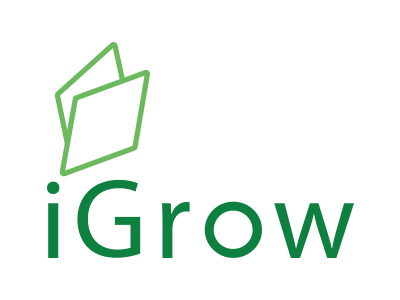
Welcome to iGrow News, Your Source for the World of Indoor Vertical Farming
Women in AI: How Does the Future of Horticulture Will Look?
But what skills are needed to work in AI tech? And what does the future of working with AI look like? Britta Meixner, Saheli De and Gosia Piekarska of Blue Radix answer these questions, and suggest how we can encourage more women to aim for tech jobs in AI or IT
August 11, 2021
Getting the best from your crop and greenhouse will increasingly become a computer responsibility. We need to make better decisions, to get better results and fix the global food problems and expertise shortages. Artificial Intelligence can help us with this. But what skills are needed to work in AI tech? And what does the future of working with AI look like? Britta Meixner, Saheli De and Gosia Piekarska of Blue Radix answer these questions, and suggest how we can encourage more women to aim for tech jobs in AI or IT.
What’s your job at Blue Radix?
Britta: “My name is Britta Meixner, and I’m a Scientific Data Engineer. I advise the Blue Radix management team on technical implementations. I keep track of new technologies enabling us to introduce innovative products to customers. I also design, build and maintain a scalable and future-proof IT environment. Other tasks include implementing proof of concepts for new technologies and setups; I design and realize solutions when we start using these new technologies. One of these is the Azure IoT Hub, which lets us send results from the Data Science Team to greenhouses, steering installations autonomously.”
“A day in a data scientist’s life entails a range of tasks,” explains Saheli De, who works as a Data Scientist at Blue Radix. “Developing new functionalities for our customers involves preparing, cleaning and analyzing the data that comes from the climate computers and other data platforms. In this phase we work closely with our product development team to understand the dynamics and strategies involved in the greenhouse. Then there’s extensive discussion of strategies to solve the business requirement, leading to building models using cutting-edge AI technologies like machine learning. The essence of the job lies in translating the horticulture industry’s business requirements into data science solutions.”
Gosia Piekarska works as a Blue Radix Test Engineer and is responsible for implementing testing procedures, shaping the testing process, and software testing. “My job is to check the quality of the infrastructure and components in both Crop Controller and the energy domain. My work is my hobby; I’m always trying to improve my software testing knowledge in my spare time. I’m particularly interested in Test Automation, Data Analysis and DevOps.”
What do you like about working with new AI tech solutions for horticulture?
Britta: “There’s often no standard way of doing something when creating new AI solutions. Every new project requires new skills and technology knowledge. I can never stop learning in my job. Staying up to speed on new developments and technologies is the key to success. This makes my job demanding, but at the same time it never gets boring.”
Adds Saheli: “The tech industry is growing rapidly, and being the flag-bearer of AI in horticulture lets you design unique and sustainable solutions. Imagine walking into a supermarket picking up a tomato that was produced with the help of your algorithms! That’s powerful!”
“I always love working on the cutting-edge technology solutions, because they introduce the innovations which are so desperately needed in our world,” says Gosia. “I think that sustainable technology in the food-growing industry is critical for people’s well-being.”
What skills are needed to work in the AI tech-field?
“You need a broad spectrum of knowledge to make our solutions work in the greenhouse, from network protocols and operating systems, databases and APIs, to data pipelines. It’s only the combination of these which enables us to steer a greenhouse autonomously,” explains Britta. “Because the IT infrastructure differs in every greenhouse, we must be able to create solutions that quickly adjust to a wide range of situations. So alongside a very broad technical knowledge, you also need to be flexible, and to understand new situations and requirements quickly.”
Saheli adds: “Data Science in particular is a mix of mathematics, statistics, and computer science skills. Horticulture-related skills are a benefit, but not mandatory in my role.”
Gosia: “Constant learning of both broad technologies and tools.. On top of that, don’t forget soft skills.”
How do you think the future of working with AI will look?
Britta: “Data Scientists now focus mainly on a deep understanding of algorithms and data sets to be able to get the most accurate results for steering the greenhouse. This is often done in controlled offline setups. But there’s still a large gap before these algorithms are ready to be integrated into production environments to produce real-world data for the greenhouse. Data science and data engineering have to work together early in the development process to close this gap. That lets us deliver new features and improvements to existing functionalities faster.”
Saheli: “As we say at Blue Radix: ‘Algorithms can feed the world’. We believe that algorithm-based solutions, like our Crop Controller, offer growers worldwide a digital brain for their greenhouse. The dream is to work towards a symbiotic utopia of growers and AI-driven solutions.”
Gosia adds: “The key will be the AI-human interaction and how to deliver AI solutions to customers who don’t necessarily have a deep technical understanding of AI systems. This is important in horticulture, because advanced controlled systems are relatively new in this industry.”
How can we generate enthusiasm among women for tech jobs in AI or IT?
Britta: “Women have different styles of working, thinking and communicating than men. While that might cause confusion here and there, it can really help a team to reach their goals faster, and to find better solutions. If we are to encourage more women to take up AI or IT jobs, it’s important to reach true equality in opportunities and pay in every job out there. We need to remove gender stereotypes in daily work, while also avoiding them in early childhood and at schools.”
Saheli: “I completely agree with Britta,; we need to generate opportunities for both genders to be able to access and experience meaningful interaction with technology from a very young age. I strongly believe that curiosity is the key to science. Stay curious and keep asking questions!”
Gosia: “We can’t shape our world if we’re not involved. Working in IT offers enormous opportunities for women to make their mark. I also believe there are great career prospects if you choose a future working in AI, IT and sustainability. There are so many great challenges, and you can really contribute to a better world. The best would be to provide successful examples and stories of women working in AI, to encourage young girls to join the field.”
"New York Is Ideally Suited For Greenhouse Production"
Intergrow Greenhouses is excited to announce the opening of its newest expansion in Upstate, NY. The 10-acre project will produce over 3 million pounds of fresh produce a year, feeding millions across the Northeast and Mid-Atlantic all of the way down to the Southeast.
August 10, 2021
Intergrow Greenhouses is excited to announce the opening of its newest expansion in Upstate, NY. The 10-acre project will produce over 3 million pounds of fresh produce a year, feeding millions across the Northeast and Mid-Atlantic all of the way down to the Southeast.
“We’ve been operating in the US since 1998, and always in New York State.” says Dirk Biemans, president of Intergrow Greenhouses. “Our European partners saw the opportunity for greenhouse-grown produce here in the US back in the 90s and we quickly set up shop. The climate here in New York is ideally suited for our greenhouse production, resulting in the best flavor, quality, and consistency for our retail partners all year. We are primed for successful growth here in NY. With nearly 60% of the US population only 24 hours from us, and growing consumer demand for local and domestically grown produce, we’ve got to be ready."
And a local company they truly are. Biemans reports over 70% of the 350 employees at Intergrow are permeant residents of New York State and that number is growing. “Labor is an extremely important part of our business model, if we can recruit, train, and retain local labor it can yield huge advantages for us.”
The new facility will be outfitted with HPS grow lights, adding to Intergrow’s ever-increasing winter offerings. It also boasts diffused glass for better light distribution and heating and fertigation systems. However, Biemans reports there were several challenges and delays that threatened the project finishing on time.
“Ocean freight is crazy right now, not only have prices increased but there’s been a huge problem with on-time arrivals and customs issues. The majority of this project came in prefabricated from Europe, which offers a lot of benefits but our team and chosen suppliers were not quite ready for the logistical challenges in 2021. However, we were able to pull through, overcoming those challenges, and working with the cards we were dealt. This project was successfully completed on time putting us at a total of 105 acres under glass.”
For more information:
Intergrow Greenhouses
www.intergrowgreenhouses.com
Lead Photo: Propagated tomato plants await their final placement in Intergrow’s Newest 10-acre greenhouse.
NL: Celebrating 15 Years of Horticultural Development At The Horti Science Park
Wageningen University & Research (WUR), the Delphy Improvement Centre, and the Municipality of Lansingerland are celebrating fifteen years of scientific development in the field of greenhouse horticulture.
August 9, 2021
Wageningen University & Research (WUR), the Delphy Improvement Centre, and the Municipality of Lansingerland are celebrating fifteen years of scientific development in the field of greenhouse horticulture. Save the date: various activities will be organized during the ’Horti Science Park Event Weeks’, held this year from 20 September to 8 October. From looking back, we are now looking forward to the role that the Horti Science Park will be playing in the future.
The autumn of 2006 saw the launch of a number of cultivation trials at the Delphy Improvement Centre and Wageningen University & Research (Greenhouse Horticulture Business Unit) sites, both located at Violierenweg in Bleiswijk (Municipality of Lansingerland). Pioneering research was conducted in support of both the Dutch and international greenhouse horticulture sector at this Horti Science Park in the past decade and a half.
In addition to devising and developing the Next Generation Greenhouse Cultivation project, a great deal of research was carried out on the application of LED lighting with a view to creating sustainable cultivation systems. The development towards digital cultivation in autonomously controlled greenhouses with the application of newly developed plant sensors is in full swing and will result in far-reaching changes regarding the management of greenhouse horticulture. The development of production systems has always been a part of this, just as several greenhouse prototypes are now being tested and scientific knowledge in the area of cultivation is being developed in support of Vertical Farming practices.
The Municipality of Lansingerland is pleased with the presence of these two leading research institutions in greenhouse horticulture and therefore wishes to further develop its position as a knowledge-intensive municipality focusing on greenhouse horticulture. It is currently collaborating with entrepreneurs and residents on a ‘Horti Science Vision’, which should comprise the basis for guiding greenhouse horticulture research and future plans on themes such as education, employment, and space.
The opening of the ‘Vertical Farming Fieldlab’ by Wageningen University & Research (WUR) and Delphy is scheduled to take place during the ‘Horti Science Park Event Weeks’, which will be held from 20 September to 8 October. In addition to the above, the Municipality of Lansingerland, WUR and Delphy, in conjunction with organizations such as Glastuinbouw Nederland and Greenport West-Holland, will be organizing at least ten other events. Examples are the Knowledge Day for entrepreneurs in horticulture, the WaterEvent and an afternoon symposium on taste research. Meet-ups on the 'Horti Science Vision' will also be planned with young people who are interested in the horticultural sector and residents of the municipality. All events will be looking towards the future based on the knowledge we have today.
For more information:
Wageningen University & Research
www.wur.nl
Welcome To Our Farm Within A Farm
But now all of the hard work and waiting has come to fruition as we are now ready to welcome you into our new Micro Farm: A Farm Within a Farm.
August 5, 2021
What is CEA?
Over the past year or so you may have heard us at Vertical Harvest referring to our “conversion” project – the construction of which has been the cause of some product delays and shortages. But now all of the hard work and waiting has come to fruition as we are now ready to welcome you into our new Micro Farm: A Farm Within a Farm.
The idea emerged when we noticed an increase in demand from our local chefs and grocery stores to supply more microgreens and petite greens. This happened to align with an internal ambition we have been fostering to implement a fully Controlled Environment Agriculture (CEA) system within our greenhouse. The new compartment has 4,000 sq feet of rack systems growing micro and petite greens fully independent of the whims of nature.
This farm is our next iteration for creating efficient and scalable growing systems. As we are seeing greater fluctuations in our local and national climates it has become increasingly important to us to delve into the capabilities of a growing system that is fully self-contained and not dependent on external changes in light and temperature. Instead, the greens will be nurtured in light and temperature conditions that are ideal to their growth cycles. This space has also increased our greenhouse production by 200%, meaning we can get our community more of the greens it loves both at home and when dining out.
Though our Maine greenhouse will incorporate some different technology, it will have a tray system that is very similar to this new compartment; so we have also reserved a portion of this new space to trial products and improve growing methods to ensure that our Westbrook greenhouse will have all the resources and information needed to hit the ground running when it plants its first seeds. We are already growing in the new space, training our employees on the new system, and getting our greens to customers. Vertical Harvest has always integrated different techniques and changed to growing demands, this project has been challenging and rewarding and will go on to influence all of our future greenhouses.
Nature Fresh Farms Featured in an Episode of YTV’s Kid Food Nation: The Show
Nature Fresh Farms joins YTV’s Kid Food Nation: The Show to educate children on greenhouse growing and fresh vegetable production.
July 20, 2021
Nature Fresh Farms joins YTV’s Kid Food Nation: The Show to educate children on greenhouse growing and fresh vegetable production.
Nature Fresh Farms will be featured in an episode during the second season of Kid Food Nation: The Show, giving the cast and the viewers at home a peek inside greenhouse and packaging facilities while exploring the many processes it takes to grow, package, and ship fresh food. Hosts Spencer and Tyra interview members of the Nature Fresh Farms team as they answer questions and share their knowledge about all things inside the greenhouse.
Kid Food Nation: The Show is in partnership with Kid Food Nation and President’s Choice Children’s Charity. The series follows Spencer, Tyra, and kid food nation heroes as they embark on culinary missions and answer questions like, "Should I eat crickets?" or "Are dandelions edible?" The jam-packed 8 episode run for Season 2 will be fun, informative, and inspirational to chefs both young and old. Like the show, the Kid Food Nation project aims to encourage Canadian kids to explore food through online recipes, activities, and videos. Founded by President’s Choice Children’s Charity, BGC Canada and Corus Entertainment, and now in its fifth year, the initiative celebrates a selection of junior chefs from every corner of Canada, featuring their family recipes in an annual contest and cookbook.
“Kid Food Nation is an amazing initiative that aligns completely with our vision of inspiring children and their families to learn about where their fresh fruits and vegetables come from while encouraging nutritional eating,” said Marketing Director, Stephanie Swatkow. “This was a great opportunity to share how we deliver fresh produce from seed to table in a fun interactive way that the program offers.”
Committed to educating consumers and helping to build healthier communities, Nature Fresh Farms believes in cultivating healthy, life-long eating habits through education and teaching important food skills so families can continually develop a healthier relationship with food.
The second season of Kid Food Nation: The Show will premiere on YTV this summer on July 28th at 6:30 pm EST. Each episode will also be uploaded on the Kid Food Nation YouTube channel at https://www.youtube.com/hashtag/kidfoodnation.
About Nature Fresh Farms
Continuously expanding, Nature Fresh Farms has become one of the largest independent, vertically integrated greenhouse vegetable farms in North America. As a year-round grower with farms in Leamington, ON, Delta, OH, and Mexico, Nature Fresh Farms prides itself on consistently delivering exceptional flavor and quality to key retailers throughout North America, while continuing to innovate and introduce more viable and sustainable growing and packaging solutions.
About Kid Food Nation
Kid Food Nation is a five-year project to excite the inner foodie in every Canadian kid. Created in partnership with President’s Choice Children’s Charity, BGC Canada, and Corus Entertainment, with the support of the Government of Canada, the Kid Food Nation online hub on YTV.com features cooking videos with kids, celebrity chefs, and local talent, tips for nutritious foods, as well as games and quizzes. In addition, topics related to the Kid Food Nation curriculum will also be available on the online hub.
The annual Kid Food Nation recipe contest encourages kids between the ages of seven and 13 from across the country to share their love of good food by submitting original, healthy recipes that highlight their culture or their Canadian pride. Each year, 26 young winners are chosen, representing every province and territory in Canada, to have their recipes and chef profiles published in the Kid Food Nation cookbook.
About Corus Entertainment
Corus Entertainment Inc. (TSX: CJR.B) is a leading media and content company that develops and delivers high-quality brands and content across platforms for audiences around the world. Engaging audiences since 1999, the company’s portfolio of multimedia offerings encompass 33 specialty television services, 39 radio stations, 15 conventional television stations, a suite of digital assets, animation software, technology, and media services. Corus is an established creator of globally distributed content through Nelvana animation studio, Corus Studios, and children’s book publishing house Kids Can Press. The company also owns an innovative full-service social digital agency so.da, and lifestyle entertainment company Kin Canada. Corus’ roster of premium brands includes Global Television, W Network, HGTV Canada, Food Network Canada, HISTORY®, Showcase, Adult Swim, NationalGeographic, Disney Channel Canada, YTV, Global News, Globalnews.ca, Q107, Country 105, and CFOX. Visit Corus at www.corusent.com.
SOURCE: Nature Fresh Farms | info@naturefresh.ca
T: 519 326 1111 | www.naturefresh.ca
There is No Soil. There Is No Growth Period. Just Add Water and Technology.
Inside, nearly £3 million of beefsteak tomatoes grow on 45-foot-high vines without a teaspoon of soil, and their roots are submerged in nutrient-rich rainwater. Other vines hold thousands of small, juicy snack tomatoes with enough pepper to impress Martha Stewart on the board. AppHarvest, a start-up company that harvests its first crop here in January and plans to open 11 more indoor farms in Appalachia by 2025.
Scott Krantz
July 10, 2021
Morehead, Kentucky — In this beautiful town on the edge of the coal country, a high-tech greenhouse large enough to cover 50 soccer fields glows pink and yellow with 30,600 LEDs and high-pressure sodium lamps.
Inside, nearly £3 million of beefsteak tomatoes grow on 45-foot-high vines without a teaspoon of soil, and their roots are submerged in nutrient-rich rainwater. Other vines hold thousands of small, juicy snack tomatoes with enough pepper to impress Martha Stewart on the board. AppHarvest, a start-up company that harvests its first crop here in January and plans to open 11 more indoor farms in Appalachia by 2025.
In a much more industrial environment near the Hackensack River in Kearny, NJ, trays filled with sweet baby butterhead lettuce and sorrel flavored with lemon and green apple are piled up in a windowless warehouse. This is known as vertical farming. Bowery, The largest vertical farming company in the United States, manipulates light, humidity, temperature and other conditions to grow produce and is funded by investors such as: Justin Timberlake, Natalie Portman, chefs Jose Andre and Tom Colicchio.
“If you taste arugula, it’s sold,” said Koricchio, who has turned to people who claim to grow delicious hydroponic produce for years. “It was very spicy and lively and surprised me.”
The two operations use technological advances such as machine learning algorithms, data analysis, and proprietary software systems to create accurate growing conditions and bring out customized flavors and textures from fruits and vegetables in a new generation of hydroponics. It is part of a cultivation farm. And they can do it almost anywhere.
These farms arrive at crucial moments. The country’s strips have withered due to the heat and drought of climate change, partly supported by certain forms of agriculture. Demand for locally sourced foods is higher than ever, and pandemics have shown that many people are not as resilient as their food supply chains may have been.
However, not everyone is participating. These huge farms grow their produce in nutrient-rich water, rather than in healthy soil, which many believe is central to both deliciousness and nutrition. They can be consumed A huge amount of electricity. Their most ardent opponents say that the claims made to hydroponics are misleading and even dangerous.
“At this point, I think the bad guys are winning,” said a Vermont farmer. Real organic project.. “Hydroponics isn’t growing because it produces healthier foods. It’s growing thanks to money. Anyone who sees this as food for people or the environment is lying. I’m just there. “
The jargon of hydroponics is controlled environmental farming, but business people call it indoor farming. What used to be simply called a farm is now called an onshore farm or field farming.
“We have perfected Mother Nature indoors by combining science and technology with agriculture,” said Daniel Malechuk, CEO of. Carrera, A company that sells whole lettuce in plastic clamshells, leaving the roots intact, at about the same price as other washed lettuce.
In March, the company opened a 77,000-square-foot facility south of Atlanta, capable of producing more than 10 million lettuce annually. Similar indoor farms in Houston, Denver, Seattle, Honolulu St. Paul, Minnesota.
According to Malechuk and other executives, the beauty of this process is not limited by the seasons. You can accurately predict the cost and growth period of your crops and build farms wherever people need fresh produce.
“We can grow in Antarctica,” he said. “We can be on the island. We can be on the moon or on the space station.”
It’s easy to imagine. There are new breeds of young farmers on the farm who wear lab coats instead of overalls and prefer computers to tractors.
Today, more than 2,300 farms growing hydroponic crops in the United States make up just part of the country’s $ 5.2 billion fruit and vegetable market. But investors who are crazy about smart farming are betting big on them.
In 2020, $ 929 million was invested in US indoor farming ventures, more than double the investment in 2019. PitchBook data. The grocery chain and California’s largest berry producer Alliance with vertical farming, also.
“There is no doubt that we are reinventing agriculture, but what we are doing is reinventing the fresh food supply chain,” said Manhattan-based indoor farm in New Jersey. Irving Fain, founder and chief executive officer of Bowery, said. One is under construction in Maryland and the other in Pennsylvania, and two research farms are in New Jersey.
Mr. Fine said his farm is 100 times more productive than traditional farms and uses 95% less water. Other companies claim that one acre can grow as much food as a traditional farm can grow at 390.
Vertical farming can be built next to the city center, so lettuce, for example, doesn’t have to sit in a truck for days when heading from California to the east coast, losing both quality and quality. Nutritional value. Vegetables are grown for flavor, not storage and yield.
The new system was designed to produce pesticide-free sanitary crops in computer-monitored sanitary buildings, forcing a major recall of Romain Lettuce in 2019 and 2020. There is little risk of contamination by bacteria such as E. coli.
Still, many farmers and scientists remain unconvincing. Chapman of the Real Organic Project was engaged in hydroponics at the US Department of Agriculture Taskforce. Five years ago, he led an effort to encourage distributors not to allow hydroponics farmers to certify their produce as organic produce. According to him and others, the very definition of organic farming depends on creating healthy soil. May, Food Safety Center, Environmental groups, led Appeal of Federal Court Decision. It upheld the policy of government agencies.
The nutritional profile of hydroponics continues to improve, but no one yet knows what long-term health implications for fruits and vegetables grown without soil. No matter how many nutrients an indoor farmer puts in water, critics say that an indoor farmer can rival the taste and nutritional value that comes from a combination of sun, healthy soil microbes, and common phytobiology. They can’t and claim they can’t offer environmental benefits-run an organic farm.
“What are the health consequences of the second generation?” Chapman asked. “This is a huge live experiment and we are mice.”
The gap between soil lovers and ag-tech futurists has spread on a much closer scale between two influential brothers, Dan and David Barber, who found and own organic farms. Masu Blue Hill Restaurants in Greenwich Village and Stoneburn, Pocantico Hills, NY
Created by David Barber in 2018 Investment fund To support new food technology companies, including Bowery. But the 2014 book “Third plate: Field notes on the future of food” dedicates the entire section to the soil and believes that truly delicious food can only come from Earth.
“I haven’t bought it,” said Dan Barber about the heat of hydroponics.
It is virtually impossible to try to fortify water with nutrients to mimic what the soil does, he said.
“We know more about the stars and the sky than the soil,” he said. “In fact, we don’t know much about nutrition.”
There are also cultural costs. For centuries, he said, cooking has been developed based on what the land and plants demand. The Mexican diet in the corn and bean-based region was born out of farmers’ awareness that corn grows better in the presence of beans that fix nitrogen in the soil.
“The technological agricultural revolution is changing this equation head-on,” Barber said. It helps efficiency in the name of feeding more people but divorces food from nature.
His brother, David, was also skeptical of hydroponics for a long time. “Most of my career has been that good soil leads to good agriculture, good systems, and ultimately good flavors,” said David Barber.
But the environmental benefits of next-generation hydroponics cannot be ignored, he said. It also does not taste better than previous hydroponic produce. “They combine outdoor and indoor thinking, and science and history to create something special,” he said. “There aren’t many winners in this area, but they will be part of our food system.”
Indoor farmers see competition as a large industrial producer producing fruits and vegetables grown to withstand processing and shipping, rather than small farmers using more natural cultivation techniques. They say the fight is against monoculture, not the farmers who maintain healthy soil and feed the community. Hydroponic farms can help develop new and more diverse plants and reduce the overall use of pesticides.
“All we’re trying to do is be as good as a farmer 100 years ago,” said hydroponic lettuce grower Malechuk.
Kentucky-born founder and CEO of App Harvest, Jonathan Webb, said indoor farming is a bet on national farming.
“American farmers are already out of date,” he said, noting that the United States imports £ 4 billion of tomatoes from Mexico each year. “Our hope is to be able to bring farmers back to US shelves.”
Coriccio also leads the campaign opposed to genetically modified foods and long advocate for smallholders, he said the two farming styles could coexist. “The toolbox needs a lot of tools,” he said.
Uita Michel Kentucky chef App Harvest likes App Harvest because the company creates jobs and grows tomatoes that they are happy to use in restaurants.
But technology will never beat the magic of the soil, she said. “There is no substitute for my summer Kentucky tomatoes.”
There is no soil. There is no growth period. Just add water and technology.
VB Ready To Double Capacity For Little Leaf Farms Again
Little Leaf Farms asked VB again to build the most modern and innovative greenhouse to date to grow leafy greens. A system that provides the smallest possible chance of disease, an optimal growing climate, and no need for human hands to be involved in the cultivation process.
July 5, 2021
Devens, Massachusetts-based Little Leaf Farms' mission is to provide fresh, locally grown lettuce grown sustainably all year round to their New England consumers. To be able to achieve this goal, it is extremely important to grow and supply products in a sustainable way all year round.
This is why Little Leaf Farms asked VB again to build the most modern and innovative greenhouse to date to grow leafy greens. A system that provides the smallest possible chance of disease, an optimal growing climate, and no need for human hands to be involved in the cultivation process. After three consecutive phases for LLF realizing an ultramodern greenhouse is a challenge that VB knows how to handle.
Inside the Little Leaf greenhouse
The climate on the US East Coast is a challenge: winters during which -25 C is no exception, and summers during which the mercury rises to +38 C. A considerable amount of energy is required to be able to cope with these extremes. The solution had to be more sustainable than transporting the lettuce by truck from the West Coast to the New England area.
With an advanced automatic cultivation system that systematically moves through the greenhouse, the sustainability challenge has been overcome. In collaboration with a team of specialists, as well as the customer, VB was able to take an in-depth look during the design process at what was needed to create an optimal growing climate inside the greenhouse.
The Little Leaf Farms greenhouse in Devens
Active cooling system
VB has integrated a unique active cooling system, with which the inside of the greenhouse can not only be kept cool during the winter through the use of outside air, but also stays cool during the hot summers. LED lighting helps compensate for the shortage of natural light during the winter. With the use of sun protection screens, excess sunlight is blocked during the summer.
The result? The climate conditions can be optimized for the cultivation process, the growth process is accelerated, there is more control over the nutrition the plants receive, available cultivation space is used in the most efficient manner, and virtually nobody needs to enter the greenhouse.
Edward Verbakel (VB) & Paul Sellew (Little Leaf Farms)
Doubling and doubling again
The first greenhouse in Devens MA was completed in 2016 and shortly after two additional phases were built by VB for Little Leaf Farms to reach 10 acres of modern growing space.
In the course of 2021 LLF and VB were able to agree again on the construction of the new Little Leaf Farms greenhouse facility in McAdoo Pennsylvania. With this expansion Little Leaf is doubling its capacity to 20 acres. Construction will start this summer and completion is expected for early Spring 2022.
McAdoo facility, Pennsylvania
For more information:
Edward Verbakel
VB Group
info@vb.nl
www.vb.nl
Signify’s Expanded GrowWise Control System Helps Growers Boost Operational Efficiencies
Signify has expanded its GrowWise Control System, allowing for higher levels of automation and reducing manual labor and operational costs
Signify has expanded its GrowWise Control System, allowing for higher levels of automation and reducing manual labor and operational costs. This can be achieved by automating the lighting planning for their crop’s full growth cycle, up to one year ahead. The software tool brings dynamic lighting to greenhouses and vertical farms and fits seamlessly with modern climate computers and greenhouse management systems. This enables growers to automatically adjust light levels to maintain consistent levels on cloudy days, save energy on sunny days and simulate sunrise and sunset throughout the day or season.
Growers, like the Italian vertical farm, Planet Farms, and the Belgium greenhouse, De Glastuin, are already using the expanded system providing additional value within their growing facility.
“Using the GrowWise Control System is ideal for us,” says Luca Travaglini, co-founder of Planet Farms. “We want to automate as many aspects of our operations as possible to become more cost efficient. Now we can easily create custom light recipes and set them to run year-round to provide the right light recipe with the right light intensity at the right time throughout the crop’s growth cycle. By automating our full light strategy during the growth cycle, for the whole year, we can run our operations very efficiently and keep our manual labor costs low. That makes it easier for us to maintain consistent quality as we scale up our production.”
The demand for the GrowWise Control System is increasing for greenhouse applications as well. “The lighting can be used much more efficient, since it gives us the flexibility to reduce light levels at any moment we need to,” says Wouter de Bruyn, owner at De Glastuin. Lettuce grower De Glastuin is using the GrowWise Control System to control the Philips GreenPower LED toplighting compact grow lights via its climate control system. “The climate computer is equipped with a daylight sensor that sends actual light measurements to the GrowWise Control System so we can adapt our light levels automatically to ensure an even light level throughout the day and season. This results in a continuous high-quality crop. In case the electricity is the limiting factor, we are still able to use the LEDs evenly for the whole greenhouse in a lesser intensity.”
“Dynamic lighting in a greenhouse is the next step in improving the cost-efficiency and quality for the cultivation process,” says Udo van Slooten, Business leader Horticulture LED solutions at Signify. “It allows growers to effortlessly maintain a consistent level of light throughout the day to produce the best possible crops. The system compensates for cloudy weather and creates a more controlled growing environment for your crop.”
For more information about the GrowWise Control System and our Philips-banded horticulture lighting, visit our horticulture pages.
Or please contact:
Global Marcom Manager Horticulture at Signify
Daniela Damoiseaux
Tel: +31 6 31 65 29 69
E-mail: daniela.damoiseaux@signify.com
About Signify
Signify (Euronext: LIGHT) is the world leader in lighting for professionals and consumers and lighting for the Internet of Things. Our Philips products, Interact connected lighting systems and data-enabled services, deliver business value and transform life in homes, buildings and public spaces. With 2019 sales of EUR 6.2 billion, we have approximately 37,000 employees and are present in over 70 countries. We unlock the extraordinary potential of light for brighter lives and a better world. We achieved carbon neutrality in 2020, have been in the Dow Jones Sustainability World Index since our IPO for four consecutive years and were named Industry Leader in 2017, 2018 and 2019. News from Signify is located at the Newsroom, Twitter, LinkedIn and Instagram. Information for investors can be found on the Investor Relations page.
Little Leaf Farms Expands Hydroponic Greens Distribution Across East Coast
Based in Massachusetts, Little Leaf Farms has doubled its hydroponic greenhouse-growing capacity to 10 acres of fields under glass capable of producing more than two million packages of lettuce each month, which will broaden the company's distribution to retailers in New York, New Jersey, Pennsylvania, and South Carolina
15-Sep-2020
By Mary Ellen Shoup
Based in Massachusetts, Little Leaf Farms has doubled its hydroponic greenhouse-growing capacity to 10 acres of fields under glass capable of producing more than two million packages of lettuce each month, which will broaden the company's distribution to retailers in New York, New Jersey, Pennsylvania, and South Carolina.
Read More At: Food Navigator
Nature Fresh Farms Releases NEW 100% Home Compostable Cucumber Wrap
An alternative to traditional polyethylene plastic, this film is an environmentally friendly compostable wrap that breaks down in a household compost without leaving behind microplastics
Leamington, ON (September 8, 2020) – Nature Fresh Farms continue their sustainable initiatives by releasing a new, 100% home compostable wrap for their Long English Cucumbers, a first in the North American market.
An alternative to traditional polyethylene plastic, this film is an environmentally friendly compostable wrap that breaks down in a household compost without leaving behind microplastics. The compostable film will prolong the shelf life of the product; however, it will do so without adding to long term landfill waste. Made from a starch-based PLA that is derived from plant-based resources including non-GMO corn starch, it is 100% compostable, breaking down naturally into CO2 and water.
Each cucumber wrap contains 0.00436 lbs of plastic; this translates to the equivalent of 23-million plastic straws saved from landfills for every 5-million Cucumbers wrapped in the compostable film. Cucumbers are packed in shrink wrap to significantly extend their life by minimizing evaporation. Through the compostable film, Nature Fresh Farms has found a packaging solution that can maintain the shelf life of the Cucumber, while meeting the demands of more sustainable packaging alternatives.
“The launch of the compostable wrap is a demonstration of our commitment to our consumer’s wants of reducing plastic usage. We are excited to be first to market with this initiative in North American and are hopeful this will start a trend with the industry while we continue to lead in sustainable packaging solutions.”
--Matt Quiring, Director of Sales
In addition, the wrap includes a PLU pre-printed on the film in compostable ink. This feature allows the entire wrap to be thrown in with backyard compost or in landfills without harming the environment. PLU stickers are commonly made of vinyl and plastic. This new wrap eliminates the need for the additional application.
“After two years of research & development and a lot of trial & error, it’s so exciting to see this film launch in the market. We are confident in this product’s ability to make a true difference
(in reducing harmful plastic waste)”
---Luci Faas, Product Development Specialist
At Nature Fresh Farms we are driven to accelerate innovation via evidence-informed sustainable packaging solutions that provide a better experience for our customers, while also helping to preserve the vitality of our planet.
-30-
About Nature Fresh Farms -
Continuously expanding, Nature Fresh Farms has become one of the largest independent, vertically integrated greenhouse vegetable farms in North America. As a year-round grower with farms in Leamington ON, Delta OH, and Mexico, Nature Fresh Farms prides itself on consistently delivering exceptional flavor and quality to key retailers throughout North America, while continuing to innovate and introduce more viable and sustainable growing and packaging solutions.
SOURCE: Nature Fresh Farms | info@naturefresh.ca T: 519 326 1111 | www.naturefresh.ca
The Basis, A Homogeneous Climate, Is Already There" Artechno Doing New Cultivation Tests In VF Chamber
Previously, the Artechno industrial hall was mainly the place to build complete water management systems for the greenhouse or harvesting lines and turnkey systems for vertical farms and deep-float systems
"Together with another colleague, I am adding green thumbs to the team that is full of technicians here", Rick van Schie laughs. As the son of a tomato grower and next year's fourth-year horticulture student, he started cultivation research in the industrial hall of Artechno in De Lier. In a AVF+ Junior climate chamber Rick researches irrigation strategies for four different substrates and the effect that far-red light has on the stretching in lettuce.
Previously, the Artechno industrial hall was mainly the place to build complete water management systems for the greenhouse or harvesting lines and turnkey systems for vertical farms and deep-float systems. “The cultivation space with deep-float facility provided insight into growth and also important key figures for the business case. By testing and growing ourselves, we can now also better serve our customers in the vertical farm industry and provide them with better data and growth recipes.”
Rick started growing in the climate chamber in mid-June. "It is often wise for a grower to first do tests in a small chamber and to collect as much information as possible about lighting, climate and irrigation before scaling up to a larger system. That is why we also offer our chambers for rent to growers."
Cameras and LED
The AVF + Junior with which Rick is currently doing tests is equipped with Philips GEN3 LED luminaires, whereby both the spectrum and the light intensity are adjustable. The chamber is also equipped with special hyper-spectral cameras (and sensors), making it possible to monitor the crop and climate without having to enter the chamber.
Homogeneous climate
Anyone who would enter the chamber will notice, according to Rick, that the climate is remarkably homogeneous. "Or actually you do not notice that much and that is positive. To demonstrate that there really is air circulation, I have hung up an A4 sheet, but you do not notice it."
Art, general director: "The aim was to realize a delta T difference of less than 1 degree Celsius difference in a 10-layer climate chamber of about 8 meters high, and we succeeded."
All this is possible thanks to the air treatment units that were developed by Artechno itself. "You want to exclude as many variables as possible in your research, so a homogeneous climate is essential."
Study 1: irrigation strategies
The first study examines the effect of different irrigation strategies on four different substrates (stone wool, foam plug, glue plug, and soil mix with 10% wood fiber). This should become the basis for other studies with various types of lettuce, Rick says.
Study 2: far-red light
The second research is conducted into the addition of far-red light. Lighting is applied with 180 micromoles for a total of 18 hours and in the last hour, far-red light is added with 10%. There is also a control group (DRB LB) without the addition of far-red light.
"The purpose of the addition of far-red light is to achieve more stretching in the leaves so that the plant makes better use of the growing surface after transplanting. This could possibly also influence the bringing forward of the growth curve."
Germination
Rick is very satisfied with the results of the sowing tests in comparison to the tests carried out in the previous two years. "96-98% germination on the various substrates is a good result, but maybe this might be surpassed by an upcoming germination chamber."
Low input, high output
The results of the tests are assessed, among other things, by measurements of fresh and dry weight, growth percentage, quality, and kilo/m2. "From these results, certain trend lines are emerging, from which the crop growth rate can be calculated. This trend line also gives us insight into the smarter use of the LED light (grams of fresh weight per mole). The ultimate aim is to be consistent with the lowest possible input to achieve the highest output (kilo/m2/year)."
Rick knows that kg/m2/year is an important factor for customers to determine the profitability of their business case. "The results of our tests are used for this, among other things. The results and experiences with certain products we always provide feedback to our suppliers and customers, so that they remain up-to-date."
Soft fruit
Meanwhile, Rick and Artechno see that, in addition to demand for research for herbs and leafy crops, there is also an increasing demand for soft fruit. "This includes, for example, growing strawberries indoors and testing with the rooting phase in, for example, the propagation of blueberry plants.
We also want to be proactive in this, so we will certainly carry out tests ourselves. For ourselves, but also for growers or suppliers to whom we rent the chambers. In addition, I can mentor them and, in consultation, help to draw up a good research plan, always with a lot of literature as a foundation, so that you are not wasting time doing research that has already been done."
For more information:
Artechno
www.artechno.nl
info@artechno.nl
Rick van Schie
rick@artechno.nl
Publication date: Fri 24 Jul 2020
© HortiDaily.com
Sakata Seed America Announces Formation of CEA Department
Leading the new division will be Tracy Lee, an 11-year veteran of Sakata Seed America with an extensive background in agriculture. At Sakata, she has played active roles specializing in product development for multiple categories, as well as handling the company’s home garden and farm market vegetable seed sales
Sakata Seed America announced the formation of a Controlled Environment Agriculture (CEA) department. This new department will focus on indoor agriculture, a growing segment of the produce industry that focuses both on traditional greenhouse production as well as specialized vertical farming.
According to Justin Davis, Sakata’s Director of Sales & Marketing, this new group is designed to bolster the company’s role in developing varieties for controlled environment ag. “We have been focused on this segment for a number of years, especially in the leafy greens category. The timing is ideal for Sakata to create this group to hone our efforts on CEA in order to bring more products to the market for Indoor ag.”
Leading the new division will be Tracy Lee, an 11-year veteran of Sakata Seed America with an extensive background in agriculture. At Sakata, she has played active roles specializing in product development for multiple categories, as well as handling the company’s home garden and farm market vegetable seed sales.
“I think there is tremendous growth opportunity in serving the Controlled Environment Agriculture segment, and I’m very pleased that Sakata is continuing its leadership in the market. This is something that I’m passionate about and have been active in for the past several years,” says Lee.
Lee completed her BA at Clemson University and earned a Master of Science in Horticulture from her alma mater. Her field of study focused on sustainable vegetable production. Prior to her work at Sakata, she held product management, marketing, and sales positions at vegetable and flower seed companies for an additional 10 years.
“I feel that my background and specific work with indoor growers gives me unique insight into the market’s needs. My goal is to harness my experience in the field and bring the right mindset back to Sakata as we develop new products created specifically for CEA,” says Lee.
For more information:
Sakata Seed America www.sakata.com
Mon 7 Sep 2020
Plants That Can Be Grown In Hydroponic Greenhouse
Vegetables grown under Hydroponic set up are in high demand, and the trend for seeking vegetables/fruits grown through this method is rising every year
31 August 2020
Most of us will know that Hydroponics is a type of “Soil-less” culture, which is a method of growing plants without soil, by using mineral nutrient solutions in a water solvent. It comes under the Horticulture discipline and has many advantages, one of them being a decrease in water usage. This method is considered as superior methods of cultivation when compared with the traditional soil-based cultivation method. In comparison to farming on the soil, the Hydroponic cultivation method requires about 80-90% lesser quantity of water.
Vegetables grown under Hydroponic set up are in high demand, and the trend for seeking vegetables/fruits grown through this method is rising every year. This system is beneficial in enabling growers to produce fresh and healthy vegetables on a controlled and consistent basis. When compared with cultivation under the soil, Hydroponics is one of the most water-efficient methods. Since the system can be designed and built according to the space available, it can be inferred that in case of lesser space, it is not a matter of concern generally. If you believe in experimenting with farming, then growing plants with the hydroponics method is most likely to catch your attention.
If new to hydroponics then is advisable to select those vegetables and plants that most growers have produced successfully. Studies and feedback from successful growers convey the possibility of larger yields through Hydroponic greenhouses than a traditional greenhouse. Here it will be important to consider that in order to maximize the chances of successful production the grower must understand which plants to grow under this method.
One should be aware of some facts that few plants may spread out too much to grow properly in a hydroponic greenhouse, and few others may be suited to cooler weather, hence may not survive under high temperatures. Also, one should also have knowledge about plants that need special attention, when growing in a Hydroponic greenhouse. There is the easy availability of the raw materials and supplies for hydroponic systems in the online and offline markets. Hydroponics not only helps a grower in designing its own system, but it also offers the opportunity to produce fresh and healthy vegetables for the entire year. Now let us know which plants can be grown in a Hydroponic Greenhouse:
Related Links
Strawberries
This type of cultivation environment is suitable for strawberries. The usual layout of the hydroponic greenhouses comfortably accommodates the fruit. Depending upon the size of the berry and desired sweetness level, there are lots of varieties to choose from.
Potatoes
Hydroponic systems can support the growth of potatoes and other root crops as well. But they should be provided sufficient depth to grow adequately. This is because there is a lot of growth in the root area, in addition to growth in stems and foliage. So if these plants are grown in lesser space, overall growth will be restricted. One can prefer smaller varieties of the root crops, in order to provide sufficient depth.
Tomatoes
Tomatoes grow well under this method. In the case of tomatoes, it is necessary to provide them a support system, similar to when cultivated in a traditional greenhouse or home garden set up.
Mint
Mint needs wet weather to grow therefore in Hydroponic greenhouses one has a greater option to choose lot many varieties. Mints should be given enough space as they spread quite a bit. With this method you can easily grow any type of mint – be it peppermint, spearmint, ginger mint etc.
Basil
Basil is a herb and can be grown in the hydroponic setup. The moist conditions provided to the herb through this system are beneficial in enhancing the herb’s flavor. Like other plants, the yield is most likely to increase using hydroponic methods of cultivation.
Lettuce
There are various types of lettuce providing different flavors. Normally the iceberg is commonly produced variety but when it comes to growing hydroponically, once can think of growing romaine, sweet butter and many more varieties, to be used in your salad menu.
Cabbage
Cabbage needs cooler temperature for proper growth, hence suitable for growing hydroponically. One may be required to adjust growing conditions for the cool weather vegetables. This would imply that it will be necessary to grow the plants according to their natural seasons. One can change the temperature settings in your greenhouse as per the crops decided for cultivation.
Green Beans
Normally the Bush-style green beans adjust quite well with the typical conditions set up in a hydroponic system, although pole beans can be grown as well. Also, the size of bush-style beans is convenient to manage versus pole beans.
Plants that require Additional Care in Hydroponic Greenhouse
Watermelon, other melons, squash, and corn are some of these vegetables which occupy greater space to grow, making it difficult to thrive well in Hydroponic greenhouses. Therefore these plants need growers addition care like pruning on a regular basis. Few varieties of pumpkin varieties allowed for the space they need. This is done by planting them outside where they can spread and increase in size accordingly.
Many plants have both male and female flowers on them therefore need the bees to pollinate them. Hydroponic setups do not have bees inside the structure, so cultivating these plants are a bit labor-intensive. Nevertheless, if the task of pollinating these plants is done by the grower himself, then chances of proper growth will be higher.
Four Storeys Up, A Commercial Vegetable Garden Thrives In A Converted Sears Warehouse
Growing food on roofs represents the future of farming, especially in these pandemic times, says Mohamed Hage, Lufa’s chief executive officer, who co-founded the company with his wife, Lauren Rathmell
DAVID ISRAELS
SPECIAL TO THE GLOBE AND MAIL
SEPTEMBER 1, 2020
The Lufa greenhouse sits atop a former Sears warehouse in Montreal's St-Laurent neighbourhood.
CHRISTINNE MUSCHI/THE GLOBE AND MAIL
In the industrial part of Montreal’s St-Laurent area, it can be hard to distinguish the bulky buildings from one another, except for one – the roof sticks out like a green thumb.
It’s a great glass greenhouse roof atop a former Sears warehouse – a giant vegetable garden, said by its creators to be the world’s biggest commercial rooftop greenhouse.
The 163,000-square-foot garden, which opened last week, is the equivalent of nearly three football fields worth of food. To date, it is the fourth and biggest commercial facility for Montreal-based Lufa Farms.
Lufa is already well known among local “Lufavores” – foodies, restaurants, and alterna-living people in the Montreal area, who value its fresh tomatoes, eggplants, and vegetables, as well as the produce it gathers from local farmers.
Growing food on roofs represents the future of farming, especially in these pandemic times, says Mohamed Hage, Lufa’s chief executive officer, who co-founded the company with his wife, Lauren Rathmell.“
When we looked at how to grow where people live, we realized that there was only one option – rooftops. It’s not sustainable to always be trucking food in from across the continent or shipping from all over the world,” Mr. Hage says.
The new building was planned and construction began well before COVID-19 hit the world, but it offers a strong response to the pandemic, he explains.“
In March 2020, we saw a doubling of demand for our food. Growing food locally on rooftops and sourcing from local farming families allows us to swiftly adjust and respond to this demand,” he says.
An employee works inside the Lufa greenhouse. | HANDOUT
Co-founder Ms. Rathmell, who is also Lufa’s greenhouse director, says it took three months to build the St-Laurent facility and grow the site.“That would normally have taken years,” she says.
“In response to COVID-19, we enacted stringent safety protocols early on, launched seven-day service, tripled our home-delivery capacity, and launched new software tools,” she says. The company also brought in more than 200 new team members, 35 new local farmers and food makers, and 30,000 new Lufavores customers.
Lufa’s new staff includes two full-time nurses to take workers’ temperatures as well as “social-distancing police” to walk around and make sure workers aren’t too close to one another, Mr. Hage says. The company has also boosted the frequency of its air exchange in all of its facilities, including the new one.
Designing and building a rooftop greenhouse is challenging, Mr. Hage says. Although some of the preparation required is not much different than getting any equipment onto a roof, some of the prep work up there is more complicated, he says.“
We have to meet national building codes, and of course, everything for the greenhouse needs to be hauled up to the roof on a crane,” he says. “Yet once it’s there, you have to do a lot of stuff manually rather than mechanically. All of this is harder than it would be to do on the ground.”
It’s also expensive. “This greenhouse costs two times as much as a ground-based greenhouse,” he says. Lufa declines to give out the cost of this latest project but says the first of its four facilities, built 10 years ago, cost $2.2-million.
Using buildings for farming is catching on, says Mike Zelkind, co-founder of 80 Acres Farms in Cincinnati, Ohio, which also operates building-based facilities in Arkansas, North Carolina, and New York.
“A field can be the least efficient place to grow food,” he says. “An indoor farm can produce more than 300 times more food, with 100-per-cent renewable energy and 97 percent less water. That’s the beauty of growing in buildings.
Montreal-area foodies value Lufa's fresh tomatoes, eggplants and various other vegetables. HANDOUT
”Similarly, in Poughkeepsie, N.Y., up the Hudson River from New York City, restaurateur, food-truck owner, and chef John Lekic pivoted as the COVID-19 lockdowns spread to launch an indoor farming business called Farmers & Chefs.“
“We use technology from an Israeli company called Vertical Field that was being showcased at the Culinary Institute of America, which is nearby,” he says. The Israeli company supplies all the materials to grow some 200 different crops on roofs and in parking lots with minimal experience required.“
We planted and installed a container in March and our first harvest was in April, Mr. Lekic says. “We’re learning fast, but it’s an easy way to grow herbs and produce.”
”Mr. Hage agrees, adding that “rooftops are superior places for an urban farm.”
“When we started [in 2009], we considered leasing parking lots for growing, but no one wanted to give them up,” he recalls. “But for most commercial building owners, rooftops are unloved – they leak, they have to be maintained and, in a cold climate like ours, you have to clean off the snow. A commercial rooftop greenhouse is a solution.”
The new St-Laurent project gives Lufa a total of about 300,000 square feet of agricultural production, and the company plans to eventually expand into Southern Ontario and the U.S. northeast.
Mr. Hage points out that a rooftop greenhouse also makes great sense in terms of environmental sustainability and reducing energy and carbon emissions.“
“We don’t use pesticides and our greenhouses use half the energy that a greenhouse at ground level would consume because we use heating from the building that rises up to the roof,” he explains.
“The biggest challenge is not the greenhouse space – who doesn’t want to walk around in a warm sunny greenhouse when it’s 20 below outside? The challenge is maximizing the warehouse space below the greenhouse,” he says.
“We’re growing so many tomatoes that the warehouses never seem to be big enough to store them.”
Urban farming in Canada is still a niche in a nationwide food industry that is primarily export-based, and accounts for 12 percent, or $62.5-billion, of Canada’s total exports every year, says Claire Citeau, executive director of the Canadian Agri-Food Trade Alliance (CAFTA).
But in a post-COVID-19 world, every bit of food production counts, she says. “We continue to see the adoption of science, technology, and innovative ways to feed people and create new economic opportunities at home and abroad.”
And if that’s not enough, just look at the place, Mr. Hage says. “Boy, do I like driving by – it sticks out like a crystal,” he says. “And when you go inside, it’s like being in a spa.”
TOPICS AGRICULTURE CORONAVIRUS GREENHOUSE MONTREAL ORGANIC FOOD
USA - COLORADO - Geodesic Growing Dome Nears Completion On CMC Campus, Benefits Multiple Programs
When it’s done, the dome will be full of trees, flowers and edible plants, offering a hands-on and in-person experience for students enrolled in the college’s sustainability studies, permaculture and culinary programs
August 27, 2020
STEAMBOAT SPRINGS — A geodesic growing dome has been erected at Bear Park on the Colorado Mountain College Steamboat Springs campus off of Crawford Avenue. The structure will serve, in part, as a greenhouse, extending the growing season and benefiting the sustainability studies program as well as others.
The dome is one part of an expansion project that was approved two years ago, allowing the college to construct the dome, a teaching pavilion, and a restroom. While the outside of the dome is complete, plumbing and electric are still being installed. The inside will take time to fill as well. Tina Evans, CMC professor of sustainability studies, expects the entire project to be completed sometime next summer.
When it’s done, the dome will be full of trees, flowers, and edible plants, offering a hands-on and in-person experience for students enrolled in the college’s sustainability studies, permaculture, and culinary programs.“
Clearly, its benefit is as an educational space, a demonstration space for growing in our region,” Evans said. “It’s really an awesome venue for learning about growing food year-round in the challenging environment in a mountain community.”
Evans said the Steamboat Springs growing season is 59 days and occurs in the summer when few students are on campus. The dome will allow year-round growing.
The design of the inside and outside gardens at Bear Park, where the dome is located, was created using permaculture, which creates beneficial relationships between all the elements of the garden. Some plants provide shade, and others offer ground cover. Some will draw in pollinators, and others repel pests. The strength of one plant benefits all of them.
“We’re trying to create systems that take care of themselves a little bit more than our food systems do in monoculture agriculture,” Evans said. “We’ll have nitrogen-fixing plants in with other plants. We’ll grow plants that provide really good mulch that pull nutrients up from the soil.”
The dome, which was funded by the Yampa Valley Electric Association’s Roundup program, the Craig-Scheckman Family Foundation, and an anonymous donor, was purchased from a Colorado company called Growing Spaces. The structure is 42 feet in diameter or nearly 1,400 square feet. The triangle panels, made of polycarbonate, are not only structurally strong but hold in heat and disperse light better than other materials like glass.
The interior of the dome will also be home to an aquaculture project of large water tanks filled with fish, although Evans isn’t sure what type of fish yet.
The water-filled with fish excrement will serve as fertilizer. The water tanks, as well as the cement, stones and the soil, are all thermal masses, or materials that absorb and release heat slowly. Having many thermal mass materials inside the dome will help the structure retain heat longer.
To help maintain an ideal temperature, a climate battery will be installed below the dome. When the dome gets too hot, the battery will pull air into the cool ground. When temperatures in the dome drop, stored hot air in the battery tubes will be released back into the structure.
“We hope to maintain a Mediterranean-like climate where it doesn’t freeze in there or freeze often,” Evans said. “We will have heaters in there for some of those days where it’s 30 below … but we expect to avoid running them.”
Evans and her colleagues won’t truly know what the climate in the dome will be like until it’s completed and they start planting.
Lead photo: A new geodesic dome on the Colorado Mountain College's Steamboat Springs campus is nearing completion.
John F. Russell
To reach Shelby Reardon, call 970-871-4253, email sreardon@SteamboatPilot.com or follow her on Twitter @ByShelbyReardon.
Producing Seedlings In An Off-Grid LED Lit Vertical Farming Facility
Plant Raisers Ltd, the largest propagator of glasshouse salad crops in the UK, has in addition to a recent expansion of its conventional glasshouse facility, partnered with sister company IGrowing Ltd to develop a system to produce seedlings using an off-grid LED lit vertical farming facility
How Plant Raisers Ltd Are Taking Propagation ‘Off Grid’
Plant Raisers Ltd, the largest propagator of glasshouse salad crops in the UK, has in addition to a recent expansion of its conventional glasshouse facility, partnered with sister company IGrowing Ltd to develop a system to produce seedlings using an off-grid LED lit vertical farming facility.
Eliminating carbon footprint
The concept has been designed to eliminate the carbon footprint associated with vertical farming and maximize the yield of seedlings per unit of electricity. To achieve this, every aspect of power demand for urban farming systems was analyzed and optimized. A key focus in developing a sustainable and efficient vertical plant production system targeted the excess heat created by the inefficiency of existing systems. Eliminating this waste energy has allowed the parasitic loads associated with heat management to be negated saving energy and unnecessary capital cost and making off-grid operation a reality.
LED fixture and power infrastructure producing negligible heat
The first task for the designers was to produce an LED fixture and power infrastructure which produced negligible heat. Collaboration with Extreme Low Energy, a UK company with knowledge and expertise in DC infrastructures provided the electrical solution and the APP-based control system that delivered crop-specific lighting recipes. Several iterations of light unit design were required before the targeted level of energy efficiency and lighting performance was achieved. The end result is a bespoke fixture that has excellent light uniformity, full spectral and intensity control and emits virtually no waste heat. The control of spectral lighting recipe and duration allows for further energy gains building on Plant Raiser’s horticultural understanding of crop requirements at each stage of growth. Additionally, as the luminaires are only 8 mm thick there is an opportunity to maximize the number of growing levels in any given space maximizing space utilization.
With no surplus heat load from the installation, controlling the environment required a different approach to the conventional HVAC systems. Instead, environmental control is provided by fans and sensors. These are switched by the App-based program which allows for remote control at any time of day or night. The app also has the ability to continuously record data to aid management decisions on the most appropriate climate and lighting settings.
Container system with low energy demand
The total energy demand of the container system is now so low that it can support off-grid production with power provided by locally mounted solar panels and/or a small scale wind turbine with a stand by gas generator available as an optional extra. Battery technology allows storage and control of the power generation. These aspects are also controlled and monitored using the app-based program.
The resulting system is the culmination of over three years' research at Plant Raisers Ltd focussed on containerized growing seedlings with the minimum energy input. The project is now fully operational and will be further developed by iGrowing Ltd for customer-specific applications. The system components can also be fitted into larger vertical farm developments looking to take advantage of the energy savings and design methodology.
For more information:
Nick Denham
iGrowing Ltd
nick@igrowing.co.uk
Agtech Sector Blooms As More Dollars And Startups Rush In
Farming has been around for thousands of years, but investments and startup activity in agricultural technology, commonly known as “agtech” or “agritech,” have only exploded over the past five years
Christine Hall | August 20, 2020.
Twitter: ChristineMHall
Farming has been around for thousands of years, but investments and startup activity in agricultural technology, commonly known as “agtech” or “agritech,” have only exploded over the past five years.
In fact, in each of the last two years, venture capitalists invested $4 billion in startups in the agtech space, according to Crunchbase data. Based on the $2.6 billion already given out as of Aug. 14 of this year, 2020 is poised to repeat or even exceed the previous years.
Better Food Ventures Partner Seana Day began tracking agtech startups more than five years ago. She said that farming is an area that isn’t typically tech-enabled. In fact, COVID-19 reminded the world about the food supply chain, she added.
“There was a disconnect between demand signals and supply, which is why you saw empty grocery shelves,” she said. “At the same time, the dairy farmers were dumping milk because they didn’t have a process in place to massively produce small consumer packaging.”
Day estimates that global food and agriculture fund managers have about $130 billion in assets under management, which is driving a surge in investments as well as a shift in thinking.
Farmers have historically been resistant to change, Day said, but at the end of the day, they are rational business people. That means that if a startup can show a farmer a product or service that will boost the return on investment—increasing revenue or decreasing costs—the company will have a better chance of making the sale.
The challenge comes in for tech companies that offer apps meant to save time and increase job productivity, areas that aren’t necessarily needed for farmers, she added.
There is also a shift in legacy food companies thinking digitally. Day points to Tyson Foods as an example. The meat producer earlier this month promoted Dean Banks to CEO. He joined Tyson as president last December from Alphabet’s high-tech incubator X.
“That is a huge signal from a company making bold moves, saying ‘we want to be a leader in this space,’” Day added.
New investments
This year has been particularly busy for the agtech innovation sector, as startups secured both big and small investments.
One of the largest went to Farmers Business Network, which raised $250 million in Series F funding earlier this month. Day said the San Carlos, California-based company was one of the pioneers in e-commerce models, helping farmers optimize their financial performances by finding demand for supply.
Meanwhile, Berkeley-based Pivot Bio announced a $100 million funding round in April, led by Breakthrough Energy Ventures and Temasek, to scale its microbial nitrogen technology. The company said the technology increases crop yields, and in turn, farmers’ revenues. Biodesign startup Geltor brought in $91.3 million in a Series B round in July, led by CPT Capital, to make proteins, such as collagen and elastin, but without animals. The startup’s products are used in beauty, and food and beverage products.
One of the newest is iFarm, a Finland-based startup providing indoor farming technology for growing fresh greens, berries and vegetables. On Thursday, it announced that Gagarin Capital led its $4 million investment with other investors including Matrix Capital, Impulse VC, IMI.VC and several angel investors.
iFarm, founded in 2017, has more than 50 ongoing projects with clients in Europe and the Middle East for 2020, Max Chizhov, co-founder and CEO, told Crunchbase News. The company will use the funding to develop its iFarm Growtune tech platform; expand into new regions in Eastern and Northern Europe and the Middle East; and will experiment with growing strawberries, cherry tomatoes, sweet peppers, radishes and other crops.
“We think this is an interesting time to be in agtech, and we think we are in the right time and right place, especially as there is more attention on food and agtech and a pipeline of investments,” Chizhov said. “We are focusing on how to change the supply chain, and we believe we are one of the solutions to solve this problem.”
Last week, we also reported on a new company, Unfold, which is focused on vertical farming. Bayer’s investment arm, Leaps by Bayer, and Singapore-based investment firm Temasek infused $30 million into the new company.
Unfold’s President and CEO John Purcell said he is bullish on the farming sector, seeing a need for genetics in vertical farming. The company has an agreement for certain rights to germplasm from Bayer’s vegetable portfolio that includes lettuce, spinach, tomatoes, peppers, and cucumbers.
“Technology has to catch up with the promise,” he said. “There has been an overall trend in produce moving toward vertical farming and greenhouse, but the hard part is you have to have the tech to make it feasible.”
The “tech” in question is lighting, mechanics and a system in place. Then it has to be competitive with the other forms of production so potential customers will see its value, Purcell added.
New areas of agtech
Purcell sees three promising areas for the agtech industry:
Major urban areas, where there is a desire for local, fresh food;
Self-sufficiency, or helping places where there is limited arable land; and
Produce supply chains, or getting food from the farm to fulfillment centers.
Ashley Tyrner, founder and CEO of Farmbox Direct, thinks there should be one more area: food as medicine. She is in the process of raising $10 million for her East Coast-based organic and natural produce delivery service.
Tyrner said she saw her business grow more than 2,000 percent during COVID-19. In that time, Farmbox also began working with Medicare to provide box services to patients identified as those who need to eat healthier to manage chronic disease.
“The climate has changed in Silicon Valley, and VCs are welcoming because we are doing food as medicine,” she added. “We were the first to find an insurance company to work with us to help patients change their eating patterns. We are creating a new space here.”
In the area of crop protection is Canada-based MustGrow Biologics, an agricultural biotechnology company taking natural compounds from mustard seeds and turning them into pesticides that fortify the soil.
The pesticide industry is valued at $65 billion, but most are synthetics, Corey Giasson, president and CEO of MustGrow, told Crunchbase News in an interview. The biologics side of the pesticide industry is growing, but is still worth only about one-sixth that amount, he said.
The slower growth is due to biologics in the past not being as effective as synthetic fertilizers, so MustGrow has been doing a lot of studies to show that its product works.
“Farmers want to use products that are healthy and safe, but need something effective to grow a crop that will suppress pests,” he said. “We also have a growing population globally, and we need to feed people, doing it in a safe, environmentally sustainable way.”
New opportunities
Crunchbase data shows that is the most active agtech venture investor, having made 20 venture investments in the agtech space since it was founded 10 years ago. It was most recently involved in India-based Intello Labs’ $5.9 million Series A round. The company uses image matching and machine learning to measure the quality of crops.
A new player is FTW Ventures, led by Brian Frank, who on Thursday announced he is raising his first “problem-focused fund” aimed at early-stage food and agricultural startups.
Frank already raised the $4 million fund, in which he will invest in 15 to 20 deals at about $200,000 to $250,000. He has already made five investments, the most recent in April as a part of Plantible Foods’ $4.6 million seed round. He was also an investor in Plantible’s pre-seed round. The San Marcos, California-based B2B food technology company is developing plant-based protein.
Frank predicts some of the hotter areas will include hardware and automation, software and SaaS, novel products–such as Plantible–and personalized nutrition. He also said that consumers are driving the way food makes its way from the farm to the fork.
“I came into this sector from mobile technology, artificial intelligence, and machine learning, with a deep-seated passion for food,” he said in an interview. “There is a major shift in consumer trends as they look for more resilient and sustainable food. Climate change is both an effect of food and it impacts food. Plants can’t just move to a new climate, so we need to help them.”
Illustration: Dom Guzman
Subscribe to the Crunchbase Daily
Darryn Keiller, Autogrow CEA And The Way Forward In A COVID-19 Reality
Autogrow is a New Zealand-based global technology company and a world leader in controlled environment farming
Autogrow is a New Zealand-based global technology company and a world leader in controlled environment farming. Most of the work they do is about moving farm operators from analog to digital management of the farm. They offer products for both smaller farms, like automation systems, and for newer, larger farms they offer a crop management platform FarmRoad and yield prediction for greenhouse based tomato production. Darryn Keiller, CEO of the company (photo right), talks about how the virus is impacting the industry and how their technologies can help growers post-COVID.
Dashboard FarmRoad
COVID-19 impacts
A major impact of COVID-19 is that virtually every greenhouse producer in the world relies on immigrant labour and there have been a lot of challenges to get labour forces across the borders everywhere. “There’s been high infection rates on large commercial greenhouse producers in North America.” There’s also been a concern about the safety of the produce.
The impacts of the virus have been very different for growers around the world. “For instance, we have two similar customers producing leafy greens and herbs, one in the US and one in Australia. They both supplied their produce to restaurants and specialty supermarkets and got hit really hard with those supermarkets and restaurants having to shut down. They had to find new ways of getting their product into the market. The one in the US started supplying directly to consumers, was able to pivot quickly. And unfortunately, the one in Australia is in a very remote location and did not have that option. They’re still operating but had to let a large portion of their staff go.”
Solutions
There were a lot of challenges in food production before COVID-19, but the virus does amplify those issues. To summarize it, farms have to become more efficient. Most of the industry is still analog, and Autogrow is creating new solutions to take growers into the digital realm. “It’s about how we apply software and data and artificial intelligence. In that regard, we’re having a lot of engagement from growers in Europe, the US, Mexico, Canada. All large enterprises looking for ways to advance the way that they operate their farms.”
Another thing that Darryn and his colleagues see it that the global crisis is invoking local business helping other local businesses. They are curious to see if those changes will stay, and expect that to become visible in the coming months or years. “And for us, it’s really about the growers who need help. Our focus is on them now. The last thirty years have been about the individual, now the situation requires us to work together and be more selfless.”
Vertical PAR
Action
The company has seen a little extra enquiry from the Middle East, but even more from India. People there are looking into hydroponics, looking to start up a hydroponic business for local productions. There is also more enquiry from South East Asia and parts of Europe. “People are taking more proactive action now, realising their own risk and wanting to do something about it.”
For more information:
Publication date: Fri 21 Aug 2020
Author: Marlies Guiljam
© HortiDaily.com
Indoor Growing vs. Traditional Greenhouse Growing
Indoor growing offers some sustainability benefits because considerable savings can be made on water, nutrients and use of pesticides
Today, in theory, there is enough food on the planet to feed approximately 12 billion people, but the way it is distributed around the world is inefficient and unsustainable. As food is transported across the entire globe, its shelf life or freshness tends to deteriorate considerably and a lot of food often goes to waste. Indoor growing is a step closer to a new situation – one in which it is possible to grow locally produced, fresh food all year round, regardless of the weather and external conditions. It may even enable us to change the face of the food industry.
However, this requires a different way of thinking. “Indoor growing is different from growing in a greenhouse in several ways,” says Fred Ruijgt, Market Development Indoor Growing. “In an automated, glass greenhouse you have to deal with external influences such as wind, rain, and sun. These variables need to be managed as effectively as possible, with or without additional technology. The grower is constantly working to achieve a stable climate for the crop. Indoor growing allows you to create your own optimal climate. The grower determines the growing conditions, from light level to air circulation.”
Fred Ruijgt
Comparing apples with oranges
According to Fred, many investors try to compare indoor growing with traditional horticulture. “In terms of investment and profitability, it is difficult to compare them,” he says. “It’s like comparing apples with oranges. It’s important to understand the differences between traditional horticultural practices and indoor growing. You can’t simply calculate what a greenhouse yields per square meter and compare it to an indoor farm. In a greenhouse you have to consider the crop cycle and in which months you can harvest and thus what you can supply to your customers. With indoor growing you can supply all year round, creating more opportunities to reach supply agreements with customers. But you also need to invest.
Indoor growing offers some sustainability benefits because considerable savings can be made on water, nutrients and use of pesticides. But, compared to a traditional greenhouse, much more artificial lighting is required. Also, the location and local sales potential should be included in the comparison. After all, a traditional greenhouse is not even an option in some countries, whereas in the Netherlands, for example, it probably costs two to three times more to grow fresh produce in an indoor farm than it does in a greenhouse.” Another difference is that traditional horticulture has traditional sales channels such as auctions, traders and cooperatives. That’s not the case with indoor growing – it’s more important to understand and collaborate with the entire chain.
Food security and food safety
The fact that indoor growing doesn’t have traditional sales channels is precisely what makes it special. “Indoor growing is clean and pesticide-free, resulting in high-quality and plannable production. An indoor farm can also be built in urban areas, which means that there’s always fresh, locally grown produce available for consumers. The product is often shipped directly from the indoor farm to, for example, the supermarket, so the route to the consumer is shorter. Therefore, in the case of indoor growing, it is important that the facility is an integrated part of the total chain: from suppliers to customers. That keeps the route nice and short,” continues Fred.
An indoor farm can be situated anywhere in the world and in any type of climate, whereas it is often not possible to build a greenhouse in certain areas. Fred: “In Singapore, for example, no more greenhouses can be built because there’s no agricultural or horticultural land available. An indoor farm offers a solution because it can be set up inside an existing building. This is an efficient alternative and it greatly reduces the dependence on food imports.”
Down to the consumer
The technology has already been proven in a number of large-scale indoor growing projects. So why isn’t this way of growing more common? “That’s because of several factors,” explains Fred. “Right now, indoor farms are mainly being integrated into existing retail chains. In addition, the demand largely comes from areas with a high average income. The existing retail chains have a vision and they always want to deliver good-quality products, so it makes sense for them to invest in this. But what are consumers prepared to pay for a fresh head of lettuce, for example,? If consumers start to value fresh and good-quality food more, entrepreneurs will be more willing to invest in a more sustainable way of producing food.”
For more information:
Priva
www.priva.com
contact.priva@priva.nl
Publication date: Tue 18 Aug 2020
August Indoor Science Cafe August 25th, Tuesday 11:00 AM EST
This month's cafe will discuss a most frequently asked question -- "Are indoor-grown veggies more nutritious?"
This month's cafe will discuss a most frequently asked question -- "Are indoor grown veggies more nutritious?"
"Nutritional Composition of CEA Leafy Greens: a Case Study on Carotenoids of Kale Grown in Field, Greenhouse, or Indoors"
by
Dr. Neil Mattson (Cornell University)
Dr. Marianne Nyman (Rensselaer Polytechnic Institute)
Please sign up so that you will receive Zoom link info.
Indoor Ag Science Cafe is an open discussion forum, organized by Chieri Kubota (OSU), Erik Runkle (MSU), and Cary Mitchell (Purdue U.) supported by USDA SCRI grants.
Sign Up Here
Cafe Archive & QA Forum
Please visit the Indoor Ag Science Cafe page in OptimIA website and ask your questions.
Submit Your General Questions for 'Indoor Ag Sci Queries'!
Please submit your questions (anonymously if you wish) about sciences and technologies of indoor farming to this submission site. Any questions are welcome! The site is always open for your questions. Selected questions will be discussed in our future Indoor Ag Science Queries series.
Indoor Ag Science Cafe is organized by the OptimIA project team funded by USDA SCRI grants program.
Previous café recordings are available in the OptimIA project website.
Please contact for more info: kubota.10@osu.edu