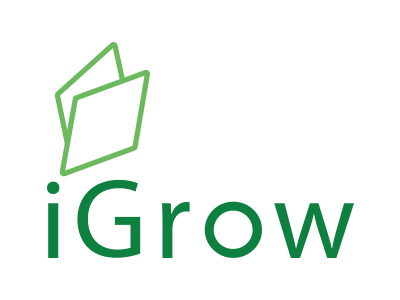
Welcome to iGrow News, Your Source for the World of Indoor Vertical Farming
KyleTalksAgTech: Small Scale Indoor Farming Systems - The Future of How And Where We Grow w/ Alexander Olesen
On this episode of the CropTalk series, #KyleTalksAgTech, Kyle Barnett sits down with Alexander Olesen of Babylon Micro-Farms, to understand the ins and outs of small scale indoor farming systems
Feb 4, 2020
On this episode of the CropTalk series, #KyleTalksAgTech, Kyle Barnett sits down with Alexander Olesen of Babylon Micro-Farms, to understand the ins and outs of small scale indoor farming systems.
Alexander shares some unique perspective and what makes Babylon's growing system and service for their clients, special.
New York City Startup Called Re-Nuble Turns Food Waste Into Fertilizer
A New York City startup is using potato peels, apple cores, and rotten tomatoes to help farmers grow fresh fruits and vegetables
It Can Be Used To Grow Crops in Indoor Hydroponic Farms.
February 5, 2020
Re-Nuble CEO and founder Tinia Pina. (Image credit: Re-Nuble video)
A New York City startup is using potato peels, apple cores, and rotten tomatoes to help farmers grow fresh fruits and vegetables.
“We take produce waste from food distributors and food processors – anything that can’t go to a food bank or farm,” says Tinia Pina, founder, and CEO of Re-Nuble.
The company converts food waste into organic fertilizer pellets that can be used in indoor, hydroponic farms.
Pina says when dissolved in water, the pellets make the nutrients immediately available to the plant, mimicking the biological nutrient systems found outdoors.
So she says the technology can help make it easier to grow organic food indoors in urban areas, where fresh local food is often scarce.
And it helps the climate. It keeps food out of landfills, where it would otherwise decompose and release methane, a potent greenhouse gas.
It also reduces the need for synthetic fertilizers, which create a lot of carbon pollution when they’re manufactured.
So far, the company has facilities in New York City and Rochester, New York, and plans to expand to the West Coast. Pina hopes to eventually help cities across the country use their food scraps to grow local, organic food.
Reporting credit: Sarah Kennedy/ChavoBart Digital Media.
US: Audio - Indoor Vertical Farm In Cincinnati Will Be Fully Automated
This year is expected to be a big one for autonomous farming where robots plant, nurture and harvest leafy greens indoors. One such farm is under construction in Ohio
January 29, 2020
Heard on Morning Edition
ANN THOMPSON
This year is expected to be a big one for autonomous farming where robots plant, nurture and harvest leafy greens indoors. One such farm is under construction in Ohio.
Wisconsin, Meet The Green Bay Woman Who’s Opening The Nation’s First Urban Snail Farm
McDonald, 65, has spent the last four years researching and getting permits for her business, Cupid's Arrow Escargot LLC. She's submitted her initial permits to the U.S. Department of Agriculture and the Food and Drug and Administration
Sandy McDonald Says Americans Can Learn To Love Homegrown Escargot
By Rob Mentzer
December 30, 2019
People have been eating snails for thousands of years.
"They're healthy," said Sandy McDonald — low in fat, high in cholesterol. "They have amino acids, Omega-3 fatty acids, niacin, iron, vitamin D complexes, magnesium. I could go on and on."
Their taste, McDonald says, is rich and earthy, like a mushroom.
Despite all these selling points, it's pretty likely that escargot, as cooked snails are known, isn't part of your regular dinner rotation.
McDonald would like to change that.
Sandy McDonald. Courtesy of Sandy McDonald
McDonald, 65, has spent the last four years researching and getting permits for her business, Cupid's Arrow Escargot LLC. She's submitted her initial permits to the U.S. Department of Agriculture and the Food and Drug and Administration. She's got a space near Green Bay's Titletown district, approved by the city for use as a site of heliciculture, which means raising snails.
She's set to become the first snail farmer in the Midwest, and the first in the nation to do it in an indoor, urban environment.
McDonald sees Cupid's Arrow as connected with the farm-to-table movement and the movement toward local food. Most of the snails served as escargot at American restaurants are imported, and it's illegal to import live snails, which means American diners are getting a less-fresh canned version. McDonald plans to sell snails to chefs around the Midwest for escargot and to harvest snail slime for use by the cosmetics industry. Over time, she hopes to sell snail eggs, too, that can be served as escargot caviar.
The reason for the government's strict controls on snail imports and cultivation is because snails are an invasive species that can harm natural ecosystems. One variety, the giant African snail, is banned from the U.S. in any form, and will be seized and removed by the government if found.
Cupid’s Arrow Escargot will be constructed with required security measures that keep the snails or their eggs from getting out of the building. The pens are escape-proof. The USDA requires the dirt to be processed before it’s disposed of, but McDonald hopes to use vermicomposting to avoid having to dispose of much at all.
It will be "a complete ecosystem," McDonald said. "They'll be born, raised and processed in the same building."
Snails need a consistent temperature of 68 to 70 degrees. They need moisture, so the pens will have humidifiers. They eat grains (McDonald hopes to get some of the byproducts of nearby Titletown Brewing such as spent hops and barley) as well as fruits and vegetables such as tomatoes and cucumbers.
McDonald plans to start with a purchase of 2,000 snails from an Irish snail farm. As long as the conditions are right, she says, they won't require a whole lot of tending.
"They just kind of do their own thing," she said.
The history behind snail-eating is no joke. Pliny the Elder, the ancient Roman historian, describes heliciculture in the first century as having been "brought to such a pitch of perfection" as to produce "fattened periwinkles" that were "quite an object of gastronomy."
Today, escargot is best known as part of French cuisine, though it's also eaten across Europe and in Morocco. In the U.S., the two certified snail farms are in Long Island, New York, and Quilcene, Washington. (She'll be buying her starter snails from Washington's Little Gray Farms.)
McDonald's application to the city of Green Bay says she'll be the only employee at first, but it's possible that she'll hire other snail-minders as the business grows.
She acknowledges that it's taken a long time to get the business up and running — a metaphor about a particular animal's pace of travel comes to mind. But it feels good to be this close to launching. Cupid's Arrow Escargot will begin operations in the spring.
In the long run, McDonald says, it's even possible that escargot could become not the sole province of fancy foodie culture, but something more mainstream.
"I'd like to hook up with a good chef," McDonald said. "Why can't there be, you know, snail poppers? (We can) bring this food into the United States."
Note: An earlier version of this story misstated McDonald's progress on getting federal permits. She has submitted her application.
Colorado School Taps Container Farm for Classroom, Food Stand
A Douglas County High School is using a refrigerated freight container converted into a hydroponic farm as an extension of the classroom. At Mountain Vista High School in Highlands Ranch, students learn how to grow leafy greens and other vegetables
Freight Farms’ hydroponic vertical container farms use nearly 99% less water than a traditional farm, running with as little as zero to five gallons per day, less than the average dishwasher. (Pixabay)
December 9, 2019
HIGHLANDS RANCH, Colo. — A Douglas County High School is using a refrigerated freight container converted into a hydroponic farm as an extension of the classroom.
At Mountain Vista High School in Highlands Ranch, students learn how to grow leafy greens and other vegetables. And David Larsen, who teaches business agriculture at the school, said other learning opportunities branch out from there.
“Then you take all the different aspects of it, like the business side, marketing, branding all those things that we want kids to have practical experience on,” Larsen said. “If you have kids that are interested in the engineering technology side of it, there's a control system and automation in there."
Students package and sell their harvests to local restaurants, students' families and staff, and any extra produce goes to retirement homes and food pantries. Larsen said students also gain soft skills such as how to be a good employee, punctuality, engagement, responsibility, and how to be the public face of a business.
Because the climate is controlled inside the container, food can be grown all school year long with a predictable commercial-scale output. A greenery unit can support 13,000 plants at a time, producing harvests of up to 900 heads of lettuce per week. Larsen said the indoor farm also is resistant to shocks such as extreme weather patterns or drought.
"The taste is incredible. When people eat our lettuces, they're like, 'Oh, wow, I didn't know lettuce could taste like that,’” he said. “There's some very interesting varieties of herbs as well. We do a lot of different arugulas. I think the freshness just really sets it apart."
The high-tech containers are the brainchild of the Massachusetts-based company Freight Farms and are well suited for Colorado. They require a considerable amount of electricity, but use nearly 99% less water than a traditional farm, running with as little as five gallons per day - less than the average dishwasher.
Eric Galatas, Public News Service - CO
AUDIO: Why A New Rooftop Farm In Paris Is A Glimpse Into The Future
The city of light may become the city of fruits and vegetables soon. French company Agripolis is slated to open a 150,000-square-foot rooftop farm in 2020, hosting 2,000 pounds of crop each day
By Tyler Kern
August 28, 2019
The City of Light May Become The City of Fruits And Vegetables Soon
French company Agripolis is slated to open a 150,000-square-foot rooftop farm in 2020, hosting 2,000 pounds of crop each day.
Urban farming and aeroponics have spread to America but this project is the most ambitious yet.
“In Europe they’ve really gone to another level with it,” Dave Schupmann, Senior Vice President of Sales and Marketing at Fortis Warranty, a roofing warranty provider, said.
Concerns about weeds and heaviness from rain and snow have traditionally been problems for rooftop farms, but advancements have made projects like this one more viable.
“Sustainability is great. The products that we’re using today, much more than ever are lasting longer. So, you’re able to put these giant farms on top of these systems without them breaking down every 10-15 years,” Schupmann said.
While green roofs are still relatively uncommon in the United States, the ability to turn a profit from them may spur more investment in the model, according to Schupmann.
“I think it’s fantastic what they’re able to do with the vegetative roofing, really making it more than just something nice to look at but making effective use of the land for the tenants around it,” he noted.
According to Curbed.com, the farm will host more than 30 different plant species. Parisians will also be able to occupy their own plots of land on the roof, creating a communal space for residents.
Tune in to Business Casual, MarketScale’s live radio broadcast, every Wednesday and Friday at 8 a.m. CST.
AUDIO: Mounting Investor Interest In Agricultural Technology
As the earth warms and the world’s population grows, more and more companies are growing food indoors in greenhouses and vertical farms
Carole Zimmer
JulY 31, 2019
Investors are paying close attention to the rapidly growing sector that is agricultural technology, or ag-tech.
As the earth warms and the world’s population grows, more and more companies are growing food indoors in greenhouses and vertical farms.
Although demand is increasing, this segment of the agricultural industry faces high costs of both labor, energy costs and equipment, for things like lighting.
Lead image: Angela Weiss/AFP/Getty Images
CO2 GRO Inc (CVE:GROW) Proprietary Foliar Spray System Boosts Yields By 25 Percent
By MIDASLETTER LIVE | APRIL 24, 2019
CO2 GRO INC
CO2 GRO Inc (CVE:GROW) (OTCMKTS:BLONF) (FRA:4O21) is developing advanced carbon dioxide technologies to accelerate plant growth. COO Aaron Archibald explains that carbon dioxide is beneficial for growth, resulting in larger and quicker-growing plants. The company’s proprietary process dissolves carbon dioxide into water, which is then applied to the foliage of plants using CO2 GRO’s foliar spray system.
Typically, growers use gas deployment systems that result in significant carbon dioxide loss as a result of venting; CO2 GRO’s foliar sprays ensure each plant receives the necessary carbon dioxide. Unlike gas deployment systems, the company’s foliar spray technology can be applied to outdoor grows and greenhouses.
Archibald reveals that using CO2 GRO’s foliar sprays regularly results in yields 25 to 30 percent higher than yields produced by using gas deployment systems. Archibald anticipates that the company’s technology will be adopted by cannabis LPs in Canada, as Health Canada is in the process of reviewing applicable regulations. CO2 GRO currently has licensing agreements in both Canada and the US, and has seen broad interest from the American hemp space since the passage of the Farm Bill.
Transcript:
Narrator: CO2 GRO is a Toronto based, precision agriculture technology company. GRO offers CO2 foliar spray systems to both indoor and outdoor growers for increasing their crop yields, safely and naturally.
The company has over 66 million shares outstanding, with management ownership at 26 percent. CO2 GRO Inc is listed on the TSX-Venture under the symbol GROW.
James West: I’m joined now by Aaron Archibald, Chief Operating Officer of CO2 Grow, trading on the TSX Venture under the symbol GROW. That’s a good symbol.
Aaron Archibald: It is, thanks!
James West: Aaron, so your business is essentially creating foliar CO2 sprays, and so just to refresh the memory of our audience, or to enlighten them for those who might not know, what is the benefit of CO2 as a foliar spray?
Aaron Archibald: Well, any grower knows that adding CO2 to plants is beneficial, and they’ll grow faster and grow bigger; it’s difficult to get CO2 to plants, though. So what we do is, we dissolve CO2 into water and apply it to the foliage of the plant. That makes it 100 percent bioavailable, and it’s driven into the plant by osmotic pressure.
James West: Okay. So interestingly, most greenhouses that beneficiate with CO2 use gas deployment systems.
Aaron Archibald: Absolutely.
James West: And that’s got to be a little bit more wasteful, because obviously the air is being changed in the environment?
Aaron Archibald: Yeah. Most of it gets vented; it’s very difficult to create a homogenic environment and get all the CO2 to every plant. It’s like HVAC systems are extremely difficult in building; most people have a forced air furnace in their home know that they have a room in the winter that’s always colder than the other ones.
James West: Sure.
Aaron Archibald: So by putting it directly into the water and putting that directly onto the plant, every plant gets CO2, and it’s just the most bioavailable means of doing it.
James West: Cool. Then, you guys, when you were last here, we were talking about this issue where Health Canada had not approved foliar-sprayed CO2 for use in commercial gardens by licensed producers in Canada. Has that changed?
Aaron Archibald: Of cannabis. They haven’t changed their regulations necessarily; they have let us know that we’re approved by GFIA, and that we don’t contravene anything. We’re not a pesticide, we’re not a herbicide. I look at it and say we’re just a novel means of applying water and CO2 at the same time. Any LP is allowed to water their plant, and allowed to use CO2.
James West: Okay, so there’s no barrier to any of the LPs using the product.
Aaron Archibald: I think it’s a matter of how you interpret the legislation, and where and when they can use it in their facilities.
James West: Okay, let me ask you this another way.
Aaron Archibald: All right.
James West: How soon till LPs are using your product over gas-delivered CO2?
Aaron Archibald: I’d say very soon. I think that Health Canada is having a long, hard look at some of their regulations, and I think they did it very quickly and did it with a broad brush. You know, you can water or foliar spray cuttings, or clones, right now; it’s just more mature plants you can’t. I think when they recognize that there’s no added pesticides, anything harmful, there wouldn’t be a problem with spraying water on a plant.
James West: Sure. So I’m curious: how do you get CO2 dissolved in water?
Aaron Archibald: We use a proprietal technology that does it very efficiently. I mean, there’s a number of different ways to put dissolved gases into liquids; we just happen to have experience doing it efficiently. We don’t need to chill it, we don’t need to compress it. You know, some of that’s proprietal, so I won’t tell everyone exactly how we do it, but we can do it extremely efficiently, at high, high levels.
James West: Wow. Okay, so then, how often does a greenhouse or a, say, cannabis plant, need to be treated with foliar CO2 in order to optimize the growth cycle?
Aaron Archibald: The more times you can apply it, the better. So what we have worked on with people is applying extremely small volumes of water more times per day, because you get more CO2 delivered to the plant that way.
James West: Okay. So is this something that you could actually create an automated misting system within a environment that would be a beneficial way to approach it?
Aaron Archibald: Absolutely. Some of our customers do that now.
James West: Oh, okay, great.
Aaron Archibald: So you – most overhead booms, you can control the volume of water, the speed of the boom, and the number of times per day that it runs, so it’s easily automatable.
James West: And your process, as you say, is proprietary, but is it patented?
Aaron Archibald: Patent pending.
James West: Patent pending. Great. So at this point, who is using your product?
Aaron Archibald: Well, a number of different growers in the States and Canada.
James West: Okay.
Aaron Archibald: Generally we do sign a non-disclosure agreement; lots of people don’t necessarily want their name put out there, but we –
James West: They don’t want their competitors to know that they’re using this secret weapon.
Aaron Archibald: Exactly, but we currently have commercial operations in Canada and the US.
James West: Uh-huh. Okay, and how much does it cost? I mean, let’s pick a unit of square footage; let’s say, per thousand square feet, is it easy to say, well, this is how much the cost is going to be per month, per thousand square feet?
Aaron Archibald: It is pretty easy. You know, we do a scoping survey with them; we have an engineering group that works with them and looks at whether or not their infrastructure is set up to use the technology, what might need to be tweaked, and then we come to a commercial arrangement. And we usually charge by the square foot per month. We can do it quarterly as well, but it’s a per square foot, or per square metre in Europe, charge.
James West: So unlike software as a service, this is like CO2 as a service, model? [laughter]
Aaron Archibald: Yes it is, yeah. We – it’s a site license/lease model that we’re doing.
James West: Very interesting. And at some point, will you have a retail option available for those growing at home?
Aaron Archibald: I could see that in the future. It would be a matter of engineering it down to a small enough size and a price point where a home grower could use it. Right now, I think it’s not very feasible, but I could see it in the near future.
James West: Really? Okay.
Aaron Archibald: Just from a cost standpoint –
James West: This is me with my hand up. I would like to grow. Heading to my NDI, this is my garden in my own home right now that is growing hydroponically, and I would love the opportunity to treat two plants with foliar spray and two plants without and see how the difference is in a measured basis.
Aaron Archibald: Well, as we talked about before we got on air, I’ll get you some equipment used for a trial. So you just have to share the data with me.
James West: Great! Yeah, of course, I’d be happy to. Okay, Aaron, then how does the revenue model, the business model, of the company work, then? You’re saying you have a per square foot plus a licensing; how does that sort of, what per user, how much – what’s your – I guess I’m babbling now. What is the projected growth of the revenue in the company?
Aaron Archibald: That’s hard to say. The market is so big. You know, the plant for food market is $9 trillion per year; you know, the focus is cannabis right now in Canada, it’s very popular, but we can help all plants grow. So whether it’s peppers or lettuce, it’s almost hard to measure what our revenues are going to be like in two years, simply because we have so much opportunity in front of us.
James West: Sure. What’s to stop me from just spraying club soda on my plants?
Aaron Archibald: You could. Technically, you’d be in violation of the process patent, but also the cost to buy club soda and spray it on your plants would be –
James West: Pretty high.
Aaron Archibald: High. Extremely high.
James West: Interesting.
Aaron Archibald: Extremely inefficient.
James West: And is the carbon content of club soda equal or similar to that, and the bioavailability, does it even apply?
Aaron Archibald: Well, not really. I mean, they chill soft drinks and put it under extreme pressure; that’s why you see bubble nucleation, so you know, if you shake it and open it, it explodes. So that’ll tend to drive the CO2 out of it, and that’s part of the experience of drinking a carbonated drink, is you like the sense of the bubbles in it.
James West: The fizz.
Aaron Archibald: What we do is different in that you won’t actually see bubbles, and bubbles won’t nucleate out; it’s done on a molecular level, and it stays in solution so that it can be utilized. If it comes out of solution, it’s just not bioavailable anymore.
James West: Sure. What kind of increase in yield, in percentage terms, can one expect from applying foliar CO2 relative to not applying any CO2?
Aaron Archibald: I’d say on average we’ve seen between 25 and 30 percent increase versus standard gassing, so 800 to 1,200 ppm in a room.
James West: Then, now with Health Canada reconsidering some of its regulations over foliar applied, let’s call it a nutrient for lack of a better descriptor – is that something that they now have to specifically give you the ability, or an LP the ability, to say, okay, you can use that now without risk of it resulting in a negative test result from your product? Is there any risk of that?
Aaron Archibald: There isn’t. See, plants take in CO2, and they keep the C, which is the carbon, which is a building block for plants, and they respire out O2, much the same way we breathe in air with O2 and respire out CO2. So there’ll be no residual CO2 left in a plant because it becomes carbon, becomes the plant. So there really is no way to test for CO2 in a plant.
James West: Right. I guess as carbon-based life forms, we have no problem dealing with carbon in our cannabis.
Aaron Archibald: Exactly right. And that’s why CO2 makes plants grow bigger and faster and yield more.
James West: Right. So I guess, then, the inflection point for your company is going to be when widespread adoption of foliar-sprayed CO2 at the commercial level takes root – the pun intended – in the cannabis industry broadly?
Aaron Archibald: Yes. Yeah, and you know, like many Canadian technologies, sometimes you go abroad before you get adoption at home. It’s an unfortunate thing, but you see it a lot. We have a phenomenal amount of interest internationally; you know, US hemp growers can’t keep up with the number of phone calls we’re getting right now. Since it’s been legalized federally in the States, they’re really, really interested, especially outdoor growers. It’s the only means to apply CO2 to a plant outdoors, is by putting it in water first and applying it to the plant.
James West: Right. Either that, or putting a coal-fired hydroelectric plant next door!
Aaron Archibald: It’d be pretty inefficient to blow it on, because the wind would just take it away. So by putting it in water, we can supply outdoor growers with CO2, hoop houses, shade houses, things that historically – like, structures that have historically not been able to use CO2 in them.
James West: Right. What about competitors? Do you have – who do you have in the competitive realm?
Aaron Archibald: Touch wood as I say it: Right now, there are no competitors! You know, it’s a novel technology. No one had ever thought to do it before, so we’re first to market with it, and you know, that’s why we’ve gone through the process of getting the IP, but I think more importantly it’s going to be first to market, having some trade secrets and penetrating the market, and becoming the company that’s known as the CO2 foliar spray technology.
James West: Interesting as ever, Aaron. We’re going to continue to follow the story, and I can’t wait to try it out on my own plants. Thanks for joining me today.
Aaron Archibald: Okay! All right, thanks very much.
[Going Green 2] How Samsung is Helping To Take Healthy Food From Farm To Table
April 25, 2019
As awareness of environmental issues grows, the impacts of the agricultural industry and our own personal food consumption are of increasing public concern. The use of pesticides, herbicides and other resources are falling out of favor and more efficient methods of food production are being explored as we strive to cultivate healthier food. Samsung Electronics is contributing to these efforts, developing technologies that can reduce the environmental impact of growing healthy food.
Horticulture LED Driving the Future of Farming
On the industrial scale, indoor farms are increasing in popularity, since they are better equipped to overcome spatial constraints and extreme climates. In such indoor farms, artificial light plays a crucial role in efficiently managing the rate of plant growth.
Drawing upon its LED technologies developed for other lighting markets, Samsung launched its Horticulture LED lineup in May of last year to provide advanced lighting solutions to indoor farms. LED lighting is more efficient and has a longer lifespan than previously existing artificial lighting solutions. It is also easy to control the light spectrum of LED lighting and LED solutions are becoming a more attractive option for indoor farms.
Samsung’s Horticulture LED Package and module
Different wavelengths of light can affect plants in different ways. For example, wavelengths of 430 to 700 nanometers are required for photosynthesis, a wavelength of 450 nanometers promotes germination, 660 nanometers stimulates growth, and 730 nanometers or more helps plants to bloom and produce fruits. It’s thanks to these properties that red wavelengths (about 600~750 nanometers) and blue wavelengths (about 400~450 nanometers) have been the prevailing trend in indoor farms.
Recent developments have also emphasized the importance of green light with a wavelength of 550 nanometers, with findings that it can penetrate the lower canopy and thus increase the photosynthesis in plants found there. Since this was observed, interaction with a blue wavelength is now actively being studied also.
Based on this research, Samsung released its White LED package last November, with an extensive spectral range, including growth-boosting blue and red wavelengths. Full-spectrum LED lights can increase the nutritional value of plants and deter disease and pests. The bright white light can also create a more pleasant work environment than narrow spectrum alternatives, allowing farmers to monitor growth and inspect for disease with relative ease.
The package is designed to deliver strong reliability, even alongside the use of chemical fertilizers or under hot and humid conditions. The package is also competitive in price when compared to red LED products, helping to reduce the cost of establishing lighting systems in indoor farms.
Samsung raised the photon efficacy level of white LED packages to the highest in the industry, thus reconfirming the company’s leadership in this field. As a result, lighting manufacturers can use 30 percent fewer packages in each luminaire to achieve the same efficacy level as other lighting equipment, ultimately reducing the costs for indoor farms.
Packages can be selected according to the types of plants and the facility’s requirements. Samsung Electronics offers five white LED packages and one white LED module. The company has also designed one blue package and two red packages with a single wavelength.
As Will Chung, a researcher in the company’s Lighting Marketing Group (LED), explained, “Although it’s been less than two years since Samsung Electronics started its horticulture LED business, we’ve already received lots of positive feedback from the market for developing high-quality LED technologies. “We’re committed to developing more innovative products that support convenient food production, and will continue to enhance our offerings with testing, studies, and experts’ advice.”
Grow Your Own
In the homes of the future, it will be possible to grow your own vegetables no matter the climate. Samsung recently showcased Chef Garden at KBIS 2019, an AI farming platform that integrates with the next generation of Family Hub. The smart indoor garden uses seed capsules, allowing people to grow small fruits, vegetables and herbs with only a small part of the plant. Chef Garden controls light, temperature and humidity to optimize plant growth. The system also utilizes fogponics technology, which creates a nutrient fog that delivers water and nutrients directly to the plants so that they can grow without the need for pesticides. With water kept to the minimum required, the inside of Chef Garden always remains clean. Chef Garden can also inform users when plants are ready to harvest and recommend recipes thanks to smart integration with Family Hub.
Fruitful Investments and Research
Samsung is supporting research and development in fields such as basic sciences, materials science and ICT through the Samsung Science and Technology Foundation. Samsung has funded 500 project grants for the Korean scientific community to explore since 2013, amongst which are technology research projects examining vertical farming and the acceleration of plant growth. In addition, it is expected that further discoveries garnered from ICT projects involving AI, IoT and LEDs will foster synergy between Samsung’s technology and industrial farming’s efforts to produce healthy food.
“One of the main objectives of this support project is to consider how technology might solve the environmental and food shortage problems society faces today,” said Doochan Daniel Eum, Head of the Samsung Research & Incubation Center for Future Technology. “It’s our intention to contribute a total of 1.5 trillion Korean Won (approximately 1.3 billion USD) by 2023, investing in technologies that can effect real change for future society.”
Artificial Lighting Solutions Going Green Healthy Food horticulture LED Indoor Farms LED lighting LED Solutions White LED Package
CO2 GRO Inc. Is Pleased To Present An Audio Interview Conducted By The OTC Markets Group With John Archibald
CO2 GRO Inc. is pleased to present an interview conducted by the OTC Markets Group with John Archibald, CEO. John presents an overview of CO2 GRO, an outlook for 2019 and the significance to the Company of the recently enacted US Farm Bill.
CO2 GRO Inc. | Suite 2400 120 Adelaide Street West Toronto, Ontario M5H 1T1
The Next Frontier of Agriculture
I gave a TEDx Talk at Wabash College that gave a glimpse as to why I chose to co-found Heliponix. We could only fit so much content in a 10 minute segment, so I saw it fitting to provide a written explanation to tell the full story. Follow the link below to see the full talk.
I was extremely fortunate to receive an internship the summers of 2014 and 2015 after my freshman and sophomore years at Purdue University working as a mechanical engineer for a company in the oil and natural gas industry that manufactured fluid control equipment in my hometown of Evansville, Indiana of about 120,000 people. Although I was surrounded by great co-workers who enriched my technical knowledge, I did not feel like this industry was right for my career.
Then one day during my junior year (Jan. 2016), I received a mass email from my college about a job opening at the horticultural college looking for an engineer familiar with fluid control systems for a hydroponic research project. I responded out of curiosity to see if I could at least learn more about other industries to strength my project experience portfolio, but I knew absolutely nothing about plant science. With luck, my email with resume and cover letter was well received, and I was invited into an interview with Dr. Cary Mitchell.
Dr. Mitchell expressed concerns for my generation's ability to grow enough food to meet the growing, global demand. Global food outputs must increase by 70% as we exceed 9 billion people in 2050 according to the UN. Agriculture accounts for 50% of land use, and 80% of freshwater consumption in the USA. To put it simply, we will run out of the land and water needed to produce enough food with our current consumption/production rates within the next thirty years.
Dr. Mitchell explained a new concept to me called CEA, controlled environment agriculture. It is exactly as it sounds, the practice of making an fully automated, indoor farm that used hydroponics. Hydroponics is a method of growing plants using no dirt, but only nutrient rich water recycled over the roots in a closed loop. By keeping the nutrients dissolved in the water in near constant curriculation, plants could grow three times faster than they would in a field. To put this in perspective, a lettuce farmer can typically grow a full head outdoors in 90 days, but hydroponics could grow lettuce in just 30 days or less in some circumstance. Most hydroponic systems are in controlled greenhouses, so a hydroponic farmer could harvest every month of the year without any pesticides and 95% less water by eliminating runoff. CEA was essentially a twelve times increase in productivity compared to conventional soil farming methods limited to one season a year. Additionally, a vertical farm that stacked layers of growing planes could multiply yields even further!
Dr. Mitchell was seeking assistance in the fluid control design for a hydroponic research apparatus called the minitron 3 funded through a NASA grant. Within my lifetime, permanent space colonies will be established on Mars which creates a need for a sustainable food supply. It is not feasible to regularly ship tons of food shipments from Earth, so they must be able to grow their own food. However, there are still challenges holding back the industry’s fruition.
The main challenge to creating a crop-growth module for space travel has been the staggering energy cost of the 600- to 1,000-watt conventional high-pressure sodium lamps traditionally used to mimic sunlight and stimulate plant photosynthesis in contained environments. The lamps also scorch plants if placed too close and require a filtration system to absorb the excess heat they create.
"Lighting was taking about 90 percent of the energy demand," Poulet said. "You'd need a nuclear reactor to feed a crew of four people on a regular basis with plants grown under traditional electric lights."
The focus of the Purdue-NASA research study was to measure the carbon dioxide concentration of air going into the minitron, and concentrations of oxygen leaving the growth chamber. This allowed researchers to measure photosynthetic efficiency rates under different wavelengths of light under an addressable LED array. If you only used LEDs of the right color plants need to grow, then you could eliminate the colors that the plants are not uptaking. The goal was to provide valuable insights about which spectrum of LEDs would be the best to reduce the energy consumption of an indoor growing operation, a major operational cost. This is why many vertical farms have “pink” lights, plants primarily need red and blue light. LEDs have become much more efficient than previous lighting options, and release little heat to greatly improve the energy efficiency of growing indoors.
With the youthful naivety of a 20 year old, I applied to every commercial, hydroponic facility in the US with little to no responses. I quickly learned that the research study I was a part of was not just an attempt to reduce the operational cost of CEA, but it was trying to make it more profitable for more people to pursue. Most indoor farming operations have access to reduced agricultural rates which is 90% less than what most residential consumers pay for energy. Without these subsidies, the industry would be reduced to very low margins, so paying for an engineering intern was out of question.
So I went back to the career fairs at Purdue desperate to find an internship opportunity anywhere outside of my hometown to see new things. I finally found my break when I was given an internship offer as a project manager in Hawaii for the summer of 2016. I immediately accepted the offer, but was told by the HR manager to not worry about the “TBD” stamp on my location of the contract I signed in March.... For the rest of the spring semester, I was ignored on all communication channels to this HR manager until I was finally called back during dead week at the end of the semester after canceling all interviews with the expectation I would be in Hawaii. I was informed that I was reassigned to build section-8 low income, government housing in El Paso, TX along the border to Juarez, Mexico.
A quick google search informed me that Juarez was a murder capital and major drug corridor for Mexican cartels bringing narcotics into the United States. The movie Sicario is based on the cartel violence in Juarez in this exact location. With no other options on the table, I packed my bags for a cross country roadtrip to the desert.
At the time, I spoke virtually no spanish and grew my beard out to appear older to the laborers working on the construction sites. My primary responsibility was to oversee a Spanish-speaking workforce for labor jobs such as toxic asbestos removal. Many of the workers had previous gang affiliations, and narcotic use was rampant. The section of El Paso I managed was originally called the “Angel's Triangle”; a triangular shaped subdivision situated between the Franklin Mountains range, the US Army’s Fort Bliss, and the border wall to Mexico. However, this portion of town was called the “devil's triangle” due to the gang activity, narcotics and prostitution that now plagues the area.
One day I woke up, and envisioned this career defining my entire life, and realized that this was not the industry for me either. I then began to look at my time in the desert as an opportunity to build a business model that could solve the food desert I was living in. A food desert is defined as, an urban area in which it is difficult to buy affordable or good-quality fresh food. Residents (who often lacked private transportation) often resorted to buying highly processed, non-perishable foods which are cheap and readily available at the local corner stores. These corner stores had little to no fresh produce which contributed to a high obesity and abnormally high diabetic rate. I knew that indoor farming could account for the poor soil quality and limited amount of water in the desert to bring these residents the fresh produce they needed, but the following points prevented this from happening.
Indoor, vertical farms require huge amounts of capital from investors to build the infrastructure with a long ROI.
Energy costs for indoor lighting greatly reduced the profitability of the facilities. Without reduced agricultural energy rates, many of these facilities would not be profitable.
Labor rates can be variable, and pose new liabilities for workman’s comp claims in the event of a workplace injury using equipment such as scissor lifts to reach top shelves. Although automation is the best solution, this is a tradeoff for an even higher infrastructure cost, and recurring maintenance cost from skilled laborers.
These points in mind, I concluded that the likelihood of a twenty-one year old being funded to build a multi-million dollar vertical farm was very unlikely. But this revelation posed a new question, “Could the technology be broken up into decentralized devices?”.
Que my TEDx talk… For inspiration I looked towards the ice industry which up until the 1800’s was made up of ice harvesters who could only cut ice from frozen bodies of water when the climate allowed water to freeze. This seasonal availability was disrupted by ice factories that could deliver ice year round in any climate. Today, 99.9% of Americans now own their own personal ice factories called refrigerators.
Much like the early ice industry, agriculture has always been dependant on the narrow window of growing seasons restricted by climates for crops to grow once a year. Since the explosion of microcontrollers and LEDs drastically increasing efficiencies and decreasing prices, indoor vertical farming has become financially viable for the first time. Much like the ice industries continual decentralization, we believe that agriculture will follow suit for many vegetables. In addition, decentralized, hydroponic farms eliminated the three concerns that limit the scalability of massive vertical farms.
Customers buy into for the hardware, not the investor.
The energy cost could be greatly reduced through a new, innovative design.
Contract manufacturing is highly competitive, and keeps manufacturing labor prices low.
This theory in my mind was validated by the success of the keurig recurring k-cup business model that could be emulated with hydroponic appliances sending monthly shipments of seed pods™ and fertilizers directly to the consumers.
Initial concept of recurring seed pod to be produced in an automated production line.
I spent the remaining time I had in El Paso creating conceptual designs this hydroponic appliance called a GroPod™. I then filed the first provisional patents on the new design before building the first prototype, and entered into business plan competitions at Purdue University my senior year. I quickly recruited my purdue-NASA-hydroponic coworker, Ivan Ball to be my Co-Founder because he was a brilliant electrical and computer engineer to close the skills gap we needed to keep improving upon our design. What happened afterwards could be a series of articles on its own, but at least this article can provide a deeper explanation of where I started, and where we are growing!
Follow us on social media as we continue growing to become the world’s largest farm without owning a single acre of land!
Instagram, Facebook, Linkedin, and Twitter: @heliponix
Urban Farm Tax Credit Plan Gets Illinois House Approval
Urban Farm Tax Credit Plan Gets Illinois House Approval
By SAM DUNKLAU • APR 30, 2018
City Farm vegetable garden and the Chicago skyline
PIUSH DAHAL VIA FLICKR / HTTPS://CREATIVECOMMONS.ORG/LICENSES/BY-SA/2.0/
The Illinois House has voted to allow tax breaks for those who take vacant land and use it for urban farming. The aim is to give an economic boost to the state’s low-income areas.
The idea comes from state Representative Sonya Harper, a Democrat from Chicago. She explained during the debate that the people she represents on the south and west sides of the city live in food deserts. That means they don’t have easy access to fresh food.
But what those neighborhoods do have is vacant land.
“Now what people are doing is they’re putting that land back to productive use, and actually reviving the local economy and bringing jobs to an area that is depressed and does not have them," she said.
Harper’s bill would allow city governments across the state to offer special incentives like tax abatements and lower utility rates. But there would be limits on the dollar amount of those incentives. Some Republicans say less tax money coming on those properties could result in higher taxes for everyone else.
The Chicago Democrat says the aim is to give people in low income communities a reason to grow their own food and create jobs.
“One of the biggest reasons why we use urban agriculture is to put our vacant land back to productive use, especially in communities that are food insecure or food deserts," she explained. "In those same communities we have tracts and tracts, and even acres, of vacant land that’s just sitting there.”
The bill now moves to the Illinois Senate.
Futuristic Vertical Farming Sprouts Up In Tennessee Greenhouses
Vertical farming is like growing vegetables in a greenhouse on steroids. The industry includes methods like aquaponics, aeroponics and hydroponics. And it's predicted to reach almost $6 billion in revenues within the next five years.
June 26, 2017 | Caroline Leland, Nashville Public Radio
Vertical farming is like growing vegetables in a greenhouse on steroids. The industry includes methods like aquaponics, aeroponics and hydroponics. And it's predicted to reach almost $6 billion in revenues within the next five years.
One of the centers of vertical farming is Tennessee, where the technique is providing locally grown vegetables year-round. Caroline Leland (@CarolineLeland) reports from Here & Now contributor Nashville Public Radio.
This segment aired on June 26, 2017.