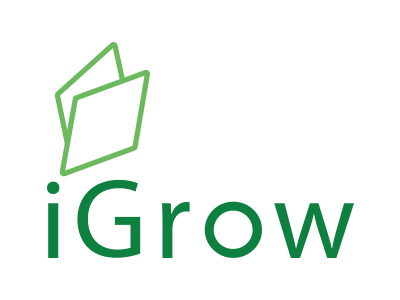
Welcome to iGrow News, Your Source for the World of Indoor Vertical Farming
Micro Lab Farms New California Cultivation Complex Approved by City of Needles
The unique facility features Gen3 GrowPods, designed to outperform other methods of cultivation, and provide rapid growth in a multi-billion dollar market
July 29, 2019
The unique facility features Gen3 GrowPods, designed to outperform other methods of cultivation, and provide rapid growth in a multi-billion dollar market
CORONA, Calif., July 29, 2019 /PRNewswire/ -- Micro Lab Farms, a premier provider of automated indoor micro-farms for rapid production of legal cannabis, announced that it has been granted a Conditional Use Permit for a two phase cultivation facility in the city of Needles, California.
The resolution was passed by the Needles City Council, and allows Micro Lab Farms to develop its California Cannabis Cultivation Complex, which will feature over 100 state-of-the-art GrowPods.
The pods, designed by GP Solutions GWPD, +0.00%, are automated, transportable, scalable micro farms that have been shown to grow cannabis at a faster rate than conventional means of agriculture.
GrowPods allow cultivation to take place year-round, and eliminate pathogens, contaminants, pesticides and chemicals, to produce clean and robust crops. The Pods also provide a sealed environment for excellent isolation of specific strains and clones.
The GrowPods will also utilize GP Solutions proprietary soil mixture, which contains no animal products. This is critical in the cannabis industry because many other soils and additives can contain harmful pathogens and bacteria that have the potential to contaminate crops and cause testing failures.
The California Cannabis Cultivation Complex also provides investment opportunities to experienced growers, entrepreneurs, and qualified individuals seeking to add the cannabis sector to their portfolios. This passive investment allows stakeholders to participate in the rapid growth of the cannabis sector, with mitigated risk.
The Conditional Use Permit allows Micro Lab Farms to develop over 35,000 square feet of cultivation space.
For more information on Micro Lab Farms, or for information on GrowPods, or for details on investing in the California Cannabis Cultivation Complex, contact Micro Lab Farms at: (951) 266-6096, or visit: www.microlabfarms.com
About Micro Lab Farms
Micro Lab Farms has made it possible to rapidly and affordably enter or expand in the legal cannabis industry with its "GrowPod" cultivation systems.
GrowPods are modular, indoor micro-farms that feature a controlled environment, state-of-the-art air and water filtration, proprietary pathogen-free living soils, and automation systems that far outperform other methods of cultivation, and produce clean, robust crops without pathogens, contaminants, pesticides or chemicals.
For information on Micro Lab Farms, call: (951) 266-6096, or visit: www.microlabfarms.com
Connect:
Website: www.microlabfarms.com
Facebook: facebook.com/MicroLabFarms
Twitter: @MicroLabFarms
View original content:http://www.prnewswire.com/news-releases/micro-lab-farms-new-california-cultivation-complex-approved-by-city-of-needles-300892124.html
SOURCE Micro Lab Farms
Copyright (C) 2019 PR Newswire. All rights reserved
GP Solutions Partners With Soilless Science to Create Premier Brand of “Living Soils”
Product line will heighten company’s brand in $262 billion organic food market
Corona, CA – March 19, 2019 – GP Solutions (OTC:GWPD), a leading developer of modular automated micro-farms, has partnered with Soilless Science to create a proprietary lineup of premium “living soils.”
These unique soil-less mediums contain no dirt and will be certified pathogen free. The mixtures will contain beneficial micro-organisms that form the foundation of highly active “living soils” that will produce abundant, healthy crops of all types.
Soil mixtures will be developed for a variety of crops - each with its own unique, beneficial composition.
The mixtures are vegan based, and use no animal products. Compare this to other products that use fish and animal waste products, which inherently contain harmful pathogens and bacteria, and can contaminate crops and potentially cause widespread illness.
As the public becomes more aware of the dangers of traditional farming and the potential harm from “dirty” soil, consumers will start demanding that their food is grown in controlled environments using healthy soil mediums.
GP Solutions will be providing this proprietary soil-less mixture to its customers of GrowPod automated farms, as well as to the general public within the near future.
GrowPod, by GP Solutions, is a unique, stackable, modular indoor micro-farm that grows clean produce in a controlled environment. By utilizing specialized air and water filtration, and its proprietary pathogen-free living soils, the GrowPod system can deliver some of the highest quality produce in the world.
“The traditional approach was to add chemicals, fertilizers, weed killers and other dangerous additives to soil and crops,” said George Natzic, President of GP Solutions. “Today, we know this can be very harmful to the public. That’s why I’m proud to be developing new living soils that are pathogen free and full of beneficial nutrients to produce high velocity, healthy crops of all kinds.”
For more information, visit: www.growpodsolutions.com, or call (855) 247-8054.
Forward-Looking Statements
This release includes statements considered “forward-looking” within securities laws. These statements represent Company’s current judgments, but are subject to uncertainties that could cause results to differ. Readers are cautioned to not place undue reliance on these statements, which reflect management’s opinions only as of today’s date. Company is not obligated to revise statements in light of new information.
Connect:
Email: info@growpodsolutions.com
Website: www.growpodsolutions.com
Facebook: facebook.com/GrowPodTechnology
Twitter: @GrowPodSolution
Vertical Farming Systems Raises $1M For Automated Agtech
April 30, 2019
Image via VFS
Australian agtech company Vertical Farming Systems (VFS) has raised $1 million for its automated indoor farming technology. Terms of the deal were not disclosed, although company co-owner Ashley Thompson told StartupSmart the investment comes from someone with “significant experience in the agriculture industry.”
Based in Queensland, Australia, VFS says its system can take plants from seedling stage to fully grown in just 28 days. Thompson, along with co-owner John Leslie, run the farm out of a warehouse facility divided into three climate cells, or insulated environments where computers control the lighting, water, and humidity levels, to give plants optimal growing conditions. The system automatically plants the seeds in trays of clay pods, then loads those trays onto stackable racks equipped with LEDs, where the plants will grow. Currently, the facility houses about eight acres’ worth of crops.
You can watch a video of the system in action here.
VFS isn’t just growing greens, however. Running with the idea that vertical farming needs to be fully automated to offset labor costs, Thompson and Leslie spent nine years developing their patented XA Series warehouse system to sell to customers around the world. The system comes in 28 different configurations, which can be matched to a customer’s business needs and expanded if need be in the future.
They’re not alone in bringing indoor farming into the spotlight of the agtech space in Australia. A company called Modular Farms sells a variety of expandable container farms, though these require a little more hands-on work from humans than VFS’ system (think Freight Farms in the U.S.) Invertigro, meanwhile, sells a modular system the company says can grow everything from leafy greens to berries.
In addition to further developing the XA system, VFS is also using the new funds to develop other technologies, including an automated fodder machine, which can feed livestock for 14 days without human intervention, and a mealworm farm system.
DelFrescoPure Introduces The LivingCube
BY DELFRESCOPURE | APRIL 19, 2019
Our exciting partnership between DelFrescoPure and CubicFarms has resulted in the LivingCube -- a system of automated vertical farming growing machines that continuously produces living lettuce, living basil and microgreens all year long.
LivingCube - Vertical Growing System
LivingCube is powered by DelFrescoPure, which produces power by using an off-the-grid electrical cogeneration system. The growing chambers are all individually climate controlled to optimize the environment for each crop to create an independent growing facility.
"We wanted to offer our retail partners innovative and local commodities and the ideal solution was to partner with CubicFarms," stated Carl Mastronardi, President of DelFrescoPure.
The LivingCube living lettuce, living basil and microgreens are always fresh, nutritious and flavor-filled. LivingCube finally offers you the freshness you love without sacrificing nutrition and flavor!
Living Lettuce
Who says you need to compromise quality for flavor? Our LivingCube allows our living lettuce to be vertically grown without pesticides in multiple varieties. Available in a 3-count lettuce bag, our living lettuce is convenient and delicious; you can grow it in your fridge or on your counter. Lettuce grow for you!
Basil Microgreens
With 12x the nutrients of mature leaves, LivingCube microgreens are a small way you can add health benefits to food! We offer multiple varieties and customized packaging combinations. Our LivingCube machines are flexible -- allowing quick crop changes that adjust seasonally. It's convenience with flavor!
"Our LivingCube microgreens allow you to add flavor, quality and fresh health benefits to your food without having to put in hard work to get it," stated Fiona McLean, Marketing Manager of DelFrescoPure.
Our packaging is made from 100% post-consumer recycled PET and comes in 50g and 100g, making our microgreens versatile and easy to buy, store and use. No need to chop, just sprinkle!
Plant Factory With Artificial Lighting: Toyoki Kozai's Brilliant Research On An Interesting Practice
According to AgriGarden, 'Plant factory is a highly efficient agriculture system which uses high precision control facilities in the continuous production of crops."
1/9/2019 9:16:19 AM
(MENAFN - GetNews) Dr. Toyoki Kozai's research work is on ' Opportunities and Challenges for Plant Factory with Artificial Lighting (PFAL) (or vertical/indoor farming). Dr Kozai graduated from Chiba University, Japan in 1967. He obtained a Master's degree in 1969, and a PhD degree of Agricultural Engineering in 1972 from the University of Tokyo in 1972. He served as Dean of Faculty of Horticulture and Director of Center for Environment, Health and Field Sciences of Chiba University. He was inaugurated as the President of the prestigious Chiba University in 2005. He resumed his career in research as a professor emeritus in an endowed chair position at the Center for Environment, Health and Field Sciences during 2009-2012. He established Japan Plant Factory Association (non-profit organization) in 2010 together with his colleague, and served as the president until 2018, and is serving as the honorary president to date.
Furthermore, Kozai's academic excellence and his scientific interest can be gauged from the multiple books he has written, namely, 'Smart Plant Factory: The next generation indoor vertical farms (2018), 'LED Lighting for Urban Agriculture (2016), 'Plant Factory: An indoor vertical farm for efficient quality food production (2015), and 'Photoautotrophic (Sugar-free) Micropropagation as a New Micropropagation and Transplant Production System (2005).
His early work on greenhouse light environments, energy savings, ventilation, computer control, knowledge engineering, integrative environment control using a heat pump, fogging and null-balance CO2 enrichment systems, and closed systems with artificial lighting for transplant production in the fields of greenhouse horticulture earned him great recognition in his field.
Kozai has recently been working on 'plant factory with artificial lighting (PFAL) and has been leading the R & D of PFAL. His continuous quest in this field allowed him to dive deeper into this subject. He has been invited as a keynote speaker on the PFAL to more than 20 international symposia during 2015-2018.
According to AgriGarden, 'Plant factory is a highly efficient agriculture system which uses high precision control facilities in the continuous production of crops."
According to Kozai, it is believed that PFAL is expected to contribute to solving the food-environment-resource-health issues concurrently. Kozai has further described the six major components of the PFAL viz., thermally well-insulated, almost closed structure, multi-tier unit with lighting and hydroponic cultivation devices, air conditioners and fans, CO2 supply unit, nutrient solution supply unit and environmental control unit. Furthermore, he has mentioned that relatively large automated PFALs have been built in Japan in the year 2018, and the number of profit-making PFALs has been increasing in Japan since 2016. Besides, there are ongoing large-scale projects in the world hence stressing the fact that this concept is gaining prominence not only in Japan but globally as well.
In addition to the above, Kozai's study throws light on the essential benefits of PFAL as well. First, that PFAL offers a high degree of freedom of environment control and that any environment can be created at minimal costs, thereby making it highly cost-effective. Second, all rates of resource supply, plant production and waste production can be measured and controlled. Then, Resource Use Efficiency (RUE) (amount ratio of resource fixed or kept in plants to the resource supplied to the PFAL) can be estimated online for each resource element including electricity, water, CO2, fertilizer and seeds. This shows the convenience and the hassle-free process.
Currently, compared to the greenhouse, the PFAL can save water consumption for irrigation per kg of produce by 95% by recycling use of transpired water vapor from plants (The transpired water vapor is condensed and collected at the cooling coil of air conditioners and returned to nutrient solution tank). The productivity of leafy lettuce per unit land area is more than 100 times higher in the PFAL than in the open field. Thanks to this high productivity per unit land area, the PFAL can be built in urban areas with non-fertile or contaminated soil, resulting in the reductions of CO2 footprint, loss of produce during transportation, and delivery time of fresh vegetables to citizens.
However amongst all the benefits, there is one issue which still remains unresolved i.e., a methodology to find an optimal set of environmental factors automatically to maximize the CP (or productivity) under given conditions is yet to be developed. To maximize the CP, unit economic value, plant growth rate, percent marketable portion, cost of each resource element, consumption and RUE of each resource element needs to be measured or estimated online, and be integrated to calculate the CP.
Kozai's excellent research suggests how the CP can be more than doubled and the impact and the expected increase this will have on the PFAL market. He has therefore proposed the reduction in cost per kg of produce, an increase in sales per m2 of cultivation space by introducing recent advanced technologies such as artificial intelligence. Currently, costs for electricity, labour and depreciation for the initial investment account for about 20%, 20% and 30%, respectively. The rest (about 20%) is for seeds, fertilizer, water, containers, maintenance, etc.
Further, Kozai has the discussed the idea of next-generation PFAL (n-PFAL) and the associated requirements, scheme for R & D, challenges and opportunities. According to him, n-PFAL needs to create unique environments for plant production to produce high-quality plants with high yields using minimum resources and minimum emission of waste by introducing advanced but inexpensive technologies. He has suggested different technologies, which can be of great use in the same. However, he has submitted some challenges and opportunities, for example, smart LED lighting, phenotyping (plant trait measurement), production management including seed processing and circadian rhythm, efficient use of resources with minimum waste, breeding using DNA markers of plants suited to PFALs, et cetera. He has defined plant phenotyping and has given a detailed account of its usage in n-PFAL. Plant traits include plant architecture, chemical components, physiological status and response, etc.
In the n-PFAL, a huge time-series dataset of plant phenotype (traits), environment and management (human and machine interventions including seed processing) is automatically accumulated in a data warehouse. The data warehouse is connected with a related genome database and other n-PFALs' data warehouse via Internet. This global and local network of n-PFALs each with semi-open database will bring about a paradigm shift of plant/food/agricultural production and breeding of plants suited to PFALs. For example, breeding of plants suited to PFALs can be speeded up using the n-PFAL. Kozai has further recommended four types of models to be implemented in the PFAL: 1) mechanistic models for photosynthesis, respiration, transpiration and growth, and for substance, energy and monetary balance, 2) multi-variate statistic models, 3) behaviour (or surrogate) models, and 4) AI (or deep learning) models.
Kozai's study has won great acclaim amongst the researchers and his brilliant research on PFAL, an upcoming innovation will be of great use not only nationally but internationally as well.
GrowPod Provides Solutions to Help Feed Earth's Growing Population
Modular micro-farms provide additional food production to meet global needs, and bring healthy produce to underserved areas.
NEWS PROVIDED BY Grow Pod Solutions
Feb 20, 2019
CORONA, Calif., Feb. 20, 2019 /PRNewswire/ -- GP Solutions (OTC: GWPD), a leading developer of automated micro-farms, announced its new systems can help meet the food production needs for the future.
Earth's population is 7.68 billion, and is expected to grow to over 9 billion within 30 years.
According to a report from the University of Minnesota, "To feed those who are currently hungry—and the additional 2 billion-plus people who will live on the planet by 2050—our best projections are that crop production will need to increase between 60 and 100 percent."
However, with scarcity of land and resources, this poses immense challenges.
"Further expansion of agriculture is a poor solution to meeting future needs because we're using nearly all of the land that's suitable for agriculture already," the report emphasized. "Relying on increased production will be an important solution, but not a sufficient one."
Additionally, food isn't being grown near where it is needed. According to the United Nations, 815 million people in the world are under-nourished.
GrowPod is part of the solution.
GrowPods are modular, scalable, transportable, indoor "micro-farms" that grow high quality, pathogen-free foods using a fraction of resources required for conventional farming.
The system utilizes both hydroponics and soil-based platforms along with proprietary air and water filtration, to create the perfect environment for growing food virtually anywhere, in any season or climate.
GrowPods can be installed in just hours, so as demand rises or shifts, it is easy to put additional pods into service.
For more information, visit: www.growpodsolutions.com, or call (855) 247-8054.
ABOUT GP SOLUTIONS:
GP Solutions designs "GrowPods" – innovative indoor micro farms that provide optimum conditions for plant cultivation with total environmental control.
Forward-Looking Statements
This release includes predictions or information that might be considered "forward-looking" within securities laws. These statements represent Company's current judgments, but are subject to uncertainties that could cause results to differ. Readers are cautioned to not place undue reliance on these statements, which reflect management's opinions only as of the date of this release. The Company is not obligated to revise any statements in light of new information or events.
Connect:
Email: info@growpodsolutions.com
Website: www.growpodsolutions.com
Facebook: facebook.com/GrowPodTechnology
Twitter: @GrowPodSolution
Hamilton Ohio Facility To Be First of Its Kind In North America
By Eric Schwartzberg - Dayton Daily News (TNS)
HAMILTON — A private investment will enable an indoor farming company to complete its previously announced Hamilton facility, which it says will be the first fully automated indoor farm in North America.
The company 80 Acres Farms received “significant investment” from San Francisco-based private equity firm Virgo Investment Group, which invests in companies transforming and disrupting high-potential industries.
Terms of the financing were not disclosed.
Founded in Cincinnati in 2015 by veteran food industry executives Mike Zelkind and Tisha Livingston, 80 Acres Farms is supported by a board of directors representing executive and leadership experience at leading food, healthcare, and other companies.
80 Acres Farms provides customers with a variety of locally grown, just-picked leafy greens, microgreens and vine crops, including the world’s only tomatoes and cucumbers grown completely indoors using solely LED lighting.
The company has developed its own artificial intelligence-powered growing system, sophisticated data monitoring, and automation technologies to deliver high quality and nutritious products at an affordable price.
By locating its indoor farms close to customers, 80 Acres Farms is able to eliminate the costs, time and environmental impact of cross-country transportation, providing customers with a fresher, longer lasting product while drastically reducing food waste, company officials said.
80 Acres distributes to major national grocers, local retailers, restaurants, and food service companies from its facilities in Ohio, Arkansas, North Carolina and Alabama.
“Virgo Investment Group joins our existing notable and experienced food industry investors in supporting the Company to rapidly commercialize the indoor vertical farming technology we have developed over the past three years,” said Mike Zelkind, co-founder and chief executive officer of 80 Acres Farms. “We are optimizing every aspect of our production processes and driving down costs, which is crucial to scaling an indoor farming business like ours.”
The first phase of the Hamilton project under construction at 7512 Hamilton Enterprise Drive is expected to be operational early this year. It will be automated from seeding to growing to harvesting to produce specialty greens, including leafy greens, culinary herbs and kale.
The Hamilton facility will feature handling robotics, artificial intelligence, data analytics, and around-the-clock monitoring sensors and control systems to optimize every aspect of growing produce indoors.
It will allow 80 Acres Farms to start to service what it said is a “substantial and growing demand” for fresh, locally grown produce year-round from both retailers and restaurants.
“Over the past three years we have provided our customers with fresh, flavorful and nutritious produce grown locally in our facilities with no pesticides and highly efficient usage of water and nutrients,” Zelkind said. “We are rapidly increasing yields for our produce, while advancing each generation of our grow zone designs to lower capital costs, production costs and reduce the use of natural resources.
80 Acres Farms’ Cincinnati location sells to Jungle Jim’s International Market in Fairfield and Eastgate, Dorothy Lane Market’s three Dayton area locations, Clifton Market in Cincinnati and Whole Foods Market locations in Cincinnati, Deerfield Twp. and Dayton. It also distributes to several local restaurants.
The company plans three additional phases at the Hamilton site. When completed, the project will comprise over 150,000 square feet of fully-automated indoor farming. The full-phase expansion will allow 80 Acres Farms to provide more product to serve its existing customers and new ones with just-picked, year-round produce.
Produce grown at the Hamilton site will supply Whole Foods Markets, Dorothy Lane Markets, Jungle Jim’s, U.S. Foods, and other retailers and food service distributors.
Zelkind said 80 Acres Farms’ facilities represent “the realization of the next generation of farming.”
“Our vision is to prove that indoor farming can be fully-automated, commercially scalable, higher-yielding, and profitable,” he said.
Eli Aheto, partner of Virgo Investment Group, said the firm is excited to partner with 80 acres to bring freshly picked produce to local markets year round.
“80 Acres Farms has created a unique and automated growing process and has built great relationships with its retail customers,” Aheto said. “We want to help accelerate the company’s growth in this multi-billion-dollar market.
The 80 Acres investment is an expression of Virgo’s long standing focus on investing in energy efficiency opportunities driven by reduced equipment costs, he said. Virgo has completed investments in utility-scale wind, community solar, electric vehicle charging and now an LED lighting driven business
Future Farming Hub Is Creating A One-Stop-Shop Vertical Farming System For ‘Anyone’
January 15, 2019
The Vertical Farming Development Centre at Stockbridge Technology Centre (a Liberty Produce consortium member)
For a company less than one year old, Liberty Produce has already taken some big strides along its path to make vertical farming a more scalable, economically feasible reality. Specifically, the UK-based agtech company hopes to not just grow food, but also create an end-to-end, automated vertical farm system that, according to founder Zeina Chapman, “anybody” could use.
On vertical farming in the UK, Chapman notes there are “really great things happening . . . but they’re all siloed.” In other words, LED companies aren’t talking to those who make HVAC systems, and thus the development of these products happens independent of one another. As technologies by themselves, they work, but when put together in one environment, are they creating the most energy- and resource-efficient way to grow the best crop yield?
It’s a question Liberty will address with its new project, the Future Farming Hub. For the £1.3 million (~$1,652,000 USD) project, Liberty will lead a consortium of 11 different partners, each focusing on a different capability of the vertical farm. Chapman wouldn’t name specific names over the phone, but she did note there were partners in Taiwan, where vertical farming is a huge industry, a major LED company, as well as companies working on sensors, nutrient delivery (for the plants), and the growbeds themselves. For the latter, a partner will redesign growbeds to reduce the amount of bacterial growth that can sometimes hinder plant growth or damage plants. Sensor technology, meanwhile, would immediately tip the grower off to there being a bacterial problem in the growbed.
Underscore that word “immediately,” as that’s the other point Liberty and the Future Farming Hub are pushing. The project will also focus on a developing a system that gives growers real-time data about the farming operation
All of this rolls up under one goal focused on, according to a press release, reducing operational costs of vertical farms by 25 percent, increasing crop yield by 30 percent, and cutting down the amount of decisions growers themselves have to make when it comes to caring for plants.
“There’s lots we don’t know about growing plants in this artificial environment and we’re not giving them optimal conditions,” says Chapman. She cites lighting as one example: “With lighting, there isn’t an option to control it in a way that maximizes plant growth. So we might be putting plants under stress.”
Chapman also wants to make it easier for virtually anybody to operate a vertical farm. When I asked if that includes an open-source framework for growing, as others have suggested, she noted this project goes a step beyond open source. “If you decide you’re going to grow basil, you just press the button and the system will take care of that,” she said. In theory, at least, Liberty will have already developed the formula for growing optimal basil and programmed it into the system, effectively taking the guesswork out of growing.
Automated vertical farming is slowly gaining momentum around the globe, and other proprietary farm systems abound. Stateside, AeroFarms’ patented system can create light “recipes” to give each plant the exact spectrum and intensity it needs to grow. Bowery, too, uses a mix of hardware, analytics, and proprietary software to produce greens year-round. They also just got a $90 million shot of fresh investment. Over on the West Coast, Plenty more than doubled that figure last year, when Softbank invested $200 million in the company’s system.
But no one’s yet come out with a one-stop-shop system that you need neither an agricultural or engineering background to operate and which relies on real-time data to do the heavy lifting.
The project doesn’t kick off until April of 2019, which makes all of this somewhat abstract at the moment. But Chapman’s optimistic. “One of the greatest things we want to achieve is to pull together a system that’s fully integrated and get all these systems to talk to each other,” she says. “We hope it can reduce the costs, which is a huge barrier to entry and also increase yield. As we increase yield, more and more products become viable.”
Chapman and Liberty aim to have a full product ready for market at the end of the 27-month project, and along with it, a more accessible, scalable approach to vertical farming.
Whole Foods Supplier Embraces Robotic Farming
By PYMNTS
2018
To supply retailers such as Whole Foods and U.S. Foods with greens, 80 Acres Farms is constructing a “fully automated indoor farm.” The project’s reported cost is in the range of $10 million to $15 million, CNBC reported.
“With the … facility, we will achieve the next-generation of indoor vertical farming,” 80 Acres Farms’ CEO and co-founder, Mike Zelkind said. “This project will deliver our proof of concept that indoor farming can be fully automated, commercially scalable, higher-yielding, and profitable.”
The first phase of construction will bring grow centers that can make products such as kale, culinary herbs and microgreens. Then, three more phases could follow. In all, the facility could grow to over 150,000 square feet — or roughly 3.5 acres.
Another vertical farming company, Smallhold, works sort of like a nursery to expedite the growing process. The company grows the produce — mushrooms, at the moment — three-quarters of the way. Then it delivers the almost-grown produce to their customers, who finish growing the fungi in their vertical growing units. The company also helps customers create the right growing conditions with WiFi enabled units that allow Smallhold to monitor and control them remotely. As a result, customers simply have to pick and serve the produce.
Smallhold’s farms also reduce the environmental impact of growing produce. Their farming units reportedly create 40 times the output per square foot compared to a traditional farm, and use 96 percent less water, according to the company.
Smallhold is not the only urban farming concept in the U.S. Boston-based agricultural tech company Freight Farms grows produce inside of shipping containers. One freight farm can grow approximately two acres worth of produce, according to the company, and that can either be sold direct to consumers (D2C) or through partnerships with local distributors, restaurants and grocery stores.
Nation’s First Fully Automated Vertical Farm Breaks Ground In Ohio
Posted by Laura Drotleff| September 25, 2018
Cincinnati-based 80 Acres Farms announced that it plans to build a large, fully automated indoor farm in Hamilton, OH, which will produce specialty greens to supply local independent retailers including Jungle Jim’s International Market and Dorothy Lane Markets, and national chain locations for Whole Foods and U.S. Foods.
The facility would be the first of its kind in the nation, according to 80 Acres. A groundbreaking was held for one of two facilities on Monday, Sept. 24. An MSNBC article stated the project would cost between $10 million and $15 million initially, and create 40 jobs would be created, which would average in the $40,000 to $50,000 range including benefits. The city discounted land in Hamilton Enterprise park for the project and is providing an Enterprise Zone property tax abatement of 75% for 10 years, MSNBC reported.
80 Acres Farms personnel will manage the facilities, which will feature robotics, artificial intelligence, data analytics, and around-the-clock monitoring sensors and control systems to optimize every aspect of growing produce indoors. The Cincinnati firm will work with its current technology partners, Signify, an LED horticultural lighting company, and Priva, which provides environmental controls and process management software, according to Tisha Livingston, President and Co-founder of 80 Acres.
The initial phase, which is to be completed later this year, will feature grow centers to produce microgreens, culinary herbs, leafy greens, and kale. Three additional phases are planned. When completed, the indoor farm is to encompass more than 150,000 square feet, which equates to nearly 3.5 acres.
The full-phase expansion of controlled environmental agriculture will enable 80 Acres Farms to provide more product to serve existing customers and new ones with fresh-picked, year-round produce. 80 Acres Farms now serves Cincinnati-area customers from its facility in Spring Grove, where it grows microgreens, culinary herbs, leafy lettuce, kale, and vine crops such as cherry tomatoes, cucumbers, and peppers.
“We already have demonstrated that we can provide to our customers the freshest, best-tasting and nutritious locally grown produce, while using renewable energy, very little water, and no pesticides,” said Mike Zelkind, CEO and co-founder of 80 Acres Farms in a September 21 release. “With the Hamilton facility, we will achieve the next-generation of indoor vertical farming. This project will deliver our proof of concept that indoor farming can be fully automated, commercially scalable, higher-yielding, and profitable. It will serve as a prototype for our ambitious plans to co-locate similar facilities with commercial customers in other parts of the country.”
Zelkind said 80 Acres Farms will work with partners such as JDL Warm Construction and Open Architecture Inc., both of downtown Cincinnati. Site Solutions Consulting of Loveland will do excavation site preparation work.
80 Acres Farms is headquartered in the Spring Grove community of Cincinnati, where the company was founded in 2015 by Zelkind and Livingston, both veteran food industry executives. It now employs more than 60 people in Cincinnati and other company research and development, engineering, and production facilities in three other states. In its mission to locally grow the best tasting, most nutritious fruits and vegetables, the company partners in research with many agrotechnology and academic research institutions.
Can Artificial Intelligence Do As Well As Farmers In The Future?
Cucumber plants to enter autonomous greenhouse of Wageningen University & Research
Tuesday 14 August marked the start of the Autonomous Greenhouses Challenge as five international teams try to grow cucumbers at a distance with the use of artificial intelligence at the facilities of Wageningen University & Research (WUR). “The goal is to convert knowledge about cultivation into algorithms that can enable computers to regulate cultivation automatically in the future, even in places where such knowledge is lacking. So the question is: can computers do as well as farmers?”
The five international teams will have four months to produce a cucumber yield remotely and without human intervention, using as little water, nutrition and energy as possible while achieving the highest possible output (i.e. production). Each team has been allocated 96 square metres in the facilities of WUR’s business unit Greenhouse Horticulture in Bleiswijk.
“The teams have partly developed their own algorithms and used them to determine output settings such as temperature, light quantity, CO2 concentration, fertilisation and several cultivation-related parameters such as plant and stem density,” says the head of the Horticulture Technology research team Silke Hemming. “The sensors and cameras – which they will be installing themselves in the week of 20 August – measure some of these cultivation data. The sensors send the information to the computer systems, allowing them to control the climate and fertilization in the greenhouse. The teams will not be allowed to enter the greenhouses apart from to install the equipment.”
The teams will collect all data remotely and be able to continuously adjust their algorithms for the software. Hemming: “The software itself will adjust the output settings like temperature where necessary. The goal is that the self-teaching software gradually takes over human decision-making.”
The challenge was organized by Wageningen University & Research Greenhouse Horticulture and the internet company Tencent. “We think we can further improve food production in greenhouse horticulture by introducing artificial intelligence,” Hemming continues. “This unique challenge lets us connect with international partners and make major strides forward. Although they are already global leaders in cultivation expertise, we believe even Dutch breeders will benefit from results of the challenge, as it will enable them to make decisions based on more carefully considered information.”
According to Hemming, the use of artificial intelligence will have an even greater impact globally. “In many countries, there is very little knowledge about complex plant production. Artificial intelligence can help people make complicated decisions, so they can locally produce vegetables and fruit with fewer means. The higher yield and production are especially important in view of the growing global population.”
Cucumber, the crop of choiceIn addition to the autonomously controlled greenhouses, the challenge will comprise a reference greenhouse where the chief grower of WUR Greenhouse Horticulture and several Dutch growers will cultivate cucumbers in an authentic way. “We settled on cucumbers as our crop of choice because they grow fast,” says Hemming. “This will enable us to obtain lots of information in four months. Cucumber plants are also very quickly affected if something is done incorrectly during cultivation. A breeding company cultivated the plants for the teams, and people from the test company of WUR Greenhouse Horticulture will put the plants in the greenhouses. The yields, their value and the associated costs and sustainability factors will be compared to the reference greenhouse.”
Supervisors from WUR Greenhouse Horticulture will provide the teams with the required digital information. Information will be shared with and output settings received from the teams via an interface produced by LetsGrow.com, one of WUR’s tech partners. WUR employees will be responsible for harvesting and communicating standard crop information, including yield weight, to the teams. An international jury will oversee the process and award points.
“Most of the points will be awarded for maximization of net profit,” Hemming explains. “Another criterion will be sustainability: energy & water consumption, CO2 levels and the use of crop protection agents.” Teams will also receive points for the use of artificial intelligence. Questions such as ‘how autonomous was the teams’ actual approach?’ and ‘how realistically could this system be applied on a large scale?’ will be the main issues evaluated by the jury in the final stage.
An exciting competition
“We expect an exciting competition in which the teams – deep_greens, AiCU, The Croperators, Sonoma, and iGrow – apply different approaches,” Hemming concludes. “For one team, for instance, the focus will be on artificial intelligence, while another team will highlight cultivation expertise.” The winner will be announced in the second week of December during the AgriFoodTech trade exhibition. “We will gain lots of new knowledge for a new cultivation method for the future.”
For more information:
Publication date: 8/15/2018
Q&A: UVA i.Lab-Supported Indoor Farming Startup Beanstalk Still Growing After Y Combinator
Q&A: UVA i.Lab-Supported Indoor Farming Startup Beanstalk Still Growing After Y Combinator
3-May-2018
Source Newsroom: University of Virginia Darden School of Business
Beanstalk Farms founders Jack and Michael Ross are building their first production facility in Northern Virginia.
By Dave Hendrick
Newswise — Indoor farming startup Beanstalk Farms has come a long way in a short period of time. Jack Ross, a 2017 graduate of the University of Virginia’s School of Engineering and Applied Science, and brother Michael Ross started their venture in the incubator program at the Darden School-hosted W.L. Lyons Brown III i.Lab in 2017, building a prototype and learning as much as they could about the complicated world of fresh produce.
After the i.Lab, the Ross brothers — both of whom trained as engineers — successfully applied for a spot at Y Combinator, the Silicon Valley-based accelerator that has helped launch companies like Dropbox, Airbnb and Instacart, among hundreds of others.
Now back on the East Coast, Jack Ross recently spoke about his experience launching Beanstalk; the UVA network on both coasts; and his quest for faster, cheaper and better-tasting lettuce and spinach.
An edited transcript of that conversation follows:
Give us the pitch for Beanstalk.
Beanstalk Farms grows heirloom produce in automated indoor farms. What that means is we bring the field inside and that allows us to control absolutely everything around the growth of the plant. We like to say it’s always 65 and sunny in our facility.
So we can grow the highest-quality food, all-year-round, and we can actually grow it faster than you can outside because it’s a perfect environment. And we can grow it anywhere, so it can be produced very close to the end consumer.
What’s the innovation you are bringing to the table? What’s different?
Beanstalk’s greatest innovation is our automation of the indoor farming process. We are not the first to grow inside. That’s been done for quite some time. It has, up to now, been very expensive. Food grown indoors has not been able to compete with the price of produce grown in the field, and the biggest reason for that is labor goes up when you grow inside. Indoor farms lose all of the technology that a company like John Deere brought to the field.
My brother and I are engineers, and we took a very different approach to farming. We created a manufacturing line that grows a plant. So the labor is very, very low.
It’s a highly automated process and, on top of that, because we don’t have to design for human labor to tend to the crops, it’s much, much denser. So, in a very small amount of space, we can grow food to feed cities.
We can put that farm right in the city, and we can grow the highest quality food, using heirloom seeds that have been cultivated for thousands of years to be incredibly tasty and very nutritious. Also, unlike field-grown food, even some organic food, we do not use pesticides. This means our food is always clean and ready to eat.
Essentially, our automated systems allow us to sell at prices competitive with traditionally farmed food, and our precise indoor environment ensures we can grow the highest quality food anywhere in the world.
What was your experience in the i.Lab like?
It was great. It’s a wonderful time when you don’t really have anything set in stone. The community was very close knit and attentive. We were just starting out as a company, and learning who we should talk to and who could help us learn more about the problem we are trying to solve. Jason [Brewster], David [Touve] and Sandra [McCutcheon] were incredible in brainstorming solutions, refining our pitch, and connecting us to people that could help us better understand the food system. The i.Lab helped us get on our feet.
During the program, we spent most of that time trying to grow plants quickly and consistently. We knew that if we could do that, the rest of it would fall in line, as the engineering is our sweet spot. The rest of time was talking to customers. We were out talking to people from all different parts of the food system.
The food system is a really complex beast. From food getting off the field, it may change hands over half a dozen times. So we wanted to talk to chefs, restaurant owners, and distributors to understand the system. We found a couple of huge problems for all people involved.
First, finding a consistent source of quality produce is a really big problem.
People are looking for local produce and it just doesn’t exist everywhere. So sourcing was a big problem. And then just the volatility of the market. From week-to-week, prices can go up 800 percent. So that kind of volatility for a restaurant owner is awful.
To us, it was pretty clear we just needed to find a way to create a consistent, high-quality product and remove the risk factors.
So the i.Lab really pushed us to get out and talk to people. Thankfully, our hypothesis was verified and we graduated from the i.Lab Incubator knowing clearly what the problem is and having a rough idea of how we wanted to solve it. So that set us up perfectly for Y Combinator.
What’s the process like for getting into Y Combinator?
It’s quick.
The application is not terribly long. It’s about half a dozen questions on the business. They wanted to know a lot about the founding team. We heard back about a month later and they basically said, “You have an interview spot; it’s in a week for 10 minutes.”
So you have to drop everything you’re doing and fly out to Mountain View for a 10-minute interview. We got organized, and the i.Lab actually helped us get out there and coordinate with people while we were out there.
I thought it was going to be more Shark Tank-style, with a lot of accusatory questions. Not at all. They asked a few hard questions, and then it turned very quickly into brainstorming. What do you guys think you can do in the program while you’re here? What’s next for you?
It was a much warmer conversation than I anticipated.
What’s the program like once you’re in it?
It’s pretty hands-off. The biggest thing they do is they want you to pick a metric, a single metric for your business. And that is kind of your guiding light for three months of the program.
We picked cost because cost is really what drives purchasing decisions. So we focused on getting the cost of production to that of the field. We said if we can reach price parity with food purchased off the field, we can put this anywhere and maintain a profit.
You meet twice a week with your partners at YC and a group of other companies and talk about what you’re doing to hit that metric and what kind of stuff is blocking you.
Was it intimidating to be in this incubator that has launched so many household names?
Intimidating is probably not far off at the beginning, because expectations are very high.
The really amazing thing is the first day they brought in Drew Houston, the founder of Dropbox, and he was gearing up for his IPO. You build up the impression of these people, and he came in and had a very pragmatic approach to how he started Dropbox and how he grew it. He was a regular guy, and he made himself very available. So that kind of demystified it a bit. The biggest thing they stress is to just keep at it. Don’t die, is what they stress. If you can just get through it, the odds are so much better that you’ll be successful.
From that first day on, it was less about meeting these ridiculous expectations and more about just figuring out what kind of support you need for your business to stay alive.
Were you tapping into a UVA or Darden network while you were out there?
Absolutely. We touched back with the i.Lab while we were out there. [BlueRun Ventures General Partner] Jonathan Ebinger (MBA ’93) was my mentor at the i.Lab, and we had connected a few times while we were in Charlottesville. But after moving out there, he helped us understand more of the pacing of these sorts of things. He’s been a venture capitalist for 20 years and has seen a lot of companies come and go, so we were able to go to him with questions. Just having someone with that experience and wisdom helped us a lot. Not to mention he helped us get a place to live while we were there for three months.
Y Combinator just wrapped up in March. Where are you all now?
We moved back just last week to set up what is going to be our first production farm. We’re setting that up in Northern Virginia and looking to go into production in pilot runs at the end of this year. Then we’ll start selling into wholesale next year. That will position us as the first vertical farm to go into wholesale markets.
To us, that’s really important. We view this as an impact or mission-focused business. So being able to sell at wholesale proves to us and to our investors and customers that this is profitable at a mass-market size. So we can sell food that everyone can afford — not just the Michelin-starred chefs.
You have a background starting technology companies. Do you consider this a tech company?
We like to say we are a technology-enabled business, as the core of our innovation is technology. However, at end of the day, we are selling produce. What we focus on day to day is how we build a better manufacturing line that grows better and more affordable food.
As you’ve been through this process, have you keyed on a particular area of weakness to address?
Certainly, continuing personal development is the most important thing. If successful, your business is going to grow exponentially. Humans do not have an intuition for exponential growth, so it’s very important to just be learning as much as you possibly can so that you can try to stay ahead of your business’ growth.
Do you end up eating a lot of your product?
We do. It’s very cool to have a company where you can eat what you work on. The past three months have been largely a salad-based diet. I was not a huge salad aficionado before, but after having tasted these heirlooms seeds and eating our food fresh off the farm, it does taste a world different.
What other lessons stand out for you from these early days?
I think the most important lesson I’ve been learning through these programs is that the time you’re there is valuable, but it’s really brief. The most important thing is the network of people you become a part of and whom you spend your time with. At UVA, I became very close with fellow i.Lab founders including Kevin Eisenfrats of Contraline, Kris Cody of Paka, and Brent Baumgartner of Helme. Even though we all run very different business, we face the same problems. It is the support from this group of fellow founders from the i.Lab, and from YC now, too, that have helped me get to where I am and keep moving forward.
About the University of Virginia Darden School of Business
The University of Virginia Darden School of Business delivers the world’s best business education experience to prepare entrepreneurial, global and responsible leaders through its MBA, Ph.D. and Executive Education programs. Darden’s top-ranked faculty is renowned for teaching excellence and advances practical business knowledge through research. Darden was established in 1955 at the University of Virginia, a top public university founded by Thomas Jefferson in 1819 in Charlottesville, Virginia.
Agriculture, Education, Entrepreneurship, Local - Virginia
KEYWORDS
The Future of Automated Urban Farming by Babylon Micro-Farms
Alexander Olesen is Founder and CEO of Babylon Micro-Farms, developing automated hydroponic systems for the restaurant and hospitality industries that grow fresh, sustainable and organic food on-site.
The Future of Automated Urban Farming by Babylon Micro-Farms
February 17, 2018 AT 12:54 PM / BY ADMIN
Podcast: Play in new window | Download (Duration: 16:00 — 22.2MB) | Embed
Subscribe: Apple Podcasts | Android | Email | RSS | More
Alexander Olesen, Founder, and CEO of Babylon Micro-Farms joins Enterprise Radio to talk about his company and why technology and hydroponics will revolutionize the way we grow food.
Listen to host Eric Dye & guest Alexander Olesen discuss the following:
- What inspired you to start Babylon?
- How do you think hydroponics will change the way we consume food?
- Why should people be paying more attention to hydroponics in 2018?
- You are working on a new product, the Micro-Farm. What can you tell me about that?
- What are you most excited about for where Babylon is headed?
Alexander Olesen is Founder and CEO of Babylon Micro-Farms, developing automated hydroponic systems for the restaurant and hospitality industries that grow fresh, sustainable and organic food on-site. The idea was conceived in a Social Entrepreneurship class at the University of Virginia in 2015. Ever since then Babylon’s mission has been to make urban farming accessible to everyone and ensure a healthier and sustainable future.
Website: www.babylonmicrofarms.com
Social Media Links:
Facebook: www.facebook.com/BabylonMicroFarms
Twitter: www.twitter.com/BabylonMF