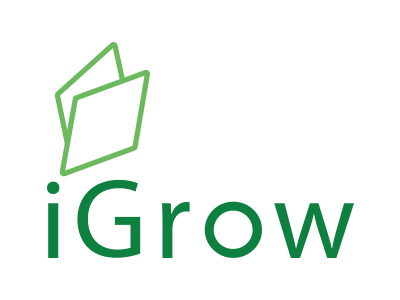
Welcome to iGrow News, Your Source for the World of Indoor Vertical Farming
How IGS Reduces Vertical Farming Costs
While vertical farming is not the ultimate solution to the world’s farming challenges, it does give control over many variables or, perhaps more accurately, the weather
December 11, 2019
Editor’s Note: Intelligent Growth Solutions (IGS) is a portfolio company of AgFunder’s and recently attracted investment from leading agtech investor Ospraie. IGS offers plug and play vertical farming technology to vertical farm operators, which they say can increase efficiencies and substantially reduce costs compared to other vertical farming operations. It can be hard to explain exactly how the technology does this, so we caught up with Niall Skinner, lead mechanical engineer at IGS to get an in-depth explanation of how the tech works.
What core challenges facing the vertical farming market does the IGS technology address, and how?
While vertical farming is not the ultimate solution to the world’s farming challenges, it does give control over many variables or, perhaps more accurately, the weather. At IGS we have gone back to basics in our technological approach to make weather control a reality, building four families of patents and patents pending along the way.
We recognised that running a vertical farm needs to be simple, even if the technology behind it is not! By its very design, a vertical farm is often a far more technical and complex environment than a traditional farm or even a glasshouse environment would be. An overly technical system can, however, be off-putting, so we have turned the thinking on its head: there are no computers, cables or capacitors in our systems.
We thought outside the box (quite literally) to work out how to bring weather from the outside in, and allow it to be controlled through a mobile phone app. Our ‘plug and play’ modular systems address the challenges of power and labour costs and offer opportunity to pre-programme ‘weather recipes’ to ensure maximum productivity across yield, consistency and quality. Core to our R&D efforts was to ensure greater commercial viability for operators and the focus on power reducing technology and automation has been paramount. Our approach has enabled us to demonstrate clearly reductions of up to 50% power usage and 80% labour costs.
In addition to our power management capabilities, we are particularly excited about our patents that address the serious challenge of ventilation in a closed space. Keeping crops at an even temperature under hot lights while balancing the CO2 they inhale and the oxygen the exhale is very tricky, but our patent-pending (in this case) technology provides a solution that delivers the required balance, even as it captures, condenses and reuses the water vapour the plants emit.
Can you explain in more detail how your technology can reduce power consumption in a vertical farm
We have developed a power-management platform that flexes with the grid in real-time, allowing it to respond to external impacts such as grid stability and power availability. This means that power can be pulled when it is cheaper or pushed back when it is more expensive and in-demand: in effect, it imitates the role of a large battery where the excess energy is converted into grown produce. The use of industrial Omron SYSMAC programmable logic controllers (PLCs) to automate our system allows automatic recovery from power loss events and means that individual towers and sites get the power they need. As a result, none of the systems need to be reset, reprogrammed or manually repositioned.
Our system has a baseline power consumption of 60 kilowatts (kW), which can be rapidly increased to 105 kW or reduced to 30 kW for short periods to optimise grid stability. Other drains on power include heating and air conditioning, but all our systems including watering are on closed loop systems to minimise power consumption. Our design reduces the need for HEPA (high-efficiency particulate air) filtration to clean large volumes of incoming air, and the heating and/or cooling of this air depending on location and season – all of which are a drain on power. In combination these efficiencies contribute to a power-saving of 50%.
With over 1000 LEDs per tray, lighting forms over two-thirds of the system’s power requirements. We were determined to develop a more efficient system to drive the LEDs, and this is where the three-phase power supply design was born. This system is more commonly used to power machinery in an industrial environment but works by transferring the power supply to a safe voltage level and transmitting it to each individual tray within the tower using aluminium tubes rather than cables. By using tubes rather than cables, we can improve transmission efficiency. Aluminium tubes are also much cheaper and lighter than comparable copper cables. By using three-phase power at a tray level, we can also further reduce losses of power and provide inherent phase balancing. This eliminates the need for costly and inefficient filtering and power factor correction, as well as the use of capacitors for single-phase conversion. These measures contribute to an increase of between 5% and 10% in driver efficiency,
Your approach to the technology replicates a more industrialised environment – why is that?
Initially, when the founding team of engineers came together at IGS, the background was more heavily based in industrial operations. This has actually been a considerable advantage in helping us look differently at the vertical farming environment; it is our industrial environment approach this is key to this. We operate our farms in large steel frame warehouses with insulated cladding walls to provide isolation from the external environment. For example, the standard buildings are 10 metres in height, which allows up to 26 trays to be stacked in towers up to 9 metres high, but we do offer a range of options in addition to this. It really is closer in style to an industrial unit than a more traditional agricultural setting; handling the trays in this environment requires no human involvement whatsoever. It is here we generate savings of as much as 80% in the area of labour.
Within each tower, we have established standalone ventilation and irrigation closed-loop systems, which automatically sterilise and recycle air and water so that the only regular inputs the system needs are power, seed, nutrients, carbon dioxide and harvested rainwater. The air is sterilised by UV filtration technology – similar to that used in clean rooms. Standard industrial chillers and cooling coils cool and dehumidify the air which is then heated as needed, also drawing on waste heat from multiple areas in the facility. Carbon dioxide can be added to this loop when required too. This optimised management right across the components of our system when compared with conventional and glasshouse environments contribute to an overall reduction of power consumption of between 40 and 50%.
All the important factors – light, heat, humidity, water, nutrients, and crop movement – are controlled by industrial programmable logic controllers (PLCs), that run on an architecture that does not need unpredictable updates. The Omron SYSMAC PLCs use feedback from sensors distributed throughout the tower and systems that is transferred to a cloud-based control system. This removes the need for computers and wiring. It makes the whole system much more simple to operate, maintain and control.
With greater control over your LED systems than many (if not all) competitors, how and why have you focused your innovation on this area? What benefits does it bring?
Lighting was always going to be a key area when we were developing our systems as this is where the greatest power consumption comes from. We have focused on light intensity and dimming particularly so we can control each individual colour in the spectrum. Our LEDs are fitted in clusters, with each cluster containing all types of LED. Our system can vary the spectrum or pulse width modulation (PWM) and intensity to simulate solar radiation. We believe this is a unique feature of our system.
Each wavelength can be turned on or off or dimmed via PWM, linear dimming or a combination of both. However, we are still at the early stages of understanding how the optimal mix of light for each crop and stage of growth can impact on different ranges of crops. This is where we use AI to measure and understand the crops’ progress in order to enhance our learning in this area. We are already making some very interesting observations across a range of crops and are showing yield improvements of up to 2-3 times increase.
Our system can also vary intensity through linear dimming or PWM. We can vary PWM infinitely in 0.01% increments over all wavelengths simultaneously and maintain 90% electrical efficiency from grid to LEDs. This means that we can really assess how the delivery of the light is impacting on how well the crops grow.
How important are AI and data aggregation in the future of vertical farming?
It is going to be absolutely pivotal, a real game-changer. It allows control, predictability and the ability to absolutely guarantee the quality, consistency, and yield of produce every single time. We have inbuilt AI and data collection capabilities in all of our systems and that makes day-to-day management considerably easier. It also allows for historic patterns to be tracked which enables us to predict future growing methods and deliver optimum data for the best growing results to our customers in the future.
Oasis Springs Runs A CSA In Every Season
Sarah and Chris Ward got their start in urban farming in 2016 when they purchased a Leafy Green Machine (the predecessor of the Greenery
7 QUESTIONS WITH SARAH
WARD OF OASIS SPRINGS FARMS
Sarah and Chris Ward got their start in urban farming in 2016 when they purchased a Leafy Green Machine (the predecessor of the Greenery). Although neither Sarah nor her husband Chris had experience in commercial farming, Sarah had over 17 years experience in marketing, public relations, and project management, and Chris had a background in information technology and engineering, so they decided to leverage their professional abilities and mutual love for local food by launching Oasis Springs Farm. Their mission? To provide fresh, healthy, local produce year-round to their community in southern New Hampshire through environmentally friendly practices and high tech resources. We recently spoke with Sarah about operating her container farm and her tricks for maintaining a loyal customer base.
Freight Farms (FF): What, if any was your experience with farming before becoming a Freight Farmer?
Sarah Ward (SW): We did a little hydroponic growing in our home the winter before to have fresh herbs and lettuce throughout the winter months. It was during all the research we did for our home operation that we came across the opportunity to scale up large enough to not only feed ourselves but our community as well.
Sarah's husband Chris learning how to harvest crops during Freight Farms' training camp for new farmers
FF: How did you find customers to buy your produce?
SW: This was one of the scariest parts of the business, trying to find interested people to buy it. We connected with local groups and businesses that have like-minded missions to bring good food to people. And we are always rewarding people with free lettuce and greens when they connect us with new businesses or CSA members. Over time we grew our membership to 50-60 shares a week, and usually have a waitlist too!
“ It amazes me every week how much we can grow. ”
FF: Who do you sell to and how do you do it?
Most of our greens go towards the CSA, although we do still have a few chef customers as well. Our customer base it varied: families, senior citizens, health-conscious shoppers, and locavores. We found this customer base by partnering with local businesses as pick-up points and using them as opportunities for co-marketing.
FF: What kinds of crops do you grow?
SW: At first we did a lot of experimentation, but ultimately found that we gave customers the best value when we provided them with everyday staples. Today we grow about five lettuce varieties, kale, some herbs, and microgreens.
FF: What’s the best piece of advice you can give to people interested in becoming Freight Farmers?
SW: Be flexible and patient! When we first started we wanted everything handed to us with the perfect formula for success, but we quickly learned that things change and you can’t always count on what you planned for. Be adaptable and open to new ideas.
FF: What was the most challenging part of becoming a Freight Farmer and how were you able to overcome it?
SW: Even with a Freight Farms unit, farming, in general, requires a lot of time. There have been many exhausting early mornings and late nights. Managing a full-time business and raising a family certainly has its challenges. We have worked hard over the last year to find the right work-life balance by trying to create a schedule that works for our family.
FF: What are your plans for the future?
SW: We plan to grow and continue to find new ways that this resource can benefit both us and the community that we live in. Most people are amazed that we do this from our backyard. The support has been amazing. I get called Lettuce Lady a lot.
Want to learn more about how Oasis Springs is operating a successful CSA? Register for our webinar with
Sarah on December 12th, 2019 from 12-12:30 PM EST.
In the meantime, follow Oasis Springs on Facebook and Instagram for updates from the farm!
China's First Intelligent LED Plant Factory in Beijing
the experts of the Chinese Academy of Agricultural Sciences and the factories responsible for researching this technology are very confident. They believe that in the future smart agriculture will become the norm, and the LED smart factory is a business card for Chinese agriculture to go international
This farm at the third ring road in Beijing is the first intelligent LED plant factory in China. The factory is highly modernized and managed by the protected agricultural IoT control system.
In more detail, there are dozens of sensors in the factory to jointly manage various parameters of the plant during its growth. Sensors and artificial intelligence cameras are also monitored throughout the process to adjust various parameters in real-time. Through the sensor and the visual analysis system equipped with artificial intelligence cameras, the parameters such as temperature, light, water and gas fertilizer are continuously optimized, and the changes of plant growth phenotypic parameters are collected and learned and calculated.
The data model of crop growth optimization is obtained, and the “plant dialogue” is implemented. The goal is to achieve maximum yield and quality with the least amount of resources.
In this “farm” built of steel the “farmland” is a row of five-layer double-row seedling racks in the house.
The person in charge of the farm said that the seedling efficiency per unit area of this seedling rack is more than 40 times that of conventional seedlings, and the seedling cycle can be shortened by 40%. Take an example of the cultivation of lettuce. From planting to harvesting, the plant factory only takes 20 days by using the so-called "Deep Flow Technique (DFT)". Besides, the output per unit area is more than 25 times that of open field cultivation, while the produce is still of high quality.
Going against tradition
In fact, this highly efficient method of cultivating vegetables is not a rare thing. As early as 1903, countries began to plant vegetables in a vertical way. But when the LED light source solved the sunshine problem in plant growth, and new technologies allowed for better control, vertical farming really started to take off.
In 2005, Yang Qichang, chief of the "Facilities Plant Environmental Engineering Team" of the Institute of Agricultural Environment and Sustainable Development of the Chinese Academy of Agricultural Sciences, found that the red and blue light combination of LED can provide an ideal spectrum for plant photosynthesis; he immediately imagined that using LEDs in plant factories instead of fluorescent lamps at that time would be a new development direction.
Since the spectral components of civil-used and plant-used LEDs were very different at that time, the team had contacted many domestic research institutes such as the Institute of Semiconductors of the Chinese Academy of Sciences and spent several times the price of civil-used LEDs to jointly develop 4 sets of LED plant light source panel systems. Since then, they have carried out many experimental pieces of researches on plant seedling, leaf vegetable cultivation, medicinal plant cultivation, and plant tissue culture, and obtained a large number of plant light formula parameters.
Afterwards, under the support of the national “863” project “Intelligent Plant Factory Production Technology Research”, the Innovation Project of the Chinese Academy of Agricultural Sciences, and 15 research units jointly tackled the problem and finally obtained a series of innovative breakthroughs: first proposed multiple light formulas for plants, and created LED energy-saving light source based on light formulas and its light environment control technology equipment; first proposed light-temperature coupled energy-saving environment control method, and created the energy-saving environmental regulation technology equipment of the plant factory; first proposed a light-nutrition regulation method for vegetable quality, and created a short-term continuous illumination to improve quality technology and technical equipment before mining; first proposed an intelligent management and control method for plant factory efficacy, energy efficiency and nutritional quality improvement, and created an intelligent management and control system based on the IoT.
Indeed, LED plant factory technology is time-consuming and labor-intensive, but this technology can help the growth of vegetables which means they can be moved indoors, completely freeing the restrictions of land, sunlight, and water. It also has the advantage of “efficient production”. Yang Qichang explained that the unit area yield can reach dozens or even hundreds of times of natural cultivation in the open field, and the water consumption is less than 5%.
However, only 10 years ago, only a few developed countries such as Japan, the United States, and the Netherlands mastered this technology. Today, as environmental and health issues are increasingly mentioned, this technology is used in all areas of agricultural production in various countries.
A long way to go
For China, although the development of this technology has good achievements, it still has obstacles on the way forward. There is a lack of professionals in this technology, and a lot of research and development funds are needed.
However, the experts of the Chinese Academy of Agricultural Sciences and the factories responsible for researching this technology are very confident. They believe that in the future smart agriculture will become the norm, and the LED smart factory is a business card for Chinese agriculture to go international.
Source: chinadaily.com.cn; sheshiyuanyi.com
Publication date: Mon 25 Nov 2019
Agritecture & Autogrow Release 2019 CEA Census Report
Agritecture and Autogrow have released their first-ever Global CEA Census Report. This is the most in-depth global survey of indoor and controlled-environment farmers to date, with 316 total respondents across 54 countries.
Despite rapid growth, data is notoriously difficult to come by in the CEA industry. According to the two companies, farm operators see the potential for improvement and are optimistic about the future, but often express frustration at not knowing where to turn to for help. Confounding this is the sentiment from farmers that many consumers, and particularly local governments, lack clarity around the benefits of local & controlled environment farming. In the report, Autogrow and Agritecture paint a clearer picture of the global CEA industry by identifying important trends and contextualizing them for a wider audience.
The Global CEA Census ran from June 4 to July 22, 2019, asking growers around the world a total of 45 questions.
Click Here For Full Report
Texas A&M Controlled Environment Agriculture Conference
This year, exclusive sponsorship opportunities are available for the 2019 Texas A&M Controlled Environment Agriculture Conference, December 5 at Texas A&M AgriLife Research and Extension, the Dallas Center (17360 Coit Rd, Dallas, TX 75252) at the Water and Land Resources Building
By urbanagnews
November 18, 2019
Texas A&M AgriLife Research and AgriLife Extension invite you attend our first annual ‘Controlled Environment: Urban Agriculture’ conference designed for new and prospective growers interested in specialty crop production under controlled environment (high tunnels, greenhouses, indoor vertical farms) and for experienced growers who want to learn more about the nuts and bolts of crop production in a controlled environment.
When: December 5, 2019
Where: Water and Land Resources Building at Texas A&M AgriLife Research and Extension Center, 17360 Coit Rd, Dallas, TX 75252
Register at 979-845-2604 or https://agriliferegister.tamu.edu/horticulture
Topics
Urban agriculture – current production systems and technologies
Mastering environment control in indoor farming: How to improve crop performance with CEA technologies
Urban agriculture in the City of Dallas
Temperature control for container-grown plant production – A grower’s perspective
Nutrients/Fertilizers
Light management
More grower’s perspective!
Speakers
Dr. Joe Masabni, Assoc. Professor, Extension Specialist-Horticulture
Dr. Genhua Niu, Professor-Urban Horticulture
Dr. Mengmeng Gu, Assoc. Professor, Extension Specialist-Horticulture
Ms. Ling Sun, Technical Manager, Denise Farms
Ms. Karla Garcia, Technical Support, Hort Americas
Mr. Robert Curry, Special Projects Manager, City of Dallas
Mr. Drew Demler, Greenhouse Manager at State Fair of Texas
November registration fee $105
Onsite registration fee $125
TNLA members— $20 discount
TOFGA members—$20 discount
AgriLife Employees—$40 discount
CEA Conference Agenda Download
Sponsorship Program
Our sponsorship program recognizes donors who support initiatives of Texas A&M AgriLife Research and the Texas A&M AgriLife Extension Service.
This year, exclusive sponsorship opportunities are available for the 2019 Texas A&M Controlled Environment Agriculture Conference, December 5 at Texas A&M AgriLife Research and Extension, the Dallas Center (17360 Coit Rd, Dallas, TX 75252) at the Water and Land Resources Building.
Event details and registration are available at https://agriliferegister.tamu.edu/Horticulture.
This conference is designed for new and prospective growers interested in specialty crop production under controlled environment (high tunnels, greenhouses, indoor vertical farms) and experienced growers who want to learn more about the nuts and bolts of crop production in a controlled environment. Contact Dr. Genhua Niu at gniu@ag.tamu.edu, Dr. Joe Masabni at jmasabni@ag.tamu.edu or Dr. Mengmeng Gu at mgu@tamu.edu for details.
Contact:
Dr. Joe Masabni at jmasabni@ag.tamu.edu or
Dr. Mengmeng Gu at mgu@tamu.edu with AgriLife Extension
Dr. Genhua Niu at gniu@ag.tamu.edu with AgriLife Research
GLASE Webinar Series: Off-Season Strawberry Production Under Controlled Environments
Strawberries production in greenhouses and indoor farms represents an uprising market that offers the potential for CEA growers to diversify and remain competitive. In this webinar, Dr. Chieri Kubota from Ohio State University will discuss the opportunities of off-season strawberry production under controlled environments
Title: Off-season strawberry production under controlled environments
Date: November 21, 2019
Time: 2 p.m. - 3 p.m. EST
Presented by: Chieri Kubota
Description:
Strawberries production in greenhouses and indoor farms represents an uprising market that offers the potential for CEA growers to diversify and remain competitive. In this webinar, Dr. Chieri Kubota from Ohio State University will discuss the opportunities of off-season strawberry production under controlled environments.
Registration link: https://cornell.zoom.us/webinar/register/WN_BW_p9oDyS7Cmx1DllSCLbA
Vertical Farming, Micro-Algae, And Bio-Reactors — The New Frontier of Sustainable Food
CEA represents a small but growing dimension of agriculture. It's attracting huge investment, particularly in the United States where venture capitalists see gains to be made in a high-tech process known as vertical farming. Vertical farms look like a cross between a factory and a laboratory. Plants are grown indoors on trays, often stacked up to 30 tiers high
RN By Antony Funnell for Future Tense
November 8, 2019
It's brunch time in the not-too-distant future. You're in your favourite cafe and you have a craving for pancakes.
You know they're delicious because you order them all the time: fluffy and light with a slightly carroty taste.
Hardly a health food, but at least they're easy on the environment — they're made with organic eggs and 100 percent locally-sourced bacteria.
The bioreactor that produces the flour is only a block away.
Like many people, you're worried about the size of your carbon footprint, so it's good to know that none of the main ingredients had to be shipped or flown in.
The coffee is good too — from a boutique plantation in an old converted office block just down the road.
It's expensive, but it's worth paying a little more to make sure the produce you eat and drink is grown right here in the city.
Your friend orders the pork and fennel sausages with a side salad — from the rooftop farm above the cafe.
Follow this story to get email or text alerts from ABC News when there is a future article following this storyline.
She often feels guilty about the amount of meat she consumes. But at least the pig she's eating was raised on micro-algae, not soybean. So, a small chunk of the Amazon is still standing because the trees in that area weren't cut down to make way for yet another enormous soya plantation.
Eating pancakes made from bacterial flour and animals raised on unicellular photosynthetic micro-organisms might seem a little out there, but these ideas are currently being explored by scientists as part of a new approach to farming called controlled environmental agriculture (CEA).
And CEA, some agricultural researchers argue, could be the best way of reducing the environmental destruction associated with modern farming, which is both land and resource-intensive.
Listen to the episode
Controlled Environmental Agriculture promises to be cleaner and greener. Future Tense examines the potential and the pitfalls.
The veggie patch goes high-tech
CEA represents a small but growing dimension of agriculture.
It's attracting huge investment, particularly in the United States where venture capitalists see gains to be made in a high-tech process known as vertical farming.
Vertical farms look like a cross between a factory and a laboratory.
Plants are grown indoors on trays, often stacked up to 30 tiers high.
Everything about the indoor environment is governed by sensors and automation, but the crucial ingredient is the artificial lighting.
"All the vertical farms operating today are using a type of lighting called LEDs, which stands for light-emitting diode," says Jeffrey Landau, the director of business development at Agritecture, an urban agriculture consultancy.
"Different types of crops prefer different types of lighting. So, your leafy greens, your vegetative crops prefer light towards the blue side of the spectrum.
"Whereas your fruiting and flowering crops, they will want something more along the red spectrum of lighting."
Each variety of plant has its own tailored lighting recipe, allowing them to photosynthesise for much longer periods of the day — up to 18 hours at a time.
In practical terms, that means more crop yields.
The major players, to date, have concentrated on producing perishable goods such as salad vegetables — crops that traditionally require large amounts of water.
But vertical farming expert Paul Gauthier believes even staples like potato and wheat could eventually be grown indoors.
"Everything is possible. I don't think there is anything in the vertical farm that we can't grow," he says.
"I was growing coffee trees inside a vertical farm.
"It's a question of which kind of design we have to make and what the economics are behind it."
Dr Gauthier, who now works for the New Jersey-based company Bowery Farming, admits both the capital and energy costs involved in vertical farming are "definitely huge".
But that needs to be put in context, he argues, because significant government subsidies have long been provided to traditional farming operations.
People in glass houses
Others aren't so convinced.
Viraj Puri sees the Silicon Valley-inspired approach adopted by companies like Bowery as unnecessarily high-tech.
"It has certainly attracted a tonne of investment, media attention, consumer interest, there's no doubt about it," he says.
"I still think the business models will require a path to profitability before it can start to attract more mainstream financing."
Mr. Puri, the CEO, and co-founder of Gotham Greens, operates five rooftop urban greenhouse facilities in New York and Chicago.
His approach to controlled environmental agriculture is to recast the classic Dutch greenhouse of an earlier age, but with 21st-century modifications.
"These are glass and steel structures controlled by computers that are able to monitor climate 365 days of the year, 24 hours a day, and make smart adjustments, data-driven adjustments, in order to maximise crop productivity, efficiency, reduce production losses," Mr. Puri says.
"They combine a lot of these advanced horticultural and engineering techniques that proponents of vertical farming espouse and promote."
And they also have the potential to achieve exponential crop yields.
"One can still get 50 times the productivity on certain types of crops. But one relies primarily on natural sunlight which is a free natural resource," Mr. Puri says.
Next year, Gotham Greens is due to open a 2,800-square-metre facility just outside Denver, Colorado, as part of a $70 million capital expansion plan.
"Some of these greenhouses are the size of dozens of football fields, so these aren't backyard hoop houses but rather very sophisticated climate-controlled buildings," Mr Puri says,
And they can get even bigger.
A French company is currently constructing a roof-top greenhouse in the centre of Paris that will cover some 14,000 square metres when completed.
Like Bowery Farms, Gotham Greens sells itself on growing pesticide-free crops, grown locally with very few transport miles.
"Urban farming is about bringing issues closer to large population centres," Mr Puri says.
"And telling the story of how agriculture is an enormous consumer of natural resources around the world and how this form of farming can play a significant role in a more sustainable future."
A revolution in the paddocks
A young farming couple find out how they can rehabilitate the natural environment while also producing healthier food.
The substitution game
For Cambridge University's Asaf Tzachor, the solution to environmental degradation lies not just in rethinking how we grow, but what we grow.
The future of food that he envisages is busy fermenting away in a bio-reactor in Iceland.
The facility is run by a company called Algaennovation, which has been experimenting with the development of a new kind of animal food supplement made from microalgae.
Dr. Tzachor estimates up to 85 percent of the soybean produced globally each year is used to feed farm animals.
Soya farming in South America is identified by environmental agencies as a major cause of deforestation.
So, the idea is to simply substitute the microalgae for soya.
"Microalgae are very interesting. They are marine organisms, which means that they don't need fresh water, unlike soybean," Dr. Tzachor says.
"And we don't have to cultivate them on terrestrial areas, so we can grow them within facilities, and these facilities can also be closed."
The savings on water alone would be significant, says Dr. Tzachor.
He says experiments at Algaennovation's facility have so far been able to achieve between 200 and 250 times more biomass per litre of water than soybean farming.
The next stage of development is demonstrating that microalgae production can be done on a mass scale.
A similar approach is being undertaken by researchers in Finland, but their focus is on producing a supplement for human food rather than stock feed.
Pasi Vainikka, from the company Solar Foods, says his company has used a bio-reactor to produce an edible flour made from fermented bacteria.
"We have a fermenter, but we don't use yeast. We use a specific microbe that doesn't eat sugar," he says.
"So instead of sugar we introduce carbon dioxide and hydrogen, and these the microbe uses for energy and carbon instead of sugars to grow.
"Then we take the liquid out of the fermenter when the microbes grow and multiply and you end up with a dry powder."
The flour, called Solein, has a 65 percent protein content, says Dr. Vainikka, and can be used as a substitute for wheat flour or soya in everything from bread to protein drinks.
"The organism has carotenoids. When you taste it raw it has a bit of an umami (savoury) taste," he says.
"When you add it to pancakes, for example, it tastes as if it would have egg, and also a bit of carrot taste."
"The production cost, according to our estimations, is around $US5 per kilogram."
But that cost, says Dr. Vainikka, could be expected to decrease as production begins to scale.
"We are about 10 times more environmentally friendly than plants and about 100 times better than animal-based proteins," he says.
"If we want to make a fundamentally more sustainable food system for the increasing population, we need to disconnect from agriculture, which usually means irrigation, use of pesticides and a lot of land use.
"So, when we disconnect from everything that has to do with these processes, the environmental benefits are huge."
Despite the promise offered by controlled environmental agriculture, Mr Puri cautions against seeing it as "panacea or a silver bullet" for the world's growing food demand issues.
"I think solutions are going to have to be varied and they have to be uniquely suited to their own geographical, economic, social and cultural contexts," he says.
"I think there's many different ways to farm sustainably and responsibly.
"Indoor farming techniques can certainly play a significant role for certain types of crops, high-value crops, crops that use a lot of water, crops that often have to be shipped in refrigerated trains, planes or trucks over great distances."
But the challenge is great. The United Nations estimates the world's population will increase to around 9.7 billion by 2050.
That's another 2 billion mouths to feed.
Element Farms Unveils New State-of-The-Art Greenhouse
New Facility Will 20x Company’s Current Capacity for Growing
Pesticide-Free, Local, and Sustainable Leafy Greens Year-Round
New York, NY -- October 31, 2019 -- Element Farms, one of the only companies capable of growing pesticide-free, local, and sustainable spinach year-round, has announced that it will begin operations at its new 70,000 square foot Lafayette, New Jersey, greenhouse facility in the coming weeks. The company will outfit its new site, once home to a horticulture company, with proprietary technology and supplemental lighting to produce a wider variety of leafy greens at a higher yield and lower cost than most competitors. At full capacity, Element Farms will produce over half a million pounds each year of pesticide-free baby spinach, arugula, baby lettuces, pea shoots, beet greens, and more.
The new facility is an evolution from Element Farms’ current home: the structure is made entirely of glass, which allows for more efficient transmission of sustainable natural sunlight, and the hilltop location moderates temperatures, bringing heating and cooling costs down during the company’s year-round production.
Most of the operation’s everyday tasks will be automated with Element Farms’ custom machinery, like seeders and harvesters, to increase yield per square foot. The new greenhouse is ideally situated on delivery routes for New York, New Jersey, and Pennsylvania’s population-dense and produce-hungry cities. As before, greens will be delivered directly to retailers within 24 hours of harvest for maximum shelf life.
“We couldn’t be more excited for our new greenhouse. We’re customizing every aspect for operational efficiencies, integrated pest management, and sustainability,” said company founder Serdar Mizrakci. “We’re also thrilled that we’ll be able to meet our ever-increasing demand and bring more pesticide-free, safe, and delicious greens to the retailers and customers who have been clamoring for it.”
The new greenhouse will have dedicated areas for research and development and fully climate-controlled space for both growing and packing. As the company grows, so will the facility: the rest of the property is similarly zoned for agriculture and can support more acres of greenhouse space. Element Farms expects to double its greenhouse team after launch and bring jobs to the surrounding area.
Mizrakci started Element Farms as an MBA student at Cornell University’s Johnson School of Management after learning that most leafy greens consumed on the east coast make a week-long trek from California and lose freshness and nutrients in transport. He envisioned and executed a better process based on his independent study work with co-founder Danny Janeczko at the College of Agriculture and Life Sciences at Cornell, his own expertise as an industrial engineer, and his passion for good food.
The Lafayette greenhouse is just the first part of Element Farms’ growth plan. The company is currently pursuing greenhouse projects in two other states where the markets for year-round local produce are ripe for disruption. Element Farms expects to announce these projects in the coming year.
About Element Farms
Element Farms launched in 2016 with a single goal: to grow the purest, best-tasting greens for the most people possible. Element Farms is one of the only indoor controlled-agriculture companies that can produce local, pesticide-free, hydroponic spinach at scale year-round.
Founder Serdar Mizrakci has solved the biggest issues in indoor agriculture--inconsistency, plant disease, and high operational costs--by bringing farming back to its most basic elements: the plant, light, nutrients, and water. The company uses proprietary technology and renewable energy to seed, grow, and harvest its produce and higher yields and lower costs than most competitors.
The Element Farms greenhouse is located in Lafayette, New Jersey. The brand’s current product line includes baby spinach, baby arugula, crispy lettuce, salad mixes, and more.
Learn more about the company at www.element-farms.com.
Images by Element Farms
3rd International Congress of Controlled Environment Agriculture Event, Held From 06-08 November 2019 Republic of Panama
We have world renowned speakers that are proven scientist, academics, businesspeople, consultants and experts on the specific topics they will impart
The theme of the Congress is: “APPLYING TECHNOLOGY IN FOOD PRODUCTION AND MARKETING.”
This third event of its kind, will continue to be the place to engage with experts from around the world, learn and apply the latest in controlled environment (CEA) for greenhouse and vertical farm owners and operators and establish lasting relationships.
SOME OF THE EXITING TOPICS WILL INCLUDE:
Growing Crops: Strawberries, leafy greens, herbs, micro greens, and more.
The biggest costs facing farms: Labor, climate and illumination.
Issues creating the most confusion: Water, nutrients, pest management and air flow.
Economic Models: How to financially manage your operation and much more!
We have world renowned speakers that are proven scientist, academics, businesspeople, consultants and experts on the specific topics they will impart. From Chiba University, to University of Arizona to Wageningen, from well known companies and in-between, the topics
Controlled Environmental Farming Inc. Guarantees Results For Its Urban Farming, Localized, Food Production Model
CEF's guarantee comes in the form of a complete investment refund for all funds applied to the proposed project, funded by the purchaser of a License
Controlled Environmental Farming Inc, (CEF) through its Licensing Business Model, will guarantee economic results for facilities placed in Urban Farming locations. The economic guarantee comes in the form of a minimum operational margin of at least 40%. In many locations, the operating margin will exceed 40%.
CEF's guarantee comes in the form of a complete investment refund for all funds applied to the proposed project, funded by the purchaser of a License. The CEF License program details (see below) can be obtained by contacting CEF at conenvfarm@gmail.com and requesting the document. Costs for the program are quoted on an individual case by case basis.
CEF intends to address the demand for urban farming facilities, providing year-round nutritious quality food at competitive and consistent pricing through the construction of locally positioned controlled environment agricultural facilities. The facilities will cultivate a wide range of fruits, vegetables, herbs, shrimp and fish, individualized for local demographics and demand. The facility engineered as a kit, can be placed anywhere geographically and integrates a variety of renewable resources to control costs while reducing its carbon footprint.
With CEF facilities, product cultivation occurs through a proprietary closed-loop, aquaponics water flow system that uses the benefits of consolidating and intensifying sustainable product growth while eliminating the risk factors that affect product quality, quantity and pricing. Processing and distribution operations are also contained within the facility which has the benefit of streamlining operations and increasing food safety.
Controlled Environmental Farming Inc.
Licensing and Consulting Operations
Innovation Hub For Controlled Environment Agriculture Launched In Dundee
CHAP partnered with Liberty Produce to develop and build the IHCEA facility with funding from Innovate UK. The facility is a series of self-contained units housing state-of-the-art equipment with a modular structure designed to create a flexible environment for research and development
10th October 2019
London, UK
Agri-tech centre Crop Health and Protection (CHAP) and farming technology company Liberty Produce have launched the Innovation Hub for Controlled Environment Agriculture (IHCEA) at the James Hutton Institute’s site in Invergowrie near Dundee.
CHAP partnered with Liberty Produce to develop and build the IHCEA facility with funding from Innovate UK. The facility is a series of self-contained units housing state-of-the-art equipment with a modular structure designed to create a flexible environment for research and development. With integrated cutting-edge LED lighting systems and patented nutrient delivery technologies, this unique research facility will enable collaboration between industry, academia, and government to effectively tackle the barriers to widespread adoption of vertical farming. Its purpose is to accelerate the development of sustainable food production year-round through resource-efficient, fully-controlled systems.
The IHCEA is a key part of Liberty Produce’s Future Farming Hub, which will offer a wide range of services, including research and development and CEA training programmes within a commercial demonstrator system, as well as industry and academic collaboration opportunities.
The James Hutton Institute has welcomed the location of CHAP’s IHCEA and Liberty Produce’s Future Farming Hub in Invergowrie, in the context of the Institute’s drive for the establishment of Open Science campuses at its sites and this has been facilitated by the creation of the Advanced Plant Growth Centre at Invergowrie as part of the Tay Cities Deal.
Fraser Black, CHAP Chief Executive, said: “We are excited to be partnering with Liberty Produce and the James Hutton Institute to establish the Innovation Hub for Controlled Environment Agriculture (IHCEA), in Invergowrie. This is a prime example of CHAP’s mission to harness game changing ideas from our creative and innovative partners to solve the problems industry is facing today and tomorrow. This is a progressive step in our ambition is enable the United Kingdom to become a global leader in CEA and augment the production of healthy food in a sustainable way.”
Zeina Chapman, Liberty Produce Co-Founder and Director, added: “Vertical farming is not yet sustainable; this partnership which has established the IHCEA and Future Farming Hub at the James Hutton Institute marks an advancement of our collective journey towards creating truly sustainable vertical farming technologies. The greater vision of Liberty Produce remains driving innovation that will enable us to meet our global crop requirements without harming the planet.”
Professor Colin Campbell, Hutton Chief Executive, commented: “This collaboration with Liberty Produce and CHAP marks the next step in the growth of the Institute's Open Science Campus initiative and brings new innovative companies to work closely with world-leading science. This has been facilitated by Tay Cities Deal announcement to create an Advanced Plant Growth centre at Invergowrie and our other new investments there and builds on our track record of engaging with industry, research partners and the public.”
UK Government Minister Colin Clark said: “I am pleased to see the opening of this new Innovation Hub at the James Hutton Institute. We know that technological innovation is the future of sustainable agriculture and Scotland is home to world-leading resources and expertise in this field. The UK Government recognises the importance of this work and remains committed to funding research and development through our modern Industrial Strategy.”
It is hoped that the synergy between CHAP, Liberty Produce and the James Hutton Institute will provide a better understanding of total controlled environment technologies, drive innovation and accelerate the growth of the vertical farming sector in the UK.
**Ends**
About CHAP
Crop Health and Protection (CHAP), funded by Innovate UK, is one of four UK Agri-Tech Centres. CHAP’s vision is for the UK to be a global leader in the development of applied agri-technologies, to help secure our future by nourishing a growing population sustainably while delivering economic, environmental and health benefits to society.
CHAP acts as a unique, independent nexus between UK government, researchers and industry, building innovation networks to identify and accelerate the development of cutting-edge solutions to drive incremental, transformative and disruptive changes in sustainable crop productivity and to establish controlled environment agriculture (CEA) as a core competency.
www.chap-solutions.co.uk/
For further information contact:
Darren Hassall
Darren.hassall@chap-solutions.co.uk
+44 (0)1904 462062
About Liberty Produce:
Liberty Produce is a farming technology company, enabling the growth of local produce year-round, using a fully-controlled, industry-leading, indoor vertical farming system. With expertise in lighting and nutrient delivery technology, Liberty develops and builds systems that reduce operational costs and improve yields of crops grown in controlled-environment farms. Their vision is to drive innovations that will enable the UK to meet our crop requirements over the next century, without harming the planet. Liberty Produce established the Future Farming Hub to enhance UK technology development and commercialization in the Controlled Environment Agriculture (CEA) sector. www.liberty-produce.com
For further information contact:
Benita Rajania
+44 20 3290 8801
About the James Hutton Institute
The James Hutton Institute is a world-leading scientific organization encompassing a distinctive range of integrated strengths in land, crop, waters, environmental and socio-economic science. It undertakes research for customers including the Scottish and UK governments, the EU and other organizations worldwide. The ongoing collaboration between the James Hutton Institute and Scottish-based vertical farm technology business Intelligent Growth Solutions Ltd resulted in the opening of Scotland’s first vertical farm at the Hutton Invergowrie campus in August 2018, and continues to be a major strength in developing the Advanced Plant Growth Centre initiative, which has been backed by a £27m transformational investment from the Tay Cities Deal. www.hutton.ac.uk
More information from Bernardo Rodriguez-Salcedo, Media Manager, James Hutton Institute, Email Bernardo.RodriguezSalcedo@hutton.ac.uk, Tel: +44 (0)1224 395089 (direct line), +44 (0)344 928 5428 (switchboard) or +44 (0)7791 193918 (mobile).
Glase Provides Analysis of CEA Market Growth To Industry Members
Using the results of the USDA’s 2007, 2012 and 2017 censuses, Mattos discussed the national market growth of food crops produced under protection with detailed analyses of the top producing states
During GLASE’s Industry Talks series presentation, executive director Erico Mattos discussed changes to the CEA market based on USDA Census of Agriculture data.
By David Kuack
One of the benefits offered by the Greenhouse Lighting and Systems Engineering (GLASE) consortium to its industry members is its Industry Talks series. This series of informal conversations are presented by academics and field experts who focus on topics suggested by the consortium’s industry members.
During the consortium’s Industry Talks presentation in August, GLASE executive director Erico Mattos reviewed controlled environment production market growth based on the results of the USDA’s Census of Agriculture. Using the results of the USDA’s 2007, 2012 and 2017 censuses, Mattos discussed the national market growth of food crops produced under protection with detailed analyses of the top producing states. The full video can be accessed by GLASE members at the GLASE.org
Increasing value of protected food crops
Total market value for all protected food crops, including tomatoes, vegetables, berries, and fresh herbs, increased 17.9 percent from 2012 to 2017. Market growth for sales of all protected food crops increased 20 percent from $634 million in 2012 to $748 million in 2017. Greenhouse tomato sales increased 4.7 percent from $400 million in 2012 to $419 million in 2017. Other greenhouse vegetable sales increased 40.6 percent from $234 million in 2012 to $329 million in 2017. Fruit and berries sales decreased 13.5 percent from $29 million to $25.1 million even though production area for these crops rose from 7.9 million square feet to 11.7 million square feet.
Greenhouse tomato production area expanded from 55.1 million square feet in 2012 to 63.9 million square feet in 2017, a 16 percent increase. For other greenhouse vegetables, production area rose from 42.8 million square feet in 2012 to 48.6 million square feet in 2017, a 13.6 percent increase.
Only other greenhouse vegetables and fresh-cut herbs saw an increase in market share from 2012 to 2017, rising from 35 percent to 43 percent. Both greenhouse tomatoes and fruit and berries saw a decline in market share between 2012 and 2017. Tomatoes fell 6 percent from 60 percent in 2012 to 54 percent in 2017. The decrease for fruit and berries was only a 1 percent drop from 4 percent in 2012 to 3 percent in 2017.
Increase in protected food crop operations, production area
The number of protected growing operations increased for all crop categories between 2012 and 2017. The number of farms producing greenhouse tomatoes rose 26 percent, up from 6,323 operations in 2012 to 7,974 operations in 2017.
The number of farms producing other greenhouse vegetables rose 36.6 percent between 2102 with 5,268 operations to 7,198 operations in 2017.
Farms producing greenhouse fruit and berries also saw a double digit increase (25.7 percent), up from 673 operations in 2012 to 846 operations in 2017.
Number of small farms increasing
Mattos said the increase in the number of protected crop operations is driven by the establishment of smaller farms.
“There are a lot of smaller farms producing greenhouse vegetables, but they represent a very small part of the market share,’ he said. “In general, as the size of the farms increases the value of sales increases until the size of operations reaches 40,000 square feet or more where there is a dramatic jump in the value of sales.”
Small size farms from 1-999 square feet represent 31.6 percent of the number of farms in the United States. These small operations only cover 1.1 percent of the square foot production area for the total industry. These farms also only represent 1 percent of total sales. They are receiving a net rate of $5.74 per square foot for what they are selling.
Operations from 1,000 to 2,999 square feet account for 32.8 percent of U.S. farms. The net rate sales are the lowest for operations from 2,000 to 2,999 square feet at $4.42.
Those greenhouse vegetable operations with 20,000 to 39,999 square feet in size are earning the most money per square foot at $11.23 per square foot. Mattos said this size category might be a good mix of technology and greenhouse management and are definitely doing something right.
Mattos said there are fewer large farms producing greenhouse vegetables, but they dominate a big part of the market. The largest operations in the U.S. with 40,000 or more square feet represent 2.7 percent of the number of farms. However, they account for 67.6 percent of the square footage (76.1 million square feet) in the U.S. These large operations also have the highest value of sales per square foot at 67.8 percent. These farms are making $6.67 per square foot.
For greenhouse tomatoes, the largest operations are the most efficient, accounting for 74.5 percent of sales and having the largest return per square foot at $7.28.
Major protected-environment producing states
On a state-by-state basis for all greenhouse vegetable categories, the top state in regards to market share value was California with 46 percent, which had a market value increase of 26 percent from 2012 to 2017. Even though the number of farms decreased from 427 to 409, the amount of square footage grew 24 percent from 28.3 million to 35.2 million square feet.
Other leading states with market share included Texas (14 percent), Ohio (10 percent), New York (9 percent), Maine (8 percent), Virginia (7 percent) and Minnesota (6 percent). Ohio had the largest rise in sales, increasing from $10.5 million in 2012 to $43.8 million in 2017, accounting for an increase of 317 percent in just five years. Virginia also experienced a large sales increase (270 percent), going from $8.5 million in 2012 to $31.5 million in 2017.
While California still had the largest market share (33 percent) for greenhouse tomatoes, it wasn’t as dominant as it was for total greenhouse production. Other states which accounted for greenhouse tomato market share included Texas (21 percent), Ohio (13 percent), New York (12 percent), Minnesota (10 percent), Arizona (6 percent) and Illinois (4 percent).
States with the largest increase in tomato share included Ohio (908 percent increase), going from $3.2 million in 2012 to $32.1 million in 2017. Illinois also saw a major rise in greenhouse tomato sales going from $1.7 million in 2012 to $10.7 million in 2017, a 517 percent increase.
For other greenhouse vegetables and fresh-cut herbs, California dominates sales ($126. 2 million) with 60 percent of the market. Virginia followed with 11 percent of the market and Illinois had a 7 percent market share. These two states had the largest growth in this crop category with sales in Illinois rising 565.8 percent from $2.2 million in 2012 to $14.3 million in 2017. Virginia saw sales grow 245 percent from $6.7 million in 2012 to $23 million in 2017.
For more: Erico Mattos, Greenhouse Lighting and Systems Engineering (GLASE), (302) 290-1560; em796@cornell.edu; https://glase.org.
David Kuack is a freelance technical writer in Fort Worth, Texas; dkuack@gmail.com.
Posted in News
Netled To Supply SweGreen With Production Units
Netled has signed a distribution agreement with Swedish technology company SweGreen. They will start providing Vera Compact Production Units for SweGreen’s urban farming destinations in Sweden. SweGreen is an innovation and technology urban farming company based in Stockholm. The company provides circular solutions for controlled-environment urban farming
Netled has signed a distribution agreement with Swedish technology company SweGreen. They will start providing Vera Compact Production Units for SweGreen’s urban farming destinations in Sweden.
SweGreen is an innovation and technology urban farming company based in Stockholm. The company provides circular solutions for controlled-environment urban farming. By integrating smart vertical farming solutions into real estate properties SweGreen provides circular energy-waste-water and carbon-absorbing systems, which enable locally grown, quality greens and help minimize the environmental footprint of facilities. Under the brand Stadsbondens, SweGreen’s CityFarm in Stockholm produces herbs for ecological-minded citizens all year round in a sustainable way.
Netled´s Vera Compact Production Units are especially well-suited for limited scale production of salads, herbs, seedlings and pot plants, and will complement SweGreen’s efforts perfectly.
For more information:
Netled
netled.fi
Publication date: Tue, 08 Oct 2019
US (AZ): Controlled Environment Indoor And Vertical Food Production Coordinated Research Conference
FarmTech Society board member Penny McBride—who chairs the FTS committee on standardization—presented on the need for standards for food safety and was honored to sit on a panel alongside NASA plant scientists Gioia Massa and Arizona Food Safety inspector Stewart Jacobson
This year’s USDA–NIFA Conference, held at Biosphere 2 outside of Tucson, AZ, from September 9 to 12, brought together a diverse set of experts in the industry—scientists, engineers, economists, business people, and policymakers—to hear from panelists and form ongoing working groups.
Hosted by the University of Arizona’s innovative Controlled Environment Agriculture Center (CEAC), the goal of the conference was to create an interdisciplinary Controlled Environment Agriculture R&D Roadmap and Coordinated Research Plan, which will help these stakeholders apply for funding from the USDA to help fast-forward the CEA industry through basic and applied research.
The conference’s keynote speakers, panels, and breakout groups focused on:
Economics
Engineering
Production systems
Plant breeding
Pest and disease management
Food nutrition and safety
Industrial ecology in closed systems
FarmTech Society board member Penny McBride—who chairs the FTS committee on standardization—presented on the need for standards for food safety and was honored to sit on a panel alongside NASA plant scientists Gioia Massa and Arizona Food Safety inspector Stewart Jacobson. How CEA production can affect health and nutrition emerged as a key line of inquiry for researchers going forward.
Fellow board member Wythe Marschall—who chairs the FTS committee on education—served as record keeper for the engineering working group. The engineering group agreed on a need for benchmarks and open standards for lights, energy, sensors, and plant breeding.
Overall, FTS was brought into a series of discussions with leading CEA experts, furthering our mission of connecting the industry at a pre-competitive level and creating a platform for amplifying industry voices at the level of university education, government research, and policy.
The final day, conference participants met to discuss the current funding landscape for CEA and form new grant-writing groups to develop specific grant proposals.
For more information:
FarmTech Society
Tom Zoellner
tz@farmtechsociety.org
farmtechsociety.org
Publication date: Fri, 27 Sep 2019
CAN (ON): University of Guelph Has A New Controlled Environments Professor
The School of Environmental Sciences is pleased to welcome Thomas Graham as the new PhytoGro Research Chair in Controlled Environment Systems
Thomas Graham is the new PhytoGro Research Chair in Controlled Environment Systems
The School of Environmental Sciences is pleased to welcome Thomas Graham as the new PhytoGro Research Chair in Controlled Environment Systems.
In this new role, created through a $1 million donation from PhytoGro Canada, a PRM Inc. company, Graham will lead cutting edge research to develop novel approaches in controlled environment plant production systems in a range of applications from urban agriculture and phytopharmaceutical applications to space exploration.
“Thomas has a strong resume with impressive industry connections,” says Prof. Jon Warland, director of the School of Environmental Sciences. “He is well known in the American, German and European space agencies for his bio-regenerative life-support research, and it is great to have his unique skill set and knowledge part of our faculty.”
One of Graham’s primary areas of focus will be the optimization and standardization of plant-based medicine production, including medicinal cannabis.
“Most of the global population still relies on plant-based medicines as their primary medical intervention,” says Graham. “This puts an enormous and unsustainable pressure on the largely wild-harvested plants. Bringing these crops into controlled environment production will improve the quality, consistency, and safety of these medical commodities while also relieving the pressure on wild populations.”
“We feel extremely fortunate to be working with Professor Graham and the whole team at CESRF,” shares Ken Clement, founder of PRM Inc. “My dreams of producing plant-based medicine to pharmaceutical standards would not be possible without the efforts of the entire team and for that, I will be forever grateful.”
“I’m very excited for the opportunity to leverage leading-edge technology to tackle many of the pressing issues of our time,” says Graham.
“The University of Guelph is in a truly unique position to make major advances in several key areas including plant-based medicine production and standardization, addressing food insecurity, and advancing human space exploration through bioregenerative life-support.”
Graham is also very passionate about how controlled environment agricultural production can solve food insecurity issues in Canada and around the globe.
Graham has been the Research and Development Manager at the University’s Controlled Environment Systems Research Facility since 2015. Prior, he held a prestigious post-doctoral research fellowship at N.A.S.A. at the Kennedy Space Centre. He received both his Ph.D. and MSc from the University of Guelph. His B.Sc. is also from the University of Guelph, with part of the degree completed through an exchange with the University of Stirling in Scotland. To date, he has published 37 peer-reviewed articles.
Publication date: Thu, 26 Sep 2019
How To Avoid Calcium Deficiency In Controlled Environment Food Crops
Tipburn and blossom end rot are symptoms of calcium (Ca) deficiency. Sometimes the first thought when a nutrient deficiency occurs is to add the nutrient that appears to be required to solve the issue
Tipburn and blossom end rot are symptoms of calcium (Ca) deficiency. Sometimes the first thought when a nutrient deficiency occurs is to add the nutrient that appears to be required to solve the issue. This isn’t always the best way to resolve the issue.
Calcium has a very important role in plant cell wall formation. If calcium cannot reach new cells in adequate time, cell wall formation cannot be completed. This can result in necrotic (dead) tissue in the leaves (tipburn) and fruit (blossom end rot) as consequence of cell death. This is why calcium uptake from roots to leaves is a very important process.
Calcium movement in plants
The main force moving calcium through plants is water. When plants transpire calcium moves. Calcium will only be present in plants when water is moving. Most cases of calcium deficiency in greenhouse crops is due to environmental conditions, not a nutrient deficiency directly related to the nutrient solution being applied.
Calcium deficiency triggers
There are several environmental conditions that can trigger calcium deficiency. The most common factors include:
Low relative humidity. When plants are exposed to low relative humidity levels, small pores in leaves called stomata close. Stomata are responsible for transpiration. Calcium movement depends entirely on stomata behavior. It is important to know optimum relative humidity levels for each crop and to keep the humidity levels as uniform and consistent as possible. The humidity in a greenhouse can be increased by running water through the evaporative cooling pads and/or by installing a fog system if necessary.
Lack of airflow over the crop. There needs to be air movement around the leaves to ensure continuous gas exchange. The airflow velocity around the plant leaves can be reduced as a result of the friction between the leaf surface and the moving air. This creates a boundary layer which is a layer of heavy air that can decrease gas exchange in plants. This reduction in gas exchange can impact calcium uptake by the plants.
This reduction in calcium uptake is common in greenhouse lettuce. Lettuce has a very tight leaf canopy. New leaves are usually exposed to a very dense boundary layer. Good airflow over the crop canopy is required to avoid tipburn. Installation of vertical fans is usually recommended to improve airflow in lettuce greenhouses. It is also important to maintain proper airflow in vertical farms. A 1 meter per second air velocity rate in each vertical layer is recommended for leafy greens.
High light intensity in vertical farms. With indoor farm production, there are many variables that need to be controlled to ensure good crop performance. Two variables that together can trigger tipburn are light intensity and the boundary layer. When plants are located close to the grow lights, the light intensity tends to increase and space for airflow decreases.
If plants are exposed to the same photoperiod during the entire production cycle, the total daily light integral (DLI) tends to increase with time. Recent research demonstrated that in indoor vertical farms when plants are exposed to a DLI that exceeds 17 moles of light per square meter per day (mol·m-2·d-1) for more than three days tipburn is triggered.
Excess humidity. Some crops including tomato show tipburn under high relative humidity environments. Transpiration from roots to leaves increases under high relative humidity levels. When the relative humidity is too high for tomato calcium uptake goes directly from the roots to the leaves bypassing the fruit. This is why sometimes blossom end rot (calcium deficiency in fruit) occurs in tomato fruit but no deficiency symptoms appear on the leaves.
Avoiding calcium deficiency
When calcium deficiency is seen in plants make sure to check that the fertigation system is operating properly. If the fertilizer stock solution is maintained in multiple tanks, check all reservoirs to ensure the same solution levels so that all nutrients are being delivered uniformly to all crops.
But remember to always monitor environmental conditions before adding calcium to any crop. Excess calcium can cause other nutrient deficiencies. If the decision is made to apply foliar calcium, then this treatment is required during the whole production cycle to avoid calcium deficiency. Foliar calcium applications to prevent calcium deficiency might be avoided if the production environment is properly controlled.
US - OHIO: Great Lakes Ag-Tech Summit - September 23, 2019
Join Urban Ag News, Hort Americas and Current, powered by GE, for the inaugural Great Lakes Ag Tech Summit on September 23rd
Don't miss the opportunity to hear from this year keynote speakers, Austin Webb (Robotany) and Chieri Kubota (The Ohio State University.)
Join Urban Ag News, Hort Americas and Current, powered by GE, for the inaugural Great Lakes Ag-Tech Summit on September 23rd. Held at the historic Nela Park campus in Cleveland, the one-day event features keynotes and panel discussions from leading researchers and innovative growers in the Great Lakes region. Connect with growers, scientists, researchers and entrepreneurs as we shape the future of food and move controlled environment agriculture forward.
Register Now!
We have added a panel to the agenda!
Hear Michel Doss, Paul Brentlinger, Dr. Chieri Kubota, Dr. Ariana Torres, Austin Webb and Chris Higgins at the end of the day as they recap and take your questions!
Location
The Institute at Nela Park
1975 Noble Rd. Cleveland, OH 44112
When
Monday, September 23, 2019
9 am to 4pm
Cost
Early bird ticket cost is $30 if you register before September 16.
Regular admission $50.
Keynotes
Optimizing Plant Production Under a Controlled Environment – Research and Education Programs at the Ohio State University
Dr. Chieri Kubota – Ohio State University
Dr. Kubota’s research mission is to serve in the development of science and technology in the area of controlled environment agriculture (CEA). Her projects are in an interdisciplinary area that encompasses plant physiology and horticultural engineering to enhance understanding and efficiency of CEA plant production systems such as greenhouses, warehouses (vertical farms), and growth chambers.
Are Consumers and Growers Putting Dollars in the Local Food Industry? Insights on Technologies and Preferences
Dr. Ariana Torres – Purdue University
Dr. Torres’ background combines field experience in agriculture with theoretical and applied research on agricultural economics. She has worked on projects looking at the impact of marketing choices on technology adoption for fruit and vegetable growers; the economic implications of social capital on entrepreneurship; and the role of community support on the resilience of small business after disasters.
Dr. Torres uses economic analysis to support the economic viability of the horticulture industry. Her research focuses on the intersection between the horticulture industry and marketing decisions. Her goal is to conduct innovative outreach and applied research in Specialty Crops Marketing, with the end of promoting economic sustainability for horticultural businesses.
Dr. Torres is currently working on a project evaluating the market, economics, and potential barriers to produce export-quality dried apricots from smallholders of southern Tajikistan. She is also working on evaluating the adoption of solar dehydrator for selected dried specialty crops in Indiana and Georgia. Lastly, she is collecting foundational data and establishing long-term pricing reports for Indiana farmers’ markets.
Agenda
Start: 9 am 09/23/19
9-9:30 am Introduction from Current
Brief history of Nela Park and Thomas Edison’s Institute
9:30-10 am Introduction from Hort Americas/Current
Chris Higgins, Owner of Urban Ag News and President of Hort Americas, LLC
Michel Doss, General Manager of Specialty at Current, powered by GE
10-10:45 am Keynote: Hear from a New Vertical Farming Company
10:45-11 am Break
11-11:45 am Panel discussion
Participants and topic TBD
11:45-1pm Lunch
1-1:45 pm Keynote: Ohio State University
Dr. Chieri Kubota
Dr. Kubota’s research mission is to serve in the development of science and technology in controlled environment agriculture (CEA). Her projects are in an interdisciplinary area that encompasses plant physiology and horticultural engineering to enhance understanding and efficiency of CEA plant production systems such as greenhouses, warehouses (vertical farms), and growth chambers.
1:45-2:30 pm Keynote: Purdue University
Dr. Ariana Torres
Ag economist focused on the marketing and economics of specialty crops, especially those grown in controlled environments. Courses instructed center on entrepreneurship, marketing and the economics of specialty crop production. Researches technology adoption for specialty crop operations, and how consumers perceive grower technologies.
2:30-2:45 pm Break
2:45-3:30 pm Panel discussion
Participants and topic TBD
3:30-3:45 pm Closing remarks
Hort Americas and Current, powered by GE
Sensing The Rise of Vertical Farming
Vertical farming is the process of food being produced in vertically stacked layers, instead of on a single level such as in a field or greenhouse. The layers are commonly integrated into urban structures like skyscrapers, shipping containers and repurposed warehouses
August 28, 2019
By Darcy Simonis, Industry Network Leader, ABB Food and Beverage
With over 7,800 high-rise buildings, the city of Hong Kong soars above all others. More than 300 of its buildings surpass 490 feet, with more people living over 15 floors above ground level than anywhere else in the world. Having a skyline in the clouds helps the densely populated metropolis to prosper where space is restricted. Agriculture has taken note of this construction technique, as vertical farming creates impressive yields.
Vertical farming is the process of food being produced in vertically stacked layers, instead of on a single level such as in a field or greenhouse. The layers are commonly integrated into urban structures like skyscrapers, shipping containers and repurposed warehouses.
Using Controlled Environment Agriculture (CEA) technology, the artificial control of temperature, light, humidity and gases makes it possible to produce a vast array of crops on an industrial scale — without any outdoor exposure.
The Sky’s the Limit
By 2050, around 80 per cent of the world’s population will live in urban areas. With agricultural space in these areas scarce or completely non-existent, how do we deliver produce?
It is estimated that one acre of vertical farming offers the equivalent production of at least four to six acres using conventional outdoor methods. As the plant’s growth is not dependent on sunlight or affected by meteorological conditions, production can continue at the same rate all year round. In terms of resources, the plants require as much as 70 per cent less water than traditional farms.
Organic crops are a huge market, with demand often outstripping supply. As vertically farmed crops are produced in a well-controlled area, there is far less need for chemical pesticides. It is also believed that vertical farming could bring fresh produce closer to urban populations, reducing the risk of nutrients diminishing during transport.
No More Soil
Hydroponics is a predominant growing method in vertical farming. The process involves growing plants in nutrient solutions that are essentially free of soil, as roots are submerged into the solution and the plants are regularly monitored to maintain the correct levels of chemical composition.
If we’re ever to fulfill futuristic plans of colonizing Mars, we’re going to need to grow our own food. So, where on Earth has the conditions to test out this method?
It may not share the same qualities as the Red Planet, but Antarctica’s nonstop winters make it impossible to grow produce outdoors, and fruits and vegetables are shipped long distances from overseas just a few times a year.
In a step closer to extraterrestrial farming, a semi-automated hydroponic facility grows plants without soil, using mineral nutrient solutions in a water solvent. Scientists on Germany’s Neumayer Station III grow produce in a 20-foot-long shipping container, cultivating greens in an area where such produce is usually limited. This is just one example of how vertical farming techniques can be used in areas affected by harsh weather conditions.
Sensing Growth
To hit high levels of production, growth conditions in vertical farms must be continuously optimized. Sensors and data must be used to effectively track variables such as climate, nutrient composition and light levels.
Climate is characterized by a combination of air temperature, humidity and carbon dioxide (CO2) levels. The effects of these factors are tremendous. The difference between plant and air temperature, for example, can tell us whether the leaves’ stomata are open. If they’re closed, the plant cannot absorb CO2 and convert it into biomass. We can also measure the light level and spectrum as perceived by the plants and the pH of irrigation water for optimal growth.
Using smart sensors that can monitor these variables will ensure that vertical farms produce yields that greatly exceed those of conventional farms, which are impacted by uncontrollable conditions.
With a skyline full of modern, gleaming constructions, Hong Kong makes the most of its space to deliver prosperity. While vertical farming still has a long way to go before it is commercially viable, it is certain that food producers can learn from the techniques it applies to help deliver produce our rising populations.
Hydroponic Farms Use Less Land, Water To Grow Vegetables
Growing lettuce and other leafy greens indoors is gaining traction nationwide, as such big players as New Jersey-based Aero Farms and Bowery, are producing huge quantities in giant warehouses fueled by millions of dollars in investment
By Susan Salisbury For The Palm Beach Post
August 12, 2019
Green Life Farms’ hydroponic greenhouse occupies nearly 3 acres. It expects to yield 750,000 pounds of premium leaf green produce throughout the year, said Mike Ferree, vice president. The greens are grown, harvested and packaged onsite. [CONTRIBUTED BY HYDRONOV}
Greenhouses Allow Year-Round Growing
And Protection From Freezes And Extreme Rainfall.
Growing lettuce and other leafy greens indoors is gaining traction nationwide, as such big players as New Jersey-based Aero Farms and Bowery, are producing huge quantities in giant warehouses fueled by millions of dollars in investment.
The push comes as farmland becomes increasingly expensive and in short supply, and consumers demand locally grown produce that’s fresher because it hasn’t been transported hundreds of miles.
In Palm Beach County two new hydroponic farms—Green Life Farms and Patagonia Green Leaf— are being launched in greenhouses off U.S. 441 west of the Lake Worth Beach/Boynton Beach area. Hydroponic farming uses no soil. Instead, crops are grown in perlite, coconut fiber or nutrient-rich water in a controlled and enclosed environment.
Art Kirstein, agricultural economic development coordinator with the Palm Beach County Cooperative Extension Service, said that hydroponic farming offers advantages such as year-round growing, increased capacity on a smaller amount of land and protection from freezes and weather events such as extreme rainfall.
Green Life Farms harvested its first crop of baby arugula, baby romaine and baby spinach in mid-July. Its greenhouse occupies nearly 3 acres and will yield approximately 750,000 pounds of premium leaf green produce throughout the year, said Mike Ferree, vice president.
Baby romaine lettuce grows in the Green Life Farms hydroponic greenhouse off U.S. 441 west of Lake Worth Beach. The company has spent $15 million on the facility.
The greens are grown, harvested and packaged onsite, then picked up or shipped directly from the farm. They are also GMO and pesticide-free.
Green Life’s head grower, Greg Graft, said the produce is mechanically harvested using an automated system.
The first crop is not available for sale. Once Green Life begins official commercial production, products will be available at local grocery stores, restaurants and other locations, Graft said.
Green Life chose Palm Beach County for its large consumer market, proximity to sales partners and an agriculture-friendly environment, Graft said. It has invested $15 million so far.
Green Life uses a deep-water floating raft technology from Hydronov, an Ashley, Ind.-based leader in the hydroponic industry with more than 30 years of experience.
The floating raft system helps to conserve water, using the oxygenated clean water in which the plants grow as a conveyor system. Green Life will be able to produce 18 harvests each year and use 90 percent less water than conventional farming.
Patagonia Green Leaf, about a mile south of Green Life, is a hydroponic farm on a former plant nursery. It’s owned by the Canosa family. They’ve farmed in the traditional way in Argentina for 10 years.
The first phase of 10 greenhouses totaling 30,000 square feet is completed. The initial crop of baby greens will be planted soon, with harvesting expected by late September.
“The idea is to harvest and deliver the product within 24 hours,” said Juan Ignacio Canosa, who lives in Boca Raton.
After visiting Miami and Fort Lauderdale on vacations, the family started coming to Boca Raton. Last year they bought 5 acres from Boynton Botanicals, whose owner was retiring.
Plants will be grown pesticide-free using a system known as NFT, (nutrient film technique) from Arcata, Calif.-based AmHydro. A pump delivers fertilized water to the growing trays, flows over the plants’ roots, then drains back into the reservoir and is recycled.
Robert Hochmuth, regional extension agent with the University of Florida’s North Florida Research and Education Center, said since the early 2000s, the number of acres of produce grown in greenhouses and other structures in Florida has increased five-fold to more than 500 acres.
Producing in protected structures extends the season and reduces insects and diseases, Hochmuth said.
“You can be a consistent supplier in the marketplace over a long period of time,” Hochmuth said.
Most of the hydroponic farms in Florida are less than an acre and tend to cater to local markets.
Hochmuth said hydroponic growing is attracting people who are new to farming.
“Because they are going with high-value specialty crops, the likelihood of profitability makes sense,” Hochmuth said.
Of course, greenhouses and other facilities are at risk of being destroyed during hurricanes or high winds. Hochmuth advises removing the plastic from the structures prior to storms because it acts as a sail.
Hydroponic farming isn’t new to Palm Beach County. Walter Ross founded Farmhouse Tomatoes west of Lake Worth in 1996 and grows heirloom tomatoes in 160,000-square-feet of greenhouses from Nov. 1 through June 30.
Thriving Needs for New Ways to Cultivate Crops Is Likely To Foster The Controlled Environment Agriculture Market At 16.9% CAGR During 2019 & 2024
Land use across the globe is shifting from agriculture to urban and industrial uses. Changing climate has also resulted in lower production yields, loss of arable land and reduced resilience
Global controlled environment agriculture market accounted for USD 57,656.6 Million in 2018 and is estimated to reach USD 1,42,222.6 Million in 2024, registering a compound annual growth rate (CAGR) of 16.9% between 2019 and 2024.
Rising Global Demand for Food
The world’s population is expected to grow to almost 10 billion by 2050. It is becoming increasingly difficult to satisfy the rising global demand for food in a sustainable manner. Due to this, in order to meet the food demand of an increasing population, the government and farmers are adopting more advanced farming techniques such as Hydroponics, Aeroponics, Aquaponics, soiled based and other hybrid methods.
The farmers are majorly growing leafy greens, tomatoes, cannabis, flowers, microgreens, strawberries, herbs, cucumbers, peppers, mushrooms, onions, leeks, hops, figs, sweet corn, eggplant, fish, insects, carrots, and shrimp. This rising popularity of controlled environmental agriculture techniques is resulting in an increase in the number of small and large indoor farms across the globe and these farms are also encouraging the consumption of other supplies such as nutrients, growing media, and others.
Loss of Agricultural Land
Land use across the globe is shifting from agriculture to urban and industrial uses. Changing climate has also resulted in lower production yields, loss of arable land and reduced resilience. Further, growing scarcities of natural resources have been encouraging the adoption of CEA since controlled environment farming an efficient way to produce more food with fewer resources than conventional farming, without being dependent on arable land availability and external climate conditions.
Strong Demand for Local Foods
Today, 55% of the world’s population lives in urban areas, a proportion that is expected to increase to 68% by 2050. Yet, the population living in urban areas are demanding locally grown foods such as fruits, vegetables, meat, etc. CEA producers across the globe are setting up their production centers near to urban consumers to take advantage of this trend due to their proximity to urban centers. Other advantages of CEA such as the requirement of less time and expense in the transportation of crop products and better product quality are also expected to strengthen the growth of global controlled environment agriculture market in upcoming years.
Remarkable Advantages of CEA
Conservation of water and nutrients is one of the many advantages of controlled environment agriculture over conventional farming methods. These advanced farming techniques such as hydroponics, aquaponics, and other soilless farming methods are effectively preventing wastage of water and overuse of nutrients. In a controlled environment, the plants have better health and faster growth, which reduces the need for pesticides and other supplements. Owing to their good health, CEA grown produces are noticeably better in both size and quality then soil-grown crops.
Barriers in CEA Market
The high cost of Nutrients used in Hydroponics
Although, CEA allows faster plant growth throughout the year, allowing larger yields. In order to do this, like any form of agriculture, CEA production is a high-risk, low margin enterprise. Establishing a CEA hydroponic vegetable operation requires considerable capital investment. Depending on the size of the operation and the level of technology involved, the investment can run into the tens of millions of dollars. This high required investment, high operating cost and high risks a huge challenge for growers and for the controlled environment agriculture market.
Lack of Awareness & Low Adoption Rate
The awareness regarding controlled environmental farming methods in underdeveloped countries is other countries which are restricting the growth of global controlled environment agriculture market. The dominance of traditional farming methods in low-income countries such as India is slowing down the growth of CEA market.
The need of skilled labors & Operational Complexity
CEA industry is witnessing a shortage of skilled labors, also the labor cost is considerably high in the case of hydroponics farming. The labor cost accounts for almost 15% of the total operation cost of hydroponics farming. Controlled environment agriculture requires great precision in monitoring. Growing in controlled environments and providing proper plant nutrition requires quality farm education. High level of operating complexity is also a major restraining factor in the growth of CEA market.