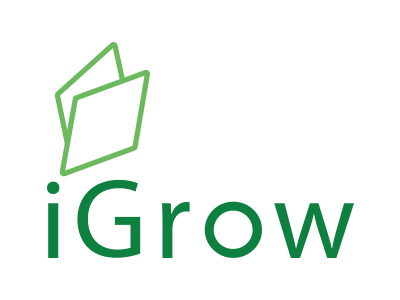
Welcome to iGrow News, Your Source for the World of Indoor Vertical Farming
2021 Virtual Plant Lighting Short Course
In each sequential module, attendees will use interactive tools to define their specific lighting requirements, hear from industry experts about available horticultural lighting systems, and learn how to compare different lighting strategies
Now Open For Registration!
Working in partnership, GLASE, OptimIA, and LAMP are excited to announce the first annual Plant Lighting Short Course! This 6-week modular short course is designed to provide participants the opportunity to learn about all aspects related to the selection, implementation, and benefits of plant lighting systems.
In each sequential module, attendees will use interactive tools to define their specific lighting requirements, hear from industry experts about available horticultural lighting systems, and learn how to compare different lighting strategies. By the end of the course, participants will be equipped to make informed decisions about the best options to meet their lighting needs.
More Info & Registration
Media Partners
Recordings Now Available
Optimizing Resource Use Efficiency in CEA Systems - July Webinar
New CEA Research Programs in the U.S. - June Webinar
GLASE Webinar Series
This short presentation will cover the history of research on photosynthetic responses to light spectrum, recent work on the importance of far-red photons, and a discussion of the implication of (not) extending the definition of PAR
The photosynthetic activity of far-red photons was discovered 70 years ago, but has largely been ignored since then. Recent research has drawn new attention to the importance of far-red photons.
This short presentation will cover the history of research on photosynthetic responses to light spectrum, recent work on the importance of far-red photons, and a discussion of the implication of (not) extending the definition of PAR. There will be ample time for discussion following the presentation.
Register Here - August 26 • 2-3 p.m. EST
Signify Announces New Philips Horticulture LED Partner Hortipar
“We are excited to be a partner of Signify and offer the range of Philips GreenPower LED grow lights to our customers”, said Aad van Ruijven, director at Hortipar
June 28, 2021
Eindhoven, the Netherlands – Signify (Euronext: LIGHT), the world leader in lighting, has signed a partnership agreement with Hortipar, an expert in realizing lighting projects for the horticultural sector worldwide. Hortipar is based in ‘s Gravenzande, the Netherlands, and operates mainly in North America, Canada, Eastern Europe, and the Netherlands.
Hortipar will now add Philips GreenPower LED grow lights to their global portfolio. Focussing on quality, flexibility, knowledge, and expertise, Hortipar offers their customers a complete solution for their greenhouse from the beginning till the end of a lighting project. With their independent advisors and team of dedicated experts, Signify is proud to add Hortipar to the global partnership network of Philips Horticulture LED.
“We are excited to be a partner of Signify and offer the range of Philips GreenPower LED grow lights to our customers”, said Aad van Ruijven, director at Hortipar. “Sustainability and innovation are of great value to us and to our network. Our customers expect the highest quality, and that we offer them the full package for their lighting installation, together with high-end advice and project management. The expertise of the team at Signify and their Philips GreenPower LED grow lights fit perfectly within these expectations and in our ambitions for the future.”
“Adding Hortipar to our global network of certified Philips Horticulture LED partners is something we are proud of”, said Udo van Slooten, Business Leader Horticulture at Signify. “According to our estimates, about 30% of the world’s greenhouse surface will be lit by 2025, and LED technology will light more than half of that surface. Therefore, we are continuously pursuing further development of our Horti LED partnerships worldwide, and Hortipar is a valuable addition.”
Signify continues to expand its Horticulture partner network, further demonstrating its commitment to lead the horticulture industry as the innovative LED lighting systems provider for greenhouses and indoor farming.
--- END ---
For further information, please contact:
Global Marcom Manager Horticulture at Signify
Daniela Damoiseaux
Tel: +31 6 31 65 29 69
E-mail: daniela.damoiseaux@signify.com
www.philips.com/horti
About Signify
Signify (Euronext: LIGHT) is the world leader in lighting for professionals and consumers and lighting for the Internet of Things. Our Philips products, Interact connected lighting systems and data-enabled services, deliver business value and transform life in homes, buildings and public spaces. With 2020 sales of EUR 6.5 billion, we have approximately 37,000 employees and are present in over 70 countries. We unlock the extraordinary potential of light for brighter lives and a better world. We achieved carbon neutrality in 2020, have been in the Dow Jones Sustainability World Index since our IPO for four consecutive years and were named Industry Leader in 2017, 2018 and 2019. News from Signify is located at the Newsroom, Twitter, LinkedIn and Instagram. Information for investors can be found on the Investor Relations page.
Why Does Energy Efficiency Matter When Selecting LED Grow Lights?
Learn the 3 things to consider when choosing energy-efficient lighting in your greenhouse or vertical farm.
Before we get started, let’s set some ground rules for this article.
1. I want to believe that everyone wants to do what’s right for the planet as long as they think their business can afford it, so we will not focus on energy efficiency and its impact on sustainability.
2. In this article I will not post the name of suppliers or the price of the lights. The price of the light will definitely impact people’s decisions and will vary widely based on the volume of lights being purchased and the supplier providing it.
3. This article is not about light quality or light spectrum. To look for information on spectrum please read this article: Why I Still Believe in Red/Blue LED Grow Lights
4. This article is written with commercial greenhouse produce growers in mind, but we do include a model which shows high output led grow lights running for long hours per day which could imply a greenhouse cannabis crop.
5. We are fully aware that when you change the amount of energy going into the light as well as the type of electric light (HPS vs LED) one is using, it will have an impact on the climate in the growing/production area. Factors like heat and relative humidity would need to be taken into consideration if one was taking a holistic approach to energy savings on the farm.
6. All lights have different output (measured in PPF.) In this article we are going to make the assumption that a grower is using the same amount of fixtures per acre regardless of output. For simplicity we are also going to assume that the grower is running the lights for the same amount of time. We are fully aware that this will have an impact on the potential yield of the crop.
7. All greenhouses can require a different amount of lights per acre to achieve the target light intensities. I am using an average of the amount of lights per acre. Height of the greenhouse, width of the bays, placement of walkways, crop layout, crop density, as well as many other variables will impact the exact number of lights per acre.
__________
There is a growing amount of discussion around the environmental sustainability of a greenhouse or a vertical farm. Much of this discussion is being driven by two or three big energy hogs inside these production facilities. This includes the grow lights and climate management equipment like heaters and cooling units.
We all know that LED grow lights are more efficient than the older HPS lights that growers have used for decades, but do we know just exactly how to measure that? And do we understand how that will have a direct impact on not only energy savings but the operational cost at the farm? For those growing in a greenhouse, understanding these numbers during dark winter months can have a huge impact on electricity bills.
3 FOCUS POINTS
1. Start by understanding the amount of light you need.
Urban Ag News recommends going to websites like Suntracker or the ESRI DLI maps site. These websites allow anyone to determine the historical DLI monthly averages for their individual locations. For this example I am going to use the area where my grandparents farm is located in southwestern Michigan. As one can see this is an area of the United States that has very dark winters.
2. Work with a trusted advisor or extension specialist to determine the amount of hours your crop needs to grow consistently year round. Remember not all crops have the same light requirements and some crops have very specific photoperiods which can determine the amount of hours one can light their crops. Use all of this information to see when you will need supplemental light and how much light you will need to supplement with.
For this example I am going to use 1 acre of greenhouse tomatoes in a glass greenhouse located in southwestern Michigan.
3. Now let’s calculate how much it’s going to cost you to run the grow lights for the estimated hours you and your advisor determined were needed per year to get the desired yields.
a) To provide a baseline, we started with traditional 1000w HPS lights which are highlighted in yellow.
b) Then we chose six different LED grow light fixtures. Because the light spectrum has an impact on how efficiently the lights run, we chose three broad spectrum fixtures and three that are red and blue only.
c) Since HPS is the baseline, the final column labeled “savings” shows how much the total savings per year one would achieve when replacing traditional HPS with the latest LED grow light technology.
d) We made a few important assumptions in this example. First, the cost per kwh is around the USA national average of $0.09/kwh. Second, the same amount of grow lights would be used even though there would be some relative differences in umols/m2/s measurements for two of the samples. We decided not to change them because that would have an impact on uniformity (the even spread of the light over one’s entire crop) and associated capital cost not addressed in this article.
IMPORTANT NOTES!
It’s important to remember the 7 assumptions made at the beginning of this article and that lights are not equal. This chart only compares ppf (output) and w (watts). We elected to account for the difference in output by changing the amount of hours we estimated you would need to run the lights. Another way to look at this would be to remember the Golden Rule of Light in which 1% increase in light is equal to 1% increase in yield.
Running these simple calculations will show you why you need to look at energy efficient lighting and in general the importance of researching energy efficient equipment in general. What these calculations do not show is the quality of some fixtures over others. Buyers must always be aware of the value of warranties, ease of returns, durability and quality of product plus accuracy of your vendor to create detailed information on the best way to use and install fixtures. We understand that this topic is intimidating for most, but this is a major purchase for your farm. Make sure to take the time to learn the math and do your homework before purchasing.
Diving into these calculations will also highlight how much energy will be required to grow a wide variety of crops consistently with uniformed yields year round in climates with low light. Hopefully in articles to come we can discuss what this means for our environment and how we might develop additional ways to lower that ecological footprint.
For help in calculating the energy efficiency of grow lights you are considering, please email us and we will connect you with professionals capable of helping you make an informed decision.
Chris Higgins is the founder of Urban Ag News, as well as General Manager and co-Owner of Hort Americas, LLC a wholesale supply company focused on all aspects of the horticultural industries. With over 20 years of commercial horticulture industry experience, Chris is dedicated to the horticulture and niche agriculture industries and is inspired by the current opportunities for continued innovation in the field of controlled environment agriculture. Message him here.
Tagged GreenhouseGreenhouse TechnologyIndoor Ag TechnologyTechnologyVertical Farming
Certhon Expands To Bring In Horticultural Experience For North American Market
Besides traditional greenhouses, indoor farming has become a professional segment that develops faster in the United States than anywhere else. In some cases, these facilities are complementary to the greenhouse, but mostly these are stand-alone setups
While celebrating its 125 years of existence this year, Certhon is far from done developing and expanding within the horticultural market. There have been a lot of developments for the company in the last few years. For example, Certhon established its own Innovation Center to research the optimization of technologies in the field of indoor farming. With a team of technology experts and agronomists, Certhon always tries to find ways to improve cultivation methods. Another development is the partnership between DENSO and Certhon that has been established last year. This collaboration is meant to accelerate the technologies used in horticulture.
We also see that projects are becoming more and more complex, large-scale, and international. Certhon is already active all over the world: from Europe to the Middle East and from Asia to North America. Because the demand for fresh greenhouse produce is still on the rise in the North American market, Certhon works to realize a stable presence in the United States. That’s why Timo Kleijwegt and Fred van Veldhoven have joined Certhon to rejuvenate and bring in experience to serve this growing market optimally. This, combined with dedicated local people and a support team based in the headquarters in Poeldijk, the Netherlands, entrepreneurs in North America can rely on the best Certhon has to offer and 24/7 support.
Left: Timo Kleijwegt, right: Fred van Veldhoven
Turn-key greenhouse projects
For expansion of an existing greenhouse, new (indoor) facility, or turnkey set up, Certhon has all the knowledge, know-how, and technologies under one roof to enable entrepreneurs to produce local, fresh food. All in accordance with the local regulations and requirements, and the wishes of the customer. One of Certhon’s solutions is the SuprimAir greenhouse, which is a semi-closed greenhouse that provides optimal growing conditions for various crops like tomatoes and peppers, but also ornamentals like orchids.
“In fact, Certhon doesn’t just design and construct a greenhouse, but creates the optimal climate and conditions to realize the best results,” says Fred van Veldhoven, who recently joined Certhon as International sales manager. “Certhon has its own developed system to obtain a complete and updated backtrack of the climatological conditions of a particular area per hour!” continues Fred. “All available data has been brought together and presents a reliable picture of the local situation. Future developments are being forecasted and extremes are being analyzed. This way, the right facility can be calculated, designed, and built for anything, anywhere.”
The American market is probably the most dynamic and demanding in the world and the consumers are used to have access to high-quality food, flowers, and ornamental plants. “Entrepreneurs choose for the total solution approach of Certhon, so they only have to turn the key,” concludes Fred.
State-of-the-art indoor farms
Besides traditional greenhouses, indoor farming has become a professional segment that develops faster in the United States than anywhere else. In some cases, these facilities are complementary to the greenhouse, but mostly these are stand-alone setups. The legalization of cannabis production in various states in the US and Canada has boosted this development. However, more and more entrepreneurs discover the benefits of fully controlled indoor food production, just around the corner.
Also within the larger agglomeration areas where fresh food is more expensive, indoor farming is part of the supply chain. Recently, Timo Kleijwegt joined Certhon as sales manager for the US market to respond to this development. Timo: “In our Innovation Centre, we have several indoor cells that are all designed differently so we can test which systems are working better for different purposes.
One of the crops we are testing and that is very interesting for indoor farming, are strawberries. Certhon has developed a unique growing concept for indoor strawberry production, which is highly profitable. Besides all the benefits that come with indoor growing, we see enormous positive results in yield and taste of growing strawberries indoors. At the moment, the final trials are being concluded. If anyone is interested in the results, they can contact me for a one-on-one presentation.”
Certhon will be present at key events in the US and Canada to share the latest developments, including the PMA in New Orleans in October. “We are looking forward to talking to ambitious entrepreneurs there,” Timo concludes.
5 Things To Check When Comparing Lighting Designs For LED Grow Lights
As a grower, you invest in supplemental LED grow lights because they power the yield and quality of your crops.
May 17, 2021
· When you compare different lighting designs, make sure to compare apples with apples.
· These are the 5 things to check when comparing lighting designs for LED grow lights.
Eindhoven, the Netherlands – As a grower, you invest in supplemental LED grow lights because they power the yield and quality of your crops. In fact, the rule of thumb is that 1% light output equals 1% crop yield. So, it is vital that your LED lighting investment delivers the full performance you paid for.
The performance is determined by the light intensity and light uniformity of the LED grow lights you use. If the installed light intensity is lower than what has been designed, there will be less yield. If the uniformity is inconsistent, individual plants will grow and develop at different rates and there will be uneven production in your greenhouse.
Before you start
When you compare different lighting designs, make sure to compare apples with apples. This means taking 3 things into account:
1. Verify the credibility of the performance claims that manufacturers make
2. Make sure that DIALux calculation software is used for the lighting design. This calculation software is independent and commonly used in the horticulture market.
3. Check which input parameters have been used for each lighting design. It is easy to tweak the input parameters and give the impression of a more positive light level and uniformity within the lighting design. So which parameters are crucial?
Most important input parameters to check
• Is the right product specified? Check if the exact product that you have selected for your project has been used in the lighting design; with the right light output (PPF in µmol/s) and spectrum (blue/red/white/far red/…)
• Are your specific design values used like the average light level at your crop (PPFD in µmol/m2/s) and the overall light uniformity?
• What are the standard settings? The height of the grow light and crop (free height), reflection factors, and size and position of the area that is used in the uniformity calculation have an impact on the average light level and overall uniformity.
#1 Check the free height
The first input parameter to check is the free height specifying the distance between the LED module and the head of the crop. The free height can seriously impact the overall uniformity value. In case of high-wire tomato crops, with a limited free height of 1.50 to 2.50m, realizing a good overall uniformity value can be a challenge. An optimistic free height or calculating uniformity on floor level as if there is no crop will positively impact the overall uniformity value.
The free height is calculated by measuring the eventual top of the crop and the mounting height of the LED grow light.
#2 Check the reflection factors
Another important parameter to check, are the reflection factors used in the lighting plan. A reflection factor indicates the amount of light that is reflected by walls and other objects in a space. DIALux calculation software has originally been designed for indoor spaces like offices, where you will get reflection off the walls, ceiling, and floors that impact the light level on your desk. To avoid being too optimistic about the outcome, the reflection values in DIALux are set at 0% for a greenhouse lighting design, because the glass in a greenhouse does not reflect the light from the grow lights.
#3 Check the area that has been used to make light intensity calculations.
The next thing to check is the defined calculation surface. The size of the calculation area and the position of the grow lights within that area will seriously impact the average amount of active photons that reaches the surface of the crop (PPFD value in µmol/m2/s). When comparing lighting design results from different manufacturers, make sure that the calculation surface shows an equal number of maximum (peaks) and minimum (dips) light intensity values. Only then you receive a realistic average PPFD value in the lighting design.
In the below example, you will see two positions of a calculation area within the same light plan, which will generate far better average light intensity values in the B situation, because the light intensity is calculated with an area that shows more grow light (peaks), and consequently less areas with the minimal amount of grow lights, which will not represent the reality after installation
Position of measurement grid defines the outcome of average light intensity
#4 Check the size of the calculation surface
Another important factor is the size of the calculation surface that will impact the overall uniformity value. When comparing lighting design results from different manufacturers, make sure the same calculation surface has been applied.
To represent a real-life situation, a calculation for the full compartment area should be made that includes the edges of the greenhouse. In case of a typical production area, a centred area is used. You may understand that a full compartment will generate lower uniformity levels, because of the lower light intensities at the edges. So, make sure you always compare either full compartments or smaller areas.
#5 Check the used uniformity
The final parameter to check is the uniformity being used. Uniformity can be expressed in different ways. When you run the DIALux lighting design software, it provides you with different types of uniformity. When comparing lighting design results from different manufacturers, make sure the same type of uniformity is applied. For a horticulture application, we prefer to express uniformity as the average light intensity divided by the maximum light intensity, which represents real-life situations best.
In Summary
When comparing lighting designs there are lots of tweaks that suppliers can possibly make to finetune their plan. In case you want to make a proper comparison, you have to take a few parameters into account.
- Is the specified product with the right spectrum and efficiency used in the calculations?
- Is the right light level for your crop used and the right overall light uniformity?
- Are the settings comparable:
o Is the free height correctly defined?
o Are the reflection factors set to 0%?
o Does the measurement grid have an even number of light and dark spots in it.
o Are you comparing full compartment or small centered area numbers?
o And is the defined uniformity similar in the lighting designs?
Read our other blog and learn how to evaluate the performance claims of an LED grow light.
Grow with the pros
You want to be sure to get a rapid return on your investment and have all aspects of your project carried out professionally. With Signify, your project is in experienced hands. Signify is the global leader in the lighting sector and has built up a substantial track record in more than 1000 projects in the horticultural lighting market since 1995. This includes over two decades of dedicated experience developing tailor-made, LED-based light recipes that help growers speed up growth, increase yield and improve the quality of plants. With cutting-edge LED innovations at our command, we can custom-build a science-based solution for you.
Pascal van Megen is an application engineer at Signify with a background in mechanical engineering. As an application engineer, Pascal ensures that growers are provided with high-end horticulture lighting designs. He is providing internal and external training to customers and partners in the application of the Philips LED Horticulture products and systems. He acts as a consultant to customers and engineers, to drive continuous improvement of Philips LED lighting solutions.
--- END ---
For further information, please contact:
Global Marcom Manager Horticulture at Signify
Daniela Damoiseaux
Tel: +31 6 31 65 29 69
E-mail: daniela.damoiseaux@signify.com
About Signify
Signify (Euronext: LIGHT) is the world leader in lighting for professionals and consumers and lighting for the Internet of Things. Our Philips products, Interact connected lighting systems, and data-enabled services, deliver business value and transform life in homes, buildings, and public spaces. With 2020 sales of EUR 6.5 billion, we have approximately 37,000 employees and are present in over 70 countries. We unlock the extraordinary potential of light for brighter lives and a better world. We achieved carbon neutrality in 2020, have been in the Dow Jones Sustainability World Index since our IPO for four consecutive years, and were named Industry Leader in 2017, 2018, and 2019. News from Signify is located at the Newsroom, Twitter, LinkedIn, and Instagram. Information for investors can be found on the Investor Relations page.
Transparent Solar Cells Boost Lettuce Farming While Decreasing Energy Use
Researchers, who have worked with the organic photovoltaic cell company NextGen Nano, believe OSCs provide a way for greenhouse cultivation without the large energy demands traditionally associated with it
New research found transparent solar cells can help greenhouse growers generate electricity and reduce energy use while cultivating crops
29 April 2021
Greenhouse farming of lettuce can be sustainable and energy-efficient under transparent solar cells.
That’s according to a new study by a team of researchers at North Carolina State University, which suggests semi-transparent organic solar cells (OSCs) can help greenhouse growers generate electricity, reduce energy use and cultivate lettuce.
Researchers, who have worked with the organic photovoltaic cell company NextGen Nano, believe OSCs provide a way for greenhouse cultivation without the large energy demands traditionally associated with it.
Published in Cell Reports Physical Science, the research found that red lettuce can be grown in greenhouses with OSCs that filter out the wavelengths of light used to generate solar power.
This means it is feasible to use transparent solar panels in greenhouses to cover their high electricity needs while not shrinking the crop yield.
Doctor Carr Ho, Research Scientist at NextGen Nano, said: “Greenhouses are used to grow plants because they drastically increase yield in non-native climates while lowering water consumption and pesticide use compared to conventional farming.
“But greenhouse glazing has poor thermal insulation, so heating and ventilation systems need to be installed to help maintain optimal conditions. Along with supplemental lighting, this lights to large, unsustainable energy consumptions.”
Lead Image: North Carolina State University
5 Learnings For Growing Top-Quality Tomatoes In A Vertical Farm
To develop an effective high-wire indoor farm, we built on our years of know-how and experience from both greenhouse growers and vertical farms. Over the past decade, tomato production has been optimized with high-tech automation and data management
Eindhoven, Nederland – In a few decades, indoor city farms or vertical farms have become popular for producing healthy food year-round in urban environments and harsh climates. Leafy greens and herbs are the most common crops in these facilities, but growers are looking to expand to a much wider variety of vegetables and fruits. In April 2019, we began a long-term series of research studies on high-wire tomatoes at our Philips GrowWise Center. Our goal? Find the optimal high-wire cultivation strategy, light recipe and best performing tomato varieties for city farms.
Building on previous tomato trials
To develop an effective high-wire indoor farm, we built on our years of know-how and experience from both greenhouse growers and vertical farms. Over the past decade, tomato production has been optimized with high-tech automation and data management. We can use this tremendous amount of knowledge and adapt and implement the same vision and technology in an indoor farm. The same construction, irrigation and cropping systems can be applied and we can even use the same kind of bumblebees for pollination. However, we should not blindly copy every aspect from a greenhouse as there are significant differences between an indoor city farm and a conventional greenhouse.
The most critical differences between a greenhouse and an indoor high-wire system, are perhaps that the latter uses active cooling and dehumidification instead of venting and uses only LED lighting instead of mostly sunlight. It is by excluding the effects of seasonal differences in temperature, humidity and light that the optimal growing environment can be created to produce a premium product year-round.
Climate optimization, selecting the right varieties, and defining growth recipes
We conducted three trials. First, we wanted to learn from our experiences in greenhouse tomato cultivation, to see what learnings on climate conditions we could repurpose and then optimize. Second, we wanted to ensure that we were growing the best-suitable varieties for growing indoor tomatoes, so we planted 20 different varieties. To finally, in our third trial, optimize for the 5 most suitable ones to find the optimal growth recipe for indoor growing.
We equipped one climate-controlled chamber with Philips GreenPower LED toplighting linear and a single row of Philips GreenPower LED interlighting. This combination of top- and interlighting is a proven solution for a uniform vertical and horizontal light distribution within the canopy. The Philips GrowWise Control System is used to plan for the right light levels throughout the growth phases of the plants.
These are the 5 learnings from our 3 trials so far:
Learning #1: Crucial to finding the right balance between light, temperature, and yield
Growing successfully indoors is all about finding the right balance between light, temperature, and yield. Increasing the light intensities might increase the yield, but that does not happen linearly. In The GrowWise Center we can achieve up to 1200 µmol/s/m2, but plants do not use all that light equally efficient. With the Philips GrowWise control system we can optimize the light intensity to the needs of the plant and seek the optimal point where the extra yield is worth more than the extra energy input from both the light and the climate system. Hence, we do not just focus on yield maximization, but rather try to achieve the most efficient system.
To steer the plant into the right balance between vegetative and generative growth it is important to adjust the temperature accordingly. Plants can be steered into a more generative state by increasing temperature. However, overcharging could result in too generative growth. The plants will put too much energy into the fruits and overload the plant, something that will cause a dip in production later on. Growing tomatoes is like walking a tight rope: correcting too fierce when in danger of falling off one side could result in falling off the other side. In a perfect strategy, only small adjustments are needed to keep the plants well balanced. Something that is undoubtedly easier without the variable influences of the climate outside.
The trial also helped us to better understand the partitioning of energy between the heat load from the LEDs and the transpired moisture from the plants. This allows us to go beyond the optimal light-use efficiency, and rather improve the total system efficiency.
Learning #2: Strong business case in place for growing high wire tomatoes in an indoor farm
Not all tomato varieties are suitable to grow in an indoor farm and not all are of interest for this form of high-tech cultivation. Some varieties are difficult to grow in a conventional system, but they might flourish in an environment with less prevalence of disease and a more stable climate. In theory, the highest production numbers could be reached with big truss and beef tomatoes, but these are certainly not suited for every market. Lower producing cherry and cocktail tomatoes or difficult to grow ‘Coeur de Boeuf’ are usually full of taste and visually appealing and therefore can serve high-end retailers or restaurant chefs.
Learning #3: Growing the right varieties can minimize handling and labor costs
In the trials, we have successfully grown over 20 cherry and cocktail varieties to select the best performing, best tasting and most robust varieties that require very little handling and pruning. This makes them ideal for vertical farmers who may not have a lot of experience in growing a certain variety of tomato and the reduced labor costs will increase the city farm’s profitability.
Learning #4: Endless potential to steer plant growth in indoor cultivation
An important benefit inherent to indoor cultivation is that we have control over plant growth. The right light spectrum, optimal light intensities, temperatures, and CO2 levels enable you to achieve an excellent balance of fruit load and vegetative plant growth. Having control over all these growth parameters means that we can really optimize for both production and taste. Moreover, the growth recipes we have developed are reproducible. This creates a consistent cultivation environment that allows reliable yield prediction. It gives growers more flexibility and security over their production and enables them to steer yields to meet market demands. In addition, creating the right environment also provides the potential to actively steer specific characteristics, such as sugar content, acidity, vitamins, and other compounds, to meet preferences for taste and nutritional value, respectively.
Learning #5: Tomatoes can now also be grown in challenging markets
Building a farm in an area that already has plenty of greenhouses or open-field production would, of course, not be very profitable. Yet, there are many places where locally grown tomatoes are not available all-year-round because of the harsh climate or other factors. A farm in the Middle East for example makes perfect sense: lots of water can be saved and the close proximity to the consumer means that the product can be super fresh and of high quality. Our trials show that it is possible to grow fresh, tasty tomatoes in an indoor, climate-controlled facility year-round, without the use of pesticides.
Blueprint for high wire tomatoes in a vertical farm
Based on the results of the trials, we now have a blueprint for growing great tasting high-wire tomatoes in a city farm with a fully controllable environment. That opens up new opportunities to grow fresh tomatoes year-round in extremely hot and cold climates. We can advise growers on how to set up their system, and how to choose the best variety based on their customers and market. With the research baseline in place, we can now focus on trials for specific concepts and markets.
Please learn about our Philips GrowWise Center or read our other blogs on growing tomatoes.
Jarno Mooren, Plant Specialist
Jarno Mooren is a Plant Specialist at Signify. He is located at the GrowWise Research Center in Eindhoven. His work focuses on setting up and carrying out trials aimed at developing growth recipes that growers can use to efficiently grow crops with desired specifications. He carries out research on light, cropping systems, climate, and nutrients for a wide range of crops for indoor farming. In this article, Jarno shares the latest results from tomato trials carried out at the GrowWise Research Center.
--- END ---
For further information, please contact:
Global Marcom Manager Horticulture at Signify
Daniela Damoiseaux
Tel: +31 6 31 65 29 69
E-mail: Daniela.damoiseaux@signify.com
www.philips.com/horti
About Signify
Signify (Euronext: LIGHT) is the world leader in lighting for professionals and consumers and lighting for the Internet of Things. Our Philips products, Interact connected lighting systems, and data-enabled services, deliver business value and transform life in homes, buildings, and public spaces. With 2020 sales of EUR 6.5 billion, we have approximately 38,000 employees and are present in over 70 countries. We unlock the extraordinary potential of light for brighter lives and a better world. We achieved carbon neutrality in 2020, have been in the Dow Jones Sustainability World Index since our IPO for four consecutive years and were named Industry Leader in 2017, 2018 and 2019. News from Signify is located at the Newsroom, Twitter, LinkedIn and Instagram. Information for investors can be found on the Investor Relations page.
Vertical Farms vs Greenhouses: Energy and LED Costs And Differences [Part 2 of 5]
Lighting is one of the biggest expenses for a vertical farm, for obvious reasons – each layer in the farm needs its own LED “suns.” Agritecture Designer, a consulting software created by Gordon-Smith’s company, estimates the need at roughly 10 LEDs per square meter
Part 2 of 5] This is the second post in a 5-part series on the differences between vertical farms and greenhouses, and the considerations that will help farming entrepreneurs decide which is right for their situation.
Last week, in the first article of this series, we discussed the basic differences between vertical farms and greenhouses, including why location is such an important factor in the decision. In short: The location of a farm governs how much space will be available for it, and the source of the energy it will use.
That last part is what you might call “the elephant in the room” when it comes to indoor farming: Energy demand, and the main reason we care about it – carbon emissions. So let’s talk about that today.
Carbon Footprint Factors: Electricity (But Not Only)
One of the leading critiques of vertical farming is that replacing natural sunlight and open-air with LED bulbs and climate control requires electricity – lots of it.
“If the source of the energy is not renewable,” points out Henry Gordon-Smith, the CEO of Agritecture, an independent consultancy that helps clients decide between vertical farms and greenhouses, “Then vertical farms have enormously more carbon footprint than greenhouses.”
But the opposite is also true – where renewables are available, vertical farming can greatly reduce the carbon footprint of foods that are normally trucked long distances, or flown in from overseas.
For example, “Norway could be huge for vertical farming, because they just have so much cheap, renewable energy,” Gordon-Smith suggested.
When you tally the emissions reductions from shorter transport distances, the reduction in fertilizer use (fertilizer production is highly carbon-intense, and Controlled Environment Agriculture uses it much more efficiently than outdoor farms), plus the reduction in food waste, it’s clear that artificial light and conditioned air inside vertical farms are not the only carbon footprint factors to consider.
Bringing the Sun Indoors: Changing Electricity Costs for Farms
Lighting is one of the biggest expenses for a vertical farm, for obvious reasons – each layer in the farm needs its own LED “suns.” Agritecture Designer, a consulting software created by Gordon-Smith’s company, estimates the need at roughly 10 LEDs per square meter.
That’s a useful figure to get started, but given the variability between types of LEDs, a more precise estimate would be about 100 watts of LED power per square meter, according to Gus van der Feltz, another CEA industry expert. Van der Feltz is a co-founder and Board Member of Farmtech Society in Belgium, and project leader for Fieldlab Vertical Farming in the Netherlands.
With these lamps operating 12 to 18 hours a day in most vertical farms, the power usage from LEDs accounts for 50 to 65% of the electricity bill.
The exact amount depends on several factors: The relative efficiency of the LEDs used, compared with the efficiency of other systems in the farm (such as climate control), as well as the light requirements of each individual crop. (For example, the total electricity required for growing light-loving strawberries in an iFarm, for example, is about 117 kWh per month for each square meter of growing space, while arugula needs only about 52 kWh.)
But whether you opt for a greenhouse or a vertical farm, you’ll be growing local produce, which means your farm may be eligible for subsidies or another form of reduced electricity rate. Be sure to check with your local government and electricity providers.
It’s also important to note that greenhouses increasingly rely on LEDs as well, especially during winter in northern climates.
This may be only supplemental light, and it will vary with the location, seasonality, and how much light each crop requires – but greenhouses are still not as energy-intensive as vertical farms.
“It takes a lot of energy to produce food (with vertical farms),” says Ramin Ebrahimnejad, vice-chair of the Association for Vertical Farming, and an expert on multiple types of urban farming.
“But,” he adds, “most vertical farms in the developed world already use renewable energy. In the long term, that’s not going to be a challenge for the industry”.
As our electricity sources become more renewable (and as LED technology improves, as we’ll discuss below) energy-intense vertical farming will become both more sustainable – less carbon-intense – and more affordable.
And we can see this evolution happening in real-time: In 2020, Europe produced more electricity from renewables than from fossil fuels for the first time.
The Cost of LEDs for Vertical Farms vs Greenhouses
LEDs themselves are another major OpEx factor in vertical farming. And even though the cost per bulb varies widely, along with the efficiency, the LEDs in a vertical farm generally have to be replaced every five to 10 years, according to the Agritecture Designer software.
However, just as the cost and carbon footprint of electricity are becoming less of a hurdle for indoor farms, the LED situation is also evolving quickly.
An idea that’s become a modern certainty is that technology gets cheaper over time. As the environmental economist William Nordhaus studied in the 1990s, the declining cost of light over the centuries – from candles, to oil lamps, to ever-more-efficient light bulbs – has been changing the world and fueling innovation for millennia.
Something similar is happening with LEDs – up to a point. Moore’s Law famously predicted computing power doubling every year, and Haitz’s Law now forecasts that the cost per lumen for LED light will fall by a factor of 10 each decade, while the light produced increases 20-fold.
However, as Van der Feltz points out, this cannot continue forever and is more limited by the laws of physics than Moore’s Law. Currently, a well-designed horticultural LED system can be up to about 55% efficient – meaning 55% of the energy put in becomes photons, which plants use to grow, and 45% becomes heat. Fifty-five percent efficiency is already impressive when compared with incandescent light bulbs, for example, where energy input produces 5% light and 95% heat.
But still, for the purpose of CEA and especially in vertical farms, the remaining 45% of the energy that becomes heat is often – though not always – useless.
“In greenhouses,” Van der Feltz explains, “the additional heat is typically not all bad. Especially since auxiliary greenhouse lighting is mostly used in the darker and cooler winter months, and there are usually plenty of options for ventilation in case it gets too warm.”
But vertical farms heat up quickly, and as closed systems where opening a window is not an option, any extra heat from LEDs must be balanced with air conditioning or creatively repurposed. Van der Feltz says some indoor farms have been designed to divert excess heat to warm an adjacent building, for example.
So LED performance can still improve marginally, but not exponentially. Van der Feltz says experts estimate that another 25% efficiency improvement is possible, but LEDs will never be able to produce light energy out of thin air.
Whatever the limits of Haitz’s Law, it’s still true that while electricity and LED light bulbs are the most expensive part of a vertical farm today, they’re also the area where improvement is most imminent. (Innovation, and the laws of supply and demand, are constantly bringing down the costs of both, regardless of how much efficiency improvement is still technologically possible.) So operating a vertical farm should still become increasingly affordable over time.
Improved technology and reduced costs for LEDs are especially good news for the potential to grow even more crops in vertical farms, as different plants use different parts of the light spectrum.
iFarm is already a leader in the industry when it comes to research and development for expanding the crop selection available to vertical farmers. As LED technology improves, we’ll be able to take those efforts even further.
Other Energy Costs: Climate Control Needs in Vertical Farms vs. Greenhouses
The high energy costs of lighting a vertical farm are obvious, but the demands of climate control are often not as clear.
Since vertical farms are closed systems, with little to no air exchanged with the outside, they must be constantly cooled and dehumidified. About 20% of the electricity used on a vertical farm is for air conditioning, while dehumidifiers account for 10%.
The need for both of these increases with each layer added to a vertical farm, in order to counter the effects of plants transpiring and increasing the heat and humidity of the system.
In temperate regions, greenhouses can save energy by using natural ventilation, as the Agritecture Designer program explains: Sidewalls can roll up to allow cool air in, while hot air escapes through vents at the top of the greenhouse. Greenhouses can also opt for an evaporative cooling system, which is still more energy efficient than a fully climate-controlled system but does add humidity – another element to be controlled.
But it’s also important to remember that greenhouses are more sensitive to outside temperatures, and therefore, the operational expenses of climate control and/or the time needed for crops to mature will vary more than they will with vertical farms – especially in cold, Northern climates.
Next, in Part 3, we’ll discuss additional cost considerations for vertical farms and greenhouses, beyond electricity.
To learn more about starting a profitable vertical farming business, reach out to our friendly team at iFarm today!
Learn more
09.03.2021
LEDs Light the Way to Efficient Urban Farming
The global pandemic has turned the world upside down, bringing unprecedented change to the way we live, work and play. But the crisis has also paved the way for important new innovations
By Mike Martens, Senior Manager, Illumination Marketing at Osram Opto Semiconductors, North America
The global pandemic has turned the world upside down, bringing unprecedented change to the way we live, work and play. But the crisis has also paved the way for important new innovations. For instance, massive disruption to the global supply chain is now compelling many nations to ramp up their indoor and urban farming efforts to secure their food supply and feed their people.
Take the desert nation of the United Arab Emirates. Amid the ongoing pandemic, the country is experiencing something of a food crisis. That’s why it recently announced a $100 million investment in cutting-edge indoor farming facilities that can help feed its population. The effort will include the creation of the world’s largest vertical farm to help solve the challenge of local food production.
A key component of vertical farming is LED technology. In places across the globe where farmland is limited, innovative LED lighting solutions offer a major advantage because they can provide the exact light composition that various plants need for ideal growth or to develop certain characteristics. Plants can also be grown in a very space-saving manner and with considerably higher yields thanks to these lighting solutions.
LEDs are more efficient
For decades, traditional high-pressure sodium (HPS) lamps were commonly used for greenhouses and other horticultural purposes but they bring with them many challenges. They have a short lifespan and are often only suitable for top lighting in greenhouses due to their high heat output.
This is a big problem for greenhouse owners because efficient energy use is essential to economic production. In traditional greenhouse and urban farming setups, HPS lights are often inefficient. They do provide light for plants, but it is often not the most efficient wavelength range because the lamps cannot be customized to provide ideal growing conditions for different types of plants.
HPS lights often generate a lot of heat , causing considerable evaporation and ultimately limiting crop yield. What’s more, due to this heat production, HPS fixtures often cannot be placed very close to plant canopy, preventing more efficient vertical-farm setups. After all, you don’t want to singe your produce.
The good news is that innovative LED technologies can alleviate many of these concerns. For starters, LEDs produce almost no radiated heat, allowing for the light fixtures to be placed closer to plants and for plants to be stacked much higher, enabling farmers to grow more produce in smaller spaces while simultaneously reducing water costs.
LED lights also offer customizable wavelengths for different plants’ needs, allowing greenhouse operators and urban farmers to grow specific plants in their optimal conditions. For instance, LEDs can be tailored to supply light with a higher amount of red or blue content, generating exactly the wavelengths the plant, such as iceberg lettuce, tomatoes and basil need for optimal growth.
Urban farming is not a new phenomenon, but LEDs have the power to take it to the next level and more efficiently feed the world. In terms of sheer numbers, LEDs have an average lifespan of 50,000 hours compared to 8,000 hours for HPS lamps, making LEDS much more economical (and better for the environment). Indeed, vertical farms that leverage LED technology can achieve 40% energy savings compared to traditional lighting methods like HPS lamps. And due to the optimized light spectrum at 450, 660 and 730 nanometers, LEDs can provide the perfect lighting for all types of plants, allowing growers to adjust the lighting exactly to the needs of various crops.
LEDs grow healthier produce
LED are the most efficient lighting technologies to date for growing produce. They not only help produce fresh food in smaller spaces without the use of pesticides, they also make it easier for consumers in urban areas to obtain fresh and healthy food quickly, a must, considering the planet’s ever-growing population and ever-decreasing farmland.
Consumers in urban areas often rely on produce grown in faraway places that is brought to them on trucks using fossil fuels. This produce is often grown with pesticides to keep insects away, as well as fertilizers, so plants can be grown throughout the year, even in suboptimal conditions. All of these factors contribute to climate change and more polluted water sources. With horticultural LEDs, these issues can be mitigated.
LEDs also provide optimal growing conditions in any environment with minimal water waste, while reducing the need for pesticides in indoor growing environments. Communities then have the ability to grow produce closer to home, which allows consumers to learn more easily what exactly goes into their food and greatly reduces the fossil fuel usage to get produce from the (urban) farm to their tables. Urban farming has great potential to make positive impacts on local environments and communities. It’s more sustainable and decreases communities’ reliance on foods shipped in at great cost from around the globe.
LEDs light the way
As we grapple with the many concerns facing our modern society, it is imperative to invest in efficient and time-saving technology of all types. LEDs are one of these technologies. Indeed, they light the way to the farms of the future. They will have an enormously beneficial impact on agriculture by dramatically increasing crop production and putting food on every table more efficiently.
Have A Look Inside Large Plant Factory on JPFA Training Course
Plant factories, or vertical farms, are grabbing the headlines lately. Learn about them on our science-based practical online course--anytime at your convenience and anywhere in the world during the course period
Have you ever visited a plant factory with artificial lighting (PFAL)? The Japan Plant Factory Association is now receiving applications for its 2021 Online Training Course on PFALs scheduled for Feb. 18-March 11. The course gives you the privilege of taking an exclusive look inside a large-scale, commercial PFAL in central Japan.
Plant factories, or vertical farms, are grabbing the headlines lately. Learn about them on our science-based practical online course--anytime at your convenience and anywhere in the world during the course period.
Besides introductory classes on the basics of PFALs, the course has the just mentioned PFAL virtual tour and the following other special content:
A lecture on phenomics and the potential of phenotyping
Hands-on technical training on PFAL business management
Tailored, further explanations on previous-course lectures,
Operational and hygiene management, future of PFALs in COVID-19 times (2020 Workshop)
Its introductory classes cover not only PFAL principles and the basics like photosynthesis, respiration, transpiration, light environment and plant growth, nutrient solution and hydroponic cultivation, but also forthcoming technologies and PFAL business management.
The JPFA oversees a plant factory hub on the Chiba University Kashiwanoha campus in Kashiwa, northeast of Tokyo. The nonprofit organization has shifted from on-site to online training due to the coronavirus pandemic.
The first-rate lecturers of the coming course include Toyoki Kozai, professor emeritus and former president of Chiba University, who is known as the father of plant factories, and Chieri Kubota, professor at the Ohio State University.
Along with lectures, the training course, run on a specified platform, encourages participants to interact each other and gives them a chance to join an online live question-and-answer session.
The course is available for anybody interested in PFALs--not only JPFA members but nonmembers as well. If you are curious, check here and apply now.
Apply Now
For more information
Japan Plant Factory Association
https://npoplantfactory.org/en/
https://npoplantfactory.org/information/news/2120/
https://npoplantfactory.org/wp-content/uploads/2020/12/Renewed-Information-for-JPFA-2021-Online-Training-Course-on-Plant-Factories-with-Artificial-Lighting-PFALs-2021.1.20.pdf
Japan Plant Factory Association
The Japan Plant Factory Association, a nonprofit organization founded in 2010, is devoted to advancing the plant factory industry and controlled-environment agriculture in and outside Japan through academia-industry collaborations.
Its mission is to develop and disseminate sustainable plant factory systems in a bid to address issues concerning food, the environment, energy and natural resources.
The JPFA oversees plant factories on the Chiba University Kashiwanoha campus in Kashiwa, northeast of Tokyo. Also, it works on about 20 R&D projects and runs workshops and training courses.
How to Become a JPFA Member
Apply for JPFA membership here. For more information, visit the JPFA website or email us at training@npoplantfactory.org. We welcome your inquiries.
Price List for JPFA 2021 Online Training Course on PFALs
Want more online educational options?
Signify Adds Automatic Intensity Adjustment Plus Year-Long Recipe Modulations To Horticultural Controls
There’s something for both the greenhouse and the vertical farm in the GrowWise tweaks, which in some cases rely on tying to other systems’ sensors.
The Signify toplights at Belgium’s De Glastuin lettuce greenhouse automatically dim or brighten as daylight levels changes. (Photo credit: All images courtesy of Signify.)
Signify has enhanced the control system for its greenhouse LED lighting so that toplights can react immediately to changes in daylight conditions and adjust brightness accordingly. The company has also added year-long control settings intended to allow vertical farmers — but not greenhouses — to program seasonal variations in LED spectral content over a 365-day period.
Both upgrades are intended to reduce manual labor and improve overall cost efficiencies, Signify said.
Until now, greenhouse farmers could dim or brighten their Signify toplights by instructing the lights to do so via the control system, called GrowWise. Signify has now modified GrowWise software so that it can take readings from daylight sensors that are part of separate systems. GrowWise then instantly and automatically adjusts artificial light intensity emitted by the toplights, called Philips GreenPower LED.
“The lighting can be used much more efficiently since it gives us the flexibility to reduce light levels at any moment we need to,” said Wouter de Bruyn, the owner of Belgian lettuce grower De Glastuin, an early user of the new automatic feature.
Whereas Signify is known in office settings to build sensors into its smart luminaires, the GrowWise controls make use of sensors that are part of climate control systems and greenhouse management systems from companies such as Priva, Hoogendern Growth Management, and Ridder, all based in Holland.
Planet Farms’ Luca Travaglini backs up Signify’s point that prescribing a year of spectral content improves efficiency and helps keep down manual labor costs in controlled environment agriculture (CEA) operations such as vertical farms.
“The climate computer is equipped with a daylight sensor that sends actual light measurements to the GrowWise Control System so we can adapt our light levels automatically to ensure an even light level throughout the day and season,” de Bruyn said at De Glastuin, based in Kontich.
“Dynamic lighting in a greenhouse is the next step in improving the cost efficiency and quality for the cultivation process,” said Udo van Slooten, business leader, horticulture LED solutions at Signify. “It allows growers to effortlessly maintain a consistent level of light throughout the day to produce the best possible crops. The system compensates for cloudy weather and creates a more controlled growing environment for your crop.”
In another upgrade to GrowWise, vertical farmers who want to prescribe modulations in spectral content are no longer limited to 24 hours of looped recipe cycles. Rather, they can order up a year’s worth of shifts for controlled environment agriculture (CEA) operations.
The year-long programming feature is aimed at vertical farmers rather than at greenhouses because the lights that Signify provides for vertical farms support controllable spectral changes, whereas the greenhouse toplights do not. Signify refers to its GreenPower LED vertical farm lights as “production modules” rather than as “toplights.” Toplights and production modules can both be programmed for intensity over a year, but the intention of the year-long feature is oriented toward spectral content.
Compared to greenhouses, vertical farms tend to make much less, if any, use of natural light. In vertical farms, the lights are mounted much closer to the crop in stacked shelves.
One of the first users of the year-round feature is Italy’s greens and lettuce grower Planet Farms.
“Now we can easily create custom light recipes and set them to run year-round to provide the right light recipe with the right light intensity at the right time throughout the crop’s growth cycle,” said Planet Farms co-founder Luca Travaglini. “By automating our full light strategy during the growth cycle, for the whole year, we can run our operations very efficiently and keep our manual labor costs low. That makes it easier for us to maintain consistent quality as we scale up our production.”
The horticultural market is a key growth sector for Signify, especially as it maps out a strategy to maintain profits in the pandemic economy, in which last week it reported a yearly rise amid rigorous cost controls that now include a small number of layoffs. CEO Eric Rondolat is targeting a big chunk of what he has quantified as a $2 billion general horticultural lighting market by 2023.
MARK HALPER is a contributing editor for LEDs Magazine, and an energy, technology, and business journalist (markhalper@aol.com).
Elevated Vertical Farming: Vaisala Sensors And The Story of Fifth Season
“When you don’t have to worry about outdoor conditions, you have the benefit of going vertical. We can grow plants year-round in urban areas close to the dense part of a city,” said Fifth Season Cofounder and CTO/COO Brac Webb
Vertical farming is looking up – quite literally. No sun, no soil, no vast expanse of land? No problem. At least not for indoor vertical farming company Fifth Season.
“When you don’t have to worry about outdoor conditions, you have the benefit of going vertical. We can grow plants year-round in urban areas close to the dense part of a city,” said Fifth Season Co-founder and CTO/COO Brac Webb
Every minute, we’re collecting Vaisala sensor data to measure and maintain the conditions most important for plant growth and using that information to build something special.
-Brac Webb, Fifth SeasonUsing a sophisticated mix of artificial intelligence (AI), sensors, data modeling and robotics, Fifth Season’s technology tends to each plant’s individual needs at high levels of efficiency and precision. But sensors and their data play the most pivotal role. “The plants are telling us exactly what they want. We just have to adjust to that,’ said Webb. “Every minute, we’re collecting Vaisala sensor data to measure and maintain the conditions most important for plant growth and using that information to build something special.”
Background
The story of Fifth Season is very much the story of the American Dream.
The startup began with three friends and entrepreneurs: cofounders Brac Webb, Austin Webb, and Austin Lawrence. Originally founded in 2016 as RoBotany Ltd., the company was incubated at Carnegie Mellon University’s (CMU) Swartz Center for Entrepreneurship.
“We really started as a tech company and looked at the vertical farming problem at first and wondered what we can do to help solve some tech problems there,” Webb said. “Much of our evolution is due to the advances of HVAC sensors and LED lights. We already had the programming. So, we said, heck, let’s just do the whole thing.”
Fifth Season is now a 60,000-square-foot, solar-powered vertical farm in the Pittsburgh borough of Braddock, PA. The company’s 25,000 square-foot grow room is equipped with 40 different robots and has 12 levels with more than 125,000 square feet of production capacity. Compared to conventional produce, which can travel thousands of miles by truck or plane, fresh produce grown in local vertical farms need only travel a few miles to reach consumers. The company produces an assortment of leafy greens, arugula, and spinach as well as ready-to-eat salads that are sold to a local clientele including Giant Eagle and numerous other retailers. They have also launched a Direct-To-Consumer model on their website.
The company uses its small army of 40 robots to streamline almost every aspect of the vertical growing operation, including storage, retrieval, harvesting, integrated pest, and disease management, scouting, seeding, media packaging, and more, according to Webb. Humans are minimally involved in the process, mostly to coordinate the robotic army to execute specific growing recipes or other tasks – which also cuts labor costs from 40% in traditional farms to just 20%.
“We have cutting-edge technology - not using traditional methods, using more of a robotics approach - and a ton of data collection with Vaisala sensors, not only for closed-loop control but also for alerting us to changes in plant growth or the environment,” Webb said.
Industry Overview
Total control of the growing environment – 24/7/365 – in small spaces governed by known and emerging technologies are farming’s oft-cited competitive advantages over other types of farming. Vertical farming also is known for efficient resource management. For example, with its hydroponics approach, growing plants in a solution of water and nutrients, Fifth Season uses 97% less land and up to 95% less water than traditional farming.
Vertical farming attempts to take the uncertainties of agriculture – pests, sunlight, soil, etc. – and makes them controllable through various combinations of AI, artificial light, sensor monitoring, climate control systems, etc. Crops are stacked in layers or rows sometimes 20 to 30 feet high. LED lights are used by all vertical farms to create a specific light recipe for each plant, giving the greens the exact spectrum, intensity, and frequency needed for photosynthesis. LEDs offer several benefits, such as: exceptional color range, longevity, low radiated heat, and energy-efficiency. They can also be recycled and don’t contain any toxic compounds or elements like mercury. Different types of crops prefer different types of lighting. For example, leafy greens and vegetative crops prefer light towards the blue side of the spectrum; whereas fruiting and flowering crops may need something more along the red spectrum.
Vaisala Sensors
The peace of mind factor is huge. You get that from Vaisala.... I never once questioned the reading that I’m getting, or that it will be just as consistent tomorrow.
-Brac Webb, Fifth Season
So, why Vaisala? “The peace of mind factor is huge. You get that from Vaisala. If we have issues with our growing environments, all our plants can die. I mean, it could kill our business,” Webb said. “I never once questioned the reading that I’m getting, or that it will be just as consistent tomorrow. But, more than that, it was also the support we received to quickly integrate your technology into our engineering and get everything up and running fast,” Webb added. In fact, tightly controlling and monitoring light, humidity, CO2, and the temperature is critically important to Fifth Season. So, data, data, data….
“We have, gosh, probably 360 of Vaisala’s HMP110 humidity and temperature probes and 36 GMP252 CO2 probes distributed throughout the entire growing environment. It’s not just about gathering data in real-time. With post-analysis of big data, we can review the growth history of those plants and learn something about them. We may learn, for example, what we thought was the best growing environment for those plants to achieve optimal conditions for taste, quality, and yield isn’t the best after all,” Webb said. “And we can course-correct.”
Future
As the world’s population expands, projected to reach 9 billion by 2050, so too does the amount of fruits and vegetables needed to sustain it. There is only so much farmland to accommodate the increase in fresh food required for life. The U.S. Department of Agriculture, investors, and entrepreneurs alike are acknowledging vertical farming as having the potential to strengthen the global food system. And startups like Fifth Season, backed by significant venture capital, are paving the way to deliver new solutions that efficiently deliver fresh and healthy food to people.
“The more we learn, the more we can improve vertical farming,” Webb said, jokingly adding: “If only we can get to the point that the computer could taste the plant.”
The story of Fifth Season is just beginning.
“We’d like to replicate these hyper-local farms. So, it isn’t just about solving the problems of having fresh produce available in Pittsburgh and making sure we can run it here. This farm is a product that we want to be able to deploy in multiple locations all over the United States, all over the world at some point, you know. That’s our grand vision.”
For Fifth Season and Webb, there’s also an underlying humanitarian goal of vertical farming that transcends business.
“As a person and an engineer, I always like reading about how (US President) Thomas Jefferson thought agriculture and engineering are intertwined: that agriculture is humanity’s first and foremost engineering problem to solve. You’re helping create jobs in that local area and we have seen how important that is to the economy. Thanks to the technology from Vaisala, you can create an environment that is perfect for the plants and help people too.”
For more information, please Contact Us.
Download the complete Customer Story below.
Elevated vertical farming: Vaisala sensors and the story of Fifth Season
The One Thing You’re Probably Overlooking In Your Greenhouse
We often overlook the value of light in southern parts of the continent.
The cost of natural sunlight is an important thing for producers to understand because there is an economic value that they should be placing on sunlight. It’s one of the main inputs to production!
If you ask a good greenhouse operator, “What is your cost of natural gas? Electricity? Building cost per square foot? Operational cost per square foot?”, he’ll give you detailed answers.
Ask him, “What is the value of the light you receive?” and you’ll get a different response.
“…Uh, what?” he might respond.
You clarify. “The light, the sunlight. What is the value of the sunlight?
“I don’t know.” He will be taken off guard because he’s never thought about it before. Why?
Because people take light for granted. After all, sunlight is free. Why place a value on it?
But light is a “free” resource!
The cost of natural sunlight is an important thing for producers to understand because there is an economic value that they should be placing on sunlight. It’s one of the main inputs to production! If they’re placing an economic value on supplemental lighting, then they should be placing an economic value on natural light.
Why do they make that mistake? Because it’s free. Most people don’t put a value on free things.
And if a person places no value on a thing, they’re not going to use it efficiently. When something is free you don’t think about trying to use it in the most economical sense. When something is free you just use it.
Why would you try to conserve something that’s free? Why would you try to maximize the value of something that’s free? In your mind, it has no value.
This is true with sunlight. Because it’s (supposedly) a free resource, people don’t place an economic value on it and then they don’t build their model to maximize that value. The problem with this is that light does have a cost that can act as a limiting factor on your operation. This inefficiency poses a significant problem.
For instance, say you want to grow in Alaska. You want to grow year round but in the middle of the winter you might only have an hour of daylight – all of a sudden the economic value of that light becomes alarmingly apparent. Because you actually have to pay to replace it in the wintertime. So if you’re growing in Alaska in the wintertime, you’re freaking out about how you get the maximum value out of that light. You’re may choose to use red and blue LEDs instead of white because you can get more efficiency from them – even if it’s at a higher initial cost. You’re going to do everything you can to maximize the value of that resource.
We often overlook the value of light in southern parts of the continent.
And that’s why, even though light is a resource like everything else, no one actually figures it into any of their calculations, including the cost of goods sold. This mistake often limits growers to much lower production, or missing out on key observations that inform their model. (Among other things.)
In reality, the value of light is high
Note that the value and the cost of light are very comparable here. The value of something can be defined by it’s cost. Keep that in mind.
If you did think about light use efficiency, you would probably find yourself at the same destination that we did: volumetric farming, and much higher production because of it.
How to Place a Value on Light
If you don’t have light, then the easiest way to calculate it is by calculating the cost of replacing that light. What is the cost of replacing it with LEDs or HID or whatever supplemental lighting you choose?
If you do have light, then you’re probably growing in a greenhouse. In that case, you can find the cost of light by comparing the cost of growing in a greenhouse (which is how you are acquiring that light) with the cost of growing in a facility without that sunlight. (So the value of the sunlight is essentially the difference in operational cost between a warehouse of the same size and a greenhouse.)
These operating costs are going to include things like replacing a covering, heating (heating a greenhouse is always a lot more expensive), and maybe things like building permits.
Those costs can add up, and you’ll find that light is a costly resource even if you don’t think about it much. When you understand the costs of light, you will begin to use it more efficiently. You’ll start thinking about maximizing light use the same way that you maximize water and electrical and natural gas and other resources.
Initially this will result in lower overall costs, but we think you’ll find that your efforts toward efficiency will lead to even more benefits.
Once you do understand the value of your light, how do you get more out of it?
To increase light use efficiency, you first have to identify the main areas of waste and eliminate them. To do that, you start by identifying what’s happening with most of the light that enters your greenhouse: absorption and reflection.
ZipGrow Towers were designed to reflect light through the mass of towers to reduce shadowing and light waste.
Absorption is happening either when the light hits photosynthesizing plants or when it hits another absorptive surface and is either used by plants or turns to heat. Reflection happens when light hits a surface and bounces back. This is what you want, because if it’s not being absorbed by plants, then we reflect it to be absorbed by plants. (The less light energy that’s converted to heat, the more is conserved for use by your plants.)
The most obvious way to promote reflectance is to use reflective surfaces wherever possible. This doesn’t necessarily mean using silver or mirror finish, but it does mean white finishes to reflect that light. It also means that we think about growing plants on multiple planes, and arranging the production apparatus to conserve light within the greenhouse through reflection as opposed to reflecting it out of the greenhouse.
If you’re growing on a horizontal plane, know that if that light doesn’t hit a plant, oftentimes light will just be reflected back up and out of your greenhouse. When we switch the plane around so that the photons are conserved to the bottom of the mass, our absorption rates are higher, we have more plants absorbing energy rather than energy just being reflected up and out of the greenhouse. That’s the idea behind volumetric farming with ZipGrow™ Towers.
Source and Photo Courtesy of Agritech Tomorrow
Understanding The Key Tech Required In Vertical Farming
Staff Reporter Jan 25, 2021
Vertical farming involves; growing crops indoors under artificial temperature and lighting conditions. This technology focuses on increasing productivity in small places. It utilizes soil-free methods like aeroponics, aquaponics, and hydroponics. Read on to understand the main tech you need for your vertical farm.
(Photo : Valcenteu Wikimedia Commons)
Lighting systems
Covered agriculture, which is the traditional method of farming uses HPS (High-Pressure Sodium) vapor lamps. These units generate a warm light, which appears as an orange-yellow glow in areas with many glasshouses. LED technologies have evolved, becoming more energy-efficient and cheaper.
LED vertical farming lighting dictates the next generation controlled environment agriculture (CEA). While HPS lamps generate orangey-yellow light, LEDs can be designed to generate light in any color or combination of choice. Today, more LED lights are specially designed for the CEA industry.
Researchers are working with manufacturers to manufacture crop-specific lights to enhance photosynthesis, guarantee crop quality, and boost yield production. When growing crops in an indoor environment without a natural or external light source, the quality and quantity of artificial vertical farming lighting for your crops is critical.
Heating, Ventilation and Air Conditioning (HVAC)
Controlling the heating, ventilation, and air conditioning is crucial in managing a vertical farm. Remember, the HVAC can influence the yield, health, and quality of your crops. Smart regulating systems are crucial for the management and maintenance of ventilation, temperature, and humidity. Installing smart enabled HVAC systems that can be incorporated into a general control system is critical.
Nutrients
Controlled environment agriculture allows farmers to regulate the frequency, levels, and nutrients they use on the crops. Commercial nutrient mixes are not only readily available but are also easy to use for your vertical farm. However, you can improve the quality of your crops and increase production with a crop-specific nutrient mix. Research and knowledge help you produce efficient nutrient mixtures for your vertical farm.
Control Systems
Control systems audit, and manage all elements of a controlled environment. Doing so allows the farmer to make proper decisions for crop-specific growing conditions. Advanced control systems give farmers crucial data on crop health, development, and the environment.
With this data, the farmer can develop different features of the growing conditions. Further, control systems facilitate the implementation of nutrient mixes and light that can change throughout growing, light intensity, and delivery of supplementary C02 (carbon dioxide).
Future vertical farms should come with integrated control systems and inline crop monitoring systems to facilitate disease management. These components will help boost conditions, enhance energy-efficiency, and increase yield.
Growing Systems
Vertical farming involves various hydroponic systems, making soil and other growing media unnecessary. Farmers can use different substrates, as seen below.
NTF (Nutrient Film Technique)
The NTF comprises narrow troughs or channels where flowing small amounts of nutrient and water solution drains to the bottom of the troughs. This process creates a thin film. Plants are hanged over the trough in net containers. They receive small amounts of the nutrient solution often per day.
The fine nutrient film solution facilitates watering of the rear of the roots without getting soaked. The top part of the roots stays dry and consumes oxygen. The nutrient film technique is ideal for baby greens, salads, leaves, strawberries, and herbs.
Flood and Ebb System
The flood and ebb system is also known as drain and flood. It involves the use of trays filled with a nutrient solution for a few minutes before the water drains. The plant roots are swayed around the nutrient solution. Using flood like circumstances allows the plants to consume nutrients and oxygen, making them healthy and strong. The flood and ebb system is ideal for producing microgreens.
Finally
Vertical farming allows farmers to grow crops throughout the year, and this facilitates maximum crop production. This technology does not rely on the weather. You can grow your crops with the help of LED lighting. Apart from being eco-friendly, vertical farming allows you to farm within limited spaces, as is the case in cities.
Vertical Farming’s Success Depends On The Cheapest Lightbulb
More than a decade ago, microbiologist Dickson Despommier floated the idea that nations with little arable land like the UAE could become self-reliant by growing food in skyscrapers with perfectly optimized artificial light and heat
The industry promised to tackle world hunger. But all it may end up delivering for now is expensive basil and perhaps some better quality marijuana.
January 16, 2021
Abu Dhabi’s giant Yas Mall isn’t the most obvious location for embracing nature. The sprawling complex, which houses a 20-screen cinema, leads to a Ferrari-themed amusement park.
At its heart is the Carrefour SA hypermarket. There’s no natural light or soil, yet floor-to-ceiling shelves offer shoppers herbs and microgreens grown right in the store. The fresh produce is a rare sight in the United Arab Emirates, which is almost all desert and imports 80% of its food. It’s marketed as a healthy way for customers to reduce the carbon emissions that would be generated transporting their groceries.
Carrefour grows herbs and microgreens such as arugula on shelves stacked floor to ceiling.
Photographer: Christopher Pike/Bloomberg
More than a decade ago, microbiologist Dickson Despommier floated the idea that nations with little arable land like the UAE could become self-reliant by growing food in skyscrapers with perfectly optimized artificial light and heat. He called it vertical farming and argued that it could reduce world hunger and restore forests depleted by commercialized agriculture. It would also eliminate planet-warming emissions caused by plowing fields, weeding, and harvesting, as well as transportation.
In the years since millions of dollars have poured into companies trying to make Despommier’s idea a reality. Agriculture and forestry account for about a quarter of the world’s greenhouse gases, while the hunt for new farming land to feed a growing global population has exacerbated deforestation. The prospect of solving both problems has enticed all sorts of investors, from tech entrepreneurs to restaurateurs and industry giants like Walmart Inc.
A record $754 million of venture capital was invested in the industry in the first three quarters of 2020, according to PitchBook data, a 34% increase from the whole of 2019. It’s drawn particular interest in Singapore and the UAE, whose governments have set goals to increase their national food production.
Mostly Leaves
Percentage of vertical farmers who say they grow a given crop
But vertical farming will have to get a lot cheaper to deliver on its lofty aspirations. While it frees up arable land and uses 95% less water, creating the ideal conditions for growing plants ends up consuming much more energy than traditional methods. Lights need to run for 12 to 16 hours a day and heating must be used in the winter. Miguel Povedano, chief operating officer at Majid Al Futtaim Retail, which runs the Carrefour franchise across the Middle East, Africa, and Asia, says vertical farms cost 20% to 30% more than traditional ones.
Investors may not be able to live up to the hype they’ve created around the industry, and see their bubble burst before they have a chance to prove themselves, says Michael Dent, an analyst at IDTechEx. “If people are expecting world-changing progress and they don’t see it in the first two or three years — and what they see is high-quality salad — there’s a chance they might pull out their investment on the field and move on to the next thing.”
His analysis shows that most vertical farmers focus on herbs and salad greens because of their rapid and simple crop cycles. Microgreens in particular are popular with consumers concerned with healthy eating, rather than in deprived areas. They’re also more likely to grow herbs like cannabis than higher-calorific squashes or melons, which need more energy and water.
A migrant worker adjusts lettuce inside an indoor hydroponic farm operated by Green Container Advanced Farming LLC (GCAF) in a Carrefour SA grocery store in Dubai, United Arab Emirates, on Monday, Nov. 9, 2020. Photographer: Christopher Pike/Bloomberg
Rather than feeding the world’s poor with high-calorific foods, the microgreens and herbs grown by indoor farms are only going to be an option for the world’s wealthy elite for many years to come. Vertically farmed produce is far more expensive than conventionally farmed goods and even most organic produce, Dent found. For example, New York-based Bowery Farming’s indoor-produced kale mix is almost three times more expensive per pound than Whole Foods Market’s baby kale option, and its cilantro is more than five times more expensive than its Whole Food’s equivalent.
Emerald Technology Ventures investor Gina Domanig says she’s more interested in backing technologies that can reduce energy costs than the farms themselves. She compares indoor farming to desalination technology — the process of removing salt from seawater to provide fresh drinking water to people in water-stressed countries such as Israel.
“When desalination came out, everybody said it’s the holy grail for freshwater,” she says. “But desalination is really energy-intensive.” Vertical farming “might be an interesting thing” if there are technologies to make it less energy-intensive, she says, but right now “it’s not economic or environmentally sound in all areas.”
Salad greens require less energy and water to grow indoors than higher calorific foods.
Photographer: Christopher Pike/Bloomberg
One option to cut costs is solar power, which has become the cheapest source of electricity in many parts of the world. In Germany, Farmers Cut has developed a combination of solar power plants and batteries so it pays less for power than it would connecting to the country’s grid, says Chief Executive Officer Henner Schwartz. The cost of storing energy can be as low as 10 or 11 euro cents per kilowatt in Germany.
“The energy issue is the key thing you need to crack,” he says. “We’re not claiming we can do carrots or watermelons any time soon at competitive prices, because it’s just not possible.”
In Abu Dhabi, Carrefour is trying to find a lightbulb supplier who can reduce its power use by as much as 65%, according to Povedano. “The kilowatts consumed in electricity is the major handicap,” he says. “It’s not only what you, as a company, want to do. It’s how you get the customer to substitute imported products for this technology, and the key is that it needs to be really affordable in terms of price.’’
— With assistance by Agnieszka de Sousa
Lead photo: LED lighting at an indoor hydroponic farm inside a Carrefour SA grocery store in Dubai.
Photographer: Christopher Pike/Bloomberg
SCOTLAND: Vertical Farming Research Gets Government Funding
EFFORTS to develop vertical farming technology are to get a share in £90million of UK Government funding allocated as part of its drive to get agriculture to 'net zero' carbon emissions by 2040
January 7, 2012
Political Affairs Editor
Light Science Technologies works with growers involved in vertical farming to provide solutions for controlled environment agriculture
EFFORTS to develop vertical farming technology are to get a share in £90million of UK Government funding allocated as part of its drive to get agriculture to 'net zero' carbon emissions by 2040.
Derby-based company Light Science Technologies is one of just 23 feasibility projects which will benefit from this cash pot from the UK’s innovation agency, Innovate UK, as part of its 'Transforming Food Production' challenge.
In partnership with Nottingham Trent University, LST will be leading the project to develop a growing sensor and transmission node for vertical farms over the next six months.
It is hoped that this ‘all in one’ indoor farm sensor will enable farms to monitor and control their environment by measuring key areas including light, water, air, temperature, humidity, oxygen, and soil to ensure optimal plant productivity and yield.
CEO of LST, Simon Deacon, said: “This is an especially important boost to our business. To be selected by Innovate UK is confirmation of the urgent need for more sustainable, productive, and cost-effective solutions in farming. Investment in UK technology and innovation in this sector is crucial in achieving a better approach to agricultural production and reducing emissions.”
Innovate UK executive chair Dr. Ian Campbell added: “There are many innovative projects in our latest feasibility competition showcasing ideas for improving productivity and cutting emissions that range across the whole agricultural sector, from arable to livestock, to sensor technology, and to new biopesticides. Our funding and support for these projects is ongoing.”
Who Will Win In Indoor Agriculture?
According to Allison Kopf, CEO of Artemis, there are five ways big players will enter indoor agriculture. "The indoor agriculture (both greenhouse and vertical farming) market is one of the fastest-growing industries
According to Allison Kopf, CEO of Artemis, there are five ways big players will enter indoor agriculture. "The indoor agriculture (both greenhouse and vertical farming) market is one of the fastest-growing industries. Big companies in agriculture and technology are trying to figure out ways to capitalize on the rapid growth of the industry."
"Artemis, the leading software infrastructure company in the industry, which allows us to have a front-row view of how the industry is growing and what the industry needs," says Allison. "Our market has historically been fragmented, where legacy companies have been growing for decades and new players have emerged more recently with innovative models to stake their ground as market leaders. Most of the growers are trying to displace traditional field-grown commodities and increase domestic (i.e. in their local country) production of fresh produce; and we’re seeing this shift, as well."
Allison says that in the 1990s in the United States, the number of tomatoes consumed grown in greenhouses was negligible. Now, only 20 years later, close to 40% are grown indoors. This shift isn’t just happening with tomatoes, it’s happening with crops best suited for indoor growth, such as lettuce, herbs, cucumbers, peppers, and increasingly berries.
"In this industry, unlike more traditional commodity markets, we have no dominant suppliers (inputs, chemicals, finance, technology) yet. Bigger companies have largely left the market open for smaller specialized companies and startups. But this is about to change. The indoor market has shown it’s a lasting and major component of our agricultural supply chain and someone will enter this market with a goal of winning. So, who will it be?"
"I believe the winner will own one or more of the areas below," says Allison.
Data
Companies who understand grower workflow, farm financials, operational data, and biological data will have a distinct advantage in the battle for the market. This creates an opportunity for folks like lighting, breeding, climate control, greenhouse manufacturers, lenders, and others.
According to Allison this isn’t just about getting closer to the farmer, it’s also an opportunity to develop technologies faster and to have commercial R&D capacity at your fingertips. "Lighting, for example, is one of the most impactful components for growing indoors. Yet, lighting companies have no access to yield information or quality information from the growers."
With access to on-farm information, lighting can become proactive and intelligent, rather than the PLC technology of the past. Signify and Osram are already leaders in horticultural lighting and are likely in a strong position to start offering intelligent lighting solutions. "Watch out for breeding companies here too. Unfold recently launched with $30m in funding from Bayer to breed indoor crops. I would expect others like Syngenta and Rijk Zwaan to follow with similar initiatives," Allison affirms.
Finance
There is an estimated $20 billion gap in project finance over the next 3-5 years for greenhouse and vertical farm construction in the United States alone. Agricultural companies who have lending capabilities, like ADM, Bunge, Cargill, Dreyfus, and others will find indoor agriculture opportunities less risky from a growing standpoint than traditional commodity investments. Lenders will need to get comfortable with the relationship-heavy buying market and the lack of offtake contracts in produce but should be able to underwrite with growers who sell to known retailers, like Costco, Walmart, and Target.
"Many growers also have a need for an operating line of credit, often needing to buy in bulk for consumables like seeds, growing media, and chemicals to obtain better pricing. With some buyers, growers face long receivables periods, which also hurt operating cash flow," says Allison.
Ultimately, legacy agriculture companies who lend to agricultural producers will win by creating financial products for the indoor agricultural space and by partnering with the technology producers who can help de-risk the investment. This opportunity will open up billions of dollars in new revenue for someone on a relatively short timeframe.
Traceability
Product recalls and supply chain blind spots hurt everyone in the ecosystem. Bigger agricultural companies have started adding traceability to their strategic plans. Many are testing out blockchain-based technologies. Allison says that others are focused on digital workflow platforms. For the most part, companies haven’t yet figured out how to stretch all the way back to the farmer and this is where the most opportunity lies with indoor agriculture, in particular.
Because indoor agriculture is more predictable, companies who can track product from input to crop to finished good and all the way through the supply chain will have a critical advantage over others. Retailers like Walmart and Target are making this a priority and have the potential to disrupt their supply chains dramatically with indoor agriculture.
"Let’s say Walmart partnered with indoor producers for 100% of their salad greens, tomatoes, cucumbers, peppers and berries. While implementing this, they set traceability standards for producers and required compliance with those standards. This would not just ensure safe products that are normally high-risk for consumers, it would also enable stable year-round supply of products (with accurate forecasting) for Walmart and would lay the groundwork to move the needle dramatically on sustainability. This means less food waste, more efficient production, stable year-round products, safer, and more sustainable production," says Allison.
It’s not just retailers who can set the bar when it comes to traceability. Large technology companies like Schneider Electric who have their technology in the hands of all the components of the supply chain, from grower to retailer, are also in a unique position to offer end-to-end traceability products.
Consumables
Consumables are another exciting opportunity for more traditional players entering the indoor agriculture market. Today, growers buy products from many individual suppliers. This drives the price up and makes reliability difficult. If one supplier is out of a product, growers are forced to buy new untested products or find another supplier on short notice.
Large greenhouse growers are often importing products from other countries and buying in bulk just to try to reduce price. And there’s a severe lack of transparency for both pricing and performance. Because the industry is moving so quickly, growers are left to buy based more on marketing claims than on actual performance.
Allison adds: "Indoor growers spend a lot of money on inputs each year and are willing to do so because quality has a direct impact on pricing. This is a drastically different approach from traditional commodity markets where yield is the prime, if not only, driver for financial performance. Because of this, growers tend to pay a premium for inputs to impact not just yield but quality as well."
Farmer’s Business Network has created a marketplace to solve for exactly this type of challenge in the inputs space. This market is ripe for an offering like this. Large chemical companies like OCP and ICL should also be paying attention to this market as specialty products will likely emerge as one of the largest product categories over the next few years.
Digital workflow
Companies like Trimble, John Deere, Syngenta, and Corteva have started making inroads in digital workflow products. None of the products designed for workflow in the field cover the workflow of indoor agricultures.
"In indoor agriculture, you need to couple the traditional cultivation processes and biology of growing with a manufacturing mindset. In indoor agriculture, the growth times are dramatically shorter than in field, so the challenges are more aligned with a factory. You’re thinking about how to manage space, time, and throughput on a continuous basis. It’s just-in-time inventory management," Allison states.
Understanding this workflow is critical to all of the other items listed above. This is what drives proper data collection, ensures traceability, and enables models like financing or a consumables marketplace. Companies who have a deep understanding of inventory management, like NetSuite, Sage, SAP, and Microsoft might do well capitalizing on this new industry. Other agricultural companies who also work in the construction and manufacturing space, like Trimble, might also win here.
For more information:
Artemis
Nathalia Delima
ndelima@artemisag.com
www.artemisag.com
Publication date: Mon 4 Jan 2021
Author: Rebekka Boekhout
© VerticalFarmDaily.com
Valoya Appoints A VP Sales North America
Valoya continues its growth trajectory with the addition of VP Sales North America, Mr. Wes Eaton. With extensive experience in horticulture and business development, Mr. Eaton will be tasked with driving Valoya’s growth in the North American market even further
Valoya continues its growth trajectory with the addition of VP Sales North America, Mr. Wes Eaton. With extensive experience in horticulture and business development, Mr. Eaton will be tasked with driving Valoya’s growth in the North American market even further.
Eaton’s horticulture industry experience is extensive, and his track record is impressive. Having worked in sales of two horticultural LED lighting companies he has a deep understanding of the horticulture lighting applications as well as the competitive landscape in North America. His experience prior to this includes working as a controlled environment agriculture consultant and developing meters and sensors for fertigation and control systems. He thus brings a deep understanding of the market and growers’ needs to the company.
In this role, he will be responsible for driving sales in crop science, cannabis cultivation, vertical farming, and greenhouse applications. Additionally, he will further develop Valoya’s North American reseller network within the cannabis market, as well as establish a local team. In meeting Valoya’s ambitious growth goals he will closely collaborate with existing customers, research partners, and distributors, to enable wider access to Valoya’s high-end LED solutions within the N.American market.
“Valoya’s ongoing commitment to deliver research-based, high-end lighting solutions is commendable. I am excited and honored to join the team and empower growers across North America to drive their plant performance to industry-leading results” says Eaton.
"We have been operating in North America since 2011 and it has always been a very important part of our business. Wes will build on this foundation to take us to the next level with his excellent experience and in-depth insight of the market", comments Mr. Lars Aikala, CEO and Co-Founder of Valoya.
Contact Mr. Eaton at – wes.eaton (at) valoya.com
About Valoya
Valoya is a provider of high-end, energy-efficient LED grow lights for use in crop science, vertical farming, and medicinal plant cultivation. Valoya LED grow lights have been developed using Valoya's proprietary LED technology and extensive plant photobiology research. Valoya's customer base includes numerous vertical farms, greenhouses, and research institutions all over the world (including 8 out of 10 world’s largest agricultural companies).
Additional information:
Valoya Ltd, Finland
Tel: +358 10 2350300
Email: sales@valoya.com
Web: www.valoya.com
Facebook: https://www.facebook.com/valoyafi/
Twitter: https://twitter.com/valoya
CANADA: Sustainable Agriculture With LED Lighting
GoodLeaf opened it’s fully commercialized, a state-of-the-art vertical farm in Guelph in 2018. This after many years of research at its pilot farm that opened in Truro, Nova Scotia in 2015
11-12-2020 | Philips Lighting
CANADA, Ontario, Guelph- GoodLeaf opened it’s fully commercialized, a state-of-the-art vertical farm in Guelph in 2018. This after many years of research at its pilot farm that opened in Truro, Nova Scotia in 2015.
We wanted a partner that could help us scale the business. ''
-Jeff McKinnon, Chief Financial Officer and Vice President | Photo Courtesy of Philips Lighting
The Challenge
For GoodLeaf it’s all about sustainability. The facility incorporated innovations to enable the use of sustainable farming practices to execute on expectional product quality. With lighting being a primary component, GoodLeaf had specific needs they expected from a lighting solution and provider. The envisioned lighting solution needed to provide scalability whilst being energy efficient. GoodLeaf was looking for a true partner.
The LED lighting solution
“We’ve been using the Philips products since Generation one back in 2013; we did a lot of testing against the T5 light bulb. The Production Module Gen 1 performed well, they held up over time compared to competitors, using them ever since”, says Jeff McKinnon, CFO and VP at GoodLeaf. Over time GoodLeaf worked with 12 different providers of LED lights but in Signify found the partner they were looking for to move forward and to scale their business.
For their 45000 SQF multilayer growing facility in Guelph, Goodleaf installed Philips GeenPower LED production modules. The light recipe was designed in collaboration with the Truleaf design team and engineers together with the plant specialists of Signify. The installed lighting system delivers optimal lighting uniformity.
Benefits
As a branded producer, GoodLeaf Farms produces and packs fresh, nutritious, and pesticide-free micro and baby greens year-round for Canadian consumers. They expect to grow and harvest approximately 1 million pounds of fresh produce per year at their automated growing facility in Guelph. Plant specialists of GoodLeaf and Signify meet monthly to discuss optimizing their crop growth recipe. As part of the partnership, GoodLeaf has greatly improved the predictability of its fresh produce. In addition, Signify and GoodLeaf worked together to obtain a sizable utility rebate from the company’s hydro provider in Ontario. McKinnon said, “The partnership with Signify has been very advantageous to GoodLeaf. We will work with them on a go-forward basis and very much look forward to that”.
GreenPower LED Production Module Static Grow Light
A static module for multilayer applications with the ideal light recipe for higher yield, better quality, higher propagation success rates, and year-round production. Suitable for multilayer, indoor cultivation of leafy greens, microgreens, and herbs.
Source: Philips Lighting
Header photo: Screenshot from GoodLeaf Farm video on youtube