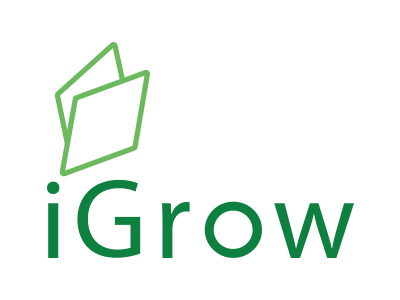
Welcome to iGrow News, Your Source for the World of Indoor Vertical Farming
Leading European Vertical Farming Company Retains Strategic Advisor to Explore Strategic Options
Award-winning Belgian vertical farming and contract research company, Urban Crop Solutions (“UCS”) has retained Contain, Inc., to explore strategic options to elevate its status as a leading European technology player in the fast-emerging global indoor farming space
Urban Crop Solutions Tech
Vertical farm & contract research co Urban Crop Solutions has retained Contain to explore strategic options to elevate its status as a tech leader in indoor ag.
We have long realised that we would need to decide between remaining independent and joining a larger organization to scale...this is the optimal time to make this move.”— Frederic Bulcaen, Chairman and founder of UCS
Urban Crop Solutions Container Farm
RENO, NV, UNITED STATES, May 19, 2021 /EINPresswire.com/ -- Award-winning Belgian vertical farming and contract research company, Urban Crop Solutions (“UCS”) has retained Contain, Inc., to explore strategic options to elevate its status as a leading European technology player in the fast-emerging global indoor farming space.
“We are delighted to have been awarded this mandate by UCS”, says Nicola Kerslake, founder of Contain. “It is a mark of the UCS management’s professionalism and dedication that they are open to exploring options from merger or acquisition to adding strategic investors to take this industry-leading firm to the next level.”
Urban Crop Solutions Grow System
UCS’ clients range from global billion-dollar companies to research institutions and start-ups across multiple industries in Europe, North America, and Southeast Asia. The growth of the business is attributed to a strong management and scientific team who have created best-in-class products and services made possible by application expertise and trade secrets. UCS expects to more than triple its revenues and reach breakeven profitability this year.
UCS offers two key solution and product channels:
-Plant biotechnology research: capabilities to simulate any growth environment and create growth recipe applications to address business and market opportunities in all crop verticals for use across numerous industries. UCS has developed innovative research applications such as growth performance of wheat, tobacco and cotton plants in controlled environments, growth recipe for green roof succulent plants on substrates and use of residual flows from waste to grow food.
-Vertical farming technology: indoor growing installations of hydroponic modules with growing surface areas ranging from 70 to over 5,000 square meters with an end-to-end customer support model. UCS has 4 different classes of product size that can be customized to meet the size or configuration requirements of any customer.
Maarten Vandecruys, founder and CTO of UCS, comments, “Now that we have our solutions and services in place, it is important that we pursue the best strategic options for the future of our organisation and team.”
“As a Board, we have long realised that we would need to decide between remaining independent and joining a larger organization to scale. There is such great momentum in indoor farming that this is the optimal time to make this move”, explains Frederic Bulcaen, Chairman and founder of UCS.
Contain Contact info:
Marilyn Jentzen
marilyn@contain.ag
+1.404.353.3754
About Urban Crop Solutions
Urban Crop Solutions BV is a privately held Belgian company founded in 2014. It offers end-to-end solutions for indoor hydroponic vertical farming via full-service customized and scalable solutions to multi-industry customers in two key product and service areas. Plant research products and services help customers select the right plant varieties or create new growth recipes for specific client needs or market opportunities. Indoor plant growing solutions and services range from concept design through business planning, manufacturing, installation, training, and after-sales servicing and support.
https://urbancropsolutions.com
About Contain, Inc.
Contain Inc is a US-based fintech platform dedicated to indoor agriculture, growing crops in warehouses, greenhouses and container farms. The Company serves the controlled environment agriculture industry in several capacities; it works with leading equipment vendors and with a wide pool of lenders to aid indoor growers in finding funding for their farms. It is also home to microlearning platform Rooted Global, which works with majors such as Danone and Dole to enable employees to grow a little of their own food at home. Most recently, the Company launched a used equipment trading platform, Equipped, to take the drama out of buying and selling used indoor farming equipment. The Company graduated from the 2019 Techstars Farm to Fork program, backed by Cargill and Ecolab.
https://contain.ag
Marilyn Jentzen
Contain Inc
marilyn@contain.ag
Visit us on social media:
Twitter
LinkedIn
Modular Hydroponic Growing Spaces In Freight Containers For Local Food Production
Freight Farms’ design was the first containerized vertical growing environment using hydroponic technology
May 17, 2021
Southeastern Pennsylvania Correspondent
A Massachusetts company has developed a unique, hydroponic growing environment in closed 40-foot freight containers that are being used world-wide to grow produce in areas with bad soil or weather conditions not conducive to outdoor growing.
Bay State natives Jon Friedman and Brad McNamara were developing rooftop greenhouses in the early 2000s when they realized a modular, hydroponic container might be a more viable solution.
Hydroponics wasn’t something new. Historians believe this soilless gardening can be traced back to hanging gardens of Babylon in Iraq built by King Nebuchadnezzar about 600 BC. Nutrient-rich water was pumped to the gardens from the Euphrates river to sustain its plants. A water-based growing thread continued through history and in the 1930s a University of California scientist, William Gericke, coined the term from the Greek word “hydro” (water) and “ponics” (work).
Friedman and McNamara, who were building outdoor, roof-based gardens on older residential buildings, looked outside the box, and turned their focus to widely available shipping containers.
They thought they could provide the equivalent of 2 acres of growing space in traditional 40-foot-by-8-foot containers and extend growing seasons year-round everywhere — especially in areas that couldn’t support traditional outdoor agriculture or in parts of the world affected most by climate change.
They named their company Freight Farms and placed their first container less than a decade ago. Now the concept is catching on worldwide.
View Photos From Freight Farms
Freight Farms’ design was the first containerized vertical growing environment using hydroponic technology. It was initially funded by a Kickstarter campaign in 2012, where they raised the funds to build a prototype to allow local food production to be available to everyone, anywhere.
The first commercial unit was installed at Boston Latin School, the oldest public school in the U.S., to produce fresh produce for the school cafeteria as well as serving as a teaching classroom for high school students.
“The company has placed 350 units in 48 states and 32 foreign countries,” Friedman said.
The company also introduced proprietary software called “farmhand” to help automate many farm processes, and is manufacturing its 10th generation container, the Greenery S, incorporating the latest technology and automation for vertical, hydroponics growing.
Growing Strong
Hydroponic Operation Supplies High-End Restaurants
Art Petrosemolo, Southeastern Pennsylvania Correspondent
Although the Freight Farms container units are capable of growing a variety of produce, leafy greens are its specialty and the best choice for farmers looking to sell their harvests year-round.
Containers also have been embraced by educational institutions to supply fresh vegetables for cafeterias and serve as learning and teaching space.
St. Joseph College in Standish, Maine, has been operating a Freight Farms unit for years to both supply fresh vegetables to its dining facilities as well as for student employment.
The site also has been a tool for community involvement with St. Joseph students working with a town Institute for Local Food System Innovation utilizing the Freight Farms container in partnership with a large hydroponic farm and commercial processing kitchen for events and agritourism.
With a decade head start in the business, Freight Farms does not have major competition in hydroponics container gardening production, although, in recent years, it has seen significant growth in multiple indoor soil- and water-based farming formats including warehouses, greenhouses and pods that are addressing growing produce year-round.
Climate change has increased concern about food production for growing populations worldwide with extreme weather conditions and higher levels of carbon dioxide in the atmosphere.
Friedman and McNamara have always been aware that the challenge to expansion for stand-alone, container gardening is the cost of power and each new rendition of their growing units has addressed both power consumption and automation to be more efficient.
Their latest Greenery S model uses growing lights that are 50% more efficient than previous models and the technology allows farmers to choose pre-set growing modes to maintain higher yields — 20% higher than earlier models — while prioritizing energy use.
Addressing affordable and clean power for customers, Freight Farms recently partnered with Arcadia, a Washington, D.C., energy company to offer affordable, renewable power options for customers.
Going forward, Friedman said growing container units will continue to become more efficient, allowing owners to increase their growing yield while having more control of their energy use to power the unit.
Slide Show Photos:
Lights and plant arrangements in Freight Farms new Greenery S model container.
Photo provided by Freight Farms
Leafy greens grow in Freight Farms’ own Greenery Farm container.
Photo provided by Freight Farms
This Freight Farms container is ready for shipment.
Photo provided by Freight Farms
Freight Farms' containers under construction in their Vermont facility.
Photo provided by Freight Farms
Lexy Basquette, Freight Farm’s on-site farmer, checks on some of her growing plants.
Photo provided by Freight Farms
Greenhouses, Vertical Farming and Urban Ag: Controlled-Environment Agriculture Has Growth Potential
Paul Post, New York Correspondent
Czech Startup Introduces New Container Farm To The Market
A container farm supplied by GreeenTech will soon be parked in Prague's Smíchov district. The hydroponic container farm will grow herbs, vegetables, and small fruits. The other two containers will go to Dubai and Shanghai
Delivering To Prague, Dubai, And Shanghai
A container farm supplied by GreeenTech will soon be parked in Prague's Smíchov district. The hydroponic container farm will grow herbs, vegetables, and small fruits. The other two containers will go to Dubai and Shanghai.
"We bring a unique and modern approach to agriculture. With vertical hydroponics we will start food self-sufficiency not only in the Czech Republic," promises co-founder of GreeenTech Karolína Pumprová, who three years ago was at the birth of the Prague urban hydroponic farm HerbaFabrica, which supplies herbs to Prague restaurants.
The co-founders of Greeentech
She was later joined by entrepreneur Dmitrij Lipovský, who, after a year-long working stay in China, where he focused on ecology and sustainability issues, saw a TV report about the HerbaFabrica farm, and was so intrigued by it that together with Karolína Pumprová and technology director Milan Souček, they created the concept of GreeenTech, a technology, and cultivation company that was officially established last July. Dmitry Lipovsky invested six million crowns of his own money in the start-up and became CEO of the company.
Modular solution
GreeenTech currently has three divisions, each with its own unique product and business and marketing direction. Urbanio is a modular system whereby the company builds an urban hydroponic farm according to the customer's requirements. The price in this case starts at one and a half million crowns and depends on the number of modules purchased and the environment where it will be built. The technology was to be officially launched at Expo 2020 in Dubai.
GreeenBoxes are containers coming with GreeenTech's technology. The price for the smallest size supplied, 13 x 3 x 3 meters, is in the lower units of millions of crowns. The third division is HerbaFabrica, which sells crops to distributors and end customers. The company intends to offer its franchise in the future.
These containers make it possible to grow crops practically anywhere and anytime, even in the desert. According to Lipovský, the company will produce three containers this year, the first of which will be located in Prague's Smíchov, while the others will also be presented at the EXPO in Dubai. It is to Dubai and also Shanghai that the company wants to expand in the medium term.
"The goal is to build full container farms and to continuously improve our technology. But we are a startup, so we are constantly in a turbulent process," smiles the CEO of the company over the next plans and reveals that the final investment round with external investors is also now underway.
Everything from the container design to the software solution is being developed in-house. Some of the technical equipment is supplied by Siemens CR, which is also a long-term technology partner.
GreeenTech wants its technology to contribute to a sustainable solution to a potential future crisis around food shortages. The founders of GreeenTech promise a recurring harvest of local vegetables full of vitamins and intense flavor. Since the crops do not undergo protective spraying, they are suitable for children and allergy sufferers.
The business model for GreeenBox and Urbanio technologies work on both a sales and rental basis. "For both options, there is an 'after-sales service, where we supply seeds, substrates, fertilizers, as well as spare components for the technology and remote farm management," Lipovský explains.
He adds that GreeenTech also started offering the HerbaShare service to businesses, shops and restaurants a month ago. This is a structure with a cold box for preserving produce, where the company regularly delivers microgreens and vegetables. "Now we want to focus more on businesses as people come back to the office. We believe this is a really interesting employee benefit and a way to have a vitamin bomb right in the workplace," he concludes.
Source: StartupJobs
For more information:
Greeentech
info@greeen.tech
www.greeen.tech
18 May 2021
N.Thing To Export Smart Farms To UAE After $3 Million Deal
The contract, set to proceed next month, will allow the firm to construct vertical smart farming containers in the UAE by December this year.
May 17, 2021
South Korean agriculture technology company N.Thing said Monday that it has recently inked a $3 million deal with Sarya Holdings in the United Arab Emirates to export smart farms.
The contract, set to proceed next month, will allow the firm to construct vertical smart farming containers in the UAE by December this year. The container can reduce the use of water up to 98 percent compared to a typical farm and cultivate crops in any environment, whether that is in Siberia, the Middle East, or Seoul.
“The UAE reached out to N.Thing as food security emerged as a key issue amid the coronavirus outbreak,” a company official said.
In February last year, Sarya Holdings conducted a proof of concept test on N.Thing’s container to verify the technology. During the test, Sarya planted four different vegetables -- batavia, kale, Boston lettuce, and oakleaf -- in eight test containers and observed their growth cycles, nutrients, quality, and more.
The test proved that N.Thing’s smart farm containers built in the UAE can produce up to 1.5 metric tons of crops per container, which was 42 percent more than initial estimates.
N.Thing received the best innovation award at the Consumer Electronics Show last year.
Lead photo: The interior of N.Thing’s smart farm container (N.Thing)
By Kim Byung-wook (kbw@heraldcorp.com)
Vertical Future And Crate To Plate Plot Fleet of Shipping Container Farms In London
Each of the 'container farms' will be able to produce up to five tonnes of leafy greens and veg each year with zero carbon footprint, the firms claim
Jessica Rawnsley
14 May 2021
Credit: Vertical Future
Each of The 'Container Farms' Will Be Able To produce Up To Five Tonnes of Leafy Greens And Veg Each Year With Zero Carbon Footprint, The Firms Claim
Urban farming specialists Vertical Future and Crate to Plate are together gearing up to rollout a fleet of indoor container farms in London, with each capable of producing zero carbon fresh salad and vegetables for swift delivery across the UK capital city, they announced yesterday.
Crate to Plate, an urban farming start-up, plans to use the 'container farms' designed by Vertical Future - a technology company focused on controlled-environment-agriculture (CEA) - across several new sites in London's Bermondsey and Stratford.
By using the container farms, Crate to Plate said it would be able to produce up to five tonnes of fresh produce - including lettuce, kale, and rocket - per year, and then deliver it to customers within 24 hours with a zero-carbon footprint, all without any use of pesticides or toxic chemicals. The firm counts Ollie Dabbous, chef-patron of Michelin-starred restaurant, HIDE, as well as independent grocers such as The Notting Hill Fish Shop and Artichoke in Hampstead among its customers.
Vertical Future's innovative farms, built within 40ft shipping containers, allow for highly-controlled indoor growing conditions, harnessing LED lighting, full climate control, and dual irrigation in order to create the optimal conditions for cultivating leafy salad and vegetables.
Proponents of vertical farming argue producing crops in such circumstances can reduce the amount of countryside land used for farming, better protect crops against the impacts of increasingly volatile outdoor climate conditions, and cut down on transport and logistics typically needed to ferry food from farms to urban centres. They also require far less water and zero pesticides.
"Our Container Labs create the optimal growth environment for growing fresh produce and can be deployed close to point of consumption, using minimal space," said Jamie Burrows, Vertical Future's CEO. "Using zero chemicals and growing crops in a controlled environment enables our partners to meet demand all-year-round, as opposed to regular food production systems which are reliant on seasonal limitations."
By shifting towards using Vertical Future's 'Container Labs', Crate to Plate's founder Sebastien Sainsbury said the firm would be able to scale up its systems across the UK while offering more efficient growing capabilities to improve both output and product quality.
"It's been incredibly encouraging and exciting to align with other dynamic, innovative, and enterprising British business, which will help us to scale up our vision and execute our exciting opportunities both nationally and internationally," Sainsbury said.
USA - ILLINOIS - Tasty, Fresh And Sustainable
There are no animals, roses, or peaches at Wiseacre Farm, a rectangular, 320-square-foot container farm inside a warehouse Sheinfeld rents in an industrial area at 1975 N. Lake Terrace, Glenview
Glenview Man's Hydroponic Farm
Uses Technology To Grow Garden Variety Produce
5/12/2021
By Dave Oberhelman
doberhelman@dailyherald.com
This is not your grandfather's farm.
It's not Aviad Sheinfeld's grandfather's farm, either -- but Wiseacre Farm is a bridge between childhood days spent on grandparents Yechezkel and Hadassah Gluzman's farm in an Israeli moshav and Sheinfeld's modern training.
That combination has resulted in some of the best greens his customers have ever tasted, grown indoors by futuristic, sustainable methods.
Whatever it is, the way you tell your story online can make all the difference.
"I don't know if it was a goal. I never thought about becoming a farmer. I was always good with computers, so working with computers was kind of the assumed path," said Sheinfeld, 49, of Glenview.
"I think my childhood experiences on the farm really gave me more of an ingrained appreciation for what it takes to grow food. The thing I remember most is the apple orchards and the peaches my grandparents grew, but they also grew roses and sheep, so also animals."
There are no animals, roses, or peaches at Wiseacre Farm, a rectangular, 320-square-foot container farm inside a warehouse Sheinfeld rents in an industrial area at 1975 N. Lake Terrace, Glenview.
Wiseacre's specialty, available by 10-week subscriptions through www.wiseacre.farm, is leafy greens. A recent delivery included six heads of lettuce of differing varieties. Another package will offer the lettuce plus herbs and other greens -- things like parsley, chives, Thai basil, red-veined sorrel, curly kale with chard.
Sheinfeld sometimes delivers his produce the day it's harvested. Reviews are strong.
"Most of our customers have remarked that they had no idea that lettuce, basil -- fill in the blank, whatever produce -- tastes that way," said Sheinfeld's daughter, Yael, who is finishing her last semester at Northeastern University in Boston, but also handling Wiseacre marketing and communications.
"I think it's hard to understand just how much the taste disappears with travel, with chemicals, herbicides, and pesticides, with just time, honestly, and sitting on a grocery store shelf," she said.
Growing crops indoors in Wiseacre Farm's controlled hydroponic environment eliminates the need for herbicides and pesticides. Serving customers within about a 10-mile radius also lends a neighborly appeal.
"It's not just buying your food from anonymous company X," Aviad said.
His father, Sam, also works on the farm. Yael -- and occasionally Aviad and Kari Sheinfeld's two teenage boys, Rahm and Lev -- are fourth-generation farmhands.
Finalizing financing and incorporation in 2018, in November 2019 Sheinfeld received his container farm from Freight Farms of Boston. He said there's a couple hundred of these repurposed shipping container farms worldwide. When he needs advice he reaches farmers in Alaska, Minnesota, Tennessee, even Tasmania.
The interior includes vertical panels about 10 feet tall in which the plants soak up rays of LED lights embedded into opposing panels. The plant panels can be removed and placed horizontally when the plants are ready for harvesting.
The media is not soil but water, to which nutrients are added automatically, manually controlled by computer. Hydroponic methods are 98% more water-efficient than traditional farming, Yael said. Through recycling irrigation water and capturing the water transpired by the plants, on average the farm uses less than 5 gallons of water a day. On very humid days, the farm will capture more water than it uses.
Nutrients, drip irrigation, temperature, humidity, lighting -- all are computer-controlled.
"As farming goes, it's kind of posh," Aviad Sheinfeld said.
"The thing about this farm is it's very technically advanced, so it kind of marries my initial interest in agriculture and my insatiable appetite for technological gadgets all into one big toy," he said.
He earned a bachelor's degree in mathematics at the University of Pennsylvania and added DePaul University master's degrees in network communications and information security and in computational finance.
First working as a software engineer with Motorola, he veered into stay-at-home dad mode after he and Kari, an attorney, started having children. The couple sent their kids to the Science & Arts Academy in Des Plaines, where Aviad served three years as board chairman. During that time, the academy explored hydroponics as part of the curriculum.
"That's kind of where I caught the bug, so to speak," he said.
No bugs at Wiseacre Farm. There is lots of energy consumption.
"We have lights that are powered by electricity and we use a lot of technology, so that is one resource that we use a lot of," Yael Sheinfeld said.
And still ...
"What's wonderful is, due to our partnership with Arcadia (Power, a renewable energy company out of Washington, D.C.) all of the electricity that we consume now is 100 percent offset with wind-generated, renewable energy. So it sort of allows us to keep that focus, knowing that's the main resource we still need to use, but doing that in a more sustainable way," she said.
For lettuce, from seed to harvest it takes only 8 weeks for the container farm to grow the equivalent of 2 acres of traditional farmland, Aviad said. He plans on about six annual growing cycles.
His first crop came through last March, right at the onset of the COVID-19 pandemic. Initially targeting restaurants for his produce, he shifted to a farm-to-table model. Customers also can now pick up goods at the farm itself on Saturdays, though preordering is a must. All packages and purchasing options are available at www.wiseacre.farm.
In its short time, Wiseacre Farm has gained acclaim beyond consumer taste buds. It won Silver for innovation in the Glenview Natural Resources Department's 2020 Environmental Sustainability Awards, and on March 28 the farm was featured in a segment of the History channel's "Modern Marvels" series highlighting "The Future of Food."
After a year, Aviad Sheinfeld said the process has become "a little less magical," but he still gets a kick out of it. Imagine what Hadassah and Yechezkel Gluzman might think.
"You put seed in a plug, and even a few days later when it pops out, I'm amazed," Aviad said.
"I do understand it, but I still don't believe how amazing it is that a plant grows out of this little, tiny seed and a few weeks later you have a head of lettuce or arugula."
Lead Photo: Wiseacre Farm owner Aviad Sheinfeld looks over some of the plants grown at his hydroponic farm in Glenview. Brian Hill | Staff Photographer
It Is Time To Grow!
In an Urban farming pilot project, we grow leafy greens in a nutritious fluid, in a container powered with 100% renewable energy outside the IKEA Malmö store in Sweden
2ndProject portfolio Leader på IKEA, Ingka, Group Sustainability
The majority of IKEA visitors enjoy the IKEA food offer and today we enable millions of people to eat healthier and more sustainably by choosing our plant-based options. We are continuously exploring how we can contribute to a better, greener, and tastier future making healthier and more sustainable food accessible and affordable for many people.
In an Urban farming pilot project, we grow leafy greens in a nutritious fluid, in a container powered with 100% renewable energy outside the IKEA Malmö store in Sweden. This will not only result in delicious, fresh, locally grown greens that IKEA visitors can enjoy but what is more important this contributes to our ambition to become people and planet positive by 2030 by using fewer natural resources compared to conventional growing methods:
90% less water
No pesticides
No farmland
Less food waste
Together with Urban Crop Solutions we have installed a controlled-environment vertical farm where plants are grown in a closed system. Water and nutrients are used instead of soil and LED-light is used instead of sunlight.
We believe that every action that enables and inspires people to live more sustainably matters and perhaps we can change the world together, one plant at the time.
Urban Crop Solutions
Freight Farms Releases Next Generation of Container Farming
Freight Farms released the 10th generation of their container farming system – Greenery S, which has several key improvements on its predecessors
4 May 2021
Freight Farms released the 10th generation of their container farming system – Greenery S, which has several key improvements on its predecessors.
Since its founding in 2013, Freight Farms has been dedicated to making modular vertical farming technology accessible to more communities around the globe in a sustainable fashion. Their systems use a hybrid of hardware, software and services to make food production possible for anyone of any background, anywhere in the world.
“Greenery S represents the apex,” Jon Friedman, COO and co-founder tell Future Farming, “leveraging the excellent design and intuitive automation to streamline workflow while driving up yields.”
LED technology
Greenery S has several key improvements on its predecessors. This includes the new Dynamic Lighting Control, which uses LED technology that allows farmers to customize the lighting spectrum, intensity and duration for optimal plant yields. It also features a brand new user-centric Workstation design making for a sleek, self-contained and multi-functional farm command center.
Text continues underneath image
LED technology allows farmers to customise the lighting spectrum, intensity and duration for optimal plant yields. - Photo: Freight Farms
More consistent harvests
This new generation also brings with it an update to Freight Farms’ farmhand software that includes a new feature called “Recipes.” This update allows farmers to obtain more consistent harvests.
“Operators simply choose the crop they wish to grow and farmhand automatically adjusts in-farm settings for that crop production,” explains Friedman. “In-farm cameras and sensors gather information and continuously improve the precision of the recipes over time, aggregating data from the entire farmer network to determine patterns that lead to exceptionally successful harvests.”
Of all their systems, Greenery S combines Freight Farms’ most optimized combination yet to allow farmers the highest possible yields at the highest quality with the fastest rates.
Lower startup costs
With lower startup costs, Freight Farms reports that their Greenery S farm system can grow an equivalent of 2.5 acres of traditional farmland with 12 harvests per year. According to Friedman, it typically takes their farmers two to three years to see returns on their initial investments.
Greenery S is now available for purchase worldwide.
Jaclyn Krymowski
Correspondent for North America
Read more about: Vertical Farming Indoor Farming Container Farming
US: TEXAS - Awty Unveils Carbon-Neutral Container Farm Thanks to Sustainability Grant From Green Mountain Energy Sun Club
Incorporating a container farm into Awty’s current operations and curriculum reinforces the school’s commitment to sustainability while providing a real-life example of environmentally sound sourcing practices to their international student body
Source: GREEN MOUNTAIN ENERGY
05/03/21
Teachers and students alike at The Awty International School are excited about the possibilities a carbon-neutral container farm brings to their campus. Awty received a $135,000 sustainability grant from the Green Mountain Energy Sun Club to implement the container farm that now provides fresh produce to the school’s cafeteria and hands-on education for students through a newly formed urban farming elective class. The school installed a 20-foot hydroponics shipping container, a 20-foot aquaponics shipping container, and a 14.4-kilowatt solar system with 48 panels to power both containers to achieve the carbon-neutral status.
Incorporating a container farm into Awty’s current operations and curriculum reinforces the school’s commitment to sustainability while providing a real-life example of environmentally sound sourcing practices to their international student body. The farm serves to demonstrate how to reduce the carbon footprint of a food operation by shortening the supply chain and reducing fuel emissions. The innovative container farm and solar-powered equipment provides Awty a year-round steady supply of fresh produce, regardless of the outside climate. The closed-loop hydroponic system also uses 98 percent less water than traditional agriculture, significantly reducing the environmental impact of food production.
“While our school community has already started to reap the benefits from the farm, one of our many goals for the container project is sharing what we have achieved with others,” stated Robert Sload, STEAM coordinator at The Awty International School. “As an international school, we certainly want to help other international, national, and local schools introduce their communities to the wonderful community-wide lessons this project provides. A larger goal is to deconstruct our efforts and refashion a much simpler and cost-effective model that could be recreated anywhere with a particular eye to school communities located in food deserts.”
Green Mountain Energy, the nation’s longest-serving renewable energy retailer, founded Sun Club in 2002 to advance sustainability by partnering with nonprofit organizations engaged in meaningful work to support the communities the company serves. Awty is one of more than 130 projects to receive a sustainability grant since Sun Club’s founding. The grants are awarded to nonprofits seeking to implement projects promoting renewable energy, energy efficiency, resource conservation, and environmental stewardship.
“Green Mountain Energy’s goal with Sun Club grants is to promote sustainability in the community, and we were excited about this project from the start as it amplifies the message to future generations through education,” said Mark Parsons, vice president, and general manager of Green Mountain Energy. “Container farming will allow Awty students the opportunity to explore innovative new approaches to food production. Farming fresh produce directly on campus powered by solar energy makes it easy to captivate students and facilitate a dialogue around farming and solar energy at the same time.”
The respect of self, of individuals, and of the environment, and the importance of contributing to the community, are the fundamental principles of Awty’s sustainability program. The program’s mission is to reduce the school’s environmental impact and become more sustainable while inspiring and challenging students to come up with innovative solutions to environmental problems. Initiatives like composting, recycling, collecting water from HVAC units, and working toward becoming a zero-waste school have allowed the school to become a Bronze Award recipient of the Eco-Schools program, an international organization that accredits schools demonstrating a commitment to sustainability.
Tags: Indoor & Vertical Farming, Processing & Supply Chain | Containers
USA: NEW YORK - When A Shipping Container Becomes A Farm
Compact, enclosed vertical farms are making their way to Hudson Valley's urban areas
Compact, Enclosed Vertical Farms Are Making Their
Way To Hudson Valley's Urban Areas
May 3, 2021
John Lekic is the chef and owner of Farmers & Chefs in Poughkeepsie and vertically grows his own produce for his restaurant in a shipping container on site. He came across the concept of shipping container farming at an exhibition at the Culinary Institute of America in 2019. Aaron Lacan
The Hudson Valley is quite familiar with what it means to be farm-to-table, but what if the farm is also practically right next to the table, even in the more urban and metro areas?
Vertical farming via high-tech shipping containers is emerging as a new solution for businesses seeking to grow their own produce in a way that shrinks the necessary agricultural footprint while maximizing yield and reducing produce travel time. Here in the Hudson Valley, a 20 by 20-foot shipping container is being used to grow up to 400 pounds of fresh produce a month at Farmers & Chefs restaurant in Poughkeepsie.
Last year, the restaurant partnered with an Israel-based agro-tech company Vertical Field to grow herbs and vegetables for its dishes in a new and innovative way. The startup, established in 2006, uses technology to create innovative growing methods to improve food supplies in urban areas around the world, working mostly in the Middle East and Europe but also recently in the United States — including right here in Dutchess County.
Poughkeepsie's Farmers & Chefs is one of the first businesses in the Hudson Valley to try shipping container farming. The restaurant's 20 by 20-foot climate-controlled container (pictured above) produces about 400 pounds of fresh produce a month. Aaron Lacan
John Lekic, chef and owner of Farmers & Chefs, grows everything from buttercrunch lettuce, kale and baby arugula to herbs like rosemary, sage and basil in his enclosed vertical farm. The container is divided into four growing fields and is set on the restaurant’s property for customers to see, which has drawn even more interest to Farmers & Chefs as of late.
So why vertical farming?
Vertical Field is just one manufacturer specializing in reimagining steel shipping containers into enclosed, climate-controlled farms that are powered by LED lights instead of the sun, essentially supercharging a growing environment. Freight Farms and Grow Pod Solutions, other manufacturers, also tout this farming approach for its lower burden on farm labor and land, and for the higher output per square foot.
Shipping container farming is climate-controlled, powered by LED lights instead of the sun, and can produce high yield in a small space. But humidity and start-up infrastructure costs can be challenges. Aaron Lacan
“It’s a dream come true for chefs to be involved from the seed to the plate,” said Lekic. “It’s a great experience when you grow your own ingredients.”
Lekic pursued vertical farming after coming across Vertical Field during an exhibition showcasing a number of Israeli-based companies involved in food and agriculture at the Culinary Institute of America in late 2019.
Before the shipping container arrived at the Poughkeepsie restaurant, Lekic sourced vegetables from nearby farms and grew herbs in small outdoor gardening beds on site. However, Lekic found that it wasn’t enough yield, especially in the summer, and he often collaborated with additional farms to fill the gap. With a shipping container for growing, the restaurant is able to produce enough of what they need and on site – a key benefit for Lekic.
“There is a huge importance of having urban farms where the demand is,” said Lekic. “The problem with today’s agriculture is that everything has to travel. Most people are not aware of it, but depletion of the nutrients in our food is a huge issue.”
If you harvest spinach, it would be full of vitamin C that same day, Lekic said. But that changes dramatically just 48 hours later, when that nutrient is mostly gone. (A 2013 study by the University of California showed that spinach could lose as much as 90 percent of vitamin C in a single day.)
Farmers & Chefs restaurant grows everything from buttercrunch lettuce, kale, and baby arugula to rosemary and sage in its on-site shipping container. Aaron Lacan
By growing the restaurant’s produce steps away from the kitchen, “it’s as fresh as it gets,” said Lekic.
Farmers & Chefs received its shipping container farm right around the same time that COVID-19 hit last year, which Lekic said actually worked out well, as it gave him a chance to learn the ins and outs of vertical farming during a period that was quiet for his restaurant. By April, he was harvesting the first crops.
“Overall, the goal of vertical farming is to reduce the cost of healthy and fresh food to the retailer and to the end buyer as well,” said Vertical Field marketing director Noa Winston. “Since vertical farming reduces transportation costs, food losses, inventory inconsistencies, and price fluctuations due to climate, natural disasters, and other crises that create shortages, the retailer with vertical farming can benefit from consistency, security, and ownership over the entire supply chain.”
In another regional example, Evergreen Market, a grocery store in Monsey in Rockland County, partnered with Vertical Field to grow vegetables that ultimately stocked the store’s produce aisles, while also inviting customers to view its micro-farm when they visit the store.
Cost and maintenance concerns
This farming approach isn’t for everyone and there are drawbacks. “While it does offer some solutions to things like land access — which is, frankly, a huge barrier to the farming we advocate for here in the Hudson Valley — there is a lot of infrastructure needed,” said Kathleen Finlay, president of Glynwood, a center for regional food and farming based in Cold Spring.
“That brings a whole other set of challenges — how to create enterprises with a high capital upfront cost, how to get sustainable systems. It’s a different suite of challenges than more land-based production.”
Indeed, the start-up costs for an on-site shipping container farms aren’t cheap, although businesses say savings can be realized downstream by the reduced costs of paying produce purveyors for food that a restaurant or business is now growing itself.
Freight Farms' 2021 Greenery S model costs $149,000, which doesn’t include the shipping fee. Additional start-up costs can vary depending on where its being shipped, training packages selected, and any extras. Vertical Field would not disclose the fees associated with its model.
Plus, there is a bit of a learning curve when farming in a shipment container. Lekic played around with different variables, like what was best to grow at the same time, to see what would produce the highest yield.
"It's as fresh as it gets," said John Lekic of Farmers & Chefs, pictured above, about the new way of farming. Aaron Lacan
“For my purposes, I learned to stick with only two to four items – mostly greens,” said Lekic about his growing. “It makes the most sense based on my demand.”
Maintenance is an ongoing effort with an enclosed growing system that requires constant electricity and temperature controls to assure optimal growing conditions. “It’s always work,” said Lekic.
Over the past year, Lekic had to work out some kinks and issues, like making sure the air conditioning and heat levels were favorable to growing produce year-round. Just like traditional farming, some seasons might require more work — a vertical farm in the summer, for example, would have increased humidity that could negatively affect plants if not properly controlled.
While some growers may need back-up plans for electricity outages, Lekic doesn't foresee issues there because he is connected to the main restaurant building, which runs on a hospital-grid electricity system. Just in case, he has two generators that he could connect to if needed.
These drawbacks are outweighed by the ability to grow such consistent produce yield himself on site, he said, and the built-in technology features like being able to water plants by pushing a button on his phone. Lekic said overall it’s pretty easy to operate and monitor, so much so that the restaurant is looking into upgrading its original container to the newer version of the same size, and purchasing a second container.
“I’m interested in doing a mushroom container,” said Lekic. “There is the possibility of that. It’s a completely different kind of experience, but we would be super excited.”
DIY shipping container farming
While the hefty price tag of some farming shipping containers might be too prohibitive for some, others are riffing off of elements of tech-first farming for their own DIY growing methods.
KC Sullivan, a New Jersey-based mushroom farmer, created his own vertical farming environment out of an abandoned 40-foot-length shipping container that was used for storage at the Whitechapel Projects in Long Branch. Sullivan, who often collaborates with Tivoli Mushrooms here in the Hudson Valley, decided to create his own container farm by spray foaming it, sealing the floors, putting in an HVAC system, adding lighting and installing a misting mechanism.
He estimated the costs to be between $15,000 and $20,000 — not insignificant but far cheaper than a new shipping container already turbo-charged for farming.
“It was challenging,” said Sullivan. “There is no real guidebook or instruction manual on how to create a container mushroom farm. It was all about brainstorming how we wanted it to be.”
While it’s only been a year since mushrooms have been grown out of this urban shipping container, Sullivan is happy with the high-yield results: he's growing around 400 to 500 pounds of mushrooms a week. Mushroom container farming is slightly different from growing vegetables or herbs; for example, Sullivan doesn’t grow compost mushrooms, so there is no dirt necessary.
“We grow hardwood varieties, so it’s exclusively on red oak saw dust that is supplemented with agricultural byproducts,” said Sullivan. “You mix the two together with water, pasteurize it to kill off any pathogens, inoculate it with the strain of mushroom you’re looking to grow. It goes through an incubation period in a separate room [outside of the container], and then it goes to the fruiting room, which is the container and where it will be harvested.”
Just like Lekic, Sullivan also has run into some maintenance hiccups. The waterlines froze during the winter, which was a “big challenge and setback,” leading to a starved off humidification system, costing him around 100 to 150 pounds of crop.
Despite that hurdle, Sullivan also says the container can stand up against storms because it’s “built like a tank,” while regular farmland could be vulnerable to severe thunderstorms and potential flooding.
“One tool in the toolbox”
While an exciting option for some, vertical farming is “one tool in the toolbox” and it’s important to not forget about the benefits of traditional farming, said Finlay of Glynwood.
Finlay applauds any effort to produce food “that aligns with environmental sustainability,” but doesn’t think vertical farming will ever replace traditional farming or even fix the lack of land available for production.
Still, any effort to grow fresh food for more people is a win overall.
“We need more healthy food, accessible and affordable to more people,” said Finlay. “As much as vertical farming can play a role to that, I think that’s wonderful.”
Written By
Cloey Callahan is a lifelong Hudson Valley resident who was born and raised in Brewster, lived in New Paltz for four years while she attended college, and now resides in Newburgh on Liberty Street. On a sunny day, she strolls through Newburgh enjoying the 19th-century architecture on her way to the Hudson River waterfront. You can reach her at cloey.callahan@hearst.com to say hi or with pitches.
US: NEBRASKA - The Bay, Beyond School Bells Launch Youth-Focused 'Freight Farm'
In partnership with Beyond School Bells, The Bay is launching The Greenery, a self-contained hydroponic farm housed in a repurposed shipping container
Apr 25, 2021
A 40-foot-long shipping container in the parking lot of The Bay will soon be filled with a whole lot of green.
In partnership with Beyond School Bells, The Bay is launching The Greenery, a self-contained hydroponic farm housed in a repurposed shipping container. Members of Beyond School Bells and The Bay gathered with local leaders Saturday to officially launch the program.
Much like The Bay’s other youth-focused programs, The Greenery is designed to allow students access to engaging, hands-on activities — in this case growing food.
“We are thrilled about the opportunity to be able to turn kids on to sustainable agriculture,” said Andrew Norman, executive director and co-founder of The Bay’s parent organization Rabble Mill. “A lot of the kids in our neighborhood have never seen anything like this; none of us have.”
The Greenery setup is designed by the Boston-based company Freight Farms. Beyond School Bells was able to purchase the unit through a partnership with the Ben Hormel Harris Foundation, said state Sen. Anna Wishart, the director of partnerships for Beyond School Bells. Several local companies and individuals donated their time to help get it up and running.
Through vertical planting that doesn’t require soil, the shipping container is able to house 13,000 plants at a time, or about as much food as a 2.5-acre farm. Throughout the container are thousands of red and blue LED lights that can be precisely controlled through the trailer’s high-tech programming to provide the perfect amount and color of light for each plant, said Doak Field, director of operations at Freight Farms.
The setup is also water-efficient, as the water that flows throughout the trailer is repumped through the cycle.
“Everything is just way more efficient than growing outside,” Field said. “You can get the exact science down to whatever you need to grow.”
Field said the team hopes to start planting the container within the next two weeks and is planning to start with greens such as lettuces and kale, as well as herbs.
The program leaders plan to sell the food grown at the Greenery at local farmers’ markets or through weekly community-supported agriculture projects. They'll also source produce to local restaurants.
While many of the similar freight farm projects that have popped up across the country have been for-profit and run by adults, Lincoln’s will be one of only a few that are not-for-profit and youth-focused, Wishart said.
Beyond School Bells works statewide to provide after-school opportunities for students like The Greenery, she said.
“Our goal is to ensure that every kid, no matter where they grow up in Nebraska, has access to quality out-of-school programming and this freight farm is absolutely an example of that,” she said.
The project will offer an opportunity for students to learn a variety of skills, Wishart said, and University of Nebraska-Lincoln honor students will also play a role in mentoring younger students working on the project.
“This also creates an incredible platform for youth to learn entrepreneurship and about sustainable, high-tech agriculture and future careers in that space,” Wishart said.
The Greenery project is part of a series of environmental-focused projects across the state that Beyond School Bells is working on, the organization's network lead Jeff Cole said.
“This will be the crown jewel,” he said. “But we're already starting to do investments in rural Nebraska around outdoor classrooms, environmental education, and a series of other things across the state.”
Lincoln Mayor Leirion Gaylor Baird said she sees the project as an example of innovative, environmentally friendly solutions that can help move the city forward.
“This is such a wonderful demonstration of how we can take better care of the Earth, create greater value for everyone in our community and hand something on to the next generation, something that they can have a leadership role in,” Gaylor Baird said.
Lead Photo: Jeff Cole of Beyond School Bells talks to visitors about the Greenery, a 40-foot-long shipping container that will operate as a high-tech hydroponic farm at The Bay. The container has space to vertically grow over 13,000 plants — the equivalent of a 2.5-acre farm. FRANCIS GARDLER, Journal Star
This Is What The Future of Farming Looks Like
Vertical farming is nothing less than exactly what it sounds like. As opposed to spreading crops out along the ground, beds are effectively turned on their side, and grown on vertical panels
Why Grow Plants Horizontally When You Can Grow Them Vertically?
What do most people think of when imagining a farm? Typically: Acres upon acres of crops, fed by an extensive irrigation system, with tons of pesticides and heavy machinery— in other words, an image of modern farming that’s simply dated. Today’s most technically advanced farms don’t require nearly as much water or chemicals and take up just a fraction of the footprint. How? The answer is simple: Vertical farming. Specifically, the brand new Greenery S hydroponic system by Freight Farms.
Vertical farming is nothing less than exactly what it sounds like. As opposed to spreading crops out along the ground, beds are effectively turned on their side, and grown on vertical panels. This isn’t exactly new; some of the earliest indigenous farmers would plant crops on layered terraces to achieve similar results. But the modern form of vertical farming is barely two decades old. While it’s proven hyper-efficient, the technological cost of entry has also traditionally proven to be high, requiring expensive lights, temperature and irrigation control systems, and enormous amounts of electricity — to say nothing of capital. Until now.
Enter Freight Farms, a fully-functional farm in a 40-foot container. Launched in 2011, Freight Farms’ mission is to build accessible, modular vertical farming technology that empowers anyone to grow fresh, healthy food in their local communities — wherever that may be. While industrial farms tend to rely on GMO seeds, extensive pesticides, and centralized distribution systems, Freight Farms has worked tirelessly to cram 2.5 acres worth of farmable land into a 320-square-foot shipping container that can be placed almost anywhere and scaled up (or down) to meet your individual needs. Whether you’re a small restaurant looking to grow your own vegetables, an entrepreneur looking to bring fresh food to a food desert, or even just a homestead hobbyist, the Greenery S by Freight Farms is here to make your vertical farm aspirations a reality.
Freight Farms brings a decade of experience to the Greenery S. The Greenery S uses 99% less water than traditional industrial farm systems, mainly because you don’t need to worry about losing so much water to evaporation over acres and acres of land. Furthermore, the Greenery S has built-in temperature controls that make farming viable year-round, with a minimum temperature of -40 degrees Fahrenheit and a maximum of 120 degrees Fahrenheit. And with over five hundred supported crop varieties, you can throw out your hardiness zone map and grow pretty much whatever you want, wherever you want.
Besides being far more cost-effective than purchasing, tilling, planting, irrigating, and harvesting multiple acres of land, Freight Farms also uses data to help you get the most out of your yield. The proprietary farmhand® software integration gives operators complete automation and control over their grow operations. The software connects hundreds of farmers and is constantly compiling data from them to help you better manage your own crops based on learnings from the entire Freight Farms network.
The Greenery S is available now, to everyone. Whether you’re a seasoned farmer looking to scale out your operation or you’re simply looking for an exciting new business opportunity, Freight Farms’ intelligent automation and exceptional design can transform any small space into a commercial-scale farm. Head here to learn more and reserve yours now.
Lead Image: Image by Freight Farms
Futurism fans: This post was paid for by Freight Farms and was written by non-editorial staff. This content does not necessarily reflect the views or the endorsement of the Futurism.com editorial staff.
As a Futurism reader, we invite you to join the Singularity Global Community, our parent company’s forum to discuss futuristic science & technology with like-minded people from all over the world. It’s free to join, sign up now!
Inside Inuvik’s New Hydroponic Greenhouse
Inuvik’s first all-season growing facility will soon be operational, offering residents year-round access to locally produced greens.
April 16, 2021
Inuvik’s first all-season growing facility will soon be operational, offering residents year-round access to locally produced greens.
Inuvik's hydroponic greenhouse is decorated with artwork by resident Adi Scott. Meaghan Brackenbury/Cabin Radio
The hydroponic greenhouse, in a trailer on land donated by Jesse and Keren Harder, is run by the Inuvik Community Greenhouse. Leafy veg like lettuce and herbs will grow using nutrient-rich water rather than soil.
“We have been working on this project for a long time, trying to get funding,” executive director Ray Solotki told Cabin Radio. “We want to be putting food in the community. We want to be hiring people in the community. We want to be doing things that are actually helpful to what our mandates are.
“This unit has been in the works with the hopes that we will produce enough food to see an actual tangible amount of difference in the communities, and also provide jobs here in Inuvik.”
Ray Solotki inside Inuvik’s community greenhouse in the summer of 2019. Ollie Williams/Cabin Radio
The greenhouse received more than $400,000 for the hydroponic facility from economic development agency CanNor last November. ColdAcre, a company that runs hydroponic greenhouses in Yukon, was contracted to construct it.
Another $100,000 from the territorial government will pay for a small solar farm to power the facility, which Solotki says will mean cheaper energy and lower-cost produce.
Solotki hopes the facility can grow as much as ColdAcre’s Whitehorse facility – about 500 lb of produce a month.
“If you consider how much spinach weighs, it’s not very heavy,” Solotki added. “That’s quite a lot of food to be bringing into the community.
Inside Inuvik’s hydroponic greenhouse. Plants are grown on shelves using nutrient-rich water that runs through a closed circuit. Meaghan Brackenbury/Cabin Radio
Kale, bok choy, Swiss chard, mizuna, and basil will be included in the greenhouse’s veggie box program, where members pay $20 a week and receive their share of the harvest. Some will be available at local grocery stores.
“I want this to be a case of once a week you get something that’s so fresh it was picked this morning, even when it’s minus-56 outside,” Solotki said.
Finding firm financial footing
The hydroponic unit will require a year-round staff member to operate it – a position Solotki said has been filled by an Inuvik resident – and offer more training opportunities for students and summer staff.
“We want to train kids from the ground up, literally, and teach them that this is a potential job,” she said.
The organization has received funding from the University of Saskatchewan for programs like bringing residents from smaller Beaufort Delta communities to teach them about hydroponics.
Shelving units inside the hydroponic greenhouse. Meaghan Brackenbury/Cabin Radio
“It doesn’t have to be in a shipping container,” Solotki explained. “You can take these out and put them in a school, you can put them in an office, you can do all sorts of things.
“But people need to understand how they work and see if it’s something they want to do.”
Meanwhile, produce sales from the hydroponic unit could help the greenhouse grow its commercial side.
Revenue that’s independently generated means less pressure to constantly fundraise, Solotki said, and could free up funding pots for other groups in the region.
“The amount of agricultural funding available per area is fixed, which means if I’m the one constantly tapping into it, other people can’t or might not have as many opportunities,” she said.
“If we could be utilizing it in better ways, and creating a better economy and creating more interesting things in the community, this is great for us.”
The greenhouse is currently seeking funding for an aeroponic facility – a system that suspends plants in the air and sprays them with nutrient-rich mist, which works well for heartier crops such as beans, potatoes, and peas.
Exploring what’s possible
Since the onset of the Covid-19 pandemic, agriculture and food security have become bigger discussions in the NWT.
Last June, a 50,000-pound donation of free potatoes to the NWT sparked debate about what northern food security should look like.
In February, three farmers in Hay River received funding for projects designed to help move the territory toward having an established agricultural sector. This month, the City of Yellowknife approved its latest food and agriculture plan after announcing a partnership with Wilfrid Laurier University to create a food hub in the city.
In Inuvik, Solotki concedes that leafy greens “won’t solve the problems of caloric intake and what you actually require for food security” – but she argues the hydroponic facility will allow the community to re-evaluate what is possible in the realm of Arctic agriculture.
“This is an idea that starts to change people’s mindsets: that we don’t have to buy from out-of-territory,” she said. “We don’t have to ship it in, we could actually do it ourselves.
“While the hydroponics is not going to be the be-all and end-all, wouldn’t it be cool to see community greenhouse hydroponics, sitting next to community greenhouse aeroponics, sitting next to the greenhouse chicken coop, sitting next to the pig barn, sitting next to the cow barn… having an actual agricultural sector that is utilizing what we need to work in our climates?”
New Freight Farms Greenery S Ushers In The Next Era of Smart Small-Space Farming
Five Specialized Systems Allow Farmers to Grow Food 365 Days a Year With Complete Control
Five Specialized Systems Allow Farmers
To Grow Food 365 Days A Year With
Complete Control
NEWS PROVIDED BY
April 21, 2021
BOSTON, April 21, 2021 /PRNewswire/ -- Earlier this month, Freight Farms, the world's leading manufacturer of container farming, unveiled its new container farm, the Greenery S. This latest model is the tenth generation of the technology since the company pioneered the small space farming concept in 2013.
The Greenery S features an exceptional new farm design which, when paired with seamless automation, unlocks powerful performance for all users. The Greenery S combines specialized space, light, air, water, and control systems to make it possible to grow 2.5 acres-worth of food in 320 square feet anywhere in the world.
Always keeping the farmer in mind, the Greenery S implements feedback drawn from in-depth customer research to execute an exceptional new farm design which, when paired with seamless automation, unlocks powerful performance for all users. The Greenery S combines specialized space, light, air, water, and control systems to make it possible to grow food anywhere in the world, thereby empowering individuals to grow food locally within their communities to decentralize the global food system.
"The Greenery S brings an entirely new level of design, control, robustness, and ease of use to our already industry-leading growing platform. It is built upon the technology we have developed over the past ten years while introducing a fresh suite of features. This farm is not just a refinement of our past models – it redefines what it means to be a farmer," said Freight Farms co-founder and COO Jon Friedman. "With the Greenery S, we hope to further simplify the process of farming to make the profession as accessible as possible to people around the world."
Industry-Leading Features for Design, Automation, and Performance
Of all the Greenery S features, the most notable are the re-imagined workspace, the enhanced farmhand® automation software, and the dynamic new proprietary LED technology.
All-New Workstation - User-Centric Design
As Freight Farms continues to define and refine what a farm can be, the company focuses specifically on optimizing workflow for their farmers with an all-new Workstation, a sleek, self-contained, and multi-functional farm command center.
Technical components – water and nutrient tanks, dosing panel, pumps – are hidden from view yet easily accessible with a simple push-to-open mechanism for instant access.
The 'Tabletop Riser' separates the workstation into two workzones, and includes an integrated, multi-functional LED bar (for tabletop illumination, plant spacing guidance, and task timing) and four full-range Bluetooth speakers.
Farmhand® Recipes - Network Learning & Automation
The latest release of Freight Farms' companion farming software–farmhand®–takes automation to the next level with the new Recipes feature.
Recipes allow farmers to achieve consistent harvests with the touch of a button: Operators simply choose the crop they wish to grow and farmhand automatically adjusts in-farm settings to optimize for that crop production.
Recipes are built by aggregating farmer network data and determining patterns that lead to exceptionally successful harvests; meaning the list of recipes will grow as the global Freight Farmer community continues to expand.
Dynamic Lighting Control - Power & Precision for Performance
The Greenery S takes a huge leap in LED technology by allowing farmers to customize the lighting spectrum, intensity, and duration of light to achieve their desired plant yields.
The Greenery S features Freight Farms' proprietary LEDs, which emit light with 60% greater intensity and 50% better efficiency compared to off-the-shelf options.
Farmers have precise control over their lights with brand new Eco (prioritizing farm efficiency by reducing power consumption), Performance (prioritizing plant growth for greater yields, and Standard (balances the two) modes.
The Most Versatile Platform in the Indoor Farming Industry
The accessibility and versatility of the Freight Farms platform allow customers to use it in a diverse range of locations and applications. The Greenery S is built with the same specifications as a standard 40-foot shipping container, making it possible to bring and install the farm in any location, such as a city center, tropical island, or area experiencing food insecurity. Once at its location, the 320 sq. ft. container becomes a commercial growing space, capable of producing 2.5 acres worth of fresh food every year. The farm's elite design, in combination with farmhand®, robust training, and access to an elite support team, ensures anyone can run a successful operation without any prior farming experience.
Freight Farms currently services more than 500 trained farmers across 48 U.S. states and more than 32 countries. For more information, visit freightfarms.com.
About Freight Farms:
In 2013, Freight Farms debuted the first vertical hydroponic farm built inside an intermodal shipping container with the mission of democratizing and decentralizing the local production of fresh, healthy food. Now with the Greenery S and integral IoT data platform, farmhand®, Freight Farms has the largest network of connected farms in the world, with global customers in 32 countries and 48 U.S. states ranging from entrepreneurs and small business farmers to corporate, hospitality, retail, education, and nonprofit sectors. To learn more, please visit freightfarms.com, or visit us on Instagram, Twitter, or Facebook.
Media Contact:
5WPR
Carinna Gano, Account Supervisor
cgano@5wpr.com
SOURCE Freight Farms
Related Links
USA: This Colorado Company Is Building Farms In Shipping Containers To Help Feed People In Need
FarmBox Foods wants people to be able to farm anywhere, allowing them to access fresh food they otherwise wouldn't be able to
Author: Jeremy Moore
April 19, 2021
FarmBox Foods Wants People To Be Able To Farm
Anywhere, Allowing Them To Access Fresh Food
They Otherwise Wouldn't Be Able To
SEDALIA, Colo. — A three-year-old Colorado company has an ambitious goal: to bring food security, safety, and sustainability to communities in need around the world.
FarmBox Foods aims to achieve that goal by connecting those communities to sustainably sourced food that's grown locally inside one of their container farms.
Their first product was a vertical hydroponic farm, or VHF, built inside a shipping container.
The company has since developed a second product: a gourmet mushroom farm, or GMF.
So far, customers in Colorado include Centura Health, Vitamin Cottage Natural Food Markets, and the C Lazy U Ranch in Granby.
FarmBox CEO Rusty Walker and COO Jake Savageau joined 9NEWS to talk about how they hope to change the way the world thinks about farming.
9NEWS also spoke with a prospective customer of FarmBox, Cori Hunt of the Denver restaurant group Edible Beats.
(Editor’s note: Responses have been edited for context and clarity.)
As a mission-driven company, what is the mission of FarmBox Foods?
Walker: Our goal and our mission is to get our products out into the communities where we can help develop food security programs. We’re looking to get into food deserts, opportunities where folks in the world might not have access to good, clean nutritional food. And so we kind of strive as a company that’s driven to feed the world one container at a time. And we’re ready to go out and manufacture thousands of these if we can.
We’re able to decentralize growing food by being mobile – being able to deploy these by just having a semi come in. We can then lift it up on a flatbed and take it to anywhere in the world. We’ve got two containers going to islands. We’ve got our first container that took off for the island of Jamaica. It’s going to Montego Bay where it’s going to be used behind mega marts on the island. And then we have another container which is our gourmet mushroom farm that’s going to be going to Tahiti where they’re going to be using that to feed the island population which does not have access to that type of food.
One big area that we’re really focusing on is the urban areas throughout the U.S. where they don’t have a lot of land to grow. These farms can go right into the parking lots, behind a church for example. We’re working with a community church on the south side of Chicago that’s looking at placing two of these containers – a vertical hydroponic farm and a mushroom farm – right outside in the parking lot outside the church.
And we think we could bring an educational spin to this where we can have the community grow their own food and supply the community themselves with highly nutritional food that ordinarily they just would not be able to get their hands on. So, we’re thinking that if this pilot program goes well this would be an application that would apply to every inner city throughout the U.S.
Farmbox Foods grows vegetables in shipping containers. Credit: Jeremy Moore, KUSA
Savageau: The mission’s always been to create products that are for the decentralized food insecurity industry. So, we want to create a product that can be deployed anywhere in the world, can run off-grid, and can feed communities. So, we have two different products – the VHF and the GMF. Every product that we develop gets us one step closer to being able to feed a community with everything they need, because you can’t feed communities forever just on leafy greens.
So mushrooms, they’re more nutrient dense, that gets us one step closer. There’s other products that we’re going to develop to get us to that point. But, I think the mission for the company is to be able to deploy these farms into communities where they’re needed, whether that’s a rural area, a food desert in the U.S., an inner city, or somewhere in Africa like Ghana or the Sudan.
We want to align with big ag and we want to help the industry get better. So we want to get food to where it’s needed. We’re looking at doing stuff with food insecurity and food inequality. That’s big with what we’re doing. So, that kind of aligns with our mission. If you look at our food system – just take for instance – you know if you look at a SNAP program or food subsidy program – you’re taking food and giving it to somebody or they’re purchasing it.
But, a lot of that food that they’re purchasing is processed, sugar – I mean, it’s poison. And if you go on a military base anywhere in the U.S., there’s fast food on the base. It’s really what you see. So, there’s a lot of reasons why we’re doing this I think. We can help fix our food system. And we can help educate the youth on how they should eat. We’re doing some stuff with an Inuit community in Alaska. They don’t necessarily know how to fix this food or prepare it or use it. So, I think education is a big part of what we’re doing.
How do these container farms work?
Savageau: When people think of farms, they don’t think of agriculture like this. Vertical hydroponics and indoor ag and controlled environments – it’s been around for a long time. I think that the way that this one works is pretty simple. The water gets fed into a tube system and the water trickles down and goes back into the tank. And where you’re standing – the seedling tray area – the water goes into a tank, into the seedling trays, gets flooded, and then back into the tank.
There’s a software that we use called Agrotech that monitors the temperature, the humidity, the lights – basically, all automated. So, it’s fairly easy to run. You need about 15 to 20 hours a week to run one farm. The GMF farms takes about 25 hours a week. It’s a little bit more intensive. The VHF is the vertical hydroponic farm and that’s the farm that we’re standing in. The GMF is the gourmet mushroom farm, which is the one that you went through earlier. You want to just keep things as clean as possible. The cleaner that you keep it the better it’s going to run.
So, we have a standard SOP, you know, that we implement with our training. Cleaning the floors. Cleaning the tubes. You don’t clean them every time. But, usually, every couple harvests you’ll take the tubes out, wash them out. You’re cleaning the tanks about every 60 days.
But, on average it’s pretty easy to maintain if you’re doing the daily checklist. The seeds are going to be in the seedling tray for about two weeks. Then, they go into the wall. And then they get harvested about 60 days after they start in the seedling tray. So, on average you’re about 60 days from seedling to harvest depending on what you’re growing.
And this farm is really setup for vertical hydroponics. So, it’s leafy greens. You can do hundreds of different types of lettuce. You can do cherry tomatoes, strawberries and peppers. There’s a lot of different things that you can grow in here. Most of our clients are only growing a couple things at one time. You don’t have to worry about weather. You don’t have to worry about if this is in a cold climate like the arctic. You know, they can’t grow food. If it’s in a desert, they can’t grow food. If it’s on an island, they can’t grow food. So, these can be deployed anywhere. And they grow 365, all day, every day. Also, the yield is very high for the square footage. So, you can put these on top of a building, inside of a building. It only takes up 320-square feet. You don’t have any pesticides. So, you don’t have to worry about pests, bugs, mildew, stuff like that’s going to effect the plant as it’s growing. It’s also decentralizing the food system.
So, you’re not having to ship food hundreds of thousands of miles from point A to point B. So, the food is right there. And the nutrients that we use are organic plant-based nutrients. And there’s no pesticides. So, the nutrient density is extremely high compared to something that you would buy – even organic – in a store.
Walker: We grow a variety of vegetables and lettuces. I believe that we’re somewhere in the area of 30 to 40 different types of vegetables and lettuces that we can grow in our farms. And, then of course we’ve got our gourmet mushroom farm which we’re currently growing anywhere from eight to nine different varieties of mushrooms. We’re in the startup phase of running that farm ourselves. So, we’re exploring the different types of mushrooms that we can grow. But, we’re very proud of the folks that are actually running these farms – our staff, very knowledgeable and they do a great job. We’re going upwards to 300 to 400 pounds a week now. We’re not competing with traditional farming. We’re actually a compliment.
Who are your customers?
Walker: One of our first customers is Centura Health. They purchased their first container – which is now sitting at St. Mary’s in Pueblo. They ordered two more containers after seeing how the first container behind their hospital worked. We actually started up a pilot program with Centura Health where we’re now running them as the FarmBox family.
We’re working with Centura Health in identifying not only their hospitals and the patients who are going to be fed through our vertical farm – but then we’re also identifying where the food deserts are and Centura Health will then help us with what we’re going to be growing, and then the communities that we’re going to be serving from those, those particular crops.
We do have a couple that’s looking at doing some farming right here in Sedalia. They’re going to use it to supplement their traditional farming, which will be an interesting pilot program for us to work with them on. We’re working with C Lazy U Ranch out of Granby, Colorado. They’ve ordered a hydroponic farm and we’re going to be manufacturing that. And they’re going to place that at the ranch. They don’t really have access to a lot of good food as far as having it grown right there on the property. So, this will be a nice compliment to the services and the customer experience that they provide their customers by having one of our farms right on site.
Centura Health is one of FarmBox Foods' first customers. Credit: Jeremy Moore, KUSA
One big area that we’re really focusing on is the urban areas throughout the U.S. where they don’t have a lot of land to grow. These farms can go right into the parking lots, behind a church for example. We’re working with a community church in the south side of Chicago that’s looking at – we’re looking at placing two of these containers – a vertical hydroponic farm and a mushroom farm right outside in the parking lot outside the church.
We can have the community grow their own food and supply the community themselves with highly nutritional food that ordinarily they just would not be able to get their hands on. So, we’re thinking that if this pilot program goes well this would be an application that would apply to every inner city throughout the United States.
Savageau: We have a customer here in Lakewood that’s going to put one in their backyard. They run a small organic farm. We’re looking all the way up into federal government and military, and everything in between.
So, Rusty was talking about FEMA, the UN, UNICEF, those are the big customers that take a long time to build a relationship with. And then we have customers that are all the way down to just an individual that wants one for their property or maybe a couple of people are going to run one for a restaurant or a developer wants one for a small development that he’s doing.
We’re working with a group in New Mexico and they’re building a huge development of about 45,000 houses. So, we’re talking about 100 of these units that are going to be deployed in that area right outside Albuquerque to feed those communities within that area over the course of about two years. We work with a grocer that’s regional. And we work with some other customers that are kind of at a government, federal government level.
I think we’ve done a lot in the last three years. I mean we haven’t gone out and raised any capitol. So, we’ve self-funded it. And I think from that point of view you know we’ve done a lot. We’re kind of at the point right now where we’re just starting to scale. So, we’ve just started our social media. You know SEO (search engine optimization), SEM (search engine marketing). We have a sales team. And orders are starting to come in. We’ve partnered with RK which is manufacturing our units. That’s giving us the ability to scale. Because before that we were building these one or two at a time in Sedalia and now we can build 100 of them. So, that’s really been a huge part of us being able to scale is the manufacturing side.
How much does it cost to purchase and operate the farms?
Jake: This VHF farm – vertical hydroponic farm – starts at $140,000. The GMF starts at $150,000. Then, you have training and deploy, getting it there. So, usually, you’re over $150,000 for a farm. So, your ROI (return on investment) in this product is going to be about 12 months to 24 months depending on what you’re growing and where it is in the world.
The GMF is going to be closer to 12 months because mushrooms tend to be more expensive – again – depending on where it’s going. We have a unit that’s going to Tahiti for example. That ROI is going to be extremely fast because they ship everything in. If there’s a market for mushrooms there, which there is with a grocer, it’s going to be quick. So, the cost of running it with labor and everything you need to grow the plants, usually around $20,000 to $40,000 a year. We’re a mission-driven company. So, money isn’t the first thing that’s important. We want to build a certain amount of these and then every x amount that we build, we build one for free and we send it to a community that maybe our social media has engaged with or given us an idea that ‘hey, this would be a good community.’ And then, we send it there. We pay for it. We train people. And that’s something that we want to do. We can’t do it yet. But, I think that’s coming in the next year.
Why is Edible Beats interested in working with FarmBox?
Hunt: We try to be as local and organic as possible and that’s what brought us here to FarmBox. We can put a box behind a restaurant and have lettuces cut and washed and put on the plate the next day.
Just to have that connection with our food and know exactly where it’s coming from and how it was produced. It’s going to be better quality because it’s not traveling. It’s not ripening in a truck coming from Mexico. Economically, what we can do to not pay the mileage on the vehicles and the gas, the inputs, the emissions, the extra packaging, the plastics.
That’s one of the best things about FarmBox – that what we can do is – if we produce food for our restaurant group – I’m not going to have to buy packaging that’s going to go into a landfill or even need to be recycled. It’ll go directly into the vessels that we’re going to store them in the cooler. We don’t have to worry about marketing and labeling and you know stickers and plastics and all this extra stuff – this hoopla that we don’t need – because FarmBox is a possibility now.
The Farmbox Foods containers allow leafy greens to grow vertically, maximizing space.
Credit: Jeremy Moore, KUSA
We are looking at lettuces and herbs, leafy greens. So yeah, like basils, sage, leaf lettuces, butter lettuces, arugula – these kinds of things that we use that could greatly help our impact. Essentially it’s a self-contained box that you can grow fruits and vegetables in – most likely leafy greens – and it’s a soilless or near soilless medium.
So, essentially you plant your seed in a very small amount of coconut core or soil or peat moss – something to hold the root structure – and that, according to with FarmBox, they’re system is a vertical farming.
So, they have vertical towers and then they put the lettuces in the towers in their small soil medium and then they drip water with enhanced nutrients mixed into the water specifically built for those vegetables. It doesn’t have a lot of soil waste.
For the amount of the surface area you can get way more production out of it and the water that goes through is recycled. Per plant, it uses far less water than any other type of growing system.
RELATED: Why Colorado agriculture groups oppose Initiative 16, an animal cruelty proposal
Foundation Farms Corp., Announces Vertical Farm Out For Delivery
The turnkey farm package has left the ZipGrow manufacturing facility for arrival at the Red Deer area site this week
April 20, 2021
NEW YORK, NY / ACCESSWIRE / April 20, 2021 / Foundation Farms, Corp., ("Foundation Farms") a subsidiary of GME Innotainment, Inc. (OTC PINK:GMEV) today announced confirmation of delivery and installation dates for the first of its many vertical farms. The turnkey farm package has left the ZipGrow manufacturing facility for arrival at the Red Deer area site this week. The installation crew is scheduled to arrive on-site next Monday and assembly and commissioning will be completed next week. Production of the first crop will begin on May 1.
Management is also excited to report that each of the company's vertical farms will become local community food hubs known as E-ROOTS CENTRES. In addition to selling its own vertical farm produce, each E-ROOTS CENTRE will buy other locally grown food products from farmers wholesale and then package, market, and distribute the locally grown food products to corporations, families, schools, restaurants, caterers, sports teams, and stores, maintaining economic growth in the community. These E-ROOTS CENTRES will develop health food brands utilizing local produce to promote nutritious diets. Mechanisms for dispatch and delivery logistics are included.
Ed Kroeker, CEO of Foundation Farms stated, "The installation and startup of our first E-ROOTS CENTRE is a wonderful milestone achievement but what I am even more excited about is the interest we are getting throughout North America from prospective joint venture partners and host communities. Demand is even greater than we anticipated. Projects are aggressively underway in Minneapolis-our important entry point for the United States as well as Regina, the Greater Vancouver Region, and the Greater Toronto Area, with the list of projects growing weekly."
Yves R. Michel, GMEV CEO applauded the milestone achievement this week and further added, "Food sustainability and reliability have become two of the most important goals within North American communities today. Foundation Farms has developed a business strategy that provides the components as well as the assembly, packaging, and distribution systems to achieve those goals in every community serviced by E-ROOTS CENTRES."
Yves R. Michel
Chief Executive Officer and Director
208 East 51st St., Suite 170
New York, NY 10022
Source: GME Innotainment, Inc. ("GMEV")
www.srcorpgroup.com/
Released April 20, 2021
OTCPink:GMEV
This press release may include certain statements that are forward-looking in nature and that involve a number of uncertainties and risks. Such forward-looking statements are within the meaning of that term in Section 27A of the Securities Act of 1933, as amended, and Section 21E of the Securities Exchange Act of 1934, as amended. The forward-looking statements in this press release are based on GME Innotainment, Inc., current expectations and projections regarding future events, which are based on currently available information. The forward-looking statements in this press release may also include statements relating to GME Innotainment, Inc.'s anticipated new developments, business prospects, financial performance, strategies and similar matters. GME Innotainment, Inc. disclaims any obligation to update any of its forward-looking statements, except as may be required by law.
SOURCE: GME Innotainment, Inc.
GME Innotainment, Inc.
USA: New Farm Brings Sustainable Farming To Northern Michigan
There's a new farm in northern Michigan that provides fresh and local produce all-year-round using environmentally friendly practices and high-tech resources. The container is home to Pine Hill Farms, a farm that uses a controlled environment agriculture system to grow produce
by Miya Ingle
April 16, 2021
To View The Video, Please Click Here:
Pine Hill Farms uses a controlled environment agriculture system to grow produce. (Miya Ingle/ WPBN)
KALKASKA COUNTY, Mich., (WPBN/WGTU) -- There's a new farm in northern Michigan that provides fresh and local produce all-year-round using environmentally friendly practices and high-tech resources.
If you're driving down Tower Road in Kalkaska, you might notice a big container.
The container is home to Pine Hill Farms, a farm that uses a controlled environment agriculture system to grow produce.
The produce is grown hydroponically instead of in the ground.
Staff at Pine Hill Farms say this growing method uses 95% fewer resources than traditional farming.
"Some of the biggest benefits to growing hydroponically versus in a traditional manner is number one; we can grow year-round, 365 days a year," Pine Hill Farms Founder Jeff Bickley said. "Number two, we're hyperlocal. Local is a really big deal. People want to support local businesses. They also benefit from the difference in freshness."
Pine Hill Farms is currently growing nine different kinds of lettuce but plans to expand its products in the future.
The farm is connecting with local restaurants to sell its produce to.
CANADA (YT): Tackling Food Insecurity Above The 60th Parallel
ColdAcre Food Systems is based in Whitehorse, Yukon, one of the northernmost provinces in Canada. The company was incorporated in August 2019 and specializes in controlled environment agriculture.
In the northernmost territories of Canada, agricultural development is underway but must contend with the cold climate, variable photoperiod and other environmental challenges. It comes as little surprise, then, that interest in controlled environment agriculture is on the rise. ColdAcre Food Systems is one of the companies that supports this endeavor and has installed multiple growing systems in northwestern Canada.
ColdAcre Food Systems is based in Whitehorse, Yukon, one of the northernmost provinces in Canada. The company was incorporated in August 2019 and specializes in controlled environment agriculture. Prior to its incorporation, ColdAcre primarily sold retrofitted shipping containers and also operated its own container farm to supply the Whitehorse market with fresh greens and herbs.
According to chief executive officer Carl Burgess, “the original intent was to sell and provide growing systems but we immediately identified an opportunity and a need to demonstrate commercial production north of the 60th parallel year-round.”
With its incorporation in 2019, ColdAcre thus based itself on four pillars:
Growing produce for the Whitehorse market and beyond
Selling prefabricated and custom growing systems for its clients
Providing consultation and pathfinding services
Active learning and engagement in various projects.
Growing produce for the Whitehorse market
When ColdAcre first began producing greens and herbs, the company started with three dozen products but have since narrowed its product line in order to have a robust supply and client demand. ColdAcre has also recently begun producing mushrooms. Explaining the Yukon’s consumer base, Carl says that the territory is the size of Spain yet is home to only 40,000 people. Whitehorse is the territory’s capital and its businesses service much of the territory, as well as southern Alaska, northern British Columbia and the western Northwest Territories.
As such, Whitehorse acts as an important hub for northern residents and has a relatively robust food demand. According to Carl, “some people drive 1,000 km to buy goods and groceries in Whitehorse a few times a year. That said, the Yukon only produces 1% of the food that is purchased and consumed in the territory.”
Importing most of its consumables carries the double burden of a heavy carbon footprint and limited nutritional quality. “When comparing the quality of fresh produce between Vancouver and Whitehorse, there is a significantly lower quality in the Yukon, which is only heightened when you go further north. Producing locally also virtually eliminates waste and the carbon footprint of production,” says Carl.
Selling growing systems
ColdAcre also continues to sell prefabricated and custom growing systems for clients through Canada’s northwestern region. While the company began with CropBox and has had success doing so, ColdAcre has found that its clients typically require more customization. Moreover, working with an American company has subjected ColdAcre to a higher degree of volatility with respect to changes in the dollar and availability of equipment, according to Carl.
With respect to its technology, Carl also explained that ColdAcre’s technology “is not necessarily unique, but that the skillset and assembly is. In the Yukon, we face the challenge of growing lettuce when it’s 40°C outside in the summer or down to -53°C. We address these extremes using high-tech and smart-tech solutions. We customize the whole management and contingency for potential crises specific to a client or area.”
Consultation and active learning
ColdAcre has also committed to providing consultation and pathfinding services to growers regardless of whether the grower is using a ColdAcre system or not. As Carl explains, “we think that our growing challenge are everyone’s challenges so if we can solve ours, we’d like to share.”
ColdAcre also has multiple research partners throughout northern Canada and while the projects are generally northern-based, the results have applications in various settings.
2020 and 2021 at a glance
In all four pillars, ColdAcre has reported increased interest in the past year. The fragility of Yukon’s food system was heightened by the COVID-19 pandemic and ensuing supply chain disruptions. As such, the interest in local food production and stabilized food system has surged in the territory. ColdAcre’s production has been sold out since October 2019 and the company will be tripling its production in the coming months. According to Carl, ColdAcre’s proximity to market channels allows the company to compete with imported commodities from California and Mexico and demand a reasonable premium. Similarly, the company is reportedly experiencing an increased demand for its systems for residential, office, and educational purposes.
Most recently, ColdAcre shipped a 53-foot container farm to Inuvik, a community in the Arctic Circle and whose community greenhouse will use the shipping container to produce fresh produce year-round.
For more information:
Carl Burgess, CEO
ColdAcre
carl@coldacre.ca
www.coldacre.ca
Publication date: Fri 9 Apr 2021
Author: Rebekka Boekhout
© VerticalFarmDaily.com
USA: Local Farm Brings Hope To Food Desert
A hydroponic produce farm in Indianapolis is filling a need in food deserts around the city. Food deserts are areas where grocery stores aren’t easily accessible. More than 200,000 people live in food deserts in Indy, according to a study published by SAVI
Q&A: Mario Vitalis
April 13, 2021
Mario Vitalis, farmer, owner, and founder of New Age Provisions, holds plants grown on his farm.
INDIANAPOLIS — A hydroponic produce farm in Indianapolis is filling a need in food deserts around the city.
Food deserts are areas where grocery stores aren’t easily accessible. More than 200,000 people live in food deserts in Indy, according to a study published by SAVI.
Mario Vitalis, farmer, owner, and founder of New Age Provisions farm, uses advanced hydroponics and vertical planting to grow year-round.
It all starts inside a shipping container on an old car lot on East 10th Street. A step inside transports visitors to a lush, green garden of produce. A variety of herbs, leafy greens, microgreens, and hemp are grown inside.
The location allows Vitalis to provide fresh produce to the community, one of the city’s many food deserts. The farm also provides produce to restaurants in Indianapolis.
“I’ve always known the city life — but there is a nagging desire to get back to my roots,” Vitalis said. “As an African American, my roots made it from slaves in the field, to sharecroppers in the South, to farming in the city.
“As a descendent of slaves, this farm enables me to get back to the type of living where our people once lived off the land. Having an urban farm allows me to connect to a long history of farming that has been forgotten.”
Vitalis shared his story with AgriNews.
Tell me a little bit about your farm.
“We are a hydroponic commercial farm. We officially started farming in August 2020.”
What was your inspiration to grow things?
“I wanted to be involved in agriculture, to be able to provide fresh food to the community independent of the supply chain, and independent of herbicides, pesticides, and contaminants.”
Indiana has several food deserts. Did that inspire you to fill a need in the community?
“Yes, it did. It provides us with the equipment to do so, as well. We’re the first company in Indiana to own this piece of equipment, the Freight Farms Greenery. We’re currently the only African American owner of the equipment. We want to be able to provide food and also provide a new way of farming. We want people to see it and have access to it.”
How does the farming system work?
“It’s called a Greenery and it’s built by Freight Farms, based in Boston. It’s essentially a hydroponic farming system in a 40-foot shipping container. If you can imagine those shipping containers that go up and down the highway, you go inside of one of these and grow vegetables. It has everything you need to do that. It has a seedling table and growth tower with different types of hydroponic methods.”
Basil grows at a hydroponic produce farm in Indianapolis.
What are some of the features of the technology?
“It has its own dosing system to control nutrients. You can control humidity, temperature and pH levels. You can check your settings and programming on a computer. There’s an app that goes with it, as well. So, you can control your farm from your phone. The technology is state of the art.”
What are some of the challenges you’ve faced as a new farmer?
“I think the biggest challenge is developing a market and getting our name out there. There’s also a learning curve to farming. I didn’t have any experience. So, I had to learn what to do and how to operate.”
What do you enjoy most about growing things?
“Seeing the plant life cycle from seed to seedling into a full plant. I also enjoy the environment. Since we’re in an enclosed environment, we can grow year-round and it’s always 65 degrees.”
Do you have any advice for minorities interested in farming?
“Right now there are so few minority farmers in general. For African American farmers, the best thing they can do is get land and find ways to cultivate the land or make use of it. Good land is becoming a scarce resource. If they’re interested in farming, there’s funding available from USDA for Black and minority farmers. There are different avenues out there. But it all starts with land and a business plan. After that you just have to have motivation and knowledge to do it.”
Anything else you’d like to share about your farm?
“Our farm is local on the east side of Indianapolis. We grow hydroponically without herbicides, pesticides or contaminants.”
How can people purchase your products?
“They can go online to our website www.newageprovisions.com. We deliver. Or, you can purchase through Market Wagon or Hoosier Harvest Market.”
How Square Roots Is Training Next-Gen Farmers During A Pandemic
The average age of the American farmer is 58 years old. If we're going to change the food system, we need to create more pathways for young people to launch successful careers in agriculture
Square Roots
10.08.20
The average age of the American farmer is 58 years old. If we're going to change the food system, we need to create more pathways for young people to launch successful careers in agriculture.
One of the many ways Square Roots invests in the future of farming is through our Next-Gen Farmer Training Program—aimed at new farmers or those at early stages in their careers. Farmers initially join Square Roots as Apprentice Growers. Through our proprietary training methodology—supported by our intuitive technology platform—Apprentice Growers rapidly learn the essential farm skills needed to move into permanent roles on the farm team and accelerate their careers.
We continuously evolve our training program to zero in on the skills and experiences that help employees become the best indoor farmers they can be. Throughout COVID-19, we have been committed to prioritizing people safety and plant safety which has led to changes in our day-to-day farming operations, as well as rewiring our in-flight farmer training programs in May and adapting how we run the Square Roots Next-Gen Farmer Training Program going forward. Also, after several years of training farmers, we’ve listened and learned to what farmers value from their experience at Square Roots and have incorporated that into our program going forward. Read more about what it’s like to be a grower at Square Roots and how the program has evolved:
Individual Pathways
Based on the needs of our farm production teams, apprentices are hired and onboarded, either individually or in pairs, on a rolling basis. By spacing out onboarding and training, our team is able to provide more attention and support to apprentices, allowing them to move more quickly through the training program and into permanent positions on our team. We expect most apprentices will complete their training in three to six months, but each will advance at their own pace.
Foundational Remote Learning
We have moved our training materials onto a virtual learning platform, which houses videos, interactive presentations, animated diagrams, virtual tours, and other types of content that can be brought to life beyond a typical presentation. Since COVID-19 restricts our ability to hold classroom-style learning, online learning can be self-serve, supporting different types of learning styles. It also drives consistency in training and terminology, reducing the burden on managers responsible for administering it.
Intensive ‘Boot-Camp’ Style Farm Immersion
Training for Apprentice Growers is laser focused on the skills required for new farmers to quickly become the best indoor farmers they can be. After the initial foundational onboarding, apprentices will jump into production, and, in parallel, will be equipped with the necessary context and complementary training to support expanded learning and competency much sooner. Apprentices will be supported by our software operating system the Farmer Toolbelt, empowering them to get up to speed much faster, engaging with data, and ultimately helping them become better growers. Throughout the training process, farmers will receive direct supervision by one of our experienced farm team members who will act as their training guide and provide professional and moral support.
Pathway to Permanent Employment at Square Roots
Central to Square Roots is our mission to empower Next-Gen leaders in urban farming, and the Next-Gen Farmer Training Program is one of the most direct ways we do that. The program is designed to bring young people with little or no experience up to speed in our proprietary indoor farms as quickly as possible and on to their careers in indoor farming—acting as an internal training program for permanent full-time employees on the Square Roots farm team.
The Apprentice Grower role is the first step in a career path to indoor farming at Square Roots. To start, apprentices will earn an hourly rate indexed to the area’s living wage, and receive 100% covered health benefits and equity in Square Roots. Once they’ve successfully mastered indoor growing fundamentals (we expect this to take three to six months), apprentices will be eligible to move into Associate Grower positions.
For more information and to learn about new open positions on our farm teams, follow us on social media and sign up for our newsletter for updates.
Tags: Next-Gen Farm / Farmer Training / COVID-19 Response / Updates