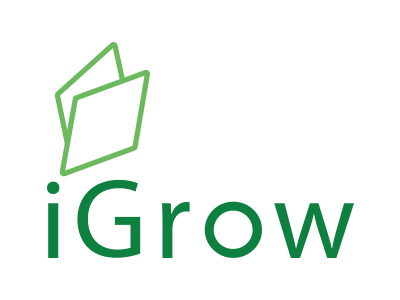
Welcome to iGrow News, Your Source for the World of Indoor Vertical Farming
VIDEO: How 2 Hong Kong Pioneers’ Hi-Tech Robotic Arms Can Transform Traditional Industries And Research
Technology created at Jonathan Cheung’s Inovo Robotics performs repetitive tasks that can cultivate sustainable crops and process foods in automated kitchens
Technology created at Jonathan Cheung’s Inovo Robotics performs repetitive tasks that can cultivate sustainable crops and process foods in automated kitchens
Eric Wong has transformed lab experiments with Nikyang’s automated tools that allow researchers to carry out a more reliable and systematic analysis
7 January 2021
While robotic technology has been widely used by big manufacturing companies to increase productivity, the high cost of getting started means many smaller businesses have yet to take advantage of its huge potential.
However, Inovo Robotics, a Hong Kong-based technology start-up, is working to solve this problem.
Since it was founded in 2016, the robotics company has been developing solutions for small- and medium-sized enterprises to help them adapt to automation in their everyday business practices.
Jonathan Cheung, the co-founder of the start-up, says his goal is to “democratize robots” and develop tools for all businesses to help them improve efficiency and remain competitive.
By submitting, you consent to receiving marketing emails from SCMP. If you don't want these, tick here
“We found that there is such a big disconnect to the market for small businesses to be able to benefit from affordable and flexible robots,” he says.
“There are a lot of businesses that are struggling to get staff to do monotonous tasks, so what we’re developing is really a tool that enables them to take away repetitive work.”
Jonathan Cheung, the co-founder of Inovo Robotics, says high entry costs mean that many small businesses have yet to take full advantage of automation’s full potential.
Disrupting traditional industries
One of the applications of the robotic arms has seen them used around the clock to carry out repetitive tasks that help grow high-quality, pollution-free vegetables at a futuristic farm in Hong Kong’s Tai Po district.
The farm, operated by indoor farming company Farm66 since 2018, is located inside a 20,000-square-foot (1,860-square-metre) factory building.
The use of the robotic arms to automatically sow seeds and harvest plants helps the farm to produce up to 200 tonnes of organic fresh produce, including cherry tomatoes, cabbage and basil, which is sold online and delivered to the city’s supermarkets and restaurants.
“Robots really improve the efficiency and speed of the products that are being made,” Cheung says. “In this competitive world, there is always a desire to drive costs down.”
In the case of vertical farming, the technology means minimal space and manpower are needed for the farming process, offering a glimpse of how technology will be able to transform farming in future.
Besides the vertical farm, the technology has also been used in an automated kitchen, where it helps with food processing to ensure cooking consistency. Inovo Robotics is also teaming up with a programming company to develop a system for high-resolution 3D scanning.
Inovo Robotics’ technology is being used to cultivate fresh organic produce at Farm66’s futuristic indoor farm inside an industrial factory building in Hong Kong. Photo: Farm66
Popularising robots for everyday use
Before setting up his own venture, Cheung spent more than a decade working as an engineer, when he witnessed first-hand how robots can help businesses scale their operations.
In 2016, Cheung and a colleague co-founded Inovo Robotics to popularise the everyday use of robot technology by businesses.
Its launch product, Modular Arm, with an adjustable system of six fully rotatable joints, gives the robot the flexibility to reach different positions. The robot’s modularity also gives customers an easy mechanism to choose longer or shorter arms, depending on their configurations.
Cheung says while large manufacturing companies often require tools that can automate a repetitive task, smaller businesses look for collaborative robots that can work alongside staff to complete different jobs at the same time.
“Smaller businesses tend to have smaller batch sizes and tighter spaces,” he says. “That is where a collaborative robot really comes into its own.”
Jonathan Cheung says Inovo Robotics’ modular robot technology offers small businesses a variety of options thanks to its adjustable flexible joints and the choice of using shorter or longer arms.
Inovo Robotics currently has two offices at Hong Kong Science Park, a government-run start-up incubator, and London, in the United Kingdom, as it seeks to tap into both the Asia-Pacific and European markets.
Cheung says Hong Kong has proved an ideal location to scale up his business because of its proximity to hi-tech research and an abundance of talent.
“[We can] be close to our supply chain, which allows us to manage it closely and deliver the best product to our customers,” he says.
“At any point in Hong Kong, you are probably within 25km to five or 10 great universities,” he adds. “There is a wealth of talent to be able to tap into – there are only a few countries with that level of accessibility.”
Revolutionizing academic research
Another Hong Kong start-up, Nikyang, has also developed fully automated laboratory equipment to help academic researchers increase the reliability of data collected in experiments.
Today, its automation technology has been applied in many settings, such as research institutes and pharmaceutical and biotechnology companies.
The venture was founded by Hongkonger Eric Wong in 1999 with the initial goal of helping researchers in traditional Chinese medicine (TCM) to conduct analysis in a more systematic way.
“The basic dream of Nikyang was originally to pursue TCM research to gain a better understanding,” says Wong, who graduated with a master’s degree in biochemistry in Canada.
“I thought we needed a more standardized way of doing analysis in TCM to collect valid and precise information.”
Eric Wong, the founder of automation company Nikyang, says the use of robotic technology allows researchers to conduct more systematic analysis.
When he started his business journey by reaching out to laboratories in Hong Kong and mainland China, he realized that researchers wanted to use machines to help them follow the correct procedure as closely as possible while carrying out repetitive work.
However, many automated instruments available then lacked the ability to carry out different steps in lab research, he says, rendering them error-prone when applied in studies.
To solve the problem, Wong collaborated with Chemspeed, a Switzerland-based provider of lab equipment, in developing specific instruments for TCM research.
His team has integrated Chemspeed’s tools with robotic arms and wearables to increase collaboration between researchers and machines in conducting the analysis.
However, he realized the company would not be sustainable if it focused solely on serving the TCM industry, so he later diversified the business and began developing solutions for different settings.
In 2008, Nikyang began receiving orders from petrochemical companies in China, which gave Wong a lifeline to sustain his business and pursue his dream in TCM research.
The venture now places an emphasis on boosting effectiveness by providing an immerse lab experience.
Its SmartLab product, which is still under development, is set to integrate sensor technology, smart wearables, and cloud data management to help researchers work more efficiently with machines.
Nikyang’s SmartLab, which is still under development, will integrate sensor technology, smart wearables, and cloud data management so researchers can work more efficiently with machines. Photo: Nikyang
Nikyang has its headquarters at Hong Kong Science Park, where it carries out most of its research and development work. To tap into the China market, it has also opened branches in Beijing, Shanghai, and Guangzhou to sell its products.
Wong says Hong Kong has served as an ideal location to grow his company because of its connectivity with China and different parts of the world.
“Hong Kong is definitely unique in terms of being a super-connector between the East and the West,” he says.
The city’s world-class financial market and sound legal system have also helped start-ups in raising capital and developing ideas as they embark on their journey.
Pioneering spirit
Both Wong and Cheung believe it is important for aspiring innovators to be passionate about their business vision to help them overcome challenges when developing and selling the products.
Wong, who spent a decade before he found a way to make his business sustainable, says it was vital to remain dedicated because many innovators experience failures before they can get their businesses on track.
“You need to have passion and a big heart to accept failure, and [an] even bigger heart to think and take risks,” he says.
Eric Wong, who spent a decade before finding a way to make Nikyang sustainable, says aspiring innovators should be passionate about their business vision – and not focus only on profits.
Wong also advises young entrepreneurs not to look only at making profits if they want to make a difference in the world.
“Money is only a by-product,” he says, adding that many successful pioneers often have to make substantial investments before they are able to disrupt the industry.
Cheung agrees that innovators must feel empowered to turn ideas into reality.
“My advice is to really focus on the business model,” he says. “It’s a very, very difficult journey to go on, and it’s very, very rewarding as well. And it’s very important to make sure you stay true to what you believe in.
“Having an idea that you believe in wholeheartedly, that you are willing to give your time and commitment to, is a good validation that you are on the right track.”
Morning Studio is the commercial content team of the South China Morning Post (SCMP). It aims to engage readers through storytelling while enabling the brand behind the content to achieve its marketing objectives. The Morning Studio team consists of specialists in various areas such as journalism, multimedia graphics, video production, digital technology, and marketing.
New Infographic From Ultimation Industries Shows
“How to Optimize Vertical Farming,” a new infographic created by Ultimation Industries LLC, highlights the benefits of vertical farming and ways to maximize the production of an indoor farming system. Ultimation has designed, manufactured, and installed conveyor systems for over 30 years and is a leader in vertical farming material handling
How To Optimize Vertical Farming
ROSEVILLE, Mich. (Jan. 6, 2021) – “How to Optimize Vertical Farming,” a new infographic created by Ultimation Industries LLC, highlights the benefits of vertical farming and ways to maximize the production of an indoor farming system. Ultimation has designed, manufactured, and installed conveyor systems for over 30 years and is a leader in vertical farming material handling.
Vertical farms can potentially achieve higher yields for the surface area dedicated to production by controlling the light, temperature, humidity, water, and nutrients the plants receive. They also reduce “food miles,” the distance food items travel from the point of production to the table and can reduce CO2 emission from transport while delivering fresher and better-tasting products.
As sustainable agricultural operations such as vertical and indoor farms become more prevalent, conveyor technology systems can be part of the solution. “Conveyors are essential to vertical farming because they can make use of all the available vertical space of a facility and can move plants through automated systems as they grow,” said Richard Canny, president, Ultimation Industries LLC. “How to optimize vertical farming is the challenge that the industry faces as it scales up.”
In addition to creating customized products for assembly operations, Ultimation offers food safe grade systems and material handling solutions for the vertical farming industry. The company has recently expanded into smaller, ‘quick ship’ products and systems that are sold through their website and in Amazon’s stores.
For more information about Ultimation Industries, visit https://www.ultimationinc.com.
About Ultimation:
Ultimation Industries, LLC is a woman-owned leader in the conveyor technology and automation industry. Founded in 1989, Ultimation designs manufactures, and installs machinery and equipment, automation devices, tire and wheel processing lines, and conveyor systems for customers throughout the Americas. The company offers a line of proprietary automation systems and is also a leading integrator of Jervis Webb Conveyor Systems. Ultimation’s e-commerce channel sells Ultimation, Interroll, Itoh Denki, Jervis Webb, and a wide range of other conveyor equipment. In 2020, Ultimation was recognized as one of Inc. 5000’s fastest-growing private companies in America. The company was a finalist for Amazon’s 2019 Woman-Owned Small Business of the Year and earned honors as one of “2019 Metro Detroit’s Best and Brightest Companies to Work For®.”
Visit https://www.ultimationinc.com/ for the latest product information and news about Ultimation.
###
For further information please contact:
Nancy Sarpolis
248-219-5651
Iron Ox Announces Next Robotic Farm In Lockhart, TX
Iron Ox has purchased nearly 25 acres of land and plans to build a new, state-of-the-art facility on the property
November 6, 2020
LOCKHART, TX, — Iron Ox, a leader in robotics and AI-enabled farming with a mission to solve food insecurity, and the City of Lockhart, Texas today announced that Iron Ox will expand their operations to the city with plans to break ground on a new facility this December, bringing new tax revenue and jobs to Lockhart.
Since 2015, Iron Ox has developed hybrid robotic greenhouses that support a range of produce offerings. To bring those produce offerings to new communities, the company identified Texas as the next state in their national expansion plan with its favorable business environment and rich history of agriculture.
“We’re proud to make Lockhart our next farm outside of California,” said Brandon Alexander, Iron Ox CEO & Co-founder. “Lockhart’s city government, as well as their planning and development staff, worked diligently with us throughout this process and made us feel right at home. In addition, the city's central location within the Texas triangle and short drive from Austin, allows for strong distribution lanes of same-day grown and harvested products throughout the entire state of Texas, making the city the ideal choice for our robotic greenhouse growing platform”.
Iron Ox has purchased nearly 25 acres of land and plans to build a new, state-of-the-art facility on the property. This new facility will house the company’s natural light greenhouses, processing operations and AI-enabled robots to bring fresh, clean and healthy food to new customers and communities throughout Texas.
“The addition of Iron Ox to the Lockhart business community represents synergy between our city’s storied history in agriculture and our growing technology sector,” said Lockhart Mayor Lew White. “The food and beverage processing industry is one of four business sectors Lockhart has targeted in its 5-year economic growth plan because our city’s unique advantages align perfectly with the needs of companies like Iron Ox.”
Mike Kamerlander, Director, Economic Development, represented the Lockhart Economic Development Corporation (CEcD) on this project.
“As Lockhart continues to grow, Iron Ox and companies like it are essential to our economic vitality and future. We thank them for their investment and commitment to Lockhart.”
About Iron Ox
Iron Ox launched the world’s first autonomous farm in October 2018, leveraging advancements in plant science, machine learning, and robotics. The Iron Ox team develops AI-enabled, autonomous technology that enables fresher, more consistent produce to be grown and distributed globally. The company’s goal is to service thousands of communities with the freshest and healthiest products, while establishing global reach and impact on food security.
For more information, visit www.ironox.com.
About Lockhart Economic Development Corporation
The Lockhart Economic Development Corporation, a department within the City of Lockhart, is designed to provide a range of business and economic development assistance. To learn more about opportunities in Lockhart, visit www.lockhartedc.com.
Contact Info:
Taylor Aldredge
570-534-4754
Babylon Microfarms Bets On Automation For The Future of Vertical Farming
What started as a humble tabletop farm at the University of Virginia has since evolved into a major company to watch in the vertical farming space, particularly when it comes to the software piece of the process
What started as a humble tabletop farm at the University of Virginia has since evolved into a major company to watch in the vertical farming space, particularly when it comes to the software piece of the process. Babylon Microfarms has over the last few years garnered quite a bit of attention for its controlled-environment farms the company now licenses to hospitals, cafeterias, and other other foodservice operations.
Based in Charlottesville, Virginia (though soon moving HQ to Richmond, VA) Babylon makes a “plug-and-play” system for hydroponic farming that automates much of the grow process and makes controlled-environment farming more accessible. The company raised a $2.3 million seed round in January of this year and, its current product is a standalone farming unit that grows leafy greens.
Of late, however, the bulk of founders Alexander Olesen and Graham Smith’s focus is on software: namely, using it to automate the growing process, which removes the more complicated aspects of vertical farming that would be off-putting to the average user.
“Growing is a cumbersome experience for many,” Olesen explained to me over the phone this week. “Removing the friction of the user experience and combining that will some of the remote management [will make] smaller forms of vertical farming possible.”
Were the average person to try and build their own high-tech grow system, it would require significant expertise in horticulture, hardware infrastructure, and software development. To name just a few examples, that would include calculating one’s one LED light recipe (which takes the place of sunlight in controlled-environment ag), controlling the temperature of the farm, and understanding how much nutrient to feed each crop and when to do that. Everyday would require a certain amount of trial and error for every plant variety.
All of this makes for prohibitively high costs when it comes to commercial greenhouse production. Olesen noted that for controlled-environment farming to go mainstream, it has to be less technically complicated for the user.
Babylon’s software is one solution addressing those complications. The company’s “seed-to-sale” system automatically dispenses the right amount of nutrients, light, and water for each crop, simultaneously collecting data on the plants so that the system can make adjustments as needed. The entire system can be controlled remotely via a mobile app.
Up to now, the company has drawn comparisons to the likes of Farmshelf, Farm.One, and InFarm, all companies that license a hardware-software farming combination out to foodservice and hospitality operations.
But Babylon’s founders told me they aren’t necessarily interested in the hardware aspect going forward. Smith says they would prefer something like teaming up with a hardware manufacturer that wants to make vertical farms but perhaps needs more expertise in software to complement their hardware capabilities.
Such a scenario is actually on its way to becoming a reality. At CES this past year, hardware giant LG announced plans for a smart-farming appliance for the consumer kitchen. At the same time, GE Appliances showcased its Home Grown concept, which featured grow systems using hydroponics and soil-based methods. Prior to CES, Miele acquired Agrilution in another play for smart farms in the appliance space.
All of these hardware developments suggest great opportunity for the accompanying software. While many companies in the vertical farming space try to do both right now, Babylon’s future focus on being “an enabling company” that offers software and services may prove a wiser bid for the long term. Besides building out distribution of its own farms, Babylon is currently interested in working with other businesses, particularly those making hardware, that want to enter the vertical farming space.
There will be no one product that wins, Olesen said, adding that instead, it will be a combination of tools working together to make vertical farming more accessible to everyone.
FILED UNDER: AG TECH BUSINESS OF FOOD EDUCATION & DISCOVERY FEATURED FOODTECH
MODERN FARMER VERTICAL FARMING
Autogrow Challenges Other Industry Players To Publish APIs
“To date, large industry players have not publicly published APIs’, but our argument is that it’s your data - you should be able to do what you want with it,” says Chief Technology Officer Jonathan Morgan
Autogrow is calling for more public APIs (Application Programming Interface), giving increased access for growers to their own data, and fostering faster innovation in the Controlled Environment Agriculture industry.
“To date, large industry players have not publicly published APIs’, but our argument is that it’s your data - you should be able to do what you want with it,” says Chief Technology Officer Jonathan Morgan.
“There can be a protectionist approach to development to dissuade people from building their own versions or integrating other products. But you will never keep up with all the customer requests or in the same timeframe as the 15 other companies working on the same improvements in the market. Access equals innovation - simple as that.”
Autogrow's FarmRoad has launched their public API on a new Developer Portal which is product agnostic and welcomes all industry players. This will allow growers to use the platform to build a ‘best of breed’ solution for their operation, no matter what their current technology providers are.
“You don’t have to rip and replace your existing technology. You just need to use an API to connect it to FarmRoad and then see all your information in one place. You can also give third parties secure access to specific areas of your information – keeping control of what you want them to see.”
“As innovation accelerates it creates a unique challenge of being able to centralize all of your data in one place – regardless of the source. We’ve been offering public APIs for over three years and are certainly the leaders when it comes to cloud technology,” notes Mr. Morgan.
Initially, the FarmRoad Developer Portal will give access to:
Measurements: Over 39 different measurement data types related to the environment and crop registration.
Events: Capturing key events or notes for example pest detection or spray regimes.
Farms/compartments/sectors: Get the full picture from different areas of the farm. Giving comparative studies, trends or with permission-based access.
“This is just the beginning for what FarmRoad will be able to offer. With API availability, growers will be able to create their own custom applications alongside the work we are doing. It’s a great developer community which can evolve and scale as businesses and the industry changes.”
For more information on the FarmRoad Developer Portal - https://farmroad.io/developer
For more information on the API documentation - https://developer.farmroad.io/
For more information on Yield Prediction by FarmRoad - https://www.farmroad.io/
11 Nov 2020
CANADA: Automated Guelph Vertical Farm Supplies Retailers With Local, Leafy Greens
An automated vertical farm in south Guelph is now fully operational. GoodLeaf Farms has the capacity to produce 800,000 units of locally grown leafy greens for Ontario retailers — including Loblaw banners, Longo’s, and Whole Foods — 12 months of the year
By Lilian Schaer
October 14, 2020
The Newly Opened Farm Grows Crops
40 to 50 Percent Faster Than Traditional Crops
There are 50 workers employed at the GoodLeaf Farms facility in Guelph. Photo: Lilian Schaer
An automated vertical farm in south Guelph is now fully operational. GoodLeaf Farms has the capacity to produce 800,000 units of locally grown leafy greens for Ontario retailers — including Loblaw banners, Longo’s, and Whole Foods — 12 months of the year.
“It’s really unique for Canada that we can grow 365 days of the year, and we can fill a gap in the market without going up against traditional farming,” said account manager Jacquie Needham during a tour of the facility on Sept. 15.
Why it matters:
The pandemic has heightened demand for locally grown foods less dependent on sometimes fragile global supply chains.
GoodLeaf’s crops include baby arugula and baby kale, along with four types of microgreens: pea shoots, Asian blend, spicy mustard medley, and arugula. While consumers are familiar with “baby” leafy greens, they’re less comfortable with what to do with microgreens, admits Needham.
“Micros are a learning curve for consumers, but they can be used to add nutritional elements to meals as garnishes, in salads or sandwiches, or as something you add to a smoothie,” she said.
“People are cooking more at home right now and experimenting more.”Vertical farming is an innovative process that naturally grows plants with hydroponics under specialized LED lights designed to maximize photosynthesis. In the GoodLeaf facility, carbon dioxide, water, nutrition, and light are carefully programmed and monitored for each specific crop.
Jacquie Needham, of GoodLeaf Farms, talked about the company’s products during a recent tour at the facility.’ photo: Lilian Schaer
According to Needham, that makes their growth cycles an estimated 40 to 50 percent shorter than traditional crops. From seed to store takes about 12 days for the microgreens and about 22 days for the baby leafy greens. That includes testing every crop for contaminants before shipping to ensure they’re safe — important at a time when North American produce recalls make headlines and can have far-reaching economic and health consequences.
Needham also pointed to the sustainability of vertical farming production. The GoodLeaf facility uses 95 percent less water than a traditional farm, doesn’t use pesticides, herbicides, or fungicides, and has no run-off issues that could impact local water supplies. The production is not organic, however.
“We are not certified organic because our production does not use soil, but we feel we have a cleaner product than organic because, in addition to being pesticide-free, it’s not exposed to wind or rain, for example,” she said. “It’s an education piece for consumers.”
GoodLeaf Farms was founded in 2011 in Nova Scotia by Gregg Curwin. That original Nova Scotia farm has now been converted into a research and development centre for the company.
The new Guelph facility employs about 50 people who work seven days a week and it’s the city’s research expertise and proximity to the Greater Toronto Area that brought GoodLeaf to the region.
The GoodLeaf building is located in an industrial area in south Guelph. photo: Lilian Schaer
“Ontario is a big hub for consumers, retail and foodservice, so we were looking for a place close to the market so we can get product to people as quickly as possible,” said Executive Director of Operations Juanita Moore. “And the University of Guelph has been a great help with research.”
Research conducted in controlled environments
GoodLeaf is working with university researchers on a number of horticulture and food safety projects, including studies on controlled environments and light spectrums. The company received $4.4 million in start-up innovation funding from Agriculture and Agri-Food Canada’s AgriInnovation Program.
“I’ve been the mayor (of Guelph) for six years now and this is one of my “wow” moments,” said Guelph Mayor Cam Guthrie following the tour. “Guelph is embracing the circular food economy and we are seeing it in action here. It’s a testament to what Guelph has to offer.”
Guelph MP Lloyd Longfield, who was also on the tour, pointed to vertical farming’s potential to help address climate change and food security issues in both urban and northern or Indigenous communities.
“This type of agriculture is consistent and gives predictability to the producers and it would be interesting to see if it could be used more widely,” he said.
CombaGroup SA, A World Leader In Automated Mobile Aeroponics, Commits to Rigorous Standards of Social and Environmental Performance, Accountability, and Transparency
CombaGroup joins the rapidly growing movement of more than 3,500 B CorpsTM from 150 industries, across 74 countries including companies like Patagonia, Alpro, Alessi, Etsy, Innocent, Too Good To Go, Opaline, and Ben & Jerry’s
Molodin, Switzerland – 17 September 2020 CombaGroup SA today announced that it has officially become a Certified B Corporation®, utilizing the power of business to address society’s greatest social and environmental challenges.
CombaGroup joins the rapidly growing movement of more than 3,500 B CorpsTM from 150 industries, across 74 countries including companies like Patagonia, Alpro, Alessi, Etsy, Innocent, Too Good To Go, Opaline, and Ben & Jerry’s.
CombaGroup has been certified by B Lab as having met the rigorous standards for B Corp Certification that represent its commitment to achieving goals beyond shareholder profit. These include verified social and environmental performance, public transparency, and legal accountability to balance profit and purpose. B Corps are accelerating a global culture shift to redesign success in business and build a more inclusive and sustainable economy.
B Corp certification covers five key impact areas: governance, workers, community, environment, and customers. The certification process is rigorous, requiring a score above 80 and providing evidence of socially and environmentally responsible practices, including energy supply, waste and water use, workers' compensation, diversity, and corporate transparency. To complete certification, the company will legally embed their commitment to a purpose beyond profit in their company articles.
The recent focus on the agro-technology industry has made CombaGroup’s B Corp Certification a milestone and underlines a shift towards greater responsibility and transparency in the sector.
"B Lab is delighted to welcome CombaGroup to the B Corp community,” said Jonathan Normand, Director of B Lab Switzerland. “CombaGroup has been a pioneer in the field of mobile aeroponic growing solutions. CombaGroup has also been acknowledged as one of Solar Impulse’s 1000 Efficient Solutions for its ability to grow crops with minimal environmental impact for maximum profitability. I look forward to seeing CombaGroup inspire other companies to join the B Corp community and use business as a force for good.”
Serge Gander, CEO of CombaGroup stated: “We are proud to be part of the B Corp community with aligned values and ways to change the world through conscious business decisions. By certifying as a B Corp, we have met the highest levels of verified social and environmental performance, transparency and accountability.
“This certification reconfirms our commitment to use our unique automated high-performance culture systems to bring efficiency, consistency, and profitability in the food supply chain with the least possible resources and minimum environmental impact.”
About B Lab
B Lab is a non-profit organization that serves as part of a global movement to redefine the notion of success in business so that one day all companies compete not only to be the best in the world, but also the best for the world.
Located on five continents, B Lab advocates for systemic change by providing a standard and tools to create a community of B Corporation certified companies.
About B Lab Switzerland
B Lab Switzerland is the Swiss branch of a global non-profit organization that supports a community of people using business as a force for good.
About CombaGroup
CombaGroup is a Swiss agro-technology company that provides farmers and industrialists with innovative mobile aeroponic farming solutions for growing fresh, environmentally- friendly, nutrient-rich vegetables.
CombaGroup’s patented technology significantly reduces water consumption and contamination risks while offering maximum productivity per square meter and minimizing environmental impact. Mechanized irrigation and spacing systems produce clean, quality, pesticide-free salads, cabbages, and aromatic plants all year round, thus providing consumers with healthy, responsible products.
For more information
contact@combagroup.com +41 21 545 99 25 www.combagroup.com
Media information online
Media information and images can be downloaded directly from combagroup.com Journalists can subscribe to our media mailings to receive information on CombaGroup’s aeroponic solutions and technology.
For the latest updates on CombaGroup, visit combagroup.com or follow on Instagram @combagroup_sa, Twitter @SmartLettuce, Pinterest, and LinkedIn
Bowery Is Sprouting In Baltimore With A New Automated Indoor Farm
Using technology that allows farming to go beyond the limits that the land imposes, the company has a mission to democratize access to fresh produce. It initially opened two farms in Kearney, New Jersey, serving the tri-state area
With a mission to democratize food access, the indoor farming startup sees the White Marsh location as a mid-Atlantic hub.
By Stephen Babcock / STAFF / 2/20/20
Inside Bowery's indoor farming operation. (Courtesy photo)
On land in White Marsh that was once associated with a working farm, new growth is taking root. But it didn’t require clearing away the building on the site: All of the growing is done inside.
“We are turning what was once an industrial warehouse back into a modern farm,” said Katie Seawell, chief marketing officer of Bowery Farming.
In early November, Bowery Farming opened a new indoor farming operation inside the warehouse on Franklin Square Drive and has been ramping up operations.
First flagged by Fast Company, it’s the third and largest farm for the New York-based startup, which in 2018 raised $90 million in a round led by Google Ventures.
Using technology that allows farming to go beyond the limits that the land imposes, the company has a mission to democratize access to fresh produce. It initially opened two farms in Kearney, New Jersey, serving the tri-state area.
With the expansion to Baltimore, the company is seeking a wider foothold in the mid-Atlantic. Seawell said the White Marsh location will open up distribution into a 150-mile radius where it can reach a potential 25 million people.
The company looks to hire locally even as it thinks regionally, and Seawell said White Marsh proved to be a transit-accessible location.
When it is fully-staffed, Bowery Farming expects to have about 80 farmers working at the space, in a mix of hourly and supervisory roles. Even for folks with no prior farming experience, Bowery looks to offer opportunities for farmers to move up within the organization as they gain skills. The farmers rotate through different roles on the farm, learning different aspects. Seawell recalled one farmer whom she met in the early days of the Kearney farm when he had a role in the packing section.
“I just ran into him last week and he was now in a support role for the ag science team,” she said.
They also seek out opportunities to support growth. In New York, the engineering team recently taught a coding class.
Inside the farm itself, hydroponics — the process of growing plants without soil — is key to the vertical farming operation, and technology plays a big role, too. CEO Irving Fain teamed with cofounders to apply technology to a big mission area. The team devised a system called BoweryOS to run the farm, which uses visual systems, sensory systems and automation. With data-gathering techniques and machine learning, the company sees its farms as a network, so the data is helping to build on what’s been done at the other two locations.
“Even though it’s the newest farm, it’s the smartest farm we’ve ever had,” Seawell said.
Bowery Farming from above. (Courtesy photo)
When it comes to the crops themselves, the farm has leafy greens and herbs in the market now. They’re available through Amazon Fresh, and Bowery is working on developing retail partnerships in the region to bring produce in the spring and summer. The company is also working to move beyond the “leafy green” category, which is often a staple of indoor farms and is testing other crops. It also has a partnership to regularly deliver hundreds of pounds of produce to the Maryland Food Bank.
Vertical farming doesn’t only upend the traditional growing model. With a wider food system that often involves food being shipped long distances, Bowery’s indoor farming approach yields lots of promise to bring production closer to where it’s eaten, employ local folks and offer a pesticide-free product.
Still, indoor farming remains new, and it’s entering an existing market with plenty of other produce players. As such, it has to make a product that’s attractive to folks, as well, and Seawell said the company has also put a lot of time and care into not just the operations, but also how it tastes.
“We believe we have a great-tasting product,” Seawell said.
FINLAND: New Chairman of The Board Appointed For Netled
Mr. Rintamäki brings solid key experience to Netled. In his previous career, he has acted in leading financial positions in various operations of Kone Oy and later in Konecranes PLC in Finland and overseas
Netled announced that Teuvo Rintamäki (M.Sc. Econ) has been elected as Netled’s new Chairman of the Board. Mr. Rintamäki brings solid key experience to Netled. In his previous career, he has acted in leading financial positions in various operations of Kone Oy and later in Konecranes PLC in Finland and overseas. Last eight in Konecranes he held a position of CFO.
Rintamäki has also next to 10 years of experience in guiding and leading start-ups as a Board Member and Chairman of the Board. He has a history of successful company listings and sales. Currently he operates as a Chairman of the Board in, for example, companies like Safedo Oyj, PowerProfPartners Oy and Saunaranta Invest Oy, as well as a Board Member and Board Advisor in various companies. In the 2000s, he also served as a member of the Committee on Strategic and Economic Affairs of the Technology in Finland.
Teuvo Rintamäki
”I´m very excited about this new position. Netled is currently in a very interesting growing phase; the company is taking off as an internationally recognised technology provider and notable player in the global market. In addition, Netled operates in a rapidly growing business field. Vertical farming is more efficient compared to traditional ways of cultivation, and it’s also more ecological and sustainable way of farming”, says Teuvo Rintamäki.
Netled’s CEO Niko Kivioja comments: ”We are extremely pleased to have Teuvo Rintamäki as our new Chairman of the Board. He has a vast know-how of globally operating technology companies as well as experience in working successfully with start-ups. We are certain that his professional background will give our company the boost for future growth.”
For more information:
Netled
netled.fi
Publication date: Tue 29 Oct 2019
Korean Ag-Tech Company Exports Smart Farming Solution To UAE
According to the source, n.thing will grow and sell Romaine lettuce in Abu Dhabi with Planty Cube
31 July 2019
The n.thing will grow and sell Romaine lettuce in Abu Dhabi with Planty Cube. (Image source: Elsemargriet /Pixabay)
South Korea’s Agricultural Technology Startup n.thing Has Started Exporting Indoor Farming Solution Planty Cube To The UAE
As reported in The Investor, the autopilot farm system is expected to allow farmers to grow greens in fully insulated indoor operations in areas with high aridity.
According to the source, n.thing will grow and sell Romaine lettuce in Abu Dhabi with Planty Cube.
Seeing the local market response, the types of greens will be diversified and production volume will rise, stated the company.
A number of smart farming companies in the Middle East is adopting smart methods to grow vegetables as the same in traditional method is very difficult due to hot arid climate, shortage of farmland and shortage of water.
US: OHIO: 80 Acres To Create 125 New Jobs As It Opens New Hamilton Headquarters
A $26.9 million investment from San Francisco private equity firm Virgo Investment Group will allow 80 Acres Farms to carry out planned phases for continued expansion of its operations in Hamilton and enable the company to create 125 new jobs in the city
July 29, 2019
Eric Schwartzberg, Staff Writer
Hamilton, Ohio
A $26.9 million investment from San Francisco private equity firm Virgo Investment Group will allow 80 Acres Farms to carry out planned phases for continued expansion of its operations in Hamilton and enable the company to create 125 new jobs in the city.
As a result of that investment and the commitment to create those new jobs, the Ohio Tax Credit Authority this morning approved a Job Creation Tax Credit for the project for 1.647 percent over eight years.
80 Acres Farms also has moved its corporate headquarters, as well as 15 employees, to newly renovated office space in downtown Hamilton, company officials said Monday. The company derives its name from its ability to grow 80 acres worth of food in a quarter of an acre space, all starting in its original location in Cincinnati.
MORE: A Hamilton facility will be the first of its kind in North America after new investment
80 Acres Farms is now producing tomatoes in downtown Hamilton. They purchased the former Miami Motor Car Co. building on S. 2nd Street in February 2017 and have renovated it to create an indoor farm facility. NICK GRAHAM/STAFF
Its vision is to establish year-round indoor farming operations in major cities around the world growing more nutritious produce, according to Mike Zelkind, 80 Acres Farms’ co-founder and CEO.
80 Acres Farms’ closed-loop, modular systems grow crops more sustainably, and their proximity to consumer locations dramatically decreases the distance produce must travel, thereby increasing shelf life and more importantly taste.
“Hamilton is a rising community looking for diversified growth and is strategically located near multiple large population centers,” Zelkind said. “Sustainability continues to be an essential part of our business, and Hamilton’s commitment to emissions-free, renewable energy through hydropower was also an important component in our decision to become an even bigger part of the Hamilton community.”
MORE: Hamilton’s large indoor growing operation is so advanced they want it around the world
Hamilton City Manager Joshua Smith said 80 Acres Farms’ decision to call Hamilton home is catalytic for three reasons.
“First, they will soon be one of our largest utility customers,” Smith said. “Second, their presence in Hamilton is attracting interest from other innovative companies. And third, their multiple locations throughout the city will have a positive impact on local businesses.”
The company was founded in 2015 by Zelkind and Tisha Livingston, two veteran food industry executives. It is supported by a board of directors representing executive and leadership experience at leading food, healthcare and other companies.
80 Acres Farms provides customers with a variety of locally grown, just-picked leafy greens, microgreens and vine crops, including the world’s only tomatoes and cucumbers grown completely indoors using proprietary technologies. That includes modular grow zones, customized LED lighting, precisely tuned climate controls and an artificial intelligence-powered growing system.
The company said that allows to produce flavorful and nutritious locally grown fruits and vegetables at affordable prices.
80 Acres Farms is now producing tomatoes in downtown Hamilton. They purchased the former Miami Motor Car Co. building on S. 2nd Street in February 2017 and have renovated it to create an indoor farm facility. NICK GRAHAM/STAFF
MORE: Dilapidated Hamilton building transforms into an industry-changing grow facility
80 Acres Farms launched renovations on the former Miami Motor Company building on South 2nd Street in early 2017, with plans to create 30,000 square feet of office and food production space downtown. The company is growing vine crops in that renovated location, where it started harvesting its first crops in April.
In September 2018, 80 Acres Farms broke ground on the first phase of its Hamilton Enterprise Park facility and in late March the first phase of the site started when the company started growing its first crop there.
It is set to become the country’s first fully automated indoor farm.
Most recently, the company moved its corporate headquarters, as well as 15 employees, to a newly renovated office space in downtown Hamilton. The company’s planned investment in Hamilton is expected to be more than $26.9 million.
MORE: Company with large Hamilton indoor growing operations joining international food effort
Future phases will add around 150,000 square feet of controlled environmental agriculture, or CEA, space. That space will allow 80 Acres to “dramatically increase” distribution with its growing list of retail and food service partners, which includes Whole Foods, Jungle Jim’s International Market, Dorothy Lane Market and Green Bean Delivery, Zelkind said.
BREAKING NEWS: Autogrow Announces First Industry Collaboration With Ridder Group And NATIVE
The collaboration is made possible with the launch of Autogrow’s new farm management platform, FarmRoadTM, which was announced by CEO Darryn Keiller at the Indoor AgTech Summit in New York today
June 20, 2019 (NEW YORK): Global automation expert Autogrow has announced a collaboration with competitor Ridder Group and New York agriculture software firm NATIVE.
The collaboration is made possible with the launch of Autogrow’s new farm management platform, FarmRoadTM, which was announced by CEO Darryn Keiller at the Indoor AgTech Summit in New York today.
“FarmRoadTM was conceived to fulfil two broad purposes. A platform for autonomous farming and secondly as a way of bringing together all disparate technologies that farmers use into one unified management tool,” explains Mr. Keiller.
“To be truly unified you need to be open and work collaboratively across the industry with buy-in from existing major players. It’s a concept we advocated two years ago when we came out with the first open API (Application Programming Interface) and I’m pleased to be in a position to say the dream is now tangible.”
“We are ecstatic that Ridder has shown the foresight and faith in us, to support what we are doing and join us in showing the industry what is possible when true collaboration occurs.”
Both Autogrow and Ridder market automation solutions for Controlled Environment Agriculture (CEA) and both will be able to integrate with FarmRoadTM.
“The Ridder Group, developer of the HortiMaX greenhouse control systems for over 40 years, supports the initiative of Autogrow,” says Joep van den Bosch, Chief Innovation Officer, Ridder Group.
“Ridder believes strongly in a connected future where systems and data is shared for the benefit of optimizing the plants growing conditions and more efficient and sustainable greenhouse operations.”
“As an industry partner, Ridder will make it possible for growers to connect their Ridder climate control and irrigation systems to the FarmRoadTM platform.”
Alongside Ridder Group, Autogrow will also be collaborating with New York based Start-Up NATIVE.
“Equally as important as an established player showing vision, is new entrants to the industry who are also bringing innovation. What NATIVE are creating delivers a fundamental industry building block, which we will integrate with FarmRoadTM,” says Mr. Keiller.
The NATIVE platform connects farms with local buyers, maximizing the value of their harvests and helping both buyers and restaurants deliver on the promise and demand of locally sourced food.
“Our partnership with Autogrow will most benefit the growers and the farmers,” says Frank Pica, co-founder, NATIVE. “FarmRoadTM users can provide NATIVE with real-time data that verifies the quantity and quality of their harvests, and NATIVE will return the true market value of the products. NATIVE then provides an outlet for growers to bring their products to premium markets within their region.”
Autogrow will work closely with Ridder Group and NATIVE over the coming months during the pilot phase. The beginning of the journey in working collaboratively with producers and growers.
“The next iterations of FarmRoadTM include flower and fruiting identification through Machine Vision and AI to provide pollination rates and flower to fruit conversion performance. We will be extending the 3rd party integration to include finance, labor management, food security and more,” says Mr. Keiller.
More information can be found on www.farmroad.io
QUERIES
General queries: (e) info@farmroad.io
Media queries: Kylie Horomia, Autogrow Head of Communications (e) Kylie.horomia@autogrow.com
(w) www.farmroad.io
About Autogrow
Autogrow leverages the power of technology, data science and plant biology to provide indoor growers affordable, accessible and easy-to-use innovation – 24/7, anywhere in the world.
Our hardware, software and data solutions support growers and resellers in over 40 countries producing over 100 different crop types.
With over 25 years in business, we have a depth of experience and passionate, fun people creating original ideas and making them a reality for our growers.
About Ridder Group
Farmers and growers worldwide need to be able to adopt their own individual approach to efficient and sustainable controlled environment agriculture. This is the promise that Ridder, as an international family-owned company, fulfils by translating more than 65 years of Dutch agri-food expertise into adaptive technology and know-how that is tailored precisely to local needs and conditions.
At Ridder, the drive to innovate is in our DNA. We are also committed to finding the best possible solution. The balanced combination of these two characteristics has enabled Ridder to evolve into the experienced market leader in technical solutions for the horticulture, intensive livestock and crop storage sectors. Today, Ridder has customers in more than 100 countries, who receive support from international offices and a global partner network.
About NATIVE
NATIVE’s mission is to empower local growers by maximizing the value of their harvests and meet the rising demand for local, transparently sourced food. NATIVE integrates real-time technology throughout the agricultural supply chain to accelerate traceability, waste mitigation, and return on investment. For more information, please visit www.nativeag.io