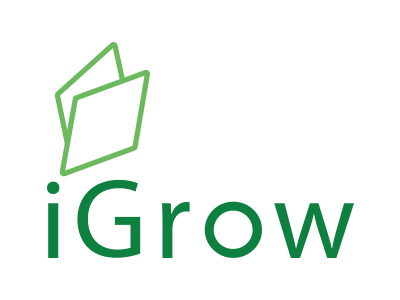
Welcome to iGrow News, Your Source for the World of Indoor Vertical Farming
"Using Variable Spectrum Luminaries Allows us to Grow a Wide Range of Plants"
Bringing food closer to consumers is no longer an option but rather a necessity, given the strain traditional agriculture and transportation place on the environment.
August 11, 2021
Bringing food closer to consumers is no longer an option but rather a necessity, given the strain traditional agriculture and transportation place on the environment. Czech grow tech company GreeenTech teamed up with Hungary’s Tungsram to provide vertical farming solutions that pave the way for sustainable crop production.
Prague-based GreeenTech was born out of this realization. The company specializes in the research and development of hydroponic technologies to be used in container farms and vertical farms set up in buildings. Established in 2000, the business aims to enable people to grow agricultural crops anytime and anywhere in the world.
They are involved in developing innovative solutions for the local production of leafy vegetables, herbs, and small fruits through their own hydroponic cultivation technology complete with an IOT control system created in cooperation with Siemens. The uniqueness of the solution provided by GreeenTech lies in the development of tailor-made hydroponic farming technology.
Finding the perfect lighting solution
"Hydroponic systems are soil-less, water-based farming processes. The technology is based on growing plants in a controlled environment where crops are fed nutrient-rich water. Crop cultivation takes place in an enclosed growing space, where sensors control conditions such as humidity, temperature, or light cycle. The result is quality crops that have not been subjected to treatment with pesticides and herbicides and the farm uses about 90% less water than conventional agriculture," the GreeenTech team explains.
Given that crops are not exposed to natural light, selecting the right lighting solution in these farms is of utmost importance. GreeenTech’s quest for the best lighting solution provider-led them to Tungsram, whose variable spectrum LED luminaries proved to be the perfect match as the light sources have been designed and created only for the purposes of a growing container.
“We were searching for a lighting solution and we realized that Tungsram’s luminaries and the automation solutions provided by them are ideal for our needs because they are well suited for research purpose. Using variable spectrum luminaries allows us to grow a wide range of plants. In addition, customers have a high degree of flexibility in deciding what kind of plants they want to grow or in switching from one crop to the other,” said Karolína Pumprová, CGO at GreeenTech.
LED lights
"Our four-channel LED lights offer the highest performance in their category and are extremely easy to install," the Tungsram team says. "The luminaries are controlled remotely and allow users to adjust the color spectrum and light intensity independently for each growing rack, which is a game-changer for large-scale urban farms."
In addition to the lights, Tungsram also provided a tailor-made lighting design with the help of the company’s engineers and designers. "Variable spectrum luminaries are a powerful tool for growers in terms of adopting a “dynamic light recipe approach,” which is a rather unique offering in the market."
Compatible with software
“Another factor that weighed heavily in favor of Tunsgram was the fact that the lighting solution developed together with them was compatible with the software and system we already had in place,” said Milan Souček, CTO at GreeenTech.
GreeenTech will use the Tungsram luminaries at the expo in Dubai, which will run from September through March. The cultivation container will be set up in a restaurant and the plants will be used in the restaurant. As part of a cooperation with the Technical University in Prague, Tungsram lights will be installed at a small hydroponic farm set up by GreeenTech where students will be conducting research and testing.
For more information:
Tungsram
Keith Thomas, Commercial Leader
keith.thomas2@tungsram.com
agritech.tungsram.com
US (CO): Container Farm at Historic Ranch to Grow Restaurant's Produce
A historic ranch in the mountains of Colorado is using a high-tech container farm to broaden its focus on farm-to-table options for guests.
August 10, 2021
A historic ranch in the mountains of Colorado is using a high-tech container farm to broaden its focus on farm-to-table options for guests.
Having been in business for 102 years, C Lazy U Ranch in Granby has a storied reputation as a luxurious, year-round mountain getaway with 8,500 acres of land for a multitude of activities. The ranch’s culinary program will soon be complemented by fresh leafy greens and herbs. The produce will be grown on-site in an automated container farm, built by Colorado-based FarmBox Foods.
“We saw an opportunity with FarmBox Foods to essentially have a year-round farm-to-table option,” said Paul Klees, assistant general manager of C Lazy U Ranch. The container farm is scheduled for delivery in mid-August.
Container purposes
Guests and members will have the opportunity to tour the farm. C Lazy U Ranch is planning to grow lettuce and culinary herbs inside the 320-square-foot farm. The sensor-based technology and insulation in the container farm are superior to greenhouses, which are susceptible to the bitter cold of the Colorado Rockies, Klees said.
The container farm is slated to be the next hands-on attraction at the ranch, where guests and members could have the opportunity to harvest their own veggies and prepare meals with a chef. “It’s interactive, it’s educational, and it builds into our vision and mission statement of having a sustainable model,” Klees said.
Purchasing a container farm is “just another step in the ranch’s continuing effort to create authentic farm-to-table dining,” Klees said.
“There are economic aspects to it because we’re shipping in all of the food, including produce,” he said. “When guests eat at our restaurants, we want the meals to resonate with them, and what people are looking for is healthy organic fresh produce.”
Horses get their share
The 200 horses on the property already benefit from C Lazy U’s sustainable approach to food sourcing; most of the hay they eat is grown on the ranch. C Lazy U is also supplied with water by its own spring and operates its own wastewater facilities.
The exterior of the container farm will be finished with a rustic scheme so it will easily blend in with its natural surroundings, which include a creek and historic structures.
For more information:
FarmBox Foods
www.farmboxfoods.com
Freight Farm To Teach Youth About Sustainable Agriculture
Beyond School Bells is partnering with the Bay in Lincoln for a new after-school program that will teach students about sustainable ag technology. "We really see Freight Farm as kind of that key, climate-change impervious tool that young people need to know about as we face an uncertain future," said Jeff Cole, Network Lead for Beyond School Bells
by Nicole Weaving
July 24th, 2021
LINCOLN, Neb. — Beyond School Bells is partnering with the Bay in Lincoln for a new after-school program that will teach students about sustainable ag technology.
"We really see Freight Farm as kind of that key, climate-change impervious tool that young people need to know about as we face an uncertain future," said Jeff Cole, Network Lead for Beyond School Bells.
An old shipping container in the parking lot of the Bay has been transformed in a self-contained hydroponic farm.
Using red and blue LED lights, this Freight Farm, known as the Greenery, creates a climate-controlled environment, where the plants grow vertically without a need for soil.
"We enrich the water with nutrients that would normally be in the soil," said Colton Harper, Organizing Manager for The Greenery. "And then in these grow walls, we've got spickets that come right through these foam and it's directly onto the roots of the plants."
Inside of the Greenery with the red and blue LED lights on. (KHGI)
According to Harper, there are currently about 6,000 plants growing in the Freight Farm, but at full capacity, it can hold 13,000 plants between the seeding area and that walls. That would produce the equivalent of a 2.5-acre farm year-round.
"Even in the winter, if there are shortages anywhere, we can turn on a dime, 7-week grow cycle and be able to provide those crops for local markets," said Harper.
The Greenery arrived in Lincoln in April, and Harper has led to two teams to get it up and running. They are currently preparing for their first harvest with items like basil, lettuce, and radishes.
"We're at about Week 7, and in 2-3 weeks, we'll have our produce at a farmer's market," said Harper.
After a few more grow cycles, the program will open to local students to teach them all aspects of sustainable farming.
"From the electrical side, the growing, the programming, computer science to the irrigation, the HVAC system, there's so many elements," said Harper. "And we're particularly well-placed with the Bay and their digital design area of focus, the students will also be able to design the packaging, design the labeling, so it's really a full-circle, interdisciplinary opportunity for the students to get involved."
The Greenery plans to hold a Harvest Party to celebrates the farm's success in the coming weeks
Central Minnesota Research Project Growing Kale Indoors
The project is a partnership with Todd-Wadena Electric Cooperative, Central Lakes College, Lakewood Health System, Great River Energy and the Electrical Power Research Institute
The project is a partnership with Todd-Wadena Electric Cooperative, Central Lakes College, Lakewood Health System, Great River Energy, and the Electrical Power Research Institute.
Written By: Rebecca Mitchell
July 21, 2021
Central Lakes College research analyst Noah Boetler shows a panel of kale plants in the Sota Grown pod during a virtual tour on July 13, 2021. Rebecca Mitchell/Pioneer Journal
STAPLES, Minn. — A community research project in Staples involving indoor gardens is set to continue growing.
The hydroponics project started in 2020 with Great River Energy, Todd-Wadena Electric Cooperative, and the Electrical Power Research Institute hoping to learn new technology and increase access to fresh produce. And even with kale as the chosen plant, local organizations rooted for the success of the hydroponics pod. The pod, planted at the Central Lakes College Staples campus, is a shipping container with room for 5,820 kale plants.
“I didn’t know how things were going to grow in here, it’s kind of a weird concept with there being no sunlight and things like that, so just seeing it go from a little seed to your big plant and harvesting it, I think that has been the coolest aspect,” CLC research analyst Noah Boelter shared with Minnesota educators in a virtual tour on July 13.
The partnership is called "'Sota Grown" and has helped develop a fully enclosed hydroponic container for growing fresh plants all year long — to supplement existing agriculture practices in communities across the state.
The pod, equivalent to one acre of crops, is a supplement to traditional farming, not a replacement, as TWEC member service manager Allison Uselman said. Although kale is the focus of the two-year project, the team has experimented with growing basil, swiss chard, lemon balm, and chives. Romaine lettuce, butterhead lettuce, and salad mixes are next on the list — and after a year of only kale, Boelter is excited for the new opportunities.
Each kale seed, planted by hand, starts in the nursery before being transplanted to vertical panels. The kale takes 12 weeks to reach maturity. The team of four staff members and interns plant and transplant on Wednesdays and harvest on Mondays.
“Kale is pretty forgiving, which is very fortunate for us,” Boelter said after sharing about a frozen pump during the winter. The kale wilted and bounced back in a matter of days. The team is also learning about flooding and nutrient dosing in the pod.
With the expected growth of indoor agriculture, Uselman said electrical companies will need to prepare for the change. For example, the pod uses the most energy when most other customers could have off-peak rates. The light and water systems run from 4 p.m. to 8 a.m. daily. The kale is watered for five minutes every 45 minutes. The electricity is about $600 a month.
“It’s education with students, it’s giving back and feeding our communities, and Todd-Wadena has the opportunity then to research all the electrical side of things and really understand this industry before it grows to a larger state,” Uselman said.
The pod’s water usage depends on the humidity levels outside, with the most water used in the winter — about 10.5 gallons every day—and about five gallons a day in the summer. The two water tanks deliver water above the panels and water behind the plants. There are also several different nutrients added, such as one to adjust pH levels.
“In the summertime, the pod does not use a whole lot of water because the HVAC unit has a dehumidifier built into it and that’s recirculating around a gallon of water an hour that gets dumped back into the pod, so it’s really efficient in the summer,” Boelter explained. “But when it’s winter, the air is so dry that’s when we use the most water.”
The indoor pod means the ability to regulate the temperature, which is a cool 65-68 degrees and having no pesticides or herbicides used on the plants since most bugs remain outside. There are some drain flies due to the algae.
The red LED lights in the Sota Grown pod at Central Lakes College are the only source of heat. The lights and water run from 4 p.m. to 8 a.m. daily. Rebecca Mitchell/Pioneer Journal, July 2021
As for sunlight, the LED lights are the only heat source in the pod, as Boelter said, though it is also insulated. The red and blue lights support stem growth and leaf density.
The process yields about 20 pounds of kale a week — and on a record week 43 pounds — or over 1,000 pounds as of July 5. All of the kale is donated to Lakewood Health System, who shares the kale through the Food Farmacy and Hilltop Regional Kitchen. The Kitchen uses the kale in specific meals for those who have tested positive for COVID-19 and people being discharged from the hospital. People can also receive free kale at the summer farmer’s market on Thursdays.
As Lakewood’s Community Health Coordinator, Amy Wiese works with about 70-100 bags of kale a week to find where it can best be served. She said the kale lasts about two weeks in the fridge.
People also receive kale recipes for new ways to enjoy the vegetable. Wiese enjoys massaging the kale to break down the bitterness and then eating it in a salad. Other favorites are kale chips and soups.
“We just see the benefits of this project and recognize the positive impact that healthy food can have on individuals and in the community,” Wiese said. The organizations also hope to address local food deserts. “It’s really amazing that we are able to provide fresh produce all year with this pod” even with snow on the ground for six months of the year.
The seeds grown and sown in the community have finished their process with new seeds set to germinate, grow to maturity, and be harvested and packaged in four to eight hours for their short drive up the road.
Photo: 1 - The kale seeds are planted in peat moss plugs and stored in the nursey for three weeks before being transplanted to the indoor panels. The planting process takes about an hour. Submitted photo
Photo: 2 - The shipping container contains an acre of kale growing hydroponically with LED lights. Photo courtesy Todd-Wadena Electric Coop
Photo: 3 - Each section has 22 panels with space for 5,820 kale plants or the resemblance of one acre of crops. Rebecca Mitchell/Pioneer Journal, July 2021
Malaysian, Smart Farm That Grows And Delivers Organic Vegetables
“The pandemic has underscored the urgency of building better food production, including fresh vegetables. Customers are increasingly aware that food choices influence both the health and the health of the planet,” the team concluded
July 15, 2021
7 years. It’s how long the farm lasts with 5G BoomGrow it has existed, but it has not always been so efficient. Founders Jay, Murali, and Shan had initially explored different cultivation methods, from simple hydroponics to aquaponics.
Image Credit: Founders of BoomGrow
“We grew our greens in small boxes. We even tried to grow them outdoors. Nothing worked, ”Jay recalled in an interview with Vulcan Post.
This trial and error lasted for five years until the co-founders discovered AI-driven vertical agriculture. With this method, they realized that they could also grow their greens in a controlled indoor environment that would make harmful chemicals such as pesticides unnecessary.
Finally, they had found it the method that allowed them to properly achieve their goals of producing clean, tasty greens.
Using 95% less resources to get the same performance
“Our systems detect how diverse contributions like the light, the water, and the pH affect the quality and the flavor of our plants. That’s what we call our plant recipes, ”said Shan.
“We then rely on machine learning and data analysis to tailor each entry to the respective plant, producing tastier greens.”
The team says its system equipped with technology is Machine Farm. It is used in all reused BoomGrow shipping containers where crops are grown on modular plant racks.
According to the team, five piles of crops on a 360-square-foot plot can produce a yield that is the equivalent of the traditional harvests of a 1-acre outdoor farm.
With this technology and efficient use of space, they can grow 20 varieties of leafy vegetables and herbs in a residential neighborhood of Ampang.
At the same time, Jay said Machine Farm uses 95% less land, water, and fuel than traditional outdoor farms.
Its technology-based agricultural approach has seen BoomGrow achieve multiple milestones, from being the country’s first 5G showcase farm to receiving benefits from government grants from SME Corp, PlaTCOM Ventures, and MDEC.
One of his most proud moments was the validation of renowned chefs working in 5-star hotels, who placed an order for their greens and have since been loyal followers.
Dedicated to clean processes and products
Clearly, there are already several agents in the precision and vertical farming industry with more union, but few are as gung-ho about clean produce as BoomGrow is.
Cleaning doesn’t just mean pesticide-free vegetables; the team decided that value should be reflected in the overall operation of their business.
Inside a Container / Image Credit: BoomGrow
As a former national athlete, Murali wanted to start BoomGrow because he knew the difference a good diet could make.
Meanwhile, Shan is a trained architect who had developed an interest in sustainable design throughout his career. Fascinated by the way modular structures had minimal impact on their environment, he wanted to explore other avenues for incorporating sustainability into everyday life.
He is the director of innovation at BoomGrow, designing and bringing its plant systems to life. On the other hand, Jay was inspired to co-found BoomGrow after many years in sustainability consulting.
He told Vulcan Post: “Throughout my career, I have had consulting experience for various agricultural and F&B manufacturing companies. This allowed me to evaluate the data around some of the practices, as well as the disconnection that people from these organizations had about sustainability. ”
Bringing the head together led the team to arrive at the current solution that is committed to implementing the 12th Sustainable Development Goal, responsible consumption, and production.
Organic vegetable packages at competitive prices
With all the investment in technology growing their organic greens, it looks like a purchase of them should cost a bomb.
But because they are able to eliminate the need for extensive land located in remote areas and a long cold chain, they can offer their vegetables at a competitive price.
BoomGrow sells 5 to 6 varieties of vegetables depending on the package you want, priced between 45 and 65 RM per package. Free delivery is offered to subscribers of weekly or fortnightly plans. Otherwise, deliveries to the Klang Valley would cost 10 RMS for purchases over 45 RM or 15 RM for those under 45 RMS.
Young Greens Growing on Modular Racks / Image Credit: BoomGrow
Compared to another vegetable delivery service with a subscription model, Plant B, BoomGrow prices are reasonable.
Floor B offers 6 types of vegetables in a box and a two-week subscription would be RM37 / week, while a 4-week subscription would be RM34 / week. Shipping costs are offered at fixed rates of RM6-RM8 depending on where you are in the Klang Valley.
For both BoomGrow and Plant B, people may not be able to choose exactly what goes into their box, but Plant B customers will be informed of the variety they can expect depending on the season and availability. You can also contact the team for exclusions.
On the other hand, BoomGrow clearly lists each variety of vegetables in a package with the assigned weight, so you’ll know exactly what you’ll get. To add, plant B does not claim that its product is organic.
Improve your B2C services during the pandemic
When the pandemic first hit in 2020, BoomGrow saw a sharp drop in overall sales as hotels and restaurants had to cut back on their orders.
Conversely, their e-commerce orders increased as more people subscribed to their vegetable packages.
“The pandemic has underscored the urgency of building better food production, including fresh vegetables. Customers are increasingly aware that food choices influence both the health and the health of the planet,” the team concluded.
They were able to meet this demand thanks to the support of MaGIC, particularly as part of cohort 4 al Global Accelerator Program.
Through it, their technology pipelines became more focused and were able to expand their digital footprints, refine e-commerce offerings, and improve their automation. Now, BoomGrow is preparing a launch of its machine factories outside of Klang Valley to reach more customers.
Outside, they will come face to face with more players in the vegetable delivery space, but perhaps their technology and mission will differentiate them in the long run and attract a segment of customers with whom their mission resonates.
Feel Confident In Starting Your Project With This 3-Part Webinar Series!
Even with effortless, turn-key container farms, there are still questions left unanswered for those interested in getting startedThis three-part webinar series will take you step-by-step through what you need to know before you start, how to select the best business model, and your options for financing the project
Even with effortless, turn-key container farms, there are still questions left unanswered for those interested in getting startedThis three-part webinar series will take you step-by-step through what you need to know before you start, how to select the best business model, and your options for financing the project.
By signing up, you will:
Hear and learn from first-hand experiences
Access knowledge and resources from Growcer and Farm Credit Canada
Break down how to get growing year-round into smaller, digestible steps
If you’re interested in growing food for your community but don’t know where to start or are stuck along the way, sign up for the webinar series today!
Register now for all three sessions:
July 13 - Getting Started
July 27 - Choosing a Business Model
August 10 - Financing your Project
Excited for you to join us,
The Growcer Team
BrightBox Farms’ Gideon Saunders Sees Alaska’s Future For Agriculture In Hydroponics
Nestled next to an otherwise ordinary house on Kodiak is a shipping container. It looks out of place, but the garden in it is even more noticeable
July 8, 2021
Nestled next to an otherwise ordinary house on Kodiak is a shipping container. It looks out of place, but the garden in it is even more noticeable. The growing area of the BrightBox Farm looks like a prop from a movie about space exploration – the vertically oriented hydroponic farm has its own perfect microclimate.
The use of this shipping box has enabled Gideon Saunders to conquer the seasons that otherwise rule Kodiak Gardens.
“There we worked with Freight Farms, who build 40-foot containers, high cubes, 2.50 m high, 2.40 m wide, standard containers, only slightly higher, very insulated, highly insulated R-28. So we agreed with them and picked out a unit and then delivered it to us, ”Saunders said.
Freight Farms made the interior of the shipping container. Inside, there are shelves with lettuce and other greens, interspersed with panels of blindingly bright ultraviolet light. A panel filled with nutrients feeds into a water tank on the back, which in turn feeds drips into the hydroponic system. The air is supplemented by a carbon dioxide tank, which ensures that the plants do not lack for anything.
The container is completely controlled by an app. And it even comes with built-in bluetooth speakers. But for the container, function is more than form – Saunders boasts that he could grow 1,000 heads of lettuce a week in less than 30 hours.
It doesn’t just look futuristic. Saunders believes systems like this will revolutionize agriculture.
“I think it’s the future. I mean, we can get into the politics of agriculture and water rights and freshwater use worldwide, and global warming and all these hot topics – 8 billion, 9 billion, 10 billion people, how do you feed them? The population is growing – how do you become more efficient with your food? Well, when it comes to vegetables and leafy greens and what we do, we use 95% less water than traditional farming. We do not use herbicides, pesticides or insecticides. So no glyphosate, no Miracle Grow. Chemically nothing bad. You can control it. So it’s the future of agriculture, ”Saunders said.
This type of production is not cheap. Saunders says the device costs around $ 100,000 with shipping and handling. But as technological advances inevitably push prices down, it becomes more cost-effective for smallholders to invest in such equipment.
And Saunders says it’s already inexpensive, although its container is complemented by a small homemade addition in its garage. He sells microgreens as a subscription service, in which he provides his subscribers with bags of greens for a monthly fee, and through sales at the local farmers’ market. Even on an island known for its horticultural and merchant shipping challenges, herbivores can enjoy fresh, locally grown produce year round.
Contain Inc Announces Finance Arrangement With Edible Beats For FarmBox Foods Container Farm
The container farm is being built and customized for Edible Beats, and will produce ingredients for all of the EB concepts, Linger, Root Down, Vital Root, El Five, and Ophelais
NEWS PROVIDED BY
July 07, 2021
Contain Inc announces a financing agreement arranged between Edible Beats Restaurant Group & a prominent lender for a FarmBox Foods container farm.
Image courtesy of FarmBox Foods
With the FarmBox Food container, we can grow hyper-local, organic, year-round produce that will be featured at all of our restaurants. We feel this is just the beginning of what we can grow”— Justin Cucci of Edible Beats Restaurant Group
RENO, NV, UNITED STATES, July 7, 2021 /EINPresswire.com/ -- Contain Inc is pleased to announce a financing agreement arranged between Edible Beats Restaurant Group and a prominent lender for a controlled-environment container farm, FarmBox Foods. Edible Beats is a locally owned Denver-based restaurant group known for its diverse menus and healthy, plant-based dishes that highlight local and seasonal ingredients. Edible Beats will be able to grow herbs, leafy greens, salad greens, and various produce organically and year-round with the container farm that will be attached to their Vital Root location.
“We have always sought opportunities to be more responsible to the sourcing, growing, and handling of the incredible ingredients that we get,” said Justin Cucci of Edible Beats Restaurant Group. “With the FarmBox Food container, we can grow hyper-local, organic, year-round produce that will be featured at all of our restaurants. We feel this is just the beginning of what we can grow, and we are eager to add the mushroom grow operation in the future”
Image courtesy of Unsplash
Edible Beats purchased the container from FarmBox Foods, a Colorado-based company that builds automated farms that grow gourmet mushrooms, leafy greens, and culinary herbs. To FarmBox, controlled-environment agriculture is the future, and this deal is one of many leading us towards a more decentralized and eco-friendly food system.
“I think we’re going to see a lot more of these types of programs going forward,” said Chris Michlewicz, Chief Public Relations Officer at FarmBox. “Restaurants are realizing that their produce is fresher and has a longer shelf life when they have a container farm on site. It’s a reliable and sustainable source of food, and it’s more eco-friendly because you no longer have to transport food in from elsewhere.”
Image courtesy of Unsplash
Likewise, Contain Inc is thrilled to support Edible Beats as it ventures into indoor ag. “We're delighted to have assisted SemiMojo and FarmBox Foods in this innovative initiative. Contain is always excited to see more fresh food made available to consumers. Customers appreciate freshness and quality produce, year round. Restaurants and container farms make this possible”, said Doug Harding, Head of Leasing & Vendor Relations at Contain Inc. “We are thrilled to have collaborated with Edible Beets and Farm Box Foods on this project. It aligns perfectly with Contain's mission of supporting the controlled environment agriculture industry in its financing needs”.
The container farm is being built and customized for Edible Beats, and will produce ingredients for all of the EB concepts, Linger, Root Down, Vital Root, El Five, and Ophelais.
About Contain Inc
Contain is out to empower the indoor ag industry of tomorrow. Our first and key mission is bringing easier and faster financing to controlled environment agriculture, but we aren't stopping there. We create platforms to move the industry forward, and most importantly, find ways to make indoor ag more accessible to farmers of all stripes.
Contact Contain:
Doug Harding, Leasing & Vendor Relations
doug@contain.ag | 760-330-1199
About Edible Beats
Edible Beats is a locally owned independent restaurant group that operates such diverse concepts as Linger, Root Down, El Five, Ophelais, and Vital Root. “Walking the walk” is important to us and the various aspects of sustainable & local food sourcing, up-cycled design, and authentic Hospitality.
About FarmBox Foods
FarmBox Foods was founded to help provide a sustainable, eco-friendly food source to places where there is a lack of access to farm-fresh produce. The company’s mission is to use container farms to decentralize the food supply chain and empower local communities.
Doug Harding
Contain Inc
doug@contain.ag
Visit us on social media:
Twitter
LinkedIn
Is Vertical Farming Cost Effective?
The technological change caused a shift in farming from conventional to container farms. Currently, farming is turning to vertical farms
The technological change caused a shift in farming from conventional to container farms. Currently, farming is turning to vertical farms.
The more exciting part is that this time round, key economy participants such as Amazon, Google’s Eric Schmidt are pumping money into the trending farming method.
Since it is a new technology, many investors are still unsure about its profitability. They have several questions on vertical farming’s viability. That is to enable them to have a better understanding of the technology.
One of the most typical questions is whether vertical farming is cost-effective. The most straightforward answer is yes. Vertical farming is cost-effective if done on a large scale.
Here, you will find out differences among the core farming technologies in terms of
initial investment,
operating costs,
appreciation, and
profit margins.
You will find it easier to decide whether to continue your current farming methods or switch to vertical farming after reading this article. Find out more below.
What Is Vertical Farming?
Understanding vertical farming requires finding out milestones of farming.
The traditional form of farming is open field farming. Here, the crops grow under direct sunlight, temperature, and humidity. Also, it does not entail artificial fertilizers.
The second milestone of farming is conventional farming, mainly called greenhouse farming. Here, you design appropriate growth conditions for the crops. For example, you introduce artificial seeds, fertilizers and shield the plants from harsh weather conditions such as an extreme cold.
The increasing scarcity of farming lands and demand for more food has caused many farmers to implement container farming. In container farming, you grow crops in soils in vessels instead of letting them grow in the open fields.
The growing technology has resulted in vertical farming. Vertical farming entails packing and growing crops indoors with the help of vertical farming lighting.
Here, you incorporate energy efficiency and customizability of LED lights— to set color, temperature, and humidity conditions for plants to thrive.
Factors that Lead to Changing Farming Criteria
The core reason for farming evolution is market demand and supply. For example, most consumers need tasty and healthy food. The plants’ growth conditions should not hurt consumer health in the long run.
They should be assured of the availability of food whenever and wherever they need it. Most importantly, the supplier should provide competitive prices.
It is on the price that many farmers question the viability of vertical framing, bearing in mind the massive cost of material needed to operate vertical farms.
Here is a summary of recent findings on vertical farming costs.
Cost Determination
Research tells that vertical farming costs three times to implement than conventional farming. The prices inflate when you cater to initial investment and operating costs.
On the other hand, you can produce twice on a vertical farm than on a convention farm. For example, investing in 70000 feet vertical farm is likely to output 1 million kilograms of vegetables annually.
Depending on market location and pricing, you are likely to propel your profit margin when you sell than in the case of conventional farming.
The more exciting part is vertical farming value appreciates twice a year compared to greenhouse farming.
So, Is Vertical Farming Effective in the Long Run?
From the above figures, you can realize that vertical farming is more profitable on a large-scale application. The appreciating value proves that the market demands its products.
The best part is that it is becoming cheaper due to smart lighting technology that becomes less expensive. What do the above findings imply?
Key Takeaways
The best time to invest in vertical farming is now. Chief economic players are channeling a wealth of money into it.
For example, leading investors such as SoftBank Vision Bank, AeroFarms, and BrightFarms recently pumped more than $200 million into vertical farming.
Large-scale investment, crops’ quick turn, and increasing food demand for the growing population make vertical farming cost-effective.
Lead photo: Image by BrightAgrotech from Pixabay
USA - WISCONSIN: Kenosha Plan Commission Backs Plans For Indoor Garden Facility Near City Airport
The Plan Commission on Thursday reviewed and advanced a proposed year-round standalone indoor garden facility adjacent to the existing Gordon Food Service distribution plant at 10901 38th St. GFS plans to partner with Square Roots, an organization specializing in urban farming, in the development. A new 8,715-square-foot facility will be used to grow fresh produce, greens, and herbs
DAVE FIDLIN
Kenosha News correspondent
June 27, 2021
A food distributor’s plans for a year-round indoor garden facility on Kenosha’s northwest side moved one step closer to reality, following a city panel’s favorable recommendation.
The Plan Commission on Thursday reviewed and advanced a proposed year-round standalone indoor garden facility adjacent to the existing Gordon Food Service distribution plant at 10901 38th St.
GFS plans to partner with Square Roots, an organization specializing in urban farming, in the development. A new 8,715-square-foot facility will be used to grow fresh produce, greens, and herbs.
Gordon has forged similar partnerships with Square Roots at other distribution centers within the U.S., the first taking place two years ago near the company’s Michigan-based corporate headquarters.
At a Thursday’s meeting, GFS representatives indicated the indoor garden facility would serve a variety of purposes, with about 60 percent of it going toward direct-to-consumer retail sales and the balance toward distribution.
Down the road, company officials have indicated the new operation could have an educational component, such as workshops on how basil is grown. Partnerships with nearby colleges and universities also were discussed as a possibility.
During deliberations, several members of the panel lauded the plans for the site. Commissioner Lydia Spottswood said she viewed Square Roots’ addition as an example of forward-thinking development.
“It seems like a brilliant opportunity for more and more (of this type of development) to happen, given the proximity to Lake Michigan,” Spottswood said. “We’re trying to brand this as a city of innovation, and this is an innovative process.”
Commissioner Charles Bradley said he, too, was pleased with the proposal, though he did weigh in on the proximity of the development, which is near the Kenosha Regional Airport.
“I’m happy, but I am a little surprised by the location,” Bradley said.!
Commissioners also discussed GFS and Square Roots’ planned building materials for the new facility, which include the use of metal shipping containers on a portion of the facility.
According to information commissioners reviewed, the shipping containers will be accessible from inside the building and will include windows cut into the ends of the containers, alongside perforated architectural metal screens along the exposed sidewalls.
The companies’ tentative plans state the shipping containers will be stacked two rows high, 10 containers wide. A portion of the facility also will be constructed with more traditional building materials, including a concrete foundation and exterior walls made of insulated metal.
“This is a really interesting, adaptive reuse,” Spottswood said.
The City Council, which has final say on the proposal, will take up the Plan Commission’s recommendation and could act on it in July.
Meeting in person
Thursday’s Plan Commission meeting was the first time the appointed body gathered in-person, since COVID-19 lockdowns forced an abrupt pivot to virtual meetings in March 2020.
As is the case with all Kenosha municipal meetings, the Plan Commission is reverting back to its pre-pandemic practices.
“I’m very excited about it,” said Ald. David Bogdala, who serves on the Plan Commission. “We’ve got a lot of work ahead of us, and I’m glad to see, for the most part, that we’re back to normal.”
Lead photo: A concept rendering of the southeast view of the proposed Square Roots and Gordon Food Service indoor garden facility adjacent to the existing GFS distribution plant at 10901 38th St.
Freight Farms And CEO Vanzura Set To Reinvent Container Farming
June 17, 2021
The global pressures exacerbated by COVID-19 and the rippling toll it takes on the international community has made one thing clear: preparedness is everything. The Coronavirus has exposed vulnerabilities in the global health network that no one could have imagined. Food production and distribution must now reset their agendas to prepare for catastrophe.
Freight Farms, a 2011 Agtech company that pioneered hydroponics-based container farming, is committed to preparing the world for the next disaster by reinventing the way we grow food.
“Fill in the blank with the institution, how prepared are you for the emerging trends that are impacting the world,” Freight Farms CEO Rick Vanzura explained. “Sustainability issues, land availability, water availability; those issues obviously preceded COVID-19, but we think there’s going to be a greater sense of urgency around folks expecting us to have an answer and be prepared for these global trends, as opposed to being reactive.”
Vanzura looks to channel his decade of experience as a restaurant executive, growing Wahlburgers from a single restaurant to a $100 million dollar institution, as well as greatly expanding Panera Bread, to redefine food production and distribution as a whole.
Freight Farms uses container-based “vertical farming” to do just that, allowing farmers to produce hundreds of high-quality local crops from a 320 square foot shipping container which automates the farming process for maximum efficiency.
Vanzura plans to expand and distribute these self-contained, sustainable farms to a wide diversity of industry segments. The priority will of course be the global communities that need them the most. “We see the Freight Farm as a perfect fit for countries with food access difficulties, short growing seasons and inherently challenging climates. There’s probably no location where having a hyper-local, highly traceable, always available solution isn’t going to make sense in some way,” he added.
In the name of access to high-quality food, in a sustainable model built to withstand a natural disaster, Freight Farms has now distributed their automated, hydroponic farms to 48 U.S states and across the world to 32 different countries, boasting success and efficiency from the Arctic wilderness, to the desert, and to concrete jungles.
Freight Farms believes that its emphasis on access, preparedness, and sustainability will be more necessary than ever in the wake of COVID-19, as well as global trends of food insecurity and environmental uncertainty. Vanzura explained that the company has already reacted to shifting demands by supporting small-scale farmers as they set up drive-through produce stations to reach customers directly.
Freight Farms CEO Rick Vanzura
“Demand during this time for that hyper-local, fresh product has certainly ramped up,” Vanzura added. “Hopefully, once people get a taste of it, they will understand the difference, and post Covid, our containers will become an industry staple.”
Vanzura sees his role as not only expanding to agriculturally vulnerable countries abroad but also increasing access to high-quality food across institutions in the United States. He wants to specifically target universities and has partnered with foodservice provider Sodexo to ensure local food is available to as many people as possible.
Vanzura says he was forced by his children to move beyond the world of crafting a restaurant chain’s vision and use his knowledge to make the world a better place. Freight Farms, with Vanzura’s leadership, has the ability to change the way we think of farming and change the world.
Freight Farms hopes to combat international uncertainty, face the threats of climate change, and provide people with fresh produce regardless of climatic constraints and difficulties. “Healthy food is a right, not a luxury,” and Freight Farms is helping make this mission statement a reality.
Lead photo: A Freight Farms container has unprecedented environmental control and exceptional ease-of-use to unlock your growing potential.
To learn more about Freight Farms and how they are reinventing container farming, visit their website.
Total Food Service is a monthly B2B foodservice publication and website covering foodservice and hospitality news, industry trends, and exclusive interviews.
USA: MASSACHUSETTS - New Partnership Will Serve Meals For 400 Youth Per Day
Town to Table, a Boston-based container farm company, announced a partnership with the Boys & Girls Clubs of Metro South, an organization that accommodates kids in out-of-school-time hours
Town to Table, a Boston-based container farm company, announced a partnership with the Boys & Girls Clubs of Metro South, an organization that accommodates kids in out-of-school-time hoursy
Town to Table, a Boston-based container farm company, announced a partnership with the Boys & Girls Clubs of Metro South, an organization that accommodates kids in out-of-school-time hours.
"Together, we are operating two Freight Farms that will serve community members, food pantries, non-profits organizations, and the Clubs’ Kids Café Healthy Meals program which provides meals for 400 youth per day and serves more than 100,000 meals annually," said Town to Table on their LinkedIn page.
The farm will also be used as an educational resource to provide hands-on learning experiences for Club members with curricula-focused food systems, food justice, nutrition, and sustainability.
For more information:
Town to Table
https://towntotable.com
Boys & Girls Clubs of Metro South
Publication date: Fri 11 Jun 2021
New AeroMax Growing Media From OASIS Grower Solutions Increases Hydroponic Crop Growth by Up to 30%
Engineered with a unique open matrix, the increased porosity of the new Horticubes® AeroMax growing media leads to greater airflow and maximizes the opportunity for oxygen to get to a plant’s root zone
(Kent, OH) – OASIS Grower Solutions, a worldwide leader in propagation and division of Smithers-Oasis Company, understands the importance of propagation. Not only helping plants grow but generating big ideas as well. The most recent of which is the revolutionary new substrate engineered for precision hydroponic farming called Horticubes® AeroMax.
New Horticubes® AeroMax growing media introduces a higher level of porosity for faster, healthier hydroponic crop root growth.
Before creating a new media to support the production of leafy greens, herbs, and other crops for hydroponic farming, Vijay Rapaka Ph.D., Global Research Manager set a rather lofty goal: “To create a smart substrate designed for today’s precision growing systems. Through extensive research over the last 24 months, we’ve achieved an ultra-low density that allows unrestricted root growth of young plants, so they can express their full growth potential of up to 30%. This innovative purpose is precisely why we named it AeroMax.”
Engineered with a unique open matrix, the increased porosity of the new Horticubes® AeroMax growing media leads to greater airflow and maximizes the opportunity for oxygen to get to a plant’s root zone. This helps crops grow faster and stronger, allowing young plants to prosper in the maximum air-filled substrate. Due to its enhanced porosity, air and nutrients constantly replenish a plant’s root zone, promoting stronger and healthier roots through each watering cycle.
The maximum airflow created with new Horticubes® AeroMax substrate helps get this young lettuce off to a great start.
Created with support from John Bonner of Great Lakes Growers, AeroMax has already delivered some impressive results. “The more porosity, the greater opportunity for air to contact the root zone,” begins Bonner. “And that happens more often with AeroMax, so we get fuzzy, almost hairy-looking roots. And when you get that type of growth, the plants simply grow faster. Since we started using AeroMax, we’ve seen faster crop growth upwards of 15%,” grins Bonner.
In addition to delivering greater oxygen to the crop’s root zone, AeroMax’s increased porosity and airflow enables it to drain more easily. This improved drainage keeps the top of the AeroMax growing media drier, dramatically reducing algae blooms and subsequent disease – creating a wonderfully clean and pathogen-free environment for young plants to grow.
Dr. Vijay Rapaka of OASIS® Grower Solutions and John Bonner of Great Lakes Growers review the incredible success of the new Horticubes® AeroMax.
AeroMax has a multitude of other functional benefits that support improved propagation. Its rich black color was strategically selected to increase the surface temperature and synergize well with photosynthetic light spectrum to produce more well-toned young plants. Plus, the less dense, almost spongy nature of AeroMax minimizes dust generation throughout the production process, making it easy to work with.
AeroMax has also been designed to separate easily at transplant through a unique etching around each cube, which also supports uniformity and precision growing. AeroMax growing media works well in NFT, Deepwater, and Vertical hydroponic systems, and is available in single-seed and multi-seed dibbled sheets of 50ct, 104ct, 162ct, and 276ct. The 50ct, 104ct, and 162ct sheets are top-grooved for easier separation.
For more information on Horticubes® AeroMax, contact Shannon Enoch, at Senoch@smithersoasis.com, customer service at 855.585.4769, or visit us online at www.oasisgrowersolutions.com/aeromax.
USA: WASHINGTON STATE - Ummah Sustained Agroecology Center - Long Time! We Have Been Getting Things Started Here On The West Coast. We Opened!
Ummah Sustained AgroEcology Center - U.S.A.C. features Washington States 1st Certified Jr Master Gardener, Youth Agroecology, and Discover through Hydroponic K8 Farm School programs
Ummah Sustained Agroecology Center, a unique opportunity for your K-8 child to be creative, and confident while building lasting friendships. Our youth development program nurtures a child’s instinctive curiosity through informal exploration learning experiences
Ummah Sustained AgroEcology Center - U.S.A.C. features Washington States 1st Certified Jr Master Gardener, Youth Agroecology, and Discover through Hydroponic K8 Farm School programs.
Our Certified Urban Permaculture center houses three hydroponic systems including Freight Farm, a greenhouse, raised beds, community garden, small session classroom, and Afrocentric resource library.
We offer volunteer opportunities through WSU Extension Snohomish County 4-H and AmeriCorp.
Vertical Roots Opens Third Indoor Hydroponic Container Farm
Vertical Roots, a vertical farming company which grows its leafy greens in repurposed shipping containers year-round, has opened its third indoor farm in Atlanta, Georgia, reducing produce transportation and expanding access to fresh, locally-grown leafy greens.
14-June-2021
By Mary Ellen Shoup
Vertical Roots, a vertical farming company which grows its leafy greens in repurposed shipping containers year-round, has opened its third indoor farm in Atlanta, Georgia, reducing produce transportation and expanding access to fresh, locally-grown leafy greens.
To Continue Reading, Please Click Here
Source Courtesy of Food Navigator-usa.com
USA - ALABAMA: Auburn College of Agriculture Using High-Tech Shipping Containers To Grow Produce For Campus Dining
Unique ‘Vertical’ Farms part of Planned 16-Acre Transformation Garden On Campus
High-tech Horticulture
Unique ‘Vertical’ Farms part of Planned 16-Acre Transformation Garden On Campus
June 10, 2021
Josh Woods | College of Agriculture
Recycled shipping containers have gained popularity in recent years, being converted into everything from houses to small stores—but the Auburn University College of Agriculture, in partnership with Campus Dining, is using them as self-contained “vertical” farms to grow produce to serve to students.
In April, the college acquired two Freight Farms shipping containers that have been converted into technologically advanced hydroponic growing stations in which plants grow vertically indoors without soil, getting their nutrition from water and light energy from powerful LEDs.
Now, the farms are producing the first crop of lettuce.
“This is state of the art,” said Desmond Layne, head of the Department of Horticulture. “We're talking growing from seed to fork in four to six weeks, depending on whether it is lettuce, arugula or another vegetable crop that can grow in there. And we can produce 15 times as much per year as we could outside in the same exact spot.”
Associate Professor of Horticulture Daniel Wells taught a vertical farming course this spring and leads operations of the vertical farms.
Wells said the containers are outfitted with a complete climate control system, which includes air conditioning and humidity control. Because they are highly insulated, the system ensures the same climate 365 days a year.
The converted containers also have an elaborate lighting system, giving all the light the plants need from two color LEDs.
“We can do any number of colors of lights,” he said. “But it turns out for photosynthesis, plants use mostly red and blue light. What’s neat about that is you can cut out a lot of the other color spectrum, creating far less heat energy. That's very efficient. It means more of the energy used is turned into light than heat.”
The containers also allow for controlled carbon dioxide levels, which accelerates plant growth.
“Ambient CO2, what you and I are exposed to every day, is about 400 ppm [parts per million],” he said. “And that’s fine, plants can grow there. But if we boost the CO2 to 1,000 ppm, they’ll grow faster. And because we’re containing the CO2, the plants can really use it. And it’s not dangerous for humans at all.”
Wells and Director of Dining and Concessions Glenn Loughridge first initiated a partnership between the College of Agriculture and Campus Dining five years ago through the Auburn Aquaponics Project, which uses hydroponics and aquaculture technologies to provide a system in which nutrient-laden wastewater from fish production is used as a food source for plant growth. Today, fish from this effort are served in dining facilities on the Auburn campus.
The new vertical farms build on that effort.
“We're in the process of finishing a $26 million dining hall in the center of campus,” Loughridge said. “It has always been foremost in my mind that we would have the opportunity to feature produce grown here on campus in that dining hall. In our biggest location, our biggest asset, we want to bring our A-game.
“This is hyper-local, on-campus sourcing,” he added. “Can you imagine being a potential student coming to tour, seeing where these products are grown, and then going to eat there? It’s incredible. We truly believe this elevates our dining experience.”
The converted shipping containers were manufactured by Freight Farms, a Boston-based company operating in 45 states and 28 countries.
“There are a few different companies out there doing this,” Layne said. “But Freight Farms is the most sophisticated. They’re the ones who have both the best product on the market and the largest production of these containers. It’s really a best-case scenario.”
Adam Lenhard, a rising senior majoring in biological agricultural technology management, said Wells’ course has been one of the most influential courses he’s taken at Auburn.
“It has been very helpful, not just in preparation for the arrival of the freights, but also in learning all about new hydroponic technologies and growing techniques,” Lenhard said. “Post-graduation, I plan to continue to work with these types of indoor, LED hydroponic systems. My primary goal after college is to normalize urban hydroponic farming, provide large, consistent yields of fresh vegetables and provide food to those in need who do not have as much access to fresh produce.”
Transformation Garden
The vertical farms are located on the College of Agriculture’s planned 16-acre Transformation Garden on the south end of the university’s campus, near the intersection of Lem Morrison Drive and Duncan Drive. The goal of the garden is to encompass every aspect of plant-based agriculture, including everything from fruits and vegetables to ornamentals to grow crops and more.
The Transformation Garden will showcase new technology and the history of agriculture, as it envelops Auburn’s Old Rotation, a single-acre research plot created in 1896. Continuously since that year, the historic landmark has been the site for testing and advancing transformative ideas that are now commonplace—ideas like crop rotation, cover crops, and low- and no-till farming.
(Written by: Kristen Bowman)
HELP DEVELOP THE TRANSFORMATION GARDEN
To help develop the new Transformation Garden, you can give online or contact Phillip Cowart, College of Agriculture director of development, at poc0001@auburn.edu or 334-844-1198.
Auburn University is a nationally ranked land grant institution recognized for its commitment to world-class scholarship, interdisciplinary research with an elite, top-tier Carnegie R1 classification, life-changing outreach with Carnegie’s Community Engagement designation and an undergraduate education experience second to none. Auburn is home to more than 30,000 students, and its faculty and research partners collaborate to develop and deliver meaningful scholarship, science and technology-based advancements that meet pressing regional, national and global needs. Auburn’s commitment to active student engagement, professional success and public/private partnership drives a growing reputation for outreach and extension that delivers broad economic, health and societal impact.
Latest Newsroom Articles
USA - Orlando, Florida: No Better Time Than Now
Kalera, one of 2020’s biggest headline makers in vertical farming, has even bigger plans for its still-under-construction nationwide network, and there’s nothing that can slow it down.
Kalera, one of 2020’s biggest headline makers in vertical farming, has even bigger plans for its still-under-construction nationwide network, and there’s nothing that can slow it down.
May 21, 2021
Matthew J. Grassi || Photos by Connor Barber
Kalera, based in Orlando, Florida, is taking the local indoor farming concept and stretching it from coast to coast during a nationwide pandemic. This all while turning out flavor and nutrient-packed and conventional crop price-competitive lettuce and leafy greens in a zero-pesticide, 95% less water-requiring closed-loop automated production system.
The highly automated vertical grower (with the slogan The Science of Great Greens) operates three indoor vertical farms, two of which are situated near its corporate headquarters in Central Florida.
The operation’s third vertical farm, located in Forest Park, Georgia, recently completed its inaugural lettuce harvest. This farm is one of the largest indoor farms in the U.S. Southeast at 77,000 square feet and is reportedly capable of churning out 10 million heads of lettuce to local Atlantans and foodservice distributors annually. Heads of lettuce pulled out of the new Atlanta facility have already made their way to local operators like Publix, Sysco and Fresh Point.
With the first harvest in Atlanta now under its belt, the nationwide farm network rollout rolls on into the summer.
The latest scoop: Kalera is pursuing a whirlwind agenda for the home stretch of 2021 and into the next year, opening new, modular farms in places like St. Paul, Houston, Denver, Columbus, Seattle and Hawaii. There, the company says the farm will be the island’s first operable commercial indoor farm when launched.
The new farm building campaign is not the only big news with Kalera. The group recently made waves by acquiring Vindara, an up-and-coming disruptor in the plant breeding world. The operation says it leverages machine learning and AI alongside traditional breeding techniques to drastically shorten the development window of new seed varieties and traits bred specifically for indoor vertical farming.
Leading and innovating
While the Kalera name is fairly new, the group is not some fly-by-night operator that just sprang up in a retrofitted warehouse one day. CEO Daniel Malechuk says the group worked for 10 years “behind the scenes in stealth mode” to develop the coast-to-coast indoor farm network concept.
“For the first time ever, an indoor farming company can offer you something from Hawaii to Seattle to Florida, and everywhere in between — which is exactly what the foodservice companies want — and it’s a consistent, quality product,” he says. “We’re bringing scale and unit economics and high yields unseen to this point in the vertical farming world, a couple of years ago people laughed at this concept, but clearly this is no longer a pipe dream.”
Malechuk has been with Kalera for just about a year now, having spent the bulk of his career in supply chain and retail purchasing across the food industry. The former VP of the supply chain for Mastronardi Produce has a firm grasp on what consumers want from an indoor produce company, and how to make that a reality in today’s world of segmented supply chains and COVID-closed borders.
“I have a lot to learn [about vertical farming] and I still do, and honestly that is what is most exciting for me — solving some of these challenges of ‘this is how we do it now, but can we do it this way’,” he says. “Can this be done at scale and with profitability? Those are the burning questions in this industry right now, and at Kalera we are answering those questions in a big way.”
Answering those questions by staying focused on providing a phenomenal produce product at a reasonable price is what sets Kalera apart in a crowded segment, according to Malechuk. “[Growing] something people can afford and not have to splurge to purchase this premium product, that is really what drives. Of course, our robotics and advanced technology is part of that focus, too, but our customer and what they care about — quality grown and sustainably produced, and at what price — that’s what gets us out of bed every morning.”
Kalera's closed-loop growing system produces crops with 95% less water used than field growing, according to the company.
Building out during a shutdown
Austin Martin is Kalera’s chief operating officer, based at the group’s first farm outside Orlando. The former big-box retail logistics professional oversees all of the far-reaching tentacles of the Kalera nationwide expansion strategy, managing the various farm buildouts as well as many aspects of the farm operations themselves.
“For those that were willing to work really hard and push the envelope to make things happen, [COVID] was actually a great opportunity for us to focus and get ahead,” Martin says when asked what it has been like managing such an ambitious rollout throughout the pandemic.
COVID did in fact alter Kalera’s go-to-market slightly. Initially, management was keenly focused on the food service retail segment as its primary customer. Then COVID hit and the bars, restaurants and local distribution networks that serve them practically grounded to a halt. Martin and his team had to quickly pivot to consumer-facing food retail to ensure a mixed-channel distribution strategy which the company will stick with once normalcy returns.
“These food retailers want to partner with a more sophisticated provider who can guarantee continuity in supply across a wide geography, yet still maintain that same level of focus on food safety,” Martin says. “They deal with a lot of regional growers and that’s really just because they don’t have another choice. They want the redundancy that a larger-scale operation can provide.”
The indoor farm's acquisition of a vertical farming genetics startup allows for customized hybrids brimming with nutrients, taste, and texture.
Seed acquisition
While Kalera’s scale and approach to vertical farming are attention-worthy attributes, what put the operation over the top was the acquisition of indoor seed genetics provider Vindara. It’s not every day that a farm can buy the company and infrastructure that provides arguably the most crucial link in the production chain.
The collaboration was born out of both familiarity and need: both companies have close ties to North Carolina State University’s ag programs — Malechuck is an alumnus — and Kalera’s leadership had realized a glaring need for genetics tailored specifically to indoor production systems.
Add Vindara president and co-founder Jade Stinson to the list of Kalera-connected executives with an interesting background. Stinson has worked in agriculture for decades, having helped with uncovering the link between mad cow disease and humans in the United Kingdom before joining BASF after college.
Vindara was founded in 2018 on the back of Stinson’s vision of becoming the premier provider of elite genetics for the vertical farming space. The fact that they figured out how to accelerate the seed trait breeding cycle from a ten-year lead time down to 18 months, while maintaining and even offering customizable yield and flavor profiles, simply cannot be oversold.
We're bringing scale and unit economics and high yields unseen to this point in vertical farming ..."
“Say we develop a new indoor lettuce seed variety today with higher yield. Ok, that’s great, but that can’t be it,” Stinson says. “LED lighting technology will evolve, there’ll be more automation and more hands-off growing style, different plant architectures. This industry is moving too fast for traditional breeding to keep up, and when you can leverage deep machine learning and analytics, you can really dive into the genetics and really start leveraging genetic diversity.”
What today’s vertical farming space requires is what Stinson calls a “systems approach” to breeding. “It’s not a one seed fits all approach. The production systems from grower to grower are so disparate, one seed in one system won’t move the needle,” she adds.
The partners share a focus on democratizing their own corners of the ag universe. Vindara is wholly-owned by Kalera, yet operates autonomously and will continue serving genetics to the entire CEA industry. Kalera wants more access to fresh, nutritious and affordable food, and Vindara wants the same for the breeding innovations side of the coin, too.
“Let’s democratize and have growers be able to call us up and say ,‘Ok I want a lettuce with dark purple color, high yield and nutrition, and it has to stay crispy in transport,” she envisions. “The Kalera vision is why should just the top 5% of the world population have access to the most nutritious food? And that’s what we believe in, too.”
Automation and technology
Having launched its first facility located at Orlando, Florida’s Marriott World Center convention area (which has a commercial irrigation and climate control system) Kalera’s chief technology officer and co-founder knew the operation required more precision and customization.
“Development and implementation of our automated HyCube growing system has been a tremendous advantage for our production cycles,” says Cris Toma, co-founder, and chief science officer. “It’s something we started to develop a couple of years ago because those off-the-shelf systems didn’t meet the requirements of our vertical farming operation and it was too difficult to extract the data.”
Today, the system is a cloud-based, mobile-optimized ecosystem of sensors and controllers and irrigation modules that are in constant interaction with the group’s closed-loop production systems.
By developing and launching its own system, the operation has cultivated a unique approach to technology via its experiences thus far.
“We like to say that we are farmers who use technology, rather than being a technology provider looking for an application in farming,” Toma says. “And that’s coming from somebody like myself with a machine learning and digital imaging processing background.”
By establishing indoor farms from coast to coast (and beyond) Kalera can offer its customers a consistent product from California to Maine.
“We do not make these statements because we do not understand technology, or have trepidation in dealing with it, rather it’s been my entire professional life,” he continues. “Yet, at the same time we need to be very careful that we don’t destroy the ROI and economic performance of each project with how we integrate technology.”
Once Kalera’s farm network is built and fully operational, the built-in advantage provided by all that aggregated production data will be a massive enablement piece for the head growers at each facility.
“We’ll create a digital data warehouse and implement big data analytics and algorithms, and those activities will drive our sensors with computer visions and AI for tracking plant health and development across all facilities,” Toma says.
While that data is important to what Kalera plans to do in 2021 and beyond, it will still rely on the tried-and-true head grower structure.
“The AI is not quite there yet for full automation, but the trend is there and will only continue to grow. And yet we still need a human in the loop for certain tasks, for the more complex tasks you still need the expert in there monitoring and making adjustments, and then you hope to build on the expert with data and analytics,” Toma says.
Bottom line
Kalera isn’t settling down anytime soon.
“I envision our expansion plans are going to continue, and we are also looking at international expansion in the years ahead,” Toma replies when asked what’s next for the operation. “We’ve got a deep pipeline of opportunities to capitalize on.”
For the CEO, it’s all about continuous improvement and never growing complacent.
“We never want to be flat organizationally, we are constantly striving to get better, learn, refine, and innovate within our business model,” Toma says. “And, if it adds value to our customers, then we’re going to do it.”
A Lot of Promise’: Vertical Farming Takes Root In Virginia
Since its inception at the turn of the millennium, vertical farming — which in its simplest form is any system where plants are grown in vertical stacks — has promised to revolutionize yields by allowing producers to multiply their crop outputs by six to eight or even more times without expanding their footprint
May 24, 2021
Imagine a field of lettuce.
Say the lettuces are all buttercrunch, and they dot the field like crisp rosettes. Each has been seeded by a farmer, kept free of pests, watered for weeks, and finally cut at the base before being rinsed and packed for transport. Each is destined for a different meal: a lazy evening salad on the porch, an artfully arranged plate at a restaurant two-top, the vegetarian alternative at grandma’s 80th.
Now imagine six of these fields, all stacked on top of one another.
The idea isn’t far-fetched. In fact, it’s already a reality in Virginia, where a new, more technologically oriented form of agriculture known as vertical farming is quietly taking root.
“There’s a lot of promise,” said Tony Banks, senior assistant director of agriculture, development, and innovation for the Virginia Farm Bureau Federation. “As we continue to watch urban encroachment and we have this demand to have food produced closer to where people actually live, we’re going to see more and more of it.”
Since its inception at the turn of the millennium, vertical farming — which in its simplest form is any system where plants are grown in vertical stacks — has promised to revolutionize yields by allowing producers to multiply their crop outputs by six to eight or even more times without expanding their footprint.
“You’re trying to use an area more intensively. Because you’re limited by horizontal space, you want to maximize vertical space,” said Leonard Githinji, a professor of sustainable and urban agriculture at Virginia State University who also works with Virginia Cooperative Extension.
The concept is flexible and scalable. The stacks can be small, nothing more than a narrow shelf installed at a restaurant or in a convenience store to grow produce within a customer’s reach. Or they can fill a warehouse, bringing an industrial dimension to agriculture.
“There’s a wide range. On one end, it’s almost you have a greenhouse that’s highly automated,” said Banks. “On the other end, you could be in a warehouse and everything is grown on huge assemblies of racks and you have complete artificial lighting and hydroponics.”
The latter type of vertical farming is “high-tech manufacturing, essentially,” said Scott Lowman, director of the Controlled Environment Agriculture Innovation Center at the Institute for Advanced Learning and Research in Danville, where scientists and other experts are exploring the promise of various types of indoor agriculture can hold for Virginia.
Hopes are high, particularly in the historic tobacco region of Southside, where state officials have been working for several decades to encourage farmers who once depended on the golden leaf to diversify their enterprises. It’s no accident that the Controlled Environment Agriculture Innovation Center was sited in a region with a rich agricultural history and an abundance of old warehouses once devoted to tobacco and now empty.
Nor was it an accident that in 2019, Gov. Ralph Northam’s office announced that vertical farming company AeroFarms had decided to build a $42 million facility in an industrial park jointly operated by Danville and Pittsylvania County. Virginia aggressively courted the project with some $1.5 million in state grant funds and incentives. In exchange, AeroFarms promised to build the facility, employ 92 people and purchase roughly $20 million of Virginia agricultural or forest products.
But while AeroFarms’ Virginia location will be the largest vertical farm in the state once built, it won’t be the only one. Over the past few years, other operations have quietly been putting down roots. Shenandoah Farms in Rockingham operates a large-scale facility that grows herbs and lettuces. In Lorton, Beanstalk grows a range of greens. Fresh Impact Farms in Arlington, which grows herbs, greens, and edible flowers, announced an expansion this spring in conjunction with the governor’s office. Babylon Micro-Farms in Richmond is developing sophisticated technology to spread small-scale vertical farms around the country. Other efforts are underway.
“We’re in a great position on the East Coast in terms of population centers,” said Lowman. “And it’s a friendly environment for business, and we have a legacy of hard-working labor.”
Controlled environment agriculture
While vertical farming is relatively new, its lineage is much longer, nesting within the family tree of controlled environment agriculture, which encompasses any type of production that takes place within a structure.
From Roman orangeries to modern-day greenhouses, controlled environment agriculture offers the advantage embedded in its first descriptor: control.
Outdoors, farmers are at the whim of the weather, plagued by pests and disease, and caught in a never-ending struggle to keep water and fertilizer confined to their fields.
Indoors, the equation changes. Because of the precision-engineered systems, controlled environment agriculture tends to require less water, less fertilizer, and few or no pesticides compared to conventional agriculture. And, depending on a particular system’s design, it can allow producers to grow crops 24/7, 365 days a year. AeroFarms has said that its technology allows it to produce leafy greens “at a rate 390 times more productive than field-grown plants.”
A vertical micro-farm known as a cropbox. (Virginia State University)
“I can now schedule my crops,” said Michael Evans, director of Virginia Tech’s School of Plant and Environmental Sciences. “I can basically optimize the environment for that crop.”
There are, of course, drawbacks. Everything nature once provided to a plant must now be provided by a human — or a machine.
“With a greenhouse, you’re taking advantage of natural sunlight. You’re not paying for that,” said Evans. “But you’re paying quite a bit for heating and cooling. When you flip to an indoor vertical system, the disadvantage is that now you have to supply the light.” Other costs diminish at the same time: without the translucent walls of a greenhouse, “your heating and cooling can go down because it’s better insulated.”
For years, prohibitively high energy costs boxed out vertical farming as a viable option for producers working in controlled environment agriculture. What would change the playing field was a technological innovation: the high-powered and highly efficient LED.
“The thing that really changed that made indoor vertical farming work and become an economic possibility was really the development of LED lighting, because that changes the energy equation a lot,” said Evans. “It makes providing the light the crops need much economically viable.”
A new generation of farmers
Despite its promise, vertical farming won’t replace conventional agriculture, experts say. Many of Virginia’s biggest commodity crops — soybeans, corn, hay — are grown at such a large scale that trying to transport them indoors would be an exercise in absurdity.
Where controlled environment agriculture has found a growing niche is in the produce most familiar to the average Virginian: lettuces, herbs, tomatoes, cucumbers, peppers, herbs, microgreens, and more. Experiments in growing strawberries indoors are also underway, and Evans pointed out that once legalized, marijuana may not be far behind, although the federal government’s continued classification of the plant as illegal will keep institutions like Virginia Tech from working with it.
For consumers of these products, the idea of local food grown only a short distance away is increasingly appealing. That can be an argument in favor of controlled environment agriculture and vertical farming, said Banks.
“When we import food into this country, what we import is fruits and vegetables that require a lot of hand labor,” he said. “So there’s opportunity there to offset some of those imports and reduce our reliance on food produced overseas.”
Both Banks and Evans also noted an unusual aspect of vertical farming: its allure for younger and often more urban Virginians.
“It’s getting a whole new generation of folks interested in agriculture. It’s a different type of agriculture, but it’s getting a lot of students,” said Evans. At Virginia Tech’s School of Plant and Environmental Sciences, he added, “we have to change our curriculum for what we’re teaching to prepare students interested in controlled environment agriculture.”
For a younger generation increasingly concerned with social and political justice, the opportunity offered by controlled environment agriculture and vertical farming to fill food deserts and involve local workers in local food systems is an attractive prospect. Many students are eager to look beyond the existing agricultural structures, said Githinji, who recently received a $600,000 grant from the U.S. National Institute of Food and Agriculture to explore the use of “micro-farms,” which incorporate vertical farming systems, as a way to address food deserts in urban neighborhoods.
It’s not unusual for extension agents to get calls in which people are saying, “‘As much as I want to grow more food, I can’t afford to buy even another quarter acre,” he said. “So you get people asking what they can do with what they have.”
The other draw is the technology. While vertical farming can be small- or large-scale, its larger applications rely on evolving and increasingly sophisticated technology that has piqued interest among the startup community.
“This is a really exciting industry that’s rapidly entering the mainstream,” said Alexander Olesen, CEO, and co-founder of Babylon Micro-Farms, a Richmond-based startup that develops indoor growing systems for institutional food service settings, such as hospitals, schools, and universities. Babylon, which in 2020 was the recipient of a $75,000 grant from the Commonwealth Research Commercialization Fund that aims to support small businesses in emerging research and technology sectors, builds small-scale vertical farms “as a sustainable amenity for these locations.”
The field’s growing popularity is also driving a need for more workers, more expertise, and more training, said many of the people interviewed for this story. The Controlled Environment Agriculture Innovation Center in Danville, itself a recipient of $365,000 in state grant funds in 2020, is key to that effort. So too are plans announced by the governor’s office last month that will see hydroponic greenhouse startup Sunny Farms build a 1.2 million square foot greenhouse in Virginia Beach — one of the largest on the East Coast — and work with Virginia Tech and the Virginia community college system to develop educational training in controlled environment agriculture.
“Our goal is really to support the controlled environment agriculture industry in Virginia, but we’re also working on creating an innovative controlled environment agriculture ecosystem in Virginia,” said Evans.
These enterprises may be only the beginning.
“Once people see that it’s working, we’re going to see them flourishing all across the commonwealth,” said Githinji.
Lead photo: Controlled digital lights help produce high-density feed grass in a Grov Olympus vertical farming machine in Utah. The Olympus Tower Farm uses a controlled environment to grow sprouted wheat and barley grass in 857 square feet of space and uses 95 percent less water to produce 5,000 to 6,000 pounds of grass per day, replacing 35-50 acres of land. (Photo by George Frey/Getty Images)
Sarah covers environment and energy for the Mercury. Originally from McLean, she has spent over a decade in journalism and academic publishing. Most recently she covered environmental issues in Central Virginia for Chesapeake Bay Journal, and she has also written for the Progress-Index, the Caroline Progress, and multiple regional publications. In 2017, she was honored as one of Gatehouse’s Feature Writers of the Year, and she has been the recipient of numerous awards from the Virginia Press Association. She is a graduate of the College of William & Mary. Contact her at svogelsong@virginiamercury.com
Squamish Nation Grows Plans For Food Security With A Hydroponic Farm
While the outside of this 40-foot container is rather striking, it’s what’s on the inside that counts. 🌱
While The Outside of This 40-Foot Container Is Rather Striking,
It’s What’s On The Inside That Counts. 🌱
May 19, 2021
By: Elisia Seeber
A big bright orange container has just landed in the Sḵwx̱wú7mesh Úxwumixw (Squamish Nation) community of X̱wemelch'stn in North Vancouver.
While the outside of the 40-foot container is rather striking, it’s what’s on the inside that counts.
The container is a Growcer hydroponic modular farm that will support the community's wellness by allowing them to grow a year-round supply of fresh produce, including leafy greens, herbs and traditional medicinal plants.
Creating a sustainable healthy source of produce and increasing food sovereignty has long been a goal for the Squamish Nation, and the hydroponic farm is another piece of the puzzle, said Kelley McReynolds, director of Squamish Nation’s Ayás Méńmen Child and Family Services.
“Part of the reason that we started to look at ways that we could [provide food] was working from our values as Squamish people and our values around food sharing,” she said.
“Traditionally, we as a community, and as families, would go out and hunt and we would gather out on the lands and the waters and we’d bring it back to our community and people would only take what they need, and the rest of it would be shared.”
Through the launch of a food distribution program about four years ago, McReynolds said the team began breaking down the stigmas and fears around food insecurity and shifting back to their traditional ways, to ensure everyone in the community felt comfortable receiving food.
“We didn't want to look at the food as being a form of charity, or only for those who don’t have food,” she said.
Hydroponic farm idea sprouts
When the COVID-19 pandemic hit, McReynolds said food security worries increased for some members and the team started thinking further outside of the box about how they could address future food scarcity.
That’s when the idea for the hydroponic farm sprouted.
Squamish Nation has looked at more traditional styles of farming, and also has 19 garden boxes set up outside of their office where they grow fruit and vegetables and a traditional medicine garden.
“We plant every year and we harvest that to give to community,” McReynolds said. “We do a lot of training with our youth and our families to help them understand the plants, gardening and harvesting."
She said a thought they always had was, “think what we could do if we had farmland, we could feed so many more people.”
“But, you know, we live in a city and you don't have access to that kind of open space,” McReynolds said.
“So, when we looked at this option of the hydroponic farm and saw that it's the size of a shipping container, we thought, ‘that's pretty cool.’ It comes with all the equipment you need inside there. And, you can get it set up and within five to six weeks you are ready to make your first harvest and it yields approximately 450 heads of produce per week. That's a lot.
“We thought, ‘wow, that's amazing.’”
The founders of the ingenious technology and social enterprise came up with the idea based on their firsthand experience of food insecurity in Nunavut in 2015 and wanted to create a system that allowed communities to grow fresh produce anytime, anywhere, in any climate.
The growing technology was first deployed in food insecure, remote communities, but has since expanded to partner with schools, non-profits, and non-remote communities who see value in growing food locally – like Squamish Nation.
The electronically run hydroponic farms cost around $180,000 to set up and will produce fresh food for around 30 years, according to Growcer.
How does the modular hydroponic farm work?
Hydroponics is a soil-free growing method that uses nutrient-rich water to grow plants using less space, time, and crop inputs.
“The modular farms are automated to provide full environmental control,” Growcer’s website states, adding that plant growth factors such as light, nutrients, temperature, humidity, carbon dioxide, and water are monitored in real-time.
Once set up, a range of 140 leafy green plants can be grown in as little as six weeks.
“It's all brand new to us,” McReynolds said, adding that Growcer would be training staff this week and continue to provide support through their hydroponic farming journey.
“We’re all really excited.”
Squamish Nation to open Food Pantry and Community Kitchen
Produce from the new farm will be shared with families serviced by Ayás Méńmen, the youth centre and the future Smeḵw'ú7ts (Food Sharing) Community Kitchen and S7ílhen (Food) Pantry, which is hoped to be up and running by the summertime.
“We will continue to do monthly food distribution, but we will also have food on our shelves and in the freezers for any of our members who are in need … whatever the situation may be,” McReynolds said.
The hope for the community kitchen is to build a healthy community by providing a safe place for members to learn and improve their food preparation and cooking skills through workshops, which may start on Zoom during the pandemic. Ayás Méńmen also plans to host a six-week program for community members to meet once a week to cook and take a meal home for their families.
“I think what excites me about that is we are such relational people,” McReynolds said. “To be able to come together and learn and share and grow and laugh and tell stories, that's so healthy and therapeutic and it brings joy to your heart just being able to be together.”
While there’s still a bit of work to be done before the hydroponic farm starts producing the goods, McReynolds has more big plans.
“I have this vision of us being able to do a Friday night or Saturday afternoon market where we can have the fresh produce, we can have music, we can maybe have food trucks and we can gather together,” she said.
“I just think it's just a great opportunity for us to celebrate who we are as farmers and come together as a community.”
Elisia Seeber is the North Shore News’ Indigenous and civic affairs reporter. This reporting beat is made possible by the Local Journalism Initiative.
Leading European Vertical Farming Company Retains Strategic Advisor to Explore Strategic Options
Award-winning Belgian vertical farming and contract research company, Urban Crop Solutions (“UCS”) has retained Contain, Inc., to explore strategic options to elevate its status as a leading European technology player in the fast-emerging global indoor farming space
Urban Crop Solutions Tech
Vertical farm & contract research co Urban Crop Solutions has retained Contain to explore strategic options to elevate its status as a tech leader in indoor ag.
We have long realised that we would need to decide between remaining independent and joining a larger organization to scale...this is the optimal time to make this move.”— Frederic Bulcaen, Chairman and founder of UCS
Urban Crop Solutions Container Farm
RENO, NV, UNITED STATES, May 19, 2021 /EINPresswire.com/ -- Award-winning Belgian vertical farming and contract research company, Urban Crop Solutions (“UCS”) has retained Contain, Inc., to explore strategic options to elevate its status as a leading European technology player in the fast-emerging global indoor farming space.
“We are delighted to have been awarded this mandate by UCS”, says Nicola Kerslake, founder of Contain. “It is a mark of the UCS management’s professionalism and dedication that they are open to exploring options from merger or acquisition to adding strategic investors to take this industry-leading firm to the next level.”
Urban Crop Solutions Grow System
UCS’ clients range from global billion-dollar companies to research institutions and start-ups across multiple industries in Europe, North America, and Southeast Asia. The growth of the business is attributed to a strong management and scientific team who have created best-in-class products and services made possible by application expertise and trade secrets. UCS expects to more than triple its revenues and reach breakeven profitability this year.
UCS offers two key solution and product channels:
-Plant biotechnology research: capabilities to simulate any growth environment and create growth recipe applications to address business and market opportunities in all crop verticals for use across numerous industries. UCS has developed innovative research applications such as growth performance of wheat, tobacco and cotton plants in controlled environments, growth recipe for green roof succulent plants on substrates and use of residual flows from waste to grow food.
-Vertical farming technology: indoor growing installations of hydroponic modules with growing surface areas ranging from 70 to over 5,000 square meters with an end-to-end customer support model. UCS has 4 different classes of product size that can be customized to meet the size or configuration requirements of any customer.
Maarten Vandecruys, founder and CTO of UCS, comments, “Now that we have our solutions and services in place, it is important that we pursue the best strategic options for the future of our organisation and team.”
“As a Board, we have long realised that we would need to decide between remaining independent and joining a larger organization to scale. There is such great momentum in indoor farming that this is the optimal time to make this move”, explains Frederic Bulcaen, Chairman and founder of UCS.
Contain Contact info:
Marilyn Jentzen
marilyn@contain.ag
+1.404.353.3754
About Urban Crop Solutions
Urban Crop Solutions BV is a privately held Belgian company founded in 2014. It offers end-to-end solutions for indoor hydroponic vertical farming via full-service customized and scalable solutions to multi-industry customers in two key product and service areas. Plant research products and services help customers select the right plant varieties or create new growth recipes for specific client needs or market opportunities. Indoor plant growing solutions and services range from concept design through business planning, manufacturing, installation, training, and after-sales servicing and support.
https://urbancropsolutions.com
About Contain, Inc.
Contain Inc is a US-based fintech platform dedicated to indoor agriculture, growing crops in warehouses, greenhouses and container farms. The Company serves the controlled environment agriculture industry in several capacities; it works with leading equipment vendors and with a wide pool of lenders to aid indoor growers in finding funding for their farms. It is also home to microlearning platform Rooted Global, which works with majors such as Danone and Dole to enable employees to grow a little of their own food at home. Most recently, the Company launched a used equipment trading platform, Equipped, to take the drama out of buying and selling used indoor farming equipment. The Company graduated from the 2019 Techstars Farm to Fork program, backed by Cargill and Ecolab.
https://contain.ag
Marilyn Jentzen
Contain Inc
marilyn@contain.ag
Visit us on social media:
Twitter
LinkedIn