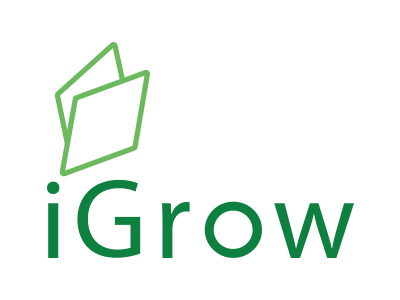
Welcome to iGrow News, Your Source for the World of Indoor Vertical Farming
April Indoor Science Cafe - Tuesday April 14th 12:00 PM EDT Photons = Flavor The Case Study of Basil
Indoor Ag Science Cafe is an open discussion forum, organized by Chieri Kubota (OSU), Erik Runkle (MSU), and Cary Mitchell (Purdue U.) supported by USDA SCRI grants
April Indoor Science Cafe
If you already signed up -- Thank you!
Tuesday, April 14th, 12:00 PM EDT
Photons = Flavor
The case study of basil
Presented by
Dr. Roberto Lopez & Kellie Walters (Michigan State University)
Please sign up so that you will receive Zoom link info.
Indoor Ag Science Cafe is an open discussion forum, organized by Chieri Kubota (OSU), Erik Runkle (MSU), and Cary Mitchell (Purdue U.) supported by USDA SCRI grants.
Sign up for April 14th Cafe
Cafe Q&A Forum
Please visit the Indoor Ag Science Cafe Q&A Forum at Public Good Ag website. OptimIA team is collaborating with Penny McBride to develop an information-sharing site with a lively discussion platform for indoor farmers and scientists.
Submit Your Questions for 'Indoor Ag Sci Queries'!
Please submit your questions (anonymously if you wish) about the sciences and technologies of indoor farming to this submission site. Any questions are welcome! The site is always open for your questions. Selected questions will be discussed in our future Indoor Ag Science Queries series.
Previous café recordings are available on this YouTube channel and OptimIA project website.
Please contact for more info: kubota.10@osu.edu
Upcoming Cafes:
April 14th, 12 PM EST [Dr. Roberto Lopez and Kellie Walters, Michigan State University]
May 26th, 11 AM EST [Nicola Kerslake, Contain Inc.]
Interested in giving a talk to share your thoughts and experiences? Please contact us!
Related Events:
July 10, 2020 - Plant Empowerment Workshop - Advanced learning to optimize crop production (Columbus, OH) [More Information]
July 11-14, 2020 - Cultivate '20 (Columbus, OH) [More information]
July 29, 2020 - OptimIA Annual Stakeholder Meeting (East Lansing, MI) [more information TBA]
September 13-17, 2020 - NCERA-101 Committee on Controlled Environment Technology and Use Annual & International Meeting (Tucson, AZ) [More Information]
May 31-June 4, 2021 - ISHS International Symposium on Light in Horticulture (Malmo, Sweden) [More Information]
Growing Up: Welcome To Vertical Farming
A new word will have to be coined to describe Zhihao Chen. Is he a farmer if there’s no farm? Chen, a chemistry instructor at Arizona State University, has created a new system for growing food. Forget farm to table. Chen has skipped the farm entirely
April 7, 2020
Closed system processes food waste and produces organic produce in record time
A new word will have to be coined to describe Zhihao Chen. Is he a farmer if there’s no farm?
Chen, a chemistry instructor at Arizona State University, has created a new system for growing food. Forget farm to table. Chen has skipped the farm entirely.
In a time when grocery stores are struggling to keep shelves full, Chen’s vertical farm could sit in the corner of a market parking lot, sending lettuce grown from a completely organic closed system to the shelves in as little as three weeks.
The system, which Chen describes as "cleantech," is contained within two standard shipping containers. One contains a system for breaking down food waste — anything from potato peels to rotten carrots to egg shells — and transforming it into fertilizer and methane gas. It’s capable of processing 2,000 pounds of food waste per day – the amount an average grocery store tosses out daily.
The second container hosts shelves of produce grown in a carefully-controlled environment.
Zhihao Chen, inside the digester container, talks about the vertical farming system he and his colleagues have developed at the Laboratory for Algae Research and Biotechnology on the Polytechnic campus. Photo by Charlie Leight/ASU Now
The 160-square-foot space can produce 1,200 heads of lettuce per month — the equivalent of two acres of farmland production. Traditionally, it takes lettuce 30 days to grow to maturity. Chen’s system produces a mature head in three weeks. It also doesn’t depend on climate. And the system uses 95% less water than traditional agriculture.
This could work on an island, in space, at sea — anywhere.
Chen came up with the idea two years ago. An instructor in the College of Integrative Sciences and Arts on ASU’s Polytechnic campus, he assembled a team to work on the project and created a startup called Homer Farms.
He takes food waste from the campus and grows lettuce, which goes back to ASU Dining Services.
“We want to achieve zero waste at ASU,” Chen said. He plans to expand operations to the other campuses. He is also in talks with grocery chains Fry’s and Kroger right now. Fry’s is interested in putting the system in their parking lots to use their food waste.
“The customer can actually see what’s going on,” he said. No pesticides, no chemicals or artificial fertilizers are used. It’s completely organic.
And, he adds, “You pretty much don’t emit any greenhouse gas emissions.”
A lattice of roots float in the fertilizer brine in the racks for the week-old butterhead lettuce at the Laboratory for Algae Research and Biotechnology. Photo by Charlie Leight/ASU Now
The process is called anaerobic digestion. Certain bacteria under a certain temperature with the proper pH will break down the carbon chain in food waste and feed the carbon into the biogas. (Biogas is a mixture of CO2 and methane.) You can combust the methane for energy to run the unit and heat it to keep growing conditions optimal.
“We process the waste, it becomes liquid fertilizer and biogas,” said faculty sponsor and Assistant Professor Taylor Weiss. “Some of the liquid fertilizer is used in algae production and some is used in the vertical farm to feed the lettuce. When the lettuce is mature, we send it to ASU Dining Services to close the loop.”
It saves long-distance transportation. How about using this in a major metropolitan area like New York or San Francisco?
“We’re able to produce on-site, so the lettuce doesn’t have to be transported from Arizona to New York,” said Chad Geelhood, assistant director of Environmental and Resource Management. “We cut down energy costs, we cut down greenhouse gas emissions, and we make the city more resilient.”
Right now, with the supply chain overwhelmed, “if you have something like that on-site, the city can self-sustain,” Geelhood said. “You don’t have to worry about waste and the food will be supplied on time."
Arizona ranks second, following California, in production of lettuce. Lettuce production in Arizona includes head, leaf and romaine lettuces and is the state's leading cash crop, averaging more than $300 million in value.
“If you air condition the container, it can be year-round in a New York environment,” Geelhood said. “Here we don’t have to add as much heat because we’re in the desert.”
The system can grow any type of vegetables.
Instructional professional Zhihao Chen (left) talks with the assistant director of the Environmental and Resource Management Chad Geelhood inside the growing room with racks of week-old butterhead lettuce, at the Laboratory for Algae Research and Biotechnology. Photo by Charlie Leight/ASU Now
“Lettuce and leafy greens are a good target because they’re high-bulk and it costs a lot to transport them relatively, but also growing them in a closed space makes them more nutritious as well,” Weiss said.
The fertilizer is super-concentrated and has to be diluted. Inside the grow container, temperature, humidity, light intensity and plant temperature are all intensely monitored.
“In that way, we can predict the quality we need,” said Yujin Park, an assistant professor in the College of Integrative Sciences and Arts who researches what types of light wavelengths are best for growing. Conditions can be optimized for different crops.
Homer Farms is currently under incubation at the University of Arizona Center for Innovation.
Top photo: Assistant Professor Yujin Park checks the week-old butterhead lettuce plants at the Laboratory for Algae Research and Biotechnology on the Polytechnic campus on March 26, 2020. The plants will be ready for harvest at three weeks. With the goal of creating a circular economy, the lab takes food waste from the university's food services and turns it into a fertilizer by way of a digester. The fertilizer is diluted and used as a hydroponic medium to grow lettuce, which is then returned to the food services. Photo by Charlie Leight/ASU Now
Solutions Polytechnic campus College of Integrative Sciences and Arts Biology Sustainability Innovation Food and Dining Healthy Living Faculty Community
UK: Vertical Farm Construction Accelerated To Help Feed Bristol During COVID-19 Crisis
LettUs Grow, an indoor farming technology provider, is fast-tracking the building of two vertical farm modules in the city of Bristol to help feed vulnerable communities during the COVID-19 outbreak
LettUs Grow, an indoor farming technology provider, is fast-tracking the building of two vertical farm modules in the city of Bristol to help feed vulnerable communities during the COVID-19 outbreak. The company is teaming up with the food redistribution charity FareShare South West to ensure the produce gets to those who need it most.
LettUs Grow expects the first of the new aeroponic farm modules to be ready to start producing fresh produce from mid-April, with the first harvests ready to be delivered to FareShare just ten days after the farm’s commissioning. A second, larger module will be following in June.
Because most of the farm’s operations are automated, they can be run with only one person on site at any given time to allow social distancing of key workers and minimizing strain on an already stretched farm labor force. The food is also produced in a high care environment with few people coming into contact with it. Once up and running, the farms will be able to provide a consistent, predictable and climate-resilient food supply to the local community all year round.
The coronavirus outbreak has shone a spotlight on the fragility of the UK’s just-in-time food supply chain. The UK only produces 50% of the food it consumes, which leaves it vulnerable to shocks in the global supply chain. The closures and lockdowns enforced due to the pandemic, have created logistical bottlenecks that ripple across these lengthy chains.
Jack Farmer, co-founder and Chief Scientific Officer of LettUs Grow said: “When we founded LettUs Grow, we wanted to enable anyone, anywhere in the world, to grow fresh produce near its point of consumption. That mission has hardly ever felt as urgent as it does today. We knew we had to get involved and help in any way we could.
“Because our farm modules can be deployed anywhere with an electricity and water supply, they are uniquely positioned to increase regions’ food supply chain resilience by diversifying local food production.”
The FareShare group provides close to 1 million meals a week to frontline charities and community groups working with vulnerable people, such as those experiencing homelessness, mental health issues, domestic violence, loneliness and families who require free school meals. As the Coronavirus situation develops, Fareshare has seen demand for their service rising, particularly in the event of closures of schools, workplaces, and public spaces and people self-isolating.
Phoebe Ruxton, Fundraising Manager at FareShare South West said: “We are absolutely determined not only to stay open but to level up our organization as far as we possibly can to stop the very worst happening.
“While supermarkets seem empty, there are thousands of tonnes of surplus food in the system. There is no other organization in the region with the capacity to redistribute this food, and FareShare South West is well placed to deliver it straight to those most in need.”
You can help FareShare South West get food to people in need during this crisis by making a financial donation here: faresharesouthwest.org.uk/coronavirus-emergency-fund/. If you’re outside the South West, you can donate here fareshare.org.uk/help-us/.
For more information:
LettUs Grow
lettusgrow.com
Publication date: Thu 9 Apr 2020
Marcel Koolen, Codema; "Food Safety, Automation And Reliability Are More Critical Than Ever"
“In this changing market, it is crucial that we provide the investor and what we call the 'corporate horticulturist' with the right information, knowledge and the proper perspective
Since 2017, Marcel Koolen has been at the head of Codema as CEO. He took over from founder Maarten de Jager, who meticulously merged various horticultural specialists into the Netherlands' leading supplier of horticultural solutions. It is his task to realize the international ambitions and at the same time, realize his own vision.
Market for horticultural solutions is changing
“We come from a world in which our customers, experienced growers who took over the company from their parents, know all about the technology. They exactly know what they need. These people choose the best solution for each individual aspect of their operation, for example, a logistics system from Hawe or a water solution from B-E De Lier. These critical cultivation systems can now be found under one roof: at Codema. This fits in well with the changing market. An increasing part of the market requires a conversation partner who comes up with a total solution.”
In recent years, horticulture has been a popular destination for the money of investors who want to invest on a large scale in, for example, medicinal cannabis, food production, and vertical farming. Floriculture and traditional growers also continue to develop and grow. Partly due to size, technical innovation must ensure higher efficiency or yield.
Conversation partner from the start
“In this changing market, it is crucial that we provide the investor and what we call the 'corporate horticulturist' with the right information, knowledge and the proper perspective. After which, we arrive at the delivery of critical cultivation systems. In the first place, this means that, from the beginning of their trajectory, we are a full conversation partner for these organizations. Our organization is now geared up for this.
Secondly, this requires an international presence. We are always building projects in America, Europe and the Asia-Pacific region with a particular emphasis on China. This goes beyond a simple sales organization, our "license to operate" depends on our ability to provide after-sales service and maintenance."
Due to these developments and continuing growth, the organization of Codema has grown strongly. "From the Netherlands, we serve and supply all over the world and on location we work as much as possible with local workers. Many beliefs converge in the latter; cost control from the customer and the influence of Nordian Capital. For example, on sustainability." However, Koolen's personal motives also make their mark:
“That does not mean that I make many difficult considerations or want to impose these on my customers. By applying new technological developments and continuing to work on both design and engineering, we already are more economical with raw materials.
Of course, it starts by considering if we can make better decisions in everything we think about and everything we do. Think about choosing green energy, solar panels, limiting flight movements, a hybrid fleet, and so on. Good business decisions that are simply better for our planet. It is no coincidence that this is also essential for our investor, Nordian Capital. Nordian’s entire investment portfolio compensates for all of its emissions through certified contracts with Land Life Company. This foundation is committed to the reforestation of around 2 billion hectares of land around the world.’’
A shared vision for the future
Originally, Marcel Koolen was an Electrical Engineer. However, he soon discovered that a wider field of vision suits him better. That theme had been a common thread in his entire career. Paired with his passion for what he calls ‘public interest’. With every step, his playing field grew larger.
‘The first time that it actually connected was with an electrical family business. There I quickly built up a department whose turnover was equal to that of the parent company and was allowed to slim it down a few years later. I have been able to face these kinds of challenges at an increasingly higher level. First at VolkerRail, during the privatization of the railways, and then at Spitzke and ABB.
When I started at Codema, significant changes were to come and therefore was an excellent fit. However, the main reason for my choice is our shared vision for the future. When I worked on the mobility of the Netherlands at VolkerRail, I noticed that serving the ‘public interest’ motivates me enormously. And at Codema we go further: we help feed the world. A good and efficient food production not only ensures that everyone has food but also makes it a lot less harmful to the environment. That is a challenge, which I would like to put my efforts into.’
Future and strategy Codema: food production
The herb cultivation market has boomed in recent years, and the legalization of the cultivation of medicinal cannabis has created a large capital inflow, which also benefited Codema. Codema realized critical cultivation systems in the largest, most advanced cannabis greenhouses in the world. These are greenhouses in which food safety and reliability, as well as automation, are more critical than ever. Codema also works in the floriculture with large cultivation organizations to apply the latest technology in areas such as software, water, lighting, and logistics. This provides knowledge and experience that Codema can directly apply to food cultivation.
“Investing in food production is a good business decision. The world population is growing, and with it, the demand for food. There are many challenges in this area that require a technical solution and where Codema can make the difference. That makes it a good investment for both investors and Codema. Since we are now active in the three major time zones, we reduce the risk of economic volatility further. That makes us future-proof.”
Cooperation in the chain
“That does not mean that Codema can do that alone. We work together with greenhouse builders and engineering -and consultancy firms, such as scientific researchers, educational institutions and market researchers. Partly because of this, Codema is able to present the final solution to the customer. This means that we go further than ever in our services. That is also what the market demands.”
When asked whether he is satisfied if, in Codema 2024 anchored her international position as a food production specialist, Koolen replies:
“We should always keep growing, but that doesn't mean it's always about financial growth. This could, for instance, be growth in the impact you have on the world. Or growth in knowledge and skills, the development of new technologies. We need to keep moving and ensure that Codema can continue to offer its customers the best proposition in the future.”
For more information:
Codema Systems Group
Oosteindsepad 8
2661 EP Bergschenhoek
The Netherlands
+31105212755
info@codemasystemsgroup.com
www.codemasystemsgroup.com
Publication date: Wed 8 Apr 2020
SINGAPORE: Coronavirus Prompts Urban Farming Interest
Millions of people across the globe have been confined to their houses because of the coronavirus (Covid-19) pandemic and some have turned to urban farming to source their fresh produce, the start of a possible trend
BY LIAM O’CALLAGH
8th April 2020, Hong Kong
With movement in many countries restricted, some consumers are turning to urban farming for their fresh produce
Millions of people across the globe have been confined to their houses because of the coronavirus (Covid-19) pandemic and some have turned to urban farming to source their fresh produce, the start of a possible trend.
According to a report from Reuters, more urban residents are resorting to growing their own fruits and vegetables as panic buying has left supermarket shelves empty.
Landscape architect Kotchakorn Voraakhom designed Asia’s largest urban rooftop farm in Bangkok, she told Reuters the current situation has the potential to drive an urban farming trend.
“More people are thinking about where their food comes from, how easily it can be disrupted, and how to reduce disruptions,” said Voraakhom.
“People, planners, and governments should all be rethinking about how land is used in cities. Urban farming can improve food security and nutrition, reduce climate change impacts, and lower stress.”
Singapore is one country that has already signaled its interest in urban farming. It imports more than 90 percent of its food but in 2019 the government set a goal to produce 30 percent of its food needs by 2030, a plan that will embrace techniques such as urban farming.
On 6 April, Singapore lawmaker Ang Wei Neng urged the country to consider its food supply, “it would be wise for us to think of how to invest in homegrown food”.
Speaking to Reuters, Allan Lim, chief executive of ComCrop, said the coronavirus had amplified the fragility of the supply chain.
“It has definitely sparked more interest in local produce. Urban farms can be a shock absorber during disruptions such as this,” Lim said.
Millions of people across the globe have been confined to their houses because of the coronavirus (Covid-19) pandemic and some have turned to urban farming to source their fresh produce, the start of a possible trend.
According to a report from Reuters, more urban residents are resorting to growing their own fruits and vegetables as panic buying has left supermarket shelves empty.
Landscape architect Kotchakorn Voraakhom designed Asia’s largest urban rooftop farm in Bangkok, she told Reuters the current situation has the potential to drive an urban farming trend.
“More people are thinking about where their food comes from, how easily it can be disrupted, and how to reduce disruptions,” said Voraakhom.
“People, planners, and governments should all be rethinking about how land is used in cities. Urban farming can improve food security and nutrition, reduce climate change impacts, and lower stress.”
Singapore is one country that has already signaled its interest in urban farming. It imports more than 90 percent of its food but in 2019 the government set a goal to produce 30 percent of its food needs by 2030, a plan that will embrace techniques such as urban farming.
On 6 April, Singapore lawmaker Ang Wei Neng urged the country to consider its food supply, “it would be wise for us to think of how to invest in homegrown food”.
Speaking to Reuters, Allan Lim, chief executive of ComCrop, said the coronavirus had amplified the fragility of the supply chain.
“It has definitely sparked more interest in local produce. Urban farms can be a shock absorber during disruptions such as this,” Lim said.
Hands-Free Cultivation At Fresh Local Produce of Ohio
Green Automation is proud to announce the realization of another project in North America
Green Automation Group's latest project in North America is completed. The fully automated growing system for hydroponic baby leaf lettuce has been installed at Fresh Local Produce of Ohio and is already producing fresh, tasty and sustainable leafy greens for local distribution in Ohio, Pennsylvania, and Indiana.
Our Hands-Free Cultivation in the controlled environment of a greenhouse checks all the boxes for safe and sustainable growing.
WELLINGTON, FLA. (PRWEB) APRIL 06, 2020
Green Automation is proud to announce the realization of another project in North America. The installation of Green Automation’s fully automated growing system at Fresh Local Produce in Hudson, Ohio was completed this winter. Fresh Local Produce of Ohio started their production of fresh baby lettuce in February and can already be found on the shelves of several grocery stores in the area. Fresh Local Produce is selling under the brand “Free! Leafy Greens”.
The name Free! Leafy Greens is referring to everything this baby leaf lettuce is free of; Free of chemical pesticides, herbicides, and fungicides, free of GMO, free of chlorine washes and even free from any hands touching the lettuce. “This is what we call Hands-Free Cultivation,” says Anthony Umina, Managing Member of Fresh Local Produce. “Food safety is at the top of everyone’s priority list today, retailers, restaurants and consumers alike. Our Hands-Free Cultivation in the controlled environment of greenhouse checks all the boxes for safe and sustainable growing” continues Umina.
“With food safety being at the focus of attention in the industry today and an essential component of any successful food production operation, we as a company are taking it upon ourselves to join the Safe Quality Food (SQF) Initiative and raise our food safety standards. By doing so we have implemented a comprehensive food safety system and are preparing for our first voluntary SQF audit to obtain the Food Safety and Quality Certification,” explains Gina Frontino, Food Safety and Quality Assurance Manager at Fresh Local Produce. “In addition to the food safety measures in place, the fully automated growing system brings an extra level of food safety to the operation, as it eliminates any human contact with the lettuce. No-one touches our leafy greens during the entire growing process. We like to call that Worry-Free lettuce,” says Frontino.
The company’s strong focus on responsibly and locally produced lettuce is aligning well with the ongoing trend toward and growing demand for fresh, safe and locally grown lettuce. “Our lettuce is in the stores within 24 hours of harvesting. It does not get much fresher than that, and you can taste the difference,” says Eric Highfield, Chief Agricultural Officer at Fresh Local Produce.
“When choosing the growing system for their operations, Fresh Local Produce asked the right questions,” says Patrik Borenius, CEO Green Automation Americas. “They looked at yield numbers, plant density, labor efficiency and the costs involved to achieve an economically viable operation. Our fully automated growing system with moving open-gutters achieves the highest plant density and operates efficiently on a commercial scale. Fresh Local Produce also chooses a strategic location for their greenhouse. The site is close to the interstate allowing for efficient distribution of their fresh greens and with a population of over 50 Million within 6 hrs. truck drive. In addition, low energy cost was secured at the site and there are opportunities to expand the operations at this location,” explains Borenius.
Free! Leafy Greens are grown and harvested every day, 365 days per year. The new greenhouse operation measures 2 acres and the site is prepared for future expansions. “Right now, we are ramping up the production of phase 1. We will take one step at the time and determine when the time is right to expand,” says Anthony Umina.
About Green Automation Group
Green Automation Group Ltd, headquartered in Finland, and it’s subsidiary Green Automation Americas LLC, based in Florida, develop, manufacture and market the most advanced greenhouse automation systems for lettuce and herb production. The systems are designed for commercial greenhouse operations with a growing area of 1 acre / 0.4 hectares and above. http://www.greenautomation.com
About Fresh Local Produce
Fresh Local produce of Ohio grows and distributes leafy greens under the brand “Free! Leafy Greens”. Free! Leafy Greens are hydroponically grown baby leaf lettuce locally sourced in Summit County Ohio! Our state-of-the-art greenhouse provides a perfect growing environment for our baby leaf, 365 days a year. Our mission is to show our customers what clean and responsibly produced lettuce should taste like. Currently serving OH, PA, and IN communities!
Professional Chefs Bring Out The Best of Madar Farms' Microgreens At Emirates Salon Culinaire
As part of the Expo Culinaire event, in collaboration with Emirates Culinary Guild, the chefs put their creative, gastronomic and artistic skills to the test in front of a judging panel
Abu Dhabi, 16 March 2020: Hundreds of professional chefs from the UAE and abroad prepared dishes using a variety of microgreens grown by Madar Farms at this year’s Emirates Salon Culinaire competition in Sharjah.
As part of the Expo Culinaire event, in collaboration with Emirates Culinary Guild, the chefs put their creative, gastronomic and artistic skills to the test in front of a judging panel.
Among the ingredients used were different ranges of microgreens that were grown in the UAE by AgTech company Madar Farms. Their local fresh produce included pea shoots, arugula, tendril peas, daikon radish, and amaranth.
Abdulaziz AlMulla, co-founder and CEO of Madar Farms, said: “As a partner, we are delighted to have been involved in this year’s Emirates Salon Culinaire. For any chef, fresh ingredients are key for preparing any type of dishes. With Madar Farms using cutting-edge farming techniques and advanced methods to grow quality produce every day, our supply of microgreens for the competition meant they were not only full of flavour but were grown here in the UAE.”
Chef Uwe Micheel, President of the Guild and Director of Kitchens Radisson Blu Hotel, Dubai Deira Creek, said: “We were privileged to have Madar Farms as one of our new partners for this year’s event. Madar Farms was our sole supplier for the microgreens and the freshness and quality of the products were very well received by the competing chefs.”
"With Our Concept, Everyone Can Be A City Farmer"
As Sweden is not on a lock-down yet, the virus is nevertheless having a great impact on jobs and the country’s economy
As Sweden is not on a lock-down yet, the virus is nevertheless having a great impact on jobs and the country’s economy. Crisis packages for jobs and transition are now being presented by the government. So far SweGreen has not noticed a great impact on business despite the COVID-19, rather the opposite. The absolute major part of SweGreen produce, based in Stockholm, is the distribution of their ‘Stadsbondens’ branded leafy greens and herbs to supermarkets. A particular increase in sales is visible, even though the company doesn’t do anything extra in-store to meet customers, besides deliveries.
Free greens
“We have some restaurants on our client list, and we see that they are suffering a lot now. We are actually delivering to them according to the agreement, but for free. We have chosen to not charge our restaurant partners anything during this crisis, just to show our compassion and goodwill,” Andreas Dahlin, CEO of SweGreen says.
The SweGreen salad mix
Stadsbondens
Stadsbondens, which means ‘The City Farmers’ in Swedish, is the leafy greens brand, that SweGreen uses for marketing their produce to supermarkets. As for now, the produce is sold at around ten supermarkets, located in Stockholm. SweGreen has recently set up service together with an online distributor which enables them to sell their fresh produce online and home-delivery of the greens. Dahlin notes: “It gives us the possibility to reach more people. Next to that customers don’t have to get out of the house, and our brand lovers can order the fresh produce no matter where they are located in Stockholm.”
Farming as a Service
SweGreen has developed its own farming service, which is a closed environment and automated in-store solution that gives customers within grocery and restaurants the possibility to be their own providers of fresh, nutritional, locally-produced greens harvested directly off the shelf.
A vertical basil wall
“Farming as a Service, as we like to call it, is the service we offer. We provide a whole system, containing both software and hardware, such as monitoring and steering. So basically with our concept, everyone can be a City Farmer as it automates the whole growing process”, Andreas Dahlin says. In Stockholm, the SweGreen city farm has been fully developed for automation. “We control everything that goes in and comes out. With a fully closed system, we also can digitally control every unit or crop that we provide to our client. One of the most important keys for Urban Farming is absolutely being able to get valid data from growing processes and having the ability to convert the data to value-shaping intelligence. We focus a lot on this now. In this way, we can improve the systems constantly together with our clients.”
A vertical fresh produce wall
Future aspect“
Our objective now is to further develop the Farming Service. Our customers really appreciate this service model and I think the circumstances right now prove the importance of factors such as sustainability, resilience and hyper-local production for the food industry."
Andreas Dahlin, CEO at SweGreen
"We have just closed our second seeding round with investors and we are planning on expanding internationally. Not only with the focus on supermarkets, because we also get a lot of interest from restaurants too. Restaurants and chefs are early adopters when it comes to the sustainable production of food”, Dahlin adds.
For more information:
SweGreenAndreas Dahlin, CEO, and partner
andreas.dahlin@swegreen.se
www.swegreen.com
Publication date: Fri 3 Apr 2020
Author: Rebekka Boekhout
© HortiDaily.com
A Journey Through The World Supply Chain With IFCO Systems
Founded in 1992, IFCO was the first pioneer to reintroduce a reusable packaging system for the entire fresh product supply chain, from producer to retailer
Founded in 1992, IFCO was the first pioneer to reintroduce a reusable packaging system for the entire fresh product supply chain, from producer to retailer. They are now the clear market leader in the world, with operations in more than 50 countries across five continents and subsidiaries in 30 countries. Their services are used by 320 of the world’s largest retail companies and over 14,000 growers and food producers. How did they grow from niche service providers to global supply chain leaders? I sat down with CEO Wolfgang Orgeldinger at FruitLogistica in Berlin to find out.
It starts with a pool of 314 million plastic containers
These containers account for 1.7 billion roundtrips per year, from one end of the supply chain to the other and back. The system is simple: first, a newly cleaned and sanitized container is sent to a grower or packer; the product is then packed and shipped to a distribution center, where it is distributed to retail outlets; the product is then sold and the container is returned to a service center where it is cleaned. Round trip complete.
The prime products are fresh fruit and vegetables, but IFCO also transports significant volumes of meat, eggs, seafood, and bread. Most containers stay in a regional pool: for example, containers will complete roundtrips for transporting cabbage in Germany, oranges in Spain, or leafed salad in Holland. But they are also used for southern hemisphere imports, bringing kiwis from New Zealand, grapes and apples from South America, and oranges from Argentina. If you ever wondered where your bananas came from, there is a good chance they came from Central America in an IFCO container.
Regional pools are flexible and scalable: you could have a specific pool for continents like North America and Europe, or scale down to a country level for Japan, Argentina, or Chile; or you could hyper-localize the pool down to a city level, for integration with vertical farms in an urban food system. To give an example, Mr. Orgeldinger cited the city of Sao Paolo, where 90% of fresh produce is grown within 100km of the city center. IFCO’s pool of containers in this region only moves within that circumference.
The operation of these pools is much more sustainable than transporting fresh products with single-use packaging.
To begin with, the containers are designed to be sturdy: each container is used for up to 120 round trips before it reaches the end of its life cycle. Small damage is repaired at servicing centers; if the container is beyond repair, the material is ground down and turned into new packaging. IFCO is the only company directly recycling its own crates to make new ones; this is possible because their crates are made out of one material and can be ground directly into the production process. This cradle to cradle system helps IFCO reduce CO2 emissions by 60%, consume 80% less energy and use up to 80% less water in its operations when compared to using single-use packaging.
But why use plastic at all? The answer is to reduce food waste. When you transport fresh products, you have to account for humidity and plastic is the best material to reduce this problem. With IFCO’s containers, the damage and spoil rates of fresh products is 90% less compared to a single-use container. A further innovation in the IFCO system is that it is totally modular: they design containers in two footprint specifications: 60X40 cm and 30X40 cm. Each footprint stacks perfectly to maximize space and reduce the likelihood of a fall. Finally, each container includes a ventilation system that extends the lifespan of the food in transit and on the shelf.
Given all the advantages of their product versus single-use packaging, it’s no wonder that customers are flocking to IFCO’s sustainable solution. ‘Customers come because the system reduces costs,’ says Mr. Orgeldinger. If you look at the cost-saving across the entire supply chain, from field to retail store, and account for all packaging related costs, all handling costs, and product damage, IFCO can save up to 27% of the total cost. Given the growing momentum of environmental concerns among consumers and suppliers, IFCO is well primed to lead the supply chain into the future. Let’s take a look at how else IFCO is innovating to help growers, producers and businesses save money and save the environment: it starts with technology.
Innovation in packaging: Apps, AI, and integration with vertical farms.
You might wonder how much technology can be packed into a plastic box. But it’s more about the technology that surrounds the box itself. Remember that pool of 314 million plastic containers? They are tagged and the new generation is readable by your smartphone. IFCO is developing a new app that enables smartphone users to identify and count all containers on a pallet. The new technology will first be rolled out in service centers and trialed in order to improve the AI algorithm. They will then provide this service to customers, enabling all participants in a given pool to act more efficiently.
Another new app enables customers to do all transactions with IFCO via their smartphone. This is an industry first, enabling growers who rely on mobile technology to participate in the supply chain more efficiently. Other technical innovations that were mentioned by Mr. Orgeldinger included integrating IFD and GPS-based systems and blockchain solutions into their producer to retailer model. But I was most interested to find out about how IFCO could integrate with innovations in other fields, like the transition of fresh food production to hyper-local vertical farms.
Vertical farms offer IFCO containers a shorter roundtrip journey
Mr. Orgeldinger told me that vertical farming is the most interesting solution for feeding the growing population who live in large urban areas. Modular, reusable plastic containers are perfect for transporting fresh produce across short distances and there is significant scope for integrating IFCO’s packaging with the shorter supply chains that are enabled by vertical farming. This is scaling down from continent to country to city, creating a whole new set of container pools for IFCO to fill. Both IFCO and the vertical farms they choose to work with will play a significant role in the sustainability of urban areas going forward. We will be watching this space closely.
Find out more about IFCO at https://www.ifco.com/
KYLE BALDOCK
View All Posts
COVID-19 Roundtable: Indoor Ag Perspectives On Coronavirus
One of indoor ag’s greatest strengths is its diversity. Under one roof — hopefully, with a rooftop garden — it unites agriculture, tech, business, tradition, and innovation in a way few other industries can match
One of indoor ag’s greatest strengths is its diversity. Under one roof — hopefully, with a rooftop garden — it unites agriculture, tech, business, tradition, and innovation in a way few other industries can match. This diversity means that when it comes to confronting something like coronavirus, people may experience the crisis in different ways. And it means a world of different people bringing their unique experiences to the monumental task of keeping people fed while the rest of the world is shut down.
With that in mind, we reached out to our friends across the industry for a (socially-distanced, email) roundtable on what they’re seeing now, and what it means for the industry.
Supply and Demand Are Changing
As shelter in place orders go out across the country, shuttering bars and restaurants, Americans are returning to eating at home, and that’s changing how they buy.
“Supply chains are disrupted and most indicators say that it will take three to four weeks to adjust to the current coronavirus situation. There is a big shift away from restaurants and toward retail food purchases and direct to consumer options. Direct-to-consumer quickly went from something grocery stores and restaurants wanted to figure out to an urgent need given the number of people that cannot or do not want to venture out of their house.
“Local produce and products from vertical farms can fit nicely into this new model. They provide local and fresh options that can fill in current supply chain gaps. Consumers tend to increase purchases of local, organic, and natural products when there is a human health or food safety concern. This spike will likely happen here. The only factor pulling it down is that these products tend to be more expensive and many people are very worried about their jobs. Over 3 million people filed for unemployment this week and that number is expected to rise dramatically in the coming weeks.” — Michelle Klieger, Strategerm Consulting
Automation Is Imperative
Whether you harvest insects, like Ÿnsect, or make agtech solutions, like Autogrow, it’s clear that this moment underscores what we’ve known for a long time: automation is one of the keys to the next generation of indoor ag.
“We have a robotized manufacturing process, where we require very, very few workers. They are wearing a full suit, so they are secure, and have a mask, like a diver. The risks of contamination are very low.” — Alain Revah, Ÿnsect
“We recently launched our new environmental sensor network, Folium, and we’re super excited to present this state-of-the-art solution to commercial growers. Launching a new product just before a global pandemic hit, who could plan for that? We are responding to this by changing channels we utilize to connect with our customer base, including more marketing and video conferencing based meetings.”
“In the current climate it’s pretty evident that if you have advanced automation systems and new smart applications to run your farm, e.g. remotely accessible environmental and crop information along with farm management tools, it gives you the freedom to make sure you are aware of what’s happening with your crops and manage them, without having to always be physically on-site. And it minimizes commercial risk. You can’t do without a grower or manager (yet) but you can certainly use solutions that can help — especially during isolation situations, reducing risk to a minimum.” — Darryn Keiller, CEO, Autogrow
Protect Your People
Our product is great food, but great food comes from great, hard-working people, and their health is always key. That means shaking up business, and how we connect with each other on an emotional level, too.
“We restricted international travel earlier in March, we could see that coming. International travel and now domestic have effectively been suspended. Cancellation of trade shows has been the biggest impact, they are how the whole industry operates in terms of customer engagement.” — Keiller
“We are dealing with anxiety and the fear of the unknown with all of the employees. We are all human and struggle with not knowing details and being out of control. So lots of communication, discussions (which are slightly more awkward as we all practice social distancing). Trying to understand all of the new rules and options for employees as we continue to process the changes that are happening on a day to day basis.” — Paul Brentlinger, President, CropKing
A Silver Lining?
There is no doubt that coronavirus is awful in just about every way, but somewhere in there is small but powerful silver lining: it’s making people think seriously about where their food comes from, and what it takes to keep stores and markets full.
As Brentlinger puts, it, “I think it shows us how prepared we need to be for any situation, and how essential we are to the world.”
Amen to that!
Learn more about Contain and funding your indoor ag business at our website, and subscribe to Inside The Box, our weekly newsletter.
Agriculture Food Supply Chain Indoor Agriculture Vertical Farming
WRITTEN BY
Nicola Kerslake
We’re Contain Inc. We use data to improve access to capital for indoor growers, those farming in warehouses, containers & greenhouses. Contain.ag
Unfazed By Covid-19, Infarm Arrives In Japan And In Canada
While centralized facilities have generally dominated the vertical farming venture capital domain, distributed and decentralized business models are gaining pace, according to AgFunder’s 2019 industry report. One in particular—Germany’s Infarm—nabbed $100 million last year to deploy its connected growing cabinets in supermarkets
March 26, 2020
Photo credit: Infarm
Strictly speaking, vertical farming has been with us since the dawn of agriculture; it would be interesting to see wheat growing any way other than vertically. But the term, despite its ambiguity, is now recognized shorthand for vertically stacked farming, where layers of crops are grown on top of each other, and where conditions like light, temperature, water or nutrients are artificially controlled indoors to allow for year-round growing.
There are two predominant visions of vertical farming: centralized and distributed. Proponents of centralized systems argue that large-scale production—and financial viability—depends on ever-bigger and higher farms. These farms, or plant factories as they are sometimes called, are proliferating, aided by huge sums of capital. Plenty scooped up a whopping $200 million in Series B funding back in 2017. US-based AeroFarms raised $100 million in late-stage funding in 2019, for example, while Fifth Season secured $50 million last year.
While centralized facilities have generally dominated the vertical farming venture capital domain, distributed and decentralized business models are gaining pace, according to AgFunder’s 2019 industry report. One in particular—Germany’s Infarm—nabbed $100 million last year to deploy its connected growing cabinets in supermarkets.
AFN has been keeping tabs on Infarm as a high-profile case study of the distributed vertical farming model. The company’s footprint already includes more than 600 cabinets in many European and US cities. During the first quarter of 2020, Infarm has been busy making progress on its global expansion strategy as well. In February, for instance, East Japan Railway Company (JR East) partnered with Infarm to deliver fresh produce grown and harvested in retail stores starting in summer 2020 (pending circumstances around the Covid-19 pandemic, of course). The partnership is Infarm’s first in Asia.
Infarm has also inked an agreement with national food distributor Muroo, which will support a phased roll-out of the Berlin-based company’s farms across Japan in 2021. Infarm has launched a new affiliate, Infarm Japan, to support its expansion in the country.
Similar plans are also afoot in Canada, where Infarm will soon launch its first fresh produce harvests at Safeway stores in Vancouver, with eventual expansion to Calgary, Edmonton, Halifax, Toronto, Victoria, and Winnipeg.
Roll-out timelines in both countries could yet be disrupted, as both Canada and Japan grapple with the Covid-19 outbreak. City lockdowns, movement restriction, and global logistics disruption may bolster the case for distributed urban growing models like Infarm’s, however.
“Urban farming by Infarm has the potential to drastically change the common practice of logistics,” Shunichiro Yamashita, the CEO of Muroo, wrote to AFN. “For produce to be consumed in large cities, such as Tokyo, we must rely on supplies from the suburbs and distant locations. By eliminating the distance between the customer and the place of origin, customers will be able to acquire fresher produce with peace of mind and safety.”
AFN caught up with Emmanuel Evita, global communications director at Infarm, (virtually, of course) to learn more about the company’s expansion strategy and the impact from Covid-19.
AFN: So how is Infarm progressing in light of the Covid-19 outbreak? How has that affected expansion, sales, and day to day operations?
Emmanuel Evita: We’re finding that the demand from many of our partners and consumers for fresh produce is increasing. In the past few weeks, for example, we were able to increase deliveries to stores with higher demand across our markets. With our hubs located in cities, as close as possible to many of the supermarkets and restaurants we serve, we’re able to keep growing and stay responsive to the needs of our partners throughout this period, whether we are growing fresh in-store or from our hub.
What did you have to adjust in your expansion strategy when thinking about Japan?
Overall, we are showing our capacity to build an operation quite quickly—from a single farming unit to hundreds of farms in supermarkets and distribution centers in cities around the world.
Japan is a nation of advanced robotics. Which synergies have you identified here with your own vertical farming offering?
There are a lot of synergies. IoT technology and Machine Learning are core to our farms, and it’s exciting to strengthen the relationship between technology and sustainable food in Japan.
In the popular imagination, Canada is a land of sweeping prairies, a place of vast outdoor agricultural production. Where would vertical farming be needed in this context?
We believe vertical farming is needed in diverse countries and cities all around the world. Modern agricultural production places an incredible burden on our environment. Not only are these processes responsible for 17% of total global CO2 emissions, but they sap plants of 45% of vital nutrients by the time they arrive in the supermarket. As climate change, soil degradation and the loss of natural ecosystems threaten to worsen these effects, we want to find another way.
Our mission is to help cities become self-sufficient in their food production while significantly improving the safety, quality, and environmental footprint of our food. We want to practice a form of agriculture that is resilient, sustainable and beneficial to our planet. And, we want to make fresh, pure, tasty and nutritious produce available to everyone.
By choosing Canada and Japan, you’re expanding simultaneously into two very different time zones, let alone cultures. How do you plan to handle and react to your growing data in real-time?
Japan and Canada mark our eighth and ninth countries, respectively, and we have more than 600 farms in stores and distribution centers around the world. Our machine learning and IoT technologies make it possible to collect huge amounts of data from our farms around the world in real-time.
With a decentralized strategy, keeping up unified growing conditions becomes difficult. How do you prevent infections at your vertical farms?
Infarm controls the farms remotely using sensors and a centralized, cloud-based platform that adjusts and improves itself continuously, so each plant grows better than the one before – providing plant seedlings with an ideal combination of light spectrums, temperature, pH, and nutrients for optimal growth. From the cloud at our Berlin headquarters, we’re able to gather up-to-the-minute information about how our plants are growing and how they respond to different growth environments on a minute scale. We can make many of the needed adjustments remotely. Our growers also offer support for the farms on-site as needed.
Infarm is the first hydroponic farming company to receive the Global G.A.P certification for the standard of quality and agricultural best practices and follow these best practices to maintain healthy plants for sale and consumption.
Is 2020 the year of hydroponics or aeroponics?
We specialize in hydroponic farms and that’s what we’re passionate about. But the Infarm approach is only one way to tackle the urgent agricultural and ecological challenges of our time.
What has been the biggest hurdle to driving down the price of indoor-grown fresh produce
Retailers set the price for the produce we provide in-store. The price does not tend to be significantly higher than their other produce offerings.
What is the ideal size of a vertical farm?
It depends on the environment. Our modular farms are easily scalable and rapidly deployable and can transform any space and fulfill any market demand, whether it’s a single unit in a restaurant or thousands of farming units chained together in a distribution center.
What can you grow? What’s been the hardest thing to grow? What’s been the craziest?
We have more than 65 herbs, micro-greens, and leafy greens as part of our catalog—from Italian Basil to Crystal Lettuce, to more special varieties like Peruvian Mint or Wasabi Rucola.
Are you collaborating with crop breeders to improve traits for indoor growing, boosting yields, taste and nutritional profiles? Can you mention any joint projects and what you have learned?
Yes, we are working with a range of responsible partners. However, we are more focused on optimized growing conditions and growing recipes than genetics at the moment as we see a huge untapped potential in improving yield, quality and consistency with that alone.
Where do you think AI will prove most useful in vertical farms by 2021?
AI can help collect and analyze data at a granularity that is remarkable for the agricultural industry. This data can be used to better plan and anticipate the growth patterns, yields and response of produce to different environmental circumstances in a way that allows farming to be implemented in a more strategic, efficient and ultimately sustainable way than ever before. Over the next several years, the marriage of real-time data capture and farming will truly revolutionize the agricultural industry.
Where will you expand to next?
We will continue to expand our operations in markets that will host the megacities of the future.
SoftBank-Backed Farming Startup Plenty Is In Talks to Raise Cash
Indoor farming startup Plenty Inc. is in talks to raise $100 million or more in a fresh round of funding, according to people familiar with the matter
(Bloomberg) -- Indoor farming startup Plenty Inc. is in talks to raise $100 million or more in a fresh round of funding, according to people familiar with the matter.
SoftBank’s Vision Fund is in discussions to lead a new fundraising round for Plenty at or below the $1 billion valuation that was ascribed to it in its most recent round, said the people, who requested anonymity because the matter is private. They cautioned that no agreement has been reached, and that one may not be finalized.
“Plenty does not comment on financing proposals and has not committed to any new financing rounds,” a spokeswoman for the South San Francisco-based company said in an emailed statement. “We are not in need of new equity financing, and evaluate any proposals opportunistically,” she added.
A representative for the Vision Fund didn’t immediately respond to a request for comment.
Plenty has raised about $400 million in capital over the past four years, according to PitchBook. In addition to the $100 billion Vision Fund, other backers include Data Collective, DCM, and funds that invest on behalf of Amazon Chief Executive Officer Jeff Bezos and former Google CEO Eric Schmidt.
The startup aims to be more efficient than traditional farms, yielding more produce in a given space, while requiring less water.
Last fall, Plenty said it intended to expand beyond the Bay Area and had identified Compton, Los Angeles, as the location for its next farm, with building slated to begin in late 2020.
SoftBank is seeking $10 billion so its Vision Fund portfolio companies can support portfolio companies battered by the coronavirus pandemic, Bloomberg News reported earlier this month.
Some of the Vision Fund’s companies have laid off employees this month including co-working giant WeWork and residential real estate brokerage Compass.
For more articles like this, please visit us at bloomberg.com
Subscribe now to stay ahead with the most trusted business news source.
©2020 Bloomberg L.P.
"A Few Weeks Ago, We Couldn't Have Imagined This Situation"
Due to the COVID-19 outbreak, the Dutch restaurants and cafes had to shut down two weeks ago
Due to the COVID-19 outbreak, the Dutch restaurants and cafes had to shut down two weeks ago.
Although food can still be picked up or delivered, it has proven to be a burden for many food suppliers and requires innovative thinking. The Duurzame Kost City Farm is located in a unique location, on an industrial heritage in Eindhoven, the Netherlands and is the largest circular indoor farm in Western Europe. It grows leafy greens, strawberries, and trout using an aquaponic growing system. The aquaponic farm produces 20,000 kg lettuce per year on a surface of 400m2.
Innovative thinking
Some distributors have created a local mini-market to supply all produce available and in this case, to sell their products. A client of Duurzame Kost, restaurant Phood, based in Eindhoven as well, has come up with a food Farm Box. Jos Hakkennes, owner of Duurzame Kost says: “Together with their other suppliers, cooks are making recipes where we get to deliver the ingredients needed. The Farm Box can be ordered at the Food restaurant and will be delivered at your home address, but there’s also a pickup point. Last week the first boxes have been delivered out and about Eindhoven. Another initiative is a ‘mini market’ located in Maarheze, which is about 10 km to the south of Eindhoven. The market serves as a fresh collection point for customers, which includes the fresh lettuce of Duurzame Kost.
Local supportHakkennes mentions, “Last week we had a big supply of fresh lettuce that could not yet be used for the mini market and the Farm Box concept. Therefore, we promoted the pick-up of our fresh produce on social networks at a fair price in order to prevent it from being thrown away. We received great support from the locals. A few weeks ago, we couldn't have imagined this situation. Nevertheless, it’s great to see creative ideas coming up and that’s really a good thing.”
Jos and an employee checking on the basil
Product innovation
Also, Duurzame Kost itself is looking to new products. "We are currently working on the possibilities within aquaponics around saltwater growing, such as sea vegetables. We see a big demand in these products from the restaurants we supply to. So there’s definitely a market for it, looking at the sales."
Strawberries, leafy greens and trout
The main product of Duurzame Kost is lettuce, but they also supply 4kg of kale year-round to a local restaurant and grow strawberries as a seasonal activity to provide to local restaurants. As the plants are put up in February, it's going to be a while before they start bearing fruit. “These strawberries take a bit more time to grow than normally, as we offer mixed fresh produce. In the first one and a half years, we have done a lot of research into crops and specific varieties that can grow next to each other.”
A freshly harvested salad with trout
“Our fruits are not very big but they taste great. As the strawberries are a seasonal side product we love providing them to our local restaurants”, Hakkennes adds. And starting next week they are also kicking off the delivery of their fresh trout straight to customers - being grown in the water used for the cultivation of the plants. "The trout is sold per 300 grams for a price of €3.95 ($4.33) each. What is being produced is directly delivered to the customers after the harvest. Because we can.”
Daycare
Duurzame Kost also serves as a care farm as we take in people with diverse disabilities and social backgrounds on a daily basis. We have around 12 people that come to our indoor farm, but the visiting days are dispersed over the week as it varies weekly. The social workplace is not canceled as it serves as a daycare for these people. “The hygiene measures are stricter than ever so we take this into account when we let people in”, Hakkennes mentions.
Lead photo: Jos Hakkennes, owner of Duurzame Kost
For more information:
Duurzame Kost
Jos Hakkennes, founder
jos@duurzamekost.nl
www.duurzamekost.nl
Publication date: Mon 30 Mar 2020
Author: Rebekka Boekhout
© HortiDaily.com
Betting The Farm: Soil-Free, Indoor Farming Might Be The Future of Healthy, Local food
Unlike companies like Amazon and FedEx that have recently brought the industry back to the grounds of the old Bethlehem Steel Plant with their distribution warehouses in Sparrows Point, Gotham Greens arrived and built a farm. An indoor, soil-free, tech-forward, 100,000-square-foot one
Lisa Elaine Held - April 2020
On a 30-degree day in January, heads of butterhead, red oak, and Tropicana green-leaf lettuce are soaking up the sun in a balmy 75-degree greenhouse so close to 695, it’s visible to drivers approaching the Francis Scott Key Bridge. “It’s pretty dreamy in here,” says Nicole Baum, director of partnerships at Gotham Greens, as a blue divider lifts and the aroma of fresh pesto welcomes us into the “basil room.”
Unlike companies like Amazon and FedEx that have recently brought the industry back to the grounds of the old Bethlehem Steel Plant with their distribution warehouses in Sparrows Point, Gotham Greens arrived and built a farm. An indoor, soil-free, tech-forward, 100,000-square-foot one.
Started on a Brooklyn rooftop in 2011, the New York City-based company is one of a hearty group of businesses now growing vegetables indoors in Baltimore year-round, turning the city into what could be, given its proximity to so many markets, a Mid-Atlantic hydroponic produce hub.
From small-scale, DIY endeavors to massive, state-of-the-art operations like Gotham Greens, these businesses say they’re increasing access to healthy, local produce while eliminating the greenhouse gas emissions, nutrient losses, and food safety concerns inherent in shipping, say, California romaine across the country to the East Coast. They also see their controlled-environment agriculture as important to food security in the era of climate change.
How they will affect the region’s food system, however, is still uncertain.
“I used to be a hacker for the Feds,” says Larry Hountz from inside his brick rowhouse off Patterson Park, where he sits on a leopard-print stool, offers guests velvet slippers, and talks about the farm he operates in his spare bedroom upstairs.
Those computer skills helped him build City-Hydro in 2013, where he now grows dozens of varieties of microgreens out of his own home. A traumatic brain injury suffered in a car accident had made focusing at a computer difficult, and urban farming seemed like it could provide opportunities for both healing and business. When he looked into indoor hydroponic systems fit for city living, though, he didn’t like what he found. “It was a lot of non-food-safe plastics and fertilizers and just things that didn’t make sense to me,” he says.
Hydroponic farming is generally done indoors. It involves placing plants in trays or towers, with the roots dropping directly into water instead of soil. Liquid nutrients are added to the water, LEDs are used for lighting, and the environment is climate-controlled for ideal growing conditions.
Hountz and his wife, Zhanna, bought their own materials, including grow lights, green plastic trays, and wire racks. Then they researched and tested designs until they landed on an efficient way to produce their seedlings, which require little space and grow to maturity quickly. He decided to sell directly to local chefs, who love microgreens for their concentrated flavor and delicate appearance. In their 10-by-15-foot room, the trays are stacked vertically, with water the only input, no pesticides, and energy-efficient lights above each.
In January, micro leeks for Cinghiale were sprouting out of coconut husk pads below micro peas headed to The Pendry and Foraged. But the farm has been significantly scaled back since its most productive days. After news coverage thrust their surprisingly simple, yet effective, system into the spotlight, the couple shifted the bulk of their business to selling the system they invented to other eager growers. “This week alone, I think we sold 60,” Hountz says, showing off a tower of boxes behind the kitchen filled with supplies that needed to be unpacked and assembled for customers. “We import a million coconut pads a year.”
They also offer free training and post YouTube videos for individuals who want to build their own farms instead of buying them, and as people from across the country visit the house to learn and report back with success stories, Hountz sees little need for what he considers big, corporate growers. “The only way we’re going to feed people [around the world] is with small, individually owned farms,” he says. “This works, and we have the people out there to prove it.”
While some hail hydroponics as an exciting new farming frontier, others are worried about the implications of growing without soil, like on the nutritional value of the vegetables produced. In the hydroponic production of full-size produce, however, growers feed their plant’s tailored fertilizers, which can lead to higher levels of some nutrients compared to soil-based farming.
Research also shows nutrient levels in all vegetables degrade over time, and produce sold in East Coast grocery stores is typically shipped long distances, especially during winter. Because hydroponic growers can harvest year-round in any locale, they are technically able to get fresher greens to consumers more quickly.
But skeptics like farmer Dave Chapman, executive director of the Real Organic Project, say soil is a complex ecosystem, home to fungi and microorganisms that interact with plant roots in ways not yet fully understood. “We are not smart enough to get the nutrient balance exactly correct,” he says. “The more we learn, the more we realize we don’t know.”
How these farms will affect the local food system is still uncertain
Then there’s the environmental impact. Hydroponic systems vary considerably, so it can be hard to make comparisons. Local distribution, no matter the farming method, can reduce greenhouse gas emissions related to transportation. Hydroponic farms generally use significantly less water and require less space, and therefore land, to produce more food. They do, however, require some energy use for systems such as lighting and climate control. Traditional outdoor farms, of course, work off natural light, but they often pollute the environment via man-made fertilizers and pesticides used to control variables and inefficiencies inherent in nature.
Organic outdoor farmers, however, have long confronted these challenges without chemicals, in ways that benefit the environment. “Organic farming is based on healthy soil,” Chapman says, back to its earliest roots, which in turn, farmers and experts say, leads to healthy plants. “The slogan is ‘feed the soil, not the plant.’”
Recently, he and other farmers have been at odds with corporate hydroponic growers who lobbied for their crops to be eligible for USDA organic certification simply based on the absence of added chemicals. Operations like Gotham Greens avoid that debate altogether: Instead of calling their produce organic, they simply state that they do not use pesticides.
In the end, some see ultra-automated, large hydroponic farms as threatening to those that are small and family-run. Others view them as an exciting way to replace the sprayed greens from far-flung places that sit on supermarket shelves.
Somewhere in the middle is Jon Shaw, a local farmer whose name comes up in most conversations surrounding hydroponic produce in Baltimore, which may be surprising to those who know him as the organic guru behind Karma Farm in Monkton.
While Shaw and his son, Nat, fully believe that soil’s magic leads to the incredible sweetness of their winter carrots, they also see hydroponic growing as complementary to their outdoor organic production. “It became clear to us that the winter was our weakness,” says Nat, who runs the farm’s hydroponic operations. “It seemed like this perfect marriage to combine hydroponics with the outdoor farm to have local, seasonal food all year.”
Like Hountz, Nat is a tech-savvy tinkerer who built proprietary systems for Karma Farm after discovering the made-to-order versions didn’t quite work as advertised. In his basement farm, where he was growing multiple basil varieties in January, he’s like a scientist showing off the gadgets in his lab, complete with timers, pumps, fans, dehumidifiers, and beneficial insects released to deal with harmful pests.
He also tends to two hydroponic farms inside shipping containers. One sits next to a Karma barn and is filled with specialty herbs like borage and cilantro, growing in vertical towers. The other is on the grounds of Sandlot, chef Spike Gjerde’s outdoor beach bar at Harbor Point, and it’s equipped to produce trays of leafy greens, which can be eaten at many restaurants, including Woodberry Kitchen.
For the Shaws, perfecting the shipping containers was a long process. Many growers find these systems difficult to master due to design flaws and the sensitive calibration of technology. So far, greens, herbs, and microgreens are the only vegetables that hydroponic farmers see as efficient enough to grow to make a profit. “It took us about two and a half years to figure out what we could grow and what will sell consistently,” Jon says.
In West Baltimore, a new, 3,000-square-foot hydroponic greenhouse that’s under construction is all about training farmers. Public charter school Green Street Academy specializes in workforce development for “green careers” and is already home to an orchard, chicken coop, fish farm, pollinator meadow, and hoop house for vegetables.
But one challenge to educating young people in agriculture has long been the school year, which is out of sync with the growing season, says JJ Reidy, CEO, and co-founder of Urban Pastoral, a local sustainable development company that’s helping Green Street build agricultural infrastructure. A greenhouse that continues to operate through the winter will give students the chance to participate in every part of the growing process.
“We should be able to do 25,000 pounds of leafy greens a year,” says Reidy, who plans to purchase them for Molina and Stem, his restaurants inside R. House in Remington. He also points out that the recent growth of hydroponic farming in Baltimore means that there will likely be more internship and job opportunities available for kids. “Indoor agriculture is a burgeoning field,” he says.
“We should be able to do 25,000 pounds of leafy greens a year.”
Across from T.J. Maxx and Petco in Nottingham, a looming gray building looks like a warehouse for storing boxes, but a worker wearing a hard hat and orange vest opens an unmarked metal door and points inside. “It’s the future of farming,” he says with a grin.
One thing is for sure: it’s futuristic farming. Started in New York City in 2015 with a mission to reduce some of the environmental impacts of agriculture, Bowery, another indoor farm setting up shop in Baltimore, now grows greens and herbs—purple bok choy, baby kale, wasabi arugula—at two farms in New Jersey.
During a winter visit, the Baltimore operation was barely up and running, but it was already clear that when founder-CEO Irving Fain says, “We stack our crops vertically from the floor to the ceiling,” he is not speaking metaphorically. The design, kept tightly under wraps, involves a dizzying grid of levels, stairways, and robotic parts moving around on their own. Fain declined to share the size of the farm or how much it cost to build, but Bowery has raised about $175 million total to date. He, too, chose the Baltimore County location for its access to markets and transportation.
“In this surrounding area, there are about 25 million people that we could serve with this farm,” he says, noting that Nottingham used to be an agricultural area. “This fulfills the mission we talk about—getting fresh food efficiently and sustainably to our population.”
Fain envisions a scalable model that would allow him to build Bowery farms that distribute locally in cities all over the world, and he emphasizes the importance of the sophisticated operating system that involves sensors, cameras, and algorithms that are constantly tracking and adjusting the plants and their environment.
“It’s like our central nervous system,” he says. “We’re collecting millions of data points in real time, and that data impacts how our crops are growing.” The company also digitally tracks each plant from seed to shelf, which reduces the possibility of an untraceable food safety scare.
While the scale and sophistication may inspire awe, the light human touch needed to operate the whole thing is apparent as well. When it’s fully up and running this spring, Bowery’s farm will create about 80 local jobs.
Gotham Greens’ farm will also employ about 60 people locally. But inside, it has less of a space-age feel, primarily because the company uses the sun instead of LEDs as its main source of light, and thus, plant energy. The space is vast, with leafy greens snuggled up to each other in rows as far as the eye can see, but it looks more like a turned-up version of a typical greenhouse. The technology used to irrigate, deliver nutrients, and move rows from seed to harvest is barely visible.
Since its launch in 2009, Gotham expanded within New York and also built farms in Chicago and Providence, Rhode Island. The Baltimore farm is the seventh, coming in around $11 million to build, and an eighth will be up and running soon in Denver. With each new location, the scale has grown, from the original 15,000 square feet to this newest iteration, which is six times the size with more advanced systems in terms of sensors, data, climate control, and automation.
CEO and co-founder Viraj Puri says the company was especially interested in Sparrows Point because urban revitalization is a part of the company’s larger goals. “We’re not single-handedly changing neighborhoods and cities,” he says. “But we are helping to raise the profile of some of these areas, to attract other businesses, and be a catalyst for additional urban renewal.”
Produce from Bowery and Gotham Greens will be sold throughout Maryland and surrounding states at various grocery stores, such as Whole Foods for the latter, and both will also court chefs throughout the region. As for small, local farms, Jon Shaw isn’t worried. “We have a relationship with restaurants. . . they want to be catered to, they want specialized [products],” he says. “And I think there’s a really strong inclination from chefs that buy locally to buy from soil-based farms.”
Plus, Fain says, “When you look at the demand for local food right now, it far, far outpaces the supply.”
HEALTH & WELLNESSTRAVEL & OUTDOORSSCIENCE & TECHNOLOGY HYDROPONIC FARMING INDOOR FARMING URBAN PASTORAL GOTHAM GREENS CITY HYDRO
Vertical Farming: How Plant Factories Stack Up Against Field Agriculture
With the world's population expected to reach nine billion by 2050, estimations project that food production must increase by 70 percent to keep up with worldwide demand. This means farmers will be required to grow more foodstuff in the next 35 to 40 years than the last 10,000 years combined
March 31, 2020
By Jeff Jurgens, AEM Director of Product Stewardship
With the world's population expected to reach nine billion by 2050, estimations project that food production must increase by 70 percent to keep up with worldwide demand. This means farmers will be required to grow more foodstuff in the next 35 to 40 years than the last 10,000 years combined. There is presently not enough farmable terrain to meet this constraint, and due to the negative environmental impacts of global deforestation (including desertification and flooding), clearing more forest for cultivation is not a sustainable option. Vertical farming, with its potential benefits, may play a major role in addressing the growing food demand while minimizing environmental impact.
VERTICAL FARMING DEFINED
Controlled Environment Agriculture (CEA), commonly known as vertical farming, is a growing system designed to weather- and climate-proof the production of food crops. CEA grows crops indoors in stacked, or standing, layers using growing systems such as hydroponics, aeroponics or aquaponics, all of which use a method of nutritious liquid delivery with minimal soil. CEA uses enclosed growing practices, controlling the environment’s temperature, illumination, gases and humidity with the goal of maximizing crop output in limited space.
CEA has become an attractive alternative to traditional farming in areas where arable land is inaccessible or scarce, including metropolitan areas where citizens wish to bring food production nearer to home. Rather than growing crops on a single level, such as in the ground or a greenhouse, CEA produces crops in vertically stacked layers, which can frequently be incorporated into other constructions like high-rise buildings, intermodal (shipping/Conex) containers or repurposed industrial space.
ENVIRONMENTAL CONCERNS
NASA reports that the majority of the world's freshwater supplies are draining faster than they are being replenished with freshwater demand set to increase by 55 percent by 2050. Currently, agriculture is responsible for 92 percent of the global freshwater usage, creating a challenge for even developed countries such as the United States, China and Australia.
A 2017 report found that more than 75 percent of Earth’s land areas have suffered from erosion and water degradation. The continual plowing of fields, combined with heavy use of fertilizers, has degraded soils across the world with erosion occurring at a rate 100 times greater than soil formation. This results in 33 percent of the world’s adequate or high-quality food-producing land being lost at a rate that far outstrips the pace of natural processes to replace diminished soil.
Collectively, this means arable land is decreasing, and poor soil health is contributing to less healthy agriculture, while water demands continue to rise.
COMMON GROUND
Approximately 1.3 billion tons of food destined for human consumption gets lost or wasted each year globally, discarded anywhere along the supply chain, from farmland to supermarkets, restaurants and home consumers. But crops for human consumption only accounts for 55 percent of all crops grown. Nine percent are used for biofuel and 36 percent used as livestock feed. Feed crops, such as hay and soy, are land and water-intensive to grow and the animals that consume them require high levels of water to thrive. Additionally, many types of livestock occupy the grazing land, which constitutes 70 percent of all agricultural land, which is not arable.
BENEFITS OF VERTICAL FARMING
Some of the obvious benefits of vertical farming for is year-round crop production for both human and livestock consumption, consistent quality, and predictable output. CEA holds other environmental benefits, requiring less fertilizer being applied to plants, reducing water usage up to 95 percent and, through weather-proofing, eliminating the need for chemical pesticides. CEA technology allows for faster growth cycles and quicker harvests, meaning more food can be grown every year, in a much smaller space than on a conventional farm. One of the highest-yielding farms grows over 350 times more food per square yard than a conventional farm.
In urban settings vertical farms utilize a farm-to-table order-based system, drastically cutting down on food waste, packaging and the fuel consumption used to transport food—known as food miles—as well. However, the carbon savings are relatively minor even with these novel approaches as at least 80 percent of the emissions for agriculture happens on the farm—not in the processing, not in the transportation. Urban gardening and vertical systems have many benefits, but it doesn’t presently have the scale that’s needed to meet human food demand or reduce environmental impact on a massive scale.
CHALLENGES OF VERTICAL FARMING
Economics is a major obstacle for the broad implementation of CEA practices. Plant factories are currently not the solution to feeding the world's increasing population as competition with crops grown in traditional systems will not be economically viable in the coming years. Plants – not just growers – will need to adapt to CEA growing conditions. Meaning, new crop genetics will need to be designed specifically for vertical farm production that addresses five traits of interest: easy and uniform fruiting; rapid biomass and multi-harvest capable crops; photoinduced quality; auto-harvest friendly traits; and dwarf plants with yield efficiency. It remains to be seen if created, the genetically modified plants would be attractive to an end consumer given the movement of non-GMO products.
CEA approaches require huge capital to launch, as they're high-risk businesses given the cost of production can be quite high per pound of product. Vertical farms are more feasible because of LEDs, but they are still energy-intensive. Proponents of vertical farms often say that they can offset the enormous sums of electricity they use, by powering them with renewable energy —, especially solar panels — to make the whole thing carbon neutral. But just stop and think about this for a second. These indoor “farms” would use solar panels to harvest naturally occurring sunlight, and convert it into electricity so that they can power…artificial sunlight? In other words, they’re trying to use the sun to replace the sun. With current technology, it makes no sense to grow food staples, such as wheat, indoors. A Cornell professor calculated that if you grew wheat indoors, just the electricity cost per loaf of bread made from that wheat would be $11.
Even if a vertical farm boom were to ensue, the output would only be a small percentage of the vegetables and fruits grown on traditional farms and none of the wheat, corn, soy, or rice, at least not in the foreseeable future. Nor will vertical farms raise livestock or grow oil palms, which are mainly what people are clearing hardwood forests to make room for.
THE FUTURE OF FIELD AGRICULTURE
The contribution of vertical farms to overall food production and environmental concerns is to be determined. The greatest potential impact is the implementation of technology in agriculture, partly due to new possibilities with data analysis. Vertical farms have a multitude of sensors measuring many parameters (from, temperature, to nutrient levels). The plants are analyzed with cameras and sensors, which monitor plant health in real-time. As a result, vertical farms are hiring data engineers and sensor specialists as a significant percentage of their workforce. Artificial Intelligence already plays a key role in many vertical farm operations. As sensors continue to get cheaper and more capable, the opportunities for field farms increases considerably.
Farmers will solve agricultural problems — like developing new methods for drip irrigation, better grazing systems that lock up soil carbon, and ways of recycling on-farm nutrients. Organic farming and high-precision agriculture are doing promising things, like the use of artificial intelligence for detecting disease, sensor-activated irrigation systems, and GPS-controlled self-driving tractors.
From the plummeting cost of robotics to the new frontiers of bioinformatics, the future landscape of farming may well look very different, indeed. While this isn't going to happen immediately, growth in the sector will accelerate as technological improvements drive down investment and operational costs.
THE BOTTOM LINE
While civilization wouldn't be where it is today without agriculture, it's a big factor in a number of society's greatest challenges. If farming practices continue unabated, the likely outcome is having to cut down more remaining forests for acreage, destroying even more land and freshwater habitats in the process. Current projections make a global water crisis almost certain.
In light of these challenges, AEM members are looking at every way to reduce the negative impact of current agricultural methods and existing equipment technology. Manufacturers are becoming technology balanced and interdisciplinary, utilizing designers, engineers, horticulturalists, and sustainability managers. AEM members can provide service from concept development to feasibility studies to education and workshops.
IoT devices are guiding precision farming to increase yields. Advanced machine communication is allowing the implementation to control the tractor for optimum efficiency. And manufacturers are developing many alternative power sources, such as advanced battery technology, cable-powered machines, and tractors powered by methane gas. Some concept machines are small enough to fit between rows, using lasers to destroy pests one by one. That is precision farming. If constraints are the catalyst for innovation, then AEM and its member companies are already rising to meet the challenge.
Subscribe to our AEM newsletters for more perspectives from AEM staff.
Farming Plenty Is In The Discussion Of Lifting $100M From Softbank Vision Fund
With the new funding, Plenty is aiming to become more efficient compared with traditional farms, and have to produce more plants in a given space with less water. Moreover, the total funding of Plenty has reached $400 million
by StartupWorld Staff
Plenty, a San Francisco-based indoor farming startup, is in the course of negotiation to lift $100 million or more in fresh funding from a Japanese-based multinational conglomerate Softbank Vision Fund. Besides, DCM, Amazon CEO Jeff Bezos and former Google CEO Eric Schmidt, and Data Collective also participated in the funding round.
With the new funding, Plenty is aiming to become more efficient compared with traditional farms, and have to produce more plants in a given space with less water. Moreover, the total funding of Plenty has reached $400 million.
In 2014, Jack Oslan, Matt Barnard, Nate Mazonson and Nate Storey founded Plenty which brings local people and communities together for planting fresh, tasty fruits and vegetables by using less amount of water, less than 1% of the land, and without using chemical pesticides and fertilizers. Besides, all the fruits and vegetables are GMO-free.
Plenty has four key features such as Next Level Freshness, Taste You Can Trust, Nature Meets Nurture and Available Year Round. In Next Level Freshness, Plenty produce fresh and flavorful fruits and vegetables. In Taste you Can Trust, it cultivates crops without using any pesticides or fertilizers. In Nature Meets Nurture, it’s plants are 100% nurtured in an indoor environment. In the Available Year Round, it grows plants indoors and the flavorful crops are always available in the season. Moreover, it also helps plants to live their best lives.
As per reports, Plenty is planning to extend over the Bay Area. Moreover, the next farm place is in Los Angeles and the operation is going to start in the second half of 2020.
This month, SoftBank is trying to get $10 billion funds. So, its Vision Fund portfolio companies can back some of the portfolio companies affected due to the COVID-19.
Some of the Vision Fund’s companies including residential real estate brokerage Compass and the co-working giant WeWork have fired their employees this month.
About Author
StartupWorld Staff
StartupWorld is the destination to learn about new and upcoming startups making waves on the web. Being an entrepreneur is as much hard work as it is fun. No one knows it better than you do. Share your story, send it in and let us showcase it to the world.
VIDEO: Indoor Microfarming: Benefits, Costs, And Profits
Microfarms are versatile. They can be created in any small room like shipping containers, bedrooms, and garages
Indoor microfarming is a trendy alternative to outdoor farming.
Outdoor, or field, farming is declining as land costs and soil erosion make it increasingly harder to start a farm. In its place, small indoor farms are popping up to meet increasing demand for locally produced food.
Did you know small farms produce more than 70 percent of the world’s food?
Microfarms are versatile. They can be created in any small room like shipping containers, bedrooms, and garages.
In this article, you’ll learn all about indoor microfarms including its benefits, costs, and how to profit from one.
Basics of Indoor Microfarming
Indoor microfarming refers to small-scale farms in urban or suburban areas.
The ability to control environmental factors like lighting, humidity, and temperature is the biggest advantage that indoor farming has over outdoor farming.
Indoor alternatives to field farming, like greenhouses, have been around for thousands of years, but it wasn’t until the 1970s that controlled environment farms emerged.
Farmers use a variety of different systems to grow plants indoors. Aquaponics, hydroponics, and aeroponics are a few of the most popular systems after using traditional soil.
Aquaponics refers to using fish to grow plants. In these systems, fish fertilize water that’s fed to the plants. The plants in turn purify the water, which is fed back into the fish tanks.
Hydroponic systems grow crops by watering plants with a nutrient-rich solution. Instead of soil, plants are grown in a nutrition-less growing medium that allows plants to absorb the nutrients from the water easier than if they were grown in soil.
In aeroponic systems, plants are grown with their roots exposed in highly misted environments. The mist is created using a nutrient solution.
We use hydroponic systems to cultivate crops in our Pure Greens container farms, which are made out of shipping containers.
Indoor microfarms are often started using spare space like an unused basement, guest room, or garage in the farmer’s home. But they can also be started in any small, indoor area like a shipping container.
The ability to use a small space to grow produce is only one of indoor microfarming’s many benefits.
Benefits of Indoor Microfarming
Indoor microfarming is beneficial because it fills demand for certain produce while saving money and stress.
As far as selling goes, demand for locally produced food across the United States is increasing.
Nielsen, a data and measurement firm, found that 48% of consumers prefer ingredients and food that have been produced locally.
Indoor microfarming fills this demand by being produced in the center of commercial areas, guaranteeing locality.
Purchasing land or buildings big enough for large-scale operations is expensive. Indoor microfarming allows people to use the buildings they already live in to start growing.
Capital expenses are also lower because you don’t have to purchase new land. Plus, equipment isn’t as expensive for microfarms due to availability of ready-for-installation systems and “Do It Yourself” (DIY) tutorials.
With smaller capital expenses comes a lower stakes environment.
When you’ve put less money into a project, there’s less pressure to succeed. Feel free to experiment with systems and crop types to find what works best for your farm.
Indoor microfarming also allows you to develop a local customer base and specialize in a niche market.
Having already secured customers and perfected a crop will help when you’re ready to expand.
Indoor microfarming also allows restauranteurs to grow their own produce onsite, reducing food waste by being able to harvest only what’s needed rather than buying in bulk. Customers will also appreciate the fresher tasting food!
Another benefit of indoor microfarming systems is that there isn’t just one way to do it.
Microfarming Systems
Because microfarming can be done using virtually any size of space, there’s a wide variety of systems to pick from.
Our Pure Greens container farms are an excellent choice for those with yard space for a 40 foot shipping container.
Our farms come outfitted with a recirculating hydroponic system, providing a low water consumption rate, and an automated controlled environment system that can be monitored via your smartphone.
For farmers with less space to work with, there are a few smaller purchasable and DIY options out there as well.
Ready-to-use hydroponic systems can be purchased online or from a local hydroponic equipment store.
One popular DIY hydroponic system for beginners is the Kratky method.
The Kratky method is easy as it doesn’t require pumps or changing the nutrient solution. In this system, plants are placed in a netted pot with a growing medium, such as coconut coir or clay balls, and then placed into a reservoir filled with water and nutrient solution.
While this method is good for farmers with very little experience, it’s only effective for growing leafy greens. Anything with flowers or fruits will need a more involved process.
The Kratky method also requires close attention to the water’s pH levels because it’s not replaced or adjusted during the grow cycle.
Aeroponic systems are also buildable but require a little bit more expertise with construction. Plants grown in these systems receive maximum nutrients.
But aeroponic systems are less common than hydroponic systems when it comes to home-growing because they require special attention to nutrient ratios and pH levels, making them not very beginner-friendly.
Scott Dekarske of Wet-Werk Hydroponics in Memphis, TN, and Master Gardener, Stephan Leonard, show how to assemble an inexpensive aeroponics system.
Aquaponic systems are a good choice for people interested in fish farming. If you raise healthy enough fish, you can sell them along with your produce.
Keep in mind aquaponic systems require more maintenance than hydroponic or aeroponic systems and they’re a little trickier.
With these systems you have to keep both the fish and the plants happy. Doing so requires finding the delicate balance of water flow between the two.
Deciding on which system to use can be tricky, but your expenses will depend heavily on the system you decide to use.
Indoor Microfarming Costs
Capital and operating expenses of indoor microfarming varies depending on the type of system and size of the operation.
The first expense is going to be buying the system itself or any materials needed to construct it. You may need to purchase tubs, pumps, and pipes.
You’ll also need to purchase light fixtures, so your plants have a light source to use for photosynthesis. During photosynthesis, plants absorb energy from light to produce glucose out of carbon dioxide and water.
There are plenty of LED lights in the market aimed specifically toward growing plants. Look for bulbs with high efficiency to conserve energy usage.
Because indoor microfarming typically relies on artificial light rather than sunlight, energy costs can be high. A 2017 survey of indoor farms found that small farms spent about $3.45 per square foot on energy alone, which was about 12% of the total budget.
Take into consideration water usage as well. Systems like recirculating hydroponics and aeroponics use considerably less water than aquaponic and soil-based systems.
Hydroponic and aeroponic systems typically require 4 gallons of water per square foot per year. Meanwhile, aquaponic systems use about 10 gallons of water per square foot per year.
Be sure to also factor in any fish costs such as a tank, food, and the animals themselves when using aquaponic systems.
Once your indoor microfarm is ready to grow, you’ll need to buy planting materials.
Planting expenses will be recurring so be sure to keep them in mind while budgeting. Purchase seeds, growing mediums, and nutrient solution online or in stores.
Growing mediums and nutrient solutions replace soil in hydroponic and some aeroponic systems. The growing medium acts as support for the plants’ roots while the solution provides essential nutrients for strong, healthy plants.
While indoor microfarming can be costly, there are plenty of strategies for growing your business.
Profiting from your Microfarm
The first step to making a profit from indoor microfarming comes before you even plant a single crop: Research.
Find demand for a product in the local market that isn’t being met. Meet with potential customers like chefs, grocery stores, and farmers’ market patrons and ask what they’d like to be able to purchase fresh.
Focus on growing specialty crops rather than common produce like lettuce.
Specialty crops can be things that are out of season, hard to grow in your climate, or something trendy such as microgreens or adaptogens.
Consider selling your products at farmers’ markets, to vendors, to wholesale distributors, and to local restaurants.
The number of farmers’ markets in the country has tripled since 2000, making it an easy choice for finding customers.
Research popular farmers’ markets in your area and learn how to set up shop. Keep in mind that some markets will charge a fee to set-up a booth.
Alternatively, approach a different produce vendor and let them sample your product. If all goes well, they will sell your product for you!
Find a middleman by selling to wholesale distributors. Distributors will find shops to sell your products for you, giving you more time to focus on growing.
Or sell your produce directly to local restaurants.
Research chefs who focus on crafting dishes using locally sourced greens. Set up an appointment with chefs to pitch your business to them and be sure to bring along your best samples.
Try to establish a rapport with the restaurant. Find out whether they’d prefer a range of products or a specific good.
After you’ve established your clientele, your indoor microfarm will blossom.
Now that you’re familiar with indoor microfarming, it’s time to get started.
Visit our website or call us at 602–753–3469 to learn more about how you can start your own container farm.
WRITTEN BY
Pure Greens Arizona LLC
Tags: Vertical Farming Indoor Farming Farming Farming Technology
Pure Greens’ container-based grow systems offer a variety of interior layouts, sizes, and options so customers can create a farm that meets their needs.
Five Reasons To Go Vertical
The rapidly increasing global population means you can be sure of two things: there’s a never-ending demand for food and a rapid reduction in the availability of land on which you can grow it
The rapidly increasing global population means you can be sure of two things: there’s a never-ending demand for food and a rapid reduction in the availability of land on which you can grow it.
The UN has predicted that the global population will surpass the 9 billion mark by 2050 which leaves government officials and scientists scratching their heads as to how we’ll provide for this colossal amount of mouths to feed. Enter vertical farming. Vertical farming presents itself as one of the answers to our population growth, which in short allows plants, fruit, and veg to grow upwards rather than outwards.
With a booming culinary industry gracing the bustling global hubs such as London, New York, and Tokyo, urban farms provide a controlled and automated climate to grow more delicate niche fruit and veg, as well as mass producing heavily demanded greens and herbs on that were once upon a time confined to their natural habitats.
Although, when it comes to vertical farming the question is not “what you can grow?”, it’s “what should you grow?”. Extensive R&D shows that leafy greens and herbs remain the most profitable and sustainable crops to mass-produce at present. Vertical farming will become a huge part of the agricultural sector in the very near future, but why is it taking off so quickly? Here are 5 reasons why:
Increase your crops per m²
Although it may look smaller than your average outdoor farm, a vertical system can equate to 4-6 X more growth surface than your standard glasshouse or polytunnel area. 1 acre of vertical farm on average produces 4-6 acres depending on the crop density and cycle duration.
Protection from the elements
Vertical farming allows the grower to exploit the advantages of growing in a fully controllable climate, safe from the natural elements such as wind, rain, and frost, meaning post-harvest spoiling and crop wastage becomes significantly less of a problem. Additionally, the secure environment results in zero pests and invasive bacteria, which allows the grower to provide organic pesticide-free produce.
Reduce water consumption
Vertical farming systems allow produce to grow with 70-95% less water required for normal plant cultivation. Taking lettuce as an example: open-field production requires 250L/kg of lettuce and greenhouse systems consume 20L/kg. However, vertical systems come in at a minimal 1L/kg of lettuce, with the only water extracted during the growth cycle being that of the plant’s consumption, with any leftover water being recycled back through the filtering system and reintroduced to the irrigation.
Standardized crop growth and yields
With vertical farming technology constantly improving, the ease of creating a completely controlled environment is increasing by the day. The use of bespoke LED spectrums, automated irrigation, and climate control allows the farm to standardize each growth cycle, producing the same amount, quality and size crop, which in turn results in standardized yields.
Local production
Being a controlled environment, vertical farms can settle wherever they choose, with climates and weather patterns becoming obsolete. Local production means a positive impact on local communities, resulting in an influx of jobs and contribution to smaller economies. Its local production and harvesting of crops reduce the amount of ‘food miles’, meaning a decrease in the global carbon footprint. Research has found that vertical farms lower overall CO2 emissions by 67-92% when compared with greenhouses.
Bridge Vertical Farming partners with Urban Crop Solutions to provide high-tech automated container farms, research facilities, and bespoke vertical farming solutions.
For more information:
Bridge Vertical Farming
Keynor Lane
Chalk Lane
Chichester
PO20 7LL
bridgeverticalfarming.co.uk
bridge@urbancropsolutions.co.uk
01243 641789
Publication date: Tue 31 Mar 2020
How To Grow Microgreens With Children
Microgreens can be taught to everyone, not just adults. Let’s face it, most children stay inside and play video games. What do children know about farming, besides crops and cows?
Microgreens can be taught to everyone, not just adults. Let’s face it, most children stay inside and play video games. What do children know about farming, besides crops and cows? This is the current stigma that has been associated with farming for the longest time. That’s great and all, but along came microgreens. Watching the microgreens sprout is really something that can’t be explained. It’s exciting and might inspire children to be urban farmers or just entrepreneurs. Introducing microgreens to children at a young age is engaging and fulfilling. It’s become a field where innovation is key and the younger generation has plenty of ideas. It’s also a fun and exciting way to connect kids with nature.
Here at Nick Greens Grow Team we worked with Kipp One Academy Charter school and had put in place a program that developed an understanding of where food comes. It was a success as the children and faculty all had to work together to make this work. This made it possible for children to connect with and appreciate the food they eat. They might even want to eat veggies if they see them in the form of microgreens. Having the microgreens program also gave children the fundamentals. The fundamentals are important because children can attempt to grow much more challenging microgreens.
Here are our steps to grow at home with your children:
Grab a 10X20 tray with drainage holes and fill it 1" thick with moist coco coir.
Weigh 14 grams of arugula microgreens Seeds into seed shaker, then broadcast evenly across the 10X20 tray.
Apply an even mist of water to the tray, then cover it with a humidity dome and place it in a dark space.
Germinate for two or three days in a dark location with at least 75% - 80% humidity. Water as described in step three at least once a day.
Remove humidity dome from the tray on day two/three. Then begin feeding plants your favorite fertilizer using a low flood/continuous flow method of irrigation.
Micro Arugula will be ready for harvest around 7-14 days, They will need about 8 to 16 hours of light with a typical fluorescent grow light about 12"-15" from the base of the plant.
It’s a fun process and gets children to get active and appreciate the world. Who knows maybe your child will start a whole urban farm in your backyard or basement.
If you enjoyed this, you might also enjoy these post:
"Guide to growing microgreens"
TAGS: #growingmicrogreens #microgreens #organicmicrogreens #microgreen #growathome #growfoodathome #microarugula #arugula #urbanfarming #urbanfarm
The Future Of Farming Might Already Be Here, Inside A Shipping Container
"We are completely protected from any natural disasters, rainstorms, pests, weeds even -- there's no pollution because all of the air is filtered," the CEO of Sprout Stack said
Ali Donaldson
10 News First Senior Reporter, 25 Mar 2020
On Hugh McGilligan's farm, it's a perfect summer's day, 16 hours a day, every single day of the year.
"We are completely protected from any natural disasters, rainstorms, pests, weeds even -- there's no pollution because all of the air is filtered," the CEO of Sprout Stack said.
It's the farming of the future, packed inside converted shipping containers on Sydney's Northern beaches.
Sprout Stack runs five farms at Brookvale -- in five shipping containers --producing as much as five hectares of traditional mainland agriculture. The shipping container farms run as closed circuits, using about five percent of the water.
But it takes just five seconds to walk from one end to the other.
And depending on the crop, they can harvest within a week to five weeks.
"Here we have purple radish," Hugh says brushing his hand across the top of a miniature forest of lush leafy greens. "That's our fastest growing crop and it takes about a week from planting through to harvesting."
"That compares to traditional farming where it takes 40 percent longer to achieve the same results."
And they're not just saving on the environment.
Sprout Stack's Mick Harder has pulled off some amazing farming equipment hacks.
"I made a harvester out of a hedge trimmer from Bunnings and some steel offcuts lying around that only cost us $1000 instead of the industrial machine that's around $100,000," Mick said while feeding his ingenious machine with the latest crop.
They don't even use soil.
Instead, everything is planted into coconut husks, which are mulched in a concrete mixer -- another hack that has saved them thousands of dollars in equipment.
And they've even tinkered with Mother Nature and the precious light she provides.
Plants only use red and blue light -- mixed together it forms a beautiful fuchsia -- for all the protein and nutrients they need. So that's all that's used on these farms.
It's about customizing the best of nature in a box, including cutting out a big chunk of the rainbow.
The farms can even be controlled over a mobile phone.
Nestled in between Sprout Stack's plant beds is its "nervous system".
"It's a farm management system that tracks the environmental conditions of the farm and the computer keeps the CO2, the temperature and the humidity of the farm ideal for growing plants," Hugh said.
"It's all run by a computer so we don't have to make any decisions -- the computer is providing the plants with the ideal growing conditions."
As we talked, the lights inside the container started switching off.
"I just go an alert," he laughs, peering through the dark at his phone.
"We turned off the air-conditioning and because we are in here the farm has got a little bit warmer and shut everything down, to ensure there are no deleterious effects on the plants."
Sprout Stack poses some interesting solutions to the modern plagues on our food bowls.
"We know that we need to provide an awful lot more food and we can't do that just throwing more resources at a strained system," Hugh says.
"We've got to get more efficient about the way that we produce food and use scarce resources like water, and we have got to produce our food closer to where it's consumed."
He then runs through the traditional vegetable supply chain -- or, as he says -- "the reason why the tomato you buy at the supermarket tends not to have very much flavour."
Hugh explains it's generally picked green about a week ago, transported cold chain from the country to the capital city you live in where it sits in a distribution centre for a day.
It then gets redistributed to another distribution centre that sends it out to your supermarket.
"At that point, it's often hit with ethylene to ripen -- basically it turns red -- but in ripening it's not really ripening it's just changing colour and in the meantime the nutritional quality of that product has declined."
He claims Sprout Stack's produce is fresher and tastier because they harvest closer to where it is being consumed.
"On average we take about 16 hours between our harvest to store, which compares to about a week for traditional agriculture."