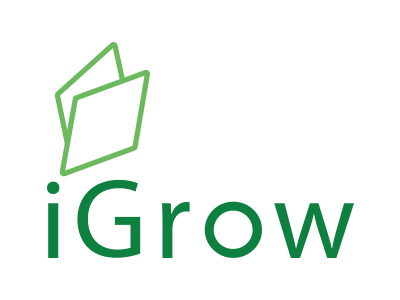
Welcome to iGrow News, Your Source for the World of Indoor Vertical Farming
Czech Startup Introduces New Container Farm To The Market
A container farm supplied by GreeenTech will soon be parked in Prague's Smíchov district. The hydroponic container farm will grow herbs, vegetables, and small fruits. The other two containers will go to Dubai and Shanghai
Delivering To Prague, Dubai, And Shanghai
A container farm supplied by GreeenTech will soon be parked in Prague's Smíchov district. The hydroponic container farm will grow herbs, vegetables, and small fruits. The other two containers will go to Dubai and Shanghai.
"We bring a unique and modern approach to agriculture. With vertical hydroponics we will start food self-sufficiency not only in the Czech Republic," promises co-founder of GreeenTech Karolína Pumprová, who three years ago was at the birth of the Prague urban hydroponic farm HerbaFabrica, which supplies herbs to Prague restaurants.
The co-founders of Greeentech
She was later joined by entrepreneur Dmitrij Lipovský, who, after a year-long working stay in China, where he focused on ecology and sustainability issues, saw a TV report about the HerbaFabrica farm, and was so intrigued by it that together with Karolína Pumprová and technology director Milan Souček, they created the concept of GreeenTech, a technology, and cultivation company that was officially established last July. Dmitry Lipovsky invested six million crowns of his own money in the start-up and became CEO of the company.
Modular solution
GreeenTech currently has three divisions, each with its own unique product and business and marketing direction. Urbanio is a modular system whereby the company builds an urban hydroponic farm according to the customer's requirements. The price in this case starts at one and a half million crowns and depends on the number of modules purchased and the environment where it will be built. The technology was to be officially launched at Expo 2020 in Dubai.
GreeenBoxes are containers coming with GreeenTech's technology. The price for the smallest size supplied, 13 x 3 x 3 meters, is in the lower units of millions of crowns. The third division is HerbaFabrica, which sells crops to distributors and end customers. The company intends to offer its franchise in the future.
These containers make it possible to grow crops practically anywhere and anytime, even in the desert. According to Lipovský, the company will produce three containers this year, the first of which will be located in Prague's Smíchov, while the others will also be presented at the EXPO in Dubai. It is to Dubai and also Shanghai that the company wants to expand in the medium term.
"The goal is to build full container farms and to continuously improve our technology. But we are a startup, so we are constantly in a turbulent process," smiles the CEO of the company over the next plans and reveals that the final investment round with external investors is also now underway.
Everything from the container design to the software solution is being developed in-house. Some of the technical equipment is supplied by Siemens CR, which is also a long-term technology partner.
GreeenTech wants its technology to contribute to a sustainable solution to a potential future crisis around food shortages. The founders of GreeenTech promise a recurring harvest of local vegetables full of vitamins and intense flavor. Since the crops do not undergo protective spraying, they are suitable for children and allergy sufferers.
The business model for GreeenBox and Urbanio technologies work on both a sales and rental basis. "For both options, there is an 'after-sales service, where we supply seeds, substrates, fertilizers, as well as spare components for the technology and remote farm management," Lipovský explains.
He adds that GreeenTech also started offering the HerbaShare service to businesses, shops and restaurants a month ago. This is a structure with a cold box for preserving produce, where the company regularly delivers microgreens and vegetables. "Now we want to focus more on businesses as people come back to the office. We believe this is a really interesting employee benefit and a way to have a vitamin bomb right in the workplace," he concludes.
Source: StartupJobs
For more information:
Greeentech
info@greeen.tech
www.greeen.tech
18 May 2021
N.Thing To Export Smart Farms To UAE After $3 Million Deal
The contract, set to proceed next month, will allow the firm to construct vertical smart farming containers in the UAE by December this year.
May 17, 2021
South Korean agriculture technology company N.Thing said Monday that it has recently inked a $3 million deal with Sarya Holdings in the United Arab Emirates to export smart farms.
The contract, set to proceed next month, will allow the firm to construct vertical smart farming containers in the UAE by December this year. The container can reduce the use of water up to 98 percent compared to a typical farm and cultivate crops in any environment, whether that is in Siberia, the Middle East, or Seoul.
“The UAE reached out to N.Thing as food security emerged as a key issue amid the coronavirus outbreak,” a company official said.
In February last year, Sarya Holdings conducted a proof of concept test on N.Thing’s container to verify the technology. During the test, Sarya planted four different vegetables -- batavia, kale, Boston lettuce, and oakleaf -- in eight test containers and observed their growth cycles, nutrients, quality, and more.
The test proved that N.Thing’s smart farm containers built in the UAE can produce up to 1.5 metric tons of crops per container, which was 42 percent more than initial estimates.
N.Thing received the best innovation award at the Consumer Electronics Show last year.
Lead photo: The interior of N.Thing’s smart farm container (N.Thing)
By Kim Byung-wook (kbw@heraldcorp.com)
Florida Native Brick Street Farms Takes On Global Agriculture With Multi-Million Dollar Investment
The Ag Tech Innovator Scales its Local Approach to More Sustainably Feed Urban Communities
The Ag Tech Innovator Scales its Local Approach to More Sustainably Feed Urban Communities
St Petersburg, FL (May 19th, 2020)- Brick Street Farms announces their new investors, Lykes Bros., a milestone championed by Florida Department of Agriculture Commissioner Nicole “Nikki” Fried, Mayor Rick Kriseman, St. Petersburg, FL, and Mayor Jane Castor, Tampa, FL. With Lykes Bros financial commitment to Brick Street Farms, the AgTech leader will scale its mission to lead the way in disrupting agriculture and reinventing possibilities to sustainably feed more people from urban locations, offer Brick Street Farm’s expertise so we can bring farm to fork in cities and contribute to healthier lives.
COVID-19 and climate change have accelerated existing strains in global food accessibility and supply chains, highlighting the need to rethink the world’s agriculture systems, particularly in dense city areas. In response to this crisis, Crunchbase News has cited that agriculture technology investments have grown 250% in the past 5 years alone. Brick Street Farms has been at the forefront of this industry because of their unique experience in both design and manufacturing of their THRIVE Containers as well as the operation of those farms for financial sustainability.
The AgTech’s ground-breaking approach is to bring to life cultivation centers, also known as Brick Street Farms hubs, which will serve as an all-inclusive onsite farming and retail shopping experience in urban cores. Brick Street Farms is reinventing urban farming with our self-contained, environmentally sustainable THRIVE Containers placed in Hubs. These hubs will grow between 16-20 acres of farmland on 1/3 acre lots. This Climate-Controlled Agriculture (CEA) maximizes output and minimizes water resources.
Brick Street Farms Founder and CEO, Shannon O’Malley observed “We could not be more honored to have Lykes Bros. as our newest investor. Brick Street Farms hubs will be the first of its kind and we can’t wait to share this innovation with the world. Our farming expertise combined with Lykes 121 years of experience in agriculture brings unparalleled leadership to feed more people ‘farm to fork’.”
“Lykes Bros. is excited to be advancing and investing in the future of agriculture. We see Brick Street Farms’ leadership and innovation in the controlled environment sector as the perfect fit for our company. They share our commitment to pioneering the future, and their hub innovation is a bold blueprint for producing healthy food locally and sustainably,” says Mallory Dimmitt, VP of Strategic Partnerships, Lykes Bros.
For more information about Brick Street Farms visit www.brickstreetfarms.com.
About Brick Street Farms
Brick Street Farms produce is grown and sold out of its St. Petersburg, Florida headquarters with a mission to ignite a sustainable farm revolution by dramatically reshaping the global population’s ability to access to clean, healthy food. Built for farming in all environments, Brick Street Farms provides healthy, fresh greens, year-round.
About Lykes Bros.:
Founded by Dr. Howell Tyson Lykes and his seven sons in 1900, Lykes Bros. Inc. is a leading Florida-based agribusiness with cattle, citrus, farming, forestry, hunting, and land and water resources operations as well as major landholdings in Florida and Texas. www.lykes.com.
Vertical Future And Crate To Plate Plot Fleet of Shipping Container Farms In London
Each of the 'container farms' will be able to produce up to five tonnes of leafy greens and veg each year with zero carbon footprint, the firms claim
Jessica Rawnsley
14 May 2021
Credit: Vertical Future
Each of The 'Container Farms' Will Be Able To produce Up To Five Tonnes of Leafy Greens And Veg Each Year With Zero Carbon Footprint, The Firms Claim
Urban farming specialists Vertical Future and Crate to Plate are together gearing up to rollout a fleet of indoor container farms in London, with each capable of producing zero carbon fresh salad and vegetables for swift delivery across the UK capital city, they announced yesterday.
Crate to Plate, an urban farming start-up, plans to use the 'container farms' designed by Vertical Future - a technology company focused on controlled-environment-agriculture (CEA) - across several new sites in London's Bermondsey and Stratford.
By using the container farms, Crate to Plate said it would be able to produce up to five tonnes of fresh produce - including lettuce, kale, and rocket - per year, and then deliver it to customers within 24 hours with a zero-carbon footprint, all without any use of pesticides or toxic chemicals. The firm counts Ollie Dabbous, chef-patron of Michelin-starred restaurant, HIDE, as well as independent grocers such as The Notting Hill Fish Shop and Artichoke in Hampstead among its customers.
Vertical Future's innovative farms, built within 40ft shipping containers, allow for highly-controlled indoor growing conditions, harnessing LED lighting, full climate control, and dual irrigation in order to create the optimal conditions for cultivating leafy salad and vegetables.
Proponents of vertical farming argue producing crops in such circumstances can reduce the amount of countryside land used for farming, better protect crops against the impacts of increasingly volatile outdoor climate conditions, and cut down on transport and logistics typically needed to ferry food from farms to urban centres. They also require far less water and zero pesticides.
"Our Container Labs create the optimal growth environment for growing fresh produce and can be deployed close to point of consumption, using minimal space," said Jamie Burrows, Vertical Future's CEO. "Using zero chemicals and growing crops in a controlled environment enables our partners to meet demand all-year-round, as opposed to regular food production systems which are reliant on seasonal limitations."
By shifting towards using Vertical Future's 'Container Labs', Crate to Plate's founder Sebastien Sainsbury said the firm would be able to scale up its systems across the UK while offering more efficient growing capabilities to improve both output and product quality.
"It's been incredibly encouraging and exciting to align with other dynamic, innovative, and enterprising British business, which will help us to scale up our vision and execute our exciting opportunities both nationally and internationally," Sainsbury said.
USA - ILLINOIS - Tasty, Fresh And Sustainable
There are no animals, roses, or peaches at Wiseacre Farm, a rectangular, 320-square-foot container farm inside a warehouse Sheinfeld rents in an industrial area at 1975 N. Lake Terrace, Glenview
Glenview Man's Hydroponic Farm
Uses Technology To Grow Garden Variety Produce
5/12/2021
By Dave Oberhelman
doberhelman@dailyherald.com
This is not your grandfather's farm.
It's not Aviad Sheinfeld's grandfather's farm, either -- but Wiseacre Farm is a bridge between childhood days spent on grandparents Yechezkel and Hadassah Gluzman's farm in an Israeli moshav and Sheinfeld's modern training.
That combination has resulted in some of the best greens his customers have ever tasted, grown indoors by futuristic, sustainable methods.
Whatever it is, the way you tell your story online can make all the difference.
"I don't know if it was a goal. I never thought about becoming a farmer. I was always good with computers, so working with computers was kind of the assumed path," said Sheinfeld, 49, of Glenview.
"I think my childhood experiences on the farm really gave me more of an ingrained appreciation for what it takes to grow food. The thing I remember most is the apple orchards and the peaches my grandparents grew, but they also grew roses and sheep, so also animals."
There are no animals, roses, or peaches at Wiseacre Farm, a rectangular, 320-square-foot container farm inside a warehouse Sheinfeld rents in an industrial area at 1975 N. Lake Terrace, Glenview.
Wiseacre's specialty, available by 10-week subscriptions through www.wiseacre.farm, is leafy greens. A recent delivery included six heads of lettuce of differing varieties. Another package will offer the lettuce plus herbs and other greens -- things like parsley, chives, Thai basil, red-veined sorrel, curly kale with chard.
Sheinfeld sometimes delivers his produce the day it's harvested. Reviews are strong.
"Most of our customers have remarked that they had no idea that lettuce, basil -- fill in the blank, whatever produce -- tastes that way," said Sheinfeld's daughter, Yael, who is finishing her last semester at Northeastern University in Boston, but also handling Wiseacre marketing and communications.
"I think it's hard to understand just how much the taste disappears with travel, with chemicals, herbicides, and pesticides, with just time, honestly, and sitting on a grocery store shelf," she said.
Growing crops indoors in Wiseacre Farm's controlled hydroponic environment eliminates the need for herbicides and pesticides. Serving customers within about a 10-mile radius also lends a neighborly appeal.
"It's not just buying your food from anonymous company X," Aviad said.
His father, Sam, also works on the farm. Yael -- and occasionally Aviad and Kari Sheinfeld's two teenage boys, Rahm and Lev -- are fourth-generation farmhands.
Finalizing financing and incorporation in 2018, in November 2019 Sheinfeld received his container farm from Freight Farms of Boston. He said there's a couple hundred of these repurposed shipping container farms worldwide. When he needs advice he reaches farmers in Alaska, Minnesota, Tennessee, even Tasmania.
The interior includes vertical panels about 10 feet tall in which the plants soak up rays of LED lights embedded into opposing panels. The plant panels can be removed and placed horizontally when the plants are ready for harvesting.
The media is not soil but water, to which nutrients are added automatically, manually controlled by computer. Hydroponic methods are 98% more water-efficient than traditional farming, Yael said. Through recycling irrigation water and capturing the water transpired by the plants, on average the farm uses less than 5 gallons of water a day. On very humid days, the farm will capture more water than it uses.
Nutrients, drip irrigation, temperature, humidity, lighting -- all are computer-controlled.
"As farming goes, it's kind of posh," Aviad Sheinfeld said.
"The thing about this farm is it's very technically advanced, so it kind of marries my initial interest in agriculture and my insatiable appetite for technological gadgets all into one big toy," he said.
He earned a bachelor's degree in mathematics at the University of Pennsylvania and added DePaul University master's degrees in network communications and information security and in computational finance.
First working as a software engineer with Motorola, he veered into stay-at-home dad mode after he and Kari, an attorney, started having children. The couple sent their kids to the Science & Arts Academy in Des Plaines, where Aviad served three years as board chairman. During that time, the academy explored hydroponics as part of the curriculum.
"That's kind of where I caught the bug, so to speak," he said.
No bugs at Wiseacre Farm. There is lots of energy consumption.
"We have lights that are powered by electricity and we use a lot of technology, so that is one resource that we use a lot of," Yael Sheinfeld said.
And still ...
"What's wonderful is, due to our partnership with Arcadia (Power, a renewable energy company out of Washington, D.C.) all of the electricity that we consume now is 100 percent offset with wind-generated, renewable energy. So it sort of allows us to keep that focus, knowing that's the main resource we still need to use, but doing that in a more sustainable way," she said.
For lettuce, from seed to harvest it takes only 8 weeks for the container farm to grow the equivalent of 2 acres of traditional farmland, Aviad said. He plans on about six annual growing cycles.
His first crop came through last March, right at the onset of the COVID-19 pandemic. Initially targeting restaurants for his produce, he shifted to a farm-to-table model. Customers also can now pick up goods at the farm itself on Saturdays, though preordering is a must. All packages and purchasing options are available at www.wiseacre.farm.
In its short time, Wiseacre Farm has gained acclaim beyond consumer taste buds. It won Silver for innovation in the Glenview Natural Resources Department's 2020 Environmental Sustainability Awards, and on March 28 the farm was featured in a segment of the History channel's "Modern Marvels" series highlighting "The Future of Food."
After a year, Aviad Sheinfeld said the process has become "a little less magical," but he still gets a kick out of it. Imagine what Hadassah and Yechezkel Gluzman might think.
"You put seed in a plug, and even a few days later when it pops out, I'm amazed," Aviad said.
"I do understand it, but I still don't believe how amazing it is that a plant grows out of this little, tiny seed and a few weeks later you have a head of lettuce or arugula."
Lead Photo: Wiseacre Farm owner Aviad Sheinfeld looks over some of the plants grown at his hydroponic farm in Glenview. Brian Hill | Staff Photographer
AmplifiedAg Increases Better Fresh Farms Production 50% With New Indoor Farm And AmpEDGE Operating System
AmplifiedAg hydroponic container farm and technologies increased leafy green production over 50% for Better Fresh Farms
By AmplifiedAg
May 6, 2021
AmplifiedAg hydroponic container farm and technologies increased leafy green production over 50% for Better Fresh Farms.
AmplifiedAg, Inc. is an agtech visionary on a mission to provide global access to safe food. (PRNewsfoto/AmplifiedAg)
CHARLESTON, S.C., May 6, 2021 /PRNewswire/ -- AmplifiedAg, Inc.®, holistic indoor farming leader with a mission to provide global access to safe food, has increased leafy green production over 50% for Metter, Georgia-based Better Fresh Farms with its automated hydroponic container farm and AmpEDGE™ proprietary Operating System.
AmplifiedAg farms sustainably grow consistent yields of 800-1000 pounds of full head leafy greens per harvest every 3 weeks.
Founded in 2016 by Grant Anderson, Better Fresh Farms is expanding its hyperlocal produce throughout Georgia with the addition of its first AmplifiedAg farm, the company's exclusive producer of leafy greens.
Anderson said, "Our AmplifiedAg farm replaced two existing models that were fairly inefficient for our goals. The new system has optimized our production in the same square footage,"
"The software is going to help us get our arms around the whole operation; there's nothing out there really like it," added Anderson. "To have tracking processes that follow produce from growth all the way through to the sale is huge. It's been cumbersome up until now, and it will save us money in the long run to have one efficient system instead of multiple programs."
AmpEDGE uniquely combines farm production and business management for an end-to-end system. 24/7 environment controls, detailed analytics, and traceability features allow farmers to easily optimize crop growth, mitigate risk, while also tracking sales forecasts, revenue streams, and daily operations. Multi-tenant software with data-driven learning capabilities, AmpEDGE can operate any type of controlled environment.
"We grow 52 weeks a year in Georgia where the majority of the time weather is extremely hot and humid," added Grant. "We're constantly trying to adapt our systems to work in an environment that they weren't designed for. AmplifiedAg understands how to adapt their containers to different weather."
Manufactured from upcycled shipping containers, AmplifiedAg's enterprise-scale farms are built to the highest global food safety certifications. The resilient architecture allows for farming in any region regardless of resources and climate. A compact 320-square feet container design promotes ultimate segmentation and risk mitigation for reliable production.
AmplifiedAg farms sustainably grow consistent yields of 800-1000 pounds of full head leafy greens per harvest every 3 weeks. The company deploys farms 70% faster and at a fraction of the cost of other CEA implementations
"This has given us a chance to start exploring larger and more legitimate sales opportunities," added Anderson.
David Flynn is the General Manager of AmplifiedAg and leader behind the company's farm and technology production. He and his team have built and deployed over 180 farm containers that services farms across the country. This includes AmplifiedAg's Vertical Roots hydroponic container farm, with produce in nearly 1,500 stores nationwide.
"We've spent the last five years developing a platform that proves our technology and shipping container farms can be used to operate a profitable produce business at scale," said Flynn.
"We're excited to share our technologies and farms with other indoor farming experts like Grant and Better Fresh Farms, and continue to refine the indoor farming process for the future."
Learn more at www.amplifiedaginc.com.
Freight Farms Releases Next Generation of Container Farming
Freight Farms released the 10th generation of their container farming system – Greenery S, which has several key improvements on its predecessors
4 May 2021
Freight Farms released the 10th generation of their container farming system – Greenery S, which has several key improvements on its predecessors.
Since its founding in 2013, Freight Farms has been dedicated to making modular vertical farming technology accessible to more communities around the globe in a sustainable fashion. Their systems use a hybrid of hardware, software and services to make food production possible for anyone of any background, anywhere in the world.
“Greenery S represents the apex,” Jon Friedman, COO and co-founder tell Future Farming, “leveraging the excellent design and intuitive automation to streamline workflow while driving up yields.”
LED technology
Greenery S has several key improvements on its predecessors. This includes the new Dynamic Lighting Control, which uses LED technology that allows farmers to customize the lighting spectrum, intensity and duration for optimal plant yields. It also features a brand new user-centric Workstation design making for a sleek, self-contained and multi-functional farm command center.
Text continues underneath image
LED technology allows farmers to customise the lighting spectrum, intensity and duration for optimal plant yields. - Photo: Freight Farms
More consistent harvests
This new generation also brings with it an update to Freight Farms’ farmhand software that includes a new feature called “Recipes.” This update allows farmers to obtain more consistent harvests.
“Operators simply choose the crop they wish to grow and farmhand automatically adjusts in-farm settings for that crop production,” explains Friedman. “In-farm cameras and sensors gather information and continuously improve the precision of the recipes over time, aggregating data from the entire farmer network to determine patterns that lead to exceptionally successful harvests.”
Of all their systems, Greenery S combines Freight Farms’ most optimized combination yet to allow farmers the highest possible yields at the highest quality with the fastest rates.
Lower startup costs
With lower startup costs, Freight Farms reports that their Greenery S farm system can grow an equivalent of 2.5 acres of traditional farmland with 12 harvests per year. According to Friedman, it typically takes their farmers two to three years to see returns on their initial investments.
Greenery S is now available for purchase worldwide.
Jaclyn Krymowski
Correspondent for North America
Read more about: Vertical Farming Indoor Farming Container Farming
What Is A Container Farm?
A container farm is usually a vertical farming system built inside a shipping container. The benefits of placing a farm within a container, rather than a building, are that it is transportable and can be squeezed into existing spaces, such as in car parks or on farmland
30-04-2021 LettUs
Container farming, vertical farming, indoor farming… What do they all mean? Are they all the same thing? In this blog, we’re going to explain exactly what a container farm is and what the benefits of growing crops in this way are.
The controlled environment agriculture club
Controlled environment agriculture (CEA) is a term for using different technologies to grow food indoors. In CEA, these technologies ensure the best growing conditions and protection for specific crops. This is slightly different to just indoor farming - by nature, indoor farms simply protect crops from external forces such as weather and pests. A container farm would be an example of CEA, as would other indoor farms such as vertical farms and high-tech commercial greenhouses.
A container farm is usually a vertical farming system built inside a shipping container. The benefits of placing a farm within a container, rather than a building, are that it is transportable and can be squeezed into existing spaces, such as in car parks or on farmland.
Since it is classified as a temporary structure, you typically don’t need planning permission for a shipping container. This can be particularly useful for those who rent their farmland. However, there are always exceptions and the necessary checks should always be made before making arrangements. As long as there is level ground, access to electricity, water & wifi, a shipping container can fit into a range of different settings.
Serving communities, big or small
Since they’re easy to transport, container farms can be easily deployed as and when they are needed. This means they could be used for research or social-impact projects, without needing to build a permanent facility. Shipping containers are also modular, which means multiple containers can be used to build a larger facility and businesses can scale their operations appropriately. They also have the potential to be bedded into existing container parks - these are dotted around the UK and are usually shipping containers made up of independent shops, cafes, and restaurants. One container farm could supply fresh produce to all of these.
In this way, container farms have the potential to be a positive disruptor within our food supply networks and strengthen our local food security by reducing our dependence on imported produce. Food waste and carbon caused by food transportation would also be reduced by strategically placing containers in key locations within communities.
The DROP & GROW container farm
LettUs Grow’s container farms are powered by aeroponic technology. This is a soil-less system that uses a nutrient-dense mist to irrigate crops - boosting oxygen levels and encouraging healthy root stock. Whilst hydroponic container farms are more common, DROP & GROW uses aeroponics to optimise crop health and increase growth rates.
Our container farms have also been designed with the grower in mind. DROP & GROW:24 includes a separate preparation area, providing ample space for the grower to do their job. Our farms have also been designed to be easy to maneuver within and check on your crops.
Celebrating vertical farming technology
DROP & GROW wasn’t designed to be inconspicuous. Quite the opposite! We think urban farming, new technologies and feeding local communities is something to shout about, so a DROP & GROW on your site is an opportunity to start a conversation and encourage your customers to learn more about the benefits of vertical farming.
If you want to take a positive step towards a more sustainable and resilient food supply chain in the UK, then talk to LettUs business development team about why a container farm might be in the right choice for you. Find out more...
Source and Photo Courtesy of LettUs Grow
How COVID-19 Fed The Dream of Growing Food At Home
Sales of hydroponic gardens boomed during the pandemic, but do high-tech solutions like those only further fuel inequality?
04-28-21
Sales of hydroponic gardens boomed during the pandemic, but do high-tech solutions like those only further fuel inequality?
This story is part of Home Bound, a series that examines Americans’ fraught relationship to their homes—and the once-in-a-lifetime opportunity to hit the reset button. Read more here.
When COVID-19 struck the United States, people rushed to grocery stores to stock up on food, only to find that many shelf-stable items like beans, rice, and flour were sold out. It was the first time many of us were forced to consider where our food comes from—and how vulnerable the global food system really is.
These food shortages spurred many Americans to consider growing their own food for the first time. Some planted vegetables in their backyards and windowsills, while others went for high-tech hydroponic gardens.
In the years before the pandemic, startups developed these compact self-watering, self-fertilizing, gardening machines that were aesthetically pleasing, to boot. During the lockdowns, sales of these products—which start around $800—spiked, prompting venture capitalists to pour millions into the industry.
But as the COVID era comes to an end, it remains to be seen whether these high-tech gardens have staying power or whether they were just a short-lived novelty. And more broadly, it’s worth asking whether these devices can be a tool for making agriculture more sustainable and equitable, or whether they’re just another toy for the Whole Foods class.
[Photo: courtesy of Freight Farms]
THE HYDROPONICS REVOLUTION
Hydroponics, which simply means growing plants in a solution of water and nutrients instead of soil, have been around since at least 600 BCE. But in the late 1920s, William Gericke of the University of California modernized these techniques, creating farms that require less space and up to 95% less water than soil-based farms but yield much bigger harvests by optimizing light, water, and nutrients. During World War II, the U.S. military built hydroponic gardens to grow vegetables for troops in locations that weren’t suited to traditional agriculture, such as Ascension Island, a refueling station in the Atlantic Ocean, where soldiers grew thousands of pounds of cucumbers, tomatoes, lettuce, and radishes each month, staving off malnutrition.
COVID-19 prompted some countries to use hydroponics to deal with disruptions in the global supply chain. The Netherlands and Singapore, which have limited agricultural land and rely largely on imports, invested billions during the pandemic to build industrial hydroponics farms on rooftops and parking lots. In the United States, hydroponics are still a small business, with about 3,000 businesses generating around $800 million in revenue, a small sliver of the $451 billion from traditional farming. But analysts are banking that the industry is poised to grow.
Over the last five years, a bevy of startups—including Rise Gardens, Gardyn, Lettuce Grow, Aerogarden, and Click-and-Grow—have launched to create hydroponic systems that can fit inside a home. That’s a departure from the focus over the past century on large-scale hydroponics farms.
The devices are expensive, and before the pandemic, it was a tough sell convincing consumers to spend nearly $1,000 on a machine that might take years to pay off. But COVID-19 changed the game, as people around the world worried about food shortages. “The pandemic made people pay attention to where their food comes from and accelerated their interest in producing their own food,” says Nina Ichikawa, executive director of the Berkeley Food Institute, which promotes food equity. “This new awareness is a good thing.”
Many of these startups doubled or tripled their sales over the past year, and some investors are capitalizing on this interest. True Ventures, which funds Peloton and Blue Bottle, invested $2.6 million in Rise Gardens; Gardyn raised $10 million from JAB Holding Company, the largest shareholder in Keurig. And right before the pandemic, Estonia-based Click & Grow received $11 million in funding from Y Combinator and Ingka Group, which operates 367 Ikea stores in Europe.
[Photo: courtesy of Lettuce Grow]
A PERSONAL HYDROPONIC GARDEN
Despite my lifelong black thumb, I decided to test Lettuce Grow, a six-foot tall hydroponic garden that looks like a white sculpture with plants artfully growing on it. I’m shocked by how much food I’ve grown: My family of three now eats freshly plucked lettuces with each meal and yet our harvest is so plentiful, we’ve had to share our veggies with neighbors.
The beauty of hydroponic systems is that they’re designed to run on their own, with minimal intervention from the owner. My machine automatically waters and fertilizes the plants by pumping a nutrient-rich solution through the system for 15 minutes every hour. The high-efficiency LED light rings control how much light the plants receive, adding only a few dollars to our monthly electricity bill. All I have to do is top up the water in the base and add a few spoonfuls of plant food every week.
When it comes to seeds, all of these hydroponic startups are also, effectively, subscription programs. You need to buy seeds or seedlings from the company for about $2 apiece to replace the plants you’ve fully harvested. This takes anywhere from three weeks to several months depending on their growth cycle. “You get to enjoy the beauty of watching living things grow, without needing any expertise in farming,” says Jacob Pechenik, who co-founded Lettuce Grow in 2019 with the actress Zooey Deschanel.
And these startups aren’t just focused on making the machines smaller, they’ve also made them beautiful. Lettuce Grow, for instance, worked with the designer Pip Tomkins—who previously designed the Nokia M Series—to create a stand with vegetables and herbs cascading from the sides, much like you’d see on a plant wall. Rise Gardens partnered with TBD Innovations, a firm made up of former IDEO designers, to create a system that looks like a white cabinet with rows of plants above it. “We knew that our garden needed to look attractive for people to consider bringing them into their homes,” says Hank Adams, founder and CEO of Rise Gardens. “We wanted it to be beautiful and minimalist, so you’d be happy to have it whether you live in your studio apartment or large home.”
Rise Gardens, Gardyn, and Lettuce Grow all created modular systems, so customers can start with just a few levels of plants and expand over time. Pechenik says his goal was for Lettuce Grow to replace up to a fifth of a household’s produce. (I can attest that our 24-plant unit easily achieves this for a family of three.) For those who can afford it, these machines generate fruits and vegetables that are far tastier and more nutritious than what you’d normally buy at a store. Studies show that most produce loses 30% of its nutrients three days after harvest, and much of what we find in the grocery is much older than that.
Hydroponics provides an alternative to industrial agriculture, which has dominated our food system since the 1960s. Factory-like farms are bad for the planet because they deplete the soil, consume a lot of water, spew toxic pesticides into the environment, and contribute to deforestation. Transporting food around the country also generates carbon emissions and creates a lot of waste, since produce goes bad along the way. Half of all U.S. produce is thrown out. For me, one of the best parts about having a hydroponic garden at home is that we’ve virtually eliminated waste and have to make fewer trips to the grocery store.
FOOD INEQUITY
For now, most of these devices have gone to people interested in small-scale gardening. But the founders believe their products have the ability to disrupt our broken food system, if they’re able to scale. “We are not in the gardening business,” says FX Rouxel, Gardyn’s founder and CEO. “We’re trying to reinvent how people can grow their own food at scale. If we have solutions that are compelling enough, we believe we can change people’s food habits and reduce their dependence on the grocery store.” Gardyn launched in early 2020, and in its first year, Rouxel says its hundreds of customers grew 70,000 pounds of produce.
But Berkeley Food Institute’s Ichikawa argues that we should be skeptical about whether these high-end hydroponic systems can actually change the food system. Most people don’t have the money to invest hundreds of dollars in this hardware, and those are exactly the people who could most benefit. A tenth of households experience food insecurity and more than 23.5 million Americans live in neighborhoods without easy access to a supermarket. “Rich people are willing to spend their money on many new-fangled technologies that don’t necessarily impact the rest of the industry for better or for worse,” she says. “It’s just a new business opportunity for these startups.”
She points out that hydroponics don’t have to be so expensive or complicated. In fact, a lot of innovation around cost-effective small-scale hydroponics came from cannabis growers, many of whom were people of color operating underground. Entrepreneurs and scientists have been developing affordable DIY hydroponics in Africa, particularly Kenya. Startups like Hydroponics Africa have built systems that don’t require electricity and use inexpensive, locally available materials, including fungi-resistant aluminum trays. “These [U.S.] startups are creating a flashier, fancier version of systems that have actually been around for a long time,” Ichikawa says. “There are a lot of low-cost solutions that have emerged from the ground up, from the communities that depend on these technologies to survive.”
For now, Pechenik tries to make his technology available to more people by donating one Lettuce Grow machine for every 10 sold to schools, nonprofits, and community organizations. He says they’ve distributed several hundred already, along with $1 million in donations. Rise Garden, meanwhile, has launched a smaller machine that starts at $279. “I compare this to the early days of personal computing when a laptop was very expensive, and yet now, laptops are widely available,” Adams says. “As hydroponic gardens scale, the cost of manufacturing will go down.”
One answer might come from systems that are large enough to feed a community, rather than a single family, and thus are more cost-effective. Take, for instance, Freight Farms, which debuted the first hydroponic farm inside a shipping container in 2012. The company sells $130,000 containers that can generate the same amount of food as three and a half acres of farmland, enough to feed hundreds of people. Long-term, these systems are more economical given their scale and could help solve food insecurity problems. The city of Boston, for instance, bought five Freight Farm systems in Mattapan, where 20% of the population lives below the poverty line, to create a high-tech farming co-op. “Our farms are being used as part of community redevelopment,” says Rick Vanzura, Freight Farms’ CEO.
[Photos: courtesy of Freight Farms]
During the pandemic, Freight Farms’ sales tripled, and the company expects business to triple again in 2021. Last year, it landed $15 million in Series B funding, bringing its total to $28 million. Vanzura believes that for hydroponics to have an impact on agriculture, there will need to be farms of different sizes, ranging from individual gardens to industrial farms. In fact, Freight Farms advised Lettuce Grow about growing techniques, drawing from its decade-worth of data. “We need to cooperate as an industry to take the best of what we each do and help each other get better,” he says.
As hydroponics grow in popularity, Ichikawa says that it’s important to remember that it is not the only, or best, solution to cultivating food for a community. The poor tend to be most impacted by problems in the food system and suffer from health issues due to lack of access to nutritious food. This is why organizations like hers advocate for food sovereignty, which means empowering communities to take charge of their own food supply through things like local ownership of grocery stores and backyard or community gardening.
While midsize hydroponic systems could be a tool for tackling food insecurity, she worries that it could create a new barrier to entry, making access to fresh food seem even more out of reach. “Food sovereignty can absolutely protect us from the instabilities from pandemics or climate change, so any way that folks can feel autonomy over their food supply is a good thing,” Ichikawa says. “But you don’t need a fancy hydroponic system to do this. You could do it just as easily with a bucket of soil by a window.”
ABOUT THE AUTHOR
Elizabeth Segran, Ph.D., is a senior staff writer at Fast Company. She lives in Cambridge, Massachusetts
[Source Images: courtesy of Lettuce Grow]
When We Started Freight Farms In 2010, There Was No Such Thing As An “Ag Tech” industry
Freight Farms has a passionate customer base of small businesses, entrepreneurs, traditional farmers, hotels, restaurants, corporate campuses, universities, and non-profits
We weren’t even sure how to explain what we were trying to do to our own friends and family! But we knew that there was a need for urban agriculture to emerge as a competitive industry in the food landscape. That’s why Freight Farms was born—to build the infrastructure and technology that would allow local food to thrive around the globe.
Less than a decade later, we are proud to be on the forefront of the fast-growing Agriculture Technology industry. Freight Farms has grown into a platform that anyone can use to supply their communities with fresh produce year-round, regardless of background or geographic location. We’ve had the pleasure of launching our container farming system in over 44 states in the US and 24 countries around the globe, creating the largest network of connected farmers.
Freight Farms has a passionate customer base of small businesses, entrepreneurs, traditional farmers, hotels, restaurants, corporate campuses, universities, and non-profits. We’d love to welcome you into our community of Freight Farmers, and our team is ready to help you get started.
Jon Friedman and Brad McNamara
Freight Farms Co-Founders
VIDEO: One Sure Way To Save Our Soil – Don’t Use Any
The advantage of container farming is the ability to create commercial-scale production within a small space the size of your standard 40-foot shipping container through vertical farming techniques
In the push for regenerative agriculture and soil rehabilitation, container farming has an important role to play.
The idea behind regenerative agriculture isn’t new, but this year it is front and center as one of the key initiatives of the official Earth Day 2021 campaign: Restore Our Earth™.
According to the Earth Day organization, overfarming has caused soil capacity in the U.S. to decline dramatically, losing soil 10 times faster than it can be replenished. The result is that in many places, the land has as few as 60 harvests left before it is completely depleted. Unfortunately, with ownership of farms increasingly concentrated in the hands of industrial or foreign producers, the promise of short-term profits wins out over long-term solutions that would prioritize soil health.
What is regenerative agriculture?
Regenerative farming takes an opposite position. As a school of thought, it is a method of farming that actively fights soil degradation by restoring carbon to the soil, which has a double benefit of renewing the viability of the land while simultaneously removing carbon dioxide from the atmosphere. There are many different types of regenerative agriculture, here’s a helpful video to explain the main three:
But between destroying the soil and saving the soil, there’s a third option: not using any soil at all. This is the premise behind container farming.
Container farming to save soil.
Container farming is a subset of the indoor farming industry, which includes everything from greenhouses and warehouses to at-home tabletop setups. The advantage of container farming is the ability to create commercial-scale production within a small space the size of your standard 40-foot shipping container through vertical farming techniques. Inside the container, plants are protected from the external elements and nurtured using nutrient-enriched water, powerful red and blue light, and optimal temperatures.
Notice anything missing? Oh yeah–soil!
Container farming with hydroponics completely eliminates the need for soil to grow food, which is great news for the whole regenerative agriculture movement. Since regenerative farming is based on the idea of protecting soil, container farming is able to take the whole idea to the logical extreme by not using any soil–period.
Not only does container farming prevent the further degradation of soil, but it actually frees up land to be actively regenerated. At Freight Farms, our containers (each capable of growing an average of 2 acres of food) have already saved 700 acres of land… which’s equal to about 530 football fields!
Additional sustainability benefits
Beyond regenerative agriculture, which is primarily focused on soil, container farming brings many additional sustainable benefits. The Greenery S is able to save:
Water: 99% less water than is used in conventional agriculture.
Food miles: we move the farms, not the food. Instead of trucking/shipping food from a centralized location, we put the farm as close to the final consumer as possible.
Carbon emissions: in addition to reducing food miles, we’ve partnered with Arcadia to make it easy and effective for our farmers to get onto the renewable energy grid and make their carbon footprint just one-quarter of what it would be if they were farming using industrial farming methods.
Regenerating communities
While regenerative agriculture may start with soil, the implications on climate change, food access, and food security are clear. In the same way, container farming is also more than just improving the sustainability of our agriculture system. In addition to saving soil, land, water and reducing food miles and carbon emissions, container farming unlocks many important social gains:
Independence: when we are not reliant on soil, land, and climate, we can make any place a farm. This makes it possible for us to create the distributed system we need to combat the harmful effects of industrial farming and centralized food systems.
Equality: independence from soil and land also creates more food equality, since individuals and communities need fewer resources (money & land) to create commercial-scale farms.
More farmers: Soil is complicated and nuanced, it takes huge amounts of experience and education to know how to do regenerative agriculture properly. With container farming, everyone can be a low-impact farmer.
More varieties: Conventional agriculture is beholden to monocropping, which improves the unit economics of growing food but also increases the risk of crop failure, blight, and soil degradation. Container farming makes it possible to grow hundreds of plant varieties, introducing people to new types of plants and growing public perception of the diversity you can have with fresh greens. This can have an overall positive effect on market demands and help move the whole system away from relying on mono-cropping.
Learn more about the Earth Day Restore Our Earth™ campaign and check out how Freight Farms is helping support the regenerative farming movement with container farming!
Freight Farms
Empowering anyone to grow food anywhere. Freight Farms makes local food accessible in any climate with the Greenery™ container farm.
April 23, 2014
Follow Earth Day Earth Day 2021 Sustainability Regenerative Agriculture Agriculture
This Is What The Future of Farming Looks Like
Vertical farming is nothing less than exactly what it sounds like. As opposed to spreading crops out along the ground, beds are effectively turned on their side, and grown on vertical panels
Why Grow Plants Horizontally When You Can Grow Them Vertically?
What do most people think of when imagining a farm? Typically: Acres upon acres of crops, fed by an extensive irrigation system, with tons of pesticides and heavy machinery— in other words, an image of modern farming that’s simply dated. Today’s most technically advanced farms don’t require nearly as much water or chemicals and take up just a fraction of the footprint. How? The answer is simple: Vertical farming. Specifically, the brand new Greenery S hydroponic system by Freight Farms.
Vertical farming is nothing less than exactly what it sounds like. As opposed to spreading crops out along the ground, beds are effectively turned on their side, and grown on vertical panels. This isn’t exactly new; some of the earliest indigenous farmers would plant crops on layered terraces to achieve similar results. But the modern form of vertical farming is barely two decades old. While it’s proven hyper-efficient, the technological cost of entry has also traditionally proven to be high, requiring expensive lights, temperature and irrigation control systems, and enormous amounts of electricity — to say nothing of capital. Until now.
Enter Freight Farms, a fully-functional farm in a 40-foot container. Launched in 2011, Freight Farms’ mission is to build accessible, modular vertical farming technology that empowers anyone to grow fresh, healthy food in their local communities — wherever that may be. While industrial farms tend to rely on GMO seeds, extensive pesticides, and centralized distribution systems, Freight Farms has worked tirelessly to cram 2.5 acres worth of farmable land into a 320-square-foot shipping container that can be placed almost anywhere and scaled up (or down) to meet your individual needs. Whether you’re a small restaurant looking to grow your own vegetables, an entrepreneur looking to bring fresh food to a food desert, or even just a homestead hobbyist, the Greenery S by Freight Farms is here to make your vertical farm aspirations a reality.
Freight Farms brings a decade of experience to the Greenery S. The Greenery S uses 99% less water than traditional industrial farm systems, mainly because you don’t need to worry about losing so much water to evaporation over acres and acres of land. Furthermore, the Greenery S has built-in temperature controls that make farming viable year-round, with a minimum temperature of -40 degrees Fahrenheit and a maximum of 120 degrees Fahrenheit. And with over five hundred supported crop varieties, you can throw out your hardiness zone map and grow pretty much whatever you want, wherever you want.
Besides being far more cost-effective than purchasing, tilling, planting, irrigating, and harvesting multiple acres of land, Freight Farms also uses data to help you get the most out of your yield. The proprietary farmhand® software integration gives operators complete automation and control over their grow operations. The software connects hundreds of farmers and is constantly compiling data from them to help you better manage your own crops based on learnings from the entire Freight Farms network.
The Greenery S is available now, to everyone. Whether you’re a seasoned farmer looking to scale out your operation or you’re simply looking for an exciting new business opportunity, Freight Farms’ intelligent automation and exceptional design can transform any small space into a commercial-scale farm. Head here to learn more and reserve yours now.
Lead Image: Image by Freight Farms
Futurism fans: This post was paid for by Freight Farms and was written by non-editorial staff. This content does not necessarily reflect the views or the endorsement of the Futurism.com editorial staff.
As a Futurism reader, we invite you to join the Singularity Global Community, our parent company’s forum to discuss futuristic science & technology with like-minded people from all over the world. It’s free to join, sign up now!
New Freight Farms Greenery S Ushers In The Next Era of Smart Small-Space Farming
Five Specialized Systems Allow Farmers to Grow Food 365 Days a Year With Complete Control
Five Specialized Systems Allow Farmers
To Grow Food 365 Days A Year With
Complete Control
NEWS PROVIDED BY
April 21, 2021
BOSTON, April 21, 2021 /PRNewswire/ -- Earlier this month, Freight Farms, the world's leading manufacturer of container farming, unveiled its new container farm, the Greenery S. This latest model is the tenth generation of the technology since the company pioneered the small space farming concept in 2013.
The Greenery S features an exceptional new farm design which, when paired with seamless automation, unlocks powerful performance for all users. The Greenery S combines specialized space, light, air, water, and control systems to make it possible to grow 2.5 acres-worth of food in 320 square feet anywhere in the world.
Always keeping the farmer in mind, the Greenery S implements feedback drawn from in-depth customer research to execute an exceptional new farm design which, when paired with seamless automation, unlocks powerful performance for all users. The Greenery S combines specialized space, light, air, water, and control systems to make it possible to grow food anywhere in the world, thereby empowering individuals to grow food locally within their communities to decentralize the global food system.
"The Greenery S brings an entirely new level of design, control, robustness, and ease of use to our already industry-leading growing platform. It is built upon the technology we have developed over the past ten years while introducing a fresh suite of features. This farm is not just a refinement of our past models – it redefines what it means to be a farmer," said Freight Farms co-founder and COO Jon Friedman. "With the Greenery S, we hope to further simplify the process of farming to make the profession as accessible as possible to people around the world."
Industry-Leading Features for Design, Automation, and Performance
Of all the Greenery S features, the most notable are the re-imagined workspace, the enhanced farmhand® automation software, and the dynamic new proprietary LED technology.
All-New Workstation - User-Centric Design
As Freight Farms continues to define and refine what a farm can be, the company focuses specifically on optimizing workflow for their farmers with an all-new Workstation, a sleek, self-contained, and multi-functional farm command center.
Technical components – water and nutrient tanks, dosing panel, pumps – are hidden from view yet easily accessible with a simple push-to-open mechanism for instant access.
The 'Tabletop Riser' separates the workstation into two workzones, and includes an integrated, multi-functional LED bar (for tabletop illumination, plant spacing guidance, and task timing) and four full-range Bluetooth speakers.
Farmhand® Recipes - Network Learning & Automation
The latest release of Freight Farms' companion farming software–farmhand®–takes automation to the next level with the new Recipes feature.
Recipes allow farmers to achieve consistent harvests with the touch of a button: Operators simply choose the crop they wish to grow and farmhand automatically adjusts in-farm settings to optimize for that crop production.
Recipes are built by aggregating farmer network data and determining patterns that lead to exceptionally successful harvests; meaning the list of recipes will grow as the global Freight Farmer community continues to expand.
Dynamic Lighting Control - Power & Precision for Performance
The Greenery S takes a huge leap in LED technology by allowing farmers to customize the lighting spectrum, intensity, and duration of light to achieve their desired plant yields.
The Greenery S features Freight Farms' proprietary LEDs, which emit light with 60% greater intensity and 50% better efficiency compared to off-the-shelf options.
Farmers have precise control over their lights with brand new Eco (prioritizing farm efficiency by reducing power consumption), Performance (prioritizing plant growth for greater yields, and Standard (balances the two) modes.
The Most Versatile Platform in the Indoor Farming Industry
The accessibility and versatility of the Freight Farms platform allow customers to use it in a diverse range of locations and applications. The Greenery S is built with the same specifications as a standard 40-foot shipping container, making it possible to bring and install the farm in any location, such as a city center, tropical island, or area experiencing food insecurity. Once at its location, the 320 sq. ft. container becomes a commercial growing space, capable of producing 2.5 acres worth of fresh food every year. The farm's elite design, in combination with farmhand®, robust training, and access to an elite support team, ensures anyone can run a successful operation without any prior farming experience.
Freight Farms currently services more than 500 trained farmers across 48 U.S. states and more than 32 countries. For more information, visit freightfarms.com.
About Freight Farms:
In 2013, Freight Farms debuted the first vertical hydroponic farm built inside an intermodal shipping container with the mission of democratizing and decentralizing the local production of fresh, healthy food. Now with the Greenery S and integral IoT data platform, farmhand®, Freight Farms has the largest network of connected farms in the world, with global customers in 32 countries and 48 U.S. states ranging from entrepreneurs and small business farmers to corporate, hospitality, retail, education, and nonprofit sectors. To learn more, please visit freightfarms.com, or visit us on Instagram, Twitter, or Facebook.
Media Contact:
5WPR
Carinna Gano, Account Supervisor
cgano@5wpr.com
SOURCE Freight Farms
Related Links
Your Quick Guide To Grow Room Controllers
A grow room controller brings together all the moving parts of your cultivation facility and allows you to automate your operation
March 5, 2021
What is a Grow Room Controller?
A grow room controller brings together all the moving parts of your cultivation facility and allows you to automate your operation. With a grow room controller, you can monitor and control your climate, lighting, irrigation, fertigation, and track your crop’s success to adjust and improve each cycle. These control systems can connect to existing equipment or come with their own set of sensors to track your environment, and adjust according to your set parameters, ultimately saving you time and money.
Grow room controllers integrate with existing systems, or can be purchased with sensors and equipment for larger operations. Some systems need only a few sensors and an application for your phone or computer, while others require larger computing and monitoring devices. Which option you choose will largely depend on the size of your greenhouse or indoor growing operation.
Being able to monitor and control your indoor or greenhouse facility is crucial for consistent and desired results. These systems are a huge benefit to all crop types, including cannabis, and can be adjusted to fit your cultivation style and desired outcomes. Not only will you be able to more accurately track and monitor your crop’s progress, but you can then take that learning and replicate it or improve upon it for your next growth cycle.
The Benefits
Grow room controllers offer you complete control and oversight of your crop. Any environmental aspect that you wish to control can be monitored and adjusted with a grow room control system. More advanced systems offer automation for your whole system, allowing you to pull yourself out of the weeds (pun intended) of trying to control everything manually. Grow room controllers are also scalable, especially if you purchase a setup with that in mind, allowing you to expand your facility but keep the same environmental parameters and automation.
All greenhouse and indoor growers know that having control over your environment is crucial to achieving desired results. This means monitoring and adjusting your lighting, climate, irrigation, and fertigation to ensure consistency, which can be time-consuming. A greenhouse control system does the monitoring and adjusting for you, ensuring all of the environmental controls work together and are adjusted accurately.
With advanced control systems, you can program light preferences for your greenhouse, so if light falls below a certain threshold your lights will adjust and will turn off if it exceeds that threshold. Indoor growing can also benefit from lighting such as timers and spectrum controls. Hydroponic sensors in your medium can tell you if you need to increase or decrease water durations. Ultimately being as efficient as possible with water and electricity, which is both environmentally and economically beneficial.
This monitoring and automation are incredibly cost-effective in the long run for your greenhouse or indoor facility. The more automation you have, the less labor you need to support your cultivation, and labor is one of the most, if not the most costly aspect of a cultivation facility. Grow room and greenhouse control systems can also schedule timers and alarms for preventative maintenance so that your equipment can receive proper downtime, preventing blowouts and loss of productivity.
How to Select a Grow Room Controller
Figure 1 from GroAdvisor Webinar
The above worksheet is an example of how you can select the right grow room controller for your needs. While many focus on cost, it’s also important to take into account which system will integrate with and enhance your facility the most. Take stock of your equipment and current manual system to ensure that your new grow room controller will add value to your operation.
Finding a grow room controller that is right for your facility will help you realize your fullest growth potential. Once you have compared and found a system that can accommodate the environmental controls you’d like to track and automate, all that’s left is the installation. Once the grow room controller is installed and your parameters are set you will no longer have to manually adjust your elements, saving time and labor, which ultimately saves money.
How Square Roots Is Training Next-Gen Farmers During A Pandemic
The average age of the American farmer is 58 years old. If we're going to change the food system, we need to create more pathways for young people to launch successful careers in agriculture
Square Roots
10.08.20
The average age of the American farmer is 58 years old. If we're going to change the food system, we need to create more pathways for young people to launch successful careers in agriculture.
One of the many ways Square Roots invests in the future of farming is through our Next-Gen Farmer Training Program—aimed at new farmers or those at early stages in their careers. Farmers initially join Square Roots as Apprentice Growers. Through our proprietary training methodology—supported by our intuitive technology platform—Apprentice Growers rapidly learn the essential farm skills needed to move into permanent roles on the farm team and accelerate their careers.
We continuously evolve our training program to zero in on the skills and experiences that help employees become the best indoor farmers they can be. Throughout COVID-19, we have been committed to prioritizing people safety and plant safety which has led to changes in our day-to-day farming operations, as well as rewiring our in-flight farmer training programs in May and adapting how we run the Square Roots Next-Gen Farmer Training Program going forward. Also, after several years of training farmers, we’ve listened and learned to what farmers value from their experience at Square Roots and have incorporated that into our program going forward. Read more about what it’s like to be a grower at Square Roots and how the program has evolved:
Individual Pathways
Based on the needs of our farm production teams, apprentices are hired and onboarded, either individually or in pairs, on a rolling basis. By spacing out onboarding and training, our team is able to provide more attention and support to apprentices, allowing them to move more quickly through the training program and into permanent positions on our team. We expect most apprentices will complete their training in three to six months, but each will advance at their own pace.
Foundational Remote Learning
We have moved our training materials onto a virtual learning platform, which houses videos, interactive presentations, animated diagrams, virtual tours, and other types of content that can be brought to life beyond a typical presentation. Since COVID-19 restricts our ability to hold classroom-style learning, online learning can be self-serve, supporting different types of learning styles. It also drives consistency in training and terminology, reducing the burden on managers responsible for administering it.
Intensive ‘Boot-Camp’ Style Farm Immersion
Training for Apprentice Growers is laser focused on the skills required for new farmers to quickly become the best indoor farmers they can be. After the initial foundational onboarding, apprentices will jump into production, and, in parallel, will be equipped with the necessary context and complementary training to support expanded learning and competency much sooner. Apprentices will be supported by our software operating system the Farmer Toolbelt, empowering them to get up to speed much faster, engaging with data, and ultimately helping them become better growers. Throughout the training process, farmers will receive direct supervision by one of our experienced farm team members who will act as their training guide and provide professional and moral support.
Pathway to Permanent Employment at Square Roots
Central to Square Roots is our mission to empower Next-Gen leaders in urban farming, and the Next-Gen Farmer Training Program is one of the most direct ways we do that. The program is designed to bring young people with little or no experience up to speed in our proprietary indoor farms as quickly as possible and on to their careers in indoor farming—acting as an internal training program for permanent full-time employees on the Square Roots farm team.
The Apprentice Grower role is the first step in a career path to indoor farming at Square Roots. To start, apprentices will earn an hourly rate indexed to the area’s living wage, and receive 100% covered health benefits and equity in Square Roots. Once they’ve successfully mastered indoor growing fundamentals (we expect this to take three to six months), apprentices will be eligible to move into Associate Grower positions.
For more information and to learn about new open positions on our farm teams, follow us on social media and sign up for our newsletter for updates.
Tags: Next-Gen Farm / Farmer Training / COVID-19 Response / Updates
AUSTRALIA: VIDEO - Shipping Container Farms: Check Out This Craze In Modified Containers
Greenhouses, hydroponics, and mushroom farms – converted shipping containers can produce protein and vegetables for all your needs
Greenhouses, hydroponics, and mushroom farms – converted shipping containers can produce protein and vegetables for all your needs. Even if you’re not an environmentalist, there are business opportunities to be had in delivering extremely fresh food to people in urban environments like Brisbane. Given the changing climate and topsoil loss we are facing, shipping container farms could well be an answer to these issues.
Over the years in the Gateway Gazette, we have published a number of stories that look at producing food in converted shipping containers. Reflecting on what we have published and looking at the detail of what can be done, let’s consider the possibilities that come with shipping container farms.
Open Top Container Greenhouse
One of the most cost-effective ways of using a shipping container as a food-producing unit is by attaching a glass top to an open-top shipping container.
In this video, Urban Farm Units looked at the concept of a greenhouse-container. An open-top 20-foot container would have a greenhouse attached to the top with shelving units directly under the glass. This allows photosynthesis to take place in the normal way.
Seedlings can be started in the lower part of the unit, which is warmed by the light and heat from the outside.
One step down from slapping a greenhouse on top of an open-top container would be to use a flat rack container and to have the greenhouse on the base (Gateway Containers can supply both open-top and flat rack containers).
The concept is an improvement on the one in the video, as long as you keep the greenhouse within the dimensions of a 20ft standard or high-cube container, it would be possible to lift and move the container farm from place to place.
This might be useful where you have an agreement with property developers or a council to use vacant plots of land in a city for agriculture. When the site is ready to be developed you can stick it all on a truck and move it to the next plot.
The concept of a shipping container greenhouse is:
Cheap to buy
Mobile
And often won’t need planning permission for a permanent site
Could this be something you’d consider? Contact us at Gateway Containers to discuss your needs!
Mushie Container Farm!
Image source: King Oyster Mushrooms Facebook
In 2019 we reported how Belgrave, Vic-based John Ford has developed a shipping container mushroom farm. This could produce protein for people as an alternative to meat or for anyone who loves the taste of freshly cut shrooms.
Mushrooms of any kind don’t store well and are best eaten as soon as possible after cutting. This is why having a mushroom farm close to restaurants could be a money-spinner.
This requires no modification from a basic shipping container, you could even install the racking inside the container yourself.
In their lifecycle, mushroom mycelium live out of sight of the world until they are stressed and get the impression that they are facing death. When stressed they flower to produce spores – those flowers are the mushrooms that many of us love to eat.
A shipping container is perfect to take advantage of such a lifecycle. Logs or other media are infected with the mycelium and left to rot for a certain time. By altering the environmental conditions, so you deliberately stress the fungi and they flower.
In our article, we reported how John Ford is producing mushroom species that are famed for their delicate taste but don’t travel well at all – shiitake and oyster mushrooms. As a sideline to his main income as a marine biologist restoring seagrass habitats near Belgrave, he produces freshly cut shrooms for local people and restaurants.
For you as an entrepreneur, mushroom growing would require buying a used shipping container and setting it up as a mushroom farm. If you are planning an urban mushroom container farm, you can take advantage of the fact that you can treat the container as a mobile unit and not as a permanent base. Shipping containers are also pretty inexpensive to buy and convert.
Hydroponics – The Rolls Royce of Shipping Container Farms
Image source: ABC
The hydroponics concept is highly developed for the use of fresh food and can be set up for high density vegetable farming in shipping containers. This requires a fair bit more modification than the two systems we describe above.
Unlike the Urban Farm Units company, several companies have managed to survive over the years selling their hydroponic container farm businesses to entrepreneurs and restaurants around the world.
Modular Farms is a company we featured in our blog originally based in Canada, but who recently set up shop over here in Australia. According to their website, they “design and manufacture container farm systems that can be used to grow food in most locations on earth.”
These systems strive to get around some of the issues we face here. Cities like Brisbane get far too much water sometimes and then face droughts for years on end. The Australian Food Services News reported, “With a focus on sustainability, Modular Farms’s hydroponic, closed-loop system uses 95% less water than a typical outdoor farm.”
Topsoil erosion is a problem, especially in prolonged droughts when it gets blown away as dust. Hydroponics use media like rock wool and even used mattresses to house the plants’ root systems and feed them nutrients via a watering system.
With our ever more extreme climate, food often has to be imported into cities from hundreds or thousands of miles away. A hydroponic container farm can enable you to grow many vegs very close to markets and restaurants.
This has been observed by global homewares retail giant IKEA, which in 2019 announced it was piloting growing vegetables in its stores for use at its restaurants. We reported, “While selling hydroponic indoor growing equipment to customers, IKEA is feeding its staff with lettuce and other vegetables grown in a container outside its Malmö and Helsingborg stores.”
Image source: ABC
There are a few downsides to hydroponics. Firstly, while some types of plants are happy enough growing in hydroponics – the simpler ones producing leaves and flowers (like broccoli!) – others aren’t so happy, such as cassava, wheat, and potatoes.
The next big issue is that for a high-intensity farm, not unlike factory farming chickens, you need to be ultra-clean in your production as the arrival of a destructive disease or fungus could wipe you out very quickly.
Container Fish Farm Too?
In theory, it is possible to run a fish farm connected to the hydroponics container farm, with you largely feeding the fish and collecting their feces and other waste to feed the plants. The plants would clean the fishes’ water and make it habitable for them as reed beds do in nature. This a concept that is in development but hasn’t caught on commercially yet.
How Can Gateway Containers Help?
We can provide and convert an insulated container for you to get started with and advise you how to best make further additions without compromising the overall structure.
If any or all of these ideas have caught your interest – or you just know about these concepts and need a shipping container to make it possible – then get in touch with us today to discuss your needs!
Posted on February 22, 2021
By Mark FinneganOtherShipping ContainerModified Shipping ContainersLeave a comment
FRANCE: How To Grow Food In A Concrete Jungle
Building flourishing farms in the heart of cities used to be just a utopian fantasy. Now it's an important step towards developing a smart, diversified food system capable of feeding a growing world population
22-03-2021 | BBC
FRANCE - Building flourishing farms in the heart of cities used to be just a utopian fantasy. Now it's an important step towards developing a smart, diversified food system capable of feeding a growing world population. Guillaume Fourdinier has lived in Paris for six years, but he still misses the taste of the fresh cereal grains, beets, carrots, and more that grow on his family's farm in Verton. There, in northern France's countryside, eating locally is a way of life – not simply a trend or a sticker on an apple at the grocery store.
“Local food is everywhere when you are in the countryside. You get fruits and vegetables with better taste, more nutritional value,” he says. “When you are in Paris, what is local food? There is nothing coming from a local farm. I think for quality of life for people living in big cities this is a big problem.”
In 2015, Fourdinier co-founded Agricool, an urban farm that's now comprised of 11 recycled shipping containers on the north side of the city. Eight farmers plant, harvest, pack, and deliver the pesticide-free lettuces, herbs, and strawberries to 60 supermarkets (though Fourdinier expects that number to grow to at least 200 retailers by the end of 2021).
Urban farms like Agricool are part of a broad collection of metropolitan agricultural efforts including everything from vertical farms to greenhouses to aquaponics to community gardens. The idea of cultivating food in or near cities is not new (see the victory gardens of both world wars, for example), but these ventures have become increasingly popular in recent years as the local food movement strengthens. After the rise of the supermarkets led many people to feel disconnected from food production, consumers are again paying more attention to how and where their food is grown, along with how far ingredients must travel between field and plate.
From Brussels to Nigeria, entrepreneurs and farmers are reimagining what farms are and conceiving innovative technology to help grow food in smaller spaces and in more sustainable ways. They're attempting to fix existing food supply chain concerns, which we've all became intimately familiar with in the past year. Images of picked-over grocery shelves and farmers tossing out produce early in the Covid-19 pandemic broadcast the failures and fragility of our current systems.
Click here to read the full article.
Photo Courtesy of BBC
Providing A Sustainable Growing Solution For Farmers, Using Renewable Energy in Container Farming
Recently, Freight Farms and Arcadia have partnered to provide Freight Farms' U.S. customers with access to clean energy for their everyday operations
“The past year has really proved our proposition as it has never been proven before,” says Rick Vanzura, CEO at FreightFarms. “The pandemic put a huge focus on supply chain security, local food access, and how to handle disruption to a supply chain, and we saw that having a modular farming solution that can be put next to people where they need food fits in perfectly. Some segments have suffered, while our farms have proven to be a great solution.” The company has seen demand going up, with 2020 being a record year: Freight Farms tripled revenue versus the prior year and set a record for orders.
Recently, Freight Farms and Arcadia have partnered to provide Freight Farms' U.S. customers with access to clean energy for their everyday operations. With this partnership, Freight Farms and Arcadia are taking strides to align their respective industries, moving indoor farming into a more sustainable future. Freight Farms’ customers can now connect the utility for their container farm to Arcadia to match 100% of the farm’s electrical usage with clean energy.
Tackling sustainability pillars
“We already have a number of current farmers that have signed up with the Arcadia energy offering. It was a really important milestone for us as sustainability has been a core mission since the founding of the company.” Rick identifies the sustainability pillars in farming as soil conservation, water conservation, food miles, and energy usage. “At Freight Farms, we have always performed very strongly in the first three categories. Our farms have no effect on soil; they use very little water (5 gallons/day, or 19 L/day), and they reduce food miles significantly, sometimes to zero. What remained for us to solve and why the Arcadia partnership is so crucial is energy,” Rick notes.
Before the Arcadia partnership, energy was the only unsolved part of the sustainability pillars Freight Farms hadn’t tackled yet. The recent partnership has given access to clean energy to all small business farmers. “With the presence of clean energy, we believe there hasn’t been a more sustainable farming solution similar to this one before.
Freight Farms looks at sustainability through the triangle of labor, yield, and power. They are increasing the output per unit of input. According to Rick, Freight Farms is far down the road in the development of greater efficiencies in their farms, focusing on optimizing for yield per unit of power and continuing to research renewable energy options. Rick says that “Everybody’s success is a collective success as we’re all relying on the industry as a whole... We’re all bound by this mission to create a more sustainable planet. Therefore, anything we can do in our own small way, we’re ready to do.”
Improving farm efficiency
On the product side, the company is doing updates to everything. “We made our farms more efficient, delivering value in several aspects, working on different renewable energy in all forms. The ROI has never been better than this farm, because of the intersection of output and efficiency gains. As we’re big believers in helping the industry as a whole for good, our ultimate goal is to be NET zero ultimately.”
While Freight Farms customers already span 46 U.S. states and 32 countries, Rick believes that the company will expand into more locations this year. This growth is stimulated by recent investment and team expansion. “By the end of 2021, we’re expecting to be in every US state and several other countries. Ospraie Ag Science led our last fundraising round, where they invested heavily in our ability to do research. Therefore, we’ve added lots of strength to the team over the last year.”
Collaborations
As a plug of vertical farming, Freight Farms is collaborating with MIT sustainability lab students together on a project. The project is about working in conjunction with the government, and public- and private partnerships around sustainability. “The goal is to be part of something where brilliant people are willing to donate their time and energy. This is just one example of many where people want to pitch in and help as we all want to have a more sustainable planet,” Rick notes.
“We’re not trying to solve for renewable energy on a location by location basis. That would be the route to go with today, but it’s a solution limited to the United States as of now,” Rick affirms. Freight Farms is always on the lookout for partners worldwide where its services can be made available.
For more information:
Rick Vanzura, CEO
Freight Farms
+1 877 687 4326
info@freightfarms.com
www.freightfarms.com
Publication date: Wed 17 Mar 2021
Author: Rebekka Boekhout
© VerticalFarmDaily.com
Eeden Farms Sees Phenomenal Market Response To Pioneering Concept
Lincoln Deal II, the founder of Eeden Farms, said: “The response has been phenomenal. Most days, we are combing growing and facilitating tours because the interest level is so high among restaurants and hotels
An Eeden Farms worker plants seeds for a sustainable future. (PHOTO: EEDEN FARMS)
NASSAU, BAHAMAS — A tech-enabled containerized farming company has seen a “phenomenal” response to its offering, according to its founder, who told Eyewitness News “the demand is definitely there”.
Lincoln Deal II, the founder of Eeden Farms, said: “The response has been phenomenal. Most days, we are combing growing and facilitating tours because the interest level is so high among restaurants and hotels.
Lincoln Deal II.
“A lot of the restaurants and hotels are enamored by how fresh the produce is, that they can get it farm-to-table and it’s Bahamian. The demand is definitely there.”
Eeden Farms, located in the BRON Business Centre, Airport Industrial Park, officially launched back in February.
The company currently utilizes three repurposed shipping containers equivalent to 15 acres of farmland and offers fresh organic produce year-round. Its farm system was created by Boston-based Freight Farms, the world’s leading manufacturer of container farm technology.
Deal defended the containerized farming concept, noting that Eeden Farms is the first company to have Freight Farm’s newest model of containerized farms.
“The technology that we are utilizing has never been used here before,” said Deal.
“We are the pioneers of this technology here in The Bahamas despite what misinformation may put out there. We were the first to receive this model from Freight Farms and they own the patent on this particular technology.”
Caroline Katsiroubas, director of marketing and community relations at Freight Farms, told Eyewitness News: “Eeden Farms represents the first entry of our technology into that region and that market. It began in 2020 but the journey didn’t start there. We have been working with him (Deal) for quite a few years, having first met at a conference in 2016.
“We’re in 32 countries right now. In terms of who our client base is, we have a very diverse kind of network of people who are interested in operating the system and it has infinite applications.”
Tags Always a headline ahead, Bahamas news, ewnews, ewnews.com, Eyewitness News, Eyewitness News Online, Nassau Bahamas, www.ewnews.com
About Natario McKenzie
View all posts by Natario McKenzie →
Lead photo: Eeden Farms. (BIS PHOTO/KRISTAAN INGRAHAM)
VIDEO: Inside A Shipping Container Vertical Farm
New farming models are cropping up around the world, including in Sydney, where Sprout Stack is transforming old shipping containers into commercial vertical farms
March 17, 2021
New farming models are cropping up around the world, including in Sydney, where Sprout Stack is transforming old shipping containers into commercial vertical farms.
With lighting in the containers designed to optimize plant growth, and sensors measuring temperature, humidity, and carbon dioxide, the approach is more productive than traditional farming — and uses 95 percent less water.