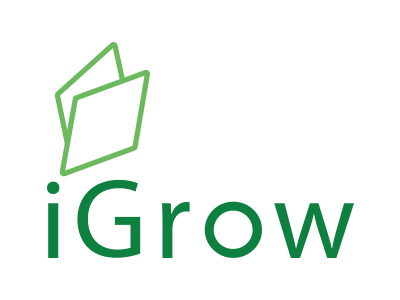
Welcome to iGrow News, Your Source for the World of Indoor Vertical Farming
Farmee Experts: Affordable Crop Consulting Online
German AgTech startup Farmee teams up with leading Dutch consulting company Delphy to support farmers remotely
German AgTech startup Farmee and well-known Dutch crop consulting company Delphy just launched the online platform Farmee Experts.
With their service, both partners provide affordable crop consulting services online. Any farmer in the world having an issue with their plants can post a question on the Farmee Experts website. Within 24 hours, the question is answered remotely by Delphy’s experienced agronomists. Farmers just have to pay for this troubleshooting without any long-term costs. All questions and answers are private and cannot be seen by other users. As a special launch deal, Farmee Experts offers the first answer for a new registered user completely free. After that, any question will be answered for a fixed price of 49 USD during the market entry phase.
“Knowledge still is the biggest challenge in agriculture today”, says Jacco van der Wekken, CEO of Delphy. “With Farmee Experts, we bring the know-how of our experts to new and innovative customer segments worldwide.” Especially innovative owners of small-sized greenhouses, indoor growers or urban farmers will benefit from having access to professional advice through an affordable service.
Florian Hassler, Co-Founder of Farmee, is looking forward to the collaboration: “We are really excited to launch our platform with Delphy as a renowned partner. We believe that sharing knowledge will help many farmers worldwide to grow better food.” In the future, Farmee Experts wants to open up their platform for other partners, becoming the world’s first open marketplace for online crop consulting.
Explainer Video
https://vimeo.com/farmee/farmee-experts-explained-in-90s
PR Contact
Farmee GmbH, Jens Schmelzle (Co-Founder), jens@farmee.io
About Farmee
Farmee is an AgTech startup from Germany. Founded in 2018, the software company develops digital solutions to enable people growing food. Farmee was selected for the Foodstars Accelerator (NL) and the EIT Food Accelerator Network.
About Delphy
Delphy stands for worldwide expertise for food & flowers. The Dutch company with over 220 employees and its own research units is the leading consulting partners, developing and offering knowledge about the cultivation of crops and expertise in all plant sectors, see www.delphy.nl
AmHydro Travels to Russia And India
The AmHydro Team was busy in December and early January with two international trips to countries eager to join the controlled environment agricultural movement. As the population continues to rise and resources become more limited, hydroponic farming is gaining huge momentum around the world.
Attendees at the Agro Greenhouse Complexes Russia Forum and Exhibition look on as speakers from various countries discuss and present to a full room about self-sustaining food technologies for the modern world.
An early December night is lit up by the Kremlin Main Tower in Moscow, Russia. With Russia's interest in sustainable ways to feed their population, could there soon be hydroponic growing systems beyond those walls?
AmHydro's Vice President Joe Swartz and CEO/President Jenny Harris both spoke on behalf of North America's contribution to the hydroponic industry. They focused on appropriate agricultural technologies for Russia, a country where average winter temperatures are in the 20s or below. They highlighted the successes of farmers around the world who have embraced hydroponics and specifically, AmHydro systems to feed their local communities.
Next in January, two of our production experts traveled all the way to Bangalor, India to help install a 1.5 acre hydroponic system that will house both leafy greens and vine crops. India is an agrarian country that, in modern times, is very interested in adopting a drought tolerant, consistent and safe way of producing food.
Now, that is a lot of NFT channels!
Bato buckets as far as the eye can see!
If you missed the webinar about Winterizing your Hydroponic Business, check it out on our YouTube page!
Get Growing! Intro to Hydroponic Crop Production Seminar (February 21 & 22 2019) | Learn to Start A Hydroponic Business!
ON SALE NOW FOR $595.00 for 2
Major SALE! $400 off plus two nights stay at the Red Lion Hotel
USE CODE: SEMFEBCOMBO
Reserve Your Spot Now!
Watch: Canada's First Vertical Mushroom Farm
In just three years, the Grugers went from farming their first mushrooms in a converted shipping container to producing about 12,000 pounds of mushrooms per month in their Nisku facility.
Published on: January 2, 2019
Rachel Gruger is co-owner of Gruger Family Fungi in Nisku, Canada’s first vertical mushroom farm.
The Nisku operation is the only indoor vertical mushroom farm of its kind in Canada. It specializes in tree-loving mushrooms so you won’t see any regular grocery store portobello or button mushrooms growing here.
In just three years, the Grugers went from farming their first mushrooms in a converted shipping container to producing about 12,000 pounds of mushrooms per month in their Nisku facility. The farm grows 10 different kinds of mushroom. Some are to eat and some are medicinal varieties meant to heal.
With files from Lisa Johnson
Indoor Farm Will Tap Solar Microgrid To Keep Plants Growing Year-Round
The Bowery Farming facility, inside a converted warehouse in Kearny, New Jersey.
WRITTEN BY Bill Opalka | January 4, 2019
PHOTO BY Bowery Farming
Bowery Farming’s New Jersey factory will include energy storage, solar panels, and on-site gas generation.
A solar-powered microgrid will soon help an urban agriculture startup grow vegetable greens inside a converted New Jersey warehouse.
Bowery Farming’s Kearny, New Jersey, facility will grow lettuce, kale and up to 100 varieties of plants, all indoors in a carefully controlled climate backed up by batteries, solar panels, on-site gas generators and technology that allows it to operate independently from the electric grid in the event of an outage or other disruptions.
“It’s really a manufacturing center with a high cost of energy in a very controlled environment,” said Don Wingate, vice president for utility and microgrid solutions with Schneider Electric, a Chicago-based company providing much of the infrastructure, controls and software for the high-tech food factory.
The microgrid will be built, owned and operated by Scale Microgrid Solutions, whose CEO Ryan Goodman said the platform is similar to what is offered in its standardized product, but it’s a first for this type of use.
“I believe no one has ever done microgrids in the indoor agricultural space like we’re doing here,” Goodman said. “There are some differences, but primarily they’re related to the load profile and how we’re using the assets.”
Microgrids are becoming increasingly popular to support uninterrupted operation of critical infrastructure like emergency and public safety buildings, hospitals, and sites that need a guaranteed power supply like data centers. In an agricultural setting, especially in the Northeast with hot summers and colder winters with shorter days, a stable, climate-controlled environment is required for plants that thrive in moderate temperatures.
The farm will run on grid power for part of its needs. Solar will provide about 15 percent of the energy required. The natural gas generator and batteries will provide the rest.
“Our assets can do a bunch of things, but in this case our natural gas product and the battery help primarily to manage peak loads,” Goodman said.
‘I believe no one has ever done microgrids in the indoor agricultural space like we’re doing here.’
The load profile is advantageous, as solar energy production peaks as overall grid demand rises and energy costs increase. Power stored in the on-site batteries could then be released to lower demand from the grid.
Goodman said the system will use the three assets in an optimal way, based on the load profile and the value proposition presented by opportunities for peak shaving and demand response.
“Generically, a solution like this would provide a 20 or 30 percent savings in energy consumption from the normal cost structure of a similar facility,” Goodman said.
Technically, the Scale system is capable of dispatching power back to the grid, but there are no plans to do that now.
The system includes Schneider Electric’s lithium-ion battery energy storage system interconnected in a behind-the-meter configuration.
“This new industry of indoor agriculture is really meaningful to society and us being able to partner in a project like this, to make repeatable solutions to make energy use much more efficient and more affordable, makes this much more exciting,” Wingate said. Schneider says it has a stable of more than 300 microgrid projects in the U.S.
Schneider Electric’s EcoStruxure Microgrid Advisor is a cloud-connected, demand-side energy management software platform that will be integrated to optimize the system’s performance. Its top layer includes cloud-connected demand side energy software that looks at current electric rate tariffs as part of its process to optimize energy use and make informed suggestions to the system. That advanced microgrid solution operates seamlessly and faster than any human being could to intervene.
The infrastructure can be built to scale and added to as necessary, Wingate said.
“As microgrids have become more cost-efficient and simpler, it’s more affordable to phase in additional pieces without having to re-engineer the entire system from the beginning,” he added.
Bowery said the indoor farm will be in production all year in a hydroponic system that uses 95 percent less water than plants grown by traditional methods out of doors. It claims crop cycles are twice as fast as traditional farming and its land footprint is 100 times less than outdoor agriculture.
The company hopes to expand to other metropolitan regions so crops can be delivered promptly to its markets. Bowery would not say how many new farms it plans or their locations.
“We’re looking forward to continuing to provide consumers with access to local, high-quality produce and drive a more sustainable future,” said Brian Donato, senior vice president for operations at Bowery Farming.
Commissioning of the Bowery microgrid project is scheduled for the first quarter of 2019.
Microgrids explained
The market for microgrids is slowly but surely expanding, and the technology is generating a lot of buzz. But how exactly do microgrids work?
ABOUT BILL OPALKA
Bill Opalka is a freelance journalist based outside Albany, New York. He has written about energy for newspapers, magazines and other publications for more than 20 years.
A TEDx Talk By Dr. Joel L. Cuello – Artificial Intelligence Does Food
By urbanagnews 2018
Dr. Joel L. Cuello, Professor of Biosystems Engineering at the University of Arizona brings us a TEDx talk on artificial intelligence as it can relate to food production for the growing global population.
Our planet sorely needs the help of artificial intelligence to achieve the increase in food production that our growing population demands in the face of scarce resources.
Vertical farming is already applying artificial intelligence and is sustainable with renewable energy.
80 Acres Farms Secures Significant Financing Round Led By Virgo Investment Group To Accelerate Indoor Vertical Farming Growth
NEWS PROVIDED BY 80 Acres Farms
January 15, 2019
Cincinnati, Ohio
80 Acres Farms, a leader in the rapidly growing indoor vertical farming industry, announced it has received a significant investment from Virgo Investment Group, a San Francisco Bay Area based private equity firm that invests in companies transforming and disrupting high-potential industries. Terms of the financing were not disclosed.
80 Acres Farms provides customers with a wide variety of locally grown, just-picked leafy greens, microgreens, and vine crops, including the world's only tomatoes and cucumbers grown completely indoors using just LED lighting. The company has developed its own artificial intelligence-powered growing system, sophisticated data monitoring, and automation technologies to deliver high quality and nutritious products at an affordable price. By locating its indoor farms close to customers, 80 Acres Farms is able to eliminate the costs, time and environmental impact of cross-country transportation, providing customers with a fresher, longer lasting product while drastically reducing food waste. 80 Acres distributes to major national grocers, local retailers, restaurants, and food service companies from its facilities in Ohio, Arkansas, North Carolina and Alabama.
"Virgo Investment Group joins our existing notable and experienced food industry investors in supporting the Company to rapidly commercialize the indoor vertical farming technology we have developed over the past three years," said Mike Zelkind, co-founder and chief executive officer of 80 Acres Farms. "We are optimizing every aspect of our production processes and driving down costs, which is crucial to scaling an indoor farming business like ours."
"We are excited to partner with highly experienced food industry leaders Mike Zelkind and Tisha Livingston to bring great tasting, freshly picked produce to local markets year round," said Eli Aheto, partner of Virgo Investment Group. "80 Acres Farms has created a unique and automated growing process and has built great relationships with its retail customers. We want to help accelerate the company's growth in this multi-billion-dollar market. The 80 Acres investment is an expression of Virgo's longstanding focus on investing in energy efficiency opportunities driven by reduced equipment costs. Virgo has completed investments in utility-scale wind, community solar, electric vehicle charging and now an LED lighting driven business."
The Virgo investment will enable 80 Acres Farms to complete the previously announced facility in Hamilton, Ohio, which will be the first fully automated indoor farm in North America. The first phase of the Hamilton project under construction is expected to be operational in early 2019. It will be automated from seeding to growing to harvesting for the highest quality and food safety standards. The Hamilton facility will feature handling robotics, artificial intelligence, data analytics, and around-the-clock monitoring sensors and control systems to optimize every aspect of growing produce indoors. The facility will allow 80 Acres Farms to begin to service the substantial and growing demand for fresh, locally grown produce year-round from both retailers and restaurants.
"Over the past three years we have provided our customers with fresh, flavorful and nutritious produce grown locally in our facilities with no pesticides and highly efficient usage of water and nutrients," Zelkind said. "We are rapidly increasing yields for our produce, while advancing each generation of our grow zone designs to lower capital costs, production costs and reduce the use of natural resources. Our facilities represent the realization of the next generation of farming. Our vision is to prove that indoor farming can be fully-automated, commercially scalable, higher-yielding, and profitable.''
About 80 Acres Farms
80 Acres Farms is an indoor farming pioneer providing customers with flavorful, and nutritious locally grown fruits and vegetables at affordable prices. Utilizing state of the art proprietary technologies, including modular grow zones, customized LED lighting, precisely-tuned climate controls, and an artificial intelligence powered growing system, the Company is able to offer customers a wide variety of pesticide free produce with a longer at home shelf life that exceeds the highest standards in food safety. 80 Acres has demonstrated early success distributing major national retailers and food service distributors. Based in Cincinnati, Ohio, the company was founded in 2015 by veteran food industry executives Mike Zelkind and Tisha Livingston who are supported by a deep team and a board of directors representing executive and leadership experience at leading food, healthcare, and other companies. For more information, please visit www.80acresfarms.com.
About Virgo Investment Group
Founded in 2009, Virgo is a thematic investor with the mission of building meaningful businesses. Virgo partners with Founder-led or Family-owned businesses where both existing owners and management have a material equity stake in the business. Virgo targets companies undergoing industry or company-specific change, which are executing on an identified inflection point in value. The Firm has invested over $1.1 billion, completing 52 investments to date.
Virgo has flexible capital that allows the Firm to provide differentiated solutions to current asset owners and existing shareholders. Virgo is an actively engaged investor. We don't just buy value; we work to create value. The Firm's Spica Alpha Unit drives value-add initiatives post-investment via a focus on human capital transformation, business process enhancement and technology implementation. We find our meaning at Virgo in creating and in reviving the soul of companies. It always starts with and ends with the soul. For more information, please visit www.virgo-llc.com.
SOURCE 80 Acres Farms
Related Links
Teshuva Agricultural Projects (TAP) Is Proud To Present the TAPKIT
Mindanao, TAPKIT
TAPKIT is a 500 m2 Hydroponic unit.
The unit , produces 6-10 Tons of leafy vegetables per you on NFT system.
Mindanao, TAPKIT
TAP developed the unit as a solution for family farming, resorts, restaurant, senior citizens homes and more. It is called the affordable hydroponic solution because of its price- $60,000- 70,000US $.
TAPKIT Korea
Since its launching on May 2018, it has been installed in Israel, S. Korea, and The Philippines, the next two units will be installed in Mauritius next month.
TAPKIT Korea
Take A Look At America’s First Robotic Farm
December 30, 2018
America’s first robotic farm claims to use less energy than other modern forms of farming. The hydroponics system uses 90% less water than traditional farming and this is while producing 30 times more crops/ac.
The farm, which is just 8,000ft² in size, is said to take a human-led, robotics first approach. This, it says, allows plants to be grown at their best from seed to harvest.
By using the hydroponics system, the farm provides the same products all year round; which are not affected by seasonality.
What is hydroponics?
Instead of soil, plants are grown using a mineral nutrient solution and misting methods. LED lights are often used as the light source.
However, hydroponic farms require a lot of labour, such as transferring individual plants at different growth stages.
To see the robots in action, take a look at the video below.
Quality Produce
Iron Ox – the company behind the robotic farm – states on its website that: “Quality shouldn’t be a luxury or compromise.”
The company claims that it is “using robotics and intelligence to grow better food for less. In a way that uses less; less of what we can’t get back or can’t afford to waste.”
The farm plans to provide a secure food supply and access to premium produce for everyone.
According to reports, the farm plans to grow 26,000 heads of lettuce, greens and herbs. Restaurants will be the first port of call for the produce, which is set to hit the market soon.
How to Sell Your Produce and Microgreens to Top Restaurants | Episode 3 - Wilson Gibbons (Farm.One)
Published on Dec 27, 2018
In our 3rd episode we chat with Wilson Gibbons, sales manager at Farm.One -
One of the most unique and innovative vertical farms in the country that grows for top Michelin starred restaurants in NYC. He gives the best sales and marketing advice so you can get your foot in the door at restaurants.
Do you have or are you thinking about starting a vertical farm?
Do you want to know how to get your produce and microgreens into some of your top local restaurants? Then you need to watch this episode!
Thanks to Wilson for taking the time and sharing his knowledge and insight.
If you have further questions you can reach out to him at wilsonrgibbons@gmail.com. Also, thanks to everyone who asked questions for this interview across Facebook, Instagram and Reddit. I tried to fit as many as I could into this interview!
ABOUT FUTURE FARMS AND FOOD
Hi everyone! My name is Albert Lin and I'm a farmer, entrepreneur and advocate for all kinds of farming technology that can help feed the world! This is part of a vlog series from VegBed where I interview farmers, entrepreneurs and academia to talk about the future of food.
If you are interested in the best hydroponic growing medium check out ours! (https://www.vegbed.com/products/vegbe...)
Connect with us! Instagram: https://www.instagram.com/vegbed/
Facebook : https://www.facebook.com/vegbed
LinkedIn: https://www.linkedin.com/company/vegbed/
Subscribe! YouTube: https://bit.ly/2EeAejT
Please make sure you hit the subscribe button and hit the notification bell so you can follow Future Farms and Food interviews!
If you would like to be on an episode of Future Farms and Food or know someone that would be a perfect fit send me an email (info@vegbed.com).
Thanks!
Category: Science & Technology
Space Tech That Feeds High-End Diners In Toronto Could Help Canada's North
Lush, leafy greens could be locally grown with innovative vertical farming system
James Dunne · CBC News · Dec 25, 2018
A look inside We the Roots vertical farm in Toronto. Wired with LED lights, the hydroponic facility can grow up to 20,000 leafy green plants at a time. (Yan Jun Li/CBC)494 comments
Technology being used to stock high-end Toronto restaurants with designer leafy greens could provide Northern Canadians with locally grown produce.
That's the view of academic experts and entrepreneurs involved with a high-tech vertical garden housed in an east-end Toronto warehouse.
"We're going to grow food using light recipes to make economic food, to make food cost-effective" says Amin Jadavji, "and I think that's the North story".
Jadavji is CEO of We the Roots, a company he co-founded in 2017 with six others, including celebrity chef Guy Rubino.
Recently, the federal government increased funding for shipping food to Northern Canada and expanded the Nutrition North program. That move comes as advances in hydroponics and LED lighting coming from research to grow food in space are expanding the prospects for northern farming.
Amin Jadavji, CEO of We the Roots, says vertical farms can produce cost-effective food, including in Canada's North. (James Dunne/CBC)
The vertical farm of We the Roots is a commercial test of the new tech. The most traditional farm-like thing about it is the pickup truck parked outside.
The structure inside a former factory is roughly 14 metres long by three metres wide and four metres tall. It houses from 15,000 to 20,000 plants at a time. "We're growing wild Italian arugula, mizuna, which is a Japanese mustard green, Tuscan kale, basil," Jadavji says, "and a little bit of cilantro."
See how hydroponic technology grows vegetables:
The operation is hydroponic and almost entirely automated. Water in the system carries nutrients and is recycled.
Plants are nested in trays and stacked seven layers high, each one under strips of LED bulbs. The bulbs provide a tailored light combination (cool white, green, deep red, ultraviolet, far red), created to bring out specific qualities in the plants, changing their size, texture and even taste.
Then there's the nutrition factor. "We can increase things like calcium and phosphorus and various vitamins by as much as 50 per cent just by changing light recipes," says Jadavji.
Young plants nestle inside the We the Roots vertical farm. The system features custom LED lighting from a company called Intravision. ( Yan Jun Li/CBC)
The system at We the Roots is the first commercial use of a concept developed by the University of Guelph in collaboration with a Norwegian company called Intravision, says Jadavji.
The university's Space and Advanced Life Support Agriculture program, which focuses on trying to grow plants in hostile environments like space, began using Intravision's LED lights in research. That developed into a stacked system that both light and water flow through.
Though this technology was created to help feed astronauts of the future, the first customers are already enjoying lunch and dinner at five upscale Toronto restaurants, including Parcheggio.
In the hierarchy everything clicks into place with this product, which is awesome.— Andrew Piccinin, Parcheggio executive chef
Parcheggio's executive chef Andrew Piccinin dropped romaine lettuce from his salad menu after California's E. coli problem. With greens from We the Roots, he doesn't worry about E. coli because hydroponics aren't vulnerable to the same contamination.
Besides safety, he loves that the greens are flavourful, local, and environmentally friendly. "In the hierarchy everything clicks into place with this product, which is awesome."
Chef Andrew Piccinin of Parcheggio displays his 'Nonna's Salad,' an old family recipe made with arugula grown in a new high-tech vertical farm. (James Dunne/CBC)
Vertical farming is part of a recent explosion in urban agriculture, a broad agriculture practice that dates back to ancient Egypt.
According to the United Nations, urban agriculture doubled from the early 1990s to 2005. Now, the UN Food and Agriculture Organization says 800 million people in cities are growing fruits and veggies or raising animals, accounting for 15 to 20 per cent of the world's food.
Vertical farming operations are a leading part of the trend.
Analysts suggest the vertical farm market will shoot up to $13 billion US a year by 2024, from just under 1.8 billion US in 2017.
Though vertical farming has seen some high-profile failures in Vancouver and Chicago, entrepreneurs and investors see fresh opportunity.
Aerofarms' massive vertical farm in New Jersey is not hydroponic, but aeroponic. It uses less water by spraying plants with mist instead of soaking the roots. (Aerofarms)
CBC News reported on a massive investment in the sector in 2016. Inside Aerofarms' large 6,500-square-metre facility in New Jersey aeroponics are used, spraying plants with mist instead of submerging them in water. The farm has the capacity to produce two million pounds of food a year.
In Canada, McCain Foods invested in a Nova Scotia vertical farm company called TruLeaf in the spring of 2018.
We the Roots plans to expand its Toronto operations next year. Jadavji is also opening two new farms, one about 135 kilometres from Toronto and one in New Jersey, each of them 1,850 square-metre facilities to produce 1.3 million pounds of greens per year.
Going big isn't the only way to get into vertical farming though.
Tiny turnkey vertical farms built inside shipping containers can be seen in cities such as Victoria, Calgary and Dartmouth, N.S.
Plants are densely packed into vertical towers inside the Very Local Greens container farm on the waterfront in Dartmouth, N.S. (Emma Smith/CBC)
Container operators can grow from 3,000 to 5,000 plants and sell at farmers' markets and to restaurants and caterers. Prices for container farms range from just over $50,000 to more than $200,000.
American container farm makers have clever names like Freight Farms and Crop Box, and Canadians are doing the same with brands such as Growcer and Modular Farms, which sells new custom containers.
While many vertical farms are in large cities, Ottawa-based Growcer has six of its high-tech containers in Alaska and three in Northern Canada, with systems in Kugluktuk, Nunavut, Kuujjuaq, Que., and Churchill, Man. Another system is going to Manitoba and one to Yellowknife as well.
Growcer's vertical farm in Churchill, Man., is made from a repurposed shipping container. The operator supplies stores, restaurants and individual or families with a weekly subscription. (Carley Basler)
Its units are insulated to function in temperatures as cold as –52 C. Growcer CEO Corey Ellis says the company began in 2015 deeply concerned about improving the supply of fresh food in the North.
It was the high food prices in the North that also gave the company a buffer period to improve its technology. The company was able to win Northern customers as it was working to lower operating costs.
"It was a great testing ground because you know with a $7 head of lettuce that's on the shelf before we show up," says Ellis, "we knew that if we could even do a $3 head we would be doing well." Ellis says Growcer's systems have advanced so much some units can match wholesale prices of greens from California.
It galls me, quite frankly, to think this Canadian technology will find its first expression in a large scale pilot in the deserts of Kuwait.— Mike Dixon, University of Guelph
Experts believe it's time to try large scale vertical gardens in the North.
University of Guelph professor Mike Dixon is frustrated technology from the school's space agriculture program isn't being used to help address Northern food security.
University of Guelph Prof. Mike Dixon believes large vertical gardens can help provide food security in Canada's North. But he says, 'It galls me, quite frankly, to think this Canadian technology will find its first expression in a large-scale pilot in the deserts of Kuwait.' (Joe Fiorino/CBC)
We The Roots wants to try the system Dixon helped create in the North, but it will be tested in extreme heat before severe cold. Why? Because Kuwait is willing to invest in it.
"It galls me, quite frankly," says Dixon, "to think this Canadian technology will find its first expression in a large-scale pilot in the deserts of Kuwait."
ABOUT THE AUTHOR
James Dunne
Producer, CBC News Business
James Dunne researches, produces and writes stories for the business unit at CBC News. He has a decade of experience in business programming including on the shows Venture and Fortune Hunters. An award winning video journalist, he's also worked on special projects and as the late lineup editor for the World at Six on CBC Radio 1.
Gulf Region, UAE: $1.2bn GCC Vertical Farming Boom Seen By 2021
New research says a growing importance is being given to vertical farming across the Gulf region
The UAE is leading the vertical farming change and has upcoming projects facilitated by the government as well as private players to help increase food security in the region.
A growing importance is being given to vertical farming across the GCC and is generating interest and increased investments from regional and overseas players, according to a new report.
Orbis Research said the region's vertical farming market is expected to reach $1.21 billion by 2021 at a compound average growth rate (CAGR) of 26.4 percent from only $380 million in 2016.
It said the UAE is leading this change and has upcoming projects facilitated by the government as well as private players to help increase food security in the region.
These include the UAE Ministry of Climate Change and Environment allotting space for 12 vertical farms to be built by Shalimar Biotech Industries, and the world’s largest vertical farm for Emirates Airlines by Crop One Holdings Inc.
With around 90 percent of food being imported in the UAE, territorial problems of water scarcity and small percentages of arable land, vertical farming is becoming increasingly vital to ensure food security within the region, the report added.
Mariam Al Mehiri, Minister of Future Food Security, also plans to create a "Food Valley" or a technology hub, dedicated to the development of food and farming automation.
The report comes ahead of AgraME 2019, a platform for the latest technology to be showcased to the regional agribusiness market.
Henry Gordon-Smith, founder and managing director of Agritecture who will be speaking at AgraME 2019, said: “The potential is certainly there to transform what has historically been a relatively small traditional farming industry into perhaps the most technologically advanced agriculture industry in the world.
"This means economic development, increased production of nutritious local produce, and lowered food costs, all with minimal water consumption and increased resilience to climate change and foreign markets.”
Samantha Bleasby, exhibition director of AgraME added that the show, which takes place in Dubai from March 5-7, is attracting key players in the industry such as Certhon, Agrotonomy, Veggitech, Wuxi, iGrowths Technology Co Ltd, Ozorganic Urban Farming and Van der Hoeven.
For all the latest tech news from the UAE and Gulf countries, follow us on Twitter and Linkedin, like us on Facebook and subscribe to our YouTube page, which is updated daily.
Singapore Changi, The World’s Best Airport To Open A Valoya Lit Indoor Garden
For 8 consecutive years Singapore’s Changi airport has been dubbed the world’s best. It is a hub for 62 million passengers annualy and is known worldwide for its indoor greenery designed to promote Singapore’s reputation as a city of gardens. The extension which is to be opened in the first half of 2019 is a futuristic looking dome of curved glass and steel with the world’s highest waterfall (40 m) placed at its center.
Photo by Jewel Changi Airport
The dome will be populated with flora that consists of 2.000 trees and over 100.000 other plants. These will receive sunlight through the glass of the dome which will be supplemented by Valoya’s luminaires, custom made for the Changi Airport. Valoya is a provider of LED grow lights for the crop science, vertical farming and medicinal plants markets globally, known for their research driven approach and high quality, wide spectra. In addition to the standard product series, Valoya offers custom made solutions developed for large scale projects such as Singapore’s renowned airport. These custom solutions are typically made for projects that are demanding and need a high degree of engineering and photobiology expertise and support.
The form factor of the luminaires resembles a compact box designed to fade into the background and not distract from the plants. Valoya’s powerful LEDs are placed inside with a spectrum optimized for the entire growth cycle of the widest variety of plants. The spectrum’s color is a warm white designed to seamlessly fuse with natural sunlight. It is safe for and pleasant to human eyes.
The construction of this dome is a 1,7 billion dollar project. The order of Valoya luminaires is already delivered to the customer and is in the installation phase. In March 2019 the dome will open its doors to the visitors.
About Valoya Oy
Valoya is a provider of high end, energy efficient LED grow lights for use in crop science, vertical farming and medicinal plants cultivation. Valoya LED grow lights have been developed using Valoya's proprietary LED technology and extensive plant photobiology research. Valoya's customer base includes numerous vertical farms, greenhouses and research institutions all over the world (including 8 out of 10 world’s largest agricultural companies).
Additional information:
Valoya Oy, Finland
Tel: +358 10 2350300
Email: sales@valoya.com
Web: www.valoya.com
Facebook: https://www.facebook.com/valoyafi/
Twitter: https://twitter.com/valoya
US Kansas: America's First Industrial Hemp Classes For Farmers
Part of the new US Farm Bill approved in Congress makes industrial hemp legal across the country
By: Alex Meachum
December 28, 2018
Kansas - Part of the new US Farm Bill approved in Congress makes industrial hemp legal across the country.
Nick Starling shows us the classes now offered to help farmers learn about growing industrial hemp.
This is America's Hemp Academy, the first of its kind in our area where future hemp farmers can come here and learn the nuts and bolts of the crop that's used for thousands of different purposes including the flour that's in this cookie.
"This is right up our ally, it's going to give our family a new opportunity," said Margit Kaltenekker-Hall, future hemp farmer.
This field of opportunity is exactly what farmer Kaltenekker-Hall needs.
"We had a very successful oriental greenhouse business and then 2009 recession knocked that out, pretty much from right under our feet," Kaltenekker-Hall said.
She hopes growing hemp will turn their family's fortunes around.
"This has potential for our family to restore some of the productivity of this incredibly fertile soil," Kaltenekker-Hall said.
She's one of 12 farmers who already tried out the America's hemp academy.
"The amount of product from one seed is mind-boggling," said Jo Bisogno, founder and CEO of America's Hemp Academy.
Founder Jo Bisogno says he see this as Kansas's next big crop.
"I see an industry that's been around for 100's of years that went away now coming back," Bisogno said.
Bisogno says the demand for these classes is high-as they teach everything from seed to sale and connect them with suppliers.
Farmers say hemp is not as easy to grow as other crops.
"It is a very difficult, delicate plant and so it's not something you're just going to put in the ground and forget about it, it's going to require a lot of attention," said Ron Keith, Shawnee.
Shawnee farmer Ron Keith hopes to start planting in April.
"I have trees in my fields now so converting some of these tree farms into hemp farms is what I'm looking at," Keith said.
While it's not a new crop-they hope hemp's restored presence will mean more green in their wallets.
"Now that we can grow it again here, it has huge potential," Kaltenekker-Hall said.
Classes start on January 14.
Nothing Is Wasted In This Greenhouse Restaurant
It has been there for a while, restaurant the Green House in the center of Utrecht (Netherlands). On April 9, the restaurant opened its doors, and since then the visitors have been able to enjoy food which is harvested above their heads in the greenhouse. The video below gives a good overview of the restaurant.
For more information, read the article published before on Horti Daily.
For more information:
The Green House
Croeselaan 16, 3521 CA Utrecht
Netherlands
+31 (0)6 2213 1447
info@thegreenhouserestaurant.nl
www.thegreenhouserestaurant.nl
Publication date : 12/13/2018
New Plug And Play Devices Deliver Dissolved Oxygen To Plant Roots
Dissolved oxygen (DO) does many things for your plant. It is a critical but often overlooked piece that helps plants uptake nutrients through the roots. Dissolved oxygen is the mechanism that allows the nutrients to be absorbed through the root membrane. "Without sufficient levels of DO, there will be no growth. It is proven that higher levels of DO help prevent “lockout” which is when your plant is getting enough water/nutrients, but not absorbing it.", says Dennis Clark with O2 Grow.
pH, TDS and EC
Dennis explains why a DO meter is an important measuring device that every grower should have. "Most growers already have pH, TDS and EC meters, but not many have a DO meter. A quality DO meter is about the only way for a grower to know if the nutrient water has enough dissolved oxygen."
DO is typically measured in either mg/L or ppm. "Most plants need a DO level of about 6 ppm to grow, some water sources such as well water can have readings as low as 2 ppm. University trials have proven that DO levels above 10 ppm will drive enhanced growth, with a better more robust root system that supports more flowering sites on each plant."
A healthier root system also enables the plant to stave off disease and other ailments common with low DO. "University of Minnesota studies revealed as much as a 30% increase in the number of peppers in a controlled study. Other studies conducted by the University of Wisconsin reported a significant increase in root mass and yield for Crown Peas grown in Nutrient Film Technique (NFT). Also noted, was the enhanced green leaf growth. The plants were simply fuller, healthier and more produced more flowering sites."
The Oxygen Research Group has introduced a product called the O2 Grow. The O2 Grow units deliver supplemental oxygen to nutrient water via the process of electrolysis. "This process converts water molecules into nano bubbles of oxygen gas", Dennis shows.
The tiny bubbles are too small to break the surface tension of the water and are therefore absorbed back into the water. "This process will saturate the nutrient water with as much dissolved oxygen as the water can hold. When measured with a DO meter, water at 20 degrees Celsius can hold as much as 14-16 ppm of oxygen. The O2 Grow units will quickly and efficiently saturate the water to the maximum amount of oxygen the water can hold."
The O2 Grow units require very little energy to operate. They are adapted to run off of a battery source which means they can be run in a field setting or off of a solar grid. "The units are quiet and compact", Dennis shows. "Units are designed to fit a specific nutrient reservoir size based on gallons of water used to water plants from as small as 10 gallons up to 250 gallons. Simply place the emitters into your nutrient water and switch the unit on. Since the units do not need to be run continuously to maintain the higher DO levels, some growers find it easier to set up the units on a timer so nutrient water is ready to go when they need it."
The O2 Grow units can be used for both hydroponic and soil based methods of growing as well as in both indoor and outdoor environments. The units are sized based on the number of gallons/litres of water that the grower will be oxygenating. Units range from 10 gallons (37.8L) up to 250 gallons (946L). There are also units designed specifically for deep water culyure (DWC). Operating the unit is easy, simply plug in and run the O2 Grow emitters prior to watering or set the units up on a schedule with a timer.
For more information:
Oxygen Research Group
15320 Minnetonka Industrial Rd
Minnetonka, MN 55345
952-474-5820
info@o2grow.com
Publication date : 12/5/2018
The Benefits of Installing Light Movers In A Grow Room
Nancy Hamilton | November 15, 2017
Source: Botany Unlimited Design Systems
Takeaway: Plants crave a natural supply of sunlight, which includes movement of the light to reach every leaf. The only way to achieve that in the grow room is to employ the use of automated light movers.
Light mover automation is an important part of the growroom set-up, and the more we automate, the better. With just a little planning, growers can free themselves and have confidence that the automation is working perfectly. With formulas for success plugged in to repeat, growers can advance with improved growth rates and yield numbers.
Complete Grow Light System Control
Automation in our growroom gives us that extra layer of perfection and protection. And, with grow light systems automated on light movers, growers can now expect much higher standards when it comes to results.
In other words, we see an even, high-yield outcome from those perfectly keyed in variables. Consistent quality and yield results are what matters most, and robotic light mover automation can provide growers with that control.
Automation is also about reducing human error, resulting in fewer mistakes in the growroom. Through automation, indoor growing systems can be dialed in for the exact results required. Specifically, a grow light system can be supercharged on light movers.
Lights Make or Break a Growroom
One thing to know by heart is this: a grow light system is the key to everything. Indoor grow lights will either make or break indoor growing results every time.
Quality of light equals quality of yield; it’s just that simple. That statement gets us to the specific details of light mover automation. Quality grow lights on light movers make all the difference in growth rates, numbers of nodes, and yield results.
Goodbye Hotspots, Goodbye Shadows
The light mover grow light system affects light as it relates to distance when the grow lights are moved along the light mover rail—it eliminates hot spots and shadows.
Without the negative impact of hot spots and zoned light overkill, we can now get our grow lights closer for maximum photosynthetically active radiation (PAR) right to the canopy.
It’s an example of the Inverse Square Law, which states the following: The farther away an object is from a light source, the effect of that light is geometrically diminished. So, a grow light that is up close is powerful and effective. But, at five feet away (1.5 meters), that same grow light is only 50 per cent as powerful.
Remember, it’s geometrically diminishing, so at four feet away (1.2 m), we are still doing poorly and are fast approaching that 50 per cent number.
Even at two to three feet away (0.6-0.9 m), we are not using the grow lights to their full potential, even though that is generally what light manufacturers recommend. However, they are giving us these numbers thinking in stationary grow light terms.
We can, however, get 3,000+ PAR right to the canopy, but we cannot do that with stationary grow lights that are multiple feet away. We can only achieve that through robotic light movers.
In other words, stationary grow light systems force us to position our grow lights at a certain distance. In doing that, and trying to avoid the hot spots while also trying for a little stationary light spread, it undermines our efforts.
It is a catch-22 for indoor grow light systems. The solution is to use light movers. That simple change allows growers to break all the stationary grow light rules.
Robotic Lights Reach Every Leaf
At the same time, light movers also affect light as it relates to leaf area. When we move our grow lights along the light mover rails, each leaf area interacts with the intensity of those moving grow lights. That interaction is for the correct period of time for each leaf surface. This is called Leaf Area Index (LAI), and it’s very important for achieving maximum yield.
Light movers, which turn indoor grow lights into robotic moving lights, get all the leaves to interact and work for the good of the plant by getting that closer, quality, improved PAR indoor plant light to reach all the leaves for the right amount of time.
To understand LAI, it’s helpful to know that there is a limit to what each leaf surface can effectively absorb. To put it simply, each leaf surface needs intermittent light.
What is ideal is to have a powerful and intense grow light interaction for a period, have it move off slightly, then return once again to being powerful and intense without the plants waiting too long for that return.
That scenario is perfect for each leaf surface, as each leaf area can only absorb light at its own pace. Only then do all the leaves work best for the good of the plant. In other words, the sun isn’t always at high noon and neither should our grow lights.
Light movers are truly the only way to get the indoor plant light to duplicate a natural supply of sunlight.
30% More Area Covered
Light movers can cover at least 30 per cent more area compared to stationary grow lights. Not only do they employ automation in the growroom, including closer coverage for maximum PAR and more leaves working for the good of the plant, but they also allow each light to cover more of the growroom. That creates efficiency and can reduce maintenance and electricity costs.
The more we automate our set-up, the better results we can achieve. This is especially true when we take the single most important variable, the grow light system, and we make it that much better. Light mover automation gives growers bang for the buck in efficiency, protection of outcome, and improved results.
Robotic light movers provide the ultimate automation and that automation is in the very area that counts the most.
Written by Nancy Hamilton
Nancy Hamilton is executive vice president of Gualala Robotics, the manufacturer of the LightRail brand. LightRail robotic light movers are instrument-grade light movers, rated for continuous duty and made in the USA since 1986. The company headquarters is based in Steamboat Springs, Colorado. Full Bio
Canadian Test Kit Promises To Identify E. coli-Contaminated Lettuce
A new rapid testing kit developed at Western University in London, Ontario, can detect E. coli in romaine lettuce long before shipments hit grocery shelves.
The Public Health Agency of Canada has warned against eating romaine lettuce because of an E. coli outbreak, forcing retailers to pull supplies from their stores.
Researchers said the Western University-developed kit detects a protein unique to the E. coli 0157 bacteria and can show results in under 24 hours. That's the same strain of bacteria causing the current outbreak in the United States and Canada.
The current test method relies on cultures being taken from possibly contaminated samples and being sent away for testing, with results taking up to two weeks to come back. By that time, the food has often been shipped to market.
Cbc.ca quoted Dr. Michael Rieder, professor at Western's Schulich School of Medicine & Dentistry and scientist at Robarts Research Institute: "This technology is not only faster, but it's less expensive, it's easy to use, and it can occur right in the processing plant."
The Western University kit has been approved by Health Canada and is now being shipped to food processing plants in North America.
Publication date : 11/26/2018
Leafy Greens From A Growing Machine
Advancements In Automated Commercial Scale Vertical Farming
Growing produce automated or nearly automated and in any possible location are some of the advantages often supplied by the vertical farming industry. The Canadian company CubicFarms shows how also traditional greenhouse companies can benefit from indoor farming techniques.
DelFresco Pure recently chose CubicFarm Systems to grow leafy greens alongside their greenhouse production of peppers, cucumbers, tomatoes and strawberries.
CubicFarms has a background in greenhouse horticulture. The British Columbia, Canada based company has developed a indoor growing system based on a conveyer rotation method, allowing indoor farming to become scalable. It is quite a mouthful, but they explain their produce to be grown safe, sustainable and self-sufficient, cost-effective and on commercial scale.
Currently CubicFarms Systems Corp. is expanding and growing with both sales of systems, and sales of produce grown in CubicFarms.
CubicFarm installation in full swing in Pitt Meadows, BC
This summer, CubicFarms finished construction of their first full-scale, completely operational, 11 machine CubicFarm System in Pitt Meadows, BC.
"With the capacity to grow over 1.5 million of heads of lettuce, or over 9 million basil plants, or over 150,000 pounds of microgreens each year, or any combination thereof, we quickly became one of the largest producers of living lettuce, herbs, and microgreens in Canada", they explain.
Plans are already in place to expand the site by 10 fold over the next 12 months.
CubicFarms in Ontario, Canada
CubicFarms recently exhibited at the PMA 2018 show in Florida with its newest customer, DelFresco Pure, of Leamington, Ontario.
DelFresco Pure recently chose CubicFarm Systems to grow leafy greens alongside their greenhouse production of peppers, cucumbers, tomatoes and strawberries. "Our system will allow DelFresco Pure to bring additional produce into their local market without disturbing their current greenhouse operations. Installation has begun and are expected to be completed by the end of January, 2019."
A mini demonstration CubicFarm growing machine was built to display in DelFresco’s huge booth at the Orlando PMA. Strawberry Sundaes with CubicFarm growing micro basil was the big flavour hit at the show.
CubicFarms in Central Alberta
CubicFarms has also recently partnered with Swiss Leaf Farms near Edmonton, Alberta. Swiss Leaf chose CubicFarms’ automated growing machines to bring local, fresh leafy greens to central Alberta.
"The machines have just been installed and will commence growing in December. Swiss Leaf will be utilising CubicFarm’s “Thriiv Local Garden” produce brand to market and sell living lettuce, herbs and microgreens."
Thriiv Local Garden
And there's more. CubicFarms' launched their lettuce, basil and microgreens into Fresh Street Market stores in October, under their proprietary “Thriiv Local Produce” brand.
"We received positive responses from customers enjoying the freshest possible produce. Their living lettuce heads are available in 3 different blends (Springtime Trio, Butter Blend and Merlot Medley) and are sold in their proprietary packaging that allows lettuce to stay alive and fresh on the windowsill or in the fridge for weeks", they explain.
The microgreens have a variety of blends, including the spicy “Fire and Ice” and “Chef’s Blend”.
Video: Hydroponic Growing of Lettuce And Spinach On PVC pipes
2018
With the constant change in climate and unfavorable conditions for food production. It makes sense to explore other alternatives that are sustainable.
The hydroponic growing of fresh fruits and vegetables offers a great solution to have a constant supply of veggies for both family and commercial purposes.
"Educator Greenhouses Foster The Perfect Learning Environment"
GrowSpan Commercial Educator Greenhouses provide a growing environment to encourage hands-on learning. The American-made structures offer an economical growing solution for instructors looking to enhance their program and teach horticulture throughout the year.
The Commercial Educator Greenhouses are 14’ wide and built to various lengths, tailoring the size of each structure to the program’s specific needs. The durable frame is made from triple-galvanized steel to prevent corrosion over time, while the clear, UV-resistant Twin-wall polycarbonate cladding is 12 times lighter than glass and accompanied by a 10-year warranty. GrowSpan is able to customize Educator Greenhouses with complete environmental control systems, including lighting, heating, ventilation and hydroponics systems as desired.
Starmont High School utilizes a GrowSpan Educator Greenhouse to take this learning a step further by organizing an annual plant sale to incorporate commerce and business experience into their program. As a GrowSpan customer, their educational program finds immeasurable value in the knowledge their students gain while working in the greenhouse.
GrowSpan understands the benefits of agricultural education for people of all ages. These greenhouses are suitable for primary and secondary schools, colleges and universities, research institutions, correctional facilities and more.
For more information:
GrowSpan Greenhouse Structures
1395 John Fitch Blvd
South Windsor, Connecticut 06074
Toll-free USA: (800) 476 9715
International: +1 860 528 9550
info@growspan.com
Publication date : 12/4/2018