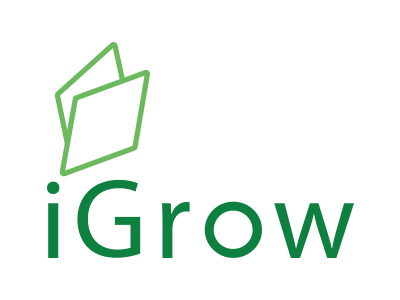
Welcome to iGrow News, Your Source for the World of Indoor Vertical Farming
Nation’s First Fully Automated Vertical Farm Breaks Ground In Ohio
Posted by Laura Drotleff| September 25, 2018
Cincinnati-based 80 Acres Farms announced that it plans to build a large, fully automated indoor farm in Hamilton, OH, which will produce specialty greens to supply local independent retailers including Jungle Jim’s International Market and Dorothy Lane Markets, and national chain locations for Whole Foods and U.S. Foods.
The facility would be the first of its kind in the nation, according to 80 Acres. A groundbreaking was held for one of two facilities on Monday, Sept. 24. An MSNBC article stated the project would cost between $10 million and $15 million initially, and create 40 jobs would be created, which would average in the $40,000 to $50,000 range including benefits. The city discounted land in Hamilton Enterprise park for the project and is providing an Enterprise Zone property tax abatement of 75% for 10 years, MSNBC reported.
80 Acres Farms personnel will manage the facilities, which will feature robotics, artificial intelligence, data analytics, and around-the-clock monitoring sensors and control systems to optimize every aspect of growing produce indoors. The Cincinnati firm will work with its current technology partners, Signify, an LED horticultural lighting company, and Priva, which provides environmental controls and process management software, according to Tisha Livingston, President and Co-founder of 80 Acres.
The initial phase, which is to be completed later this year, will feature grow centers to produce microgreens, culinary herbs, leafy greens, and kale. Three additional phases are planned. When completed, the indoor farm is to encompass more than 150,000 square feet, which equates to nearly 3.5 acres.
The full-phase expansion of controlled environmental agriculture will enable 80 Acres Farms to provide more product to serve existing customers and new ones with fresh-picked, year-round produce. 80 Acres Farms now serves Cincinnati-area customers from its facility in Spring Grove, where it grows microgreens, culinary herbs, leafy lettuce, kale, and vine crops such as cherry tomatoes, cucumbers, and peppers.
“We already have demonstrated that we can provide to our customers the freshest, best-tasting and nutritious locally grown produce, while using renewable energy, very little water, and no pesticides,” said Mike Zelkind, CEO and co-founder of 80 Acres Farms in a September 21 release. “With the Hamilton facility, we will achieve the next-generation of indoor vertical farming. This project will deliver our proof of concept that indoor farming can be fully automated, commercially scalable, higher-yielding, and profitable. It will serve as a prototype for our ambitious plans to co-locate similar facilities with commercial customers in other parts of the country.”
Zelkind said 80 Acres Farms will work with partners such as JDL Warm Construction and Open Architecture Inc., both of downtown Cincinnati. Site Solutions Consulting of Loveland will do excavation site preparation work.
80 Acres Farms is headquartered in the Spring Grove community of Cincinnati, where the company was founded in 2015 by Zelkind and Livingston, both veteran food industry executives. It now employs more than 60 people in Cincinnati and other company research and development, engineering, and production facilities in three other states. In its mission to locally grow the best tasting, most nutritious fruits and vegetables, the company partners in research with many agrotechnology and academic research institutions.
Young Fijian Makes Good Use Of Govt Scheme
A Fijian who studied in India has made the most of Government’s Young Entrepreneurship Scheme and embarked on a journey to combine engineering and agriculture.
September 22
18:56 2018
by SWASHNA CHAND , SUVA
Entrepreneur, Rinesh Sharma.
A Fijian who studied in India has made the most of Government’s Young Entrepreneurship Scheme and embarked on a journey to combine engineering and agriculture.
Rinesh Sharma, 25, is an entrepreneur living in Lautoka who has started up something unique.
“While studying in India, I came across a software engineer who had an indoor hydroponics farm in Goa,” he said.
“After reading his success story, I made up my mind to do the same back home.”
Hydroponics is a method of growing plants without soil by using mineral nutrient solutions in a water solvent.
“Engineering combined with agriculture allows me to grow plants in its special conditions and parameters, maximising faster yields,” he said.
“I grow include strawberries, mint, coriander, coral lettuce and butter crunch lettuce. The idea of hydroponics came to me in my third year of engineering.
“Since then, I have researched every day about executing this project on a commercial scale in Fiji.”
Mr Sharma said he came back to Fiji in May and started an automated hydroponics system, in which he grew green leafy vegetables in his backyard.
“This was a challenging process because it was almost impossible to find hydroponic system supplies in Fiji, but regardless I made a small prototype where I can harvest 372 plants per month,” he said.
“Doing farming is the best thing I have done and perception really does matter because we have a lot of people who left farms and moved to the urban life and this has created a huge gap to fill in the field of agriculture.”
Mr Sharma said for him it was a mission to feed the world and he was going to start with his country.
“Upon my arrival in Fiji, I had applied for the YES entrepreneurship scheme run by the Ministry of Trade, Tourism and Industry with the intention to begin an automated hydroponics farm in Fiji on a commercial scale and got a grant of $20,000,” he said.
He is thankful to the Government for providing him with the assistance.
“The assistance is motivating and encouraging for us the younger generation to do step forward and do something,” he said.
“I keep challenging myself with growing the most impossible edible items such as blueberries, raspberries and apples as well.
“It is important that people of Fiji are able to afford proper nutritional meals every day and that to at low cost.
“So, as a hydroponics farmer, I am able to control any device in my farm through a single touch on my phone via internet and I am also able to receive any data changes that may occur, such as change in PH, moisture, temperature.
“It was a privilege to be given a scholarship by the Indian High Commission where I got to learn so much.
“I came back to Fiji with the intention of working with the Government and their expertise to change and shape farming methods in Fiji.”
Edited by Epineri Vula
Feedback: swashna.chand@fijisun.com.fj
Hydroponic Seed Starting 101: A Primer For Beginners
Starting your seeds hydroponically has many benefits, but many people are unsure how to go about it. Shannon McKee gives us a primer on the basics of starting your own seeds to expand on what you’re currently growing.
Shannon McKee | July 10, 2017
Takeaway: Starting your seeds hydroponically has many benefits, but many people are unsure how to go about it. Shannon McKee gives us a primer on the basics of starting your own seeds to expand on what you’re currently growing.
Many people skip starting their own seeds because of the time and effort to get them started, but there are some great reasons to start your own seeds hydroponically. It’s so much easier to just go to the store to pick up some seedlings to pop into your system and get growing, right? Well, store-bought seedlings do have some downsides that can be avoided if you start your own.
The first is that you’re limited to what you can grow in your system. You have to choose from the options available at the store. However, if you start your own seeds, you can grow anything. This means you can grow your favorite heirlooms or even rare plants that aren’t found at many nurseries.
Adding seeds to your hydroponic system means that they won’t go through any trauma or root damage from being transplanted into your system. This process may also introduce diseases or bugs into your hydroponic system from the store.
Also, you get the satisfaction of growing a plant from a tiny seed rather than just picking up a seedling. Plus, a packet of seeds can grow a number of plants for just a few bucks, whereas the cost of only one seedling can be the same amount.
Seeds are also more cost-effective than buying one or two seedlings in the long run, as you can save some for the following year. The germination rate can decrease over time, but often, you can still get quite a few to sprout over the years until you have to buy your next seed packet.
What You Need to Start Seeds in a Hydroponic System
The first time you start your own seeds for your hydroponic system may be a bit more expensive at the beginning because you need to buy more materials than in future years. Seeds need water, light, oxygen, and heat to grow. You really don’t need anything too special to grow your own seeds.
You can use a grow tray with a dome for your own miniature greenhouse to create an ideal environment. If you’ll be growing your seeds in an area that is cooler, you may want to invest in a heating mat that goes underneath the grow tray to keep it warm as this is a necessary condition for sprouting to occur. Light is good to have as well as this will help your seeds sprout.
Inside of your grow tray, it can be beneficial to use a pot that works for your seeds and their future as seedlings in your hydroponic set-up. You’ll want to use starter cubes, such as those made of stonewool (rockwool). The key here is to use something that can withstand being immersed in water without dissolving, as it could clog up your system after transplanting.
Step by Step Instructions for Sprouting Seeds in a Hydroponic System
The first thing that you’ll want to do is to soak your starter cubes in clean water for about an hour. After they’ve been given a chance to soak, put a few seeds into the cube’s hole. You’ll want to add several just in case you have some seeds that don’t germinate. Once they sprout, you can thin out the weaker plants to allow the strongest to grow.
Prepare your grow tray with about an inch of clean water or nutrient solution that is at half strength. Arrange the light source and heating mat as needed. You can keep the lid on to keep the heat and moisture in the tray.
Put these planted cubes into the grow tray and add water or the half strength nutrient solution as the level goes down in the grow tray.
After about four days, you’ll start to see some sprouts emerging.
Some people prefer to use a Ziploc bag, rather than a grow tray, when trying to get the seeds to germinate as it functions like a greenhouse. Seal the bag with a little bit of air and put it in a dark place for about four days to get the seeds sprouted. Then, you can put the starter cubes with sprouted seeds into the grow tray.
Step by Step Instructions on Transplanting
Keep your tiny seedlings growing strong with your hydroponic nutrient solution. Once they’ve gotten bigger, you don’t have to make the nutrient solution half strength.
You’ll start to see the seedlings’ roots coming out of the bottom of the cube, and this is the sign you’ve been waiting for, as it means you can start transplanting. This can take about two to four weeks depending on what plants you’re growing.
Clear up a spot in your hydroponic system’s growing media for the seedling – cube and all. Gently transfer the starter cube into your growing media, and cover it gently.
Give the root system a chance to naturally seek out the water and nutrients in your system by top watering it for a few days to give it a chance to grow the root system.
Voila! You grew your own seedlings into a strong plant for your hydroponic system. Depending on the type of plant, you’ll be able to get your first harvest about four to eight weeks from the time you transplanted your seedlings.
Cut out the dependency of only being able to grow the types of plants that are available as seedlings at your favorite gardening store. Take a little extra time to nurture your seeds so that they become strong seedlings ready to transplant into your system. You’ll be able to take pride in your efforts with how healthy your plants are and your overall system’s health.
What Are The Best Plants To Grow With An Ebb and Flow (flood and drain) Hydroponic System?
Hybrid seeds will give you significantly higher yields and multiple disease-resistant properties.
Written by Lynette Morgan
Q:
I have an ebb and flow (flood and drain) hydroponic system. I have tried growing many types of plants, but the best performers in the system were lettuce, cucumbers and tomatoes. As I only have a 320 square foot greenhouse and wish to share the produce with my family, I want to grow the most productive plants. Can you suggest the best seeds for me to purchase for lettuce, cucumbers and tomatoes? I live in northern Florida. Thank you!
A:
The best varieties for a small, hydroponic greenhouse in your climate would be hybrid types of tomato and cucumber plants, and heat-tolerant cultivars of lettuce. Hybrid seeds will give you significantly higher yields and multiple disease-resistant properties. They perform well under hydroponic growing conditions where they receive the ideal levels of advanced nutrition. Lettuce is essentially a cool-season crop and can struggle in warm growing conditions, so selecting more heat-tolerant or bolt-resistant types is recommended to help prevent problems such as upward stretching, or the development of tip burn under high temperatures. The following would be my seed recommendations for a hydroponic system in Florida:
Tomatoes
Beefsteak: Trust F1 and Geronimo F1. These are both grown commercially in greenhouses and are ideal for hydroponics. The fruit is large, so fruit trusses may need some support due to their weight. These varieties also have multiple disease-resistant properties. Hybrid tomato plants need plenty of potassium when the fruit is developing, so I recommend using a high-quality fruiting or bloom nutrient formulation at this stage.
Cherry: Flavorita F1 or Sakura F1. Both are red cherry tomatoes with a good, sweet flavor and multiple disease-resistant properties. They are less prone to splitting or cracking than other cherry types.
Cucumbers
There is quite a wide range of cucumber types that can be grown hydroponically. Here are some of my top recommendations:
Long, seedless Dutch type: Tyria F1. Fruit are 14 inches long, great-tasting, thin-skinned and non-bitter. They also have some resistance to powdery mildew, which is a huge advantage when it comes to cucumbers.
American slicer type: Corinto F1. Fruit are 7-8 inches long, have good disease resistance and are highly productive in hydroponics.
Mini cocktail type: Iznik F1. Harvested when just 2-3 inches long, and also called snack cucumbers, these cucumber seeds are a good variety for hydroponics as they produce a lot of thin-skinned fruits.
Lettuce
It pays to try growing a wide range of lettuce types, depending on your personal preferences, of course. However, the following types are proven performers in hydroponic systems:
Green butter lettuce: Pelleted Rex seeds are the best in terms of handling and germination. This lettuce is ideal for Florida’s climate. It is slow to bolt and very reliable. It also tolerates downy mildew.
Green frilled type: Muir. It is a medium-sized, light green, open and slow-growing variety. Muir is fairly heat tolerant and has a good flavor.
Salanova: For a mix of different lettuces and a surefire way to impress friends and family, the latest hydroponic lettuce trend is the Salanova lettuce types that produce compact heads of leaves that are all totally uniform in size and shape. I recommend the Salanova Home Garden Mix pelleted seed that will produce a range of colored Salanova types. This seed is a little more expensive than other lettuce types since it is a reasonably new development, but it is well worth the investment, particularly with the deep red types.
All of these seed varieties are available online from Johnny seeds (johnnyseeds.com) in different-sized packs. Good luck with your hydroponic greenhouse this season!
Have a question? Ask us here.
View all questions from Lynette Morgan.
Urban Crop Solutions Offers A Glowing And Growing Global Future For Indoor Farming
A start-up that engineers and builds fully automated indoor vertical farms inside shipping containers and buildings.
by S. Virani
25 September 2018
“Imagine yourself standing inside a climate-controlled, high-ceiling warehouse. In front of you stands a tower with 8 irrigated levels, on each of which lettuces, herbs, micro greens, and baby greens grow under LED lights. Robotics move trays with young plants from outside this grow room into the right position in the grow tower, while on the other end fully grown crops are taken out, ready to be harvested. Can you see it? You are standing in Urban Crop Solutions' Plant Factory — the state-of-the-art in indoor vertical farming technology. A highly engineered manufacturing plant producing not goods, but crops.” — Urban Crop Solutions.
Meet Urban Crop Solutions: A start-up that engineers and builds fully automated indoor vertical farms inside shipping containers and buildings. They also provide clients that have bought a system with carefully selected and tested seeds, substrates, nutrients and comprehensive software grow recipes. The result: year-round production of fresh and healthy crops.
The start-up’s goal is to create an optimum environment for plants to grow, with the right combination of climate, lighting and nutrients throughout their growth cycle.
From left, Frederic Bulcaen, co-founder and chairman at Urban Crop Solutions, with Brecht Stubbe, global sales director and Maarten Vandecruys, co-founder and CEO with at European FoodNexus Award Ceremony
Headquartered in Belgium, with regional offices in Miami (USA) and Osaka (Japan) as well as a network of sales agents in various territories, Urban Crop Solutions will take part in the World Agri-Tech Innovation Summit to be held from October 16-17 in London, selected as one of the 13 start-ups to present their innovative solutions.
Produce Business UK sat down with Brecht Stubbe, global sales director of Urban Crop Solutions, to understand the technology that the start-up has developed, as well the growth of the vertical farming market in general, challenges that farmers face now and will face in the future, and Urban Crop Solutions’ formulas to combat food shortage in the future.
How did the Urban Crop Solution concept come about?
By 2050, more than 70 per cent of all people will live in cities. The population will grow from 2.5 billion to over 9.8 billion, leading to a need to produce 70 per cent more food. In 2012, 80 per cent of the land suitable for agriculture was already in use. Due to these facts, it was safe to say that something needed to change.
That is when our co-founder (Maarten Vandecruys) started thinking: “What if we could use technology to grow any plant, year-round and independent of local climate? What if we could do this using 95 per cent less fresh water? What if we could do this using zero pesticides and herbicides?” Together with Frédéric Bulcaen, the other co-founder who acted as a business angel, they set out to explore this further.
With the above goals in mind, modular solutions were developed at Urban Crop Solutions: A fully controlled and automated resolution that can be placed anywhere and which can grow any plant. Imagine a closed box or warehouse with crisp white walls in which plants are grown using LED lights, as well as without soil.
In lieu of the Agri-Innovation Summit, where you will present alongside a dozen or so other start-ups, what is it about your technology that stands out and set up apart? Essentially what is your unique selling point?
Urban Crop Solutions has a total turnkey solution, as well the latest technology in terms of indoor farming systems. A big difference with other competitors is the fact that we have plant scientists that develop recipes for more than 180 crop varieties. We also offer all the consumables — seeds, substrates, nutrients — to help you grow your crops.
Finally, we have experience all over the globe, from Belgium to Japan to Miami.
So when we look at our unique selling propositions, these would be the consistent high quality of produce combined with our biological know-how of how to grow them, as well as the use of automation to bring down labour costs.
Let’s talk about your clientele and the sorts of industries that you have worked with? Furthermore, would you say there has been a growth in demand for this over the years?
A first category of clients are the entrepreneurs, people who see the opportunity this technology offers and plan to start from scratch. For example, those who want to build a produce brand growing vertically and indoors.
Another category are R&D institutions and corporate departments as well as crop science companies that use our technology to conduct relevant research while being able to manage all variables precisely to their needs.
A third important category is the existing vertical farmers who are looking for a high-quality, third-party solution provider to help them scale.
We would also include the category of existing traditional farmers that are looking to capture the new market this technology offers by complementing their existing production methods. For example, open-field and greenhouse farming.
Do you see other start-ups competing in this space?
Not really. There are a lot of vertical farmers focused on growing and integrating technology themselves. However, they are not any qualitative total solution providers like Urban Crop Solutions, that have the ability to design and build a tailored, fully automated efficient solution the world over.
We just did a piece about the new Emirates Airlines vertical farm. It provides an example of how other industries can apply and utilize the vertical farm. What are your thoughts on that?
This is a good example of disruptive new business opportunities and vertical integration into supply chains. Zooming out, the broader definition of this case can be defined as food catering companies (a subcategory of food processing companies) integrating produce farming into their business. The technology allows them to capture an additional margin by adding the value themselves as opposed to buying the produce from a third party and enables them to perform just-in-time production with reductions in waste and certainty of ability to deliver.
You have various solutions on your website: The Farmflex Container, The Farmpro Container? The Plant Factory. What are the main differences between all of them?
We have two different product categories:
Off-the-shelve product
This includes our FarmPro & FarmFlex container. These are mainly used as a first stepping stone/proof of concept for companies that would like to grow commercially or conduct research on a larger scale in the future.
FarmPro container: The Urban Crop Solutions FarmPro is a 40-foot, fully automated freight container with a state-of-the-art leafy green growing system. This system gives a four-layer growing solution. Its design is primarily focused on growing lettuce and individual herbs.
FarmFlex container: This system has a state-of-the-art leafy green growing rack setup. It gives a fully automated, four-layer growing solution with maximum flexibility as to what you can grow. For this reason, educational and research institutions have the highest demand for this product, as it allows growth of almost anything: lettuce, herbs, micro greens, baby greens and more.
Then we have custom-made large-scale solutions:
PlantFactory: Our Urban Crop Solutions PlantFactory allows you to grow in any available space, whether it is a basement or a warehouse. This way, you can produce leafy greens year-round on an industrial scale or set up complex large-scale R&D infrastructure.
In an Urban Crop Solutions PlantFactory, everything is designed and engineered according to the available space, as well as to the customers’ needs. For example, the cultivation area, our innovative LED growing technology, ingenious irrigation systems and climate control.
In terms of industries, what industries do you work with, and what would you say are the industries most relevant for now in 2018?
Agricultural food production and crop science research are the most relevant industries for 2018 based on the demand they produce for us.
As a B2B publication focused on produce, we are interested in how vertical farming truly can affect the industry as a whole. What are some predictions you might have about the effect of vertical farming on produce? Are there particular fruits or vegetables that will thrive in this environment and produce higher yields?
There exists a distinction between what we can grow from a technical standpoint (almost everything – even strawberries, cucumbers, tomatoes, peppers, etc.) Then, however, there is the commercial standpoint. The latter is more limited because obviously one needs a positive cash flow. The capital-investment cost and substantial operational costs (e.g. electricity) require that one selects a crop that has a short grow cycle, high density and harvests the full biomass created.
As a result, the current commercially viable food production crops are the leafy greens such as lettuce, herbs, baby greens and micro greens.
Just how good, just how efficient are these farms?
The farms can be tailored to include carefully selected and tested seeds, substrates, nutrients and a comprehensive software tool automatically providing the plants with the right combination of climate, lighting and nutrients throughout their growth cycle. Our solution leads to higher yields, higher nutritional value, food safety and security, higher water efficiency. This can actually be up to 95 per cent less than open-field farming.
On your home page, you make the following claim: “Urban Crop Solutions envisions to become the global independent reference of the fast-emerging vertical farming industry." How would you say this is possible?
At this time, vertical farmers are trying to juggle two widely different business plans: on the one hand, they spend capital developing and integrating an engineered solution and the biological corresponding know-how. On the other hand, they then apply this research to construct a vertical farm, operate it as farmers, and earn back the investment not only of the infrastructure, but also of the R&D that precedes it, as well as continues afterwards. In our opinion, this is a poor business plan because they have to earn back their R&D and their operational infrastructure investment with the sale of crops.
If we look at the more mature greenhouse industry, we get a sense of where the sector of vertical farming will eventually evolve. A greenhouse tomato grower that wants to set up a new production facility will not develop his own technology, but instead turn to the 15 best greenhouse project developers, ask for quotes, and select the one he feels most confident about. In that setup, we see technology companies focusing on providing systems, and growers focusing on farming. We start seeing a change in the mindset of vertical farmers along those lines today as well.
Let’s talk briefly about the upcoming World Agri-Tech Innovation Summit. What will you be presenting there?
We will begin with a company introduction, present our unique selling points, newest technology, projects and achievements.
While creating all these solutions, there indeed have to be challenges that need solutions. What would you then say are some of the actual challenges that farmers face today?
Traditional farmers are combating unreliable climate conditions, increased labor costs, crop diseases, crop pests, soil degradation and much more. Our solutions provide reliable alternatives to all of these concerns.
Existing vertical farmers from their end are struggling with the high labor costs associated with running non-automated vertical farms — requiring scissor lifts or stairs to harvest the higher levels of crop cultivation areas — as well as inconsistent quality in their production due to poor control of the different variables. Our fully automated and well-engineered system reduces labour costs and deviations from the ideal settings, respectively.
The vertical farm model is certainly a rising trend amongst start-ups. How did this movement come about?
Well, it’s like I said from the beginning. By 2050, more than 70 per cent of all people will live in cities. Added to that, in 2017 almost 300 million USD has been invested in vertical farming, creating more and more momentum.
To put things into perspective globally, which regions would you say have the biggest influence on the vertical farm boom?
In North America and South East Asia, we see the most vertical farms. In South East Asia, there is a lack of land to farm on and a variety of food safety issues. In North America, there are a lot of business opportunities with vertical farming technology due to the willingness of consumers to pay a premium for locally produced healthy crops.
Hydroponics Gives Local Veg Production Further Boost
It is learnt that hydroponics systems, a technology suitable for Qatar’s environment even during the summer, can grow watermelons extremely well, producing big and sweet varieties.
September 28 2018 08:18 PM
Prominent Qatari agriculturist Nasser Ahmed al-Khalaf showing the watermelons in his farm near Al Khor.
Qatar’s aim for self-sufficiency in food production has got a major fillip as a local farm succeeded in growing and improving the quality of certain types of vegetables and fruits with hydroponics system.
Prominent Qatari agriculturist Nasser Ahmed al-Khalaf told Gulf Times that his farm will harvest in the coming weeks melons and water melons, grown for the first time in the country using hydroponics.
"We have as well increased the (production of various types of) herbs,” disclosed al-Khalaf, who is also the owner and managing director of Agrico.
A private Qatari agricultural development company established in 2011, Agrico produces organic vegetables and fruits year-round in Al Khor using hydroponics systems and aims to help Qatar achieve food security.
Al-Khalaf said that they will be harvesting between 800kg and 1,000kg of watermelons per week from next week while melons would take 30-45 days more. These types of fruits are grown separately in two greenhouses.
Agrico now produces large-size watermelons with hydroponics system
It is learnt that hydroponics systems, a technology suitable for Qatar’s environment even during the summer, can grow watermelons extremely well, producing big and sweet varieties.
While some local farms also produce melons, al-Khalaf pointed out that Agrico uses hydroponic system and aims to grow vegetables and fruits year-round.
“Any new item we introduce we try to make it sustainable in order to supply the market on a daily basis,” he stressed.
In the mushroom family, the company now added shiitake and oyster mushrooms in its production. By next year, it will also grow some hard vegetables such as carrots and beetroots.
Agrico also plans to experiment with growing bananas by the end of this year, apart from organic papayas and other fruits such as lemon and pomegranate.
Al-Khalaf noted that Agrico’s operations expanded substantially in the previous season to further increase its production and meet the growing demand for fresh produce. It is now exporting various vegetable items to Kuwait and Oman.
After proving it can produce year-round in the past years, even during the summer, he pointed out that they developed other greenhouse systems in a much economical price.
“Our aim in 2018 was to focus more in developing our agriculture system in other farms, which we did by developing over 20,000sqm of greenhouses under our own operation,” al-Khalaf said.
“Besides Agrico, we are also keen in developing other farms using our technology and transferring this know-how to improve the farms in Qatar to make production sustainable,” he observed.
Around 300 of the 1,400 farms are continuously increasing their production of various vegetables since last year and this number is also growing, according to al-Khalaf.
"Qatar residents will also see a huge difference in the quality of existing items this season, especially in tomatoes, cucumber, zucchini, capsicum, and eggplant," the agriculturist added.
Geothermal Energy May Make Indoor Farming Work in The Future
The farms of the future may be possible even in an urban setting with the right alternative energy.
September 27, 2018 By JULIE CAMPBELL
The farms of the future may be possible even in an urban setting with the right alternative energy.
Technology and geothermal energy advances are sending farming indoors on an increasing basis. This is the case both with urban greenhouses on a smaller scale or larger scale greenhouses.
The primary challenge with these types of greenhouse have to do with the energy they need.
Greenhouse operation is energy intensive, with high demands for electricity because of lighting, but, more importantly, heating. It is in the area of heating that geothermal energy presents a significant opportunity.
As populations rise and the demand for local food production increases, indoor farming may become much more important even in urban settings, according to a recent World Economic Forum article. That said, in order to make that financially feasible, producers need to look to affordable alternative energy options.
These urban operations rely on using every square inch to its greatest potential, as space is much more limited. Moreover, everything must operate on less water. That said, as these indoor farms – small or large in size – have the same heating and lighting requirements as a traditional farm. This requires affordable sources of energy.
Many in the industry believe geothermal energy will be among the leading solutions for indoor farming.
Among the reasons that many will look to geothermal energy is that there are already many success stories with this technology. It is not only receiving increasing attention from those in the industry, but it has also already proven itself in many examples.
For example, one of the largest flower producers in Kenya, called Oserien, uses geothermal power for heating as well as small-scale electricity production. In the Netherlands, energy is becoming increasingly expensive, so geothermal wells are being drilled for many greenhouse operators that need heat. Iceland has widespread geothermal energy heating in its greenhouses to make it possible to grow vegetables throughout the year.
Germany is home to several geothermal power projects being developed to use this resource for their greenhouse operator heating. A new effort has also been underway in Pagoda Springs, Colorado, where it is being used for vegetable production on top of broadening economic development.
Reusing Shipping Containers: Thinking Outside The Box
Let us introduce you to some of the creative-minded people who - literally - think outside the box!
By: AJOT | Oct 04 2018 | Intermodal News
Boots are made for walking and containers are made for shipping, right? Well, not if you ask everyone! Today, we see an exhilarating creativity in the reuse of shipping containers - living spaces, hotels, bars, pop-up stores, emergency shelters, bridges, art projects, and urban farming - the list goes on. Greencarrier Liner Agency loves the idea of recycling and innovation. Let us introduce you to some of the creative-minded people who - literally - think outside the box!
Urban farming – growing crops inside shipping containers
Freight Farms has found a way to grow crops inside shipping containers. Their hydroponic farming system called The Leafy Green Machine uses hi-tech growing technology to transform discarded shipping containers into mobile farm units. Each farm can produce as much food as a two-acre plot of land on a much smaller plot than is required by traditional crops.
As the outdoor climate has no impact on the conditions inside the container, food can be produced throughout the year and in any location. The project truly taps into the growing trend for urban farming and reduces the ecological footprint of food production.
Life uncontained – living inside Evergreen Line shipping containers
For the claustrophobic reader, it is now time to cover your eyes! After spending years not knowing what to do with their lives, this couple decided to chase what made them happy. Inspired by their past road trips, the hippies of the seventies, and Elon Musk, they chose to risk everything: They sold their traditional home, quit their jobs, and moved from Florida to Texas to build their dream debt-free net zero shipping container home using a couple of Evergreen Line Shipping containers. Are you intrigued? Follow their journey on YouTube!
A piece of container artwork you just can’t take your eyes off
As a part of his project “Women are Heroes,” the French artist JR turned shipping containers into a stunning piece of floating art. The picture assembled on the containers represents the eyes of a woman called Elisabeth who lives in the Kibera slums in Nairobi. When JR met and photographed her, she said “Make my story travel with you.” Using thousands of strips of paper placed by dock workers on the sides of the containers, JR created two eyes gazing at the world while travelling the oceans – two eyes belonging to women who will never travel across those oceans – made possible by art.
Container skyscrapers to replace slum housing
CRG Architects have come up with the concept for Container Skyscraper. The idea is to provide temporary accommodation to replace slum housing in developing countries. As many cities are facing unprecedented demographic, environmental, economic, social and spatial challenges, stacking recycled shipping containers to create cylindrical-looking towers can create high-density, cost-effective housing in urban areas. This is a truly innovative idea both in terms of CSR and the environment.
Container village startup hub for young companies
Dutch architect Julius Taminiau has created a temporary startup hub in Amsterdam using shipping containers. He has turned a derelict patch of land into a low budget, temporary space for young companies. In this dynamic village, the startups will inspire, collaborate across sectors, exchange knowledge and produce unexpected and paradigm-shifting creations. As the containers are placed upon concrete tiles, everything can be reused when the village is taken apart in the future and no trace will be left – an eco-friendly and innovative solution, which we are all about at Greencarrier Liner Agency!
3 reasons for reusing shipping containers.
As exemplified above – shipping containers can be so much more than just a box to ship commodity in. The reason for reusing shipping containers for other purposes than shipping is not only that they are extremely flexible, can solve a bunch of problems and be used in such innovative, unique, creative and cool ways – there is much more to it.
When containerisation conquered the global trade, shipping containers were standardised for intermodal freight transport. The standardisation made it possible to transport larger freight volumes and use different modes of transport without having to unload or reload the goods. Today, shipping containers still serve their purpose, but also provide great advantages when used as Intermodal Steel Building Units (ISBU).
1. Shipping containers are excellent construction material
From a structural point of view, containers are excellent construction material. As they spend the majority of their lifetime outdoors, the material is ideal for exposure to the elements of nature. The steel construction and design provide protection and strength as well as structural support and a long lifespan. The corner assemblies and locking mechanism also provide stability when multiple containers are being used in the construction of a building.
2. Buying empty shipping containers can be cost-efficient
Looking at costs, the reuse of shipping containers can be cost-efficient. A shipping container’s initial purpose is to carry cargo at sea, therefore it has to be cargo worthy throughout its lifespan. Most containers are finished as shipping containers after ten years in service and they are being replaced. Even though container stock is tight for most shipping lines, there is a big aftermarket for those replaced units retired from service at sea. To use those units as building material is inexpensive compared to traditional materials, such as wood, bricks or steel.”
3. Reusing shipping containers is sustainable construction practice
Recycling of any sort is eco-friendly. This is especially true when it comes to reusing shipping containers. It is, without doubt, sustainable construction practice; recycling unused containers for construction material puts an unused product to use while at the same time cleaning up spaces such as ports and shipyards. Shipping containers are also excellent for making use of solar power and can be insulated with eco-friendly materials.
CubicFarm Systems Readies For Expansion Into Cannabis Sector As Bevo Agro Prepares To Become Zenabis Global
Bevo introduces CubicFarm Systems Corp. (CubicFarms), an agriculture technology business that was developed by the Bevo management team.
On October 4, 2018, Bevo Agro announced that it had signed an Arrangement Agreement with Sun Pharm for a reverse take-over of Bevo, and announced its intent to change its name to Zenabis Global. Zenabis will have nearly 3.5 million square feet of available production space.
Now, Bevo introduces CubicFarm Systems Corp. (CubicFarms), an agriculture technology business that was developed by the Bevo management team. As part of the Arrangement Agreement cited above, Bevo's ~43% equity ownership in CubicFarms will be spun out to Bevo's existing shareholders, and CubicFarms intends to simultaneously list on the TSXV as a separate company. Zenabis (through Sun Pharm) also holds a stake in CubicFarms that it will retain post-amalgamation. This investment will be held by Zenabis Ventures, Zenabis' wholly-owned cannabis venture platform.
CubicFarms is the developer of patented technology that automates large-scale commercial farming operations in climate controlled growing chambers. By recycling water, each crop uses a fraction of the water required under traditional farming methods. Further, each machine is constructed inside an individually climate controlled growing chamber, allowing optimized climate, lighting, nutrients and other plant-specific needs, leading to faster growing cycles and year-round production. Utilizing CubicFarms' patented "undulating path" conveyor system, all plants are brought to those harvesting and planting, reducing labour significantly and increasing yield per cubic foot compared to other growing systems.
CubicFarms currently grows lettuce and leafy greens; microgreens; and basil and herbs. CubicFarms is also exploring cannabis cultivation applications in a joint venture with Zenabis named ZenCube. In addition, CubicFarms is further optimizing the technology for the nutraceutical and animal feed space.
CubicFarms has been building and selling systems since 2016, with its systems shipped from a state-of-the-art manufacturing facility. This facility is ramping up production to meet CubicFarms' growing global sales pipeline. CubicFarms operates its own commercial scale CubicFarm system, which it installed this summer in Pitt Meadows, British Columbia. This facility grows and sells a wide variety of leafy greens to the local retail and wholesale market, and also accommodates research and development.
"I am delighted that Zenabis sees the value in automating the growing process and reducing the space and labour requirements through utilizing CubicFarms technology to advance their growing capacity," said Dave Dineson, CEO of CubicFarm Systems Corp. "The joint venture between CubicFarms and Zenabis will make available cannabis-optimized growing machines for global customers who want to lower their growing costs, increase yields, reduce labour, water and energy usage, eliminate pesticides, and enjoy consistent quality growing."
"It's exciting that CubicFarms can expand on its patented technology to enter into a whole new vertical market," said Leo Benne, Chief Growing Officer of Bevo (Zenabis Global). "CubicFarms offers growers unparalleled accuracy and predictability, so that no crop ever goes to waste, while saving money and time by using a fraction of the resources."
"As a leading licensed producer of cannabis, we have long admired the pioneering technology introduced by CubicFarms," said Rick Brar of Sun Pharm Investments, the new CEO of Zenabis. "We look forward to working in partnership to help CubicFarms expand into worldwide markets as Zenabis continues to meet the growing global demand for cannabis."
For more information:
CubicFarms
cubicfarms.com
Publication date : 10/11/2018
First Automated Indoor Farm In The U.S. Will Grow Greens For Whole Foods
America is about to get its first fully automated indoor farm.
BY KRISTIN HUNT
1 MONTH AGO
America is about to get its first fully automated indoor farm. This one-of-a-kind site will use robotics and artificial intelligence to grow fresh produce for supermarkets across the United States, including national chains like Whole Foods.
The farm is underway in Hamilton, Ohio — a city just 20 miles away from Cincinnati, where the company behind this innovative project is based. 80 Acre Farms has been on the vertical indoor farming scene since 2015, but this expansion will mark a dramatic increase in production.
The new farm will span over 150,000 square feet, or roughly 3.4 acres, and grow crops ranging from microgreens to kale. Once construction is complete, 80 Acres Farms will supply Whole Foods, Jungle Jims, U.S. Foods, Dorothy Lane Markets, and other food sellers and distributors with veggies year-round.
"We already have demonstrated that we can provide to our customers the freshest, best-tasting and nutritious locally-grown produce, while using renewable energy, very little water, and no pesticides," Mike Zelkind, co-founder and CEO of 80 Acres Farms, said in a press release.
"With the Hamilton facility we will achieve the next-generation of indoor vertical farming using best of breed technology. This project will deliver our proof of concept that indoor farming can be fully-automated, commercially scalable, higher-yielding, and profitable.
"It will serve as a prototype for our ambitious plans to co-locate similar facilities with commercial customers in other parts of the country."
80 Acres Farms uses a hydroponic system that nourishes plants with minimal resources. Hydroponic farming typically requires no soil, no pesticides, and much less water than traditional growing methods, making it the technique of choice among many sustainable food makers.
Indoor farms also allow for better temperature control. With four walls and a roof, growers can keep the environment as warm, cool, or mild as they like — meaning no crop is ever out of season.
They’re also not an energy drain. Thanks to efficient LED lights that nurture the plants’ growth, 80 Acres can manage its power needs. That efficiency extends to the day-to-day operations, which will be bolstered by artificial intelligence, data analysis, robotics, monitors, and control systems.
Despite the robot assistance, the farm will create 40 jobs with an average $40,000 to $50,000 salary — plus benefits.
"Hamilton thanks 80 Acres Farms for its investment in our city," Pat Moeller, the mayor of Hamilton, said in the release.
"80 Acres' high-tech indoor farm efficiently grows fresh produce that will continue to be sold locally. I have had the opportunity to purchase 80 Acres produce and really enjoyed the fresh, flavorful taste."
According to CNBC, the farm’s projected cost is somewhere between $10 and $15 million. Hamilton officials and 80 Acres Farms expect the first phase of the project to wrap by the end of this year, with three additional phases to follow after that.
It’s unclear when the new farm will be open and ready for business, but once it is, it could have a significant impact on the way the U.S. grows and sells food.
Indoor Farm Celebrates Groundbreaking in Welland
A new indoor farm is coming to Welland, phase 1 of the 20,000 sq. ft. industrial facility is about to get underway.
June 26, 2018 | Posted by: Erie Media
A new indoor farm is coming to Welland, phase 1 of the 20,000 sq. ft. industrial facility is about to get underway.
Niagara Holdings Canada announced Monday June 25/2018 that construction is about to get underway. They celebrated the start of this phase with a ground breaking ceremony at the Enterprise Industrial Subdivision at Hwy. 140 and Ridge Rd.
” Well connected infrastructure, ready access to markets, business friendly incentive programs like the Gateway Community Improvement Plan and the proactive and dynamic attitude of officials from the City of Welland and Niagara Foreign Trade Zone, are the main reasons we chose Welland”, said Clarence D’Souza, President of Niagara Holdings in a press release.
Local and federal dignitaries attended the celebration.
Niagara Holdings held it’s groundbreaking ceremony Monday at the location of its new facility in Welland. Photo submitted
Niagara Centre M.P. Vance Badawey congratulated all those involved in bringing the project to Welland.
“Great work by all partners to bring this all together,” Badawey said.
”This project exhibits investor confidence in South Niagara,” he said. “This confidence is a reflection of our current designations as a Gateway Economic Centre and Foreign Trade Zone and our overall proximity to markets. Our ability to work together continues to strengthen our economic performance, globally.
The “purpose built” facility will be the housing for “sophisticated and automated indoor farms in the world,” the press release said.
It is the first on this scale in Canada.
The design is for high volume production of leafy green vegetables. Romaine, Arugula, Kale and Basil are the primary products to be produced at this facility.
The operators for the facility are going to be Intravision Greens (Canada).
“lntravision Greens (Canada), together with lntravision Group Norway (http:/ /www.intravisiongroup.com/), is a leading provider of technology featuring broad spectrum lighting and full system integration. Backed by technology perfected at the University of Guelph’s Controlled Environment Systems Research Facility, the company’s focus is on multi-band and spectrum variable LED lights, enabling biological control and optimization of plant responses to specific wavelengths between UV A and IR light,” the press release said.
“The location in Welland, with its ability to scale up rapidly, it’s green and clean environment and close proximity to several key markets, is of considerable strategic value”, said Amin Jadavji, President of lntravision Greens (Canada) in the release.
The building contract has been award to Timbro, “one of Welland’ s best known engineering firms, with over l 00 years of experience in Ontario,” the release said.
Operations are targeted to begin in the first quarter of 2019.
Moleaer Helps Big Tex Urban Farms Donate More to Local Community With Oxygen Nanobubbles
Big Tex Urban Farms wanted to incorporate an innovative solution that would help them grow more food per square foot to provide more produce to their local community.
By urbanagnews -
October 3, 2018
Moleaer, the leading manufacturer of industrial-scale nanobubble generators, announces that the Big Tex Urban Farms has installed its Boost nanobubble generator to increase crop production. Throughout the growing season, Big Tex Urban Farms donates all its produce to local Dallas area organizations.
Big Tex Urban Farms wanted to incorporate an innovative solution that would help them grow more food per square foot to provide more produce to their local community. After evaluating several options, they chose Moleaer’s nanobubble generator. The generator boosts the deep-water culture’s dissolved oxygen content through oxygen-enriched nanobubbles. When roots are exposed to oxygen- enriched nanobubbles combined with elevated dissolved oxygen content, they can absorb nutrients more effectively, translating into higher yields and ultimately, more food for the local community.
When Big Tex Urban Farms lost power, temperatures in the greenhouse soared above 110 degrees Fahrenheit. The nanobubble-infused water was able to mitigate the effects. Nanobubbles are unique because they are neutrally buoyant and remain suspended in water for long periods of time. In this capacity, they act like a battery, maintaining dissolved oxygen in the water beyond the point of aeration. When the farm lost power, the nanobubbles saved the crop by keeping the plants healthy until power was restored. The tank that did not incorporate a nanobubble generator experienced significant losses, demonstrating a unique benefit of nanobubbles in high-temperature applications.
Moleaer Inc., nanoBoost-enhanced roots on far left
“Big Tex Farms State Fair Project is all about growing, harvesting, and donating produce. We give everything that we grow away to the local community,” said Drew Demler, Director of Horticulture at the State Fair of Texas. “We are trying to feed people and we think that the Moleaer nanobubble system is going to be a big part of how we can get more fresh produce to South Dallas.”
About Moleaer
Moleaer (Latin for tiny air) is a Los Angeles based company that develops industrial scale nanobubble generators to enhance a wide range of processes. Nanobubbles do not float, have immense surface area and stay suspended in water for long periods of time resulting in an unprecedented high rate of gas transfer. These extraordinary properties are proven to help farmers grow more food, oil and mining companies recover more valuable resources and operators treat wastewater more cost effectively.
If Farms Are to Survive, We Need to Think About Them as Tech Companies
We’re not experiencing a food shortage—it’s a shortage of people to farm it.
By Brandon Alexander October 3, 2018
CEO of Iron Ox and former engineer at Google X's drone-delivery program, Project Wing
Growing up on my granddad’s farm—he grows cotton, peanuts, and potatoes in Texas—I often heard that technologies like genetically modified crops were required to scale food production. My granddad believed that organic practices do not scale and will not feed the world at an affordable price point. Given the state of technology then, I believe he was right.
But the industry has changed with much more than the seasons, and we need more than an iterative improvement on past technologies. We are reaching a plateau in food production. According to research published in Nature, about one third of the world’s agricultural lands have maxed out the amount of rice, wheat, and corn farmers can grow.
At the same time, the World Resources Institute suggests we will need to double our food production by 2050 to feed nearly 10 billion people. In order to boost yield, we need to systematically improve the entire grow process and maximize the potential of every plant. To enable this next age of agriculture, we will need to rely on two new advances: machine learning and robotics.
The amount of data available to farmers has skyrocketed. In addition to collecting data at a macro level from satellite or drone imagery, we can also capture data at the micro level, thanks to a combination of cheaper, lower-powered sensors. These sensors provide farmers with insights like hyperlocal measurements on soil conditions, for example.
AP PHOTO/RICH PEDRONCELLI
Farmers have already been using drones to spray crops for years—what tech will come next?
But a firehose of data does not equate to insights, and that’s where the newer methods of applied machine learning come in. Companies like Descartes Labs and Farm Logs are applying machine learning and computer vision to glean insights from these new data streams, providing farmers not just pretty graphs, but actionable information to increase yield.
Machine learning and computer vision enables us to scan each plant in acres of land, detecting plant diseases before they spread and significantly minimizing yield loss and the need for pesticides. For example, traditionally a farmer would inspect parts of a plot of land for plant diseases like powdery mildew or signs of pest pressure like aphids. Because it was physically impossible for them to inspect each plant on acres of land, they would have to extrapolate their findings across the entire plot. Now, modern computer-vision techniques can take multiple images of every plant and stitch them together for a full 3D reconstructed model of the produce.
Data may give us the information we need to improve yield, but something still needs to perform the action. And it’s increasingly not humans.
We are experiencing a growing labor-shortage epidemic. According to the US Census, the average farmer is 58.3 years old, and new generations are not inspired to take on the laborious task that their elders did—even those who have generations of farmers in their family, like myself. This issue isn’t a shortage of food: It’s of people. Crops are rotting on bushes and vines because there aren’t enough staff to maintain and pick them. Considering that one in nine people onEarth aren’t getting adequate nutrition every day, it’s devastating.
This means that though there are more mouths to feed than ever, there will be less land to provide them food, and less calloused hands to tend to the crops that will feed them. So what do you do when you have little land to work with and fewer hands to help? You turn to technology.
Automation allows for a more accurate work environment with little human oversight. It will involve hardware that is more agile than the human eye or hand, and it will be able to give each and every plant the unique attention it needs.
Recent advancements in computing power, dexterity, motion planning, and computer vision are enabling a new generation of robotic applications. Robotics excel at rapidly performing repetitive tasks, but combined with computer vision, robots can start making real-time decisions on a per plant basis, from adjusting the nutrients to pruning. Companies like Blue River have successfully automated tasks like weeding (a manual process for non-GMO crops) to great effect, which is why John Deere bought the company for over $300 million last year.
DAVE GERSHGORN/QUARTZ
A sample of Iron Ox’s automated grow operation.
At Iron Ox, we’ve designed the entire grow process with a robotics-first approach. That means not just adding a robot to an existing process, but designing everything, including our own hydroponic grow system, around the robotics. In an indoor farm, tasks like seeding or harvesting are happening thousands of a times a day. These labor intensive, repetitive tasks are perfect for robotics. And by integrating machine learning and computer vision, we’re able to have the robots respond to an individual plant’s needs. For example, our robot can quarantine a plant if it shows early signs of pest pressure before it contaminates others nearby or change the nutrition recipe for a plant based on phenotyping.
And we don’t even need arable land: By creating indoor farmhouses with these technologies, we can open farmhouses in any location. This means we will be able to control the weather and take chance out of the growing process; currently, we’re losing more and more crops every year to drought, extreme heat and cold, and spontaneous weather incidents. We will also be able to grow crops closer to the communities that need them, reducing the amount of miles travelled to consumers’ kitchens and the industry’s carbon footprint writ large—and for much cheaper.
If farms are to survive, we need to think about them as tech companies. And that means they should be taking advantage of what many other industries are already harnessing: automation.
This story is part of What Happens Next, our complete guide to understanding the future. Read more predictions about the Future of Food.
Israeli Companies Promoting Urban Agriculture Techs
Dubi Raz, agronomy director of Israeli drip irrigation giant Netafim Global.
Source: Xinhua| 2018-10-13 03:09:37|Editor: yan
by Nick Kolyohin
JERUSALEM, Oct. 12 (Xinhua) -- Israeli companies and experts are part of a global effort to promote and develop urban agriculture technologies. They believe urban farming is the way to secure food supply around the world.
"There are three main technological ways to do urban agriculture, and we are involved in all of them by working with most of startups and companies in these field around the world," Dubi Raz, agronomy director of Israeli drip irrigation giant Netafim Global, said in an interview with Xinhua.
The technology which makes urban agriculture possible is the ability to grow crops without the need for land and sun. It is a revolutionary technology which makes it possible to produce food anywhere in the universe.
Instead of the sunlight, there is a special artificial light which is designed and adjusted to crop individually. This modification ensures perfect growing conditions.
The second revolutionary part of urban farming is the use of water or special substrate instead of soil to grow vegetables and fruits. These technologies make it possible to grow crops on walls or vertical layers.
Although the technology exists, it is still an expensive practice in most cases.
"Because it is costly to grow crops inside the city. It doesn't make sense to produce sample wheat, tomatoes or any other plants, which consume lots of expensive energy to provide the artificial conditions," Raz said.
"That's why most of the urban agriculture is applied to leafy vegetables with really short growing cycle," Raz explained.
However, not everyone takes economic factors as top priority.
Tagit Klimor is a founding partner of Knafo Klimor Architects and a senior lecturer at the Faculty of Architecture and Town Planning at the Israeli Technion Institution.
Knafo Klimor Architects designed a huge vertical productive wall at Expo 2015 exhibition in Italy, showing the world the possibility of growing wheat, rice and corn in building walls.
"In a sustainable economy, we need to put into consideration the damage to the nature, pollution, energy consumption and so on," said Klimor.
"In urban agriculture, we are giving exact amount of water and ingredients the crops need ... for example, all the water are coming from the growing facility usage," Klimor added.
For health issues, urban agriculture products are more fresh with more nutrition ingredients.
However, Israeli government wants to encourage local farmers to grow crops in the countryside instead of cities.
"There are only a handful of urban agriculture places in Israel, and they are pretty lame," Avigail Heller, head of Urban Agriculture Community Branch at the Israeli Ministry of Agriculture and Rural Development, told Xinhua.
Heller said that the Israeli government is not encouraging the urban farming. Taxes on urban farmers are higher than traditional agriculture farmers.
"Israel is a small country where the farm fields are a half-hour drive from the cities. So there is no initiative to grow crops in cities where the land is much more expensive," said Zvi Alon, director general of Israel Plants Board.
"Our mission is to continue to lead and improve our techniques of making more crops by using less water and soil. It is the real solution to the food shortage crisis," concluded Alon.
Leafy Greens are Grown by Machines at New, Automated Silicon Valley Farm
Called Iron Ox, the farm aims to produce leafy greens — romaine, butterhead, and kale, alongside various herbs
Luke Dormehl POSTED ON 10.13.18 - 1:00PM
Did you hear the one about the Google software engineer who packed it all in to start a farm? No, it’s not the setup for a joke. Nor is it the premise for some quirky Sundance comedy, probably telling the story of a stressed-out programmer who rediscovers their happiness by moving to the country. It’s a real, honest-to-goodness farm, which just opened in San Carlos, around 20 miles outside San Francisco. Called Iron Ox, the farm aims to produce leafy greens — romaine, butterhead, and kale, alongside various herbs — at a rate of roughly 26,000 heads per year. Oh yes, and it’s staffed almost exclusively by robots.
“This is a fundamentally different way of approaching farming,” CEO and co-founder Brandon Alexander, 33, told Digital Trends. “Traditionally, the farming process means that you seed, you wait a few months, you come back, you harvest, and you distribute. That hasn’t changed a whole lot in hundreds, if not thousands, of years.” Until now, at least.
Iron Ox’s indoor farm measures around 8,000-square-feet. That makes it paltry compared to the thousands of acres occupied by many traditional farms, but, through the use of some smart technology, it promises a production output that’s more in line with an outdoor farm five times its size. To achieve this, it has a few tricks up its sleeve. For starters, Iron Ox is a hydroponics farm, a method of growing plants without soil, using mineral nutrient solutions in a water solvent. Unlike a regular farm, hydroponic farms grow their produce in vertical and horizontal stacks; every element minutely controlled through the use of glowing LED lights and jets of water to affect the crops’ size, texture, and other characteristics.
In place of a farmer, Iron Ox employs a giant, 1,000 pound robot called Angus. It’s Angus’ job to move the heavy 800 pound, water-filled tubs of fresh produce without spilling them. A robot arm is used to tend the crops, making this the agricultural equivalent of Elon Musk’s automated Tesla factory in Fremont, CA.
“We’ve taken a robotics-first approach to the growing,” Alexander continued, in what can only be described as an understatement. “Everything is designed with that in mind.”
DISRUPTING THE FAMILY BUSINESS
When he was a kid, Alexander was shipped off each summer to his grandfather’s family farm in the Texas and Oklahoma area. Looking back at it today, it’s a cherished memory. At the time, not so much.
Iron Ox
“I’ll be honest: I hated it,” he said. “All my friends were going on vacation and I was the one who was stuck on a farm.” When his buddies were sleeping in, he was getting up at the crack of dawn. When they were on the beach, he was on a tractor. Years later, when he and his co-founder and CTO Jonathan Binney, 34, were busy planning out Iron Ox, he called his grandfather. Now 83 and still running a farm, Alexander told him about his plans for roboticizing the work that his family had done by hand for generations.
But this isn’t a story about a guy who decided to take revenge for summers of hard labor by disrupting the industry. Far from it. Alexander has a deep respect for farming, evident from the reverent way that he speaks about a profession that has looked after his family for years.
“[My grandad is] technophobic; he doesn’t know how to use an iPhone [or about machine learning or computer vision],” Alexander said. “But when I explained what I was doing, he said, ‘This is inevitable.’ That kind of surprised me, but it shouldn’t. When he was a kid, and his dad was farming, they managed 40 acres. Now him and his crew are managing 6,000 acres. He’s seen the progression.”
JUST-IN-TIME FARMING
Farming isn’t an industry that’s at the forefront of many people’s minds in Silicon Valley. It probably should be, though, because the emphasis on farm-to-table produce is only growing. When Alexander and Binney speak to chefs, they regularly hear stories about customers wanting to know exactly where a particular bit of produce has been sourced from, or how old it is.
That typically gets an unsatisfactory answer in the U.S., where the average distance travelled by fresh fruit and vegetables is around 2,000 miles. “There are relatively few places that have the right conditions for growing,” Alexander explained. “Everyone else gets week-old produce.”
Iron Ox
Iron Ox aims to change that by building farms within easy reach of cities. Using its autonomous technology, customers can get fresh greens grown in their neighborhood. Better yet, they can get it year round, since an indoor farm isn’t subject to the same seasonal conditions as traditional farms are.
“We call this just-in-time farming,” Alexander said. He is using terminology that is usually applied to manufacturing, pioneered by automaker Toyota in Japan during the 1960s and 70s. What makes just-in-time manufacturing special is that it focuses on making items to meet demand, rather than creating surplus in advance of need. It means less waste with overproduction, less waiting, and less excess inventory. That works well for cars, computers, or smartphones. The Iron Ox team hope it will work great for crops, too.
“In a traditional greenhouse, you’re committed to growing a thousand or tens of thousands of a particular varietal,” Alexander said. “Our systems gives us the ability to fine-tune the nutrients for each crop. We’re only committed to growing a hundred of something at a time. That’s important. Previously you would committed to, for example, kale. ‘Kale’s going great,’ you say. ‘Let’s go all-in on kale.’ But trends change. If we suddenly notice a big demand for purple bok choy or Italian basil, our system can adapt to that consumer demand very quickly.”
Overseeing the farm, like a green-fingered HAL 9000 from 2001: A Space Odyssey, is what Alexander calls “The Brain.” This is a cloud-based, A.I. which constantly monitors information relating to nitrogen levels, temperature, and the location of robots. Over time, it will expand this to take into account data pertaining to food orders, or more general information about food-based trends.
Weighing up all this data, it can then make decisions about exactly what should be growing — and in what quantities — in each of the modular tanks.
THE ROAD FROM HERE
Right now, Iron Ox is starting to take chef’s orders for the two dozen-plus varieties of leafy greens that it is growing from the start. It aims to be in full production by the end of the year. This is still the beginning of the journey, but it’s one that Alexander and his co-founder are happy to be on.
“We had some pretty good, cushy jobs at Google and whatnot,” Alexander said. “We wanted to make sure that, when we took the next step, it was something we were passionate about. It’s not about staying passionate for one year; it’s about whether or not this was something we could put decades of our life into? That’s a different metric, for sure.”
How does he feel about the impact of automation on jobs in the farming community as a whole?
“I think farming is a fairly unique space in this regard,” he said. “Agriculture is one of the few industries right now where they can’t get enough help. That was something that surprised Jon and myself when we first started. When we quit our jobs, we spent four months roadtripping California, talking to farmers. We talked to dozens of outdoor and indoor farmers. One of the questions we asked was ‘what’s your biggest pain point?’ 100 percent of them said that it was labor scarcity. They could not get enough help for their farms.”
Added to this is the fact that, in the United States, the average age of a farmer is 58. “It’s a bell curve distribution, and it keeps shifting over to older and older,” he said.
Those jobs are not being replaced in equal numbers by the younger generation. “There simply aren’t enough people wanting to do this,” he continued. “And I don’t blame them. It’s hard, back-breaking work. It’s just where it’s going.”
Iron Ox isn’t the only startup applying the latest technology to farming. Other companies and researchers are building self-driving tractors for farms, using CRISPR gene editing to improve the efficacy of crops, and building robots that are capable of picking a variety of fresh produce without damaging it. But Iron Ox’s business model nevertheless represents an enormous step potential forward in U.S. agriculture and the way that it works.
In 1820, more than half of the United States population lived and worked on farms. Today, this is fewer than 2 percent of the population, with the overwhelming majority having moved to the city. Thanks to companies such Iron Ox, people may no longer have to choose between farm and city. If people won’t leave the city for farms, then the farms will just have to come to them.
US (HI): Researchers Help Waimānalo Families Use Aquaponics, Improve Health
Three researchers at the University of Hawaii at Mānoa have won a national fellowship and will receive $350,000 funding over three years to assist Waimānalo families with backyard aquaponics to sustainably produce healthy food.
The project will connect the modern technology of aquaponics with Native Hawaiian food practices. Aquaponics taps into the power of the natural symbiotic relationship between fish and plants, and combines the raising of plants in water with raising fish in tanks to create a sustainable, contained food production system.
From left, Ilima Ho-Lastimosa, Ted Radovich and Jane Chung-Do
The fellowship was awarded by the Robert Wood Johnson Foundation, a nonprofit organization that works to promote health equity in the U.S.
The research team is comprised of Jane Chung-Do, an associate professor with the UH Mānoa Office of Public Health Studies in the Myron B. Thompson School of Social Work; Ilima Ho-Lastimosa, community coordinator at the Waimānalo Learning Center and an education specialist in the Department of Tropical Plant and Soil Science (TPSS) in the College of Tropical Agriculture and Human Resources; and Ted Radovich, a TPSS associate specialist.
They will expand their work with families in Waimānalo to develop an aquaponics program to grow fresh fruits and vegetables and raise fish that families can use to prepare meals and Hawaiian medicines. This builds on the decade-long work that Ho-Lastimosa has been promoting in her community of Waimānalo.
The researchers will recruit Native Hawaiian families in Waimānalo to participate in aquaponics lessons and will guide the families in building and maintaining backyard systems. The researchers will follow up to see whether the systems are successful in helping the participants increase their intake of and access to fresh fruits, vegetables and fish, as well as promote healthy eating habits. In addition, impacts on participants’ mental wellness, cultural identity, family strength and community connectedness will be measured.
Ilima Ho-Lastimosa feeds fish in an aquaponics set-up, while Jane Chung-Do looks on.
“Our goal is to restore Native Hawaiian practices related to food and community,” said Chung-Do. “The study embraces the perspective that health is holistic and interconnected with our culture, families, communities and the ʻāina.”
As a public health scientist, Chung-Do has worked to enhance the wellness of children and families in Hawaii, especially in rural and minority communities.
Radovich was born and raised in Waimānalo and holds a PhD in horticulture. His expertise is in sustainable and organic farming systems.
Ho-Lastimosa grew up on the Waimānalo Homestead and holds masters degrees in social work and acupuncture; she is also a master gardener. The community leader and cultural practitioner in Waimānalo founded God’s Country Waimānalo, a group that initiated a food sovereignty and sustainability movement in the community.
Source: University of Hawai'i (Theresa Kreif)
Publication date : 10/11/2018
Desktop NFT System
Grow fresh, high-quality leafy greens on your desktop or kitchen counter.
Our unique hydroponic desktop NFT system has all the capabilities of a traditional sized NFT system allowing you to grow fresh, high-quality leafy greens on your desktop or kitchen counter. Perfect for schools, hobby growers and anyone looking for fresh produce year-round!
This system features:
• A removable top cap (lid) makes the channels easy to use and easy to clean.
• End caps on both ends of the channel, keeping light out & preventing algae growth.
• Constructed of non-toxic, food grade, UV-stabilized plastic.
• A standard electric plug – no additional power source required.
• Square top cap holes that are made for 1" seedling cubes.
Specs:
• Measures 16'L x 11'W x 4'H
• Weighs 3.5 lbs when the tank is empty & 12 lbs when it’s full.
System Includes:
• (2) 1' x 4 ⅝' grow channels
• 6 plant sites
• Pump
• Feed line
• 1 ½ gal tank
• Fertilizer & Rockwool cubes
$49.95
Get yours today by calling 330-302-4203!
*volume and educational discounts available
CropKing.com
Pure Flavor® Breaks Ground on New Georgia Distribution Center
Georgia greenhouse, Pure Flavor® announced recently that they have broken ground on a new 60,000 sq. ft distribution center just 10 minutes away from their new greenhouse facility off of I-75 in Peach County, GA.
Fort Valley, GA - November 1st, 2018
With fresh tomatoes coming to life in its new Fort Valley, Georgia greenhouse, Pure Flavor® announced recently that they have broken ground on a new 60,000 sq. ft distribution center just 10 minutes away from their new greenhouse facility off of I-75 in Peach County, GA.
“We are strategically growing our business across North America and in doing so, need to support this growth with regional facilities that reduce food miles for our greenhouse grown vegetables. Our new distribution center in Peach County will allow us to better serve our retail & foodservice customers throughout the southeast year-round”, said Jamie Moracci, President. As a vertically integrated vegetable company, Pure Flavor®’s family of growers produce greenhouse tomatoes, peppers, cucumbers, eggplants and a wide variety of USDA certified Organic items at farms in Canada, USA, and Mexico.
The new Georgia distribution center will serve as a consolidation point which will provide an opportunity for a greater assortment of Pure Flavor® greenhouse grown vegetables to retailers & foodservice partners in the southeastern US region starting in early 2019. Pure Flavor® operates distribution centers in Leamington, ON, Romulus, MI, and San Antonio, TX to support its vast network of growers throughout North America.
A little over 14 months ago, Pure Flavor® broke ground on a 75-acre, $105 million-dollar greenhouse facility in Fort Valley, GA. Phase 1 of 25 acres is now complete with the first crop of Georgia Grown tomatoes to be picked in a few weeks’ time. Pure Flavor®’s Long English & Mini Cucumber crop will also be ready for picking in November.
“Our team has been hard at work building a state of the art, high tech greenhouse facility in Georgia. What has been accomplished in the past year has been remarkable”, said Moracci. “Our goal to grow greenhouse tomatoes & cucumbers in Georgia is becoming a reality, we look forward to promoting Georgia Grown vegetables this winter”, said Jamie Moracci.
To learn more about Pure Flavor®’s Georgia greenhouse project and to see photos of the construction of both projects, visit GeorgiaGrownFlavor.com.
Pure Flavor® is a family of greenhouse vegetable growers who share a commitment to bringing A Life of Pure Flavor™ to communities everywhere. Our passion for sustainable greenhouse growing, strong support for our retail & foodservice customers, and focus on engaging consumers is built on a foundation drawn from generations of growing expertise.
SOURCE: Chris Veillon | chris@pure-flavor.com
Chief Marketing Officer | Pure Flavor®
T: 519 326 8444
Seven-Figure Order for Ultra-Wide Spectrum Cannabis LEDs
As a company specialized in fine tuned spectra development, Valoya has independently tested and optimized Valoya Canna+ through a series of trials.
Earlier this month, Valoya, manufacturer of high end LED grow light solutions, introduced Valoya Canna+ to the market – a line of LED luminaires with an ultra-wide spectrum designed for professional cultivation of cannabis. As a company specialized in fine tuned spectra development, Valoya has independently tested and optimized Valoya Canna+ through a series of trials. The result is a balanced spectrum for consistent yields and cannabinoid expressions inside state-of-the-art LED luminaires. Valoya says its Canna+ is the widest spectrum available on the market at the moment covering the range from 380nm (UV-A) to 780nm (Far red) thus resulting in superior cannabinoid profiles.
The order is of 6400 pieces of Valoya Canna+ 120 fixtures which are high intensity, 4’ (120 cm) long bars that with 132 W produce a total output of 320 µmols. Delivery of this order is due before the year end.
“This 7 figure order comes less than a month after the product launch giving a good signal about the value the Valoya Canna+ line brings to the cannabis market. As the cannabis market is developing so are growers’ needs for solutions enabling them to bring superior offerings to the market. Cannabis growers are looking for high yields with superior secondary metabolite and terpene compositions with fixtures that do not consume much energy and are reliable.” – Mr. Rabbe Ringbom, VP Sales and Marketing at Valoya.
The order is realized through Innovative Growers Equipment (IGE), Valoya’s North American distributor for the cannabis market. IGE is an equipment supplier to commercial growers in North America. Their products include ebb and flow and expanded metal benches, Valoya’s LED grow lights, plant support systems, automated fertilizer injectors etc.
For more information:
Valoya Oy, Finland
Tel: +358 10 2350300
sales@valoya.com
www.valoya.com
Innovative Growers Equipment
+1 (815) 991-5010
sales@innovativegrowersequipment.com
www.innovativegrowersequipment.com
Could the Future of Farming be Vertical?
Vertical farming is greener and more efficient than traditional agriculture, writes Natalie Mouyal
Photo: BrightAgrotech, Pixabay
Vertical farming promises a more sustainable future for growing fruit and vegetables. Instead of planting a single layer of crops over a large land area, stacks of crops grow without soil or sunlight.
The nascent technology enables farmers to grow more food on less land. Among the benefits, it reduces the environmental impact of transportation by moving production from the countryside to the cities, where most people live.
Dilapidated warehouses and factories around the globe are being transformed into urban farms to grow salads and other leafy greens at a rate that surpasses traditional farming techniques. LEDs provide the lighting plants need to grow, while sensors measure temperature and humidity levels. Robots harvest and package produce.
At one vertical farm in Japan, lettuce can be harvested within 40 days of seed being sown. And within two towers measuring 900 m2 each (actual cultivation area of 10 800 m2 and 14 400 m2), the factory can produce 21 000 heads of lettuce each day.
Indoor farming is not a new concept, as greenhouses have long demonstrated. It has existed since Roman times and can be found in various parts of the world.
Greenhouses are described in a historic Korean text on husbandry dating from the 15th century and were popular in Europe during the 17th century. In modern times they have enabled the Netherlands to become the world’s second largest food exporter.
Vertical farming offers a new take on indoor farming. Popularized by the academic Dickson Despommier, its proponents believe that vertical farming can feed millions of people while reducing some of the negative aspects associated with current agricultural practices: carbon-emitting transportation, deforestation and an over-reliance on chemical fertilizers.
Vertical farming is defined as the production of food in vertically stacked layers within a building, such as a skyscraper or warehouse in a city, without using any natural light or soil. Produce is grown in a controlled environment where elements including light, humidity, and temperature are carefully monitored.
The result provides urban dwellers with year-round access to fresh vegetables since they can be grown regardless of weather conditions, without the need for pesticides and have only a short distance to cover, from farm to plate.
Initially conceived by Despommier with his graduate students as a solution to the challenge of feeding the residents of New York City, vertical farming has since taken off around the world, most notably in the United States and Japan. According to the research company Statista, the vertical farming market is expected to be worth USD 6,4 billion by 2023.
High-tech farming
According to the UN Food and Agriculture Organization, food production worldwide will need to increase by 70% by 2050 to feed a projected global population of 9,1 billion. Vertical farming seeks to address the dual challenges of feeding a growing population that, increasingly, will live in urban centres.
By repurposing warehouses and skyscrapers, these ‘high-tech’ greenhouses reuse existing infrastructure to maximize plant density and production. One vertical farm in the United States claims that it can achieve yields up to 350 times greater than from open fields but using just one percent of the water traditional techniques require.
In general, two methods for vertical farming are used: aeroponics and hydroponics.
Both are water-based with plants either sprayed with water and nutrients (aeroponics) or grown in a nutrient-rich basin of water (hydroponics). Both exhibit a reliance on advanced technology to ensure that growing conditions are ideal for maximizing production.
So as to produce a harvest every month, vertical farms need to control the elements that affect plant growth. These include temperature, requisite nutrients, humidity, oxygen levels, airflow and water.
The intensity and frequency of the LED lights can be adjusted according to the needs of the plant. A network of sensors and cameras collects data with detailed information about the plants at specific points in their lifecycle as well as the environment in which they grow.
This data is not only monitored but also analyzed to enable decisions to be taken that will improve plant health, growth and yield. Data sets sent to scientists in charge of the growing environment enable decisions to be made in real-time, whether they are onsite or at a remote location.
Automation can take care of tasks such as raising seedlings, replanting and harvesting. It can also be used to provide real-time adjustments to plant care. One factory plans to automate its analytical process with machine learning algorithms so that real-time quality control can take into account a diverse range of data sets.
While each of these farms will implement varying levels of technology, it can be expected that as these technologies become more widespread, their adoption will increase. The use of artificial intelligence and cloud computing is not yet extensive but is likely to become increasingly important to ensure production yields remain high.
Growing pains
Despite the enthusiasm for vertical farming, its business model is not yet proven. The initial investment needed to launch a vertical farm and the electricity required to power the 24-hour lights, sensors and other technologies can be costly.
Depending on the source of the electricity used to run the equipment, it may not necessarily prove environmentally cleaner than traditional farming techniques. For this reason, a shift towards renewable energy sources could support the claim that these farms have a positive environmental impact.
At this stage, vertical farms are used primarily for growing crops that attract high market prices, such as herbs, medicinal plants and baby greens. They have not been used to grow the wheat, beans, corn or rice which feed much of the world. Its scale is not yet sufficient to meet food demands.
Vertical farming is still in its infancy. No large scale studies have yet been completed to allow a full comparison with traditional farming techniques. Despite this, it has generated much enthusiasm and, more recently, significant financial support, which may enable vertical farming to create a niche market for the supply of fresh produce to city dwellers.