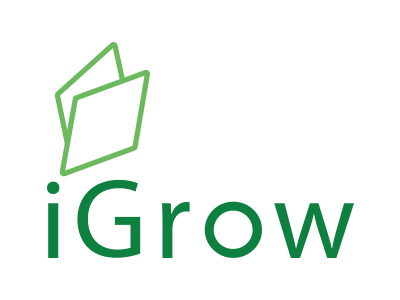
Welcome to iGrow News, Your Source for the World of Indoor Vertical Farming
2021 GLASE Webinar Series
The production of high nutrient density crops in controlled environments (such as greenhouses and plant factories) allows for high density, local, year-round food production
Urban CEA: Optimizing Plant Quality,
Economic And Environmental Outcomes
Date: February 25, 2021
Time: 2 p.m. - 3 p.m. EDT
Presented by: Dr. Neil Mattson (Cornell University)
Click Here To Register
The production of high nutrient density crops in controlled environments (such as greenhouses and plant factories) allows for high density, local, year-round food production. Mattson leads a National Science Foundation project that seeks to better understand the benefits and constraints of urban CEA including: economics, natural resource use, carbon footprint, and nutrition. Mattson will discuss research that seeks to optimize crop performance, nutrition, and resource use through strategic LED lighting and CO2 supplementation. Finally, Mattson will discuss efforts of the NSF project to define workforce development needs by the nascent urban CEA industry and a new USDA workforce development project to expand training opportunities in CEA for 2-year colleges and lifelong learners.
Special thanks to our Industry partners
Join today
If you have any questions or would like to know more about GLASE,
please contact its executive director
Erico Mattos at em796@cornell.edu
TURKEY: The Goal Is To Establish a Million Square Meters of Agriculture Factory
Vertical farming practice is a method of soil-free farming, unlike traditional methods. Agriculture can be done completely with water without using any soil
The rapidly increasing world population causes an increase in the demand for food. People expect to consume fresh fruits and vegetables throughout their lives. It is getting harder every year to meet the fresh food demand of people due to the declining fertile lands due to the increasing urbanization and industrialization, the climate changes, and the inadequate irrigation of agricultural lands. While more production is made with the hormone drugs and other pesticides used to meet this demand, the yield and quality of the fresh foods produced decrease.
HGT Tarım, a Pimtaş establishment, started the works to establish an agricultural factory of 1 million square meters in order to prevent all these problems and to meet the increasing demand for fresh and organic food. All necessary work is underway for the Vertical Agriculture project, which is carried out jointly with PİMARGE and Gebze Technical University.
Smart Agricultural Investment
Vertical farming practice is a method of soil-free farming, unlike traditional methods. Agriculture can be done completely with water without using any soil. Thanks to the Vertical Farming system, there is no need for agricultural land, and the water used is used continuously by using the recirculation system. It allows us to obtain more efficiency with less water usage.
The products that meet our mineral needs in water will be made efficient by lighting with special LEDs without using any fertilizer drugs. While lettuce soil yields 60 crops in 1 day in our latest works, this period is reduced to 15 in 1 day with the Smart Agriculture system.
Products that are constantly working and controlled by automation with special software are indispensable for customers who want to buy fresh products at affordable prices, apart from being 100% organic.
Our project will stimulate the economy
The arable land requirements of traditional farming are too large and invasive to remain sustainable for future generations. With rapid population growth rates, arable land per capita is expected to decrease by approximately 2050% in 1970 compared to 66. Vertical farming allows more than ten times the crop yield per acre compared to traditional methods. Unlike traditional farming in non-tropical areas, indoor farming can produce crops year-round. All seasonal farming increases the productivity of the field surface 4 to 6 times depending on the crop.
All processes are environmentally friendly
All products that will be used in the system are completely recycled. Environmental problems are becoming less dangerous for the agricultural industry with vertical farming. Farmers do not use chemicals such as pesticides, so the whole process runs environmentally friendly. Vertical farming has an important role in a sustainable environment. In addition, it enables the production of fresh and healthy products and production for 365 days without the need for agricultural knowledge.
Speaking about the project, our Chairman of the Board of Directors Şamil Tahmaz said, 'Thanks to this project, which we will implement with 100% domestic and national means, we will protect our country's natural resources and ensure that our nation can access the food products they need most whenever they want. He said to produce what our country needs most and to produce more. ''
Growing Sprouts In A Former Slaughterhouse
Grow Up FARM has recently launched a new product, named Eat-Grow-Repeat: small pea shoots that grow on a small hemp-square in a bag. "Rip off the upper section of the bag, and the bottom of the bag is now the pot," Lasse Vilmar, Chief Executive Grower of the company, explains
Grow Up FARM has recently launched a new product, named Eat-Grow-Repeat: small pea shoots that grow on a small hemp-square in a bag. "Rip off the upper section of the bag, and the bottom of the bag is now the pot," Lasse Vilmar, Chief Executive Grower of the company, explains. "Place the bottom of the bag with pea plants on your table and the growth will continue. Harvest completely fresh pea sprouts for your salad bowl. Keep watering and within a week they will grow out once again."
Developing innovative packaging is a new field for Grow Up FARM, as the company has been working with mainly sprouts for three generations already. The Ringsted-based family business started with Lasse’s grandparents growing sprouts in the ‘60s. Lasse himself took over in 2013. “At that time, we were looking for new products to shoot the market. Our eyes fell on Koppert Cress and other companies that were doing microgreens. All of a sudden, it was like a light bulb that went off, and it felt like a natural direction to pursue”.
GrowUp FARM owners Jens Essemann and Lasse Vilmar
The new product had already been planned for quite some time, but the launch was accelerated the world-wide plot twist that the pandemic created. “We had just geared up and planned everything for the summer season to start, with all its parties and weddings. In the end, we only got to deliver one or two full batches before the lock-down”.
Although the company for years had focused on companies rather than local customers, selling to people in the area got them through the first lock-down. “We searched for Facebook community pages to advertise to local customers. Luckily we got rid of most of our stock that way, even though we only sold in large commercial-sized boxes. We combined different varieties in one box so that people had a chance to eat all of it. I even borrowed a van from a nearby car dealer on which I taped some of our roll-up banners. Like an old-school farmer I stood there, selling my produce. It was a fun period, but also nerve-wracking because we had no ideas when we could be able to continue our regular growing process again”.
Unlike the sprouts that Lasse has been working with for years, the microgreens are grown in a vertical farm. The building once was a poultry slaughterhouse, and the coolers have been turned into growing chambers. Isolation is important, as sprouts are grown completely in the dark. Even more importantly, isolation is needed for strict hygiene reasons.
“Growing sprouts is considered high-care production in the EU. The beans need a warm and moist environment, which are ideal circumstances for bacteria and molds. You need to be sure that the equipment is sterilized and that the water is drink-water quality. It takes a lot of control and procedures”. Most of the watering, which takes 400 liters every 3 hours per batch, is for cooling purposes. “The temperature in the core of the sprout-mass can rise to 70 degrees, so the sprouts could basically cook themselves”.
The sprouts are sold to both supermarkets and retailers, which makes it less vulnerable regarding covid-restrictions. Also, the Eat-Grow-Repeat plants are sold exclusively to supermarkets. “We’re doing 2000 bags delivery each week, and in a month we will launch the product to other supermarkets. The reviews have been raving, so we are quite proud of what we have achieved so far”.
Keeping an eye on the environment
The company strives to keep its packaging material as environmentally friendly as possible. The foodservice products are 100% recyclable, consisting only of FSC-cardboard and organic biodegradable hemp. Its current consumer packaging only consists of 6g of recyclable PE-plastic and organic biodegradable hemp, no pots or cardboard.
The Eat-Grow-Repeat product, with pea shoots
“Our farm is not much different from other vertical farms,” says Lasse. We are entirely electrified, and we have chosen an energy company (NaturEnergi) that pushes sustainable energy. This way our energy is constantly getting more sustainable.” In 2019 approximately 50% of the energy produced in Denmark came from wind and solar. “Ultimately we aim to plaster our roof with solar panels,” Lasse adds.
For more information:
Grow Up FARM
Lasse Vilmar, Owner and Chief Executive Grower
lasse@growupfarm.dk
www.growupfarm.dk
Source: Publication date: Thu 11 Feb 2021
Source: Author: Rebekka Boekhout
© VerticalFarmDaily.com
US - SOUTH CAROLINA: VIDEO: Columbia Vertical Farm Uses Technology To Cut Plastic Pollution And Boost Sustainability
With the use of agricultural technology, Vertical Roots farm in West Columbia created a packaging system for its leafy greens that cut down the company’s plastic usage by 30% and extends the shelf life of the lettuce
FEBRUARY 01, 2021
Vertical Roots is the largest hydroponic container farm in the country. They grow and package lettuce varieties and have recently implemented a packaging process that reduces plastic with a resealable film. TRACY GLANTZ TGLANTZ@THESTATE.COM
With the use of agricultural technology, Vertical Roots farm in West Columbia created a packaging system for its leafy greens that cut down the company’s plastic usage by 30% and extends the shelf life of the lettuce.
In 2015, high school friends Andrew Hare and Matt Daniels created the idea for Vertical Roots, now the largest hydroponic container farm in the country. Hare is the general manager of the company and Daniels acts as the chief horticulturist.
The first Vertical Roots opened in Charleston and expanded with its second farm site in West Columbia in 2019. Vertical Roots parent company, AmplifiedAg, manufactures the container farms and farm technology of which Vertical Roots operates.
The farms are part of a growing industry called controlled environmental agriculture (CEA) that uses technology to ramp up nutrient-rich food production year-round.
Hydroponics helps the farm uses 98% less water than traditional farming, according to Hare. Their technology creates an indoor environment to grow lettuce on the East Coast. Most lettuce in the U.S. comes from California and Arizona, where temperatures do not fluctuate much throughout the year, traveling 2,000 miles from farm to table. Vertical Roots offers a solution for local lettuce.
“Our mission is to revolutionize the way communities grow, distribute and consume food,” said Hare. As populations grow, Hare said the ability to produce enough food is a global concern.
VERTICAL ROOTS AGRICULTURAL INNOVATION
As a company committed to sustainability, Vertical Roots had to address its plastic usage and the consumer demand for environmentally friendly products.
“I think everyone can agree that the amount of plastic that’s consumed and used globally is a bit of a problem,” said Hare.
If Vertical Roots were to completely opt-out of using plastics, as much as 40% of the lettuce would be damaged in transportation to the retailers, Hare said. So the company decided to still use plastic containers in order to cut out food waste, but it changed the amount and type of plastic used.
By replacing the conventional “clamshell” plastic lids that you see on a container of lettuce at the grocery store, Vertical Roots cut down more than 30% of plastic usage by creating a resealable film lid. The new packaging comes at no extra cost to the customer and will be cheaper in the long-run for Vertical Roots, according to Hare.
The farm also uses recycled plastic that can also be recycled again after use. Tiny perforations in the film lid of the packaging allows air to leave the lettuce container and extends the product’s freshness, making Vertical Roots lettuce last around 14 days on the shelf.
“We tested respiration and condensation with each lettuce variety, and ultimately found that we could extend the freshness and shelf life of our salad mixes even more,” said Hare.
GROWTH IN THE AGRICULTURAL TECHNOLOGY INDUSTRY
In the first three quarters of 2020, a record $754 million of venture capital was invested in the vertical farming industry, according to PitchBook data. This was a 34% increase from the entire previous year, Bloomberg reported in a January article.
A 2019 report from Global Market Insights showed that the vertical farming market size, or the number of potential customers or unit sales, surpassed $3 billion in 2018 and said it, “will exhibit a massive compound annual growth rate (CAGR) of over 27% from 2019 to 2026.”
In vertical farms, crops are harvested on several vertical layers indoors, where farmers can grow year-round by controlling light, temperature, water, and other factors, according to the U.S. Department of Agriculture.
Vertical agriculture is also seen as a growing industry because it “could help increase food production and expand agricultural operations as the world’s population is projected to exceed 9 billion by 2050,” according to the USDA.
However, some are skeptical about the future of vertical farming for several reasons. The farms use LED light bulbs to grow the crops, which require a lot of energy and money to operate.
Also, the farms mostly produce greens, which are low in calories because they take less water and light. The new farming technology is marketed as a way to combat world hunger, but in poorer countries, low-calorie greens are not as beneficial, according to Bloomberg.
THE FUTURE OF VERTICAL ROOTS
Despite a tough year due to COVID-19, Vertical Roots will open two more indoor, container farms in Georgia and Florida in 2021.
The company lost revenue from foodservice customers like restaurants, schools, and universities during the pandemic, said Hare.
Those food service customers accounted for about half of Vertical Roots’ business, Hare said. Grocery store business stayed steady and even grew during the pandemic. As schools and restaurants are slowly reopening, Vertical Roots is gaining business back.
The West Columbia farm location produces about $1.5 million pounds of produce per year, said Hare. Vertical Roots lettuce is in 1,200 different grocery stores in 11 states, including Lowes Foods stores, Publix, Harris Teeter, and Whole Foods Market chains.
Hare said the company is constantly working on sustainable initiatives, including figuring out a way to reduce light energy consumption by 20-25%, thinking about compostable packaging systems and finding ways to use less water at the farms.
In the future, Vertical Roots hopes to offer a larger variety of produce. The team is experimenting with growing foods like tomatoes, cucumbers, peppers, herbs and mushrooms to see if they could be viable products.
USA: Wichita, Kansas - Fidelity Bank’s New ‘Car Park’ Adding Ground-Floor Restaurant, Rooftop Urban Farm
Called Rise Farms, it will include 5,000 square feet of space where fresh vegetables and herbs will be grown in raised beds, large planters, and a 24x70-foot long hoop house
Fidelity Bank is embarking on a $51 million project to build a 10-story tower next to its existing five-story headquarters at Main and English. It also plans a new 505-stall parking garage. BY JAIME GREEN
The ground level of Fidelity Bank’s new five-story “car park” on Market between Waterman and English will soon have a new 4,000-square-foot restaurant on its main level.
And that’s not even the biggest news to come out of the project this week.
In addition to the restaurant — which Fidelity isn’t ready to share details about quite yet — the new parking garage will also be home to a rooftop urban farm that bank officials say will be the largest in the Midwest.
Called Rise Farms, it will include 5,000 square feet of space where fresh vegetables and herbs will be grown in raised beds, large planters, and a 24x70-foot long hoop house. The food the farm produces will be used not only by the new ground-level restaurant tenant but also by other restaurants around Wichita. Fidelity Bank employees also will be beneficiaries of the produce, and the first crops should be ready by fall.
The rooftop project will include a private event center with retractable garage doors where Fidelity can house small events and gatherings during warm weather seasons as well as a 5,622 square-foot solar farm featuring 204 solar panels, which produce 380 watts each. The panels, which weigh about 35,000 pounds, are already up and running and producing enough energy to provide the power for the car park and its first-floor tenants.
A rendering of what Fidelity Bank’s rooftop Rise Farms will look like Courtesy FIDELITY BANK
The car park, which has 405 stalls, 24 electric car charging stations employees can use, and daytime public parking on the ground level, just opened and is the first part of a $51 million Fidelity Bank expansion project that also will include a new 10-story, 135,000 square-foot office tower at 100 E. English, where the bank’s parking deck is. Construction on that hasn’t started yet.
The idea for the rooftop farm came about after Fidelity polled its employees about what types of tenants they would like to see move into the 17,000 square feet of retail space on the car park’s ground level, said Aaron Bastian, Fidelity’s president, and CEO. Overwhelmingly, they said they’d want a restaurant.
In the course of meeting with potential restaurant tenants, Bastian said, one suggested the idea of raising fresh produce on the roof.
Bastian, who said that local food culture is a topic he’s passionate about, liked the idea, but bank leadership decided they’d need to consult with an expert to pull it off.
“When we started talking about this idea, we wanted to go out and find people we could partner with to help create what we think could really be a cool downtown amenity,” Bastian said.
Fidelity has since partnered with Leah Dannar-Garcia, the owner of Firefly Farm at West 21st Street North and North 159th Street East, who already raises produce that she sells to about 38 Wichita restaurants. She’ll be in charge of the farm and will offer its produce for sale to restaurants on her route. The ground-floor restaurant, though, will get first dibs.
Fidelity Bank’s new car park in downtown Wichita just opened to employees. By fall, it will have a ground-floor restaurant and a rooftop farm. Courtesy FIDELITY BANK
Dannar-Garcia has been working with the bank for about a year, she said and has mapped out her growing plans in detail. Once it gets going, she’ll have plants growing in beds and containers along both the north and west sides of the building as well as in the climate-controlled hoop house. The bank envisions a program in which Fidelity employees will be able to volunteer to work the farm, and they’ll also set up some type of program where employees can get boxes of fresh produce to take home.
Once it’s fully functioning, the farm will produce vegetables like beets, carrots, broccoli, cauliflower, sweet potatoes, and Brussels sprouts as well as greens like arugula, Swiss chard, and spinach. It’ll also grow herbs, including parsley, cilantro, and Greek oregano.
“We’re going to grow in all four seasons on this farm, so we’ll have spring, summer, fall, and winter crops,” Dannar-Garcia said.
The project is a “natural extension” of the bank’s health, wellness, and green initiatives, it says. One goal of the farm is that it produces zero wasted food.
“Whether that means it gets donated, we haven’t defined that yet,” said Melissa Knoeber, executive vice president at Fidelity who is also the bank’s director of culture and talent. “But that’s really important to us.”
Construction on Rise Farms should start in the spring, and the first crops should be ready by fall.
COURTESY FIDELITY BANK
DENISE NEIL
316-268-6327
Denise Neil has covered restaurants and entertainment since 1997. Her Dining with Denise Facebook page is the go-to place for diners to get information about local restaurants. She’s a regular judge at local food competitions and speaks to groups all over Wichita about dining.
PUERTO RICO: Indoor Vertical Farming Jumpstarts Agribusiness
Francisco Santana founded Grupo Vesan in 2015 with a simple concept: farming differently and more effectively. He looked to indoor vertical farming and became the first company in Puerto Rico to adopt that model
Grupo Vesan Seeks To Provide Food Security
With Sustainable Practices
Unlike other lettuce produced in Puerto Rico, the ones grown via vertical farming are unaffected by saltpeter, a naturally occurring nitrate. Courtesy of Grupo Vesan
January 13, 2021
A small business in the southern region of Puerto Rico is seeking to revolutionize agribusinesses with sustainable practices while providing food security and reducing the need for imported produce.
Francisco Santana founded Grupo Vesan in 2015 with a simple concept: farming differently and more effectively. He looked to indoor vertical farming and became the first company in Puerto Rico to adopt that model. As previously reported by THE WEEKLY JOURNAL, indoor vertical farming allows farmers to generate fresh food items in a controlled environment with smaller required spaces.
“Everything is with artificial lights and it works with 62 degrees F of temperature. It is a completely different environment. We regulate the humidity and even the oxygen level is controlled. The concept of all these parameters is completely different from what one usually finds in the market,” Santana explained.
In its beginnings, Grupo Vesan started with a 40-foot wagon and is now producing a variety of fruits and vegetables in Canas Industrial Park in Ponce, working with a 20-foot ceiling and 14 different parameters that allow for a broader range of products. Even after Hurricane Maria devastated nearly 70 percent of the island’s hydroponics, the company stood strong.
As such, Santana hopes that more agribusinesses incorporate this system so that residents have access to fresh food in times of crisis. “One of the benefits of this system… is that it provides food security. What we project is that agriculture should move indoors,” he said.
“Agriculture in Puerto Rico is not where it should be. That is the main issue of food security tied to this subject of indoor vertical farming. On the other hand, at the technology level, we are the pioneers in this process. We promote the idea of impacting the agriculture of Puerto Rico for new generations. [The idea that] new generations are not going to go to traditional agriculture; that is not true. We have, for example, an alliance with the Catholic University of Ponce and they send students here. They are working in air conditioning, in a white coat, like a pharmacist. They are doing scientific research, but they are really doing agriculture,” he added.
Islandwide Agriculture
Another benefit of indoor vertical farming is that it can be employed virtually anywhere in Puerto Rico, regardless of the soil’s fertility or if the area is prone to flooding or droughts. In fact, Grupo Vesan was founded while the island was experiencing a drought that prompted the Aqueduct and Sewer Authority (Prasa) to ration water.
Indoor vertical farming is also tied to the concept of “urban farming,” which is gaining popularity in Europe. That is, residents in any corner of Puerto Rico, including the San Juan metropolitan area or beachy municipalities like Dorado, can start their own agribusiness.
Likewise, this type of farming can be applied in spaces labeled as “brownfields,” which are areas that are contaminated and, therefore, unsuitable for traditional farming practices. Grupo Vesan even sells wagons for these purposes because one of their aims is to popularize this technique.
Environmental Impact
According to Santana, if more agribusinesses emerge with this model, the island would drop its carbon dioxide (CO2) emissions because there wouldn’t be a need to transport fresh food via long distances. “It also provides fresher food to consumers and businesses like restaurants could apply the farm-to-table concept,” he said.
Moreover, Grupo Vesan packs its agricultural products with its roots in a pouch with water. This allows the product to have greater longevity, thus reducing food waste and allowing for financial savings by not having to purchase fresh fruits or vegetables as often. As an example, Santana stated that the lettuce produced by his company can last “two or even three weeks” without spoiling.
Apart from lettuce, Grupo Vesan also grows spinach, tomatoes, cilantro, peppers, broccoli, carrots and a variety of other agricultural products.
“Revenue, a sense of community, and environmental impact; those are the components of a sustainable company. In our case, we don’t use any insecticide or pesticide, none of that. Our products are practically organic,” he affirmed.
He added that the company is currently developing a project to grow strawberries, noting that indoor vertical farming could eventually minimize the need to import foods that can’t be grown in Puerto Rico via traditional farming.
Reporter for The Weekly Journal. She is a journalist with experience in social media management, translations, and digital marketing.
Follow Giovanna Garofalo, The Weekly Journal
Signify Adds Artechno To Its Philips Horticulture LED Partner Network To Lower Bar For Future Vertical Farmers
“Partnering with Signify is a logical choice for us,” said Art van Rijn, Owner of Artechno
January 4th, 2021
Signify Chooses Artechno As its New Philips
Horti LED Partner For The Unique Modular
Turnkey Vertical Farming Solutions That it Provides
· Lowers bar for growers and entrepreneurs to start a new vertical farm
· Helps to automate the production process for diverse crops from seed to harvest
Eindhoven, Netherlands – Signify (Euronext: LIGHT), the world leader in lighting, has signed a partnership agreement with Artechno, global provider of scalable Automated Vertical Farming systems, to make it easier for growers and entrepreneurs to start a state-of-the-art vertical farm using Philips GreenPower LED lighting. Artechno, headquartered in De Lier, the Netherlands, is an engineering company that develops and realizes unique automated cultivation systems based on hydroponic substrates for clients across the globe.
“Partnering with Signify is a logical choice for us,” said Art van Rijn, Owner of Artechno. “We’re a winning combination as we offer our customers the highest efficiency and highest reliability, while Signify provides energy-efficient lighting solutions that perform 24/7, 365 days a year. Together this will help our customers to grow tasty, high-quality produce year-round.”
Artechno has channeled 100+ years of combined experience in horticulture into its flagship product, Automated Vertical Farming, or AVF+. It offers a fully automated solution for producing a variety of crops from seed to harvest. Artechno has automated all processes to ensure low labor costs and consistent crop production. AVF+ is a modular system that can be customized to the needs of the crop, available space, or desired production volume. Growers and entrepreneurs can start with a few key components and scale up their automation and operation as they grow.
“We’re proud to expand our partnership network with the knowledge and expertise of Artechno,” said Udo van Slooten, Business Leader Horticulture at Signify. “They share our values of innovation, quality and reliability. This partnership will help us lower the barriers for growers and entrepreneurs who are considering a vertical farm by enabling us to offer Philips GreenPower lighting within fully modular and automated systems for every aspect of their operations.”
Signify continues to expand its horticulture partner network, further demonstrating its commitment to lead the horticulture industry as the innovative LED lighting systems provider for the indoor farming industry.
--- END ---
For further information, please contact:
Global Marcom Manager Horticulture at Signify
Daniela Damoiseaux
Tel: +31 6 31 65 29 69
E-mail: daniela.damoiseaux@signify.com
About Signify
Signify (Euronext: LIGHT) is the world leader in lighting for professionals and consumers and lighting for the Internet of Things. Our Philips products, Interact connected lighting systems and data-enabled services, deliver business value, and transform life in homes, buildings, and public spaces. With 2019 sales of EUR 6.2 billion, we have approximately 37,000 employees and are present in over 70 countries. We unlock the extraordinary potential of light for brighter lives and a better world. We achieved carbon neutrality in 2020, have been in the Dow Jones Sustainability World Index since our IPO for four consecutive years, and were named Industry Leader in 2017, 2018 and 2019. News from Signify is located at the Newsroom, Twitter, LinkedIn and Instagram. Information for investors can be found on the Investor Relations page.
"Leading The Next Frontier of Farming And This Investment Further Accelerates Our Momentum"
“The addition of our new farm to the network is a critical next chapter in our growth,” said Irving Fain, founder, and CEO of Bowery Farming
“The addition of our new farm to the network is a critical next chapter in our growth,” said Irving Fain, founder, and CEO of Bowery Farming. “It will expand our reach and ability to be a reliable source of local produce for more communities. We’re leading the next frontier of farming, and this investment further accelerates our momentum.”
Bowery Farming is building its newest commercial farm in Bethlehem, Pennsylvania. Joining its network of farms in Kearny, New Jersey, and Nottingham, Maryland, Bowery’s new Bethlehem farm will be its largest, most technologically-advanced commercial farm yet.
Driven by explosive demand for safer, traceable pesticide-free produce, and propelled by the BoweryOS- which integrates software, hardware, sensors, computer vision systems, machine learning models and robotics to orchestrate and automate the entirety of operations - the strategic location of Bowery’s Bethlehem commercial farm will expand the company’s reach in the region.
This farm will feature a number of developments that build on previous Bowery technology, further automating the growing process from seed to store, and enhancing the efficiency of Bowery’s network such as, Water Conservation: A state-of-the-art, comprehensive water transpiration system will recapture almost all water used throughout Bowery’s growing process, with the goal of reclaiming and repurposing nearly all of the water in the farm.
The facility will also focus on more efficient LED Lighting amplifying Bowery’s holistic approach to sustainability and features industry-leading environmental improvements like energy-reducing LED lighting throughout.
"It's the smartest farm yet, powered by the BoweryOS, this farm will leverage billions of data points collected from Bowery’s network of farms to grow a reliable supply of consistently delicious produce year-round. Laying the groundwork for the next chapter in smart, scalable indoor farming, the Bethlehem farm will feature next-level technological capabilities unlike any Bowery farm to date, deepening the integration of the BoweryOS across all aspects of the business."
Furthermore, it offers restoration to the community. Bowery is working with the Commonwealth of Pennsylvania to transform the Bethlehem location from a non-arable industrial site into productive, modern farmland—stimulating economic revitalization that will provide year-round sustainable farming jobs for the community.
Since the beginning of 2020, Bowery has experienced more than 600% brick and mortar sales growth, and more than doubled sales with e-commerce partners, including Amazon. Bowery’s produce is harvested year-round at peak freshness and delivered to stores within a few days of harvest — a stark contrast to the 90% of leafy greens grown in the U.S., which are transported over 3,000 miles to consumers on the East Coast.
With this new farm, Bowery’s Protected Produce will be available to the 49 million people living within the farm’s 200-mile radius, advancing the company’s goal of expanding access to local, traceable, pesticide-free food to people in every major city in the U.S. and around the world.
For more information:
Bowery Farming
Shelby Farahan, Communications
sfarahan@boweryfarming.com
www.boweryfarming.com
Publication date: Fri 18 Dec 2020
Author: Rebekka Boekhout
© VerticalFarmDaily.com
Infarm Raises $200 Million To Add “Farm” to Cities
heir environment-controlled and automated growing chambers grow food such as leafy greens inside the supermarket, so it’s fresh, without your food accumulating food miles
Infarm’s Israeli founders take on Berlin and the farm to table movement with high-tech farms.
Infarm, a company that grows fresh produce inside supermarkets, has recently announced a $170 million USD funding round to help the company expand across Europe. Their environment-controlled and automated growing chambers grow food such as leafy greens inside the supermarket, so it’s fresh, without your food accumulating food miles.
The company was founded by three Israelis in Berlin in 2013, and they announced this astounding investment achievement despite the Covid plague destroying global markets. Food, we understood, is something that must stay constant. The need for food which is grown locally, and available fresh now resonates at a time of uncertainty and the basic need for survival.
The company has raised $200 million USD total in their Series C round funding which was by LGT Lightstone, Hanaco, Bonnier, Haniel, and Latitude, Atomico, TriplePoint Capital, Mons Capital, and Astanor Ventures.
With a mix of equity and debt financing, the fresh capital brings Infarm’s total funding to date to more than $300 million, underscoring consumer and retailer appetite for Infarm’s approach to fresh, sustainable, and local food production in the wake of this year’s pandemic.
By 2025, Infarm’s farming fridge network is expected to reach more than 5,000,000 square feet to become the largest distributed hydroponic network in the world as it builds towards helping cities become self-sufficient in their food production. Competition includes Freight Farms in the US, and BrightFarms, also American.
“The coronavirus pandemic has put a global spotlight on the urgent agricultural and ecological challenges of our time,” says Erez Galonska, Co-founder and CEO of Infarm. His brother Guy Galonska is also a founder: “At Infarm, we believe there’s a better, healthier way to feed our cities: increasing access to fresh, pure, sustainable produce, grown as close as possible to people,” adds Erez.
The investment will be used to deepen the regional and local penetration of Infarm’s global farming network and complete development of Infarm’s new generation of vertical cloud-connected farms, capable of generating the crop-equivalent of acres of farmland and amplifying the diversity of produce currently available through vertical farming. Vertical farming is also known as hydroponic farming or controlled environment agriculture.
The technology has become developed and well-known over the years thanks to cannabis growers who used this energy-intensive and “stealth” mode of farming to grow cannabis with high concentrations of the active ingredient THC. When it was illegal to grow in Canada, young entrepreneurs were inspired by early blueprints from NASA and farming in space and found ways to set up a soil-less system in basements and closets. To their surprise, they could grow better quality cannabis, faster as inputs such as lighting, humidity, and nutrients could be tightly controlled.
And growing food became the next natural step for people who wanted to grow fresh food year-round even though it’s usually not cost-effective to grow tomatoes or lettuce this way unless you do it at scale.
Hydroponics and variations of it, using just water, a semi-solid coir medium or Styrofoam and/or with fish added, has become the promise for growing food in far-flung locations like Antarctica and food deserts where chocolate bars are available at bodegas, but fresh greens are not. This is according to mothers I have met in Harlem, New York. The hydroponic method is not that complicated at all in theory but in practice, it is hard to achieve good results without know-how in chemistry, engineering, and biology.
An integration of advanced engineering, software, and farming technology, the Infarm farms will save labour, land, water, energy, and food-miles, while contributing to a more sustainable food system, the company proposes.
Partnering with Aldi, Marks & Spencer, Sobeys
While companies like Farmigo founded in New York (also by an Israeli) wanted to put supermarkets out of business, in the past year Infarm has been working to keep them relevant and formed new partnerships with the world’s largest retailers, including Albert Heijn (Netherlands), Aldi Süd (Germany), COOP/Irma (Denmark), Empire Company Ltd (Sobeys, Safeway, Thrifty Foods – Canada), Kinokuniya (Japan), Kroger (United States), Marks & Spencer (United Kingdom) and Selfridges (United Kingdom).
With operations across 10 countries and 30 cities worldwide, Infarm harvests 500,000+ plants monthly, while using 99.5% less space than soil-based agriculture, some 95% less water, 90% less transport, and zero chemical pesticides. Today, 90% of the electricity use throughout the Infarm network is from renewable energy and the company has set a target to reach zero emissions from their production next year.
With the cost of lighting typically very high in hydroponics systems, I’d be curious to know how they will do that without buying carbon credits. Consider this Stanford research paper that mentioned the cost of hydroponic lettuce to be about 8KG of carbon compared to 150g if grown conventionally. The research is a few years old and certainly, there can be ways to improve energy efficiencies.
What organic farmers think?
Proponents of organic farming, regenerative agriculture, and permaculture don’t love hydroponics farming because it relies on petroleum-based fertilizers and nutrients as additives, and while there may be no or few bugs in the grow chambers, there is a risk of fungus and bacteria; in nature, there is always free natural sun (unless you are in Finland in the winter) and natural interactions between plant, soil; and even among small biota like mycorrhizal fungi which play a role in the uptake of micronutrients to the roots and the overall essence of what we call a plant. There is one school of thought that says the “organic” label can only be applied to soil-based farming. Lawyers are debating the issue now.
The answer will be somewhere in the middle. Like most things in life the middle way will help us. The dream is many one-acre regenerative farms to feed us healthily and to feed the planet too but meanwhile there is a gap. How do we feed everyone else who can’t afford to buy at Whole Foods?
We need to improve our local supply chain for food. When you live in a country like Israel, Egypt or Jordan with ample sun, growing food inside a supermarket fridge makes no sense, although hydroponics does. See this project in Jordan, funded by the USAID. Or the one that has changed lives in Harlem.
I had a hydroponics robotics venture (see this article on Bloomberg) and I took it to New York a few years ago and found myself running in circles trying to explain why eating local is good for the planet, it’s good for a circular economy that might one day be about survival. Venture Capitalists laughed at me. They said my technology and vision was a vitamin and not a bandaid –– “a nice to have” but not “a necessary to have”, especially in cities like New York. Then Covid thinking happened.
Here is what investors in Infarm say now (and kudos to the team who worked hard building physical farms and maintaining the pilots):
“We are excited to partner with the Infarm team to accelerate their urban vertical farm vision, ultimately creating a more sustainable food system for a growing population,” says Dharmash Mistry, Partner of LGT Lightstone: “With over $1bn of customer demand, partnerships with 17 of the top 50 global grocers, Infarm is set to revolutionise the market behind a unique ‘demand led’ modular business model.”
Let’s hope. Another Israeli called Benzi Ronen came from Silicon Valley and started a farm-to-table venture in New York and was on top of the world. He had just raised $26 million to grow Farmigo into the Amazon for fresh food and I spoke with him at one point when he warned me to stay in Israel and work there locally for a couple of years before moving stateside. That’s me in the biodome below, growing bok choy for future Martians on my roof in Tel Aviv. I didn’t listen.
I had a venture in robotics to help cannabis farmers (even Mars farmers grow cannabis in space – see this article in Fast Company) and city hydroponic farmers. Farmigo was trying to eliminate supermarkets, by connecting farmers to consumers at drop off points throughout the city. The model was valorous –– who doesn’t want the freshest farm picked veggies every morning? The modern CSA? And it supported local farming, just like what Michael Pollan wants us to do. And to compete with Amazon? Yes. Yes. Yes.
Farmigo raised millions and then the company’s vision to be the Amazon of fresh food could not compete with Amazon. Farmigo changed its business model and now sells software.
I saw the challenges of the business in supplying fresh food. The mechanics of the machines, the lack of willing labor, software needed, the logistics, the importance of food safety. The fungus, the bacteria. The good bacteria. The bad. The responsibility. The chemicals needed to feed the plants, to keep the systems “clean” and safe. So much is hard to control when you are talking about living things.
I always said that if hydroponics or farmers that come from Microsoft want to make city farming work the model will look like the cellphone industry: different players supplying various parts like Qualcomm, Verizon, 3M, Broadcom, and Texas Instruments does. Even to make iPhones work.
Can and will Infarm do it all?
“We see a massive demand in the market for sustainable, environment-friendly, and healthy food – and Infarm has just the right team in place to make this happen,” says Pasha Romanovski, Co-founding Partner of Hanaco Ventures.
More about Infarm
Founded in Berlin in 2013 by Osnat Michaeli and the brothers Erez and Guy Galonska, Infarm is dedicated to creating a future where local super fresh produce is available for everyone. The farms are placed in various locations in the city, like supermarkets, restaurants, and distribution centers, so that vegetables grow and are harvested close to the moment of purchase or consumption. People like Elon Musk’s brother Kimbal Musk has been doing this in New York with a project called Square Roots. They train young entrepreneurs to dream up all sorts of business models inside the shipping container farms built by Freight Farms.
Some in the VC world I have talked with question the viability of the business model of these containers. While it’s a nice idea it’s hard to get the return on the upfront investment.
But when it comes to specialty products and “farms” you can find the Infarm service model in all sorts of permutations in the United States. I got to spend some ample time in meetups with a pile of entrepreneurs building an urban farming project in New York. There I met Andrew Carter, now growing mushrooms in a warehouse in Williamsburg. There is also Farm.One which grows papalo, minutina and all the boutique and hipster greens any chef could dream up in the center of New York City. They deliver.
Lastly and most easily is to try out growing fresh greens at home without the supermarket, or less of the supermarket. I met the founder of Hamama when she was in Israel via MIT helping kids in Israel grow their own food using hydroponics at The Greenhouse. (After I wrote this story in 2008 <— kids from the US were writing me about how to donate their Bar Mitzva money to Noam Geva).
Over at The Greenhouse Camille had her head inside an aeroponics system she’d rigged up last time I saw her. She brought a few of her MIT geek friends over to my house in Jaffa and we talked about hydroponics changing the world. And now she helps people in the easiest way to grow microgreens at home. That’s a hyper simplified way to do hydroponics. She was one of the most inspiring people I met in hydroponics and urban farming.
In fact many in the business are. They are people who want to change the world. Have you met Henry?
Go out and meet someone, start a farm. Grow something. That’s how we change the world.
Now over to Infarm: good luck!