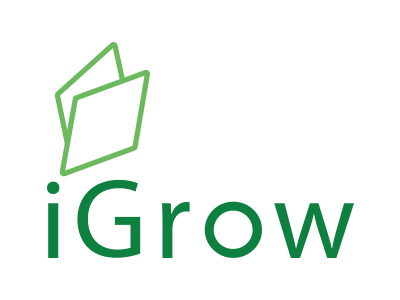
Welcome to iGrow News, Your Source for the World of Indoor Vertical Farming
Is A Vertical Farm Cost Effective To Build And Operate?
A common question we’re often asked is a vertical farm cost effective to build and operate? There is no categorical answer to this complex question, which often requires a detailed feasibility study to resolve.
Author: Robert Colangelo.
Founding Farmer at Green Sense Farms Holding, INC.
A common question we’re often asked is a vertical farm cost-effective to build and operate? There is no categorical answer to this complex question, which often requires a detailed feasibility study to resolve.
The answer Starts With The 4 Cs -
Crop, Capacity, Climate, and Capital Budget.
Crop: What is the intended crop and how many varieties will be grown? At this time vertical farms can economically grow leafy greens (lettuces, baby greens, herbs, and microgreens), starter plants, and cannabis. To grow a cultivar well its best to design a farm with individual grow rooms where set points can be optimized to the monocrop. Many customers ask us to build farms that can grow a wide range of crops. We suggest specializing in growing large volumes of a few crops, that you can grow well and build a brand. This will also make production more efficient increasing the profitability.
Capacity: What is the desired output and frequency of harvest? The answer to this question is key to sizing a farm design. Understanding the production schedule and how many crop rotations a farm will hold will assist in laying out the farm. Capacity is also key to calculating the unit production cost. The bigger the farm typically the lower the unit cost.
Climate: One of the advantages of a vertical farm is that it can be built anywhere from the cold-dry climate in the South Pole to the hot- humid climate in Southeast Asia. The more humid the climate the more expensive mechanical equipment will be required to control Temperature and Relative Humidity. A good farm design can take into consideration the outside cool-dry climate and use it to reduce capital and operating expenses. In addition, cooler drier climates tend to have less bugs which will reduce operating costs when it comes to Integrated Pest Management (IPM) programs.
Capital Budget: A rule of thumb is that if you spend more on capital expense then you will reduce your operating expense. A well-built farm that is designed to optimize crop growth will lower the daily operating cost. To do this it greatly helps to have an anchor customer identified, define the crop (s) that will be grown, the harvest frequency/delivery and how it will be packaged so that these variables all be factored into the farm design.
Many other factors play a role in setting and building a farm. This includes location, automation, and labor. The 4C’s will get you off to a good start and will allow the development of an initial financial proforma so that you can predict the size of the farm, output, and the capital required to build and operate the farm profitably. I have learned that sometimes the best projects are the “ones not done.” Building a farm too big or too small can be a disaster. Starting backwards to first identify and understand the customers’ needs is a good way to begin. With adequate research and planning a vertical farm can be built to operate profitably and be a project worth doing!
This Startup Wants Vertical Farmers To Hire A Robot Gardener
“By automating the production with robotics and remote monitoring, we can lower labor costs and offer solutions for food producers that are economically viable and environmentally sustainable,” the company claims on their website.
Arugula micro greens are grown at AeroFarms on February 19, 2019, in Newark, New Jersey.
Photo: Photo by Angela Weiss (Getty Images)
In recent years, vertical farming has emerged as a futurist’s solution to the world’s agricultural problems. The growing trend seeks to use controlled environments to boost food production, leveraging indoor labs where temperature, light, and nutrients can be mechanically controlled.
Yet while vertical farms have gained in popularity, they are also still very expensive. When compared to conventional farming, these farms necessitate the purchase of pricey equipment to aid human labor—a fact that, when paired with other economic pressures, has apparently led to an industry “littered with bankruptcies.”
One company hopes to change this dire picture. Enter Watney the robot.
Watney was designed by start-up Seasony. The company, which was featured today at this year’s Alchemist Accelerator’s Demo Day, has sought to make the tech-farming trend more accessible by automating away some of the more difficult labor involved.
Image: Screenshot: Youtube/TV2LORRY
“By automating the production with robotics and remote monitoring, we can lower labor costs and offer solutions for food producers that is economically viable and environmentally sustainable,” the company claims on their website.
Indeed, Watney is designed to augment (and, in many ways, replace) a human labor force—currently one of the biggest expenditures for vertical farms. Essentially an intelligent, automated cart, the robot was designed to “move and transport plant trays” within a farming hub. In techno-jargon, it is an autonomous mobile manipulation robot (AMMR), a type of machine known for moving and manipulating items on its own. It is also equipped with a camera that captures image data and sends it back to farm management software for human analysis. Watney also gathers valuable horticultural data to help farmers optimize yields, said Christopher Weis Thomasen, Seasony’s CEO and Co-Founder, in an email.
From left to right: Erkan Tosti Taskiran, Servet Coskun and Christopher Weis Thomasen.
Photo: Photo from Seasony.
“We are doing for vertical farming what the integration of autonomous mobile robots did to amazon. We are able to decrease the costs of growing food in a vertical farm by alleviating the logistics pains of working from scissor lifts,” said Thomasen.
Thomasen, a mechanical engineer, and his two co-founders electrical engineer Servet Coskun and business specialist Erkan Tosti Taskiran, were inspired to create the business while brainstorming what it would take to sustain life in outer space (Watney the robot is named after Mark Watney, the astronaut in the movie The Martian, who, after being stranded on the Red Planet, fertilizes potatoes with his own poop to survive).
“It quickly evolved to Seasony setting up a vertical farming lab and exploring the technical challenges facing the new industry. Reducing the costs related to labor is key in order to scale vertical farming and make agriculture more sustainable,” Thomasen said.
There is, of course, some debate in the farming community about the social costs incurred through the large-scale displacement of human labor.
Presumably, we will have to wait to see what that cost-saving process looks like. Seasony, which is still getting off the ground, plans to do a pilot trial with the largest vertical farm in Europe in April. It has plans to conduct further testing with several smaller vertical farms, as well, Thomasen said.
Lucas Ropek
Staff writer at Gizmodo
Indoor Farming: How Can You Ensure Success?
Any business can fail for any number of reasons, but indoor farming is an incredibly delicate organism that depends on many disparate factors being perfectly aligned and in balance
Any business can fail for any number of reasons, but indoor farming is an incredibly delicate organism that depends on many disparate factors being perfectly aligned and in balance. This increases the risk of failure for those unaware of the number of plates that need to be kept spinning in perfect time. This list is not definitive but gives you a good idea of the most common mistakes to avoid.
1. Avoid a Trial and Error Approach to Design
There are multitudes of factors that are naturally managed and balanced with indoor farming. The sun cannot be changed, irrigation to every plant is different as weather patterns can change from moment to moment and even the nutrition in the soil can vary across the area of the field. Planning your farm therefore gives you the ultimate control but also dramatically increases the variables that you can and must consider.
These variables start with the facility’s very layout, such as the size of growing space, plant distribution, airflow and more. Additionally, without having the right models in place to determine the exact light recipe and combination of CO₂, nutrients and water required to grow a successful crop, growers can find themselves wasting time and money on testing phases to try to maximize yield and revenue. Once you have developed a model for your vertical farm, you should then put it through a testing phase on a smaller scale to ensure it is viable.
2. Pick the Right Crop
It’s far easier to develop a profitable and scalable facility if you know the needs of your crop inside and out. That ideally means specializing in one type of crop that you can design your facility around, electing the right growth spectrum and studying that particular plant’s biology to better understand how to optimize irrigation, nutrition, air flow, CO₂ concentration and propagation in order to maximize elements such as taste, nutritional content, visual appeal, potency or shelf life.
Too many growers have tried to hedge against perceived risk by trying to grow multiple crops. By default, it is extremely difficult to have one installation that is optimized for a wide variety of plants, and therefore the returns from each crop are lower than they could have been. The facility then may have to suffer through downtime as the technology is tweaked and optimized for the next crop — eating into profitability and adding unnecessary costs.
3. Location, Location, Location
The old adage that location is half the battle has never been more relevant than in vertical farming today. Vertical farms have a key advantage in their ability to be located close to their customer, whether they are selling to food processors, supermarkets or local shops. Removing the vast transport logistics associated with today’s food supply chain slashes costs and helps appeal to an increasingly conscientious customer. The lack of transport costs also helps counter the higher production costs resulting from higher energy and labor inputs.
At city planning level, there are also many advantages of co-locating a vertical farm with other facilities such as office buildings, shops or residences — which could draw the vertical farm’s excess heat to reduce demands on other sources of energy.
4. Simplify Your Business Model
Proximity to customers and the ability to produce crops year-round at a sustainable rate is a strong advantage in the market, whether you’re growing for the food or pharmaceutical sectors. Therefore, consider the opportunities available through establishing exclusive contracts with customers at a fixed rate that will offer more financial security as you build your business.
5. Be Realistic About Operational Cost
Setup and fit-out costs represent a high initial outlay for any indoor farming entrepreneur, but the ongoing operational costs (energy, labor, inputs, maintenance, etc.) are also significant. Businesses not only need to find creative ways to mitigate these risks (e.g. growing through the night when energy tariffs are lower and the outdoor climate is cooler to assist HVAC systems’ efficiency), but also consider the cost-benefits of different configurations and process flow.
6. Set Prices Based on What Consumers Will Pay
At the 2017 inaugural AgLanta Conference11, PodPonics’ CEO admitted that the company missed out on higher potential margins as it priced its crops to compete with conventional growers, ignoring the price premium that food traceability, pesticide-free growing and local production can increasingly attract from consumers in some markets.
7. The Skills Gap
In many cases, those who have embraced the promise of indoor farming have not been traditional growers but rather tech entrepreneurs, engineers or hobbyists. Vertical farming requires a unique mix of skills to be successful: big data scientists, systems integrators, project managers, engineers, growers and plant scientists all have a role to play in addition to the core functions that any business needs to be successful (financial strategists, marketing and business development, etc.). From the leadership perspective, experience at replicating and scaling a business is critical. Ignoring any one of these functions leaves a serious gap in business capability that could undermine the overall success of the operation.
8. Remember What You’re Selling
In a bid to capitalize on the new technology and growth models offered by vertical farming, some growers have forgotten that their primary focus should be on growing and selling the highest quality food. Instead, they have tried to recoup their investment by trying to commercialize their vertical farm’s technology, process and methodology. Unfortunately, as we have seen, every vertical farm is different with potentially very different needs. The trick is to not to try and do many different things at once, but instead keep a clear focus on doing one thing as well as possible.
Source: www.currentbyge.com/ideas