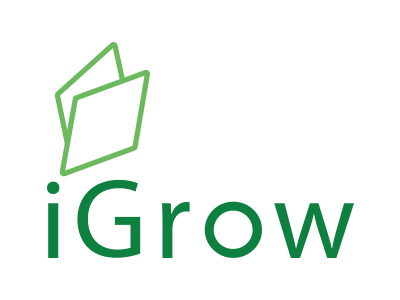
Welcome to iGrow News, Your Source for the World of Indoor Vertical Farming
Infarm Raises $170M In Equity And Debt To Continue Building Its ‘Vertical Farming’ Network
That’s likely a testament to the speed of new retail partnerships over the last 12 months. They include Albert Heijn (Netherlands), Aldi Süd (Germany), COOP/Irma (Denmark), Empire Company’s Sobeys, Safeway and Thrifty Foods (Canada), Kinokuniya (Japan), Kroger (U.S.) and Marks & Spencer and Selfridges (U.K.)
September 17, 2020
Image Credits: Infarm
Infarm, the vertical farming company that has built a network of urban farms to grow fresh food closer to consumers, has raised $170 million in new investment in a “first close” of a Series C.
Leading the round — which is expected to reach $200 million and is a mixture of equity and debt — is LGT Lightstone, with participation from Hanaco, Bonnier, Haniel, and Latitude. Existing Infarm investors Atomico, TriplePoint Capital, Mons Capital, and Astanor Ventures also followed on. It brings the company’s total funding to date to more than $300 million.
That’s likely a testament to the speed of new retail partnerships over the last 12 months. They include Albert Heijn (Netherlands), Aldi Süd (Germany), COOP/Irma (Denmark), Empire Company’s Sobeys, Safeway and Thrifty Foods (Canada), Kinokuniya (Japan), Kroger (U.S.) and Marks & Spencer and Selfridges (U.K.).
With operations across 10 countries and 30 cities worldwide, Infarm says it now harvests more than 500,000 plants monthly, and in a much more sustainable way than traditional farming and supply chains. Its modular, IoT-powered vertical farming units claim to use 99.5% less space than soil-based agriculture, 95% less water, 90% less transport, and zero chemical pesticides. In addition, 90% of the electricity used throughout the Infarm network is from renewable energy and the company has set a target to reach zero emission food production next year.
Founded in 2013 by Osnat Michaeli, and brothers Erez and Guy Galonska, Infarm’s “indoor vertical farming” system is capable of growing herbs, lettuce and other vegetables. It then places these modular farms in a variety of customer-facing city locations, such as grocery stores, restaurants, shopping malls and schools, thus enabling the end-customer to actually pick the produce themselves. To further scale, it also installs Infarms in local distribution centers.
The distributed system is designed to be infinitely scalable — you simply add more modules, space permitting — whilst the whole thing is cloud-based, meaning the farms can be monitored and controlled from Infarm’s central control center. It’s also incredibly data-driven, a combination of IoT, Big Data and cloud analytics akin to “Farming-as-a-Service.”
The idea, the founding team told me back in 2017 when I profiled the nascent company, isn’t just to produce fresher and better-tasting produce and re-introduce forgotten or rare varieties, but to disrupt the supply chain as a whole, which remains inefficient and produces a lot of waste.
“Behind our farms is a robust hardware and software platform for precision farming,” explained Michaeli at the time. “Each farming unit is its own individual ecosystem, creating the exact environment our plants need to flourish. We are able to develop growing recipes that tailor the light spectrums, temperature, pH and nutrients to ensure the maximum natural expression of each plant in terms of flavor, color and nutritional quality.”
On that note, I caught up with two of Infarm’s founders to get a brief update on the Berlin-headquartered company and to dive a little deeper into how it will continue to scale.
TechCrunch: What assumptions did you make early on that have turned out to be true or, more interestingly, not panned out as expected?
Osnat Michaeli: When we first chatted about four years ago, we were 40 people in Berlin, and much of the conversation centered around the potential that our approach to urban vertical farming might have for retailers. While for many it was intriguing as a concept, we couldn’t have imagined that a few years later we would have expanded to almost 10 countries (Japan is on its way) and 30 cities, with partnerships with some of the largest retailers in the world. Our assumptions at the time were that retailers and their customers would be attracted to the taste and freshness of produce that grew right in front of them in the produce section, in our farms.
What we didn’t anticipate was how much and how quickly the demand for a sustainable, transparent, and modular approach to farming would grow as we, as a society, begin to feel the impact of climate change and supply chain fragility upon our lives, our choices and our food. Of course, we also did not anticipate a global pandemic, which has underscored the urgency of building a new food system that can democratize access to high-quality, amazing-tasting food, while helping our planet regenerate and heal. The past few months have confirmed the flexibility and resilience of our farming model, and that our mission is more relevant than ever.
In terms of signing on new retailers, based on your progress in the last 12 months, I’m guessing this has gotten easier, though undoubtedly there are still quite long lead times. How have these conversations changed since you started?
Erez Galonska: While lead times and speed of conversations can vary depending upon the region and retailer. In mature markets where the concept is familiar and we’re already engaged, deal conversations can reach maturity in as little time as three months. Since we last spoke we are already working with most of the leading retailers that are well established in Europe, the U.K., and North America. Brands which in each of their markets are both forerunners in a retail industry rapidly evolving to meet the demand for consumer-focused innovation, while proving that access to sustainable, high-quality, fresh, and living produce is not only possible, but can be available in produce aisles today, and every day of the year, with Infarm.
I’m interested to understand where Infarms are installed, in terms of if the majority is in-store and consumer-facing or if the most scalable and bulk of Infarm’s use cases are really much larger distribution hubs in cities or close to cities, i.e. not too far away from places with population/store density but not actually in stores. Perhaps you can enlighten me on what the ratio looks like today and how you see it developing as vertical farming grows?
Erez Galonska: Today across our markets, the split between our farms in stores and in distribution centers is roughly 50/50. However, as you anticipate, we will be expanding our network this year with many more distribution hubs. This expansion will likely lead to an 80/20 split as early as next year, with the majority of our regions being served with fresh, living produce delivered throughout the week from centrally located hubs. This not only offers retailers and restaurants flexibility in terms of volumes of output, and the ability to adapt the presentation of our offerings to floor areas of different sizes, but it also allows us to begin to serve whole regions from our next-generation farms under development today.
Based in our hubs, these farms will deliver the crop equivalent of an acre or more of fresh produce on a 25 m2 footprint, with significant further savings in energy, water, labor and land use. We believe this technology will truly challenge ideas of what is possible in sustainable, vertical farming and we look forward to talking about it more soon.
Lastly, what are the main product lines in terms of food on the shelves?
Osnat Michaeli: We have a catalog of more than 65 herbs, microgreens, and leafy greens that is constantly growing. Our offerings range from the known and common varieties like Coriander, Basil, or Mint, to specialty products like Peruvian Mint, Red Veined Sorrel or Wasabi Rucola.
Because our farms give us excellent control over every part of a plant’s growth process and can imitate the complexity of different ecosystems, we will be able to expand the diversity of Infarm produce available to consumers to include root vegetables, mushrooms, flowering crops, and even superfoods from around the world in the near future. What you see today with Infarm is still only the beginning.
“We Are Developing A Sustainable Technology That Uses 75% Less LED Lighting”
Verde Compacto, a Mexican start-up, producer of container farms and indoor farming growing technologies, has seen significant demand for their growing systems during the pandemic
Verde Compacto, a Mexican start-up, producer of container farms and indoor farming growing technologies, has seen significant demand for their growing systems during the pandemic.
"COVID is driving this market forward because people want to know what is behind their food and their diets. Logistic chains in countries like South Korea and Arab countries are really dependent on imports. They are trying to implement urban technologies to strengthen their supply chains. As we’re focusing on growing systems, we are trying to turn this into reality. We are growing food in a more sustainable way where everyone can benefit from it”, Juan Gabriel Succar, Co-Founder and CCO of Verde Compacto says.
The company has an R&D container farm, Huvster, with several labs and small scale systems. The company sells some of its crops locally to better understand the urban business model, as Verde Compacto is educating the future indoor growers.
The Huvster growing container
Succar continues: “We are providing the knowledge to any grower that wants to have an urban farm and we are helping them throughout the process by constructing a farm to their needs.” The company does not only build container farms, which is their standard model but also provides custom made projects such as warehouses or buildings. Or on a smaller scale like supermarkets and restaurants. “We provide the knowledge to install a farm at any size”.
Decreasing LED use
Verde Compacto is looking to improve the electricity use for its growing solutions. “We are developing a sustainable technology that uses 75% less LED lighting, which is part of a sustainable R&D project. The tests are still running but they have delivered positive results. In the end, our technology used for indoor farms allows us to rotate the lamps. Rather than using four lamps at one spot, Verde Compacto can use one light that is constantly rotating. That's why we can make such a big impact on light usage”, Succar affirms.
Lack of quality and water
“Every business model and location has different benefits. As we are one of the largest agricultural countries in the world, we can offer excellent fresh produce quality. The sad story is that all the good fruits and vegetables are exported, thus there is a lack of quality products here in Mexico”, Succar says.
Succar says that Verde Compacto’s technology can build a profitable business model to deliver excellent quality and healthy food to the Mexican society. He notes that the central Mexican region sees a big challenge: a large water shortage. “With our solution, companies still see an opportunity to grow food and maintain their quality by using fewer resources”, Succar notes.
Sustainability
“We always try to give the best options possible regarding our client’s budget, business model, and capabilities. Verde Compacto is cooperating with solar panels to give access to clients for installing these solutions. “Renewable energy, in the end, really depends on the client. Our goal is to make vertical farming as sustainable as we can”, Succar states. At the end of October this year the company will install the first urban farm in Salamanca, Mexico which will be run on 100% solar energy.
Price opportunities
Succar: “In Mexico, we provide our produce at a lower price level than supermarkets. This is done on purpose, to get people to know about vertical farming. Sometimes we are on the same price level.”
Olivier Kappetein, EU representative at Verde Compacto notes: “We have a financial stimulator and we found out that we can bring product prices down. Consumers would pay less compared to supermarket prices as they are unbelievably high. In the United Arab Emirates, locally grown products are unfindable. An iceberg lettuce costs around €7.60 (9 USD) or more. We could get that price down by at least 350% and still make a profit if we were to sell our produce there. We are aiming to sell high-quality food and that’s what they are looking for.”
Pre- and post COVID story
Verde Compacto has a pre- COVID story and a post-COVID story regarding any company expansions. The pre-COVID story was to expand to all Latin American countries, as a priority. They started several alliances and promoted the Verde Compacto technology in Latin America. However, the economy in Latin America was really affected during the pandemic.
“Thus, countries depending on imports saw a great opportunity in our technology for constant production. We didn’t get behind on the expansion actually. Right now, we are working with associations to open different commercial offices in several countries in Latin America. We will be expanding there at the beginning of next year. We are also exploring different options in different parts of the world, expanding globally. One of the regions is Northern Europe because we saw the need for farming technology in those countries. Especially in Luxemburg, where there’s limited fresh produce available.
“The most common problem in vertical farming is the unawareness of the consumer”, Kappetein adds. “They don’t know what it has to offer. It’s still an investment that needs to be made. There is still a greater focus on organic produce as they are aware of the great benefits that come along.”
The Verde Compacto team
Forage
Verde Compacto has been developing its own R&D department, generating knowledge that is also used for new product lines. Succar continues: “We are developing indoor farming systems that are not limited to leafy greens and herbs, but also for forage e.g.. Forage is eaten by grazing cattle mostly. With our hydro system, we can feed cows e.g. with using fewer resources in a more profitable way. The meat and milk industry is impacting the ecosystem significantly. Implementing this technology will help us to make this type of agriculture more sustainable.” The company is also exploring the opportunities of launching indoor strawberries, with the greatest focus on Europe.
For more information:
Verde Compacto
Juan Gabriel Succar, Co-founder, and CCO
juan.gabriel@verdecompacto.com
Olivier Kappetein, EU representative
olivier.kappetein@verdecompacto.com
Phone: +316 14 62 13 10.
www.verdecompacto.com
Publication date: Tue 8 Sep 2020
Author: Rebekka Boekhout
© HortiDaily.com
Breakthrough In Artificial Photosynthesis Lets Scientists Store The Sun's Energy As Fuel
Plants have a seemingly effortless skill – turning sunlight into energy – and scientists have been working to artificially emulate this photosynthesis process
29 AUGUST 2020
Plants have a seemingly effortless skill – turning sunlight into energy – and scientists have been working to artificially emulate this photosynthesis process. The ultimate benefits for renewable energy could be huge – and a new approach based on 'photosheets' could be the most promising attempt we've seen so far.
The new device takes CO2, water, and sunlight as its ingredients, and then produces oxygen and formic acid that can be stored as fuel. The acid can either be used directly or converted into hydrogen – another potentially clean energy fuel.
Key to the innovation is the photosheet - or photocatalyst sheet - which uses special semiconductor powders that enable electron interactions and oxidation to occur when sunlight hits the sheet in water, with the help of a cobalt-based catalyst.
No additional components are required for the reaction to occur, and it's fully self-powered.
"We were surprised how well it worked in terms of its selectivity – it produced almost no by-products," says chemist Qian Wang, from the University of Cambridge in the UK.
"Sometimes things don't work as well as you expected, but this was a rare case where it actually worked better."
The device in action. (University of Cambridge)
While the prototype photosheet only measures 20 square centimetres (3 square inches), the scientists who invented it say it should be relatively easy to scale up without incurring huge costs.
Ultimately, they think these sheets could be produced in large arrays, similar to those on solar farms. What's more, the resulting formic acid can be stored in a solution, and from there converted into different types of fuel as needed.
It achieves something that isn't always guaranteed in conversion systems like this – a clean and efficient process without any unwanted by-products. Any extra waste produced has to be dealt with, which can negate the positive effects of the initial reaction.
"It's been difficult to achieve artificial photosynthesis with a high degree of selectivity so that you're converting as much of the sunlight as possible into the fuel you want, rather than be left with a lot of waste," says Wang.
A team from the same lab was also responsible for developing an 'artificial leaf' material in 2019. While the new photosheet behaves in a similar way, it's more robust and easier to scale up – and it produces fuel that's more straightforward to store, too (last year's system created syngas).
That doesn't mean the new photosheet is ready to go commercial just yet: The researchers need to make the process a lot more efficient first; they are also experimenting with different catalysts that may be able to produce different solar fuels.
The need for a full transition to clean energy is more urgent than ever, but we're encouraged by how many projects are in the pipeline. However, as is the case with this new process, figuring out the science is just the start of producing a fuel that will work practically.
"Storage of gaseous fuels and separation of by-products can be complicated – we want to get to the point where we can cleanly produce a liquid fuel that can also be easily stored and transported," says chemist Erwin Reisner, from the University of Cambridge.
"We hope this technology will pave the way toward sustainable and practical solar fuel production."
The research has been published in Nature Energy.
Pablo Bunster, Co-founder and CCO of AgroUrbana “In Our Next Farm, We Will Be Able To Use 100% Renewable Energy”
As Chile has been in a complete lockdown since mid-May, AgroUrbana is lucky to continue its operations. “It’s not easy, because you have to change the way of operating, the interactions, and in-farm activities, even when food safety was already key to the company culture
As Chile has been in a complete lockdown since mid-May, AgroUrbana is lucky to continue its operations. “It’s not easy, because you have to change the way of operating, the interactions, and in-farm activities, even when food safety was already key to the company culture. Our customers have been ordering through home delivery”, Cristián Sjögren, Co-founder and CEO of AgroUrbana says.
Renewable energy
Bunster notes: “It took us from the energy market, from renewable energy, to farming. We believe that this is the perfect testing round to see what vertical farming can do.” Chile has drought, cheap labor, we have competitive, available and abundant renewables. Which is always a discussion around vertical farming. We manage sunlight here as we use 100% renewable energy PPA. However, we cannot do this with our pilot because the overall consumption is too low, so we have to regulate it. In our next farm, we will be able to go 100% renewable. That puts a lot toward sustainability for vertical farming.” The urban population is growing fast in Latin America. AgroUrbana believes that vertical farming can accommodate that food demand.
“Our next stage is, going commercial to a scale where we can bring costs down”, Bunster continues. “First, we thought of a small community distributed model with a few small blocks around, such as container farms. But, we believe that scale is still required as you can become more competitive with higher efficiency.
“First, we’re farmers and technology comes to serve that purpose be the best farmers! We are developing some technologies internally to run our farms, but our focus now is how we can actually rate the curve of cutting costs to make our products increasingly competitive. We want to stay out of the commodity but still reach the masses. Our mantra is to deliver better quality food to everyone”, Sjögren adds.
Pablo Bunster harvesting some fresh lettuce
Pilot farm
Sjögren states: “We started with a pilot farm, because vertical farming is something completely new in Latin America.” Before launching a new category for Agriculture in Chile, Sjögren and Bunster wanted to understand the economics of vertical farming. They took an approach of technology-agnostic by building a 3000 sq. ft pilot farm, where different technologies are tested. The 18-month pilot phase will be completed by the end of this year.
“We are integrating our own recipe that combines the seeds nature provides us with its nutrition and environmental parameters. Next to that, we are constantly improving and optimizing our operations in order to drive down costs”, Bunster adds. These quantities are allocated in a 3000 sq. ft farm which is not a large production, Sjögren noted, but this is done to test the market, integrate and develop our technology and do R&D in new varieties. AgroUrbana is planning on scaling up throughout Chile in 2021 with an aim to further expand into the new markets, mainly large urban areas, in the region in the next years.
“Chile is a perfect testing ground to start, test and stress what vertical farming can do, due to the Mediterranean weather we have, favorable to open farming, but also abundant and competitive renewable energy. We both spent our last ten years in the wind- and solar energy industry. Renewables will help AgroUrbana close the gap between traditional agriculture and vertical farming”, Sjögren says.
The country has suffered from climate change, with a 10-year drought that highly affected Chilean agriculture. AgroUrbana has achieved surprising improvements in its yield. “We are planning to transfer all this knowledge to our next farm, a 30,000 sq. ft commercial-scale farm. In the upcoming months, we are doing funding rounds in order to help us realize this farm.
Sjögren says that AgroUrbana is going to pilot in the berry space as well, such as strawberries. “We are starting a pilot to test the different varieties of strawberries. Next to that, we are developing edible flowers and some microgreens”, Sjögren affirms. Most of the volume is lettuce, but we will be rolling out other leafy greens and we will see how it goes with the other crops.
Carmelo platform
“There are many components such as climate control, irrigation, growing structures, and so on. We want to put all the pieces together and operate these very efficiently”, Sjögren states. The company is developing a technology ‘Carmelo’, a platform of sensors with hardware and software to monitor and control our operations. “We are at a level of precision, where we are able to handle the microclimates within the farm. Using Carmelo, we are collecting data already for over one year which is helping us to become even more precise and consistent.” All data gathered will be used for our first large scale commercial farm planned for 2021.
“We’re all about technology and data because that’s how you drive down the costs. We are combining genetics, giving the perfect climate, and the perfect environment. Carmelo is all about finetuning the recipe we’re creating, through managing a farm, and having consistent quality food, every day of the year”, Bunster adds.
Product pricing
“Our team is in good spirits as we have been keeping up production. The pandemic hit us hard, but we were able to relocate all production to different distribution channels, such as e-commerce, supermarkets and subscriptions”, Bunster states. We were planning on doing that already, but we accelerated our go-to-market because of the current situation. “There’s no going back on e-commerce because customers are getting used to it. If we can take our produce to e-commerce, keep our customers satisfied and easy about always getting the perfect product, they’ll always order it online. It’s something we already wanted to do and we are currently testing and proving it. So far, we’re doing okay”, Bunster adds.
AgroUrbana has two markets, one of them being retail with a fast pace opening of new distribution for their products, with 100% recyclable packaging. Furthermore, the company delivers its products to restaurants. Since one year, AgroUrbana has launched its own house mix of lettuce.
Cristián Sjögren and his colleague preparing the plugs for planting
Bunster mentioned that AgroUrbana is selling to restaurants that are price sensitive. Meaning that they care about food quality and the costs. “Here’s where food waste comes into play. We do not have any food waste. We’re coming to the point where most of what we grow, we’re able to process and sell. In restaurants only, we’re saving between 25-35% food of waste in leafy greens. We are very efficient in logistics as we don’t truck. We move food for a few miles from our farms to the kitchens of different clients. This helps us to make numbers for a competitive market.”
Focusing on the next generation
“It has been exciting to put our team together because nobody has a vertical farming degree on its resumé. We’re really excited to prepare the next generation of vertical farmers. We’re putting together different skills and attracting the next generation of farmers that want to move from the countryside to the city. It’s an attractive way to get a generation back to growing veggies in the city with a lot of interaction with technology”, Sjögren ends.
For more information:
AgroUrbana
Cristián Sjögren, Co-Founder and CEO
cristian.sjogren@agrourbana.ag
Pablo Bunster, Co-Founder and CCO
pablo.bunster@agrourbana.ag
www.agrourbana.ag
Publication date: Tue 25 Aug 2020
Author: Rebekka Boekhout
© HortiDaily.com
Farming In The Desert: Are Vertical Farms The Solution To Saving Water?
When I told people I was going to grow tomatoes in the desert, they thought I was crazy," Sky Kurtz, founder of Pure Harvest Smart Farms, told DW
Jul. 23, 2020
By Isabelle Gerretsen"
When I told people I was going to grow tomatoes in the desert, they thought I was crazy," Sky Kurtz, founder of Pure Harvest Smart Farms, told DW.
With just an average 12 days of rain a year, less than 1% arable land, a desert location, and an 80% import rate for food, the United Arab Emirates (UAE) seems an unfavorable place to set up a farm.
Kurtz is one of several entrepreneurs using high-tech farming techniques to boost crop production in the Emirates. Pure Harvest built the first climate-controlled greenhouse in Abu Dhabi in 2017.
Prompted by arid conditions and a desire for greater food security, the country is investing millions in technologies — such as vertical farming — that could make it an unlikely agricultural pioneer.
Vertical farms can grow a rich variety of different crops by stacking them in layers under LED lighting in climate-controlled greenhouses and watering them with mist or drip systems. The process is tailored to each crop's specific needs, resulting in high-yield, year-round harvests."
It takes 30 to 40 days to grow leafy greens out in the field. We can grow that same crop in 10 to 12 days," says Marc Oshima, co-founder of Aerofarms. The company received funding from the Abu Dhabi Investment Office to build the capital's largest indoor vertical farm, with 800 different crops, by 2021.
Water Scarcity and Fossil-Fuel Reliance
The technology uses minimal land and up to 95% less water than conventional agriculture.
The hydroponics system places the plants' roots directly into a water-based and nutrient-rich solution instead of soil. This "closed-loop" system captures and recirculates all the water, rather than allowing it to drain away — useful for a country like the UAE suffering from extremely high water stress.
Globally, agriculture accounts for 70% of freshwater withdrawals, and UAE is extracting groundwater faster than it can be replenished, according to the International Center for Biosaline Agriculture (ICBA)."
Water is very expensive over in the UAE, but energy is cheap as it is subsidized," says Jan Westra, a strategic business developer at Priva, a company providing technology to vertical farms.
The artificially controlled environment is energy-intensive because the air conditioning and LED lights need a constant source of electricity.
This bringing forth of life in the desert could come at a high environmental cost. Most of that energy comes from carbon-emitting fossil fuels, even as the Middle Eastern country feel the effects of climate change.
By 2050 Abu Dhabi's average temperature is predicted to increase by around 2.5°C (36.5 F) in a business-as-usual scenario. Over the next 70 years, patterns of rainfall are also expected to change.
Integrating Renewable Energy
Although Pure Harvest is building a solar-powered farm in neighboring Saudi Arabia, its UAE operations get electricity from the carbon-intensive national grid.
Investing more in renewables "is a goal of ours," Kurtz told DW. He said the company has not set a clean energy target but is working on various green power projects, including a plan to integrate solar power generated in UAE into its operations.
However, Willem van der Schans, a researcher specializing in short supply chains at Wageningen University in the Netherlands, says sustainability and clean energy should be "inherent in the technology and included in plans when starting a vertical farm."
He argues that many vertical farming companies are not sustainable in terms of energy as they still view clean power as an optional "add-on."
Ismahane Elouafi, director-general of the government-funded ICBA in Abu Dhabi, acknowledges that vertical farming has some way to go before achieving "real sustainability," but she believes the innovations are "promising."
Improved battery storage, increasingly efficient LED lights, and cheaper solar panels will help, she adds.
Local Solutions
By 2050, the UAE government wants to generate almost half its energy from renewable sources.
Fred Ruijgt, a vertical farming specialist at Priva, argues that it's important to factor transport and refrigeration into the energy equation. Vertical farming uses more energy to grow crops than traditional agriculture, but because crops are grown locally, they do not have to be transported by air, sea, or truck over long distances."
The energy-saving is difficult to calculate exactly, but the advantages of locally grown crops are huge," he says, adding that those grown in vertical farms not only use less water and pesticides but that they also have a longer shelf life due to minimal transportation time.
Food Security and Coronavirus
In 2018, the UAE set out its vision to become a hub for high-tech local food production.
Companies and investors have flocked to the region, attracted by the 0% corporate tax rate, low labor costs, and cheap energy. With their help, the UAE aims to reduce its reliance on imports and make its food system more resilient to shocks like climate change and pandemics.
Oshima from Aerofarms says the coronavirus pandemic has brought "greater appreciation of how fragile the supply chain is and raised questions about food safety and security."
When the UAE went into lockdown in April, imported supplies of perishable goods like vegetables fell and business boomed for local suppliers.
ICBA's Elouafi said they have helped keep the UAE well-stocked during the pandemic."With the help of local food production and adequate imports, there has been absolutely no shortage of food in the UAE," Elouafi told DW.
Climate change, however, poses an altogether more complex threat to the country in the long-term. Given climate change's likely impact on food production, she says vertical farming has shown it is "an economically viable proposition even with harsh climatic conditions."
Reposted with permission from Deutsche Welle.
RELATED ARTICLES FROM ECOWATCH
Vertical Farms: The Future of Agriculture? -
EcoWatch ›Inside the Nation's Largest Organic Vertical Farm - EcoWatch ›
5 Ways Vertical Farms Are Changing the Way We Grow Food ...
RELATED CONTENT AROUND THE WEB
Investing In Vertical Farming: Five Take-Aways ›
This company wants to build a giant indoor farm next to every major ... ›
TAGS: farming farmers water food food security agriculture renewable energy
The Underwater Habitat With A Greenhouse
Swiss designer Yves Behar has unveiled his design for French ocean conservationist Fabien Cousteau's underwater pressurised research station that will be "the ocean's equivalent to the International Space Station".
29-07-2020 | Msn News/ India Block
Swiss designer Yves Behar has unveiled his design for French ocean conservationist Fabien Cousteau's underwater pressurised research station that will be "the ocean's equivalent to the International Space Station".
Behar designed the station, which is called Proteus, for the Fabien Cousteau Ocean Learning Center. It will have its own greenhouse to allow scientists to grow their own food 18 metres under the sea near Curaçao, an island in the Caribbean.
Up to 12 researchers and aquanauts – scientists who remain underwater breathing pressurised air for over 24 hours – will be able to live in Proteus at a time.
Like the International Space Station, Proteus will allow scientists to collaborate and make new discoveries in an inhospitable environment.
"The research station will enable the discovery of new species of marine life, create a better understanding of how climate change affects the ocean, and allow for the testing of advanced technologies for green power, aquaculture, and robotic exploration," Behar told Dezeen.
Living underwater in a pressurised environment, rather than just diving in, allows scientists to spend far more time in the water and only decompress at the end of their assignment.
Proteus is the result of Behar's studio Fuseproject being commissioned by Cousteau, and his non-profit the Fabien Cousteau Ocean Learning Center (FCOLC).
"We needed to understand the constraints that come from building underwater and the challenges of living in an underwater structure," Behar said.
"The social isolation, the humidity, the lack of light and lack of exercise all needed to be addressed," he explained. "I learned about these challenges from Fabien, who had the record as the person who lived longest in an underwater habitat."
© Provided by Dezeen Proteus by Yves Behar
Cousteau broke the record, previously set by his grandfather, with a 31-day-long stay in an underwater laboratory off the coast of Florida called Aquarius.
Behar used Cousteau's experience to inform the design of Proteus, which has two levels connected by a curving ramp with pods set around the edges.
Circular-shaped main spaces are designed to encourage teamwork and social interaction for the scientists. Pods around the perimeter are designed to hold specific laboratories, bathrooms and areas for sleeping.
"Both circular floors are offset to allow as much natural light as possible through skylights and portholes, and are connected by a sloping ramp which creates the opportunity for physical activity," said Behar.
Social spaces will be kept separate from the more humid areas of the wet labs and the moon pool – the space in an underwater habitat where occupants can access the water directly in a protected environment.
© Provided by Dezeen Proteus by Yves Behar
An underwater greenhouse will allow occupants to grow their own food, allowing them to stay underwater for longer and cope more comfortably with the confines of a pressurised environment where no open flames for cooking are allowed.
Behar deliberately gave the underwater habitat a retrofuturist vibe in keeping with the way science fiction has traditionally imagined underwater living.
"Fabien and I looked at many exploratory designs from the 60s and 70s, a golden era of interest for the oceans pioneered by the Cousteau family history," Behar told Dezeen.
"We felt that Proteus could incorporate a new visual language based on modern hull and composite building technology, as well as be a state-of-the-art scientific environment while delivering a comfortable social interior space."
In keeping with the Cousteau dynasty's ocean conservation goals, Proteus will be powered by renewable energy. The habitat will use a mixture of wind, solar, and Ocean Thermal Energy Conversion (OTEC), a process that produces electricity using the difference in temperature between warm water on the surface and cold water from the deep ocean.
Cousteau will head to Curaçao to map the site as soon the borders shut due to the coronavirus pandemic open, hopefully in September. Behar estimates it will then take 36 months to build and lower Proteus to the ocean floor.
Behar hopes Proteus will be one of a series of marine habitats dedicated to research and conservation. As well as scientists, the designer hopes the facility will be able to welcome civilian visitors.
"Proteus is designed to be a scientific environment, but also to create that desire in people to want to visit," he said.
"For me, it’s a lot more exciting to visit Proteus than going to Mars."
Behar embraces technology with his designs, which include plans for 3D-printed houses for impoverished farmers and a wearable UV sensor to protect against skin cancer.
The post Proteus is an underwater habitat with a greenhouse designed by Yves Behar appeared first on Dezeen.
Source: Msn News/ India Block
Photo Provided by Dezeen
FREE WEBINAR: CEO Panelists To Discuss "How To Get Indoor Farm Up and Running" on July 22, 2020 @ 2 PM EST
Whether just starting out or looking for fresh new ideas to bolster a current operation, the CEO panelists joining the July 22, 2020, Indoor Ag-Conversations free webinar series from Indoor Ag-Con will offer participants a wealth of business-building ideas to get a farm going and growing
Leaders From Kalera, Vertical Harvest, Artesian Farms, & Danforth Plant Science Center Join Indoor Ag-Conversations Webinar Series
LAS VEGAS (July 13, 2020) –Whether just starting out or looking for fresh new ideas to bolster a current operation, the CEO panelists joining the July 22, 2020, Indoor Ag-Conversations free webinar series from Indoor Ag-Con will offer participants a wealth of business-building ideas to get a farm going and growing. Moderated by Claire Kinlaw, Director of Innovation Commercialization, The Donald Danforth Plant Science Center, "How To Get An Indoor Farm Up & Running" webinar panelists include Daniel Malechuk, CEO, Kalera; Nona Yehia, CEO & Co-Founder, Vertical Harvest; and Milan Kluko, CEO, Artesian Farms LLC.
During the 60-minute session, the panel will cover a number of topics and issues like:
Crops: types, traits, sourcing
Customers: profiles, targets, buying interests
Selling: direct to consumer, distributors, grocery chains
Technology: what’s best suited for geography, crop, scales of production
Founding Team Skills: technical, agronomic, sales/marketing, biology/genetics
CapEx – How and where to access funds to get established
Indoor Ag-Conversation webinars are free to industry members. To register for the upcoming July 22, 2020 session, visit www.indoor.ag/webinar. Indoor Ag-Conversations presenters include:
Claire Kinlaw, Director of Innovation Commercialization, Danforth Plant Science Center --Claire combines science research and business knowledge along with experience with startup companies to support commercialization of innovative technologies in agriculture. She began work at the Danforth Center in February of 2019. She promotes the commercial impact of the Center’s intellectual property through such activities as patent filing, license agreements, and oversite for an innovation incubation program (IN2, funded by the Wells Fargo Foundation). IN2 accelerates early-stage agriculture technologies into the market through the execution of validating research for companies in collaboration with the Danforth Center.
Daniel Malechuk, CEO, Kalera -- A food industry veteran, Daniel Malechuk has spent his career managing and growing several of the world’s leading food, grocery, and produce companies. As a leader in the industry, Daniel has worked in both sales and supply chain optimization and has built sustainability programs for companies such as Shamrock Foods, Kalera HyCube, Keysource Foods, and ALDI. While at Shamrock Foods, Malechuk led the retail division and drove explosive revenue and profitability growth and expansion across the Southwest. Daniel also served as Vice President at Keysource Foods, where he led company strategy and sales operations and negotiated contracts with some of the world’s largest food companies, including ConAgra, Carnival Corporation, PF Chang’s, ALDI, and Sysco.
Nona Yehia, Co-Founder & CEO, Vertical Harvest -- Nona Yehia is uniquely positioned in the vertical farming sphere. She is at once a practicing Architect and the Co-Founder and CEO of the 1st vertical hydroponic greenhouse in the United States. Vertical Harvest of Jackson Hole is a cutting-edge commercial-scale greenhouse that not only grows food for communities, in communities~ but futures for those who need it most.
Following her passion for local food and experiences growing up with a brother with developmental disabilities, Nona conceived of a three-story hydroponic greenhouse that employs people with developmental disabilities while producing local food for the community year-round. In 2016 Vertical Harvest opened its doors.
Milan Kluko, CEO & Co-Founder, Artesian Farms LLC & Berrien Processing Solutions (BPS) -- Milan Kluko has been in the environmental engineering, alternative energy, agriculture, and solid waste industry as an engineering consultant, developer, vendor, and technology supplier for 38 years. For nearly four decades he has worked on developing recycling and solid waste reduction programs, sustainable agriculture, renewable energy, and low impact development projects worldwide. From 2001-2015 Mr. Kluko worked on worldwide projects as a sustainability consultant for the Coca Cola Company. During the past several decades his focus has been primarily on “project-based” assignments gaining significant expertise with a wide variety of environmental, agriculture, alternative energy, and recycling systems starting in 1982.
Indoor Ag-Con LLC created the new Indoor Ag-Conversations series to share content originally planned for its May 2020 in-person annual conference that was postponed due to the Covid-19 pandemic. More details on the upcoming and future sessions, as well as recordings of previous webinars, are available at www.indoor.ag/webinar.
ABOUT INDOOR AG-CON LLC
Founded in 2013, Indoor Ag-Con touches all sectors of the business, covering produce, legal cannabis, hemp, alternate protein, and non-food crops. In December 2018, three event industry professionals – Nancy Hallberg, Kris Sieradzki, and Brian Sullivan – purchased Indoor Ag-Con LLC, setting the stage for further expansion of the events globally. For more information, visit: www.indoor.ag
Vertical Agriculture in Chile
Urban agriculture is beginning to take off in Chile, where the AgroUrbana start-up has just closed a $ 1 million seed capital round, raising its total capital to $ 1.5 million, to create a vertical farm, according to the Association for Vertical Agriculture
Urban agriculture is beginning to take off in Chile, where the AgroUrbana start-up has just closed a $ 1 million seed capital round, raising its total capital to $ 1.5 million, to create a vertical farm, according to the Association for Vertical Agriculture.
Leading the round with a 33% cash contribution was the CLIN Private Investment Fund managed by Chile Global Ventures, the venture capital arm of Fundacion Chile, a public-private initiative for innovation and sustainability in the country. Funding also came from CORFO, Chile's economic development agency, and private investors.
The funds will go to the construction of a 280-square-meter pilot facility in the suburbs of Santiago, where tests are being carried out with hydroponic crops and led lights powered by renewable energy. Green leafy fruits and vegetables are grown there.
According to company sources, the closure of restaurants due to COVID-19 made them focus on e-commerce and direct sales to consumers. In the long term, the owners plan to expand the facility to 3,000 square meters, which they speculate could be financed with funds from new capitalization rounds before the end of this year. Design and production will depend on the results of their pilot tests.
Source: Bioeconomia.info / agrositio.com.ar
IGS Completes Deal With Vertegrow to Build Scotland’s First Commercial Vertical Farm
A 245 m2 insulated superstructure will accommodate four nine-metre-high towers alongside a 1,600 m2 service area on Vertegrow’s site at Waterside Farm in Aberdeenshire. This will provide approximately 1,343 m2 of growing space, producing up to 70 tonnes of produce per annum when fully operational
New Vertical Farming Operator to Adopt IGS Agritech
Platform in Scotland
Edinburgh, Scotland – 08 July 2020 - Indoor agritech specialist IGS has today announced the completion of a deal with new vertical farming operator Vertegrow. The four-tower system will be built in Aberdeenshire in Scotland in late 2020.
A 245 m2 insulated superstructure will accommodate four nine-metre-high towers alongside a 1,600 m2 service area on Vertegrow’s site at Waterside Farm in Aberdeenshire. This will provide approximately 1,343 m2 of growing space, producing up to 70 tonnes of produce per annum when fully operational.
This is the first move into vertical farming for Vertegrow, diversifying alongside existing agricultural operations, currently growing crops including barley and rye in open fields.
Vertegrow was established through Steadman Partners, the UK-based private investment office set up by BrewDog co-founder Martin Dickie. Located in Scotland, Steadman Partners has a wide range of interests and investments throughout the UK and beyond.
The IGS platform was selected after a rigorous analysis of the market and considered to be the most advanced, efficient, and scalable to meet Vertegrow’s requirements. The plug-and-play vertical farming product developed by IGS offers them a highly controllable platform, designed specifically to maximize productivity whilst minimizing energy consumption and allowing the production of consistently high-quality produce at scale.
The towers, which are expected to be operational in early 2021, will grow a variety of crops that are intended to service the local food supply chain. Vertegrow will work with a range of local customers including retailers, caterers, restaurateurs, and other local services, to deliver fresh, nutritious, high-quality produce all year round.
IGS CEO David Farquhar commented: “This is an exciting step for IGS and for Vertegrow as we set out to deploy a new vertical farm for a new operator in this space. With proven experience in traditional farming and extensive involvement, through its owners, in the food and drink sector, we are confident that this will bring a new and top-quality offering to the local market. Such re-localization of the food supply chain is a feature of post-coronavirus planning we are seeing all over the world.”
“We were delighted that the IGS platform was selected for this project. It is proof that our rigorous commitment to engineering design excellence and our unique patented systems deliver what customers want – a system that is highly pragmatic, flexible, modular, and scalable. We look forward to getting underway with the deployment of our Growth Towers with the Vertegrow team.”
Graeme Warren, of Vertegrow commented: “Vertegrow is delighted to be working with IGS on this innovative project as we position our farm business to address the challenges of the modern food supply chain. We have spent considerable time identifying the right partners and systems, and the IGS platform stood out as a quality solution that could be configured for our needs. Growing quality, nutritious food in North East Scotland will allow us to reduce food miles for our customers. Combined with our renewable energy sources and rainwater harvesting, the efficiency of the IGS system is a key part of our ambition to grow crops in a carbon-neutral way. We look forward to continuing to work with IGS as we construct the facility later this year.”
The team at IGS will continue to work closely with its new customer in the construction and deployment phases over the coming months.
Ends
Notes to editors:
For more information: please contact Kate Forster, IGS on kate@intelligentgrowthsolutions.com or call +44 7787 534999.
About IGS:
Founded in 2013, IGS brought together decades of farming and engineering experience to create an agritech business with a vision to revolutionize the indoor growing market. Its commitment to innovation has continued apace and it has evolved the applications of its technology beyond agriculture to create solutions for a wide variety of indoor environments that enhance life for plants.
IGS launched its first vertical farming demonstration facility in August 2018.
For more information visit www.intelligentgrowthsolutions.com or connect with us on Twitter and LinkedIn.
About Vertegrow
Vertegrow represents the indoor growing arm of an existing productive arable farm in North East Scotland. It is committed to producing high-quality food sustainably, responsibly, and ultimately in a carbon-neutral way. Vertegrow expects to sell its first crops in early 2021 and then to expand and improve its crop range through research and development.
More information will be available from www.vertegrow.com as the facility approaches completion. Connect with us on Twitter, Instagram or contact hello@vertegrow.com
Future of Indoor Vertical Farming With Microgrids
Schneider Electric’s Don Wingate discusses how microgrids can help the indoor vertical farming movement realize its full potential
09-07-2020 | Microgrid Knowledge
Schneider Electric’s Don Wingate discusses how microgrids can help the indoor vertical farming movement realize its full potential.
While indoor agriculture has steadily gained traction in recent years as the world seeks alternative ways to feed growing populations, the uncertainty of today’s global pandemic has accelerated a rethinking of the way we obtain our food. In the last few months, modern supply chains experienced volatility like never before and it wasn’t long before we started to see the impact beyond medical gear and personal protective equipment and began to affect food production. According to the Institute of Supply Chain Management, 75% of companies reported some kind of supply chain disruption due to COVID-19.
Indoor vertical farming is emerging as an alternative to conventional farming because it both requires lower land-use and introduces the opportunity to bring agricultural production closer to consumers — shortening supply chains and increasing footprint productivity. This is especially important during times of turmoil, which is broader than the current pandemic as weather events and changing climate patterns continue to put constant strain on traditional farming practices. In addition to shortening supply chains, indoor farming has many other advantages in comparison to traditional agriculture such as using zero pesticides, employing 95% less water, and reducing food waste. Health benefits also include fresher food, increased urban availability, and pollution reduction.
Despite the major advantages, there is one looming barrier to mainstream adoption: the process is very energy-intensive.
Solving for the energy intensity problem
Vertical farming presents a unique opportunity to grow food on already developed land and increase domestic food production, but the energy demand required to power these facilities is much higher than other methods of food production. In fact, we’ve identified indoor agriculture as one of the four major drivers that will increase electricity consumption in the next decade, along with electric vehicles, data centers, and the electrification of heat. This is why more of today’s modern farming companies are turning to microgrids as a possible solution to ease their energy challenges.
Although most of today’s facilities are not equipped to meet the electricity needs of an indoor agriculture operation, microgrids can provide dynamic energy management and the resources required to support maximum productivity, sustainability, and energy efficiency. They can provide localized power generation and utilize renewable distributed energy resources to help deliver power and reach clean energy goals, while also allowing users more control and reliability. Additionally, microgrids can capture and repurpose CO2 emissions to help in crop production.
Moreover, microgrids provide resilience from unexpected outages that could result in a loss in production. A key advantage of vertical farms is their ability to allow crops to grow year-round, and communities rely on their ability to deliver on this promise. Microgrids not only have several clean energy benefits, but they also increase business continuity that maximizes output. Given their ability to operate either in conjunction with or as an island from the utility grid, they can keep the farm producing even when the grid goes down.
The case for investment: Securing an affordable solution
Building and operating a vertical farm requires various technologies that can translate to high startup cost and design complex processes. At the same time, it is more expensive to maintain a vertical farming operation than traditional field farming. Microgrids offer a compelling value proposition, but they’re inherently complex machines and not many companies have the upfront capital or in-house expertise needed to make the investment. Fortunately, innovative business models such as energy-as-a-service (EaaS) help provide price certainty and make the investment attainable.
For example, a modern farming company, Bowery Farming, created a facility wherein crop production is 100 times more efficient than traditional farmland. This generated a need for a greater need for reliable, efficient power. Thus, the company made the decision to integrate a hybrid microgrid system that would feature a rooftop solar array, natural gas generator, and a lithium-ion battery energy storage system through an EaaS business model. Through EaaS, Bowery Farming saved upfront capital that can be used toward additional operational investments.
By 2050, the world’s population is expected to grow by another 2 billion people, and feeding it will be a major challenge. According to the projections of the Food and Agriculture Organization, we have to increase overall food production by 70% by this timeline. Coupled with new concerns that have surfaced as a result of today’s global pandemic and unstable weather, vertical farming will play a key role in future food production and institutions will take notice. However, the technology that will help ease some of the industry’s ongoing energy challenges will be just as important to aid the transition.
Don Wingate is the VP of utility and microgrid solutions at Schneider Electric.
Source: Microgrids Knowledge
Photo Courtesy of Microsoft News
VIDEO: IGS Intelligent System Design – FTS Finds Out More
IGS has, as a company, focused from the outset on automation, intelligent system design, and the energy equation of CEA vertical farming
July 6, 2020
IGS has, as a company, focused from the outset on automation, intelligent system design, and the energy equation of CEA vertical farming. This has garnered them a reputation as one of the leading and most innovative companies in the industry. We took some time to have a chat with them and find out a bit more about how this all works in practice.
FTS: Hello and thanks for taking the time to talk with us. Can you briefly introduce IGS, its history as well as its outlook?
IGS: IGS was founded in 2013 bringing together decades of farming and engineering experience with a vision to revolutionize the indoor growing market. The two founders, farmer Henry Aykroyd and our CTO Dave Scott had an appetite for innovation and realized that there were significant gaps in the provision of scalable technology for the sector.
Henry knew how to grow and understood the challenges which faced traditional farming: Dave knew how to manage automation and power controls in an industrial environment. The opportunity to bring greater climate control to a growing environment was significant. The ability to manage power consumption was revolutionary. The simplicity of its implementation and use is pivotal.
We opened our first vertical farm demonstrator in Scotland in 2018. Artificial intelligence determines optimal nutritional input and the exact combination or ‘recipes’ of weather: lighting, watering, and ventilation. Data is collected continuously and machine learning used to make iterative adjustments, all of which is monitored through a web-based app. The whole Intelligent Growth platform is IOT-enabled to automate system control and management. Our degree of control is so fine that each 6m2 growth tray has its own microclimate. Technical simplicity is at the heart of our mechanical design.
Our commitment to innovation has continued apace and we have evolved the applications of our technology beyond agriculture to create solutions for a wide variety of indoor environments, developing the Intelligent Grid platform.
The Intelligent Grid uses the same IOT-enabled power and controls platform to manage and monitor lights, sensors, cameras, and communications for complete climate control and reporting. It too has a very simple, clean, and elegant design for application in any commercial building, greenhouse or livestock shed. In contrast to the vertical farm, we use our same core technology through the Intelligent Grid to create whole-space macroclimates.
Both IGS demonstrators are based at the James Hutton Institute, a world-renowned crop, and plant science research facility. IGS and the Hutton collaborate closely to help advance the understanding of plant science for indoor growing.
Until 2018 IGS had invested approximately £7m in R&D to ensure that its platforms offered the greatest levels of control and achieved levels of economic viability, scale, and minimal environmental impact compared to other systems on the market. In 2019 IGS raised £7 million in institutional capital to enter production and take its systems to global markets. We continue to invest over £1m per annum in R&D.
FTS: You have recently shared news of two reseller partnerships – one in the Middle East and one in the UK and Italy with TEP Renewables. Can you tell us briefly a bit more about them?
IGS: We have been talking to International Real Estate Partners (IREP), the international facilities management firm for some time in the Middle East, and we’re really pleased to recently sign this referral agreement which is specifically focused on indoor vertical farming for the UAE and Saudi Arabian markets.
We also have an opportunity to extend into Asian markets in the future. It gives us a greater capacity to service the Middle East market and secure and deploy vertical farming platforms across the region. IREP’s presence in this market is well established with many existing customers across agriculture, retail, and construction and it is a very positive development for both companies we believe.
The agreement with TEP Renewables is an MOU (Memorandum of Understanding) or a reseller-type partnership if we identify customers who would like to operate solar-powered vertical farms in Italy or the United Kingdom that we will work with them.
FTS: Fantastic! In the end, any vertical farm (indeed any farm!) is only as environmentally sustainable as its energy equations. But it is also only as financially sustainable as its energy cost. You have focused quite intensely on this energy cost question. As we see this dramatic collapse of fossil fuel energy production return on investment, it seems that NOW is the time to have renewable energy options on hand for CEA. Do you believe that renewable energy can be cost-competitive – both in terms of installation, sustainable life-cycle and with regard to the price of the final product for the consumer?
IGS: We consider a variety of power distribution and supply methods. Renewables can have considerable benefits from an environmental perspective and also specific to grants and other financial support for utilizing renewable energy resources.
The “virtual power plant” capabilities of our systems indicate strong Demand Side Response (DSR) potential. We can manipulate our growth cycles to respond to power availability and respond to inherent instabilities in power networks. This is already having an influence on our engagement in circular energy projects to utilize spare energy for growing and allows for more renewable power sources to be adopted.
FTS: Labor cost is the other biggest outlay for any vertical farm. You have invested heavily in automation. Is the trade-off of increased capital expenditure for automation worth the reduction in operational expenditure for labor, in your experience?
IGS: Absolutely. Driving down the farm gate price is the ultimate goal and while labor costs vary from region to region, we believe that this investment in the automation (and indeed the associated patents) within our growing operations is imperative and differentiates our systems considerably.
FTS: You’ve set about designing modular and intelligent systems. Such a bespoke system offers advantages of course, as we’ve seen above. But it can also present challenges if it cannot be integrated with other equipment and systems later. Do you future-proof your systems to be able to accommodate such updates and integrations over time?
IGS: We have thought about this from the outset, and our systems are designed in a plug and play model, rather than being bespoke as such. Scalability is paramount for our customers and this has been a consideration throughout our R&D development. Rather than using proprietary systems for processes such as sowing and harvesting, we use off-the-shelf equipment and components. This means we can keep startup and maintenance costs down by providing items with which farmers are already familiar. If a section of the vertical farming system needs to be replaced or upgraded, such as a water filter, a lighting panel or a tray, it can be done with almost no interruption.
However, what is also imperative to think about in terms of future proofing, and a hugely important part of our approach, is how we work so closely with the science community to better understand plant light interactions. The level of control we have designed into our hardware systems allows us to flex and adapt as we need to deploy the most up to date plant light information through our software development, which is continuously evolving.
The approach of our software development has also involved maximising security of our systems and ensuring simplicity of operation. This will be continuously updated, but with seamless integration for our customers.
FTS: Along with FTS, you’ve joined a number of other associations and similar collaborative groups. Why is this important to you as a company, and how do you balance the proprietary needs of your company against this desire to cooperate?
IGS: Collaboration and cooperation across this sector is essential. Our vision is that sustainable change will only be delivered not only when we collaborate, but when we are all open and honest about the limitations, as well as the opportunities for this sector. We want to work alongside technology vendors with complementary products, and with growers and producers, supported by science and greater understanding of growing plants indoors, all backed by far-sighted investors.
We firmly believe that through innovation, collaboration and investment we can create an economically and environmentally sustainable global indoor food industry.
FTS: Thanks so much for taking the time to talk with us today. We wish you every success and look forward to working with you in the future.
IGS: Thanks very much indeed. We look forward very much to be part of Farmtech Society as we all move forward in the development and innovation of agricultural technology.
For IGS
David Farquhar
CEO
Vertical Farming In LatAm: AgroUrbana Closes $1m Seed Funding
Access to vertical farming technologies is deepening and widening across the world, bringing down the costs and hassle of locally producing anything from Singapore strawberries to Arctic tomatoes
July 2, 2020
Access to vertical farming technologies is deepening and widening across the world, bringing down the costs and hassle of locally producing anything from Singapore strawberries to Arctic tomatoes.
In Latin America, however, indoor vertical farms are still largely written off on a continent known for its abundant fertile soil and plentiful sunlight. Why need of artificial light or indoor automation when the sun is free and labor is cheap?
That said, there are early signs of a LatAm vertical farming awakening in Chile, where AgroUrbana has just raised a $1 million seed round, bringing its total capital raised to $1.5 million. AgroUrbana is South America’s first vertical farm, according to the Association for Vertical Farming.
Leading the round by contributing 33% of the cash was the CLIN Private Investment Fund administered by Chile Global Ventures, the venture capital arm of Fundación Chile, a public-private initiative for innovation and sustainability in the country. Support financing also came from CORFO (Chile’s Development Agency) and private investors like company builder and VC Engie Factory, the country’s largest telecommunications company Entel, and sustainability investor Zoma Capital.
In a video call with AFN, AgroUrbana f0unders Cristián Sjögren and Pablo Bunster described how the funds would be put to work at their 3,000 square feet pilot facility in the suburbs of Santiago, where testing is ongoing on layered stacks of hydroponically grown, LED-lit, renewable energy powered leafy greens and fruits. AgroUrbana’s first big offtake deal had just been inked with a major Chilean grocery retailer, they said.
A pre-planned switch from restaurant to retail
“It’s been run, run, run,” recalled Bunster, describing the political turmoil in Chile that brought curfews and shuttered restaurants months before Covid-19 locked down the country. That earlier disruption, he added, had actually had its upsides, as it got them thinking more about e-commerce and direct-to-consumer sales — so when the team’s restaurant deals dried up during the Covid-19 pandemic, the switch to retail was already scoped out.
As to scaling up further, Sjögren envisioned an eventual 30,000 square foot facility that would be bankrolled by a Series A that they plan to work towards later this year; the design and output would depend on the results of their pilot trials.
This size of farm sets the team somewhere in the middle of the two dominant visions of vertical farming: centralized versus distributed. Proponents of centralized systems argue that large-scale production—and financial viability—depend on ever-bigger and higher farms. These farms, or plant factories as they are sometimes called, are proliferating, aided by huge sums of capital. Plenty scooped up a whopping $200 million in Series B funding back in 2017. US-based AeroFarms raised $100 million in late-stage funding in 2019 while Fifth Season secured $50 million last year.
Although centralized facilities have generally dominated the vertical farming venture capital domain, distributed and decentralized business models are gaining pace, according to AgFunder’s 2019 industry report. One in particular—Germany’s Infarm—nabbed $100 million last year to deploy its connected growing cabinets in supermarkets. The theatricality of these cabinets harmoniously glowing in office buildings or hospitals in a post-corona world also holds sway in the popular and corporate imagination of 2020, with companies like Square Mile Farms recently crowdfunding over $300,000 on the promise of re-kitting office spaces like those of Microsoft’s London premises with fresh produce. In New York, Farmshelf has its own grow cabinets deployed in WeWork FoodLabs.
Learning from cash-heavy first movers
Mention of giants like Plenty or InFarm could be daunting for newer companies like Square Mile Farms or AgroUrbana and their hitherto modest sums raised. But there is perhaps an advantage in starting late — so long as the team learns from the costly mistakes and hubris of earlier endeavors. Here, both Bunster and Sjögren see parallels with the renewable industry, where they worked previously, and see the arrival of cheaper, more sustainable energy and capital in Chile as crucial to making vertical farming competitive.
AgroUrbana is exploring three options for solar going forward: either establish a PPA, in which they buy renewable energy from an existing plant; to finance a power plant which will sell to them later; or build their own solar farm. But they acknowledge that the larger the facility, the less feasible it is to have solar onsite.
The pair described how some Chilean outdoor farming is already lean and competitive, yet much of it has been geared towards high-value crops like avocados — and that stuff is primed for export. For the urbanizing local market, they see gaps for hyper-local fresh produce, where the competition would actually be with low-tech smallholder farmers with less traceable supply chains. In the context of Covid-19 and an ensuing consumer embrace of e-commerce options, better nutrition, less water use, and fewer pesticides, the pair reckon there is much to gain from providing produce that is consistently fresh 365 days a year.
Any chance of the world’s first vertically-farmed avocados any time soon? Unlikely, replied Bunster. As for gene editing, where Latin America is known to have more lax regulations than North America, Bunster said the plan was to work with what nature already provides, and just give them “the conditions of spring every day of the year.”
Exelon Invests In Reducing Indoor Ag Energy Needs And Costs With GrowFlux
“GrowFlux specifically can increase yields in indoor farming making it more economical for city centers and where it can serve often underserved communities fresh and healthier foods.”
June 11, 2020
A welcome impact from the Covid-19 pandemic has been clearer skies and returning wildlife to usually polluted areas after industry, transport systems, and more shut down across the world, reducing carbon emissions.
Today marks two months since the UK’s electricity industry last used coal; the longest period since the Industrial Revolution began more than 200 years ago and well beyond the 18 days, 6 hours and 10 minutes record which was set in June last year, according to the BBC. Renewable and nuclear energy have stepped in to make up the shortfall in a trend that’s been particularly pronounced in the US where renewables supplied more energy than coal for the first time ever this year.
Agriculture’s impact on the environment, particularly surrounding its carbon emissions, has been flung into the spotlight in recent years, particularly by alternative meat and animal products startups keen to promote the environmental credentials of their plant-based or cultivated alternatives. But of course, even a plant-based diet has carbon emissions associated with it, from the fertilizer and pesticides applied in the production process, to its transport to end markets. Plant-based products and diets are also not always affordable or accessible to certain demographics who may live in food deserts.
Indoor agriculture has long been a potential solution to food deserts and many of the carbon emissions related to crop production, making it an interesting prospect for city planners and city-based corporates. But the energy consumption associated with the production system, specifically related to lighting and climate control systems, has left much to be desired; not least because the costs involved have stunted the growth of viable business models.
Further, energy demand from these indoor farms is only set to increase as the need for more localized production in certain regions across the world has been highlighted during the Covid-19’s disruption of traditional supply chains; Singapore is a case in point.
“With over 8.6 terrawatt hours of energy consumed by horticultural lighting systems in emerging indoor farms and greenhouses in the US in 2019, utility companies are hard-pressed for rapidly scalable energy management tools that meet the needs of growers,” says Eric Eisele, CEO of GrowFlux. GrowFlux is an agtech startup focused on smart lighting controls for the horticulture industry working to significantly reduce the cost of lighting automation and its energy needs.
GrowFlux, a Philadelphia-based startup, was therefore immediately of interest to Exelon, the nuclear energy provider that claims to have the largest number of electricity and natural gas customers in the US after it launched a new startup incubator late last year aimed at reducing greenhouse gas emissions and bolstering urban centers. GrowFlux is part of the first cohort of Exelon’s $20 million Climate Change Investment Initiative (2c2i) and recently received $100,000 in cash as well as in-kind services such as legal and advisory as part of the program.
“When we think about food & ag, we think about there being a mitigation and adaptation benefit from helping to advance the indoor ag industry for food. [By growing food close to city centers] there’s a climate change mitigation benefit from the decreased emissions related to traditional, carbon-intensive farming methods of harvesting, planting and transporting food from rural areas to cities,” Exelon Corp SVP Chris Gould told AFN. Indoor ag, where farming environments can be completely controlled, is also a good mechanism to adapt to climate change, he added.
“GrowFlux specifically can increase yields in indoor farming making it more economical for city centers and where it can serve often underserved communities fresh and healthier foods.”
GrowFlux says its technology allows even the smallest farms and upstarts to build advanced controlled environment agriculture automation without millions in venture funding. Its approach is different from the traditional high-level objective of optimizing climate control towards a constant set point; instead it aims to respond more dynamically to crops’ needs via distributed sensor data and cultivar specific crop models. “Crop responsive environmental controls have the potential to result in tremendous resource efficiency, creating opportunities to grow new crops in greenhouses, reducing the operating cost of existing CEA, and reducing the capital costs associated with CEA,” reads the company website.
“We reduce cost with cloud-based control (as opposed to cloud-connected control), which is new to the industry. This strategy is unique from our competition, which are essentially boutique engineering firms that do a full range of automation services using on-site controls that are slow to scale and come at a significantly higher cost,” added Eisele.
2c2i is a partnership between Exelon and its foundation and involves $10 million in funding from the foundation and $10 million in-kind contribution of pro-bono services from the corporation, such as mentorship and access to the company’s venture capital and R&D departments.
“Our partnership with Exelon Foundation will help GrowFlux advance its energy savings and energy management solutions, and allow our customers to drive down their operating costs and carbon footprint associated with greenhouse and indoor agriculture,” said Eisele about the investment. “We believe their guidance on energy management strategy is just as valuable, if not more valuable than the cash.”
2c2i is focused on innovations that will positively impact the cities in which Exelon operates, including Atlantic City, Chicago, Baltimore, Philadelphia, Washington, D.C., and Wilmington. Innovations must also have the potential to mitigate greenhouse gas emissions; boost the resiliency of urban infrastructure (e.g., the power grid, transportation systems, buildings, vacant land) against flood, stormwater, and rising temperatures; help cities, businesses and communities adapt to climate change; or help achieve a state or city’s specific sustainability and climate goals. External consultant Freshwater Advisors selected a shortlist to pitch in front of the Exelon team.
“We also consider and have selected startups from outside of our cities, but in that regard we ask them to have a line of sight on one of our cities, with hope of attracting them to region to set up an office,” said Gould.
Microgreens Launched By Vertical Farmer April Sun
Just in time for this year’s winter season, vertical farmer April Sun launched its range of sustainably grown microgreens from its new commercial-sized micro-farming facility in Melbourne
Food & Beverage | June 4, 2020
Just in time for this year’s winter season, vertical farmer April Sun launched its range of sustainably grown microgreens from its new commercial-sized micro-farming facility in Melbourne.
With a philosophy of true sustainability and paired with cutting-edge technology, the local farm wants to provide the community with a range of nutrient-packed microgreens available year-round to their nearby community.
Co-founder Darren Nichol, April Sun visionary of Australia’s cleanest and highest nutritional food supply who has a wealth of knowledge due to his agricultural background, says, “This is a particular focus of the Darebin Council. They have an actual goal to increase food production within its municipality.”
These super foods are grown without pesticides and utilise 95 percent less water than traditional farming methods due to a hydroponic based (closed loop) watering system. Co-founder Ty Dickson, April Sun technologist and facility designer, said this system guarantees the plants do not receive too little or too much water.
“The watering targets each individual plant or root system and is drained back to the holding tanks,” he said. “Traditional farming methods would see water being lost to the ground and you would use more water to achieve the same level of fertigation without the ability to recapture the excess.”
With custom-spectrum lights developed in-house, the microgreens are grown in their ideal conditions, allowing for year-round production and minimal waste.
“We use a combination of specific wavelengths of blue, red, far red and full spectrum light to stimulate the chlorophyll A and B of the plants, while giving the right signals to ensure proper colour, increased nutrients through stress and, above all, a very healthy plant,” Dickson said.
“We are a non-single use plastics company; we opt for PLA compostable packaging. Our facility uses the highest efficiency components and equipment available. We do run on electricity, although we are engaging in using 100% renewables, and are in preliminary talks with the Darebin Council to implement 100kW of solar panels on our warehouse roof.” said Dickson.
In traditional farming, external factors such as drought, pollution, soil erosion and more can impact crop success. However, the world of vertical farming is “most often done indoors in a controlled environment”, he adds. “Vertical farming when done sustainably has less impact on the environment, there are significant reductions in water usage, land usage, gas usage and many other resources. This is all achieved whilst controlling the indoor growing environment with minimal impact to it outside.”
“By controlling every factor in the plant’s environment, you end up with a high-quality product on a number of levels,” said Nichol.
“We can grow to a timeline and the removal of variables such as the weather allows us to more accurately forecast and grow to our customers’ demands. This can reduce the amount of waste and also increase consistency of supply to customers. This is a huge problem for traditional farming and is the cause for the large price jumps and shortages of produce on the market.”
To see more, click here.
Google Just Made The Largest Ever Corporate Purchase of Renewable Energy
Two years ago, Google became the first company of its size to buy as much renewable electricity as the electricity it used. But as the company grows, so does its demand for power
09.19.19
Two years ago, Google became the first company of its size to buy as much renewable electricity as the electricity it used. But as the company grows, so does its demand for power. To stay ahead of that demand, Google just made the largest corporate renewable energy purchase in history, with 18 new energy deals around the world that will help build infrastructure worth more than $2 billion.
[Photo: courtesy Google]
The projects include massive new solar farms in places like Texas and North Carolina where the company has data centers. “Bringing incremental renewable energy to the grids where we consume energy is a critical component of pursuing 24×7 carbon-free energy for all of our operations,” Google CEO Sundar Pichai wrote in a blog post today. While most of the renewable energy the company has purchased in the past has come from wind farms, the dropping cost of solar power means that several of the new deals are solar plants. In Chile, a new project combines both wind and solar power, making it possible to generate clean energy for longer each day.
The package of new projects will supply a total of 1,600 megawatts of electricity, bringing Google’s total renewable portfolio to 5,500 megawatts—the equivalent of a million roofs covered in solar panels. Pichai writes that the company’s clean energy projects will be able to produce more electricity than is used by the city of Washington, D.C., or the entire country of Lithuania.
Device Recycles Waste Heat Into Light To Boost Solar Systems
Arrays of aligned single-wall carbon nanotubes could channel wasted heat and greatly raise the efficiency of solar energy systems, report researchers
JULY 16TH, 2019
Arrays of aligned single-wall carbon nanotubes could channel wasted heat and greatly raise the efficiency of solar energy systems, report researchers.
The new invention is a hyperbolic thermal emitter that can absorb intense heat that would otherwise spew into the atmosphere, squeeze it into a narrow bandwidth, and emit it as light that can be turned into electricity.
The discovery rests on another that Junichiro Kono’s group at the Brown School of Engineering at Rice University made in 2016 when it found a simple method to make highly aligned, wafer-scale films of closely packed nanotubes.
A scanning electron microscope image shows submicron-scale cavities patterned into films of aligned carbon nanotubes. The cavities trap thermal photons and narrow their bandwidth, turning them into light that can then be recycled as electricity. (Credit: Naik Lab)
WASTE HEAT
Discussions with Gururaj Naik, an assistant professor of electrical and computer engineering, led the pair to see if the films could be used to direct “thermal photons.”
“Thermal photons are just photons emitted from a hot body,” Kono says. “If you look at something hot with an infrared camera, you see it glow. The camera is capturing these thermally excited photons.”
ABOUT 20 PERCENT OF OUR INDUSTRIAL ENERGY CONSUMPTION IS WASTE HEAT. THAT’S ABOUT THREE YEARS OF ELECTRICITY JUST FOR THE STATE OF TEXAS.
Infrared radiation is a component of sunlight that delivers heat to the planet, but it’s only a small part of the electromagnetic spectrum.
“Any hot surface emits light as thermal radiation,” Naik says. “The problem is that thermal radiation is broadband, while the conversion of light to electricity is efficient only if the emission is in a narrow band. The challenge was to squeeze broadband photons into a narrow band.”
The nanotube films presented an opportunity to isolate mid-infrared photons that would otherwise be wasted. “That’s the motivation,” Naik says. “A study by [co-lead author and graduate student] Chloe Doiron found that about 20 percent of our industrial energy consumption is waste heat. That’s about three years of electricity just for the state of Texas. That’s a lot of energy being wasted.
CARBON NANOTUBES CAN TAKE THE HEAT
“The most efficient way to turn heat into electricity now is to use turbines, and steam or some other liquid to drive them,” he says. “They can give you nearly 50 percent conversion efficiency. Nothing else gets us close to that, but those systems are not easy to implement.” Naik and his colleagues aim to simplify the task with a compact system that has no moving parts.
The aligned nanotube films are conduits that absorb waste heat and turn it into narrow-bandwidth photons. Because electrons in nanotubes can only travel in one direction, the aligned films are metallic in that direction while insulating in the perpendicular direction, an effect Naik called hyperbolic dispersion. Thermal photons can strike the film from any direction, but can only leave via one.
“Instead of going from heat directly to electricity, we go from heat to light to electricity,” Naik says. “It seems like two stages would be more efficient than three, but here, that’s not the case.”
Naik says adding the emitters to standard solar cells could boost their efficiency from the current peak of about 22 percent. “By squeezing all the wasted thermal energy into a small spectral region, we can turn it into electricity very efficiently,” he says. “The theoretical prediction is that we can get 80 percent efficiency.”
Nanotube films suit the task because they stand up to temperatures as high as 1,700 degrees Celsius (3,092 degrees Fahrenheit). Naik’s team built proof-of-concept devices that allowed them to operate at up to 700 C (1,292 F) and confirm their narrow-band output. To make them, the team patterned arrays of submicron-scale cavities into the chip-sized films.
“There’s an array of such resonators, and each one of them emits thermal photons in just this narrow spectral window,” Naik says. “We aim to collect them using a photovoltaic cell and convert it to energy, and show that we can do it with high efficiency.”
A paper on the technology appears in ACS Photonics. The Basic Energy Science program of the Department of Energy, the National Science Foundation, and the Robert A. Welch Foundation supported the research.
Source: Rice University
Lead Photo: (Credit: James Moran/Flickr)
Original Study DOI: acsphotonics.9b00452
TAGS
Swiss Retail Migros: "All Greenhouses To Be Heated Fossil-Free By 2025"
Retailer Migros is serious: From 2025 onwards, the greenhouses supplying the Swiss retail chain are only to be heated with renewable energy. "With this pioneering work, Migros and its producers are showing that it is possible to phase out heating oil and fossil gas," said WWF CEO Thomas Vellacott earlier this year. "We need this kind of joint effort to meet the Paris Climate Agreement and curb climate change, which sets an example for Migros - also for other sectors."
Nowadays, the greenhouses are mostly heated by oil or natural gas. An estimated 100 companies supply the various cooperatives of Migros throughout Switzerland. "In the future, every company should use the optimum mix of renewable energy sources for its location", Migros explained. "Heat pumps, wood heaters, bio-gas, geothermal energy and solar energy are in the foreground."
Heating swiss horticulture
Greenhouses are heated especially at the beginning and end of the Swiss season to extend the domestic season. Since most growers have improved the insulation and energy use of their greenhouses in recent years, they have reduced their emissions. Nevertheless, greenhouse production continues to be one of the most carbon intensive sectors in Switzerland. "With annual savings of up to 75,000 tonnes of CO2 thanks to the use of renewable-heated greenhouses, regional production in cultivation is significantly strengthened",
The schedule to heat all greenhouses from 2025 fossil-free is ambitious. For this reason, the conversion takes place in close cooperation between Migros and the producers. Migros invests one million francs a year in the project. "With the money producers are financially supported in the conversion. In addition, thanks to clear commitments regarding the future scope of supply, producers are given planning certainty. Migros welcomes the commitment of all those involved to work together for a climate-friendly future", the retailer explained.
These energy changes in the glasshouses, however, have their price. There is a rumbling in the vegetable industry. Nobody wants to comment publicly, but behind the scenes, the very short deadline that the largest retailer in the country poses to its producers is being criticized, says SRF.ch.
Climate friendly lettuce
On the other hand, Migros' demand did not catch all producers cold. Patrick Forster, Managing Director and owner of the Forster Group, has already taken all kinds of steps by himself.
Hydroponic lettuce. The vegetable garden of the future?
When he built a modest new greenhouse a few years ago, he installed a waste heat installation instead of a conventional one. According to Forster, the greenhouse emits around 700 tonnes less CO2 per year. That's as many greenhouse gases as about 700 single households emit annually.
Sustainable Hydro Lettuce
In the Forster's greenhouse, lettuces are lined up next to other lettuces. Forster delivers them to the Migros. This so-called Hydro Lettuce production facility is already very sustainable, because it functions with a minimum use of water, pesticides and fertilizer, says Forster. The climate-friendly heating mode completes this sustainable project.
His greenhouse is situated next to a waste incineration plant in the district of Oftringen in the canton of Aargau. A special pipeline transports warm water to the greenhouse, where it creates the necessary temperatures. This heating system was twice as expensive as a conventional heating system, says Forster. However, the vegetable growers will have earned back the investment costs within five years.
After that, the heating system is quite a bit cheaper: "This way, we have realized an economically and environmentally sensible project," says the vegetable grower and entrepreneur. But not everyone can build a greenhouse like him, next to a waste incineration plant. "For some companies it will be almost impossible to find a solution," Forster thinks.
For more information:
A. Trachsel AG - Forster Gruppe
Inh. Patrick Forster
Gewerbe Brunnmatt 7
6264 Pfaffnau (CH)
+41 62 746 93 00
www.trachsel.ch
Publication date: 5/8/2019
Geothermal Energy May Make Indoor Farming Work in The Future
The farms of the future may be possible even in an urban setting with the right alternative energy.
September 27, 2018 By JULIE CAMPBELL
The farms of the future may be possible even in an urban setting with the right alternative energy.
Technology and geothermal energy advances are sending farming indoors on an increasing basis. This is the case both with urban greenhouses on a smaller scale or larger scale greenhouses.
The primary challenge with these types of greenhouse have to do with the energy they need.
Greenhouse operation is energy intensive, with high demands for electricity because of lighting, but, more importantly, heating. It is in the area of heating that geothermal energy presents a significant opportunity.
As populations rise and the demand for local food production increases, indoor farming may become much more important even in urban settings, according to a recent World Economic Forum article. That said, in order to make that financially feasible, producers need to look to affordable alternative energy options.
These urban operations rely on using every square inch to its greatest potential, as space is much more limited. Moreover, everything must operate on less water. That said, as these indoor farms – small or large in size – have the same heating and lighting requirements as a traditional farm. This requires affordable sources of energy.
Many in the industry believe geothermal energy will be among the leading solutions for indoor farming.
Among the reasons that many will look to geothermal energy is that there are already many success stories with this technology. It is not only receiving increasing attention from those in the industry, but it has also already proven itself in many examples.
For example, one of the largest flower producers in Kenya, called Oserien, uses geothermal power for heating as well as small-scale electricity production. In the Netherlands, energy is becoming increasingly expensive, so geothermal wells are being drilled for many greenhouse operators that need heat. Iceland has widespread geothermal energy heating in its greenhouses to make it possible to grow vegetables throughout the year.
Germany is home to several geothermal power projects being developed to use this resource for their greenhouse operator heating. A new effort has also been underway in Pagoda Springs, Colorado, where it is being used for vegetable production on top of broadening economic development.
Study Shows How Badly Smog Can Cripple Solar Farms
New research finds that severe air pollution can eliminate all profits from solar panel installations.
Aug 30, 2018
A lot can keep solar panels from generating electricity, from cloud cover blocking the sun to simply being nighttime. But according to recent research, one of the biggest obstacles facing solar farms is smog and haze from air pollution.
It’s not surprising that air pollution can make solar panels less effective since it can cut down on visibility and reduce the amount of sunlight reaching the ground. In the past, researchers have found that air pollution can lead to dust buildup on solar panels that can dramatically reduce their effectiveness.
This new research, from scientists at MIT and Singapore, calculates how much solar energy is lost due to smog in many of the world’s biggest cities. In the city of Delhi, one of the world’s most polluted cities, electricity generation is reduced by more than 10 percent the study finds, which translates to a cost of more than $20 million.
The problem is more than just inefficiency. A loss of this size could spell doom for many urban solar farms by seriously inhibiting their ability to turn a profit. Pollution can turn a money-making solar farm into a money sink.
Even worse, the lack of a solar alternative naturally just increases reliance on smog-generating fossil fuels and could serve to lock entire regions into a vicious cycle. This gives us another reason to keep our air clean, just in case we didn’t have enough.
Source: Energy and Environmental Science
The Rise Of The Urban Rooftop
With space at a premium, cities are exploring new ways to make better use of their rooftops.
The rooftops of our cities are wowefully under-utilised, despite the constant-battle for land (Image credit: Shutterstock)
With space at a premium, cities are exploring new ways to make better use of their rooftops.
Our cities have never been denser, taller, or busier than they are now, and with that, comes the constant battle for land. Whether you’re a city dweller, developer, transport planner, or farmer, you’re forced to compete for dwindling amounts of available space. And with two-thirds of the world’s population predicted to live in cities by 2050, the stress on urban infrastructure looks set to outpace even the most carefully-laid plans. But if we look at aerial images of any city center, we can quickly spot plenty of unused space – the rooftops. Speaking to Scientific American, Steven Peck from a non-profit called Green Roofs for Healthy Cities, describes the roofscapes of our cities as “the last urban frontier – (representing) 15 to 35 % of the total land area.”
So what can we use this precious resource for? In a growing number of high-density cities, some of it is dedicated to recreation – everything from bars and pools, to soccer pitches and running tracks can now be found atop skyscrapers. Others host smog-eating roof tiles or questionable wind turbines, while in China, a large shopping mall has 25 villas on its roof. But when a rooftop offers access to sunlight, there are two more obvious candidates for its use – agriculture and solar power.
Green Cities
Green roofs have been growing in popularity for more than a decade, and in some cases, growing in scale too – atop a convention center in Manhattan sits the city’s largest, covering an area of 89,000 m2. Usually comprised of planted beds, or carpet-like tiles that encouraged the growth of low profile vegetation, green roofs can provide a habitat for birds and insects in an otherwise hostile environment. They also act as thermal insulation for the building, and reduce storm water runoff that can otherwise cause havoc in urban sewers.
Green roofs come with the added benefit of mitigating the dreaded urban heat island effect, whereby, as a result of heat-absorbing materials like asphalt and concrete, cities can be several degrees warmer than the surrounding countryside. In contrast, trees and green spaces can absorb shortwave radiation, and use it to evaporate water from their leaves – a kind of ‘double cooling’ effect. There are countless studies that back up this idea. One of the most interesting came from researchers at the University of Georgia. In 2015, they showed not only that ‘green’ cities are cool cities, but that networks of small urban green spaces, such as parks, gardens and green roofs, were more effective at reducing a city’s temperature than a singular park of the equivalent size.
In some European and US cities, councils now offer significant financial incentives to developers who install a green roof – in Hamburg, building owners can receive subsidies of 30–60% of its installation costs. And from 2020, green roofs will be considered compulsory for all new, large-scale builds in the city. (CONTINUED...)
uilding-intergrated PVs are growing in popularity. But are they always the best option? (Photo by Thomas Imo/Photothek via Getty Images)
As food security and urban nutrition creep ever-higher on the agenda for the United Nations, there’s also a worldwide movement of using green roofs for hyper-local food production. In regions with suitable climates, hundreds of different vegetables, fruits, herbs and salad leaves can be grown on rooftops. Beehives and chicken coops are also becoming commonplace amongst the high-rises. But not all rooftop farms are equal, as we’ll discuss.
Power Up
But first, what about solar power? With so many cities now divesting from fossil fuels, and the costs of solar panels dropping dramatically, photovoltaic (PV) systems have become the ‘go to’ option for generating distributed power in built-up areas. And, even with standard commercial panels, the energy gains are dramatic. The US National Renewable Energy Laboratory (NREL) have estimated that rooftop PV systems could generate almost 40% of electricity demands nationwide. NREL also developed a very cool visualization tool called PVWatts to help people discover if solar panels would work for them. In 2012, Dutch researchers calculated that building-integrated photovoltaics could deliver 840 TWh of electricity – that’s more than a fifth of the total annual demand for all of the EU-27 countries.
In 2011, a fascinating map was published by the City University of New York. Assembled from images taken by a LIDAR-enabled (Light Detection and Ranging) aircraft, it showed that at the time, 66.4% of New York’s buildingshad roof space suitable for commercial photovoltaic systems. Furthermore, they estimated that, even with NYC’s changeable weather, rooftop installations could meet close to 14% of the city’s annual electricity consumption.
And cities have certainly taken note of this data – in many cases, making such installations compulsory, as in Sao Paulo, where Brazil’s Ministry of Cities announced that future low-income housing developments should include rooftop photovoltaics.
Which one to choose?
There’s no doubt that in both cases, a network of ‘productive rooftops’ could benefit the local community by supplying a portion of a necessary resource – either food or electricity – while also reducing their environmental burden. But is one better than the other? (CONTINUED...)
This was the question posed by researchers from MIT and the University of Lisbon in a recent paper in the journal Cities. Focusing on the rooftops of a mixed-use neighborhood in Lisbon, they carried out a Cost-Benefit Analysis for four scenarios – 1. Open-air rooftop farming, 2. Rooftop farming in low-tech greenhouses, 3. ‘Controlled environment agriculture’ (farming in high-tech greenhouses) or 4. Solar PV energy generation. Starting with existing data on everything from installation costs and resources used, to carbon footprint and yield, they modelled the impact that each installation would have on the local community over a period of 50 years.
The researchers took a footprint of one square meter of roofing, considered a population of 17,500 residents, and for the farms, looked only at a single crop – tomatoes. The fruit is not only incredibly popular in the Portuguese diet – with an average of 10.4 kg eaten per year, per person – there’s also a large body of data available on their growing requirements and yields. For solar power, they considered standard single-crystalline silicon PV modules, arranged on flat or pitched roofs. They also assumed that the PVs installation would act as part of the grid – in other words, though generated locally, the electricity would be distributed via existing infrastructure.
Urban farming might add value to a neighbourhood far beyond what had been previously assumed (Photo by John S Lander/LightRocket via Getty Images)
Here are a few highlights from their study:
The benefits of food production varied according to the supply chain, except for high-tech rooftop farms, which were predicted to be profitable regardless. Open-air and low-tech greenhouses were found to only profit when the crops are sold directly to consumers.
If the demand for tomatoes in Lisbon was to be met through rooftop farming, you’d require 1.89 square meters for organic field cultivation (#1), 0.37 m2 for soil-less cultivation in unconditioned greenhouses (#2), or 0.15 m2 for controlled-environment agriculture (#3)
A rooftops farm could potentially create five times as many local jobs as a rooftop PV system, but would involve much higher operation and maintenance costs
The electricity yield for PVs installed on south-oriented unshaded rooftops was calculated to be approximately 300 kWh/m2/year.
So, both options seem pretty good. But it’s when we look at the bigger picture that the differences start to show. I’ve written about the questionable profitability of urban farming in the past, but that was only ever as measured on individual farmers, which – I say, with the benefit of hindsight – doesn’t make all that much sense in the context of a city.
This study, however, takes a broader, and much more sensible view – it looks at rooftop installations as part of an interconnected network. And it’s which measures the overall value – in terms of economics and the environment – to both the building owner, and the community around it. And by looking at it that way, they concluded that for Lisbon, the use of rooftops for food production could yield significantly higher local value than solar PV energy generation or standard green roofs. Of course, this is very site-specific – in another city, you might come to exactly the opposite conclusion, but that’s kind of the point. There is no one-size-fits-all solution to make cities more sustainable, and anyone who tells you otherwise is massively over-simplifying a complex issue.
There are lots of things that will help anywhere – e.g. moving from private cars to mass transit, making renewable energy the default option, being smarter with how we use water, reducing our reliance on concrete, minimizing our waste footprint, and reserving single-use plastics for very, very specific applications. But when it comes to ‘other’ questions, like should we use our rooftops for energy generation or farming, the answers are a lot less black-and-white. By adopting research like the study I’ve featured here, we can get much closer to making the right decision for our specific circumstances. The authors said that their study “…aims to provide decision-makers with a basis for systematic and integrated comparison of these productive uses of rooftops.” Now, all I hope is that some of those decision makers start using it.