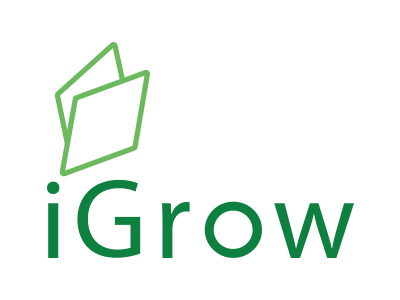
Welcome to iGrow News, Your Source for the World of Indoor Vertical Farming
The Foody Benefits of Farming Vertically
The answer, foodies say, is to go back to a better, gentler age, when farmers worked with nature and did not try to dominate it
More Variety, New And Old Tastes
August 31, 2019
Many foodies pin the blame for farming’s ills on “unnatural” industrial agriculture. Agribusinesses create monocultures that destroy habitat and eliminate historic varieties. Farmers douse their crops with fertiliser and insecticide, which poison streams and rivers—and possibly human beings. Intensive farms soak up scarce water and fly their produce around the world in aeroplanes that spew out carbon dioxide. The answer, foodies say, is to go back to a better, gentler age, when farmers worked with nature and did not try to dominate it.
However, for those who fancy some purple-ruffles basil and mizuna with their lamb’s leaf lettuce, there is an alternative to nostalgia. And it involves more intensive agriculture, not less.
A vast selection of fresh salads, vegetables and fruit is on the way, courtesy of a technology called vertical farming. Instead of growing crops in a field or a greenhouse, a vertical farm creates an artificial indoor environment in which crops are cultivated on trays stacked on top of each other (see article). From inside shipping containers in Brooklyn, New York, to a disused air-raid shelter under London’s streets and an innocuous warehouse on a Dubai industrial estate, vertical farms are sprouting up in all sorts of places, nourished by investment in the business from the likes of Japan’s SoftBank and Amazon’s founder, Jeff Bezos.
This should cheer anyone who wants organic produce that has been grown without pesticides and other chemicals, and which has not been driven hundreds of miles in refrigerated lorries or flown thousands of miles in the belly of a plane. Such farms can greatly reduce the space needed for cultivation, which is useful in urban areas where land is in short supply and expensive. Inside, climatic conditions are carefully controlled with hydroponic systems supplying all the nutrients a plant needs to grow and recycling all but 5% of their water—which is incorporated in the crop itself. Specially tuned led lighting generates only the wavelengths that the plants require to prosper, saving energy. Bugs are kept out, so pesticides are not needed. Foliage and fruit can be turned out in immaculate condition. And the harvests last all year round.
There is more. As they will remain safe and snug inside a vertical farm, long-forgotten varieties of fruit and vegetables can stage a comeback. Most of these old-timers have been passed over by varieties bred to withstand the rigours of intensive farming systems. A cornucopia of unfamiliar shapes, colours and flavours could arrive on the dinner table.
This glimpse of Eden is still some way off. The electricity bill remains high, principally because of the cost of powering the huge number of leds required to simulate sunlight. That means vertical farming can, for the time being, be profitable only for high-value, perishable produce, such as salad leaves and fancy herbs. But research is set to bring the bill down and the costs of renewable energy are falling, too. In a hot climate such as Dubai’s extensive solar power could make vertical farms a valuable food resource, particularly where water is scarce. In a cold climate thermal, wind or hydroelectric power could play a similar role.
Some field crops, including staples such as rice and wheat, are unlikely ever to be suitable for growing in vast stacks. But as its costs fall thanks to further research, vertical farming will compete more keenly with old-fashioned greenhouses and conventional, horizontal farms where crops grow in the earth. As an extra form of food production, vertical farming deserves to be welcomed, especially by the people whose impulse is to turn their back on the future. ■
This article appeared in the Leaders section of the print edition under the headline "Plant power"
New Ways To Make Vertical Farming Stack Up
From the outside it looks like a tall, metal-clad barn. But step in, through a large airlock designed to keep out the bugs, and a kaleidoscopic scene emerges
Cultivating Fresh Produce In An Artificial Environment
Is Getting Cheaper
August 31, 2019 | INVERGOWRIE
From the outside it looks like a tall, metal-clad barn. But step in, through a large airlock designed to keep out the bugs, and a kaleidoscopic scene emerges. A central aisle is flanked by two pairs of towers. Each tower is stacked with a dozen or so trays on which are growing strawberries, kale, red lettuce and coriander. And each tray is bathed in vibrant light of different colours, mostly hues of blue and magenta. Douglas Elder, who is in charge of this artificial Eden, taps some instructions into an app on his mobile phone and, with a short whirr of machinery, a tray of lush, green basil slides out for his inspection.
Mr Elder is product manager for Intelligent Growth Solutions (igs), a “vertical farming” company based at Invergowrie, near Dundee, in Scotland. Each of the nine-metre-high towers in the demonstration unit that he runs occupies barely 40 square metres. But by stacking the trays one on top of another an individual tower provides up to 350 square metres of growing area. Using his phone again, Mr Elder changes the colours and brightness of the 1,000 light-emitting diodes (leds) strung out above each tray. The app can also control the temperature, humidity and ventilation, and the hydroponic system that supplies the plants, growing on various non-soil substrates, with water and nutrients. Armed with his trusty phone, Mr Elder says he can run the farm almost single-handedly.
Plant power
Vertical farming of this sort is not, of itself, a new idea. The term goes back to 1915, though it took a century for the first commercial vertical farms to be built. But the business is now taking off. SoftBank, a Japanese firm, Google’s former boss Eric Schmidt and Amazon’s founder Jeff Bezos have between them ploughed more than $200m into Plenty, a vertical-farming company based in San Francisco. And in June Ocado, a British online grocery, splashed out £17m ($21.3m) on vertical-farming businesses to grow fresh produce within its automated distribution depots.
The interest of investors is growing just as technology promises to turn vertical-farming operations into efficient “plant factories”. The high-tech leds in igs’s demonstration unit are optimised so that nary a photon is wasted. The hydroponics, and the recycling that supports them, mean the only water lost from the system is that which ends up as part of one of the plants themselves. And towers mean the system is modular, and so can be scaled up. Most of the systems which igs hopes to start delivering to customers early next year will consist of ten or more towers.
Some people, however, remain sceptical about how much vertical farms have to offer that good-old-fashioned greenhouses do not. Vertical farms are certainly more compact—a bonus in places like cities where land is expensive. Since sales of fresh produce to the urban masses are often touted as one of vertical farming’s biggest opportunities, that is important. But a greenhouse gets its light, and much of its heat, free, courtesy of the sun. And modern greenhouses can also use solar-powered supplementary led lighting to extend their growing seasons and hydroponic systems to save water, says Viraji Puri, co-founder of Gotham Greens, an urban-farming company that operates greenhouses on the roofs of buildings in New York and Chicago. As for food miles, they could not get any shorter for Gotham Greens’s rooftop greenhouse in Brooklyn, which supplies the Whole Foods Market located downstairs.
The biggest drawback of vertical farming is the high cost of the electricity required to run the large number of leds. This has meant that production has been commercially viable for high-value, perishable produce only, such as salad leaves and herbs. That, nevertheless, is a market not to be sniffed at. But for a broader range of produce, it can prove too expensive. In 2014 Louis Albright, an emeritus professor of biological and environmental engineering at Cornell University in America, calculated that a loaf of bread made from wheat grown in a vertical farm would be priced at about $23.
Blue is the colour
One way of saving electricity is to use leds that generate only the colours that plants require, instead of the full spectrum of plain white light. Plants are green because their leaves contain chlorophyll, a pigment that reflects the green light in the middle of the spectrum while absorbing and using for photosynthesis the blue and red wavelengths at either end of it.
The vertical farm at Invergowrie takes this idea further. It uses leds that are highly tuneable. Although the lights produce mostly blue and red wavelengths, researchers now know that other colours play an important role at various stages of a plant’s development, says David Farquhar, igs’s chief executive. A dose of green at an appropriate moment produces a higher yield. A timely spot of infrared can improve the quality of foliage. The lights can also produce various blue/red mixes.
To operate these leds efficiently, the company has developed a low-voltage power-distribution system. This, says Mr Farquhar, can cut energy costs to about half of those incurred by existing vertical farms. As a result, all four towers can produce 15-25 tonnes a year of herbs, salad leaves, fruit and vegetables. This, the company claims, is between two and three times more than a conventional greenhouse with an equivalent but horizontal growing area, and equipped with supplementary lighting and heating, could manage. And the system can grow all this produce at a similar cost-per-kilogram.
One of the jobs of the Invergowrie unit is to develop lighting regimes tailored to individual crops. Another is to develop algorithms to control, in an equally bespoke way, the climatic conditions preferred by different crops. The idea is to design crop-specific weather “recipes” in order to boost the yield and quality of whatever varieties are grown in the vertical farm. All the processes involved are engineered to be efficient. Irrigation, for instance, relies on captured rainwater. This is cleaned and recycled, but only 5% gets used up by each harvest—and most of that as the water-content in the plants themselves. Ventilation is also a closed loop, harvesting surplus heat from the leds while managing humidity and oxygen levels.
By reducing running costs, the system should make it profitable to grow a wider variety of produce vertically. The firm has already succeeded with some root vegetables, such as radishes and baby turnips. Bulk field crops, such as wheat and rice, may never make sense for a vertical farm, and larger, heavier vegetables would be tricky to raise. This means full-grown potatoes are probably off the menu, at least with existing technology.
Seed potatoes, though, are a good candidate, says Colin Campbell, head of the James Hutton Institute, a plant-science research centre backed by the Scottish government. It is based next door to igs and works with the company. Many fields around the world, Dr Campbell observes, are suffering a growing burden of pests and disease, such as potato-cyst nematode. In the controlled environment of a vertical farm, from which both pests and diseases can be excluded, seed potatoes could be propagated more efficiently than in the big, bad outdoor world. This would give them a head start when they were planted out in fields.
The institute’s researchers are also looking at plant varieties that might do particularly well indoors, including old varieties passed over in the search for crops which can withstand the rigours of intensive farming systems. By dipping into the institute’s gene banks, Dr Campbell thinks it may find some long-forgotten fruits and vegetables that would thrive in the security of a vertical farm.
All this could go down well with foodies, and unlock new and forgotten flavours. Shoppers might even find some exotic varieties growing in supermarket aisles. In Berlin a company called Infarm provides remotely controlled shelved growing cabinets for shops, warehouses and restaurants. Herbs and salad leaves, including exotics such as Genovese basil and Peruvian mint, are resupplied with seedlings from the company’s nursery as the mature plants are picked.
Vertical farming then will not feed the world, but it will help provide more fresh produce to more people. It may even be that, as vertical-farming systems improve further, miniature versions will be designed for people to put in their kitchens—thus proving that there is nothing new under either the sun or the led. Such things used once to be called window boxes.■
This article appeared in the Science and technology section of the print edition under the headline"Growing brighter"
Testing The Waters - Is Public Drinking Water Safe For Hydroponic Production?
The quality of the irrigation water with respect to chemical, microbial and physical properties affects crop quality and health. No matter what, test the chemical parameters of your irrigation water!
Fig. 1. Sensitivity of Petunia x hybrida to free chlorine in irrigation water. Plants were irrigated with 0, 2 and 4 ppm free chlorine with every irrigation. Chlorosis was observed at 4 ppm or greater.Photos courtesy of Rosa E. Raudales, Cora McGehee and Juan Cabrera
The quality of the irrigation water with respect to chemical, microbial and physical properties affects crop quality and health. Growers producing edibles are also concerned about the risk of spreading waterborne human pathogens during production and postharvest. Many growers resolve to use water from public water systems to lower the risk of foodborne illnesses and avoid the hassle of testing and treating water. However, growers must always monitor the chemical parameters of irrigation water to grow high-quality crops. This article explains why growers should test “clean” water.
Public drinking water must meet the Environmental Protection Agency (EPA) drinking water standards established in the Safe Drinking Water Act. EPA sets regulatory limits for microbial contaminants, among others. The Food and Drug Administration (FDA) indicates that “water that meets the microbial standards for drinking water is considered safe and sanitary” and is recommended in the Good Agricultural Practices (GAP) and Good Handling Practices (GHP) certification guidelines. The Food Safety Modernization Act (FSMA) waives microbial testing of water if the source comes from a public water system and has a certification of treatment and sampling. Hence, many growers adopt public drinking water for irrigation and postharvest. However, public water facilities inject chlorine, also an EPA-regulated contaminant, to control microbes in drinking water. Chlorine in irrigation water can be toxic to crops.
Chlorine chemistry
Chlorine is an effective germicidal agent for removing pathogens from water. Chlorine is added to water as a gas, liquid (e.g. sodium hypochlorite, AKA bleach) or solid (e.g. calcium hypochlorite), or generated via membrane electrolysis. All chlorine sources react with water and form hypochlorous acid (HOCl). Further dissociation of HOCl will result in hypochlorite (OCl-) and hydrogen (H+) ions. The sum of HOCl and OCl- is known as free chlorine; both are sanitizing agents. Hypochlorous acid is the strongest form of chlorine sanitizer.
Hypochlorous acid reacts with nitrogen-containing compounds, both organic and inorganic, to form chloramines. Chloramines are a combined chlorine form. Chloramines have a lower disinfection efficacy and longer residual effect than free chlorine.
The sum of free and combined chlorine is total chlorine. Growers can measure all forms of chlorine with colorimetric kits.
Fig. 2. Sensitivity of lettuce to free chlorine in irrigation water. Plants were irrigated with 0, 0.5 and 1 ppm free chlorine with every irrigation.Photo courtesy of Rosa E. Raudales, Cora McGehee and Juan Cabrera
Phytotoxicity
In separate experiments, our team from the University of Connecticut and researchers at the University of Guelph and the University of Florida, have established that most container-grown crops can be irrigated with up to 2 ppm (or mg/L) free chlorine without causing phytotoxicity (Fig. 1). Target doses to control plant pathogens and phytotoxicity thresholds vary by crop-pathogen combination.
Chlorine demand is the difference between the initial (applied) and residual (measured after a given contact time) concentration. The organic matter in the substrate reacts with chlorine and exerts chlorine demand. Hence the recommendations for container-soilless media cannot be directly applied to hydroponically grown crops.
We tested the sensitivity of lettuce to chlorine in hydroponic production. We observed reduction in plant weight when the concentration was as low as 0.5 ppm free chlorine (Fig. 2).
The phytotoxicity symptoms caused by chlorine on hydroponically grown young lettuce plants can be confused with root rot or nutrient deficiencies (Fig. 3). In contrast, the symptoms in mature plants are not very distinctive (Fig. 2). For this reason, sending symptomatic (and healthy) plants to a diagnostic clinic and monitoring the chemistry of nutrient solutions is an important part of the diagnosis.
Fig. 3. Lettuce seedling with phytotoxicity caused by chlorinePhoto courtesy of Rosa E. Raudales, Cora McGehee and Juan Cabrera
Testing and treating the waters
The maximum chlorine level allowed in drinking water is 4 ppm. Public water treatment facilities can change chlorine residual levels, reaching up to 4 ppm combined or free chlorine, without notifying the end-user. Therefore, growers using public drinking water must include chlorine in their standard water-testing practice.
Hanna Instruments, Hach and similar companies have developed kits that can be used to measure chlorine in-house.
For more information
Good Agricultural Practices and Good Handling Practices
We do not know yet the phytotoxicity thresholds of free or combined chlorine for most hydroponically grown crops. For this reason, we recommend that growers measure total chlorine.
Growers using public water should have a water treatment option to remove chlorine from the water. The options include activated carbon filters, sodium thiosulfate and aeration.
Take-home message: No matter what, test the chemical parameters of your irrigation water!
Rosa (rosa.raudales@uconn.edu) is an assistant professor at the University of Connecticut and Cora and Juan are Ph.D. students at the University of Connecticut.
Disclaimer: Trade names are included in this publication as a convenience to readers and to illustrate examples of technologies. The use of brand names and any mention or listing of commercial products or services does not imply endorsement by the University of Connecticut, nor discrimination against similar products or services not mentioned.
Sensing The Rise of Vertical Farming
Vertical farming is the process of food being produced in vertically stacked layers, instead of on a single level such as in a field or greenhouse. The layers are commonly integrated into urban structures like skyscrapers, shipping containers and repurposed warehouses
August 28, 2019
By Darcy Simonis, Industry Network Leader, ABB Food and Beverage
With over 7,800 high-rise buildings, the city of Hong Kong soars above all others. More than 300 of its buildings surpass 490 feet, with more people living over 15 floors above ground level than anywhere else in the world. Having a skyline in the clouds helps the densely populated metropolis to prosper where space is restricted. Agriculture has taken note of this construction technique, as vertical farming creates impressive yields.
Vertical farming is the process of food being produced in vertically stacked layers, instead of on a single level such as in a field or greenhouse. The layers are commonly integrated into urban structures like skyscrapers, shipping containers and repurposed warehouses.
Using Controlled Environment Agriculture (CEA) technology, the artificial control of temperature, light, humidity and gases makes it possible to produce a vast array of crops on an industrial scale — without any outdoor exposure.
The Sky’s the Limit
By 2050, around 80 per cent of the world’s population will live in urban areas. With agricultural space in these areas scarce or completely non-existent, how do we deliver produce?
It is estimated that one acre of vertical farming offers the equivalent production of at least four to six acres using conventional outdoor methods. As the plant’s growth is not dependent on sunlight or affected by meteorological conditions, production can continue at the same rate all year round. In terms of resources, the plants require as much as 70 per cent less water than traditional farms.
Organic crops are a huge market, with demand often outstripping supply. As vertically farmed crops are produced in a well-controlled area, there is far less need for chemical pesticides. It is also believed that vertical farming could bring fresh produce closer to urban populations, reducing the risk of nutrients diminishing during transport.
No More Soil
Hydroponics is a predominant growing method in vertical farming. The process involves growing plants in nutrient solutions that are essentially free of soil, as roots are submerged into the solution and the plants are regularly monitored to maintain the correct levels of chemical composition.
If we’re ever to fulfill futuristic plans of colonizing Mars, we’re going to need to grow our own food. So, where on Earth has the conditions to test out this method?
It may not share the same qualities as the Red Planet, but Antarctica’s nonstop winters make it impossible to grow produce outdoors, and fruits and vegetables are shipped long distances from overseas just a few times a year.
In a step closer to extraterrestrial farming, a semi-automated hydroponic facility grows plants without soil, using mineral nutrient solutions in a water solvent. Scientists on Germany’s Neumayer Station III grow produce in a 20-foot-long shipping container, cultivating greens in an area where such produce is usually limited. This is just one example of how vertical farming techniques can be used in areas affected by harsh weather conditions.
Sensing Growth
To hit high levels of production, growth conditions in vertical farms must be continuously optimized. Sensors and data must be used to effectively track variables such as climate, nutrient composition and light levels.
Climate is characterized by a combination of air temperature, humidity and carbon dioxide (CO2) levels. The effects of these factors are tremendous. The difference between plant and air temperature, for example, can tell us whether the leaves’ stomata are open. If they’re closed, the plant cannot absorb CO2 and convert it into biomass. We can also measure the light level and spectrum as perceived by the plants and the pH of irrigation water for optimal growth.
Using smart sensors that can monitor these variables will ensure that vertical farms produce yields that greatly exceed those of conventional farms, which are impacted by uncontrollable conditions.
With a skyline full of modern, gleaming constructions, Hong Kong makes the most of its space to deliver prosperity. While vertical farming still has a long way to go before it is commercially viable, it is certain that food producers can learn from the techniques it applies to help deliver produce our rising populations.
Worker-Owned Greenhouse Grows Its Business In First Year
The largest urban commercial greenhouse in Massachusetts is marking its first year of production
he Wellspring Harvest greenhouse built on a "brownfields" site in Springfield, Massachusetts using hydroponic farming technology. At peak production it can put out 10,000 heads of lettuce a month.
CREDIT WAMC
Listen
The largest urban commercial greenhouse in Massachusetts is marking its first year of production.
Wellspring Harvest, a hydroponic greenhouse built on the once-badly contaminated former Chapman Valve property in Springfield’s Indian Orchard neighborhood, made its first delivery of lettuce to four Big Y supermarkets just about one year ago.
Like many new businesses, the first year has been a learning experience, according to Fred Rose, co-director of Wellspring Cooperative Corporation.
"We have learned an enormous amount about growing, about selling to different markets, about building our work team," said Rose.
The greenhouse now sells to over 25 stores including Whole Foods and seven institutional customers that include area colleges and two hospitals.
"That has been the real success, to get in the door in lots of important places," said Rose.
Wellspring, a non-profit that develops worker-owned cooperative businesses in low-income neighborhoods, initially spent over $1.2 million to purchase the 1- acre site and construct the greenhouse. An additional $250,000 had to be raised to subsidize operations as production ramped up during the first year.
" I think this fall we will get to full production and sales and break even by early spring. That is the idea," said Rose.
One of the greenhouse’s biggest customers is River Valley Co-op market in Northampton. General Manager Rochelle Prunty said there is a growing brand recognition for the lettuce with the Wellspring Harvest label.
" Produce is one of our biggest categories and we specialize in local produce. This lettuce to have it year-round is really special," said Prunty.
Mercy Medical Center in Springfield was an early investor in the greenhouse project. Now, Doreen Fadus, regional executive director of Trinity Health New England, said she’s trying to convince more of the organization’s hospitals to buy the lettuce.
" It is great lettuce," said Fadus. " No one is doing anybody a favor by buying it. It is a great product."
Eight people work at the greenhouse. Alicia Brown, who lives right across the street, was one of the first people hired. Now, after a year of learning the business she has become a worker-owner.
"It feels good to say I'm a part-owner," said Brown.
Wellspring has two other worker-owned cooperatives in Springfield: a furniture repair and re-upholstery business and a window restoration shop.
TAGS: WELLSPRING HARVEST WELLSPRING COOPERATIVE CORPORATION HYDROPONICS
New Ways To Make Vertical Farming Stack Up
From the outside it looks like a tall, metal-clad barn. But step in, through a large airlock designed to keep out the bugs, and a kaleidoscopic scene emerges
Cultivating Fresh Produce In An Artificial Environment
Is Getting Cheaper
August 31, 2019 | INVERGOWRIE
From the outside it looks like a tall, metal-clad barn. But step in, through a large airlock designed to keep out the bugs, and a kaleidoscopic scene emerges. A central aisle is flanked by two pairs of towers. Each tower is stacked with a dozen or so trays on which are growing strawberries, kale, red lettuce and coriander. And each tray is bathed in vibrant light of different colours, mostly hues of blue and magenta. Douglas Elder, who is in charge of this artificial Eden, taps some instructions into an app on his mobile phone and, with a short whirr of machinery, a tray of lush, green basil slides out for his inspection.
Mr Elder is product manager for Intelligent Growth Solutions (igs), a “vertical farming” company based at Invergowrie, near Dundee, in Scotland. Each of the nine-metre-high towers in the demonstration unit that he runs occupies barely 40 square metres. But by stacking the trays one on top of another an individual tower provides up to 350 square metres of growing area. Using his phone again, Mr Elder changes the colours and brightness of the 1,000 light-emitting diodes (leds) strung out above each tray. The app can also control the temperature, humidity and ventilation, and the hydroponic system that supplies the plants, growing on various non-soil substrates, with water and nutrients. Armed with his trusty phone, Mr Elder says he can run the farm almost single-handedly.
Plant power
Vertical farming of this sort is not, of itself, a new idea. The term goes back to 1915, though it took a century for the first commercial vertical farms to be built. But the business is now taking off. SoftBank, a Japanese firm, Google’s former boss Eric Schmidt and Amazon’s founder Jeff Bezos have between them ploughed more than $200m into Plenty, a vertical-farming company based in San Francisco. And in June Ocado, a British online grocery, splashed out £17m ($21.3m) on vertical-farming businesses to grow fresh produce within its automated distribution depots.
The interest of investors is growing just as technology promises to turn vertical-farming operations into efficient “plant factories”. The high-tech leds in igs’s demonstration unit are optimised so that nary a photon is wasted. The hydroponics, and the recycling that supports them, mean the only water lost from the system is that which ends up as part of one of the plants themselves. And towers mean the system is modular, and so can be scaled up. Most of the systems which igs hopes to start delivering to customers early next year will consist of ten or more towers.
Some people, however, remain sceptical about how much vertical farms have to offer that good-old-fashioned greenhouses do not. Vertical farms are certainly more compact—a bonus in places like cities where land is expensive. Since sales of fresh produce to the urban masses are often touted as one of vertical farming’s biggest opportunities, that is important. But a greenhouse gets its light, and much of its heat, free, courtesy of the sun. And modern greenhouses can also use solar-powered supplementary led lighting to extend their growing seasons and hydroponic systems to save water, says Viraji Puri, co-founder of Gotham Greens, an urban-farming company that operates greenhouses on the roofs of buildings in New York and Chicago. As for food miles, they could not get any shorter for Gotham Greens’s rooftop greenhouse in Brooklyn, which supplies the Whole Foods Market located downstairs.
The biggest drawback of vertical farming is the high cost of the electricity required to run the large number of leds. This has meant that production has been commercially viable for high-value, perishable produce only, such as salad leaves and herbs. That, nevertheless, is a market not to be sniffed at. But for a broader range of produce, it can prove too expensive. In 2014 Louis Albright, an emeritus professor of biological and environmental engineering at Cornell University in America, calculated that a loaf of bread made from wheat grown in a vertical farm would be priced at about $23.
Blue is the colour
One way of saving electricity is to use leds that generate only the colours that plants require, instead of the full spectrum of plain white light. Plants are green because their leaves contain chlorophyll, a pigment that reflects the green light in the middle of the spectrum while absorbing and using for photosynthesis the blue and red wavelengths at either end of it.
The vertical farm at Invergowrie takes this idea further. It uses leds that are highly tuneable. Although the lights produce mostly blue and red wavelengths, researchers now know that other colours play an important role at various stages of a plant’s development, says David Farquhar, igs’s chief executive. A dose of green at an appropriate moment produces a higher yield. A timely spot of infrared can improve the quality of foliage. The lights can also produce various blue/red mixes.
To operate these leds efficiently, the company has developed a low-voltage power-distribution system. This, says Mr Farquhar, can cut energy costs to about half of those incurred by existing vertical farms. As a result, all four towers can produce 15-25 tonnes a year of herbs, salad leaves, fruit and vegetables. This, the company claims, is between two and three times more than a conventional greenhouse with an equivalent but horizontal growing area, and equipped with supplementary lighting and heating, could manage. And the system can grow all this produce at a similar cost-per-kilogram.
One of the jobs of the Invergowrie unit is to develop lighting regimes tailored to individual crops. Another is to develop algorithms to control, in an equally bespoke way, the climatic conditions preferred by different crops. The idea is to design crop-specific weather “recipes” in order to boost the yield and quality of whatever varieties are grown in the vertical farm. All the processes involved are engineered to be efficient. Irrigation, for instance, relies on captured rainwater. This is cleaned and recycled, but only 5% gets used up by each harvest—and most of that as the water-content in the plants themselves. Ventilation is also a closed loop, harvesting surplus heat from the leds while managing humidity and oxygen levels.
By reducing running costs, the system should make it profitable to grow a wider variety of produce vertically. The firm has already succeeded with some root vegetables, such as radishes and baby turnips. Bulk field crops, such as wheat and rice, may never make sense for a vertical farm, and larger, heavier vegetables would be tricky to raise. This means full-grown potatoes are probably off the menu, at least with existing technology.
Seed potatoes, though, are a good candidate, says Colin Campbell, head of the James Hutton Institute, a plant-science research centre backed by the Scottish government. It is based next door to igs and works with the company. Many fields around the world, Dr Campbell observes, are suffering a growing burden of pests and disease, such as potato-cyst nematode. In the controlled environment of a vertical farm, from which both pests and diseases can be excluded, seed potatoes could be propagated more efficiently than in the big, bad outdoor world. This would give them a head start when they were planted out in fields.
The institute’s researchers are also looking at plant varieties that might do particularly well indoors, including old varieties passed over in the search for crops which can withstand the rigours of intensive farming systems. By dipping into the institute’s gene banks, Dr Campbell thinks it may find some long-forgotten fruits and vegetables that would thrive in the security of a vertical farm.
All this could go down well with foodies, and unlock new and forgotten flavours. Shoppers might even find some exotic varieties growing in supermarket aisles. In Berlin a company called Infarm provides remotely controlled shelved growing cabinets for shops, warehouses and restaurants. Herbs and salad leaves, including exotics such as Genovese basil and Peruvian mint, are resupplied with seedlings from the company’s nursery as the mature plants are picked.
Vertical farming then will not feed the world, but it will help provide more fresh produce to more people. It may even be that, as vertical-farming systems improve further, miniature versions will be designed for people to put in their kitchens—thus proving that there is nothing new under either the sun or the led. Such things used once to be called window boxes.■
This article appeared in the Science and technology section of the print edition under the headline"Growing brighter"
Crop One Grows Food Hydroponically With Unique Formulas For Each Plant
Crop One is a vertical farming holding company for two subsidiaries – FreshBox Farms, Millis, Mass., and a joint venture with Emirates Flight Catering, Dubai South, United Emirates
Crop One is hardware agnostic but develops its own proprietary software and data analytics platform that governs its growing process as well as it farms.
Hydroponic Technology and Data Analytics in Vertical Farming
Dave Vosberg, CFO & SVP Strategy | Crop One
07/30/19 Indoor & Vertical Farming
Tell us about Crop One and your role with the company.
Crop One is a vertical farming holding company for two subsidiaries – FreshBox Farms, Millis, Mass., and a joint venture with Emirates Flight Catering, Dubai South, United Emirates. Crop One has been in commercial production longer than any other major vertical farmer in the U.S. It produces the highest crop yield per square foot, at 25% of the capital cost, of any vertical farm, due to its unique combination of proprietary technology platform and best-in-class plant science. For more information about Crop One and vertical farming follow the link to CropOneHoldings.com. Crop One’s mission is to solve the world’s food problems one crop at a time. The first crop we are successful with is leafy greens, but soon we will be growing fruits, proteins, some cereals and many specialty crops. My role with the company is as CFO and SVP Strategy, helping to provide the vision for corporate financial success.
Please tell us what advantages and benefits Crop One provides?
Crop One Holdings is transforming the ag tech industry, using advanced hydroponic technology and proprietary data analytics to provide pure, safe and consistent produce year round. Crop One’s differentiated technology stack and growing process make it the most advanced company in the vertical farming space. The company delivers industry-leading environmental benefits with technology that is centered around lowering costs and increasing yields. Additionally, the company is also actively experimenting with growing new crop types and cultivars, and has partnered with leading seed and research companies to develop seeds specifically bred for the controlled indoor environment.
Since sustainably feeding a growing population is a paramount interest globally, what type of international interest do you have for your farms?
Crop One Holdings, the world’s leading vertical farm operator through its FreshBox Farms brand and Emirates Flight Catering (EKFC), announced a $40 million joint venture the build the world’s largest vertical farm in Dubai, United Arab Emirates. The 130,000 square foot controlled environment facility will produce three US tons (6,000 pounds) of high quality, herbicide and pesticide-free leafy greens, harvested daily, using 99 percent less water than outdoor fields. Its location will enable quick delivery of fresh products within hours of harvest, maintaining the food’s nutritional value and reducing carbon emissions associated with transportation.
How big of an issue is distribution?
Distribution is the key issue. Crops are now grown far from the point of consumption often times traveling weeks before reaching supermarkets and are vulnerable to disruptions related to climate, pathogens, and chemical intervention. Addressing these challenges will require a combination of plant science, AI, agtech, software analytics, environmental sustainability and operations management to address. Crop One’s differentiated technology stack and grow process makes it the most scalable company in the vertical farming space, delivering industry-leading environmental and economic benefits.
What role have Sensors and LEDs played?
Vertical farming that can control the environment in which it grows can be liberated from climate and geography enabled by the advent of cheap LED lighting and cheap sensors. Both have allowed us to improve economics of leafy greens and will continue to allow us to permanently change the infrastructure of agriculture, one crop at a time.
What are the innovative aspects or the technological advances that make Crop One unique?
Crop One grows food hydroponically with unique formulas for each plant. Crop One is hardware agnostic but develops its own proprietary software and data analytics platform that governs its growing process as well as it farms. Crop One is technology enabled and plant science forward - it has a strong plant science team led by Dr. Deane Falcone, enabling the company to manage its cost and increase yields. The company’s plants are supported by more than 250M+ data points for maximum growth and give the exact, correct amount of water, light, and nutrients, all grown without the use of soil. The final products (leafy greens) are fresher, safer and cleaner.
What are the biggest hurdles currently facing Vertical Farming and its expansion?
To date, the biggest hurdle facing Vertical Farming has been operators who can demonstrate consistent operational and financial success in order to attract debt financing. This is an asset-heavy industry, and without debt or third-party project capital, the business is un-scalable. Crop One has consistently proven its operations and financial performance being the only vertical farm that has consistently delivered product every week for the past four years, and at positive gross margins the past two and a half years. As such, Crop One is now on a growth trajectory to significantly expand production.
Where do you see Vertical Farming and Crop One 5 years down the road?
5-10 years from now, Vertical Farming will supply roughly 50% of the value of the leafy greens market. It will also have made inroads into fruits, proteins, cereals and specialty crops. Similar to data centers, we are at the beginning of this industry and vertical farms will soon become as plentiful. Crop One will be a leader in this space, but this is a multi-winner market. Crop One will be distinguished by its leadership in plant science, technology and business model innovation.
About David Vosburg, CFO & SVP Strategy
Dave has spent his life's work founding, growing and scaling technology businesses. Crop One Holdings, trading as FreshBox Farms, is his fifth successful startup he has lead at the CXO level. As CFO and SVP Strategy for Crop One, Dave leads the finance and strategy of the company.
Dave is passionate about businesses which use technology to disrupt markets while creating significant social value. Previously, Dave was CFO of Southern Africa's largest money transfer company, outside of South Africa, CEO of Zambia's leading HR consulting and outsourcing company and CCO of an Ed-Tech startup which translated the entire Zambian primary curriculum into 5,000 flash-animated lessons.
Mr. Vosburg also served as the past President of the American Chamber of Commerce in Zambia and holds a BA from the University of Notre Dame and an MBA from Yale University."
The content & opinions in this article are the author’s and do not necessarily represent the views of AgriTechTomorrow
Purdue Field Day Provides Info On Small-Farm Crops
According to attendees and organizers alike, this year’s Purdue Small Farm Education Field Day, which consisted of lectures and on-farm demonstrations, provided excellent guidance for small-scale growers
August 19, 2019
Petrus Langenhoven is explaining to attendees how to grow sweet peppers in a high tunnel and reflects on results from a high tunnel bell pepper variety trial that was conducted in 2018 at the Purdue Student Farm. (Courtesy photo)Download image
WEST LAFAYETTE, Ind. – According to attendees and organizers alike, this year’s Purdue Small Farm Education Field Day, which consisted of lectures and on-farm demonstrations, provided excellent guidance for small-scale growers.
Hosted by Purdue’s Department of Horticulture and Landscape Architecture, the field day featured lectures on planting and sustainability, soil care, high tunnels, cover crops, small-scale equipment, food safety and more. The day started in a classroom and ended with participants watching and listening to demonstrations put on by Purdue staff at the Student Farm.
“The event was a resounding success,” said Petrus Langenhoven, Purdue’s horticulture and hydroponics crop specialist in the Department of Horticulture and Landscape Architecture. “Attendees love the fact that they can learn some theory in the classroom in the morning and then go for a hands-on session at the farm. It’s like you can feel the energy and passion of growers when they attend our field day.”
Langenhoven said the event attracted three times as many participants than the first, which was held last summer.
“We were surprised that interest has grown so much in one year, but it clearly shows that horticulture farmers in Indiana are in need of information to increase the profitability of their farming businesses,” he said. “Attendees were very engaged and showed lots of interest during the on-farm tours. Some of them have told me it was the best field day they have attended and that they will be back next year.”
Chris Adair, the Purdue Student Farm manager, demonstrates to attendees the different applications of a power harrow and rototiller when used in conjunction with a walk-behind tractor. (Courtesy photo) Download image
Lori Jolly-Brown, Extension events and communications coordinator, said, “We had more new attendees this year who complimented us on the program. Return attendees said they appreciate keeping up on new educational information to put to good use on their farms.”
Participants of the program were a diverse group — from beginners and experienced growers, to hobbyists and small business practitioners. Rocio Rodea, a teacher from Gary, came looking for advice she could apply to a community garden she helped establish and eventually will use as a tool for her students. She was particularly interested in the morning food safety session. Langenhoven said attendees in general were very attentive and asked a lot of good questions in the morning sessions.
“I was super interested in the food safety portion because Gary has started to put on several farmers markets throughout the week, so every urban farm or garden will have its turn to host,” Rodea said.
Sierra Yeary, a participant hoping to grow some vegetables for a brewery restaurant she is opening next year, learned about cool and warm season vegetables for the first time.
“I didn’t even realize that we should be planting cover crops,” she said. “We only do tomatoes now, and they were saying in the session that we should be planting cool season veggies too, to keep the soil going. I had no idea.”
Along with a networking lunch, the afternoon consisted of six informational stations where attendees learned about high tunnel tomato and bell pepper production, the practical applications of leaf mold composting, field production of onions and tomatoes, the use of solar dryers for postharvest processing and vegetable wash station design.
“The student farm was a hive of activity with over a hundred people enjoying the perfect weather and exchanging all manner of tricks of the trade,” said Steve Hallett, a professor of horticulture who presented one of the afternoon stations.
Johnny Washington, a grower with a small vegetable market in Gary, said he learned new techniques to implement on his operation during the afternoon stations.
“I don’t have a hoop house, so sometimes when it rains hard the dirt splashes up onto the leaves, and I learned that can cause diseases,” he said. “A light bulb sort of went on in my head — so I’ll be looking more closely into putting plastic around the base of the plants.”
Shelly Janowski and her husband attended the field day to learn new techniques and planning for their already-established small fruit and vegetable farm.
“We’re looking at some of their techniques of planting, weed suppression and harvesting,” she said. “This has been very valuable. If you can learn something to make things easier, to have it take less time or increase your production, that could be a game-changer.”
Demonstrations on how to use a rototiller, power harrow and tractor-mounted seeder were also part of the afternoon stations.
“We can’t afford to spend $40,000 on a piece of equipment,” said Janowski’s husband, Mark. “But if there’s something small or used we can get, or something to use in a way other than what was intended, that’s very helpful.”
Langenhoven, who initiated the Small Farm Education Program, has plans to expand its reach to other Indiana cities, especially those with large numbers of urban and peri-urban farms such as Gary, Fort Wayne and Indianapolis. He and his collaborators would like to find more funding and the right partners to move that plan forward. For now, the next Field Day is scheduled July 30, 2020, at the Purdue Student Farm, and will showcase additional technologies and information useful to horticulture growers.
Sources: Lori Jolly-Brown, ljollybr@purdue.edu
Petrus Langenhoven, plangenh@purdue.edu
Steven Hallett, halletts@purdue.edu
Agricultural Communications: 765-494-8415;
Maureen Manier, Department Head, mmanier@purdue.edu
Urban or Rural: Where To Build A Greenhouse
Drawing from experience, Lefsrud points out that governments across the world, not just in Quebec, have largely been slow to consider using urban greenhouses as a legitimate food generator
‘You need political will, and it takes time’ – urban greenhouses could benefit from more direct support from governments, experts say.
August 20, 2019
Written by Doug Johnson
Montreal’s Lufa Farms now has three locations and around 17,000 customers.IMAGES: Lufa Farms
The first two floors of 1400 Rue Antonio Barbeau in Montreal look like they belong on any other low-density commercial building – blocky, covered in mottled brown brick and windows gazing into a beige interior. Just over the lip of its roof, though, peeks long walls made of glass and metal, and inside them, rows of vegetables.
Around a decade ago, the building was a full floor shorter. That was before Lufa Farms – a Montreal-based urban farm and food delivery service – began. It touts itself as the world’s first commercial greenhouse located on a rooftop.
Now, Lufa Farms has three locations spread across Montreal – others are in the Laval and Anjou neighbourhoods – and around 17,000 customers that the company has dubbed ‘Lufavores.’
But back when it first started, urban agriculture, in- or outside of a greenhouse, was something new and untested. Even Lufa Farms – which is now often pointed to as a model of what urban agriculture could be – had a rough time finding a home and traversing the untested waters of starting a farm of its size in a city.
“The biggest thing [was], there was no proof of concept ... Everything from finding a suitable building – because it was something that hadn’t been done – to an open building owner to city and zoning. It was very out-of-the-box,” says Lauren Rathmell, Lufa Farms’ co-founder and greenhouse director.
Quebec’s agriculture department, Ministre de l’Agriculture, des Pêcheries et de l’Alimentation (MAPAQ), recently released a report on the state of greenhouse-grown produce in the province. The report noted that only 31 per cent of greenhouse vegetables consumed in Quebec were grown in the province – Rathmell, and other urban agriculture dignitaries, say there’s potential here. The report also notes that the increased demand for organic foods presents Quebec with another area due for growth, and that Ontario has not actively pursued it.
While many of Montreal’s neighbourhoods now vie for a Lufa Farms location, its growing pains are familiar to many sizeable urban agriculture efforts.
Mark Lefsrud has studied different ways of growing food for more than 20 years. He is an associate professor at McGill University’s Macdonald Campus where he is a leader of the Biomass Production Laboratory and worked on the design of the Advanced Plant Habitat on the International Space Station.
Drawing from experience, Lefsrud points out that governments across the world, not just in Quebec, have largely been slow to consider using urban greenhouses as a legitimate food generator.
“It was an unknown – that’s the best way to describe it. They’re used to external, outside-of-the-city food production systems and field conditions. The idea of [using] full, controlled environments wasn’t in their comfort [zone],” he says.
However, the idea of turning unused space in urban centres into something that could aid food security is not an old one. It’s been around for maybe a decade, and agricultural ministries around the world are increasingly eyeing it as a path to feed and employ people – particularly in food deserts.
Lufa Farms’ earlier struggles were largely logistical ones, and the Gouvernement du Québec hasn’t particularly helped or hindered the business’ growth, Rathmell says. While the situation has improved in recent years, there are still challenges that face the industry as a whole.
Cost is a big issue – perhaps more so than other more traditional businesses. Besides the normal run of fees paid by every business, urban agricultural operations above a certain size need to pay to construct a specialized facility. However Rathmell notes that it has become cheaper as acceptance has grown.
Rooftop greenhouses are a bit of a different beast. There’s also the added difficulty of physically moving the building materials onto the roof. And, as much as they encourage people to give a useful purpose to a previously unused space, they come with a dossier of regulations. Functionally, they’re treated like an entirely new floor of a building.
The facility on this new floor needs a sprinkler system, and it needs to be sturdy enough to bear a lot of snow during the winter – [all] in all, it’s a hefty structure, Rathmell says.
Many places are not zoned for greenhouses or other agricultural activities like aquaponics, according to Rathmell. Historically, most urban planning in cities rarely took urban agriculture into consideration.
The land itself is also more expensive in urban areas than it is in rural ones. Lefsrud has a rough calculation for this. In rural operations, a plant usually costs between $0.05 and $0.10 to grow, compared to urban greenhouses, where the cost per plant can be as high as $0.45, depending on the season.
Vertical farming somewhat offsets this. Though there is a larger initial price tag to get started, after a while the density of plants – three dimensions as opposed to two – pays for the added costs. Traditionally, the companies that lend credit to agriculture ventures, like Farm Credit Canada and more recently Desjardins, have been wary of providing credit to urban agriculture efforts, but according to Lefsrud they are beginning to catch on.
Some costs can be offset in a city, though. It’s easier to find labour in high population centres, and the ambient warmth lowers the price of heating somewhat – either from the urban heat island effect or, more directly and in the case of rooftop greenhouses, the floors in the building below.
Regionally-based energy company Énergir – formerly Gaz Métro – offers grants for natural gas boilers, something which Lufa has taken advantage of to generate further warmth for its operations.
MAPAQ notes that Hydro Québec offers an incentive for growers with supplemental lighting. Designed for greenhouse operators who use all or part of their electricity supplied by Hydro Québec for photosynthetic lighting, this rate option is ideal for customers who can adjust their production to help manage their electricity consumption. According to the report, around 40 per cent of the greenhouse vegetable area in Quebec uses supplemental lighting, a tool that can help extend the growing season and, in turn, help growers take advantage of better market prices.
According to MAPAQ, the department has also established a network to aid urban agriculture across Quebec. As the province only obtains 31 per cent of its greenhouse produce from local sources, the remaining 69 per cent that is imported could potentially be met by local production.
However, according to Olivier Demers-Dubé, founder and CEO of Écosystèmes Alimentaires Urbains (ÉAU), around 80 per cent of greenhouses in Quebec grow for only three out of four seasons every year, limiting the sector’s potential.
“I think we’re producing a very low percentage of what we’re actually eating, even more so in [the] winter. These numbers ... that’s year-round,” he says of the information provided by MAPAQ.
Since it began five years ago, ÉAU has helped 10 communities in Quebec design aquaponic systems. This includes an Indigenous community in the north of the province, Whapmagoostui. ÉAU also works with private investors and pre-established food producers looking to attach a fish farm to their greenhouse or vice versa.
“We have this goal to bring back food production to where humans live, and humans live mainly in cities,” Demers-Dubé says.” We have this strong belief that food production need[s] to be close to where we live. We need to have contact, we need to interact with it. Eating is what we do most in our lives, minus breathing.”
According to Demers-Dubé, there are facets of starting an urban greenhouse that are becoming easier, but at a basic level, it’s still more difficult to set up a sizeable facility in the city than it is elsewhere. Further, he says, though many governments offer programs and funding that coincide with urban agriculture, there are still precious few initiatives that specifically seek to aid those operations.
“You need political will, and it takes time,” he says.
Going forward, one of the biggest challenges to urban agriculture comes in a fairly innocuous form. Now that Canada has legalized recreational cannabis, most of the thought and attention paid to greenhouses in general, by both businesses and governments, is dedicated to this relatively new industry.
“Right now, one of our biggest challenges is cannabis taking all the air out of the room,” Lefsrud says.
HAREDI HYDROPONICS: Technology And Sustainability Meet At The Diaspora Yeshiva
“Probably many of these guys have never had kale before,” comments Robin Katz, founder and CEO of Start-Up Roots, the nonprofit that runs hydroponic gardens here and at two haredi (ultra-Orthodox) schools in Jerusalem
JACOB SCHONZEIT checks the roots of greens growing in the hothouse. (Photos: Jordana Benami)
• JORDANA BENAMI
AUGUST 16, 2019
In the courtyard of a 2,000-year-old stone building on Mount Zion, a sign taped to a tiny black door announces the unlikely scene found within: The Diaspora Yeshiva Hydroponic Garden.
Inside, two agronomists in white shirts and black kippot tend tiers of vibrant kale, basil and romaine lettuce. The strings of their tzitzit gently sway as they climb up and down, adjusting nutrient and pH levels, preparing new seedlings and checking lights and filters.
The hyper-local and hyper-fresh greens, grown in a soil-less medium bathed in nutrient-enriched water, will be harvested and carried across the courtyard to the yeshiva’s kitchen to find their way into a variety of dishes.
“Probably many of these guys have never had kale before,” comments Robin Katz, founder and CEO of Start-Up Roots, the nonprofit that runs hydroponic gardens here and at two haredi (ultra-Orthodox) schools in Jerusalem. “I’ve had some kids look at let- tuce and say, ‘Are you sure this is kosher? I’ve never seen it in my house.’”
Katz, a Chicago émigré, is a lawyer and teacher by profession. Since 2015, her organization has been installing hydroponic systems in schools and providing a multidisciplinary curriculum that teaches how to care for the produce, how to incorporate it into nutri- tious meals and how to monetize the bounty. A photo-journalism element allows the students to create visual documentation of the growth process.
The Diaspora Yeshiva setup was donated by Irving Backman of Massachusetts, an international benefac tor of sustainability and advanced technology initiatives through his DATT (Developers of Advanced Technology Today) group. Backman’s grandson, Rabbi Yaakov Kent, is the son-in-law of the Rosh Yeshiva of the Diaspora Yeshiva and the study partner of Katz’s son, Rabbi Zechariah Kaplan, at the nearby Yeshivas Bircas HaTorah.
“Irving Backman & Associates sent over the equipment for a hydroponic garden at the Diaspora Yeshiva, and Mr. Backman’s assistant, Ameth Alzate, asked me to help shepherd it through customs,” says Katz, who had worked with him previously.
With Backman’s blessing, she took the project under the wing of Start-Up Roots, and the garden was inaugurated on her birthday, June 12.
The site is professionally managed by Ari Waldman, chief operating officer of Start-Up Roots, with daily assistance from Jacob Schonzeit, another study partner of Katz’s son at Bircas HaTorah. “Jacob had a background in permaculture, so we trained him in hydroponics,” says Katz.
Diaspora Yeshiva students, who range in age from 17 to 70-plus, may choose to spend an hour or two every day helping to tend the system.
Daniel Levin, 36, found out about the garden when he saw Katz carrying supplies in the courtyard and offered to help. Now he volunteers regularly.
“When Robin showed me what was happening here, I thought it was cool because in South Africa I lived on a farm where we tried growing different plants and trees. It also combines other experiences I’ve had working with electricity and water pumps and salts and nutrients. We’re looking at what works well and could be most viable to grow efficiently and that would most benefit the yeshiva menu,” says Levin.
SEEDLINGS ARE started in a growing medium called rock wool, and incubated before being planted in the trays.
RABBI YOSEF GOLDSTEIN: Spending time in the hydroponic garden ‘helps our students get close to God.’
KATZ SEES all the Start-Up Roots projects as a strategy toward ensuring a healthier future.
“Chemical pesticides are killing us,” she says. “Israel has the highest chemical pesticide usage in the OECD.
We also have a high poverty rate and a high malnutrition rate, and we’re right behind America with a rising obesity rate. I really believe that schools can be a great agent for change.”
Katz discovered hydroponics several years ago and realized it could solve multiple problems at once: The veggies provide vitamins, minerals and fiber often missing in impoverished families’ diets; the plants don’t leave carbon footprints since they are grown on premises and aren’t trucked in; and the students work- ing in the enterprise gain valuable skills they could use to earn a living.
Moreover, during the shmita (agricultural sabbatical) year, when most haredi Israelis buy only imported pro- duce, the greens raised in the school gardens can be cultivated, harvested and consumed without worry because they don’t grow in the ground. The absence of soil and the indoor environment adds another benefit year-round in keeping the plants largely insect-free.
START-UP ROOTS CEO Robin Katz with the greens growing in the hydroponic garden at the Diaspora Yeshiva.
“You don’t need chemical pesticides. The idea is to control the environment so that insects aren’t such a problem,” says Katz. Before entering the growing area, all visitors cover their shoes with paper booties so as not to track in bugs or other contaminants.
She also explains that in a water-stressed region, growing in water actually makes good ecological sense.
“Hydroponics saves 90% of the water of regular agriculture because the water goes directly to the roots and not into the ground,” explains Katz.
Speaking of roots, the word in the name of the organization has more than one layer of meaning. “Many children think that lettuce comes from the grocery store. They have no concept of the chain behind it. So we try to connect kids with the source of their food,” says Katz.
Beyond that are the roots of Torah teachings involving agriculture. Religious schoolchildren learn the laws of tithing, for example, but rarely or never have the opportunity to pick fresh produce and perform the ceremony. It’s all been done at a distant packing house.
And on a more spiritual level, Katz adds, “By watching how the tiny seeds develop, kids learn that the universe is more complicated and bigger and more awesome than they ordinarily take time to stop and think about. They learn that if they don’t put in the effort nothing will grow, but there are also aspects that are beyond their control.”
Rabbi Yosef Goldstein, spiritual adviser at the Diaspora Yeshiva and son of its founder, says spending time in the hydroponic garden “helps our students get close to God.
It’s a way to clean their minds and to be surrounded by nature. Even learning next to the plants for an hour in the morning helps them grow spiritually. I love to come in here and see what’s growing and breathe in all the oxygen. And afterward, we get to eat this healthy nutritious food.”
GOLDSTEIN, WHO is also a practitioner of Chinese medicine, hopes the garden will raise herbs in the future. In only a few months, the site has produced vegetables including cucumbers, radishes, green beans and chard.
“We have 200 students from all over the world from many different backgrounds, and I believe this project can also be a way to build a future source of parnassa [income] especially in the shmita year,” adds Goldstein. “It will be nice for religious people to go into agriculture.”
Levin says that volunteering in the garden “gives me a new dimension of looking at what I am learning in the Torah.”
The connection between faith and farming is entrenched in Judaic sources. The 13th century Tosafist Talmudic commentators expressed it like this: “The farmer who sows seeds places his faith in the life-giver of all the worlds, for he trusts that God will provide all that is needed for his crops to grow.”
The Torah also admonishes against waste, Levin points out. “When you know where food comes from and how much goes into growing something that takes five minutes to eat, you are motivated not to waste anything.”
Katz extracts additional lessons from the hydroponic growing experience.
“In an indoor controlled environment, we’re putting nutrients directly into the water exactly what the plant needs – and we measure it every day along with the pH of the water because that affects how the plants absorb the nutrients,” she says.
“We use that as a metaphor for absorbing information in the learning environment. We encourage kids to think how they can optimize their own ‘pH level.’ They see that if you take care of something it thrives, and they can apply the same principle to themselves.”
Aside from the project at the Diaspora Yeshiva, Start-Up Roots has established hydroponic gardens at two haredi girls’ schools in Jerusalem. The schools’ science teachers present the science part of the curriculum, while a Start-Up Roots dietitian presents hands- on sessions to enable students to discover the impact of the food choices they can make.
“The students enjoy the nutritious food that they are growing, which enables them to incorporate the greens into their own diets in tasty ways,” says Katz.
Shiran Iluz, vice chairman of the IDC Entrepreneurship Club, came to one of these schools to help the students develop a viable business plan around the veggies.
“One girl thought of selling a green drink. Initially, the others thought it sounded awful but when they tried making it with our nutritionist, they discovered that they loved it. Then they named it and learned how to pitch it and sell it to their classmates. They had to learn how to network with kids outside their social circles, and this project totally changed the social dynamics of the school.”
In the fall, Start-Up Roots will implement a hydroponic garden at a pluralistic school in the Sharon region.
“Food is a great unifier and our environment is a great unifier,” says Katz. “I’m very happy that every segment of Israeli society is embracing our initiative and our curriculum.”
Nature Inspires Some of The Coolest Things
Unlike many other vertical farms, which are located in artificially lit warehouses and cut off from the outside world, Vertical Harvest makes use of natural sunlight and ventilation
By Chip Giller on August 3, 2019
Hey there,
I know what you’re thinking. Reading a nature-themed climate change newsletter from a guy who shows up to business meetings looking like he’s just finished up a hike is a little on-the-nose.
But hear me out. Nature’s got a lot more to offer us than a great place to eat trail mix.
Very Smart People everywhere are learning that natural processes and ecosystems offer great models for the world that we create: Think a biodegradable Michelin tire based on coral growth, Adidas shoes meant to one day be recycled into a new pair, even a flood-friendly courtyard tile dreamt up by a group of middle schoolers and inspired by … potatoes. (Weirdos like me sometimes call the concept biomimicry.)
Read on to learn more about nature-inspired design — how can you resist the allure of a kelp-based tank top or a seed-inspired monocopter you can make yourself?! You don’t need a pair of hiking boots to find inspiration in what already works.
— Chip, Grist Founder
1. Your New Hero
Nona Yehia is CEO and co-founder of Vertical Harvest in Jackson, Wyoming. The company produces Bumble Bee tomatoes, rainbow chard, butterhead lettuce — as much bounty as a 10-acre traditional farm, all in a state-of-the-art, hydroponic greenhouse that takes up only one-tenth of an acre of land. And it does it with a lot of help and inspiration from nature.
Unlike many other vertical farms, which are located in artificially lit warehouses and cut off from the outside world, Vertical Harvest makes use of natural sunlight and ventilation. The company even uses “bug-on-bug warfare” to fend off insect pests, Yehia says.“We have parasitic wasps that are right now patrolling to take care of white flies and aphids.”
Vertical Harvest’s design and business model — many of the company’s employees are people with disabilities— have garnered attention from around the globe.
Check out our recent conversation with Yehia, a 2016 Grist 50 Fixer.
Blue Sky Science: How Do Plants Grow Without Dirt?
The principal purpose of soil is to provide mineral nutrition for the plant. About 20 elements make up the mineral nutrition requirements for plants, and if you can provide those, you’re providing a lot of what soil is giving to the plant
Aug 7, 2019
Q - How do plants grow without dirt?
— Ruby Taggart, Merrimac, Wis.
A - Simon Gilroy, professor in the department of botany at the University of Wisconsin-Madison:
The principal purpose of soil is to provide mineral nutrition for the plant. About 20 elements make up the mineral nutrition requirements for plants, and if you can provide those, you’re providing a lot of what soil is giving to the plant.
A long time ago, plant researchers found out that you can get plants to grow perfectly fine without soil if you provide water and the mineral nutrition. That’s the idea of hydroponics, where we can grow plants in a soil-less environment. We’re providing what they need: water and the minerals that allow them to grow.
Soil also provides structural support, so to replace soil we have to provide support in some other way. The classic way for hydroponics is to have plants growing in a plug, some inert material that provides the support. The roots grow down into a liquid. The liquid provides the minerals that the plant needs. All you need at that point is to power plant growth by photosynthesis, which is providing it with air and sunlight.
You can take that to the extreme. Some of the research being done at UW-Madison is related to figuring out how plants can be optimized to grow in space. Researchers are interested in growing plants in the space station to perhaps sustain astronauts for incredibly long journeys.
But growing in that weightless environment is not how plants evolved. Think about growing plants off the Earth where there is no soil. Think about growing them, for instance, on Mars or on the moon, where you can grow them in the dust that coats the surface of those bodies.
Providing you can balance the unique environment and added stresses, maybe add a little bit of fertilizer, you can grow plants perfectly happily under those conditions.
With minerals, water, sunlight and air, you can make a plant grow.
Blue Sky Science is a collaboration of the Wisconsin State Journal and the Morgridge Institute for Research.
Disruption In The U.S. Fast Food Sector Creates Prospects For A New (And Lucrative) Market Opening For The Vertical Farming Industry
Plant-based alternative meats are gaining increased traction with customers owing to their smaller environmental footprint compared with traditional meat production
AUGUST 2, 2019
KYLE BALDOCK
By Joel L. Cuello, Ph.D.
U.S. fast food customers’ growing expectations for healthier, ethical and more environmentally sustainable options directly correspond with the values and produce that the Vertical Farming industry provides.
As the vertical farming industry in the United States grows, its market segments correspondingly diversify and widen.
Aerofarms, Gotham Greens and Square Roots, for instance, all deliver their produce to local grocers as well as to Whole Foods Market.
Plenty sells its leafy greens through the online retailer Good Eggs, San Francisco’s Faletti Foods as well as to fine-dining restaurants, including Atelier Crenn and the Michelin-starred Protege in Palo Alto, among others.
New-Jersey-based Greens Do Good, whose entire profits go to helping people with autism through an innovative and socially-responsible business model, delivers the bulk of its produce to a partner golf country club.
Meanwhile, Crop One Holdings has recently and emphatically helped push the market frontiers for vertical farming by forming a joint venture with Dubai’s Emirates Flight Catering to supply 105 airlines and 25 airport lounges at Dubai International Airport with a full array of greens for catering services.
A Great Convergence
In a parallel industry universe, the U.S. fast food sector is in the midst of experiencing arguably its biggest disruption in decades caused by the tectonic shifts in customers’ preferences and expectations. With customers’ growing demand for healthier, ethical and more environmentally sustainable options, the industry’s major players from McDonald’s to Burger King to Carl’s Jr., among others, have taken notice and are promptly strategizing and responding.
McDonald’s, the largest fast food chain in the United States, now exclusively offers antibiotics-free chicken, cage-free eggs, cow milk unadulterated with artificial growth hormones, and buns devoid of high fructose corn syrup, among others.
And in direct response to mounting customer discomfort with the health, environmental and ethical costs of meat, Burger King has introduced its vegetarian burger Impossible Whopper using the plant-protein-based meat supplied by Impossible Foods.
Plant-based alternative meats are gaining increased traction with customers owing to their smaller environmental footprint compared with traditional meat production. It is well known, for instance, that livestock production for meat and dairy accounts for close to 15 percent of the global greenhouse gas emissions annually. That animal ranching also consumes exorbitant amounts of water, feed, land and energy further exacerbates the sustainability deficits of traditional meat production.
Burger King currently sells its Impossible Whopper to 59 restaurants in the St. Louis area, and plans to swiftly make it available in all of its 7,200 locations nationwide.
Carl’s Jr. now also offers a vegetarian burger by the alternative-meat maker Beyond Meat at over a thousand of Carls’ Jr. restaurants, while White Castle has been selling a Slider version of the Impossible burger since last year in its over 380 stores.
Earlier this month, Dunkin’ began serving its meatless Beyond Sausage Breakfast Sandwich in some of its restaurants in New York City with plans to sell it eventually nationwide.
Even KFC is currently exploring adding plant-based fried chicken as part of its standard offerings.
And McDonald’s, while still currently weighing whether to add a meatless burger on its menu in the United States, has now added a vegan burger — called the Big Vegan TS — as part of its permanent offerings in Germany. Nestle sources the meatless burger to McDonald’s restaurants in the country, one of the company’s top five international markets.
For true meat lovers who prefer their burger to be actually animal-derived and non-vegan — but ethical and environmentally sustainable just the same — Memphis Meats is currently at work in perfecting its lab-grown meat constituted from actual beef cells. This innovation is still very much in development, however, that the meat product is not expected to be made available in the market any time soon.
It’s One Small Step for Wendy’s
The rising convergence of AgTech innovations in the U.S. fast food industry — a direct result of the aforementioned customers’ evolving and more enlightened expectations and preferences — certainly received a recent big boost when Wendy’s finally decided to source all of its tomatoes from indoor hydroponic greenhouses located in the U.S. and Canada for all of its 6,000 restaurants in the United States.
In keeping with Wendy’s motto of Always Fresh, the decision ensures superior quality as well as enhanced food safety, predictability, reliability and product traceability for the American international fast food’s fresh tomato supply.
Wendy’s, the second largest burger fast food chain in the U.S., also has plans over time to source its other fresh vegetable ingredients from similar indoor crop production systems.
One Giant Leap for U.S. Vertical Farms?
Could Wendy’s one small step translate into one giant leap for both the U.S. fast food industry and vertical farming industry?
The likelihood is real in part given their now shared product values and since the economy of scale involved helps provide impetus and cushion to both industries
For U.S. fast food, partnerships with vertical farms would help meet the former’s customer expectations on the health, ethical and sustainability fronts, while also ensuring produce quality, nutrient value, consistency and supply reliability even as they help reinforce local jobs creation.
For U.S. vertical farms, partnerships with U.S. fast food would help effectively reduce their price of produce through the expanded economy of scale even as they also help strengthen local jobs creation.
The size, of course, of the U.S. fast food industry is gargantuan, with approximately 500 million Americans eating at fast food restaurants every day, generating annual sales of about $200 billion at 200,000 fast food locations across the country. Indeed, just the top 10 U.S. burger and chicken fast food chains — namely, McDonald’s, Wendy’s, Burger King, Chick-fil-A, Sonic, KFC, Carl’s Jr./Hardee’s, Jack in the Box, Popeyes Louisiana Chicken, and Whataburger — post a combined annual sales of over $84 billion (2016).
The entry of U.S. vertical farms into the U.S. fast food industry would certainly provide the former a momentous and immense market opportunity that it seeks.
One hopes that the continuing convergence of AgTech innovations in the U.S. fast food industry would help launch both the U.S. fast food and vertical farming industries into a jointly reinvigorated sustainability trajectory for people, planet and proft.
*****
Dr. Joel L. Cuello is Vice Chair of the Association for Vertical Farming (AVF) and Professor of Biosystems Engineering at The University of Arizona. In addition to conducting design and research on vertical farming and cell-based bioreactors, he teaches “Globalization, Sustainability & Innovation” and “Integrated Engineered Solutions in the Food-Water-Energy Nexus”. Email cuelloj@email.arizona.edu.
CO2 GRO Inc. Is Pleased To Present An Interview With John Archibald, President And CEO Conducted At The Recent TSX Venture 50 Conference
John discusses the 2019 outlook and CO2 GRO's significant innovations in the agtech industry
Dear Shareholders, Stakeholders
And Interested Parties
CO2 GRO Inc. is pleased to present an interview with John Archibald, President and CEO conducted at the recent TSX Venture 50 Conference. John discusses the 2019 outlook and CO2 GRO's significant innovations in the agtech industry.
To view the interview please click here www.co2gro.ca/pages/investors.
For more information please contact Sam Kanes, VP Communications at 1-416-315-7477 or sam.kanes@co2gro.ca
©2019 CO2 GRO Inc. | Suite 5800 40 King Street W Box 1011 Toronto Ontario M5H 3S1
Veggies Grown In Nevada's Massive Indoor Farm Are Now On Sale To Las Vegas Locals
Nevada does not have particularly fertile lands, but that didn't stop Oasis Biotech when they opened a 215,000-square-foot indoor farm to the public last July
by Phillip Moyer
July 30th 2019
The facility uses hydroponics and environmental control to reduce environmental impact. (PHOTO: Nathan O'Neal)
Nevada does not have particularly fertile lands, but that didn't stop Oasis Biotech when they opened a 215,000-square-foot indoor farm to the public last July.
Designed to be sustainable and environmentally-friendly, the facility uses hydroponics to use 90 percent less water than traditional farming, and have a completely controlled environment to eliminate the need for pesticides.
Guests had the chance to sample the vegetables after its openings, but until now, the food was only widely available to high-end restaurants in the Las Vegas Valley.
Today, the farm announced that they'll be selling eight-ounce bags of its baby leaf Spring Mix and Romaine Mix blends to consumers under its "Evercress" brand name.
“Over the last year, we have been working hard to perfect our crops and growing methods to bring the community and our customers the freshest salad greens in Las Vegas,” says Michelle Howell, Sales & Marketing Manager at Oasis Biotech. “We had over 1,000 people attend last year’s grand opening and the big question everyone asked us was “When can we buy it?” so we are thrilled to now offer the Evercress salad greens to Las Vegas locals."
The blends can beat Oasis Biotech's farming facility, located at at 6225 Annie Oakley Drive in Las Vegas.
In an effort to stay true to its mission to “Feed the World, Better.,” any product not sold to current customers or purchased by the public will be donated to local charities.
Scientists Play With Light And Water To Speed Up Crop Breeding
A number of challenges face crop production around the world, including drought, diseases, pests and limited land. Scientists are tasked with breeding varieties that will produce higher yields but use less land and fewer resources
BY DTN Grains - Loren Lindler | July 27, 2019
OMAHA (DTN) — This twice-monthly column condenses the latest news in the field of crop technology, research and products. Researchers say that by 2050, there could be 10 billion people in the world. A number of challenges face crop production around the world, including drought, diseases, pests and limited land. Scientists are tasked with breeding varieties that will produce higher yields but use less land and fewer resources. To aid in this, some international researchers are experimenting with two new techniques to speed up the breeding process: LED technology and hydroponics.
PLEASE, SIR, CAN I HAVE SOME MORE LIGHT?
Lee Hickey, a plant geneticist at the University of Queensland in Australia, is combining breeding and light-emitting diode (LED) technology to produce a form of “speed breeding.”
Plant breeding can often take years. With speed breeding, researchers are able to use LED lights that are ideal for photosynthesis, which allows researchers to grow crops three times faster, creating more generations in a single year.
Botanists started growing plants under artificial light over 150 years ago. As the years passed, LED technology has vastly advanced, allowing scientists to be more precise by customizing light settings to individual crop species. The Australian researchers exposed their crops to 22 hours of continuous blue and red LED lights, under ideal temperatures, which essentially convinced the plants to flower early. A generation of crops can take months, or even a year, to breed with traditional methods. However, with the use of LED lights and speed breeding, scientists were able to grow six generations of wheat, barley, chickpeas and canola in a year.
A WATERY WONDER
To obtain the fastest breeding results in their greenhouses, scientists at the John Innes Centre in the U.K. are using hydroponics, the practice of growing crops without soil, usually with the use of a water-nutrient solution. Hydroponic techniques allow nutrients and oxygen to reach plant roots quicker.
Many researchers have found that hydroponic plants grow 30% to 50% faster than a plant grown in soil. The ample amount of oxygen in a hydroponics system allows the roots to absorb nutrients much faster, stimulating root growth. The U.K. researchers are taking advantage of this faster-growing time to speed up their evaluation of the genomes of wild relatives of modern crops, which can hold valuable disease-resistance genes.
You can learn more about the LED technology and plant breeding with hydroponics: https://www.nowscience.co.uk/…
Hydroponic Farming Gaining Success In Bangladesh
The founder of Agro Circuit at Uttara has no problem selling 25-30 kg of exotic green vegetables he produces every day and that too at premium prices. Tanvir’s clients include Gourmat Bazaar, Unimart and families at Uttara and Gulshan
21 July, 2019
FAISAL MAHMUD, Dhaka
Amid stories of agrarian crisis everywhere, Tanvir Hossain Siddiqui has a happy tale to tell.
The founder of Agro Circuit at Uttara has no problem selling 25-30 kg of exotic green vegetables he produces every day and that too at premium prices. Tanvir’s clients include Gourmat Bazaar, Unimart and families at Uttara and Gulshan.
If Tanvir’s story sounds different at a time when farming is becoming unsustainable due to falling yields, increasing costs and low prices along with water scarcity and soil degradation, his farm looks different too.
Green leafy vegetables such as spinach, tomato and lettuce grow on a one-foot bed of flowing water—and, no soil—in a specially designed 2,000-sq-ft greenhouse at Agro Circuit Farm.
There is no need to spray insecticide or pesticide, or even use fertilizers. The nutrition for plant growth comes from 8,000 freshwater fish—Telapia and Carp—cultivated in separate water tanks inside the greenhouse.
Fish & Veggies
Tanvir uses what is called ‘aquaponics’ to grow leafy vegetables.
The method combines aquaculture—cultivating fish and other aquatic animals in tanks—with hydroponics, in which plants are cultivated in water.
The water from the fish tank is pumped onto the beds where the plants grow. While the fish excretions provide nutrients for the plants, the clean water is recirculated back to the fish tank. While the initial cost to set up the facility would be high, the recurring cost is low in aquaponics and there are two sources of revenue: fish and vegetables.
Moreover, the water requirement is as less as a tenth of that in conventional agriculture.
Tanvir who completed his bachelors in electrical engineering from Ahsanullah University of Science and Technology in Dhaka, went to Australia in 2010 to complete his masters. There he quickly developed an interest for agriculture, especially for aquaculture and hydroponic agriculture.
“When I used to go to Australian supermarkets, I saw that the most fresh and priciest vegetables were tagged as hydroponic vegetables. They were also the juiciest and tastiest. Then I started studying about hydroponic agriculture,” he told The Independent.
Tanvir said studying about hydroponics was not that hard. “These days, studying about anything is easy. You just need to do a Google search or search for it in YouTube. There are numerous tutorials and learning materials.”
He, however, added that the practical work is obviously a bit challenging than learning through a virtual medium. “I first bought a two planter startup kit from a farmers’ market in Sidney and started growing kale on an experimental basis. I succeeded and it boosted my confidence. Then in 2015, I came back to Bangladesh and started building the greenhouse in my father’s Uttara house,” he said.
Challenges of Hydroponics Farm
Tanvir said the first climate management challenge that hydroponic farmers must overcome is figuring out how much cooling, dehumidification and heating are required to manage the temperature and humidity of the space for growing.
“In an aquaculture or hydroponic farm, lighting is the greatest source of heat, followed by motors used to operate fans, pumps and automation. Because hydroponic farms are often well-insulated and designed to operate day and night throughout the year, cooling is usually required 24/7 and year-round to remove the heat generated inside the space,” he said.
Dehumidification is also constantly required to remove moisture added to the air via evapotranspiration from the plants and irrigation system. The rate and quantity of evapotranspiration depends on several variables, including light intensity, air temperature and humidity (or vapor pressure deficit), air movement and the irrigation method, he explained.
The second biggest challenge is figuring out how to deliver the conditioned air everywhere within the hydroponic farm to create a uniform growing environment. “When racks are spaced tightly together—both vertically and horizontally—it is difficult to create uniform conditions everywhere,” said Tanvir.
The third biggest challenge is to properly set up the location of the cooling equipment or the HVAC equipment of the hydroponic farm. HVAC equipment can include air conditioners, dehumidifiers, circulation fans, ductwork, chillers, boilers, pumps and pipes.
The cooling and dehumidification equipment are best located outside the building, where heat and moisture can be ejected to the outdoor air. Some equipment (air conditioners, dehumidifiers, etc.) are ideally located on the roof of the building or on the ground outside and next to the room they serve, helping to limit ductwork.
“No matter what crop is grown, managing humidity control and air movement in a hydroponic farm is essential to plant productivity, harvesting schedules, quality control and, ultimately, profitability,” Tanvir added.
A Growing Trend
Many aspiring young farmers like Tanvir are taking to hydroponic farming professionally. The Facebook page “Hydroponic in Bangladesh” has over 1,900 members and they engage in various discussions on different problems and prospects of hydroponic agriculture.
Dohar-based Mizanur Rahman, who is a textile businessman, is an amateur hydroponic vegetable grower. He has a 3000-sq-ft green house at Dohar in which he cultivates tomato through the hydroponic system with technical help from the local agriculture department and Agriculture Research Institute.
The nutritional requirements of the plants in his system of soilless farming are met by the nutrient mixtures, called hydroponics fertilizer mixtures, added to the water in which the plant roots are kept submerged. These mixtures are made of chemical plant nutrients.
“I grow my tomatoes without the use of any pesticide, so they are very organic. They taste better than any other tomatoes in the market,” he said.
Mizanur said some hydroponics enthusiasts abroad have been experimenting with various kinds of organic manures and mixtures of plants, but successful and commercially viable organic hydroponics models are still not available. “In fact, even globally accepted principles for certifying organic hydroponics products are also not yet available,” he said.
Highlighting the advantages of hydroponic farming, agriculturist and Professor of Bangladesh Agricultural University in Mymensingh Dr Abdus Salam told The Independent, “It requires 90 per cent less water than the conventional soil-based farming. Since it is water based, it has macro and micronutrients directly fed to the plants and they grow 50 per cent faster and also have a better yield.”
Giving an example, he explained, “If lettuce grown conventionally requires 60 days, lettuce grown using hydroponics yields double the produce in 28-30 days.”
Emphasizing on its water efficiency, Salam said, “Regular soil-based farming with 1,500 plants would require about 200 liters of water a day, but with hydroponics, only 20 liters of water is enough.”
EA
The Future of The Agriculture Industry Is Vertical Farming
It’s only a subtle whiff in the air that indicates something might be hidden beneath the surface. But more than 100 ft below a nondescript building in south London’s district of Clapham, vegetables and herbs are growing in former raid shelters.
Vertical farming uses LED lights and nutrient-infused water to create optimal growing conditions for plants. Credit: Jeff Gilbert
23 July 2019
It’s only a subtle whiff in the air that indicates something might be hidden beneath the surface. But more than 100 ft below a nondescript building in south London’s district of Clapham, vegetables and herbs are growing in former raid shelters.
“You will hear trains rumbling four storeys above us, that's the Northern line,” says Steven Dring, co-founder of Growing Underground, a vertical farming start-up.
The shelters, built between 1939 and 1942 in tunnels under one of London’s busiest train lines, became a place of refuge for 8,000 people fleeing the Luftwaffe aircraft over the skies of London during the Battle of Britain.
Nearly a century later, the underground space has seen a radical transformation, as a pinkish hue now floods the tunnels lined with trays growing the garden-variety of produce: pea shoots, red mustard, fennel, radishes, rocket leaves, coriander, baby leaves and more.
For Growing Underground, so-called vertical farming promises to change the way food is produced through facilities that optimise vegetable growth and bring production within touching distance of town centres.
The industry itself is expected to be worth more than $11bn in just over six years, and has seen a commitment in the UK from the government, which is preparing to invest $24.8m through its Industrial Strategy Challenge Fund in innovative projects that boost agricultural productivity at a time when traditional farming is facing an uphill battle.
The average cost per acre of agricultural land has jumped almost 5,000pc from 1966 to $9,800 in 2017, while the amount of land available for farming has declined, as almost 450,000 hectares were lost to urban developments last decade.
“It's efficiency, this is how we need to grow,” Dring says. “It's about controlling that environment forensically to give the plants exactly what they want all the way through their life.”
To grow its produce, the Clapham-based company first sows seeds into a recycled piece of carpet that acts as a substrate for germination to take place in the dark.
Once the seeds have started to spring to life, they are incubated in vertically stacked trays, which are exposed to LED lights dialled into the exact brightness needed by the plants, and a carefully-crafted infusion to optimise growth, taste and yield.
“All the nutritional composition you would have in soil we put into water through a nutrient mix that is exactly what's required by the plants,” Dring says.
Credit: Jeff Gilbert
The company has found success with its products, becoming a key supplier to supermarket giants such as Waitrose, Whole Foods and Marks and Spencer, and are far from the only ones taking advantage of this new way of producing food, as a host of companies have started to experiment with vertical farming - all while swooning investors.
AeroFarms, a New Jersey-based vertical farming company, raised $100m at the start of the month in a funding round led by the investment vehicle of IKEA-owner, Ingka Group. It’s a move that brings the firm a step closer to “unicorn” status with a post-funding valuation of $500m, and will help it boost the production of its pesticide-free produce.
Meanwhile online food retailer Ocado, which announced an almost $1bn tie-up with Marks and Spencer earlier this year around its delivery business, declared its intention to step into vertical farming after revealing a $21m investment in the space last month, including in Scunthorpe-based Jones Food Company, operator of Europe’s largest indoor farm.
At the time, Tim Steiner, chief executive of Ocado, said that he hoped locally-grown herbs and vegetables could one day be delivered “to a customer’s kitchen within an hour of it being picked”.
But the influx of money into vertical farming didn’t always seem likely. According to Dring, the agriculture sector was “under-optimised” just a decade ago, with little attention directed towards the disruptive potential of technology.
Some keen-eyed investors caught a glimpse of potential early on. Take Graham Ramsbottom, chief executive of Wheatsheaf, the agricultural investment arm of the centuries-old Grosvenor Estate, headed by the Duke of Westminster.
Set up in 2012, Wheatsheaf took an early bet on Aerofarms when its first facility was “in a disused disco”. Ramsbottom, who has been involved in the agriculture industry for more than 30 years, said he saw little change in the way food was produced in that time, but found the data-led, precision approach on offer from vertical farming to be an interesting road forward.
“We grow food in open environments that have huge variability around climate,” he says. “If you take one acre of land from one side of the field to the other, you can have huge variation in terms of shading, temperature, type of soil, pest damage.”
The shift away from traditional agriculture has indeed picked up pace, but some criticism has been levelled at vertical farming, with concerns about the amount of energy needed to maintain facilities that are essentially growing plants 24/7.
“There's no doubt the energy equation is one of the big calculations that anyone looking to set up a facility like this does need to do at the outset,” says Belinda Clarke, director of trade body Agri-Tech East. Ramsbottom also claimed that he was “cognizant” of the issue before investing.
The growth of lettuce in a vertical farm, for example, requires 3,500kWh a year of energy for each square metre it is grown in due to the demands of artificial lighting, versus the 250kWh of energy needed to grow lettuce in a greenhouse.
As Clarke points out, managing these kinds of facilities “does require a degree of sophistication” that ensures management of the appropriate conditions, delivery of water, and correct humidity, all while keeping pests and diseases out.
But there could be workarounds to the energy conundrum. Prioritising the use of low-energy LED lights and recycling water can cut costs, while more innovative solutions can support the industry too. Clarke points to a facility run by Japanese tech giant Fujitsu, which uses “spare heat” to warm up a vertical farming system producing lettuce.
Another issue at hand is the high capital input cost involved in the initial setup of a facility, which is why the Agri-Tech East director thinks vertical farms need to be deployed in an “appropriate” way.
For some farmers eyeing up the opportunities in vertical farming for crops like wheat, potatoes or sugar beet, the benefits may not stack up, while for others in more challenging climates, the business case is evident.
“If you're in an environment which is very environmentally inhospitable, for example, or in a disaster recovery zone or something like that, then there is a real opportunity to augment the food production,” Clarke says.
The case for vertical farming has gone beyond just business. According to the United Nations, the world population is expected to reach 9.7bn by 2050, and the carbon intensive demands of current agricultural processes will be unsustainable if climate change is to be tackled.
“It's getting really hard to deny climate change [and] there’s going to be another India and China effectively on the planet by 2050,”says Dring.
Growing Underground has seen a “significant focus” from Asia and the Middle East, regions which are moving “to protect their food security and supply chains” as swelling middle-class populations will demand more and better quality produce.
It’s one reason why vertical farming is likely to stick around, but ultimately, any reason to produce food more effectively is one to grab a hold of.
“It's really doing what plants have always done,” says Ramsbottom, “in an environment where you can truly understand it.”
Growing Plants Without Soil
Have you ever thought of growing plants without soil? Sounds weird? There’s a new technology doing rounds in the agriculture market, which could change both the course and future of farming
Have you ever thought of growing plants without soil? Sounds weird? There’s a new technology doing rounds in the agriculture market, which could change both the course and future of farming
BHUBANESWAR: For millennia, the state of Odisha has been a pioneer in farming. The farmers have cultivated plants, grew various kinds of crops, and developed different farming techniques with the help of advance science and technology.
Now there’s a new method, by which the state farmers can develop a self-sustaining farm even without the need of soil. Through the process of Hydroponics, one can grow plants in water without using soil. The main components used by plants are water and nutrients, which makes it possible to grow a plant without soil.
Once all the essential nutrients which are required by plants are provided through some other source like a water solution (nutrient-rich solution) containing all the necessary nutrients, one can eliminate the use of soil to grow plants.
According to latest research, there is advanced agronomy technology with Hydroponics. People all around the world seek healthy food grown in a safe environment, where Hydroponics seems to be fulfilling that need. Orissa Post interacted with agriculturist Ekadasi Nanda who said that Hydroponics is the game changer in the agriculture industry. The main concern is to bring the plant in direct contact with the nutrient-rich water solution.
One can start Hydroponics as a mean of additional income by growing and selling plants without much hassle. This technology is all set for commanding a formidable position in the agriculture industry as it doesn’t demand any particular skill required for growing plants. Also, there’s no prior cost involved. By adopting this technology, you can utilize your space and reduce the use of chemical fertilizers for the growth of plants.
This technology has proven to be one of the best for growing crops in urban areas. With all the advantages of Hydroponics system, there are fair chances that this can change the course of the future by restructuring the cities and making them more environment-friendly. Hydroponics can be a game changer for the agriculture industry.
However, it’s not a cakewalk as it seems like, one needs to have access to the proper guidance of subject matter experts to grow and maintain the plants through Hydroponics. My Urban Greens (an initiative by IFFCO Kisan), for instance, is serving similar kinds of services to the urban population and progressive farmers by providing them a customised solution as per their requirements.
Sandeep Malhotra, MD and CEO, IFFCO Kisan, said, “There has been a great hue and cry about the scarcity of water; Hydroponics is emerging as a boon in the agriculture industry as well as in common households. Through this process, plants consume less amount of water in comparison to the conventional gardening system. It’s not just about saving water, but it is observed that plants grown by hydroponics technique consist of 50% more vitamins and it grows faster than traditionally grown plants. It is more profitable for farmers to grow plants through this technology.”
He further added, “IFFCO Kisan provides experts’ advice and services to urban people, FPO’s and progressive farmers related to the right and best practices of Hydroponics farming. We have initiated crop specific advisory services and support in vernacular languages to make this technology easily understandable to the farmers and urban people. We are encouraging and supporting them to adopt this technology and in alignment with that, several training programs are also lined up across different states of the country.”
Tags: HydroponicsInnovative technology
New Raft For Hydroponic Crops Such As Basil
"They are designed to optimize processes, logistics, maintenance, cleaning operations and, most of all, to increase productivity per square meter."
Rosa Plast has introduced a new raft to grow basil hydroponically. Developed in collaboration with Cammelli, the companies claim that the productivity increases by 25%. "They are designed to optimize processes, logistics, maintenance, cleaning operations and, most of all, to increase productivity per square meter."
Using the panel leads to a 25% increase in productivity, 10% less time used for harvesting, a 15% drop in transplant time and a 30% drop in cleaning time. Its long-lastingness was assessed at +400%."
"Thanks to our lengthy experience and our collaboration with Cammelli, we developed a panel for the cultivation of basil. The great performances were confirmed by both agronomists and producers," explains plant manager Attilio Cattaruzza.
"In addition, no sanitation is required and the material used is entirely recyclable. The panel was designed to be used with an automated system and can be stacked."
Rosa Plast was set up in the 1960s and specializes in the construction of plastic component molds and equipment for the processing of plastic materials. A few years ago, it also started focusing on the indoor forming sector, with particular attention to designing rafts for soil-less hydroponic crops.
"Our recent experiences and the collaboration with expert producers of highly-automated systems meant we could develop a few products for hydroponic crops. We registered two patents for salad and basil rafts."
Contacts:
Rosa Plast Srl
Z.I. Nord- Via Valcellina 1,
33097 Spilimbergo (PN) Italy
Tel.: (+39) 0427 595311
E-mail: attilio.cattaruzza@rosagroup.com
Website: www.rosagroup.com
Publication date: 7/1/2019
© HortiDaily.com