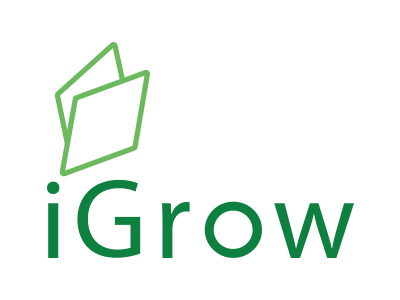
Welcome to iGrow News, Your Source for the World of Indoor Vertical Farming
No Sun, No Soil, And Robot Farmers: Is This Tomorrow’s Food Crop?
Even by the unconventional standards of modern-day urban agriculture, Geert Hendrix’s set-up is unorthodox. It is in an Alphington warehouse, with no windows and no soil, and is filled with the most diminutive of crops
By Megan Backhouse
July 2, 2021
Even by the unconventional standards of modern-day urban agriculture, Geert Hendrix’s set-up is unorthodox. It is in an Alphington warehouse, with no windows and no soil, and is filled with the most diminutive of crops.
Tiny purple radish stems, miniscule basil leaves and microscopic watercress seedlings are the heavy hitters here. Their stems strain towards LED lights and their roots stretch down through hemp fibre and coconut coir into fish-tanks.
Geert Hendrix with one of his indoor growing systems. CREDIT: JUSTIN MCMANUS
Other leafy greens are growing on illuminated shelves that have nutrient-rich water recirculating inside them. Lettuces are being cultivated – in a sealed glass cabinet – on nothing but air and a regular misting of another nutrient solution. Other plants are tended by robot.
Freewheeling, this place is not. Space is carefully allocated, lighting is monitored and close tabs are kept on waste. Nothing is left to chance. Hendrix, part of a growing band of people working to make food production more sustainable and reliable, is using his indoor farm at the Melbourne Innovation Centre to help turn traditional methods of food production on their head.
He says the range of growing systems – some of which are at more experimental stages than others – is predominantly aimed at showing high-school students what is possible.
Purple radishes growing in trays of hemp fibre atop a fish tank. CREDIT: JUSTIN MCMANUS
As anyone growing vegetables as microgreens in trays of soil in a sunny spot in their kitchen will tell you, growing baby plants doesn’t have to be high-tech. You need to be rigorous with your twice-daily rinsing, but then, in little more than a week, you will invariably have a good yield of aromatic, nutritionally dense miniature greens at the ready.
Hendrix says it’s the very ease and speed of growing microgreens that makes them such a powerful educational tool. “I see them as a gateway to help people become full-spectrum farmers in the future.” He expects that, over the next 10 years, big shifts in agricultural processes will create new opportunities for farming, and he wants to inspire young people to take advantage of them.
Lead photo: Lettuces growing in a sealed glass cabinet. CREDIT: JUSTIN MCMANUS
Robots Take Vertical Farming To New Heights
Braddock, Pa., is where Andrew Carnegie first mass-produced steel. The city, now one-tenth its former size, is home to a new kind of industry: robotic farms that grow greens inside buildings
Braddock, Pa., Is Where Andrew Carnegie First Mass-Produced Steel. The City, Now One-Tenth Its Former size, Is Home To A New Kind Of Industry: Robotic Farms That Grow Greens Inside Buildings.
June 28, 2021
A decades-long decline of industry in Braddock has left the western Pennsylvania town in ruins. Ten miles upriver from Pittsburgh in the Mon (Monongahela) Valley, most of the city’s factories, businesses and homes were abandoned long ago and leveled. Among the ruins, a sprawling steel mill, built by Andrew Carnegie in 1874, is still producing slabs of steel, 24 hours a day, seven days a week. It’s stained blue walls and maze of giant, rust-colored pipes and vents stand in contrast to the brand-new, block-long, gleaming white structure directly across the street. The mill’s neighbor is Fifth Season, a vertical farm growing greens indoors by stacking racks of plants on top of each other.
Fifth Season is the brainchild of brothers Austin and Brac Webb, and co-founder Austin Lawrence. “We view vertical farming as really a smart manufacturing system,” says Austin Webb. “We just happen to manufacture living organisms.”
The partners consider their fledgling enterprise as more than a means to feed people, but also a chance to work with a community in need. Almost none of the old steel plant’s employees live in Braddock. Conversely, everyone hired to work at Fifth Season lives close by and in the surrounding communities. “We’re creating a workforce of the future,” Webb says. “It’s an entirely new ag-manufacturing job that hasn’t existed before.”
Since the collapse of the steel industry in Braddock, the borough has struggled to attract new business and residents.(David Kidd/Governing)
Automated City Farming
Two shifts of 20 people oversee operations at the vertical farm. And like the steel maker across the road, the work never stops. Dressed in blue scrubs and lab coats, with heads covered and gloves on their hands, workers inside the plant look more like medical research professionals than farmers. The entire process, from seed to harvest, is controlled robotically. “What we have built is the industry first, and industry only, end-to-end automated platform,” says Webb.
Fifth Season’s proprietary software allows efficiencies otherwise not attainable. Spinach, arugula and other greens move around the 60,000-square-foot facility in plastic trays, each with its own unique ID. Sensors are constantly monitoring everything from nutrient mix, carbon dioxide levels and light spectrum, in order to ensure that the greens follow their prescribed grow recipe. Every plant can be traced from any point in the process, at any time.
Webb is quick to tout the advantages of vertical farming. Fifth Season uses up to 95 percent less water and 98 percent less land than conventional farming. Water from the municipal system is filtered and proprietary nutrients added before getting to the plants directly through their roots. “It means you can replicate any form of soil environment,” he says. Whatever water is not used by the plants is retreated and recirculated, with nutrients added as needed. A peat mix is used to support the roots, but all the nutrients are in the water, not the “soil.”
“We use no herbicides and no pesticides,” Webb says. “And that’s because we have hermetically sealed environments.” The possibility of contamination is all but eliminated. Fifth Season recently received a perfect score from the Safe Quality Food (SQF) program, an international, independent body that certifies food safety management. “The second time in 25 years they gave 100 percent,” he says.
With only their faces exposed, employees work among the various conveyor belts that crisscross the high, white-walled rooms of Fifth Season’s production floor. But there are no humans in the adjacent grow room, where tightly spaced racks, supporting trays of plants, are stacked 30 feet high, bathed in an otherworldly purple-magenta glow. The dramatic color comes from the LEDs that replicate the most useful parts of the spectrum of sunlight. “You can’t control the sun,” Says Webb. “But what you can control are LEDs.”
Fifth Season’s proprietary systems allow more plants to be grown in less space. The purple-magenta LED lighting replicates the most useful parts of the spectrum of sunlight, improving growth of the greens.(Fifth Season)
Every few minutes, a robot glides forward and back along a raised guideway that runs down the center of the room, dividing the stacks in half. The machine is not much more than a plain box, just a few feet tall. A metal beam rises from its back, extending to the ceiling. Its task is to place and remove trays of plants, taking its instructions from the all-knowing software. Because they are so tightly spaced, more trays can be stacked on top of each other, resulting in greater production.
“Compared to some other vertical farms out there, we have a lot more density,” says Webb. “We’re able to have more racks that grow inside the same space.” Moving trays is a task well-suited to a machine. Not only does the robot fit into places no human could, it always knows where every tray of greens should be, and for how long.
Vertical Farming Comes to Braddock
After a five-year career in finance, Austin Webb enrolled in an MBA program at Carnegie Mellon University in Pittsburgh. “I believe that robotics will possibly disrupt every industry in the world,” he says. “And so I went to C.M.U., specifically because it’s the No. 1 school in computers, science and robotics.”
There he met Austin Lawrence, who shared his interest in controlled environment agriculture. Together they visited a few vertical farms, coming to the conclusion that what was needed was an entire robotic platform, something the two of them could not accomplish on their own. Webb’s brother Brac, a self-described engineer and entrepreneur, was soon recruited to help. Their new business was incorporated in 2016, initially as RoBotany, which later morphed into Fifth Season.
With financial backing in hand, the partners looked for a place to build, quickly settling on nearby Braddock. They broke ground in May of 2019, were installing equipment less than a year later and were at full production before the end of 2020. “I think there’s a lot of opportunity for resurgence in a place like this,” says Webb. “A lot of folks that stayed are passionate around Braddock being able to grow and thrive and we want to be a part of that.”
In the foreground, Fifth Season’s new structure stands in contrast to the steel plant behind it that still dominates the town.(David KIDD/Governing)
Andrew Carnegie’s mill was the first of many that would proliferate in the Mon Valley, making it the nation’s steel capital. The churches, schools, stores and restaurants that served the town’s 20,000 inhabitants are mostly gone now. Shops and services are few and far between for the 2,000 that remain. “The nearest grocery store is up the hill, two towns over,” says Braddock Mayor Chardae Jones. “And most people don’t have cars.” It’s a hot day in June when a few of the locals gather in a brand-new park along Braddock Avenue. Everyone agrees the park is nice, but it’s no consolation for the hospital that used to stand on the site.
Many years ago, steelworkers and their families lived close to the mill.(David Kidd/Governing)
A few blocks away, an ever-present din still emanates from Carnegie’s steel mill, and a parade of trucks continues to roll past the boarded-up stores and empty lots that line the borough’s main thoroughfare. “We have a lot of vacant buildings,” says Mayor Jones. “That’s our biggest issue.” But there are signs of a revival among the ruins.
Present Day Braddock
Against the backdrop of empty and dilapidated storefronts, “The Ohringer,” a former furniture store built in the streamline moderne style of the 1940s, has recently been completely rebuilt and modernized as apartments and studio space for artists. Applicants are expected to present their work for review and answer a few questions, one of which is “why are you interested in becoming part of Braddock’s resurgence?”
Not only does Braddock lay claim to Andrew Carnegie’s first steel mill, but also the first Carnegie library, dedicated in 1889. Narrowly escaping demolition in the 1970s, the impressive stone structure is today undergoing a comprehensive restoration and modernization. Bright yellow notices of this year’s street sweeping schedule are affixed to telephone poles near the library and all over town, an indication that the local government is still functioning.
A repurposed furniture store now provides updated living and studio space to area artists.(David Kidd/Governing)
Further up the avenue, more official-looking signs are attached to random telephone poles. “NOTICE, WRITE MORE LOVE LETTERS” says one. “NOTICE, LOVE IS FREE,” says another. The signs were placed there, unofficially, by Gisele Fetterman, wife of former mayor and current Lt. Governor John Fetterman. Among her many initiatives to improve the lives of people in Braddock, she founded the Free Store nine years ago, a place where “surplus and donated goods are received and redistributed to neighbors in need.”
Fifth Season is a regular contributor to the Free Store, having recently given them a new refrigerator and donating 100 pre-packaged salads every Thursday. “We’re treated like we’re a customer,” says Gisele Fetterman. “We’re not getting things that didn’t sell, or surplus. Our families get to come in and choose. They can feel like they are at a grocery store. There is great dignity in the process of being able to choose.”
Offering “produce grown in soil by humans in Braddock,” workers at Braddock Farms do it the old-fashioned way.(David Kidd/Governing)
There are more signs along Braddock Avenue. “BE ALERT: VEGETABLES AHEAD.” Another simply says “TURNIPS.” Back in 2007, when John Fetterman was the mayor, he encouraged a nonprofit group of community gardeners to establish a farm in Braddock. Bisected by a side street, the organic farm has expanded to a little less than an acre in size, growing greens, tomatoes, onions, peppers and eggplant. This is Nick Lubecki’s fourth year as manager of the farm. “We’re here in Braddock, so the people in Braddock are our main focus,” he says. “We want to be useful.”
At best, the little farm on Braddock Avenue can produce 13 plantings of greens in a year. It is entirely different from the computer-controlled, machine-driven, non-stop production that takes place a few blocks away at Fifth Season, where a half-acre indoors can produce the equivalent of nearly 100 acres of farmland. But higher yields don’t matter as much if a significant portion is ultimately lost in transit to the table.
Serving a Market
Localized food production means less spoilage and waste. “If it takes anywhere from five to eight days to go from California to Pittsburgh, you’ve just lost five to eight days of shelf life,” says Austin Webb. Most of what Fifth Season produces is consumed in the Pittsburgh area. “The day after it was cut, not 10 days later.” Their ready-to-eat salads can be purchased at a local supermarket chain, or delivered directly to the consumer at home, a direct response to the pandemic. Local restaurants, hospitals and universities are also customers.
Convinced they have successfully demonstrated the viability of their proprietary technology, the three partners are looking to expand beyond western Pennsylvania. “We can build these anywhere… even larger than what we have here today,” says Austin Webb. “And we don’t have to re-create the wheel. It’s not like it would take us another five years.”
Conversations are already taking place about licensing the technology, proceeding in partnership with someone else, or going it alone. “That will allow us to build a facility just like we built in Braddock, in other parts of the U.S., and other parts of the world, even faster.”
A Job You Can Walk to
Andrew Carnegie built his steel mill in the Mon Valley because he needed the river, the raw materials, and access to labor. His plant was expressly designed to use the Bessemer Process, the first method to inexpensively mass-produce steel. Nearly 150 years later, the Webb brothers and their partner Austin Lawrence chose the exact same location to showcase their own new manufacturing technology and to fill a need in the community. “Knowing that we could build these anywhere, we wanted to build in Braddock because we knew that we could create jobs,” says Austin Webb. “That we could create this new workforce of the future.”
Employed since January, John Davis lives less than a block away from Fifth Season. “I have family in Braddock. They’re very happy I’ve got a job.”(David Kidd/Governing)
Braddock resident John Davis may or may not think of himself as part of the workforce of the future. But he’s happy to have a good job. Covered head to toe in his surgical outfit, he works in the seeding department at Fifth Season, a job he’s held since January. He’s lived here for 20 years, and this is the first job he’s had that didn’t involve a commute. He walks to work from his house, half a block away.
Davis is 32 years old and anxious to put the past behind him. “To have a job that you like, where you live, it’s comfortable,” he says. “And you can see that this is going to change Braddock for the better because it gives the residents jobs and new innovations. It’s going to bring life.”
While awaiting their fate, many of Braddock’s empty buildings provide space for murals and artwork.(David Kidd/Governing)
Lead photo: Greens leave the grow room at robot farm Fifth Season, ready for harvest. (Fifth Season)
Tags: Economic DevelopmentFood AssistanceTechnology
David Kidd is a photojournalist and storyteller for Governing. He can be reached at dkidd@governing.com.
Autonomous Delivery Startup Nuro Hits $5 Billion Valuation On Fresh Funding of $500 Million
Nuro, the autonomous delivery startup founded by two former Google engineers, has raised $500 million, suggesting that investors still have an appetite for long-term pursuits such as robotics and automated vehicle technology
Kirsten Korosec@kirstenkorosec / November 9, 2020
Image Credits: Nuro
Nuro, the autonomous delivery startup founded by two former Google engineers, has raised $500 million, suggesting that investors still have an appetite for long-term pursuits such as robotics and automated vehicle technology. Nuro now has a post-money valuation of $5 billion.
The Series C round was led by funds and accounts advised by T. Rowe Price Associates, Inc., with participation from new investors including Fidelity Management & Research Company and Baillie Gifford. The round also includes existing investors such as SoftBank Vision Fund 1 and Greylock.
Nuro was founded in June 2016 by former Google engineers Dave Ferguson and Jiajun Zhu. While the startup was initially bootstrapped by Ferguson and Zhu, it has never struggled to attract investors. Nuro completed its first Series A funding round in China in 2016, a deal that gave NetEase founder Ding Lei (aka William Ding) a seat on Nuro’s board. A second, U.S.-based, round in June 2017 raised Nuro’s total Series A funding to $92 million. But it was the monster $940 million investment made by the SoftBank Vision Fund in February 2019 that catapulted Nuro ahead of numerous other startups attempting to commercialize autonomous vehicle technology. Nuro had a $2.7 billion valuation following the SoftBank investment, meaning its value doubled in about 18 months. That money has helped it grow to more than 650 employees.
Unlike many other startups in the AV industry, Nuro has focused its effort on designing a low-speed electric self-driving vehicle that transports packages, not people. Some of Nuro’s first tests and pilots were with Toyota Prius vehicles equipped with its self-driving system. Nuro partnered in 2018 with Kroger to pilot a delivery service in Arizona. The pilot, which initially used Toyota Prius vehicles, transitioned to its R1 delivery bot. Nuro has also partnered with companies like CVS, Domino’s, and Walmart.
The company has since developed a second-generation vehicle, known as the R2. This delivery bot, which is designed for local delivery service for restaurants, grocery stores, and other businesses, received an exemption from the federal government earlier this year that allows it to operate as a driverless vehicle.
“We are witnessing an unprecedented shift in consumer demand for safe and affordable local delivery services,” Zhu, CEO, and co-founder of Nuro said in a statement. “This funding, which brings us together with many of the world’s top investors, positions Nuro confidently toward a future where our world-class technology is adopted into people’s everyday lives.”
The company, which is testing and operating R2 on public roads in Arizona, California, and Texas, told TechCrunch that the new funding will allow it to “confidently grow for years to come, with multi-year runway to build in multiple cities and scale across multiple markets.” Nuro’s near-term focus is on scaling its service in Houston and implementing R2 into commercial service.
Bay Area Brothers Hope to Feed The World With Their Robotic Indoor Farming Technology
Their entrepreneurial “garage” is a two-story-tall indoor vertical farm in San Jose, California, where we met up with CEO Samuel (a Santa Clara University graduate) and Chief Technology Officer John (Westmont College, Technical University of Munich)
June 28, 2020
By Linda Zavoral
Mercury News
(San Jose)SAN JOSE, Calif. – You’ll forgive the Bertram brothers if their Silicon Valley elevator pitch is as fast-paced as a doubles match. After all, they moved from Melbourne, Australia, to the United States to play collegiate tennis, then developed a love for engineering and robotics – and a lofty goal to meet the world’s nutritional needs.
Less than a decade after arriving in California, they co-founded OnePointOne, an agricultural technology company, and Willo, their direct-to-consumer health and lifestyle brand.
Their entrepreneurial “garage” is a two-story-tall indoor vertical farm in San Jose, California, where we met up with CEO Samuel (a Santa Clara University graduate) and Chief Technology Officer John (Westmont College, Technical University of Munich). After checking out the technology, gawking at the hundreds of red mizuna plants carefully nurtured by growers, engineers, and robots, and nibbling on just-harvested, state-of-the-art basil, it was time to ask some questions.
Q: How did you two hit upon this idea for a vertical farming start-up?
Sam: There are 1.1 billion people that began this millennium malnourished. Think about that number for a moment. Galvanized by its magnitude, John and I named our vertical farming company OnePointOne, or OPO, as a constant reminder of what we are aiming to solve. Compounding the problem: Poor nutrition kills more people in the USA than anything else, including cigarettes. Plants have always been and will continue to be, the solution to the problem of malnourishment and diet-related disease. Our technology – through production and plant research – intends to solve these problems.
Willo is the first revolutionary step in this direction. It is the direct-to-consumer brand of our company. By allowing you to configure and control what you grow in your Willo Farm Plot, we can work together to personalize your nutrition, and use plant-based food as the primary tool for preventative medicine that it has always been.
Q: How does Willo’s OnePointOne technology differ from other indoor farming methods?
John: Willo’s high-performance indoor farming technology is different from any other indoor or outdoor farm. We use LED lights to supplant the sun, we use a nutrient-rich mist to replace the soil, and a clean-room environment to keep the plants safe, comfortable, and away from the dangers of the outdoors. We are the only organization in the world to grow plants out of tall vertical towers using aeroponics (which is a form of hydroponics using a nutrient-rich mist). And we use fleet robotics to perform many of the functions inside of our farm – everything from plant seeding, plant movement, and plant inspection.
Q: An early client of yours is chef David Kinch’s new Mentone restaurant in Aptos.
He calls basil the “spirit animal” for that Cal-Mediterranean concept. So you’ve got a three-Michelin-starred chef who wants high-quality basil year-round. No pressure there! How did you develop a basil that meets his standards?
Sam: Chef Kinch offered us a challenge to replicate the quality of a specific basil variety grown in Pra, Italy. Through many months of varying the size, shape, taste, and texture of the basil, we arrived at precisely the product he was looking for. Now we are the sole supplier of Ligurian Genovese basil to his restaurant.
Funnily enough, now that we have the “recipe” to grow Mentone’s basil, the pressure is off. Since we control the plant’s experience so closely, the replicability and consistency of the product is guaranteed.
Q: Are there nutritional studies that have compared vegetables and herbs grown this way with those grown conventionally outdoors in soil?
Sam: Yes, and we are in the process of compiling an extensive study on Willo’s produce in comparison to outdoor-grown produce. What I can say is that organic farms use pesticides and often contain heavy metals. Willo’s produce never will.
To be clear, conventionally and “organically” grown produce is still far better for you than almost any other food, and the farmers/workers that grow it for you are modern-day superstars. The problem is one of sustainability. Massive consumption of water, large-scale contamination of water, soil degradation, and pesticide poisoning are all very serious problems that Willo’s farming technique eliminates.
Q: How do you mitigate the effects of the agricultural job losses this technology creates?
John: In every facility that Willo builds, there will be a host of new employment opportunities for a wide variety of skill sets – growers, engineers, scientists, and operators. These facilities are set to create jobs in each location we build, not eliminate them. Indoor farming is the last thing farmers and their laborers have to worry about. Without our technology, there is already a shortage of workers and an average age of 57. Willo ensures that in the midst of these statistics, consumers will continue to receive access to fresh produce.
Q: You’re now starting to grow produce for the public. How does this membership work and what will customers receive?
Sam: You get to subscribe directly to Willo’s Farm and claim a Farm Plot of your own. You’ll first receive a home-delivered Welcome Box filled with our first generation of crops; 5 oz. kale, 5 oz. mizuna, 5 oz. protein crunch, 5 oz. microgreens and a 5 oz. salad mix of the combination of products. Within seven days you’ll be given the opportunity to configure your farm with the crops you enjoy most or to continue with the Welcome Box farm configuration. Depending on your subscription, Willo delivers these five 5 oz. packages weekly or bi-monthly directly to your door.
Willo is currently developing an app to connect you directly to your Farm Plot. There, you’ll be able to watch your plants grow through time-lapse imagery, add new crops to your Farm Plot, trade Farm Plots with your neighbors, and donate Farm Plots to Willo’s charitable partners among many other things.
SWITZERLAND: Migros Basel And Growcer Launch Joint Vertical Farming Project
Switzerland's first "Robotic Vertical Farm" is currently being built in a hall located on the Wolf site in Basel. From sowing to irrigation and harvesting, machines take over the work fully automatically
“Vertical Farming Meets The Demand
For More Sustainability And Regionality"
Together with the Migros Basel cooperative, Growcer is developing the first "Robotic Vertical Farm" in Switzerland, in order to grow regional foodstuffs there in the future, independent of weather conditions, pesticide-free and water-saving, and - thanks to the shortest transport routes - to deliver them quickly to the Migros branch. The start of production is imminent, and the first products are expected to be available exclusively in the MParc Dreispitz in the summer.
Switzerland's first "Robotic Vertical Farm" is currently being built in a hall located on the Wolf site in Basel. From sowing to irrigation and harvesting, machines take over the work fully automatically. The production chambers are sealed off from the environment, which means that production can take place all year round without soil, without any pesticides and with up to 90 percent less water.
In addition to all this, land consumption is, of course, minimal, as the cultivation beds can be stacked. This creates around 1,000m2 of cultivated area on a surface area of just 400m2. The farm can produce leafy vegetables and herbs all year round and, thanks to the immediate proximity of the sales point in the MParc Dreispitz, these can be delivered absolutely fresh within hours of being harvested.
Regionality and continuity
"Switzerland, like many countries, is dependent on imports. Via Growcer we bring regionality and continuity into it. In addition, pesticides are a problem for the population and nature, which we can solve by doing without them. With Migros Basel we have found a partner who supports our values and goals and is committed to the introduction of a new generation of sustainable products", says Marcel Florian, CEO of Growcer AG.
"Vertical farming is a trend that meets the demand for more sustainability and regionalism", says René Lori, Head of Supermarkets/Catering at Migros Basel. "The cooperation with Growcer gives us the opportunity to invest in an innovative and future-oriented project".
Year-round production
The production facility on the Wolf will be completed next spring, and the first products are expected to be available exclusively at Migros in the MParc Dreispitz in the summer. It is planned to produce further vegetables or fruit all year round at a later date and to supply other branches.
Migros Basel and Growcer are looking forward to the cooperation.
Source: Migros Basel
Publication date: Fri 17 Jan 2020
Sustainability In Three Dimensions
Picture a snow globe. Inside its crystalline sphere, the conditions are always ideal for a winter wonderland—even in the hottest days of summer. So, what if farmers could take this idea and use it to create optimal, self-contained cultivation environments that allowed them to grow their crops during the dead of winter?
Technology Spotlight December 20, 2018
Picture a snow globe. Inside its crystalline sphere, the conditions are always ideal for a winter wonderland—even in the hottest days of summer. So, what if farmers could take this idea and use it to create optimal, self-contained cultivation environments that allowed them to grow their crops during the dead of winter?
A traditional approach to this challenge is greenhouse farming, in which glass domes heighten and retain solar energy within a growing environment that’s closed off from the surrounding atmosphere. As a result, the temperature inside the dome is warmer and more stable, allowing farmers to cultivate warm-weather crops during the cold seasons.
If farmers can grow their crops through the winter, what if they could grow them through the night?
WHAT IF GROWERS COULD CREATE THE INFRASTRUCTURE TO GET 10 ACRES WORTH OF PRODUCTION FROM ONLY ONE ACRE OF LAND?
It may sound improbable to grow plants in closed environments without relying on the sun, but modern agriculture is already making incredible strides in bringing 24/7 cultivation to reality by augmenting existing practices with indoor vertical farms and robotic technologies.
In fact, vertical farms are on the rise. There are currently 2.2 million square feet of indoor farms operating across the globe, and that number is expected to increase almost tenfold to 22 million square feet in the next five years. Will vertical farming replace conventional farming practices? No, but this dramatic rise in indoor farms will add even more of a boost to our future food production capabilities, complementing the incredible innovations that are being made in traditional sun-soaked, outdoor crops.
Why such the exponential increase in interest and investment in both vertical farms and robotics? In short, this pairing offers profound potential to help agriculture achieve sustainability in the environmental, economic, and societal spheres.
To read the entire article, Please Click Here
Stacked Farm, Australia's First Fully Robotic End-to-End Vertical Farm
Australia may have one of the world's lowest population densities and plentiful farmland, but as farmers know all too well, water is and will continue to be a great challenge for the country's food supply
Written on the 3 December 2019 by Matt Ogg
Whether it be Bowery Farming backed by Google's parent company Alphabet, Square Roots which was founded by Elon Musk's brother Kimbal, or the innovative startup InFarm with leafy green-growing modules installed in supermarkets, vertical farming is a fertile space for development right now.
Australia may have one of the world's lowest population densities and plentiful farmland, but as farmers know all too well, water is and will continue to be a great challenge for the country's food supply.
Innovations abound in the sector, most notably Sundrop Farms in South Australia which has become a global leader in sustainable agriculture by powering its greenhouse with solar power and sourcing irrigation from desalinated seawater.
Now another Australian company Stacked Farm is set to join the ranks of innovators pioneering food solutions for the future.
After four years of research and development, the Gold Coast-based group's fully automated end-to-end vertical farm will soon be supplying leafy greens to national wholesalers including Sumo Salad, QSR, Dnata, Crown Resorts and Morco Fresh.
This means Stacked Farm's urban-grown produce from Burleigh Heads will be supplied to casinos, in-flight airline catering and retail outlets around the country, with plans for expansion with new facilities in 2020.
A spokesperson for the company says the facility is likely the first of its kind in the world to be fully automated.
"Other vertical farms might have a component of automation but one or two components are done by hand whether that's seeding, cutting or packing," she says.
Stacked Farm CEO Conrad Smith (pictured) says the farm is commercially viable, scalable and competitive, from seedling through to packaging with leading-edge technology.
"A good crop is not weather dependent and can be grown using up to 95 percent less water than conventional farming. It eliminates the use of pesticides and other climate-related hazardous processes as the growing is fully contained and controlled," says Smith.
"We also take sustainability very seriously and renewable power is already contributing up to 30 percent of what it takes to power the farm."
"Drought has wiped out so many primary producers in the country. Water is always going to be an issue in Australia it's our most valuable commodity. Vertical farming can help support our farmers in times of drought or crisis."
Efficient water usage is just one of the sustainable aspects that makes this operation appealing to food wholesalers in Australia. Produce growth is fast and shelf-life longer, with the entire process from seed to bag taking only 16-21 days.
"Produce life is increased due to the controlled growing environment, the technology and the fact it's packed within seconds of harvest and there's no need to wash it - which can be a big degrader of product quality," he says.
"It's great for growing in the city, as we can deliver within kilometres of the produce being grown, not like most farms who rely heavily on lengthy transport distances."
While the current facility can produce a couple of tons of produce a week equating to a 20-acre farm in output. Smith doesn't see this as working against traditional agriculture but rather as a means to complement it.
It's a game-changer for the cattle industry. We have identified that we can grow livestock feed en masse very quickly, and again using up to 95 percent less water. A 1000sqm vertical farm will have enough output to feed hundreds of cattle daily."
"The impact that this could have on farming communities that are suffering through the drought is enormous."
While the production is currently focused on leafy greens, herbs and livestock feed, Stacked Farm is also working with the CSIRO to develop additional products suited for indoor vertical farm growth.
Discussions are also underway with property owners in Victoria and Queensland to build farms suitable for produce growing, as well as a major farming operator in NSW to grow livestock feed.
Roto-Gro on track for Freshero JV and first facility
In other recent horticultural news, ASX-listed Roto-Gro International announced Friday that it had made significant progress in negotiations for a joint venture with Freshero, an aspiring organic produce grower with longstanding relationships across the wholesale, retail and foodservice space in Australia, Southeast Asia and the Middle East.
The company expects to execute the terms of an agreement by the end of 2019, in a move that will see the construction of a fully automated state-of-the-art facility Roto-Gro's patented and proprietary cultivation technology with standard agricultural seeding and harvesting equipment.
This technology includes rotational garden systems, fertigation units, the company's iGrow Software as well as material management systems.
Roto-Gro said Freshero CEO Tony Mahoney had strategically positioned Freshero to lead the development of organic urban vertical farming and distribution centres for fresh organic produce grown in proximity to large urban centres.
Despite the positive news, the RGI share price is currently less than half of what it was a year ago, most likely due to the collapse of cannabis stocks to which its growing technology is also closely aligned.
Can Cutting Costs, Via Robotics, Unlock Vertical Farming Profits?
Despite the enthusiasm of the investment community for vertical ag in recent years, the indoor vertical farming industry has yet to deliver an economically viable business model
October 15, 2019
Donald Marvin Contributor
GETTY
Despite the enthusiasm of the investment community for vertical ag in recent years, the indoor vertical farming industry has yet to deliver an economically viable business model. No matter how well funded they might be, most indoor vertical farms struggle to be profitable. The reasons are simple: high operating costs, especially for labor and energy.
One of the newest entrants to the vertical ag scene, Fifth Season, has designed its first 60,000-square-foot indoor vertical farm, now being constructed near Pittsburgh, and is looking ahead toward solving the profitability challenge. The company got its start under the name RoBotany while in the incubator program at Carnegie Mellon University’s (CMU) Swartz Center for Entrepreneurship, which supports innovation coming out of the university's renowned robotics, business and other schools. Drive Capital and other investors with connections to CMU have helped supply over $35 million in total funding to date to help Fifth Season commercialize its innovative technology platform.
Co-founder and CEO Austin Webb, a CMU alum and former investment banker with B. Riley FBR, said it took the company three years to develop and perfect its platform technology at two indoor R&D farms, working out of an old warehouse in Pittsburgh. Webb and his team—plant scientists and robotics and AI engineers—designed their facility to achieve the goal of producing greens, including spinach, arugula, lettuce and herbs, to be sold locally, at affordable prices and at a profit.
Fifth Season's first commercial, large-scale indoor vertical farm will begin operation in early 2020. It is a welcomed participant in the revitalization of the riverside town of Braddock, longtime home of U.S. Steel’s Edgar Thomson Works, one of the oldest still-operating steel plants in the Monongahela Valley.
Webb and his colleagues noticed early on that, after an initial surge of investments in vertical farming, funders have more recently been posing very pointed questions about profitability. Accordingly, said Webb, his team has been designing with profitability as the paramount objective.
“Consumers are all in for locally produced, clean food that’s affordable,” Webb noted. “But to be sustainable and profitable long-term, you’ve got to prove favorable ‘all-in’ per-unit costs. And that’s what makes us different in the industry.”
That is where robotics come in. In their due diligence, Webb and colleagues saw that routine work in the full production chain could be turned over to robotics to help drive down costs. That’s most opportune, given that somewhere from 40% to 60% of a typical vertical farm’s operating costs are for labor. Fifth Season has targeted 20% and less, courtesy of robotics.
“We said, let's take an empty warehouse and design a system—from seed to harvest to package to destination,” Webb said. Their resulting proprietary design strings together an “Internet of things” of about 40 different robotic components, or “bots”—in Webb’s words, “a fully integrated solution of robotic hardware and software.”
Energy is another big cost factor in vertical growing, and Fifth Season’s team designed its operation with cost efficiency in mind there, too. Energy costs are reduced via solar collectors, which help provide the power supply not only to the robotics and IT, but for grow lights, which are in use 16 or more hours a day in a typical indoor vertical farm.
Fifth Season is collaborating with GE Current, a Daintree Company, to employ the most efficient lighting technology to its operation. In an interview, Michel Doss, general manager of specialty at Current in Montreal, said he believes a vertical-farming approach that can drive energy and labor costs down toward those of outdoor farming will be the big winner.
“I'm definitely convinced 100% that vertical farming will work,” Doss said in an interview. “But nobody knows exactly when as a date on a calendar. But the economics have to be there for it to happen.”
In addition to working with Fifth Season, Doss's division did the lighting for two of the largest vertical farms in the world: Mirai Co. of Japan and the U.K.’s Jones Food Co.
Doss called the advent of LED lighting a “missing link” that has enabled indoor farming. But, he added, lighting is only one factor, along with seeds, ventilation, humidity control and airflow, among others: “The entire ecosystem for indoor growing is critical. The technology is still evolving as it’s being tested in the field.”
Lighting alone is a work in progress, he said: “We’ve historically done a mix of deep red, which has a 660-nanometer range, and blue, a regular blue that’s readily available and seems to be yielding good results with leafy greens. But we still need more studies. What about adding green? What about white, and what kind of white, because all white isn't equal? We're just at step one of a 10,000-step journey in the space.”
Webb’s team at Fifth Season, along with Doss’s Current lighting crew and other vendors and collaborators, are still tweaking many variables, always with a sidelong glance at the elusive holy grail of indoor growing: tasty and sustainable profits.
Follow me onTwitter.
I am president and CEO of Concentric, a developer and producer of proprietary biological and plant nutrient inputs for specialty and broadacre crops. Concentric was named one of the Forbes Top 25 Most Innovative Agtech Startups in 2018. I report on agtech developments based on my more than 30 years’ experience in building and leading bioscience and agtech companies. Prior to joining Concentric in 2014, I was CEO at IdentiGEN, Inc., a provider of DNA-based solutions to the agriculture and food industries. Earlier in my career, I co-founded the Nasdaq-traded Orchid BioSciences, a pioneer in human DNA identity testing and was president and CEO of Diatron Corporation, a biomedical company developing fluorescence-based instrument systems for the clinical diagnostics industry. I have raised in excess of $350 million in both private and public financings and completed over a dozen M&A transactions. I earned my B.S. in microbiology from Ohio State University and an MBA from Iona College.
This Startup Is Building A Massive Indoor Farm In A Rust Belt Steel Town
The farm, from a startup called Fifth Season, will begin selling spinach, lettuce, and other leafy greens early next year, using a robot-based system that the founders say is cost-competitive with growing and transporting the same crops from a traditional farm
Fifth Season will begin selling spinach, lettuce, and other leafy greens—all grown inside with the help of robots—early next year.
[Photo: courtesy Fifth Season]
10.22.19
In a vacant lot next to one of the last remaining steel mills in Braddock, Pennsylvania, a town just south of Pittsburgh, a massive new indoor farm is taking shape. The farm, from a startup called Fifth Season, will begin selling spinach, lettuce, and other leafy greens early next year, using a robot-based system that the founders say is cost-competitive with growing and transporting the same crops from a traditional farm.
It’s more affordable, they argue than some others in the vertical farming industry. “We looked at vertical farming and realized that the industrywide struggle to make the economics work was a huge factor, and something that would really prevent the industry from truly taking off,” says Austin Webb, co-founder, and CEO of Fifth Season, which incubated its first farm at Carnegie Mellon University. “The per-unit economics don’t work. Companies are losing money for every pound that they sell. And that obviously needs to change.”
[Photo: courtesy Fifth Season]
Like others in the space, the startup touts the advantages of growing indoors. It’s possible to use only a tiny fraction of the water that’s used to grow greens in fields; most lettuce is currently grown in drought-prone California and Arizona. (In Arizona, farmers will also soon start losing access to water from the Colorado River.) Growing indoors eliminates the need for pesticides. It eliminates food safety hazards like E. coli contamination. And if crops are grown close to end markets—in this case, restaurants and stores in Pittsburgh—it also eliminates the emissions from trucks traveling thousands of miles and the problem of less-than-fresh produce that may be more likely to be thrown out because it’s already starting to wilt. “When we look at the food distribution system, we looked at it and saw an overly complicated broken system, where no one’s connected to their food, and there’s a lot of food waste,” Webb says.
[Photo: courtesy Fifth Season]
Some past efforts at indoor farming have failed because of high costs, such as FarmedHere, near Chicago, which shut down in 2017 in part because of the cost of labor. “When you look at vertical farms and labor is 40% to 60% of their cost—labor for them is actually more than the all-in delivered cost of Western-grown field produce—it’s just not going to work,” he says. The company’s system, which it has running now at another location and which it’s recreating at the new location, uses around 40 robots. “Together, they’re completely integrated so that our facility is, in a sense, one robotic system.”
Robots plant seeds in trays and deliver trays to grow rooms, where automated systems control everything from the amount of nutrients the plants receive to the schedule of lighting and the amount of carbon dioxide in the air. When a crop is ready, it goes into an automated harvesting system, and then to an automated packaging system, and the trays are sent back to be automatically cleaned and sanitized and then replanted. “We essentially looked at it and said that we should create an automated fulfillment center,” says Webb. “The difference being that instead of pallets of boxes, it should be trays of plants.” Solar panels on the roof and a battery backup system means that the facility can continue operating even if extreme weather takes out the electric grid.
[Photo: courtesy Fifth Season]
Other companies in the industry are also developing automated systems, including Plenty, a Softbank-funded Silicon Valley startup that now has a suite of state-of-the-art custom robotics. Plenty hasn’t shared the details of the cost of its system. But Fifth Season estimates, as an example, that its own robot used for storing and retrieving plants may cost two to three times less. It also uses space more efficiently than some other companies; because everything is automated and humans don’t need to access rows of produce on scissor-lift equipment, the aisles between plants can shrink, growing more produce in the same amount of space. (The new farm is 60,000 square feet, a little smaller than the 69,000-square-foot farm run by another company called Aerofarms.) During its first full year of operation, it expects to grow half a million pounds of greens and herbs, with prices in line with organically grown produce. At that price point, the payback period of the full system will be less than two years.
[Photo: courtesy Fifth Season]
In Braddock, where the population has shrunk more than 90% since its high point in the 1920s to around 2,000 people today, the new farm can provide some new jobs, despite the automation. Three shifts a day will employ 20 workers each. “These are manufacturing-like jobs where we’ve got folks that are helping us operate our machinery,” Webb says. “We’ve got folks that are monitoring the health of the equipment. All of that is something where someone can come from a previous job and you’re not necessarily saying you’re going to do something that’s totally completely different, such as sit at a computer and write code.” As the company expands, it will also hire more engineers and plant scientists.
The startup hopes to replicate the new facility, designed as a modular system, throughout the country. “We’re able to take what we’re building in Braddock and take those blueprints and really hit the repeat button quickly,” he says.
ABOUT THE AUTHOR
Adele Peters is a staff writer at Fast Company who focuses on solutions to some of the world's largest problems, from climate change to homelessness. Previously, she worked with GOOD, BioLite, and the Sustainable Products and Solutions program at UC Berkeley, and contributed to the second edition of the bestselling book "Worldchanging: A User's Guide for the 21st Century."
You Might Also Like:
Robots are already farming crops inside this Silicon Valley warehouse
Live in your own farm in the sky in this plant-covered apartment building
Video: The most crucial advice Patreon CEO Jack Conte has for any struggling creator
SPONSORED: OLD DOMINION
How Old Dominion is using technology to better serve its customers
Shenandoah Growers Opens Next Generation USDA Certified Indoor Biofarms In Virginia
The new BioFarms will solve persistent problems in the fresh product supply chain – delivering peak freshness, longer shelf life, enhanced food safety, reduced food miles, and year-round organic supply.
ROCKINGHAM, Va. — Shenandoah Growers, Inc., the US leader in indoor USDA certified organic agriculture, has begun harvests at its next generation BioFarm facilities in Rockingham and Elkwood, Virginia. The company will now grow, pack and ship locally grown, premium quality organic produce from its sustainable indoor farms to its customers in the Mid-Atlantic region 365 days a year.
Shenandoah Growers BioFarm Basil Plants
The new BioFarms will solve persistent problems in the fresh product supply chain – delivering peak freshness, longer shelf life, enhanced food safety, reduced food miles, and year-round organic supply. Shenandoah’s sustainable growing technology uses bioactive soil and fresh water, just like in nature, producing healthy organic plants and delivering on the company’s mission to reduce its carbon footprint and lead in environmental stewardship.
The Rockingham BioFarm will supply 100% of Shenandoah’s basil in the Mid-Atlantic region, marking the transition away from traditional field production. Basil is not only the best-selling herb, but it is also the most difficult to grow and ship nationally due to its vulnerability to weather volatility, disease and temperature damage. The Elkwood BioFarm will supply the company’s new line of local organic lettuces to Mid-Atlantic customers.
“Being able to grow the totality of our basil demand inside our pack house and not fly or truck hundreds or thousands of miles from the field was inconceivable when I entered the business over 20 years ago,” says Tim Heydon, CEO.
While Shenandoah Growers are pioneers in indoor organic agriculture, they are quick to emphasize that the company has been farming and operating in the industry for over 30 years. Chief Customer Officer Steven Wright intoned, “It’s one thing to be able to grow indoors, it’s quite another to harvest, pack and deliver with consistent quality 7 days a week, 52 weeks a year while meeting demand during peak seasons.”
The company points out that its indoor production units, many of which have been in operation for over 4 years, are proven efficient. According to company President, Phillip Karp, “Fundamentally we are about the democratization of sustainably grown organic produce, and for the promise of indoor agriculture to truly unlock its great potential, it must achieve cost parity with traditional farming. Anything we launch from our indoor farms will be scalable and profitable for us and our customers and affordable for the shopper.”
The company is in the process of accelerating its indoor farming capacity with a clearly defined plan to deploy additional next generation USDA certified organic Biofarms across its entire national platform of operating locations.
About Shenandoah Growers, Inc.
Founded in 1989, Shenandoah Growers is the leading grower and marketer of fresh organic culinary herbs in the United States, providing sustainable, USDA certified organic, regionally grown produce to retailers coast-to-coast. The Rockingham, Virginia-based company has developed the nation’s largest commercial indoor organic growing systems and continues to redefine how to bring fresh, organic, and sustainably farmed produce to market—operating across a nationally integrated platform of farms, production, and logistics facilities. For more information, please visit www.shenandoahgrowers.com.
Under the THAT’S TASTY® BRAND, Shenandoah Growers provides USDA organic, non-GMO, regionally grown, and sustainably farmed fresh culinary herbs and greens. Launched in 2017, the THAT’S TASTY BRAND offers consumers ways to add Pure Organic Flavor™ to their everyday cooking by offering a full line of products including living organic herb plants, fresh cut herbs, herb purees, lettuces and microgreens. www.thatstasty.com
2 Day Webcast Series: New Ag International Digital Week
Join us 14 & 15 October 2019 for New Ag Digital Week, a global 2-day series of live educational webcasts and downloadable resources providing the latest insights on Biostimulants, Biocontrol, specialty fertilizers, Irrigation and new/the latest Greenhouse and Precision Ag technologies
Join us 14 & 15 October 2019 for New Ag Digital Week, a global 2-day series of live educational webcasts and downloadable resources providing the latest insights on Biostimulants, Biocontrol, specialty fertilizers, Irrigation and new/the latest Greenhouse and Precision Ag technologies.
Day 1: Monday, October 14, 2019
The Impact of Swarm Robotics on Arable Farms
9am EDT / 2pm BST / 3pm CEST
Does deficit irrigation work in annual crops? Best practices learned from Spain
10am EDT / 3pm BST / 4pm CEST
Day 2: Tuesday, October 15, 2019
New Biostimulant Technologies Focus on Efficiency
9am EDT / 2pm BST / 3pm CEST
Development of New Biological Control Agents Against Apple Scab and Powdery Mildew
10am EDT / 3pm BST / 4pm CEST
REGISTER NOW
To sponsor future digital events, contact partners@knect365lifesciences.com or request details.
RoBotany Builds 60,000-Square-Foot Vertical Farm In Braddock, Plans Nationwide Expansion As Fifth Season
The company's first urban farm, incubated at Carnegie Mellon University, uses proprietary robotics technology to grow affordable fresh produce for Pittsburgh-area grocery stores and restaurants
The company's first urban farm, incubated at Carnegie Mellon University, uses proprietary robotics technology to grow affordable fresh produce for Pittsburgh-area grocery stores and restaurants
NEWS PROVIDED BY Fifth Season
September 24, 2019
PITTSBURGH, Sept. 24, 2019,/PRNewswire/
Fifth Season, an indoor farming pioneer, announced plans for its first highly efficient, commercial-scale indoor vertical farm, which will open in early 2020 in Braddock, a historic steel town near Pittsburgh.
Fifth Season, originally founded as RoBotany Ltd., is a consumer-focused technology company that was incubated at Carnegie Mellon University's (CMU) Swartz Center for Entrepreneurship—an alliance of CMU's business, robotics, and other schools focused on fostering innovation. The company has raised over $35 million to date led by Drive Capital and other private investors with close ties to CMU. Its leadership team has deep expertise in plant science, robotics, AI and systems engineering.
Austin Webb, Fifth Season's co-founder, and CEO
Austin Webb, Fifth Season's co-founder, and CEO said the company's 60,000-square-foot Braddock farm will set a new vertical agriculture standard for efficient, safe and sustainable production of pesticide-free leafy greens and herbs in urban communities.
Fifth Season developed and perfected its technology with two R&D vertical farms in Pittsburgh's South Side neighborhood. Their leafy greens have been sold at local retailers, such as Giant Eagle and Whole Foods Market, along with popular Pittsburgh restaurants Superior Motors, honeygrow and Kahuna.
Produce from the flagship production farm coming to Braddock will also be available in Pittsburgh-area grocery stores and restaurants.
"The goal through our first three years of development was to prove we could bring fresh food to urban customers at prices competitive with conventionally grown produce," Webb said.
"We have developed fully integrated, proprietary technology to completely control the hydroponic growing process and optimize key factors such as energy, labor usage and crop output," Webb added. "The result is a vertical farm design that has over twice the efficiency and grow capacity of traditional vertical farms. Our unprecedented low costs set a new standard for the future of the industry."
Webb said the Braddock farm's ideal growing environment will deliver perfect, pure produce, in any season. It will produce over 500,000 pounds of lettuce, spinach, kale, arugula and herbs from its 25,000-square-foot grow room during the first full year of operation. The facility is partially solar-powered and requires 95 percent less water compared to traditional growing operations.
Webb said the company is planning a staged expansion in additional, similar-sized cities across the U.S.
Photos and graphics to accompany this announcement can be downloaded at this link: https://www.dropbox.com/sh/8ucvpnvlln10o7x/AADzxmH2iA3rr9LGNO_BrMc1a?dl=0
Contact:
Grant Vandenbussche, Fifth Season (248) 240-4694, grant@robotany.ag
or
Michele Wells, Wells Communications (303) 417-0696 or mwells@wellscommunications.net
SOURCE Fifth Season
The Scottish Innovations Tackling The World’s Food Shortage
Invergowrie-based Intelligent Growth Solutions (IGS) has created Scotland’s first vertical farm, pictured here, and the company has recently harvested a £5.4 million cash boost from the Scottish Investment Bank, agri-food investor S2G and online venture capital firm AgFunder
Intelligent Growth Solutions' purpose-built facility is being constructed at the James Hutton Institute near Dundee.
SARAH DEVINE
19 September 2019
Scotland’s agriculture sector is changing rapidly, with rural businesses across the country driving forward groundbreaking innovations in attempts to address the myriad challenges of the land.
Globally, some 113 million people across 53 countries reportedly experienced food poverty last year, and it is expected that the world’s population will reach 9.8 billion by 2050, according to the UN.
However, inventive organizations across Scotland are devising new and creative ways to tackle the global food shortage.
Invergowrie-based Intelligent Growth Solutions (IGS) has created Scotland’s first vertical farm, pictured here, and the company has recently harvested a £5.4 million cash boost from the Scottish Investment Bank, agri-food investor S2G and online venture capital firm AgFunder.
The firm, which is based at the James Hutton Institute situated on the outskirts of Dundee, provides vertical farming technology to enable efficient food production through indoor crops around the world, having built its demonstration facility at Invergowrie last year.
It features stacked layers, LED lights and app-controlled air vents to create the perfect conditions for crops to thrive all year round.
The early-stage company states that its patented Internet of Things-enabled power and communications platform is able to reduce an organization’s energy usage by up to 50 percent and labor costs by up to 80 percent, in comparison to other indoor growing environments, and can produce yields of 225 percent compared to crops that have been grown under glass.
IGS experimented with colored LED lights, growing basil plants at the indoor facility in an impressive 20 days.
Its chief executive, David Farquhar, explains that such developments are urgently needed because at present an astonishing 30 percent of the world’s food is put to waste.
“Vertical farming allows experimentation to take place in order to impact the yield or cost of production, flavor, nutrients, appearance or a combination of those things,” he says.
“Producers want consistency, assurance of supply, and to know they are going to fill supermarket shelves or supply those Michelin-starred restaurants every day of the week. Those are things that farmers struggle with all the time.”
Farquhar adds: “If there is a forecast for bad weather and a supermarket decides to only take half of their delivery, what are they going to do with the rest of the produce?”
Using the vertical farm, a crop’s growth can be slowed down or sped up to prevent waste.
“People have been talking about vertical farms for several years, but we are now at the starting point. Over the next six months, we will get going with the first technology in the world that is capable of delivering this on an industrial scale.”
The firm, which was formed in 2013, plans to use this recent funding to create jobs in areas such as software development, engineering, robotics, and automation.
Investment into such areas is also needed across Scotland because dietary demand is changing, according to David Ross, chief executive of Edinburgh-based Agri-EPI Centre.
“Environmental sustainability is personal now for everyone and therefore there are challenges for primary producers to adapt to the needs of the consumer, the needs of society and the overall sustainability of the planet,” he says.
FARMPRO: Fully Automated And Climate Controlled 40' Container Farming
The Urban Crop Solutions FarmPro is a 40 ft fully automated freight container with a state-of-the-art leafy green growing system. This system gives you a fully automated 4-layer growing solution
FARMPRO by Urban Crop Solutions
A FULLY AUTOMATED AND
CLIMATE CONTROLLED 40' FREIGHT CONTAINER
The Urban Crop Solutions FarmPro is a 40 ft fully automated freight container with a state-of-the-art leafy green growing system. This system gives you a fully automated 4-layer growing solution.
HYDROPONICS AND OWN GROWTH RECIPES FOR 200+ CROPS
To deliver healthy crops, our closed-loop irrigation system:
Minimizes the use of fresh water
Increases plant nutrient uptake and can work with up to 70 organic nutrients and minerals
Provides optimal root growth, aeriation and nutrient delivery
Allows to grow microgreens and super-large crops
CLIMATE CONTROLLED ENVIRONMENT
In/outflow of air is controlled to limit unwanted elements while optimizing climate conditions.
Closed production plants have minimal external elements influencing the indoor climate
Monitoring the in- and outflow of air allows for the best possible crops
Flavour can be tailored to market demand by influencing climate, light and nutrients
CUSTOM-MADE LED TECHNOLOGY
Our own LED lights provide the optimal spectrum for your plants, using limited energy.
The photosynthetic active radiation (PAR) range, enables photosynthesis in the 400-700nm range
Using energy-efficient LEDs, our crops receive just the right light spectrum to grow efficiently
ROBOTIZED AND CONTROLLED PROCESS
Our top-notch industrial standards allow full control over monitoring and automation.
Minimize human intervention to achieve higher levels of pro
STANDARD FUNCTIONS
40 ft insulated container
Climate control
SIZE: 40” - LAYERS: 4
1 irrigation system
Continuous monitoring
Custom-made LEDs
4 cultivation layers
Handling area and technical room
Fully automated growing process
Online crop and process management
OPTIONS
Custom outside colour
Personalized logo on container
Up to 2 different water systems
1 or multiple windows
1 or multiple webcams
Back-up power system
WHAT YOU GET
80 M² GROWING SURFACE
1.6K- 3.6K CROPS PER GROWING CYCLE
24K - 54K CROPS PER YEAR
To View Our Videos, Please Click Here
ARE YOU INTERESTED IN A FARMPRO?
Would You Like To Receive Additional Information?
3 Ways Technology Is Changing The Food-Growing Industry
It's happening right before our eyes -- robots have submitted their resumes and are taking over human jobs. Robotics is certainly the change that we can neither deny nor refuse, the very next thing in technology
The Phenomenon of Uncontrollable
Weather And Farming Conditions Demand A Solution.
CONTRIBUTOR
Consumer Goods Entrepreneur, Freelance Writer
August 2, 2019
Opinions expressed by Entrepreneur contributors are their own.
It's happening right before our eyes -- robots have submitted their resumes and are taking over human jobs. Robotics is certainly the change that we can neither deny nor refuse, the very next thing in technology.
The effect of this "next level" is not limited to any industry. Apart from the threat it poses to human labor, which might imply job loss for many, these machines serve to ensure efficiency and effectiveness of processes and products, reduce lag time and increase output.
Related: How Visionary Tech Can Help Prevent Climate Change
This is particularly true for the agricultural industry. With vertical farming came the use of controlled-environment area (CEA) technology for growing food. The phenomenon of uncontrollable weather and farming conditions received a solution with this technology-powered innovation. Skyscrapers, hitherto used or abandoned warehouses, and shipping containers were transformed into farmlands.
Within this farmland, the environment is controlled and techniques similar to greenhouses adopted. The augmenting of natural light with artificial lighting is not uncommon here. Most recently, LED lights are made to mimic sunlight for the purpose of growing foods. Call it a sneak peek into the future; below are three ways technology is changing food growing today.
1. Surprise technological advancements
We live in the computer age, and computer-powered machines are the new labor force. Tasks that depend solely on human labor are reducing by the day. We're looking at times when tractors and other farm machines drive themselves, and nothing is done the same way anymore. Over the last twenty years, the agricultural industry has experienced tremendous changes; you would be surprised to learn shocking ways AI is shaping the food growing industry.
This is good news, as machine intelligence is sure to condense the inefficiencies related to human labor. It's amazing how these technological advancements are running on auto-update even in the agricultural sector.
Related: No One Knows It But These 3 Industries Now Depend on AI
With vertical farming, urban areas don’t have to depend on rural farmers for their entire food consumption. While the former lacks the large expanse of land for farming, they can utilize the spaces in her high-rise building, abandoned containers or simply create some, to grow her food.
The lag time wasted on irrigation and fertilization at different times has been collapsed into fertigation, which is a process that combines fertilization and irrigation. Fertilizer is added into an irrigation system, and is most commonly used by commercial growers.
2. Weed control made easy
For small farms, human effort is effective for weed control. This is because of the time given to "seeing" and eliminating weeds across the farmland. Large scale food growing cannot afford the time and resources needed to pull it off. Hence, the use of herbicides and the devising of machines to aid in spraying.
Regular spraying leaves a lot of unnecessary herbicides lying around on the farm, which is both a waste of resources and labor effort squandered. The solution would be a weed-control process that targets the weeds alone, is fast, efficient, and has no effect on the farm yield.
Related: How has Technology Sown the Seeds for Advancements in Agriculture
With the advent of the seed and spray machines, computer vision and machine learning are combined to redefine weed control. The see and spray smart machine is the new way to control weed, as it jettisons 90% of the herbicide used while making sure weeds are eliminated. It comes with a "sense and a decide" function that sees every plant and decides the appropriate treatment for them, while the robotic nozzles target unwanted weeds in real-time as the machine drives through.
3. Robotic plant grafting and agricultural drones
Artificial Intelligence is all about speed, efficacy and convenience. With AI, once-stressful tasks are handled by robots. According to this report, vegetable expert Richard Hassell led a team of scientists at Clemson University's Coastal Research and Education Center who unveiled a robotic system that grafts disease-resistant roots to robust plant tops as quickly as you can say chop-chop.
On the other hand, agricultural drones allow farmers and the drone pilots that operate them to increase efficiency in certain aspects of the farming process, from crop monitoring to planting, livestock management, crop spraying, irrigation mapping and more. These drones are useful for land scouting, spot treating of plants and general farm management.
Related: What Is AI, and Will It Take Over Your Service-Based Business Job?
Precision agriculture seeks to use new technologies to increase crop yields and profitability while lowering the levels of traditional inputs needed to grow crops (land, water, fertilizer, herbicides and insecticides).
In conclusion, we can choose to either focus on the potential human job loss that this future implies, or we can embrace the change. The fact is, this is the future of food growing, and artificial intelligence is driving it.
Lead Image Credit: Sompong Sriphet | EyeEm | Getty Images
An Agricultural Robot Makes Its Debut In Fujian
The white agricultural robot, with 5G technology and many sensors, can move between two rows of green leafy vegetables in a greenhouse, collect data on the plants and send them to the control room
Online People 2019: 07
Fuzhou, 07/11/2019 (The People Online) - While industrial robots have become commonplace in factories throughout eastern China, the country's agricultural sector is seen by some as a place where few technologies they can take root, due to the high cost and the sophisticated natural environment involved in the cultivation of food.
But a research institute and a start-up based in Fuzhou, capital of Fujian province, east of China, are determined to change perception by jointly developing an agricultural robot.
The white agricultural robot, with 5G technology and many sensors, can move between two rows of green leafy vegetables in a greenhouse, collect data on the plants and send them to the control room.
Developed by the Academy of Agricultural Sciences of Fujian and Fujian Newland Era Hi-Tech Co Ltd, the robot is part of its efforts to build a functioning autonomous farm.
Unlike industrial plants where robots can follow pre-established routes and perform fixed jobs, such as feeding standardized electronic parts, agricultural environments are much more complex, said Zhao Jian, deputy head of the Institute of Digital Agriculture of the Academy of Agricultural Sciences of Fujian .
"Agricultural robots also have to adapt to a wide variety of crops, livestock and highly differentiated aquatic products," said Zhao.
To solve the challenges, the research institute and Newland have jointly developed a more sophisticated artificial intelligence system. The computer algorithms, as well as the positioning hardware, map construction, route design and avoid obstacles, have been optimized to adapt to the agricultural environment, taking into account fertilization, plant irrigation, bumpy roads and other factors natural.
The robot's head is equipped with two 5-megapixel cameras that make "eyes" and two 7-megapixel cameras that make "ears." With the sensors at the top of its head and mouth, the robot can also detect wind speed, carbon dioxide levels, humidity, temperature and other data about the natural environment of the greenhouse.
The farm robot has succeeded in verifying its compatibility with 5G mobile communication technology, which allows data to be analyzed by computers enabled by artificial intelligence in the control room more efficiently.
"Currently, the robot can automatically inspect farms and collect data samples that are used to drive various applications. It can determine the health condition of the plants and decide if pest control measures are required," said Chen Li, deputy director of Newland Marketing.
According to Chen, the robot remains a prototype and, based on this, the two sides hope to increase investments to develop versatile robots that can even harvest fruit with a bionic hand in the future.
"Based on the mass agricultural data and images we have acquired, we hope to build a plant growth model optimized to achieve automatic control of the growth environment and early warning of pests and diseases," Chen added.
China is now the largest industrial robot market in the world. As labor costs continue to rise, the demand for robots will be stronger in China, said Wang Tianmiao, president of the Intelligent Manufacturing Research Institute of Beihang University.
Lead Photo: An agricultural robot moves between two rows of plants in a greenhouse in Fuzhou, capital of Fujian Province. [Photo provided to China Daily]
VIDEO: This Robotic Farm Uses 90% Less Water Than Traditional Farming
There are multiple advantages of our approach to farming. With hydroponics, we can grow near consumption, near people. And with robotics, we can make sure that we're getting a consistently, great product every week
Iron Ox's robotic farm uses 90% less water than traditional farming.
The plants are grown without soil in sensor-connected, hydroponic trays.
Following is the transcript of the video.
This robotic farm uses 90% less water than traditional farming.
According to the World Resources Institute, the world population will be 10 billion by 2050.
That's 2.4 billion more mouths to feed than today.
That's a challenge that start-up Iron Ox is tackling.
Iron Ox wants to create more sustainable farming by combining robotics and hydroponics.
Hydroponics is the process of growing plants without soil.
Brandon Alexander: There [are] multiple advantages of our approach to farming. With hydroponics, we can grow near consumption, near people. And with robotics, we can make sure that we're getting a consistently, great product every week.
With Huge New Vertical Farm, Plenty’s Produce Could Hit More Shelves
Just outside the LED-lit depths of the Bay Area’s newest and most futuristic indoor farm, a robot arm grabs a row of seedlings and sticks them into a hydroponic planter. An even larger robot arm then flips the planter vertically and sends it onward to become one thin sliver of a 20-foot-tall wall of arugula, baby kale and beet leaves
June 20, 2019
Plants grow on vertical towers inside Tigris.Photo: Plenty
Just outside the LED-lit depths of the Bay Area’s newest and most futuristic indoor farm, a robot arm grabs a row of seedlings and sticks them into a hydroponic planter. An even larger robot arm then flips the planter vertically and sends it onward to become one thin sliver of a 20-foot-tall wall of arugula, baby kale and beet leaves.
South San Francisco vertical farm company Plenty has unveiled its biggest, most efficient and most automated farm yet in its hometown. Called Tigris, it grows produce hydroponically — without soil — with LED lights year-round. Unlike outdoor farmers, Plenty’s engineers don’t have to think about the seasons, pests or what plants will grow best locally. While Tigris is specifically designed for leafy greens, Plenty CEO Matt Barnard said the company has test-grown nearly 700 varieties of plants within the last year.
Related Stories
BY JONATHAN KAUFFMAN
U.S.’s first robotic farm opens in the Bay Area
BY LEENA TRIVEDI-GRENIER
The novice farmer whose search for his roots led to an organic...
BY TARA DUGGAN
The Bay Area company building world’s largest vertical farm...
There are more than 20 companies erecting indoor farms around the country — another Bay Area player is San Mateo’s Crop One, which is building a giant farm in Dubai. Industry leaders say vertical farms can be a solution at a time when labor shortages, drought and climate change threaten outdoor agriculture as well as bring fresh produce to regions that lack arable land. These farms are springing up all over the world, including Japan, the Netherlands and Antarctica.
According to Plenty, the new farm can grow 1 million plants at a time in a facility around the size of a basketball court and process 200 plants per minute, thanks to strides in automation. The new farm means Plenty will be able to greatly widen its distribution to grocery stores and restaurants.
Plenty’s newest vertical hydroponic farm Tigris in South San Francisco can grow 1 million plants at a time in a facility about the size of a basketball court.Photo: Plenty
Plenty, which operates one other farm in South San Francisco as well as farms in Wyoming and Washington, plans to open farms all over the world, and has received $226 million in funding, according to Crunchbase. Plenty’s engineers designed ways to control the environment of each individual plant at the new farm, from the temperature to the amount of light, which impacts flavor.
“On the farm I grew up on, we didn’t measure any of the things we measure here because at the end of the day, there was nothing we could do about it,” said Barnard, who was raised on a cherry and apple farm in Wisconsin.
Inside these vertical farms, everything is intentional and nothing happens by chance, according to engineers.
“We have only one sun outside, but here we can choose the exact light spectrum and intensity based on what we want the plant to taste like,” added Izabelle Back, an engineering manager at Plenty.
In 2018, the company started selling greens through online retailer Good Eggs, San Francisco market Faletti Foods and Roberts Market in Woodside. Barnard said Plenty could expand to as many as 100 grocery stores in the Bay Area by late 2019. He also said prices should continue to drop due to the farm’s efficiency — on Good Eggs right now, a 5-ounce box of salad greens goes for $4.99.
Barnard also hopes to work with more chefs. Plenty supplies San Francisco robot burger spot Creator and fine dining restaurant Atelier Crenn.
Anthony Secviar, chef-owner of Michelin-starred Palo Alto restaurant Protege, described Plenty’s greens as “delicious, vibrant, luscious” and “aesthetically immaculate.” He also remarked on their unusually lengthy shelf life and the lack of need to wash them as being a huge boon for busy chefs.
“We’re begging them to get in the restaurant industry because they’re going to change the game,” Secviar said.
The new farm holds rows and rows of tall green walls, which alternate with walls of bright, colorful LED displays you’d expect to see at Burning Man. Combined with the climate-controlled environment, it clearly racks up a higher energy bill than outdoor farms.
Barnard prefers to look at the entire environmental footprint, including carbon footprint. Since Plenty’s business model is based on distributing only in a farm’s immediate region, its produce travels far fewer miles than, say, avocados from Mexico.
Barnard said Plenty has taken steps to grow more efficient, with the new farm being five times as energy efficient as the company’s other farm one year ago. “We are now roughly on par with a field farm when you look at the total footprint.”
Plenty plans to implement solar and wind power at future farms. The company also claims Tigris uses less than 1% of the amount of land and less than 5% of water compared with conventional outdoor farms.
Because the vertical farming industry is so new, there isn’t much in the way of academic research into its viability. In 2017, Cornell researchers received a three-year, $2.4 million grant to comprehensively study indoor farms, including their environmental impacts compared with outdoor farms. The results are still to come.
Plenty is pushing forward regardless. The company has started experimenting with strawberries and tomatoes and expects to respond to consumers’ increasing interest in plant-based protein with legumes within the next few years.
Some crops, like wheat, are too expensive to grow indoors at scale to be realistic ventures, but the vertical nature of Plenty’s farms doesn’t represent a barrier, according to Plenty chief scientific officer Nate Storey. He said plants adapt to the verticality and support themselves — Plenty has even grown watermelon, which didn’t start dropping to the floor until they reached 20 pounds.
“There’s nothing that won’t work,” he said. “The question is, do the economics make sense today?”
Janelle Bitker is a San Francisco Chronicle staff writer. Email: janelle.bitker@sfchronicle.com Twitter: @janellebitker
Follow Janelle on: https://www.facebook.com/SFChronicle/janellebitker
Janelle Bitker joined The San Francisco Chronicle in 2019. As the food enterprise reporter, she covers restaurant news as well as Bay Area culture at large through a food lens. Previously, she served as a reporter for Eater SF, managing editor at the East Bay Express, and arts & culture editor at the Sacramento News & Review. Her writing has been recognized by the California Newspaper Publishers Association and Association of Alternative Newsmedia.
Past Articles from this Author:
Does AI Hold The Key To A New And Improved “Green Revolution” In Agriculture?
Producing enough healthy food to feed the world—on a changing planet—is going to be a steep challenge. These researchers are giving farmers AI-driven techniques and tools to find solutions
Producing enough healthy food to feed the world—on a changing planet—is going to be a steep challenge. These researchers are giving farmers AI-driven techniques and tools to find solutions.
BYJACKIE SNOW FEBRUARY 19, 2019 NOVA NEXT
Automation in agriculture may soon make robots as common in greenhouses as they are on factory floors. Photo credit: Shutterstock
On a stretch of highway in the Netherlands not far outside of Amsterdam, a row of greenhouses at Wageningen University & Research (WUR) poke up like knuckles along the flat landscape. The Dutch university is known for its cutting-edge agricultural research, but some of these greenhouses recently ran an experiment that’s novel even for them: autonomous growing.
Stepping into a humid box from a brisk autumn day, you hear the noises of machines adjusting themselves mixing with the sounds of leaves rustling. The amount of light, water, fertilizers, and carbon dioxide—along with the temperature of the greenhouse—are all set by deep learning algorithms and executed by machines. Humans are still responsible for moving vines up the lattices as they grow, as well as pruning and harvesting.
But it’s pretty clear who—or rather, what—is calling the shots.
The Future of Farming?
By 2050, we’ll need to feed nine billion people with about a third less arable land than we had in the 1970s, experts estimate. Farmers will need all the help they can get, including insights gleaned from artificial intelligence, or AI. Developed carefully—and with the people who will be using it taken into account—AI can be part of the solution to feeding a growing world, according to the Refresh report, a document put together by researchers from Google, university professors, nonprofits, and farmers. And as an added bonus, some of the unsustainable practices developed over the past 70 years could be reversed with more efficient, AI-driven technology.
The Green Revolution was a set of advances that started in the 1950s in areas like high-yield crops, synthetic fertilizers, and irrigation technology that greatly increased food production, especially in developing countries—saving an estimated one billion people from starvation. But it left in its wake a culture of pesticides, reduced agricultural biodiversity, and overuse of chemical fertilizers that deplete the soil and poison waterways.
“It was never meant to be used in the long term,” says Danielle Nierenberg, the president of Food Tank, a non-profit working to build a better food system that also worked on the Refresh document. Farmers were supposed to transition back to organic, Nierenberg adds: It just never happened because increased yields generated by industrial-scale farming put pressure on smaller farms to follow suit.
One of the main ways AI could help agriculture transition out of practices forged in the Green Revolution and into a more sustainable future is with precision farming. Until now, there hasn’t been an easy way for farmers to learn from historical or real-time data. But AI-powered programs can combine data on weather patterns, crop yields, market prices, and more to guide farmers to planting at the right time, adding the appropriate level of fertilizers, and harvesting at peak ripeness.
WUR is one of the places where big data approaches to growing food are being tested. Last fall, five teams of AI researchers and biologists from around the world competed in growing cucumbers in separate 96-square-meter greenhouses, with a sixth grown manually as a reference. Each team trained its own algorithm, although the teams had the ability to decide how closely to follow the solutions that their AI models came up with. The teams kept an eye on their crops with sensors and cameras, and could feed the algorithms new data and tweak them as needed. To win, teams had to maximize total yield and net profits while minimizing the use of resources.
The winner was a team called Sonoma, made up of Microsoft Research employees and students from Danish and Dutch universities. According to Silke Hemming, head of the scientific research team for greenhouse technology at WUR, Sonoma’s plan used more artificial light earlier and kept carbon dioxide levels higher than a typical gardener might. But other teams also discovered counterintuitive ways to increase yield, such as pruning smaller cucumbers close to harvest or letting bigger ones have a chance to grow a little more.
Like all problems in AI, growing cucumbers and other crops by algorithm demands a food source of its own: data—and lots of it. The cucumber contest was a start at putting information together that other researchers can build on with future projects.
“You have a dataset you would never have,” Hemming says. “You can learn so much from that.”
The researchers organizing the competition chose cucumbers because they are a fast-growing crop cultivated worldwide, and problems like blight show up in them immediately. But this project could transform how other indoor crops are grown. It’s a first step in finding ways to combine humans and AI technology to produce more food, more efficiently.
“It’s not all about winning.” Hemming says. “It’s also about learning.”
FARMWAVE Founder and CEO Craig Ganssle uses its smartphone app with an automated kernel count feature to assess corn yield. Photo credit: FARMWAVE
AI on the Farm
“Farming is a lot more complicated than other industries,” says Joshua Woodard, an agricultural business and finance professor at Cornell and founder of the farming data company Ag-Analytics. “It’s a really complex system of environment and management practices."
Ag-Analytics’s wants to bridge that gap with easy-to-use data analysis tools to help farmers plan and monitor their fields. Their farm management platform takes data from sensors in John Deere farm equipment and combines it with other datasets, like satellite imagery and weather forecasts, to develop predictions for individual farms.
Algorithms working from afar could make a huge impact for less tech-heavy farms, too. Farmers in the developing world are working with minimal data and stand to make leaps in productivity with algorithms in the cloud instead of expensive machinery in their fields. According to the United Nations, 20 to 40 percent of crop yields are lost each year due to pests and diseases. AI tools like Plant Village and FARMWAVE allow farmers to take photos with their phones of sickly plants, bugs, and weeds, and then have computer vision-powered algorithms diagnose the problem from afar in seconds. FARMWAVE is already working with farmers in countries across the world, who, despite their distance, are all dealing with similar problems that AI can spot.
"Army worm in corn looks the same in Africa versus the U.S.,” says Craig Ganssle, the founder and CEO of FARMWAVE.
In India, a team at the International Crops Research Institute for the Semi-Arid Tropics (ICRISAT) is working on providing real-time pest predictions to help Indian farmers take specific actions to protect their crops. ICRISAT uses cloud computing, machine learning, and data from IoT (short for the “Internet of Things”) sensors to come up with personalized predictions about pest risks.
Dr Avijit Tarafdar of ICRISAT converses with chickpea farmer Mr Srinivasa Boreddy in Adilabad District, Telangana. Photo credit: D Chobe, ICRISAT
“Whenever [farmers] see the pests in the field, they simply go for pesticides,” says Dr. Mamta Sharma, a principal scientist at ICRISAT. “It will help them reduce the amount of sprays that farmers are applying."
ISCRISAT has offices in Africa that could eventually use the tool, with interest coming from South America as well. As these offices collect more data, Sharma says, it could be used to spot new risks due to climate change.
“It helps us recognize emerging threats,” she says.
Robot Green Thumbs
Indoor farming currently occupies around 2.3 million square feet worldwide. But based on information from growers, the analysis firm Agrilyst predicts this number will balloon to 22 million square feet over the next five years. Despite the expense of setting up these spaces and the limited types of produce that can currently be profitably grown, much of AI research is being done in greenhouses and other indoor spaces because, with the reduction of arable land, these production methods will become more critical. Indoor farming can also produce up to 20 times as much fruit and vegetables per square foot as outdoor farming, while using up to 92 percent less water, according to one study, with one company claiming it needs 99 percent less water.
In San Carlos, California, two robots cruise within a hydroponic farm developed by the start-up Iron Ox. These robots, which plan, care for, and harvest produce, are overseen by a computer program affectionately nicknamed “the Brain.” Even before the advent of AI, hydroponic systems were known to use less water, need fewer pesticides, grow faster, and produce more plants in less space. However, hydroponics are notoriously labor-intensive, requiring plants to be moved to different vats throughout the growing phase. Training robots for this monotonous task could make razor-thin profit margins a little less tight.
“A lot of things that weren’t feasible outside of a lab five years ago are possible now,” says Brandon Alexander, the CEO of Iron OX.
In the end, improved agricultural processes lead to better food options. And making small indoor farms more efficient could open up the possibilities of food grown closer to city centers. Most produce travels an average of 2,000 miles from farm to shelf in the U.S., which forces farmers to plant fruits and vegetables that can handle being transported—not necessarily those that taste good.
“Fresh produce isn’t that fresh,” Alexander says.
After improving its robotic systems, Alexander says, Iron OX’s long-term plans include breeding plants using data currently being gathered on its farm. Algorithms crunching this data and other local information, like what sells best, could replace tasteless, homogenized tomatoes and lettuce with more varieties suited to different communities’ tastes.
“We could make delicious, extra healthy things that people want to eat,” Alexander says.
Firm Takes Leap Into Future With Robot Strawberry Picker
PUBLISHED: February 2019
Dr Vishuu Mohan at the University of Essex Picture: VICKY PASSINGHAM
A prototype fruit-picking robot being developed on an Essex jam maker’s farm has featured in a report on farming of the future.
Wilkin and Sons’ Farms manager Andrey Ivanov has been working with Dr. Vishuu Mohan, a computer science and engineering lecturer at the University of Essex, to develop the robotic strawberry picker.
“The researchers at the university, like many across the world, are trying to develop a robotic piece of equipment that will be capable of identifying when a strawberry is ready to be picked then make a decision and pick the fruit by snapping the stem without damaging or touching the actual berry to avoid bruising,” said Mr Ivanov.
The challenge for the researchers is developing a robot capable of picking strawberries of all sizes in all weathers and conditions. “Dextrous manipulation in unstructured environments is a big challenge for robotics today,” admitted Dr Mohan.
The study is featured in a new report from the National Farmers’ Union (NFU), which looks at what the food and farming industry might look like in 20 years, with robots, vertical farms and virtual fencing.
The Future of Food 2040 report highlights the importance of establishing a future domestic agricultural policy which enables the industry to increase its productivity, profitability and resilience.
Looking beyond Brexit to how the country will evolve socially, technologically and environmentally, it delves into how changing trends will affect food production
The Tiptree plant’s collaboration is one of three case studies featured.
NFU East Anglia Regional Director Rachel Carrington said: “Agriculture is a progressive and forward looking industry and farmers in East Anglia have always been quick to adopt new technology.
“Our farmers already utilise satellite-guided tractors, drones to survey crops and soil structures, probes to monitor moisture in fields and robots in glasshouses. However, there are still many jobs that have to be done by hand and cannot be replaced by technology, at least in the short-term.
“This report provides an exciting glimpse of the future, but, to get there, it is crucial that farm businesses are not only given the support they need to survive and thrive now, but they start to plan and prepare for the challenges and opportunities ahead.”
Agri-Tech East director Dr Belinda Clarke said: “This NFU report rightly positions agri-food production as an industry with enormous potential. Measures to improve the use of finite resources such as soil and land and to increase productivity are to be encouraged and Agri-Tech East welcomes this report.
“However, to encourage the wider adoption of new technology it is vital to establish the business case for farmers and growers. We would like to see a process for independent evaluation of the return on investment.
“We agree, as stated in the report, that innovation needs to meet regulatory approval, but also understand that this can be problematic if the science is progressing ahead of the regulators. We would recommend creating advisory panels that include scientists and technologists as this would be beneficial to all.”
Topic Tags: