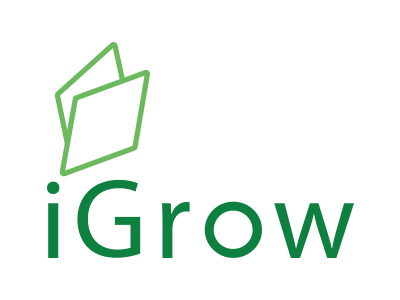
Welcome to iGrow News, Your Source for the World of Indoor Vertical Farming
USA: Virginia - Controlled Environment Agriculture On The Rise
March 17, 2019
Growing food indoors has been trending for several years, and some farmers are weighing the benefits of moving production indoors.
Innovations in greenhouse and vertical farming operations were discussed at the 2019 Virginia Smart Farming Conference, held March 12 at the Virginia Farm Bureau in Goochland County. Keynote speaker Dr. Neil Mattson of Cornell University shared research and information about controlled environment agriculture businesses.
Controlled environment agriculture is an innovative method of growing plants by creating an optimized aerial and root zone environment and focusing on production benefits. The merits of producing foods in a controlled environment include high plant quality, predictable crop timing and consistently available quantity with limited environmental impact. Many operations use hydroponics—growing plants without soil and using a mineral nutrient solution in a water solvent.
According to the 2014 U.S. Department of Agriculture Census of Horticultural Specialties, the top crops grown under protection include tomatoes, strawberries, peppers, lettuce, herbs and cucumbers. Tomatoes were grown the most in a controlled environment, with 96,265 tons; of that amount, 82,797 tons were produced hydroponically. Cucumbers were the second-largest crop at 36,310 tons produced and 33,101 produced hydroponically.
Mattson said there were 37 stacked plant facilities and rooftop greenhouses in the United States in 2017. Stacking indicates the plants, usually shorter crops, are grown in multiple layers stacked one above another.
While there are benefits to growing in a controlled environment, barriers also exist. “Accessing capital and the high up-front costs of getting started are the biggest barriers to overcome, because this is still somewhat new,” Mattson explained. It can be hard to show realistic business models, he added.
Accessing the market also can be tricky because “consumers are well-served by the conventional market,” Mattson said. “You need to show value to the table to get produce buyers to buy these crops.”
He said the energy required to grow the crops, and the labor force needed, can be daunting. “It’s a different type of labor,” Mattson said. “The sheer numbers for harvesting, packaging and educating growers to optimize production systems and push production” can be challenging.
Jerry Conner of Four Oaks Farms in Franklin County started a hydroponic greenhouse operation in 2012, planting the first seeds in April 2014. Four Oaks Farms grow lettuce and other leaf crops, including microgreens and herbs, as well as other vegetables. Conner sells produce at farmers’ markets and to area schools.
He said hydroponic operations require significant capital investment; computer, electrical, mechanical and plumbing knowledge; and 100 percent commitment 24 hours a day, seven days a week. “Plants don’t take Christmas or Thanksgiving off or anything like that, so I classify it as a labor of love.”
Food Security On Rise In Gulf
BY RICHIE SANTOSDIAZ
19th March 2019, London
The Agra Middle East exhibition in Dubai demonstrated the growth of vertical farming in the region, as well as other environmentally smart production methods
According to the organisers of the Agra Middle East exhibition in Dubai, which took place at the start of March, vertical farming is gaining in importance across the Gulf region, along with other Controlled Environment Agriculture (CEA) methods, and is generating interest and a rise in investment from across the globe.
The vertical farming market in the Middle East and Africa is expected to reach US$1.21bn by 2021 at a combined annual growth rate of 26.4 percent from only US$0.38bn in 2016, according to Orbis Research.
One of the GCC countries leading this is the UAE, having upcoming projects facilitated by the government, in addition to private players, helping increase food security.
The UAE Ministry of Climate Change and Environment, for instance, has allocated space for 12 vertical farms to be built by Shalimar Biotech Industries. There is also the world’s largest vertical farm for Emirates Airlines by Crop One Holdings.
As 90 per cent of food in the UAE is imported, and given territorial problems over water scarcity and available arable land, vertical farming is pivotal to ensuring food security within the region.
Food security equally forms part of the national strategy of Saudi Arabia, as well as wider economic development and diversification, as witnessed by its Saudi Vision 2030.
At a recent preparatory workshop for next year’s G20 meeting, which Saudi Arabia will be hosting, Abdulrahman bin Abdulmohsen Al-Fadhli, Minister of Environment, Water and Agriculture, said that digital technologies and artificial intelligence would have a growing role in the Kingdom’s efforts to maintain food security. Arab and foreign institutions were looking for modern and innovative technologies and solutions, he said, with the aim of discovering alternative food resources.
The agriculture sector faces major challenges, from price increases of agricultural products to climate change. A big part of the G20 discussions under the Kingdom’s presidency in 2020 includes topics such as the development of natural resources to reduce degradation, sustainable food security and water scarcity, to name a few.
Agra Middle East, which took place at Dubai’s World Trade Centre, brought some of the leading innovators and urban farming experts to the UAE to provide the industry with valuable information and knowledge.
Exhibition director Samantha Bleasby commented: “With the aim of increasing food security in the Middle East and attaining the UN Sustainable Development Goal (SDG) of zero hunger, we are excited to present the industry with new technologies from around the globe and free-to-attend learning and networking opportunities that will increase productivity in the region with sustainable use of water and land resources.”
Greenhouse Co2 Measurements For Higher Productivity And Higher Quality
We have collected the essential facts for you to take into account when selecting an instrument or searching for the optimal instrument location.
Greenhouses are demanding environments for measurement devices. We have collected the essential facts for you to take into account when selecting an instrument or searching for the optimal instrument location.
The following topics are covered in the document:
The importance of CO2 measurement control in a greenhouse
CO2 for plant growth
Tips for selecting an instrument for a greenhouse
Tips for transmitter placement in the greenhouse
Fill in the form given in the link below to download the PDF document and learn about greenhouse CO2 measurements to optimize plant growth.
https://www.vaisala.com/en/lp/greenhouse-co2-measurements-higher-productivity-and-higher-quality?utm_medium=referral&utm_source=GreenhouseManagement&utm_campaign=&utm_content=CO2MonitoringInGreenhouses
Will Controlled Environment Agriculture Disrupt The Value-Chain?
Is there a business case for widescale commercial vertical farming in the UK or will it remain a niche opportunity for high-end restaurants and retail? This is the challenge to be discussed by early adopters at the Agri-Tech East conference ‘Innovating for Controlled Environment Agriculture’ 19 March. Advances in logistics and the falling cost of LED lighting may enable year-round growing of undercover produce in the UK, but will energy costs and technical issues delay scale-up and integration within the food supply chain?
Potential to be commercially viable
“We do think there is the potential for indoor farming to be commercially viable and there are some immediate gains for growing crops such as leafy salads in high hygiene environments,” comments Lindsay Hargreaves, MD of Frederick Hiam, a farming and fresh produce business with farms in Suffolk and Cambridgeshire. “Growing indoors provides greater control of quality and quantity and fewer inputs of plant protection products.
“There is also the matter of growing crops closer to the point of consumption. Being able to grow more exotic crops in East Anglia close to distribution centres would reduce the food miles. Additionally, there are opportunities to grow crops for pharmaceuticals, cosmetics and vaccines within a controlled environment.”
There are many approaches to indoor cultivation, such as deep-water hydroponics, vertical soilless cultivation, and aeroponics, where exposed roots are sprayed with nutrients. All of these methods are to be discussed at the conference along with advances in monitoring and robotics.
However, despite the news that Sterling Suffolk, one of the UK’s most technically-advanced glasshouses, is set to produce millions of tomatoes starting in February 2019, the cost (£30M) and the technical challenges mean there are few commercial installations in the UK.
Also, it is proving difficult to demonstrate to retailers that controlled environment agriculture (CEA) can bring tangible benefits to their supply chain.
Aquaponics provides fish with a side salad
Kate Hofman, co-founder of GrowUp Farms, which from 2015 to 2017 operated ‘Unit 84’, a commercial-scale aquaponic urban farm inside an industrial warehouse. The 8,200 square feet of growing space could produce enough for 200,000 salad bags and 4,000kg of fish each year. It sold directly into restaurants, through a New Covent Garden distributor and also through bricks and mortar supermarkets and Farmdrop, the online supermarket.
Kate comments: “A key learning over the last six years is that we can’t just focus on technology – we have to partner along the supply chain to create a business model that ultimately delivers commercial success for growers and retailers.
“One of the major challenges for CEA is to optimise operations to bring down the cost of production to match existing imported products. Our prototype urban farm showed that it was possible to use CEA commercially, and we were able to demonstrate the demand for the produce we could grow. This ranged from specialist micro-greens and cut herbs through to mixed baby leaf salad.
“We are now working on scaling up our business. This will involve relocating, so that our production is co-located with a renewable energy plant and working in partnership with more traditional farming businesses to integrate their experience and expertise.”
There are also technology challenges to be addressed when trying to meet the highly variable consumer demand for high quality, fresh produce.
Year around UK production?
G’s Fresh supply baby leaf crops all year round, with much of the winter supply grown in Spain and Italy to ensure security of delivery. In summertime it produces a huge amount of outdoor salad crop, particularly lettuces and celery in the UK. Ben Barnes is investigating how controlled environment agriculture can increase the long-term viability and profitability of both of those parts of the business.
The organisation has a large standard greenhouse facility that is used to propagate seedlings for planting out into the field. It is running two projects: Smart Prop, which is looking at increasing the efficiency of the propagation facility to improve growth and make stronger plants so they transplant better back into the field. And Winter Grow, a pre-commercial trial, to see if it is feasible to produce baby leaf crops during the winter at an affordable price point.
Ben explains: “I’m going to be talking at the Agri-Tech East event about the commercial journey, in terms of the go and no-go decision-making process and what the key things are that we need to learn in order to be able to make those kind of investment decisions.
“One element of this is the development of ‘lighting recipes’ to enhance plant growth characteristics. We’ve got multi-spectrum LED lights, so we can turn up the different amounts of red, blue, green and white, and even far red light. These are fairly expensive, so once we have worked out what works best we can buy fixed spectrum lights, which are a tenth of the cost.
“You think LEDs are very efficient, but they still generate a heck of a lot of heat when you’ve got them turned up to full. It is more about keeping the space cool, and the plants obviously are transpirating so we’ve got dehumidifiers in there sucking the moisture out of the air.
“One of the biggest problems with the vertical farming concept is this interaction between moisture and temperature. You’ve got the two factors constantly fighting against each other and that ends up sucking up huge amounts of energy if you’re not careful.”
How will it integrate with the value chain?
Dr Belinda Clarke is director of Agri-Tech East, an independent membership organisation that is facilitating the growth of the agri-tech sector, comments that the commercial challenges need addressing along with the technical and agronomic aspects: “The promise of CEA is sustainable, intensive production but achieving that may require a different type of value chain.
“It could be that supermarkets of the future allow you to pick your own fruit and baby leaf instore, or we may see large-scale distribution of veg boxes, with produce grown indoors in optimum conditions or perhaps traditional growers would have more flexibility to grow a greater range of produce all year around with less waste.
“These ideas all have potential but also require significant capital investment and creative solutions for energy management. These are some of the themes we will discuss in the conference.”
‘Bringing the outside In – Innovating for Controlled Environment Agriculture’ taking place on 19 March from 10.00 – 16.00 at Rothamsted Research, Harpenden.
It will look at the different growing systems, emerging technologies, the challenges of implementing a system and the logistics involved with integrating a controlled environment agriculture into the food value chain
Container In Limassol Is The Future of Farming
FEBRUARY 20, 2019
Remember when you were little, and dreamt of the space age future promised on TV; a bright time in which everything was hip, high-tech, and healthy? In just a few decades, we were told, we’d be making phone calls from our watches (check), travelling in driverless cars (almost check), and eating produce grown in high-tech vertical farms (Hmm.). Well, two out of three isn’t bad. Though, if Herbanleaf Farms have anything to do with it, we’re heading strongly towards three for three…
Located in Parekklisha village, this farm is a one-of-a-kind, growing super fresh, healthy greens with a difference… Everything – all the planting, seeding, growing, tending and harvesting – takes place in an upcycled, 40-foot shipping container. And it’s all thanks to the miracle of hydroponics…
A sustainable indoor hydroponics farming company, Herbanleaf is the brainchild of the Timveos family: dad, mum and daughter all working diligently to provide clean, premium leafy greens and herbs grown inside a controlled environment. “This really is a family affair,” explains Myrianthi, the 32-year-old daughter. “My Mum Maria and I work full-time on the farm, while my dad, Panayiotis, helps out whenever he can. In fact, though we’re all as a family very into healthy eating, this whole venture was originally my Dad’s idea: he’s always been into organic gardening, growing vegetables in the backyard, planting seeds and feeding family and friends.”
Inspired by Panayiotis’ research into alternative methods of farming, this environmentally-conscious family came across the Freight Farms venture in 2016, a company which offers complete hydroponic farming solutions for families and businesses all over the world. “My parents went to the regional Freight Farms outlet in Holland, decided to forge ahead with the idea, and next thing we knew our shipping container and equipment had arrived on the island, along with a couple of trainers to teach us the basics…
“It all arrived in November 2017, and by December of that year we were up and running,” Myrianthi reveals. “Granted, we didn’t originally realise what we were in for,” she laughs, “but now we’ve been at this for a while, we love what we do: it’s a real passion…”
Focusing on providing better quality and healthier leafy greens and herbs using the latest sustainable farming techniques Herbanleaf’s innovative methods include the use of non-GMO seeds, grown without the use of harmful chemicals, pesticides, or fertilisers.
“Because we control the growing conditions so completely, we have an amazing range of products that Cyprus doesn’t usually see,” Myrianthi notes. “Mustard greens such as wasabina, which has a spicy flavour, and adds a wonderfully spicy note to salads and eggs; the electric daisy, an edible flower native to Brazil which has antiseptic, analgesic, anti-bacterial and anti-fungal properties and boasts a delightfully citrus flavour; and both green and purple pak choi! We also grow everything from fresh, crisp lettuce, to four varieties of kale, swiss chard, red-veined sorrel, leaf beet and all sorts of herbs such as dill, wild rocket, and coriander. There are,” she adds, “other hydroponics farms on the island, but they’re using greenhouses rather than a specialised, environmentally controlled farm, and that’s what makes us different…”
Saving more than 90 per cent of the water used in traditional farming, delivering the produce equivalent to that grown on 7,284 square metres of land, and able to grow all year round, the Herbanleaf hydroponics system is a marvel of space-age innovation. The plants are grown vertically, in 256 towers. “It’s very futuristic!” smiles Myrianthi. “It’s almost like a spaceship inside: there’s a constant of purple haze from the red and blue LED lights we use – the optimal wavelengths for photosynthesis. There’s also a lot of agrotech involved: special programming which controls the functioning of the farm, oversees the nutrient, seedling, and main tanks, as well as sensors for everything from pH to water temperature. It’s definitely hard work, but we have a real passion for what we’re doing and it’s good to know we’re helping to promote a healthy, environmentally-friendly island!”
From seeds to harvest, Herbanleaf not only delivers sustainable agriculture, it also offers its clients a transparent overview of where and how their food is grown. “Come summer, much of the produce you buy in supermarkets has been imported,” explains Myrianthi. “Now, that ups your carbon footprint and, at the same time, adds a dimension of uncertainty to the food you’re eating. In fact, even produce grown right here on the island may be covered in harmful chemicals. I think a lot of people are under the impression they’re buying healthy food for their families but, unless you ask the right questions and really do your research, you might be very surprised by what you’re consuming!”
At Herbanleaf, however, customers know exactly what they’re getting and how their food has been grown: there’s complete transparency to the growing process. And, by using non GMO seeds and eschewing the use of harmful chemicals, the venture is able to offer a safer, healthier option to all sectors of the community. “‘Fresher, healthier, and tastier’ is what we do,” Myrianthi adds. “It’s right there in our logo, and we stand by it!”
Not only do the family enjoy these fresher, healthier greens themselves, they also sell to individuals and outlets all over the island. Chefs at various hotels purchase from Herbanleaf on a weekly basis, as does Frutopia in Limassol, and the Alchemy bartending school (apparently the edible flowers are a hit in cocktails!). Then there’s the monthly Peyia Market, at which individuals can get their shot of healthy greens direct from the family, as well as a service which sees the produce delivered all over the island.
“So far,” Myrianthi concludes, “we’ve been very successful. There’s an excellent market out there of health conscious individuals, chefs looking for a premium product, and people who want to know exactly how their food is grown. In fact, if you’d like to see the farm for yourself, we’re always more than happy to show visitors round, give them different flavours to taste and teach them about the wonders of hydroponics. This, I believe, is the future of farming!”
For more information on Herbanleaf Farms,
visit https://www.herbanleaffarms.com
or the Faceook page ‘HerbanLeaf Farms’
Pick-Your-Own Fruit And Veg At A Retail Park?
Source: Holdsworth Associates PR
03/02/19
Is there a business case for widescale commercial vertical farming in the UK or will it remain a niche opportunity for high-end restaurants and retail? This is the challenge to be discussed by early adopters at the Agri-Tech East conference ‘Innovating for Controlled Environment Agriculture’ next month (19 March). Advances in logistics and the falling cost of LED lighting may enable year-round growing of undercover produce in the UK, but will energy costs and technical issues delay scale-up and integration within the food supply chain?
GrowUp Farms' vertical lettuce growing | credit: GrowUp Farms
“We do think there is the potential for indoor farming to be commercially viable and there are some immediate gains for growing crops such as leafy salads in high hygiene environments,” comments Lindsay Hargreaves, MD of Frederick Hiam, a farming and fresh produce business with farms in Suffolk and Cambridgeshire. “Growing indoors provides greater control of quality and quantity and fewer inputs of plant protection products.
“There is also the matter of growing crops closer to the point of consumption. Being able to grow more exotic crops in East Anglia close to distribution centres would reduce the food miles. Additionally, there are opportunities to grow crops for pharmaceuticals, cosmetics and vaccines within a controlled environment.”
There are many approaches to indoor cultivation, such as deep-water hydroponics, vertical soilless cultivation, and aeroponics, where exposed roots are sprayed with nutrients. All of these methods are to be discussed at the conference along with advances in monitoring and robotics.
However, despite the news that Sterling Suffolk, one of the UK’s most technically-advanced glasshouses, is set to produce millions of tomatoes starting in February 2019, the cost (£30M) and the technical challenges mean there are few commercial installations in the UK.
Also, it is proving difficult to demonstrate to retailers that controlled environment agriculture (CEA) can bring tangible benefits to their supply chain.
Kate Hofman, co-founder of GrowUp Farms, which from 2015 to 2017 operated 'Unit 84', a commercial-scale aquaponic urban farm inside an industrial warehouse. The 8,200 square feet of growing space could produce enough for 200,000 salad bags and 4,000 kg of fish each year. It sold directly into restaurants, through a New Covent Garden distributor and also through bricks and mortar supermarkets and Farmdrop, the online supermarket.
Kate comments: “A key learning over the last six years is that we can’t just focus on technology – we have to partner along the supply chain to create a business model that ultimately delivers commercial success for growers and retailers.
“One of the major challenges for CEA is to optimise operations to bring down the cost of production to match existing imported products. Our prototype urban farm showed that it was possible to use CEA commercially, and we were able to demonstrate the demand for the produce we could grow. This ranged from specialist micro-greens and cut herbs through to mixed baby leaf salad.
“We are now working on scaling up our business. This will involve relocating, so that our production is co-located with a renewable energy plant and working in partnership with more traditional farming businesses to integrate their experience and expertise.”
There are also technology challenges to be addressed when trying to meet the highly variable consumer demand for high quality, fresh produce.
G’s Fresh supply baby leaf crops all year round, with much of the winter supply grown in Spain and Italy to ensure security of delivery. In summertime it produces a huge amount of outdoor salad crop, particularly lettuces and celery in the UK. Ben Barnes is investigating how controlled environment agriculture can increase the long-term viability and profitability of both of those parts of the business.
The organisation has a large standard greenhouse facility that is used to propagate seedlings for planting out into the field. It is running two projects: Smart Prop, which is looking at increasing the efficiency of the propagation facility to improve growth and make stronger plants so they transplant better back into the field. And Winter Grow, a pre-commercial trial, to see if it is feasible to produce baby leaf crops during the winter at an affordable price point.
Ben explains: “I'm going to be talking at the Agri-Tech East event about the commercial journey, in terms of the go and no-go decision-making process and what the key things are that we need to learn in order to be able to make those kind of investment decisions.
“One element of this is the development of ‘lighting recipes’ to enhance plant growth characteristics. We've got multi-spectrum LED lights, so we can turn up the different amounts of red, blue, green and white, and even far red light. These are fairly expensive, so once we have worked out what works best we can buy fixed spectrum lights, which are a tenth of the cost.
“You think LEDs are very efficient, but they still generate a heck of a lot of heat when you’ve got them turned up to full. It is more about keeping the space cool, and the plants obviously are transpirating so we've got dehumidifiers in there sucking the moisture out of the air.
“One of the biggest problems with the vertical farming concept is this interaction between moisture and temperature. You’ve got the two factors constantly fighting against each other and that ends up sucking up huge amounts of energy if you're not careful.”
Dr Belinda Clarke is director of Agri-Tech East, an independent membership organisation that is facilitating the growth of the agri-tech sector, comments that the commercial challenges need addressing along with the technical and agronomic aspects: “The promise of CEA is sustainable, intensive production but achieving that may require a different type of value chain.
“It could be that supermarkets of the future allow you to pick your own fruit and baby leaf instore, or we may see large-scale distribution of veg boxes, with produce grown indoors in optimum conditions or perhaps traditional growers would have more flexibility to grow a greater range of produce all year around with less waste.
“These ideas all have potential but also require significant capital investment and creative solutions for energy management. These are some of the themes we will discuss in the conference.”
'Bringing the outside In – Innovating for Controlled Environment Agriculture' taking place on 19 March from 10.00 – 16.00 at Rothamsted Research, Harpenden. It will look at the different growing systems, emerging technologies, the challenges of implementing a system and the logistics involved with integrating a controlled environment agriculture into the food value chain
www.agritech-east.co.uk/upcoming-events/
About Agri-Tech East: www.agritech-east.co.uk
Agri-Tech East is a business-focused membership organisation that is supporting the growth of a vibrant agri-tech cluster of innovative farmers, food producers & processors, scientists, technologists and entrepreneurs.
Agri-Tech East brings together organisations and individuals that share a passion for improving the productivity, profitability and sustainability of agriculture. It aims to help turn challenges into business opportunities and facilitate mutually beneficial collaboration.
Vertical Farming: Pick-Your-Own Fruit And Veg At Retail Parks?
Is there a business case for wide scale commercial vertical farming in the UK or will it remain a niche opportunity for high-end restaurants and retail? This is the challenge to be discussed by early adopters at the Agri-Tech East conference‘Bringing the outside in - Innovating for Controlled Environment Agriculture’ next month (19 March).
19/02/2019
Advances in technology, from more energy efficient LEDs to better sensors and advances in soilless cultivation, are enabling the expansion of novel farming methods, but how might controlled environment agriculture disrupt the value-chain? Agri-Tech East's 'Bringing the outside in' investigates.
Is there a business case for wide scale commercial vertical farming in the UK or will it remain a niche opportunity for high-end restaurants and retail?
This is the challenge to be discussed by early adopters at the Agri-Tech East conference‘Bringing the outside in - Innovating for Controlled Environment Agriculture’ next month (19 March). Advances in logistics and the falling cost of LED lighting may enable year-round growing of undercover produce in the UK, but will energy costs and technical issues delay scale-up and integration within the food supply chain?
“We do think there is the potential for indoor farming to be commercially viable and there are some immediate gains for growing crops such as leafy salads in high hygiene environments,” comments Lindsay Hargreaves, MD of Frederick Hiam, a farming and fresh produce business with farms in Suffolk and Cambridgeshire. “Growing indoors provides greater control of quality and quantity and fewer inputs of plant protection products.
“There is also the matter of growing crops closer to the point of consumption. Being able to grow more exotic crops in East Anglia close to distribution centres would reduce the food miles. Additionally, there are opportunities to grow crops for pharmaceuticals, cosmetics and vaccines within a controlled environment.”
There are many approaches to indoor cultivation, such as deep-water hydroponics, vertical soilless cultivation, and aeroponics, where exposed roots are sprayed with nutrients. All of these methods are to be discussed at the conference along with advances in monitoring and robotics.
However, despite the news that Sterling Suffolk, one of the UK’s most technically-advanced glasshouses, is set to produce millions of tomatoes starting in February 2019, the cost (£30M) and the technical challenges mean there are few commercial installations in the UK.
Also, it is proving difficult to demonstrate to retailers that controlled environment agriculture (CEA) can bring tangible benefits to their supply chain.
Kate Hofman, co-founder of GrowUp Urban Farms, which from 2015 to 2017 operated 'Unit 84', a commercial-scale aquaponic urban farm inside an industrial warehouse. The 8,200 square feet of growing space could produce enough for 200,000 salad bags and 4,000kg of fish each year. It sold directly into restaurants, through a New Covent Garden distributor and also through bricks and mortar supermarkets and Farmdrop, the online supermarket.
Kate comments: “A key learning over the last six years is that we can’t just focus on technology – we have to partner along the supply chain to create a business model that ultimately delivers commercial success for growers and retailers.
“One of the major challenges for CEA is to optimise operations to bring down the cost of production to match existing imported products. Our prototype urban farm showed that it was possible to use CEA commercially, and we were able to demonstrate the demand for the produce we could grow. This ranged from specialist micro-greens and cut herbs through to mixed baby leaf salad.
“We are now working on scaling up our business. This will involve relocating, so that our production is co-located with a renewable energy plant and working in partnership with more traditional farming businesses to integrate their experience and expertise.”
There are also technology challenges to be addressed when trying to meet the highly variable consumer demand for high quality, fresh produce.
G’s Fresh supplies baby leaf crops all year round, with much of the winter supply grown in Spain and Italy to ensure security of delivery. In summertime it produces a huge amount of outdoor salad crop, particularly lettuces and celery in the UK. Ben Barnes is investigating how controlled environment agriculture can increase the long-term viability and profitability of both of those parts of the business.
The organisation has a large standard greenhouse facility that is used to propagate seedlings for planting out into the field. It is running two projects: Smart Prop, which is looking at increasing the efficiency of the propagation facility to improve growth and make stronger plants so they transplant better back into the field. And Winter Grow, a pre-commercial trial, to see if it is feasible to produce baby leaf crops during the winter at an affordable price point.
Ben explains: “I'm going to be talking at the Agri-Tech East event about the commercial journey, in terms of the go and no-go decision-making process and what the key things are that we need to learn in order to be able to make those kind of investment decisions.
“One element of this is the development of ‘lighting recipes’ to enhance plant growth characteristics. We've got multi-spectrum LED lights, so we can turn up the different amounts of red, blue, green and white, and even far red light. These are fairly expensive, so once we have worked out what works best we can buy fixed spectrum lights, which are a tenth of the cost.
“You think LEDs are very efficient, but they still generate a heck of a lot of heat when you’ve got them turned up to full. It is more about keeping the space cool, and the plants obviously are transpirating so we've got dehumidifiers in there sucking the moisture out of the air.
“One of the biggest problems with the vertical farming concept is this interaction between moisture and temperature. You’ve got the two factors constantly fighting against each other and that ends up sucking up huge amounts of energy if you're not careful.”
Dr Belinda Clarke is director of Agri-Tech East, an independent membership organisation that is facilitating the growth of the agri-tech sector, comments that the commercial challenges need addressing along with the technical and agronomic aspects: “The promise of CEA is sustainable, intensive production but achieving that may require a different type of value chain.
“It could be that supermarkets of the future allow you to pick your own fruit and baby leaf instore, or we may see large-scale distribution of veg boxes, with produce grown indoors in optimum conditions or perhaps traditional growers would have more flexibility to grow a greater range of produce all year around with less waste.
“These ideas all have potential but also require significant capital investment and creative solutions for energy management. These are some of the themes we will discuss in the conference.”
'Bringing the outside In – Innovating for Controlled Environment Agriculture' taking place on 19 March from 10.00 – 16.00 at Rothamsted Research, Harpenden. It will look at the different growing systems, emerging technologies, the challenges of implementing a system and the logistics involved with integrating a controlled environment agriculture into the food value chain.
Agri-Tech East is an independent business-focused cluster organisation for the East of England. It is creating a global innovation hub, to improve the international competitiveness of plant and crop-based agriculture and catalyse economic growth.
Controlled-Environment Growers Power Their Operations With Cogeneration Systems
Cogeneration systems can deliver the electricity, heat and supplemental carbon dioxide that controlled-environment growers can use to produce edible, ornamental and medical cannabis crops more efficiently and more profitably.
January 30, 2019
By David Kuack
The highest density of cogeneration systems in greenhouses is in the Netherlands. Cogeneration systems in Dutch greenhouses represent almost 25 percent of the electricity produced in the country.
“Cogeneration is a technology that converts natural gas into useful energy for greenhouses, which includes inside power generation to heat the greenhouses and the production of supplemental carbon dioxide that can be used to increase plant growth,” said Dick Kramp, founder and CEO of AB Greenhouse Power Netherlands. AB GPN is acting as a vertical cultivation center of excellence for the global AB organization. Over the last three decades AB GPN developed a standardized cogeneration solution for greenhouses which is fully integrated with the cultivation system.
“The cogeneration system purifies the exhaust gases to produce carbon dioxide. The carbon dioxide can be used to supplement atmospheric carbon dioxide for the production of vegetables, ornamentals and medical cannabis. For the production of cannabis, cogeneration is being used to generate electricity to operate the grow lights. Also, heat from the cogeneration system can be converted into chilled water to cool the greenhouses.”
The majority of greenhouse operations that have installed cogeneration systems have done so to support the electrical power they cannot get from the grid.
Photo courtesy of AB Greenhouse Power Netherlands
The cogeneration system is based on the burning of natural gas.
“Fortunately natural gas is relatively cheap at this time,” Kramp said. “Right now cogeneration is the most economical way of producing energy. The founders of AB GPN started with this technology in Europe and have done over 1,000 unit installations in greenhouses.
“In greenhouses the two major costs are labor and energy. Cogeneration is an additional income stream by selling electricity to the grid and/or energy savings for growers to reduce their price of growing. To operate grow lights growers have to purchase electrical power from the grid. They have to have boilers to heat the greenhouses. They have to have chillers to cool down/dehumidify the greenhouses. With cogeneration on site growers can produce electricity so that they don’t have to buy it from the grid and they can produce the electricity themselves for a lower price. Growers save on their energy bill thereby lowering their cost of production. This enables growers to be more competitive.”
Greenhouse, indoor farm applications
Cogeneration systems can be used in greenhouses and in indoor farms.
“A cogeneration system is not just an engine and a generator,” Kramp said “It’s a total system that is integrated into a greenhouse or building. Ninety percent or higher of every Btu of natural gas is converted into useful energy. Cogeneration is the most economical way of converting natural gas into energy.
“With an indoor farm, it’s more energy intensive because it is not making use of sunlight. On the other hand, an indoor farm allows for the creation of its own climate because the building is more controlled. But it is more expensive to create that climate because it is not making use of the sunlight and grow lights have to be installed to light the crops.”
Kramp said the majority of greenhouse operations are using cogeneration to support the power that they cannot get from the grid.
“In Canada, we have sold more than 50 megawatts of cogeneration in Ontario,” he said. All of the cogeneration systems there are supplying power back to the grid as intermittent power.
“Cogeneration was driven by the need for flexible power supplied to the grid. There is a lot of wind-generated electricity in Ontario and there was a need for integrated flexible power. Cogeneration systems were installed in greenhouses to supply electricity back to the grid when it was needed when there was no wind.”
The carbon dioxide produced by cogeneration systems can be used to supplement atmospheric carbon dioxide for the production of vegetables, ornamentals and medical cannabis. Photo courtesy of SunSelect Produce
A vegetable greenhouse in California has a contract with its utility company to supply electricity back into the grid. The electricity generated by the company’s cogeneration system produces heat, carbon dioxide and enough electricity to power its 64-acre operation plus an additional 2,300 homes.
“This greenhouse is creating an income stream out of selling power to the grid,” Kramp said. “The cogeneration engines run during the day to produce electricity. The heat that is generated is captured and stored in a heat storage tank. This heat can be extracted from the tank at night when the engines are not operating. The engines also produce carbon dioxide that can be used during the day to increase crop productivity.”
Need for more electricity
Kramp said many medical cannabis growers in the U.S. and Canada are installing cogeneration systems.
“The biggest driver of cogeneration in this industry is the shortage of power,” he said. “Right now in the U.S. and Canada they are installing cogeneration systems because they cannot get the electricity from the grid that they need to light their crops. Many growers are installing cogeneration systems in order to guarantee that they have enough power.”
Kramp said growers who have installed cogeneration systems will see the value of the systems as the price of produce begins to drop.
“Currently growers are not really interested in reducing their energy bills by generating electricity at a cheaper price,” he said. “The value of medical cannabis will eventually decrease and will become a commodity like other crops. When it becomes a commodity, then the growers will have to lower their energy bills by installing cogeneration to stay competitive.”
Financial incentives
Kramp said the amount of money growers can save using cogeneration depends on the price of natural gas and electricity.
“Substantial savings can be achieved by installing cogeneration,” he said. “Depending on the price of gas, a kilowatt of electricity can usually be produced for a lower price than buying it from the grid. It really depends on the price of natural gas. The exact savings will be determined in a feasibility study that is done before a cogeneration system is advised.”
In addition to the savings that growers will realize from generating their own electricity, Kramp said many states offer financial incentives for installing cogeneration systems. Both the U.S. Department of Energy and EPA promote incentive programs related to cogeneration, which is referred to as combined heat and power.
“Each state has its own cogeneration program where there are different rebate programs available,” Kramp said. “The incentive program in Massachusetts is called Mass Save. The Department of Energy is supporting cogeneration. The agency has a special group that is available to do feasibility studies for growers interested in installing cogeneration systems.
“Massachusetts is also offering rebates for the installation of LED lights. To apply for these rebates a feasibility study has to be submitted. This is usually done by an engineering company. The state is only awarding the rebates when it is supported by a feasibility study that shows the savings from installing LED lights. Growers can work with the lighting companies to determine what types of rebates are available with the state. Combining LED lights with cogeneration is a great way to maximize efficiency.”
For more: AB Greenhouse Power Netherlands, (31) 631635065; dick.kramp@gruppoab.com; https://www.gruppoab.com/en/greenhouse.
David Kuack is a freelance technical writer in Fort Worth, Texas; dkuack@gmail.com.
How GLASE is Blazing A New Frontier in Lighting
By Erico Mattos | January 25, 2019
Primary organizers of the GLASE consortium are Tessa Pocock of the Rensselaer Polytechnic Institute (left) and Neil Mattson (center) and Erico Mattos of Cornell University.
Lighting control is the last frontier in controlled environment agriculture (CEA). Well-designed horticulture lighting systems can reduce energy use in greenhouses and indoor farms, thereby increasing production and profitability. Light-emitting diode (LED) technologies have the potential to improve energy efficiency and therefore energy costs of greenhouses, but in many ways the hardware capabilities are further ahead than our understanding of how to best operate these systems.
Working in the rapidly growing CEA industry, the Greenhouse Lighting and Systems Engineering (GLASE) consortium is a public-private partnership to develop, transfer, and implement advanced energy-efficient LED lighting systems with improved environmental controls for more efficient and sustainable greenhouse production. Formed by Cornell University, Rensselaer Polytechnic Institute (RPI), and Rutgers University, GLASE is supported by the New York State Energy Research and Development Authority (NYSERDA). The consortium’s mission is to advance CEA through a holistic approach, bringing together different areas of expertise from academia and the marketplace, and creating a hub for technology and information exchange among industry stakeholders and key players.
First-Year Focus: Research and Participation
The combination of engineering practices with plant science is being recognized as valuable, if not critical, to the field of horticultural lighting. During its first operational year in 2018, GLASE developed a series of multidisciplinary activities aimed to optimize CEA systems. Recent technologies developed by consortium researchers include:
• The use of a remote chlorophyll fluorometer to monitor plants relative growth rates
• A proposed standardized horticultural lighting label to facilitate the comparison of lamps across manufacturers
• Improvements to the Lighting and Shade System Implementation (LASSI)
• A control system to optimize lighting control and reduce greenhouse energy consumption
• Light-spectrum optimization for plant growth
The participation of industry stakeholders is paramount in guiding GLASE research and bringing the innovations to market. GLASE is working with industrial partners to commercialize and accelerate the adoption of new energy-efficient technologies nationwide. Since April 2018, 21 industrial members have joined the consortium. The participants are a combination of commercial greenhouses, indoor farms, lighting manufacturers, and service providers. With $5 million secured for research and outreach for the next five years, GLASE will continue to work with industry partners to further develop and implement new energy-efficient technologies to achieve energy-related improvements in greenhouse system operations by optimizing energy efficiency, crop yield, and quality.
What’s Next for GLASE
Future GLASE activities include:
• The development of automated lighting and shade control systems integrated with control of wavelengths for optimal crop growth
• The use of CO2 enhancement in greenhouses
• Investigation of LED use to alter plant physiology and morphology to increase yield or the production of chemical compounds that increase crop value
• The design of novel prototype luminaires for greenhouses
• The development of software that includes whole greenhouse systems management to synergistically control lighting, ventilation , and humidity.
GLASE also works with commercial pilot facilities to test technology adoption in real-world production settings. To ensure the development and implementation of effective technologies, GLASE is supported by a scientific advisory board (SAB) and an industrial advisory board (IAB). The SAB identifies new areas of research and vets GLASE-developed technologies, whereas the IAB offers the consortium guidance on the optimal path to market and provides a source of technical and market intelligence.
Working toward industry standardization, GLASE has established a partnership with Intertek to offer its industrial partners a complementary lighting test to characterize horticultural lighting fixtures following the proposed lighting label published by A.J. Both, et al. This is an effort to provide growers with a reliable comparative platform to select among the available lighting technologies that best fit their unique needs.
Through the development of strategic partnerships and increased industry participation, GLASE is expanding its activities in 2019. In addition to having the opportunity to work with other GLASE partners, members of the consortium receive the benefits of a seat on the GLASE Industrial Advisory Board, early notice of invention disclosures (IP), quarterly technical reports and industry meetings, access to Cornell University and RPI research facilities, networking, marketing, and educational and training programs.
How You Can Participate
As part of the consortium outreach activities, GLASE is developing a national greenhouse energy benchmark database. The aggregated data will be used to support the development of new energy incentive programs, guide national funding opportunities, and allow GLASE researchers and other academic institutions to identify new areas of improvement in Controlled Environment Agriculture systems. Participating greenhouse and indoor growers will have the opportunity to benchmark their production systems against a national database to identify areas of improvement to increase operations’ profitability.
To learn more about GLASE and how to join the consortium, go to Glase.org.
Erico Mattos (em796@cornell.edu) is the Executive Director of GLASE. See all author stories here.
Van Gelder Fruits & Vegetables And PlantLab Establish Indoor Farming Collaboration
RIDDERKERK (NL), 31 January 2019
Foodservice supplier Van Gelder and indoor farming specialist PlantLab have entered into a partnership to produce various types of fresh vegetables in PlantLab’s fully controlled Plant Production Units (PPUs).
Within the Experience Center located at Van Gelder’s new facilities which will incorporate aspects of knowledge sharing, innovation and experience, Van Gelder will showcase specialty crops. Cultivation will take place within two Plant Production Units designed and developed specifically for these purposes by PlantLab. Next to this, PlantLab will produce various crops in large volumes at its own production facilities for Van Gelder. These exclusive crops will enable chefs currently working with Van Gelder to provide new and exciting culinary experiences to their guests.
More vegetables on the table
“In today's world everyone is focused on eating healthier, but this has been a primary focus of Van Gelder for many years. Since early 2011 we have been actively promoting a healthy lifestyle which is a fundamental philosophy to our new facilities”, says Managing Director Gerrit van Gelder. “Together with our growers, suppliers and partners, it is our responsibility to ensure the products we deliver are high in quality, healthy and fresh. This also means that we are constantly looking for products with better taste and higher nutritional value.” Gerrit van Gelder continues: “During this search we encountered indoor farming and in PlantLab we have found a highly qualified partner.”
Indoor Farming at PlantLab
Indoor farming is a new cultivation method which allows crops to be grown in a multilayer system within a completely enclosed environment. “At PlantLab we refer to this as Plant Paradise®; the optimum growing conditions for the most flavorful and nutrient rich produce,” according to Ard Reijtenbagh from PlantLab. Our fresh produce is grown close to the consumer year round irrespective of climate or season. Ard Reijtenbagh explains: “This allows us to reduce transport-related CO2 emissions and waste in the supply chain. Furthermore, we only harvest once our crops have reached their peak in flavour. PlantLab’s products are grown pesticide-free and we utilise up to 95% less water during production”. This local and sustainable manner of growing fresh produce is a perfect fit in Van Gelder’s new facilities.
Partnership
The partnership between Van Gelder and PlantLab has a strong emphasis on sustainable production and delivery of fresh, flavourful, nutrient rich (vitamins and minerals) vegetables with a constant focus on food safety. Furthermore, both organisations will focus on innovation of new products at the Experience Center in Ridderkerk (NL). The newly designed and developed Experience Plant Production Units will provide inspiration for indoor farming, new products, new flavours and vegetables that contain higher nutritional values.
Gerrit van Gelder enthusiastically explains, “Together with our clients we will search for new products with exceptional new flavours. By doing this we can distinguish ourselves with exclusive, high-quality products. PlantLab will collaborate with us in the field of production, product innovation, technology, software and cultivation”. PlantLab’s Ard Reijtenbagh explains: “It’s of great importance for us to be in touch with the market, partnerships such as with Van Gelder enable us to do so”.
About Van Gelde
Van Gelder groente & fruit is a vegetable and fruit supplier located in Ridderkerk, the Netherlands. Founded as a family business, Van Gelder has developed into a foodservice wholesaler with national coverage, with its own growing and production facilities. Using this model Van Gelder has seen substantial growth over recent years and all signs point to further expansion in the future. In order to be able to continue practicing all activities, Van Gelder is currently constructing its new hyper modern facilities. The new Van Gelder facilities form the entrance to the new business park, Nieuw-Reijerwaard, the most sustainable business park in Europe. This is on the same location where Leen van Gelder sr. once started growing Brussels sprouts.
The new Van Gelder facilities will be a place for education, innovation, inspiration and experience focused on fresh! Alongside growing, packaging, processing, storing and transporting vegetables and fruit, the family business will also share knowledge on nutrition, health and sustainability in a unique way.
Seeing, tasting, smelling, feeling and hearing: all the senses will be stimulated at the Experience Center; the meeting place for healthy nutrition.
About PlantLab
PlantLab produces fresh vegetables in its indoor farm systems known as Plant Production Units (PPUs). PlantLab’s technology is developed in-house at its R&D center in ’s-Hertogenbosch (NL). PlantLab supplies products to various supermarkets and foodservice companies in Europe and North America from its Plant Production Units on location.
"Labor Is The Number One Topic In All The Conversations We Are Currently Having"
“…Being a wholesaler and being constantly aware of the need to add value to our customers’ businesses, we are focused on finding the winning innovation of tomorrow”
As we begin 2019, the moment is here to take a general look at the industry, and who better to discuss today’s topics with than Chris Higgins? With Hort Americas continually competing to be one of the leading wholesalers in North America, and Chris being a complete horti-geek, he’s on top of the industry’s topics of today and tomorrow. And there’s much to cover at the moment. “For us, Hort Americas, the only constant thing we see is change. Being a wholesaler and being constantly aware of the need to add value to our customers’ businesses, we are focused on finding the winning innovation of tomorrow”, he explains.
Drew Demler (State Fair of Texas), Chris Higgins and Stephen Ritz (Green Bronx Machine) (photo Hort Americas)
Anniversary
It's been almost a decade since Hort Americas was founded. In April 2009, a group of young American entrepreneurs united with the Dutch suppliers of Horticoop and started bringing horticultural products to the quickly growing horticultural industry of the USA and Canada. Operating as a wholesaler, the company made many products accessible to bigger and smaller companies.
Within their client base you can find vegetable growers, ornamental growers as well as a wide variety of growers implementing a wide variety of innovative techniques used to produce an even wider variety of crops. However, there are various topics that unite them. “Labor is the number one topic in all the conversations we are currently having. It does not seem to matter if we are talking about commercial horticulture, field agriculture or vertical farming. This trend seems constant. In vegetable production as well as in ornamental horticultural production – the quality, availability and cost of labor is the number one topic in North America”, Chris explains. To the company, being on top of these trends and offering solutions to them is key.
“We have a fairly narrow focus on a niche market and we are in contact with our client base daily. This allows us to understand their needs intimately and find and deliver solutions that make our customers more profitable and more successful.” He continues, “This includes new emerging markets as well as established industries that are evolving to meet demand and stay relevant, like indoor farming of medicinal crops and the hydroponic production of soft fruits.”
On a side note he offers, “I do believe that out of these new or evolving grower populations, we are going to see some all stars: people that do things differently - apply new technology, or operate their business in a different way - and become the leaders. But, as common throughout history, it will only be a small percentage of the companies that change the industry. And it is not our desire nor our goal to pick winners. To us, the focus is the complete industry: seeing the similarities between the companies and the way trends and novelties impact their operation. Within these topics, we select products that are winners to us: that can add value to most growers' businesses. That’s how we’re serving the industry and how we are on the look-out for our own product range.”
Role as a wholesaler
The company's vision sounds clear - but there’s challenges in the market. In 2018 Horticoop, the Dutch partner of Hort Americas, announced it would resign their wholesale activities and focus on production only. Whilst this does not affect the Hort Americas business, it did urge the company to rethink their role as a wholesaler. Adding value is key, Chris explains. “Being a distributor is more than just selling or providing products. To us it is offering growers solutions to better their business in both the short and the long term.” To do so, HortAmericas puts a lot of effort in helping growers with their specific challenges and, if needed, educate them about the solutions. “Before, being a supplier meant supplying products. Now it’s about understanding what our growers need and value, then finding ways to fulfill those needs as a service: educating, improving the crop(s) quality, creating a better more efficient work environment, and eventually helping growers find ways to become more profitable.”
Demo Greenhouse
It’s not just a vision to Hort Americas. Besides being active continuously in educating growers and researching a lot, the company (which two years ago started their own demo greenhouse) is focused on creating positive change within their community while at the same time improving the knowledge of the Hort Americas team and their ability to communicate that knowledge with both their vendors and their grower partners.
“Thanks to our relationship with the State Fair of Texas (better known as Big Tex Urban Farms), who’ve continuously supported our business, we’ve been able to combine our efforts, energies and resources to create a demo greenhouse at the fairgrounds based in Dallas, Texas. As long as you have scheduled an appointment, it is open for both the community and growers year round. It is in production year round. It is in a constant state of learning and development. But most importantly it is contributing free, safe and healthy food to members of the south Dallas community in need.”
Night time before the start of the Texas State Fair, where more than 200 thousand people are estimated to visit the greenhouse each year. This pond uses Current, Powered by GE LED Top Lights and the Moleaer Nanobubble Generator. (photo Hort Americas)
Hot summer
When asked why Dallas, Texas, Higgins responds, “We are testing products and trying to prove their value. The hot Texas summers offer a tough and difficult environment to grow in. If we can make it work in Dallas, we are confident in the quality of these products and their abilities to perform in some of the most harsh circumstances.” From their commitment to have a positive social impact to their commitment to playing an important role in both the success of their vendors and their grower partners, Higgins is excited and enthusiastic about the future.Then there’s the social aspect: adding value to the local community.
Chilling the rootzone
In the demo greenhouse the Moleaer system is shown - one of Hort Americas' most talked about products at the moment. “We’ve focused on the limiting factors in producing the best possible crops 12 months of the year. One of the biggest issues in Dallas turned out to be controlling temperature of the root-zone. Chilling the rootzone is not cost-effective in most scenarios. Adding dissolved oxygen to it, turned out to do the trick.”
To Chris, the Moleaer product range offered a typical Hort Americas solution. “It can benefit many growers in an affordable, easy way and it is applicable in a wide area of the countries we service”, he explains. “With Hort Americas, we want to be there for a large group of growers. Products that are only accessible to a small part of the market are not a good fit to us. We are looking for the products that help the average grower in their business.”
Add value by specializing
He explains how the North American industry on one hand consists of big companies, in need of tailor-made solutions. “Then there is a large amount of smaller scale customers. These farming operations do not follow the same pattern of upscaling or monocropping. Instead they add value by specializing in specific groups of products, serving local communities with locally grown product or whatever business model proves them to be right. Whilst we are capable of supplying the large customers, we also want to bring suitable products and services to the farms and greenhouses of all shapes and sizes.”
The Sudlac product portfolio is another example of a product line that is effective for large and small greenhouse ranges as well as hydroponic vegetable production and ornamental horticulture. The demand for the various shading solutions has been on the rise. “Creating a better production climate is of course important to growers everywhere in the world. The added value at the moment is in innovative second generation shading products that not only reduce the amount of light in the greenhouse, but can manipulate and improve light in ways that can enhance crop quality.”
USDA Fresh Herbs Grant Planning Meeting held during the 2018 Texas State Fair. (photo Hort Americas)
Relationships with suppliers
The importance of a good and stable relationship isn’t a one way road. Relationships with suppliers are of high importance to Hort Americas. “Obviously the product itself is important in our selection, but it’s not just that... it cannot be just that. Trust between us and our valued suppliers has continued to evolve into a vital part of our business model. We look for specific relationships with suppliers. We look for companies that we can count on and trust, and vice versa. We ask ourselves, ‘Can the manufacturer add value to the chain? Can we help them market their products in the better ways? Do the manufacturers understand the needs of the market?’ Again we want to create partnerships. Partnerships lead to better business for everyone involved.”
A perfect example of this is Hort Americas' relationship with Current by GE (LED grow light solutions). Adding lighting to the crop is an important topic for many growers wanting to lengthen their season and increase their production. “This goes for vegetables, but for sure is not exclusive to vegetable crops. Managing light intensity, light quality and photoperiod is important in all crop production. LED lighting has helped everyone from tree nurseries (for example) becoming more efficient in growing maple trees to tissue culture facilities producing ornamental and medicinal crops.
"Investing in LED is all about effectiveness and efficiency - making it a perfect Hort Americas product catalog. And the engineering team at Current has helped us to develop a variety of fixtures perfect for many (not all) applications. We are working towards that.” Higgins’ excitement about the GE partnership carries over to other partners that are helping them produce innovative fertilizers and have provided them with opportunities to explore new technologies like 30MHZ (sensor products offering growers a better control and more insights on their crop).
Leafy Greens being grown under Current, Powered by GE LED Grow Lights (Arize Lynk LED Grow Lights) (photo Hort Americas)
Keeping up is a challenge
With the Hort Americas client base being super diverse, staying on top of the various needs in the industry is of vital importance. “Keeping up with all the issues along with the wide range of crops and topics indeed is a challenge”, Chris confirms. “On the other hand, trends are similar across the categories. Labor (again) is something affecting the complete industry: the quality, availability and cost of it is the number one topic in North America at the moment. The biggest difference between the various sub-segments within industries are access finance and the pace of developments and investments - depending on both the maturity of the sectors and what their opportunity for profits look like. But in the end the demand of growers is the same in all crops. It all comes down to the smart use of technology and how that technology lets the grower achieve a sound ROI. That’s the main question we are all trying to answer. This will always be the question we are trying to answer.”
For more information:
Hort Americas
Chris Higgins
chiggins@hortamericas.com
www.hortamericas.com
Publication date : 1/15/2019
Author: Arlette Sijmonsma
© HortiDaily.com
Greenhouse In An Auchan Hypermarket
In Italy, Auchan is testing the installation of a greenhouse in a hypermarket. Fresh herbs and salads grow directly on the shelves and customers do their own “harvesting”.
In Italy, Auchan is testing the installation of a greenhouse in a hypermarket. Fresh herbs and salads grow directly on the shelves and customers do their own “harvesting”.
Agricooltur, a young company from the Turin region, is the originator of this scheme. The neighboring Auchan hypermarket placed the installation in its market area at the end of November; it is a spectacular complex of about thirty meters square. The plants are grown by aeroponics: the roots are hanging loose and are sprinkled with a nutrient solution.
Also in late November, Casino installed a showcase in which an assortment of fresh herbs were grown in its supermarket in La-Varenne-Saint-Hilaire, France.
Source: internationalsupermarketnews.com
Publication date : 1/17/2019
Considering Growing Controlled Environment Edible Crops?
By David Kuack, UrbanAgNews.com
January 17, 2019
Regardless of whether specialty crops are grown in hoop houses, greenhouses or indoor vertical farms, growers are incorporating technology to improve production and profitability.
When it comes to technology, most controlled environment growers are looking for ways to produce their crops as efficiently and as economically as possible. Purdue University horticulture and agricultural economics professor Ariana Torres is focused on the marketing and economics of specialty crops, especially those grown in controlled environments.
“Because of my educational background in controlled environment I focus more on that type of production,” Torres said. “I have three appointments at the university. I teach entrepreneurship. I do research on technology adoption for specialty crop operations, including vegetables, ornamentals, herbs and organic agriculture. I also investigate how consumers perceive grower technologies. My extension appointment allows me to bring the findings from my research to growers and other stakeholders.
“I collect information on farmers markets every week. I have an extension program called Horticulture Business with a website that is hosted by Purdue University. I am also working on developing financial tools like online enterprise budgets and financial calculators where growers can learn about risk and the break-even analysis of various crops.”
Purdue University horticulture and agricultural economics professor Ariana Torres tours Big Tex Urban Farms at the State Fair of Texas in Dallas.
Photos courtesy of Ariana Torres, Purdue Univ.
As a graduate student at Purdue, Torres studied controlled environment production learning that light requirements and nutrition not only vary by crop, but also by variety.
“I can transfer those learning skills to other crops,” she said. “Ninety percent of my current research is on edible crops and 10 percent is on ornamentals. This split also reflects what is happening in the industry. Greenhouse growers and ornamental growers are slowly transitioning to edible crops as well. Many hydroponic systems that were developed for greenhouses and poly houses were designed for ornamental production.
“Of the specialty crop growers I’m working with, 50 percent are controlled environment and 50 percent are outdoor field growers. I initially started working with field crop growers and have transitioned more into controlled environment systems.”
Focused on cost-efficient technology
Torres is focusing on how growers can adopt cost-efficient technologies. She is particularly interested in assisting growers in accessing information about the cost efficiency of technologies.
“I am also interested in finding out how these technologies are perceived by consumers,” she said. “I am starting to study consumers’ perceptions and their willingness to pay for specialty crops.
“One project I’m particularly interested in studying is related to value-added technologies. There are specialty crop growers who sell wholesale in bulk while other growers cut, wash, dry and label products. Value-added can be defined as any physical or labeled transformation of a product. I’m evaluating the transformation of the identity of a crop. Anything related to whether a crop is non-GMO, organic, pesticide-free, locally grown or domestically produced.”
Differences in operation size, customer base
Torres said that small and large specialty crop growing operations have very different market channels.
“The goal of most large operations is to produce large volumes,” she said. “That involves a lot of efficiency—producing the highest value crops that can provide the highest profits selling large volumes to one or two customers.
“Small hydroponic growers are not only looking for a higher profit, they are also looking to access different market channels than large operations. They tend to diversify their number of crops and their number of market channels. For example, small operations tend to sell to restaurants, farmers markets, independent grocery stores, community supported agriculture and they may also sell online.”
Torres said once small operations incorporate technology they tend to stick with it for as long as possible to recover their investment.
“At small hydroponic operations there tends to be less technology and lower investments,” she said. “They also tend to grow more edible crops, including tomatoes and other small fruit, and try to capitalize on higher prices for locally-grown hydroponic crops.
“Large operations are aiming to produce fewer crops and larger volumes with potentially smaller profit margins than small operations. These large operations grow fewer crops and their technologies tend to be more expensive. For example, large growers tend to use more expensive sensors, substrates, irrigation systems, lighting fixtures, and they are usually more willing to experiment with newer technologies. These operations also tend to be more efficient as a result of technological efficiencies.”
Automation limitations
Torres said Europe still leads the way in agricultural automation.
“More technology will be coming from Europe, but I’m not sure if it will come from European companies,” she said. “There are more U.S. researchers and companies doing research on automation and its impact on controlled environment agriculture.
“The Dutch have been very innovative on controlled environment technologies for automation. One of the successes for the Dutch growers is that they are very specialized. A grower has one crop, two crops at most. If a grower is producing one crop like tomatoes, then automation makes a lot of sense. In the U.S. it’s more difficult because growers are more likely to produce a larger number of different crops. The challenge is when growers produce multiple crops like baby kale, microgreens and tomatoes. These are crops that have different production requirements, different stages and different pest pressures. In regards to automation, what works in Europe may not necessarily work in the U.S.”
Factors affecting profitability
Torres said the type of structure and facility can also impact investment and profitability.
“With hoop houses there is usually less technology and fewer investments compared to greenhouses,” she said. “There also tends to be less technology and lower investments at small operations. If these small growers capitalize on higher prices for hydroponic crops, they can be profitable relatively quickly.”
Ariana Torres and a visiting scholar collect prices of specialty crops sold at Indiana farmers markets.
Torres said indoor vertical farms tend to take longer to be profitable because of the startup costs. There can be a large investment in technology.
“Even though greenhouse growers typically need more employees than vertical indoor farms because their operations are larger, most vertical farms are dealing with a higher level of technology requiring more qualified labor resulting in higher labor costs,” she said.
“Energy costs are also going to be higher for vertical indoor farms. The reason profitability is harder to reach for large indoor farms in the first and second year is a reflection of the investment and operational costs.
“Customer base also impacts profitability. A bag of lettuce may cost $4 at a farmers market and $5 at Whole Foods. The prices are not that different considering that selling at a farmers market allows a grower to capture a higher share of the consumers’ dollars. Also considering that operational costs for growers selling wholesale are very different, it is evident why profitability is harder to reach for large growers. If growers sell to wholesalers, the price they receive can be considerably lower than the price paid by consumers. In addition, labor costs per square foot tend to be higher for indoor farms and operational costs can be higher. However, these indoor farms can produce a lot of product so that they are able to supply large volumes.”
Vertical farms can be profitable
Torres said she has been able to collect limited information on indoor vertical farms.
“Small vertical farms tend to sell to independent grocery stores and local farmers markets,” she said. “The vertical farms I have seen in the Midwest tend to be small and their level of technology they usually have built themselves and/or recycled a lot of equipment. They can be very profitable because they are small and are able to capitalize on high prices for locally-grown crops like leafy greens and microgreens.
“Even though these vertical farms are producing on a small scale, they can be very profitable because they are rotating crops every four to six weeks. They can have as many as 12 crop cycles, which is a lot of production.”
Ariana Torres is visiting urban hydroponic operations like this one in Indianapolis.
Torres said where these indoor vertical farms start to run into trouble is when they look to scale up production.
“When small operations scale up, they are going to become a full time job and may need to start hiring employees,” she said. “Once they start to scale up because of increased demand for their product or just because they want to expand their business, that’s when they are likely to run into financial stress. They would need to invest in more technology and their customer base is going to change, moving from direct-to-consumer markets to wholesale or retail. When growers move into bigger market channels and start selling to larger retailers and wholesalers, their business model changes and with that their financial performance.
“With indoor vertical farms, scaling up may involve a lot of investment, especially going from a small to large operation. In field agriculture, it is much easier to scale up to increase profit and revenues. For large indoor vertical farms, for the first three to five years depending on how much money is invested, they are going to just break even or maybe generate negative numbers. Those indoor farms that are able to succeed during the first three years usually have investors with deeper pockets who are willing to see the operations through the long term.”
For more: Ariana Torres, Purdue University, Horticulture and Landscape Architecture, West Lafayette, IN 47907; (765) 494-8781; torres2@purdue.edu; https://www.purdue.ag/hortbusiness.
This article is property of Urban Ag News and was written by David Kuack, a freelance technical writer from Fort Worth, TX.
TAGS Education Greenhouse Technology Indoor Ag Technology Plants Purdue University
Princeton Environmental Institute Urban Challenges Awards $509,000 To New Urban Sustainability Projects
Vertical farms in post-industrial America, origami-based noise-pollution barriers and cement made from burned waste make up the latest round of projects funded by the Princeton Environmental Institute (PEI) Urban Grand Challenges program
Morgan Kelly, Princeton Environmental Institute
January 18, 2019
Vertical farms in post-industrial America, origami-based noise-pollution barriers and cement made from burned waste make up the latest round of projects funded by the Princeton Environmental Institute (PEI) Urban Grand Challenges program. Totaling $509,000, the new awards are active through September 2020 and are described below.
The Urban Grand Challenges program combines the study of the natural and built environments to address the interrelated environmental and social issues facing the world’s rapidly expanding urban areas in a world of increasing environmental volatility. Urban Grand Challenges supports and encourages interdisciplinary faculty and student research at Princeton in the environmental sciences, engineering, architecture, the humanities, policy, the creative arts and the social sciences.
Results from these projects are not only published, but also form the basis of community outreach efforts. In addition, each project includes an educational component — particularly in the form of Princeton courses and PEI internships — that perpetuate the knowledge needed for a sustainable future.
The Princeton Vertical Farming Project was established by Paul Gauthier, associate research scholar in geosciences and the Princeton Environmental Institute, to study how vertical farms can be implemented in communities, particularly in cities.
Photo by Nick Donnoli, Office of Communications
The sustainability of vertical farming in the cities of tomorrow
Paul Gauthier, associate research scholar in geosciences and PEI, is building on the Princeton Vertical Farming Project (PVFP) he established in 2017 to study how vertical farms can be implemented in local communities, particularly in cities. He is working with the nonprofit Isles Inc. based in Trenton, New Jersey, and the 1,200-square-foot Kêr Farms based in Hamilton, New Jersey, to develop a 1,200-square-foot vertical farm and a “food hub” in Mill One, a former industrial building in Trenton. The goals of the project are to prove the feasibility of establishing vertical farms in former industrial buildings, study the social impacts of vertical farming on underserved communities, and better identify the energy and environmental costs of vertical farms. Most importantly, the farm will serve as a source of fresh food for local residents and be used to teach Trenton and Princeton communities about the benefits of vertical farming and the nutritional benefits of “hyper-local” organic food. Gauthier will build on the PVFP’s current partnerships with Hopewell Elementary School and Princeton Public Schools to develop an educational program at Isles Youth Institute designed to help students learn the necessary skills to become a successful farmer.
AmHydro Travels to Russia And India
The AmHydro Team was busy in December and early January with two international trips to countries eager to join the controlled environment agricultural movement. As the population continues to rise and resources become more limited, hydroponic farming is gaining huge momentum around the world.
Attendees at the Agro Greenhouse Complexes Russia Forum and Exhibition look on as speakers from various countries discuss and present to a full room about self-sustaining food technologies for the modern world.
An early December night is lit up by the Kremlin Main Tower in Moscow, Russia. With Russia's interest in sustainable ways to feed their population, could there soon be hydroponic growing systems beyond those walls?
AmHydro's Vice President Joe Swartz and CEO/President Jenny Harris both spoke on behalf of North America's contribution to the hydroponic industry. They focused on appropriate agricultural technologies for Russia, a country where average winter temperatures are in the 20s or below. They highlighted the successes of farmers around the world who have embraced hydroponics and specifically, AmHydro systems to feed their local communities.
Next in January, two of our production experts traveled all the way to Bangalor, India to help install a 1.5 acre hydroponic system that will house both leafy greens and vine crops. India is an agrarian country that, in modern times, is very interested in adopting a drought tolerant, consistent and safe way of producing food.
Now, that is a lot of NFT channels!
Bato buckets as far as the eye can see!
If you missed the webinar about Winterizing your Hydroponic Business, check it out on our YouTube page!
Get Growing! Intro to Hydroponic Crop Production Seminar (February 21 & 22 2019) | Learn to Start A Hydroponic Business!
ON SALE NOW FOR $595.00 for 2
Major SALE! $400 off plus two nights stay at the Red Lion Hotel
USE CODE: SEMFEBCOMBO
Reserve Your Spot Now!
"The Crop is Ready for the Darkest Period"
LEDs for bell pepper cultivation
Only two more weeks and the days will get longer again on the Northern hemisphere, making it quite a challenge for growers these days to keep their crop up and running.
The team at the Delphy Improvement Centre is doing their best as well. They're currently conducting a light test in which the first bell peppers were harvested at the end of November. The plant load is now at around 28 fruits/m2. This is also the maximum plant load calculated for the darkest period with the 200 μmol/m2/s light intensity. The most difficult phase is only just beginning, according to BTO, and the current crop is a good start for the next cultivation phase.
During cultivation they've tried to regulate the amount of light according to the needs of the plant. "This way, we wanted to ensure that the crop did not become too heavy during the period that the supply of assimilates was greater than the demand, so that in the first few weeks light was shielded based on the sum of realized light. Starting in week 42 (4 weeks after planting) the number of exposure hours is slowly increased and from week 47 on we will use the lighting for the maximum 18 hours per day."
Fruit thinning
The challenge of the coming period is that the crop will not experience a dip in fruit production. A plan has therefore been drawn up for the number of fruits that are allowed per week, and fruit thinning is the solution. "The plan is to have a maximum of 3.5 fruits/m2 per week. As bell peppers don't always take every node, thinning is a precision job. But when we look back at the plant load, the plan worked well. We currently have fruit hanging in all stages, which should ensure that we get an even production through the winter."
No difference between departments
There are currently no differences between the two departments (full LED compared to a combination of LED and SON-T lighting). In half of each greenhouse there is extra far-red lighting. So far this provided slightly more stretching and less anthocyanin formation on the stem.
The fruits of the first and second nodes are currently harvested. The fruit weight of the main variety Mavera is around 220 grams and the fruits are very thick-walled. These fruits were harvested within 6 weeks after setting. "Two weeks before the first harvest the setting was somewhat lower, but this week we see this again."
Source: Kas als Energiebron
Publication date : 12/17/2018
Applied Technology: Putting The Hyper In Local
December 21, 2018
For some retailers and restaurants, proximity to local food is key—like next door, on the next floor, or on the roof— and you can’t get much fresher than that.
This technology is already gaining traction across the nation and worldwide with vertical farms in skyscrapers, vegetable and herb gardens at restaurants or near retailers, and container farms in areas where growing can be nearly impossible.
Local Roots, a Los Angeles-based startup, has created a twist on greenhouse growing. The company does grow produce and herbs in a protected setting, but instead of a greenhouse, the indoor farms are in 40-foot shipping containers.
The four student founders say that by using robotics, microbiology, and data analytics, their indoor container “TerraFarms” produce up to 300 times higher per square foot densities than traditional farms.
The containers “have also achieved cost parity with greens and other produce grown out in the field,” says Gary Hawkins, founder and CEO of the Los Angeles, CA-based Center for Advancing Retail & Technology, LLC.
Better yet, he says, “they use a fraction of the water and no pesticides or herbicides.”
Local Roots believes it has eliminated many hazards of the supply chain and is partnering with area businesses, restaurants, and retailers, notably Walmart.
And if a retailer or processor has the desire, Local Roots will not only sell and set up a TerraFarm, but oversee the entire growing process from seed to harvest for the freshest, local vegetables and herbs.
The Vegetable Farmer from the Antarctic
Paul Zabel from the German Aerospace Center operates a greenhouse in the Antarctic, where tomatoes, lettuce and cucumbers flourish
By Dirk Asendorpf
The greenhouse EDEN: tomatoes, cucumbers and lettuce grow up to -40 degrees outside. (DLR)
Paul Zabel from the German Aerospace Center operates a greenhouse in the Antarctic, where tomatoes, lettuce and cucumbers flourish. For future space missions, plant cultivation is to be tested under difficult conditions.
"Zabel. Hello. "- A call in Antarctica. Just started there the polar day.
"We have 24 hours of sunshine when we have no clouds. Today it is very nice. We have the second right summer week. It's only
about minus 13 degrees. " In recent months, Paul Zabel had to cope with significantly worse weather conditions. For one polar winter, he was responsible for the research greenhouse of the German Aerospace Center. This is located 300 meters from the German Neumeyer Station in a container.
"We had the lowest temperature with minus 43.4 degrees in August. There were a few days where there were stronger storms, and I did not go because that was just too dangerous. "
He has a satellite connection at all times in the greenhouse 13,500 kilometers away in the view. A dozen screens fill a wall of the control room.
"We can not touch the plant itself. But we could say for example: The container is now two degrees warmer, we put this here and then the container would be up to two degrees warmer. We could control the light and, for example, we could also give a different nutrient mix to the plant. We can control everything from here. "
A full greenhouse for the first visitors to Mars
The complete remote control of vegetable cultivation in a hermetically sealed container is the prerequisite for its application to future interplanetary space missions.
"Scenarios provide that the greenhouse system flies to Mars in advance, unfolds there automatically and already plants are grown automatically. And when the first humans come to Mars, they can almost find a fully grown greenhouse. That's the theory. "
The tomatoes and salad are well grown. Only the strawberries and peppers did not really thrive in the EDEN greenhouse. (DLR)
However, the practice was still a long way away. Almost every day Paul Zabel had to look to the right in the Antarctic greenhouse.
"For example, we had a broken LED lamp from the plant LEDs relatively early in the year. I could then replace it with a spare part. We had several failures of electrically controlled valves and pumps in our cooling system, which are now being replaced by other models. "
The repairs will be carried out by project manager Daniel Schubert personally in January. Then he also brings the seeds for the next test run, including seeds for ten different types of lettuce that Nasa has already tested on the International Space Station. In the Antarctic container they should germinate and grow as independently as possible. A gardener will not exist in the next polar winter.
The greenhouse should be completely remotely controlled
"We could not find anyone who would like to hibernate again. And then we thought: Could we do a self-sufficient mission? So really just observe and control the greenhouse system only from Bremen, out of our mission control center. And we say to the overwinterers: Only go in an emergency - or to harvest. "
Paul Zabel flies back in mid-December to Bremen. There he missed a century summer.
"I also talked regularly with my colleagues and then I was a bit jealous here and there. But I was just a year in the Antarctic. But chirping birds and being able to go out into the forest again, these are things that you just can not do here. And I'm definitely looking forward to that. "
Belgian Supermarket to Introduce In-Store Vertical Farms
The retail group sees multilayer cultivation as part of its wider aim of pursuing more sustainable products, shortened chains and innovation.
Colruyt Group is testing a system developed in-house for 'vertical farming' or multilayer cultivation in climate-controlled conditions. The retail group sees multilayer cultivation as part of its wider aim of pursuing more sustainable products, shortened chains and innovation. Colruyt Group aims to start stocking the shelves of its retail formula Bio-Planet with the first herbs from its vertical farm from the autumn of 2019, under its own label Boni Selection, which is strongly committed to a sustainable product range.
Ambition: herbs with a very small ecological footprint
Consumers are making increasing demands regarding responsible consumption. Colruyt Group wants to offer a possible solution using vertical farming. "Our multilayer cultivation creates the perfect conditions for plants", explains Stefan Goethaert, Director at Colruyt Group and responsible for product sustainability. "Air, light, water and nutrients are dosed in the ideal quantities. As a result, we only use the amount of energy and raw materials that is strictly necessary, whilst still allowing the plant to achieve optimum growth. And it's no longer necessary to use pesticides. The plants are therefore 100% natural. Moreover, they reach maturity twice as fast than when conventionally cultivated. And the quality remains high throughout the year, regardless of the weather conditions."
The first results after a year of testing confirm the story, says Stefan Goethaert. "We are already using 90% less water and 50% less nutrients than in conventional cultivation. We reuse all of the nutrients that the plant doesn't use. Moreover, we only work with filtered rainwater. Our LED lighting is twice as efficient as the current standard on the market. And the system runs on green electricity from our own wind turbines and solar panels." It is Colruyt Group's ambition to sell herbs that have a very small ecological footprint. That's why the entire lifecycle of the plants is looked at, from seed to consumer's home. The retailer is therefore also working on recyclable packaging and a long shelf life, and will minimise the number of kilometres driven by integrating the vertical farm in a distribution centre in the future.
Home-grown innovative technology
Colruyt Group is the first retailer in Belgium to test a vertical farm that was developed in-house. The technology used has been fully developed within its own R&D department. In the current test set-up, biotechnologists and engineers continue to work on optimising growing conditions.
For Colruyt Group, this project isn't a leap into the unknown: recent innovation projects around water purification, LED lighting, renewable energy, automation, eco-design and refrigeration have formed the basis. In addition, the R&D department works together with a number of knowledge institutions. "We are also in talks with potential partners", adds Stefan Goethaert. "We also want to make some of the plants available to innovative entrepreneurs who work on food trends. Together we can explore the possibilities for using our products."
First trial at Bio-planet in 2019
"We are still in the testing phase, but the goal is to sell the first herbs at Bio-planet within a year", says Jo Ghilain, business unit manager of Bio-planet. "Vertical farming fits perfectly with our brand positioning. Bio-Planet stands for healthy, natural and local products. Furthermore, our customers are early adopters and are looking for added value. They are the people demanding products with a sustainable story." The herbs are currently grown using certified organic seed and substrate. "That was a decisive argument, in addition to the sustainability score of the plants", says Jo Ghilain.
Meanwhile, Bio-Planet customers were the first to taste test basil plants in three stores: on 27 November in Uccle, on 28 November in Grimbergen and Jambes. Jo Ghilain emphasises the added value of this co-creation: "The people of Uccle, Grimbergen and Jambes will help us determine the eventual flavour of the plants. Based on their opinions, we will adjust the cultivation process and the taste. This means that our customers actually choose the end result themselves."
For more information:
Colruyt Group
www.colruytgroup.com
Publication date : 12/5/2018
US (MA): Lettuce Grower Decreases Crop Cycle by 30%
Fresh Roots Greenhouse is a hydroponic lettuce, herb and leafy greens grower based in Chelmsford, Massachusetts. After 40 years in the pharmaceutical industry, Fresh Roots’ owner Bill Evans wanted to give back to his community during his retirement years. He found himself drawn to how cooperative-run greenhouses like Evergreen Cooperatives and WellSpring Cooperative created jobs for underserved members in addition to providing local produce, which inspired him to build Fresh Roots Greenhouse. Fresh Roots’ state-of-the-art Harnois greenhouse uses an AmHydro Nutrient Film Technique (NFT) system to grow arugula, kale, basil, and several varieties of lettuce.
The potential to direct plant growth
Since Bill’s goal is to run his greenhouse year-round, he needed the most energy-efficient lighting system possible. His experiences growing with HPS and fluorescent lights at other facilities had been suboptimal. While the fixtures grew plants, Bill could tell that the plants were not growing as quickly and that the red varieties were not coloring up as expected. Bill felt that LEDs were the most practical financial choice – while LEDs cost a bit more up front, they would save him money on electricity and labor in the long run. After Bill learned about spectrum and LumiGrow through Melanie Yelton, Vice President of LumiGrow Research, at a hydroponic tomato growing course at the University of Arizona, he was eager to learn more and stayed in touch. He was impressed with LumiGrow Research’s depth of knowledge and hands-on approach to helping customers implement the latest lighting strategy research. As a result, LumiGrow was top of mind for Bill when he began to search for the right LED lighting system for Fresh Roots Greenhouse.
“I really believe in the promise of spectral science,” says Bill, “From the time I met Melanie [at University of Arizona] and learned about LED lighting’s potential to direct plant growth, I’ve wanted to work with LumiGrow.”
Extending photoperiod to maximize growth
Bill implemented LumiGrow fixtures across the Fresh Roots entire greenhouse. He uses them for all NFT stages of plant growth. Bill was eager to start growing and immediately began using the lights to extend his plants’ photoperiod to 21 hours.
“Keeping the light on for 21 hours keeps the plants awake,” explains Bill, “If they’re kept awake, we maximize their growth period.”
Fresh Roots lettuce varieties reach harvest size about 30% faster than their typical light exposure seen in soil farming. The seed manufacturer reports a typical harvest after 50-55 days, whereas the LumiGrow-lit lettuce is ready after about 35-40 days. Bill has had success growing a wide variety of lettuces, from green butterhead to green leaf to romaine. Depending on the variety, the finished lettuce heads weigh between 7-10 oz. Each variety grows a bit differently under the LumiGrow lights.
Bill has also successfully reduced his basil’s crop cycle by over 35-40%. The basil plants reach harvest size in 35-42 days – unlit greenhouse-grown basil can take up to 56-68 days as reported by the seed manufacturer.
Additional savings using smartPAR Light Sensors
Bill has moved past simple daylight extension and is using LumiGrow fixtures to automate his lighting strategy to improve production. Bill is using LumiGrow smartPAR Light Sensors to constantly monitor the light levels inside the greenhouse and adjust the fixture intensity to achieve a daily light integral (DLI) of 17 μmol·m−2·s−1 over the course of each 21-hour photoperiod. Once the target DLI is reached, the LumiGrow smartPAR Wireless Control System turns down the fixtures’ light intensity to minimize electricity use while keeping the plants awake for the full photoperiod. Bill is happy to see that his plants are thriving under the LumiGrow fixtures.
Bill was even happier to discover that in addition to consistently reaching his lighting goals, the smartPAR Light Sensors are maximizing his LumiGrow fixtures’ energy efficiency. After Fresh Roots’ smartPAR Light Sensors were installed, Bill noticed that his electricity bill was significantly lower than when he was simply turning the fixtures on at the end of the day to extend photoperiod. Bill can rest easy knowing that he can rely on his smart lighting to deliver the appropriate amount of light every day while saving him money each month.
Bill also appreciates the flexibility that LumiGrow adjustable spectrum offers. While Bill prefers to use his LumiGrow smartPAR Light Sensors to automate his greenhouse’s lighting, he likes that the LumiGrow smartPAR Wireless Control System also gives him the option to adjust each spectral channel to create custom spectral strategies. His LumiGrow fixtures’ versatility and user-friendly software make it simple to fine-tune his spectral programs as leafy greens research continues to develop. Bill likes that smartPAR enables him to easily create new lighting zones, which opens the possibility of growing new varieties of leafy greens under different ratios of light spectrum
In the meantime, Bill will continue to provide high-quality, locally-grown leafy greens to the local community in Massachusetts and share his passion for LumiGrow technology.
“I love sharing the many properties of these lights with people, particularly the science and engineering behind them,” says Bill, “Year-round supplemental lighting is not something a lot of greenhouses in this area have yet.”
For more information:
LumiGrow
800-514-0487
info@lumigrow.com
www.lumigrow.com