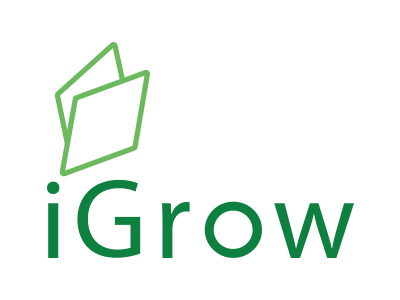
Welcome to iGrow News, Your Source for the World of Indoor Vertical Farming
These Shipping Container Farms Will Soon Be In Grocery Store Lots Across The U.S.
03.06.19
Kimbal Musk’s Square Roots’ partnership with Gordon Food Service will bring hundreds of container-style farms directly to distribution centers and stores.
[Photo: Square Roots]
Since 2016, Square Roots–the indoor urban farming startup founded by Kimbal Musk and entrepreneur Tobias Peggs–has been producing a steady output of fresh herbs and greens. In 10 shipping containers in a Brooklyn parking lot, the Square Roots team harvests the produce for local distribution to New York grocery stores, and educates young people interested in learning this new, tech-driven method of agriculture.
Musk and Peggs aren’t the only entrepreneurs growing greens indoors and hydroponically: AeroFarms and Bowery, both based in New Jersey, are just a two of the many other companies using similar tactics to grow kale and basil. It’s an increasingly popular idea: Bowery and AeroFarms have raised $118 and $138 million, respectively. But some more traditional organic agriculture advocates, like Dan Barber, have criticized the method for failing to contribute to the effort to remake farming in a more environmentally healthy way, in favor of leaning on new technology.
[Photo: Square Roots]
But despite that criticism, enthusiasm for a more sci-fi approach to growing greens does not appear to be slowing down. In fact, it will only become more mainstream, and Square Roots’ newest collaboration will play a critical role in that.
The farming tech company (or “accelerator,” as Musk and Peggs call it) is partnering with Gordon Food Service, which manages distribution facilities across North America as well as 175 retail store locations. Through the partnership, Square Roots will set up its shipping container farming systems on or very near GFS’s distribution and retail locations. The idea is to create a very short pipeline for fresh, local greens to reach GFS customers. And through Square Roots’ Next-Gen Farmer Training Program, which will expand along with the growing operations, Peggs says the number of young people the company will be able to train and employ will increase dramatically.
[Photo: Square Roots]
The way the partnership came about, Peggs says, is tied up with another project of Musk’s: his nonprofit Big Green, which educates young kids about food and growing by installing gardens in schools. GFS, which is based in Grand Rapids, Michigan, sponsors Big Green in Detroit. Around nine months ago, GFS’s CEO, Rich Wolowski, traveled to Brooklyn to visit the Square Roots facility to investigate the possibility of a partnership.
“GFS understands that there’s an increasing consumer demand for locally grown food, and changes in climate mean that we need to be thinking about new and innovative forms of agriculture,” Peggs says. “So they came to the farm and literally tasted the basil. It was obvious that the companies were mission-aligned: We both want to bring good quality food to a great number of people.”
[Photo: Square Roots]
The partnership evolved very quickly, and not all of the details are final. Square Roots and GFS, for now, are not announcing which distribution centers and retail stores will be the first to get a farm on their property. But they do have a sense of what the impact could be: Each Square Roots farm “campus” might contain 10 shipping containers, each of which will create one job for a local person interested in the Next-Gen Farmer Training Program. Each container can grow around 50,000 pounds of produce per year, which will feed directly into the local food supply. The farms are all connected, so as more come online, Peggs says the company will receive more data about what conditions lead to the best yields, and will be able to use that knowledge to increase efficiencies and introduce more diverse crops to their operations.
Square Roots and GFS are not placing a ceiling on how many farm containers each property might receive: That, Peggs says, can quickly develop in accordance with customer demand. “We’ll start with putting 10 containers down in a market, and as demand for locally grown produce increases, we can very quickly expand our footprint by adding more modules,” he says.
The greatest potential for the partnership between GFS and Square Roots, perhaps, is that it represents a truly localized supply chain for fresh produce. In the U.S., food travels an average of 1,500 miles to reach people’s plates. Those 1,500 miles represent excess carbon emissions from transport and electricity use from cooling needs along the way. If food, instead, can be grown and distributed in the place it is produced, as the GFS and Square Roots partnership aims to accomplish, we could begin to walk back some of the environmental costs of accessing food. “It’s going to take more than Square Roots and GFS to fix the food system,” Peggs says, but he’s hopeful that the partnership and prospective growth signal a real shift toward more localized food production and distribution.
ABOUT THE AUTHOR
Eillie Anzilotti is an assistant editor for Fast Company's Ideas section, covering sustainability, social good, and alternative economies. Previously, she wrote for CityLab.
You Might Also Like:
Container In Limassol Is The Future of Farming
FEBRUARY 20, 2019
Remember when you were little, and dreamt of the space age future promised on TV; a bright time in which everything was hip, high-tech, and healthy? In just a few decades, we were told, we’d be making phone calls from our watches (check), travelling in driverless cars (almost check), and eating produce grown in high-tech vertical farms (Hmm.). Well, two out of three isn’t bad. Though, if Herbanleaf Farms have anything to do with it, we’re heading strongly towards three for three…
Located in Parekklisha village, this farm is a one-of-a-kind, growing super fresh, healthy greens with a difference… Everything – all the planting, seeding, growing, tending and harvesting – takes place in an upcycled, 40-foot shipping container. And it’s all thanks to the miracle of hydroponics…
A sustainable indoor hydroponics farming company, Herbanleaf is the brainchild of the Timveos family: dad, mum and daughter all working diligently to provide clean, premium leafy greens and herbs grown inside a controlled environment. “This really is a family affair,” explains Myrianthi, the 32-year-old daughter. “My Mum Maria and I work full-time on the farm, while my dad, Panayiotis, helps out whenever he can. In fact, though we’re all as a family very into healthy eating, this whole venture was originally my Dad’s idea: he’s always been into organic gardening, growing vegetables in the backyard, planting seeds and feeding family and friends.”
Inspired by Panayiotis’ research into alternative methods of farming, this environmentally-conscious family came across the Freight Farms venture in 2016, a company which offers complete hydroponic farming solutions for families and businesses all over the world. “My parents went to the regional Freight Farms outlet in Holland, decided to forge ahead with the idea, and next thing we knew our shipping container and equipment had arrived on the island, along with a couple of trainers to teach us the basics…
“It all arrived in November 2017, and by December of that year we were up and running,” Myrianthi reveals. “Granted, we didn’t originally realise what we were in for,” she laughs, “but now we’ve been at this for a while, we love what we do: it’s a real passion…”
Focusing on providing better quality and healthier leafy greens and herbs using the latest sustainable farming techniques Herbanleaf’s innovative methods include the use of non-GMO seeds, grown without the use of harmful chemicals, pesticides, or fertilisers.
“Because we control the growing conditions so completely, we have an amazing range of products that Cyprus doesn’t usually see,” Myrianthi notes. “Mustard greens such as wasabina, which has a spicy flavour, and adds a wonderfully spicy note to salads and eggs; the electric daisy, an edible flower native to Brazil which has antiseptic, analgesic, anti-bacterial and anti-fungal properties and boasts a delightfully citrus flavour; and both green and purple pak choi! We also grow everything from fresh, crisp lettuce, to four varieties of kale, swiss chard, red-veined sorrel, leaf beet and all sorts of herbs such as dill, wild rocket, and coriander. There are,” she adds, “other hydroponics farms on the island, but they’re using greenhouses rather than a specialised, environmentally controlled farm, and that’s what makes us different…”
Saving more than 90 per cent of the water used in traditional farming, delivering the produce equivalent to that grown on 7,284 square metres of land, and able to grow all year round, the Herbanleaf hydroponics system is a marvel of space-age innovation. The plants are grown vertically, in 256 towers. “It’s very futuristic!” smiles Myrianthi. “It’s almost like a spaceship inside: there’s a constant of purple haze from the red and blue LED lights we use – the optimal wavelengths for photosynthesis. There’s also a lot of agrotech involved: special programming which controls the functioning of the farm, oversees the nutrient, seedling, and main tanks, as well as sensors for everything from pH to water temperature. It’s definitely hard work, but we have a real passion for what we’re doing and it’s good to know we’re helping to promote a healthy, environmentally-friendly island!”
From seeds to harvest, Herbanleaf not only delivers sustainable agriculture, it also offers its clients a transparent overview of where and how their food is grown. “Come summer, much of the produce you buy in supermarkets has been imported,” explains Myrianthi. “Now, that ups your carbon footprint and, at the same time, adds a dimension of uncertainty to the food you’re eating. In fact, even produce grown right here on the island may be covered in harmful chemicals. I think a lot of people are under the impression they’re buying healthy food for their families but, unless you ask the right questions and really do your research, you might be very surprised by what you’re consuming!”
At Herbanleaf, however, customers know exactly what they’re getting and how their food has been grown: there’s complete transparency to the growing process. And, by using non GMO seeds and eschewing the use of harmful chemicals, the venture is able to offer a safer, healthier option to all sectors of the community. “‘Fresher, healthier, and tastier’ is what we do,” Myrianthi adds. “It’s right there in our logo, and we stand by it!”
Not only do the family enjoy these fresher, healthier greens themselves, they also sell to individuals and outlets all over the island. Chefs at various hotels purchase from Herbanleaf on a weekly basis, as does Frutopia in Limassol, and the Alchemy bartending school (apparently the edible flowers are a hit in cocktails!). Then there’s the monthly Peyia Market, at which individuals can get their shot of healthy greens direct from the family, as well as a service which sees the produce delivered all over the island.
“So far,” Myrianthi concludes, “we’ve been very successful. There’s an excellent market out there of health conscious individuals, chefs looking for a premium product, and people who want to know exactly how their food is grown. In fact, if you’d like to see the farm for yourself, we’re always more than happy to show visitors round, give them different flavours to taste and teach them about the wonders of hydroponics. This, I believe, is the future of farming!”
For more information on Herbanleaf Farms,
visit https://www.herbanleaffarms.com
or the Faceook page ‘HerbanLeaf Farms’
Cadets Create Indoor Farm Inside Shipping Containers
From the confined space of a shipping container, military college cadets grow and harvest hundreds of heads of lettuce per week for staff and students.
By Jennifer Albert and Dalia Martinez
February/March 2019
The project helps cadets gain hands-on experience in business, chemistry, engineering, and growing food. Photo by The Citadel.
Inside three shipping containers on the campus of The Citadel, a military college in South Carolina, cadets are learning how to grow lettuce crops in a controlled indoor “farm” setting, producing organic produce in an environment that can withstand unpredictable weather conditions and disease. The cadets’ hands-on education comes from The Citadel Sustainability Project, in which the first shipping container functions as a hydroponic cultivation system for lettuce crops, the second container is a testing ground for various growing systems, and the third container will be outfitted by cadets who design and build the growing equipment as part of a corresponding independent study.
The Citadel STEM Center of Excellence initiated the project in 2016 as an interdisciplinary collaboration. Of the 20 or so students who are members of the Sustainability Club, several are STEM Scholars. We also have electrical engineers who are completing a design project on hydroponics. We’ve had students from almost every campus department — engineering, biology, business — who have worked with the project.
Prior to their graduation, Alex Richardson, who studied engineering, and Cameron Brown, who studied business, managed the growing container with the help of other students motivated by a passion for the environment.
“Cadets are excited about The Citadel Sustainability Project because it incorporates biology, chemistry, computer science, business, engineering, and community outreach. It gives us the opportunity to collaborate with students outside of our own programs on a project focused on global population needs,” Richardson says. “And seeing people on campus eat and enjoy our crops is gratifying.”
A Sustainable Food Source
We’re currently growing more than 4,400 plants in the shipping containers, including collards, lettuce, spinach, and herbs. The nutrients used to grow the crops are recycled within the system’s 100-gallon reservoir and are managed through a smartphone application. The app tracks the metallic minerals in the water and sends nutrients to the plants every 10 minutes. It also displays the water’s temperature and the container’s carbon dioxide and pH levels.
More than 4,400 plants, including collards, lettuce, spinach, and herbs, grow in the container. Photo by Stefanie Swackhammer.
The transformation from seed to harvest inside the shipping container farm occurs in five weeks, compared with the 10 weeks the crops would need in an outdoor environment. Thanks to high-density crop production, the cadets harvest more than 800 heads of lettuce per week for the campus restaurant’s salad bar as well as events. Additionally, cadets get to eat the fresh lettuce in the student mess hall. If the growing container is running at full capacity, the 320-square-foot space can yield about 40,000 heads of lettuce per year.
Each container is valued at $115,000 after it’s outfitted. The cadets intend to make the project sustainable by putting profits from the crops toward the purchase of more containers.
“Our self-propagating irrigation system uses up to 98 percent less water than conventional industrial farming does,” says Brown, who wrote the project’s business plan. “We want to expand, grow more, and sustain this Earth-friendly initiative, making our healthy produce available to more members of our community.
In addition to providing a sustainable food source, the goal of the project is to help young entrepreneurs and members of other disciplines gain hands-on experience.
We also try to bring in high school students. Last spring, students from Burke High School, which is next door to our campus, incorporated the indoor farm into one of their projects. Then, a 10th grade economics class wrote business plans for the container with data we provided, and followed up with two field trips to the container.
The container farm is installed in a corner of campus, leaving room for expansion. Photo by The Citadel.
The shipping container farm is located in a back corner of campus near the marsh, with plenty of room for expansion. We’ve submitted a National Science Foundation grant application with The GEL Group, AmplifiedAg, and SuperGreen Solutions to design a system that would filter excess nutrients out of treated wastewater and incorporate sustainable energy so the system could be viable anywhere. Ultimately, we’d like to expand the project to be able to produce more fresh food for the South Carolina Corps of Cadets, which comprises the college’s undergraduate population.
Jennifer Albert is the director of The Citadel STEM Center of Excellence. Dalia Martinez graduated from The Citadel in May 2018, and is now a researcher at The Medical University of South Carolina.
CEA Advisors Announces Formation of New Division Focused on Cannabis Industry
The company has completed the design process for the first shipping container farm specifically designed and built for cloning and young plant production.
March 5, 2019
After nine years of designing and marketing custom-made Growtainers and providing consultant services for commercial clients worldwide, CEA Advisors has announced that it has formed a new division to focus on the cannabis Industry. Recently the company has completed the design process for the first competitively priced shipping container farm specifically designed and built for cloning and young plant production.
“Although I grew indoors many years ago, I spent more than a year discussing today’s technology and the specific requirements of this crop with industry experts and component manufacturers and when I was sure we could execute, we began the design and manufacturing process” said Glenn Behrman, founder of Greentech Agro LLC and CEA Advisors LLC.
Each fully equipped, plug and play 20-foot fully insulated container-based Clone Facility has a separate utility area and provides climate controlled vertical production space for cloning and mother plant storage. Each unit is specially designed for maximum efficiency and workflow. Besides the dedicated technology for the ebb and flow irrigation system installed, a state-of-the-art water monitoring and dosing system and high-pressure fog system, each production area is equipped with energy efficient LED production modules, offering wavelength and intensity specifically designed for cloning and vegetative growth.
The LED environment for cloning provides light levels from 50 to 100 micromoles with an incremental increase as the plant becomes established and the mother plant storage area provides up to 700 micromoles for faster vegetative growth. In addition, each clone factory provides a warm, humid LED lit micro climate for germinating seeds. Based on the current configuration, each unit is capable of producing 1,080 four-inch pots per cycle or substantially more in standard 1020 trays.
CEA Advisors is in the process of finalizing agreements with some of the world’s top cannabis consultants to provide technical support for our clients. The company has already brought on board a container modification expert with over 20 years of hands-on experience to manage its agreement with the world’s largest container manufacturer to provide large quantities of ISO certified 20 foot, 40 foot and 45 foot Container Farms for quick deployment for all stages of growth in the food production, research and international cannabis market.
For more information contact us by email at GB@cea-advisors.com
How Freight Farms Plans To Grow Sales (And More Veggies) With Its Next-Gen Farm In A Box
Brad McNamara (left) and Jon Friedman, co-founders of Freight Farms, in front of their new Greenery, a high-tech, hydroponic farm built inside of a shipping container.FREIGHT FARMS
Almost a decade ago, the cofounders of Boston-based Freight Farms pioneered the idea of outfitting used shipping containers with everything a farmer needs to grow greens and herbs in a pesticide-free, climate-controlled environment– without soil. These hydroponic vertical farms, which grow plants in nutrient-enriched water, are turnkey operations that enable a farmer to get up and running in a matter of days. And the whole thing takes up just 320 square feet.
Co-founders Jon Friedman and Brad McNamara formed their company in 2010, raised their first funds on Kickstarter in 2011 and introduced their Leafy Green Machine a year later. Freight Farms has since raised about $12 million from VC firms. To date, it has sold more than 250 of those shipping-container farms, which use off-the shelf parts and their own proprietary software, in more than 15 countries.
"After about four years of working with that model and pushing it as far as we could go, we realized we needed to make a more quantum leap," said Friedman, who is chief operating officer.
Freight Farms says its new LED lighting system produces higher yields and heavier plants FREIGHT FARMS
Today Freight Farms will announce its next-gen product, called the Greenery. Instead of using recycled shipping containers, the units are built from the ground up for Freight Farms with all new components. Growing racks can now be configured to accommodate bigger plants, such as tomatoes. Lighting has improved too. Its energy-efficient LED arrays, with three times the power of the old ones, result in heavier plants and greater yields, according to the company.
Water and energy usage are also more efficient than the old design. The farm's new climate-control system condenses and recycles ambient moisture. The company said it offers 70% more growing space, among other features. Its IoT-connected sensors continuously send the farmer data on temperature, lighting, moisture content, CO2 levels and other environmental variables to allow them to monitor and adjust conditions remotely from a smart phone.
I first wrote about Freight Farms in December 2015, when revenue was about $3 million and the company had about 50 customers. Granted, the business is still small, but it's growing steadily and adapting, much as plants do, to a changing environment. The company declined to disclose its revenue this time around, citing intense industry competition. Indeed, a quick Google search shows they aren't alone anymore in the shipping-container farm business. Competitors include the CropBox and Growtainer. Customers might also opt for other types of vertical, hydroponic systems that don't use a shipping container.
In 2015, Leafy Green Machines had a base price of $76,000. The new Greenery costs $104,000.
Some of the most enthusiastic customers of the freight-container farms are big corporations, who see it as an extension of health and wellness programs or social action initiatives. You can find a Leafy Green Machine on the Google campus in Mountainview, Calif., where it's used to grow greens and edible flowers. In Detroit, Ford Motor Company Fund, the automaker's philanthropic arm, also has a freight farm, that it's operating in partnership with a nonprofit to help supply its community kitchen with fresh produce and provide job training. Everlane, the clothing company, uses its shipping-container farms in Vietnam to provide food for its workers.
Academic institutions find freight farming particularly appealing, said McNamara, who is CEO. "We're seeing more and more of the education segment who want onsite local high quality produce and want to connect students and employees to where their food is coming from."
The University of Georgia has just ordered two Greenery farms to help supply their dining halls with local greens more efficiently and sustainably while educating students about where their food comes from, the school told me in an email.
Of course, not every university or corporation wants to actually do the work of farming, the co-founders realized. So, in late 2018, they launched Grown by Freight Farms, where customers sign up for a service contract. "We provide them with a farm and a farmer," said McNamara, who is CEO.
Small farmers are also an important market for Freight Farms. In Guam, a farmer uses his Leafy Green Machine to supply Wendy's with lettuce. In North Carolina, Heather David and John Peters, who sell pasture-raised meat to chefs from their WhyNot Farms with two locations in North Carolina and a new one in Tennessee, are among the first in line for a Greenery. They expect to receive delivery in May.
"We were looking to diversify our business in a way that would be less labor intensive, and we wanted something that would weigh less than cows or pigs," said Davis. 'We're middle-aged and felt it would be more sustainable for us to be raising vegetables."
Heather Davis and John Peters, owners of Whynot Farms, are buying a Greenery from Freight Farms to diversify from grass-fed animals into vegetables. WHYNOT FARMS
Davis, president and chief investment officer at Nuveen Private Markets in Charlotte, N.C., moonlights as her husband's farmhand on weekends and she happens to have a local vertical, hydroponic farming operation in her portfolio. There were plenty of options for Davis to consider for their own hydroponic system, which they hope to power mostly with solar energy.
"What appealed to me about Freight Farms is that they are very focused on the sustainability aspect and conservation of water," she said. "It's in a compact unit, and they just drop it on your site."
Davis also liked the fact that the company provides intensive farmer support and education.
"It's not clear to me yet the extent of what we'll be able to grow in this," she said. "I'll grow what anybody will buy as long as it's not a total pain in the neck and I can make a profit."
Robin D. Schatz is a New York-based writer focusing on food, nutrition, business and health care. Follow her on Twitter @Robin_Schatz. Read her Forbes stories here.
Robin D. Schatz Contributor
I'm a prize-winning business journalist, most recently working as an assistant managing editor at Crain's New York Business, where I managed health care coverage. I've been a staff writer and editor at Bloomberg News, Businessweek and other publications and a freelance writer for a broad media clientele. I'm also a weekend organic farmer in the Catskill Mountains with a keen interest in sustainable agriculture, plant-based eating and the future of food.
After a long break from blogging about food entrepreneurs, I'm happy to be relaunching on Forbes' food and wine vertical. I'll still be writing about game-changing entrepreneurs, those who are trying to figure out how we'll feed a planet of 9 billion people and others are just trying to make a living producing something healthy and delicious. I'll also be looking at the nexus of nutrition, public health and business.
Read More
Franchise Farms: Champion or Disrupter of Grocery Stores?
Coauthor: Jonathan Hua
Over the past few years, we’ve seen e-commerce aggressively challenge brick and mortar stores across industries. Despite this market trend, the food and grocery industries still heavily rely on in-store experiences, led by big box chains such as Walmart, Target and Costco. This is attributed to the high perishability of produce, two-thirds of which are grown in California which requires an extensive supply chain and energy intensive refrigeration sections to constantly account for losses. In the United States and Canada, around 40 percent of wasted food is thrown out by consumers according to United Nations Food and Agriculture Organization.
But is it too far-fetched to imagine a world where next-gen farming solutions could one day replace brick and mortar grocery stores? As it turns out, with rising obesity rates, dwindling natural resources and a lackluster set of options for fresh produce, we may need to consider the efficacy of indoor agriculture solutions to help feed the world’s population sooner rather than later.
To put this concept into perspective, it makes sense to take look closer at one of the causes of the food production problem. Across mid-America, “small-box” retailers such as Dollar General have moved into communities deemed too small to be profitable by large retailers such as Walmart. This is only possible by carrying a limited stock of prepared foods; in fact, Dollar General is now feeding more people than grocery chains like Whole Foods! Dollar General has now become one of the fastest growing franchises in the United States, but has consequently caused these rural communities to see an increase in obesity, as few options for fresh produce remain.
To exacerbate this problem further, seasonal climates simply do not offer the consistent growing seasons needed to grow vegetables throughout the year due to long winters with harsh conditions. This situation may sound bleak, but we may already be well on our way to a viable long-term solution: indoor agriculture. This is a topic that hasn’t drawn as much attention as buzzwords such as “blockchain” or “automation”. However, the case can be made that indoor agriculture is, indeed, the most viable solution to the food production climate because of an ability to provide Controlled Environment Agriculture in a dynamic climate. According to Maximum Yield, indoor agriculture is a method of growing crops or plants, usually on a large scale, entirely indoors. The primary challenge of indoor farming is that many of these facilities require skilled engineers on staff to maintain these complex operations, and plant scientists to ensure the biological needs of the plants are met. Although the massive vertical farms of the world are cautious to not share information about their margins, it can only be assumed they are around 4–5% at best.
Without the agricultural, reduced energy rates, it is unlikely any of these facilities would be profitable at all with the exception of specialty crops. Many US companies have access to state-level agricultural energy pricing which can be as low as $.015 per KWH. Residential americans pay almost 90% higher rates or $0.12 per KWH. They are directly competing with farm gate pricing in order to maintain positive cash flow in a complex supply chain that must account for the margins of growers, processing/packaging facilities, and ultimately the retailers. The digital revolution has provided transparency by immediately tracking outbreaks of foodborne illnesses to the source. This will result in more costly outdoor growing operations, which will be required to be equipped with sensors to monitor environmental conditions and alert the growers when pathogen outbreaks occur. The implementation of sensors and computer controlled apparatuses is tantamount to a controlled environment farming operation.
Therefore, decentralized, indoor agriculture is the most viable solution to bring fresh produce to the masses! Perhaps the best opportunity for vertical agriculture would be a vertically integrated supply chain, as shown by the headlines made by SweetGreen recently.
The Fourth Industrial Revolution is defined by the combination of mechanical systems from the first industrial revolution, powered by electricity from the Second Industrial Revolution, given a rudimentary nervous system of digital sensors in the Third Industrial Revolution, and now a consolidation of complex tasks into a cohesive automation platform that historically required a dedicated team of experts. This is particularly advantageous for indoor agriculture companies that can now eliminate the largest risk factor of any growing operations, which is the human input itself.
The primary value proposition of indoor farming operations is clean produce that does not carry pesticide residues. Despite the benefits of eating clean food, these chemicals are very effective at killing pests. Indoor farmers are required to follow a disciplined pest management protocol with near clean room sanitation standards to prevent a single pest from breaching the operations. Robotics can now eliminate the exposure of the clean plants to the outside world and, more importantly, eliminate the knowledge of operating an indoor farm if coupled with a computer vision system to diagnose nutrient deficiencies or pH imbalances in real-time. Agriculture is now being democratized into a franchise business model.
This is happening now with computer vision companies such as IUNU offering a complete growing platform to provide constant monitoring of plant needs without an extensive background of indoor agriculture required. These machine learning algorithms will only become more efficient as they gather more data to refine the operational output. Another company, 80 Acres, has now secured funding to build what it claims to be the first fully autonomous, indoor farm. The future of agriculture will certainly be less human, and more like kiosk business models. Perhaps there will even be kiosk growing systems that emulate the Redbox business models which can be stationed at these Dollar General store locations or Sweet Green restaurants. History often repeats itself.
Source: Heliponix
Many species of produce will no longer be shipped in its final stage of growth, but instead as a zip file for food or a compostable seed pod like a keurig k cup from an automated production facility that contains all essential macro and micro nutrients with growing media for consistent yields. Our dependence on refrigeration at brick and mortar grocery stores will be greatly reduced by consuming produce directly from the source of a personal farm. They may even have the ability to learn from a user’s feedback to optimize the growing conditions to meet the their taste expectations. Keeping the plants alive until the moment of consumption will maximize the nutritional content and taste for the user which can only be assumed to increase fruit and vegetable consumption for residents across mid-America who were deemed too remote or sparsely populated to keep a constant supply of fresh produce on demand.
Generation Z and Alpha Farmers
The invention of the lightbulb made the need for oil (in the form of kerosene for lanterns) obsolete, but quickly met a new demand for gasoline in automobiles. The internet made paper mail obsolete through email, but revived the need for mail logistical services through e-commerce marketplaces more than ever. For all we know, people may re-adopt the agrarian lifestyles of our ancestors through these automated farming appliances at a consumer level in the new gig economy.
To engage the CoAuthors
'It's A Blizzard Outside And We're Growing Lettuce': Busby Area Farmers Grow Vertical
A unique farm has opened near Busby growing leafy greens in fabricated shipping containers
Travis McEwan · CBC News · Feb 02, 2019
Greens are expected to grow at Swiss Leaf Farms out of 14 different shipping containers. (Trevor Wilson/CBC)
An indoor farm near Busby, Alta. is harvesting leafy greens in the middle of winter using a system called vertical farming and fabricated shipping containers.
David and Alyssa Pfaeffli of Swiss Leaf Farms have been growing lettuce, microgreens, and herbs in a 9,500-square-foot warehouse for the past couple of months. The system they are using will allow them to grow year-round.
The growing machines are developed by a company in Langley, B.C. and an irrigation system waters each tray as it rotates past a water spout. A single row of growing lights sit on the top of the container.
A heating and cooling system ensures the plants grow at the right temperatures.
CBC News Edmonton | A Busby, Alberta farmer uses a vertical farming system to grow leafy produce all year round.
Within the warehouse, there are 14 growing machines that grow different varieties of leafy greens. Each container holds 4,000 heads of lettuce, with each head of lettuce taking a month to grow. The microgreens are harvested every six days.
The farm just had their first harvest last week and have delivered greens to grocery stores in Westlock, Barrhead and Edmonton.
"We can provide the same produce that's fresher, tastes better, it's healthier and there's zero pesticides. It's better for the planet," said David Pfaeffli. "You're not driving a diesel rig all over North America to deliver lettuce."
Alyssa and David Pfaeffli of Swiss Leaf Farms started the vertical farm a few months ago. Their 14 shipping containers have the capacity to grow 4,000 heads of lettuce per container. (Trevor Wilson/CBC)
The couple say they're able to grow a lot within a small space, as a traditional garden will take up a lot more land. Within their building, they can also control the temperatures with a heating and cooling system.
"This system allows us to do that here now, whereas before in Alberta where would you be able to do that? It's a blizzard outside and we're growing lettuce." said Alyssa Pfaeffli.
The cost of vertical farming
Financing the vertical farm was the biggest challenge for the couple, said David Pfaeffi. Without large farming equipment, he didn't have a lot of collateral if things dried up.
"Agricultural lending outfits weren't too eager to lend a large sum of money on equipment like this because they'd have a hard time recouping their costs. It's not a combine," David said.
The Pfaeffli's are excited about their new farming venture, but at the moment they're trying to not get too ahead of themselves.
"We want to grow not only plants but we want to grow the business. We want to keep adding on phases of growing machines. I'd like to see 50 acres of growing containers eventually," David Pfaeffi said.
Their greens are sold in grocery stores like Freson Bros. in Stony Plain. The Swiss Leaf Farms product fills a void of locally-produced lettuce in the winter months.Their latest order sold within 24 hours.
"We try to have an Alberta item everywhere. As soon as we get something like this, there are [consumers] willing to pick it up and try it," said Dan Pazder, Freson Bros. produce director.
Busby is approximately 71 kilometres northwest of Edmonton.
With files from Trevor Wilson
Giving Shipping Containers A Second Life
View inside an Agricool cooltainer. © Agricool
BY MAREX 2019-01-20
CMA CGM is supporting the financial and industrial development of Agricool, a young company specializing in urban agriculture, in order to enable it to launch its industrialization phase.
Founded in 2015 in Paris, Agricool aims to create urban farms in recycled containers. With its agricultural model, the young company wishes to produce fruit and vegetables without pesticides, picked and sold on the same day. Several containers are currently being tested.
In Paris, Agricool grows strawberries and saves on water and nutrients by 90 percent compared to classical agricultural methods. The system uses renewable energy only. The strawberries contain an average of 20 percent more sugar and 30 percent more vitamin C more than retail store strawberries.
In the Fall of 2018, the CMA CGM Group provided its first concrete support to Agricool by offering technical and logistical support for the delivery and installation of a "cooltainer" in Dubai.
In December, Agricool completed a €25 million ($28 million) fundraising campaign to finance the industrialization of its innovative project. At the time, CMA CGM acquired an equity stake in the company through its investment fund, CMA CGM Ventures.
In parallel, CMA CGM wants to support Agricool's development by providing it with its industrial and logistics expertise. The Group thus becomes the main supplier of containers and the primary logistics and supply partner for the company.
The collaboration is part of the innovation support strategy implemented by Rodolphe Saadé, Chairman and CEO of the CMA CGM Group. The strategy involves equity investments and commercial partnerships with start-ups with strong entrepreneurial values and innovative industrial projects. In line with CMA CGM's commitment to sustainable development, this solution allows the company to recycle containers and give them a second life.
US: New Modular Indoor Agricultural System Grows Food In Clean, Pure Environment
Grow Pod Solutions announced that its new modular indoor agricultural systems can grow herbs and vegetables without contamination frequently associated with other farming methods.
The modular, stackable pods feature proprietary technology to monitor every detail of plant growth, including light intensity, nutrient delivery, and oxygen levels.
"We are leading the drive to provide consumers with 'Super Foods' that are clean and healthy," said George Natzic, President of Grow Pod Solutions. "Our exclusive high-grade clean agricultural system eliminates harmful pathogens, and grows food with farm-to-table freshness and 100% traceability."
'Know the grow'
GrowPod allows businesses, entrepreneurs, restaurateurs, grocery stores, schools, hotels, neighborhoods and organizations to grow fresh, clean food on-site that is free from disease, pesticides and dangerous chemicals. This allows consumers to "Know the Grow" and have confidence that their food is fresh, clean, and healthy.
The GrowPod agricultural system uses sterile water and purified air in a sealed and filtered environment, thus eliminating the sources of contamination. The company's patented bipolar air ionization reduces airborne pollutants by delivering charged oxygen molecules that neutralize chemical compounds and sterilize pathogens, mold and bacteria, to create the optimum environment for growing.
Grow Pod Solutions also announced that the company is shortening its name to GP Solutions in conjunction with its move from a privately held to a publicly traded company. GP Solutions is traded on the OTC markets under the ticker symbol: GWPD.
For more information:
GP Solutions
(855) 247-8054
info@growpodsolutions.com
www.growpodsolutions.com
Publication date : 1/4/2019
How Abu Dhabi Found A Way To Grow Vegetables In 40-Degree Heat
January 17, 2019 by World Economic Forum
This article is brought to you thanks to the collaboration of The European Sting with the World Economic Forum.
Author: Emma Charlton, Writer
Could you grow your lunch in an old shipping container? One that’s situated in 40-degree desert heat?
A project underway in Abu Dhabi aims to encourage people to do just that – pairing old shipping containers and high-tech hydroponics to overcome the region’s hostile climate and increase local food production.
(Unsplash, 2019)
A new solution for farming in hostile conditions / Image: CustomWeather
While food security issues are climbing up the agenda globally, they are felt particularly acutely in the United Arab Emirates, where temperatures are high and rain levels low. Creating vertical farms inside shipping containers could help communities grow more of their own produce and cut down on the cost of transporting food to the region.
In Masdar City – an urban development project in Abu Dhabi – Madar Farms are using hydroponic systems that require much less water than traditional farms, to grow lettuce, herbs and brassicas. The project is being showcased at Abu Dhabi Sustainability Week.
Because the plants are growing in a controlled environment inside the container, with nutrients coming from enriched water, pesticides and insecticides are not required. LED lighting with deep red and blue hues mimics sunlight and cycles on and off to simulate periods of day and night for the plants.
LED lighting mimics sunlight and switches off to simulate night. / Image: Madar Farms
According to proponents of the idea, shipping-container-based farming uses 95% less water than traditional farming. The containers, which are 12.2 metres long and 2.4 wide, are stackable, durable and easy to modify. It’s an idea that’s taking hold elsewhere as well, with CropBox offering a similar idea in the United States.
Some people argue that becoming dependent on such methods creates a reliance on a secure energy supply to power the boxes, while others point out it could disrupt ecosystems and harm pollinators.
Despite these reservations, vertical farming systems like this one, where grow towers hang vertically, and others, where crops are stacked, are seen as essential for the future of sustainable farming.
The vertical farming market is forecast by Global Market Insights to grow to $13.9 billion a year in 2024, from $2.5 billion in 2017.
Vertical farming is a key growth area / Image: Global Market Insights
Shaping the Future of Food is one of the World Economic Forum’s key initiatives, since it anticipates the global population will have swelled to 9.8 billion by 2050, resulting in a need for 70% more food than is consumed today. Leadership, innovation and collaborative action are needed to meet the challenge, it says.
“Food systems do not currently provide nutritious food in an environmentally sustainable way,” the initiative says. “At the same time, food production, transportation, processing and waste are putting unsustainable strain on environmental resources.”
Masdar City's Steel Urban Allotments Could Help Solve Food Security Crisis
Vertical farms and eco-villas to be profiled at Abu Dhabi Sustainability Week could help UAE grow more of its own crops
Abu Dhabi’s Masdar City is piloting a project that could see urban communities growing their own food in an allotment, but with a very modern day twist.
A pilot future farming facility built from recycled shipping containers could solve the region’s food production crisis by allowing communities to grow produce, despite the harsh desert climate.
Masdar City, which was built to be one of the world's most sustainable communities, is collaborating with Madar Farms, who try to find sustainable solutions to the GCC's food security issues, to develop vertical farming inside shipping containers. They are equipped with hydroponic systems that can operate using minimal water.
“With the world’s population expected to exceed 9 billion by 2050, efficient and sustainable production and distribution of food is becoming increasingly important,” said Yousef Baselaib, executive director of Masdar City.
“This is particularly true for countries with arid climates and harsh environmental conditions like ours.”
Hydroponics systems allow tonnes of greens to be grown in small spaces. Antonie Robertson / The National
The 1.5 acre plots inside each 12-metre container have the capability to grow crops using less than 40 litres of water a day.
The crops are constantly monitored by the latest technology within a sealed environment, shortening the growing cycle.
Temperature and carbon dioxide levels can be regulated via a mobile phone app, with an automated nutrient delivery system to produce the best possible results.
“We have begun investing in technologies and partnerships focused on sustainable agriculture with the aim of commercialising farming techniques,” said Mr Baselaib.
“These systems can be applied to urban areas to encourage people in the UAE to eat home grown produce.”
Read more:
Abu Dhabi Sustainability Week to place spotlight on real environmental change, says minister
Smart cities look well set to power global economy
Neighbourhood Watch: Farming grows sense of community at Dubai's Sustainable City
Food security and sustainable farming will be one of the key focuses of Abu Dhabi Sustainability Week (ADSW), which begins on Saturday.
The technology and methods used by Madar Farms use approximately 95 per cent less water and land than conventional farming, making the company one of the most efficient and sustainable growers in the GCC.
The initiative joins other similar schemes such as one run by Agricool in Sustainable City in Dubai, where they are growing fresh strawberries for the local community in hydroponic grow room inside shipping containers.
Masdar City first engineered ideas of productive landscapes in 2008 to address food security issues.
Since then, community gardening plots have been developed to allow for plant research, agricultural education and to encourage people to grow their own food.
Masdar’s agricultural strategy hopes to encourage traditional farming methods and the growth of indigenous plants.
An eco-villa has been built in the eco-friendly city to show how green living could be used in the home on a wider scale.
Kyle Wagner, head of operations at Madar Farms, checks the growth of crops grown in a retrofitted shipping container. Antonie Robertson / The National
“The villa is an example of Masdar’s commitment to sustainability and is a pilot project conceived as a template for affordable, energy- and water-efficient residential villas,” said Mr Baselaib.
By this month, they also hope to have implemented home farming technologies and they will be showcasing the project at ADSW.
The eco-villa uses about 72 per cent less power and 35 per cent less water than a typical villa in Abu Dhabi, displacing an estimated 63 tonnes of carbon dioxide annually.
During ADSW, Masdar will also show other projects focused on vegetable and livestock farming, water harvesting and recycling, waste recycling and how to use energy for cooking.
Less than 1 per cent of the region is arable and permanent crop land, and more than 40 per cent of the UAE’s food is imported.
Importing that volume of food will cost more than US$100 billion (Dh367b) by 2030.
The crops are grown inside shipping containers. Antonie Robertson / The National)
More than 40 per cent of natural water sources have been lost in the past 20 years through overuse and despite water scarcity, 84 per cent of water is used for agriculture and irrigation, which contributes less than 1 per cent to GDP.
That has left conventional farming unsustainable in the UAE, forcing the development of alternative models.
Masdar has paired up with the UAE Office for Future Food Security to rubber stamp its commitment to addressing the most important environmental issues likely to impact the nation.
Other sustainable farming methods are being developed in a Central Park project, using vertical farming techniques, solar-powered greenhouses, a self-contained farmers’ market and edible maze.
“Tackling the challenge of food security is a priority for Masdar and one that we are addressing in a holistic manner by looking at solutions in energy, food and water,” said Mr Baselaib.
Applied Technology: Putting The Hyper In Local
December 21, 2018
For some retailers and restaurants, proximity to local food is key—like next door, on the next floor, or on the roof— and you can’t get much fresher than that.
This technology is already gaining traction across the nation and worldwide with vertical farms in skyscrapers, vegetable and herb gardens at restaurants or near retailers, and container farms in areas where growing can be nearly impossible.
Local Roots, a Los Angeles-based startup, has created a twist on greenhouse growing. The company does grow produce and herbs in a protected setting, but instead of a greenhouse, the indoor farms are in 40-foot shipping containers.
The four student founders say that by using robotics, microbiology, and data analytics, their indoor container “TerraFarms” produce up to 300 times higher per square foot densities than traditional farms.
The containers “have also achieved cost parity with greens and other produce grown out in the field,” says Gary Hawkins, founder and CEO of the Los Angeles, CA-based Center for Advancing Retail & Technology, LLC.
Better yet, he says, “they use a fraction of the water and no pesticides or herbicides.”
Local Roots believes it has eliminated many hazards of the supply chain and is partnering with area businesses, restaurants, and retailers, notably Walmart.
And if a retailer or processor has the desire, Local Roots will not only sell and set up a TerraFarm, but oversee the entire growing process from seed to harvest for the freshest, local vegetables and herbs.
Future Farm: Crops Grown With LED Lighting Might Lead To New Markets
The plan is to see if the cost of using electricity to power the new frontier of “indoor agriculture” is feasible compared to traditional agriculture.
By Powergrams - 2018
Alabama Power engineer Blair Farley and Cheryl McFarland, Commercial and Industrial Marketing Support manager, inside the hydroponic container where they're testing the feasibility of indoor agriculture. (Joseph De Sciose/Powergrams)
Alabama Power’s penchant for pushing the innovation envelope can be seen in a refurbished Freight Farms shipping container outside the Technology Applications Center at the General Services Complex in Calera.
Employees are growing lettuce and other vegetables, herbs and edible flowers in an insulated container retrofitted with LED lighting and climate-control equipment. The plan is to see if the cost of using electricity to power the new frontier of “indoor agriculture” is feasible compared to traditional agriculture.
Alabama Power engineer Blair Farley steps out of the indoor agriculture unit in Calera where the company is test-growing lettuce, carrots, basil, dill, arugula and radishes. (Joseph De Sciose/Powergrams)
Indoor agriculture could be a game-changer for farmers, stores, restaurants, consumers and Alabama Power, in part because:
Crops could be grown in a controlled environment year-round with nutrients in circulated water without soil and few or no pesticides.
Crops could be grown in urban settings and areas classified as food deserts (locations where fresh food is not easily accessible).
Transportation costs could be drastically reduced or eliminated, as food could be grown near consumers and stores.
Indoor farming can produce 12 more lettuce harvests a year, and uses up to 90 percent less water, than a traditional outdoor farm.
Energy-efficient LED lighting and other components can be programmed for off-peak hours to take advantage of cheaper electric rates.
With electricity needed to operate the lighting and climate control systems, indoor farming could usher in a new stream of opportunities for the company.
From an economic development standpoint, vacant warehouses or buildings, including those with existing utilities, could be repurposed for controlled-environment agriculture, providing jobs for Alabamians.
Other advantages include growing during drought or excessive rainfall; producing fruits and vegetables not native to a geographic area; and uninterrupted growing seasons.
Engineer Blair Farley and Cheryl McFarland, Commercial and Industrial Marketing Support manager for Alabama Power, walk alongside the modified shipping container where the company is testing the feasibility of indoor agriculture. (Joseph De Sciose/Powergrams)
There is a viable market in Alabama, with $67 million spent on lettuce annually for households and about 70 percent of people buying organic products.
“Indoor agriculture can be a great addition to the already thriving agriculture industry in our state,” said Cheryl McFarland, Commercial and Industrial Marketing Support manager.
But there are challenges. Like any new, fast-growing concept, scarce data is available to determine long-term pros and cons. High startup costs and unavailable labor could be viewed as making it a financial risk. Vague or unfavorable city laws could be a barrier to an indoor agriculture operation.
Cheryl McFarland and Blair Farley monitor the towers where they’re growing vegetables inside a refurbished shipping container. (Joseph De Sciose/Powergrams)
Exploring the container farm concept at Alabama Power originated from an increasing interest in indoor agriculture and the need to fully understand the benefits of using electricity to enhance the process.
Alabama Power employees installed a 40-foot hydroponic container in January 2017 and began producing lettuce one month later. The container has a seed germination table and 256 vertical towers holding up to 17 small heads of lettuce each. Food production at the GSC is not limited to lettuce and includes basil, arugula, carrots, dill and radishes.
Because of automation, the APC container is fairly self-sufficient. However, one to two employees with other work responsibilities spend a little of their time each week planting, harvesting and performing routine maintenance in the container.
“Interest in indoor agriculture or controlled-environment agriculture is growing either in completely enclosed settings, such as our container, augmented greenhouses or empty buildings, like a vacant mall or Walmart,” McFarland said. “It’s a great way to provide access to fresh foods and jobs in rural communities and urban settings, particularly in areas of food deserts.”
Alabama Power’s next move on the chessboard that is indoor agriculture is to assess produce production and water and electricity usage, then compare findings with similar projects within Southern Company.
“We feel the interest in indoor agriculture is continuing to grow as consumers demand more fresh, local and healthy food options in stores and restaurants,” McFarland said. “Alabama Power has always tried to find ways to improve the way of life for our customers, and indoor agriculture is another avenue we are exploring.”
Space Tech That Feeds High-End Diners In Toronto Could Help Canada's North
Lush, leafy greens could be locally grown with innovative vertical farming system
James Dunne · CBC News · Dec 25, 2018
A look inside We the Roots vertical farm in Toronto. Wired with LED lights, the hydroponic facility can grow up to 20,000 leafy green plants at a time. (Yan Jun Li/CBC)494 comments
Technology being used to stock high-end Toronto restaurants with designer leafy greens could provide Northern Canadians with locally grown produce.
That's the view of academic experts and entrepreneurs involved with a high-tech vertical garden housed in an east-end Toronto warehouse.
"We're going to grow food using light recipes to make economic food, to make food cost-effective" says Amin Jadavji, "and I think that's the North story".
Jadavji is CEO of We the Roots, a company he co-founded in 2017 with six others, including celebrity chef Guy Rubino.
Recently, the federal government increased funding for shipping food to Northern Canada and expanded the Nutrition North program. That move comes as advances in hydroponics and LED lighting coming from research to grow food in space are expanding the prospects for northern farming.
Amin Jadavji, CEO of We the Roots, says vertical farms can produce cost-effective food, including in Canada's North. (James Dunne/CBC)
The vertical farm of We the Roots is a commercial test of the new tech. The most traditional farm-like thing about it is the pickup truck parked outside.
The structure inside a former factory is roughly 14 metres long by three metres wide and four metres tall. It houses from 15,000 to 20,000 plants at a time. "We're growing wild Italian arugula, mizuna, which is a Japanese mustard green, Tuscan kale, basil," Jadavji says, "and a little bit of cilantro."
See how hydroponic technology grows vegetables:
The operation is hydroponic and almost entirely automated. Water in the system carries nutrients and is recycled.
Plants are nested in trays and stacked seven layers high, each one under strips of LED bulbs. The bulbs provide a tailored light combination (cool white, green, deep red, ultraviolet, far red), created to bring out specific qualities in the plants, changing their size, texture and even taste.
Then there's the nutrition factor. "We can increase things like calcium and phosphorus and various vitamins by as much as 50 per cent just by changing light recipes," says Jadavji.
Young plants nestle inside the We the Roots vertical farm. The system features custom LED lighting from a company called Intravision. ( Yan Jun Li/CBC)
The system at We the Roots is the first commercial use of a concept developed by the University of Guelph in collaboration with a Norwegian company called Intravision, says Jadavji.
The university's Space and Advanced Life Support Agriculture program, which focuses on trying to grow plants in hostile environments like space, began using Intravision's LED lights in research. That developed into a stacked system that both light and water flow through.
Though this technology was created to help feed astronauts of the future, the first customers are already enjoying lunch and dinner at five upscale Toronto restaurants, including Parcheggio.
In the hierarchy everything clicks into place with this product, which is awesome.— Andrew Piccinin, Parcheggio executive chef
Parcheggio's executive chef Andrew Piccinin dropped romaine lettuce from his salad menu after California's E. coli problem. With greens from We the Roots, he doesn't worry about E. coli because hydroponics aren't vulnerable to the same contamination.
Besides safety, he loves that the greens are flavourful, local, and environmentally friendly. "In the hierarchy everything clicks into place with this product, which is awesome."
Chef Andrew Piccinin of Parcheggio displays his 'Nonna's Salad,' an old family recipe made with arugula grown in a new high-tech vertical farm. (James Dunne/CBC)
Vertical farming is part of a recent explosion in urban agriculture, a broad agriculture practice that dates back to ancient Egypt.
According to the United Nations, urban agriculture doubled from the early 1990s to 2005. Now, the UN Food and Agriculture Organization says 800 million people in cities are growing fruits and veggies or raising animals, accounting for 15 to 20 per cent of the world's food.
Vertical farming operations are a leading part of the trend.
Analysts suggest the vertical farm market will shoot up to $13 billion US a year by 2024, from just under 1.8 billion US in 2017.
Though vertical farming has seen some high-profile failures in Vancouver and Chicago, entrepreneurs and investors see fresh opportunity.
Aerofarms' massive vertical farm in New Jersey is not hydroponic, but aeroponic. It uses less water by spraying plants with mist instead of soaking the roots. (Aerofarms)
CBC News reported on a massive investment in the sector in 2016. Inside Aerofarms' large 6,500-square-metre facility in New Jersey aeroponics are used, spraying plants with mist instead of submerging them in water. The farm has the capacity to produce two million pounds of food a year.
In Canada, McCain Foods invested in a Nova Scotia vertical farm company called TruLeaf in the spring of 2018.
We the Roots plans to expand its Toronto operations next year. Jadavji is also opening two new farms, one about 135 kilometres from Toronto and one in New Jersey, each of them 1,850 square-metre facilities to produce 1.3 million pounds of greens per year.
Going big isn't the only way to get into vertical farming though.
Tiny turnkey vertical farms built inside shipping containers can be seen in cities such as Victoria, Calgary and Dartmouth, N.S.
Plants are densely packed into vertical towers inside the Very Local Greens container farm on the waterfront in Dartmouth, N.S. (Emma Smith/CBC)
Container operators can grow from 3,000 to 5,000 plants and sell at farmers' markets and to restaurants and caterers. Prices for container farms range from just over $50,000 to more than $200,000.
American container farm makers have clever names like Freight Farms and Crop Box, and Canadians are doing the same with brands such as Growcer and Modular Farms, which sells new custom containers.
While many vertical farms are in large cities, Ottawa-based Growcer has six of its high-tech containers in Alaska and three in Northern Canada, with systems in Kugluktuk, Nunavut, Kuujjuaq, Que., and Churchill, Man. Another system is going to Manitoba and one to Yellowknife as well.
Growcer's vertical farm in Churchill, Man., is made from a repurposed shipping container. The operator supplies stores, restaurants and individual or families with a weekly subscription. (Carley Basler)
Its units are insulated to function in temperatures as cold as –52 C. Growcer CEO Corey Ellis says the company began in 2015 deeply concerned about improving the supply of fresh food in the North.
It was the high food prices in the North that also gave the company a buffer period to improve its technology. The company was able to win Northern customers as it was working to lower operating costs.
"It was a great testing ground because you know with a $7 head of lettuce that's on the shelf before we show up," says Ellis, "we knew that if we could even do a $3 head we would be doing well." Ellis says Growcer's systems have advanced so much some units can match wholesale prices of greens from California.
It galls me, quite frankly, to think this Canadian technology will find its first expression in a large scale pilot in the deserts of Kuwait.— Mike Dixon, University of Guelph
Experts believe it's time to try large scale vertical gardens in the North.
University of Guelph professor Mike Dixon is frustrated technology from the school's space agriculture program isn't being used to help address Northern food security.
University of Guelph Prof. Mike Dixon believes large vertical gardens can help provide food security in Canada's North. But he says, 'It galls me, quite frankly, to think this Canadian technology will find its first expression in a large-scale pilot in the deserts of Kuwait.' (Joe Fiorino/CBC)
We The Roots wants to try the system Dixon helped create in the North, but it will be tested in extreme heat before severe cold. Why? Because Kuwait is willing to invest in it.
"It galls me, quite frankly," says Dixon, "to think this Canadian technology will find its first expression in a large-scale pilot in the deserts of Kuwait."
ABOUT THE AUTHOR
James Dunne
Producer, CBC News Business
James Dunne researches, produces and writes stories for the business unit at CBC News. He has a decade of experience in business programming including on the shows Venture and Fortune Hunters. An award winning video journalist, he's also worked on special projects and as the late lineup editor for the World at Six on CBC Radio 1.
Saskatoon Company Develops ‘Space-Age Farming’ Tech To Grow Crops Indoors
WATCH ABOVE: Farm Boys Design Corp. creates customizable indoor ecosystems to produce fresh crops using automation.
December 20, 2018
By Rebekah Lesko Reporter Global News
Kale, radishes, chives and basil are among the leafy greens and herbs growing in a shipping container in a parking lot at Innovation Place in Saskatoon.
It’s the first prototype unit that Farm Boys Design Corp. has been using for testing purposes in the past year.
“It initially started as a basic idea of having affordable food in areas where it’s hard to get fresh produce,” Farm Boys CEO Chad Fischl said.
The AeroPod prototype has been used for testing purposes for the last year.
Devin Sauer / Global News
The unit runs on automation, with the light, air and water controlled.
“This environment is optimized to grow plants,” explained Lena Syrovy, the research and development agronomist with Farm Boys.
“The roots, actually most of the time, are exposed to air. The plants are in this Rockwool medium and the roots grow out of the Rockwool into the middle of these columns and then, based on a set schedule, the water and nutrient solution is pumped to the top of the columns and then it trickles over the roots.”
Fischl said the aeroponic system Farm Boys created uses up to 98 per cent less water than growing crops outdoors.
Leafy greens, microgreens and herbs are growing in the AeroPod prototype.
Devin Sauer / Global News
RELATED
Next year, Farm Boys plans to work with communities in the Middle East and northern Canada, according to Fischl.
“We’re just trying to make fresh produce that traditionally comes from areas like California and places like Central America, more readily available to areas like the north, so you can get highly nutritious, nutrient dense food in areas of the north that doesn’t have to get transported,” Fischl said.
The company has been in talks with the country of Qatar to start a pilot facility there in early 2019.
READ MORE: Soil-free gardens at Grant MacEwan growing fast (2015)
Fischl said there is also a big opportunity for the units to be used by licensed producers in the cannabis industry.
“With the new micro cultivation rules, where you can grow in a smaller setting, a smaller foot print,” Fischl said. “Something like this has great application for that.”
Herbs, such as chives, can be grown with the Farm Boys automation technology.
Devin Sauer / Global News
“The idea of space-age farming is what we’re after,” Fischl said.
“It’s about automation and it’s about growing in an effective way that can be reproduced on a massive scale.”
© 2018 Global News, a division of Corus Entertainment Inc.
Ikea Sweden To Start Growing Lettuce
Ikea Sweden will grow its own lettuce next year at two of its locations. In cooperation with waste processing company Bonbio, Ikea will begin cultivating in containers in Malmö and Helsingborg in the course of 2019. Part of the plant food will come from organic waste. The goal is for the lettuce to be served in Ikea restaurants.
"More than 25 percent of carbon dioxide emissions come from food. This project is in line with Ikea's ambition to find innovative and sustainable solutions to environmental problems," says Jonas Carlehed, Sustainability Manager at Ikea. Ikea Sweden already supplies organic waste to various recycling companies, including a biogas plant in Helsingborg from OX2 Bio, a sister company of Bonbios.
"Because we can regulate light, temperature, supply of water and food, we are unaffected by weather influences and we can guarantee a large quantity of fresh locally grown vegetables all year round," says Fredrik Olrog, director of Bonbio. Ultimately, the Ingka group, the largest franchisee of the Ikea brand, hopes to become self-sufficient in terms of lettuce and other leafy vegetables. "This way we avoid transport costs and we don't need soil or crop protection. The required electricity comes from our own wind power plants," says Catarina Englund, innovation manager at the Ingka group.
Bonbio will use a cultivation container of 30 m2 for this project, but will create a total cultivation area of 80 m2. They achieve this by growing vertically on four floors. Each floor has 45 gutters and there is room for 20 cultivation bins in each gutter. It's grown hydroponically, using only 10 percent of the amount of water needed for traditional cultivation. The climate parameters, such as light and carbon dioxide, are controlled by sensors. After five to six weeks, they expect about 18 kg of lettuce to be harvested per container.
Source: www.mynewsdesk.com
Publication date : 12/19/2018
This Year Our Farms Went Where No Farm Have Gone Before!
We went oversees to Vietnam, cross-country to Alaska, and even underground in the Caribbean! We also launched a brand new managed farming service, set a record for fastest sale (18 hours!), and performed a container farming first by transporting a growing farm to NYC for the Future of Everything Festival
Freight Farms
We went oversees to Vietnam, cross-country to Alaska, and even underground in the Caribbean! We also launched a brand new managed farming service, set a record for fastest sale (18 hours!), and performed a container farming first by transporting a growing farm to NYC for the Future of Everything Festival.
We hosted five open houses, gave 150+ private farm tours, and trained 80+ new farmers…good thing we also added seven new employees to the team to help out!
Some of our notable new customers included: Ford Motors and Cass Community, NBA player Ekpe Udoh and his non-profit, SEFCU, AppHarvest, and IDEA schools… it was amazing to see how these organizations are adding a modern twist to what it means to farm.
Keep reading for ALL the stats
A Greenhouse In The Eternal Ice: Vegetable Gardening In The Antarctic
Paul Zabel from the German Aerospace Center is operating a greenhouse in the Antarctic, where tomatoes, lettuce and cucumbers flourish. For future space missions, plant cultivation is to be tested under difficult conditions.
Photo: DLR
In the past few months, Paul Zabel had to cope with bad weather conditions. For a whole polar winter, he was responsible for the research greenhouse of the German Aerospace Center. This is located in a large container, 300 meters from the German Neumeyer Station.
"We had the lowest temperature in August, with minus 43.4oC. There were a few days where there were stronger storms, and I did not go out because that was just too dangerous. "
Through a satellite connection, the situation in the greenhouse, 13,500 kilometers away from Europe, is monitored continuously.
Photo: DLR
"We can not touch any of the plants, but we can say for example: The container should be two degrees warmer. Let's make an adjustment and then the container would be up two degrees. We can control the lighting and we can also give a different mix of nutrients to the plants. We can control everything from here."
The complete remote control of vegetable cultivation in a hermetically sealed container is a prerequisite for its application to future interplanetary space missions.
"The scenarios demand that the greenhouse system could fly to Mars in advance, unpacking there automatically and making sure that plants would grow automatically there. When the first humans arrive on Mars, they would find an almost fully functioning greenhouse. That's the theory."
Source: Deutschlandfunk Kultur
Barbados: Government To Start Veggie Project ‘Early Next Year’
December 19, 2018
Article by Barbados Today
A high-tech farming project is set to kick-off early next year that could slash demand for imported vegetables by over 80 per cent.
The Government project to be set up in the new year, comes as a private firm owned by young farmers uses technology in an agricultural project that is intend to eventually feed the entire country while withstanding the threat of natural disasters, said Agriculture Minister Indar Weir.
Operating out of a 40-foot shipping container at Hastings, Christ Church, the directors of Ino Grow have developed a hydroponic farm, which currently produces lettuce, herbs and other leafy greens.
The company is producing non-genetically modified organisms (non-GMO) and herbicide-free crops, which can be grown every day of the year.
After a tour of the small facility, an excited minister for food security revealed the project had won the support of Government. Weir has invited Ino Gro directors Warren Kellman and Rishi Pajwani to be part of a similar programme, to be rolled out by Government at the beginning of the New Year.
“We are going to get together and we’re going to pull all of the costing together… and take agriculture to the next level. But more importantly, we need the scale,” said Weir.
Government’s ultimate goal is to produce almost 80 to 90 per cent of some of the vegetables currently being imported, Weir declared.
Minister Indar Weir (left) under the artificial sunlight provided by the agricultural farm, being schooled by Ino Gro co-directors Rishi Pajwani (left) and Warren Kellman (second from right) as mentor Ayub Kola looks on.
“I speak of tomatoes and lettuce of all varieties, and then we are going to look at broccoli as well, because broccoli is one of the vegetables that we import and we have to address that. If I am able to pull all of this together in short time, we then start looking at reducing our food import bill,” he said.
Amid the worldwide threat of global warming, Weir praised the new technology for responding to the growing need for “climate-smart” initiatives.
“We have to look at what climate change is doing to the Caribbean islands and indeed Barbados is vulnerable to climate change and if we’re going to get into climate smart agriculture, then this is the way we have to go,” according to the agriculture and food security minister.
“So that if we get a climate event, we don’t find ourselves without food for extended periods of time . . . . We have to be able to protect the amount of food that we are going to need to get through a climate event. We have to protect the seedlings to make sure that we have them at our disposal so that we can continue to grow,” he stressed, while indicating that the use of green energy will also be key to the development of similar initiatives.
Weir is particularly excited about the promise of climate smart agriculture for youth. “It excites the younger mind; those people who are coming out of school, who would have traditionally stayed away from agriculture, because they didn’t see it as a career option. But if we could replicate this right across Barbados, all of a sudden we are addressing a 21st century need, where we can create entrepreneurs, through having young people now graduating from university and getting involved in projects like these as businesspeople,” he said.
Ino-Gro co-director Rishi Pajwani thanked Weir for giving them a platform to show off the young farm initiatives. He also assured Barbadians that his company is up to the task of reducing the country’s “enormous” food import bill.
“We wanted to cut that down as well as educate the youth here in Barbados about agriculture – Traditional agriculture. Agriculture is no longer outside, hot sun and breaking your back. It’s now become labour efficient and easy, so we wanted to inform everyone and the youth to re-innovate the industry and get back into agriculture, because this is where Barbados was born,” said Pajwani.
But the new private sector initiative has not come without obstacles. As co-director Warren Kellman put it, the idea was so peculiar to Customs officials that they were sceptical when equipment started coming in.
“Customs had never seen something like that before. So when they saw certain pieces of equipment . . . they said they’ve never seen something like this attached to farming. We had to work closely with Customs as well, and actually create new entries in their system, so that people who are interested in this type of innovative farming, when they do bring in systems like this in the future, they wouldn’t face issues that we faced, because we tried to pave the way,” he said.
Making the process easier is the knowledge that they have the backing of Government in their quest to revolutionise Barbadian farming, Kellman said.
The Urban Farming Startup Created By Kimbal Musk — Elon’s Brother — Lets You Scan Your Produce To See Where It Came From. Take A Look Inside
Business Insider/Jessica Tyler
December 19, 2018
Square Roots farmers sell their crops to local customers.
Business Insider/Jessica Tyler
Elon Musk's brother, Kimbal, is on a mission to reduce the global food shortage and train the next generation of urban farmers.
His Brooklyn-based company, Square Roots, delivers fresh herbs that are grown inside 320-square-foot shipping containers.
In the wake of the romaine E. coli outbreak, Square Roots is determined to substitute the opaque practices of the industrial food industry.
The company now allows you to scan its crops and learn exactly when they were produced — and who made them.
While his brother, Elon, dreams up moonshot projects like colonizing Mars and building a tunnel for autonomous vehicles, Kimbal Musk's thoughts are rooted in a much more immediate crisis: the global food shortage.
Though he's on the board of both Tesla and SpaceX, he'd much prefer to talk about Square Roots, the urban farming startup that he co-founded with friend and entrepreneur Tobias Peggs.
Since 2016, Square Roots has been delivering fresh herbs to retail stores across New York City. The company also pioneered a training program that walks young entrepreneurs through every step of the indoor farming process, from planting seeds to selling crops.
Read more: Kimbal Musk predicts a movement of millennial workers fleeing desk jobs for farms
One of the advantages of indoor farms is that they can control climate conditions to reduce the risk of contamination in the water or air.
Square Roots is taking this a step further by offering customers some peace of mind about how, when, and where their food is being grown — adding in the kind of transparency that could one day prevent incidences like the recent romaine E. coli outbreak, which resulted in more than 50 reported illnesses across 19 states.
By scanning a QR code on the back of an herb, customers can learn the name of the Square Roots farmer who grew it, and exactly when the growing process started.
The new scanning system makes Square Roots an industry standout, even among the numerous vertical farms popping up across the nation.
Earlier this year, Business Insider took a tour of the Brooklyn-based indoor farming compound. Take a look.
Square Roots is headquartered in Brooklyn, but its non-GMO, pesticide-free herbs are also sold in Manhattan and Queens.
Business Insider/Jessica Tyler
The company is more than just a collection of indoor farms.
Business Insider/Jessica Tyler
"There's an incredible opportunity to re-envision the food system," said co-founder Tobias Peggs.
Business Insider/Jessica Tyler
In an interview with Business Insider, Musk said he expects a growing number of young Americans to join him in the local farming movement.
Peggs said Square Roots plans to have one of its farms in every city in America, before going global.
Business Insider/Jessica Tyler
Even on a rainy day, visitors crowded around the steel shipping-containers that house Square Roots' produce.
Business Insider/Jessica Tyler
Each shipping container has its own programmable climate, which is controlled by Square Roots farmers.
Business Insider was given a peek at the herbs being harvested inside.
Business Insider/Jessica Tyler
The company's hydroponic growing system uses 90% less water than conventional agriculture.
Business Insider/Jessica Tyler
LED lights illuminate the crops, but they don't run 24-7 like some other vertical farms.
Business Insider/Jessica Tyler
Peggs said operating the farm is intuitive, like using an iPhone.
Business Insider/Jessica Tyler
"You press a few buttons and it's magic," he said. The company's software allows farmers to monitor the growth process, adjust temperature conditions, and conserve resources in real time.
Square Roots has access to historical records that can tell it when and where the best crops were grown.
Business Insider/Jessica Tyler
If you tasted the basil in Northern Italy in 2006, the company can research and replicate the temperature conditions to give you a similar product.
Peggs said the average apple takes nine months to get through the food system.
Business Insider/Jessica Tyler
The typical storage time for lettuce is around one to four weeks, but certain produce can be stored for up to a year.
To keep an apple from rotting, distributors often coat it in wax or treat it with a pesticide-active ingredient that slows down the growing process.
Business Insider/Jessica Tyler
In those instances, Peggs said, consumers think they're making a healthy choice, when "you're actually just eating a waxy ball of sugar."
Like apples (which are not offered by Square Roots) herbs begin to lose their nutrients if they're stored for too long.
Business Insider/Jessica Tyler
The company delivers its herbs to retail stores within 24 hours of harvest, which is critical to keeping them fresh.
Business Insider/Jessica Tyler
Square Roots let us try their freshly-grown chives, which were some of the yummiest we've ever tasted.
Business Insider/Jessica Tyler
"When people try real food, they don't go back to industrial food," Musk said. "It just doesn't taste good."
The company also produces herbs like mint, oregano, thyme, and basil.
Business Insider/Jessica Tyler
The scanning system gives a detailed timeline of the crop from seed to shelf.
Business Insider/Jessica Tyler
That may sound like simple information, but food labeling laws in the United States are notoriously lax.
Business Insider/Jessica Tyler
It was only after the latest E. coli outbreak that the Food and Drug Administration finally asked producers to label romaine with a harvest date and region of origin.
All you have to do is point your iOS camera at the bar code on the back of the package.
Business Insider/Jessica Tyler
From there, you'll gain access to more than just data.
Business Insider/Jessica Tyler
The timeline offers links to learn more about the farmers and their growing techniques.
"At the heart of everything we do are the farmers," Peggs said. "You have to love the arugula to make it grow better."
More: Features BI Innovation Indoor Farm Kimbal Musk