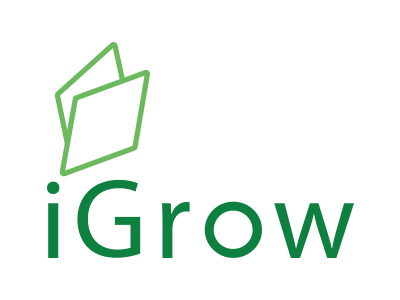
Welcome to iGrow News, Your Source for the World of Indoor Vertical Farming
Ground Broken on New Hydroponic Facility To Serve The Marginalized Communities in Torrington CT.
The mission of the farm is to provide entry-level, safe, clean “green jobs” to members of the community
Published on July 6, 2020
Joe Swartz
Vice President/Lead Horticulturalist at AmHydro - 36 years as Controlled Environment Ag Consultant and Commercial Grower
June 30, 2020, was an exciting day for the local Connecticut organization, New Opportunities. http://www.newoppinc.org/ After years of planning, the ground was broken on a new hydroponic farm project called "CT Food4Thought" that is going to bring fresh, nutritious, pesticide-free food to local food banks, shelters, soup kitchens, and schools to communities throughout Connecticut. In addition to that, the farm will also supply retail grocery stores and co-ops with fresh produce as a way to generate income for programs through selling the produce grown. New Opportunities partnered with industry-leading Controlled Environment Agriculture Technology company AmHydro of Arcata, CA. (https://amhydro.com/ )
The groundbreaking marked the start of three greenhouses, containing AmHydro’s soilless hydroponic growing systems, being constructed in partner with Borghesi Engineering with plans to expand up to 12 greenhouses in the future. AmHydro VP Joe Swartz and the Commercial Growing Team at AmHydro will provide on-going support and grower training to ensure a successful project and economic sustainability.
New Opportunities is a social service organization that serves marginalized and low-income communities throughout Connecticut. The mission of the farm is to provide entry-level, safe, clean “green jobs” to members of the community. Specifically, CT Food4Thought wants to offer these job opportunities to those with developmental disabilities, those who have been previously incarcerated, and those who are unemployed as a way to provide a path to higher-level employment opportunities in both this industry and others, such as: the field of nutrition, food safety, environmental management, and horticulture.
Dr. James H. Gatling, Ph.D., CEO of New Opportunities, speaks prior to breaking ground.
New Opportunities Foundation had a vision and worked directly with hydroponic industry leader AmHydro to develop the most optimum growing system and production methods available. This hydroponic farm will use 90% less water than conventional field agriculture and will be able to produce more than 10 times the amount of produce that traditional growing methods yield. The farm will also be able to operate year-round due to the environmental controls inside the greenhouse that can simulate the perfect growing conditions for plants even in the dead of winter. This will allow people in Connecticut to have access to fresh, local produce all year in comparison to the normal outdoor growing season in the area that lasts approximately 120 days.
Bill Rybczyk, New Opportunities, Joe Swartz, AmHydro, Jon Jensen, the Corporate Advisory at the project site this Spring.
AmHydro is proud to partner with New Opportunities on their new project CT Food4Thought and is excited to continue to be a part of and support the project through providing training to members of New Opportunities and members of the community.
Quote, from Bill Rybczyk, Director of Research, Planning, and Development for New Opportunities Inc : “We’re planting seeds for lettuce and other herbs, but we’re also planting seeds into people’s lives, and they can then take that, and they begin to grow….and that impacts not only their lives but their children’s lives and their grandchildren’s lives into the future…..and that’s what this project is all about."
For more information, please contact Joe Swartz, VP, AmHydro at Joe@AmHydro.com
Published by
Vice President/Lead Horticulturalist at AmHydro - 36 years as Controlled Environment Ag Consultant and Commercial Grower
Please check out this amazing project that American Hydroponics is proud to be a part of. New Opportunities will be producing fresh, pesticide-free food, local "green jobs," and economic empowerment to marginalized communities.
Truly wonderful. hashtag#LocalFood hashtag#LocalFarms hashtag#WeGotThis hashtag#HelpingOthers hashtag#SustainableFarming
Farm Box Foods - Digital Farming Entrepreneurs
In 2017, an unlikely group of friends—a real estate agent, a solar energy entrepreneur, and a fabricator, decided to take action. From the drive to decentralize food supply chains and assist communities to produce more locally grown, healthy food, FarmBox Foods was born
OUR MISSION
We want to empower communities to produce their own locally grown produce year-round.
We strive to change the way people farm by merging technology and agriculture into a system that greatly reduces water usage and transportation costs while maximizing space.
We see a future where communities have achieved food independence by producing their own healthy food and distributing it locally – no longer relying on centralized food systems.
Our Story
Our planet is in trouble, and we need to find new, innovative approaches to food production.
In 2017, an unlikely group of friends—a real estate agent, a solar energy entrepreneur, and a fabricator, decided to take action. From the drive to decentralize food supply chains and assist communities to produce more locally grown healthy food, FarmBox Foods was born.
Our founders knew they had to search for agricultural innovations. At the heart of this new approach lies the shipping container. Our goal was to develop the most efficient, high-yielding container farm on the market. Early in our research and development, we saw the appeal of vertical farming—this design principle would allow us to maximize limited space. Bringing all these ideas together, FarmBox Foods created a hydroponic farm with an elegant and user-friendly design.
With our hydroponic farm on the market, FarmBox Foods is now looking for new ways to bring more healthy food options to communities. Enter mushrooms. With their myriad health benefits and culinary versatility, mushrooms are the perfect crop for sustainable food systems. Our first-of-its-kind gourmet mushroom farm will debut in 2020 and boost access to this superfood.
FarmBox Foods is changing the way we think about growing food, one shipping container at a time.
It comes down to what’s inside, the “Plant Force One” is built inside of a recycled 40-foot container. Helping the environment and help you change the way you farm
Jersey City May Have The U.S.'s First Municipal Vertical Farm. Experts Share How it Can Thrive
The city has signed a three-year contract with the Newark-based vertical farming company AeroFarms and plans to begin growing leafy greens in 10 locations including senior centers, schools, public housing complexes and municipal buildings later this year
Rebecca King | NorthJersey.com
June 26, 2020
Jersey City is on track to implement the country’s first municipal vertical farming program.
The city has signed a three-year contract with the Newark-based vertical farming company AeroFarms and plans to begin growing leafy greens in 10 locations including senior centers, schools, public housing complexes, and municipal buildings later this year.
“A lot of people don’t go for regular physicals,” said Jersey City Mayor Steven Fulop. “They’re not checking their sugar levels, blood pressure or cholesterol. Having people be more diligent about their diet will hopefully increase their lifespan, long-term.”
Once the microgreens start sprouting, members of the community will be able to sign up to receive free produce. They’ll be encouraged to attend seminars about healthy eating and get regular health tests done through Quest Diagnostics, which has also partnered with the city.
Because crops are stacked at this AeroFarms facility, the company says it can produce 390 times the crops from a traditional farm.~Courtesy of AeroFarms
“It’s important to be doing this prior to people getting diseases or sicknesses,” said Fulop. “A lot of what we’re doing is based on education. Many people aren’t aware of the bad foods they’re putting in their bodies on a regular basis.”
Vertical farming is one method of hydroponic controlled environment agriculture. Instead of being grown outside in soil, plants in vertical farms are stacked on shelves inside, misted with nutrients and lit with LED lights in lieu of sunlight.
Garrett Broad, an assistant professor at Fordham University whose research focuses on new food technology, food justice, and community-based organizing, says vertical farming has many sustainability boons.
Because the environment is completely controlled, the weather cannot destroy or affect crops. Vertical farming saves water. It reduces runoff. There’s no need for pesticides. And any kind of crop can be grown year-round. Fulop predicts Jersey City’s program will produce 19,000 pounds of food annually.
“The idea is that by doing vertical stacking, you can get a lot of productivity out of a very small area,” Broad said.
Farmers tend plants at AeroFarms with the help of platforms that can rise and fall.~Courtesy of AeroFarms
But, there are downsides. Vertical farming is extremely energy-intensive. Even energy-saving LED lights require a huge amount of power to shine on the crops. According to Fulop, Jersey City has no way to offset the impact of this energy use yet. Many of the farms are housed in decades-old buildings that have not been updated to include solar panels or other energy-saving technologies.
“It’s something we need to consider in the future,” said Fulop.
The other issue with vertical farming is that leafy greens are essentially the only plants worth growing, said Broad. Larger, heavier fruits and vegetables have too much biomass and require too much artificial light and nutrients to grow in a cost-effective way.
Indeed, Fulop confirmed that greens are the “easiest base material” to grow and will be the focus of Jersey City’s vertical farms.
That said, vertical farms do have the ability to create change in a community when done right, said Broad.
“Vertical gardens are similar to other urban farming projects we see,” he said. “They exist on a sort of spectrum. Some are total failures, some are a fun project and some are actually part of a social change.”
Projects that don’t receive enough funding or attention rank as “total failures.” Small community gardens rank in the “fun project” category -- “They provide small scale change. People get to know their food a bit more, they learn some horticultural skills, but it doesn’t drastically change the community,” said Broad.
According to Broad, Jersey City will have to do extensive community outreach to make vertical farming a long-term success – which means reaching out to faith leaders, schools and groups that are trusted by the community and getting them involved with the distribution of produce.
It means talking to residents about what vegetables they actually eat; planning cooking classes at times when people aren’t working; making dishes at those classes that the attendees will actually cook in their own homes.
As technology continues to improve, the company expects vertical farming to become even more cost-effective. | Courtesy of AeroFarms
“Did we ask to see if the people who are actually the target of this project have working kitchens? Are we making sure they have pots and pans? Are we growing food that’s culturally relevant to them? If we don’t ask these questions, a lot of times vertical farming projects stay in the ‘nice and fun’ category,” Broad said.
Jersey City has launched a few food initiatives in past years. The city gave grants to bodegas and corner stores to redesign display cases, putting fruits and vegetables next to their counters instead of snacks and candy to encourage healthy eating. Another program involved walking senior citizens around a supermarket and teaching them to read the labels on the back of packaged foods. At the end of the tour, they were given money and encouraged to purchase healthy meals.
Areas in which there is an extreme lack of nutritious, affordable food have been called “food deserts.” But, those who study farming technology have been moving away from that term, which brings up images of scarcity and used-up land. Instead, “food swamp” is now used to describe cities and towns that have food available, but few healthy options. Others use the term “food apartheid” to draw attention to food inequality. Poorer neighborhoods are usually the places that lack fresh, affordable food.
Jersey City is one such place, said Broad. If given the right attention, he added, a vertical farming initiative could be a step toward addressing poverty and food inequality.
“This is the kind of thing that can be fun and flashy and get media attention,” he said. “But, it’s up to us to apply pressure to the government and say, ‘OK, show us how this is part of something bigger.’”
Rebecca King is a food writer for NorthJersey.com. For more on where to dine and drink, please subscribe today and sign up for our North Jersey Eats newsletter.
Email: kingr@northjersey.com Twitter: @rebeccakingnj Instagram: @northjerseyeats
June 26, 2020
Indoor Vertical Farming is The Future Says Irish Agritech Start-Up
Farmony says Ireland can become self-sufficient in leafy greens, herbs and microgreens thanks to its approach to vertical farming
Farmony Says Ireland Can Become Self-Sufficient in Leafy Greens, Herbs, and Microgreens Thanks to its Approach to Vertical Farming
Jun 25, 2020
Olive Keogh
Farmony co-founders Rodrigo Andrade, Dan O’Brien, and John Paul Prior
Animals grazing peacefully in the fields and serried rows of crops stretching far into the distance are what usually come to mind when we think about farming. It’s a pastoral image deeply embedded by tradition and worlds away from how they do things at the agritech start-up Farmony, which builds high output, controlled environment vertical farms to produce leafy greens and herbs.
On a Farmony farm, the crops are grown indoors on multiple layers of tiered shelving. The method is ideally suited to growing salad leaves and microgreens and a unit can produce in 55sq m (592sq ft) what would normally occupy five acres if conventionally farmed. It also only uses about 5 percent of the water required by traditional growing methods and a unit can be operational 365 days a year.“Vertical farming is not new. In fact, it’s been around forever. Just look at the Hanging Gardens of Babylon or rock faces or the seashore with plants growing, irrigated and fed by water,” says Farmony co-founder John Paul Prior.
So, in the strictest sense, vertical farming isn’t new but its commercialization is. The first large-scale commercial application only came on stream in Singapore in 2012 and Farmony is joining this nascent industry at a time when it is increasingly seen as part of the answer to sustainably and economically feeding the world’s growing population.
What makes Farmony’s approach innovative is twofold. Firstly, it has designed its system to support multiple crops requiring different growing conditions. Secondly, it has put everything a grower needs together in one turnkey package. “In a nutshell, we build customized, controlled environment vertical farms and use our own hardware and software operating system to improve growing efficiencies,” says Prior, who set up Farmony with co-founders Daniel O’Brien and Rodrigo Andrade in November 2018.
The idea for Farmony was O’Brien’s and he spent about 18 months developing the concept before bringing Prior (a friend from college with a marketing background) and business graduate Andrade (a former colleague at the Kerry group) on board. O’Brien’s background is in agriculture and economics and he had seen the start of commercial vertical farms in Asia and the Far East while working abroad.
The Farmony growing units are modular and can be built to any size
Modular units
Potential customers for Farmony include existing and would-be farmers, schools, colleges, community enterprises, and even individuals with €1,500 to spare who can produce a steady supply of fresh greens from a mini-unit in their own home. Anywhere there’s free space is a potential site and controlled farming environments have been created around the world in many unusual places: from tunnels and disused air raid shelters to vacant car parks.
The growing units are modular so farms can be built to any size. A fully kitted out facility, roughly the size of two 40ft (12m) containers joined together, would cost in the region of €86,000. “We land the farm in someone’s yard or put it together in an available outbuilding – such as an unused mushroom house – hook it up to the [existing] power and water supply and they are ready to start growing,” Prior says.“Growers have no problems with weather or seasonality and don’t have to worry about levels of watering or plant nutrition as this is all controlled for them. With our system it’s not the growing that’s the issue. It’s the selling. They need to have thought out their route to market for the volume they’re planning to produce because if they go for microgreens they’d have crops ready for harvesting every 7-10 days. But if they went for something like basil it’s between 21 and 25 days to harvest so it’s less labor-intensive.”With their shiny growing trays, distinctive LED lighting, and humans dressed in white coats with gloves and hair coverings, a Farmony unit looks more like a plant factory than a farm. However, high levels of hygiene mean the growing environment can be kept pesticide-free. It’s all very quiet and even a little bit eerie as the low labor requirement means people are thin on the ground. Making everything as automated as possible was a priority for the company so the labor input for a 20-module unit would be 25-30 hours a week between seeding, transplanting, harvesting, and cleaning.
Farm dashboard
While the uniform rows of little green plants are the visible manifestation of the Farmony method, they are just one side of the story. The other is the intelligent monitoring system that’s whirring away in the background and measuring all the key metrics, providing minute-by-minute detail about the crops as they grow so environmental tweaks can be made as needed.
Each grower has an individual farm dashboard that gives them updates on their crops and offers advice on things like workflow planning. The dashboard can also be used to reorder raw materials such as seeds and growing mats.
Farmony’s units can be remotely controlled from anywhere in the world from any network. This is different to most smart technology farm systems that require the user to be closer to home. The company’s platform is open source and can be used over GSM phone networks and any wifi or internet connection. Customers can choose to operate alone with just back-up support from Farmony or they can become part of the interconnected Farmony “family”, which among other things uses aggregated data from growers to help them further improve growing efficiencies and gain insights into crop behavior.“
In Ireland alone we import around €300 million in fresh produce that we could be growing here given the right conditions,” Prior says. “With our solution this produce could be grown locally all year round, creating jobs and reducing food miles. There is no reason why Ireland can’t become self-sufficient in leafy greens, herbs and microgreens.”Investment in the business has been about €250,000 so far with support coming from the Department of Agriculture, Fingal Local Enterprise Office, and Teagasc. e
Farmony will make its money from selling hardware and from monthly SaaS subscriptions based on farm size with over-the-air updates and tiered reporting levels available.
In May, Farmony signed a European distribution agreement with the US-based Sananbio, a vertical farming technology company that makes growing modules and horticultural lighting. The plan is for Farmony to start selling its solution across Europe using Sananbio’s equipment and it has already opened a satellite office in Poland to kick-start the process. The company expects to have about five farms up in running in Ireland by the end of the year and already has one in the US with another to follow and one about to come on stream in the UK.
JPFA Webinar June 30 - The Challenges And Impact of COVID-19
The Japan Plant Factory Association (JPFA) is organizing its 138th online workshop. The workshop is free of charge
Japan Plant Factory Association / JPFA
Japan Plant Factory Association (JPFA) is a non-profit organization founded in 2010 and is devoted to academic and business advancements in the global industry of plant factory/controlled environment agriculture. Our mission is to develop and disseminate sustainable systems that can address global challenges: food, environment, energy, resource and people's health. With international industry-academia collaborations, we manage around 20 R&D projects, workshops, training courses, etc. based in a Chiba University campus in Kashiwanoha, a smart city in Japan.
Monthly workshops are one of our important education/knowledge sharing activities with JPFA members and others. We have been organizing workshops since 2010 on a wide variety of topics, including plant physiology, new technologies towards next generation, cultivation methodology on multiple crops, business case studies of commercial plant factory operations, to name just a few.
The Japan Plant Factory Association (JPFA) is organizing its 138th online workshop. The workshop is free of charge.
Some sessions include the presentation of 80 Acres Farms on tomato production in indoor farms, a survey report on the impact of COVID-19 by JPFA and a lively panel discussion with leading plant factory companies from Japan and China. Such as, 808 Factory, Greenland, Saladbowl, and Future Agro-Tech, all together with researchers on plant factory and indoor breeding from JPFA and Chiba University.
Date
Scheduled to be released on June 30, 2020.
Free viewing will be available from 13:00 (JST) on June 30 to 13:00 (JST) July 15, 2020.
Theme
As the coronavirus disease (COVID-19) creates challenges worldwide, we feel concerted effort is crucial to our sector more than ever before.
The global challenges/impacts of COVID-19 in the sector, the future role, possibilities and direction of plant factory will be discussed to rethink about what we can do together for our future.
Outline
I. Keynote: “beyond leafy greens: tomato crop production in indoor farms” by Mike Zelkind, 80 Acres Farms + Q & A Session
II. “Report on COVID-19 survey by JPFA” Eri Hayashi (JPFA)
III. Panel discussion: “the challenges and impact of COVID-19, future role and direction of Plant Factory”
*Please kindly note that some contents might be only in Japanese.
Panelists:
Bai Baosuo (Future Agro-Tech (Beijing)
Katashi Kai (Shinnippou, 808 Factory)
Susumu Tanaka (Saladbowl)
Toyoki Kozai (JPFA)
Toru Maruo (Chiba University)
Yuhei Shimada (greenLand)
Moderator: Eri Hayashi (JPFA)
Fee Free of charge
How to watch
Advanced registration is required.
Registration deadline: 13:00 (JST) on July 14, 2020
Please register at https://select-type.com/e/?id=n2duYvX-Gas
After the registration, you will receive the link with access to the workshop videos a day before the release. Please apply one by one. If you cannot access the registration website, please send us the email with your "name", "organization", "country" and "questions to the webinar speaker/panelists (optional)" to info.english@npoplantfactory.org
For more information on the workshop:
JPFA Workshop website
https://select-type.com/s/JPFA-Training
https://npoplantfactory.org/information/1499/
If you have not joined the survey yet, please take the survey, Urgent Survey on the Impact of COVID-19 (Vol.1) before the workshop/online viewing starts.
For more information:
Japan Plant Factory Association (JPFA) International Relations & Consulting
Nozomi Hiramatsu, Eri Hayashi
info.english@npoplantfactory.org
Sunway Goes Into Agritech
Sunway Group is venturing into agricultural technology (agritech) to help reduce Malaysia’s food import bill and encourage and reduce the carbon footprint on the food consumed in the country
By Jennifer Jacobs | The Edge Markets | June 5, 2020
Sunway Chief Innovation Officer and Sunway iLabs Director, Matt van Leeuwen
Sunway Group is venturing into agricultural technology (agritech) to help reduce Malaysia’s food import bill and encourage and reduce the carbon footprint on the food consumed in the country.
It is building a 50,000 sq ft urban farming innovation hub, Sunway FutureX, to help urban farming professionals, tech companies, researchers and young talents collaborate and create solutions for food and agritech. The hub should be completed by the third quarter of this year.
Sunway FutureX, an initiative led by Sunway Innovation Labs (Sunway iLabs), will be located in the heart of Sunway City Kuala Lumpur and it will feature FutureX Farm, an indoor and outdoor smart farming area, FutureX Talent, a research and development centre, and FutureX Campus, a training and collaborative space.
“Bringing together a wide pool of expertise and resources from ecosystem players, Sunway FutureX will aim to create decentralised urban farms to serve local communities, and to address supply chain challenges and the distance between the farm and the fork.
“We hope to build new innovations, which will contribute to improved long-term food security and sustainability in our nation,” says Matt Van Leeuwen, the Sunway Group chief innovation officer and Sunway iLabs director, in a press release.
It is looking to create an agritech ecosystem and one of its first partners will be Sunway Property. “We aim to nourish our communities with the fresh produce grown at our farms and educate them on sustainable living and urban farming.”
Ultimately, it hopes to empower homeowners to grow their own food. “This will be a model for Sunway Property to replicate throughout their cities in Malaysia and allow us to scale up quickly.”
The press release quoted reports that claimed Malaysia imports most of its food from countries such as China, India, Thailand, Indonesia and New Zealand because only about 8% of its agricultural land is used for agro-food production.
“Malaysia’s food import bill has grown significantly over the last two decades and exceeded RM52 billion in 2018. Research shows that imported food loses an alarming amount of nutrients during processing, packaging and transportation before it reaches consumers.
“In addition, traditional farming methods and existing logistics involved in the supply chain contribute in a big way to the carbon footprint. With the world experiencing unprecedented challenges amid the global Covid-19 pandemic, the threat to food security has increased,” the press release adds.
It goes on to say that in urban cities like the Klang Valley where land is limited and expensive, Sunway sees the potential of harvesting the power of talent and technology to build urban farms in underutilised spaces such as rooftops, car parks and even within buildings.
Sunway adds that recent developments in technology have enabled efficient urban farming techniques that require less water and no pesticide to produce consistent yields while revitalising underutilised spaces. “In recent years, urban farming has rapidly gained attention in cities all over the world as a feasible instrument in realising food sustainability and sustainable development.”
FutureX Farm will partner with Thought For Food (TFF), a global non-profit organisation dedicated to entrepreneurial innovation for food and agriculture.
“We see many exciting opportunities to collaborate with Sunway iLabs to provide a sandbox for start-ups from our global TFF innovation platform to carry out pilot projects to test out their solutions to fit local market needs,” Thought For Food chief executive officer (CEO) Christine Gould says.
Thought for Food will be partnering with Sunway iLabs to launch various programmes, including the TFF Digital Asean Lab, to engage, empower and accelerate the next generation of purpose-driven food and agritech innovators.
Sunway Group embarked on its journey towards food sustainability last year by repurposing 40 hectares of undeveloped land in Sunway City Ipoh for food and agriculture. Located at The Banjaran Hotsprings Retreat, Sunway Organic Gardens produces pesticide-free fruits and vegetables with fresh water from mountains for its guests, locals who work there and their communities.
Sunway Pyramid, Sunway Real Estate Investment Trust (REIT) and Sunway Hotels & Resorts have also joined forces to introduce the "Food CPR — Compost. Plant. Reduce." campaign aimed at tackling the food waste problem in Malaysia. Food waste will be channelled into Sunway Pyramid and Sunway Hotels & Resorts on-site compost machines to be processed into fertilisers. The compost will be free for the public to collect at Sunway Pyramid’s compost collection area at B1 Blue Zone Carpark Lobby.
Expert Insights: Advancing Indoor and Vertical Farming Opportunities during COVID-19
The indoor and vertical farming industry has fast-tracked many opportunities to help feed consumers during a global pandemic. The virtual Indoor AgTech Innovation Summit will identify how the world’s leading farm operators found a gap in the market to meet consumer demand and deliver fresh and healthy produce with discussions led by Lipman Farms, Gotham Greens and Smallhold.
The indoor and vertical farming industry has fast-tracked many opportunities to help feed consumers during a global pandemic. The virtual Indoor AgTech Innovation Summit will identify how the world’s leading farm operators found a gap in the market to meet consumer demand and deliver fresh and healthy produce with discussions led by Lipman Farms, Gotham Greens and Smallhold.
Here’s what our experts have to say about the current crisis:
Elyse Lipman, Director of Strategy, Lipman Farms, USA
Will the legacy of COVID 19 be further automation in the food production sector? Will we ever reach a contactless food system? COVID-19 has raised awareness about prospects of automation, but it’s also reinforced the importance of people in this business. At Lipman, each and every stage of the value chain requires coordination and care by our team members. The human element of what we do is important for providing food for people to eat – and we know that the quality of our products and sustainability of our company depends on the people behind the scenes. That said, where there are opportunities for automation that make sense such as machines in packing houses and indoor environments. I think it’s fair to say that humans can be relieved of those tasks and refocused on others. To help us stay ahead of the curve on food safety, for example, we use a web-based training platform that helps customize training, track completions, and easily identify opportunities for improvement. COVID-19 has only reinforced how technology can serve as valuable tools, while also creating new roles for people that are still safe and distanced across the food system.
At Lipman, we’ve diversified our farming techniques over the decades with indoor, outdoor, and hybrid growing environments. We know that growing produce in any capacity requires ingenuity, a learning mindset, and constant adaptation. Two years ago we acquired Huron Produce and while our Suntastic hot house brand continues to deliver high-quality products on the retail shelf, some of the most exciting learnings for us have come from the collaborations between teams. We see indoor ag as both distinct and complementary to our conventional farming practices. I think COVID-19 also revealed to our customers the vulnerabilities of relying on any one supply source, and the value in being able to source from multiple channels.
Viraj Puri, CEO and Co-Founder, Gotham Greens, USA
Demand for local and resilient supply chains is growing, how can indoor agriculture capitalize on this opportunity? Given current pressures on the U.S. food system, one thing is clear: the importance of strengthening our country’s food supply chain through decentralized, regional supply chains. Our business model has enabled us to remain nimble during these unprecedented times and continue to deliver fresh, locally grown produce to customers and our communities. Growing produce indoors certainly has an increasing role to play in the future of sustainable food production. While indoor farming may not represent the future of all fresh produce production, for certain types of crops like leafy greens, herbs, tomatoes and cucumbers, it will become more prevalent.
Gotham Greens has been rapidly expanding our footprint across the US, including opening four new greenhouses in the past 6 months. Today Gotham Greens operates 500,000 square feet of greenhouse across five U.S. states with more than 350 employees. Just last month we opened our newest greenhouse in the Denver Metro area. Although we never envisioned our Denver greenhouse opening during a global pandemic, we’re proud to be providing people in the Mountain Region and across the country with healthy, safe and fresh food options they can get excited about.
Andrew Carter, CEO, SMALLHOLD, USA
Although somewhat harder to find, consumers are still out there. How have Smallhold gone about finding them?
Strangely, consumers have found us. People who try our mushrooms love them and tell their friends. While we scrambled a bit in the beginning, we kept moving full steam. Instead of shutting down, we implemented South Korean-style measures for our warehouse, farm, and office. Then, we launched a new nationally distributed product that allows folks to grow mushrooms at home rather than travel to the grocery store. Now Smallhold is in homes in every state as we gear up for a national expansion of our retail presence in 2020. The product was featured in Bon Appetit, Vice’s Garage, and HypeBeast and is still going strong, although it is not a core business line for us, we continue to see it grow.
How can a grower best manage the expectations of their investors in times as uncertain as these?
Fortunately, as we mentioned above, things are weirdly going well for us. There was a brief period during which we were uncertain, but once our DTC campaign results came in, we became our investors’ case study for what to do in situations like these. As with many things in life, communication is key. At Smallhold, we’ve always had an open dialogue with our investors, and the pandemic hasn’t changed that. Even as the global outlook changes week by week, we’ve worked to provide our investors with a regular cadence of communication and data alongside a clear narrative and plan of action that makes them feel comfortable with the quick decisions we have to make every day. When the world shifts, success can take many forms, and our stakeholders are happy with how we’ve managed it.
CubicFarms Leverages Its Expertise In Controlled-Environment Agriculture And Announces Launch of new Control Room System And Sale To Career Field Farmer And Entrepreneur
CubicFarms’ Control Room is assembled inside its proprietary stainless steel, fully insulated growing chamber with the option to customize features such as lighting, automated irrigation and nutrient delivery, and full climate control for temperature, humidity and carbon dioxide levels
VANCOUVER, BC, JUNE 18, 2020 – CubicFarm® Systems Corp. (TSXV:CUB) (“CubicFarms” or the “Company”) is pleased to announce the launch of its new Control Room system for sale to growers looking to grow crops more efficiently by controlling every aspect of the growing environment.
CubicFarms’ Control Room is assembled inside its proprietary stainless steel, fully insulated growing chamber with the option to customize features such as lighting, automated irrigation, and nutrient delivery, and full climate control for temperature, humidity, and carbon dioxide levels. The system has a variety of sensors available, all of which can be remotely monitored and controlled.
Photo: Inside a CubicFarms Control Room, complete with LED light fixtures, an automated heating, cooling and ventilation system, and wired environmental controls.
The Control Room enables growers to have complete control over the growing environment that is so crucial for high yields and quality – a capability especially well suited for research and development purposes. The temperature, humidity, lighting, and airflow can be properly calibrated to suit crop requirements.
“We are pleased to launch a new product that allows growers to conduct their own growing trials inside a controlled-environment chamber. We’ve had numerous inquiries for this kind of solution and are pleased to be able to support our customers with this technology. We see good market potential for this solution that helps growers fine-tune the optimal environmental parameters for growing crops indoors,” commented CubicFarms CEO Dave Dinesen.
“We are confident that once growers experience the consistency and quality of yields achieved in the Control Room, they will seek to automate growing inside our Fresh Produce system, which is essentially the Control Room plus motorized rows of trays containing crops that follow a patented path inside the chamber to ensure all sides of the crop are evenly bathed in light to maximize growth.”
CubicFarms control rooms can be placed inside an existing warehouse or greenhouse to serve as controlled-environment growing chambers to test and develop crop varieties. They can also be placed outside in many environments. It is well-suited for many types of growers, including:
Photo: CubicFarms control rooms being installed at the customer’s site.
Greenhouse growers and vertical farmers who have a need to hold larger plants in an environment separate from their existing facility. As an example, a hemp grower who would like to hold the mother plant used for cloning in an ideal environment;
Growers in the floral or nursery industry who need to hold plants or bulbs at a specific temperature or humidity; and
Growers undertaking research activities that require different environmental controls than their typical growing space.
CubicFarms announces first sale and installation of control rooms to BC-based field farmer and food entrepreneur
The Company is pleased to announce that it has sold three control rooms to a customer in British Columbia. The control rooms were recently installed at the customer’s site. The customer, an experienced field farmer, and consumer packaged foods expert, plans to engage in controlled-environment growing trials of various crops that have traditionally been grown in the field. Mr. Dinesen added: “I’m very excited that CubicFarms can support our customers by leveraging technology we already have, but in this unique way. Our customers never cease to amaze me in how creative and inspiring they are when looking to grow their businesses.”
Neither the TSX Venture Exchange nor it’s Regulation Services Provider (as that term is defined in the policies of the TSX Venture Exchange) accepts responsibility for the adequacy or accuracy of this release.
About CubicFarm® Systems Corp.
CubicFarm Systems Corp. (“CubicFarms”) is a technology company that is developing and deploying technology to feed a changing world. Its proprietary technologies enable growers around the world to produce high-quality, predictable crop yields. CubicFarms has two distinct technologies that address two distinct markets. The first technology is its patented CubicFarm™ System, which contains patented technology for growing leafy greens and other crops. Using its unique, undulating-path growing system, the Company addresses the main challenges within the indoor farming industry by significantly reducing the need for physical labor and energy, and maximizing yield per cubic foot. CubicFarms leverages its patented technology by operating its own R&D facility in Pitt Meadows, British Columbia, selling the System to growers, licensing its technology and providing vertical farming expertise to its customers.
The second technology is CubicFarms’ HydroGreen System for growing nutritious livestock feed. This system utilizes a unique process to sprout grains, such as barley and wheat, in a controlled environment with minimal use of land, labor, and water. The HydroGreen System is fully automated and performs all growing functions including seeding, watering, lighting, harvesting, and re-seeding – all with the push of a button – to deliver nutritious livestock feed without the typical investment in fertilizer, chemicals, fuel, field equipment, and transportation. The HydroGreen System not only provides superior nutritious feed to benefit the animal but also enables significant environmental benefits to the farm.
Cautionary statement on forward-looking information
Certain statements in this release constitute "forward-looking statements" or "forward-looking information" within the meaning of applicable securities laws, including, without limitation, statements with respect to the market potential of the Control Room system and system capabilities. Such statements involve known and unknown risks, uncertainties, and other factors including evolving market conditions, which may cause the actual results, performance, or achievements of CubicFarm Systems Corp., or industry results, to be materially different from any future results, performance, or achievements expressed or implied by such forward-looking statements or information including the Company obtaining the approval of the Offering from the TSX Venture Exchange. Such statements can be identified by the use of words such as "may", "would", "could", "will", "intend", "expect", "believe", "plan", "anticipate", "estimate", "scheduled", "forecast", "predict", and other similar terminology, or state that certain actions, events, or results "may", "could", "would", "might", or "will" be taken, occur, or be achieved.
These statements reflect the Company's current expectations regarding future events, performance, and results and speak only as of the date of this news release. Consequently, there can be no assurances that such statements will prove to be accurate and actual results and future events could differ materially from those anticipated in such statements. Except as required by securities disclosure laws and regulations applicable to the Company, the Company undertakes no obligation to update these forward-looking statements if the Company's expectations regarding future events, performance, or results change.
Kimberly Lim
VP, Corporate Communications & Investor Relations
Mobile: 236.858.6491
Office: 1.888.280.9076
Email: kimberly@cubicfarms.com
ONLINE WORKSHOP - The Ohio State University Empowerment Plant Workshop, July 9-10, 2020
The goal of this Workshop is for growers to empower crop production through a balanced growing method, through an integrated approach based on physics and plant physiology, for high yields, quality, saving energy, and profitability in greenhouse controlled environments
— Live Education —
The Ohio State University, in partnership with Gotham Greens and Hort Americas, will be organizing the Plant Empowerment Workshop Online on July 9-10, 2020 (10 am – 2:30 pm EDT).
Advanced learning and discussion for growers towards “an integrated approach based on physics and plant physiology, leading to a balanced growing method for high yields, quality, saving energy, and profitability in greenhouse controlled environments
Instructor: Dr. Peter van Weel
Author of ‘Plant Empowerment’
Expert in greenhouse climate control
Former PI at Wageningen UR, The Netherlands
Host: Dr. Chieri Kubota
The Ohio State University
Ohio CEA Center
The goal of this Workshop is for growers to empower crop production through a balanced growing method, through an integrated approach based on physics and plant physiology, for high yields, quality, saving energy, and profitability in greenhouse controlled environments
Textbook (optional): ‘Plant Empowerment’ available at www.plantempowerment.com
Plant Empowerment Workshop Online
10 a.m. to 2:30 p.m. (EDT), July 9-10, 2020
Thursday, July 9, 2020 | 10 a.m. to 2:30 p.m. (EDT)
Part 1: Introduction to Plant Empowerment, The Theories
Basic knowledge about physics and physiology that play an important role in a greenhouse and for plantsPlant empowerment, from experience-based control to sensor-based control
Friday, July 10, 2020 | 10 a.m. to 2:30 p.m. (EDT)
Part 2: The Practical Applications of Plant Empowerment
Introduction to the sensors, the software tools and the value of data analysis
Registration is open through July 1.
Workshop fee is $20 per person.
Register now!
For more information, contact Dr. Chieri Kubota, kubota.10@osu.edu
Sustaining The Future of Indoor Vertical Farming With Microgrids
While indoor agriculture has steadily gained traction in recent years as the world seeks alternative ways to feed growing populations, the uncertainty of today’s global pandemic has accelerated a rethinking of the way we obtain our food
June 15, 2020, By Guest Post
Schneider Electric’s Don Wingate discusses how microgrids can help the indoor vertical farming movement realize its full potential.
Don Wingate, vice president of utility and microgrid solutions at Schneider Electric
While indoor agriculture has steadily gained traction in recent years as the world seeks alternative ways to feed growing populations, the uncertainty of today’s global pandemic has accelerated a rethinking of the way we obtain our food. In the last few months, modern supply chains experienced volatility like never before and it wasn’t long before we started to see the impact beyond medical gear and personal protective equipment and began to affect food production. According to the Institute of Supply Chain Management, 75% of companies reported some kind of supply chain disruption due to COVID-19.
Indoor vertical farming is emerging as an alternative to conventional farming because it both requires lower land-use and introduces the opportunity to bring agricultural production closer to consumers — shortening supply chains and increasing footprint productivity. This is especially important during times of turmoil, which is broader than the current pandemic as weather events and changing climate patterns continue to put constant strain on traditional farming practices. In addition to shortening supply chains, indoor farming has many other advantages in comparison to traditional agriculture such as using zero pesticides, employing 95% less water, and reducing food waste. Health benefits also include fresher food, increased urban availability, and pollution reduction.
Despite the major advantages, there is one looming barrier to mainstream adoption: the process is very energy-intensive.
Solving for the energy intensity problem
Vertical farming presents a unique opportunity to grow food on already developed land and increase domestic food production, but the energy demand required to power these facilities is much higher than other methods of food production. In fact, we’ve identified indoor agriculture as one of the four major drivers that will increase electricity consumption in the next decade, along with electric vehicles, data centers and the electrification of heat. This is why more of today’s modern farming companies are turning to microgrids as a possible solution to ease their energy challenges.
Although most of today’s facilities are not equipped to meet the electricity needs of an indoor agriculture operation, microgrids can provide dynamic energy management and the resources required to support maximum productivity, sustainability, and energy efficiency. They can provide localized power generation and utilize renewable distributed energy resources to help deliver power and reach clean energy goals, while also allowing users more control and reliability. Additionally, microgrids can capture and repurpose CO2 emissions to help in crop production.
Moreover, microgrids provide resilience from unexpected outages that could result in a loss in production. A key advantage of vertical farms is their ability to allow crops to grow year-round, and communities rely on their ability to deliver on this promise. Microgrids not only have several clean energy benefits, but they also increase business continuity that maximizes output. Given their ability to operate either in conjunction with or as an island from the utility grid, they can keep the farm producing even when the grid goes down.
The case for investment: Securing an affordable solution
Building and operating a vertical farm requires various technologies that can translate to high startup cost and design complex processes. At the same time, it is more expensive to maintain a vertical farming operation than traditional field farming. Microgrids offer a compelling value proposition, but they’re inherently complex machines and not many companies have the upfront capital or in-house expertise needed to make the investment. Fortunately, innovative business models such as energy-as-a-service (EaaS) help provide price certainty and make the investment attainable.
For example, a modern farming company, Bowery Farming, created a facility wherein crop production is 100 times more efficient than traditional farmland. This generated a need for a greater need for reliable, efficient power. Thus, the company made the decision to integrate a hybrid microgrid system that would feature a rooftop solar array, natural gas generator, and a lithium-ion battery energy storage system through an EaaS business model. Through EaaS, Bowery Farming saved upfront capital that can be used toward additional operational investments.
By 2050, the world’s population is expected to grow by another 2 billion people, and feeding it will be a major challenge. According to the projections of the Food and Agriculture Organization, we have to increase overall food production by 70% by this timeline. Coupled with new concerns that have surfaced as a result of today’s global pandemic and unstable weather, vertical farming will play a key role in future food production and institutions will take notice. However, the technology that will help ease some of the industry’s ongoing energy challenges will be just as important to aid the transition.
Don Wingate is the VP of utility and microgrid solutions at Schneider Electric.
Exelon Invests In Reducing Indoor Ag Energy Needs And Costs With GrowFlux
“GrowFlux specifically can increase yields in indoor farming making it more economical for city centers and where it can serve often underserved communities fresh and healthier foods.”
June 11, 2020
A welcome impact from the Covid-19 pandemic has been clearer skies and returning wildlife to usually polluted areas after industry, transport systems, and more shut down across the world, reducing carbon emissions.
Today marks two months since the UK’s electricity industry last used coal; the longest period since the Industrial Revolution began more than 200 years ago and well beyond the 18 days, 6 hours and 10 minutes record which was set in June last year, according to the BBC. Renewable and nuclear energy have stepped in to make up the shortfall in a trend that’s been particularly pronounced in the US where renewables supplied more energy than coal for the first time ever this year.
Agriculture’s impact on the environment, particularly surrounding its carbon emissions, has been flung into the spotlight in recent years, particularly by alternative meat and animal products startups keen to promote the environmental credentials of their plant-based or cultivated alternatives. But of course, even a plant-based diet has carbon emissions associated with it, from the fertilizer and pesticides applied in the production process, to its transport to end markets. Plant-based products and diets are also not always affordable or accessible to certain demographics who may live in food deserts.
Indoor agriculture has long been a potential solution to food deserts and many of the carbon emissions related to crop production, making it an interesting prospect for city planners and city-based corporates. But the energy consumption associated with the production system, specifically related to lighting and climate control systems, has left much to be desired; not least because the costs involved have stunted the growth of viable business models.
Further, energy demand from these indoor farms is only set to increase as the need for more localized production in certain regions across the world has been highlighted during the Covid-19’s disruption of traditional supply chains; Singapore is a case in point.
“With over 8.6 terrawatt hours of energy consumed by horticultural lighting systems in emerging indoor farms and greenhouses in the US in 2019, utility companies are hard-pressed for rapidly scalable energy management tools that meet the needs of growers,” says Eric Eisele, CEO of GrowFlux. GrowFlux is an agtech startup focused on smart lighting controls for the horticulture industry working to significantly reduce the cost of lighting automation and its energy needs.
GrowFlux, a Philadelphia-based startup, was therefore immediately of interest to Exelon, the nuclear energy provider that claims to have the largest number of electricity and natural gas customers in the US after it launched a new startup incubator late last year aimed at reducing greenhouse gas emissions and bolstering urban centers. GrowFlux is part of the first cohort of Exelon’s $20 million Climate Change Investment Initiative (2c2i) and recently received $100,000 in cash as well as in-kind services such as legal and advisory as part of the program.
“When we think about food & ag, we think about there being a mitigation and adaptation benefit from helping to advance the indoor ag industry for food. [By growing food close to city centers] there’s a climate change mitigation benefit from the decreased emissions related to traditional, carbon-intensive farming methods of harvesting, planting and transporting food from rural areas to cities,” Exelon Corp SVP Chris Gould told AFN. Indoor ag, where farming environments can be completely controlled, is also a good mechanism to adapt to climate change, he added.
“GrowFlux specifically can increase yields in indoor farming making it more economical for city centers and where it can serve often underserved communities fresh and healthier foods.”
GrowFlux says its technology allows even the smallest farms and upstarts to build advanced controlled environment agriculture automation without millions in venture funding. Its approach is different from the traditional high-level objective of optimizing climate control towards a constant set point; instead it aims to respond more dynamically to crops’ needs via distributed sensor data and cultivar specific crop models. “Crop responsive environmental controls have the potential to result in tremendous resource efficiency, creating opportunities to grow new crops in greenhouses, reducing the operating cost of existing CEA, and reducing the capital costs associated with CEA,” reads the company website.
“We reduce cost with cloud-based control (as opposed to cloud-connected control), which is new to the industry. This strategy is unique from our competition, which are essentially boutique engineering firms that do a full range of automation services using on-site controls that are slow to scale and come at a significantly higher cost,” added Eisele.
2c2i is a partnership between Exelon and its foundation and involves $10 million in funding from the foundation and $10 million in-kind contribution of pro-bono services from the corporation, such as mentorship and access to the company’s venture capital and R&D departments.
“Our partnership with Exelon Foundation will help GrowFlux advance its energy savings and energy management solutions, and allow our customers to drive down their operating costs and carbon footprint associated with greenhouse and indoor agriculture,” said Eisele about the investment. “We believe their guidance on energy management strategy is just as valuable, if not more valuable than the cash.”
2c2i is focused on innovations that will positively impact the cities in which Exelon operates, including Atlantic City, Chicago, Baltimore, Philadelphia, Washington, D.C., and Wilmington. Innovations must also have the potential to mitigate greenhouse gas emissions; boost the resiliency of urban infrastructure (e.g., the power grid, transportation systems, buildings, vacant land) against flood, stormwater, and rising temperatures; help cities, businesses and communities adapt to climate change; or help achieve a state or city’s specific sustainability and climate goals. External consultant Freshwater Advisors selected a shortlist to pitch in front of the Exelon team.
“We also consider and have selected startups from outside of our cities, but in that regard we ask them to have a line of sight on one of our cities, with hope of attracting them to region to set up an office,” said Gould.
Agri-Khalifa: Agriculture Skyscraper For Dubai
Skyscraper is a perfect medium for vertical farms, especially in the desert climate condition. We utilize space as much as possible. No winter in the desert, so we omit the curtain wall of the building, making use of the natural condition of Dubai
Editors’ Choice
2020 Skyscraper Competition
Zeng Shaoting, Liu Chenyang
China
Dubai is one of the most popular cities in the world, lies directly within the Arabian Desert. With sandy desert surrounded, Dubai has a hot desert climate. Summers in Dubai are extremely hot, windy, and humid, with an average high around 41 °C (106 °F) and overnight lows around 30 °C (86 °F) in the hottest month, August. Most days are sunny throughout the year. Winters are comparatively cool with an average high of 24 °C (75 °F) and overnight lows of 14 °C (57 °F) in January, the coolest month. Desert terrain, extremely high temperatures, and limited rainfall have historically made agriculture unworkable in Dubai and the United Arab Emirates
Dubai currently imports over 80% of its food. The main food influences were from nearby countries such as Saudi Arabia, Oman, Iran, East Africa, and Indian. In order to reach the city’s targets, locally grown food not only has to expand its growth rapidly, but it also has to meet the uncompromising health standards of the UAE, and cater to the diverse population that enjoys a wide variety of international food.
The Burj Khalifa, known as a skyscraper in Dubai, has been the tallest structure and building in the world since its topping out in 2009. Our skyscraper project is Agri Khalifa aimed to use innovative agricultural technology to find ways to grow locally-sourced produce in Dubai and change its current state.
Agri Khalifa is a vertical farm located in the desert area of Dubai, going with a big factory that includes energy, transportation system. There is sufficient solar and wind energy in the desert, and we build a series of energy collect system to supply electricity to the farm. We apply many advantages of current vertical farm technologies, such as lighting system, which uses a series of variable color LEDs, for instance, we can use ultra-violate light to shorten the span of plant growth to improve the production.
Skyscraper is a perfect medium for vertical farms, especially in the desert climate condition. We utilize space as much as possible. No winter in the desert, so we omit the curtain wall of the building, making use of the natural condition of Dubai.
We use robotic arms and elevators to pick up mature plants automatically. There are rail trails beneath the building, and we can use railway transportation to conduct remote carriage to the urban and living area of Dubai.
Up to 20 units of outdoor farmland per unit of vertical farming could return to its natural state, due to vertical farming’s increased productivity. Vertical farming would reduce the amount of farmland, thus saving many natural resources.
Deforestation and desertification caused by agricultural encroachment on natural biomes could be avoided. Producing food indoors reduces or eliminates conventional plowing, planting, and harvesting by farm machinery, protecting soil, and reducing emissions.
Traditional farming is often invasive to the native flora and fauna because it requires such a large area of arable land. One study showed that wood mouse populations dropped from 25 per hectare to 5 per hectare after harvest, estimating ten animals killed per hectare each year with conventional farming. In comparison, vertical farming would cause nominal harm to wildlife because of its limited space usage.
An Aussie Vertical Farm Company Has Gained International Interest Amid Concerns About Food Supply Chain During The Coronavirus Pandemic
Aussie company Stacked Farm, a fully automated vertical indoor farm, has been gaining international interest amid the coronavirus pandemic
By Sharon Masige | Business Insider | 5 June 2020
Stacked Farm, an Australian automated vertical indoor farm, has received international interest during the coronavirus pandemic amid concerns about the continuity of food supplies.
The farm produces salad greens and has the capacity for tomatoes and strawberries.
CEO Conrad Smith told Business Insider Australia Stack Farm received significant interest from the Middle East.
Aussie company Stacked Farm, a fully automated vertical indoor farm, has been gaining international interest amid the coronavirus pandemic.
Stacked Farm, founded in 2017, produces salad greens and herbs like lettuce and rocket and has the capacity to produce tomatoes and strawberries. It's even looking at testing out a type of blueberry next year.
The company has been receiving a lot of interest during the coronavirus pandemic amid concerns about virus clusters breaking out in the food supply chain. Back in May, a coronavirus cluster broke out at Melbourne's Cedar Meats abattoir, which was linked to 62 cases, according to the ABC.
"People are more concerned than ever about who is handling their food, where it’s coming from and how many stops it made before arriving on supermarket shelves," Stacked Farm CEO Conrad Smith said in a statement.
The company is headquartered in Burleigh Heads, Queensland and has plans to open up farms across Australia as well. "A scaled-up farm in Victoria will be our first major commercial farm," Smith told Business Insider Australia. Its farm is fully automated, with the produce packed and sealed once its harvested by robotic farming.
"It doesn’t pass through the usual supply chains either – greens and herbs can go directly to wholesalers, retails, hotels and restaurants, unlike traditional produce which passes through a number of hands before reaching our shelves," Smith said in a statement.
Stacked Farm has a partnership with fresh produce supplier Morco Fresh and counts Dnata as one of its clients as well, which provides aircraft services like flight catering.
"We are not too dissimilar to a normal farm where we go through markets and we go through wholesalers and food service distributors," Smith said.
And while it mainly supplies to the food service industry, Stacked Farm is looking at a move into retail so people can grab its produce from supermarket shelves as well. "We haven't got the capacity to do that at the moment," Smith said. "But when we scale up to our Victorian farm, we will certainly have the capacity to do that and we'll be looking for retail partners to jump on the journey that we're on."
The farms are temperature controlled and automated
Stacked Farm grows its produce 12 months a year, without relying on different seasons. Its products are grown in a temperature-controlled environment that is fully automated from seeding to harvesting. The company is looking at post-harvest automation as part of its next business phase.
Stacked Farm also makes barley-based livestock feed. "In a drought-vulnerable country like Australia, there's a lot of opportunity there because while we all think about human consumption, animals are a massive part of the food chain that needs to be considered," Smith said.
The company's employees are mainly in the science and tech field rather than traditional farm labourers.
"We're not like traditional farms where we require pickers, packers and harvesters," Smith said. "We employ more labour leaning towards engineering, software engineering, mechanical engineering, CAD designers [and] horticultural scientists."
The company has been receiving interest from the Middle East
Stacked Farm has received international interest in its farm during the coronavirus pandemic, mainly thanks to concerns over food safety, quality and security.
"There's a lot of food chains that have been broken throughout this COVID-19 pandemic, and we've had interest from the Middle East to set up farms there," Smith said.
"We have been very enthused by the interest from particularly a couple of states in the Middle East that have governments that really support local industry and local farming." Smith gave the example of Dubai which relies predominantly on imports. According to Bloomberg, the United Arab Emirates imports up to 90% of its food.
Smith explained that in Dubai, "a lot of produce can't travel by sea".
"They've immediately recognised that there's a problem in their food chain and they need to bring tech businesses to their country to support feeding their people." And, in the case of Stacked Farm, can help feed livestock too.
Smith added that Stacked Farm can support the future of food production, particularly in extremely hot and dry or extremely cold climates. He explained that one in nine people go hungry around the world. According to the Food and Agriculture Organisation of the United Nations, by 2050 world food demand is expected to rise by 70%.
"Having urban indoor vertical farms is definitely [an] exciting prospect for the future," Smith said. "We can literally shave days off out of the logistics process, we can extend the shelf life of products so there's less wastage and that in turn will benefit the community."
Microgreens Launched By Vertical Farmer April Sun
Just in time for this year’s winter season, vertical farmer April Sun launched its range of sustainably grown microgreens from its new commercial-sized micro-farming facility in Melbourne
Food & Beverage | June 4, 2020
Just in time for this year’s winter season, vertical farmer April Sun launched its range of sustainably grown microgreens from its new commercial-sized micro-farming facility in Melbourne.
With a philosophy of true sustainability and paired with cutting-edge technology, the local farm wants to provide the community with a range of nutrient-packed microgreens available year-round to their nearby community.
Co-founder Darren Nichol, April Sun visionary of Australia’s cleanest and highest nutritional food supply who has a wealth of knowledge due to his agricultural background, says, “This is a particular focus of the Darebin Council. They have an actual goal to increase food production within its municipality.”
These super foods are grown without pesticides and utilise 95 percent less water than traditional farming methods due to a hydroponic based (closed loop) watering system. Co-founder Ty Dickson, April Sun technologist and facility designer, said this system guarantees the plants do not receive too little or too much water.
“The watering targets each individual plant or root system and is drained back to the holding tanks,” he said. “Traditional farming methods would see water being lost to the ground and you would use more water to achieve the same level of fertigation without the ability to recapture the excess.”
With custom-spectrum lights developed in-house, the microgreens are grown in their ideal conditions, allowing for year-round production and minimal waste.
“We use a combination of specific wavelengths of blue, red, far red and full spectrum light to stimulate the chlorophyll A and B of the plants, while giving the right signals to ensure proper colour, increased nutrients through stress and, above all, a very healthy plant,” Dickson said.
“We are a non-single use plastics company; we opt for PLA compostable packaging. Our facility uses the highest efficiency components and equipment available. We do run on electricity, although we are engaging in using 100% renewables, and are in preliminary talks with the Darebin Council to implement 100kW of solar panels on our warehouse roof.” said Dickson.
In traditional farming, external factors such as drought, pollution, soil erosion and more can impact crop success. However, the world of vertical farming is “most often done indoors in a controlled environment”, he adds. “Vertical farming when done sustainably has less impact on the environment, there are significant reductions in water usage, land usage, gas usage and many other resources. This is all achieved whilst controlling the indoor growing environment with minimal impact to it outside.”
“By controlling every factor in the plant’s environment, you end up with a high-quality product on a number of levels,” said Nichol.
“We can grow to a timeline and the removal of variables such as the weather allows us to more accurately forecast and grow to our customers’ demands. This can reduce the amount of waste and also increase consistency of supply to customers. This is a huge problem for traditional farming and is the cause for the large price jumps and shortages of produce on the market.”
To see more, click here.
Online Course: Wednesday, June 17 - Plant Response to CEA Variables - 3 PM CST
Learn how plants respond to different environmental variables and how to apply this knowledge to improve your indoor system management and crop production!
Learn how plants respond to different environmental variables and how to apply this knowledge to improve your indoor system management and crop production!
Instructor: M.S. Karla Garcia
- Hort Americas Technical Service
- Master in Plant Sciences from The University of Arizona
- Recognition by ISHS in strawberry hydroponic research
- Editor: Book Roadmap to Growing Leafy Greens and Herbs
- CEO at Microgreens FLN
DATE: Wednesday, June 17, 2020
Schedule: 3 pm to 5 pm (Central Standard Time)
Platform: ZOOM US
Price: $50 US
Once you have registered, we will make contact to provide access to our LIVE session.
Course Content
-Advantages of controlled environment agriculture
-Energy balance
-Light
a) Solar radiation
b) Artificial lighting
c) How improve net photosynthetic rate
-Wind
a) Fans/ Air circulation
-Humidity
a) Plant transpiration
-Temperature
a) Effect in plant metabolism
b) How plants respond to temperature?
c) Treatments
-CO2
-Nutrients
a) Nutrient function and uptake
-Oxygen in root zone
-Water and root zone temperature
Research For Workforce Development in Controlled Environment Ag: What Makes a Successful Indoor Farm Manager?
As indoor agriculture has grown, finding, training, and retaining a skilled workforce has emerged as an important challenge to the industry. A unique combination of plant production, tech troubleshooting, and innovation is needed among employees managing these operations
By urbanagnews
June 8, 2020
As indoor agriculture has grown, finding, training, and retaining a skilled workforce has emerged as an important challenge to the industry. A unique combination of plant production, tech troubleshooting, and innovation is needed among employees managing these operations.
What are the critical skill sets, and how can we create a larger pipeline of individuals trained in these skills so that they can contribute to CEA business success?
At Cornell University, a group led by Professor Anu Rangarajan (Director, Small Farms Program) seeks to provide answers as part of a National Science Foundation-funded research project on CEA Viability in Metro Areas.
Rangarajan’s team has conducted extensive research to date in order to understand the workforce needs of the hydroponics industry, including greenhouses and indoor vertical farms—and the research continues.
With the long-term goal of creating robust curricula for training CEA employees in mind, a team from Cornell University conducted many in-depth interviews with professional CEA growers in 2018 and 2019.
The team then organized a workshop, in consultation with The Ohio State and Agritecture Consulting, that invited a focus group of CEA operations managers to model in detail the diverse activities that they perform on the job.
The resulting chart is a detailed, peer-reviewed list of duties (responsibilities) and tasks (activities, skills) that describe the work of the expert Indoor Farm Operations Manager.
The chart is currently being reviewed by peer growers worldwide, who are asked to verify how important each skill is, and how frequently it is conducted.
Based on this input, the Indoor Farm Operations Manager chart will be used as a starting point for prioritizing future CEA training modules. After that, a deeper analysis of key individual skills will be conducted in order to translate the foundational research into a teachable vocational curriculum.
Right now, however, Rangarajan’s team is actively seeking more responses to the verification survey.
“We need your help,” she emphasizes, speaking to professional CEA growers. “We want to learn your priorities for a CEA curriculum that will enhance the skills of current or future employees.”
The survey takes approximately thirty minutes to complete and can be completely anonymously. CEA growers who complete the survey will also be provided with an Amazon gift card for $25 as a token of appreciation, although they must provide their names and email addresses in order to receive this gift.
To take the survey, register here. The Cornell team will send a survey link directly from Qualtrics.
As Rangarajan notes, “Grower input will help us prioritize the core education and training relevant to indoor agriculture,” helping provide the industry with the skilled workforce it will need to scale.
For more information about this study regarding the future of the CEA workforce, please contact project lead Anu Rangarajan (ar47@cornell.edu) or research associate Wythe Marschall (wmarschall@fas.harvard.edu).
Shenandoah Growers - Bringing Nature Indoors
At Shenandoah Growers, we believe in the power of technologically-controlled indoor environments to sustainably transform the future of fresh produce. As the only large scale USDA Certified Organic soil-based indoor growing system in the United States, we are passionate about leveraging cutting-edge science and technological innovation to ensure that our customers receive the freshest, healthiest, most affordable organic produce possible year-round.
Working with (not against) nature to create an optimal environment for plants to thrive
What Sets Us Apart?
At Shenandoah Growers, we believe in the power of technologically-controlled indoor environments to sustainably transform the future of fresh produce. As the only large scale USDA Certified Organic soil-based indoor growing system in the United States, we are passionate about leveraging cutting-edge science and technological innovation to ensure that our customers receive the freshest, healthiest, most affordable organic produce possible year-round. With twelve growing locations across the country, we couldn’t be prouder to provide organic, local produce to over 18,000 stores every day.
Why Indoor Controlled Agriculture?
There’s nothing quite like the great outdoors—at Shenandoah Growers, we know there’s something better. Our LED-powered indoor bioponic growing platform increases yields and reduces waste, enabling us to make fresh herbs available year-round across the country. Plus this proprietary system is environmentally conscious, conserving water and land, and avoiding harmful pesticides.
How Do We Do It?
Some call it “Know-How”. We call it “Grow-How”
Our proprietary bioponic growing process mimics nature but enhances it with carefully controlled temperatures, light levels, humidity, and water exposure. And because we use just what we need to keep our plants healthy and no more, we conserve valuable environmental resources and set our industry up for a sustainable future.
USA: Indoor Growers Wanted For CEA Survey
"The current step in our research plan is to verify the details of this chart with peer growers worldwide via a survey", explains research associate Wythe Marschall. "It invites indoor farm managers to tell us how important each skill is, and how frequently it is conducted
A Cornell team is leading a new project to investigate how Controlled Environment Agriculture (CEA) compares to conventional field agriculture in terms of energy, carbon and water footprints, profitability, workforce development and scalability. Strategic FEW (food, energy, water) and Workforce Investments to Enhance Viability of Controlled Environment Agriculture in Metropolitan Areas is funded by a three-year, $2.4 million grant from the National Science Foundation, through its new funding initiative called Innovations at the Nexus of Food, Energy and Water Systems.
The workforce development research, led by Professor Anu Rangarajan (Director, Small Farms Program), consisted in 2018 and early 2019 of interviews and an intensive two-day workshop with industry experts. During that workshop, a focus group of indoor farm operations managers produced this chart detailing the duties (responsibilities) and tasks (activities, skills) that describe their work.
Survey
"The current step in our research plan is to verify the details of this chart with peer growers worldwide via a survey", explains research associate Wythe Marschall. "It invites indoor farm managers to tell us how important each skill is, and how frequently it is conducted. The survey can be completed anonymously, or growers can provide us with their names and emails to receive a $25 Amazon gift card as a token of our appreciation."
To take this survey, register here. The Cornell team will send a survey link directly from Qualtrics. Respondents may provide their names and emails to receive a $25 Amazon gift card as a token of appreciation.
Online workshops
"We are also interested to ask growers if they would be interested in a series of upcoming online workshops to help us detail what specific, teachable steps (activities) are contained within each important skill needed by indoor farm operations managers", Wythe adds. "For example, we'll ask growers to dive into the specific skill, 'Manage crop fertigation (e.g., mixing nutrients, monitoring pH, monitoring water temp),' breaking this down into teachable, specific components.
"This series of workshops will be compensated, and we are beginning to schedule it now. Any CEA farm manager is invited to participate, regardless of location or modality."
For more information about this study regarding the future of the CEA workforce, please contact project lead Anu Rangarajan (ar47@cornell.edu) or research associate Wythe Marschall (wmarschall@fas.harvard.edu).
Publication date: Tue 9 Jun 2020
AeroFarms Reveals To California North Coast Food Producers Its High-Tech Controlled Environment Agriculture
Imagine a farming method so efficient that you could grow a variety of leafy greens in half the time it traditionally takes — without any pesticides, herbicides or fungicides — and where the sun has no role
NORTH BAY BUSINESS JOURNAL March 2, 2020
CHERYL SARFATY
Imagine a farming method so efficient that you could grow a variety of leafy greens in half the time it traditionally takes — without any pesticides, herbicides or fungicides — and where the sun has no role.
It’s all done indoors, and it’s a growing trend known as controlled environment agriculture (CEA). The biggest player in the space is AeroFarms, a Newark, New Jersey-based operation that was among the businesses that participated at the Feb. 25 North Coast Specialty Food & Beverage Conference.
“We track everything that happens to the plants, from its genetics all the way to harvest. And by measuring along the way, we can use that data to learn more about what makes plants grow,” said AeroFarms Chief Financial Officer Guy Blanchard. “The ability to do this is transformative, it’s brand new if you think of the difference with field farming, where you can’t control the temperature and you can’t control the weather. You’re really reacting and trying to respond to the things that Mother Nature is throwing at you.”
In addition to AeroFarms, which is privately held, there are a variety of CEA players in the marketplace, including Bright Farms, Little Leaf Farms, Bowery Farms, Revol Greens and Plenty, which is based in South San Francisco. The majority of these businesses are headquartered in the Midwest and further east, where bad weather makes it impossible to grow the greens outdoors.
There are a variety of growing methods within the CEA category, the two most common being hydroponics and aeroponics. With hydroponics, plants are grown with mineral nutrients in a water base rather than in soil. Aeroponics, which is AeroFarms’ method, also uses no soil, instead of planting seeds in fabric and misting them with mineral nutrients.
AeroFarms grows 800 varieties of edible greens, such as lettuce, arugula, and spinach. The plants require 95% less water than on farms and are completely grown in 12 to 14 days, rather than 30 to 45 days in the field. The company’s retail brand, Dream Greens, is sold in grocery stores in New Jersey and New York.
Blanchard declined to disclose the company’s financial metrics. According to ROI-NJ, a New Jersey business publication, AeroFarms raised $40 million in 2017.
The vertical farming market size was valued at $2.23 billion in 2018 and projected to hit $12.77 billion by 2026, according to Allied Marketing Research.
There’s going to be change, but I don’t want to lose our small farmers.
Pegi Ball, Santa Rosa Original Certified Farmers Market
Pegi Ball and Janet Ciel, who each run farmers markets in the North Bay, said at the conference they wonder how the CEA industry might someday impact the region’s farmers“.
There’s going to be change, but I don’t want to lose our small farmers,” said Ball, who manages the Santa Rosa Original Certified Farmers Market at the Luther Burbank Center for the Arts. “It’s more than just lettuce and that sort of thing. It’s the culture, it’s the tradition, it’s our community, so that’s what concerns me.”Ciel, who manages the Healdsburg Certified Farmers Market and also works with the Agricultural Institute of Marin’s Stonestown Farmers Market in San Francisco, came away impressed by Blanchard’s presentation, but also curious about how traditional farming and controlled environment agriculture could potentially coexist.
“I think the technology is brilliant,” Ciel said.
“I just think the small farmer is … dealing with the weather and pests and (various other factors), and they don’t have the funding or the education to pull something like this off. Is there something there that is for them?”
Blanchard views the growing CEA industry to be more comparable to — and therefore more competitive with — commercial food-processing operations than traditional farming because of the costs involved, from investing in capital equipment to staffing, of which AeroFarms employs about 160 people.
“If you’re going to have a farm manager, a safety manager, a shipping manager and a maintenance manager (among the staff), you may be up to like $600,000 a year in wages and benefits before you’ve even gotten to anything really related to the farm,” Blanchard said. “In many ways, even though the processes are different, this isn’t different than some other food-processing (businesses) necessarily, and you’ve got to manage it.”
I’m certain we’ll continue to see new and different commodities take advantage of innovative growing techniques of a controlled environment.
Mary Coppola, United Fresh Produce Association
Another reason CEA poses little to no threat to farmers, at least at this point in time, is because food grown in this vertical indoor environment is limited primarily to leafy greens. Greenhouses have more latitude.
“There are a number of companies who are growing greenhouse strawberries, peppers, cucumbers and tomatoes with much success,” said Mary Coppola, vice president for marketing and communications at United Fresh Produce Association. The Washington, D.C.-based organization was founded in 1904 and advocates for companies in the fresh produce supply chain. “I’m certain we’ll continue to see new and different commodities take advantage of innovative growing techniques of a controlled environment.”
And where agriculture industry experts laud controlled environment agriculture for its renewable and sustainable efforts, such as conserving land and water, there are other cost concerns.“
They rely a lot on artificial lighting, so obviously energy consumption is an issue,” said Humberto Izquierdo, agricultural commissioner, and sealer of weights and measures for Napa County. “I think the economics have to be there.”
Guy Blanchard, chief financial officer of AeroFarms, explains how the New Jersey-based startup gets dozens of turns of fresh produce annually through its vertical indoor farm, speaking at North Bay Business Journal’s North Coast Specialty Food and Beverage Industry Conference on Tuesday, Feb. 25, 2020, at Doubletree Hotel by Hilton Sonoma Wine Country in Rohnert Park. (Jeff Quackenbush / North Bay Business Journal)
Blanchard said he doesn’t view energy consumption as a challenge for AeroFarms.“I think when people think about energy or environmental footprint, it’s tough to see how much is really embedded in traditional agriculture when you have all the energy going to root watering, soil and soil degradation, and the energy that goes into fertilizers and harvesting a field,” Blanchard said, as well as transporting, cooling and washing.
Marc Oshima, AeroFarms co-founder, and chief marketing officer said the company and its competitors are focused on strengthening the overall agriculture industry, such as sharing their expertise about how to grow greens safely to avoid contamination. They also formed their own group, called the Controlled Environment Agriculture Food Safety Coalition.
“(It) was a critical step to establishing best practices and educating the FDA and customers on why indoor farming has so many more safeguards versus traditional field farming, and less exposure that often occurs with co-mingling at the major leafy greens processors, who are sourcing from multiple growing regions both domestically and internationally,” he said.
The coalition also has partnered with Foundation for Food and Agriculture Research on a $2 million, three-year program to identify stressors of leafy greens in order to optimize taste and nutrition, he said.
Staff Writer Cheryl Sarfaty covers tourism, hospitality, health care, and education. Reach her at cheryl.sarfaty@busjrnl.com or 707-521-4259.
FOR SALE - 2018 Freight Farm Computer Controlled Hydroponic Grow System - Atlanta, Georgia
The Leafy Green Machine is a complete hydroponic growing system built entirely inside a shipping container with all the components needed for commercial food production. The system is designed and engineered for easy operation, allowing users of all backgrounds to immediately start growing.
Make & Model - 2018 Freight Farm Computer Controlled Hydroponic Grow System
Manufacturer - Freight Farms
Location - Atlanta, Georgia
Price - $75,000
Description
Well maintained 2018 LGM purchased from Freight Farms.
This LGM has been a reliable producer of healthy produce.
The Leafy Green Machine is a complete hydroponic growing system built entirely inside a shipping container with all the components needed for commercial food production. The system is designed and engineered for easy operation, allowing users of all backgrounds to immediately start growing.
Current Uses
• Perfect for starting a small produce business, growing for restaurants or supplementing existing produce production.
• Restauranter who wants to grow custom greens for rotating menus 365 days a year. Farm to Table? How about Parking Lot to Table!
• Universities and schools have created programs for students to learn to grow while supplementing dining facilities with fresh greens.
The Highest Standard in Controlled Environment Agriculture
• Pre-built system designed to maximize operational efficiency and streamline workflow
• Perfect environment is achievable 365 days a year, regardless of geographic location
• Automated scheduling reduces the amount of labor required to operate
• Remote monitoring & control capabilities through the Farmhand AppTM
Operation Requirements
Space- The LGM dimensions are 40’ x 8’ x 9.5’. We suggest putting the farm on either trap rock or a concrete pad.
Electrical- 60 amp, 120/240-volt single phase or 120/208V three phase connection.
Water- A designated water source is suggested such as a garden hose or hardline water plumbing.
Labor- 15 to 20 hours a week for farming and upkeep.
It is recommended growing smaller compact crops with a high turnover rate, like head and loose leaf lettuces, herbs and heartier greens like kale and swiss chard.
LGM Accessories
Replaced sink with a 4 row, direct lighting microgreen station.
Website of previous owner being sold at additional cost. The website is currently set up for the business of this local farmer, and upon purchase can be changed to the meet the purchaser’s new brand.
Crop Examples
Butterhead lettuce, Oakleaf lettuce, Swiss Chard, Mustard Greens, Cabbage Leaves, Arugula, Cilantro, Mint, Dill, Oregano, Kale, Endive, Basil, Chives and Thyme
Yields
800+ heads of lettuce weekly
12 heads per tower (256 vertical towers)
1 LGM= 1.8 acres
Numerous additional extras included.
Numerous warranties still in effect
Training, website and ongoing support available through Freight Farms.
Visit Freight Farms (Website) for more information.
2018 - Freight Farms LGM Information Booklet
For Additional Information And To Arrange A Viewing:
(909) 942-9594
Spencer.Hoff@iGrow.News
1. ALL-WEATHER CONSTRUCTION
Steel frame with stainless interior, 40' x 8' x 9.6' overall footprint.
2. AUTOMATIC DOSING
Programmable nutrient & pH dosing for perfect growing conditions.
3. CUSTOM WORKBENCH
TIG-welded stainless workbench with integrated seedling growth stage.
4. COMMERCIAL VOLUME
Thousands of growing sites across 256 irrigated vertical towers.
5. HIGH-EFFICIENCY LED ARRAY
5:1 red / blue LED lighting optimized for green leafy growth.
6. INSULATED ENTRY
Padlock-proof safety door with controlled-environment insulation.
All information is from sources deemed reliable but is subject to errors, omissions, changes in price, prior sale or withdrawal without notice.
No representation is made as to the accuracy of any description.
All measurements, yields and square footages are approximate and all information should be confirmed by the customer.