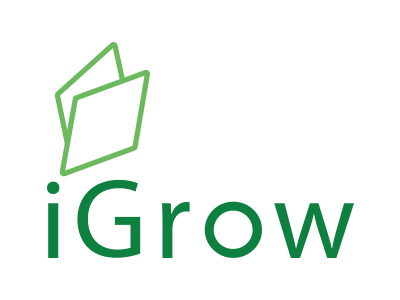
Welcome to iGrow News, Your Source for the World of Indoor Vertical Farming
‘Greenhouse Of The Future’ With Special Solar Glass Coming To Netherlands
‘Greenhouse Of The Future’ With Special Solar Glass Coming To Netherlands
A ‘Greenhouse of the Future’ will soon be built on the Floriade site in Venlo. The greenhouse, made possible with various subsidies, will be energy and CO2 neutral and can even generate energy. To achieve this, the latest technological innovations in the field of Het Nieuwe Telen (Next Generation Cultivation) such as Air & Energy and LED systems are combined with Dye-Sensitized Solar Cells (DSSC) nanotechnology.
The greenhouse, a prototype covering a total of 1200 m2, will be built by Maurice Kassenbouw. Michel La Crois, director at Maurice Kassenbouw: "All designs are ready, and we only have to wait for the special glass in the right dimensions."
Solar panel
The special glass has been developed by Brite Solar Technologies from Greece. Nick Kanopoulos, the man behind Brite Solar Technologies: "The glass we make has a special, transparent coating that transmits 70 to 75 percent of light in the frequencies that are important for photosynthesis. The glass also features special stripes, similar to what you seen in the rear window of a car. These are solar cells that generate energy from sunlight, so the glass actually functions as a solar panel. An additional advantage is that the glass also has improved insulating properties, so less energy is needed to heat the greenhouse. "
Energy gain
In Greece the glass has already been tested on a small scale on a 100 m2 greenhouse. Many growers feared that the glass letting through less light would have a negative effect on crop yield, but this turned out to not be true in those tests. There were as many kilograms from the test greenhouse in Greece as from comparable greenhouses without special glass. In addition, the glass also generated an energy gain of 5,400 kilowatt hours per year during the test.
The glass will larger on the Dutch prototype greenhouse. Where the glass panels in Greece measured 50 x 50 cm, they will now be 1 x 1.2 m. The results of the project will be closely monitored by Brite Solar Technologies, both remotely and by people on the ground. Nick: "All kinds of sensors will be placed in the greenhouse, so that we can monitor the results from anywhere in the world."
Self-sufficient
Although the first prototype has not even been built yet, Maurice Kassenbouw already has a second project lined up for another two hectares. However, they need to wait on the results of the first greenhouse. "In the south of Europe in particular, I expect a high energy yield. There is already interest in this type of greenhouse in Dubai, and we expect that we will soon be able to build these types of greenhouses on a large scale."
The glass is now 6 mm thick, but in order to be able to replace existing glass in existing greenhouses, they are working on glass with the conventional thickness of 4 mm.
Ultimately, the goal is for these greenhouses to be self-sufficient in terms of energy and to be a solution to the problem of food scarcity. Michel: "The question that we are jointly facing is: how are we going to feed nine billion people by 2050?"
European innovation program
The construction of the greenhouse is part of the European Innovation Program Southern Netherlands (PROJ-01061).
For more information:
Brite Solar Technologies
www.britesolar.com
info@britesolar.com
Maurice Kassenbouw
www.kassenbouw.com
maurice@kassenbouw.com
Publication date: 5/2/2018
Scientists Discover Hormone That Helps Plants Sense Drought
Wonderful weed: Scientists at the Riken Center for Sustainable Resource Science in Tsukuba, Ibaraki Prefecture, have detected a hormone that senses drought in thale cress. | GETTY IMAGES
Scientists Discover Hormone That Helps Plants Sense Drought
BY ROWAN HOOPER
SPECIAL TO THE JAPAN TIMES
- APR 26, 2018
Plants deserve more credit. They can’t move to find food or water or to escape a predator. But that doesn’t mean they are helpless — far from it. They don’t have eyes, ears, a nose or mouth, but they can sense the world remarkably well — in some cases better than we can.
For example, as you might expect, plants are highly sensitive to light. Humans have three different kinds of light-receptors in their eyes to sense light; plants have 15. Plants can monitor light levels very precisely, from the ultraviolet to the infrared.
Plants’ powers of communication are also extraordinary. A plant being eaten by a predator such as a caterpillar will release ethylene, and this warns other plants that there is a threat nearby. If you look at a tree infested by herbivores and nearby trees that are untouched, you’ll find that the uneaten trees have produced protective chemicals that render them unpalatable to predators.
Ethylene is also produced as fruit ripens, and the gas is sensed by other plants and promotes ripening in them, too. It means fruits ripen at the same time, which attracts the animals needed to eat them and disperse the seeds.
If you cut a tomato plant, proteins are produced in response in many distant parts of the plant. There is also evidence of electrical processing of information in the roots of plants that is analogous to what we see in the animal brain.
Now, from the Riken Center for Sustainable Resource Science (CSRS) in Tsukuba, Ibaraki Prefecture, comes the discovery of a hormone that helps plants sense drought. It’s a reminder that plants are far more sophisticated than we often give them credit for.
“People think that plants are static because they do not move,” says Fuminori Takahashi, of CSRS. “However, in plants there is close and active communication between tissues separated by large distances.” The root can tell the shoot what is going on in the soil, and the information allows the plants to adapt when environmental conditions turn stressful. Plant scientists suspected this communication was going on but, until Takahashi’s discovery, they didn’t know how.
A lack of water is one of the most important factors that limits plant growth. The hormone identified by Takahashi and colleagues helps plants retain water when none is available in the soil.
The hormone moves through the plant circulatory system in an analogous way to how animal hormones move through the body. For example, if you have low blood pressure, your body produces the hormone vasopressin. The hormone circulates through the body in the blood and causes your arteries to constrict, which increases your blood pressure back to normal levels. Takahashi’s study shows, for the first time, that plants have a similar mobile hormone that can travel through the plant’s body.
“The hormone modulates root-to-shoot communications in response to drought stress conditions,” says Takahashi, “and transmits information about the lack of water in soil from root to leaves, to prevent water loss.”
Now they have identified the hormone, the team plans to modify it.
“We are working on modified peptides that are more effective for stress resistance than the natural ones,” Takahashi says. The team is also working on ways to mix hormones into fertilizer to enhance drought and salt resistance of crops in the field.
Scientists have shown in the past that communication goes on between plants. If plants are subjected to drought conditions, those that are in contact via the root system close the stomata, the holes on the leaves that let the plants breathe but which also allow water vapor to escape. The plants are basically shutting up shop in preparation for drought. Perhaps the signal is a hormone such as the one discovered by Takahashi — but this remains to be discovered.
The Tsukuba scientists use a plant called Arabidopsis, which is more commonly known as thale cress. It’s a weed; you might see it growing in a crack in the road and think nothing of it. But it was the first plant to have its complete genome sequenced and is grown in labs all over the world. That such a humble and boring-looking plant can yield such deep discoveries is a reminder of how much we still have to learn about the living world.
Rowan Hooper is managing editor of New Scientist magazine. He tweets at @rowhoop and his new book, “Superhuman: Life at the Extremes of Mental and Physical Ability,” is out in May.
NATIONAL / SCIENCE & HEALTH | NATURAL SELECTIONS ARTICLE HISTORY
E. Coli Outbreak In Romaine Lettuce Underscores Need For Change And Technology
APR 29, 2018
E. Coli Outbreak In Romaine Lettuce Underscores Need For Change And Technology
Phil Lempert, CONTRIBUTOR cover issues, and trends in the food and agriculture sectors.
Opinions expressed by Forbes Contributors are their own.
Freshly picked and chilled arugula being poured into a sorting bin to be washed. (Photographer: Mark Elias/Bloomberg)
The Food and Drug Administration and the Centers for Disease Control and Prevention have reported that 98 people in 22 states have become ill from eating romaine lettuce grown in the region of Yuma, Arizona.
Forty-six of those individuals have been hospitalized, including 10 who have developed a type of kidney failure. The difficulty of discovering just how and when the lettuce was contaminated is due to the fact that, at least in the case of the people sickened at an Alaska correctional facility, the contamination occurred not at the farm where the whole-head lettuce was grown and harvested but elsewhere in the packaging and distribution chain, according to the FDA.
‘Farm to table’ is a common phrase that is used to describe high quality and fresh foods. Along this path for all foods, there are many instances where foods can be contaminated. In the case of this lettuce, which was harvested, put in boxes, shipped to another facility (or multiple ones), stored under refrigeration, washed, chopped and then packaged in bags that may include plain romaine or various salad mixes (that could contain other lettuces or vegetables grown from other farms) that contained the romaine. Many touch points that could be the culprit of the contamination.
Food production is complex, and following proper food safety handling techniques is very difficult. Since April 1, 2018, there has been 38 food recalls from the FDA ranging from having undeclared ingredients in protein bars to Listeria monocytogenes in mini éclairs to Salmonella in organic coconut flour to this lettuce recall due to E. coli.
The CDC has told consumers to avoid eating and restaurants and retailers to stop selling or serving chopped, baby, organic, whole head, hearts, of romaine lettuce, or any salad mixes that contain romaine if it comes from Yuma, or if it cannot be identified where it comes from. The CDC estimates that nearly half of all food-borne illnesses are caused by produce and in a 2013 report wrote that leafy vegetables (which includes lettuces) were the number one source of food poisoning.
There have been brands that have never recovered from having their products pulled from shelves. The FDA ordered the shutdown Bon Vivant Soup Company’s plant in Newark, New Jersey on July 7, 1971, after Samuel J. Cochran died as a result of botulism poisoning traced by Federal Food and Drug Administration investigators and State Health Department. Five cans of soup out of 324 that they found were contaminated with botulinum toxin, all in the initial batch of vichyssoise that was recalled.
The recall destroyed public confidence in the Bon Vivant name. Peter Pan peanut butter has never gained back their market share since their initial recall back in 2007 where they had to recall three years of production from store shelves due to a nationwide salmonella outbreak that sickened at least 625 people in 47 states, was missing from stores for 6 months and more than a decade later had to pay the largest criminal fine in a US food safety case of $11.2 million.
On September 14, 2011, FDA issued a press release to announce that Jensen Farms issued a voluntary recall of Rocky Ford Cantaloupe because the cantaloupes have the potential to be contaminated with Listeria and may be linked to a multi-state outbreak of listeriosis which resulted in 33 deaths and a pregnant women’s miscarriage – the source was found to be improper equipment that washed the cantaloupes before shipping to retailers for sale.
There are solutions that could help to avoid and more rapidly discover where these outbreaks occur.
All our foods start in agriculture, where our food comes from. Our land, water, soil and environment are all under siege and the USDA says that climate change is going to create challenges. The location where we grow our foods, on dirt farms, is where many of the food safety recalls occur can change. At the same time, we are seeing more consumers opting for more of a plant-based diet. There is also a new breed of younger farmers entering the fields – the USDA’s latest Census of Agriculture reports that the number of farmers aged under 35 is increasing – that’s only the second time that’s happened since 1900, and 69% of them have college degrees – far higher than the 40% of the general population that has graduated from college. Younger, smarter farmers will bring us into a new era of agriculture and food safety.
By 2050 the world’s population will reach 9.6 billion with 65% of us living in urban areas.
Most of the lettuces sold in the US are shipped from California. The bagged lettuce you buy in a bodega or supermarket in Manhattan had to travel 3,000 miles, hopefully in a truck that was immaculate and under the proper temperature.
Vertical indoor farming is more efficient bringing more farms closer to where people live, reducing expense and environmental impact.
Kate Hofman of GrowUp Urban Farm, producing fresh fish, salads, and herbs using a combination of aquaponic and vertical growing technologies, in London in 2016. (Photo by Miles Willis/Getty Images)
In Linkoping Sweden, a multi-use building will open in 2020 with 16 stories of farms to offices at a 3:1 ratio, with a retail store and a wholesale operation and a controlled environment which would greatly reduce the risk of contamination. This farm also is much more energy efficient and saves 1,100 tons of CO2 emissions and 13 million gallons of water while producing 4 to 6 times the yield as one outdoor acre, and can be built in downtown Manhattan and deliver to that bodega or supermarket that is just a few miles away. Of course, these types of vertical farm buildings are expensive and take years to build.
In the meantime, blockchain technologies can be used to more efficiently track our foods across the supply chain. IBM is developing the IBM Food Trust food safety solution which consists of digital information including farm details, batch numbers, factory and processing data, expiration dates, storage temperatures and shipping detail which are digitally connected to food items and the information is entered into the blockchain along every step of the process. According to IBM’s Shanker Ramamurthy, General Manager Global Strategy & Market Development, in a blog post “the information captured in each transaction is agreed upon by all members of the business network; once there is a consensus, it becomes a permanent record that can’t be altered. Each piece of information provides critical data that could potentially reveal food safety issues with the product. The record created by the blockchain can also help retailers better manage the shelf-life of products in individual stores, and further strengthen safeguards related to food authenticity.” Which clearly would speed up the discovery process and likely result in less illnesses and deaths.
Blockchain is an initiative that must be fast-tracked in order to reduce food borne illnesses and reinforce consumer trust in our food supply.
Phil is known as "The SupermarketGuru" and writes and reports on food trends. Check out SupermarketGuru.com for more insights into the world of food and his new food product reviews
New Technologies Change The Business Landscape
New Technologies Change The Business Landscape
Mar 27, 2018
Kathy Gibson at Dell EMC Forum, Sandton – New technologies are going well beyond helping businesses to improve or change their processes – they are fundamentally changing the business itself.
According to Nigel Moulton, EMEA chief technology officer: converged platforms and solutions division at Dell EMC, this means all businesses are going to have to look at embracing new and innovative technologies that are now becoming mainstream.
“For instance, the business case for Internet of Things (IoT) is everything,” he says. “IoT can have a profound impact on just about every business.”
He cites the example or Aero Farms, a vertical farming operation that is talking about using IoT and analytics to improve crop yields by a staggering 100%.
“Think about IoT in healthcare,” Moulton adds. “To a large extent, we are already there with wearables that monitor heart rate, temperature and much more.”
IoT can be used in any application where something can be measured, monitored and made more accurate, he says. “Can I derive a set of results that allow me to be more accurate? And if I can, will that offer the opportunity to improve the process? Because then it’s a use case for IoT.”
IoT proponents often talk about the concept of the digital twin, where a digital version of something or someone represents the physical.
Moulton believes this concept can be extended.
On the one hand, he says, there is the digital twin that represents a person. “This is a holographic representation of the person who can be in one place, but projected to another at the same time.”
The second iteration, which is starting to gain ground now, is the digital mapping of physical infrastructure.
“For example, you could have a digital model of the road network. If you have to do work on the road, you can use modally to predict the best way to reroute people; or to predict the most optimal time t do the work.
“This type of digital twin lets you simulate and predict based on real-world data.”
Another technology that is fast gaining traction, and that threatens to disrupt a lot of industries, is artificial intelligence (AI).
“AI is about teaching a machine to think like a human,” Moulton explains. “We are already seeing this in advanced chatbots, some of which are advanced enough to respond exactly like a human.”
AI has allowed voice to become the primary interface for communicating with computer devices, he adds. “We already have AI assistants with no screen or keyboard, which we interface with using natural language.”
What’s apparent about many of the new technologies that are about to go mainstream is that they are relatively new. “These changes are geometric in nature – they are not linear,” Moulton says.
“We don’t think geometrically, but we are teaching machines to do so. This means machines are able to tackle mathematical problems that are out of our league.”
Tupperware And Techshot Develop Plant Growth Chamber For NASA
Tupperware And Techshot Develop Plant Growth Chamber For NASA
An improved system for growing plants in space, developed for NASA by Tupperware Brands and Techshot is expected to launch to the International Space Station (ISS) April 2 aboard a commercial SpaceX Dragon cargo capsule from Florida's Cape Canaveral Air Force Station.
Mizuna growing inside plant growth chambers developed for NASA by Tupperware and Techshot. Six of the chambers are visible inside a Veggiemini-greenhouse at the Kennedy Space Center.
Since 2014, astronauts aboard the ISS have been growing a variety of leafy vegetables and colorful flowers inside the Vegetable Production System, otherwise known as the 'Veggie' facility. NASA is always seeking to improve upon existing technologies, while reducing its need for resources, such as crew time. In an effort to reduce the frequency that an astronaut must water plants growing in space, Dr. Howard Levine and his colleagues at the NASA Kennedy Space Center (KSC) began exploring new design concepts for the component of Veggie that holds the root structure of the plants - the so-called 'plant pillows'. Research at KSC led to a semi-hydroponic design concept dubbed the Passive Orbital Nutrient Delivery System (PONDS).
Iconic kitchen and housewares company Tupperware Brands, and Techshot Inc., a commercial space enterprise, partnered to further develop the concept and manufacture spaceflight-qualified PONDS plant growth units for use aboard the ISS. Up to six can be installed in Veggie at one time. Like the plant pillows, the PONDS devices are single-use items, which can be discarded after the plants are grown and harvested on orbit. However, unlike the plant pillows, PONDS can also be returned, refurbished, and reflown in space.
The seven PONDS modules launching on SpaceX mission CRS-14 in April comprise three variations on a common design. Four black "opaque" modules will grow red romaine lettuce, the same lettuce that has been grown previously in the Veggie facility. The two "shrouded" modules, also growing red romaine lettuce, each includes a clear window and a removable cover that allows astronauts to periodically observe root growth in the hydroponic reservoir. One "clear" module, which does not contain a plant, will be used to perform testing and videography to characterize the movement of water within the reservoir while in space.
Six more modules are expected to launch in May from Wallops Island, Virginia, aboard a commercial Orbital ATK Cygnus cargo spacecraft. These six will grow another leafy vegetable called Mizuna. Both sets of hardware will provide a validation of the device's performance, in advance of its use in a comprehensive research campaign by NASA scientists in November.
Tupperware applied its deep knowledge and longstanding success of design for manufacturability, injection molding, and food-safe construction materials to yield a system that utilizes capillary forces and unusual internal geometries to replace gravity. The result is a product that is expected to provide plants grown in space with a near functionally-equivalent growing environment to their terrestrial counterparts.
"Tupperware products have included smart technology features for nearly 70 years," said Tupperware Brands Vice President of Research and Innovation David Kusuma. "Our product evolution goals have always been to meet today's needs for consumers, whether that includes microwaveable grills or food processors that require no electricity; we are proud to now say that this includes sustainable vegetation growth in space. This has been one of our most exciting and unique collaborations, and we are honored to have worked alongside NASA and Techshot on the advancement and success of the PONDS project."
With nearly 30 years of experience developing equipment for human spaceflight, Techshot assisted with requirements management, safety, verification and integration tasks, and some light manufacturing and assembly. It also provided Tupperware designers with access to subject matter experts in areas such as low-gravity fluidics.
"It's been great working closely with the talented teams of engineers, designers and scientists at NASA and Tupperware on the project," said Dave Reed, Techshot's PONDS project manager and the company's director of launch operations. "And while it's always a thrill watching new hardware launch into space, seeing the first crop of PONDS-grown lettuce harvested aboard the ISS will be the real payoff after more than a year of hard work."
For more information:
www.Techshot.space
www.tupperwarebrands.com
Publication date: 3/28/2018
Crop Enhancement Company BioLumic To Invest $7 Million In Business
Crop Enhancement Company BioLumic To Invest $7 Million In Business
JILL GALLOWAY
March 29, 2018
BioLumic chief executive Warren Bebb and founder Jason Wargent have received some significant financial backing.
BioLumic chief executive Warren Bebb and founder Jason Wargent have received some significant financial backing.
Palmerston North-based company BioLumic, which has developed a world first system of using ultraviolet (UV) light on crops, will invest $7 million to grow the business.
Chief executive Warren Bebb said the company would be able to employ more people as a result of the funds from a group of American and local investors.
He said a few days of light improves growth development, more consistent yields and disease resistance in seedlings.
The patents existed and it was charged out per seedling, but while the system was being developed he would not say how much each treated seedling cost.
READ MORE:
* BCC launches Young Enterprise Scheme for 2018
* Palmerston North startup BioLumic attracts significant overseas funding
The light system was being trialled and developed in a Massey University-owned glass house at its plant growth unit.
"We are already in large scale trials with growers in Mexico, the United Kingdom and California and achieving yield gains of up to 22 per cent."
Warren Bebb, BioLumic chief executive, in the glasshouse where seedlings are treated with UV light. | PHOTO: DAVID UNWIN/STUFF
Bebb said just one treatment made a huge difference to plants, making them more robust to wet, as well hot, sunny weather.
He said the exciting thing about the investment as it would allow them to further ramp up the company, which currently has 10 employees.
"It is a great connection for us. They are strategic partners but it also puts us in touch with customers."
"We have an agronomist in Mexico at the moment, but this will allow us to have another one based in the United States, who will cover Europe as well. And it also allows us to employ more engineering staff ."
Bebb said the money would allow BioLumic to do more research and development.
He said the investment would be used to aggressively expand the BioLumic team in both New Zealand and its US office in California, and to intensify the global deployment of its UV technologies.
The investment will lead to more job opportunities and research and development.
PHOTO: DAVID UNWIN/STUFF
BioLumic was founded by Dr Jason Wargent, a world-renowned photobiologist specialising in UV/plant interactions, and spun out of leading AgTech research from Massey University in Palmerston North with support from local incubator Building Clever Companies (BCC) and seed funding from MIGAngels. The technology is the result of more than a decade of Wargent's research into UV photomorphogenesis, a process whereby a precise UV treatment induces plant root and leaf development and activates secondary metabolism.
It is focused on lettuce, broccoli, strawberry and tomato seedlings which are kept in a glasshouse and dosed regularly with UV light.
Agtech is one of the hottest global growth markets, and New Zealand is already a world leader in agricultural production. It is estimated that more than 8.6 billion people will populate the planet by 2030, and the world will need to produce 50 per cent more food by 2050.
"It is an exciting development but they we would not have got anywhere without help from the BCC and and the Manawatu Investment Group," Bebb said.
The contributions came from Finistere Ventures, Radicle Growth, Rabobank's recently-launched Food and Agri-Innovation Fund, along with New Zealand investors that have already contributed money.
- Stuff
Saint Lucia Launches Climate-Smart Greenhouse Project
Saint Lucia Launches Climate-Smart Greenhouse Project
The SLCSI has received grant funding in the amount of USD$50,000 under the Global Environment Facility (GEF) program for the implementation of the first-ever “Climate Smart Greenhouse” project.
The two-year project is aimed at using technology to create a sustainable climate-smart system which can be used by farmers in Saint Lucia.
The experimental project is the first of its nature in the Caribbean. It is an integration of agriculture and technology that will demonstrate effective protected organic farming practices, using a specially-designed greenhouse to cushion plants from weather elements and provide an environment that can be easily manipulated.
The project utilizes an integrated, automated farm management system that gives insight into production and the farm business.
The first instalment of the grant is in the amount of USD$50,000. A further grant of USD$150,000 is contingent on the success of the project.
Publication date: 3/28/2018
FarmBot v6.3.0 Software Update
FarmBot v6.3.0 Software Update
Over the last week, we rolled out version 6.3.0 of our software stack with a host of new features and improvements that make working with FarmBot faster, easier, and more fun.
Photos taken with FarmBot's camera are now rendered in the farm designer map if the camera has been calibrated. Map images can be filtered by date and time via the map menu using date and time inputs or a date slider.
FarmBot OS and Arduino firmware parameters are now stored in the backend API, allowing for greater reliability and easier account switching.
FarmBot can now read messages out loud through your computer or a speaker plugged into the Raspberry Pi. This is great for demonstrations!
Dropdown menus throughout the application have been organized, with some now including Peripherals and Sensors to make configuring your FarmBot faster and more intuitive.
Ready to get your own FarmBot?
We're now manufacturing v1.4 FarmBot Genesis and Genesis XL devices. Visit our shop to learn more and place your pre-order before our March sale ends!
Who Will Create The First Self-Cultivating Greenhouse?
Who Will Create The First Self-Cultivating Greenhouse?
Wageningen University & Research organizes an international challenge to boost vegetable production using artificial intelligence and autonomous greenhouses. The challenge is sponsored by Tencent, a leading provider of internet services in China and David Wallerstein, Chief Exploration Officer (CXO) of Tencent. The world is facing a rapid increase in human population and Wageningen University & Research is working with Tencent to explore breakthroughs that can help feed more people, deliver greater food security and create more food with fewer resources.
Open for registration
The challenge is open for multi-disciplinary teams from all over the world. Teams can subscribe from 19 March to 15 April at www.autonomousgreenhouses.com and can consist of people like scientists, R&D specialists, and students, from different disciplines like artificial intelligence, sensor technology, and crop physiology.
The teams participating in the challenge will run a greenhouse compartment in which a computer and machine learning algorithms or computer models make all kind of decisions on distance with limited human interaction.
Safe products without residues
In order to supply consumers with fresh products produced close to large cities, greenhouse production is a very efficient way to supply fresh vegetables and fruit with a high content of vitamins and minerals requiring only a small production area. Production in greenhouses is typically up to 10 times higher than in open field and uses much less water. Recent research results of Wageningen University & Research have shown that in extremely controlled greenhouses only 5 litres of water is used to produce 1 kilogram of tomatoes, while it would be up to 40 more litres in open field production. The controlled environment enables the reduction of pesticide use to a minimum and leads to the production of safe products without residues.
In the future even more greenhouses are needed to produce our food. For that the “green fingers”, or the knowledge and experience of a grower, is essential. At the same time, it is hard to find enough skilled workers in many countries worldwide. Automation, ICT and AI can help the grower to oversee all the information needed and help to make complex decisions.
Tencent and Wageningen University & Research believe that autonomous greenhouses can boost vegetable production and bring greenhouse production to a next level. Autonomous greenhouses can bring further improvement to yield and quality of greenhouse vegetable crops and a substantial reduction of the needed input in terms like energy, water, and crop protection at the same time.
In autonomous greenhouses the computer will decide about the optimum greenhouse climate set points, based on a wide range of sensors and cameras, self-learning software will partly take over human decisions. AI will help the grower to run the greenhouse in an optimal way, enable him to manage his greenhouses at a distance in various parts of the world.
Start in June
The first part of the challenge will start in June to select the five best teams and will run May-December 2018. From August till the end of December, five selected teams will run their own crop in their own greenhouse compartment at the greenhouse facilities of Wageningen University & Research. The experts of Wageningen University & Research will monitor the results of the teams: resources input and crop production output.
Source: Wageningen University & Research
Publication date: 3/20/2018
New Partnership To Drive Innovation In Perennial Fruits
New Partnership To Drive Innovation In Perennial Fruits
14 March 2018
AgTech solutions company Autogrow and Plant & Food Research today signed a Memorandum of Understanding (MoU) confirming their intention to collaborate in the development of protocols to maximize yield and enable continuous production of perennial fruits.
The agreement was signed by Autogrow CEO Darryn Keiller and Dr Kieran Elborough, General Manager Science - New Cultivar Innovation for Plant & Food Research.
“We are incredibly excited to be working with Plant & Food Research and see collaborations like this as fundamental to furthering our industry, ultimately benefiting both growers and consumers. Plant & Food Research are responsible for some of the best cultivars to come onto the global market and their scientific expertise combined with our knowledge of controlled environment agriculture will take perennial fruits to the next level,” said Mr. Keiller.
Autogrow’s Director of Plant Science and Agronomy Dr Tharindu Weeraratne will head up Autogrow’s team as part of the MoU.
Speaking at the signing, Dr. Elborough said, “Working with a global company like Autogrow has the potential for us to match new breeding strategies with future growing systems that deal with numerous horticultural challenges such as climate change, sustainable food production and reducing land availability.”
IMAGES: Mr. Keiller (in black) and Dr. Elborough (in white). High-resolution images available upon request
About Autogrow
Autogrow leverages the power of technology, data science and plant biology to provide indoor growers affordable, accessible and easy-to-use innovation – 24/7, anywhere in the world.
Our hardware, software and data solutions support growers and resellers in over 40 countries producing over 100 different crop types.
We have over two decades of experience and passionate, fun people creating original ideas and making them a reality.
About Plant & Food Research
Plant & Food Research is a New Zealand-based company providing research and development to enhance the value and productivity of the horticultural, viticultural, arable, seafood and food and beverage industries. With more than 900 people based at sites across New Zealand, as well as in the USA and Australia, at the heart of the Institute is a goal to support the growth of plant and marine-based food industries through the successful application and commercialization of research-based innovation.
Our science supports the sustainable production of high quality produce that earns a premium in international markets, as well as driving the design and development of new and novel functional foods that offer benefits to human health and wellbeing.
In its 90 year history, Plant & Food Research has bred a range of new fruit, vegetable and arable cultivars that are now marketed globally, including Jazz™ and Envy™ brand apples, Zespri® Sungold Kiwifruit and Moonlight potatoes.
For more information:
Autogrow
sales@autogrow.com
www.autogrow.com
Plant & Food Research
www.plantandfood.co.nz
New Climate Screen Offers More Light And Lower Energy Costs
New Climate Screen Offers More Light And Lower Energy Costs
Ridder Climate Screens introduces a new energy-conserving screen fabric that offers 2% more light transmission – without detriment to its energy conservation properties.
More light
Ridder Climate Screens’ new RES 10+ FR climate screen fabric has been developed in response to the demand for more light in dark, cold growing periods.
Ridder's Mario Scherpenzeel explains: "Obviously, growers use energy-saving screens to minimize heat losses from their greenhouse in the winter. However, they also want to let the maximum possible light into the greenhouse that their crops need to achieve optimum growth and yields. These needs gave us cause to give careful consideration to the available technological options for the optimization of our Ridder Energy Saving (RES) screens. Our efforts have resulted in the development of a new type of screen fabric that offers growers the same energy conservation properties together with an increase in light transmission of no less than 2%."
Extra energy savings
Growers opting for RES 10+ FR screens are able to lengthen daytime screening periods in the darker seasons of the year and benefit from the extra energy savings. Vegetable growers, in particular, can also achieve higher winter yields. Moreover, the additional amount of light ensures that new, young plants become productive earlier in the cultivation period.
Moisture balance
Mario Scherpenzeel adds that the RES 10+ FR screen fabric not only increases light transmission by 2%, but also improves the climate in the greenhouse. "The screen fabric's moisture permeability properties enable growers to retain adequate control of the moisture balance in the greenhouse. This is also beneficial to crop yields."
RES 10+ FR will be available from Ridder Climate Screens, from stock, as from July of this year. Contact your installer or greenhouse builder for more information about the benefits of this new translucent, energy-conserving screen fabric.
For more information:
Ridder Climate Screens
Honderdland 131 – 2676 LT
Maasdijk – The Netherlands
T +31 858 338 333
info.rcs@ridder.com
www.ridderclimatescreens.com
Italy: SAIM Service's Vacuum Cooling Technology
Italy: SAIM Service's Vacuum Cooling Technology
Vacuum cooling uses the principle of low-temperature evaporation of a fraction of the humidity found in a product. This results in a quick stress-free pre-cooling that guarantees a reduced drop in weight while hastening commercialization times.
"Leaf vegetables can be cooled in 20-30 minutes, taking them from 25 to 3-5°C without stress," explains Yuri Simonelli from SAIM Service.
How vacuum cooling works - Click photo to enlarge
The company has been working in the post-harvest technology sector for 30 years - from cold storage units, ozone gas applications for the sanitation of air and water, detanning and modified atmosphere to hydro and pressure cooling.
The vacuum cooling technology
In 2017, SAIM Service added vacuum cooling to the vast range of technology supplied thanks to its partnership with Dutch company Weber Cooling.
Vacuum cooler models - Click photo to enlarge
This type of cooling is particularly suitable for products with a high surface/weight ratio such as leaf lettuce, spinach, mushrooms, sprouts as well as more compact products such as green beans, broccoli, celery, and corn.
Vacuum cooling works from the core of the product, extending its shelf-life and storage time. This, in turn, makes it easier to ship it to foreign markets.
"Different internal and final temperatures are needed according to storage and shipping times: a cooling temperature of 5°C or higher is enough for short times and distances while longer storage times and long distances require a temperature closer to 1°C."
Such conditions can be achieved and managed using refrigerated storage and transport in combination with vacuum cooling.
Vacuum cooler models - Click photo to enlarge
The company has a flexible demo machine (small quantities) for those wishing to test the technology.
More than just vegetables…
SAIM Service's partnerships with companies both in Italy and abroad and its attentiveness towards new market needs have led it to developing new applications. Compost for mushroom cultivation and heavy products such as peat for grass-turf can also be cooled with this technology. And there's more: it is also suitable for pre-baked bread and flowers.
Some of the products vacuum cooling can be used for
In 2018, SAIM Services also extended its headquarters and hired new personnel. In addition, it is active on Facebook, Twitter, LinkedIn and YouTube.
Contacts:
Yuri Simonelli
Cell.: +39 335 6270026
SAIM Service
Via Pantanello, 19 (Z.I)
04022 Fondi (LT)
Tel.: +39 (0)771 510470
Fax: +39 (0)771 532029
Email: info@saimimpianti.com
Web: www.saimimpianti.com
Publication date: 3/14/2018
This Local AGTech Startup Wants You To Forget Everything You Know About Farming
This Local AGTech Startup Wants You To Forget Everything You Know About Farming
By Andrew Moore
March 15, 2018
In November 2016, Tyger River Smart Farm constructed a 13,000-square-foot greenhouse and 3,500-square-foot harvesting facility on 30 acres in Greer. The expansion has increased the farm’s production capacity tenfold. Photo by Will Crooks.
Industrial agriculture has allowed farmers to maximize the potential yield of their crops for centuries. But it has done so at a major cost to the environment — a cost characterized by a steady decline in soil productivity, reduced water quality, elevated levels of carbon dioxide, habitat loss, and more.
Unfortunately, the negative consequences of industrial agriculture are set to worsen in the coming decades as the national population grows and urban sprawl continues to swallow large swaths of productive farmland. The American Farmland Trust, a group working to promote healthier farming practices, estimates that 24 million acres of agricultural land have been developed since 1982.
As a solution, an increasing number of entrepreneurs are turning to controlled-environment agriculture (a combination of engineering, plant science, and computer-managed greenhouse control technologies) to optimize plant growing systems, plant quality, and production efficiency.
One company that’s leveraging the power of CEA is Tyger River Smart Farm.
The Greer-based operation grows a variety of lettuces, chard, kale, and basil through the use of hydroponics — the method of cultivating plants without soil by instead using a nutrient-rich solution to deliver water and minerals to their roots.
“I don’t have a problem with people who adhere to conventional farming methods,” said Ryan Oates, owner and founder of Tyger River Smart Farm. “But I do think growing crops with hydroponics is more beneficial to both the consumer and the environment.”
Growing a business
Despite being the first person in his family to farm, Oates is no stranger to plants.
Oates studied plant biology at Clemson University and conducted numerous research projects at the Genomics Institute. He then enrolled at Miami University in Ohio to pursue a graduate degree in plant molecular biology but decided to drop out after becoming disenchanted with academia.
Upon his return to the Palmetto State, Oates spent several years as a financial planner in his father’s business. He then worked in commercial cabinetry for nearly a decade. In 2012, Oates stumbled onto the concept of hydroponic farming and decided to install a system in an existing greenhouse behind his parents’ home in Duncan.
“My mom loves to garden, so she built the greenhouse as a hobby,” Oates said. “But she was no longer using it, so I thought I would give hydroponics a try. It just seemed like something I would enjoy doing as a full-time job.”
Ryan Oates
Oates eventually outfitted his mother’s 1,300-square-foot greenhouse with fans, an evaporative cooling system, a propane heater, overhead LED lights, and hydroponics equipment. He officially launched Tyger River Smart Farm in August 2013. But the new venture didn’t come without challenges, according to Oates. A power outage, for instance, stopped the flow of water for about two hours and decimated about 70 percent of his crop. Oates outfitted the greenhouse with a generator shortly after.
Following the first harvest in February 2013, Oates had to give away most of his produce to neighbors due to a lack of customers. But then Tyger River Smart Farm was accepted into the TD Saturday Market in downtown Greenville. The market, which runs on Main Street on Saturday mornings from May 6 through Oct. 28, has become a signature event since its launch in 2002 and typically features more than 75 vendors that sell farm-fresh produce, baked goods, meats, cheeses, seafood, and other specialty foods.
“We owe a lot of our success to the TD Saturday Market,” Oates said. “The market not only helped us sell our produce that summer. It also helped us get our name out there and gain new customers.”
Tyger River Smart Farm has since become a vendor at the Greer Farmers Market and Hub City Farmers Market in Spartanburg, according to Oates.
The farm also sells fresh produce to a variety of local restaurants and grocers, including the Swamp Rabbit Café and Grocery in Greenville, Tandem Creperie and Coffeehouse in Travelers Rest, The Farmer’s Table in Spartanburg, Stella’s Southern Bistro in Simpsonville, Cribbs Kitchen in Spartanburg, Restaurant 17 in Travelers Rest, Adam’s Mobile Market in Easley, and GB&D in the Village of West Greenville.
Farming as a science
As the farm’s reputation and customer base continued to grow over the years, Oates realized that Tyger River Smart Farm would need to scale to survive.
In November 2016, Oates expanded his operation by constructing a 13,000-square-foot greenhouse and 3,500-square-foot harvesting facility on 30 acres in Greer. The expansion has increased the farm’s production capacity tenfold, according to Oates.
Oates said the new greenhouse relies heavily on automation. The facility features natural gas heaters, recirculating fans, exhaust fans, mechanical vents, and an evaporative cooler that aids in controlling the temperature and humidity. It also features a retracting shade system that helps with temperature control and light levels.
“Traditional farming isn’t easy,” Oates said. “But our CEA system requires us to monitor our plants on a real-time basis and watch how they react to different conditions. It’s much more process-oriented, so all the automation really helps.”
He added that the farm’s greenhouse uses carbon dioxide generators, which enrich the surrounding air if the levels become low, and more than 100 LED lights, which provide supplemental lighting during the winter months when solar light levels are too low for growing crops. It also uses an environmental controller, which is responsible for sensing environmental conditions and integrating all of the equipment through computer logic to produce a consistent environment year round.
As for growing the produce, Tyger River Smart Farm employs a Nutrient Film Technique (NFT) system, a soilless technique that bathes the roots of the plants in water infused with carefully monitored nutrients.
Tyger River Smart Farm uses over 100 LED lights to provide plants with supplemental lighting during the winter months when solar light levels are too low for growing crops. Photo by Will Crooks.
Oates typically begins the process by purchasing seeds from Johnny’s Selected Seeds in Maine or Paramount Seeds in Florida. The seeds are then germinated in a propagation room, which is completely enclosed and controlled with central heat and air.
After basking in the pink glow of LED lights for one to two weeks, the seedlings are relocated into nursery channels in the greenhouse, which sits on a well and 600-gallon underground tank. The water from the tank is then mixed with nutrients and sent down the channel, where it flows over the roots of the plants. Excess water is then collected at the end of the channels and returned to the water tank.
The nutrient water is then pumped from the main storage tanks back into the plastic channels, according to Oates. Thus, no water or nutrients is ever wasted. The same environmental controller in the greenhouse is responsible for maintaining optimum nutrient and pH levels in the storage tanks.
When the produce is harvested, it is packaged and sold with the roots in order to maintain the plant’s lifespan and nutritional value. During the peak of the season, Oates harvests between 8,000 and 9,000 plants a week, but he continues to produce plants all year round.
“The best part about hydroponics is that I get to harvest plants during the winter months when other farms are buried under the snow,” Oates said. “It definitely helps me stay ahead of the competition.”
The farm’s hydroponic system also has various environmental benefits, according to Oates. About 1,500 square feet of the greenhouse, for instance, is dead space reserved for an insect screen, which allows the farm to not use any toxic pesticides, insecticides, or herbicides during the growing process. And the recirculation process from the farm’s NFT system uses about one-tenth of the water a traditional farm usually uses. And since soil is not used, there is no chance of contamination through runoff.
Tyger River Smart Farm also utilizes various methods to conserve energy. Last year, for instance, Oates purchased and installed a large solar array behind the greenhouse that’s capable of producing enough electricity to power the entire operation.
Planning for the future
While hydroponic farming can be more lucrative than traditional farming and beneficial to the environment, it can also be challenging. Plants, for instance, require over a dozen essential nutrients that must be administered according to species, growth stage, and local conditions, such as water hardness.
“Hydroponic farmers have to understand how plants and nutrients interact in order to be successful,” Oates said. “We use a lot of automation, but we’re still dealing with living things that react to the environment. Luckily, I have a background in plants and can tell pretty quickly whether or not I need to make an adjustment to the system.”
Oates has hired three full-time employees since launching the farm in 2012, but he still spends up to 70 hours a week tending to plants in the greenhouse. “Hydroponics is a double-edged sword,” he said. “We get to farm year-round, which gives us a leg-up on the competition. But we don’t really get vacations or holidays because we have to get the work done when the plants demand it.”
Tyger River Smart Farm grows a variety of lettuces, chard, kale, and basil through the use of hydroponics — the method of cultivating plants without soil by instead using a nutrient-rich solution to deliver water and minerals to their roots. Photo by Will Crooks.
The industry forecast, however, makes all the hard work worthwhile, according to Oates.
The U.S. hydroponic industry has grown consistently the past five years and is projected to continue into 2022, according to market research group IBISWorld. Industry revenue rose 3.4 percent to a total of $848 million the past five years ending 2017. Its outlook declined to a yearly rate of 0.2 percent until 2022.
Oates hopes to reach new customers in the coming years by selling produce through local distributors. The farm has already partnered with a wholesale distributor to sell basil at numerous Ingles supermarkets across the Upstate and Western North Carolina.
He also plans to expand the farm by constructing another 13,000-square-foot greenhouse in 2019. “It will just be an addition to what we have now,” Oates said. “We really want to become an industrial operation, and we’re pretty close to that now, but this addition will pretty much complete that transition.”
Keeping Plant-Cell Motors On Track
Keeping Plant-Cell Motors On Track
Molecular brakemen keep transporter proteins in check until it’s their turn to move
By Talia Ogliore March 13, 2018
Biologists at Washington University in St. Louis have discovered the molecular brakeman that holds kinesins in check until it’s their turn to move. (From left:) Ram Dixit, Anindya Ganguly, Graham Burkart and Yuanwei Fan. (Photo: Joe Angeles/Washington University).
Fluorescent dyes light up the areas of activity for regulator IMB4 (red) along green microtubules in a growing plant cell. (Image: Dixit lab)
Within both plant and animal cells, motor proteins act like the engines in a busy train system. They shuttle material in the cell from one location to another. And just as commuter trains travel a predictable route in a defined direction, their volume of transport is commensurate with need. At rush hour, more trains are in operation. At midnight, there’s no point in running trains every 10 minutes.
In a growing plant cell, motor proteins called kinesins work as transporters that haul materials built in one part of the cell to the place where they are needed. Kinesins travel along tracks of polymers known as microtubules to get where they are going. Moving cargo costs the cell energy and resources, and this process is closely controlled to prevent waste.
Now biologists at Washington University in St. Louis have discovered the molecular brakeman that holds kinesins in check until their cargo is needed.
Ram Dixit (right), with postdoctoral fellow Anindya Ganguly. (Photo: Joe Angeles/Washington University)
The importin IMB4 is a regulator that controls a kinesin specifically involved with building the plant cell wall. It works by physically binding to the kinesin, said Ram Dixit, associate professor of biology in Arts & Sciences. IMB4 holds the kinesin in an inactive state — protecting it from degrading while it waits — and prevents the kinesin from traveling along a microtubule until its cargo is needed. The new research is published in the journal Developmental Cell.
“The cell wall is like the plant’s exoskeleton, and building it is one of the growing plant’s most important functions. We have identified a key molecular regulator that closely controls cell wall deposition by physically binding to a kinesin,” Dixit said. “We still don’t know what signals cause IMB4 to release the brakes, but we now understand how it holds kinesins back until they are needed.”
Ready movers
A rigid cell wall is an essential and energetically expensive investment for a plant. The cell wall confers strength and enables the cell to withstand the turgor pressure that is necessary for growth.
In Arabidopsis plants, cell wall deposition depends on a kinesin-4, called Fragile Fiber 1 or FRA1. FRA1 was identified more than a decade ago, but a 2015 study in Dixit’s lab confirmed that its motility and abundance were correlated with cellular growth rates.
Postdoctoral fellow Anindya Ganguly, lead author of the paper, was intrigued by what the research team had seen. In rapidly growing cells of seedling stems, they saw lots of FRA1 kinesins moving along microtubules. But further down the stem, where the cells had ceased to elongate, the motor proteins were gone.
“Similar to rush hours, when plants are rapidly growing, you need to deliver a lot of cell wall material to keep up with growth,” Ganguly said. “Efficient, high-volume transport depends on having a lot of motor proteins. The regulator we discovered keeps a surplus of these transporter proteins around during times of rapid growth.”
Postdoctoral fellow Anindya Ganguly hand-pollinates Arabidopsis plants. (Photo: Joe Angeles/Washington University)
Ganguly and co-authors discovered that the importin IMB4 binds directly to the motor domain of the FRA1 kinesin. Then, using a combination of mutant analysis, microscopy of FRA1 within living cells and protein biochemistry, the team showed that this interaction inhibits the movement of FRA1.
“This importin essentially jams the motor, the engine of the kinesin,” Dixit said. “You inhibit mobility by virtue of prohibiting its association with its track.”
“The site where we think it binds, based on some analysis we did here, includes amino acids that are very conserved in other kinesin families in both plants and animals,” Dixit said. “So we think that there’s a good chance that this mechanism might be generally applicable.”
Twisted sister
With a handle on IMB4, researchers now have a better understanding of the mechanical workings of the engines of cell wall deposition. Another study published by the Dixit lab this month identifies a regulator involved in building the scaffold on which kinesins move.
In this study, the researchers examined a mutant Arabidopsis plant that exhibits a twisted growth pattern. Its leaves and stems swirl back in on themselves; its roots are tangled and skewed.
These so-called spiral mutants suffer from misaligned microtubules (the “tracks” that the kinesins walked along in the other study). In the mutant, severing proteins were thought to snip and shorten the microtubules at the points where they cross over each other.
Postdoctoral fellow Yuanwei Fan is lead author of a new study that discovered a protein that regulates the minus-end dynamics of microtubules. (Photo: Joe Angeles/Washington University)
But when Dixit and postdoctoral fellows Yuanwei Fan and Graham Burkart set out to parse intracellular activity in the spiral mutant, they uncovered a more interesting and nuanced mechanism. Importantly, they discovered that the plant-specific SPR2 protein regulates the minus-end dynamics of microtubules in the mutant.
Microtubules have a fast-growing and more dynamic end, identified as a “plus” end, and a slow-growing, less dynamic “minus” end. Microtubules grow and shrink from the plus side, while the minus side has generally been considered static in plants — until now.
Remarkably, in the spiral2 mutant, the minus-ends are extremely dynamic and shorten at much higher rates compared to wild-type plants.
Graham Burkart in the lab. (Photo: Joe Angeles/Washington University)
“Not only did we find that this protein localizes to the minus end, in plants, and regulates the minus-end dynamics, but we were able to recapitulate that behavior in vitro,” Dixit said. “We can say that this protein and this protein alone is sufficient to localize to the minus ends, track the minus ends, and stabilize them.”
Interestingly, the SPR2 plant protein shares some characteristics with mammalian proteins that stabilize the minus ends of microtubules in the tissues that line the surfaces of organs and in neurons.
This separate, microtubules work is funded by the National Institutes of Health, and is published online in advance of the March 19 issue of the journal Current Biology.
Keeping track of cell shapes and functions
Taken together, this new research on the regulators of motor proteins and microtubules helps explain the inner workings of plant cells that gives rise to their shape and enables them to alter their growth in response to developmental and environmental signals.
RELATED STORY
NSF announces new Science and Technology Center
The work on IMB4 and the FRA1 kinesin is part of Dixit’s effort with the Center for Engineering MechanoBiology (CEMB), a National Science Foundation-funded science and technology center jointly led by Washington University and the University of Pennsylvania. Within CEMB, Dixit leads a research cohort focused on determining how cells adapt to, and change, their mechanical environment.
“The center’s focus is really to uncover, understand and ultimately be able to control the role of mechanical forces writ large on biological systems,” Dixit said.
“One of the thing that’s unique about the center is that it brings together both plant and animal systems. That hasn’t been done before,” Dixit said. “The idea is that we will be able to uncover some universal principles that are applicable to both kingdoms.”
The Center for Engineering MechanoBiology (CEMB) is a multi-institutional Science and Technology Center funded by the National Science Foundation (NSF) to advance the study of mechanical forces in molecules, cells and tissues in plants and animals. Washington University partners with University of Pennsylvania to lead the CEMB; other partners include: the University of Maryland; the New Jersey Institute of Technology; Bryn Mawr College; Alabama State University; and Boston University.
Funding for this research was provided by: Current Biology publication: This work was supported by National Institutes of Health (NIH) (R01 GM114678) Developmental Cell publication: This work was supported by the Monsanto/Norman Borlaug Corporate Fellowship; the Center for Lignocellulose Structure and Formation, an Energy Frontier Research Center funded by the U.S. Department of Energy, Office of Science, Basic Energy Sciences (DE–SC0001090); and the National Science Foundation (MCB–1121287) and the Center for Engineering MechanoBiology (CMMI-1548571).
ARTS & SCIENCESBIOLOGYCELL BIOLOGYCENTER FOR ENGINEERING MECHANOBIOLOGY (CEMB)MECHANOBIOLOGY
Media Contact: Talia Ogliore
John Kerry And Howard Schultz to Headline The 4th Edition of Seeds&Chips
SEEDS &CHIPS 2018:
John Kerry And Howard Schultz to Headline The
4th Edition of Seeds&Chips
· The Summit opens on May 7th with Howard Schultz, Starbucks Executive Chairman, one of the largest and most influential companies in the advancement of CSR.
· On May 8th, Former US Secretary of State John Kerry will discuss the impact of the food system on global affairs and sustainable policy initiatives.
Milan, 2018 Feb 22th - Former Secretary of State John Kerry and Starbucks Executive Chairman Howard Schultz have been announced as two of the Keynote speakers to appear at Seeds&Chips - The Global Food Innovation Summit, the largest food tech event in the world. The fourth edition of the Summit, the brainchild of Seeds&Chips founder Marco Gualtieri, will take place at MiCo, Milano Congressi, from 7 to 10 May 2018.
Howard Schultz, Executive Chairman of the largest coffee chain in the world, will open the Summit on May 7th. Milan holds a special place in Mr. Schultz’s career path, as it was on a visit to the city that he understood that coffee was more than a beverage, it was an experience. Schultz was convinced that the Italian experience of coffee beverages like lattes and cappuccinos, and the community that develops around this shared passion, was a valuable formula ripe for international export. He departed from Starbucks and took his enthusiasm for coffee cultures to Il Giornale, a coffee bar chain that grew into a very successful brand. It was so successful in fact, that Il Giornale purchased Starbucks in 1987, and Schultz became President and CEO of the company that first inspired him. Today, Starbucks is one of the world’s most successful companies, valued at $77 billion, with more than 21,000 stores around the world.
Former Secretary of State John Kerry drawing on his vast experience in International Affairs Kerry will address the Summit on May 8th, where he will discuss the importance of climate change to the food system and the challenges that we face in securing a sustainable future. Exploring solutions to environmental challenges has been a central theme in Kerry’s political career as well as his subsequent humanitarian work. John Kerry’s appearance on the Seeds&Chips stage follows the 2017 keynote address by President Barack Obama, who chose The Global Food Innovation Summit to deliver his first post-presidency remarks. The Global Food Innovation Summit represents an important opportunity for Secretary Kerry’s message to reach an important sector of the tech world, as food becomes an increasingly important aspect of sustainability.
Marco Gualtieri, Founder, and Chairman of Seeds&Chips, said this about the 2018 Summit: “This year’s edition of Seeds&Chips has four incredible international figures taking the stage on each of its four days. We are honored to officially announce the first two, Howard Schultz and John Kerry, who set the standard for the quality of Keynote speakers at the Summit. Last year President Obama, with his extraordinary charisma, paved the way towards uniting the goals sustainability with food, the environment, and the climate in a debate which raised the level of international discourse. Seeds&Chips is committed to continuing along this path with the knowledge that our message and the new models, innovations, and opportunities related to food must reach every corner of the planet"
John Kerry
Exploring solutions to environmental challenges has been a central theme in Kerry’s political career. In 2009, he was appointed as the Chairman of the Senate Foreign Relations Committee where he assumed a key leadership role on foreign policy and national security issues facing the United States. Upon his appointment as Secretary of State under President Barack Obama in 2013, the United States made climate change and sustainability a central feature of their foreign policy portfolio. Kerry spearheaded the bilateral talks between the US and China in 2014 which resulted in a cooperation agreement between two of the most powerful nations in the world. Most notably, Kerry was instrumental in securing US participation in the 2015 Paris Agreement, a sweeping international accord to reduce carbon emissions that were signed by almost 200 countries around the world. In his work since leaving office, John Kerry has been a tireless advocate for environmental awareness and has founded a number of initiatives aimed at tackling the challenge of climate change. Kerry’s ‘Our Oceans’ Foundation has generated commitments valued at $9.24 billion and committed to protecting 9.9 million square kilometers of the world’s oceans.
Howard Schultz
Growing up in a working-class family in Canarsie, Brooklyn, Mr. Schultz experienced first hand the struggles that American families face in order to make ends meet. Coffee figured early in his career: upon graduating with a Bachelors of Science degree, Schultz worked for Hammarplast selling European coffee machines in the United States. His position led to his first encounter with The Starbucks Coffee Tea and Spice Company, a small operation founded in 1971 that sold high-quality beans to retail outlets. In 1982 he was hired as the Director of Retail Operations and Marketing for the young company, and in 1987 he became CEO of the company. Under Schultz’s stewardship, Starbucks has been an early proponent of corporate social responsibility, and its 2016 Global Social Impact Report outlined the company’s vision for the future with a particular emphasis on sustainability, greener retail, and community engagements. In May 2016, Starbucks issued a $495.6 million sustainability bond to use its influence in the coffee supply chain to improve working conditions for farmers and combat the environmental risks to coffee farms around the world.
***
Seeds&Chips, The Global Food Innovation Summit, founded by entrepreneur Marco Gualtieri, is the largest Food Innovation event in the world. The Summit is a showcase entirely dedicated to promoting innovative food solutions and talent from around the world, with an exhibition hall for innovators to present their work. Together, actors from all points in the global food chain discuss the themes and projects that are changing the way in which food is produced, transformed, distributed, consumed, and recycled. At the 3rd edition of the Global Food Innovation Summit, President Barack Obama made his first post-presidency appearance as a Keynote speaker, taking his place among 300 speakers and 240 exhibitors from around the world. In four days, the Summit recorded 15,800 visitors and 131 million social media impressions. The fourth edition of The Seeds&Chips Global Food Innovation Summit takes place at MiCo, Milano Congressi, from May 7-10, 2018. Among the speakers scheduled to appear are Former US Secretary of State John Kerry and Howard Schultz, Executive Chairman of Starbucks.
This Startup Is Building The Techiest Indoor Farm In The World
This Startup Is Building The Techiest Indoor Farm In The World
Vertical farming startup Bowery says it's building the most technologically sophisticated indoor farm in the world. Courtesy of Bowery
By BETH KOWITT
February 28, 2018
Indoor vertical farming startup Bowery is in the process of building a second facility which it claims will be the most technologically sophisticated indoor farm in the world.
The operation will be in Kearny, N.J., and grow 30 times more produce than its current indoor farm that’s located nearby, and supply 100 types of leafy greens and herbs for customers like Whole Foods and Foragers.
In May, the New York City-based startup raised a $20 million Series A from investors including General Catalyst, GGV, and GV (formerly Google Ventures), with capital from the round going toward building the new farm.
Bowery is applying robotics, machine learning, and predictive analytics to the agriculture sector, a segment of the economy that has been slow to adopt technology and digital advancements.
The company has developed what is says is a proprietary software system, complete with a robust network of sensors that takes in data in real time to determine outcomes like the quality, texture, color, and yield of its plants. “The software is the brains of the farm,” says Bowery CEO and founder Irving Fain.
Small adjustments—water flow, light intensity, temperature, humidity—can then be made in response to data inputs to impact outcomes like taste and flavor, such as growing a mustard green that’s got a spicier pick.
“These changes get pushed out automatically into our system,” says Fain. “The precision and level of control is unparalleled.”
Fain says that Bowery is more than 100 times more efficient than a square foot of farmland, in large part because the startup can grow 365 days a year independent of season in a completely controlled environment. Bowery doesn’t use any pesticides or agri-chemicals. Normally out in a field that would lead to reduction in yield, but Bowery has more crop cycles per year, grows twice as fast as a field, and has higher yield per crop cycle, says Fain.
The Bowery model is also predicated on a growing demand for local food. Since the farm is located in New Jersey, its produce goes out to the tri-state area. “We see very strong demand nationally and internationally right now for high quality locally produced consistent produce,” Fain says.
Because the produce is grown close to the point of consumption, “not as many players sit between us and the final consumers.” That level of efficiency helps keep costs down, Fain explains.
The National Organic Standards Board recently voted on whether hydroponics—essentially crops not grown in soil—could be certified as organic. While the board voted yes, Fain says that Bowery wasn’t involved in those conversations and isn’t focused on the organic certification.
“We’re growing post-organic produce,” he says. “It’s the next evolution.” Organic, he explains, still allows for pesticides—something his operation does not use
“It’s a better product for us and better way of growing and less destructive to the earth,” says Fain. “We’re using technology to grow the purest food possible.”
Indoor Vertical Farming: Digging Deep in Data
Indoor Vertical Farming: Digging Deep in Data
Geoff Spencer | Microsoft Writer
February 27, 2018
When it comes to farming, Ken Tran digs deep – not in dirt, but in data. He doesn’t drive a tractor and he doesn’t pull a plow. But he is helping to sow the seeds of a new type of agriculture – one that is nurtured by machine learning and artificial intelligence.
Ken is a Principal Research Engineer with Microsoft Research and his mission is to help perfect new ways of growing food and feeding the world scientifically, sustainably, and profitably.
In its way, digital technology is writing a new chapter in the story of agriculture. Once upon a time, about 12,000 years ago, humans began to give up hunter and gatherer lifestyles for farming. Across the ages, more secure food supplies saw the number of the people on the planet grow from maybe a few million people in Neolithic times to more than 7 billion today.
And through all those millennia, farmers have literally battled the elements. They have read the seasons and bred new crop types largely through trial and error. By the late 20th century we had increased food production with mechanization, fertilizers, herbicides, pesticides, irrigation and a lot more. Today, humankind is growing more food than ever. But, here’s a crucial question: How long can we keep farming like this?
Ken Tran, Principal Research Engineer, Microsoft Research
Ken has his doubts. “The planet’s population is growing, and the amount of arable land is diminishing. There are threats from climate change and pressure on resources, like water,” he explains. “At the same time, our cities are expanding. More and more consumers want food that is fresh, safe, nutritious, varied and available.”
In short, agriculture is being squeezed at one end by pressure on finite resources, and at the other by never-ending demand.
Moreover, there is so still a lot we don’t know about the vagaries of the environment, and even about plants themselves. We still “hope” for good harvests. We still “pray” for rain, and we still “worry” about early frosts, late snow, unexpected floods, prolonged droughts, tenacious weeds, and hungry pests. The natural world is full of uncertainty and lot of farming is still based on good luck and guesswork.
The game-changing component here is the ability to collect high-quality data and very quickly.
When we are confronted with big issues like this, science and knowledge often offer a better way. And for Ken, and technologists like him, that better way lies in digital transformation. Agriculture, he argues, is one of many sectors of human endeavor that is falling under the spell of the 4th Industrial Revolution. Like so much else in the modern world, farming is being disrupted by data that can supply answers and produce solutions.
In many locations around the world, new data-driven techniques anchored in the cloud are being introduced to farm life. Microsoft is leading the movement through its Farm Beats program. For instance, small plot farmers in India rely on digital tools to work out when best to sow their crops and so enjoy more bountiful harvests. In New Zealand, farmers are using the Internet of Things to best deploy spraying to best irrigate their fields.
Ken, who is originally from Vietnam and is now based at Microsoft’s headquarters in Redmond in the U.S. state of Washington, is part of this overall effort. But he occupies a different place: His research is indoors.He is focused on improving the output and efficiency of “indoor vertical farms”. These are enclosed spaces where everything that is required to grow crops – light, atmosphere, temperature, water, and nutrients – is supplied, controlled and constantly monitored to produce data that in turn is used to develop better techniques and better results.
Indoor vertical farms, which are sometimes called “plant factories”, rely on hydroponics. This soil-less water-based way of growing plants has been around for decades. What is different now is the arrival of cloud computing, which has given rise to data-based techniques aimed at producing better yields and better food at cheaper cost and in sustainable ways.
“The game-changing component here is the ability to collect high-quality data and very quickly,” he said on the sidelines of an international conference on indoor agriculture that was recently held in Singapore. “With big data, we use machine learning in the cloud to analyze and produce models with optimal configurations – say for the intensity of light to create better yields, or lower electricity costs, or what is the best ratio of nutrients that we should provide the plant to produce good food and higher yield.”
Indoor vertical farm technology is still being perfected and there are many variations. In theory, all crops could be grown this way. But the greatest potential is for leafy green vegetables, along with some fruits and herbs. High-calorie foods, including cereals, like rice and wheat, and vegetables, like potatoes, are probably best grown in the field – albeit under more optimal, data-driven conditions.
Eri Hayashi from the Japan Plant Factory Association
Eri Hayashi, of the Japan Plant Factory Association, specializes in airtight and thermally insulated rooms where “control” is a crucial factor. And, it is here that data comes into its own.
“On a traditional outdoor farm, environmental factors control how plants grow,” she explains. “In a plant factory, we can control the environmental factors – so we control how plants grow rather than the other way around. And, a closed environment is a great way to collect data quickly. We call the needs of a plant ‘a plant recipe’. The plant needs light, carbon dioxide, nutrients, and water. There are so many combinations. Until now we have only been able to find set points on some of the combinations. So, we need AI’s help to find more combinations for numerous plant recipes.”
Both Ken and Eri see opportunities to trial new ways of doing things. For example, “in a closed plant factory, we can pump in extra carbon dioxide to promote faster plant growth with oxygen produced as a byproduct. That might mean using a greenhouse gas for good,” says Ken.
Closed environments also mean better control of pests and disease – and the elimination of chemical pesticides and herbicides. Water, which is largely lost to the soil and atmosphere on a conventional farm, can be used sparingly in a closed continuous cycle.
“We can reduce water usage by 99 percent or more compared with land farms. We can also reduce the use of nutrients and waste by minimizing input and maximizing out,” Ken says.
AI-controlled indoor vertical farming also opens up the prospect of farms in urban and industrial areas that can be productive in all seasons and in cost-controlled ways in all sorts of building and spaces. And, that could significantly change the way cities source food and feed themselves. By way of example, let’s look at a supermarket not far from where Ken and Eri were being interviewed in Singapore, a city-state with virtually no space for conventional farming of its own. Its shelves were stocked with produce from around the world, like lettuce from Australia, strawberries from South Korea, beans from the European Union, and grapes from Peru. Local indoor farms potentially could reduce that dependence on imports that are now constantly flown or shipped in.
Acknowledging the advantages, Asian cities, particularly in China and Japan, are fast-adopting this technology with hundreds of indoor vertical farms – and Ken only sees this trend growing there as well as across North America and Europe.
READ: AI for Earth can be a game-changer for our planet
Automation – through AI, machine learning, and robotics – promises to bring down the cost of labor and other operations at a time when the age of farmers is climbing around the world and the economics of agriculture is fluctuating. This will allow smaller entrepreneurial farmers, as well as big operators, to establish niche on-demand services for customers. It could be lifestyle-changing.
“In 10 years it is very possible that many apartment buildings in cities will have their own indoor farms,” Ken says. “In a few years’ time, there will be a lot more online delivery companies. So, you can grow indoors and package at your farm. Your customers will just go online and order a delivery. The time from farm to your fridge could be around two hours or so – just like a pizza delivery now.
“It means fresh, locally available, cheaper and healthier food for potentially millions of people.”
- Additional images featured in this report are of indoor vertical farming activities conducted by SananBio in Xiamen, China.
The EDEN-ISS Laboratory Starts Its Greenhouse Operations
The First Seedlings Have Been Planted
The EDEN-ISS Laboratory Starts Its Greenhouse Operations
Now it's getting serious: The EDEN ISS laboratory in Antarctica has been set up, the first seedlings are placed in the growth cabinets, and the majority of the team of the German Aerospace Center (DLR) is back in Germany after eight weeks of travel. For DLR scientist Paul Zabel, who will be the only member of the EDEN ISS team to stay in the Antarctic until the end of 2018, this means that wintering in the Neumayer Station III of the Alfred Wegener Institute (AWI) begins.
Cucumbers, tomatoes, and peppers will start as the first cultivated plants on the southern-most point of the world. "Our goal is to make sure there will always be something to harvest in the coming months," explains DLR project manager Daniel Schubert. With those proceeds, the diet of the ten-man wintering crew will be supplemented
Photo: DLR German Aerospace Center
The last few weeks have been exhausting for the scientists and engineers who assembled a working greenhouse for the eternal cold of Antarctica from the delivered container parts. Minus 5 to minus 10 degrees Celsius and a decent wind made the work much more exhausting than in Bremen, where the EDEN ISS laboratory was tested for the first time. And these temperatures will drop significantly in the coming weeks.
In addition to the adverse weather conditions, however, the isolated location, which makes the delivery of fresh food impossible, brings the scenario close to a mission to Mars. With Paul Zabel, just nine overwinterers will be living in the Antarctic station over the next few months - a team on a space mission would also be small. "But that's exactly what we wanted to test - with our laboratory, under realistic environmental conditions, we want to produce space tomatoes and space lettuce in an environment like this," says Daniel Schubert from the DLR Institute of Space Systems.
Photo: DLR German Aerospace Center
From basil to lemon balm
In addition to tomatoes, cucumbers, and strawberries, the scientists are planting leafy lettuce, rucola, radishes, peppers, basil, chives, parsley, lemon balm, and mint. The plants are growing under artificial light. Instead of soil, that would have no place on a long-term space mission, a nutrient solution is feeding the cultivated vegetables and herbs. The water in this closed life support system is recycled - it will only leave the container inside the harvested greens.
"All subsystems such as lights, irrigation, air circulation system and cameras are tested and are working properly." However, the harsh environment in which the greenhouse is located has also caused some problems: the researchers had to look for a solution when condensation was precipitated in their containers. "It is just quite different if the container is in a city or in the Antarctic," says Schubert. Building the structure was troublesome. If a tool was needed, someone had to walk 400 meters, back to the Neumayer Station. Not only did all of this make for a strenuous time for DLR's team, but it also brought a wealth of experience needed for a later mission into space.
More photos and information about the project on the DLR website.
Need For Modern Technology Use In Agriculture Stressed
Use of modern techniques and technologies in Agriculture is the need of the hour which carries equal significance for both the businessmen and the men of science and technology.
Need For Modern Technology Use In Agriculture Stressed
Rukhshan Mir (@rukhshanmirpk) February 14, 2018
Use of modern techniques and technologies in Agriculture is the need of the hour which carries equal significance for both the businessmen and the men of science and technology
LAHORE, (UrduPoint / Pakistan Point News
Use of modern techniques and technologies in Agriculture is the need of the hour which carries equal significance for both the businessmen and the men of science and technology.
It was the upshot of the speeches delivered at a seminar on 'High-Value Agriculture' held here at Lahore Chamber of Commerce & Industry on Wednesday. The LCCI President Malik Tahir Javaid, Ceo Yuksel Seeds, Turkey Yaqub Yuksel, Convener LCCI Standing Committee on Mechanized & High Value Agriculture Mian Shafqat Ali, Ex-vice Chancellor Arid Agriculture University, Rawalpindi Dr Rai Niaz Ahmed, Dr Khawaja Asif, Mian Shaukat Ali, Faisal Iqbal Sheikh and Naeem Hanif also spoke on the occasion.
The experts said that there was a dire need for reforms in the agriculture sector and addition in the cropped area as a country could not afford to stay where it was today in terms of cropped areas and per hectare yield, because it was already running well short of per capita food availability.
They said that yield gap in the four major crops of Pakistan was three times from the best producers in the world such as China and Egypt.
They said that low yield had contributed to the poverty in rural areas besides forcing the country to import agriculture produces to feed its population.
Malik Tahir Javaid said the agriculture sector of Pakistan continued to be the single largest and dominant driving force for growth which contributed almost 19.5 percent in Gross Domestic Product.
It was the main source of livelihood for 42.3 percent of total labour force despite the fact that agriculture mechanization in Pakistan was very limited. He said that area under cultivation for important crops accounted for 23.85 percent of the value added in overall agriculture.
Wheat accounted for 9.6 percent of the total value added in agriculture and cotton production was 10.67 million bales. For the sake of increasing the share of agriculture sector in GDP, the existing area of cultivation had to be increased on war-footing.
Malik Tahir Javaid said that due to lack of technology usage in the agriculture sector, we face the problem of crops yields gaps. The average yields production in the agriculture sector of Pakistan was far below the level of those countries that used the technology in their agriculture sector, he said, citing that level of yields of different crops was 50 to 83 percent lower than the average of other countries of the world.
He said the prospects of Pakistan's economic prosperity heavily depended on the performance of agriculture sector. It had to be evaluated that government was giving subsidy to farmers at various stages of purchasing fertilizers, pesticides, seeds as well as selling their output at support prices but still this sector had not succeeded in enhancing the level of productivity.
He said that in the present scenario of water scarcity, the sustainable food security of Pakistan had to be ensured by way of adopting new techniques. "There are many developing countries like Pakistan which are encouraging corporate farming and in parallel to that, they are fostering high-value agriculture that includes vertical farming, hydroponics farming, aquaponics farming and arctic farming etc.
If government helps the farmers in acquiring these technologies at affordable prices then it is highly likely that new employment opportunities will be created and the productivity will also increase." Mian Shaukat Ali said that Chamber of Commerce and Industry played an important role to promote agriculture sector of any country.
All Chambers of Commerce and industry of Pakistan should pay attention to agriculture so that they could highly contribute to the development of this sector. He said that another problem of the agricultural sector was lack of agricultural graduates or their non-seriousness towards agricultural developments, adding that had they worked for the development of this sector seriously it would be beneficial for the country.
What If We Could Grow Delicious, Nutrient-Dense Food, Indoors Anywhere In The World?
This Computer Will Grow Your Food In The Future
What if we could grow delicious, nutrient-dense food, indoors anywhere in the world? Caleb Harper, director of the Open Agriculture Initiative at the MIT Media Lab, wants to change the food system by connecting growers with technology. Get to know Harper's "food computers" and catch a glimpse of what the future of farming might look like.