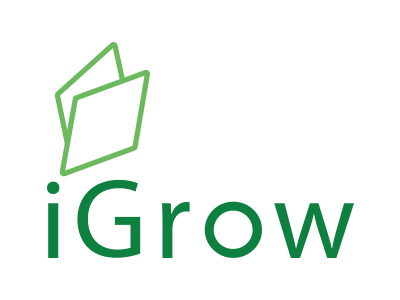
Welcome to iGrow News, Your Source for the World of Indoor Vertical Farming
Worms, Fish Farms, Hydroponics, Aeroponics Help Fuel Oregon Hotel
Many of the celebrities that stay at The Nines have requested tours of the food lab and their private chefs that travel with them are fascinated at what the restaurant is doing.
Author: Nina Mehlhaf
November 19, 2018
PORTLAND, Ore. — Some believe that the future of food combines technology and transparency, so diners know where their food comes from, and that it shouldn't come from far away. A Portland hotel is experimenting with how to do it.
Jeff Brown, the general manager of food and beverage at The Nines Hotel, is leading the charge at his facility.
And he's doing it far from the hotel lobby, and deep underground from the restaurants and kitchens of The Nines hotel.
The Nines, a luxury hotel in downtown Portland, is growing much of its own food in hydroponic facilities in the basement of the hotel. Photos by Nina Mehlhaf, KGW 2018
"Let's go feed our fish," Brown says enthusiastically as he punches in the code to unlock the keypad to a food lab in the sub-basement of the hotel. "These are tilapia, they are about 8 months old," he says of a tank full of open-mouth fish eager for food.
They're part of the farm of the future. The goal for those who embrace food-based technology growing practices is to allow food to be produced even in outer space or catastrophic climate situations.
The fish poop provides nitrate which acts as a fertilizer and is filtered through into water for some small tomato plant and basil starts nearby. It's known as aquaponics.
And hydroponics grows plants without fish, just water, LED lights to mimic the sun and no soil. Lettuce and basil grown in the hydroponic tubs in the basement are being served on the menu at Urban Farmer restaurant, one of the hotel's two signature restaurants.
"This is what I'm most excited about," says Brown as he opens the double doors to a purple-hued lit cabinet, much taller than he is. A sophisticated setup that soon, hotel guests will get to see when it's moved up to a room near the lobby. This is the aeroponics garden.
The Nines, a luxury hotel in downtown Portland, is growing much of its own food in hydroponic facilities in the basement of the hotel. Photos by Nina Mehlhaf, KGW 2018
"So these are just misters and it's just misting the root." It's the same way Matt Damon survived on Mars in the movie "The Martian." Artificial light, mist, no soil. Brown and his chefs have beta-tested 102 types of vegetables, fruit and flowers in the past year, experimenting with which method works best.
"The chefs love that they can grow specific foods and grab it themselves and don't have to worry about foods being wilted or old and they can speak to it to customers, it's the transparency component," said Brown.
"If you think about it, it's simply, it's just seeds, light and water yet people are fascinated by it. We eliminate the carbon footprint this way. But the staff feel like they're part of something bigger. They can contribute to the guest's dining experience."
Another basement-level down, in the hotel's huge trash room, another hotel is humming along. Urban Farmer and Departure, the hotel's restaurants, compost salad scraps, coffee grounds and newspaper into a huge plastic bin for red wiggler worms. The worms eat the scraps and make a nitrate-rich soil that fertilizes the plants in the food lab. The tilapia also eat the worms.
Brown loves technology almost as much as he loves food. He has ideas for augmented reality at the restaurant dinner table as well that would get rid of the high cost and trees of printing menus every day.
"You would get your phone out and look at a marker, that's what they call it, on the table for instance. And the menu would pop up on their phone and you can move it around and learn more about things through other markers around the restaurant. What farm their steak comes from, or more about the process of how their vegetables were grown here in Oregon."
Many of the celebrities that stay at The Nines have requested tours of the food lab and their private chefs that travel with them are fascinated at what the restaurant is doing.
© 2018 KGW
Local Lettuce Grower Has A Safer Way Through Hydroponics
Acting on the CDC’s recommendation, grocers nationwide are pulling suspect romaine lettuce product from store shelves.
By Bill Hudson November 21, 2018 at 6:41 pm Filed Under:Bill Hudson, Center For Disease Control And Prevention, Local TV, Revol Greens, Romaine Lettuce
MINNEAPOLIS (WCCO) — The nationwide recall of romaine lettuce couldn’t have come at a worse time. As families prepare for their Thanksgiving Day feasts, romaine lettuce is being pulled from their tables.
On Tuesday, the Centers for Disease Control and Prevention issued a nationwide romaine recall based on 32 recent illnesses in 11 states and 18 reported illnesses in Canada.
All are likely linked to eating romaine lettuce contaminated by E. coli. It’s believed the field-raised lettuce may have been contaminated by irrigation water that contained the E. coli 0157 strain.
Acting on the CDC’s recommendation, grocers nationwide are pulling suspect romaine lettuce product from store shelves.
But in Medford, the nine-month old Revol Greens company has safer way to grow leafy greens – by raising the lettuce hydroponically indoors.
“We have eight or nine different varieties here that we grow,” said company president Jay Johnson.
Johnson says that unlike lettuce that is grown outdoors in massive fields in Arizona and California, their crops are grown hydroponically – under glass and in pools of irrigation water which they sterilize with ultra violet (UV) light.
“We started from the beginning with food safety in mind, and this is the safest way,” said Johnson. “That’s why it’s difficult to be grouped in with the broad romaine alert.”
RELATED: Romaine Recall Leaves Mpls. Nonprofit Looking For Nutritious Replacement
It’s also why Revol is working with the industry’s lobby to ask federal regulators to exempt indoor grown lettuce from the recall. Arguing that unlike field-raised crops, their romaine lettuce is never exposed to possible contamination sources from birds or animals.
“E. coli comes from the intestines of animals and birds. So [unlike] a bird flying over your field or an animal running through your field, we are enclosed with this glass greenhouse,” explained Johnson.
Even without more clarity from the CDC, Johnson says other lettuce varieties, such as iceberg and baby arugula are not impacted by the recall and will remain on grocers shelves.
Finally, Revol Greens wants to assure customers who might have its romaine lettuce in their refrigerators that it is safe to eat. Because it is grown not in a farm field, but in the company’s controlled and sterile environment.
Rooftop Greenhouse Teaches, Nourishes and Empowers Students
The nation’s first student-run rooftop greenhouse with the capacity for year-round food production helps stock the UA Campus Pantry.
By Emily Dieckman, UA College of Engineering
Nov. 20, 2018
Gene Giacomelli, left, former director of the UA's Controlled Environment Agriculture Center, talks tomatoes with Todd Millay, director of the Arizona Student Unions, in the greenhouse on the Student Union roof.
EXTRA INFO
The UA Campus Pantry has food distribution days from noon to 7 p.m. on Wednesdays and from 11 a.m. to 3 p.m. during the academic year. Tours of the rooftop garden are available on Wednesday mornings at 10 a.m. and can be signed up for at the Arizona Student Unions information desk.
Stacy Tollefson, project and production manager for the greenhouse and a professor of practice in the Department of Biosystems Engineering, tends the crops in the greenhouse atop the UA student union building.
Twice a week in the basement of the Student Union Memorial Center, about 500 students, faculty and staff pick up free groceries at the University of Arizona Campus Pantry.
Twice a week on the roof of the student union, UA students and future commercial growers harvest cucumbers, tomatoes and bell peppers from the Rooftop Greenhouse and send the vegetables down to the Campus Pantry. This student-designed, and mostly student-run, controlled-environment facility is the first rooftop campus greenhouse in the nation that can produce food year-round, with 10 times the productivity of an outdoor garden.
“We harvest on the same days the campus pantry does distribution and bring the food right down, so the produce is super fresh,” said Stacy Tollefson, project and production manager for the greenhouse and a professor of practice in the Department of Biosystems Engineering, as well as an expert vegetable grower for the UA’s nationally recognized Controlled Environment Agriculture educational program.
Seed of an Idea
Student volunteer Maggie Lacross, UA Campus Pantry operations chair, offers some nutrition guidelines.
When Todd Millay became director of the Arizona Student Unions in December 2016, he was excited to see there was a small outdoor garden on the roof being run by staff. When he heard about the Campus Pantry, which was serving about 30-40 people every few weeks, he offered pantry volunteers a central campus location in the Student Union, but noticed they weren’t receiving many fresh produce donations. The potential for connection seemed clear.
“Why don’t we just make a better garden on the roof and send the food down?” he thought. “And maybe instead of Student Union employees figuring out how to do this, we could ask students how to build it.”
Millay and some Student Union colleagues partnered with the UA Office of Student Engagement and launched a four-month competition. Twenty-five groups of five students each were given a hypothetical $50,000 budget to design a cost-effective, productive and sustainable system to grow fresh produce for the Campus Pantry. Coca Cola, Shamrock Farms, the UA Student Union, the UA Student Services Fees Grant and the UA Green Funds Grant helped finance the competition and the eventual greenhouse.
The winning team, composed of four UA College of Engineering students and one UA College of Agriculture and Life Sciences student, proposed a 750-square-foot temperature-controlled greenhouse that would grow tomatoes, cucumbers and bell peppers. Design advice from Gene Giacomelli, a professor of biosystems engineering and the former director of the Controlled Environment Agriculture program, combined with donations from companies like Autogrow, Formflex, Grodan, Wadsworth Control Systems and Polytex Inc., led to the greenhouse’s construction in 2018.
The Tech Behind the Tomatoes
The greenhouse is temperature-controlled and could yield produce year-round, but the team harvests for nine months and takes the summer off to prepare for new student recruits and start afresh. In those nine months, Tollefson expects the greenhouse to yield 3,000 pounds of cucumbers, 1,200 pounds of tomatoes, 800 pounds of cherry tomatoes and 250 pounds of bell peppers.
The plants don’t get their nutrients from soil, but from two large tanks of solution with just the right mix of nitrogen, phosphorous, potassium and other nutrients. Any solution that isn’t absorbed by the greenhouse’s four rows of plants is recirculated back into the tanks, revitalized and fed back to the plants.
“We’re saving tons of water with this recirculating hydroponic system because we’re only losing maybe 5 percent to evaporation, and we’re saving tons of nutrients,” Tollefson said.
In addition to conserving water and nutrients, the recirculation system ensures that no fertilizer water is discharged into the environment. Another hi-tech feature is that the greenhouse climate and irrigation control systems are connected to the internet: The greenhouse team can log in and monitor the nutrient solution for pH, electrical conductivity and temperature from their phones.
Efforts Bearing Fruit
Tollefson, who has a Ph.D. in agricultural and biosystems engineering, said working at the greenhouse has been an excellent learning experience, even for her – this is the first time she has grown hydroponic tomatoes while recirculating the nutrient solution, so both she and the students are learning how to manage plant nutrition more efficiently. Student interns are learning hydroponic cultivation techniques and greenhouse management techniques that translate to valuable career skills.
“There’s a tremendous demand out in the industry for people who know how to operate these greenhouses because of the recent interest in locally grown and urban agriculture,” Giacomelli said.
Tollefson oversees two interns – plant sciences major Chris Patzke and veterinary science major Tyler Rodriquez – and full-time greenhouse manager Quinn Waltz, a senior majoring in agricultural technology management.
The greenhouse team makes frequent visits to the greenhouse to check on the hydroponic system, care for the plants and monitor the environmental conditions, and harvest, weigh and deliver the crops to the Campus Pantry. The idea is to make sure everything is running smoothly – and it certainly is. This fall, the cucumber plants were growing about 2 feet a week, and the tomato plants about 18 inches. The tomatoes and bell peppers are just starting to ripen, but they’re already delivering about 50 pounds of cucumbers to the pantry each week.
“We keep the conditions just right,” Patzke said. “Happy plants grow really fast.”
The students in the greenhouse say they love knowing their work is making a difference in the Wildcat community.
“It’s inspiring and humbling to know we are the first ones working on this project,” Waltz said. “We are setting the foundation for future students who want to be a part of something that impacts others, and want to learn about how and where their food comes from.”
Technological Supplier THORILEX Is Looking For Partners And Distributors
THORILEX launched several new products this summer including reusable THORILEX Hydroponics baskets for an automatic vertical THORILEX Hydroponics system and the company is looking for partners and distributors now.
“We can see a huge opportunity on the vertical farming market that is still moving forward with a significant growth at a CAGR of 22%. The vertical farming market is projected to grow from present 2,45 billion € to 6.54 billion € till the year 2023. We would like to find great partners and distributors to grow.” Explains Marek Hrstka from THORILEX
“I know that we have truly great products that are now placed in the THORILEX Farm in the biggest glass house complex in our country and it is possible to visit the farm to see the products in operation. Finding truly great partners or distributors is important to achieve our strategy.”
“It will take some time to find the right one. We are looking for someone who haS similar thoughts, likes, innovations and have experience in the horticulture industry. It can be a big or a small company or even an individual.
We are looking for a win-win situation where both sides are prospering from mutual cooperation.” Concludes Marek
The Salvation Army Teaches Children How To Grow Indoors
Mark Lindberg, social enterprise ministry specialist at Salvation Army
Photo: Patrick Williams
With help from CropKing, the organization offers educational programs for at-risk youth at its Fresh Face Farm in Akron, Ohio.
November 15, 2018
GIE Media Horticulture Group
Children in and around Akron, Ohio, could help develop systems that could one day be used to grow food on Mars, upload blueprints for “food computers” and grow produce for wholesale and food pantries.
It’s all part of the studies they’re undertaking with the Salvation Army Summit County Area Services (SCAS), which opened Fresh Face Farm, an indoor growing facility, at its Akron Fort Romig location in January 2018.
The indoor farm provides the children learning opportunities in Science, Technology, Engineering and Math (STEM), culinary arts and other subjects, says Major Kevin Jackson, SCAS coordinator. Jackson says about 90 percent of these students are “at-risk,” which the Journal of General Internal Medicine defines as populations that may have low literacy rates, be economically disadvantaged, face abuse or persecution, or experience other issues. SCAS has partnered with Akron Public Schools (although participation at the farm isn’t limited to children in the district), the University of Akron, NASA and MIT. CropKing provided automated hydroponics systems, sole-source lights and other materials.
“The kids are pretty much involved in every aspect,” Jackson says. “Technology is what drives their world, so the CropKing system was perfect for us in terms of the computer and the sensors, and the automation that came with it.”
The students range in age from 18 months to 18 years, Jackson says. Younger students start out learning about aquaponics and ebb-and-flow systems — which take up about 6,000 square feet of the 18,000-square-foot Fort Romig warehouse. Once the students reach about first or second grade, they begin working in a walled-off 7,000-square-foot commercial grow room in the warehouse that The Salvation Army has outfitted with CropKing’s nutrient film technique (NFT) and Bato bucket hydroponic systems.
In the grow room, lettuce and leafy greens flourish under LEDs, while tomatoes prosper under high-pressure sodium (HPS) lights. Mark Lindberg, social enterprise ministry specialist and the operation’s only full-time employee, says the lights run from about 5 p.m. — after the students have gone home — until the early morning hours. Fresh Face Farms sells most of its produce wholesale, but it sends some to food pantries or home with students.
Basil growing in NFT systems under LED lights at Fresh Face Farm
Photo: Patrick Williams
The idea behind Fresh Face Farms began when Jackson, who has been involved with The Salvation Army his whole life, was given an assignment: to come up with a model to break intergenerational poverty. At the time, he was working throughout the western United States, and he tried growing outdoors in Montana. After weeks of 60-degree temperatures, he planted his crops, then in early June, six inches of snow fell. His wife, Linda, who is now also SCAS coordinator, suggested they try a new approach to farming.
After transferring to Akron, Jackson says he ran an online search for a possible equipment supplier and found CropKing in nearby Lodi, which he calls “sheer luck.” He applauds CropKing’s customer service and expertise, calling the business “not just a vendor.” “You know what's amazing to me?” he asks. “Every once in a while, they’ll just be driving by, and they’ll just stop by [and say] ‘Hey, how's it going? Can we take a look around?’”
Lindberg says he has had similar experiences interacting with CropKing. “Paul calls me on my cell phone,” he says. “It’s like, ‘Hey, Mark, I'm going over that way. You going to be there tomorrow?’ ‘Sure!’”
Growing up in Ashland County — a mostly rural area in Ohio — Lindberg says his parents had a garden, and he was interested in horticulture from a young age. He went on to work in facilities management, but after more than a decade with The Salvation Army, the opportunity presented itself for him to work at Fresh Face Farms. In preparation, he took CropKing’s Grower Workshop to familiarize himself with controlled environment agriculture (CEA).
Lindberg has passed some of the information he learned in the workshop onto the students at Fresh Face Farms. One lesson included how to adjust the alkalinity of water to get it to a desired pH range. On a related note, but one not taken straight from his CropKing Grower Workbook, Lindberg also had students guess the pH of orange juice and milk and then assess the pH of those liquids. “That’s one of the things I love, is this is all hands-on [education],” he says. “This is not just show and tell, but it's experiencing.”
The technology and the hands-on education come together to form a learning experience that shows promising results for inspiring children to explore new avenues of interest and excel in their lives and careers, Jackson says. Some of his former students out west have even gone on to study growing in hopes of making it a career. “When you say, ‘Salvation Army,’ it’s just not what you’re thinking,” he says. “That’s The Salvation Army of the future.”
LEDs HPS Lighting Hydroponics Tomato Indoor agriculture Food nutritionLocal food Education Food security CEA Dutch buckets
What’s The Difference: Hydroponics Vs. Aquaponics Vs. Aeroponics
Three distinct systems – all vying for the top spot in the niche of alternative growing systems.
May 9, 2018
By Heather
Three distinct systems – all vying for the top spot in the niche of alternative growing systems.
What differentiates these three systems from one another? What makes them work? These are the areas that we will be tackling today.
Hydroponics vs. aquaponics vs. aeroponics – which one is the superior system?
Hydroponics
What Is It?
The principle of hydroponics is the oldest among the three because the use of soil-less setups has been around since the age of the Hanging Gardens of Babylon.
A hydroponics system has two main parts: the grow beds and the reservoir.
The reservoir contains the nutrient solution or the water mixed with various nutrients that plants need in order to grow successfully in the media bed. The grow beds, on the other hand, contain the media and the ‘cups’ that will hold the plants in place.
To clarify, growth media will replace soil in a hydroponics setup. There are many kinds of growth media to choose from: coconut coir, perlite, organic-polymer composites, rockwool, etc.
Among the beginning enthusiasts market, the most popular is coconut coir because it’s 100% organic, expands tremendously with water and can accommodate plants easily – with spectacular results.
Perlite, on the other hand, is hailed as a near-perfect medium for growing plants but it is particularly light, which makes it problematic for flood and drain systems as it can easily float away along with the small current of the water in the grow bed.
Organic-polymer combos/composites like Perfect Starts are becoming increasingly popular because they’re easy to use and are not deformed when germinating plants are transferred from the growth trays to the main growing beds.
And finally, we have rockwool. Rockwool is a type of reusable media as it can be sanitized with steam washing after every growing season.
Rockwool is actually melted rock spun into slabs and other shapes/sizes for the purpose of growing plants.
The main point of contention with rockwool is that it’s not very environmentally friendly and thus, it goes against the main principle of switching to a more environmentally friendly method of cultivating plants.
The type of media used in a hydroponic system is so important because it will dictate the efficiency in which plants will be able to absorb the nutrients from the solution.
One of the key problems with hydroponics is that roots sometimes succumb to low oxygen levels, which predisposes crops to premature death.
A solution that growers have found effective in dealing with poor aeration and oxygen zone issues is combining two kinds of media to get the best attributes of each one.
Our personal recommendation would be to combine 50% coconut coir with 50% perlite.
Perlite is amazing when it comes to absorbing and delivering moisture plus it also improves the overall aeration of the plant’s root area. Both are highly regarded in the hydroponics community and both are also widely available to growers everywhere.
Tip: Coconut coir can be made more effective with the addition of perlite.
Hydroponics Pros And Cons
The main advantage of hydroponics is it’s designed for long-term cultivation of almost any kind of crop.
Commercial hydroponic growers harvest hundreds of kilograms of crops easily using large rockwool slabs.
The system simply works and can be easily expanded if you want to make money off your hydroponics system.
The downside is that with the booming interest in hydroponics in recent years, the price of the chemical compounds needed to create a viable nutrient solution has been steadily rising due to the over-mining of these minerals.
Another problem with hydroponics is that it uses relatively more water because after a time the buildup of salts becomes too much for the system and water has to be replaced so as not to kill the plants.
Also, there is a need to check the electrical conductivity of the water every day to make sure that the pH of the water is just right. Fluctuations in the pH level of the water can damage plants and eventually cause a die-off.
Aquaponics
Aquaponics is a hybrid system that combines the best of aquaculture and hydroponics. System-wise, it looks like a hydroponic system, but instead of relying on a main reservoir that contains a nutrient solution, the source of nutrients will be a vat of live, swimming fish.
How does this work? When you feed fish, the fish will naturally excrete waste. The waste mixes with the water, increasing the ammonia levels.
Obviously, this waste has to be mediated and reduced, so as not to kill the fish. Normally, fish tanks are regulated by biological filters and other types of filters that neutralize ammonia and reduce the impact of feces on the fish.
In an aquaponics setup, water from the fish tank is recirculated throughout the system so that it passes through the grow beds, where crops are steadily being cultivated.
The plants absorb dissolved nutrients in the water and process ammonia, which is highly toxic to fish in increased levels.
Bacteria residing the in the roots of plants, as well as good bacteria from the gut of fish work together to establish a balanced ecosystem where both fish and plants will survive.
After about half a year, the mini-ecosystem formed by an aquaponics setup will begin to show signs of high-level, self-regulation.
This will be the time when both fish and plants will begin to truly flourish. There will be great increases in both fish yield and plant yield, and the maintenance of the system will become even easier.
Tip: Be sure to check the roots of plants for signs of rot.
Aquaponics Pros And Cons
The best thing about aquaponics is you will be essentially hitting two birds with one stone – you will be raising fish and growing crops at the same time.
Fish waste, which is something that is regulated in aquaculture, will no longer be considered a problem because it becomes a sought-after source of nutrition for the plants.
Without fish waste, plants wouldn’t have nutrients.
The plants, on the other hand, will serve as a 24/7 ammonia control center for the fish tank, reducing the ammonia load and preventing toxicity in the water.
Fish are sensitive to ammonia and even a small increase in the ammonia content in the water can cause stress, shock, and disease.
Additionally, aquaponics growers now add red worms to the grow beds to increase the efficiency of waste breakdown and subsequently, the distribution of nutrients to plants.
Red worms are first grown on soil and upon adulthood, they are then soaked/washed and then transferred to the growth bed of an aquaponics setup.
The process of breaking down physical waste into smaller particles through the digestive action of red worms is – you got it right, composting!
Yes, it is amazing to imagine that you can actually compost organic material on a grow bed, on stuff that isn’t actually soil.
But there you have it – red worms do the job quite splendidly.
In addition to helping improve the nutrient levels of the water being fed to the plants, there is another big reason why red worms are now being regularly included in aquaponics systems: e. coli.
E. coli is a common pathogen/bacteria found in fish feces. E. coli infections can bring down a full-grown, healthy adult and bring him to the hospital.
Imagine what a widespread e. coli outbreak can do to a tank full of fish, with no other place to hide from the swimming bacteria.
E. coli colonizes fish feces, so these need to be broken down more quickly to prevent an e. coli outbreak from taking over the system.
Red worms can do this perfectly because they need to eat fish feces to survive.
Is there a downside to an almost perfect system? One of the downsides of aquaponics culture is you have to be very specific with the design of the system so you won’t have to shut it down during the winter.
Obviously, you can’t move large equipment and vats indoors, unless you have a really big house (or garage) but all the same, it’s an issue since frozen water can easily kill fish and winter does the same to plants.
Another downside to the system is even if you only want to grow crops for consumption or sale, you still have to tend to your fish well enough so they don’t continually die off.
Fish care can be learned and if you are a natural hobbyist and if you don’t mind looking at another component in a system, then tending to your fish won’t be much of a problem.
Aeroponics
What is It?
Aeroponics is a variation of hydroponics, but instead of using a grow bed filled with media, the plants are instead suspended, with roots facing a sprinkler system connected to the main nutrient reservoir.
Depending on the plant and the design, aeroponics systems generally use little to no media at all.
Now, you may already be wondering – what is the point of all this?
Why not just use media like everyone else? Why do you have to install a sprinkler system that periodically sprays the roots of plants with the nutrient solution?
It all boils down to oxygen. Believe it or not, even if the roots of the plants are down there in the soil, these still need oxygenation in order to thrive.
One of the limitations of hydroponics is because the roots are also submerged in water and the media, there is often poor oxygenation, which hampers plant growth.
Aeroponics solves this problem by completely liberating the roots of the plants and allowing it to come into contact with pure air.
The results are astounding.
Crops grow two to three times their normal size and yields are simply amazing.
Root formations are also incredible. Normally, the taproot of plants only have a moderate amount of root hairs around them.
In plants grown using the aeroponics method, the roots flourish widely and the root hairs become really thick – a tangle of healthy root hairs just enjoying the exposure to oxygen.
Aeroponics Pros And Cons
As with any system, aeroponics has its own set of ups and downs. The main advantage of this system is crops grow incredibly quickly and the yields are high.
If you are after high yield and shorter growing periods, aeroponics is certainly something to think about, especially if you are already investing in equipment and space for this endeavor.
Aeroponics also uses the least amount of water over time and all excess water that isn’t used by the roots of the plants are simply drained back to the nutrient tank.
Tip: Always have backup power and an extra pump in an aeroponics setup.
The nutrient tank is checked daily, much like a conventional hydroponics system.
The pump and spray system is submerged in the water and through a simple timing mechanism, is able to deliver short mists of water to the roots of the plants.
And now for the downsides. Room air doesn’t store water, even if it’s really humid. Humidity is not enough to sustain the roots of plants at all.
Aeroponics is extremely dependent on the misting system. If something should happen to the misting system, then the plants can die easily as a result of dried up roots.
To avoid this, you have to plan ahead. The misting system needs to have backup power and you need to have a backup misting system too, in case the first one fails for some reason. This usually means having an identical pump waiting in store to replace the main once it breaks down.
The misting heads also need to be checked periodically for clogs. We recommend replacing these misting heads instead of just cleaning them to get optimum results.
Remember – your plants are at the mercy of the misting system. They’re not submerged in water and plants are like fish out of water when there’s periodic misting taking place.
Young Fijian Makes Good Use Of Govt Scheme
A Fijian who studied in India has made the most of Government’s Young Entrepreneurship Scheme and embarked on a journey to combine engineering and agriculture.
September 22
18:56 2018
by SWASHNA CHAND , SUVA
Entrepreneur, Rinesh Sharma.
A Fijian who studied in India has made the most of Government’s Young Entrepreneurship Scheme and embarked on a journey to combine engineering and agriculture.
Rinesh Sharma, 25, is an entrepreneur living in Lautoka who has started up something unique.
“While studying in India, I came across a software engineer who had an indoor hydroponics farm in Goa,” he said.
“After reading his success story, I made up my mind to do the same back home.”
Hydroponics is a method of growing plants without soil by using mineral nutrient solutions in a water solvent.
“Engineering combined with agriculture allows me to grow plants in its special conditions and parameters, maximising faster yields,” he said.
“I grow include strawberries, mint, coriander, coral lettuce and butter crunch lettuce. The idea of hydroponics came to me in my third year of engineering.
“Since then, I have researched every day about executing this project on a commercial scale in Fiji.”
Mr Sharma said he came back to Fiji in May and started an automated hydroponics system, in which he grew green leafy vegetables in his backyard.
“This was a challenging process because it was almost impossible to find hydroponic system supplies in Fiji, but regardless I made a small prototype where I can harvest 372 plants per month,” he said.
“Doing farming is the best thing I have done and perception really does matter because we have a lot of people who left farms and moved to the urban life and this has created a huge gap to fill in the field of agriculture.”
Mr Sharma said for him it was a mission to feed the world and he was going to start with his country.
“Upon my arrival in Fiji, I had applied for the YES entrepreneurship scheme run by the Ministry of Trade, Tourism and Industry with the intention to begin an automated hydroponics farm in Fiji on a commercial scale and got a grant of $20,000,” he said.
He is thankful to the Government for providing him with the assistance.
“The assistance is motivating and encouraging for us the younger generation to do step forward and do something,” he said.
“I keep challenging myself with growing the most impossible edible items such as blueberries, raspberries and apples as well.
“It is important that people of Fiji are able to afford proper nutritional meals every day and that to at low cost.
“So, as a hydroponics farmer, I am able to control any device in my farm through a single touch on my phone via internet and I am also able to receive any data changes that may occur, such as change in PH, moisture, temperature.
“It was a privilege to be given a scholarship by the Indian High Commission where I got to learn so much.
“I came back to Fiji with the intention of working with the Government and their expertise to change and shape farming methods in Fiji.”
Edited by Epineri Vula
Feedback: swashna.chand@fijisun.com.fj
Hydroponic Seed Starting 101: A Primer For Beginners
Starting your seeds hydroponically has many benefits, but many people are unsure how to go about it. Shannon McKee gives us a primer on the basics of starting your own seeds to expand on what you’re currently growing.
Shannon McKee | July 10, 2017
Takeaway: Starting your seeds hydroponically has many benefits, but many people are unsure how to go about it. Shannon McKee gives us a primer on the basics of starting your own seeds to expand on what you’re currently growing.
Many people skip starting their own seeds because of the time and effort to get them started, but there are some great reasons to start your own seeds hydroponically. It’s so much easier to just go to the store to pick up some seedlings to pop into your system and get growing, right? Well, store-bought seedlings do have some downsides that can be avoided if you start your own.
The first is that you’re limited to what you can grow in your system. You have to choose from the options available at the store. However, if you start your own seeds, you can grow anything. This means you can grow your favorite heirlooms or even rare plants that aren’t found at many nurseries.
Adding seeds to your hydroponic system means that they won’t go through any trauma or root damage from being transplanted into your system. This process may also introduce diseases or bugs into your hydroponic system from the store.
Also, you get the satisfaction of growing a plant from a tiny seed rather than just picking up a seedling. Plus, a packet of seeds can grow a number of plants for just a few bucks, whereas the cost of only one seedling can be the same amount.
Seeds are also more cost-effective than buying one or two seedlings in the long run, as you can save some for the following year. The germination rate can decrease over time, but often, you can still get quite a few to sprout over the years until you have to buy your next seed packet.
What You Need to Start Seeds in a Hydroponic System
The first time you start your own seeds for your hydroponic system may be a bit more expensive at the beginning because you need to buy more materials than in future years. Seeds need water, light, oxygen, and heat to grow. You really don’t need anything too special to grow your own seeds.
You can use a grow tray with a dome for your own miniature greenhouse to create an ideal environment. If you’ll be growing your seeds in an area that is cooler, you may want to invest in a heating mat that goes underneath the grow tray to keep it warm as this is a necessary condition for sprouting to occur. Light is good to have as well as this will help your seeds sprout.
Inside of your grow tray, it can be beneficial to use a pot that works for your seeds and their future as seedlings in your hydroponic set-up. You’ll want to use starter cubes, such as those made of stonewool (rockwool). The key here is to use something that can withstand being immersed in water without dissolving, as it could clog up your system after transplanting.
Step by Step Instructions for Sprouting Seeds in a Hydroponic System
The first thing that you’ll want to do is to soak your starter cubes in clean water for about an hour. After they’ve been given a chance to soak, put a few seeds into the cube’s hole. You’ll want to add several just in case you have some seeds that don’t germinate. Once they sprout, you can thin out the weaker plants to allow the strongest to grow.
Prepare your grow tray with about an inch of clean water or nutrient solution that is at half strength. Arrange the light source and heating mat as needed. You can keep the lid on to keep the heat and moisture in the tray.
Put these planted cubes into the grow tray and add water or the half strength nutrient solution as the level goes down in the grow tray.
After about four days, you’ll start to see some sprouts emerging.
Some people prefer to use a Ziploc bag, rather than a grow tray, when trying to get the seeds to germinate as it functions like a greenhouse. Seal the bag with a little bit of air and put it in a dark place for about four days to get the seeds sprouted. Then, you can put the starter cubes with sprouted seeds into the grow tray.
Step by Step Instructions on Transplanting
Keep your tiny seedlings growing strong with your hydroponic nutrient solution. Once they’ve gotten bigger, you don’t have to make the nutrient solution half strength.
You’ll start to see the seedlings’ roots coming out of the bottom of the cube, and this is the sign you’ve been waiting for, as it means you can start transplanting. This can take about two to four weeks depending on what plants you’re growing.
Clear up a spot in your hydroponic system’s growing media for the seedling – cube and all. Gently transfer the starter cube into your growing media, and cover it gently.
Give the root system a chance to naturally seek out the water and nutrients in your system by top watering it for a few days to give it a chance to grow the root system.
Voila! You grew your own seedlings into a strong plant for your hydroponic system. Depending on the type of plant, you’ll be able to get your first harvest about four to eight weeks from the time you transplanted your seedlings.
Cut out the dependency of only being able to grow the types of plants that are available as seedlings at your favorite gardening store. Take a little extra time to nurture your seeds so that they become strong seedlings ready to transplant into your system. You’ll be able to take pride in your efforts with how healthy your plants are and your overall system’s health.
What Are The Best Plants To Grow With An Ebb and Flow (flood and drain) Hydroponic System?
Hybrid seeds will give you significantly higher yields and multiple disease-resistant properties.
Written by Lynette Morgan
Q:
I have an ebb and flow (flood and drain) hydroponic system. I have tried growing many types of plants, but the best performers in the system were lettuce, cucumbers and tomatoes. As I only have a 320 square foot greenhouse and wish to share the produce with my family, I want to grow the most productive plants. Can you suggest the best seeds for me to purchase for lettuce, cucumbers and tomatoes? I live in northern Florida. Thank you!
A:
The best varieties for a small, hydroponic greenhouse in your climate would be hybrid types of tomato and cucumber plants, and heat-tolerant cultivars of lettuce. Hybrid seeds will give you significantly higher yields and multiple disease-resistant properties. They perform well under hydroponic growing conditions where they receive the ideal levels of advanced nutrition. Lettuce is essentially a cool-season crop and can struggle in warm growing conditions, so selecting more heat-tolerant or bolt-resistant types is recommended to help prevent problems such as upward stretching, or the development of tip burn under high temperatures. The following would be my seed recommendations for a hydroponic system in Florida:
Tomatoes
Beefsteak: Trust F1 and Geronimo F1. These are both grown commercially in greenhouses and are ideal for hydroponics. The fruit is large, so fruit trusses may need some support due to their weight. These varieties also have multiple disease-resistant properties. Hybrid tomato plants need plenty of potassium when the fruit is developing, so I recommend using a high-quality fruiting or bloom nutrient formulation at this stage.
Cherry: Flavorita F1 or Sakura F1. Both are red cherry tomatoes with a good, sweet flavor and multiple disease-resistant properties. They are less prone to splitting or cracking than other cherry types.
Cucumbers
There is quite a wide range of cucumber types that can be grown hydroponically. Here are some of my top recommendations:
Long, seedless Dutch type: Tyria F1. Fruit are 14 inches long, great-tasting, thin-skinned and non-bitter. They also have some resistance to powdery mildew, which is a huge advantage when it comes to cucumbers.
American slicer type: Corinto F1. Fruit are 7-8 inches long, have good disease resistance and are highly productive in hydroponics.
Mini cocktail type: Iznik F1. Harvested when just 2-3 inches long, and also called snack cucumbers, these cucumber seeds are a good variety for hydroponics as they produce a lot of thin-skinned fruits.
Lettuce
It pays to try growing a wide range of lettuce types, depending on your personal preferences, of course. However, the following types are proven performers in hydroponic systems:
Green butter lettuce: Pelleted Rex seeds are the best in terms of handling and germination. This lettuce is ideal for Florida’s climate. It is slow to bolt and very reliable. It also tolerates downy mildew.
Green frilled type: Muir. It is a medium-sized, light green, open and slow-growing variety. Muir is fairly heat tolerant and has a good flavor.
Salanova: For a mix of different lettuces and a surefire way to impress friends and family, the latest hydroponic lettuce trend is the Salanova lettuce types that produce compact heads of leaves that are all totally uniform in size and shape. I recommend the Salanova Home Garden Mix pelleted seed that will produce a range of colored Salanova types. This seed is a little more expensive than other lettuce types since it is a reasonably new development, but it is well worth the investment, particularly with the deep red types.
All of these seed varieties are available online from Johnny seeds (johnnyseeds.com) in different-sized packs. Good luck with your hydroponic greenhouse this season!
Have a question? Ask us here.
View all questions from Lynette Morgan.
Step Inside The Hydroponic Farm Supplying Greens To Legacy Hall
Sprouting up: Margot Masinter holds a flat of microgreens grown inside a recycled shipping container. Billy Surface
With Doodle Farms, Margot Masinter is ready to give North Texas something homegrown to graze on. First stop: Legacy Hall.
BY STACY GIRARD
PUBLISHED IN D MAGAZINE JULY 2018
Growing up, Margot Masinter had little interest in dresses or dance classes. Instead, when she wasn’t dodging hockey pucks shot at her by her two older brothers, you could find her outside, digging in the dirt. It’s how she earned her family nickname, Doodlebug.
It was while in high school, during her first summer job working on a farm in Asheville, North Carolina, when she considered her interest might be more than just a recreational pastime. Proof came while attending Middlebury College, pursuing a degree in environmental studies. Her passion and education were further shaped through courses in farming and food policy, and part-time jobs: growing crops at Dallas’ Eat the Yard, establishing new colonies for the Texas Honeybee Guild, and working at an apple orchard in Vermont.
Trading acres for square feet, Masinter purchased a refurbished and recycled shipping container from Dallas-based Growtainer.
In Masinter’s case, some things never change. The 23-year-old natural beauty still prefers planting to primping and faithfully answers to her pet name—a name that opportunely serves as the DBA for her urban farming start-up, Doodle Farms, which supplies local restaurants with sustainably grown produce.
“We need more small-scale farmers,” she says. She expressed her convictions to her father, Mark Masinter, a successful real estate investor and developer and a partner in the 250-acre Legacy West development. The conversation yielded the idea of an on-site hydroponic farm that would service the Legacy Hall food stalls and area restaurants.
Trading acres for square feet, Masinter purchased a refurbished and recycled shipping container from Dallas-based Growtainer to house her chemical-free greens and herbs. The 53-by-10-by-9 metal box is docked on the Hall’s second floor, overlooking the outdoor Box Garden and music stage. Outfitted with LED lights, grow racks, fertilizing tanks, an irrigation system, and an AC unit with fans that control airflow and regulate temperature, the Growtainer provides a perfectly controlled growing environment.
Before she’d harvested her first crop, Masinter had already secured business with Legacy Hall’s Whisk & Eggs, Bravazo Rotisserie, and Détour, as well as other local restaurants—Sixty Vines, Haywire, The Ranch at Las Colinas, Whiskey Cake, Shinsei, Town Hearth, and Imōto, Tracy and Kent Rathbun’s new Pan-Asian concept. And her dad is such a believer in his daughter and the container-to-table concept that he became her partner in the company. “I loved the idea and wanted to be a part of it,” he says.
Masinter’s fast-cycle microgreens and other highly perishable crops—able to be harvested every eight to 28 days—are densely planted and require very little fertilizer. Masinter admits it is not the most sustainable way to farm—“You still have to use electricity,” she says—but growing in an urban environment requires compromises. “I’ll learn a lot this year and make any changes I need to,” Masinter says. “If anything, it will be a good experiment.”
Her next sustainable urban farm, a procession of raised beds, is already planned on a Henderson Avenue plot across from Gemma. This time, she’ll be back on terra firma and doing what she loves most—digging in the dirt.
Hydroponics Gives Local Veg Production Further Boost
It is learnt that hydroponics systems, a technology suitable for Qatar’s environment even during the summer, can grow watermelons extremely well, producing big and sweet varieties.
September 28 2018 08:18 PM
Prominent Qatari agriculturist Nasser Ahmed al-Khalaf showing the watermelons in his farm near Al Khor.
Qatar’s aim for self-sufficiency in food production has got a major fillip as a local farm succeeded in growing and improving the quality of certain types of vegetables and fruits with hydroponics system.
Prominent Qatari agriculturist Nasser Ahmed al-Khalaf told Gulf Times that his farm will harvest in the coming weeks melons and water melons, grown for the first time in the country using hydroponics.
"We have as well increased the (production of various types of) herbs,” disclosed al-Khalaf, who is also the owner and managing director of Agrico.
A private Qatari agricultural development company established in 2011, Agrico produces organic vegetables and fruits year-round in Al Khor using hydroponics systems and aims to help Qatar achieve food security.
Al-Khalaf said that they will be harvesting between 800kg and 1,000kg of watermelons per week from next week while melons would take 30-45 days more. These types of fruits are grown separately in two greenhouses.
Agrico now produces large-size watermelons with hydroponics system
It is learnt that hydroponics systems, a technology suitable for Qatar’s environment even during the summer, can grow watermelons extremely well, producing big and sweet varieties.
While some local farms also produce melons, al-Khalaf pointed out that Agrico uses hydroponic system and aims to grow vegetables and fruits year-round.
“Any new item we introduce we try to make it sustainable in order to supply the market on a daily basis,” he stressed.
In the mushroom family, the company now added shiitake and oyster mushrooms in its production. By next year, it will also grow some hard vegetables such as carrots and beetroots.
Agrico also plans to experiment with growing bananas by the end of this year, apart from organic papayas and other fruits such as lemon and pomegranate.
Al-Khalaf noted that Agrico’s operations expanded substantially in the previous season to further increase its production and meet the growing demand for fresh produce. It is now exporting various vegetable items to Kuwait and Oman.
After proving it can produce year-round in the past years, even during the summer, he pointed out that they developed other greenhouse systems in a much economical price.
“Our aim in 2018 was to focus more in developing our agriculture system in other farms, which we did by developing over 20,000sqm of greenhouses under our own operation,” al-Khalaf said.
“Besides Agrico, we are also keen in developing other farms using our technology and transferring this know-how to improve the farms in Qatar to make production sustainable,” he observed.
Around 300 of the 1,400 farms are continuously increasing their production of various vegetables since last year and this number is also growing, according to al-Khalaf.
"Qatar residents will also see a huge difference in the quality of existing items this season, especially in tomatoes, cucumber, zucchini, capsicum, and eggplant," the agriculturist added.
Skyscraper Farms, Solution To World's Rising Food Demand, Set To Go Global
In a suburb of Kyoto in Japan, surrounded by technology companies and startups, Spread Co is preparing to open the world’s largest automated leaf-vegetable factory.
At vertical farms sealed room protects the vegetables from pests, diseases and dirt
The problem has always been reproducing the effect of natural rain, soil and sunshine at a cost that makes the crop competitive with traditional agriculture
Bloomberg Last Updated at October 31, 2018
In a suburb of Kyoto in Japan, surrounded by technology companies and startups, Spread Co is preparing to open the world’s largest automated leaf-vegetable factory. It’s the company’s second vertical farm and could mark a turning point for vertical farming — bringing the cost low enough to compete with traditional farms on a large scale.
For decades, vertical farms that grow produce indoors without soil in stacked racks have been touted as a solution to rising food demand in the world’s expanding cities. The problem has always been reproducing the effect of natural rain, soil and sunshine at a cost that makes the crop competitive with traditional agriculture.
Spread is among a handful of commercial firms that claim to have cracked the problem with a mix of robotics, technology and scale. Its new facility in Japan will grow 30,000 heads of lettuce a day on racks under custom-designed LED lights. A sealed room protects the vegetables from pests, diseases and dirt. Temperature and humidity are optimised to speed growth of the greens, which are fed, tended and harvested by robots. “Our system can produce a stable amount of vegetables of a good quality for sale at a fixed price throughout the year, without using pesticides and with no influence from weather,” Spread President Shinji Inada, 58, said in an interview at the company’s existing facility.
Inada won the Edison Award in 2016 for his vertical-farming system. He expects the new factory to more than double the company’s output, generating 1 billion yen in sales a year from growing almost 11 million lettuces.
About 60 per cent of indoor-farm operators in Japan are unprofitable because of the cost of electricity to run their facilities. Most others only turn a profit because of government subsidies or by charging a premium to consumers for vegetables that are chemical-free. Spread sells lettuces for 198 yen a head to consumers, about 20 to 30 percent more than the normal price for conventionally grown varieties, according to Inada.
First Published: Wed, October 31 2018
Leafy Greens are Grown by Machines at New, Automated Silicon Valley Farm
Called Iron Ox, the farm aims to produce leafy greens — romaine, butterhead, and kale, alongside various herbs
Luke Dormehl POSTED ON 10.13.18 - 1:00PM
Did you hear the one about the Google software engineer who packed it all in to start a farm? No, it’s not the setup for a joke. Nor is it the premise for some quirky Sundance comedy, probably telling the story of a stressed-out programmer who rediscovers their happiness by moving to the country. It’s a real, honest-to-goodness farm, which just opened in San Carlos, around 20 miles outside San Francisco. Called Iron Ox, the farm aims to produce leafy greens — romaine, butterhead, and kale, alongside various herbs — at a rate of roughly 26,000 heads per year. Oh yes, and it’s staffed almost exclusively by robots.
“This is a fundamentally different way of approaching farming,” CEO and co-founder Brandon Alexander, 33, told Digital Trends. “Traditionally, the farming process means that you seed, you wait a few months, you come back, you harvest, and you distribute. That hasn’t changed a whole lot in hundreds, if not thousands, of years.” Until now, at least.
Iron Ox’s indoor farm measures around 8,000-square-feet. That makes it paltry compared to the thousands of acres occupied by many traditional farms, but, through the use of some smart technology, it promises a production output that’s more in line with an outdoor farm five times its size. To achieve this, it has a few tricks up its sleeve. For starters, Iron Ox is a hydroponics farm, a method of growing plants without soil, using mineral nutrient solutions in a water solvent. Unlike a regular farm, hydroponic farms grow their produce in vertical and horizontal stacks; every element minutely controlled through the use of glowing LED lights and jets of water to affect the crops’ size, texture, and other characteristics.
In place of a farmer, Iron Ox employs a giant, 1,000 pound robot called Angus. It’s Angus’ job to move the heavy 800 pound, water-filled tubs of fresh produce without spilling them. A robot arm is used to tend the crops, making this the agricultural equivalent of Elon Musk’s automated Tesla factory in Fremont, CA.
“We’ve taken a robotics-first approach to the growing,” Alexander continued, in what can only be described as an understatement. “Everything is designed with that in mind.”
DISRUPTING THE FAMILY BUSINESS
When he was a kid, Alexander was shipped off each summer to his grandfather’s family farm in the Texas and Oklahoma area. Looking back at it today, it’s a cherished memory. At the time, not so much.
Iron Ox
“I’ll be honest: I hated it,” he said. “All my friends were going on vacation and I was the one who was stuck on a farm.” When his buddies were sleeping in, he was getting up at the crack of dawn. When they were on the beach, he was on a tractor. Years later, when he and his co-founder and CTO Jonathan Binney, 34, were busy planning out Iron Ox, he called his grandfather. Now 83 and still running a farm, Alexander told him about his plans for roboticizing the work that his family had done by hand for generations.
But this isn’t a story about a guy who decided to take revenge for summers of hard labor by disrupting the industry. Far from it. Alexander has a deep respect for farming, evident from the reverent way that he speaks about a profession that has looked after his family for years.
“[My grandad is] technophobic; he doesn’t know how to use an iPhone [or about machine learning or computer vision],” Alexander said. “But when I explained what I was doing, he said, ‘This is inevitable.’ That kind of surprised me, but it shouldn’t. When he was a kid, and his dad was farming, they managed 40 acres. Now him and his crew are managing 6,000 acres. He’s seen the progression.”
JUST-IN-TIME FARMING
Farming isn’t an industry that’s at the forefront of many people’s minds in Silicon Valley. It probably should be, though, because the emphasis on farm-to-table produce is only growing. When Alexander and Binney speak to chefs, they regularly hear stories about customers wanting to know exactly where a particular bit of produce has been sourced from, or how old it is.
That typically gets an unsatisfactory answer in the U.S., where the average distance travelled by fresh fruit and vegetables is around 2,000 miles. “There are relatively few places that have the right conditions for growing,” Alexander explained. “Everyone else gets week-old produce.”
Iron Ox
Iron Ox aims to change that by building farms within easy reach of cities. Using its autonomous technology, customers can get fresh greens grown in their neighborhood. Better yet, they can get it year round, since an indoor farm isn’t subject to the same seasonal conditions as traditional farms are.
“We call this just-in-time farming,” Alexander said. He is using terminology that is usually applied to manufacturing, pioneered by automaker Toyota in Japan during the 1960s and 70s. What makes just-in-time manufacturing special is that it focuses on making items to meet demand, rather than creating surplus in advance of need. It means less waste with overproduction, less waiting, and less excess inventory. That works well for cars, computers, or smartphones. The Iron Ox team hope it will work great for crops, too.
“In a traditional greenhouse, you’re committed to growing a thousand or tens of thousands of a particular varietal,” Alexander said. “Our systems gives us the ability to fine-tune the nutrients for each crop. We’re only committed to growing a hundred of something at a time. That’s important. Previously you would committed to, for example, kale. ‘Kale’s going great,’ you say. ‘Let’s go all-in on kale.’ But trends change. If we suddenly notice a big demand for purple bok choy or Italian basil, our system can adapt to that consumer demand very quickly.”
Overseeing the farm, like a green-fingered HAL 9000 from 2001: A Space Odyssey, is what Alexander calls “The Brain.” This is a cloud-based, A.I. which constantly monitors information relating to nitrogen levels, temperature, and the location of robots. Over time, it will expand this to take into account data pertaining to food orders, or more general information about food-based trends.
Weighing up all this data, it can then make decisions about exactly what should be growing — and in what quantities — in each of the modular tanks.
THE ROAD FROM HERE
Right now, Iron Ox is starting to take chef’s orders for the two dozen-plus varieties of leafy greens that it is growing from the start. It aims to be in full production by the end of the year. This is still the beginning of the journey, but it’s one that Alexander and his co-founder are happy to be on.
“We had some pretty good, cushy jobs at Google and whatnot,” Alexander said. “We wanted to make sure that, when we took the next step, it was something we were passionate about. It’s not about staying passionate for one year; it’s about whether or not this was something we could put decades of our life into? That’s a different metric, for sure.”
How does he feel about the impact of automation on jobs in the farming community as a whole?
“I think farming is a fairly unique space in this regard,” he said. “Agriculture is one of the few industries right now where they can’t get enough help. That was something that surprised Jon and myself when we first started. When we quit our jobs, we spent four months roadtripping California, talking to farmers. We talked to dozens of outdoor and indoor farmers. One of the questions we asked was ‘what’s your biggest pain point?’ 100 percent of them said that it was labor scarcity. They could not get enough help for their farms.”
Added to this is the fact that, in the United States, the average age of a farmer is 58. “It’s a bell curve distribution, and it keeps shifting over to older and older,” he said.
Those jobs are not being replaced in equal numbers by the younger generation. “There simply aren’t enough people wanting to do this,” he continued. “And I don’t blame them. It’s hard, back-breaking work. It’s just where it’s going.”
Iron Ox isn’t the only startup applying the latest technology to farming. Other companies and researchers are building self-driving tractors for farms, using CRISPR gene editing to improve the efficacy of crops, and building robots that are capable of picking a variety of fresh produce without damaging it. But Iron Ox’s business model nevertheless represents an enormous step potential forward in U.S. agriculture and the way that it works.
In 1820, more than half of the United States population lived and worked on farms. Today, this is fewer than 2 percent of the population, with the overwhelming majority having moved to the city. Thanks to companies such Iron Ox, people may no longer have to choose between farm and city. If people won’t leave the city for farms, then the farms will just have to come to them.
Desktop NFT System
Grow fresh, high-quality leafy greens on your desktop or kitchen counter.
Our unique hydroponic desktop NFT system has all the capabilities of a traditional sized NFT system allowing you to grow fresh, high-quality leafy greens on your desktop or kitchen counter. Perfect for schools, hobby growers and anyone looking for fresh produce year-round!
This system features:
• A removable top cap (lid) makes the channels easy to use and easy to clean.
• End caps on both ends of the channel, keeping light out & preventing algae growth.
• Constructed of non-toxic, food grade, UV-stabilized plastic.
• A standard electric plug – no additional power source required.
• Square top cap holes that are made for 1" seedling cubes.
Specs:
• Measures 16'L x 11'W x 4'H
• Weighs 3.5 lbs when the tank is empty & 12 lbs when it’s full.
System Includes:
• (2) 1' x 4 ⅝' grow channels
• 6 plant sites
• Pump
• Feed line
• 1 ½ gal tank
• Fertilizer & Rockwool cubes
$49.95
Get yours today by calling 330-302-4203!
*volume and educational discounts available
CropKing.com
United States and Israel Collaborative Research: Safe Recycle of Aquaponics and Hydroponics Water
Scientists from the University of Illinois and Agricultural Research Organization, Israel are collaborating to reduce the use of water in aquaponics and hydroponics.
USA.- Scientists from the University of Illinois and Agricultural Research Organization, Israel are collaborating to reduce the use of water in aquaponics and hydroponics. To prevent plant pathogens from spreading in these soilless environments, water disinfection is required.
The researchers found that disinfection with ozone created lower toxic effects than with chlorine. They also found that lower concentration of disinfectants over a longer exposure time created lower toxicity in the recycled water. The results were presented to aquaponics and hydroponics producers in Illinois.
'The Next Evolution of Farming Has Already Begun'
By Austin Stankus - Wednesday, October 10, 2018
The world population continues to grow with ever-increasing urbanization predicted to reach 80 percent by 2050. The U.N. predicts that human population will reach nearly 10 billion by 2050. This increasing population is also growing richer — and hungrier.
To feed this population using traditional farming practices, much more land would need to be brought under cultivation. But, already much farmland around the world has been degraded from poor management practices, and lands remaining available for food production are decreasing from the effects of erosion, salt buildup and pollution.
As you read this today, tens of millions of children are going to bed hungry, with the Food and Agriculture Organization of the United Nations estimating the number of hungry in 2018 at 812 million or approximately one out of 9 people.
Something needs to change. Food production needs to get more efficient, more equitable and more environmentally minded. Moreover, food production should follow the population to the cities, or as Dickson Despommier, a forerunner of this movement, simply states: “Put the food where the people live.”
Indoor farming through controlled-environment agriculture (CEA) will be an important component towards establishing local food systems that can address this pending crisis in global food insecurity. CEA, simply put, is using smart, sustainable farming practices inside of high-tech greenhouses. This is nothing new, and these modern greenhouses are an established technology and can be found around the world. In fact, much of the lettuce, tomatoes, peppers and cucumbers in the EU come from CEA in the Netherlands and Spain.
These greenhouses have incredible benefits compared to traditional farming: They use less water because they are protected from the sun and wind, they use fewer pesticides because insects and disease can be kept outside, and there is less waste because production can be matched exactly to consumer demands.
If hydroponics or other soil-less practices are used, the farmer does not need to use tractors for tilling, plowing and reaping, so the oil bills and energy consumption are lower. In addition, the fertilizer usage is reduced, and all the fertilizer the farmer uses is consumed by the plants, thereby reducing nutrient-rich runoff that can pollute watersheds.
Known as eutrophication, this nutrient pollution is a huge problem for coastal communities in the Chesapeake Bay and Gulf of Mexico and has impacted fisheries, recreational activities and livelihoods around the world.
However, CEA greenhouses can occupy a lot of space. So, the next logical evolution is stacking these modern greenhouses, one atop the other.
Vertical farming, as greenhouses stacking is called, has additional benefits. Reducing the footprint means that more food can be grown in a smaller area and therefore can be brought closer to the people eating that food. As populations move toward the cities, it makes sense for the food to follow.
Part of the vision of vertical farms is the reconnection of the producer and the consumer plus the restructuring of food value chains to become more transparent and responsive to the needs and wants of the people.
An added benefit of farming inside of skyscrapers is the option of having mixed-use buildings. When combined with a wholesale market, the skyscraper can not only produce the food but get it to the consumer faster. Less time in storage, less transportation and less handling means fresher produce and reduced need for postharvest treatments like irradiation and chemical fumigation.
There are still some daunting challenges as well as some encouraging recent developments.
Unleashing the innovative power of American small businesses has jump-started the transition to modern farming, and the public desire for local, healthy food is an economic engine driving the industry toward change. In fact, there are currently so many vertical farm startups that a shortage of qualified workers is now the main hurdle to accelerating the establishment of new indoor farms. On one hand this is a challenge to the industry, but on the other it presents an enormous opportunity for job creation in urban areas if an inclusive, enabling environment is codeveloped with the vertical farms to provide vocational training and career advancement prospects.
On a technical level, there is a significant energy demand needed for pumping water, maintaining good environmental conditions like temperature and humidity, and powering the grow lights to keep producing year-round. However, with smart buildings wired on intelligent platforms, the energy consumption can be monitored and controlled to maximize efficiency — and by tying into other green enterprises like photovoltaic and biogas generation, this energy demand is decreasing day by day. In fact, with the new innovations in LED lighting technology, the power demand has been reduced tenfold in the last few years.
The next evolution of farming has already begun, and big players are already involved. In fact, the National Grange wrote a letter to Congress with their support to public-private funding mechanisms to accelerate the modernization of agriculture, specifically highlighting the potential of vertical farming.
With this type of buy-in from large agribusinesses, national and international agricultural organizations, funded with innovative financial mechanisms, and driven by the innovative spirit and technological power only found in the U.S., vertical farming will feed tomorrow’s children with healthy, safe food; protect the environment while being resistant to environmental shocks; and spur economic growth in the process.
For a detailed look at one such startup, see the centerfold story on Skyscraper Farm.
• Austin Stankus, an integrated farming specialist, is chief science officer at Skyscraper Farm LLC.
China Reaches Top of Global Food Safety List
China moved from fourth place to the top of the list. This announcement explained that this development is due to China being a high-income economy with low custom tariffs for agricultural import products, which helps to reduce the import costs.
The Economist Intelligence Unit recently announced the "Global Food Safety Index". It ranks the food safety level of 113 countries based on an investigation of food origin, product quality, and safety. China moved from fourth place to the top of the list. This announcement explained that this development is due to China being a high-income economy with low custom tariffs for agricultural import products, which helps to reduce the import costs.
However, the announcement also stated that China's food supply is easily disturbed by weather conditions and natural disasters. For example, if weather changes, soil quality, and water supply are included in the investigation, then China drops to number 16 on the list.
Apart from this, China's food supply is also vulnerable because the majority is imported from around 180 countries, so that trade and supply chain problems can easily disturb China's food supply.
Source: News and Current Trends
Publication date : 10/22/2018
As Director of The New School of Plant and Environmental Sciences, Mike Evans Wants to Create an Environment Where Creative Collaborations Lead to Innovative Discoveries
As director of the new School of Plant and Environmental Sciences, Mike Evans wants to create an environment where creative collaborations lead to innovative discoveries.
Mike Evans grew up in rural Pittsylvania County, Virginia, where he spent his summers pulling tobacco and running a soybean drill for his grandparents and neighbors.
He saved enough money during those hot summers to buy his first car — a 1980 Ford Pinto — which he proudly parked in the Cage during his first year at Virginia Tech. He’d been exposed to the university through his high school’s Future Farmers of America program, which brought him to campus to take part in horticultural competitions.
As a student majoring in horticulture, he fell in love with researching the plants he’d been surrounded by his entire life. The intensive laboratory work he did during his undergraduate years at Virginia Tech prepared him well for the rigors of graduate school at the University of Minnesota, where he earned a master’s degree and a Ph.D.
Evans went on to a career in higher education that involved research to help industries thrive, Extension outreach programs that impacted local communities, and academic programs that prepared the next generation of students for the challenges of facing the world.
Now, the Hokie alumnus has returned to Virginia Tech to use all the skills he’s acquired to lead the College of Agriculture and Life Sciences’ latest strategic initiative.
Evans is the director of the newly formed School for Plant and Environmental Sciences, which combines three former departments — horticulture; crop and soil environmental sciences; and plant pathology, physiology, and weed sciences — under one administrative roof.
“When we bring people together you get something new called ‘creative collisions.’ These intersections lead to innovation on a level that changes the paradigm of what is possible,” Evans said. “We want to create an environment in the school where the silos are broken down and people are interacting in unique ways to allow opportunities for more of these creative collisions to occur. This benefits everyone from students and professors to industry leaders and local producers.”
Though faculty and administration have been involved in planning the school via committees, public forms, and other outlets for three years, it becomes officially operational on July 1.
“Mike’s experience makes him the perfect person to lead the school and help our faculty, staff, students, and Extension professionals find new ways to work together to make an even greater impact on our college, the state, and the world” said Alan Grant, dean of the college.
Evans most recently worked at the University of Arkansas, where he was an interim associate dean in the Dale Bumpers College of Agricultural, Food, and Life Sciences. Prior to Arkansas, Evans was a professor at Iowa State University. At both institutions, he was a horticulture faculty member, teacher, and researcher who focused on controlled agricultural environments, such as greenhouses, and how to use hydroponic techniques to increase yields of food crops. He started his career as a researcher at the Gulf Coast Research and Education Center with the University of Florida where he conducted research and Extension programs related to greenhouse crops and ornamental plants.
Evans points to projects he did as a horticultural researcher that show how collaboration can lead to greater impact.
A few years ago, he was researching how lettuce is best grown in a controlled environment using hydroponics. He started to talk with a plant pathologist who was trying to find ways to combat powdery mildew on spinach. The two began to collaborate on ways to grow the spinach in a greenhouse, which allowed for faster growing cycles. This development in the greenhouse helped the plant pathologist do quicker scientific trials than it would have been possible in the field. The teamwork between disciplines was what made the solution possible.
“You never know what innovative, cross-disciplinary solutions are possible until you tear down the walls that exist and build a space where ideas can freely flow — and new ideas can be born,” he said.
Similarly, the school will merge three former departments and bring researchers, faculty, and staff together to use their diverse experiences and skillsets to tackle issues ranging from increased crop production to ways to grow healthier food throughout the world.
None of the majors or degrees offered by the three former departments will change, though Evans said the school will explore creating new majors that build upon the expertise of the faculty and meet the demands of students and industry. All clubs and student organizations will remain as they currently operate. The school also will focus on ways to expand the college’s physical footprint, such as constructing new greenhouses or the future Human and Agricultural Biosciences Building 2.
“I believe that by creating a space where new relationships can form and risk-taking in the name of innovation is encouraged, there is unlimited potential to make a lasting impact in plant and environmental sciences,” he said.
Contact:
South Korean Road Tunnel Smart Farm No Rose-Coloured Pipe Dream
Behind a blue wall that seals a former highway tunnel stretches a massive indoor smart farm bathed in rose-tinted light.
AP | 30 August 2018
Behind a blue wall that seals a former highway tunnel stretches a massive indoor smart farm bathed in rose-tinted light.
Fruits and vegetables grow hydroponically — with no soil — in vertically stacked layers inside, illuminated by neon-pink LEDs instead of sunlight.
Operators of this high-tech facility in South Korea say it is the world’s first indoor vertical farm built in a tunnel.
It’s also the largest such farm in the country and one of the biggest in the world, with a floor area of 2300sqm, nearly half the size of an American football field.
Indoor vertical farming is seen as a potential solution to the havoc wreaked on crops by the extreme weather linked to climate change and to shortages of land and workers in countries with ageing populations.
The tunnel, about 190km south of Seoul, was built in 1970 for one of South Korea’s first major highways.
Once a symbol of the country’s industrialisation, it closed in 2002.
An indoor farming company rented the tunnel from the government last year and transformed it into a “smart farm”.
Instead of the chirrups of cicadas, Claude Debussy’s Clair de Lune resonates in the tunnel in hopes of stimulating the crops’ healthy growth.
“We are playing classical music because vegetables also love listening to music like we do,” said Choi Jae Bin, head of NextOn, the company that runs the vertical farm.
Head of NextOn Choi Jae Bin explains how his high-tech tunnel-based vertical indoor farm NextOn in Okcheon, South Korea, could be a potential solution to the havoc wreaked on crops by the extreme weather linked to climate change, and to shortages of land and workers as the country ages.Picture: AP
Sixty types of fruits and vegetables grow in optimised conditions using NextOn’s own growth and harvest systems.
Among them, 42 are certified as no-pesticide, no-herbicide and non-GMO products, said Dave Suh, NextOn’s chief technology officer.
He said the tunnel provided temperatures of 10 to 22 degrees celsius, enabling the company to optimise growing conditions.
High-tech smart farms, used also in places like Dubai and Israel where growing conditions are challenging, can be a key to developing sustainable agriculture, experts said.
“Society is ageing and urbanisation is intensifying as our agricultural workforce is shrinking,” said Son Jung Eek, a professor of plant science at Seoul National University.
Smart farming can help address that challenge, he said, as well as make it easier to raise high-value crops that are sensitive to temperature and other conditions.
Only slightly more than 16 percent of South Korea’s land was devoted to farming in 2016, according to government statistics.
The rural population has fallen by almost half over the past four decades, even as the overall population has grown nearly 40 per cent.
The Agriculture Ministry announced earlier this year it would invest in smart farm development nationwide, expanding their total area to 7000ha from the current 4010ha.
Turning a profit can be challenging for indoor vertical farms given the high cost of construction and infrastructure.
NextOn cut construction costs in half by using the abandoned tunnel and developing its own LED lights and other technologies.
Sesame leaves grow on a vertically stacked styrofoam layer.Picture: AP
The proprietary technologies reduce water and energy use and the need for workers, cutting operation costs, Suh said.
Sensors in each vertical layer measure variables such as temperature, humidity, light, carbon dioxide and micro-dust levels to maintain an optimised environment for each crop.
The crops will cost less than conventionally grown organic vegetables, Suh said.
The farm will begin supplying vegetables to a major food retailer and a leading bakery chain beginning in late August, NextOn said.
Suh said the medicinal plant market was currently dominated by a few countries and regions.
“Our goal is to achieve disruptive innovation of this market by realising stable mass production of such premium crops,” he said.
Are Hydroponics The Future of Agriculture?
Unlike traditional agriculture, hydroponic systems use a solution of hydroponic nutrients in water to grow plants. A few benefits have been associated with hydroponics, such as saving time and providing healthier crops
Unlike traditional agriculture, hydroponic systems use a solution of hydroponic nutrients in water to grow plants. A few benefits have been associated with hydroponics, such as saving time and providing healthier crops. This has helped the market to grow and be expected to keep growing for the following years.
According to a report by Research and Markets, in 2017 the global hydroponics market reached a value of US$411.88 million. It’s expected that the market will have a value of US$752.57 million by 2022.
Eco-Friendly Farming
Hydroponics eliminates any need for sunlight, soil, or rain. With many pests originating from the soil, hydroponics reduces the likelihood of pests attacking plants. This also reduces the need for herbicides, insecticides, and pesticides. Additionally, the lack of topsoil use prevents topsoil erosion, which increases the difficulty of soil supporting plant growth and storing water.
With arable land decreasing, it’s vital to have a solution that allows for plants to grow in smaller areas. In traditional farming, plant’s roots tend to spread out and expand so that plants can find oxygen and nutrients. Hydroponics, however, soaks plants’ roots in a nutrient solution full of oxygen, allowing plants to be grown closer together.
Possible Anywhere, at Any Time
Independent of climate and weather, making it possible to be done anywhere and at any time. Occupies less land than traditional farming by growing plants in containers and vertically.
Similar to greenhouses, hydroponics allows for complete climate control. Humidity, temperature, air composition, and lighting is adjusted according to plants’ needs. Crops can be grown anywhere and at any time regardless of the weather or the season.
Faster Plant Growth
Hydroponics are more efficient than traditional farming methods, as less water is used than with traditional agriculture. Water used in hydroponics can be recycled many times. This re-circulation prevents wastage and evaporation, as the water reaches the plants’ roots.
Plants grow faster, which allows for bigger yields in short periods of time. Crops flourish in a controlled environment and, with hydroponics having a shorter growing cycle, yields can easily be doubled or tripled.
Healthier Crops
Protection from pests and diseases provides healthier crops and stops the fear of the former spreading to other plants or future crops. Powdery mildew and root rot, for example, can affect the following year’s crops and hinder recovery.
Additionally, hydroponics remove the uncertainty of why plants may be struggling. You have control over your plants’ environment and you can easily balance their pH levels, the nutrient solution, and create a customised environment for every crop.
Control Over Nutrients
With complete control over all resources and nutrients needed by the plants, hydroponics help plants receive more nutrients than through traditional farming. Specific values of nutrients for specific plants are easily mixed with water, reducing the nutrient changes or losses naturally occurring in the soil.
This futuristic concept of growing plants in vertically-stacked layers is often done in indoors through growing methods such as hydroponics. Even in extreme and challenging environments, hydroponics might be a solution for unavailable land for agriculture.