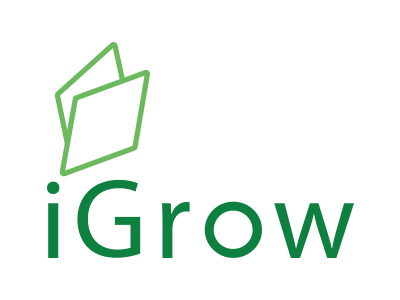
Welcome to iGrow News, Your Source for the World of Indoor Vertical Farming
Miljøgartneriet, Norway's Largest Nursery, Grows Even More Tomatoes And Peppers Year-Round By Using Philips LED Lighting
For many years, Signify has studied lighting and plants and has found the perfect lighting recipe for tomatoes, peppers, cucumbers, and other fruits and vegetables
April 6, 2021
Eindhoven, the Netherlands – Norwegian consumers are currently eating fruits and vegetables that have traveled thousands of kilometers from Southern Europe before they reach the shelves in Norwegian stores, which results in more imported food and a greater carbon footprint from its transport, compared to locally-grown crops. Now, Miljøgartneriet, Norway's largest nursery, together with its partner LOG and Signify’s horticulture LED department, are taking the first steps in shortening the farm to fork distance by growing tomatoes and peppers year-round locally, under LED lights.
The goal is to increase opportunities for local production and reduce the climate impact that comes from importing foreign produce. Signify has supplied Philips GreenPower LED toplighting compact for the 70.000 square meter greenhouse in Naerbø, Rogaland, Norway. With LED lighting, Miljøgartneriet gets the best possible conditions in the greenhouse. This is important since the lighting affects the plants' photosynthesis, and that makes proper lighting extremely important for how well the plants grow and thrive.
For many years, Signify has studied lighting and plants and has found the perfect lighting recipe for tomatoes, peppers, cucumbers, and other fruits and vegetables. Miljøgartneriet can therefore provide the plants with the right spectrum and light intensity at the right time. In this manner, they can control growth, planning and not least of all, increase productivity.
"Many supermarket chains want to be able to offer their customers fresh and tasty fruits and vegetables with a significantly lower carbon footprint than those that come from Southern Europe. This is something we can provide all year, thanks to our cooperation with Signify," said Kåre Wiig from Miljøgartneriet. "We chose Signify because they can do more than just providing LED lighting. We have a good, close cooperation with their plant experts in order to get the most out of the lighting solution so that the vegetables get the best possible growing conditions. This means that we can easily adjust production as we get better at growing vegetables and Signify can also bring in different experts if necessary."
Miljøgartneriet has installed Philips GreenPower LED toplighting compact, in combination with the GrowWise control system. This makes it possible to dim the lights so that growers can provide even light levels throughout the day and production cycle. Growers can also dim the lights when necessary. Either to save energy or when there is sufficient daylight.
Innovation in horticulture
Miljøgartneriet starts with 1 hectare of tomatoes and 0.4 hectares of peppers,and intends to eventually expand this. The vegetables are already being harvested now and on their way to the stores throughout Norway.
Even though Signify has worked witFphilh LED lighting for greenhouses since 2012, there are many producers that are still not ready for the newest greenhouse lighting technology. Henrik Nørgaard, who is the Commercial Operations Manager for Agriculture at Signify, hopes that this cooperation with Miljøgartneriet, which is one of the leading actors in the market, can inspire other growers to install Signify Horti LED lighting and increase production.
"We are really proud that Miljøgartneriet sees the potential of cultivating with our lighting. Our lighting solutions should be seen as a cornerstone of production. We start with defining what is grown, the physical framework of the greenhouse and the production goal, and based on this we create an optimal mix of micromoles, spectrum and timing; the light recipe, together with the grower. With the solution, we can avoid the overuse of both water and electricity, as well as the environmental burden with transport from Southern Europe, and instead can get fresh, locally-produced vegetables in Scandinavia year-round," said Nørgaard.
Supporting food availability through Horti-LED illustrates Signify's commitment to supporting good health and well-being (SDG3) and is the key to their commitment to double the percentage of earnings for a brighter life that benefits society, to 32%, as part of the program Brighter Lives, Better World 2025, that they launched in September of 2020.
--- END ---
For more information, please contact:
Global Marcom Manager Horticulture at Signify
Daniela Damoiseaux
Tel: +31 6 31 65 29 69
E-mail: daniela.damoiseaux@signify.com
Signify Nordics, PR Manager
Anne-Cathrine Tjørnehøj
Tel: +45 40330806
E-mail: anne-cathrine.tjornehoj@signify.com
About Signify
Signify (Euronext: LIGHT), a world leader in lighting for the professional market, the consumer market, and lighting for the Internet of Things. Our Philips-products, Interactive lighting systems, and data-activated services add value to businesses and transform private homes, buildings and public spaces. In 2020, we had sales of 6.5 billion EUR and approximately 38,000 employees in 70 countries. We utilize the full potential of light to offer a brighter life and contribute to a better world. We were carbon-neutral in 2020 and have been on the Dow Jones Sustainability World Index for four consecutive years since our listing. WE were also named Industry Leader in 2017, 2018 and 2019. News from Signify is availabel at Newsroom, Twitter, LinkedIn and Instagram. Investor information is available on the Investor page.
Babylon Micro-Farms Expanding Its Impact With New Partnership
Babylon Micro-Farms makes indoor growing aimed at providing more farm-fresh options for college students. It is now partnering with Harvest Table Culinary Group to bring fresh produce to more colleges
April 1, 2021
CHARLOTTESVILLE, Va. (WVIR) - A company that started at the University of Virginia is hoping to expand its impact.
Babylon Micro-Farms makes indoor growing aimed at providing more farm-fresh options for college students. It is now partnering with Harvest Table Culinary Group to bring fresh produce to more colleges.
“Self-contained vertical farms use hydroponics to grow plants with 90% less water. There are no pesticides or chemicals. We can grow plants 2-3 times more quickly,” Babylon Micro-Farms CEO Alexander Olesen said.
The planting of the farms is mostly done by designated operators assigned by Babylon, but they often get students involved.
Green Life Farms Breaks Ground On Second Hydroponic Greenhouse
The hydroponic technology allows Green Life Farms to grow leafy greens in oxygenated water – without soil – then harvest and package them in a controlled environment, reducing the risk of contamination and preserving flavor and freshness
04.05.2021
By Emily Park
LAKE CITY, FLA. - Green Life Farms announced on April 1 that the company is building a second hydroponic greenhouse in Lake City, Fla.
The hydroponic technology allows Green Life Farms to grow leafy greens in oxygenated water – without soil – then harvest and package them in a controlled environment, reducing the risk of contamination and preserving flavor and freshness.
Following the success of its flagship hydroponic greenhouse in Lake Worth, Fla., and significant customer demand for its products, the new greenhouse will be 400,000 square feet and is expected to begin commercial operations in early 2022.
“Following our very successful launch in South Florida, we are proud to announce this new facility to serve North Central Florida - the Jacksonville, Gainesville, and Tallahassee regions,” said Forrest Sawlaw, chief operating officer of Green Life Farms. “In light of ongoing food safety concerns across the country, now more than ever customers are looking for locally grown, clean produce. Our innovative hydroponic technology will deliver the cleanest and freshest leafy greens, all free from GMOs, pesticides and contaminants.”
Green Life Farms will incorporate specialized ozone water management technology to filter, sanitize and store rainwater for use in the growing process, and will rely on Florida sunshine – meaning the facility will use significantly fewer natural resources.
The new greenhouse will be able to produce 18 harvests each year and use 90% less water than conventional farming. At full maturity, the greens are gently moved using a floating conveyor system to be harvested, cooled, and packaged to reach customers within a few days of harvest, instead of the 8 to 10 days it may take conventionally farmed produce to reach customers in the region.
Green Life Farms’ products include Baby Arugula, Baby Kale, Baby Romaine, Farmer’s Blend, and Butterhead Lettuce, and are currently sold at more than 120 grocery store locations throughout South Florida.
Invitation To F&A Next 2021: The Impact of Innovation!
While our aim was to physically host the upcoming edition of F&A Next at the Campus of Wageningen University & Research, another virtual summit is today’s reality. Postponing is definitely not an option. Irrespective of Covid-19, a great deal happened in 2020. Investments in global food- and agtech were increased by over 30% to some USD 26 bilion!
F&A Next invites investors, entrepreneurs, and experts to address the next challenges of our sector on Wednesday, 26 May 2021 at the 6th annual F&A Next Summit. We look forward to showcasing the next scaling food and agtech companies. Yes, we‘ll miss meeting you in person, but we’ll make sure that dialing in will be as close as possible to the real thing!
During this year's 3-hour live, virtual summit we will
bring you up to speed on the Impact of Innovation in the agrifood industry,
present eight 'Next Heroes in Food- & Agtech', and
offer you ample opportunity to virtually connect and meet with (other) startups, scale-ups, investors, and corporates in the agrifood space.
GET YOUR EARLY-BIRD TICKET WITH A 25% DISCOUNT
Book your ticket before 12 April to get a 25% discount! Apply the code: FaN@21
Stay safe, stay healthy!
The partners of F&A Next
2021 Theme: "The impact of Innovation"
Get Your eTicket to F&A 2021, 26 May
Food & Ag Innovation only started around 2014 and has definitely gained momentum ever since. in 2020 investments in global food and agtech have risen, irrespective of Covid-19 influences. The pandemic did, however, trigger changes in consumer behavior. Has ‘life as we know it’ irrevocably changed? And what about the much-needed innovation earlier in the value chain?
At F&A Next, Rob Leclerc, founding Partner of Agfunder and Nick Ferreday, Executive Director Food & Agribusiness at Rabobank, will compare notes.
Our Monthly Webinar For April Is “Training The Next Generation of Aquaponic Farmers” From Researcher Sarah Milliken At The University of Greenwich, U.K.
Ms. Milliken will introduce an open access aquaponics curriculum, Aqu@teach, specifically developed for college students with a focus on entrepreneurial and transferable skills
The Webinar Will Take Place Live, Saturday,
April 17 From 11 am To 12 pm EST And Feature A Live Q&A.
Click Below To Register:
REGISTER: Training the Next Generation of Aquaponic Farmers
Ms. Milliken will introduce an open access aquaponics curriculum, Aqu@teach, specifically developed for college students with a focus on entrepreneurial and transferable skills. As soilless food production technologies become increasingly important in light of climate change and the threat of food insecurity, there is an urgent need to provide an appropriately trained workforce.
The Webinar is free to the public during the live broadcast. The Webinar will remain available for free, in perpetuity, to all Aquaponics Association Members in the Member’s Area of our Community Site.
Special thanks to Ed "Aqua-Eddie" Tivnan, Association Director of STEM Aquaponics, for organizing the webinar.
Hope to see you there!
Brian Filipowich, Chairman
Aquaponics Association
The Aquaponics Association
1240 Evarts Street, NE
Washington, DC 20018
How Square Roots Is Training Next-Gen Farmers During A Pandemic
The average age of the American farmer is 58 years old. If we're going to change the food system, we need to create more pathways for young people to launch successful careers in agriculture
Square Roots
10.08.20
The average age of the American farmer is 58 years old. If we're going to change the food system, we need to create more pathways for young people to launch successful careers in agriculture.
One of the many ways Square Roots invests in the future of farming is through our Next-Gen Farmer Training Program—aimed at new farmers or those at early stages in their careers. Farmers initially join Square Roots as Apprentice Growers. Through our proprietary training methodology—supported by our intuitive technology platform—Apprentice Growers rapidly learn the essential farm skills needed to move into permanent roles on the farm team and accelerate their careers.
We continuously evolve our training program to zero in on the skills and experiences that help employees become the best indoor farmers they can be. Throughout COVID-19, we have been committed to prioritizing people safety and plant safety which has led to changes in our day-to-day farming operations, as well as rewiring our in-flight farmer training programs in May and adapting how we run the Square Roots Next-Gen Farmer Training Program going forward. Also, after several years of training farmers, we’ve listened and learned to what farmers value from their experience at Square Roots and have incorporated that into our program going forward. Read more about what it’s like to be a grower at Square Roots and how the program has evolved:
Individual Pathways
Based on the needs of our farm production teams, apprentices are hired and onboarded, either individually or in pairs, on a rolling basis. By spacing out onboarding and training, our team is able to provide more attention and support to apprentices, allowing them to move more quickly through the training program and into permanent positions on our team. We expect most apprentices will complete their training in three to six months, but each will advance at their own pace.
Foundational Remote Learning
We have moved our training materials onto a virtual learning platform, which houses videos, interactive presentations, animated diagrams, virtual tours, and other types of content that can be brought to life beyond a typical presentation. Since COVID-19 restricts our ability to hold classroom-style learning, online learning can be self-serve, supporting different types of learning styles. It also drives consistency in training and terminology, reducing the burden on managers responsible for administering it.
Intensive ‘Boot-Camp’ Style Farm Immersion
Training for Apprentice Growers is laser focused on the skills required for new farmers to quickly become the best indoor farmers they can be. After the initial foundational onboarding, apprentices will jump into production, and, in parallel, will be equipped with the necessary context and complementary training to support expanded learning and competency much sooner. Apprentices will be supported by our software operating system the Farmer Toolbelt, empowering them to get up to speed much faster, engaging with data, and ultimately helping them become better growers. Throughout the training process, farmers will receive direct supervision by one of our experienced farm team members who will act as their training guide and provide professional and moral support.
Pathway to Permanent Employment at Square Roots
Central to Square Roots is our mission to empower Next-Gen leaders in urban farming, and the Next-Gen Farmer Training Program is one of the most direct ways we do that. The program is designed to bring young people with little or no experience up to speed in our proprietary indoor farms as quickly as possible and on to their careers in indoor farming—acting as an internal training program for permanent full-time employees on the Square Roots farm team.
The Apprentice Grower role is the first step in a career path to indoor farming at Square Roots. To start, apprentices will earn an hourly rate indexed to the area’s living wage, and receive 100% covered health benefits and equity in Square Roots. Once they’ve successfully mastered indoor growing fundamentals (we expect this to take three to six months), apprentices will be eligible to move into Associate Grower positions.
For more information and to learn about new open positions on our farm teams, follow us on social media and sign up for our newsletter for updates.
Tags: Next-Gen Farm / Farmer Training / COVID-19 Response / Updates
PODCAST: Vertical Farming Podcast - Season 3 Episode 28 - Robert Laing. Rob Is The Founder And CEO At Farm.One
Join Harry Duran, host of Vertical Farming Podcast, as he welcomes to the show founder, leader, and author, Robert Laing. Rob is the Founder and CEO at Farm.One, an organization that has reinvented specialty farming, and now supplies some of the best chefs in New York.
In this episode, Harry and Rob discuss Rob’s background in design and how Rob’s entrepreneurial drive led him to launch Farm.One. Rob talks about how the pandemic impacted his business and how he was able to pivot to different business models to combat those challenges. Rob shares the work he and his organization are doing to help underrepresented groups as well as the work they’re doing with Google to address sustainability.
Listen & Subscribe
Season 3 Title Sponsor
If you are starting a vertical farm and don't know where to begin, or which technology would suit your needs, Cultivatd can help. As indoor farm brokers, they help connect you to the right technology and ensure your project is successful. Best of all, their service is free. They work on behalf of their partners.
Polygreens Podcast Episode: 19 Grahame Dunling - WorldWide Local Salads
Grahame Dunling, together with son Matthew, has launched WorldWide Local Salads, bringing vertical farming to the city where the rich rural hinterlands served his family well for more than 100 years
Joe Swartz & Nick Greens | 3/26/2021
In this episode Joe and Nick interview Grahame Dunling about his extensive career in vertical farming. Vertical farming allows us to grow healthy, accessible foods within a few acres of land, close to home.
Grahame Dunling, together with son Matthew, has launched WorldWide Local Salads, bringing vertical farming to the city where the rich rural hinterlands saw the family well for more than 100 years.
More about Grahame Dunling:
LinkedIn: https://www.linkedin.com/in/grahame-dunling
More about Joe Swartz:
Website: https://amhydro.com/
Twitter: https://twitter.com/HydroConsultant
More about Nick Greens:
Website: https://www.nickgreens.com
Twitter: https://twitter.com/InfoGreens
Support the show (https://www.patreon.com/nickgreens)
Latest Episode
Introducing Low-Cost Farming Models To The Philippines
“I am convinced that we found a system that works perfectly here for the local climate conditions, with minimal cost of electricity and well suited for the skill level of the labor force, whilst delivering the highest quality produce
Through Local Sourcing
And The Use of Natural Resources
The Philippines is one of the greatest exporter of coconuts, mangoes, and pineapples worldwide, it is quite a surprise that a large number of vegetables are imported from surrounding countries. “Fresh herbs and leafy greens, in particular as they’re much more expensive here and low-quality,” says Ralph Becker, CEO and founder of Urban Greens. “Our climate is not ideal for some specific vegetable cultivation because of the extreme heat, torrential typhoons and other natural disasters. However, there is growing awareness regarding a healthy lifestyle, whereas the demand for vegetables is increasing noticeably.”
After spending a decade in corporate technology with Sony Electronics, Ralph Becker decided to shift his focus. “When I left the shelter of corporate life and moved back to the Philippines, I noticed that lots of food was imported. It made me think whether that could be done more efficiently with a smaller carbon foodprint and eventually better food quality.”
Ralph Becker
Sourcing locally
Hydroponic material and equipment is easily obtainable in most western countries but less so in the Philippines and particularly when he started his venturesome 4 years ago, which is why Ralph and his team designed everything themselves from the ground up.
“I am convinced that we found a system that works perfectly here for the local climate conditions, with minimal cost of electricity and well suited for the skill level of the labor force, whilst delivering the highest quality produce. One of the benefits for us is that the equipment can easily be repaired from parts available in a local hardware shop, for instance.
Contrary to other players who brought in technology from abroad that was not particularly designed for these temperature and humidity conditions, such as container farms which heat up in this tropical climate and take a lot of electricity to cool down – cost that has to be recovered on a slim profit margin to start with. We have our own technology and we’re able to scale it, without having to rely on outside technology.”
The new warehouse
With the brand-new warehouse farm right in the city center, the company will soon be delivering more than 1,5 tons of fresh produce per month. “Everything we’ve learned thus far in previous smaller units is now replicated in our new farms implementing the same model. The Philippines is a big country with many cities that rely quite heavily on imports, which is the main market we want to target,” says Ralph.
Ralph had always been interested in plant growing ever since being exposed to hydroponic farming in Japan and the US. Once he relocated to the Philippines he started doing some experiments with growing herbs. Posting about his project on social media many people reached out as they wanted him to grow for them too. Ralph says that restaurants and hotels were eager to validate the demand of high-quality local produce.
Pilot model
Urban Greens is building the new warehouse farm with a bigger purpose in mind, namely, as a pilot model for more farms. People interested in the vertical farming space can come and visit the farm. Ralph adds, “We want to inspire visitors by showing the possibilities of these new farming models. After all, we need young farmers to come into the industry. The younger generation isn’t that interested in farming because of the hard labor and low wages. We want to prove them wrong by showing that farming can be lucrative and modern too.”
Apart from cost-effectiveness, reliability is one of Urban Greens’ greatest assets. “Consistency of supply gets easily interrupted due to tropical storms, which is both bad for the farmer and for those who rely on it. Reducing food miles is of essential importance to food availability,” Ralph states. This also happened during COVID, when many supply chains were cut and the company noticed a strong increase in demand. “We turned hardship into an opportunity,” says Ralph. “Once we’ve finished up this warehouse farm in the heart of Makati, people will see that vertical farming can be viable in the Philippines. This country has 7000 islands, and I think each of them is in need of an Urban Greens farm.”
For more information:
Ralph Becker, CEO
Urban Greens
ralph@eaturbangreens.com
www.eaturbangreens.com
Publication date: Mon 29 Mar 2021
Author: Rebekka Boekhout
© VerticalFarmDaily.com
RUSSIA: iFarm Supports Urban Greenhouse Challenge At TPU
iFarm, the winner of The Europas Awards 2020 as the Hottest Ag/FoodTech startup, has supported Urban Greenhouse Challenge: Reforest, an international competition held at Tomsk Polytechnic University
By avborovskaia
March 27, 2021
iFarm, the winner of The Europas Awards 2020 as the Hottest Ag/FoodTech startup, has supported Urban Greenhouse Challenge: Reforest, an international competition held at Tomsk Polytechnic University.
iFarm creates technologies to grow fresh herbs, berries and vegetables throughout the year, including modular automated vertical farms and iFarm Growtune IT-platform. and has offices in Novosibirsk, Moscow, and Amsterdam, along with a showroom in Finland. The herbs, grown using iFarm technologies, are sold in all federal chain stores of Russia.
iFarm is a winner of the CovHack-2020 Virtual Innovation Challenge in the Best Startup category, a winner of the Nordic Startup Awards in the Best Social Impact Startup category, an Overall Indoor Farming Solution Provider of the Year in AgTech Breakthrough-2020 Awards in the Indoor Farming category and others.
“Urban farming arises at the intersection of multiple technological disciplines: agricultural engineering, engineering, and IT. We consider that similar competitions help teams to dive into such a multidisciplinary environment, master their skills, and further, together with us, change approaches to plant growing. It does not matter if it is about trees or food products, the set of technologies will be approximately the same,” Kirill Zelenski, iFarm Europe Managing Director, says.
“The events like Urban Greenhouse Challenge are an investment in the development of a new industry, staff training and highlighting really crucial problems, that humanity is going to face soon,” Kirill Zelenski emphasizes.
Besides the lecture part, the iFarm representatives will take part in mentoring the teams over the period of the competition. The company is interested in involving as many students from different countries as possible in this new industry.
“Non-specialists are usually the ones who change technological approaches to various fields of life. For instance, it was Henry Ford who made a revolution in people transportation but not the companies, which had been constructing carts and carriages for centuries. iFarm is a striking case in point. It is an IT-company that creates automated vertical farming technologies applying knowledge and approaches that have almost never been used in agriculture before. Therefore, what we expect from students is different, even the most incredible but well-elaborated ideas, which we will help them implement,” the expert says.
“We wish the participants not to be afraid to ask questions and try to understand things that they are not good at yet. Only such an audacious approach leads to the emergence of new and breakthrough solutions,”
Fashion Giant Makes Foray Into Leafy Greens
25th March 2021, London
New Investment In Vertical Farming Company Ljusgårda AB
Comes From Platform Owned By Chairman of H&M
The investment platform owned by H&M chairman, Karl Johan Persson, has invested in Ljusgårda AB, the Swedish vertical farming business based in Tibro.
Reports published by HortNews indicate the vertical farming company is backed by a number of investors, including Philian, which is the investment platform owned by Persson.
Ljusgårda, which produces crispy bagged salads, is planning to use the new investment to expand its production area in order to produce more products.
“We will grow from a cultivation area of 300m2 to 2,500m2, and thus from cultivating two tonnes a month to 60 tonnes when the factory is in full swing after the summer,” Ljusgårda marketing manager Maria Hillerström told reporters. “We will expand with more products this spring.”
Ljusgårda’s chief executive, Andreas Wilhelmsson, added the company is ambitious to expand. “We are looking at a number of possible new locations. As our first factory will soon start producing, it’s time to start financing the growth plans.
“The interest is huge out there. On the one hand, we are joining the sustainability trend, food-tech is starting to become very popular at the same time as this type of company out in the countryside where we are is not so common.”
Lead Image credit: Hort News
Enjoyed this free article from Eurofruit Magazine and its team of editors? Don't miss out on even more in-depth analysis, plus all the latest news from the fresh produce business. Subscribe now to Eurofruit Magazine.
Three Way To Maximize A Vertical Farm's Potential
Population growth and urbanization are forcing global food production to a crossroads
17 March 2021
By Abhay Thosar, Ph.D., director of horticulture services for Fluence by OSRAM
Previously published in the February 2021 issue of Inside Grower.
Population growth and urbanization are forcing global food production to a crossroads. Overall, migration to high-density areas increases access to health care, higher-paying jobs, education, and other socio-economic opportunities. But it also places more strain on existing infrastructure and demand for resources, leading to greater water scarcity, energy consumption, waste, and, perhaps most importantly, threats to the food supply, prices, and quality.
The economically disadvantaged will be the first to pay the price of increased urbanization. As prices increase and access to quality food sources decreases, the nutritional health of poor populations will decline. Over the next several years, the responsibility of bridging the gap between projected food supply and demand in urban areas will largely fall on vertical farms, an industry that is expected to nearly quadruple by 2025 to about $16 billion. The COVID-19 pandemic could accelerate that growth rate even further.
The vertical farming industry still has challenges to overcome. Production costs remain relatively high and, as a young market, knowledge gaps in operational best practices in critical areas like facility design and environmental conditions threaten long-term sustainability and profitability. The evolving economic dynamic with supermarkets is forcing vertical farms to scale quickly as they attempt to grow and supply a wider variety of crops while maintaining the buyer’s standards around produce size, quality, and nutritional value.
And, as we look to the future, new innovations in lighting strategies, facility design, cultivation best practices, and automation mean that vertical farming operations have to be constantly adapting and seeking new operational advantages. This is just as true for new market entrants and relatively established players alike, and each will be critical to not only maintaining profitability, but ensuring that food production in urban areas can increase with demand.
With that in mind, here are three critical factors vertical farmers need to consider to meet market expectations, improve efficiency and ultimately grow, cultivate and distribute larger quantities of quality food to more people in a smaller area.
Facility design as a function of market demand
The history and growth of the vertical farming market are largely driven by two trends at the consumer and buyer levels. A decade ago, consumers asking questions about how, where, and when their food was grown was practically unheard of. Things are different today. People want to know the provenance behind the food they buy and ensure it is chemical-free and safe to eat. Every product has become more than a label, it’s become a story that consumers want to hear, and one that has an equally significant impact in where they shop and what they buy.
Supermarkets have taken notice. Beyond that, though, vertical farming operations have given supermarkets one more option in addition to the existing supply chains on which they’ve relied for food production and distribution. Vertical farms play an even more important role during large-scale disruption events like the COVID-19 pandemic or massive recalls. As a result, supermarkets—which value the consistent supply of produce above all—are turning to their local vertical farming operations and, in some cases, even investing in them directly. The increased attention, however, comes at a cost (literally and metaphorically). Supermarkets are demanding that the vertical farms supplying them grow a wider variety of crops—lettuce, tomatoes, cucumbers, leafy greens, microgreens, herbs—more consistently while also meeting unique specifications around weight, aesthetic, nutritional value and a variety of other factors that are ultimately dictated by the vertical farm’s environment and the grower’s expertise.
Vertical farmers are quickly realizing they need to expand their portfolio from potentially a handful of crops to a few dozen or more, raising a range of questions on how to design or retrofit their facilities and adjust environmental conditions that favor any given crop.
The first decision many vertical farmers face is the growing technique that will be most scalable and viable for their operation. Hydroponics, aeroponics and aquaponics have all emerged as viable options with varying degrees of success, but they’re far from interchangeable.
In the end, there is no universal solution for every vertical farm. Cultivators should closely consider their buyers’ expectations, and how those expectations might change over time. Then, cultivators must assess the full range of their crops’ needs and how each might respond differently to various environmental factors and lighting strategies.
Strike a balance between environmental factors
The next set of factors governing facility design, investment and day-to-day operations should always be the environmental conditions themselves.
How air flows into and across each rack of a vertical farm is one of the most unique and important challenges vertical farms have to solve. Ignoring or failing to closely monitor airflow is often a death blow to entire sections of crops and to profitability, yield, and consistency as a result. Air movement helps to maintain temperature, humidity, and transpiration at each rack, and lack of it creates wide temperature swings or large gaps between crops at the bottom and crops at the top. It’s an incredibly fragile balance to strike. Everything from the number of access points into a warehouse—there should only be one access point—to HVAC and circulation systems affect air movement.
As a best practice, the maximum difference between the temperature at the top-most rack and the bottom-most rack should be no more than two degrees Fahrenheit. In practical scenarios, cultivators facing large temperature fluctuations can also consider placing crops that prefer relatively warmer temperatures—such as basil, oregano, chives, sage or thyme—at the top and simply let the laws of thermodynamics do the rest.
Carbon dioxide enrichment is a slightly easier condition to manage but no less important and changes based on temperature and lighting strategy. CO2 enrichment, too, can fluctuate based on the number of access points into a warehouse (again, there should only be one). Enriching a cultivation environment with carbon dioxide stimulates photosynthesis and plant growth, the rate of which is critically dependent on the difference between CO2 concentrations in the air and in the leaf cells.
The law of diminishing returns puts a cap on the amount of carbon dioxide cultivators should be introducing. CO2 is by no means the only factor governing plant growth, but vertical farms have the advantage of being able to closely monitor and control CO2 levels. To do so properly, however, they shouldn’t shy away from significant investments in both handheld devices—which allow cultivators to measure carbon dioxide levels at each rack, each plant, and each leaf—but also large-scale control systems that can measure and track CO2 throughout the entire warehouse.
Humidity levels govern a plant’s transpiration rate and the aperture sizes of its stomata, ultimately affecting how much water it moves from its root zone to release back into the warehouse. When a plant’s stomata open, they release water while also collecting carbon dioxide, making the balance of humidity, temperature, and carbon dioxide all the more crucial. Different plant types in different growth stages have different transpiration rates, adding even more complexity to how a vertical farm is designed and managed. The most common way to express humidity is relative humidity, the percentage of water vapor in the air at a given temperature compared to the total amount of water the air can hold at that temperature. In vertical farming, however, vapor pressure deficit (VPD) is the more accurate way to gauge humidity’s effect on plant growth. VPD remains an interesting discussion among researchers as the industry seeks to understand the differences between VPDs for air and leaves as well as exact VPD calculations.
Every environmental factor in a vertical farm affects the others to some degree. Nearly everything can be controlled; it’s both the advantage and the challenge native to the market. No factor, however, is more important to photosynthesis than its primary driver: light. Each factor—CO2, temperature, airflow, humidity, fertilizer, irrigation, VPD—need to be fine-tuned with changes to light quantity and quality to optimize plant performance and response.
Designing an effective lighting strategy
The design and implementation of an effective lighting strategy is and always will be the primary driver of your vertical farm’s success. In environments as complex as vertical farms, identifying the correct light intensity, spectra, photoperiod, and configuration will determine how other environmental factors work together to optimize a facility for plant yield and quality.
The first of these, the fixtures themselves, carry more implications for vertical farms than other cultivation spaces; in a vertical farm, plants receive no other source of light. The sun isn’t the safety blanket that it is for greenhouses. This simple and obvious fact means that vertical farmers have to find efficiencies in ways others don’t, which can manifest across a variety of operational metrics. Light efficacy, for instance, becomes more important. Most vertical farms are located in urban areas and are likely paying a premium for electricity. Maximizing micromoles per watt and reducing energy waste becomes more than a sustainability initiative, it’s critical to overall profitability.
Similarly, vertical farms operating warehouses measuring in the tens of thousands of square feet need fixtures with a good form factor without sacrificing light intensity. The right configuration means vertical farms can squeeze more racks into their facilities while also putting the lights closer to the plants for better results.
Beyond the hardware specifications, lighting design and strategy consist of several key factors: light intensity, light quality (or spectra), and light bar configuration. Each should be rooted in a facility’s overarching goals—typically defined by the consumer or buyer. Lighting strategies can be customized by crop, yielding specific plant chemistries or changes in biomass. Differences in spectra and light intensity can affect a crop’s coloration, shelf life, taste, and smell. Desired crop characteristics should be determined upfront in conjunction with the prospective buyer, therefore guiding a lighting designer to identify the optimal strategy to accomplish a facility’s goals.
Light quantity is the first and foremost aspect when it comes to optimizing the productivity of the crop. It is important to target the correct mols/day for each crop. Light quality (or spectra) is defined by measuring light’s wavelength in nanometers (nm). Wavelengths of light that drive photosynthesis are primarily found within 400 to 700nm—a range identified as photosynthetically active radiation (PAR). In a vertical farming environment, broad, white light has proven effective for tissue culture, propagation, and vegetative growth—while also serving the more practical function of making it easier for human eyes to diagnose and observe crops day in and day out. As the body of research into LED applications has expanded, it’s become clear that lighting strategies need to shift based on the growth stage. The days of bombarding plants with the same intensity and spectra are quickly fading. More and more research is showing that different cultivars respond to different lighting strategies at different stages of their maturation. More nuanced, customized lighting strategies are increasingly leading to tangible business outcomes for cultivators: longer shelf life, improved aesthetic, enhanced nutritional value, faster cycle times, and higher yields.
LED improvements will continue to drive costs down, while more in-depth research will discover and confirm a new set of lighting strategies and operational best practices to help vertical farmers meet future market demand for increased food production while also improving profitability. Overall, the future for vertical farms is bright and ripe for even broader innovation. Automation—the final frontier of food production—will mean even greater control of agricultural environments. That future is on the horizon. For now, though, vertical farms just need to stick to what they can control, which is pretty much everything else.
About Abhay
Abhay Thosar is the director of horticulture services at Fluence by OSRAM, where he is responsible for managing a team of horticulture specialists that enhances how cultivators grow their crops, optimize their lighting strategies and increase profitability in their operations. He holds a Ph.D. in plant physiology from Gujarat Agricultural University and spent more than a decade at leading greenhouses and nurseries throughout the U.S.
Vertical Growing Solutions That Are Easily Multiplied Increasing The Management Scale of Each Grower
GrowSpec offers three main products, each with numerous product lines contained therein. These three products include LED grow lights, vertical grow systems, and container farms
GrowSpec is an indoor farming equipment supplier established in 2015. GrowSpec offers three main products, each with numerous product lines contained therein. These three products include LED grow lights, vertical grow systems, and container farms. According to GrowSpec CEO Alvis Ma, these products can be used to produce a variety of crops indoors.
LED Grow Lights
GrowSpec offers six different types of LED lighting: AgriSpec, AgriBar, Sun Ray, Panel, SlimSpec, and Quantum. According to the company’s website, AgriSpec is a high-performance top-lighting solution with dimmable capabilities to allow growers to transition from vegetative to regenerative growth (i.e., flowering). The lights’ slim configuration enables installation in low rooms, racking systems, etc. While AgriBar and Sun Ray are both advertised as applicable for greenhouses as well as indoor farms, Panel is more specifically designed for indoor growing as the wide panels are somewhat wide for greenhouse use yet provide high light uniformity for indoor environments.
Vertical Grow Systems
GrowSpec also designs a number of vertical grow systems, all consisting of racks with integrated power supply, control system, and PVC trays so that each 4’x 8’ tray can be managed independently. Among these product lines in VertiDrip, a modular rack consisting of GrowSpec’s lighting, drip irrigation, airflow system, power supply, and touchscreen controls. The company’s VertiGro follows similar principles. GrowSpec’s main grow system, which was previously featured in IGrow (Combining Hydroponic And Aeroponic In Vertical Farming — iGrow) is VertiAero, which uses aeroponic technology. According to Alvis, VertiAero is patent pending in both the United States and Europe and offers various savings to growers.
“VertiAero reduces operational costs by 40%. In terms of electricity, we use 30% less. With nutrients, we save 85% because we use aeroponics rather than soil, so the root area is sealed and water losses are reduced. Our vertical grow systems are designed to optimize farm’s operation, they can match up with different irrigation systems so as to meet growers’ different preferred cultivation skills, and easily multiplied increasing the management scale of each grower,” explains Alvis.
Moreover, Alvis explained that having an integrated ventilation system in every rack of GrowSpec’s vertical grow systems helps to decrease plant disease.
“With inadequate ventilation, some plants will have diseases like powdery mildew or botrytis. But if you have full ventilation and every leaf can be blown with air, you will seldom have those diseases,” says Alvis.
Alvis also explained that the racks are space-efficient by both having an adjustable height and by being horizontally mobile using a mechanical assist. This, according to Alvis, allows growers to fit more racks into a grow room.
Container Farms
GrowSpec’s third product offering is container farms, which are equipped with GrowSpec’s vertical grow systems. According to Alvis, GrowSpec’s container farms are ideal both for production and for research as the conditions are highly modifiable and allow growers to test various things.
“If people want to do research, they can use this container to do so. They can set up irrigation, lighting, temperature of the root zone, temperature of the canopy, light intensity, etc. It is the perfect toy for them.”
Efficiency and scalability as priorities
Across GrowSpec’s three product types (LEDs, vertical grow systems and container farms), the company has emphasized improved resource use efficiency and scalability so that growers can easily increase production over time.
“For installation, we design our systems in modules so that they are very easy to install. It is a complex system yet easy to install. And it is scalable. It is easy to design the grow room because every rack is independent. The rack height is also customizable, and the power is integrated so that there is one main cable per rack, this allows requires the systems to be easy to maintenance ” explains Alvis.
GrowSpec also reports increased crop productivity by allowing growers to produce seven crops per year rather than four crops in traditional farming systems.
For more information:
USA: ILLINOIS - Glenview's Wiseacre Farm To Be Featured On History Channel
"We were connected to this opportunity through Freight Farms, a hydroponic farming container company in Boston. Our farm was built and distributed by Freight Farms," said Yael Sheinfeld, whose father, Aviad, founded Wiseacre Farm
This Sunday's Episode of "Modern Marvels"
Will Highlight Innovative Hydroponic Techniques
March 23, 2021
The Wiseacre Farm crew (left to right): Sam Sheinfeld, Yael Sheinfeld and Aviad Sheinfeld. (Photo by Wiseacre Farm)
GLENVIEW, IL — Back in December of last year, a television production crew from the History Channel made a special visit to Glenview. Wiseacre Farm, a family-owned hydroponic farm, will be featured this Sunday as part of the network's "Modern Marvels" program.
Yael Sheinfeld, who handles marketing for the farm at 1975 N Lake Terrace, said the team at Wiseacre hasn't seen the episode titled, "Future of Food," yet. It is set to air at 9 p.m.
"We were connected to this opportunity through Freight Farms, a hydroponic farming container company in Boston. Our farm was built and distributed by Freight Farms," said Yael Sheinfeld, whose father, Aviad, founded Wiseacre Farm. "We're so grateful for the experience, and are very excited for the episode to air."
Aviad Sheinfeld shows off Wiseacre Farm during an episode of "Modern Marvels" on The History Channel. (Courtesy of Wiseacre Farm)
Sunday's episode of "Modern Marvels," hosted by food author and culinary entrepreneur Adam Richman, showcases Wiseacre's innovative hydroponic farming process as the future of food, highlighting the farm's mission to grow clean, fresh produce within the community that it serves.
"It was exciting for the film crew to visit the farm. Our farming team (Aviad Sheinfeld and his dad, Sam Sheinfeld) talked through each step of the plant life cycle and delivery process while the crew filmed," Yael Sheinfeld said. "[We also] participated in sit-down interviews where we discussed the concept behind the farm, how we started it, etc."
Yael Sheinfeld said that due to COVID-19 restrictions, the entire film crew for the episode was local.
Founder Aviad Sheinfeld talks about Wiseacre Farm during the episode of "Modern Marvels" titled, "Future of Food." (Photo by Wiseacre Farm)
Wiseacre Farm works to shorten the path from farm to table, promote and practice environmental sustainability, and educate consumers about the origins of their food.
"We're a family-owned hydroponic farm in Glenview that provides fresh, hyperlocal greens to the community," Yael Sheinfeld said. "We currently offer home delivery and farmside pickup options."
Wiseacre greens are available through home delivery subscriptions and weekly farmside pickup. Wiseacre Farm also makes frequent donations to local food pantries, working to ensure that fresh greens are accessible to all.
More information about Wiseacre Farm can be found here: https://www.wiseacre.farm/.
Could Depletion of Fertile Soil Trigger A Bigger U.S. Food Crisis?
U.S. farmland in the Midwest has lost over one-third of the soil necessary to sustain crop production, according to scientists at the University of Massachusetts, Amherst
By Ted Kelly
March 9, 2021
U.S. farmland in the Midwest has lost over one-third of the soil necessary to sustain crop production, according to scientists at the University of Massachusetts, Amherst. The study concluded that fertile soil has been destroyed — not as a result of natural wind and water erosion, but by a century of overplowing. (tinyurl.com/wps8c99c)
Topsoil is the “black, organic, [carbon and mineral] rich soil that’s really good for growing crops,” said Evan Thaler, a Ph.D. student at UMass. Topsoil accumulates over centuries and is teeming with microorganisms.
The healthy and fertile soil was effectively managed and stewarded by Indigenous peoples of the region for centuries, if not millennia. But after a few hundred years of hyper-exploitation, first, by European colonial settlers and later big agribusiness, a third of all the topsoil across Illinois, Iowa, Indiana, and Minnesota is now gone according to a study reported in the Proceedings of the National Academy of Sciences. (tinyurl.com/3yxy4v9d) This figure is much higher than has been reported by the U.S. Department of Agriculture. Lead researcher Thaler said, “I think the USDA is dramatically underestimating the amount of loss.” (NPR)
This assessment is corroborated by a 2006 study from Cornell University which found fertile soil is disappearing faster than it’s being replaced, stating: “Each year about 10 million hectares of cropland are lost due to soil erosion, thus reducing the cropland available for food production. The loss of cropland is a serious problem because the World Health Organization reports that more than 3.7 billion people are malnourished in the world. Overall soil is being lost from land areas 10 to 40 times faster than the rate of soil renewal imperiling future human food security and environmental quality.” (tinyurl.com/cpav2xj9) [One hectare is the equivalent of 100 acres.]
This follows a global trend that has caused a drastic reduction in fertile farmland due to capitalist overdevelopment. Almost all food production — 99.7%, according to the Cornell study — depends on healthy topsoil. But half of it has been destroyed in the last 150 years according to the World Wildlife Federation. (tinyurl.com/pxkcx37b)
An impending food crisis is not the only issue at stake. Low-nutrient soil produces low-nutrient crops. Food today simply does not have as many vitamins and minerals as it did a few decades ago.
Another study, conducted by the University of Texas at Austin, found “‘reliable declines’ in the amount of protein, calcium, phosphorus, iron, riboflavin (vitamin B2) and vitamin C” in dozens of fruits and vegetables since 1950. (tinyurl.com/3nhwhzza)
Corporate genetic modification of plant species, like corn, is aimed at making more profitable — not healthier — produce. “Efforts to breed new varieties of crops that provide greater yield, pest resistance and climate adaptability have allowed crops to grow bigger and more rapidly, but their ability to manufacture or uptake nutrients has not kept pace with their rapid growth,” the UT study claimed.
Cuba shows the way
There is a model, however, for soil replenishment and food production that could point to a way forward that would avoid famine and nutritional starvation. And it comes, unsurprisingly, from the socialist world.
The “Special Period” in the history of revolutionary Cuba refers to the great upheaval immediately after the dissolution of the Soviet Union, which socialist states around the world had depended on.
In 1993, the Cuban Communist Party formed agricultural cooperatives to manage hundreds of state-owned farms. The goal was to increase domestic food production, while providing jobs and housing to Cuban workers, and to rely less on imported chemical pesticides and other synthetic farming techniques.
“The land redistribution program has been supported by solid research-extension systems that have played key roles in the expansion of organic and urban agriculture, and the massive artisanal production and deployment of biological inputs for soil and pest management,” writes Miguel Altieri, one of the founders of the Cuban Association of Organic Agriculture. (Monthly Review, “The Paradox of Cuban Agriculture,” Jan. 1, 2012)
Even more impressive is the growth of food production on urban farms, or organopónicos. “Cuba’s achievements in urban agriculture are truly remarkable — there are 383,000 urban farms, covering 50,000 hectares of otherwise unused land and producing more than 1.5 million tons of vegetables . . . using no synthetic chemicals. . . . Urban farms supply 70% or more of all the fresh vegetables consumed in cities such as Havana and Villa Clara.”
Capitalism is at a dead-end by every conceivable metric. Socialist societies point the way forward to providing healthy, nutritious foods for all without a profit motive.
AUSTRALIA: VIDEO - Shipping Container Farms: Check Out This Craze In Modified Containers
Greenhouses, hydroponics, and mushroom farms – converted shipping containers can produce protein and vegetables for all your needs
Greenhouses, hydroponics, and mushroom farms – converted shipping containers can produce protein and vegetables for all your needs. Even if you’re not an environmentalist, there are business opportunities to be had in delivering extremely fresh food to people in urban environments like Brisbane. Given the changing climate and topsoil loss we are facing, shipping container farms could well be an answer to these issues.
Over the years in the Gateway Gazette, we have published a number of stories that look at producing food in converted shipping containers. Reflecting on what we have published and looking at the detail of what can be done, let’s consider the possibilities that come with shipping container farms.
Open Top Container Greenhouse
One of the most cost-effective ways of using a shipping container as a food-producing unit is by attaching a glass top to an open-top shipping container.
In this video, Urban Farm Units looked at the concept of a greenhouse-container. An open-top 20-foot container would have a greenhouse attached to the top with shelving units directly under the glass. This allows photosynthesis to take place in the normal way.
Seedlings can be started in the lower part of the unit, which is warmed by the light and heat from the outside.
One step down from slapping a greenhouse on top of an open-top container would be to use a flat rack container and to have the greenhouse on the base (Gateway Containers can supply both open-top and flat rack containers).
The concept is an improvement on the one in the video, as long as you keep the greenhouse within the dimensions of a 20ft standard or high-cube container, it would be possible to lift and move the container farm from place to place.
This might be useful where you have an agreement with property developers or a council to use vacant plots of land in a city for agriculture. When the site is ready to be developed you can stick it all on a truck and move it to the next plot.
The concept of a shipping container greenhouse is:
Cheap to buy
Mobile
And often won’t need planning permission for a permanent site
Could this be something you’d consider? Contact us at Gateway Containers to discuss your needs!
Mushie Container Farm!
Image source: King Oyster Mushrooms Facebook
In 2019 we reported how Belgrave, Vic-based John Ford has developed a shipping container mushroom farm. This could produce protein for people as an alternative to meat or for anyone who loves the taste of freshly cut shrooms.
Mushrooms of any kind don’t store well and are best eaten as soon as possible after cutting. This is why having a mushroom farm close to restaurants could be a money-spinner.
This requires no modification from a basic shipping container, you could even install the racking inside the container yourself.
In their lifecycle, mushroom mycelium live out of sight of the world until they are stressed and get the impression that they are facing death. When stressed they flower to produce spores – those flowers are the mushrooms that many of us love to eat.
A shipping container is perfect to take advantage of such a lifecycle. Logs or other media are infected with the mycelium and left to rot for a certain time. By altering the environmental conditions, so you deliberately stress the fungi and they flower.
In our article, we reported how John Ford is producing mushroom species that are famed for their delicate taste but don’t travel well at all – shiitake and oyster mushrooms. As a sideline to his main income as a marine biologist restoring seagrass habitats near Belgrave, he produces freshly cut shrooms for local people and restaurants.
For you as an entrepreneur, mushroom growing would require buying a used shipping container and setting it up as a mushroom farm. If you are planning an urban mushroom container farm, you can take advantage of the fact that you can treat the container as a mobile unit and not as a permanent base. Shipping containers are also pretty inexpensive to buy and convert.
Hydroponics – The Rolls Royce of Shipping Container Farms
Image source: ABC
The hydroponics concept is highly developed for the use of fresh food and can be set up for high density vegetable farming in shipping containers. This requires a fair bit more modification than the two systems we describe above.
Unlike the Urban Farm Units company, several companies have managed to survive over the years selling their hydroponic container farm businesses to entrepreneurs and restaurants around the world.
Modular Farms is a company we featured in our blog originally based in Canada, but who recently set up shop over here in Australia. According to their website, they “design and manufacture container farm systems that can be used to grow food in most locations on earth.”
These systems strive to get around some of the issues we face here. Cities like Brisbane get far too much water sometimes and then face droughts for years on end. The Australian Food Services News reported, “With a focus on sustainability, Modular Farms’s hydroponic, closed-loop system uses 95% less water than a typical outdoor farm.”
Topsoil erosion is a problem, especially in prolonged droughts when it gets blown away as dust. Hydroponics use media like rock wool and even used mattresses to house the plants’ root systems and feed them nutrients via a watering system.
With our ever more extreme climate, food often has to be imported into cities from hundreds or thousands of miles away. A hydroponic container farm can enable you to grow many vegs very close to markets and restaurants.
This has been observed by global homewares retail giant IKEA, which in 2019 announced it was piloting growing vegetables in its stores for use at its restaurants. We reported, “While selling hydroponic indoor growing equipment to customers, IKEA is feeding its staff with lettuce and other vegetables grown in a container outside its Malmö and Helsingborg stores.”
Image source: ABC
There are a few downsides to hydroponics. Firstly, while some types of plants are happy enough growing in hydroponics – the simpler ones producing leaves and flowers (like broccoli!) – others aren’t so happy, such as cassava, wheat, and potatoes.
The next big issue is that for a high-intensity farm, not unlike factory farming chickens, you need to be ultra-clean in your production as the arrival of a destructive disease or fungus could wipe you out very quickly.
Container Fish Farm Too?
In theory, it is possible to run a fish farm connected to the hydroponics container farm, with you largely feeding the fish and collecting their feces and other waste to feed the plants. The plants would clean the fishes’ water and make it habitable for them as reed beds do in nature. This a concept that is in development but hasn’t caught on commercially yet.
How Can Gateway Containers Help?
We can provide and convert an insulated container for you to get started with and advise you how to best make further additions without compromising the overall structure.
If any or all of these ideas have caught your interest – or you just know about these concepts and need a shipping container to make it possible – then get in touch with us today to discuss your needs!
Posted on February 22, 2021
By Mark FinneganOtherShipping ContainerModified Shipping ContainersLeave a comment
UAE: “Hydroponic Farming Is Not Yet Deployed At A Meaningful Scale”
Greener Crop was founded in September last year with the goal of enabling hydroponic farming in the Middle East and Africa
“While hydroponic farming is extremely relevant to the water-poor Middle East, and incentives for agriculture such as energy and water subsidies have been put in place, the technology has not been deployed at a meaningful scale yet,” Alexander Kappes, founder of Greener Crop states.
Greener Crop was founded in September last year with the goal of enabling hydroponic farming in the Middle East and Africa. Alexander was working at an investment office prior to Greener Crop which brought his attention to the long-existing problem: the country is too dependent on food imports. “We wanted to enable local sustainable farming here as well.” Greener Crop offers farm management solutions, removing entry barriers.
The company offers four key solutions for existing or aspiring farmers: development of crop strategy, input management, physical farm management, and crop marketing. From Container farms to greenhouses and indoor vertical farms, Greener Crop supports their clients from finding the right supplier and setup, to selling the crops in the market. “It’s a great solution if you’re looking for an experienced partner to get your farm up and running, whether it’s short or long term,” says Alexander.
Alexander Kappes
There has been a strong push from local governments to develop alternative farming methods. The government in the UAE has invested over $200 million to support the development of growing facilities. This is a highly valuable approach, however, it is important to keep in mind that even a $40m indoor vertical farm can only contribute 0.03% of the local annual fruit & vegetable consumption. Farming is a highly democratized industry and requires not only a handful of a large farm but thousands of small and medium-sized farms that enable a country to be self-sufficient,” Alexander claims.
Removing barriers
Whether farmers want to expand or convert their farm into a hydroponic farm or an outsider investor, Greener Crop is here to help. The company connects farmers to suppliers and manufacturers, they can either run the farm, handle the supply chain and in some cases, handle the sales. “Clients no longer have to figure out everything on their own – we are here to support them with the operations and even sale of their crops. In many cases, clients are self-consumers such as hotels and restaurants,” Alexander explains.
The company sits together with their clients, comes up with a plan, ticks off the boxes, and starts setting things up, given the customer budget. Based on the expected yield, an approximate selling price per kg can be provided to clients. “We can always predict with a certain degree of accuracy. In this way, we can sketch revenue, utility costs, including labor, etc., which eventually leaves us to the expected profits. After the preliminary proposal is given, we reach out to potential suppliers as we understand what they offer in terms of yield, cycles, crop analyses, costs, and input.”
Green Crop has the ability to run a farm completely independently, however, the client can decide how hands-on they want the company to be. Clients can set foot on the farm at any time. “We can also operate certain parts of the operation such as maintenance for instance. Our benefit is that we come in, with trained staff, they do the work and go out.
Finding a suitable market
Alexander says, “The difficulty is not in selling all of the produce, but whether you are able to sell it at the right price. The smaller the farm, the higher the production costs. Being able to sell something at the price where it covers all costs is the main goal.” The challenge this therefore to gauge the available client-base for your produce, as well as the competition and their prices. Similarly, a thorough crop strategy must account for seasonal price fluctuations and ensure that we seed to harvest at the right time.
Often, the biggest challenge, according to Alexander, for smaller individual farmers is sourcing the right seeds and nutrients. Finding suppliers of quality products is often a challenge, and in most cases, they require you to buy large quantities that exceed the farms' annual consumption. “There are large differences in quality between suppliers and often when farmers choose the most affordable solution, this results in high costs for maintenance and replacements. For many new manufacturers, hydroponic farming looks like an easy enough industry to get into, but they underestimate the complexity of fine-tuning an indoor farm for efficient farming, and it’s often the farmers that pay the price for this,” Alexander notes.
Greener Crop started operations in the UAE and is now expanding into Saudi Arabia and Qatar, with the rest of the Middle East and all of Africa in their sights. Alexander adds: “As the region in the world most under threat from water stress and shortages, conventional farming is often not a sustainable option. It is for that reason that we chose to focus on enabling hydroponic farming in this area.”
For more information:
Alexander Kappes, Founder and CEO
Greener Crop
alexander@greenercrop.com
www.greenercrop.com
Publication date: Mon 22 Mar 2021
Author: Rebekka Boekhout
© VerticalFarmDaily.com
PODCAST: Vertical Farming Podcast - Season 3 Episode 27 - Allison Kopf - Founder and CEO of Artemis
Hosted by Harry Duran
The Vertical Farming Podcast is the #1 show dedicated to the Vertical Farming market. Tune in every week for fascinating conversations with CEOs, Founders, and luminaries from the exciting and fast-growing world of Vertical Farming. Vertical farming is a revolutionary approach used to produce food and medicinal plants in vertically stacked layers such as in a skyscraper, used warehouse, or shipping container. It facilitates production of huge quantities of nutritious and quality fresh food without relying on favorable weather, high water usage, skilled labor, and high soil fertility.
This ensures reliable yield and consistency in crop production year-round with climate control, and no effects of external environment factors such as diseases, pests, or predator attacks.
The Vertical Farming industry is projected to generate $12.77 Billion, Globally, by 2026 with a compound annual growth rate (CAGR) of 24.6%.
Subscribe and learn more by visiting Vertical Farming Podcast
Listen & Subscribe
US: NEW YORK - 21st Century Fund Awards FeedMore WNY $100,000 For Expanded Freight Farms Greenery
In 2020, FeedMore WNY served more than 16 million meals to WNYers who were homebound due to quarantine
by queenseyes
March 17, 2021
Recognizing the needs of the community is an integral component of the 21st Century Fund. Making sure that those needs are met is another. The Fund – “a giving circle open to anyone who wants to give back in Western New York” – designates significant awards to worthy organizations that submit applications for consideration. This year, FeedMore WNY is the recipient of $100,000, which will allow the non-profit to continue on with its efforts to feed those struggling during the pandemic.
In 2020, FeedMore WNY served more than 16 million meals to WNYers who were homebound due to quarantine. This was accomplished via the group’s 300 pantries, soup kitchens, emergency shelters, etc., throughout Erie, Niagara, Cattaraugus, and Chautauqua counties.
FeedMore WNY will be using the significant funds to expand its GrowMore for Good project, by allowing the organization to double its capacity, which in turn will ensure that fresh produce will be available to over 129,000 individuals. The expansion of a FeedMore-operated Freight Farms Greenery™ (the organization’s second hydroponic container farm) means that FeedMore will be able to produce 200 lbs. of produce each week. The group’s initial hydroponic “container farm” will supplement the effort. This food will be harvested and distributed within 24 to 48 hours, according to FeedMore.
This is an incredible effort that will allow more people to access healthy foods, instead of relying upon less wholesome canned foods.
In order to receive the crucial funding, FeedMore WNY made it to the final four, out of a streamlined pool of 30 applicants, before coming away with top honors. Homespace, Jericho Road, and OLV Charities were the other three finalists – all four projects can be found here.
Members* from across the country ended up casting their votes for FeedMore WNY, knowing how imperative it is to get healthy foods into the hands and onto the tables of disadvantaged households. The existence of ‘food deserts’ and the fight for ‘food justice’ go hand-in-hand. Compounded by the pandemic, it’s more important than ever to offer people food security, for healthier futures.
“FeedMore and all the clients we serve across Erie, Niagara, Cattaraugus and Chautauqua counties are overwhelmingly grateful for the generous support from the 21st Century Fund which will allow us to purchase our second container farm. The indoor, vertical growing, hydroponic farm will allow us to double our output of crops to enable us to put fresh, nutritious and fragile produce into our clients’ hands within 48 hours of harvest,” said Tara A. Ellis, FeedMore president and CEO.
“Our giving circle is a great way to introduce people to philanthropy,” said Ted Borowiak, 21st Century Fund Co-Chair. “We are always accepting members and encourage anyone including families, school groups or organizations to learn more about our membership options. Once you are a member, you are a member for life, allowing you to stay informed on new projects underway and make an impact in our community over and over again.”
The next 21st Century Fund grant process will open in the fall of 2021. For more information about the 21st Century Fund and membership details, visit www.21stcenturyfund.org.
*Members pay a one-time fee to join the 21st Century Fund and come together every other year to vote on awarding a $100,000 grant to one deserving organization for a specific project that will benefit the community. The 2018 winner chosen by members was the Niagara Falls Boys & Girls Club’s 17th Street Clubhouse Revitalization Project.
Tagged with:21st Century Fund, FeedMore WNY, food deserts, Freight Farms Greenery, GrowMore for Good, Tara A. Ellis, Ted Borowiak
Providing A Sustainable Growing Solution For Farmers, Using Renewable Energy in Container Farming
Recently, Freight Farms and Arcadia have partnered to provide Freight Farms' U.S. customers with access to clean energy for their everyday operations
“The past year has really proved our proposition as it has never been proven before,” says Rick Vanzura, CEO at FreightFarms. “The pandemic put a huge focus on supply chain security, local food access, and how to handle disruption to a supply chain, and we saw that having a modular farming solution that can be put next to people where they need food fits in perfectly. Some segments have suffered, while our farms have proven to be a great solution.” The company has seen demand going up, with 2020 being a record year: Freight Farms tripled revenue versus the prior year and set a record for orders.
Recently, Freight Farms and Arcadia have partnered to provide Freight Farms' U.S. customers with access to clean energy for their everyday operations. With this partnership, Freight Farms and Arcadia are taking strides to align their respective industries, moving indoor farming into a more sustainable future. Freight Farms’ customers can now connect the utility for their container farm to Arcadia to match 100% of the farm’s electrical usage with clean energy.
Tackling sustainability pillars
“We already have a number of current farmers that have signed up with the Arcadia energy offering. It was a really important milestone for us as sustainability has been a core mission since the founding of the company.” Rick identifies the sustainability pillars in farming as soil conservation, water conservation, food miles, and energy usage. “At Freight Farms, we have always performed very strongly in the first three categories. Our farms have no effect on soil; they use very little water (5 gallons/day, or 19 L/day), and they reduce food miles significantly, sometimes to zero. What remained for us to solve and why the Arcadia partnership is so crucial is energy,” Rick notes.
Before the Arcadia partnership, energy was the only unsolved part of the sustainability pillars Freight Farms hadn’t tackled yet. The recent partnership has given access to clean energy to all small business farmers. “With the presence of clean energy, we believe there hasn’t been a more sustainable farming solution similar to this one before.
Freight Farms looks at sustainability through the triangle of labor, yield, and power. They are increasing the output per unit of input. According to Rick, Freight Farms is far down the road in the development of greater efficiencies in their farms, focusing on optimizing for yield per unit of power and continuing to research renewable energy options. Rick says that “Everybody’s success is a collective success as we’re all relying on the industry as a whole... We’re all bound by this mission to create a more sustainable planet. Therefore, anything we can do in our own small way, we’re ready to do.”
Improving farm efficiency
On the product side, the company is doing updates to everything. “We made our farms more efficient, delivering value in several aspects, working on different renewable energy in all forms. The ROI has never been better than this farm, because of the intersection of output and efficiency gains. As we’re big believers in helping the industry as a whole for good, our ultimate goal is to be NET zero ultimately.”
While Freight Farms customers already span 46 U.S. states and 32 countries, Rick believes that the company will expand into more locations this year. This growth is stimulated by recent investment and team expansion. “By the end of 2021, we’re expecting to be in every US state and several other countries. Ospraie Ag Science led our last fundraising round, where they invested heavily in our ability to do research. Therefore, we’ve added lots of strength to the team over the last year.”
Collaborations
As a plug of vertical farming, Freight Farms is collaborating with MIT sustainability lab students together on a project. The project is about working in conjunction with the government, and public- and private partnerships around sustainability. “The goal is to be part of something where brilliant people are willing to donate their time and energy. This is just one example of many where people want to pitch in and help as we all want to have a more sustainable planet,” Rick notes.
“We’re not trying to solve for renewable energy on a location by location basis. That would be the route to go with today, but it’s a solution limited to the United States as of now,” Rick affirms. Freight Farms is always on the lookout for partners worldwide where its services can be made available.
For more information:
Rick Vanzura, CEO
Freight Farms
+1 877 687 4326
info@freightfarms.com
www.freightfarms.com
Publication date: Wed 17 Mar 2021
Author: Rebekka Boekhout
© VerticalFarmDaily.com