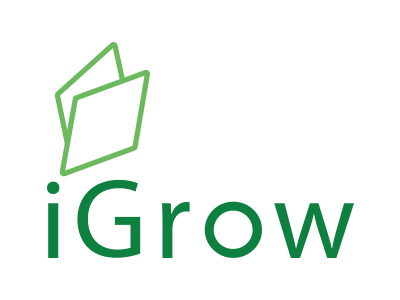
Welcome to iGrow News, Your Source for the World of Indoor Vertical Farming
RotoGro (ASX:RGI) Updates Market On Vertical Farming Tech
The RotoGro Garden System is the core of the company's technology with the ability to maximize plant surface growing area by situating a spherical garden around a centrally placed lighting system
Source: RotoGro
RotoGro (RGI) provides an update of its vertical farming technology with encouraging results from recent trials
The company says recent data indicates its garden systems produce more yield per square meter when compared to other indoor vertical farming methods
Further, trials of RotoGro 710 are said to be progressing well and the team is trialing how to further reduce water and energy usage
RGI is also encouraged by its studies and customer feedback for its RotoGro 420 system which it says validates commercial-scale cultivation of lawful cannabis
Shares were trading 2.3 percent higher at 4.4 cents apiece
RotoGro designs and manufactures cultivation solutions for indoor vertical farming, operating in perishable foods and lawful cannabis.
The RotoGro Garden System is the core of the company's technology with the ability to maximize plant surface growing area by situating a spherical garden around a centrally placed lighting system.
The systems can be stacked, maximizing the yields per square meter when compared to the ground space occupied.
RGI said data collected from recent crop trials conducted in collaboration with agriculture company Verity Greens and herb grower and distributor Fresh Leaf indicates its garden systems produce more yield per square meter when compared to other indoor vertical farming methods.
Specifically, RotoGro projects yields 3.8 to 15.3 times the yield per square meter compared to industry-leading farming producers and greater in contrast to greenhouse and conventional farming.
CEO Michael Di Tommaso said ventures like the ones with Verity Greens and Fresh Leaf will "strengthen RotoGro’s market presence by successfully penetrating the burgeoning indoor vertical farming industry with its technology offerings".
Further, internal trials of the company's most recently developed garden system, the RotoGro 710, are said to be progressing well with cultivation of 48 kilograms of basil and 26.5 kilograms of cilantro in a single harvest cycle.
After multiple trials cultivating leafy greens, the agronomy team repeatedly achieved yields of 124 kilograms in a fully planted RotoGro 710, indicating single harvest yields of 372 kilograms could be achieved when the technology is at full capacity, stacked three-high.
The team is trialing shorter full crop cycle lengths while maintaining yields and aims to refine the plant irrigation schedules to further minimize water usage and refine the environmental controls to ensure enhanced energy efficiencies.
In other news, RotoGro has enabled full automation of its lawful cannabis cultivator, RotoGro 420.
The company's software controls the wheel revolution speed, lighting cycles, and spectrum variations, direct CO2 injection as well as the plant irrigation processes and environmental controls including temperature, air conditioning, and humidification.
Notably, the 420-garden system has been able to consistently produce 10.2 kilograms of dried cannabis flower in a single 56-day crop cycle when stacked three-high.
RGI said its studies in combination with its customer’s data validates the commercial viability of RotoGro 420 in the commercial-scale cultivation of lawful
cannabis.
Mr Di Tommaso said RotoGro is continuing to develop relationships globally to expand its presence in both the perishable foods and lawful cannabis markets.
Shares were trading 2.3 percent higher at 4.4 cents apiece at 1:31 pm AEST.
Latest ZipGrow Inc. Product Introduces Vertical Indoor Farming To New Growers
Controlled Environmental Agriculture (CEA) is currently undergoing an upturn in public interest as the general population begins to appreciate the importance of locally produced food from sustainable sources
September 9, 2020
ONTARIO, CA - Controlled Environmental Agriculture (CEA) is currently undergoing an upturn in public interest as the general population begins to appreciate the importance of locally produced food from sustainable sources. ZipGrow Inc.’s new product offering, the Introduction to Commercial Growing package, is designed to make commercial growing more accessible to farmers and businesses wanting to get into the CEA industry.
“As interest grows in improving food security, we wanted to make commercial growing more accessible to newcomers to the hydroponics world”, explains Eric Lang, President of ZipGrow Inc. “This new package is an accessible, and affordable entry-level product for anyone interested in testing out if controlled environmental agriculture is right for them.”
The new product package includes a discounted set of everything you need to get started, including 90 patented 8’ ZipGrow™ Towers, steel ZipRacks, LED growing lights, a seedling area, a comprehensive plumbing system, and an automatic doser from Atom Controllers. This package is not only all-inclusive, but also modular to be able to expand as the operation grows.
“This package can set someone up to produce up to 100 pounds of leafy greens or herbs such as lettuce or basil each week, and is a great way to test a pilot system in your local community”, adds Lang. “Since the start of COVID-19 we have seen interest in sustainable food sources skyrocket, and this is one way we are trying to encourage more people to see if hydroponic farming is right for them.”
The Introduction to Commercial Growing package has a flat rate shipping option for all locations within Canada and the continental United States, with shipping to other locations available at custom rates. The package will be fully installed on-site, with costs varying dependent on location. ZipGrow team members will work with customers to ensure the product is the right fit for them and ensure all training and ongoing education needs are fulfilled.
ZipGrow Inc. is an international leader in indoor, vertical farming technology. Our flagship product, the ZipGrow™ Tower, is a core component of many of the world’s most innovative farms; from indoor hydroponic warehouses to vertical aquaponic greenhouses and high-density container farms.
For more information contact Gina Scandrett at hello@zipgrow.com or at 1-855-ZIPGROW.
A Brief Insight Into Thailand’s Vertical Farming Sector
"There’s quite a big difference between Thailand and other Asian countries in terms of the advancements in vertical farming technology and business”, Siriwat Sakhonwasee says
by Dr. Siriwat Sakhonwasee
"There’s quite a big difference between Thailand and other Asian countries in terms of the advancements in vertical farming technology and business”, Siriwat Sakhonwasee says. After obtaining his Ph.D. on plant biology from the University of California Davis in 2009, Sakhonwasee is now a lecturer and researcher in the faculty of agricultural production at Maejo University, Chiang Mai, Thailand.
Sakhonwasee's university lab research on seed production of petunia under LED lights
Increase of interest
“When I started doing research on vertical farming about 10 years ago, people in Thailand thought that I was pursuing a useless hobby. However, in other Asian countries such as Japan, Korea and Taiwan, vertical farming was already a serious business concept. Today, vertical farming is becoming a new trend where a number of companies are interested to place their bet on. The concept of vertical farming in Thailand receives a lot of influence from Japanese technology. This is why most people use the word “Plant factory”, a jargon, originated from Japan to describe vertical farming.” Last month, Thailand’s Board of Investment (BOI) announced that it officially will support investments on Plant Factories by reducing the tax burden on businesses involved with this technology. Sakhonwasee continues: “I see this as a good sign for vertical farming in Thailand as the same thing happened in Japan a decade ago.
More demandIn terms of Thailand, now there are many more research projects regarding vertical farming than five years ago. “I sometimes have to review research proposals for funding agencies and I can easily tell that nowadays research projects, involving vertical farming concepts, are more frequently submitted”, Sakhonwasee notes. This means that researchers in Thailand will have more chances to explore the science behind the concept of vertical farming. He continues: “Hopefully, this will lead to the development of innovative techniques that are suitable for the country. From a global perspective, people are integrating much more sophisticated technology into vertical farming, such as IoT and AI. The concept is not just growing a plant on the shelves using artificial light anymore. It is about collecting the data and constantly improving the vertical farming system.”
Dr. Siriwat Sakhonwasee
“One thing I see as a clear improvement is the business model of vertical farming. More diverse business models are applied such as a decentralized model by Infarm, harvest on demand by Farmers Cut.” For Thailand, 3 prominent vertical farming startup companies also use a different business model to sell their produce, namely, Wangree Fresh which uses a subscription model to sell their vegetables, NoBitter which is using online channels to engage with its customers and LED Farm which uses a retail hypermarket channel to sell its produce through.
Current industry struggles“I think that making people understand the value of a vertical farming product, is a common problem for vertical farming worldwide. Recently, Irvin Fain founder of Bowery used the word “post-organic” to explain the value of their fresh produce. This is such a good way to describe produce from vertical farming that is pesticide-free and very clean so customers do not need to wash before eat.” Sakhonwasee adds: “My colleague recently spoke with Mr. Chingchai Konthansakul founder of LED Farm of Thailand. He has an interesting way of thinking regarding vertical farming produce. He explained that he will never compare vegetables from his vertical farm with traditional farming fresh produce. Instead, he shows off his fresh produce as a novel product. This helped LED Farm to design a proper marketing strategy for consumers who were always skeptical about the safety of fresh produce.”
Mr. Chingchai Konthansakul, founder of LED Farm
Future vision
“In Thailand, I believe that vertical farming will never completely replace traditional farming, in terms of feeding the population. We are blessed with great natural resources that are suitable for almost every aspect of agriculture. But, vertical farming might play a big role in the production of premium produce for high-end consumers. However, to achieve this concept a certification process must be established, like organic produce. I think we will see more diversity in the application of vertical farming systems such as speed breeding and production of medicinal substances from herbs or genetically modified plants.
In other Asian countries, vertical farming will probably play a more prominent role in terms of food production. For example, a small country like Singapore just set a 30 by 30 goal last year. This was done to support the local food production to meet 30% in demand of the Singaporean population by the year 2030. In this case, the cultivation area is a big issue and vertical farming is expected to play a significant role in Singaporean food production. Other examples are countries in the Middle East where the majority of land is desert and not arable. Again, vertical farming can overcome this limitation and could provide food security for these countries.”
For more information:
Dr. Siriwat Sakhonwasee, assistant professor
tongscpl@yahoo.com
Publication date: Wed 12 Aug 2020
Author: Rebekka Boekhout
© HortiDaily.com
CANADA: Local Leaf Farms To Open Vertical Farming Site In Kingston
Purchasing local produce will become easier year-round after Local Leaf Farms opens their newest vertical farming site on Innovation Drive. Their innovative take on farming removes the need for a lot of land, and our Canadian dependency on weather
Credit: localleaffarms.com
Purchasing local produce will become easier year-round after Local Leaf Farms opens their newest vertical farming site on Innovation Drive. Their innovative take on farming removes the need for a lot of land, and our Canadian dependency on weather.
Local Leaf Farms is on a mission to change the way food is produced and distributed in Canada, growing superior quality food that’s safer, fresher, and more sustainable. Using vertical farming technology first invented by NASA, they are able to provide Canadians with pesticide and herbicide-free, hyper-local produce (grown within the city it is sold) year-round. With a model that has them delivering the product directly to store shelves within hours of harvest, they ensure maximal freshness of the product, while reducing both food waste and the carbon footprint of transportation.
Packed in 100% plastic-free, compostable containers, their innovative technology provides retailers & consumers with a fully traceable food source, via a QR code on the package, that allows instant access to all details about how the product in a specific package was grown, when and by whom.
Kingston Economic Development and the City of Kingston are pleased to welcome this new business to our community in the St. Lawrence Business Park. “I’m absolutely delighted to welcome Local Leaf Farms to Kingston,” says Mayor Paterson. “This is a company that brings an exciting and innovative approach to local food that will bring great benefits to our residents, and will further position Kingston as a leader in food security and sustainability.”
The Local Leaf facility will be located in a new development at 800 Innovation Drive and is anticipated to open in late October of this year. This business is a $450,000 investment in the Kingston community in terms of start-up costs and is expected to create seven (7) full-time jobs locally.
“We’re proud to have Local Leaf Farms joining the innovative businesses that will be sharing one roof at 800 Innovation Drive when it opens this fall,” says Ben Pilon, President of BPE Group. “Their focus on sustainability and food security aligns nicely with our business philosophy, making this agreement a natural fit. With tenants like Local Leaf, 800 Innovation Drive, will see job creation, strengthen our local economy, and show the world that good things grow in Ontario.”
“As we scale to build 20 production facilities across the country by 2025, Kingston was an obvious choice. As a gateway to eastern Ontario, Kingston represents the perfect mix of a City whose municipal government understands the importance of both innovation and the food sector, an Economic Development Office that is exceptional in supporting out of town businesses in their relocation and a community that values sustainable, quality food products. It was an obvious choice that we are excited to commence upon,” says Steve Jones, President, and CEO of Local Leaf Farms.
“We are excited that Local Leaf Farms selected Kingston as a new site for their 7,000 sq. ft. facility. Their business mission aligns with the City of Kingston’s vision for innovation, entrepreneurship, and food security making it a great fit in the community,” says Shelley Hirstwood, Business Development Officer, Attraction & Aftercare with Kingston Economic Development Corporation. “The Kingston Economic Development team is looking forward to continuing to work with Local Leaf Farms as they became established.”
While you’re here …
…Can we take two minutes of your time?
More Kingstonians than ever are relying on Kingstonist for their local news. But we need your help to keep it going.
A few years ago, two big media conglomerates, Torstar and Postmedia, “swapped assets” and promptly shuttered one of Kingston’s main newspapers. We saw talented journalists displaced and years of recorded Kingston history destroyed by a decision made in another city, with interests not grounded in what was best for the Kingston community.
And we resolved that we would not permit that to happen again.
That’s when we decided to take the Kingstonist, at that time a popular Kingston community blog, and reimagine it as the dedicated, independent local news provider you see now.
Today, businesses everywhere are struggling under the burdens of COVID-19, and we are no different. So we’re asking you to support us. Help us in our mission to: hold our local governments accountable; provide voices for those fighting against social injustice; fight against misinformation; and provide news not censored by the influence of corporate bias.
We believe that access to news is an integral component of a healthy community. If you believe the same, click here to subscribe to Kingstonist.
Farming In The Desert: Are Vertical Farms The Solution To Saving Water?
When I told people I was going to grow tomatoes in the desert, they thought I was crazy," Sky Kurtz, founder of Pure Harvest Smart Farms, told DW
Jul. 23, 2020
By Isabelle Gerretsen"
When I told people I was going to grow tomatoes in the desert, they thought I was crazy," Sky Kurtz, founder of Pure Harvest Smart Farms, told DW.
With just an average 12 days of rain a year, less than 1% arable land, a desert location, and an 80% import rate for food, the United Arab Emirates (UAE) seems an unfavorable place to set up a farm.
Kurtz is one of several entrepreneurs using high-tech farming techniques to boost crop production in the Emirates. Pure Harvest built the first climate-controlled greenhouse in Abu Dhabi in 2017.
Prompted by arid conditions and a desire for greater food security, the country is investing millions in technologies — such as vertical farming — that could make it an unlikely agricultural pioneer.
Vertical farms can grow a rich variety of different crops by stacking them in layers under LED lighting in climate-controlled greenhouses and watering them with mist or drip systems. The process is tailored to each crop's specific needs, resulting in high-yield, year-round harvests."
It takes 30 to 40 days to grow leafy greens out in the field. We can grow that same crop in 10 to 12 days," says Marc Oshima, co-founder of Aerofarms. The company received funding from the Abu Dhabi Investment Office to build the capital's largest indoor vertical farm, with 800 different crops, by 2021.
Water Scarcity and Fossil-Fuel Reliance
The technology uses minimal land and up to 95% less water than conventional agriculture.
The hydroponics system places the plants' roots directly into a water-based and nutrient-rich solution instead of soil. This "closed-loop" system captures and recirculates all the water, rather than allowing it to drain away — useful for a country like the UAE suffering from extremely high water stress.
Globally, agriculture accounts for 70% of freshwater withdrawals, and UAE is extracting groundwater faster than it can be replenished, according to the International Center for Biosaline Agriculture (ICBA)."
Water is very expensive over in the UAE, but energy is cheap as it is subsidized," says Jan Westra, a strategic business developer at Priva, a company providing technology to vertical farms.
The artificially controlled environment is energy-intensive because the air conditioning and LED lights need a constant source of electricity.
This bringing forth of life in the desert could come at a high environmental cost. Most of that energy comes from carbon-emitting fossil fuels, even as the Middle Eastern country feel the effects of climate change.
By 2050 Abu Dhabi's average temperature is predicted to increase by around 2.5°C (36.5 F) in a business-as-usual scenario. Over the next 70 years, patterns of rainfall are also expected to change.
Integrating Renewable Energy
Although Pure Harvest is building a solar-powered farm in neighboring Saudi Arabia, its UAE operations get electricity from the carbon-intensive national grid.
Investing more in renewables "is a goal of ours," Kurtz told DW. He said the company has not set a clean energy target but is working on various green power projects, including a plan to integrate solar power generated in UAE into its operations.
However, Willem van der Schans, a researcher specializing in short supply chains at Wageningen University in the Netherlands, says sustainability and clean energy should be "inherent in the technology and included in plans when starting a vertical farm."
He argues that many vertical farming companies are not sustainable in terms of energy as they still view clean power as an optional "add-on."
Ismahane Elouafi, director-general of the government-funded ICBA in Abu Dhabi, acknowledges that vertical farming has some way to go before achieving "real sustainability," but she believes the innovations are "promising."
Improved battery storage, increasingly efficient LED lights, and cheaper solar panels will help, she adds.
Local Solutions
By 2050, the UAE government wants to generate almost half its energy from renewable sources.
Fred Ruijgt, a vertical farming specialist at Priva, argues that it's important to factor transport and refrigeration into the energy equation. Vertical farming uses more energy to grow crops than traditional agriculture, but because crops are grown locally, they do not have to be transported by air, sea, or truck over long distances."
The energy-saving is difficult to calculate exactly, but the advantages of locally grown crops are huge," he says, adding that those grown in vertical farms not only use less water and pesticides but that they also have a longer shelf life due to minimal transportation time.
Food Security and Coronavirus
In 2018, the UAE set out its vision to become a hub for high-tech local food production.
Companies and investors have flocked to the region, attracted by the 0% corporate tax rate, low labor costs, and cheap energy. With their help, the UAE aims to reduce its reliance on imports and make its food system more resilient to shocks like climate change and pandemics.
Oshima from Aerofarms says the coronavirus pandemic has brought "greater appreciation of how fragile the supply chain is and raised questions about food safety and security."
When the UAE went into lockdown in April, imported supplies of perishable goods like vegetables fell and business boomed for local suppliers.
ICBA's Elouafi said they have helped keep the UAE well-stocked during the pandemic."With the help of local food production and adequate imports, there has been absolutely no shortage of food in the UAE," Elouafi told DW.
Climate change, however, poses an altogether more complex threat to the country in the long-term. Given climate change's likely impact on food production, she says vertical farming has shown it is "an economically viable proposition even with harsh climatic conditions."
Reposted with permission from Deutsche Welle.
RELATED ARTICLES FROM ECOWATCH
Vertical Farms: The Future of Agriculture? -
EcoWatch ›Inside the Nation's Largest Organic Vertical Farm - EcoWatch ›
5 Ways Vertical Farms Are Changing the Way We Grow Food ...
RELATED CONTENT AROUND THE WEB
Investing In Vertical Farming: Five Take-Aways ›
This company wants to build a giant indoor farm next to every major ... ›
TAGS: farming farmers water food food security agriculture renewable energy
Vertical Farming in LatAm: AgroUrbana Closes $1m Seed Funding
Access to vertical farming technologies is deepening and widening across the world, bringing down the costs and hassle of locally producing anything from Singaporean strawberries to Arctic tomatoes
July 2, 2020
Access to vertical farming technologies is deepening and widening across the world, bringing down the costs and hassle of locally producing anything from Singaporean strawberries to Arctic tomatoes.
In Latin America, however, indoor vertical farms are still largely written off on a continent thought of in terms of its abundant fertile soil and plentiful sunlight. Why pay for artificial light or indoor automation when the sun is free, and labor and land are cheap?
That said, there are early signs of a Latin American vertical farming awakening in Chile, where AgroUrbana has just closed a $1 million seed round, bringing its total capital raised to $1.5 million. The startup has created South America’s first vertical farm, according to the Association for Vertical Farming.
Leading the round by contributing 33% of the cash was the CLIN Private Investment Fund administered by Chile Global Ventures, the VC arm of Fundación Chile, a public-private initiative for innovation and sustainability in the country. Support financing also came from CORFO, Chile’s economic development agency, and private investors like company builder and VC Engie Factory, the country’s largest telecommunications company Entel, and sustainability investor Zoma Capital.
In an interview with AFN, AgroUrbana founders Cristián Sjögren and Pablo Bunster described how the funds would be put to work at their 3,000 square feet pilot facility in the suburbs of Santiago, where testing is ongoing on layered, renewable energy-powered stacks of hydroponically grown, LED-lit leafy greens and fruits. AgroUrbana’s first big offtake deal has just been inked with a major Chilean grocery retailer, they said.
A pre-planned switch from restaurant to retail
“It’s been run, run, run,” Bunster recalls, describing the political turmoil in Chile that brought curfews and shuttered restaurants months before Covid-19 locked down the country. That earlier disruption, he adds, actually had its upsides, as it got them thinking more about e-commerce and direct-to-consumer sales — so when the team’s restaurant deals dried up during the Covid-19 pandemic, the switch to retail was already scoped out.
As to scaling up further, Sjögren envisions an eventual 30,000 square foot facility to be bankrolled by Series A funding they plan to work towards later this year. The design and output would depend on the results of their pilot trials.
This size of farm sets the team somewhere in the middle of the two dominant visions of vertical farming: centralized versus distributed. Proponents of centralized systems argue that large-scale production — and financial viability — depend on ever-bigger and higher farms. These farms — or plant factories as they are sometimes called — are proliferating, aided by huge sums of capital. Plenty scooped up a whopping $200 million in Series B funding back in 2017. AeroFarms raised $100 million in late-stage funding in 2019 while Fifth Season secured $50 million last year.
Although centralized facilities have generally dominated in terms of raising capital, distributed and decentralized business models are gaining pace according to AgFunder’s 2019 industry report. One in particular, Germany’s Infarm, nabbed $100 million last year to deploy its connected growing cabinets in supermarkets.
The theatricality of these cabinets harmoniously glowing in office buildings or hospitals in a post-coronavirus world also holds sway in the popular and corporate imagination of 2020. Companies like Square Mile Farms recently crowdfunding over $300,000 on the promise of re-kitting office spaces like Microsoft’s London premises with fresh produce. In New York, Farmshelf has its own grow cabinets deployed in WeWork FoodLabs.
Learning from cash-heavy first movers
Mention of relative giants like Plenty or InFarm could be daunting for newer entrants such as Square Mile Farms or AgroUrbana and their hitherto modest sums raised. But there is perhaps an advantage in starting late, so long as the team learns from the costly mistakes and hubris of earlier endeavours. Here, both Bunster and Sjögren see parallels with the renewable energy industry — where they worked previously — and see the arrival of cheaper, more sustainable energy and capital in Chile as crucial to making vertical farming competitive.
AgroUrbana is exploring three options for solar going forward: either establish a power purchase agreement, in which they buy renewable energy from an existing plant; finance a power plant which will sell energy to them later; or build their own solar farm. But they acknowledge that the larger the facility, the less feasible it is to have solar on-site.
The pair describe how some Chilean outdoor farming is already lean and competitive, yet much of it has been geared towards high-value crops like avocados – and that stuff is primed for export. For the urbanizing local market, they see gaps for hyper-local fresh produce, where the competition would actually be with low-tech smallholder farmers with less traceable supply chains. In the context of Covid-19 and an ensuing consumer embrace of e-commerce options, better nutrition, less water use, and fewer pesticides, the pair reckon there is much to gain from providing produce that is consistently fresh, 365 days a year.
Any chance of the world’s first vertically-farmed avocados any time soon? Unlikely, replies Bunster. As for gene editing, where South American jurisdictions are known to have more lax regulations than their North American counterparts, Bunster says the plan was to work with what nature already provides, while giving “the conditions of spring every day of the year.”
UAE Agricultural Firm Uses Technology To Help With Food Security
Smart Acres aims to support the UAE’s food security program by using high-tech vertical farming to produce approximately 8,000 kilograms of lettuce per cycle
KATERYNA KADABASHY
July 13, 2020 | DUBAI
Smart Acres aims to support the UAE’s food security program by using high-tech vertical farming to produce approximately 8,000 kilograms of lettuce per cycle.“
In the expansion phase, we will have 78 modules, which comes to a total of 88,320 pots. Each lettuce, for example, will weigh 100 grams. So, that is approximately 8,000 kilograms of crops per cycle,” the company’s CEO Abdulla Al-Kaabi told Arab News.
The vertical farm — currently in the proof-of-concept stage — is expected to launch in the third quarter of 2020, producing 12 cycles of crops annually and expanding from Abu Dhabi to the rest of the country. In this type of farming, plants are stocked vertically, providing more produce per area and resembling something similar to the green walls sometimes seen in malls.
Smart Acres collaborated with South Korean vertical farming technology n.thing in their farming processes. (Supplied)
The company collaborated with South Korean vertical farming technology n.thing to employ the Internet of Things in their farming so as to efficiently use water and monitor humidity, temperature, and nutrients.“
Vertical farms, in general, save over 90 percent of water compared to traditional farming methods. There is constant water flow across all the little pots, and the water is filled with all the nutrients necessary for the plant to grow,” Lead Project Manager Aphisith Joe Phongsavanh said.
The high-tech design of the farm allows Smart Acres to produce clean crops without any pesticides and with minimal intervention.“
Since we are growing our crops in a 100 percent closed environment, we don’t have to use pesticides at all. That’s exactly what we mean by clean food: non-adulterated food products that go through minimal processing,” Phongsavanh said.
However, this closed environment in which the plants grow requires staff and visitors to wear protective gear before entering the premises in order to preserve the sterility of the area.“
It is almost like going into a very high-tech factory. You have to wear lab coats and go through an air shower, where one door is closed and the other door only opens after 10 seconds of disinfection,” Director of Smart Acres Sean Lea said.
Currently, the company does not have any investors, but Al-Kaabi said that the expansion phase “of course will require an investment,” expected to cost around AED16.7 million ($4.5 million).
It will not just include a larger number of crops, but also a research and development center with a vision to start cultivating baby spinach, mature spinach, baby arugula, strawberries, and potato seeds.
Earlier in July, Abu Dhabi’s Crown Prince Mohammed bin Zayed Al-Nahyan visited some local farms and met with agricultural entrepreneurs.“
I was pleased to meet some of the UAE’s aspiring agricultural entrepreneurs who are pioneering sustainable and resilient farming practices using modern technology,” Al-Nahyan tweeted.
The UAE is pushing for local production of crops and livestock.
According to Khaleej Times, the Abu Dhabi Agriculture and Food Safety Authority provided over $174 million to “138,000 families, 30,632 breeders and farmers, and 259 small-scale producers and commercial animal farms in Abu Dhabi” to support the industry in June.
Lead Photo: Smart Acres’ vertical farming technology enables it to produce approximately 8 tons of lettuce per cropping cycle. (Supplied)
VIDEO: IGS Intelligent System Design – FTS Finds Out More
IGS has, as a company, focused from the outset on automation, intelligent system design, and the energy equation of CEA vertical farming
July 6, 2020
IGS has, as a company, focused from the outset on automation, intelligent system design, and the energy equation of CEA vertical farming. This has garnered them a reputation as one of the leading and most innovative companies in the industry. We took some time to have a chat with them and find out a bit more about how this all works in practice.
FTS: Hello and thanks for taking the time to talk with us. Can you briefly introduce IGS, its history as well as its outlook?
IGS: IGS was founded in 2013 bringing together decades of farming and engineering experience with a vision to revolutionize the indoor growing market. The two founders, farmer Henry Aykroyd and our CTO Dave Scott had an appetite for innovation and realized that there were significant gaps in the provision of scalable technology for the sector.
Henry knew how to grow and understood the challenges which faced traditional farming: Dave knew how to manage automation and power controls in an industrial environment. The opportunity to bring greater climate control to a growing environment was significant. The ability to manage power consumption was revolutionary. The simplicity of its implementation and use is pivotal.
We opened our first vertical farm demonstrator in Scotland in 2018. Artificial intelligence determines optimal nutritional input and the exact combination or ‘recipes’ of weather: lighting, watering, and ventilation. Data is collected continuously and machine learning used to make iterative adjustments, all of which is monitored through a web-based app. The whole Intelligent Growth platform is IOT-enabled to automate system control and management. Our degree of control is so fine that each 6m2 growth tray has its own microclimate. Technical simplicity is at the heart of our mechanical design.
Our commitment to innovation has continued apace and we have evolved the applications of our technology beyond agriculture to create solutions for a wide variety of indoor environments, developing the Intelligent Grid platform.
The Intelligent Grid uses the same IOT-enabled power and controls platform to manage and monitor lights, sensors, cameras, and communications for complete climate control and reporting. It too has a very simple, clean, and elegant design for application in any commercial building, greenhouse or livestock shed. In contrast to the vertical farm, we use our same core technology through the Intelligent Grid to create whole-space macroclimates.
Both IGS demonstrators are based at the James Hutton Institute, a world-renowned crop, and plant science research facility. IGS and the Hutton collaborate closely to help advance the understanding of plant science for indoor growing.
Until 2018 IGS had invested approximately £7m in R&D to ensure that its platforms offered the greatest levels of control and achieved levels of economic viability, scale, and minimal environmental impact compared to other systems on the market. In 2019 IGS raised £7 million in institutional capital to enter production and take its systems to global markets. We continue to invest over £1m per annum in R&D.
FTS: You have recently shared news of two reseller partnerships – one in the Middle East and one in the UK and Italy with TEP Renewables. Can you tell us briefly a bit more about them?
IGS: We have been talking to International Real Estate Partners (IREP), the international facilities management firm for some time in the Middle East, and we’re really pleased to recently sign this referral agreement which is specifically focused on indoor vertical farming for the UAE and Saudi Arabian markets.
We also have an opportunity to extend into Asian markets in the future. It gives us a greater capacity to service the Middle East market and secure and deploy vertical farming platforms across the region. IREP’s presence in this market is well established with many existing customers across agriculture, retail, and construction and it is a very positive development for both companies we believe.
The agreement with TEP Renewables is an MOU (Memorandum of Understanding) or a reseller-type partnership if we identify customers who would like to operate solar-powered vertical farms in Italy or the United Kingdom that we will work with them.
FTS: Fantastic! In the end, any vertical farm (indeed any farm!) is only as environmentally sustainable as its energy equations. But it is also only as financially sustainable as its energy cost. You have focused quite intensely on this energy cost question. As we see this dramatic collapse of fossil fuel energy production return on investment, it seems that NOW is the time to have renewable energy options on hand for CEA. Do you believe that renewable energy can be cost-competitive – both in terms of installation, sustainable life-cycle and with regard to the price of the final product for the consumer?
IGS: We consider a variety of power distribution and supply methods. Renewables can have considerable benefits from an environmental perspective and also specific to grants and other financial support for utilizing renewable energy resources.
The “virtual power plant” capabilities of our systems indicate strong Demand Side Response (DSR) potential. We can manipulate our growth cycles to respond to power availability and respond to inherent instabilities in power networks. This is already having an influence on our engagement in circular energy projects to utilize spare energy for growing and allows for more renewable power sources to be adopted.
FTS: Labor cost is the other biggest outlay for any vertical farm. You have invested heavily in automation. Is the trade-off of increased capital expenditure for automation worth the reduction in operational expenditure for labor, in your experience?
IGS: Absolutely. Driving down the farm gate price is the ultimate goal and while labor costs vary from region to region, we believe that this investment in the automation (and indeed the associated patents) within our growing operations is imperative and differentiates our systems considerably.
FTS: You’ve set about designing modular and intelligent systems. Such a bespoke system offers advantages of course, as we’ve seen above. But it can also present challenges if it cannot be integrated with other equipment and systems later. Do you future-proof your systems to be able to accommodate such updates and integrations over time?
IGS: We have thought about this from the outset, and our systems are designed in a plug and play model, rather than being bespoke as such. Scalability is paramount for our customers and this has been a consideration throughout our R&D development. Rather than using proprietary systems for processes such as sowing and harvesting, we use off-the-shelf equipment and components. This means we can keep startup and maintenance costs down by providing items with which farmers are already familiar. If a section of the vertical farming system needs to be replaced or upgraded, such as a water filter, a lighting panel or a tray, it can be done with almost no interruption.
However, what is also imperative to think about in terms of future proofing, and a hugely important part of our approach, is how we work so closely with the science community to better understand plant light interactions. The level of control we have designed into our hardware systems allows us to flex and adapt as we need to deploy the most up to date plant light information through our software development, which is continuously evolving.
The approach of our software development has also involved maximising security of our systems and ensuring simplicity of operation. This will be continuously updated, but with seamless integration for our customers.
FTS: Along with FTS, you’ve joined a number of other associations and similar collaborative groups. Why is this important to you as a company, and how do you balance the proprietary needs of your company against this desire to cooperate?
IGS: Collaboration and cooperation across this sector is essential. Our vision is that sustainable change will only be delivered not only when we collaborate, but when we are all open and honest about the limitations, as well as the opportunities for this sector. We want to work alongside technology vendors with complementary products, and with growers and producers, supported by science and greater understanding of growing plants indoors, all backed by far-sighted investors.
We firmly believe that through innovation, collaboration and investment we can create an economically and environmentally sustainable global indoor food industry.
FTS: Thanks so much for taking the time to talk with us today. We wish you every success and look forward to working with you in the future.
IGS: Thanks very much indeed. We look forward very much to be part of Farmtech Society as we all move forward in the development and innovation of agricultural technology.
For IGS
David Farquhar
CEO
Indoor Vertical Farming is The Future Says Irish Agritech Start-Up
Farmony says Ireland can become self-sufficient in leafy greens, herbs and microgreens thanks to its approach to vertical farming
Farmony Says Ireland Can Become Self-Sufficient in Leafy Greens, Herbs, and Microgreens Thanks to its Approach to Vertical Farming
Jun 25, 2020
Olive Keogh
Farmony co-founders Rodrigo Andrade, Dan O’Brien, and John Paul Prior
Animals grazing peacefully in the fields and serried rows of crops stretching far into the distance are what usually come to mind when we think about farming. It’s a pastoral image deeply embedded by tradition and worlds away from how they do things at the agritech start-up Farmony, which builds high output, controlled environment vertical farms to produce leafy greens and herbs.
On a Farmony farm, the crops are grown indoors on multiple layers of tiered shelving. The method is ideally suited to growing salad leaves and microgreens and a unit can produce in 55sq m (592sq ft) what would normally occupy five acres if conventionally farmed. It also only uses about 5 percent of the water required by traditional growing methods and a unit can be operational 365 days a year.“Vertical farming is not new. In fact, it’s been around forever. Just look at the Hanging Gardens of Babylon or rock faces or the seashore with plants growing, irrigated and fed by water,” says Farmony co-founder John Paul Prior.
So, in the strictest sense, vertical farming isn’t new but its commercialization is. The first large-scale commercial application only came on stream in Singapore in 2012 and Farmony is joining this nascent industry at a time when it is increasingly seen as part of the answer to sustainably and economically feeding the world’s growing population.
What makes Farmony’s approach innovative is twofold. Firstly, it has designed its system to support multiple crops requiring different growing conditions. Secondly, it has put everything a grower needs together in one turnkey package. “In a nutshell, we build customized, controlled environment vertical farms and use our own hardware and software operating system to improve growing efficiencies,” says Prior, who set up Farmony with co-founders Daniel O’Brien and Rodrigo Andrade in November 2018.
The idea for Farmony was O’Brien’s and he spent about 18 months developing the concept before bringing Prior (a friend from college with a marketing background) and business graduate Andrade (a former colleague at the Kerry group) on board. O’Brien’s background is in agriculture and economics and he had seen the start of commercial vertical farms in Asia and the Far East while working abroad.
The Farmony growing units are modular and can be built to any size
Modular units
Potential customers for Farmony include existing and would-be farmers, schools, colleges, community enterprises, and even individuals with €1,500 to spare who can produce a steady supply of fresh greens from a mini-unit in their own home. Anywhere there’s free space is a potential site and controlled farming environments have been created around the world in many unusual places: from tunnels and disused air raid shelters to vacant car parks.
The growing units are modular so farms can be built to any size. A fully kitted out facility, roughly the size of two 40ft (12m) containers joined together, would cost in the region of €86,000. “We land the farm in someone’s yard or put it together in an available outbuilding – such as an unused mushroom house – hook it up to the [existing] power and water supply and they are ready to start growing,” Prior says.“Growers have no problems with weather or seasonality and don’t have to worry about levels of watering or plant nutrition as this is all controlled for them. With our system it’s not the growing that’s the issue. It’s the selling. They need to have thought out their route to market for the volume they’re planning to produce because if they go for microgreens they’d have crops ready for harvesting every 7-10 days. But if they went for something like basil it’s between 21 and 25 days to harvest so it’s less labor-intensive.”With their shiny growing trays, distinctive LED lighting, and humans dressed in white coats with gloves and hair coverings, a Farmony unit looks more like a plant factory than a farm. However, high levels of hygiene mean the growing environment can be kept pesticide-free. It’s all very quiet and even a little bit eerie as the low labor requirement means people are thin on the ground. Making everything as automated as possible was a priority for the company so the labor input for a 20-module unit would be 25-30 hours a week between seeding, transplanting, harvesting, and cleaning.
Farm dashboard
While the uniform rows of little green plants are the visible manifestation of the Farmony method, they are just one side of the story. The other is the intelligent monitoring system that’s whirring away in the background and measuring all the key metrics, providing minute-by-minute detail about the crops as they grow so environmental tweaks can be made as needed.
Each grower has an individual farm dashboard that gives them updates on their crops and offers advice on things like workflow planning. The dashboard can also be used to reorder raw materials such as seeds and growing mats.
Farmony’s units can be remotely controlled from anywhere in the world from any network. This is different to most smart technology farm systems that require the user to be closer to home. The company’s platform is open source and can be used over GSM phone networks and any wifi or internet connection. Customers can choose to operate alone with just back-up support from Farmony or they can become part of the interconnected Farmony “family”, which among other things uses aggregated data from growers to help them further improve growing efficiencies and gain insights into crop behavior.“
In Ireland alone we import around €300 million in fresh produce that we could be growing here given the right conditions,” Prior says. “With our solution this produce could be grown locally all year round, creating jobs and reducing food miles. There is no reason why Ireland can’t become self-sufficient in leafy greens, herbs and microgreens.”Investment in the business has been about €250,000 so far with support coming from the Department of Agriculture, Fingal Local Enterprise Office, and Teagasc. e
Farmony will make its money from selling hardware and from monthly SaaS subscriptions based on farm size with over-the-air updates and tiered reporting levels available.
In May, Farmony signed a European distribution agreement with the US-based Sananbio, a vertical farming technology company that makes growing modules and horticultural lighting. The plan is for Farmony to start selling its solution across Europe using Sananbio’s equipment and it has already opened a satellite office in Poland to kick-start the process. The company expects to have about five farms up in running in Ireland by the end of the year and already has one in the US with another to follow and one about to come on stream in the UK.