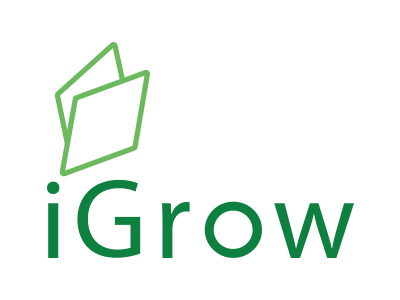
Welcome to iGrow News, Your Source for the World of Indoor Vertical Farming
Why Lettuce Greenhouse Sector's Growth Is Focused In The U.S.
Greenhouses for lettuce and leafy greens are being built at a rapid pace across the U.S. In contrast, in neighboring Mexico there is no similar greenhouse production and in Canada there is very little — the primary exception being 11-acre Whole Leaf Farms located in Coaldale, Alberta.
By Peter Tasgal
August 10, 2021
Greenhouses for lettuce and leafy greens are being built at a rapid pace across the U.S. In contrast, in neighboring Mexico there is no similar greenhouse production and in Canada there is very little — the primary exception being 11-acre Whole Leaf Farms located in Coaldale, Alberta.
Based on my research, the primary driver for this U.S. phenomenon is investor comfort in making U.S.-based investments in leafy greens greenhouses, which are more expensive to build compared to tomato, cucumber and pepper greenhouses.
For example, AppHarvest’s latest tomato greenhouse is expected to be 63 acres and valued at $139 million — just over $50 per square foot. In contrast, Bright Farms’ 280,000-square-foot leafy greens greenhouse in North Carolina cost $21 million, or $75 per square foot. Gotham Greens built a 100,000-square-foot leafy greens greenhouse in Providence, Rhode Island, that cost $12.2 million, or $122 per square foot.
In addition to investor interest in the U.S. market, other potential factors affecting this phenomenon include:
Temperature variance;
Pricing certainty;
Equilibrium capital leading the charge; and
Generational knowledge in Canada.
Temperature variance
Lettuce and leafy greens perform best at cooler temperatures, up to 70 degrees Fahrenheit. Tomatoes, cucumbers and peppers, in comparison, grow best at temperatures in excess of 70 degrees Fahrenheit.
As the U.S. has a more moderate climate than either Canada or Mexico, a band of greenhouses across the U.S. takes advantage of the more temperate climate. Historically, leafy greens greenhouses have been built in the middle and upper sections of the U.S. However, boundaries have moved. Revol Greens, for example, has a 10-acre greenhouse in Minnesota and is expected to build a 20-acre greenhouse in Austin, Texas, to be completed in 2022.
Historically it has been more costly to keep a greenhouse cool rather than to heat it. However, alternative sources of energy and energy pricing incentives in parts of the southern U.S. have made it increasingly cost competitive to build greenhouses in this area.
Pricing certainty
The cost to build a leafy greens greenhouse is more than a tomato, pepper or cucumber greenhouse on a per square foot basis and on a per pound basis. As a reference, the cost of AppHarvest’s tomato greenhouse is approximately $3 per one year’s production of pounds of tomatoes. In comparison, Bright Farms’ recent leafy greens greenhouse is over $10 per one year’s production of pounds of lettuce and leafy greens.
This large cost structure variance requires greenhouse-grown lettuce to be priced at a premium. In contrast, greenhouse-grown tomatoes can and are priced directly with field-grown tomatoes. In the U.S. today, greenhouse-grown tomatoes make up the majority of fresh tomato sales.
The risk for an investor in a premium product is demand fluctuation. Economic and other market conditions will have a greater effect on premium product demand compared to product with more commodity-like traits.
Equilibrium Capital leading the charge
Equilibrium Capital is a leading investor in the North American controlled environment agriculture sector. It closed its second fund (CEFF II) this past month, with a capacity of $1.022 billion. Its first fund, CEFF I, had a capacity of $336 million. Recent investments made by Equilibrium include:
AppHarvest: $91 million non-dilutive investment to support the building of its second tomato greenhouse in Kentucky.
FINKA: Expansion capital for the Mexican greenhouse company, which operates tomato, pepper and cucumber greenhouses, the product of which is primarily sold into the U.S. and Canada. This was Equilibrium’s first investment outside of the U.S.
Little Leaf Farms: $90 million of debt and equity financing for the company, which is currently building a lettuce and leafy greens facility in Pennsylvania and is expected to follow with a facility in North Carolina.
Revol Greens: $110 million of debt and equity capital to support its building of a large lettuce and leafy greens greenhouse in Texas.
FINKA is Equilibrium’s only investment outside of the U.S. to-date.
Generational knowledge in Canada
According to the Ontario Greenhouse Vegetable Growers’ website, the organization formed in 1967 has “220 members who grow greenhouse tomatoes, cucumbers and peppers on over 3,000 acres.”
Two of the largest growers in Canada, Mastronardi Produce and Mucci Farms, have invested primarily in building their current greenhouses. To the extent each has branched out, it has been primarily to berries and eggplants. Mastronardi and Mucci have little to no owned lettuce and leafy greens production across North America.
Of note, in 2019 AppHarvest entered into a Purchase and Marketing Agreement with Mastronardi, under which “Mastronardi will be the sole and exclusive marketer and distributor of all tomatoes, cucumbers, peppers, berries and leafy greens” at its Morehead, Ky., facility (currently producing only tomatoes).
Per the 10-year agreement, Mastronardi has a right of first refusal for any additional facilities established in Kentucky or West Virginia. The take-away is Mastronardi is willing to distribute and market greenhouse-grown leafy greens, venturing a reputational risk, but has not yet chosen the investment risk of operating its own greenhouses.
Speaking to the OGVG, most greenhouse operators in Ontario have chosen to put their resources into products they already know. When asked specifically about lettuce and leafy greens, OGVG said the cost to build this type of greenhouse is very expensive per unit of output.
Recap
Some of the most seasoned greenhouse operators in North America are growing a range of produce types in the Ontario, Canada, area largely focused on tomatoes, cucumbers and peppers.
Each of these products grows best at higher temperatures than lettuce and leafy greens. Canadian operators who have been in the business for generations are potentially willing to distribute and market leafy greens, yet they have not been willing to make significant investments in the area.
While leafy greens were once only grown in the Northern parts of the U.S., Revol Greens, backed by Equilibrium Capital, is building one of the largest greenhouses in Texas. Equilibrium Capital, the “smart money,” has only invested in U.S. CEA companies to-date. The exception is FINKA, which operates in Mexico but sells exclusively to the U.S. and Canada.
Based on my research, until lettuce and leafy greens greenhouse production can be priced competitively with field-grown product, it will continue to be a U.S. phenomenon. At least until that time, Canadian and Mexican operators will leave greenhouse lettuce and leafy greens production to U.S. operators.
Peter Tasgal is a Boston-area food agriculture consultant focused on controlled environment agriculture.
Lettuce: Meet The Salad Kings of SA
Back home in East London in 1978, he made the decision to become a farmer, an option that was met with criticism from family and peers who did not have farming backgrounds.
By Glenneis Kriel
August 6, 2021
Not knowing what to do after finishing his military service back in the 1970s, Michael Kaplan set off to work on a kibbutz in Israel, where he was exposed to banana, dairy and chicken production.
From there, he backpacked through Europe, and was particularly impressed by the new technologies that farmers in the Netherlands were using to protect their crops and improve production efficiencies.
Back home in East London in 1978, he made the decision to become a farmer, an option that was met with criticism from family and peers who did not have farming backgrounds.
“My mother, Ethel, was a doctor and my father, Lewis, a lawyer, so they thought I was completely bonkers when I told them I wanted to farm,” recalls Kaplan.
In pursuit of his dream, he wanted to study agriculture at the Elsenburg Agricultural
Training Institute in the Western Cape, but entries had already closed by the time he applied. So he began working at what was then the English Trust Company farm in Stellenbosch, thanks to an introduction from his childhood friend, Bruce Glazer, who already worked there.
Dew Crisp was co-founded by childhood friends Michael Kaplan (left) and Bruce Glazer.
“It really was a case of being in the right place at the right time, as the English Trust Company was one of the first to introduce farming tunnels in South Africa.
“They produced tomatoes using the nutrient film technique [NFT] and experimented with the gravel flow technique [GFT] to grow butter lettuce and celery,” says Kaplan.
These hydroponic techniques, he explains, are similar in that both entail the circulation of a nutrient solution in a closed system. The difference is that with GFT, gravel is used as a growth medium, whereas, with NFT, plants are suspended and their roots exposed.
Early days
Kaplan worked at the English Trust Company for two years. He then learnt that the Joburg Market sold up to three times more vegetables than its Cape Town equivalent.
Deciding it was time to spread his wings, he drove up to Johannesburg, where he began looking for a business partner and land on which to grow his own produce.
“My mother lent me R10 000, which I used to rent land near Heidelberg [about 50km south-east of Johannesburg] and produce celery under 2 000m² of nets using GFT,” says Kaplan.
In 1981, Heidelberg was hit by a severe snowstorm. It destroyed almost all of Kaplan’s infrastructure, but he managed to save most of the crop and used the income from the sale to rebuild his operation.
“I kept costs low by doing almost everything myself, and using the income to grow the operation, reaching 8 000m² by the third year of production,” recalls Kaplan.
In his fourth year of operation, he started looking for land closer to the Joburg Market and with more favourable production conditions.
“These are actually two of the most important prerequisites for farming success; you need to be close to the market, and farm in a region where the climatic and production conditions are suited to the crop you want to grow. I learnt the hard way that the Highveld is unsuited to salad production in winter,” he says.
Financing
With a clearer idea of what he required, Kaplan bought land near Nooitgedacht and applied to the Land Bank for a loan.
Being unfamiliar with hydroponic production, the bank declined his application, but Kaplan managed to secure a loan from First National Bank at an interest rate of 26%. Fortunately, the market was far less competitive and demanding in those days, which enabled him to repay the loan quickly.
“It would be almost impossible to accomplish the same today; land, labour, infrastructure and production costs are exorbitant. And you buy everything in dollars and euros but get paid in rands,” he says.
Costs are driven up even further by international production standards and auditing programmes such as GlobalGAP and HACCP, which are required to supply most markets today, while market access is complicated by retailers and big buyers demanding huge supply volumes all year round.
An impressive growth path
In the intervening years, Glazer had studied agriculture at Elsenburg and thereafter also worked on a kibbutz in Israel. On his return in 1984 he bought a farm near Kaplan’s, and two years later the two decided to amalgamate their businesses to create better economies of scale.
The new company was called Dew Crisp. To add value to their produce, they sold ready-to-eat lettuce in pillow packs, a market they dominated for over six years.
Since then, Dew Crisp has grown into one of the largest value-added salad suppliers in South Africa, expanding their geographical footprint over time to lengthen their production season and mitigate climate and production risks.
Today, they have 10ha under production in Muldersdrift, 200ha near Bapsfontein and 140ha near Philippi, as well as processing plants in the West and East Rand of Gauteng and in Franschhoek in the Western Cape.
Dew Crisp also sources produce from between 15 and 20 selected farmers across geographically diverse regions, some of whom have been supplying the business for over 25 years.
The company’s empowerment arm, Rural Farms, supports and sources produce from five previously disadvantaged smallholder farmers.
In 2009, Agri-Vie, the Africa Food & Agribusiness Investment Fund, bought a 49% share in Dew Crisp, which enabled Kaplan and Glazer to grow the business and place greater emphasis on financial administration and corporate governance.
“We realised that it wasn’t enough to simply follow the market; we had to create our own destiny by becoming market leaders.
“To achieve this, we needed to be innovative and have a really good understanding of consumer trends. We’ve introduced many firsts on the market,” says Kaplan.
Glazer and Kaplan have also drastically diversified their market risks by supplying all the major retailers, various prepared-meal manufacturers such as the Rhodes Food Group, and food service companies such as KFC, McDonald’s, Nando’s and Burger King.
Production
Dew Crisp’s produce is grown under nets, in plastic tunnels and in open fields.
“Tomatoes, English cucumbers and peppers don’t like water or cold [air] on their leaves, so we generally produce them under plastic,” says Kaplan.
Shade nets are used in the production of salad vegetables, as these are sensitive to sunlight, heat and wind. The nets also protect against hail and bird damage while reducing the impact of rain by breaking up the droplets. In addition, they help to absorb heat and keep the production area cool.
Open-field production is highly seasonal and limited to hardier vegetables such as sweetcorn, onions and cabbage.
Most of the produce is grown in hydroponic systems, where the plants are supplied with nutrients via a nutrient solution. In most cases, Dew Crisp uses closed hydroponics (recycled water).
“Closed hydroponics is used for salad production in GFT, whereas open hydroponics is used in the production of tomatoes and cucumbers, as they are really sensitive to diseases that might spread with the water. For this reason, each of these plants has access to its own dripper,” explains Kaplan.
Sawdust and coco peat are used as growth mediums in the open hydroponic systems.
“Some farmers sterilise these mediums to reuse them, but I prefer using them only once to prevent disease outbreaks. We do, however, reuse the gravel in the open gravel system, after cleaning it with a chlorine solution at the end of each production cycle.”
In the same way, the crops that are planted in the soil are rotated to prevent a build-up of diseases.
Water quality largely determines the success of a hydroponic system, so a farmer should not even think of using it if the irrigation water is of poor quality or has high levels of chlorine or sodium. Water can be pretreated to rectify mineral imbalances, but this drives up costs. Water should, in any case, be filtered before use.
Dew Crisp has worked with scientists for years to refine its plant feeding programmes based on the nutritional requirements of various crops during different development phases.
“The trick is to supply exactly what the plant needs. An undersupply leads to plant deficiencies, while an oversupply is wasteful and might result in damage to the system and plants. To prevent this, we constantly monitor the recycled solution, plant growth and climatic conditions, and tweak the nutritional programme accordingly,” says Kaplan.
Achieving this with open-field crops is even more challenging due to soil differences. Soil, nonetheless, has a higher buffering capacity and is thus more forgiving.
The farm does not employ any climate-control technology because of its high capital and running costs. Instead, tunnel windows are opened and closed to augment ventilation and reduce the interior temperature.
Even without climate-control technology, production is energy-intensive, as the water has to be recycled continuously. Back-up generators are a necessity, as most of the salads will die within hours if water flow is interrupted.
Advice
Farming, and especially farming under protection, has become highly specialised over the years, with low profit margins leaving little room for error.
“In the past, when a buyer ordered a hundred frilly lettuces, we could plant 150 and it didn’t really have an impact on the bottom line. These days, production costs are so high that we plant to order and programme,” says Kaplan.
The shift has also made it increasingly important for farmers to make use of consultants to fill their knowledge gaps.
“If you want to be successful today, you need to surround yourself with people who are better skilled than you are in their respective jobs.”
Email Michael Kaplan at mkaplan@dewcrisp.com.
Lead Photo: Shade nets are used in the production of salad vegetables, as these are sensitive to sunlight, heat and wind. Photo: Dew Crisp
Where All Grow Corn, This Farm Grows Lettuce
The farm that I got to visit was True Food Farms, an 8600 sq. ft hydroponic farm based in Stanton, Iowa
by Shubham
About 5 years ago in 2016 when I landed in Iowa, I couldn't fathom the magnitude of corn farms that I saw here stretching in all the directions, as they disappeared into the horizon. It took me a few months to normalize and make peace with Iowa, the heart of the corn belt. So a week ago, when I came across a local farmer growing lettuce, I knew this was something different.
Visiting an indoor farm has been at the top of my bucket list ever since I claimed the title of being an indoor farming armchair expert. Writing a few blogs, and reading countless articles about the topic acting as my credentials. As all the big guns of the indoor farming industry are either on the west coast in San Francisco, or are spread throughout the east coast. A few of them are scattered through the Midwest, but none of them near me. So when an opportunity came knocking on my door, here in southwest Iowa, I couldn't let it pass.
The farm that I got to visit was True Food Farms, an 8600 sq. ft hydroponic farm based in Stanton, Iowa. It is run by Darren Barkman who originally hails from Canada and grew up on a farm in Manitoba. Darren, who has been farming indoors for the last 20 years was gracious enough to spend an hour of his time giving me a tour of his farm.
How did you decide to grow lettuce in Iowa? I moved with my family to the Stanton area about 5 years ago and was in the indoor farming business in Tennessee before that. The different varieties of lettuce we grew there are more popular in the urban areas. Around this region, however, Iceberg and Romaine are the only two popular varieties, so the market has tremendous potential for the other varieties that we grow. Also, the traditional lettuce is typically grown in the warm climate of the Salinas Valley in California. Once harvested, these lettuce heads travel 1500 miles on a truck taking anywhere between 5 and 10 days to reach the store shelves in Iowa.
True Food Farms is changing that with hydroponically grown lettuce that hits the local grocery shelves within 24 hours of harvesting. Also, we are bringing several different varieties of lettuce like Butterhead, French Crisp, Frisee among others. It will help the locals experience True Food that is clean, healthy, and safe to eat and is grown year-round locally. It doesn't get any better than this.
How would you grow through the winter months?
A hydroponic greenhouse crop doesn't need soil to grow and needs 95% less water than a traditional farm. Being in Iowa that has a gloomy winter for about 6 months, where the sun doesn't show up most of the time between November and March. But a plant needs light to grow, so we have installed LED lights for the winter. These lights emit a spectrum of light that is needed for plant growth. They are controlled by an automated dimming system that reacts to the intensity of the light outside the farm. Also, based on the recipe for the lettuce it will adjust the light emitted to create the perfect growing conditions all throughout winter.
What about the harsh cold of the winters?
When the temperatures drop below a certain number, the heating system kicks in. The floor is heated by hot water running through the pipes spread throughout the floor. It is a highly controlled environment and nothing is left to the unpredictable outside climate giving the ability to grow fresh lettuce even through the cold winters.
What is your biggest cost for the farm?
Until a few years ago, the seeds for growing lettuce indoors were the same as those used for growing outdoors. But nowadays the seeds are bred to suit the indoor farms. Although they are not super expensive, but for the volume of seeds we go through in a year, it can add up.
However, the capital needed to set up the greenhouse is the highest piece of the cost pie. In order to control the environment inside, we had to install all the automated systems, the lights, heating, all these consume electricity, making the power bill it's the biggest number.
What happens when the power goes out?
Since it is a highly automated system that needs a lot of power, we have backup generators that are capable of supporting the farm to run the systems. If the generators fail to switch on in the middle of a winter blackout, we have about an hour before losing the produce.
What is your biggest challenge on the farm?
We are still in the initial stages of setting up the farm but getting it up and running smoothly is the current big challenge. An indoor farm faces the challenge of bugs and diseases, you cannot keep the bugs out but only delay them from coming in. Using helpful insects like ladybugs that fight and eat away the harmful bugs is a healthy option for pest control.
In order to control the diseases, experience is needed to control and monitor the nutrient and pH levels of the water circulated to the crop. Since the whole farm is supplied by the same nutrient solution, any significant change can affect the whole crop.
You will always have problems, you need to keep on top of them. If you let a problem grow, only then it becomes a big problem.
Where do you plan to sell your produce?
Although we are not operating at full capacity, we sell our current production under our brand True Food Farms itself. We are currently supplying our delicious leafy greens to the southwest Iowa region at Hy-Vee stores at Redoak, Clarinda, Shenandoah, and Omaha. We are in talks with Fareway waiting on their corporate approval.
What is next for True Food Farms?
Focus for now is on this farm, to get it up and running at full capacity. We will be hiring more people to help with the harvesting and packaging of the produce. In order to reach more stores, we plan on expanding and adding more farms in the area.
After watching all the videos about indoor farms on the internet, being able to tour a hydroponic farm in person has just increased my curiosity about the indoor farming industry. I was able to get a high-level understanding of operating and setting up a hydroponic farm. Darren has promised to let me bug him again in a few months when the farm is fully operational and I will be back with an update to this post.
Shubham | May 9, 2021
Tags: featured | Categories: AgTech | URL: https://wp.me/p3uM6F-12p
Kalera Announces The First Harvest For Atlanta Vertical Farming Facility That Will Produce Over 10 Million Heads of Lettuce Per Year
The new facility will supply schools, restaurants, grocery stores, hospitals, retailers, and more with safe, fresh, nutrient-dense, locally-grown greens
The new facility will supply schools, restaurants, grocery stores, hospitals, retailers, and more with safe, fresh, nutrient-dense, locally-grown greens
April 27, 2021
Source: Kalera
ATLANTA, April 27, 2021 (GLOBE NEWSWIRE) -- Kalera (Euronext Growth Oslo ticker KAL, Bloomberg: KSLLF), one of the fastest-growing US vertical farming companies in the world and a leader in plant science for producing high-quality produce in controlled environments, today celebrated their first harvest in their Atlanta-area facility. Its largest farm to date — and the largest vertical farm in the Southeastern United States — the facility is 77 thousand square-feet and has the capability of producing over 10 million heads of lettuce per year. Located in Forest Park, GA, the farm was built in just eleven months thanks in large part to the company’s modular building approach and has created dozens of new jobs in the Atlanta area.
“Our new Atlanta facility is open and performing in line with our expectations and we are eager to begin offering our local, fresh, safe, sustainable greens to the Georgia market,” said Daniel Malechuk, CEO of Kalera. “Our customers are telling us that there has never been a better time to ensure supply continuity, locally, than now and we are grateful Kalera can provide this.”
Kalera’s optimized nutrient and light recipes allow them to grow high-quality, pesticide-free, non-GMO produce at accelerated growth cycles. Planting at the Atlanta facility began in early March, and the first harvest began successfully last week. Kalera has so far experienced optimal operating efficiencies in Atlanta, particularly in terms of lighting productivity. All growth systems, environmental equipment, and technology have operated effectively since opening the facility on March 11. Due to strong sales indications in the region from both retail and foodservice customers, Kalera is implementing a faster ramp-up schedule than originally planned.
The facility’s location near the urban center of Atlanta cuts down on travel times for retailers, restaurants, and other customers who want access to the freshest, non-GMO, clean living lettuces and microgreens. Royal Food Service, a leading produce distributor in the state, is one of Kalera’s top partners bringing “pick-to-plate” greens to restaurants, hotels, schools, and other businesses including Ansley Golf Club, The Ritz-Carlton at Reynolds, Lake Oconee, The Georgia World Congress Center, several restaurants and many others. The lettuce is also available on the shelves of Publix Supermarkets.
“As the former Governor of Georgia, I could not be more excited that Kalera’s delicious greens are now available in the Atlanta area,” said Sonny Perdue, former U.S. Secretary of Agriculture, who joined Kalera’s Board of Directors earlier this year. “Kalera is leading the pack in a booming vertical farming industry. It’s a perfect example of the power of American innovation, creativity, and entrepreneurship to develop different, innovative ways to grow and provide food at home and around the globe.”
Kalera currently operates three growing facilities – two in Orlando and one in Atlanta and is building facilities in Houston, Denver, Columbus, Seattle, Minnesota, and Hawaii. Kalera is the only controlled environment agriculture company with coast-to-coast facilities being constructed, offering grocers, restaurants, theme parks, airports, and other businesses nationwide reliable access to locally grown clean, safe, nutritious, price-stable, long-lasting greens. Once all of these farms are operational, the total projected yield is several tens of millions of heads of lettuce per year. Kalera uses a closed-loop irrigation system which enables its plants to grow while consuming 95% less water compared to field farming.
Recently, Kalera also acquired Vindara, a seed company that uses genomics, machine learning, and computational biology along with traditional breeding methods to meet the market need for produce that is non-GMO, nutritious, high-yielding, and delicious. Explicitly intended for the new high-tech indoor growing environments, Vindara seeds offer growers the opportunity to capitalize on significantly higher yield potential, production efficiencies, and product customization — in a fraction of the time through reducing the grow cycle.
ABOUT KALERA
Kalera is a technology-driven vertical farming company with unique growing methods combining optimized nutrients and light recipes, precise environmental controls, and cleanroom standards to produce safe, highly nutritious, pesticide-free, non-GMO vegetables with consistently high quality and longer shelf life year-round. The company’s high-yield, automated, data-driven hydroponic production facilities have been designed for rapid rollout with industry-leading payback times to grow vegetables faster, cleaner, at a lower cost, and with less environmental impact.
Media Contact
Molly Antos
Phone: (847) 848-2090
Email: molly@dadascope.com
US: INDIANA - Hi-Tech Indoor Farm In South Bend Taking On Lettuce Market
inside a new six-acre building on West Calvert Street in South Bend, Matt Gura is keeping a close watch over a sea of baby plants that fill a greenhouse about the size of two big-box retailers, or 174,000 square feet
By ED SEMMLER South Bend Tribune
March 27, 2021
SOUTH BEND — It’s a chilly, wet, and windy day – enough to remind us that winter still isn’t too far in the rearview mirror.
But inside a new six-acre building on West Calvert Street in South Bend, Matt Gura is keeping a close watch over a sea of baby plants that fill a greenhouse about the size of two big-box retailers, or 174,000 square feet.
It’s like a warm day in early summer inside the building, which uses computers and monitors to control light, liquid nutrients, temperature, humidity, and even plant-loving carbon dioxide.
Gura, director of operations at Pure Green Farms – a hydroponic indoor farm on the city’s southwest side – touts it as the “most technologically advanced leafy green greenhouse in the world.”
“And it’s in South Bend,” he says.
Though it might seem odd to build a massive indoor farm in northern Indiana – considering the cold weather and the perma-cloud that seemingly hangs over the region each winter – leaders at South Bend-based Ceres Partners, an agricultural investment firm, studied the project for years.
They believe there is an opportunity to disrupt the lettuce trade, which is largely dominated by growers in California who ship products to markets in the Midwest.
There’s more sunlight here than most of us realize, and the fact that it doesn’t get too hot in the summer means that the cost of trying to keep the building cool won’t be out of line, Gura said.
A combination of LED and high-pressure sodium lights will supplement the light needs of the plants, and there’s an automated shade that can be used to cut down on light coming in or out of the greenhouse as needed.
In the winter, the indoor farm will use offal heat from the nearby South Bend Ethanol plant, and discussions are underway to possibly use carbon dioxide produced by the facility if it makes economic sense for both businesses.
Ceres also liked the location because it’s near its headquarters near the University of Notre Dame as well as major transportation links that will be crucial to getting the leafy greens produced by Pure Green Farms to grocers, restaurants, and other customers throughout the region, said Brandon Zick, chief investment officer for the firm.
“There’s 55 million people within a 300-mile radius,” said Joe McGuire, a seasoned produce distribution executive who was brought in to serve as CEO of Pure Green Farms. “There’s 75 million people within 400 miles.”
That distance gives Pure Green a significant shipping advantage over traditional leafy green producers that are located in California, Arizona and other far-away locations.
By the time lettuce is harvested and processed in California, for example, it might take 10 days to reach store shelves in the Midwest. Conversely, the romaine, arugula and leaf lettuces grown at Pure Green could be on store shelves in a couple of days or even less.
“We think there’s going to be strong demand for fresher produce that’s grown in the market,” McGuire said.
The first shipments have gone out to Kroger stores in Indiana, and it won’t be long before Pure Green is available at Martin’s Super Markets and other grocers.
Beyond the freshness factor, Pure Green believes it can separate itself from other salad providers because it is not using pesticides or other sprays that might be needed to control bugs and plant diseases outdoors.
Plant protection and eliminating chances for contamination are of paramount importance at the South Bend facility, which currently has 20 workers.
Employees crossing into the greenhouse walk through a tray of shoe sanitizer and wear gloves, coats and hairnets.
After seeds are inserted into a blend of sanitized peat and wood fiber by machine, the planting trays move into the greenhouse, where they are given a nutrient drink while germinating under less intense light and then growing up under full light.
Depending on the variety, it will take about 25 days for the romaine, arugula and leaf lettuces to reach the stage where they are harvested by lightning-fast cutters, blended together, packaged and boxed for shipment.
“From planting to packaging, it’s never touched by human hands until it’s opened by the consumer,” McGuire said.
Nothing is wasted. The nutrient mix that isn’t consumed by the plants is collected, cleaned, tested and reused; the peat material in the growing trays will be composted and used for other agricultural purposes.
“We use 90 percent less water than field-grown lettuces,” said Gura, who previously served as director of operations at Ceres-owned Hop Head Farms in Baroda, Michigan, before joining the team at Pure Green. “I believe it’s the future of growing.”
Though current laws don’t allow the lettuce to be labeled as organic, Zick and McGuire indicated there could be court challenges as controlled-environment growing facilities continue to spring up around the country.
“It’s not classifiable as organic because we don’t put it into the ground,” McGuire said.
Though indoor facilities have been used to produce tomatoes and other crops, producing leaf lettuces at a significant volume is a more recent phenomenon, brought about by shipping distances, food safety and the push for locally produced food.
Beyond the freshness factor, lettuces produced at Pure Green Farms could eliminate 500,000 truck miles annually and up to 300,000 pounds of food waste each year, according to figures provided by Ceres.
Ariana Torres, an assistant professor of agricultural economics at Purdue University, said the timing is right for ventures such as Pure Green because people are consuming more salad and insisting on higher quality produce.
“Consumers want something that is local and fresher,” Torres said. “People also are more aware of food safety, and the pandemic showed that there can be disruptions in the supply chain.”
Though there are competitors in the market – such as Gotham Greens in New York and Chicago, and Little Leaf Farms in Massachusetts – Pure Green is still at the front-edge of a what could be an enormous trend in the future, Zick said.
“The market is huge and only a tiny fraction is grown indoors,” said Zick, the Ceres executive. “Though we won’t be the first to do it, we’re still getting into it early and gaining important experience.”
Looking ahead, the business needs to dial in its efficiencies by fine-tuning its highly-automated growing, harvesting and packaging processes, Gura said.
About $25 million already has been spent on the project, but up to three additional phases are planned. Eventually, Green Farms could have about 16 acres of enclosed greenhouse and about four acres under roof for planting, processing, and packaging.
With 64 acres owned by Green Farms and an additional 280 adjoining acres owned by its parent organization – Ceres – there’s plenty of room for growth, including the possibility of bringing in other operators that are experienced in growing tomatoes, strawberries, and other produce.
“We’ve been interested in developing an ag-tech campus there,” said Zick, adding that partnerships could be developed with Purdue, Notre Dame and other universities to work on problems associated with controlled-environment agriculture.
South Bend Mayor James Mueller was impressed by what he saw during a tour of Pure Green Farms on Friday.
“A lot of people would be surprised by what’s going on there and the level of technology,” Mueller said. “It’s part laboratory, part agriculture, and part advanced manufacturing.”
And he said he’s looking forward to seeing the South Bend-produced lettuces on store shelves.
“Their farm will serve as a model for sustainable and advanced farming techniques,” he said.
VIDEO: Havecon Introduces Havelettuce Projects: Standardized Turn-Key Lettuce Greenhouses Make Entering Greenhouse Industry Easier
Havelettuce will not only take on the build of a greenhouse but the complete project realization, offering a plug and play concept for starting a lettuce greenhouse enterprise. With this new initiative, the door into the horticultural industry will open more easily, CEO Henk Verbakel explains
Havecon has been known as a turnkey greenhouse supplier for many years now, but as of now they'll take turnkey to a new level under the name of “Havelettuce Projects”. Havelettuce will not only take on the build of a greenhouse but the complete project realization, offering a plug and play concept for starting a lettuce greenhouse enterprise. With this new initiative, the door into the horticultural industry will open more easily, CEO Henk Verbakel explains.
Reduce food miles
"Growing hydroponic vegetables closer to consumers will reduce food miles and help reverse the trend of foreign produce imports. Together with our partners and suppliers we bring over 100 years of combined experience in developing large-scale hydroponic greenhouses for several kinds of fruit, vegetables and medicinal cannabis. With Havelettuce Projects, we're using this knowledge to offer 1-2 and 2-4 hectare standardized, turn-key hydroponic lettuce greenhouses," says Henk.
With this new concept, they're answering to the growing demand for local food production and helping investors and other newcomers to the industry find an easy entrance. "We'll manage the entire project from start to finish. This means you only deal with one company," says Jon Adams, Vice President North America. "Furthermore, we provide project anonymity to our customers to provide a competitive edge by being the face of the project until it goes live."
Investors
The horticultural industry has become of interest for many investors and according to the Havelettuce team, it's not difficult to see why. "It is a proven method of growing plants in a soilless environment by relying on a nutrient-rich water solution," Jon explains. "Hydroponics can rapidly help serve unmet demands for fresh vegetables by being grown close to their markets. And it's a sound investment: with investment sizes of 20-50 million dollars for a 1- 4 ha projects we can show a 10-year average EBIDTA of 30 – 45%."
Hydroponic advantages
He adds how growing produce in a hydroponic greenhouse has many advantages. "Greenhouse temperatures and inputs can be precisely controlled, allowing plants to grow faster and face fewer diseases than their outside soil counterparts. Furthermore, a closed-loop irrigation system results in major water savings and uses less fertilizers. This prevents pollutants from entering soil and groundwater as seen with open-field production."
And it's not just the existing industry players anymore that see these opportunities. Many new people are entering the industry. To make it easy for them to do so and to avoid reinventing the wheel, Havelettuce has been created. "Our team has built over 400 greenhouse facilities throughout the world from project as small as 0.1 to over 100 hectares. And now we combine our expertise in hydroponic farming with that of our partners. With the standards we created, Havelettuce Projects makes lettuce cultivation in greenhouses possible for everyone in any climate," he shows.
This means that location, climate, utility load studies, feasibility studies, and all other things you can think of like the community outreach and education, the permitting and incentive procurement will be taken on by our team and by doing so relieve the investors, just as of course the engineering and constructing, project management, crop and harvest advice, and grower consulting and training. "We will provide all of the necessary tools needed to succeed in this industry."
For more information:
Havelettuce
info@havelettuce.com
www.havelettuce.com
Linkedin
Twitter
Publication date: Mon 4 Jan 2021
Author: Arlette Sijmonsma
© FreshPlaza.com
E. coli Strikes Again
On November 10th, the CDC issued a statement alerting us that E.coli has struck again, this time in a pre-packaged single-head romaine after several people became ill from eating E. coli contaminated lettuce
The World Is Scary Enough Without Our Lettuce Trying To Kill Us.
On November 10th, the CDC issued a statement alerting us that E.coli has struck again, this time in a pre-packaged single-head romaine after several people became ill from eating E. coli contaminated lettuce.
This calls us back to the past two Novembers where salad mix and commercial romaine were mass-recalled surrounding the most popular eating holiday in the US: Thanksgiving.
You might remember, the shelves all looked like this:
No lettuce as far as the eye can see. Photo: Washington State University
Lucky for us, the food system is slowly changing (too slowly), so that when E.coli strikes some lucky consumers can turn to small-scale indoor farmers in their area for salad greens that are not only safe, but also very tasty.
We know E. coli is bad... but what, exactly, is it?
E. coli is a bacteria found in the intestines of humans and animals.
That’s right...it’s inside of us.
Before you freak out, most strains of the bacteria are completely harmless. Unfortunately, the bad one that makes you sick (E. coli 0157:H7) is the one that’s currently in our lettuce. Womp-womp.
E. coli makes its way into the outside world… through poop. If the poop makes contact with food, you’ve got an E. coli contamination. If the poop makes contact with a lot of food, it becomes a full-on outbreak.
This isn’t just gross, it's dangerous. E. coli 0157:H7 causes intestinal infections (read: diarrhea, abdominal pain, nausea, vomiting, fever, and fatigue). In severe cases it can cause bloody diarrhea (*silent scream*), dehydration, kidney failure… even death.
This is awful. How the heck did it get on our lettuce?
The best explanation we have is animal or human poop infected the soil or water source at a big romaine farm. The scary thing is, this is only an educated guess. Since people might not start getting sick until several weeks after harvest, it’s hard to go back and try to figure out what actually happened at Ground Zero (or even where Ground Zero is).
Feel like you’re having deja-vu?
That’s because this happened literally the past two years! In 2018 we had three E. coli outbreaks in romaine alone, the worst of which was in the spring: There were reported outbreaks in 36 states with 210 infected, 96 hospitalized and 5 dead. Only months later, another outbreak struck 12 states with 43 infected and 19 hospitalized just after Thanksgiving. Since then, romaine-related Ecoli has been popping up all over the place. The most frustrating part is that it usually takes the CDC months to investigate, meaning we don’t even hear about these outbreaks until well after the dangerous food is long-forgotten.
By now you’re probably thinking…
Before you denounce all salad, forever, we may have a solution.
The problem is with the system as a whole.
The reason that E. coli outbreaks are so widespread is because we source 95 percent of our leafy greens from a few farms in California and Arizona. Those greens (romaine included), get harvested and amassed at big distribution points before making their way cross-country to stores and restaurants. This means zero transparency into where the E. coli originated, making it difficult to eradicate. Not to mention, a lack of regulations prevents any actual accountability. The result? We keep eating the nasty stuff, and more people get sick.
One solution is surprisingly simple… decentralization.
This problem wouldn’t exist if we moved away from a centralized food system to a distributed one with small indoor farms. Here's why:
(1) Small, indoor farms create total environmental control with all types of fancy filters and regular water tests. Plus, this prevents exposure to two common sources of E. coli: contaminated soil and animal waste.
(2) Decentralization = transparency. Lettuce from small farmers isn’t changing hands, like, a million times. In the event of an outbreak, we can easily trace it back to its source to confirm that it’s safe to eat. With a shorter supply chain, this process take days, not months.
(3) While chances of contamination in a small indoor farm are much, much, much smaller… it is theoretically possible. Distributed production means, even if you do have one contaminated small farm, the exposure is contained, so it’s still safe to eat lettuces from other local farms.
Cultivar Boston | Massachusetts, @chefmarydumont @cultivarboston
These are all things we know a lot of our farmers' customers appreciate about the Leafy Green Machine. Throughout this whole ordeal, they've had access to safe greens in their neighborhoods.
It’s always rattling to see how fragile our food system can be, and we hope this whole hoopla motivates policymakers, wholesalers, and shoppers to think more about how we source our food.
Want to be the change you want to see in the world?
Become a farmer
Is Your Lettuce Crop Starving For Calcium?
Tip burn is a common problem in lettuce crops lacking calcium. Young leaves can develop In lettuce, calcium deficiency often manifests as tip burn on developing leaves
By Erica Hernandez|
August 12, 2020
Tip burn is a common problem in lettuce crops lacking calcium. Young leaves can develop In lettuce, calcium deficiency often manifests as tip burn on developing leaves. Tip burn gives leaf margins a burned or crinkled appearance and will affect their appearance throughout development.
Calcium, though not a macronutrient, is essential for proper plant development. Plants absorb calcium both through their roots from nutrient solutions and through leaves and shoots during foliar applications. Xylem, the water-carrying network of cells within plants, transports calcium from the point of absorption upward through plant tissue.
Transpiration powers this upward flow as the plant photosynthesizes and releases water molecules into the environment. Calcium serves several important purposes within plants. Strong cell walls require calcium to be incorporated in their structure, with adequate supplies leading to well-formed, healthy leaves and stems. Several biological processes also employ calcium as a signaling molecule, keeping plant development on-track, or responding to changing environments.
Lettuce is a long-cultivated crop; calcium requirements have been well documented and the differences between field and greenhouse production understood. Hydroponic lettuce production calls for 100 to 150 ppm calcium throughout the growth cycle. The calcium must be supplied by the water rather than obtained from field soil. Tap water contains some calcium, but often not enough to hit this target.
Hydroponic producers may incorporate a calcium-nitrate-based fertilizer to provide both calcium and nitrogen to their crops. Calcium chloride at 1 pound per 100 gallons can also be applied as a foliar spray to help deliver calcium to leaves when transpiration is low.
Know the Symptoms
In lettuce, calcium deficiency often manifests as tip burn on developing leaves. Tip burn gives leaf margins a burned or crinkled appearance and will affect their appearance throughout development. The damage continues to affect new leaves until the cause of the deficiency is remedied. Damaged tissue can go on to become necrotic, providing a potential point of entry for secondary Botrytis infection. Overall, tip burn reduces the health, appearance, and shelf-life of lettuce heads and leaves.
Pinpoint the Root Cause
Identifying the cause of calcium deficiency in lettuce can be a tricky topic, as it is not always caused by a lack of applied calcium. Since water carries calcium through the plant as transpiration occurs, calcium movement is dependent solely on transpiration rates. It will not matter how much calcium you supply to the root zone of your crop if you are growing in a humid, low-transpiration environment. Conversely, overly dry conditions causing plants to close their stomates and cease transpiration may also lead to calcium deficiency.
Head lettuce is particularly susceptible to tip burn in humid environments. As lettuce heads develop, they enclose the apical meristem, or growing point, in an envelope of leaves. This creates a pocket of stagnant air, which can be resistant to outside air movement. Stagnant air cuts down on transpiration at the growing point, leading to less calcium being delivered and developing leaves becoming misshapen and tip burned. Alternatively, in high-light, low-humidity environments, lettuce will experience a surge in photosynthesis while closing off stomates to cut down on water loss. Again, the movement of calcium is impeded within the plant even though there may be enough at the root zone.
Remedying calcium deficiency first relies on identifying the cause. Step one is looking at the nutrient solution. Is there a high or low level of calcium in the base water? Is there a calcium source included in the recipe? Calcium is available over a wide pH range, so pH changes are often not necessary. Next, look at the environmental conditions. Appropriate airflow is essential, though it may require different equipment than other crops.
Successful lettuce growers often utilize vertical airflow fans over horizontal airflow. The downward direction of airflow allows air to be forced into and around the protected growing point of head lettuce. A gentle and constant flow is all that is necessary — high airspeeds can lead to stomatal closure and tip burn once more. Finally, make sure photoperiods and light levels are appropriate for lettuce. A daily light integral (DLI) of 17 mols/m2/d is ideal for lettuce production, with a photoperiod between 14 to 18 hours.
Erica Hernandez is a Controlled Environment Agriculture Technical Specialist at Griffin. After obtaining her advanced degree in Horticultural Biology from Cornell University, she came to work with the GGSPro team supporting greenhouse growers across the country. She works to bring proven horticultural techniques to growers and increase production efficiencies through knowledgeable advice.
See all author stories here.
Lead Photo courtesy of Griffin
USA: Tanimura & Antle Recalls Romaine, Michigan Reports E. Coli Cases
“At Tanimura & Antle, food safety is a number-one priority and the company prides itself on its preventative measures,” according to the company’s notice posted on the Food and Drug Administration’s website. “It is unlikely that this product remains at retail establishments due to the shelf life of lettuce and the number of days that have passed.”
November 8, 2020
A state agency in Michigan is advising residents not to eat Tanimura & Antle brand romaine lettuce packed as single heads, and the company has issued a recall of the lettuce.
The Michigan Department of Agriculture and Rural Development on Nov. 6 issued its advisory, the same day the Salinas, Calif.-based company recalled single heads of romaine.
Random testing by the state’s agriculture department found a sample with E. coli, and more testing by the Michigan Department of Health and Human Services laboratory determined the strain is “highly related” to the strain linked to two cases being investigated in Michigan, according to a news release from the state’s agriculture department.
Tanimura and Antle’s recall covers almost 4,000 cases of single heads of romaine with the Universal Product Code of 0-27918-20314-9. The Produce Traceability Initiative codes on the cartons are 571280289SRS1 and 571280290SRS1.
“At Tanimura & Antle, food safety is a number-one priority and the company prides itself on its preventative measures,” according to the company’s notice posted on the Food and Drug Administration’s website. “It is unlikely that this product remains at retail establishments due to the shelf life of lettuce and the number of days that have passed.”
The sample was collected at a Walmart in Comstock Park, according to the Michigan agriculture department. According to the Tanimura & Antle notice, its recall “is based on the test result of a random sample collected and analyzed by the Michigan Department of Agriculture and Rural Development as part of their routine sampling program.”
The Tanimura & Antle recall, however, does not list Michigan as a destination for the recalled romaine. The single heads of romaine were packed on Oct. 15-16 and were shipped to Alaska, Oregon, California, Texas, Arkansas, Oklahoma, Indiana, Nebraska, Missouri, Tennessee, Wisconsin, New Mexico, South Carolina, Washington, North Carolina, Ohio, Virginia, Massachusetts, Illinois, and Puerto Rico.
The recall and Michigan advisory comes as the FDA is investigating two E. coli outbreaks involving separate strains of the pathogen that “are recurring, emerging or persistent strains,” according to an Oct. 28 news release.
Those two strains are “genetically related” to E. coli outbreaks related to romaine lettuce: one from a 2019 outbreak that led to 23 illnesses, and another from a 2018 outbreak that led to 21 illnesses and one death. Each of the current outbreaks have two cases reported in Michigan, according to the Centers for Disease Control and Prevention.
In the Oct. 28 announcement, the FDA said there was no evidence to link the outbreaks to any specific foods, and that a pathogen strain being linked to a food safety event in the past does not prove a link to a current outbreak.
Related story:
FDA says E. coli outbreaks have strains
Lead photo: ( Courtesy FDA )
NEW ZEALAND: Southland Lawyer-Turned Lettuce Farmer Expanding Hydroponics Business
Aviation lawyer Angela Beazer, who has been working for the Civil Aviation Authority part-time, was a recent recipient of a $2.5 million Provincial Growth Fund loan
1 November 2020
Otago Daily Times
By: Mary-Jo Tohill
A Southland lawyer-turned lettuce farmer is looking forward to devoting all her time to expanding her hydroponics business.
Aviation lawyer Angela Beazer, who has been working for the Civil Aviation Authority part-time, was a recent recipient of a $2.5 million Provincial Growth Fund loan.
While flying high, the 45-year-old has her feet firmly on the ground. With plans afoot to triple the lettuce farm's production, it had become clear to her she could no longer do both jobs and would have to quit one.
"But now I'm ready for change. I've been trying to juggle both, but they're not complimentary.
"I have a life many people would envy. I can work on my own schedule. I can be there to pick up my daughter from school, but as I say, they (lawyer/lettuce growing) are not complementary. I could not give 100 percent to both. If I do something I like to do it properly.
"I'm quite looking forward to focusing just on the lettuces."
If someone had told the former career professional eight years ago that she was destined to become a lettuce farmer, she would have laughed.
"I pictured lettuces sown out in the middle of the muddy paddock. Not my cup of tea at all."
She and her partner, Craig Macalister, had already taken a big leap of faith when they moved from Wellington to Invercargill so that he could take up a new position with financial advisory and accountancy firm Findex.
However, it was their frustration at not being able to find a suitable rural lifestyle block that led them to a property in Myross Bush.
Shoulder-tapped by a real estate agent, they went out and looked at a place that happened to have a hydroponics setup — Drysdale Hydroponics.
"I knew nothing about growing lettuces. We'd been down here about a year. I had a plot where I grew some veggies — a bit of broccoli, some cauliflower, a few potatoes. Actually, the potatoes were already there. That was about the extent of my horticultural experience."
Fast forward eight years and now she grows lettuce by the hundreds at her farm Southern Hydroponics, still trading as Drysdale Hydroponics, near Invercargill.
And with the expansion that will employ another 30 people, she's set to grow more, and other vegetable crops, including capsicums and tomatoes.
"We're been producing a fairly fixed amount of product. The business does need to expand because there's more competition. The minimum wage's gone up, so you either shut down or you expand and make it worthwhile."
Increasing production and lowering costs made for better economies of scale. Beazer liked the concept of hydroponics as an efficient way of growing food on a large scale.
However, while it had been a great move, it was also a huge lifestyle change,
"I think sometimes, 'why am I doing it?' But you're working at waist height — you're not having to bend and I quite like working undercover, but still feeling like you're working outdoors.
"On the other hand, this is a 24/7, 365-day operation. Someone has to be here watching all the time. There's a lot that goes on behind the scenes."
It was sometimes hard to close the greenhouse door and walk away when you had to be constantly checking things like nutrients and temperature, she said.
"One thing I'm really looking forward to is being able to move to a heat pump from the boiler, with the expansion."
There might also be time to take up some interests again — like Zumba.
"I was doing it, but since lockdown and everything I haven't got back into it and I've been a bit of a lazy bum and not been doing it."
Lead photo: Angela Beazer surveys her hydroponic lettuces. Photo / Supplied
Living Lettuce, Vertical Gardening: This Startup Is Using AI For Organic Farming
Analytics India Magazine got in touch with Shivendra Singh, founder and CEO of Barton Breeze, who believes that in the future the vegetable greens will likely come from the building next to you
13/10/2020
Srishti currently works as Associate Editor at Analytics India Magazine.…
The interest and popularity of organic and sustainable farming are increasing drastically. While the consumers are often skeptical about the food products that they consume, Dubai and New Delhi-based Barton Breeze is growing safe, delicious, and healthy food while relying on analytics and AI. It offers top-quality products that are grown locally in nutrient-rich water without pesticides. The crops are harvested weekly and delivered to sales outlets within a couple of hours.
Following the principle of ‘living lettuce’, it follows a method where roots are left intact, which makes it last longer. The startup also follows vertical gardening where it uses vertically stacked growing beds, up to five levels high using less than 1% of the space required by the conventional growing, a precious commodity in densely populated urban areas.
Analytics India Magazine got in touch with Shivendra Singh, founder and CEO of Barton Breeze, who believes that in the future the vegetable greens will likely come from the building next to you.
The Journey
After graduating from IIM Ahmedabad, Singh started working on a pilot project around hydroponics and set up two container farms in Dubai. “During this time I thought, a country like India with profound climate changes needs this technology more than anyone else,” he says.
Soon after, Barton Breeze was established in 2015 in Dubai, UAE, with a mission for technology innovation in agriculture. As Singh recalls, the journey initially was challenging and well expected, but with the right vision, it became unstoppable. In addition to the lack of proper information, availability of funds, market volatility, the task to create consumer confidence was critical. Another challenge was that hydroponics was a new technology to adapt, and the existing unprofessional quality and high prices made it difficult to find the right customer in the market.
Overcoming these challenges, Barton Breeze is now the market leader in the sector and has expanded operations to India.
Data Science And AI Is At The Core
Barton Breeze team includes experts from deep data science to engineering, and from marketing to producing. “When we started, people had no idea about this new technology. And whatever talent was available, they had to unlearn. Training and building our staff from the ground up, we are now a team of six core members, supported by 25 field farms,” added Singh.
Explaining how Barton Breeze uses analytics and AI to increase the farm produce, Singh shares the areas as below:
Smart Farms: Each smart farm is backed with the expertise of the chief technology officer, a dedicated R&D team, plant scientists, microbiologists, mechanical engineers, and design engineers.
Cloud Architecture and Data Center: Barton Breeze collects hundreds of data points at each of its farms to its data center, which allows it to quickly alter its indoor precision control for taste, texture, color, and nutrition. It also helps in adjusting variables like temperature and humidity to optimize its crop yields. Barton also collects all yield and harvest data into the cloud to calculate sales projections and market trends.
Using Artificial Intelligence and IoT (Internet of things): Barton uses software with a device clipped on the stems and leaves of each plant. It informs the nutrients or mineral needs of the plants.
Highlighting other venues where AI is used, Singh shares that they have perfected their algorithm for optimal taste, texture, color, and nutrition so one can taste the science of flavor in every delicious bite of leafy greens. “We do this by leveraging plant science, engineering, and lighting to optimize our plants while also using 85% less water, 5x productivity, and zero pesticides,” he added.
He further shares that Barton Breeze carefully monitors the health and quality of plants daily to optimize taste, texture, color, nutrition, and yield to deliver a better product using AI. “Barton’s growing techniques can be highly customized,” he said.
The startup has also developed iFarm, a cloud-based data and farm output AI software. It allows the clients to get all their farm and production details on the cloud at home or office. “Our farm dashboard and IoT uses artificial intelligence and data analytics to measure important indicators that help in food/crop planning and hence help connect in the food security ecosystem,” he said.
Some areas where AI and IoT are used at Barton:
SMS alert system
Data logging facility
Online monitoring and control
Sensor-based control system
Environment management system
Water temperature management
Sunlight monitoring system
Crop management system
Farm system efficiency dashboard
Nutrition management system
Barton team includes members with deep expertise in science, engineering, technology, food safety, crop physiology, microbiology, and more to help deliver rapidly deployable and scalable solutions.
“Being first and one of a kind in the segment of agri-tech, we at Barton Breeze are trying to create and promote healthy lifestyle’ To achieve it, we are working into the whole ecosystem in the form of B-FRESH, B-FARM and B-HOME,” shares Singh.
Growth Story
With experienced and known names in the team, Barton Breeze has increased team members, post-COVID to increase the outreach. “Currently we are in 10 states, and Barton Breeze is planning to enter five more states in the next couple of months,” shared Singh. The startup takes pride in increased customer query by 200% and increased consumer awareness by 10X post COVID.
Singh further shares that there has been an increase in the interest level from angel investors and venture capitals for Barton Breeze with VC calls gone up by 150%. The startup is closing 1.5 million USD funding within this year.
“Our goal is to achieve 360-ton produce marketing per year by the end of March 2021 while adding 25 more clients. We are targeting 50 crores revenue @CAGR 800%. We would also be coming up with ten new commercialized farms apart from doing R&D on 50 crop varieties,” concluded Singh on an ambitious note.
Srishti currently works as Associate Editor at Analytics India Magazine. When not covering the analytics news, editing, and writing articles, she could be found reading or capturing thoughts into pictures.
Canada Requires Romaine From Parts of California To Be Tested For E. Coli
Effective October 7, 2020, the CFIA will require importers to either provide proof that romaine lettuce destined for import into Canada does not originate from counties in the Salinas Valley, or provide an official certificate of analysis from an accredited laboratory confirming that the lettuce has below-detectable levels of E. coli
Thanks in part to imported products, Canadians can enjoy fresh produce year-round. From 2016 to 2019, romaine lettuce from California was linked to outbreaks of E. coli illnesses in the USA and Canada. Food safety investigations by Canadian and US authorities identified the Salinas Valley growing region as a recurring source of the outbreaks.
To mitigate risk in the event of another outbreak this fall, the Canadian Food Inspection Agency (CFIA) is implementing temporary import measures aimed at preventing contaminated food from entering the marketplace.
Effective October 7, 2020, the CFIA will require importers to either provide proof that romaine lettuce destined for import into Canada does not originate from counties in the Salinas Valley, or provide an official certificate of analysis from an accredited laboratory confirming that the lettuce has below-detectable levels of E. coli.
CFIA is working closely and collaboratively with the US Food and Drug Administration to identify and respond to any potential outbreaks and continues to put in place effective preventive controls.
The testing applies to romaine lettuce as well as mixed salads containing romaine and will be required until December 31, 2020.
The program adds an extra layer of controls to the food safety measures in place under the Safe Food for Canadians Regulations (SFCR).
On January 15, 2020, SFCR requirements came into force for most businesses in the fresh fruits or vegetables (FFV) sector that import, export or engage in interprovincial trade.
Under the SFCR, FFV businesses are required to obtain a Safe Food for Canadians licence and maintain:
preventive controls that address food safety hazards;
preventive control plans that document risks to food and how they are addressed; and
traceability documentation that tracks the movement of food one step forward and one step back in the supply chain.
Additional safeguards
Canada maintains specific import requirements to minimize potential hazards associated with romaine. For example, the importation of leafy greens from California is limited to products supplied by certified members of the California Leafy Greens Marketing Agreement (LGMA). LGMA certified members must adhere to food safety requirements subject to regular audits by the California Department of Food and Agriculture.
In addition, the CFIA has a regular monitoring program for E. coli O157:H7 in fresh vegetables and is also testing 1,000 more samples of lettuce and products containing lettuce per year.
For more information, read the CFIA's guidance Import requirements for romaine lettuce from the United States.
Source: Canadian Food Inspection Agency (CFIA)
Quick Facts
The CFIA plays a critical role in safeguarding a healthy food supply system, ensuring the foods Canadians eat are safe and facilitating the trade of food and food products internationally.
More than 50,000 shipments of romaine lettuce or salad mixes containing romaine lettuce were imported into Canada from June 2019 to July 2020.
Romaine is associated with elevated food safety risks. In Canada, there have been seven documented outbreaks of illnesses associated with romaine lettuce, and 16 recalls of romaine lettuce or products containing romaine lettuce due to E. coli O157:H7 from 2010 to 2019.
Under this new requirement, romaine from Salinas must be tested in a laboratory accredited by the Standards Council of Canada (SCC), the Canadian Association for Laboratory Accreditation (CALA) or another accreditation body that is a signatory to the International Laboratory Accreditation Cooperation (ILAC) Mutual Recognition Agreement (MRA).
Related Products or Associated Links
GreenFactory Emirates: The Largest Indoor Farm In The World To Be Developed In Abu Dhabi
GreenFactory Emirates will develop an innovative indoor farming with the world's most advanced indoor growing system from The Netherlands
Barendrecht (The Netherlands) and Abu Dhabi (UAE)
September 22, 2020
A joint venture between GrowGroup IFS from Barendrecht (The Netherlands) and RainMakers Capital Investment LLC from Abu Dhabi (UAE) will build the largest indoor farm in the world in the desert of Abu Dhabi. The GreenFactory Emirates will produce 10,000 tons of fresh produce per year on a plot of 17.5 hectares and a cultivation area of 160,000 square meters.
GreenFactory Emirates will develop an innovative indoor farming with the world's most advanced indoor growing system from The Netherlands. It is a combination of vertical and flat farming and solves the normal cultivation restrictions due to extreme climates in regions as the UAE. The facility will involve numerous leading agro-technological companies in its construction as best of breed for each component will be sourced through top-tier Dutch companies. It is now possible to cultivate high-quality vegetables 100% pesticide-free, all year round and anywhere on the planet: “Quality of Holland – Local Grown.” From seeding, harvesting, processing to "ready to eat" products will take place under one roof.
The joint venture also plans to build other indoor farms in other regions of the world where extreme climates are a challenge to normal cultivation.
Water, Co2, and waste
The GreenFactory will be saving 95% of water consumption as opposed to standard methods of cultivation as well as reducing its Co2 footprint up to 40%. By growing fresh produce locally, GreenFactory Emirates will also contribute to reducing waste in various other areas. Its contribution to slowly reducing reliance on fresh foods imports will in turn reduce waste of produce occurring during the transport process while reducing logistical traffic.
Research and development
GreenFactory Emirates will include a built-in research and development component that will help ramp up the production beyond the 56 current varieties of lettuces, leafy greens, herbs, and kale. It will also optimize its production by collecting real-time data to inform future global expansion of indoor farming. With confirmed partnerships with GAAS Wageningen and Delphy in The Netherlands, GreenFactory will benefit from live feedback provided by some of the best students and Academia in the field.
Food security
Food security is high on the UAE’s agenda. The country aims to be number 1 on the Global Food Security Index by 2051. In 2019, the UAE ranked on the 21st place on the Index, jumping an impressive 10 places from number 31 in 2018. Boosting local production and creating an enabling environment for agri-tech is a top priority for the government. The UAE strives to become a knowledge hub with regards to food production in heat, high humidity, and high salinity soil. The private sector (supermarket chains and the hospitality industry) has also set ambitious targets for itself in order to sell more local produce.
Partnership
The partnership between GrowGroup and rainMKRS is initiated and a result of an introduction made by the Embassy of the Kingdom of The Netherlands in the United Arab Emirates and the Monarch Group which has played an instrumental role in seeking opportunities and nurturing relationships.
Expo 2020 Dubai
The total project amounting to 650M AED (150M EURO) is planned in different phases in 3 years. Phase 1 will be operational before Expo 2020 Dubai in October 2021, so GreenFactory Emirates can show the world its innovations. A kick-off for more similar projects and innovations worldwide.
GrowGroup IFS
GrowGroup IFS (Innovative Farming Solutions), founded by CEO John Breedveld in Barendrecht in The Netherlands, is specialized in developing indoor farming based on the most advanced Dutch innovative farming solutions, especially in regions where normal cultivation is restricted by extreme climate and or limited space.
rainMKRS Capital Investment LLC
With offices in Abu Dhabi (UAE) and Montreal (Canada), rainMKRS is an entrepreneurial catalyst co-founded by a group of Emirati and Canadian entrepreneurs. Led by Mohamed Jouan Al-Dhaheri, Sultan Al-Nassour, Sebastien Leblond, and Jonathan Mérineau Gosselin, rainMKRS brings together the world’s most impactful companies and projects in the food and agriculture sector and UAE’s economic, educational, and investment stakeholders. rainMKRS’ objective is to help bridge the gap between these stakeholders in order to accelerate the progress on critical and strategic components in support of the UAE desire to achieve food security.
GreenFactory Emirates is its first of many initiatives in the field.
IGS Signs Significant Export Deal With Jungle To Supply French Retail Market
The first growth towers will be in production by early 2021, scaling incrementally to a minimum of 17 towers by the end of 2021
Scottish Technology to Create One of
Europe’s Largest Vertical Farms
Edinburgh, Scotland – 17 September 2020 - Indoor agritech specialist IGS has today announced a significant export deal with experienced French urban agriculturalists, Jungle. The multi-million-pound deal will introduce IGS indoor growing platforms to Jungle’s operations, initially outside Paris, to grow a variety of crops to supply major French retailers.
The first growth towers will be in production by early 2021, scaling incrementally to a minimum of 17 towers by the end of 2021. Jungle will grow a range of herbs and salads to supply select retailers across France. The company will utilize the patented IGS plug-and-play vertical farming platform to widen its portfolio and produce new varieties through an ongoing program of crop trials.
Jungle’s indoor growing operations will also develop a variety of botanicals to provide natural ingredients to a world-leading flavor and fragrance business.
Jungle’s ethos is focused on sustainable food production, with superior quality of crops grown through a more efficient model, re-localizing the supply chain, considerably reducing waste and using no chemicals. With extensive experience in the indoor growing space, the company has achieved recognition in the highly competitive retail market in France for the quality of its produce.
To increase the scale of production sustainably, while maintaining its commitment to high-quality, delicious, and pesticide-free produce, the company conducted an extensive search to identify the best technology partner.
After a thorough and competitive review of the market, IGS was selected as the most economically viable and environmentally friendly system capable of meeting Jungle’s requirements to reach the industrial scale required by its customers. IGS offers its customers a highly controllable platform, designed to maximize productivity whilst minimizing energy and water consumption.
When completed, the nine-meter-high growth towers will be housed alongside a 1,500 m2 service area on Jungle’s site outside Paris. This will provide approximately 5,200 m2 of growing space, producing up to 425 tonnes per annum when fully operational, making it one of the largest vertical farms in Europe.
IGS CEO, David Farquhar, commented: “In recent months, global markets have been challenged considerably and export agreements have become more difficult to fulfill. The announcement of this deal is an exciting one not just for IGS, but also for the UK’s Agri-tech sector as we showcase our international capability to support economic recovery post-coronavirus. The Jungle team has a strong reputation for excellence and sustainability both of its produce and approach.
“Jungle needs a reliable, productized system that can meet its ambitious growth plans in France and beyond and IGS has proven to be exactly that, following a rigorous selection process. This deal is proof that our unwavering commitment to innovative, practical design, based on a deep understanding of delivering optimum growing conditions, is what customers want. The deployment of the system for Jungle begins immediately and I am encouraged by how well our teams are collaborating as we move forward together.”
Gilles Dreyfus, CEO of Jungle commented: “This partnership agreement is a significant step forward for Jungle and our ability to deliver at scale for our customers. We have established Jungle as a grower of superior produce with major French retailers and have plans to build on this reputation as we look at operations in other regions. We are proud to be innovators in our sector and it is important that we find people and organizations that share this same vision.
“We undertook a very serious assessment of the market and IGS was a clear leader in our eyes. What we can offer our customers through the partnership with IGS puts us at a different level in terms of scale, flexibility, and potential to expand and develop our produce portfolio. The IGS approach, both with the technology and the team, is such that we feel completely aligned and able to work collaboratively now and into the future.”
IGS has received recognition from the Scottish Government for the exciting export opportunities it is bringing to the Scottish market. Trade Minister Ivan McKee MSP said: “This significant contract underlines IGS’ standing as a global leader in agricultural innovation which will help everyone farm more sustainably. IGS’ growth has been driven by a focus on quality, innovation and scientific expertise and shows what Scottish companies can achieve with the right support in place.
“International exports have a central role to play in our economic recovery from COVID-19. The Scottish Government has set an ambitious target of increasing the value of exports from 20 percent to 25 percent of GDP by the end of the decade and I look forward to IGS helping us achieve that goal.”
In addition, Scottish Enterprise which has worked closely with IGS since 2018, welcomes this strategic export announcement. Neil Francis, International Trade Director at Scottish Enterprise, said: “We congratulate IGS on securing this export deal, which will ensure the company’s innovative technology is delivered to a global marketplace.
“Scottish Enterprise has worked closely with IGS over the past couple of years, both through our investment arm, the Scottish Investment Bank, and Scottish Development International. We look forward to continuing support IGS as it demonstrates its capabilities in the agritech sector.
“International trade will be key to Scotland’s economic recovery and help deliver the future, sustainable growth we all want to see. Working with our partners, Scottish Enterprise will continue to do all we can to support companies access overseas markets.
Ends
Notes to editors:
For more information: please contact Kate Forster, IGS on kate@intelligentgrowthsolutions.com or call +44 7787 534 999 or Gilles Dreyfus, Jungle on gdreyfus@jungle.bio.
About IGS:
Founded in 2013, IGS brought together decades of farming and engineering experience to create an agritech business with a vision to revolutionize the indoor growing market. Its commitment to innovation has continued apace and it has evolved the applications of its technology beyond agriculture to create solutions for a wide variety of indoor environments which enhance life for plants and people alike.
IGS launched its first vertical farming demonstration facility in August 2018.
For more information visit www.intelligentgrowthsolutions.com or connect with us on Twitter and LinkedIn.
About Jungle:
Jungle originated in Portugal in 2016 and maintains a Research and Development facility in Lisbon. It identified strong demand from the retail market in France and opened operations there in 2019. Further European operations are under consideration as the demand for healthy, sustainable and locally-sourced produce increases.
Little Leaf Farms Expands Hydroponic Greens Distribution Across East Coast
Based in Massachusetts, Little Leaf Farms has doubled its hydroponic greenhouse-growing capacity to 10 acres of fields under glass capable of producing more than two million packages of lettuce each month, which will broaden the company's distribution to retailers in New York, New Jersey, Pennsylvania, and South Carolina
15-Sep-2020
By Mary Ellen Shoup
Based in Massachusetts, Little Leaf Farms has doubled its hydroponic greenhouse-growing capacity to 10 acres of fields under glass capable of producing more than two million packages of lettuce each month, which will broaden the company's distribution to retailers in New York, New Jersey, Pennsylvania, and South Carolina.
Read More At: Food Navigator
It's Hard To Grow Vegetables In This Mountain Town. Then This Farmer Had An Idea
Operating an indoor farm in the snowy northwest corner of Wyoming wasn't exactly the job Yehia had envisioned for herself years ago. In 2008, after the New York City-based architect moved to Jackson to start a new firm, Yehia wanted to try something innovative in her new community
By Jeremy Harlan, CNN
September 14, 2020
Jackson, Wyoming (CNN) It was a no-brainer when it came to finding the best job for Ty Warner.
"Ty is our tomato guy," said Nona Yehia, co-founder and CEO of Vertical Harvest, an innovative three-story greenhouse in downtown Jackson, Wyoming.
Nona Yehia, the founder of Vertical Harvest in Jackson, Wyoming.
As she watched the slender 6'5" Warner carefully weave his way through a towering canopy of plants, pulling ripe tomatoes hanging above, Yehia smiled with pride. "Ty is good at every part of growing tomato plants. It is really impressive."
Operating an indoor farm in the snowy northwest corner of Wyoming wasn't exactly the job Yehia had envisioned for herself years ago. In 2008, after the New York City-based architect moved to Jackson to start a new firm, Yehia wanted to try something innovative in her new community.
"We really wanted to address the local sustainable source of food," she said.
The idea To Go Up
Jackson sits at an elevation just over 6,000 feet, nestled between Grand Teton National Park, Yellowstone National Park, and the Teton National Forest, and its location means there is very little space and conducive weather for farmers to grow fresh produce for the bustling tourist town.
"We came together to look for an out-of-the-box solution and that's where the idea to go up came from," Yehia said.
"Up" was on a 1/10 of an acre lot abutting an existing parking garage.
In July, Nona Yehia, CEO and co-founder of Vertical Harvest, announced a second vertical farm in Westbrook, Maine. The second Vertical Harvest will be five times larger than the original Wyoming farm and will open in 2022.
In the spring of 2016, Vertical Harvest began growing its first lettuce, microgreens, and tomato plants. The farm's current staff of 40 now grows year-round and cultivates the amount of produce equivalent to ten acres of traditional outdoor farming.
Yehia says all of the produce grown is distributed to 40 local restaurants and four grocery stores.
"Nona has approached it as bringing something unique to chefs that they then can use and feature all year round," said Ben Westenburg, the executive chef and partner of Persephone West Bank in nearby Wilson, Wyoming. "It's just so easy to call up Vertical Harvest and be like, 'I need some salad greens and tomatoes and some really beautiful microgreens.' And they're like, 'Okay, we'll be there tomorrow.'"
'We're pairing innovation with an underserved population'
Ty Warner, a Vertical Harvest employee, is tasked with picking and pruning hundreds of the indoor farm's tomato plants.
While planning for a new greenhouse, Yehia and her design team realized they had to do more with the project than just grow fresh greens for locals.
"There was a bigger problem," Yehia said. "People with physical and intellectual disabilities in our town who wanted to work, who wanted to find consistent and meaningful work, were not able to do so. We're pairing innovation with an under-served population and really creating a sea change of perception of what this population is able to do."
Half of Vertical Harvest's workers have physical or intellectual disabilities. Yehia, whose older brother is disabled, says every single employee, including Warner -- who is autistic -- is critical to keeping Vertical Harvest functioning.
"We can empower the most under-served in our communities just by giving them a chance and giving them something to be able to give back to," Yehia explained.
"It's hard for people with disabilities to find a job," says Sean Stone, who used to wash dishes at several restaurants in town before joining Vertical Harvest as a farmer. "I'm glad to help the community and grown them fresh produce to have."
Growing beyond Wyoming
In July, Yehia announced Vertical Harvest would be expanding to serve a second community. The new farm located in Westbrook, Maine, will open in 2022 and will be five times larger than the original Wyoming greenhouse.
The goal is to grow a million pounds of produce each year for local restaurants, grocery stores, hospitals, and schools.
Mycah Miller, a Vertical Harvest employee, packages lettuce greens to be delivered to one of four grocery stores the vertical farm services in Jackson, Wyoming.
"In moving to Maine and having a much larger space, we're excited to play out the model of providing local produce at an urban scale," she says.
Yehia believes the global pandemic this year has forced consumers and communities around the country to explore new ways to get fresher produce from closer sources.
"COVID has shined a spotlight on what we knew ten years ago when we were looking at this vertical model: We have a centralized food system and it's kept us from getting fresh, local, good-tasting food," Yehia said. "I think Covid-19 has forced people to ask why that is and how they now can get locally-grown food they like in the summertime and get it year-round. It's exactly what Vertical Harvest is about."
Smart Acres CEO On The Latest Addition To The Hydroponic Vertical Farming Industry In Abu Dhabi
The launch of Smart Acres, the UAE’s latest addition to the hydroponic vertical farming industry, this week means that a line of the freshest, most nutrient-dense greens for UAE residents and businesses alike is now being produced in containers on the Armed Forces Officers Club in Abu Dhabi, with the aim to expand across the UAE
Smart Acres is here with lettuce at the helm. In an exclusive interview with Abu Dhabi World, Smart Acres CEO Abdulla al Kaabi reveals what this means to Abu Dhabi and the farming community on the whole.
If you love healthy produce, and who doesn’t, then this news is going to please you and your tastebuds no end. The only drawback at the moment is they’re not for sale in supermarkets just yet, but it won’t be long before they are.
The launch of Smart Acres, the UAE’s latest addition to the hydroponic vertical farming industry, this week means that a line of the freshest, most nutrient-dense greens for UAE residents and businesses alike is now being produced in containers on the Armed Forces Officers Club in Abu Dhabi, with the aim to expand across the UAE.
So we headed over to the St. Regis Abu Dhabi to meet Smart Acres CEO Abdulla al Kaabi to find out more.
Tell us about your background?
I am from a tech and farm background. My father has a passion for farming and gardening; he’s very strict about anybody who messes around with his garden or farm. My father has a few farms across the UAE, where he grows crops and dates. When he heard that I was pursuing a project in the agriculture sector he got excited and actually gifted me a farm, which I am grateful for and will keep. However, Smart Acres, rather than the farm my father gifted me, is an urban farm.
How was Smart Acres first developed?
CEO Abdulla al Kaabi (centre)
Smart Acres was founded in 2017 and local testing began in July 2019. Smart Acres was developed by a team of experts, including myself, Director Sean Lee, and Lead Project Manager, Aphisith Phongsavanh with the aim of improving food security within the United Arab Emirates and developing the country’s farming capabilities, providing a solution to potential socioeconomic threats such as pandemics and climate limitations the Middle East currently endures.
Tell us more
We planted lettuce and after a few harvests, we decided to expand from two containers to eight containers. From the two insulated containers, the yield was 3.5 tons annually, which was our proof of concept. For the proof of concept, our target weight for each lettuce head was 140g. However, we have reached an average of 200g per head. I don’t think any other vertical farm here reached that quality or weight in terms of vegetables at this size.
How would you describe Smart Acres?
It is a one-of-a-kind agriculture system that is designed to produce some of the highest yields of crops within the UAE’s vertical farming industry while introducing a new future for clean foods and allowing both business to business (B2B) and business to consumer (B2C ) sectors to locally sourced produce.
Tell us about the containers
We invested heavily in the containers, not just financially, and it took us a while to partner up with n.thing, a South Korean vertical farming technology company, to bring the best vertical farm here in the UAE. We had talks with other companies before and we decided to go with this one, in terms of risk, in terms of technology they are using. And the system we are using in the containers is hydroponics (growing plants without soil) which has been used by growers for hundreds of years.
Techno advancements mean we were able to implement the Internet of Things for operations, which helps us to monitor the entire farm in terms of humidity, temperature, and even the nutrients that go inside the plants. Now we have our expansion plan from eight to 78 containers, which eventually will produce more than 140 tons of produce annually. We are currently in talks with private and public entities in terms of the expansion. We are also planning to have a research and development center in order to start growing our own potato seeds in a controlled environment.
Will Smart Acres just be growing lettuce?
In our current eight containers, we grow four types of lettuce; Lolo rosso , green glace, oakleaf Batavia, but we are able to grow 30 types of lettuce. Currently, we are testing new methods to improve the quality and weight of the existing lettuce. The results of last month’s test resulted in lettuce whose individual heads weighed more than 200 grams on average. However, we aim to grow more than just lettuce. We have plans to eventually grow baby spinach, mature spinach, and baby arugula. Smart Acres’ vision is to expand to meet the demand of popular produce in the region such as strawberries, and, as I previously mentioned, a shift and emphasis on cultivating potato seeds.
Where can we buy your smart lettuces?
We are now supplying restaurants and hotels for free to get ourselves known, and we have had great feedback from them. We have also partnered with several restaurants and cafes around the country including Inked and Fae Cafe, and have plans to have our produce in the kitchen of dozens of other F&B outlets. The recent initiative by HH Sheikh Mansour bin Zayed, Deputy Prime Minister, Minister of Presidential Affairs, and Abu Dhabi Agriculture and Food Safety Authority (ADAFSA), stating that all major grocery stores in the capital must allocate space for local produce mean we are perfectly poised to enter local supermarkets. We have had lots of offers from Abu Dhabi Holding and other government entities that are members in the food security committee to buy our whole produce. Currently, we are focused on our actual produce itself, in terms of quality, weight.
Facebook Twitter Linked In Pinterest Tumblr Reddit Digg Email Print Share
Posted in Features, Food, Life, News
Tagged agriculture system Abu Dhabi, CEO Abdulla al Kaabi, Clean foods UAE, food security UAE, SMART ACRES Abu Dhabi, st regis abu dhabi, UAE Climate Change Risks and Resilience, UAE farms, UAE’s vertical farming industry, vertical farming Abu Dhabi
Publix And Its GreenWise Stores Go After Hydroponics In Big Ways
Publix partnered with St. Petersburg-based Brick Street Farms on the initiative, a good fit because of Brick Street’s focus on quality and sustainability
September 9, 2020
by: Grier Ferguson
Sarasota-Manatee Editor
The Lakeland-Based Grocery Giant Is
Targeting Customers
Who Want Fresh, Local Products
There was a time when hydroponic farming seemed almost futuristic, like flying cars or underwater houses. But not anymore. The future is now for hydroponics.
Hydroponics, which involves growing plants without soil, is becoming more prevalent, including with Lakeland-based grocery giant Publix and the company’s GreenWise Market stores that sell organic, natural, and specialty groceries. Publix operates GreenWise stores in Lakeland, Tallahassee, Boca Raton, Ponte Vedra, and Odessa as well as in Mountain Brook, Ala., and Marietta, Ga. It closed two GreenWise stores in South Carolina in late August, citing the locations’ space constraints, but it plans to open a store in South Florida in the fourth quarter.
Publix and GreenWise are biting into hydroponics in some big ways, hoping it pays off with customers seeking fresh, local products.
Courtesy. Lettuce grown in the hydroponic container farm at Publix’s GreenWise Market in Lakeland is sold in the store.
In one major move, the company installed a 40-foot hydroponic container farm in front of its Lakeland GreenWise store. The container, added at the beginning of March, uses mineral-rich water instead of soil to grow lettuce plants. Publix partnered with St. Petersburg-based Brick Street Farms on the initiative, a good fit because of Brick Street’s focus on quality and sustainability efforts, Publix Business Development Director for Produce and Floral Curt Epperson says.
One key feature of the container is a viewing window on the side that allows people to see the plants growing. Along with showing off the growing process to customers and store employees, GreenWise also wants to use it during educational tours for schoolchildren. The image of the fresh product is key, Epperson says. “You have a good visual of farming at its best inside a container,” he says.
The hydroponic farm is near an outdoor sitting area, encouraging people to mingle and see what it's all about. “There’s certainly been some interest in that,” Epperson says. People are also attracted to the system’s sun-emulating lighting. “It really has an iridescent grow to it,” he says. “It draws you into the container. It’s hard to walk by it and not say, ‘What is that?’”
The lettuce, which takes about five weeks to grow, is harvested right in the container. GreenWise has a grower on site who works with Brick Street and harvests the product three days a week, amounting to about 720 heads of lettuce each week. The same day it’s harvested, the lettuce is taken into the store to be sold. “It really brings a new level of freshness and sustainability to the customer,” Epperson says.
Sustainability can be a key selling point for consumers who are becoming savvier and more knowledgeable about where their food comes from. Because the lettuce from the hydroponic container only has to travel mere feet to end up on store shelves, the product uses fewer resources and has a reduced carbon footprint.
Customers are already responding well. The lettuce grown in the container has done well at the store, Epperson says, and currently, all of it is purchased at that location. Once the lettuce is harvested, more is planted, continuing the cycle.
Other GreenWise stores are getting in on the hydroponic action, too. Brick Street, for instance, is providing lettuce for other locations. Publix has also worked with South Carolina-based Vertical Roots on a mobile hydroponic farm that it brought to stores, giving people the chance to walk inside the farm. The mobile educational tool is on hold during the pandemic, but it’s expected to come back. “It’s really just a cool opportunity to bring the farming concept to the customers,” Epperson says.
Courtesy. Publix worked with South Carolina-based Vertical Roots on a mobile hydroponic farm that it brought to stores, giving people the chance to walk inside.
In another hydroponic effort, Publix has partnered with vertical farming company Kalera to distribute the lettuce it grows hydroponically in Orlando.
Other crops might be involved in the future as well; growers are working on expanding beyond lettuce. “Each of these growers are looking at other ways to grow other commodities,” Epperson says. “I think you’ll see more trials into tomatoes, cucumbers, and peppers going forward.”
Epperson says Publix is working with more hydroponic growers, too, in states including Florida, Georgia, South Carolina, and North Carolina. “Every day, we’re outsourcing product,” he says. “It’s a great way to support communities that are supporting the growers and us. It’s great for the customer, great for the grower, and great for Publix.”
Food Revolution With Dubai Vertical Farms
There is a growing need for local produce to be safe and fresh, and warehouse farms like Uns are responding to that demand. As the CEO of Uns Grahame Dunling puts it
Zubina Ahmed
September 4, 2020
An Al Quoz-based indoor vertical farm is setting a new template for food production. (Photo: Shihab/KT)
Imagine an ultra-modern, high-tech farm right in the middle of a desert, where fresh vegetables are being grown without soil or sunlight. Al Quoz-based facility Uns Farms is an indoor vertical farm that is growing high quality, pesticide-free, farm-fresh local produce in a controlled, indoor environment using hydroponic technology and LED lights. Produce includes greens like kale, mustard, basil, lettuce, eggplant, and capsicum, as well as a wide variety of crops ranging from leafy to microgreens. The farm, which began production in January last year, is on a 3,000 sqm plot of land in one of Dubai's main industrial areas and produces crops equivalent to 5,000 sqm of land. The idea is to create natural, healthy, and safe food options that can be produced with optimal resources throughout the year, even during peak summers.
"Agriculture has progressed drastically over the decades," says Mehlam Murtaza, executive director of Uns Farms. "It went from field farming to greenhouses, but both these models demand nature's aid. The Middle East is challenged in terms of the weather. It's hot, humid and there's a scarcity of water. Vertical farming, on the other hand, is a model that can be adopted anywhere in the world. It is resource-efficient and the climate and temperature are controlled, which, in the context of the GCC, is perfect.
"The sprawling indoor facility in Al Quoz uses three stages of farming to grow crops. Mehlam explains the first stage as being one where seeding is done. "That's where we are more efficient because we put one seed per plug." In the subsequent nursery stage, the seed grows into a small baby plant, which is then ready for transplanting. "That's when the root has developed into a certain amount as the plant requires more space to grow," says Mehlam. The final stage is when the crops grow. After the harvest, the plants are processed and packaged for distribution.
An indoor farming environment demands appropriate lighting. "In terms of light, the farm has energy-saving LED spectrums, which have different biological effects on the plant. For example, the red spectrum elongates the plant, the blue spectrum makes it thick, the green spectrum aids in health and immune system of the crop," says Mehlam
.Vertical farming also has a solution to concerns related to water. "What you see in soil farming is that you would drip-irrigate or spray water on the floor. A lot of that water goes into the earth and is lost. Hydroponics feeds the root and drains out into a tank and goes into a circular system, where the water is reused and that's how we save 90 percent of water."
There is a growing need for local produce to be safe and fresh, and warehouse farms like Uns are responding to that demand. As the CEO of Uns Grahame Dunling puts it, "We are very local and centralized with no outdoor influences. So, if there is anything in the atmosphere, it doesn't affect our crops." In fact, Covid-19 has brought about a renewed focus on vertical farming. "In pre-COVID times, we had difficulty in explaining to consumers what indoor farming really is, but the pandemic made us realize the fragility of the supply chain.
A lot of our customers had issues importing food, and with the UAE being a major food importer, it seemed to be a very big challenge. Because of COVID, we were able to expand and show people the importance of locally-owned produce," says Mehlam.
Today, Uns produces anywhere between 1,000 to 1,500kgs of vegetables every day and supplies to gourmet chefs, hotels, restaurants, supermarkets, and hypermarkets. Much to his gratification, Grahame notes that his modern farm is a 'choice for the future'.
zubina@khaleejtimes.com
Singapore's Temasek Bets on 'Skyscraper Farms' As Growth Market
Temasek and German pharmaceutical major Bayer established Unfold, a 50-50 joint venture, last month. The company will develop and market seeds for vertical farming both in Singapore and at its California headquarters
Joint Venture With Bayer To Develop Seeds
To Boost Food Security In City-State
TAKASHI NAKANO, Nikkei staff writer
September 10, 2020
SINGAPORE -- Singapore's state-backed investment group Temasek Holdings has extended its business portfolio into urban farming, a concept that will aid the city-state in its quest to become more agriculturally self-sufficient.
Temasek and German pharmaceutical major Bayer established Unfold, a 50-50 joint venture, last month. The company will develop and market seeds for vertical farming both in Singapore and at its California headquarters.
Singapore produces less than 10% of the food it consumes. The government plans to raise the ratio to 30% by 2030.
Vertical farming, officials believe, is crucial to attaining that goal. The technique grows agroponic layers of crops under artificial light inside skyscrapers. Because the plants are not dependent on weather, the method is expected to generate large yields in a relatively quickly.
"Temasek is recognized as one of the leading investors in the food and agriculture segment," said Jurgen Eckhardt, head of Leaps by Bayer -- an investment arm of Bayer. "They have investments in, and relationships with, a range of vertical farming companies."
Bayer will provide plant genetic data to Unfold, which will first develop new varieties of lettuce, spinach and tomatoes, among other crops. The company will sell seeds to food producers.
Temasek will introduce companies to the technology and expertise at Unfold and other investment targets. Temasek holds a stake in Sustenir Agriculture, a Singaporean urban farming company, providing a channel for Sustenir to cultivate Unfold's high-yield seeds.
Vertical farming is projected to grow into a $12.77 billion market in 2026, according to Allied Market Research, up from $2.23 billion in 2018.
Temasek invested 3 billion euros ($3.7 billion) into Bayer in 2018 -- funding which helped Bayer complete the acquisition of U.S. seed producer Monsanto.
The company anticipates further investments in the agricultural sector.
"Whether it's in the area of an alternative protein, aquaculture, or crop science, it's an area that requires actually more capital," said Temasek International CEO Dilhan Pillay Sandrasegara. "So far it's done well for us and we're still keen to invest more in it."
Temasek has expanded its portfolio of life sciences and agribusiness investments. Allocation in the domains stood at 8% at the end of March, or five points higher than five years earlier. The size of the holdings is about $17 billion.
The coronavirus pandemic has heightened concerns over food security. Thailand and other trading partners temporarily imposed restrictions on exports. The Singaporean government doled out 30 million Singapore dollars ($22 million) in subsidies this April to help companies produce more eggs, leafy vegetables and fish.
"In Singapore, with less than 0.8% arable land, vertical farming innovation is critical," said Unfold CEO John Purcell.
This year, Temasek has invested in startups that develop meat and fish substitutes, as well as plant-based milk. GIC, another Singaporean state investor, in May picked up shares in Apeel Sciences, a U.S. company that developed an artificial peel for fruits and vegetables to extend shelf life.
The less-than-stellar portfolio performance has also factored in Temasek's investments into agribusiness. For the year ended March, the company reported a return of minus 2.3%, the first negative result in four years. Declining stock values of domestic companies such as the banking group DBS Group Holdings and the conglomerate Sembcorp Industries were behind the setback.
When Singapore Airlines sought to raise up to S$15 billion in rescue funds this March, Temasek was the first to indicate it would sign on in light of its status as a major investor in the carrier. Saddled with its role as a financial provider of last resort, the state investment group's ability to reap returns from investments in agriculture and other growth sectors will sway its performance.
Temasek has also stepped up investment in advanced medical fields such as biopharmaceuticals in the past year, with stakes in 10 companies revealed in 2020 so far.
Vertex Venture Holdings, a Temasek unit that oversees a fund specializing in the medical field, has invested in more than 20 healthcare-related startups, including American drug developer Elevation Oncology in July.
"COVID-19 has shone a light on the importance of continued R&D investment," said Lori Hu, managing director of Vertex Ventures HC. "It has revealed critical unmet needs in the health care industry. We continue to actively look at new deals."
Leveraging its broad network, Vertex took a stake in Israeli telemedicine platform operator Datos Health in April and invested in India's IVF Access Hospitals, which specializes in infertility treatments, two months later.
Through its investments in the medical field, Temasek is also involved in the global race to develop coronavirus treatments. It was part of a group of investors to pour $250 million into Germany's BioNTech, which is jointly developing a COVID-19 vaccine candidate with Pfizer. South Korean drugmaker Celltrion, in which Temasek holds a roughly 10% stake, has brought a diagnostic kit to market in the U.S. last month.
Investments in biopharmaceutical developers carry high risks, but the payoff can be large when a treatment successfully reaches the market. Holdings in unlisted companies accounted for 48% of Temasek's portfolio as of March-end, up six points from a year earlier.
Lead photo: Courtesy of Unfold - Vertical farms use hydroponics to grow crops inside buildings.