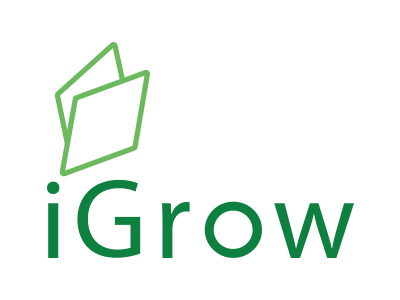
Welcome to iGrow News, Your Source for the World of Indoor Vertical Farming
Investment Brings New Life, New Jobs For RecoveryPark
After working for more than a decade to launch its first social enterprise, RecoveryPark is poised to break ground in November on a commercial-scale hydroponics greenhouse that will create jobs and eventually, equity ownership for Detroiters facing employment barriers
September 08, 2019
Project has attracted investments from three high-profile investors
Will establish Detroit's first commercial-scale hydropronics grower
Expected to sow and harvest first crop, baby leaf lettuce, in August 2020
Justin Phillips, farm associate at RecoveryPark, harvests greens from the nonprofit's pilot hydroponics growing operation. Photo: Bill Bowen
After working for more than a decade to launch its first social enterprise, RecoveryPark is poised to break ground in November on a commercial-scale hydroponics greenhouse that will create jobs and eventually, equity ownership for Detroiters facing employment barriers.
The $10 million project on East Palmer Street near Chene will bring farming — albeit a different type — back to a part of the city that was once home to flower and vegetable seed producer D.M. Ferry & Co. and establish Detroit's first commercial-scale hydroponics grower.
It's attracted three high-profile investors: Stephen Polk, CEO of Birmingham investment company Highgate LLC.; Jim M. Nicholson, co-chairman, PVS Chemicals Inc.; and Walter Tripp Howell, retired international director of Jones Lang LaSalle in Washington, D.C., and an ex-pat of the Detroit area, who learned of the project during the 2018 Detroit Homecoming.
Detroit-based Nextek Power Systems is also considering an equity investment, its CEO Paul Savage confirmed.
Those investments will make up about a third of the $12.5 million raised to cover bridge operational funding for the nonprofit RecoveryPark over the past several months and construction and startup costs for the climate-controlled greenhouse operation, which is set to launch in August 2020, RecoveryPark CEO Gary Wozniak said last week.
A 28-year loan backed by the U.S. Department of Agriculture and U.S. Small Business Administration and a 10-year loan backed by the U.S. Small Business Administration, both made through the Greater Nevada Credit Union's Greater Commercial Lending arm to for-profit company RecoveryPark JV LLC, are set to close in October, rounding out funding, Wozniak said.
Wozniak projects the greenhouse operation, run by the for-profit company, will yield $6 million in revenue its first year and $18 million annually within four years with two planned expansions that will triple its "acres under glass."
RecoveryPark has already proven the business model through pilot hydroponics and high-tunnel or soil-based growing operations a couple of blocks away near its headquarters on Chene, Wozniak said. It has contracts to supply lettuce to Detroit wholesale distributor Del Bene Produce that produced $180,000 in revenue last year and are set to do about the same this year.
It's now in talks with retailers including Nino Salvaggio and Meijer, Wozniak said.
Next to tomatoes, leafy greens are the second most in-demand vegetable, he said. And recent romaine lettuce recalls have spurred demand for hydroponically grown lettuce and greens even more.
The greenhouse will help RecoveryPark achieve its social mission, said Wozniak, who is himself a recovering addict and ex-offender.
"Our mission is to create jobs for people with barriers to employment: people coming out of prison and/or drug treatment programs," Wozniak said. "Our vision is to do that by creating jobs in the food industry and eventually we'll transfer majority ownership to the workforce in those businesses."
The new greenhouse will also help change the way consumers view food by establishing local, hyper-fresh options and local accountability for the quality of that food, he said.
Joint venture
RecoveryPark JV will be jointly owned by the nonprofit RecoveryPark as minority owner and the equity investors holding a combined 70-percent stake. RecoveryPark will look to buy back equity from the investors over 10 years, before transitioning ownership to employees, Wozniak said.
Charles Motley, COO, RecoveryPark JV LLC; and Gary Wozniak, president and CEO of the nonprofit RecoveryPark. Photo: Bill Bowen
Automotive and manufacturing veteran Charles Motley has joined the new company as COO.
Motley, 47, brings 25 years of experience at manufacturing companies, most recently serving as vice president of manufacturing at Wixom-based gun sight manufacturer Trijicon Inc.
With his experience and expertise in construction and team management, process flow, lean systems and continuous improvement skills, "he's taking us from being a church committee to being a real business," Wozniak said.
Motley, a native Detroiter, said he was attracted by the opportunity to give back at this point in his career.
"We're committed to taking ... not just the greenhouse (but) the whole area ... from being blighted to being a stronger economic centerpiece for the city," he said.
Beyond their investments, each of the equity investors brings specific expertise and is helping mentor the startup greenhouse company, Wozniak said. Polk has given advice on managing the stress of pulling together financing for the greenhouse while balancing operational and funding needs for the nonprofit. Nicholson was instrumental in driving to hire someone like Motley to lead the greenhouse operations. Howell has brought an understanding of the farm-to-table movement and marketing for the food industry.
The RecoveryPark greenhouse venture has a lot of interesting facets and is a good approach to helping Detroit, Polk said. "It's early on, (but) we're excited about it."
When you look at the neighborhood where the new greenhouse will be located, it's a tough area to build a food economy, he said. But RecoveryPark's plan will reclaim land and put it to good use.
The goal of helping people come back from addiction and other challenges is also a beneficial project for Detroit, Polk said.
And the opportunity to turn it into a profitable venture is also interesting. "They've had a good start getting their products from the existing test facility into local restaurants. People like the homegrown aspect of it," he said.
"With the local food scene in Detroit, I think the drive for local produce will continue to grow."
Howell said he's been interested in agriculture since he was growing up in Grosse Pointe. That interest and his desire to make a difference in Detroit drew him to the RecoveryPark greenhouse project.
"I've been an investor in a series of restaurants in the Washington, D.C., region, and I've found that the lettuce product is hard to get a hold of, expensive, and when we receive it on the East Coast, there's so much that's thrown away," he said.
The opportunity to have something grown locally, harvested locally and consumed within days of being harvested is attractive, he said.
Coupled with that, "I think the fact that the Department of Agriculture is getting involved in a farm that's in an urban setting ... is a next-generation move," Howell said.
"The way the social side meets the for-profit side is just a good model for so many things. I really want to see this succeed."
Demolition of a former Kroger store and former potato chip manufacturing building at 2259 East Palmer St. near Chene, about two miles north of Detroit's Eastern Market, is underway to make room for the new, 2-acre greenhouse. Site preparation is set to begin Nov. 1.
The hydroponics greenhouse will be located in an Opportunity Zone, but the deferment of capital gains tax associated with those low-income zones was not a factor in attracting the initial investments to the greenhouse project, Wozniak said.
Gakon Horticultural Projects
RecoveryPark and a group of investors plan to break ground Nov. 1 on Detroit's first commercial-scale hydroponics greenhouse, similar to this Gakon Horticultural Projects building in the Netherlands.
The greenhouse itself will be assembled from a kit shipped here by Netherlands greenhouse manufacturer Gakon Horticultural Projects.
Hamilton Anderson Associates is the local architect on the project and O'Brien Construction as general contractor.
Next summer, Motley said, he'll look to hire and train 12-15 people coming out prison and/or drug recovery programs. Through a contract with the nonprofit RecoveryPark, they'll be lined up with supportive services like transportation.
The greenhouse will operate year-round with a continuous growth cycle, with seeding at one end of a large pond of water and trays of plants slowly moving across the water over 12-14 days for harvesting on the other end.
Motley projects the annual costs to operate the greenhouse will run about $800,000.
RecoveryPark will get three cents of every dollar of revenue from the joint venture as a royalty, he said, projecting that will be about $350,000 the first year and increase with each expansion. The joint venture company will also pay a set amount each month per employee to RecoveryPark to provide wrap-around support services.
By the time the greenhouse has 6 acres of crops, RecoveryPark should be receiving about $1 million each year from the for-profit joint venture, enough to be self-sustainable, Wozniak said.
While the greenhouse takes shape, Motley is working with Detroit companies Skidmore Studio and Nebulous Concepts LLC on brand development and marketing. He believes it's important to include RecoveryPark's mission on packaging, if possible, to help people understand why buying the product is important, he said.
The new company plans to take taste testing of its leafy product — possibly under the "RecoveryPark Farms 313" brand — directly to retail locations in January and hopes to have contracts with retailers in place by about the end of the first quarter, Motley said.
"We're building brand awareness through wholesale, (but) expect to see retail sales really be a big part of the growth."
Initially, the greenhouse will focus on growing baby leaf lettuce "but we're doing a lot of research over the next three or four months to say 'OK, these are other options that consumers are looking at that might fit our portfolio,'" Motley said.
Going forward
As Motley takes on oversight of the greenhouse operations, Wozniak and RecoveryPark will look to new pastures.
The nonprofit will look to shift the high-tunnel growing it's done in recent years to a niche farming business or education and community gathering program, Wozniak said.
The nonprofit will shrink to four to six employees. It will focus on providing support services for greenhouse employees and developing other social enterprise pilots such as new lines of tomato seeds, an indoor fish farm and/or a small greenhouse to grow starter plants for other growers.
RecoveryPark currently operates on a $1.2 million budget with nine full-time employees after laying off employees last year when it shut down the high-tunnel growing operation to save money on heating costs over the winter and let the ground regenerate.
Part of moving forward will be settling old debts.
"We've got a lot of debt on our balance sheet and are looking for creative ways (to settle it)," Wozniak said.
RecoveryPark has pitched the idea of converting debt to stock ownership in RecoveryPark Farms, the nonprofit's holding company for the social enterprises, and is working on deals to convert $1.8 million of debt into stock ownership in the holding company. If it's successful in those conversions, it will be left with 57-percent ownership in the holding company.
The Max M. and Marjorie S. Fisher Foundation, which made a $400,000 program-related investment loan to the nonprofit in 2016, is in the process of looking at the conversion terms, said Meredith Freeman, who is serving as interim executive director of the Fisher Foundation while Executive Director Doug Stewart is on sabbatical.
Max M. and Marjorie S. Fisher Foundation
Meredith Freman
"I really applaud them for their commitment not only to the city and the neighborhood but to keeping that social aspect in place around making sure they are employing those who have challenges to employment. ... they've never let that go," she said.
"It could have been easier business-wise to let that go, but they made that commitment, stuck to it, and we are really happy to support that."
Letter
Intensive Course In Hydroponic Lettuce And Leafy Greens At University of Arizona
The controlled Environment Agriculture Center Is Offering An Intensive Course In Hydroponic Lettuce And Leafy Greens October 5th Through The 9th
By urbanagnews
September 4, 2019
The Controlled Environment Agriculture Center is offering an intensive course in Hydroponic Lettuce and Leafy Greens October 5th through the 9th.
Lettuces and leafy greens – we eat them every day! (or we SHOULD!) But how do we grow them sustainably with delicious flavor? Join the Controlled Environment Agriculture Center to answer these questions and more during our Intensive Hydroponic Lettuce and Leafy Greens course.
Our esteemed staff and faculty will provide 40+ hours of classroom time and hands on application in the Greenhouses on the CEAC Campus to ensure your hydroponic leafy greens are a success.
About CEAC: The Controlled Environment Agriculture Center (CEAC) is a research institution of The University of Arizona. The CEAC provides Education, Research, Outreach, and Extension activities, and is heavily involved with Agriculture & Biosystems Engineering, Plant Sciences/ES, and Agricultural Technology Management Departments.
Dates: October 5th through 9th 2019
Cost: $1,195
Instructor: Myles Lewis
Location: Controlled Environment Agriculture Center 1951 E. Roger Rd, Tucson, AZ, 85719
For more information on our upcoming courses visit https://ceac.arizona.edu/events/intensive.
To register for this exciting event visit here. Please contact Megan Dragony With any further questions at dragonym@email.arizona.edu or 520-626-9566.
Ultra-Locally Grown - Urban Farming Takes Off In Germany
Recent experiments in sustainability mean you can now purchase shrimp from Bavaria and pike perch from Berlin. "Urban gardening" promises healthy and fresh products without long transportation routes
Recent experiments in sustainability mean you can now purchase shrimp from Bavaria and pike perch from Berlin. "Urban gardening" promises healthy and fresh products without long transportation routes.
Photos: Diephotodesigner.de
September 03, 2019
When Christian Echternacht gets invited to dinner, he likes to bring tilapia and basil rather than wine or flowers. His friends have grown used to it by now. They know that the fish and the plants have something in common: Both are harvested by Echternacht himself. They make great fish burgers topped with basil mayonnaise.
The ingredients prosper in the urban farm that Echternacht has run with his partner, Nicolas Leschke, for several years. It's located in central Berlin, on the grounds of the Malzfabrik, a startup hub in the city's Schöneberg district.
Tilapia at various stages of growth swim around in 13 different tanks, their skin varying shades of silver and pink. The fish don't weigh much when they arrive at Echternacht's ECF Farmsystems, as his company is called, but after a few months in his tanks, they plump up to half a kilogram (1.1 pounds) and are ready for harvesting.
Next door on this warm summer's day, shirtless gardeners are working in the greenhouse where they grow basil from seed, an intensely aromatic sea of leaves. The plants sit atop gigantic grow tables onto which water from the fish tanks is diverted -- filtered and full of nutrients. The water contains ammonia from fish excrement and is transformed into optimal fertilizer by bacteria. This symbiotic circuit made up of fish farming (aquaculture) and plant cultivation in water (hydroponics) is called aquaponics, a technique that is thought to have been used hundreds of years ago in China and by the Mayans.
The Berlin duo markets their products as "capital city tilapia" and "capital city basil," and they are part of an international movement that seeks to bring food production closer to consumers in the city, thus making it more sustainable. Doing so is an absolute necessity, because traditional rural agriculture and forestry is responsible for 23 percent of manmade greenhouse gas emissions.
Bringing Production Closer to Home
Alternative forms of food production, such as city farms, are currently just as popular as modern aquaculture facilities. Saltwater shrimp are being raised in the village of Langenpreising, near Munich; and in supermarkets and restaurants, one increasingly finds futuristic glass cabinets from the Berlin-based startup Infarm, where consumers can watch herbs and lettuce grow and buy them freshly harvested.
All the producers are united by the mission of producing high-quality natural foodstuffs using modern technology and unconventional methods. In their indoor gardens, they use no pesticides for growing vegetables and eschew antibiotics in aquaculture facilities. Aquaponics has the added benefit that 90 percent of the water is reused. Shorter transportation routes result in fresher food and lower emissions, especially due to the reduced need for refrigeration.
A surprising number of those involved in such production are self-taught or mid-career beginners and don't have backgrounds in agriculture.
That also holds true for Christian Echternacht. He initially studied medicine before founding an internet agency in the mid-1990s. Later, he spent a few years on the road with Roxy Music icon Brian Eno, helping out with his video installations.
His new career was born out of his interest in high-quality foodstuffs, the 48-year-old explains, and the beginnings were rather modest. He initially used a shipping container for the fish tanks, and he built a greenhouse on his roof. The remains of this container farm can still be seen on the premises of the Malzfabrik in Schöneberg, just a few meters from the current facility, which is 1,800 square meters in size (almost 20,000 square feet) and cost around 1.4 million euros to build. The money came from private investors and from the Investitionsbank Berlin, a state owned development bank.
The early years were difficult. The city farmers soon had to abandon their hopes of a completely circular economy in which nutrient-rich fish water would be cleaned by the plants' roots and sent back to the fish tanks. "We realized that for optimal results growing the plants and raising the fish, we needed water with different pH values."
They also experimented with a wide variety of different sorts of vegetables -- from eggplants to tomatoes to peppers -- before ultimately arriving at basil. And why did they choose a fish species that originated in Africa? Primarily because it is particularly efficient at utilizing food: 1.4 kilos of food produces 1 kilo of fish. Furthermore, the species is rather undemanding. "We would also like to raise pike perch," Echternacht says, "but they are sensitive, require peace and quiet and are quick to stop eating if conditions aren't perfect."
'The Experimentation Phase Is Over
Echternacht and his partner also experienced a steep learning curve when it came to marketing their products. Initially, they tried to sell on-site in addition to offering a subscription produce box for 15 euros a week. For a time, they also had a stand at a market hall in the district of Kreuzberg. But it was a partnership with the supermarket chain Rewe that provided the breakthrough. Rewe now buys up the farm's entire production of basil, with 7,500 plants per week ending up in stores in the region just one day after harvest. The price at the store is around 2 euros per plant. Currently, more than 400,000 basil plants and around 30 tons of fish are produced each year at the facility right in the heart of Germany's capital city.
"The experimentation phase is over and we're going to be profitable this year," says Echternacht, though the work done by the three gardeners and two fish farmers is only part of the business plan. The farm, after all, is also a showroom, with tours almost every day for schoolchildren and people interested in the facility from around the world. Just recently, Echternacht hosted a delegation from Bangladesh who were interested in learning more about aquaponics.
Echternacht and his partner have also branched out into consulting, offering feasibility studies for individual projects at a price of 15,000 euros in addition to planning complete facilities. Farms designed by the team are currently operating in Brussels and in Bad Ragaz, Switzerland.
Traditional farms will always cover the lion's share of the demand, Echternacht says, but he says his farms show that agriculture in city centers is also a viable option. Far from being a short-lived trend, he believes the model presents a real alternative. "It makes economic sense for any Germany city with a population of more than 500,000, so they will spread."
Another Berlin-based produce start-up is located just a few kilometers away -- one that is currently working on an international growth strategy. The founders of Indoor Urban Farming, known as Infarm for short, have only recently secured funding for their expansion. The venture capital firm Atomico invested tens of millions, accounting for a significant share of a financing round totaling $100 million. It would seem that even large investors from the tech industry have faith in the concept of urban produce cultivated indoors.
Infarm was founded by three Israelis who moved to Berlin six years ago from La Gomera in the Canary Islands, where they grew a broad array of vegetables for their own consumption. Once they moved to Berlin, they were put off by the quality of standard vegetables at the supermarkets. "The vegetables only had an echo of the flavor that we had grown used to from our own," says co-founder Osnat Michaeli. But they were faced with the problem of too little sun and no garden of their own. So, they began growing lettuce and cherry tomatoes in their apartment -- and the very first harvest was so good that they decided to professionalize the operation.
'We Sell Living Plants'
They developed mini greenhouses that look a bit like glass display cases. Inside, the herbs and lettuce grow on plastic trays, arranged on seven levels -- a principle known as vertical farming, the goal of which is to grow lots of produce in a tight space.
"We have a specific strategy for each seed," says head biologist Ido Golan as he stands in the corridor between dozens of growing cabinets at company headquarters. "The basil here is currently sleeping," he says, pointing to an incubator where the grow lamps have been switched off. The incubators are computer controlled in an effort to create the ideal growth conditions for each plant, which can mean simulating a Mediterranean climate for many of the herbs.
The plants' roots are in water into which nutrients are added by way of canisters in the floor of the cabinets. That means that each of the miniature greenhouses is completely autonomous from the others. Once the lettuce and herb plants reach maturity, they are only separated from their root balls at the supermarket. "We sell living plants, which makes a huge difference," says Golan. Standard produce, he says, loses valuable vitamins and antioxidants during transportation. "Normal growing practices are focused primarily on keeping produce fresh longer so they can withstand the transportation and storage phases. Nutrition and taste are last on the list of priorities."
There are already around 200 connected and remote-controllable Infarm cabinets in German supermarkets, with an additional 150 at wholesalers. The company hopes that the number will rise to over 1,000 by the end of the year and they are currently focusing on expansion throughout Europe. It's not the vertical farms themselves that Infarm is selling, though, but the produce inside. Supermarket operators and wholesalers then sell the produce onward at a markup. Infarm employees take care of the harvesting and restocking, referring to the business model as "farming as a service."
Yet the reliance on grow lamps raises questions about energy consumption -- concerns that Infarm head Michaeli immediately counters: "We rely on green energy and our CO2 footprint is less than 20 grams per plant. A traditionally produced head of iceberg lettuce is responsible for many times more than that.
At its production site in the Berlin district of Tempelhof, the company isn't just producing seedlings for supermarkets, but also for Germany's star chef Tim Raue, whose name is written on two of the vertical farming units. At the moment, they contain Peruvian basil, a special type of coriander and a kind of edible flower. Because he farms independently of climactic zones and seasons, Golan is also able to handle special requests. The biologist pulls a stalk of arugula from a harvest container that produces a wasabi-like aroma in your mouth. He also raves about a rare type of oregano found in the Middle East and coveted by Moroccan chefs.
Restaurants are important buyers for most of the new urban farming operations. They include the one belonging to Fabian Riedel, who has established a modern aquaculture facility in Langenpreising, located just northeast of Munich. The 36-year-old is actually a lawyer by training, but these days, his mobile phone contains the numbers of several high-end chefs, who are able to place orders directly via WhatsApp. As proof, he reads a recent message from a chef on Austria's Wörthersee lake: The previous day, the chef wrote, Jon Bon Jovi ate at his restaurant and praised his food. Now, the chef needed to lay in fresh supplies.
Raising Shrimp in Bavaria
The supplies grow in a large warehouse in an industrial zone in the town, not far from the Munich airport. Behind a hygienic gate that leads to rooms containing eight shallow pools, the climate is tropical, with high humidity and temperatures above 30 degrees Celsius (86 degrees Fahrenheit). That's how the pool residents, of the species litopenaeus vannamei, prefer it. The shrimp species is native to mangrove forests, but here in Bavaria, the grayish-blue animals seem to be doing just fine. The edges of the pools are lined with white curtains because the creatures can sometimes jump quite high out of the water.
Riedel buys the shrimp as larvae for around 15 euros per 1,000 and then spends three to four months feeding them a nutritious diet of peas, wheat and sustainably produced fish meal. They are then caught in fish traps, killed with electricity and packed by hand to be sold in select supermarkets and through the company's own online shop. About half of the shrimp go to restaurants.
Riedel says that although his operation "may not be romantic, it is a contemporary industrial farming enterprise." In contrast to production in Asia, he says, no mangroves are harmed, no water is polluted and no antibiotics are used -- and because transportation distances are short, there is no need to freeze the shrimp. They can even be eaten raw in the form of sashimi or tartare.
'Indoor Farming Will Play a Significant Role'
The launch of his exotic business concept of raising shrimp in Bavaria wasn't exactly easy. The state of Bavaria provided a significant financial grant, but Riedel's co-founder soon backed out for health reasons. Later, there was a several-month period with larvae supply difficulties. Riedel says he also initially underestimated the seasonal demand for fish. "Having only a single product is risky," he says. These days, his brand CrustaNova also sells caviar, lobster and salmon from other producers with similar quality standards. He says the company has become profitable and is investing in growth. His facility can be expanded modularly and he has secured the neighboring property.
For now, Riedel only sells around 30 tons of product each year, making him something of a niche producer, just like the urban farmers in Berlin. But it doesn't have to stay that way. In the United States and Asia, larger aquaponic facilities are in operation and one company is trying to establish a mass-production shrimp farm on land.
Infarm co-founder Michaeli says she believes the development is unavoidable. "Because of climate change and depleted soil, we need methods to produce more with fewer resources. Indoor farming will play a significant role."
Vertical Farming, The Future For Food Production
The cost price for vertical farmers (wherever they are in the world) needs to be reduced. All experts are in agreement about this. Enza Zaden would like to help with this
Vertical Farms would appear to be a Valhalla for plant cultivation. Growing crops under the perfect climate (always the same) conditions, throughout the year. Continuous production with constant quality. And then preferably in multiple layers on top of each other. Or perhaps are Vertical Farms, not the Holy Grail that they at first appear?
Setbacks
All new developments go through their teething problems. And the first Vertical Farming companies suffered quite a few setbacks resulting in some having to close again due to technical problems, high costs and disappointing sales results. And yet, the number of new Vertical Farms is growing steadily. At least 200 were established worldwide over the last two years; a trend that Enza Zaden's Senior Product Specialist Jan van Kuijk expects to continue over the next decade.
24/7 monitoring and adjustment
This is because things are developing rapidly: ‘Fluorescent lighting has been replaced by more efficient LED lighting and companies have - together with the lighting industry - developed various light recipes tailored to specific crops,’ summarised colleague and Lettuce & Endive Portfolio Manager, Anh Nguyen. ‘In the 3rd development phase, we will see customised light recipes and remote crop management. Using sensors, vision, smartphones and apps, the cultivation process can - in principle - be monitored and managed from anywhere in the world, 24/7.’ She is expecting the technology to become increasingly cheaper, with increasingly higher output, enabling Vertical Farms to reduce their cost price and compete with conventional growing.
Big in the East
The latter expectation will take somewhat longer in Europe than in the East, where countries such as Taiwan, Singapore, China and Korea are already very enthusiastic about vertical farming. ‘In Japan and Taiwan, consumers in large cities have an urgent need for fresh vegetables that are guaranteed to be clean and safe. Due to the high standard of living, they are willing and able to pay a lot for this,’ explained Jasper den Besten (Lecturer at HAS University of Applied Sciences in Den Bosch and Board Member of the globally active Association for Vertical Farming). ‘In addition, these countries are very focused on new technology. It is therefore not surprising that vertical farming has taken off in these countries in particular. Japanese cities already have about 200 plant factories and there are about 100 in Taiwan. Together, this is more than in the rest of the world.’ In North America, it is mainly investors and marketeers that find the concept interesting, and interest in Europe is somewhere in between, according to Den Besten. ‘For European countries, the cost price is too high for now, but the consistent quality that you can achieve in a Vertical Farm is still very interesting. Because supermarkets don’t like the fluctuating product quality that is associated with conventional production methods.’
Vertical Farming at Enza Zaden
The cost price for vertical farmers (wherever they are in the world) needs to be reduced. All experts are in agreement about this. Enza Zaden would like to help with this. ‘Seed companies have always selected their varieties under varying climatic and light conditions,’ explained Van Kuijk. ‘In a Vertical Farm, these conditions are in principle always constant. In order to know how varieties will perform under such conditions, they should also be tested under these conditions. So that’s what we’re doing. And we are already seeing that this results in different choices than in the selection programmes for conventional cultivation methods.’
Leafy greens behind the glass wall
Area Manager Japan & Korea, Young Han, encountered a new phenomenon in the metro stations of Seoul this year: lettuce factories behind glass walls, with machines that allow hungry commuters to take a locally grown, automatically harvested and freshly packaged head of lettuce from the wall. Every day, millions of commuters see there how the crops grow under LED lights and how they are automatically harvested and packaged. Maybe a great idea for the long walkways at Schiphol?
For more information
Publication date: 9/2/2019
AmHydro’s Joe Swartz On The “Shiny Object” Problem Plaguing Indoor Ag
All photos courtesy of American Hydroponics and Joe Swartz. Joe Swartz, Vice President of Contain vendor American Hydroponics (AmHydro), is a fourth-generation farmer from Western Massachusetts. When it came time for him to take over, he went looking for a way to do things differently
All photos courtesy of American Hydroponics and Joe Swartz.
Joe Swartz, Vice President of Contain vendor American Hydroponics (AmHydro), is a fourth-generation farmer from Western Massachusetts. When it came time for him to take over, he went looking for a way to do things differently. His family had faced numerous challenges with conventional outdoor agriculture, from the state’s short, 120-day growing season, to an uncle who died prematurely due to pesticide exposure.
Joe decided the solution was indoor agriculture, and since 1984, he’s grown just about everything you can imagine with every possible setup. We caught up with Joe to talk about why it’s important to educate the public about indoor ag, and how media hype can distract from the fundamentals of good farming.
What’s AmHydro’s approach, and what makes it unique?
Ironically, AmHydro started about the same time I started to grow, unbeknownst to each other. We have always focused on the philosophy of making growers successful by employing the correct technologies in the appropriate situation, not trying to sell this system or that system, but looking at a given situation and assembling the correct technologies to effectively grow.
In fact, I think AmHydro has more successful growers around the world than any other hydroponics company. We have growers in 66 countries around the world, soon to be 67, and we’re really very, very pleased with that.
What are some of the most common challenges about getting started in indoor agriculture?
There are lots of different technology companies trying to get your attention. The biggest challenge I see right now is a lot of inappropriate technology that’s being promoted, especially in the media and online, because people think certain things look really interesting or cool. We call it “shiny object” technology. These are not effective technologies.
A lot of vertical farming technology, where you’re essentially trying to cram as many plants into a give area as you can, from a horticultural standpoint, that isn’t correct. Plants have very specific needs in terms of environmental management and space management, and a lot of these systems ignore the basic horticultural concepts that are required for successful production.
You’re saying you think all vertical farms and plant factories don’t work?
Not all plant factories, but unfortunately that model is by far—and I mean by a factor of thousands—by far the most challenging segment of controlled environment agriculture in terms of making an economic return.
If you look at the industry, look at where the expansion is in hydroponics. Companies like Gotham Greens and BrightFarms are expanding rapidly because they have a cost-effective production model. Tomato operations such as Houweling’s and NatureFresh and Sunset are all expanding rapidly. Again, they’re utilizing effective technology.
What’s been the main benefit of working with Contain?
We were actually one of the first companies that Contain worked with. They believed in our model, and we believed in the model they had, which was helping provide financing solutions so that more people could enter this industry. We thought it was a great model — people who understood controlled environment agriculture and were offering financing models. Good people and proper technology is a good combination.
We’ve had a few projects where there would have been difficulty in locating financing, and they went through Contain and were able to do it, so it was an effective model. We hope to do more of that in the future.
What advice do you wish you got when you started growing?
I think I would’ve pushed myself to focus on the basics of correct horticulture. That means to learn as much about the lifecycle of the plant, the lifecycle of insect and disease pests, to understand the different living ecosystems that go on in a facility like that. At the end of the day this is still farming. With a lot of the technological advances, people forget that.
Why are some banks and investors reluctant to get into indoor ag, and how can we change that as an industry?
It’s a very capital-intensive business. It is expensive to set up and to get started. That’s always been one of the big pain points of getting into the industry.
And I do think that investment and interest in technologies that are not productive damages the industry. In the 1980s, Weyerhaeuser and Pepperidge Farms and General Electric and all these huge corporations began building large greenhouses here on the East Coast, and utilizing the pond system, and talking about lettuce factories, and these are all automated systems, and by 1990 all of our food is going to be grown in these indoor food factories. They all failed spectacularly, and millions and millions of dollars in investment were lost, and it damaged the credibility of the industry. It’s taken a long time for the industry to recover. Unfortunately, we’re heading down the same path today.
AmHydro does a lot of public education. Why is that important?
We feel very strongly that education is the key to everything. Basically you are looking at a very intensive form of growth that requires knowledge in terms of growing and business management to be successful. The more we educate our growers, the more successful they are.
What’s the most exciting trend in indoor agriculture?
The most exciting trend is the level of public awareness about the business, both from a consumer buying hydroponically grown produce, to people who want to get involved in the industry. This is the highest level ever.
When I was in agricultural college in the ‘80s, I was in a classroom of young people with 30, 35 students. I come back now to the University of Massachusetts and I lecture to 300 students, so the level of involvement has skyrocketed, and that’s tremendous, and I couldn’t be more excited.
This conversation transcript has been lightly edited for length and clarity. Learn more about Contain and funding your indoor ag business at our website.
Tags: Agriculture Indoor Agriculture Startup Finance Contain
WRITTEN BYNicola Kerslake
We’re Contain Inc. We use data to improve access to capital for indoor growers, those farming in warehouses, containers & greenhouses. https://www.contain.ag/
CO2 Enrichment, Acclimation, And Efficiency In Hydroponic Growing
Carbon dioxide (CO2) is an essential requirement for photosynthesis and can be somewhat overlooked by newer growers. Being odorless, invisible, and only a small fraction of our atmosphere, CO2 often doesn’t get the same attention as nutrients, lights, and other plant-growth factors
Lynette Morgan | August 23, 2019
Takeaway: While many commercial growers use carbon dioxide to boost crop quality, yield, and growth rates, Lynette Morgan explains how home hydroponic horticulturists can also take advantage of CO2 enrichment.
Carbon dioxide (CO2) is an essential requirement for photosynthesis and can be somewhat overlooked by newer growers. Being odorless, invisible, and only a small fraction of our atmosphere, CO2 often doesn’t get the same attention as nutrients, lights, and other plant-growth factors.
The use of CO2 enrichment to boost yields, quality, and growth rates under hydroponic production is, however, widely used in commercial greenhouse horticulture and has an even greater potential in enclosed growing spaces. While simply pumping in some additional CO2 may seem like a straightforward option, the use of this technology is a little more complex if its potential is to be maximized and problems minimized.
CO2 Enrichment
Ambient CO2 levels in air are a little more than 400 ppm (or 0.04 per cent by volume), however, plant tissue contains an average of 45 per cent carbon that comes entirely from CO2. By boosting CO2 levels surrounding the leaf surface, above ambient levels, the rate of photosynthesis increases up until the point where some other factor, such as the speed at which plant enzymes will work, is reached.
Email Newsletter
Join thousands of other growers who are already receiving our monthly newsletter.
Essentially, the transfer of CO2 from the surrounding air to the reaction centers in the leaf chloroplasts depends both on the concentration difference between the air and these sites, and the intervening biochemical resistance in various leaf tissues. This means that while CO2 enrichment will boost photosynthesis, there comes a point were further increases will not occur and plant damage becomes a possibility. Determining this optimal level of CO2 enrichment for a particular plant or stage of growth is where the application of CO2 needs some careful thought.
Carbon dioxide enrichment has become more popular in recent times with hydroponic growers using a range of low- and high-tech options to boost CO2 levels. The most common methods of generating CO2 include burning hydrocarbon fuels and the use of compressed, bottled CO2. Smaller growers with a very limited growing space may use dry ice (solid, very cold CO2) which releases CO2 as it “melts” under warm conditions.
Fermentation or the decomposition of organic matter (composting and fungi) are still effective but less accurate ways of boosting CO2 levels through natural processes. Whichever method is used to generate CO2, levels should be regularly monitored, either with a hand-held CO2 meter or as part of the environmental control system in the growing area.
Read also: The Benefits of Adding CO2 During the Cloning Stage
Enrichment levels
If CO2 enrichment is to be applied, then determining the correct level is as important with this gaseous element as it is with nutrient levels. The benefits and levels of CO2enrichment is crop dependent, but most plants respond well to levels in the range of 500–1,500ppm. Below 200ppm, CO2 begins to severely limit plant growth, but more than 2,000ppm of CO2 becomes toxic to many plants.
More than 4,000ppm is a risk to humans. An excess of CO2 will cause crop damage in the form of CO2 toxicity, which is often misdiagnosed as mineral deficiencies or disease symptoms. Mild CO2 toxicity can cause stunting of growth, or leaf-aging type symptoms, while excessive levels may cause leaf damage such as chlorosis (yellowing), necrosis (death of leaf tissue), curling and/or thickening of the leaves.
There is much debate over which level of enrichment is ideal for each crop, under various different growing conditions, however, the most economic use of CO2 is in enriching crops to above ambient levels, but not more than 1,200ppm. Most commercial growers enrich to within the range of 600-800ppm where an increase in growth and yields of between 20-30 per cent are common.
While CO2 enrichment is largely used on fruiting crops such as tomatoes, capsicum, and cucumber, it can benefit a wide range of plant species. Indoor gardens with ornamental, potted, and flowering plants also respond to CO2 enrichment with increased rates of growth and leaf area, increased rates of flowering, more lateral breaks, earlier flowering, greater flower number, reduced flower drop, and increased flower diameter as well as improved leaf color and reduced time to maturity. Carbon dioxide also assists with root development on cuttings and clones in many species and may be applied via enrichment of the air or through the use of carbonated mist.
CO2 Efficiency
To make the most of CO2 enrichment, other growth factors need to be considered and manipulated. Carbon dioxide enrichment will produce the best results in terms of plant growth, yield increases, and shortening the time to maturity where there is high light to power rapid levels of photosynthesis.
If light is insufficient or below the light saturation point for the crop, then boosted CO2levels cannot be fully utilized by the plants. Temperature also plays a role in the efficient use of CO2. Under conditions of high light and CO2 enrichment, temperatures can be run higher than they would normally, and this maximizes the effect of additional CO2.
Studies have shown that for tomato plants, a threefold level of CO2 enrichment will increase net photosynthesis by about 50 per cent in both dull and bright light, but if leaf temperature is also raised (to 86°F), the increase in net CO2 fixation can be as high as 100 per cent in bright light. This means that while boosting CO2 in an indoor hydroponic system will boost growth rates, consideration should be given at the same time to manipulation of the other environmental factors of light and temperature if the valuable CO2 is to be used with the highest degree of efficiency.
Another often overlooked factor is CO2 distribution around the plants. Simply releasing or generating CO2 for enrichment into the growing area is often not sufficient to get the maximum rate of photosynthesis unless this is directed and circulated over leaf surfaces. A stale boundary layer of moist air, depleted in CO2 due to photosynthesis, can form directly around the leaf surface and this needs frequent removal and replenishment.
Whatever source of CO2 generation is being used, it is vital that the enriched atmosphere is thoroughly mixed so the valuable CO2 is delivered to plant surfaces for uptake and assimilation. Small mixer fans can be used to gently circulate the air away from the source of CO2 generation and toward the crop.
To monitor this process, hand-held CO2 meters are useful to check levels in and around the canopy rather than just at the point of CO2 release. Keeping a check on CO2 levels inside a small growing area is vitally important, no matter what the source of CO2 used. It can be difficult to judge how much CO2 the plants are taking up and in tightly sealed growing environments, CO2 accumulation can occur and cause plant damage.
Read also: The Symbiotic Relationship Between CO2 and Ventilation
CO2 Acclimation
CO2 enrichment is undoubtedly a great growth-promoting tool for hydroponic growers, however, it has its limitations and risks.
Plants have the ability to adjust and adapt to increasing CO2 levels, so that over time, acclimation occurs. When CO2 enrichment is first introduced to a crop, there is a rapid increase in photosynthesis and growth, but as plant growth continues, the effect of the increased CO2 levels becomes less and less so that by the time the crop is completed, overall yields were not as high as the increase in early yield.
Numerous studies have reported this effect with plants grown continuously at high CO2 levels having a photosynthetic rate that tends to decrease with time. If a crop grown at elevated CO2 levels is suddenly given only ambient CO2, it will recover back to normal rates of photosynthesis within five days.
Some growers have attempted to prevent this acclimation of crops to high CO2 levels by only supplying CO2 intermittently, or avoiding the use of CO2 enrichment until a vital stage of development, such as flowering or fruit set, has been reached when the boost in photoassimilate is most valuable to yields. Studies have shown the problem of CO2 acclimation can be reduced or eliminated if the plant has strong “sinks” for the assimilate produced in the leaves.
These sinks for assimilate include rapidly developing tissues such as buds, flowers, and fruits. Plants with a low sink strength often end up with carbohydrate accumulating in the leaves under CO2 enrichment, which in turn triggers acclimation and a reduction in photosynthesis. Despite the issue of plant acclimation to high CO2levels limiting the overall potential boost to growth, CO2-enriched plants still produce photosynthetic rates higher than those grown at ambient CO2 levels.
Carbon dioxide enrichment is a worthwhile tool for indoor and greenhouse growers which is well proven in a wide range of crop species to increase growth rates and yields. However, as with most high-tech techniques, it requires monitoring, attention to detail, and careful consideration of the effect on biochemical processes. If CO2 is to be used at maximum efficiency, correct rates of application, adjustments to light and temperature, timing of enrichment, and consequences of CO2 acclimation all need consideration.
Written by Lynette Morgan
Dr. Lynette Morgan holds a B. Hort. Tech. degree and a PhD in hydroponic greenhouse production from Massey University, New Zealand. Lynette is a partner with Suntec International Hydroponic Consultants and has authored several hydroponic technical books. Visit suntec.co.nz for more information. Full Bio
VIDEO: Indoor Vertical Farming Praised As Future Source of Produce
With drought gripping much of the country, there are calls for the government to support new and emerging methods of agriculture
July 9, 2019
With drought gripping much of the country, there are calls for the government to support new and emerging methods of agriculture. Indoor vertical farming is being touted as a future source of fresh produce, but fledgling companies in Australia are struggling to move beyond the startup phase.
COLORADO: Precision Farming With The Help of Technology - By The Numbers
Steve and Soozie Arnold used to run cattle on 30,000 acres in the San Juans. Now, they grow butter lettuce and other delicious greens on three acres just north of Spring Creek Road near Montrose
By Michael Cox Special to the Montrose Daily Press
August 22, 2019
Soozie and Steve Arnold pose with part of their hydroponic Garden at the Eatin’ Greens farm. The system they use is considered precision farming. (Michael Cox/ Special to the Montrose Daily Press)
Steve and Soozie Arnold used to run cattle on 30,000 acres in the San Juans. Now, they grow butter lettuce and other delicious greens on three acres just north of Spring Creek Road near Montrose.
They do it hydroponically. Steve can irrigate his crops from his smart phone. Soozie sells greens and things at the farmers' markets, Gold's Gym, several restaurants, and to other customers, taking plastic payment and processing it with The Square on her phone. She counts the beans on QuickBooks. Steve reads the Wall Street Journal online, which is where he found out about the growing system they use.
Without the internet, broadband or otherwise, life would not be the same for small and large ag operations alike. The Arnolds are part of the precision farming movement. It’s farming and ranching with much less guess work and fewer surprises. Growers with a few acres, like the Arnolds, and cattle outfits, like the one Steve used to run, are getting more yield, using less water and taking fewer chances because they have the internet and tools like phoning in your irrigation.
Soozie Arnold helps a Farmers Market customer “pick” her own greens from their hydroponic “farm field.”
(Michael Cox/ Special to the montrose Daily Press)
No more root cellars
When the refrigerator replaced the root cellar and the icebox back in the 1930s, everything from the way farmers finished crops to the way consumers bought them changed for the better. That came about when the Rural Electrification Act set the stage for energy being delivered to rural farms and ranches.
“A similar shift is upon us with the advent of digital technology and next generation precision agriculture, resulting in increasing productivity with fewer inputs, better market access and healthier rural communities,” said Megan Nelson of the American Farm Bureau Federation.
Nelson is all about pushing the idea of broadband for everybody. But what is broadband?
The dictionary definition is, “A high-capacity transmission technique using a wide range of frequencies, which enables a large number of messages to be communicated simultaneously.” In terms more of us can understand, it's like having a digital party line where everyone can talk at once and still get the message straight. In the unseen operations, the data — words, pictures, numbers, etc. — move at light speed in computer-assigned packets. The problem is the network that does this magic is not in place everywhere.
“Just recently the Federal Communications Commission admitted that the maps they have are wrong,” Nelson said, “We really donít know who has broadband available and who doesn’t.”
The FCC has promised to get the maps up-to-date as quickly as possible. In bureau speak that could be next year or the third June of 2021.
Australia: This Car Park Turned Urban Farm Has Grown 300 kg of Produce For People In Need
Forget the assumption that cities have a lack of space available to grow fresh produce. This experimental urban farm proves that it's possible to grow masses of vegetables in a space as small as a car park
Produce grown in the urban farm in Port Melbourne. (William Hamilton-Coates)
28 August 2019
Forget the assumption that cities have a lack of space available to grow fresh produce. This experimental urban farm proves that it's possible to grow masses of vegetables in a space as small as a car park.
By Yasmin Noone
An urban farm project in Melbourne, powered by coffee compost and food waste that would otherwise go to the landfill, has successfully reached its target and grown around 300 kilograms of vegetables and herbs for people in need.
The farm, spread across two empty car spaces in Port Melbourne industrial parking lot, was originally intended to be a 12-month experimental project run by Cirrus Fine Coffee, Biofilta and Australian Ecosystems.
But having already generated 360 kilograms of produce in under eight months and donated more than 90 per cent of food grown to OzHarvest, the farm will now remain functioning on-site indefinitely.
"So an urban farm like this aims to tackle the existence of food deserts in cities like Melbourne, and improve the nutrition of people in need.”
“In our cities, we have food deserts – areas where there are high concentrations of fast food outlets,” says Brendan Condon, director of the three sustainability companies involved in the collaboration.
“But many people can’t get access to nutrient-dense, high-quality food. So an urban farm like this aims to tackle the existence of food deserts in cities like Melbourne, and improve the nutrition of people in need.”
OzHarvest collects the produce grown at the urban farm in Port Melbourne. (Image: William Hamilton-Coates)
The small farm will now be used as a test case for a much bigger scale rooftop farm, Melbourne Skyfarm, to be built on a larger parking lot in the heart of the city in 2020.
“We tend to think that cities are congested places with no space, but in Melbourne, we have huge amounts of spare, under-utilised space to be growing food,” explains Condon.
“On top of that, we have huge streams of organic waste streams that come out of our cities, as well as massive amounts of water running off our rooftops. We could be using the water and organic waste and putting it back into urban farming.
“This small project proves that cities can be really food abundant and we can grow huge amounts of food in small spaces.”
How coffee compost and food waste is charging this urban farm
The farm's recipe for success is multifactorial. Firstly, it uses water-efficient wicking beds. But the real secret seems to lie in the soil, featuring composted coffee grounds and coffee chaff from the company’s roaster, as well as composted organic waste from South Melbourne Market.
Composted coffee grounds contain a large amount of minerals such as potassium, magnesium and phosphorus, calcium and iron, making them a good additive into compost. They are also a valuable source of nitrogen.
The organic waste from the markets includes fish residues. “That’s fish guts, heads, bones and innards,” he says. “Fish residues turbocharges your garden, as it’s high in nitrogen.”
Off-cuts from produce stalls at South Melbourne Market also make it into the farm’s compost heap.
“Fish residues turbocharges your garden, as it’s high in nitrogen.”
South Melbourne Market stall-holder, Alan Li from Fruits on Coventry, tells SBS he contributes masses fruit and vegetable waste to the farm.
“We sell around 45-50 tonnes of fresh food a week,” says Li. “So we fill around three green bins a day of green waste, plus two extra bins of green waste from the oranges we juice for our customers. In total, that’s about 5 big bins of green waste a day. That’s a lot of green waste that we produce, which doesn’t end up in landfill.”
Li explains leaves, off-cuts and leftover produce from the stall goes into green waste bins, before being hot composted and then donated to the urban farm for fertiliser.
“We are using our green waste to create a benefit for the community as most of the food grown at the urban farm goes towards feeding the homeless and people in need. I’m really happy with the outcome.”
Volunteers work on the urban farm, spread across two car spaces in the Cirrus Fine Coffee parking lot in Melbourne. (Image: William Hamilton-Coates)
Since the project started in January this year, the double car-park garden has grown heritage varieties of tomatoes, corn, zucchini, pumpkin, spring onion, beetroot, rainbow chard, spinach, silverbeet, flowers to attract beneficial insects and also a range of herbs like chives, basil, oregano and coriander.
Although winter has been slow, Condon believes that spring will reap a plentiful harvest.
“We can’t grow all of the diverse food plants that comprise the entire modern diet,” says Condon.
“But by volume, weight and value, we can punch a big hole in city food demands within city limits by using readily available organics that we currently treat as waste.”
Hydroponics: Pros And Cons of Hydroponic Gardening
Hydroponic farming is one of the most misrepresented farming methods around the world. I mean, it sounds like an alien if not a futuristic concept growing food without a single grain of soil
Guest post by Dan Chabert
Ben Eagle
Hydroponic farming is one of the most misrepresented farming methods around the world. I mean, it sounds like an alien if not a futuristic concept growing food without a single grain of soil.
One of the major reasons hydroponics has been gaining a foothold is because studies have shown that this farming type may soon overtake conventional field farming. For example, it has recently emerged that hydroponically grown plants are of high quality, require less space and are not as resource-intense as their field counterparts. Goes without saying that urban and indoor gardening has witnessed new horizons with no sight of the ending.
What is hydroponics?
Hydroponics is a soilless farming method where planting takes place in a controlled aquatic-based environment. To many, the concept of soilless plant growing may seem like a smack to the plant’s nutritional needs. However, they actually do exceptionally well as they are sufficiently supplied with water and nutrients, which are essential for any plants to thrive.
To provide these nutrients, a nutrient solution is fed to the plants through the roots resulting in normal and healthy plants. With that said, there are multiple hydroponics systems and others don’t necessarily require substrates.
How does it work?
There are different hydroponics systems although the basics are the same. The systems allow the roots of the plants to directly come into contact with nutrients and oxygen without factoring in the soil. As a replacement for the soil, the system uses clay pebbles, stonewool, coco coir, or vermiculite to support the roots.
For the nutrients, there is a water-based solution that’s rich in nutrients delivered directly to the plants through the roots. As a solution to the light which is essential for growth, some hydroponic systems utilize natural lighting while others solely rely on artificial lighting.
Most often people tend to mostly focus on the bias which essentially overshadows the positive characteristics. However, just like any other culture system out there, it has its good side and its ugly side.
Initially, it can prove extremely difficult to kick-start and maintain hydroponic gardens but once you have honed the skills the pros outweighs the cons.
What are the pros and cons of hydroponic gardening?
Pros
One of the most outstanding benefits of hydroponic gardening is the fact that it happens indoors. As such, planting can be done irrespective of the season and production can take place all year round. Additionally, the plants yield double compared to the soil-based farming thanks to the constant growth cycle.
With increasing concern of the food security around the world, public and private sectors are looking for farming methods that can outperform traditional farming methods. Although water and water-based solutions play an important role in producing better yields, hydroponics systems use less water as its possible to re-use and recycle.
In addition to using less water, the system doesn’t produce run-off which can destroy and degrade the environment. Even better, hydroponic farms don’t require deep wallets for upkeep and maintenance compared to traditional farms. For example, since it’s done in controlled environments susceptibility to soil-borne diseases and pests is limited.
Thanks to the compact spaces, hydroponics gardening is ridiculously cheap in terms of labor as a few individuals can harvest and replant in a snap.
Cons of hydroponic gardening
Although hydroponics farming comes with a bit of disadvantages, the advantages far outweigh the bad side. One of the major letdowns of hydroponic farming is the high initial set-up costs.While most small-scale farmers can buy or build relatively cheap equipment, large-scale farms require specialized equipment that comes with a steep price tag that can run into millions.
The second letdown although not a deal breaker is that the farms require constant monitoring and supervision. These large farms are like toddlers who need pampering in terms of constantly keeping track of the lighting, nutrient solution, and oxygen levels. We have to agree in unison that such a modern farm is prone to unusual factors that aren’t common in traditional farms. For example, a power outage in a single day could lead to untellable losses.
The take home
As it appears, hydroponics has clear advantages and some disadvantages. However, I think that the benefits outweigh the demerits since it is a great alternative for food production in areas with poor soil. It’s also a hallmark of other great characteristics like efficiency, it is less costly, and more economical in space.
About Dan:
Dan Chabert – Dan is an entrepreneur, husband and ultramarathon distance runner. He spends most of his time co-managing home sites like Contractor culture, That Sweet Gift, Borncute, health sites such as Runnerclick, Nicer Shoes and The Gear Hunt. He has also been featured on runner blogs all over the world.
Central Illinois Fresh Hydroponic Greens Bring New Life To Geier Florist Shop
Something is flourishing inside the old Geier Florist building. Sam Hendricks and Brandon Neuzil are partners in a new business growing microgreens in an urban agriculture environment. Their business is called Central Illinois Fresh
By Brady Johnson / of the Journal Star
August 18, 2019
WEST PEORIA — Something is flourishing inside the old Geier Florist building.
Sam Hendricks and Brandon Neuzil are partners in a new business growing microgreens in an urban agriculture environment. Their business is called Central Illinois Fresh.
The 28-year-old Neuzil had been looking for space last year to try out his idea and had been in contact with Geier Florist. When that longtime West Peoria business at 2002 W. Heading Ave., shut down earlier this year, Neuzil bought out the first floor of the building.
In February, he and Hendricks got into contact and their business began to come to fruition in April. The duo have been selling microgreens and leafy greens since the beginning of June, including at the Riverfront Farmers Market in Peoria each Saturday — selling out their stock there during many weeks.
“We wanted to get involved in the food movement in Peoria,” Neuzil said.
It’s a business he’s completely new to, with no experience running a greenhouse or using commercial hydroponics, though Hendricks has farmers’ market experience.
“Hydroponics we do for all of our lettuce,” Neuzil said. “NFT system, which means Nutrient Film Technique, is our process. We get our equipment from a manufacturer in Ohio. We purchase from them and then set it up to fit our greenhouse layout.”
The system works as produce is placed into pipes where their roots interact with a small line of nutrient-mineral water. The process doesn’t need potting soil because all of the nutrients needed are mixed into the water system. Neuzil and Hendricks just have to replenish the tank of mineral water every week.
“Hydroponics is still relatively new to agricultural,” Neuzil said. “Currently we are producing 870 heads of lettuce. We have 870 holes to work with.”
The method allows for consistent production throughout the year.
“I think a way that will separate ourselves from other farmers is that come winter time urban agricultural will be able to produce year round,” Hendricks said. “There are a lot of limitations with the seasons and weather. We are trying to produce strong quality products year round.”
Microgreens do not require a lot of time to produce, with an average growth rate of two weeks compared to produce that can take 45 to 90 days, Neuzil said.
The result comes in trays filled with cabbage, radishes and red Russian kale.
“Microgreens can be produced in almost any building as long as it is climate controlled and you have good water. You can do it in your garage or below ground,” Neuzil said. “There is a hydroponics company that produces lettuce hundreds of feet underground in a mine shaft. As long as you have water and power and some air flow you can make your own microgreens.”
The produce has even started to appear on local restaurant plates.
They’re growing a great product,” says Dustin Allen, who operates Edge in Peoria Heights. His usual order is 10 to 12 pounds of leafy greens and several pounds of microgreens.
He and Hugh Higgins at Hearth up the street in the Heights are two restaurant owners using Central Illinois Fresh’s produce.
“For us and our business model, we have no national suppliers at all in our restaurant,” Allen said. “It takes us over 60 family farms to run this restaurant on a yearly basis. To me, they are just another part of that, part of our system.”
The prospect of a year-round supply has made Allen a very happy restaurant owner.
“What we are excited about is that they have the ability to provide yearly to us.,” Allen said. “That opens up a segment to our menu that in years past has been very small.”
Neuzil, meanwhile, hopes to educate youth in the area about sustainable farming like microgreens. He sees the idea of urban agriculture as an important one to the next generation.
“You don’t have to use much,” Neuzil said. “You just sprinkle some on your salads and flatbreads and you can also eat it plain on crackers. We have people who come to us and tell us about their microgreen experiments in cooking. We are wanting to get feedback from everyone.”
For now, both men run the business on the side, with Neuzil working for Cazenovia Salt and Hendricks at Kaufman Wellness Center. But they’d like to add in a storefront to allow for more business, and they’re laying plans for an open house and concert at their venue sometime next month.
Scientists Grow Tastier Vegetables Just By Changing Light Falling On Them, No Gene-Edit Needed
In order for farmers to make a decent profit on their crops, they need to have a reliable produce. Of course, they only have limited land to work with, so limited number of plants need to have enough weightage of output. Unfortunately, that can result in tasteless produce
Gwyn D'Mello April 16, 2019
In order for farmers to make a decent profit on their crops, they need to have a reliable produce.
Of course, they only have limited land to work with, so limited number of plants need to have enough weightage of output. Unfortunately, that can result in tasteless produce.
Think of a simple vegetable (fruit?) like tomato. You might see two different varieties of it in your local market, where one is much larger but the smaller ones are tastier. That's due to something scientists called the "dilution effect", where there's an overlap between the compounds a plant requires to produce more or produce tastier fruit.
That's why you're more likely to see this happen with a large scale farm as opposed to when you grow tomatoes in your garden. But apparently, it doesn't have to be that way, at least according to researchers at MIT.
Scientists at the University's OpenAG group have been researching basil plants in particular, led by principal researcher Caleb Harper. They've been trying to change the various stress factors acting on basil plants to see how it changes the flavour. "If you took the same basil seed and you put in 50 different countries, you would have started with the same genetics but you would get 50 different flavors," he told Digital Trends.
The process behind tastier vegetables
What these researchers, in partnership with the University of Texas, found is that exposing basil to light 24 hours a day made them the most flavourful. The constant light produced more secondary metabolites. These are organic compounds the plants don't necessarily need to survive, but can help them keep away animals that eat them. And the presence of these are affected by everything from drought to the presence of certain insects, ultimately changing how the plants taste.
The researchers had no reason to believe 24-hour light exposure would make the basil tastier, they instead went with 18 hours to begin with. It was a custom-developed AI algorithm, developed by MIT and Cognizant, that analysed all the factors and made the suggestion. In fact, that same AI was originally used by the startup that developed it (before being acquired by Cognizant) for hedge fund trading.
The basil was grown in hydroponic boxes, full of sensors and circuits, allowing the scientists to completely control everything from temperature, to humidity, to the light intensity and exposure.
But ultimately this experiment wasn't just about making industrial agriculture plants tastier. Using the AI, researchers can possibly even have the plants develop in other ways. For instance, Harper talks about his dream for "diabetes basil", grown in such a way that it's rich in proteins found to be helpful in treating the illness.
"That's kind of amazing that we could design flavor from climate," he said. "And now we're going to see can we design nutrition."
IMAGES COURTESY: MIT
Join FarmBoxFood, Iot.Atl, Ponix, & New City Properties On The Eve of Smart City Expo Atlanta
FarmBoxFoods and Ponix Farms is developing end-to-end local food ecosystems focused on reclassifying food as a utility, much like water or electricity
Join FarmBoxFoods, IoT.ATL, Ponix, & New City Properties to help revolutionize the future of food with Vertical Hydroponic Farms in shipping containers| Tuesday, September 10th | 4 -7 pm | 725 Ponce De Leon, Atlanta, Georgia
FarmBoxFoods is proud to take the next step in building resilient communities by connecting people, companies and technology to forge a stronger path for the future.
On September 10th, partners from IoT.ATL, leaders in smart city technology, and community mavericks will converge at 725 Ponce in Atlanta to celebrate the innovation of FarmBoxFoods, Ponix Farms and the opening of the first IoT.ATL Living Lab!
FarmBoxFoods, a new and revolutionary manufacturer of Vertical Hydroponic Farms in shipping containers with Ponix Farms, a winner of the IoT.ATL AgTech Challenge, is identifying scalable AgTech solutions to address the need for resilient food systems and illuminate how technology can be used to solve the pressing social issues of our time. Through this lens, they will change the future of food and urban agriculture to benefit communities across the globe as the world urbanizes.
FarmBoxFoods and Ponix Farms is developing end-to-end local food ecosystems focused on reclassifying food as a utility, much like water or electricity.
Join us in celebrating this monumental product launch on the eve of Smart City Expo Atlanta at 725 Ponce, just steps off the Atlanta Beltline - across from Ponce City Market.
Thank you to our core partners; New City Properties, Georgia Power, Invest Atlanta, AGCO, Metro Atlanta Chamber, City of Atlanta, and the Atlanta Beltline for their tremendous support and sponsorship.
About IoT. ATL
The IoT.ATL Living Labs program is focused on testing and validating IoT and technology solutions to help ensure equity and inclusion in the wave of strong economic growth.
The future success of smart communities lies in the collaborative projects the region creates and the public-private partnerships like IoT.ATL that drive innovation forward.
The IoT.ATL Living Labs project was founded by Georgia Power, City of Atlanta, Invest Atlanta, the Atlanta BeltLine, the Metro Atlanta Chamber and AGCO to help address pressing challenges in the community and leverage technology for good. For more information, visit iot-atlanta.com.
VIDEO: Plants Ready To Go In At New Russian Indoor Farm
iFarm is a Russian vertical farming company that both operates farms and supplies the techniques to do so, as well as conducting a lot of research to get the best out of leafy greens, vegetables, berries and flowers
Plants can go in any day now at the newly installed vertical farm by the Russian company iFarm. The project, which is located in the city of Novosibirsk, is eight layers high and is the first project of this size conducted by the iFarm team.
“Our technologies for vertical farming have passed another test", co-founder Konstantin Ulyanov shares proudly. "Earlier we projected and built small farms which we tested the automation on, sampled the taste quality and contents of the lettuce and herbs. We learned to scale the technology (three times for this particular project), and increased the amount of varieties that could be grown in our farm."
iFarm is a Russian vertical farming company that both operates farms and supplies the techniques to do so, as well as conducting a lot of research to get the best out of leafy greens, vegetables, berries and flowers. Earlier this year they opened a laboratory for edible flowers. Currently they are also realizing projects near Moscow. Construction of three farms will start this month. "The next step is to launch such farms via distributors, like we already do abroad", Konstantin adds. For example, an iFarm showroom is being realized in Helsinki.
Some serious numbers
The new farm is located in the building of a former car dealer. To get this one ready for indoor growing, 20 tons of construction materials have been brought to the site, of which 90 stacks with 8 layers each have been installed. In it also 3 kilometers of wiring, 20 square meters of partitions and 1000 meters of pipeline. It took 10 people working in two shifts to assemble the racks in 30 days - working without a day off. They drilled 3333 holes and connected 60,0000 parts to assemble the 90 racks.
The first seeds will be planted at the end of August. Six types of leafy greens will be grown on 749 shelves: romaine lettuce, kale, chards, leaf lettuce, basil and bok choy. The overall growing area will comprise 1000 square meters, and planned production capacity is 42 thousand pots a month.
Pesto
The new production site will be equipped with a processing center to create pesto from the rucola and basil, as well as healthy chips, oils and fresh juices. Another part of the farm will be turned into a showroom: the visitors will be able to see the greenery growing process through glass partitions.
The vertical farm has been constructed with the help of attracted private investments. The projected payback period for a vertical farm of this size should be reached within 5 years. The farm will be producing 25 to 30 tons of greenery a year, the production margin being 27%. The first crops should be collected in October 2019.
Company Vega-Absolut acts as a strategic and technological partner of iFarm. The first vertical iFarm with a showroom of 300 square meters growing area is currently operational at the Novosibirsk science campus.
UK ‘Closing In’ On Large-Scale Vertical Lettuce Production
As investment increases and the cost of production comes down, vertical farming has the potential to replace imports in leafy salads
29th August 2019 London
BY FRED SEARLE
Vertical farm director says indoor production of salad heads in Britain has potential to replace imports from Spain as sector gathers steam
As investment increases and the cost of production comes down, vertical farming has the potential to replace imports in leafy salads.
This is the view of Vernon Mascarenhas, a director at the London-based vertical farming company GrowUp Farms, which has specialised in growing microgreens, salads and herbs for the restaurant sector and is now focused on applying its know-how to industrial-scale salad production.
Several companies in the UK and abroad are making good progress on the challenges of making vertical farming work at scale, said Mascarenhas, who believes we are no more than a few years away from produce grown in industrial-scale vertical farms becoming an established part of the UK supply chain.
Also a commercial director at New Covent Garden catering supplier Nature’s Choice, he stressed that if UK growers can start growing salad heads year-round in Britain, the implications of not having to import large volumes from Spain in the winter will be huge.
“If companies like G’s don’t invest multi millions, they will have a real problem,” he said. “As soon as we get up and running and can produce gem and cos in the UK in the winter, it’s going to replace supply from Murcia, and this will increase suppliers’ margins.
“The price of a two-pack of gem in a supermarket is around 75p, and to bring it over from Murcia costs around 28p. Instead of wasting this 28p per pack on long-distance haulage, we can use it to pay off the capital investment required to build vertical farms where we will soon be able to produce gems for around 12p.”
Mascarenhas also said UK supermarkets are on the verge of having vertical farms in store, on their rooftops or in their car parks that not only showcase food production, but also provide significant supply – in wholehead salads as well as herbs.
In Britain he thinks Ocado, Amazon or possibly Asda could be the first to invest in vertical production, predicting that Asda’s owner Walmart could soon be taken over by Amazon – “Amazon will invest whatever they need to in this kind of thing,” he said.
Indeed it has already been announced that Berlin-based start-up Infarm is set to launch its in-store vertical farms withsome of the UK’s largest online and brick-and-mortar supermarkets in September, adding to its network of over 200 in-store farms across Germany, Switzerland and France.
Although many are sceptical about the financial viability of growing vertically, Mascarenhas is confident the cost of production will come down quickly in the next few years as technology advances, operational knowhow improves, and large investments are made in the sector. For example, in June Ocado invested £17 million in two vertical farming businesses, with plans to grow herbs and leafy greens next to its distribution centres.
Up until now, only micro greens and herbs have proven financially viable for vertical production in the UK, but such developments will allow mainstream salad produce to be grown domestically for the retail sector – both in store and, more importantly, in big warehouses – starting with baby leaf and moving into gem and cos lettuce, lollo rossa, oakleaf and other salad leaves.
“These vertical farms will be completely automated," he said. "The salad seeds will be sown, grown, watered, harvested and packaged without a human hand and the products will be grown in controlled conditions, with no pests or chemicals.
“We have all that technology already and established horticultural companies are heavily involved in making this happen.”
Produced vertically, a gem lettuce will only take 28 days to grow from sowing to harvesting, according to Mascarenhas, and once this has been achieved, producers can move on to rocket and spinach, which he says will be possible to produce in just 18 days.
He added that as well as allowing for more consistent year-round production, vertical farming can deliver higher quality and safer products than are currently available since they are grown in a controlled environment.
“Leafy products are just the tip of the iceberg,” he said. “Trials are currently happening around Europe on fruiting crops such as strawberries, raspberries, tomatoes and cucumbers, although these are still very early stage and it will be a while before the know-how and technology gets to a place where it makes commercial sense to grow them in a vertical farm.
“Basically, anything that grows as a root crop doesn’t work, but anything that grow upwards might. There’s a possibility that products like courgettes, beans and peas could be grown vertically but we have no idea yet what the economics of that would look like.”
US: Utah - World’s First Commercial, Indoor Strawberry Farm Coming To Murray
It could be the world’s first private, commercial, vertical, indoor strawberry farm, and the Murray City Council approved it during their June 18 meeting. In a first for an urban Utah city, the City Council amended the Murray City Municipal Code to allow for indoor, vertical farming
August 29, 2019 ● By Shaun Delliskave
By Shaun Delliskave s.delliskave@mycityjournals.com
It could be the world’s first private, commercial, vertical, indoor strawberry farm, and the Murray City Council approved it during their June 18 meeting. In a first for an urban Utah city, the City Council amended the Murray City Municipal Code to allow for indoor, vertical farming.
This clears the way for Chihan Kim, a businessman whose holdings include a Sandy coffee shop, to develop what would be Utah’s first large-scale commercial, indoor, hydroponic farm in a vacant warehouse building located at 158 E. 4500 South.
“(I) will collect all the material to build the facility and…grow vegetables and some fruits, like strawberries, that will benefit from the omittance of herbicides,” Kim told the Murray City Planning Commission on May 2.
Vertical farming has become a buzzword in agriculture. The process includes producing food in vertically stacked layers, such as in a skyscraper, unused warehouse, or stacked shipping containers, with controlled-environment agriculture technology, where all environmental factors can be controlled. Such facilities utilize artificial light control, environmental control (humidity, temperature and gases) and fertigation. Some vertical farms use techniques similar to greenhouses, where natural sunlight can be augmented with artificial lighting and metal reflectors.
One of the most successful vertical farming operations is in Jackson, Wyoming. There, Vertical Harvest produces 100,000 pounds of vegetables a year on a plot 30 feet high by 150 feet long. Their 1/10th-of-an-acre site grows an annual amount of produce equivalent to 10 acres of traditional farmland. However, other ventures have failed.
Vertical farms are expensive to set up and take a long time to expand. Technology is changing at such a rapid pace that a newly opened competitor in the field could offer produce at a lower rate than an established producer. Still, indoor farming is appealing as a sustainable solution to growing food with little need for pesticides, water and land.
Before the code change, “Indoor Farming” was not listed as an allowable use in any zone in Murray City. For Kim to move forward with his zoning request, he needed to go through the extreme measure of having Murray change its code to allow for such a business.
This won’t be the first vertical, indoor farm in Utah, as an 11,000-square-foot facility sits on farmland in Charleston. Strong Vertical Garden supplies produce from that building to Smith’s grocery stores and microgreens to several chefs and restaurants in Utah.
The building that Kim intends to transform into an indoor farm is the former Electrical Wholesale Supply building. That building will allow Kim’s company, City Farm, to have 40,609 square feet for operations. LED lighting will be the primary source of light for the plants.
Murray City planning staff noted in their recommendation to the City Council that the indoor farm, “…will create the best opportunities to adaptively re-use and potentially revitalize older buildings and vacant spaces… (and) have the potential to place year-round access to fresh food closest to populations with limited transportation options, creating a positive impact on public health.”
“The main crops that we are considering at this moment are strawberries,” Kim said. Strawberries, he said, are one of the most contaminated fruits because of outdoor pesticides. This process will save them from harmful chemicals that get trapped in their seeds and pores and don’t all wash out with water.
“The farm operations will be maximum automation. Pollination—I am going to use drones. Drones will produce wind that will promote pollination. The farm will be open to the public with large windows. Strawberries will be supplied to grocery stores, but we will also make strawberry smoothies and food like that,” Kim said.
Councilwoman Diane Turner stated, “I think it is a great idea. I am really pleased you are doing this in Murray.”
Lead photo: An example of vertical farming shows stacks of crops growing in an indoor building. (Photo courtesy Murray City)
Hydroponic Farming Having A Huge Impact On Agri Sector
Hydroponics farming has created a huge impact on Qatar’s agriculture sector as local fresh produce is becoming sustainable all-year round, prominent Qatari agriculturist and Agrico managing director Nasser Ahmed al-Khalaf has said
August 19, 2019
Nasser Ahmed al-Khalaf
Hydroponics farming has created a huge impact on Qatar’s agriculture sector as local fresh produce is becoming sustainable all-year round, prominent Qatari agriculturist and Agrico managing director Nasser Ahmed al-Khalaf has said.
“We continue to grow and develop more farms (in Qatar) even during the summer. We never stop and have been producing every day since 2015,” he told Gulf Times.
Agrico, a private Qatari agricultural development company established in 2011, aims at helping the country achieve self-sufficiency.
The company developed a highly sophisticated hydroponics system capable of producing various types of organic and pesticide-free vegetables and fruits such as tomatoes, cucumbers, lettuces, green leafy vegetables, spring onion, egg plants, zucchinis, mushrooms, hot and sweet peppers, and melons, among others, all year long.
Al-Khalaf said all their production is hydroponic-based, which gives higher yield, better quality of vegetables and fruits, and consumes 90% less water compared to conventional system of farming.
Between farms and backyards, he noted that eight different areas (and still increasing) in the country are being developed for hydroponic farming.
“We have three major farms, which we developed other than Agrico, and they are now producing even during the summer,” al-Khalaf stressed.
“I have one farm at 20,000sqm and still increasing in size. Another farm at 10,000sqm and another farm at 100,000sqm, he added.
“All these farms have been developed, operated and marketed by Agrico using its technology,” al-Khalaf said. “We provide for them the total solution from development, operations and marketing.”
It is learnt that local farms recorded a substantial increase in the production of fresh vegetables since the blockade on Qatar.
According to al-Khalaf, similar hydroponic systems designed for backyard farming are also being built, which aims to sustain every family’s vegetable needs.
The development of farms in the country is also unlocking their full potential and further increase yields that would meet the growing demand for fresh produce, according to al-Khalaf.
He encouraged compatriot entrepreneurs to invest in agriculture, especially in hydroponics farming. He described it as “a good and healthy” business.
“Hydroponics is the future of agriculture”, al-Khalaf stressed.
Have You Seen 'Hydroponically Grown' On Your Produce? Here's What It Means
Have you been perusing the produce area at your store and noticed fruits or vegetables that say “hydroponically grown?” They just kind of popped up one day, and we noticed there wasn’t much explanation
By Dawn Jorgenson - Graham Media Group
August 21, 2019
Image by engin akyurt from Pixabay.
Have you been perusing the produce area at your store and noticed fruits or vegetables that say “hydroponically grown?” They just kind of popped up one day, and we noticed there wasn’t much explanation.
If you’re anything like us, you may have bypassed it just because you’re unsure about what a hydroponically grown product is.
As it turns out, unless you’re attempting to try this growing process yourself (spoiler alert: it can be tricky), the advantages seem to outweigh the disadvantages.
How it works
The fruits or vegetables are grown in a liquid solution that contains minerals they need to thrive. There is no soil used, and instead, the root system is supported by a medium such as perlite, rockwool, clay pellets, peat moss or vermiculite, according to Full Bloom Hydroponics. Doing so allows the plant roots to have direct contact with the nutrient solution, as well as access to oxygen.
The process allows the plant to not work as hard to obtain the nutrients, therefore allowing it to mature 25% faster and produce up to 30% more than the same plant growing in soil.
Growing plants hydroponically also uses less water than soil-based produce because the system is enclosed, preventing much evaporation.
Are hydroponically grown produce good for you?
Because hydroponic fruits and vegetables are not exposed to outdoor elements, they do not need the same level of pesticides to protect the plants from insects or pathogens, according to LiveStrong.com. This often allows organic farming methods.
This is good news, but there does seem to be a possible drawback to hydronic produce. Because of the high humidity of the greenhouses, the produce can be more susceptible to salmonella contamination. However, washing and cooking vegetables thoroughly should remove and help destroy any possible salmonella.
LiveStrong made a special note to remind consumers that even though hydroponic farming appeals to some because of environmental concerns, any diet high in vegetables can improve health, regardless of whether it was grown conventionally or hydroponically.
Have you tried hydroponically grown produce? What did you think about it? Let us know in the comment section below.
Modular Farms Australia Will Be The Training Partner For The Greenhouse Technical Management Course Hosted by Graeme Smith And Rick Donnan In Conjunction With Gotafe
Modular Farms Australia is pleased to announce that they will be the training partner for the Greenhouse Technical Management Course hosted by Graeme Smith and Rick Donnan in conjunction with gotafe
Modular Farms Australia is pleased to announce that they will be the training partner for the Greenhouse Technical Management Course hosted by Graeme Smith and Rick Donnan in conjunction with gotafe.
Whether you're considering becoming a modular farmer or already own a farm, this hydroponics course covers all you need to know about growing the most delicious hydroponic crops!
Email: LTaig@gotafe.vic.edu.au
Website: http://www.gotafe.vic.edu.au/
SIGN UP NOW
If you would like further information please contact the course coordinator Leigh Taig on the above details.
Email: LTaig@gotafe.vic.edu.au
INDIA: Growing Crops Without Soil: Here’s How Hydroponics Works
At HMA Greens Hydro Farm there are over 14 varieties of greens being grown at any given point using hydroponics. Launched in early 2018 by 30-year-old Akil Murthi, the farm started with three varieties of lettuce before scaling up to its present stage
AUGUST 05, 2019
We head to HMA Greens Hydro Farm to understand how hydroponics works
The air in the polyhouse is thick with the fragrance of basil. A variety of lettuce, baby spinach, arugula, mustard greens, kale, mint and the aforementioned basil thrive in little net pots, nestled in troughs with varying levels of water.
Workers are busy checking the roots and shoots of the plants before deciding whether to move them to the next stage. All one can hear is the gentle whirring of fans, constantly running to maintain a conducive temperature inside the polyhouse. It is hard to believe that bustling OMR is just 500 metres away from these lush surroundings.
Meeting market demand
At HMA Greens Hydro Farm there are over 14 varieties of greens being grown at any given point using hydroponics. Launched in early 2018 by 30-year-old Akil Murthi, the farm started with three varieties of lettuce before scaling up to its present stage.
“I first came across hydroponics when I was doing my MBA in Singapore. I wanted to replicate it since we didn’t have anything of the sort here then. Land is becoming premium and you can do so much more with hydroponics: better quality control, more yield in a smaller patch of land and lower water usage as well,” he says, adding, “It took about eight months to get the project moving.”
Akil explains how hydroponics allows one to tailor crops as per market demand. “There was a report by the World Economic Forum that stated that a lot of Southeast Asian countries grow crops that are not really required in the market at that point of time. This leads to wasted produce,” he says. He adds, “With hydroponics we can change that, since harvesting times are a lot shorter than in traditional farming.”
In hydroponics it takes an average of 45 days to harvest crops like lettuce, basil and baby spinach. The same would take around 90 days when grown the traditional way. Water consumed to grow these crops is 90% less. “A nutrient solution is mixed into the water in the control room. From here it is pumped into troughs which house the net pots with the crops. Since the water directly reaches the roots, it is absorbed much better and you need much less water as well since nothing is lost in soil absorption,” says Akil.
Less water, good yield
Typically, HMA Greens farm uses around 700-800 litres of water a day. In winter that consumption goes down to 500 litres. This is why his farm has managed to consistently produce good yield despite the water scarcity in the city this year.
No chemicals are used in the farm and only natural ingredients such as neem oil are used to keep away pests. “We also use sticky pads and a solar powered insect trap,” says Akil.
They also use the Nutrient Filled Technique (NFT) system, which Akil says is ideal to grow crops like salad greens. The polyhouse also uses the pad and fan technology — cooling pads line the wall on one side, while on the opposite wall are fans — to maintain temperature and humidity levels inside. “Since this was a pilot project we did not get into vertical farming. If we decide to, it’d mean changing our entire system and bringing in LED lights for the plants.”
On an average the HMA farm produces a total yield of 2,500 kilograms during summer and in the cooler months manages to churn out as much as 4,000 kilograms. Excess produce is turned into compost. HMA farm delivers to customers’ doorsteps for a fixed charge. Alternatively, customers can pick up their orders from the office at HMA Land, Thapar house, 37, Montieth Road, Egmore. 28553550.