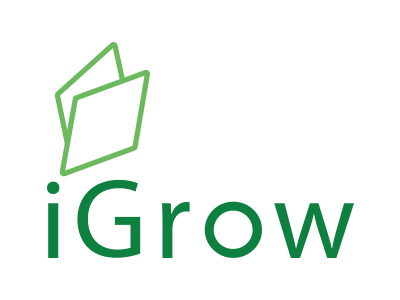
Welcome to iGrow News, Your Source for the World of Indoor Vertical Farming
Applied Technology: Putting The Hyper In Local
December 21, 2018
For some retailers and restaurants, proximity to local food is key—like next door, on the next floor, or on the roof— and you can’t get much fresher than that.
This technology is already gaining traction across the nation and worldwide with vertical farms in skyscrapers, vegetable and herb gardens at restaurants or near retailers, and container farms in areas where growing can be nearly impossible.
Local Roots, a Los Angeles-based startup, has created a twist on greenhouse growing. The company does grow produce and herbs in a protected setting, but instead of a greenhouse, the indoor farms are in 40-foot shipping containers.
The four student founders say that by using robotics, microbiology, and data analytics, their indoor container “TerraFarms” produce up to 300 times higher per square foot densities than traditional farms.
The containers “have also achieved cost parity with greens and other produce grown out in the field,” says Gary Hawkins, founder and CEO of the Los Angeles, CA-based Center for Advancing Retail & Technology, LLC.
Better yet, he says, “they use a fraction of the water and no pesticides or herbicides.”
Local Roots believes it has eliminated many hazards of the supply chain and is partnering with area businesses, restaurants, and retailers, notably Walmart.
And if a retailer or processor has the desire, Local Roots will not only sell and set up a TerraFarm, but oversee the entire growing process from seed to harvest for the freshest, local vegetables and herbs.
The Next Frontier of Agriculture
I gave a TEDx Talk at Wabash College that gave a glimpse as to why I chose to co-found Heliponix. We could only fit so much content in a 10 minute segment, so I saw it fitting to provide a written explanation to tell the full story. Follow the link below to see the full talk.
I was extremely fortunate to receive an internship the summers of 2014 and 2015 after my freshman and sophomore years at Purdue University working as a mechanical engineer for a company in the oil and natural gas industry that manufactured fluid control equipment in my hometown of Evansville, Indiana of about 120,000 people. Although I was surrounded by great co-workers who enriched my technical knowledge, I did not feel like this industry was right for my career.
Then one day during my junior year (Jan. 2016), I received a mass email from my college about a job opening at the horticultural college looking for an engineer familiar with fluid control systems for a hydroponic research project. I responded out of curiosity to see if I could at least learn more about other industries to strength my project experience portfolio, but I knew absolutely nothing about plant science. With luck, my email with resume and cover letter was well received, and I was invited into an interview with Dr. Cary Mitchell.
Dr. Mitchell expressed concerns for my generation's ability to grow enough food to meet the growing, global demand. Global food outputs must increase by 70% as we exceed 9 billion people in 2050 according to the UN. Agriculture accounts for 50% of land use, and 80% of freshwater consumption in the USA. To put it simply, we will run out of the land and water needed to produce enough food with our current consumption/production rates within the next thirty years.
Dr. Mitchell explained a new concept to me called CEA, controlled environment agriculture. It is exactly as it sounds, the practice of making an fully automated, indoor farm that used hydroponics. Hydroponics is a method of growing plants using no dirt, but only nutrient rich water recycled over the roots in a closed loop. By keeping the nutrients dissolved in the water in near constant curriculation, plants could grow three times faster than they would in a field. To put this in perspective, a lettuce farmer can typically grow a full head outdoors in 90 days, but hydroponics could grow lettuce in just 30 days or less in some circumstance. Most hydroponic systems are in controlled greenhouses, so a hydroponic farmer could harvest every month of the year without any pesticides and 95% less water by eliminating runoff. CEA was essentially a twelve times increase in productivity compared to conventional soil farming methods limited to one season a year. Additionally, a vertical farm that stacked layers of growing planes could multiply yields even further!
Dr. Mitchell was seeking assistance in the fluid control design for a hydroponic research apparatus called the minitron 3 funded through a NASA grant. Within my lifetime, permanent space colonies will be established on Mars which creates a need for a sustainable food supply. It is not feasible to regularly ship tons of food shipments from Earth, so they must be able to grow their own food. However, there are still challenges holding back the industry’s fruition.
The main challenge to creating a crop-growth module for space travel has been the staggering energy cost of the 600- to 1,000-watt conventional high-pressure sodium lamps traditionally used to mimic sunlight and stimulate plant photosynthesis in contained environments. The lamps also scorch plants if placed too close and require a filtration system to absorb the excess heat they create.
"Lighting was taking about 90 percent of the energy demand," Poulet said. "You'd need a nuclear reactor to feed a crew of four people on a regular basis with plants grown under traditional electric lights."
The focus of the Purdue-NASA research study was to measure the carbon dioxide concentration of air going into the minitron, and concentrations of oxygen leaving the growth chamber. This allowed researchers to measure photosynthetic efficiency rates under different wavelengths of light under an addressable LED array. If you only used LEDs of the right color plants need to grow, then you could eliminate the colors that the plants are not uptaking. The goal was to provide valuable insights about which spectrum of LEDs would be the best to reduce the energy consumption of an indoor growing operation, a major operational cost. This is why many vertical farms have “pink” lights, plants primarily need red and blue light. LEDs have become much more efficient than previous lighting options, and release little heat to greatly improve the energy efficiency of growing indoors.
With the youthful naivety of a 20 year old, I applied to every commercial, hydroponic facility in the US with little to no responses. I quickly learned that the research study I was a part of was not just an attempt to reduce the operational cost of CEA, but it was trying to make it more profitable for more people to pursue. Most indoor farming operations have access to reduced agricultural rates which is 90% less than what most residential consumers pay for energy. Without these subsidies, the industry would be reduced to very low margins, so paying for an engineering intern was out of question.
So I went back to the career fairs at Purdue desperate to find an internship opportunity anywhere outside of my hometown to see new things. I finally found my break when I was given an internship offer as a project manager in Hawaii for the summer of 2016. I immediately accepted the offer, but was told by the HR manager to not worry about the “TBD” stamp on my location of the contract I signed in March.... For the rest of the spring semester, I was ignored on all communication channels to this HR manager until I was finally called back during dead week at the end of the semester after canceling all interviews with the expectation I would be in Hawaii. I was informed that I was reassigned to build section-8 low income, government housing in El Paso, TX along the border to Juarez, Mexico.
A quick google search informed me that Juarez was a murder capital and major drug corridor for Mexican cartels bringing narcotics into the United States. The movie Sicario is based on the cartel violence in Juarez in this exact location. With no other options on the table, I packed my bags for a cross country roadtrip to the desert.
At the time, I spoke virtually no spanish and grew my beard out to appear older to the laborers working on the construction sites. My primary responsibility was to oversee a Spanish-speaking workforce for labor jobs such as toxic asbestos removal. Many of the workers had previous gang affiliations, and narcotic use was rampant. The section of El Paso I managed was originally called the “Angel's Triangle”; a triangular shaped subdivision situated between the Franklin Mountains range, the US Army’s Fort Bliss, and the border wall to Mexico. However, this portion of town was called the “devil's triangle” due to the gang activity, narcotics and prostitution that now plagues the area.
One day I woke up, and envisioned this career defining my entire life, and realized that this was not the industry for me either. I then began to look at my time in the desert as an opportunity to build a business model that could solve the food desert I was living in. A food desert is defined as, an urban area in which it is difficult to buy affordable or good-quality fresh food. Residents (who often lacked private transportation) often resorted to buying highly processed, non-perishable foods which are cheap and readily available at the local corner stores. These corner stores had little to no fresh produce which contributed to a high obesity and abnormally high diabetic rate. I knew that indoor farming could account for the poor soil quality and limited amount of water in the desert to bring these residents the fresh produce they needed, but the following points prevented this from happening.
Indoor, vertical farms require huge amounts of capital from investors to build the infrastructure with a long ROI.
Energy costs for indoor lighting greatly reduced the profitability of the facilities. Without reduced agricultural energy rates, many of these facilities would not be profitable.
Labor rates can be variable, and pose new liabilities for workman’s comp claims in the event of a workplace injury using equipment such as scissor lifts to reach top shelves. Although automation is the best solution, this is a tradeoff for an even higher infrastructure cost, and recurring maintenance cost from skilled laborers.
These points in mind, I concluded that the likelihood of a twenty-one year old being funded to build a multi-million dollar vertical farm was very unlikely. But this revelation posed a new question, “Could the technology be broken up into decentralized devices?”.
Que my TEDx talk… For inspiration I looked towards the ice industry which up until the 1800’s was made up of ice harvesters who could only cut ice from frozen bodies of water when the climate allowed water to freeze. This seasonal availability was disrupted by ice factories that could deliver ice year round in any climate. Today, 99.9% of Americans now own their own personal ice factories called refrigerators.
Much like the early ice industry, agriculture has always been dependant on the narrow window of growing seasons restricted by climates for crops to grow once a year. Since the explosion of microcontrollers and LEDs drastically increasing efficiencies and decreasing prices, indoor vertical farming has become financially viable for the first time. Much like the ice industries continual decentralization, we believe that agriculture will follow suit for many vegetables. In addition, decentralized, hydroponic farms eliminated the three concerns that limit the scalability of massive vertical farms.
Customers buy into for the hardware, not the investor.
The energy cost could be greatly reduced through a new, innovative design.
Contract manufacturing is highly competitive, and keeps manufacturing labor prices low.
This theory in my mind was validated by the success of the keurig recurring k-cup business model that could be emulated with hydroponic appliances sending monthly shipments of seed pods™ and fertilizers directly to the consumers.
Initial concept of recurring seed pod to be produced in an automated production line.
I spent the remaining time I had in El Paso creating conceptual designs this hydroponic appliance called a GroPod™. I then filed the first provisional patents on the new design before building the first prototype, and entered into business plan competitions at Purdue University my senior year. I quickly recruited my purdue-NASA-hydroponic coworker, Ivan Ball to be my Co-Founder because he was a brilliant electrical and computer engineer to close the skills gap we needed to keep improving upon our design. What happened afterwards could be a series of articles on its own, but at least this article can provide a deeper explanation of where I started, and where we are growing!
Follow us on social media as we continue growing to become the world’s largest farm without owning a single acre of land!
Instagram, Facebook, Linkedin, and Twitter: @heliponix
How to Sell Your Produce and Microgreens to Top Restaurants | Episode 3 - Wilson Gibbons (Farm.One)
Published on Dec 27, 2018
In our 3rd episode we chat with Wilson Gibbons, sales manager at Farm.One -
One of the most unique and innovative vertical farms in the country that grows for top Michelin starred restaurants in NYC. He gives the best sales and marketing advice so you can get your foot in the door at restaurants.
Do you have or are you thinking about starting a vertical farm?
Do you want to know how to get your produce and microgreens into some of your top local restaurants? Then you need to watch this episode!
Thanks to Wilson for taking the time and sharing his knowledge and insight.
If you have further questions you can reach out to him at wilsonrgibbons@gmail.com. Also, thanks to everyone who asked questions for this interview across Facebook, Instagram and Reddit. I tried to fit as many as I could into this interview!
ABOUT FUTURE FARMS AND FOOD
Hi everyone! My name is Albert Lin and I'm a farmer, entrepreneur and advocate for all kinds of farming technology that can help feed the world! This is part of a vlog series from VegBed where I interview farmers, entrepreneurs and academia to talk about the future of food.
If you are interested in the best hydroponic growing medium check out ours! (https://www.vegbed.com/products/vegbe...)
Connect with us! Instagram: https://www.instagram.com/vegbed/
Facebook : https://www.facebook.com/vegbed
LinkedIn: https://www.linkedin.com/company/vegbed/
Subscribe! YouTube: https://bit.ly/2EeAejT
Please make sure you hit the subscribe button and hit the notification bell so you can follow Future Farms and Food interviews!
If you would like to be on an episode of Future Farms and Food or know someone that would be a perfect fit send me an email (info@vegbed.com).
Thanks!
Category: Science & Technology
Abandoned Mines Could Become The Farms of The Future
Academics are exploring the use of abandoned mines and other subterranean facilities in the UK and China as alternatives to traditional agricultural land.
December 22, 2018 | By John McKenna
Coal mines and inner-city tunnels could be transformed into farms to help feed the planet’s growing population.
Academics are exploring the use of abandoned mines and other subterranean facilities in the UK and China as alternatives to traditional agricultural land.
“There are millions of redundant coal mines and tunnels in the world which could be linked to new tunnels for crop production,” says Professor Saffa Riffat, Chair in Sustainable Energy at the University of Nottingham.
“In the UK there are over 1,500 redundant coal mines, and in China, there are over 12,000 abandoned coal mines (0.6 million m3), 7.2 billion m3 of tunnels and about one billion m3 of civic air defence tunnels.”
Farm demand
The United Nations predicts the world’s population will grow by 1 billion to reach 8.6 billion in 2030, and 9.7 billion by 2050.
This increase – coupled with an expanding global middle class that is demanding higher-quality food – will require a near doubling of current food production levels, which today still leave 815 million people chronically undernourished.
Instead of simply doubling the amount of agricultural land and all of the economic and environmental implications that would come with that, farmers and scientists are exploring new techniques for growing our food.
Riffat and his University of Nottingham colleagues are embarking on a two-to-three-year study of underground facilities in the UK and China.
They claim that a variety of crops could be grown in the subterranean farms using hydroponic planters, where plant roots are fed with nutrient-rich water. This water could be sourced from groundwater used directly or water that is condensed from ambient air.
Coloured LED units would enable photosynthesis in the absence of sunlight, while plants could breathe CO2 that has been captured from industrial emissions and stored underground.
Dome grown
Growing food inside in artificial conditions is nothing new: in Iceland, where winter can last for six months, crops have been produced in geothermal domes all year round for the past 20 years.
However, today hydroponics is being combined with digital technology to make indoor farming more efficient than ever before, leading some to call it the future of agriculture.
And in many cities – where the majority of the planet’s projected population growth will occur – vertical farms are appearing. These “skyscraper farms” are claimed to yield more than 32 times the level of crops per square metre as agricultural land.
However, Riffat warns that “vertical farming systems are expensive to manufacture and install, and require a large amount of water and energy for heating and cooling”.
“They are also vulnerable to extreme weather conditions, wars and terrorism,” he adds.
He argues that underground farms would be less exposed to many of these risks.
Such underground farms already exist: in London one company has converted old Second World War air raid shelters into a hydroponic farm that produces herbs and salads for London’s hotels, restaurants and supermarkets.
The article was published on the World Economic Forum’s website.
Photo credit: Daniel Mennerich on Foter.com / CC BY-NC-NDCopy
How Do You Stop Diseases On Controlled Environment Edible Crops?
Controlling the environment is a key component of preventing diseases on edible crops.
As an increasing number of growers start growing edible crops in controlled environment structures they may be facing some diseases that they haven’t encountered before. For ornamental plant growers who are adding edible crops, they will not have as many or as effective chemical controls as they have access to with their ornamental crops.
“Growers currently don’t have a good complement of products for edible crops being grown in greenhouses or other controlled environment structures,” said Michigan State University plant pathologist Mary Hausbeck. “And if there are chemical controls available, growers may want to spray all of their herbs together. For instance, if the rosemary needs to be sprayed to protect against Botrytis, it’s wise to make sure that other nearby herbs are also listed on the fungicide label. Otherwise, growers need to make sure that their employees who are going to be spraying know which herbs they can and cannot spray with a particular product. Fungicides labels can be complicated.”
Hausbeck said growers should be cautious about using pesticides in greenhouses and other controlled environment structures like warehouses, vertical farms and plant factories.
“Previously, EPA required that use in greenhouses had to be specifically stated on a pesticide label in order for greenhouse growers to use it. But states varied in their interpretation and so usage was determined on a state-by-state situation. Several years ago EPA determined that if the label doesn’t restrict use in greenhouses, then a pesticide can be applied to a greenhouse-grown crop. In Michigan, our state agency views greenhouses and other controlled environment structures similarly. Just make sure that the label doesn’t prohibit the use of a fungicide in a greenhouse.”
Optimizing environmental control
Because of the limited number of chemicals available to greenhouse growers of edible crops, Hausbeck said it is critical for growers to use environmental control to limit disease.
“Environmental control has to be part of the equation,” she said. “Powdery mildew, downy mildew and Botrytis have a tremendous capability to reproduce in large numbers via spores. A microscope is needed to see one spore, but when there are many spores, the eye can see the fuzziness of the mildew or grey mold on the plants. The spores are moved around the greenhouse via air currents.
“Powdery mildew and downy mildew tend to be specific as to what plants they will infect. Powdery mildew is a problem on tomatoes, cucurbits and peppers. Downy mildew can be a problem on basil, cucumber and lettuce. Botrytis has a much broader host range.”
Botrytis is in a lot of growing environments because it can take advantage of plant tissue whether it is alive or dead. Downy mildew and powdery mildew won’t colonize dead plant tissue that is lying on the floor or sitting in a trash pile. Botrytis will infect plant parts that are still attached or have been discarded.
Powdery mildew, downy mildew and Botrytis prefer cooler temperatures.
“Occasionally I have seen Botrytis sporulate in coolers,” Hausbeck said. “Older leaves that are mature and are senescing may be in direct contact with moist growing media and may lead to Botrytis infection. Plants growing in a moist environment with high humidity and extended periods of leaf wetness are at particular risk of Botrytis infection. For instance, Botrytis can cause stem blight on rosemary and other herbs leading to significant losses.”
Hausbeck said Botrytis has a fairly broad temperature range in which it can infect plants.
“Growers who effectively use environmental control to keep conditions dry and unfavorable for Botrytis can get by without fungicides,” she said. “Botrytis needs leaf wetness to infect plants. Moisture is key.
“At 80-85 percent relative humidity even a small drop in temperature can lead to Botrytis issues. If the relative humidity is maintained at a low level, Botrytis won’t be successful in becoming established. Growers should do everything possible to keep Botrytis at low levels.”
Botrytis can cause stem blight on rosemary leading to significant losses.
Photo courtesy of Mary Hausbeck, Mich. St. Univ.
Botrytis can also come in as a secondary problem. It may become a problem as a result of the plants undergoing an environmental stress that results in some leaf browning. Botrytis can take advantage of this dead tissue.
Hausbeck said Botrytis can be an issue with rosemary propagated by vegetative cuttings.
“Growers should try to lower the humidity immediately following taking cuttings from rosemary stock plants for 24 to 48 hours,” she said. “Botrytis infection can occur on the wounded stems of stocks plants leading to dieback. Growers can raise the temperature in the greenhouse by a degree or two to reduce the relative humidity. Growers should try to drop the humidity below 70 percent or as low as possible depending on the circumstances of the greenhouse. They should also provide good air movement around the plants. Having good airflow movement around the plants helps to prevent all types of diseases, including Botrytis, bacterial diseases, powdery mildew and downy mildew.
“It doesn’t take a lot of expensive technology to keep the relative humidity low and the plants dry. Avoid overwatering and keep the leaves dry by watering at a time of day when they can dry rapidly. Keep the air in the greenhouse moving so that there aren’t pockets of high humidity. Ensure there is good drainage so there is no standing water on the greenhouse floors. In areas of the greenhouse where there is standing water, the relative humidity in these areas can be increased by as much 15 percent.”
Correctly identifying the disease
Hausbeck has encountered times when some of the problems growers have reported were caused by environmental stress.
“In some cases growers have been able to send me really good pictures and I can make a diagnosis based on the photos,” she said. “If it appears the plants have a potential disease I’ll recommend that growers send samples to a diagnostic lab. There are some symptoms that don’t look like a pathogen at all. I ask the growers about their growing systems and to describe when the symptoms first appeared and the pattern they are seeing across the crop.”
Having good airflow movement around plants applies to preventing all types of diseases, including basil downy mildew. Photo courtesy of Mary Hausbeck, Mich. St. Univ.
Hausbeck said as more edible crops are being grown, she expects to see some “oddball” diseases showing up that she hasn’t seen before.
“Some of these are fungal pathogens,” she said. “I have seen Septoria, which is a fungal leaf blight, on a couple of herbs. As herbs are being grown in greater volume, it’s likely that we are going to see more problems develop just by the sheer amount of plant material being grown. It’s important for growers to recognize in some situations this is still a relatively new arena for plant disease.
“We don’t know everything about the range of crops that can be impacted and what the disease symptoms might look like. If growers see a problem with a crop they really should connect with a diagnostic lab sooner than later. In the case of a disease problem, the recommendation may be to toss the plants and not try to save them because there isn’t a good complement of fungicides. Growers may sit on a crop trying to nurse it along with different growing regimes, not recognizing that it is a pathogen that is destroying their crop. This could result in costing them more time and more money.”
More control options available
Hausbeck and her laboratory at Michigan State have developed a reference chart for “Registered Products for Common Greenhouse Diseases on Vegetables and Herbs.”
“We have compiled this “cheat sheet” for products that can be used on edible crops,” she said. “We have grouped the crops according to brassica, cucurbit, leafy greens, fruiting and herbs. It is only meant to be used as a guide. Growers must read the pesticide labels carefully.
“What we have learned is that there is not a blanket product that can be used on all herbs. If a product can be used on herbs, it may or may not include basil. The situation is getting better with these crops and registered products in terms of having more options.”
For more: Mary Hausbeck, Michigan State University, Plant Biology Laboratory; hausbec1@msu.edu; https://veggies.msu.edu.
Hort Americas works with a wide variety of vendors that help controlled environment gorwers manage the climate inside their greenhouses and vertical farms. Learn more about fan, ventilation equipment and other products available from Hort Americas.
This article is property of Hort Americas and was written by David Kuack, a freelance technical writer in Fort Worth, TX.
Saskatoon Company Develops ‘Space-Age Farming’ Tech To Grow Crops Indoors
WATCH ABOVE: Farm Boys Design Corp. creates customizable indoor ecosystems to produce fresh crops using automation.
December 20, 2018
By Rebekah Lesko Reporter Global News
Kale, radishes, chives and basil are among the leafy greens and herbs growing in a shipping container in a parking lot at Innovation Place in Saskatoon.
It’s the first prototype unit that Farm Boys Design Corp. has been using for testing purposes in the past year.
“It initially started as a basic idea of having affordable food in areas where it’s hard to get fresh produce,” Farm Boys CEO Chad Fischl said.
The AeroPod prototype has been used for testing purposes for the last year.
Devin Sauer / Global News
The unit runs on automation, with the light, air and water controlled.
“This environment is optimized to grow plants,” explained Lena Syrovy, the research and development agronomist with Farm Boys.
“The roots, actually most of the time, are exposed to air. The plants are in this Rockwool medium and the roots grow out of the Rockwool into the middle of these columns and then, based on a set schedule, the water and nutrient solution is pumped to the top of the columns and then it trickles over the roots.”
Fischl said the aeroponic system Farm Boys created uses up to 98 per cent less water than growing crops outdoors.
Leafy greens, microgreens and herbs are growing in the AeroPod prototype.
Devin Sauer / Global News
RELATED
Next year, Farm Boys plans to work with communities in the Middle East and northern Canada, according to Fischl.
“We’re just trying to make fresh produce that traditionally comes from areas like California and places like Central America, more readily available to areas like the north, so you can get highly nutritious, nutrient dense food in areas of the north that doesn’t have to get transported,” Fischl said.
The company has been in talks with the country of Qatar to start a pilot facility there in early 2019.
READ MORE: Soil-free gardens at Grant MacEwan growing fast (2015)
Fischl said there is also a big opportunity for the units to be used by licensed producers in the cannabis industry.
“With the new micro cultivation rules, where you can grow in a smaller setting, a smaller foot print,” Fischl said. “Something like this has great application for that.”
Herbs, such as chives, can be grown with the Farm Boys automation technology.
Devin Sauer / Global News
“The idea of space-age farming is what we’re after,” Fischl said.
“It’s about automation and it’s about growing in an effective way that can be reproduced on a massive scale.”
© 2018 Global News, a division of Corus Entertainment Inc.
Beyond Garnish: How Science Helps An Indoor Farm Amp Up Flower Flavor
December 26, 2018
WHITNEY PIPKIN
At the restaurant Siren by Robert Wiedmaier, pastry chef Maddy Morrissey uses marigold as the base for a Japanese dessert served with nasturtium leaves, flower petals and pineapple sage shortbread. | Brian McBride/RWRestaurant Group
From inside the overly-lit interior of a 1960s strip mall, software programs and science are helping an urban farm fire up the flavor of fennel fronds and control the size of nasturtium leaves. By carefully monitoring each variable and its impact on the way a plant tastes, looks and grows, Fresh Impact Farms is inching closer to its goal: delivering edible flowers and herbs catered to the taste preferences of top-tier chefs.
To that end, nutrient mix, water temperature, light spectrum and countless other variables are regularly tweaked to produce more of the thumb-sized, lily-pad-shaped leaves chefs prize from nasturtium, each packed with a peppery punch. Lights at the "far red" end of the spectrum shine down on the same plant to coax its orange and vermilion blooms to appear earlier and more often. Every change is an experiment, and every aspect of the plant a potential moneymaker.
But, even though everything grown at the 1,000-square-foot farm in Arlington, Va., will likely be the last element placed onto the plate and the first pop of color a restaurant diner sees, "this isn't a [typical] garnish farm," says owner Ryan Pierce.
Fresh Impact Farm owner Ryan Pierce (left), and operations chief Matt McKinstry (right), stand in the 1,000-square-foot space in a suburban strip mall where they grow up to 60 varieties of edible flowers, herbs and greens at a time for restaurants.
Whitney Pipkin for NPR
"We didn't set out to just grow things that are pretty," adds Pierce, who, at 32, looks like an off-duty surgeon in blue scrubs, disposable gloves and a hat worn for food safety. "We set out to grow things that become an element of the flavor of the dish. We want to give chefs a palette to elevate their food."
Pierce comes to the field of hydroponic growing from a career in cloud computing, where he learned to make sense of a dizzying number of data points. He saw in indoor farming an opportunity to apply that background while producing edibles in a way that uses less water and land, reducing pollution and waste in the process.
Those same factors have fueled the hydroponic industry's meteoric growth in recent years. For urban farmers looking to make the most out of limited spaces, microgreens are often the crop of choice. But shoots and sprouts comprise only a small fraction of Pierce's business.
A purple ice plant flourishes under a spectrum of light designed to help it flower and thrive in an indoor environment at Fresh Impact Farms in Arlington, Va. / Whitney Pipkin for NPR
Instead, he has found a way to infuse surprising flavor into the plate-topping flowers, herbs and greens restaurants are already accustomed to buying.
Take one of the many varieties of hyssop that Fresh Impact grows, says D.C. Chef Robert Wiedmaier, whose high-end D.C. flagship Marcel's was the farm's first customer. "You close your eyes, taste that and it's like, 'Wow. What is that? Boom.' "
The hyssop, which smacks of mint and licorice-y anise, tops pan-seared scallops at Wiedmaier's Michelin-starred restaurant, Siren, and makes cameos in cocktails. Wiedmaier is such a booster of Pierce's business that he hosted a five-course dinner featuring the farm at Siren this fall. There, candy apple sorrel-flavored meringue topped a black sea bass dish and bright orange marigolds starred in a Japanese dessert with pineapple sage shortbread.
But Wiedmaier says: "You can't throw flowers on just anything." These garnishes must be used with care or they could overpower a dish. The musty marigold can be a challenge to deploy correctly, even if it's pretty.
Some of Fresh Impact's products pack such a flavor punch, they should come with a warning label. But chefs can't seem to get enough of the hard-to-grow and equally potent wasabi arugula. And, at the Japanese tasting room Nasime in Alexandria, Va., chef-owner Yuh Shimomura isn't timid about plating tiny yellow flowers from the toothache plant, so named because of their intense saliva-increasing, tongue-numbing effect.
Since launching in 2016, the farm has experimented with 250 plant varieties and currently grows between 50 and 60 at a time. Many of the successful varieties were originally suggested by chefs — some of them new to the concept that a farm could tweak the flavor of an herb or flower they thought they knew so well.
Ryan Pierce holds one of the nasturtium blooms prized by his chef-customers for decorating and flavoring dishes at high-end restaurants. / Whitney Pipkin for NPR
When Johnny Spero, executive chef and owner of Reverie in Washington, D.C., first requested that Pierce grow huacatay, a feathery plant used in Peruvian stews and sauces, he expected it to taste as pungent as varieties he'd tried elsewhere.
But Pierce's was milder, and Spero initially asked if he could make it more intense.
Adding "intensity" entails stressing the plant, something that is hard to do in a controlled environment where the plants are protected from the elements. Pierce can mimic that stress with an imbalance of nutrients, by applying different spectrums of light or by harvesting leaves from older plants—but every crop is different.
"Our goal is, as we collect data, to understand how small shifts change the overall flavor and success of the crop," he says. "Ultimately, we want to get to a point where we can tweak those crops on demand to produce specific flavor outcomes."
The farm's latest experiment? The succulent iceplant. Its leaves look like water droplets have frozen, still dewy, on the surface, and biting into one of them delivers a blast of hydration. One of Siren's chefs has said he wants the largest leaves possible for a dish he's dreaming up. Meanwhile, chefs at D.C.'s two-Michelin-starred minibar by José Andrés say they want the tiny clusters of leaves the plant produces before it blooms.
"If we can get it to production, we already know we have two customers interested in different parts of the plant," says Pierce.
The farm worked with a company to develop its own software that tracks the feedback received from chefs for each crop. If a chef thought a batch of bronze fennel was too bitter or too sweet, that information is stored and considered for the next crop.
Eventually, Pierce wants to bring all of that data into real-time — with chefs providing feedback through an app. Already, monitors on each of the water basins report data on its Ph, temperature and overall nutrient level to a computer every four seconds. The goal is to eventually measure each of the 17 nutrients essential for plant growth — all the time.
"The challenge is for us to drill down to that level," says Pierce, who'd like to get the flavor-changing equation down to a science. It's not going to be easy, he admits. "If you feel like you have this down already, then you're not doing something right."
garnish strip mall Farm fine dining microgreens flavor chefs
Introducing Living Food Company: The Future of Food
India’s Food Supply Chain is Not Working
Why is India, one of the fastest growing economies, undergoing a nutrition and health crisis? India has the largest micronutrient deficiency among all countries and among the highest disability-adjusted lost years of life from micronutrient deficiencies. Diets low in nutrition are the leading cause of this current health and nutrition crisis. Fresh food that is nutrient-dense is surprisingly difficult to find in India, particularly for the urban consumer.
We don’t know where our food comes from, what it contains and how long it takes to reach us.
The food we consume has been designed to be stored and shipped in containers over long distances. The industrial food supply chain is extremely complex and is plagued by inefficient supply management and wastage at the distribution stage. The agriculture system is failing us by producing food that contains harmful chemicals in the form of pesticides and fertilizers.
On an average, Indians consume close to 42000 metric tonnes of pesticides in a year, including those that are banned in other countries for their carcinogenic effects.
In June 2017, more than 40 cotton farmers died after inhaling chemicals while spraying pesticides in Maharashtra in one agricultural season.
Micronutrient deficiency in India. Source: http://unicef.in/Whatwedo/8/Micronutrient-Nutrition
We now depend upon cheap, low-nutrient food that sacrifices quality for quantity at the cost of our health and the environment. Global crop production has more than tripled since the 1960s. This has led to the depletion of water resources for irrigation, soil pollution from overwhelming fertilizer application and rising greenhouse gas emissions.
The average concentration of pollutants in the Indian soil is almost twice the amount found globally.
Such high levels lead to long-term damage in the central nervous system, immune and reproductive systems, while also being one of the leading causes of cancer.
The organic food movement, tries to address some of the health risks by eliminating the use of fertilizers. Yet, organic produce that is grown in soil can’t prevent harmful chemicals from entering our bodies. Contaminated groundwater containing dangerous proportions of heavy metals such as Arsenic is still used in organic farming and can cause long-term damage to our cells and immune systems. Simply put, organic food doesn’t solve the problem.
We are what we eat
In June 2017, my life took a drastic turn. My mother was diagnosed with Thyroid cancer and had to undergo a painful surgery. Less than a year later, on 20th March, my father was diagnosed with Stage 4 Peritoneal cancer.
This personal tragedy shook me to the core and I started investigating into this deadly disease. The more I read, I found out — how less I knew. I had never imagined that the everyday food that we eat can either strengthen our immune system or completely break it down making us susceptible to life threatening diseases, such as cancer. Everything I read brought me to the same point — we are what we eat.
Real food is about trust and transparency. It is also about ensuring quality and traceability at every step. Living food Company was born to provide food that we can trust. Our produce is grown with passion, care and precision and by controlling the entire process we guarantee high quality produce that can be traced at every step.
Living Food Company: The Future of Food
Living Food Company was born from the need to take control of our food production systems. We decided to grow microgreens, 10–12 day old baby plants that are extremely rich in nutrients, anti-oxidants and essential vitamins and minerals. They contain upto 40 x the nutrition found in their mature counterparts.
We focus on growing extraordinarily highly nutritious microgreens such as Kale, Broccoli, Mizuna (Japanese mustard), Pink Radish, Red Chard and 15 other powerful varieties. We make these nutrient rich foods affordable and accessible for the average urban Indian consumer and democratize access to superfoods.
Akash K. Sajith
CEO & Founder at @LivingFood, building the future of food.
Trouble In The High-Rise Hothouse
Big indoor farms are attracting big investments. But transforming agriculture might depend on putting nanofarms everywhere — maybe even in your home.
Editor-in-chief, Ideas: The Magazine of the Aspen Institute, senior editor, The Atlantic, five-time James Beard Journalism Award winner, restaurant critic
December 6, 2018
Paul Gauthier launched Princeton’s Vertical Farming Project to explore the economics of indoor agriculture. Photo by Lauren Lancaster
Big indoor farms are attracting big investments. But transforming agriculture might depend on putting nanofarms everywhere — maybe even in your home.
This was written for NEO.LIFE in association with NOVA Next/WGBH Boston.
Paul Gauthier, a plant physiologist at Princeton University, took a short drive up the New Jersey Turnpike to try to figure out whether the biggest vertical farm on the East Coast is succeeding. The answer isn’t as clear as you might think.
AeroFarms, which runs a 70,000 square-foot operation in Newark, is one of the highest-profile companies founded on the premise that growing crops indoors will transform agriculture. These aeroponic indoor farms stack leafy greens and herbs on racks that nurture the produce with sprays of mist and light from LEDs or high-pressure sodium lamps. They use no soil or pesticides, and can operate year-round. For further efficiency, AeroFarms mechanizes the seeding, harvesting, packaging, and cleaning of its produce.
It requires a great deal of electricity to give plants the light and heat they could get for free outdoors. But the idea is that vertical farms in big urban centers will be less costly—both economically and for the environment—because of the inputs they avoid, like toxic chemicals and long-distance transportation to consumers.
So do they actually come out ahead? Gauthier studies the science and the economics of growing food indoors, and he wants it to work. But the indoor farms getting glamour-puss investments refuse to release their numbers. And after touring several of them, digging into their methods to weigh the costs and the benefits, he’s suspicious about whether the numbers add up.
If you ask him whether the farms are making money or on track for any real financial viability, Gauthier, raised in Nantes and trained there and in Paris, where he earned his Ph.D, does a French thing with his mouth that translates to an existential shrug. “Who knows? So they say.” But he’s pretty sure that economics is a “major part of what’s stopping vertical farms from growing.”
Feeding 10 billion people in a world stressed by the rapidly changing climate is going to require constant innovations in how food is produced—a new green revolution, just this time not involving methods that wreck soil and water. But while vertical farms might work as a technical concept, thriving as businesses is another matter.
The problem, Gauthier suspects, is that the future of indoor agriculture might not look like a venture capitalist’s dream, with microgreens and other fancy kinds of lettuce sold at macro markups. To have a truly global impact, the startups ideally would also be researching how to grow staple crops threatened by climate change and trying to maximize their nutritional value. And, Gauthier and others argue, these agricultural startups should be thinking small at the same time—encouraging cottage and studio-apartment farmers to raise indoor tomatoes and strawberries themselves and join what could become an information-sharing revolution.
“Stupid designs”
Gauthier, who has been at Princeton’s geosciences department for six years, has a typical academic’s curiosity but also a French touch of mischief. He considered medical school, he says, but “then someone told me that even if we cure all the diseases on earth, people will still have to eat. Plus plants are cool.”
A set of test shelves in Gauthier’s lab. Photo by Lauren Lancaster
And nothing sounded cooler than saving the world by growing its food indoors, right where rapidly expanding urban populations need it. But he was baffled by the wildly optimistic predictions he read and heard for vertical farming. A widely cited 2013 study by German economists at the Macrothink Institute made the case that vertical farms in high-density urban areas, particularly in India and China, could be cost-effective because of the transport costs they would save. And they could increase access to food and reduce hunger in the bargain.
But the claims being made for the majority of vertical farms were, Gauthier says, unbacked by current, deep, and comparative data. “As a scientist, this wasn’t acceptable,” he says. “A lot of what they said was just marketing.” So two years ago he launched Princeton’s Vertical Farming Project to understand what can and can’t work economically.
He regarded with a beady eye the Ivy League grads applying for investment and Silicon Valley venture capitalists funding indoor vertical farms. Where they see a future full of urban warehouses and exurban hangars repurposed to grow food, he sees a bubble likely to burst too soon, with all those massive buildings more likely to be eventually repurposed for marijuana — the one indoor crop guaranteed to turn a profit.
Lettuce, microgreens, and herbs—the primary crops of vertical farms—have a high markup relative to, say, brussels sprouts, and being highly perishable suits them to very short transport time from indoor farm to store. But not many other commercial crops check those same boxes. Some vertical farms market kale, which is an odd choice, because it’s dirt cheap. Why bother? Gauthier leans over as if imparting a big secret: “Because anyone can grow kale, and it grows everywhere.”
Vertical farms might work as a technical concept. Thriving as businesses that transform agriculture is another matter.
Anything grown in a vertical farm might sell in China, where contaminated-food scandals mean consumers will pay a premium for food they consider to be safe, like that of fast-food chains. Vertical farms use little water and don’t need pesticides or fertilizers, all of which can be sources of contamination. So it could be smart that the most highly capitalized vertical farm company — Plenty, based in San Francisco, which has raised more than $200 million — plans to build 300 vertical farms in China.
It also would be wise to diversify the number and kind of crops in vertical farms. That optimistic German study from 2013 was based on a simulation of a farm that would grow not just vegetables but also tilapia, in tanks. Variety of output protects any business against the collapse of any one product — but that isn’t the current practice in vertical farms. Why? Perhaps because new startups follow the examples of others that seem to be successful. Perhaps because research on protein-rich products like chickpeas or fish is less evolved than it is for easy-to-grow, easy-to-sell bagged lettuce. Perhaps because different crops require different amounts of light, humidity, and nutrients and thus make for less-efficient production in a single space. David Rosenberg, cofounder and CEO of AeroFarms, says his company has experimented with growing 700 different plants, but his production is still heavily concentrated on microgreens that can fetch $40 a pound. He also sells baby greens, which he’s proud to have turned profitable, as they usually go for a much lower price to stay competitive—just $6 a pound.
Inside AeroFarms’ facility in Newark. The company’s CEO has said most startups in the industry won’t survive three years. Photo courtesy of AeroFarms
More diversified crops are possible to grow together in vertical farms — and economically safer in the long run, Gauthier thinks. But the business models might be trickier to construct for startups looking for funding. He has two indoor test gardens, one on wire shelves in a side room off his lab in the atmospherically collegiate Princeton geosciences building, and one a bit outside of the tony, horsey town of Princeton. In these little indoor gardens he grows particularly sweet strawberries he’s proud of. They don’t grow efficiently enough, though, to appeal to today’s commercial vertical farms.
Though Rosenberg won’t disclose whether AeroFarms is profitable, he shares much of Gauthier’s general skepticism about many of his competitors in vertical farming. In a keynote address to an indoor-farming conference last year, he predicted that 60 to 90 percent of indoor farms would fold within three years of starting. Some already have gone bankrupt.
Rosenberg says not enough of them truly understand how costly their build-outs and operations will be before their first robot plants a seed in ecologically ultra-responsible growth medium. He says he and his team of 120 workers, most of them engineers, have learned this from several years of expanding into four buildings in downtown Newark. “Biological systems scale in non-obvious ways,” he says.
In the last year alone, he says, four companies that were going out of business approached him to buy their assets. Those companies had “stupid designs,” he says. “They lost before they got going.”
Lettuce, microgreens, and herbs have a high markup, and being highly perishable suits them to very short transport time from indoor farm to store. But not many other commercial crops check those same boxes.
In general, Gauthier says, energy for lighting and climate control accounts for as much as 60 to 70 percent of operational overhead in a vertical farm. Add in labor costs, which are higher in the urban areas where vertical farms are located, and the farm is likely to have, at best, a profit margin of 4 to 5 percent. That’s more than what’s reaped by most U.S. farms, which are strapped by international competition and the current trade war. Even 4 to 5 percent, though, is nothing to venture funders, who look for profitability of 10, 15, 20 percent and beyond. (Rosenberg, without disclosing specifics of AeroFarms’ business, says those fatter profit margins are indeed possible—but only if debt-service and real-estate costs are low, and if many processes are mechanized.)
Peppers harvested from Gauthier’s lab. He tinkers with the pH of the growth medium to manipulate the peppers’ spiciness. Photo by Lauren Lancaster
The danger, Gauthier thinks, is not that a few well-funded farms will turn only a modest profit growing niche crops to be sold by boutiques whose customers can afford high markups. It’s that many indoor farms will fail, because anyone who tries the things he thinks would best serve the industry — crop diversity within the same indoor space, research into lower-margin staples like wheat that are threatened by climate change, efficient techniques for growing high-protein crops — won’t appeal to funders who expect too much too soon.
Micro-farm in the rec room
Vertical farmers might have a better chance of nailing the math if they had real-world data about what works. And that’s hard to come by. Those well-funded indoor farms keep their data secret: the costs of buildout and climate control and labor; how plant growth varies with the nutrients they feed plants; the amount and color of the light and heat and humidity and growing time for each one, the prices the harvests fetch.
What if a lot more of that data were widely available to anyone who wanted to transform agriculture by bringing it indoors, anywhere in the world? How expensive are the lights, shelves, aeration, and hydration and climate-control systems? How long do they take to amortize? How do different plants grow indoors in different places and conditions — not just the sterile, ultra-controlled-atmosphere buildings stacked 37 stories high, the utopia conjured in endless vertical farm stories?
Gauthier checks the roots on two new plants. Photo by Lauren Lancaster
Gauthier envisions a much broader ecosystem: a future of thousands upon thousands of farms, in basements and bedroom corners, growing strawberries and basil and lettuce and tomatoes, uploading data to central servers that help cottage growers all over the world as well as larger-scale indoor farmers. “Everybody has a basement or a corner,” Gauthier says. Only 15 minutes of tending a day max, he promises. And if the climate isn’t perfect and the lighting is not custom-tailored for one plant, well, people’s gardens in real life aren’t so tailored either.
These micro-farms in every rec room, study nook, and garage would be simple — no need for the colored lights that large-scale vertical farms use. Just full-spectrum LEDs of the kind Gauthier has in his pocket-sized lab farm. The vivid light in the space makes it warm and inviting, unlike the compact fluorescent light over his research assistants in the next room. “People come here and say, ‘I could put my desk here,’” he says. Just being here and fussing with his leggy strawberry and basil plants visibly brightens Gauthier’s mood.
Why would you follow his suggestion and buy the makings for your own basement or closet? The same reason that inspires window-box and patio gardeners everywhere: to have fresh food you’ve grown yourself, for pennies on the dollar and the kind of brightness of flavor those bright lights suggest. And unlike with window boxes and mini-terraces, indoor gardens would flourish independent of weather.
Turning basil into data
Caleb Harper, of MIT’s Media Lab, also has very large ambitions for very little indoor farms all over the world. He founded the Open Agriculture Initiative, or OpenAg, with open-source data, hardware, and software as founding principles. He wants to create more “digital farmers” around the world by making how-to information and tools easily available to them, and he hopes to connect them so they do the neighborly tip-sharing that used to take place at the feed and seed store.
One of Harper’s first moves, in 2015, was to release designs for a prototype “food computer,” a kit that creates a milk-carton-sized, digitally controlled hydroponic growing environment for even, say, one stalk of basil. That was version one, and the costs for materials ran from $2,500 to $4,000 for a souped-up model. The most recent version, V3, costs about $500. Its starter equipment includes a “central nervous system” that incorporates a printed circuit board, USB camera, LED lights, fans, and sensors to measure temperature, humidity, and carbon dioxide. Wi-Fi-connected processors in the box upload millions of pieces of data about the plant’s progress to cloud servers that help others replicate and share their results.
One of Caleb Harper’s “food computers” that captures data about growing conditions. Photo by MIT Open Agriculture Initiative (CC-BY-NC-SA 4.0)
Harper’s idea, like Gauthier’s, is that the more information that indoor farmers around the world share — the levels of irrigation, minerals, nutrients, light, and temperature that together he calls the “climate recipe” — the faster the field can keep up with what Harper calls mounting climate and ecological pressures.
The VC firms funding vertical farms, Harper says, seem to believe that they need to hoard the best and most efficient technology and formulas to farm indoors. But little to none of the materials that go into vertical farms are much farther evolved than the off-the-shelf equipment used in greenhouses and what his food computers require. Few if any processes are likely to be so different from what anyone else is using as to create windfalls, he thinks.
Even so, companies won’t disclose data about indoor farming. They’re saying to Harper, “Why are you telling the Muggles our secrets?” His operative answer: “I want to make vertical farming work. And I see how often claims are completely baseless — and the number of bankruptcies over the past 10 years.”
OpenAg operates two sets of food computers at MIT, one in miniature in the glossy, glassy Media Lab building and another in three repurposed shipping containers in a former storage warehouse for a disused linear accelerator. Harper himself is all over the world all through the year, raising awareness and raising money. He researches what his funders want. So one of the shipping containers at MIT has an extra-tall growing chamber to fit hazelnut trees for Ferrero, the hugely profitable, family-owned maker of Nutella. Harper recently dispatched half his team to India to rig out a shipping container to grow cotton for Welspun, a sheets and towels manufacturer that hopes to enlarge the limited supply of sustainably grown cotton. But even though his high-profile clients are usually secretive, all the research the MIT team conducts is, by the Open Agriculture Initiative’s contract, open-source.
“Why are you telling the Muggles our secrets?”
Hildreth England, OpenAg’s assistant director, has a diplomacy major’s fluency of expression and comes from a multi-generational engineering family. As she explains the uses of the 3.5 million data points she says the food computers produce per plant every growing cycle, her head is illuminated by a mesmerizing light show emanating from the box behind her. The food computer can be programmed to cycle through green, red, yellow, blue, and white lights shining on a basil plant viewable from a little window inside the black honeycomb cube, like something in Hamburg’s Reeperbahn. Various colors of light can make the plant express more of the volatile essential oils and fragrances it produces in reaction to the stress that microbes in dirt, wind, and drought inevitably impose — “in a sad, sad way we’re stressing the plants out,” she says — and these compounds can be valuable in dietary supplements and medicines. She and Harper expect indoor farms to someday grow high-profit plant-based derivatives for the pharmaceutical industry, alongside tomatoes bred to express more cancer-resisting lycopene thanks to data uploaded by thousands of growers.
In a collaboration with the United Nations World Food Programme, the Initiative put food computers in Syrian refugee camps in Amman, Jordan, to provide fresh food where people aren’t allowed to make changes to the land. A professor who was a refugee had the idea of experimenting with how to create a climate recipe that would increase the active ingredients in St. John’s wort to treat depression and anxiety: for many people, drinking herbal tea is more culturally acceptable than taking Prozac.
The uses of indoor farming, then, can be as unexpected and ingenious as the places it appears and the people who tend the plants. The underlying technology might be similar the world over, Gauthier says. But think of the iPhone: Everyone uses it a little differently, and Apple collects that data so it can make the next generation easier to use. Large leaps and small serendipities might well come from the tiny plots both he and Harper envisage — the ones that can turn the latest sexy innovation into tomorrow’s world-changing revolution.
CAN (SK): Herb Grower Talks About Switch To Marijuana
If everything goes according to plan, Brian Bain will convert his Saskatoon market garden to a marijuana nursery by next year.
He said it's a matter of economics.
"All of a sudden, you have a crop that comes along, that you can pay your employees better, you can pay yourself better and the business itself will do better," he told CBC Radio's Saskatoon Morning. "It's really hard not to make that switch."
Right now, Bain grows herbs like mint, chives, dill and basil and sells them to grocery stores across western Canada. He plans to convert his hydroponic garden to a nursery that will sell live pot plants to licensed stores.
Bain said margins in the produce business are tight and it can be difficult to make money.
Publication date : 12/13/2018
Ship To Plate, Food Grown Onboard Cruise Condo Ships
What else can you add to the cruise ship to make it more like home? A fresh produce farm. Storylines will have ship-to-plate food using some of the latest technologies in hydroponic food production. This will enable portions of the menu and indeed whole dishes to be grown right onboard the cruise condo ship.
Side benefits of this are better quality and better tasting food with a lower carbon foot print as food produced this way only travels a few feet, not thousands of miles.
Guests will be able to get involved in this process if they choose, so even the green thumbs in the community will be catered too. A big part of the Storylines offer is the fact that "anything you can do in your land based living, you should be able to do onboard our ships." This hydroponic garden is just an extension of that.
The garden itself will be over 2 levels and radiate a warm UV type light into the surrounding areas as it will be encased in glass. It will sit in pride of place right in the center of the main dining lounge so as guests are ordering their meal, the chef may be in the garden picking the ingredients to go on the plate. The lower level will be glassed in on a condo deck adding the feeling of a cosy home to those living nearby.
For more information:
www.storylines.com
Publication date : 12/11/2018
On November 2018 MG Magazine Published An Article Written By Chief Strategist of D Branding - Dino H Carter
As someone with extensive experience, Dino knows how important brand thinking is for an industry that grows so rapidly like the Cannabis industry.
Here are some of the highlights:
The foundation of every company is its brand. No matter how booming the industry or what a company produces, if its brand is not solid the business will find surviving—much less thriving—in a competitive environment difficult. Make no mistake: The cannabis industry is becoming more competitive by the day.
So, what is a brand? Is it the company’s logo? A product’s name?
It’s neither.
Brands are intangible. Logos, product names, packaging, marketing, advertising, and customer service are some of the tangible assets that help build a brand. The brand itself is much more: a “feeling” customers associate with a service or product; a concept, an idea…an experience.
For your business to become a brand, it must develop a personality beyond its products and services, and that personality must align with consumers’ wants and needs. Who are your customers? What benefits do you deliver to them? How do your products and services make them feel about themselves? As you consider your brand, focus outward; see your brand from consumers’ point of view. Remember: They have all the power. They probably can buy products very similar to yours whenever they want, wherever they want, and for a price with which they feel comfortable. What—besides the nebulous and ubiquitous “high quality”—makes your brand so special they should buy from you? Even the smallest companies can build a strong brand with devoted customers simply by creating an identity that resonates with their target market.
Your brand isn’t about your company—it’s about who your customers want to be. Nike’s brand, for example, has less to do with shoes than with excellence in sports. Check out the company’s ads sometime. You won’t find the benefits of the product in big, bold type. In fact, you may not even notice the product at all. Instead, you’ll see action shots of professional athletes doing what they do best. Nike’s customers don’t buy shoes—they buy a dream.
(to read the whole article click here)
Business Owner:
If you don't get good results from your marketing activities
If you don't get the business results you desire
If sales are down
If you are launching a new product in 2019
You should work on your brand strategy. Book a free consultation call with Dino H Carter, Chief Strategist of D Branding.
Click here to book your free session now.
BREAKING NEWS: Heliponix Wins Second Stage Investment From Purdue University Venture Ag-Celerator Fund. Midwest AgTech Investments On The Rise.
Midwest indoor agriculture startup, Heliponix (Evansville, IN) has won a second stage investment of $50k from the Purdue Ventures Ag-Celerator fund in West Lafayette, IN
By iGrow News | December 19, 2018
Midwest indoor agriculture startup, Heliponix (Evansville, IN) has won a second stage investment of $50k from the Purdue Ventures Ag-Celerator fund in West Lafayette, IN. The company, Heliponix provides consumers rotary aeroponic™ appliances called GroPods®. Although the appliance is the size of a dishwasher, it is capable of yielding a full head of leafy green vegetables on a daily basis by staggering harvests. These unprecedented yields are achieved by constantly replacing the non-perishable seed pods supplied by a monthly subscription. Not only is the appliance is able to grow CLEAN plants faster and more reliably than outdoors, but it only uses $7 of energy per month, and 6 gallons of water per month! It can even be configured to grow fruiting plants, or dwarf varieties of specialty crops.
The advanced IoT algorithms completely automate the farming process for consumers who have no previous knowledge or time to spend catering to the needs of plants. “We turn black thumbs green by collecting an incredible amount of data from the sensors in the GroPods deployed across the USA which is then fed into our machine learning algorithm”, siad CTO and Co-Founder Ivan Ball. “We then use this data to simulate and maintain environmental conditions for specific plants over WiFi without any additional maintenance from the user”.
Time lapse video generation included in the mobile application of each GroPod user.
This is only possible through the former NASA student engineers’ multiple utility patents which were filed after Co-Founders Scott Massey and Ivan Ball began prototyping designs in their apartment as undergraduate students at Purdue University. They had met while previously designing hydroponic growth chambers researching the optimal light spectrum to grow plants using LEDs with the least amount of energy. This research study was sponsored by a NASA grant across several universities to advance interplanetary, agricultural technologies under Dr. Cary Mitchell. However, Massey and Ivan went against the graduate route of most engineers in this position, and co-founded the company on a theory that the evolution of agriculture is on an irreversible trajectory towards consumer aeroponics appliances.
Young farmers inspecting their harvest of genova basil in their GroPod.
“If you wanted ice in the 1800’s, you needed to wait until winter when the climate allowed freezing temperatures. This was the status quo until the invention of refrigeration allowed ice to be made in centralized, ice factories that could produce year round. Ice factories defined the ice industry until personal ice factories, or refrigerators eventually became the standard means to produce ice, said Massey. “Much like the ice industry, agriculture is completely dependant on a stable climate in a world with a climate less stable than before. This was true until micro controllers and LEDs needed to farm indoors made recent, giant leaps in efficiencies/cost, so vertical farming could be more profitable than ever before. Despite the overwhelming amount of capital being invested into massive vertical farms, there are few instances in history where a decentralized version of a technology did not greatly disrupt the market share for centralized business models. By overcoming the knowledge gap that regular people lack about farming with sensors, IoT software, and automation; we have opened a new frontier for Agriculture, and we will take a giant leap into the future of food”.
GroPod at Forbes AgTech Summit in Indianapolis.
The aeroponic appliance, consumer business model has many inherent advantages. The nonperishable seed pods are manufactured in an automated k-cup packaging facility that drop ships directly to consumers to consolidate the entire supply chain through their proprietary software. Paying consumers invest into the hardware as opposed to institutional investment dollars for large vertical farms that are capital intensive with employees on payroll needed to maintain operations. There are no building or construction permits required for this business model that can be scaled to potentially millions of Americans without extensive capital investments beyond initial tooling, operating capital for inventory, and marketing needs. Although these benefits are all welcomed in the age of toxic outbreaks, the appliance is still listed at $2k which Massey explains is normal for any new product launch.
“The toxic Ecoli outbreak that killed too many people is symptom of a much larger problem in our current food system. Consumers are demanding transparency and accountability as the trust in organic labeling continues to fall with more scandals, and these toxic outbreaks become more common. This reactionary food system is only alerted after a death or ailment has been linked to a plant which often times goes unnoticed as the cause of the illness. We believe farming is a basic human right that every individual is entitled to, and we have a proactive solution for this global problem. When our farmers calculate the return on their investment (typically 1-2 years depending on the crop), they often find an immediate return on their investment when including the health benefits of eating safe and fresh produce that tastes better for themselves or their families”, according to Massey.
Harvest of a customer’s romaine lettuce, red russian kale, arugula, spinach, and genova basil.
Massey attributes their success in fundraising, team building, and sales through the resources available to entrepreneurs in the state of Indiana. The Purdue foundry, Agrinovus Indiana, CoWork Evansville, the Indiana Small Business Development Center, Purdue WestGate, Centric Indiana, Techpoint, the Vectren Foundation, the Mandela Washington Fellowship, and Elevate Ventures among many other entities have given exposure, capital, and industry introductions needed to not only start, but scale an AgTech company. The convergence of these resources in Indiana’s AgBioScience sector have amounted to an entrepreneurial hotbed throughout the state, and it’s Time To Tell
CEO, Scott Massey (center) speaking at the recent Agrinovus Innovation Summit.
Brooklyn's Diversity Shines Through Urban Agriculture And Retail Trends
As part of the 2018 New York Produce Show schedule, FreshPlaza attended the Brooklyn Retail and Urban Agriculture Tour on December 13. The tour visited five different places in various parts of the borough, showing the diverse range of produce activities happening now in Brooklyn. From an urban greenhouse to an open air market, there are a lot of dynamic developments here, which could make Brooklyn a barometer for the future of the American produce landscape.
Urban greenhouse strives to attract young people into agriculture
Urban greenhouses are becoming less of a novelty and more of an accepted option for locally-grown produce. This is certainly the case in Brooklyn, with a number of urban greenhouses popping up in recent years. One of these is Square Roots, which was the first stop on the tour. Square Roots is located in a former Pfizer factory in the Williamsburg district and grows primarily herbs along with other greens in shipping containers that have been climate controlled and fitted out with grow lights, water systems and atmosphere control.
The company uses plenty of technology to help it operate and delivers within the local area to stores and restaurants. One of the primary drivers of the company is to draw in more young people into agriculture. "The average age of the American farmer is 58," noted tour leader Karsten Ch'ien of Square Roots. "Growing produce in an urban greenhouse attracts more young people with a passion for farming. A combination of high-tech equipment, the fact that more young people live in large cities with limited land area, and the interest in healthy and locally-grown food has helped drive the growth of urban greenhouses. Square Roots offers training programs and skill building in agriculture to give young people with a passion for fresh produce an opportunity to be a farmer."
On-the-go and convenience prominent
As a busy metropolis in its own right, the trend of convenient, on-the-go produce has established itself firmly in Brooklyn. Two of the stores visited as part of the tour, City Acres in Williamsburg, and Brooklyn Fare in the downtown area, were heavily stocked with a range of pre-packaged salads, healthy meals as well as juices and other healthy drinks.
In City Acres, along with a significant range of organic options, was a section devoted to fresh-cut fruits and vegetables in clamshells. They were all common produce items such as watermelons, cantaloupe, broccoli, cauliflower, and many others, cut up in store to serve the busy patrons. Brooklyn Fare offered cut vegetables and prepared salads by the pound. Each store had a large organic section as well as offering a diverse range of exotic and on-trend fruits and vegetables.
Traditional style open-air markets still have a place
After visiting the gentrified Williamsburg area, the tour continued to the southwest of Brooklyn to one of the few remaining open-air markets in New York City - Three Guys From Brooklyn. Established in 1975, the store never closes and despite the wintry conditions, the array of fruits and vegetables displayed brought a burst of color into the grey day. Here the owners have kept their traditional method of selling high-volume, low-cost fruits and vegetables to serve the local community, from which many nations are represented.
"This is a very diverse neighborhood and our customers prefer the traditional feel and experience of purchasing fruits and vegetables," explained Philip Penta of Three Guys. "Although the cut and prepared market is a growth point, we also focus on growing our wholesale business with local restaurants and hotels. When modernizing, we are careful what we add to make sure we retain the character of the market while also keeping up with modern trends like loyalty cards and home deliveries."
Running this type of market comes with its challenges, but Penta said it is working well for them. "It's very difficult to remain open 24/7 every single day of the year. However, we need to have staff overnight to accept deliveries so we might as well stay open. 25 percent of our business occurs between 10pm and 6am which is remarkable to think about."
New York City's only mushroom farm
After having lunch at Wholefoods and observing the Gotham Greens greenhouse on the store's rooftop, the tour continued towards the Navy Yard to a simple red brick building with no other sign than "No Parking" on the garage. Inside was an entirely different world as we stepped into not only the only organic farm in New York City, but also the only mushroom farm - Smallhold. Not only that, but this farm operates very differently to the traditional grow and sell method. As the name suggests, Smallhold sets up micro-mushroom farms on customers' premises, to offer what is described as "hyper-local" produce. From there, Smallhold maintains control of the farms from its Brooklyn office and workshop.
"We provide a service whereby stores and restaurants can grow their own mushrooms right on the premises," explained co-founder Adam Carter. "If it's a store, they can sell the mushrooms to customers, or in the case of a restaurant, use them in dishes. We nurture the mycelium from which the mushrooms grow until they are ready to grow, then deliver them to the customer's climate-controlled mushroom farm which we set up. Smallhold maintains control of all systems, including airflow, CO2, and temperature. We currently grow ten different mushroom varieties, with oyster being the most popular."
Brooklyn's diversity offers many opportunities
With modern produce trends, customers are seeing more convenience and on-the-go offerings in stores. But Brooklyn is home to many different cultures and backgrounds and therefore the traditional high volume, low-cost, open-air markets are still thriving. The tour also demonstrated there are many young people and other urban dwellers with a passion for agriculture and they have embraced urban farming as a way in which "locally-grown" will have a viable future in big cities.
CO2 GRO Announces The Signing Of Its First Commercial Agreement
TORONTO, ON – December 12, 2018
Toronto based CO2 GRO Inc. (“GROW”) (TSX-V: GROW, OTCQB: BLONF, Frankfurt: 4021) is pleased to announce the signing of its first Commercial Agreement.
GROW has granted a technology site license to US based Tumbleweed Farms a greenhouse grower for a patent protected CO2 Foliar Spray system. The technology site license term is perpetual. Engineering installation starts immediately for completion in January 2019. The date of the agreement is December 4, 2018.
Fees upon start-up will be paid monthly on a per square foot basis. Fees charged will cover engineering support, installation, monitoring and telemetry of GROW’s Foliar Spray technology as well as the technology site license.
This US grower was more than satisfied with all of GROW’s plant science research and commercial grow trial results so went directly to a commercial installation.
John Archibald, CEO, stated “This is the first of a series of expected Commercial Agreements in four plant verticals GROW is targeting for 2019 – indoor and outdoor cannabis, hemp, flowers and leafy vegetables in North America. While the revenues from this technology site license will be modest initially there is the potential for revenues to grow significantly over time”.
About http://www.co2gro.ca/
Inc.
GROW's mission is to accelerate all indoor and outdoor value plant growth naturally, safely, and economically using its patented advanced CO2 Foliar Spray technologies. GROW’s global target plant markets are retail food at $8 trillion per year (Plunkett Mar 2017) and retail non-food at an estimated $1.2 trillion per year with retail tobacco at $760 billion (BA Tobacco estimate), floriculture at $100 billion by 2022 (MarketResearch.Biz estimate) and legal cannabis at $50 billion per year by 2022 (Bay St. Analyst estimates).
GROW's CO2 technologies are commercially proven, scalable and easily adopted into existing irrigation systems. GROW's proven crop yield enhancements and revenue model are compelling for growers and Agri-industrial partners.
GROW's sole focus is working with its plant grower and Agri-industrial partners in proving and adopting its CO2 technologies for specific growers’ plant yield needs.
The CO2 technologies work by transferring CO2 gas into water and foliar spraying water across the entire plant leaf surface area, which is a semi permeable membrane. The dissolved concentrated CO2 then penetrates a leaf's surface area naturally like nicotine naturally dissolves through human skin from a nicotine patch.
Foliar spraying of natural water, dissolved nutrients and chemicals on plant leaves has been used for over 60 years by millions of indoor and outdoor plant growers. To date, outdoor growers have not had any way to enhance plant CO2 gas uptake for faster growth.
Indoor use of CO2 gassing has enhanced plant yields for over 60 years. However, about 60% of the CO2 gas is typically lost through ventilation. Current greenhouse CO2 gassing levels of up to 1500 PPM are also not ideal for worker health and safety. GROW's safer infused CO2 foliar spray can be used by indoor and outdoor plant growers with minimal CO2 gas lost and much greater plant bioavailability resulting in higher yields.
Forward-Looking Statements This news release may contain forward-looking statements that are based on CO2GRO's expectations, estimates and projections regarding its business and the economic environment in which it operates. These statements are not guarantees of future performance and involve risks and uncertainties that are difficult to control or predict. Therefore, actual outcomes and results may differ materially from those expressed in these forward-looking statements and readers should not place undue reliance on such statements. Statements speak only as of the date on which they are made, and the Company undertakes no obligation to update them publicly to reflect new information or the occurrence of future events or circumstances, unless otherwise required to do so by law.
Neither the TSX Venture Exchange nor its Regulation Services Provider (as that term is defined in the policies of the TSX Venture Exchange) accepts responsibility for the adequacy or accuracy of this release.
For more information, please visit www.co2gro.ca or contact Sam Kanes, VP Business Development at 416-315-7477.
Farm Bill Creates Office For Urban Agriculture and Innovative Production
By Brian Filipowich
The 2018 Farm Bill (H.R.2) passed both the House and Senate and will be signed into law by the President imminently. The Bill creates the USDA Office of Urban Agriculture and Innovative Production which should boost aquaponics, hydroponics, and other sustainable growing methods.
The Bill establishes the Office “to encourage and promote urban, indoor, and other emerging agricultural production
practices.” Related to this new Office, the Bill:
Provides for the assignment of a farm number for rooftop, indoor, and other urban farms.
Provides authority to award competitive grants to operate community gardens or
nonprofit farms, educate a community on food systems, nutrition, environmental impacts,
and agricultural production, and help offset start-up costs for new and beginning farmers.Establishes an Urban Agriculture and Innovative Production Advisory Committee.
Establishes pilot projects to increase compost and reduce food waste, and create urban
and suburban county committees.
In addition to the Office for Urban Agriculture, the Farm Bill also establishes the Urban, Indoor, and Other Emerging Agriculture Production Research, Education, and Extension Initiative. This Initiative does the following:
Authorizes competitive research and extension grants to support research, education, and
extension activities for the purposes of enhancing urban, indoor, and other emerging
agricultural production.Provides $4 million mandatory for each fiscal year 2019-2023.
Requires the Secretary to conduct a census of urban, indoor, and other emerging
agricultural production.
Unfortunately, there is plenty of bad along with the good: this Farm Bill continues negative policies that stifle smaller growers and wastefully support large industrial monoculture growers. Nevertheless, it is welcome to see the Federal Government acknowledging the need for investment in urban and sustainable growing.
Hopefully the Office of Urban Agriculture and Innovative Production can meaningfully support the expansion of aquaponics!
Brian Filipowich serves as Chairman of the Aquaponics Association
Hemp, High-Speed Internet And Other Highlights From The New Farm Bill
December 13, 2018
Congress passed a 10-year, $867 billion farm bill Wednesday that would reauthorize a variety of agricultural programs and food aid for low-income Americans.
Debate on the legislation took months, with funding for the food stamp program one of the major sticking points during negotiations. The Senate approved the bill on 87-13 vote Tuesday. The House passed the measure with a 369-47 vote Wednesday, sending the bill to President Donald Trump’s desk.
Here’s what is in the legislative package, which Trump is expected to sign next week:
Rejects limits to the Supplemental Nutrition Assistance Program, better know as food stamps. The bill final left out a proposal from House Republicans and the president to impose stricter work requirements that would have cut roughly 1.1 million households from the program, according to a 2018 study by Mathematica Policy Research. The program currently serves more than 40 million low-income Americans.
Expands the safety net for dairy farmers. The bill lowers insurance premiums in the dairy margin protection program, a risk management programauthorized by the 2014 farm bill that protects farmers’ revenues when when production margins fall. The renewed support comes as the dairy industry faces a fourth year of depressed milk prices.
Legalizes the cultivation of industrial hemp. Senate Majority Leader Mitch McConnell, R-Ky., played a key role in negotiations to remove the crop from the federal list of controlled substances. The new classification will benefit McConnell’s home state of Kentucky, whose farmers are part of a growing hemp industry that’s predicted to expand into a $20 million industry by 2020.
Extends forest management. The finalized bill did not include a proposal by House Republicans and the Trump administration to ease environmental rules to allow more logging and forest-thinning projects, something they argued could help prevent wildfires. But it does create a program to encourage utility companies to clear bush near power lines on federal land.
A host of other, lesser-known provisions also made it into the bill:
Permanent funding for veteran and minority farmers. The bill guarantees $435 million in permanent funding to educate military veterans, socially disadvantaged and beginner farmers by tripling the current budget of the Farming Opportunities Training and Outreach Program.
The bill provides other benefits for veterans as well, including decreasing the price of risk management tools, improving access to capital and land, and improving access to training.
Urban farming. The farm bill establishes a new office at the Department of Agriculture to advocate for and promote urban and indoor agriculture, such as community gardens, rooftop farms, and hydroponic and aquaponic farms. The office’s responsibilities also include helping identify best practices for navigating local urban farming policies and enhance existing business training programs for urban farmers.
Funding for organics. The bill permanently secures $50 million in annual funding for a Department of Agriculture research program that focuses on organic farming practices and expanding organic agriculture. It also offers funding to support farmers transitioning to organic production.
Scholarships at historically black colleges and universities. About $40 million in new funding will be allocated for new scholarships at 19 African-American land-grant universities for students to pursue careers in agricultural and food sciences.
The bill also provides $50 million for at least three “centers of excellence” based at HBCUs with specific areas of focus, including farming systems and emerging technologies.
Rural high-speed internet. Under the bill, funding for high-speed internet in rural communities will increase from $25 million to $350 million annually.
Funding for specialty crop farmers. The bill continues a number of research, disease control and grant programs fort specialty crop farmers (such as fruit, vegetable and tree nut producers.) It also provides $125 million in funding over five years for a new research program into citrus pests and diseases.
Left: Dairy cows eat their breakfast after their morning milking at EMMA Acres dairy farm, in Exeter, Rhode Island, U.S., 7 April, 2018. REUTERS/Oliver Doyle
Related
House passes farm bill and sends it to Trump’s desk
By Juliet Linderman, Associated Press
For farmers, talking about mental health used to be taboo. Now there’s #AgTwitter
By Courtney Vinopal
Go Deeper
Valoya Has One Of the Largest Patent Portfolios of the Horticultural Lighting Industry
Since its founding in 2009 Valoya’s focus has been on research in plant biology and technology for the purpose of creating the best possible LED lighting solutions for growers worldwide. In this process Valoya has accumulated 86 patents making it one of the greatest patent holders in the horticultural lighting industry, globally.
‘None of our spectra are ‘off-the-shelf’ but rather results of years of research. Thus far we have tested more than 60 spectra variations before we commercialized the 6 that we offer at the moment. We believe that a finely balanced spectrum can make all the difference for growers and enable them to bring superior products to the market. This stands for the crop science field as well as the emerging markets such as vertical farming and cannabis’ says Nemanja Rodic, the Marketing Manager of Valoya.
Nowadays the number of LED lighting providers is growing rapidly creating confusion for growers when making their purchase decisions. Furthermore, as LED technology evolves, technical specifications among various manufacturers’ products are converging. One way for growers to identify superior lighting providers is to analyze the amount of research they have conducted and published in plant biology and technology fields as well as the number of patents the company holds. This ensures that claims made by that lighting manufacturer can be substantiated with data and are not just replicated industry standard figures e.g. a 50 000 hour life span of the luminaire, which few manufacturers could show actual light-decay-over-time data on.
Valoya’s research has partially been done in-house and partially in collaboration with various partners, companies and research institutes around the world. This commitment to research has earned it high profile clients including 8 out of 10 world’s largest agricultural companies in addition to countless other partners in the 51 countries Valoya has sold to thus far.
Next year the company will celebrate its 10th anniversary making it one of the most experienced horticultural LED lighting companies in the market. The commitment to research and development continues, especially nowadays in the time of Valoya’s rapid expansion.
To see the full list of Valoya’s patents, please go to: valoya.com/patents
About Valoya Oy
Valoya is a provider of high end, energy efficient LED grow lights for use in crop science, vertical farming and medicinal plants cultivation. Valoya LED grow lights have been developed using Valoya's proprietary LED technology and extensive plant photobiology research. Valoya's customer base includes numerous vertical farms, greenhouses and research institutions all over the world (including 8 out of 10 world’s largest agricultural companies).
Additional information:
Valoya Oy, Finland
Tel: +358 10 2350300
Email: sales@valoya.com
Web: www.valoya.com
Facebook: https://www.facebook.com/valoyafi/
Twitter: https://twitter.com/valoya
CO2 GRO Announces Dramatic Improvement In Resistance To Pathogens and Pests from Employing CO2 Foliar Spray
TORONTO, ON – December 06, 2018
Toronto based www.co2gro.ca
. (“GROW”) (TSX-V: GROW, OTCQB: BLONF, Frankfurt: 4021) is pleased to announce dramatic plant resistance improvement against common pathogens and a common predator using CO2 Foliar Spray. Bacterial (E. coli) and fungal (F. oxysporum) numbers showed a reduction by two orders of magnitude (over 90%) while a significant reduction in aphid counts was also identified.
Foliar Spray plants once infected with powdery mildew had over a 100% increase in days of plant survival post infection versus plants grown conventionally and CO2 gassed plants. The CO2 gassed plants had similar low results to conventional plants showing minimal pathogen resistance improvement using CO2 gas.
These pathogen and pest results will add to grower confidence to use GROW’s natural CO2 Foliar Spray which is proven to sharply enhance plant growth and value. It could lead to the reduction of the amount of chemical pesticides, insecticides and fungicides used for optimal plant growth with CO2 Foliar Spray use.
CO2 FOLIAR SPRAY SCIENTIFIC TRIAL METHODOLOGY
Antipathogen experimentation considered bacterial (E. coli), fungal (F. oxysporum) Powdery Mildew strains and aphids (insects). Six individual experiments were conducted at St. Cloud State University under Dr. Matt Julius. Two grew pathogens directly on agar plates (one E. coli and one F. oxysporum). Four used peppers as a host for the pathogens; one used E. coli, one used F. oxysporum and one used Powdery Mildew. The sixth experiment used predator aphids.
CO2 Foliar Spray at 800 PPM dissolved was applied every fifteen minutes for three hours per day. E. coli, fungi, and aphid trials were five days long while the powdery mildew trials were 21 days in length.
With the powdery mildew trial, three variations were considered. A control, CO2 gassing at 1200 PPM, and CO2 foliar infusion at 800 PPM. Plants were infected with Powdery Mildew and days to mortality were counted for each experimental plant.
All experiments were compared with standard statistical methods and found major increases in resistance for all pathogens and predators trialed.
CANNABIS TRIALS PENDING
Several LP cannabis growers waiting to trial CO2 Foliar Spray following approval expressed concerns that its use could increase powdery mildew risk with limited Health Canada powdery mildew treatment options. These non-cannabis plant scientific results using powdery mildew prove the opposite.
The next series of scientific pathogen and predator resistance trials will be performed at two legal US cannabis facilities in early Q1, 2019. Results will be filed with Health Canada in support of approving the Canadian usage by LPs of CO2 Foliar Spray during plant cutting transplant and vegetative growth phases for superior pathogen and predator resistance.
Dr. Matt Julius concluded “These results are consistent with the hypothesis that CO2 Foliar Spray use inhibits the growth of E. Coli, fungus and Powdery Mildew and retards insect grazers.”
John Archibald, CEO of GROW stated "These results add further confidence to our potential cannabis and non-cannabis plant growers of the dramatic plant value superiority using CO2 Foliar Spray over no CO2 gassing as well as over plants CO2 gassed.”
About CO2 GRO Inc.
GROW's mission is to accelerate all indoor and outdoor value plant growth naturally, safely, and economically using its patented advanced CO2 foliar technologies. GROW’s global target plant markets are retail food at $8 trillion per year (Plunkett Mar 2017) and retail non-food at an estimated $1.2 trillion per year with retail tobacco at $760 Billion (BA Tobacco estimate), floriculture at $100B by 2022 (MarketResearch.Biz estimate) and legal retail cannabis at $50 billion per year by 2022 (Bay St Analyst estimates).
GROW's CO2 technologies are commercially proven, scalable and easily adopted into existing irrigation systems. GROW's proven crop yield enhancements and revenue model are compelling for growers and Agri-industrial partners.
GROW's sole focus is working with its plant grower and Agri-industrial partners in proving and adopting its CO2 technologies for specific growers’ plant yield needs.
The CO2 technologies work by transferring CO2 gas into water and foliar spraying across the entire plant leaf surface area, which is a semi permeable membrane. The dissolved concentrated CO2 then penetrates a leaf's surface area naturally like nicotine naturally dissolves through human skin from a nicotine patch.
Foliar spraying of natural water, dissolved nutrients and chemicals on plant leaves has been used for over 60 years by millions of indoor and outdoor plant growers. To date, outdoor growers have not had any way to enhance plant CO2 gas uptake for faster growth.
Indoor use of CO2 gassing has enhanced plant yields for over 60 years. However, about 60% of the CO2 gas is typically lost through ventilation. Current greenhouse CO2 gassing levels of up to 1500 PPM are also not ideal for worker health and safety. GROW's safer infused CO2 foliar spray can be used by indoor and outdoor plant growers with minimal CO2 gas lost and much greater plant bioavailability resulting in higher yields.
Forward-Looking Statements This news release may contain forward-looking statements that are based on CO2 GRO's expectations, estimates and projections regarding its business and the economic environment in which it operates. These statements are not guarantees of future performance and involve risks and uncertainties that are difficult to control or predict. Therefore, actual outcomes and results may differ materially from those expressed in these forward-looking statements and readers should not place undue reliance on such statements. Statements speak only as of the date on which they are made, and the Company undertakes no obligation to update them publicly to reflect new information or the occurrence of future events or circumstances, unless otherwise required to do so by law.
Neither the TSX Venture Exchange nor its Regulation Services Provider (as that term is defined in the policies of the TSX Venture Exchange) accepts responsibility for the adequacy or accuracy of this release
The Indoor Farming Market Is Becoming Increasingly Diverse With A Huge Range of Variants Performing Industries
Mrudula.k October 25, 2018
Indoor Farming Market report gives statistical analysis on current trends, market size and shares, Revenue value and volume within the geographical regions and leading manufactures. Indoor Farming Report lets you to understand the key strategies to survive in the industry during forecast period.
The global Indoor Farming market is expected to register a CAGR of about 14.4 % during the forecast period of 2018-2023.
Indoor Farming Market report focuses on global major leading industry players with information such as company profiles, product picture and specification, capacity, production, price, cost, revenue and contact information. Upstream raw materials, equipment and downstream consumer’s analysis is also carried out. What’s more, the Indoor Farming industry development trends and marketing channels are analysed. Major key players are given in the report are: Aerofarms , Bowery Farming , Contain Inc. , Freshbox Farms , Garden Fresh Farms ,Indoor Farms of America , Philips Lighting
In this Indoor Farming Report development policies and plans are discussed as well as manufacturing processes and cost structures. This report also states import/export, supply and consumption figures as well as cost, price, revenue and gross margin by regions and other regions can be added as follows: US, Canada, Germany, France, UK, China, India, Japan
For the sake of making you deeply understand the Indoor Farming industry and meeting you needs to the report contents, Global Indoor Farming Industry Situation and Prospects Research report will stand on the report reader’s perspective to provide you a deeply analysis report with the integrity of logic and the comprehensiveness of contents. Indoor Farming report will provide to the report reader a professional and in-depth industry analysis no matter you are the industry insider potential entrant or investor.
Indoor Farming Market Report Includes these important TOC points:
Introduction: Market Definition
Research Methodology: Indoor Farming Market size and forecast determination efforts
Executive Summary: Interviewing the key executives from the industry
Key Inferences: Sources like reference book, directories, and records
Indoor Farming Market Overview: Current Market Scenario, Porter’s Five Forces Analysis
Indoor Farming Market Dynamics: Drivers, Restraints, Opportunities, Key Challenges
Market Segmentation: By Device Type, By Application, By Geography
Competitive Landscape: Mergers & Acquisition Analysis, Agreements, Collaborations, and Partnerships, New Products Launches
Key Players
Future of the Market
Finally, the feasibility of new investment projects is assessed, and overall research conclusions are offered. At the end Indoor Farming report provides major statistics on the state of the industry and is a valuable source of guidance and direction for companies and individuals interested in the Indoor Farming market.