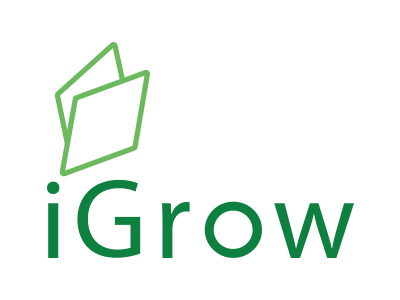
Welcome to iGrow News, Your Source for the World of Indoor Vertical Farming
Bowery Expands Indoor Farming To Baltimore Area With An Eye Towards More Sustainable Production Globally
18-Nov-2019 By Elizabeth Crawford
Uncomfortable with the idea that agriculture is a necessary evil with the demand for food outweighing the negative environmental impact of traditional farming and ranching, the co-founder and CEO of Bowery is expanding his revolutionary approach to food production through indoor farms that use proprietary technology to improve sustainability and produce quality.
To Read The Entire Article, And View The Video, Please Click Here
Produce Grown Is Served In On-Campus Dining Locations
Housing and Food Services, along with the student organization OUr Earth, have joined together to bring the Leafy Green Machine to campus
Freight Farms
Housing and Food Services, along with the student organization OUr Earth, have joined together to bring the Leafy Green Machine to campus. Housed in an upcycled shipping container, it is the first hydroponic farm at a Big 12 university. Produce grown is served in on-campus dining locations.
Singapore Agritech Startup Sustenir Now Serving Hong Kong With Locally Grown, Low Emissions Kale
Earlier this year, Singapore-based agri-tech company Sustenir made headlines with its lab-grown strawberries and arugula in its hydroponic facility. Now, the startup has just expanded into Hong Kong to start vertical farming in the city, producing two kinds of kale at their Tuen Mun facility
By Sally Ho November 12, 2019
Earlier this year, Singapore-based agri-tech company Sustenir made headlines with its lab-grown strawberries and arugula in its hydroponic facility. Now, the startup has just expanded into Hong Kong to start vertical farming in the city, producing two kinds of kale at their Tuen Mun facility. Sustenir’s vertical farming technology presents an alternative to the current food system operating in hot and humid climates like Hong Kong and Singapore. By growing non-native crops in lab-controlled settings, the startup hopes to alleviate dependence on foreign food imports, which generates additional carbon emissions, and food waste in the transportation process.
After its latest round of Series A funding, which attracted US$15.4 million in investment from venture capital firms including Grok Ventures and Tamesek Holdings, Sustenir has recently launched a new 30,000 square foot hydroponic farming facility in Tuen Mun, Hong Kong. The produce currently launched in the city include “Kinky Kale” and “Toscano Kale”. The company is also looking to bring in new offerings in the near future, including kale juice and pesto, both of which they sell in Singapore.
Commenting on the reasons behind their launch in Hong Kong, co-founder and CEO of Sustenir Benjamin Swan told Green Queen that “Hong Kong has similar constraints to space as Singapore and has a similar reliance on imported produce. Our mission has always been to be present in countries and communities with heavy reliance to imports, so we can produce locally and lessen carbon emissions from import transportation.”
The company, which was founded in Singapore in 2013, produces crops that are in local demand using laboratory-controlled vertical farming methods based on artificial intelligence and LED lighting, which helps photosynthesis in plants. Using this technology, the shelf-life of Sustenir’s farmed crops can be extended, which helps to reduce food wastage. In addition, by growing non-native crops in a local facility, the concept minimizes the carbon footprint involved in transporting foods, as well as wasted food that often results in the logistical process of importing fresh produce. This is particularly relevant for Hong Kong, where over 90% of the city’s food supplies are imported from abroad, and for the wider Asian region, which is responsible for over half of global waste.
To cater to Hong Kong tastes specifically in their first launch outside of Singapore, Swan said to Green Queen: “When we enter a country, we always make sure that we tailor our products to the tastes and wants of the people so we can truly give a product made in Hong Kong for Hong Kong.”
Now that their first international foray under their belt, Sustenir hopes to be able to first increase their product offerings in the facility, including growing other leafy greens like lettuce, spinach, arugula and basil, and to continue to launch more urban vertical farms across Asian cities.
Lead image courtesy of ST Photo/ Lim Sin Thai.
Produce Will Grow On Site At Kroger's QFC Stores.
The Kroger Co. is teaming with urban farming network Infarm to bring modular living produce farms to North America, which will result in offering produce picked so fresh that consumers will be able to see the roots
Kroger Launching Living Produce Farms This Month
11/19/2019
Produce will grow on-site at Kroger's QFC stores.
The Kroger Co. is teaming with urban farming network Infarm to bring modular living produce farms to North America, which will result in offering produce picked so fresh that consumers will be able to see the roots.
The partnership between Cincinnati-based Kroger and Berlin, Germany-based Infarm marks the first-of-its-kind in the United States, according to the two entities.
The living produce farms will launch this month at two of the 15 stores planned at QFC, a Kroger banner, at locations in Bellevue and Kirkland, Washington. Using hydroponic technology, the produce will grow on site at the participating QFC stores, removing the need for extended transportation and storage and producing a more eco-conscious product, according to Kroeger. The farms are designed to scale and will provide shoppers the freshest and most sustainable living produce options available.
"Kroger believes that everyone deserves to have access to fresh, affordable and delicious food, no matter who you are, how you shop or what you like to eat," said Suzy Monford, Kroger's group vice president of fresh. "Our partnership with Infarm allows us to innovate by combining ground-breaking in-store farming technology with our passion for fresh, local produce and ecological sourcing. Kroger is excited to be first to market and offer the best of the season."
"We want to make fresh, pure, tasty and nutritious produce available and affordable for everyone," said Erez Galonska, CEO and co-founder at Infarm. "Kroger's commitment to innovation, quality and flavor makes them the perfect partner with which to launch our business in the United States and for the first time in North America."
Vertical Farming: On The Up
The cost of energy – financially and environmentally – remains the greatest challenge to scaling up vertical farming. Even using off-peak energy, and with ever more efficient LEDs coming on the market, the energy requirements are high
Ramona Andrews Author
24th April 2019
Standing 12 metres high and with 17 stacked levels of indoor growing space, lit with LEDs in a mixture of red, white and blues – is this really the future of farming?
Lincolnshire-based Jones Food Company’s (JFC) vertical farming system is capable of producing over 400 tonnes of baby leaf salad a year in about 5,000 square metres of indoor space. While there has been development in growing berries, tomatoes and other fruiting plants through these systems, the technology is not yet there to make these crops scalable and JFC is concentrating efforts on baby leaf and herbs. As co-founder Paul Challinor explains, the intention is to make the business commercial from the beginning “rather than having a trial shipping container to look at how it could develop”.
Other city hydroponic growers, such as New York’s Sky Vegetables, a rooftop farm in The Bronx and Growing Underground, a hydroponic farm located 33 metres below the streets of Clapham in London, see their role as an incredibly short supply chain for produce directly into the city.
But not everyone has the same end goal – Grow Bristol has built a vertical farm inside a shipping container on disused land, offering an opportunity for public engagement and connecting urban communities to food, rather than to provide high quantities of salad to the city.
The Jones Food Company grows over 400 tonnes of salad a year. Image Holly Challinor
The sky isn’t the limit
The cost of energy – financially and environmentally – remains the greatest challenge to scaling up vertical farming. Even using off-peak energy, and with ever more efficient LEDs coming on the market, the energy requirements are high.
Jaz Singh of Innovation Agri-Tech Group, behind an indoor farm in Bracknell, Berkshire, says: “It doesn’t really matter what time of day your energy is getting produced. It’s about how you cycle it. You can turn the evening into effectively daytime if you’re doing it in a fully closed environment.”
For Grow Bristol’s Oscar Davidson, the future of vertical farming must be in renewables, such as biogas or through anaerobic digestion, and ideally on-site generation. This is echoed by another hydroponics expert Kate Hofman, of GrowUp Urban Farms, who says: “From my point of view, the only purpose of doing this kind of farming is to be able to grow food more sustainably…you’ve got to use renewable energy and at the moment it’s too expensive to buy off the grid, so we’ve got to be co-located.”
GrowUp tested a pilot aquaponics urban farm (aquaponics combines raising fish with hydroponics, feeding the plants fish waste), but the system has not proved financially sustainable in its original East London location due to high land rental costs. For Hofman, in theory, the more production moved indoors, the more land can be freed up for other uses, less intensively farmed and even used for carbon sequestering.
Moving beyond salad
Described by Davidson as a “gateway crop to the technology”, salad greens are easy and quick growing (baby leaf salad takes four to five weeks to mature, microgreens just over two weeks), require minimal nutrients and provide multiple crops per season.
Oscar Davidson and Dermot O’Regan of Grow Bristol
But will we be seeing more than just baby leaf and herbs anytime soon? There has been researching into crops including sweet potatoes and broccoli, and Singh says he has had some success trialing strawberries. But this poses a greater financial risk with the longer growing time required, and the extra light hours needed.
It all comes back to considering the whole cycle of growing and supply, including energy use. Vertical farming is becoming ever more environmentally and economically sustainable, and if these startups continue to develop at the current rate, a lot more of the food in our fridge could be grown in the tower block down the road.
Is vertical farming organic?
Vertical farming often uses hydroponic growing systems that do not use soil
The Soil Association does not currently class hydroponic growing as organic – in the UK, plants classified as organic need to be grown in soil, whereas in the US, the United States Department of Agriculture (USDA) does not make this requirement.
That said, there are no pesticides involved in the growing at JFC and other hydroponic farms, and the no pesticide factor is often a major motivator for people choosing organic. Hofman says: “I would wonder that the organic movement’s reliance on soil was good for the time it was created, but there’s actually the opportunity to think a bit more broadly about how both systems might be able to coexist or work together.”
Davidson adds: “There are other things to consider, where has that been grown, what was the conditions of the workers who have grown that crop? So yes, we use a lot of energy to grow our crops with our lighting, but we don’t use big agricultural machinery that uses diesel, we don’t use petrol fertilizers, and we don’t use endless amounts of groundwater.”
How Indoor Ag Is Growing A Resilient Food Revolution
We're at a pivotal moment in an important trend for sustainable food systems: the emergence of sustainably grown food in urban environments. As the growth and maturity of these operations continue, they could play a critical role in food security amid a changing climate as well as the continuing shift in global trade patterns
November 12, 2019
We're at a pivotal moment in an important trend for sustainable food systems: the emergence of sustainably grown food in urban environments. As the growth and maturity of these operations continue, they could play a critical role in food security amid a changing climate as well as the continuing shift in global trade patterns.
They also could be key in eliminating food deserts, neighborhoods that lack a supermarket selling produce, serviced only by convenience stores that stock nutrient-poor packaged foods and beverages.
A great deal of the technology that enables indoor growing was developed and honed over the past two decades by cannabis farmers, who learned how to grow plants at scale in confined (and usually hidden) spaces. They use controlled-environment agriculture, including hydroponics — growing plants without soil — a technology as ancient as the fabled Hanging Gardens of Babylon thought to be the first example of soilless gardening.
Today, such technologies are used on the International Space Station to study plant growth outside the Earth’s atmosphere and how best to supply food and oxygen for future colonization missions to Mars and beyond.
Growing leafy greens, specialty herbs, tomatoes and other produce indoors using hydroponics consumes up to 95 percent less water than growing them outdoors and uses fewer pesticides.
Even on Spaceship Earth, such technologies make a lot of sense. Growing leafy greens, specialty herbs, tomatoes and other produce indoors using hydroponics consumes up to 95 percent less water than growing them outdoors and uses fewer pesticides — sometimes none at all. Hydroponics has long been central to the Dutch and Japanese food systems, but the relatively cheap cost of land and water in the United States, combined with the costly energy intensity of lighting, made hydroponics too expensive for growing anything but high-value cash crops (such as cannabis).
That’s changing. Today, there is the new breed of indoor ag companies sprouting up all over, many using tricked-out shipping containers, LED lighting and a simple continuous-flow watering system. Environmental controls ensure that temperature, airflow, carbon dioxide, and humidity levels remain optimized.
In the East Ward neighborhood of Ironbound in Newark, New Jersey, for example, AeroFarms built the world’s largest vertical farm using aeroponics, in which racks of crops are grown indoors using neither soil nor water. Most of the seed money for the operation came from Goldman Sachs’s Urban Investment Group.
AeroFarms' 69,000-square-foot facility, in a former steel factory, can grow 2 million pounds of leafy greens annually, all without using a speck of dirt or a ray of sunlight. The company says the same seed that would take 30 to 45 days to grow in the field can grow in 12 to 16 days indoors, enabling up to 30 crop turns a year.
Rising tide
Operations such as AeroFarms are a perfect example of the need for a distributed network that can provide security and resilience in the face of societal shocks — in particular, extreme weather events.
Case in point: Most of the food that finds its way into New York City — cabbage from New York, oranges from California, blueberries from Chile, bell peppers from the Netherlands, beef from Australia, fish from Nova Scotia — passes through a single facility: the Hunts Point Food Distribution Center in the South Bronx. Opened in 1967, and home to 8,500 workers at 115 companies, it is the largest food market in the United States, feeding more than 23 million people throughout the region.
The million-square-foot facility is not just critically important, but also vulnerable. It sits on a peninsula with the East River on two sides and the Bronx River on the third and is subject to storm surge during high tides.
If Hurricane Sandy had hit 12 hours earlier, during high tide, the food supply for all five boroughs would have been disrupted.
In fact, if Hurricane Sandy had hit 12 hours earlier, during high tide, Hunts Point would have been flooded, the facility would have lost power and the food supply for all five boroughs would have been disrupted. As a result, AeroFarms offers an additional route to bring food into New York — food produced locally, indoors, year-round — enabling the region's food supply chain to be more adaptive to challenging circumstances.
It’s important to note that few of these operations rely on federal dollars or subsidies to grow their businesses. (As Haggerty notes, the 2018 U.S. Farm Bill allotted $10 million annually to develop an Office of Urban Agriculture and Innovative Production at the U.S. Agriculture Department, a pittance but a start. Among other things, it requires the ag secretary to conduct a census of urban, indoor and other emerging agricultural production sites). Indeed, when it comes to creating the new menu for how America grows and consumes food, Uncle Sam is largely absent from the table.
Instead, these companies were built by innovators and entrepreneurs chasing market opportunities, helped along by nonprofit and for-profit incubators, food aggregation and distribution centers catering to smaller operators, and local tax breaks for landowners who lend or lease their property to urban farmers.
And, of course, a healthy appetite for locally produced food that will only continue to grow.
For more on these topics, I invite you to follow me on Twitter, subscribe to my Monday morning newsletter, GreenBuzz, and listen to GreenBiz 350, my weekly podcast.
Topics: Food & Agriculture Climate Change Cities Risk & Resilience
Jeff Bezos-Backed Vertical Agriculture Startup Plenty ‘Hibernates’ Plans For Seattle Farm
The indoor agriculture startup backed by high-profile tech executives — including Amazon CEO Jeff Bezos — has canceled plans to open a major Seattle-area farm, GeekWire learned this week
By inventiva - November 15, 2019
Plenty Is Rethinking Its Growth Strategy
The indoor agriculture startup backed by high-profile tech executives — including Amazon CEO Jeff Bezos — has canceled plans to open a major Seattle-area farm, GeekWire learned this week. Plenty said it changed plans because the Kent, Wash., facility could no longer accommodate its next-generation vertical farm. The company is continuing to grow in its home state of California but has no plans in the immediate future to launch a farm in Washington.
“We decided that the best course of action would be to hibernate Seattle,” said Christina Ra, Plenty’s senior director of integrated marketing.
In the two years since announcing plans to build a 100,000 square-foot vertical farm in the Seattle region, Plenty developed Tigris, a new facility near its San Francisco headquarters. Tigris is too tall to fit in the Kent facility that Plenty leased in 2017, according to Ra.
“As a relatively lean company, we had to just make a decision about where we were going to put our focus and we felt like building Tigris, while also focusing on Seattle as a new and really important market, was something that we couldn’t do well,” Ra said.
Plenty grows its plants in tall towers inside a climate-controlled facility with LED lights. It does not use pesticides, herbicides, synthetic fertilizers, or GMOs. The system uses thousands of infrared cameras and sensors to collect data in the farms that is analyzed using machine learning to optimize growth.
The five-year-old startup promises its new Tigris farm can produce fruits and vegetables using less than 5 percent of the water and 1 percent of the land required in traditional agriculture.
It’s a prospect that has attracted some of the biggest names in tech. Backers of the company’s last fundraising round include SoftBank (via its Vision Fund); Alphabet Chairman Eric Schmidt (through Innovation Endeavors); Bezos (through Bezos Expeditions); DCM Ventures; Data Collective; Finistere Ventures; and Louis Bacon. Plenty has raised more than $200 million in venture funding.
Ra said Plenty ceased operations in Kent a year ago. Some employees were given the opportunity to relocate to San Francisco. Today, none of the employees who worked in Kent are still with Plenty. Ra said it is unlikely that Plenty will circle back to the Kent facility but the company still maintains its lease on the building.
Last month, Plenty announced plans to open a next-generation farm in Los Angeles. With the Seattle-area operation defunct, LA will be Plenty’s first expansion beyond its home markets in South San Francisco and Wyoming.
“Seattle’s still on our roadmap,” Ra said. “It’s a really important market for us. It was just a decision we had to make to prioritize and focus as a small company and the limited resources that we had.”
Indoor farming remains an untested industry with plenty of casualties.
Local Garden Vancouver, a similar crop-yielding greenhouse concept, declared bankruptcy a few years ago. Another startup called Aerofarms pledged to build 25 indoor farms over five years in 2015. To date, it has only built one farm outside its headquarters, according to Fast Company. Other startups in the space have struggled over the years.
Source: Geek Wire
Early History of Indoor Agriculture & Associated Technology Development
This month’s Indoor Ag Science Café was about the history and current technology status of indoor farming. The beginning seems to be in Syracuse, NY, where General Electric developed an indoor hydroponic farm funded by DoD in 1973
By urbanagnews
October 17, 2019
By Dr. Cary Mitchell (Purdue University)
This month’s Indoor Ag Science Café was about the history and current technology status of indoor farming. The beginning seems to be in Syracuse, NY, where General Electric developed an indoor hydroponic farm funded by DoD in 1973. Then there was a large commercial indoor farm for leafy greens in Dekalb, IL, owned by General Mills, which was closed in the 1990s. The longest survived may be the one in Japan (TS Farm by Kewpie Co.) where they use HID lamps and aeroponics since 1989. Most significant technological improvements are two ways – one in lighting and another in rack/shelving systems. Dr. Mitchell also introduced the contributions that NASA indoor farming studies made over the past 30+ years, as one of the contributors in the space.
Indoor Ag Science Café is supported by the USDA SCRI grant program and designed to create a precompetitive communication platform among scientists and indoor farming professionals. The Café presentations are available from YouTube channel. Contact Chieri Kubota at the Ohio State University (Kubota.10@osu.edu) to be a Café member to participate.
US - Indiana - Lafayette Resident Grows Produce Without Soil For Community
At Lafayette Produce farm on Wabash Avenue, 25 vertical, aeroponic towers produce basil, kale and other crops. Austin Kasso, Lafayette Produce owner, said he hopes to increase the farm to hundreds of towers as they become a year-round source of local, organic produce for Lafayette residents
BY LUCAS BLEYLE Staff Reporter
November 11, 2019
At Lafayette Produce farm on Wabash Avenue, 25 vertical, aeroponic towers produce basil, kale and other crops. Austin Kasso, Lafayette Produce owner, said he hopes to increase the farm to hundreds of towers as they become a year-round source of local, organic produce for Lafayette residents.
Lafayette Produce's vertical aeroponic system involves growing plants in towers, with the roots of the plants extending into the interior of soilless, cylindrical towers. Every 15 minutes, water mixed with an all-natural nutrient solution trickles down over the roots.
“With vertical aeroponics, we can grow 150 different fruits, vegetables, fruits, herbs and flowers,” Kasso said. “We can do a great variety of things that people ordinarily don't have access to around here. We could do five different kinds of basil and five different types of tomatoes.”
Because the water-nutrient mix is reused and trickled through multiple times, none of the water or nutrients are wasted like they might be in soil-based agriculture, Kasso said. The resulting produce is healthier because the plants are never subjected to nutrient deficiencies while they grow, he said.
“(Aeroponic towers) use 98% less water than traditional farming and they can grow 150 different crops in about 50% less time with about 30% greater yield on average,” Kasso said.
“Yields in soilless systems are typically higher and you can reduce the crop cycle time, especially with the leafy vegetables if it's your fruiting crops,” said Petrus Langenhoven, horticulture and hydroponic crop specialist for Purdue's horticulture and landscape architecture department.
Up until last year, Kasso had worked with community members and the organization Habitat for Humanity to fundraise and purchase his first 12 aeroponic towers. Since he began in 2013, Kasso has experimented with numerous crops including tomatoes, kale, basil and zucchini.
In 2018, Kasso was approached by his current business partner, Bob Corbin, to start an aeroponic farm for Corbin’s Corner Market, a store on Wabash Avenue selling local goods such as handmade candles, raw honey and West Lafayette BONZ BBQ sauce.
Kasso said Wabash Avenue used to be considered the “armpit of Lafayette.” Historically, it was the part of the city that had little development and lots of crime. Over the last few years, community planners have worked to bring new life to the area, inviting artists to adorn buildings with murals and expanding the local park.
“I was inspired to start it here because I realized there's a food insecurity problem in Indiana as well,” Kasso said. “It needs to be addressed and I believe local food and urban farming are the answer to that.”
Langenhoven said the closer farming is to cities, the better.
“Urban farming is great," Langenhoven said. "I think the closer we can get to the major city centers, the better it is for that supply chain."
He said there is a potential for urban farming to help meet the demand for fresh produce. Two controlled-environment farms — Green Sense Farms in Portage, Indiana, and Gotham Greens in Chicago — both successfully supply produce year-round to the Chicago area.
Local produce often sells at a premium because customers are drawn to its superior taste and freshness.
“I'm a big fan of (local farming), because I like fresh produce,” Langenhoven said. “I know what fresh produce tastes like because I grow this stuff and I eat what I grow, and everybody else in the department ... they're always like, ‘Wow, this is so different from what it tastes like in the store.’ And it's really because it was picked this morning or yesterday and I've waited until it was fully mature to actually pick it.”
Langenhoven said customers are often willing to pay a premium for local produce that helps make capital- and energy-intensive controlled cropping systems such as aeroponics more viable.
“First thing to note about aeroponics is that it's actually a very management-intensive system," Langenhoven said. "Anything can go wrong if you don't have backups. You (can) have total crop failure because the roots are hanging in the air.”
Any sort of power outage can devastate a crop if proper electricity backup systems aren’t in place. These backup systems and the other controls needed to have a functional production system makes aeroponics very expensive, Langhoven said.
Due to the productivity and efficiency of his system, Kasso said he is able to make up for the increased infrastructure and energy costs, especially when compared to produce shipped from California. His goal is to sell produce at an affordable cost.
“Instead of charging more for organic, local, it's going to be similar to what you'd find at Pay Less or Walmart,” Kasso said.
Lafayette Produce currently sells basil to two local restaurants, Bruno’s Pizza and Town & Gown Bistro.
Bowery Grows With New Facility In Maryland
By increasing efficiencies around R&D, computer vision and automation, Bowery will continue experimenting beyond leafy greens and herbs, and focus on crops that are very limited by seasonality and traditionally grown outdoors, from root vegetables (turnips, radishes, kohlrabi) to fruiting crops (peppers, cucumbers)
Bowery announced its new indoor farm in the Baltimore-DC area - the brand's first farm outside the tristate region - with distribution of leafy greens and herbs to local retailers starting early next year. This new farm is 3.5x larger than Bowery's last facility, and the urban density of the new farm's surrounding area of White Marsh, MD provides access to a population of 26 million people within a 150-mile radius.
New crops
By increasing efficiencies around R&D, computer vision and automation, Bowery will continue experimenting beyond leafy greens and herbs, and focus on crops that are very limited by seasonality and traditionally grown outdoors, from root vegetables (turnips, radishes, kohlrabi) to fruiting crops (peppers, cucumbers).
Expanded distribution
In addition to moving to the Baltimore/DC region, Bowery recently expanded distribution at Whole Foods in the tri-state area, growing from availability in 12 locations to 31. Bowery leafy greens and herbs are now available in retail locations on Long Island, Connecticut, West Chester and in all Manhattan locations. On the heels of this expansion news also comes Bowery’s announcement of $50M in a B+ funding round.
For more information:
Bowery Farming
contact@boweryfarming.com
boweryfarming.com
Publication date: Thu 7 Nov 2019
iGrow - Op Ed / Opinion: by: Bruce Carman - Founder of Controlled Environmental Farming Inc.
I recently read an article in Fast Company entitled "This Google Ventures-backed indoor farming startup just opened its biggest farm yet" by Adele Peters a staff writer (11.06.19)
November 17, 2019
by: Bruce Carman
I recently read an article in Fast Company entitled "This Google Ventures-backed indoor farming startup just opened its biggest farm yet" by Adele Peters a staff writer (11.06.19).
In the article, Ms. Peters identifies a few of the larger indoor farming operations, Bowery, Plenty, to name a few and where these entities are today versus their projections from a couple of years ago. In most cases, these entities have fallen short of their own growth projections in terms of the number of facilities they predicted would be operational at this point in time.
As an owner/operator and the developer of Indoor Agriculture Technology for Urban Farming locations, I would like to share my vision of indoor agriculture. First, location, location, location, it is very important. Facilities should be placed geographically where the consumer is. Urban Farming, within its truest form, means that facilities will be placed in the downtown districts of a municipality, next to the opera house or the sports stadium. I realize this is disruptive to conventional operations but, doing so provides reduced transportation costs, fresher more nutritional product with less food waste, greater affordability, and sustainable economical development. Carbon footprint reduction is a huge winner within this concept.
Second, facilities need to offer product diversity. Leafy greens alone will not provide the necessary product variety for a successful Urban Farming entity. How often do you go to the store for just one item? The Urban Farm is no different, you don't go to just acquire leafy greens. When you go, you want to be able to purchase locally grown fruit, vegetables, herbs, shrimp and fish. In short, you would like to be able to purchase an entire meal and just not the core of the salad.
Third, Urban Farming entities should be closed-loop operationally. The ability to produce locally grown, organic products, is the true ideal model for Urban Farming facilities. Resources, like water, are conserved, reclaimed and re-used beneficially. Pollution is reduced or eliminated. Food safety, food security, and affordability are increased within the local community. The closed-loop system provides for protein-based food production, naturally, efficiently, while also providing product diversity. The economic model for the Urban Farm is enhanced and the community benefits.
Please don't misunderstand my thoughts. Developing cultivation technology is very important and necessary for the evolution of Urban Farming to get where it needs to be, quickly. Equally important, in my view, is food production that occurs outside the box. That provides for new locations, zoning regulations, structures, methods, systems, distribution models and product diversity outside of leafy greens. If we don't invest in those facets of food production too, we will not meet the challenges that are upon us now.
Controlled Environmental Farming Inc.
In This Finnish Farm, Strawberries Grow On Multiple Levels
Despite fall being in full bloom, the strawberry cultivation in Lappträsk, Finland is running full throttle. Robert Jordas believes it is interesting to try new cultivation methods
Robert Jordas Performs 'Secret' Experiment In His Greenhouse
Despite fall being in full bloom, the strawberry cultivation in Lappträsk, Finland is running full throttle. Robert Jordas believes it is interesting to try new cultivation methods.
One of the new methods is the vertical cultivation of strawberries: the strawberries grow on different levels. In the space, around 30 square meters in size, strawberry plants are hanging with flowers, unripe, and ripe fruit. Because of the colorful lighting, it reminds of a disco.
The high air humidity immediate fogs up your glasses, but the temperature is not tropical. it looks more like the Finnish Indian summer.
All plants are looking well, because every level has its own lighting. Jordas: "We want the plants to grow optimally and to keep the climate around the plant as optimal as can be."
Secrets, pink light, and the perfect cultivation circumstances
The optimal climate for a strawberry plant means the right light and the right heat and air humidity. The plant also requires CO2, nutrients, and water.
Jordas: "The interesting thing is that we, focused or the growth requirement, can control everything."
Much of the project is still secret. One of the secrets is LED lighting. The plants need a lot of light; LED lighting produces less heat than other lamps and can be placed closer to the plant so you can create more levels.
Jordas: "There are many advantages to growing on multiple levels: a larger harvest on a smaller surface, being able to control the spectrum of the lamps. We try to learn as much as possible and find the right cultivation method."
Robert Jordas wanted to grow strawberries because he likes them, but he is not completely satisfied with the taste his strawberries have at the moment.
Jordas: "We are going to test this cultivation method for a year. Continuous harvesting is possible, when one plant has flowers, the other has ripe fruits."
But is it environmentally friendly to grow strawberries in Finland in the middle of winter?
According to Jordas, that depends on how the electricity is generated. "If we use sustainable energy, it is better than importing vegetables and fruit from other countries. Also, strawberries are fresh products and it is important to consume them as soon as possible."
Source: Svenska
Publication date: Fri 8 Nov 2019
© HortiDaily.com
Vertical Farming, Micro-Algae, And Bio-Reactors — The New Frontier of Sustainable Food
CEA represents a small but growing dimension of agriculture. It's attracting huge investment, particularly in the United States where venture capitalists see gains to be made in a high-tech process known as vertical farming. Vertical farms look like a cross between a factory and a laboratory. Plants are grown indoors on trays, often stacked up to 30 tiers high
RN By Antony Funnell for Future Tense
November 8, 2019
It's brunch time in the not-too-distant future. You're in your favourite cafe and you have a craving for pancakes.
You know they're delicious because you order them all the time: fluffy and light with a slightly carroty taste.
Hardly a health food, but at least they're easy on the environment — they're made with organic eggs and 100 percent locally-sourced bacteria.
The bioreactor that produces the flour is only a block away.
Like many people, you're worried about the size of your carbon footprint, so it's good to know that none of the main ingredients had to be shipped or flown in.
The coffee is good too — from a boutique plantation in an old converted office block just down the road.
It's expensive, but it's worth paying a little more to make sure the produce you eat and drink is grown right here in the city.
Your friend orders the pork and fennel sausages with a side salad — from the rooftop farm above the cafe.
Follow this story to get email or text alerts from ABC News when there is a future article following this storyline.
She often feels guilty about the amount of meat she consumes. But at least the pig she's eating was raised on micro-algae, not soybean. So, a small chunk of the Amazon is still standing because the trees in that area weren't cut down to make way for yet another enormous soya plantation.
Eating pancakes made from bacterial flour and animals raised on unicellular photosynthetic micro-organisms might seem a little out there, but these ideas are currently being explored by scientists as part of a new approach to farming called controlled environmental agriculture (CEA).
And CEA, some agricultural researchers argue, could be the best way of reducing the environmental destruction associated with modern farming, which is both land and resource-intensive.
Listen to the episode
Controlled Environmental Agriculture promises to be cleaner and greener. Future Tense examines the potential and the pitfalls.
The veggie patch goes high-tech
CEA represents a small but growing dimension of agriculture.
It's attracting huge investment, particularly in the United States where venture capitalists see gains to be made in a high-tech process known as vertical farming.
Vertical farms look like a cross between a factory and a laboratory.
Plants are grown indoors on trays, often stacked up to 30 tiers high.
Everything about the indoor environment is governed by sensors and automation, but the crucial ingredient is the artificial lighting.
"All the vertical farms operating today are using a type of lighting called LEDs, which stands for light-emitting diode," says Jeffrey Landau, the director of business development at Agritecture, an urban agriculture consultancy.
"Different types of crops prefer different types of lighting. So, your leafy greens, your vegetative crops prefer light towards the blue side of the spectrum.
"Whereas your fruiting and flowering crops, they will want something more along the red spectrum of lighting."
Each variety of plant has its own tailored lighting recipe, allowing them to photosynthesise for much longer periods of the day — up to 18 hours at a time.
In practical terms, that means more crop yields.
The major players, to date, have concentrated on producing perishable goods such as salad vegetables — crops that traditionally require large amounts of water.
But vertical farming expert Paul Gauthier believes even staples like potato and wheat could eventually be grown indoors.
"Everything is possible. I don't think there is anything in the vertical farm that we can't grow," he says.
"I was growing coffee trees inside a vertical farm.
"It's a question of which kind of design we have to make and what the economics are behind it."
Dr Gauthier, who now works for the New Jersey-based company Bowery Farming, admits both the capital and energy costs involved in vertical farming are "definitely huge".
But that needs to be put in context, he argues, because significant government subsidies have long been provided to traditional farming operations.
People in glass houses
Others aren't so convinced.
Viraj Puri sees the Silicon Valley-inspired approach adopted by companies like Bowery as unnecessarily high-tech.
"It has certainly attracted a tonne of investment, media attention, consumer interest, there's no doubt about it," he says.
"I still think the business models will require a path to profitability before it can start to attract more mainstream financing."
Mr. Puri, the CEO, and co-founder of Gotham Greens, operates five rooftop urban greenhouse facilities in New York and Chicago.
His approach to controlled environmental agriculture is to recast the classic Dutch greenhouse of an earlier age, but with 21st-century modifications.
"These are glass and steel structures controlled by computers that are able to monitor climate 365 days of the year, 24 hours a day, and make smart adjustments, data-driven adjustments, in order to maximise crop productivity, efficiency, reduce production losses," Mr. Puri says.
"They combine a lot of these advanced horticultural and engineering techniques that proponents of vertical farming espouse and promote."
And they also have the potential to achieve exponential crop yields.
"One can still get 50 times the productivity on certain types of crops. But one relies primarily on natural sunlight which is a free natural resource," Mr. Puri says.
Next year, Gotham Greens is due to open a 2,800-square-metre facility just outside Denver, Colorado, as part of a $70 million capital expansion plan.
"Some of these greenhouses are the size of dozens of football fields, so these aren't backyard hoop houses but rather very sophisticated climate-controlled buildings," Mr Puri says,
And they can get even bigger.
A French company is currently constructing a roof-top greenhouse in the centre of Paris that will cover some 14,000 square metres when completed.
Like Bowery Farms, Gotham Greens sells itself on growing pesticide-free crops, grown locally with very few transport miles.
"Urban farming is about bringing issues closer to large population centres," Mr Puri says.
"And telling the story of how agriculture is an enormous consumer of natural resources around the world and how this form of farming can play a significant role in a more sustainable future."
A revolution in the paddocks
A young farming couple find out how they can rehabilitate the natural environment while also producing healthier food.
The substitution game
For Cambridge University's Asaf Tzachor, the solution to environmental degradation lies not just in rethinking how we grow, but what we grow.
The future of food that he envisages is busy fermenting away in a bio-reactor in Iceland.
The facility is run by a company called Algaennovation, which has been experimenting with the development of a new kind of animal food supplement made from microalgae.
Dr. Tzachor estimates up to 85 percent of the soybean produced globally each year is used to feed farm animals.
Soya farming in South America is identified by environmental agencies as a major cause of deforestation.
So, the idea is to simply substitute the microalgae for soya.
"Microalgae are very interesting. They are marine organisms, which means that they don't need fresh water, unlike soybean," Dr. Tzachor says.
"And we don't have to cultivate them on terrestrial areas, so we can grow them within facilities, and these facilities can also be closed."
The savings on water alone would be significant, says Dr. Tzachor.
He says experiments at Algaennovation's facility have so far been able to achieve between 200 and 250 times more biomass per litre of water than soybean farming.
The next stage of development is demonstrating that microalgae production can be done on a mass scale.
A similar approach is being undertaken by researchers in Finland, but their focus is on producing a supplement for human food rather than stock feed.
Pasi Vainikka, from the company Solar Foods, says his company has used a bio-reactor to produce an edible flour made from fermented bacteria.
"We have a fermenter, but we don't use yeast. We use a specific microbe that doesn't eat sugar," he says.
"So instead of sugar we introduce carbon dioxide and hydrogen, and these the microbe uses for energy and carbon instead of sugars to grow.
"Then we take the liquid out of the fermenter when the microbes grow and multiply and you end up with a dry powder."
The flour, called Solein, has a 65 percent protein content, says Dr. Vainikka, and can be used as a substitute for wheat flour or soya in everything from bread to protein drinks.
"The organism has carotenoids. When you taste it raw it has a bit of an umami (savoury) taste," he says.
"When you add it to pancakes, for example, it tastes as if it would have egg, and also a bit of carrot taste."
"The production cost, according to our estimations, is around $US5 per kilogram."
But that cost, says Dr. Vainikka, could be expected to decrease as production begins to scale.
"We are about 10 times more environmentally friendly than plants and about 100 times better than animal-based proteins," he says.
"If we want to make a fundamentally more sustainable food system for the increasing population, we need to disconnect from agriculture, which usually means irrigation, use of pesticides and a lot of land use.
"So, when we disconnect from everything that has to do with these processes, the environmental benefits are huge."
Despite the promise offered by controlled environmental agriculture, Mr Puri cautions against seeing it as "panacea or a silver bullet" for the world's growing food demand issues.
"I think solutions are going to have to be varied and they have to be uniquely suited to their own geographical, economic, social and cultural contexts," he says.
"I think there's many different ways to farm sustainably and responsibly.
"Indoor farming techniques can certainly play a significant role for certain types of crops, high-value crops, crops that use a lot of water, crops that often have to be shipped in refrigerated trains, planes or trucks over great distances."
But the challenge is great. The United Nations estimates the world's population will increase to around 9.7 billion by 2050.
That's another 2 billion mouths to feed.
Fresh Greens From A Shipping Container In Alaska’s Aleutian Islands? Believe It
A young family has begun selling the first year-round, locally grown commercial produce in the unforgiving climate of Unalaska in the Aleutian Islands. Aleutian Greens co-owner Blaine Shaishnikoff said last week that two storms had just blown through the community — and the lettuce and herbs, nestled inside shipping containers set up as hydroponic farms, were unscathed
November 11, 2019
A young family has begun selling the first year-round, locally grown commercial produce in the unforgiving climate of Unalaska in the Aleutian Islands.
Aleutian Greens co-owner Blaine Shaishnikoff said last week that two storms had just blown through the community — and the lettuce and herbs, nestled inside shipping containers set up as hydroponic farms, were unscathed.
“You wake up and there‘s a couple inches of snow on the ground, and it kind of makes you think about it for a minute,” Shaishnikoff said.
Shaishnikoff, 28, and his wife, Catina, grew up in Unalaska, the treeless island community where fresh produce is shipped in from Seattle, more than 2,000 miles away.
“It takes a lot of shelf-life off of the product,” Shaishnikoff said.
Sometimes grocery stores run out of certain vegetables. Members of the community have long discussed how fresh produce is hard to come by, he said.
The Shaishnikoffs started Aleutian Greens with funding from the Aleutian Housing Authority. The plants are grown hydroponically inside standard shipping containers.
Aleutian Greens is growing lettuce, herbs and other produce in shipping containers in Unalaska. The plants are grown hydroponically. (Photos provided by Aleutian Greens)
Each shipping container measures 40 feet long, 8 feet wide and 9 feet 6 inches high. A single container can produce 450 heads of lettuce every week or combinations of leafy greens and herbs.
So far, the butterhead and green leaf lettuces have been popular, Shaishnikoff said. They are also growing parsley, dill, arugula, kale, chives, basil, Thai basil, cilantro, bok choy and mizuna, a spicy mustard green.
Since its first harvest Oct. 28, Aleutian Greens has been selling to the Grand Aleutian Hotel and Harbor View Bar and Grill for their restaurants.
In January, the company will expand its reach, and Unalaska residents will be able to buy the produce at Alaska Ship Supply, one of two grocery stores in town.
“Being able to buy and sell locally grown fresh produce is something that you never even thought would be an option in the Aleutians,” Bob Owens, Alaska Ship Supply owner, wrote in an email.
Unalaska‘s 4,400 residents live about 800 miles southwest of Anchorage.
Imported produce takes two weeks to arrive from Seattle, Owens said. With Aleutian Greens, the store will have the produce on the same day it is harvested.
“Slight difference,” Owens wrote.
Owens wrote that the prices will be comparable to produce already on the shelves.
The growing units came from Anchorage-based company Vertical Harvest Hydroponics, which specializes in creating vertical farms in shipping containers.
Why shipping containers? Cameron Willingham, Vertical Harvest Hydroponics founder, and Chief Technology Officer, offered two reasons.
First, shipping containers are tough — “pretty much bombproof” — which makes them ideal for rough conditions, Willingham said. Second, the farms must be small enough to fit on a barge or plane to be shipped to rural Alaska.
The hydroponics systems are set up for quick-cycling plants like herbs and greens. “We never set out to compete with carrots or potatoes,” Willingham said, which can be stored longer.
“We set out to go after the crops that just don‘t travel well, that just don‘t grow in the winter up here, that just don‘t store,” Willingham said.
The two containers sit on land owned by the Aleutian Housing Authority that was previously vacant – and happens to be a “stone‘s throw” from Shaishnikoff‘s house, he said.
So far, the couple operates the business along with a couple volunteers. Shaishnikoff has kept a second job working at a rock quarry, he said.
In late November, a third shipping container was en route to Unalaska that will be used for harvesting and packaging, Shaishnikoff said.
“That‘s really going to benefit us,” Shaishnikoff said.
Getting Off The Grid: Alternative Energies For Hydro Systems
With solar cells dropping in price and battery systems improving all the time, there are considerable benefits to looking at alternative energy sources for your growing needs
Chris Bond | October 29, 2019
Takeaway: With solar cells dropping in price and battery systems improving all the time, there are considerable benefits to looking at alternative energy sources for your growing needs. Chris Bond provides an overview of what is out there for those curious about unplugging from the grid and taking power into their own hands.
Nearly all the components of a hydroponic system can be partially or fully powered by alternative energies. Any system that runs on electricity or battery power ---such as lighting, pumps, filters, agitators, and timers--- can be altered to run on off-the-grid power sources.
Not all energy sources are practical for all systems, and many may be too cost-prohibitive to implement with complete efficiency.
But for the majority of alternative systems, there is usually a DIY version or an online hack out there that can help you to grow your greens without using petroleum or non-renewable energy sources.
Join thousands of other growers who are already receiving our monthly newsletter.
The systems outlined below are just an overview of the different types of alternative energies available and should not be considered a how-to. Most of the energy systems will generate direct current (DC). An inverter is required to convert the DC into alternating current (AC) to be useful for most of the appliances that a hydroponic system runs on. Another option is to consider converting your components to be compatible with DC.
Solar Energy
The effectiveness of any solar energy collection system for your growroom depends on how much sunlight you receive and how large of a collection system you can install. If you can put solar panels on the south-facing slope of your roof that aren't blocked by any large shade trees, then you will likely have enough power for more than just your hydroponic system.
Many homes, especially older ones, aren't suited for this type of installation. Solar panels can be placed on other buildings or as free-standing units in your yard. Their effectiveness then becomes reliant on factors such as the time of year or amount of cloud cover in your area.
The benefit of adding a solar collection system to your hydroponic set-up is that solar panels and other solar collection devices continue to improve as technology and demand increase. Simple systems can be installed to manually (or automatically) turn to follow the path of the sun.
Other solar collection devices are designed to warm the water by heating the pipes instead of converting sun energy into a current. This system can either expel heat or simply reduce the amount of energy required to heat your water.
Solar has come a long way in the last 20 years and there is an application for almost every scenario. It is also a type of alternative energy that can easily be added onto. You could, for instance, attempt to power just one aspect of your hydro system and keep building from there until the entire hydroponic system runs on stored energy derived from the conversion of solar power into usable current.
Wind Energy
Most people can imagine the way wind energy works as the concept is fairly simple. As the wind blows, a rotor or turbine spins. The energy derived from spinning is converted by a generator into usable power. The number of materials used to create a wind turbine also makes the prospect accessible to many and encourages creativity.
Wind turbines can be made from parts of 55-gallon drums, old satellite dishes, canvas sails, and almost anything that can cup the wind and spin freely. But the difficulty lies in the actual application of harnessing the wind power on a small scale and its practicality. Both of these depend on your location.
If you have an open piece of land that is an acre or more in size, wind power may be practical. If you live in an urban setting, in one of the tallest buildings, and have access to the roof, wind power may be practical. In a typical suburban setting, however, only very small scale energy applications are usually worth your time and investment. In these environments, it may make more sense to try to power only a portion of your hydro system with wind and then store whatever energy it creates into a battery.
Hydro Power
Yes, you can run your hydroponic system on hydropower; that is, if you have access to a source of running water on your property. In a nutshell, a portion of the flowing water gets diverted into a pipe (conveyance) where it is delivered to a pump or waterwheel. This then converts the flow of the water into rotational energy. An alternator or generator then converts the rotational energy into electrical current.
This system could be modified to run on stored water from a reservoir, but most hydro power systems take advantage of the natural flow of a body of water.
The initial investment will vary greatly depending on both the distance from the water source and how many kilowatts (kW) the system will generate. Many farm-based systems can produce up to 100kW, but even a modest 10kW is more than adequate to power a small growing operation.
Geothermal
Using geothermal energy in your hydroponic system is not as common as using solar, wind, or hydro energies, but it is still worth considering. If you are already paying for the energy it takes to heat your growroom, or are in the position of building a new hydroponics system, it pays to employ geothermal heating if you can.
Basically, geothermal heating takes advantage of underground soil or water temperatures. It draws this heat up from the ground into your structure and greatly reduces the amount of supplemental energy need to heat or cool the space around it.
There are many downsides to geothermal. Even though the temperature underground is fairly consistent throughout the country, accessibility is not reliable. Even if you do live in an area where the Earth’s underground warmth can be used, you will be unable to take advantage of this technology if you do not own the building or possess the right to dig beneath it.
However, if it is an option for you, you should consider tapping into this geothermal energy. It has a relatively quick payback period; you should immediately see the cost of heating or cooling your hydroponic space reduces.
Bioenergy
Making your own biofuels to either power some aspect of your operation or to heat the space you are growing in is probably the least likely of all the alternative energies listed here.
It is worth exploring, however, as most people create enough organic waste to power such a system. Grass clippings, food scraps, animal manures, and other organic wastes can be put into a digester to create biogas, which is a renewable alternative to natural gas.
While not practical for most people at the moment, bioenergy may represent a viable way to generate much of the energy needed to run your growing operation—maybe even your entire household—as the technology gets more widely utilized in coming years.
Rain Harvesting
Though not truly an alternative energy, collecting rainwater belongs in a discussion of using alternatives for a hydroponic system. Like the wind turbine, rain harvesting systems can be made from a wide variety of materials—five-gallon buckets, food-grade containers, or any collection tank that can hold water. Multiple small containers can be linked in series so that as one fills, the overflow goes into the next.
Most plants thrive better in rainwater than from city or well water. A hydroponic system can be supplemented, or filled entirely, with rainwater. As with any water source, careful scrutinizing of the pH and EC levels are called for. It is also important to maintain periodic agitation to prevent the development of algae or promote the breeding of insects.
Extra Considerations
No matter the type of alternative energy you consider to power your hydroponic system, there are a few things to keep in mind. Permissions range widely from municipality to municipality and you will need to know what your area’s zoning laws allow for, what requires a permit, and what is forbidden under any circumstances.
If you are considering installing a wind turbine, there are likely building codes to follow. The same goes for the installation of solar panels and collectors. However, many small-scale ventures into alternative energy can be done without affecting your neighbor’s view or without constructing large structures.
If you intend to harness the power of any stream, creek, river, or public body of water, you will need to obtain the appropriate permissions and may need to invest in equipment or components that measure your water usage and prevent backflow into the streams.
If any of these strategies sound appealing, but you lack the requisite building or engineering skills, there are more and more professional companies springing up that specialize in alternative energy installations for almost any application. Some of these strategies may even offer tax incentives. Check with your tax professional before claiming any alternative energy credit first, however, as many such programs are specific around how to qualify.
Written by Chris Bond
Chris Bond’s research interests are with sustainable agriculture, biological pest control, and alternative growing methods. He is a certified permaculture designer and certified nursery technician in Ohio and a certified nursery professional in New York, where he got his start in growing.
UK: Vertical Farming Now Aiding Beer Brewing
For vertical farmers, the question of “what can we do with all of this excess heat from the LED lights?” is a reoccurring question. One firm in the Midlands decided to put their thinking caps on and come up with a solution when posed with that exact dilemma
For vertical farmers, the question of “what can we do with all of this excess heat from the LED lights?” is a reoccurring question. One firm in the Midlands decided to put their thinking caps on and come up with a solution when posed with that exact dilemma.
In a bid to take more eco-friendly steps, the firm Astwood Group, formed a business idea, making expert use of all of that wasted heat.
Enter Lab Culture, a microbrewery based in the Midlands, UK. An idea born from a team brainstorm at the pub (we recognize the irony), that boasts a range of beers brewed directly from their neighboring vertical farm, Vertivore.
Read the full article at Urban Ag News
Publication date: Fri 8 Nov 2019
US: Texas Schools Tap Container Farms To Fill Cafeterias With Fresh Produce
Texas schools are using refrigerated freight containers converted into hydroponic farms as an extension of the classroom. At IDEA charter schools, students learn how to grow leafy greens and other vegetables, and deliver their harvests directly to the school cafeteria
Texas students are getting hands-on, high-tech experience growing fresh produce inside converted shipping containers. Photo: Freight Farms
by Eric Galatas
SAN ANTONIO, Texas – Texas schools are using refrigerated freight containers converted into hydroponic farms as an extension of the classroom. At IDEA charter schools, students learn how to grow leafy greens and other vegetables, and deliver their harvests directly to the school cafeteria.
Caroline Katsiroubas – director of community relations at Freight Farms, the company that developed the technology – says schools are using the farms in part to shift traditional food culture and improve health by giving students nutritious options.
“In the San Antonio IDEA school’s campus, they don’t use salt or pepper in their cafeteria,” says Katsiroubas. “And they’re growing herbs specifically in their farm to make a seasoning.”
The University of North Texas also is using the container farms as a lab for a wide range of hands-on learning opportunities in biology, organic chemistry, nutrition, and culinary arts, as well as business, computer science, and marketing.
Many schools have developed certificate programs and majors around sustainable food production, which gives graduates a leg up on joining the growing ag-tech field or starting their own farm.
Because the climate is controlled inside the container, food can be grown all school year long with a predictable commercial-scale output. Greenery units can support 13,000 plants at a time, producing harvests of up to 900 heads of lettuce per week.
Katsiroubas says the technology is useful in a state such as Texas and notes Houston freight farmers played a critical role in providing food during Hurricane Harvey.
“These container farms act as a way to control the food supply chain, and make it resistant to shocks like extreme weather patterns or hurricanes or drought,” says Katsiroubas.
Katsiroubas says the container farms also are helping lower schools’ overall carbon footprint. Harvests happen just steps from the dining hall, which all but eliminates transportation emissions and packaging.
She says the farms use 99% less water than a traditional farm, running with as little as five gallons per day, less than the average dishwasher.
Did you like this? Share it:
Written by: admin on November 8, 2019.
The Vertical Farming Industry Is Growing Deeper Roots
The urban indoor vertical farm industry is at an important juncture. Automation is taking root, long-term contracts with creditworthy retail and foodservice distributors are in the works and vertical farms are preparing to scale up. Also, the industry is about to get its first trade group, the American Association for Urban and Vertical Farming
November 11, 2019
Plenty plans to build a global network of vertical farms, starting with the west coast of the United States.
The urban indoor vertical farm industry is at an important juncture. Automation is taking root, long-term contracts with creditworthy retail and foodservice distributors are in the works and vertical farms are preparing to scale up. Also, the industry is about to get its first trade group, the American Association for Urban and Vertical Farming.
"The vertical farming industry in the U.S. is at a point where — if provided facilitation in terms of industry coordination, information exchange, innovation, education, training, funding, etc. — ... it can be enabled to reach critical mass," said Joel Cuello, a University of Arizona professor of biosystems engineering and vice chair of the Munich-based Association for Vertical Farming (AVF).
Just as important: a trade association can advocate for the industry and help it secure more funding.
In the 2018 U.S. Farm Bill, an annual allotment of $10 million was established to develop an office of urban agriculture and supporting projects, said Neil Mattson, controlled environment agriculture director and associate professor/greenhouse extension specialist at Cornell University. That’s a relatively small amount that includes everything from vertical farms to urban community gardens.
Whether industry-wide collaboration is needed or wanted at this stage is unclear. Sharing information could accelerate the industry’s development, but it also could dilute the value of a firm’s propriety research and development efforts.
Technology is important to reduce cost and to improve yields and quality, and therefore to provide a better return on investment.
The existence of New York City’s Agriculture Collective — which counts AeroFarms, Bowery Farming, Smallhold and Square Roots as members — illustrates that there are ways for the urban farming industry to share knowledge.
Having a city or regional dimension to collaborative efforts is key, especially when it comes to working in cities, said Henry Gordon-Smith, founder and managing director of Agritecture Consulting. For example, there is often a need for new zoning for indoor farming because it is not a permissible use of a building in an urban area, he added.
The new vertical farm trade association will be affiliated with the AVF, but the exact affiliation has not been negotiated yet.
A compelling story
Vertical farming does a very good job of tapping into customers’ interest in tasty, fresh and locally grown food. "Customers love it," said Chris Manca, Whole Foods Market’s local program coordinator for the Northeast region. "It connects with people who are passionate about local food and the environment."
Since 2014, Whole Foods has cultivated a high-tech Gotham Greens greenhouse farm on the rooftop of its Gowanus, Brooklyn, store. Leafy greens, microgreens and herbs grown in this rooftop greenhouse are sold in its store downstairs, in other nearby Whole Foods locations and at local restaurants. In addition, for the last year and a half, the Whole Foods location in Bridgewater, New Jersey, also has been selling mushrooms grown in an in-store vertical farm unit developed by the Brooklyn-based organic mushroom farming company, Smallhold. More recently, a second Smallhold in-store mushroom growing unit was added in a Whole Foods store in Brooklyn.
Gotham Greens
Gotham Greens operates a network of greenhouses across the Northeast, Mid-Atlantic, Midwest, New England, Mountain West and beyond.
The chief selling points of indoor vertical farm-grown fruits and vegetables are that they are pesticide- and herbicide-free, require only a little water and land to produce, offer flexible supply dynamics, have short grow cycles, offer year-round production and have easy product traceability, according to those interviewed for this article. Grocers or producer purveyors also might be able to claim greater price certainty and a longer shelf life.
"We look at [vertical farms] as a growing trend and a unique opportunity to partner with up and coming brands," Whole Foods’ Manca said.
But some farms need to get their prices in line with traditional produce, and it is becoming clear that vertical farms must start offering a wider variety of produce. Many are experimenting with growing berries and vine crops, such as tomatoes and cucumbers. To date, leafy greens, microgreens and herbs have been vertical farms’ cash crops because they offer more competitive pricing due to high yields and the fact that they require less energy to grow.
The growing appetite for indoor growing
Five Mediterranean climates — including California’s — supply all of the world’s fresh fruit and vegetables, and these climates are dealing with changing weather patterns. That is forcing more scrutiny of the vertical and indoor farming sectors.
"Today, the world can only grow enough fresh fruits and vegetables to feed two-thirds of the global population what is required for a healthy diet. That's with 7.5 billion people on Earth," said Christina Ra, senior director of integrated marketing at Plenty, the San Francisco-based indoor vertical farming company that in 2017 raised $200 million in Series B funding from Softbank, Amazon’s Jeff Bezos and Eric Schmidt, the former chairman of Alphabet.
Already, there is not enough, and the global population is expected to reach almost 10 billion in 2050, Ra pointed out.
Vertical farms alone cannot fill the gap, but new technologies and innovations, including more efficient LED lighting, robotics, machine vision and artificial intelligence, are making vertical farms more efficient and productive.
"Technology is important to reduce cost and to improve yields and quality, and therefore to provide a better return on investment," said Charlie Wang, president and CEO of Oasis Biotech, an Albuquerque-based company that owns vertical farms in Las Vegas, China and Albuquerque. It also develops and sells LED lights and hydroponic grow systems under SANANBIO brand.
During the last three years, LED lighting costs have dropped considerably amid a 20 percent improvement in energy efficiency. Looking ahead, over the next three years, similar advances in energy efficiency are expected, and developments in precision farming and automation are also expected to help the vertical farm industry eke out additional efficiency gains.
"We can do precision agriculture within a precise environment," said Grant Vandenbussche, senior business development strategist at Fifth Season, a fully automated indoor vertical farm company based in Pennsylvania. "This allows us to isolate variables to optimize for specific desired outcomes rapidly. We know how each factor is impacting things like plant growth, coloring, and flavor. … It's a true 'smart manufacturing' system."
Operating a fully-automated vertical farm can put a vertical farm's labor cost on par with field-grown produce, Cornell’s Mattson said.
We have been very forward [about how] energy requirements are a potential limiting factor for the industry.
According to Vandenbussche, automation helped Fifth Season reduce its labor from 40-60 percent of costs to 20 percent of costs. Fifth Season also said that the energy required from its automation processes is negligible within its system.
Indoor vertical farms’ energy needs for lighting and HVAC are considerable, however. For example, leafy greens grown in vertical farms in the Northeast currently have a carbon footprint that is two times higher than the carbon footprint for the same product grown in a field in California and then shipped 3,000 miles across the country, Mattson said.
There is also research and data that points to vertical farming being more energy-intensive than greenhouse-grown produce.
"We have been very forward [about how] energy requirements are a potential limiting factor for the industry," Vandenbussche said. "We're paying very close attention to our energy requirements as we launch our new farm, and we are implementing as many energy savings solutions as possible."
Sourcing all of a vertical farm’s energy needs from renewable sources through local utility providers can be challenging. Microgrids are an obvious alternative, but for some vertical farms, the initial capital cost is prohibitive.
For its farm, Fifth Season partnered with Scale Microgrid Solutions, a firm that provides turnkey microgrids, on a solar-microgrid solution. "[They have] a shared savings solution that allows you to capture the benefits of a microgrid without the upfront capital cost," Vandenbussche said.
Another workaround could involve geothermal energy, which can help control the air temperature. But for indoor vertical farms, the largest energy cost is electricity for lighting, which geothermal cannot address.
Plenty of paths
The indoor vertical farm industry has seen a lot of investment, but the business models are still sorting themselves out.
"There has been a big push on technology, but technology might not be the differentiating factor. The business models matter" said Ian Copeland, managing director at Ultra Capital, a San Francisco- and Philadelphia-based firm that focuses on small to midsize sustainable infrastructure projects in the agriculture, energy, waste and water sectors.
Investors want data-rich businesses that are responding to climate change, Gordon-Smith of Agritecture Consulting said. Consumers and retailers, meanwhile, want produce that they can trust will be clean and local, he added.
According to Whole Foods Market’s Manca, one big driver of the vertical farming trend is people wanting to know where their food comes from. "Especially for people in urban areas, I think that it’s really appealing to know that fresh produce is now being grown nearby and available at local stores at the peak of freshness," he said.
When it comes to vertical farming, venture capital is important, but project financing is critical, Oasis Biotech’s Wang said.
Project finance investors want to see long-term contracts with creditworthy counterparts; cost-competitive products and revenue predictability are also important.
Most vertical farms, including Plenty, initially have focused on leafy greens such as kale. Plenty
"Thanks to our modular platform — where we build farms inside refurbish shipping containers — we can quickly pop up in a new city with relatively little capital vs competitors,” said Tobias Peggs, co-founder, and CEO of Square Roots.
Earlier this month, Square Roots and Gordon Food Service (GFS), North America’s largest privately-owned foodservice distributor, forged a strategic partnership and opened its first co-located farm at GFS’ headquarters in Michigan.
"First, we want to refine and evaluate the proof of concept [at the co-located headquarters farm]. Assuming that we meet or exceed the projections going in, we hope to begin adding more locations next year," said Sean Walsh, GFS’s director of North America category management.
GFS trucks food to more than 100,000 restaurants, schools, hospitals/healthcare facilities, cruise ships and summer camp customers in the eastern half of the United States and Canada. GFS also runs a regional network of stores that service small businesses, caterers and walk-in consumers.
Other indoor farming companies are also in an expansionary mode. For example, Gotham Greens, which operates five high-tech greenhouse farms in New York City and Chicago, is opening new locations in Providence, Rhode Island; Chicago and Baltimore in the coming months. It says its retail presence will have grown to about 2,000 retail doors by the end of this year.
And in late October, Plenty, which concentrates on the West Coast, announced plans for a farm in the heart of Los Angeles. The new facility will create about 50 local jobs, ranging from growers to operations manager.
FOR SALE - 2014 Freight Farm - Computer Controlled Hydroponic Grow System - Texas
The Leafy Green Machine is a complete hydroponic growing system built entirely inside a shipping container with all the components needed for commercial food production. The system is designed and engineered for easy operation, allowing users of all backgrounds to immediately start growing.
FOR SALE - 2014 Freight Farm - Computer Controlled Hydroponic
Grow System - Texas
Manufacturer - Freight Farms
Model - 2014 Leafy Green Machine (LGM)
Price - $29,950
Location: Texas
The Leafy Green Machine is a complete hydroponic growing system built entirely inside a shipping container with all the components needed for commercial food production. The system is designed and engineered for easy operation, allowing users of all backgrounds to immediately start growing.
Current Uses
• Perfect for starting a small produce business, growing for restaurants or supplementing existing produce production.
• Restauranter who wants to grow custom greens for rotating menus 365 days a year. Farm to Table? How about Parking Lot to Table!
• Universities and schools have created programs for students to learn to grow while supplementing dining facilities with fresh greens.
The Highest Standard in Controlled Environment Agriculture
• Pre-built system designed to maximize operational efficiency and streamline workflow
• Perfect environment is achievable 365 days a year, regardless of geographic location
• Automated scheduling reduces the amount of labor required to operate
• Remote monitoring & control capabilities through the Farmhand AppTM
Operation Requirements
Space- The LGM dimensions are 40’ x 8’ x 9.5’. We suggest putting the farm on either trap rock or a concrete pad.
Electrical- 60 amp, 120/240-volt single phase or 120/208V three phase connection.
Water- A designated water source is suggested such as a garden hose or hardline water plumbing.
Labor- 15 to 20 hours a week for farming and upkeep.
It is recommended growing smaller compact crops with a high turnover rate, like head and loose leaf lettuces, herbs and heartier greens like kale and swiss chard.
Crop Examples
Butterhead lettuce, Oakleaf lettuce, Swiss Chard, Mustard Greens, Cabbage Leaves, Arugula, Cilantro, Mint, Dill, Oregano, Kale, Endive, Basil, Chives and Thyme
Yields
800+ heads of lettuce weekly
12 heads per tower (256 vertical towers)
1 LGM= 1.8 acres
Freight Farms technology makes it easy to bring farming closer to where people live. The result is local, year-round production featuring fresh, sustainably-grown, and flavorful greens.
Freight Farms is exactly what it sounds like–a farm in a repurposed freight container.
These old containers are retrofitted with vertical, hydroponic components to make farming possible anywhere in the world, regardless of the outside climate.
LGM Included Accessories:
2 (two) new Freight Farm chem panels; with AgrowDose pumps. Pumps where primed with water but never used. New sensors also.
2 (two) A/C units: Unit #1 is Factory the other is a MrCool Oasis ES Series Ductless Mini-
Split Heat Pump System 230V 19 SEER - 24,000 BTU. If you don’t need 2nd A/C unit remove it & reinstall exhaust fan. All tubing, wires where run into the farm through exhaust port hole so as to keep farm integrity.
1 Dehumidifier Model HCWH-90 Whole Home Dehumidifier
1 (one) ClearView pump to manage the condensate.
2 (two) (Floor fan tubes (2ea. for both sides)
2 (two) 800cfm fans; only one installed
4 (four) Westpointe fans not installed
2 (two) Co2 Generators, 1 MiniGen; 1 Autopilot
1 (one) Evolution RO1000 High Flow Reverse Osmosis Water Filter by HydroLogic
1 (one) BIGboy Ultra Violet Sterilizer Kit by HydroLogic.
2 (two) Seedling Doser Panel & Main Doser Panel w/sensors
2 (two) sets pH probe - EC probe - Temp probe -
Seedling & Main delivery tanks; replaced All of them 8 are new
Illumitex - Eclipse Gen2 8 LED Grow lights & Eclipse Gen2 12 LED Grow lights - 3ea. Over the seedlings area NEW
10 LED light strips 7 replacements
Agrowtek – Hydro Transmitter and sensors; (All New)
Cradle Point (AT&T) Cell for Internet into LGM has ??? router that works with Farmhand.
4 port switch
Laptop cradle w/swing arm not installed
Lots of spare parts
Misc. PVC fittings most treaded a few slip on
2 aux pumps, small volume, 2 air pumps,
Training, website and ongoing support available through Freight Farms.
Visit www.freightfarms.com for more information.
Everything You Will Need To Grow Seedling And Microgreens And Then Some
Materials For Growing Hydroponic Plants - Additional $7,500.00 USD
Seedling Cart & Racks (DIY) 6 trays, 1 sump, lights (mix of LED’s & T5) Bright Agrotech design ($500)
Illumitex - Eclipse Gen2 8 LED Grow lights & Eclipse Gen2 12 LED Grow lights** ($4,000)
20 (twenty) K5 fluorescents lights 4’
Agrobrite 2’x1’ 4 bulbs
Multiponics High-End Cycle Timer in waterproof box ($250)
Multiponics Aquatec CDP 8800 pump w/psi guage in waterproof box ($300)
ProSeries 5 stage Reverse Osmosis Water Filter System 1 ea. w/expansion tank (5gal.); 50GPD ($350)
4 stage Reverse Osmosis Water Filter System 1 ea. w/expansion tank (4.4gal) ($250)
Trays w/holes 50 ea. Trays w/ holes (diamond pattern)
Trays seedling (200ea. cells) 20ea. Trays w/o holes $20 ea.
Q Plugs 20/60 4K per case 1ea. case by IHort
Microgreen grow Pads & roll
Propagating Chamber model PC-22 by PRO-GROW ($2,200)
Zipgrow Farm Walls: 2ea. 4’ & 1ea. 8’ complete by Bright Agrotech ($1,500)
Tower Garden growing system ($500)
1ea. 30”x30”x6” tub
Pumps; Aerators; Timers; Tubing and fittings (1/4” / 3/8” / ½”)
PSI gauges
pH & EC probes handheld w/solution
Light Meter (Apogee Instruments) Full-Spectrum Quantum sensor ($500)
** (Seeds Included 1 Year Old)
Attached Documents:
Freight Farm Twitter Feed
LGM Cut Sheets
See All Photos And Videos Here
All information is from sources deemed reliable but is subject to errors, omissions, changes in price, prior sale or withdrawal without notice.
No representation is made as to the accuracy of any description.
All measurements, yields and square footages are approximate and all information should be confirmed by the customer.
Disclaimer of Warranty - The 2017 Freight Farms LGM hydroponic farming container is being sold “as is” and the Seller disclaims all warranties of quality, whether express or implied, including the warranties of merchantability and fitness for particular purpose.
This Google Ventures-Backed Indoor Farming Startup Just Opened Its Biggest Farm Yet
The Baltimore farm is 3.5 times as large as Bowery’s formerly largest farm—and is the latest attempt to make indoor farming work as a way to disrupt the agricultural system
11.06.19
The Baltimore farm is 3.5 times as large as Bowery’s formerly largest farm—and is the latest attempt to make indoor farming work as a way to disrupt the agricultural system.
If you live in the U.S., the last time you ate a salad, the lettuce inside it almost certainly came from California or Arizona. But the geography of leafy greens is very slowly starting to change as the trend of indoor farming—growing greens in large warehouses using artificial light and automated technology—expands. The latest farm to open is in Baltimore. It’s the largest, so far, from the New York-based, tech-heavy startup Bowery.
[Photo: Bowery]
The company, which just announced that it raised another $50 million from investors, grows what it previously called “post-organic” produce in sprawling warehouses (it no longer uses the phrase, but the greens are grown without any pesticides). It’s one of a handful of startups trying to make a dent in some of the challenges of traditional agriculture. The industry isn’t moving as quickly as some predicted. Aerofarms, for example, said in 2015 that it hoped to build 25 farms over the next five years; so far, it has two large farms, an R&D farm and a small farm at a school. The same year, FarmedHere said that it planned to expand to 18 farms but went out of business two years later. Boston-based Fresh Box Farms said in 2017 that it planned to expand to 25 farms in five years but still has only one farm. Plenty, a Silicon Valley-based indoor farming startup that has raised $226 million, has one farm.
Bowery, which launched in 2015, opened its first farm in New Jersey in 2017, followed by another farm at the same location, roughly 30 times larger, in 2018. The new farm in Baltimore is around 3.5 times larger than the last (the company won’t disclose specific square footage). The company is ramping up operations in Baltimore this week and planting crops, with the first sales to begin at local retailers early next year. Like others, the startup also hasn’t moved quite as quickly as it has suggested—last year, it said that it planned to open multiple farms in new cities by the end of 2019, though the Baltimore farm will be the only one to open this year—but it offers evidence that the field is continuing to grow. Another large indoor farm, from Gotham Greens, will also open in Baltimore late this year inside a former steel mill. In Pittsburgh, a robot-run farm from another startup called Fifth Season is scaling up in an industrial neighborhood.
“We’ve been really measured and thoughtful at Bowery in the way that we’ve scaled and grown the business, and that’s not just the farms themselves but the development around our technology . . . I think that really is rooted in the recognition that the problem that we’re solving and the opportunity that we’re focusing on is a large one, and ultimately, we’re running a marathon, not a sprint,” says Bowery CEO Irving Fain.
If the business model can succeed, it could help farming become more sustainable. “When you look at the footprint of agriculture globally, it’s the largest consumer of resources in the world by a quite a wide margin,” says Fain. The majority of the world’s water is used for agriculture—often in places like California that struggle with frequent drought and where droughts will increase with climate change. Indoor growing systems can shrink water use by more than 95%.
Because the crops grow in a pristine environment, they also don’t require any pesticides, fungicides, or herbicides. (Growing inside a controlled environment also eliminates the risk of contaminated produce, such as an E. coli outbreak in conventionally grown lettuce in 2018 that made 210 people sick and left five people dead.) Bowery estimates that its system is 100 times more productive than a traditional farm on the same amount of land. And while indoor farming uses a significant amount of energy for climate control and lighting, the technology is becoming more efficient. “I think you’re going to see us really fulfill our energy needs with more and more renewable energy over time,” he says.
[Photo: Bowery]
Like others in the space, Bowery relies heavily on technology. The company uses a custom-built operating system to carefully monitor plants and automatically make changes to improve yield and quality. Cameras track plant growth. “That plant vision system is taking photos of our crops in real-time,” Fain says. “It runs those photos through deep learning algorithms that we’ve developed. It both analyzes and understands what’s happening with the crops today but also predicts what will happen to the crops in the future. And then all that data runs through other machine learning algorithms, which essentially say, these are the adjustments and tweaks and changes that we want to make to this crop.” The software also manages farmers, making it possible, he says, to hire people who have no previous experience in growing food.
As the company expands, it can use the data it has already collected to improve each new farm. “In essence, what we’re doing is we’re building this distributed network of farms, and every new farm comes online with the benefit of all the prior farms that have come before it,” says Fain. “And then that farm itself also is now contributing data into that network and strengthening the network itself. What that means is better produce, more efficiency, new taste and flavors, and new varieties, and all those things are sort of translating from the learning that we’re getting through the Bowery operating system and the systems themselves.”
All of this, he says, can happen at a cost-competitive with growing in the field. Right now, the company’s leafy greens sell through 100 retailers for around the same price as organically grown produce. Fain says that he expects the cost to eventually be at par with any produce. “When I started Bowery, one of the things that was really important to me was really ensuring that we could ultimately democratize access to high quality, fresh produce,” he says. “To get there, we had to be able to sell a product that was already competitive today . . . We’ve spent a lot of time really carefully and meticulously focusing on not only the way we run our farms but the systems inside of our farms, the automation, the technology and the software, and how that directly ties into the unit economics of the farms themselves. And so we can today be at or below field organic pricing with a very healthy economic model for our farms.”
ABOUT THE AUTHOR
Adele Peters is a staff writer at Fast Company who focuses on solutions to some of the world's largest problems, from climate change to homelessness. Previously, she worked with GOOD, BioLite, and the Sustainable Products and Solutions program at UC Berkeley, and contributed to the second edition of the bestselling book "Worldchanging: A User's Guide for the 21st Century."
[Photos: Bowery]