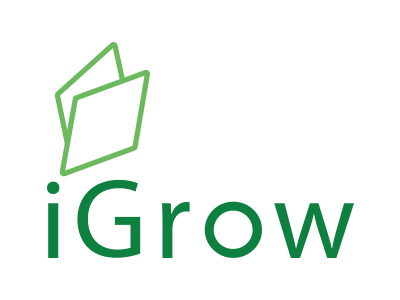
Welcome to iGrow News, Your Source for the World of Indoor Vertical Farming
Urban Crop Solutions Awarded As Best-In-Class Vertical Farming Solution Provider
Urban Crop Solutions has been awarded a ‘Best-in-Class’ award for their production systems by the Center of Excellence for Indoor Agriculture. They were selected as the winners for the category of ‘systems starting between $250k-$500k’.
August 2021
Urban Crop Solutions has been awarded a ‘Best-in-Class’ award for their production systems by the Center of Excellence for Indoor Agriculture. They were selected as the winners for the category of ‘systems starting between $250k-$500k’. Each finalist went through a rigorous review process and was evaluated according to several criteria. Emphasis was given to sustainable farms and equipment manufacturers that efficiently use resources such as land, energy, labour and water to produce the highest yields at an affordable price in indoor farm settings.
“The award is definitely a recognition for our team that is continuously working on state-of-the art growing solutions which optimise the sustainability of our industry, whether this is in an existing building or for a greenfield project.” says Maarten Vandecruys, Founder and CTO, Urban Crop Solutions.
“Today we are rewarded with a prize for our approach, but to be successful for our customers, the knowledge of the plant science is as equally important as the engineering part. We keep on striving for a more sustainable impact, not just on the consumption of our natural resources, but also the yield, which positively impacts the financial sustainability” he adds.
"We are enormously proud of the entire team! A team that works together for the future. A team that is there for each other, to give the best of themselves. Looking at our latest realisations, the ModuleX and the FarmLab, and our 24/7 support both technically and biologically, as a team leader you can look forward with a broad smile!" says Jean-Pierre Coene, CEO, Urban Crop Solutions.
Jean-Pierre Coene operating the ModuleX
ABOUT UCS
Urban Crop Solutions is a Belgium based pioneer in the fast-emerging technology of indoor vertical farming. It has developed over the past six years, 220+ plant growth recipes in its research centre in Waregem, Belgium. To date, UCS has delivered over 25 projects in multiple global locations. Their farms are being operated both for commercial and research purposes. Uses range from the production of leafy greens, microgreens and herbs for food retail, service and industrial use, and scientific research across multiple institutions.
Website: www.urbancropsolutions.com
Facebook: www.facebook.com/urbancropsolutions
Twitter: www.twitter.com/U_C_Solutions
LinkedIn: www.linkedin.com/company/urbancropsolutions
CONTACT
Filip Meeuws – Sales Director, Urban Crop Solutions
fime@urbancropsolutions.com
Maarten Vandecruys – Co-founder & CTO, Urban Crop Solutions
maarten.vandecruys@urbancropsolutions.com
Jean-Pierre Coene – CEO, Urban Crop Solutions
jpco@urbancropsolutions.com
Lead Photo: Maarten Vandecruys in the UCS Research Centre
European Pension Managers Go Big For Indoor Ag as Equilibrium Closes $1.1bn CEA Fund
Equilibrium Capital, a US-based private sustainable finance and ESG funds manager, has closed its second indoor ag fund on just over $1 billion – well beyond its $500 million target.
By Louisa Burwood-Taylor
July 8, 2021
Equilibrium Capital, a US-based private sustainable finance and ESG funds manager, has closed its second indoor ag fund on just over $1 billion – well beyond its $500 million target.
Controlled Environment Foods Fund II (CEFF II) raised $1.02 billion from a group of institutional investors, mostly pension funds, with a strong showing from Europe, according to Equilibrium CEO Dave Chen. Sweden’s AP4 was one of five anchor investors that took over half of the total fund alongside two large UK pension managers, he added.
CEFF II will invest in high-tech greenhouses, indoor, vertical farms, and other sectors that need controlled environment agriculture (CEA) facilities such as alternative proteins and aquaculture.
“The strong investor demand reflects a drive to real assets” and sustainability by large institutional investors, combined with an “interest in agriculture and food systems,” Chen told AFN.
“There is a sense that ag is going through several simultaneous disruptions and that creates an opportunity.”
A press release announcing the fund closing states that investors and retailers “are increasingly looking for more sustainable, and less volatile, ways to invest in and scale agriculture.
“CEA shifts agriculture from a land-centered industry where the land, geography, and weather determines what can grow, into a climate-resilient industry that can now focus on the consumer’s demand for the fresh, safe, and regional fruits and vegetables they want to eat,” it continues.
For Portland, Oregon-based Equilibrium — which has funds across environmental and sustainability verticals including ‘green’ real estate, water, wastewater, and outdoor agricultural production — CEA is a compelling investment opportunity for its ability to dramatically increase the productivity of food production “per unit of resource input [and] land use,” said Chen.
“The ability to ride a tech innovation curve, locate farms regionally for quality and resilience, adapt to climate change, and capture demand from retailers and food service” also make it attractive, he added.
Asked where he expects the market share for CEA-produced food to be in five years, he estimated upwards of 30-50%. “Tomatoes are already there,” he said.
Equilibrium is predominantly a real assets investor, owning or investing in indoor farming facilities and greenhouses, but it also buys equity stakes in operating companies. CEFF II will invest between $10 million and $125 million per deal, primarily across North America. It has made three investments to date — two in the US and one in Mexico — mostly in mature high-wire crops like tomatoes, peppers, and cucumbers, as well as the emerging categories of leafy greens and berries.
Equilibrium’s $336 million Fund I portfolio includes indoor ag companies such as AppHarvest — which went public earlier this year via a SPAC merger — Revol Greens, and Little Leaf Farms.
Sakata Seed America Announces Formation of CEA Department
Leading the new division will be Tracy Lee, an 11-year veteran of Sakata Seed America with an extensive background in agriculture. At Sakata, she has played active roles specializing in product development for multiple categories, as well as handling the company’s home garden and farm market vegetable seed sales
Sakata Seed America announced the formation of a Controlled Environment Agriculture (CEA) department. This new department will focus on indoor agriculture, a growing segment of the produce industry that focuses both on traditional greenhouse production as well as specialized vertical farming.
According to Justin Davis, Sakata’s Director of Sales & Marketing, this new group is designed to bolster the company’s role in developing varieties for controlled environment ag. “We have been focused on this segment for a number of years, especially in the leafy greens category. The timing is ideal for Sakata to create this group to hone our efforts on CEA in order to bring more products to the market for Indoor ag.”
Leading the new division will be Tracy Lee, an 11-year veteran of Sakata Seed America with an extensive background in agriculture. At Sakata, she has played active roles specializing in product development for multiple categories, as well as handling the company’s home garden and farm market vegetable seed sales.
“I think there is tremendous growth opportunity in serving the Controlled Environment Agriculture segment, and I’m very pleased that Sakata is continuing its leadership in the market. This is something that I’m passionate about and have been active in for the past several years,” says Lee.
Lee completed her BA at Clemson University and earned a Master of Science in Horticulture from her alma mater. Her field of study focused on sustainable vegetable production. Prior to her work at Sakata, she held product management, marketing, and sales positions at vegetable and flower seed companies for an additional 10 years.
“I feel that my background and specific work with indoor growers gives me unique insight into the market’s needs. My goal is to harness my experience in the field and bring the right mindset back to Sakata as we develop new products created specifically for CEA,” says Lee.
For more information:
Sakata Seed America www.sakata.com
Mon 7 Sep 2020
Why Soil And Not Hydroponics, And Vice Versa
Hydroponics, in a nutshell, is a method of growing plants without soil
I have decided that is high time we tackle this topic as my next article because in fact is a pretty hot topic of conversation. Especially in Berlin, where we have incredible startups like infarm, who specialize in hydroponic production in urban areas, supplying restaurants, supermarkets, and much more, and therefore cutting down on the food miles as in most places their setup is installed in-house.
Also, I’m finding that friends left right and center are getting themselves home hydroponic kits to grow exciting salad varieties. So we’ve often find ourselves talking about why we use soil instead of hydroponics, and so we wanted to give a bit of an overview of the pros and cons of soil versus hydroponics.
So then let’s go back to basics, what is hydroponics? Hydroponics, in a nutshell, is a method of growing plants without soil, where you use mineral nutrient mixes in a water solution (hence the word ‘hydro’). Generally, the plants are grown with their roots exposed, whereby the water and nutrient mix is introduced by either the roots sitting within the mixture, being sprayed or in some cases having partial drying and partial immersion. In other cases where plants require support to their root systems perlite, rock wool and gravel can be used. The nutrient solutions utilized can be those produced by the multiple companies that have begun specializing in this, or you can mix up your own (with access to a lab-type stock of elements), by-products of aquaculture farms, fish waste, etc. can also be used. Generally, hydroponic systems that most homeowners utilize for home gardening are a fully controllable unit including lighting. Therefore enabling growers to control and produce a very efficient plant in the best conditions that you choose.
Economic investment
This all might sound ideal to some, but actually, there are a few things to consider here. Firstly the economic investment required in the beginning is rather substantial. These systems are not always cheap. Or let me put it this way, if you want good lighting which are in the right ‘spectrum’ and are not going to give you leggy unhealthy plants, you want a good system that has been produced by a trustworthy company. And whilst these sure exist, say Ikea even does great systems their not cheap, it adds up financially. Whilst in comparison when you’re doing home balcony soil based gardening you can do so without investing tons of money in the beginning but build it up slowly, all you need is some seeds and soil and you can recycle egg cartons to your hearts delight for seedling trays and bang you’re on your way in springtime!
Energy reliance/plant compounds
Now another thing to be concerned about in terms of hydroponics is that its energy reliant. So if you’re in a place where the electricity tends to cut out, or you don’t fancy using unnecessary energy but conserving then this is really something to consider. If your lights go out, your plants will die. Sadly that’s just the reality, it’s a very fine-tuned system and you can get great productivity out of it, but at the same time, these plants produced in such systems are not as resilient as those grown in natural conditions. And that brings us to the next major point to consider. Natural conditions tend to enable plants to develop a buffer capacity against changes in temperature, lack of water, etc. They toughen up and produce all kinds of amazing secondary metabolite plant compounds that help protect them from the stress. And guess what- science is just discovering how healthy some of these compounds are for us, humans! Secondary metabolites called ‘glucosinolates’ in the broccoli family have been found to have anti-carcinogenic properties! So plants toughening up to growing conditions can be a good thing for them and for us.
Maintenance / disease
Now whilst there is a whole hype in controlling ‘lighting’ recipes that LED’s can now create for plants, and some home growers are tweaking their tomato plants for example to increase flavonoid secondary compounds. This is realistically a bit more on the advanced side. And essentially hydroponics can be even harder for the novice gardener because the plants are not very resilient or forgiving. They are fragile beauty queens that have never had a stress in their life and really throw a temper tantrum when things go a bit unusually out of schedule. This importantly enough brings us to another point, that hydroponic systems are very controlled clean and uncontaminated. This usually means then that if one plant gets a disease, a virus or is afflicted by something you can pretty much count on all the other plants being afflicted or struck down by the same thing within days. All plants are grown in the same water mixture and this just causes disease and contamination to spread extremely fast. So you have to really be quick on the draw in identifying a malady or symptom when it crops up.
Organic?
Now another aspect if you were not aware of it, an interesting fact, organic produce will not be certified so if grown using hydroponics. Why you might ask? Because one of the underlying most important rules for organic certification is that organic produce in grown in soil. There has been a huge push to get this removed as there have been increasingly more sustainable organic fertilizers and nutrient mixes being made for hydroponics that were not available a few years ago. But I must say that I think it might be an important gold standard to keep in play. Soil is so important, and actually is also such a reserve of all kinds of micro life and activity that when cared for and given back to in exchange for the harvests and bounties you are getting out of your balcony or garden, can become enriched and magical. There is a whole micro magical world of fungi and organisms that aid in the breakdown and transport of nutrients from the air into the soil and to your plant’s roots that are just mind-boggling. So when you create a healthy balanced soil you are in for a win-win situation of constant giving in exchange for a bit of compost and humus content every year. It’s pretty satisfying I must say!
Big companies?
Also back onto the topic of minerals and fertilizers, this is not so far off from the monoculture system many of us are trying to not support by, in fact, growing our own and sidestep the big agri-companies. Hydroponics sadly is fertilizer based, and one very important aspect to consider even when using organic biofertilizers is where and how is this product produced? It’s very often the result of mining activities in a developing country where workers are not living in healthy socially justifiable conditions. Additionally, a lot of ‘producers’ of chemicals required for the creating of these mixtures are big pharmaceutical companies. And essentially I still have a hard time justifying such high externalities when liquid manures and composts can be created so easily at home in even space limited flats. Additionally, the production of hydroponics growing facilities and systems is very energy-intensive to ‘build’ or manufacture. And so if you have access to a windowsill or balcony with sunlight or even semi sunlight I would be more in favor of encouraging gardeners to branch out and explore that area first. I especially cannot wait in spring for those first warm days to go and begin organizing and sowing and get growing. There’s nothing better than fresh air and sunlight and actual dirt under nails in my opinion but that’s just me. Also, let’s not forget how much the insects and bees thank us for the plants and flowers that are provided to them from our outdoor growing activities.
Cons of hydroponics
Now I know I’ve banged on about the cons of hydroponics a bit and I going to try and redeem myself here a bit. Because trust me living in Berlin and being an urban gardener by profession, the idea of growing things indoors in winter really is starting to get under my skin. So for me, this is where the plus can come in. If you have no balcony or sunny windowsills then these systems can be incredible. In fact, I’ve even visited fantastic bars that grow all their medicinal plants indoor year long using beautifully handmade hydroponic shelving systems. So I have been secretly scouting out a section in our flat for a little homemade DIY winter growing because let’s be honest, this green thumb gets super itchy and would love to have some things to play within the winter. I also really like the idea of homegrown winter veg and salads during the winter and being able to see the results of lighting and nutrients first hand, and sadly my flat is incredibly dark year-round with not an inch of sunlight all day. Now my only constraint is all the points I’ve mentioned beforehand, especially as I am blessed enough to have an urban garden here in Berlin that I share with friends. But you know where I think the pay of is going to come? In the summer because fantasizing about all the amazing seedlings I could start of early with a hydroponics system here in the flat. So I guess to finish off- to each their own. But for me personally? Nothing beats being outdoors with dirt under my nails!
Lead photo by Emile-Victor Portenart on Unsplash
Natasha Weddepohl
From market gardening to urban permaculture projects, Natasha has been involved in a multitude of projects linked with food growing and sustainability, for over 12 years. Originally from South Africa, she has gained her experience in sustainable food production through hands-on work worldwide. She is currently based in Berlin, assisting a few projects, whilst completing an MSc in Horticultural Science.
Micro-Naps For Plants: Flicking The Lights On And Off Can Save Energy Without Hurting Indoor Agriculture Harvests
A nighttime arrival at Amsterdam’s Schiphol Airport flies you over the bright pink glow of vegetable production greenhouses. Growing crops under artificial light is gaining momentum, particularly in regions where produce prices can be high during seasons when sunlight is sparse.
The Netherlands is just one country that has rapidly adopted controlled-environment agriculture, where high-value specialty crops like herbs, fancy lettuces and tomatoes are produced in year-round illuminated greenhouses. Advocates suggest these completely enclosed buildings – or plant factories – could be a way to repurpose urban space, decrease food miles and provide local produce to city dwellers.
One of the central problems of this process is the high monetary cost of providing artificial light, usually via a combination of red and blue light-emitting diodes. Energy costs sometimes exceed 25% of the operational outlay. How can growers, particularly in the developing world, compete when the sun is free? Higher energy use also translates to more carbon emissions, rather than the decreased carbon footprint sustainably farmed plants can provide.
I’ve studied how light affects plant growth and development for over 30 years. I recently found myself wondering: Rather than growing plants under a repeating cycle of one day of light and one night of darkness, what if the same daylight was split into pulses lasting only hours, minutes or seconds?
Short bursts of light and dark
So my colleagues and I designed an experiment. We’d apply the normal amount of light in total, just break it up over different chunks of time.
Of course plants depend on light for photosynthesis, the process that in nature uses the sun’s energy to merge carbon dioxide and water into sugars that fuel plant metabolism. Light also directs growth and development through its signals about day and night, and monkeying with that information stream might have disastrous results.
That’s because breaking something good into smaller bits sometimes creates new problems. Imagine how happy you’d be to receive a US$100 bill – but not as thrilled with the equivalent 10,000 pennies. We suspected a plant’s internal clock wouldn’t accept the same luminous currency when broken into smaller denominations.
And that’s exactly what we demonstrated in our experiments. Kale, turnip or beet seedlings exposed to cycles of 12 hours of light, 12 hours dark for four days grew normally, accumulating pigments and growing larger. When we decreased the frequency of light-dark cycles to 6 hours, 3 hours, 1 hour or 30 minutes, the plants revolted. We delivered the same amount of light, just applied in different-sized chunks, and the seedlings did not appreciate the treatment.
The same amount of light applied in shorter intervals over the day caused plants to grow more like they were in darkness. We suspect the light pulses conflicted with a plant’s internal clock, and the seedlings had no idea what time of day it was. Stems stretched taller in an attempt to find more light, and processes like pigment production were put on hold.
But when we applied light in much, much shorter bursts, something remarkable happened. Plants grown under five-second on/off cycles appeared to be almost identical to those grown under the normal light/dark period. It’s almost like the internal clock can’t get started properly when sunrise comes every five seconds, so the plants don’t seem to mind a day that is a few seconds long.
Just as we prepared to publish, undergraduate collaborator Paul Kusuma found that our discovery was not so novel. We soon realized we’d actually rediscovered something already known for 88 years. Scientists at the U.S. Department of Agriculture saw this same phenomenon in 1931 when they grew plants under light pulses of various durations. Their work in mature plants matches what we observed in seedlings with remarkable similarity.
A 1931 study by Garner and Allard tracked the growth of Yellow Cosmos flowers under light pulses of various durations. J. Agri. Res. 42: National Agricultural Library, Agricultural Research Service, U.S. Department of Agriculture., CC BY-ND
Not only was all of this a retread of an old idea, but pulses of light do not save any energy. Five seconds on and off uses the same amount of energy as the lights being on for 12 hours; the lights are still on for half the day.
But what would happen if we extended the dark period? Five seconds on. Six seconds off. Or 10 seconds off. Or 20 seconds off. Maybe 80 seconds off? They didn’t try that in 1931.
Building in extra downtime
It turns out that the plants don’t mind a little downtime. After applying light for five seconds to activate photosynthesis and biological processes like pigment accumulation, we turned the light off for 10, or sometimes 20 seconds. Under these extended dark periods, the seedlings grew just as well as they had when the light and dark periods were equal. If this could be done on the scale of an indoor farm, it might translate to a significant energy savings, at least 30% and maybe more.
Recent yet-to-be published work in our lab has shown that the same concept works in leaf lettuces; they also don’t mind an extended dark time between pulses. In some cases, the lettuces are green instead of purple and have larger leaves. That means a grower can produce a diversity of products, and with higher marketable product weight, by turning the lights off.
One variety of lettuce grew purple when given a 10-second dark period. They look similar to those grown with a five-second dark period, yet use 33% less energy. Extending the dark period to 20 seconds yielded green plants with more biomass. J. Feng, K. Folta
Learning that plants can be grown under bursts of light rather than continuous illumination provides a way to potentially trim the expensive energy budget of indoor agriculture. More fresh vegetables could be grown with less energy, making the process more sustainable. My colleagues and I think this innovation could ultimately help drive new business and feed more people – and do so with less environmental impact.
July 22, 2019 6.58am EDT Updated July 22, 2019 2.40pm EDT
This article was updated with a corrected legend on the photograph of the plants grown in 1931.
These 4 Reasons Tell Us Why It’s Time To Shift To Indoor Farming
Though growing indoors can never be a replacement for outdoor agriculture, it can certainly help in growing certain vegetables, herbs, microgreens, and more
By Ecochirp Foundation in Environment
6th August 2020
Traditionally, agriculture was done on large open farms, having a large dependence on external environmental factors. In recent times, there is a new vertical emerging in agriculture, giving promising results i.e., Indoor farming or vertical farming. Particular challenges that were faced in conventional cultivation techniques have been resolved with indoor agriculture. Though growing indoors can never be a replacement for outdoor agriculture, it can certainly help in growing certain vegetables, herbs, microgreens, and more.
Let’s have a comparative study of indoor growing vs. outdoor growing.
Weather Dependence
Traditional outdoor growing is largely dependent on weather conditions. Only seasonal crops can be grown. Weather conditions can be the biggest nightmares for farmers as things like thunderstorms, floods, droughts can damage crops overnight. By growing indoors, we eliminate our dependence on the weather. Instead, growers can control the climate inside the indoor growing system creating the ideal environment for maximum outputs. Using a wide range of sensors, indoor growers can check their plants at all times.
Pesticides And Herbicides Requirement
Do you also wear a mask while consuming those??
The crops are more prone to pests and other animal damage as they are exposed to the outer environment. We recently saw the locust attack that happened; it devastated large areas of crops. We saw how fast they traveled and farmers couldn’t take measures in time. They had to spray large amounts of pesticides to protect the remaining crops that eventually went into our systems. The pesticides and chemical fertilizers used are a root cause of major ailments like cancers, immune disorders, infertility, and cardiovascular diseases.
Indoor grown edibles need fewer chemical additives to grow well. Being indoors, they are not prone to pests. Also, the environment is controlled; therefore, there is no need for pesticides or herbicides. Therefore, the vegetables are pure.
About 70% of the world’s freshwater goes to agriculture. And with increasing populations, this water requirement is expected to go up by 15% by 2050. This is a thing we should be afraid of, as the freshwater resources are declining. If things keep going in the same way, there is a possibility that we might not be able to keep up with the requirements. Taking the case of indoor growing, techniques such as hydroponics take up to 90-95% less water. They use a closed-loop system, where there is no wastage, and resources are optimally utilized.
The Nutritional Content Of Edibles
The current agriculture system is centralized. Therefore, fruits and vegetables have to travel thousands of miles before they reach us. In the meanwhile, they lose a considerable amount of nutritional content. For example, spinach loses about 50-90% of its vitamin C within 24 hours of being harvested, which means the vegetables and fruits we eat at our homes in cities is not as nutritional as it should be.
In the case of indoor growing, which is generally done in cities near our homes, transportation time is less than 5-6 hours. Therefore, they are fresh and highly nutritious.
Pre And Post-Harvest Losses
About 40% of the world’s food is wasted due to the pre and post-harvest losses. Pre-harvest losses occur before harvesting begins, and may be due to insects, weeds, and rusts. Post-harvest losses occur between harvest and the moment of human consumption. Fruits and vegetables are perishable products and tend to get spoiled or degraded with time and unfavorable factors. Indoor growing has very low wastage as they rarely get diseases; they are near to cities and therefore, have lower transportation times. The edibles are consumed soon after they are harvested.
This comparison is just a brief glimpse of how growing indoors is more beneficial as compared to conventional growing. However, this article does not mean that indoor growing can replace proper farming. Outdoor farming can not be eliminated but can be decentralized, and with the help of indoor growing techniques, we can revolutionize the current agriculture system for the better.
About the author: Palak Kumar is an insatiably curious Mechanical Engineering student, passionate about flying, clouds, literature, and plants, working towards revolutionizing Indoor Vertical Growing.
Is The Future of Farming Indoors?
The global population is predicted to reach 9.7 billion by 2050, and to feed everyone, it’s estimated that global food production will need to increase by up to 70% in the next 30 years
July 14, 2020
Brian Kateman Contributor
I write about sustainable and ethical technology and consumer trends.
The global population is predicted to reach 9.7 billion by 2050 and to feed everyone, it’s estimated that global food production will need to increase by up to 70% in the next 30 years.
There are many challenges to overcome before fears of a worldwide food shortage can be allayed, including rising temperatures and more frequent droughts caused by global warming. These obstacles are making traditional farming methods increasingly inefficient and unpredictable.
Traditional farming has also been hit hard by the COVID-19 pandemic. According to the FAO, border closures, quarantines and disruptions to supply chains are limiting some people's access to food, especially in countries hit hard by the virus or already affected by high levels of food insecurity.
There’s an emerging consensus that the agriculture industry needs to adapt to use less water and chemicals, make crops less vulnerable to changes in the climate, and produce more reliable yields. Part of the answer may lie in the emerging start-ups growing produce in indoor environments, where growing conditions can be better managed.
The indoor farming technology market was valued at $23.75 billion in 2016, and is projected to reach $40.25 billion by 2022. Yields are typically much higher than traditional farming methods. Crops from indoor farming are grown in three dimensions, rather than two – and can be grown all year round, independent of external weather conditions.
Square Roots next-generation farmers growing basil. CRAIG VANDER LENDE
One of Square Roots’ indoor farms, for example, produces the same amount of food as a two- or three-acre farm annually, just from 340 square feet. This yield is achieved by growing plants at 90 degrees, and by using artificial intelligence (AI) to ensure the environment is optimal for each specific plant, including the day and night temperatures and amount of CO2 needed.
“Our indoor farms are living biosystems, constantly adapting to maintain optimal climates for growing specific crops. We’re then able to understand how changes in the climate can impact yield taste and texture,” says Tobias Peggs, Square Roots’ chief executive.
Not only could indoor farming help adapt to a warming planet, but it has the potential to help slow down climate change by being more sustainable – using less water and producing fewer emissions. While estimates vary widely, according to the United States Environmental Protection Agency, agriculture accounted for 10% of all greenhouse gas emissions in 2018; it is also highly dependent on, and a pollutant of, water.
Square Roots’ pop-up farms are built in shipping containers in cities, often in parking lots. They serve local communities, which means reduced emissions compared to traditional agriculture, which often involves transporting food much further. For example, it has 10 farms in Brooklyn that serve 100 retail stores all within five miles of the farm.
At the Plenty headquarters in South San Francisco, leafy greens use up one percent of the land and five percent of the water compared to traditional outdoor farms, says Matt Barnard, the start-up’s Chief Executive Officer, and Co-Founder.
AeroFarms’ indoor farm in New Jersey grows greens including baby kale, baby arugula, and baby watercress using 95% less water than conventional agriculture on just one percent of the land required. The crops grow under LED light with no pesticides and a fraction of the fertilizer used on traditional farms.
AeroFarms environmentally-controlled indoor farms can grow all year round independent of climate and ... [+] AEROFARMS
Marketing director Alina Zolotareva says being able to produce have ready-to-eat produce that doesn’t require rinsing helps to reduce water usage.
“This is a transformational innovation for agriculture at large,” she says, “as access to fresh water for growing food is one of the most pressing challenges of our time.”
As well as fewer miles and less water, indoor farming doesn’t require pesticides. This is better for the environment and human health as it eliminates the risk of water contamination due to run-off, and is in line with increasing consumer demand for non-GMO produce.
Plenty eliminates the need for pesticides with LED lights, which are synced with the crop’s growth, Barnard says, to provide the ideal spectrums and exposure and minimize energy usage.
“Our sensor system ensures each plant gets exactly the amount of purified water it needs, and any excess water is recycled through a closed-loop irrigation system resulting in greatly reduced water consumption and zero waste,” he says.
Nanobubbles super-saturates the water with oxygen, making the plant roots healthier. This promotes ... [+]
MOLEAER
Other farms are using nanobubble technology, such as Moleaer, which has allowed more than 100 indoor farms to connect their irrigation systems to generators that provide oxygen via sub-micron gas-containing cavities to the plant’s roots to provide chemical-free water. These nanobubbles result in healthier roots, more resilient plants, and increasing crop yields, says Nick Dyner, CEO of Moleaer.
“Our oxygen transfer efficiency provides the most cost-effective solution to elevate oxygen levels in the water, which in turn promotes beneficial bacteria and root development,” he says.
The company is also working on a new NASA-approved space farming research project, exploring how astronauts on the International Space Station can grow their own food in microgravity using nanobubble technology.
There are concerns that it’s an expensive investment, but Dyner says Moleaer has various systems so it’s accessible to all sizes of indoor farms, high- and low-tech. Some products do, however, require growers to connect an external source of oxygen, which must come from a gas supply company or an onsite oxygen generator, which Moleaer provides.
“In many cases, traditional farmers may have more to gain by using our technology, since the capital investment is significantly less than the most advanced growing technologies available today, which are often out of a typical farmer’s budget,” Dyner says.
“Nanobubble technology is a cost-effective, chemical-free, and scalable solution that allows growers to increase crop yields and shorten cultivation time - which will be much needed to feed our growing population in the future.”
Peggs says Square Roots is also focused on ensuring its technology makes farming an accessible career path for young people who live in urban areas.
“If you’re a new young farmer at Square Roots, our app will guide you through what to do; what’s growing, what state is in it, what do we need to do today based on where things are in the growth cycle. Through our app and our training program we’re able to bring new people into our team, even folks with zero horticulture experience, and get them ready to go in about six weeks.”
Indoor farming is putting the youth back in agriculture. PLENTY
But despite being an emerging option for youth in the city, Barnard predicts most will remain traditional farmers.
“The world still needs the field and will need the field forever. We support the field by growing in addition to the field. Over time, [indoor] farming systems will become more accessible and affordable. Both field and indoor farming will be necessary to support global food demand.”
Viraj Puri, Co-Founder, and CEO of Gotham Greens, a pioneer in urban indoor agriculture that operates over 500,000 square feet greenhouses in 5 U.S. states, echoes this sentiment: “Growing produce indoors certainly has an increasing role to play in the future of sustainable food production. While indoor farming may not represent the future of all fresh produce production, for certain types of crops such as tomatoes, cucumbers, leafy greens, and herbs, it will become more prevalent. Customers are increasingly recognizing the reliability, consistency, and high quality of greenhouse-grown produce that’s grown in close proximity to large population centers using fewer natural resources. Other agricultural commodities like grains or fruits or root vegetables, however, can’t yet be produced.”
However, Dyner predicts that, eventually, the majority of agriculture will move to indoors, in vertical farms— the practice of growing crops in vertically stacked layers—in urban areas.
“These settings enable traditional farming to shift to controlled growing conditions, using new technology and automation, and reducing the risk of exposure to harsh climate conditions,” he says.
Plenty's goal is to build vertical farms in urban hubs and distribute each farm’s harvest locally ... [+]
PLENTY
Start-ups like Square Roots, Plenty, and AeroFarms currently practice vertical farming, which is a form of indoor farming that relies on artificial lighting such as LEDs instead of drawing on natural sunlight.
Other indoor farming companies like Gotham Greens grow produce in high-tech glass-clad greenhouses that primarily rely on natural sunlight for plant photosynthesis. According to Puri: “vertical farming is a more nascent technology within the indoor farming sector and the costs of running a vertical farm with artificial lighting and air conditioning is currently not as cost-effective as relying on natural sunlight in greenhouses.”
Gotham Greens takes a different approach, relying on natural sunlight rather than the artificial ... [+]
GOTHAM GREENS AND JULIE MCMAHON
“Greenhouse indoor farming technology has been in operation globally for 20 to 30 years and is proven to be commercially viable. That being said, the costs around artificial lighting and other vertical farming technologies have been coming down significantly in the past few years,” he adds.
Nonetheless, indoor farm technology start-ups, broadly speaking, don’t see themselves as disruptive, but as being on the same side of traditional farms, for the wider cause.
“The common enemy is the industrial food system, shipping food from one part of the world to the other, rather than locally produced food,” Peggs says.
Indoor farms don’t work in competition with each other, either; they work collaboratively by forming a network that shares data. For example, AeroFarms is collecting data on a research project with the non-profit Foundation for Food & Agriculture Research to understand the sensory and nutritional characteristics of leafy greens for the benefit of the entire agriculture industry.
However traditional and AI-based indoor farming work together in the future, there’s little doubt that indoor farming is helping to meet the needs of a growing global population and support traditional farming, which is both at the mercy of and exacerbating a warming planet. Only one method will find itself in space – but there’s space for them both.
I am co-founder and president of the Reducetarian Foundation, a nonprofit organization dedicated to reducing consumption of animal products.
Lead Photo: The world’s current agricultural practices are unsustainable, and indoor farming may offer solutions ... [+] PLENTY
Future of Indoor Vertical Farming With Microgrids
Schneider Electric’s Don Wingate discusses how microgrids can help the indoor vertical farming movement realize its full potential
09-07-2020 | Microgrid Knowledge
Schneider Electric’s Don Wingate discusses how microgrids can help the indoor vertical farming movement realize its full potential.
While indoor agriculture has steadily gained traction in recent years as the world seeks alternative ways to feed growing populations, the uncertainty of today’s global pandemic has accelerated a rethinking of the way we obtain our food. In the last few months, modern supply chains experienced volatility like never before and it wasn’t long before we started to see the impact beyond medical gear and personal protective equipment and began to affect food production. According to the Institute of Supply Chain Management, 75% of companies reported some kind of supply chain disruption due to COVID-19.
Indoor vertical farming is emerging as an alternative to conventional farming because it both requires lower land-use and introduces the opportunity to bring agricultural production closer to consumers — shortening supply chains and increasing footprint productivity. This is especially important during times of turmoil, which is broader than the current pandemic as weather events and changing climate patterns continue to put constant strain on traditional farming practices. In addition to shortening supply chains, indoor farming has many other advantages in comparison to traditional agriculture such as using zero pesticides, employing 95% less water, and reducing food waste. Health benefits also include fresher food, increased urban availability, and pollution reduction.
Despite the major advantages, there is one looming barrier to mainstream adoption: the process is very energy-intensive.
Solving for the energy intensity problem
Vertical farming presents a unique opportunity to grow food on already developed land and increase domestic food production, but the energy demand required to power these facilities is much higher than other methods of food production. In fact, we’ve identified indoor agriculture as one of the four major drivers that will increase electricity consumption in the next decade, along with electric vehicles, data centers, and the electrification of heat. This is why more of today’s modern farming companies are turning to microgrids as a possible solution to ease their energy challenges.
Although most of today’s facilities are not equipped to meet the electricity needs of an indoor agriculture operation, microgrids can provide dynamic energy management and the resources required to support maximum productivity, sustainability, and energy efficiency. They can provide localized power generation and utilize renewable distributed energy resources to help deliver power and reach clean energy goals, while also allowing users more control and reliability. Additionally, microgrids can capture and repurpose CO2 emissions to help in crop production.
Moreover, microgrids provide resilience from unexpected outages that could result in a loss in production. A key advantage of vertical farms is their ability to allow crops to grow year-round, and communities rely on their ability to deliver on this promise. Microgrids not only have several clean energy benefits, but they also increase business continuity that maximizes output. Given their ability to operate either in conjunction with or as an island from the utility grid, they can keep the farm producing even when the grid goes down.
The case for investment: Securing an affordable solution
Building and operating a vertical farm requires various technologies that can translate to high startup cost and design complex processes. At the same time, it is more expensive to maintain a vertical farming operation than traditional field farming. Microgrids offer a compelling value proposition, but they’re inherently complex machines and not many companies have the upfront capital or in-house expertise needed to make the investment. Fortunately, innovative business models such as energy-as-a-service (EaaS) help provide price certainty and make the investment attainable.
For example, a modern farming company, Bowery Farming, created a facility wherein crop production is 100 times more efficient than traditional farmland. This generated a need for a greater need for reliable, efficient power. Thus, the company made the decision to integrate a hybrid microgrid system that would feature a rooftop solar array, natural gas generator, and a lithium-ion battery energy storage system through an EaaS business model. Through EaaS, Bowery Farming saved upfront capital that can be used toward additional operational investments.
By 2050, the world’s population is expected to grow by another 2 billion people, and feeding it will be a major challenge. According to the projections of the Food and Agriculture Organization, we have to increase overall food production by 70% by this timeline. Coupled with new concerns that have surfaced as a result of today’s global pandemic and unstable weather, vertical farming will play a key role in future food production and institutions will take notice. However, the technology that will help ease some of the industry’s ongoing energy challenges will be just as important to aid the transition.
Don Wingate is the VP of utility and microgrid solutions at Schneider Electric.
Source: Microgrids Knowledge
Photo Courtesy of Microsoft News
VIDEO: IGS Intelligent System Design – FTS Finds Out More
IGS has, as a company, focused from the outset on automation, intelligent system design, and the energy equation of CEA vertical farming
July 6, 2020
IGS has, as a company, focused from the outset on automation, intelligent system design, and the energy equation of CEA vertical farming. This has garnered them a reputation as one of the leading and most innovative companies in the industry. We took some time to have a chat with them and find out a bit more about how this all works in practice.
FTS: Hello and thanks for taking the time to talk with us. Can you briefly introduce IGS, its history as well as its outlook?
IGS: IGS was founded in 2013 bringing together decades of farming and engineering experience with a vision to revolutionize the indoor growing market. The two founders, farmer Henry Aykroyd and our CTO Dave Scott had an appetite for innovation and realized that there were significant gaps in the provision of scalable technology for the sector.
Henry knew how to grow and understood the challenges which faced traditional farming: Dave knew how to manage automation and power controls in an industrial environment. The opportunity to bring greater climate control to a growing environment was significant. The ability to manage power consumption was revolutionary. The simplicity of its implementation and use is pivotal.
We opened our first vertical farm demonstrator in Scotland in 2018. Artificial intelligence determines optimal nutritional input and the exact combination or ‘recipes’ of weather: lighting, watering, and ventilation. Data is collected continuously and machine learning used to make iterative adjustments, all of which is monitored through a web-based app. The whole Intelligent Growth platform is IOT-enabled to automate system control and management. Our degree of control is so fine that each 6m2 growth tray has its own microclimate. Technical simplicity is at the heart of our mechanical design.
Our commitment to innovation has continued apace and we have evolved the applications of our technology beyond agriculture to create solutions for a wide variety of indoor environments, developing the Intelligent Grid platform.
The Intelligent Grid uses the same IOT-enabled power and controls platform to manage and monitor lights, sensors, cameras, and communications for complete climate control and reporting. It too has a very simple, clean, and elegant design for application in any commercial building, greenhouse or livestock shed. In contrast to the vertical farm, we use our same core technology through the Intelligent Grid to create whole-space macroclimates.
Both IGS demonstrators are based at the James Hutton Institute, a world-renowned crop, and plant science research facility. IGS and the Hutton collaborate closely to help advance the understanding of plant science for indoor growing.
Until 2018 IGS had invested approximately £7m in R&D to ensure that its platforms offered the greatest levels of control and achieved levels of economic viability, scale, and minimal environmental impact compared to other systems on the market. In 2019 IGS raised £7 million in institutional capital to enter production and take its systems to global markets. We continue to invest over £1m per annum in R&D.
FTS: You have recently shared news of two reseller partnerships – one in the Middle East and one in the UK and Italy with TEP Renewables. Can you tell us briefly a bit more about them?
IGS: We have been talking to International Real Estate Partners (IREP), the international facilities management firm for some time in the Middle East, and we’re really pleased to recently sign this referral agreement which is specifically focused on indoor vertical farming for the UAE and Saudi Arabian markets.
We also have an opportunity to extend into Asian markets in the future. It gives us a greater capacity to service the Middle East market and secure and deploy vertical farming platforms across the region. IREP’s presence in this market is well established with many existing customers across agriculture, retail, and construction and it is a very positive development for both companies we believe.
The agreement with TEP Renewables is an MOU (Memorandum of Understanding) or a reseller-type partnership if we identify customers who would like to operate solar-powered vertical farms in Italy or the United Kingdom that we will work with them.
FTS: Fantastic! In the end, any vertical farm (indeed any farm!) is only as environmentally sustainable as its energy equations. But it is also only as financially sustainable as its energy cost. You have focused quite intensely on this energy cost question. As we see this dramatic collapse of fossil fuel energy production return on investment, it seems that NOW is the time to have renewable energy options on hand for CEA. Do you believe that renewable energy can be cost-competitive – both in terms of installation, sustainable life-cycle and with regard to the price of the final product for the consumer?
IGS: We consider a variety of power distribution and supply methods. Renewables can have considerable benefits from an environmental perspective and also specific to grants and other financial support for utilizing renewable energy resources.
The “virtual power plant” capabilities of our systems indicate strong Demand Side Response (DSR) potential. We can manipulate our growth cycles to respond to power availability and respond to inherent instabilities in power networks. This is already having an influence on our engagement in circular energy projects to utilize spare energy for growing and allows for more renewable power sources to be adopted.
FTS: Labor cost is the other biggest outlay for any vertical farm. You have invested heavily in automation. Is the trade-off of increased capital expenditure for automation worth the reduction in operational expenditure for labor, in your experience?
IGS: Absolutely. Driving down the farm gate price is the ultimate goal and while labor costs vary from region to region, we believe that this investment in the automation (and indeed the associated patents) within our growing operations is imperative and differentiates our systems considerably.
FTS: You’ve set about designing modular and intelligent systems. Such a bespoke system offers advantages of course, as we’ve seen above. But it can also present challenges if it cannot be integrated with other equipment and systems later. Do you future-proof your systems to be able to accommodate such updates and integrations over time?
IGS: We have thought about this from the outset, and our systems are designed in a plug and play model, rather than being bespoke as such. Scalability is paramount for our customers and this has been a consideration throughout our R&D development. Rather than using proprietary systems for processes such as sowing and harvesting, we use off-the-shelf equipment and components. This means we can keep startup and maintenance costs down by providing items with which farmers are already familiar. If a section of the vertical farming system needs to be replaced or upgraded, such as a water filter, a lighting panel or a tray, it can be done with almost no interruption.
However, what is also imperative to think about in terms of future proofing, and a hugely important part of our approach, is how we work so closely with the science community to better understand plant light interactions. The level of control we have designed into our hardware systems allows us to flex and adapt as we need to deploy the most up to date plant light information through our software development, which is continuously evolving.
The approach of our software development has also involved maximising security of our systems and ensuring simplicity of operation. This will be continuously updated, but with seamless integration for our customers.
FTS: Along with FTS, you’ve joined a number of other associations and similar collaborative groups. Why is this important to you as a company, and how do you balance the proprietary needs of your company against this desire to cooperate?
IGS: Collaboration and cooperation across this sector is essential. Our vision is that sustainable change will only be delivered not only when we collaborate, but when we are all open and honest about the limitations, as well as the opportunities for this sector. We want to work alongside technology vendors with complementary products, and with growers and producers, supported by science and greater understanding of growing plants indoors, all backed by far-sighted investors.
We firmly believe that through innovation, collaboration and investment we can create an economically and environmentally sustainable global indoor food industry.
FTS: Thanks so much for taking the time to talk with us today. We wish you every success and look forward to working with you in the future.
IGS: Thanks very much indeed. We look forward very much to be part of Farmtech Society as we all move forward in the development and innovation of agricultural technology.
For IGS
David Farquhar
CEO
AmHydro’s Joe Swartz On The “Shiny Object” Problem Plaguing Indoor Ag
All photos courtesy of American Hydroponics and Joe Swartz. Joe Swartz, Vice President of Contain vendor American Hydroponics (AmHydro), is a fourth-generation farmer from Western Massachusetts. When it came time for him to take over, he went looking for a way to do things differently
All photos courtesy of American Hydroponics and Joe Swartz.
Joe Swartz, Vice President of Contain vendor American Hydroponics (AmHydro), is a fourth-generation farmer from Western Massachusetts. When it came time for him to take over, he went looking for a way to do things differently. His family had faced numerous challenges with conventional outdoor agriculture, from the state’s short, 120-day growing season, to an uncle who died prematurely due to pesticide exposure.
Joe decided the solution was indoor agriculture, and since 1984, he’s grown just about everything you can imagine with every possible setup. We caught up with Joe to talk about why it’s important to educate the public about indoor ag, and how media hype can distract from the fundamentals of good farming.
What’s AmHydro’s approach, and what makes it unique?
Ironically, AmHydro started about the same time I started to grow, unbeknownst to each other. We have always focused on the philosophy of making growers successful by employing the correct technologies in the appropriate situation, not trying to sell this system or that system, but looking at a given situation and assembling the correct technologies to effectively grow.
In fact, I think AmHydro has more successful growers around the world than any other hydroponics company. We have growers in 66 countries around the world, soon to be 67, and we’re really very, very pleased with that.
What are some of the most common challenges about getting started in indoor agriculture?
There are lots of different technology companies trying to get your attention. The biggest challenge I see right now is a lot of inappropriate technology that’s being promoted, especially in the media and online, because people think certain things look really interesting or cool. We call it “shiny object” technology. These are not effective technologies.
A lot of vertical farming technology, where you’re essentially trying to cram as many plants into a give area as you can, from a horticultural standpoint, that isn’t correct. Plants have very specific needs in terms of environmental management and space management, and a lot of these systems ignore the basic horticultural concepts that are required for successful production.
You’re saying you think all vertical farms and plant factories don’t work?
Not all plant factories, but unfortunately that model is by far—and I mean by a factor of thousands—by far the most challenging segment of controlled environment agriculture in terms of making an economic return.
If you look at the industry, look at where the expansion is in hydroponics. Companies like Gotham Greens and BrightFarms are expanding rapidly because they have a cost-effective production model. Tomato operations such as Houweling’s and NatureFresh and Sunset are all expanding rapidly. Again, they’re utilizing effective technology.
What’s been the main benefit of working with Contain?
We were actually one of the first companies that Contain worked with. They believed in our model, and we believed in the model they had, which was helping provide financing solutions so that more people could enter this industry. We thought it was a great model — people who understood controlled environment agriculture and were offering financing models. Good people and proper technology is a good combination.
We’ve had a few projects where there would have been difficulty in locating financing, and they went through Contain and were able to do it, so it was an effective model. We hope to do more of that in the future.
What advice do you wish you got when you started growing?
I think I would’ve pushed myself to focus on the basics of correct horticulture. That means to learn as much about the lifecycle of the plant, the lifecycle of insect and disease pests, to understand the different living ecosystems that go on in a facility like that. At the end of the day this is still farming. With a lot of the technological advances, people forget that.
Why are some banks and investors reluctant to get into indoor ag, and how can we change that as an industry?
It’s a very capital-intensive business. It is expensive to set up and to get started. That’s always been one of the big pain points of getting into the industry.
And I do think that investment and interest in technologies that are not productive damages the industry. In the 1980s, Weyerhaeuser and Pepperidge Farms and General Electric and all these huge corporations began building large greenhouses here on the East Coast, and utilizing the pond system, and talking about lettuce factories, and these are all automated systems, and by 1990 all of our food is going to be grown in these indoor food factories. They all failed spectacularly, and millions and millions of dollars in investment were lost, and it damaged the credibility of the industry. It’s taken a long time for the industry to recover. Unfortunately, we’re heading down the same path today.
AmHydro does a lot of public education. Why is that important?
We feel very strongly that education is the key to everything. Basically you are looking at a very intensive form of growth that requires knowledge in terms of growing and business management to be successful. The more we educate our growers, the more successful they are.
What’s the most exciting trend in indoor agriculture?
The most exciting trend is the level of public awareness about the business, both from a consumer buying hydroponically grown produce, to people who want to get involved in the industry. This is the highest level ever.
When I was in agricultural college in the ‘80s, I was in a classroom of young people with 30, 35 students. I come back now to the University of Massachusetts and I lecture to 300 students, so the level of involvement has skyrocketed, and that’s tremendous, and I couldn’t be more excited.
This conversation transcript has been lightly edited for length and clarity. Learn more about Contain and funding your indoor ag business at our website.
Tags: Agriculture Indoor Agriculture Startup Finance Contain
WRITTEN BYNicola Kerslake
We’re Contain Inc. We use data to improve access to capital for indoor growers, those farming in warehouses, containers & greenhouses. https://www.contain.ag/
Not All LEDs Are Equal: How Greener Roots Farm Is Growing Faster With Horticulture Lighting From Current
From a small window sill to an empty storage closet, to a rooftop utility room and, finally, to a spacious warehouse and greenhouse, Founder and President Jeffrey Orkin has been growing Greener Roots Farm one harvest at a time since 2012
Meet the light bars behind “the best damn lettuce you’ve ever tried.”
From a small window sill to an empty storage closet, to a rooftop utility room and, finally, to a spacious warehouse and greenhouse, Founder and President Jeffrey Orkin has been growing Greener Roots Farm one harvest at a time since 2012. As the first commercial-scale hydroponic vertical farm in Nashville, Tennessee, Greener Roots supplies herbs and leafy greens to local establishments year-round, including fresh lettuce and flavorful pea shoots, sunflower sprouts, sorrel and more that are picked and delivered within two days, never traveling more than 50 miles.
For Orkin, consistency is the key to Greener Roots’ steady success, measured in predictable crop yields and high-quality, nutrient-dense produce with no seasonal fluctuations. It’s what keeps local grocery stores and restaurant owners racing back to fill new orders, and it’s why Orkin relies heavily on LED lighting to help his business thrive. However, when a big investment in a new system started to go bad, Current, powered by GE, stepped in with a brighter solution.
Rising Above the Rest
Greener Roots cultivates over 14 tons of produce a year, with most of the greens being raised in racked hydroponic beds stacked high to the ceiling. Between its warehouse and greenhouse, the indoor operation totals nearly 7,000 square feet of grow space, requiring more than 300 LED light bars to provide optimal illumination for plant health. According to Orkin, it’s all part of producing “the best damn lettuce you’ve ever tried.”
“Some chefs are adamant about soil, but we’re showing them you can grow very flavorful things without soil, and having extremely high and uniform light levels is critical to that,” he says.
Greener Roots was growing fast, and new and better lighting technology was hitting the market. With help from Hort Americas, a leading commercial greenhouse and hydroponics supplier, he started to test an array of new LED options including horticulture lighting from Current. Immediately, Orkin gravitated to Current’s Arize™ LED growing system for its ease of installation, long life and proven results in improving production yields.
“The new lights from Current are very reliable and are producing faster growth, and now we can get red leaf varieties to turn red, where we couldn’t do that before,” Orkin said.
“The new lights from Current are very reliable and are producing faster growth, and now we can get red leaf varieties to turn red, where we couldn’t do that before.”
– Jeffrey Orkin, Founder and President, Greener Roots Farm)
“The Arize system also puts off less heat, so we can add more layers to our vertical beds if we choose. And what’s convenient is how you can daisy-chain the product end-to-end to make installation much simpler, which we really liked, having done all the work ourselves.”
Growing the Future
By isolating and combining different light wavelengths to replicate and accelerate natural photosynthesis, Arize LEDs can shorten growth cycles and enable different growth patterns, allowing urban farmers to tailor the light to the specific needs of every crop. Including LED tubes, light bars, suspended fixtures and lamps, the full Arize product family features everything needed for indoor vertical and greenhouse farming.
“Overall, we’re getting more biomass from every harvest,” says Orkin. “It’s all about ensuring the correct light intensity throughout the day, and how many photons we’re ‘feeding’ to the plants essentially. Current’s LEDs help us create the ideal condition for each crop.”
“Overall, we’re getting more biomass from every harvest.”
Orkin notes that Greener Roots is now pulling over 2,500 heads of lettuce a week from its greenhouse as more local customers discover the soil-free urban farm flourishing in their city. In fact, the new greenhouse―located on the outskirts of Nashville in nearby Franklin, Tennessee―is part of a large agritourism destination dubbed Southall Farms. This farm-to-table rural retreat will feature an inn, guest cottages, an event center and an agricultural barn, adding up to over 160,000 square feet of relaxed destination space where people will be able to savor experiences that celebrate culture, community and craft.
“There’s been an undercurrent for urban farming for some time, whether that’s someone raising a garden at home or a small farm making more fresh food options available to people,” Orkin says.
Rooted in Results
Orkin still drives the delivery truck that drops off freshly picked foods to his customers each day because to this entrepreneur, relationships are the seeds of success. It’s an approach that has taken the landscape-architect-turned-urban-farmer from a single planter in a kitchen window to a sprawling production system that ensures sustainable produce is always in stock.
“Having Current and Hort Americas there to support us, to answer our questions and try new things, it’s been huge,” says Orkin. “We’re trying to have the biggest impact on the local food scene we can, and that takes partners who understand the importance of durable and reliable technologies, such as LED.”
Learn more about how Current, with its deep expertise in LED technology, is helping indoor farmers reach new heights.
Are you ready to talk about
the right growth spectrum for your business?
START THE CONVERSATION
Want Chemical-Free Vegetables? Vertical Farming Might Be The Answer
These vertical farming towers developed by the Telangana State Centre of Excellence may be the answer to the increasing demand for chemical-free leafy green vegetables
JULY 01, 2019
The Telangana State Centre of Excellence (TSCoE) in Jeedimetla feels like an oasis, in contrast to the barren highway that leads to the area and the humble residential colony in its vicinity. The 10.35-acre facility managed by the department of horticulture is a hub of experiments for cultivation of vegetables and flowers.
In one of the poly houses covered by a UV-stabilising film, more than 800 PVC pipes have been converted into vertical farming towers. Each of these pipes have been filled with a mix of coco peat, red soil, neem cake, vermicompost and micronutrients that help plant growth. Each pipe has more than 20 slots from which small branch-like extensions emanate, it is in these that green leafy vegetables are grown.
The CoE designed and tested such prototypes in December 2018, approved by the department of horticulture authorities and a technical committee of agriculture experts; it has so far grown coriander, amaranthus, bacchali (Malabar spinach) and palak (spinach). At the moment, the 800-plus towers grow spinach, some of them ready to harvest.
A retail counter near the entrance of the premises sells fresh greens and vegetables grown at the centre and it’s a big hit with the neighbourhood. Palak is sold at ₹40 per kg, double the price of wholesale market, but there are many takers since these greens are free of chemical pesticides. There have been days when the centre sold 400 to 600 bunches of leafy greens.
Around the world
Singapore: The vertical urban farm called Sky Greens, located in Lim Chu Kang, harvests 500kg of green leafy produce every day. According to a Straits Times report, the yield in this farm is 10 times that of traditional farms, as it uses tiered metal towers up to nine metres tall. The rotation of these towers in glass buildings allows all the plants to get uniform sunlight.
San Francisco: Tigris, a hydroponic vertical farm in San Francisco, is a futuristic project focusing on growing leafy greens. The new farm reportedly can grow one million plants at a given time.
While vertical ornamental gardens add aesthetics to premises, vertical farming is more utilitarian. CoE intends to encourage residential colonies in urban areas and farmers at the district and zilla parishad levels to grow more greens using vertical farming.
The CoE feels that having several small crop colonies in urban pockets and rural areas might help meet some of the growing demand for vegetables in the state. Leafy greens, tomatoes, brinjals, chillies and okra, for instance, can be cultivated in balconies and terrace gardens to meet individual home needs.
In addition, enterprising farmers in both urban and rural areas can do vertical farming to grow greens that meet the needs of their neighbourhoods, believes the CoE. “Green vegetables are the need of the hour. They perish easily and don’t withstand long-distance transport. A lot of greens available in the market are also laced with chemical pesticides. There’s an increasing awareness today about safe food. Growing your own greens will ensure safe food and reduce food miles,” says K Latha, assistant director of horticulture, CoE.
Traditional farmers can use vertical farming towers to step up the yield. “In flat-surface farms, it’s tough to harvest green leaves during monsoon. Leafy vegetables can be harvested every 25 to 30 days, so ideally you can aim for 12 harvests a year. In flat cultivation farmers only manage eight or nine harvests. Using these towers and a poly film roof, greens can be grown all round the year,” she says.
K Latha, additional director of horticulture, COE, with agriculture engineering students at the vertical farming polyhouse | Photo Credit: K V S Giri
The coco peat and nutrient mixture in these towers can be replenished after three or four harvests to get quality produce. To counter weeding, the CoE uses a weeding mat on the ground. Small outflow pipes from each of the towers drain excess water.
To make vertical farming economical, the CoE uses non-ISI mark PVC pipes that cost ₹400 to 500 each, as opposed to ISI-certified ones that cost around ₹5000. However, the non-ISI pipes stand the risk of damage when exposed to prolonged heat. The UV-stabilising poly film roof counters this problem.
Latha points out that there are several smart vertical farming methods worldwide, including those that use hydroponics and aeroponics. “There are various designs of vertical farming towers too, across the world. The indigenous technology we developed is one of the methods,” she says, signing off.
Planet Healers celebrates eco-conscious initiatives. If you know an eco warrrior, write in to hydmetroplus@thehindu.co.in
Best New Field Technology And Best New Indoor Growing Technology
Innovation Award finalists - Part 2
United Fresh announced 48 new products as finalists for the United Fresh Produce Association’s 2019 Innovation Awards. This year’s finalists will compete in seven categories for the title of Best New Product at United Fresh 2019, June 10-12 in Chicago, where attendees will be able to vote for those winners during the trade show.
Earlier, FreshPlaza presented the finalists for Best New Fruit product and Best New Vegetable product, and today we look at the finalists for Best New Field Technology and Best New Indoor Growing Technology.
Best New Field Technology
Automated Storage and Retrieval System (ASRS)
Stemilt Growers, LLC – Booth # 6015
"Stemilt’s new distribution center welcomes a piece of technology they call the “brains” of the operation: the automated storage and retrieval system (ASRS). ASRS is the one-stop-shop for order fulfillment to make the process flawless and speedy, resulting in an experience that is delightful from farm to table."
Produce Plan
Frontera Produce – Booth # 13046
"This technology enhances your supply chain data visualization, actively updates production plans, and protects your crop investment through cultural practice performance monitoring. Soil moisture, heat units and estimated harvest dates per field and lot are just a few examples of how this technology can change traditional farming."
RipeTime
RipeTime – Booth # 18045
"RipeTime has developed world-first patented technology that measures and reports in real-time of ethylene in post-harvest operations from 1PPB. This monitoring and alerting allows post-harvest operators to make decisions to assure the quality of their fruit and assist with prioritizing the load-out operations."
SC iOn™ Trak SC1204
CalAmp – Booth # 18025
"The SC iOn Trak™ SC1204 eliminates the manual processes of automatically logging location and environmental condition data using a wireless gateway (fixed or mobile) that can communicate with several Bluetooth tags for transport and storage applications. The solution is reusable, which helps to increase the technology investment ROI."
Best New Indoor Growing Technology
Hoogendoorn Analytics
Hoogendoorn America Inc. – Booth # 18045
"Our online platform for data storage and data analysis. Convert real-time data into valuable information that can give you the possibility of producing more and better. We use this information to track the growth of the plants and look for the best combination to achieve high yield production."
LivingCube™
Del Fresco Produce Ltd. – Booth # 12027
"The LivingCube™ is a system of automated vertical growing machines that continuously produces living lettuce, living basil and microgreens all year long. It's powered using an off-the-grid electrical cogeneration system, which is environmentally sustainable due to its minimal footprint, reduction in greenhouse gases, usage of recycled water and pesticide-free integration."
Virgo
Root AI – Booth # 9028
"Root AI is building autonomous systems that care for specialty crops. Our first product, Virgo, uses the latest advancements in robotic hardware and artificial intelligence software to delicately harvest tomatoes with precision, efficiency, and dependability."
The 2019 United Fresh Innovation Awards finalists will be displayed on the trade show floor at United Fresh 2019 in Chicago, where attendees will have the opportunity to cast their votes for their favorite new and innovative products on Tuesday, June 11 and Wednesday, June 12. United Fresh will announce winners from the Main Stage on Wednesday, June 12 at 2:00 pm at Chicago’s McCormick Place Convention Center.
For more information:
Mary Coppola
United Fresh Produce Association
Ph: +1 (202) 303-3425
mcoppola@unitedfresh.org
www.unitedfresh.org
Publication date: 5/14/2019
Photos: The Beauty of High-Tech Horticulture
The Danish magazine Foresight Climate & Energy has something nice to show you. They dove into the Dutch efforts to reduce carbon footprint of their tomatoes and tulips.
"As the world pushes to decarbonise energy systems and the Netherlands aims to end its 50-year-old love affair with gas, greenhouse companies and the municipality of Westland are looking for cleaner heating solutions, such as geothermal heat and heat pumps, to reduce the carbon footprint of their tomatoes and tulips", they write
The attention for the efforts of the horticultural industry to better the world are nice - but there's more.
Take a look at the beauty of horticulture in these photos.
Publication date: 5/9/2019
Author: Arlette Sijmonsma
© HortiDaily.com
Relationships And Trust Help Hort Americas Mark 10 Years In Controlled Environment Agriculture
Horticultural distributor Hort Americas is celebrating its 10th anniversary of working with controlled environment growers. General manager Chris Higgins said it has been 10 years of forming trusting relationships with the growers and vendor suppliers that Hort Americas works with
Hort Americas 10 years of providing controlled environment growers with timely technical information and innovative products to solve their problems.
Horticultural distributor Hort Americas is celebrating its 10th anniversary of working with controlled environment growers. General manager Chris Higgins said it has been 10 years of forming trusting relationships with the growers and vendor suppliers that Hort Americas works with.
“Hort Americas doesn’t make a single product,” Higgins said. “What Hort Americas does do is we use our technical expertise to assist in the development of new products used to solve growers’ problems. This process takes a lot of trust. Our customers have to trust us about sharing their information. Some of that information could be proprietary. It could be information about their business that they need to be comfortable sharing. It could be information that allows us to look into the future and identify problems growers see coming up. By partnering with our grower customers and vendor suppliers, Hort Americas has been able to develop the technology, products and services that help controlled environment growers.”
At the same time that growers have to be able to trust Hort Americas, Higgins said a similar relationship has to exist between Hort Americas and its suppliers.
“Whether it’s working with our suppliers to develop new substrates or lighting fixtures, Hort Americas often has to share sensitive information. We need to have trust that sensitive information is going to turn into products that are going to be equitable in terms of helping everyone along the supply channel grow their businesses profitably.
“There is a lot of trust involved and that trust can’t be built off of non-disclosure agreements. That trust needs to be built off of years of experiences, cooperation and deliverables. If someone can’t deliver what they say they are going to deliver when they say they are going to deliver it, then trust is going to be lost. And the desire to want to cooperate is going to be lost too.”
Forming trusting business relationships
Higgins said forming a trusting business relationship should not have anything to do with the size of the company whether it’s a grower or supplier.
“Many businesses find themselves on a one-way street,” he said. “Many business people today only care about the value they create for their own business. And while it has probably always been this way, it feels this is more the case today than ever before.
“Trust takes years to build, seconds to break, and forever to repair.” – Author unknown
“This can happen with suppliers that haven’t set up a true supply channel management strategy. Distribution partnerships may seem needed, but are truly not necessary. Therefore some suppliers don’t really care about the health or well-being of their partners or partnerships. They just want to get as much of their product out the door as possible. Fortunately for Hort Americas we have been able to find those suppliers that are exceptions to the rule. Hort Americas must then remember that it is on a two-way street. We must create a situation that is not only good for our grower customers, but are vendor partners as well.”
Chris Higgins, general manager at Hort Americas, with Daniel Lee, sales development manager at Current, powered by GE.
Partnerships in the Information Age
Higgins said today’s Information Age also creates challenges for companies trying to form strong partnerships.
“In this Information Age companies don’t necessarily see the value of networking,” he said. “They don’t see the value of how long it takes to build trust along the supply channel.
“Hort Americas goes out on a limb every time it takes on a new business relationship whether it’s with a grower or supplier. Every time we begin to build a new partnership we have to expect we may never receive the invested money or time back. There’s two to three years of never knowing whether all of the resources we have invested are going to take on any sort of return.”
Higgins said there is an inherent amount of risk that one takes when forming business relationships.
“Sometimes companies build these relationships and they go very well for five to six years,” he said. “Then one person at the top changes the management strategy of an entire company and everything implodes. This could be a change in personnel. This could be a stress fracture created by the need to find increased profitability. There could be a change in market dynamics such as competition, demand or price. Based on this list of changing conditions, companies need to be able to find the ability to trust each other.
“Partnerships are based on trust and that takes time. Hort Americas and GE have been working together for 5 years and we could not be happier with what we have been able to accomplish together.” —Dan Lee, Current, powered by GE
“Just like in a marriage, if something drastic happens, the marriage can end in divorce. Being able to maintain that relationship has to do with the ability to change and adapt. The way you treat somebody, the professionalism and the ability to be empathetic to the position that a customer might be in, those are going to speak volumes in terms of one’s ability to create strong business relationships.”
From bicycles to horticulture
William Fry, who is Hort Americas longest serving employee, started as the customer service manager in 2012.
“I came from the world of bicycles, Fry said. “Bicycles were a passion of mine, including riding bikes all the time. That led me to the business side of bicycles. I owned a bicycle shop and worked with a bicycle parts distribution company. That experience translated well into horticultural distribution when I came to Hort Americas. It doesn’t really matter what the commodity is that you are trying to get from one side of the world to the other, it’s very similar.
“Coming to Hort Americas I had no knowledge of greenhouse technology–what went where, what was needed for each crop, etc. But since I had learned about thousands of bicycle parts, I figured I could learn anything I needed to know about what goes inside a greenhouse.”
Fry, who is now Hort Americas operations manager, said the reasons he has stayed with the company is it’s a fun place to work and he really enjoys working in the horticulture industry.
“Hort Americas and the industry constantly challenge me, both by the technology that is coming out and how they are ever evolving,” he said. “I have to constantly educate myself from a product standpoint.
“From a logistics standpoint, our products are shipped from all over the world. The challenge is to bring them in in a logical way. I’m constantly trying to beat myself as to how I can do things more efficiently and bring costs down for us and for our customers.”
Trying to grow its customers’ business
Fry said one of the major reasons that growers enjoy working with Hort Americas is the company is constantly trying to bring new technology to market.
“We’re trying to bring proven technology to market,” he said. “We aren’t just going to have an idea that a product might work and then offer it to growers. We are going to test it in a research greenhouse first. We are going to send it to growers who we have great relationships with for them to trial. And we are going to work with universities to prove that these products will serve a purpose in this market and work before we bring them to market. That has been fun and interesting.”
Hort Americas general manager Chris Higgins (center) with the Hort Americas team look to provide their grower customers with the expertise they have acquired on controlled environment production.
Another benefit that Hort Americas offers its grower customers is its efforts to be very economical.
“We try to buy at the best price, sell at the best price and ship at the best price,” Fry said. “We are constantly working to provide excellent customer service and to save people money. We are trying to help our customers grow their business so that our business can grow. We try to be a cheerleader for our customers. I have always tried to value every single sale that we have made and try to make our customers that much better so that as they grow we grow.
“Developing our own network of logistics partners has given Hort Americas the ability to cherry-pick the best combination of price vs. speed depending on the situation. With this network we feel confident that we can respond to whatever needs our customers have, whether it is saving money on shipping or delivering an emergency order to them ASAP. We can lean not only on our logistics network, but also on our network of vendors who have much larger buying power.
Looking for supportive suppliers
Fry said good vendor/suppliers provide a consistent, high quality product in a timely manner with logistical excellence.
“Good vendors back us with sales and marketing materials and trial materials for our customers who want to try a product to prove it will work for them,” he said. “They also have a good customer service team on their end as well.
“I’m looking for vendors who treat us as a customer and as a partner, not as a middleman. The same thing that I expect Hort Americas to deliver to our customers, I expect from our vendors. Offer good products, deliver them to us in the best manner possible and help us market and promote them. Be there as a partner and work with us as a team to accomplish a goal. The training that has been by provided by GE lighting engineers along with the hands-on installation of new GE fixtures and factory tours with Grodan representatives to understand the rockwool production process have been invaluable.”
Kyle Barnett (left), regional sales manager at Hort Americas, talks with Bruno D’Amico, design and product manager at GE, about the lighting company’s newest LED fixtures.
Fry said Hort Americas tries to pull from its staff’s experiences when developing new products and working with its vendors to develop these products.
“Sometimes we find a product and it really works well,” he said. “Sometimes we decide the market just isn’t big enough for a product. Or a product may not work in trials as well as we thought it would and we scrub it before ever bringing it to market. We are always looking for those products that make us special to our grower customers. We have also been much more responsive in how we bring on new products in order to lower costs for our customers and for Hort Americas.
“The other half of this product development is training our staff to work with the products. Our staff has a lot of hands-on experience with the products. Depending on the supplier, they may not have the employees who understand the niche industry that we’re in. That is where Hort Americas comes in with staff members who are experts in controlled environment agriculture.”
This article is property of Hort Americas and was written by David Kuack, a freelance technical writer in Fort Worth, TX.
For Indoor Ag Startup Freight Farms, Competing With The Mass Market Produce Industry Was Never The Plan
Indoor agriculture, a generalized term used to refer to farms inside structures such as greenhouses, container farms, and multi-level warehouse operations housing thousands of rows of plant space, has been touted as a way to meet the demand for local food, help consumers learn more about food production, and provide a fresher source of produce with fewer food miles.
But some are skeptical about the scalability of an inherently localized industry and whether it will ever truly compete with traditional mass market produce, especially when it comes to container farming where production is housed in an old shipping container.
“The confines of the retrofit shipping container make it inherently inefficient compared to other forms of CEA (controlled environment agriculture) and therefore the audience for container grown produce will be a highly niche one over the long term,” agriculture consultant Peter Tasgal recently wrote in the AgFunderNews guest post What is the Future of Container Farming?
Tasgal also noted that there are significant costs involved with container farming, including retrofitting the box, labor, and the cost of power for the LED lights. He concludes that container farming is at least four times as expensive per pound to produce leafy greens in a container compared to traditional farming methods.
“There is technological innovation that will improve the efficiency of container farming, but I don’t see anything on the horizon that will allow container-grown produce to compete with the quick turning leafy greens sold at your local grocery store or those sold by wholesale distributors,” Tasgal wrote.
Did you know that AgFunder is one of the most active agrifood tech investors?
We are democratizing access to venture capital. Learn how you can invest with us.
Funding for novel farming systems like indoor agriculture and insect farming dropped between 2018 and 2017 according to AgFunder’s AgriFood Tech Funding Report 2018, which you can download here, raising $596 million. There were 17% fewer deals and only two of those deals were over $100 million after US vertical farming operation Plenty closed a record-breaking $200 million round in 2017.
Different Routes to Market
Indoor ag companies’ route-to-market approaches differ just as much as their approaches to cultivating produce under a roof. Some companies like BrightFarms and Bowery, for example, are offering packaged salads to local retailers to compete with traditional supermarket produce offerings.
But for Boston-based Freight Farms, however, competing with grocery store produce was never the plan.
Founded by Brad McNamara and Jonathan Friedman, Freight Farms has been a longstanding player in the container farming space, raising over $12 million in venture capital funding to-date, including backing from accelerator group Techstars, Right Side Capital Management, Spark Capital, Morningside Group, and The Startup Playbook author Will Herman.
As many startups often say, the idea is to disrupt existing markets, not necessarily to conquer them. For a startup that spends most of its time thinking about how to grow food inside a box, its technology is based on thinking outside of the traditional produce cultivation box.
“They compare container farming to the iceberg lettuce industry. We are not interested in that market,” Friedman told AgFunderNews. “We are interested in a distributed food system and some of the incredible changes that are happening throughout the whole food system like ugly produce, food waste, yield maximization. The entire system is in flux and that’s exciting.”
Introducing Greenery, the Leafy Green Machine 2.0
Freight Farms offers a ready-made shipping container called the Leafy Green Machine (LGM) that can be placed in a wide variety of locations including dense metropolitan areas. It just launched its newest product, Greenery, which is the first deviation from the LGM model.
Within the same 320-square-foot space as the LGM, Greenery boasts 70% more growing space and new IoT technology driven at improving yield, efficiency, and automation. With its real-time transparency feature, a single head of romaine can be traced back through every growing stage to the exact hour its seed was planted. It also features recipes that allow farmers to replicate ideal environmental conditions for specific crops like non-native produce. It supports a variety of crops beyond greens, as well, including tomatoes and root vegetables.
The University of Georgia has already purchased two Greenery containers. An independent farmer operating WhyNot Farms, which supplies pasture-raised meat to chefs in North Carolina and Tennessee, also made a purchase.
Although the duo has been pleased with the LGM’s success, Greenery was developed in response to their clientele’s feedback and ever-changing needs. Freight Farms has diverse users throughout the world, including schools, hospitals, NGOs, corporations, and private owners who develop niche businesses offering locally grown produce to restaurants and chefs in the area.
“The joys of standardizing something is that you get a lot of feedback. We have a network of 200 farmers around the world including Guam, Puerto Rico, Europe, and UAE. When we talk about greenhouse farming or traditional farming, no one farms the same way so it’s hard to collect these metrics,” Friedman says. “We looked at workflow considerations and where operators were spending the most time such as fixing things or having to remove a column to replace a part.”
“We benefited from having hundreds of customers in all these varied segments but at the end of the day, there is overlap among what they want, like more yield, fewer operating costs, flexibility, and customization. Our core, bread-and-butter customers are small business entrepreneurs,” McNamara told AgFunderNews. “And because we had experience developing four generations of the LGM, we were able to move faster and to save development dollars because we had real experience. Something John and I talk about all the time is human centric design. When it came to Greenery’s design process, it was equal parts human and plant-centric.”
Tech Developments
Some of the biggest differences between the LGM and Greenery have to do with workflow and appearance. Greenery has mobile LED light boards and grows rows that are both adjustable. This allows farmers to grow a larger variety of crops and makes it easier to maneuver through the grow rows.
“After the fourth evolution of the LGM, there was a significant design jump to increase yield, bring in new tech, and to hit the metrics that all of our customers want, which are things like increased yield and improved workflow,” Friedman adds. “One of the bigger things we ran into is that we felt like we had exhausted as much of the off-shelf tech as we could. We realized we had to go back to the beginning and build from the ground up.”
As a testament to its outside-the-box ethos, NASA selected Freight Farms for a Small Business Technology Transfer grant to fund work with Clemson University exploring how to grow food in extreme climates. NASA is hoping that Freight Farms can help create an off-grid crop production unit that would help facilitate deep space exploration.
It’s a Dynamic Time for Agriculture
As far as the future of container farming, McNamara and Friedman want to remind people that the industries are not static entities, especially when they are so heavily focused on technological innovation.
“What frustrates us is that articles are written as if everything is in a static state. We are in a dynamic time for indoor agriculture. If you could have told us back in 2010 how things would be today, it would have been beyond our wildest dreams,” McNamara says.
“With LGM and Greenery, we offer a new way of growing to build a distributed food system, which is exciting to us. You can lower the bar to entry for agriculture with this technology, making it possible for people who want to get into this professionally but who don’t want to build a warehouse or who don’t have a background in ag,” says Friedman. “If they want to grow their own brand or have a private label deal for a restaurant, we want to give them the tools to achieve that and to bring the other half of the world into farming and agriculture.”