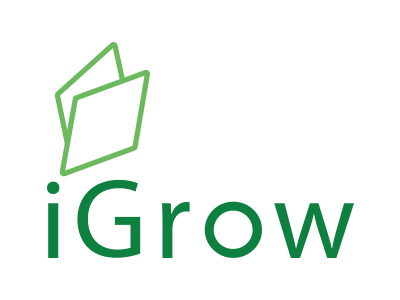
Welcome to iGrow News, Your Source for the World of Indoor Vertical Farming
International Partnership For New Certificate For CEA-Grown Produce
The FarmTech Society and GlobalGAP recognize each other in their membership programs, initiating a new open partnership to develop and implement a certification specifically for new “indoor” high tech systems with natural and artificial lights
The FarmTech Society and GlobalGAP recognize each other in their membership programs, initiating a new open partnership to develop and implement a certification specifically for new “indoor” high tech systems with natural and artificial lights.
The partnership is open to all industry stakeholders small and large to help advance a comprehensive new certificate for innovative production systems.
Innovative production systems in CEA require new standards
The partners have identified the need for all stakeholders active in the production of produce in CEA systems to form a working group at a pre-competitive level to address critical challenges, such as climate change, consumer trust and food security facing the industry. The partnership will develop best-practice standards for the certification process, recognizing the need for a multidisciplinary/multi-stakeholder approach in developing a certificate – by and for industry stakeholders in CEA.
The partnership will strengthen the existing well-established foundation of the GlobalGAP Integrated Farm Assurance (IFA) process by adding criteria for new technologies and cultivation methods, inserting dynamic data collection applications and adapting to the potential of the digital era, keeping future options valid.
The main goal of the GlobalGAP revision process is to deliver a standard that will take into account producers’ practices and the risks presented. The unique challenges presented by vertical farming or more generally, produce grown in controlled environments will be addressed to ensure appropriate user experience. Additionally, the group will focus on implementing real-time monitoring and data-driven solutions to facilitate the certification process, enabling transparency and traceability.
Taking into consideration the limits in technology by engaging with growers, retail, innovators and proven experts in the supply chain, the certification target will enhance the advantages of the end products and differentiate them in the marketplace.
The development roadmap will have three milestones: The first phase “open call for design and information gathering” will be kicked-off with a press conference at Fruit Logistica 2020, on February 6th, 2020. The second phase commences in June 2020 with the conclusion of the public consultations with multiple partners, and extensive international stakeholder meetings. The third phase is scheduled for the fall of 2020 with pilot testing in key supply chains followed by a market-wide peer review and introduction in 2021.
For more information:
www.globalgap.org
www.farmtechsociety.org
www.ukuat.org
www.cultinova.com
www.integar.de
Publication date: Mon 3 Feb 2020
FOR SALE - 2014 Freight Farm - Computer Controlled Hydroponic Grow System - Texas
The Leafy Green Machine is a complete hydroponic growing system built entirely inside a shipping container with all the components needed for commercial food production. The system is designed and engineered for easy operation, allowing users of all backgrounds to immediately start growing.
FOR SALE - 2014 Freight Farm - Computer Controlled Hydroponic
Grow System - Texas
Manufacturer - Freight Farms
Model - 2014 Leafy Green Machine (LGM)
Price - $29,950
Location: Texas
The Leafy Green Machine is a complete hydroponic growing system built entirely inside a shipping container with all the components needed for commercial food production. The system is designed and engineered for easy operation, allowing users of all backgrounds to immediately start growing.
Current Uses
• Perfect for starting a small produce business, growing for restaurants or supplementing existing produce production.
• Restauranter who wants to grow custom greens for rotating menus 365 days a year. Farm to Table? How about Parking Lot to Table!
• Universities and schools have created programs for students to learn to grow while supplementing dining facilities with fresh greens.
The Highest Standard in Controlled Environment Agriculture
• Pre-built system designed to maximize operational efficiency and streamline workflow
• Perfect environment is achievable 365 days a year, regardless of geographic location
• Automated scheduling reduces the amount of labor required to operate
• Remote monitoring & control capabilities through the Farmhand AppTM
Operation Requirements
Space- The LGM dimensions are 40’ x 8’ x 9.5’. We suggest putting the farm on either trap rock or a concrete pad.
Electrical- 60 amp, 120/240-volt single phase or 120/208V three phase connection.
Water- A designated water source is suggested such as a garden hose or hardline water plumbing.
Labor- 15 to 20 hours a week for farming and upkeep.
It is recommended growing smaller compact crops with a high turnover rate, like head and loose leaf lettuces, herbs and heartier greens like kale and swiss chard.
Crop Examples
Butterhead lettuce, Oakleaf lettuce, Swiss Chard, Mustard Greens, Cabbage Leaves, Arugula, Cilantro, Mint, Dill, Oregano, Kale, Endive, Basil, Chives and Thyme
Yields
800+ heads of lettuce weekly
12 heads per tower (256 vertical towers)
1 LGM= 1.8 acres
Freight Farms technology makes it easy to bring farming closer to where people live. The result is local, year-round production featuring fresh, sustainably-grown, and flavorful greens.
Freight Farms is exactly what it sounds like–a farm in a repurposed freight container.
These old containers are retrofitted with vertical, hydroponic components to make farming possible anywhere in the world, regardless of the outside climate.
LGM Included Accessories:
2 (two) new Freight Farm chem panels; with AgrowDose pumps. Pumps where primed with water but never used. New sensors also.
2 (two) A/C units: Unit #1 is Factory the other is a MrCool Oasis ES Series Ductless Mini-
Split Heat Pump System 230V 19 SEER - 24,000 BTU. If you don’t need 2nd A/C unit remove it & reinstall exhaust fan. All tubing, wires where run into the farm through exhaust port hole so as to keep farm integrity.
1 Dehumidifier Model HCWH-90 Whole Home Dehumidifier
1 (one) ClearView pump to manage the condensate.
2 (two) (Floor fan tubes (2ea. for both sides)
2 (two) 800cfm fans; only one installed
4 (four) Westpointe fans not installed
2 (two) Co2 Generators, 1 MiniGen; 1 Autopilot
1 (one) Evolution RO1000 High Flow Reverse Osmosis Water Filter by HydroLogic
1 (one) BIGboy Ultra Violet Sterilizer Kit by HydroLogic.
2 (two) Seedling Doser Panel & Main Doser Panel w/sensors
2 (two) sets pH probe - EC probe - Temp probe -
Seedling & Main delivery tanks; replaced All of them 8 are new
Illumitex - Eclipse Gen2 8 LED Grow lights & Eclipse Gen2 12 LED Grow lights - 3ea. Over the seedlings area NEW
10 LED light strips 7 replacements
Agrowtek – Hydro Transmitter and sensors; (All New)
Cradle Point (AT&T) Cell for Internet into LGM has ??? router that works with Farmhand.
4 port switch
Laptop cradle w/swing arm not installed
Lots of spare parts
Misc. PVC fittings most treaded a few slip on
2 aux pumps, small volume, 2 air pumps,
Training, website and ongoing support available through Freight Farms.
Visit www.freightfarms.com for more information.
Everything You Will Need To Grow Seedling And Microgreens And Then Some
Materials For Growing Hydroponic Plants - Additional $7,500.00 USD
Seedling Cart & Racks (DIY) 6 trays, 1 sump, lights (mix of LED’s & T5) Bright Agrotech design ($500)
Illumitex - Eclipse Gen2 8 LED Grow lights & Eclipse Gen2 12 LED Grow lights** ($4,000)
20 (twenty) K5 fluorescents lights 4’
Agrobrite 2’x1’ 4 bulbs
Multiponics High-End Cycle Timer in waterproof box ($250)
Multiponics Aquatec CDP 8800 pump w/psi guage in waterproof box ($300)
ProSeries 5 stage Reverse Osmosis Water Filter System 1 ea. w/expansion tank (5gal.); 50GPD ($350)
4 stage Reverse Osmosis Water Filter System 1 ea. w/expansion tank (4.4gal) ($250)
Trays w/holes 50 ea. Trays w/ holes (diamond pattern)
Trays seedling (200ea. cells) 20ea. Trays w/o holes $20 ea.
Q Plugs 20/60 4K per case 1ea. case by IHort
Microgreen grow Pads & roll
Propagating Chamber model PC-22 by PRO-GROW ($2,200)
Zipgrow Farm Walls: 2ea. 4’ & 1ea. 8’ complete by Bright Agrotech ($1,500)
Tower Garden growing system ($500)
1ea. 30”x30”x6” tub
Pumps; Aerators; Timers; Tubing and fittings (1/4” / 3/8” / ½”)
PSI gauges
pH & EC probes handheld w/solution
Light Meter (Apogee Instruments) Full-Spectrum Quantum sensor ($500)
** (Seeds Included 1 Year Old)
Attached Documents:
Freight Farm Twitter Feed
LGM Cut Sheets
See All Photos And Videos Here
All information is from sources deemed reliable but is subject to errors, omissions, changes in price, prior sale or withdrawal without notice.
No representation is made as to the accuracy of any description.
All measurements, yields and square footages are approximate and all information should be confirmed by the customer.
Disclaimer of Warranty - The 2017 Freight Farms LGM hydroponic farming container is being sold “as is” and the Seller disclaims all warranties of quality, whether express or implied, including the warranties of merchantability and fitness for particular purpose.
What Is Hydronic Cooling?
“As Surna’s projects have become larger and more complex, we have added several products to our fan coil product family to meet the climate control needs of our customers”
Boulder, Colorado, August 27, 2019 — Surna Inc. (OTCQB: SRNA) introduces a full line of purpose- built fan coil products providing a wide range of choices for both ducted and ductless applications for small to large commercial indoor cannabis cultivation facilities.
“As Surna’s projects have become larger and more complex, we have added several products to our fan coil product family to meet the climate control needs of our customers”. These new products are part of our strategy to enhance our position as a trusted climate control advisor to our customers and offer more products and services to meet their specific requirements,” said Troy Rippe, Surna’s Director of Engineering and R&D.
The introduction of the IsoStreamTM product family allows Surna to serve:
Ductless environments where climate control systems circulate water, not air.
Ducted environments that provide economical solutions while still serving multiple grow
rooms.
Surna provides efficient and economical environmental control systems across a larger array of indoor cannabis cultivation facilities. Our new, whisper quiet fan coil units use electronically commutated motors to optimize airflow while specialized chilled water modulating valves are used to fine-tune for minimizing energy consumption.
If you want to learn more about our full line of Surna IsoStreamTM fan coils, please contact us at
www.surna.com
About Surna
Surna Inc. (www.surna.com) designs, engineers and manufactures application-specific environmental control and air sanitation systems for commercial, state- and provincial-regulated indoor cannabis cultivation facilities in the U.S. and Canada. Our engineering and technical team provides energy and water efficient solutions that allow growers to meet the unique demands of a cannabis cultivation environment through precise temperature, humidity, and process controls and to satisfy the evolving code and regulatory requirements being imposed at the state, provincial and local level.
Veggies Grown In Nevada's Massive Indoor Farm Are Now On Sale To Las Vegas Locals
Nevada does not have particularly fertile lands, but that didn't stop Oasis Biotech when they opened a 215,000-square-foot indoor farm to the public last July
by Phillip Moyer
July 30th 2019
The facility uses hydroponics and environmental control to reduce environmental impact. (PHOTO: Nathan O'Neal)
Nevada does not have particularly fertile lands, but that didn't stop Oasis Biotech when they opened a 215,000-square-foot indoor farm to the public last July.
Designed to be sustainable and environmentally-friendly, the facility uses hydroponics to use 90 percent less water than traditional farming, and have a completely controlled environment to eliminate the need for pesticides.
Guests had the chance to sample the vegetables after its openings, but until now, the food was only widely available to high-end restaurants in the Las Vegas Valley.
Today, the farm announced that they'll be selling eight-ounce bags of its baby leaf Spring Mix and Romaine Mix blends to consumers under its "Evercress" brand name.
“Over the last year, we have been working hard to perfect our crops and growing methods to bring the community and our customers the freshest salad greens in Las Vegas,” says Michelle Howell, Sales & Marketing Manager at Oasis Biotech. “We had over 1,000 people attend last year’s grand opening and the big question everyone asked us was “When can we buy it?” so we are thrilled to now offer the Evercress salad greens to Las Vegas locals."
The blends can beat Oasis Biotech's farming facility, located at at 6225 Annie Oakley Drive in Las Vegas.
In an effort to stay true to its mission to “Feed the World, Better.,” any product not sold to current customers or purchased by the public will be donated to local charities.
Ag Foundation Funds Groundbreaking Indoor Farming Research
April 08 , 2019
The Foundation for Food and Agriculture Research (FFAR) is pushing the boundaries of traditional agriculture with a new public-private partnership that will develop crops specifically suited for indoor environments.
To achieve this, the Precision Indoor Plants (PIP) Consortium is studying the environmental and genetic factors that help agriculture thrive indoors, says FFAR’s executive director Sally Rockey.
According to Rockey, this research will provide unique insight for the industry as most other studies on this type of farming focus on design elements for indoor systems, such as vertical productions facilities and lighting, rather than the plants themselves.
The PIP collaborative has joined together world-class indoor growers, breeders, genetics companies, and agricultural equipment leaders, including AeroFarms, BASF, and Benson Hill Biosystems, among others. These participants are pooling resources to fund research on the best means to present nutritious, flavorful crops that can grow anywhere, year-round, profitably.
Specifically, PIP says its research will explore how to improve nutrient content and yields, decrease the amount of energy needed for production, and help crops perform their best in indoor conditions.
So far, FFAR has committed to investing US$7.5 million in PIP, and with matching funds from participants, the consortium will grant a minimum of US$15 million to its studies.
This move is just part of the growing trend of indoor agriculture, also called controlled environmental agriculture (CEA).
The “booming” interest in this type of agriculture has been attributed to the new needs of our growing world. The challenge of feeding a rapidly rising global population in a sustainable way has influenced researchers to examine innovative food production approaches, says PR Newswire.
Producing crops indoors could also be a solution for challenges arising from a changing climate, adds the company.
Today, lettuce and other leafy greens have successfully become profitable CEA, while PIP’s research seeks to expand this to include a variety of other crops, such as herbs, tomatoes, strawberries and blueberries.
Initial PIP projects will focus on increasing nutritional content and changing the size and shape of the plant.
“This research has implications for a wide variety of agricultural environments, including outdoor agriculture and space,” the entity said.
“For farmers planning outdoors, PIP’s research has the potential to reduce strain on the environment, make crops more resilient to stresses, bolster food and nutritional security and shorten the supply chain for producers.
“The research is also useful for government agencies and corporations interested in growing food in space for long-term space exploration.”
How Can Controlled-Environment Growers Improve Energy Efficiency And Grow Light Optimization?
Greenhouse Lighting and Systems Engineering (GLASE) consortium researchers are looking for ways to reduce grow light electricity use and improve light uniformity to maximize controlled-environment crop yields.
April 3, 2019
By David Kuack
Are you using or thinking about using grow lights to produce your controlled environment crops? If so, would you be interested in how to reduce the amount of electricity needed to operate those lights?
Researchers with the Greenhouse Lighting and Systems Engineering (GLASE) consortium at Cornell University in Ithaca, N.Y., are studying the use of control algorithms to optimize the light used on controlled-environment crops while reducing the amount of electricity used to operate grow lights.
“These control algorithms that deal with lighting were developed over 20 years ago,” said research associate Dr. Kale Harbick. “Unfortunately, this technology, which was under patent until about four years ago, never achieved large scale commercial use.
“The algorithms are related to delivering a constant amount of light to the plants every day, which is called daily light integral (DLI). Controlled-environment crops like lettuce prefer to receive a constant amount of light every day. This enables the plants to maximize their growth and helps to avoid problems with tipburn, which can make the crops unsalable.”
Even though this technology is off patent, Harbick said some growers are still hesitant to incorporate it into their environmental control systems.
“As part of the GLASE research program we are putting this control technology into two commercial pilot facilities in New York,” he said. “We are going to run multi-year experiments so that the growers in those facilities can compare the performance under our control system with what they are currently using. Incorporating this technology, we are looking to demonstrate a large amount of energy savings for the crop yields produced.
“We’re specifically focused on lettuce, tomato and strawberry. The first two pilot facilities are growing leafy greens, primarily lettuce. Lettuce is the crop the Cornell controlled-environment agriculture group has studied the longest and we understand the best. Tomato and strawberry are newer crops to us so we are doing a lot of greenhouse experiments right now with these plants to analyze the relationship between light, carbon dioxide and growth. We have the information well established for lettuce, but it’s not as well established for fruiting crops. We would eventually like to roll out pilot programs for tomatoes as well. We have some tomato growers in the state who have expressed interest in using the technology.”
GLASE researcher Dr. Kale Harbick is studying the use of control algorithms to optimize light while reducing the amount of electricity used to operate grow lights.
Photos courtesy of Kale Harbick, Cornell Univ.
Harbick said New York State Energy Research and Development Authority (NYSERDA), which is financially supporting GLASE, is interested in trying to meet greenhouse gas emission production targets. CEA has the potential to use a lot of energy. Any energy savings that the GLASE research can realize has a corresponding large reduction in greenhouse gas emissions.
Lack of light uniformity
One of the problems that Harbick often sees with grow lights is growers don’t install enough fixtures.
“The most basic problem is light intensity,” he said. “We often see greenhouses where growers are trying to produce lettuce with grow lights, but they only have installed half the number of fixtures they should have in order to grow lettuce optimally. What that means is even if they ran those lights 24/7 they wouldn’t be able to achieve the DLI needed to reach the target amount.”
Harbick said the issue of not installing enough lights is related to measuring light.
“Trying to measure the light is not a trivial thing to assess,” he said. “If there is an array of lights that are regularly spaced in the same plane, the problem is the light is not uniform on the crop. It kind of has a bullseye effect where there is a lot of light in the center and not very much on the edges. Lighting manufacturers and designers often provide growers with designs that show the light intensity at the center of the space, which is not representative of the light that is received in the rest of the space. The lights might be sized according to that center spot which is just fine, but everything else is undersized. We hear regularly from growers who’ve spent a lot of money on a lighting system and then realize later that it was undersized.”
Harbick has done a lot of work on lighting uniformity to try to address this issue of undersizing.
“We’ve looked at techniques to change the positon of the lights to make it more uniform,” he said. “We’ve looked at changing the brightness of the lights depending on where they are in the space to make the light more uniform. We have a couple of greenhouse spaces at Cornell that have this uniformity optimization. These are the only greenhouses on campus to have uniform lighting.”
One of the common issues encountered by growers who have installed grow lights is the lack of light uniformity which can be caused by undersizing the number of fixtures.
Harbick said this lack of light uniformity is not often noticed because of the way humans see light distribution.
“We could look out at a crop and the lighting looks uniform to our eyes because our eyes are so good at attenuating brightness levels,” he said. We don’t notice these differences very easily. The brightness level differences have to be measured.”
Although the lack of light uniformity can be related to the number of light fixtures installed, Harbick said there could be other factors involved.
“In the research greenhouse that we have optimized light uniformity, initially we received a design from the manufacturer that called for 20 LED fixtures,” he said. “I modified the design using a computer program that I wrote that was able to reduce the number of fixtures to 16, but improved the light uniformity. The light is much more uniform and we were able to do it with fewer fixtures.
“It’s not always a case of installing more fixtures to increase light uniformity. It can also be things like changing the brightness of the fixtures or changing the position of the fixtures. There are other possibilities to improve uniformity besides the number of lights.”
Loss of crop yields
One of the reasons that there continues to be light uniformity issues is how the fixtures are spaced in greenhouses and indoor farms.
“It’s a status quo thing,” Harbick said. “Lights have always been placed in a plane and regularly spaced out. This is how it has always been done. Until recently most grow lights have had a fixed intensity. Under those conditions it is difficult to overcome this light uniformity problem.
“Lack of light uniformity is less of problem in large greenhouses because there is a lot of interior space and not much edge space. However, this is a major problem in indoor farms where there are long rows or shelves. These indoor farms don’t have the background natural light like greenhouses to mitigate some of these effects. I have seen warehouses where they were growing a high DLI crop and the plants in the center of the room were a foot taller than the plants on the edge. It was simply because the plants in the center were receiving more light. In indoor farms, whether it’s lettuce, tomatoes or other high DLI crops, that is where the payoff really comes for optimizing light uniformity. For indoor farms light uniformity is something that people aren’t looking at yet. They just kind of live with it. They just move plants around to try and even out the growth. But that creates a lot of extra labor and logistic issues. They’re not optimizing the total yield of the crops. Every plant on the edges that is shorter than the ones in the center of the room is lost sales.”
GLASE researchers are conducting greenhouse experiments on tomato and strawberry to analyze the relationship between light, carbon dioxide and plant growth.
Harbick said that the issues with light uniformity may improve as changes are made to lighting fixtures.
“As the lights become more capable in terms of adjusting brightness and spectrum, there are opportunities for GLASE researchers to share some of that optimization technology with lighting manufacturers to try to get these improvements out to the industry. But it’s going to take some time. We’re still doing a lot of the research ourselves. We don’t have an active grant in this area right now so this is something that I have been doing on my own. It’s definitely an opportunity for future study.”
For more: Kale Harbick, Cornell University, School of lntegrative Plant Science, Horticulture Section, Ithaca, NY 14853; kh526@cornell.edu.
David Kuack is a freelance technical writer in Fort Worth, Texas; dkuack@gmail.com.
US (NY): Cornell University Hosts CEA Conference
April 22, 2019
Geneva, New York
Cornell University is hosting a CEA conference on Friday April 26. The Cornell Controlled Environment Agriculture (CEA) advisory/stakeholder group was formed to address the increasing demands of consumers for fresh, local, and year-round produce. In the Northeast, meeting this demand means incorporating various technologies to extend the growing season.
The CEA advisory/stakeholder meetings are designed to address this challenge with a multifaceted approach made possible by the diversity of its participants, which include: New York State producers, agribusiness professionals, supermarkets, government agencies, financial management companies, and Cornell faculty and faculty/staff from the Cornell AgriTech, the Charles S. Dyson School of Applied Economics and Management, the School of Integrative Plant Science, and the Department of Biological and Environmental Engineering.
The April 26, 2019 conference is designed to explore possibilities that could enable New York State to become a leader in the industry. Participants will hear from industry experts and leading academics about how they can create and capture economic synergies that will provide tremendous lasting value for New York State and beyond.
The meeting will be held at the Jordan Hall Auditorium at Cornell AgriTech, 614 W North St., Geneva, N.Y. Parking is free and located directly behind the building.
Precision Indoor Plants (PIP) Consortium to Revolutionize Agriculture
Foundation for Food and Agriculture Research (FFAR) is launching the Precision Indoor Plants (PIP) Consortium, a public-private partnership that transcends the bounds of traditional agriculture to develop flavorful, nutritious crops specially intended for indoor agriculture
First-of-its-Kind Consortium Develops Crops Intended for Indoor Agriculture
WASHINGTON (April 3, 2019) – The Foundation for Food and Agriculture Research (FFAR) is launching the Precision Indoor Plants (PIP) Consortium, a public-private partnership that transcends the bounds of traditional agriculture to develop flavorful, nutritious crops specially intended for indoor agriculture.
Sustainably feeding a growing global population requires researchers to examine innovative food production approaches. One approach gaining traction is controlled environment agriculture (CEA), also known as indoor agriculture. Worldwide, interest in indoor agriculture is booming. Yet, CEA research largely focuses on design elements for the indoor systems, such as vertical productions facilities and lighting, not the plants themselves.
“The majority of the crops grown indoors have been developed over thousands of years for outdoor production,” said Sally Rockey, FFAR’s executive director. “While understanding the indoor system’s design elements is important, PIP seeks to understand which environmental and genetic factors help crops thrive indoors.”
The PIP collaborative convenes a diverse array of participants representing aspects of the indoor agriculture industry. The collaborative pools resources to fund joint research that produces nutritious, flavorful crops that can grow anywhere, year-round, profitably. PIP’s research will explore increasing nutrient content and yields, growing crops with less energy and understanding how crops perform best in CEAs.
“Do you remember the taste of tomatoes from your childhood? If you’re like me, every summer you complain that commercial tomatoes today are not the same. Commercial tomatoes are abundant, shelf-stable and disease resistance – but not perceived as tasty as they once were,” noted John Reich, FFAR Scientific Program Director. “However, PIP’s research could produce a tomato plant that grows quickly indoors, tastes great and is highly nutritious. This plant would require less energy to grow indoors, potentially increasing affordability, and could be grown anywhere regardless of environmental constraints.”
With a growing population, shifts in consumer demand for healthier, tastier food and challenges arising from a changing climate, producing crops indoors can mitigate these challenges and meet demand. CEA is successfully growing lettuce and other leafy greens profitably. PIP’s research seeks to make CEA an option for growing a variety of crops, including leafy greens and herbs, tomatoes, strawberries and blueberries. Initial PIP projects will focus on improving nutritional content and changing the size and shape of the plant.
This research has implications for a wide variety of agricultural environments, including outdoor agriculture and space. For farmers planning outdoors, PIP’s research has the potential to reduce strain on the environment, make crops more resilient to stresses, bolster food and nutritional security and shorten the supply chain for producers. The research is also useful for government agencies and corporations interested in growing food in space for long-term space exploration.
FFAR is investing $7.5 million in PIP, and with matching funds from participants, the consortium will invest a minimum of $15 million to develop flavorful, nutritious crops for indoor agriculture. PIP’s participants represent world-class indoor growers, breeders, genetics companies and agricultural equipment leaders, including AeroFarms, BASF, Benson Hill Biosystems, Fluence Bioengineering, Intrexon, Japan Plant Factory Association and Priva.
About the Precision Indoor Plants Consortium
Precision Indoor Plants (PIP) is a public-private partnership created by the Foundation for Food and Agriculture Research (FFAR) to produce new flavorful, nutritious crops specially intended for indoor agriculture. By focusing on innovative science and technology, the consortium’s research efforts will increase our ability to produce crops that are high-value, of consistent quality, and desired by consumers. Ultimately, PIP can help food producers grow flavorful, nutritious food indoors.
FFAR’s initial $7.5 million investment is matched by the PIP participants for a total investment of $15 million to develop flavorful, nutritious crops for indoor agriculture. PIP’s participants include AeroFarms, BASF, Benson Hill Biosystems, Fluence Bioengineering, Intrexon, Japan Plant Factory Association and Priva.
Fluence Bioengineering - Quote From Dave Cohen, CEO
Fluence is proud to be a founding member of the Precision Indoor Plants Consortium. Our cultivation and engineering teams are aggressively innovating how growers use LED lighting solutions to cultivate nutritious, high-quality produce. PIP is an important initiative to verify research into photobiology for commercial applications and enable more growers to profitably cultivate plants for people that do not normally have access to fresh vegetables, herbs and fruits,” said Dave Cohen, CEO, Fluence Bioengineering.
Farms In The City: How A Chinese Firm Uses Tech To Boost Yield
By Feng Yilei
2018-12-01
An appetite for clean, fresh greens is growing with the burgeoning population in Chinese cities and towns. But feeding the rising demand is a challenge, partly because of the country's massive shift from being an agrarian to urban economy.
In the next 15 years, over 200 million Chinese are expected to move from rural areas into urban and suburban environments. This will greatly reduce the labor force on China's arable lands, which some say calls for a revolution in farming methods in order to create sustainable food production.
Beijing COFCO wisdom farm. /COFCO Photo
In suburban Beijing, a number of plant factories built with innovative techniques have incorporated farming into urban growth.
Dr. Wei Lingling, a researcher at the Chinese Academy of Agricultural Sciences, said controlled environmental agriculture (CEA) aims to get the most output with the least resources at the highest efficiency. They use technology like artificial intelligence (AI) and the Internet of Things (IoT) to precisely control production.
On a small plot of indoor space, plants are rooted on layered shelves vertically and bathe in light continuously during the day. Sensors linked to automatic irrigation and temperature control systems provide optimal conditions for growing.
Planned production means a higher yield resource-wise, space optimization, and labor savings. Dr. Wei believes CEA technologies will be more accurate in the future to better balance cultivation and the environment with less energy consumption.
“And in this closed production system, we circulate water and fertilizer to cut emissions, and improve sustainability of agriculture,” she added.
Plant factory using artificial light. /VCG Photo
While many believe this industrialized and intelligent way of farming will gradually replace extensive farming, which relies heavily on manual work and land usage for mass production, ordinary Chinese may have to accept difficulties in their daily lives during the process of moving on to the next stage.
For individual farmers that own the country's hundreds of millions of small plots, some have temporarily transferred their leaseholds to these high-tech farms and are adapting to their new roles.
Villager Wang Xiangang said that he got paid for both his land and working on the farm as an employee meaning he no longer worries about natural disasters and has time to learn about organic farming. He doesn't make as much as he used to, but it is stable.
And when conditions are ripe – will consumers be ready to pay a higher price for the products? Experts say the public will recognize the value of these crops as awareness of food safety and environmental stewardship rises. And once the demand rises, more players are expected to use tech-based food production, which will drive down prices.
The Salvation Army Teaches Children How To Grow Indoors
Mark Lindberg, social enterprise ministry specialist at Salvation Army
Photo: Patrick Williams
With help from CropKing, the organization offers educational programs for at-risk youth at its Fresh Face Farm in Akron, Ohio.
November 15, 2018
GIE Media Horticulture Group
Children in and around Akron, Ohio, could help develop systems that could one day be used to grow food on Mars, upload blueprints for “food computers” and grow produce for wholesale and food pantries.
It’s all part of the studies they’re undertaking with the Salvation Army Summit County Area Services (SCAS), which opened Fresh Face Farm, an indoor growing facility, at its Akron Fort Romig location in January 2018.
The indoor farm provides the children learning opportunities in Science, Technology, Engineering and Math (STEM), culinary arts and other subjects, says Major Kevin Jackson, SCAS coordinator. Jackson says about 90 percent of these students are “at-risk,” which the Journal of General Internal Medicine defines as populations that may have low literacy rates, be economically disadvantaged, face abuse or persecution, or experience other issues. SCAS has partnered with Akron Public Schools (although participation at the farm isn’t limited to children in the district), the University of Akron, NASA and MIT. CropKing provided automated hydroponics systems, sole-source lights and other materials.
“The kids are pretty much involved in every aspect,” Jackson says. “Technology is what drives their world, so the CropKing system was perfect for us in terms of the computer and the sensors, and the automation that came with it.”
The students range in age from 18 months to 18 years, Jackson says. Younger students start out learning about aquaponics and ebb-and-flow systems — which take up about 6,000 square feet of the 18,000-square-foot Fort Romig warehouse. Once the students reach about first or second grade, they begin working in a walled-off 7,000-square-foot commercial grow room in the warehouse that The Salvation Army has outfitted with CropKing’s nutrient film technique (NFT) and Bato bucket hydroponic systems.
In the grow room, lettuce and leafy greens flourish under LEDs, while tomatoes prosper under high-pressure sodium (HPS) lights. Mark Lindberg, social enterprise ministry specialist and the operation’s only full-time employee, says the lights run from about 5 p.m. — after the students have gone home — until the early morning hours. Fresh Face Farms sells most of its produce wholesale, but it sends some to food pantries or home with students.
Basil growing in NFT systems under LED lights at Fresh Face Farm
Photo: Patrick Williams
The idea behind Fresh Face Farms began when Jackson, who has been involved with The Salvation Army his whole life, was given an assignment: to come up with a model to break intergenerational poverty. At the time, he was working throughout the western United States, and he tried growing outdoors in Montana. After weeks of 60-degree temperatures, he planted his crops, then in early June, six inches of snow fell. His wife, Linda, who is now also SCAS coordinator, suggested they try a new approach to farming.
After transferring to Akron, Jackson says he ran an online search for a possible equipment supplier and found CropKing in nearby Lodi, which he calls “sheer luck.” He applauds CropKing’s customer service and expertise, calling the business “not just a vendor.” “You know what's amazing to me?” he asks. “Every once in a while, they’ll just be driving by, and they’ll just stop by [and say] ‘Hey, how's it going? Can we take a look around?’”
Lindberg says he has had similar experiences interacting with CropKing. “Paul calls me on my cell phone,” he says. “It’s like, ‘Hey, Mark, I'm going over that way. You going to be there tomorrow?’ ‘Sure!’”
Growing up in Ashland County — a mostly rural area in Ohio — Lindberg says his parents had a garden, and he was interested in horticulture from a young age. He went on to work in facilities management, but after more than a decade with The Salvation Army, the opportunity presented itself for him to work at Fresh Face Farms. In preparation, he took CropKing’s Grower Workshop to familiarize himself with controlled environment agriculture (CEA).
Lindberg has passed some of the information he learned in the workshop onto the students at Fresh Face Farms. One lesson included how to adjust the alkalinity of water to get it to a desired pH range. On a related note, but one not taken straight from his CropKing Grower Workbook, Lindberg also had students guess the pH of orange juice and milk and then assess the pH of those liquids. “That’s one of the things I love, is this is all hands-on [education],” he says. “This is not just show and tell, but it's experiencing.”
The technology and the hands-on education come together to form a learning experience that shows promising results for inspiring children to explore new avenues of interest and excel in their lives and careers, Jackson says. Some of his former students out west have even gone on to study growing in hopes of making it a career. “When you say, ‘Salvation Army,’ it’s just not what you’re thinking,” he says. “That’s The Salvation Army of the future.”
LEDs HPS Lighting Hydroponics Tomato Indoor agriculture Food nutritionLocal food Education Food security CEA Dutch buckets
As Director of The New School of Plant and Environmental Sciences, Mike Evans Wants to Create an Environment Where Creative Collaborations Lead to Innovative Discoveries
As director of the new School of Plant and Environmental Sciences, Mike Evans wants to create an environment where creative collaborations lead to innovative discoveries.
Mike Evans grew up in rural Pittsylvania County, Virginia, where he spent his summers pulling tobacco and running a soybean drill for his grandparents and neighbors.
He saved enough money during those hot summers to buy his first car — a 1980 Ford Pinto — which he proudly parked in the Cage during his first year at Virginia Tech. He’d been exposed to the university through his high school’s Future Farmers of America program, which brought him to campus to take part in horticultural competitions.
As a student majoring in horticulture, he fell in love with researching the plants he’d been surrounded by his entire life. The intensive laboratory work he did during his undergraduate years at Virginia Tech prepared him well for the rigors of graduate school at the University of Minnesota, where he earned a master’s degree and a Ph.D.
Evans went on to a career in higher education that involved research to help industries thrive, Extension outreach programs that impacted local communities, and academic programs that prepared the next generation of students for the challenges of facing the world.
Now, the Hokie alumnus has returned to Virginia Tech to use all the skills he’s acquired to lead the College of Agriculture and Life Sciences’ latest strategic initiative.
Evans is the director of the newly formed School for Plant and Environmental Sciences, which combines three former departments — horticulture; crop and soil environmental sciences; and plant pathology, physiology, and weed sciences — under one administrative roof.
“When we bring people together you get something new called ‘creative collisions.’ These intersections lead to innovation on a level that changes the paradigm of what is possible,” Evans said. “We want to create an environment in the school where the silos are broken down and people are interacting in unique ways to allow opportunities for more of these creative collisions to occur. This benefits everyone from students and professors to industry leaders and local producers.”
Though faculty and administration have been involved in planning the school via committees, public forms, and other outlets for three years, it becomes officially operational on July 1.
“Mike’s experience makes him the perfect person to lead the school and help our faculty, staff, students, and Extension professionals find new ways to work together to make an even greater impact on our college, the state, and the world” said Alan Grant, dean of the college.
Evans most recently worked at the University of Arkansas, where he was an interim associate dean in the Dale Bumpers College of Agricultural, Food, and Life Sciences. Prior to Arkansas, Evans was a professor at Iowa State University. At both institutions, he was a horticulture faculty member, teacher, and researcher who focused on controlled agricultural environments, such as greenhouses, and how to use hydroponic techniques to increase yields of food crops. He started his career as a researcher at the Gulf Coast Research and Education Center with the University of Florida where he conducted research and Extension programs related to greenhouse crops and ornamental plants.
Evans points to projects he did as a horticultural researcher that show how collaboration can lead to greater impact.
A few years ago, he was researching how lettuce is best grown in a controlled environment using hydroponics. He started to talk with a plant pathologist who was trying to find ways to combat powdery mildew on spinach. The two began to collaborate on ways to grow the spinach in a greenhouse, which allowed for faster growing cycles. This development in the greenhouse helped the plant pathologist do quicker scientific trials than it would have been possible in the field. The teamwork between disciplines was what made the solution possible.
“You never know what innovative, cross-disciplinary solutions are possible until you tear down the walls that exist and build a space where ideas can freely flow — and new ideas can be born,” he said.
Similarly, the school will merge three former departments and bring researchers, faculty, and staff together to use their diverse experiences and skillsets to tackle issues ranging from increased crop production to ways to grow healthier food throughout the world.
None of the majors or degrees offered by the three former departments will change, though Evans said the school will explore creating new majors that build upon the expertise of the faculty and meet the demands of students and industry. All clubs and student organizations will remain as they currently operate. The school also will focus on ways to expand the college’s physical footprint, such as constructing new greenhouses or the future Human and Agricultural Biosciences Building 2.
“I believe that by creating a space where new relationships can form and risk-taking in the name of innovation is encouraged, there is unlimited potential to make a lasting impact in plant and environmental sciences,” he said.
Contact:
Vertical Farming: Bursting With Promise -- But Unknown Costs
By Dr. Michael Evans - - Wednesday, October 10, 2018
The production of food crops such as fresh greens (like lettuce and arugula) and herbs (such as basil) in vertical production facilities is part of a larger field of agriculture often referred to as controlled environment agriculture (CEA). In addition to production of these types of crops in vertical facilities, production also occurs in such facilities as greenhouses and plant factories inside of converted warehouses and shipping containers. The types of crops most commonly grown in CEA production include tomatoes, peppers, cucumbers, strawberries and fresh greens and herbs.
Depending on the crops being grown, different types of production systems might be used in CEA, but the most common systems are nutrient film technique, floating beads, Dutch bucket systems and various types of gutter systems. These systems might be true hydroponic systems — in which the plant roots are suspended in a static or recirculating fertilizer solution — or a system that uses an artificial soil or substrate in which the plant roots grow.
Across all of the types of controlled environment structures, systems and crops, the production of food crops in CEA has been experiencing rapid growth in the U.S. In fact, Rabobank, a Dutch multinational banking and financial services company, reported that the value of U.S. greenhouse-grown food crops exceeded $3 billion in 2013 and is expected to exceed $4 billion by 2020.
The U.S. Department of Agriculture’s statistics also support the conclusion that greenhouse-grown produce production has been rapidly increasing. Many factors have been reported to be responsible for the growth in greenhouse food crop production including reducing water and fertilizer inputs needed to grow crops, an ability to better program and have predictability of crops in CEA versus open fields, the ability to grow crops year-round and thus better serve the local markets, the ability to potentially better use biorational disease and pest control, the ability to grow food crops on nonarable land, the ability to produce higher volumes of produce on limited land (especially with vertical farms), and the potential for reducing food safety issues as compared to open field production.
In addition to these factors, the growth of CEA was reported as being fueled by market and human factors. Karen Halliburton Barber of Rabobank noted in a report that, “There is a growing preference among U.S. retail and food service buyers for greenhouse produce.” She also noted that, “The buyers are seeking the quality and reliability of supply that greenhouse products provide.”
As a type of CEA, vertical farming affords the opportunity to produce larger volumes of these crops per area than traditional field production. This is achieved by both the potential for year-round production and the multiple levels of production systems employed. Vertical systems also allow for the production of produce crops in areas where land is very limited or very expensive as is often the case with highly urbanized areas. However, compared to both field production and even traditional greenhouse (single level production) hydroponic production, the fixed costs and variable costs of production will be different for vertical farming. Some costs are likely to be significantly higher while others might be lower. Costs are likely to be spread over higher levels of crop production.
It is important to understand these costs. It is important also to understand the market. What is the target market? What crops does the market want? How large is that market and what are the prices for a given product that the market will tolerate are all important questions before deciding to move forward with any type of CEA operation — including vertical farms. Having a strong understanding of the crops to be grown, the level of production achievable, the costs of production and the market will increase the chances for a successful CEA business venture.
• Michael Evans, Ph.D., is director of the School for Plant and Environmental Sciences in the College of Agriculture and Life Sciences at Virginia Tech (@VTCals).
'The Next Evolution Of Farming Has Already Begun'
By Austin Stankus - Wednesday, October 10, 2018
The world population continues to grow with ever-increasing urbanization predicted to reach 80 percent by 2050. The U.N. predicts that human population will reach nearly 10 billion by 2050. This increasing population is also growing richer — and hungrier.
To feed this population using traditional farming practices, much more land would need to be brought under cultivation. But, already much farmland around the world has been degraded from poor management practices, and lands remaining available for food production are decreasing from the effects of erosion, salt buildup and pollution.
As you read this today, tens of millions of children are going to bed hungry, with the Food and Agriculture Organization of the United Nations estimating the number of hungry in 2018 at 812 million or approximately one out of 9 people.
Something needs to change. Food production needs to get more efficient, more equitable and more environmentally minded. Moreover, food production should follow the population to the cities, or as Dickson Despommier, a forerunner of this movement, simply states: “Put the food where the people live.”
Indoor farming through controlled-environment agriculture (CEA) will be an important component towards establishing local food systems that can address this pending crisis in global food insecurity. CEA, simply put, is using smart, sustainable farming practices inside of high-tech greenhouses. This is nothing new, and these modern greenhouses are an established technology and can be found around the world. In fact, much of the lettuce, tomatoes, peppers and cucumbers in the EU come from CEA in the Netherlands and Spain.
These greenhouses have incredible benefits compared to traditional farming: They use less water because they are protected from the sun and wind, they use fewer pesticides because insects and disease can be kept outside, and there is less waste because production can be matched exactly to consumer demands.
If hydroponics or other soil-less practices are used, the farmer does not need to use tractors for tilling, plowing and reaping, so the oil bills and energy consumption are lower. In addition, the fertilizer usage is reduced, and all the fertilizer the farmer uses is consumed by the plants, thereby reducing nutrient-rich runoff that can pollute watersheds. Known as eutrophication, this nutrient pollution is a huge problem for coastal communities in the Chesapeake Bay and Gulf of Mexico and has impacted fisheries, recreational activities and livelihoods around the world.
However, CEA greenhouses can occupy a lot of space. So, the next logical evolution is stacking these modern greenhouses, one atop the other.
Vertical farming, as greenhouses stacking is called, has additional benefits. Reducing the footprint means that more food can be grown in a smaller area and therefore can be brought closer to the people eating that food. As populations move toward the cities, it makes sense for the food to follow.
Part of the vision of vertical farms is the reconnection of the producer and the consumer plus the restructuring of food value chains to become more transparent and responsive to the needs and wants of the people.
An added benefit of farming inside of skyscrapers is the option of having mixed-use buildings. When combined with a wholesale market, the skyscraper can not only produce the food but get it to the consumer faster. Less time in storage, less transportation and less handling means fresher produce and reduced need for postharvest treatments like irradiation and chemical fumigation.
There are still some daunting challenges as well as some encouraging recent developments.
Unleashing the innovative power of American small businesses has jump-started the transition to modern farming, and the public desire for local, healthy food is an economic engine driving the industry toward change. In fact, there are currently so many vertical farm startups that a shortage of qualified workers is now the main hurdle to accelerating the establishment of new indoor farms. On one hand this is a challenge to the industry, but on the other it presents an enormous opportunity for job creation in urban areas if an inclusive, enabling environment is codeveloped with the vertical farms to provide vocational training and career advancement prospects.
On a technical level, there is a significant energy demand needed for pumping water, maintaining good environmental conditions like temperature and humidity, and powering the grow lights to keep producing year-round. However, with smart buildings wired on intelligent platforms, the energy consumption can be monitored and controlled to maximize efficiency — and by tying into other green enterprises like photovoltaic and biogas generation, this energy demand is decreasing day by day. In fact, with the new innovations in LED lighting technology, the power demand has been reduced tenfold in the last few years.
The next evolution of farming has already begun, and big players are already involved. In fact, the National Grange wrote a letter to Congress with their support to public-private funding mechanisms to accelerate the modernization of agriculture, specifically highlighting the potential of vertical farming. With this type of buy-in from large agribusinesses, national and international agricultural organizations, funded with innovative financial mechanisms, and driven by the innovative spirit and technological power only found in the U.S., vertical farming will feed tomorrow’s children with healthy, safe food; protect the environment while being resistant to environmental shocks; and spur economic growth in the process.
For a detailed look at one such startup, see the centerfold story on Skyscraper Farm • Austin Stankus, an integrated farming specialist, is chief science officer at Skyscraper Farm LLC
New Forum With CEA Scientists
By urbanagnews
September 21, 2018
Join three CEA scientists (Chieri Kubota, Erik Runkle and Cary Mitchell) who are organizing an online monthly forum series, called ‘Indoor Ag Science Café’. This online forum has been designed to discuss the science and technologies that can contribute to indoor controlled environment agriculture (AKA vertical farms). According to Chieri, “we wish to make the forum develop as a non-competitive, informal communication platform among indoor agriculture industries”.
Please contact Chieri Kubota (kubota.10@osu.edu) if you would like to join the Café.
The most recent topic presented by Erik Runkle at the Café is now available:
University of Arizona - Hydroponic Intensive Workshops
For more information:
Registration at CEAC.ARIZONA.EDU/INTENSIVE
Email: danaem@email.arizona.edu
Call Danae, Program Coordinator, (520) 626-9566
Sustenir Sows The Seeds of Success
Company plows efforts into high-tech methods of farming to maximize land-use and yield while reducing wastage.
July 31, 2018
Sustenir is an urban farming company that uses controlled environment agriculture to grow non-native plants in Singapore. Seen here are regional sales manager Jack Moy (left) and co-founder Benjamin Swan. The company is also looking at using AI to monitor plant growth. BT PHOTO: LEE JIA WEN
GROWING cold-weather crops such as strawberries and kale in Singapore might seem impossible to many, but that is exactly what Sustenir Agriculture is doing.
Since 2014, Sustenir has been using high-tech methods such as controlled environment agriculture (CEA), vertical farming, and hydroponics to grow a variety of non-native plants indoors.
For co-founder Benjamin Swan, this unlikely agricultural venture is far from frivolous. He sees it as an important environmental move: "It was really my opportunity to do the right thing, to fight the good fight, you know. This was something that needed to happen."
Cultivating an idea
The idea first came to Mr. Swan when he read an article about vertical farming on his MRT ride home from work in 2012 - and felt that current methods were not efficient enough.
"The illustrations that I saw, they were wasting a lot of space. It may work in the United States where there is a lot of space, but in Singapore and Hong Kong, where land is scarce and rent is high. It just wouldn't work wasting space like that," he says.
That night, the then-engineer and project manager designed more compact versions.
Much of that early design work has translated to Sustenir's commercial farm in Admiralty today, which covers an area of 10,000 square feet (approximately 930 square metres).
While keeping his day job, the budding indoor farmer spent his weekends and after-office hours connecting with academics and farmers from all over the world to learn more about this industry.
"I took bites from what everyone was doing, because everyone was doing things so differently, and from that, I just formed my own hypothesis on how growing would happen."
With the knowledge gained, he focused on "growing impossible products at impossible places".
His first impossible place was the basement of a swimming facility in April 2013. There, he experimented with varying light wavelengths, nutrient solutions, carbon dioxide levels, and many other variables to find the optimum conditions for different species of plants to grow.
"I was growing kale by tricking the plant into thinking it was cold by chilling the water. It was there that I learned the power of a controlled environment. You just need to think outside the box."
After seeing the fruits of his labor, he decided to become a full-time farmer. The construction of Sustenir's facility in Admiralty started in October that year.
Mr. Swan wanted to use the budding technology of CEA to address the growing issue of environmental sustainability.
"If we keep going with farming the way it's being done right now, we're going to need farming land the size of Brazil by 2050 to feed the growing population. That means more deforestation, more pesticide run-off into rivers killing fish - it's not great.
"It's not to say that traditional farming is the devil, but we're saying that we need to fix it because it's not sustainable."
Through Sustenir's methods of vertical farming, land can be optimized to obtain more yield.
In an area of 54 square metres, Sustenir produces 1 tonne of kale or 3.2 tonnes of lettuce per month.
According to some reports, this can be 14 to 127 times more than the yield produced through traditional farming on the same area of land, depending on the climate.
Unlike traditional outdoor farming, vertical farming is not affected by seasonal changes. This allows for continuous production.
This form of farming also reduces water consumption, as the harvested crops do not need to be washed before they are consumed.
Sustenir keeps the plants clean by keeping external air pollutants out of the growing area and by having staff put on clean-room suits before they enter. This cleanliness is then maintained by packing the produce in airtight containers.
Producing non-native plants locally also reduces the ecological footprint from transport and food waste.
"Thirty-three percent of produce is wasted in the logistics alone before it even gets to the merchants," says Mr. Swan. "Then the merchants also have wastage as well. It's what they call shrinkage."
Sustenir further reduces wastage by using all of its yields. Physically imperfect specimens are made into juice instead of being thrown away.
"Sometimes during the harvesting process, we could be a bit rough and the leaves are not perfect, so we don't sell those to retail," says general manager Jack Moy. "What we do is find a way to repurpose this, because they taste equally good and they have the same nutrition."
To support Singapore's self-sustainability - at least where greens are concerned - Sustenir does not grow local produce. Instead, the firm aims to grow imported veggies which are popular among residents.
"We put our customers at the heart of all our decisions," says Mr. Swan.
For instance, after learning that many Singaporeans are fans of Japanese and Korean strawberries, Sustenir made that fruit its newest project.
Officially launched on June 20 this year, the strawberries have enjoyed substantial demand - so much so that Sustenir plans to allocate more space in its farm for growing the fruit.
Unfortunately, not all its products were equally well-received.
Upon the launch of its kale, the Sustenir team gave out samples at Cold Storage stores, only to find that many locals do not enjoy the vegetable's tough texture and bitter taste.
Mr Swan then went back to the "grow room" - as the growing area is dubbed - and altered the environment to reduce these unpopular attributes of kale, resulting in a softer-leaf, less bitter product.
The team also visits farmers' markets to study customer preferences. This feedback is used to modify produce, for instance by cultivating sweeter strawberries or milder arugula.
Mr. Swan hopes to apply the same CEA methods to maximize the nutrients in plants and grow them for medicinal purposes, too.
Sustenir is also working on developing local grapes and wine.
Leveraging technology
Apart from its own techniques, Sustenir taps external technologies for greater efficiency.
Through Spring Singapore - now Enterprise Singapore, after its merger with International Enterprise Singapore - Sustenir partnered PBA Systems to create robotic arms for seeding. One robotic arm does the work of three people.
Sustenir also works with educational institutions such as the National University of Singapore (NUS) and the Singapore Institute of Technology (SIT) to boost awareness of and interest in the industry.
After learning about vertical farming and CEA, students get the opportunity to develop projects and help the company in its green journey.
Says Mr. Moy: "It's kind of like an internship. We even bring NUS (students) onto the business side where they can help with the marketing."
Ideas which the firm finds feasible will be commercialized, he adds. "So it's really cool for the students. They can be proud to share that they worked with Sustenir to create a new innovation that customers love."
In line with its zero-waste policy, Sustenir is working with SIT to find the most suitable way to turn physically imperfect kale into kale powder.
The company is currently exploring different ways of drying the vegetable - from spray drying to vacuum drying - to find one that retains the most nutritional value.
Another technology Sustenir is looking at is artificial intelligence, which can be used to monitor plant growth and detect problems so they can be nipped in the bud.
Says Mr. Swan: "We're working with companies right now to work on our own in-house AI technology, to not only help us monitor and track plant growth, but to also help with the whole farming system. Everything from upstream with the resource materials to downstream with the ERP (enterprise resource planning) system." He declined to reveal the companies.
Sustenir also plans to create an online platform, Sustenir Life, to educate consumers on health, fitness, and vertical farming.
The company will work with health and fitness professionals, environmentalists and charities to share their stories and promote their causes on the blog-like platform.
All this is in the service of a larger, industry-level goal: changing the nature of outdoor farming, too.
"That's really the future of Sustenir," says Mr. Swan. "It's to take technology and help outdoor farmers - through our center of excellence in indoor farming - to apply smart technology into their farms, to optimize their farming programmes."
This is another reason Sustenir does not grow local produce. This ensures it does not compete with local farmers, instead of complementing their existing products.
Currently, Sustenir's cold-weather crops can be found at select Cold Storage outlets and online at Redmart. Sustenir also supplies food chains, restaurants and hotels such as SaladStop!, Les Amis and Shangri-La.
Mr Swan hopes to expand to other countries. "We're going to start with Asia-Pacific. In all heavily urbanized cities in Asia, we want to have Sustenir."
The company is building a 50,000 square foot facility in Hong Kong and is working with local farmers in Indonesia and Malaysia to integrate smart technology - such as the robotic seeding arm - into their traditional methods.
Outdoor farmers can also tap Sustenir's research findings for optimal growth, for instance by varying the pH levels of water in response to changes in climate and temperature.
Ultimately, Mr. Swan envisions Sustenir broadening its reach to the whole world: "It's time for a change in agriculture."
Brought to you by The Future Economy Council
Webinar Series - Funding Opportunities For CEA Energy Efficiency
The GLASE Consortium Webinar Series features the latest technological innovations and best practices in the CEA field providing the audience the opportunity to discover new solutions and to connect with field experts.
Webinar Series
Funding Opportunities For CEA Energy Efficiency
This webinar will introduce some key funding opportunities to help CEA growers install energy efficient equipment. Growers and manufacturers will learn how to leverage federal, state, and utility funding to identify opportunities for energy efficiency and contribute towards the installation cost of the identified projects. Attendees will also learn about utilizing the joint GLASE/EnSave software tool to share operational details of their CEA facility to further the GLASE mission.
Date: July 12th, 2018
Time: 2 pm EST
Presented by: EnSave
Register here
EnSave is the United States' leading designer and implementer of agricultural energy efficiency and greenhouse gas reduction programs. Since 1991, EnSave has worked with a variety of clients including federal agencies, state government, energy utilities, and industry organizations to help drive sustainable growth within the agricultural sector. We are proud to be a GLASE industrial member.
What Are The Production And Training Issues Facing Controlled Environment Agriculture Growers?
What Are The Production And Training Issues Facing Controlled Environment Agriculture Growers?
Exclusives from Urban Ag News
Ohio State University professor Chieri Kubota is focused on helping to resolve the production and training challenges facing controlled environment growers.
Trying to produce vegetables in hot, humid conditions can be difficult for controlled environment growers whether growing in a greenhouse or a warehouse.
“The challenges of greenhouse growing in Ohio and the Midwest are different than the challenges faced by growers in Arizona,” said Ohio State University horticulture professor Chieri Kubota. Kubota, who joined the faculty at Ohio State this past June will continue the controlled environment agriculture research she was doing while at the University of Arizona.
“Some people think I’m an expert at dealing with heat stress because I was doing my research in an Arizona greenhouse,” she said. “But in Arizona growers don’t really have to worry about the heat inside a greenhouse if they are using an evaporative cooling system to lower the temperature. In Arizona, the outside temperature can be 110ºF, but the temperature in the greenhouse can be lowered to 75ºF-80ºF (25ºC-27ºC) as long as the air is dry enough and water is available. In Arizona the dryness can be a challenge, causing tip burn on sensitive crops such as lettuce and strawberry.
“I really didn’t have to deal with heat stress much in Arizona. But there are other parts of the country like the Midwest and East Coast that have to deal with hot, humid summer conditions and very cold winters. I would like to work on those issues and develop technologies, including climate control strategies that can mitigate the issues of growing crops year-round. In Ohio and the Midwest summer heat stress is a major issue for crops causing all kinds of physiological disorders including incomplete pollination and fruit ripening disorders. During the winter, heating and humidity can also be an issue. There is also an issue with low light levels so supplemental lighting is more important.”
Ohio State University horticulture professor Chieri Kubota is planning to continue the controlled environment research she started at the University of Arizona and plans to expand her program to study LED lighting and new crops.
Photos courtesy of Chieri Kubota, Ohio St. Univ.
Because of the limited optimum growing season in greenhouses in the Midwest, Kubota said using indoor productions systems makes more sense compared to Arizona.
“In this part of the country it is very difficult to maintain the optimum temperature range year round,” she said. “And because of the increased interest in vertical farming, I expect to put more effort in warehouse production systems, including the use of LED lighting.”
Improving vegetable grafting
Some of the projects Kubota started at the University of Arizona that she will continue to work on our vegetable grafting and hydroponic strawberry production. She is a member of a research team led by North Carolina State University plant pathologist Frank Louws that is working on vegetable grafting.
“I am continuing my research on improving grafting methods and the handling of grafted plants so that they can be shipped long distances,” Kubota said. “I am also creating a simple tool for growers to schedule grafted plant production. Having the grafted plants ready at exactly the same size is always a challenge for growers. The research group is working to develop a simple plant growth model based on environmental conditions to predict how many days are needed to finish a grafted crop.”
Kubota said the grafting research team is looking at a variety of plants, including tomato, watermelon, cucumber, eggplant, pepper, and muskmelon.
“Growers are commercially producing grafted tomato and watermelon plants, but there are many more crops that can use grafting technology to reduce loss from soil-borne diseases and to increase yields. My program is looking at all of these potential crops.”
Kubota said the grafting research also has application to greenhouse crops.
“The grafting technology was originally developed for soil-based production, but greenhouse vegetable growers discovered that even though they are doing soilless production, using grafted plants can increase crop yields,” she said. “In North America, greenhouse growers were the first group who started using grafting technology. The field growers are now more interested since they have fewer means to control disease. In terms of potential market, field production in the U.S. is much larger in terms of number of plants.
“Currently tomato accounts for the majority of grafted plants in greenhouses. Increased tomato yields have been the driver for greenhouse growers to use grafted plants. Some greenhouse growers have been trialing grafted cucumbers and some research has shown that grafted eggplants can increase yields.”
Improving strawberry production
Kubota who has been working on greenhouse strawberry production for nine years will continue working on this crop with an interest in the use of LEDs.
Chieri Kubota will continue her greenhouse strawberry research with an interest in increasing yields using supplemental light.
“Strawberry fruit production is not as productive as leafy greens or tomatoes in terms of dollars of return relative to the input of light,” she said. “I’m interested in studying the increase in yields relative to the increase in light. What is the dollar value of that increase of yield by adding for example, 1 mole of light? Unless there is an improvement in lighting technology, it may not make sense to grow strawberries under supplemental lighting.
“I would like to come up with a smart lighting system to reduce the lighting cost based on the understanding of strawberry physiology and how plants are grown in a greenhouse. I think we could reduce lighting energy use and costs quite a bit by doing that. Strawberries are physiologically unique in terms of light saturation and also in terms of the sink-and-source relationship of how much sugar can be translocated from the leaves so that the photosynthetic rate can be maximized.”
Developing new crops
Another area that Kubota would like to expand for CEA production is the development of new crops.
“Controlled environment growers whether they are growing in greenhouses or warehouses need to diversify and increase the number of crops they are producing,” she said. “Although I don’t have any new crop projects coming up, I am particularly interested in small fruits. Since Ohio and the Midwest have a cold climate, there may be an opportunity to do more with small fruit crops like raspberries, blueberries, blackberries and other berry crops for greenhouse production.”
Kubota is also interested in revisiting the study of spinach production in greenhouse and warehouses.
“Controlled environment growers seem to have a particularly difficult time managing diseases including Pythium on spinach,” she said. “I am interested in determining if there is a practical way to manage these diseases. Cornell University researchers had previously done a lot of studies on this issue years ago. I wanted to see what the difference was between the successful hydroponic growing of spinach in Asia and other countries and why U.S. growers can’t do that too.”
Expanding professional training, research programs
As part of her extension efforts at Ohio State, Kubota wants to expand the opportunities for growers to receive professional training.
“I want this training to go beyond Ohio and to go nationwide and even international,” she said. “I’m interested in training professionals with online courses and other programs at a reasonable cost.
“The heart of the horticulture industry is in this part of the country. There are many different types of growers, supporting vendors and technology providers here. They are well connected.”
Chieri Kubota said having an extensive group of CEA researchers and extension specialists at Ohio State will enable her to expand training programs for growers not only in the state but potentially worldwide.
Kubota said at the University of Arizona research in the plant science department was focused more on basic science such as how a particular gene functions in plants, but not necessarily horticultural plants.
“Here at Ohio State I am in the horticulture and crop science department so the other faculty members understand what horticulture is,” she said. “There are a number of people here working on controlled environment agriculture including horticulture, which covers floriculture, hydroponics, and high tunnels, and ag engineering, entomology, plant pathology and food safety. There is a complete set of researchers and extension specialists who can work on a variety of controlled environment agriculture issues related to horticulture crops. This makes it advantageous for not only developing research projects together, but also professional training for commercial growers.”
For more: Chieri Kubota, The Ohio State University, Department of Horticulture and Crop Science, kubota.10@osu.edu; http://u.osu.edu/cepptlab; https://hcs.osu.edu/our-people/dr-chieri-kubota; https://www.facebook.com/CEPPTLAB.
That Healthful Looking Green Leafy Stuff in Your Fridge May Not Be As Great For You As You Think.
That Healthful Looking Green Leafy Stuff in Your Fridge May Not Be As Great For You As You Think.
How could that be you ask? Well…Let me explain.
Firstly, a brief ecology lesson;
- Healthy organic soil contains microorganisms* or microbes
- These microbes work to break down plant matter in the soil
- This breakdown of vegetation creates humate deposits in the soil
- Humate deposits are rich in the amazing fulvic acid and humic acids (also known as minerals)
*Soil microorganisms can be classified as bacteria, actinomycetes, fungi, algae and protozoa. Each of these groups has characteristics that define them and their functions in soil.
So, how does this relate to my lettuce?
Right now, less than 4% of the soil in North America is certified organic farmland, and worldwide chemically based farming practices are continually polluting the soil.
This means the valuable microbes are being killed off by things like herbicides and pesticides, fertilizers, ultimately leading to mineral depletion. Without these precious microbes even re-mineralizing the soil is futile, as the humates and fulvic acid are still missing.
Ok, on to that lettuce finally! Chances are it was grown in an environment that was lacking microbes, and thus the creation of humates and fulvic minerals are almost nil to very low. As a result, the lettuce is lacking in minerals even though it may look lush and green.
I get it, sick soil = means my lettuce is lacking
But what effect does this have on my health? And what’s this fulvic acid stuff you keep talking about?
Patience please, your answers are on the way in our next couple emails while your waiting you can watch today's message from our founder HERE.
Let's make tiny farming not so tiny!
WINNERS ANNOUNCED: Hackathon to Grow Crops on Mars Sees ‘Duckweed’ Take Prize for Best Solution
WINNERS ANNOUNCED: Hackathon to Grow Crops on Mars Sees ‘Duckweed’ Take Prize for Best Solution
7 November 2017, San Francisco, USA
Hackathon team ‘Just Food’ and their innovative solution for utilizing the aquatic plant duckweed, took the win Sunday night at the inaugural 2017 Autogrow #CropsOnMars Hackathon.
Global ag-tech company Autogrow acknowledged the solution was incredibly well thought out, achievable and original.
“The team did an impressive job researching how they could not only grow duckweed in a challenging environment but how it could realistically sustain life on Mars,” said Autogrow CEO Darryn Keiller.
“The judges all agreed that, while duckweed wasn’t the most appetizing food source, they couldn’t argue with the nutrient value or the innovative prototype of super thin LED lit grow beds they had created.”
‘Just Food’ and nine other teams hacked for two days on software, data or design solutions involving plant biology, controlled environment agriculture and the Mars environment. The judges looked for originality, sustainability, scalability and the potential for reproducibility on Earth.
Teams had the support of mentors and event organizers Autogrow and Silicon Valley Forum over the two days.
“I was privileged to be a mentor covering all aspects of plant biology and lighting. It was also great hackers had access to other mentors from NASA, IBM, Microsoft, Plenty, Orange Silicon Valley and Western Growers to name a few. And of course, the support of event partner Silicon Valley Forum who found a wonderful venue to hack. Like plants, people thrive in the right environment and we had a great growing environment,” said Autogrow Director of Crop Science and Agronomy Tharindu Weeraratne.
The race for the win was so tight that two teams took the runner-up slot with one advocating collapsible growth chambers and the other a rapid deployable enclosure to be set up prior to astronaut arrival using robotic technology.
Mr. Keiller noted that although teams were competing against each other there was an impressive amount of support for one another.
“The Hackers (predominantly millennials) gave us great hope for the future due to their creativity, their outlook to the future and to put things right for our planet’s ecosystem while meeting the needs of our growing population.”
“As organizers of the event, the most unexpected and visceral emotion of the collective teams was the spirit of unity around the daunting challenge we put in front of them. Here were people from perhaps 20 nations; students, startup founders, academics and business owners, all coming together to do something that was substantially beyond any one of them. The strength of their ideas was in their diversity as people and their willingness to collaborate.”
With the success of the inaugural event under their belt, Autogrow will announce new dates early in the year for the next #CropsOnMars hackathon, likely to be scheduled for late 2018 and held in Silicon Valley.
WINNING TEAM ‘JUST FOOD’
Wyatt Smith
Michelle Jia
Deger Turan
Santiago Perez
Zandra Vinegar
JUDGING PANEL
Dr. Nate Storey, Chief Science Officer – Plenty
Jeffrey Law, Chief Technology Officer – Autogrow
Dr Ioana Cozmuta, Industry Engagement, Commercial Space Partnerships – NASA
Andrew Scheurmann, CEO – Arch Systems
Greg Chiocco, Director of Product Management - Climate Corporation
Dr Rosie Bosworth, Strategic Communications – Sustain Ltd
MENTORS
Bilind Hajer, Data Engenieer - Product School
Tobi Ogunaikee, Software Engineer
Isabel Chamberlain, Compliance Specialist and Grower - Plenty
Akihiro Ishimura, Senior Consultant/ AgTech Expert - Fujitsu
Miika Mantyvaara, Global Marketing, Business Development and Innovation - The Vault
Robert (Bruce) Pittman, Chief System Engineer - NASA
Bilind Hajer, Data Engineer - Product School
Anna Propas, Software Engineer Lead Instructor - Coding Dojo
Juanita Dion, Software Engineer - IBM
Dennis Donohue, President at Royal Rose Radicchio - Western Growers Association
Ulrika Lidstorm, Research Scientist & Program Coordinator - Dupont Pioneer
Davies Odu, Software Engineer - Microsoft
Itiya Aneece, PhD Researcher - USGS
Hugo Wagner, Partner - Orange Silicon Valley
Erica Riel Carden, AgTech & FoodTech Advisor - Global Capital Markets
Davies Odu, Software Engineer - Microsoft