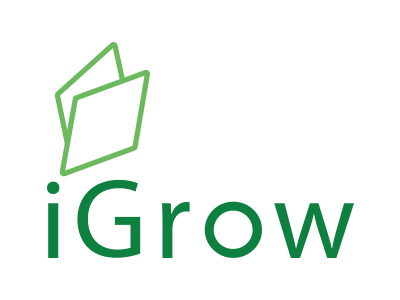
Welcome to iGrow News, Your Source for the World of Indoor Vertical Farming
Why Vertical Farming Won’t Grow Without More Data
January 3, 2019
Image courtesy of Princeton University
Vertical farming got a lot of attention at the very end of 2018, from Bowery’s $90 million funding round to news of major corporations starting their own farms.
But amid all those numbers and names, one vital piece of information was (and is) missing: We don’t actually know how well the vertical farming market as a whole is doing — if it’s on track to reach its projected $13 billion marketshare by 2024, and if the concept is even as promising a food source as the headlines would have you believe.
That’s where universities come in to play — Princeton University, to be exact. The Princeton Vertical Farming Project (PVFP) researches what the most optimal growing conditions are for indoor farming and how to produce the best crop yield while using the fewest amount of resources (e.g., water, electricity). Led by Paul P.G. Gauthier, an associate research scholar in plant physiology and environmental plant metabolism, PVFP also wants to provide a model for other initiatives and companies by releasing data on their experiments about what works in vertical farming, and what doesn’t.
“I just wanted to study and provide data,” Gauthier said in a phone interview. “Yes, we’re putting [farms] indoors. We never talk about where the waste water is going, how we get the water. Is it really worth it?”
If you’re a startup operating under the pressure of turning a profit, that’s a scary question. However, Gauthier and his PVFP team are free of that burden, so they can afford to ask questions and conduct more experiments: whether that’s trying to grow wheat or questioning the very value of, say, hydroponics, the current darling of the vertical farming startup scene. “It seems that hydroponic would be more efficient, but that’s never really been proven that that’s true,” says Gauthier. The industry as a whole tends to claim things that aren’t, he says, necessarily backed up by data.
The answer, as he sees it, is open-source vertical farming. That is, turning current data about vertical farming into a framework other projects and startups can use to guide their own efforts in the space. Gauthier would like to see PVFP provide an open-source model for vertical farming so the industry can start to answer some of those tough questions and gain a better understanding of the future.
Tied to that ideal is also the need for data to tell us about the not-so-successful stories. For every AeroFarms out there, there are others who go under for various reasons: operational costs, failure to break even, etc. We know very little, for example, about why Chicago-based startup FarmedHere shuttered in 2017. But the answer could help other vertical farming companies operate more successfully.
Gauthier agrees: “A lot of the small companies have something to tell, and we should hear their story.”
He’s quick to point out, though, that even with more robust data to learn from, vertical farming shouldn’t be treated as a savior come to end world hunger. “There’s really a lot of possibility and a lot of strategy, but it’s important to put everything into a context,” he says. Right now, leafy greens and cannabis are the most successful crops grown in vertical farms; neither make for a meal by themselves, particularly when you look at them in the context of food-insecure populations who need higher-calorie food as fuel.
That said, Gauthier does believe there’s a place in our agricultural future for vertical farming. “It will save us space,” he explains. “And eventually in the future, some of the space we’re using for [traditional] agriculture we can restore to forestry and improve biodiversity.” And initiatives like PVFP can also help train a new generation of labor to understand the science and process behind caring for plants, especially in this indoor context.
Right now, PVFP is working towards realizing that open-source model mentioned above, though no data is currently available publicly as of yet. Currently, the project fuels student theses at Princeton, and the greens produced by their experiments are making their way around campus eating establishments, most notably at the Terrance F. Club, one of Princeton’s dining clubs. PVFP would like to eventually supply all of the school’s dining outposts with vertically farmed greens.
There remains a lot of debate around the merits of vertical farming. I could write a 95-page opus on the complexities of the space, and how it’s neither a worrying distraction nor the robot-manned future of indoor agriculture, and instead lies somewhere in between those two extremes. But I don’t have to: research initiatives like PVFP — not to mention a growing number of others, including University of Arizona and Cornell University — are already delving deep into those complexities as they harness data that gets to the heart of vertical farming’s real value.
Newsletter: The Road to CES and Plant-Based Meat Mania January 4, 2019In "Around The Web"
Future Farming Hub Is Creating a One-Stop-Shop Vertical Farming System for 'Anyone' January 15, 2019In "Ag Tech"
How Cannabis Farmers Helped Create the Indoor Farming Industry November 28, 2017In "Ag Tech"
Jennifer (Jenn) is a writer, editor, and ghostwriter based in NYC. At The Spoon she covers agtech, sustainable food issues, and restaurant tech. She is obsessed with IKEA.
The Future of Farming Is Up In The Air
David Thorpe | 14 February 2019
Food that’s grown in the air instead of soil could soon appear on plates in Britain and other parts of the world.
A new investment deal worth $1.8 million to build indoor farms uses technologies developed by a company called LettUs Grow, a Bristol, UK-based startup that designs irrigation and control technology for vertical farms.
The startup will partner with ECH Engineering, which manufactures controlled environment technology, traditionally in refrigeration, and urban agriculture experts from Grow Bristol. Bristol has made a name for itself as Britain’s greenest city.
The company is one of a number of startups in the fast-expanding area of indoor growing who are supplying farm management software, crop analysis and testing services, through to full indoor farm design and build.
A glimpse of the pilot aeroponics project in Bristol showing a variety of produce being tested using the system.
Following earlier seed funding, if you’ll pardon the expression, it’s now scaling up operations to produce its aeroponic system, which suspends plants in the air and feeds the roots via a nutrient-dense mist. This technique results in faster growth rates than conventional hydroponics.
“The nutrients we use are made with mineral salts, not chemicals,” co-founder and managing director of LettUs Grow Charlie Guy told The Fifth Estate.
“They’re formulated for the vegetative stage of growth in hydroponics and aeroponic systems and precisely balanced and manufactured for great results.
“In our system we reclaim and recycle most of our water and any nutrients not absorbed by the plants. Due to this recapture and reuse, we use about 95 per cent less water than traditional field-based agriculture and 30 per cent less than typical hydroponics with our unique aeroponic technology.”
Since the plants are indoors, pest control is possible without pesticides and fungicides, making the production process organic. Previous trials have seen crop yield increases of over 70 per cent compared to conventional techniques for leafy greens, salads and herbs.
Yields and crop cycle times vary from crop to crop. The shortest is just five days for certain microgreens, to just over 30 days for head lettuce from seed.
A pilot project involving Grow Bristol involved an indoor hydroponic vertical farm that produced 100 kilograms of nutrient dense leafy greens every month without the use of pesticides and with minimal environmental impact. It tested over 50 crop varieties and sold the products to over 60 customers.
Having tested over 40 different varieties LettUs Grow’s core crops are: coriander (micro), fennel (micro), leek (micro), kale, pea shoots, sunflower shoots, radish, red cabbage, lettuce (many varieties), coriander, watercress, basil, and pak choi. “They’re our main crops, but we’re also growing rooting and fruit crops too (strawberries, spring onions and carrots, for example),” Guy says.
“We are expanding this facility in 2019 by over 10 times, to allow the testing of more and more crops and to expand our work into strawberries and root crops,” he adds.
Government funding
The $718,810 government funding is derived from the UK’s innovation agency, Innovate UK, and will be matched by $157,918 from other sources and research grants.
The grants came hot on the heels of the disruptive startup’s most recent investment round, where they raised $835,179 from ClearlySo, Europe’s leading impact investment bank, which has an extensive network of high-net-worth individual and institutional investors.
“Our investors see the value, both in terms of financial and environmental/social returns from tackling this systemic global problem. That’s why they got involved in LettUs Grow. LettUs Grow provides the technological innovation piece to the vertical smart farming movement that is currently trending rapidly in the urban context,” investment manager at ClearlySo Matias Wibowo says.
The company has ambitions to supply a rapidly growing global market for efficient and sustainable farming technology.
By 2050, humanity has to increase food production by 70 per cent to feed over 9 billion people without breaking the planet’s life-support systems, which would happen if present agricultural and food industry logistics trends continue. Aeroponics can help to address the colossal degree of waste that presently exists throughout the supply chain.
“The global agri-tech industry is very exciting right now, all stemming from the necessity to improve the economic and environmental sustainability of food production. We are fielding enquiries from all around the world from food producers and farmers who want to experience the benefits of our technology across a growing range of crops,” Charlie Guy says.
The environmental footprint
The Fifth Estate asked Charlie Guy about the environmental footprint of the technology and the energy used in a given system, compared to a soil based or hydroponic system.
He says that it depends on a number of factors, including choice of crop, choice of technology, retail route, geography, climate and season. “One of the key benefits of indoor growing, over traditional methods, is the massively reduced supply chain length. This cuts the carbon footprint of produce substantially.”
LettUs Grow are working on integrating indoor and vertical growing with renewable energy technologies to further reduce energy costs and the carbon footprint.
“Indoor, vertical growing generally acts as a substitute for imported produce,” Guy says, quoting studies claiming that CO2 reductions of up to 90 per cent are achievable by growing produce at its point of consumption using hydroponics, compared to the carbon cost of importing the same product from Europe.
He also refers to independent, academic studies into the startup’s technology that have shown that its patent-pending aeroponic technology can reduce the carbon cost of production against traditional hydroponic vertical farms by between 60 and 90 per cent.
But can the operation scale up? “Scale of operation is one of these determining factors and the vertical growing industry is still some way off the scale currently reached in glasshouse growing,” Guy says.
“The productivity increases demonstrated by LettUs Grow’s aeroponic technology represent another step-change in economic viability of farms. This enables smaller farms to deliver a return on investment up to 50 per cent faster than traditional hydroponic indoor farms.
“Energy and labour are two of the greatest operational costs of running an indoor farm and LettUs Grow are working on solutions to bring these two costs down substantially. LED lighting continues to fall in price and increase in efficiency and advanced automation processes are reducing labour costs further still.”
However, Guy says his system is “lighting agnostic”. “Anyone can use our system with any lighting. In fact, you can use our aeroponic technology without any lights, such as in glasshouses.”
To reduce costs, the company is investigating automation, not dissimilar to that found in giant Amazon warehouses. “We have designed our own automated farm management system called Ostara. It is breaking down barriers to entry for indoor farming and aeroponics. Aeroponic technology has historically been seen as complex and difficult to implement. Ostara makes aeroponics easy.”
The company plans to license its technology in the future. Watch out for indoor farms springing up near you in the not too distant future.
David Thorpe is the author of the book The One Planet Life and the forthcoming book One Planet Cities.
Tags: energy, farming, food, technology
New Greenhouse Concept: Multispan, Foil and Semi-Closed
During this year's Sival, a new greenhouse concept was launched by CMF Groupe. The GreenPush BioActive is a semi-closed multispan concept. "We want to limit the pest pressure and offer a more homogeneous climate", Corenthin (Felix) Chassouant with CMF Groupe explains.
IPM
As shown at the Sival and in the video above, the GreenPush BioActive is equipped with insect nets, in the roof and windows. A constant airflow into the greenhouses creates over-pressure, making it impossible for insects to enter the greenhouse and thus creating favorable conditions for IPM.
The air entering into the greenhouse is controlled by a high-tech climate management system, offering extra control over the greenhouse air. "Temperature, humidity and CO2 can be optimized in an easy way, offering growers extra tools to control their climate", Felix continues. "Since the air is dehumidified before it enters the greenhouse anyhow, it offers opportunities to recycle the air various times and create a homogeneous, favorable climate for the crop while ensuring optimal heating conditions and using the energy to the best. In warmer periods and with the use of cooling pads, it's also possible to cool the outside air being brought into the greenhouse."
The GreenPush BioActiv is equipped with the oval tubes - like the GreenPush concept that was launched last year. The ovalized tube makes higher widths possible and thus more volume in the greenhouse. "This concept is for both glass as well as foil greenhouses", Felix tells us. "The larger widths & higher volume gives a better humidity and temperature control within the greenhouse, whereas the amount of shadow is significantly lower thanks to the larger distance between posts. With the GreenPush BioActiv we take the next step."
Like CMF's other options, the CMF’s GreenPush BioActiv turnkey solution can be adapted to all climatic conditions to obtain more homogeneous crops by reducing or even eliminating chemical products.
For more information:
Author: Arlette Sijmonsma
© HortiDaily.com
Are You A Teenager Who Is Passionate About Technology And The Environment?
This is your time to shine!
Seeds&Chips and Fondazione Francesca Rava - NPH Italia Onlus
launch the Call for Teenovators
Applicants have the chance to speak at the next edition of the Summit and meet with the innovators and world leaders who are shaping the future of the planet
The deadline for applications is April 10th 2019:
https://seedsandchips.com/#call-teenovator
Milan, February 14th 2019 - Seeds&Chips - The Global Food Innovation Summit – the largest food innovation summit in the world – in collaboration with Fondazione Francesca Rava - N.P.H. Italia Onlus, a charitable non profit foundation that helps children in serious need in Italy and worldwide, is launching the Call for Teenovators.
The objective is to find the most passionate and dedicated teenagers (ages 13 to 19), determined to change the food system and address the most pressing global issues in accordance with the UN Sustainable Development Goals. These teenagers will inspire the current and next generation of leaders at the fifth edition of Seeds&Chips, from May 6-9, 2019 in Milan, Italy at Fiera Milano, Rho.
At the Summit, Teenovators will have the chance to open the conference sessions for our exceptional speakers – heads of state, entrepreneurs, opinion leaders and innovators – from around the world, and share their thoughts and experiences with them.
Giving a voice to young people has always been a priority for Seeds&Chips. As ambassadors for the next generation, they are spokespeople for the fundamental changes that we must undertake, and symbols of the incredible potential we have to meet these challenges. It is them, after all, who have the most influence on the future, not just from a food innovation point of view. In addition to involving many teenagers, Seeds&Chips 2019 is also calling for Young Pioneers (age 20-25) to share with the world their current projects and plans for the future.
“The world needs to take inspiration from young people,” says Marco Gualtieri, Chairman and Founder of Seeds&Chips. “In the years to come new generations will have to face great challenges: soil degradation, biodiversity loss, pollution, access to water and climate change pose very serious threats to the future of humanity as we know it. With their choices and efforts, new generations have the power to help humanity transition to a better food system and to reverse the environmental damages that are threatening life on Earth. Luckily, research shows that Generation Z is poised to become the most entrepreneurial generation ever, bound to influence the next big wave of innovation and fully achieve the United Nations Sustainable Development Goals.”
“We’re enthusiastic about the synergy with Seeds&Chips because an important part of the Fondazione Francesca Rava – N.P.H. Italia Onlus is educating young people about respecting themselves, others and the environment that surrounds them,” says President Mariavittoria Rava. “N.P.H. Nuestros Pequeños Hermanos, which represents the Francesca Rava Fouundation in Italy has been changing people’s lives for over 60 years, with the motto one child at a time, from the streets to the degree.
Through our work in schools and campuses, we listen to the motivated voices of many young people who don’t often get the chance to express themselves and be valued.
The partnership with Seeds&Chips, thanks also to the support of Eco Eridania, allows us to give many deserving young people the opportunity to bring their ideas to the world stage with and be influencers for a better tomorrow.”
Seeds&Chips and the Fondazione Francesca Rava – N.P.H. Italia Onlus are thus launching a worldwide call to all teen innovators who are motivated to shape the future of the planet and of humanity.
Are you ready to impact the future?
Complete and submit the application form available on our website https://seedsandchips.com/#call-teenovator no later than April 10th, 2019.
Seeds&Chips - The Global Food Innovation Summit, founded by entrepreneur Marco Gualtieri, is the largest food innovation event in the world. Every year since 2015, the Summit has brought together and expanded an ecosystem of startups, companies, universities, organizations, investors, accelerators and incubators, opinion leaders and policy makers from all over the world. It functions as an international meeting point for innovators, influential experts and global leaders from the public and private sector to develop and implement solutions for the most pressing issues in food production and supply.
It showcases the latest ideas and state-of-the-art technologies that hold the potential to transform our food system and help achieve the targets set by the Sustainable Development Goals. In 2017, Seeds&Chips’ keynote speaker President Barack Obama delivered inspiring remarks on the importance of food innovation and the impact of climate change and sustainable practices on our global food system. T
he 2018 edition saw more than 300 international speakers, among them former US Secretary of State John Kerry, President of IFAD Gilbert Houngbo, Minister of Agriculture of the Kingdom of The Netherlands Carola Schouten, former European Commission President and Italian Prime Minister Romano Prodi, Starbucks’ former CEO and Chairman Howard Schultz and Intellectual Ventures Founder Nathan Myhrvold.
Fondazione Francesca Rava Fondazione Francesca Rava – N.P.H. Italia Onlus is an independent, non political, charitable non profit foundation whose mission is to help children in serious need, in Italy and worldwide, through children sponsorship, fundraising projects, volunteers and educational programs. In Italy the Foundation represents N.P.H. (Nuestros Pequenos Hermanos – Our little brothers and sisters) a charitable organization for orphaned and abandoned children in Latin America, founded in 1954 by Father William Wasson, from Phoenix, Arizona. NPH philosophy was even studied by Doctor Erich Fromm, a renowned German social psychologist. In more than 60 years, more than 25,000 orphaned and abandoned children have been saved, nourished, raised with love and educated in the N.P.H. orphanages in Mexico, Haiti, Guatemala, Honduras, Nicaragua, El Salvador, Dominican Republic, Peru and Bolivia. The Francesca Rava Foundation was born in 2000 in the name of Francesca, a bright and generous young woman who suddenly died in a car crash, after her sister Mariavittoria, a lawyer, met N.P.H. and decided to dedicate her life to help children. Since then, an outstanding amount of projects were supported from Italy, accomplished in Haiti, where the Foundation is particularly committed, and in other countries in Latin America to support N.P.H. children.
"Fresh Lettuce Even With Snow On The Ground"
CubicFarms is growing again
CubicFarms has completed its latest CubicFarm System near Edmonton, Alberta. Located in Weslock, AB, Swiss Leaf Farms founder and CEO David Pfaeffli is now selling his CubicFarms produce under the Thriiv Local Garden brand to a variety of stores and restaurants. Swiss Leaf Farm’s 14 machine CubicFarm System is capable of growing over a million and a half heads of lettuce a year, along with microgreens, basil and more.
Even though snow is on the ground, and temperatures are dipping below -20 oC, fresh, crisp, local lettuce and microgreens are now available.
David and Alyssa Paeffli and family in front of one of their CubicFarm Machines
DelFresco Pure installation has begun
Ontario CubicFarm customer Del Fresco Pure has completed their building, and 14 CubicFarm growing machines have been delivered to one of Ontario’s largest greenhouse operators. Del Fresco and CubicFarms are partnering together on several exciting projects and were recently together at the CPMA in Orlando where they featured a fully functional “Demo CubicFarm” complete with live produce. Passers by were memorized by the lettuce, basil, and microgreens growing before their eyes. The booth featured Del Fresco’s wide range of greenhouse crops, including strawberries. The ice cream machine was a hit and we featured Del Fresco strawberries and Cubic’s “Microbasil” as toppings.
Del Fresco expects to bring their CubicFarms grown produce to the Ontario market in the next 2 months, including lettuces and microgreens.
The Del Fresco Pure and CubicFarm Systems teams at the Orlando PMA
CubicFarms is working on its public listing on the TSX V
CubicFarms was approximately 40% owned by Bevo Farms, but in late 2018 that ownership was spun out as a one-time special dividend to shareholders. CubicFarms expects to be listed as a publicly traded company in the next month or so, making it one of the first publicly traded vertical farming companies.
For more information:
CubicFarms
1-888-280-9076
info@cubicfarms.com
www.cubicfarms.com
Publication date : 2/1/2019
EDEN ISS Antarctic Grower Paul Zabel Returns
365 days on the eternal ice flows.
365 days in the Antarctic, of which 257 days cut off from the outside world. Antarctic grower Paul Zabel from the German Aerospace Center (DLR) has tested vegetable cultivation, suitable for Moon and Mars environments in the EDEN-ISS greenhouse. There, he harvested peppers, tomatoes, cucumbers and various lettuces and herbs, grown with the use of artificial light.
Now Paul Zabel has returned to Germany and, at a press conference at the DLR Bremen site, he spoke for the first time since his arrival of his efforts and deprivations of recent months, as well as the joys of plant breeding in extreme situations and his life on the seventh continent.
"The Antarctic is a fascinating place and I am very happy that I could be one of the few people who had the opportunity to spend the winter there, having experienced many unique impressions and challenges over the past 12 months. Now it is great to be back home, seeing family, friends and colleagues again," said Zabel.
"Antarctic grower" Paul Zabel returned after a stopover at the Antarctic Novo Airbase and a short stay in Cape Town shortly before celebrating Christmas in his home in the Brandenburg Spreewald. "Having spent Christmas 2017 in the Antarctic, it was very special to spend Christmas Eve and New Year's Eve at home." Zabel left for the Antarctic on 16 December 2017, with three other members of the EDEN-ISS team. After a two-month build-up phase, he remained there from February 18, 2018 on German Antarctic station Neumayer III with nine other overwinterers of the AWI.
Working in the Antarctic cold
Day by day, Zabel set off on the commute to the EDEN-ISS greenhouse, about 400 meters from the station. Only during the strongest storms, of which Zabel experienced many during the Antarctic winter, the greenhouse was monitored and controlled automatically by people in the Bremen control center. "From Bremen, we were in daily contact with Paul," reports EDEN-ISS's Daniel Schubert from the DLR Space Systems Institute. "He has done a great job over the past months. Although it has taken up quite a lot of his time, the EDEN-ISS project and he himself will be thanked by future astronauts."
Other members of the AWI hibernation team also helped Paul Zabel with his work. They aided him with the sowing of the plants and supported him with the numerous experiments. "After more than a year in the Antarctic, we can look back on successful overwintering." The work in the greenhouse and the fresh vegetables have enriched our time at the Neumayer Station III," says station manager Bernhard Gropp.
Rich harvest
A detailed evaluation of the studies on plant breeding in Antarctica is currently in full swing. The extensive results, including technical, botanical, microbiological and psychological analysis, are expected in May 2019. It is already clear that Paul Zabel has repeatedly been able to harvest a rich harvest, again supported by the other AWI overwinterers. For example, on Neumayer III over the past year, the crew wwere able to eat 67 kilograms of cucumbers, 46 kilograms of tomatoes, 19 kilograms of kohlrabi, 8 kilograms of radishes, 15 kilograms of herbs and 117 kilograms of lettuce.
The station continues to be open to researchers from all over the world. In the next two years, DLR, AWI and other research partners will further develop the production processes in the EDEN-ISS greenhouse, with the goal to offer future stations on the Moon and Mars an optimized greenhouse concept. The continuation of the project is open to researchers from all over the world. "Soon we will hand over the greenhouse to the new overwinterers who will continue the EDEN-ISS project in the Antarctic and look after the crop," says dr. Daniel Schubert. "We will monitor and control the greenhouse from Bremen." Schubert and his team will again travel to the Antarctic in mid-January 2019 to maintain the EDEN-ISS greenhouse and update it technically for the continuation.
EDEN-ISS: Food supply of the future
World food production is one of the key societal challenges of the 21st century. An increasing world population and simultaneous upheavals caused by climate change call for new ways of cultivating crops, even in climatically unfavorable regions. For deserts and areas with low temperatures, as well as space missions to the Moon and Mars, a greenhouse, closed of from the weather, the sun and the seasons, will allow independent harvests, less water consumption and the abandonment of pesticides and insecticides. With the project EDEN-ISS, such a greenhouse of the future can be tested under Antarctic extreme conditions.
Source: www.gemuese-online.de
Publication date : 1/15/2019
Technology Will Make The UAE One of The World's Most Food-Secure Countries By 2021
From vertical farms to artificial intelligence, the nation is embracing cutting-edge innovations to achieve this ambitious goal, says the UAE Minister of State for Food Security
Food security is without doubt one of humankind’s most pressing concerns and the issue is one that is felt particularly keenly in the UAE. Although considered food secure – primarily because it enjoys a high degree of economic and political stability – the UAE still faces significant challenges. These stem from its arid climate, its shrinking groundwater levels and the volatility of the wider region. Added to these geographic and geopolitical stressors is the country’s spectacular growth. As its population has expanded exponentially, increasing from about 300,000 in 1971 – the year the UAE was founded – to more than nine-and-a-half million today, the need to provide for its residents has increased correspondingly.
My responsibility as UAE Minister of State for Food Security is to ensure that the nation continues to enjoy an adequate food supply for its citizens as it develops and to elevate its current position of 31st on the global ranking for food security to the top 10 by 2021. In order to achieve this, we are championing trade facilitation and enabling technology-based production and supply of food. The initiatives to support strategic goals are anchored in diversification of supply, alternative supply sources, technology-enabled enhancement of local production and international trade links, among others. Thus, a major part of my mandate is involved in incorporating agricultural technology – also known as “AgTech” – into the country’s food security agenda. This agenda is enshrined in the UAE’s recent launch of its National Food Security Strategy.
Variously defined as “transforming the global food system through digital technology” and “smart farmers getting smarter using digital technology”, AgTech encompasses advanced agricultural methods that differ distinctly from the traditional ways of farming practised for millennia. Increasingly seen as a solution to the UAE’s food security issues, my office is now placing a strong focus on adopting AgTech in the country’s agricultural sector, as part of a concerted effort to considerably reduce the 90 per cent of food that the country currently imports.
The AgTech government accelerator project, with its two components, is one such initiative. The first component is the promotion of the use of “controlled-environment agriculture” (CEA), which is a technology-based approach toward food production that utilises highly efficient technologies to properly manage agriculture inputs and maximise output. It involves agricultural industry entrepreneurs working alongside government bodies to provide tangible solutions to promote CEA, primarily through implementing an enabling business environment that is conducive to innovation.
The second component of the project is aquaculture, which is farming in controlled conditions of fish, crustaceans, molluscs, aquatic plants, algae and other organisms in freshwater and saltwater. With agriculture in general being the world’s thirstiest industry, accounting for approximately 72 per cent of total freshwater consumption, aquaculture represents one of the best uses of what is the region’s most precious resource. To this end, the UAE has established a vibrant aquaculture sector with an investment of more than Dh100 million to develop hatcheries and fish farms.
Vertical farming is another AgTech component that my department is promoting and one that has been identified as offering a solution to the UAE’s food security issues. The concept involves plants being grown in vertically stacked layers in an indoor environment where environmental factors can be controlled. Vertical farms typically use artificial light, humidity regulation, temperature control and minimum use of pesticides, enabling the production of vegetables in large quantities all year round without the need for soil, sunlight and chemicals. The commercial applications of vertical farming are already being realised in the UAE, with the opening of the Gulf region’s first-of-its-kind facility in December 2017. Located in the Al Quoz industrial area of Dubai, the 8,500sq ft farm produces 18 varieties of micro-greens, including rocket, kale, radishes, red cabbage, basil and mustard.
Remote-controlled drones have become an accepted presence in the skies above the UAE, with the ubiquitous flying machines used by the authorities to – among other things – monitor traffic and deliver post. Now they are providing benefits for the country’s agricultural sector, with unmanned aerial vehicles (UAVs) being used to map farming areas across the country. Announced in June 2017, the pilot project sees UAVs being used to create a highly accurate agricultural database that supports decision-making and forward planning by enabling the best use of resources and determining the optimum areas for crop growth.
Perhaps the most prevalent form of AgTech being incorporated in the UAE’s agricultural sector is the use of sensors, with their adoption resulting in increased yields in both large-scale agricultural projects and smaller organic farms. Sensor-equipped gyroscopes, accelerators and GPS monitors are being employed to enhance crop production by making the most of land and water use – precision irrigation that is highly effective in reducing water waste. A good example is an organic farm in Sharjah that relies heavily on sensors to determine the salinity and mineral content of the soil to ensure optimum crop growth with minimal use of water. Another prime example is a household name Japanese electronics manufacturer that is creating a farm in Dubai to grow strawberries, with the facility incorporating light-emitting diodes for controlled lighting, air distillation technology and other appliances to check room temperature and humidity.
Aquaculture, vertical farming, drone use and sensors are just four of the technologies that are being utilised in the UAE to maximise crop production while ensuring good husbandry of resources. This is only the start of what will be an expanding role for AgTech in the country’s agricultural sector. The office of food security is currently evaluating how emerging areas of technology, such as robotics, can play a part. Automation combined with artificial intelligence is an exciting field that we are currently assessing. One company in the US has produced a robot that mimics what a fruit picker in the field does. It uses AI to determine which fruit is ripe and ready to be picked, leaving unripe fruit in place on the vine. We are closely following such developments as part of the National Food Security Strategy and will be assessing how rapid technological changes that form part of the Fourth Industrial Revolution can be best incorporated to ensure food security for all.
Mariam Al Mheiri is the UAE's Minister of State for Food Security
Updated: January 16, 2019 04:25 PM
Green Life Farms Hires Head Grower
Green Life Farms Hires Head Grower
Industry veteran brings more than 15 years of experience growing produce in indoor hydroponic greenhouses to team
Boynton Beach, FL (January 28, 2019) – Green Life Farms, the state-of-the-art hydroponic produce greenhouse under construction in Boynton Beach, FL, has hired Gregory Graft as its Head Grower. Graft will play a significant role in helping the organization prepare to begin commercial operations in the first half of 2019. Green Life Farms is slated to be the largest indoor hydroponic produce grower in the southeast.
“Gregory is a seasoned expert in all aspects of the hydroponic industry,” said Mike Ferree, Vice President, Green Life Farms. “His 17 years of hands-on experience in managing a hydroponic greenhouse makes him a vital addition to the Green Life Farms team, as we work to establish ourselves as an industry leader in sustainable farming practices.”
After serving in the United States Marine Corp, Graft was the Vice President and General Manager of Grateful Greens Hydroponic Farm in Clarksville, IN. There, he designed, built and maintained the hydroponic farm, managing every aspect from assessing plant health to developing client relationships. Graft also served as a production supervisor at Enjoy Life Foods in Jeffersonville, IN, assuming responsibility for product quality, planned volume and line efficiency.
As Head Grower for Green Life Farms, Graft will oversee the facility and lead the day-to-day operations. He will be directly involved with growing operations and maintaining the greenhouse’s infrastructure and hydroponic equipment. In addition to his immersion in the daily processes, Graft will take a holistic approach to managing the facility, analyzing data to evaluate its performance and recommending adjustments. He will also hire, train and supervise a staff of 16 greenhouse employees. Graft will work closely with the rest of the team to continue to drive sales.
Green Life Farms baby leafy greens will set new standards for cleanliness, freshness, and taste. Grown locally, using sustainable farming practices combined with the most advanced AgTech practices, and kept free from GMOs, pesticides and contaminants, Green Life Farms baby leafy greens are good for your body, family, community, and planet.
For more information about Green Life Farms, visit GreenLifeFarms.ag. Contact Elayne@GreenLifeFarms.ag for sales and Ray@GreenLifeFarms.ag for investor relations.
About Green Life Farms
Green Life Farms is constructing a 100,000 square foot state-of-the-art hydroponic greenhouse in Boynton Beach, Florida, with additional expansion planned in Florida and beyond. Commercial operation is expected to begin in the first half of 2019. By incorporating agriculture with technology, Green Life Farms will provide consumers with premium-quality, fresh, local, flavorful and clean baby leafy greens that are good for their bodies, families, communities and planet – year-round.
Singapore Aiming To Become Region's Urban Agriculture Technology Hub: Koh Poh Koon
January 15, 2019
SINGAPORE - Singapore has the "right ingredients" to make it the urban agriculture and aquaculture technology hub in the region, Dr Koh Poh Koon, Senior Minister of State for Trade and Industry, said on Tuesday (Jan 15).
In a keynote speech at the Indoor Ag-Con Asia conference at Marina Bay Sands Expo and Convention Centre, which is being held in Singapore for the fourth time, Dr Koh said Singapore is in a strong position to "catalyse technological and business innovations", as it has a climate for innovation, strong talent base and strategic location which can transform agriculture and aquaculture in the Asia-Pacific region.
"Where arable land is scarce, innovating how we produce food is critical in helping us overcome our farming constraints and better contribute to our food sustainability and traceability efforts," he said.
Senior Minister of State for Trade and Industry Koh Poh Koon said Singapore is in a strong position to "catalyse technological and business innovations".PHOTO: LIANHE ZAOBAO
"Investments in agri-tech can also help to reduce our reliance on food imports and allow us to enjoy seasonal produce while lowering our carbon footprint."
To boost the agri-tech sector, Dr Koh announced that Enterprise Singapore, through its investment arm Seeds Capital, has appointed seven investment partners under Startup SG Equity - a scheme that encourages private sector investment for start-ups.
Seeds Capital aims to spur the growth of emerging and strategic sectors such as agri-tech, by stimulating investment in innovative local start-ups.
Under this partnership, more than S$90 million worth of investments will go into early-stage tech start-ups with food and agri-tech solutions.
The appointed partners are AgFunder, Hatch, ID Capital, Openspace, The Yield Lab, Trendlines and VisVires New Protein.
With Seeds Capital, the partners will assist early-stage start-ups, such as by introducing new business partners and providing support to enter new markets.
Seeds Capital will also provide co-funding of up to $4 million per deep tech start-up under Startup SG Equity.
Dr Koh said: "We are building a vibrant agri-tech start-up environment to uncover more talent, anchor experts, partners, investors and accelerators into our ecosystem, and expand the pool of knowledge and resources.
"We are developing relevant research capabilities in areas such as seed formulation and fish nutrition, advanced biotech-based protein production and food safety science. (Furthermore) we are establishing a high-tech physical cluster in Kranji to support operations in urban agriculture and aquaculture."
One of the Singapore agri-tech companies at the conference was Protenga, an insect farming company that produces animal feed. It has incorporated data sensors into its farms to help determine the right feeding frequency and amount, increasing the quality and volume of produce.
Another company VertiVegies, an indoor vertical farming firm, also displayed its modular planting system that uses technology to ensure efficient plant growth, while taking up minimal space and giving Singapore the potential to achieve food security.
"Singapore's journey to become a leader in agriculture technology is still in the early days, and there is much more for us to do," added Dr Koh. "I encourage industry representatives and leaders to carry on your good work in leading the development of solutions and standards for the sector, to provide fertile ground for the germination of new ideas, technology matching and transfer, capability development."
A Method To Monitor Indoor Crop Health No Matter What Planet You're On
A user-friendly, cost-effective protocol to use SI-NDVI imaging for early, remote detection of plant stress.
PUBLIC RELEASE: 17-DEC-2018
BOTANICAL SOCIETY OF AMERICA
IMAGE: SINGLE-IMAGE NORMALIZED DIFFERENCE VEGETATION INDEX (SI-NDVI) ANALYSIS ENABLES EARLY DETECTION OF PLANT RESPONSE TO STRESS, PRIOR TO WHITE LIGHT-VISIBLE DETECTION. SI-NDVI IMAGES OF ARABIDOPSIS PLANTS SHOW RESPONSE TO SALT STRESS... view more
CREDIT: NICOLE S. BEISEL, JORDAN B. CALLAHAM, NATASHA J. SNG, DYLAN J. TAYLOR, ANNA-LISA PAUL, AND ROBERT J. FERL. 2018. UTILIZATION OF SINGLE-IMAGE NORMALIZED DIFFERENCE VEGETATION INDEX (SI-NDVI) FOR EARLY PLANT...
As the world urbanizes and technologies such as LED grow lights bring down costs, indoor farming is becoming an increasingly important part of the food supply. Eventually, indoor farming techniques could help humans maintain a healthy diet in space. However, because of the completely closed systems in which indoor crops are grown, imbalances in soil nutrients, salinity, temperature, and other factors must be caught quickly to avoid losing a whole crop. In work published in a recent issue of Applications in Plant Sciences, Dr. Robert Ferl and colleagues at the University of Florida Space Plants Lab developed a light-based tool to assess plant health quickly, accurately, and inexpensively.
Not surprisingly for work coming from the Space Plants Lab, this study was conducted with an eye toward extraterrestrial farming. "Imagine a greenhouse being robotically maintained on Mars," said Dr. Ferl, corresponding author on the study. "The only data we can get back from that greenhouse is electronic. No sample return. Under those conditions it becomes really beneficial to derive as much data as possible from the photons that are coming off the leaves of plants." These photons make distinctive light signatures that can tell quite a bit about how a plant is doing, when analyzed using the normalized difference vegetation index (NDVI).
The NDVI is a widely used metric of plant health and photosynthetic rate that was originally developed for satellite-based monitoring of plant growth. This metric compares the plants' absorption of different spectra of light; healthy plants give off an identifiable light signature, absorbing light in the photosynthetically active region of light spectra, and reflecting near-infrared light. "[NDVI] proved to be an interesting starting point for the project simply because there is a large dataset and collective understanding that underpins the idea of using different spectral components to understand plant health," said Dr. Ferl. They adapted single-image NDVI (SI-NDVI), a low-cost version of this analysis, to see if it would be practical for monitoring crop health in indoor farming conditions.
Dr. Ferl and colleagues assessed the efficacy of this monitoring technique by exposing two different plants (arugula and the model plant Arabidopsis thaliana) to two different stressors (salinity and a high-concentration ammonium nitrate treatment) that create distinctive and well-understood stress responses. "Using these well-controlled stresses that have a well-defined biochemical basis for their responses is allowing us to probe the root causes of NDVI difference detections of stress or health responses," said Dr. Ferl. They were able to detect stress signatures from both treatments well before stress was visible to the naked eye, proving the utility of these techniques as early monitoring systems that can be deployed remotely and relatively inexpensively.
While these authors were primarily motivated by an interest in growing plants in space, the monitoring technique they developed could prove useful here on earth for indoor farmers looking to catch problems in the grow room quickly. "Single-image NDVI offers the opportunity to derive spectral character from a single RGB image. This keeps costs down," said Dr. Ferl. "It also opens the door to a large community of citizen scientists and applications developers that are interested in using SI-NDVI concepts commercially." This means that this method could be adapted to monitor a variety of crops grown under indoor conditions, which could mean less expensive, healthier salad greens on your table, whether that table be here or on Mars.
New York Vertical Farm Aims To Instill Consumer Trust With Transparency
Starting today, consumers can just point their camera app at the QR code, or type in the lot number, found on all Square Roots food packaging to trace their food’s path from seed to sale.
By Laura Drotleff| December 19, 2018
Consumers can simply scan the QR code with the camera on their phones to get the full story on when, where, and how Square Roots’ herbs are produced in Brooklyn, NY.
In the wake of the romaine lettuce recall, Square Roots, a Brooklyn, NY-based vertical farm with famous co-founders, has launched new labeling that will allow consumers to access the full backstory for when, where, how, and by whom their food was grown with a simple scan.
Starting today, consumers can just point their camera app at the QR code, or type in the lot number, found on all Square Roots food packaging to trace their food’s path from seed to sale, with the aim of bringing a “whole new level of transparency” to the food chain.
Co-founded by Tobias Peggs and Kimbal Musk (yes, Elon’s brother), Square Roots is a seed-to-sale indoor urban farm that produces a variety of fresh, pesticide-free herbs that are hand-harvested, self-packaged, and same-day-delivered to retail stores in New York City. The company was built on the premise of reconnecting city dwellers with the “comfort, nourishment, and taste of food and the people who grow it.” In addition to growing and selling herbs, Square Roots has taken it upon itself to groom next-generation farmers and future leaders in urban farming through its training platform that requires a one-year commitment to the company.
The Why Behind Square Roots’ Transparency Timeline
Musk wrote in a blog-post revealing Square Roots’ reason for launching its new scan-able label is that the operation wants to provide consumers with the transparency they’re demanding about where and how their food is grown.
Following the E. coli outbreak that resulted in the recall of all romaine lettuce grown in the U.S., consumers were put at risk, and the complexities and lack of traceability in the agricultural supply chain resulted in it taking weeks for federal agencies to track down the source of the bacteria.
Meanwhile, by growing in controlled environments, indoor food producers can provide advantages to minimizing the occurrence of outbreaks. Musk says by promoting this, Square Roots’ customers can enjoy the operation’s locally grown products “with the comfort and confidence of being able to see exactly how and where your food was grown and who grew it.”
Grown hydroponically inside climate-controlled, refurbished shipping containers, Square Roots’ end-to-end system monitors and controls every aspect of the production process, Musk says. The operation’s technology stack surrounds its farmers with data, tools, and insights to make smart decisions in real time, allowing them to sustainably produce food year-round.
Musk says while there’s a lot of excitement around the possibilities that blockchain offers for food traceability that could improve the current supply chain, consumers are turning to locally grown produce because there are fewer steps and less time involved from farm to fork.
“We, like many local farmers, don’t need to utilize blockchain architecture to give the consumer what they want today – total transparency, without the buzzword BS.”
Read Musk’s full article on the Square Roots blog, and learn about the company on its website. Stay tuned for more stories on how indoor producers are promoting food safety and transparency on GreenhouseGrower.com.
Evansville, A Home For Business
Back text: “E — Scenic View of Ohio River, V — Reitz Memorial High School, A — Vandenburgh County Courthouse, N — Adm. Bldg., Evansville College, S — Evansville National Guard Armory, V — Dade Park Race Track, I — Electric Fountain, Garvin Park, L — Greyhound Bus Station, L — Lions Den, Mesker Park Zoo, E — Dress Plaza”
After graduating from Purdue University in May 2017, I continued to rent co-work space on campus in West Lafayette working for Heliponix full-time until my apartment lease ended at August 2017. At the time, I was hyper focused on the engineering design tasks at hand for Heliponix to debut a new prototype GroPod™ at the Forbes AgTech Summit. After the summit ended, I brought all of my possessions back to Evansville. It occurred to me I was once again living in Evansville only after I had moved back home. Upon moving back, I was asked to speak at Evansville’s Tech on Tap weekly entrepreneurial meetup where I was asked why I came back. I answered, “Evansville is home, and I can continue working on my company without paying myself by living with my parents.” This seemingly obvious answer spurred a new found sense of urgency that if I were to scale a technology company, than I must leave southern Indiana for greener pastures. I then began to look for every possible reason why I should move away from Evansville for the benefit of Heliponix. I identified the following four reasons why I could not headquarter Heliponix in Evansville, Indiana.
Early adopter customers for new technologies do not live in the midwest.
Tech companies need investors. Evansville did not have venture funds.
Tech companies need top tier software engineering talent. Evansville did not have individuals with this skill set on hand.
Hardware companies such as Heliponix need to manufacture overseas to be cost competitive in the marketplace.
Customers
Heliponix (formerly Hydro Grow) team picture after winning first place at the Schurz Innovation Prize at Purdue University. Left to Right: Scott Massey (CEO), Jimmy Carlson (Software Engineering Intern), Ivan Ball (CTO)
Starting a company without experience or the money needed is comparable to charging into a battle unarmed and unaware of the terrain with dangers ahead. I was acutely aware of my limitations, and spent my senior year at Purdue University delivering newspapers at night for about $9/hour, and competing in business plan competitions between classes for cash awards. Although we were very lucky to have successfully secured over $80k over the course my senior year and a little under $100k from competitions post graduation, the money was the second most valuable aspect of winning these pitch competitions. For every competition we won, at least two or three articles from local media publications would cover the story with our name on the front title. We jumped at every opportunity to showcase our prototypes at schools, STEM career fairs, and also leveraged my position as the lowly delivery boy to publish articles in the Exponent to grasp as much publicity as possible for an early stage company.
Scott Massey giving a STEAM (Science, technology, engineering, agriculture, and math) career talk about indoor agriculture to middle and high school students Our Lady of Providence School in New Albany, Indiana.
For every article and interview that was published, I received an email from random Indiana residents interested in purchasing a GroPod when it became available for purchase. I kept a running list of these potential customers, and reached out to collect a $500 pre-order deposit when we had finally landed on a GroPod design that worked reliably. We had definitively proven that a pre-revenue startup company could launch an expensive product in Indiana if they are able to achieve enough publicity to convert impressions into executed sales. Although there are many more wealthy individuals in major cities who could buy an early stage product; we did not yet have the production capabilities to meet this demand, and still had product development to refine before we would be ready for a massive user base.
Funding
Inside Indiana Business interview with Dr. K and Gerry Dick
Although we had been veryfortunate to secure some funding from business plan competitions for patents and prototype development, we had reached the ceiling of competition funding available in Indiana for an idea not yet generating revenue. My Co-Founder, Ivan Ball accepted a full-time, electrical controls engineering job offer upon graduation to pay off student loans at GPC (Grain Processing Corporation, an ethanol and grain alcohol processing plant in Washington, Indiana) after interning and co-oping as a student for several years prior. Together we worked exhausting hours for a full year to refine the GroPod design until we created a functional product able to generate revenue in Ivan’s garage.
One of many harvests from the fourth generation GroPod™. ALL RIGHTS RESERVED. HELIPONIX©
Ivan Ball at his electrical work station in an unheated garage assembling the fourth generation GroPod™. ALL RIGHTS RESERVED. HELIPONIX©
This marked a major turning point for the company after three generations of failed prototypes. When asked if we both worked on Heliponix full-time to this point, I would honestly say yes. Our individual hours spanned 50–70 hours weekly even though Ivan had a full-time day job that took 40–45 hours per week. At this time, we had spent almost all competition award winnings on patents, prototyping, travel for events, or other business expenses. We simply did not have the capital needed to cover materials to assemble the first GroPod betas. I then approached Eric Steele, my Entrepreneur in Residence with Elevate Ventures (Indiana’s state venture fund) seeking capital needed to fund inventory. Eric referred us to the ISBDC (Indiana Small Business Development Center) who advised the Vectren Foundation Grow Local loan program for small businesses. After working with Douglas Claybourn and Kim Howard, we sent an application to the Vectren Foundation board to build the first GroPods. After waiting patiently, we were approved for a loan needed to build these GroPods with very favorable terms for any company, let alone a startup with zero cash flow history. We used the loan to buy all the parts needed, and collected the remaining $1,500 left on each GroPod order with early adopters to sell out of the beta models assembled by hand. We 3D-printed all parts, wrote our own code, soldered our boards, assembled every aspect of the product Ivan and I had designed entirely by ourselves, and delivered each GroPod in person to the early adopters. There was so many GroPod parts laying around Ivan’s home, I had to deflate my air mattress to make more room, and slept on his couch for months.
Ivan Ball installing a camera on the fifth generation GroPod™. ALL RIGHTS RESERVED. HELIPONIX©
GroPod™ assemblies consuming every square foot of Ivan Ball’s home in Washington, Indiana. ALL RIGHTS RESERVED. HELIPONIX©
Ivan Ball (Left), Scott Massey (Right) with first functional GroPod. ALL RIGHTS RESERVED. HELIPONIX©
At this point Ivan quit his job at GPC, to work solely at Heliponix, and sold his house in Washington, Indiana to be fully committed to the company. Today, I am pleased to announce that the risk the Vectren Foundation took on us for funding the loan is being paid back in full plus interest. This market validation thrusted us into the long sought after post-revenue status, which did not go unnoticed by local and regional angel investors; however, this is a story for another day. Despite the undeniable fact that the largest investment funds are in major cities, very few early stage hardware companies receive those investments due to the amount of competitors who rarely manufacture products within these cities, let alone the state. It is much better to refine the product and user experience until a sizable MRR (monthly recurring revenue) is established before approaching these funds which are beginning to invest outside of their states to leverage the capital efficiency of a midwest startup.
Talent
Delivering the first GroPods was just the beginning of a long troubleshooting learning curve with paying customers… Internet connectivity with a connected, IoT (Internet of Things) device will come with many software bugs as well as faulty sensor failures when buying in low quantities from Chinese suppliers. The problems that you are both unaware of, and unable to solve are the hardest any startup will encounter. It is incredibly important to find these problems by getting your product in the hands of early adopters as soon as possible to identify and solve. The dilemma of an underfunded hardware startup company is that you will more than likely need to sell a product that doesn’t yet have all the features needed to make it “perfect” in order to stay cash flow positive. The reality is that no garage startup will be fully ready, and you will certainly find excuses to not be ready if you look for them. This is called the MVP (minimum viable product). Then something amazing happened, customers began to complain less each day as we solved problems one after another, until I began to hear feedback that their GroPods were growing more food than they could consume! This major milestone was met with interest from angel investors who provided the capital needed to hire a full-time software development lead. Unfortunately, there is not a plethora of software developers in Evansville at this time, so we needed to look for a remote employee. After interviewing several developers, Ivan and I decided to hire Bryan Lemon, a PhD computer scientist from West Virginia University living in South Carolina. Bryan’s experience with IoT device companies translated very well into solving problems, creating new features that kept customers happy, and attributed to our zero-percent churn rate. Despite never meeting Bryan in person, we were quickly able to determine his technical ability by first hiring him as an independent contractor for an agreed upon milestone. I strongly encourage that early stage technology companies consider remote software developers to save cost, expand your professional network, and reach a wider pool of candidates to only hire top talent. You do not need to go to the bay area or other major cities to find top talent, and the operational cost of your business will increase by multiples if you move to a larger city.
Manufacturing
Whirlpool Refrigeration Plant on Highway 41. Source: Courier and Press
I remember all too well the day that the Whirlpool plant in Evansville shut down for the last time, a major manufacturing hub for appliances that employed several thousand people. At a very young age, this instilled the idea that hardware manufacturing companies must leave the United States in order to find competitive manufacturing prices. That is why I took a flight to Shenzhen, China to tour contract manufacturing plants. This massive manufacturing city is often called the hardware capital of the world based upon its speed, competitive labor, and material rates. After returning and considering the cost of manufacturing overseas, I began to factor in the not-so-obvious costs of building products outside of Evansville. The language barriers requires a translator to be present, and often leads to misunderstandings that can be very costly mistakes. The logistical challenges, uncertain trade relationship, and intellectual property theft quickly amounted to a cost that far exceeded that of domestic contract manufacturers. Most startup companies fail by aimlessly pursuing random goals without strategy as capital dwindles.
I have discovered that the resources I need to prototype and manufacture are widely available within the Midwest ecosystem. We then began to look locally for contract manufacturers within the Evansville-Cincinnati-Louisville trifecta that had worked at GE and Whirlpool appliance manufacturing plants and engineering design centers. Without disclosing trade secrets, we can confirm that the midwest has manufacturing capabilities that are very competitive with international rates. In our case, we were able to source almost all parts needed in manufacturing from Indiana, Illinois, and Kentucky. In addition to Evansville and Louisville being the former appliance manufacturing capitals of the world; we have been able to find top tier talent and industry partners with relative ease. Eventually, most hardware companies manufacture overseas when they exceed 1,000–10,000 units per year, but automation is the equalizer in a world where labor can be bought for a few dollars per hour, or be subsidized by a country in the process of industrialization. Indiana is uniquely positioned to be an entrepreneurial hotbed with several investment groups, and countless angel investors in one of the top manufacturing states in total manufacturing GDP (Gross Domestic Product).
Conclusion
After speaking to countless successful and not-so-successful entrepreneurs; I believe that starting a company requires two things.
The drive to achieve your goals
The means to achieve your goals
This has led to a new revelation about Evansville; it is not a good place to start a company… it’s a great place to start a company. It is uniquely large enough to have the means to fund a startup company, but not so large that the means become unobtainable to newer companies. The cost of living combined with these resources will triple to quintuple how far your dollar will go as opposed to a startup in a major city.
I now proudly say that Heliponix is based in Evansville, and we intend to stay here for the foreseeable future. We will continue to directly and indirectly create new jobs as operations expand. This only leaves one question from me to you, “Why not stay in Evansville?”.
Indiana entrepreneurial resource map, courtesy of Drew Peyronnin.
Indiana entrepreneurial resource map, courtesy of Drew Peyronnin.
The infographic above shows just some of the many resources available for startups in Indiana that has helped Heliponix many times in the past, present, and future. Purdue Foundry, Elevate Ventures, Purdue Polytechnic Institute, Blue Sky Capital, CoWork Evansville, APPCOM/BIZCOM, SVBIG, Certificate Entrepreneurship and Innovation — Purdue University, Burton D Morgan Business Plan Competition, Foundry@WestGate, GAGE, Agrinovus, Centric, IU IP Clinic, E is for Everyone, SouthWest Indiana Chamber of Commerce, Innovation Connector, TedxWabashCollege, Schurz Innovation Prize, Center for Entrepreneurship — PNW, Vectren Foundation, iGrow.news, and prospectively the MakerStation which conveniently holds many of these resources in one building; Innovation Pointe.
Scott Massey
Founder and CEO of Heliponix™. Purdue University, class of 2017. Mandela Washington Fellowship Alumni.
Osram Presents New Near-Infrared LED for Smart Farming Application
Oslon Black SFH 4736 near-infrared LED (NIRED) helps farmers harvest at the right time.
12/12/18, 10:38 AM | Indoor & Vertical Farming, Monitoring & Growing
Osram, a leader in the optoelectronic industry, today announced its new Oslon Black SFH 4736 near-infrared LED (NIRED). When installed in a smartphone or tablet, the NIRED offers a simple way for farmers to scan fruit, vegetable or grain crops, generating reliable information about the sugar, water and fat content. One of the most important decisions for farmers and vineyard owners is picking the right time to harvest. This not only ensures that the produce has the best possible taste, but also saves precious time and money during the processing and shipment stages.
Determining ripeness is made possible by near-infrared spectroscopy. This process involves scanning the content of various types of fruit, vegetables and grains - and takes only a few seconds. For example, a farmer would select a random ear of wheat, scan it with a smartphone, and just a few seconds later read the results on the display.
The NIRED irradiates the sample with a defined spectrum of light. Depending on its precise composition, the sample will reflect only a certain proportion of that light. The spectrometer then processes the information and integrates it into the smartphone or tablet. The reflected light can be considered a kind of "photometric fingerprint." These measurements indicate the existence and quantity of certain nutrients, allowing farmers to take samples and easily monitor the progress of their crops in real time so they can plan the ideal time for harvest.
"By focusing on making progress for farmers, the new Oslon Black SFH 4736 near-infrared LED takes farming technology to the next frontier," said Karl Leahy, Director of Emitters, Lasers and Sensors at Osram Opto Semiconductors. "Our unique NIRED allows farmers to optimize their crop yield, as well as enhance harvest efficiency while keeping costs down."
In late 2016, Osram Opto Semiconductors unveiled the SFH 4735 as the worlds first broadband emitter of its kind. The previous model is being used in various applications including in SCiO, one of the first near-infrared micro-spectrometers for the consumer market from Consumer Physics. The SFH 4736, which achieves almost twice the output thanks to its newly integrated lens, is also suitable for use in the professional sector and can provide valuable assistance to farmers.
ABOUT OSRAM
OSRAM, based in Munich, is a leading global high-tech company with a history dating back more than 110 years. Primarily focused on semiconductor-based technologies, our products are used in highly diverse applications ranging from virtual reality to autonomous driving and from smartphones to smart and connected lighting solutions in buildings and cities. OSRAM uses the endless possibilities of light to improve the quality of life for individuals and communities. OSRAMs innovations enable people all over the world not only to see better, but also to communicate, travel, work and live better. OSRAM has approximately 27,400 employees worldwide as of end of fiscal 2018 (September 30) and generated revenue of more than €4.1 billion. The company is listed on the stock exchanges in Frankfurt and Munich (ISIN: DE000LED4000; WKN: LED 400; trading symbol: OSR). Additional information can be found at www.osram.com.
On the Heels of Digital Sales Boost, Kroger Launches First-Ever Unmanned Delivery Service
Since August, the companies have operated a self-driving grocery delivery service in Scottsdale, AZ, with an autonomous Prius fleet accompanied by vehicle operators.
Nuro and The Kroger Co. announced the launch of the first-ever unmanned delivery service available to the general public.
Since August, the companies have operated a self-driving grocery delivery service in Scottsdale, AZ, with an autonomous Prius fleet accompanied by vehicle operators. The autonomous vehicles have completed nearly one thousand deliveries to the general public.
With this launch, the fleet is expanding to include Nuro's custom unmanned vehicle known as the R1. The R1 travels on public roads and has no driver, no passengers and only transports goods. Nuro has been developing the R1 since 2016, and announced its partnership with Kroger, America's largest supermarket retailer, in June.
"Nuro envisions a world without errands, where everything is on-demand and can be delivered affordably. Operating a delivery service using our custom unmanned vehicles is an important first step toward that goal," explained Nuro President and co-founder Dave Ferguson.
"Kroger customers are looking for new, convenient ways to feed their families and purchase the products they need quickly through services like pickup and delivery," said Yael Cosset, Kroger's chief digital officer. "Our autonomous delivery pilot with Nuro over the past few months continues to prove the benefit of the flexible and reliable technology. Through this exciting and innovative partnership, we are delivering a great customer experience and advancing Kroger's commitment to redefine the grocery experience by creating an ecosystem that offers our customers anything, anytime, and anywhere."
Kroger experienced 60 percent digital sales growth in the third quarter, and its seamless coverage area now reaches more than 90 percent of customer households.
Square Roots Implements “Transparency Timeline” for Greens
An indoor farm in Brooklyn, N.Y., wants to do its part to restore consumer confidence in greens.
Tom Karst December 19, 2018
Urban farm Square Roots has unveiled what they call a transparency timeline, accessed via QR code on their packaging.
( Square Roots )
An indoor farm in Brooklyn, N.Y., wants to do its part to restore consumer confidence in greens.
Urban farm Square Roots has unveiled a new food packaging system that the company says will give consumers a comprehensive story of how the firm’s basil, sage, chives, and mint traveled from seed to the retail shelf.
In a Dec. 19 blog post by co-founder Kimbal Musk (younger brother of Elon Musk) headlined “After the Romaine recall nightmare, here’s how Square Roots is going to get Americans to trust their food again," the company said it was introducing a labeling program that would allow consumers to see “the complete story of where and how their food was grown, and who grew it, with a simple #knowyourfarmer scan.”
“By simply scanning a QR code or typing in the lot number found on every package of Square Roots fresh produce, you are now able to see the complete story of where and how your food was grown and who grew it — tracing the entire path from seed-to-store,” Musk said in the blog post.
The QR code scan — readable by most smartphone cameras — informs consumers of what Musk called the “transparency timeline” for the commodity. The timeline includes information about the crop’s development, including:
Seeding: the scan tells where the seeds were sourced from, when and where they were seeded and the first name of the worker who seeded the commodity;
Nursery: The date the commodity was placed in the company’s climate-controlled nursery in the specified farm and the first name of the individual that transferred the tray;
Transplant: The date the seedlings were moved from the nursery to the hydroponic grow towers i in the specified farm, and the name of the worker who moved them;
Harvest: The date the herb commodity was hand-harvested and the first name of the worker that harvested it;
Packing: Date of packing and first name of the worker who packed it; and
Delivery: Date of delivery to retail store, with a note that delivery was done with “low impact transport.”
Musk said future versions of the transparency timeline could add information about the specific climate that food was grown in, recycling information relevant to the packaging for the product and perhaps other data. “If you would like see any other information added to the timeline, just let us know,” he said in the post.
With recent the recent E. coli outbreak linked to romaine lettuce — the third outbreak in two years — Musk said that consumers are at risk from foodborne illnesses.
“The situation was compounded by opaque supply chains in the Industrial Food System, making it ridiculously difficult to accurately trace the source of guilty pathogens,” he said in the blog post. “To their credit, the big lettuce producers did eventually react, and agreed to start labeling their products with a mark of the state in which their products are grown. But that’s not enough. Consumers demand — and deserve — to know more.”
Musk said that indoor climate-controlled farming “has many advantages” over open field growing when it comes to minimizing the risk of such outbreaks. He said that Square Roots’ distributed, modular farm network reduces that risk even further.
“Square Roots customers can enjoy our products not just because they taste great and are grown hyper-locally, but also because they come with the comfort and confidence of being able to see exactly how and where your food was grown and who grew it,” he said.
Musk said blockchain technology has created buzz but so far hasn’t delivered much information to consumers.
“We’re optimistic on that long-term vision (of blockchain), and we know many of the people working hard on blockchain solutions right now,” he said in the post. “But the reality is that initial implementations, while heavily buzzword-compliant, have been distinctly underwhelming in terms of the information they provide.”
Trouble In The High-Rise Hothouse
Big indoor farms are attracting big investments. But transforming agriculture might depend on putting nanofarms everywhere — maybe even in your home.
Editor-in-chief, Ideas: The Magazine of the Aspen Institute, senior editor, The Atlantic, five-time James Beard Journalism Award winner, restaurant critic
December 6, 2018
Paul Gauthier launched Princeton’s Vertical Farming Project to explore the economics of indoor agriculture. Photo by Lauren Lancaster
Big indoor farms are attracting big investments. But transforming agriculture might depend on putting nanofarms everywhere — maybe even in your home.
This was written for NEO.LIFE in association with NOVA Next/WGBH Boston.
Paul Gauthier, a plant physiologist at Princeton University, took a short drive up the New Jersey Turnpike to try to figure out whether the biggest vertical farm on the East Coast is succeeding. The answer isn’t as clear as you might think.
AeroFarms, which runs a 70,000 square-foot operation in Newark, is one of the highest-profile companies founded on the premise that growing crops indoors will transform agriculture. These aeroponic indoor farms stack leafy greens and herbs on racks that nurture the produce with sprays of mist and light from LEDs or high-pressure sodium lamps. They use no soil or pesticides, and can operate year-round. For further efficiency, AeroFarms mechanizes the seeding, harvesting, packaging, and cleaning of its produce.
It requires a great deal of electricity to give plants the light and heat they could get for free outdoors. But the idea is that vertical farms in big urban centers will be less costly—both economically and for the environment—because of the inputs they avoid, like toxic chemicals and long-distance transportation to consumers.
So do they actually come out ahead? Gauthier studies the science and the economics of growing food indoors, and he wants it to work. But the indoor farms getting glamour-puss investments refuse to release their numbers. And after touring several of them, digging into their methods to weigh the costs and the benefits, he’s suspicious about whether the numbers add up.
If you ask him whether the farms are making money or on track for any real financial viability, Gauthier, raised in Nantes and trained there and in Paris, where he earned his Ph.D, does a French thing with his mouth that translates to an existential shrug. “Who knows? So they say.” But he’s pretty sure that economics is a “major part of what’s stopping vertical farms from growing.”
Feeding 10 billion people in a world stressed by the rapidly changing climate is going to require constant innovations in how food is produced—a new green revolution, just this time not involving methods that wreck soil and water. But while vertical farms might work as a technical concept, thriving as businesses is another matter.
The problem, Gauthier suspects, is that the future of indoor agriculture might not look like a venture capitalist’s dream, with microgreens and other fancy kinds of lettuce sold at macro markups. To have a truly global impact, the startups ideally would also be researching how to grow staple crops threatened by climate change and trying to maximize their nutritional value. And, Gauthier and others argue, these agricultural startups should be thinking small at the same time—encouraging cottage and studio-apartment farmers to raise indoor tomatoes and strawberries themselves and join what could become an information-sharing revolution.
“Stupid designs”
Gauthier, who has been at Princeton’s geosciences department for six years, has a typical academic’s curiosity but also a French touch of mischief. He considered medical school, he says, but “then someone told me that even if we cure all the diseases on earth, people will still have to eat. Plus plants are cool.”
A set of test shelves in Gauthier’s lab. Photo by Lauren Lancaster
And nothing sounded cooler than saving the world by growing its food indoors, right where rapidly expanding urban populations need it. But he was baffled by the wildly optimistic predictions he read and heard for vertical farming. A widely cited 2013 study by German economists at the Macrothink Institute made the case that vertical farms in high-density urban areas, particularly in India and China, could be cost-effective because of the transport costs they would save. And they could increase access to food and reduce hunger in the bargain.
But the claims being made for the majority of vertical farms were, Gauthier says, unbacked by current, deep, and comparative data. “As a scientist, this wasn’t acceptable,” he says. “A lot of what they said was just marketing.” So two years ago he launched Princeton’s Vertical Farming Project to understand what can and can’t work economically.
He regarded with a beady eye the Ivy League grads applying for investment and Silicon Valley venture capitalists funding indoor vertical farms. Where they see a future full of urban warehouses and exurban hangars repurposed to grow food, he sees a bubble likely to burst too soon, with all those massive buildings more likely to be eventually repurposed for marijuana — the one indoor crop guaranteed to turn a profit.
Lettuce, microgreens, and herbs—the primary crops of vertical farms—have a high markup relative to, say, brussels sprouts, and being highly perishable suits them to very short transport time from indoor farm to store. But not many other commercial crops check those same boxes. Some vertical farms market kale, which is an odd choice, because it’s dirt cheap. Why bother? Gauthier leans over as if imparting a big secret: “Because anyone can grow kale, and it grows everywhere.”
Vertical farms might work as a technical concept. Thriving as businesses that transform agriculture is another matter.
Anything grown in a vertical farm might sell in China, where contaminated-food scandals mean consumers will pay a premium for food they consider to be safe, like that of fast-food chains. Vertical farms use little water and don’t need pesticides or fertilizers, all of which can be sources of contamination. So it could be smart that the most highly capitalized vertical farm company — Plenty, based in San Francisco, which has raised more than $200 million — plans to build 300 vertical farms in China.
It also would be wise to diversify the number and kind of crops in vertical farms. That optimistic German study from 2013 was based on a simulation of a farm that would grow not just vegetables but also tilapia, in tanks. Variety of output protects any business against the collapse of any one product — but that isn’t the current practice in vertical farms. Why? Perhaps because new startups follow the examples of others that seem to be successful. Perhaps because research on protein-rich products like chickpeas or fish is less evolved than it is for easy-to-grow, easy-to-sell bagged lettuce. Perhaps because different crops require different amounts of light, humidity, and nutrients and thus make for less-efficient production in a single space. David Rosenberg, cofounder and CEO of AeroFarms, says his company has experimented with growing 700 different plants, but his production is still heavily concentrated on microgreens that can fetch $40 a pound. He also sells baby greens, which he’s proud to have turned profitable, as they usually go for a much lower price to stay competitive—just $6 a pound.
Inside AeroFarms’ facility in Newark. The company’s CEO has said most startups in the industry won’t survive three years. Photo courtesy of AeroFarms
More diversified crops are possible to grow together in vertical farms — and economically safer in the long run, Gauthier thinks. But the business models might be trickier to construct for startups looking for funding. He has two indoor test gardens, one on wire shelves in a side room off his lab in the atmospherically collegiate Princeton geosciences building, and one a bit outside of the tony, horsey town of Princeton. In these little indoor gardens he grows particularly sweet strawberries he’s proud of. They don’t grow efficiently enough, though, to appeal to today’s commercial vertical farms.
Though Rosenberg won’t disclose whether AeroFarms is profitable, he shares much of Gauthier’s general skepticism about many of his competitors in vertical farming. In a keynote address to an indoor-farming conference last year, he predicted that 60 to 90 percent of indoor farms would fold within three years of starting. Some already have gone bankrupt.
Rosenberg says not enough of them truly understand how costly their build-outs and operations will be before their first robot plants a seed in ecologically ultra-responsible growth medium. He says he and his team of 120 workers, most of them engineers, have learned this from several years of expanding into four buildings in downtown Newark. “Biological systems scale in non-obvious ways,” he says.
In the last year alone, he says, four companies that were going out of business approached him to buy their assets. Those companies had “stupid designs,” he says. “They lost before they got going.”
Lettuce, microgreens, and herbs have a high markup, and being highly perishable suits them to very short transport time from indoor farm to store. But not many other commercial crops check those same boxes.
In general, Gauthier says, energy for lighting and climate control accounts for as much as 60 to 70 percent of operational overhead in a vertical farm. Add in labor costs, which are higher in the urban areas where vertical farms are located, and the farm is likely to have, at best, a profit margin of 4 to 5 percent. That’s more than what’s reaped by most U.S. farms, which are strapped by international competition and the current trade war. Even 4 to 5 percent, though, is nothing to venture funders, who look for profitability of 10, 15, 20 percent and beyond. (Rosenberg, without disclosing specifics of AeroFarms’ business, says those fatter profit margins are indeed possible—but only if debt-service and real-estate costs are low, and if many processes are mechanized.)
Peppers harvested from Gauthier’s lab. He tinkers with the pH of the growth medium to manipulate the peppers’ spiciness. Photo by Lauren Lancaster
The danger, Gauthier thinks, is not that a few well-funded farms will turn only a modest profit growing niche crops to be sold by boutiques whose customers can afford high markups. It’s that many indoor farms will fail, because anyone who tries the things he thinks would best serve the industry — crop diversity within the same indoor space, research into lower-margin staples like wheat that are threatened by climate change, efficient techniques for growing high-protein crops — won’t appeal to funders who expect too much too soon.
Micro-farm in the rec room
Vertical farmers might have a better chance of nailing the math if they had real-world data about what works. And that’s hard to come by. Those well-funded indoor farms keep their data secret: the costs of buildout and climate control and labor; how plant growth varies with the nutrients they feed plants; the amount and color of the light and heat and humidity and growing time for each one, the prices the harvests fetch.
What if a lot more of that data were widely available to anyone who wanted to transform agriculture by bringing it indoors, anywhere in the world? How expensive are the lights, shelves, aeration, and hydration and climate-control systems? How long do they take to amortize? How do different plants grow indoors in different places and conditions — not just the sterile, ultra-controlled-atmosphere buildings stacked 37 stories high, the utopia conjured in endless vertical farm stories?
Gauthier checks the roots on two new plants. Photo by Lauren Lancaster
Gauthier envisions a much broader ecosystem: a future of thousands upon thousands of farms, in basements and bedroom corners, growing strawberries and basil and lettuce and tomatoes, uploading data to central servers that help cottage growers all over the world as well as larger-scale indoor farmers. “Everybody has a basement or a corner,” Gauthier says. Only 15 minutes of tending a day max, he promises. And if the climate isn’t perfect and the lighting is not custom-tailored for one plant, well, people’s gardens in real life aren’t so tailored either.
These micro-farms in every rec room, study nook, and garage would be simple — no need for the colored lights that large-scale vertical farms use. Just full-spectrum LEDs of the kind Gauthier has in his pocket-sized lab farm. The vivid light in the space makes it warm and inviting, unlike the compact fluorescent light over his research assistants in the next room. “People come here and say, ‘I could put my desk here,’” he says. Just being here and fussing with his leggy strawberry and basil plants visibly brightens Gauthier’s mood.
Why would you follow his suggestion and buy the makings for your own basement or closet? The same reason that inspires window-box and patio gardeners everywhere: to have fresh food you’ve grown yourself, for pennies on the dollar and the kind of brightness of flavor those bright lights suggest. And unlike with window boxes and mini-terraces, indoor gardens would flourish independent of weather.
Turning basil into data
Caleb Harper, of MIT’s Media Lab, also has very large ambitions for very little indoor farms all over the world. He founded the Open Agriculture Initiative, or OpenAg, with open-source data, hardware, and software as founding principles. He wants to create more “digital farmers” around the world by making how-to information and tools easily available to them, and he hopes to connect them so they do the neighborly tip-sharing that used to take place at the feed and seed store.
One of Harper’s first moves, in 2015, was to release designs for a prototype “food computer,” a kit that creates a milk-carton-sized, digitally controlled hydroponic growing environment for even, say, one stalk of basil. That was version one, and the costs for materials ran from $2,500 to $4,000 for a souped-up model. The most recent version, V3, costs about $500. Its starter equipment includes a “central nervous system” that incorporates a printed circuit board, USB camera, LED lights, fans, and sensors to measure temperature, humidity, and carbon dioxide. Wi-Fi-connected processors in the box upload millions of pieces of data about the plant’s progress to cloud servers that help others replicate and share their results.
One of Caleb Harper’s “food computers” that captures data about growing conditions. Photo by MIT Open Agriculture Initiative (CC-BY-NC-SA 4.0)
Harper’s idea, like Gauthier’s, is that the more information that indoor farmers around the world share — the levels of irrigation, minerals, nutrients, light, and temperature that together he calls the “climate recipe” — the faster the field can keep up with what Harper calls mounting climate and ecological pressures.
The VC firms funding vertical farms, Harper says, seem to believe that they need to hoard the best and most efficient technology and formulas to farm indoors. But little to none of the materials that go into vertical farms are much farther evolved than the off-the-shelf equipment used in greenhouses and what his food computers require. Few if any processes are likely to be so different from what anyone else is using as to create windfalls, he thinks.
Even so, companies won’t disclose data about indoor farming. They’re saying to Harper, “Why are you telling the Muggles our secrets?” His operative answer: “I want to make vertical farming work. And I see how often claims are completely baseless — and the number of bankruptcies over the past 10 years.”
OpenAg operates two sets of food computers at MIT, one in miniature in the glossy, glassy Media Lab building and another in three repurposed shipping containers in a former storage warehouse for a disused linear accelerator. Harper himself is all over the world all through the year, raising awareness and raising money. He researches what his funders want. So one of the shipping containers at MIT has an extra-tall growing chamber to fit hazelnut trees for Ferrero, the hugely profitable, family-owned maker of Nutella. Harper recently dispatched half his team to India to rig out a shipping container to grow cotton for Welspun, a sheets and towels manufacturer that hopes to enlarge the limited supply of sustainably grown cotton. But even though his high-profile clients are usually secretive, all the research the MIT team conducts is, by the Open Agriculture Initiative’s contract, open-source.
“Why are you telling the Muggles our secrets?”
Hildreth England, OpenAg’s assistant director, has a diplomacy major’s fluency of expression and comes from a multi-generational engineering family. As she explains the uses of the 3.5 million data points she says the food computers produce per plant every growing cycle, her head is illuminated by a mesmerizing light show emanating from the box behind her. The food computer can be programmed to cycle through green, red, yellow, blue, and white lights shining on a basil plant viewable from a little window inside the black honeycomb cube, like something in Hamburg’s Reeperbahn. Various colors of light can make the plant express more of the volatile essential oils and fragrances it produces in reaction to the stress that microbes in dirt, wind, and drought inevitably impose — “in a sad, sad way we’re stressing the plants out,” she says — and these compounds can be valuable in dietary supplements and medicines. She and Harper expect indoor farms to someday grow high-profit plant-based derivatives for the pharmaceutical industry, alongside tomatoes bred to express more cancer-resisting lycopene thanks to data uploaded by thousands of growers.
In a collaboration with the United Nations World Food Programme, the Initiative put food computers in Syrian refugee camps in Amman, Jordan, to provide fresh food where people aren’t allowed to make changes to the land. A professor who was a refugee had the idea of experimenting with how to create a climate recipe that would increase the active ingredients in St. John’s wort to treat depression and anxiety: for many people, drinking herbal tea is more culturally acceptable than taking Prozac.
The uses of indoor farming, then, can be as unexpected and ingenious as the places it appears and the people who tend the plants. The underlying technology might be similar the world over, Gauthier says. But think of the iPhone: Everyone uses it a little differently, and Apple collects that data so it can make the next generation easier to use. Large leaps and small serendipities might well come from the tiny plots both he and Harper envisage — the ones that can turn the latest sexy innovation into tomorrow’s world-changing revolution.
CO2 GRO Announces Dramatic Improvement In Resistance To Pathogens and Pests from Employing CO2 Foliar Spray
TORONTO, ON – December 06, 2018
Toronto based www.co2gro.ca
. (“GROW”) (TSX-V: GROW, OTCQB: BLONF, Frankfurt: 4021) is pleased to announce dramatic plant resistance improvement against common pathogens and a common predator using CO2 Foliar Spray. Bacterial (E. coli) and fungal (F. oxysporum) numbers showed a reduction by two orders of magnitude (over 90%) while a significant reduction in aphid counts was also identified.
Foliar Spray plants once infected with powdery mildew had over a 100% increase in days of plant survival post infection versus plants grown conventionally and CO2 gassed plants. The CO2 gassed plants had similar low results to conventional plants showing minimal pathogen resistance improvement using CO2 gas.
These pathogen and pest results will add to grower confidence to use GROW’s natural CO2 Foliar Spray which is proven to sharply enhance plant growth and value. It could lead to the reduction of the amount of chemical pesticides, insecticides and fungicides used for optimal plant growth with CO2 Foliar Spray use.
CO2 FOLIAR SPRAY SCIENTIFIC TRIAL METHODOLOGY
Antipathogen experimentation considered bacterial (E. coli), fungal (F. oxysporum) Powdery Mildew strains and aphids (insects). Six individual experiments were conducted at St. Cloud State University under Dr. Matt Julius. Two grew pathogens directly on agar plates (one E. coli and one F. oxysporum). Four used peppers as a host for the pathogens; one used E. coli, one used F. oxysporum and one used Powdery Mildew. The sixth experiment used predator aphids.
CO2 Foliar Spray at 800 PPM dissolved was applied every fifteen minutes for three hours per day. E. coli, fungi, and aphid trials were five days long while the powdery mildew trials were 21 days in length.
With the powdery mildew trial, three variations were considered. A control, CO2 gassing at 1200 PPM, and CO2 foliar infusion at 800 PPM. Plants were infected with Powdery Mildew and days to mortality were counted for each experimental plant.
All experiments were compared with standard statistical methods and found major increases in resistance for all pathogens and predators trialed.
CANNABIS TRIALS PENDING
Several LP cannabis growers waiting to trial CO2 Foliar Spray following approval expressed concerns that its use could increase powdery mildew risk with limited Health Canada powdery mildew treatment options. These non-cannabis plant scientific results using powdery mildew prove the opposite.
The next series of scientific pathogen and predator resistance trials will be performed at two legal US cannabis facilities in early Q1, 2019. Results will be filed with Health Canada in support of approving the Canadian usage by LPs of CO2 Foliar Spray during plant cutting transplant and vegetative growth phases for superior pathogen and predator resistance.
Dr. Matt Julius concluded “These results are consistent with the hypothesis that CO2 Foliar Spray use inhibits the growth of E. Coli, fungus and Powdery Mildew and retards insect grazers.”
John Archibald, CEO of GROW stated "These results add further confidence to our potential cannabis and non-cannabis plant growers of the dramatic plant value superiority using CO2 Foliar Spray over no CO2 gassing as well as over plants CO2 gassed.”
About CO2 GRO Inc.
GROW's mission is to accelerate all indoor and outdoor value plant growth naturally, safely, and economically using its patented advanced CO2 foliar technologies. GROW’s global target plant markets are retail food at $8 trillion per year (Plunkett Mar 2017) and retail non-food at an estimated $1.2 trillion per year with retail tobacco at $760 Billion (BA Tobacco estimate), floriculture at $100B by 2022 (MarketResearch.Biz estimate) and legal retail cannabis at $50 billion per year by 2022 (Bay St Analyst estimates).
GROW's CO2 technologies are commercially proven, scalable and easily adopted into existing irrigation systems. GROW's proven crop yield enhancements and revenue model are compelling for growers and Agri-industrial partners.
GROW's sole focus is working with its plant grower and Agri-industrial partners in proving and adopting its CO2 technologies for specific growers’ plant yield needs.
The CO2 technologies work by transferring CO2 gas into water and foliar spraying across the entire plant leaf surface area, which is a semi permeable membrane. The dissolved concentrated CO2 then penetrates a leaf's surface area naturally like nicotine naturally dissolves through human skin from a nicotine patch.
Foliar spraying of natural water, dissolved nutrients and chemicals on plant leaves has been used for over 60 years by millions of indoor and outdoor plant growers. To date, outdoor growers have not had any way to enhance plant CO2 gas uptake for faster growth.
Indoor use of CO2 gassing has enhanced plant yields for over 60 years. However, about 60% of the CO2 gas is typically lost through ventilation. Current greenhouse CO2 gassing levels of up to 1500 PPM are also not ideal for worker health and safety. GROW's safer infused CO2 foliar spray can be used by indoor and outdoor plant growers with minimal CO2 gas lost and much greater plant bioavailability resulting in higher yields.
Forward-Looking Statements This news release may contain forward-looking statements that are based on CO2 GRO's expectations, estimates and projections regarding its business and the economic environment in which it operates. These statements are not guarantees of future performance and involve risks and uncertainties that are difficult to control or predict. Therefore, actual outcomes and results may differ materially from those expressed in these forward-looking statements and readers should not place undue reliance on such statements. Statements speak only as of the date on which they are made, and the Company undertakes no obligation to update them publicly to reflect new information or the occurrence of future events or circumstances, unless otherwise required to do so by law.
Neither the TSX Venture Exchange nor its Regulation Services Provider (as that term is defined in the policies of the TSX Venture Exchange) accepts responsibility for the adequacy or accuracy of this release
New Plug And Play Devices Deliver Dissolved Oxygen To Plant Roots
Dissolved oxygen (DO) does many things for your plant. It is a critical but often overlooked piece that helps plants uptake nutrients through the roots. Dissolved oxygen is the mechanism that allows the nutrients to be absorbed through the root membrane. "Without sufficient levels of DO, there will be no growth. It is proven that higher levels of DO help prevent “lockout” which is when your plant is getting enough water/nutrients, but not absorbing it.", says Dennis Clark with O2 Grow.
pH, TDS and EC
Dennis explains why a DO meter is an important measuring device that every grower should have. "Most growers already have pH, TDS and EC meters, but not many have a DO meter. A quality DO meter is about the only way for a grower to know if the nutrient water has enough dissolved oxygen."
DO is typically measured in either mg/L or ppm. "Most plants need a DO level of about 6 ppm to grow, some water sources such as well water can have readings as low as 2 ppm. University trials have proven that DO levels above 10 ppm will drive enhanced growth, with a better more robust root system that supports more flowering sites on each plant."
A healthier root system also enables the plant to stave off disease and other ailments common with low DO. "University of Minnesota studies revealed as much as a 30% increase in the number of peppers in a controlled study. Other studies conducted by the University of Wisconsin reported a significant increase in root mass and yield for Crown Peas grown in Nutrient Film Technique (NFT). Also noted, was the enhanced green leaf growth. The plants were simply fuller, healthier and more produced more flowering sites."
The Oxygen Research Group has introduced a product called the O2 Grow. The O2 Grow units deliver supplemental oxygen to nutrient water via the process of electrolysis. "This process converts water molecules into nano bubbles of oxygen gas", Dennis shows.
The tiny bubbles are too small to break the surface tension of the water and are therefore absorbed back into the water. "This process will saturate the nutrient water with as much dissolved oxygen as the water can hold. When measured with a DO meter, water at 20 degrees Celsius can hold as much as 14-16 ppm of oxygen. The O2 Grow units will quickly and efficiently saturate the water to the maximum amount of oxygen the water can hold."
The O2 Grow units require very little energy to operate. They are adapted to run off of a battery source which means they can be run in a field setting or off of a solar grid. "The units are quiet and compact", Dennis shows. "Units are designed to fit a specific nutrient reservoir size based on gallons of water used to water plants from as small as 10 gallons up to 250 gallons. Simply place the emitters into your nutrient water and switch the unit on. Since the units do not need to be run continuously to maintain the higher DO levels, some growers find it easier to set up the units on a timer so nutrient water is ready to go when they need it."
The O2 Grow units can be used for both hydroponic and soil based methods of growing as well as in both indoor and outdoor environments. The units are sized based on the number of gallons/litres of water that the grower will be oxygenating. Units range from 10 gallons (37.8L) up to 250 gallons (946L). There are also units designed specifically for deep water culyure (DWC). Operating the unit is easy, simply plug in and run the O2 Grow emitters prior to watering or set the units up on a schedule with a timer.
For more information:
Oxygen Research Group
15320 Minnetonka Industrial Rd
Minnetonka, MN 55345
952-474-5820
info@o2grow.com
Publication date : 12/5/2018
Backyard Farms’ Northeast Expansion Sets Record
December 04, 2018
Mastronardi Produce Ltd. is expanding the Backyard Farms brand with the introduction of a high-tech greenhouse in New York, one the largest-ever single builds in North America.
“This expansion allows us to meet the incredible loyal consumer and retailer demand for this brand," said Paul Mastronardi, president, chief executive officer and the fourth-generation family member to lead Mastronardi Produce. “It also ensures that all Northeasterners can enjoy what New Englanders have come to expect: fresh-from-the-vine Backyard Farms tomatoes delivered within hours.”
The 71.6-acre glass greenhouse is only Phase I of the company’s mission to satisfy customer appetites — and exceed flavor expectations — for locally grown Backyard Farms tomatoes.
The new, industry-leading greenhouse more than doubles Backyard Farms’ greenhouse growing acreage and increases Mastronardi Produce’s internal greenhouse network to seven locations across the United States. In total, Mastronardi produces and delivers fresh, flavorful produce to retailers from more than 4,000 productive acres of growing capacity.
New-York-grown Backyard Farms tomatoes are planned to hit stores in Fall 2019
NASA Technology To Grow Crops Faster
NASA has created a new technology to grow crops on other planets with the prospect of establishing colonies on Mars or another planet in the future. A group of scientists from the John Innes Center, the Earlham Institute, the Quadram Institute in the United Kingdom, and the University of Queensland have tested the application of this technology in terrestrial crops.
They have applied the new technology in a greenhouse at the John Innes Center in Norwick (United Kingdom). Researchers conducted rapid genetic improvements using shorter crop growth and harvest cycles, in addition to improved LED lighting. The research, which was published in the scientific journal Nature Protocols, shows that this method of cultivation can produce crops that are resistant to diseases, climate challenges, and that are more nutritious to feed a growing world population.
This technique uses improved LED illumination and day regimes of up to 22 hours to optimize photosynthesis and promote rapid crop growth. It accelerates the plants reproduction cycle: for example, it allows producers to grow six crops of wheat in a year, well above the two crops per year that are achieved with traditional improved farming methods.
By shortening breeding cycles, the method allows scientists and plant breeders to make accelerated genetic improvements, such as increasing yields, disease resistance and tolerance to climate change in a variety of crops, such as wheat, barley, rapeseed, and pea.
Source: lavanguardia.com
Publication date : 11/29/2018