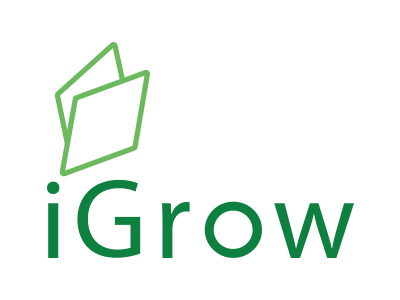
Welcome to iGrow News, Your Source for the World of Indoor Vertical Farming
Gardyn Aims To Make At-Home Vertical Farming Small, Simple, and Stylish
Thanks to disruptions in the food supply chain, panic-buying sprees, and the general uncertainty of the times, growing food at home seems like a pretty good idea of late
Thanks to disruptions in the food supply chain, panic-buying sprees, and the general uncertainty of the times, growing food at home seems like a pretty good idea of late. Trouble is, many consumers don’t have the know-how to cultivate their own leafy greens and other produce in the backyard. Even those who do often lack adequate space.
A company called Gardyn is addressing both of those issues with an at-home vertical farming system that requires minimal input from the user and can easily fit inside a small apartment if need be. The idea, as Gardyn founder and CEO FX Rouxel explained to me over the phone last week, is to make growing food in one’s own home as simple and straightforward as possible. To do that, the company has built a farm that relies on AI to do much of the heavy lifting in terms of monitoring and maintaining an edible crop of food. Or as Rouxel said, “The system is managing everything for you.”
Gardyn’s system is made up of two parts: a compact vertical tower, which can grow as many as 30 plants, and an accompanying app powered by an AI assistant named “Kelby.” Users only have to order seeds and “plug” the seedpods into the vertical towers. The system automatically circulates water and nutrients to the plants, while Kelby monitors plant growth and sends reminders when it’s time to add water to the garden or harvest the plants.
Right now, available crops from Gardyn’s site include mostly leafy greens and herbs, some flowers, cherry tomatoes, and jalapeños. Customers can also use their own seeds if preferred.
The system uses what Rouxel calls “a hybrid of different hydroponic technologies,” including the deepwater method and aeroponics. (The company brands its approach as “hybriponics.”) By themselves, these different methods have certain limitations in the at-home setting. Deep water, where plant roots are fully submerged in nutrient-enriched water, requires a lot of space. Aeroponics is a great setup for outdoors, but once indoors it requires lighting, which gets expensive very quickly. Gardyn pulled elements from both to create a system that takes up only two square feet of space and doesn’t require any extra hardware. “Within just two square feet, you can produce a lot of food,” says Rouxel, adding that Gardyn’s units have produced “over 25,000 pounds of produce” during the last few months.
That quest to grow a lot of leafy greens in a small amount of space is an area with plenty of competition these days. Farmshelf recently unveiled its first-ever farm for the home, and companies like Rise Gardens and Agrilution (the latter recently bought by Miele) also offer promising solutions for the consumer space.
And while historically, investment in vertical farming has mainly gone towards the industrial-scale indoor farms (think AeroFarms), at-home farms are fast becoming a lucrative area. Investors, Rouxel explained to me, see traditional agriculture as a risky business that’s less insurable because its success is in part dependent on the weather outside. With climate change triggering more extreme weather, investors will look more and more to alternative solutions in controlled-environment agriculture.
“I am absolutely convinced we are going to see in the coming two years a total disruption in the way we grow things,” he says. Chiefly, that will be growing the food in much closer proximity to consumers, whether through at-home systems like Gardyn’s, in-store farms at grocery retailers, rooftop gardens, and high-tech greenhouses. “In future, we’re going to have a spectrum of solutions,” Rouxel noted.
Getting these vertical farms closer to consumers and in their own homes will require bringing the price of the machines down. At the moment, Gardyn’s system is roughly on par pricewise with other systems out there that can realistically feed a family of four: $799 for the base model all the way up to $1485 for the “Plus” model.
Rouxel is aware that the cost is still too high for many consumers. “We don’t want this to be only for well-off people,” he told me. “It’s important that we find ways that anyone can afford this.”
Many companies, including Gardyn, offer financing options on their farms now. And more investment dollars going into the space in the future could mean companies have the time and space to innovate on ways to make their system cheaper for the average consumer.
While pricing remains a question, one thing that’s certain is that at-home vertical farming is on the path to becoming a regular part of the kitchen, rather than just a trend. “What we want is to develop solutions that will quickly change the way people access food,” said Rouxel. “We won’t solve everything, that’s for sure, but we want to be part of the solution for how we shape food.”
FILED UNDER: AG TECH BUSINESS OF FOOD EDUCATION & DISCOVERY FEATURED FOODTECH
“We Are Developing A Sustainable Technology That Uses 75% Less LED Lighting”
Verde Compacto, a Mexican start-up, producer of container farms and indoor farming growing technologies, has seen significant demand for their growing systems during the pandemic
Verde Compacto, a Mexican start-up, producer of container farms and indoor farming growing technologies, has seen significant demand for their growing systems during the pandemic.
"COVID is driving this market forward because people want to know what is behind their food and their diets. Logistic chains in countries like South Korea and Arab countries are really dependent on imports. They are trying to implement urban technologies to strengthen their supply chains. As we’re focusing on growing systems, we are trying to turn this into reality. We are growing food in a more sustainable way where everyone can benefit from it”, Juan Gabriel Succar, Co-Founder and CCO of Verde Compacto says.
The company has an R&D container farm, Huvster, with several labs and small scale systems. The company sells some of its crops locally to better understand the urban business model, as Verde Compacto is educating the future indoor growers.
The Huvster growing container
Succar continues: “We are providing the knowledge to any grower that wants to have an urban farm and we are helping them throughout the process by constructing a farm to their needs.” The company does not only build container farms, which is their standard model but also provides custom made projects such as warehouses or buildings. Or on a smaller scale like supermarkets and restaurants. “We provide the knowledge to install a farm at any size”.
Decreasing LED use
Verde Compacto is looking to improve the electricity use for its growing solutions. “We are developing a sustainable technology that uses 75% less LED lighting, which is part of a sustainable R&D project. The tests are still running but they have delivered positive results. In the end, our technology used for indoor farms allows us to rotate the lamps. Rather than using four lamps at one spot, Verde Compacto can use one light that is constantly rotating. That's why we can make such a big impact on light usage”, Succar affirms.
Lack of quality and water
“Every business model and location has different benefits. As we are one of the largest agricultural countries in the world, we can offer excellent fresh produce quality. The sad story is that all the good fruits and vegetables are exported, thus there is a lack of quality products here in Mexico”, Succar says.
Succar says that Verde Compacto’s technology can build a profitable business model to deliver excellent quality and healthy food to the Mexican society. He notes that the central Mexican region sees a big challenge: a large water shortage. “With our solution, companies still see an opportunity to grow food and maintain their quality by using fewer resources”, Succar notes.
Sustainability
“We always try to give the best options possible regarding our client’s budget, business model, and capabilities. Verde Compacto is cooperating with solar panels to give access to clients for installing these solutions. “Renewable energy, in the end, really depends on the client. Our goal is to make vertical farming as sustainable as we can”, Succar states. At the end of October this year the company will install the first urban farm in Salamanca, Mexico which will be run on 100% solar energy.
Price opportunities
Succar: “In Mexico, we provide our produce at a lower price level than supermarkets. This is done on purpose, to get people to know about vertical farming. Sometimes we are on the same price level.”
Olivier Kappetein, EU representative at Verde Compacto notes: “We have a financial stimulator and we found out that we can bring product prices down. Consumers would pay less compared to supermarket prices as they are unbelievably high. In the United Arab Emirates, locally grown products are unfindable. An iceberg lettuce costs around €7.60 (9 USD) or more. We could get that price down by at least 350% and still make a profit if we were to sell our produce there. We are aiming to sell high-quality food and that’s what they are looking for.”
Pre- and post COVID story
Verde Compacto has a pre- COVID story and a post-COVID story regarding any company expansions. The pre-COVID story was to expand to all Latin American countries, as a priority. They started several alliances and promoted the Verde Compacto technology in Latin America. However, the economy in Latin America was really affected during the pandemic.
“Thus, countries depending on imports saw a great opportunity in our technology for constant production. We didn’t get behind on the expansion actually. Right now, we are working with associations to open different commercial offices in several countries in Latin America. We will be expanding there at the beginning of next year. We are also exploring different options in different parts of the world, expanding globally. One of the regions is Northern Europe because we saw the need for farming technology in those countries. Especially in Luxemburg, where there’s limited fresh produce available.
“The most common problem in vertical farming is the unawareness of the consumer”, Kappetein adds. “They don’t know what it has to offer. It’s still an investment that needs to be made. There is still a greater focus on organic produce as they are aware of the great benefits that come along.”
The Verde Compacto team
Forage
Verde Compacto has been developing its own R&D department, generating knowledge that is also used for new product lines. Succar continues: “We are developing indoor farming systems that are not limited to leafy greens and herbs, but also for forage e.g.. Forage is eaten by grazing cattle mostly. With our hydro system, we can feed cows e.g. with using fewer resources in a more profitable way. The meat and milk industry is impacting the ecosystem significantly. Implementing this technology will help us to make this type of agriculture more sustainable.” The company is also exploring the opportunities of launching indoor strawberries, with the greatest focus on Europe.
For more information:
Verde Compacto
Juan Gabriel Succar, Co-founder, and CCO
juan.gabriel@verdecompacto.com
Olivier Kappetein, EU representative
olivier.kappetein@verdecompacto.com
Phone: +316 14 62 13 10.
www.verdecompacto.com
Publication date: Tue 8 Sep 2020
Author: Rebekka Boekhout
© HortiDaily.com
What Are The Pros And Cons of Hydroponics?
Hydroponics is a type of aquaculture that uses nutrients and water to grow plants without soil. It is an increasingly popular growing method in urban areas and regions with extreme climates
AUGUST 28, 2020
Hydroponics is a type of aquaculture that uses nutrients and water to grow plants without soil. It is an increasingly popular growing method in urban areas and regions with extreme climates. There are many benefits to hydroponics as an alternative form of agriculture, including fewer chemicals, higher yields and greater water efficiency.
However, hydroponics is not a perfect solution. The initial setup is expensive, and the whole growing system is heavily dependent on access to electricity and a clean water source. Here are just a few pros and cons of hydroponics.
Pros
The benefits of hydroponics are myriad and include:
1. More Water Efficient
Growing plants can require a lot of water, and conventional agriculture is historically wasteful of this resource. For example, a single walnut requires almost 5 gallons of water, and an orange uses nearly 14 gallons. Globally, over 70% of freshwater is used for agriculture.
Compared to traditional growing methods, hydroponic systems are much more water-efficient. Growing in a climate-controlled environment allows cultivators to use the exact amount of water required for healthy plants, without any waste. Overall, hydroponics utilizes 10 times less water than conventional agriculture.
2. Higher Yields
Since crops are grown in a climate-controlled environment, hydroponic farmers are not limited by extreme weather or annual rainfall, resulting in higher crop yields. There’s more control over the setup of the system, and crops aren’t limited to a specific growing season.
Additionally, when comparing vegetables grown in soil, hydroponics can sometimes grow plants at up to 16 times higher density. Hydroponics allows growers to do this without using significantly more nutrients or other inputs.
3. Less Space
Some crops require a lot of space, and many conventional forms of agriculture are inefficient when it comes to using land. For example, row crops like soybeans and corn take up most of the arable land in the United States, but the harvest is used mostly for livestock and processed food, not human consumption.
In contrast, hydroponic systems focus on cultivating fruits and vegetables, providing nutrient-dense food for consumers without taking up significant amounts of space. Additionally, researchers at NASA are studying how to incorporate hydroponic systems for longer-duration space missions by providing the right balance of light, carbon dioxide, and water.
4. Community Resilience
Many cities have significant food deserts, and access to quality and affordable items is significantly limited. Urban hydroponic systems enable communities to cultivate their own crops, increasing food security for vulnerable populations.
While hydroponics requires significant operational costs, there is also some proof that it may be a possible solution for countries that struggle with food insecurity or need back-up options during months of extreme drought.
For example, in the United States, many agricultural enterprises grow food in one region but ship it to another for consumption. Many rural communities struggle with access to healthy produce because of this. Hydroponics may help foster community resilience by setting up an accessible system.
5. Fewer Chemicals
Many advocates of hydroponic systems stress that hydroponics reduces the need for synthetic chemicals. Since plants are most often grown in greenhouses with strictly controlled environmental inputs, pest pressure is almost nonexistent. Considering the detrimental impact of pesticides on the environment, using fewer chemicals is a huge advantage for hydroponics compared to traditional growing systems.
However, there is an ongoing debate regarding how to qualify hydroponic crops, and whether they are eligible for organic certification. According to the USDA, this refers to the care and maintenance of soil without chemicals. Since hydroponics do not use earth, many traditional organic growers feel that they are not eligible. Regardless of how crops are labeled, the fact that hydroponics uses fewer chemicals is a definitive advantage compared to conventional agriculture.
Cons
Despite the many positives, hydroponics also has some challenges to overcome.
1. Technology Reliance
Hydroponics is a high-tech process. Most commercial operations utilize specialized equipment that regulates water temperature, as well as acidity and nutrient density. Because plants are cultivated in a completely climate-controlled environment, there is a significant reliance on technology. Hydroponics is considerably more high-tech than other growing methods, and there is an opportunity in agtech to improve yields and decrease inputs. However, the amount of tech also makes it cost-prohibitive for beginning growers.
2. Initial Investment
The hydroponics market is expected to grow from $9 billion to $16 billion in the next five years, so there is certainly an opportunity for investors to consider vertical farming as a viable operation. In traditional agriculture, is it hard for new and beginning farmers to get started, as many face difficulties with land access and infrastructure investments.
However, getting into hydroponics is not necessarily any easier or cheaper. Despite a growing market, the initial investment in hydroponic systems is steep, especially on a commercial scale. For this reason, many of the largest growers are established agriculture corporations that already have capital in place. The initial investment limits profitable hydroponic operations to a few large farms, making it tricky for smaller growers to enter the market.
3. Organic Debate
As mentioned above, there is an ongoing debate in the farming community about whether hydroponic produce can be labeled organic according to USDA standards. Without a clear definition of the nutrient profile of hydroponics, nor stringent guidelines on which fertilizers or chemicals are permissible, many consumers remain cautious about hydroponic produce. This affects the industry’s success, as many consumers don’t know how crops are grown or what’s added to the water.
Without a clear definition from the USDA, there remains some question over self-labeling of hydroponic crops as organic when synthetic chemicals may still be added.
4. Equipment Requirements
While a home gardener can easily utilize some plastic bottles and storage containers to build a small hydroponic system, commercial farmers have significant equipment requirements. In addition to the initial costs of setup for infrastructure, there are also necessary and costly machines to consider. Pumps, tanks, and other controls can be expensive, not to mention electricity and access to filtered water.
5. Waterborne Diseases
While hydroponic systems may reduce or eliminate pest pressure, certain waterborne diseases are more prevalent in hydroponically grown produce. The most common ones affect the plant’s root structure, such as Pythium, which includes several water mold species.
Proper hygiene and cleaning practices can reduce the risk of plant disease, but it is often impossible to avoid completely. Because of this likelihood, many hydroponic growers incorporate bio fungicides to prevent breakouts.
Soil-Free Growing
Hydroponic growing can increase crop yields while reducing water usage. The benefits of hydroponics are significant, and the industry is expected to grow astronomically in the next five years. However, there are also some disadvantages to growing hydroponically. Improving access to infrastructure and making technology more accessible will enable more beginning growers to enter the market.
Aquaponics Can Have Both Environmental And Cost Benefits
Although aquaponics systems, which combine conventional aquaculture with hydroponics, have become a hotly debated topic in future food production, data on the economic feasibility of aquaponics is relatively limited
Aquaculture is the farming of fish and other aquatic animals, while hydroponics involves growing plants without any soil. Both approaches have been successful on their own, however, combining fish and vegetable production — so-called aquaponics — could also be profitable, according to a new analysis published on 19 May in the journal Aquaculture Research (1).
Although aquaponics systems, which combine conventional aquaculture with hydroponics, have become a hotly debated topic in future food production, data on the economic feasibility of aquaponics is relatively limited.
To figure out how realistic the approach might be, researchers from the Leibniz-Institute of Freshwater Ecology and Inland Fisheries (IGB) analyzed one year of real production data from an existing aquaponics system — the “Mueritzfischer” — located in Waren (Müritz) in Germany. The research system was build as part of INAPRO, an EU-funded project led by IGB aimed at demonstrating the viability of an innovative aquaponics system.
The 540-square-meter facilities produce fish and vegetables on a large scale in a combined recirculating system. The fish and plants are grown separately within the two recirculating systems and sensors are used to continuously monitor can connect the two systems when needed to create optimal growth conditions.
The authors examined two different scenarios and performed an extensive profitability analysis. One scenario showed that the aquaponics approach can be profitable if facilities are sufficiently large. Using this scenario, the researchers developed a model case, which they used to calculate figures for different sized facilities.
Under the right conditions, aquaponics can have both environmental and cost benefits, according to the authors. The main barriers to the commercialization of aquaponics are the high investment costs and high operating costs such as for fish feed, labor, and energy, particularly in countries like Germany. Another challenge is that profitability largely depends on the market environment and the production risks, which can be difficult to predict.
Lead author Goesta Baganz believes there might be huge potential for aquaponics in urban areas: “The already profitable model case would cover an overall space of about 2,000 square meters. This would mean that professional aquaponics would also be possible in urban and peri-urban areas, where space is scarce and often relatively expensive.”
“If, therefore, urban aquaponics can make a profit on such a scale, there is even greater opportunity for local food production, which is becoming increasingly important throughout the world as urbanization progresses”, Baganz explained.
In a global context, Professor Werner Kloas, who led the project, said: “Considering current problems like climate change, population growth, urbanization as well as overexploitation and pollution of natural resources, global food production is the largest pressure caused by humans on Earth, threatening ecosystems and the stability of societies. Consequently, one of the key societal goals is to achieve eco-friendly, efficient food production,”
(1) Baganz, G. et al. Profitability of multi‐loop aquaponics: Year‐long production data, economic scenarios and a comprehensive model case. Aquaculture Research (2020). DOI: 10.1111/are.14610
VIDEO: Growing Healthy Food Indoors
How many of us live in apartments or townhomes and long for a big backyard to start a garden?
How Many of us Live in Apartments or
Townhomes And long For a Big Backyard to Start a Garden?
Well with new technology, indoor herb growers give anyone the chance to grow their own food. You don't even need a backyard anymore to grow healthy foods.
Now, you can do it all from the comfort of your home. In this article, we're going to talk about our favorite indoor herb grower right now and why you should try it for yourself!
Read more
Food Safety And E. coli in Aquaponic And Hydroponic Systems
This document is The Aquaponics Association’s response to a recent publication on E. coli in Aquaponic and Hydroponic systems
This document is The Aquaponics Association’s response to a recent publication on E. coli in Aquaponic and Hydroponic systems.
PDF Version: Food Safety and E. Coli in Aquaponic and Hydroponic Systems
April 27, 2020
By Tawnya Sawyer; Nick Savidov, Ph.D.; George Pate; and Marc Laberge
Overview of the Study
On April 6, 2020, Purdue Agriculture News published a story about a study related to the contamination risk of Shiga toxin-producing E. coli (STEC) in Aquaponic and Hydroponic production. The full study was published in MDPI Journal Horticulturae in January 2020.
Researchers conducted the study from December 2017 through February 2018. The Study consisted of side-by-side aquaponic and hydroponic systems in a controlled environment lab growing lettuce, basil, and tomatoes with tilapia. The purpose of the study was to identify the food safety risks associated with soilless systems. The study indicates that both the aquaponic and hydroponic systems contained Shiga toxin-producing E. coli (STEC) at the time of sampling. It did not find the presence of Listeria spp., or Salmonella spp.
The authors contend that the aquaponic system and specifically the fish feces were likely the sources of E. coli. However, we believe that there is no evidence to prove that this was the actual source of contamination since the authors admit traceback was not performed, and there were several other possible introductions.
The pathogen was present in the water and on the root system of the plants. The researchers did not detect it in the edible portion of the plants. However, if the water is positive for a contaminant, and it accidentally splashes onto the edible portion of the crop throughout its life, or during harvest, this could still result in a food safety concern.
History of E. coli in Soil-less growing systems
Until now, researchers have only discovered environmental E. coli in soilless growing systems. It is essential to note that there are hundreds of types of non-fecal coliform bacteria in the air, water, soil, as well as the fecal coliform bacteria represented mostly by E.coli in the waste of all mammals, humans, and some birds. A vast majority of these coliforms are perfectly harmless.
The E. coli found in this Study — Shiga toxin-producing O157:H7 — historically has been associated with warm-blooded mammals, more specifically bovine fed corn in feedlots (Lim JY et al. 2007), as well as swine and turkeys. Further research must be performed to prove that cold-blooded, non-mammal aquatic species such as tilapia can harbor this strain of pathogenic E. coli. A wide group of studies, university professors, and industry professionals currently refute the possibility that tilapia can harbor this strain. The lack of evidence detailing the ability of aquatic animals to harbor E. coli makes the fish contaminated with this specific strain of bacteria very rare and suspect.
Many foodborne illnesses from fresh produce such as romaine lettuces, green onions, herbs, and sprouts, are traced back to the soil; the irrigation water used in these crops (Solomon et al. 2002); the seed stock; or poor sanitation in handling facilities.
There are a wide variety of community and commercial aquaponic and hydroponic growing facilities that routinely perform pathogen testing and have not identified this pathogen present. If it was present, traceback procedures would be followed to identify and remove the source, as well as any necessary food safety precautions and recalls performed.
Our Position
The Aquaponic Association and its members agree that food safety and proper handling practices are critical to commercializing our industry and the safety of our customers. One thing that the study points out is that a contaminant can occur in a soilless system, which creates a potential food safety concern. We agree on this; however, we have numerous concerns with the procedures and statements made in the publication.
We have reached out to the professional investigator on this study Hye-Ji Kim to get answers to essential questions that the study publication does not adequately address. There are significant gaps and questions with the study.
Concerns About the Study Findings and Publication
Lack of Traceability
The study group is unsure how the pathogen was introduced into the two systems. They admit that no traceback was performed to identify the source of contamination. They speculate both in the study and in their email response that this pathogen was:
1) Accidentally introduced
2) That it is from the fish feces in the aquaponics system that splashed into the hydroponic system through the open top of the fish tank during feeding,
3) that it was from contaminated fish stock (which were provided by the Purdue Animal Sciences Research and Education Center)
4) That it was human contamination from visitors or operator handling issues.
A traceback was not conducted as it was not within the scope of the study (Kim personal communications). We disagree; the discovery of O157:H7 strain in the university greenhouse with the suspicion of fish being contaminated should have resulted in immediate action in order to track down the source of contamination and prevent infection of the university students and staff. Outside of a University setting, traceback would have been mandatory in a commercial facility. It is questionable that the University did not perform these procedures because it was “out of the scope of the study”.
Questioning Fish Feces as the Source of Contamination
Blaming fish feces as the contaminating source seems incredibly misleading when so many other options exist, and no traceback proved that as the source. The contents of the fish intestines were tested for the presence of E. coli, and none was found (Kim personal communications). It seems that if the fish does not have STEC E. coli inside its gut, then it is more likely the fish feces being positive would be related to the contaminated water that the feces was floating in.
In wild fish species, levels of E. coli appear to follow trends similar to ambient water and sediment concentrations; as concentrations in their environments rise, so do concentrations within the fish (Guillen et al., 2010).
Furthermore, it seems very suspect that a two-month-old system in a controlled environment lab could have been so quickly contaminated. It is well-known that E.coli cannot survive in a biologically-active environment, such as an anaerobic digester or aquaponic system (T.Gao et al., 2011). E. coli are outcompeted by other microorganisms, which adapted to survive in the environment outside animal guts much better than E. coli. Thus, E. coli O157:H7, which is specially adapted to live in cattle guts, will inevitably be replaced by other microorganisms.
As for the hydroponic system showing positive results, this also seems suspect if the nutrients were synthetic, as there would be very little chance for the E. coli to survive without a biological host or continuous contamination source being present. An accidental exposure in the hydroponic system would have become diluted over time, or the pathogen died off to the point that they would have been undetectable. The fact is the organic matter in hydroponics is virtually absent and, therefore, provides a poor environment for E. coli growth and propagation (Dankwa, 2019). Therefore. one would need a continuous source, not an accidental one (like splashing), in order to maintain the E. coli population in hydroponics.
Since both systems were contaminated, we suggest that there is a more likely common pathogen source that the researchers did not correctly identify and remove. The source of contamination could be from source water, filtering system, repurposed equipment, airborne in the greenhouse or HVAC system, human vector, lab equipment, the seed stock, nutrients, or other inputs.
The Purdue Animal Research and Education Center, where the researchers sourced the fish, is an operation that also has swine, cattle, and poultry production. Research suggests that pathogenic E. coli can travel 180 m through airborne exposure (Berry et al., 2015). Airborne exposure poses a more significant risk to controlled environments as pathogens can persist in the HVAC system (Riggio et al., 2019). STEC has the potential to live in dust particles for up to 42 weeks, which can act as a possible vector of contamination if there is a continuous source. Therefore, even a slight possibility of the pathogenic Shiga-producing O157:H7 strain of E. coli transfer from the Animal Research and Education Center resulting in the uncontrolled cross-contamination of other research labs and facilities certified below Biosafety level 2 not designed to work with the pathogenic bacteria would raise a serious concern about the existing safety practices (Boston University).
Lack of 3rd Party or Peer University Test Verification
It has also been recognized that there is a high frequency of false-positive signals in a real-time PCR-based “Plus/Minus” assay (Nowrouzian FL, et al., 2009). Hence the possibility that the PCR verification method may have resulted in inaccurate results. The pathogen was not verified by a 3rd party lab to be actual STEC E.coli O157:H7. Only positive or negative results were obtained for this study.
We recommend several other universities and third-party labs to run samples and validate the results. However, no samples have been provided, which may be impossible to obtain based on the study being conducted in early 2018. Without this verification, there are questions about the possibility of false-positives due to the presence of environmental E.coli, fecal coliforms, or a wide variety of other bacteria commonly found in nutrient-rich environments (Konstantinidis et al., 2011).
Impact of Sterilization
The study conclusion suggests that sterilization efforts are critical. “Our results indicated that contamination with bacterial pathogens could likely be reduced in aquaponic and hydroponic systems if the entire systems were thoroughly sanitized before each use and pathogen-free fish were used for the operation.” This statement is inaccurate and could be detrimental to proper food safety practices. As the microflora of the system develops, it creates an environment that can suppress phytopathogens (Bartelme et al., 2018) and other zoonotic pathogens as a result of antibiotic compounds released by beneficial bacteria (Compant et al., 2005). In Recirculating Aquaculture Systems (RAS), some microbial communities take over 15 years to develop (Bartelme et al., 2017), resulting in greater stability over time.
Many papers support this hypothesis with regards to probiotics in wastewater treatment, aquaculture, and hydroponics. Microbial community analysis also depicts a greater microbial diversity in aquaponics over decoupled or aquaculture systems (Eck et al., 2019), indicating a more significant potential for suppression of pathogens in coupled aquaponic systems over RAS or decoupled aquaponic system. No pathogens were discovered in a mature coupled aquaponics system during 18 years of continuous research in Canada since 2002 (Savidov, personal communications).
These findings support the argument that more biologically mature systems are less likely to develop pathogens and that periodic sanitation should not be done outside of initial start-up unless a zoonotic pathogen (Henderson 2008), is detected. If a pathogen is found, producers should follow proper sanitation and recall procedures.
Conclusion
Overall, this and other research into food safety are ongoing, and new information becomes available continuously to help shape the best practices for proper greenhouse management. As the Aquaponic Association, we hope to provide the most accurate and reliable resources for this purpose. At the same time, we hope to reduce the possibility of studies like this creating unnecessary fear, or unsubstantiated claims that could harm the growth of the aquaponic (and hydroponic) industry. When a document like this is published, it will be quoted by the media, and referenced in other studies as if it is an absolute. Other research must be performed to validate or negate this study’s outcomes.
Our findings conclude that while there is a low chance of the persistence of a pathogen in properly designed aquaponic and hydroponic systems, there is still a potential concern. No agricultural system is immune to this. Compared to soil production, soil-less crops grown in a controlled environment are far less likely to become infected pathogens from mammals, birds, and other creatures which are difficult to prevent in field crop production. Human contamination or poor handling practices are of significant concern (Pattillo et al., 2015). The best way to avoid risk is to adhere to food safety guidelines set forth by the USDA, GlobalGAPs, the Aquaponic Association, and other accredited organizations.
contact: info@aquaponicsassociation.org
References
Bartelme, R.P., McLellan, S.L., Newton, R.J., 2017. Freshwater Recirculating Aquaculture System Operations Drive Biofilter Bacterial Community Shifts around a Stable Nitrifying Consortium of Ammonia-Oxidizing Archaea and Comammox Nitrospira. Front. Microbiol. 8. https://doi.org/10.3389/fmicb.2017.00101
Bartelme, R.P., Oyserman, B.O., Blom, J.E., Sepulveda-Villet, O.J., Newton, R.J., 2018. Stripping Away the Soil: Plant Growth Promoting Microbiology Opportunities in Aquaponics. Front. Microbiol. 9, 8. https://doi.org/10.3389/fmicb.2018.00008
Berry, E.D., Wells, J.E., Bono, J.L., Woodbury, B.L., Kalchayanand, N., Norman, K.N., Suslow, T.V., López-Velasco, G., Millner, P.D., 2015. Effect of Proximity to a Cattle Feedlot on Escherichia coli O157:H7 Contamination of Leafy Greens and Evaluation of the Potential for Airborne Transmission. Appl. Environ. Microbiol. 81, 1101–1110. https://doi.org/10.1128/AEM.02998-14
Compant, S., Duffy, B., Nowak, J., Clément, C., Barka, E.A., 2005. Use of Plant Growth-Promoting Bacteria for Biocontrol of Plant Diseases: Principles, Mechanisms of Action, and Future Prospects. Appl. Environ. Microbiol. 71, 4951–4959. https://doi.org/10.1128/AEM.71.9.4951-4959.2005
Dankwa, A.S., 2019. Safety Assessment of Hydroponic Closed System 127. https://digitalcommons.library.umaine.edu/cgi/viewcontent.cgi?article=4052&context=etd
Eck, M., Sare, A., Massart, S., Schmautz, Z., Junge, R., Smits, T., Jijakli, M., 2019. Exploring Bacterial Communities in Aquaponic Systems. Water 11, 260. https://doi.org/10.3390/w11020260
Guillen, Wrast, Environmental Institute of Houston, 2010, Fishes as Sources of E. coli Bacteria in Warm Water Streams, https://www.uhcl.edu/environmental-institute/research/publications/documents/10-015guillenetalfishreport.pdf
Henderson, H., 2008. Direct and indirect zoonotic transmission of Shiga toxin-producing Escherichia coli. J. Am. Vet. Med. Assoc. 232, 848–859. https://doi.org/10.2460/javma.232.6.848
Konstantinidis, Chengwei Luo, 2011. Georgia Tech Institute, Environmental E. coli: New way to classify E. coli bacteria and test for fecal contamination, https://www.sciencedaily.com/releases/2011/04/110411152527.htm
Lim JY et al., Escherichia coli O157:H7 colonization at the rectoanal junction of long-duration culture-positive cattle. Appl Environ Microbiol. 2007;73:1380–1382 https://www.ncbi.nlm.nih.gov/pmc/articles/PMC1828644/
Boston University Agent Sheet E.coli EHEC or STEC) (https://www.bu.edu/researchsupport/safety/rohp/agent-information-sheets/e-coli-0157h7-agent-information-sheet/).
Nowrouzian FL1, Adlerberth I, Wold AE., 2009 High frequency of false-positive signals in a real-time PCR-based “Plus/Minus” assay. https://www.ncbi.nlm.nih.gov/pubmed/19161539
Riggio, G., Jones, S., Gibson, K., 2019. Risk of Human Pathogen Internalization in Leafy Vegetables During Lab-Scale Hydroponic Cultivation. Horticulturae 5, 25. https://doi.org/10.3390/horticulturae5010025
Solomon et al., Effect of Irrigation Method on Transmission to and Persistence
of Escherichia coli O157:H7 on Lettuce Journal of Food Protection, Vol. 65, No. 4, 2002, Pages 673–676 https://www.ncbi.nlm.nih.gov/pubmed/11952218
Gao*, T. Haine, A. Chen, Y. Tong, and X. Li, 2011, 7 logs of toxic strain of E. coli were removed by mesophilic AD process while ~ 5 logs increase of the strain were seen in water control with the same condition for 7 days
Pattillo*, Shaw, Currey, Xie, Rosentrater, 2015, Aquaponics Food Safety and Human Health, https://southcenters.osu.edu/sites/southc/files/site-library/site-documents/abc/aquaponics_workshop/AquaponicsFoodSafetyandHumanHealthAllenPatillo.pdf
Five Reasons To Go Vertical
The rapidly increasing global population means you can be sure of two things: there’s a never-ending demand for food and a rapid reduction in the availability of land on which you can grow it
The rapidly increasing global population means you can be sure of two things: there’s a never-ending demand for food and a rapid reduction in the availability of land on which you can grow it.
The UN has predicted that the global population will surpass the 9 billion mark by 2050 which leaves government officials and scientists scratching their heads as to how we’ll provide for this colossal amount of mouths to feed. Enter vertical farming. Vertical farming presents itself as one of the answers to our population growth, which in short allows plants, fruit, and veg to grow upwards rather than outwards.
With a booming culinary industry gracing the bustling global hubs such as London, New York, and Tokyo, urban farms provide a controlled and automated climate to grow more delicate niche fruit and veg, as well as mass producing heavily demanded greens and herbs on that were once upon a time confined to their natural habitats.
Although, when it comes to vertical farming the question is not “what you can grow?”, it’s “what should you grow?”. Extensive R&D shows that leafy greens and herbs remain the most profitable and sustainable crops to mass-produce at present. Vertical farming will become a huge part of the agricultural sector in the very near future, but why is it taking off so quickly? Here are 5 reasons why:
Increase your crops per m²
Although it may look smaller than your average outdoor farm, a vertical system can equate to 4-6 X more growth surface than your standard glasshouse or polytunnel area. 1 acre of vertical farm on average produces 4-6 acres depending on the crop density and cycle duration.
Protection from the elements
Vertical farming allows the grower to exploit the advantages of growing in a fully controllable climate, safe from the natural elements such as wind, rain, and frost, meaning post-harvest spoiling and crop wastage becomes significantly less of a problem. Additionally, the secure environment results in zero pests and invasive bacteria, which allows the grower to provide organic pesticide-free produce.
Reduce water consumption
Vertical farming systems allow produce to grow with 70-95% less water required for normal plant cultivation. Taking lettuce as an example: open-field production requires 250L/kg of lettuce and greenhouse systems consume 20L/kg. However, vertical systems come in at a minimal 1L/kg of lettuce, with the only water extracted during the growth cycle being that of the plant’s consumption, with any leftover water being recycled back through the filtering system and reintroduced to the irrigation.
Standardized crop growth and yields
With vertical farming technology constantly improving, the ease of creating a completely controlled environment is increasing by the day. The use of bespoke LED spectrums, automated irrigation, and climate control allows the farm to standardize each growth cycle, producing the same amount, quality and size crop, which in turn results in standardized yields.
Local production
Being a controlled environment, vertical farms can settle wherever they choose, with climates and weather patterns becoming obsolete. Local production means a positive impact on local communities, resulting in an influx of jobs and contribution to smaller economies. Its local production and harvesting of crops reduce the amount of ‘food miles’, meaning a decrease in the global carbon footprint. Research has found that vertical farms lower overall CO2 emissions by 67-92% when compared with greenhouses.
Bridge Vertical Farming partners with Urban Crop Solutions to provide high-tech automated container farms, research facilities, and bespoke vertical farming solutions.
For more information:
Bridge Vertical Farming
Keynor Lane
Chalk Lane
Chichester
PO20 7LL
bridgeverticalfarming.co.uk
bridge@urbancropsolutions.co.uk
01243 641789
Publication date: Tue 31 Mar 2020
Elevate Farms Inc.: Tech-Based Vertical Farming Company Completes Capital Funding to Scale Operations and Secure IP
A tech-based vertical farming company focused on cost-effectively growing leafy green vegetables at mass scale, Elevate Farms Inc. (“Elevate Farms”) is pleased to announce the closing of a $1.8M funding led by Brightspark Ventures
By urbanagnews
February 14, 2020
PRESS RELEASE – Toronto, CANADA / A tech-based vertical farming company focused on cost-effectively growing leafy green vegetables at mass scale, Elevate Farms Inc. (“Elevate Farms”) is pleased to announce the closing of a $1.8M funding led by Brightspark Ventures.
Elevate Farm’s unique solution uses hydroponics and a proprietary automation system, paired with photobiology, to grow high-quality leafy greens (such as arugula, kale, and basil) in a climate-controlled environment.
Elevate Farms’ system aims to deliver a product that is larger, tastes better and has higher nutritional content than traditionally-grown leafy greens – all at a lower cost. The produce grown by Elevate Farms also has the benefit of being local, completely non-GMO, as well as pesticide and chemical free.
“Elevate Farms represents the next generation of indoor farming: their system solves some of the biggest problems the first wave of vertical farms experienced,” says Mark Skapinker, Managing Partner at Brightspark Ventures. He continued, “their edge is their ability to cost-effectively create a tasty and nutritious product – and grow it at a mass-market scale. We invested because we saw meaningful potential, being a team of world-leading experts that can execute, proven technology, and true science being applied into a massive marketplace.”
Elevate Farms is the first to commercially implement an automated climate-controlled environment for plant-production that utilizes far less labor than other indoor farms.
Amin Jadavji, Elevate Farm’s CEO stated: “With the new funding, the company is now ready to scale significantly. This financing will allow us to execute on our currently secured flagship facilities in New Jersey and Niagara, each projected to produce in excess of one-million pounds of leafy greens annually.” Mr. Jadavji continued: “The funding will also fuel our plans to scale the business, grow our team, build and secure new and existing IP, prepare for business partnership opportunities, as well as finalize initial major orders and operational financing.”
Travis Kanellos, Elevate Farm’s Chief Strategy Officer added: “This is a major milestone for our North American operations. It also allows us to forge ahead on our global partnerships, as well as execute our global plan to build out facilities internationally over the next 12-months.”
ABOUT ELEVATE FARMS
Elevate Farms Inc., previously operating corporately as Intravision Greens Inc., is a technology-driven vertically-stacked indoor farming enterprise focused on a mass scale and cost-effective operations with patent secured and patent-pending technology as well as over a decade of advanced photobiology research deployed.
ABOUT BRIGHTSPARK VENTURES
Brightspark is one of Canada’s top-performing venture capital firms, actively investing in exceptional entrepreneurs since 1999. We provide growth capital and expertise to disruptive, market-transforming Canadian tech companies in seed to growth stages. Since inception, Brightspark has invested across traditional VC Funds, and more recently under an investment model open to individual and non-institutional investors.
A.G. Kawamura Joins Board of Indoor Growing Tech Company
“A.G.’s extensive expertise in innovative farming and sustainable agriculture will be invaluable to the Agt3 Holdings Board,” CEO Ed Horton said in the release
February 7, 2020
Agt3 Holdings, a Laguna Niguel, Calif., indoor vertical growing technology company, has appointed former California Secretary of Agriculture A.G. Kawamura to its board.
Kawamura, who led the California Department of Food and Agriculture from 2003-10, is a founding member of Orange County Produce. The Agt3 Holdings board is made of agriculture industry leaders with “unparalleled experience and expertise in sustainable, economically strong urban farming,” according to a news release.
“A.G.’s extensive expertise in innovative farming and sustainable agriculture will be invaluable to the Agt3 Holdings Board,” CEO Ed Horton said in the release.
Kawamura is involved in numerous agriculture groups and is a co-chairman of Solutions From the Land, a member of AGree Initiatives’ Ag Advisory Committee, a member of the Board on Agriculture and Natural Resources, a Western Growers board member, a member of the advisory committee for the Agricultural Sustainability Institute at the University of California-Davis, and a trustee for the Council on Agriculture, Science, and Technology.“
With the rapid expansion of urban agriculture, innovative vertical farms like Agt3 Holdings offer a solution to the changing landscape,” Kawamura said in the release. “I look forward to collaborating with Ag t3 Holdings and its board of like-minded visionaries.”
Lead Photo and logo courtesy Agt3 Holdings; graphic by Amelia Freidline )
Related Topics: Greenhouse Produce Tech
Are In-Home Vertical Farms The Next Big Appliance For Connected Kitchens?
Whether you’re contemplating your own home grow system or just curious, here’s a look at what’s available and what’s in the pipeline
A little less than a year ago, The Spoon looked at a number of hydroponic farming devices that could fit into the average person’s apartment. These were, for the most part, table-top models or units that could hang on a wall. At the time, the concept of having a grow system in your own home seemed more than a little novel.
Fast forward to now and things have changed. Putting an indoor vertical farm in the average consumer’s home isn’t yet a mainstream concept, but as more startups and major appliance-makers alike have shown over the last 12 months, the idea is making its way into the Everyman’s kitchen with more speed these days. Now, thanks to a bunch of concepts shown off at this year’s CES, suddenly the idea of having a smart farm in your kitchen doesn’t seem so novel.
Whether you’re contemplating your own home grow system or just curious, here’s a look at what’s available and what’s in the pipeline.
Aspara
If you’re like me, you have minimal space (almost none, really) in the home for adding much in the way of smart farming systems. Aspara’s hydroponic growing device could potentially solve that problem because it’s small — 14 inches high and 21 inches wide — and could reasonably fit on a countertop, shelf, or even on top of the refrigerator. The system uses a combination of LEDs, an auto-watering feature, and sensors that detect nutrient levels, humidity and air, and other factors to create the optimal grow “recipe” for the plants.
After a user does the initial planting of the seeds, the Aspara app manages most of the grow process, notifying the user when it’s time to refill the water tank and harvest the plants. It also includes tips and recipes for growing and lets you monitor multiple Aspara farms at the same time.
The device is currently available in Hong Kong, the United Kingdom, Canada, and the U.S. through online retailers. For U.S. buyers, the device currently goes for $259.99 on Amazon for just the machine and $339.99 with a starter seed kit included.
Rise Gardens
Chicago, IL startup Rise Gardens is one of those companies aiming to make a truly “plug in and go” indoor vertical farming system for the home. This one is a standalone console that can be purchased with one, two, or three “levels” for plants and weighs between 60 and 106 pounds depending on the size.
A user assembles the garden — much as you would a piece of furniture from IKEA, from the looks of it — then downloads the app, which controls the lighting and nutrients schedule and reminds the user when it’s time to water the plants. Each garden comes with a starter pack of 12 plant pods that can be inserted directly into the grow trays.
Price ranges from $549 for a single-level console to $949 for a triple.
Agrilution’s Plantcube
Not to be confused with Plantycube (see below), the Plantcube made headlines at the end of 2019 when its maker, a German company called Agrilution, was acquired by appliance-maker Miele. Less device than full-on kitchen appliance, the Plantcube automates temperature, light, climate, and water levels of the indoor vertical farm, and can be controlled from within the Agrilution app.
The appliance looks like a wine cooler and is about the same size. However, unlike a wine cooler or any of the systems listed above, the Plantcube is meant to be built directly into your kitchen cupboards or beneath a countertop. That would perhaps explain the price point: €2,979 (~$3,300 USD), a figure most consumers wouldn’t spend on an indoor farm right now. Even for those who would, the device is currently only available to those in Germany, Austria, Belgium, Luxemburg or the Netherlands.
Even so, the concept Plantcube pushes is one to watch. It’s entirely possible that appliances like these eventually become as common in the home kitchen as microwaves. The price point would have to come way down for that to become a reality, which is one reason we’re watching Plantcube closely in the future.
GE Home Grow
As The Spoon’s Mike Wolf wrote recently, CES 2020’s standout in the consumer kitchen was GE because, “rather than create product demos designed as show-off vehicles for new technologies, GE illustrated how these technologies could be employed in a cohesive, systematic way to provide consumers answers to some of their biggest problems.”
Among those technologies was Home Grown, GE’s indoor gardening concept that uses a combination of hydroponics, aeroponics, and soil-based grow systems that are built directly into the kitchen design. For each of the three systems, water, nutrient, and light delivery are controlled through an app, which also guides the user through the seeding and harvesting stages of the grow process.
The system also offers consumers information on the health benefits of each plant as well as how to prepare herbs and greens in meals once they are harvested.
Home Grow is purely conceptual at this stage, so there’s no price point on these systems. Like the Plantcube, however, GE is thinking bigger than the just-another-appliance concept and imagining a system that can encourage healthier eating, reduce food waste, and increase consumer education around the foods they’re eating.
Honorable Mentions
We’ve covered these in-depth already, but LG and Plantycube are also at the forefront of bringing vertical farming technology into the consumer kitchen. Both showed off products at CES this year.
LG’s forthcoming appliance is the size of a fridge and, as I wrote recently, “takes many of the functions found in commercial-scale indoor farming and applies them to a device specifically made for the average consumer.”
N.thing’s Planty Cube, meanwhile, is a highly modular indoor farming system that can be small enough to fit on a countertop or large enough to serve cafeterias at schools, offices, and other institutions.
Since things are never as simple as they seem, there are obviously still a lot of questions around these “plug-in-and-grow” systems. Will they raise consumers’ utility bills significantly? What happens if they break? Are they worth the cost if they can only grow leafy greens and not more substantial veggies, like carrots or broccoli?
Many more questions will sprout up as companies introduce new systems to the consumer market, and it’s ok that those questions won’t get answered immediately. The more important point here is that entrepreneurs and corporations both are testing new ways to make food cleaner, more local, and more in the consumer’s control. Right now, we need concepts as compact as an Aspera and as conceptual as GE’s Home Grown right now to help get us there.
Farmshelf Takes Growers From Seed to Plate
Kitchen gardens are going high-tech as the development of smart, efficient hydroponic grow systems helps both novice and experienced growers from seed to plate
Farmshelf is A Smart, Automated Farm For Hotels,
Restaurants And Corporate Cafes
BY CORRIS LITTLE ON JANUARY 15, 2020
BROOKLYN, NY—Kitchen gardens are going high-tech as the development of smart, efficient hydroponic grow systems helps both novice and experienced growers from seed to plate. One such company is Farmshelf, based here, which builds smart indoor farms that enable people to grow leafy greens, herbs and flowering crops where they live, work and eat.
“Our bookcase-sized smart, indoor farms are small enough to fit into a restaurant and powerful enough to provide pounds of fresh produce every week. Farmshelf brings the outdoors inside and grows food two to three times faster than conventional farming,” said J.P. Kyrillos, co-founder, Farmshelf.
Farmshelf’s bookcase-style growing system was invented by Andrew Shearer, Farmshelf co-founder, and CEO. He found inspiration through his passion for food, technology, engineering, and community.
“He married his years of volunteering experience to fund education in agriculture in Nicaragua’s food-insecure communities, and professional tech experience in Silicon Valley to build a tool that allows people to grow healthful, flavorful food anywhere, any time and know its source,” said Kyrillos.
As a result, the hospitality industry has taken notice. At HX: The Hotel Experience Powered by AAHOA, Farmshelf was the winner of the Best of Show award. Farmshelf has also captured the attention of hotel chefs and high-profile New York restaurateurs like Marcus Samuelsson of Red Rooster and Jose Andres of Mercado Little Spain, who have entered into partnerships with the company.
“They find as much value in the five to six pounds of leafy greens and herbs the units produce weekly as they do the organic marketing value,” Kyrillos said. “Our partners in the hospitality space share with us that the units add beauty to whatever space they are in. We designed Farmshelf to be eye-catching, and we often see hotel guests and diners in the restaurants that house Farmshelf taking time to really look at the unit, discover what it is and admire what it provides.”
Kyrillos also noted that the chefs at the hotels where Farmshelf is stationed regularly praise the accessibility and freshness of the produce.
“We aim to shorten the distance between farm to plate—a journey that’s often hundreds or thousands of miles—and having fresh herbs and greens right at your fingertips not only allows for speedy and easy access, it provides superior freshness,” he said.
Sustainability is a key facet of the Farmshelf business.
“Farmshelf helps minimize food waste because you know exactly how much produce you are able to harvest at any time, and no food expires in transit,” he said. “Nearly 40% or more of the food we grow in the U.S. ends up in a landfill. That equates to millions of dollars and pounds of food that could have otherwise been used. It’s a solvable problem, and we’re working to lay the building blocks to address it in a scalable way. In addition, Farmshelf uses 90% less water in comparison to traditional soil growing. By enabling you to harvest just what’s needed, Farmshelf also eliminates packaging, environmental impacts from transportation, and food waste.”
Kyrillos noted that the Farmshelf leadership team has seen firsthand the devastation that a lack of access to food causes.
“At Farmshelf, we are passionate about ensuring people have access to fresh, healthful food, anywhere and anytime,” he said. “And, while we are still a young company, we are working to scale our technology so that more people can have access to food.”
Andrew Shearer Farmshelf food waste garden Gardening HX: The Hotel Experience Hydroponic J.P. Kyrillos Sustainability
This UVA-Born Startup Is Revolutionizing The Home Farming Industry
Imagine a world where you can grow your own produce right in your kitchen. That world might be closer than we think
December 23, 2019
Share Facebook Twitter Linkedin
Imagine a world where you can grow your own produce right in your kitchen. That world might be closer than we think.
Alexander Olesen, CEO of Babylon Micro-Farms, and his business partner Graham Smith, CTO, started exploring hydroponics in 2016 while in school at the University of Virginia in terms of its hypothetical applications to grow crops in refugee camps.
“We realized that this was an incredibly efficient way of growing crops,” Olesen said.
Upon researching into how large commercial greenhouses use this technology, Olesen and Smith began looking into how it could be used on a smaller scale. While the technology never made it into refugee camps, they started looking into practical applications in their community and researching the minimum square foot of farming space needed to feed one person, feed a family or sustain a business.
Image courtesy of Babylon Micro-Farms.
When they realized those measurements could fit into a home or business, the idea of the small vertical farming modules utilizing unique hydroponics technology that Babylon Micro-Farms creates today was born.
Named for the famed ancient Hanging Gardens, Babylon Micro-Farms produces self-contained vertical farming units that can easily fit into a home or business. The company sends weekly “meal-prep style” subscription packages of produce kits and remotely manages the units, including the airflow, irrigation, sunlight-mimicking grow lights, fertilizer mixes and pH for the acidity of the water. Customers lease the farming space on a 24-month contract, which includes an all-inclusive monthly fee.
“We’ve essentially automated the need for a green thumb,” Olesen said.
The company just this year finalized a $2.4 million seed round of fundraising from investors including CIT GAP Funds and Plug and Play Ventures, following a $600,000 pre-seed round in 2018. Additionally, Babylon received a $25,000 grant to continue their research this year from the National Science Foundation.
Grown out of UVA, the company is still based in Charlottesville but hopes to begin expanding its operations into Richmond soon. The company is focusing on building their core market in Virginia and expects to see the growth of customers in commercial food service and corporate dining.
While Olesen and Smith have ambitions to bring their farming units into the household, the business currently targets clients in industries such as institutional food service and restaurants, higher education and corporate dining. Babylon’s products are already in use at companies including Dominion Energy, Commonwealth Senior Living, and Hampton Roads Academy, to name a few.
Currently, the company has 14 employees with a heavy emphasis on software and mechanical engineering, developing their patented software platform, app, hardware product, and weekly subscriptions.
Olesen believes this is just the beginning of a booming industry, similar to the way in which solar panels have become popular for use even on residential homes.
“We’re in the infancy of an industry for fresh produce or herbs,” Olesen said. “Vertical farming is going to disrupt that industry and become the status quo given how inefficient things are today. We see what we’re doing as a sustainable infrastructure play that is going to become a necessity.”
Image courtesy of Babylon Micro-Farms
CubicFarm Systems Corp. Announces Strategic Acquisition of HydroGreen, Inc.
Vancouver, BC – (AccessWire – December 11, 2019) – CubicFarm® Systems Corp. (TSXV:CUB) (“CubicFarms” or the “Company”) is pleased to announce that it has entered into a binding purchase agreement effective December 10, 2019, to acquire HydroGreen, Inc. (“HydroGreen”), an arms-length private company headquartered in South Dakota
December 11, 2019
Vancouver, BC – (AccessWire – December 11, 2019) – CubicFarm® Systems Corp. (TSXV:CUB) (“CubicFarms” or the “Company”) is pleased to announce that it has entered into a binding purchase agreement effective December 10, 2019, to acquire HydroGreen, Inc. (“HydroGreen”), an arms-length private company headquartered in South Dakota (the “Acquisition”).
HydroGreen is a manufacturer of fully-automated hydroponic growing systems that produce live, green animal feed, prioritizing animal health and performance. HydroGreen’s unique process sprouts grains, such as barley and wheat, in a controlled environment with minimal use of land, labor, and water. Its system performs all growing functions including seeding, watering, lighting, harvesting, and re-seeding – all with the push of a button – to deliver animal feed without the typical investment in fertilizer, chemicals, fuel, field equipment, and transportation.
Overview of Acquisition
The Acquisition will be completed by way of a reverse triangular merger of CubicFeed Systems U.S. Corp., a wholly owned subsidiary of the Company, and HydroGreen, resulting in HydroGreen being renamed “of CubicFeed Systems U.S. Corp” and becoming an indirect and wholly-owned subsidiary of the Company. The new CubicFarms subsidiary will operate the existing business of HydroGreen moving forward.
Under the terms of the merger agreement, holders of HydroGreen shares (“HydroGreen Shareholders”) will be entitled to receive an aggregate of 11,000,000 common shares of CubicFarms (the “Consideration Shares”), subject to an adjustment related to working capital. Of the Consideration Shares, 10,000,000 will be issued on closing of the Acquisition with the remaining 1,000,000 shares being issued on the six-month anniversary of closing, subject to any set-off relating to indemnification. None of the current shareholders of HydroGreen will hold more than 5% of the common shares of the Company pursuant to the Acquisition.
The implied value of the CubicFarms common stock issued to HydroGreen is C$1.50 per share. Following closing, principals of HydroGreen holding in excess of 80% of the Consideration Shares will enter into a pooling agreement with respect to their Consideration Shares. Under the terms of the pooling agreement, 25% of their Consideration Shares will be released on the closing of the Acquisition and an additional 25% will be released on each of the dates which are 6 months, 12 months and 18 months following the closing of the Acquisition.
In 2018, HydroGreen recorded unaudited sales revenues of approximately US$1.2 million and an unaudited gross profit of approximately US$700,000.
The Acquisition will require the approval of HydroGreen Shareholders at a special meeting expected to take place in late December (the “HydroGreen Meeting”). In order to become effective, the Acquisition must be approved at the HydroGreen Meeting by HydroGreen Shareholders holding greater than 50% of the HydroGreen shares entitled to vote at the HydroGreen Meeting. HydroGreen Shareholders holding approximately 75% of the issued and outstanding HydroGreen shares have entered into voting and support agreements with CubicFarms in support of the Acquisition. The board of directors of HydroGreen has unanimously approved the Acquisition and will recommend that HydroGreen Shareholders vote FOR the Acquisition. The merger agreement includes representations, warranties, and covenants typical of a transaction of this nature, including with respect to non-solicitation.
In addition to approval of HydroGreen Shareholders, the Acquisition is subject to the approval of the TSX Venture Exchange and other customary closing conditions. It is not anticipated that the Acquisition will be classified as a Reviewable Transaction under TSX Venture Exchange Policies.
The Acquisition is expected to close in December 2019 following the HydroGreen Meeting.
About HydroGreen
The HydroGreen growing system consists of a 10-feet by 8-feet rack with 8-feet by 6-feet growing surfaces stacked 6 layers high to a total height of 10 feet. This is the smallest, one-section system available for sale – two-section up to six-section systems that are 50 feet long, 8 feet wide and 10 feet high are available. The modular system allows farmers to combine multiple systems to feed hundreds or thousands of livestock.
Image 1: The HydroGreen automated three-section growing system for animal feed.
Seeding one growing surface each day with 1.8 bushels of seed can produce 487 pounds of animal feed every six days. A one-section system could produce enough feed for a 20 to 25-cattle farm, while a three-section system could potentially provide most of the feed for a herd of 100.
The HydroGreen growing system’s automated seeder spreads half an inch of small grain seed on the growing surface. A fine mist of water is sprayed from above to initiate growth, followed by a gentle-rain automated irrigation system to feed the plants as they sprout. After six days, fresh green feed on the growing surface is rolled off and harvested at the push of a button on the touchscreen control panel.
As the feed layer is rolled off the surface, it is sliced into pieces with a water jet, ready to be blended with a feed ration or fed directly to livestock. Once the harvest cycle is complete, the surface is automatedly cleaned and reseeded with a new seedbed, ready to be irrigated – setting in motion another grow cycle.
Image 2: The HydroGreen system takes seed to feed in six days.
While growing feed hydroponically is not a new concept, traditional rack-and-stack systems are labor-intensive and are sensitive to mold. Mold tends to grow on seeds in warm, damp or humid conditions. Traditional hydroponic systems rely on human labor to manually clean the growing pans and soak, spread and water the seed, resulting in significant potential for human error and potential for mold to develop. The HydroGreen technology alleviates both problems as it requires only one second of labor per tonne of feed produced – to push a button on the touchscreen control panel. Through its automated process, the system applies a sequence of eleven procedures dedicated to controlling mold, stretching from seed selection to harvest, reducing the potential for human error and for mold to develop.
Economic, environmental and nutritional benefits of hydroponic animal feed
The HydroGreen system provides local, on-demand availability of fresh green feed 365 days a year, unaffected by drought, snow or rain. Hydroponic feed that is fed directly to livestock results in a significant reduction of feed waste since the entire root mass is consumed with the grass.
In addition to savings from reduced labor and water, the system’s vertically stacked surfaces allow for high yields in a very small area, increasing farmers’ independence by growing food for their livestock without the need for cultivated land.
When wheatgrass and barley are sprouted, they release many vitamins and minerals as well as convert hard-to-digest starches into easily digestible proteins. Sprouting results in increased enzyme levels in the ration, which aids digestion and absorption of nutrients; increased levels of vitamins; increased mineral bioavailability and increased fatty acids (quality energy) and amino acids (quality protein). These nutrients are critical to animal health, growth, milk production and reproduction.
Sales and marketing strategy for the HydroGreen system
CubicFarms has signed an authorized reseller agreement with Artex Feed Solutions. Artex Feed Solutions is a joint venture company which is 25% owned by CubicFarms and 75% owned by Artex Barn Solutions, a leader in agricultural supplies for over 40 years. Artex Barn Solutions was founded by John de Jonge – also a board member of CubicFarms – who purchased Artex Barn and grew it into a global provider of cattle handling equipment, ventilation and cow cooling. He has deep expertise in establishing and scaling up multiple manufacturing facilities in China and North America.
Artex and Mr. de Jonge plan to market the HydroGreen system to their existing dealership network in the USA and Canada, and to qualified leads in China, Indonesia, and the Middle East – areas with substantial market potential due to changing food consumption patterns and supportive government policies toward agricultural technology.
Internationally, Artex dealers will target existing agriculture animal producers looking to enhance profitability and environmental sustainability, early-stage farmers with minimal capital and land constraints, small- to medium-size farms seeking feed alternatives to benefit their operations and urban farmers without access to land.
The arrangement with Artex Feed Solutions may be considered a related-party transaction subject to TSX-V Policy 5.9 and Multilateral Instrument 61-101. The Company will be exempt from the need to obtain minority shareholder approval and a formal valuation as required by MI 61-101 as the Company is listed on the TSX Venture Exchange and the fair market value of the transaction with Artex is far below 25% of the Company’s market capitalization.
While remaining on CubicFarms’ board of directors, Mr. de Jonge will transition from his current role as the Company’s Chief Design and Installation Officer to Chief Executive Officer of CubicFarms subsidiary CubicFeed Systems, effective immediately. Rodrigo Santana, CubicFarms’ Chief Operating Officer, will assume oversight of machine design and installations, supported by a management team with significant field expertise.
Dave Dinesen, Chief Executive Officer of CubicFarms, commented: “This landmark transaction with HydroGreen is a catalyst for continued growth at CubicFarms. Having already established a robust sales pipeline for our fresh produce vertical, this acquisition will enable us to capitalize on technology and automation synergies with HydroGreen to capture the animal feed space, which we believe could be a larger market than fresh produce. Approximately two-thirds of the world’s agricultural land is used for grazing and animal feed production. HydroGreen’s “land on a stand” system helps reduce the vast amounts of land required to grow feed.
“While the CubicFarms system is ideal for growing fresh produce, the advancements made in the HydroGreen system in the areas of harvesting, reseeding and self-cleaning, make it particularly well-suited for the production of animal feed. This transaction positions us to be a leading ag-tech company providing controlled-environment growing systems in four diversified verticals – fresh produce, animal feed, hemp/cannabis, and nutraceutical ingredients.”
Dihl Grohs, Chief Executive Officer of HydroGreen, commented: “I am incredibly proud of HydroGreen’s growth trajectory since our first system prototype was built in 2014 in Sioux Falls, South Dakota, then progressively refined to achieve today’s 98% reliability rating and the system’s ability to monitor and correct issues in advance.
“The technology is poised for large-scale commercialization and this merger represents an ideal next step to bring HydroGreen systems to international markets. I am confident that CubicFarms’ global leadership in automated vertical-farming solutions, combined with the go-to-market ability of Artex Feed, will result in significant uptake of our systems as farmers learn how this technology enhances the productivity of their operations.”
John de Jonge, President of Artex Feed Solutions, and Chief Executive Officer of CubicFeed Systems commented: “As a lifelong dairy industry participant, I believe the animal feed market is ripe for disruption, urgently requiring predictable, year round production of nutritious feed while minimizing the inputs of land, labor, and water. I am excited to lead the expansion of CubicFarms’ animal feed business by leveraging Artex’s broad network of dealers in 40 countries to bring the HydroGreen solution to market.”
Neither the TSX Venture Exchange nor it’s Regulation Services Provider (as that term is defined in the policies of the TSX Venture Exchange) accepts responsibility for the adequacy or accuracy of this release.
This news release does not constitute an offer to sell or a solicitation of an offer to buy any securities in the United States. The Consideration Shares to be issued as part of the Acquisition have not been, nor will be, registered under the United States Securities Act of 1933, as amended (the “U.S. Securities Act”), and such securities may only be offered or sold within the United States pursuant to an exemption from the registration requirements under the U.S. Securities Act and all applicable state securities laws.
About CubicFarm® Systems Corp.
CubicFarm® Systems Corp. (“CubicFarms”) is an ag-tech company commercializing large scale, vertical farming solutions for global industrial markets. Founded in 2015, the Company’s mission is to provide industries around the world with efficient growing systems capable of producing predictable crop yields. CubicFarms offers turnkey, commercial scale, hydroponic, automated vertical farm growing systems that can grow predictably and sustainably for 12 months of the year virtually anywhere on earth. CubicFarms enables its customers in the fresh produce, animal feed, nutraceutical, and hemp/cannabis industries to grow locally and to provide their markets with safe, sustainable, secure and fresh ingredients that are consistent in color, size, taste, nutrition and allows for longer shelf life. Further support and value is provided to customers through the Company’s patent-pending germination technology and proprietary auto harvesting and processing methods.
Using its unique, undulating growing system, the Company addresses the main challenges within the indoor farming industry by significantly reducing the need for physical labor and energy, and maximizing yield per cubic foot. The Company has sold and installed systems in Canada and the US and is currently negotiating with a global pipeline of prospective customers. It also operates one wholly owned facility in Pitt Meadows, British Columbia, and sells its produce in the province to retail and wholesale customers under the brand name Thriiv Local Garden™.
Information contact
Kimberly Lim
kimberly@cubicfarms.com
Phone: +1-236-858-6491
www.cubicfarms.com
Cautionary statement on forward-looking information
Certain statements in this release constitute “forward-looking statements” or “forward-looking information” within the meaning of applicable securities laws, including, without limitation, statements with respect to the closing of the Acquisition and HydroGreen’s sales and growth prospects. Such statements involve known and unknown risks, uncertainties, and other factors which may cause the actual results, performance, or achievements of CubicFarm Systems Corp. and its subsidiaries, or industry results, to be materially different from any future results, performance, or achievements expressed or implied by such forward-looking statements or information. Such statements can be identified by the use of words such as “may”, “would”, “could”, “will”, “intend”, “expect”, “believe”, “plan”, “anticipate”, “estimate”, “scheduled”, “forecast”, “predict”, and other similar terminology, or state that certain actions, events, or results “may”, “could”, “would”, “might”, or “will” be taken, occur, or be achieved.
These statements reflect the company’s current expectations regarding future events, performance, and results and speak only as of the date of this news release. Consequently, there can be no assurances that such statements will prove to be accurate and actual results and future events could differ materially from those anticipated in such statements. Except as required by securities disclosure laws and regulations applicable to the company, the company undertakes no obligation to update these forward-looking statements if the company’s expectations regarding future events, performance, or results change.
Urban Crop Solutions Celebrates it's 5th Anniversary
The company is a total solution provider and offers container farms and plant factories and all products and services that growers need to grow healthy crops in an indoor farm
Today, Urban Crop Solutions celebrates its 5th anniversary. On this occasion, a movie was released with testimonials from customers around the globe. Urban Crop Solutions is proud to be a pioneer in the emerging market of indoor vertical farming with a unique business model. The company is a total solution provider and offers container farms and plant factories and all products and services that growers need to grow healthy crops in an indoor farm.
The story of the founding of Urban Crop Solutions starts in 2012 when the founders were experimenting with rooftop farming in urban areas. Only in 2014, the choice was made to focus on indoor vertical farming after some successful tests where done in the warehouse of one of the founders. Since then the company was taken on a rollercoaster and the company evolved from a local AgTech startup to an international scale-up with unique commercial products and services.
Link to the 5 years anniversary movie with testimonials from over the globe.
https://youtu.be/KnqLMtNrr7w
From its incorporation, the company’s vision was always that the knowledge of plant growth is key. Today, the company operates 10 labs, 1 demo plant factory and 1 demo container farm for its research operations.
“Over the last 5 years, we have conducted over 800 cultivar trials. Some tests with seeds failed miserably.” explains dr. Oscar Navarrete, chief plant scientist and the first employee of Urban Crop Solutions. “But through our continuous work to tweak seed selection, LED spectrum, irrigation, substrate and nutrition, we have developed more than 200 plant growth recipes that are available for our clients.”
The design of the plant growth infrastructure that Urban Crops Solutions is building for its clients is the result of the know-how the plant scientists transfer to the mechanical engineers to achieve optimal plant growth in an indoor vertical farm environment. In February 2016, the Flemish Minister-President Geert Bourgeois opened Urban Crop Solutions’ automated indoor farm which was the largest in Europe. This installation was built and is operated by Urban Crop Solutions for research purposes.
“We’ve been at the forefront of this emerging industry since the beginning. Some of our engineering concepts lacked robustness, but by listening to the feedback of our customers we’ve upgraded numerous components to improve the reliability, the operational efficiency, and food safety”, says Maarten Vandecruys, founder and CTO of Urban Crops Solutions. “We now have 24 containers in operation with our customers, of which about half in Europe and half in the USA. We are proud to have collaborations with large corporates and with several scientific institutions”.
Urban Crop Solutions caught in the past 5 years much attention by media, by trendwatchers, by large corporates, by politicians, and by royals. In November 2018, the company could present its technology to the French president Emmanuel Macron and the Belgian King Filip. In September 2019, the company realized a series A capital round, marking the start of the international commercialization of its products and services portfolio.
“It is clear that indoor vertical farming is still an early-stage industry. With the current high initial cost involved, it requires finding the right market niche for the right crop in order to achieve an attractive ROI.” Explains CEO and co-investor Tom Debusschere. “However, the world is changing very fast and besides the obvious food industry we see a lot potential for our products and services in some high-value end-markets like food supplements, fragrances, cosmetics, aromatics and phyto-pharmaceuticals.”
The technology and the products of Urban Crop Solutions are best explained as at “the crossroads between plant biology and factory engineering”. In the coming years, the company will continue to invest in products and services for ‘killer applications’ (revolutionizing market segments) and ‘moonshot crops’ (developing indoor plant growth recipes with large impact) in order to realize its mission: ‘Urban Crop Solutions contributes to the solutions for the challenges caused by global urbanization, the growing world population and the lack of agricultural land in the world’.
For more information on this press release, on Urban Crop Solutions or on the products and services of Urban Crop Solutions you can contact Tom Debusschere, Managing Director (tode@urbancropsolutions.com), or Maarten Vandecruys, Co-founder and CTO (mava@urbancropsolutions.com ) or visit our website ( www.urbancropsolutions.com ):
European headquarters: American headquarters:
Grote Heerweg 67 800 Brickell Avenue, 1100 Suite
8791 Beveren-Leie (Waregem) Miami (FL 33131)
Belgium Florida
(+32)56 96 03 06 +1 (786) 408-6027
Facebook: www.facebook.com/urbancropsolutions
Twitter: www.twitter.com/U_C_Solutions
LinkedIn: www.linkedin.com/company/urbancropsolutions
YouTube channel: http://www.youtube.com/c/UrbanCropSolutions
OASIS Grower Solutions Moves Florida Manufacturing
This new facility gives the company 30% more space, providing for anticipated growth in the southern region of the country, as well as for additional capacity and warehousing
To gear up for what's anticipated to be an exciting year for OASIS® Grower Solutions in 2020, it has moved its Florida offices and manufacturing from Mt. Dora to a much larger and more modern facility at 5454 Foliage Way, in Apopka, Florida. This new facility gives the company 30% more space, providing for anticipated growth in the southern region of the country, as well as for additional capacity and warehousing. www.oasisgrowersolutions.com
Babylon Is Excited To Share That We Have Made It Onto The FoodTech 500's Shortlist!
The final list will be released in February, so keep an eye out for our final ranking
The list recognizes companies in all sectors of the AgriFoodTech industry, that are entrepreneurial success stories and have disrupted norms within the industry. The final list will be released in February, so keep an eye out for our final ranking.
hashtag#FoodTech hashtag#Agtech hashtag#futureoffood hashtag#babylonmicrofarms hashtag#successstories
Hydroponic Indoor Gardening Kit Allows You To Grow Vegetables All Year Round
The Swedish company IKEA has developed a hydroponic system that would allow anybody to grow vegetables all year round without the need for a traditional garden
November 04, 2019
The Swedish company IKEA has developed a hydroponic system that would allow anybody to grow vegetables all year round without the need for a traditional garden. Users without immediate access to a garden now have the chance to grow their own foods via IKEA's indoor hydroponic garden. It's easy to use and requires no prior gardening experience and knowledge.
A hydroponic farm
The hydroponic system in order to function requires only adequate sunlight and water. With this, the user is able to grow much produce found in the aisles of their local grocery stores. Within the hydroponic system lies absorbent foam plugs that coat the seed. The specially created foam enables the seed to fully hydrated, keeping them moist enough without overwatering them which could be detrimental to their growth. Once germination is complete, they would then be transferred to a separate pot that is filled with pumice rock and water to complete the growth process.
Indoor gardening kit
Subsequently, the pots are then moved to a growing tray that is equipped with a solar lamp. The addition of the solar lamp is beneficial for places where sunlight is not readily available. The internal water sensor ensures that the plants are receiving sufficient water. According to, Helena Karlen, from the Swedish University Of Agricultural Science, the main objective was to make a hydroponic system that could be easily utilized by the average consumer. The series of a hydroponic device referred to as KRYYDDA/VAXER, was designed by a team consisting of Swedish agricultural scientist and was marketed to persons who live in apartments and those who want fresh produce during winter months.
Additionally, the product was designed to be a more sustainable, healthier and eco-friendly mean of growing and harvesting produce. Whether you live in China, North America or Northern Sweden, the product creators believe that you should be able to produce freshly harvested produce. Upon purchasing the basic VAXER series, the user will get seeds, starter plugs, nursery boxes, cultivation insert sets, fertilizer, pumice stones, cultivation light fixtures, and cultivation light. Additionally, the VAXER hydroponic system is more affordable when compared to traditional means of produce harvesting. It's also the company's first departure from traditional household items like bookshelves and tables. The head of the sustainable department of the Swedish company states that the device is the first of many that will be placed on the market in an attempt to provide a more eco-friendly and sustainable life for users.
CubicFarm Systems Announces Global Reseller Agreement With Groviv With Minimum Sales Threshold of 200 Machines
The new partnership significantly expands CubicFarms’ machine sales pipeline into strategic international markets
New partnership significantly expands CubicFarms’ machine sales pipeline into strategic international markets
Vancouver, BC – (AccessWire – November 6, 2019) – CubicFarm® Systems Corp. (TSXV: CUB) (“CubicFarms” or the “Company”) is pleased to announce that it has entered into a global Reseller Agreement (the “Agreement”) with Groviv, a leader in the science and technology of controlled-environment agriculture (CEA). Groviv, a division of Nu Skin Enterprises – a minority investor in CubicFarms – will lead global sales for CubicFarms and has appointed Joe Huston, its Vice President of Business Development to direct the effort. Mr. Huston has extensive retail sales and distribution experience, working with brands such as Walmart, Kroger and Costco.
The authorized Reseller Agreement, while global in nature, will be focused initially on the sales of vegetable-growing machines in key territories such as China, the Middle East, and other strategic areas. The Agreement complements CubicFarms’ own sales and marketing efforts for its machines. CubicFarms is also focused on growing machine sales in its other verticals – animal feed, hemp/cannabis, and nutraceutical ingredients – through its own sales pipeline or in partnership with other resellers.
In January 2019, CubicFarms signed a binding term sheet with Nu Skin to work together in the long term to market and sell CubicFarms systems in China. This Reseller Agreement expands upon CubicFarms’ relationship with Nu Skin to allow its Groviv division to act as an exclusive, authorized reseller globally, with the provision that Groviv fulfills a minimum semi-annual sales threshold of 60 and 140 CubicFarms growing machines by June 30, 2020 and December 31, 2020, respectively.
“The expansion of the China binding term sheet to this global Reseller Agreement is a testament to Nu Skin and Groviv’s confidence in CubicFarms’ patented technology. We are excited to work with Joe and his team to bring the best automated vertical farming technology to China, the Middle East and other strategic areas where population growth, water, soil and farmland challenges present a huge need for high-value leafy vegetables, herbs and other crops,” said Dave Dinesen, Chief Executive Officer of CubicFarms.
“Joe and the rest of the Groviv team have already established relationships with key growers, customers and partners worldwide, resulting in a significant sales pipeline. Joe’s leadership experience in building businesses and driving revenue, coupled with his deep experience operating in China, are an enormous boon to our partnership.”
Steve Lindsley, President of Groviv, stated: “We are excited to combine both our sales and marketing expertise with CubicFarms. Together we have the science, technology and experience to provide sustainable solutions that will grow safe, clean and nutritious fresh produce around the world.”
Neither the TSX Venture Exchange nor its Regulation Services Provider (as that term is defined in the policies of the TSX Venture Exchange) accepts responsibility for the adequacy or accuracy of this release.
About CubicFarm® Systems Corp.
CubicFarm® Systems Corp. (“CubicFarms”) is an ag-tech company commercializing large scale, vertical farming solutions for global industrial markets. Founded in 2015, the Company’s mission is to provide industries around the world with efficient growing systems capable of producing predictable crop yields. CubicFarms offers turnkey, commercial scale, hydroponic, automated vertical farm growing systems that can grow predictably and sustainably for 12 months of the year virtually anywhere on earth. CubicFarms enables its customers in the fresh produce, animal feed, nutraceutical, and hemp/cannabis industries to grow locally and to provide their markets with safe, sustainable, secure and fresh ingredients that are consistent in colour, size, taste, nutrition and allows for a longer shelf life. Further support and value is provided to customers through the Company’s patent-pending germination technology and proprietary auto harvesting and processing methods.
Using its unique, undulating growing system, the Company addresses the main challenges within the indoor farming industry by significantly reducing the need for physical labour and energy, and maximizing yield per cubic foot. The Company has sold and installed systems in Canada and the US, and is currently negotiating with a global pipeline of prospective customers. It also operates one wholly owned facility in Pitt Meadows, British Columbia, and sells its produce in the province to retail and wholesale customers under the brand name Thriiv Local Garden™.
Information contact
Kimberly Lim
kimberly@cubicfarms.com
Phone: +1-236-858-6491
www.cubicfarms.com
Cautionary statement on forward-looking information
Certain statements in this release constitute "forward-looking statements" or "forward-looking information" within the meaning of applicable securities laws, including, without limitation, statements with respect to Groviv, a division of Nu Skin Enterprises – a minority investor in CubicFarms – will lead global sales for CubicFarms; and the authorized Reseller Agreement, while global in nature, will be focused initially on the sales of vegetable-growing machines in key territories such as China, the Middle East and other strategic areas. Such statements involve known and unknown risks, uncertainties, and other factors which may cause the actual results, performance, or achievements of CubicFarm Systems Corp., or industry results, to be materially different from any future results, performance, or achievements expressed or implied by such forward-looking statements or information. Such statements can be identified by the use of words such as "may", "would", "could", "will", "intend", "expect", "believe", "plan", "anticipate", "estimate", "scheduled", "forecast", "predict", and other similar terminology, or state that certain actions, events, or results "may", "could", "would", "might", or "will" be taken, occur, or be achieved.
These statements reflect the company's current expectations regarding future events, performance, and results and speak only as of the date of this news release. Consequently, there can be no assurances that such statements will prove to be accurate and actual results and future events could differ materially from those anticipated in such statements. Except as required by securities disclosure laws and regulations applicable to the company, the company undertakes no obligation to update these forward-looking statements if the company's expectations regarding future events, performance, or results change.
Rise Gardens Helps You Grow The Perfect Tomato In Your Living Room
After becoming frustrated with growing fruits and veggies outdoors, Hank Adams tried his hand at building his own in-home hydroponic system, a device that grows plants in a reservoir of moving water and organic materials
October 31, 2019
Maintaining a garden in Chicago is difficult. Not only is the region plagued with a short growing season and unpredictable weather, but figuring out how to provide fruits and vegetables with the perfect amount of water, sunlight and nutrients can be confusing.
After becoming frustrated with growing fruits and veggies outdoors, Hank Adams tried his hand at building his own in-home hydroponic system, a device that grows plants in a reservoir of moving water and organic materials.
“It was a really frustrating experience,” Adams said. “It actually took a fair amount of research to figure it out. And what I ended up with was a system that really belonged in my basement.”
The system was “ugly,” he said. “It was nothing I wanted to show off.”
A Rise Gardens system (Photo via Katherine Davis)
But the experience led to Adams launching Rise Gardens, a Chicago startup creating an indoor, IoT-connected hydroponic system that is attractive enough to put in your living room and simple enough for anyone to grow a perfect head of lettuce.
Adams began making prototypes for Rise Gardens in 2017, working out of Chicago startup incubators 1871 and mHub, and began selling the final product in August. Adams is a board member of 1871 and also the former CEO of Sportsvision, a Chicago-based graphics company best known for inventing the yellow first-down marker in football broadcasts.
Rise Garden systems can be bought online or in the startup’s pop-up shop at 20 W. Kinzie St., which opened in early October.
The modular system is made out of hardwood and heavy-gauge, powder-coated steel. It has a built-in water pump, seed sockets and a programmed LED light system that automatically shifts on and off to give plants the perfect amount of light.
Once consumers purchase their hydroponic system, they are encouraged to subscribe to Rise Gardens’ subscription service, which sends them seed pods every month and gives them access to the company’s mobile app that reminds users when to add water or nutrients. The startup sells seeds for a range of vegetables and herbs, including kale, lettuce, tomatoes, peppers, basil, and rosemary.
“We’ve made it simple,” Adams said. “If you follow the instructions, it grows really robustly.”
Adams said plants grow 20 percent faster in his system than they could in soil or outdoors, adding that users can expect to grow arugula in 14 days and a head of lettuce in 25 days.
A Rise Garden system (Photo via Katherine Davis)
Though small, counter-top hydroponic systems are common, Adams says Rise Gardens’ large size allows for users to actually grow a significant amount of fresh food.
Since launching, Adams said he has sold 70 systems and is now working with retailers to sell the device in more locations. The system starts at $549 for one level and goes up to nearly $950 for three.
In his own Rise Gardens system at home, Adams grows lettuce, carrots, beets, tomatoes, peppers, and strawberries. Often times, he says he uses his produce in homemade salads, pastas and pizzas.
“It’s really nutritious and it tastes great,” Adams said. “Compared to a lot stuff that we’re used to getting in grocery stores, you’re surprised by the taste.”
Hank Adams, founder of Rise Gardens, with his hydroponic system (Photo via Rise Gardens)
The Farmshelf Corridor Dubbed The “Garden of Eden” by Katie Couric At The Next50 Event Celebrating The Work of José Andrés And World Central Kitchen
Farmshelf was honored to play a small part in an event that kicks off the next 50 years of World Central Kitchen and its mission to mobilize chefs after natural disasters to deliver a hot plate of food when it’s needed most
The Farmshelf corridor dubbed the “Garden of Eden” by Katie CouricOctober 4, 2019
Jean-Paul KyrillosFollow
Co-founder/ CRO at Farmshelf
Farmshelf is rolling into new cities and big events.
Next50 at The Shed, Hudson Yards, NY
Last week, guests of José Andrés got to enjoy tapas with Farmshelf greens harvested on-demand as they wandered through the Farmshelf corridor. Farmshelf was honored to play a small part in an event that kicks off the next 50 years of World Central Kitchen and its mission to mobilize chefs after natural disasters to deliver a hot plate of food when it’s needed most.
Stop Food Waste NYC at the Javits Center
Jacob K. Javits Convention Center, New York, NY
Our partners from Cultivated NY had their brand new Farmshelfs on display as part of their larger effort to showcase ways that their parent company Compass Group is fighting food waste. With Farmshelf, no greens or herbs are lost in transit and chefs harvest only what is needed, so food waste from spoilage is virtually eliminated.
Oh hey, CA...
Renaissance Esmeralda Resort & Spa, Indian Wells, CA
As we get ready for our west coast launch, Farmshelf was at the Society for Hospitality and Foodservice Management conference in Palm Springs, CA. While we had some fun being outdoors, this was just a cameo. Farmshelf is designed for onsite growing inside your restaurant, hotel or café.
Wondering when we arrive in your city?
Available Now: NYC, DC, Philadelphia, Texas
October 2019: Chicago, Milwaukee
January 2020: SF Bay Area, Boston, Florida
March 2020: Portland, Seattle
Summer 2020: Top 20 U.S. Markets
Farmshelf connects you to your food by making growing simple and enjoyable. Available now for businesses only.
Subscribe to our newsletter for more live updates on Farmshelf and our partners!