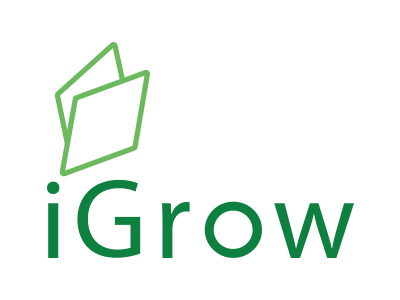
Welcome to iGrow News, Your Source for the World of Indoor Vertical Farming
Rensselaer Polytechnic Institute Lighting Research Center Releases New Report on LED Horticultural Lighting Systems
The Lighting Research Center (LRC) at Rensselaer Polytechnic Institute has published a new report on the energy and economic performance of LED horticultural luminaires.
Rensselaer Polytechnic Institute Lighting Research Center Releases New Report on LED Horticultural Lighting Systems
By urbanagnews
May 16, 2018
The Lighting Research Center (LRC) at Rensselaer Polytechnic Institute has published a new report on the energy and economic performance of LED horticultural luminaires. The LRC evaluated key factors such as power demand, life-cycle cost, luminaire intensity distribution, and luminaire shading. Of particular importance is the fact that the LRC considered the effectiveness of the entire lighting system for a controlled growing environment.
The research team found that for a given growing area, energy savings were possible with some of the tested LED horticultural luminaires compared to the tested high-pressure sodium (HPS) and metal halide (MH) horticultural luminaires, when meeting the same photosynthetic photon flux density (PPFD) criterion, but there was remarkably wide variation among products.
The LRC chose PPFD as the primary metric for the evaluation because, for plants, PPFD is analogous to photopic illuminance on a work surface in an architectural application. Just as it is only valid to compare the power densities of alternate lighting systems at equal illuminance levels on the work plane, the power densities of alternate horticultural luminaires should only be compared when they provide the same PPFD on the plant canopy. The LRC found that, on average, approximately three times as many LED horticultural luminaires would be needed to provide the same PPFD as a typical 1000-watt HPS horticultural luminaire layout.
For this project, the LRC developed an equal-PPFD-based framework for evaluating and comparing horticultural luminaires, which includes 11 luminaire-specific metrics and 5 application-specific metrics to provide growers with the most accurate information regarding any given horticultural luminaire’s performance. The LRC used this framework to evaluate a total of 14 horticultural luminaires, including 10 LED products. The evaluation included photometric testing, application simulations, and life-cycle cost analysis.
The results of the evaluation show that stakeholders can be misled by considering luminaire efficacy alone. Rather, the luminaire intensity distribution and layout to reach a criterion PPFD are necessary for an accurate life-cycle cost analysis. The LRC report provides a technology-neutral framework that stakeholders can use to evaluate lighting systems.
“Upon analyzing our data, we were intrigued by how intensity distribution and layout emerged as key factors in system performance,” said LRC Research Scientist Leora Radetsky, who authored the report.
When choosing a lighting system for a greenhouse, growers should consider the size and number of luminaires needed, because luminaires block the daylight from reaching the plants. The LRC shading analysis found an increase in shading from LED luminaires compared with HPS luminaires due to the size of the luminaires and the fact that more are needed to provide the same PPFD. The shading from LED luminaires reduces daylight in a greenhouse by up to 55% compared with a 5% reduction in daylight from HPS luminaires, thus more electric energy could be needed for lighting with the LED systems, depending upon the available daylight.
In a recent LRC survey, 75% of growers identified the cost of LED horticultural lighting to be a barrier to adoption, therefore it was important to include a life-cycle cost analysis in the report. The LRC found that three of the tested LED horticultural luminaire lighting systems had lower life-cycle costs and the remaining seven had higher life-cycle costs than either of the two 1000-watt HPS lighting systems that were tested.
“Energy use and life-cycle costs vary widely among LED and HPS lighting systems used in controlled environment horticulture,” said Radetsky. “It has been the standard approach for many years in the field of architectural lighting, and is becoming readily apparent in horticultural lighting, that we must conduct complete system energy and life-cycle cost analyses to generate an accurate picture of which technology would work best for each particular application.”
The project was funded by the Lighting Energy Alliance and Natural Resources Canada. Members of the Lighting Energy Alliance include Efficiency Vermont, Energize Connecticut, National Grid, and the Northwest Energy Efficiency Alliance.
View the LED and HID Horticultural Luminaire Testing Report.
About the Lighting Energy Alliance
The Lighting Energy Alliance (LEA) at Rensselaer Polytechnic Institute’s Lighting Research Center is a collaboration of members who pool their funds to advance lighting research and education that is of common interest. Since launching in 2014, LEA has worked to identify effective new ways to save energy, quantify the savings, and support its members in implementation.
About the Lighting Research Center
The Lighting Research Center (LRC) at Rensselaer Polytechnic Institute is the world’s leading center for lighting research and education. Established in 1988 by the New York State Energy Research and Development Authority (NYSERDA), the LRC has been pioneering research in solid-state lighting, light and health, transportation lighting and safety, and energy efficiency for more than 30 years.
LRC lighting scientists with multidisciplinary expertise in research, technology, design, and human factors collaborate with a global network of leading manufacturers and government agencies, developing innovative lighting solutions for projects that range from the Boeing 787 Dreamliner to U.S. Navy submarines to hospital neonatal intensive-care units. LRC researchers conduct independent, third-party testing of lighting products in the LRC’s state of the art photometric laboratories, the only university lighting laboratories accredited by the National Voluntary Laboratory Accreditation Program (NVLAP Lab Code: 200480-0).
In 1990, the LRC became the first university research center to offer graduate degrees in lighting and today, offers an M.S. in lighting and a Ph.D. to educate future leaders in lighting. With 35 full-time faculties and staff, 15 graduate students, and a 30,000 sq. ft. laboratory space, the LRC is the largest university-based lighting research and education organization in the world.
About Rensselaer Polytechnic Institute
Rensselaer Polytechnic Institute, founded in 1824, is America’s first technological research university. The university offers bachelor’s, master’s, and doctoral degrees in engineering; the sciences; information technology and web sciences; architecture; management; and the arts, humanities, and social sciences.
Rensselaer faculty advance research in a wide range of fields, with an emphasis on biotechnology, nanotechnology, computational science and engineering, data science, and the media arts and technology. The Institute has an established record of success in the transfer of technology from the laboratory to the marketplace, fulfilling its founding mission of applying science “to the common purposes of life.”
Veteran Tesla Engineer Leaving For Greener Pastures: AgTech Startup Plenty
Nick Kalayjian, a high-ranking Tesla engineer who joined in its shambolic early days before Elon Musk was CEO and has worked on all its products from the Roadster through the Model 3, is joining Plenty, an ag-tech startup backed by SoftBank and Jeff Bezos that hired another top Tesla veteran last year.
JUN 7, 2018 The Little Black Book of Billionaire Secrets
Veteran Tesla Engineer Leaving For Greener Pastures: AgTech Startup Plenty
Plenty
Long-time Tesla engineer Nick Kalayjian is leaving the carmaker after nearly 12 years to help design highly efficient vertical farms for San Francisco startup Plenty.
Nick Kalayjian, a high-ranking Tesla engineer who joined in its shambolic early days before Elon Musk was CEO and has worked on all its products from the Roadster through the Model 3, is joining Plenty, an ag-tech startup backed by SoftBank and Jeff Bezos that hired another top Tesla veteran last year.
A vice president of engineering reporting to Doug Field, Tesla’s engineering chief who’s currently on leave, Kalayjian becomes San Francisco-based Plenty’s senior vice president of engineering this month. He's not leaving Tesla because of dissatisfaction or friction, but a desire to tackle another big societal challenge after working to advance clean vehicles and energy for nearly 12 years, he told Forbes.
“The mission of Plenty is potentially bigger than the electrification of transportation or the grid,” he said. “The energy consumed, the impact on the environment of farming all over the world is massive, and it's a problem that needs a kind of engineering focus Tesla applies to vehicles. I think there's a lot of opportunity to have a big impact.”
Plenty
Nick Kalayjian, a Tesla vice president of engineering, is switching gears to design Plenty's indoor, vertical farms.
The company he joined in 2006 has evolved from a shoestring operation that avoided death in 2008 into a leader in electric vehicles with a $54 billion market cap and over 37,000 employees worldwide. Yet Tesla has struggled to fulfill Musk’s long-held promise of mass-producing vehicles average carbuyers can afford, namely $35,000 Model 3s. And regardless of his motivation, Kalayjian is one of many notable exits this year. They include Matthew Schwall, an engineer working with federal investigators reviewing an Autopilot-related crash who joined Alphabet’s Waymo; the departure of Chief Accounting Officer Eric Branderiz and vice president of finance Susan Repo; Autopilot chief Jim Keller who joined Intel ; and former global sales and service chief Jon McNeill, who took a job at Lyft in February.
Still, Tesla shares jumped 9.7% on June 6 after Musk told attendees at the company’s annual shareholder meeting that Model 3 output would hit a goal of 5,000-units/week by the end of the first half and that $35,000 versions of the car could be built in volume in early 2019. An emotional Musk was also visibly relieved that proposals to remove him as Tesla chairman and oust three board members failed to win shareholder support.
Kalayjian will find familiar faces at his new company, which has more than a dozen former Tesla staff, including Kurt Kelty, who until last year was a core member of its battery tech team and essential to Tesla’s partnership with Japan’s Panasonic. Kelty joined Plenty in October as senior vice president of operations and market development.
"Productizing" Farms
Co-founded by CEO Matt Barnard, Plenty is a unicorn in the fast-developing indoor agriculture space, luring Silicon Valley talent and capital to create high-yield vertical farms that use a fraction of the energy and water needed for field-grown crops. SoftBank Vision Fund was lead investor in Plenty’s $200 million Series B round in 2017, pushing total funding to $226 million. The company has started generating revenue from its South San Francisco farm and adds a commercial growing operation in Seattle this year. It will then expand across the U.S. and into international markets.
Kalayjian is a Stanford University-trained engineer, who also has a degree in physics and multiple patents for work done both at Tesla and Apple, his previous employer. So why does a company planning high-yield indoor farms that grow affordable produce close to where it will be sold and consumed need someone with cutting-edge engineering chops?
“We're ‘productizing’ farms,” Barnard said in an interview. “These are very dense, highly resource-efficient farms. It's a very complex engineering problem.”
Plenty
Plenty co-founder and CEO Matt Barnard says the company needs cutting-edge engineering to create its high-tech "productized" indoor farms.
“It's super important for us to have a production system to grow food at prices that fit into everyone's budget,” he said. “Few people in the world that have led engineering development and productization processes that move as fast for systems that are as dense and complex as what Nick and his teams at Tesla have done.”
From the outside, Plenty farms look like warehouses or big box stores, and range in size from 100,000 square feet to 250,000 square feet, or the equivalent of 2.3 to more than 5 acres. Inside, plants grow sideways on vertical columns between 7 feet and 20 feet high.
With precise use of water, nutrients, temperature control and light, its farms "can grow anywhere from a couple hundred acres to 1,000 acres of conventional field production on a volume basis over the course of a year," Barnard said. And they do that using 1% of the water a traditional farm would. Growing close to where the crops are consumed also cuts shipping costs, fuel use and carbon exhaust.
Like at Tesla, the initial focus will be on higher-end products: organic produce priced in line with the field grown variety. But Plenty aspires to build farms to feed parts of the world that currently have to import produce because of climate and local growing conditions that aren't optimal.
"When I joined Tesla it was the appeal to really cause a revolution in the transportation industry," said Kelty, who worked on its battery team from March 2006 until last August. A doezen years later, with most major global automakers planning to electrify their model lines, "that revolution is happening," he said.
Plenty "is very similar to the early days at Tesla, where we're going to revolutionize the agriculture industry. And it's an industry that's bigger than the EV industry," Kelty said. "The impact on people is going to be much greater. The impact we can have on impoverished areas, especially in Africa, is just huge.
Plenty
Plenty's indoor farms, set up inside warehouse-like buildings take up just a few acres but can produce the volume of a conventional farm growing on hundreds of acres of land, while using just a fraction of the water.
New System Significantly Reduces Power Consumption of Vertical Farms
New System Significantly Reduces Power Consumption of Vertical Farms
30 May 2018
The energy efficiency of vertical farms could soon be boosted by as much as 20 percent, thanks to a new system developed by a student from Brunel University London.
©Brunel University London
vFarm, by design student Jonny Reader, uses OLEDs – organic light-emitting diodes – and smart automation to significantly reduce the amount of power used in vertical farming.
The new system will be unveiled at Made in Brunel in June.
“Current agriculture uses 70 percent of the world’s pumped water, and accounts for 70 percent of water contamination and 33 percent of global warming,” according to Reader.
“Vertical farming is a way of taking it inside – you use five percent of the water traditional farming uses and don’t need pesticides, because you’re in an enclosed environment.”
Current vertical farms use traditional LEDs, however, vFarm uses OLEDs, which produce less heat and have a higher energy efficiency. Importantly, OLED panels are also significantly thinner than their LED equivalents, meaning greater yields can be achieved at shorter heights.
While the price of OLEDs is currently prohibitive in most circumstances, Reader predicts costs will fall as the technology gains traction.
vFarm also aims to increase efficiency and yield through the use of automation, using a series of sensors to help control factors such as temperature and humidity.
“It can read the current temperature, how much water there is in the reservoir, light intensity and how much power it’s drawing,” said Reader. “Everything is automatic.”
While vFarm is currently in the prototype phase, Reader has been invited to take part in an official Knowledge Transfer Partnership with Hydrogarden.
“Right at the start of the project I went up to Hydrogarden to do some general research and find out about their gardens,” said Reader.
“When I finished I took it back up to show them, and they said they’d been trying to do something similar with small control units. If it all goes through, I’ll be working with them for the next three years, developing this kind of technology.”
vFarm, along with a host of other innovative new devices designed by final-year design students from Brunel, will be on display at Made in Brunel, which runs at the Bargehouse, Oxo Tower Wharf, London, from June 15–17.
How Technologies Can Save Our Earth’s Resources
It’s not a secret that within a bit more than a century, the world science has made a quantum leap that led to numerous technical and technological inventions in various fields and industries.
How Technologies Can Save Our Earth’s Resources
By Ansh Sharma
May 17, 2018
It’s not a secret that within a bit more than a century, the world science has made a quantum leap that led to numerous technical and technological inventions in various fields and industries.
Today, we can hardly imagine our life without the Internet, mobile telecommunications, wireless connections, and a whole variety of gadgets and items that make our life easier, work more efficiently, and leisure more enjoyable. However, the biggest paradox about this vigorous technological breakthrough is that technologization and industrialization severely impact the environment and exhaust natural resources. In fact, we are slowly “killing” the Earth, which is our common home, with our own hands.
Initially aimed at life improvement, today, the technological progress might lead to a global disaster. Greenhouse effect, freshwater, and food shortage as well as the lack of other vital resources are not a myth anymore but rather a frightening reality. For this reason, the world leading scientists and inventors join their efforts to stop this and make technologies work for the humanity and help solve our environmental problems.
Renewable Energy
Solar water heaters, solar chargers, and solar powered outdoor lights, as well as other major and minor heating and lighting solutions based on the solar energy, are already common things for many households and even enterprises all over the world. With the energy and fuel being the biggest issues, modern technologies are being maximized and optimized to efficiently turn the power of wind, sun, and water into energy to replace traditional energy sources.
Let’s Drive Electric Cars
Carbon dioxide (CO2) emissions destroying the ozone layer are the biggest hazard for the atmosphere. Industrial plants powered by natural gas, coal and other types of fuel as well as ordinary vehicles, quickly growing in numbers, are the major CO2 generators. While it is still pretty hard to find a truly functional technological solution for factories and large-scale plants, today, we can easily replace a gasoline-powered vehicle by an electric car to cut at least some part of harmful CO2 emissions. Recently, scientists have also introduced a device that can recycle CO2 emissions to obtain a hydrocarbon fuel.
Living in Smarter Homes
There has been developed a great many technologies to set up a so-called smart and environmentally friendly home. These are mostly intended to reduce energy loss and, as a result, energy consumption by controlling heating, air conditioning, lighting, and ventilation systems operation.
Growing population needs more food while growing cities leave less land for traditional agriculture. Vertical farms that can be arranged in urban skyscrapers will help produce crops all year round even in non-agricultural areas. Meanwhile, robots designed specifically for farming can handle anything from simple planting to complex monitoring that will let greatly optimize basic processes.
Though many environmental technological inventions still require optimization, improvement, and enhancement to become viable and fully functional, great chances are that in a decade or so, they will become mainstream and will seem the only correct solutions.
WUR In Front Window Amsterdam Bookstore
WUR In Front Window Amsterdam Bookstore
The front window of the Athenaeum bookstore in Amsterdam is being transformed into a WUR-themed display over the next two weeks. Not only does it showcase photos of food and agriculture, it also features items such as a custom-made vertical farm. The display window is being decorated as a way of familiarising the major urban centres in the west of the Netherlands regarding important Wageningen research domains in celebration of the hundred-year anniversary of Wageningen University & Research.
Organised byWageningen University & Research
Date: Mon 28 May 2018 until Sun 10 June 2018
Would you like to take a look at the bookstore yourself? That is no problem at all. Virtual visitors can also get a preview of this special display window via a webcam. Of course, there is no space large enough to house a complete representation of what the experts in Wageningen are working on, but it does provide others with an idea of the hundreds of research projects that are currently underway.
Examples of our research
What needs to be considered for vertical farming with LED lighting? What exactly would printing food involve? These are some examples of topics that researchers at Wageningen University & Research are addressing every day.
Food and agriculture are the primary research domains at Wageningen University & Research. Wageningen is practically synonymous with agriculture. This comes as no surprise, as Wageningen has been at the top of the list in various significant rankings related to the field of agricultural research.
Agriculture and food
When accounting for the big picture, agriculture and food cannot be approached separately. For instance, just think about the challenge facing all of humanity in the future: feeding 10 billion people by 2050. Others have put it this way: we (the farmers) will have to produce more food in the period from now until 2050 than we have since agriculture first came into existence. Not to mention that we have to do it as efficiently and sustainably as possible.
Preview of this special display window via a webcam
- www.myfoscam.com
- Login: info@tupola.nl
- Password: Fosc@m890
- Or use the Foscam App on your phone
Vertical farming
Today’s rapidly urbanising societies challenge our food system to feed cities. Vertical Farming can provide a secure and sustainable route to provide cities with fresh food. In a vertical farm plants are grown under fully controlled conditions in buildings in many stacked layers without solar light. Advantages of vertical farms are: no pesticides, no nutrient emission, only 2-4 litres of water per kg produce, much less land use, less waste, and lower food mileage, though electricity use is still high. Vertical farming not only allows to greatly improve quality (taste, aroma, appearance, shelf life, nutritional value, safety) but also to provide guarantees on vegetable quantity and quality every day of the year independent of weather, climate change, or location.
LED Lighting
Vertical farming has become possible due to rapid developments in LED technology. LEDs are energy efficient and are available in different colours, which can be used to control the growth and quality of the plants.
The plants can utilize all the visible light for photosynthesis, i.e. the production of sugars in leaves which are the basis for growth of the plant. Red is often more efficient for photosynthesis than other colours.
The plant has also a number of photoreceptors that can sense different colours of plant, which can greatly affect the growth, development and quality of plants. Which mixture is optimal for the plants, may depend on many conditions and is being researched in depth at the moment.
3D food printing
Innovation in food and agriculture has come a long way in the past century, resulting in the production of more food than ever before. However, the food industry is facing new challenges due to rapid societal changes: in 2040 there will be 9 billion people to feed; there is an increasing demand for personalized, nutritious, and healthy food; and food production should be done in an affordable way without harming the environment. Radical innovations are required to meet the demands of the near future. 3D printing provides the food industry the opportunity to adapt and change their production processes. In order to accelerate and facilitate the application of 3D food printing, three Dutch research organizations, TNO, Wageningen University & Research and Eindhoven University of Technology, have joined forces to develop a comprehensive 3D food printing research program.
State-of-the-art
3D food printing is an innovative manufacturing process. A complete 3D object is built up layer by layer, based on a 3D computer design, and without the use of moulds or assembly steps. 3D printing was initially used in the manufacturing industry, where materials like metals and plastics were used. However, over the past years a much wider range of printable materials and thus applications have emerged. Over the last years Wageningen Food & Biobased Research and TNO has been jointly developing and applying 3D printing technologies in food production. In multiple international research projects we have shown great potential for the layer wise building of food products. The 3D food products are well-structured and based on multiple materials by using different types of base ingredients. 3D printing has the unique capability to use precise amounts of materials in very specific 3D locations. It gives food manufacturers the opportunity to make improved or even completely new food products with novel shapes, textures, structures, and flavours. Based on our knowledge 3D food printing, currently developed applications are being implemented in supermarkets and out-of-home settings. Supermarkets are testing the 3D printing of customized cakes and candies, and various start-up companies have been established that either sell 3D food printers or offer 3D printed pasta, candy and chocolate.
Western Dakota Tech Grads Seek Solution To Food Deserts
Western Dakota Tech Grads Seek Solution To Food Deserts
May 24, 2018 | By JOHN CONWAY
RAPID CITY, S.D.
Food deserts in Rapid City are nothing new, but they were back in the headlines last year when three full-service grocery stores announced they were closing their doors.
Now, a group of young engineers and entrepreneurs think they have found a cost-effective solution to the problem. And they're finding it right here in Rapid City.
The closure of Prairie Market and two Family Thrift grocery stores in October greatly expanded the food deserts of Rapid City. Food deserts are places where people do not have reasonably convenient access to full-service grocery stores that sell a variety of nutritious food options.
In the absence of full-service grocery stores, convenience stores - which are abundant in these areas – have become a primary food source for the local residents. Mary Corbine, food security manager with Feeding South Dakota, says this situation is far from ideal.
"Convenience stores just don't have access to all the nutrition that a person needs, and they tend to be more expensive," Corbine said. "So, therefore, they're utilizing [more of] people's resources."
And without that balanced nutrition, people in food deserts tend to have higher rates of preventable disease.
"If you are eating higher calorie foods, [processed foods] and higher sugary foods, you probably will have more obesity, more heart disease and also more diabetes due to increased weight," said Cindy Gates, a clinical dietitian at Regional Health Rapid City Hospital.
The problem caught the attention of electrical trades students at Western Dakota Technical Institute (WDT). They are using their skills to develop a new system to help provide healthy food options to the residents of food deserts all year.
"The great thing with our system is that we can set it down there within the communities,” said Nick Smith, a member of the WDT aquaponics team. “Therefore, we eliminate the transportation costs of getting food to them."
Aquaponics is a combination of aquaculture and hydroponics. An aquaponics system raises fish and uses the fish excrement to feed plants. An aquaponics system produces not just fresh fish, but also fresh fruits and vegetables more effectively than traditional agriculture. The system can grow produce anywhere in the world, year-round.
"The yield first would be much greater than a normal garden, like a community garden,” Smith said. “We can grow plants twice as fast and produce about three times as much as a normal garden."
Aquaponics isn't new, but it has required a lot of human labor to operate and maintain the filters and pumps and monitor things like water levels. The WDT aquaponics team is working to automate the system, requiring less human input.
"We pretty much train the computer to do [the work] for them,” Smith said. “The computer takes care of all that, and all they have to do is come in and harvest [the produce]."
The system, if successful, will also recycle its own water and bring year-round fresh food to not only food deserts, but actual deserts where water is scarce, reducing the cost of nutritious food options.
"The only water input we have is when we initially build it,” said Joseph Cattin, another member of the WDT aquaponics team. “After that, it should be totally off the grid and not need any other input."
The team also hopes to eventually develop a solar power source for the system, allowing it to be installed in areas without access to electricity, making the system entirely self-sustaining.
The team’s work on the aquaponics technology has won them a spot as a finalist in the National Science Foundation Community College Innovation Challenge. They will travel to Alexandria, Va. in June to present their project to industry and members of Congress.
This 'Carbon Farm' Grows Plants Using CO2 Harvested From People Inside The Building Below
This 'Carbon Farm' Grows Plants Using CO2 Harvested From People Inside The Building Below
May 15, 2018 By Bruce Gellerman
The fifth-floor stairwell at Boston University's College of Arts and Sciences opens up to the sky.
Here, amid heating and air conditioning vents and ducts, an unusual crop is being collected, says Nathan Phillips, professor of earth and environment.
"We're growing food on the rooftop at BU and we're harvesting the carbon that comes out of the breath of all of the people inside of the building," he says. "And we're breathing it out every day at 40,000 parts per million in our breath."
In the atmosphere, CO2 — now at record levels, the highest in recorded history— is a powerful heat-trapping gas responsible for the rapidly changing climate. But carbon dioxide is also a critical factor in growing plants.
About a decade ago, Phillips got the idea of putting the high levels of CO2 that build up in classrooms to good use.
The carbon farm with spinach plants ready for harvesting (Bruce Gellerman/WBUR)
"We supercharge the photosynthetic process when we breathe on our plants," he says.
High concentrations of CO2 can make you sleepy, even kill you, but green plants love the stuff. In fact, it's essential for photosynthesis. That's the process by which plants use sunlight to convert carbon dioxide, minerals and water into the food they need — and produce life-sustaining oxygen for us.
The BU rooftop is dotted with metal mushroom air vents.
"The vents in many buildings, they have to exhaust the air, so they're blowing it out anyway," Phillips says. "We're just capturing it."
"I don't know of anyone else who's doing this," says Sarabeth Buckley, Phillips' grad student. "We're calling it the carbon farm at the moment."
The carbon farm is Buckley's Ph.D. research project, and she's collecting data.
Mechanical engineering students from BU laid coiled conduit from building vents. They carry carbon dioxide-rich classroom air. They also built ambient collectors that act as experimental controls. At the end of the pipes are spinach plants set in milk buckets at different distances.
"We're still working out the best physical system to move the air to the plants," Buckley says. "But at least in terms of the pilot study that I did, where I kept the plants closer to the vent, I did get some positive results from that. So the plants grew larger next to the vent, versus away from the vent."
The largest plants are at the end of eight coiled conduits. They look like octopus arms, carrying a strong and steady flow of waste CO2 from the academic hot air vents to leaves.
The possibilities of carbon dioxide-fed plants are literally breath-taking.
Urban greenhouse gardens are becoming increasingly popular. Hospitals, restaurants, even supermarkets are turning empty acres of space atop buildings into food-producing farms. But roofs are stressful environments. Hit with direct sun, they're hot, dry and windy, and rain can run off quickly.
But Buckley's yields in earlier tests have shown substantial improvements over typical rooftop crops. The possibilities of carbon dioxide-fed plants are literally breath-taking.
"For our initial pilot study there was around a 50 percent increase in growth," she says. So: faster, cheaper, better.
Buckley will harvest the plants, carefully count and weigh them, and put them in an oven to dehydrate, and weigh them again two more times.
"You also need the dry weight because that's what's most commonly reported in science," she says, "so we'll just have to dry them and then they'll become little crispy spinach plants, and that's not very tasty."
So while Buckley may be able to enjoy the fruits of her Ph.D. labors from her carbon farm experiment, she won't be eating these veggies.
This segment aired on May 15, 2018.
Related:
- Climate Summit For Mayors To Be Held In Boston In June
- How The New England Aquarium Seeks To Urge Visitors To Act On Climate Change
- Most Mass. Voters Say Climate Change Is Bringing More Frequent Or Severe Storms
- Report: Boston Sea Level Projected To Rise 1.5 Feet By 2050
Bruce Gellerman Reporter
Bruce Gellerman is an award-winning journalist and senior correspondent, frequently covering science, business, technology and the environment.
The Benefits of Wireless Technology In Hydroponics
The Benefits of Wireless Technology In Hydroponics
Hydroponic growing has certain inherent advantages. Plants grown in a nutrient solution will mature up to 25 percent faster and deliver up to 30 percent more yield than plants grown in soil. Wireless IoT systems are a key element of achieving these kinds of results.
Hydroponic growing depends on control. As an indoor growing method, hydroponics requires fine management of environmental factors such as heat and humidity. This soilless style of growing depends on careful control of nutrient dosing and water flow.
Wireless IoT connectivity makes it possible for a grower to implement the necessary levels of control without having to be constantly on site. Automation drives productivity in the hydroponic grow, and wireless connectivity is what enables automation, giving the grower the ability to set schedules, receive up-to-the-minute information on grow conditions, and have remote control capabilities.
Wireless IoT systems deliver off-site connectivity, typically via a smartphone app. With the ability to monitor off-site and adjust settings in response to environmental needs, the grower can exercise a high degree of control. Likewise, a system of alerts can be established to automatically signal the grower if conditions need to be adjusted.
Wireless IoT basics
The essential wireless IoT system requires only a few components. They may be purchased individually, but it’s more common these days for a farmer to acquire a single integrated system that delivers all of the needed elements, in order to ensure a seamless deployment.
At the heart of the system is a wireless controller that pulls data from various sensors and monitors, and delivers it to the end user—typically the farmer with a smartphone.
The system also includes various sensors designed to track environmental factors, such as heat, temperature, and humidity. Other sensors may track pH in the nutrient mix or monitor water levels across the hydroponic grow.
This ability to remotely monitor water quality is of critical importance. In traditional soil-based growing, plants take in nutrients from the earth. Hydroponically grown plants pull their nutrients from enriched water, which must be closely monitored so that nutrient levels never drop too low or rise toxically high.
Setting up a well-regulated hydroponic system can take a lot of time and requires some finesse. Some growers may find the need to constantly monitor and balance pH and nutrient levels daunting, but wireless can help overcome these challenges.
A pre-configured wireless IoT system with all the needed components can simplify the process of getting a hydroponic grow up and running. Over the long term, wireless control significantly eases the management burden, making it possible to achieve positive outcomes while lowering the overall time and effort required to sustain a successful grow.
For more information:
Growlink
875 Kalamath
Denver, CO 80204
+800-432-0160
info@growlink.com
growlink.com
Publication date: 5/24/2018
Montreal-Based Start-Up Motorleaf Enables Greenhouse Farmers to More Accurately Forecast Their Future Harvests Using Artificial Intelligence
Montreal-Based Start-Up Motorleaf Enables Greenhouse Farmers to More Accurately Forecast Their Future Harvests Using Artificial Intelligence
It all started in 2016 in rural Sutton (Quebec) when Ramen Dutta, now CTO of Motorleaf, had trouble finding friends to water his plants while he was away on vacation.
With a US$2.85 million round of financing, artificial intelligence start-up Motorleaf can revolutionize greenhouse growers’ crop planning, achieving major productivity gains and reducing greenhouse gas (GHG) emissions. The financing round comprised notably Radicle Growth, Desjardins Capital, Real Ventures, Fluxunit and BDC Capital. With their support, Motorleaf can be a game changer in this agri-food sector niche in industrialized countries.
Motorleaf develops yield-predicting algorithms and indoor growth sensors. Using these advanced technologies that monitor plant growing conditions, greenhouse vegetable and tomato producers can make better business decisions and reduce costs, energy in particular, as well as water consumption, a critical factor in many regions around the world.
“We’re ready to distribute our technology so farmers can meet their fullest potential and acquire an innovative cost-cutting tool within the controlled-environment agriculture sector,” said Alastair Monk, co-founder, and CEO of Motorleaf.
Predicting the amount of vegetables from a harvest is currently a time-consuming process. Agronomists count samples of vegetables, leaves, and flowers in a small area and that sample then serves to estimate the expected yield of the entire grow operation. Often imprecise, farmers are unsure if they will produce enough vegetables to meet contract obligations or know how much labour they will need to package their produce. If they produce too much, farmers try to sell their perishable goods quickly at rock-bottom prices. Using Motorleaf’s artificial intelligence and machine-learning algorithms, the digital agronomist software can acquire data from indoor growing conditions. In turn, the algorithms learn growing patterns in the greenhouse, which then can predict the size of future harvests.
Cutting harvest prediction errors by half
Harvest yield-predicting algorithms are the latest technology born from Montreal’s booming artificial intelligence sector. With this financing round, Motorleaf aims to further develop its software and sensors so that its equipment can acquire additional data from common indoor climate control and irrigation systems. Farmers can now adopt this technology with a small addition of Motorleaf equipment but without the need for dramatic changes to their greenhouse infrastructure.
“Better yield prediction is only the beginning for Motorleaf’s added value to this sector,” says Alastair Monk. “We’re ultimately producing dynamic grower protocols, which help manage everything from light and nutrients to predicting greenhouse diseases before they happen, and optimized growing conditions that increase return on investment – all based on real-time data.”
Initial trials of the technology since October 2017 in a 70-acre California greenhouse cultivating tomatoes demonstrated its value to farming. Client SunSelect reduced its error in predicting weekly tomato yield by half, resulting in significant cost savings for the grower. As a result of the improved predictability using Motorleaf’s technology, SunSelect has since abandoned manual yield predictions in favour of Motorleaf’s algorithms. See the SunSelect case study at https://bit.ly/2IxxeF9.
The province of Quebec has 900 greenhouses, half of which have an area of under 999 square metres
Data compiled by the Ministère de l’Agriculture, des Pêcheries et de l’Alimentation (MAPAQ) shows 900 greenhouses in 2016, including 356 specialized in vegetables, 388 in flowers and 156 mixed greenhouses, for a total area of 297.2 hectares (ha). The same data shows that the three regions with the largest greenhouse areas were Montérégie (77.8 ha or 26%), Laurentians (54.3 ha or 18%) and Laval(34.8 or 12%). As for the number of farms, Montérégie had 226 (or 25%), Laurentians 117 (or 13%), Chaudière-Appalaches 72 (or 8%), Centre-du-Québec 59 (or 7%), Laval and Lanaudière with 55 each (or 6%) and the Eastern Townships 51 (or 6%).
Inspired by dead plants
The idea for Motorleaf stems from the heartbreak of returning home to find your prized plants dried out. Living in rural Sutton, Ramen Dutta, CTO of the Montreal start-up, had trouble finding friends that could drive to his home and water his indoor plants while he was away on vacation. Being an agricultural engineer, he built an automated, sensor-controlled irrigation system that would become the foundation of Motorleaf’s technology.
SOURCE Desjardins Capital
US (NY): Startups Look To Redefine Indoor Agriculture
June 20-21, New York
US (NY): Startups Look To Redefine Indoor Agriculture
Six international agtech start-ups have been selected to pitch their technologies to a panel of ‘Sharks’ and an audience of 200 leading international indoor and vertical farming operators, agri-food businesses and VC investors at the upcoming Indoor AgTech Innovation Summit on June 20-21 in Brooklyn, New York.
AgTech Accelerator, a unique start-up venture development fund focused on discovering and developing emerging agricultural technology companies, is the Innovation Partner for the summit. Novel farming systems, such as those being showcased, have the potential to transform and modernize the global food system and are among AgTech Accelerator’s key strategic focus areas.
“Our mission is to identify and shape breakthrough research efforts that will improve efficiencies in the agricultural value chain, fuel the future of farming and enhance human health,” said John Dombrosky, CEO of AgTech Accelerator, who will serve as a Shark for the Technology Showcase.
“As the summit’s Innovation Partner, we’re supporting ground-breaking technologies that hold the promise to catalyze the global growth and adoption of indoor and vertical farming, a rapidly evolving space that provides an innovative way to increase food production in a healthy, sustainable and local way. The world of agriculture is moving toward a more sustainable model and we are steadfast in building the next generation of companies discovering and developing innovative farming solutions.”
Following a call for entries, six start-ups were chosen to present based on their fresh ideas and approaches as well as their robust go-to-market strategy. They will each have seven minutes to present their solution and outline business plan, followed by questions from the panel and audience. The presenting companies are as follows:
- Arugga, a start-up company from Israel, is developing an autonomous ground robot for the global greenhouse farming market, focusing first on tomato greenhouse farming. The Arugga robot will harness artificial intelligence to monitor and treat every individual plant, serving as an invaluable tool to pollinate flowers, optimize yield prediction and detect pests, diseases and other stress conditions with immediate treatment.
- City Farm Systems (CFS)’s protected IP offers the most sustainable, environmentally friendly and economically viable urban farms. The UK company’s CloudGro® approach uses cloud computing to manage automated, lightweight greenhouses. This eliminates the costs of distribution for the hardest to transport fresh produce by growing at the point of need using unproductive space and resources. AI and machine learning create grow-to-order crop plans and allow harvests to be buffered to match immediate demand, reducing waste and increasing sales.
- LUNA by iUNU is a comprehensive platform that combines continuous imaging with AI, machine learning and computer vision to give indoor growers advanced insights into plant health, readiness, yield forecasting, incipient disease, nutrient deficiency and pest detection. Called a ‘gamechanger’ by Greenhouse Grower magazine, LUNA creates an unparalleled integration of the growing operation to business support tools such as inventory, space and labor management.
- Phospholutions has developed an OMRI certified soil amendment to enhance growing substrate for improved fertilizer efficiency. The controlled-release technology soaks up key nutrients in the soil, maintaining plant availability, improving nutrient retention and plant uptake, and stimulating root growth. Less fertilizer needs to be applied, with up to 98% staying in the soil until it is taken up by the plant. The amendment can be recharged with nutrients for years to come offering benefits to the soil and cost-savings over the long term.
- PLANTX, based in Tokyo, Japan, is an indoor agriculture technology company that develops plant science and technology for vegetables in a pesticide free environment, and plant machinery which enables vegetables to grow five times more efficiently.
- Smart Spectrum develops intelligent software and sensor solutions that improve the quality, predictability and profitability of indoor horticulture through autonomous systems. Its core technology, AgEYE is the largest and most accurate deep learning platform completely dedicated to agriculture; which is used to modify environmental factors to produce uniquely different harvest characteristics of plants.
The summit will welcome major international operators from across the United States, Canada, Europe, the Middle East and Asia including Plenty, Shenandoah Growers, AeroFarms, InFarm, Gotham Greens, Badia Farms, Bright Farms, Church Brothers Farms, Bowery, FreshBox Farms, Square Roots and associations including the Japan Plant Factory Association (JPFA) and Association of Vertical Farming (AVF).
Co-located with Future Food-Tech (June 19-20), the Indoor AgTech Innovation Summit is part of the World Agri-Tech Innovation Series of summits hosted by Rethink Events, focused on international networking and deal-making for food and agribusinesses, solution providers, entrepreneurs and investors.
For more information:
Publication date: 5/24/2018
First Lettuce Harvested In Bio4safe Biostimulant Project
First Lettuce Harvested In Bio4safe Biostimulant Project
The Bio4safe biostimulant pilot project started off in August 2017. It's a collaboration between various partners from Belgium, France and the United Kingdom and is coordinated by the Belgian Test Center for Horticulture (PCS). They are researching the effects of biostimulants on nutrient use, tolerance against abiotic stress and crop quality. The aim of the project is to reduce water and fertilizer use by applying biostimulants in combination with innovative sensors.
In order to measure the effects of the biostimulants, various tests are being conducted with different crops, including tomatoes, lettuce, strawberries, chrysanthemums, and tulips. The lettuce tests take place at Pôle Légumes Région Nord in France. The first lettuce was harvested last week and is currently being examined by Yncréa Hauts de France, établissement ISA Lille (France).
Chrysanthemum trials
In a few weeks, Proeftuin Zwaagdijk will finish the first trials with chrysanthemums, which are investigating the effects of four different seaweed products and a mycorrhizal fungus. In addition to measuring the branch length and the fresh and dry weight, they will also analyze nitrogen absorption. A certain amount of the nitrogen isotope 15N has been applied to the potting soil in which the chrysanthemums are grown. By measuring the amount of this isotope present in the plants at the end of the test, it can be determined whether the biostimulants increased nitrogen absorption.
Seaweed as a biostimulant?
In addition to carrying out these tests, Noordzeeboerderij has worked on mapping both the existing and the potential biostimulant market. The potential of this market appears to be very substantial. Moreover, further research will be done about using seaweed as a biostimulant. For example, which varieties are being cultivated, and are they suitable for use as biostimulants?
Source: Proeftuin Zwaagdijk
Publication date: 5/21/2018
Photo Report: 6th Annual Indoor Ag-Con
Photo Report: 6th Annual Indoor Ag-Con
Networking opportunities, interesting speakers and exploring new technologies. On the sixth edition of the Indoor Ag-Con it was al present and we will inform you completely on it. But first get ready for some photos!
Organizer Newbean Capital every year unites the indoor farming industry in the Las Vegas Convention Center and on May 3rd & 4th this year it was no different. Networking opportunities were the main reason for many visitors to come to the event, but also the talks of the big players in the industry were visited very well.
The emerging indoor growing market attracts also many opportunists and it becomes clear during the event a lot is still to explore in the indoor farming market. From financing to closing the chain and from special bred varieties to focussing on the market, the indoor farming industry is developing rapidly but offers many opportunities for further growth.
An important topic in the industry is the rise of new crops. After the leafy greens of course, cannabis is also a settled crop by now, but what else is on the horizon? Strawberries for sure, but also other medical plants and growing opportunities are talk of town.
Over the next couple of weeks, we'll update you completely on the opportunities in this growing industry. Let's take a look at some photos first!
Check out the photo report here.
Publication date: 5/7/2018
Author: Arlette Sijmonsma
Copyright: www.hortidaily.com
UK: Will EDEN ISS Plant Cultivation Technologies Deliver Terrestrial Applications?
UK: Will EDEN ISS Plant Cultivation Technologies Deliver Terrestrial Applications?
The EDEN ISS research project in Antarctica is designed to help astronauts grow food in space and on other planets. It has produced its first crop: 3.6kg of lettuce, 70 radishes and 18 cucumbers. But will the new technologies the project aims to develop be useful on Earth?
Evolution and Design of Environmentally-closed Nutrition Sources (EDEN)
The ISS EDEN plant cultivation project is led by the Institute for Space Systems (ISS), a consortium of experts in human spaceflight and controlled environment agriculture from academia and industry.
The ISS also aims to identify possible developments of closed or nearly closed-loop plant cultivation systems that would enable terrestrial agriculture to be conducted in regions that are currently unsuitable.
It’s not the first research project to attempt to grow food in conditions similar to those in space – and astronauts are already growing individual plants on the International Space Station - but the consortium is researching key technologies that it hopes will be relevant to large-scale food production in space and on Earth. These technologies include:
- Nutrient delivery systems
- Bio-detection and decontamination systems
- Food quality and safety
- High-performance LED lighting systems
- New UK research into LED lighting
Dr Jim Monaghan, Director of the Fresh Produce Research Centre at Harper Adams University, is working with Cambs Farm Growers (part of the G’s group) to develop the use of LED lighting in the commercial propagation of young vegetable transplants and production of leafy crops.
LED lighting could enable optimised transplant production for field crops and allow year round production of leafy crops in vertical or indoor production systems.
Normally, transplants of lettuce and celery are grown under protection (such as glass) in the UK but seasonal light and temperature changes influence the production time. By manipulating the light environment it is possible to control the duration of propagation as well as characteristics of the transplant that may be beneficial when planted on into the field.
Currently, baby leaf crops are mainly field-grown in the UK in spring and summer then imported in winter. Using indoor growing technologies may enable UK growers to supply a year-round crop with potentially enhanced nutritional status.
Dr Monaghan said: “We have seen how we can manipulate plant growth rates and morphology through using different LED light spectra. These effects may have significant benefits when the plants are moved into the field. One challenge is the cost of LED systems and it will be interesting to see the LED developments produced by EDEN ISS and how much energy is required to power them.
In addition to his work at Harper Adams University, Dr Monaghan also teaches fresh produce courses offered through the Agrifood Training Partnership. Topics include post-harvest quality and advanced agronomy. Last year Dr Monaghan was involved in a series of training workshops for growers focussed on managing food safety risks in the production of fresh produce crops.
Training opportunities with the Agrifood Training Partnership
The range of crops that make up fresh produce is wide, covering root crops, leafy vegetables, bush fruit and tree fruit. The fresh produce sector of agriculture is fast moving, innovative and high value. The constant pressure to improve efficiency and come up with new crops has led to significant innovations and refinements in growing methods.
The Agrifood Training Partnership offers a range of short and full-time courses on crops and fresh produce including production, quality management, plant pathogens, sustainability and agricultural drones.
Short courses starting soon
- Applied Precision Crop Production starts 27 May
- Advanced Agronomy for Fresh Produce starts 3 June
- Fresh Produce Postharvest Quality Management starts 4 June
Winter courses
- Advanced Sugar Beet Production Management starts 31 October
- Potato Production and Management starts 21 November
For more information about our short courses, contact us on 0330 333 4530.
For more information:
AgriFood Training Partnership
The University of Reading
PO Box 226, Whiteknights
Reading RG6 6AP
T. +44 (0)330 333 4530
www.aftp.co.uk
Publication date: 5/7/2018
Tomatoes From Space Stations, Desert And Polar Regions
Tomatoes From Space Stations, Desert And Polar Regions
Have you ever dreamt of taming the desert? Of flying to the moon and back? Come and meet the pioneers of tomorrow’s world at the “Revolution in Food and Biomass Production (REFAB)”, October 1 and 2 in Cologne (Germany). The required technologies are available. Their smart integration pushes our limits beyond imagination and opens up a world full of possibilities. Even here on our planet. Bitter cold or burning heat, a smart integration of technologies allows crop cultivation even in the most extreme conditions on Earth or, taking it one step further, in space stations and on Mars.
Challenges
Following new pathways, previously unknown challenges have to be met with innovative solutions: LED lighted greenhouses, desalinization of seawater (in combination with aeroponic, hydroponic and aquaponic systems) as well as solar technologies and closed biomass cycles open up completely new areas for food production. These topics are one of the focal points of the REFAB conference, 1 – 2 October 2018, Cologne (Germany). Fully automated and controlled environments for agriculture are no longer just a dream.
Developed in the science laboratories of space agencies, first commercial systems are available. Key technologies are so-called hydroponic or aeroponic systems which allow growing plants without soil and with plant nutrition and water supply that perfectly fits the plants requirements. Research in this field is ongoing: Scientists of the European MELiSSA project developed systems for growing vegetables in Antarctica and even on space stations: LED illumination combined with temperature and nutrient control create a suitable environment for cultivating tomatoes, cucumbers or lettuce. Developed for life in space, these technologies enable food production basically everywhere.
Food for Mars
Researchers at Wageningen University (NL) are looking into the vision of food production and supply for a future Martian colony: How can future inhabitants sustainably produce sufficient food within the existing conditions? Which resources will be available? More importantly, what will be missing? The scientists are testing the cultivation of vegetables in a simulated Martian soil. An important issue is the usage of the available resources as efficiently as possible, e.g. organic waste and excrement. In addition, the scientists enrich bacteria and fungi in the soil to optimize the nutrient supply of the plants and breed bumblebees for pollination. The cultivation of potatoes, tomatoes, radishes and many more plants has already been successfully tested. The aim is to develop a sustainable ecosystem for the food supply of future colonies on Mars.
Christophe Lasseur from the MELiSSA programme as well as Wieger Wamelink and Joep Frissel from Wageningen University will present ways to sustainable agricultural ecosystems for Mars and the Moon at the REFAB conference.
Mankind’s old dream of a green and blooming desert is now within reach. Integrating and adapting different traditional and innovative technologies into various environmental conditions plays an important role to achieve this goal.
Although agriculture has always been practiced in arid areas, soil availability and quality as well as water availability remain limiting factors. The consequences of agriculture are salinisation and erosion of soil as well as decreasing groundwater levels.
Projects in the desert
Regions including large desert areas are intensively researching new ways to bring the desert to life in a sustainable way: In hydroponic systems, plants grow in a special nutrient solution so that vegetable cultivation is also possible on infertile land. In addition, these systems allow water savings of over 90% in fruit and vegetable cultivation. Several companies in the MENA region are already successfully commercializing these systems. Teshuva Agricultural Projects from Israel will present its solutions for agriculture under extreme conditions at REFAB.
The Sahara Forest Project from Norway will present its own vision of greening the Sahara at the conference. The heart of this project is the combined use of Concentrated Solar Power (CSP) and salt-water cooled greenhouses. These systems can be supplemented by various systems: Aquaculture/algae, salt-resistant hedges/trees as well as seawater desalinisation form an integrated saltwater-based food supply system in arid areas.
Agrophotovoltaics reinvents the classic stratification of natural vegetation. Fraunhofer ISE realized a project where photovoltaic systems and conventional crops are combined vertically on a shared patch of land. While wheat, potatoes or clover grass grow on a ground layer, photovoltaic systems are installed at a top layer in a few meters height. Resulting yield losses of both systems are more than compensated by the combined area use: This is a central milestone in increasing land use efficiency.
These and more projects and prominent companies will be presented at the conference “Revolution in Food and Biomass Production (REFAB)”, 1-2 October in Cologne, Germany. Altogether, 50 speakers and 30 exhibitors will show the future of food and biomass production (www.refab.info). The call for papers is open until mid of May, the preliminary program can be found online.
For more information:
Nova-Institut GmbH
www.nova-institute.eu
Italy: ENEA Patents Field Simulator To Grow Plants Indoor
Italy: ENEA Patents Field Simulator To Grow Plants Indoor
Science and technological innovation are advancing day by day and often change our lifestyles. First and foremost, they benefit producers, although the concept of cultivation is no longer strictly connected to open fields. What used to be a simple veggie plot could potentially turn into a super-Hi Tech micro-plot that can be kept in the house.
Microcosm cultivation
ENEA patented and developed the first microcosm for the indoor and extreme-environment cultivation of plants with a root and an aerial part (fruit-bearing trees, lettuce, basil, tomatoes, potatoes). It's a true Hi Tech field simulator that makes it possible to grow plants in environments that would usually be unsuitable for plant growth such as airports, undergrounds and shopping malls as well as in extreme environments such as the Poles, desert areas or within space missions. It replicates the growth pattern, production of beneficial properties and biomass that occurs in nature.
Created in collaboration with private entrepreneur Gruppo FOS, this innovative smart-agriculture system differs from greenhouses and traditional growth chambers for a series of elements, starting from architecture, the network of sensors that monitor environmental control, plant growth and reproduction to the LED precision lighting system employing selected wavelengths.
Luigi d'Aquino from ENEA's Nanomaterial and Device Laboratory
"The main innovation is the double independent chambers. One is a subterranean chamber destined to the growth of the root system and rhizosphere (i.e. organisms that live in the soil where roots grow) and the other is an above-ground chamber destined to the cultivation of the aerial part of plants and the phyllosphere (i.e. organisms living in the air)," explains Luigi d'Aquino from ENEA's Nanomaterial and Device Laboratory.
Although the chambers are independent and can be managed separately, they are actually interconnected - just like it happens in nature - thanks to the geseous exchanges through the root growth substrate (soil, compost or peat).
"We're currently experimenting the effectiveness of the microcosm paired with precision lighting. We have sowed and cultivated a field of basil plants of the same variety in a pot in our lab (a typically inhospitable environment for plants), in a microcosm under white light (they grew much more) and in a microcosm under precision lighting (plants developed a biomass dozens of times higher, with higher chlorophyll levels and even started the reproductive phase)."
Ecosystems that can replicate nature
Microcosms are true ecosystems that can faithfully replicate what happens in open fields. Specific environmental conditions are set and there are organisms that interact with vegetable functions such as pathogens or parasites.
Microcosms have been developed within the TRIPODE public private laboratory and are currently being developed further within the ISAAC Project, co-financed with over €4.7 million by Horizon 2020 and PON Imprese & Competitività 2014-2020 (ENEA, FOS and BECAR, a subsidiary of Beghelli, are part of it).
"Over the next three years, the ISAAC Project also aims at developing an innovative lighting system to effectively grow, develop and reproduce plants indoor and in extreme environments as well as supporting the well-being of human beings. We will go from a TRL 4 (Technology Readiness Level) to a TRL 7, i.e. from lab prototypes to practical application prototypes."
Practical applications
"Our patent could be the base to develop prototypes for research labs studying plant physiology, pathology and parasites, ecophysiology, ecotoxicology and soil ecology but could also be useful to develop prototypes to promote plant cultivation in unconventional environments with excellent market and commercial potential."
Publication date: 5/7/2018
Energy Is A Major Expense In Greenhouse Productions (between 10% and 25%).
Energy Is A Major Expense In Greenhouse Productions (between 10% and 25%).
Several solutions currently exist on the market to help reduce this energy bill. The dilemma is how to choose an optimal configuration adapted to the external climate, inner climate, and crop(s).
Hortinergy is the first online software that can simulate energy consumptions of an existing or planned greenhouse anywhere worldwide.
It is suitable for a diversity of clients, from growers to agricultural consultants or greenhouse equipment manufacturers. It takes less than 10 minutes to enter your parameters.
The library includes the major equipment available on the market: glass, plastic films, climate screens, etc. Equipment manufacturers can spotlight their branded products for select pre-set parameters to simplify the user experience.
Hortinergy is a decision-making tool to calculate the required dimensions of equipment and optimize the investment: users compare economical and technical scenarios with a simple online interface. A detailed report is sent for each scenario.
Hortinergy allows users to determine optimal configurations for energy savings, which can be up to 50% for renovations, and more than 70% for innovative greenhouse concepts.
In most cases, existing software programs offer only qualitative analyses. While a few are quantitative in nature, they are either not suitable for daily use or they provide limited modeling options.
Hortinergy is a real scientific breakthrough with:
ï Innovative algorithms that take into account greenhouse-specific parameters, such as: light transmission through the transparent cover, external and inner climate, canopy evapotranspiration, and crop types.
ï Dynamic calculations generated with GPS position anywhere worldwide.
ï Most of the functions of a climate computer regulation: day/night climate, screens, vapor pressure deficit, etc.
ï Models that simulate classic equipment (water tank, combined heat, and power (CHP), etc.) as well as innovative equipment (semi-closed greenhouse, active ventilation).
ï Outputs that include heating consumptions, dehumidification needs, photosynthetically active radiation (PAR) reaching canopy, etc. for hourly, monthly or annual periods.
ï Results validated by research centers with measurement campaign in classic and semi-closed greenhouses in France and in the Netherlands.
Multiple add-ons will complete our software.
For more information please contact us : alexandre@hortinergy.com - +33 (0)4 79 72 40 59 Agrithermic 17 avenue du Lac Léman – Savoie Technolac BP 60 269 -73 375 Le Bourget du Lac cedex - France
Scientists Want to Replace Pesticides With Bacteria
April 16, 2018
Scientists Want to Replace Pesticides With Bacteria
Indigo’s microbes could change Big Agriculture forever.
By Elizabeth G Dunn
Healthy microbiomes are increasingly recognized as critical to our overall health.
SOURCE: INDIGO AG
Fresh snow coats the sidewalks outside Indigo Ag Inc.’s Boston offices, but inside the temperature is calibrated to mimic spring in the Midwest. Hundreds of almost identical soy seedlings sit beneath high-intensity arc lamps, basking in the artificially sunny 60F weather.
The plants aren’t destined to stay identical for long. “We haven’t imposed the stress yet,” says Geoffrey von Maltzahn, the company’s lanky 37-year-old co-founder. The MIT-trained microbiologist gestures toward photos showing what happens when you apply Indigo’s signature product—a coating of carefully chosen microbes—to some seeds but not others before planting, then dial back the water supply: One shows a tall, flourishing stalk; the other, what looks like a tangle of shriveled leaves.
In humans, a healthy microbiome—the universe of bacteria, fungi, and viruses that lives inside all of us—is increasingly recognized as critical to overall health. The same is true of the plant world, and Indigo is among the dozen or so agricultural technology startups trying to take advantage of the growing scientific consensus. Their work is enabled by advances in machine learning and a steep reduction in the cost of genetic sequencing, used by companies to determine which microbes are present. Approaches vary: AgBiome LLC, with funding from the Bill & Melinda Gates Foundation, is studying how microbes can help control sweet potato weevils in Africa, while Ginkgo Bioworks Inc. announced a $100 million joint venture with Bayer AG to explore how microbes can encourage plants to produce their own nitrogen.
The grow room at Indigo Ag. SOURCE: INDIGO AG
Indigo is the best-funded of the bunch, having raised more than $400 million. To develop its microbial cocktails, Indigo agronomists comb through normal fields in dry conditions to see which plants seem healthier than average. They take samples of the thriving plants and “fingerprint” their microbiomes using genetic sequencing; once they’ve done this with thousands of samples, they use statistical methods to pick out which microbes occur most often in the healthiest plants. These proceed to testing, then large-scale field trials.
The company’s first commercial products are focused on improving drought tolerance, one of the most difficult traits to address through genetic modification. “It’s like a symphony,” founder von Maltzahn says of a plant’s reaction to water stress, “and GMOs are like slamming down on one note on one instrument.” Drought conditions are likely to become a greater threat to agriculture because of global warming. Indigo is also investing heavily in research and development efforts to see how microbes influence factors such as nitrogen use and pest resistance, aiming to reduce or even eliminate the use of synthetic pesticides and fertilizers as well as genetically modified seeds. With the general public rejecting chemical treatments and GMOs in favor of “natural” foods, Indigo is counting on a potentially multibillion-dollar market. So far, its microbe coatings have boosted cotton yields by an average of 14 percent in full-scale commercial trials in Texas and wheat yields by as much as 15 percent in Kansas.
Indigo’s microbe coatings have boosted cotton yields by an average of 14 percent in commercial trials in Texas. SOURCE: INDIGO AG
Indigo Chief Executive Officer David Perry doesn’t want to just market a suite of seed treatments, however. He wants to reshape the structure of the agriculture industry completely, competing not only with chemical companies such as Monsanto and Dow Chemical but also with agricultural distributors like Cargill and Archer Daniels Midland. Perry, a biochemist who grew up on a small farm in rural Arkansas, founded two pharma-related companies, a drugmaker he eventually sold for multiple billions of dollars and an online marketplace for research supplies that went public in 1999. After joining Indigo in 2015, Perry quickly zeroed in on a fundamental business challenge: Most farmers have no choice but to sell their harvest at commodity prices. Without the opportunity to earn more for using environmentally sustainable methods, they have little incentive to alter their ways.
For farmers to adopt Indigo technology, they’d need a buyer willing to pay a premium for non-GMO, pesticide-free products. So, Perry reasoned, Indigo would facilitate the sale. Today the company contracts upfront with hundreds of farmers to buy their entire harvest of, say, Indigo Wheat, at a hefty premium. “Now you’re growing a value-added product, and that starts to go directly to farm profitability,” he says. Indigo then sells the wheat to end users such as breweries, flour mills, and food companies, which have become more interested in transparency and control when it comes to the origin of their grains. Perry says he’s betting on a long-term shift away from commodity agriculture and toward specialty markets, as the coffee and cocoa industries are seeing.
While the science behind microbiome treatments is promising, Indigo has a long road ahead. Its success depends on proving that microbes can meaningfully influence more than just drought tolerance while at the same time scaling up to the kind of sprawling, complex operation that can buy and sell millions of bushels of grain from tens of thousands of farms.
Michael Dean, chief investment officer for the venture capital investment platform AgFunder Inc., sees Indigo’s technologies as potentially disruptive but suggests that one of the biggest challenges the company will face is persuading farmers to turn their back on comfortable relationships with Big Ag. “Farmers have tended to buy seed from the guy their dad bought from, and sold it to the same grain elevator,” Dean says. “This is going to make waves, and not everyone will be happy about it.”
BOTTOM LINE - Leveraging the plant microbiome to improve crop yields is more and more promising, but any upstarts will have a hard time getting between farmers and Monsanto.
Can A Nozzle Provide The Breakthrough Indoor Farming Has Been Waiting For?
Can A Nozzle Provide The Breakthrough Indoor Farming Has Been Waiting For?
3 May 2018, by Gavin McEwan
A British company says it can greatly extend the range of crops grown in indoor growing formats beyond the established leafy greens and herbs.
Images: Airponix
Discussions on the potential of urban and indoor farming invariably mention the need to feed a growing global population, forecast to reach 10 billion by the middle of the century, against a backdrop of climate change and depleted land and other resources.
But so far, for technical and economic reasons, the movement has largely targeted leafy greens and herbs — relatively high-value but low-mass, low-calorie crops. Indeed, one successful London grower specialises in "micro-salads" sought by higher-end retailers and restaurants that, for all their merits, are unlikely to displace much conventional farming or address food supply in the developing world.
This may be about to change though, thanks to a technological breakthrough by a British company. West London-based Airponix says it has overcome an obstacle to growing more high-calorie crops, thanks to spray nozzles adapted from printers.
Aeroponics is a variant of hydroponic growing in which plants’ roots are exposed to a nutrient-rich mist within a chamber, rather than sitting in a circulating water-and-nutrient solution. Like other indoor growing technologies, aeroponics has so far found a market in hobby growing more readily than in commercial horticulture, with several UK suppliers offering variants on the format on a range of scales.
That said, aeroponics is also the basis of what is claimed to be the world's largest commercial indoor growing facility, run by AeroFarms in a former steel mill in New Jersey, USA, and employing its own multi-tiered variant of the technology in combination with LED lighting to produce up to 900 tonnes of fresh produce a year.
But this too grows only salads. What has so far restricted aeroponic growing to such crops, Airponix explains, is that the size of the droplets in the chamber causes them to coalesce, precipitate out of the air and form larger droplets on the roots, inhibiting the uptake of nutrients and encouraging the growth of wastefully long roots.
Nutrient-rich 'fogs'
To address this, Airponix has worked with a developer of piezoelectric inkjet technology to engineer print heads that can emit nutrient-rich "fogs" — a term that Airponix contrasts with the "mists" of conventional aeroponics — comprising droplets that can be greatly reduced in size to below 20 microns, and indeed optimised to the needs of the particular crop.
These print heads also require less energy than other fog-making methods, are highly reliable and easy to install or replace under field conditions, says Airponix.
This allows the technology to extend into growing soft fruits, grapes, brassicas, root crops and even the cereal staples of rice, wheat and maize. Airponix says its own small-scale potato-growing trials show typical yields are around 50 times greater per hectare per year than from conventional farming, without the expense of heavy machinery, diesel or crop-protection products. Rather than capital-intensive glasshouses, or tech-heavy enclosed controlled growing environments, the growing system can be housed in simple polytunnels.
Airponix chief executive Michael Ruggier says: "Trials of our breakthrough technology show that we can produce crops such as potatoes with lower production costs and higher quality, competing strongly against conventionally grown new baby potatoes."
He adds: "The potential cost of the system is very low and requires little energy to operate. Manual labour is also greatly reduced because harvesting is a simple, clean process and root crops don't need washing."
Ruggier co-founded the company in 2016 with John Prewer, now its technical director, who developed and patented an early form of aeroponic growing more than 40 years ago, while its horticulturist and operations manager Barry Robertson was previously head of controlled environment horticulture at the John Innes Centre.
The technology has already garnered awards, including being named the overall winner in the Rushlight Awards for novel, clean technologies in January.
A-frame units
Airponix has now equipped a 1,000sq m glasshouse in Norfolk with its A-framed potato-growing units for development, testing and demonstration, thanks to a half-million-pound loan from Centrica Innovations. The glasshouse incorporates further growth-enhancement techniques such as imparting an electrostatic charge on the droplets for better adherence to and absorbption by the plants’ leaves and roots. A smart, fully automated system, operated by a mobile phone app, is also being developed.
The aim initially is "to demonstrate the yield quantities and the costs associated so that next year Airponix will be in a position to licence the technology", says a company representative, adding that it will also provide samples of the first crop, due next month, to supermarket retailers for evaluation.
"The type of potatoes that Airponix can grow and harvest are unlike anything currently being sold anywhere and has huge potential in both the fresh-produce and snacks categories," he points out. The company also hopes that selling this year’s remaining crop will provide revenue to enable it to extend its own glasshouse space and growing facilities next year.
Q&A: UVA i.Lab-Supported Indoor Farming Startup Beanstalk Still Growing After Y Combinator
Q&A: UVA i.Lab-Supported Indoor Farming Startup Beanstalk Still Growing After Y Combinator
3-May-2018
Source Newsroom: University of Virginia Darden School of Business
Beanstalk Farms founders Jack and Michael Ross are building their first production facility in Northern Virginia.
By Dave Hendrick
Newswise — Indoor farming startup Beanstalk Farms has come a long way in a short period of time. Jack Ross, a 2017 graduate of the University of Virginia’s School of Engineering and Applied Science, and brother Michael Ross started their venture in the incubator program at the Darden School-hosted W.L. Lyons Brown III i.Lab in 2017, building a prototype and learning as much as they could about the complicated world of fresh produce.
After the i.Lab, the Ross brothers — both of whom trained as engineers — successfully applied for a spot at Y Combinator, the Silicon Valley-based accelerator that has helped launch companies like Dropbox, Airbnb and Instacart, among hundreds of others.
Now back on the East Coast, Jack Ross recently spoke about his experience launching Beanstalk; the UVA network on both coasts; and his quest for faster, cheaper and better-tasting lettuce and spinach.
An edited transcript of that conversation follows:
Give us the pitch for Beanstalk.
Beanstalk Farms grows heirloom produce in automated indoor farms. What that means is we bring the field inside and that allows us to control absolutely everything around the growth of the plant. We like to say it’s always 65 and sunny in our facility.
So we can grow the highest-quality food, all-year-round, and we can actually grow it faster than you can outside because it’s a perfect environment. And we can grow it anywhere, so it can be produced very close to the end consumer.
What’s the innovation you are bringing to the table? What’s different?
Beanstalk’s greatest innovation is our automation of the indoor farming process. We are not the first to grow inside. That’s been done for quite some time. It has, up to now, been very expensive. Food grown indoors has not been able to compete with the price of produce grown in the field, and the biggest reason for that is labor goes up when you grow inside. Indoor farms lose all of the technology that a company like John Deere brought to the field.
My brother and I are engineers, and we took a very different approach to farming. We created a manufacturing line that grows a plant. So the labor is very, very low.
It’s a highly automated process and, on top of that, because we don’t have to design for human labor to tend to the crops, it’s much, much denser. So, in a very small amount of space, we can grow food to feed cities.
We can put that farm right in the city, and we can grow the highest quality food, using heirloom seeds that have been cultivated for thousands of years to be incredibly tasty and very nutritious. Also, unlike field-grown food, even some organic food, we do not use pesticides. This means our food is always clean and ready to eat.
Essentially, our automated systems allow us to sell at prices competitive with traditionally farmed food, and our precise indoor environment ensures we can grow the highest quality food anywhere in the world.
What was your experience in the i.Lab like?
It was great. It’s a wonderful time when you don’t really have anything set in stone. The community was very close knit and attentive. We were just starting out as a company, and learning who we should talk to and who could help us learn more about the problem we are trying to solve. Jason [Brewster], David [Touve] and Sandra [McCutcheon] were incredible in brainstorming solutions, refining our pitch, and connecting us to people that could help us better understand the food system. The i.Lab helped us get on our feet.
During the program, we spent most of that time trying to grow plants quickly and consistently. We knew that if we could do that, the rest of it would fall in line, as the engineering is our sweet spot. The rest of time was talking to customers. We were out talking to people from all different parts of the food system.
The food system is a really complex beast. From food getting off the field, it may change hands over half a dozen times. So we wanted to talk to chefs, restaurant owners, and distributors to understand the system. We found a couple of huge problems for all people involved.
First, finding a consistent source of quality produce is a really big problem.
People are looking for local produce and it just doesn’t exist everywhere. So sourcing was a big problem. And then just the volatility of the market. From week-to-week, prices can go up 800 percent. So that kind of volatility for a restaurant owner is awful.
To us, it was pretty clear we just needed to find a way to create a consistent, high-quality product and remove the risk factors.
So the i.Lab really pushed us to get out and talk to people. Thankfully, our hypothesis was verified and we graduated from the i.Lab Incubator knowing clearly what the problem is and having a rough idea of how we wanted to solve it. So that set us up perfectly for Y Combinator.
What’s the process like for getting into Y Combinator?
It’s quick.
The application is not terribly long. It’s about half a dozen questions on the business. They wanted to know a lot about the founding team. We heard back about a month later and they basically said, “You have an interview spot; it’s in a week for 10 minutes.”
So you have to drop everything you’re doing and fly out to Mountain View for a 10-minute interview. We got organized, and the i.Lab actually helped us get out there and coordinate with people while we were out there.
I thought it was going to be more Shark Tank-style, with a lot of accusatory questions. Not at all. They asked a few hard questions, and then it turned very quickly into brainstorming. What do you guys think you can do in the program while you’re here? What’s next for you?
It was a much warmer conversation than I anticipated.
What’s the program like once you’re in it?
It’s pretty hands-off. The biggest thing they do is they want you to pick a metric, a single metric for your business. And that is kind of your guiding light for three months of the program.
We picked cost because cost is really what drives purchasing decisions. So we focused on getting the cost of production to that of the field. We said if we can reach price parity with food purchased off the field, we can put this anywhere and maintain a profit.
You meet twice a week with your partners at YC and a group of other companies and talk about what you’re doing to hit that metric and what kind of stuff is blocking you.
Was it intimidating to be in this incubator that has launched so many household names?
Intimidating is probably not far off at the beginning, because expectations are very high.
The really amazing thing is the first day they brought in Drew Houston, the founder of Dropbox, and he was gearing up for his IPO. You build up the impression of these people, and he came in and had a very pragmatic approach to how he started Dropbox and how he grew it. He was a regular guy, and he made himself very available. So that kind of demystified it a bit. The biggest thing they stress is to just keep at it. Don’t die, is what they stress. If you can just get through it, the odds are so much better that you’ll be successful.
From that first day on, it was less about meeting these ridiculous expectations and more about just figuring out what kind of support you need for your business to stay alive.
Were you tapping into a UVA or Darden network while you were out there?
Absolutely. We touched back with the i.Lab while we were out there. [BlueRun Ventures General Partner] Jonathan Ebinger (MBA ’93) was my mentor at the i.Lab, and we had connected a few times while we were in Charlottesville. But after moving out there, he helped us understand more of the pacing of these sorts of things. He’s been a venture capitalist for 20 years and has seen a lot of companies come and go, so we were able to go to him with questions. Just having someone with that experience and wisdom helped us a lot. Not to mention he helped us get a place to live while we were there for three months.
Y Combinator just wrapped up in March. Where are you all now?
We moved back just last week to set up what is going to be our first production farm. We’re setting that up in Northern Virginia and looking to go into production in pilot runs at the end of this year. Then we’ll start selling into wholesale next year. That will position us as the first vertical farm to go into wholesale markets.
To us, that’s really important. We view this as an impact or mission-focused business. So being able to sell at wholesale proves to us and to our investors and customers that this is profitable at a mass-market size. So we can sell food that everyone can afford — not just the Michelin-starred chefs.
You have a background starting technology companies. Do you consider this a tech company?
We like to say we are a technology-enabled business, as the core of our innovation is technology. However, at end of the day, we are selling produce. What we focus on day to day is how we build a better manufacturing line that grows better and more affordable food.
As you’ve been through this process, have you keyed on a particular area of weakness to address?
Certainly, continuing personal development is the most important thing. If successful, your business is going to grow exponentially. Humans do not have an intuition for exponential growth, so it’s very important to just be learning as much as you possibly can so that you can try to stay ahead of your business’ growth.
Do you end up eating a lot of your product?
We do. It’s very cool to have a company where you can eat what you work on. The past three months have been largely a salad-based diet. I was not a huge salad aficionado before, but after having tasted these heirlooms seeds and eating our food fresh off the farm, it does taste a world different.
What other lessons stand out for you from these early days?
I think the most important lesson I’ve been learning through these programs is that the time you’re there is valuable, but it’s really brief. The most important thing is the network of people you become a part of and whom you spend your time with. At UVA, I became very close with fellow i.Lab founders including Kevin Eisenfrats of Contraline, Kris Cody of Paka, and Brent Baumgartner of Helme. Even though we all run very different business, we face the same problems. It is the support from this group of fellow founders from the i.Lab, and from YC now, too, that have helped me get to where I am and keep moving forward.
About the University of Virginia Darden School of Business
The University of Virginia Darden School of Business delivers the world’s best business education experience to prepare entrepreneurial, global and responsible leaders through its MBA, Ph.D. and Executive Education programs. Darden’s top-ranked faculty is renowned for teaching excellence and advances practical business knowledge through research. Darden was established in 1955 at the University of Virginia, a top public university founded by Thomas Jefferson in 1819 in Charlottesville, Virginia.
Agriculture, Education, Entrepreneurship, Local - Virginia
KEYWORDS
Smithers-Oasis Company Announces Partnership With Agrilyst
Smithers-Oasis Company Announces Partnership With Agrilyst
Smithers-Oasis Company, a worldwide leader in providing solutions throughout the plant and flower supply chain from propagation to consumer, announces its partnership with Agrilyst, leading provider of a software as a service (SaaS) product for greenhouses and vertical farms that allows growers to track crops, labor, inventory and other metrics.
Oasis Grower Solutions products will be included in Agrilyst and offered to growers that subscribe to the software, which helps them manage their crops and provides data-driven insights to make more profitable production decisions.
“With Agrilyst, we bring to the industry an understanding of how to leverage data, making it easier for growers to manage and scale their businesses,” said Allison Kopf, CEO of Agrilyst. “Including Oasis® Grower Solutions products in our platform will enable indoor growers to know when and what to order so they can perform optimally.”
The Agrilyst platform puts the power of precision agriculture in the hands of any grower, no matter what its size. The cloud-based platform leverages knowledge from other growers and offers a mobile app for ease of use. Indoor growers are able to extract data that helps them take control of their operations and improves their supply chain management.
“Using Agrilyst, growers can spend their time and expertise focused on their flowers and vegetables, rather than trying to maintain their supply chain,” said Bill Riffey, general manager, grower operations, Americas, Europe and Africa. “As the industry moves more and more towards indoor growing because of climate changes, it is important for Smithers-Oasis to be involved in the latest technologies that innovative growers are using to help grow their businesses.”
Oasis® Grower Solutions horticulture products provide for the strong, healthy, clean start and post-harvest care and handling of plants and flowers throughout their lifecycle to ensure the best user experience. The entire plant journey includes the breeder, propagator, growers, retailers, distributors and finally, the end consumer.
For more information
Agrilyst
www.agrilyst.com
Smithers-Oasis
www.smithersoasis.com
Publication date: 5/3/2018