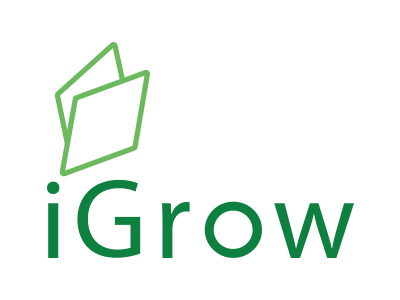
Welcome to iGrow News, Your Source for the World of Indoor Vertical Farming
Micro Farm, Macro Impact
March 25, 2019
Brooke Bilyj | Photography by Erin Elliott, except where noted
Micro Farms in Nappanee, Indiana, Hopes to Revolutionize Food Production With its Patented Hydroponic System.
From left to right: Nick Graber, Steve Kiefer and Dion Graber
Nestled in the heartland of northern Indiana’s Amish country sits a shimmering glass greenhouse where fresh produce is grown, 365 days a year, without any pesticides or herbicides. Although the facility occupies a mere quarter of an acre, the owners of Micro Farms hope to revolutionize global food production with their innovations.
“Our big-picture goal for Micro Farms is to develop technology and growing systems to provide wholesome food to people globally,” says Loren Graber, who established the hydroponic greenhouse about five years ago.
“There are too many people who go to bed hungry,” adds Dion Graber, Loren’s son and head grower. “With all the technology and resources available, we should be able to feed them.”
Building on a long farming history, the Graber family has been producing food on this property for generations. Back in the ’80s, before Dion was born, Loren ran the family’s corn, soybean and dairy farm in Nappanee, Indiana. One day, he jokingly mentioned to the farm’s agronomist, Steve Kiefer, that he would start a greenhouse operation someday.
But then, soon after Dion was born, milk prices plummeted — forcing Loren to find work in another field. At the time, he didn’t realize that his new job in vinyl fencing would inspire the innovation to bring his greenhouse to life.
“Since he was in the vinyl business and he has PVC connections, vertical farming was right up his alley,” Dion says. “He’s always been an inventor at heart, and he has multiple patents. He just loves thinking outside the box and trying to come up with new things that are more efficient.”
Leveraging his inventive curiosity, his knowledge of vinyl and his drive to make traditional agriculture more efficient, Loren designed and patented his own vertical hydroponic/aeroponic tubes. He asked Kiefer to team up with him again, and they established Micro Farms in late 2013 with the dream of farming differently. Dion jumped onboard as head grower, and several years later, his younger brother Nick joined the family business to execute their father’s dream.
Lettuce growing at Micro Farms
“Vertical” integration
Loren considered using traditional, single-layer hydroponic systems that used floating rafts — deep water culture (DWC) — or the nutrient film technique (NFT), where nutrient-rich water circulates past the bare roots of plants in enclosed channels. But these horizontal layouts required too much space — pointing him toward vertical farming instead.
“You get so much more product per square foot when you grow vertically,” Dion says. “We have 320 tubes in a 4,000-square-foot area, and we can fit 46,823 plants in that 4,000 square feet. That’s roughly 10 plants per square foot.”
Micro Farms’ “Verti Tubes” are 12 feet tall and eight inches in diameter. Loren’s patented design features removable growing cups and trays that pop out of the tube for cleaner, easier harvesting. Prongs in each cup hold a foam cube in place to support the plant’s roots, and a small groove in the bottom of each cup channels water down as it trickles through the tube.
“The biggest thing that separates us when it comes to our Verti Tubes is the removable cup,” Dion says. “Most of them are molded in and you can’t take them out, so our design is better for cleaning purposes. It’s easier to harvest your plants, because if the roots are too long, they’ll get caught when you try to pull them out.”
The foam cubes can be removed with the roots still intact, allowing Micro Farms to harvest and sell living lettuce with a shelf-life of at least two weeks — leaving minimal cleanup behind.
Micro Farms’ Verti Tube Home Growing System
Finding the right mix
The Grabers broke ground in fall 2012, and then a team of builders from Rough Brothers constructed the Venlo greenhouse in 2013. The glass structure contains a 3,000-square-foot head house for seed-starting, a 4,000-square-foot space filled with Verti Tubes, and another 4,000-square-foot space for vertical vine crops.
Dion didn’t have any experience with hydroponics, so he and Kiefer attended the Controlled Environment Agriculture Center at the University of Arizona for a “quick crash course” that packed “six months’ worth of college courses into five days, and then another four months in two days,” he says. “That’s where my knowledge started, but at least 80 percent of my growing knowledge is just hands-on.”
When Dion started growing, he experimented with 23 varieties of leafy greens that he seeded weekly. Through trials, he whittled that collection down to 10 varieties, based on what grew and sold best.
The front half of the greenhouse is dedicated to leafy greens like butterhead and oakleaf lettuce, kale and pak choi grown in Graber’s hydroponic/aeroponic Verti Tubes. In the back half, vine crops like tomatoes, red bell peppers and snacker cucumbers are strung up toward the ceiling from hydroponic Bato buckets below — which are filled with recycled glass Growstone that can be rinsed and reused.
Dion and Nick continue to explore new varieties together — switching up greens in the summer to include basil and other heat-loving plants. They’re even trying strawberries in the Verti Tubes.
“We’re constantly experimenting,” Dion says.
Micro Farms grows tomatoes in addition to its Verti Tube-grown lettuce.Photo: Brooke Bilyj
Watering the natural way
In addition to Loren’s innovation, the design of the greenhouse also drives efficiency at Micro Farms.
For example, each peak of the Venlo greenhouse roof has a vent on each side. “Whichever way the wind blows, the opposite side opens, so you don’t have a dramatic change in temperature,” Dion explains. “And then every valley has a gutter where we collect rainwater, which is stored in a 25,000-gallon tank under the floor of the headhouse.”
The roof of the warehouse next door also collects rainwater to supplement the operation. They have access to well water, if needed, but they rarely need to tap into that supply.
“The plants just respond better to rainwater,” says Dion, who also uses an O2 Grow system to “supercharge” the water with dissolved oxygen. “We’re trying to imitate exactly what a plant would get out in the ground, but with no soil.”
To that end, Kiefer formulated a mix of granular fertilizers mined from the ground — including Epsom salt, potash, potassium nitrate, monopotassium phosphate and calcium nitrate — that’s added to the water.
Building on a long farming history, the Graber family has been producing food in Indiana for generations.Photo: Brooke Bilyj
Bugging out for pest control
To keep greenhouse insects in check, Dion and Kiefer rely on beneficial bugs to provide biological pest control at Micro Farms.
“We try to keep our population up, so when pests come, we’re ready for them,” Dion says. “Pests seem to multiply quicker than your beneficial bugs, so we’re constantly ordering them.”
Dion regularly releases parasitic wasps to control pesky aphids. Meanwhile, small sachets of swirski mites hang from the plants, inviting the tiny predators to go after the eggs of thrips that can threaten crops. Beneficial insects are released once or twice a month, negating the need for sprays.
“One thing that separates us is that we do not spray any pesticides or herbicides on our plants,” Dion says. “We don’t even have to rinse our produce after harvesting, because nothing was sprayed on it.”
Ronda Kuhns, greenhouse worker at Micro Farms, harvests lettuce from its Verti Tubes.
Harvesting fresh for market
Using scissor lifts to access crops all along the 12-foot-tall tubes, Micro Farms employees harvest produce daily. While some is sold fresh to local restaurants and retail customers, Micro Farms also sells produce through an online farmers market called Market Wagon.
Founded by a fellow former dairy farmer, the online platform allows customers throughout the state to order locally grown or handmade products from various vendors, who get to set their prices and availability weekly. Then, orders are either delivered directly to consumers’ doorsteps or to local pickup points.
There are too many people who go to bed hungry. With all the technology and resources available, we should be able to feed them. — Dion Graber
Every Thursday morning, Dion drives a truckload of produce to the Market Wagon hub in Indianapolis, two hours south of Micro Farms. On the way home, he swings by another hub in LaPorte, an hour west. At each hub, he distributes orders into customers’ bags, which are delivered after every vendor drops off their goods.
Market Wagon extends Micro Farms’ reach across the northern half of Indiana. But word travels fast in the small, rural town of Nappanee — and local consumers started asking how they could get fresh hydroponic produce, too. So last November, Micro Farms began selling to the public on Saturday mornings from 9 a.m. to noon.
“At 9, you’ll see half a dozen buggies and a dozen cars in the parking lot,” Dion says. “Local people have responded very well to our products.”
Photo: Brooke Bilyj
Looking to the future
The Graber family is eager to share their hydroponic innovations with other growers. The first phase of this long-term plan is their home growing unit, which is slated to hit the retail market later this year.
A smaller version of their greenhouse Verti Tubes, the home hydroponic units, are mounted on a rolling cart that can be wheeled outside. Or, the unit can sit in a kitchen, using an optional LED strip and rotating function to provide sufficient light inside. The home unit features Loren’s patented removable cups and trays, allowing consumers to hydroponically grow 24 plants with minimal mess or maintenance.
Looking even further into the future, the Grabers’ dream of improving food production around the world by providing greenhouse supplies, resources and knowledge to communities in underserved nations like Haiti and Africa, where they’ve been involved in mission work.
“We want to teach other people how to grow. Ultimately, our big goal is to feed the hungry by educating them and setting them up for success,” Dion says. “Because our tubes maximize product per square foot, we think it could definitely make a difference.”
Brooke is a freelance writer based in Cleveland.
Vertical farms Irrigation Hydroponics Aeroponics Cucumber Lettuce
Kale Bok choy Basil Pepper
USDA National Organic Program Holds Firm Against Efforts to Impose Special Restrictions Against Growers Using Container and Hydroponic Methods
Groups opposed to certification of production systems incorporating containers and hydroponics failed in their most recent attempts in the last few weeks to convince the USDA and the National Organic Standards Board to initiate the process for new standards for those production systems.
Several groups including the Real Organic Project, the Organic Farmers Association, the National Organic Coalition and others presented testimony at the recent National Organic Standards Board meeting in Seattle and in recent press campaigns to call for a moratorium on certifications for organic production systems using containers and hydroponics. The moratorium would be followed by the revocation of certification for existing operations. However, if the USDA does not agree to those terms, the groups insist that new more restrictive regulations must be drafted, implemented and then applied to container and hydroponic organic production systems.
Those groups have begun the tactic of inventing hypothetical scenarios about production practices, and they then ask for clarification from USDA regarding the legality of such an approach. USDA indicated that they would not likely give opinions regarding hypothetical situations, but USDA will look at specific cases and instances of operations performing actual activities to review for compliance. The CSO expects that opponents of certifications for containers will refer operations for review, and USDA will respond regarding those practices.
However, this activity will not be unofficial rule making or regulations that are created without any opportunity for public input. USDA does not have the authority to implement standards through the guidance process that would create special restrictions for container operations. Any new restrictions would have to go through the formal rule making process.
Organic producers must follow all applicable USDA standards for organic production systems. Specifically, growers need to show that their production system is managed to respond to site-specific conditions by integrating cultural, biological, and mechanical practices that foster cycling of resources, promote ecological balance, and conserve biodiversity.
Here are the requirements copied from 7 CFR 205.201 that lay out the elements required to be included in the organic production and handling systems plan.
§205.201 Organic production and handling system plan.
(a) The producer or handler of a production or handling operation, except as exempt or excluded under §205.101, intending to sell, label, or represent agricultural products as “100 percent organic,” “organic,” or “made with organic (specified ingredients or food group(s))” must develop an organic production or handling system plan that is agreed to by the producer or handler and an accredited certifying agent. An organic system plan must meet the requirements set forth in this section for organic production or handling. An organic production or handling system plan must include:
(1) A description of practices and procedures to be performed and maintained, including the frequency with which they will be performed;
(2) A list of each substance to be used as a production or handling input, indicating its composition, source, location(s) where it will be used, and documentation of commercial availability, as applicable;
(3) A description of the monitoring practices and procedures to be performed and maintained, including the frequency with which they will be performed, to verify that the plan is effectively implemented;
(4) A description of the recordkeeping system implemented to comply with the requirements established in §205.103;
(5) A description of the management practices and physical barriers established to prevent commingling of organic and non organic products on a split operation and to prevent contact of organic production and handling operations and products with prohibited substances; and
(6) Additional information deemed necessary by the certifying agent to evaluate compliance with the regulations.
(b) A producer may substitute a plan prepared to meet the requirements of another Federal, State, or local government regulatory program for the organic system plan: Provided, That, the submitted plan meets all the requirements of this subpart.
Your Membership and Activity Still Needed
The efforts of growers and other members of the organic community like yourself helped to create more regulatory certainty and to safeguard your rights to select the most appropriate growing methods in your organic operations continues.
Join the CSO if you have not done so already. Our sustained efforts on behalf of the hydroponic, aquaponics and container industry around the country and in Washington, DC rely on dues from farming operations like yours.
UK: Sheffield Scientists Are Growing Food Ten Times Faster Without Soil At An Urban Farm in Tinsley
Jacob Nickles at the urban farm in Tinsley where scientists are using pioneering hydroponics techniques to grow food without soil. Picture by Chris Etchells.
By BEN BARNETT
05-19-19
“It is estimated that 35 Mount Everest’s
worth of soil a year is lost to erosion.”
Ceaseless world population growth and worrying levels of soil erosion mean new ways of producing food perhaps matches mitigating climate change as the biggest global challenge of our time.
Some 24 billion tons of fertile soil is being lost globally to erosion every year and such is the mounting crisis that academics at the University of Sheffield predict the UK has fewer than 100 harvests left.
Enter hydroponics, the science of growing plants using nutrient solutions in a controlled unit without using soil. It is a ground-breaking technique that is now gaining greater traction internationally as scientists explore ways of ensuring the world does not go hungry in the future.
An attempt to harness the potential of hydroponics is underway on the border of Sheffield and Rotherham, where a team of scientists are using a disused building at the former Tinsley Infant School to grow a range of fresh produce, from salad to tomatoes, using specialist foams that chemically, physically and biologically resemble soil - a product developed by University of Sheffield PhD student Harry Wright.
Such has been the so-called “urban farm” project to date that scientists have found that they can grow plants up to 10 times faster than in soil.
A public open day at the facility was held on Saturday, where project leader Jacob Nickles, a knowledge exchange associate from Sheffield University’s new Institute for Sustainable Food, explained how the system worked.
“This technology is the way forward,” Mr Nickles said.
“By 2050, we are facing having to feed 10bn people worldwide and we don’t have the space or resources to do so. Both hydroponics - and aquaponics to raise fish - solve a number of issues in one go.
“For example, you can build these units upwards rather than outwards.”
He said there was “absolutely” still a place for traditional farming methods but it was important globally to help soils recover.
“The whole purpose of using synthetic soil is an attempt to move away from conventional soils,” the scientist explained.
“It is estimated that 35 Mount Everests worth of soil a year is lost to erosion. We need to give our soil time to recover by pulling some of the growth away from traditional technology.”
Mr Nickles has grand hopes for the technology.
“The unit we have here is small at the moment but an ambition for the future is to repurpose an derelict urban building, like a warehouse, so that people can use it for hydroponic growing.”
He anticipated a mixed reaction to soil-free food production from the public.
“Most people mistrust something foreign to them but we have done a lot of analysis and this system can produce food that is just as healthy, if not more so. It’s about getting the knowledge out there.”
CAN (ON): Video Tour of An Ontario Based Cannabis Operation
James E. Wagner Cultivation Corporation President and CEO Nathan Woodworth gave a tour of the company’s new facility located in Kitchener, Ontario. Woodworth also talks about the company’s GrowthSTORM system and stresses that its high density, low-cost system is the most effective way to control the plant’s growth cycle. GrowthSTORM is a multi-part system that uses aeroponic and hydroponic techniques to optimize yield and plant growth.
“The degree of standardization that we can achieve with this system is proof that we have discovered a way to control the total plant growth cycle,” said Woodworth. “We’ve created a high-density, low-cost growth system which results in a 98 percent success rate after 11 to 14 days.”
Woodworth explained the process behind the system and its advantages. According to Woodworth, the plants are moved into GrowthSTORM baskets once they are fully rooted. The baskets allow the plant to form complex root systems throughout its life. Once the plants have reached full production size, they are moved to a low-density array until the flowering cycle is complete. Woodworth also talked about JWC’s latest innovation, the Dual Droplet system, which distributes a large and a small nutrient droplet. These droplets help KWC optimize the delivery and uptake of nutrients. The cannabis plants are then flat trained, ensuring standardization of yield per square foot and maximizing the quality of the finished product.
JWC’s facility has eight grow rooms that are capable of producing up to 50 kilograms per growth cycle with less than one percent crop loss. The company’s 29 strains, which feature four unique phenotypes, are all being grown using the GrowthSTORM system.
For more information:
JWC
1-888-594-4272
info@jwc.ca
jwc.ca
Publication date: 5/15/2019
Testing Saffron in Hydroponic Cultivation
Saffron (Crocus sativus L.) is cultivated worldwide. Its stigmas represent the highest-priced spice and contain bioactive compounds beneficial for human health
Saffron (Crocus sativus L.) is cultivated worldwide. Its stigmas represent the highest-priced spice and contain bioactive compounds beneficial for human health. Saffron cultivation commonly occurs in open field, and spice yield can vary greatly, from 0.15 to 1.5 g m-2, based on several agronomic and climatic factors.
A new study evaluated saffron cultivation in soilless systems, where plants can benefit from a wealth of nutrients without competition with pathogens or stresses related to nutrient-soil interaction. In addition, as plant nutrient and water uptake can be enhanced by the symbiosis with arbuscular mycorrhizal fungi (AMF), researchers also tested two inocula: a single species (Rhizophagus intraradices) or a mixture of R. intraradices and Funneliformis mosseae.
After one cultivation cycle, they evaluated the spice yield, quality (ISO category), antioxidant activity, and bioactive compound contents of saffron produced in soilless systems and the effect of the applied AMF inocula. Spice yield in soilless systems (0.55 g m−2) was on average with that produced in open field, while presented a superior content of several health-promoting compounds, such as polyphenols, anthocyanins, vitamin C, and elevated antioxidant activity.
The AMF symbiosis with saffron roots was verified by light and transmission electron microscopy. Inoculated corms showed larger replacement corms (+50% ca.). Corms inoculated with R. intraradices performed better than those inoculated with the mix in terms of spice quality (+90% ca.) and antioxidant activity (+88% ca.). Conversely, the mixture of R. intraradices and F. mosseae increased the polyphenol content (+343% ca.).
Thus, soilless systems appeared as an effective alternative cultivation strategy for the production of high quality saffron. Further benefits can be obtained by the application of targeted AMF-based biostimulants.
Publication date: 5/9/2019
Update On Glyphosate And Organic Certification
The debate on the failing integrity of the National Organic Program has become international, as heard on last night's program on BBC World. Click here to hear Dave Chapman, farmers from Holland and India, and General Mills discuss the controversies in organic
The debate on the failing integrity of the National Organic Program has become international, as heard on last night's program on BBC World. Click here to hear Dave Chapman, farmers from Holland and India, and General Mills discuss the controversies in organic.
I was honored to be a part of this show. It is clear that we are ALL affected by the failures of the USDA organic program, from California to Singapore.
A certified hydroponic organic blueberry "farm."
In my last letter, I quoted NOP director Jenny Tucker as saying that there is no transition period for hydroponics. After reading my letter, some withheld judgment until the Seattle meeting of the National Organic Standards Board. Jenny promised she would address the issue of hydroponics and glyphosate at that meeting. No transition period means that a hydroponic producer could use ANY chemical on their land or greenhouse that is allowed in conventional agriculture. They could do this the week before bringing in new substrate and still qualify for immediate organic certification.
A Driscoll's certified organic blueberry "farm" of coco coir pots.
Substrate is the fancy word for the growing medium in the pot. Hydroponic producers choose materials to grow in like shredded coconut husks (called coir) because they don’t rot. They also don’t provide any nutrition to the plants. The coir holds the roots and the water. All the nutrition is provided as a near-constant liquid feed in the irrigation water. Hydroponics can happen in a container on the ground or on a table. For some crops, it even happens without any container at all. At its most extreme form, called aeroponics, the roots are suspended in the air and sprayed with the nutrient solution. There is no nutritional difference between spraying the roots in the air or watering them in a container of coir or a bucket of water. The difference is in the time the plant can survive if the electricity goes off. With an “aeroponic” system, it is a matter of minutes. With a container system, it is a matter of hours. It is the same nutrition.
Jenny’s comment created quite a stir as the implications became clear. In the new USDA interpretation, “certified organic” no longer defines how the land is farmed. It now only defines how a pot of coco coir is “farmed.”
How twisted will the USDA "new organic" standards become? Will they look something like the political machinations we see in this district map of Maryland?
The new USDA definition of organic is becoming a form of gerrymandering. Gerrymandering is the process by which a group of political officials manipulates the drawing of an election map in a way that benefits them. The result is a complex, illogical map that makes sense only to those who will profit. This principle is applied to many areas of government. When the allowable levels of glyphosate were being crossed in conventional farm products, the EPA simply increased the “safe” level. In the case of "organic" hydroponics, we are ending up with a convoluted set of regulations that look like the latest Congressional district designed to keep one party in power.
Or we are left with no regulations at all, with every certifier making up their own? That is the case until the USDA answers our questions.
Wasn't preventing such a "Wild West" scenario the justification for the NOP in the first place?
Real organic blueberry production. Soil-grown blueberries must be free of prohibited substances for 3 years before being eligible for organic certification. This is referred to as a "3 year transition period."
The reason for this is because hydroponics CAN’T fit into the real meaning of organic. Organic farming is based on the principle of stewarding the life in the soil in order to provide superior nutrition for plants, animals, and humans. I would now add climate to that list of benefits. It is, in fact, the opposite way of farming from “conventional.” This foundation of soil stewardship is well understood in the rest of the world, as clearly defined by IFOAM (The International Federation of Organic Agriculture Movements). The United Arab Emirates has just joined the rest of the world in prohibiting hydroponic from being certified as organic. It is also well understood in our own law, the Organic Food Production Act. And yet, the USDA continues to be the rogue nation embracing hydroponic as organic.
Hydroponic is the opposite way of farming from organic. Being a hydroponic organic producer is like being an illiterate book critic. They just don’t fit together.
Jenny Tucker speaking this winter at an event on organic integrity.
So people came to Seattle ready for answers. They got none. Jenny Tucker has given the seemingly contradictory statements that glyphosate would never be tolerated in organic AND that there was no transition time for hydroponics, thus allowing glyphosate (and hundreds of other pesticides) to be used immediately before certification. And there are no standards prohibiting hydro producers from going out of certification for a week during the crop changeover so they can spray whatever they want, and then being immediately recertified when they bring in new pots.
Laura Batcha of the OTA and Dave after speaking together on a panel in Washington this Spring. We often agree to disagree. Photo courtesy of Charles E. DeBourbon/The Hagstrom Report.
The Organic Trade Association (OTA) delivered a letter to the USDA signed by members, including the leading USDA organic hydroponic producers. It demanded that USDA make clear that glyphosate is not permitted in organic certification. Which of course, it is not. Dr. Tucker was happy to make that clear. The letter briefly mentions the question of whether glyphosate is allowed the week before organic certification. Which it is, in the absence of applying the three year transition period to hydroponic and container operations. Yet the three year transition period is a cornerstone of the Organic Foods Production Act.
Just to be clear, the OTA continues to strongly support certification for its hydroponic members such as Driscoll's and Wholesum Harvest. Although OTA has publicly opposed certifying “hydroponics,” their definition of hydroponics is a perfect example of “rebranding.” In the strange world of OTA, hydroponics is limited to plants growing with their roots in water or in the air. Clearly, this is not what the rest of the world means by that word. No wonder they are so confused. In their private world, “Hydroponic is what we say it is. Organic is what we say it is.”
CCOF President Phil LaRocca at the 2017 Jacksonville NOSB meeting.
Phil LaRocca, President of CCOF, testified in Seattle, where he clearly expressed his genuine outrage that this “no transition period” was being allowed. He said that he had been told by CCOF’s Executive Director that, indeed, no transition time was being required by some certifiers for hydroponics. As the largest certifier in the world, CCOF (California Certified Organic Farmers) would know. Phil asked that Jenny clarify the USDA National Organic Program position.
She would not.
Over and over people, including members of the National Organic Standards Board, pressed Dr. Tucker to respond and clarify the NOP position. Over and over Jenny responded that she would not respond to a question about “hypotheticals.”
It seems to me that when the NOSB and the President of CCOF ask what the USDA policy is on organic transition time, it is not a hypothetical.
I have wondered why Jenny refused to set the record straight and answer a simple question about policy? She did say that she misspoke in answering my question, but she would not disavow her statement! All she had to do was say, “I was wrong. A three year transition period is required for ALL organic production, and always has been.”
That answer would then lead to the decertification of those certified with no transition time. Probably that would lead to lawsuits. But if the USDA continues to allow this, that will also probably lead to lawsuits. It looks to me like the USDA is going to get sued (again), one way or the other.
The final testimony at the meeting came from Lee Frankel, the lobbyist for the misnamed Coalition For Sustainable Organics. They should be called the Coalition For Hydroponic Organics. They just don’t want you to know that. The desire to keep us in the dark seems to be the hallmark of the “hydroponic organic” producers. Lee asked what the logic was of requiring a three-year transition for hydroponics? It is interesting to note that Wholesum Harvest, the leader of the Coalition, is calling on the NOP to enforce a three-year transition in the OTA letter. On the same day, the Executive Director of the Coalition is questioning whether a three-year transition makes any sense.
Is there a logic in requiring a three year transition period for a pot of coco coir? The problem with this whole circus is that it doesn't make any sense certifying hydroponic as organic in the first place. Organic and hydro are opposite systems of growing. Let the hydro producers make their own label. Let them proudly offer their products to consumers.
But that transparency isn’t going to happen, is it? The large hydro growers run from honesty with their customers. The whole reason they want the organic label is to avoid being transparent.
Real Organic dairy at Radiance Dairy in Iowa.
People have said that real organic farmers are afraid of honest competition. I say bring it on. But let’s make sure it is HONEST. Let every hydroponic tomato and berry have an image above of plants growing in buckets of coco coir sitting on black plastic. Let every CAFO (concentrated animal feeding operation) produced container of milk or eggs have a picture of animals in confinement on the front. And real organic farmers will put pictures of our reality on our products, of plants growing in soil and animals eating fresh grass. Then we will see who wins the support of the customers.
Aurora Dairy in Colorado which, according to the Washington Post, is fake organic. For their investigation, the only cows found on pasture were "dry cows," not producing milk. Which milk would you buy? Photo courtesy of Washington Post.
Of course, this would be no contest. The HYDROs and CAFOs would go out of business. The farmers growing real organic would be unable to keep up with market demand. The stores would be falling over themselves to buy locally from real organic farmers. Real organic farmers would multiply.
The whole reason that we shouldn’t allow hydroponics to take over American organic vegetable production is that we want to be honest. We want to protect the customers from fraud. We want to protect the farms and farmers. We want to protect the land.
So I invite all in the organic community to come together.
If you are a consumer, demand that local real organic products are on the shelves of your grocery store.
If you are a member of CCOF, demand that your organization stops certifying hydroponics. Throw out CAFOs while you are at it.
If you are a member of OTA, demand that your organization publicly calls for an end to ALL hydroponic certification, including hydroponic containers. Throw out CAFOs while you are at it.
When that day comes, perhaps we can take back the organic seal in America. Oh, and we will need to elect a new President as well. I never said this was going to be easy.
In the meantime, please support the Real Organic Project.
Greece: Hydroponic Workshops Launched In Corfu
Hydro Fresh Produce Announces The Launch of
Hydroponic Workshops In sunny Corfu, Greece
The workshops will take place at their hydroponic farm in central Corfu, Greece. The farm is located just 5 km from Corfu International Airport and 7km from the historic UNESCO city centre. Accommodation is available just a five minute walk from the farm or select your own.
The workshops last four days and will cover everything from setting up the system, implementation, maintenance, crop types, water and nutrient management and much more. The course will provide all of the information required to enable anyone to start their own hydroponic production, whether on a small scale at home for the family, or on a larger commercial basis. The official launch date for the workshops is Tuesday 4th of June 2019.
Ivor de Lloyd of Hydro Fresh Produce Corfu says about the project that it "started with yet another 'Ivor, don’t even think about it!' And here we are – 3 years into it and proving them wrong yet again.
"Hydro Fresh Produce hydroponic farm is a logical addition to my culinary career. How many chefs can say they grow their own greens, not to mention using innovative technologies? We supply local shops and taverns with the freshest produce in Corfu. If you choose the right restaurant, your salad will still have been growing this morning!
"Now, the next step. Hydroponic Workshops right here in beautiful Corfu.
"Enjoy the beauty of Corfu on a holiday with something extra…
“Learn how Hydroponics works and gain the knowledge to do it yourself!"
Hydro Fresh Corfu believe that this is a valuable addition to the thriving eco/agri-tourism movement and is aimed at individuals, couples or groups interested in learning about hydroponic production, with a view to setting up themselves.
For more information:
Hydro Fresh Produce (Corfu)
Ivor de Lloyd
+30 26610 56226
+30 693 099 7873
idelloyd@yahoo.com
www.hydro-fresh.com
Publication date: 5/22/2019
Waste Heat From Berlin Biomass Plant Will Help Grow Hydroponic Greens
The biomass power plant in Berlin is getting half a million dollars from the state to build a waste heat recovery system that will soon power a new greenhouse
PHOTO: Wood chips wait to be turned into electricity – and excess thermal energy – at the Burgess BioPower plant in Berlin.
Photo By CORI PRINCELL / NHPR
By ANNIE ROPEIK • 05-17-19
The biomass power plant in Berlin is getting half a million dollars from the state to build a waste heat recovery system that will soon power a new greenhouse.
The Burgess Biopower plant burns wood chips to make steam, which turns turbines and generates electricity.
It also makes a lot of excess heat – 500 million BTUs an hour, enough to keep roughly 10 million square feet warm. Right now, that heat is released to the atmosphere.
Burgess operations manager Dammon Frecker says the new grant, from the state Public Utilities Commission, will help them build a system to harness that waste heat and put it to good use.
"We're very excited about not only the economic development, but in doing something novel with Burgess BioPower,” he says. “Not only producing electrical renewable energy, but thermal renewable energy."
One application for that thermal energy will be a hydroponic greenhouse that’ll grow more than a million pounds a year of baby leafy greens – like spinach, kale and arugula – for sale locally.
"Particularly in a Northern climate, a greenhouse will need heat ... for growing the produce,” he says. “So this thermal energy recovery system has been designed just to meet those heating demands in the cooler weather."
The 4-acre greenhouse is set to be built next year and will be operated by a third party, which Frecker declined to name.
The city of Berlin also wants to use some waste heat to melt snow and ice on its sidewalks. Frecker says these kinds of “synergies” have been one of Burgess’ goals since it was built.
And he says even these two projects combined will only use about 20 percent of the heat the power plant generates.
Burgess has space left on its campus for future businesses that could use the heat. Frecker says it could also theoretically be distributed beyond their facility, with other infrastructure upgrades.
TAGS: BERLIN BURGESS BIOPOWER BIOMASS
RELATED CONTENT
Berlin City Manager Hopes To Harness Steam From Biomass Plant To Melt Sidewalk Snow
By SARAH GIBSON • JAN 18, 2019
SARAH GIBSON FOR NHPR
On cold days, Berlin City manager Jim Wheeler can stand on the steps of city hall and see plumes of steam billowing from the wood chip burning plant Burgess BioPower.
The plant sits on the former site of the city’s pulp mill factory on the Androscoggin River.
“One of the things about biomass plants is that they make a lot of steam, and that's energy that goes to the sky,” Wheeler says.
Now, Wheeler wants to harness the heat that makes this steam for a snowmelt system.
In A Basement in Stockholm, The Inhabitants Grow Their Own Fish and Vegetables - Cycling Cultivation Provides Extremely Grown Food
PUBLISHED FÖR 14 DAGAR SEDAN.
Different forms of urban cultivation are becoming increasingly popular and Dag-Tore Johannessen from the Circulation Company is testing aquaponics in a basement room. Photo: Yle / Linda Söderlund
In a few months the residents of Solberga in Stockholm can go and catch the dinner fish in the basement. At the same time, they can harvest salad, tomatoes and herbs. The cycling plant is tested to get locally produced food in town.
You first go through a bicycle cellar and then you come to a basement room, where the former storehouse was kept. An aquaponic cultivation has now been built, which provides both the fish and vegetables for the needs of the tenants.
THIS IS HOW AQUAPONI WORKS
- I jumped on the project right away. I am interested in food production and I also work with it. It seemed interesting to have friends with neighbors and raise fish and plants in the basement, says Markus Jantunen, one of the tenants in Solberga.
Torbjörn Frisö and Markus Jantunen read about the various hydroponic cultivation techniques. Photo: Yle / Linda Söderlund
The entire plant is a biological system that works with bacteria. The plants get nourishment from the fish bait, and at the same time the plants help to clean the water so that it can return to the fish farm.
In two open tanks, tilapia swims, one of the world's most cultured fish. Tilapia grows fast and thrives on a small surface and one expects to get 200 kg of fish a year from here.
Tilapia is an African fish that is grown a lot in especially Asia and the USA. Photo: Yle / Linda Söderlund
The fishermen sprinkle and swim up to the surface when Torbjörn Frisö pours half a cup of fish feed into the water.
- The only thing we add to the culture is oxygen and fish food, says Frisö.
Frisö founded Kretsloppsbolaget and he and Dag-Tore Johannessen have built the cultivation plant in the basement. Cultivation is part of the EU project Green Solberga and here in southern Stockholm several different climate-smart and sustainable innovations are tested.
The cultivation can provide 1500 basil pots per year
In the basement, three different hydroponic cultivation beds are tested, where one grows in water. Here grow lush basil, tomatoes, sugar peas, fennel and chili.
Basil is the main product right now and one expects 1500 basil pots per year.
The NFT technology with pipes is especially suitable for growing herbs. Photo: Yle / Linda Söderlund
THREE DIFFERENT HYDROPONIC CROPS
The big challenge is to maintain the balance in the biological system.
- Secondly, it is important to raise the level of bacteria, which converts the fish's poo ammonium to nitrite and then to nitrate. The pH value is important, as is the alkalinity, says Torbjörn Frisö.
With climate change, interest in urban cultivation is growing
Markus Jantunen believes that in the future it will become increasingly important that one can also produce their own food in the cities.
- We city dwellers do not have many options, compared to people living in rural areas. Then such solutions are needed to become self-sufficient in food.
He also appreciates the social part, to do something for the climate together with the neighbors.
- We are destroying our soil, we are depleting the soil and surpassing them elsewhere and we are fishing out of the sea. Then it is this that will be the future.
Ebb and river technology are suitable for different types of perennials, such as tomatoes. Photo: Yle / Linda Söderlund
The ecocycle company also believes that interest in urban cultivation continues to grow. People are becoming increasingly aware of climate change and want to influence themselves with active choices.
It is hoped that this type of aquaponic plant will be built in several basements around Stockholm. According to the circuit company, the plant has many advantages.
- This food is extremely popular if you think of the tenants living in Solberga. Water consumption is smaller than in normal cultivation and so we have the premises that are already heated, says Dag-Tore Johannesson.
The cultivation requires supervision a few times a week
Now the inhabitants are learning how to manage the cultivation. It is a group of about ten people who have been allowed to register and eventually they take over the responsibility for the cultivation from the Circulation Company.
- It requires supervision two or three times a week, depending on how the plant has been set up. It takes some time, but at the same time it is fun, so I think it will be fine, ”says Jantunen.
Photo: Yle / Linda Söderlund
Torbjörn shows Markus how to best sow basil. He uses regular seed soil and seeds sold for commercial use, they have much better germination than regular seeds.
- The first pots we put - oh, oh, as soon as it grew! It is amazing !, describes Torbjörn and shows with his hands how quickly the basilica grew.
"So the problem is that it gets so much that you don't know what to do about it?" Asks Markus.
- No, it's just eating it! We usually make pesto at home, it will be fine, Torbjörn tips and laughs.
The Green Solberga project also includes cultivation in pallet collars, a project with water stairs that can take advantage of stormwater and to test a biotechnology that removes bad odor during waste sorting. The project is run by IVL Svenska Miljöinstitutet and Stockholmshem.
Meet Mexico’s Biggest Producer of Hydroponically Grown Food
When you meet Leo Lobato, co-founder of Karma Verde Fresh, the first thing that you will notice is his charisma and warm-hearted charm
When you meet Leo Lobato, co-founder of Karma Verde Fresh, the first thing that you will notice is his charisma and warm-hearted charm. Leo’s energy for life and his well-earned passion for indoor growing has not only allowed him to start what may prove to become Mexico’s biggest producer of hydroponically grown food but has also allowed him to create some great allies along the way.
by Jens Ruijg
May 17, 2019
I sat down with Leo at NCERA-101, meeting in May to learn more about the newest Farmtech Society member.
Leo grew up in the farming and ranching community of Durango, Colorado, where he learned the balance of life eating produce grown in his Irish grandfather’s garden. His journey took Leo to Jalapa, Veracruz, Mexico in 1974, as a study abroad student from the University of Colorado. In 2004 Leo launched his atmospheric science business which is now a major contractor to the country’s National Weather Service, with exclusive representation of some of the World Meteorological Organization’s largest technology committee members. His post as the President of the Membership Committee for the American Chamber of Commerce of Mexico, and as a founding board member of the Ag-Industry Sector of CANACINTRA (Mexico’s largest industrial chamber) he has fostered many connections; it was a thoughtful conversation with a fellow member that inspired him to begin his exploration into indoor farming.
Beginning in 2015 until 2018, Lobato Kelly headed abroad to understand the landscape of indoor farming. Starting at the agriculture focused Milan World Fair, followed with trips to Rome and Munich, and finally landing at the Japanese Plant Factory Association summit, he consulted with some of the world’s best indoor farming experts. In order to understand the impact of hunger on violence in society Lobato Kelly visited the Peace Institute in Washington.
This long journey resulted in Leo securing a critical location for production in Mexico, a head grower, and essential industry connections that helped him to Karma Verde Fresh’s proof of concept site in 2018.
Truly embodying the spirit of the Farmtech Society, Karma Verde Fresh began collaborating with key universities throughout the region and has donated GrowRacks sourced from Hort Americas to expand educational opportunities. Thanks to the Enterprise-University-Enterprise (E-U-E) Collaboration Model and key industry guidance, Karma Verde Fresh has carried out 5 separate training courses preparing 163 local students, professionals and citizens for indoor growing.
Lobato is marketing lilies grown with his university partners to 10 Home Depot stores to help generate funding for ag school student food and transportation scholarships and for funding further vertical agriculture R&D.
Thanks to the success of the E-U-E at the UANL in Monterrey, and the university interest in further development of Mexico as a thought leader in Controlled Environment Agriculture, in 2019 the team at Karma Verde begins their Proof of Production phase of 10,000 square feet at the Marin Campus, within 30 minutes of the Central Distribution Centers of the major grocery store chains. The company has plans to expand into full production into the first of 2 of 30, 100,000 sq ft facilities between Monterrey and Mexico City beginning in 2020.
With an undeniable knack for creating community, the Farmtech Society is excited to partner with this growing company to help expand Ponics VET, which is based on the Erasmus+ vocational training credentials, and will serve to augment the course materials for certifying students in controlled environment agriculture across Mexico.
FarmTech Society will organize a series of panel discussions during Greentech Amsterdam 2019. On Tuesday June 11, Tom Zöllner will host a discussion on Plant Nutrition – Extra Natura, focusing on how we can grow the best possible plants in a controlled environment with speakers from Rijk Zwaan, Valoya, INTAG and Signify.
On Wednesday the 12th, Daniel Podmirseg of the Vertical Farming Institute will host speakers from The European Commission, Priva, Liberty Produce, Cultinova and Vertimis to discuss Energy and Building Topology for controlled environment agriculture.
Finally on Thursday June 13, Gus van der Feltz will host a discussion on Vertical Farming Business cases and Consumer Acceptance with speakers from Valoya, 80 Acres, Wageningen University, and Innovation Quarter.
For more information:
FarmTech Society
Place du Champs de Mars 5, 1050 Ixelles
+32 487 90 79 54
contact@farmtechsociety.org
farmtechsociety.org
Publication date: 5/16/2019
Student Design for Space Colony Greenhouse Wins NASA Praise
Student-designed inflatable dome folds and collapses for transport, racks plants vertically.
IMAGE COURTESY OF DARTMOUTH THAYER SCHOOL OF ENGINEERING
May 8, 2019
A radiation-shielded, inflatable greenhouse with a hydroponic growing system designed by undergraduate students at Dartmouth College’s Thayer School of Engineering could sustain four astronauts on a 600-day mission to Mars as soon as 2030.
The students’ Deployable, Enclosed Martian Environment for Technology, Eating and Recreation (DEMETER) concept—the acronym is also the name of the Greek goddess of the harvest—won first place in the 2019 NASA Breakthrough, Innovative and Game Changing (BIG) Idea Challenge, the agency announced on April 24.
The team pitched their idea to scientists at NASA and the National Institute of Aerospace (NIA) in competition with four other finalist teams.
NASA and NIA are seeking innovative ideas for the design, installation and sustainable operation of a habitat-sized Mars greenhouse, with the primary purpose of food production, according to NASA. The agency says an efficient and safe greenhouse design could assist with Mars missions and long-term lunar missions.
The 8-meter-high by 16-m-wide DEMETER includes an automated hydroponic growing system that uses a 3-m-tall cylinder inside of a torus, with the cylinder storing the water and nutrient delivery and recycling systems. A running track for astronaut recreation circles the vertically integrated assembly of growing trays.
The team used a 1⁄6-scale prototype to show folding methods for 1.5-m-long hydroponic growing trays, which nest against the central cylinder during transport. It also tested growing crops in a nutrient film technique hydroponic system to refine their design.
Dartmouth edged ahead when scored on the completeness of the proposed design, low system mass, optimization for food production and design simplicity, says Kevin Kempton, NASA program element manager and one of seven judges.
The team used “top-notch systems engineering throughout,” Kempton says. “That began with a systems overview that identified their system of interest relative to external systems, such as sunlight, heat, and water in the Martian environment.”
Kempton says another strength is that the components all appear relatively low risk and are based largely on a habitat design developed in a 2017 NASA feasibility study, which was the basis for the competition. “The team estimates it would take three to four missions to become a cost-effective option,” versus the cost of transporting food from Earth, Kempton says.
The team also scored high marks for innovation for the proposed concept of operations and for system deployment, which begins with robotic transport of the packaged greenhouse payload from the landing site to the deployment site. The design “seemed to have the highest level of technical maturity and it would likely require less technology development effort to get a DEMETER-base design up and running for the initial Martian outpost,” Kempton says.
NASA plans to send astronauts to the moon by 2024, with future missions in the 2030s, when a Mars greenhouse concept would potentially be viable, says Drew Hope, NASA program manager.
MIT placed second for its Biosphere Engineered Architecture for Viable Extraterrestrial Residence (BEAVER) concept. Plans include a spiral hydroponic design track in a multilevel facility featuring an enclosed waterfall for astronaut relaxation. Other finalists included designs from three state universities, California Davis, Colorado Boulder and Michigan Ann Arbor.
The finalist teams receive a shot at five NASA internships, recognition and a $6,000 stipend to travel to NASA’s Langley, Va., research center to present. All original ideas and concepts are credited to the student teams, but NASA has the option to take any portion of the ideas for use in future NASA mission planning, Hope says.
KEYWORDS Greenhouse /Hydroponic / Mars / NASA /Space Colony
Getting The Growing Bug
Adam Green
Photo courtesy of Adam Green
Adam Green took a "winding road" through college, but found his niche growing microgreens and other crops at AGreen Farms.
May 8, 2019
Before he founded his own vertical farm in his apartment building,, Adam Green’s journey through college was, as he calls it, “a winding road.” He started out at Drexel University in his native Philadelphia before he transferred to Syracuse University in Upstate New York, where he changed his major “three or four times.” Green then transferred again — this time to Temple University, back home in Philadelphia — and graduated with a degree in vocational development.
“When I was at Drexel, I was a film major,” he says. “Then I guess it went from being a screenwriter and not falling in love with the film industry so much, so I wanted to be a writer. I wanted to write fiction novels, so I became an English major. Then that didn't work out.” At Syracuse, he got the "science bug" – and switched to geology – before majoring in phycology when he transferred to Temple.
It was at Temple that horticulture got onto Green’s radar. Along with his girlfriend, who majored in horticulture, Green started shopping at farmers markets in Philadelphia and volunteering at Backyard Eats, an urban garden company in the Chestnut Hill neighborhood, in 2017. Today, Green has launched his own business — AGreen Farms — a hydroponic indoor farm in Philadelphia growing microgreens, herbs, edible flowers and more.
“I think that college is kind of now become, for a lot of Millennials, a place where you find what you don't want to do — and that's kind of what it was for me for sure,” Green says. “By finding out what I didn't want to do, I found out what I was most passionate about, and that was food.”
Gaining experience
After he transferred to Temple, Green wanted to switch to horticulture as a major. But due to his previous majors, he was unable to take the requisite sciences classes. When Green graduated last May he sought out any growing experience he could. He says he applied to pretty much “any indoor farm that was a moderate success in the country.” Only one got back to him: Farm.One, a New York City specialty crop producer whose primary customers are restaurants in the Big Apple.
“When I went there I had a really great sales manager in Wilson [Gibbons] and he showed me the ropes of what it's like to walk into a restaurant unannounced with a bunch of rare and exciting products, and I was just totally bitten by the sales bug,” he says. “It was funny that I wanted to be a paid farmhand at Farm.One and they didn't have a position open, so I took what I could."
Green returned to Philadelphia in August and started applying for jobs at different farms in the area, but without a horticulture degree or science background, no opportunities presented themselves. But after a conversation with his dad Bill, a career entrepreneur, AGreen Farms was born. Initial funding came from Bill.
“We had been talking about me starting my own farm for a few years, but we wanted to get, obviously, as much experience before I took such a daring venture on, for sure,” he says. “Things just fell into place; the timing was just kind of right.”
Mapping out a business plan
Philadelphia — like New York — has a burgeoning restaurant scene where chefs crave locally-grown produce for their restaurants, Green says. It helped that the elder Green had helped finance restaurateur Michael Schulson. Schulson had just opened Giuseppe & Sons, an Italian restaurant, and needed microgreens and AGreen Farms had its first customer.
“With my time at Farm.One, the specialty herbs started to excite me, and the edible flowers started to excite me, so it's really the unique flavors and the strong flavors that really interested me the most, and they became items that I was pretty good at selling because they're so hard to access for chefs while also being local and of really high quality,” he says.
Green estimates that were he able to add other notable area chefs and restaurants to this client list — a process that’s already begun — the farm would be set-up for long-term success. As the business begins, professional chefs and some hospitality establishments are the clientele Green is after.
To get the farm itself built, and Brandon Merrill was hired as farm manager. Merrill previously worked for Oasis Biotech, a Chinese-owned corporate growing company, and urban farming company Gotham Greens.
“We're totally giving him a ton of creative freedom, and that's why we got him on board to build this farm and not wait until the farm was built and then him say, ‘You know what? I wouldn't have done it this way,’” Green says.
The 5,000-square-foot growing space — outfitted with “bare bones” technology to keep costs down — is in Green’s apartment building. The company that owns his building, Post Brothers, was willing to lease him the space (and allow the farm to be built) in part because of an existing business relationship with Schulson. Green adds that, as opposed to other potential farm sites that wanted him to sign a five-year lease, Post Brothers allowed him to sign a more flexible lease. The plan is to prove the concept, take on investment and move into a bigger growing space to continue growing the company.
“It's going be a grind for sure, and it's not going to be easy. It's going to be about getting the right people in place, having a really great team, and just hauling ass,” Green says. “We're going to be developing relationships with chefs that we haven't met and have connections with, by walking into their restaurants three days a week and knowing what products they're already purchasing from distributors from across the country, and just bringing it to them more locally, more fresh and with better quality."
Purdue Startup Assists Cameroon With Developing Hydroponic Farming Methods, Entrepreneurship
May 15, 2019
A second visit by Heliponix startup to the African continent strives to develop new agricultural processes, self-reliance for countries.
WEST LAFAYETTE, Ind. - Cameroon, a West African country in the Congo region, has long relied on foreign aid to feed its citizens due to the extreme desert climate in some areas and a continued influx in refugees and orphaned children from neighboring nations.
Through support from the Mandela Washington Fellowship, Scott Massey, a Purdue University graduate and founder of Heliponix, recently completed a workshop to provide Cameroon residents and farmers with practical advice and resources to develop low-cost hydroponic farms to increase the production of agricultural products and encourage entrepreneurship to advance self-reliance while using local materials.
Scott Massey, founder of Heliponix, steps over some pipes at the beginning of a hydroponic farm workshop at the University of Ngaoundéré in Cameroon. Massey, a Purdue University graduate, traveled to Cameroon to teach people about hydroponics and entrepreneurship. He is the co-founder of Heliponix, which makes the GroPod, an innovative appliance that fits under a kitchen counter and grows produce year-round. (Photo provided) Download image
Massey’s company makes the GroPod, an innovative appliance that fits under a kitchen counter and grows produce year-round.
“Organizations providing food for some of the most at risk groups in Cameroon are reliant on nonprofits, which can make it difficult for them to always have a consistent source of quality food ,” Massey said. “We built hydroponic farms at certain locations to allow them to grow their own food, have some degree of independence from foreign aid, and overcome the extreme desert climate that often makes it difficult to grow crops.”
Massey credited the Mandela Washington Fellowship, which seeks to promote business development and civic engagement through the academic and entrepreneurial empowerment of African people, with the advancement of his contributions to the area and other programs to help the country feed its population while fostering independence. The program provides young entrepreneurs and leaders with the chance to travel to the United States for a short period of time for an opportunity to develop their skills and learn from mentors in American colleges and universities.
Massey, a graduate of the Purdue Polytechnic Institute in Mechanical Engineering Technology with a Certificate in Entrepreneurship and Innovation, was accepted into the program in 2017 and was later granted the status of American Professional, which made him eligible for the Reciprocal Exchange Grants. That led to his recent three-week trip to Cameroon.
Joseph Daliwa (left), Bello Mohamadou (center) and Scott Massey (right) work on a hydroponic system for orphans in Cameroon displaced by regional conflict. Daliwa and Massey got involved in helping in Cameroon through the Mandela Washington Fellowship, which seeks to promote agricultural empowerment of African people. Mohamadou is an English and science teacher in Ngaoundere, Cameroon. (Photo provided)Download image
During that trip, modular farms also were built at farm build at the University of Ngaoundéré with the purpose of teaching students how to build and maintain the farms. Massey adapted the GroPod device in these modular farms using the same concept but taking into consideration the availability of different resources. A video about his work is available here.
“There are some concepts from the GroPod that we have incorporated into these designs, but it was important that we design the device with local materials so that they would be able to build it and replicate it themselves,” Massey said.
He also lectured at the University of Yaoundé, teaching students about hydroponic technologies and basic entrepreneurial skills. Through these lectures, Massey was able to share his experiences as an entrepreneur and offer advice that could help guide students in their own entrepreneurial ventures.
Massey’s lectures also focused on teaching the students how to pitch their ideas, an ability he said is essential to attract investors and grow a company.
“For any entrepreneur, the art of pitching is vital. As an entrepreneur, it is important to be able to properly articulate what the problem is that you are solving, what makes your solution unique, and what the opportunity is behind the solution. Having this clear articulate story-telling ability is what we were trying to help the students achieve, and that’s something that the Purdue Foundry does very well. Going through their program was a tremendous help for me and I am sharing this knowledge where I can,” Massey said.
Massey said taking part in programs at the Purdue Foundry, an entrepreneurship and commercialization accelerator in Discovery Park's Burton D. Morgan Center for Entrepreneurship at Purdue, was essential in helping get his company off the ground.
This was Massey’s second trip to Africa through the Mandela Washington Fellowship’s Reciprocal Exchange Grant, which gives recipients the opportunity to travel to different sub-Saharan countries in the continent. In 2018, Massey traveled to Togo, where he assisted in developing sustainable agriculture methods.
About Purdue Foundry
The Purdue Foundry is an entrepreneurship and commercialization accelerator in Discovery Park’s Burton D. Morgan Center for Entrepreneurship whose professionals help Purdue innovators create startups. Managed by the Purdue Research Foundation, the Purdue Foundry was co-named a top recipient at the 2016 Innovation and Economic Prosperity Universities Designation and Awards Program by the Association of Public and Land-grant Universities for its work in entrepreneurship. For more information about funding an investment opportunities in startups based on a Purdue innovation, contact the Purdue Foundry at foundry@prf.org.
Writer: Zeina Kayyali, zmkayyali@prf.org
Purdue Research Foundation contact: Tom Coyne, 765-588-1044, tjcoyne@prf.org
Source: Scott Massey, scott@heliponix.com
Growing The Future: High-Tech Farmers Are Using LED Lights In Ways That Seem To Border On Science Fiction
Mike Zelkind, chief executive of 80 Acres Farms, grows tomatoes and other produce with artificial-light recipes made possible with new LED technology. (Maddie McGarvey for The Washington Post)
By Adrian Higgins Nov. 6, 2018
Mike Zelkind stands at one end of what was once a shipping container and opens the door to the future.
Thousands of young collard greens are growing vigorously under a glow of pink-purple lamps in a scene that seems to have come from a sci-fi movie, or at least a NASA experiment. But Zelkind is at the helm of an earthbound enterprise. He is chief executive of 80 Acres Farms, with a plant factory in an uptown Cincinnati neighborhood where warehouses sit cheek by jowl with detached houses.
Since plants emerged on Earth, they have relied on the light of the sun to feed and grow through the process of photosynthesis.
But Zelkind is part of a radical shift in agriculture — decades in the making — in which plants can be grown commercially without a single sunbeam. A number of technological advances have made this possible, but none more so than innovations in LED lighting.
“What is sunlight from a plant’s perspective?” Zelkind asks. “It’s a bunch of photons.”
Diode lights, which work by passing a current between semiconductors, have come a long way since they showed up in calculator displays in the 1970s. Compared with other forms of electrical illumination, light-emitting diodes use less energy, give off little heat and can be manipulated to optimize plant growth.
In agricultural applications, LED lights are used in ways that seem to border on alchemy, changing how plants grow, when they flower, how they taste and even their levels of vitamins and antioxidants. The lights can also prolong their shelf life.
“People haven’t begun to think about the real impact of what we are doing,” says Zelkind, who is using light recipes to grow, for example, two types of basil from the same plant: sweeter ones for the grocery store and more piquant versions for chefs.
For Zelkind, a former food company executive, his indoor farm and its leading-edge lighting change not just the way plants are grown but also the entire convoluted system of food production, pricing and distribution in the United States.
High-tech plant factories are sprouting across the United States and around the world. Entrepreneurs are drawn to the idea of disrupting the status quo, confronting climate change and playing with a suite of high-tech systems, not least the LED lights. Indoor farming, in sum, is cool.
It has its critics, however, who see it as an agricultural sideshow unlikely to fulfill promises of feeding a growing urbanized population.
Grower David Litvin picks tomatoes at 80 Acres Farms in Cincinnati. The vines grow in a high-tech environment that includes LED lamps with customized light recipes. The plant factory produces 200,000 pounds of leafy greens, vine crops, herbs and microgreens annually in a 12,000-square-foot warehouse. (Maddie McGarvey/For The Washington Post)
Zelkind agrees that some of the expectations are unrealistic, but he offers an energetic pitch: He says his stacked shelves of crops are fresh, raised without pesticides and consumed locally within a day or two of harvest. They require a fraction of the land, water and fertilizers of greens raised in conventional agriculture. He doesn’t need varieties bred for disease resistance over flavor or plants genetically modified to handle the stresses of the field. And his harvest isn’t shipped across the country in refrigerated trucks from farms vulnerable to the effects of climate change.
“We think climate change is making it much more difficult for a lot of farms around the country, around the world,” he says, speaking from his office overlooking a demonstration kitchen for visiting chefs and others.
In addition to shaping the plants, LEDs allow speedy, year-round crop cycles. This permits Zelkind and his team of growers and technicians to produce 200,000 pounds of leafy greens, vine crops, herbs and microgreens annually in a 12,000-square-foot warehouse, an amount that would require 80 acres of farmland (hence the company’s name).
Zelkind says he can grow spinach, for example, in a quarter of the time it takes in a field and half the time in a greenhouse. Growing year-round, no matter the weather outside, he can produce 15 or more crops a year. “Then multiply that by the number of levels and you can see the productivity,” he said.
Zelkind and his business partner, 80 Acres President Tisha Livingston, acquired the abandoned warehouse, added two shipping containers and converted the interior into several growing zones with sophisticated environmental systems that constantly monitor and regulate temperature, humidity, air flow, carbon dioxide levels and crop health. Grown hydroponically, the plant roots are bathed in nutrient-rich water. The moisture and unused nutrients exhaled by the plants are recycled.
But it is the LED lighting that has changed the game. Conventional greenhouses have relied on high-pressure sodium lamps to supplement sunlight, but HPS lights can be ill-suited to solar-free farms because they consume far more power to produce the same light levels. They also throw off too much heat to place near young greens or another favored factory farm crop, microgreens. Greenhouses, still the bulk of enclosed environment agriculture, are moving to a combination of HPS and LED lighting for supplemental lighting, though analysts see a time when they are lit by LEDs alone.
In the past three years, Zelkind says, LED lighting costs have halved, and their efficacy, or light energy, has more than doubled.
Production in the Cincinnati location began in December 2016. In September, the company broke ground on the first phase of a major expansion 30 miles away in Hamilton, Ohio, that will eventually have three fully automated indoor farms totaling 150,000 square feet and a fourth for 30,000 square feet of vine crops in a converted factory. (The company also has indoor growing operations in Alabama, North Carolina and Arkansas, which acted as proving grounds for the technology.)
“We feel the time is right for us to make the leap because the lighting efficiency is there,” Livingston says.
Grower Julie Flickner inspects kale at 80 Acres Farms. Growing year-round, no matter the weather outside, the vertical farm can produce 15 or more crops annually. The produce is sold in Cincinnati-area grocery stores and restaurants. (Maddie McGarvey/For The Washington Post)
The visible spectrum is measured in minuscule wavelengths, shifting at one end from violet-blue light through green to red at the other. For decades, scientists have known that photosynthesis is optimized within the red band, but plants also need blue lightwaves to prevent stretching and enhance leaf color. A barely visible range beyond red, known as far red, promotes larger leaves, branching and flowering. With advances in LED technology, light recipes — determining the number of hours illuminated, the intensity of photons directed at plants and the mix of colors — can be finely tuned to each crop and even to each stage in a crop’s life.
Given the evolving nature of the technology and its enormous commercial potential, light manufacturers and universities, often in collaboration, are actively involved in research and development.
“We have a completely new era of research,” says Leo Marcelis, a horticulture professor at Wageningen University in the Netherlands. Tweaking light recipes has allowed researchers to manipulate crops in a way never seen before. In the lab, chrysanthemums have been forced into bloom without the traditional practice of curtailing their daily exposure to daylight. This will allow growers to produce bigger plants in flower.
“It’s to do with playing around with the blue light at the right moment of the day,” Marcelis says. “Its internal clock is affected differently, so it doesn’t completely recognize it’s still day. There are so many amazing responses of the plant to the light.”
Lettuce, for example, likes as much as 18 hours of light per day, but basil prefers brighter light for 15 hours, says Celine Nicole, a researcher for Signify, formerly Philips Lighting. “Every plant has its own preference,” says Nicole, who conducts research at the company’s high-tech campus in Eindhoven, Netherlands. She has already tested 600 types of lettuce.
Although the permutations are still under study, the sun suddenly seems so analog. “The spectrum from sunlight isn’t necessarily the best or most desirable for plants,” says Erik Runkle, a plant scientist at Michigan State University. “I think we can produce a better plant” with LED lights, he says. “The question becomes: Can you do it in a way that is cost-effective considering the cost of plants indoors?”
“People haven’t begun to think about the real impact of what we are doing.”
Mike Zelkind, chief executive of 80 Acres Farms
The answer seems to be yes. LED light shipments to growers worldwide are expected to grow at an annual average rate of 32 percent until 2027, according to a market report by analysts with Navigant Research in Boulder, Colo. Shipments of LED lights will overtake those of legacy lights starting next year, says Krystal Maxwell, who wrote the report with Courtney Marshall.
Most of the growth will be as supplemental lighting in greenhouses, but vertical farms are seen as an alternative production system that will develop alongside greenhouses, not displace them, Marcelis says.
Runkle estimates there are 40 or more vertical farms in the United States, and new ones are opening every year with the help of deep-pocketed investors. In some of the biggest deals, AeroFarms, headquartered in Newark, last year raised a reported $40 million. Plenty, a grower based in South San Francisco, raised $200 million in 2017 for a global network of vertical farms. (One of the backers is a venture capital firm created by Amazon founder Jeffrey P. Bezos, who also owns The Washington Post.)
Zelkind declined to reveal his capital costs, but for start-up entrepreneurs, LED-driven vertical farms can be one of the most lucrative forms of agriculture. “Based on manufacturers and growers I have talked to, that’s where the money is,” Marshall says.
Critics argue that a lot of the hype around indoor farming is unwarranted, saying it won’t fulfill promises of feeding an increasingly urbanized planet and reverse the environmental harm of industrialized agriculture, not least because most staples, such as corn, wheat and rice, cannot be grown viably indoors.
Also, to build enough indoor farms for millions, or billions, of people would be absurdly expensive.
Runkle says vertical farming “shouldn’t be considered as a way to solve most of our world’s food problems.” But it is a viable way of producing consistently high-quality, and high-value, greens and other plants year-round.
Zelkind says what he’s doing may be novel, but it’s just one component of how we feed ourselves in this century. “We shouldn’t overblow what we do. Eventually it’s going to become more important, but vertical farming alone isn’t the cure-all.”
He adds, however, that “there’s no reason today to ship leafy greens from California to Ohio.”
Livingston likens LED-raised food to the advent of smartphones. “Five years from now everyone is going to be living with indoor farming and wonder how we did without it,” she says.
David Litvin, left, inspects vine crops while farm operations tech Devon Brown prepares labels for retail packaging. (Maddie McGarvey/For The Washington Post)
Additional credits:
Lettering by Craig Ward for The Washington Post; animation by Sarah Hashemi; photo editing by Annaliese Nurnberg; design and development by Elizabeth Hart.
US - Pennsylvania - BrightFarms To Open Hydroponic Greenhouse in Snyder County
BY MELINA DRUGA | APRIL 25, 2019
New York-based BrightFarms recently announced plans to open a 250,000-square-foot hydroponic greenhouse in Snyder County.
© Shutterstock
The greenhouse will serve the company’s four primary facilities and will grow leafy greens and herbs. BrightFarms will invest more than $20 million, and the project is expected to create 54 jobs over the next three years.
“BrightFarms is extremely grateful for the support we have received while searching for our next location in Pennsylvania,” Paul Lightfoot, BrightFarms CEO, said. “This is an exciting chapter for our company as we push forward with our mission of providing more Americans access to the freshest, tastiest and most responsibly grown local produce through their supermarkets. Our next step will be recruiting members of the community to fill over 50 ‘green-collar’ jobs at the greenhouse. These employees will receive competitive pay, industry-leading benefits and world-class training from our team members.”
The Department of Community and Economic Development submitted a $24,300 grant proposal to BrightFarms for workforce training.
The Pennsylvania Industrial Development Authority has encouraged BrightFarms to apply for a $2.95 million low-interest loan to assist with the purchase of land, machinery, and equipment.
BrightFarms grows using sustainable farming methods in four states: Pennsylvania, Ohio, Virginia, and Illinois.
INDIA: Roots of Labour: IIM Alumni's Startup Barton Breeze Brings Farms To Your Doorstep
Gurugram-based Barton Breeze sets up fully-automated hydroponic farms using its in-built technologies to grow clean and pesticide-free vegetables.
22nd Apr 2019
We all know that home-cooked food is the best. But what we really don’t seem to consider is the backend process – vegetables grown using chemicals, pesticides, and insecticides to increase their yield. These chemicals get accumulated in the soil, and in turn, increases the plant's uptake of chemicals. As a result, by the time the food reaches our plate, it would have lost half its nutritional value, and we might be consuming vegetables with high pesticide residues.
Solving this pain-point is Gurugram-based Barton Breeze. Started by Shivendra Singh (31) in 2016 in Dubai, UAE, with a mission to bring technology innovation in the farming sector, Barton Breeze focuses on Hydroponics. It is a method of growing plants without soil by making use of mineral nutrient solutions. It reduces water consumption as well as increases yield.
Shivendra Singh, Founder
The company, which started operating in India by the end of 2017, wants to give ‘clean food’ to its customers throughout the year, without being affected by the changing seasons.
At present, Barton Breeze grows 28 varieties of crops, including edible flowers, eight different coloured bell peppers, lettuce, different varieties of tomatoes, and micro-greens at its farms across India.
The beginnings
After graduating from IIM Ahmedabad, Shivendra worked with the Landmark Group in Dubai. Later, in 2016, he started working on a pilot project around hydroponics and set up two container farms in Dubai. Shivendra says, it was then he met Ratnakar Rai (49), an Agro Technologist, in an agri-tech meet.
“We shared our thoughts on the need for hydroponic and clean food in India, and soon he joined me on my second research project,” says Shivendra.
After setting up a branch in India, Ratnakar, who specialises in Controlled Environment Agriculture, joined the company as the Co-founder.
Shivendra and Ratnakar Rai (L-R)
“Ratnakar can do magic in agri-support and operation. But we needed tech support for faster growth, and that’s when Dheeraj joined us,” Shivendra adds.
Dheeraj Joshi (35) has over 14-years of experience working with software and automation companies in India, the UK and Singapore.
While keeping Dubai farms operational, Barton Breeze entered the Indian market by the end of 2017. The company has developed six fully-automated farms within a year in four states namely Haryana, Rajasthan, Uttar Pradesh, and Uttarakhand.
However, “Getting skilled operators was impossible, and we had to train and build our own ground staff team. We are now a team of six core members, supported by 14 field farms,” says Shivendra.
Quality control using tech
Barton Breeze builds farms, operates it, and directly sells the produce to the customer. This end-to-end operation not only reduces the final cost to the consumers, but also ensures total control over quality.
The team claims to have built fully-automated farms using its in-built technology.
“We have built a software where we clip a device on the leaves and stem of each plant. The software is connected to the computers, and informs the user when a particular plant needs more nutrients or minerals,” says Shivendra.
However, the journey wasn’t as easy for the team. “The supplier base was limited, and so we developed products ourselves and encouraged vendors to develop a few,” says Shivendra.
As a result, Barton Breeze has five hydroponic products developed in-house. This includes Nutrient Film Technique channels, home gardening essentials, and consumables like plat nutrition, net pots, and grow media.
Inside a Barton Breeze farm
The startup is now a retail supplier of these products, and this “adds up to 15 percent of our revenue,” Shivendra adds.
Debolina thinks life is all about seeking that one "great
perhaps". She considers herself a foodie and wants to
have her own food and travel column in a magazine someday
Hydroponic Farming: Why the Future of Food Is Indoors
Hydroponic farming needs a fraction of the water and space needed
to grow crops compared to conventional farming.
Hydroponics could help meet the world’s growing food pressure.
Pixabay
There are about 7.5 billion people on the face of the planet. With every new person born, there’s a new mouth to feed.
In just a few decades, we might just hit a Full-Earth scenario.
By 2100, the global population will be around 11 billion. To feed this many people, we need 0.22 hectares of cultivated land on average per person. That gives us 2.4 billion hectares. Currently, there are 1.5 billion hectares of cultivated land in the world. So, we need about 1 billion more hectares of farmland, roughly the size of the United States.
That’s not even thinking about all of the water needed to irrigate these crops and the strain this will put on the world’s water resources.
Besides being unfeasible, it’s just an unsustainable model that we used and tested for a very long time.
Non-conventional agriculture systems, like vertical farming and urban farming, could help produce more food, while also easing environment issues related to food production.
Hydroponic farming is another method that allows growing plants to not only meet quantity needs but also quality standards.
Indoor Hydroponic Farms: no Soil, no Pesticides, and Very Little Water
If hydroponic farming sounds futuristic, the concept itself is about as old as agriculture with many instances of hydroponic farms throughout history and civilizations.
The Hanging Gardens of Babylon, one of the Seven Wonders of the Ancient World, is the first known example of hydroponic farming. The Aztec built chinampas, floating farms that used hydroponic systems.
Hydroponics is basically an irrigation system that allows growing plants without soil.
Leveraging robotics and data analytics, many companies are taking indoor hydroponic farming to levels never before reached.
One such company is Bowery Farming, a startup founded in 2014 in New York that specializes in indoor farming.
The company claims its farming system to be 100 times more productive than traditional farming while using 95% less water and zero pesticides.
A combination of tech solutions enable Bowery to produces a wide variety of crops, twice as fast, and take them to market within a few days after harvest.
Irving Fain, Bowery CEO and co-founder, told Clean Technica:
“BoweryOS, our proprietary software system, uses vision systems, automation technology, and machine learning to monitor plants and all the variables that drive their growth 24/7, while combining software and automation with industrial process management to optimize production, fulfillment and distribution. By applying proprietary machine learning algorithms to millions of points of data collected by an extensive network of sensors and cameras.”
Because indoor farms offer a closed and controlled environment for greens to grow, there’s more to these products than just their little resources requirements.
They are safer to eat because controlled environment technology minimizes the risk of contamination from different sources, like animal waste, water, or irrigation run-off.
In the case of Bowery products, because they control “the entire process from seed to store, our greens aren’t matriculated through large distribution and fulfillment centers that often lead to additional exposure to contaminants”.
Zayan Guedim
Trilingual poet, investigative journalist, and novelist. Zed loves tackling the big existential questions and all-things quantum.
Italy: Thirteen Hectares of Lettuce Grown On A Floating System
All types of lettuce are grown with the floating system on an area of 13 hectares. The whole system is automated to produce salad marketed under the brand name Ninfa. The location is Standiana, (Ravenna), near the large amusement park Mirabilandia, famous in Italy. "Here we also have fun with water - and we produce lettuce with water", entrepeneur Gianluca Rossi says.
The owner Gianluca Rossi
High quality
A production site of this size, with these technologies is not often seen in Europe. According to Rossi he gets positive responds on his systems, even from the major seed companies in the world.
"The 13 hectares are part of a 100-hectare farm. The design took more than six years to complete and I did it myself together with the leading experts. I made many trips abroad before it was done", he recalls.
Here is how the roots appear in the support, just removed from the water
On the track, oriented in the direction of the processing warehouse, the panels with the lettuce.
Gianluca shows how everything is done with utmost care. "Our greenhouses only serve as protection, not to anticipate cycles. The production runs from mid-April to December, while in the winter months it is suspended."
The cultivation takes place with floating panels certified for contact with food. The roots are immersed in water. Nutrition is carried out with the classic triad of elements N, K, P and microelements. Weed killers are not needed, of course. Defence follows the technique of integrated control.
Watch the video!
The positioning of the panels with lettuce on the railroad.
180 hectare land
"With traditional methods, adds Rossi - considering also the rotations, in the open field - it would take 180 hectares of land to produce what we can do in 13 hectares of floating system. In our case, the rotation is nothing more than the replacement of the "old" water that is not wasted but returned to the fields of the remaining 87 hectares of our company".
No water waste
At first glance, it might seem that there is a waste of water, but that is not the case. "Careful management allows for prolonged and waste-free use. With the same number of plants produced, the reduction in water consumption varies between 70 and 80% compared to a traditional method".
Here are some other numbers: 9 million cultivated plants expected in 2019, 4000 tons of products and 169,000 floating support panels. "Our history goes back a long way, Rossi points out, because it was my father, from a very young age, who dedicated himself to the trade in vegetables. At a national level, we are already known for our activity as traditional producers, and now we want to make ourselves known for this new reality".
Aerial view of the Standiana farm. There are 13 hectares of greenhouses with lettuce grown in floating systems
Minerals
Water, like the earth, does not of itself, contain enough nutrients, but they are both a means of mixing, holding and conveying them. Unlike traditional methods, in the tank, the mineral salts are available only to plants that absorb according to their daily needs, excluding leaching, waste and dispersion into the surrounding environment or in the aquifers.
"More yields, less waste of nutrients, less water consumption, no forcing, concludes Rossi. There is a difference, even from an organoleptic point of view. The panel tests carried out on the Ninfa salad have shown a higher percentage of mineral salts than traditional crops, with a significant increase in shelf life.
Ikea Harvests First Hydroponically-Grown Lettuce
Courtesy of Ikea & Bonbio
4th April 2019
Ikea has harvested and served its first “home-grown” lettuce as part of a year-long trial exploring how food can be served more sustainability.
The Swedish furniture giant is growing lettuces in containers outside its department stores in Malmö and Helsingborg, Sweden, working alongside circular farming expert, Bonbio.
Each container conceals a high-tech growing operation comprising 3,600 lettuce plants in an area of 30 m2.
The container has four levels and is full of different sizes of lettuce. The seeds are sown in batches, so there is always lettuce available for harvesting.
No pesticides are needed during the growing process because the farming takes place in a closed system.
The lettuce is grown hydroponically in water containing liquid plant nutrients extract from organic waste – including food waste from Ikea’s restaurants.
This, Ikea said, means the lettuces require 90% less water and less than half the area than those that have been conventionally growth.
“It is not every day that we have a harvest celebration at Ikea and it is really fun for us to finally be able to serve our own lettuce. It is fresh, crisp and has a bit more taste than regular lettuce,” said Ann Holster, responsible for Ikea Sweden’s restaurant operations
“We will start serving the lettuce in our staff canteens, but hope to soon be able to offer it to our customers.”
Spreading Hydroponic Farming Technologies Across India
AmHydro And Farms 2050
On April 9th, Farms 2050 of Bangalore and AmHydro of Arcata, CA celebrated the grand opening of what is the largest commercial hydroponic farm in India to date.
A rich agricultural heritage that has been challenged by a harsh climate, water scarcity and a rapidly growing population to feed has created an urgent need for newer, more sustainable farming methods in the region. In response to this need, Farms 2050 and AmHydro partnered to develop effective controlled environment agricultural (CEA) facility that provides local growers with the ability to produce large volumes of nutritious, high quality crops, all while using 95% less water than conventional farming techniques.
Construction nearly complete on state of the art greenhouse and packing house facilities
The first (of many) new hydroponic farms in Bangalore include a 45,000+ square foot climate controlled greenhouse, highly productive AmHydro hydroponic growing systems, and a 5,000 square foot packing house with processing, cooling, and shipping facilities. Each technology was carefully chosen to provide the highest level of performance while also remaining economically sustainable and providing growers with a fast return on investment. The initial farm features systems to produce both leaf crops (culinary herbs, lettuce, and greens), as well as vine crops (peppers, tomatoes, and cucumbers).
High performance AmHydro NFT leaf crop system, ready to plant
Prior to the grand opening event, AmHydro CEO Jenny Harris and VP Joe Swartz traveled from California, USA to Bangalore to fine tune and test the greenhouse and hydroponic growing system. When this was complete, they trained the local farming team in all aspects of high level hydroponic crop production; from proper seed selection, germination, crop production techniques to harvest, processing, storage and food safety. Professional film crews were on hand to assist in the production of instructional videos, providing present and future farmers with growing guidance and information.
Instructional videos of microgreens seeding techniques being filmed
In a lavish public ceremony, Farms 2050 and AmHydro then signed a mutual MoU with the support of Indian government officials to develop additional sustainable, high producing hydroponic farms across the region. Sharing the stage with the Minister of Water Resources, Minister of Revenue, and the Minister of Agriculture, Farms 2050 CEO Basan Patil and AmHydro CEO Jenny Harris signed a historic MoU to develop more hydroponic farms and controlled environment agricultural technologies in various locations within India. The primary goal of this venture is to dramatically improve the economic empowerment of local farmers as well as providing high quality vegetables, greens, and fruits to their communities.
Left: Indian Government Officials along with Farms 2050 and AmHydro Right: AmHydro CEO Jenny Harris
The signing event receiving national press attention
On the final day of the visit, local religious leaders stopped by to bless the new operation with good luck and success. Planting is now underway and plans for the next farm are already in development.
For more information:
AmHydro
amhydro.com