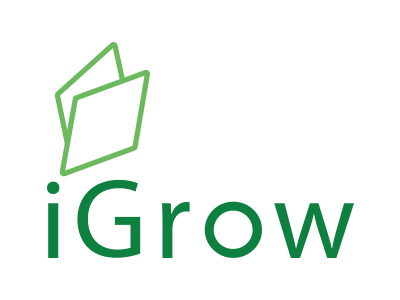
Welcome to iGrow News, Your Source for the World of Indoor Vertical Farming
‘Greenhouse Of The Future’ With Special Solar Glass Coming To Netherlands
‘Greenhouse Of The Future’ With Special Solar Glass Coming To Netherlands
A ‘Greenhouse of the Future’ will soon be built on the Floriade site in Venlo. The greenhouse, made possible with various subsidies, will be energy and CO2 neutral and can even generate energy. To achieve this, the latest technological innovations in the field of Het Nieuwe Telen (Next Generation Cultivation) such as Air & Energy and LED systems are combined with Dye-Sensitized Solar Cells (DSSC) nanotechnology.
The greenhouse, a prototype covering a total of 1200 m2, will be built by Maurice Kassenbouw. Michel La Crois, director at Maurice Kassenbouw: "All designs are ready, and we only have to wait for the special glass in the right dimensions."
Solar panel
The special glass has been developed by Brite Solar Technologies from Greece. Nick Kanopoulos, the man behind Brite Solar Technologies: "The glass we make has a special, transparent coating that transmits 70 to 75 percent of light in the frequencies that are important for photosynthesis. The glass also features special stripes, similar to what you seen in the rear window of a car. These are solar cells that generate energy from sunlight, so the glass actually functions as a solar panel. An additional advantage is that the glass also has improved insulating properties, so less energy is needed to heat the greenhouse. "
Energy gain
In Greece the glass has already been tested on a small scale on a 100 m2 greenhouse. Many growers feared that the glass letting through less light would have a negative effect on crop yield, but this turned out to not be true in those tests. There were as many kilograms from the test greenhouse in Greece as from comparable greenhouses without special glass. In addition, the glass also generated an energy gain of 5,400 kilowatt hours per year during the test.
The glass will larger on the Dutch prototype greenhouse. Where the glass panels in Greece measured 50 x 50 cm, they will now be 1 x 1.2 m. The results of the project will be closely monitored by Brite Solar Technologies, both remotely and by people on the ground. Nick: "All kinds of sensors will be placed in the greenhouse, so that we can monitor the results from anywhere in the world."
Self-sufficient
Although the first prototype has not even been built yet, Maurice Kassenbouw already has a second project lined up for another two hectares. However, they need to wait on the results of the first greenhouse. "In the south of Europe in particular, I expect a high energy yield. There is already interest in this type of greenhouse in Dubai, and we expect that we will soon be able to build these types of greenhouses on a large scale."
The glass is now 6 mm thick, but in order to be able to replace existing glass in existing greenhouses, they are working on glass with the conventional thickness of 4 mm.
Ultimately, the goal is for these greenhouses to be self-sufficient in terms of energy and to be a solution to the problem of food scarcity. Michel: "The question that we are jointly facing is: how are we going to feed nine billion people by 2050?"
European innovation program
The construction of the greenhouse is part of the European Innovation Program Southern Netherlands (PROJ-01061).
For more information:
Brite Solar Technologies
www.britesolar.com
info@britesolar.com
Maurice Kassenbouw
www.kassenbouw.com
maurice@kassenbouw.com
Publication date: 5/2/2018
Largest Rooftop Solar Project In Nation To Begin Soon At Stuyvesant Town-Peter Cooper Village
The 3.8-megawatt solar energy system will span across the property’s 22 acres of rooftops. Once completed, the rooftop solar project at Stuyvesant Town-Peter Cooper Village will triple Manhattan’s current solar generation capacity.
Largest Rooftop Solar Project In Nation To Begin Soon At Stuyvesant Town-Peter Cooper Village
NOVEMBER 9, 2017 | BY JOHN JORDAN
The 3.8-megawatt solar energy system will span across the property’s 22 acres of rooftops. Once completed, the rooftop solar project at Stuyvesant Town-Peter Cooper Village will triple Manhattan’s current solar generation capacity.
A rendering of the rooftop solar project at Stuyvesant Town and Peter Cooper Village. Photo courtesy of Stuy Town Property Services.
NEW YORK CITY—Work will begin this winter on what has been described as the largest private multifamily rooftop solar project in the United States at the Stuyvesant Town-Peter Cooper Village here.
Owner Blackstone and Ivanhoe Cambridge announced the launch of the project that will be run by StuyTown Property Services, the property management company of the more than 11,200-unit Stuyvesant Town and Peter Cooper Village complex. A representative of the ownership tells Globest.com that the rooftop solar project’s cost will be approximately $10 million.
The 3.8-megawatt solar energy system will span across the property’s 22 acres of rooftops. Once completed, the rooftop solar project at Stuyvesant Town-Peter Cooper Village will triple Manhattan’s current solar generation capacity. New York City-based renewable energy developer Onyx Renewable Partners is the project developer for the installation. The project is expected to be completed in 2019. Stuyvesant Town-Peter Cooper Village is the largest private rental apartment complex in the U.S., with more than 11,200 multifamily units and houses more than 27,000 residents in 56 buildings across 80 acres in Manhattan’s East Village.
“We are incredibly proud of the long-term partnership we are building with the StuyTown community,” says Nadeem Meghji, head of real estate Americas at Blackstone. “In 2015 we made a commitment to preserve StuyTown’s unique heritage and be responsible stewards of its future. This innovative solar project is one of many initiatives we designed and implemented to make the community more sustainable and environmentally friendly.”
The installation will consist of 9,671 high-efficiency solar panels and will generate enough energy to power more than 1,000 New York City apartments annually. The project is expected to offset approximately 63,000 tons of carbon dioxide emissions, which is comparable to removing 12,000 cars from the road for a year, Stuyvesant Town officials state.
“Working to make communities more sustainable underpins many of our business decisions. We are especially proud of this initiative and congratulate our partners Blackstone and the team at SPS. Stuyvesant Town Peter Cooper Village is a very special place and continues to be a leader in New York City,” says Daniel Fournier, chairman, and CEO, Ivanhoé Cambridge.
Previous energy-saving initiatives have earned Stuyvesant Town-Peter Cooper Village an ENERGY STAR certification three years in a row for its energy management technologies. Other sustainable initiatives at the property have included the installation of LED lighting, high-efficiency hot water heat exchangers, elevator shaft louvers to minimize heat loss and domestic water flow control valves, as well as incorporating the use of a centralized building management system to control steam heating distribution and manage all of its sustainable initiatives.
The development’s compost waste pickup is averaging a little over 10,000 pounds of organic material collected weekly, which represents 17% of all residential compost waste collected in Manhattan. Stuyvesant Town-Peter Cooper Village has also reduced on-site greenhouse gas emissions by 10% since 2007, which will be increased once the solar rooftop project is complete.
John Jordan
John Jordan is a veteran journalist with more than 30 years experience in newspaper and web publishing. He is a contributing writer for Real Estate Forum and GlobeSt.com. johnjord@aol.com
Startup Iron Ox Mixes Robotics and Hydroponics to Futurize Farming
Silicon Valley-based startup Iron Ox is utilizing autonomous robotics to fundamentally change the nature of greenhouse-based agriculture. While the exterior of the Iron Ox greenhouse in San Carlos, California is far from remarkable, the cost-cutting integration of hydroponics, solar energy, robotics, and space-conscious farming is more than noteworthy.
Startup Iron Ox Mixes Robotics and Hydroponics to Futurize Farming
Photo Credit: Jirakan Jiherb/123RF
Silicon Valley-based startup Iron Ox is utilizing autonomous robotics to fundamentally change the nature of greenhouse-based agriculture. While the exterior of the Iron Ox greenhouse in San Carlos, California is far from remarkable, the cost-cutting integration of hydroponics, solar energy, robotics, and space-conscious farming is more than noteworthy.
Iron Ox
By using autonomous robots to plant, seed, water, and even harvest their hydroponically grown crops, Iron Ox’s system provides uniformity and rapidity which conventional, human-centric farming methods can’t match. Iron Ox greenhouses’ daily harvesting and proximity to urban centers, grocery stores and produce suppliers diminishes the nutrient loss and often bland taste which results from produce being shipped hundreds or thousands of miles from farm to store.
Founders Brandon Alexander, a former Google X engineer and John Binney, who holds a PhD in robotics, check all the boxes when it comes to consumer demand for non-GMO, pesticide-free produce. Alexander, Iron Ox’s CEO, is uniquely qualified as the leader of this farming revolution. His work on Google’s Project Wing included exploring and implementing ways for autonomous robots to work in combination. With the proper technology in place, Alexander estimates that set-up of one of Iron Ox’s urban greenhouses takes only three to four months, on average.
Luiz Ribeiro Ribeiro/123RF
The master plan is to expand Iron Ox greenhouses manned by autonomous robot-farmers to as many American cities as possible, providing a fresher, potentially cheaper source of produce that traditional farms located far from these cities would be hard-pressed to compete with. Consider that, according to Alexander, a single square-acre Iron Ox greenhouse can match the annual yield of 30 acres of traditional farmland. It also stands to reason that the products created in these robotic greenhouses are less vulnerable to insects and parasites, eliminating the need to use harmful chemicals used to protect outdoor-grown crops.
Like so many industries that have long been a staple of the American and world economies, the application of robotic technology in agriculture will likely mean a drastic shift away from dependence on human labor. The proliferation of companies like Iron Ox carries clear benefits, but it will almost certainly mean structural unemployment for those who depend on traditional means of agriculture as a livelihood. That said, it’s not a matter of if, but a matter of when we see this shift toward autonomous greenhouse farming on a mass scale.
Solar Greenhouses Generate electricity and Grow Crops at The Same time, UC Santa Cruz Study Reveals
Electricity-generating solar greenhouses are outfitted with transparent roof panels embedded with magenta luminescent dye that absorbs light and transfers energy to narrow photovoltaic strips, where electricity is produced. A new study shows that this novel technology, which has the potential to take greenhouses offline, didn't interfere with plant growth or production.
Plants grown in this "smart" greenhouse fared as well or better than plants grown in conventional greenhouses. (Photo by Nick Gonzales)
The first crops of tomatoes and cucumbers grown inside electricity-generating solar greenhouses were as healthy as those raised in conventional greenhouses, signaling that "smart" greenhouses hold great promise for dual-use farming and renewable electricity production.
"Plants are sensitive not just to the intensity of light but also to color," says Michael Loik. "But it turns out the plants grow just as well."(Photo by Nick Gonzales)
"We have demonstrated that 'smart greenhouses' can capture solar energy for electricity without reducing plant growth, which is pretty exciting," said Michael Loik, professor of environmental studies at the University of California, Santa Cruz, and lead author on a paper that appears in the current issue of the American Geophysical Union's journal Earth's Future.
Electricity-generating solar greenhouses utilize Wavelength-Selective Photovoltaic Systems (WSPVs), a novel technology that generates electricity more efficiently and at less cost than traditional photovoltaic systems. These greenhouses are outfitted with transparent roof panels embedded with a bright magenta luminescent dye that absorbs light and transfers energy to narrow photovoltaic strips, where electricity is produced. WSPVs absorb some of the blue and green wavelengths of light but let the rest through, allowing the plants to grow. WSPV technology was developed by coauthors Sue Carter and Glenn Alers, both professors of physics at UC Santa Cruz, who founded Soliculture in 2012 to bring the technology to market.
Loik's team monitored photosynthesis and fruit production across 20 varieties of tomatoes, cucumbers, lemons, limes, peppers, strawberries, and basil grown in magenta glasshouses at two locations on campus and one in Watsonville, California.
"Eighty percent of the plants weren’t affected, while 20 percent actually grew better under the magenta windows," said Loik. Tomatoes and cucumbers are among the top greenhouse-produced crops worldwide, he said.
In additional experiments, small water savings were associated with tomato photosynthesis inside the magenta glasshouses. "Plants required 5 percent less water to grow the same amount as in more conventional glasshouses," he said.
"I thought the plants would grow more slowly, because it's darker under these pink panels. The color of the light makes it like being on the Red Planet," said Loik. "Plants are sensitive not just to the intensity of light but also to color. But it turns out the plants grow just as well."
Reducing the energy consumed by greenhouses has become a priority as the global use of greenhouses for food production has increased six-fold over the past 20 years to more than 9 million acres today—roughly twice the size of New Jersey, according to Loik. "It's big and getting bigger," he said. "Canada relies heavily on greenhouses for vegetable production, and their use is growing in China, too." Plastic greenhouses are becoming popular for small-scale commercial farming, as well as for household food production, he added.
Greenhouses use electricity to control temperature and power fans, lights, and other monitoring systems. "This technology has the potential to take greenhouses offline," said Loik, who specializes in climate change, plant physiology, water resources, and sustainable technologies. Cost per panel of WSPV technology is 65 cents per watt—about 40 percent less than the per-watt cost of traditional silicon-based photovoltaic cells.
"If greenhouses generate electricity on site, that reduces the need for an outside source, which helps lower greenhouse gas emissions even more," said Loik. "We're moving toward self-sustaining greenhouses."
Additional coauthors include Catherine Wade, who participated as a graduate student, Carley Corrado, who participated as a postdoctoral researcher, and undergraduates David Shugar and Devin Jokerst, all of UC Santa Cruz; and Carol Kitayama, senior grower at Kitayama Brothers Growers.
Amazon’s Seattle Campus Is Using Data Center Next Door As A Furnace. It’s Pretty Neat
Using “waste heat” from digital infrastructure to stay warm downtown.
Amazon’s Seattle Campus Is Using A Data Center Next Door As A Furnace. It’s Pretty Neat
Using “waste heat” from digital infrastructure to stay warm downtown.
Updated by David Roberts@drvoxdavid@vox.com Nov 22, 2017
The hippest new technology: big pipes carrying hot water. Jordan Stead/Amazon
Retail giant Amazon has a rather mixed reputation among progressives, to say the least. There are ongoing debates about its labor practices and its ruthless competitive tactics, which have driven competitor after competitor out of business. Among environmentalists, opinion is also divided — some argue that online shopping (and shipping) has accelerated wasteful consumer culture, others that it has reduced the carbon footprint of shopping that was going to happen anyway.
Putting those broader disputes aside, there is one area where the company is making substantial and undeniable progress. After years of what could charitably be called benign neglect, Amazon has recently moved aggressively toward corporate sustainability.
It plans to have 15 rooftop solar systems, with a total capacity of around 41 MW, deployed atop fulfillment centers by the end of this year, with plans to have 50 such systems installed by 2020.
Amazon was the lead corporate purchaser of green energy in 2016. That year, it also announced its largest wind energy project to date, the 253 MW Amazon Wind Farm Texas. Overall, the company says, it has “announced or commenced construction on wind and solar projects that will generate a total of 3.6 million megawatt hours (MWh) of renewable energy annually.”
(Of particular interest to Vox nerds: The company also signed on to an amicus brief in support of Clean Power Plan, Obama’s signature climate policy, which the Trump administration wants to kill.)
But what recently caught my eye is the clever way that Amazon’s giant new campus in downtown Seattle will keep its occupants warm in the winter — a pleasingly low-tech solution that sits squarely at the intersection of several of my enduring obsessions: the importance of smart design, the benefits of urban density, and the need for electrification of the power system.
Juicy! Let’s take a look.
Hot water is so hot right now
Amazon is building a giant four-block campus in downtown Seattle’s Denny Triangle, which will eventually encompass five towers and five million square feet. This schematic is fromGeekwire (which has its own excellent story on Amazon’s project).
That’s a lot of space to heat during the dreary Pacific Northwest winters.
Good fortune! Just across 6th Avenue from Doppler Tower is the 34-story Westin Building Exchange, a regional telecom “carrier hotel” that houses computer and server hardware for some 250 telecom and internet companies. About 70 percent of the building is occupied by data centers.
All that hardware creates an enormous amount of heat. Lacking any better options, Westin has been venting that heat into the Seattle air, through giant cooling towers, at considerable expense.
Waste heat, meet heat consumer.
Amazon and the co-owners of the Westin — Seattle’s Clise Properties and San Francisco’s Digital Realty Trust — struck a deal: Amazon would buy some of the Westin’s waste heat.
As winter approaches, an innovative heat source will be keeping our Seattle headquarters warm. #greenenergyhttp://amzn.to/2j2t8pI
The technology is impressive at this scale, but conceptually, it’s pretty simple. Water circulates in PVC pipes throughout the Westin, gathering heat. It is then sent beneath the street (city waivers had to be granted to cross public rights of way, a huge problem for waste-heat projects historically) to Doppler tower.
Beneath Doppler, a series of large heat exchangers run the Westin’s warm water next to cool water from Amazon, heating it up (exchanging the heat). That warmed water is around 65 degrees, so it is run through a series of five heat-reclaiming chillers to raise the temperature to 130 degrees (also reducing the volume of water).
Amazon’s five big chillers, chilling.
That hot water is then circulated beneath the floors of the campus buildings via radiant heating systems, providing more than three-quarters of the heating required by the campus, at about four times the energy efficiency of a comparable HVAC system.
The cooled water then returns to the basement to gather more heat, and lo, the cycle continues.
Westin’s building manager told the Seattle Times that the building generates the heat equivalent of about 11 megawatts per day. During winter, Amazon will siphon off about 5 megawatts of that.
In effect, Westin is replacing Amazon’s need for natural gas boilers to heat the water, which would have run close to a million dollars annually in fuel and maintenance costs. Another way of looking at it: the system will allow Amazon to avoid the purchase of some 4 million kilowatt-hours of electricity a year.
What’s more, the data center is a rock-solid, reliable source of heat; it is guaranteed to always be running (unless the grid goes down). Amazon has a couple of efficient natural gas boilers for backup, but at least over the past two winters, it says they have rarely been run.
In exchange, during the winter, Amazon’s campus is serving as a giant cooling tower for the Westin, substantially reducing its cooling bill — and paying for the privilege.
It is, to risk cliché, a win-win.
To pull all this off, Amazon and Clise had to create an “ecodistrict” (navigating a thicket of city bureaucracy). The coolest part is that there’s lots more heat to use, so there’s no reason the district couldn’t be extended to more Amazon buildings, or to surrounding buildings.
An aerial view of Amazon’s Doppler Tower and Meeting Center (with its green roof). Note the “biospheres,” which will be filled with plants. (Amazon)
Old technology with intriguing new applications
There’s nothing new about “district heating” — i.e., heating multiple buildings using a single source and a network of pipes. The concept dates all the way back to the Roman Empire. In the Industrial Era, such systems were frequently used to exploit the heat from small in-city power plants. A number of modern cities, from Paris to Tokyo to Vancouver, BC, have district heating systems in use today, fueled by everything from biomass to sewer water to solid waste incineration.
What is somewhat novel about Amazon’s arrangement is the use of an electricity consumer — a data center — as the heat source. (Waste heat from data centers is used in other places, though Amazon says this is the first contract between a data center and a heat consumer with different owners.)
As I mentioned, this sits right at the intersection of three of my enduring obsessions.
First, it represents enormous energy savings with relatively old and reliable technology — it’s just water run through pipes. What produced the savings was not some whiz-bang tech innovation, but simple design. Cities produce enormous amounts of waste heat and then import enormous amounts of energy to warm themselves. It’s kinda crazy. Smarter design could help close that loop, reducing the need for imports, reducing emissions, and bringing more of a city’s energy management under its own control.
Second, along the same lines: cities! Cities are everything this century. State, provincial, and national governments are often captured by rural or corporate interests, creating substantial status quo bias. In cities, however, constant change is a fact of life and governments are at least somewhat more nimble — and that’s especially true when it comes to experimentation and innovation around the clean-energy transition. The more cities can generate and manage their own energy, the less hostage they are to state and national policy shifts.
With that in mind, why not bring more highly energy-intensive operations — not just data centers, but, oh, indoor farms, or marijuana grow operations — into dense urban areas? They have traditionally been built in the hinterlands, where land and power are cheap, but if they could make a substantial second income selling their waste heat, they might be able to justify urban locations.
That would reduce shipping supply lines. It would bring tax-paying, profit-making industrial facilities that don’t pollute into urban boundaries and budgets. It could potentially reduce urban HVAC bills, if the facilities are hooked up to district heating systems. And it would give cities more direct control over their energy fate.
Indoor farming generates lots of waste heat. Plenty
Third: Amazon explicitly decided against an electricity-based heating system, instead opting for hydroponic (fluid-circulating) system, which must draw on local sources of heat. Is this an exception to my “electrify everything” mantra?
Yes and no. Mostly no. The key difference here is that the local source of heat is itself electrical — a data center. So in that sense, Amazon is using electricity for heat. In fact, it is helping Seattle use its electricity more efficiently, getting more work out of the same kWh.
The expert community is divided on the possibility, or advisability, of moving all HVAC to electricity (like heat pumps). It would require an enormous amount of capital and produce an enormous new electricity load. Limitations on both probably mean that we’ll need zero-carbon HVAC alternatives that still draw on heated water or combusted fuel, which can substitute more easily in retrofits of today’s buildings.
Perhaps some of that fuel can itself come from electricity — it is increasingly possible tosynthesize liquid fuels that way. But a great deal of the heated water can come from existing and planned sources of waste heat, preferably drawing on electrical sources.
Making sunlight and CO2 into methane and other liquid fuels. MIT
If electricity is zero carbon, then all subsequent derivatives, from waste heat to synthetic liquid fuels, will be zero carbon as well. That is the magic of clean electricity.
Better design, urban density, and electrification all require far-seeing investment
There’s a telling line in Amazon’s blog post on this project:
Because of the up-front investment to build it, the ecodistrict isn't currently delivering heat that's any cheaper compared to a typical system, according to [Mike Moriarty, the Senior Engineering Manager who leads operations and maintenance for campus], but “the price of electricity is only going to go up.”
This is like so many clean-energy technologies: The upfront investment is high relative to the alternatives, but it pays back many times over throughout its life.
As Amazon adds buildings to the system — and maybe someday, as Seattle expands the system beyond Amazon’s campus — the savings will pile up ever higher, eventually dwarfing the upfront investment.
A robust district energy system could save Seattle money for a hundred years. Again, it’s just pipes with water, a technology that has stood the test of time. All that’s needed is policy coordination and good design.
Whatever its other sins, Amazon has shown itself willing to make patient investments; that’s why it keeps growing but never makes much profit. It invests for the long term.
Almost more than anything, it is that mentality — the willingness to sink upfront investment into long-term savings — that can move corporations (and society) toward sustainability. For that reason alone, I hope this project pays off for Amazon.
And I hope Amazon carries the lesson over to its next headquarters.
Renewable Energy: Smart Greenhouses Generate Solar Power and Grow Crops At The Same Time
Renewable Energy: Smart Greenhouses Generate Solar Power and Grow Crops At The Same Time
BY SYDNEY PEREIRA ON 11/6/17
Tomatoes and cucumbers appear to grow just fine—and just as healthily—in smart, solar-powered greenhouses that capture solar energy for electricity.
Scientists from the University of California, Santa Cruz, have shown how crops can grow as healthily in these new greenhouses as they do in conventional greenhouses.
"Plants are sensitive not just to the intensity of light but also to color," says Michael Loik. "But it turns out the plants grow just as well."(Photo by Nick Gonzales)
"We have demonstrated that 'smart greenhouses' can capture solar energy for electricity without reducing plant growth, which is pretty exciting," Michael Loik, professor of environmental studies at UCSC, said in a press release. Loik is the lead author for the paper, published in the American Geophysical Union's journal Earth's Future.
Solar Power Trapped by a Red Roof
Bright magenta panels cover the tops of the greenhouses, soaking up sunlight and transferring the energy to photovoltaic strips. From there, electricity is produced.
The greenhouses are able to take sunlight for energy and leave the rest, allowing plants to grow using a technology called Wavelength-Selective Photovoltaic Systems (WSPVs). The technology, developed by co-authors Sue Carter and Glenn Alers, is less expensive and more efficient than traditional photovoltaic systems.
The team tested the growth and fruit production across 20 varieties of tomatoes, cucumbers, lemons, limes, peppers, strawberries and basil at two locations at the Santa Cruz campus and one in Watsonville, California. Scientists reported that 80 percent of the plants were unaffected by the slightly darker lighting from the magenta panels, and 20 percent of the crops grew better. Tomato plants needed 5 percent less water under the magenta panels.
Reducing the energy used in greenhouses is crucial since the use of greenhouses to grow food has increased by sixfold in the past 20 years, according to Loik.
Solar-powered greenhouses are one of several developments for new ways of farming in recent years.
Plants grown in the smart greenhouse were just as good as plants grown in conventional greenhouses.NICK GONZALES
Smart Greenhouse Detects Infestations
Another company, NatureSweet, has outfitted its greenhouses in Arizona with artificial intelligence, reported CNN. The plants are monitored with 10 cameras installed in the greenhouse ceilings which continuously take photographs to detect insect infestations or dying plants.
The software, developed by a company called Prospera, recognizes those problem spots and sends feedback 24/7. Previously, reported CNN, NatureSweet's employees walked through the greenhouse in order to spot issues with the plants.
Green roofs are another method of growing food in an attempt to utilize space and close gaps in access to foods in urban areas.
In Washington, D.C., Up Top Acres has opened five urban farms on the rooftops of buildings since 2015, reported Washington City Paper. Green roofs improve storm-water collection, habitat protection and energy preservation, in addition to providing food. The company's co-founder, Kathleen O'Keefe, told the paper that the company may not produce enough food for the city, but green roofs can change the way people think about food, in addition to utilizing unused space.
Future of the Prairie
FUTURE OF THE PRAIRIE
October 11, 2017 at 5:00 am | By DEVIN HEILMAN Staff Writer
LOREN BENOIT/Press From left, Coeur CEO Tom McNabb, Coeur Greens operations manager Kelly Lattin and Innovation Collective founder Nick Smoot pose for a photo in front of house at 1915 E. Mullan Ave in Coeur d’Alene. The house is a prototype for a future sustainable living community in Hayden.
A mixed-use sustainable village destined for Hayden is starting with a little old house in downtown Coeur d'Alene.
Coeur, a company that focuses on sustainable resources including power and food, recently purchased the house at 1915 E. Mullan Ave. to serve as a prototype for a sustainable living community and industrial campus in Hayden. Coeur purchased the 35 acres at the southeast corner of Hayden Avenue and Huetter Road in early 2016 and plans to start construction in the spring.
Coeur CEO Tom McNabb and Innovation Collective founder Nick Smoot, a partner in the project, are using the Mullan house as a demo site for the village.
"It's a simple model to see what we can do for starters," McNabb said Tuesday. "The word ‘sustainability,’ you never really know what it is, but we figure we’d try and figure it out."
Smoot said the community will be built on three core principles: outbound, sustainable and intellectual.
"Most people of this next generation want to live an outbound life in nature and having experiences in their community," Smoot said. "The idea of creating a whole village of people who have that mentality is something that's interesting as a housing development."
The "sustainable" principle is built upon dedication to low-cost, low-impact living where power sources such as wind and solar are maximized, gray water (mostly clean waste water from sinks, baths and kitchen appliances) is recycled, and native landscaping is used. Those involved in the project are researching and working on ways to expand even further into the sustainability aspect.
The third principle is "intellectual," meaning home owner associations and covenants, conditions and restrictions would encourage residents to read books, watch documentaries, help pay for educational guest speakers and otherwise maintain an intellectually stimulated community.
Smoot said he can imagine riding his bike into such a community, parking it at the community bike corral and walking to his house through a neighborhood where community fire pits generate conversation and serve as social gathering places. The houses are small (500 to 1,200 square feet), but provide enough space for their residents, and the community dining hall provides even more opportunities for people to meet and get to know each other.
"It makes me very happy," Smoot said. "That's the kind of place you want to live."
The solar-powered Coeur Technology Campus will be located just west of the village. It will house a solar farm to generate power for schools and public buildings, vertical farms to grow local produce, and a bottling plant to bottle local water at the source. It will also serve as a space where entrepreneurs and forward-thinkers can share ideas and put them into action.
"A lot of people don’t know it, but we have more sun hours per year than Florida,” McNabb said, “Solar, about five years ago, was 2 cents off because the rates for hydropower were cheap, but in the last five years the rates (for hydropower) are going up and the rates of hardware have gone down about 40 percent, so all of a sudden it makes sense.”
The 630-square-foot house on Mullan, built in 1930, would probably have been torn down if it had not been selected for this project. McNabb explained that the original structure will be kept as the inside is remodeled to be a studio-type dwelling that can be rented out on a short-term basis to give people an experience in sustainable living.
Tanks will be installed to recycle the gray water and help with temperature. The roof will be lined with solar panels, and energy-efficient appliances and products will be used, among other forward-thinking alterations that will boost the home's sustainability.
McNabb said a more precise estimate could be given near the house's completion date in the spring, but he believes the cost of giving the house a sustainable makeover will be somewhere around $50,000 or $60,000. About 20 people representing a wide variety of talent and expertise have already expressed interest in contributing to the project, he said.
The community is welcome to attend an open house from 11 a.m. to 1 p.m. Saturday to check it out prior to its sustainable makeover and exchange ideas with those leading the project.
Info: www.coeurllc.com
There’s An Indoor Farm Growing From 2,000 Solar Panels On A South Philly Roof
The farm is the product of Metropolis Farms, a technology company that specializes in creating both indoor and outdoor vertical farming systems. The idea is to give farmers the chance to grow produce year-round, regardless of weather, while also making the technology affordable for any community.
USER @CLIMATEGROUP/TWITTER
Solar energy prices have dropped significantly as the technology figures to assume a key role in the global energy mix of the future.
OCTOBER 04, 2017
There’s An Indoor Farm Growing From 2,000 Solar Panels On A South Philly Roof
It's the only solar-powered indoor farm the world has ever known
SOLAR URBAN FARMING PHILADELPHIA EQUITY TECHNOLOGY FARMING SOUTH PHILADELPHIAURBAN GARDENING
BY MARIELLE MONDON
PhillyVoice Staff
Not far from the South Philly Target, more than 2,000 solar panels cover about 100,000 square feet of roof – creating the only solar-powered indoor farm the world has ever known.
The farm is the product of Metropolis Farms, a technology company that specializes in creating both indoor and outdoor vertical farming systems. The idea is to give farmers the chance to grow produce year-round, regardless of weather, while also making the technology affordable for any community.
According to a post on the company’s blog, the roof’s solar panels will capture enough sunlight to supply more than half a megawatt of energy, allowing the indoor vertical farm just below on the fourth floor to grow what’s equivalent to 660 acres’ worth of crops.
“Before starting this project, the fourth floor of this building was only growing pigeons,” the company’s blog post reads.
“But now, using our innovative technology that can uniquely grow everything, this solar-powered indoor farm will be growing fresh tomatoes, strawberries, lettuce, herbs, broccoli, and other crops for local Philadelphians.”
Metropolis Farms says there are currently about eight acres of urban farmland in Philadelphia, and that's not unique to many other large cities. If more cities have the opportunity to farm locally, the company posits, it will improve the quality of food across all communities, offer fresher meals and help boost local economies.
Metropolis Farms President Jack Griffin is an ex-banker originally from Philly who launched the company early last year, seeing the project as a method of civic engagement for the city.
“Instead of being a customer, we have to become our own supplier,” Griffin told the Philadelphia Citizen in 2016. “That way, we can keep our money moving within our own city.”
In less than two weeks, Philly will host its first-ever Indoor Ag-Con on Oct. 16, a daylong event scheduled to be held at the Pennsylvania Academy of the Fine Arts that will feature presentations from various indoor agricultural professionals, including Griffin.
Solar energy prices have dropped significantly as the technology figures to assume a key role in the global energy mix of the future.
World’s First Solar Powered Indoor Vertical Farm Comes To Philadelphia
World’s First Solar Powered Indoor Vertical Farm Comes To Philadelphia
October 3rd, 2017 by Steve Hanley
It’s always sunny in Philadelphia, according to the title of a popular television show. If so, it’s the perfect place for the world’s first solar powered indoor vertical farm.
Metropolis Farms has constructed a 500 kilowatt solar array made up of 2003 solar panels on the roof of a building in The City of Brotherly Love. On the fourth floor, it is constructing a vertical farm that will be powered entirely by electricity coming from the roof. It plans to grow the equivalent of 660 outdoor acres worth of crops in less than 100,000 sq feet. “The panels are already installed and turned on, now we’re building out the farm. The first crops will be planted in November,” the company says.
Before Metropolis Farms took over the space, the only things growing on the fourth floor were pigeons. But soon, crops of fresh tomatoes, strawberries, lettuce, herbs, and broccoli will flourish there for the benefit of the citizens of Philadelphia and environs. “We feel this inherently demonstrates the wonder of this new industry we’re helping create, the industry of indoor farming.”
The company goes on to say,
“To this point, the city of Philadelphia has only ~8 acres of urban farming, mainly because there’s no available land for growing crops traditionally. By bringing the growing process indoors, in line with our mission of social responsibility, we are revitalizing abandoned spaces and are using them for local food production. We are empowering a new generation of farmers to grow food for cities, in cities.
“This technology democratizes the ability to grow local food in any community, regardless of location or climate. We’re doing this because local food is just better. Local food is more nutritious than food that’s packed in a truck and travels for weeks, it tastes better, and growing food in the communities where it’s eaten helps stimulate the local economy.”
Detractors of indoor farming point out the high cost of powering all the lights and circulation pumps needed, but Metropolis Farms thinks its rooftop solar array will answer the critics.
“The truth is, like any technology, indoor farming is constantly improving upon itself. We have gained efficiencies through innovative lighting (not LEDs), BTU management systems, and other means to dramatically reduce the amount of energy our farms are using.
“And we are on the cusp of a breakthrough in a technology that will reduce our energy usage even further. We hope to demonstrate this new technological advancement at this year’s Indoor Ag-Con, hosted for the first time in Philadelphia. We are pushing the envelope by attempting to build a zero-carbon farm. Through water recapture techniques, renewable energy production, advanced energy systems, and most importantly by farming locally, we are on the right track.”
Another benefit of vertical gardening is a dramatic decrease in the amount of pesticidesneeded to grow fresh food. Not only will the crops not be covered in chemicals, neither will the environment surrounding the vertical garden. That’s a huge benefit that should not be discounted. “We hope others will follow our lead and start building farms of the future, so communities everywhere can benefit from having a quality local food source that grows crops responsibly,” say the leaders of Metropolis Farms.
Property Owners Reap Cost Savings With Green Building
Green infrastructure is an umbrella term for anything that helps manage stormwater naturally and often includes rain gardens, green roofs, cisterns and rainwater recycling.
Property Owners Reap Cost Savings With Green Building
June 27, 2017 | Julie Littman, Bisnow Bay Area
Eco-friendly features are cropping up on buildings around the country. In addition to green roofs and solar panels, private-public partnerships are increasingly building more efficient and cost-effective stormwater systems. And owners are reaping major monetary rewards for their efforts.
ULI The roooftop at Gerling Edlen's Meier Frank building in Portland, Ore.
Green infrastructure is an umbrella term for anything that helps manage stormwater naturally and often includes rain gardens, green roofs, cisterns and rainwater recycling. Stormwater runoff, which often contains oil, grease and fertilizer, is among the most consistent pollutants of local waterways, according to the U.S. National Research Council. With more development in urban areas consisting of concrete and other impervious surfaces, stormwater often has no place to go other than down the local sewage channel. Without mitigation, the stormwater can overflow channels, flooding streets.
With this in mind, local governments are starting to require some kind of green infrastructure within commercial development and are creating coordinated green infrastructure networks that include public and private sites.
The Urban Land Institute, which reviewed several water management and green infrastructure systems in a recent report, found in addition to benefiting the city, green infrastructure is adding value for property owners.
“We found that green infrastructure was capable of creating value,” ULI Senior Director of Urban Resilience Katharine Burgess said. “It created an enhanced user experience, improved placemaking opportunity and improved development yield of land to be used more efficiently.”
These additional amenities, such as green roofs, parks and water features, will often lead to rental increases. A 200-unit apartment complex at 1330 Boylston in Boston garnered an additional $300 to $500/month in rent for units that overlooked the green roof. The green roof cost $113K to build and the extra rent nets $120K/year, according to the ULI report.
Savings Initiative
Courtesy of Katharine Burgess ULI Senior Director, Urban Resilience Katharine Burgess
Partnering with private developers creates a more affordable way for cities to address green infrastructure, which studies show is more cost-effective than implementing graywater infrastructure (where sewage mains and tunnels collect and treat stormwater and sewage before discharging). New York City estimates gray strategy would cost $6.8B compared to a green strategy that would cost $5.3B to implement. Burgess said she expects stormwater management and green infrastructure to become increasingly more prominent until one day it is part of business as usual.
"Real estate developers are taking really effective approaches on requirements or desires to achieve sustainability practices,” Burgess said.
Several developers have already noticed savings in building costs since implementing various green infrastructure.
In 2016, Gerling Edlen was able to harvest rainwater at its 180K SF Meier & Frank building in Portland, Oregon, that met 93% of the building’s non-potable water needs. The company saved more money than it paid the city. Annual savings equaled 107% on the building’s total annual water cost, according to Gerling Edlen Director of Sustainability Renee Loveland. The building owner also uses the stormwater system as a marketing tool with tenants. The renovation benefited from a local green investment fund grant.
This historic building, which is LEED Platinum certified, has an underground rainwater collection tank, a 12K SF green roof, a 112-kilowatt solar array and bioswales at grade.
Retail Owners Follow The Trend
ULI Burbank Water and Power EcoCampus
The retail center Market at Colennade in Raleigh, North Carolina, uses three cisterns and a water reuse system, bioretention swales, an efficient irrigation system and a detention basin as part of its water management system. It is so efficient that of the 30.6 inches of rainfall captured in one year, only 0.6 inches flowed out of the system, according to Regency Centers Vice President of Investments Chris Widmayer.
Among the biggest benefits of this project was its ability to partner with anchor tenant Whole Foods, which uses the cistern to help market the grocery store’s green culture, Widmayer said.
For Burbank Water and Power, the green infrastructure helped attract younger employees to the company's campus, Burgess said. The campus, which was renovated in 2000, operates on 100% recycled water, using green roofs that absorb 70% of rainwater and save the facility about $14K/year, according to ULI’s report.
Eindhoven Unveils Plans For A Solar-Powered City Block With Living Roofs And Urban Farms
Billed as a contemporary and hyper-modern development, Nieuw Bergen will add 29,000 square meters of new development to Eindhoven city center. The sharply angled and turf-covered roofs give the buildings their jagged and eye-catching silhouettes that are both modern in appearance and reference traditional pitched roofs. The 45-degree pitches optimize indoor access to natural light.
Eindhoven Unveils Plans For A Solar-Powered City Block With Living Roofs And Urban Farms
by Lucy Wang
The Dutch city of Eindhoven just selected MVRDV and SDK Vastgoed (VolkerWessels) to create Nieuw Bergen – a super green block of homes and businesses topped with living roofs and solar panels. Located in the inner city area around Deken van Someren Street, the project’s seven buildings will comprise 240 new homes, 1,700 square meters of commercial space, 270 square meters of urban farming, and underground parking.
Billed as a contemporary and hyper-modern development, Nieuw Bergen will add 29,000 square meters of new development to Eindhoven city center. The sharply angled and turf-covered roofs give the buildings their jagged and eye-catching silhouettes that are both modern in appearance and reference traditional pitched roofs. The 45-degree pitches optimize indoor access to natural light.
“Natural light plays a central role in Nieuw Bergen, as volumes follow a strict height limit and a design guideline that allows for the maximum amount of natural sunlight, views, intimacy and reduced visibility from street levels,” says Jacob van Rijs, co-founder of MVRDV. “Pocket parks also ensure a pleasant distribution of greenery throughout the neighborhood and create an intimate atmosphere for all.”
Related: The Sax: MVRDV unveils plans for a ‘vertical city’ in Rotterdam
Each of Nieuw Bergen’s structures is different but collectively form a family of buildings that complement the existing urban fabric. Gardens and greenhouses with lamella roof structures top several buildings. A natural materials palette consisting of stone, wood, and concrete softens the green-roofed development.
Sun Bandit Produces Solar Hot Water In Sub-Zero Temperatures to Heat Dwellings and Grow Fresh Produce North of the Arctic Circle
Sun Bandit Produces Solar Hot Water In Sub-Zero Temperatures to Heat Dwellings and Grow Fresh Produce North of the Arctic Circle
Freeze-Resistant Properties Allow World’s First Certified PV-Powered Solar Water Heating System to Heat Water, Channel Stored Energy to Feed Radiant Wall and Floor Heating and Extend Growing Season for Hydroponically Produced Fresh Vegetables In Sub-Zero Temperatures
The world's first solar hydroponic trailer to grow fresh produce north of the Arctic Circle.
LAFAYETTE, COLORADO (PRWEB) JUNE 23, 2017
Next Generation Energy’s Sun Bandit celebrated the Summer Solstice by shedding light on the first off-grid photovoltaic (PV) solar water heating solution to heat water, channel stored energy into radiant heating and hydroponically grow fresh vegetables in sub-zero temperatures -- NORTH of the Arctic Circle.
Freezing temperatures are no longer a barrier to solar hot water production.
The 26-foot Solar Hydroponic Trailer manifesting this innovation is located in the enterprising village of Kotzebue, Alaska, the hub of 11 Native Alaskan villages in the state’s Northwest Arctic Borough. Kotzebue is 26 miles north of the Arctic Circle, in the Land of the Midnight Sun. It’s an inspiring time to celebrate the power of solar energy -- and Sun Bandit’s expanded solar applications.
The Solar Hydroponic Trailer is the brainchild of Ingemar Mathiasson and solar thermal veteran Mark Houston, founder and CEO of Anchorage-based The Comforts of Home, LLC. A Passive House Institute (PHIUS)-certified* contractor/energy rater, Houston has been advising clients on energy conservation and alternative energy concepts for 30 years.
“For the first time, we can keep the trailer at 74 degrees in sub-zero temperatures, which allows growing to begin as early as March,” said Houston. “We are collecting solar energy, converting it to heat, and running it through a glycol-based radiant floor and wall panel that provides all of the heat we need to grow a bounty of fresh produce in often-dark, bitter-cold conditions for about nine months of the year.”
The project was inspired when Mathiasson, the energy coordinator representing the Inupiat village of Kotzebue, asked Houston to build a sustainable, cost-effective solution to keep a trailer warm enough to grow fresh vegetables throughout the year.
It’s a tall task, as temperatures in Kotzebue swing from a bitter 40 degrees below zero in winter to a chilly 54 degrees Fahrenheit in the summer. Even during the summer, it’s simply not warm enough to sustain a large community garden. With an average daily temperature of 21.8 degrees Fahrenheit, the best ‘vehicle’ to consistently serve the village with fresh produce was a hydroponic trailer.
The desire to grow fresh vegetables in many remote areas of Alaska isn’t new; Alaskans import up to 95% of their food. Houston says there are companies shipping hydroponic growing containers to Alaska, but they’re overly-sophisticated for the market. They have rotating racks and a bevy of bells and whistles. And they use oil, which can run from $6 to $11 a gallon, depending on the location. Not only is oil expensive for many Alaskans (it has to be refined and then delivered by ship or flown to remote villages), it is finite. It can be a long wait for a delivery truck trekking across the tundra to replenish one’s fuel reservoir – or any household goods for that matter.
Kotzebue had tried using oil to heat their hydroponic trailer, but when it came time to ventilate the space to eliminate water vapor emitted by the plants, the ventilation systems (sometimes as rudimentary as simple fans) rid the trailer of moisture, but took the heat as well, fostering less than ideal growing conditions.
To solve the heat loss problem, Houston introduced a Minotair Air Source Heat Pump (ASHP) to remove unwanted moisture and contaminants and replenish the trailer with fresh outdoor air. Before leaving the trailer, the ASHP heats the stale, damp exhausting air to 150 degrees. The heated air blends with fresh incoming air (whose temperatures can be as low as 40 degrees below zero), warming it to 66 degrees Fahrenheit before returning it to the growing area. This is a critical process, as air colder that that would damage or kill the plants.
When village elders got wind of Sun Bandit, they asked Houston to conceive of a cleaner concept using Sun Bandit as the primary heat source. “They didn’t need anything fancy. They just wanted a place they could reliably grow things. And they wanted to heat it without using oil,” Houston said. “Burning oil (and the cash that goes with it) wasn’t working for them.”
By integrating Sun Bandit’s solar electric hybrid water heating and storage solution with hydronic heating hybridized with a Sanden Air Source Heat Pump and air sealing with urethane foam, Houston has delivered a lower cost, oil-free innovation that provides fresh vegetables year-round in a difficult growing climate – and with a reduced carbon footprint.
Seven to eight months of the nine-month Solar Hydroponic Trailer growing season will be supported using free solar hot water and radiant heat from stored Sun Bandit energy. Sun Bandit optimizes energy production with an arsenal of built-in back-up options for days when the sun doesn’t shine. In off-grid situations, Sun Bandit solar hybrid water heaters can be configured with a small wind turbine or battery backup to heat water and – as the Kotzebue project illustrates -- support radiant floor heating and hydroponics. Sun Bandit is equipped to use grid-fed electricity when solar is not available as well. View a detailed slide presentation of Houston’s solution by clicking here.
Sun Bandit was selected for this project because it performs where old-school solar water heating systems can’t, eliminating fluids, leaks, pump stations, overheating, stagnation, freezing and the complicated installation and maintenance issues that can plague traditional mechanical solar water heating systems.
“The exciting takeaway here is that freezing temperatures are no longer a barrier to solar hot water production -- even in extreme conditions,” said Next Generation Energy CEO Dave Kreutzman. See Sun Bandit’s white paper on “Redefining Solar Hot Water Efficiency” by clicking here.
As a small business owner, installer and energy rater, Houston sees the broader market potential for Sun Bandit-centered solar hot water and heating solutions in homes; he's already working with clients eager to begin.
“I’ve been in this business for decades. The Kotzebue project demonstrates that PV-powered Sun Bandit is a much better product to use in colder regions: it’s simple, low-maintenance and it can be installed in one third the time. It’s really the only one that works in the coldest, darkest of climates. And in its solar heating applications, Sun Bandit is four times more efficient than regular electric heat,” Houston said. “At the end of the day --- particularly the longest day of the year -- people don’t want to have to fix things in freezing temperatures. They just want them to work. That is where Sun Bandit shines.”
About Next Generation Energy's Sun Bandit® : Sun Bandit is a trademark-registered, patented product innovation of Colorado-based Next Generation Energy (NGE®), whose expertise in PV, solar thermal and off-grid system design and engineering have been delivering high-performing, money-saving renewable energy solutions to commercial, utility-scale, governmental, individual and multi-family housing interests for over 30 years. Learn more by calling 877-NGE-4SUN – or visit http://www.ngeus.com. Find Sun Bandit at http://www.sunbandit.us.