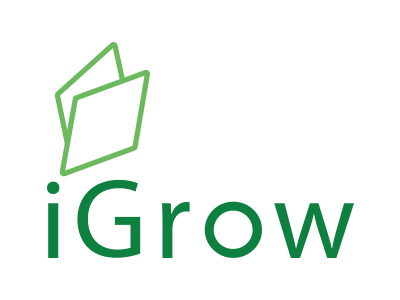
Welcome to iGrow News, Your Source for the World of Indoor Vertical Farming
USA (CA) - Iron Ox Raises $20 Million To Grow Robotic Greenhouse Operations
The funding will be used to open additional robotic growing facilities in California and other parts of the U.S., according to company co-founder and CEO Brandon Alexander
Khari Johnson @kharijohnson
September 9, 2020
Robotics farming company Iron Ox today announced the close of a $20 million funding round. The funding will be used to open additional robotic growing facilities in California and other parts of the U.S., according to company co-founder and CEO Brandon Alexander. The funding will also be used to hire additional machine learning and robotics experts as well as growers and scientists who work with plants.
“We’re now competing on price with field farms, but we think we can do even better and take this to more people,” he said.
Iron Ox employs a 1,000-pound mobile transport system roughly the size of a car to move trays of growing vegetables and tend to plants using a robotic grasper while computer vision systems monitor the plant growth cycle. The semi-autonomous system still relies on humans for a part of its seeding, pruning, and inspection process, Alexander said, but the goal is for Iron Ox to someday be fully autonomous.
While startups like Bowery practice indoor vertical farming in urban facilities near New York and Baltimore, Iron Ox has turned its focus toward greenhouse farming since the company was founded in 2015 as a way to lower energy costs. Earlier this year, Iron Ox opened its first greenhouse, a 10,000-square foot facility in Gilroy, California, the company’s second location. Iron Ox currently provides produce to 15 Whole Foods stores in the San Francisco Bay Area.
Though Gilroy is known as the garlic capital of the world, Iron Ox does not currently grow any garlic. Instead, the company focuses on leafy green vegetables like lettuce and some herbs.
Alexander said Iron Ox’s biggest challenge is how to use data collected by sensors to train AI systems that produce higher yields at lower costs.
“I would say in agriculture as a whole it’s not just collecting data, it’s not just taking an image, but it’s actually how do you include that data into the decision making process?” Alexander said. “I would say that is the biggest challenge in ag is how do you respond to these each individual plants and the variety and all these little variables.”
The $20 million funding round was led by Pathbreak Ventures with participation from Crosslink Capital, Amplify Partners, Eniac Ventures, R7 Partners, Tuesday Ventures, and At One Ventures. Iron Ox is based in San Carlos, California. The company currently has 30 employees and has raised $45 million to date.
Field farming today is still the most efficient way to grow produce. However, concern about shrinking field yields and instability due to climate change has spurred interest in indoor farming. In 2018, international teams from companies like Microsoft and Tencent competed against each other to find out who could grow the highest yield of cucumbers inside a greenhouse using AI and automation. (Spoiler: The Microsoft team won.)
In other AI and agriculture news, last month the startup iFarm raised $4 million for its AI-driven urban farming solution, and in June the startup Burro began rolling out its autonomous farm robot in southern California to assist in grape harvesting.
Image credits: Iron Ox
Latest ZipGrow Inc. Product Introduces Vertical Indoor Farming To New Growers
Controlled Environmental Agriculture (CEA) is currently undergoing an upturn in public interest as the general population begins to appreciate the importance of locally produced food from sustainable sources
September 9, 2020
ONTARIO, CA - Controlled Environmental Agriculture (CEA) is currently undergoing an upturn in public interest as the general population begins to appreciate the importance of locally produced food from sustainable sources. ZipGrow Inc.’s new product offering, the Introduction to Commercial Growing package, is designed to make commercial growing more accessible to farmers and businesses wanting to get into the CEA industry.
“As interest grows in improving food security, we wanted to make commercial growing more accessible to newcomers to the hydroponics world”, explains Eric Lang, President of ZipGrow Inc. “This new package is an accessible, and affordable entry-level product for anyone interested in testing out if controlled environmental agriculture is right for them.”
The new product package includes a discounted set of everything you need to get started, including 90 patented 8’ ZipGrow™ Towers, steel ZipRacks, LED growing lights, a seedling area, a comprehensive plumbing system, and an automatic doser from Atom Controllers. This package is not only all-inclusive, but also modular to be able to expand as the operation grows.
“This package can set someone up to produce up to 100 pounds of leafy greens or herbs such as lettuce or basil each week, and is a great way to test a pilot system in your local community”, adds Lang. “Since the start of COVID-19 we have seen interest in sustainable food sources skyrocket, and this is one way we are trying to encourage more people to see if hydroponic farming is right for them.”
The Introduction to Commercial Growing package has a flat rate shipping option for all locations within Canada and the continental United States, with shipping to other locations available at custom rates. The package will be fully installed on-site, with costs varying dependent on location. ZipGrow team members will work with customers to ensure the product is the right fit for them and ensure all training and ongoing education needs are fulfilled.
ZipGrow Inc. is an international leader in indoor, vertical farming technology. Our flagship product, the ZipGrow™ Tower, is a core component of many of the world’s most innovative farms; from indoor hydroponic warehouses to vertical aquaponic greenhouses and high-density container farms.
For more information contact Gina Scandrett at hello@zipgrow.com or at 1-855-ZIPGROW.
KUALA LUMPUR, Malaysia: This Vertical Farm Was Born In The Pandemic. Sales Are Up
The Vegetable Co. in Kuala Lumpur, Malaysia, grows vegetables under LED lights in a shipping container. “We were a nascent product in an uncertain market,” one of its founders said
The Vegetable Co. in Kuala Lumpur, Malaysia, grows vegetables under LED lights in a shipping container. “We were a nascent product in an uncertain market,” one of its founders said.Credit...Ian Teh for The New York Times
The Vegetable Co. Sits In A Shipping Container On The Edge of A Malaysian Parking Lot. It’s One of Many Small Farms Around The World Selling Directly To Consumers.
By Ian Teh and Mike Ives
Sept. 3, 2020
KUALA LUMPUR, Malaysia — The setup of the two friends’ agricultural venture was unusual. Their farm sat next to a gas station, inside a shipping container where the plants grew in vertically stacked shelves. And the timing of their first sales — during the early days of Malaysia’s coronavirus outbreak — seemed less than ideal.
“We were a nascent product in an uncertain market,” said Shawn Ng, 28, a co-founder of the vertical farm, the Vegetable Co. “We weren’t too sure if it would take off.”
“But somehow,” he added, “the market kind of played in our favor. ”As in-person shopping wanes during the pandemic, Mr. Ng’s Malaysia-based operation is one of many small farms around the world that are selling fresh produce directly to consumers in ways that bypass brick-and-mortar grocery stores.
Some farms sell on e-commerce platforms like Amazon or Lazada, Alibaba’s online emporium for Southeast Asia, or through smaller ones like Harvie, a Pennsylvania-based website that connects consumers with individual farms across the United States and Canada.
ImageShawn Ng, one of the Vegetable Co.’s founders, loaded freshly harvested produce into a car for delivery.Credit...Ian Teh for The New York Times
Others, like the Vegetable Co., sell directly to customers. “I was very ‘kan cheong’ during the lockdown period,” said one of Mr. Ng’s regular customers, Ayu Samsudin, using a Cantonese word for anxious. “Having fresh vegetables delivered to your doorstep was such a relief.”
The Vegetable Co. consists of a 320-square-foot shipping container on the edge of a parking lot in Kuala Lumpur, Malaysia’s largest city. It opened for business, with just a handful of customers, about a month before the country’s restrictive lockdown took effect in mid-March.
Revenue grew by 300 percent in the first few weeks, and the shipping container is now approaching production capacity because of high demand, said Mr. Ng’s business partner, Sha G.P.Apart from the gas station, the shipping container’s other neighbors are a driving range and an oil palm plantation. Inside, tightly packed shelves with hydroponic lettuce, sprouts and other vegetables grow under LED lights.
Mr. Ng on a delivery run in Kuala Lumpur. Malaysia has weathered the pandemic relatively well, at least compared with other Southeast Asian countries.Credit...Ian Teh for The New York Times
The wallpaper outside the growing chamber shows blue sky and clouds, evoking the view from an old-fashioned farm. But employees pace the chamber’s narrow corridor wearing rubber gloves, surgical masks and white lab coats, as if it were a hospital ward.
The founders have scant experience with traditional farming, and they speak about their work with Silicon Valley-like jargon.
Mr. Sha, who has a master’s degree in management, said he first became interested in vertical farming after watching “The Martian,” the 2015 film in which an American astronaut played by Matt Damon is stranded on Mars and learns to grow his own food.
“I was lost in awe about the degree of precision in the technology along with the elegance of the solution to grow vegetables in a zero-gravity environment,” he said. “Since then, I have gone down the rabbit hole of independent research.”
Gudrun Olafsdottir, a Kuala Lumpur resident from Iceland, said the Vegetable Co. was one of the local businesses she was supporting with a “financial hug” during the pandemic.Credit...Ian Teh for The New York Times
The coronavirus took off in Malaysia in March, after an Islamic revivalist group’s gathering there became one of the pandemic’s biggest vectors in Southeast Asia. Since then, the country of about 32 million has weathered the outbreak relatively well, at least compared with some of its neighbors. As of Thursday, it had reported fewer than 10,000 confirmed cases since the pandemic began, according to a New York Times database.
Malaysia’s initial lockdown allowed only one person per household to go outside for essential errands, and the police enforced local travel restrictions with roadblocks.
But even though the rules were gradually loosened to let most businesses reopen, many urban Malaysians have maintained the online shopping habits they developed during the initial lockdown, said Audrey Goo, the founder of MyFishman, an e-commerce platform that connects fishermen from villages along the country’s west coast with consumers in Kuala Lumpur.
Gudrun Olafsdottir, a Kuala Lumpur resident from Iceland, said the Vegetable Co. was one of the local businesses she was supporting with a “financial hug” during the pandemic.Credit...Ian Teh for The New York Times
“Not many end users are willing to go back to the wet market,” said Ms. Goo, adding that her company’s sales had roughly doubled during the pandemic. “So I think the whole business model will continue to change.”
Mr. Ng said the Vegetable Co.’s parent company, Future Farms, was now seeking seed capital to finance an expansion into a larger facility. He recently hired an architect and a software developer to design it. For now, though, the operation remains modest. On a recent afternoon, Mr. Ng climbed into his car for a delivery run that snaked through low-rise residential neighborhoods, as the sun sank below Kuala Lumpur’s hazy downtown skyline.
One of the customers on the 40-plus-mile route, Gudrun Olafsdottir, said that along with yoga and meditation, greens from the Vegetable Co. were part of a routine that helped her keep physically and mentally fit during the pandemic.
Ms. Olafsdottir, who is from Iceland and works in retail, found the farm on Facebook through a local chef who specializes in raw and vegan cooking. She said it was one of several local businesses that she was supporting these days with a “financial hug.”
“I think that we could do so many things to support those in need if we just consciously choose how we spend our time and money,” she has written on her blog. “A hug and a squeeze.”
The farm is in a 320-square-foot shipping container near a gas station, a driving range and an oil palm plantation.Credit...Ian Teh for The New York Times
Ian Teh reported from Kuala Lumpur and Mike Ives from Hong Kong.
VIDEO: USA, WYOMING - Cody’s Vertical Garden Enhances Downtown
“It’s just to get the community involved in growing edibles, besides a dirt base,” Butler said. “And it’s more of an art form, too, just to enhance this plaza that we have it in.”
August 31, 2020
By Wendy Corr
Visitors to Cody this summer might be able to pick their own salad greens straight from the garden – downtown.
This summer, a hydroponic garden was installed in Bell Plaza, a public space in the heart of downtown Cody. Bernie Butler works for the city but is volunteering her time to take care of the vertical garden that has been placed for the benefit of the community.
“It’s just to get the community involved in growing edibles, besides a dirt base,” Butler said. “And it’s more of an art form, too, just to enhance this plaza that we have it in.”
A vertical garden is just what it sounds like — plants placed in upward reaching rows instead of spread out across the ground. The plants are raised in a hydroponic system that uses nutrient-rich water for nourishment rather than dirt.
Butler said Cody is one of several Wyoming cities to embrace the vegetable growing technique.
“They partnered with Travis Hines out of Pinedale, he has Bio-Logic Designs,” she said. “He built this frame for it, brought everything down, we planted the plants, which he supplied, and filled up the tank – we have fish and aqua plants in there. He just got us going.”
The funds for the garden came from the U.S. Department of Agriculture, funneled through the Wyoming Business Council. Amy Quick, the Northwest Regional Director for the Business Council, said the project benefits communities in a number of ways.
“Eleven different communities throughout the state are participating, including, of course, Cody, but Sheridan, Rock Springs, Casper are a few other examples,” Quick said. “And it’s just a really great opportunity to get some community involvement, focus on nutrition, education, economic development.”
Butler pointed out that the produce from the garden is available to anyone.
“I do have a couple of older people that come by almost every night, and they take some lettuce and some kale, and the mint is their favorite.”
Butler adds that once colder weather arrives, the garden will move to Eastside Elementary, where students there will take over the process – and the produce.
Future of Farming: Vertical Harvest Announces Plans For New Location In Westbrook, Maine
Maine’s first vertical farm, Vertical Harvest, is dedicated to jobs serving the underemployed population and enhancing community access to exceptional farm-fresh foods year-round using less land, water, and fuel
Maine’s first vertical farm, Vertical Harvest, is dedicated to jobs serving the underemployed population and enhancing community access to exceptional farm-fresh foods year-round using less land, water, and fuel
Westbrook, Maine (July 28, 2020) – Born from the creative minds of a group of women in Jackson Hole, Vertical Harvest became the first vertical greenhouse in the United States. In the last four years, Vertical Harvest has perfected the urban farm model and will bring their second location to Westbrook, Maine. The project will start construction in 2021 in partnership with the City of Westbrook.
Vertical farming is a growing industry that uses environmentally sound practices to produce nutrient-dense food grown locally year-round, and yields more crops per-square-foot than traditional farming. Vertical Harvest has a company mission to grow both food and futures. The company pairs innovative growing technologies of vertical farming with jobs for the underemployed population in what has been proven in Jackson to be a successful model for uplifting local economies, providing fresh nutritious produce to schools, hospitals, restaurants, markets, and consumers, and embodies a commitment to civic participation, health, and the environment.
Co-founder Nona Yehia stated, “We have felt a kinship with Maine for quite some time. At our beginning stages 10 years ago, Vertical Harvest Jackson engaged the same engineer as Backyard Farms in Madison, Maine. Wyoming and Maine have more in common than just a four-to-five month grow season and drastic seasonal climates – they have polar rural and urban areas, there is deep-rooted respect for the environment, the farming and food communities are a source of pride, and there is a sense of responsibility to serve the job and food insecure population. With our second location for Vertical Harvest, we feel honored to become a part of this special state and Westbrook community.”
Pictured: Co-founders Nona Yehia (right) and Caroline Estay (left)
Vertical Harvest will generally not compete with local Maine growers. Instead, the farm lowers the need for out-of-state produce imports into Maine (representing over 90 percent of the State’s consumption), and the out-of-state jobs these imports benefit, thereby helping to strengthen the overall business base of Maine’s economy. Vertical Harvest will also support local businesses for its growing supplies, increase food security, and be part of the solution to fulfill objectives for the Maine State Economic Plan focusing on talent and innovation. In addition, Vertical Harvest will strengthen the Maine businesses it will serve by providing a stable, consistent source of produce, year-round at competitive prices.
Co-founder Caroline Estay said, “At Vertical Harvest, we have reimagined the food systems and the jobs they create to make them more nourishing, resilient, and sustainable. Maine has an impressive history of changemakers in the food and farming industry and inspiring culinary thought leaders – we are excited to bring Vertical Harvest to Westbrook and work alongside valued community members in these industries and beyond.”
The company anticipates bringing 50 full-time equivalent jobs to Westbrook, in addition to currently working with Portland-based architect and engineering firm, Harriman (in partnership with GYDE Architects in Jackson, WY where Nona Yehia is partner/co-founder).
City of Westbrook Mayor Michael Foley stated, “This exceptional mixed-use project, anchored by Vertical Harvest’s four-story greenhouse, will provide significant private commercial investment and job creation, expanded residential presence and expansion of free public parking to support growth and development of other businesses in our downtown. We are excited about the partnership and welcome Vertical Harvest to the City of Westbrook. “
Pictured: New employees get an orientation tour at Vertical Harvest Jackson Hole (L); two employees harvest produce in the greenhouse (R).
The 70,000 square-foot Vertical Harvest Westbrook located on Mechanic Street will initially grow a variety of microgreens and lettuces. It’s estimated this vertical farm will produce a million pounds of produce per year. In addition to wholesale partnerships with hospitals, corporate cafeterias, schools, chefs, restaurants, caterers and more, the Westbrook location will also have a consumer marketplace and plans for a presence at farmer’s markets.
Pictured L to R: Varieties of microgreens and lettuces grow in the Vertical Harvest flagship, Jackson Hole. Microgreen Kale (middle) is packaged for consumers.
For more information please follow @verticalharvest on Instagram, Facebook, and visit www.verticalharvestjackson.com
###
About Vertical Harvest:
Vertical Harvest is a vertical farm that provides consistent, meaningful employment for people with intellectual and physical disabilities by cultivating nutritious food for the community. The Vertical Harvest company's impact is much larger, joining private investment, public resources, and philanthropy as a model to create positive economic and social impact for communities. Vertical Harvest’s focus is to create partnerships to build cost-effective, profitable hydroponic farms that will not only act as innovative urban models for growing fresh food but will have a substantial social impact. The first of these is a state-of-the-art, three-story hydroponic farm in Jackson Hole, Wyoming.
The second location will be in Westbrook, Maine. In 2020, a documentary on Vertical Harvest was released on PBS called Hearts of Glass: https://www.heartsofglassfilm.com/
About Vertical Farming:
Vertical farming is an industry that can work to supplement traditional agriculture by developing controlled indoor growing environments that save space, water, and energy use. The UN Food and Agriculture Organization estimates that by 2050 the human population will increase by 3 billion people demanding a 70% increase in agricultural production. Globally, over 80% of arable land is in use. At the same time, food deserts, where affordable and healthy food is difficult to obtain, are becoming more common in urban neighborhoods. Hydroponic agriculture uses a fraction of the water and energy of field agriculture.
Additional Press:
Farms that grow up—rather than spread out
Vertical Harvest seeks to grow jobs for disabled in city
Is Vertical Farming The Future of Herb Cultivation?
“With vertical farming, I can plant a herb, and can be sure it'll ready to sell in five weeks,” says Berjelle. “You also have certainty about your product’s quality. That’s because the product is optimally controlled. The plant grows evenly, thanks to the LED lighting, so it tastes better too."
Berjelle van Namen, Van Namen Specialties
Berjelle van Namen’s roots lie primarily in mushroom cultivation. His father, Johan, has a farm on the banks of the Maas river in the Netherlands. Yet, a few years ago, Berjelle decided to add herb cultivation. Not in a greenhouse or in full soil; in a converted mushroom cultivation cell.
The room is illuminated with violet-colored LED bulbs, and the containers holding the herbs are stacked, one atop the other. This can clearly be considered vertical farming. This concept is gaining increasing popularity among farmers - especially those who grow herbs, leafy and micro vegetables, and edible flowers.
There have even recently been trials with soft fruit. It’s been standard practice in the mushroom world for some time now. Hence the relationship between Van Namen mushrooms and the herbs of Van Namen Specialties.
For Berjelle, it started as an experiment. He encountered this cultivation method during his internship in Finland. There, at Robbe’s Little Garden, they grow lettuce, herbs, and micro vegetables in this way. According to Berjelle, vertical farming offers numerous advantages over traditional herb cultivation.
Vertical farming’s advantages
“With vertical farming, I can plant a herb, and can be sure it'll ready to sell in five weeks,” says Berjelle. “You also have certainty about your product’s quality. That’s because the product is optimally controlled. The plant grows evenly, thanks to the LED lighting, so it tastes better too."
"It satisfies clients, who are increasingly demanding just-in-time delivery of products like herbs. Of course, we mustn’t forget the sustainable character of this cultivation method. Especially since farming like this uses very little gas and no pesticides. We’re looking for ways to be highly energy-efficient too.”
There was a demand for herbs
Berjelle now grows about 12 kinds of herbs and has added a second cell. “In this way, we can vary cultivation conditions like using different temperatures," explains van Namen. "Basil is our top seller. It’s a popular herb that sells well. It’s followed by herbs such as parsley and mint.”
Berjelles sells his herbs under the company’s own brand, Pika Surprisa, and Esperanto for ‘spicy surprises’. Still, Berjelle points out that it’s mainly enjoyable to cultivate and experiment with these herbs. “It’s not quite profitable yet. To achieve this, you’d have to seriously consider scaling up and adding rooms."
"You’d also have to see if you want to grow only one variety. We chose to grow herbs mainly because of the increasing demand for year-round delivery and consistent quality. Vertical farming guarantees this. You can also be relatively lazy with your purchases. You know what you’ll get on the day you want it."
"From the cultivation side, there aren’t as many operational issues either. Although you always have to deal with that. The only thing is, it doesn’t save labor; hands are still needed in that cell,” admits Berjelle.
Herb sales differ from those of mushrooms. “We’ve attracted many new clients who really only buy herbs, and we’ve noticed fewer clients buying both. We keep these two products separate. That’s why the herbs fall under Van Namen Specialties. For example, we export mushrooms to countries like Germany and the UK, but not yet our herbs. Perhaps we will in the future.”
For the coming months, Van Namen’s main goal is to make it through the corona crisis successfully. “The mushroom market was very volatile in these unusual times. It’s slowly recovering, but it still has a long way to go. There aren’t any major developments planned for the rest of the year, either. Now, it's mostly a matter of serving our clients well,” Berjelle concludes.
More information:
Van Namen Specialties
www.vannamenspecialties.nl
Berjelle van Namen
berjelle@vannamenspecialties.nl
Publication date: Thu 27 Aug 2020
Author: Thom Dobbelaar
© FreshPlaza.com
Micro-Naps For Plants: Flicking The Lights On And Off Can Save Energy Without Hurting Indoor Agriculture Harvests
A nighttime arrival at Amsterdam’s Schiphol Airport flies you over the bright pink glow of vegetable production greenhouses. Growing crops under artificial light is gaining momentum, particularly in regions where produce prices can be high during seasons when sunlight is sparse.
The Netherlands is just one country that has rapidly adopted controlled-environment agriculture, where high-value specialty crops like herbs, fancy lettuces and tomatoes are produced in year-round illuminated greenhouses. Advocates suggest these completely enclosed buildings – or plant factories – could be a way to repurpose urban space, decrease food miles and provide local produce to city dwellers.
One of the central problems of this process is the high monetary cost of providing artificial light, usually via a combination of red and blue light-emitting diodes. Energy costs sometimes exceed 25% of the operational outlay. How can growers, particularly in the developing world, compete when the sun is free? Higher energy use also translates to more carbon emissions, rather than the decreased carbon footprint sustainably farmed plants can provide.
I’ve studied how light affects plant growth and development for over 30 years. I recently found myself wondering: Rather than growing plants under a repeating cycle of one day of light and one night of darkness, what if the same daylight was split into pulses lasting only hours, minutes or seconds?
Short bursts of light and dark
So my colleagues and I designed an experiment. We’d apply the normal amount of light in total, just break it up over different chunks of time.
Of course plants depend on light for photosynthesis, the process that in nature uses the sun’s energy to merge carbon dioxide and water into sugars that fuel plant metabolism. Light also directs growth and development through its signals about day and night, and monkeying with that information stream might have disastrous results.
That’s because breaking something good into smaller bits sometimes creates new problems. Imagine how happy you’d be to receive a US$100 bill – but not as thrilled with the equivalent 10,000 pennies. We suspected a plant’s internal clock wouldn’t accept the same luminous currency when broken into smaller denominations.
And that’s exactly what we demonstrated in our experiments. Kale, turnip or beet seedlings exposed to cycles of 12 hours of light, 12 hours dark for four days grew normally, accumulating pigments and growing larger. When we decreased the frequency of light-dark cycles to 6 hours, 3 hours, 1 hour or 30 minutes, the plants revolted. We delivered the same amount of light, just applied in different-sized chunks, and the seedlings did not appreciate the treatment.
The same amount of light applied in shorter intervals over the day caused plants to grow more like they were in darkness. We suspect the light pulses conflicted with a plant’s internal clock, and the seedlings had no idea what time of day it was. Stems stretched taller in an attempt to find more light, and processes like pigment production were put on hold.
But when we applied light in much, much shorter bursts, something remarkable happened. Plants grown under five-second on/off cycles appeared to be almost identical to those grown under the normal light/dark period. It’s almost like the internal clock can’t get started properly when sunrise comes every five seconds, so the plants don’t seem to mind a day that is a few seconds long.
Just as we prepared to publish, undergraduate collaborator Paul Kusuma found that our discovery was not so novel. We soon realized we’d actually rediscovered something already known for 88 years. Scientists at the U.S. Department of Agriculture saw this same phenomenon in 1931 when they grew plants under light pulses of various durations. Their work in mature plants matches what we observed in seedlings with remarkable similarity.
A 1931 study by Garner and Allard tracked the growth of Yellow Cosmos flowers under light pulses of various durations. J. Agri. Res. 42: National Agricultural Library, Agricultural Research Service, U.S. Department of Agriculture., CC BY-ND
Not only was all of this a retread of an old idea, but pulses of light do not save any energy. Five seconds on and off uses the same amount of energy as the lights being on for 12 hours; the lights are still on for half the day.
But what would happen if we extended the dark period? Five seconds on. Six seconds off. Or 10 seconds off. Or 20 seconds off. Maybe 80 seconds off? They didn’t try that in 1931.
Building in extra downtime
It turns out that the plants don’t mind a little downtime. After applying light for five seconds to activate photosynthesis and biological processes like pigment accumulation, we turned the light off for 10, or sometimes 20 seconds. Under these extended dark periods, the seedlings grew just as well as they had when the light and dark periods were equal. If this could be done on the scale of an indoor farm, it might translate to a significant energy savings, at least 30% and maybe more.
Recent yet-to-be published work in our lab has shown that the same concept works in leaf lettuces; they also don’t mind an extended dark time between pulses. In some cases, the lettuces are green instead of purple and have larger leaves. That means a grower can produce a diversity of products, and with higher marketable product weight, by turning the lights off.
One variety of lettuce grew purple when given a 10-second dark period. They look similar to those grown with a five-second dark period, yet use 33% less energy. Extending the dark period to 20 seconds yielded green plants with more biomass. J. Feng, K. Folta
Learning that plants can be grown under bursts of light rather than continuous illumination provides a way to potentially trim the expensive energy budget of indoor agriculture. More fresh vegetables could be grown with less energy, making the process more sustainable. My colleagues and I think this innovation could ultimately help drive new business and feed more people – and do so with less environmental impact.
July 22, 2019 6.58am EDT Updated July 22, 2019 2.40pm EDT
This article was updated with a corrected legend on the photograph of the plants grown in 1931.
Smart Acres CEO on The launch of The UAE’s Latest Vertical Smart Farm
The launch of Smart Acres, the UAE’s latest addition to the hydroponic vertical farming industry, this week means that a line of the freshest, most nutrient-dense greens for UAE residents and businesses alike is now being produced in containers on the Armed Forces Officers Club in Abu Dhabi, with the aim to expand across the UAE
Smart Acres Is Here With Lettuce At The Helm. In An Exclusive Interview With Abu Dhabi World, Smart Acres CEO Abdulla al Kaabi Reveals What This Means To Abu Dhabi And The Farming Community On The Whole.
words Derek Issacs
If you love healthy produce, and who doesn’t, then this news is going to please you and your tastebuds no end. The only draw back at the moment is they’re not for sale in supermarkets just yet, but it won’t be long before they are.
The launch of Smart Acres, the UAE’s latest addition to the hydroponic vertical farming industry, this week means that a line of the freshest, most nutrient-dense greens for UAE residents and businesses alike is now being produced in containers on the Armed Forces Officers Club in Abu Dhabi, with the aim to expand across the UAE.
So we headed over to the St. Regis Abu Dhabi to meet Smart Acres CEO Abdulla al Kaabi to find out more.
Tell us about your background?
I am from tech and farm background. My father has a passion for farming and gardening; he’s very strict about anybody who messes around with his garden or farm. My father has a few farms across the UAE, where he grows crops and dates. When he heard that I was pursuing a project in the agriculture sector he got excited and actually gifted me a farm, which I am grateful for and will keep. However, Smart Acres, rather than the farm my father gifted me, is an urban farm.
How was Smart Acres first developed?
CEO Abdulla al Kaabi (centre)
Smart Acres was founded in 2017 and local testing began in July 2019. Smart Acres was developed by a team of experts, including myself, Director Sean Lee and Lead Project Manager, Aphisith Phongsavanh with the aim of improving food security within the United Arab Emirates and developing the country’s farming capabilities, providing a solution to potential socioeconomic threats such as pandemics and climate limitations the Middle East currently endures.
Tell us more
We planted lettuce and after a few harvests, we decided to expand from two containers to eight containers. From the two insulated containers the yield was 3.5 tons annually, which was our proof of concept. For the proof of concept, our target weight for each lettuce head was 140g. However, we have reached an average of 200g per head. I don’t think any other vertical farm here reached that quality or weight in terms of vegetables at this size.
How would you describe Smart Acres?
It is a one-of-a-kind agriculture system that is designed to produce some of the highest yields of crops within the UAE’s vertical farming industry, while introducing a new future for clean foods and allowing both business to business (B2B) and business to consymer (B2C ) sectors to locally source produce.
Tell us about the containers
We invested heavily in the containers, not just financially, and it took us a while to partner up with n.thing, a South Korean vertical farming technology company, to bring the best vertical farm here in the UAE. We had talks with other companies before and we decided to go with this one, in terms of risk, in terms of technology they are using. And the system we are using in the containers is hydroponics (growing plants without soil) which has been used by growers for hundreds of years. Techno advancements means we were able to implement the Internet of Things for operations, which helps us to monitor the entire farm in terms of humidity, temperature, and even the nutrients that goes inside the plants. Now we have our expansion plan from eight to 78 containers, which eventually will produce more than 140 tons of produce annually. We are currently in talks with private and public entities in terms of the expansion. We are also planning to have a research and development centre in order to start growing our own potato seeds in a controlled environment.
Will Smart Acres just be growing lettuce?
In our current eight containers, we grow four types of lettuce; Lolo rosso , green glace, oakleaf Batavia, but we are able to grow 30 types of lettuce. Currently we are testing new methods to improve quality and weight of the existing lettuce. The results of last month’s test resulted in lettuce whose individual heads weighed more than 200 grams on average. However, we aim to grow more than just lettuce. We have plans to eventually grow baby spinach, mature spinach, and baby arugula. Smart Acres’ vision is to expand to meet the demand of popular produce in the region such as strawberries, and, as I previously mentioned, a shift and emphasis on cultivating potato seeds.
Where can we buy your smart lettuces?
We are now supplying restaurants and hotels for free to get ourselves known, and we have had great feedback from them. We have also partnered with several restaurants and cafes around the country including Inked and Fae Cafe, and have plans to have our produce in the kitchen of dozens of other F&B outlets. The recent initiative by HH Sheikh Mansour bin Zayed, Deputy Prime Minister, Minister of Presidential Affairs, and Abu Dhabi Agriculture and Food Safety Authority (ADAFSA), stating that all major grocery stores in the capital must allocate space for local produce means we are perfectly poised to enter local supermarkets. We have had lots of offers from Abu Dhabi Holding and other government entities that are members in the food security committee to buy our whole produce. Currently we are focused on our actual produce itself, in terms of quality, weight.
Posted in Features, Food, Life, News
Tagged agriculture system Abu Dhabi, CEO Abdulla al Kaabi, Clean foods UAE, food security UAE, SMART ACRES Abu Dhabi, st regis abu dhabi, UAE Climate Change Risks and Resilience, UAE farms, UAE’s vertical farming industry, vertical farming Abu Dhabi
US (NY): Wall-To-Fork Fresh Produce Comes To Monsey
The iconic Evergreen Market is debuting a revolutionary 20-foot high geoponic (soil-based) wall farm that lets customers not only choose clean, fresh-picked produce but also see exactly where it comes from
The world of freshly harvested greens and herbs is looking up – literally – in Monsey, NY. The iconic Evergreen Market is debuting a revolutionary 20-foot high geoponic (soil-based) wall farm that lets customers not only choose clean, fresh-picked produce but also see exactly where it comes from.
The pesticide-free lettuce, kale, arugula, basil, and cilantro from Evergreen’s on-site farm are sold at competitive prices in individual pots, making the “buying local” experience more convenient than ever. Pesticide-free and grown in soil that is never exposed to bugs, all products are Star-K Kosher Certified for purity.
“We are gratified to be the first kosher supermarket in the country to introduce the Vertical farm,” said Malki Levine of Evergreen. “Our customers are very much looking forward to buying fresh produce that is grown in our own backyard rather than being transported on long hauls from farms across the country. They will also appreciate the significantly reduced level of infestation, a major concern of kosher consumers.”
Shoppers can visit the thriving vertical farm when they visit the store. The state-of-the-art system features a controlled, sterile environment with soil beds containing a proprietary mix of minerals and nutrients. Advanced sensors constantly monitor, irrigate, and fertilize the crops throughout every growth stage.
Evergreen’s wall farm is the latest installation from Vertical Field, an Israeli ag-tech company that produces innovative vertical agricultural solutions that help the environment, improve human health conditions, and make fresh, delicious produce available all year round.
Geoponic (soil-based) vertical farming yields a new crop every few days, ensuring that fresh greens and herbs will always be in season in Monsey. The sustainable and eco-friendly method produces cleaner, healthier, tastier veggies than those shipped from miles away. And, reduced soil-to-plate time means a longer shelf life and fewer hands involved – a welcome benefit in the age of Covid-19.
“We are extremely excited with the partnership with Evergreen,” said Guy Elitzur, the CEO of Vertical Field. “They are precisely the type of supermarket that has the right customer base and will successfully integrate the latest technological advances in geoponic farming.”
For more information:
Vertical Field
info@verticalfield.com
www.verticalfield.com
Publication date: Tue 18 Aug 2020
Temasek Backs US $30m Firm For Vertical Farming Innovation to Boost Singapore's Food Supply
Called Unfold, it is a tie-up between Singapore state investment firm Temasek and a unit of German pharmaceutical and life sciences giant Bayer
Temasek Is Partnering With A Unit of Bayer To Form A US $30 Million
Company To Develop Breakthroughs In Vertical Farming.
August 12, 2020
SINGAPORE - A new US $30 million (S$41.2 million) company has been formed to develop breakthroughs in vertical farming, a move that will help to further reinforce Singapore's food supply.
Called Unfold, it is a tie-up between Singapore state investment firm Temasek and a unit of German pharmaceutical and life sciences giant Bayer.
The Straits Times understands that they will have an equal share of the company, which is incorporated in the United States.
Its primary focus is on improving the quality and variety of food as well as boosting the efficiency of its production, including that of popular vegetables such as lettuce and spinach.
In doing so, it will ensure the safe and reliable supply of food, something that is vital for countries with little arable land and in times of crisis like the Covid-19 pandemic, said Bayer on Wednesday (Aug 12), when announcing the union between its investment unit Leaps by Bayer and Temasek.
Temasek's head of agribusiness, Mr. John Vaske, noted that food security is a priority for Singapore, pointing to the country's "30 by 30" goal, which is to produce 30 percent of its nutritional needs locally by 2030.
He also told The Straits Times that Singapore has been formative in developing vertical farming. "So, we have insights and knowledge of the industry that Unfold can benefit from through the set-up of its commercial, research, and development operations here."
These operations will also be established in California, where Unfold will be headquartered in the city of Davis.
The focus on the genetic potential of vertical farming also sets the company apart from most vertical farming start-ups, which invariably concentrate on developing more efficient infrastructures, Bayer said.
The aim of the venture is to improve the quality and variety of food as well as boost the efficiency of its production. PHOTO: BAYER STOCK PHOTOS
Unfold has already entered into an agreement for specified rights to germplasm, or seed genetics, from Bayer's vegetable portfolio, a move that will enable it to develop new varieties of seeds. It also plans to come up with agronomic advice that is tailored for growing crops in the unique indoor environment of vertical farms.
These farms, also known as indoor farms, leverage on artificial light to grow crops, are less dependent on man-made chemicals, and optimize the use of water.
The company's chief executive officer is Dr. John Purcell, who was previously Bayer Crop Science's head of vegetable seeds research and development, said Bayer in its statement.
Dr. Purcell said that Unfold's investment in germplasm and crop growth models is timely as the two fields are "largely underserved"."
Some technology companies do not have access to germplasm resources. The power of Unfold is that we will combine the expertise and 100 percent focus on the genetics for vertical farming, with access to the best in class germplasm of the Bayer vegetable seed business," he added.
www.bayer.com
www.leaps.bayer.com
www.temasek.com.sg
unfold.ag
Lead Photo: PHOTO: BAYER STOCK PHOTO
Infarm, The New Generation of Farm
Labeled as the new generation of farm, German startup Infarm farms everywhere—in supermarkets, restaurants, bars and warehouses—lowering the carbon print by cutting out millions of miles between the farm and the final consumer
Labeled as the new generation of farmers, German startup Infarm farms everywhere—in supermarkets, restaurants, bars and warehouses (Credit: Infarm)
by Melanie Epp
August 11, 2020
Infarm was founded in 2013 by Osnat Michaeli and brothers Erez and Guy Galonska. They built the world’s largest in-store farm in Metro’s flagship store in Paris.
(This article was first published in our sister publication AgriExpo)
Labeled as the new generation of farm, German startup Infarm farms everywhere—in supermarkets, restaurants, bars, and warehouses—lowering the carbon print by cutting out millions of miles between the farm and the final consumer.
It all started when two people from Israel came to Berlin and couldn’t find their typical herbs—and couldn’t understand why, when they tried, the herbs wouldn’t grow in Berlin. They picked up the idea of vertical farming and a hydroponic method of farming to create their farming system which resembles a giant glass-door fridge. They understood, then, that people would no longer need to import herbs from distant countries because they could be grown on-site, explained Key Account Manager at Infarm Jakob Peter
“We can grow herbs throughout the year at the same price. We’re focusing on cities for our pilot projects, but we’ll go into rural areas and plan on producing 1000 farms in the next years.”
The startup always looks for places in need before deciding where they should implement their idea in order to fill in the gaps. They’ve already put their farm in restaurants, including Good Bank Restaurant in Berlin, with several other projects underway. They’re currently operating more than 50 farms across Berlin in supermarket aisles, restaurants kitchens, and distribution warehouses.
The company has deployed operational farms in Copenhagen, London, and Seattle. One thousand in-store farms are being rolled out in Germany alone. Infarm is expanding to other European markets every day, partnering with leading supermarket chains, and planning its North America expansion program. For co-founder Osnat Michaeli,
“Recognizing the requirements of our customers, we have recently launched a new product: the DC farm, a ‘Seed to Package’ production facility tailored to the needs of retail chains’ distribution centers.”
Courtesy of Infarm
How the Farm Functions
The farms are connected to the internet and information is exchanged via the cloud. So they can “communicate with all the farms” no matter where they are. This hyper-connected solution is all about urban precision farming.
It’s 2m² with several levels and can produce 1,200 herbs per month (per farm), or 800 heads of lettuce at 800 grams each. It’s a modular system and can have both herbs and lettuce. It can be placed in offices, dead space, storage facilities and idle buildings.
The farm allows exact monitoring of light, climate, pH value of water, etc. and can be tailored depending on the type of produce. The company ensures transportability and availability of herbs and lettuce via the information stored in the cloud, attributing the system the title “harvest on demand”. Infarm generates transparency for end-users and can initiate discussion between family members when they see the farm. But the product has to be good for this concept to work.
“A fancy vertical farm with the best LED lighting system would be useless if the end result equalled bad produce.”
Its hydroponic system uses 90% less water than conventional farming and only needs water replacement twice a month for hygiene purposes. No pesticides are needed and the product can be taken directly from the farm, so it’s convenient. Herbs are always delivered with the roots and must be placed in water to remain fresh and good for two days. The door of the farm is always locked and only trained InFarm employees can open the door for hygiene reasons.
“We offer a service. We don’t sell a farm. We own the farm and you pay a monthly rent. We harvest for you. Our technicians come when there are issues with the farm.”
As each member thinks like a farmer, having a background in farming, they define themselves as a farming business. They even produced all the technical products involved in the farming system themselves.
Courtesy of Infarm
Retailers willingly welcome the concept as it provides a larger variety for clients, and an added bonus is that retailers can set their own prices.
After introducing the concept of in-store farming to the world from Metro Cash & Carry in Berlin, Infarm and Metro partnered again. In 2018, they inaugurated the world’s largest in-store farm in Metro’s flagship store Paris. The 80 m2 vertical farm produces approximately 4 tonnes of premium quality herbs, leafy greens, and microgreens annually. Metro will become completely self-sufficient in its herb production with its own in-store farm.
This urban farming solution of in-store farming impacts the environment in a positive way: It reduces CO2 simply by cutting down the supply chain, avoiding major transportations from various countries. The startup is currently in contact with universities to do research on how much CO2 they’re reducing compared to the typical supply chain.
Basil at Metro
Fifth Generation Grower Follows In His Father's Footsteps
Worldwide LocalSalads is a new vertical farming company, currently raising funds to build their first fully commercial warehouse farm
Matthew, son of Grahame Dunling
Worldwide LocalSalads is a new vertical farming company, currently raising funds to build their first fully commercial warehouse farm. The company was started by Matthew Dunling, who is the 5th generation grower of his family and son of Grahame Dunling. He has a passion to follow in his father’s footsteps and is powered by the knowledge that he has been taught by a pioneer in the industry.
Building his own view
Matthew has been working quietly behind the scenes as he builds what he calls a game-changing view on how vertical farming should be operating. "For the past few years I have been watching how vertical farms are being set up and operated and I still believe that so far from a truly commercial perspective they are a long way from being what experienced growers would call a commercial farm." Matthew’s view stems from his family's long involvement in commercial horticulture and growing up surrounded by commercial glasshouses in Yorkshire in the 1990s.
"I think when we are talking about sustainability, we have to realize that there are three elements to sustainability – social, environmental, and economical. Each of these has to have a positive impact and be profitable to allow the business to survive on its own and not on needing a constant stream of investment to allow it to survive."
Project and business model
What is looking like an exceptional project and business model with huge scale for growth and expansion is an exciting venture for someone who has so much family history in the industry.
"This farm will consist of a minimum of 2000 square meters, containing a fully automated system where we can produce quality produce which will bring the flavour back to salads. We have the most advanced technology allowing us to track, trace, and control every element in our warehouses from any location in the world. We can do this by using our custom computer system which has all the control parameters integrated on-board to realize the required conditions from climate, CO2, irrigation to lights, and nutrition.
"This feedback will be presented in data and graphical overviews allowing us to make decisions according to the required circumstances, and then via dashboards, the required settings can be made. So, a unit in the UAE can be controlled from the UK and every measurement unit changed remotely. Our track and trace system will also allow me to see daily sowings, harvest, and sales from anywhere in the world, therefore allowing us to anticipate and measure every detail from seed to harvest. With all this data we can guarantee the perfect crop for every punnet.
"The exciting part of this technology is that it is constantly learning and adapting based on crop requirements and growing results in combination with our domain knowledge and AI. Our product line to start with will be a combination of baby leaf salads and triple head lettuce, we will then introduce other crops which we have run successful trials on. We can produce the same quality and quantity daily and this ensures a 365-day supply chain allowing the consumer to have confidence in our brand."
Partnering with other companies
Matthew has partnered LocalSalads with some of the largest horticultural leaders from commercial growing on large scale projects around the world. "We have joined together some of the best companies in the world of horticulture, each with decades of experience, to create a bespoke commercial grow system that is unique to the industry. The ability to fully understand the ins and outs of growing and supplying an exceptional standard of crop to supermarkets while reducing our impact on the environment is the most important factor to me."
Worldwide LocalSalads are currently seeking investment to establish a commercial warehouse and to begin their expansion phase.
For more information:
Worldwide LocalSalads
Matthew Dunling, CEO
matthew@localsalads.com
Publication date: Fri 14 Aug 2020
Hydroponics – The Pros And Cons of Growing In Soilless Medium
Hydroponics is the practice of growing food with no soil involved. Hydroponic operations may bring food to places where it would be difficult to obtain. It may also assist in the flaws of our current food system
Posted by: Alejandro Gutierrez
Hydroponics is the practice of growing food with no soil involved. Hydroponic operations may bring food to places where it would be difficult to obtain. It may also assist in the flaws of our current food system.
In 2018, the CDC and the FDA issued two safety alerts for Romaine Lettuce in seven months. Consumers across the United States were urged to avoid Romaine lettuce because of E. coli infection concerns. It took weeks for the FDA to announce that the agency found the source of the contamination. The advisory prompted many food stores, including Whole Foods to remove all Romaine lettuce from their shelves.
Image by Gerd Altmann from Pixabay;
Situations like these are scary for consumers. And not surprisingly, they’re also angry. People are frustrated about how little they know about the source of fresh produce they buy at grocery stores. Urban farming ventures are taking advantage of concerns about the safety of fresh food. Food miles also become relevant. Consumers desire to avoid fresh food that may have been grown with unfavorable conditions. In some cases, pesticide drift from near farms also poses a threat.
Hydroponics offers an answer and a solution to all these concerns. And it presents an opportunity for healthy and eco-conscious people to gain control over the source of their fresh food.
Photo by Harits Mustya Pratama on Unsplash
Let’s look at the pros and cons of hydroponics. We’ll look at the advantages and disadvantages that apply to urban farming companies catering to local consumers. Followed by those to home gardeners who are involved in hydroponics on a vastly smaller scale.
The Pros and Cons of Hydroponics for Urban Farms
Advantages
In many cities, urban farms bring business to abandoned buildings and decaying neighborhoods. Their presence benefits the area and encourages the restoration of unused and abandoned buildings.
Urban farms create jobs in areas with limited or non-existent job opportunities.
Hydroponic growing offers training opportunities for young people in the community, providing skills they can be used in later life.
Community growing brings fresh food to “food deserts,” eliminating the excuse that area residents had for not eating healthier foods.
Growing hydroponically within the city gives people access to locally grown food that doesn’t have to travel so far.
Food grown on urban farms is picked at the peak of freshness, so it’s higher in nutrition.
Urban farms lower the carbon footprint of food production. Because they use so water efficiently, hydroponic systems are far eco-friendlier. And the food doesn’t have to travel as far. The use of LED lights increases the energy-efficiency of hydroponic systems.
Government officials have instant access to information about hydroponic produce and its path from the controlled environment to the consumer.
Consumers have the assurance that there won’t be any problems with bacterial contamination. They can trust the source of the produce they buy.
Access to high-quality fresh, locally grown produce means that they don’t have to buy more than they can use. This ensures they’re not wasting food or throwing money away.
Hydroponics eliminates the need to use chemical pesticides and insecticides
Photo by Nolan Issac on Unsplash
Photo by Fitleaf
Empty/Abandoned warehouse has the potential for Hydroponic Growing
Disadvantages
Urban agriculture doesn’t solve the problems of gang violence and crime in low-income neighborhoods but it’s a great start.
Businesses that want to establish urban farms in big cities have to go through lengthy applications. From the business license to the zoning permit, it may be a tedious process.
An urban agriculture venture isn’t likely to bring lots of jobs to the community in the short run. It is not until it establishes itself that results come in the long-run.
It will take time for the company to create the conditions for growing conditions. Assembling a hydroponic system that can handle large scale food production will also require some effort.
The company will need to consider transportation and parking needs for the employees. There may be concerns regarding parking for workers; having an impact on the parking situation for people who live in the neighborhood. However, a good solution with be biking
There may be a high cost of installing a backup power system (like generators). This is necessary because the damage of potential power failures would inflict significant losses.
Pros and Cons of Hydroponics for Home Growers
Positive Benefits of Hydroponic Gardening at Home
Hydroponics brings plants into the home, and the presence of plants improves air quality and overall health.
Hydroponics encourages people to take an interest in the origin of their food. It also gives them insight on what it takes to bring it to their tables.
Individuals who have hydroponics systems in their homes have access to better quality, fresher, and more nutritious food.
When you have a hydroponic system at home, you’re able to pick fresh produce just before using it. There is then less chance that fresh vegetables will sit in your refrigerator because you forget about them.
Because you can pick fresh food when you need it, you’ll cut the cost of your weekly grocery bills. The money you save from buying fewer groceries can go towards clearing debts or in savings.
You’ll get a tremendous and invaluable sense of satisfaction from being able to be more self-sufficient.
Since you’re buying the seeds for your hydroponics system, you can be certain of their origin.
You can plant and harvest fruits and vegetables grown at your own standard. You are free of paying the premium that is standard for food products that bear the “certified organic” label. This label usually carries the charge to the consumer.
Negatives of Hydroponic Gardening at Home
The cost of purchasing equipment. Regardless of whether you buy kits like the Tower Garden, or buy the components to build your own. While building a system isn’t cheap, the process is educational and fun.
Unless you buy a kit that provides instructions, you’ll have a harder time assembling your system and getting it started.
If you buy a kit, you’ll eventually need to purchase replacement parts, additional accessories, and supplemental nutrients. You should factor these things into the total cost of buying and operating a hydroponics system at home.
No matter how energy-efficient your system manufacturer claims it is, there will be an extra load on your electrical system. A hydroponic system will increase your utility bill throughout the year. With this issue, eco-friendly alternatives arise, such as solar panels which should be implemented if possible.
Unless you buy a system that is fully automated, you’ll have to constantly monitor nutrient and water levels. You may also have to turn the lights on or off. Don’t expect to have a productive hydroponic garden unless you’re willing to put the effort in. Checking your plants every day is a must. Observing them will ensure that their growing conditions are acceptable.
Failing to add water when the reservoir needs it, may burn your motor out, and you may weaken or kill the plants. That would be a significant financial setback.
A power failure will alter the growing conditions in your hydroponic unit. An extended power failure will deprive your plants of light, water, and oxygen. That’s a recipe for their death.
Hydroponics is no different from traditional gardening in that you get what you put into it. Some of the most significant advantages include being able to grow what you want and when you want to grow it, not being tied to traditional gardening seasons, and not having to do as much maintenance as you would if you tried to grow your food in the ground. A well-maintained hydroponic garden will give you access to healthy and nutritious food at any time. You’ll never have to rush to the grocery store for something because you don’t have it on hand.
Photo by Fitleaf
Bowery Farming Wants To Make Lettuce Safe, Smart And Tasty
Grown indoors, lettuces, greens and herbs are non-GMO, free from pesticides “and grown with complete transparency,” says Katie Seawell, Chief Marketing Officer
August 12, 2020
For decades, consumers have been on a quest for cleaner, safer produce — and agricultural methods that are good for both the palate and the planet.
Bowery Farming, the New York-based indoor farming start-up, thinks it’s mastered the recipe, especially given increasing safety concerns.
Grown indoors, lettuces, greens, and herbs are non-GMO, free from pesticides “and grown with complete transparency,” says Katie Seawell, Chief Marketing Officer. “We are deeply committed to increasing access to high-quality delicious food. We’re going to build an enduring brand — we hope a generational brand — that emotionally connects with consumers.”
Its main selling point? “Our produce tastes better, too, and that means a lot to our core audience.”
At present, the vast majority of produce isn’t branded, “and highly commoditized, not unlike coffee used to be,” she says. “I spent 15 years at Starbucks before joining Bowery a year ago, and I see a lot of similarities. Starbucks is a very mission-driven company, and so is Bowery. We are committed to disrupting the food-supply vision. And through technology, we want people to think differently about how we grow the food we eat.”
Currently, Bowery is selling its products in retail chains such as Walmart, Giant, and Whole Foods Market. It’s also available on Amazon Fresh and believes e-commerce will be one of its biggest sources of growth. “It’s a great cross-section of retailers, and part of our goal-to democratize access to our produce.”
Seawell says it is preparing ads set to break later this year, based on consumer research that uncovered ongoing concerns about widespread lettuce recalls for problems like E. coli and Cyclospora infections.
Mustache is the ad agency, and it also worked with Red Antler for a brand refresh and a new website.
Seawell says the pandemic has also intensified interest in safer, healthier foods. It’s also accelerated awareness of America’s gaping inequalities and inefficiencies in the food system.
So far, Bowery has two farms in Kearny, New Jersey, and the a outside of Baltimore. With its modular technology, it hopes to expand soon. Providing fresh food for underserved communities is also part of its mission, which translates into partnerships with nonprofits, including DC Central Kitchen and Table to Table.
Correction: An earlier version of this story misspelled CMO Paula Seawell’s name, as well as the location of two of its farms. They are in Kearny, New Jersey.
Albertsons To Bring Plenty Leafy Greens To 400-Plus Stores
Plenty products are already available in some Safeway and Andronico’s locations in the Bay Area, and the plan is for more of the company’s stores in California — Albertsons, Vons and Pavilions locations — to also carry Plenty products as supply increases
August 12, 2020
Boise, Idaho-based Albertsons has entered into an agreement with South San Francisco, Calif.-based Plenty Unlimited to bring its leafy greens to more than 430 California stores.
Plenty products are already available in some Safeway and Andronico’s locations in the Bay Area, and the plan is for more of the company’s stores in California — Albertsons, Vons and Pavilions locations — to also carry Plenty products as supply increases, according to a news release.
Stores plan to carry four Plenty products to start: baby arugula, baby kale, crispy lettuce and mizuna mix.
“We pride ourselves on offering fresh, quality products that surprise and delight our customers,” Geoff White, executive vice president of merchandising for Albertsons, said in the release. “Plenty’s data-driven and sustainable methods are truly innovative, and we look forward to bringing their unique and exciting products to more customers in California as they scale their operations.”
The company’s indoor vertical farm is powered by wind and solar energy, and its operation leverages customized lighting, machine learning and data analytics, per the release. The farm can grow a million plants at a time and process 200 plants per minute.
Lead Photo: Albertsons and Plenty announced a new partnership. ( Albertsons and Plenty )
Related Topics: Produce Retail Sustainability Lettuce
VIDEO: CubicFarms Customer Spotlight: Swiss Leaf Farms
Swiss Leaf is supplying retailers across Western Canada, including Safeway, IGA, Thrifty Foods, Freson Bros. and FreshCo, with fresh lettuce, herbs, and microgreens grown inside a CubicFarms system
We are proud to spotlight our awesome customer – family-owned Swiss Leaf Farms in Busby, Alberta.
Swiss Leaf is supplying retailers across Western Canada, including Safeway, IGA, Thrifty Foods, Freson Bros., and FreshCo, with fresh lettuce, herbs, and microgreens grown inside a CubicFarms system.
Watch our short video on Swiss Leaf here!
Publix Grows Hydroponic Produce At Greenwise Store
Publix has partnered with local hydroponics firm Brick Street Farms to grow, pack and harvest hydroponic lettuce in a container farm located outside its Lakeland, Florida Greenwise Market store
Krishna Thakker@krishna_thakker
Aug. 3, 2020
Dive Brief:
Publix has partnered with local hydroponics firm Brick Street Farms to grow, pack and harvest hydroponic lettuce in a container farm located outside its Lakeland, Florida Greenwise Market store.
The 40-foot container farm will grow an equivalent of 2.5 to 3 acres of lettuce and can operate 365 days a year in any weather conditions, Brick Street Farms told Grocery Dive in an emailed announcement. It substitutes soil for mineral-rich water, which means no pesticides are needed. The container farm uses 90% less water than a traditional farm and produces 720 heads of lettuce each week.
Customers can watch the produce grow through a window on the side of the container and purchase heads of lettuce inside the store.
Explore how the current landscape is impacting coffee manufacturers and how organic and fair trade can help ensure long-term success of the industry.
Dive Insight:
Publix has recently stepped up its partnerships in alternative agriculture. Earlier this year, the company began hosting Vertical Roots' interactive mobile hydroponic farm in the parking lots of its grocery stores and Greenwise locations. In March, Publix began selling microgreens from Kalera, a hydroponic farm on top of a Marriott hotel that lost all its business due to coronavirus, at 165 stores.
Hydroponic farming has been plagued by inefficiencies and high costs in the past, but improvements in technology are helping suppliers better meet retailers' demands for pricing and scale. On-site farms also add a bit of theater that can draw curious shoppers to stores.
Publix isn’t the only food retailer exploring this field. Kroger last year installed mini hydroponic farms in a handful of Seattle stores in partnership with Infarm, a start-up based in Germany. Around the same time, Gordon Food Service and indoor farming startup Square Roots opened their first co-located hydroponics farm on Gordon’s headquarters in Wyoming, Michigan. H-E-B and Whole Foods have also experimented with hydroponics in and around their stores.
Having a hydroponic farm at the store removes the need for transportation and storage of lettuce before it hits shelves, according to Brick Street Farms. It also allows Publix to sell the produce in-season all year round, providing some supply stability.
Although omnichannel business is booming for grocers like Publix right now, many are looking for ways to drive traffic to their stores, where they can make the most money per order. Grow farms and other safe, eye-catching attractions could be one way to accomplish this.
Follow Krishna Thakker on Twitter
Lead Photo: Permission granted by Publix
Filed Under: Fresh food Natural/organic
Local Company Providing Fresh Produce, Tools to Grow It All Year Long
Since opening its doors last July, Cold Acre Food Systems has been perfecting its indoor hydroponic growing systems for greens and herbs that can be harvested continually throughout the year.
August 6, 2020
The Yukon isn’t the place in the world most suited to year-round farming, given its long winters and short, unpredictable summers, but one local company is trying to change that.
Since opening its doors last July, Cold Acre Food Systems has been perfecting its indoor hydroponic growing systems for greens and herbs that can be harvested continually throughout the year.“
Hydroponics is a very old growing system and can be done in different methods,” said Carl Burgess, Cold Acre Food Systems CEO. “It’s essentially nutrient water delivered to roots to grow plants.”
The benefit of it in food production for a community sense is that there is less soil management because there is no soil management and in that way it can stabilize production year-round,” Burgess added.
The company does the majority of its farming in two shipping container-style growing facilities located on Titanium Way in the Marwell industrial area.“
Right now we are operating 6,000 planting spaces,” Burgess said. “One of those (containers) is basically equivalent to an acre of a market garden,” and “one container can give, at minimum, a weekly supply of greens to about 100 to 200 people.”
Denise Gordon, Cold Acre Food Systems lead grower, holds trays of microgreens in front of their growing unit in Whitehorse on July 26, 2020. (Crystal Schick/Yukon News)
Environmentally, the system uses 10 to 20 percent less water than the traditional method of growing, Burgess said. The carbon footprint is also greatly reduced since produce only has to travel a couple of blocks to its destination compared to being shipped on trucks, food waste is almost nonexistent because of the high reliability of growing indoors, the company uses compostable packaging, and there are no storage facilities.“
We harvest and go,” Burgess said. “It’s usually within two hours of harvesting that the produce is in the grocery stores or dropped off at someone’s home.”
What began as some test lettuce crops have turned into a diverse selection of leafy greens, like bok choy, arugula, kale, mizuna, and rainbow chard, as well as several different types of microgreens, which are similar to sprouts in appearance, and basil. The company is also experimenting with growing edible flowers and mushrooms.
Cold Acre Food Systems currently sells the vegetables it grows to several grocery stores in Whitehorse, restaurants, and cafes, and through a subscription box.“
The last year of business has been lots of fun,” Burgess said. “We went from being a very small food producer to a medium-sized food producer (in the Yukon).”
But selling the vegetables it grows isn’t the end game for this company. Building, selling, and installing growing systems is also part of Cold Acre’s business model. The company can build custom growing facilities for just about any client, from smaller at-home units to the larger commercial shipping container-style units.
Right now there are two large units that will soon be providing fresh produce to Yukon communities. The first, in partnership with the University of Calgary, is at the Kluane Lake Research Station near Silver City. Once it is up and running it will provide food to the Haines Junction and Burwash Landing areas. The second, currently still in Whitehorse, is owned by Na-Cho Nyäk Dun Development Corporation (NNDDC) and will be ready to feed people in the Mayo area this spring.
Leafy greens grow under neon lights in a shipping container style facility in Whitehorse on July 26, 2020. (Crystal Schick/Yukon News)“
We are currently fabricating a small-scale unit for demonstration/growing inside the Mayo Foods Store as part of the NNDDC project,” said Burgess.
The objective of Cold Acre Food Systems is to reduce food scarcity in the North and to enable everyone access to fresh produce year-round. “Success will be twofold,” said Burgess. “Our goal is to activate indoor growing. So success will look like a handful of growing facilities around that we either deployed or helped deploy. And success for us looks like a large growing facility that’s displacing a number of food products that right now are coming up the road and doing that cost effectively for consumers.”
Contact Crystal Schick at crystal.schick@yukon-news.com
Tall Lettuce Farm To Rise in Houston Industrial Building
It will be the fourth facility for the company, which opened a large Orlando location this year after proving the concept with The HyCube, a modular vertical farm built to supply the Marriott Orlando World Center on-site in 2018
July 31, 2020
Kalera, an Olrando, Fla., company, has selected a new industrial building in the northeast Houston submarket for what would be its largest hydroponic farm yet, producing nearly 5 million pounds of artisan lettuces a year as part of a strategy to grow food near where it is consumed in a high-tech, earth-friendly manner.
It will be the fourth facility for the company, which opened a large Orlando location this year after proving the concept with The HyCube, a modular vertical farm built to supply the Marriott Orlando World Center on-site in 2018.
At 83,436 square feet, the building, at 7159 Rankin Road in Humble, will be 2½ times the size of the newest Orlando farm, and about 12 percent larger than one going up in Atlanta. The vertical farms are part of a plan to scale the company across North America and globally.
“What we’re doing is bringing back what used to always be the normal, which is to eat where you are, and to eat produce that is not weeks old,” said Daniel Malechuk, CEO of Kalera.
Kalera wants to take a bite out of the lettuce market, which is concentrated on traditional farms in California and Arizona. Its cleanroom technology process eliminates both the need for pesticides and washing and processing the lettuces to prepare them for shipment up to 1,200 miles or more by truck.
The Kalera farms, which grow lettuces by stacking them in LED-lit warehouses, are designed to use 95 percent less water than traditional farms. It takes six weeks from seed to harvest, shaving about two weeks off the traditional timeline. The process also protects against pathogens such as E. coli.
With COVID-19, consumers have a heightened concern for where products come from and how many people have touched them, said Malechuk.
When it opens in late spring 2021, Kalera will work with local grocers and major food distribution companies to deliver produce to stores, restaurants, schools, hotels, hospitals, and cruise lines the same day harvested. The prices will be in line with traditional artisan lettuces, Malechuk said.
The facility, which will employ 55 to 70 people, will serve Houston as well as markets within a few hours away by truck. Lettuce harvested in the morning could be served at a restaurant in Dallas the same evening.
Kalera is the first tenant in Parc 59, a two-building development of Jackson-Shaw and Thackeray Partners off U.S. 59, just north of Beltway 8. It’s leasing the rear-load building with a clear height of 28 feet. A cross-dock building with 196,064 square feet and clear height of 32 feet is available for lease. The building is suited for warehousing, manufacturing, distribution, and assembly.
“The building’s prime location in Houston was the perfect fit for all of Kalera’s needs to serve its customers seamlessly and deliver high quality, fresh products to the Houston market and regionally,” Grant Pearson, vice president of development at Jackson-Shaw, said in an announcement.
Jason Dillee and Nathan Wynne of CBRE represented the landlord, while Mike Spears and Derek Riggleman of Lee & Associates represented Kalera in the 10-year lease. Terms were not disclosed.
The Parc 59 project team includes Cadence McShane as a general contractor and Powers Brown Architecture.
katherine.feser@chron.com
twitter.com/kfeser
PHOTOS:
1. Malechuk holds a head of lettuce at HyCube, Kalera’s vertical farm on-site at the Photo: Kalera
2. Kalera uses cleanroom technology and processes to eliminate the use of chemicals at its vertical farms. The Orlando-based company says its lettuces consume 95 percent less water compared to field farming. Photo: Kalera
3. Kalera, a vertical farming company, leased a new 83,436-square-foot building in Parc 59 at 7159 Rankin Road in Humble. Jackson-Shaw developed the two-building, 279,500-square-foot Parc 59 with equity partner Thackaray Partners . Photo: Jackson-Shaw
Katherine Feser
Follow Katherine on:
http://www.facebook.com/home.php?ref=home#!/katefeserkfeser
Katherine Feser covers a variety of subjects for the Houston Chronicle Business section. She coordinates some of the paper's most popular special sections, including the Chronicle 100, Home Price Survey, and Top Workplaces. She compiles many of the staples of the section, including the daily markets page, People in Business, event listings and real estate transactions.
Past Articles from this Author:
US: NEW JERSEY - Will NJ's Million Dollar Investment In Vertical Farming Yield Long Term Growth?
Amidst the growth of urban farming projects in the US, a notable development took place earlier in June with the announcement that Jersey City, New Jersey, is to fund the construction and operation of 10 vertical farms in the city; the first municipal vertical farm program in the country
Written By: Theo Longsdon, Agritecture Intern
Amidst the growth of urban farming projects in the US, a notable development took place earlier in June with the announcement that Jersey City, New Jersey, is to fund the construction and operation of 10 vertical farms in the city; the first municipal vertical farm program in the country.
The city has partnered up with AeroFarms in a three-year contract worth $987,000 - with just over half of this sum funding the construction of the farm units and the rest covering the project’s maintenance. The farms will use aeroponics to grow a range of vegetables and will be situated at senior centers, schools, public housing complexes, and municipal buildings across the city, taking six weeks to install, and the first vegetables being ready just two weeks after.
The principal motive behind the program is the recognition that there is a growing need to enhance access to locally grown nutritious food and improve the diet and overall well being of citizens. This is in part related to the impact of Covid-19, which according to Steve Fulop, the mayor of Jersey City, has had a “disproportionate impact on people with pre-existing heart conditions, high blood pressure, obesity and diabetes which is directly linked to a person’s diet”. The venture will seek to counter these issues and promote a healthy, sustainable lifestyle through producing 58,000 lb of fresh vegetables over three years – roughly equating to 100,000 servings – and through holding dietary workshops and health screenings for participants. The hope is that a surge in awareness about healthy eating practices, coupled with the distribution of fresh, nutritious produce, will drive a change in people’s eating habits that leads to improvements in the wider, long-term health of the community.
The creation of jobs will be a further benefit of the program. AeroFarms are significant job providers; they have created about 120 jobs through their projects in Newark, and their new indoor vertical farming facility in Danville is projected to generate 92 jobs for the area. Whilst there has been no indication about the exact number of jobs that will be created as part of the program, with the introduction of 10 farms across the city it is clear a number of employment opportunities will arise, thus helping to stimulate economic development in the area.
Yet despite these upbeat anticipations, the cost of constructing and maintaining the 10 vertical farms is high, with the contract worth just under $1m. By AeroFarms’ own estimation the 10 farms will produce around 58,000 lb of produce over their 3 years, meaning that it will cost the city about $17 to produce one lb of produce. This is a colossal sum and represents an expensive economic venture in a time when the city faces a $70m budget shortfall as a result of Covid-19.
In such a climate, an alternative option for the city would be to invest money in supporting local farms and promoting the distribution of their produce. A quick look at local farms in the region highlights how this may be a far more cost-effective option: Alstede Farms, a 600-acre farm based in Chester Township retails a wide range of fresh organic vegetables at a significantly lower price – selling a bunch of their spinach for $2.99; a bunch of kale for $2.99; and a pound of beans for $3.99. Another organic farm in the region – Terhune Orchards - offers similarly low prices, retailing a bunch of their kale for $3.25 per bunch, a Romaine lettuce head for the same price, and a head of green cabbage for $2.95. If the city was seeking a more cost-friendly way of promoting healthy consumption patterns, then taking such an approach may have been the more viable option.
But whilst they may represent the more costly option, vertical farms hold a number of advantages over traditional soil farms. Crop yields tend to be higher, as crops can be grown all year round and conditions can be controlled to maximize growth. Having this controlled environment reduces the susceptibility to climate and local weather conditions that is a major drawback of traditional soil farming. The land area needed to cultivate the produce is far lower, as the vegetables can be stacked vertically – a major benefit at a time of increasing pressure on land. Vertical farms also use much less water as they facilitate the production of crops with 70-95% less water compared to traditional cultivation practices. Finally, the generation of local, year-round farmworker jobs is a clear advantage over conventional outdoor farms in the NJ area that depend primarily on seasonal labor. Taking such factors into account may indeed justify the higher cost of produce associated with the program.
One notable stipulation of the program is that those wanting to gain free access to the produce must partake in healthy eating workshops and quarterly health screenings. This entails the obvious risk that the city has overestimated the demand for education and health monitoring amongst Jersey City residents, which could mean that the uptake is lower than anticipated. If the demand does fall short of what the city anticipates, then issues of distribution may arise and the program’s effectiveness may be undermined. Its success will, therefore, depend to a large extent on the willingness of residents to spend time participating in these workshops and regular health screenings.
Jersey City’s newly launched program represents a pioneering attempt to combat deficiencies in access to locally grown, nutritious produce and awareness about healthy dietary patterns. The decision by the municipal body to step in and sponsor the vertical farms is ambitious and unprecedented in the US, but it also throws up some major questions. For example; will the plan of action lead to a long-term alteration in the diets and lifestyles of those involved? Do the associated benefits outweigh the cost of the program? And ultimately, is it a city’s duty to feed people through its own asset, or should it instead focus on policies, incentives, and programs that encourage the growth and support of local farms?