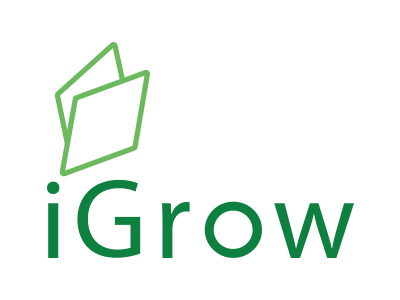
Welcome to iGrow News, Your Source for the World of Indoor Vertical Farming
US, New York, Seeds of Sustainable Future Planted at Third Hydroponic School Lab Opening In Astoria
Hydroponic labs are spaces where student can grow plant life without the use of soil and offer hands-on lessons on biology, ecology and agriculture. Studies have shown that students who physically experience scientific concepts are more likely understand them better.
Photo by Alejandra OConnell-Domenech/QNS
January 15, 2019
The seeds of a sustainable future have been planted at P.S. 84 – Steinway in Astoria, where Councilman Costa Constantinides helped opened a new hydroponic science lab on Jan. 14.
“Environmental changes are increasingly making science a component of every industry, so we must make sure our leaders of tomorrow get the hands-on experience now to solve problems of the future,” said Constantinides.
Hydroponic labs are spaces where student can grow plant life without the use of soil and offer hands-on lessons on biology, ecology and agriculture. Studies have shown that students who physically experience scientific concepts are more likely understand them better.
This was apparent during Constantinides visit to P.S. 84 – Steinway, as grade-school children guided him through their new lab explaining the biology behind plant growth.
“These are the best lessons in life,” said P.S. 84 – Steinway Principal John Buffa. “[This] develops a love of learning because when children take ownership of their learning, they are going to take it from beginning to end.”
Besides teaching students to take responsibility for their own learning, hydroponic science labs teach children how to think sustainably. According to Manuela Zamora, the executive director of New York Sun Works, the nonprofit that built the hydroponic lab at P.S. 84, each school equipped with a lab also receives a curriculum with appropriate ways of teaching complex scientific concepts to depending on their age.
Zamora used ladybugs to exemplify this. If the plants P.S. 84 – Steinway become infested with a pest such as aphids, “[we] will bring in ladybugs who will eat the aphids so that we don’t have to use pesticides.” This creates a teachable moment about the harms of pesticides and alternative methods of pest removal.
New York Sun Works, offers curriculum for kindergarten through 12th grade.
The new lab represents a broader push by Constantinides to enhance science curriculum, educational technology and renewable energy in its schools. As chairman of the City Council’s Environmental Protection Committee, Constantinides has also allocated funding to cover STEM lab updates, solar panels. He also recently announced a push to have the city study how it can shut down gas-fire power plants across the five boroughs by the end of 2020.
But opening the plant at P.S. 84 – Steinway is more than just politics for the councilman; it’s also personal.
“This is repaying a debt,” said the councilman, an alum of the elementary school.
According to Constantinides, the New York Power Authority (NYPA) has agreed to fund the hydroponic lab at P.S. 84 – Steinway.
“NYPA has had preliminary conversations to discuss the possibility of giving programmatic support to schools in the councilman’s district that are near its power facility and meet further criteria,” said NYPA in an email to QNS. ” However, discussions are still ongoing with both NY Sun Works and the councilman’s office to identify which schools, in Queens as well as other areas of the city, can be supported in 2019.”
Topics: Astoria climate change Councilman Costa Constantinides eating green
Evansville, A Home For Business
Back text: “E — Scenic View of Ohio River, V — Reitz Memorial High School, A — Vandenburgh County Courthouse, N — Adm. Bldg., Evansville College, S — Evansville National Guard Armory, V — Dade Park Race Track, I — Electric Fountain, Garvin Park, L — Greyhound Bus Station, L — Lions Den, Mesker Park Zoo, E — Dress Plaza”
After graduating from Purdue University in May 2017, I continued to rent co-work space on campus in West Lafayette working for Heliponix full-time until my apartment lease ended at August 2017. At the time, I was hyper focused on the engineering design tasks at hand for Heliponix to debut a new prototype GroPod™ at the Forbes AgTech Summit. After the summit ended, I brought all of my possessions back to Evansville. It occurred to me I was once again living in Evansville only after I had moved back home. Upon moving back, I was asked to speak at Evansville’s Tech on Tap weekly entrepreneurial meetup where I was asked why I came back. I answered, “Evansville is home, and I can continue working on my company without paying myself by living with my parents.” This seemingly obvious answer spurred a new found sense of urgency that if I were to scale a technology company, than I must leave southern Indiana for greener pastures. I then began to look for every possible reason why I should move away from Evansville for the benefit of Heliponix. I identified the following four reasons why I could not headquarter Heliponix in Evansville, Indiana.
Early adopter customers for new technologies do not live in the midwest.
Tech companies need investors. Evansville did not have venture funds.
Tech companies need top tier software engineering talent. Evansville did not have individuals with this skill set on hand.
Hardware companies such as Heliponix need to manufacture overseas to be cost competitive in the marketplace.
Customers
Heliponix (formerly Hydro Grow) team picture after winning first place at the Schurz Innovation Prize at Purdue University. Left to Right: Scott Massey (CEO), Jimmy Carlson (Software Engineering Intern), Ivan Ball (CTO)
Starting a company without experience or the money needed is comparable to charging into a battle unarmed and unaware of the terrain with dangers ahead. I was acutely aware of my limitations, and spent my senior year at Purdue University delivering newspapers at night for about $9/hour, and competing in business plan competitions between classes for cash awards. Although we were very lucky to have successfully secured over $80k over the course my senior year and a little under $100k from competitions post graduation, the money was the second most valuable aspect of winning these pitch competitions. For every competition we won, at least two or three articles from local media publications would cover the story with our name on the front title. We jumped at every opportunity to showcase our prototypes at schools, STEM career fairs, and also leveraged my position as the lowly delivery boy to publish articles in the Exponent to grasp as much publicity as possible for an early stage company.
Scott Massey giving a STEAM (Science, technology, engineering, agriculture, and math) career talk about indoor agriculture to middle and high school students Our Lady of Providence School in New Albany, Indiana.
For every article and interview that was published, I received an email from random Indiana residents interested in purchasing a GroPod when it became available for purchase. I kept a running list of these potential customers, and reached out to collect a $500 pre-order deposit when we had finally landed on a GroPod design that worked reliably. We had definitively proven that a pre-revenue startup company could launch an expensive product in Indiana if they are able to achieve enough publicity to convert impressions into executed sales. Although there are many more wealthy individuals in major cities who could buy an early stage product; we did not yet have the production capabilities to meet this demand, and still had product development to refine before we would be ready for a massive user base.
Funding
Inside Indiana Business interview with Dr. K and Gerry Dick
Although we had been veryfortunate to secure some funding from business plan competitions for patents and prototype development, we had reached the ceiling of competition funding available in Indiana for an idea not yet generating revenue. My Co-Founder, Ivan Ball accepted a full-time, electrical controls engineering job offer upon graduation to pay off student loans at GPC (Grain Processing Corporation, an ethanol and grain alcohol processing plant in Washington, Indiana) after interning and co-oping as a student for several years prior. Together we worked exhausting hours for a full year to refine the GroPod design until we created a functional product able to generate revenue in Ivan’s garage.
One of many harvests from the fourth generation GroPod™. ALL RIGHTS RESERVED. HELIPONIX©
Ivan Ball at his electrical work station in an unheated garage assembling the fourth generation GroPod™. ALL RIGHTS RESERVED. HELIPONIX©
This marked a major turning point for the company after three generations of failed prototypes. When asked if we both worked on Heliponix full-time to this point, I would honestly say yes. Our individual hours spanned 50–70 hours weekly even though Ivan had a full-time day job that took 40–45 hours per week. At this time, we had spent almost all competition award winnings on patents, prototyping, travel for events, or other business expenses. We simply did not have the capital needed to cover materials to assemble the first GroPod betas. I then approached Eric Steele, my Entrepreneur in Residence with Elevate Ventures (Indiana’s state venture fund) seeking capital needed to fund inventory. Eric referred us to the ISBDC (Indiana Small Business Development Center) who advised the Vectren Foundation Grow Local loan program for small businesses. After working with Douglas Claybourn and Kim Howard, we sent an application to the Vectren Foundation board to build the first GroPods. After waiting patiently, we were approved for a loan needed to build these GroPods with very favorable terms for any company, let alone a startup with zero cash flow history. We used the loan to buy all the parts needed, and collected the remaining $1,500 left on each GroPod order with early adopters to sell out of the beta models assembled by hand. We 3D-printed all parts, wrote our own code, soldered our boards, assembled every aspect of the product Ivan and I had designed entirely by ourselves, and delivered each GroPod in person to the early adopters. There was so many GroPod parts laying around Ivan’s home, I had to deflate my air mattress to make more room, and slept on his couch for months.
Ivan Ball installing a camera on the fifth generation GroPod™. ALL RIGHTS RESERVED. HELIPONIX©
GroPod™ assemblies consuming every square foot of Ivan Ball’s home in Washington, Indiana. ALL RIGHTS RESERVED. HELIPONIX©
Ivan Ball (Left), Scott Massey (Right) with first functional GroPod. ALL RIGHTS RESERVED. HELIPONIX©
At this point Ivan quit his job at GPC, to work solely at Heliponix, and sold his house in Washington, Indiana to be fully committed to the company. Today, I am pleased to announce that the risk the Vectren Foundation took on us for funding the loan is being paid back in full plus interest. This market validation thrusted us into the long sought after post-revenue status, which did not go unnoticed by local and regional angel investors; however, this is a story for another day. Despite the undeniable fact that the largest investment funds are in major cities, very few early stage hardware companies receive those investments due to the amount of competitors who rarely manufacture products within these cities, let alone the state. It is much better to refine the product and user experience until a sizable MRR (monthly recurring revenue) is established before approaching these funds which are beginning to invest outside of their states to leverage the capital efficiency of a midwest startup.
Talent
Delivering the first GroPods was just the beginning of a long troubleshooting learning curve with paying customers… Internet connectivity with a connected, IoT (Internet of Things) device will come with many software bugs as well as faulty sensor failures when buying in low quantities from Chinese suppliers. The problems that you are both unaware of, and unable to solve are the hardest any startup will encounter. It is incredibly important to find these problems by getting your product in the hands of early adopters as soon as possible to identify and solve. The dilemma of an underfunded hardware startup company is that you will more than likely need to sell a product that doesn’t yet have all the features needed to make it “perfect” in order to stay cash flow positive. The reality is that no garage startup will be fully ready, and you will certainly find excuses to not be ready if you look for them. This is called the MVP (minimum viable product). Then something amazing happened, customers began to complain less each day as we solved problems one after another, until I began to hear feedback that their GroPods were growing more food than they could consume! This major milestone was met with interest from angel investors who provided the capital needed to hire a full-time software development lead. Unfortunately, there is not a plethora of software developers in Evansville at this time, so we needed to look for a remote employee. After interviewing several developers, Ivan and I decided to hire Bryan Lemon, a PhD computer scientist from West Virginia University living in South Carolina. Bryan’s experience with IoT device companies translated very well into solving problems, creating new features that kept customers happy, and attributed to our zero-percent churn rate. Despite never meeting Bryan in person, we were quickly able to determine his technical ability by first hiring him as an independent contractor for an agreed upon milestone. I strongly encourage that early stage technology companies consider remote software developers to save cost, expand your professional network, and reach a wider pool of candidates to only hire top talent. You do not need to go to the bay area or other major cities to find top talent, and the operational cost of your business will increase by multiples if you move to a larger city.
Manufacturing
Whirlpool Refrigeration Plant on Highway 41. Source: Courier and Press
I remember all too well the day that the Whirlpool plant in Evansville shut down for the last time, a major manufacturing hub for appliances that employed several thousand people. At a very young age, this instilled the idea that hardware manufacturing companies must leave the United States in order to find competitive manufacturing prices. That is why I took a flight to Shenzhen, China to tour contract manufacturing plants. This massive manufacturing city is often called the hardware capital of the world based upon its speed, competitive labor, and material rates. After returning and considering the cost of manufacturing overseas, I began to factor in the not-so-obvious costs of building products outside of Evansville. The language barriers requires a translator to be present, and often leads to misunderstandings that can be very costly mistakes. The logistical challenges, uncertain trade relationship, and intellectual property theft quickly amounted to a cost that far exceeded that of domestic contract manufacturers. Most startup companies fail by aimlessly pursuing random goals without strategy as capital dwindles.
I have discovered that the resources I need to prototype and manufacture are widely available within the Midwest ecosystem. We then began to look locally for contract manufacturers within the Evansville-Cincinnati-Louisville trifecta that had worked at GE and Whirlpool appliance manufacturing plants and engineering design centers. Without disclosing trade secrets, we can confirm that the midwest has manufacturing capabilities that are very competitive with international rates. In our case, we were able to source almost all parts needed in manufacturing from Indiana, Illinois, and Kentucky. In addition to Evansville and Louisville being the former appliance manufacturing capitals of the world; we have been able to find top tier talent and industry partners with relative ease. Eventually, most hardware companies manufacture overseas when they exceed 1,000–10,000 units per year, but automation is the equalizer in a world where labor can be bought for a few dollars per hour, or be subsidized by a country in the process of industrialization. Indiana is uniquely positioned to be an entrepreneurial hotbed with several investment groups, and countless angel investors in one of the top manufacturing states in total manufacturing GDP (Gross Domestic Product).
Conclusion
After speaking to countless successful and not-so-successful entrepreneurs; I believe that starting a company requires two things.
The drive to achieve your goals
The means to achieve your goals
This has led to a new revelation about Evansville; it is not a good place to start a company… it’s a great place to start a company. It is uniquely large enough to have the means to fund a startup company, but not so large that the means become unobtainable to newer companies. The cost of living combined with these resources will triple to quintuple how far your dollar will go as opposed to a startup in a major city.
I now proudly say that Heliponix is based in Evansville, and we intend to stay here for the foreseeable future. We will continue to directly and indirectly create new jobs as operations expand. This only leaves one question from me to you, “Why not stay in Evansville?”.
Indiana entrepreneurial resource map, courtesy of Drew Peyronnin.
Indiana entrepreneurial resource map, courtesy of Drew Peyronnin.
The infographic above shows just some of the many resources available for startups in Indiana that has helped Heliponix many times in the past, present, and future. Purdue Foundry, Elevate Ventures, Purdue Polytechnic Institute, Blue Sky Capital, CoWork Evansville, APPCOM/BIZCOM, SVBIG, Certificate Entrepreneurship and Innovation — Purdue University, Burton D Morgan Business Plan Competition, Foundry@WestGate, GAGE, Agrinovus, Centric, IU IP Clinic, E is for Everyone, SouthWest Indiana Chamber of Commerce, Innovation Connector, TedxWabashCollege, Schurz Innovation Prize, Center for Entrepreneurship — PNW, Vectren Foundation, iGrow.news, and prospectively the MakerStation which conveniently holds many of these resources in one building; Innovation Pointe.
Scott Massey
Founder and CEO of Heliponix™. Purdue University, class of 2017. Mandela Washington Fellowship Alumni.
Teshuva Agricultural Projects (TAP) Is Proud To Present the TAPKIT
Mindanao, TAPKIT
TAPKIT is a 500 m2 Hydroponic unit.
The unit , produces 6-10 Tons of leafy vegetables per you on NFT system.
Mindanao, TAPKIT
TAP developed the unit as a solution for family farming, resorts, restaurant, senior citizens homes and more. It is called the affordable hydroponic solution because of its price- $60,000- 70,000US $.
TAPKIT Korea
Since its launching on May 2018, it has been installed in Israel, S. Korea, and The Philippines, the next two units will be installed in Mauritius next month.
TAPKIT Korea
Denver, Colorado: A Look Inside Rino's Rooftop Urban Farm
January 8, 2019
If you’ve recently walked down Lawrence Street in RiNo, you have probably have been stopped in your tracks by the sight of a rooftop garden. At the very least, you’ve probably wondered what was going on above Uchi. This beautiful greenhouse space is home to Altius Farms. As one of the largest vertical aeroponic rooftop gardens in the country, Altius currently grows varieties of lettuce, herbs and edible flowers galore.
Part of the new S*Park condo community, Altius landed at the RiNo location where the land historically has been farmed since the 1930s. The greenhouse itself offers 8,000 square feet to run operations, and the community garden outside will double the growing space once the spring comes. S*Park and Altius are planning to team up for great farm-to-table events and community dinners come warmer temperatures.
Sally Herbert, co-founder of Altius, is excited to open the flagship location of Altius Farms in Denver and partner with S*Park to do so. Short for Sustainability Park, the condo community is an incubator for sustainable living and community development. Centered around wellness for human bodies and the earth, Altius Farms is a great addition to the RiNo living complex.
Herbert commented that their mission is to “bring urban farming back into our communities.” They are currently focusing on their partnerships with restaurants to do so. Altius works with some of Denver’s top-rated restaurants – including Beast + Bottle, Butcher’s Bistro and Urban Farmer. The team at Avanti Food & Beverage asked Herbert to grow a mix of greens to pair well with a particular dressing the restaurant is concocting for a special event.
“There’s a real demand for produce that’s safe, nutritionally dense, that’s got good flavor, that doesn’t have 1,500 food miles on it,” Herbert explained. Most of Altius’ customers are located in the surrounding neighborhoods, so the produce is fresh when restaurants receive their orders. This cuts back on food waste both within the farm and in restaurants – however the produce that Altius can’t sell before its prime, they donate to We Don’t Waste and Denver Food Rescue.
“We are a for-profit company with a social impact mission,” Herbert commented. And in addition to engaging the community in learning more about their food, Altius operates on a sustainable business model. The aeroponic tower system uses 10 percent of the water and 10 percent of the space to produce 10 times the yield of a conventional soil farm. Herbert also gets to see an eye-level view of each plant every day – making it easy to identify the needs of particular plants throughout the greenhouse.
The greenhouse itself was designed to recognize the plants needs by pooling the environment. Sensors around the greenhouse cue the processing system to turn on fans or heaters, open up roof and side vents to adjust the humidity and temperatures to make the greenhouse the perfect environment for growing leafy greens.
The greenhouse also provides a controlled environment for their plants to grow. Altius Farms has a separate water system and a controlled environment that is not affected by the state of surrounding farms. In result, Altius was able to supply their customers with romaine when the rest of the country was having an e. coli scare.Transversely, if Altius had a scare in their own farm, it wouldn’t affect any growing site except the greenhouse location.
The horticulturalist for Altius, Don Dwyer, has been in the growing business since the 1970s. More and more he sees that people want to “establish a relationship with their food.” Altius helps facilitate a positive relationship with food by providing fresh produce with interesting flavor profiles to Denver residents. Dwyer also understands that so many Denverites want to support local farms and Altius gives residents a way to learn about growing food in an urban location.
As Altius approaches full growing capacity, they are looking forward to living into their mission and engaging the community in their work. “Food is important in [illness] recovery and in education and just having nutritious meals for our kids,” Herbert explained. Once they have the capacity, Altius hopes to serve the community beyond restaurants – including schools and medical centers.
For the time being, Altius takes great care of their restaurants. Herbert enjoys offering tours and tasting to their chef partners and helping them to design a menu around Altius greens. With flavors like wasabi arugula to mustard greens and a number of edible flowers, Altius Farms caters to many chefs and their various dish innovations.
These partnerships excite Herbert, who has never worked with chefs in this way. “What’s been interesting,” Herbert commented, “is that they are – pun intended – hungry for this kind of food. They want to have the conversation with us.” In the future, Altius wants to expand their produce and grow specific plants for restaurants – working with chefs from the inception of a dish idea to the culmination.
Altius Farms is located at 2500 Lawrence Street #200, Denver. Their restaurant customers in RiNo and LoDo are Urban Farmer, Uchi, Crema, HiTide Poke, Port Side, Stowaway, Famous Original J’s Pizza, Butcher’s Bistro, Goed Zuur, Beast + Bottle and Dio Mio. Altius greens are available in both Marczyk’s Fine Foods.
All photography by Evans Ousley.
ABOUT THE AUTHOR
When not working one of her three jobs, Evans walks the streets of Denver to discover more about the city's food scene. On the weekends, Evans loves to stroll around Denver's many parks – mostly to obsess over all the dogs she can't have.
Conventional Problems, Unconventional Solutions: Birth of Triton Foodworks
03 January, 2019 By: Sheetal Dhamecha
The conventional problems associated with agriculture can be solved through unconventional means, the belief was turned into reality by the young entrepreneurs in Delhi. Deepak Kukreja, Dhruv Khanna, Ullas Samrat, and Devanshu Shivnani, the friends who wanted to do something that was economical and ecological gave birth to Triton Foodworks.
What an idea! But how this idea?
Back in 2014, Ullas was keen on developing a farm in Mohali as a defense mechanism for his mother diagnosed with Interstitial Lung Disease. The doctors however advised that the life on farmhouse shall cause more harm than good due to dust and various issues linked to farming. He was then determined to find ways to make a clean farm for his mother. Dhruv, then based in Singapore did a lot of field research there and the two of them zeroed in on Hydroponics. They later collaborated with Deepak and Deevanshu to look after tech and finances.
Started as an experiment in the urban landscape, Triton Foodworks works on clean, accountable and reliable farming methods. The founders define a new generation of farmers, farmers who live in apartments, hang out in bars, and are social media addicts but also care deeply for the environment.
Say Hello to Hydroponics and Aeroponics
Hydroponics is the science of growing plants without soil. Nutrients are supplied to the plant through the water. In the present scenario of depleting water resources, hydroponics has an advantage over traditional farming. It consumes around 90 per cent less water, in turn, prevents topsoil erosion, requires no pesticides, and provides a better yield. Along with hydroponics, Triton uses aeroponics, a method of growing plants without a growing medium. The roots are suspended in air and nutrients are given through fine mist.
Both techniques are win-win methods, sustainable and profitable methods of food production.
Triton Foodworks now operates around 150,000 ft. of greenhouses in India and has managed to produce more than 700 tonnes of vegetables and fruits on their hydroponic farms. Be it bell peppers or strawberries, tomatoes or mint, they offer it right.
Related Links:
US (RI): University Launches Hydroponics Educational Program
Acopia Harvest International, member of Irving A. Backman & Associates and University College at Roger Williams University are partnering to create hydroponics education and training programs for students, military personnel, senior citizens, homemakers and career-chasers.
The new program provides opportunities for students to receive an education enabling them to join one of the fastest-growing industries worldwide. Programs begin in summer 2019.
Hydroponics, the art and science of growing plants in water, is an effective learning tool stimulating students of all ages by allowing them to engage in and explore all areas of STEMM (Science, Technology, Engineering, Math and Manufacturing). Students develop transferable skills in water management, plumbing, electricity, agriculture, nutrition, sustainability, marketing, business management and economics.
According to Ameth Alzate, Acopia International Founder, "Hydroponics is a rapidly-developing industry providing year-round plant growth. Delivering fresh, locally grown produce at all times of the year is a key strategy for growing food in parts of the world with harsh environments and/or limited growing seasons."
Jamie E. Scurry, RWU's Vice President of University College said, "University College is pleased to partner with Acopia because hydroponics technology provides knowledge and training to pursue this proven method of cultivation."
For more information:
ibaglobal.co
www.rwu.edu
Publication date : 12/18/2018
Salmon Arm Business To Provide Fresh Greens Year Round
Wolf Wesle and Karen Dow show a tray of microgreens in front of a rack of lettuce, both of which are being grown by Living Leaf Growers located at the Westgate Public Market. (Jodi Brak/Salmon Arm Observer)
Area Residents Invited To Participate In Test Market To Help Develop Signature Salad Mix
December 15, 2018
Salad lovers will be able to access locally grown greens and microgreens, thanks to Living Leaf Growers.
Located at Westgate Public Market, co-owner Karen Dow says the company has been working on developing a commercial hydroponic system for two years under the direction of Wolf Wesle of Green Croft Gardens organic farm in Enderby.
While the produce will not be certified organic, Dow says it is as good as organic.
“It’s all done in water, no chemicals; it’s grown with just nutrients,” she says. “We are testing different types of nutrients as some are better than others.”
The produce will be grown in racks that go 24 feet high, consisting of seven rows, in four different sections. At the moment, Living Leaf is running about 25 per cent of the system but planning to be up to 50 per cent soon.
“We have eight different lettuce types that feed into a salad mix and we want to test different combinations of colours, types, textures and tastes,” she says. “We want to come up with their own best seller and we need help to do that.”
For the next two or three months while production ramps up, Living Leaf will prepare sample mixes of lettuce and invite a test group to buy a bag of salad or microgreens for $1 and provide feedback on how long it lasts in the fridge, texture and taste.
As well as lettuce and microgreens, Living Leaf is planning to grow strawberries and probably cherry tomatoes.
Microgreens are a vegetable green, harvested after sprouting as shoots, that are used as a component or ingredient to enhance the attractiveness and taste of dishes with their delicate textures and distinctive flavours.
“We have the capacity to grow 28,000 heads of lettuce a month and 700 strawberry plants and I don’t know what the numbers are, but we can grow a lot of microgreens year round,” says Dow. “Lettuce, mixed salad lettuce and strawberries will be available all year round, but the strawberries won’t be available until next spring.”
Dow says the first batch of lettuce will be harvested on Dec. 17, with lots more becoming available in January and February.
To join the test market and register for the lettuce and microgreen program, go online to www.westgatepublicmarket.com, click on the Living Leaf Growers page and fill out the registration form.
“When we have lettuce and/or microgreens available, we will notify you by email to come in and pick up your bag,” Dow says, noting people may only buy one bag at a time and will be required to fill out a questionnaire before they can buy more.
Introducing Living Food Company: The Future of Food
India’s Food Supply Chain is Not Working
Why is India, one of the fastest growing economies, undergoing a nutrition and health crisis? India has the largest micronutrient deficiency among all countries and among the highest disability-adjusted lost years of life from micronutrient deficiencies. Diets low in nutrition are the leading cause of this current health and nutrition crisis. Fresh food that is nutrient-dense is surprisingly difficult to find in India, particularly for the urban consumer.
We don’t know where our food comes from, what it contains and how long it takes to reach us.
The food we consume has been designed to be stored and shipped in containers over long distances. The industrial food supply chain is extremely complex and is plagued by inefficient supply management and wastage at the distribution stage. The agriculture system is failing us by producing food that contains harmful chemicals in the form of pesticides and fertilizers.
On an average, Indians consume close to 42000 metric tonnes of pesticides in a year, including those that are banned in other countries for their carcinogenic effects.
In June 2017, more than 40 cotton farmers died after inhaling chemicals while spraying pesticides in Maharashtra in one agricultural season.
Micronutrient deficiency in India. Source: http://unicef.in/Whatwedo/8/Micronutrient-Nutrition
We now depend upon cheap, low-nutrient food that sacrifices quality for quantity at the cost of our health and the environment. Global crop production has more than tripled since the 1960s. This has led to the depletion of water resources for irrigation, soil pollution from overwhelming fertilizer application and rising greenhouse gas emissions.
The average concentration of pollutants in the Indian soil is almost twice the amount found globally.
Such high levels lead to long-term damage in the central nervous system, immune and reproductive systems, while also being one of the leading causes of cancer.
The organic food movement, tries to address some of the health risks by eliminating the use of fertilizers. Yet, organic produce that is grown in soil can’t prevent harmful chemicals from entering our bodies. Contaminated groundwater containing dangerous proportions of heavy metals such as Arsenic is still used in organic farming and can cause long-term damage to our cells and immune systems. Simply put, organic food doesn’t solve the problem.
We are what we eat
In June 2017, my life took a drastic turn. My mother was diagnosed with Thyroid cancer and had to undergo a painful surgery. Less than a year later, on 20th March, my father was diagnosed with Stage 4 Peritoneal cancer.
This personal tragedy shook me to the core and I started investigating into this deadly disease. The more I read, I found out — how less I knew. I had never imagined that the everyday food that we eat can either strengthen our immune system or completely break it down making us susceptible to life threatening diseases, such as cancer. Everything I read brought me to the same point — we are what we eat.
Real food is about trust and transparency. It is also about ensuring quality and traceability at every step. Living food Company was born to provide food that we can trust. Our produce is grown with passion, care and precision and by controlling the entire process we guarantee high quality produce that can be traced at every step.
Living Food Company: The Future of Food
Living Food Company was born from the need to take control of our food production systems. We decided to grow microgreens, 10–12 day old baby plants that are extremely rich in nutrients, anti-oxidants and essential vitamins and minerals. They contain upto 40 x the nutrition found in their mature counterparts.
We focus on growing extraordinarily highly nutritious microgreens such as Kale, Broccoli, Mizuna (Japanese mustard), Pink Radish, Red Chard and 15 other powerful varieties. We make these nutrient rich foods affordable and accessible for the average urban Indian consumer and democratize access to superfoods.
Akash K. Sajith
CEO & Founder at @LivingFood, building the future of food.
Barbados: Government To Start Veggie Project ‘Early Next Year’
December 19, 2018
Article by Barbados Today
A high-tech farming project is set to kick-off early next year that could slash demand for imported vegetables by over 80 per cent.
The Government project to be set up in the new year, comes as a private firm owned by young farmers uses technology in an agricultural project that is intend to eventually feed the entire country while withstanding the threat of natural disasters, said Agriculture Minister Indar Weir.
Operating out of a 40-foot shipping container at Hastings, Christ Church, the directors of Ino Grow have developed a hydroponic farm, which currently produces lettuce, herbs and other leafy greens.
The company is producing non-genetically modified organisms (non-GMO) and herbicide-free crops, which can be grown every day of the year.
After a tour of the small facility, an excited minister for food security revealed the project had won the support of Government. Weir has invited Ino Gro directors Warren Kellman and Rishi Pajwani to be part of a similar programme, to be rolled out by Government at the beginning of the New Year.
“We are going to get together and we’re going to pull all of the costing together… and take agriculture to the next level. But more importantly, we need the scale,” said Weir.
Government’s ultimate goal is to produce almost 80 to 90 per cent of some of the vegetables currently being imported, Weir declared.
Minister Indar Weir (left) under the artificial sunlight provided by the agricultural farm, being schooled by Ino Gro co-directors Rishi Pajwani (left) and Warren Kellman (second from right) as mentor Ayub Kola looks on.
“I speak of tomatoes and lettuce of all varieties, and then we are going to look at broccoli as well, because broccoli is one of the vegetables that we import and we have to address that. If I am able to pull all of this together in short time, we then start looking at reducing our food import bill,” he said.
Amid the worldwide threat of global warming, Weir praised the new technology for responding to the growing need for “climate-smart” initiatives.
“We have to look at what climate change is doing to the Caribbean islands and indeed Barbados is vulnerable to climate change and if we’re going to get into climate smart agriculture, then this is the way we have to go,” according to the agriculture and food security minister.
“So that if we get a climate event, we don’t find ourselves without food for extended periods of time . . . . We have to be able to protect the amount of food that we are going to need to get through a climate event. We have to protect the seedlings to make sure that we have them at our disposal so that we can continue to grow,” he stressed, while indicating that the use of green energy will also be key to the development of similar initiatives.
Weir is particularly excited about the promise of climate smart agriculture for youth. “It excites the younger mind; those people who are coming out of school, who would have traditionally stayed away from agriculture, because they didn’t see it as a career option. But if we could replicate this right across Barbados, all of a sudden we are addressing a 21st century need, where we can create entrepreneurs, through having young people now graduating from university and getting involved in projects like these as businesspeople,” he said.
Ino-Gro co-director Rishi Pajwani thanked Weir for giving them a platform to show off the young farm initiatives. He also assured Barbadians that his company is up to the task of reducing the country’s “enormous” food import bill.
“We wanted to cut that down as well as educate the youth here in Barbados about agriculture – Traditional agriculture. Agriculture is no longer outside, hot sun and breaking your back. It’s now become labour efficient and easy, so we wanted to inform everyone and the youth to re-innovate the industry and get back into agriculture, because this is where Barbados was born,” said Pajwani.
But the new private sector initiative has not come without obstacles. As co-director Warren Kellman put it, the idea was so peculiar to Customs officials that they were sceptical when equipment started coming in.
“Customs had never seen something like that before. So when they saw certain pieces of equipment . . . they said they’ve never seen something like this attached to farming. We had to work closely with Customs as well, and actually create new entries in their system, so that people who are interested in this type of innovative farming, when they do bring in systems like this in the future, they wouldn’t face issues that we faced, because we tried to pave the way,” he said.
Making the process easier is the knowledge that they have the backing of Government in their quest to revolutionise Barbadian farming, Kellman said.
Developer Plans $33 Million Indoor Farm, Microgrid Project In Former Paper Mill
DECEMBER 20, 2018
Arcadia Energy Corp. wants to transform the former Florelle Tissue Corp. plant, pictured here in 2010, into an up to $33 million indoor farm and energy complex.
WATERTOWN DAILY TIMES
BROWNVILLE — A Rochester microgrid developer plans to build an up to $33 million indoor hydroponic farm and energy complex in a former paper mill on the Black River.
Acadia Energy Corp. wants to repurpose the 100,000-square-foot mill that once housed Florelle Tissue Corp., which closed in 2013, for a vertical farm and a microgrid.
John Bay, CEO of Acadia Energy, said for the farm, which would occupy only 10,000 square feet, he envisions growing produce like lettuce, tomato and arugula in bins of seven to 15 feet with rotating trays. The microgrid would produce electricity and thermal energy using natural gas, although Mr. Bay said he wants to transition to using hydroelectric and solar to generate power down the road.
“We’re very excited about this opportunity. This marketplace is an up-and-coming marketplace,” Mr. Bay said. “We’re excited to work with and serve people in the greater Watertown area.”
The state awarded Acadia Energy $415,000 through the Regional Economic Development Council program Tuesday, which will help fund the vertical farm.
The firm has already secured preliminary commitments from banks to finance the overall project, which would include about $3.5 million for the farm and $20 million to $30 million for the energy complex. Mr. Bay said, however, the firm must take several more steps before opening the complex, including purchasing the building, updating it and finishing the engineering designs.
“It’s been probably three years in the process and we’re probably another 12 to 18 months before we bear fruit,” Mr. Bay said. “We’re not certain at this point if we’re going to own the hydroponics (farm) or put somebody in as a tenant.”
Building the farm and energy complex inside the former Florelle Tissue mill is not Arcadia Energy’s first north country project. The firm, which has an office in the Watertown Center for Business and Industry, has also been designing the Jefferson County Industrial Development Agency’s microgrid to supply electricity to tenants in the Jefferson County Corporate Park.
“One reason we’re down there is the welcome we got from the county and town” of Watertown and Hounsfield, Mr. Bay said about his project in the mill.
Hydroponic Farming Lets You Grow Your Food Indoors
By Kristine Wen | Published on Friday, December 7, 2018
Urban farming is hardly a new concept. Watch “Edible City,” and you’ll discover the trend was really taking root (see what we did there?) around 2008. But today, tonier restaurants on both coasts have gone beyond simply growing mint on the roof or kale next to the patio. Indoor farming, or sometimes called vertical farming, a highly technological, grow-your-own-indoors method, has been having a moment the last couple of years.
Glass-paneled hydroponic vertical farms, often doubling as interior designporn or art pieces, grow fresh produce—think butter lettuce, wasabi, cucumbers—in soil-less containers next to where your Manhattan is being made. Water and nutrients are delivered directly to a plant’s roots, allowing food to be grown in perfectly controlled conditions inside.
Former college roommates Andrew Carter and Adam DeMartino started their own indoor farming business called Smallhold in 2016, with the aim of growing hard-to-find mushroom varieties they knew chefs were on the hunt for. Smallhold grows a dozen different mushroom varieties, from coral-like pink oyster clusters to the cloud-shaped formations of young lion’s mane, in shipping containers in Bushwick. (Similar to fellow Brooklynite indoor farm Square Roots.) Before they are ready to harvest, the mushrooms are distributed to customers in what Smallhold dubs “minifarms,” which house the fungi in climate-controllable encasements as they continue to grow. Like the custom installations of Melbourne’s Farmwall, Smallhold’s minifarms are designed and built to match their customers’ aesthetic needs. At New York’s beloved Mission Chinese, for example, the minifarm’s display of amorphous, brightly-colored mushrooms is part art installation, part fresh mushroom vending machine.
Smallhold
It sounds complicated, but that’s kind of the point. “Our customers don’t have to understand how to grow mushrooms,” says Carter. “With our technology, we’re able to tell what’s going on, on a shelf-by-shelf basis in each of our minifarms. We can also run programs depending on the species we put in—changing the humidity, the CO2 levels—to create the best growing conditions for each type of mushroom,” adds DeMartino. All chefs and vendors have to do is pick the mushrooms when they’re ready to harvest, serving food that’s grown-to-order.
So why only mushrooms? “Restaurants like Bunker Vietnamese and Mission Chinese are looking for quality produce first and foremost,” says DeMartino. “It’s really hard to get high-quality mushrooms. You might start out with high-quality harvested mushrooms, but by the time they’ve gone through the harvesting and shipping processes, their taste and appearance have deteriorated quite a bit.”
And when you’re ready to try these grown-to-order mushrooms yourself, DeMartino has a few suggestions. “You can’t go wrong with the Mission Chinese mushroom fried rice,” he says. “And one of the best chefs in New York, Tara Novell of Honey’s, makes a tempura from the lion’s mane mushrooms we grow. The lion’s mane is perfectly encapsulated in the batter. You can taste the full mushroom, but with that tempura crunch.”
All featured products are curated independently by our editors. When you buy something through our retail links, we may receive a commission. For more great hand-picked products, check out the Chowhound Shop.
Header image courtesy of Farmwall.
You Can't Legally Trade In Cannabis In South Africa Yet, But The dagga business is booming Anyway After Possession Was Decriminalised By The Constitutional Court
Hydroponics suppliers that would not speak on the record about their current trade or plans hinted at everything from massive import orders to local manufacturing
The Dagga Business Is Booming Already – Even Though Nobody Is Officially Selling Any Yet
Phillip de Wet , Business Insider SA
December 04, 2018
You can't legally trade in cannabis in South Africa yet, but the dagga business is booming anyway after possession was decriminalised by the Constitutional Court.
Hydroponics systems are suddenly very popular.
A Cannabis Expo in Pretoria next week is sold out – even though it will have a strict no cannabis rule.
Next week, The Cannabis Expo will open in Menlyn, Pretoria, for three days of "industry, health, and agriculture" exhibits.
Early ticket sales, at R150 a pop, point to a visitor attendance of around 20,000 people, organiser Silas Howarth told Business Insider South Africa, double what exhibitors had been promised. And exhibition space is long sold out while a waiting list for spots that open up due cancellations continues to grow. A similar exhibition in Cape Town in April is likely to be three times the size of the Gauteng event.
"It's been insane," says Howarth. "It's getting to the point where we're quite quickly turning away certain types of exhibitors."
Interest in the expo has been big even though the organisers have been very clear: no actual marijuana will be allowed on the premises. As best legal experts can tell it remains illegal to trade in dagga, or in seeds, following a historic Constitutional Court ruling that effectively legalised cultivation and possession in personal spaces.
Exhibition visitors are liable to be searched on entry - they may have the right to carry cannabis on their person, but the owners of private spaces can still impose restrictions.
See also: 5 things you need to know about growing dagga at home
"This is an ordinary exhibition, just like any other exhibition," where organisers could ban legal alcohol or guns, says Howarth. "That is what people in the industry have been fighting for, for cannabis to be treated like anything else."
Many industry players are playing their cards very close to their chests as they prepare for what is expected to be a flood of business following full legalisation of dagga. Even so, it is clear that a great deal of frantic preparation is underway.
Several organisations at the Cannabis Expo will be seeking investors to fund rapid expansion and one, the White Lion Seed Company, will be launching a brand for a company that can not yet sell its primary wares, cannabis seeds.
Specialist fertiliser companies are gearing up, consultants are offering advice, legal firms are positioning themselves as experts, and even packaging-design companies are putting themselves in line for business that is already trickling in, ahead of an expected flood.
One headline exhibitor, Cape Town based Hydroponic.co.za business has been selling home hobbyists equipment to grow better vegetables since 1994. It is just hiring another staffer, after adding two new employees recently.
"We don't know what people are using it for," Megan Hinde, manager for the shop with a strong online presence, told Business Insider South Africa. "We don't ask."
But equipment is certainly flying off the shelves, more so than seems likely to have been caused by the breaking of the Western Cape drought and an uptick in interest in hydroponic vegetables.
See also: Smoking dagga is being decriminalised, but you can still be fired for it – maybe
"People often phone and ask advice, but even then sometimes you don't know what they are growing; tomatoes grow very similarly to cannabis plants," she says. "If lighting is involved it is a little bit it of a clue, but people also want to grow vegetables all year round."
Hydroponics suppliers that would not speak on the record about their current trade or plans hinted at everything from massive import orders to local manufacturing.
Video: Hydroponic Growing of Lettuce And Spinach On PVC pipes
2018
With the constant change in climate and unfavorable conditions for food production. It makes sense to explore other alternatives that are sustainable.
The hydroponic growing of fresh fruits and vegetables offers a great solution to have a constant supply of veggies for both family and commercial purposes.
Farms In The City: How A Chinese Firm Uses Tech To Boost Yield
By Feng Yilei
2018-12-01
An appetite for clean, fresh greens is growing with the burgeoning population in Chinese cities and towns. But feeding the rising demand is a challenge, partly because of the country's massive shift from being an agrarian to urban economy.
In the next 15 years, over 200 million Chinese are expected to move from rural areas into urban and suburban environments. This will greatly reduce the labor force on China's arable lands, which some say calls for a revolution in farming methods in order to create sustainable food production.
Beijing COFCO wisdom farm. /COFCO Photo
In suburban Beijing, a number of plant factories built with innovative techniques have incorporated farming into urban growth.
Dr. Wei Lingling, a researcher at the Chinese Academy of Agricultural Sciences, said controlled environmental agriculture (CEA) aims to get the most output with the least resources at the highest efficiency. They use technology like artificial intelligence (AI) and the Internet of Things (IoT) to precisely control production.
On a small plot of indoor space, plants are rooted on layered shelves vertically and bathe in light continuously during the day. Sensors linked to automatic irrigation and temperature control systems provide optimal conditions for growing.
Planned production means a higher yield resource-wise, space optimization, and labor savings. Dr. Wei believes CEA technologies will be more accurate in the future to better balance cultivation and the environment with less energy consumption.
“And in this closed production system, we circulate water and fertilizer to cut emissions, and improve sustainability of agriculture,” she added.
Plant factory using artificial light. /VCG Photo
While many believe this industrialized and intelligent way of farming will gradually replace extensive farming, which relies heavily on manual work and land usage for mass production, ordinary Chinese may have to accept difficulties in their daily lives during the process of moving on to the next stage.
For individual farmers that own the country's hundreds of millions of small plots, some have temporarily transferred their leaseholds to these high-tech farms and are adapting to their new roles.
Villager Wang Xiangang said that he got paid for both his land and working on the farm as an employee meaning he no longer worries about natural disasters and has time to learn about organic farming. He doesn't make as much as he used to, but it is stable.
And when conditions are ripe – will consumers be ready to pay a higher price for the products? Experts say the public will recognize the value of these crops as awareness of food safety and environmental stewardship rises. And once the demand rises, more players are expected to use tech-based food production, which will drive down prices.
Prince Edward Officially Opens New Hydroponics Unit
20th November 2018
By Lauren Jones Multimedia Reporter
A state-of-the-art hydroponics unit in Ellesmere Port has been officially opened by the Earl of Wessex.
The Bridge Community Wellness Gardens and Farm welcomed Prince Edward on Monday, November 19 to officially open the 'The Earl of Chester Hydroponics Unit.'
First of its kind in Cheshire, the new hydroponics unit will grow plants without soil by using mineral nutrient solutions in water solvent.
Plants can be grown with only their roots exposed to the solution and the farm's staff are growing fruit,vegetables and exotic micro greens for restaurants in Cheshire.
Farm and wellness gardens manager Clair Johnson said: “It was fantastic to have a visit from Prince Edward and to show him the amazing work we do here.
“The hydroponics unit is an exciting addition for us because it allows us to grow plants indoors without soil, gives us faster growth all year round and saves on water usage.
“We love to encourage our wellness clients to overcome their mental health and learning difficulties and find new skills.
"And they do every day. It’s so inspiring!”
During his visit, Prince Edward was given a tour of the farm where he met staff and volunteers working in the routing shed, the bee friendly Mandala Garden, the seeding tunnel, solar dome and polytunnel.
He also unveiled a plaque on the site marking the official Royal visit.
Chairman of Bridge Community Wellness Gardens and Farm Francis Ball said: “I’m incredibly proud of what Clair and her team of staff and volunteers have achieved here.
“Pretty well every day we are reduced to tears by the gratitude of a client, or client’s parent or carer, who gain so much benefit from spending just a few hours with us.
"It’s inspiring and it drives us on to Grow Better Lives.”
Prince Edward also paid a visit to pupils at Neston High School on Monday.
New Hydroponics Project Lets Students Learn As Crops Grow
By Kathy Brown, Gillette News Record (via Wyoming News Exchange)
Gage Terrell prepares to harvest lettuce from a hydroponic plant holder in the hydroponics room at Lakeview Learning Center. Rhianna Gelhart, Gillette News Record
GILLETTE — The Adventurarium in Gillette is growing plants and feeding many of its animals through a new hydroponics room.
The Campbell County School District’s science center is open throughout the school year for Family Science Nights and serves students ranging from pre-school through sixth grade. The new hydroponics room with lights, a top-drip vertical wall system and a floating deep water culture system (now growing tomato plants) are featured in the hydroponics room.
There, Gage Terrell, 17, a senior at Thunder Basin High School, tests the systems for pH levels, harvests the lettuce and herbs growing in the top-drip system and helps science center director Jodi Crago-Wyllie keep up with the planting, harvesting and production from the hydroponics.
It’s Terrell’s second year as a mentor student at the science center. Each morning he feeds the plants and checks their pH levels. He’s become a right-hand man for Crago-Wyllie, who also serves as the elementary level science facilitator for the district.
It is an affordable hydroponics system that uses PVC pipe, painted used aquariums and similar inexpensive parts that grow plants year-round.
The science center staff, including Crago-Wyllie and Terrell, are learning as they grow.
“You really have to be on top of it,” Crago-Wyllie said. “It’s kind of like a pet.”
Everything in the room is grown without soil, she said. Material to start the seedlings is similar to carpet or compost material. Those are then planted in the vertical wall.
“We don’t bring in any plants with soil on the roots,” Crago-Wyllie said, adding that soil can transfer diseases or bugs.
Each week, Terrell and Crago-Wyllie harvest the lettuce and herbs and replant. The system uses overhead lights that can be raised or lowered with another track of lights aimed at the wall system, which can be moved closer or further away from the plants as needed.
That’s where they are continuing some experimentation, along with growing herbs ranging from oregano to parsley. Crago-Wyllie said she hopes to plant some peppers in the deep water system once she has harvested the tomatoes, which are showing dramatic growth each week.
She’ll also have to see how to add stakes to help support the tomato plants, she said.
“It’s become such a big thing now,” Crago-Wyllie said of hydroponics. “So many kids don’t know where their food comes from.”
The hydroponics room is a way to show them. There are three types of lettuce being grown in the eight vertical rows of plants in the top drip system. The room is kept at between 70 to 81 degrees and a fan helps circulate air.
“It’s cool,” Terrell said. “You can see how food is grown and we can feed it to the animals who eat it." (Terrell’s) parents don’t garden, but his grandmother does. And he’d like to show her how this hydroponics room works.
Terrell’s favorite? The tomatoes, he said. “I like these because you can see them grow every day.”
The plants doubled in growth over the past three-day weekend. It won’t be long before he is raising the lights or adding stakes to the aquariums and lightweight, floating rocks (similar to lava).
“I think it’s something we can do in my house,” Terrell said about building his own hydroponic garden.
Among the herbs growing at the science center is cilantro, he said, adding that “hopefully we can make some salsa.”
It is a class Terrell said he loves.
“It’s cool to do different things. I do something different every day,” he said. “I like it in here. It’s like a science experiment.”
Terrell remembers coming to the science center and Adventurarium as a younger student in Campbell County.
“I thought of it as a museum of sorts. If I’d known, I’d have come every day,” he said of the Adventurarium, which each elementary school class visits at least once a year.
The class works well with what he hopes to do in the future. “I thought about being a teacher. A science teacher would be fun,” he said.
He plans to start at Gillette College, attend two years there, then move on to the University of Wyoming, Terrell said.
He repainted the aquariums black to start the deep water culture system. The air pumps from those former fish tanks are very responsive, Crago-Wyllie said.
The baskets they found to hold the rocks and the tomato plants fit perfectly and cost about $10, she said. Overall, the two systems in the room cost about $1,500 and will grow plants year-round.
A daily dose of nutrients helps the plants grow better and faster under the lights, she said. If the plants are less acidic, they absorb more nutrients, which means quicker growth.
“It sounds easy, but you have to keep up with it,” Crago-Wyllie said. “It’s so fun and so much different than I imagined.”
Terrell grows the lettuce to feed the animals in the science center, including his favorite, Cedric, a parrot. He also will sing to the animals when he feeds them.
“Cedric loves him. He loves Gage and he doesn’t love anyone,” Crago-Wyllie said of the formerly abused parrot.
The idea of building a hydroponic garden came to Crago-Wyllie a year ago. Now both she and Terrell are learning as they go.
“Yeah, I still don’t really know how that works,” Terrell said.
“You have to be a bit of everything,” Crago-Wyllie said. “A chemist ... and more, not just a gardener.”
With that, she and Terrell added a new row of lettuce to try Tuesday, including Caesar, Simpson and butter crunch.
Technology Distilled To Grow The Hydroponics Industry
By Chad Campbell
November 16, 2018
When Horticulture Assistant Professor Krishna Nemali joined Purdue in July 2016, he immediately began to develop a program as new to the school as he was. Nemali studied agriculture in India before earning his Ph.D. from the University of Georgia and spending nine years as a scientist in controlled environment crop physiology at Monsanto. All these experiences combined to provide him with the range of experience necessary in his current position coordinating research and Purdue Extension activities in Controlled Environment Agriculture (CEA).
CEA harnesses technology to grow plants like vegetables and ornamentals in conditions maximizing the efficient use of water, light, labor and space. Hydroponics, the method most commonly associated with CEA, minimizes water, nutrient and labor requirements to grow plants. It can also reduce other needs, such as pesticides. Researchers like Nemali work to discover the perfect combinations of water, light, nutrients, temperature and additional factors to make sure there is no wasted energy or potential. Nemali’s goal is to answer the question,
“How do you make that technology easily accessible to everybody?”
Nemali is working to harness the potential of smartphones, specifically new apps and add-on devices, to provide growers access to these processes. “There are companies and some apps already there that just take a picture and show some data. That’s not what we’re trying to get at. We have these expensive imaging stations and we are developing technologies that match that high-quality data.” A combination of research, calibration and algorithms takes place behind the scenes to provide farmers with valuable, yet easy-to-understand information, everything using their smartphones.
One app Nemali is creating will use background processing to measure plant growth. The plant’s size is calculated through pictures the user takes and algorithms designed by Nemali. With daily use, the app generates growth curves. “It’s like when you take your kids to a doctor, and they take a weight and height measurement.They put the numbers on a standard chart. 90th percentile height, 70th percentile weight. You can create standard curves for different species and plot this data under the standards.”
Nitrogen is essential in plant processes, including photosynthesis, yet the equipment needed to measure nitrogen levels in plants is cost-prohibitive. Nemali’s lab is currently creating a similar device for smartphones, available for less than $150. Nemali hopes to create widely adopted and applied technology to reach independent growers.
Through Purdue Extension, Nemali also works with Indiana farmers to capitalize on the untapped potential hydroponics provides. The industry is small, but rapidly growing at 3.5% annually in the US. For example, Nemali sees a wealth of opportunity in leaf lettuce production. The USDA estimates people eat about 11 pounds of leaf lettuce per year. With 6.7 million Hoosiers and a $1.00 wholesale valuation on each pound of lettuce, that’s over $70 million.
Indiana imports nearly all its leaf lettuce from places like Arizona and California. “We want that money to stay within Indiana," Nemali shared. We want our growers capitalizing on this. There is a demand there. Grow lettuce locally, sell lettuce locally, keep the money local. That money spread out among the 300 lettuce growers in Indiana, that’s going to improve their livelihood. That’s what sustainability, in my opinion, is.” He organizes workshops that provide both classroom style training and experiential learning to farmers.
The methods and technology Nemali creates produce a level of precision that can set hydroponic farmers apart. Even small adjustments to the levels of red, green and blue artificial light provided to grow plants can have significant effects on the growth, color and nutritional value of plants. Nemali tells his growers, “Don’t say simply that your lettuce is crisp and fresh. Everybody says that. How do you find a niche? Use technology to grow lettuce that has more nutritional value, antioxidants, and less nitrates. Show the value. Health. That’s what attracts millennials.” The results of this research are integrated into Nemali’s apps to bolster the intelligence of the technology.
Nemali also uses hydroponics and vertical farming techniques to address problems like childhood obesity. A few years ago, Nemali’s son participated in a multi-week summer camp where the children planted and harvested their own vegetables, making salads and soups.
“For the next couple of months,” says Nemali, “he was all about eating healthy. That told me something. Give kids that exposure to plants: how you seed them, sow them, you see them grow, you harvest them and clean them. That may change their attitudes and behaviors from a less favorable attitude towards eating healthy, and that’s what we’re trying to do.” He collaborates with schools to setup small indoor growing facilities for children using hydroponics.
As the benefits of hydroponics become increasingly apparent, nations around the world are studying, researching and building hydroponic facilities of their own. Scarcities of land and water are critical issues in many countries. Hydroponics are incredibly efficient in both respects. Vertical farming is a common practice in hydroponic facilities. Warehouses may accommodate 15 to 20 levels of plants. It is reasonable to expect five to ten times more production in such spaces.
Hydroponics brings researchers across the globe together to work toward a common goal. Nemali embraces the spirit of hydroponics by making the most of current resources and rapidly producing new resources to grow the industry.
Want to try hydroponics at home?
Create your own simple hobby garden.
Category: Agricultural & Biological Engineering, Agricultural Economics, Agronomy, Botany & Plant Pathology, Extension, Food Science, Forestry & Natural Resources, Giant Leaps, International Programs in Agriculture, Office of Multicultural Programs, Research, Teaching, Uncategorized
Local Startup Making High-Tech Gardens Grow
JOSH MANDELL @joshuamandell
November 19, 2018
Babylon Micro-Farms has created an indoor growing system that allows customers to farm organic foods inside their home or business. Credit: Andrew Shurtleff, The Daily Progress
Babylon Micro-Farms has created an indoor growing system that allows customers to farm organic foods inside their home or business. Credit: Andrew Shurtleff, The Daily Progress
When Charlottesville’s Silk Mills building opened in 1895, it brought a new manufacturing business to a local economy that still was based upon agriculture.
Today, the building on Harris Street houses a team of “farmers” who build circuit boards and write code as they tend to their crops.
Another tenant, Babylon Micro-Farms, hopes to bring the technology used by large-scale urban farms to small businesses and individual consumers.
“We want to make advanced, controlled agriculture accessible to more people,” said Alexander Olesen, Babylon Micro-Farms co-founder.
(From left) Babylon Micro-Farms Will Graham, Graham Smith, Alexander Olesen and Sam Korn stand in front of a new indoor growing system. Credit: Andrew Shurtleff, The Daily Progress
Since its creation in 2017, Babylon has installed automated hydroponic systems at several Charlottesville eateries, including Corner Juice and Yoga, Three Notch’d Craft Brewery and Kitchen and the University of Virginia’s Observatory Hill dining hall. The company currently is finishing its most complex project to date inside the Boar’s Head Resort’s Trout House.
Dale Ford, Boar’s Head’s executive chef, said he expects the hydroponic farm to produce 300 heads of lettuce each week — enough for all of the resort’s dining locations.
“Putting together a small urban farm inside what we consider to be a legendary, iconic building for our property was a great combination,” Ford said. “The thought that we could grow produce from an heirloom seed and track the analytics and data from germination to harvest and tell the story of that food to our guest — that is pretty special.”
Olesen and co-founder Graham Smith built their first micro-farm for a social entrepreneurship course at UVa. That wooden, pool table-sized prototype has given rise to tall, transparent setups that can be precisely programmed to provide water and nutrients to multiple crop varieties at once.
Will Graham, Babylon’s director of marketing and sales, said the company ships pre-seeded trays and programs the micro-farms in advance to make indoor farming a “plug-and-play” experience for its clients.
Credit: Andrew Shurtleff, The Daily Progress
Many other companies are trying to capitalize on the efficiency and environmental sustainability of hydroponics. A handful of urban farming startups have attracted enormous investments this year.
BrightFarms, which operates a 250,000-square-foot greenhouse in Culpeper County, raised a $55 million Series D investment round in June. Gotham Greens, based in New York and Chicago, raised $29 million in an investment round this past summer.
Beanstalk, another indoor farming startup founded by UVa graduates, participated in the Y Combinator accelerator program this year.
While Beanstalk hopes to disrupt the wholesale market for produce, Babylon Micro-Farms is targeting individual restaurants and health-conscious consumers. The company is scheduled to unveil a residential model of its micro-farm in December, with an estimated starting cost of $3,500.
“When we looked at the industry, we saw that it was confined to massive commercial industrial operations and small DIY kits,” Olesen said. “That doesn’t make any sense, and it reflects the problems of the larger agricultural system.”
Babylon Micro-Farms soon will sell its own produce at local farmers markets and groceries. It has donated greens to the Blue Ridge Area Food Bank.
“We grow hundreds of crops and experiment with all sorts of rare varieties and herbs that you can’t get in Charlottesville,” Olesen said. “If we say it’s that easy, why wouldn’t we be doing it ourselves?”
Green Life Farms Announces Innovative Partnership with Hydronov for Sustainable Ag-Tech Greenhouse
Flagship hydroponic farm will feature Hydronov’s industry-leading deep-water floating raft technology to grow premium baby greens year-round
Boynton Beach, FL (November 19, 2018) – Green Life Farms has selected Hydronov, a Pranger Company, to design, construct and provide technology for its state-of-the-art hydroponic farm in Boynton Beach, FL. This agreement marks an important milestone as Green Life Farms prepares to begin commercial operation in the first half of 2019. Green Life Farms will grow premium baby leafy greens year-round from its Boynton Beach facility.
Green Life Farms has selected Hydronov, a Pranger Company, to design, construct and provide technology for its state-of-the-art hydroponic farm in Boynton Beach, FL. Green Life Farms will use Hydronov’s pioneering deep-water floating raft technology (pictured above), which is cost effective and environmentally friendly.
Green Life Farms has selected Hydronov, a Pranger Company, to design, construct and provide technology for its state-of-the-art hydroponic farm in Boynton Beach, FL. Green Life Farms will use Hydronov’s pioneering deep-water floating raft technology (pictured above), which is cost effective and environmentally friendly.
Green Life Farms will use Hydronov’s deep-water floating raft technology (FRT) to grow baby leafy greens for supermarkets, restaurants, cruise ships, and other customers from its state-of-the-art hydroponic greenhouse in South Florida. Hydronov is a pioneer in the hydroponic sector, leading the way with this cost-effective and environmentally-friendly method of hydroponic growing.
“Partnering with Hydronov and leveraging the company’s leading technology will help us realize our vision for Green Life Farms – growing sustainable and delicious leafy greens for consumers in South Florida and beyond,” said Mike Ferree, Vice President, Green Life Farms. “Green Life Farms will grow baby leafy greens that are good for your body, family, community, and planet. Creating a sustainable facility by using leading Ag-Tech methodology, along with green energy and other environmentally-friendly practices, brings our mission to life.”
FRT helps to conserve water, allowing a buffer for fertilization and oxygen control, and provides an integrated Harvest Transportation System which uses the water in which the plants grow as a conveyer system, eliminating the costs and maintenance associated with mechanical conveyers. No water is lost through soil or growing media; there is no direct evaporation by the sun, no dumping of growing solution and no dripping gutters. The FRT system leads to higher productivity, producing up to 18 crop harvests per year versus the five harvests per year with soil-based greenhouse growers.
Hydronov is an industry leader in the design and construction of hydroponic growing facilities. With more than 30 years of experience in hydroponics and aquaponics, the company brings industry-leading expertise to the innovative project with Green Life Farms.
“We’re excited to partner with Green Life Farms on this state-of-the-art project,” said Gabe Pranger, owner of Hydronov. “Growing leafy greens in South Florida presents a number of unique challenges, but we’re confident that the combination of Hydronov’s technology and construction management expertise with Green Life Farms’ strategy will result in great success.”
Green Life Farms produce will set new standards for cleanliness, freshness, and taste. Grown locally, using sustainable farming practices combined with the most advanced AgTech practices, and kept free from pesticides and contaminants, Green Life Farms baby leafy greens are good for your body, family, community, and planet.
For more information about Green Life Farms, visit GreenLifeFarms.ag. Please contact Elayne@GreenLifeFarms.ag for sales and Ray@GreenLifeFarms.ag for investor relations.
About Green Life Farms
Green Life Farms is constructing a 100,000 square foot state-of-the-art hydroponic greenhouse in Boynton Beach, Florida, with additional expansion planned in Florida and beyond. Commercial operation is expected to begin in the first half of 2019. By incorporating agriculture with technology, Green Life Farms will provide consumers with premium-quality, fresh, local, flavorful and clean baby leafy greens that are good for their bodies, families, communities and planet – year-round.
About Hydronov
Hydronov LLC was purchased by Nick Pranger and Gabe Pranger in 2017. Since its beginnings in the 1980s with founder Luc DeRochers, Hydronov has focused on innovation in the greenhouse industry. The success of a small research project developed into Hydronov’s unique growing system, Deep Water Floating Raft Technology. Today, Hydronov’s technology is a cost-effective, environmentally friendly, and profitable way to grow hydroponic lettuce, herbs, and produce. Hydronov is headquartered in Ashley, Indiana. Learn more about Hydronov’s floating raft technology at www.hydronov.com.
Tips On Designing The Best Hydroponics System
November 1, 2018
To design the best hydroponics system, one must look at the host of factors contributing to plant growth, roughly these are the environment, temperature, nutrient delivery and protection from damaging agents.
Hydroponics farming in India looks to the use of Greenhouses as a solution to manage these factors. Greenhouses are large structures built over tracts of flat land to accommodate the protected farming techniques, that use climate control methods and such to grow seasonal crops in unseasonal weather. In hydroponics, an additional technology used is water chillers as a cool root zone promotes aeration and root health.
For ambient temperature fan and pad cooling systems are effective in dry and hot weather. The system works by drawing air in through a cellulose pad placed all along one side of the polyhouse structure, water is trickled through this cellulose pad to provide the evaporative cooling effect. The air is sucked in by large fans and blown out of the greenhouse.
The material a greenhouse is made of can also greatly help with removing trapped heat from the structure, commonly used material is polycarbonate which, while being significantly more expensive than a poly sheet, it has the best heat transfer ability and hence is the best for climate control. Polycarbonate is also more durable but can be tough to work with due to its rigidity. The ultimate in greenhouse material technology is Glass greenhouses, both the most expensive and the best to control temperature and climate. A Glass greenhouse would ultimately require less frequent maintenance than any other type of greenhouse material. A glass greenhouse would be ideal for doing hydroponics in Gurgaon or Delhi which have very varying climates.
When looking at doing large scale hydroponics in India it is important to remember that we undergo usually intense summers followed by pleasant winters. Heating is not a necessary concern except in very extreme cold climates, but these climate zones are restricted to a few pockets and usually, the market for hydroponics is not present in these areas. This, however, should not discourage potential hydroponic farmers as the colder climates help with growing high-value exotics. These have great export and commercial value in urban areas.
Automation is a key aspect of designing any hydroponics system, water is reactive and transpiration and evaporation can change key water parameters of ph and EC and hence it is necessary standing monitor systems like the Bluelab Guardian monitor. When looking at automatic dosing the requirement stems from the need to reduce labor and time spent on maintaining the system thereby freeing up labor for harvest, maintenance, and packaging of the produce. Automation can be achieved through master controllers and peristaltic pump dosers.
These control panels like the Bluelab Pro Controller are very efficient at monitoring and controlling dosing pumps such as the Bluelab Peripod to maintain the all-important parameters of pH and EC. The Bluelab connect software is a remote monitoring and control software that helps growers record data and control their dosing remotely.
The Pro controller is a versatile device that can control up to 12, 3 or 4 pump dosing units and can be used to do up to 3 nutrients and one pH solution, this has great application for automating fruiting vegetable crop production. The Pro controller can set an individual on/off times for each of the pumps thus enabling the grower to maintain the right NPK mix for his crops throughout the growing cycle.
The Hydroponics system itself should be designed according to the crop to maximize efficiency and space. For example, Tomatoes need larger root spaces with changes to their NPK ratios during flowering but lettuce can be grown close together on pipes with very little nutrient use.
Thus we use different hydroponic techniques for these plants, tomatoes are grown on DWC rafts or BATO bucket systems and NFT systems are used to grow leafy greens and herbs. The type of crop dictates the type of vessel the crop is grown in. While cheap and cost-effective, DWC trays may be cumbersome to maintain and flimsy meaning frequent repairs and upgrades. NFT and BATO systems are easier to maintain and dose, they also use water and space more efficiently.
One important factor of the use of all these technologies is the ability to monitor the factors affecting crop growth and thus giving us the necessary data to improve our crop growing process to produce better yields and more quality crops.
The use of technology could help us mitigate the damage that factory farming over vast tracts of land has done to our environment. The introduction of a data-based A+B= C formula is only possible with careful data monitoring and interpretation to make a replicable plant growing formula for great yields and quality produce.
FutureFarms Pvt. Ltd
4/640, 12th Link, 3rd Cross Street
Nehru Nagar, Venkateswara Colony
Perungudi, Chennai, India 600 096