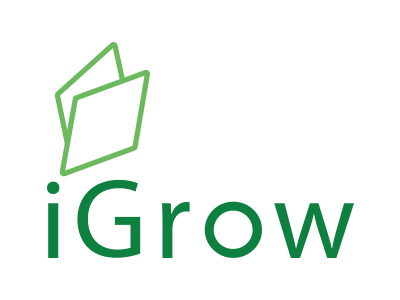
Welcome to iGrow News, Your Source for the World of Indoor Vertical Farming
Spotlight On Urban, Vertical And Indoor Agriculture
Should food be grown in cities? If so, how? These questions have a long history, with the last few hundred years taking in the Garden City movement where towns were designed to include homes, industry and agriculture, the ‘Victory Gardens’ of the First and Second World Wars and, more recently, the food miles debate
By Helen Breewood, originally published by Food Climate Research Network
January 22, 2019
Should food be grown in cities? If so, how? These questions have a long history, with the last few hundred years taking in the Garden City movement where towns were designed to include homes, industry and agriculture, the ‘Victory Gardens’ of the First and Second World Wars and, more recently, the food miles debate.
Meanwhile, futuristic visions of the food system often feature city-centre skyscrapers full of fresh fruit and vegetables, carefully tended by a fleet of robots, with precise doses of fertiliser, water and exactly the right wavelengths of light administered by an intelligent computer – and perhaps open to city dwellers looking to unwind among some greenery or learn how their food is produced. Entrepreneurs Peter Diamandis and Steven Kotler, for example, paint a rosy picture in their book Abundance, in which they claim that just 150 thirty-storey farms could feed the whole city of New York.
But look closer, and the picture becomes less clear. Isn’t urban farming an old tradition, in the form of allotments or community gardens? Aren’t commercial greenhouses already highly automated? Is it really more efficient to build a huge structure and use artificial lights, instead of just transporting food from farmland using rapid modern supply chains? If high-tech skyscraper farms are really more efficient (in terms of resource use or environmental impacts per unit of output) than field-based farming, why limit them to urban areas where land is expensive?
This purpose of this blog post is to disentangle some of the many intertwined concepts here: urban, indoor and vertical farming. The diagram below is one attempt at showing how several different forms of food production can be classified as urban, indoor, vertical or a combination. I’ll outline some of the main factors and questions surrounding their implementation. This post does not aim to answer all the questions raised, nor make a judgement on which types of urban, vertical or indoor farming are ‘best’ or most sustainable. Its purpose rather is to stimulate ideas and discussion among FCRN members. Do give your thoughts and feedback via the FCRN Google Group.
This post focuses mostly on high-tech farming rather than, say, allotments. It also focuses on higher-income countries. However, urban farming is of great importance in the context of lower-income countries – see, for example, the paper Sustainable urban agriculture in developing countries. A review and the work of the RUAF Foundation, which is a “global partnership on sustainable urban Agriculture and Food Systems”. For more information on different aspects of urban, indoor and vertical farming, see the resources listat the end of this post.
Image: one possible way of classifying agriculture according to whether it is urban, indoor, vertical or a combination of these. An alternative visualisation of these categories could be a 3D graph with three axes: rural to urban, outdoor to indoor, and horizontal to vertical. In this latter option, individual items could be placed at the appropriate point along each axis, instead of being classified as strictly urban or rural (say).
Urban agriculture
Image: Fadi Hage, Greenhouses at Lufa Farms, the world’s first commercial rooftop greenhouses. Montreal neighborhood of Ahuntsic-Cartierville. Wikimedia Commons.
The location of agriculture can be defined on a spectrum from rural to urban, with urban or semi-urban encompassing a wide variety of situations such as windowsills, allotments, private gardens, public parks, multi-storey farms, industrial estates, rooftop gardens and even disused underground rail tunnels or ‘guerrilla gardens’ (areas of land that people cultivate without having formal legal rights to do so, such as unused building sites).
Proponents of urban agriculture claim that it has both environmental and social benefits.
On the environmental side, these include lower transport emissions, introducing green areas and biodiversity into cities, food waste reductions, greater efficiency of water use, and greater ease of using urban waste streams as a farming resource or linking with renewable energy production.
On the social side, listed benefits include fresher food, community cohesion, stress relief and mental health improvements, training and employment opportunities, and increased access to fresh fruits and vegetables. Matt Barnard, CEO of hydroponics startup Plenty argues that fruit and vegetables can be made cheaper by cutting out transport costs – and that therefore more people might be able to afford to buy them.
However, not all these benefits have a strong evidence base, not all apply to all types of urban agriculture, and there are also potential disadvantages to consider.
An example of a benefit that only applies to a specific form of urban agriculture is aesthetics. Anna Birgitte Milford, Research Scientist in the Division of Food Production and Society at NIBIO, is currently studying rooftop greenhouses in Bergen, Norway. She argues “A rooftop greenhouse can also, if done well, become an aesthetic landmark in any city, and this has a lot of social value.” However, commercial urban farms might not be open or visible to the public – and, as Milford points out, the aesthetic aims of a greenhouse may conflict with achieving optimal plant growing conditions. Mike Hamm, who is C.S. Mott Professor of Sustainable Agriculture at the Centre for Regional Food Systems, Michigan State University, adds that while one of the arguments used to promote some urban farms is that organic agriculture would be easier because pests can be excluded, this attribute would be absent in the case of open green spaces.
Similarly, while employment opportunities may be created by some types of urban farming, highly automated urban farms may not create many jobs. Nevertheless, social enterprises can be designed specifically to provide educational opportunities, access to green space or other social benefits (see for example the box below about Gorgie City Farm).
There could be trade-offs between emissions savings from transport reduction and the high energy or material use of some forms of urban agriculture (for more on the resources used by indoor agriculture, see below).
According to Milford, it is difficult for rooftop greenhouses to be economically viable because of the additional material cost required to safely construct rooftop greenhouses and because of the higher costs of urban compared to rural land. However, successful examples do exist: Lufa Farms, which operates commercial rooftop greenhouses in Québec, claims to be running a profitable business.
While Hanna Tuomisto, Associate Professor at the University of Helsinki, says that freshness is one possible advantage of urban agriculture (indeed, many urban agriculture companies focus on freshness as a selling point, including Plenty, Lufa Farms and Farm.One), freshness is only important for some types of crops, such as salad leaves and soft fruit. There will almost certainly be little advantage in growing less perishable crops, such as grains, in urban locations.
Image: GroCycle Urban Mushroom Farm, Grocycle press kit
According to Peter Wootton-Beard, Lecturer in Agri-Technology at Aberystwyth University, another advantage of urban farming is that it becomes easier to use so-called ‘co-located’ resources or waste streams as inputs for the farm, including “nutrient recycling technologies such as anaerobic digestion, insect production, micro algae production (both for protein) and the use of waste heat and CO2 from CHP [combined heat and power] plants or electricity generation.” Thinking along similar lines, Diamandis and Kotler have suggested that the energy to run artificially-lit urban farms could be extracted from sewage, a waste stream that is readily available in urban areas. Another enterprise taking advantage of urban resource streams is GroCycle, which uses waste coffee grounds from cafes as a substrate to grow mushrooms in a disused office building. It would be less practical to transport the coffee grounds to a rural area, because they go mouldy quickly.
Gorgie City Farm: An example of urban agriculture
Image: Kim Traynor, Gorgie City Farm, Geograph, Creative Commons Attribution-ShareAlike 2.0 Generic
Gorgie City Farm in Edinburgh, UK, is an urban farm designed to promote education, volunteering opportunities and social inclusion. It offers free entry to visitors along with educational tours and workshops. As well as selling fruit and vegetables to local shops and restaurants, the farm showcases traditional animal farming methods. The farm is a charity and accepts donations rather than being economically self-sustaining through food production.
Indoor agriculture
Image: NASA/GSFC/METI/ERSDAC/JAROS, and U.S./Japan ASTER Science Team, Surrounding the town of El Ejido, Almeria Province, southern Spain is a sea of greenhouses, stretching for tens of kilometres.
Indoor farming encompasses a range of food production methods such as cold frames, polytunnels, unheated greenhouses, heated greenhouses and so-called controlled environment agriculture (CEA), with tight control over many aspects of the growing environment (e.g. LED lighting with tuneable wavelengths to replace or supplement sunlight). What these methods have in common is a greater ability to control the growing environment than with outdoor production.
Some claimed advantages of indoor farming include better working conditions (e.g. less heat stress compared to working outdoors), greater control over pests and diseases, improved food safety, less vulnerability to extreme weather, the ability to produce all year long, lower emissions of pollutants such as excess nutrients and pesticides to the air, soil or waterways, and the ability to fine-tune crop flavours by adjusting growing conditions.
However, the energy and resource use of indoor farming can be high, depending on climate. For example, it takes so much energy to heat greenhouses in France that tomatoes grown in them have a higher carbon footprint than imported tomatoes grown in unheated greenhouses in Morocco, even after accounting for transport (Payen et al., 2015).
Speaking of relatively high-tech indoor systems, Mark Bomford, who is Director of the Yale Sustainable Food Programme, says “CEA comes at a higher energy cost per unit than field production for the same thing, which in most analyses means a higher environmental cost”, citing the thesis of Yoshihiko Wada, who in 1993 used real-world data to calculate the environmental impacts of tomato production in comparable hydroponic systems with conventional open-air farming. According to Bomford, Wada found that “sustaining the production of 1t tomatoes in a high-yield CEA system would actually require 15 times the ‘ecological footprint’ land for the same 1t of tomatoes in a low-yield field system [emphasis added]”. Bomford has advised several CEA startups, and mentions that these startups have generally viewed the high environmental impacts of CEA as a challenge to be overcome through greater efficiency.
Bomford does think that CEA has some advantages – namely, making working conditions safer and employment more seasonally stable – but suggests CEA may be best suited to single-storey sun-lit systems on relatively cheap rural land, and that multi-storey CEA farms on expensive urban land – i.e. the popular futuristic skyscraper farm vision – may be limited to a small market niche. Hamm agrees.
The relative ease of automation in indoor systems raises questions over control and ownership of technology and knowledge. For example, Infarm remotely controls all of its growing units (see box below). Although cofounder Erez Galonska says that the system will “re-empower the people to take ownership of their food”, might it actually mean that growers no longer develop expertise in recognising and responding to a plant’s needs? Plenty won’t share details of its hydroponics technology (source), but Liverpool’s Farm Urban, in contrast, gives out free instructions for building mini aquaculture kits.
Infarm: an example of indoor farming
Image: Infarm, First vertical farm to table restaurant opens its doors, Instagram
Berlin-based startup Infarm makes modular, automated farming systems that are designed to be used in locations close to consumers, such as supermarkets, restaurants, bars and schools. Infarm happens to be not just indoor but also vertical and – generally – urban.
The systems are remotely run by Infarm’s central control system to provide the right light spectrum, temperature, pH and nutrient levels for the crops. Retailers and others who hire the growing units won’t have to control the units themselves, other than to harvest the produce.
Infarm claims that one in-store farming unit is equivalent to 250 m2 of farmland (presumably in terms of production capacity) but uses 95% less water, 75% less fertiliser and no pesticide. It isn’t clear how Infarm’s carbon footprint or energy use compare to field-based farming.
There are also economic implications if the demand for manual labour decreases through automation. While it may benefit farmers in some circumstances – for instance, some UK farmers are concerned that there may be a labour shortage under the UK’s proposed post-Brexit immigration system – might automation also put people out of jobs or contribute to the concentration of wealth in the hands of those who own the technology?
Wootton-Beard says that indoor farming “means the possibility of near complete control over the environment, opening up the possibility to tailor the environment to alter flavour, nutritional profile and other characteristics of food plants.” However, such a tightly controlled growing environment may imply strict biosecurity and hygiene measures and a lack of public access – which would preclude some of the social benefits cited by promoters of urban and indoor farming. Wootton-Beard notes the discrepancy between public perceptions and what might realistically happen, saying people “have seen the concepts for urban skyscrapers and food production integrated with living accommodation, which whilst not impossible, is much less economically viable [than] a factory style production line approach.”
Another question is reliability: while Wootton-Beard points out that indoor farming is “agnostic of climate change, political instability, trade deals, and supply chain complexities”, might high-tech indoor systems instead be vulnerable to failure through mechanical breakdown, electronic faults, or malicious hacking of the control systems? Are these risks higher or lower than the risks of pests and extreme weather in outdoor systems?
Some indoor farming businesses say that fewer pollutants are released to the environment, compared to outdoor systems. For example, hydroponics startup Plenty says its system means “absolutely zero pesticides going into the soil, groundwater, and your food.” However, Bomford suggests that comparing controlled environment agriculture (CEA) to conventional farming is “not really fair” unless the same crops are being compared, saying “Advocates of CEA often miss their targets in their marketing material, pointing to the environmental abuses of agricultural sectors that will never be viable indoors (i.e. they might invoke the ‘dead zone’ in the gulf of Mexico, despite the fact that CEA tech will not change corn and soy practices, or invoke the subsidence of land in California due to groundwater removals, despite the fact that CEA tech will not change tree nut, cotton, or alfalfa growing practices) and then present a solution for a completely different sector – generally niche specialty crops.”
Vertical agriculture
Image: Farm. One press kit
Vertical farming can refer both to multi-level farms where the plants grow on stacked shelves of horizontal substrates, and to systems where the growth substrate itself is vertical, as in the Leafy Green Machine™, a ‘farm in a box’ where vertical strips of plants hang under artificial light in a converted shipping container (see the box below for more information). ‘Green walls’ of plants are also used for decoration, air purification, cooling of buildings or reducing stress, and less commonly for food production (e.g. the Edible Walls exhibit at Sydney’s Powerhouse Museum, curated by FCRN member Judith Friedlander). Vertical farming is highly compatible with growing techniques such as hydroponics, aquaponics and aeroponics, which don’t need soil.
One significant benefit of vertical farming is space-saving, relative to conventional ‘horizontal’ farming. This is particularly useful in urban areas, where land is more expensive than in rural areas. Vertical farming therefore offers the possibility of providing very fresh food by squeezing into urban locations near consumers – albeit perhaps at a premium, due to the energy use and high land costs. Perhaps vertical farming could compensate for some farmland lost to urbanisation. However, Tuomisto points out that some people are concerned “whether the plants from hydroponics have the same nutritional value [as] plants grown on soil.” For further discussion of this question, see this piece from the New York Times: Are Hydroponic Vegetables as Nutritious as Those Grown in Soil?
On the other hand, perhaps urban land would be better used to provide housing to reduce emissions from commuting – particularly since urban land is expensive compared to rural land. Furthermore, the space-savings benefits of vertical farming could also be applied in non-urban settings, such as growing food in cargo ships which would otherwise be empty on their return journey.
As Tuomisto tells me, vertical farming generally requires artificial lighting because otherwise the lower layers of plants would not receive enough sunlight. For this reason, vertical farming systems also tend to be indoor systems (although outdoor multi-level cropping systems could conceivably be classified as a form of vertical farming). Artificial lights, together with cooling systems to remove the heat they produce, require a lot of energy. Tuomisto says generating this energy sustainably may be a challenge, but adds that vertical farming systems may become more efficient in future through optimisation of lighting, cooling and fertiliser and water usage. However, Hamm suggests that gains in energy efficiency can’t beat using sunlight.
The cooling requirements of vertical farms are a contrast to horizontal heated greenhouses. In the latter, the relatively large ratio of surface area to volume means that a lot of light can get in, but that heat is lost rapidly (at least in a cold climate).
Perhaps there is an optimum shape of vertical greenhouse (maybe with only a few layers) where the heat produced by both natural and artificial lighting is approximately balanced by the greenhouse’s passive rate of heat loss. Such a greenhouse might need relatively little additional heating or cooling.
Tuomisto also cites high material costs as a disadvantage of vertical farming, raising questions as to whether vertical farming provides environmental benefits (see below for a discussion of the carbon footprint of one vertical farming system). We may have some answers soon, as Tuomisto is in the early stages of conducting a Life Cycle Assessment study of a four-layer hydroponic system in Finland. As well as considering the direct environmental impacts of novel farming systems, we should also consider interactions with the wider food system. For example, might land spared by vertical farming become available for carbon sequestration, e.g. through reforesting or BECCS?
Freight Farms: an example of vertical farming
Image: LED lights, Freight Farms Press Kit
The Leafy Green Machine™ (LGM) produced by Freight Farms is a vertical hydroponic growing system inside a shipping container. It has been used in urban areas such as Paris and Oslo and has also been placed on some conventional rural farms, where it adds the ability to grow herbs and salads all year round.
Freight Farms claims that its system, which has an area of around 30 m2, can produce as much food in one year as two acres of farmland (it isn’t clear whether this is measured by weight) and uses 90% less water use compared to conventional agriculture. The system costs $85,000 to buy and around $13,000 per year to run (including electricity, water and growing supplies), according to Freight Farms.
Freight Farms gives some illustrative figures for inputs and outputs, although these vary according to the outside climate: per week, 875 kWh of electricity, 160 litres of water, 15-20 hours of labour and $75 worth of nutrients can produce (for example) 52 kg of butterhead lettuce or 23 kg of spinach.
Freight Farms doesn’t give the carbon footprint of growing food with the LGM. However, if as a very rough estimate we take a carbon intensity of 414 g CO2 eq. per kWh of electricity (the UK’s electricity mix on 3 January 2019, according to Electricity Map), then the electricity to run the Leafy Green Machine™ for a week would cause emissions of roughly 362 kg CO2 eq. That’s around 7 kg CO2 eq. per kg of lettuce, or nearly 16 kg CO2 eq. per kg of spinach – only accounting for electricity, not fertiliser, water or construction of the LGM.
How does that compare to conventional production? According to Clune et al., who reviewed the carbon footprints of food production across the world, typical carbon footprints are 3.70 kg CO2 per kg of lettuce (based on heated greenhouse production) and only 0.54 kg CO2 eq. per kg of spinach. That means food produced in the LGM has a carbon footprint at least 2 to 30 times higher than for conventional production, not accounting for transport.
Does reduced transport compensate for the increased carbon footprint of growing food in an LGM? It seems unlikely: transporting food across several thousand kilometres might only produce around 0.7 kg CO2 eq. per kg of lettuce, according to Mike Hamm.
Of course, if the LGM were to be used with lower-carbon electricity, the carbon footprint of the food produced would fall. In France, for instance, where the large contribution of nuclear power means the electricity mix produces only 74 g CO2 eq. per kWh (3 January 2019, Electricity Map), the LGM carbon footprints would fall to (as a minimum) 1.2 kg CO2 eq. per kg of lettuce and 2.8 kg CO2 per kg of spinach – which, for spinach, is still much higher than conventional production.
The LGM may have some advantages, but climate impact is not necessarily one of them.
In conclusion
There is a great deal of enthusiasm for new forms of farming. Milford even tells me “I have probably never been met with more enthusiasm when searching for stakeholders to a project.” However, perceptions are not always realistic. Wootton-Beard says “I have found that people tend to be orientated towards the utopian visions for indoor farming, and imagine it to be some sort of science fiction strangeness”, while Bomford claims “Public perception of CEA often seems a fantastical construction.”
Urban, indoor and vertical farming encompass a wide variety of systems, each of which have different benefits and drawbacks. Perhaps many of the systems considered here do have some role to play in our future food system, with each type being suited to serving different environmental, social or economic goals.
Acknowledgements
Many thanks to our interviewees and to other FCRN members who have helped to produce this blog post by pointing out useful resources, including Anna Birgitte Milford, Hanna Tuomisto, Peter Wootton-Beard, Mark Bomford, Mike Hamm, Judith Friedlander, Annie Leymarie, Steve Gillman and Angelika von Heimendahl.
Tags: building resilient food and farming systems, urban agriculture, vertical farms
Green City Growers Names Christopher Grallert As Company President
Grallert has 25 years of experience in the sustainable agriculture industry globally. Since joining GCG in 2015, Grallert has served in multiple roles for the organization, starting as a investor and advisory board member, then moving in to a more intensive operational role in 2017
SOMERVILLE, Mass., Aug. 20 /CSRwire/
Green City Growers (GCG) has announced the promotion of Christopher Grallert to the position of Company President. According to GCG’s CEO and Founder Jessie Banhazl, “Chris’s extensive background in business management, agricultural systems, fresh produce, and operations, combined with his vision of what future food systems can look like, make him a great fit to lead the company through the next phase of growth.”
Grallert has 25 years of experience in the sustainable agriculture industry globally. Since joining GCG in 2015, Grallert has served in multiple roles for the organization, starting as a investor and advisory board member, then moving in to a more intensive operational role in 2017. Since then, Chris has overseen the building out of the back office and operational components of the company. He has led GCG’s commercial growth and has been instrumental in tactical and strategic developments. Grallert’s efforts, Banhazl said, “have helped to take Green City Growers from a Massachusetts-focused business to a regional company that has almost tripled in size since his involvement.”
In assuming the company president position, Grallert will manage GCG’s overall business operations and staff. Grallert will continue to support Banhazl as she continues to take on a larger role in shaping GCG’s strategic growth, overseeing marketing efforts, and driving business development.
“I’m very excited about the future of GCG and proud to have been chosen to lead the company,” Grallert said. “As urban ag continues to gain traction nationally, we will continue to focus on innovations that will bring integrated food production to more and more communities”.
“I couldn’t be more excited to have Chris taking the lead on the day to day operation. We’ve been working together side-by-side for a few years now, and I feel 100% confident in his ability to lead us as we continue to grow,” Banhazl said. “It feels amazing to know the company I founded is in such good hands.”
Green City Growers was founded in 2008 to provide edible landscaping and urban farm installation and maintenance. The company has evolved to serve a wide array of commercial businesses, including global property management and real estate companies and manages farms on top of Whole Foods Market and at Fenway Park. The company was just awarded a USDA Farm to School Grant to continue a multi-town school gardening program.
With more than 100 sites throughout MA RI, CT, and NY, GCG annually grows 35,000 lbs of organic produce, converts over 20,000 sq ft of unused space into food-producing landscapes, teaches 2,000 kids how to grow their own food, and engages ½ million individuals in urban farming through their programs.
Can Vertical Farming Feed The World And Change The Agriculture Industry?
Can Vertical Farming Feed The World And Change The Agriculture Industry?
Year after year, cities expand and pristine natural habitats are turned into farms and pastures to support the world’s growing population. But despite our encroachment into the environment, we still struggle to feed everyone. Vertical farms could offer a solution by producing higher crop yields year-round in less space than conventional agriculture.
What Is Vertical Farming?
With land for crops and pastures growing scarce — plus the threat of pesticides and herbicides taking a toll on our health and the environment — people are exploring new ways to grow food, such as urban agriculture. In general, this is the process of growing food within city limits – whether on rooftops, in backyards or on balconies. The goal is to provide families with fresh, healthy food that isn’t laced with chemicals — and when you grow your own crops, you can control these elements.
Vertical farming is a type of urban agriculture – but vertical farms are often constructed indoors in extremely controlled environments. Crops are grown on shelves that extend upward instead of outward, and the environment is carefully monitored, so crops grow year-round.
In addition to growing crops, some vertical farmers have developed ways to grow fish in a self-sustaining system. Water from the plants is recycled into fish tanks, and the waste from the fish becomes fertilizer for the plants. Then, both the plants and fish can be harvested for food.
The benefits of vertical farming
The benefits of vertical farming are numerous. Farmers can control the crops’ environment in vertical farms, so the plants aren’t subjected to nasty weather conditions or droughts. Humidity, nutrients and water are administered to growing plants to achieve optimum growing conditions. Because of the controlled environment, crops can be harvested more than once a year, resulting in higher yields than traditional farming.
Related: The GCC’s first commercial vertical farm launches in Dubai
Vertical farms are more sustainable than conventional farms because they use less water (which is often recycled through the system), they take up less space and they use less fossil fuels because they don’t rely on heavy machinery such as tractors and harvesters.
Technology helps vertical farmers get the best output from the farm. Tailored lamps help plants get more light exposure, which encourages them to grow faster than crops that rely on the sun. Vertical farms also provide greater protection from insects, thus decreasing the need for harmful chemical products.
Downsides to vertical farming
While vertical farms can help with local hunger issues and sustainability, there are some barriers that may keep them from gaining worldwide traction. The cost of setting up a vertical farm can be prohibitive. Conservative estimates put the initial start-up cost at around $110,000, but there are estimates upward of millions of dollars.
Finding an abandoned warehouse or building in an urban setting for a reasonable price might be difficult. Since vertical farms rely on electricity for growing lamps and strict environmental controls, the location has to have reliable power — not just any old abandoned building will do. Vertical farms also depend heavily on technology, which can be costly. Keeping the lights on and the environmental controls running will impact energy use — and your budget.
Not every crop that is grown traditionally can be raised successfully in a vertical farm. Leafy greens and herbs do the best in an indoor environment, while staple crops like wheat and potatoes are difficult to grow indoors, as are some fruits and vegetables. The crops that can be harvested from a vertical garden are limited.
Growing food to feed the hungry is a noble gesture, but it also has to be profitable, especially when the initial cost to set up a vertical farm is so high. If there isn’t a market in your area, it’s a waste of time to grow large amounts of food that you won’t be able to sell.
The Verdict
Despite the downsides, the positives are plentiful. In addition to embracing sustainability and helping combat hunger, vertical farms can also encourage support for local economies. These farms can create jobs, turn a profit and provide a healthy source of food for locals.
As technology continues to advance, new approaches will improve the efficiency and productivity of vertical farms. If nothing else, the idea sparks the conversation about changing the agricultural industry and gives us a place to start for finding better, more sustainable ways to grow food.
Images via Depositphotos, Aqua Mechanical and Mike Chino for Inhabitat
under Agriculture, Features, Innovation, Sustainable Food, Urban Farming
Urban or Rural: Where To Build A Greenhouse
Drawing from experience, Lefsrud points out that governments across the world, not just in Quebec, have largely been slow to consider using urban greenhouses as a legitimate food generator
‘You need political will, and it takes time’ – urban greenhouses could benefit from more direct support from governments, experts say.
August 20, 2019
Written by Doug Johnson
Montreal’s Lufa Farms now has three locations and around 17,000 customers.IMAGES: Lufa Farms
The first two floors of 1400 Rue Antonio Barbeau in Montreal look like they belong on any other low-density commercial building – blocky, covered in mottled brown brick and windows gazing into a beige interior. Just over the lip of its roof, though, peeks long walls made of glass and metal, and inside them, rows of vegetables.
Around a decade ago, the building was a full floor shorter. That was before Lufa Farms – a Montreal-based urban farm and food delivery service – began. It touts itself as the world’s first commercial greenhouse located on a rooftop.
Now, Lufa Farms has three locations spread across Montreal – others are in the Laval and Anjou neighbourhoods – and around 17,000 customers that the company has dubbed ‘Lufavores.’
But back when it first started, urban agriculture, in- or outside of a greenhouse, was something new and untested. Even Lufa Farms – which is now often pointed to as a model of what urban agriculture could be – had a rough time finding a home and traversing the untested waters of starting a farm of its size in a city.
“The biggest thing [was], there was no proof of concept ... Everything from finding a suitable building – because it was something that hadn’t been done – to an open building owner to city and zoning. It was very out-of-the-box,” says Lauren Rathmell, Lufa Farms’ co-founder and greenhouse director.
Quebec’s agriculture department, Ministre de l’Agriculture, des Pêcheries et de l’Alimentation (MAPAQ), recently released a report on the state of greenhouse-grown produce in the province. The report noted that only 31 per cent of greenhouse vegetables consumed in Quebec were grown in the province – Rathmell, and other urban agriculture dignitaries, say there’s potential here. The report also notes that the increased demand for organic foods presents Quebec with another area due for growth, and that Ontario has not actively pursued it.
While many of Montreal’s neighbourhoods now vie for a Lufa Farms location, its growing pains are familiar to many sizeable urban agriculture efforts.
Mark Lefsrud has studied different ways of growing food for more than 20 years. He is an associate professor at McGill University’s Macdonald Campus where he is a leader of the Biomass Production Laboratory and worked on the design of the Advanced Plant Habitat on the International Space Station.
Drawing from experience, Lefsrud points out that governments across the world, not just in Quebec, have largely been slow to consider using urban greenhouses as a legitimate food generator.
“It was an unknown – that’s the best way to describe it. They’re used to external, outside-of-the-city food production systems and field conditions. The idea of [using] full, controlled environments wasn’t in their comfort [zone],” he says.
However, the idea of turning unused space in urban centres into something that could aid food security is not an old one. It’s been around for maybe a decade, and agricultural ministries around the world are increasingly eyeing it as a path to feed and employ people – particularly in food deserts.
Lufa Farms’ earlier struggles were largely logistical ones, and the Gouvernement du Québec hasn’t particularly helped or hindered the business’ growth, Rathmell says. While the situation has improved in recent years, there are still challenges that face the industry as a whole.
Cost is a big issue – perhaps more so than other more traditional businesses. Besides the normal run of fees paid by every business, urban agricultural operations above a certain size need to pay to construct a specialized facility. However Rathmell notes that it has become cheaper as acceptance has grown.
Rooftop greenhouses are a bit of a different beast. There’s also the added difficulty of physically moving the building materials onto the roof. And, as much as they encourage people to give a useful purpose to a previously unused space, they come with a dossier of regulations. Functionally, they’re treated like an entirely new floor of a building.
The facility on this new floor needs a sprinkler system, and it needs to be sturdy enough to bear a lot of snow during the winter – [all] in all, it’s a hefty structure, Rathmell says.
Many places are not zoned for greenhouses or other agricultural activities like aquaponics, according to Rathmell. Historically, most urban planning in cities rarely took urban agriculture into consideration.
The land itself is also more expensive in urban areas than it is in rural ones. Lefsrud has a rough calculation for this. In rural operations, a plant usually costs between $0.05 and $0.10 to grow, compared to urban greenhouses, where the cost per plant can be as high as $0.45, depending on the season.
Vertical farming somewhat offsets this. Though there is a larger initial price tag to get started, after a while the density of plants – three dimensions as opposed to two – pays for the added costs. Traditionally, the companies that lend credit to agriculture ventures, like Farm Credit Canada and more recently Desjardins, have been wary of providing credit to urban agriculture efforts, but according to Lefsrud they are beginning to catch on.
Some costs can be offset in a city, though. It’s easier to find labour in high population centres, and the ambient warmth lowers the price of heating somewhat – either from the urban heat island effect or, more directly and in the case of rooftop greenhouses, the floors in the building below.
Regionally-based energy company Énergir – formerly Gaz Métro – offers grants for natural gas boilers, something which Lufa has taken advantage of to generate further warmth for its operations.
MAPAQ notes that Hydro Québec offers an incentive for growers with supplemental lighting. Designed for greenhouse operators who use all or part of their electricity supplied by Hydro Québec for photosynthetic lighting, this rate option is ideal for customers who can adjust their production to help manage their electricity consumption. According to the report, around 40 per cent of the greenhouse vegetable area in Quebec uses supplemental lighting, a tool that can help extend the growing season and, in turn, help growers take advantage of better market prices.
According to MAPAQ, the department has also established a network to aid urban agriculture across Quebec. As the province only obtains 31 per cent of its greenhouse produce from local sources, the remaining 69 per cent that is imported could potentially be met by local production.
However, according to Olivier Demers-Dubé, founder and CEO of Écosystèmes Alimentaires Urbains (ÉAU), around 80 per cent of greenhouses in Quebec grow for only three out of four seasons every year, limiting the sector’s potential.
“I think we’re producing a very low percentage of what we’re actually eating, even more so in [the] winter. These numbers ... that’s year-round,” he says of the information provided by MAPAQ.
Since it began five years ago, ÉAU has helped 10 communities in Quebec design aquaponic systems. This includes an Indigenous community in the north of the province, Whapmagoostui. ÉAU also works with private investors and pre-established food producers looking to attach a fish farm to their greenhouse or vice versa.
“We have this goal to bring back food production to where humans live, and humans live mainly in cities,” Demers-Dubé says.” We have this strong belief that food production need[s] to be close to where we live. We need to have contact, we need to interact with it. Eating is what we do most in our lives, minus breathing.”
According to Demers-Dubé, there are facets of starting an urban greenhouse that are becoming easier, but at a basic level, it’s still more difficult to set up a sizeable facility in the city than it is elsewhere. Further, he says, though many governments offer programs and funding that coincide with urban agriculture, there are still precious few initiatives that specifically seek to aid those operations.
“You need political will, and it takes time,” he says.
Going forward, one of the biggest challenges to urban agriculture comes in a fairly innocuous form. Now that Canada has legalized recreational cannabis, most of the thought and attention paid to greenhouses in general, by both businesses and governments, is dedicated to this relatively new industry.
“Right now, one of our biggest challenges is cannabis taking all the air out of the room,” Lefsrud says.
US: Bronx, New York - Video - Green Bronx Machine Presents The Blooming Bloomberg Salad
Green Bronx Machine builds healthy, equitable, and resilient communities through inspired education, local food systems, and 21st Century workforce development
Green Bronx Machine
July 31, 2019
Visit https://greenbronxmachine.org
WE GROW VEGETABLES... AND STUDENTS! One student at a time, one classroom at a time, one school at a time.
DONATE: https://greenbronxmachine.org/donate
Green Bronx Machine builds healthy, equitable, and resilient communities through inspired education, local food systems, and 21st Century workforce development. Dedicated to cultivating minds and harvesting hope, our school-based model using urban agriculture aligned to key school performance indicators grows healthy students and healthy schools to transform communities that are fragmented and marginalized into neighborhoods that are inclusive and thriving.
Like us on Facebook: https://www.facebook.com/green.BX.mac...
Follow us on Twitter: https://twitter.com/greenBXmachine/
Like us on Instagram: https://instagram.com/greenbronxmachine/
Donation FAQ: https://support.google.com/youtube/?p...
Category Education
US: Chicago - Vertical Farming Brings High-Tech Approach To Metropolitan Agriculture
"We're doing for farming what Henry Ford did for the automobile," said entrepreneur Jake Counne
A Local Entrepreneur Has A High-Tech Take
On Agriculture That Could Change What Ends Up On Our Plates
By Meghan Kluth
Thursday, August 15, 2019 CHICAGO (WLS)
You could call it farming for the future.
A local entrepreneur has a high-tech take on agriculture that could change what ends up on our plates.
"We're doing for farming what Henry Ford did for the automobile," said entrepreneur Jake Counne.
Counne has found a way to grow produce locally, even when it's below 50 outside. He said the answer is using cameras, software and a conveyor belt in what's called a vertical farm.
"I came across vertical farming and I was just enamored with the ability to exponentially out produce the natural ability of that land," said Counne, who is the founder and CEO of Backyard Fresh Farms.
Six types of lettuce are stacked on a four level tower under the glow of purple LED lights in his Back of the Yards facility.
The farm produces three tons of greens in one year's time, which is what a farmer could do with Soldier Field but in just four parking spaces.
Counne's vertical farm reduces costs of energy, labor, and his produce has proven to last weeks.
"We've already beat the cost of a field farmed equivalent products," Counne said.
An automatic lift collects trays of ready plants and brings them to an assembly line of workers for harvest. It has reduced labor by 80% compared to the first vertical farms of its kind.
"We are quite literally building an assembly line of greens," Counne said.
Counne has nine patents pending that are helping him create the perfect environment for a plant every day of its life.
"The software here is looking to try to figure out what the optimal amount of light. It's also looking for early signs of stress in the new growth," said Counne.
Some of the cities high end restaurants are already using Counne's produce and when put to the taste test, it's clear this is not your average lettuce.
Counne's plan is to expand and open 100,000 square foot facilities near every major metropolitan area around the country
Kimbal Musk’s Goal: Grow Fresh Food In Containers In Every American City
Musk’s newest venture — alongside his co-founder Tobias Peggs — combines food and technology to empower the next generation of farmers. Square Roots is a seed-to-sales urban farm, connecting people in cities to locally grown whole foods. The farm also runs a farmer-training program, which creates opportunities for more people to become urban farmers.
August 22, 2019
Kimbal Musk | SUSAN FRANCE
Standing out in Boulder is not an easy thing to do. From famed world athletes to politicians, the city has its share of notable residents, but when a 6-foot-4-inch man wearing a cowboy hat walks around town, people notice. Some know who he is; some don’t. It’s Kimbal Musk, food entrepreneur and owner of The Kitchen restaurant chain.
Musk’s newest venture — alongside his co-founder Tobias Peggs — combines food and technology to empower the next generation of farmers. Square Roots is a seed-to-sales urban farm, connecting people in cities to locally grown whole foods. The farm also runs a farmer-training program, which creates opportunities for more people to become urban farmers.
Currently, Square Roots farmers grow a variety of fresh herbs in indoor, vertical farms inside containers, right in the heart of Brooklyn. They hand-harvest, self-package and deliver to retail stores across New York City. The herbs are non-GMO and pesticide-free, developed through human-centered farming technology that surrounds farmers with data, insights and tools so they can grow high-quality food, all year-round, using the fewest resources possible.
The system uses a water-efficient hydroponic growing system within vertical modular farms in shipping containers, which means there is no need for pesticides. Plus, Musk says, it requires about one-tenth the amount of water compared to traditional gardening.
Musk started to really think about urban gardening 16 years ago when he opened The Kitchen in Boulder alongside partner and chef Hugo Matheson. According to Musk, they worked with local farmers from the beginning because the food simply tasted better. Along the way, they ended up learning about the sustainability ethos and how much local farmers care about the land, as well as how important it was to have local food production.
The idea behind Square Roots, Musk says, was to create something that would enable the best quality herbs while empowering young farmers to grow food in the city.
“Most of our young farmers are in big cities,” Musk says. “They are not in the countryside.”
But every new technology comes with a cloud of doubts and skepticism, and Square Roots is not immune. Critics have questioned whether or not Square Roots will require more fossil fuel energy to grow food inside, as well as the limits to the type of food that can be produced without soil, and the unrealistic possibility of feeding millions of people with a technology that cannot produce food for the masses.
Musk says that Square Roots’ electricity consumption is mitigated because the containers use electricity at night when power plants have excess energy.
“The energy is being produced anyway,” Musk says. “The farms don’t pull more energy from the grid, which allows us to get electricity at a much lower price.”
For farmer Maxwell Carmack, a Square Roots graduate, the future of vertical farming seems promising. Aware of the critics, he says the carbon footprint of the transportation and refrigeration costs currently in use to move food across the country is worse than the electricity needed to run the indoor farms. Still, he is looking forward to incorporating sustainable energy production technologies to the industry of vertical farming to take it to the “next step.”
While critics may think it will be impossible to feed cities out of containers, Carmack, an engineer who decided to stay on with Square Roots after graduating the program, is excited to prove them wrong.
“I spend my time making all of the marginal gains that can add up,” he says. “In fact, in the past year we’ve doubled the production. I see improvement every day. In the end, as an engineer, I care about what might be possible and not what might not.”
Since its founding two and half years ago, the Square Roots program has graduated 30 people, and many graduates have taken the path of entrepreneurship, from rooftop garden installations to catering. And it’s expanding, as urban farmers in Grand Rapids, Michigan, will soon start producing fresh herbs as well.
Musk says the ultimate goal over the next 10 years is to have Square Roots systems in every U.S. city and to graduate around a thousand new urban food farmers, while continuing to improve the technology. While he’s aware that Square Roots can’t feed America alone, he hopes it’s the start of a vertical revolution with its roots in Boulder.
New York City’s Largest Rooftop Farm Sprouts Up In Brooklyn
In addition to growing produce, which will go to restaurants and farmers markets, the new facility — operated by Brooklyn Grange — offers a “Swiss army knife” of benefits for the city, according to co-founder Anastasia Plakias
August 13, 2019 | Scott Enman
Brooklyn Grange's newest farm in Sunset Park is the largest of its kind in New York City. Photo courtesy of Brooklyn Grange
Tomatoes, carrots and cucumbers are only a few of the many fresh options now growing on New York City’s largest rooftop farm: a 140,000-square-foot facility in Sunset Park.
In addition to growing produce, which will go to restaurants and farmers markets, the new facility — operated by Brooklyn Grange — offers a “Swiss army knife” of benefits for the city, according to co-founder Anastasia Plakias.
Environmentally, rooftop farms can cut energy costs, decrease combined-sewer-overflow, reduce urban heat island effect, create a habitat for wildlife, absorb air pollutants and lessen noise pollution.
The farm’s close proximity to Green-Wood Cemetery will also give migratory and native birds a place to take refuge.
Plakias said that while it’s difficult to stop New York from expanding upwards, residents could help the city grow in a different type of way.
“It’s impossible to ignore the piece of development in this city,” she told the Brooklyn Eagle. “Development will never cease in New York City. There will always be change happening, but we have an opportunity to influence the direction and shape that that change takes. Now is a really critical time for New York City to be a leader.”
The space at 850 Third Ave. is the company’s third farm. The first opened in 2010 in Long Island City, and the second came to the Brooklyn Navy Yard in 2012.
A paver system is installed at the Brooklyn Grange’s Sunset Park farm. Photo courtesy of Brooklyn Grange
The Sunset Park green roof acts like a giant sponge, managing roughly 175,000 gallons of storm water in a single rainfall — helping to reduce the amount of CSO entering New York’s waterways.
(The Brooklyn Navy Yard facility, in comparison, can manage about 100,000 gallons of water per storm.)
Because of its ability to reduce CSO, the roof was partially paid for by the Department of Environmental Protection’s Green Infrastructure Grant Program.
The new space, located adjacent to the Metropolitan Detention Center and overlooking the Sims Municipal Recycling, will also host weddings and other special occasions.
An event space and kitchen are currently under construction, and co-founder Ben Flanner said the farm would ideally host parties in the future using fresh herbs to garnish drinks.
Plants grow on the new farm. Photo by Ian C. Roberts
Borough President Eric Adams said that it was crucial for similar operations like Brooklyn Grange to open in low-income communities. “We don’t need fast food. We need farm food, and it’s right here in the heart of our city,” he said. “This is profitable to be able to grow food in an urban environment: Not only isolated in communities that are gentrified, but also in Brownsville, East New York and Bedford-Stuyvesant.
“There’s no reason we can’t have a Brooklyn Grange on the top of every NYCHA building so they can grow healthy food and live a healthy lifestyle. We can’t grow new land but we can better utilize our rooftops.”
The space, which officially opens on Sunday, will be open to the public every Sunday through October from 11 a.m. to 4 p.m.
Follow reporter Scott Enman on Twitter.
Many Have Tried And Failed To Make Vertical Indoor Farming Work. One Chicago Entrepreneur Thinks He Can Do It
Leafy greens typically don’t get kids excited. So Jake Counne knew he’d grown something special in his indoor vertical farm when his children, aged 5 and 7, were snacking on fresh spinach “like it was a bag of chips.”
August 07, 2019
Jake Counne, 31, founder of Backyard Fresh Farms, an indoor vertical farming facility located inside The Plant that houses food and agricultural startups in the Back of the Yards neighborhood of Chicago on July 11, 2019. The farm grows lettuce, kale, arugula and and other greens using innovative manufacturing processes to make the operation more efficient and profitable. (Zbigniew Bzdak / Chicago Tribune)
Leafy greens typically don’t get kids excited. So Jake Counne knew he’d grown something special in his indoor vertical farm when his children, aged 5 and 7, were snacking on fresh spinach “like it was a bag of chips.”
Other, more refined palates also have been impressed by Counne’s spicy wasabi arugula, tart red sorrel and horseradish-tinged red mizuna — all grown under the purple glow of LED lights in a windowless office in Chicago’s Back of the Yards neighborhood.
“The flavors coming out of these leaves were unbelievable," said Steve Lombardo III, chairman of Gibsons Restaurant Group, one of Counne’s first customers. "We were talking about them like we were talking about fine wines.”
Counne, a real estate investor before his interest turned to agriculture, is launching Backyard Fresh Farms during a period of heightened consumer and investor interest in produce grown locally in controlled environments that are less subject to contamination, waste and unpredictable weather.
High costs have killed similar ventures attempted in Chicago. But as he prepares for a significant expansion to bring his greens into stores, Counne said he believes his hydroponic farm has the technology to succeed where others have failed to make large-scale indoor vertical farming a profitable business
“The ey to what we’ve done here is being able to scale it to a point that not only can we grow it, we can grow it at an affordable price,” said Counne, 31.
Farm technician Sergio Arroyo tends to the vertical farm at Backyard Fresh Farms on July 11, 2019. (Zbigniew Bzdak / Chicago Tribune)
Counne currently operates a pilot farm in a 250-square-foot space at The Plant, a food business incubator housed in a former meatpacking factory in the shadow of the old Union Stockyards. There, he is testing cameras and artificial intelligence software to improve the quality and quantity of produce grown, as well as robotics to reduce the amount of time workers spend climbing ladders to tend to plants. For example, an automated lift collects trays of ready plants and brings them to an assembly line of workers for harvest.
The process has reduced labor costs by 80% compared with a first-generation vertical farm, Counne said. Combined with lower energy costs from other efficiencies, and a farm-to-retailer model that cuts out the distributor, he said he can price his product to compete with high-quality organic greens grown in the field — which are typically priced at about $3 to $3.50 for a five-ounce package of lettuce, he said.
Counne is in discussions with landlords in Chicago and Calumet City, where he hopes to lease 35,000 square feet in which he says could yield 6 million pounds of produce a year, in towers stacked 21 feet high, with only six laborers. His long-term vision is to open 100-square-foot facilities near major metropolitan areas around the country.
“We wanted to treat this more like a manufacturing process rather than a farming process," Counne said.
A sample of red mizuna greens at Backyard Fresh Farms on July 11, 2019. (Zbigniew Bzdak / Chicago Tribune)
Growing produce in controlled environments, including greenhouses and indoor vertical farms, has gained steam as a sustainable solution to the food needs of a growing population because it uses less land and far less water than traditional farming and can be done year-round near cities, reducing the distance the food travels.
Food safety is another benefit. Controlled environments protect against contaminants from air, runoff or insects that can lead to recalls in field-grown greens, such as the mass romaine recall last year after E. coli exposure sickened more than 40 people. In addition, such produce is pesticide-free, has a longer shelf life and tends to be high quality because growers can control the variables.
Commercial-scale production of indoor- and greenhouse-grown produce has ramped up as growers gain capital and retail distribution, and as technological advancements make it more cost-effective.
More than $300 million in venture capital has been invested in greenhouses and indoor vertical farms during each of the last three years, up from $100 million in 2016, according to CleanTech Group, an industry market research and consulting firm based in San Francisco.
But the farms are expensive to set up and take a long time to expand, so many are unprofitable. In search of viable business models, some growers partner with distribution firms or grow produce inside of supermarkets themselves, said CleanTech associate Chris Sworder.
In Chicago, Gotham Greens grows lettuce and herbs in a 75,000-square-foot rooftop greenhouse in the Pullman neighborhood, while BrightFarms greens and MightyVine tomatoes grow in greenhouses in suburban Rochelle.
Indoor vertical farms, which take up a smaller footprint than greenhouses, don’t rely on sunlight and generally are more expensive to operate, are rarer in the Midwest. Most of the large operations — California-based Plenty, Ohio-based 80 Acres and Bowery and Aerofarms, both based in New Jersey — don’t sell their products in Chicago.
FarmedHere in suburban Bedford Park was the world’s largest indoor vertical farm when it shuttered in 2017 because of high labor costs and inconsistent yields. Its co-founder and former chief operating officer, Steve Dennenberg, is on the board of advisors of Backyard Fresh Farms.
Dennenberg compared the technology his company had to “Gordon Gekko’s phone,” referring to the giant block of a 1980s cell phone carried by Michael Douglas’ character in “Wall Street.” Much has changed in just two years to make indoor farming commercially viable, and he believes Counne can make it profitable.
Farm technician Sergio Arroyo works with red mizuna greens at Backyard Fresh Farms on July 11, 2019. (Zbigniew Bzdak / Chicago Tribune)
“Everybody has the artificial technology now, but Jake (Counne) has the robots,” said Dennenberg, who is working on a medical marijuana greenhouse in Michigan. “We had neither.”
Counne has nine patents pending for the software and hardware he is testing at his pilot space, where he has grown 100 different varieties of vegetables from bok choy to radishes.
Currently, six types of lettuce for a spring mix are stacked on a four-level tower, growing under the watchful eye of mounted cameras that lock into the center of each plant and watch for signs of stress twice per minute. An algorithm analyzes the data the camera has gathered and prompts the environment — temperature, humidity, water nutrients, light intensity, carbon dioxide levels — to automatically adjust to optimize the plants’ healthy growth. A supervisor can watch on a monitor and is alerted when something is wrong.
“Instead of a human looking at the plant and trying to adjust parameters, it’s the plant itself talking to the system, the plant itself becomes the sensor,” he said. “We like to call this plant-based intelligence.”
Counne has developed a roving camera that travels from level to level by itself, which cuts down on the need for multiple cameras, as well an automated lift system that collects trays of ready plants and brings them to an assembly line of workers, who are able to harvest in a fraction of the time it takes where workers must travel to the plants. The empty trays, traveling on a conveyer belt, continue through an automated sanitation tunnel before an another robot transplants new plugs and another lift transfers the newly planted tray to the nursery.
Backyard Fresh Farms is one of six vertical farms operating in The Plant, which houses a variety of businesses including a brewery and a coffee roaster, but it is the most technologically advanced, said John Edel, founder of the incubator. Though several local indoor farms have failed as they tried to scale, Edel thinks technology and lighting have improved to the point where Counne can make it economically viable.
“Oh, I think it will work,” Edel said. “He has a lot of things figured out.”
Sergio Arroyo, a farm technician at Backyard Fresh Farms who used to work at an aquaponics greenhouse, said the efficiencies make a big difference. One worker can produce the same amount of lettuce in the 250-square-foot space as three people could in a 10,000-square-foot greenhouse, in the same amount of time, he said. And unlike greenhouses, which in summer could reach 115 degrees, causing plants to grow too fast, indoor farms can be controlled to a more precise degree, he said.
The high level of control allows Counne and his team of four to grow greens with distinct flavor profiles. For example, they have found that giving arugula more light than it needs makes it spicier.
Eventually Counne expects he can grow exclusive greens like red mizuna and red sorrel, currently available only to chefs, for food stores. He also hopes to create chef-sponsored mixes that play with different flavors.
Bob Mariano, founder and former CEO of the Mariano’s grocery store chain, said Counne’s focus on cutting costs so he can sell the greens at a reasonable price will broaden the appeal of what he said is an “outstanding product.” He is also on the board of Backyard Fresh Farms.
“I’ve tasted a lot of food in my career — it’s difficult to explain,” Mariano said about sampling Counne’s greens. “It was so fresh, refreshing and tasty. It was very unusual.”
“People don’t eat enough greens because they don’t taste very good,” Mariano said. “The process that he has creates such a fresh product that people have never had that taste in their mouth.”
Counne, who has mostly self-funded the seed money for his company and is in the process of raising $10 million, came to indoor farming through his interest in real estate.
A Miami native and orthodox Jew, he was living in Israel when he decided to move to Chicago in 2011 to help areas hit hard by the housing crash by buying homes people had lost to foreclosure, renovating them and renting them back to the community. His company, Medallion Properties, now manages 600 units, mostly single-family homes on the South and West sides of Chicago.
Hoping to invest in commercial or industrial properties, Counne was touring the massive former Libby, McNeill and Libby canning plant in Blue Island when the property owner mentioned a potential tenant had considered opening a small vertical farm inside. Counne researched the idea and it struck him that vertical farms could be a productive use for vacant old buildings in Chicago.
“That (Libby) building was the inspiration for everything we built,” Counne said. “We want to take existing buildings and fit our technology into it.”
Though the goal is to sell in retail stores, Counne’s first step was to prove his product to discerning tastebuds in the restaurant scene.
At Gibsons Restaurant Group, which owns the classic Gold Coast steakhouse as well as Hugo’s Frog Bar, LuxeBar and Gibsons Italia, corporate executive chef Daniel Huebschmann said he was “blown away” by a test run of Backyard Fresh Farm’s lettuces. He left a bag of kale and romaine in his refrigerator for 10 days and it was still high quality at the end. Counne said his greens can last for a month without spoiling.
“To acquire a product of that quality, you have to order from somebody like Chef’s Garden,” said Huebschmann, referring to a specialty grower for professional chefs based in Ohio. “You pay crazy dollars to get the stuff shipped to you.”
Gibsons, which goes through some 30 to 40 cases of romaine a day, only buys such high-end produce for special events because it’s so expensive. The bulk of its lettuce travels some 2,000 miles to its doorstep from California’s Salinas Valley.
“If this can be scaled on a cost effective basis, it is a game changer for the industry, for sure,” said Lombardo, whose restaurants have been serving Backyard Fresh Farm’s microgreens, baby kale and mixed greens in its salads and garnishes for the past six months. “Not just restaurants but the food industry.”
aelejalderuiz@chicagotribune.com
Twitter @alexiaer
Alexia Elejalde-Ruiz
CONTACT
Alexia Elejalde-Ruiz covers the food industry for the Chicago Tribune's business section. Prior beats include workplace issues, the retail sector and lifestyle features, plus stints at RedEye, the Daily Herald and the City News Service. Alexia grew up in Washington, D.C., and has her degree in international relations from Brown University.
Hong Kong Start-Ups Are Using Hydroponic Technology And Vertical Farming To Bring Fresh And Healthy Food To Citizens
The green movement is a growing revolution across the world and particularly Hong Kong. A part of this change is the ground-breaking farming technology that cuts lengthy supply chains to allow easy access to fresh produce rich in nutrients and bursting with flavour
Hong Kong Growing Urban Farming Tech
The green movement is a growing revolution across the world and particularly Hong Kong. A part of this change is the ground-breaking farming technology that cuts lengthy supply chains to allow easy access to fresh produce rich in nutrients and bursting with flavour.
A Hong Kong-based urban farming technology company launched in January 2018, has been offering herbs, microgreens, and edible flowers to restaurants, hotels and home cooks. It will take things to the next level in a couple of weeks with the launch of its first “mobile farm”.
Using hydroponic technology, the greens will grow in-store so that consumers know exactly where their food is coming from – they can actually see their vegetables as they grow. The pilot mobile farm will be launched in mid-August at an organic convenience store in Sai Kung.
Hydroponic basically refers to the way that the plants absorb nutrients, which is through water instead of soil. The start-up uses organic nutrients bought from the United States which has US Federal Drug Administration approval and adds it to water. An advantage of indoor farming is that it is extremely sanitary and water-saving.
Soil-based farming often sees the loss of a lot of water (which goes underground), hydroponic farming saves 90 per cent more water.
Hong Kong imports an astounding 98.3 per cent of its vegetables, with 70 per cent of the imports coming from China and 28 per cent flown in from around the world. All the emissions involved in getting our greens into Hong Kong is a massive black mark in terms of sustainability – and it’s also bad for health.
Another issue is that as soon as produce is harvested, the roots stop supplying water to the leaves and stem and the plant start losing their nutrient content. A benefit of a mobile farm is the ability to buy greens with the roots still intact, take the produce home and use it while it’s still fresh.
The start-up’s team have been using the Causeway Bay operation for research and development and a base in Cyberport to develop the mobile farm technology.
Beyond the hydroponic technology, the team is developing even more sustainable and efficient farming technology, but they’ve taken it slow the first year to develop their understanding of the crops they are growing.
According to an earlier report, a hi-tech vegetable farm in Hong Kong’s Tai Po district is thriving inside a converted factory building and produces four tonnes of lettuce, wild rocket, endive and cabbage for salads each month.
Its workers, most of them in their 20s and 30s, tend to neat rows of racks, each 30cm tall and 10 tiers high, filled with potted greens lit by low-energy light-emitting diode (LED) lamps and connected to fish tanks on the floor.
Instead of shovels and hoes, they work with computers and drones. The farm’s co-founder noted that they farm with technology, not ploughs. This is farming 4.0.
This start-up offers a glimpse of the future of farming by harnessing technology and using less space than traditional, long regarded a sunset industry in Hong Kong.
Primary industries, mainly comprising farming, fishing, mining and quarrying, accounted for HK$502 million last year, a tiny fraction of the city’s total gross domestic product of HK$2.65 trillion.
But the start-up’s co-founder, who is optimistic about the prospects for aqua-farming, said that Hong Kong is a service-based city, but still needs healthy food. This is a viable business in Hong Kong because of the demand for healthy produce and the growing awareness of food safety.
Fresh Out of The Box
Shipping containers, the vectors of globalisation that were forged in the first instance to ferry goods thousands of miles around the earth, are now being used to grow fresh produce that will be consumed in their immediate vicinity
Wednesday 14th August 2019, London
As interest in urban farming continues to grow, modular, closed-loop production units could spark a horticultural revolution
A growing phenomenon that is reshaping fresh produce supply chains. Shipping containers, the vectors of globalisation that were forged in the first instance to ferry goods thousands of miles around the earth, are now being used to grow fresh produce that will be consumed in their immediate vicinity. What’s more, having made international markets more accessible to all, the containers now house technology so advanced that even someone with the most basic, rudimentary knowledge of horticulture can control and oversee the cultivation within.
Excitement about the potential of urban farming continues to build, with the idea of producing closer to market – using fewer resources and arguably boosting quality in the process – attracting plenty of interest, not to mention investment. Earlier this year, Italian start-up Planet Farms unveiled a plan to build Europe’s largest and most advanced vertical farm by spring 2020 in Cavenago, halfway between Milan and Bergamo. The farm will eventually extend across 9,000m2 and supply 40,000 packs of residue-free produce per day.
It’s a trend that is by no means confined to Europe or North America. In Shanghai, a group called Orisis is working with joint venture Infinite Acres – comprising British online retailer Ocado, Dutch horticultural tech specialist Priva and US plant science firm 80 Acres Farms – to build what it says will be the city’s first indoor vertical farm, producing lettuce and other leafy greens.
However, it’s the arrival of closed-loop, container-based systems, which theoretically allow anyone to become a grower, that could really revolutionise this area of the fresh produce business. In June 2019, furniture retail giant Ikea revealed it was preparing to harvest its first hydroponically grown lettuces and serve them to customers at two of its in-store restaurants in Helsingborg and Malmö. The vegetables are grown under led lights inside specially retrofitted shipping containers using a so-called circular farming system developed by partner company Bonbio. Days later, Swedish supermarket chain ICA announced a similar venture at its Maxi Högskolan store in Halmstad, between Gothenburg and Helsingborg, using a container system called Greenery configured by Boston-based vertical farming start-up Freight Farms.
In this exclusive interview, fresh focus tech speaks to Freight Farms co-founder Brad McNamara about the company’s recent dramatic growth, about the trends he says are driving that expansion and about a future that might eventually see fresh produce cultivation become something that practically anyone with access to a laptop or smartphone can manage and control.
Brad, can you tell us what inspired you and co-founder Jon Friedman to create Freight Farms?
Brad McNamara: We were originally looking at how we could bring food production closer to the urban centre. We were looking at greenhouses, but really it came down to a better way to create accessibility and transparency in the food system. So for us, the idea was to move away from the constraints of a rooftop greenhouse to a more user-friendly model that allows a wider population to grow locally in a particular place. That’s really where it all came from.
Were you involved in horticulture in any way prior to that?
BM: Not specifically, although I had been growing on my own for some time. I got an undergrad degree from Northeastern University in Boston, then an MBA in sustainability and environmental science. Jon’s background was industrial design, so the two kind of married well. The big thing for us was, when we first started the market potential for local, transparent, sustainable, chemical-free was just at the beginning. Everybody was talking about it, but no-one had a solution for how to produce in those ways while increasing the quality and consistency of the supply chain.
The business you created, was it a fairly large operation from the start?
BM: No, at the start it was Jon and I plus a small team, very much your classic startup, starting in a simple parking lot. We knew we needed to build the technology from the ground up with the market and the farmer in mind, and we knew it had the potential to empower anyone to grow food anywhere. We built our first prototypes in 2012 and went into commercial manufacturing in 2014.
To whom did you show this original proof of concept?
BM: Well, anyone that would look in the early days! What we did was grow a wide variety of crops to test the stability and the flexibility of the system, as well as some of the concepts within it. I was constantly bringing people from the produce industry by, so we made a lot of connections with cold supply chain, produce distributors, regional specialists, as well as some of the markets around us. We talked to a lot of the wholesalers and asked them, ‘Is this product ready? or ‘Is this crop specifically what you would look for, or maybe something different?’ That was really the guiding light, to know what the market would accept. The feedback was phenomenal. Much of the time they would say ‘this is fresher, brighter, crisper than anything I’m getting now’ and they got very excited about that.
Were there any areas in which you needed to improve?
BM: Well, once we got the plants in their mouths, there weren’t really any doubts left. You know when you eat something and it’s really good? I think in the early days it was more about general education in the market, in terms of growing crops indoors, hydroponics and all of the more technical pieces which by now have been more established. On the institutional side, the concept of needing to supply more locally grown food was not something we had to explain. They were getting hammered by their customers to provide higher quality, locally sourced, clean, healthy and consistent produce.
Brad McNamara (left) with Freight Farms co-founder Jon Friedman
Around 2012, there was a lot of talk about vertical farming as a concept that might eventually see production centres constructed as entire buildings in cities. Were you aware of this trend bubbling away?
BM: We were right there at the early stage of vertical farming, so we had the benefit of building systems while seeing those conceptual drawings of space-age technology. That was great, because it was almost like watching a sci-fi movie while you’re doing it in real life. Some of those concepts did apply but we had that functional knowledge we needed to satisfy.
Many people at the time said it was science fiction, but we kept very quiet about the fact that we were already accomplishing it with our unit. That made us feel like we were on to something. We were early enough that we were growing, we had customers and we had market insight. Technology for technology’s sake wasn’t going to serve our customers appropriately.
With any transition to a new technology, there can be resistance from certain quarters. Did you encounter any concerns about bringing traditional horticulture into an urban, indoor environment?
BM: What people want to understand is about traceability – where exactly did it come from, who grew it, how was it grown. That’s been the driving question in the conversation, and less about whether it’s grown in soil or not. Indoor-grown, whether in a greenhouse, warehouse or decentralised module is pretty much mainstream at this point.
The full interview with Brad McNamara of Freight Farms is published in Fruitnet's annual fresh produce technology supplement Fresh Focus Tech.
To order your copy, contact subscriptions@fruitnet.com or +44 20 7501 0311.
Part two of this interview will be published on Monday 26 August.
CIT Gaps Funds Invests In Charlottesville, Va.-Based Babylon Micro-Farms
The provider of an on-demand indoor farming service said it will use the investment to expand operations with new hires in product, sale and marketing.
By Michelai Graham / STAFF
A Babylon Micro-Farms' location at Boar's Head Resort in Charlottesville, Va. (Photo via @BabylonMF on Twitter)
The Center for Innovative Technology (CIT) announced that CIT GAP Funds made an investment in Charlottesville, Va.-based Babylon Micro-Farms, provider of an on-demand indoor farming service.
Center for Innovative Technology - VA@CITorg
Very pleased to announce a new @CITGAPFunds investment in Babylon Micro-Farms! @BabylonMF provider of on-demand indoor farming services https://bit.ly/2KOe0Ky #UrbanFarming #MicroFarms #Cville #innovation
"Tech to inspire a new generation of urban farmers" #sustainability #food
See Center for Innovative Technology - VA's other Tweets
Founded in 2017, Babylon provides small growers and businesses with indoor agriculture modules through on-demand farming services using their patented IoT tech. The financial terms of the investment were not disclosed but Babylon said in a press release that it plans to use this investment from CIT GAP Funds to expand their operations with new hires in product, sales and marketing.
Alexander Olesen, co-founder and CEO of Babylon Micro-Farms, said the startup’s idea was born in a University of Virginia (UVA) classroom when he and co-founder Graham Smith were asked by their professor to develop a high impact, low cost product that could help refugees.
“I quickly discovered and became interested in hydroponics, a way to grow plants without soil, use less water, and grow crops faster,” Olesen said in a statement. “Our mission is to develop technology that will inspire a new generation of urban farmers to grow their own fresh, affordable, sustainable produce at the push of a button. We are grateful for the support of CIT GAP funds at this stage of our development.”
The startup provides 24/7 farming support for the patented IoT system that remotely controls the customizable farming ecosystems. Babylon provides farmers with a guide to take them through the indoor farming process. Some of the startup’s customers include a UVA dining hall, The Boar’s Head’s Resort and Corner Juice.
“Being able to grow any kind of produce year round within our communities, such as for local food service industries, education and assisted living, or community farms to name a few, is a game changer for the state of sustainable urban agriculture. CIT is very confident in Babylon’s future success, and we look forward to being part of their journey,” Thomas Weithman, managing director of CIT GAP Funds and president and CEO of MACH37, said in a press release.
Companies: Center for Innovative Technology
Projects: CIT Gap Funds
World's Largest Urban Farm To Open – On A Paris Rooftop
The 14,000m² farm is set to open in the south-west of Paris early next year
The 14,000m² Farm Is Set To Open In The
South-West of Paris Early Next Year
The new rooftop farm in Paris will be the largest of its kind in the world. Photograph: Valode & Pistre Architectes Atlav AJN
13 August 2019
It’s a warm afternoon in late spring and before us rows of strawberry plants rustle in the breeze as the scent of fragrant herbs wafts across the air. Nearby, a bee buzzes lazily past. Contrary to appearances, however, we are not in an idyllic corner of the countryside but standing on the top of a six-storey building in the heart of the French capital.
Welcome to the future of farming in Paris – where a whole host of rooftop plantations, such as this one on the edge of the Marais, have been springing up of late. Yet this thriving operation is just a drop in the ocean compared to its new sister site. When that one opens, in the spring of 2020, it will be the largest rooftop farm in the world.
Currently under construction in the south-west of the city, this urban oasis will span approximately 14,000 sq metres (150695 sq feet) – also making it the largest urban farm in Europe. With the plan to grow more than 30 different plant species, the site will produce around 1,000kg of fruit and vegetables every day in high season. Tended by around 20 gardeners, they will also be using entirely organic methods.
The aim is for the farm to be a global model for sustainability. Photograph: Valode & Pistre Architectes Atlav AJN
“The goal is to make the farm a globally-recognised model for sustainable production,” says Pascal Hardy, founder of Agripolis, the urban-farming company at the centre of the project. “We’ll be using quality products, grown in rhythm with nature’s cycles, all in the heart of Paris.”
Located on the top of a major exhibition complex currently under redevelopment in the 15th arrondissement, the Paris Expo Porte de Versailles, the farm will also have its own on-site restaurant and bar with capacity for around 300 people. Run by Paris’s renowned chain of rooftop venues, Le Perchoir, this aerial eatery will offer panoramic views over the capital – and, needless to say, the menu will feature seasonal produce grown on the site.
The Cityscape: get the best of Guardian Cities delivered to you every week, with just-released data, features and on-the-ground reports from all over the world
“Our fresh produce will be used to feed the inhabitants across the south-west of the city – either directly, through veg-box schemes or via shops, hotels and canteens – thereby helping to reduce food miles,” Hardy says. “Furthermore, we won’t be using any pesticides or chemicals, so the farm will be a haven for biodiversity.”
The farm will also offer a range of services related to urban agriculture, including educational tours, team-building workshops and special events. Last but not least, there will be the opportunity for local residents to lease small vegetable plots of their own – in specially-devised wooden crates – helping to reconnect city-dwellers with their food source.
Local residents will also have an opportunity to lease small plots of their own. Photograph: Valode & Pistre Architectes Atlav AJN
“Our guiding principle with all our farms is to help foster environmental and economic resilience in tomorrow’s cities,” says Hardy, who expects the farm to start making a profit within its first year. “If we can create a model that is commercially viable, rather than having to rely on goodwill and subsidies, that will help urban farms to become sustainable in their own right.”
While large-scale urban farming is nothing new in itself, with major sites in The Hague, Detroit and Shanghai, among others, this new flagship farm in Paris will be ground-breaking in several ways. Not only will it be the largest rooftop farm in the world but they will also be pioneering their own technique in aeroponic ‘vertical’ farming.
Apart from not requiring pesticides, this method uses a closed water system and no soil – therefore minimising the risk of any pollutants. Furthermore, by supplying people right on the doorstep, the farm will have an exceptionally low carbon footprint.
Strawberries growing at one of the other rooftop farms in Paris run by Agripolis. Photograph: Agripolis
“Our vision is a city in which flat roofs and abandoned surfaces are covered with these new growing systems,” says Hardy. “Each will contribute directly to feeding urban residents who today represent the bulk of the world’s population.”
For now at least, urban farming seems to be thriving here in all its forms. In fact, the City of Paris has committed to planting 100 hectares of vegetation across the capital by 2020, through its Parisculteurs project, with one third of this devoted to urban agriculture. For example, new for this year, a farming promenade is set to be created beneath the aerial métro line at Barbès.
Among the other imaginative agricultural sites across the city is the eco-farm of La Recyclerie, installed along the old railway line at Porte de Clignancourt, and the organic mushroom operation, La Caverne, located in an underground car park at Porte de La Chapelle. Even the capital’s much-maligned Montparnasse Tower is rumoured to be getting its own growing space.
Red Sox President & CEO Sam Kennedy And Fenway Sports Group Partner Linda Henry Dish On The Five-Year Anniversary Of Fenway Farms
What started out as a dream of having a spot at Fenway Park to grow sustainable and organic produce has turned into a 10,600-square foot rooftop farm churning out organically grown vegetables and fruit to diners at Fenway Park’s Dell/EMC Club restaurant (as well as throughout the park)
Photo Credit: Billie Weiss/Boston Red Sox
What started out as a dream of having a spot at Fenway Park to grow sustainable and organic produce has turned into a 10,600-square foot rooftop farm churning out organically grown vegetables and fruit to diners at Fenway Park’s Dell/EMC Club restaurant (as well as throughout the park).
Located on the roof of the Front Office on the third base side of the EMC Level, it is here where the team at Green City Growers tends to this sustainable spot at America’s most beloved (and now greenest) ballpark. Celebrating its fifth year, Fenway Farms has produced 21,000 pounds of produce since inception that Aramark Executive Chef Ron Abell uses to prepare dishes from carrot hummus to scallion pancakes.
Photo Credit: Maddie Malhotra/Boston Red Sox
How did Fenway Farms come to be? “About six years ago, Red Sox Chief Operating Officer Jonathan Gilula and I were sitting in a game in the suite about 100 yards from here,” said Red Sox President & CEO Sam Kennedy at the five-year anniversary celebration yesterday. “Linda, who we had worked with for a long time at that point, who is passionate about lots of Fenway sports group issues and Boston and works on a variety of different things, especially sustainability, especially engaging kids and works closely with everyone in the front office, said, ‘Guys, guys, I have an idea.’ She said, ‘Come out, I want to show you something.’ We walked out here and she said, ‘What do you think about Fenway Farms and putting a garden here? Wouldn’t that be incredible?'”
Photo Credit: Maddie Malhotra/Boston Red Sox
And the rest, as they say, is history. “When I was growing up, I remember summer nights of just having our fresh tomatoes,” said Linda Henry, Fenway Sports Group Partner and Red Sox Foundation Board Member. “We had this one problem there. We were at the losing end. We had this epic battle with this gopher in our backyard and I have a brilliant dad and he worked so hard. We put up netting; we put up traps and we were not winning. In fact, my dad found the spiciest hot peppers he could find and planted them just for the gophers. The gophers left us the hot peppers, but took everything else. I never lost my passion for gardening and the appreciation for what real fresh vegetables are.
I was captivated by what Green City Growers was doing because they were finding a way to bring rooftop gardens in an inexpensive and accessible way. This is something very attainable. We wanted to show this was something incredibly productive without a huge investment. What better way to show the potential for sustainable living than growing organic produce right here. If it can work in a place where hot dogs, peanuts and Cracker Jacks are considered three square meals, then we felt others would join us and that’s really what happened, which has really been amazing. Fenway Farms for me represents a daily miracle. Whoever imagined a working vegetable garden on the roof of the oldest ballpark in Major League Baseball?”
INDIA: Urban Kisaan Brings Commercial Hydroponic Farming To Visakhapatnam
The Hyderabad-based startup, Urban Kisaan, specialises in soil-less gardening also known as hydroponics that is particularly popular in urban centres as it allows people to grow fresh vegetables even if they don’t have a garden
AUGUST 02, 2019
With Hydroponic Farming, Even Those
Without Gardens Can Grow Their Own Greens
As soon as you enter the office of Urban Kisaan in MVP Colony, you are swamped by the greenery and the sound of flowing water. The Hyderabad-based startup, Urban Kisaan, specialises in soil-less gardening also known as hydroponics that is particularly popular in urban centres as it allows people to grow fresh vegetables even if they don’t have a garden.
The fresh palak, methi and gongura shrubs at their office make a compelling case of why one should consider trying farming at home. The objective of hydroponic farming is to cultivate vegetables with minimal use of soil and water.
Urban Kisaan has come lately to Visakhapatnam. It provides the infrastructure to grow plants at home. The base model has three hydroponic channels in tiers on a metal stand. Above them, there are six plants growing in plastic nets that allows the roots to reach to the water in the channels below them. The water is circulated into in the channels through a 20 litre-reservoir tank. The water is mixed with a nutrient solution for maintaining its acidic content. (see infobox)
Set up the plants and channels in an area that gets eight to 10 hours of sunlight
Check pH/EC values once in three days
Ensure that reservoir tank is sealed; flush the tank every three months
Top up the tank with water and add nutrient each week
The kit needs to be placed where plants get eight to 10 hours of sunlight. Depending on the plant and climatic conditions, you get the yield once in two weeks. For instance each plant of palak gives a yield of 250 grams once in two weeks. They are also prototyping a set-up where plants can be grown in artificial light. Any numner of leafy vegetables can be cultivated. Basil, Bok choy , lettuce , parsley, kale, spinach, sorrel leaves, coriander, mint, and fenugreek are some that have done well with hydroponics.
The kit comprises two bottles of nutrient solution, a digital pH scale (to determine the pH balance of the water-based solution) and an electrical conductivity metre. There are instructions on how to set up and dismantle the structure. The smallest set-up which can hold 18 plants costs around ₹10,000.
Urban Kisaan has managed to sell about 10 kits in July. Says its CEO Vihari Kanukollu, “In coming months, we plan to set up a farm in Visakhapatnam where people can harvest vegetables before purchasing them.” Urban Kisaan has expanded its operations to Bengaluru as well.
Saras Chandra, learnt about hydroponics after a YouTube algorithm guided him towards hydroponic videos while he was searching for gardening tips. He is now growing 24 varieties of plants using this technique in his balcony. “I was fascinated with the technology. I now grow palak, methi and gongura. Over the last two weeks, he has harvested palak twice. So taken is Saras with his success in growing his own food that he has left his full time job at a bank to explore business opportunities in hydroponic farming.
The Urban Kisaan technology also flourishes on the rooftop of Karuna Shree, a city based lawyer. She says, “My terrace not only looks green but also gives me fresh vegetables.” According to her, the set up is sturdy and can easily endure few days of heavy rainfall.
Each drop counts
Vertical farming uses 70-95 percent less water as compared to traditional cultivation method.
New York: An Aerial Farm Sprouts In Manhattan At Essex Crossing
Something’s taking root on a Manhattan terrace — namely, carrots, turnips, radishes and all kinds of leafy greens.The garden with a view is the latest addition to Essex Crossing, the $1 billion mega-development project that will eventually cover nine city blocks around the intersection of Delancey and Essex Streets
By CARLA ROMAN
NEW YORK DAILY NEWS | JUL 30, 2019
(L-R) Linda Bryant, president of Project EATS, Rick Smith, Project EATS Director of Farm Operations, and L+M Vice Chair, Debbie Kenyon, pose in the quarter-acre Essex Crossing Farm on top of the Essex Market on Monday in Manhattan, New York. (Barry Williams/for New York Daily News)
Something’s taking root on a Manhattan terrace — namely, carrots, turnips, radishes and all kinds of leafy greens.
The garden with a view is the latest addition to Essex Crossing, the $1 billion mega-development project that will eventually cover nine city blocks around the intersection of Delancey and Essex Sts.
The airy green space is perched atop the 6th floor deck of The Essex, one of the nine developments that will populate the Lower East Side when the project is finished in 2020.
The quarter-acre plot ― already resplendent with organic arugula and kale, and soon to welcome tat-soi and bok choy — is being farmed by Project Eats, which runs a network of 10 urban farms around the city with an eye toward feeding and involving surrounding communities.
Although not very large, the Essex Crossing’s farm is the second biggest in Manhattan, second only to another green garden on Randall’s Island. Essex Crossing’s first ready-to-eat crop — arugula —will go on sale this Saturday at its farm stand in Essex Crossing Park.
Katie Archer, director of Community Relations for Delancey Street Associates, a conglomerate of developers building Essex Crossing, said a big goal of the garden is to connect with seniors and local youth groups.
Astro Arugula plants grow in the raised bed in the quarter-acre Essex Crossing Farm on top of the Essex Market Monday in Manhattan. (Barry Williams/for New York Daily News)
Despite the farm being in early stages, PE had over 40 applications for its spring after-school PEAS (Project Eats After School) program, with many kids coming from the 5 city high schools located on a campus right across the street.
The program teaches and develops farming skills and health awareness. From the 40 applications, 28 students were selected and three are now full time summer employees at the farm stand.
Other students from the program now serve as community health educators, trying to teach residents about the different types of vegetables available to eat.
The produce is also available at a “Farmacy” stand in the Essex Crossing Park near its farm stand. Working in partnership with nearby Gouverneur Hospital and other local medical providers, patients will get a dietary prescription detailing which veggies would be most beneficial for them to eat. These prescriptions are then filled at the “Farmacy” at a subsidized cost via Health Bucks, a SNAP benefit program.
Project EATS Director of Farm Operations, Rick Smith, picks some Astro Arugula from the garden Monday morning. (Barry Williams/for New York Daily News)
Essex Farm will also provide free breakfast on Saturdays using the produce on the farm – hoping to spark an appetite for green-eating while demonstrating to the community how to use the crops in their cooking. The first community breakfast will be on the Essex Farm roof in late August when the vegetation is ready to harvest.
For now, the breakfast program is for seniors. But by 2020 families with children will also be included.
The farm and roof will also host other community programs like farm yoga, cooking demonstrations, and “Up On the Roof” a commissioned public art project featuring local artists, according to Linda Bryant, president and founder of PE.
Rover radish plants grow in the raised bed in the quarter-acre Essex Crossing Farm Monday morning. (Barry Williams/for New York Daily News)
A REIT's New Amenity: A CSA Program From A Rooftop Farm
Perhaps most interesting is one of the amenities the REIT is offering: namely an opportunity to join a CSA (community-supported agriculture) program at the largest soil-based rooftop farm in the Mid-Atlantic region
The office space has been designed by Wingate Hughes Architects.
By Erika Morphy | July 29, 2019
BETHESDA, MD—Federal Realty Investment Trust has unveiled renderings of its new headquarters at 909 Rose, an office building located in its Pike & Rose mixed-use project. The office space was designed by Wingate Hughes Architects.
The locally-based REIT’s new office include an abundance of natural light from floor to ceiling windows, authentic materials and integration within the 24-acre Pike & Rose neighborhood.
Perhaps most interesting is one of the amenities the REIT is offering: namely an opportunity to join a CSA (community-supported agriculture) program at the largest soil-based rooftop farm in the Mid-Atlantic region. These programs, found across the country, are usually subscription-based, allowing members to receive fresh produce on the regular from local farms.
Other touches: There is an interconnecting staircase between Federal’s two floors, a raised lounge featuring living room seating, strong acoustic privacy and natural “bump into” space, according to Gavin Daniels, principal of Wingate Hughes.
The second office building in the LEED ND neighborhood, 909 Rose will be 11-stories and offer Class A, LEED Silver designated space, which is being designed by Hickok Cole Architects.
Erika Morphy
Erika Morphy has been writing about commercial real estate at GlobeSt.com for more than ten years, covering the capital markets, the Mid-Atlantic region and national topics. She's a nerd so favorite examples of the former include accounting standards, Basel III and what Congress is brewing.
Manila's Urban Greens Plans To Bring The Airbnb Model To Urban Farming
Urban Greens is the brainchild of Luxembourg-born entrepreneur Ralph Becker. The man behind the plan went to university in the UK, Paris and Singapore, before taking on a corporate job with Sony Electronics
AUGUST 5, 2019
KYLE BALDOCK
Ralph Becker’s struggle to modernise agriculture in the Philippines
Introducing Ralph Becker of Urban Greens
Urban Greens is the brainchild of Luxembourg-born entrepreneur Ralph Becker. The man behind the plan went to university in the UK, Paris and Singapore, before taking on a corporate job with Sony Electronics. During his 10-year tenure working in business and product development, he crossed the world, working everywhere from Berlin to Barcelona, from San Francisco to Tokyo.
Through all this experience, Becker always had in mind that he wanted to do something more impactful. In March, 2016, he quit Sony Mobile and moved to the Philippines, the birthplace of his mother. There was no concrete plan- he just wanted to get involved in something exciting and meaningful, and Manila’s start-up scene beckoned.
The Struggle to Modernise Agriculture in the Philippines
The Philippines, with a lush tropical climate and soil capable of growing a vast array of crops, has a rich agricultural tradition. But pressures on this tradition are growing: outdated food production methods are failing to keep pace with explosive population growth; climate change is impacting the variability of monsoon rainfall and increasing the severity of droughts; rapid industrialisation is shifting employment to the urban centres; and some within the country are worried that agriculture is being left behind.
Cursory online research alludes to a stagnant industry, struggling with such factors as an ageing workforce; lack of effective training and education; dependency on imported fertilisers and seeds that carry high prices; and poorly developed infrastructure including irrigation, transport and processing centres. The sum result is an overall agricultural system that leaves farmers unsupported, underfunded and de-incentivised.
Becker told me: ‘Other countries in Southeast Asia, especially Thailand, Indonesia and Vietnam, have found success modernising their agricultural systems, but the Philippines has lagged behind.’ There is no doubt that this situation hurts society as a whole: fresh produce is more expensive in the Philippines than in the U.S. or Europe, even compared to the relative dollar or euro price.
This Isolated Island Population Imports as much as 50% of its Fresh Food.
The Philippines has an abundance of fresh fruit but most vegetables are shipped in from afar, including the U.S., Europe, New Zealand and China to reach the commercial centre of Manila. The carbon footprint from transport, warehousing and refrigeration is huge, and the associated costs are passed on to the consumer. It is clear that this island nation, like many others across the world, needs to restore a sustainable system of food production based on local needs. Becker, ever the optimist, looks at these problems and sees opportunities.
Agriculture as a Tool for Urban Transformation
While working in Japan and the U.S., Becker was exposed to hydroponics and the concepts of urban farming. This interest grew into a hobby and he began growing fresh vegetables in his apartment in central Manila, using a custom-built hydroponic system. When he posted his experiments on social media, he noticed there was a lot of interest and friends encouraged him to do it full time.
He started speaking to friends in the Food & Beverage Industry, who told him of their troubles securing high-quality produce throughout the year. He then looked around at Manila’s urban sprawl- it is one of the most densely populated cities in the world- and noticed all the idle space on rooftops and in basements; entire empty buildings seemed to be calling out for utilisation. Becker wondered: what if we could reclaim all those underutilised, un-monetised spaces and turn them into profitable urban farms- a sort of Airbnb of Urban Farming.
The Perfect Island-Based Food Production System
Thus Urban Greens was founded in October 2016 with the mission of revolutionising the Philippines’ food production mentality. They design closed-environment growing systems that are modular and scalable, adapting to the space required. All systems are run with IoT sensor technology, allowing the team to remotely monitor crop growth within each setup, providing maintenance and service only when necessary. They have so far built several growing systems in private buildings including schools and the national science museum; at the time of writing, projects with several major hotel chains in Manila are lined up. They are also in partnership with property developers working on large-scale projects that integrate AgriTech food production from the start.
Outside of Manila, the opportunities are endless. Many of the Philippines’ islands have resorts and hotels that struggle to source their food; produce usually calls in at Manila first, before being shipped to these remote destinations, adding yet another link in the transport chain. Ralph sees the Urban Greens model of modular, scalable systems as being the perfect island-based food production system. Resorts could ideally cut out the middle men by growing a proportion of their food onsite, thus commanding a higher price premium because of the quality and freshness. But before every resort in the Philippines is equipped with its own vertical farm, a systemic change is needed, starting with the way people think about the entire concept of food.
A Culture in Transition
The Filipino diet is traditionally meat-centric, with lower rates of fruit and vegetable consumption than other countries in the region. Partly due to its heritage of American influence, the Philippines have the highest number of fast food chains per square mile in the region; accordingly, it also suffers from high rates of childhood obesity and type-2 diabetes.
But young Filipinos are socially aware and active- they absorb everything on social media, including the current trend of vegan/vegetarianism and healthier lifestyles. As Ralph puts it: ‘there was no questioning before; now the younger generation is questioning everything.’ There is growing demand for fresher food from this younger demographic, but where will this fresh produce come from?
Becker believes that the answer lies in unlocking the potential of urban farming. He and his team are slowly but surely introducing the concepts of cleaner, fresher greens grown locally, with the use of hydroponics. He runs a series of workshops, seminars and programmes to introduce these concepts and get people growing on a small scale in their own homes.
What’s next for Urban Greens?
These are still early days for Urban Greens, as they look to turn their start-up vitality into the bedrock concept for a modern, Filipino agriculture. As they validate this business model, they are actively seeking partnerships and investment to realise their dream.
Read more about Urban Greens: https://www.eaturbangreens.com/
You can contact Ralph Becker by email: ralph@eaturbangreens.com
Support Urban Greens by following them on Facebook: @EatUrbanGreens
EMAIL US AT INFO@VERTICAL-FARMING.NET
TAGS: AVF MEMBERS, VF INDUSTRY
Dave Riddell Grows Greens In A Storage Container
Riddell grew up in Needham, Massachusetts outside Boston. Both his mom and his aunt were passionate gardeners. His fascination began early with the plant world. He graduated from the University of Maine after a course of study that included communications and forest recreation management
August 7, 2019
Owner Dave Ridill holds a tower of growing lettuce inside his hydroponic farm, housed in an upcycled, 40-foot shipping container in Tetonia, Idaho. Riddell has been in business for three years and grows a variety of hardy greens like lettuce, Swiss chard, arugula and others. It happens 365 days a year.
Greens sprout from towers in Riddell’s hydroponic farm at Clawson Greens.
REBECCA NOBLE / NEWS&GUIDE photos
It was quite a while back, actually, that my dear friend Ken retired from Grand Targhee Resort’s ski patrol and moved to Salt Lake City. It was then that he told me it would be a good idea for me to become acquainted with his fellow patroller, Dave Riddell. Ridill had started a new business, Clawson Greens, growing greens inside shipping containers in Tetonia, Idaho. Now just how unlikely is that scenario?
Ridill and I spoke on the phone a few times before I met him, with me repeatedly promising it would be soon that I would come check out his scene. Around Christmas time of 2017 we met while he was delivering his beautiful produce to Hand Fire Pizza as I was interviewing the chef and manager for a column. Hand Fire serves one simple and delicious salad. It is made of Clawson Greens.
Ridill grew up in Needham, Massachusetts outside Boston. Both his mom and his aunt were passionate gardeners. His fascination began early with the plant world. He graduated from the University of Maine after a course of study that included communications and forest recreation management.
One college spring break Riddell accompanied his brother and some friends to Jackson Hole to ski. While in the neighborhood he applied for a summer job at Grand Targhee on the wilderness crew of the U.S. Forest Service in the Jedediah Smith Forest. That continued until 2018, when Clawson Greens began consuming more of his time.
That winter of 2007 Ridill started a winter job of as ski patroller at Grand Targhee that he still enjoys. He was later a bike patrolman for six years but, after breaking his back in four places, he decided that job was not for him. He also worked as part of Teton County, Idaho’s fire department.
In 2016 he was about to attend paramedic school in Boston when his neighbors approached him with an outlandish proposal. They had discovered a company that used shipping containers to grow food in a controlled environment. They loved the idea and yet believed it more appropriate for someone much younger than they were to embark on such project of that scope. Thus they shared the idea with their favorite neighbor.
Ridill became more intrigued and educated about the possibilities. There are countless shipping containers all over the planet. Many are abandoned or fallen into disuse. Why not repurpose, up-cycle these already existing units in a productive manner?
Ridill connected with Freight Farms. As fate would have it, the founder of the company grew up a couple miles from Ridill’s family home. They went to the same high school although five years apart. It was as if it was meant to be.
After he returned from training with Freight Farms the first shipping container grow room arrived at its final home in Tetonia, Idaho. In the winter of 2017 Ridill had his first restaurant customer.
It’s simple to check out Freight Farms’ website online. It is amazing to look at the possibilities of the future of farming and food, though it’s much more impressive in person.
The system uses a fraction of the water used in most agriculture. The drip irrigation waters the vertical tube, and it all recycles. The environment is temperature and humidity controlled for a growing season of 52 weeks a year. Beautiful organic produce is available mud- and insect-free using no pesticides.
It is an eight-week process from planting the seeds in tiny plugs to harvesting the heads of greens with their root ball attached. The variety of plants ranges from red-veined sorrel and wasabi arugula to rainbow chards and many lettuce varieties. All are vibrantly alive and remain in excellent condition for use for a couple weeks. As chefs plan their seasonal menus, Ridill provides specialty greens in a timely fashion.
There are now three grow room containers that supply 10 local restaurants. Last winter the customers at Phoenix and Dragon were impressed enough that they requested greens for home use. Eric and Zarina Sakai, who own Phoenix and Dragon, put together a little CSA. Ridill brought greens and everyone was happy. I hope they do it again next winter. It is true that the salads at the restaurant are particularly tasty. The small plate of summer rolls and their KFC, or Korean Fried Chicken, sent me into a dreamy state the other evening. Their summer schedule serves lunch Monday through Friday and dinner Tuesday through Saturday.
Ridill has not become a paramedic and yet he is caring for our health in a different way. It’s pretty exciting. 
Where to find Clawson Greens
The Phoenix and the Dragon
Hand Fire Pizza
Forage Bistro & Lounge (Driggs, Idaho)
Butter Cafe (Victor, Idaho)
Citizen 33 Brewery (Driggs)
Warbirds Cafe (Driggs)
Huntsman Springs (Driggs)
Royal Wolf (Driggs)
Branding Iron Cafe (Bondurant)
Visit ClawsonGreens.com or FreightFarms.com for more information.
Bru, who cooks for private clients, writes about the valley’s talented chefs.
Veggies Grown In Nevada's Massive Indoor Farm Are Now On Sale To Las Vegas Locals
Nevada does not have particularly fertile lands, but that didn't stop Oasis Biotech when they opened a 215,000-square-foot indoor farm to the public last July
by Phillip Moyer
July 30th 2019
The facility uses hydroponics and environmental control to reduce environmental impact. (PHOTO: Nathan O'Neal)
Nevada does not have particularly fertile lands, but that didn't stop Oasis Biotech when they opened a 215,000-square-foot indoor farm to the public last July.
Designed to be sustainable and environmentally-friendly, the facility uses hydroponics to use 90 percent less water than traditional farming, and have a completely controlled environment to eliminate the need for pesticides.
Guests had the chance to sample the vegetables after its openings, but until now, the food was only widely available to high-end restaurants in the Las Vegas Valley.
Today, the farm announced that they'll be selling eight-ounce bags of its baby leaf Spring Mix and Romaine Mix blends to consumers under its "Evercress" brand name.
“Over the last year, we have been working hard to perfect our crops and growing methods to bring the community and our customers the freshest salad greens in Las Vegas,” says Michelle Howell, Sales & Marketing Manager at Oasis Biotech. “We had over 1,000 people attend last year’s grand opening and the big question everyone asked us was “When can we buy it?” so we are thrilled to now offer the Evercress salad greens to Las Vegas locals."
The blends can beat Oasis Biotech's farming facility, located at at 6225 Annie Oakley Drive in Las Vegas.
In an effort to stay true to its mission to “Feed the World, Better.,” any product not sold to current customers or purchased by the public will be donated to local charities.