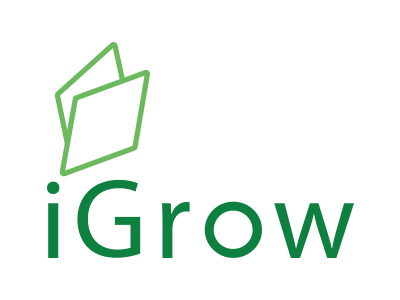
Welcome to iGrow News, Your Source for the World of Indoor Vertical Farming
Freight Farms And CEO Vanzura Set To Reinvent Container Farming
June 17, 2021
The global pressures exacerbated by COVID-19 and the rippling toll it takes on the international community has made one thing clear: preparedness is everything. The Coronavirus has exposed vulnerabilities in the global health network that no one could have imagined. Food production and distribution must now reset their agendas to prepare for catastrophe.
Freight Farms, a 2011 Agtech company that pioneered hydroponics-based container farming, is committed to preparing the world for the next disaster by reinventing the way we grow food.
“Fill in the blank with the institution, how prepared are you for the emerging trends that are impacting the world,” Freight Farms CEO Rick Vanzura explained. “Sustainability issues, land availability, water availability; those issues obviously preceded COVID-19, but we think there’s going to be a greater sense of urgency around folks expecting us to have an answer and be prepared for these global trends, as opposed to being reactive.”
Vanzura looks to channel his decade of experience as a restaurant executive, growing Wahlburgers from a single restaurant to a $100 million dollar institution, as well as greatly expanding Panera Bread, to redefine food production and distribution as a whole.
Freight Farms uses container-based “vertical farming” to do just that, allowing farmers to produce hundreds of high-quality local crops from a 320 square foot shipping container which automates the farming process for maximum efficiency.
Vanzura plans to expand and distribute these self-contained, sustainable farms to a wide diversity of industry segments. The priority will of course be the global communities that need them the most. “We see the Freight Farm as a perfect fit for countries with food access difficulties, short growing seasons and inherently challenging climates. There’s probably no location where having a hyper-local, highly traceable, always available solution isn’t going to make sense in some way,” he added.
In the name of access to high-quality food, in a sustainable model built to withstand a natural disaster, Freight Farms has now distributed their automated, hydroponic farms to 48 U.S states and across the world to 32 different countries, boasting success and efficiency from the Arctic wilderness, to the desert, and to concrete jungles.
Freight Farms believes that its emphasis on access, preparedness, and sustainability will be more necessary than ever in the wake of COVID-19, as well as global trends of food insecurity and environmental uncertainty. Vanzura explained that the company has already reacted to shifting demands by supporting small-scale farmers as they set up drive-through produce stations to reach customers directly.
Freight Farms CEO Rick Vanzura
“Demand during this time for that hyper-local, fresh product has certainly ramped up,” Vanzura added. “Hopefully, once people get a taste of it, they will understand the difference, and post Covid, our containers will become an industry staple.”
Vanzura sees his role as not only expanding to agriculturally vulnerable countries abroad but also increasing access to high-quality food across institutions in the United States. He wants to specifically target universities and has partnered with foodservice provider Sodexo to ensure local food is available to as many people as possible.
Vanzura says he was forced by his children to move beyond the world of crafting a restaurant chain’s vision and use his knowledge to make the world a better place. Freight Farms, with Vanzura’s leadership, has the ability to change the way we think of farming and change the world.
Freight Farms hopes to combat international uncertainty, face the threats of climate change, and provide people with fresh produce regardless of climatic constraints and difficulties. “Healthy food is a right, not a luxury,” and Freight Farms is helping make this mission statement a reality.
Lead photo: A Freight Farms container has unprecedented environmental control and exceptional ease-of-use to unlock your growing potential.
To learn more about Freight Farms and how they are reinventing container farming, visit their website.
Total Food Service is a monthly B2B foodservice publication and website covering foodservice and hospitality news, industry trends, and exclusive interviews.
USA: MASSACHUSETTS - New Partnership Will Serve Meals For 400 Youth Per Day
Town to Table, a Boston-based container farm company, announced a partnership with the Boys & Girls Clubs of Metro South, an organization that accommodates kids in out-of-school-time hours
Town to Table, a Boston-based container farm company, announced a partnership with the Boys & Girls Clubs of Metro South, an organization that accommodates kids in out-of-school-time hoursy
Town to Table, a Boston-based container farm company, announced a partnership with the Boys & Girls Clubs of Metro South, an organization that accommodates kids in out-of-school-time hours.
"Together, we are operating two Freight Farms that will serve community members, food pantries, non-profits organizations, and the Clubs’ Kids Café Healthy Meals program which provides meals for 400 youth per day and serves more than 100,000 meals annually," said Town to Table on their LinkedIn page.
The farm will also be used as an educational resource to provide hands-on learning experiences for Club members with curricula-focused food systems, food justice, nutrition, and sustainability.
For more information:
Town to Table
https://towntotable.com
Boys & Girls Clubs of Metro South
Publication date: Fri 11 Jun 2021
CANADA: Thursday, July 8th, 2021 - 12:00 PM EST
Sit back and learn more about Growcer's beginnings, our farm's uses, and essential considerations for starting your own Growcer project. It will be an informal opportunity to ask our team questions and learn more!
Every first Thursday of the month, we'll be hosting a Meet and Eat that anyone can join; however, we're going to have it on the second Thursday in July to accommodate for the statutory holiday on Thursday, July 1st.
Register Now →
Sit back and learn more about Growcer's beginnings, our farm's uses, and essential considerations for starting your own Growcer project. It will be an informal opportunity to ask our team questions and learn more!
SIGN UP TODAY
Thursday, July 8th, 2021
12:00 PM EST
USA: WASHINGTON STATE - Ummah Sustained Agroecology Center - Long Time! We Have Been Getting Things Started Here On The West Coast. We Opened!
Ummah Sustained AgroEcology Center - U.S.A.C. features Washington States 1st Certified Jr Master Gardener, Youth Agroecology, and Discover through Hydroponic K8 Farm School programs
Ummah Sustained Agroecology Center, a unique opportunity for your K-8 child to be creative, and confident while building lasting friendships. Our youth development program nurtures a child’s instinctive curiosity through informal exploration learning experiences
Ummah Sustained AgroEcology Center - U.S.A.C. features Washington States 1st Certified Jr Master Gardener, Youth Agroecology, and Discover through Hydroponic K8 Farm School programs.
Our Certified Urban Permaculture center houses three hydroponic systems including Freight Farm, a greenhouse, raised beds, community garden, small session classroom, and Afrocentric resource library.
We offer volunteer opportunities through WSU Extension Snohomish County 4-H and AmeriCorp.
Vertical Roots Opens Third Indoor Hydroponic Container Farm
Vertical Roots, a vertical farming company which grows its leafy greens in repurposed shipping containers year-round, has opened its third indoor farm in Atlanta, Georgia, reducing produce transportation and expanding access to fresh, locally-grown leafy greens.
14-June-2021
By Mary Ellen Shoup
Vertical Roots, a vertical farming company which grows its leafy greens in repurposed shipping containers year-round, has opened its third indoor farm in Atlanta, Georgia, reducing produce transportation and expanding access to fresh, locally-grown leafy greens.
To Continue Reading, Please Click Here
Source Courtesy of Food Navigator-usa.com
CANADA: The Value of Hyper-Local Produce
At Yellowknife Co-op, produce is grown steps away from the store in a container farm!
The hyper-local food trend is more than just a fad: there’s a reason that hyper-local food is catching on in a big way. If you’re thinking about growing hyper-local food, it’s important to understand the value of the product and its market position.
At Yellowknife Co-op, produce is grown steps away from the store in a container farm!
BUT FIRST, WHAT IS HYPER-LOCAL FOOD?
Where does that ‘local’ head of lettuce you pick up from the grocery store actually come from? The Canadian Food Inspection Agency (CFIA) defines ‘local food’ as being grown in the province where it’s being sold, or within 50km of the border. But hyper-local food is even more local than being from the same province or being Canadian-grown. It is usually grown within the same town or city, or a short distance from where it’s being sold (sometimes even right behind the store!).
BENEFITS OF HYPER-LOCALLY GROWN FOOD
LOWER FOOD MILES
Hyper-local produce is usually grown within the same town or city, or a short distance from where it’s being sold.
As consumers are becoming more and more aware of the environmental impact of our food choices, the demand to lower food miles is also growing. A food mile can be thought of as the distance that food travels from the grower to the consumer. As a metric, it helps to assess the environmental impact of the foods we consume. A 2012 study showed that on average, 30% of food is imported in Canada, leading to annual emissions of 3.3 million metric tonnes of CO2.
Growing food hyper-locally can result in significantly lower food miles (and as few as zero food miles!) in both urban centres and rural communities. This reduces the carbon footprint of what you eat.
SUSTAINABLY GROWN
Growing hyper-locally in a hydroponic farming system has further benefits. Water in a closed hydroponic system is captured and reused, resulting in 90% less water use, and 95% less land than conventional farming.
TRACEABLE FOOD CHAIN
Growing hyper-local is completely traceable. This means you know exactly what’s going into your product. There are no synthetic pest control products, less risk for E.Coli, and a shorter supply chain to manage.
FRESHER PRODUCE WITH A LONGER SHELF LIFE
Growing food hyper-locally also means fresher produce and a longer shelf-life. Instead of wilting in a truck for hundreds of kilometers, hyper-local produce is shelf-ready immediately. This has a marked effect on the quality, as most produce loses 30 percent of nutrients just three days after harvest.
Life Water Gardens, a container garden project in Norway House Cree Nation, sells locally-grown produce at the Northern Store. Click here to learn more about the project and hear from its growers!
“When you get your hands on the fresh produce and taste it, you know it’s a good thing for your community in general. It’s really easy to get excited and pumped about [this project].” - Ian Maxwell from Norway House.
“When you get your hands on the fresh produce and taste it, you know it’s a good thing for your community. It’s really easy to get excited and pumped about [this project].”
— Ian Maxwell, co-manager of Life Water Gardens
WHERE IS HYPER-LOCAL PRODUCE POSITIONED IN THE MARKET?
For growers, it’s important to keep in mind that hyper-local food isn’t competing with foreign produce that you typically find in grocery stores. Between locally-grown vs imported food, the wholesale price for foreign produce is cheaper than local produce.
Keep in mind that grocery stores buy produce at wholesale prices, which means that they may buy produce from you at a certain cost, and then sell it with a 30% margin added to the price. When you walk into a grocery store and see produce being sold for $4.99, the reality is that the grocery store-bought it for $3.50 and added a mark up to the final price to help cover their costs of operations.
To find price-compatible products for market research in your area, look for products that will match your future products, such as living lettuce, other hydroponic greens, and other hyper-local, organic produce. Growcer greens belong in the hyper-local, value-added produce category.
GETTING STARTED WITH HYPER-LOCAL FOOD
Growing hyper-local food has many benefits: not only is it fresher, healthier, and better for the planet, it can also be a profitable investment for growers. When crafting your financial projections, keep in mind the value of hyper-local produce and where it sits in the market.
Interested in learning more about our hyper-local hydroponic growing systems? Find out more.
Vertical Roots Expands To Atlanta, Partners With Two Wholesalers
The company partnered with two of the leading Southeastern produce suppliers, Collins Brothers Produce BB #:128652 and Phoenix Wholesale Foodservice BB #:134241, to place the farm directly at their facilities
June 11, 2021
CHARLESTON, S.C., June 10, 2021 /PRNewswire/ — Vertical Roots, the largest hydroponic container farm in the U.S. sustainably growing fresh leafy greens year-round, opened its third indoor farm in Atlanta, Georgia this June.
The company partnered with two of the leading Southeastern produce suppliers, Collins Brothers Produce BB #:128652 and Phoenix Wholesale Foodservice BB #:134241, to place the farm directly at their facilities.
The new Atlanta farm site will eliminate the need for produce transportation to the distributor and allow Vertical Roots lettuce to be delivered to local customers the same day it’s harvested.
Located within the Atlanta State Farmers Market, this is phase one of the company’s Atlanta expansion. With farm production underway, Vertical Roots Georgia Grown™ lettuce will be available in grocery stores in July 2021.
Crisp, sweet, tender, or buttery, Vertical Roots lettuces are nutritious, pesticide-free, and come in a wide variety of flavors, colors, and textures for culinary masterpieces and everyday meals. With long lasting freshness, produce is in the hands of consumers within one to three days of being harvested and has up to a 21-day shelf life.
Vertical Roots’ mission is to revolutionize the ways communities grow, distribute, and consume food. Farming directly at distribution hubs is a part of Vertical Roots’ distinctive strategy to eliminate a massive leg of produce transportation in order to reduce emissions and provide communities with fresh, locally-grown produce.
The new Atlanta farmsite will reduce produce transportation by an estimated 300 miles per delivery and will help meet the company’s retail demand that services thousands of grocery stores across the Southeast and Mid-Atlantic, as well as restaurants, universities, and schools.
“A large part of our mission is to grow food as close to the point of consumption as possible, and this farmsite accomplishes just that,” said Andrew Hare, co-founder, and general manager of Vertical Roots. “The Collins family are esteemed produce industry leaders for three generations, and we’re ecstatic about the unique grower-supplier partnership that we’ve cultivated.”
David Collins, President of Collins Brothers & Phoenix Wholesale Foodservice, said, “At Collins Brothers and Phoenix Wholesale, we’ve had the privilege to work with dedicated farmers across the country for decades. We’re thrilled to partner with Vertical Roots as they bring an innovative way of farming to the agriculture industry. We look forward to this relationship as we share a like-minded mission in providing our customers with high quality, fresh, local produce.”
Vertical Roots’ state-of-the-art indoor farms are manufactured from upcycled shipping containers at the company’s headquarters in Charleston, SC. The farm containers made their way to Atlanta on June 8, where farmers started seeding and transplanting to produce Vertical Roots lettuce within weeks.
A small footprint with a large output, the new farm will produce half a million heads of lettuce this year. Each 320-square-foot container maximizes the growing space with 3,400 plants per harvest, and up to 17 harvests per year.
Vertical Roots farms operate with the highest globally recognized food safety standards, eliminating the need for pesticides of any kind.
An AmplifiedAg, Inc.® company, Vertical Roots operates farms with proprietary software and technology. The farms don’t rely on soil, use up to 95% less water and grow crops 25% faster, compared to traditional farming methods.
About Vertical Roots:
An AmplifiedAg, Inc. company, Vertical Roots is the country’s largest hydroponic container farm and is revolutionizing the ways communities grow, distribute and consume food. Sustainably-grown indoors and pesticide-free, Vertical Roots leafy greens are fresh, clean, nutritious, and delivered to your local grocery store within one to three days of being harvested. Vertical Roots produce is available at thousands of leading grocery stores in 12 Southeastern states, educational institutions, restaurants, and other food service organizations. Vertical Roots operates farms in Charleston, S.C., Columbia, S.C. and Atlanta, Ga.
Tagged greenhouse, lettuce, vertical farming
USA - ALABAMA: Auburn College of Agriculture Using High-Tech Shipping Containers To Grow Produce For Campus Dining
Unique ‘Vertical’ Farms part of Planned 16-Acre Transformation Garden On Campus
High-tech Horticulture
Unique ‘Vertical’ Farms part of Planned 16-Acre Transformation Garden On Campus
June 10, 2021
Josh Woods | College of Agriculture
Recycled shipping containers have gained popularity in recent years, being converted into everything from houses to small stores—but the Auburn University College of Agriculture, in partnership with Campus Dining, is using them as self-contained “vertical” farms to grow produce to serve to students.
In April, the college acquired two Freight Farms shipping containers that have been converted into technologically advanced hydroponic growing stations in which plants grow vertically indoors without soil, getting their nutrition from water and light energy from powerful LEDs.
Now, the farms are producing the first crop of lettuce.
“This is state of the art,” said Desmond Layne, head of the Department of Horticulture. “We're talking growing from seed to fork in four to six weeks, depending on whether it is lettuce, arugula or another vegetable crop that can grow in there. And we can produce 15 times as much per year as we could outside in the same exact spot.”
Associate Professor of Horticulture Daniel Wells taught a vertical farming course this spring and leads operations of the vertical farms.
Wells said the containers are outfitted with a complete climate control system, which includes air conditioning and humidity control. Because they are highly insulated, the system ensures the same climate 365 days a year.
The converted containers also have an elaborate lighting system, giving all the light the plants need from two color LEDs.
“We can do any number of colors of lights,” he said. “But it turns out for photosynthesis, plants use mostly red and blue light. What’s neat about that is you can cut out a lot of the other color spectrum, creating far less heat energy. That's very efficient. It means more of the energy used is turned into light than heat.”
The containers also allow for controlled carbon dioxide levels, which accelerates plant growth.
“Ambient CO2, what you and I are exposed to every day, is about 400 ppm [parts per million],” he said. “And that’s fine, plants can grow there. But if we boost the CO2 to 1,000 ppm, they’ll grow faster. And because we’re containing the CO2, the plants can really use it. And it’s not dangerous for humans at all.”
Wells and Director of Dining and Concessions Glenn Loughridge first initiated a partnership between the College of Agriculture and Campus Dining five years ago through the Auburn Aquaponics Project, which uses hydroponics and aquaculture technologies to provide a system in which nutrient-laden wastewater from fish production is used as a food source for plant growth. Today, fish from this effort are served in dining facilities on the Auburn campus.
The new vertical farms build on that effort.
“We're in the process of finishing a $26 million dining hall in the center of campus,” Loughridge said. “It has always been foremost in my mind that we would have the opportunity to feature produce grown here on campus in that dining hall. In our biggest location, our biggest asset, we want to bring our A-game.
“This is hyper-local, on-campus sourcing,” he added. “Can you imagine being a potential student coming to tour, seeing where these products are grown, and then going to eat there? It’s incredible. We truly believe this elevates our dining experience.”
The converted shipping containers were manufactured by Freight Farms, a Boston-based company operating in 45 states and 28 countries.
“There are a few different companies out there doing this,” Layne said. “But Freight Farms is the most sophisticated. They’re the ones who have both the best product on the market and the largest production of these containers. It’s really a best-case scenario.”
Adam Lenhard, a rising senior majoring in biological agricultural technology management, said Wells’ course has been one of the most influential courses he’s taken at Auburn.
“It has been very helpful, not just in preparation for the arrival of the freights, but also in learning all about new hydroponic technologies and growing techniques,” Lenhard said. “Post-graduation, I plan to continue to work with these types of indoor, LED hydroponic systems. My primary goal after college is to normalize urban hydroponic farming, provide large, consistent yields of fresh vegetables and provide food to those in need who do not have as much access to fresh produce.”
Transformation Garden
The vertical farms are located on the College of Agriculture’s planned 16-acre Transformation Garden on the south end of the university’s campus, near the intersection of Lem Morrison Drive and Duncan Drive. The goal of the garden is to encompass every aspect of plant-based agriculture, including everything from fruits and vegetables to ornamentals to grow crops and more.
The Transformation Garden will showcase new technology and the history of agriculture, as it envelops Auburn’s Old Rotation, a single-acre research plot created in 1896. Continuously since that year, the historic landmark has been the site for testing and advancing transformative ideas that are now commonplace—ideas like crop rotation, cover crops, and low- and no-till farming.
(Written by: Kristen Bowman)
HELP DEVELOP THE TRANSFORMATION GARDEN
To help develop the new Transformation Garden, you can give online or contact Phillip Cowart, College of Agriculture director of development, at poc0001@auburn.edu or 334-844-1198.
Auburn University is a nationally ranked land grant institution recognized for its commitment to world-class scholarship, interdisciplinary research with an elite, top-tier Carnegie R1 classification, life-changing outreach with Carnegie’s Community Engagement designation and an undergraduate education experience second to none. Auburn is home to more than 30,000 students, and its faculty and research partners collaborate to develop and deliver meaningful scholarship, science and technology-based advancements that meet pressing regional, national and global needs. Auburn’s commitment to active student engagement, professional success and public/private partnership drives a growing reputation for outreach and extension that delivers broad economic, health and societal impact.
Latest Newsroom Articles
CubicFarms Announces Closing of $25.3 Million Equity Financing
This financing allows us to fully capitalize on our accelerating sale pipeline growth and market-leading R&D program.”
CubicFarm Systems announced today the closing of its previously announced bought deal equity offering of common shares of the company. The net proceeds from the offering of approximately C$23.8 million will be used to support CubicFarms’ continued global growth, research, and development efforts to optimize machine yields, automation, and functionality, expand addressable crop varieties, and for working capital and other general corporate purposes.
Pursuant to the offering, the company issued a total of 18,740,742 common shares at a price of C$1.35 per common share for gross proceeds to the company of C$25,300,001, which includes the exercise, in full, by the underwriters of the over-allotment option granted by the company to purchase an additional 2,444,445 common shares at a price of C$1.35 per common share.
“We are thrilled by the overwhelming support by our global institutional shareholders, like Handelsbanken, and their confidence in our vision,” said Dave Dinesen, Chief Executive Officer, CubicFarms. “The strong demand for this bought deal financing allowed us to upsize and fully allocate the over-allotment option with the closing of $25.3 million. This financing allows us to fully capitalize on our accelerating sale pipeline growth and market-leading R&D program.”
CubicFarms completes previously announced debt reduction
CubicFarms also announced that further to its news release dated May 3, 2021, the company has completed its previously announced issuance to Business Development Bank of Canada of 128,205 common shares of the company at a deemed price of $1.56 per common share.
“We’re pleased to work with our long-term lending partner on reducing the debt associated with our C$2.5 million growth capital loan with more favorable terms for the Company,” said Dave Dinesen, CEO, CubicFarms. “This demonstrates continued confidence in our ongoing development and the growth of the Company.”
CubicFarms approves grant of options
The Company also announced today that its board of directors has approved the grant of 700,000 stock options to certain directors and officers of the company pursuant to the company’s stock option plan. The options have an exercise price of $1.47 per share, vest as to one-third n each of 12, 24, and 36 months from the date of grant, and have a 5-year term. The grant of the options is subject to the approval of the TSX Venture Exchange.
For more information:
CubicFarms
1-888-280-9076
info@cubicfarms.com
www.cubicfarms.com
Publication date: Fri 4 Jun 2021
It's Harvest Time! Yukon's 1st Off-Grid, No-Dirt, Hydroponics Farming Unit Produces Crops
The unit is 8 by 40 feet and can hold up to 2,800 mature plants and 1,000 seedlings
The First Harvest of Crops Comes After Only 6 Weeks of Planting The First Round of Seeds
Chris MacIntyre · CBC News · Jun 06, 2021
'It's awesome to see what you put into the project, you get out,' said Brittany Weber, the agricultural operations coordinator at the Kluane Lake Research Station. (Chris MacIntyre/CBC)
The Kluane Lake Research Station located between Haines Junction and Destruction Bay is known for its studies on climate change and the impacts it has on wildlife and the ecosystem.
Now, they're taking a look at food sustainability in the North.
It's been months of work but their off-grid hydroponic containerized farming unit is now producing leafy greens and herbs.
The first harvest of crops comes after only six weeks of planting the first round of seeds.
Brittany Weber is the agricultural operations coordinator for the research station.
And she's responsible for taking care of the crops.
'It's kind of a bit of an optical illusion when you walk in. It's super cool,' says the station's agricultural operations coordinator, Brittany Weber. (Chris MacIntyre/CBC)
"We grow plants without the use of dirt," she explained.
"Instead we use this nutrient-rich water solution. Using pumps and gravity, we wash the water over the roots of the plants and that provides them with everything they need.
Weber says because the system is containerized it is a controlled environment so pesticides and herbicides aren't used.
Inside the container
The unit is 8 by 40 feet and can hold up to 2,800 mature plants and 1,000 seedlings.
"We have six shelves going all the way from the floor to the ceiling," said Weber during the tour of the unit.
Entering into the container is described as an optical illusion.
"The trays are actually sloped so you'll stand there and see the next tray in the back row and it'll be a foot off of the first tray but really that's the gravity so the water can flow naturally down these trays," Weber said.
The plants are arranged in a "cascading of age".
The front of the container holds the big greens while the back of the unit will have the newly planted seedlings.
"You'll be able to see the different life cycles of the plants," Weber said.
A look inside of the off-grid hydroponic containerized farming unit. (Chris MacIntyre/CBC)
The entrance of the container has been made into a processing area called an Arctic entrance.
This allows the vegetables and greens to be processed in freezing temperatures, without worrying about frostbite or losing any leaves.
"We have a little bit of a processing area called an arctic entrance,"
Harvesting the crops
Approximately 350 plants will be harvested next week.
Produce include kale, lettuce, spinach, Swiss chard, basil, cilantro, and dill.
Henry Penn, manager of the research station and the project lead, says the next step is to get the produce out into the community.
"The plan for the first number of harvests, they will be gathered up into a few small sample bags," Penn said.
"We'll be bringing them to locations around the Kluane region and offering them up to anyone that would like one free of charge."
'People are more than welcome to come by the Kluane Lake Research Station and have a tour, see the facility and learn all about the project,' said manager Henry Penn. (Chris MacIntyre/CBC)
The goal behind this is to let people try the product, understand how it is grown, and to provide feedback on what sort of produce is needed and wanted in the community.
Penn says now that the project is up and running, the public is invited to visit the station and see how everything works in person.
"People are more than welcome to come by the Kluane Lake Research Station and have a tour, see the facility and learn all about the project," Penn said.
Shipping Container Farm by CropBox
Lead photo: Yukon's first off-grid hydroponic containerized farming unit. This unit can hold up to 2,800 mature plants. (Chris MacIntyre/CBC)
CBC's Journalistic Standards and Practices|About CBC News
Report Typo or Error
VIDEO: World Food Prices Rise At Fastest Pace In A Decade As Inflation Concerns Continue In U.S.
What's driving the increase? Drought in key growing regions including the western U,S. and Brazil, slowing vegetable oil production in Southeast Asia along with increasing costs for livestock producers and soaring Chinese demand
AgDay 06/04/21 - Food Prices
By AGDAY TV June 4, 2021
The United Nations issued a warning this week as world food prices are rising at their fastest pace in a decade.
The data comes from the UN's Food and Agriculture Organization (FAO)'s Food Price Index for May. The Index surged in May with prices rising at their fastest monthly pace since October of 2010. Global food prices have risen for 12 consecutive months and now sit at their highest level since September of 2011.
What's driving the increase? Drought in key growing regions including the western U,S. and Brazil, slowing vegetable oil production in Southeast Asia along with increasing costs for livestock producers and soaring Chinese demand.
Arlan Suderman of StoneX Group says inflation is also part of the equation.
"It definitely is a factor," says Suderman. "And we saw after the Beige Book report [Federal Reserve] came out this past week talking about inflation pressures, how money came into the commodity sector in the overnight trade following that report's release, and it's a hedge against inflation. However, whenever that causes the dollar to rise sharply because interest rates start to go up, then they start to pull back because the fear factor takes hold, we're not going to compete. Longer-term, though, the trend is inflation tends to be positive for the commodity sector, particularly those with a story."
Suderman says data indicates wage inflation is also having an impact. He says wage inflation is increasing at rates the U.S. hasn't seen since the 12th Federal Reserve Chair Jimmy Volcker held his position from 1979 to 1987, under U.S. presidents Jimmy Carter and Ronald Reagan.
"I still see momentum building on the flip inflation pressures right now," Suderman adds. "And a lot of people talk about it being transitory, the Fed talks a lot about that supply lines refilling, that's not what we're seeing in ag, this is a build up a demand that's been building up over time. And then when you look at wage inflation, the last four quarters in a row combined, the strongest wage inflation we've seen in four decades going back to the Paul Volcker era."
FAO says the world food price surge comes with a warning as it echoes similar moves in 2008 and 2011, when high costs led to food riots across some 30 nations.
USA - COLORADO: Sedalia-Based FarmBox Foods Sending Container Farms All Over The World
FarmBox Foods’ short-term goals include partnering with institutions that help provide the biggest possible impact for the most people, including food banks, schools, and hospitals
Posted by Chris Michlewicz
May 28, 2021
With increasingly unpredictable weather patterns impacting crops and a continuing global food crisis affecting millions, a Colorado company is using tech-based indoor farming to make sure no one goes without a reliable, secure source of nutrient-rich food.
FarmBox Foods, based in Sedalia, has spent the last four years developing automated farms in shipping containers to grow organic leafy greens, culinary herbs, tomatoes, and now pine tree seedlings. The company also has a first-of-its-kind gourmet mushroom farm that produces around 400 pounds of mushrooms per week.
The mission-driven company is focused on helping feed those living in food deserts while empowering local communities and providing jobs and educational opportunities. FarmBox Foods’ patented vertical hydroponic watering systems use 90% less water than traditional farms and yield the equivalent of 2 – 2.5 acres of farmland. The repurposed shipping containers that house these systems can be placed virtually anywhere in the world — from island nations to college campuses to the frozen reaches of Alaska — and produce food year-round.
The fully controlled enclosed growing environment is protected from pests and pathogens, which reduces and can eliminate entirely the need for pesticides, allowing people to harvest and eat untainted farm-fresh produce. Setting up containers in or near populated areas also reduces food waste, as the food is able to get to the table more quickly and can better retain its nutritional value.
“The real mission in this whole thing is to be able to feed the world in places that ordinarily wouldn’t be able to grow food,” said Rusty Walker, CEO of FarmBox Foods.
FarmBox Foods’ short-term goals include partnering with institutions that help provide the biggest possible impact for the most people, including food banks, schools, and hospitals.
Learn more at www.farmboxfoods.com.
Posted in Arapahoe County, Douglas County, Douglas County Business, Douglas County Front, Featured, Jefferson County, South Jeffco
Tagged agtech, climatecontrolledfarming, Colorado, coloradobusiness, containerag, containerfarms, eatorganic, farmboxfoods, farmboxfoodscolorado, farming, farmtotable, fooddeserts, foodinequality, foodinsecurity, foodsecurity, growyourownfood, indoorfarming, indoorfarms, mushroomcultivation, mushroomfarm, mushrooms, organic, sedalia, urbanfarming, verticalhydroponicfarm, verticalhydroponics
About the Author: Chris Michlewicz
USA - KENTUCKY: Elliott County High School Receives New Container Farm Through AppHarvest
The curriculum provided by AppHarvest will cover topics such as high-tech growing and an introductory course on local food systems and food resiliency
May. 29, 2021
SANDY HOOK, Ky. (WSAZ) - Some students at Elliott County High School will soon be able to help grow food -- not only for themselves but for the entire region.
The Elliott County High School container farm is the fourth addition to AppHarvest’s program in 2021 and the sixth educational container farm to date.
The container farm program was launched in 2018 and demonstrates AppHarvest’s ongoing commitment to cultivating interest in high-tech farming as it seeks to create America’s AgTech capital from inside Appalachia. Each retrofitted shipping container acts as a hands-on agricultural classroom for students, allowing them to grow and provide fresh leafy greens to their classmates and those in need in their communities.
AppHarvest has opened container farms in Eastern Kentucky at Madison Central High School in Richmond; Breathitt High School in Jackson; Shelby Valley High School in Pikeville; and Rowan County Senior High School and AppHarvest’s flagship farm at Rockcastle County High School in Morehead.
Elliott County High School’s container farm includes space to grow up to 2,760 seedlings and 2,960 mature plants, all at once in a nutrient film technique (NFT) system. NFT is a water-saving system in which plant roots are continuously fed all necessary water and nutrients by a shallow stream, also called “film.” Excess water drains to a holding tank and is then recirculated. This system of high-tech growing sets the Elliott County container apart from AppHarvest’s other educational containers, which have operated hydroponically and vertically.
“One of our goals at AppHarvest is to build an AgTech capital right here in Appalachia,” said Jonathan Webb, AppHarvest Founder, and CEO. “We want to see communities across the region use technology to bring farms to life. And in five years from now, it’ll be leaders from these very programs coming to us with ideas on how we continue to evolve and change agriculture.”
Makayla Rose, Elliott County High School agriculture teacher, will lead the newest container program.
The curriculum provided by AppHarvest will cover topics such as high-tech growing and an introductory course on local food systems and food resiliency.
“This is exciting. Some students who might not like to get in the dirt have a different way of growing vegetables,” said Garret Barker, president of Elliot County’s FFA chapter. “It’s different than my farm at home. It doesn’t depend on outside factors like the rain. It’s all controlled by an app.”
Lead Photo: Elliott County High School receives new container farm through AppHarvest (Kimberly Keagy/ WSAZ)
Brick Street Farms Expands Through Florida and East Coast
“We really wanted to bring food production to the point of consumption, so we’re focused on embedding our farms in urban areas,” says Shannon O’Malley, CEO, and co-founder of Florida-based container farming company, Brick Street Farms
"We Are As Much A
Technology Company
As We Are A Farm Operator”
“We really wanted to bring food production to the point of consumption, so we’re focused on embedding our farms in urban areas,” says Shannon O’Malley, CEO, and co-founder of Florida-based container farming company, Brick Street Farms.
The company was founded by Shannon and her husband Bradley, who combined her expertise in electrical engineering with his background in software development to design their own shipping container farms.
According to Shannon, a major differentiator of Brick Streets Farms is that the company manufactures and operates its own shipping container farms.
Brick Street Farms Hubs
Brick Street Farms has recently secured a significant investment from Lykes Brothers, which is reportedly one of the largest and longest-running private agricultural companies in the United States. During the official announcement last week, the financial investment will be used to aggressively expand Brick Street Farms hubs, which are the combination of container farms with a retail front in densely populated areas.
Click here to Zoom the photo. (Photo courtesy of Brick Street Farms)
According to Shannon, this expansion will begin in west-central Florida then expand to the east coast. From these hubs, Brick Street Farms will also introduce home delivery and will support restaurant partners located within 50-100 miles of the hubs. Already in 272 Publix supermarkets, Brick Street Farms will continue this partnership and plans to expand into additional product categories.
Building a resilient, multi-channel sales strategy
Brick Street Farms was first developed in 2015, and during its early years, the company predominantly sold its products to restaurants and directly to customers. However, the pandemic-induced shutdown in 2020 resulted in the loss of 70% of Brick Street Farms’ clients due to restaurant closures. As Shannon explains, Brick Street Farms was already selling its products in the GreenWise section at Publix supermarkets, which is reportedly the largest employee-owned supermarket chain in the US. This partnership allowed Brick Street Farms to quickly pivot following the mandated closure of restaurants.
“In the same month that Florida went into lockdown, grocery stores saw an incredible jump in demand so we were able to quickly pivot and provide our vegetables to grocery stores within a week. We are currently in 272 Publix stores and are working to expand into west-central Florida,” says Shannon. The state of Florida has since reopened and Brick Street Farms was able to bring back its previous accounts and sign new ones, according to Shannon.
Brick Street Farms also has its own gourmet market located at the farm that is open six days per week. Consumers can shop either on-site or online, with contactless delivery available. Shannon also explains that the company has adopted a unique twist to community-supported agriculture. By subscribing to a farm membership, consumers receive a discount and support the recently approved non-profit, Desert Farms Foundation.
“We established Desert Farms Foundation to help us bring container farms to food deserts within the United States. With a farm membership, 1% of the proceeds go to Desert Farms Foundation to really support community agriculture,” explains Shannon.
Thrive Containers
“Our containers are under the name Thrive Containers, which is wholly owned by Brick Street Farms. Our containers are the equivalent of 2-3 acres of traditional farmland. They use very little water, are energetically efficient, produce very little waste and use no chemicals. Since our products are wash-free, our customers get the benefits of long-lasting produce,” explains Shannon.
According to Shannon, Brick Street Farms is as much an agtech company as it is a farm operator. The company decided to establish Thrive Containers as its own entity within Brick Street Farms in order to differentiate between the food production and manufacturing aspect of the company. “When people see Brick Street Farms, we want them to think of butterhead lettuce, basil and our other vegetables,” notes Shannon.
Thrive Containers does not sell its container farms to third parties, but instead continuously improves the farm design for current and future installations. As Shannon explains, the company focuses on designing intelligent systems that can adjust to indoor and outdoor environmental conditions. Thrive containers have more than 120 sensors in and around the farm to monitor and respond to ambient temperature, humidity, carbon dioxide, vapor pressure deficit, etc.
Brick Street Farms and Thrive Containers work closely, with the engineers and designers having all undergone farmer training to ensure that the systems designed truly respond to the needs of Brick Street Farms’ growers.
Why Florida?
While warm and sunny Florida may seem ideal for outdoor agriculture, Shannon explains that soil conditions make soil-based agriculture somewhat difficult. She says that Florida soils are rather degraded and sandy, lack nutrients and lack natural bacteria, meaning farmers need to spend significant time and effort on rebuilding soils. Also, water sources are highly saline because of our position at level, near the coast, and with a low water table. Finally, the lack of winter makes it difficult to regulate pest cycles.
Lead photo: Co-founders Brad Doyle and Shannon O’Malley
For more information:
Madeline McNaughton, Head of Business Development
Brick Street Farms
madeline@brickstreetfarms.com
www.brickstreetfarms.com
Publication date: Thu 27 May 2021
Author: Rebekka Boekhout
© VerticalFarmDaily.com
USA: Vertical Field Signs Agreement To Provide Vertical Farms of Fresh Vegetables To Senior Living Homes In California
Vertical Field has developed and commercialized unique soil-based, vertical farms that operate in 20 and 40-foot containers that produce freshly harvested and pesticide-free produce
Company To Deliver Unparalleled Produce Quality Via
Freshly-Harvested On-site Vertical Farms in 8 Calson
Management Nursing Homes Across The State
News & Photos by: Vertical Field
May 26, 2021
RA'AANA, Israel, May 26, 2021 /PRNewswire/ -- Vertical Field - ("VF" or the "Company"), a global ag-tech company that develops vertical farming systems, has signed an agreement with Calson Management to supply assisted living homes with on-site vertical farming units. According to the agreement, Vertical Field will provide a demo unit to the Glen Cove senior living lodge in Vallejo, California, and after a successful pilot will expand to seven other centers.
Vertical Field has developed and commercialized unique soil-based, vertical farms that operate in 20 and 40-foot containers that produce freshly harvested and pesticide-free produce. The VF indoor farms are capable of growing a variety of fresh greens and other crops year-round with no seasonality barriers while minimizing supply chain logistics and storage, eliminating the need for transportation, and minimizing inventory losses.
Vertical Field's urban farms use 90% less water and 30 times less land than conventional farming methods. Each portable unit is made up recycled shipping containers that grow produce in controlled conditions. Advanced sensors and monitors, climate control technology, and state-of-the-art lighting create the optimum conditions for crops to grow quickly and efficiently year-round, regardless of the weather.
The Company provides vertical farming for supermarkets, restaurants and multi-site facilities in the United States, Ukraine, United Arab Emirates, Israel, Russia, and others.
"We are very excited to launch our first partnership with an assisted living center, providing senior citizens freshly harvested, high-quality produce grown right outside their residence" says Guy Elitzur, Vertical Field's CEO. "This partnership supports our values of ensuring that nutritious produce reaches the homes of all people- no matter where they live. We look forward to continuing to expand to many other assisted living centers, and to making delicious and quality food accessible to senior citizens and other marginalized communities throughout the world."
About Vertical Field: Vertical Field is an ag-tech company that develops innovative and proprietary vertical growing systems for the urban environment. Our urban farms make efficient use of city space by growing crops vertically and on-site, bringing healthy, fresh, and local produce all the way to the consumer.
About Calson Management:
Calson Management provides a full suite of services and solutions for every aspect of a Senior Living project, and is committed to excellence in providing personal services in a warm, loving, and supportive environment. The Reyes family (partners and managers) have been involved in Senior Living for more than 30 years, and is dedicated to creating unique, specialized communities for seniors throughout California. Our family and our team members work to provide safe, engaging, and comfortable communities.
"Enhancing the health and wellbeing of our seniors is a priority at Calson Management, which is why partnering with Vertical Field to supply senior living homes with fresh, nutritious, and on-site produce was a natural decision. By bringing the farm all the way to our residents, seniors can see where the food grows and enjoy high-quality produce, furthering a living home's ability to create a happy, safe, and comfortable community." – Jason Reyes, Principal, Calson Management
For further information https://www.verticalfield.com
News & Photo Source: Vertical Field
USA - FLORIDA: St. Pete’s Brick Street Farms Gets Multi-Million-Dollar Investment From Lykes Bros
Lykes Bros., one of the oldest and largest agribusinesses in Florida, is putting a big bet on the future of farming as it invests in Brick Street Farms, an urban farm, and market in St. Petersburg
May 20, 2021
Photo credit: Brick Street Farms
Lykes Bros., one of the oldest and largest agribusinesses in Florida, is putting a big bet on the future of farming as it invests in Brick Street Farms, an urban farm and market in St. Petersburg.
Lykes is making a “significant” investment in Brick Street Farms, the two companies announced at a news conference Thursday. The amount of investment was not disclosed, but a news release described it as “multi-million dollar” investment. Lykes will take a 20 percent ownership stake in Brick Street Farms because of the deal, Mallory Dimmitt, vice president of strategic partnerships at Lykes, told the St. Pete Catalyst.
Brick Street Farms will use the investment to accelerate the expansion of Brick Street Farms hubs, an all-inclusive onsite farming and retail shopping experience in urban cores, said Shannon O’Malley, founder and CEO. The company has self-contained, environmentally sustainable THRIVE containers that will be placed in each hub. Each hub will grow between 16 to 20 acres of farmland on one-third acre lots.
Mallory Dimmitt, vice president at Lykes Bros., announces investment in Brick Street Farms while Nikki Fried, Florida Ag Commissioner, looks on.
The first new hub will open in St. Petersburg’s Warehouse Arts District in late 2021, with an expansion to Tampa in early 2022 followed by more hubs on the east coast, O’Malley said.
“We are the future of farming, and our new investors have the perfect expertise to help us take our successful business model in sustainable farming to feed more people healthy food,” O’Malley said.
The two companies first connected in November at the Florida-Israel Agriculture Innovation Summit, hosted by the Florida Department of Agriculture and Consumer Services, said Nikki Fried, Florida Department of Agriculture Commissioner.
The collaboration meets several goals, including feeding people in urban locations, fighting urban food deserts and food insecurity, bringing farm-to-fork produce closer to people and bringing cutting edge agriculture technology to everyone.
From left, Tampa Mayor Jane Castor, St. Petersburg Mayor Rick Kriseman and Shannon O’Malley, founder and CEO, Brick Street Farms
Brick Street Farms is a hub of innovation and creativity and is the only female-founded and led company in the vertical farming industry, said St. Petersburg Mayor Rick Kriseman. He also highlighted the work of the company’s non-profit Desert Farms Foundation.
“Not only is Brick Street Farms working to make us healthier by providing us some of the best and freshest food around, but through its 501c3, Brick Street Farms is working to end food deserts through the Tampa Bay area,” Kriseman said.
Every urban environment struggles with food deserts, said Tampa Mayor Jane Castor.
“The problems that occur from those food deserts are often times for many communities insurmountable. This is a solution to so many problems,” Castor said.
She also praised the company’s business model. It is financially successful by providing produce to a number of restaurants, Castor said.
While an urban focus might seem like an unusual fit for company like Lykes, which owns hundreds of thousands of rural acres throughout the state, “We know from our experience that innovation is what moves the agriculture industry forward,” said Dimmitt, who will join the Brick Street Farms board of directors.
“In addition to innovations in sustainable production and the technology it uses, the job opportunities and related job training and skills are key to Florida’s future and to our health and wellness,” Dimmitt said. “What could be better medicine than high-quality nutrient-dense greens grown close to the consumer where they have direct access, all while creating community.”
Brick Street Farms, at 2233 3rd Ave. S. was founded in 2016 by O’Malley and her husband, Brad Doyle. Read more about O’Malley in St. Pete Catalyst‘s Hustle profile.
Indoor Vertical Farming Grows Up
Bryan Walsh, author of Future
Indoor vertical farming, where crops are raised in automated stacks, often in or near cities, offers a way to sustainably meet the growing demand for food — if its energy demand can be reduced.
Why it matters: With the global population still rising — albeit more slowly — and more people moving to urban areas, the world needs ways to produce more food without clearing land for conventional farms.
Driving the news: New York-based vertical farming startup Bowery Farming on Tuesday announced a new $300 million funding round — the largest in the industry's history — that values the company at $2.3 billion.
The deal accelerates the momentum in venture capital funding for vertical farming companies, which hit nearly $1.9 billion globally in 2020, almost tripling investment from the year before.
"We're going to need 50–70% more food over the next 30 years, according to the UN," says Irving Fain, the CEO, and founder of Bowery Farming, which has two commercial vertical farms in New Jersey and Maryland and sells its leafy greens to 850 grocery stores. "Indoor farming is not the only answer to that challenge, but it's part of the solution."
How it works: Food has been grown indoors in greenhouses for decades, and it's industrialized to the point that the Netherlands has become the second-largest vegetable exporter in the world chiefly through greenhouses.
Vertical farming takes greenhouses to the next level —literally — with crops grown in tower-like walls of plant-holding cells that require no soil. Like an apartment tower versus a suburban tract, that means more food can be grown on a smaller footprint, which is ideal for cities.
Water and nutrients are delivered to crops either aeroponically — via the air through misting — or hydroponically, in which the plants are grown in nutrient-rich water. "You get high density and high output, while using 90% less water" than conventional farming, says Micki Seibel, VP of product at the vertical farming startup Unfold.
Growing light is delivered via LED lamps. While more expensive than sunlight — which currently remains free — the LED lamps aren't weather-dependent, and like water, nutrients and temperature in the vertical farms, the light can be controlled precisely, vastly enhancing yield and reducing grow times.
Because vertical farming uses so little space, "we can move the farm to the people rather than the food," says James Woolard, chief marketing officer at Freight Farms, which develops mobile hydroponic freight containers modified for indoor farming.
By the numbers: There are more than 2,000 vertical farms in the U.S. Most are run by small growers with a few bigger players, including Bowery Farming, Newark-based AeroFarms, and Wyoming-based Plenty.
Internationally, says Seibel, "Japan has looked at vertical farming as a way to increase food security and reclaim production lost during the tsunami, while Singapore — which imports 90% of its food — is making significant investments in the sector to increase its own food security."
A recent report pegs the size of the vertical farming market at $240 million in 2019 and projects it will grow to over $1 billion by 2027.
The catch: Even with that growth, vertical farming will likely still remain a niche player — the output of U.S. farms alone was worth $136 billion in 2019.
In part because of the price of supplying artificial light, vertical farms have struggled to break even in the past, and they chiefly produce comparatively priced leafy greens rather than the commodity crops that make up the backbone of the food system.
What's next: Second-generation vertical farms are taking advantage of efficiency advances in LED technology, as well as automation and sensors that can reduce labor and setup costs and enhance yield.
The ability of vertical farms to maintain the ideal environment for high-quality crops like tomatoes or lettuce anywhere in the world at any time of the year is turning agriculture into a high-tech industry.
"All the externalities that have been uncontrollable [in farming] historically are now very much controllable," says Bowery's Fain.
What to watch: The development of AeroFarms's 136,000-square-foot Model 5 facility in Virginia, which is set to be the largest and most technologically advanced vertical aeroponic farm when it is scheduled to be completed in mid-2022.
The bottom line: Agriculture made cities possible. Now vertical farming holds out the possibility that cities could become farms themselves
Lead Illustration: Shoshana Gordon/Axios
Purpose At Work: How Square Roots Is Growing A Sustainable Food Movement
How can we reduce the climate impacts of our food system? How can we get the freshest produce to people in urban areas? How can we offer fulfilling jobs to today’s youth? These are all issues that Square Roots is working to address
May 24, 2021
Purpose At Work: How Square Roots Is Growing A Sustainable Food Movement
PHOTO PROVIDED BY SQUARE ROOTS
How can we reduce the climate impacts of our food system? How can we get the freshest produce to people in urban areas? How can we offer fulfilling jobs to today’s youth? These are all issues that Square Roots is working to address.
“The mission of the company is to bring locally grown food to people in cities, all across the world while empowering the next generation of leaders in urban agriculture,” Tobias Peggs, Co-founder, and CEO of Square Roots, tells We First.
The agriculture startup’s modular and technology-first design is transforming how food is grown and distributed in amazing ways. The scalability and data-driven approach make Square Roots an excellent example of a company demonstrating how to scale business growth and impact.
Founding story
Before Square Roots, Tobias received a Ph.D. in machine learning and had worked for a number of successful startups, one of which was acquired by Walmart. “I worked as a data scientist there for a year. One of the projects they had me do was study global grocery buying behaviors.” With around 300 million customers, Tobias had a massive amount of data to pull insights from.
“That's a lot of bananas flying all over the world,” he says. “You begin to think about the impact of transportation on the planet. “As food is traveling, nutrients are breaking down and maybe the quality of food isn't as good at the end of long supply chains as it would be for local food. Customers don't have any idea of where that food comes from. The sense of community around food was just lost.”
MORE FOR YOU
Vertical Indoor Farms Make Sense
The insights Peggs was having lit a spark in his entrepreneurial engine. “People want food from all over the world. That's not going to change,” he says. “Instead of shipping food, how about we ship environmental data from one part of the world to the other?” By collecting data on the best growing conditions, Tobias could hypothetically grow anything at any time of year in a controlled indoor environment made from repurposed shipping containers and deliver that to a nearby retail store on the day it’s picked. “It looks and smells amazing, which also means all the nutrients are intact,” he says. “That was the idea behind Square Roots.”
Peggs cofounded the company with Kimbal Musk, “He would say, ‘Can it feed the world? And are we going to make a massive positive impact? If so, let's figure out how to get this done,’” Peggs recalls. The two innovators began by working together in a WeWork office. “With the experience of being involved in a number of startup companies before—some successful, some failure—I know for sure that if you don't get started, you're going to fail.”
In the two-man brainstorming sessions, Peggs and Musk would visualize the business at scale. “We saw these modular farms in every city across the world. That is the way that we're able to think about feeding every consumer on the planet with locally-grown food,” Peggs says. “There was a missing piece of the puzzle. There wouldn't be enough farmers to hire to staff all of those farms.” That realization was the foundation of the second pillar of Square Roots’ purpose, “To provide pathways for young people to come into the farming industry and become the future leaders,” he shares.
Leading with purpose
Purpose At Work: How Square Roots Is Growing A Sustainable Food Movement
PHOTO PROVIDED BY SQUARE ROOTS
Square Roots’ core business was structured to address some of the world’s biggest challenges. Food is interconnected with climate, which also poses risks on outdoor crops. It is also fundamental to public health and prosperity. As the global population rises, our planet’s carrying capacity will be tested. We need to innovate to meet that rising global demand for food.
The model relies on able-bodied young people to tend to the crops. The talent pool of skilled farmers in the U.S. is aging. The average farmer is 58 years old. “Who the hell is going to grow all the food when our current farmers retire in five or 10 years’ time? ” Tobias proposes. “We had to figure out a way to bring young people into the industry and train them quickly so they could be not just productive farmers, but feel infused about a career in a completely new industry.”
To overcome the hurdle, the founders developed hardware, software and teaching methods. “We had an investment banker who was bored sitting behind a spreadsheet all day. He quit his job to join Square Roots because he wanted to make an impact on the world. He was growing the most delicious kale, you've ever tasted in your life,” Peggs says. “That was six months after making the transition, it was magic to see that.” Within a year they trained 10 people, many with no previous farming experience.
In addition to creating purpose-driven employment opportunities, Square Roots is addressing climate through transportation and waste. “Forty percent of food from industrial systems is wasted. We waste around 3%,” Tobias says. A significant portion of wasted food is discarded before it even hits the shelf, due to damages during shipping or spoiling quickly. “Because we're indoor, there's a lot of precision, a lot of control. We can grow food for demand.”
Modular design
Square Roots’ structure allows it to be replicated and optimized from a systems approach. It's a distributed model. “We deploy clusters of these modular farms together so there's some operational scale and the business economics work,” Peggs explains. “Each farm serves its local market and runs its own independent business entity, set on top of a standard technology platform.” Every compound grows, harvests packages and delivers produce to local retailers. “We look after everything from seed to shelf.”
The growing startup has set up operations in Brooklyn, New York, and Grand Rapids, Michigan with plans for expansion across the Midwest, the North East in cities around the world where demand is large enough. People can see inside the shipping containers and when Covid-19 is under control, you can schedule a farm tour. “While its a very scalable platform, the consumer experience is a hyper-local one.”
Leveraging data & technology
When it comes to deciding what to grow, Square Roots focuses on crops that require the least amount of energy. “Walk into a supermarket. Lineup every single fruit and vegetable from the lightest to the heaviest. And that's essentially our product roadmap for the next 20 years,” Peggs says.
They also choose crops based on economic yields based on competitive market prices. “This is where data science and technology marry,” Tobias says. “Outdoor farmers can’t suddenly look at the sun, make it twice as efficient and reduce costs or double their yield. Indoor farmers can.”
Integration of AI machine learning empowers Square Roots to optimize at scale. “We're building a network of cloud-connected modular farms,” Tobias says. The company monitors and collects data from each of those farms every second. “We’re looking at temperature, humidity, nutrients, yield, taste and texture,” Peggs says. “ If in one particular box, a farmer did something or we changed an environmental parameter that increased yield or improves efficiency, we can spot that information from the data and push that new instruction out across the whole network. The whole network is learning how to farm better as we go about building the business.”
Building community
Food has the potential to unite people. While Square Roots farms are indoors, they connect and share knowledge with outdoor farmers. “ I'll give you an example,” Tobias says. “A good technique in organic farming is known as integrated pest management, where a farmer might release beneficial insects onto the crop, essentially ridding the nasty insects that we don't want. We use that technique inside the farm.”
“The farmers that we work with are very much on the same mission, which is how do we get people more connected with where their food comes from? How do we build that sense of community around food? And I think the common enemy is the industrial food system,” Peggs says. That common enemy also resonates with employees, consumers and other key stakeholders who join together around a set of core values.
“I know pretty much every founder or CEO of every indoor farming company. There's remarkable alignment around that mission,” Tobias says. “Everybody understands that we've got to change the food system and if we're helping each other out, it's better for all of us,” Tobias mentions companies like Gotham Greens and Oishii that are also innovating in the indoor farming space.
Purpose also informs Square Roots’ investor strategy. “We’re a venture-backed company. When we're talking with investors, we want to make sure that they're mission aligned. I can’t tell you how many investors have talked to me about considering cannabis. It’s not aligned with our mission.” A lot of people don't realize that the power of purpose is just as compelling in terms of what you don't do, as opposed to what you do.
The takeaway here is that building your community around shared purpose fosters goodwill amongst team members and customers. It also presents collaborative opportunities with other brands and organizations working towards the same goal.
Challenges and opportunities
With the opaque information in the industrial food system and increased health consciousness, consumers are looking for transparency. In addition to its open invitation to check out the farms, the company includes a QR code on each product. You can scan the code and learn all about where it's made and the value chain.
Purpose At Work: How Square Roots Is Growing A Sustainable Food Movement
PHOTO PROVIDED BY SQUARE ROOTS
Covid-19 has also presented challenges for businesses across sectors and Square Roots is no exception. Before the pandemic, they trained new hires to be farmers in classrooms. “If we didn't have our mission, it would have been easy to say, ‘We got to keep growing, forget this farmer training stuff. We're just going to go hire experienced people.’ Or we could have developed a robot to do part of the job of a farmer,” Tobias says.
“The mission allowed us to focus on solving issues with our current business model,” he continues. “It was already misaligned. Everyone was able to get behind it very quickly. And we were actually able to solve problems and put in place new programs and new policies ridiculously quickly. Never waste a good crisis.”
Despite adversity, the startup has started true to its mission and transitioned to digital and socially distanced training, and built a more robust system than before.
The future of food
Technology and data are a critical aspect of emerging agriculture trends. “Food is a $12 trillion industry,” Peggs states. “There's about 20 companies that have raised a bunch of money and are doing this stuff in America.”
“Indoor farming actually reminds me of the internet in the early '90s,” he says. “We know this thing is inevitable, but no one can quite yet tell you what shape it's going to take in the future. Indoor farming is like that. We're all helping each other figure out how this eventually feeds every consumer in the world.”
While innovation is budding, “The food system has to become a lot more responsible and sustainable,” Peggs says. “The current food system cannot feed the new future world, which has 10 billion people, 70% living in urban areas that are not near these industrial farms.”
We’ve seen changes over the last two decades with the organic food movement, which now grosses $25 to $30 billion annually, Tobias says. He thinks that Covid-19 will accelerate the shift towards healthy and sustainable food. “People were forced to stay at home and cook. You get more curious about the food that you're buying, and you observe how long it lasts in your refrigerator. You get more educated,” Tobias says. “We are in the first inning of indoor farming. We're just getting started.”
Lessons for entrepreneurs
With his experience from Square Roots and beyond, Tobias Peggs’ insights offer valuable lessons for entrepreneurs looking to Lead With We. Here are three teachings from Peggs on how to build a successful startup.
“Be prepared to be told, "No, we're not interested."
“You have to be a bit of a missionary and sign up for having a lot of stamina. Just be consistent with the drumbeat that this idea—no matter how crazy it might seem—you can do it.”
“There are going to be bumps in the road, there are going to be things that don't go quite right. If there's a shared purpose articulation of what the mission is, you move through those things and you make it happen. Purpose is a very powerful multiplier.”
Simon Mainwaring is the founder and CEO of We First, a strategic consultancy that accelerates growth and impact for purpose-driven brands by putting 'We' first. I specialize in brand strategy, culture building and impact storytelling for startups, high-growth companies, and Fortune 500 corporations. My national podcast is LeadWithWe.com on Spotify, Google and Apple. My book, We First: How brands and consumers use social media to build a better world is a New York Times, Wall Street Journal, and Amazon bestseller, and strategy+business named it the Best Business Marketing Book of the Year. I deliver keynotes, training, and workshops that help brands define, integrate and activate their purpose to drive growth and scale impact.
Visit SimonMainwaring.com for speaking and WeFirstBranding.com for consulting
Vertical Farming: Disrupting Agriculture
A New Agricultural Revolution Could Forever Change The Planet
24 May 2021
Vertical farming leverages cutting-edge technology to grow food in a new and better way.
One of its many benefits is that it can increase crop yield by 700 percent.
Vertical farming can help relieve pressure on scarce resources and boost Earth's biodiversity.
One day soon, you could eat bananas grown in downtown Manhattan.
It's a way of growing food that turns traditional agriculture on its head. With the required technologies now rapidly maturing, vertical farming is sprouting across the globe.
While there are still unresolved issues with this marriage of technology and agriculture, its promise may be irresistible. If it gets off the ground — literally — in a major way, it could solve the problem of feeding the Earth's 7.9 billion people. And that's just one of the benefits its proponents promise.
Vertical farms could take over the world | Hard Reset by Freethink www.youtube.com
Agriculture through time
When humankind began planting crops for nutrition about 12,000 years ago, the nature of our hunter-gatherer species fundamentally shifted. For the first time, it's believed, people began staying put.
With agriculture as their central mission, communities formed, with the now-familiar arrangement of residential areas surrounded by land dedicated to growing food. Even today, with modern transportation making the widespread consumption of non-local foods common, this land-allocation model largely survives: population centers surrounded by large areas for growing vegetables and fruit and raising livestock.
Credit: Genetics4Good / Wikimedia
Challenges facing traditional agriculture
As our population has grown, traditional agriculture has begun facing some big challenges:
Farmland takes up a lot of space and destroys biodiversity. Our World in Data reports that half of all habitable land is used for agriculture. As Nate Storey of Plenty, Inc., a vertical farming startup, puts it, "It is probably one of the most defining acts of humanity: We literally changed the ecosystem of the entire planet to meet our dietary needs."
The demand for farmland — both for produce and livestock — has led to a dangerous deforestation in several parts of the world. This also results in biodiversity loss and contributes to an increase in the greenhouse gases that drive climate change.
Degradation of farmland, such as through soil erosion, poses a threat to agricultural productivity.
Agriculture consumes copious amounts of water, which exacerbates water shortages. (Obviously, water shortages also reduce agricultural productivity.)
Fertilizer run-off causes substantial environmental damage, such as algal blooms and fish kills.
Pesticides can degrade the environment by affecting non-target organisms.
The effects of climate change are already making agriculture more challenging due to significant shifts in weather, changes to growing seasons, and realignment of water supplies. Our climate is continuing to change in unexpected ways, and the only predictable aspect of what lies ahead is unpredictability.
Vertical farming proponents expect that a re-think of how we grow food can ultimately solve these problems.
What is vertical farming?
Credit: Freethink Media / Plenty, Inc.
Vertical farming is a form of agriculture that grows plants indoors in floor-to-ceiling, tower-like walls of plant-holding cells. Instead of growing plants in horizontal fields on the ground, as in traditional farming, you can think of vertical farming's "fields" as standing on the edge and extending upward toward the ceiling. The plants need no soil or other aggregate medium in which to grow; their roots are typically held in a cell lining, often composed of coconut fiber.
Vertical flora is grown either aeroponically, in which water and nutrients are delivered to plants via misting, or hydroponically, in which plants are grown in nutrient-rich water. These are incredibly efficient systems, requiring 95% less irrigation than soil-grown plants. With vertical farming, Storey says that 99 percent of the moisture transpired by plants can be recaptured, condensed, and recirculated.
Plants, of course, also need light to grow, and vertical farms use increasingly efficient LED bulbs to keep plants thriving.
Vertical farms can increase crop yields by 700 percent
Credit: pressmaster / Adobe Stock
If vertical farming takes off the way its supporters believe it should and will, it may solve many of the aforementioned challenges facing agriculture.
Crop yields with vertical farming far exceed what's possible with traditional agriculture. Plenty, Inc.'s Shireen Santosham notes that the highly controlled growing environment of vertical farming has allowed her company to reduce the growing time for some crops to as little as 10 days. Without needing to consider whether or even sunlight, combined with the ability to operate 365 days a year, their system increases the potential annual yield by about 700 percent.
The land requirement for vertical farming is a mere fraction of that for traditional agriculture. Santosham says it can be done in a building the size of a big-box retail store that can be built pretty much anywhere that has adequate utilities, including within major urban centers. The tightly controlled environment of a vertical farm should also eliminate the need for applied pesticides.
Yet another benefit of vertical farming is the return of land currently needed for food production back to the planet. This could help facilitate Earth's recovery from deforestation and return much-needed habitat to threatened or endangered species. Of course, if we ever colonize the moon or Mars, vertical farming will be the go-to option for feeding the colonists.
Several vertical farming company pioneers are already getting their high-quality crops into the hands, and mouths, of consumers. Plenty, Inc. has an eponymous line of greens, and Aerofarms has their FlavorSpectrum line. Both companies claim that their products are exceptionally tasty, a result of their carefully controlled growing environments in which computer-controlled lighting can be optimized to bring out the most desirable qualities of each crop.
Credit: Alesia Berlezova / Adobe Stock
The history of vertical farming
The idea of vertical farming isn't new, and experts have been questioning its viability since the term was first coined in 1915 by Gilbert Ellis Bailey, who was obviously way ahead of the available technology at the time. The first attempt to grow produce in a constructed environment was a Danish farmhouse factory that was built to grow cress, a peppery green related to mustard, in the 1950s.
The modern concept of a vertical farm arose in the New York classroom of Columbia University's Dickson Despommier in 1999. He presented the idea as a theoretical construct, a mental/mathematical exercise imagining how to farm in an environmentally sound manner. His class began with the notion of a rooftop garden before considering a "high-rise" version that might theoretically be able to grow enough rice to feed two percent of Manhattan's population at the time. The eureka moment was a question Dispommier asked: "If it can't be done using rooftops, why don't we just grow the crops inside the buildings? We already know how to cultivate and water plants indoors."
With the technological advances of the last few decades, vertical farming is now a reality. Our sister site, Freethink, recently paid Plenty, Inc. a visit. (See video above.)
Vertical farming today
Credit: Nelea Reazanteva / Adobe Stock
Today, growers across the globe are developing vertical farms. While the U.S. has more vertical farms than any other country, the industry is blooming everywhere.
There are currently over 2,000 vertical farms in the U.S. While more than 60 percent of these are owned by small growers, there are a few heavyweights as well. In addition to Wyoming's Plenty, Inc. and Newark's Aerofarms, there's also New York's Bowery Farming. There are also companies such as edengreen, based in Texas, whose mission is to help new entrants construct and operate vertical farms.
Japan comes in second, with about 200 vertical farms currently in operation. The largest vertical farming company there is SPREAD. Across Asia, vertical farms are operating in China, South Korea, Singapore, Thailand, and Taiwan. In Europe, vertical growers are in Germany, France, Netherlands, and the U.K. Germany is also home to the Association for Vertical Farming, "the leading global, non-profit organization that enables international exchange and cooperation in order to accelerate the development of the indoor/vertical farming industry."
In the Middle East, whose desert land and scarcity of water present a particularly challenging agricultural environment, vertical farming is taking root, so to speak. The United Arab Emirates' Badia Farms is now producing more than 3,500 kilograms of high-quality produce each day and expects to increase that yield going forward. In Kuwait, NOX Management launched in the summer of 2020 with plans to produce 250 types of greens, with a daily output of 550 kg of salads, herbs, and cresses.
The economics of vertical farming
Credit: meryll / Adobe Stock
Building and operating a vertical farm is a costly endeavor, requiring a substantial initial investment in state-of-the-art technology, real estate, and construction. AgFunderNews (AFN) estimates that it can cost $15 million to construct a modern vertical farm. Fortunately, investors see the potential in vertical farming, and the industry has attracted more than $1 billion in investments since 2015. That includes $100 million for Aerofarms. Plenty, Inc raised $200 million in 2017 from a fund backed by such respected forward-thinkers as Jeff Bezos and Alphabet chairman Eric Schmidt.
AFN is particularly excited by the potential of what they call second-generation vertical farming technology. They cite advances in LED technology — expected to increase energy efficiency by 70 percent by 2030 — and increasingly sophisticated automation that can streamline the operation of vertical farms. AFN anticipates operating cost reduction of 12 percent due to improvements in lighting and another 20 percent from advances in automation.
BusinessWire says that the vertical farming produce market was valued at nearly $240 million in 2019, and they expect it to grow 20 percent annually to over $1 billion by 2027.
A welcome disruption
Vertical farming will be disruptive.
Vertical farming would eliminate the need for the arduous work of harvesting crops by hand from vast tracts of farmland. Current picking jobs, the company says, can be replaced by better-paying, full-time jobs available 365 days a year in better working conditions — and in the variety of geographic locations in which vertical farms can operate.
There are two caveats, however. First, the number of people needed to manage and harvest vertical farm crops will be far fewer than the many farmworkers required for less efficiently planted traditional fields. Second, with automation becoming ever-more capable — and perhaps a key to eventual profitability — one wonders just how many new jobs ultimately will be created.
But the societal benefits far outweigh any costs. As Plenty's Storey muses, "Like most everything in the world, we can only save our species if it makes economic sense." Thankfully, it does make economic sense
Lead photo: Credit: Freethink Media / Plenty, Inc..
A Lot of Promise’: Vertical Farming Takes Root In Virginia
Since its inception at the turn of the millennium, vertical farming — which in its simplest form is any system where plants are grown in vertical stacks — has promised to revolutionize yields by allowing producers to multiply their crop outputs by six to eight or even more times without expanding their footprint
May 24, 2021
Imagine a field of lettuce.
Say the lettuces are all buttercrunch, and they dot the field like crisp rosettes. Each has been seeded by a farmer, kept free of pests, watered for weeks, and finally cut at the base before being rinsed and packed for transport. Each is destined for a different meal: a lazy evening salad on the porch, an artfully arranged plate at a restaurant two-top, the vegetarian alternative at grandma’s 80th.
Now imagine six of these fields, all stacked on top of one another.
The idea isn’t far-fetched. In fact, it’s already a reality in Virginia, where a new, more technologically oriented form of agriculture known as vertical farming is quietly taking root.
“There’s a lot of promise,” said Tony Banks, senior assistant director of agriculture, development, and innovation for the Virginia Farm Bureau Federation. “As we continue to watch urban encroachment and we have this demand to have food produced closer to where people actually live, we’re going to see more and more of it.”
Since its inception at the turn of the millennium, vertical farming — which in its simplest form is any system where plants are grown in vertical stacks — has promised to revolutionize yields by allowing producers to multiply their crop outputs by six to eight or even more times without expanding their footprint.
“You’re trying to use an area more intensively. Because you’re limited by horizontal space, you want to maximize vertical space,” said Leonard Githinji, a professor of sustainable and urban agriculture at Virginia State University who also works with Virginia Cooperative Extension.
The concept is flexible and scalable. The stacks can be small, nothing more than a narrow shelf installed at a restaurant or in a convenience store to grow produce within a customer’s reach. Or they can fill a warehouse, bringing an industrial dimension to agriculture.
“There’s a wide range. On one end, it’s almost you have a greenhouse that’s highly automated,” said Banks. “On the other end, you could be in a warehouse and everything is grown on huge assemblies of racks and you have complete artificial lighting and hydroponics.”
The latter type of vertical farming is “high-tech manufacturing, essentially,” said Scott Lowman, director of the Controlled Environment Agriculture Innovation Center at the Institute for Advanced Learning and Research in Danville, where scientists and other experts are exploring the promise of various types of indoor agriculture can hold for Virginia.
Hopes are high, particularly in the historic tobacco region of Southside, where state officials have been working for several decades to encourage farmers who once depended on the golden leaf to diversify their enterprises. It’s no accident that the Controlled Environment Agriculture Innovation Center was sited in a region with a rich agricultural history and an abundance of old warehouses once devoted to tobacco and now empty.
Nor was it an accident that in 2019, Gov. Ralph Northam’s office announced that vertical farming company AeroFarms had decided to build a $42 million facility in an industrial park jointly operated by Danville and Pittsylvania County. Virginia aggressively courted the project with some $1.5 million in state grant funds and incentives. In exchange, AeroFarms promised to build the facility, employ 92 people and purchase roughly $20 million of Virginia agricultural or forest products.
But while AeroFarms’ Virginia location will be the largest vertical farm in the state once built, it won’t be the only one. Over the past few years, other operations have quietly been putting down roots. Shenandoah Farms in Rockingham operates a large-scale facility that grows herbs and lettuces. In Lorton, Beanstalk grows a range of greens. Fresh Impact Farms in Arlington, which grows herbs, greens, and edible flowers, announced an expansion this spring in conjunction with the governor’s office. Babylon Micro-Farms in Richmond is developing sophisticated technology to spread small-scale vertical farms around the country. Other efforts are underway.
“We’re in a great position on the East Coast in terms of population centers,” said Lowman. “And it’s a friendly environment for business, and we have a legacy of hard-working labor.”
Controlled environment agriculture
While vertical farming is relatively new, its lineage is much longer, nesting within the family tree of controlled environment agriculture, which encompasses any type of production that takes place within a structure.
From Roman orangeries to modern-day greenhouses, controlled environment agriculture offers the advantage embedded in its first descriptor: control.
Outdoors, farmers are at the whim of the weather, plagued by pests and disease, and caught in a never-ending struggle to keep water and fertilizer confined to their fields.
Indoors, the equation changes. Because of the precision-engineered systems, controlled environment agriculture tends to require less water, less fertilizer, and few or no pesticides compared to conventional agriculture. And, depending on a particular system’s design, it can allow producers to grow crops 24/7, 365 days a year. AeroFarms has said that its technology allows it to produce leafy greens “at a rate 390 times more productive than field-grown plants.”
A vertical micro-farm known as a cropbox. (Virginia State University)
“I can now schedule my crops,” said Michael Evans, director of Virginia Tech’s School of Plant and Environmental Sciences. “I can basically optimize the environment for that crop.”
There are, of course, drawbacks. Everything nature once provided to a plant must now be provided by a human — or a machine.
“With a greenhouse, you’re taking advantage of natural sunlight. You’re not paying for that,” said Evans. “But you’re paying quite a bit for heating and cooling. When you flip to an indoor vertical system, the disadvantage is that now you have to supply the light.” Other costs diminish at the same time: without the translucent walls of a greenhouse, “your heating and cooling can go down because it’s better insulated.”
For years, prohibitively high energy costs boxed out vertical farming as a viable option for producers working in controlled environment agriculture. What would change the playing field was a technological innovation: the high-powered and highly efficient LED.
“The thing that really changed that made indoor vertical farming work and become an economic possibility was really the development of LED lighting, because that changes the energy equation a lot,” said Evans. “It makes providing the light the crops need much economically viable.”
A new generation of farmers
Despite its promise, vertical farming won’t replace conventional agriculture, experts say. Many of Virginia’s biggest commodity crops — soybeans, corn, hay — are grown at such a large scale that trying to transport them indoors would be an exercise in absurdity.
Where controlled environment agriculture has found a growing niche is in the produce most familiar to the average Virginian: lettuces, herbs, tomatoes, cucumbers, peppers, herbs, microgreens, and more. Experiments in growing strawberries indoors are also underway, and Evans pointed out that once legalized, marijuana may not be far behind, although the federal government’s continued classification of the plant as illegal will keep institutions like Virginia Tech from working with it.
For consumers of these products, the idea of local food grown only a short distance away is increasingly appealing. That can be an argument in favor of controlled environment agriculture and vertical farming, said Banks.
“When we import food into this country, what we import is fruits and vegetables that require a lot of hand labor,” he said. “So there’s opportunity there to offset some of those imports and reduce our reliance on food produced overseas.”
Both Banks and Evans also noted an unusual aspect of vertical farming: its allure for younger and often more urban Virginians.
“It’s getting a whole new generation of folks interested in agriculture. It’s a different type of agriculture, but it’s getting a lot of students,” said Evans. At Virginia Tech’s School of Plant and Environmental Sciences, he added, “we have to change our curriculum for what we’re teaching to prepare students interested in controlled environment agriculture.”
For a younger generation increasingly concerned with social and political justice, the opportunity offered by controlled environment agriculture and vertical farming to fill food deserts and involve local workers in local food systems is an attractive prospect. Many students are eager to look beyond the existing agricultural structures, said Githinji, who recently received a $600,000 grant from the U.S. National Institute of Food and Agriculture to explore the use of “micro-farms,” which incorporate vertical farming systems, as a way to address food deserts in urban neighborhoods.
It’s not unusual for extension agents to get calls in which people are saying, “‘As much as I want to grow more food, I can’t afford to buy even another quarter acre,” he said. “So you get people asking what they can do with what they have.”
The other draw is the technology. While vertical farming can be small- or large-scale, its larger applications rely on evolving and increasingly sophisticated technology that has piqued interest among the startup community.
“This is a really exciting industry that’s rapidly entering the mainstream,” said Alexander Olesen, CEO, and co-founder of Babylon Micro-Farms, a Richmond-based startup that develops indoor growing systems for institutional food service settings, such as hospitals, schools, and universities. Babylon, which in 2020 was the recipient of a $75,000 grant from the Commonwealth Research Commercialization Fund that aims to support small businesses in emerging research and technology sectors, builds small-scale vertical farms “as a sustainable amenity for these locations.”
The field’s growing popularity is also driving a need for more workers, more expertise, and more training, said many of the people interviewed for this story. The Controlled Environment Agriculture Innovation Center in Danville, itself a recipient of $365,000 in state grant funds in 2020, is key to that effort. So too are plans announced by the governor’s office last month that will see hydroponic greenhouse startup Sunny Farms build a 1.2 million square foot greenhouse in Virginia Beach — one of the largest on the East Coast — and work with Virginia Tech and the Virginia community college system to develop educational training in controlled environment agriculture.
“Our goal is really to support the controlled environment agriculture industry in Virginia, but we’re also working on creating an innovative controlled environment agriculture ecosystem in Virginia,” said Evans.
These enterprises may be only the beginning.
“Once people see that it’s working, we’re going to see them flourishing all across the commonwealth,” said Githinji.
Lead photo: Controlled digital lights help produce high-density feed grass in a Grov Olympus vertical farming machine in Utah. The Olympus Tower Farm uses a controlled environment to grow sprouted wheat and barley grass in 857 square feet of space and uses 95 percent less water to produce 5,000 to 6,000 pounds of grass per day, replacing 35-50 acres of land. (Photo by George Frey/Getty Images)
Sarah covers environment and energy for the Mercury. Originally from McLean, she has spent over a decade in journalism and academic publishing. Most recently she covered environmental issues in Central Virginia for Chesapeake Bay Journal, and she has also written for the Progress-Index, the Caroline Progress, and multiple regional publications. In 2017, she was honored as one of Gatehouse’s Feature Writers of the Year, and she has been the recipient of numerous awards from the Virginia Press Association. She is a graduate of the College of William & Mary. Contact her at svogelsong@virginiamercury.com