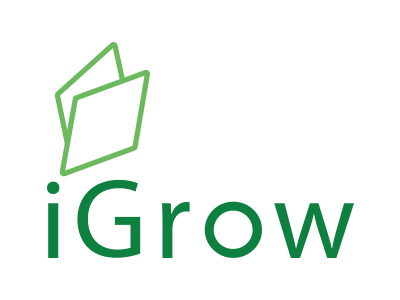
Welcome to iGrow News, Your Source for the World of Indoor Vertical Farming
2nd Urban Agri Africa 2018
The world’s population is expected to increase by about 3 billion by 2050 and it is forecasted that nearly 80% of that population will live in urban centers.
Africa’s urban growth rate is at 3.5% the highest in the world and doubles the world average. The challenge of growing enough healthy food for Africa’s growing cities is enormous. At the same time, the stresses of climate change, and the declining availability of arable land and fresh water are challenging conventional agriculture as never before.
Many countries and companies are expressing strong interest in vertical farming business and urban agriculture. It is a solution to the weather and pests problems, food security, climate change and environmental preservation. Commercialization of vertical farming is catching on in Asia, Europe, USA, Russia and now Africa.
Many private companies are interested in growing crops in hydroponics, aquaponics and aeroponics systems in warehouses, greenhouses, containers and high scrapers. There is also a burgeoning interest in the production of medicinal plants in vertical farms.
Africa has unique opportunities for vertical farms. Feeding Africa’s rapidly growing urban population will continue to be a daunting challenge, but vertical farming – and its variations – is one of the most innovative approaches that can be tapped into as part of an effort to grow fresh, healthy, nutritious and pesticide-free food for consumers.
Learn more at 2nd Urban Agri Africa 2018 to be held on September 25-26 in Johannesburg, South Africa. The latest joint ventures and partnerships will be highlighted, case studies shared and strategies robustly debated. New trends, opportunities, and technologies will be showcased, once again providing the perfect platform for extraordinary networking opportunities for all Summit participants.
Find out more at 2nd Urban Agri Africa 2018.
To register or request event details... Contact
Jose at +65 6846 2366 or jose@magenta-global.com.sg today.
Record Harvest At Antarctic Greenhouse
77 kilograms fresh lettuce, 51 kilograms cucumbers, 29 kilograms tomatoes
The Antarctic greenhouse EDEN ISS has weathered the polar night – as well as Antarctic storms and temperatures below minus 40 degrees Celsius – in its practical test under the direction of the German Aerospace Center (Deutsches Zentrum für Luft- und Raumfahrt; DLR). It has been yielding herbs, lettuce and freshly harvested vegetables to the 10-member overwintering crew in the Alfred Wegener Institute’s Neumayer Station III for the first time since the beginning of 2018.
After more than half a year of operation in Antarctica, the self-sufficient greenhouse concept appears to be effective for climatically demanding regions on Earth, as well as for future manned missions to the Moon and Mars.
DLR researcher Paul Zabel is overcoming challenges, as well as acquiring knowledge from cultivating plants under such harsh conditions. To the overwintering team, the fresh greens are a welcome change during their long-term isolation. Zabel reported on his experiences in a live transmission from Antarctica on 13 September 2018.
Plenty of lettuce and tomatoes, few peppers, and no strawberries yet
“The harvests are now so plentiful that some of it does not always make it straight to the table, and we now have the luxury of spreading out our consumption of some refrigerated lettuce and herbs over several days,” Zabel says. “The overwintering team members are always looking forward to their next fresh meal.” Indeed, the lettuce, tomatoes, cucumbers and herbs thrive especially well under the conditions of 21 degrees Celsius and 65 percent relative humidity in the greenhouse. Seventy-seven kilograms of lettuce, 51 kilograms of cucumbers, 29 kilograms of tomatoes, 12 kilograms of kohlrabi, five kilograms of radishes and nine kilograms of herbs have been grown and harvested on a cultivation area of about 13 square metres.
“What astonished us was the failed harvest for peppers and strawberries,” Zabel says. The pepper and strawberry plants grow quickly in Antarctica as well, but the artificial pollination causes some problems, whereby only a few fruits or – in the case of strawberries – none at all have been produced. EDEN ISS Project Manager Daniel Schubert adds: “The pepper plants bore ample fruit during the greenhouse trial run in Bremen last year. This shows how important and instructive the greenhouse’s extreme test under Antarctic conditions is.”
Greenhouse technology in extreme conditions
Quite often, a storm prevents Zabel from making the 400-metre outdoor trip from the Neumayer Station III to the greenhouse. Under these circumstances, the control centre in Bremen takes complete responsibility for monitoring the plants and supervising the greenhouse. However, this has been necessary on no more than three consecutive days so far, so Zabel has been able to do a good job of ensuring that the plants receive continuous care. The importance of his presence on site has been demonstrated repeatedly at times when the greenhouse technology has run into difficulties under the extreme conditions and urgent assistance has been needed. “On one occasion, for example, I had to go to the greenhouse quickly because a screw had come loose in the thermal system, and the lamp cooling was no longer sufficiently ensured.” Small repairs like these are hardly foreseeable and teach the researchers about the greenhouse concept and how to make its design more robust in future.
“It is important for us to be able to react when there are complications with the existing tools and resources on site. After all, the sound operation of a greenhouse on the Moon and Mars would be essential for survival,” says Schubert, the Project Manager. Forty different experiments are currently running in the greenhouse. This means a lot of work for Zabel, as he extensively analyses the cultivation of vegetables. His tasks include taking regular microbiological samples, examining the precise quality of the harvest, and periodically checking all systems, such as light, temperature regulation, and the nutrient- and carbon dioxide-enriched air supply. He also documents how fresh food is affecting the health of the overwintering team members.
Sharing the fun live with strawberries and peppers, and providing tips
Gaining insights into Antarctic plant cultivation has so far been reserved for the international researchers on the project, but everyone will have this opportunity in the future. “Until now, we in the control centre have received daily images of the individual plants through 32 cameras in the greenhouse. The researchers involved have access to these images and can provide the relevant tips,” Schubert says. “Now, we are opening these plant images to the public via an online tool on the EDEN ISS project website. Anyone who is interested can take part live in our vegetable cultivation in the Antarctic.” Every day, photos of the individual plant cultivation boxes are automatically taken at a specific time and under special lighting conditions. These images are then transmitted to the mission control centre in Bremen and made available online. The plant growth can be followed via an interactive timeline. In this way, people can interactively participate in a technology that will become more important in the future.
Positive effect is noticeable
Eberhard Kohlberg from the Alfred Wegener Institute, who is the logistics manager for the Neumayer Station III and has been a member of the overwintering crew on several occasions, says how pleasant it is to have a garden with lettuce and herbs just around the corner: “Otherwise, the menu just consists of long-life products from the freezer and storage room.” Only at the end of October 2018 will the first supply aircraft be able to provide the overwintering team with fresh food items from the outside world once again. Neumayer III station manager Bernhard Gropp adds: “We greatly value and enjoy the fact that regularly fresh salad, herbs and vegetables from the greenhouse enrich our diet. The positive effect is noticeable.” The last part of the winter is particularly challenging for the crew, as they gradually have to switch back to normal operation with many people at the station.
For more information:
EDEN ISS
Are Hot Springs The Future of Farming?
A small Colorado town is using its hot springs for an unusual purpose: growing food year-round. And with geothermal energy in abundance, this could be a model used across the US.
By Daliah Singer - 10 September 2018
The tomatoes aren’t cooperating. Instead of growing up the trellis, the plants are weaving all over the garden bed and arching, menacingly, toward a young grapevine. On a hot August afternoon, Pauline Benetti and Diane Kelsey are trying to coach the fruit upward by tying its stems to the wood-and-metal trellis.
It’s high season for the juicy red spheres, but these two volunteers – both shorter than the vines they’re trying to wrangle – aren’t just struggling with these plants for the final farmers’ markets of the summer. They want to train the tomatoes to grow in the right direction inside this greenhouse all year long.
Their work is part of a five-year effort by the Geothermal Greenhouse Partnership (GGP) in Pagosa Springs, Colorado. The volunteer-run nonprofit, in coordination with the south-west Colorado town, is transforming the world's largest and deepest geothermal hot spring into something much more than just a travel destination: it’s using the renewable energy source to grow food year-round for the community.
Pagosa Springs is well-known in the western United States for its unique approach to geothermal energy, which is energy harnessed from the Earth’s heat. Geothermal food growing, though, is a new enterprise.
You might also like:
• How vertical farming reinvents agriculture
• Are forgotten crops the future of food?
• The most extreme geothermal plant in the world
In the center of the small downtown, on the banks of the San Juan River, sit three conspicuous, geodesic greenhouses, each 42ft (13m) in diameter. They stand in stark contrast to the old-timey buildings on the road above. All will house gardens, but each has a different mission.
The project’s three greenhouses use geothermal energy to help grow plants even in Colorado’s cold-weather months (Credit: Daliah Singer)
The first, the Education dome, was built in 2016. It is the only one of the trio that’s currently operational. Volunteers stop by to prune and plant every day; more than 300 students have visited the site to learn about the plants and to practice their maths or science skills; and the public is welcome from 11:00 to 14:00 on Tuesdays and Saturdays.
“Everything we do is [focused on] teaching sustainable agriculture to the next generation and growing food year-round – which is pretty special” at an altitude of 7,150 feet (2,180m), says Sally High, a former environmental educator and GGP board treasurer.
The geothermal water comes from town wells via a lease agreement with Pagosa Springs. A heat exchanger inside each greenhouse uses the geothermal liquid to heat domestic water, which is piped through the floor of the greenhouse in cold-weather months. The geothermal fluid then resumes its natural path.
Inside of the Education dome, volunteers prune and plant every day (Credit: Daliah Singer)
The closed-loop system is as close to non-consumptive as possible – meaning almost no water is consumed during the process, with most of it returning to the ground – and allows the greenhouse to maintain a consistent temperature that ranges from 58F (around 14C) on the coldest winter nights to 90F (32C) on a sweltering summer day. (A pond, fans, misting system, and windows also help regulate the temperature.) That means the squash, kale and beets can grow in any month – a major benefit in a high-elevation mountain town where the average frost-free growing season spans less than 80 days.
The method will be similar in the Community Gardens greenhouse, which is expected to open before the end of 2018. Local civic organisations and community groups, such as food banks and veteran-focused associations, will have their own garden beds in which they’ll grow food to help feed their communities.
The Innovation greenhouse, slated to open in 2019, has a different purpose. It will house an aquaponic growing environment, raising fish and plants together in a symbiotic system in which the fish waste acts as a food source for the plants while the plants filter the fish’s water, one that uses about one-tenth of the water required for conventional soil growing. It’s a controlled environment, so the dome will be closed to the public except during special demonstrations or tours.
Our geothermal resource is underused and undervalued – Sally High
“Farmers’ markets are seasonal. This takes Colorado’s agriculture [towards being] very local and year-round,” says High, who sees Pagosa’s greenhouse endeavor as both an economic and tourism driver for the town. “Our geothermal resource is underused and undervalued.”
First discovered in the 1800s, the hot springs are popular for therapeutic purposes (Credit: Getty Images)
The Ute Indians first discovered the area’s therapeutic waters in the 1800s. More than a century later, in 1982, the town, with help from the US Department of Energy (DOE), launched a geothermal heating system that uses the geothermal water to provide heat to about 60 local businesses and residences and melt snow on the sidewalks in the small downtown. (There are around 20 such systems in the country, including in Boise, Idaho, and San Bernardino, California.)
“It’s a 24/7/365 power source; it’s not intermittent, like solar or wind,” High says. “This direct-use project… it’s absolutely replicable.”
Pagosa Springs isn’t alone in growing food geothermally. But the process is still rare in the US. In its most recent look at geothermal direct-use installationsin the country, which dated to February 2017, the National Renewable Energy Laboratory (NREL) counted just 29 greenhouses.
“One thing that’s unique about geothermal is, in addition to the ability to provide power, it can provide these other services to a community that allow them to be more self-sustaining,” says Katherine Young, NREL’s programme manager for geothermal energy.
Since 1982, the hot springs have been used to provide heat to buildings in downtown Pagosa Springs (Credit: Daliah Singer)
Most conversations about geothermal energy focus on Iceland, where the natural resource accounts for about 25% of the country’s total electricity production and where 90% of homes are heated geothermally. Other European countries have access to mostly intermediate- to low-temperature geothermal resources, which restricts them somewhat, as higher heats are better suited to electricity production. Even so, at least 13 countries tap into them for greenhouses, among other uses.
But the US hasn’t fully realised its geothermal potential. According to the DOE, “the US leads the world for installed geothermal capacity, with more than 3.7 gigawatts” – most of which is concentrated in the West. But a 2006 Massachusetts Institute of Technology study found that technology investment could open up access to more than 100 gigawatts in the next five decades, providing more than 10% of the country’s electricity demand. (The DOE announced a $4 million [£3.1m] investment in six deep direct-use feasibility studies last year.)
There’s a ton of heat everywhere beneath the US, and it can be harnessed – Katherine Young
“There’s a ton of heat everywhere beneath the US, and it can be harnessed everywhere,” Young says. “It can play a significant role in the US energy economy.”
Thus far, the GGP project has been primarily grant-funded – including a recent $174,500 (£135,000) infusion from the Colorado Water Plan and Colorado Water Conservation Board – and volunteer-driven. But as the final domes inch closer to completion, the team wants to hire a site manager, its first employee. Funds will come from private donations as well as by selling produce from the Innovation dome to local restaurants and at farmers’ markets. (Visitors can also buy tomatoes and lettuce from the Education dome on the two days a week it’s open; some of that produce winds up at the farmers’ markets, too.)
This past summer, vegetables grown in the Education greenhouse’s salad garden were part of the meals in the free summer food programme for kids in need. Community events at Centennial Park, where the greenhouses sit, have ranged from cooking classes to breakfasts to educational speakers.
Vegetables grown inside of this greenhouse helped feed local children this summer (Credit: Daliah Singer)
For local youth like Tucker Haines, the Education greenhouse affords more than just an opportunity to learn about eating – and growing – fresh foods. Every Monday last school year, the 13-year-old would walk from Pagosa Springs Middle School to the GGP park. His maths teacher thought hands-on learning might help the formulas and fractions finally click with the students. Tucker and his classmates measured the garden beds and plants and kept calendars which outlined when the seeds were going to germinate; they also planted and harvested kale, red cabbage and cauliflower. “My regular math class I couldn’t quite understand,” Tucker says. Suddenly, though, the numbers started to make sense. “It made math enjoyable,” says his mother Nancy Haines.
Tucker’s experience is the kind of broader community benefit High and the rest of the GGP were hoping for when they set out on this mission a decade ago. “It’s this living laboratory that we have right smack in the middle of town,” says Cindy Schultz, Pagosa’s associate planner. “It gives people a sense of what’s possible.”
Join 900,000+ Future fans by liking us on Facebook, or follow us on Twitter or Instagram.
Plans Advancing For $16M-$17M High-Tech Greenhouse Along Prince Street Garage
TIM STUHLDREHER | Staff Writer
September 4, 2018
Plans for a hydroponic vertical greenhouse in downtown Lancaster are moving ahead, its backers say, and the facility, budgeted at $16 million to $17 million, could start operating in the fall of 2020.
“This is our flagship project,” said Corey Fogarty, president of the nonprofit Lancaster Urban Farming Initiative.
The aim is not only to produce fresh, healthy vegetables in an environmentally friendly and economically sustainable manner but to employ people with physical and developmental disabilities as part of a diverse, inclusive workforce.
Nona Yehia, co-founder and CEO of Vertical Harvest, the Wyoming-based company partnering on the project, said it has the potential “to create a model that can affect communities all over the globe.”
Lancaster Chamber President Tom Baldrige said he’s impressed by the way the project combines Lancaster County’s agricultural heritage with the area’s expanding high-tech capabilities.
“It sets a vision for our future,” he said.
West Orange Street site eyed
Fogarty is an experienced entrepreneur; he is managing partner of the Federal Taphouse, among other endeavors.
The greenhouse would be built on a narrow strip of Lancaster Parking Authority property on West Orange Street along the facade of the Prince Street Garage.
Fogarty credits former Mayor Rick Gray with originating the idea, saying Gray suggested it when Lancaster UFI met with him a few years ago to discuss rooftop farming.
In 2016, the parking authority board gave the go-ahead for a feasibility study. Last month, after a follow-up presentation, the board agreed to begin contract negotiations for use of the tract.
For a vertical greenhouse, "it's almost uncanny how perfect it is," Fogarty said, with its central location and copious southern exposure.
Indeed, the layout would be almost identical to Vertical Harvest of Jackson Hole, a 13,500-square-foot structure adjoining a parking garage in Jackson, Wyoming. Opening in 2016, it has ironed out various technical kinks and converted skeptics, including a local Tea Party official.
Lancaster would be Vertical Harvest's second location. Originally, a greenhouse similar in size to Jackson's was envisioned here, with a budget of roughly $5 million. The plan has since scaled up considerably, to about 42,000 square feet.
It would be five or six stories high, and roughly 30 feet wide, Fogarty and Yehia said. A rendering shows it extending over much of the block, pedestrians strolling underneath.
It would grow crops year-round, conservatively yielding about 200,000 pounds a year, Yehia said, including vine vegetables (tomatoes, cucumbers and the like), leafy greens and microgreens — high-nutrition vegetables harvested early in the growing cycle.
They would be sold to groceries and local restaurants; there would be a small retail store as well. The idea is to complement, not compete with, the area’s existing agricultural operations, Fogarty said.
The facility is expected to create 40 or more full-time-equivalent jobs. In Jackson, about half the work force consists of people with “different abilities,” and the goal here would be the same, Yehia said.
Vertical Harvest of Jackson Hole adjoins a parking garage in Jackson, Wyoming.
Provided
Financing
The $16 million to $17 million project budget has been thoroughly vetted, and incorporates what's been learned from building and operating Vertical Harvest Jackson Hole, Fogarty said: "These are real numbers."
Projections call for breaking even in the third year of operations, he said.
A variety of funding sources are being explored, he and Yehia said, including two state subsidy options: the Redevelopment Assistance Capital Grant and the City Revitalization & Improvement Zone programs.
The project could receive up to $10 million from the former. Funding for the latter would depend on the tax revenue the business generates. A project can only take advantage of one of the programs.
If it turns out that all the startup capital has to be raised from private sources, that’s fine, too, Fogarty said.
“We have private money that’s willing to step up,” he said. “We’re very confident that our money will be in place by the third quarter.”
Design and engineering is to start soon, with a goal of starting construction in the fall of 2019 and opening about a year after that.
Vertical Harvest of Jackson Hole partners with a nonprofit to employ people with disabilities in its work force. Provided
Farming for a crowded world
Vertical farming has attracted extensive interest in recent years. Advocates tout its efficiency and say its small-footprint, high-output model is an idea whose time has come in a rapidly urbanizing world beset by water scarcity, soil depletion and energy challenges.
“It will never replace traditional agriculture, but it can be a supplement,” Yehia said.
Robert Berghage, a professor of horticulture at Penn State, said he supports urban agriculture in all its forms, but cautioned that it can be extremely challenging to make the economics of vertical farming work.
‘It’s tough to compete with a regular greenhouse,” he said. The industry has seen its share of hype and setbacks, and entrepreneurs need to be ruthlessly realistic about their costs and revenue projections.
Fogarty said that's what his team has done.
"We are confident it will be a sustainable business," he said.
Parking authority executive director Larry Cohen said the organization is pleased to help advance a progressive initiative "that should be exciting for everyone in the community."
Randy Patterson, director of economic development and neighborhood revitalization, said city government is supportive of the project.
Way To Grow: Urban Farms Are An Amenity At Many Developments
2018 Margaret Jackson, Bisnow Denver
As people increasingly demand to know where their food comes from, more developers are jumping on board to integrate urban farms into their projects.
Courtesy of Tracy Weil
RiNo Art District Creative Director Tracy Weil grows heirloom tomatoes at Farm 39 in RiNo
Take S*Park. Named for its heritage as Sustainability Park, the 99-unit residential project in Denver’s Curtis Park neighborhood includes a 7,200 SF greenhouse with 340 aeroponic towers that will grow leafy greens.
The greenhouse will be operated by Altius Farms, which will offer residents a vegetable subscription program, greenhouse tours and classes and community dinners with Denver celebrity chefs. Altius also will provide neighborhood restaurants with produce from the greenhouse.
Courtesy of Altius Farms
Altius Farms will grow leafy greens on towers like these at Scissortail Farms in Tulsa, Okla.
Altius Farms founder and CEO Sally Herbert said the tower system at S*Park will produce 75,000 pounds of leafy greens a year — the equivalent of 1.5 acres of conventional farming each month. The towers use 10% of the water of a traditional farm and produce 10 times the yield, and the produce is much fresher than what consumers find in grocery stores, she said. Colorado imports 97% of its produce, and after it spends seven to 14 days in transport, between 20% and 40% of it is discarded.
“When restaurateurs receive produce that’s come in from Arizona or California, it’s been harvested early and gets wilty or bruised,” she said. “You have to throw away the crappy stuff.”
NAVA Real Estate Development is taking a different approach at Lakehouse, its 12-story, 196-unit condominium project at Sloan’s Lake. The produce from its second-floor garden will be available only for residents of the 12-story building.
“We are growing a certain amount of vegetables and herbs on-site that will be professionally managed and harvested,” NAVA co-founder and CEO Brian Levittsaid. “We’ll have a harvest room where people can be part of a harvest. There will be opportunities where people can reach over and pick something and put it in their salad. There will be a juicing center and sauna where people can sit and enjoy the juice.”
Bisnow/Margaret Jackson
The greenhouse at S*Park will provide produce to residents and nearby restaurants.
The garden is just one component of NAVA’s efforts to ensure a healthy environment for residents of Lakehouse, which is seeking Well Building certification. It also must meet standards for air and water quality and fitness, among other things.
Urban Ventures has launched a wellness program that includes food production at Aria Denver development. Aria Denver has partnered with Regis University to launch the Cultivate Health program at its development in northwest Denver. Food production, in both gardens and greenhouses in the neighborhood, is just one component of the program, which is designed to support the health and wellness of residents living in the multi-generational, mixed-income community. Its food production partners are UrbiCulture Farms and Groundwork Denver.
Courtesy of Tracy Weil
Farm 39 in RiNo sells about 8,000 tomato plants a year.
Urban farming is a growing trend both in new developments and city neighborhoods.
Artist Tracy Weil, creative director of the RiNo Art District, co-founded Heirloom Tomato Farms with Carolyn Jansen in 2004 when they weren’t able to find the produce they wanted. They started with 175 plants, which they sold and gave to friends. Weil was on the board of The GrowHaus, a nonprofit indoor farm, marketplace and educational center in Denver’s Elyria-Swansea neighborhood. The GrowHaus, based in a historic 20K SF greenhouse, agreed to give him enough space to expand to 1,200 plants.
But then aphids from the herbs in The GrowHaus infested Weil's tomato plants, so he built his own greenhouse — Farm 39 — on an eighth of an acre at 3611 Chestnut Place in RiNo. Jansen started The Sparrow in Capital Hill. The combined farms are known as Heirloom Tomato Farms. Now, people line up every spring to purchase some of the 8,000 plants the two farms grow before they sell out.
“It’s been kind of a nice supplemental income,” he said. “As an artist, I wanted to diversify my income stream.
A Suffolk Greenhouse The Size of 11 Football Pitches
A company’s multi-million pound investment is about to turn Suffolk into a major producer of vine tomatoes.
Cliff Matthews, a director of Sterling Suffolk Ltd., inside the giant glasshouse being built on land between Great Blakenham and Bramford. The new greenhouse will be used to grow vine tomatoes by hydroponic
A company’s multi-million pound investment is about to turn Suffolk into a major producer of vine tomatoes.
Cliff Matthews, a director of Sterling Suffolk Ltd., inside the giant glasshouse being built on land between Great Blakenham and Bramford. The new greenhouse will be used to grow vine tomatoes by hydroponics
In the first stage of a £30m project, at Great Blakenham near Ipswich, Sterling Suffolk Ltd has built a massive Dutch-style glasshouse with the dimensions of an aircraft hangar - or 11 football pitches.
It is on track for the first tomatoes to be planted in December, and for the first cropping to begin from mid February 2019.
The plan is to produce tomato vines by hydroponics - without soil, but perhaps coconut matting (coir), and fed water and nutrients that are carefully controlled.
This giant greenhouse is similar to those seen in parts of Holland and France, and used to produce a range of salad vegetables, fruit and flowers.
Cliff Matthews, a director of the developers, Sterling Suffolk Ltd, said: “It has been great to start this, seven years ago, and to be here to see it coming to fruition,
“There are some bigger ones in the country of course. This phase one is the size of 11 football pitches.
“It is the most environmentally efficient glasshouse in the UK. The first of its kind here.
“There are a number in France and Holland.
“Real glass is more efficient for this.
“This is agriculture on a industrial scale. There is an art and science to growing tomatoes and we have a very good expert involved, Richard Lewis, one of the best in the UK.”
Vine tomatoes, with clumps of tomatoes still attached to the vine, would be harvested and supplied to supermarkets and the restaurant trade.
“We aim to produce 50,000 vines per week. It is more about the taste than the quantity.” he added. “These will be top of the range quality.”
The 5.6 hectare building is phase one of a three-phase project, costing around £30m in all, over the next three years.
When complete there will be 17 hectares of production glasshouses, plus office, packaging and production on site.
The first giant 8,3 metre tall house has been constructed since March, despite the bad weather.
Now it will be fitted out with blinds and hydroponics equipment ready for the first planting in December.
It would be very environmentlly friendly, he said, with air ciculation systems and the water for the hydroponics collected from the roof and stored in a reservoir.
The tomatoes would grow in natural light, with a season from March through to October, and one hectare of plants would grow under lights at other times.
The site would employ between 40 and 50 people, he said. “And we will employ more when we get growing and expanding.
“We have spent about half a million pounds in the local environment so far, with more to follow.
“Over the years it is gooing to benefit all of the community,”
The project attracted some local opposition during the planning process.
Mr Matthews added: “Personally I don’t think it looks too bad in the countryside. There are trees and we are goiong to plant more for screening.”
This project will not be the largest in the region, at Wissington in Norfolk British Sugar has an 18 hectatre glasshouse - and products there include medicinal cannabis.
Is Warehouse Farming The Future Of Agriculture?
No matter what industry you’re in, you need to be looking ahead for technological changes, the cost-effectiveness of your competition, changing customer behavior, and potential government regulation.
One threat to the status quo I would like to explore is the potential for large-scale warehouse or vertical farming. Could it reduce the need for row-crop production?
If so, what kinds of crops will be first to face competition? And, what kinds of crops may never be grown indoors?
Because of shortages of arable land in some places, like Asia, indoor vegetable production has been in play for years. Alibaba.com, a Chinese internet retailer, advertises that it offers 2,466 vegetable warehouse products, including pre-fabricated buildings.
Companies like Philips are developing red and blue spectrum LED lights specifically for growing plants, while others are building sensors that detect optimal lighting levels for various crops.
Some companies on the West Coast are growing fruit and vegetables in 20-foot-tall towers inside of climate-controlled facilities with LED lights.
They claim to use no pesticides, herbicides, synthetic fertilizers, or GMOs. They do use thousands of infrared cameras and sensors to collect data in order to optimize lighting, water supply, and temperatures. Some warehouse type growers claim that this technology can achieve yields that are many multiples of traditional farming.
However, vertical farming still has one inefficient component: electricity usage. Without sunlight, plants require intense artificial lighting for 16 or more hours a day. That adds up to sky-high energy bills. Improvements in lighting efficiency may bring the overall cost of warehouse-grown crops into competition with outdoor crops, but that tech is still in the works.
You may not have heard of it, but there is an Association for Vertical Farming. On the group’s website, it states that they expect crop productivity for indoor farms to double every five years in the near future.
You can find many articles about the following crops being grown indoors: lettuce, kale, herbs, tomatoes, green beans, and peppers.
One company is growing greens on the roof of a Whole Foods in Brooklyn, New York. Another company claims to be growing 2 million pounds a year of greens in a 70,000-square-foot warehouse in Newark, New Jersey. There is also a 215,000-square-foot indoor ag facility in Las Vegas growing 16 types of greens and 11 types of herbs.
One company is even putting hydroponic farming systems inside of 40-foot shipping containers. They claim you can grow about 3 tons of herbs and greens out of it in one year.
On the flip side, you can find examples of vertical farms shutting down.
In the Chicago area there was a company called FarmedHere that was maintaining a 90,000 sq ft indoor farming operation and selling to about 100 grocery stores. It shut down a couple of years ago due to lack of profitability. Like any business, some operators figure out how to make it work, and others don't.
With labor shortages in some vegetable producing states, like California, it’s easy to envision warehouse production of vegetables becoming cost-effective eventually due to reduced labor requirements – plants covering fewer square feet, harvests happening year-round, and stationary robot vegetable pickers.
However, could warehouse production ever supplant the traditional row-crop production of corn, soybeans, or wheat? Answer: Probably not any time soon. I haven’t found any examples of commercially viable indoor grain production.
One executive with a vertical farm tech company suggested the optimal indoor crop mix as 80% greens and 20% herbs. Why? They need crops that turn fast and grow year-round. They need crops with high per-pound values in order to cover the labor, power, building, and equipment costs.
Waiting four to five months for an ear of corn is a big cash flow problem for a warehouse farm.
Three Advantages of ACRYLITE® Resist Diffuse High-Impact Acrylic
This light-transmitting, heat-insulating and weather-resistant sheet is available with diffusion properties.
July 19, 2018
Edited by the GIE Media Horticulture Group
ACRYLITE® Resist high-impact acrylic is a light transmitting, heat-insulating and weather-resistant sheet made of impact modified acrylic (polymethyl methacrylate, PMMA) polymer. This 16-millimeter multi-skin acrylic sheet is now available with diffusion properties, and ideal for commercial greenhouse applications where diffused light is desirable for optimized crop growth, while maintaining overall high light levels.
Here are three advantages it offers growers who add it to their operation.
1. It scatters light.
Because it scatters light, ACRYLITE® Resist high-impact acrylic offers growers a more homogeneous light distribution that penetrates deeply into the plant canopy. This wraps the plants in light and activates more photosynthesis. The result is fewer hot spots and shady spots in the greenhouse. It also means better growth, stronger plants and brighter colors.
2. It provides increased light.
Growers know that the morning and evening can be difficult for growing due to the low angle of light. But ACRYLITE® Resist high-impact acrylic allows more light into the greenhouse at those two points in the day when the plants need it the most. It also helps reduce greenhouse temperatures in the summer and thus reduces the need for shade cloth.
3. A high-quality product.
As with all ACRYLITE® Resist high-impact multi-skin sheets, the ACRYLITE® Resist high-impact acrylic features excellent protection against excessive amounts of UV radiation; comes with a 30-year warranty against yellowing, and is hail-resistant with a 10-year guarantee for withstanding hailstones with a kinetic energy of 1 joule. It also offers growers up to 50 percent energy savings, minimizes CO2 emissions and is treated with a nontoxic, biologically neutral anti-algae application.
Plus, on its way to greenhouses and when it is assembled, it is guaranteed to be impact resistant.
For more information on ACRYLITE®, click here.
Photo courtesy of Evonik
"New Responses To The Way We Grow Food Are A Must To Respond To The Challenges Of The Future."
Nona Yehia, Vertical Harvest
With rising global urban populations, existing food infrastructure systems are rapidly becoming unsustainable. Some of those looking for alternative solutions note food’s potential to act as an organizer of urban systems and catalyst for change. Tapping into this potential, architects and designers have been using urban farming as a vehicle to speculate about “green” futures. However, sustainability is often sidelined in photorealistic images where designs are ‘decorated’ with organic matter, designs that are unlikely to be viable.
Architecture should and can go beyond that image, as it provides the built accommodation for both plants and people, and hence plays a crucial role in creating the important social, economic and ecological infrastructure for sustainable and healthy cities. During this session, the opportunities and challenges in optimizing this role - in cooperation with other stakeholders and disciplines - is discussed and explored. What is the role of design in realizing sustainable food production and promote health in metropoles? Do architects need to play a leading role in developing sustainable urban farms that bring benefits for all?
Wageningen University & Research asked it to Nona Yehia, Co-Founder/CEO of Vertical Harvest, and Principal at GYDE Architects.
I envision a future where vertical greenhouses are an integral part of the urban fabric, that cities have embraced this model as a necessary tool to achieve sustainable and successful futures.
By 2050, 80% of the world’s population will live in cities, this fact is at once a substantial challenge and an opportunity.
"New responses to the way we grow food are a must to respond to the challenges of the future."
At the same time, food deserts, where affordable and healthy food is difficult to obtain, are becoming more common in urban neighborhoods. Add to this the fact that available land, healthy topsoils, and water are becoming scarce commodities, and that costs of energy and transporting food are increasing, new responses to the way we grow food are a must to respond to the challenges of the future.
Architect and visionary
I’m an architect, and from my professional view, I see the opportunities in this field are much more than just about creating space. Architecture has the potential to respond to a community need, but at the same time, reflect a community’s values and have great impact beyond the limitations of the building. It is this belief that architecture can be the physical act of social change that cemented my dedication to the idea of vertical farming. In the past ten years, the focus of my work has been to create a viable model to build cost-effective hydroponic vertical greenhouses in urban areas that not only act as innovative, environmentally sustainable models for growing fresh food but have a substantial social impact.
Innovative investment
We need innovative partnerships to support this vision. At this juncture, urban food production in the form of vertical farming is challenged by the cost of land, capital costs and the cost of energy. Public/private partnerships with vertical farming businesses and municipalities can help mitigate these barriers to entry by working with operators to secure unused land, invest in this unique and productive type of public infrastructure, and create opportunities to use renewable energy. Our cities' leaders need to invest in tools to help drive the impact they want to see in their communities.
Sustained success
Commercial scale urban agriculture, much like traditional agriculture, is riddled with potential pitfalls and challenges. How to run a successful vertical farm, and then following - how to sustain that success is based on experience. In this nascent and exciting industry, it is by learning from each other’s experiences that we will be able to collectively achieve and sustain success of the industry as a whole. Until the industry is able to embrace a truly collaborative approach, we will be vulnerable to the multiple challenges that we all face.
"It is by learning from each other’s experiences that will we be able to collectively achieve and sustain success."
Year round fresh produce
Vertical Harvest of Jackson Hole in Wyoming USA responds to two significant needs in our community: Jackson has a 4-month growing season and imports the majority of its produce from outside of Wyoming. Jackson is now home to one of the world’s first vertical greenhouses located on vacant land next to a downtown parking garage. This 13,500 sq. ft. three-story stacked greenhouse utilizes a 1/10 of an acre to grow an annual amount of produce equivalent to 10 acres of traditional agriculture. Our project enables the community to grow produce 365 days a year despite difficulties posed by the harsh climate.
Do good, do well
Our community impact model cultivates an empowered, healthy, sustainable, and connected community. We sell locally grown, vegetables year-round to Jackson restaurants, grocery stores and directly to consumers. In addition to fresh produce, Vertical Harvest produces jobs for individuals with different abilities. Our mission is simple – we provide consistent, meaningful employment for people with disabilities (typically a 78% unemployment rate) by cultivating nutritious food for the community. Our impact is much larger – we utilize public/private partnerships as a model to create positive economic and social impact for communities.
We do good by doing well.
One of the primary reasons vertical farms fail is due to labor challenges, however, we are resisting the trend of moving towards greater automation and are instead looking at our labor model as an opportunity to achieve success. Employees benefit from multiple dividends; this a positive effect on our co-workers, the company’s bottom line and the community. We do good by doing well.
Metric-driven growers
We see ourselves as growers first and foremost. Technology with regards to vertical farming is advancing at an astonishing rate, and while efficiency and optimization in production is always a key priority, understanding how to evaluate all of the options available to our farms is particularly challenging. Our dual mission of employing a unique population in conjunction with growing as much food as possible resulted in multiple efficiencies and innovations in our design that strengthens the bottom line of everything we are doing.
Vertical Harvest is essentially 3 greenhouses stacked on top of one another – this creates different microclimates on each floor. This structure allows for the development of a portfolio of crops that have different price points as well as risk factors. Take our lettuce carousels: these are continuous rotating systems that span the vertical southern façade of our building as well as move horizontally into the 30’ depth of our building.
These unique growing systems solve three problems at once. They balance natural and artificial light, essential to managing energy costs, add a fourth floor to our three-story greenhouse, and finally bring the plant directly to our farmers for transplanting and harvesting. We strive to use this metric to evaluate all of our choices in terms of technology.
Source: WUR
Publication date: 9/5/2018
NatureFresh™ Farms Partners With Forgotten Harvest To Reduce Food Waste Footprint
Leamington, ON (August 30th, 2018) – In an organized effort to reduce their food waste footprint, NatureFresh™ Farms has partnered with Forgotten Harvest, a perishable food rescue, and redistribution organization, to deliver nutritious food to people in need. So far in 2018 2018, NatureFresh™ Farms has successfully donated over 150,000 pounds of produce to the Forgotten Harvest program.
The issue of food waste, both at the commercial and consumer level, is beginning to gain more recognition as a serious global problem. Every year, roughly 1.3 billion tons of food gets thrown out globally, and this food ends up in landfills where it is not used and begins to emit greenhouse gases (primarily methane). As food wastage becomes a more recognized problem, consumers and businesses in the food industry are improving their efforts to curb the issue of food waste.
The NatureFresh™ Farms team has made a firm commitment to consistently collecting and donating greenhouse-grown products that cannot be sold at the retail level but are still nutritious and fully edible, to Forgotten Harvest. The food rescue organization then gleans and repackages the produce into family-friendly sizes that are redistributed within their network of food banks.
Justin Guenther, the Allocation/Shipping Manager at NatureFresh™ Farms, has been a driving force for this program’s development: “The initial creation of this donation program saw some obstacles, as every new program does, but once people started to realize how much food we were saving, it really opened their eyes to the good we could do as a company.” In 2018, NatureFresh™ Farms is projecting that they will reallocate roughly 600,000 pounds of produce to feed food insecure families through Forgotten Harvest’s food bank network.
NatureFresh™ Farms has been donating produce to Forgotten Harvest since 2011, but the food rescue organization has been feeding members of the metro-Detroit area since 1990. With 35 tracks, over 16,000 annual volunteers, and a massive local and international network, Forgotten Harvest is committed to providing food insecure families with fresh, nutritious food as quickly as possible. Chris Ivey, Director of Marketing & Public Relations at Forgotten Harvest, cites the importance of their partnership with NatureFresh™ Farms: “As metro Detroit’s only fresh food rescue, our partnership with NatureFresh™ is a critical portion of our supply chain. Because of these efforts, Forgotten Harvest can deliver on the promise of providing a fresh nutritious mix of food, delivered free of charge, to the over 250 partner agencies we support in our community.”
Forgotten Harvest’s mission to provide people with access to essential foods is a mission that Peter Quiring, the Founder and CEO of NatureFresh™ Farms, also champions: “Working with an organization like Forgotten Harvest, as well as many other community food banks, means that our company can help even more people live healthier lives. To build strong communities, it’s essential to work hand in hand with like-minded organizations.”
In addition to their work with Forgotten Harvest, NatureFresh™ Farms constantly seeks to engage with local food banks and food rescue organizations, including Southwestern Ontario Gleaners.
Kara Badder
Marketing Project Manager
10 Reasons to Choose ACRYLITE®
From high light transmission to hail protection, these are some of the reasons growers are choosing ACRYLITE®.
July 19, 2018
Edited by the GIE Media Horticulture Group
Originally designed for use in the commercial greenhouse industry more than 40 years ago, the technology behind ACRYLITE® acrylic multi-skinned sheet has been continually improved through ongoing research and development in cooperation with the world’s leading growers.
The result is the most advanced, state-of-the-art glazing material available today which delivers decades of performance and exceptional return on investment. Commercial growers of all crop types operating in both cold and warm climates recognize the critical role that ACRYLITE® glazing plays in the long-term success and profitability of their operations.
These are 10 reasons to choose ACRYLITE® for your greenhouse.
1. High light transmission for growth results
ACRYLITE® acrylic multi-skin sheet transmits up to 91 percent percent of photosynthetically range (PAR) into the greenhouse. The exceptional clarity of ACRYLITE® provides the most natural growing conditions and promotes vigorous and vibrant bloom color. Optimum growth response and shorter maturity time provide economic advantages that help you grow your profits.
Comparisons between a conventional double-covered greenhouse and a structure glazed with ACRYLITE® show that ACRYLITE® transmits 20 percent more light – a distinct advantage, particularly in the winter months. The ribbed design of ACRYLITE® also diffuses light over the crop canopy, eliminating harsh “hot spots” associated with growing under glass.
ACRYLITE® will retain its light transmission and clarity for decades; in fact, even after 10 years of use, acrylic glazing transmits more light than brand new polycarbonate.
All ACRYLITE® acrylic multi-skin sheets block UV light penetration. However, in applications where UV light transmission is desirable, ACRYLITE® Alltop is one of the only glazing materials available in a UVT version that transmits the full spectrum of light including ultraviolet.
2. Never yellows
ACRYLITE® acrylic will not yellow, become brittle or degrade — a promise we back with our 30-year no-yellowing guarantee — the best in the industry.
Yellowing of plastics is caused by the sun’s UV rays breaking down the glazing, but ACRYLITE® acrylic is 100 percent naturally UV-stable. Polycarbonate and other plastic covers need a UV barrier or coating to delay yellowing, but must often be replaced after a few years of installation because they have turned yellow. UV barriers are often thin and are highly prone to failure. But ACRYLITE® acrylic is composed of 100 percent naturally UV-stable molecules throughout the material that stabilizes it from the inside out and protects the entire sheet, not just its surface.
ACRYLITE® high impact acrylic doubleskin sheet is the ideal choice for replacing yellowed polycarbonate or weathered fiberglass. Ask us for our comparison kit containing samples of ACRYLITE®and polycarbonate that have been removed from greenhouses after the same number of years of use and see for yourself.
3. Protection from hail
ACRYLITE® high impact acrylic is strong enough to withstand hail impact — a promise that we back with our 10-year warranty. In fact, because our proprietary polymers are ten times more impact resistant than traditional acrylics, our hail warranty is not prorated. Glass and weathered, fragile polycarbonate cannot protect your greenhouses from damaging hail. ACRYLITE® protects not only your crops from hail damage, but protects your bottom line from replacement costs.
4. Energy savings of up to 55 percent* per year
Energy is a critical cost factor for commercial greenhouse operators. In North America, growers spend an average of $1 to $2 per square foot on heating their greenhouses. With ACRYLITE® multi-skin acrylic sheet’s natural insulative qualities, you’ll save up to 55 percent* in annual energy and heating costs when compared to single glazing.
The money you save on energy costs will pay for your investment in ACRYLITE® glazing within a few years of installation. Over ACRYLITE’s® long service life of 30+ years, you will fully recover the capital cost of your building project and save hundreds of thousands, even millions of dollars in heating costs.
*This figure is confirmed by the Institute of Agricultural and Environmental Engineering (IMAGDLO), which established that energy savings of 24 to 55 percent can be achieved using ACRYLITE® acrylic sheet.
5. Patented anti-condensate technology, with anti-algae technology
Thanks to our No-Drip anti-condensate technology, ACRYLITE® multi-skin acrylic sheets maintain optimal transparency even in bad weather. This water-dispersing layer causes condensation to flow off as a continuous self-cleaning film, resulting in the highest possible light transmission and eliminating uncontrolled dripping that can result in crop damage and disease. Unlike coatings on other glazing products that wear off, our manufacturing technology makes the patented No-Drip feature an integral part of ACRYLITE® acrylic sheets.
6. Strength and durability
The unique polymers of acrylic combined with the geometry of ACRYLITE® multi-skin sheets makes them inherently stronger than other multi-walled glazing. Thicker walls and ribs create a more rigid sheet of greater overall weight designed to provide high live-load carrying capabilities while allowing for greater span distances. ACRYLITE® meets or exceeds snow and wind requirements offering durability in extreme climates.
7. Reduces additional equipment needs
ACRYLITE® multi-skin acrylic sheet naturally holds heat in, reduces shadows, hot spots and burning. Not only will you require less initial capital investment in heating systems, lights and curtains, you’ll also save on costly maintenance over decades of use.
8. Life expectancy of 30+ years
ACRYLITE® multi-skin acrylic sheet has been proven to perform consistently over decades of use in all types of climates throughout the world. ACRYLITE® acrylic’s long service life means less replacement costs when compared to inferior glazing materials that must be replaced more frequently, often after just a few years of use.
9. Environmental protection
Glazing with ACRYLITE® helps contribute to a healthier environment through reduced energy use, reduced emissions, environmentally-sound manufacturing processes, certified facilities and elimination of harmful chemicals. Long product life means less old glazing going to landfill sites due to premature failure, but if it must be replaced, ACRYLITE® is recyclable for use in making consumer goods.
Upon combustion, other plastic coverings produce thick smoke and toxic gases that are harmful to people and the environment. Deterioration from UV rays changes the burning characteristics in many plastics, but thanks to ACRYLITE®’s UV stability, its characteristics do not, so in the event of fire, ACRYLITE® burns cleaner with less smoke and has no release of toxic or corrosive gases.
10. The best warranties in the industry
ACRYLITE® high impact acrylic is backed with the industry’s best warranties. Our non-prorated, full replacement 30-year non-yellowing, 10-year light transmission and 10-year hail warranties protect both your investment in ACRYLITE® and your bottom line.
For more information on ACRYLITE®, click here.
Photo courtesy of Evonik
Arctic Agricultural Technologies: 'Smart' Greenhouses And Light On Demand
August 13, 2018
© Viktor Drachev/TASS
TASS, August 13. Scientists of the Tomsk Polytechnic University designed "smart" greenhouses for the Arctic regions, where growing vegetables does not depend on climate conditions or sunlight. The scientists told TASS about how the Arctic regions may grow vegetables for own needs and what other technologies may be used there.
Hydroponic vegetables
The "smart" greenhouses for the Arctic have automatic processes and do not depend on the climate or any other outside conditions, Director of the University’s Engineering School Alexei Yakovlev told TASS. The Tomsk project will use for lighting vegetables, which in regular conditions are short of light, polycrystalline LED materials - thus giving to vegetables the light of a necessary spectrum.
"Plants are sensitive to the spectrum, which is different for human eyes," the scientist said. "Our task is to offer to vegetables a comfortable spectrum." The equipment is programmed so that it will offer automatically more light for example on overcast days, he added.
The vegetables will grow not in the soil, but hydroponically. "We are using hydroponic systems," the expert said.
The scientists are beginning tests - they will try growing cucumbers in the greenhouse. Besides, they will study how plants react to various lights.
Supply and demand
People, living in the Yamalo-Nenets Region, consume every year 11,000 tonnes of cucumbers and tomatoes, while the local greenhouses produce only 18 tonnes a year, the regional governor’s press service told TASS. The gap is filled by supplies from the Krasnodar, Stavropol, Tyumen, Kirov, Moscow regions, and from the CIS countries.
A new greenhouse complex, which will open in Salekhard in 2020, will take an area of one hectare.
"This project, a public-private partnership, continues, and the complex will produce about 1,000 tonnes of vegetables a year," the press service said, adding the local authorities are interested in new agricultural technologies, in automatic "smart" greenhouses.
In the Arkhangelsk Region, two companies grow vegetables. The regional agricultural ministry told TASS the annual production there is 1-1.2 thousand tonnes of vegetables. The vegetables and herbs are sold in Severodvinsk, Arkhangelsk and Novodvinsk.
The Nenets Agricultural Company (in the Yamalo-Nenets Region) produces 70 tonnes of cucumbers, tomatoes and herbs. "The locally produced vegetables are supplied mostly to Naryan-Mar," the regional Department of Natural Resources, Ecology and Agriculture told TASS. "As we have nomadic population, the locally produced vegetables make only 12% of the demand, and the rest is brought from outside the region."
Komi’s Vorkuta, which is north of the Polar Circle, develops the project on hydroponic vegetables.
"We produce about 200 kg of herbs a month - lettuce, salad, basil, mint," the project’s head Elena Smirnova told TASS. "We supply them to cafes and restaurants, to some shops; the trade chains are only watching us yet."
"Anyway, we see the demand and plan to expand the production," she added.
New formats
Russian regions have other projects related to growing in the Far North of plants, which are not typical for those regions. Director General of the iFarm Company, working in Novosibirsk, Alexander Lyskovsky said his company, which produces greenhouses, eyes making vertical greenhouses, where every garden bed is above another. They are installed in absolutely dark spaces.
"Probably, it may be more correct to install the vertical farms using fully artificial light - anyway, there is so little sunlight in those regions," he said. "Vertical farms are organized in basements, hangars, to where the sunlight would not come, and there you install garden beds one above another."
"It is more complicated to grow there cucumbers or tomatoes, as they require much space, but it is quite possible to grow herbs and strawberry there," he added. iFarm’s specialists plan to test the technology and materials in Norilsk, where the authorities have expressed interest in greenhouses.
"Smart" greenhouses for the Arctic regions are also designed in St. Petersburg. The Defense Ministry is interested in portable complexes for growing any amounts of vegetables, the project’s head Gayane Panova told TASS.
"At the request from the Defense Ministry, we have initiated a waste-free energy-effective technology for growing greengrocery (parsley, dill, lettuce, other herbs, tomatoes, and cucumbers)," she said. "We were allowed to state tests in the Arctic." However, due to problems with an investor, the Arctic tests did not happen and the scientists are looking for new investors.
More:
http://tass.com/economy/1017011
Mucci Farms Opens In San Antonio!
August 23rd, 2018 | San Antonio, Texas
Mucci Farms announces the opening of a brand new distribution facility in San Antonio, Texas, strategically located to optimize service in the southern United States. “We are thrilled to continue our expansion into the US with a southern facility that can help us service the region effectively,” said Joe Spano, Vice President of Mucci International Marketing. “As a company committed to efficient execution, our main focus was to reduce food miles as well as our carbon footprint to better serve our partners and customers.” The company plans to begin operations over the next 8-10 weeks.
With an appetite for a larger US footprint, the announcement comes on the heels of their first harvest from Phase 1 of a 3-Phase 60-Acre Huron, Ohio expansion. The organization has been actively searching for a strategic opportunity to serve current and potential clients in the south and the southwestern United States. “San Antonio was a logical city for us because it is a major southern crossing, and this location will help us increase efficiencies and assist with logistics,” remarked Danny Mucci, President of Mucci International Marketing. “Through this facility, we’ll be able to distribute our full lineup of products to the region in a timely manner, allowing consumers to take advantage of maximum shelf life and high quality of our produce.”
Growing fresh produce for over 50 years, Mucci Farms is a vertically integrated Greenhouse farming company with over 200 acres of Lettuce, Tomato, Pepper, Cucumber and Strawberry farms in Canada and the United States. Headquartered in Kingsville, Ontario, the Award Winning company is dedicated to continual investments in automation and technology along with a high level of research and development to offer consumers the most flavourful fruit and vegetable varieties in the world.
French Homeless Shelter Plans To Build Rooftop Greenhouse
An urban farm could be installed on the roof of a French shelter, in order to develop agriculture in the city and to supply the social restaurant of the shelter in particular. It’s located on the Island of Nantes. The association Les Eaux Vives will open this project in 2019, which will be called "5 Ponts (5 Bridges)".
Homeless people will be offered hour-based work contracts. Missions will be proposed within the urban farm, the Emmaus boutique, the restaurant, or the green spaces of the site.
Next, to the restaurant, Les Eaux Vives now offers a day stop and a night stop, and an emergency shelter on three different addresses in Nantes.
The 5 Bridges project is organized around a covered street to facilitate the meeting of different audiences. The project is supported by the City of Nantes, and the European Union as part of the UIA (urban innovative action) project.
Publication date: 8/14/2018
NASA Awards UbiQD Contract To Develop Greenhouse Films For Space Missions
PRESS RELEASE PR Newswire
Aug. 13, 2018
LOS ALAMOS, N.M., Aug. 13, 2018 /PRNewswire/ -- UbiQD, Inc., a New Mexico-based nanotechnology development company, announced today that it has been awarded a Small Business Technology Transfer Program (STTR) Phase I contract by the National Aeronautics and Space Administration (NASA). The contract will provide funding for UbiQD's collaborative research and development with the University of Arizona to explore using quantum dots (QDs) to tailor the spectrum of sunlight for optimized crop growth for in-space and planetary exploration missions.
"We are excited to be working with UbiQD to explore this innovative approach in managing wavelengths of light from light source to plant leaf within a food plant production application," said Dr. Gene Giacomelli, professor in the Department of Biosystems Engineering Department and the Controlled Environment Agriculture Center at the University of Arizona. "This technology has the potential to improve the PAR light source efficiency, thereby becoming a game-changer for indoor crop production."
UbiQD has quietly been developing its QD agriculture films after receiving funding from Breakout Labs in 2017 to explore the concept. The company is now aiming to launch a retrofit version of its film product in late 2018 under the UbiGro™ brand. The UbiGro™ Film is designed to promote vegetable production and accelerate plant growth.
"With NASA's support we will work with the University of Arizona controlled Environment Agriculture Center in their College of Agriculture and Life Sciences to evaluate our quantum dot agriculture films for improved lettuce production," said Dr. Matt Bergren, Chief of Product at UbiQD and Principal Investigator for the project. "We have already been testing the films, in both research and commercial greenhouses in the U.S., and we've seen yield improvements for tomatoes on the order of 20-30 percent."
About UbiQD, Inc.
UbiQD is a nanotechnology company based in Los Alamos, New Mexico that manufactures high-performance cadmium-free quantum dots and composite materials. The company uniquely focuses on applications that utilize its nanomaterials to manipulate sunlight, enabling solar windows and spectrum-controlled greenhouses. Spun out of technology developed at Los Alamos National Laboratory, Massachusetts Institute of Technology, the University of Washington, and Western Washington University, UbiQD envisions a future where quantum dots are ubiquitous in a wide spectrum of applications. For more information visit UbiQD.com and UbiGro.com.
About University of Arizona Controlled Environment Agriculture Center
The Mission of the Controlled Environment Agriculture Center (UA-CEAC) is to develop economically, environmentally and socially sustainable agricultural systems that will provide food of high quality for helping to feed the world. Engineers and scientists focus on CEA production agricultural practices within greenhouse, growth rooms and vertical farms to provide the desired aerial environment and the necessary root zone environment using hydroponic production techniques. Resource use efficiency of water, energy and plant nutrients are improved within automated systems.
About NASA STTR Program
The NASA STTR program is sponsored by its Space Technology Mission Directorate (STMD) and managed at NASA's Ames Research Center in California's Silicon Valley. STMD is responsible for developing the cross-cutting, pioneering, new technologies and capabilities needed by the agency to achieve its current and future missions. For more information about the SBIR/STTR program, including the selection list, visit sbir.nasa.gov/. To learn more about the other missions and programs NASA's Kennedy Space Center supports, visit www.nasa.gov/kennedy.
MEDIA CONTACTS
UbiQD, Inc.
info@ubiqd.com | 505.310.6766
View original content with multimedia:http://www.prnewswire.com/news-releases/nasa-awards-ubiqd-contract-to-develop-greenhouse-films-for-space-missions-300695852.html
SOURCE UbiQD, Inc.
Gotham Greens, Natalie’s Juices And Red Sun Farms Tomatoes Sprouting In Strack's Produce Department
August 9, 2018
What’s new in the Strack & Van Til produce department? A fresh crop of locally grown, sustainable and made clean products to offer customers more choices. These include Gotham Greens, Red Sun Farms Tomatoes and Natalie’s Orchid Island Juices.
Gotham Greens are premium quality produce grown under the highest standards of food safety and environmental sustainability in a climate-controlled, urban rooftop greenhouse facility in Chicago.
The proximity of the Chicago greenhouse to Northwest Indiana ensures that the Gotham Greens lettuces and leafy greens you buy at Strack & Van Til are at peak freshness.
“Products are harvested just a few hours before they reach our shelves," said Bob Hylka, Strack & Van Til director of produce. "They’re grown responsibly, which means they’re free of harmful chemicals like pesticides, insecticides, and herbicides.”
Hylka said Gotham Greens also contain no GMOs; in fact, they’re verified by the Non-GMO Project, a nonprofit organization committed to preserving and building sources of non-GMO products, educating consumers and providing verified non-GMO choices.
Because nothing says healthy goodness like biting into a juicy, red ripe tomato, Strack & Van Til is proud to add Red Sun Farms Tomatoes to its produce department, with varieties hand selected for their unique characteristics to deliver the best quality and taste.
Red Sun Farms Tomatoes are grown by the largest greenhouse operation in North America, which controls the entire process from seed selection to harvest to delivery to your local Strack & Van Til store. “That means our consumers can depend on safety, freshness, and flavor,” Hylka said.
You can also be sure that 100 percent of Red Sun Farms Tomato seeds are non-GMO, plus they’re grown sustainably in high-tech, climate-controlled greenhouses. All water and nutrients not consumed by the plants are recycled; the water is conditioned and sterilized before being fed back into the greenhouse. No pesticides, insecticides, or herbicides are used in the growing process.
Fresh fruits and vegetables are just some of the items you’ll find in the Strack & Van Til produce department; check out the delicious varieties of natural juices on the shelves, including the new, award-winning Natalie’s Orchid Island Juices.
Hylka noted that Natalie’s Orchid Island Juices are minimally processed. “That translates into fresh, clean label juice.”
Natalie’s uses quality ingredients, by hand selecting and sourcing the finest fruits and vegetables available. It handcrafts its juice in small batches to ensure authentic freshness and clean, nutritious juice made with integrity.
Owned by women and family driven, Natalie’s has provided families with a source of authentic nutrition for more than 30 years, and now customers can enjoy that deliciousness and quality when shopping at Strack & Van Til.
Stanford Seed Startup Future Farms Is Out To Solve India’s Food Crisis With Clean, Soil-Less Farming
Sohini Mitter July 8, 2018
Chennai-based Future Farms was one of the first agri startups in India to utilise hydroponics and set up rooftop farms that produce clean food crops.
At a Glance
Startup: Future Farms
Founder: Sriram Gopal
Year it was founded: 2014
Where it is located: Chennai
The problem it solves: Pesticide-free, soil-less farming for “clean” food
Sector: Agritech
Funding raised: Bootstrapped
Sriram Gopal was running Synamen Thinklabs, an IT firm, in Chennai when he stumbled upon videos of soil-less farming and rooftop farms on YouTube. The year was 2014, and Sriram’s seven-year-old IT venture, which offered business consulting and go-to-market strategies to tech startups, was enjoying a good run with a turnover of about Rs 2 crore.
Sriram was keen to do more, and to experiment, even as his top team at Synamen Thinklabs was content sticking to their core business. It was then that the Caledonian Business School (UK) alumnus began scouting for newer ideas and opportunities, and discovered hydroponics.
Sriram Gopal, Founder & CEO, Future Farms
Hydroponics is the practice of growing plants without soil, using mineral nutrient solutions in a water solvent. It not only helps reduce water consumption and increase yield, but also ensures pesticide-free farming, making it a cleaner, greener agri solution.
“I was fascinated. It looked more like engineering than agriculture,” Sriram tells YourStory. “Hydroponics had existed in Southeast Asia for nearly 15 years. But no Indian company was doing it. I wondered why,” he says.
Bringing precision farming to India
YouTube videos and reading matter on the web led Sriram to develop small DIY hydroponics kits. His father, who was the owner of a printing factory in Chennai, aided him in the activity. They would soon go on to acquire the distributorship of a foreign company that sold hydroponics kits in India.
“We listed on Trade India and other online directories. But sales were low because the kits were expensive,” Sriram recalls.
However, it helped him network with “like-minded people” that included engineers, biotechnologists, agronomists, and some with a simple interest in gardening. About 8-10 of them were willing to join Sriram in his hydroponics “adventure” and they formed a company in late 2014.
Each of them, “core team members” as they are referred to, now own shares in Future Farms, which has grown to be a 70-member startup in four years. It has executed over “32 commercial projects” for companies, including the Adani Group, Parry Agro, Dabur, Kalpataru Group, Aries Agro, and others, essentially pioneering hydroponics in Indian agriculture.
Future Farms now grows 16 crop varieties, classified under English Exotic, Asian Exotic and Indian Exotic, across 15 acres of land spread over 10 states. It recorded a $1 million turnover last year.
Future Farms' hydroponics cultivation in Kotagiri, Tamil Nadu
Sriram says,
“The focus is mostly on leafy vegetables and we have farms in every corner of the country from Delhi and Gujarat to Maharashtra and Tamil Nadu. We have grown significantly in the past two years.”
The Stanford Seed effect
Founder-CEO Sriram attributes much of Future Farms’ recent growth to the Stanford Seed Program, a year-long leadership programme designed for high-potential Indian business leaders and startup founders to scale their ventures. “Stanford Seed has been phenomenal. It helped us in being taken seriously by the VC community, which usually favours the IIT-IIM labels,” Sriram says.
He adds,
“Half the systems that we are running today were non-existent before Stanford Seed happened. They have given a format and a structure to our organisation, extended support and validation. They also helped us network with VCs in the Silicon Valley and put us on the Stanford Seed Angel Network.”
Future Farms has gone on to execute a pilot in Sri Lanka, and has a few more international projects lined up this year.
Davis Albohm, Associate Director, Global Operations, Stanford Seed, tells YourStory,
“The Seed Transformation Program was designed to provide critical skills and support to business leaders in India, with the goal of empowering talented entrepreneurs by growing their companies, developing new products and services and creating new jobs. The success of Sriram and Future Farms is a testament to the great promise and economic potential of India, and we’re thrilled to follow his continued growth and successes.”
The measurable impact
Future Farms claims to have brought down water consumption by a whopping 90 percent, cut down farming cost by half, increased yield (it says it manages four acres worth of produce in a single acre), accelerated the growth cycle (seed to plant takes about 35 days now), and improved the overall produce (120-160 tonnes to 250-270 tonnes annually).
Sriram says,
“This urban farming technique is 100 percent clean. It leaves no pesticide residue, has zero bio-toxicity or metal contamination. It involves lesser labour and input cost, but gives a greater yield. After all, why should people pay a premium for clean food? Isn’t it their right?”
The United Nations estimates that there are over 820 million “hungry” people in the world, and a huge chunk of them are in India. The affordability and accessibility of food is poor, but with hydroponics and other modern farming solutions, it is likely to improve.
Market opportunities
According to Transparency Market Research, the global hydroponics market will reach $12.1 billion by 2025, with Asia-Pacific being the growth driver. The study states,
“Growing awareness about the advantages of this form of cultivation over traditional farming has been propelling the global market. Hydroponics save water, land, use lesser fertilisers, and are a simple solution to problems of climate change.”
Hence, for Future Farms, the world is a stage. In the domestic market, especially, it is one of the few hydroponics startups to have executed commercial projects (BitMantis Innovations, Letcetra Agritech, Triton Foodworks, and Junga FreshnGreen being the others).
Bootstrapped till now, Future Farms is close to sealing a $1 million fund-raise from angels. It is looking to ramp up its agri-technology and expand its farms in India and abroad. “We are a group of people solving a global food crisis,” Sriram says.
Urban Farm Coming To Former Sparrows Point Steel Mill Site In Baltimore County
Gotham Greens, a Chicago-based urban farm operation, is opening a large greenhouse at Sparrows Point. (Gotham Greens/Julie McMahon)
A former Baltimore County steel mill is going green, as a New York-based urban farming operation looks to transform a portion of Sparrows Point into a large greenhouse.
Gotham Greens is opening a 100,000-square-foot hydroponic greenhouse at Tradepoint Atlantic, the massive redevelopment project planned for Sparrows Point, according to a news release.
Using recycled water and renewable energy sources, the climate-controlled facility will grow produce for restaurants, grocers, and other food services throughout the Mid-Atlantic.
Baltimore County will become the third market for Gotham Greens, which also has greenhouses in Chicago and New York.
The Sparrows Point urban farm is expected to open early next year and generate 60 full-time jobs. It’s part of Tradepoint Atlantic’s efforts to create 17,000 jobs in the area.
“Urban agriculture, at its core, is about reconnecting with the community through food, jobs and economic development,” Viraj Puri, co-founder, and CEO of Gotham Greens said in a statement. “To that end, we’ve found a great partner and are proud to be part of the American industrial turnaround story taking place at Tradepoint Atlantic.”
Under Tradepoint Atlantic, the former steel mill site aims to become a hub for shipping, manufacturing, and distribution. A joint venture of the local investment firm Redwood Capital Investments and Chicago-based Hilco bought the property in 2014. Since then, FedEx, Under Armour and Pasha Automotive have moved in to Sparrows Point. Amazon is also building* a distribution warehouse there.
The county has been focused on developing the site for distribution and retail, but Gotham Greens will add diversity to the site, said Will Anderson, Baltimore County’s director of economic and workforce development.
”Something this creative and adaptive in really difficult industrial development is just one more piece in a diverse set of solutions,” Anderson said. “These products that are going to come out of land that was once a challenge for us are now ending up at AmazonFresh and Whole Foods and Target.”
Anderson said the hydroponic greenhouse will build on Baltimore County’s tech strength.
“It’s kind of a home run on a number of different levels that would be unexpected at a former [Bethlehem] Steel site,” he said.
The Sparrows Point steel mill, once owned by Bethlehem Steel, closed in 2012, and its facilities have fallen into disrepair.
Tradepoint Atlantic recently received $20 million from the U.S. Department of Transportation to upgrade the property. The project will include upgrades to the site’s port, such as dredging to allow larger ships to use Tradepoint’s berths. The $20 million grant will only cover a portion of the work at the 3,100-acre property; Tradepoint will foot the bill for an additional $30 million.
Baltimore Sun reporter Pamela Wood contributed to this story.
Mega Greenhouse Marks First Harvest That Will Be In 'Major Retailer' By October
BrightFarm's Wilmington greenhouse will be able to grow one million pounds of produce each year.BRIGHTFARMS
By Hannah Poturalski – Managing Editor, Dayton Business Journal
Aug 5, 2018
A mega greenhouse in Wilmington marked its first harvest this week in the $10 million hydroponic facility.
BrightFarms' 120,000-square-foot farm will have the capacity to grow one million pounds of produce each year and will supply supermarkets in Ohio.
"BrightFarms will be available at a major retailer this October and hopes to bring its fresh, local produce to a variety of retailers in the region," the company said in a release. The retailer was not disclosed.
An event with speakers and tours was held Aug. 3 to mark the first harvest of produce at the hydroponic greenhouse. Produce will include Sunny Crunch, an iceberg, and leafy green hybrid; Happy Beet, beet greens; arugula, romaine, kale, spinach and basil. Friday's harvest was sent to the Ohio State Fair.
"If consumers would like to see BrightFarms in their grocery store, they can contact the store's customer service to let them know," the release continued.
Speakers at the event included Mitch Heaton of Dayton Development Coalition; Wilmington Mayor John Stanforth; Clinton County Commissioner Brenda Woods; and representatives for Ohio Senators Rob Portman (R) and Sherrod Brown (D).
"As consumer demand for local produce has increased, BrightFarms is playing a key role for retailers that have struggled to source locally year-round," the company release said. "BrightFarms estimates that its Wilmington greenhouse will use 80 percent less water, 90 percent less land, and 90 percent less shipping fuel when compared to salad farms located in California or Arizona."
New York-based BrightFarms has three other greenhouse farms outside of Chicago, Washington, D.C., and Philadelphia. DBJ previously reported in May the greenhouse was hiring for 30 jobs.
Quality, Quantity of Qatar's Fresh Produce Have 'Substantially Improved' This Summer
August 04 2018
*Company exported products to Kuwait nearly five weeks ago and is now in talks with Oman: Qatari agriculturist
Both the quality and quantity of fresh produce in Qatar have significantly improved this summer compared to the same period in previous years, prominent Qatari agriculturist Nasser Ahmed al-Khalaf has told Gulf Times.
Al-Khalaf, managing director of local Qatari agricultural development company Agrico, attributed the feat to research and development.
“We have been constantly improving the system to produce more and meet the increasing demand for fresh vegetables in the country,” he noted. “It (greenhouse) is developed by us and our research and development (in indoor farming) continues.”
Agrico, which operates a 120,000sqm (12 hectares) organic farm in Al Khor, has been at the forefront of helping the country achieve food security. It produces organic vegetables all year long, using locally made and state-of-the-art hydroponic greenhouses.
The company exported products to Kuwait by sea nearly five weeks ago and is now negotiating with Oman, according to al-Khalaf.
“Hopefully, within the next three weeks we will start our first shipment to Oman since the blockade,” he added.
Al-Khalaf also disclosed that they are currently developing a greenhouse system with solar energy, which could supply a substantial amount of electricity to his farm near Al Khor. “If we are able to generate enough power, then we can produce all types of vegetables in the greenhouse.”
He noted that such a plan, which is still in the design phase, aims to take advantage of the greenhouse structure and use new types of solar panels to generate power.
Al-Khalaf said the company is now modifying its seasonal net greenhouses, which built for the winter this year, to produce even during the summer.
The company has constructed an additional 120,000sqm of these seasonal net greenhouses to grow more fresh vegetables during the winter season, in addition to its 120,000sqm facility, which operates all year round.
“We have actually planted (in) the net greenhouse in mid-July and waiting for the production in the end of August,” he said. “If we succeed, we can guarantee a long season that can last 10 months or more of production, getting a high yield at a very low cost.
“My target today is to increase the yield per square metre in different types of greenhouses and produce new varieties such as strawberries.”
According to al-Khalaf, his farm now also produces good-quality papayas, which can be bought in the local market.
Agrico is also planning to experiment with growing bananas by the end of this year, apart from melons and watermelons.