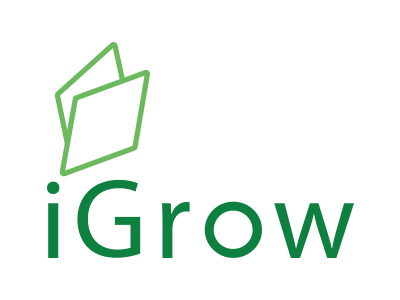
Welcome to iGrow News, Your Source for the World of Indoor Vertical Farming
Indoor Farm Grows Produce In Outer Space
Indoor Farm Grows Produce In Outer Space
The plant cultivation technology will help provide food for crew members on board the International Space Station.
6 Nov 2017
Most people take the ability of walking to the supermarket to buy food for granted, but that simply isn’t a possibility for many who are based – quite literally – in the middle of outer space. Engineers at the German Aerospace Center (GAC) saw this gap in the market and created the EDEN ISS project, which aims to advance controlled environment agriculture technologies beyond the state-of-the-art. EDEN ISS is a 4-year project under the European Union‘s Research and Innovation Action program Horizon 2020. The goal of the project is to develop safe food production for on-board the International Space Station (ISS) and for future human space exploration vehicles and planetary outposts.
The project will develop an advanced nutrient delivery system, a high performance LED lighting system, a bio-detection and decontamination system, and food quality and safety procedures and technologies. A mobile container-sized greenhouse test facility will be built to demonstrate and validate different key technologies and procedures necessary for safe food production within a semi-closed system. The plant cultivation technologies will initially be tested in a laboratory setting. The next phase will see the high-tech greenhouse container shipped to the German Neumayer Station III in Antarctica, which will begin crop cultivation experiment in December.
Technology has placed itself in the middle of those who are in need of a service and the creation of the required service, with nothing seeming impossible. The mobility of the less able in poverty-stricken countries, for example, has been tackled by one company, who created an all-terrain wheelchair, while the Finnish government has teamed up with a startup tohelp refugees with their finances. How has technological advances in the past 12 months boosted your business’ operations?
Website: www.eden-iss.net
Contact: www.eden-iss.net/index.php/contact
iUNU’s Computer-Vision Greenhouse Management Solution LUNA
iUNU’s Computer-Vision Greenhouse Management Solution LUNA
Adds Rail Network and Autonomous Camera System
Greenberg: “Our technology helps growers optimize greenhouse farming through images and data, improving performance and demand-driven agriculture. Simply put: Luna has got your back.”
Seattle, WA — Following the launch of iUNU’s [www.lunapowered.com] flagship LUNA greenhouse management platform, the company unveiled its latest innovation, the Luna rail network and autonomous camera system today. This revolutionary tool leverages how machines and computers emulate the human brain and eyes to create images and understanding about the growing process and operation.
Luna works by using a rail-mounted, autonomous mobile camera that captures close-up, high-definition plant images, and high-definition emplaced cameras that watch and keep track of the total growing process. This, combined with visual information data points gathered from in-canopy sensors, tells you what is actually happening. At the same time, Luna is building models of real-time growth curves and proactively notifying the team if subsequent crops deviate from established standards. By coupling these alerts with workflow management dashboards, managers can easily assign tasks and track all the care required for a specific crop. Luna is easily accessed through any Internet-connected device through a native mobile application or a desktop browser.
“Our technology helps growers optimize greenhouse farming through images and data, improving performance and demand-driven agriculture. Simply put: Luna has got your back,” said iUNU CEO Adam Greenberg. “The Luna rail network and camera are the latest grower focused, plant-centric solutions from iUNU, and we are just getting started,” Greenberg continued. “Over the coming months you will continue to see updates and enhancements added to the software management suite as well as extending functionality and reach with hardware developments. The team driving this company is the best in the emerging ag-tech sector,
combining decades of experience from companies like Amazon, Boeing, Honeywell, Intel, IBM, HP, Adobe, Mozilla and some of the largest greenhouse operations in the country. We are applying the same approach that revolutionized manufacturing to the commercial greenhouse market – turning recipes into measured, repeatable, industrial processes.”
The arrival of the rail network and camera augments the Luna software platform’s computer-vision and machine learning technologies to continuously build detailed models of individual plants throughout the day while addressing greenhouse-wide operations issues. Using high-resolution imagery, as well as bioinformatics, this system provides an innovative approach to monitoring tiny changes in plant behavior, allowing for more proactive management. The reality is greenhouse growers must deal with pests, diseases and other environmental threats to plants – now Luna offers a solution that enables them to operate as modern, demand-based, information-driven, manufacturing facilities.
The Luna system begins to learn, and remember, the moment cameras and sensors are turned on, giving growers historical records of every detail of every plant in the system, as well as live information – everything they need to make the best possible business decisions.
LUNA is AVAILABLE NOW. Check us out at www.lunapowered.com.
###
Founded in 2013, iUNU (“you knew”) is an industrial computer vision company headquartered in Seattle, with offices in San Francisco and San Diego. Connecting plants, facilities, and people through a single interface, LUNA turns commercial greenhouses into precise, predictable, demand-based manufacturers. An AI born in the heart of Seattle; trained in Silicon Valley and the greenhouses of Skagit Valley; and now accessible from everywhere. The team at IUNU looks forward to introducing you to her.
NatureFresh™ Farms Signs Agreement With Netherland’s Van der Knaap Group
NatureFresh™ Farms signed an agreement with Netherlands-based specialists in high quality rooting and growing media Van der Knaap Group to grow peppers organically using a patented sustainable organic cultivation system.
NatureFresh™ Farms Signs Agreement With Netherland’s Van der Knaap Group
Leamington, Ontario (Oct 6th, 2017)
NatureFresh™ Farms: Committed to Investing in Innovation
NatureFresh™ Farms signed an agreement with Netherlands-based specialists in high quality rooting and growing media Van der Knaap Group to grow peppers organically using a patented sustainable organic cultivation system. This agreement supports NatureFresh™ Farms plans increase it’s organic peppers lineup from 9 acres to 15 acres in 2018, and further this effort with 30 acres of organics by 2019.
Sustainable Organic Cultivation: Seven Years in the Making
Van der Knaap’s R&D team has been working with their partners to develop a cultivation system for growing organically above the soil. This effort has been led by Karel de Bruijn, R&D Manager of Van der Knaap who developed a reactor that converts proteins into nitrates (NO3) nitrogen. This nutritional solution produced with the reactor is free from organic residue, fungi and bacteria.
Applying Global Best Practices to Local Growing
“Our team strives to constantly innovate in order to improve our growing practice.” says John Ketler, General Manager of NatureFresh™ Farms. Working with Van der Knaap’s cultivation system underscores NatureFresh™ Farms commitment to improving the quality of its organics offering by applying the latest technologies from across the globe. “Sustainability is core to our business and this partnerships allow us the ability to think globally and grow locally.” says Peter Quiring, CEO & Owner of NatureFresh™ Farms.
-30-
About NatureFresh™ Farms
NatureFresh™ Farms has grown to become one of the largest independent, vertically integrated greenhouse vegetable growers in North America. Growing in Leamington, ON and Delta, OH, NatureFresh™ Farms prides itself on exceptional flavor & quality. Family-owned NatureFresh™ Farms ships Non-GMO greenhouse grown produce year-round to key retailers throughout North America. Learn more at www.naturefresh.ca/about/innovation
About Van der Knaap Group
Van der Knaap is a group of companies specialised in high quality rooting and growing media. Van der Knaap Group offers professional horticulture solutions in the field of natural rooting and growth media. Van der Knaap consciously chooses raw materials that are recyclable and therefore environmentally friendly.
Why Eating Local Produce Just Got More Innovative
Why Eating Local Produce Just Got More Innovative
November 10, 2017 | HOUSTON, TX
When Dish Society restaurant owner Aaron Lyons prepares his food for patrons, he knows that 75 percent of what's on the plate is from the Houston area.
"Locally sourced ingredients taste better, they're more nutritious, and we like to support the local economy," said Lyons.
His lettuce vendor is Sustainable Harvesters in Hockley.
"I love the fact that it's - the whole procedure is better for the environment," Lyons explained.
Sustainable Harvesters grow their produce in a greenhouse without the use of chemicals or pesticides.
"We're in about 12,000 square feet of space, that's a quarter of one acre of land. In that quarter acre, we can produce up to 7,000 heads of lettuce a week. That's a tenth of the land required for a traditional farm outdoors, but not only a tenth of the land. We use a tenth of the water," explained Sustainable Harvesters Co-Founder Matthew Braud.
They also save on labor.
"This entire system is run by a greenhouse manager and greenhouse technician," said Braud.
So, how is it possible to run an entire farm with only two people? It's because of the aquaponics technique they use.
"Aquaponics is the combination of aquaculture, or raising fish in a controlled environment, and hydroponics, which is growing plants in a soil-less environment," Braud said.
The process starts with over 2,000 tilapia in each tank fed a high-protein diet.
"That food ultimately gets consumed by the fish and converted into a waste product that we can use through filtration as a concentrated form of nitrate for them to take up," explained Braud.
The water then flows into two filters.
"From these filters, the water flows below these plants and gets consumed by the roots and then ultimately cleaned before that water flows back into the fish tank as a clean source of water," he explained.
Then, the lettuce is delivered to vendors with the root still intact. Even when Hurricane Harvey hit the Houston area, the torrential rain and floods didn't affect their farm.
"This structure keeps us safe from not only floods, but also rain, bad weather including wind, and especially pests," said Braud.
So, for them, even after Harvey, it was business as usual, producing the freshest of lettuce so restaurateurs like Lyons could dish out the best-tasting entrees.
"It's a better product. It's a better quality product," said Lyons.
USDA Advisory Board Blocks Ban Against Using Hydroponics In Organic Farming
USDA Advisory Board Blocks Ban Against Using Hydroponics In Organic Farming
Constantine Spyrou
November 7, 2017
Hydroponics is one of the fastest-growing fields in agriculture today. By growing plants in water and "feeding" them solutions of nutrients they need, crops can grow at higher yields over a faster period of time while drastically reducing water consumption and land space. While it's an amazing tool for the future of food, one question has been in the minds of several industry members: Can food grown via hydroponics be classified as USDA Organic?
In a recent 8-7 ruling, the National Organic Standards Board (NOSB) ruled against a ban on hydroponics in organic farming. In doing so, the board, which makes recommendations to the USDA on rules for the organic industry, clears the way for organic, hydroponically grown produce to proliferate in supermarkets. The USDA does still have to receive an official recommendation and choose to act on it or not, however.
If they do so, it could be huge for hydroponics, but would harm organic soil farmers. Hydroponics, with its faster growth rate and decreased water and land use, is already taking a significant market share away from the soil farmers. Nowadays, most organic tomatoes are grown through hydroponics and similar methods, and organic farmer Dave Chapman voiced fears to NPR that even more space in supermarkets will be given to hydroponically-grown produce.
"What will happen, very quickly, is that virtually all of the certified organic tomatoes in supermarkets will be hydroponic. Virtually all of the peppers and cucumbers [will be hydroponically grown]. A great deal of the lettuce. And most of the berries."
On the other hand, the innovative technology can be used to keep up with growing organic demand. It also is more sustainable than traditional farming since it doesn't utilize as many natural resources, making it the ideal choice for environmentalists and scientists focused on preserving the planet.
At the center of the debate, though, is the true definition of what it means to be "organic." Hydroponic farms claim that they are organic because they don't use synthetic pesticides and can grow year-round at a cheaper price. Traditional farmers, however, argue that the true core of organic farming is nurturing and taking care of the soil itself, something that hydroponics doesn't even involve.
When it comes to what it really means to be "organic," for now, it seems that the NOSB is willing to include hydroponics within that definition based on their recent decision.
Shenandoah Herb Grower is Expanding Across The U.S.
Shenandoah Herb Grower is Expanding Across The U.S.
October 27, 2017
Shenandoah Growers produces organic plants in greenhouses and
indoor growing rooms. Courtesy Shenandoah Growers Facebook
Shenandoah Growers, a Harrisonburg-based organic herb grower, continues to expand its system of automated greenhouses and indoor LED growing rooms around the country.
The company’s Rockingham County farm complex serves as the eastern hub of operations, with spokes in the mid-Atlantic, Midwest and South Central markets. It recently opened its third indoor growing facility in Sherman, Texas. The other two are in Virginia and Indiana.
The combination of greenhouses and indoor growing rooms changes the way highly perishable produce can be grown and distributed, says CEO Timothy Heydon. Shenandoah Growers is able to produce more than 30 million certified-organic plants per year — from arugula to thyme — under these controlled conditions.
With the latest expansion, “we start the plants in Virginia and then we ship partially finished plants to Indiana and Texas. They finish growing fresh there for the markets,” Heydon says. “With the advances in growing with LED lights, we can get a high-quality plant, good value and good shelf life.”
Shenandoah Growers also plans to implement an indoor farming hub and spoke system on the West Coast next year. A location has not yet been chosen.
“LED growing is only part of our system. We use it as tool where it makes the most sense,” Heydon says. “Our approach is to use LED at the more critical stages of growth. When plants germinate, we put them into the LED room, where we can control plants at a younger stage of development. The plants then are transferred to greenhouses.”
The benefit of this approach, he says, is that “we can have a smaller unit in a regional facility, without having to build an entire infrastructure from seed. It’s a more efficient way to use resources.”
Since the company was founded in 1990, “we’ve evolved. We put a lot of emphasis on research. We’re organic USDA certified. Our systems are built on the principles of sustainability,” Heydon says. For example, “we collect rainwater from our buildings and use it to irrigate our plants.”
The company now has more than 1,200 employees working at farms, production facilities and logistics operations in 11 states.
NatureFresh™ Farms & Eminent Seeds NL Introduce “The World’s Smallest Tomato”
NatureFresh™ Farms and Eminent Seeds NL reached a proprietary agreement within North America. NatureFresh™ Farms will exclusively grow and market Tomberry® tomatoes in Canada, United States and Mexico.
NatureFresh™ Farms & Eminent Seeds NL Introduce “The World’s Smallest Tomato”
NFF-Tomberries-30 Oct 2017 NatureFreshFarms
Leamington, ON (October 30th, 2017) This past PMA Fresh Summit in New Orleans, NatureFresh™ Farms and Eminent Seeds NL reached a proprietary agreement within North America. NatureFresh™ Farms will exclusively grow and market Tomberry® tomatoes in Canada, United States and Mexico. Jan van Heijningen, Director at Eminent Group, and John Ketler, Farm Manager at NatureFresh™ Farms, finalized the agreement during the tradeshow.
In the spring of 2018 NatureFresh™ Farms will begin growing and commercially marketing this exciting new variety of tomato from its Leamington Ontario Greenhouse. Plans are to expand the production of the Tomberry® tomato over the next few years, as the category grows to meet consumer demands for snacking tomatoes.
This past year NatureFresh™ Farms trial and development team has worked with Eminent NL Seeds to explore new tomato varieties that would fit the growing trend in the snacking category. Not only does the Tomberry® deliver in flavor, it brings a new look and ingredient to the culinary world of food service. These attractive berries are very versatile in the use of salads, hot dishes, and visually appealing. “The World’s Smallest Tomato”, The Tomberry® tomato is about 0.5 to 1 cm in diameter with an average fruit weight of 1 to 2 grams, perfect for snacking.
“The Tomberry® is unique in size and has caught the interest of our retail partners” explained Matt Quiring, Executive Retail Sales Manager. “The snacking trend in North America has exploded and we continue to search for new items that will help grow our snacking category. This pearl sized fruit’s unique size is something hard to miss and even more difficult to pass by without picking up. Once a consumer tries them, we are confident that they will be coming back for more. Visually, it is candy to the eyes. From a sensory standpoint, we can back that up.”
“We are pleased to partner with Eminent NL” said Peter Quiring, President and Owner of NatureFresh™ Farms. “This is a perfect fit to complement our TOMZ® snacking category and our brand strategy. We want to grow and market the best tasting tomatoes, peppers, and cucumbers and we are excited to offer this for the first time from our Leamington Ontario greenhouse starting next spring. Our research team works hard at identifying these new varieties that taste exceptional, and we look forward to the new opportunities they provide for future consumers.”
Over the next few months, NatureFresh™ Farms will be developing packaging and branding for a launch scheduled in spring 2018. For more information about this exciting new tomato contact NatureFresh™ Farms Sales. 519-326-1111
Eminent Seeds NL ABC Westland 118 2685 DB Poeldijk the Netherlands
NatureFresh™ Farms 634 Mersea Rd. 7 Leamington, Ontario Canada, N8H 3V8 www.naturefresh.ca
About NatureFresh™ Farms -
NatureFresh™ Farms has grown to become one of the largest independent, vertically integrated greenhouse vegetable growers in North America. Growing in Leamington, ON and Delta, OH, NatureFresh™ Farms prides itself on exceptional flavor & quality. Family owned NatureFresh™ Farms ships Non-GMO greenhouse grown produce year-round to key retailers throughout North America.
SOURCE: Ray Wowryk | rayw@naturefresh.ca
Director of Business Development | NatureFresh™ Farms T: 519 326 1111 | www.naturefresh.c
Mucci Farms Expansion to Create Largest Greenhouse Strawberry Grower in North America
The company that mainly grows greenhouse tomatoes, cucumbers and peppers wants to grow strawberries year-round using artificial lights in the expanded acreage and is banking on freshness and not using pesticides to compete with field berries. Greenhouses tend to use native insect predators for pests.
Mucci Farms Expansion to Create Largest Greenhouse Strawberry Grower in North America
SHARON HILL, WINDSOR STAR
Published on: October 26, 2017
Mucci Farms is spending $12 million on top of its $24-million investment in greenhouses built just for strawberries to become the largest strawberry grower in North America under glass.
The company that mainly grows greenhouse tomatoes, cucumbers and peppers wants to grow strawberries year-round using artificial lights in the expanded acreage and is banking on freshness and not using pesticides to compete with field berries. Greenhouses tend to use native insect predators for pests.
“Mucci Farms can proudly say we are putting Kingsville, Ontario, on the map for having the largest strawberry greenhouse not only in Canada but in North America,” Joe Spano, a vice-president of sales and marketing, said before a Thursday ribbon-cutting ceremony.
Danny Mucci, the other vice-president of sales and marketing, said the 36 acres of greenhouses — when 12 acres are added next year to the 24 acres of strawberries under glass at the Road 2 East site — may end up being the largest indoor production of strawberries in one spot worldwide.
The $12-million expansion will include artificial lights and getting a lower electricity price was key in the decision to expand, Spano said. Mucci Farms is building greenhouses in Ohio where hydro is cheaper but those greenhouses won’t grow strawberries, he said.
“We’ve come to terms with Ontario Hydro on a couple pilot projects that they’ve supplied some discounted pricing allowing us to expand our footprint here,” Spano said.
He said without the pilot project, the company likely wouldn’t have been able to expand in Kingsville. Spano didn’t divulge details of that agreement.
Mucci Farms employs about 1,200 people in Leamington and Kingsville and will add about 100 workers since 300 are needed to pick strawberries at the peak harvest times.
Mucci said the farm may grow other fruits. The berries are sold as Smuccies Sweet Strawberries.
“We think we can (compete). We have a superior product. The quality’s going to be fantastic. If they have inclement weather outdoors — whether it’s rain or too hot of temperatures — we feel that we still have a better berry,” Mucci said.
“It is the cleanest strawberry out in the marketplace because we do not spray any pesticides.”
Unlike California berries that are trucked over days to grocery stores, Spano said Smuccies will be on shelves within 24 hours and the marketing in Canada and the United States will focus on freshness. It won’t hurt that Christmas, New Year’s and Valentine’s Day fall in the winter.
“Local strawberries on Valentine’s Day would be a win-win for everybody,” Spano said.
Smuccies were sold at $4.99 and $5.99 for a 12-ounce clamshell container in local stores and Spano said they were competing with California berries in a slightly smaller one pound container at $5.
“We were selling out so the consumers are speaking volumes. They like the cleanliness. They like the sweet flavours,” Spano said. “We can compete, yes. I think actually they’re going to have a problem competing with us.”
Greenhouse strawberries have been big in Europe for more than a decade and Mucci said the European strawberry market is about 65 per cent from greenhouses.
While other local greenhouses grow strawberries, they aren not on the scale of Mucci Farms.
The Thursday announcement included a media peek at the first harvest in Phase 2 of the expansion and treats including chocolate-covered strawberries and champagne poured over strawberries.
GLASE Seeks Industry Involvement in Research of Controlled Environment Agriculture
Lighting and Systems Engineering Consortium, is a partnership among growers, plant physiologists and horticulturists, trade groups, produce buyers, agriculture engineers, lighting manufacturers, government agencies, and others to pioneer and commercialize breakthrough technologies that deliver greenhouse crop and energy solutions.
GLASE Seeks Industry Involvement in Research of Controlled Environment Agriculture
GLASE, the Greenhouse Lighting and Systems Engineering Consortium, is a partnership among growers, plant physiologists and horticulturists, trade groups, produce buyers, agriculture engineers, lighting manufacturers, government agencies, and others to pioneer and commercialize breakthrough technologies that deliver greenhouse crop and energy solutions.
Established in 2017 by Cornell University and Rensselaer Polytechnic Institute and supported by the New York State Energy Research and Development Authority (NYSERDA) and the Center for Lighting Enabled Systems & Applications (LESA) at Rensselaer, GLASE unites world-class engineers and horticultural researchers with private and public stakeholders to transform the way greenhouses operate, dramatically reducing their energy use while increasing yields and crop quality through greenhouse lighting and energy management systems that are integrated with carbon dioxide supplementation, ventilation, and humidity control.
GLASE has secured $5 million for research for the next seven years and is now inviting industry members to join the consortium and step into the future of controlled environment agriculture today.
Benefits of joining GLASE
GLASE is a unique technology and information hub where members receive exclusive and early access to:
- Invention disclosures and preferential licensing rights to GLASE-conceived and developed intellectual property.
- Technical reports, presentations, data and information on new and emerging engineering and crop research.
- Training opportunities and educational programs including webinars, short courses and research symposia at reduced registration rates.
- Grant opportunities, investment opportunities and energy audit programs.
- Professional networking opportunities among thought leaders and researchers.
Members sit on GLASE’s Industry Advisory Board, which meets quarterly and provides input on research directions based on members’ priorities.
Areas of research
Applied Engineering: LED fixture design, thermal management, driver design, high refractive index LED encapsulants.
Photobiology: Crop-specific spectrum testing, biochemical analyses, maximizing the potential of light-driven plant growth and development and improved nutritional content in crops.
Energy modeling: Greenhouse energy profiling, standardize protocols for testing light fixtures.
Integrated controls: Growth chambers and greenhouses, light-shade-CO2 controls.
For more: Erico Mattos, executive director, Greenhouse Lighting and Systems Engineering Consortium, (302) 290-1560; em796@cornell.edu; www.glase.org.
Alexandre Novi of Exploitation NOVI About Water-Grown Lettuce
Alexandre Novi of Exploitation NOVI About Water-Grown Lettuce
“We are looking into this exciting technique”
Exploitation NOVI exports 95% of their winter lettuce. This family-run business specialises in varieties of lettuce. “We have, in addition to our open fields, almost 11 hectares of greenhouses on two farms”, says Alexandre Novi, sales manager at the company, which is based in Provence, France.
“We export mainly to Germany and Switzerland”, he says. “We also sell to the Netherlands, the United Kingdom and, sometimes Belgium. We would like to increase our presence in the Netherlands and Belgium.” Their clients include importers and supermarkets.
They start their season with a new concept: “mix box”. “This is a small box with four heads of four different varieties of lettuce”, explains Alexandre. Exploitation NOVI grows lollo rossa, lollo bionda, green and red oak leaf, green and red batavia, red lettuce and salanova, a very leafy lettuce variety. They also pack in poly bags and flowpacks.
The company starts with the French salads at the beginning of November. After the lettuce seeds are planted, it takes six to eight weeks before they can be harvested. “We cut the lettuce in the morning, then prepare the pallets”, says Alexandre. “We use a cooling system that incorporates total immersion. The lettuce is sent to our clients on that same day.”
Alexandre says they have had no rain since May. “The weather in the Provence is an advantage for our growing process. The dry environment and sunshine allows a nice and good development of roots and of the salads.” He added that like some other growers, Exploitation NOVI is also looking to develop stronger crops and stronger textures for their lettuce “This helps reduce pathogens as well as insect infestation. Insects don't like the stronger textures, so they go elsewhere.”
‘We are looking into the exciting technique of water-grown lettuce”, says Alexandre. “We have no experience in it yet, but we have seen other businesses in the sector build these kinds of greenhouses. It is very interesting because you can increase efficiency, while at the same time, reducing the number of phytosanitary products you need. It would be really nice to use this cultivation technique, here in Provence.” “Our priority is to provide fresh lettuce on a regular basis,” says the Sales Manager. “We are committed to customer trust and satisfaction. The best quality at the best price.”
For more information:
Alexandre NOVI
Exploitation Novi SAS
Mob: +33 6 12 93 25 02
Publication date: 10/20/2017
Author: Sander Bruins Slot
Copyright: www.freshplaza.com
Is Indoor Farming The Future of Appalachia?
Is Indoor Farming The Future of Appalachia?
Courtesy of AppHarvest
On an abandoned mine near a small town in Kentucky, one company will soon be growing millions of pounds of tomatoes.
October 17, 2017
On an abandoned mountaintop mine in Kentucky, Jonathan Webb sees the future of Appalachia, and it tastes like tomatoes.
Webb is founder and CEO of AppHarvest, a company currently constructing a 1.8 million square-foot indoor farm near the town of Pikeville, in Kentucky's struggling Southeast. Mining jobs, once the lifeblood of the region, have been drying up for decades—could farming be the answer? And while 600 jobs—the number the company expects to create and sustain—pales in comparison to the more than 10,000 jobs lost in this rural, sparsely populated region over the past decade, it's certainly a start.
Tomatoes will be the stock in trade; AppHarvest will partner with the leading greenhouse grower in North America, SUNSET Produce, to get the job done in five, high-tech greenhouses which will amount to a total of 160 acres of indoor farm, all under glass.
While the project has the potential to do good things for the community (starting with increased access to fresh produce during the off-season), that's not the sole reason AppHarvest is here—Central Appalachia, while often perceived as an isolated place, is actually a relatively strategic location, located within a day's drive of a majority of the population (nearly 70 percent) in the United States. This makes growing produce here a smart and cost-effective alternative to importing from other places. (Labor in Mexico, for example, is cheaper, but the cost of getting the produce to market is lower, not to mention the fact that it won't take very long to get it there.)
If all goes to plan, Webb is optimistic that the Pikeville project could be the first of many operations within the region; it's certainly going to get a great deal of attention, once the first site is completed—in just this one location, AppHarvest estimates that they'll be able to produce so many tomatoes, it could actually put a dent (small, but not insignificant) in the import market.
Here’s Why Technology Could Be a Double-Edged Sword for Agriculture
MUCH HAS BEEN MADE of the impact of technology and its capability to drive high growth and amazing results in short periods of time, but there’s a big question mark as to whether or not everyone should be jumping in to incorporate the latest and greatest technologies promising the sun and the moon for their bottom lines.
By Samantha Cheh | 13 October, 2017
MUCH HAS BEEN MADE of the impact of technology and its capability to drive high growth and amazing results in short periods of time, but there’s a big question mark as to whether or not everyone should be jumping in to incorporate the latest and greatest technologies promising the sun and the moon for their bottom lines.
This was especially true when you think about some pretty expensive systems, such as machine learning and automation programs meant to take off the slack on human employees. These are great systems that can have a real monetary cost to them that might not necessarily be beneficial to the company if it results in driving up costs.
Executives and decision makers in companies need to really focus on what tech will work positively for their companies, especially if there isn’t any significant ROI to speak of.
A farm in Singapore drew particular focus on the issue, as the owners battle with whether or not to bring in technologies that could potentially benefit their business. The Jurong Frog Farm, the only place in Singapore that breeds American bullfrogs, is weighing the wisdom of integrating a new recirculating aquaculture system that could help them continue their business should they be moved off their current land when their lease ends.
The problem at the heart of it is that the Singaporean government is implementing a new policy that would weight farmers’ adoption of sustainable and productivity-boosting technologies as a factor in the land-lease bidding process.
Some farms in Norway and overseas are experimenting with indoor farming. Source: Shutterstock
A tender released in August will evaluate bids partly on the basis of these farmers’ ability to harness innovation and sustain production, a challenge for many small, independent farms that may not be able to afford such investments.
According to the farm directors, the aquaculture system – which relies on a single stock of water that is repeatedly treated and recycled – could cost hundreds of thousands of Singaporean dollars as it’ll need to be refitted to suit the needs of a frog farm. Estimates and initial sums indicate that the small farm would not be able to afford such an investment, and it could actually set them back, according to Chelsea Wan who is the director of Jurong Frog Farm.
“Even with government subsidies at implementation, the running cost of such a system might force us to eventually pass on costs to customers, who may simply turn to other farms in the region, which have plenty of land and water,” she said to the Straits Times.
As the only American bullfrog suppliers in Singapore, the loss of Jurong Farm could affect sources of live frogs and frog meat to consumers in the nation state. Wan said that she was looking into other low-tech solutions, including relying on sources in other countries with the necessary land and resources.
Regardless, her story is emblematic of a little-discussed problem: what happens when tech doesn’t work?
Let’s set the record straight first: technology can make a huge difference for many players in many industries. It’s worked wonders for the financial industry, as well as those in logistics. However, not all industries are made the same, and agriculture is a particularly sensitive one especially since it deals with food sources.
However, as with the Jurong Frog Farm example, the swift introduction of technology into an important and fragile industry could prove dangerous especially since outcomes have significant impacts on livelihoods and welfare. For instance, the introduction of new production management systems or new fishing cages may have affected fish supplies.
According to Singapore’s Agri-Food and Veterinary Authority (AVA), local fish stocks fell from 5,272 tonnes in 2015 to 4,851 in 2016.
All things considered though, technology could still bring massive improvements to agricultural output in the long run. AVA said that the fish farms will likely see improved results in the future once snags in the system have been smoothed out.
A spokesperson for the agency said that the new technology could see the implementation of sensors and robotics that will be able to automate menials tasks such as net cleaning, which will boost efforts to increase fish farming system threefold sometime down the line.
The integration of technology into farming may also not be a matter of personal choice anymore, though, as climates globally shift, thus creating havoc in our natural ecosystems and disrupting agricultural production.
“Agriculture is sensitive to weather conditions. Climate change may impact food supplies,” said climate scientist Benjamin Grandey to tge Straits Times. Heworks at the Singapore-MIT Alliance for Research and Technology.
Technology may be a way to fend off the harsher effects of climate change on our food sources. Farms in countries like Norway are already introducing new best practices such as closed containment systems and indoor farming systems the mimic natural environments without the dangers of being exposed to extreme weather.
“We cannot control the weather. But we can control how we want to manage the risks,” said a senior minister for National Development, Dr. Koh Poh Koon, in a Facebook post.
“I urge all our farmers to work together with government agencies to transform our farming sector into a more resilient and productive one. Your long-term viability and our food security are intertwined.”
Your Next Head of Lettuce, Grown By A Robot
Your Next Head of Lettuce, Grown By A Robot
You could drive past and never see the only farm in San Carlos, California. The tiny city of 30,000 that sits between San Francisco and Silicon Valley has all the charms of suburbia—sprawling office parks and single-story homes—but doesn’t seem a likely suspect for agriculture.
The farm, run by startup Iron Ox, is nestled between three stonemasons and a plumber in a nondescript office park building; there’s no greenhouse, no rows of freshly-tilled soil, or tractor parked outside. Only peeking in the large bay door reveals the building’s tenants: a few hundred plants and two brightly-colored robot farmers.
Iron Ox looks a lot like a tech company. One of its co-founder is an ex-Google engineer and it raised $1.5 million in pre-seed venture capital from Y Combinator, Pathbreaker, and Cherubic Ventures in April 2016. Instead of fake food, or plant-based meat meals, or even a food delivery service tethered to an app, Iron Ox is reinventing farming, raising real, not faux, food. Think hydroponically raised lettuce and basil, like what you’d get at an ordinary farmers market.
Iron Ox plans to build a network of autonomous, robot-run greenhouses near major US cities, complete with a fleet of trucks to ensure same-day delivery. Traditional outdoor farms don’t mesh with suburban sprawl, but the planned square-acre greenhouses have a small footprint that can easily fit into dense urban or suburban areas. The robots plant, raise, and harvest the crops.
Iron Ox founders Jon Binney, left, and Brandon Alexander. (Iron Ox)
Pod lettuce
Co-founder and CEO Brandon Alexander, who worked on Google’s Project Wing, figuring out how to make multiple robots work together, says it takes just three or four months to set up one of its farms. Plants take six weeks to mature. One of these modular, square-acre farms could provide the same yearly yield as 30 acres of traditional farmland, Alexander says.
“We want to have the most efficient farm out there,” says Alexander. “In some ways this is just the natural evolution of [farming].” Growing up, Alexander spent summers working on his grandfather’s peanut, potato, and cotton farm that straddles Texas and Oklahoma. He’s seen his grandfather adopt self-guided tractors and other new technologies, giving the ability to scale the family farm from 40 to 5,000 acres in one generation.
While raising crops has evolved from the time of small family farms, it’s still inefficient, Alexander says. Vegetables waste a large portion of their shelf lives traveling 2000 miles to get from farm to store. In addition, the pool of labor for existing centralized farms is aging and diminishing. The average US farmer is 55 years old, and the average crop worker is 33. “There’s just not enough labor to go around,” Alexander says.
Iron Ox isn’t the only company trying to revolutionize food production. Plenty, another Bay area startup, recently received $200 million from the Softbank Vision fund with a similar mission of distributed farms near metropolitan areas. Plenty’s buzzword isn’t automation, but vertical farming: growing crops up walls to save space. AeroFarmswants to disrupt hydroponics with nutrient-filled mist. Freight Farmswill grow crops in shipping containers.
The robots
Iron Ox plans to use three robots powered by artificial intelligence to work each square-acre of greenhouse. Two robots, without official names but referred to as transporters, will lift and ferry trays of plants over to the third robot, a robotic arm. The robotic arm will plant seeds, cycle juvenile plants into larger growing plots, image the plants to check for disease, and harvest the crop. Iron Ox plans to grow leafy greens like the lettuce and basil varieties it is testing now. Large-field crops like corn aren’t on the roadmap.
Iron Ox is using a hydroponic system called deep water culture; the plants, seated in plastic cones, float on a raft in a tray of water, their roots submerged in nutrient-rich water.
These trays are the key to Iron Ox’s indoor farm; while many deep water culture systems are built around large, stationary pools of water, these trays allow the plants to be moved to and from the robotic arm. The company developing the three components—robotic arm movement, transporter robot, and automated hydroponic system—separately. Humans now do the work slated for the robots, but the pre-robot farming provides a valuable runway of data for Iron Ox about optimal growing conditions.
Half a dozen data points are collected from each water tray per second, plus air temperature and quality, ambient light, humidity. The brains of the system are in the robotic arm. If it knows certain plants need more space, the transporter can be summoned to collect them for transplanting. If it’s time for harvest, the trays come to the arm.
The arm, which stands between two trays, moves with serpentine ease only occasionally interrupted by a mechanical lurch. As I watch, it’s controlled by CTO Jon Binney, but can be set to autonomously shuffle plants around from tray to tray. The goal is to only have one robot arm per acre of greenhouse, able to switch out its end effector, or hand, for specialized tools based on the task. Universal Robots is the arm’s manufacturer, but it runs custom code for motion planning. The stereoscopic cameras used to image the produce are installed and integrated by Iron Ox, and the end effectors used to inject and transplant are built custom-built by the company as well.
The transporter’s job is to hulk over a tray of plants, tuck the tray into its belly, and carefully transport it to a space next to the arm. It glides around the warehouse with a precise, mechanical grace, seemingly able to drift in any direction on its Mecanum wheels. These specialized wheels mean the trays can be just inches apart on the entirety of the greenhouse floor, since the transporter doesn’t need space to turn.
The process
The plants start as seeds, which are injected by the robotic arm into small, foam-like cubes seated in a plastic cone. The plastic cone protects the base of the plant from the robotic arm’s grippers, which giving each plant a standardized place to grip the plant while moving it around.
When the seeds have sprouted and grown for about two weeks, they are brought to the arm by the transporter. The robotic arm then picks up the plants and transplants them to a tray with more room between each plant. Each tray is outfitted with augmented reality tags (that allow the arm to recognize which tray it’s working with, and the bounds of where it can and can’t put plants.)
Two weeks later, the transplant process occurs again, and then again two weeks after that. Each time a plant is moved, two cameras on the arm build a 3D model of it, which is analyzed to check for disease and to ensure it’s growing normally. After the plant is fully grown, the arm pulls it—roots and all—from its plastic cone, and places it in a plastic clamshell container to be shipped.
The company has yet to launch its first fully-functioning greenhouse, and it currently donates its hydroponically-grown produce at a local San Carlos food bank in addition to supplying the company salad bar. IronOx wants to build the first greenhouse by the end of 2017, sell to local chefs in the Bay Area, and then scale to grocery stores in early 2018.
No Dirt, No Weeds, Just Organic Greens - Floor To Ceiling
NO DIRT, NO WEEDS. JUST ORGANIC GREENS – FLOOR TO CEILING
October 4, 2017
By Gretchen C. Van Benthuysen |
Theresa Reid, owner of Beyond Organic, plans to open a juice bar in the building in front of her 3,500 square-foot greenhouse at 89 Howell Road in Howell where she grows 15,000 plants in aeroponic towers. All photos by Gretchen Van Benthuysen
Beyond Organic started small and grew and grew.
“My daughter lives in L.A. and I would go out there to visit her and the produce was so beautiful and delicious,” explained Theresa Reid, owner of Beyond Organic in Howell. “I craved having that all the time.”
So she bought a 4 1/2-foot tall indoor Tower Garden by Juice Plus that uses aeroponics (water, liquid nutrients and a soilless growing medium).
Seedlings that were germinated in rockwool, a soilless growing medium, will be transplanted into the towers where water and liquid nutrients circulate feeding the plant as it grows.
“It was great,” she said. “It was the middle of winter and I was getting fresh thyme and parsley and lettuce from my tower.”
Then she had another idea that began to grow. She wondered how she could bring locally grown, delicious, organic greens, microgreens and herbs to the local community. Maybe even open an organic juice bar.
“I knew they did this (aeroponics) on a commercial scale,” she said. “So we looked into it and nobody was doing this north of Georgia at the time, nor east of Oklahoma.”
“We” included her husband David Reid, the owner of Reid Sod Farm, Freehold, and a fourth generation farmer, and her son Matt Engleke, who works closely with her at Beyond Organic. Two years later, Reid has a 3,500-square-foot greenhouse with 15,000 plants that grow in 144 aeroponic 10-foot tall towers filled with nutrient rich water. Radiated heating in the floor enables growing throughout the winter. The initial investment was $350,000 for the greenhouse and towers that use 90 percent less land and water than a conventional farm, she said.
Matt Engleke, Theresa Reid’s son, tends to some of the greens and herbs grown in vertical aeroponic towers at Beyond Organic.
There’s no weeding, but strict monitoring of the pH balance and nutrients is a must.
Ladybugs and grasshoppers take care of any bugs in the summer and organic Neem oil does the job in the winter.
“But if your plants are healthy they’re not going to be susceptible to disease and bugs and that results in a higher percentage of crop success,” Reid said. “We’ve learned a lot. I came from corporate sales and I knew nothing about gardening.”
On a recent hot summer day the windows were open, the fans were blowing and the sound of dripping water all around you was soothing.
“I like to grow stuff I can’t find in grocery stores, like lemon basil, Thai basil, garlic chives, tangerine edible marigolds, escarole that is sweet, and thin stalks of celery that are amazing,” she said. “We have butter crunch (lettuce) growing that has a really mild butter aftertaste. It’s delicious. Everything here is about flavor.
“This arugula is going to have a kick to it,” she warns as she hands me a leaf I pop into my mouth that immediately wakes up my tongue. “And that’s our mild guy.”
Mustard leaves have been popular recently, she noted, especially one with a spicy horseradish kick that can bring tears to the eyes.
There is no mistaking the distinctive tangerine taste of a marigold leaf. She grows them at the request of Fresh Kitchen in Sea Girt.
Chef Meg LaManna at 26 West on the Navesink in Red Bank requested red sorrel for its tart lemon taste.
Theresa Reid, owner of Beyond Organic, plans to open a juice bar in the building in front of her 3,500 square-foot greenhouse at 89 Howell Road in Howell where she grows 15,000 plants in aeroponic towers.
“We make sure we grow plenty and always have that ready for them,” Reid said.
Currently 12 restaurants are clients, including Kitch Organic in Red Bank; d’jeet in Shrewsbury; Blue Grotto in Oceanport; Rooney’s and Trama Trattoria in Long Branch; Tre, 618 and the Metropolitan Cafe in Freehold; the Shipwreck Grill in Brielle; and Local Urban Kitchen in Point Pleasant Beach.
“Most of the restaurants contacted me,” she said. “Even if they are not about organic, it’s the flavor. And it’s fresh.”
But chefs don’t get all the fun.
Greens, herbs and microgreens (including pea shoots and wheat grass) are available to the public in a 4-ounce bag. Seedlings are available at $2 each.
“It’s funny. Now people are buying nasturtium for their dishes at home,” she said. “Normally that’s the thing they push aside on their dish in the restaurant. Everybody’s getting an education.” That includes Girl Scout and Boy Scout troops and a special education school group that toured the greenhouse.
“They plant a seed. They do a taste test. They’re willing to eat it because they’re working with their hands and it brings them back into farming,” Reid said. “We’re eating clean. We’re eating organically.”
Adults are learning as well. Farm-to-table dinners held in the greenhouse are popular and bookings for private parties are increasing.
For the dinners, a guest chef prepares a multicourse meal paired with wine inside and cooks on an old propane tank converted into a wood-fired grill with an oven and two burners outside the greenhouse overlooking 210 acres of the sod farm that also includes Reid’s home.
“White linen tablecloths. Live music. The setting sun. People love it,” Reid said. “They sit at these long tables and they talk to each other. They take each other’s number and come back in groups. It’s a lot of fun.
“Dinners were not part of the plan, but they are now,” she said, adding she plans to expand with a tent, add a container organic vegetable garden and book more events next summer.
“We will also have a juice bar opening out front,” she said. “I can grow and juice it and now I know how good the flavors are going to be. If it’s there, people will eat healthy.”
Last Sunday, Beyond Organic hosted an 80th birthday party.
“We’re just getting a lot of requests. People are asking about having baby showers, bachelor parties. They’re looking for something different to do,” she said. “And I think the younger generation want local, fresh food. And so many of them are vegans as well.”
It just keeps growing and growing.
This article was first published in Sept. 14 – Sept. 21, 2017 print edition of The Two River Times.
BrightFarms Set to Break Ground on 4th Greenhouse
Ohio, October 16, 2017
BrightFarms Set to Break Ground on 4th Greenhouse
With consumer demand for local produce and value-added products at an all-time high, New York-based BrightFarms, Inc. is set to break ground on its fourth greenhouse this month. "We have emerged as the nation’s leading producer of locally grown salad greens as it continues to disrupt the incumbent salad industry on the West Coast," says Paul Lightfoot, CEO. “We have seen demand for our local greens climb sharply as retailers have come to rely on the stability and consistency of our product." Though many companies look to occupy the locally grown salad space, SPINS data shows BrightFarms is the leader, exceeding others in this space by millions of dollars in annual sales.
Preference for local
The success BrightFarms is experiencing is part of a larger national trend towards local produce. The Food Marketing Institute’s 2017 Power of Produce report listed both organic and local as two of the largest drivers for growth in fresh, but noted that consumers have a significant preference for local. Researchers found when quality and appearance are controlled with no price differential, 60% of consumers chose the local option versus just 32% for organic.
However, Lightfoot notes that most retailers are unable to gain access to reliable year-round supply of local produce. “There is a large opportunity for the supermarket produce department to grow if they can source locally,” he says. “BrightFarms sees a clear opportunity in the market to expand our model for local produce across the country.”
Wilmington, Ohio
BrightFarms’ Wilmington, Ohio, greenhouse is slated to break ground this month and will encompass 120,000 square-feet. The operation will provide locally grown salad greens and herbs to supermarkets in the Cincinnati, Dayton and Columbus metropolitan areas. “We will also be creating 30 permanent green collar jobs that provide a living wage and full healthcare benefits to members of the community.” says Lightfoot. “A model for the future of local, low-impact farming, the greenhouse will be the most sustainable source of local year-round salad greens in the Ohio market.”
In keeping with its commitment to health and sustainability, BrightFarms is sponsoring the 5K Race for Talent at Produce Marketing Association’s Fresh Summit in New Orleans. “We hope everyone will come out for this great event whether to run or to support someone who is running,” says Lightfoot. “We look forward through this event and our other market inroads to continuing as an innovative leader in produce and retail.”
For more information
BrightFarms, Inc
349 5th Ave
New York, NY 10016, USA
Tel: +1 212-358-1100
Heading Off To The Eternal Ice
Heading Off To The Eternal Ice
EDEN ISS Greenhouse En Route to Antarctica
10 October 2017 | Credit: DLR (CC-BY 3.0).
The loading at the port of Hamburg begins
- DLR scientist Paul Zabel moves to the Antarctic for one year with the EDEN ISS greenhouse
- Test run in Bremen produces more than 40 kilograms of fresh vegetables
- Plant cultivation without soil, with optimised light, carbon dioxide content and closed water cycle
- Focus: Space, biosystems
The venture to cultivate plants in the Antarctic is gathering momentum: on 8 October 2017 the special EDEN ISS greenhouse container, packed safely away on a cargo ship, left the Port of Hamburg en route to the Ekström ice shelf in the Antarctic. The journey will last approximately 11 weeks. The EDEN ISS team is expected to receive the high-tech greenhouse at the German Neumayer Station III of the Alfred Wegener Institute (AWI) shortly before Christmas. In this project, the German Aerospace Center (Deutsches Zentrum für Luft- und Raumfahrt; DLR) is collaborating with international partners to investigate the fully self-sufficient cultivation of vegetables to supply food in harsh climatic environments and for future manned missions to the Moon and Mars.
Rich harvest in the trial run
Cucumbers, tomatoes, radishes, peppers, lettuce and herbs flourished in the 12-metre container greenhouse during the trial run from late June until August 2017. "The trial run at the DLR site in Bremen yielded a rich harvest," says Project Coordinator Daniel Schubert from the DLR Institute of Space Systems. "We are confident that everything will proceed smoothly in the harsh environment of the Antarctic as well."
In total, the researchers produced over 40 kilograms of fresh vegetables over the course of the test phase. What makes it so fascinating? There is no loss of water. The only water that leaves the self-sufficient greenhouse system is in the harvested fruits. The rest is recycled and reintroduced into the plants. Under special artificial light, in a temperature-controlled environment without soil and supplied with selected nutrient solutions, the plants can grow faster and more productively than in their natural environment.
Vegetables #MadeinAntarctica
The actual crop cultivation experiment in Antarctica will begin at the end of December 2017. DLR scientist Paul Zabel will move to the Antarctic, where he will live for one year at the Neumayer III research station and work at the EDEN ISS greenhouse. He will be part of the winter crew staffing the Neumayer III Antarctic station operated by the Alfred Wegener Institute (AWI). "Scientists live and working all year round in the research station, despite the harsh Antarctic. During the summer, there are up to 50 people at the station. In the winter, however, only nine people remain there: one cook, three engineers, one doctor and four scientists," says the long-time Station Manager Eberhard Kohlberg. This is the winter team that Zabel will join as the tenth member.
Team colleagues from the EDEN ISS project will help Zabel with the construction and commissioning of the greenhouse, before leaving him in charge of running the greenhouse and cultivating the crops. The harvest during the months of darkness will enrich the diet of the people at the Neumayer III station. At the same time, the project will imitate the supply scenario for a manned mission to Mars.
"The preparations for the winter sojourn are exciting and already account for much of my day's work," says Zabel. “It gives you an idea of just how painstaking the preparations for a space mission are, when every eventuality has to be considered and one must be prepared for everything." Zabel has already completed survival training in the Alps as a member of the Neumayer III winter team. He has also attended a number of seminars on the technical systems at the station and a one-week fire-fighting training course. And there is still a lot of preparatory work ahead before his departure in December.
Food production of the future
Global food production is among the key societal challenges of the 21st century. The world's rising population, coupled with the simultaneous upheaval associated with climate change, demand new methods to cultivate crops, even in climatically inhospitable regions. A closed greenhouse system will enable crop growth independent of the weather, Sun and season in deserts and low-temperature regions – as well as for future manned missions to the Moon and Mars – while also reducing water consumption and eliminating the need for pesticides and insecticides. The EDEN ISS project will put this model for a future greenhouse through its paces for one year during a long-term trial in the extreme conditions of the Antarctic. System assembly is planned for late December 2017 to February 2018. Research operations will follow and are scheduled to run through the Antarctic winter and until December 2018.
International cooperation in EDEN ISS
The EDEN ISS project will be conducted during an overwintering mission at the German Antarctic station Neumayer III, in collaboration with the Alfred Wegener Institute, Helmholtz Center for Polar and Marine Research (AWI). A large number of other international partners are contributing to a research consortium under the auspices of DLR, ensuring that the greenhouse will work smoothly in the Antarctic: Wageningen University and Research (Netherlands), Airbus Defence and Space (Germany), LIQUIFER (Austria), the National Research Council (Italy), the University of Guelph (Canada), Enginsoft (Italy), Thales Alenia Space (Italy), Arescosmo (Italy), Heliospectra (Sweden), the Limerick Institute of Technology (Ireland) and Telespazio (Italy) all form part of the consortium of the EDEN ISS project. The project is financed with funds from the EU Framework Programme for Research and Innovation under project number 636501.
Last modified:
10/10/2017 13:28:37
Contacts
Falk Dambowsky
German Aerospace Centre (DLR)
Media Relations, Aeronautics
Tel.: +49 2203 601-3959
Daniel Schubert
German Aerospace Center (DLR)
DLR Institute of Space Systems
Tel.: +49 421 24420-1136
Paul Zabel
German Aerospace Center (DLR)
DLR Institute of Space Systems
Tel.: +49 421 24420-1273
Dr. Eberhard Kohlberg
Alfred Wegener Institut (AWI)
Tel.: +49 471 4831-1422
Meet 10 People Who Are Influencing Different Segments of The Produce Industry
In every industry, there are outstanding individuals who go above and beyond to improve the world around them. Produce is no different. From ag-tech to marketing to urban farming, these people are propelling the industry forward. In this month’s cover story, meet 10 of the leading People in Produce.
People In Produce
Meet 10 People Who Are Influencing Different Segments of The Produce Industry
October 3, 2017
In every industry, there are outstanding individuals who go above and beyond to improve the world around them. Produce is no different. From ag-tech to marketing to urban farming, these people are propelling the industry forward. In this month’s cover story, meet 10 of the leading People in Produce.
Do you know someone you think should be recognized in a future issue? Drop us a line at cmanning@gie.net. We’d love to know who you think is making a difference.
Specialty crops
Andrew Carter, CEO and co-founder, Smallhold
Photo courtesy of Andrew Carter
The authority on New York City mushroom production offers customers hyperlocal subscription-based farms.
graduate of the University of Vermont with a degree in ecological design and environmental sciences, Andrew Carter says that in college he learned a lot about mushroom production — a prime educational example of bioremediation. Following graduation, he worked in greenhouses, growing primarily hydroponic leafy greens and herbs, and consulted for vertical, container and warehouse farmers. A couple years ago, things came full-circle when he saw how he could launch the only operating mushroom farm in New York City.
Along with Adam DeMartino, Carter began Smallhold, which grows mushrooms in a container farm by Brooklyn’s East River and ships subscription-based “Minifarms” to restaurants and grocery stores throughout New York City. “I read a lot,” he says about the research he had to conduct before being able to corner the New York mushroom-growing market. “I went out to a few big farms and spoke with the operators there.”
Although Smallhold is still in its early stages, Carter hopes to expand its markets beyond the five boroughs and also potentially begin growing leafy greens and herbs. “In my opinion, as far as the ag market is concerned, you have to be competitive on freshness and price,” he says.
Smallhold’s roughly six-foot-tall Minifarms include rack row chambers that the company has developed in-house that are equipped with WiFi, LED lights, climate control and irrigation, Carter says. “It’s mostly automated, but when we want to update parameters or we want to change anything, we take care of that,” he says.
Carter calls Smallhold’s nine mushroom varieties gourmet and exotic, and they encompass everything from shiitakes to lion’s mane to oyster to pioppino — a delicacy in Italy. The company sells the mushrooms at a competitive price, and due to their proximity to the end consumer, they are very fresh.
“What we’re really figuring out is a way to bring the freshest produce humanly possible to our customers,” Carter says. “By growing it right there, there’s nothing better than that. We’re really working on ways of streamlining that process, making it affordable and making it easy for everyone to have their food growing right there.” — Patrick Williams
Vertical Farming
Photo courtesy of Henry Gordon-Smith
Henry Gordon-Smith,
Founder and managing director, Agritecture Consulting
Henry Gordon-Smith found his niche in agriculture by chasing new opportunities.
enry Gordon-Smith spent his childhood overseas. He was born in Hong Kong, and lived in Japan, Germany, the Czech Republic and Russia before attending university in Canada. While he was not directly engaged in agriculture while growing up, his international experiences primed him for his current career as the managing director of Agritecture Consulting, a company that helps to plan, design and implement urban agriculture projects around the world.
“I grew up in big cities, and big cities force you to think about how you’re using space,” Gordon-Smith says. “You have the chance to engage with so many different cultures and ways of thinking that it forces you to think in a more diverse approach, which I think is a big part of my philosophy.”
Gordon-Smith was first exposed to urban farming and its benefits while studying at a university in Vancouver, Canada. Involvement in local sustainable farming efforts and his own studies lead him to found a blog focused on vertical and urban farming issues called Agritecture (agritecture.com) while also volunteering at various urban ag operations to obtain hands-on- growing experience. Recently, Agritecture merged with Blue Planet Consulting — where Gordon-Smith served as managing director — to form Agritecture Consulting.
After graduation, he bought a one-way ticket to New York City to become an urban farmer. Despite not landing a job immediately, he stayed there, spent time studying at Columbia University under industry pioneer Dickson Despommier and ultimately found his current niche as a consultant. Now, five years after moving to New York, he wants to help people embark on their own journeys into urban agriculture as he continues his own.
“I want to be known as someone who's excited about this [industry], in it for the long-term and is ready to help people progress,” Gordon-Smith says. — Chris Manning
Technology
Dr. Nate Storey
Co-founder and chief science officer, Plenty
Photo courtesy of Plenty
Storey works to bring local, clean produce to communities around the world.
Dr. Nate Storey first made his mark on the produce industry by developing the ZipGrow Tower, a vertical farming system, at Bright AgroTech, a vertical farming equipment manufacturer he founded. Now, as a co-founder and the chief science officer at Plenty, a high-tech indoor farming company, he’s part of a team that’s trying to give everyone access to local food.
Storey started in agriculture by studying aquaculture-integrated hydroponics at the University of Wyoming, where he earned his bachelor’s degree, master’s degree and Ph.D. There, he was able to pursue research projects specific to his interests — projects that lead him to found Bright AgroTech and develop the ZipGrow Towers over a two-year period while he earned his Ph.D.
“[The university] supported my research,” Storey says. “This wasn’t research other universities were interested in or saw as valuable.”
Now, at Plenty, he’s continuing the work he did at Bright AgroTech — which was recently purchased by Plenty — and taking it further. Plenty’s goal is to bringclean, local food to communities across the world that’s grown in its vertical container farms. And, despite only being a young company, Plenty is already a success story.
According to Storey, Plenty is already competitive with field-grown pricing on different greens and herbs and should eventually be able to replace “a good portion” of what field growers currently produce. Publications such as The Wall Street Journal, Fast Company and Bloomberg say Plenty is a model business in a rapidly evolving industry.
This year, it also received a $200 million investment — the largest ever for an ag-tech company, according to TechCrunch — from a venture capital group that includes Amazon founder Jeff Bezos.
And while Storey understands that it’s not “free money,” he knows and appreciates that his work can make an impact beyond the checkbook.
“I love that I’m impacting the future of humanity,” he says. “I am not powerless to see my ideas come to life.” — Chris Manning
Association leadership
Lauren M. Scott
Photo courtesy of Lauren M. Scott
Chief marketing officer, Produce Marketing Association
A foodie from the beverage industry breaks into a leading produce and floral organization.
Self-proclaimed foodie and experienced marketer Lauren M. Scott appears to have found her dream job. A year ago, she was named chief marketing officer for the Produce Marketing Association (PMA). In her new role, she has the unique opportunity to help all businesses in the produce and floral industry prosper.
“I’ve always been a foodie and I’ve worked in the beverage business at Pepsi and Diageo most of my career,” says Scott. “When the PMA opportunity came my way, it gave me the chance to work with leaders in two of the most popular categories in culture today — produce and floral. I wanted to contribute my talent, energy and skills to help these industries grow and prosper worldwide.”
Scott says she’ll be working with her colleagues at PMA to help members by:
- Examining the landscape: consumer/industry research, including the role culture plays in this space.
- Offering actionable insights on strategic marketing: how it complements existing sales and marketing efforts and can be used as a discipline to grow a business.
- Providing resources companies can use to build their businesses, such as eat brighter! (pma.com/events/eat-brighter) and more.
“Our industry is operating in a highly competitive, dynamic food marketplace,” Scott says. “We have to understand that marketplace and then break through the clutter so that our member companies can perpetually thrive.”
In addition to helping established companies prosper, PMA is working to encourage young people to seek careers in the produce industry. It has set up a foundation called the Center for Growing Talent to “attract and retain the best talent for the industry.”
“PMA is committed to making the produce and floral industries the best place to work,” says Scott. “We have significant programs that target college students and we’ve had great success bringing them into member companies where they are contributing to growth.” — Neil Moran
Marketing
Chris Veillon
Photo courtesy of Chris Veillon
Chief marketing officer, Pure Flavor
In a new role with an expanding grower, this marketer conducts a top-down approach to branding.
Chris Veillon, who recently took the position as chief marketing officer for Pure Flavor, sees exciting times ahead for the company and offers some key insights into the future of the produce industry.
Founded in 2003 in Leamington, Ontario, Pure Flavor grows and markets a variety of greenhouse vegetables, including tomatoes, bell peppers, cucumbers, eggplant and living lettuce grown in the United States, Canada and Mexico. In his new role as CMO, Veillon hopes to take the brand to the next level, in part by taking on specific roles with promotions, advertising, content creation and digital marketing.
“The opportunity to grow with Pure Flavor, not only from a brand and product perspective, but professionally, was something I could not pass up,” Veillon says, citing an upcoming $105 million investment into a 75-acre greenhouse build in Georgia as just one growth opportunity for the brand.
Veillon got his start in marketing in the tourism industry. After 10 years in tourism, he was ready for a change. He says he was contacted “out of the blue” by a produce company that was looking to build a marketing department. Over the last 10 years, he was able to “create, strategize and build” a variety of brands that are developing into household names.
At Pure Flavor, Veillon says he gets to see the company from the 10,000-foot level. He sees opportunities to expand the company’s message, but hasn’t lost sight of the most important thing on consumers’ minds: great taste.
“Flavor drives repeat sales, hands down. Great packaging will attract, but what they bite into is what will determine their next move,” Veillon says. “In a space where there is an S-O-S, or ‘sea of sameness’ as I like to call it, there has to be a unique experience for you to retain that customer.”
As consumers become more savvy, they want to know where their fruits and vegetables come from, Veillon says. “Brands that resonate with consumers are the ones that have a unique value proposition,” he says. “It’s not about smoke and mirrors to get the sale, it is about authenticity to create a customer for life.” — Neil Moran
Sustainability
Photo courtesy of Nathan Kaufman
Nathan Kaufman
Director of living systems, The Perennial
This grower feeds flies to fish to fuel an environmentally friendly farm-to-table experience.
The husband-and-wife restaurateur duo of Karen Leibowitz and Anthony Myint started Mission Chinese Food and Commonwealth before founding The Perennial, a restaurant in San Francisco that sheds light on climate change and practices sustainability. Taking advantage of environmentally friendly food production and service methods such as carbon ranching and offering Kernza, a perennial grain, outdoor farmers and onsite employees do their part. But much of the work takes place across the San Francisco Bay with grower Nathan Kaufman.
As director of living systems, Kaufman runs The Perennial’s roughly 1,000-square-foot greenhouse and 2,000-square-foot outdoor production space in West Oakland. The greenhouse stands out for its highly nontraditional greenhouse crops — everything from turmeric to Australian finger lime to dwarf cardamom to papalo.
“In the year that we had for buildout, there was just so much give and take and discussion,” Kaufman says. “Initially, Anthony and Chris [Kiyuna], the executive chef, hit me with a wish list, and there would be stuff like jackfruit on there. I’m like, ‘Ok, guys. We’re not in Southeast Asia, and that’s going to take like 40 years for me to start getting fruit on it. That’s an 80-foot-tall tree, guys.’”
To boost sustainability efforts, Kaufman takes leftover food prep that the back of house staff has divided into two categories (the first being produce and the second being being meat, dairy and bread) and composts it. He uses worms to break down the produce and black soldier flies to break down the meat, dairy and bread. In turn, he feeds the fly larva to sturgeon and catfish that power aquaponic systems.
Kaufman is also executive director of The Perennial's nonprofit, the Perennial Farming Initiative, which educates others on sustainable efforts. But not every diner wants to hear about environmentalism while eating dinner. “Sometimes if you’re just getting a cocktail after work and you just want a great environment, hey, that’s totally fine by me,” he says. “For us, just by supporting us with your dollar, you’re voting with your buck. In that way, we can really engage with folks wherever they’re at.” — Patrick Williams
Leadership
Dr. Roberta Cook,
Photo courtesy of Dr. Roberta Cook
Director, Village Farms
A longtime academic economist now advises an industry-leading grower.
After 31 years working at University of California, Davis, Dr. Roberta Cook remains as passionate about the produce industry as when she was still a graduate student at Michigan State University.
“In my career at UC Davis, I was tasked with looking at all the key supply and demand trends affecting markets for fresh produce in California,” says Cook, who held the position of extension economist in the Department of Agriculture and Resource Economics. She is now on the board of directors at Village Farms and Ocean Mist Farms.
Her research and consultations have allowed her to gain key insights into the trends affecting the produce industry — information that should be valuable to both growers and retailers. Cook says consumers became very value-conscious during the recession and haven’t reverted to earlier buying practices, making competitive pricing even more important for retailers, which puts pressure on suppliers.
One of the biggest trends she sees affecting the industry, which will most likely continue for years to come is “channel blurring,” or the advent of more and more types of competing retail outlets for fresh produce, beyond the conventional supermarket of old.
“From Walmart Supercenters to club stores, dollar stores, convenience stores, drug stores, online sales and limited assortment stores, such as Aldi and Trader Joe’s, the proliferation of store formats is still expanding,” Cook says. — Neil Moran
Education
Stephen Ritz
Photo courtesy of Stephen Ritz
Founder, Green Bronx Machine
A teacher with a big heart incorporates indoor ag into the classroom.
A teacher with more than 30 years of experience, Stephen Ritz embraced project-based learning decades ago through environmental restoration and community gardening with over-age, under-credited students. Now, the founder of Green Bronx Machine, a native of New York City’s northernmost borough, grows produce in Tower Gardens with primary school age children in the National, Health, Wellness & Learning Center at Community School 55.
In his lessons, Ritz aligns food production with academic standards, and his students are excited to take part. “We took targeted students that had 40 percent attendance and moved them to 93 percent attendance and a 100 percent graduation rate,” Ritz says. “But beyond that — and realize that we are in the poorest congressional district in America, in the least healthy county in New York State, with the highest percentage of homeless and transitional children in New York City — we have record attendance at this school.”
A 2015 Global Teacher Prize Top Ten finalist, Ritz — who is recognizable by his bowties, cheese hat and noticeably trimmer frame than when he carried 300 pounds in the early days of Green Bronx Machine — has visited the White House and worked in his classroom with former White House chef William Yosses. Ritz has also met Pope Francis, former President Bill Clinton, Virgin Group founder Richard Branson and journalist Fareed Zakaria, among other influential public figures and celebrities. Author Michael Pollan featured Ritz in his book “In Defense of Food.” In May 2017, Ritz released his own book, “The Power of a Plant,” which details the path he took to champion for students to become more engaged in learning, make healthier diet decisions and contribute to society in a meaningful way.
When it comes to production output, Ritz and his students don’t skimp. They grow enough food indoors to send 100 bags of groceries home with students weekly. In addition to indoor production, they grow about 5,000 plants outdoors. Their 37 crops include gourmet lettuces, a variety of tomatoes, eggplants, peppers, pickles, collard greens, squash, cucumbers, celery, oregano, basil, nasturtiums, corn, string beans and cilantro. And the food doesn’t go to waste. In partnership with Memorial Sloan Kettering Hospital, Ritz and his students are growing about 5,000 pounds of produce for food-insecure, recovering cancer patients in the Bronx.
As a full-time volunteer, Ritz doesn’t expect payment for his work. This, he says, is to “step apart from” the system in order to fix it. “We need to go from a world that once loved people and used things and now kind of loves things and uses people — we’ve got to get back to our roots, literally,” he says. “Imagine if we refreshed our soil and our farmers the way we took care of our precious laptop screens. The world would be a better place. To me, this is about dignity and respect, growing something greater. Yes, I grow food, but really what we grow is hope and opportunity. I like to say I grow vegetables, but my vegetables grow students, schools and resilient communities and give everybody a chance to sit at the table.” — Patrick Williams
Research
Dr. Kevin Folta,
Professor and chairman, University of Florida’s IFAS Extension
Photo Courtesy of Dr. Kevin Folta
This professor pushes the development of horticultural lighting forward by pursuing unique research projects.
Dr. Kevin Folta grew up knowing that science, in some way, would be part of his career. When he started college at Northern Illinois University, he studied DNA and genetics. But as he interned at different companies as an undergrad, he developed a passion for agriculture and decided to get his graduate degree in biology, and then a Ph.D. in molecular biology, to apply to agriculture research.
In 2002, Folta moved to the University of Florida, where he currently serves as a professor and chairman of the horticultural sciences department. It was at UF where began working on the type of research he’s best known for — LED lighting, and how it can be used to improve plant growth
“That’s where it all came together,” he says.
Folta’s research explores the relationship between lights and plants and specifically how growers can use LED lighting to “talk” to plants. According to his research, a grower can use a specific light color — red, for example — to communicate specific instructions to a plant. This level of precision, in theory, would allow growers to get specific results from each plant in the greenhouse. That could even mean using a specific light color to draw out a specific flavor profile from a crop in the greenhouse.
“You’ve got something people need, something people want and something that makes money for the people who grow it and supply it,” he says.
In addition to his research, Folta also co-hosts podcast called “Talking Biotech” (talkingbiotechpodcast.com) and does it for the same reason he does his research: He loves it. “My one hobby is recording a podcast,” Folta, who records on Saturdays as early as 4 a.m., says. “So that’s why I do it.” — Chris Manning
To hear more from the People in Produce, be sure to check out The Hort Report podcast. Past guests include Dr. Gary Stutte, Dr. Kevin Folta and Dr. Jill Calabro. There is also coverage of industry events attended by the Produce Grower staff such as United Fresh and Indoor Ag-Con. You can find all of the podcasts at bit.ly/2fA8Umr and/or on iTunes at bit.ly/hortreportpodcast
Community Outreach
Photo courtesy of Mario Cambardella
Mario Cambardella
Director of urban agriculture, Atlanta
A career adjustment lead Cambardella towards his current role in shaping urban agriculture in Atlanta.
After graduating college, Mario Cambardella did what most people do after college: look for a job, secure a job and then work towards advancements. For Cambardella, who studied landscape design at the University of Georgia, that meant working at a company called Valley Crest as a designer and project manager for landscape developments in the Atlanta area.
But four years into his career, UGA created a new master’s program called “Environmental Planning and Design,” and the program’s dean recruited him personally for the program. While there, he completed that program, met his future wife, decided to stick around while she finished law school and completed a second master’s in landscape design while starting his own business, Urban Agriculture, which combined his design skills and new interest in sustainable city planning. After graduation, he turned that business into a full-time career for four years.
That business lead him to be hired by the city of Atlanta in 2015, where he now works for the city as the director of urban agriculture. There, he plays a key role in developing “Aglanta,” a digital food hub for Atlanta residents. That also includes the Aglanta Conference, which had 272 attendees in 2017, its first year, and the Aglanta Forum, an annual event where residents can learn about sustainability and healthy eating. (Editor's note: To learn more about the Aglanta Conference, listen to “Previewing Aglanta” here)
“Developing urban agriculture spaces within our city is, I think, a dream job,” Cambardella says. — Chris Manning
LumiGrow Partners With Nectar Farms to Light 40 Hectares of Greenhouse in Australia
LumiGrow Partners With Nectar Farms to Light 40 Hectares of Greenhouse in Australia
Sydney, Australia – Nectar Farms Headquarters – October 4, 2017
Nectar Farms, an Australian agri-business, has selected LumiGrow as their lighting partner for its first 40 hectares of greenhouse developments, representing the largest greenhouse installation in the southern hemisphere. LumiGrow will be the exclusive provider of LED lighting systems comprised of both LED hardware and software for the facility growing vine crops and other vegetables in Victoria, Australia.
The agri-business aims to transform the Australian farming model by using smart lighting techniques and other advanced technologies. “When considering an effective lighting solution there are a number of variables,” says Stephen Sasse, Managing Director and CEO of Nectar Farms. “Having completed a structured technology and vendor selection process we have chosen to partner with LumiGrow. We believe that their systems and technology are leading-edge.”
Nectar Farms’ lighting strategy promises to go well beyond traditional techniques. The greenhouses will be equipped with adjustable LEDs, controlled through the LumiGrow smartPAR cloud-based software. The spectrum, intensity, and photoperiod of the LEDs will be managed dynamically along with plant growth stages, to elicit beneficial plant characteristics and respond to plant stress. Additionally, the smartPAR software will be integrated with LumiGrow smartPAR Light Sensor Modules, to maximize utilization of the sun’s energy and reduce energy costs.
“After encountering soaring prices for grid-based electricity and gas, electrical efficiency became particularly important for us,” says Stephen. To bolster the glasshouses’ sustainability and to save on electrical costs, Nectar Farms has partnered with French renewable energy company Neoen in the Bulgana Green Power Hub. The partnership comprises a 196MW wind farm and a 20MW/34MWh battery storage facility to ensure uninterrupted supply, which will make Nectar Farms one of the largest sustainably-operated greenhouses in the world.
Smart horticultural lighting will be an integral component of Nectar Farms’ smart farming initiative, beyond simply energy savings from the LEDs. Their high-tech and sustainable model will use light’s characteristics to maximize exportable produce and reduce inefficiencies of supply and pricing to meet growing global demand. Nectar Farms and LumiGrow will be working in close partnership with Costa Group who will provide an off-take marketing alliance for the sales, marketing, and distribution of the produce.
“We know that LED light can profoundly improve our crop production and be used to increase efficiency,” says Stephen. “With smart horticultural LEDs, we also have a tool to direct our crops’ growth and meet our quality and production goals. The partnership with LumiGrow is working effectively already, and we particularly value the support from their in-house research department.”
LumiGrow, a smart horticultural lighting company, will work with Nectar Farms as their lighting partner, a level of designation traditionally reserved for development, design, construction, and distribution entities.
“The future of horticultural lighting is here, and it’s through smart lighting technology deployed by our qualified spectral scientists that growers are going to see exceptional value,” says Shami Patel, CEO of LumiGrow. “As our company drives the industry’s understanding of how plants interact with light, we continue to apply the latest research to our lighting solution. With the release of our newest sensor technology, Nectar Farms will be able to gather and respond to solar data for a largely automated lighting solution. We feel inspired to be working with Nectar Farms. Finding partners who value the impact that technology can make on crop production is key. It’s truly smart farming meets smart lighting, and we’re thrilled to see LED lighting come this far.”
Learn more about LumiGrow smart horticultural lighting technology here: https://www.lumigrow.com/technology/
Check out LumiGrow's newest light sensor product, the smartPAR Light Sensor Module: https://www.lumigrow.com/technology/smartPAR-light-sensor-module/
About LumiGrow Inc.
LumiGrow, Inc., the leader in smart horticultural lighting, empowers growers with the ability to improve plant quality, boost crop yields, and achieve cost-saving operational efficiencies. LumiGrow offers a range of proven grow light solutions for use in greenhouses, controlled environment agriculture and research chambers. LumiGrow solutions are eligible for energy-efficiency subsidies from utilities across North America.
LumiGrow has the largest horticultural LED install-base in the United States, with installations in over 30 countries. Our customers range from top global agribusinesses, many of the world’s top 100 produce and flower growers, enterprise cannabis cultivators, leading universities, and the USDA. Headquartered in Emeryville, California, LumiGrow is privately owned and operated. For more information, call (800) 514-0487 or visit www.lumigrow.com.
How To Invest In Leafy-Green Indoor Agriculture
How To Invest In Leafy-Green Indoor Agriculture
Editor’s Note: B. David Vosburg is CFO and SVP Strategy of Crop One Holdings, an indoor farming technology company and producer of high-quality leafy greens in the Boston, MA area of the US under the brand FreshBox Farms. Vosburg is a serial entrepreneur and has an MBA from Yale University.
The lettuce industry in the US is worth just under $6 billion per year. If it follows the tomato industry, 50% of leafy greens will be grown indoors by 2030, a $3 billion opportunity. This transformation is inevitable with the ongoing trend of higher efficiency LEDs.
Indoor farming in cities and suburbs is giving new meaning to the term “local.” These operations are producing crops which had previously been grown only in certain geographies, because of the constraints of available land, water, and weather. This industry is now able to grow anything year-round, anywhere in the world.
In our growing units, we have measured a 99% reduction in water usage, and a 90%+ reduction in land use, compared to Salinas Valley lettuce farms, and since most indoor operations grow locally without any pesticides/herbicides/fungicides and 30 day+ shelf lives, indoor farming is a difficult proposition not to believe in.
And investors are starting to put some big bucks behind it. Indoor farming startups growing fruits and vegetables globally have raised $285 million since the start of 2017, with particularly large rounds for US-based vertical farms pushing the sector to its highest ever investment levels, according to AgFunder data.
The question is, who will win this market in the end?
No doubt you’ve seen several indoor agriculture companies that claim to be the best at growing leafy greens (lettuces, herbs, etc.) indoors. For any number of reasons, they claim to be better than their peers who are also vying for your funding dollars. But how do you tell the difference between them?
Here are seven simple metrics that will tell you if the company is worth your investment dollars.
1. Capital Density (CAPEX/plant site)
Most companies will tell you they grow more capital efficiently than everyone else, but you have to do the math. Calculate the number of plant sites they have per square foot, and the CAPEX required (all-inclusive) to build/buy that square foot of grow space.
Things to look for include companies that grow in vertical channels: the encasement and spacing take up so much space, they’re not able to achieve anything close to market-leading densities. Think cubic feet, not square feet.
If then it appears that that company is growing produce for a fraction of their competition’s Capex per farm, you will know they have a better ability to scale and turn over capital faster. For example, if a company grows for 25% of their competition’s CAPEX/plant site – the farm location — they can scale to four times the size with the same capital and will turn over that capital four times as fast.
2. Form Factor
There are now many players in the space building indoor farms in various formats: Pond greenhouses, Aquaponics, Warehouse growers, and Modular growers; each with its own inherent set of risks, particularly around contamination.
Pond greenhouses grow with sunlight — and at times some LED augmentation — in one, large single pond. They are the most susceptible to contamination as all plants share the same room. From a build-out perspective, it can take over 2.5 years to build one farm!
Aquaponics growers do control for contamination. However, plants are provided nutrients from fish feces, which can lead to contamination. The water temperature at which fish live is in the upper 70s Fahrenheit, several degrees above what is ideal for lettuce, so these growers will be limited in what they can grow and the yields they can achieve.
Warehouse growers can mass produce plants because they can grow them at high density to be some of the most efficient indoor farmers. Contamination can be a risk here as well; if a pest gets into a warehouse, an entire building of produce could be lost or recalled, costing the company tens or hundreds of thousands of dollars. There are several examples of hydroponic warehouse growers that have lost entire operations to a single pest or pathogen.
Modular growers come in many flavors, from divided warehouses to shipping containers. These growers can find a balance between controlling for infestation while growing efficiently. They can also match warehouse growers for density. In whatever shape or size they come, this appears to be the preferred growing approach for indoor farming – assuming that density inside the modular unit can be achieved. However, watch out for modular growers that sub-divide their farms into too many rooms as this will increase labor costs.
Be aware of form factors and decide which style best suits your investment needs.
3. Energy Efficiency (g/KWH)
Energy can be one of the most expensive components, if not the most expensive, of a completely indoor growing operation. This is a large part of the input costs of a labor efficient, completely indoor, growing operation. The common unit of measurement is how many grams of product a company can grow with one KWH of energy input.
What to watch for: many US companies have access to state-level agricultural energy pricing which can be as low as $.015 per KWH. Make sure the company is not ‘efficient’ because they simply have a low energy rate. We’ve all suffered through the end of subsidies in other industries, especially clean-tech!
Identify the number of grams that can be grown on the farm in a given month, then divide this by the number of KWH consumed per month. If the number is south of 40 or 50 – half the peak scientists have achieved in R&D labs– do not proceed unless there is a very clear technology roadmap showing how the company will achieve higher numbers soon.
4. Automation
Hiring is another expensive cost for indoor growers and will only increase in many urban places where indoor agriculture is applied. Automation is, therefore, going to become a critical aspect of reducing costs to increase gross margins. Some of the questions to ask:
1. How many dollars are spent in labor to grow one pound of lettuce?
2. How many hours does it take one person to seed, transplant, harvest, pack, and clean per unit of production?
3. Does the company use automation, and do they own that technology?
4. What is the company doing to find experienced/appropriate labor?
5. Plant Science
Farms grow living organisms. This is not an industry that produces widgets, no matter what anyone tells you. An experienced plant scientist is critical to any successful indoor farm. Identify this person and understand their background, knowledge, experience, and ability to control mold/fungus/pests as well as grow indoors in controlled environment and leverage plant stressors for yield.
The right person will understand every lever that can be pulled to increase yield and reduce costs: light spectrum, humidity, CO2, various micro-nutrients, water oxygenation, micro-pulsing, shadow-less lighting, sunsetting/sunrising, photoperiod and much more. This can contribute to a 50%-75% increase in yield over the competition, something competitors cannot finance their way out of.
Look for companies building competitive advantages around the non-commoditized aspects of growing – lighting, HVAC, and automation have plenty of very clever people around the world focused on improving efficiency in their own industries.
6. Commercial Approach
Brand is King. Those who have the consumer’s mindshare will be the ones to take home the value. Currently, grocery stores in the US are white-labeling many leafy green products so they can switch suppliers at will and reduce retail costs while maintaining margins. The consumer and the grocery store benefit; lettuce growers do not.
If the consumer is unaware of the brand, the company is not worth financing and will never be able to have the leverage to negotiate the price necessary for a venture return — and possibly not even a profitable business.
Ask a company about its consumer-facing products or plans.
7. Speed of Evolution
How quickly can a company change technologies? LEDs, farm management practices, controls and different types of automation are developing exponentially, industry-wide. Can you responsibly invest in a company that takes over two years to build out infrastructure?
The number of lumens/watt an LED produces is projected to quadruple in the next fifteen years, an annual compounded efficiency improvement rate of 10%. This means investing in a two-year project today will result in having lighting technology that is 21% less efficient than new entrants.
Keep track of technological advances and ask companies how they’re planning to stay on top.
Meeting The Environmental Challenge of Growing Food Crops
Meeting The Environmental Challenge of Growing Food Crops
SEPTEMBER 21, 2017 DAVID KUACK
More predictable production levels and harvest dates are driving growers to adopt controlled environment agriculture.
Even though most greenhouse vegetable growers are producing fewer types of crops than ornamental plant growers, trying to control the environment of these food crops can be a much bigger challenge.
“The environmental control challenges for vegetables are much tougher because the produce is going to be consumed,” said University of Guelph professor Mike Dixon, who is director of the Controlled Environment Systems Research Facility in Guelph, Ontario, Canada. “The fact that they are destined to be a food commodity requires more attention to things like pest control.
“For vegetable production, since the margins are typically small for food crops, growers are trying to tightly control inputs as much as they can without compromising the quality and productivity of the commodity. This is a significant challenge and requires a great amount of detail to environmental control than for typical ornamental crops. Ornamental commodities, since they are not eaten, are not subject to the same kinds of stringent controls, especially with pesticide residues. But it’s more than that. The food safety regulations for food crop inputs and production outputs (e.g. nutrient runoff) are much tighter than they are for ornamental commodities. That means that environment control is a key factor in maintaining production standards and quality standards in a competitive market.”
Meeting market expectations
Dixon said part of the issue with trying to maintain the proper environment for vegetable production is consumer expectations for “perfect” fruits and vegetables.
“Consumers have been conditioned by generations of what today are considered environmentally unacceptable cultural management practices, using chemicals and pest management protocols, that occasionally leave residues,” he said. “Consumers don’t want peppers with spots on them. Consumers don’t want roses with blemishes on the flower petals. In the minds of consumers, they expect virtual perfection and don’t appreciate that the means to achieve this are not necessarily environmentally correct today.
“There is a transition between the old ways of doing things and the new ways of doing things. In terms of controlled environment agriculture, growers are transitioning to production practices that don’t compromise quality and productivity and yet meet environmental standards as well. That can be a tough balance.”
Dixon said that growing food crops in the northern latitudes year-round requires some type of controlled environment production.
“In Canada, six months out of the year food crops can’t be produced unless they’re grown in a controlled environment,” he said. “This requires that the growing has to be done in a nearly subtropical environment in which many disease pathogens and insects thrive. These pests gravitate toward these ideal controlled environment conditions. It’s the growers’ challenge to maintain some kind of balance and still meet the quality and production requirements of the market.”
Minimizing costs, maximizing production
Dixon said the degree of sophistication that is achievable with today’s technology should really be taken advantage of by growers especially in regards to minimizing labor.
“Labor is the top line in the cost of production in a controlled environment commodity,” he said. “Automation, including computer controlled environments and automated irrigation can mitigate the labor bill. Energy is a close second in regards to major costs.”
Dixon said the winter environment in the northern areas of the United States and in Canada is a major challenge for controlled environment growers.
“Winter production in these areas requires a higher level of technical sophistication than is needed for operations located further south,” he said. “The farther south an operation is located the issue then becomes heat extremes. In the middle latitudes, which include a large portion of the United States, environment control challenges are not as extreme as they are in Canada, Mexico and South America.
“In more moderate climates, growers tend to be slower in adopting more sophisticated technology because the cost benefit is harder to justify. Labor costs will be the major factor that will drive the conversion to automation for a lot of middle latitude growers. Up until recently they haven’t been required. What has changed is that the capital cost requirements for a lot of technology enhancements or retrofits in older greenhouses have become very attractive. For example, the cost of LED lighting is not only energy conservative, but it can also enhance productivity with the appropriate technology and application information.”
More predictable, profitable production
Dixon said since the margins on food crops are relatively small compared to many ornamental crops, growers need to have relatively large greenhouse operations in order to be profitable.
“We’re talking on the order of 50-200 acres of controlled environment greenhouses,” he said. “To consider manually managing that scope of a greenhouse production system is prohibitive. It’s not realistic, growers couldn’t do it. It’s absolutely required that that they engage some form of automation, controlling especially irrigation, lighting and conventional environment control including opening vents, etc. The largest controlled environment food production area in North America is in the Leamington area in southwest Ontario. This area is typified by very large, highly sophisticated controlled environment agriculture systems for the production of tomatoes, peppers and cucumbers.”
Dixon said automating irrigation to reduce labor costs and automating basic temperature and humidity control in the greenhouse will significantly enhance the production system.
“It comes down to the cost benefits analysis,” he said. “Each grower has to look at it on the basis of their own specific case. It depends on the commodity. It depends on the local market and the margins growers can obtain with a more homogenous quality that they realize with automation. Automation offers more predictable production levels and predictable harvest dates. These are the kinds of issues that drive the adaptation to controlled environment computer automation and even robotic systems.
“Adding more sophistication gives more reliability in some cases as well as predictability in terms of production and quality. And that can only enhance a grower’s attractiveness to the market.”
Dixon said automating irrigation to reduce labor costs and automating basic temperature and humidity control in the greenhouse has been shown to significantly enhance the production system of a grower’s greenhouse.
“That’s really the goal,” he said. “Look at the capital cost requirement to obtain that level of technical sophistication and amortize over a reasonable three- to five-year period. Then look realistically at the labor savings, energy savings and the environmental impact savings including waste and runoff that would be realized by doing it. If it makes economic sense then there’s the answer.
“Sometimes it’s difficult to line up all of the things that need to be considered in a cost-benefit analysis. Depending on the size of an operation, if it’s a small-scale operation, it may not make economic sense to incorporate this automation because the cost-benefit is probably going to take 10 years to realize. But as the scale of the operation goes up, generally the justification for automating the system and reducing labor costs is greater.”
Bringing space technology back to Earth
One of the major elements of Mike Dixon’s research program at the University of Guelph’s Controlled Environment Systems Research Facility is the development of technologies for food production (i.e. life support) in the context of long term human space exploration missions. Dixon said the technologies being transferred from his program to the greenhouse sector are those that were developed for these missions.
“These technologies are being adapted to terrestrial agri-food sector applications in as economical a way as possible,” Dixon said. “Some of the technologies being developed include LED systems, environment control protocols, recycling systems, environment sensors and imaging systems for diagnostics.Terrestrial agriculture is benefiting greatly from research activities taking on the challenge of growing food on the Moon and Mars.”
For more: Mike Dixon, University of Guelph, Ontario Agricultural College, School of Environmental Sciences, Controlled Environment Systems Research Facility, Guelph, Ontario, Canada N1G 2W1; (519) 824-4120, Ext. 52555; mdixon@uoguelph.ca; http://www.ces.uoguelph.ca.
David Kuack is a freelance technical writer in Fort Worth, Texas; dkuack@gmail.com.