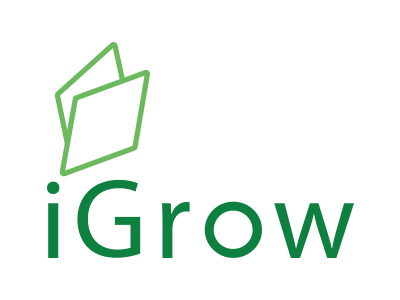
Welcome to iGrow News, Your Source for the World of Indoor Vertical Farming
5 Steps For Setting Up A Valuable LED Lighting Trial
2018
Philips Lighting
76% of growers growing under LEDs agree that LEDs have improved the quality of crops at their location
If you’re thinking about taking the first step with LEDs, the process can seem daunting. There are so many claims and so much information being shared that you may find it difficult to wade through the information with confidence and true understanding.
The reality is that LED technology is here, and regardless of the crops you grow, it’s time to begin seriously thinking about and preparing for the eventual transition to LEDs that will take place in your greenhouse operation.
You can begin the transition by starting with a small trial area in your greenhouse operation. As with other processes in the greenhouse, it isn’t quite as intimidating when broken down into smaller, more manageable steps. Follow these five steps to set up this trial area.
Step 1: Identify your challenge.
Some crops have higher values, meaning they generate more revenue or higher margins, than others. It could be that there is a high demand for a specific crop or that a crop brings in higher margins but presents some unique challenges when growing. Consider the following factors when selecting the crop/cultivar for your trial:
Production volume
Economics of production
Propagation challenges
Step 2: Determine a location to set up your trial.
Select a location in your greenhouse, ideally in a typical growing area. To get an appropriate sample size and maintain environmental conditions, it is recommended that the trial area for plug trays be approximately 1,000 to 1,500 square feet. If you’re conducting a lighting trial over potted plants, a larger space may be required.
Step 3. Set up comparative lighting scenarios.
You’ll want to work with a lighting supplier to determine the best way to set up a trial that allows you to compare your current lighting situation to a new lighting scenario.
Start by measuring the inside light levels of your current lighting and compare them to the daily light integral (DLI) for optimal growth of the crop being grown in the trial. This will help you determine if part of the lighting trial is to track the results of delivering increased light levels, or if the trial is to see the results of growing under a different spectrum. You want to see the effect of more light as well as understand the crop response to the focused red and blue spectrum of LEDs.
Step 4. Track the results.
Plan to track the data to not only document the effect on crop growth but also to understand how other crop inputs are affected by the LED lighting. Note adjustments that are made. It is recommended that measurements or data be recorded once a week. (See chart.) Be sure to have the same person measure and record the data at the same time every week during the trial.
Also, take side-by-side photographs of the crops to capture the difference in rooting, basal branching, coloration, speed of flowering, etc.
Step 5. Review the trial results
Let the results inform your decision. Did you see an uptick in the fill rate? Did you note faster flowering? Were you able to decrease the application of PGRs? Once the improvement in crop growth is translated into quantitative and/or qualitative results, you can then calculate the true ROI of an LED installation. This information will help you develop a plan for converting to energy-efficient LED lighting.
Check out this video of John Bonner, owner of Great Lakes Growers, explaining how he conducted a trial to compare and evaluate growing lettuce under HPS to growing under LEDs.
Ready to give LEDs a try? Contact a certified Philips LED horti partner to get started. Learn more about Philips horticulture products.
Workshop Iberia 2018 Light, The Right Element - Grow Your Life
The horticultural and agricultural industry is undergoing a transformation in the way plants are grown. Behind these changes, there are innovations in the field of LED lighting that use new technologies to boost plant growth, maximize production and minimize energy consumption.
These LED lighting solutions are making it possible to have crops almost anywhere, from big cities to people's homes. Wherever we look, from vertical crops and hydroponic greenhouses to the cultivation of algae, green facades and small farming systems - LED solutions are increasingly present.
At the seminar of Osram Opto Semiconductors, "LEDs for horticulture - growing green", researchers from the CSIC ("Higher Council of Scientific Research"), Osram partners and specific experts of Osram Opto Semiconductors will present from a didactic and practical perspective the benefits and latest advances in LED technology in the field of horticulture.
We will also provide a vision of the market, as well as the opportunity to talk with our partners and exhibitors about real applications.
Do not miss the opportunity to benefit from the knowledge and experience of our experts. Interacting with them and with our partners, you can give added value and gain inspiration for your existing and future projects.
Come visit us, "and let's grow green together!"
Sign up for free!
The horticultural and agricultural industry is undergoing a transformation in the way plants are grown. Behind these changes, there are innovations in the field of LED lighting that use new technologies to boost plant growth, maximize production and minimize energy consumption.
These LED lighting solutions are making it possible to have crops almost anywhere, from big cities to people's homes. Wherever we look, from vertical crops and hydroponic greenhouses to the cultivation of algae, green facades and small farming systems - LED solutions are increasingly present.
At the seminar of Osram Opto Semiconductors, "LEDs for horticulture - growing green", researchers from the CSIC ("Higher Council of Scientific Research"), Osram partners and specific experts of Osram Opto Semiconductors will present from a didactic and practical perspective the benefits and latest advances in LED technology in the field of horticulture.
We will also provide a vision of the market, as well as the opportunity to talk with our partners and exhibitors about real applications.
Do not miss the opportunity to benefit from the knowledge and experience of our experts. Interacting with them and with our partners, you can give added value and gain inspiration for your existing and future projects.
Come visit us, "and let's grow green together!"
Sign up for free!
Partners that participate:
"Smart Lighting Makes Growing Easier And More Cost Effective"
After being in the LED market for years, ITC is now expanding in to horticulture with the Amplify and Amplify Plus product lines. Remarkable is how their smart LED lighting solution can be steered on the actual weather conditions at individual locations.
"Our research resulted in grow light products, specifically intended to reduce energy usage, increase yield, and enhance plant strength", the team with ITC explains while showing their new Amplify product line. "It offers multiple, scientifically proven spectrums and lamp configurations to provide a solution for greenhouse or controlled environment growers."
The LEDs used in the Amplify product line are optimized for light distribution and plant level light intensity. The spectrum options are focused on the light needs of different cultivars at different points of development. "These are key to consistent and even growth patterns, that produce better yields and quicker turns. While the finned heatsink design of the lamp dissipates the minimal heat and the whale tail feature provides an additional protective shield for water and dirt intrusion."
Extra attention is paid to the design of the fixtures. "The simple hang and plug single and double lamp options are great for narrower spaces or long runs. Both are available in 80 or 150 degree light spreads. The 5-Lamp fixture gives consistent light placement across larger areas while reducing the number of electrical drops needed. This feature reduces install labor and can comply with existing infrastructure of greenhouses."
Smart lamps
And then there's the smart technology. "Many experts continue to explore the complexities that climate change and environmental factors are having on our food growing capabilities. These factors are making the consistency within food production environments a necessity.
Nebula Controls modules
Nebula Controls, a technology company, is providing artificial intelligent wireless controls for ITC Horticulture’s Amplify Plus smart LED lighting. This partnership is enabling the ability to program and reprogram the cloud based lighting control operation from mobile devices for enhanced growth and energy savings.
"Based on weather conditions at individual locations or programmed zones the Nebula Control smart control system is able to maximize efficiencies and reduce energy usage with minimal human dependency", the team explains. "Both ITC Horticulture’s Amplify Plus smart LED lighting and Nebula Controls are working to elevate supplement and controlled environmental horticulture lighting to a new level by using a new state-of-the-art smart lighting control system that contribute to consistent high performing food production environments. This way we are working to make growing easier and more cost effective for today and tomorrow."
For more information:
Nebula Controls
519-749-3373
contact@nebulacontrols.ca
Publication date : 11/16/2018
The Cutting-Edge Technology That Will Change Farming
Thousands of young collard greens are growing vigorously under a glow of pink-purple lamps in a scene that seems to have come from a sci-fi movie, or at least a NASA experiment.
WASHINGTON POST
NOVEMBER 6, 2018
Mike Zelkind, chief executive of 80 Acres Farms, grows produce with artificial-light made possible with new LED technology.
Mike Zelkind stands at one end of what was once a shipping container and opens the door to the future.
Thousands of young collard greens are growing vigorously under a glow of pink-purple lamps in a scene that seems to have come from a sci-fi movie, or at least a NASA experiment. But Zelkind is at the helm of an earthbound enterprise. He is chief executive of 80 Acres Farms, with a plant factory in an uptown Cincinnati neighborhood where warehouses sit cheek by jowl with detached houses.
Since plants emerged on Earth, they have relied on the light of the sun to feed and grow through the process of photosynthesis.
But Zelkind is part of a radical shift in agriculture - decades in the making - in which plants can be grown commercially without a single sunbeam. A number of technological advances have made this possible, but none more so than innovations in LED lighting.
“What is sunlight from a plant’s perspective?” Zelkind asks. “It’s a bunch of photons.”
Diode lights, which work by passing a current between semiconductors, have come a long way since they showed up in calculator displays in the 1970s. Compared with other forms of electrical illumination, light-emitting diodes use less energy, give off little heat and can be manipulated to optimize plant growth.
In agricultural applications, LED lights are used in ways that seem to border on alchemy, changing how plants grow, when they flower, how they taste and even their levels of vitamins and antioxidants. The lights can also prolong their shelf life.
“People haven’t begun to think about the real impact of what we are doing,” says Zelkind, who is using light recipes to grow, for example, two types of basil from the same plant: sweeter ones for the grocery store and more piquant versions for chefs.
For Zelkind, a former food company executive, his indoor farm and its leading-edge lighting change not just the way plants are grown but also the entire convoluted system of food production, pricing and distribution in the United States.
High-tech plant factories are sprouting across the United States and around the world. Entrepreneurs are drawn to the idea of disrupting the status quo, confronting climate change and playing with a suite of high-tech systems, not least the LED lights. Indoor farming, in sum, is cool.
It has its critics, however, who see it as an agricultural sideshow unlikely to fulfill promises of feeding a growing urbanized population.
Zelkind agrees that some of the expectations are unrealistic, but he offers an energetic pitch: He says his stacked shelves of crops are fresh, raised without pesticides and consumed locally within a day or two of harvest. They require a fraction of the land, water and fertilizers of greens raised in conventional agriculture. He doesn’t need varieties bred for disease resistance over flavor or plants genetically modified to handle the stresses of the field. And his harvest isn’t shipped across the country in refrigerated trucks from farms vulnerable to the effects of climate change.
“We think climate change is making it much more difficult for a lot of farms around the country, around the world,” he says, speaking from his office overlooking a demonstration kitchen for visiting chefs and others.
In addition to shaping the plants, LEDs allow speedy, year-round crop cycles. This permits Zelkind and his team of growers and technicians to produce 200,000 pounds of leafy greens, vine crops, herbs and microgreens annually in a 12,000-square-foot warehouse, an amount that would require 80 acres of farmland (hence the company’s name).
Zelkind says he can grow spinach, for example, in a quarter of the time it takes in a field and half the time in a greenhouse. Growing year-round, no matter the weather outside, he can produce 15 or more crops a year. “Then multiply that by the number of levels and you can see the productivity,” he said.
Zelkind and his business partner, 80 Acres President Tisha Livingston, acquired the abandoned warehouse, added two shipping containers and converted the interior into several growing zones with sophisticated environmental systems that constantly monitor and regulate temperature, humidity, air flow, carbon dioxide levels and crop health. Grown hydroponically, the plant roots are bathed in nutrient-rich water. The moisture and unused nutrients exhaled by the plants are recycled.
But it is the LED lighting that has changed the game. Conventional greenhouses have relied on high-pressure sodium lamps to supplement sunlight, but HPS lights can be ill-suited to solar-free farms because they consume far more power to produce the same light levels. They also throw off too much heat to place near young greens or another favored factory farm crop, microgreens. Greenhouses, still the bulk of enclosed environment agriculture, are moving to a combination of HPS and LED lighting for supplemental lighting, though analysts see a time when they are lit by LEDs alone.
In the past three years, Zelkind says, LED lighting costs have halved, and their efficacy, or light energy, has more than doubled.
Production in the Cincinnati location began in December 2016. In September, the company broke ground on the first phase of a major expansion 30 miles away in Hamilton, Ohio, that will eventually have three fully automated indoor farms totaling 150,000 square feet and a fourth for 30,000 square feet of vine crops in a converted factory. (The company also has indoor growing operations in Alabama, North Carolina and Arkansas, which acted as proving grounds for the technology.)
“We feel the time is right for us to make the leap because the lighting efficiency is there,” Livingston says.
The visible spectrum is measured in minuscule wavelengths, shifting at one end from violet-blue light through green to red at the other. For decades, scientists have known that photosynthesis is optimized within the red band, but plants also need blue lightwaves to prevent stretching and enhance leaf color.
A barely visible range beyond red, known as far red, promotes larger leaves, branching and flowering. With advances in LED technology, light recipes - determining the number of hours illuminated, the intensity of photons directed at plants and the mix of colors - can be finely tuned to each crop and even to each stage in a crop’s life.
Given the evolving nature of the technology and its enormous commercial potential, light manufacturers and universities, often in collaboration, are actively involved in research and development.
“We have a completely new era of research,” says Leo Marcelis, a horticulture professor at Wageningen University in the Netherlands. Tweaking light recipes has allowed researchers to manipulate crops in a way never seen before. In the lab, chrysanthemums have been forced into bloom without the traditional practice of curtailing their daily exposure to daylight. This will allow growers to produce bigger plants in flower.
“It’s to do with playing around with the blue light at the right moment of the day,” Marcelis says. “Its internal clock is affected differently, so it doesn’t completely recognize it’s still day. There are so many amazing responses of the plant to the light.”
Lettuce, for example, likes as much as 18 hours of light per day, but basil prefers brighter light for 15 hours, says Celine Nicole, a researcher for Signify, formerly Philips Lighting. “Every plant has its own preference,” says Nicole, who conducts research at the company’s high-tech campus in Eindhoven, Netherlands. She has already tested 600 types of lettuce.
Although the permutations are still under study, the sun suddenly seems so analog. “The spectrum from sunlight isn’t necessarily the best or most desirable for plants,” says Erik Runkle, a plant scientist at Michigan State University. “I think we can produce a better plant” with LED lights, he says. “The question becomes: Can you do it in a way that is cost-effective considering the cost of plants indoors?”
The answer seems to be yes. LED light shipments to growers worldwide are expected to grow at an annual average rate of 32 percent until 2027, according to a market report by analysts with Navigant Research in Boulder, Colorado. Shipments of LED lights will overtake those of legacy lights starting next year, says Krystal Maxwell, who wrote the report with Courtney Marshall.
Most of the growth will be as supplemental lighting in greenhouses, but vertical farms are seen as an alternative production system that will develop alongside greenhouses, not displace them, Marcelis says.
Runkle estimates there are 40 or more vertical farms in the United States, and new ones are opening every year with the help of deep-pocketed investors. In some of the biggest deals, AeroFarms, headquartered in Newark, last year raised a reported $40 million. Plenty, a grower based in South San Francisco, raised $200 million in 2017 for a global network of vertical farms. (One of the backers is a venture capital firm created by Amazon founder Jeff Bezos, who also owns The Washington Post.)
Zelkind declined to reveal his capital costs, but for start-up entrepreneurs, LED-driven vertical farms can be one of the most lucrative forms of agriculture. “Based on manufacturers and growers I have talked to, that’s where the money is,” Marshall says.
Critics argue that a lot of the hype around indoor farming is unwarranted, saying it won’t fulfill promises of feeding an increasingly urbanized planet and reverse the environmental harm of industrialized agriculture, not least because most staples, such as corn, wheat and rice, cannot be grown viably indoors.
Also, to build enough indoor farms for millions, or billions, of people would be absurdly expensive.
Runkle says vertical farming “shouldn’t be considered as a way to solve most of our world’s food problems.” But it is a viable way of producing consistently high-quality, and high-value, greens and other plants year-round.
Zelkind says what he’s doing may be novel, but it’s just one component of how we feed ourselves in this century. “We shouldn’t overblow what we do. Eventually it’s going to become more important, but vertical farming alone isn’t the cure-all.”
He adds, however, that “there’s no reason today to ship leafy greens from California to Ohio.”
Livingston likens LED-raised food to the advent of smartphones. “Five years from now everyone is going to be living with indoor farming and wonder how we did without it,” she says.
What Do Investors Need To Know About The Future of LED Grow Light Technology?
NOVEMBER 16, 2018 PATRICK FLYNN
Editor’s Note: Patrick Flynn created Urbanvine.co in 2016 to help urban dwellers learn how to start urban farming without any previous experience. As the site grew, he discovered that “urban farming” was actually a general term that can include a wide variety of concepts, including grow lights and hydroponics, topics which the site now covers in depth.
The horticultural lighting market is growing, and growing rapidly. According to a September press release from Report Linker, a market research firm specializing in agribusiness, the horticultural lighting market is estimated grow from a $2.43 billion market this year to $6.21 billion in 2023.
One of the key factors driving current market sector growth is increased development of LED grow light technology. LEDs (light emitting diodes) were first developed in the 1950s as a smaller and longer-lasting source of light compared to the traditional incandescent light bulb invented by Thomas Edison in 1879.
LEDs last longer, give off less heat, and are more efficient converting energy to light compared to other types of lights, all features that can result in higher yields and profits for indoor growers.
But until recently, LEDs were only used to grow plants indoors experimentally, largely because the cost was still too high for commercial businesses. Many commercial growers still use HID (High Intensity Discharge) lights such as High Pressure Sodium, Metal Halide, and Ceramic Metal Halide; all lights that have a high power output but are less durable than LED lights, generate far more heat, and have less customizable light spectra.
Today, LEDs are fast becoming the dominant horticultural lighting solution. This is due primarily to the one-million fold decrease in fabrication cost of semiconductor chips used to make LED lights since 1954.
For investors more familiar with field-based agriculture, it can certainly be a minefield to know where LED lighting technology for horticulture is going in the future. Although it is no longer the “early days” of LED technology development, current trends are still shaping the future of LED technology.
So what does the intelligent agtech investor need to know about the current state and future of LED grow light technology?
I interviewed Jeff Mastin, director of R&D at Total Grow LED Lighting, to discuss what the future of LED grow light technology for agriculture looks like, and how investors can use current trends to their advantage in the future.
What is your background – how did you get involved in grow light technology at Total Grow?
The company behind TotalGrow is called Venntis Technologies. Venntis has, and still does, specialize in integrating touch-sensing semiconductor technologies into applications.
Most people don’t realize LEDs are semiconductors; you can also use them for touch-sensing technologies, so there’s a strong bridge to agricultural LED technology.
Some of the biggest technical challenges in utilizing LEDs effectively for agriculture include LED glaring, shadowing and color separation.
We have used our expertise in touch-sensing LEDs to expand into horticultural LEDs, and we have developed technology that addresses the above challenges better, giving better control over the spectrum that the LED makes and the directional output of the light in a way that a standard LED by itself can’t do.
My personal background is in biology. When TotalGrow started exploring the horticultural world, that’s where being a biologist was a natural fit to take a lead on the science and the research side of the development process for the product; that was about 7 years ago now.
If you were going to distill your technical focus into trends that you’re seeing in the horticultural lighting space, what are the main trends to keep an eye on?
The horticultural lighting industry is really becoming revolutionized because of LEDs. Less than 10 years ago, LEDs in the horticultural world were mainly a research tool and a novelty.
In the past, they were not efficient enough and they were definitely not affordable enough yet to really consider them an economical general commercial light source.
But that is very quickly changing. The efficiencies are going up and prices down and they are really right now hitting the tipping point where for a lot of applications, but definitely not all applications, the LED world is starting to take over horticulture and indoor agriculture.
How do you view the translation of those trends into actionable points? For investors or technology developers in the agriculture technology space, how do they make sure that the LED light technology they are investing in isn’t going to be obsolete in a year or two?
With LEDs, the key question is still cost-efficiency, and there’s only so far the technology can improve.
Why? There are physical limitations. You can’t make a 100% efficient product that turns every bit of electricity into photons of light. At this point, the efficiency level of the top of line LEDs are up over 50%.
Can we ever get up to 70 or 80%? Probably not any time soon with an end-product, not one that’s going to be affordable and economical generally speaking.
So to answer your question, it’s not a category where you’re going to say, “well this is obsolete, I can get something three times better now.” The performance improvements will be more marginal in the future.
Ten years from now the cost will be cheaper. But that again doesn’t make current LED technologies obsolete. In terms of that fear, I don’t think people have to worry about current LED light technologies becoming obsolete.
In a large commercial vertical farming set up, what is the ballpark cost of horticultural LEDs currently?
To give just an order of magnitude sort of number, you’re probably going to be someplace in the $30 per square foot number for lights for a large facility. It can be half that or it can be double that.
That’s just talking within the realm of common vertical farming plants like greens and herbs, or other plants similar in size and lighting needs.
If you start talking about tomatoes or medicinal plants, then the ability to use higher light levels and have the plants make good use of it skyrockets. You can go four times higher with some of those other plants, and for good reason.
What type of horticultural lighting applications are LEDs still not the best solution for now and in the foreseeable future?
There are at least 3 areas where LEDs still may not make sense now and in the near future.
First, if the LED lights are not used often enough. The more hours per year the lights are used, the more quickly they return on their investment from power savings and reduced maintenance. Some applications only need a few weeks of lighting per year, which makes a cheaper solution appropriate.
Second, in some greenhouse applications, LED’s may not be the best choice for some time to come. Cheaper lights like high-pressure sodium have more of a role in greenhouses where hours of use are less and higher hang heights are possible. (Many greenhouses will still benefit strongly from LEDs, but the economics and other considerations make it important to consider both options in greenhouses.)
Lastly, some plants are not the best in vertical farming styles of growing where LEDs have their most drastic advantages. At least at this point it is not common to attempt to grow larger fruiting plants like tomatoes or cucumbers totally indoors, though when attempted that is still more practical with LEDs than legacy lights.
Thanks Jeff!
To learn more about Total Grow, visit www.totalgrowlight.com
AEssenseGrows Introduces ‘The Perfect Grow Light’ For Cannabis
AErix Line Brings Broad Spectrum and High Photon Efficacy
that Help Plants Grow Superior Buds
SUNNYVALE, Calif., Nov. 12, 2018 -- AEssenseGrows, an AgTech company specializing in automated precision aeroponic platforms for consistent high-yield plant production, today introduced a unique new line of grow lights optimized for premium value plants like cannabis. The AErix LBR003 grow light delivers the specifications required to improve the quality of buds grown indoors along with all of the automation features large cultivation facilities desire.
AErix lights offer a balanced broad spectrum coupled with high photon efficacy, making them ideal for premium leafy plants. The lights will be showcased Wednesday through Friday at MJBizCon in Las Vegas at the AEssenseGrows booth, #2473.
“Science has come a long way in pinpointing the role lighting plays in plant growth, and our new AErix line is built around these findings,” said Phil Gibson, AEssenseGrows’ vice president of marketing. “The best quality buds grow under balanced broad-spectrum light--light that contains sufficient amounts of blue, green, yellow, and red—and that’s what AErix lights deliver. That’s why we call them the perfect grow light.”
AErix lights (dimensions: 40”x50”) provide intense output with wide wavelength coverage and full light spectrum with an average PPFD of 1,000 µmol/s/m2 when placed 6 to 12 inches above the plant canopy—optimal for cannabis. With a maximum power usage of 700W, the lights are less than 3 inches thick including the power supply with no fan required. All AErix lights include an IP65 water repellant rating covering everything you want in a high humidity-intensive grow room.
The AErix lights drew praise from Joel Cuello, professor of Agricultural and Biosystems Engineering at the University of Arizona and a global expert in indoor farming.
“The AErix LBR003 indoor grow light spans the wavelength range of the photosynthetically active radiation with a spectral output distribution that remarkably conforms with the significant portions of the average plant's photosynthetic response curve to light,” Cuello said. “Its excellent spectral quality distribution combined with its high photon flux output makes it a superior indoor grow light.”
The new networked lights include many automation features and are optimized for the AEssenseGrows AEtrium-4 Bloom System. Fully controlled by the Guardian Grow Manager central control system software, the AErix lights include 0-100% dimming through an integrated AES link for complete scheduling and intensity automation. When connected, the lights automatically daisy chain to the network and can be sequenced in massive grow rooms to soft-start, one row at a time, without complex relays or programming.
Also included is a wide range 100-277V universal input power connection so the light is ideal for all power grids and geographies. The AErix lights will deliver as much as 16-24 pounds of dry trimmed bud per light per year, at below $150 per pound at scale. The complete AEssenseGrows system will be on display this week at MJBizCon Las Vegas.
The lights are automated to enable scheduling at various intensity levels. They are built for longevity and require little to no maintenance. The AErix light is verified by the Electrical Testing Laboratories (ETL) safety certification, exceeding or surpassing all Standards for Safety published by UL and other standards bodies.
For more information about the AErix lights, including a data sheet and user manual, visit the AEssenseGrows website or contact Gibson at pgibson@aessensegrows.com or 669.261.3086.
Ackrell Capital listed AEssenseGrows as one of the firm's Top 100 Private Cannabis Companies for 2018.
AEssenseGrows (pronounced "essence grows"), founded in 2014, is a precision AgTech company based in Sunnyvale, CA. AEssenseGrows provides accelerated plant growth SmartFarm platforms and software automation delivering pure, zero pesticide, year-round, enriched growth to fresh produce and medicinal plant producers globally. With AEssenseGrows, you can precisely control your production operations at your fingertips from anywhere in the world.
CAM Led Lighting, A Division of CAM Mfg., A California Company, Announces It’s Agreement To Market And Distribute The Wand.
Latest Product News for InDoor Growers, Farmers and Commercial Horticulture Operators
Los Angeles, CA, October 16, 2018:
CAM Led Lighting, a Division of CAM Mfg., located in Murrieta, CA is proud to announce their partnership with BioRadiance Grow Science, a cutting- edge Science & Technology Company based in the UK. BioRadiance offers cost-effective straight forward solutions to urgent, destructive, very costly and sometimes life-threatening sickness problems caused by harmful pathogens.
The “Wand” delivering BRe3, is a Patented Light Energy Science that prevents Pathogen infection and cures infected plants, vegetables, cannabis & seeds & extends the lives of flowers, cut vegetables/plants by organically destroying fungi and bacteria. The non-visible WaveLength light is safe for use from Seed 2 Sale, has no residues or toxins to leave behind and is safe for all humans, animals and plants. Growers can maximize crop potential and eliminate the use of pesticides and chemicals allowing them to grow clean and healtheir produce/plants and cannabis.
The Wand is a LED Emitter Light Bar, approximately 48” L x 1- 1/ 2” W, installs along side current grow lights, or can be used as a stand-alone LED Grow Light + Pathogen Control. The Light source uses the non-visible spectrum of light and delivers natural occuring wavelengths, covering up to a 6’ x 4’ area at a distance of 24” away from the plant(s), or as close as 6” away from the plant(s) covering a smaller footprint of 4’ x 2’ for quicker results. The Bar has an IP65 rating and can be also be installed in outside grows under cover with structural support for attachment.
Several Certified Lab Tests have been conducted in commercial grow rooms and results are available upon request. Please email Director of Marketing, Judi Randall, @ info@camledlighting.com, for more information on Test Results.
“We are excited and thrilled to be offering such an amazing product to the Indoor Grower’s Industry, particularly here in California where regulations on Pesticides are on the forefront and may detour good quality growers from entering into the market. We believe this product and it’s science is the answer to grow/production issues relating to the quality, control and the safety of plants, vegetables, fruit, flowers, insects and related products to the Public.” States, Judi Randall.
Judi can be contacted @ their CA company headquarters, 1-951-837-4776 or by email info@camledlighting.com for additional information, pricing or ordering.
## END ##
Indoor Farm Celebrates Groundbreaking in Welland
A new indoor farm is coming to Welland, phase 1 of the 20,000 sq. ft. industrial facility is about to get underway.
June 26, 2018 | Posted by: Erie Media
A new indoor farm is coming to Welland, phase 1 of the 20,000 sq. ft. industrial facility is about to get underway.
Niagara Holdings Canada announced Monday June 25/2018 that construction is about to get underway. They celebrated the start of this phase with a ground breaking ceremony at the Enterprise Industrial Subdivision at Hwy. 140 and Ridge Rd.
” Well connected infrastructure, ready access to markets, business friendly incentive programs like the Gateway Community Improvement Plan and the proactive and dynamic attitude of officials from the City of Welland and Niagara Foreign Trade Zone, are the main reasons we chose Welland”, said Clarence D’Souza, President of Niagara Holdings in a press release.
Local and federal dignitaries attended the celebration.
Niagara Holdings held it’s groundbreaking ceremony Monday at the location of its new facility in Welland. Photo submitted
Niagara Centre M.P. Vance Badawey congratulated all those involved in bringing the project to Welland.
“Great work by all partners to bring this all together,” Badawey said.
”This project exhibits investor confidence in South Niagara,” he said. “This confidence is a reflection of our current designations as a Gateway Economic Centre and Foreign Trade Zone and our overall proximity to markets. Our ability to work together continues to strengthen our economic performance, globally.
The “purpose built” facility will be the housing for “sophisticated and automated indoor farms in the world,” the press release said.
It is the first on this scale in Canada.
The design is for high volume production of leafy green vegetables. Romaine, Arugula, Kale and Basil are the primary products to be produced at this facility.
The operators for the facility are going to be Intravision Greens (Canada).
“lntravision Greens (Canada), together with lntravision Group Norway (http:/ /www.intravisiongroup.com/), is a leading provider of technology featuring broad spectrum lighting and full system integration. Backed by technology perfected at the University of Guelph’s Controlled Environment Systems Research Facility, the company’s focus is on multi-band and spectrum variable LED lights, enabling biological control and optimization of plant responses to specific wavelengths between UV A and IR light,” the press release said.
“The location in Welland, with its ability to scale up rapidly, it’s green and clean environment and close proximity to several key markets, is of considerable strategic value”, said Amin Jadavji, President of lntravision Greens (Canada) in the release.
The building contract has been award to Timbro, “one of Welland’ s best known engineering firms, with over l 00 years of experience in Ontario,” the release said.
Operations are targeted to begin in the first quarter of 2019.
ASABE Announces The Publication Of A New Lighting Standard For Horticulture
November 1, 2018
ST JOSEPH, MICHIGAN— The American Society of Agricultural and Biological Engineers (ASABE) has published the second in a three-part series of standards relating to LED radiation measurements for plant growth and development.
ANSI/ASABE S642, Recommended Methods for Measurement and Testing of LED Products for Plant Growth and Development, describes the methods used for measurement and testing of LED packages, arrays, and modules; LED lamps; and any other LED optical radiation devices.
This standard was preceded by the first document in the series, S640, Quantities and Units of Electromagnetic Radiation for Plants (Photosynthetic Organisms), which presented definitions and descriptions of metrics for plant growth and development. The final standard in the series will focus on performance criteria for LED systems used in horticulture.
ASABE members with standards access and those with site-license privileges can access the full-text of the standard by electronic download within the next few weeks. Location for the download is on the ASABE online Technical Library at: elibrary.asabe.org. Others can obtain a copy for a fee directly from the library or by contacting ASABE headquarters at OrderStandard@asabe.org.
ASABE is recognized worldwide as a standards developing organization for food, agricultural, and biological systems, with more than 260 standards currently in publication. Conformance to ASABE standards is voluntary, except where required by state, provincial, or other governmental requirements, and the documents are developed by consensus in accordance with procedures approved by the American National Standards Institute.
For information on this or any other ASABE standard, contact Scott Cedarquist at 269-932-7031, cedarq@asabe.org.
A current listing of all ASABE standards projects can be found on the ASABE web site at www.asabe.org/projects.
ASABE is an international scientific and educational organization dedicated to the advancement of engineering applicable to agricultural, food, and biological systems.
Further information on the Society can be obtained by contacting ASABE at (269) 429-0300, emailing hq@asabe.org or visiting www.asabe.org/.
Seven-Figure Order for Ultra-Wide Spectrum Cannabis LEDs
As a company specialized in fine tuned spectra development, Valoya has independently tested and optimized Valoya Canna+ through a series of trials.
Earlier this month, Valoya, manufacturer of high end LED grow light solutions, introduced Valoya Canna+ to the market – a line of LED luminaires with an ultra-wide spectrum designed for professional cultivation of cannabis. As a company specialized in fine tuned spectra development, Valoya has independently tested and optimized Valoya Canna+ through a series of trials. The result is a balanced spectrum for consistent yields and cannabinoid expressions inside state-of-the-art LED luminaires. Valoya says its Canna+ is the widest spectrum available on the market at the moment covering the range from 380nm (UV-A) to 780nm (Far red) thus resulting in superior cannabinoid profiles.
The order is of 6400 pieces of Valoya Canna+ 120 fixtures which are high intensity, 4’ (120 cm) long bars that with 132 W produce a total output of 320 µmols. Delivery of this order is due before the year end.
“This 7 figure order comes less than a month after the product launch giving a good signal about the value the Valoya Canna+ line brings to the cannabis market. As the cannabis market is developing so are growers’ needs for solutions enabling them to bring superior offerings to the market. Cannabis growers are looking for high yields with superior secondary metabolite and terpene compositions with fixtures that do not consume much energy and are reliable.” – Mr. Rabbe Ringbom, VP Sales and Marketing at Valoya.
The order is realized through Innovative Growers Equipment (IGE), Valoya’s North American distributor for the cannabis market. IGE is an equipment supplier to commercial growers in North America. Their products include ebb and flow and expanded metal benches, Valoya’s LED grow lights, plant support systems, automated fertilizer injectors etc.
For more information:
Valoya Oy, Finland
Tel: +358 10 2350300
sales@valoya.com
www.valoya.com
Innovative Growers Equipment
+1 (815) 991-5010
sales@innovativegrowersequipment.com
www.innovativegrowersequipment.com
Growing Microgreens With LED Grow Lights In Sonora, Mexico
Written by, admin
Urban grower Karla Garcia is proud to announce the creation of her new company, Microgreens FLN based in Sonora, Mexico. Karla is a recent graduate with honors and a master's degree in plant science from the University of Arizona. She is proud of her company's commitment to specializing in microgreens production using an indoor vertical farming strategy. Microgreens are an emerging class of specialty leafy greens and herbs. The crops are harvested when the cotyledons are fully developed and in some cases when the young plants have one true leaf.
Studies have shown that microgreens are an excellent source of vitamins (Sun et al., 2013; Xiao et al., 2012) that offer a variety of flavors, textures and colors. For this reason they are quickly gaining in popularity among foodies, salad lovers and top chefs around the world. Karla and Microgreens FLN are currently focused on producing a wide variety of microgreens, including broccoli, mustard, coriander, beetroot and radish.
Creating the proper growing environment
Climate management is key in allowing Karla and her team to grow consistently and year round. Their specifically designed grow room enables them to maintain production throughout the year regardless of the outside temperature. The room is conditioned with fans and a cooling system to maintain seedlings at an average temperature of 21 ° C (70 ° F). Growracks are used to stack the crops and maximize the square foot production area.
Microgreens FLN is also working with Hort Americas to create the proper light intensity and light spectrum with ARIZE LED grow lights from GE in combination with white fluorescent lamps . This combination enables the company to provide at least one daily light integral DLI of 12 mol / m / d in order to maintain quality, predict growth and reduce energy costs.
How-to tips
For growers interested in trying to grow microgreens, Karla offers the following tips.
1. Ensure a clean area by disinfecting trays, seeds (in case they need it) and shelves.
2. Germinate seed by keeping trays in dark and humid conditions for the first three days.
3. After germination, place seedlings under grow lights for about two weeks and then harvest.
Harvesting techniques
Microgreens FLN has two different harvesting techniques. Some customers request that their microgreens be delivered live, still growing in trays filled with substrate which provides a longer shelf life. Other customers prefer that the crop be harvested with sterilized scissors and packaged in a plastic clam shell. The delivered product is protected ready to be washed and served.
Microgreens FLN's goal is simple: offer a fresh, healthy, environmentally-friendly product that is nutritious and flavorful.
"Take care of your body, take care of the planet, eat microgreens!" Said Karla.
Urban farmer Karla Garcia is proud to announce the creation of her new company, Microgreens FLN in Sonora, Mexico. Karla (recently graduated with honors and a Masters in Plant Sciences from the University of Arizona) is proud of her company which is committed to specializing in the production of shoots using vertical farms as a strategy. For those who do not know the term buds. The shoots are a new class of vegetable product, which consists of edible seedlings grown from vegetable seeds or herbs, which are harvested at the end of the development of tender leaves called cotyledons.
Studies have shown that shoots are an excellent source of vitamins (Sun et al., 2013; Xiao et al., 2012), also offering a range of colors, flavors and textures. Reason why this product has quickly gained interest in consumers of vegetable products, salad lovers and top chefs around the world. Karla and Microgreens FLN are currently focused on the production of different types of shoots such as: Mustard, broccoli, radish, beet and cilantro.
Creating the right environment to grow
The control of the environment is the cornerstone that allows Karla and her team to grow shoots throughout the year. This team has been dedicated to design a quarter of growth to maintain its production during the year regardless of the outside temperature. The room is conditioned with fans and cooling system to maintain seedlings around 21 ° C on average. They use a shelf system to maximize production per area. Microgreens FLN also collaborates with Hort Americas to create the right lighting environment using GE "Arize LED" lights for plant growth with a combination of fluorescent bulbs. This combination allows Karla and her team to maintain quality, predict growth (Managing at least one DLI of 12 mol m -2 d -1 ) and in turn to reduce energy costs.
Tips to grow
For those wondering how they can do shoots at home, Karla gives the following tips:
The first step for the production of shoots is to ensure a clean area, by disinfection of trays, seeds (if necessary) and shelves. Second, induce germination by keeping the trays in a dark and humid place. After germination, the seedlings are placed under the growth lights for two weeks and then harvested.
Harvesting techniques
Microgreens FLN has two different harvesting methods. Some consumers demand to keep their buds alive, growing on the substrate, which generates a longer shelf life. Other consumers prefer that Microgreens FLN harvest the product, by cutting with sterile scissors, being packed in plastic containers. The delivered product is then ready to be washed and consumed.
The goal of Karla and Microgreens FLN is simple, to offer a product full of nutrients and flavor that is fresh, healthy and friendly to the environment. Quoting Karla: "Take care of your body, take care of your planet, consume Microgreens FLN!"
Tagged
Kimbal Musk Is Reinventing Food One Shipping Container At A Time
Interesting dresser, marketing pro, rich dude, brother to the most famous man in tech: Musk is changing food production, one shipping container at a time. And it's starting to work.
By Kevin Dupzyk
Oct 24, 2018
DAVID SCOTT HOLLOWAY
The low-slung building on Evans Avenue with the greenhouse roof blends into the surroundings in an uninspiring stretch of Denver, all nondescript retail and pockets of ranch homes. It’s a hydroponic farm, run by partners Jake Olson and Lauren Brettschneider. The produce is all on tables at waist height, and the plumbing is subtle and minimalist. There is no soil anywhere. From the street it’s easy to miss Rebel Farm; inside, it looks like an Apple Store hosting a farmer’s market.
One afternoon this summer, Kimbal Musk, a tall, lanky man in a cowboy hat, ducked in through the front door. He was here to see about the produce for his Denver-area restaurants. Unlike, perhaps, the average restaurateur, he’d brought a couple of assistants, who used smartphones to photograph his entrance, and his greeting with Olson and Brettschneider, and the huge smile he put on when he surveyed the farm. He’d never been to Rebel Farm before, but the operation was already providing him gem lettuce, a trendy green, and now he wanted to see what else it might offer. Olson and Brettschneider start walking him up and down the aisles. The building’s southern exposure is a heat-exchanging wall, and they start there, in the cool-climate crops.
“We just can’t get spinach to grow,” the Rebel guys say.
“Really?” Musk asks. “What about kale?”
Arugula’s easy. “The gateway green,” they all agree.
Musk surveys the farm and talks hydroponic technology in the manner you expect his older brother, Elon Musk, might approach a tour of NASA’s Jet Propulsion Laboratory. Like his brother, Musk is a billionaire entrepreneur, but since 2004 he’s made his living in food.
Musk tastes hydroponically-grown greens at Rebel Farm, an urban farm in Denver, CO.
DAVID SCOTT HOLLOWAY
At each new crop, Olson and Brettschneider tear off a few leaves for Musk to try, and he takes each bouquet, contemplates it, smells it deeply, eyes closed, takes a bite, and stares off into the middle distance. For a moment it’s like he is absorbing the simple life of the leaf, just sun, soil, and water, the way cannibals eat the hearts of others to imbibe their essence.
Of course, this also makes for good photos. And Instagram Live opportunities. He asks Olson and Brettschneider to do a short live video with him, and they oblige him behind a planting of sunflower sprouts on a sheet of geometric growing foam called Horticubes. An assistant gets in position with her smartphone, and as soon as they start recording, Musk comes to life, a perfect host, asking leading questions and making sure that the brands’ audience gets to know Olson and Brettschneider and their strange urban farm of delicious hydroponic crops.
Video over, tour back on, and Musk quickly turns to logistics. “Do you know how much production you do?” he asks.
Musk has a particular interest in this farm that goes beyond his restaurant chains, The Kitchen and Next Door. Musk also cofounded an urban farming startup based in Brooklyn, called Square Roots. Square Roots develops hydroponic farms housed in shipping containers that use high-tech lighting systems and offer precise, scientific control of light and every other relevant variable, like water and nutrients. Then it teaches a new breed of farmer—think Brooklyn hipster with a back-to-the-land mentality—to use them.
“Well, this is 15,000 square feet,” says Olson.
“Right, so that’s about one third of an acre,” Musk says. “At Square Roots we’re able to take a shipping container and get two acres of productivity out of it.”
“That’s some big shipping container,” Brettschneider says, not quite getting what Musk’s driving at. Musk is speaking entrepreneur, but Olson and Brettschneider are just two people who left pretty good day jobs to work the land. (As it were.)
Sprouts on a low-water growth medium. DAVID SCOTT HOLLOWAY
Musk’s goal isn’t just to produce food, or just to produce food that’s good. It’s to produce what he calls “real food”—“food you can trust to nourish your body, trust to nourish the farm, and trust to nourish the planet”—as efficiently as possible. The way he sees it, the last few decades have seen two food movements, opposites, both misguided. There’s the precious food movement, which aims to set the table only with food grown in the immediate community. The problem with that is that it’s pretty much restricted to wealthy people in fertile places.
Then there’s the feed-the-world movement, which produces more food than we need, most of it processed, unhealthy, and untasty, leading to health problems like diabetes and obesity. Musk is trying to shoot the gap, and unlike the cornucopia of restaurateurs in most midsize or larger cities these days offering local kale, he has the background and resources to implement a grander vision. Kimbal opened The Kitchen, a fine-dining restaurant, in 2004 before conceiving of Next Door, which sources ingredients with the same principles but offers food with a tad less pretention and a bit more fun, at prices—generally under $15 an entrée—that most Americans can afford. And Musk has ancillary enterprises that lay the groundwork. He founded a nonprofit, Big Green, that installs learning gardens in schools to educate kids about real food. Then there’s Square Roots. Musk points out that with shipping-container farms, which lock out all the traditional encumbrances of farming—drought, locusts, 24-hour cycles of day and night—optimization of food is possible. Unlike a traditional farmer, who may work his land for 50 years and in that time get only 50 growing seasons to experiment with, a Square Roots farmer can iterate endlessly until: spinach.
As we’re getting ready to leave, Olson and Brettschneider ask if they can show off some of their more specialized crops, and we make our way to the hot north end of the farm. They take us to a rack covered with huge serrated leaves and tangles of thick stalks. Brettschneider pulls some of the tangle away and points at a smooth purple ball from which the stalks emanate.
“What is that?!” Musk asks.
“Kohlrabi!” Olson says, uprooting one and handing it to Musk, who holds it in one of his big hands and examines it from every side. Olson launches a disquisition on all the ways you can cook up kohlrabi, and while Brettschneider says it isn’t exactly her favorite veggie, even she’s clearly pleased to be showing off their crop. Musk smiles, pondering all the uses of this strange orb, and his assistants fire up the smartphones to catch him mugging with the vegetable.
“It’s a pretty good job I have,” Musk told me earlier that day, on the way into a shopping center in a neighborhood in South Denver. “I get to go drop off food at children’s hospitals.”
Just across the street is a branch of Children’s Hospital Colorado, and we’ll be heading there soon—just as soon as we finish at this shopping center, where we’re checking out what will soon be the newest Next Door. So far it’s a plywood husk. The whole time Musk walks around the interior, he’s being photographed. He throws on a hard hat and walks slowly from room to room, exaggerating looks of surprise. The check-in is as much photo op as inspection, part of the constant hard work of building a business.
I ask him if he ever gets tired of being photographed. “Oh, with Instagram, it’s all the time,” he says, in a way that might be wistful if one could be wistful through such a radiant smile. “Not just journalists.”
DAVID SCOTT HOLLOWAY
When every conceivable angle has been captured for social, he says—cheerfully—“Let’s go meet the neighbors!” When Musk opens a new location, he likes to scout the other businesses nearby. The shopping center is a quad, with rows of stores around each of four sides. We skip the eyelash store next door to Next Door, which isn’t open yet, and go into a clothing boutique one storefront down.
Musk asks the woman behind the counter at the boutique how long they’ve been open, and how things have been going, and which tenants are in already. You know—small talk. This is the thing about Musk: Everything he does has a purpose.
The woman mentions the parking situation, which is that there isn’t enough of it. “Yes,” Musk says. “I did notice that it seems like not quite enough spaces for the businesses here.” He looks out the glass walls of the boutique, a little troubled. We proceed to the Orangetheory Fitness on the adjacent side of the quad. Musk mentions the parking, and the young man and woman working agree that, yes, it really does seem like there are a lot of cars here. Musk peeks into the last two stores on that side of the lot and then works his way back to a Starbucks on the far corner, popping his head into more shops along the way. He eyes the full lot suspiciously as he walks, first on the way into the Starbucks, and again on the way back out, cup in hand.
When we finally climb through gull-wing doors into the backseat of a white Tesla Model X, Musk looks around for a moment before pushing a button on the back of the center console to release two cup holders.
“Have you given your input into the design of the cars?” I ask. (Musk serves on Tesla’s board of directors.)
“Oh yes, I’ve been quite involved,” he says. “Once there was a design with no consideration of cup holders. That was a terrible idea.”
In 1999 Kimbal and Elon sold Zip2, the company they cofounded, to Compaq for $307 million. Elon took his and became Tony Stark; Kimbal took his and moved to New York, where he enrolled at the French Culinary Institute. He was living blocks from the World Trade Center on 9/11—close enough that he had a security pass to get into the zone around the Twin Towers that shut down for rescue and cleanup. That’s the first of the foundational stories about Musk and food: that he used that pass and the good suggestion of a Culinary Institute colleague to spend weeks feeding firefighters at Ground Zero. He opened The Kitchen in Boulder three years later. The second foundational story about Musk and food happened in 2010. At the time, Musk was still working for tech companies in addition to working in food. He was tubing in the snow with his family when his tube flipped and he broke his neck. He was paralyzed for three days, and found himself contemplating all the big things one contemplates in such circumstances. It was time to get out of tech, he realized. Food was his passion.
As we pull out of our parking space, he asks his assistant, who’s driving, to exit the shopping center between a Shake Shack and a Torchy’s Tacos, a different way than we came in. He doesn’t know Torchy’s but he’s heard it’s popular. He gets a call as we’re leaving. “The problem with this place is going to be the parking,” he says into the phone. He bobs his head down to look at the patios of the Shake Shack and the Torchy’s, which are both full of customers, and registers approval.
Musk’s finishing up the call when we pull into the parking lot at the children’s hospital. On the way in, he shakes a few hands and takes more pictures. We wind our way back to a conference room, where Hal Reynolds, Next Door’s regional operations manager, and Brad DeFurio, development chef, are rotating in fresh trays of roasted veggie quinoa bowls, ancho chile chicken bowls, curry chicken sliders, and chips and guac and hummus for hospital staff. Musk greets Colin Ness, director of operations: Parking is going to be a problem, he tells him. Musk does more photos and a TV spot and grabs some food. I ask him what he recommends. He assures me that it’s all good.
THIS IS THE THING ABOUT MUSK: EVERYTHING HE DOES HAS A PURPOSE.
“This is really great for us,” he says, pausing to chew. I expect something about what fighters the kids are, and how pleased he is to have such an admirable neighbor. Instead: “Because we’re trying to add catering, and this is a good test.”
Musk never lost the skills he honed at Zip2 and the other tech companies he worked for. At Zip2, he was director of product marketing, and he tells me he’s still a product guy at heart. He figures out what he’s selling and how to position it. He makes himself an embodiment of the brand, which these days is about food and connection. When Kimbal Musk wants to reconnoiter a shopping center, he says, “Let’s go meet the neighbors!” When he needs a test run for catering, he finds a children’s hospital.
That night Musk works the open-air upper level at Next Door Glendale, a location in another corner of suburban Denver. Next Door hosts a school fundraiser series called 504U: On certain nights, when a school brings in business to the restaurant, they get to keep 50 percent of the profit. Tonight is the pre-school-year event to rev up the educators for another season of philanthropy. Musk goes from group to group of buzzed teachers and gorged administrators and expertly makes conversation and offers hugs.
Then Ness comes over and speaks to him semiprivately, voice a hush. Musk’s eyes grow wide with amusement, and he puts his hands over his mouth. From the looks of things, some part of tonight’s itinerary has gone wrong. Musk and Ness whisper, and then Musk shrugs, and Ness dashes off to fix it. Musk goes back to work. He greets everyone like he knows them. He’s mixing and greeting and good-humoring—even when a guest, like the fanboy wearing a ball cap emblazoned with “The Boring Company,” the name of one of the many projects of Musk’s brother, doesn’t seem so interested in the fundraising as in a real-life audience with a Musk.
Soon Reynolds comes walking slowly and carefully through the crowd, gingerly carrying a bucket and some kind of cloth-covered implement, which radiates heat. Ness follows, and he gets Musk’s attention. Musk jumps up on a chair and draws in the crowd. “We call this a branding party,” he says. “And we’re going to take an actual brand, like you’d use on an animal, and put a brand on the restaurant.”
“The catch is,” he says, “the handles burned off.”
MUSK GOES FROM GROUP TO GROUP OF BUZZED TEACHERS AND GORGED ADMINISTRATORS AND EXPERTLY MAKES CONVERSATION.
Musk hops down from the chair and walks over to the bucket. The charred remnants of the brand’s dual wooden handles have been wrapped in a few layers of towel and tied fast with string. What wouldn’t Elon give to fix a problem so easily? It’s not a bad gig Kimbal’s got, having expressed the Musk curiosity and faith in technology through a product that still has the most visceral, tangible kind of accountability—Does it taste good?—and now he’s got these restaurants and he’s teaching children to eat well and he’s pursuing his own dream of a previously unimaginable future, one in which a trendy city kid says “Welcome to my farm!” and cranks open the door of a shipping container in some gritty, hollowed-out urban district and runs his hands through hanging fields of chard.
Musk grabs the towel handles with both hands and presses the brand hard into the wood frame of a large chalkboard menu hanging on the restaurant’s wall. He splays his great long legs wide to form a base of support and pushes hard. At first, nothing seems to be happening, and Musk is straining, long arms taut. Then you start to smell it. Wood. Wood burning. Musk’s body quivers with the effort. It’s been a long day. Smoke starts to rise from the brand and the smell intensifies, that burning wood smell of chips in charcoal. Musk holds the brand in place a second longer, then pulls back. A perfect “ND” is burned into the wood. “Ha!!” he shouts. He lets loose a primal scream. He smiles a big, toothy smile. He’s made his mark.
Musk has made his mark.
DAVID SCOTT HOLLOWAY
The next morning, Kimbal invited me and David Scott Holloway, a photographer, to hike his commute: from his home in a Boulder neighborhood, up the side of Mount Sanitas, and back down to the original Kitchen and Next Door in downtown Boulder.
Looking east from just above the treetops of Kimbal’s neighborhood.
Kevin Dupzyk: So Square Roots attacks the farming problem with technology. Do you think of Square Roots as more of a technology company or a food company?Kimbal Musk: I think it’s not a meaningful distinction. In order to do anything great today, you have to be a technology company. But on the food side, you’ve got to grow something that tastes great and is super-nourishing. That people trust. If they don’t like it, they don’t like it. You can’t solve a product-quality problem by talking about the technology.
KD: You said yesterday that even when you were doing tech stuff, the marketing thing was what you were really good at. Where did that come from?
KM: I’d say product, marketing, and sales are what I was better at. I don’t know where it came from. I had a painting business in university, so that taught me a lot about sales. I don’t know. There’s this thing I learned from Steve Jobs—I didn’t know him, but I learned from reading about him—if you do what you love, success generally comes from that. And I just love product.
KD: You have chalkboards in your restaurants that list the sources of your ingredients. A lot of places do that now, but I’ve heard speculation that you were the first.
KM: I believe so, yeah. We actually designed those chalkboards for the menu. And our menu changes every day, and we didn’t quite get to the operational challenge of that—erasing a menu and writing it out every day. And so we had the idea to put our farmers on there because it would still change, but it wouldn’t change every day. And that really sort of hit a nerve.
We descend back down to the streets of Boulder, and we’re walking through a residential neighborhood just a few blocks from downtown.
KD: Because this is a food you’ve mentioned a couple times over the last two days . . . I have to confess I really don’t like tomatoes. KM:Well you’re probably eating bad tomatoes. Most tomatoes are pretty bad.
KD: That’s what the tomato people are always trying to tell me.
David Scott Holloway: Kimbal, are there any foods you don’t like?
KM: Um . . . I don’t like things that are too processed. And that’s more of, like, an aversion.
KD: Come on—there’s not one vegetable you don’t like?
KM: Let me think . . . I don’t think so, because I know how to cook pretty much any vegetable to make it taste good. But if I eat vegetables other people cook, I often don’t like them.
DSH: My family was definitely part of that convenience generation. If my mom could get it out of a can, or if it could go into a microwave, she was feeding it to me.
KM: Yeah, they idolized convenience for so long. And people still want convenience. But it got to such a point of convenience where you’re just sitting by yourself all alone in front of a TV eating a TV dinner, and that’s kind of where our life ended up.
KD: I still kind of feel like it’s a treat when I eat a TV dinner.
KM: Really?! Oh my God! That grosses me out!
KD: It’s just because when I was a kid, it was like—we’re going to watch TV while we eat, and there’s a brownie in there!
KM: Well, I admit, I don’t think I’ve ever had a TV dinner.
KD: You’ve got to try it.
KM: You eat a tomato, I’ll eat a TV dinner.
KD: I’m fascinated by this thing that Square Roots hints at, where our idea of what a farmer is really changes. Do you think the mix of factory farms and these other models is going to shift significantly by, say, 2050?
KM: I’m already seeing in Colorado a lot of family farms are coming back. These are farms that might have a top line of $500,000 in revenue. They’ll sell to restaurants, farmers’ markets, and they’ll live on the farm with a cash flow of maybe $100K after all expenses are paid. That’s a pretty good lifestyle. Not everyone wants that lifestyle, but it is a pretty good lifestyle. But if you want to live in the city, like New York, the family farm doesn’t really exist.
[Smiles broadly with a realization.] Actually—I take that back. Rebel Farm was a family farm! That was a couple, with their kids, running that farm in downtown Denver. So it can be done. It’s just, I think, a little more unusual.
Musk stops walking. We’re in the bustling center of downtown Boulder, right in front of The Kitchen and Next Door.
KM: So here’s Next Door. This is where I end up. That’s my commute.
Kimbal Musk on his commute to work. DAVID SCOTT HOLLOWAY
'The Next Evolution of Farming Has Already Begun'
By Austin Stankus - Wednesday, October 10, 2018
The world population continues to grow with ever-increasing urbanization predicted to reach 80 percent by 2050. The U.N. predicts that human population will reach nearly 10 billion by 2050. This increasing population is also growing richer — and hungrier.
To feed this population using traditional farming practices, much more land would need to be brought under cultivation. But, already much farmland around the world has been degraded from poor management practices, and lands remaining available for food production are decreasing from the effects of erosion, salt buildup and pollution.
As you read this today, tens of millions of children are going to bed hungry, with the Food and Agriculture Organization of the United Nations estimating the number of hungry in 2018 at 812 million or approximately one out of 9 people.
Something needs to change. Food production needs to get more efficient, more equitable and more environmentally minded. Moreover, food production should follow the population to the cities, or as Dickson Despommier, a forerunner of this movement, simply states: “Put the food where the people live.”
Indoor farming through controlled-environment agriculture (CEA) will be an important component towards establishing local food systems that can address this pending crisis in global food insecurity. CEA, simply put, is using smart, sustainable farming practices inside of high-tech greenhouses. This is nothing new, and these modern greenhouses are an established technology and can be found around the world. In fact, much of the lettuce, tomatoes, peppers and cucumbers in the EU come from CEA in the Netherlands and Spain.
These greenhouses have incredible benefits compared to traditional farming: They use less water because they are protected from the sun and wind, they use fewer pesticides because insects and disease can be kept outside, and there is less waste because production can be matched exactly to consumer demands.
If hydroponics or other soil-less practices are used, the farmer does not need to use tractors for tilling, plowing and reaping, so the oil bills and energy consumption are lower. In addition, the fertilizer usage is reduced, and all the fertilizer the farmer uses is consumed by the plants, thereby reducing nutrient-rich runoff that can pollute watersheds.
Known as eutrophication, this nutrient pollution is a huge problem for coastal communities in the Chesapeake Bay and Gulf of Mexico and has impacted fisheries, recreational activities and livelihoods around the world.
However, CEA greenhouses can occupy a lot of space. So, the next logical evolution is stacking these modern greenhouses, one atop the other.
Vertical farming, as greenhouses stacking is called, has additional benefits. Reducing the footprint means that more food can be grown in a smaller area and therefore can be brought closer to the people eating that food. As populations move toward the cities, it makes sense for the food to follow.
Part of the vision of vertical farms is the reconnection of the producer and the consumer plus the restructuring of food value chains to become more transparent and responsive to the needs and wants of the people.
An added benefit of farming inside of skyscrapers is the option of having mixed-use buildings. When combined with a wholesale market, the skyscraper can not only produce the food but get it to the consumer faster. Less time in storage, less transportation and less handling means fresher produce and reduced need for postharvest treatments like irradiation and chemical fumigation.
There are still some daunting challenges as well as some encouraging recent developments.
Unleashing the innovative power of American small businesses has jump-started the transition to modern farming, and the public desire for local, healthy food is an economic engine driving the industry toward change. In fact, there are currently so many vertical farm startups that a shortage of qualified workers is now the main hurdle to accelerating the establishment of new indoor farms. On one hand this is a challenge to the industry, but on the other it presents an enormous opportunity for job creation in urban areas if an inclusive, enabling environment is codeveloped with the vertical farms to provide vocational training and career advancement prospects.
On a technical level, there is a significant energy demand needed for pumping water, maintaining good environmental conditions like temperature and humidity, and powering the grow lights to keep producing year-round. However, with smart buildings wired on intelligent platforms, the energy consumption can be monitored and controlled to maximize efficiency — and by tying into other green enterprises like photovoltaic and biogas generation, this energy demand is decreasing day by day. In fact, with the new innovations in LED lighting technology, the power demand has been reduced tenfold in the last few years.
The next evolution of farming has already begun, and big players are already involved. In fact, the National Grange wrote a letter to Congress with their support to public-private funding mechanisms to accelerate the modernization of agriculture, specifically highlighting the potential of vertical farming.
With this type of buy-in from large agribusinesses, national and international agricultural organizations, funded with innovative financial mechanisms, and driven by the innovative spirit and technological power only found in the U.S., vertical farming will feed tomorrow’s children with healthy, safe food; protect the environment while being resistant to environmental shocks; and spur economic growth in the process.
For a detailed look at one such startup, see the centerfold story on Skyscraper Farm.
• Austin Stankus, an integrated farming specialist, is chief science officer at Skyscraper Farm LLC.
Bell Pepper Year Round With LED or Hybrid Lighting
Sander Hogewoning (Plant Lighting) about lighting test Bell peppers are hardly grown year round in The Netherlands. Growing year round has advantages for the market, but also a number of challenges. In the past results of tests with lighted bell pepper growth were mixed, with sometimes difficult fructification and insufficient stretching of the bud. By combining cultivation knowledge (Delphi and growers), plant physiological support (Plant Lighting) and light knowledge (Signify), we hope to realize successful year round cultivation.
The basis of the research is that the quantity of assimilates are being produced by the variety in balance with the demand for assimilates by the developing fruits. In a regular unlighted cultivation, daylight and plant taxation increase simultaneously. In the lighted test the results are exactly reversed: shortly after planting there is lots of daylight and little need for assimilates.
The plant tends to produce lots of fruits. Then the plant taxation will increase, and also the demand for assimilates, but daylight is diminishing. The hypothesis is that a too large plant taxation in the beginning will lead to imbalance-related problems later on.
Tight schedule
That is the reason why plant taxation is built up according to a tight schedule, and any overage of fruits is immediate cut away. The lighting is geared as much as possible to the shortage of daylight to meet the assimilate demand. Aided by photosynthesis measurements and crop models the assimilation of the crop is calculated as precise as possible. Furthermore, part of the crops are being used for experiments with directional light to measure the effect on stretching in the bud.
The crop is looking healthy now, and the first fruits have set. The goal is to end up with around 40 kg production. It will be exciting how the growth will proceed around the shortest day and in the following period.
The program Kas als Energiebron, Signify, and crop cooperation Paprika financed the research.
Source: Kas als Energiebron
Publication date : 10/16/2018
Current, Powered by GE and Stockbridge Technology Centre Partner to Research the Farm of the Future
Stockbridge Technology Centre’s Vertical Farming Development Facility to enable growers to test and model their individual urban farm setup prior to investment
Aims to propel the success of the vertical farming industry, projected to be worth $13.9 billion USD in 20241 and generate more “farmable land” to address future global food production pressures
Current by GE’s Arize LED horticulture solution will help researchers test growth of crops such as leafy greens and herbs in different conditions
Stockbridge Technology Centre's Vertical Farming Development Facility (Photo: Business Wire)
October 16, 2018
LONDON--(BUSINESS WIRE)--Current, powered by GE (NYSE: GE) today celebrated the opening of CHAP’s new Vertical Farming Development Facility, supported by Innovate UK and based at Stockbridge Technology Centre (STC), which leverages the company’s Arize horticultural lighting solution to propel commercial urban farming success in the UK. The state-of-the-art research facility, located in Selby, North Yorkshire, is designed to help entrepreneurs, growers and investors gain deeper insight into the technology and environmental parameters needed to optimise crop yields before breaking ground on their own vertical farming operations.
We can help growers create more farmable space in industrial and urban areas in a way that is commercially and environmentally sustainable - Malcolm Yare, Current by GE
Modelling the Farm of the Future
In its 2017 report, Global Market Insights, Inc. predicted that the vertical farming industry (both indoor and outdoor applications) will grow from revenue of $2.5 billion USD in 2017 to $13.9 billion USD in 20241 and the new facility is designed to support this trend. By testing the latest technology and approaches relevant to this production model, the STC will improve the industry’s understanding of ideal indoor farming crop light requirements and growing conditions.
Potential investors and vertical farmers can work with STC’s plant scientists and vertical farming experts to identify and test the perfect vertical farm setup to maximise their planned harvest’s size, nutritional value and visual appeal. In a controlled environment, they are able to monitor and tweak parameters such as the length of the growing day, C02 concentration, humidity, nutrients and temperature, to ensure that their proposed farm will be commercially sustainable prior to construction. The resulting data supports business planning activity and minimises risks previously associated with vertical farming.
This “farm of the future”, built by systems integrator GrowStack working in conjunction with TCE Electrical Ltd., is the latest research initiative to be led by CHAP and Stockbridge Technology Centre (STC), a pioneer in experimental and applied horticulture research since the 1950s. Since its inception, STC has acted as a bridge between academia and commerce, sharing valuable research and insight that has helped to revolutionise farming practice in the UK.
The installation contains two identical grow rooms - a total growing area of 228m2 - with full climate control and a recirculating hydroponics system as well as futuristic propagation and germination rooms. Four tiers of cropping racks are lit by 780m of Arize LED lighting, delivering a balanced spectrum of red and blue wavelengths that will help boost the development of a broad range of plants.
“As cities’ populations grow at an exponential rate, the demand for fresh produce grows as well,” states Dr Rhydian Beynon-Davies, head of novel growing systems at STC. “We have the potential to grow more produce at an industrial scale within our cities and the focus of this new facility is to support the growers who are taking this bold step into the future of farming. By developing controlled environment grow systems integrated with LED lighting, we can demonstrate how, through technology, urban farming can improve the supply and nutritional value of food in a way that is commercially viable.”
Shining a Light on the Potential of Urban Farming with Arize
“Over the years, Stockbridge Technology Centre has been at the forefront of innovation, devoted to one of the most fundamental industries in the UK – that of feeding the population,” comments Malcolm Yare, Horticulture Business Development Manager for Current by GE. “Light is critical to the success of any crop and by focusing on combining the most effective wavelengths with the optimal environmental conditions, we can help growers outpace traditional methods by creating more “farmable space” in industrial and urban areas, increasing global harvests in a way that is both commercially and environmentally sustainable.”
The Arize range of horticulture solutions has been developed based on Current by GE’s experience in intelligent, connected industrial lighting, combined with extensive research and collaboration with horticulture and agriculture experts. The lights have been designed for easy, plug-and-play installation and are also fully sealed and IP66 UL Wet rated for easy cleaning in high-care, cleanroom environments. Arize lighting is one of the most energy-efficient solutions on the market, using less energy to power the LEDs and generating less heat to tax the facility’s cooling systems. With a 36K-hour lifetime (L90) and five-year warranty, the horticulture lighting solutions allow growers to amortise their capital expenditure over a longer period for greater return on investment.
Notes to editors:
The Vertical Farming Development Facility has been developed in partnership between the Crop Health and Protection Centre (CHAP) and Stockbridge Technology Centre and is supported by Innovate UK.
About Current, powered by GE
Current is the digital engine for intelligent environments. A first-of-its-kind start-up within the walls of GE (NYSE: GE), Current blends advanced LED technology with networked sensors and software to make commercial buildings, retail stores and industrial facilities more energy efficient & digitally productive. Backed by the power of Predix*, GE’s platform for the Industrial Internet, and a broad ecosystem of technology partners, Current is helping businesses and cities unlock hidden value and realize the potential of their environments. www.currentbyge.com
For more information about Stockbridge Technology Centre
www.stockbridgetechnology.co.uk
1 Global Market Insights, Inc. Insights Report 2017, “Vertical Farming Market Size by Product, Fruits, Vegetables & Herbs, Aquatic Species, By Technology, By Application, Industry Analysis Report, Regional Outlook, Growth Potential, Price Trends, Competitive Market Share & Forecast, 2018 – 2024” www.gminsights.com/industry-analysis/vertical-farming-market
Contacts
Current, powered by GE
Karen O’Neil, +1 857-265-9113
karen.oneil@ge.com
or
Racepoint Global
Jenna Keighley, +44 208 811 2151
CurrentEU@racepointglobal.com
Valoya Canna+, Ultra-Wide LED Spectrum For Superior Chemical Expression in Cannabis
The research into the interaction of the cannabis plant and light is growing but is yet not abundant due to bans which still exist in most places around the world. One thing we do know for sure is that high quality light will result in a high quality plant, one with a good chemical expression.
Valoya, the manufacturer of LED grow lights, known for their research based approach, has been testing and developing a variety of plant spectra over the past ten years. In the last three years, Valoya has conducted research on light interaction on cannabis, independently as well as in collaboration with research institutes and customers. The result is a new line of LED grow lights, designed to help growers achieve high quality cannabis plants, consistently, cycle after cycle. Valoya has placed emphasis on finding the right wavelengths for particular growth phases to achieve optimal growth. After having tested more than 60 LED spectra, Valoya has commercialized 5, earning it customers in 51 countries so far including 8 out of 10 world’s largest agricultural companies. Valoya Canna+TM is Valoya’s latest innovation which is a line of luminaires with a spectrum optimized for professional cannabis cultivation.
The spectrum is a wide (also known as full, broad or continuous) spectrum extending outside the commonly used PAR area. The range encompasses radiation between 380 and 780 nanometers which means the entire PAR area plus the far-red and the UV-A wavelengths. The benefit of these additional wavelengths is that the spectrum that is wider and fuller, contains more information and thus stimulates the plants more than a simpler spectrum would. The far red radiation is important for quick development of healthy plant biomass that can then later support large flower formations where most of the valuable secondary metabolites are. The UV-A creates a small amount of stress for the plant. The plant responds by strengthening its defense mechanisms i.e. creating more secondary metabolites. In addition to that, small pathogens cannot withstand the UV-A radiation thus the growing environment becomes less prone to outbreaks of powdery mildew and other such problems.
Valoya Canna+TM comes in two form factors:
- A 135 W bar LED grow light for indoor (single or multitier) cultivation and
- A 392 W box LED grow light for greenhouse (sea of green) cultivation
Valoya Canna+ 120
Valoya Canna+ 120 is a 4’ (120 cm) long, high intensity bar that reaches 2,4 µmol/W (PPF 320 µmol/m2/s). It is sealed shut, has no deep fins or fans that collect pathogens so it can be easily cleaned even with harsh chemicals. This makes it suitable even for the most demanding, GACP/GMP compliant grows. On both of its ends are pressure and temperature stabilizing vents thanks to which the luminaire will work even longer than the industry standard 50000 hours.
Valoya Canna+ 400
Valoya Canna+ 400 is a 13.7” x 15” (35 cm X 38 cm) high intensity light that reaches 2,3 µmol/m (PPF 880 µmol/m2/s). It is compact and robust thus suitable for greenhouse and sea of green cultivation. With excellent thermal dissipation properties this luminaire will last at least 50000 hours.
Both are dimmable and project light at a 120° angle making it possible to install them close to the canopy (Valoya Canna+ 120 only 4” / 10 cm and Valoya Canna+ 400 only 25” / 50 cm from the canopy). Instead of a silicone coating which expands and contracts in heat and deteriorates quickly, these luminaires’ LED chips are protected by tempered glass. AR (anti-reflection) coated glass is used which increases light transmission efficiency to about 98%.
As this emerging industry is rapidly growing, a need arises for high quality lighting solutions with which growers will be able to create consistent yields and cannabinoid expressions year after year. This is particularly so for the pharmaceutical grade cannabis and all large scale cannabis cultivation operations. Valoya provides a solution to this challenge with its new line of products. Valoya has published a spectrum quality guide which outlines the small permitted variations within the spectrum across production batches and generations of products. For growers this means that when they acquire Valoya luminaires for cannabis they can rest assure that all their future purchases, or replacements of products will be with the same spectrum, thus resulting in consistent yields.
The Valoya Canna+TM is available immediately, globaly. It will be introduced at the upcoming Marijuana Business Conference and Expo in Las Vegas in November (14-16). Valoya will be exhibiting at booth 3468.
For the North American customers, Valoya Canna+TM line is available through Innovative Growers Equipment, Valoya’s distributor
sales@innovativegrowersequipment.com
(815) 991 – 5010
About Valoya Oy
Valoya is a provider of high end, energy efficient LED grow lights for use in crop science, vertical farming and medicinal plants cultivation. Valoya LED grow lights have been developed using Valoya's proprietary LED technology and extensive plant photobiology research. Valoya's customer base includes numerous vertical farms, greenhouses and research institutions all over the world (including 8 out of 10 world’s largest agricultural companies).
Additional information:
Valoya Oy, Finland
Tel: +358 10 2350300
Email: sales@valoya.com
Web: www.valoya.com
Facebook: https://www.facebook.com/valoyafi/
Twitter: https://twitter.com/valoya
Alabama Power Looks Into Economic Feasibility of Indoor Agriculture
October 16, 2018
Alabama Power an electric utility company, has taken on a research project that is virtually unprecedented among utility companies. The power company is looking into the use of LED lighting to grow crops. A refurbished Freight Farm shipping container outside the Technology Applications Center at the General Services Complex in Calera is the location of the project.
Alabama Power engineer Blair Farley and Cheryl McFarland, commercial and industrial marketing support manager
In a specially customized, insulated and climate controlled shipping container, employees grow lettuce and other vegetables, as well as herbs and edible flowers. The goal of the project is to see if the cost of using electricity for indoor agriculture is economically feasible compared to traditional agriculture.
Exploring the container farm concept at Alabama Power originated from an increasing interest in indoor agriculture and the need to fully understand the benefits of using electricity to enhance the process.
Potential Advantages of Indoor Agriculture
It is thought that indoor agriculture could be a revolutionary for farmers, stores, restaurants, consumers. Alabama Power asserts that crop could be grown year-round in a controlled environment with nutrients in circulated water. Soil would not be necessary and few or no pesticides would be needed.
Furthermore, crops could be grown in urban settings and areas categorized as food deserts (locations where fresh food is not easily accessible). Also, transportation costs could be dramatically reduced or eliminated with food possibly grown near consumers and stores.
Alabama Power says for example that indoor farming can produce 12 more lettuce harvests a year, and needs up to 90 percent less water, than a traditional outdoor farm.
One way of saving on electricity, according to the company, is to use energy efficient LED lighting and other components which can be programmed to operate during off-peak hours to take advantage of cheaper electric rates. Alabama Power speculates that with the electricity needed to operate the lighting and climate control systems, indoor farming could present a new range of opportunities for the company.
Indoor Farming Could be Done in Repurposed Buildings and Warehouses
In theory, Repurposed vacant warehouses or buildings, including those with existing utilities, could be utilized for controlled-environment agriculture, providing jobs for Alabamians. Other potential advantages include growing crops during periods ofdrought or excessive rainfall; producing fruits and vegetables not native to a geographic area; and having uninterrupted growing seasons.
“Indoor agriculture can be a great addition to the already thriving agriculture industry in our state,” said Cheryl McFarland, commercial and industrial marketing support manager.
But there are challenges. Like any new, fast-growing concept, scarce data is available to determine long-term pros and cons. High start-up costs and unavailable labor may make it a financial risk. Additionally, vague or unfavorable city laws could pose a barrier to an indoor agriculture operation.
Shipping Container Farming Operation
In January 2017, Alabama Power employees installed a 40-foot hydroponic container and began producing lettuce one month later. The container has a seed germination table and 256 vertical towers holding up to 17 small heads of lettuce each. However, the food production is not limited to lettuce and includes basil, arugula, carrots, dill, and radishes.
With the help of automation, the APC container is relatively self-sufficient. However, one to two employees with other work responsibilities spend a little of their time each week planting, harvesting and performing routine maintenance in the container.Alabama Power plans to assess produce production and water and electricity usage, then compare findings with similar projects.
“We feel the interest in indoor agriculture is continuing to grow as consumers demand more fresh, local and healthy food options in stores and restaurants,” McFarland said.
“Interest in indoor agriculture or controlled environment agriculture is growing either in completely enclosed settings, such as our container, augmented greenhouses or empty buildings, like a vacant mall or Walmart,” McFarland added. “It’s a great way to provide access to fresh foods and jobs in rural communities and urban settings, particularly in areas of food deserts.”
New Vertical Farming Light Bar/Panel Hybrid Designed To Maximize Yields With Less Space
The team of lighting experts at TotalGrow have announced the launch of the new TotalGrow Stratum. The features and benefits of this new light include:
Thin profile to maximize space under 4” from canopy to shelf
Full spectrum and modular design for extra versatility
Broad panel/bar hybrid for improved uniformity and penetration in tight spaces
Simple mounting and electrical installation to save time and costs; up to 80 lights per plug
Cost effectiveness, waterproofing and warranty for economic sustainability
The 40W TotalGrow Stratum is designed and refined to maximize yields, space and versatility while minimizing costs. The spectrum and size are ideal for low/no-sunlight growing in virtually any vertical farm, growth chamber, propagation system, tower garden and more. Exceptional efficiencies and light delivery potential, along with long, low maintenance lifespans provide long-term sustainability.
Custom wiring harnesses create the cleanest, simplest power distribution for your operation. An example is shown for a typical 250 µmol*m-2*s-1 setup over several 4’x8’ shelves.
Spectrum customization available
For more information:
TotalGrow
Jeff Mastin – Biologist
315.373.9716
jeffm@venntis.com
totalgrowlight.com
Climate Cell On Wheels Helps Dutch Growers With LED Dilemma
"Everybody wants to do 'something' with LED and has the feeling something has to be done with it, but what? There's so much going on and being offered - how to get started and what to do?" That's why the Hortilux & Green Simplicity teams created a research solution for the industry. Currently they're on the road with it: for two weeks, a climate cell on wheels is shown at various companies. This Thursday it will be shown at Hortilux themselves.
The roadshow is fully booked, and every day two or three companies are visited: breeders, seed growers, research institutes and growers of course. For example De Ruiter and Syngenta are being visited. The climate cell on wheels drives there, and the possibilities of LED in horticulture, places without daylight, research and vertical farming are discussed. There's a lot of interest and many colleagues are visiting the climate cell. "We're not getting bored", the Hortilux / Green Simplicity teams agree.
"For example the roadshow offers an insight on the possibilities in research, but also how to translate it to a solution for production: going hybrid with SON-T or LED only, in a greenhouse or a vertical farm. With Hortilux & Green Simplicity we can have a fair amount of knowledge and can help with this."
This Thursday the roadshow will be at Hortilux, (Vlotlaan 412) and their employees can take a peek. Between 10:00 - 13:00 everybody is welcome to enter, also other people / companies with interest. Just send a message to Martin Moes or leave a voicemail (+31(0)6-22981504) in advance.
For more information:
LED'S RESEARCH
www.leds-research.com
US (MA): Horticultural Lighting On Show At Tech Festival
October 8-14 Boston
OSRAM will bring its technology to Boston’s City Hall Plaza in early October as the Gold Sponsor of HUBweek, a weeklong festival and civic initiative that explores the intersections of art, science and technology.
OSRAM will showcase smart horticulture lighting solutions, Human Centric Lighting (HCL) glasses and an HCL light ceiling in its shipping container; and will include pop-up experiences and exhibit participation with collaborative partners such as Workbar, Dan’s Power Plant, Corner Stalk Farm and FreshBox Farms. OSRAM technology experts also will take part in panel discussions and other events throughout the week. OSRAM will be centrally located at The HUB, across from the Hall of the Future, during HUBweek, held Oct. 8-14, 2018, on Boston’s City Hall Plaza.
“HUBweek has proven to be a hot spot for innovators. This year OSRAM is showing how some of its coolest technologies are at the heart of it all, including smart horticultural lighting for urban farms and human centric lighting glasses, which have been used by BMW M Motorsports race car drivers and the German ski team during the 2018 Winter Games,” said Lori Brock, OSRAM Head of Innovation, Americas Region. “Ten years ago, nobody could have predicted the impact of such technologies. Today, Urban Farming and HCL are increasingly making their way into the mainstream, providing a critical first step in fundamentally changing how we live our lives and build a healthier, more sustainable future.”
Brock will take part in a curated panel focusing on the impact of technology on health, along with other notable experts. The panel discussion will take place at Center Stage at The HUB at 2:30 p.m. Wednesday, Oct. 10, 2018.
Horticultural lighting solutions
Due to limited natural resources, indoor farming soon will become more prevalent, providing fresh produce closer to urban environments like Boston. Visitors of the OSRAM showcase at HUBweek will learn how growing plants indoors with smart LED-based lighting technology can save water and energy.
The horticultural lighting solutions also can help growers improve flavor and nutrition profiles, better manage the growth cycle, and increase yield – either on-site or remotely. LED technology and advanced sensors ensure plant growth 365 days a year and supports local food production while helping to significantly reduce the environmental footprint.
OSRAM will be located across from the Hall of the Future in The HUB during HUBweek, held Oct. 8-14, 2018, on Boston’s City Hall Plaza. For more information about OSRAM, visit www.osram.us, and for more information about HUBweek 2018 and to purchase one of three pass types to unlock all types of experiences during HUBweek, visit hubweek.org.
Publication date : 10/1/2018