanzura as CEO who will also join the company’s Board of Directors, while cofounder Brad McNamara will remain as Freight Farms’ President. The company also welcomes automation and robotics specialist Jake Felser as Head of Engineering.
The need to simplify supply chains and ensure reliable access to healthy, traceable food at a local level has become more crucial for communities worldwide. Expansion of Freight Farms’ team follows a year of strong momentum for the company as forward-thinking organizations, particularly at the institutional level, recognize the benefits of a secure, distributed, and transparent food supply. As the company scales for growing demand at speed, expansion of Freight Farms’ leadership is positioned to quicken new extensions of its technology platform and deepen market reach.
“Freight Farms’ innovation addresses issues like urban land scarcity, traceability and the need for hyper-local solutions with speed to market. The current environment demonstrates more than ever the value of Freight Farms’ offerings.”
— Rick Vanzura, CEO of Freight Farms
“What excites me about Freight Farms is the ability to join a passionate, mission-driven business that is already perfectly positioned to address the growing critical need for sustainable, hyper-local food production,” says Vanzura. “Freight Farms has an incredible technology platform as the originator of container farming, as well as a global footprint driving numerous sources of value. Beyond providing a meaningful solution across industries, Freight Farms’ innovation addresses issues like urban land scarcity, traceability and the need for hyper-local solutions with speed to market. The current environment demonstrates more than ever the value of Freight Farms’ offerings.”
Vanzura has driven value for companies from start-up to Fortune 5 across technology, restaurant, retail, and entertainment sectors. With a focus on leveraging innovation and developing new market channels, he led strategy for Panera, General Motors Information Services and GameStop, and as the original CEO of Wahlburgers, he built the company from a single unit into one of America's fastest-growing restaurant brands. Vanzura’s 20 years in President and C-level roles include a decade in food service working with markets central to Freight Farms’ business. He also brings significant international experience to his role, having run Borders Group’s nearly $1 billion international business.
“As co-founders, Jon Friedman and I have taken Freight Farms from an idea to help decentralize the food system to being the leader in containerized vertical farming that’s truly putting the power of hyper-local food production into people’s hands,” said McNamara. “Rick has amplified growth across interconnected industries, and his international experience lends itself to our ongoing global expansion. His personal alignment with Freight Farms’ mission was crucial for us as well—he’s a welcomed addition to the team as we scale.”
“Rick has amplified growth across interconnected industries, and his international experience lends itself to our ongoing global expansion.”
— Brad McNamara, President of Freight Farms
“The potential is extraordinary,” Vanzura added, “I’m excited to be working with Brad, Jon and the team on the spectacular opportunities ahead, all while doing our part to help build a better, more sustainable food system for all.”
Jake Felser, former VP of Engineering for eatsa (now Brightloom), has also joined the Freight Farms team as Head of Engineering. With teams across hardware and software, Felser led robotics R&D and the development of eatsa’s shelf-style pickup system from conception to deployment across the company’s network of partners. Prior to eatsa, Felser was Senior Engineer and Product Manager at Cooper Perkins and has worked in hydraulics, refrigeration, structural optimization, design for development, and agriculture for companies including Blue Origin, Promethean Power Systems, and AGCO. With a passion for sustainable development, Felser is focused on automation, IoT, and machine learning-based integrations for Freight Farms growing technology portfolio.
Company growth, including ten new roles across all departments in Q1, also follows Freight Farms’ recent launch of the Greenery. Nearly 100 have been adopted by customers in 9 countries to date, bringing Freight Farms’ global footprint to more than 300 container farms around the world. The innovation also spurred interest from Sodexo in a strategic national partnership to grow food onsite at educational and corporate campuses nationwide and new investment from Ospraie Ag Science.
Coronavirus Pandemic Highlights Vital Need For Vertical Farms In World Cities
Although the sources and sourcing of food in North America and Western Europe are currently generally secure, what might soon become a prodigious concern is that their workers in the production, distribution and retail segments of the food supply chain may eventually succumb to coronavirus infection
MARCH 25, 2020
by Professor Joel Cuello, Ph.D.
Image modified from Martin Sanchez/Unsplash
The speed with which the coronavirus outbreaks in Asia, Europe, and North America metastasized into a full-blown global pandemic — catching many world governments by surprise and with little preparation — underscores just how our world today is highly interconnected and how, in order to contain and stem the surging pandemic, temporary disconnection from the physically-networked world by cities, regions and even entire nations has become an urgent imperative.
With confirmed coronavirus cases globally now exceeding 370,000 and the number of deaths surpassing 16,000, many world cities have become throbbing epicenters of the surging pandemic. Accordingly, various countries, states, and cities have enforced lockdown or stay-at-home orders with drastic measures including banning public gatherings, restricting restaurants to take-out and delivery only, and closing schools, bars, theaters, casinos and indoor shopping malls, among others.
Such orders, or their looming possibility, have consequently intensified the panic-buying urges of consumers for food and household essentials particularly in North America and Western Europe, giving occasions for daily photos of empty grocery-store shelves splashed ubiquitously from across news networks to social media platforms. The availability of food in North America and Western Europe during the ongoing coronavirus pandemic, however, remains generally secure, at least in the near term of the pandemic.
Food Sourcing
New York City, for instance, normally has food supply amounting to approximately 8.6 million tonnes (19 billion pounds) annually as purveyed by a network of regional and national food distributors, which then is sold at about 42,000 outlets across the city’s five boroughs, according to a 2016 study sponsored by the city.
Over half of the outlets are made up of approximately 24,000 restaurants, bars, and cafes through which consumers access almost 40 percent of the city’s food by volume annually. The rest of the outlets are chain supermarkets, bodegas, and online grocery stores. The study reported that the city’s annual food supply feeds over 8.6 million city residents, over 60 million tourists plus daily commuters in the hundreds of thousands from the tri-state area of New York, New Jersey, and Connecticut.
With millions of tourists and commuters now staying away from the city, however, and with the city’s hotels at just 49 percent occupancy for the week ending March 14, an excess of the food supply is readily available for diversion into the city’s grocery stores and other retailers to meet the surge in demand by local residents. In the case of Germany, the country imports food that accounts for nearly 8 percent of its US$1.3 Trillion imported goods in 2018. Germany procures from abroad about 3 million tonnes of fresh vegetables annually — with cucumbers and tomatoes accounting for 40 percent of the import volume — at a value of around 3.5 billion Euros, mainly from the Netherlands and Spain. Indeed, approximately 30 percent of the 2.6 million tonnes of exported Dutch-grown fresh vegetables go to Germany.
Meanwhile, approximately 80 percent of the United Kingdom’s food and food ingredients are imported. The U.K. imports approximately 2.4 million tonnes of fresh vegetables each year from Spain (33 percent), the Netherlands (28 percent), France (10 percent) and from various parts the world (29 percent).
Access to Food
Although the sources and sourcing of food in North America and Western Europe are currently generally secure, what might soon become a prodigious concern is that their workers in the production, distribution and retail segments of the food supply chain may eventually succumb to coronavirus infection. In such events, coupled with the potential for lockdown bureaucracies to slow down the flow of cargo between countries and between cities, severe delays in delivery — or real delivery shortages — could well become an actual possibility.
Local Vertical Farms
The coronavirus pandemic lockdowns have laid bare if fortuitously, the crucial importance of partial local food production in or around world cities in the context of urban resilience. The following salient features of vertical farms have become especially significant toward buttressing a city’s resilience in the event of a pandemic lockdown:
(1) Local — production of safe and fresh produce can take place within the lockdown zone, obviating the hurdles and perils of going in and out of the red zone;
(2) Automation-Amenability — impact of severe labor shortage which can be expected as the pandemic surges as well as direct physical contact between workers and fresh produce can be significantly minimized or eliminated;
(3) Controlled-Environment — infection risks to both workers and crops are significantly reduced through clean and controlled operations;
(4) Modular Option — crops may be grown in modular production units, such as shipping containers, which may be conveniently transported to neighborhoods located either farther away or in areas of stricter isolation; and,
(5) Reliability — Dependability, and consistency of high-yield and high-quality harvests throughout the year is virtually guaranteed independently of season and external climate conditions.
Fortunately for New York City, even as it sources most of its fresh vegetables from California and Arizona, the New York greater area now serves as host to the highest concentration in the United States of commercial urban vertical farms — including Aerofarms, Bowery Farming, Bright Farms, Farm.One, Square Roots and Gotham Greens, among others — that operate as controlled-environment farms year-round and independently of the variable effects of climate and geography. While conventional outdoor farming can produce three vegetable harvests per year, some of these vertical farms can achieve up to 30 harvests annually.
New York City and other world cities could certainly use more vertical farms.
Indeed, the urban planning and design of every world city should incorporate vertical farms, in and/or around it, not only for promoting food security — but for fostering disaster resilience as well. During a pandemic when a temporary period of social distancing between cities and nations becomes critically necessary, vertical farms can serve as helping outposts of resilience for cities and regions on lockdown as they brave the onslaught of the pandemic until it runs its course and duly dissipates — at which time the enfeebled ties of cooperation between cities, states and nations across the globe can once again be mended and made even stronger than before. Thus, not only locally, but in fact also globally, vertical farms can serve as helping vanguards of protection for all of our communities.
Dr. Joel L. Cuello is Vice-Chair of the Association for Vertical Farming (AVF) and Professor of Biosystems Engineering at The University of Arizona. In addition to conducting research and designs on vertical farming and cell-based bioreactors, he also teaches “Integrated Engineered Solutions in the Food-Water-Energy Nexus” and “Globalization, Sustainability & Innovation.” Email cuelloj@email.arizona.edu.
UAE: Growing Salads In Dubai
With the world in Lockdown Local warehouse farms can come into their own and show their value, by growing staple salads and not just Microgreens
Uns is the largest operational farm in the UAE and was designed with the intention of providing fresh high-quality produce to the masses of the UAE.
Here at Uns Farms, we took a different approach to the typical ‘concept’ warehouse vertical hydroponic farm, as we believed that these types of projects need to be large in order to make a real impact and actually address food security. To do this, we took the bold step and built a large-scale vertical farm inside a warehouse complex. Uns farm has some 2,000 ebb n flow benches that have 2.88m2 growing area each. This makes Uns one of the largest warehouse growers with over 5,700 m2 of growing space available now.
A global crisis like the COVID19 virus has really highlighted the importance of local produce and the stability it can provide.
Uns Farms being a large operation, has always meant that we grew products for all segments of the market. So, from the start, we had three main product lines or divisions.
Gourmet for the HORCEA industry, Premium for the mass supermarket industry then our specialty lines for all markets. The HORCEA industry has been impacted in a big way, however, there is still a market given the home delivery of food from the Restaurants. Our premium baby leaf market has seen an increase in market share due to the supermarket sales increasing, so people although not eating out still have access to our produce through our distribution in local supermarkets.
Uns is focused on growing the best quality mixture of leaves which we pack as baby leaf’s in a range of six mixes. These are grown for quality, taste & texture. Our micro herbs have always been grown to order so by doing this the slowing down of the market our damage has been limited. Distributors take care of the sales in both the HORECA and retail, while we take care of the growing. Therefore, we are diversified and not too dependent on anyone's market segment.
Customers can reach us for our products through some large chain supermarkets and we are exploring online platforms, but we are constantly battling to expand our reach through as many mediums as possible.
We also have a steady flow of sales directly from the farm and people are welcome to purchase our products directly from the farm as well.
So as one door has closed in hospitality, we have other doors of opportunity and are always looking for the next one. Innovation is not just growing, but sales and distribution are key.
One benefit of indoor warehouse growing is we have more food security, However, we are based in Dubai so now as the summer is arriving we are seeing ‘Normal’ greenhouse farms slowing production down due to the heat and humidity. Here at Uns Farms we are actually increasing production and expanding. Our quality increases due to us being able to control the conditions that we grow in. So we aim to continue to provide our fresh salad and expand our range as indoor growing allows us to be relatively safe from outside elements.
Our products are salad mixes and we have designed them to cater to multinational tastes and cuisines to fit the diverse community of the UAE.
Uns farms were built as a large-scale commercial facility, with the intention of supplying high-grade consumer-based salad products. We were built with the vision to address the masses and to help the UAE fight its dependence on imports and build food security. Given that this farm is the largest in the country,
we only aim to grow larger and cement the UAE as an agricultural powerhouse in the region.
THE ARCTIC CIRCLE - This Greenhouse In A Sea Can In Gjoa Haven Is Powered by Wind And Solar Energy
Betty Kogvik and Susie Kununak are making sure those little fruits — which will mark the second harvest from the community's new agricultural research station — have all the warmth and light they need, despite the dark winter outside
'It was so fresh, not like what we get in the store,' says technician at shipping container research station
Beth Brown - CBC News
These sea cans in Gjoa Haven are actually a new research station and grow pod used for growing vegetables. The solar and wind-powered project is called Naurvik, which means, the growing place. (Submitted by Thomas Surian)
In a sea can outside Gjoa Haven, Nunavut, there are rows of ripening cherry tomatoes working to grow from green to red.
Betty Kogvik and Susie Kununak are making sure those little fruits — which will mark the second harvest from the community's new agricultural research station — have all the warmth and light they need, despite the dark winter outside.
The two women are technicians, or guardians, for a new wind and solar-powered greenhouse that the Kitikmeot community named "Naurvik." That means "the growing place" in Inuinnaqtun.
The first harvest, of lettuce, grew in around four weeks. It was given to Gjoa Haven elders who have played a large role as advisors for the Naurvik project, which is led by the not-for-profit group, the Arctic Research Foundation.
One elderly lady even danced with joy when she got her lettuce.- Betty Kogvik"It was so fresh, not like what we get in the store. Sometimes when we get [lettuce] in the stores it is almost rotten. The ones we harvested are really fresh and tasty," Kogvik said. "One elderly lady even danced with joy when she got her lettuce."
Agriculture could grow new economy
The research station is built of two sea cans (shipping containers brought up on the summer sealift), two windmills and a row of solar panels. It has a generator for backup when the wind and sun both fall short.
It's on a hill, near a bay, in a place that elders said gets a lot of wind, and is only a few minutes ride by snowmobile from town.
Naurvik technician Betty Kogvik harvests the first lettuce grown in the sea can greenhouse in Gjoa Haven. (Submitted by the Arctic Research Foundation)
Every day, the technicians, including Kogvik's husband Sammy, spend time monitoring the station. The current harvest only uses a quarter of what the station could grow. Come summer, they want to run a trial growing cloudberry and blueberry plants, and other tundra plants used for medicine and tea.
"At the beginning, it was really confusing," Kogvik said. "We didn't know what to do, but we've got the hang of it now."
In the spring, Sammy says he wants to travel to Taloyoak to help that community start its own version of the Naurvik grow pod.
For the Arctic Research Foundation, the focus of Naurvik is on improving food insecurity, and on researching how to most efficiently grow food in remote and harsh environments, said project lead Adrian Schimnowski.
But it's also meant to foster the economy. Schimnowski said he'd like to see a local product grown to a scale where it's ready for export. For now, he's working to be able to employ and train students, as well as community-based technicians.
The Arctic Research Foundation is calling its new Naurvik greenhouse project in Gjoa Haven the most northern agriculture pod to be powered by wind and solar electricity. (Submitted by Thomas Surian)
The foundation is funding the program with help from Agriculture and Agri-Food Canada, the National Research Council of Canada, and the Canadian Space Agency.
"It's a mini, mobile research station. We can add as we expand," said Schimnowski. "It's directed by the wishes of the community."
Space agency looks to Gjoa Haven
Because Naurvik is working on more efficient technology to grow vegetation in an environment it usually wouldn't survive in, that same research can also be used to help scientists understand how to grow food in harsh environments — like space.
"We are hoping to find strategies that could help astronauts grow food in space," Christian Lange, head of exploration strategic planning with the Canadian Space Agency, said in a news release. Research from "extreme or remote environments," like Gjoa Haven, could be part of that, he said.
This crop of potted cherry tomato plants are thriving under LED grow lights. They will be the second kind of plant harvested at the Naurvik grow pod in Gjoa Haven. (Submitted by the Arctic Research Foundation)
The research station itself is built to be hyper-efficient, project lead Schimnowski said.
"It's very narrow and tight, similar to what it would be like in a spaceship, but everything is well organized and everything has purpose."
While gardening isn't an Inuit tradition, using the land to care for and store food is. Elders who are working with Naurvik said using the green energy to run the research station made them think of a community freezer, the kind built into the ground. Those elders said the hill near the station could be used to build a traditional freezer.
"When I first heard of [the project] I thought it would never work up here," Gjoa Haven elder Peter Akkikungnaq is quoted in the news release. "Not in this 40 below zero. Now I know anything is possible if you have the right idea ... I had a taste of the vegetation. It was fresh."
Vertical Farming: The Advantages of Growing Up, Not Out
Vertical farming refers to growing crops in multiple vertical layers in controlled indoor environments, such as repurposed buildings, growth chambers and even shipping containers
We share this planet with more than 7 billion people, and the UN forecasts that by 2050 we will need to feed over 9.7 billion. If you’re like me, you’re wondering what we can do to scale farming to meet the needs of the future. That’s where vertical farming comes in, along with innovative technologies that make growing up, not out, a more viable option.
by Ali Ahmadian, CEO Heliospectra
Vertical farming refers to growing crops in multiple vertical layers in controlled indoor environments, such as repurposed buildings, growth chambers, and even shipping containers. While growing crops in the greenhouse have its own merits, depends on the crop and technology used vertical farming has advantages over single-layer crops grown in a field or greenhouse:
Vertical farming enables growers to optimize their costs per square meter and produce more within the same footprint. A vertical format could potentially produce a harvest that is 3- to 4-times larger (or more!) than a field the same size could produce.
Vertical farming is done in an automated, controlled environment, which eliminates many of the risks involved with traditional field farming. Variables such as seasonal weather and environmental issues are taken out of the mix to produce a thriving crop year-round – no matter what’s happening outdoors.
Crop yields are standardized in vertical farming, with every harvest cycle producing the same quantity, quality, flavor and appearance that customers expect.
Vertical farming enables growers to meet changing market demands, by easily introducing new crops or varieties based on consumer or retail preferences.
Due to its smaller footprint, vertical farming is a viable and environmentally sound solution for feeding cities. The UN predicts that close to 70% of the population will be living in urban areas by 2050. To reduce the carbon footprint of our food, we need to think of ways to bring food production closer to the dining table. A LCA is necessary to weigh in such decision making.
While we continue to build larger and larger cities to accommodate our growing population, arable farmlands will be pushed further out. Vertical farming can ensure our cities have plentiful locally grown food – food that has a predictable harvest, optimizes costs per square meter, looks beautiful, fresh and tastes delicious.
Source: LinkedIn
Publication date: Fri 6 Mar 2020
UAE: Armela Farms Gears Up To Open 3 ha Automated Lettuce Farm
After launching in August 2016, the Armela team has spent more than two years in Research and Development regarding techniques, varieties of produce and optimum climate conditions, before celebrating their first harvest in August 2018
After launching in August 2016, the Armela team has spent more than two years in Research and Development regarding techniques, varieties of produce and optimum climate conditions, before celebrating their first harvest in August 2018. Since then, the team has advanced its process to achieve over 250% of an increase in production and is currently finalizing the opening of a new facility for Q1 2021, which will boast over 3 hectares of fully automated advanced lettuce farm, making it the largest facility of its kind in the GCC.
Armela Farms will also partner with several leaders in the Dutch agriculture sector to build the largest automated data-driven growing facility in the United Arab Emirates. Located in Abu Dhabi, the farm will be able to create over 9,000,000 lettuce heads per annum; that’s equivalent to 2,300 tonnes per annum.
Dutch tech
Armela Farms has chosen Van der Hoeven Horticultural Products to supply the project. In conjunction, Armela Farms will be using specialist technologies from a variety of suppliers like Hoogendoorn, Patron Agri Systems, Green Production Systems, Rijk Zwaan, Jiffy, Koppert, due to the expertise and experience by each company in their individual fields.
Mr. Avir Shah, CEO, and Founder of Armela Farms states, “Our aim is to produce products which exceed our community's expectation and reduce the reliance of imported highly-priced products by bridging the supply and demand gap with affordable price. We can achieve this vision by utilizing available resources and transforming it into a hi-tech, sustainable food production facility in accordance with the country’s vision of National Food Security and self-sustainability.”
Mr. Yazan Abu Jaish, General Manager of Armela Farms: “The new facility, for example, will enable us to monitor the evaporation of a single plant at any given time and many other advanced parameters required for optimum plant grown and output. Armela Farms is now moving from traditional hydroponic farming to data-driven farming.”
Mr. Gerard Oorthuys of Van der Hoeven Horticultural Projects: “I was very impressed by the sheer knowledge of the Armela farms team and wanted to show them one of our constructed greenhouses to show our capability. From our regional experience, we understand the climatic challenges more than any other company and we are confident we will deliver them a fantastic project.”
For more information:
Armela Farms
armelafarms.com
Publication date: Mon 9 Mar 2020
Coalition for Sustainable Organics Disappointed in Latest Attempts Center for Food Safety to Restrict Supplies Organic Foods Through Lawsuit
Lee Frankel, the executive director of the CSO stated, “It is disappointing to see groups target pioneering organic farmers that use the most appropriate organic growing methods adapted to their site-specific conditions on their farms to meet the needs of consumers
SAN DIEGO, CALIFORNIA March 3, 2020 – The Coalition for Sustainable Organics (CSO) is saddened by the latest attempts by the Center for Food Safety and their allies to limit fair competition and organic supplies in the market through legal action.
Lee Frankel, the executive director of the CSO stated, “It is disappointing to see groups target pioneering organic farmers that use the most appropriate organic growing methods adapted to their site-specific conditions on their farms to meet the needs of consumers. The members of the CSO are strongly committed to the integrity of organic standards and the organic label. The groups behind the lawsuit failed to convince the members of the National Organic Standards Board (NOSB) to prohibit container and hydroponic production methods after significant industry debate and submission of public comments. Instead of unifying the industry after the decision made by representatives of the organic community at the NOSB, the CFS is seeking to eliminate public input to achieve their goals of restricting competition to drive up the price of organics for organic consumers to allow favored producers to increase their profit margins.”
Frankel continued, “Growers using containers adhere to the U.S. Department of Agriculture organic standards under the National Organic Program (NOP) and have been allowed to grow certified organic produce since the initiation of the NOP more than 25 years ago. After extensive study in 2010, the USDA through the NOP opted not to change these high standards for certifying organic produce – and affirmed that organic produce can be grown through containerized methods. After additional review in 2015-2017, the National Organic Standards Board voted to reject a proposed prohibition on container and hydroponic systems.”
Karen Archipley of Archi’s Acres of Escondido, California added “Our production systems are managed in accordance with the federal organic law. We chose to incorporate hydro-organic methods at our operations since it is the most appropriate way to promote ecological balance by drastically reducing our water use, conserve biological diversity by preserving valuable habitat while still incorporating the microbial processes described by organic pioneers to recycle nutrients to nourish our crops. Every choice we make and every input we use must be audited and approved by USDA-accredited certifying agents like any other Organic Farmer.”
Archipley continued “Changing the rules now would limit the amount of organic produce available to the public – just as the public is demanding more organic produce. This is not an issue that should be settled in the courts or politicized. If a grower meets USDA standards for organic certification, they should be able to market organic produce, whether they grow in soil or any other sustainable, certified organic growing media.”
#######
The Philadelphia Zoo Is Running A Farm Inside A Converted Shipping Container
Tua lives at the Philadelphia Zoo, the first zoo in the country with its own on-site vertical garden used to grow leafy greens for its animals. And she loves the produce they’re feeding her
by Brianna Baker, For The Inquirer, March 4, 2020
Kristen Waldren, director of strategic initiatives at The Philadelphia Zoo, walks through the zoo's new "Cropbox" — a vertical farm being used to grow plants that are harvested to feed animals. MARGO REED
If you’re a fan of homegrown arugula and mustard greens, you just may have the same taste as Tua, a 27-year-old Sumatran orangutan.
Tua lives at the Philadelphia Zoo, the first zoo in the country with its own on-site vertical garden used to grow leafy greens for its animals. And she loves the produce they’re feeding her.
The garden is located in a retrofitted shipping container in the Urban Green, the zoo’s open-air food marketplace. A mural, by Philly-based environmental artist and activist Eurhi Jones, transforms the front of the shipping container into a colorful collage of the animals who’ll chow down on the vegetation.
But the real beauty is inside, where stacked, tidy shelves hold rows of plants that are grown hydroponically, in nutrient-rich water instead of soil. LED lights, a substitute for sunlight, shine 18 hours a day. Farm operators use a mobile app to remotely control the container’s light, temperature, and humidity levels.
Kristen Lewis-Waldron, director of strategic initiatives at the zoo, said the vertical farm is far more sustainable than bringing in food from outside sources. It uses 70% to 90% less water than traditional farming, has no need for pesticides or herbicides, and cuts greenhouse gas emissions out of the equation since no motor-powered transportation is necessary to get the food to the zoo.
“It really kind of creates this farm-to-table [model] — in this case, shipping container-to-exhibit,” she said of the project, which is in a pilot phase.
Want to know what's going on in Philly? Find out about upcoming concerts, shows, and other events with our weekly newsletter.
Lewis-Waldron is short on farming experience but knows a thing or two about feeding animals. She landed her first role at the zoo 23 years ago as a nutrition intern. She went on to work for, and eventually lead, the zoo’s conservation department, before transitioning to her current position. Growing greens for the animals makes her feel like she’s come full circle, she said.
A peacock at the Philadelphia Zoo walks past the "Cropbox," a converted shipping container being used to grow plants being used to help feed the animals. MARGO REED
To launch the project, she enlisted the services of CropBox (which is also what the zoo calls the vertical farm), a North Carolina company that provides all the equipment customers need, including the shipping container, and helps set up the system.
Lewis-Waldron also consulted with industry experts, including those who operate their own vertical farms, to learn best practices and how to troubleshoot technical challenges. All in all, the preparation process took about a year.
In its nine months of operation, the CropBox has fed 20 animal species with its microgreens. It produces 275 pounds of leafy greens a month, which is only 10 percent of the zoo’s monthly requirement. But that number, Lewis-Waldron said, will grow once the pilot year concludes and the project is expanded.
“You can take over a vacant warehouse or vacant building and convert it,” she said. “You could take six of these and make a dent in the requirements of our collection.”
The CropBox also benefits the zoo economically by replacing a collection of food it would otherwise purchase.
But perhaps most importantly, the greens grown in the vertical farm are rich in nutrients. The zoo takes animals’ diets very seriously and even employs a full-time nutritionist. By feeding leafy greens to the animals, the zoo is keeping their health in shape.
Still, that doesn’t mean the greens are every species’ favorite snack. Just like humans, animals have unique palates. And the current variety growing in the CropBox — a stir-fry mix that includes arugula and mustard greens — isn’t always a crowd-pleaser.
“It’s got a little kick to it, a little bit of spice. Our emus were a little hesitant,” Lewis-Waldron said. “But our monkeys, langurs, apes, gorillas, orangutans, tortoises absolutely love it. So it’s interesting, and we’ll continue to test out different types of greens.”
Brianna Baker, For The Inquirer
Fireside Chat With Square Roots CEO & Co-Founder Tobias Peggs: Scaling Indoor Farming At Speed
Indoor Ag-Con is excited to announce that Square Roots Co-Founder & CEO Tobias Peggs has joined our conference line-up for the May 18-20, 2020 edition! Tobias will join Nicola Kerslake, Indoor Ag-Con Founder and Co-Founder, Contain, for the afternoon Fireside Chat: Scaling Indoor Farming At Speed
Square Roots Co-Founders Tobias Peggs and Kimbal Musk Empowering Next-Gen Farmers
Indoor Ag-Con is excited to announce that Square Roots Co-Founder & CEO Tobias Peggs has joined our conference line-up for the May 18-20, 2020 edition! Tobias will join Nicola Kerslake, Indoor Ag-Con Founder and Co-Founder, Contain, for the afternoon Fireside Chat: Scaling Indoor Farming At Speed. If our industry is to bring high-quality, local produce to customers all year round, we must collectively understand how to scale farming at speed to reach as many people as possible. Using a unique and scalable ‘farmer-first’ technology platform, Square Roots is doing just that. Tobias will share how this tech-enabled urban farming company is training and empowering the next generation of leaders in urban agriculture to grow local food that is delicious, responsible, nutritious, and profitable. And, be sure to check out the story further down in this issue highlighting our special guest blog post from Square Roots Co-Founder Kimbal Musk, too!
CHECK OUT FULL CONFERENCE SCHEDULE >>>
During Indoor Ag-Con, we’ll be featuring the panel presentation, What Is the Next Technical Frontier for LED Lighting” on Monday, May 18 from 10 – 10:45 am. Moderated by Dr. Morgan Pattison, SSLS, Inc., the panel will include Blake Lange, Signify, formerly Philips Lighting – City Farming; Brandon Newkirk, LumiGrow; and Xander Yang, Sananbio.
Ahead of the session, we reached out to our participants to find out, from an LED perspective, what is the next hot thing in lighting?
WHAT'S THE NEXT HOT THING IN LED LIGHTING? >>>
KIMBAL MUSK: 10 WAYS SQUARE ROOTS' FARM-TECH PLATFORM EMPOWERS THE NEXT GENERATION OF FARMERS
Ahead of Square Roots CEO & Co-Founder Tobias Peggs' Fireside Chat at Indoor Ag-Con, Co-Founder & Exec Chairman Kimbal Musk has shared a guest blog post with us.
"There are a lot of smart people in this industry, many with different visions for the optimum architecture and model for indoor farming (e.g. plant factories)," says Musk. "But all working hard to bring better food to market — which, given our wider vision to bring real food to everyone, is wonderful to see. The more of us working on the real food revolution the better — and we want all of these systems to flourish. But here are 10 reasons why we think container farming rocks.....”
10 WAYS SQUARE ROOTS' FARM-TECH PLATFORM EMPOWERS NEXT-GEN FARMERS>>>
YOU COULD WIN 2 TICKETS TO BIOSPHERE 2!
When you arrive at Indoor Ag-Con, be sure to enter for your chance to win two general admission tickets to Biosphere 2 and an overnight stay at B2 cabanas!
The winners will get to tour one of the world’s most unique facilities dedicated to the research and understanding of global scientific issues. The Biosphere 2 facility serves as a laboratory for controlled scientific studies, an arena for scientific discovery and discussion, and a far-reaching provider of public education.
What’s more, as part of the package, the University of Arizona Controlled Environment Agriculture Center (UA-CEAC) would like to also extend an invitation for the recipients to its vertical farm research and educational facility (UAgFarm) at UA-CEAC and other UA-CEAC projects/facilities as an additional welcome!
SEE WHO'S SPEAKING | SEE WHO'S EXHIBITING
INSIDE INDOOR AG | INDUSTRY NEWS HARVEST
PRODUCE GROWER: Elevate Farms Closes on $1.8 Million In Round Of Funding
GREENHOUSE GROWER: Gotham Greens Opens Another Massive Greenhouse
NEW YORK POST: I Tasted A Bug Diet, the Sustainable Protein That Could Save The WorldIGROW NEWS --CubicFarm Systems Announces Largest Sale To Date
SPECIAL THANKS TO OUR GROWING ROSTER OF
SPONSORS, MEDIA ALLIES & INDUSTRY PARTNERS
In addition, Indoor Ag-Con is proud to be a member of the Hemp Industries Association.
US: New Jersey - Hope Cahill Starts As Coordinator At Hydroponic Farm
A hydroponic farm, in the middle of a municipal center? Well, it all started in 2016, when Robbinsville Mayor Dave Fried found out about hydroponic farming in freight containers
By Lois Levine
March 1, 2020
A hydroponic farm, in the middle of a municipal center? Well, it all started in 2016, when Robbinsville Mayor Dave Fried found out about hydroponic farming in freight containers.
“He loved the idea and thought it would be beneficial to the township in terms of feeding programs and education on how to grow greens and learn more about nutrition,” said Kevin Holt, recreation manager for the Robbinsville Township.
Hope Cahill, the new coordinator of Robbinsville’s hydroponic farm, holds some of the farm’s yield.
Now, the farm has a new coordinator—Hope Cahill, who took over for original caretaker Kyle Clement in January.
“We can grow anything that is a leafy green,” Cahill said. “Here we are growing butterhead, oak leaf, and lollo lettuce, as well as spring mix.”
The farm also grows some herbs, basil, and cilantro. Cahill, 25, is certified in aquaponics, an off-breed of hydroponics.
After graduating high school, she got certified in a variety of different areas of agriculture, and before taking this position working as a naturalist at various garden centers, as well as with the Monmouth County Park system. Born and raised in Tinton Falls, Cahill will be soon moving to Freehold.
Hydroponic farming is farming done without soil. Plants typically get all their nutrients from the soil. In hydroponic farming, however, nutrient-rich water takes the place of the soil, enriching the seedlings as they grow into fully mature plants and watering them at precise times through a computerized system.
With the system that the Robbinsville Township purchased, known as the Leafy Green Machine, lettuces and herbs are grown in a vertical hydroponic farm that lives within a recycled, refrigerated, insulated, custom-built shipping container.
Between the nutrient-rich water and light energy from powerful LEDs, greens can be independent of the need for land, climate and season, growing in a modular design that is also mobile and can theoretically live anywhere.
The container consists of insulation, where it maintains an average internal temperature of 70 degrees Fahrenheit in extreme climates; climate control, built with an integrated “economizer” that saves energy by drawing in cool outside air when appropriate and also doubling as an intake fan; a dehumidifier to maintain optimal humidity levels and decreasing the farms overall water consumption; airflow ducts, consisting of two fans that distribute cool carbon dioxide enriched air evenly; and a carbon dioxide regulator with a safety shut-off feature, providing plants with exactly the right amount of carbon dioxide needed for photosynthesis.
In addition, the greenery’s LED lights provide the plants with the best quality light at its most efficient point. The LED boards are designed to emit only particular wavelengths of red and blue light, which are the colors that plants are able to absorb most easily for photosynthesis (red light is essential for stem and leaf growth, while blue light helps develop thick stems and dark green foliage).
Just as it is in nature, Cahill and her team start with the seeds, which begin in a flowing hydroponic system and are placed into compressed peat moss, known as grow plugs. The peat-moss plugs act as a sponge for absorbing nutrient-rich water. The seeds soak for 10 minutes, are covered with a humidity dome and sit under grow lights for about a week.
At that point, the seeds have become sprouts, with small roots, short stems, and a few young leaves. They then move up to the next level, a flow troth, where the roots “get completely soaked,” Cahill said. Now actual seedlings, taller and sturdier than they had been, with a secure root system, the plants sit in that troth for another two weeks, getting consistent water and light to develop strong stems needed to support the plant’s weight later in its life cycle.
After this time period, the seedlings are harvested and transplanted into the main cultivation area, where they are now in the towers, growing vertically for the first time. The roots, which are still in the peat-moss grow plugs, are wedged into stiff foam panels, which provide firm support, with the plant facing outward towards the LED light, encouraging the leaves to grow. Here, in this final destination, they spend from two to five weeks until they are ready for their harvest..
A view of the produce inside of the shipping container that houses Robbinsville’s hydroponic farm
“It is a continual cycle of putting new lettuce and herbs in, taking grown ones out,” Cahill said.
Every week, the team has something to harvest.
“What is nice about the system is that it is computerized so that plants get exactly the nutrients it needs at the right time,” Cahill said. “Sensors on the computer know when they might need nitrates or some other nutrient.”
Freight Farm, the company that built the hydroponic farm equipment, also developed an app that can be used via a person’s iPhone or desktop computer to keep an eye on all sensor data.
Holt admits he did not know much about hydroponic farming until Fried asked him to look into purchasing a machine.
“I did a ton of research on what hydroponic farming is, to educate myself, and then looked into what companies are out there to make these container farms,” he said. “We talked to a lot of companies, and decided on Freight Farm, out of Boston. At the time, they told us we were the only municipality they had ever sold a freight farm container to.”
Once Cahill and Holt have the finished products, the lettuce and herbs get donated back to the Robbinsville Senior Center.
“We also give some of the produce to Meals on Wheels, and also Mercer Street Friends, who disperse it to schools,” Cahill said. “They distribute it to about a dozen schools in the Trenton area.”
And how does the finished product taste?
“It is honestly the best lettuce you can ever eat,” Holt said. “You really can see and taste the difference between this produce and the produce you buy in a supermarket.”
It looks good and feels good, too, Cahill said.
“Before we distribute it, we take care to remove any brown or damaged leaves,” she said. “There are, of course, no pesticides, no chemicals that the greens were treated with, so it is very safe and very clean.”
Both Cahill and Holt rave about how green and fresh the lettuce is, “with so much more taste to it than what you get in the stores, which by comparison, tastes so bland,” Holt said.
Since starting the farm at the municipal center in 2017, companies have come through to see the set-up, expressing interest in buying machines for themselves. Holt said the township has also hosted schools and colleges, as well as field trips and local education programs.
“Our mission is to grow, educate and unite: we grow the lettuce, give it away, educate the community about how hydroponic farming works, and unite people by asking them to volunteer or hold events, which is a catalyst for bringing people together,” Holt said. “This has been a huge win-win for the community.”
Cahill said she is always seeking volunteers and visitors, as well.
To schedule a tour or for more information, visit robbinsville.net/recreation or send an email to hcahill@robbinsville.net.
80 Acres Farms Will Grow Tomatoes On Fifth Avenue In Guggenheim Exhibition
Based in Hamilton, Ohio, 80 Acres Farms is a leader in technology-assisted indoor growing and a multi-farm operator marketing a wide variety of freshly picked vegetables and fruits to retailers such as Giant Eagle, Kroger, Whole Foods, Jungle Jim’s and Dorothy Lane Markets
80 Acres Farms will grow tomatoes on one of the busiest streets in New York City outside the Solomon R. Guggenheim Museum as part of the Guggenheim’s new exhibition in collaboration with Rem Koolhaas, “Countryside, The Future.”
Along with its commercial partners Infinite Acres and Priva Holding BV, 80 Acres Farms will grow cherry tomatoes in an indoor grow module right outside the museum on Fifth Avenue.
Based in Hamilton, Ohio, 80 Acres Farms is a leader in technology-assisted indoor growing and a multi-farm operator marketing a wide variety of freshly picked vegetables and fruits to retailers such as Giant Eagle, Kroger, Whole Foods, Jungle Jim’s and Dorothy Lane Markets.
The company was founded by veteran food industry executives Mike Zelkind and Tisha Livingston, who are supported by a deep team and a board of directors representing executive and leadership experience at leading food, healthcare and other companies.
Window on tomato production
People in New York will be able to look through a large window in the indoor farm to view a crop of fresh tomatoes being grown continuously during the next six months under precise LED lighting and other controlled conditions.
The first tomatoes will be ready for harvest by late-March.
The grow module will demonstrate how indoor farming can benefit the world through growing fresh, pesticide-free food near populations, anywhere in the world while using fewer natural resources.
The “Countryside, The Future” exhibition will examine political forces, social issues and environmental factors altering landscapes across the world, including traditional farmlands.
80 Acres Farms is a founding member of the Infinite Acres partnership venture, along with Netherlands-based Priva Holding BV, a leading provider of technology solutions, services and automation systems to horticultural and other industries; and Ocado Group, one of the world’s largest dedicated online grocery retailers, operating its own grocery and general merchandise retail businesses.
That partnership is now building large-scale, fully automated indoor farms in the U.S., Asia and Europe.
“We believe that what we are doing is about the future of food. We are changing the way fruits and vegetables are grown and harvested locally then delivered to grocers the very next day,” Zelkind said.
“There is an enormous market and consumer appetite around the world for produce that our crop scientists and other food experts have been perfecting during the past five years,” he said. “Our participation in this exhibition will allow New York residents and visitors to experience how the freshest, tastiest locally grown tomatoes can be grown year-round indoors in one of the busiest cities in the world.”
700-square-foot grow center
For the Guggenheim exhibition, 80 Acres Farms, Infinite Acres, and Priva Holding have collaborated on the 700-square-foot grow center and all of the state-of-the art ag-technology within it.
While in operation for the next six months outside the Guggenheim, the Infinite Acres grow module is expected to grow 50,000 tomatoes.
Additional tomatoes will be donated to City Harvest, a New York City food rescue organization that safely recovers excess food and distributes it to people in need.
“Countryside, The Future” will be open to the public through Aug. 14.
US: Texas - Personal Growth As Well As Leafy Greens Thrive in San Antonio Nonprofit’s New Hydroponic Farm
A group of people crowded around a shipping container in the parking lot of the San Antonio Clubhouse, a community and resource center for adults with mental illness. Inside the 40-foot long container is a hydroponic farm, which produces as many crops as a three-acre farm, simply with water and lights
March 7, 2020
A group of people crowded around a shipping container in the parking lot of the San Antonio Clubhouse, a community and resource center for adults with mental illness.
Inside the 40-foot long container is a hydroponic farm, which produces as many crops as a three-acre farm, simply with water and lights.
But the best part of Clubhouse Grows — the new indoor water-based, high-tech farm — isn’t that it sprouts an abundance of leafy greens. It’s that it also serves as a recovery-oriented volunteer opportunity for the people the nonprofit serves.
“We are working together as a Clubhouse community on this farm,” said Mark Stoeltje, the executive director of San Antonio Clubhouse. “It is providing meaningful work for our members, but it is also providing a product.”
Clubhouse Grows, which was unveiled Friday, was made possible with a $100,000 grant from Impact San Antonio, a women’s philanthropic non-profit that awards grants to local organizations.
Jennifer Bennett, president of Impact SA, said one of the reasons the group chose to award Clubhouse a grant was “because of the multilayered benefits that it delivers to the community.”
“A lot of our citizens who have mental health challenges do not get the degree of support that they need to help them live lives that feel good to them,” Bennett said. “Clubhouse is really unique to doing that in our community.”
The plants in the 320-square-foot freight container do not rely on soil. Instead, they grow on 88 black foam and metal panels, which have water pumped through them. Powerful LED red and blue lights that emulate the sun are on 18 hours a day. And the climate-controlled space remains stable between 65 and 68 degrees.
“The extra sunlight, combined with the fact that it’s never cloudy and we don’t have to worry about different seasons, really helps accelerate the plants’ growth,” said Brandon Wagner, a staff member and project lead for Clubhouse Grows.
On ExpressNews.com: South San Antonio elementary students growing food with a larger goal in mind
Crops planted include five types of lettuce, kale, beets, arugula, basil, oregano, and even some flowers.
Wagner, who has been prepping the new farm and working with it for around a month, said he has found it to be very therapeutic.
“You zone out and just concentrate on the work,” he said. “You are planting 300, 400 or up to 500 seeds at a time, so there is a very meditative workflow.”
While the farm only uses about 25 gallons of water a month, Wagner said, it can grow 550 small and crisp heads of lettuce alone each week.
“I love lettuce, but that is more lettuce than we can eat,” Stoeltje said.
So, in addition to using the produce at the Clubhouse facility, the organization plans to donate some to local non-profits.
Stoeltje said while healthy eating is important, the farming process — seeding, maintaining, relocating and harvesting crops — is also a chance for Clubhouse members to work hard, work together, hone new skills, reach goals and ultimately feel a sense of accomplishment.
San Antonio Clubhouse, which was founded in 2003, operates under a national model that's based on the belief that everyone deserves to be part of a caring community and has talents to share.
The non-profit helps its more than 2,000 members gain work experience through volunteering at the center, job training, résumé building, job-search assistance and advocating to potential employers.
“This is the perfect project for us because we are founded on two principles,” Stoeltje said, “meaningful relationships and rewarding work.”
sara.cline@express-news.net
Sara Cline
Follow Sara on: https://www.facebook.com/sara.cline.5494SaraLCline
Sara Cline is a staff writer for the San Antonio Express-News through the Hearst Fellowship Program.
She previously worked at the Times Union under the program. She also worked at the Brockton Enterprise, in Massachusetts, as a general assignment reporter. She has also contributed to newspapers and magazines in Arizona, Massachusetts and Rhode Island.
Sara graduated from the University of Arizona in 2016 with a B.A. in journalism.
Past Articles from this Author:
CropKing Partners With Urban Crop Solutions To Grow Vertical Container Farm Showcase
CropKing, a full-service hydroponic company located in Lodi, OH, specializing in controlled-environment agriculture and hydroponic growing, will operate the Urban Crop Solutions’ FarmPro vertical container farm as a showcase, continued research, and testing facility
March 4, 2020
CropKing and Urban Crop Solutions have announced plans to collaborate on a controlled-environment agriculture project in the U.S., leveraging the extensive hydroponic experience of CropKing with the high-quality controlled-environment technology in vertical farming of Urban Crop Solutions.
CropKing, a full-service hydroponic company located in Lodi, OH, specializing in controlled-environment agriculture and hydroponic growing, will operate the Urban Crop Solutions’ FarmPro vertical container farm as a showcase, continued research, and testing facility. The first FarmPro container arrives in March at the Lodi headquarters, where CropKing will start testing it with the help of in-house plant scientists.
“We are excited to be working with Urban Crop Solutions and for the opportunity to validate the effectiveness of automated container farming,” said CropKing President Paul Brentlinger in a press release from Urban Crop Solutions. “
Their personal and custom-made approach could fulfill the needs of many clients. The shipping container system offers advantages like climate control, irrigation system, and automated growing process, which has captured our interest for the past few years.”
Urban Crop Solutions, a turn-key solutions provider that offers biological know-how in the indoor vertical farming industry, recently celebrated its 5th anniversary and already has 28 active projects across the world. In the last five years, it has developed more than 200 plant growing recipes, for a variety of industries, through its in-house research center.
Paulina Murrath, Business Development Manager of Urban Crop Solutions, will serve as a point of contact for the North American market at the company’s offices in Miami, FL.“
It’s a great honor to start a collaboration with CropKing and Paul Brentlinger, who is a controlled-environmental agriculture expert with extensive knowledge of growing high-quality food products,” Murrath said in the press release. “CropKing shares the same values that we consider as important, like bringing higher yields, nutritional value, food security, local production, and consumption, to different industries. That’s why we believe our collaboration will be rewarding.
”The Vertical Farming Industry Needs Proven Technology
CropKing will put the FarmPro vertical container through a rigorous testing process, which includes assessing items such as plant pathology and system yield, as well as validating the true return on investment (ROI) of the unit, according to Brecht Stubbe, Global Sales Director at Urban Crop Solutions.
The FarmPro vertical container CropKing will receive is a fully automated and climate-controlled 40-foot freight container with a four-layer, state-of-the-art growing system for leafy greens and herbs. The insulated container includes features such as climate control and an irrigation system, continuous monitoring, custom-made LEDs, a handling area and technical room, as well as online crop and process management. Plants grow in a nutrient film technique (NFT) hydroponic system.“
Technological failures and resulting bankruptcies have been a problem in the vertical farming industry,” Stubbe says. “With CropKing’s 30 years of experience in the greenhouse industry, we can prove that this technology and our growing recipes can provide the ROI to growers. We don’t want this technology to fail for our clients.”
Collaboration a Strong Match for Exploring New Markets, Including Floriculture
This collaboration is only phase one for CropKing and Urban Crop Solutions. Stubbe says the companies hope to work together on more projects to explore new markets and opportunities in the vertical farming sphere
.Urban Crop vertical farming technology is already being used for research into medical plants for compound extraction. On the floriculture side, Stubbe says Urban Crop Solutions is currently conducting some promising research in Belgium. The latest growth trials with strawberries, for example, resulted in sweet fruits with a Brix value averaging between 11 and 16.“
They are growing azaleas at the trialing facility and now to a very high extent can control the temperature and bring crops just to the point of flowering, which helps increase their shelflife when they go to retail,” Stubbe says. “This type of technology could allow flowers to be grown across the globe, instead of shipped internationally to supply those markets.”
When asked about how the unit might be integrated into a controlled-environment greenhouse operation, Stubbe said he sees several applications and benefits, two being maximizing germination space with multilayer growing and eliminating risk factors involved with plant handling. For people growing in high tunnels or the field, the unit could help them diversify their operation into new crop segments. A grower could also use the unit to provide products locally on a year-round basis.
Janeen Wright is managing editor for Greenhouse Grower. You can email her at jwright@meistermedia.com. See all author stories here.