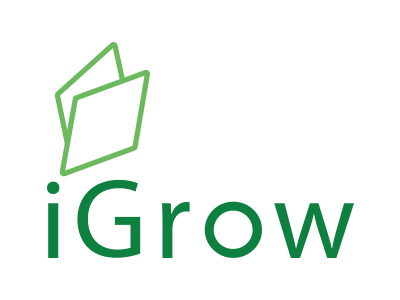
Welcome to iGrow News, Your Source for the World of Indoor Vertical Farming
Farms in the City: How a Chinese Firm Uses Tech to Boost Yield
In suburban Beijing, a number of plant factories built with innovative techniques have incorporated farming into urban growth.
By Feng Yilei
2018-12-01 08:01 GMT+8
Updated 2018-12-01 09:06 GMT+8
An appetite for clean, fresh greens is growing with the burgeoning population in Chinese cities and towns. But feeding the rising demand is a challenge, partly because of the country's massive shift from being an agrarian to urban economy.
In the next 15 years, over 200 million Chinese are expected to move from rural areas into urban and suburban environments. This will greatly reduce the labor force on China's arable lands, which some say calls for a revolution in farming methods in order to create sustainable food production.
Beijing COFCO wisdom farm. /COFCO Photo
In suburban Beijing, a number of plant factories built with innovative techniques have incorporated farming into urban growth.
Dr. Wei Lingling, a researcher at the Chinese Academy of Agricultural Sciences, said controlled environmental agriculture (CEA) aims to get the most output with the least resources at the highest efficiency. They use technology like artificial intelligence (AI) and the Internet of Things (IoT) to precisely control production.
On a small plot of indoor space, plants are rooted on layered shelves vertically and bathe in light continuously during the day. Sensors linked to automatic irrigation and temperature control systems provide optimal conditions for growing.
Planned production means a higher yield resource-wise, space optimization, and labor savings. Dr. Wei believes CEA technologies will be more accurate in the future to better balance cultivation and the environment with less energy consumption.
“And in this closed production system, we circulate water and fertilizer to cut emissions, and improve sustainability of agriculture,” she added.
Plant factory using artificial light. /VCG Photo
While many believe this industrialized and intelligent way of farming will gradually replace extensive farming, which relies heavily on manual work and land usage for mass production, ordinary Chinese may have to accept difficulties in their daily lives during the process of moving on to the next stage.
For individual farmers that own the country's hundreds of millions of small plots, some have temporarily transferred their leaseholds to these high-tech farms and are adapting to their new roles.
Villager Wang Xiangang said that he got paid for both his land and working on the farm as an employee meaning he no longer worries about natural disasters and has time to learn about organic farming. He doesn't make as much as he used to, but it is stable.
And when conditions are ripe – will consumers be ready to pay a higher price for the products? Experts say the public will recognize the value of these crops as awareness of food safety and environmental stewardship rises. And once the demand rises, more players are expected to use tech-based food production, which will drive down prices.
Danone Among Backers of French Urban Farming Start-Up Agricool
French urban agriculture start-up Agricool has secured $28 million in its latest funding round, including an investment from Danone’s investment arm, Danone Manifesto Ventures.
Posted By: Contributor on: December 07, 2018
French urban agriculture start-up Agricool has secured $28 million in its latest funding round, including an investment from Danone’s investment arm, Danone Manifesto Ventures.
In the past three years, Agricool has developed a technology to grow local fruits and vegetables more productively and within small and controlled spaces, known as ‘Cooltainers’ (recycled shipping containers transformed into urban farms).
The Paris-based business said it is responding to reports which suggest that by 2030 20% of products consumed worldwide will come from urban farming – compared to 5% today.
Other investors in the round – which adds to $13 million previously raised – include Bpifrance Large Venture Fund, Antoine Arnault via Marbeuf Capital, Solomon Hykes and a dozen other backers.
With the new funding, Agricool aims to position itself as a key player in the vertical farming sector. The start-up hopes to multiply its production by 100 by 2021, in Paris first, then internationally, starting in Dubai, where a container has already been installed in The Sustainable City.
Agricool said that its challenge, and that of urban farming, is to help develop the production of food for a growing urban population which wants to eat quality produce, while limiting the ecological impact of its consumption.
In a statement, the start-up said: “Agricool strawberries are harvested when perfectly ripe and contain on average 20% more sugar and 30% more vitamin C than supermarket strawberries.
“The production technique makes for strawberries which require 90% less water to grow compared to traditional agriculture, with zero pesticides, and a reduced transportation distance reduced to only a few kilometers between the place of production and point of sale.”
Agricool co-founder and CEO Guillaume Fourdinier said: “We are very excited about the idea of supporting urban farming towards massive development, and it will soon no longer be a luxury to eat exceptional fruits and vegetables in the city.”
Agricool Is 'Growing Food In The Cities Where You Live'
Agricool grows fruit in shipping containers in urban areas
Alex LedsomContributor
Agricool is a Parisian startup on a mission to grow delicious strawberries in inner city areas, at scale and for profit, which can be transported ‘from field to fork’ in just 20 km. What’s more, it’s a sustainable business that be replicated worldwide.
Agricool grows fruit in shipping containers in urban areasAGRICOOL
Agricool grows its strawberries in shipping containers using vertical farming methods; this is where food is grown in vertical shelves or on walls, to maximise the surface area used for cultivation. Founders Guillaume Fourdinier and Gonzague Gru are the sons of farmers from the north of France. As CEO Fourdinier explains, he arrived in Paris at age 20 and it wasn’t long before he was seriously missing ‘quality fruit and vegetables’ from the countryside. Strawberries are notoriously challenging to grow well, he says; they are fragile with a growing cycle and post-harvesting process which can be difficult to manage. Also, with increased urbanisation, more and more food is transported into city areas pumped with pollutants to ensure they survive the journey which usually means they are less tasty. He is convinced that ‘strawberries have got lost in the last 30 years’.
Founders Guillaume Fourdinier and Gonzague GruAGRICOOL
And so the two partners began to see if it was possible to find a way to harvest the highest quality strawberries under urban conditions. Fourdinier is keen to point out that this business didn’t start as a shipping container business — the idea to use containers was much more practical and organic. They had previously used containers on their families’ farms and once they had used up all the room in their apartment, it was ‘the easiest room to find’ and highly functional because the size is standardised, you can transport it easily, and you can scale up profitably.
The inside of a cooltainerAGRICOOL
Growing strawberries in containers is an incredibly technical process with an extraordinary amount of factors to control. The fruit has a three-month cycle; two months from the day of planting to the first harvest, and then there is one month where the fruit can be harvested every day. Climate-wise, the temperature, air humidity and carbon dioxide must all be varied in quantity over the course of the three-month cycle. Agricool uses a closed-loop water system, meaning that they fill a tank for three months and use the same water over that period, which uses 99% less water. When strawberries are grown in a field, they are planted in soil where the roots soak up moisture. Agricool uses aeroponics instead of a soil-based system, where the plants’ roots are directly exposed to the air, taking in moisture from mist sprays. Agricool doesn’t aim for having a completely bacteria-free environment — believing this to be impossible, it grows its own ‘friendly’ bacteria, putting ‘friendly fungi in the water and friendly insects into the containers’, to protect against the risk of damaging insects finding a way inside. In this sense, the containers grow their own antibodies. Finally, the lighting is key. Agricool uses LED lights, not just to regulate the intensity of light but also the spectrum of light that the strawberries receive. Fourdinier says that one of the biggest challenges for vertical farming is to get this intensity just right. And never mind the calculations for the number of bees in bee boxes required for pollination... The one drawback always levelled at vertical farming is the amount of energy it consumes but Agricool counter this argument by using renewable energy. They believe it is better to grow food locally in large cities with artificial lighting rather than transporting produce from far away, where it loses its taste and chalks up the food miles.
Harvesting strawberriesAGRICOOL
The business model is to sell directly to the customer, without a middleman and this strategy appears to be working; French customers have been abandoning poorer quality fruit and vegetables sold in some French supermarkets, and so chains have been very receptive to Agricool’s new agricultural model. The company produced its first box of strawberries in October 2015 and now have over 60 staff.
The strawberries look like artAGRICOOL
Funding came in two funding rounds from European venture capitalists. Its CEO adds that it isn’t possible to be profitable if you are not vertically integrated; that is to say, you must own and produce the products you use in your supply chain. And this has been where the real challenge lies, as to develop the best possible LED light for its containers, in the most profitable way, Agricool has had to develop its own technology. They now design and manufacture their own LEDs, which are three times more efficient for their lighting needs at the energy spectrum they require than other LEDs they could find.
A cooltainer in Bercy, ParisAGRICOOL
Urban vertical farming is incredibly on-trend. Just like like the mushroom farms in New York, people are turning to more sustainable farming in urban areas for the quality and ethos but also the urban aesthetic — under the luminous lights, this fruit looks more and more like art. The difference between Agricool and its competitors is that it believes it has the recipe to scale up. Fourdinier explains,
Indeed, Agricool already operates a container in Dubai from its French headquarters.
The end result AGRICOOL
The downsides are really the same as the upsides in that the opportunities are immense but the technology makes each stage a huge challenge. It isn’t a straightforward business; a truth highlighted by the fact that 70% of its staff are in R&D.
The harvest AGRICOOL
And the statistics are impressive for this startup aiming to ‘feed the cities of tomorrow’. Its strawberries have 30% more vitamins than conventional strawberries and contain 20% more sugar. Its containers can yield 10 times as much as a greenhouse and 120 times as much as a field. And while Agricool is keen to point out that farming today is mostly woods and rice, which are difficult to grow vertically at the moment, it believes in 30 years time, about 30% of what we grow will be farmed in cities, for cities. Today Agricool sells about 200kg of strawberries each week but in one years' time, they expect this to be 2,000kg, ten times as much. As Agricool begins to branch out into tomatoes, which are similar in complexity to strawberries, its slogan ‘we grow food where you live’ has never been more true or more deliciously tempting.
Propagating Floriculture Crops Under Sole-Source Lighting
This production method allows growers to strictly control the growing climate to best meet the needs of a given plant throughout the day.
September 18, 2018
Leontiene van Genuchten
In the last 10 years, many companies have sprung up to grow herbs and greens in climate-controlled vertical farm or city farm facilities which are daylight-free. As a plant specialist for floriculture with Signify(formerly known as Philips Lighting), I’ve watched these developments with great interest. But I have wondered if a vertical farm can also benefit cultivation of young plants from floriculture crops.
Cultivating floriculture crops without daylight
Growing plants under daylight is the standard practice in conventional greenhouses. But as the popularity of vertical farms has increased, we as plant specialists have been asking ourselves if it is possible to grow floriculture crops without the influence of daylight. Why would growers want to do this? In a greenhouse, the sun affects both the amount of light that the plant receives as well as the temperature and humidity of the growing environment. A controlled environment removes the influence of daylight on the plant’s growth. This would allow growers to strictly control the growing climate to best meet the needs of each plant throughout the day.
Cultivating in a controlled environment also allows growers to optimize other factors, like plant quality and growth speed, and reduce water usage. Since fewer diseases and bacteria come into the controlled environment, vertical farming can also help stop the use of insecticides and fungicides.
Set-up of floriculture trial
These benefits prompted us to conduct a floriculture trial in our climate-controlled test facility at BrightBox in Venlo, The Netherlands. Most of the requests we receive are from growers of young plants, so we ran a trial on the propagation phase of flowers. We chose a wide range of annual and perennial plants, including begonias, petunias, calibrachoas, dianthus, gerberas, celosias, alternatheras and impatiens.
For this trial, we translated the cultivation conditions of a greenhouse to a climate-controlled environment and added the experience of our colleague City Farm plant specialists. Light levels were chosen based on the reference greenhouse environment with daylight, as well as scientific literature and the experience of growers. The light spectra used in the test were aligned with a number of growers to meet their quality standards for the different varieties of flowers. Growth speed is one requirement from growers, but good plant quality is the first priority. In this case, a plant is considered good if it has a compact shape, enough leaves and branches and a good root system. In addition, a good plant should be able to quickly establish roots and bloom as it moves to its next growth phases.
By drawing upon our experiences and the scientific literature we were able to extract enough insights to develop light recipes that would produce these plant characteristics. For example, many plants react to a higher amount of blue light by becoming more compact. The length of the internodes becomes shorter. Some plants benefit from far red light by germinating faster and developing stronger roots, while other react by bolting and drooping.
Read the results of our trial on the Philips horticulture blog
Leontiene van Genuchten is plant specialist at Signify (formerly known as Philips Lighting).
5 Steps For Setting Up A Valuable LED Lighting Trial
2018
Philips Lighting
76% of growers growing under LEDs agree that LEDs have improved the quality of crops at their location
If you’re thinking about taking the first step with LEDs, the process can seem daunting. There are so many claims and so much information being shared that you may find it difficult to wade through the information with confidence and true understanding.
The reality is that LED technology is here, and regardless of the crops you grow, it’s time to begin seriously thinking about and preparing for the eventual transition to LEDs that will take place in your greenhouse operation.
You can begin the transition by starting with a small trial area in your greenhouse operation. As with other processes in the greenhouse, it isn’t quite as intimidating when broken down into smaller, more manageable steps. Follow these five steps to set up this trial area.
Step 1: Identify your challenge.
Some crops have higher values, meaning they generate more revenue or higher margins, than others. It could be that there is a high demand for a specific crop or that a crop brings in higher margins but presents some unique challenges when growing. Consider the following factors when selecting the crop/cultivar for your trial:
Production volume
Economics of production
Propagation challenges
Step 2: Determine a location to set up your trial.
Select a location in your greenhouse, ideally in a typical growing area. To get an appropriate sample size and maintain environmental conditions, it is recommended that the trial area for plug trays be approximately 1,000 to 1,500 square feet. If you’re conducting a lighting trial over potted plants, a larger space may be required.
Step 3. Set up comparative lighting scenarios.
You’ll want to work with a lighting supplier to determine the best way to set up a trial that allows you to compare your current lighting situation to a new lighting scenario.
Start by measuring the inside light levels of your current lighting and compare them to the daily light integral (DLI) for optimal growth of the crop being grown in the trial. This will help you determine if part of the lighting trial is to track the results of delivering increased light levels, or if the trial is to see the results of growing under a different spectrum. You want to see the effect of more light as well as understand the crop response to the focused red and blue spectrum of LEDs.
Step 4. Track the results.
Plan to track the data to not only document the effect on crop growth but also to understand how other crop inputs are affected by the LED lighting. Note adjustments that are made. It is recommended that measurements or data be recorded once a week. (See chart.) Be sure to have the same person measure and record the data at the same time every week during the trial.
Also, take side-by-side photographs of the crops to capture the difference in rooting, basal branching, coloration, speed of flowering, etc.
Step 5. Review the trial results
Let the results inform your decision. Did you see an uptick in the fill rate? Did you note faster flowering? Were you able to decrease the application of PGRs? Once the improvement in crop growth is translated into quantitative and/or qualitative results, you can then calculate the true ROI of an LED installation. This information will help you develop a plan for converting to energy-efficient LED lighting.
Check out this video of John Bonner, owner of Great Lakes Growers, explaining how he conducted a trial to compare and evaluate growing lettuce under HPS to growing under LEDs.
Ready to give LEDs a try? Contact a certified Philips LED horti partner to get started. Learn more about Philips horticulture products.
Container Farms: A New Type of Agriculture
Innovators within the produce industry are breaking the boundaries of food production
August 20, 2018 6:00 AM, EDT
Innovators within the produce industry are breaking the boundaries of food production — by growing crops not in fields, but in recycled shipping containers.
This modern twist on farming is designed to bypass some of the challenges and restrictions that farmers traditionally have faced, such as extreme weather, pests and limited growing seasons.
By overcoming these limitations, farming operations are capable of producing more food and growing certain crops in regions that otherwise would have had to import them.
By growing this food locally, suppliers are able to cut out the long travel distances often necessary to transport these foods to certain markets.
According to Jeff Moore, vice president of sales at produce supplier Tom Lange Co., shorter travel distances provide numerous benefits, such as fresher product, reduced transportation costs, less waste and fewer empty shelves at markets.
The use of innovative farming methods also is being pushed in Canada. Grocery retailer Loblaw Companies Ltd. announced plans to spend $150 million more each year with Canadian farmers by 2025. As part of that effort, the company pledged to help farmers implement growing techniques that will enable them to produce fruits and vegetables in Canada that the country has traditionally imported.
Freight Farms and Tiger Corner Farms are two companies that are growing produce in shipping containers through the use of hydroponics and aeroponics — methods of growing plants without the use of soil.
Freight Farms is working with NASA to find ways to grow produce in space. (Freight Farms)
Both companies use nutrient-rich water as a substitute for soil, but beyond that, their container farms are quite different.
Tiger Corner Farms’ farming units consist of five shipping containers; four are used for farming and the fifth one is used as a working station where the plants germinate and as a post-harvest station.
Tiger Corner Farms, based out of Summerville, S.C., is a family company that began with the combined interest of Stefanie Swackhamer, the general manager, and her dad, Don Taylor.
Through Grow Food Carolina, a nonprofit organization focused on preserving farming in South Carolina, Tiger Corner Farms has partnered with two other companies: Vertical Roots and Boxcar Central. Tiger Corner Farms manufactures farming units from recycled shipping containers, Boxcar Central works on the automation of the hardware and software used for these container farms, and Vertical Roots deals with the production of the produce.
With Tiger Corner Farms’ shipping container farms, Vertical Roots can increase food production. Having 13 farms in total, Vertical Roots is able to produce about 40,000 heads of lettuce in about half the time it would take a traditional farm.
Vertical Roots sells its produce to grocery stores such as Whole Foods and Harris Teeter.
Vertical Roots says it can produce 40,000 heads of lettuce in about half the time of a traditional farm. (Tiger Corner Farms)
For Vertical Roots, founded by Andrew Hare and Matt Daniels, working with Tiger Corner Farms was a no-brainer.
“Providing cleaner, fresher, better access to food was something all four of us were wanting to do. They wanted to provide jobs and educate people on the importance of sustainable agriculture, and we wanted to do the same thing,” said Hare, Vertical Roots’ general manager. “We wanted to bring transparency and education and empowering our community in knowing where their food comes from and how important the freshness and quality is.”
Meanwhile, Boston-based Freight Farms offers a hydroponic “farm in a box,” dubbed the Leafy Green Machine, built entirely inside a single 40-foot shipping container.
The company, founded in 2010 by Brad McNamara and Jon Friedman, also offers a farming service and mobile app, Farmhand, to aid farmers in monitoring their farms.
Freight Farms’ customers range from individual farmers to universities and corporations.
One of those customers is Kim Curren of Shaggy Bear Farm in Bozeman, Mont., which provides local restaurants with leafy greens that aren’t grown in the region.
Someday, hydroponic farming might even play a role in space exploration and colonization.
Freight Farms is working with NASA and Clemson University to improve the efficiency of its farming units in the hopes of eventually using them in space.
Joshua Summers is one of the professors at Clemson that worked on the project. Professors Cameron Turner and John Wagner and students Doug Chickarello, Malena Agyemang and Amaninder Singh Gill also worked on the project.
Lettuce grows inside a climate-controlled container farm from Tiger Corner Farms. (Tiger Corner Farms)
In order to enable the farming units to work in space, the Clemson team is focusing on making it a closed-loop system by looking at thermal and electrical loads of the LED lights as well as the heating, ventilation and air conditioning unit.
While working on this project, there is one major issue that Summers said needs to be taken into consideration.
“One of the major issues in moving into space is gravity. As you move away from gravity, a lot of their growing patterns are based on plants growing in a specific way,” Summers said. “Now you don’t know exactly how they are going to grow, so it’s going to be a bit more random, so we have to change some of the geometric layout to make it more efficient in terms of volume.”
Clemson, NASA and Freight Farms are working on a new proposal to continue this project.
Through its work with individual farmers as well as organizations such as NASA, Freight Farms is taking steps toward its goal of empowering anyone to grow food anywhere.
Farm in a Box
Local agricultural technology may change the way we eat
(Clockwise from top left) A lighting system nurtures infant greens; Tiger Corner Farms general manager Stefanie Swackhamer and her dad, AmplifiedAg CEO Don Taylor; green oak lettuce, nearly ready to harvest.
For conscientious eaters, the holy trinity of organic, local, and in-season can be difficult to come by. Leafy greens, in particular, are tricky to grow in the Lowcountry, and thus tough for the likes of schools and grocers to obtain. Local start-up Tiger Corner Farms has a solution: aeroponic farms built inside shipping containers, where humidity, light, nutrients, and carbon dioxide levels can all be controlled, yielding a year-round supply.
Controlled environmental agriculture is booming nationwide, but Tiger Corner has an edge: it’s part of a parent company called AmplifiedAg founded by former Benefitfocus CTO Don Taylor. AmplifiedAg’s two other divisions are Boxcar Central, an automation software platform that lets users dial in exact specifications for any plant, and Vertical Roots, whose growers operate farms in Summerville, off Clements Ferry Road, and outside Daniel Island eatery Dockery’s (which serves the greens).
“We have a continuous feedback loop that allows us to quickly make adjustments to our product to best serve the farmers,” says Tiger Corner general manager Stefanie Swackhamer about Vertical Roots, which sells to GrowFood Carolina and retailers like Whole Foods, Harris Teeter, and Earth Fare. They also supply greens to Dorchester District Two schools, and “This school year, we’re implementing a farm at Ashley Ridge High School to allow students to get involved in the growing process,” says Swackhamer.
Head Count
How many farms—and leafy green plants—is Tiger Corner Farms producing? Take a look at the numbers:
A full, turnkey farm—including 4 pods and a “clean room”—takes about 4 weeks to build and costs $550,000.
Each pod yields 3,800 to 7,000 plants (depending on variety) per month.
Tiger Corner has built 18 pods since 2016, making its very first sale to The Citadel.
Resources:
Photographs by (4) Melissa Sommer
Hydroponic Intensive Workshops At The Controlled Environment Agriculture Center
For more information:
Registration at CEAC.ARIZONA.EDU/INTENSIVE
Email: danaem@email.arizona.edu
Call Danae, Program Coordinator, (520)626-9566
CubicFarm Systems Readies For Expansion Into Cannabis Sector As Bevo Agro Prepares To Become Zenabis Global
Bevo introduces CubicFarm Systems Corp. (CubicFarms), an agriculture technology business that was developed by the Bevo management team.
On October 4, 2018, Bevo Agro announced that it had signed an Arrangement Agreement with Sun Pharm for a reverse take-over of Bevo, and announced its intent to change its name to Zenabis Global. Zenabis will have nearly 3.5 million square feet of available production space.
Now, Bevo introduces CubicFarm Systems Corp. (CubicFarms), an agriculture technology business that was developed by the Bevo management team. As part of the Arrangement Agreement cited above, Bevo's ~43% equity ownership in CubicFarms will be spun out to Bevo's existing shareholders, and CubicFarms intends to simultaneously list on the TSXV as a separate company. Zenabis (through Sun Pharm) also holds a stake in CubicFarms that it will retain post-amalgamation. This investment will be held by Zenabis Ventures, Zenabis' wholly-owned cannabis venture platform.
CubicFarms is the developer of patented technology that automates large-scale commercial farming operations in climate controlled growing chambers. By recycling water, each crop uses a fraction of the water required under traditional farming methods. Further, each machine is constructed inside an individually climate controlled growing chamber, allowing optimized climate, lighting, nutrients and other plant-specific needs, leading to faster growing cycles and year-round production. Utilizing CubicFarms' patented "undulating path" conveyor system, all plants are brought to those harvesting and planting, reducing labour significantly and increasing yield per cubic foot compared to other growing systems.
CubicFarms currently grows lettuce and leafy greens; microgreens; and basil and herbs. CubicFarms is also exploring cannabis cultivation applications in a joint venture with Zenabis named ZenCube. In addition, CubicFarms is further optimizing the technology for the nutraceutical and animal feed space.
CubicFarms has been building and selling systems since 2016, with its systems shipped from a state-of-the-art manufacturing facility. This facility is ramping up production to meet CubicFarms' growing global sales pipeline. CubicFarms operates its own commercial scale CubicFarm system, which it installed this summer in Pitt Meadows, British Columbia. This facility grows and sells a wide variety of leafy greens to the local retail and wholesale market, and also accommodates research and development.
"I am delighted that Zenabis sees the value in automating the growing process and reducing the space and labour requirements through utilizing CubicFarms technology to advance their growing capacity," said Dave Dineson, CEO of CubicFarm Systems Corp. "The joint venture between CubicFarms and Zenabis will make available cannabis-optimized growing machines for global customers who want to lower their growing costs, increase yields, reduce labour, water and energy usage, eliminate pesticides, and enjoy consistent quality growing."
"It's exciting that CubicFarms can expand on its patented technology to enter into a whole new vertical market," said Leo Benne, Chief Growing Officer of Bevo (Zenabis Global). "CubicFarms offers growers unparalleled accuracy and predictability, so that no crop ever goes to waste, while saving money and time by using a fraction of the resources."
"As a leading licensed producer of cannabis, we have long admired the pioneering technology introduced by CubicFarms," said Rick Brar of Sun Pharm Investments, the new CEO of Zenabis. "We look forward to working in partnership to help CubicFarms expand into worldwide markets as Zenabis continues to meet the growing global demand for cannabis."
For more information:
CubicFarms
cubicfarms.com
Publication date : 10/11/2018
Meet CropKing’s Nick Greens And Jake Emling
The two New Hires At CropKing Bring A Variety Of Experiences To the Lodi, Ohio-Based Operation.
September 18, 2018
CropKing, based in Lodi, Ohio, recently announced that it has expanded its team, with the addition of Nick Greens in the role of horticulturist/consultant, and Jake Emling in the role of horticulturist. The two new hires recently shared with Produce Grower their backgrounds and excitement about their new roles.
Nick Greens, horticulturist/consultant, based out of Lodi, Ohio
Horticulturist/consultant Nick Greens began his growing career in 2002 as an apprentice grower for a hydroponics shop. In 2007, Greens moved to Humboldt County, California, to work as an assistant grower for a collective of greenhouses, where he began experimenting with a vortex brewer to develop several recipes for compost teas.
In 2010, Greens moved back to Chicago to start growing produce for Blue Star Produce, where he perfected his compost tea recipes and became a pioneer in organic microgreens and leafy greens production. When he started growing microgreens in 2010, Greens used CropKing systems. He worked for and advised many Chicago indoor farms, including BrightFarms, Garfield Produce, Plant Chicago, Windy City Greens and Nick Greens Grow Team.
Greens has created many growing opportunities for youth in urban Chicago. He installed an indoor growing system at Kipp One Academy Charter School, and helped design and build the Food Science Lab at Schurz High School.
Having helped different microgreens operations get off the ground, Greens says he knows what it takes for small farming businesses to succeed. Now that he’s working at CropKing, Greens says he is excited to help customers solve their problems.
“Now that I’ve been at CropKing for a few months, I’ve really enjoyed the workshops,” Greens says. “Getting to meet potential growers and talk through their questions while also teaching about ways to provide heathy and sustainable food is one of the things I like best.”
Jake Emling, horticulturist, based out of Lodi, Ohio
Horticulturist Jake Emling developed a love of nature and the outdoors while growing up in the Upper Peninsula of Michigan. He attended Michigan State University, where he received both a bachelors and masters of science in horticulture. While at Michigan State, Emling researched various fruit crops in intensive growing systems. He also has worked in the fertilizer industry as well as with greenhouses, grower education and entomology.
Emling has worked throughout the United States with numerous crops and growers, and he says he is excited to pull from those experiences to help CropKing customers. “It is always interesting to me how the different cultural practices are used to produce the same crop in different locations,” he says.
In his spare time, Emling works in his one-third-acre vineyard. Additionally, he has experience working with computer-aided design. “Over the last few years I have been able to use my knowledge of engineering principles and horticulture to help improve different designs and layouts of greenhouses. I have been building things and tinkering all my life, so applying this skill with my background in horticulture has allowed me to solve problems for growers.”
At the end of the day, Emling says he is drawn to controlled environment agriculture (CEA) because of the range of experiences it presents. “I like the flexibility of different tasks that are needed to successfully produce a crop,” he says. “Also, [I like] the wide range of plants that you can grow in CEA. You are only limited to how much time you want to spend taking care of the needs of those specific plants.”
Virginia Smart Farming Conference on Using Controlled Environment Agriculture
August 8, 2018, created by Joyce Latimer
Join us for the 2018 Virginia Smart Farming Conference on Using Controlled Environment Agriculture to be held on Thursday, September 13, 2018, at the Institute for Advanced Learning and Research (IALR) in Danville, VA.
From farms to greenhouses to warehouses, controlled environment agriculture is growing in the field of agriculture. Join academic and industry experts for this one-day event focused on the latest advances in protected culture, sensor technology, lighting, computer vision, automation, and vertical farming. Hear from technical experts as well as Virginia producers who have been successful in incorporating controlled environment agriculture into their business models.
Neil Mattson, Ph.D., Director of the Cornell University Controlled Environment Agriculture group will kick the conference off with his Keynote Address on Building a Controlled Environment Agriculture Business: Site, Structure, Crops, and Growing System. Later Neil will talk about niche markets filled by successful vertical farms and energy modeling in vertical farms and greenhouses.
In addition, Chris Higgins of Hort Americas will be joining us as a Special Guest Speaker for the Smart Farming Conference with an update on LED lighting options for commercial vertical farms as well as a presentation in the greenhouse track on using technology for climate control and reducing labor needs.
With speakers on using CEA on the farm, in the greenhouse, and in vertical/indoor farms, there is something for everyone. Check out the full program, speaker bios, and registration link on our website.
https://www.hort.vt.edu/sfcea/
Pre-registration ends September 4, 2018. Space is limited. Exhibitor space and sponsorship opportunities are still available.
About the Author:
Joyce Latimer
Professor, Horticulture, Virginia Tech
Joyce Latimer is a Professor and Greenhouse Extension Specialist at Virginia Tech in Blacksburg VA. Her specialty is in perennials production, problem solving, and plant growth regulation of herbaceous perennials under greenhouse and nursery conditions. Joyce also works with greenhouse energy efficiency education and implementation programs.
Joyce has been recognized for her Extension service to the industry with the Alumni Award for Outreach Excellence (Virginia Tech, 2010), Horticultural Initiative Award (Southeast Color Connection, 2010), and the Outreach Excellence Award (Virginia Tech College of Agriculture and Life Sciences, 2007).
What’s So Special About Controlled Environment Agriculture Cucumbers And Corn?
Controlled Environment Agriculture (CEA) has become nearly a household term during this decade. That’s not to say CEA is new, but rather it has become significantly more visible in research, teaching, and consumer awareness.
By Peter Konjoian|
July 13, 2018
In, July 2014, I wrote an article on “Indoor Agriculture: Opportunities to Imagine”. In it was a discussion stating that as Earth’s human population reaches nine billion by 2050, current agricultural systems and practices may not be capable of feeding everyone.
It’s All in the Terminology
Controlled Environment Agriculture (CEA) has become nearly a household term during this decade. That’s not to say CEA is new, but rather it has become significantly more visible in research, teaching, and consumer awareness
The agriculture community has made progress in educating urban, suburban, and rural consumers about the ultimate importance of future food production to every person on the planet. Still, more education and collaboration are needed between farmer and consumer. That aside, consumer awareness and interest in CEA’s emerging applications for indoor (warehouse) agriculture, greenhouse production, and urban agriculture in general signals impressive progress.
To be clear, CEA includes greenhouse production. Any of us growing crops in greenhouses, ornamental or edible, are indeed controlled environment agriculturists as, by definition, horticulture is a branch of agriculture. While indoor agriculture is receiving much of the attention, greenhouse production will also play an important role as we meet the challenge of feeding nine billion people.
Feeding the world is not a zero-sum game where one system of food production will become the only system. Industrial-scale field agriculture will maintain a significant share of global production due to sheer food volume necessity. While sounding contradictory, applying sustainable practices to our industrial model will help. But supplementing and complementing industrial output with greenhouse and indoor production located in and around urban consumption centers will be required. With these comments as today’s backdrop, let’s talk about cucumbers and corn.
How CEA Cucumbers Are Grown
What’s so special about the cucumbers shown in Figure 1 (see slideshow)? After a quick glance, most would respond that there’s nothing special about them. Some might suggest that they could be darker green, or that they’re not straight enough, or should be more uniform. All are accurate and welcomed comments, but they’re not the correct answer. What’s different about these three cukes is that they were harvested from plants grown without a single photon of sunlight.
Greenhouse and indoor edible crop production revolves around proper cultivar selection. The cucumber ‘Salad Bush’ was used in this experiment and was provided by Harris Seeds, Rochester, NY. As implied by its name, this cultivar is a dwarf, bush-type vine growing to a length of three feet.
Figures 2 and 3 (see slideshow) show the indoor growth room equipped with 2-foot-long light emitting diode (LED) light fixtures. During early seedling growth, the fixtures were hung above the young plants in a traditional horizontal orientation. As the vines developed, they were trained along bamboo stakes mimicking traditional greenhouse-trellised cucumber production. The light fixture orientation was changed to vertical as well to provide uniform light intensity to the vertical vines. Figure 2 shows the lights in growth mode, where red and blue diodes provide most of the light. Figure 3 shows the fixtures in view mode, where all diodes except white are powered down to allow for normal viewing.
The cucumbers were sown in plug trays on a greenhouse propagation bench and transferred to the indoor growth room upon transplant into 6-inch pots using Jolly Gardener Proline C/B growing mix (Northeast Nursery and Greenhouse Supply, division of Northeast Nursery, Peabody, MA).
Flood and drain irrigation was used to deliver 150 ppm nitrogen from a 13-2-13 JR Peters soluble fertilizer formulation. Multiple flood cycles were used as plants grew. A 16-hour daylength was used with light intensity of approximately 400 umoles of PAR via the LED source yielding a daily light integral of approximately 23 moles. Growth room temperature set point was 70°F.
What About CEA Corn?
The two ears of corn pictured in Figure 4 (see slideshow), referenced by a 6-inch chef’s knife, do not appear to be any more special than the cucumbers. Some might suggest that the ears are not long enough, that pollination was incomplete, or they should be more uniform. Again, all are accurate and welcomed comments, but not the correct answer. Unlike the cukes, these ears of corn were harvested from plants that did receive sunlight. However, the plants were not grown outdoors in a field but on a greenhouse bench in pots containing a soilless mix.
Figures 5 and 6 show the crop during production. Ten-inch pots contained three plants using the same Jolly Gardener mix as the cucumbers. Pictured is a 4 foot-by-8 foot flood tray holding 15 pots (45 plants). Accounting for overhang, the plant density for this experiment was approximately 1.2 plants/square foot. The cultivar ‘Revelation’ was also provided by Harris Seeds.
Flood cycles were adjusted as the crop developed, and the nutrient solution contained 200 ppm nitrogen,150 ppm from 13-2-13, and 50 ppm from 15-0-0. The crop was grown during summer months without night heat, with a greenhouse ventilation set point of 75°F. The temperature set point was exceeded on sunny days. Figure 5 (see slideshow) shows the crop several weeks after transplant, and Figure 6 shows the crop several weeks after that. Air movement from greenhouse ventilation facilitated pollination.
Again, What’s so Special?
Your answer to the question ‘What’s so special?’ about these two common vegetable crops may be simple, but there’s nothing special about them. Cucumbers are already a major greenhouse crop, so imagining indoor production isn’t too hard of a stretch. I agree, but still, knowing that progress is being made that will soon allow any of us as consumers to repurpose our canned-goods pantry next to the kitchen into an indoor CEA unit is pretty exciting.
Fresh salad ingredients 3 feet away from the kitchen counter will define farm to table in an exciting way. This isn’t suggesting that commercial field, greenhouse, and indoor production will become obsolete. Remember, we have nine billion mouths to feed. We are going to need every type of sustainable food production system in the arsenal.
Regarding the corn, your answer to ‘What’s so special?’ might be that greenhouse production of an agronomic-like crop is silly and not at all feasible. Okay. But hold on a second, here’s another perspective.
For the past year, I have been working on a project with a team of engineers at MIT. The project, called OpenAg, is focused on indoor CEA. Last July (2017), the project took the MIT team and me to NASA to participate in a two-day CEA workshop. For me, working with NASA scientists and engineers was a once-in-a-lifetime, humbling experience.
Out of This World
The most jaw-dropping objective NASA presented during the two days is that we need to have food growing on the surface of Mars by 2029 when the first astronauts are scheduled to arrive. This target date is dependent upon funding, and the NASA folks repeatedly told us that support from Washington, DC, changes from one administration to the next. Nevertheless, 2029 is our next “JFK 1960s charge of going to the Moon and returning safely” rally point.
A few minor details set the stage. We were schooled repeatedly that the cost of placing something, anything, in space is exorbitant. As a plant scientist, I needed to be reminded that inputs used on earth, like water and fertilizer, cannot be put into space in the amounts needed. Much ingenuity is required. Another consequence of this reality is that we cannot afford to send much more food than will be required to get the astronauts to Mars. Before they arrive, food needs to be there, growing.
Robotic crop production will need to be there well before our first explorers arrive. That means that during this decade and the next, we’ll be practicing on the Moon’s surface. How cool is that? Does CEA corn and cucumber production seem so far-fetched with this in mind?
How does this affect any of us currently in commercial greenhouse production? Think of decades of technology from the space program trickling down to everyday life. Lightweight and strong composite metals, high-tech fabrics, Tang, freeze-dried food, cordless power tools, memory foam — we were reminded while at NASA that all these products and many others were spun from the space program.
Another recurring message in the From Flowers to Food series is that greenhouse and indoor food crop production are limited, in my opinion, by a single factor: our imagination. Figure 7 (see slideshow) is a picture that, within the next decade, might travel electronically over 30 million miles after being taken on the surface of Mars.
Peter Konjoian received his B.S. from the University of New Hampshire and M.S. and Ph.D. from The Ohio State University. He is president of Konjoian's Floriculture Education Services in Andover, Mass. See all author stories here.
Q & A With Frank Sharp, Senior Technical Leader, The Electric Power Research Institute, Inc.
Q & A With Frank Sharp, Senior Technical Leader, The Electric Power Research Institute, Inc.
Background on EPRI:
The Electric Power Research Institute, Inc. (EPRI, www.epri.com) conducts research and development relating to the generation, delivery and use of electricity for the benefit of the public.
An independent, nonprofit organization, EPRI brings together its scientists and engineers as well as experts from academia and industry to help address challenges in electricity, including reliability, efficiency, health, safety and the environment. EPRI's members represent more than 90 percent of the electricity generated and delivered in the United States, and international participation extends to 40 countries. EPRI's principal offices and laboratories are located in Palo Alto, Calif.; Charlotte, N.C.; Knoxville, Tenn.; and Lenox, Mass.
Q&A: Frank Sharp, Senior Technical Leader, Energy Utilization, EPRI.
- What is the best form factor in this industry?
-
- EPRI is researching CEA because of its potential to address issues related to population growth, food security, food safety, water access, water use, sustainability, grid load, local job creation, land usage, and smart city integration, all for community benefit.
- That said, we see three primary emerging forms and each have benefits:
- The converted warehouse, vertical farm, custom building
-
- This provides opportunity to use underutilized or underperforming real estate in areas that often have limited economic potential.
- These facilities offer the ability to yield high quality produce in large volumes near population centers via their use of technologies to maintain ideal growing conditions.
- Converted shipping containers or pods
- This approach is highly mobile, is often modular, and utilize modern technologies to maintain growing conditions.
- These facilities offer the ability to reliability deliver fresh produce to targeted communities and applications and use minimal resources
- Augmented greenhouses where heat and lighting are added to keep the greenhouse operating year-round.
-
- This format has lower operational cost per square foot since it’s lighting load is only utilized when sunlight is not available
- These facilities have the ability to deliver crops in large scale and deliver fresh produce year-round to markets. We found a lot of unanswered questions about each of these types of controlled environment agriculture and they all warrant significantly more research as we move forward. We are working with utilities and CEA groups to better leverage current technology to forward each of these formats for the public benefit.
- That said, we see three primary emerging forms and each have benefits:
- In addition to these three forms there are other forms developing like aquaculture, indoor shrimp production, and insects for protein.
- Note, established industries like traditional greenhouses and floriculture operations are also very common and will continue to expand and be utilized. These operations are typically not researched by EPRI since their operations and technologies are well established. EPRI does follow work in these areas and will engage to evaluate new process and technologies in these operations if they emerge.
- With major e coli and other pathogen outbreak concerns plaguing the food landscape, CEA is a viable solution if implemented correctly. What measures are you implementing now to reduce the likelihood of a pathogen outbreak, or warn a consumer that the food is not safe?
- Controlled environment agriculture can reduce the likelihood of the spread of food borne pathogens due to its ability to control the environment and limit exposure to outside factors. But there is still risk and all agriculture facilities (indoor or out) should remain vigilant to maintain food safety and security in the future. Continued research into efficacies and future technologies will help reduce this risk further.
- Energy is one of the most expensive component for an indoor growing operation. What is your number of grams that can be grown on the farm in a given month, then divide this by the number of KWH consumed per month. Please give more configuration details, pictures, and growth trial data from these trials.
- While energy is one of the more significant costs for growing indoors, this industry has great potential to expand. This expansion will be driven by need for fresh produce by expanding population, but the CEA industry must focus on improving its operational efficiency where it can be a vital part of a further efficiently electrified economy.
- Benefits derived from improved operational efficiency and higher yield can also help CEA facilities minimize labor costs, which are typically they highest costs.
- The combination of improved technologies, operational efficiency improvements, and maximized labor costs can help assure CEA facilities that their products are competitive.
- CEA integration with an electrified economy will also make CEA a key part of future smart cities.
- The smart city integration of CEA will be further enhanced by use of grid integrated renewable energy and other distributed energy. As these resources come online, access to affordable and clean energy resources will help shift the energy costs of CEA facilities. We will be exploring this aspect of CEA in great detail during our 2018 Electrification conference in Long Beach this summer.
- With further electrification and demand on the grid, additional research is critical to learn how to support grid stability and reliability as more CEA operations come online.
- We are working with utilities and CEA operations around the world to learn more about emerging technologies and identifying proper placement of these operations on the existing grid.
3rd Greenhouse and Hydroponic Technical Management Course for India
3rd Greenhouse and Hydroponic
Technical Management Course for India
"Delish Veggies, Graeme Smith Consulting and Future Farms are pleased to announce the 3rd Greenhouse and Hydroponic Training Program in Pune India after the grand successes of our two training courses in 2017.
We received a phenomenal response for both training programs due to the presence of renowned international trainers from Australia and practical farm tours whereby we hosted many international participants, multiple Indian states, and 60 participants and received “extremely satisfied” feedback from all the participants.
Delish Veggies had to decline many participants in these training programs due to limited seats, therefore due to popular demand we are organizing a 3rd course this June (4th to 8th) and have again included many interesting topics and commercial farm set up sessions."
The course will again be conducted by two highly experienced Australian industry presenters Graeme Smith and Rick Donnan.
Graeme is the proprietor of Graeme Smith Consulting, he consults throughout the world, runs regular study tours to Holland/EU and North America, and is the past Chairman of Protected Cropping Australia. Recent international greenhouse projects include Hyderabad, Abu Dhabi, China and Rajasthan.
Rick owns Growool Horticultural Systems and is the Q&A columnist in the world’s leading hydroponic industry publication- Practical Hydroponics and Greenhouses magazine and provides consultancy services.
The course assists participants to improve their ability to understand the key principles in a commercial greenhouse and hydroponic production by:
• understanding the principles of controlled production systems
• using correct strategies and technologies to manage
greenhouse climates and irrigation
• understanding plant growing requirements and plant
production techniques
• developing new strategies for plant protection and integrated
pest & disease management
• understanding plant nutrition and fertigation programs
• identifying the risks and opportunities of climate change
Topics Include:
• Media types & characteristics • Plant structure
• Nutrition & nutrient management • EC & pH
• Water quality and treatment • Plant physiology
• Environmental management • Irrigation management
• Greenhouse business and marketing plan • Plant health
• Greenhouse design and layout • Pest and disease control
Greenhouse Technical Management Course Details
Greenhouse Technical Management Course Photos
Location: Pune, India
Dates: June 4th to 8th 2018 (5 days)
Course cost: Rs. 50,000 excluding 18% GST. (Lunch, as well as morning and afternoon tea, will be provided throughout the course)
To register your interest, please contact the course Coordinator, Uday Mathapati on +91 9130098714 or email: udaymathapati@gmail.com or visit www.delishveggies.com for further information
Qatar Could Export Vegetables In Future: US Agriculture Expert
Glenn Behrman; Some of the leafy vegetables produced through indoor farming
Qatar Could Export Vegetables In Future: US Agriculture Expert
Qatar could become an exporter of several agricultural products at some point in the future, an expert from the US told Gulf Times.
“There are tremendous opportunities for the country,” claimed horticulture specialist Glenn Behrman, a proponent of controlled-environment indoor farming concept called 'Growtainer'.
It features a container - a highly engineered modular and mobile vertical production environment, custom-built for a wide variety of crops, botanical products, and business models. In the high tech facility, plants are grown in nutrient-enriched water through vertical farming. They can be grown in shipping containers, warehouses or such enclosed areas.
“We can recreate nature. If the plants want rain, there will be rain, if there is no need of wind, there will be no wind and can even provide the best light for the plant. It is fully controlled by computers. Some crops grow 18- 20 hours a day and the yield is dramatically higher,” said Behrman.
In Qatar to explore the possibilities of introducing the new method, the expert had several rounds of meetings with the royal family members, government officials, potential partners, and investors as well as business people in the country.
“We have had several rounds of discussions. They had visited me in the US and invited me to come over here. Now, we are moving into the next stage of co-operation. I am hopeful that we will be able to start the project in less than six months,” noted Behrman.
According to Behrman, most types of vegetables can be grown using the technology. “The normal space between the rows in a shipping container is about 18-20 inches. You can grow anything with shallow roots. Lettuce, tomatoes, radish, herbs, spices and leafy vegetables are some of them,” he explained.
The expert also pointed out that the produce from the system are healthier and cleaner than organic products. “It is also less expensive than organic food. They grow 30 to 40% faster than other food items,” he described.
“The technology is very much water conserving and does not waste any water. It uses about 750 gallons of water for a certain number of plants whereas in a farm the same number might need 60,000 gallons of water. We can also grow many vegetables that are yet to be grown in Qatar,” he added.
CoBank: Controlled Environment Agriculture Experiencing Rapid Growth
CoBank: Controlled Environment Agriculture Experiencing Rapid Growth
USAgNet - 05/16/2018
Technological advancements and consumer demand for fresh, local and year-round supplies of high-quality produce are growing the controlled environment agriculture (CEA) industry across the U.S., according to a new report from CoBank's Knowledge Exchange Division.
CEA, a technology-based approach toward food production to use optimal growing conditions, often indoors, occurs in all 50 states, but the vast majority of the large facilities growing tomatoes, cucumbers and peppers are in the Northeast, West, and Southwest.
"The rising demand for local, high-quality food and the need for a year-round supply of it-is creating market opportunities," said Christine Lensing, senior analyst for CoBank's KED. "Although there is a steep learning curve, high cost and other barriers to CEA, this segment is likely to continue growing for the next five years."
Those barriers are not stopping CEA growers from entering the market at high rates according to the report, partially due to the realization of price premiums and significantly higher yields that the technology, such as hydroponics, provides.
"What has happened with tomatoes over the last 20 years, where about 50 percent of all domestic tomatoes are grown using CEA, is starting to happen in other industries," said Lensing. "There are significant opportunities in leafy greens, microgreens, herbs and other novelties such as turmeric and ginger. However, as new ventures are coming online, they must be very aware of three things, the high cost of operating, fluctuations in the market and competition in this growing space."
According to the report, CEA is an efficient way to produce food locally, save on costs like transportation, meet consumer demands and diversify current operations. This technology will not likely take place of the conventional agriculture of the future, but all indications point to it being an important tool for meeting rising consumer demand for quality produce year-round.
Click for a brief video synopsis of "Controlled Environment Agriculture: Farming for the Future?"
The full report is available at cobank.com.
UAE Tries Vertical Farming To Produce Food With Little Water
UAE Tries Vertical Farming To Produce Food With Little Water
Sustainable agriculture is a challenge in the arid United Arab Emirates, but a new indoor approach to farming may be the key to supplying the region with food without overdrawing from its limited water stores.
Anwar Mirza/Reuters
May 10, 2018
- By Rabiya Jaffery Reuters
ABU DHABI
When people picture the United Arab Emirates (UAE), what likely comes to mind are desert sands, skyscrapers, and a blue sea under a shimmering sun. Agriculture does not.
There are good reasons for this: The federation of seven emirates is hampered by high temperatures, a lack of arable land, salty soil, and steep production costs. And that is without accounting for the occasional voracious locust swarm.
So it is hardly surprising that the UAE imports nearly 90 percent of its food needs, according to the Abu Dhabi Global Environmental Data Initiative, a data research organization.
This reliance on the global food trade brings opportunity, said Saudi Arabian entrepreneur Omar Al Jundi, who has built the Middle East's first commercial vertical farm in Dubai.
Badia Farm – the word means 'oasis' in Arabic – grows greens like radish, kale, mustard, basil, and arugula in a controlled, indoor environment using hydroponic technology and LED lights.
"As a region that has struggled to grow crops due to largely hostile desert landscapes, our farm offers a viable solution to farming that produces harvests 365 days of the year," he said.
"The produce will not only be cheaper than imported goods but fresher too, as the farms will be producing all year round."
The farm, which began production late last year, is on an 800-square-meter plot of land in one of Dubai's main industrial areas and produces two hundred boxes of green vegetables a day.
Though this pales in comparison to the world's largest vertical farm – which operates on 6,500 square meters of a former steel factory in New Jersey in the United States – it marks a big step for alternative farming in this region.
Vertical farming is taking off elsewhere, too: Europe's first commercial farm opened near Amsterdam last year, and Shanghai will next year start a 250-acre agricultural district with skyscrapers dedicated to growing fruit and vegetables.
Vertical farming brings some important benefits, said Mr. Al Jundi: because produce is grown in a controlled environment there is no need for pesticides or chemicals. And they use much less water – 90 percent less than open-field farming.
Growing food locally for the firm's 30 UAE clients – mainly restaurants and hotels – means a smaller carbon footprint, and saves on transport costs.
"It makes no sense to order produce that arrives in boxes in the back of a ship from as far as tens of thousands of miles away when it can be grown at home," he said.
Even though the UAE imports most of its food, the emirates are food secure, according to the United Nations Food and Agriculture Organization (FAO).
However, its food security is not without risk, said Hina Kamal, a research analyst at the UAE University's College of Food & Agriculture, as it is reliant on vulnerabilities in supplier countries and on the international food trade market.
Another concern is climate change, which is likely to increase food prices in the years ahead, said Majid Sultan Al Qassimi of the UAE's ministry of climate change and environment.
Although the UAE has strategic reserves in place to protect it from short-term disruptions, he said, "ensuring global food security will be challenging in the future due to impacts of climate change."
Part of the solution, he said, is to boost domestic production through sustainable means; another is "to diversify imports and investments to ensure that the country is food secure in the long-run."
Other solutions include setting up storage facilities abroad and acquiring farmland in Africa, Europe, and Asia. Emirates NBD, a large regional bank, says UAE investors were part of at least 28 deals in the past 50 years covering about 1 million hectares of farmland globally.
The Emirates' drive to secure land abroad to assure its food supply is not risk-free, Ms. Kamal said and could be undone by political conditions in those countries or by climate change.
"It is possible that some of [the countries] will be highly affected by climate change – both through more extreme weather events and reduced productivity over time."
Droughts or food shortages could, for example, see host governments impose export bans, she said, which is why boosting productivity at home is the lowest-risk way to ensure food security in the decades to come. It is also more sustainable.
The UAE will need to improve its agricultural productivity in the coming decades to meet demand, said Mr. Qassimi, and to do so in the face of rising global temperatures that are expected to worsen extreme weather events.
"All of this has a direct impact on agricultural production, affecting both food producers and those who depend on them. The UAE is no exception," he said.
Nor, for that matter, is the Gulf region, noted a report last year from the Emirates Wildlife Society and World Wildlife Fund (EWS-WWF), which evaluated the likely effects of climate change on food security.
The UAE is a major regional hub for the re-export of food commodities, it pointed out, and the consequences of climate change, including hotter weather, could affect those facilities.
Any resultant food price spikes would hurt the poorest the most, and that could drive a long-term need for food subsidies.
There are other factors too, not least water. The UAE's agricultural sector accounts for just 1 percent of its economy, the EWS-WWF report noted, yet uses about one-third of its water – vastly disproportionate to its GDP contribution, said Fanack Water, a research group.
Given that water is more expensive than electricity in the UAE – and given that regular farmers benefit from subsidies for water Al Jundi of Badia Farm said ending such breaks would make vertical farming a cheaper solution.
"The money spent on powering vertical farms is relatively much lower than of the cost of water used in open fields."
That said, Badia does use plenty of electricity: from pumping water to powering the artificial lighting and computers that monitor temperatures. But looking ahead, said Al Jundi, it is working with the government on a shift to renewable energy.
The impact one vertical farm can have, though, is limited, and will be felt only on the margins: It will not change the UAE's reliance on countries such as Brazil, India, Iran, and South Africa for cereals, sugar, and food oils, for example.
But what it represents – a better way of growing produce in a region that is facing significant challenges from climate change – is important, Al Jundi said.
"This technology will be a major contributor to agriculture sustainability, food diversity, and security as it enhances crop production and lowers their cost," he said.
This story was reported by The Thomson Reuters Foundation.
Controlled Environments: The Future of Small-Scale Agriculture
Controlled Environments: The Future of Small-Scale Agriculture
April 25, 2018 | By Ted Tanner, CEO and Co-Founder | Agriculture, Technology
Many experts believe small-scale agriculture is the future of growing. For those who choose that path, success may be closely tied to controlled environments and the use of agricultural technologies.
To understand how ag-tech drives success in small-scale farming, it's important to first take a closer look at small-scale agriculture: what it is, how it works, and why some envision it as the logical next step for the agricultural industry..
Thinking Small
For decades, agriculture has been dominated by a push toward larger farms with bigger grow operations that leverage various means to produce massive yields at low costs. But this kind of farming, sometimes called “factory farming,” has come with a price.
This mode of agriculture is devouring resources such as land and water. In the U.S. alone, agriculture accounts for 80 percent of ground and surface water usage, according to the United States Department of Agriculture's (USDA) Economic Research Service. In many Western states, that number is as high as 90 percent. Big farms require a lot of labor, at a time when available farm labor is shrinking. Big farms also tend to be geographically removed from consumers, which increases food costs and the level of greenhouse gases produced because goods are trucked long distances to consumers.
Small-scale farms offer an attractive alternative.
With smaller farms, there are more options available. Farming can happen all over the world—even in more densely populated areas. With small-scale farming, food is fresh and grown locally year-round. Smaller agricultural systems are also more flexible, adapting to changing climate conditions and showing a greater resilience than large farms, according to small-scale farmers like California farmer Nikiko Masumoto.
A smaller grow enterprise can bring a new economic dimension into play, making agriculture a more commercially viable endeavor.
“Since small scale farmers tend to sell their products directly to consumers, they manage to avoid the middlemen. This means they can offer locally-grown, affordable, fresh, and sustainable food anywhere year-round,” according to Farming Solutions, a site that champions sustainable farming solutions for the future
How Ag-Tech Helps
Although big farms generate vast quantities of agricultural goods, small farms are making inroads. Globally, the Food and Agriculture Organization of the United Nations reports that farms of less than one hectare account for 72 percent of all farms. The USDA National Agricultural Statistics Service Census of Agriculture, which occurs every five years, revealed in 2012 that small-scale family farms account for 88 percent of all U.S. farms.
Technological innovation can be a key driver of success for the small-scale farm, because a smaller grow space is inherently more controllable than a vast span of acreage. By applying agricultural controls, the grower can drive bigger yields with less effort at a lower cost.
A controlled environment allows for a small-scale farmer to manage a range of variables that might otherwise prove a detriment to productivity. Nutrients and irrigation, soil quality, and pest control all can be managed effectively using sensors for environmental monitoring and app-based smartphone systems for automation and 24/7 remote access.
Using the latest ag-tech, a grower can keep a watchful eye on variables such as heat, light, humidity, and soil conditions—without being present on-site. The grower can adjust conditions remotely and program automated routines to maximize efficiency and predictability in agricultural activities.
Smart systems take advantage of the small-scale farm’s inherent advantages: its smallness and self-contained nature. The small-scale farm is by design a manageable space, and growers who implement ag-tech solutions to manage the land can drive dramatically enhanced results.
There is a trend to break away from industrial agriculture. Consumers have grown skeptical of the factory farm, with its weighty environmental impacts and commoditization of the agricultural process. There is a call for something more authentic, something simpler and closer to home.
Growers who tap into that trend can find a valuable niche among consumers. By going small and using technology to maximize profitability, savvy growers can establish a unique position for themselves in an increasingly competitive marketplace.
Thrive Agritech, Leading LED Horticulture Lighting Innovator, Secures $2 Million Capital Injection
Latest Investment Round, led by New York-based Rose Capital, to Accelerate Adoption of Thrive’s Unique Lighting Technology into Global Horticulture Market
NEW YORK (PRWEB) April 30, 2018
Thrive Agritech, Inc., a technology company focused on leading innovations in LED horticulture lighting (“Thrive”), today announced that it has received an additional $2 million in equity capital to accelerate the development and deployment of its LED technology in controlled environment agriculture. The investment round was led by Rose Capital, a New York-based institutional investor. In conjunction with the investment round, Rose Capital has also joined Thrive’s Board of Directors.
The financing round – and a new partnership with Rose Capital – follows an exceptional year for Thrive Agritech, which saw a rapidly expanding customer base with lighting installations in greenhouses, vertical farms and cannabis production facilities across North America.
Rose Capital noted, “We are excited about this investment based on the extraordinary customer adoption that Thrive has experienced since its first product launch in 2015. Thrive has established a successful track record of commercializing best-in-class LED lighting products – having launched a new product every year since the Company’s inception. We look forward to partnering with Thrive to continue to break down traditional industry barriers and commercialize some of the most innovative products in the global horticultural market.”
The United Nations Food and Agriculture Organization estimates that food production must increase by 70% over the next forty years to satisfy increasing demand. The total market in North America for LED lighting solutions for greenhouses is expected to grow from 2.5 million square feet in 2015 to more than 50 million square feet in 2021. In response to these trends, companies like Thrive are introducing high output lighting solutions to change the efficiency dynamic for global growers.
“Our biggest challenge today is responding to the overwhelming number of opportunities with which we are being confronted,” said Thrive Agritech CEO Brian Bennett. “As we close this investment round, we will be aggressively hiring sales, marketing, and operations support, and leveraging Rose Capital’s expertise, to exceed the expectations of our customers and further develop our product portfolio and core technologies. Additionally, we will be expanding operations into Europe to capture growth in the emerging greenhouse supplemental lighting market.”
Thrive Agritech was founded at the Y Combinator accelerator in Silicon Valley, with a mission to enhance sustainability for controlled environment agriculture. The company’s industry leading energy efficient lighting products have already made significant reductions in the carbon footprint from older lighting technologies. Further, all Thrive Agritech products have an optimized horticulture light spectrum, high reliability, and most importantly improve efficiency and longevity of horticultural crop growth.
About Thrive Agritech
Thrive Agritech is a leading developer and manufacturer of innovative products for the controlled environment agriculture industry. The company’s patent-pending technologies enable unique advantages for horticultural solid-state lighting and controls. Corporate headquarters are located in New York City. For more information, visit http://www.thriveagritech.com
About Rose Capital
Rose Capital is a strategic advisor and investment firm focused on the global medical and adult use legal cannabis sector. It is funded by a small consortium of partners looking to access the industry through a diversified long-term, value-focused cannabis fund. Rose Capital manages an ecosystem of best-in-class operating assets across the data, analytics & compliance, distribution & logistics, and consumer products & contract manufacturing verticals of the US cannabis market, expanding globally. Please visit us at http://www.boldrosecapital.com.
The Role of LEDs in Speed Breeding
The Role of LEDs in Speed Breeding
Some of the most important crops for feeding the ever-increasing global population include wheat and barley. In order to meet the future demand, scientists have a task of finding ways to improve efficiencies in breeding these and other, similar plant species. Typically, more than 10 years are needed to develop novel cultivars with an advanced agronomic performance. On one hand, it is because several generation cycles are required to obtain genetically stable lines from selected parent material and on the other hand it is because we are limited in how many generation cycles we can carry out annually.
John Innes Centre scientists have found a way to reduce the amount of time needed for new cultivar development. They call it speed breeding and with it the time needed for one generation cycle is cut in half. They ran tests on wheat (Triticum aestivum), durum wheat (Triticum durum), barley (Hordeum vulgare), chickpea (Cicer arietinum), pea (Pisum sativum) and canola (Brassica napus). The findings show that it is possible to have up to 6 generations annually for the first five species listed and up to 4 for canola, as opposed to the 2-3 generations annually under normal greenhouse conditions.
To achieve this, they used a controlled environment set-up with a light/dark period of 22/2 hours as opposed to the plants grown in greenhouses with no supplementary light. The plants subjected to the speed breeding conditions progressed to the flowering stage in approximately half the time of those in the greenhouse conditions. The 22-hour daily photoperiod was achieved by using LED illumination as a supplementary source of light. The spectrum in question is Valoya’s NS1, a patented wide spectrum that is a close replica of the wavelengths produced by the Sun on a clear sky day. Additionally, a Far-Red spectrum was used in combination with the NS1 so as to induce flowering. This is because a low R: FR (red: far red) ratio has been found to reduce the time to flowering in plant species such as wheat, barley, grain legumes and many others.
This approach will enable seed companies to significantly cut costs and to produce results faster. Implications could thus be significant for the global food production. It is important to note that the effect on seed quality and quantity was similar to the slower/conventional breeding cycles. Furthermore, it was possible to show that the phenotype for traits such as loss of awn suppressor, dwarf genes, reduced glaucousness or progression of fusarium could be recapitulated under the speed breeding conditions.
Learn more about speed breeding here.
The full study is available here.
The official press release of the John Innes Centre is available here.
Valoya will be hosting the LEDs & Innovators Conference 2018 at the upcoming GreenTech in Amsterdam. The conference is free-of-charge and the topic of Speed Breeding will be presented by Valoya’s biologist, Ms.Stefanie Linzer. To learn more and to reserve your seat, please click here.
About Valoya Oy
Valoya is a provider of high end, energy efficient LED grow lights for use in crop science, vertical farming, and medicinal plants cultivation. Valoya LED grow lights have been developed using Valoya's proprietary LED technology and extensive plant photobiology research. Valoya's customer base includes numerous vertical farms, greenhouses and research institutions all over the world (including 8 out of 10 world’s largest agricultural companies).
Additional information:
Valoya Oy, Finland
Tel: +358 10 2350300
Email: sales@valoya.com
Web: www.valoya.com
Facebook: https://www.facebook.com/valoyafi/
Twitter: https://twitter.com/valoya