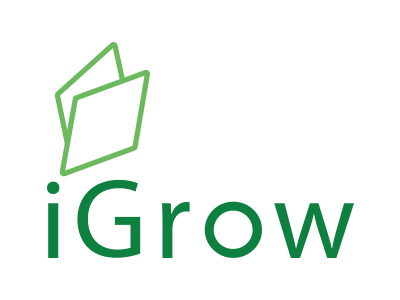
Welcome to iGrow News, Your Source for the World of Indoor Vertical Farming
Investment Projects On Construction And Modernization of Greenhouse Complexes Will Be Presented At The 5th Anniversary International Forum And Exhibition Greenhouse Complexes Russia & CIS 2020
The well-being of our guests and participants is the top priority for our company, so this year “Greenhouse Complexes of Russia and CIS” Forum will be held in “hybrid format”. The event will take place on 2-4 December 2020
Date: 2 - 4 December 2020
Place: Moscow, Baltschug Kempinski
Organized by: Vostock Capital
Tel.: +44 207 394 3090
E-mail: Events@vostockcapital.com
Website: https://www.greenhousesforum.com/en/
The well-being of our guests and participants is the top priority for our company, so this year “Greenhouse Complexes of Russia and CIS” Forum will be held in “hybrid format”. The event will take place on 2-4 December 2020. We are delighted to welcome the participants at the traditional venue – Baltschug Kempinski hotel and on the online platform at the same time. Every delegate will be able to choose the most convenient format of networking.
We have already held a successful event in this format. More testimonies to link.
5th Anniversary International Forum and Exhibition Greenhouse Complexes Russia & CIS 2020 – is an established professional international platform for attracting investment in the Greenhouse Industry of Russia, discussing industry development strategies, exchanging experience between key market players, and signing new win-win contracts.
The Forum is supported by the Ministry of Agriculture of the Russian Federation.
Silver sponsor: SVETOGOR. Bronze sponsors: Unitec, Pylot, FITO. Onsite Visit Sponsor: Osram.
Onsite Visits Partners: “Agrokultura Group” Greenhouse Complex, “Podosinki” Greenhouse Complex.
The Forum unites investors from Europe and the CIS, initiators of greenhouse projects for from all regions of Russia, senior executives from federal and regional agricultural holdings, representatives of Russian regulating agencies, heads of the regions, top managers from retail chains and service companies, presidents of national unions and associations as well as investors from Asia.
Among the confirmed companies 2020: ECO-Culture, Stavropol Flavour, Greenhouse, Ovoschevod, Grow Group Azerbaijan, Yagodnaya Dolina, Tander, X5 Retail Group, Agricultural Complex Gorkovskiy, Agrocombine Moskovskiy, MC AgroPark Plody s Gryadki, Yug-Agro, ECO-farm Mazilovo, Trading House Vyborgec, Green Farmer, Sun Valley, Growth Technology, Yagodnaya Dolina, Udmurt Flowers, FITO, MWM RUS, Horti XS BV, Pylot, AgroBioTechnology, and many others.
Register Now - https://www.greenhousesforum.com/en/registration/
Forum Highlights 2020:
• 500+ senior executives of major commercial greenhouses and agriholdings from Russia and the CIS – Kazakhstan, Uzbekistan, Belarus, Armenia, Azerbaijan, as well as investors, government officials, chief agronomists, heads of retails chains and service providers
• NEW! 2 ONSITE VISITS to state-of-the-art greenhouse complexes - “AGROKULTURA GROUP” (vegetable farming) and “PODOSINKI” (flower cultivation)
• Leaders debate: The Ministry of Agriculture of the Russian Federation, agriholdings, investors, initiators. How will the greenhouse industry evolve after the pandemic?
• Greenhouse investment projects on construction and modernisation to be developed in 2021-2025 from all Russian regions and the CIS
• NEW! CITY FARMING. Development prospects of the city farming trend in Russia and the CIS
• FOCUS-SESSION: Diversification – MICROGREENS, LETTUCE, PARSLEY, DILL, AND OTHER GREEN CROPS. If not cucumbers and tomatoes, what else can grow in a greenhouse?
• HOW MODERN GREENHOUSE TECHNOLOGIES CAN OPTIMISE PRODUCTION? How can innovations boost the greenhouse industry?
• GREENHOUSE MARKETING. How to sell food from the greenhouse properly? Success formula by major producers
• IMPORTANT! POWER SUPPLY IN THE GREENHOUSE INDUSTRY. How to cut power expenses?
• SELLING GREENHOUSE PRODUCTS How to build cooperation with retail chains?
• AGRONOMY DAY - specialized workshops on growing vegetables. How to boost plant fertility and resistance?
• Specialised exhibition of advanced equipment and technology for greenhouses by the lead companies from the Netherlands, Israel, Germany, Italy, Spain, and other countries
• Fast and efficient! Roadshow of innovative technologies and equipment by the global leaders
• Evening cocktails
Register now - https://www.greenhousesforum.com/en/registration/
Folium 2.0 Hits The Market Ahead of Schedule
“F2 gives growers that next level microclimate data. Traditionally, microclimates described the farm, then it was the greenhouse, but now with F2 it is down to the level of the plant itself. Each sensor can gather a monumental amount of data making it the most comprehensive sensor network on the market.”
19 November 2020
Autogrow has launched the second generation of its Folium Smart Sensor Network, ahead of schedule to meet customer demand for greater access to data in the cloud.
“Since the initial launch of Folium in February we have had fantastic feedback from customers requesting further features. Because of our focus on usability and our approach to design; we have been able to deliver F2 significantly ahead of our timeline and incorporate the most requested items which is incredibly exciting,” says Chief Technology Officer Jonathan Morgan.
“F2 gives growers that next level microclimate data. Traditionally, microclimates described the farm, then it was the greenhouse, but now with F2 it is down to the level of the plant itself. Each sensor can gather a monumental amount of data making it the most comprehensive sensor network on the market.”
The Autogrow team focused on the most requested features for F2 including the addition of plant temperature readings, substrate moisture readings, and actual VPD (Vapor Pressure Deficit).
“With the release of our Folium public API (Application Programming Interface) in August, we were able to integrate other sensor technology like Plant Temperature sensors and Substrate Moisture Sensors to the platform. Growers don’t need to buy seven or eight different sensors any longer to get all of these readings. Everything is available in F2.”
F2 introduces new features including:
Connecting a Plant Temperature Sensor
Connecting a Substrate Moisture Sensor
Receiving actual VPD (Vapor Pressure Deficit) readings as opposed to estimated.
Dew Point calculation.
As well as delivering the existing readings for:
Climate Temperature
Relative Humidity
CO2
PAR (Photosynthetically Active Radiation)
RAD (Radiation)
Barometric pressure
“All of the readings and microclimate visualization are presented in the cloud on one platform. When you’re looking for precision in agriculture you need to understand the levers you can pull to further increase your yield and F2 is what’s going to get you there.”
For more information on F2 - https://autogrow.com/products/folium-f2
MEDIA QUERIES
Kylie Horomia, Head of Brand & Communications
(e) Kylie.horomia@autogrow.com
(w) www.autogrow.com www.farmroad.io
Sales queries – sales@autogrow.com
About Autogrow
Autogrow leverages the power of technology, data science, and plant biology to provide indoor growers affordable, accessible, and easy-to-use innovation – 24/7, anywhere in the world.
Our hardware, software, and data solutions support growers and resellers in over 40 countries producing over 100 different crop types.
We are the experts in Controlled Environment Agriculture (CEA) and continue to stay ahead of a rapidly evolving landscape.
Autogrow, Building 3, Level 1, 61 Constellation Drive, Mairangi Bay, Auckland, Auckland 0632, New Zealand
Green Tech Farm Settles On Singapore
Hong Kong-based vertical and urban farming innovator Green Tech Farm has announced it will open a new display and sales center in Singapore. The Singapore site was chosen from a shortlist of five major cities and countries in Asia and the Middle East
BY LIAM O’CALLAGH
19th November 2020, Hong Kong
Vertical farming specialist will construct a new display and sales center in Singapore
Hong Kong-based vertical and urban farming innovator Green Tech Farm has announced it will open a new display and sales center in Singapore.
The Singapore site was chosen from a shortlist of five major cities and countries in Asia and the Middle East.
Green Tech Farm, which manufactures and sells leading-edge hydroponics units with advanced lighting, heating, cooling, and AI-controlled robotics and control systems said that the city-state's geographical location and commitment to sustainable development made it a highly suitable choice.
"We settled on Singapore for a number of reasons, one of which was its own reputation for driving environmental sustainability,” Green Tech Farm said in a release.
“We felt that Singapore would be more inclined to embrace the principles behind what we are trying to achieve given their own efforts over the years.”
The Singapore center will house several fully operational examples of the HydroPod, the company's shipping container-based vertical farming solution while also functioning as a support and learning hub for regional customers.
The site will also showcase a fully operational HydroFactory - Green Tech Farm’s, modular offering which can be expanded to fill any large space - and give visitors the opportunity to see the system perform its many functions on a far larger scale than that available in the smaller, self-contained HydroPods.
According to Green Tech Farm, the center will be operational by the third quarter of 2021.
80 Acres Farms Finalist At 2020 Red Herring Top 100 North America
Finalists for the awards are among the continent’s brightest and most innovative private ventures. Red Herring’s editorial team has chosen their place among North America’s tech elite
11.15.2020 (80 Acres Farms) has been selected as a finalist for Red Herring’s Top 100 North America award, one of the technology industry’s most prestigious prizes.
Finalists for the awards are among the continent’s brightest and most innovative private ventures. Red Herring’s editorial team has chosen their place among North America’s tech elite, during the months-long process that takes into account criteria including disruptive impact, proof of concept, financial performance, market footprint, and quality of management.
For over two decades Red Herring’s team has seen through the tech sector’s hype to select brands that have become industry benchmarks. Previous Top 100 finalists have included Alibaba, Facebook, Google, Skype, SuperCell, Spotify, Twitter, and YouTube.
The Top 100 North America has become not only a springboard for some of tech’s biggest names, but a valued and trusted tool for venture capitalists, experts, and analysts predicting trends at the industry’s sharpest edge.
“Selecting finalists for this year’s Top 100 has proved more difficult than ever,” said Alex Vieux, publisher and chairman of Red Herring. “North America has been tech’s beating heart for years–but never have I seen such an exciting, disruptive, and innovative generation as we have in 2020. “
“80 Acres Farms fully deserves its place among our finalists, and I’ve every confidence it will make a significant impact in the tech world,” added Vieux.
"We are thrilled to be recognized by Red Herring for our world-class technology that grows the cleanest and most nutritious fruits and vegetables in our vertical farms for customers in our local communities," said Mike Zelkind, CEO, and Co-founder of 80 Acres Farms.
About Red Herring
Red Herring is a global media company which unites the world’s best high technology innovators, venture investors, and business decision-makers in a variety of forums: a leading innovation magazine, an online daily technology news service, technology newsletters, and major events for technology leaders around the globe. Red Herring provides an insider’s access to the global innovation economy, featuring unparalleled insights on the emerging technologies driving the economy.
About 80 Acres Farms
80 Acres Farms is a vertical farming leader providing customers with the freshest, and most nutritious fruits and vegetables at affordable prices. Utilizing world-class technology and analytics, the Company offers customers a wide variety of pesticide-free food with a longer shelf-life that exceeds the highest standards in food safety.
For further information, please contact us at:
rebecca.haders@eafarms.com | +1 513-910-9089
S. Korea’s Indoor Farming Technology Helps Crop Production In The Middle East
This may look like a regular shipping container, but in fact, it’s an indoor vertical farm exported to the United Arab Emirates by a South Korean company. The 12-meter long container is filled with vertical racks of crops, including Romaine lettuce. Named ‘Planty Cube’, the farm replaces conventional farming methods with digital technology
2020-11-12
This may look like a regular shipping container, but in fact it’s an indoor vertical farm exported to the United Arab Emirates by a South Korean company. The 12-meter long container is filled with vertical racks of crops, including Romaine lettuce.
To View The Video, Please Click Here
Named ‘Planty Cube’, the farm replaces conventional farming methods with digital technology.
Natural sunlight is replaced with artificial lighting and water levels, air temperatures, and humidity can be adjusted with just a few clicks.
"It also operates under a hydroponic system, where nutrients are mixed into water so that crops can grow without soil."
Farms can also be monitored remotely from South Korea, even from a smartphone, and conditions can be adjusted to optimize plant growth.
This way of farming can produce quality food all year round, without being affected by the weather, natural disasters, or disease.
There has been high demand for South Korean indoor vertical farms in the Middle East.
Two indoor vertical farms were first set up in July 2019 as part of a pilot project.
Now a total of 10 are stationed in Abu Dhabi with more planned to be shipped next year.
"We are actually planning to export our farm in the next first quarter about 50 cultivation modules… Also, we're getting a lot of requests from other GCC (Gulf Cooperation Council) areas, such as Saudi Arabia, Oman, and Kuwait. "
South Korea launched a set of programs last year to export its smart farm technologies.
It aims to become a key player in the industry, along with the U.S. and the Netherlands.
Min Suk-hyen, Arirang News.Reporter : shmin@arirang.com
본 저작물 중 본문에 해당하는 뉴스 스크립트(텍스트)는 공공누리 제1유형-출처표시 조건에 따라 이용할 수 있습니다.
The Future of Farming Is Inside This Bomb Shelter
The farm is known as Growing Underground (GU), and it’s located 108 feet below the main street in Clapham, a south London suburb
Ten Stories Underneath London,
Thousands of Plants Are growing
BY ROB KEMP
PHOTOGRAPHY BY KATE PETERS
NOV 12, 2020
Deep beneath the streets of London, in a complex of bomb shelters left abandoned since World War II, something is growing. Thousands of green sprouts burst from their hydroponic trays, stretching toward glowing pink lights that line the arched ceilings. These plants, along with tens of thousands of other salad crops, are being grown from seed without soil or sunlight, in tunnels transformed into a high-tech commercial farm.
The farm is known as Growing Underground (GU), and it’s located 108 feet below the main street in Clapham, a south London suburb. Every year, in 6,000 square feet of old bomb shelter, more than 100 tons of pea shoots, garlic chives, cilantro, broccoli, wasabi mustard, arugula, fennel, red mustard, pink stem radishes, watercress, sunflower shoots, and salad leaves are sown, grown, and prepared for dispatch.
London’s unique move toward re-localizing agriculture—feeding its growing population while cutting the environmental impact of producing and transporting crops—is the brain-child of entrepreneur Richard Ballard and his business partner Steve Dring.
The tunnels consist of two portions - a larger upper level, where growing and processing takes place, and a smaller lower level, shown here, which is used for storage. KATE PETERS
“The United Nations predicts that we need 70 percent more food by 2050,” says Ballard. “But how are we going to achieve this when only 10 percent of the Earth’s surface is suitable for agriculture and we use a third of that to grow livestock feed?”
Ballard’s journey to becoming a pioneering subterranean farmer is an unusual one. After his ethical garden furniture business went bust in 2008, he moved closer to his old friend, Dring, and the pair would regularly sit in the pub and discuss ideas for start-ups. Both men were intrigued by the idea of vertical farming as an efficient way to feed people, especially in urban areas.
These farms are not susceptible to weather, and crops can be protected from food contamination and grown without herbicides and pesticides. Transport costs are minimal, harvesting is often automated, and much of the water used to grow crops can be recycled.
But the question of how to build it in a city where living space is at such a high premium presented their first major challenge.
At that time, London’s Crossrail line was in its construction stages. The excavations for the 73-mile-long high-speed railway across the city regularly featured on the TV news—especially as secrets to the city’s past were being unearthed, including plague pits, Roman artifacts, and unexploded World War II bombs. It led Ballard and Dring to consider going underground.
Cilantro sprouts under the pink growing lights. KATE PETERS
They worked with the management company for the city’s underground railway network, Transport for London (TfL), to find the Clapham site. “As long as we weren’t building an underground nightclub, they were happy for us to trial a small farm to see if a tunnel could work as a growing environment,” Dring says.
A crowdfunded campaign raised more than $900,000 to develop the site. After a successful trial in one small section of the shelters, Ballard and Dring negotiated a nearly 20-year lease from TfL and began operating in 2015.
The entrance to GU is within an unassuming brick office at street level. In here sit four of the site’s seven aboveground staff; they work at computers taking orders from retailers and arranging deliveries. It’s also the spot where visitors are asked to remove any jewelry and sign a consent form confirming that they are in good health, have never carried typhoid, and are not bringing any nuts onto the site.
From there, it’s a trip into a cramped elevator with barely enough room for two people. It descends slowly, 10 stories belowground, to where visitors step out into a tunnel of whitewashed corrugated arches that contrast brightly with the eerie elevator shaft. Through a row of rubber strips hanging from a tunnel entrance, the kind you see in an industrial refrigerator, a bright pink light glows. Coupled with a sound of hard-core punk music coming from another passageway, this farm has the feel of the illicit nightclub their landlords had feared.
The working farm currently occupies an eighth of its potential 45,000 square feet of growing space. The entire site is two parallel tunnels, each 1,640 feet in length. Built at the height of the Blitz between 1940 and 1942 and capable of accommodating 8,000 people, the space was already connected to electricity and the London water supply before Growing Underground moved in.
Pea shoots are planted in the recycled growing medium. KATE PETERS
Belowground the next set of safety precautions sees visitors putting on white rubber boots, disposable hair nets, another net to cover any facial hair, and white lab coats.
“It’s a controlled environment. We don’t need pesticides but we can’t afford contamination,” says Jess Moseley, GU’s operations coordinator and tour guide. “We ask visitors to remove their jewelry to prevent any possibility of any foreign body contamination. We don’t want tiny gemstones in our salad.” Visitors wash their hands thoroughly with soap and use an alcohol-based sanitizer on them, and then are free to enter the farm.
Moseley works alongside a team of growers, all wearing the same hair net and rubber boots combo. Four of them, dressed in blue, stand in a line at polished-metal weighing scales picking bunches of harvested herbs and packing them for distribution.
“There are 16 production staff and two growers who organize the sowing,” Moseley explains, as the electronic scales beep and another box of fresh herbs is sealed and stacked. These micro greens are the intensely flavored early stages of plants that are usually harvested later in their life cycle. They’re especially popular with restaurants that serve dishes with very little on the plate. “We switched pea shoots to tendril pea shoots, which are frillier, because the chefs prefer them,” says Moseley.
The trays in the foreground hold crops that are ready for the harvest, while those under the lights are still growing. KATE PETERS
Most of GU’s crops are micro herbs—there are only two larger crops, pea shoots and sunflower shoots. Most full-size produce such as carrots or bok choy could be grown here, but they take too long to grow to make them profitable. However, more research into alternative lighting spectrums may make these a possibility, says GU operations manager Alex Hamilton-Jones.
"OUR PEA SHOOTS CAN BE HARVESTED UP TO 60 TIMES IN A YEAR. OUTDOORS YOU GET THREE OR FOUR HARVESTS A YEAR; IN A GREENHOUSE, AROUND 30."
“Larger crops require a change to the growing equipment, like the height of the stacks and light intensity,” Moseley says. “This is going to be a part of the next iteration of the farm.”
Within its short existence, Growing Underground’s team has expanded its variety and reduced turnaround time on crops. That’s due in no small part to a number of technological innovations that optimize growing conditions on the farm.
“Our pea shoots can be harvested up to 60 times in a year,” Ballard says. “Outdoors you get three or four harvests of those in a year; in a greenhouse, around 30.”
To help plants grow quickly, the correct lights are key. Ballard and Dring tried seven different LEDs during their R&D and found that the system they settled on—spectrum AP673L LEDs from Valoya of Finland—produced the best yield and greatest flavors.
These LEDs utilize a red:far-red (R:Fr) spectrum ratio that targets the red and far-red light-absorbing photoreceptors on the plant leaf. The light resembles sunlight at its peak level, which delays the flowering of herbs and allows the plant to focus its energy into fast biomass development.
The result is a compact, intensely flavored product grown in a short time in conditions that not only suit the plant but meet the needs of the growers, too. “The cycle for growing coriander has gone from 21 to 14 days,” explains Riley Anderson, the site’s team leader. “Some plants can be harvested after just six days in the growing tunnel, which beats anything a farm aboveground can achieve consistently through the year.” They toyed with duller tones than the vivid pink that now illuminates the growing tunnel, but found that the reduction in visibility meant having to lift each plant tray out off of its bench to do quality checks. It slowed the process and didn’t enhance the crop.
Jess Moseley, GU’s operations coordinator and tour guide, checks on some of the crops. KATE PETERS
“We wanted to source the lowest energy-consuming lighting system we could find,” explains Ballard. “The LEDs do not use the same amount of energy nor do they create the high direct heat that conventional (high-pressure sodium) lights do, which means we’re able to grow the plants in shelves closer together.”
The power comes from Good Energy, which only uses renewable sources. “As it’s a closed-loop system of farming, anything that’s added—nutrients or fertilizers—stays within the circuit,” says Ballard. The only farm waste—the substrate recycled carpet leftover from harvesting the herbs—is sent to SELCHP, a waste-to-energy converter in southeast London. “Zero carbon output has been the Key Performance Indicator we chose to work to from the very start because any business starting today needs to think about its impact on the environment,” says Ballard.
This 700-recipe cookbook will have you eating every last bit of your bounty. This is an actual problem at our house. Cooking everything takes creativity.
In addition to high-tech lighting, there are several other adaptations that allow plants in the tunnels to grow so quickly. It starts when the seeds are sown, without the aid of conventional soil: Workers place two-inch-thick rectangular growing mats—called Growfelt and made from pulped floor carpet—into shallow trays. The mats are sprinkled with seeds by hand.
Once sown, the seed trays are stacked onto carts and left in a dark section of the same tunnel for propagation. For a short time, they sit in complete darkness, covered with plastic wrap. This “fools” the seeds into thinking they’re beneath the earth. This is where germination begins. Within a day or two, the seed shoots appear. By the fourth day, the trays are transferred to shelves known as benches under the banks of LEDs in the crop-growing tunnel.
Garlic chive seeds are sewn into the recycled carpet seed bed. KATE PETERS
There’s no music playing in the growing area—workers seldom spend much time in here, as the plants are doing all the work on their own. Instead, the only noise in this long, flamingo-pink chamber is the whirring of the axial fans dangling from the ceiling. Although the fans help keep the farm at a settled temperature of around 59°F, the plants beneath the glare of the LEDs feel the warmth of up to 77°F.
“There’s a slight variance throughout the farm,” says Anderson. “We place the crops strategically to optimize growth. Our radishes prefer to be right at the front of the farm, where it is coolest. Our most robust crop, the pea shoot, grows well wherever it is positioned within the farm.”
On either side of the tunnel are trays bristling with herbs at different stages of growth. In each tray, a handwritten sign identifies the type of crop, along with a P date of propagation, an L for the day it was put under the lights (when transferred to the farm from propagation), and B for the bench the tray is assigned to.
The warming glow provides “sunlight” for 18 hours a day. Rain comes in the form of hydroponics. A faucet fills each tray of plants with a water-and-nutrient mix five times a day. The roots in the trays grow down through the matting to absorb the mix and then water is filtered through tanks beneath the benches. “We use 70 percent less water than conventional field farming,” says Moseley.
The garlic chive crop is harvested and ready for packing. KATE PETERS
The night before a harvest, workers put the plants on carts in the middle of the farm, which has the best airflow, Anderson says. That dries them overnight to the point of being packable without them breaking down quicker.
CROPS HERE CAN BE HARVESTED, PACKED, DELIVERED, AND SERVED ON A PLATE ALL WITHIN FOUR HOURS.
To harvest, fresh herbs are sliced from their roots, shaken off of the matting that served as their soil bed, and placed into a blue bowl. From there the crop is weighed and packed into transparent tubs made from rPET—recycled plastic—and labeled with the GU logo and contents.
Above each growing bench is a round, yellow sensor the size of a large coin that records temperature, humidity, and illumination, and sends the data to the University of Cambridge’s engineering department. The results are fed back to GU, which compares them with the crop yields to determine which conditions are working best for growth.
“We monitor yields every day when we cut,” says Ballard. “A platform with machine learning capability collects the data from all the sensors and alerts you to any anomalies. It gives us access to the sort of technology being used in big agricultural projects, but that would be too expensive for us to put together.”
Crops here can be harvested, packed, delivered, and served on a plate all within four hours. The reduced time spent in transit means GU products have a longer shelf life than those grown outside of the capital. As a result, they’re sold in some of the U.K.’s major food retailers and wholesalers.
A number of renowned London chefs use GU produce, too, including Michelin-starred Michel Roux Jr. He not only uses their herbs in his dishes at Le Gavroche, a French restaurant in the Mayfair area of London, but he also came on board as a founding supporter. He describes the shoots and leaves that it provides as “mind-blowingly good.”
For distribution to smaller restaurants, GU goes underground as well. “We send our delivery guys off with all these bags of orders onto the subway trains,” says Anderson. “Food that’s been grown in a Tube tunnel is delivered through one as well, further reducing the carbon footprint.”
Tours of the tunnels take place outside of the production cycle, with chefs, students, and potential investors visiting during the week and members of the public shown around on Saturday afternoons. “We’ve had farmers from Scotland, mainland Europe, and as far as America come and visit us,” adds Anderson. In the past five years that the farm has been operating, technology has improved a lot—more efficient LED lighting, water recycling, and air management systems, Anderson says. “But the principle of what we’re doing is remarkably simple, giving crops the nutrients they need and a medium to grow in.”
Ballard is now busy sourcing funding to expand farther into the tunnels while investigating sites for other controlled-environment farms in other parts of the world and in different structures.
“When we started, the plan was to produce a supply for London,” Ballard says. “But as the retailers have taken an interest, we’re now looking to serve their distribution centers beyond the M25 [London’s encircling motorway].”
As GU grows, it looks to similar farms for inspiration. In South Korea, subterranean vegetable farms are cropping up at underground stations on the Seoul metro, thanks to a start-up called Farm8, while in Tokyo, abandoned utility tunnels built to service a skyscraper city that never materialized have also been converted into GU-style farms. In Hamburg, Germany, a vertical farm called &ever uses methods similar to GU’s to harvest salad crop using just 5,920 square feet of indoor growing space. Producing an equivalent yield outdoors would require 161,458 square feet of open field.
Increasingly crowded cities are getting imaginative when it comes to farmland. “But these farms don’t have to be underground at all,” says Ballard. “It can be in an abandoned factory or disused warehouse aboveground. The model is simply redundant space.” Even so, with at least six more abandoned tunnels beneath London alone, GU’s subterranean farm may not be the only game of its type in town, or underneath it, for much longer.
SOUTH AFRICA: 'We See Hydroponics As The Future of Farming’
Getting children to learn how to grow vegetables at school is an idea that is growing in popularity across Mzansi
By Terry van der Walt
November 10, 2020
Getting children to learn how to grow vegetables at school is an idea that is growing in popularity across Mzansi.
The topic is close to the heart of Branden Gee and his business partner Cameron Blair, who also have a hydroponic set-up in Pinetown outside Durban, as well as an e-commerce business.
“Our major ambition is to get either a hydroponic system or a 100 percent organic and sustainable vegetable patch in every school in the country. That’s the reason we do it for free. We want everyone to learn how to grow their own food and self-sustain.
“Each project deals with a different aspect that contributes to a greater goal, and that goal is sustainable living,” said Gee.
This past Friday they visited Curro Hillcrest Independent School and taught learners the basic building blocks of permaculture, and introduced a worm farm to the school.
“Worms are arguably the most important organisms to life on our planet. They convert organic matter into valuable nutrients that your plants will thank you for later,” he said.
The worm farm makes use of vegetable scraps which the worms feed on, which creates a nutrient-rich liquid - worm wee - which helps build fertile soil, resulting in thriving crops.
On Saturday the duo hosted Thomas More College learners at their Geeshydro hydroponic farm and grow store.
“We use the farm as an educational tool to teach anyone and everyone who is wanting to learn more about hydroponics.
“We see hydroponics as the future of farming since it uses 90% less water than traditional farming, and it can grow a surplus of food in a smaller area using vertical grow towers,” he said.
Brenden Gee and Cameron Blair, in front, are getting learners to grow food. Picture: Supplied
Their e-commerce website called Our Local Market is free to vendors in the upper highway area and was set up to create and support opportunities for young entrepreneurs to thrive by offering them a platform to sell their products with no risk.
“We want the next generation to not only learn how the natural world works, but also how to use it to create a business.
“By using nature the kids can learn how to create a vegetable garden that can thrive. We teach them how to build soil, how to harvest worm wee, how to grow seedlings to sell, growing chickens and learning how to harvest the eggs, as well as selling their produce,” he said.
Learners from Thomas More College get the low-down on hydroponics. Picture: Supplied
Their business is structured around three major principles: Earth care, People care, Fair share.
Gee hopes to adopt more schools and relies on donations to make it happen.
If you want to help go to: https://gf.me/u/y6gtkm
“I know money has been harder to come by this year but I’ve been getting a little from all over, so any donation makes a huge difference, every little bit helps,” he said.
Lead photo: The hydroponic set-up uses a fraction of water and is used as an educational tool for visiting schools. Picture: Supplied
Thrive Containers Launched Operations With Its New Intelligent Container Technology - Shipping Container Farm
Our vision is to not only bring accessibility to farming but to offer a great return on investment for the AgTech industry.”
Thrive Containers launched operations today with its new intelligent container technology, aiming to disrupt the commercial farming industry. COVID-19 and climate change have accelerated existing strains in global food accessibility and supply chains, highlighting the need to rethink the world’s agriculture systems.
Our founder and CEO Shannon O'Malley has been at the forefront of this change through six years of container farm innovation here at Brick Street! O’Malley observed “Thrive Containers is redefining shipping container farming technology.
Our vision is to not only bring accessibility to farming but to offer a great return on investment for the AgTech industry.” Thrive Container's farm system uniquely excels in software automation, customer experience ease of use, and adaptability engineered by industry-leading experts. The result is maximized, year-round crop growth, reducing up to 90% of freshwater resources used in traditional agriculture practices. Shannon Quotes
Thrive Launch
“Thrive Containers is redefining shipping container farming technology. Our vision is to not only bring more accessibility to farming but to offer a great return on investment for the AgTech industry.”
“We want to bring this cutting-edge technology to the masses, to build a farm whose technology is firmly centered on the grower experience.”
Ohio Container
“The Ohio Container is the first breakthrough container model that focusses on leafy greens and herbs providing industry leading yields to the shipping container farms market.”
“Rivers are the inspiration for our model naming convention. Since Thrive container technology supports cleaner, healthier waterways, we want to celebrate, acknowledge, and highlight our commitment to our planet.”
Industry Evolution
“The Agtech industry is currently situated where the .com legacy once was. We are in an industry that is in a race to define who the main players are.”
Investment opportunity
“In the Agtech industry, shipping container farming is wide open, with key competitors that are raising and looking for market share. Each competitor has its own unique business model and approach, focused on different paths to success. Our focus is decentralizing the commercial food system at the point of consumption while utilizing large scale grocers in minimal spaces.”
Supply chain
“By growing the highest producing yield containers, we are bringing production to the point of consumption to provide access to the masses. We are mobile and focused on the urban core. Vs competitors buying large acreage and trucking produce out.”
THE LINE-UP
Thrive Containers provide a multitude of container farm systems for all types of growing solutions. Our in house manufacturing continues to explore the endless possibilities of technology + agriculture.
The most efficient leafy green hydroponic container on the planet. Built for ROI, Ohio’s production efficiencies and low reliability on resources yield higher, while maximizing profit and planet.
COMING SOON: The most efficient micro green hydroponic container on the planet. Built for ROI, Yukon’s production efficiencies and low reliability on resources yield higher, while maximizing profit and planet.
COMING SOON: The most efficient cannabis/hemp hydroponic container on the planet. Built for ROI, Colorado’s production efficiencies and low reliability on resources yield higher, while maximizing profit and planet.
Thrive Container Website!
Follow us on Instagram @thrivecontainers
Click the link below to check out the Thrive website!
Linkedin
Twitter
Infarm Raises $200 Million To Add “Farm” to Cities
heir environment-controlled and automated growing chambers grow food such as leafy greens inside the supermarket, so it’s fresh, without your food accumulating food miles
Infarm’s Israeli founders take on Berlin and the farm to table movement with high-tech farms.
Infarm, a company that grows fresh produce inside supermarkets, has recently announced a $170 million USD funding round to help the company expand across Europe. Their environment-controlled and automated growing chambers grow food such as leafy greens inside the supermarket, so it’s fresh, without your food accumulating food miles.
The company was founded by three Israelis in Berlin in 2013, and they announced this astounding investment achievement despite the Covid plague destroying global markets. Food, we understood, is something that must stay constant. The need for food which is grown locally, and available fresh now resonates at a time of uncertainty and the basic need for survival.
The company has raised $200 million USD total in their Series C round funding which was by LGT Lightstone, Hanaco, Bonnier, Haniel, and Latitude, Atomico, TriplePoint Capital, Mons Capital, and Astanor Ventures.
With a mix of equity and debt financing, the fresh capital brings Infarm’s total funding to date to more than $300 million, underscoring consumer and retailer appetite for Infarm’s approach to fresh, sustainable, and local food production in the wake of this year’s pandemic.
By 2025, Infarm’s farming fridge network is expected to reach more than 5,000,000 square feet to become the largest distributed hydroponic network in the world as it builds towards helping cities become self-sufficient in their food production. Competition includes Freight Farms in the US, and BrightFarms, also American.
“The coronavirus pandemic has put a global spotlight on the urgent agricultural and ecological challenges of our time,” says Erez Galonska, Co-founder and CEO of Infarm. His brother Guy Galonska is also a founder: “At Infarm, we believe there’s a better, healthier way to feed our cities: increasing access to fresh, pure, sustainable produce, grown as close as possible to people,” adds Erez.
The investment will be used to deepen the regional and local penetration of Infarm’s global farming network and complete development of Infarm’s new generation of vertical cloud-connected farms, capable of generating the crop-equivalent of acres of farmland and amplifying the diversity of produce currently available through vertical farming. Vertical farming is also known as hydroponic farming or controlled environment agriculture.
The technology has become developed and well-known over the years thanks to cannabis growers who used this energy-intensive and “stealth” mode of farming to grow cannabis with high concentrations of the active ingredient THC. When it was illegal to grow in Canada, young entrepreneurs were inspired by early blueprints from NASA and farming in space and found ways to set up a soil-less system in basements and closets. To their surprise, they could grow better quality cannabis, faster as inputs such as lighting, humidity, and nutrients could be tightly controlled.
And growing food became the next natural step for people who wanted to grow fresh food year-round even though it’s usually not cost-effective to grow tomatoes or lettuce this way unless you do it at scale.
Hydroponics and variations of it, using just water, a semi-solid coir medium or Styrofoam and/or with fish added, has become the promise for growing food in far-flung locations like Antarctica and food deserts where chocolate bars are available at bodegas, but fresh greens are not. This is according to mothers I have met in Harlem, New York. The hydroponic method is not that complicated at all in theory but in practice, it is hard to achieve good results without know-how in chemistry, engineering, and biology.
An integration of advanced engineering, software, and farming technology, the Infarm farms will save labour, land, water, energy, and food-miles, while contributing to a more sustainable food system, the company proposes.
Partnering with Aldi, Marks & Spencer, Sobeys
While companies like Farmigo founded in New York (also by an Israeli) wanted to put supermarkets out of business, in the past year Infarm has been working to keep them relevant and formed new partnerships with the world’s largest retailers, including Albert Heijn (Netherlands), Aldi Süd (Germany), COOP/Irma (Denmark), Empire Company Ltd (Sobeys, Safeway, Thrifty Foods – Canada), Kinokuniya (Japan), Kroger (United States), Marks & Spencer (United Kingdom) and Selfridges (United Kingdom).
With operations across 10 countries and 30 cities worldwide, Infarm harvests 500,000+ plants monthly, while using 99.5% less space than soil-based agriculture, some 95% less water, 90% less transport, and zero chemical pesticides. Today, 90% of the electricity use throughout the Infarm network is from renewable energy and the company has set a target to reach zero emissions from their production next year.
With the cost of lighting typically very high in hydroponics systems, I’d be curious to know how they will do that without buying carbon credits. Consider this Stanford research paper that mentioned the cost of hydroponic lettuce to be about 8KG of carbon compared to 150g if grown conventionally. The research is a few years old and certainly, there can be ways to improve energy efficiencies.
What organic farmers think?
Proponents of organic farming, regenerative agriculture, and permaculture don’t love hydroponics farming because it relies on petroleum-based fertilizers and nutrients as additives, and while there may be no or few bugs in the grow chambers, there is a risk of fungus and bacteria; in nature, there is always free natural sun (unless you are in Finland in the winter) and natural interactions between plant, soil; and even among small biota like mycorrhizal fungi which play a role in the uptake of micronutrients to the roots and the overall essence of what we call a plant. There is one school of thought that says the “organic” label can only be applied to soil-based farming. Lawyers are debating the issue now.
The answer will be somewhere in the middle. Like most things in life the middle way will help us. The dream is many one-acre regenerative farms to feed us healthily and to feed the planet too but meanwhile there is a gap. How do we feed everyone else who can’t afford to buy at Whole Foods?
We need to improve our local supply chain for food. When you live in a country like Israel, Egypt or Jordan with ample sun, growing food inside a supermarket fridge makes no sense, although hydroponics does. See this project in Jordan, funded by the USAID. Or the one that has changed lives in Harlem.
I had a hydroponics robotics venture (see this article on Bloomberg) and I took it to New York a few years ago and found myself running in circles trying to explain why eating local is good for the planet, it’s good for a circular economy that might one day be about survival. Venture Capitalists laughed at me. They said my technology and vision was a vitamin and not a bandaid –– “a nice to have” but not “a necessary to have”, especially in cities like New York. Then Covid thinking happened.
Here is what investors in Infarm say now (and kudos to the team who worked hard building physical farms and maintaining the pilots):
“We are excited to partner with the Infarm team to accelerate their urban vertical farm vision, ultimately creating a more sustainable food system for a growing population,” says Dharmash Mistry, Partner of LGT Lightstone: “With over $1bn of customer demand, partnerships with 17 of the top 50 global grocers, Infarm is set to revolutionise the market behind a unique ‘demand led’ modular business model.”
Let’s hope. Another Israeli called Benzi Ronen came from Silicon Valley and started a farm-to-table venture in New York and was on top of the world. He had just raised $26 million to grow Farmigo into the Amazon for fresh food and I spoke with him at one point when he warned me to stay in Israel and work there locally for a couple of years before moving stateside. That’s me in the biodome below, growing bok choy for future Martians on my roof in Tel Aviv. I didn’t listen.
I had a venture in robotics to help cannabis farmers (even Mars farmers grow cannabis in space – see this article in Fast Company) and city hydroponic farmers. Farmigo was trying to eliminate supermarkets, by connecting farmers to consumers at drop off points throughout the city. The model was valorous –– who doesn’t want the freshest farm picked veggies every morning? The modern CSA? And it supported local farming, just like what Michael Pollan wants us to do. And to compete with Amazon? Yes. Yes. Yes.
Farmigo raised millions and then the company’s vision to be the Amazon of fresh food could not compete with Amazon. Farmigo changed its business model and now sells software.
I saw the challenges of the business in supplying fresh food. The mechanics of the machines, the lack of willing labor, software needed, the logistics, the importance of food safety. The fungus, the bacteria. The good bacteria. The bad. The responsibility. The chemicals needed to feed the plants, to keep the systems “clean” and safe. So much is hard to control when you are talking about living things.
I always said that if hydroponics or farmers that come from Microsoft want to make city farming work the model will look like the cellphone industry: different players supplying various parts like Qualcomm, Verizon, 3M, Broadcom, and Texas Instruments does. Even to make iPhones work.
Can and will Infarm do it all?
“We see a massive demand in the market for sustainable, environment-friendly, and healthy food – and Infarm has just the right team in place to make this happen,” says Pasha Romanovski, Co-founding Partner of Hanaco Ventures.
More about Infarm
Founded in Berlin in 2013 by Osnat Michaeli and the brothers Erez and Guy Galonska, Infarm is dedicated to creating a future where local super fresh produce is available for everyone. The farms are placed in various locations in the city, like supermarkets, restaurants, and distribution centers, so that vegetables grow and are harvested close to the moment of purchase or consumption. People like Elon Musk’s brother Kimbal Musk has been doing this in New York with a project called Square Roots. They train young entrepreneurs to dream up all sorts of business models inside the shipping container farms built by Freight Farms.
Some in the VC world I have talked with question the viability of the business model of these containers. While it’s a nice idea it’s hard to get the return on the upfront investment.
But when it comes to specialty products and “farms” you can find the Infarm service model in all sorts of permutations in the United States. I got to spend some ample time in meetups with a pile of entrepreneurs building an urban farming project in New York. There I met Andrew Carter, now growing mushrooms in a warehouse in Williamsburg. There is also Farm.One which grows papalo, minutina and all the boutique and hipster greens any chef could dream up in the center of New York City. They deliver.
Lastly and most easily is to try out growing fresh greens at home without the supermarket, or less of the supermarket. I met the founder of Hamama when she was in Israel via MIT helping kids in Israel grow their own food using hydroponics at The Greenhouse. (After I wrote this story in 2008 <— kids from the US were writing me about how to donate their Bar Mitzva money to Noam Geva).
Over at The Greenhouse Camille had her head inside an aeroponics system she’d rigged up last time I saw her. She brought a few of her MIT geek friends over to my house in Jaffa and we talked about hydroponics changing the world. And now she helps people in the easiest way to grow microgreens at home. That’s a hyper simplified way to do hydroponics. She was one of the most inspiring people I met in hydroponics and urban farming.
In fact many in the business are. They are people who want to change the world. Have you met Henry?
Go out and meet someone, start a farm. Grow something. That’s how we change the world.
Now over to Infarm: good luck!
Global Warming, Decreased Crop Yields, And The Food Waste Industry
With the withdrawal of the US from the Paris Agreement and the proposal of the Green New Deal, concerns continue to grow over global warming and the stability of our food supply
November 4, 2020
Written by Daniel Cunniffe
With the withdrawal of the US from the Paris Agreement and the proposal of the Green New Deal, concerns continue to grow over global warming and the stability of our food supply.
Will global warming affect crop yields?
Among the many impacts of global warming, the two that would likely affect crop yields the most are rising sea levels and more severe, unpredictable climate conditions. Rising sea levels would reduce the land available for farming and severe, unpredictable climate conditions such as strong tropical storms, floods, drought, altered growing regions, or even less rain during the year could decrease crop yields, change the types of crops traditionally grown on a farm, or even make that land unusable for farming.
Smaller crop yields and a smaller food waste industry
The food waste industry depends on the food industry and its crops for raw materials. A decreased crop yield means less food, less food waste, and a decreased food waste industry. One impact of a decreased food waste supply is greater competition between food waste businesses for fewer raw materials. Additionally, if crop yields decrease, the price of food increases, leading consumers to utilize more of a food’s edible potential - a secondary decrease in food waste. Bones, eggshells, and banana peels are commonly thrown away, yet all of these are edible and are more likely to be consumed under conditions of food scarcity.
Different climate conditions, different crops, different food waste industry
Traditionally, farms were handed down from father to son or daughter, where the parent would teach the children what types of crops they could grow along with all of the intricate details and tricks to growing those crops.
Crops that a farm can grow is largely based on the climate conditions of the growing region they’re in, which in turn affects things like soil type, humidity level, etc - all of which are prime factors that allow for healthy crop growth. Global warming will likely shift these growing zones for certain crops. For example, say global warming turns the climate of Canada to that of Mexico, where once Canadian farmers could only grow cold weather crops, now they instead grow oranges.
The idea is that a farm may experience changes in the types of crops they can grow and thus this changes the crops available to local food waste companies. Companies that use waste from a single crop, may have to move locations, ship that food waste from a distant farm, or go out of business altogether as growing zones shift. This will in turn affect the food waste supply chain in ways that the industry may not be prepared for. Growing zones are not concerned with political borders.
If a company depends on a certain crop and the growing region of that crop shifts outside of the country, that company may have to ship food from outside of the country and take on additional costs, such as customs and taxes.
What can the food waste industry do about global warming?
Enter soilless systems - They can be grown indoors and protect crops from severe weather conditions like, droughts, pathogens, and pests. Additionally, companies like Re-Nuble are reducing the carbon footprint of the food supply chain through closed loop agriculture which allows us to avoid further global warming and empower farmers to increase crop yields. This will further ensure a stable food supply, healthy environment, and healthy food for our future.
Tags: closed loop, crop yields, food supply chain, global warming
Lead Image Source: https://sustyvibes.com/impact-climate-change-agriculture
Vertical Farming Made Easy With Sarab From Ecotwigs
Sarab lives in Mumbai, India. In 2017, she completed an internship in Canada at the In.Genius Farms, a small-scale vertical farm in Laval, Quebec. Mentored by Khaled Majouji, aka The Plant Charmer, she learned about the potential of vertical farming. Once back home, she decided to be the change she wanted to see in her country
August 5, 2020
Sarab lives in Mumbai, India. In 2017, she completed an internship in Canada at the In.Genius Farms, a small-scale vertical farm in Laval, Quebec. Mentored by Khaled Majouji, aka The Plant Charmer, she learned about the potential of vertical farming. Once back home, she decided to be the change she wanted to see in her country.
Inspired by her experience in Canada, Sarab started her own startup: Ecotwigs. With the help of her father, Gurmukh Singh, an entrepreneur in computer numerical control (CNC) machinery, they designed and developed a ready-to-assemble vertical farming system.
It can be produced on an industrial scale, delivered wherever it is needed, and easily deployed upon reception.
Sarab at her vertical farm near Mumbai
As in many countries, the COVID-19 pandemic has disrupted the mobility of agricultural workers in India, adding pressure to food supply chains and compromising the food security of the most vulnerable populations. The situation raised awareness on the importance of local farming and shorter supply chains.
Sarab vertical farming solution comes at the right time. It aims to solve a few problems at once:
requires less land;
reduces the workload and dependence on seasonal foreign workers;
increases yields per square-foot;
improves food salubrity;
simplifies traceability;
and fosters profitability.
Given the current pandemic, such a farming system, which also requires limited interactions and manipulations while operated, would be more than handy.
How it all started
Sarab studied sciences in Junior college. “It was the rational choice”, she said. However, her real dream was to become a pastry chef. She had always been fascinated by big wedding cakes, but convincing her dad about this career choice was challenging.
Nonetheless, while in college she started a side gig as a freelance pastry chef. She liked it so much that after college, she did a bachelor’s degree in Hotel and Hospitality Administration. While studying, she spent a semester working as an intern at the Danat Jebel Dhanna Resort on the outskirts of Abu Dhabi in Ruwais city.
Before completing her bachelor’s degree, a research topic on lifestyle diseases based on our diets shed a different light on her passion. “I realized that what I was loving [baking cakes] was making people diabetic”, she said. “I thought I was giving people joy, but I was giving them diabetes”, she added.
Sarab explained that although she still enjoys baking and has nothing against eating pastries, it may not be the purpose she wanted in life. When she graduated, suddenly she felt like she didn’t want to follow this path anymore.
One day, while waiting for a friend near a market, she was watching how the food was handled. Among other things, she noticed bunches of cilantro unloaded directly on the dirty pavement of a street in Mumbai. Given that cilantro is a garnish in almost every Indian dish, she thought that she could do better. She started to crawl Youtube and looked at hours of videos on how to grow food. The first thing she tried was to grow kiwis from seeds. “I never stopped after that”, she said.
She made a rooftop garden, but without any background in agriculture, she admitted her results were suboptimal. Nevertheless, she was determined to pursue this new path. In 2017, she was following Khaled, aka The Plant Charmer, on Instagram. When she saw a post about an internship opportunity at his new vertical farm, she jumped on it.
The Instagram post that caught Sarab’s attention
Although it sounded like a crazy idea to her parents, generating some fuss in her family, they ended up being supportive of her choice. “Going to Khaled’s farm was the best decision in my life”, she said.
When I was at Khaled’s farm it struck me: this is the future of farming. – Sarab
Sarab wanted to see the full cycle, from seedling to harvesting, including everything in between. “I was supposed to do a one-month internship only”, she explained. “But I was so fascinated on how the system works, I asked to stay longer”, she added.
Sarab at the In.Genius Farm in Laval, QC, Canada
At the end of her internship, another big decision was awaiting Sarab. She had to decide whether to stay in Canada and apply for permanent residence, or to return to India. “The greatest accomplishment in our country is to leave”, Sarab said. “With everything I learned, I felt like the right thing to do was to bring back this knowledge and do something for my country”, she added.
When she returned home, she faced a few challenges. The same as any small-scale urban farming entrepreneurs would encounter in India and elsewhere: access to land, in or near the city, is difficult.
The real estate in Mumbai and other major Indian cities is as expensive as any major city in North America or Europe. It makes farming possible only in remote and often deficiently developed regions. Moreover, a lot of lands in or near the cities and suburbs are highly contaminated, making agriculture beyond gardening nearly impossible. Luckily, Sarab’s uncle provided her with the opportunity to develop her project on an 18,000 sq.-ft plot of land he owns, only 20 minutes away from Mumbai’s suburbs.
Why vertical farming
A new climate report from the United Nations has warned that the world might face a food crisis due to climate change and overexploitation of land and water resources. The vertical farming infrastructure proposed by Sarab aims to enable growing food wherever there is place while reducing pressure on farmlands and fostering soil regeneration.
Without farming the land itself, the annual yields are still calculated in metric tons on less than an acre. By growing above the ground, pest damage and diseases are drastically reduced without the need for any pesticides or harmful chemicals.
For Sarab, vertical farming as she learned it at the In.Genius Farms makes organic farming way easier. “It reduces operational costs, requires fewer resources [human and natural], while increasing yields and margins”, she explained.
“Vertical farming with my infrastructure can be done by anybody because the hard work factors of conventional farming were removed”, she said. “There’s no kneeling, no bending, and no weeding”, she added. From her experience at In.Genius farms, Sarab thinks that 1 worker for every 100 units is more than enough (100 units cover about 10,000 sq.-ft.).
Business model
Once back from her internship at In.Genius Farms, Sarab realized something: she didn’t want to start a farm, she wanted to become the vertical farming infrastructure provider.
I want to be the person who set [up] vertical farms for others because that’s the future. – Sarab
Sarab explains that going through the process of figuring out vertical farming by yourself can be daunting. “Of course some could do it by themselves, but it would turn out to be expensive and time-consuming”, she said. “I want to make things simple and affordable to those wishing to start a vertical farm”, she added.
Her business model is to provide customers with a turnkey vertical agricultural infrastructure and technical assistance to ensure they reach the full yield potential. Therefore, land use and the time, effort, and money spent would be optimized.
As what IKEA does to home furniture, Ecotwigs does to farms by designing and selling ready-to-assemble vertical farms. – Sarab
Sarab’s main market for her vertical farming infrastructure will be existing farmers, but also a new generation of food entrepreneurs who own small plots of land and wish to start small-scale farming businesses. For Sarab, too many farmers in India (and elsewhere) are not treating their farm as a business, and when they do, it is often not managed efficiently. Thus, she wants to provide them with proper customer support to create lasting prosperity.
Vertical Farming Systems
As Sarab’s father noticed her enthusiasm for vertical farming, he decided to help her in her venture. He helped her design and engineer a new system following her experience in Canada.
This A-frame is made of inert material. Suitable for outdoor and indoor farming, it is lighter than wood and easier to assemble (or disassemble if needed). Moreover, it is made to last a minimum of 10 years.
A 100 units farm can be assembled within a week by 2 people. – Sarab
One unit can be assembled by 2 people in 30 minutes. Each A-frame unit includes 10 rammers that are 12 feet long (or 3.90 meters). There are 5 rammers on each side. Working 7.5 hours per day, it would take two people about 7 days to set up a 100 unit vertical farm on 10,000 sq.-ft.
Depending on the crop and location, each unit can generate from $400 to over $1000 in revenue per season. The price to buy a unit is not yet settled. Nevertheless, the price range will be established to allow clients to get a great return on investment (ROI).
Our challenge was to design the most profitable, eco-friendly, food-safe, sturdy, and long-lasting farming system. – Sarab
The rain gutters, as used on the In.Genius Farms’ A-frame, are replaced by a custom made rammers. For marketing purposes, Sarab and her father decided to change the name of this component, which is the channel used to grow food. “In India, when you say gutters, it is associated to a filthy place”, she explained. “It is not the place where people would want their food to grow”, she added.
The rammers’ length, width, and depth were increased to allow higher yields per unit and the growth of a wider variety of crops. The angle of the rammers was set to get a maximum sun or LED light exposure. The system can be deployed either as a few units in a backyard, on rooftops, or at scale on acres.
The next steps
Sarab currently operates a 30 unit vertical farm. It serves as a research and development lab. “That is where data are validated”, she said. Sarab is growing varieties of lettuce and spinach, arugula, peanuts, sweet bell peppers, edible flowers, and eggplants. She will also experiment with growing strawberries, which is unusual for Mumbai’s climate.
As the rammers are longer, deeper, and wider than the model she experienced at the In.Genius farms, bigger crops like cauliflower, celery, and zucchinis will be tested as well. The food harvested at her farm will be for friends and family. With 30 vertical farming units, Sarab already knows that she will not have the volume necessary to consistently supply clients like chefs or grocery stores.
Her focus is on supplying the infrastructure and acting as a vertical farming consultant to her clients. Thus, operating the farm to gather data is the priority. The system will be continuously tested to make sure it can perform well, and that yield expectations are accurate.
Sarab explained that “when a client is looking to invest in infrastructure like this, we need to give them the proper numbers. And I know that at one point, the numbers will speak for themselves”.
Sarab is well aware of the Canadian winter. “Made of inert material, these A-frames do not react much to temperature fluctuations”, she explained. She also knows how robust the system needs to be to endure the cold temperature of northern countries, as well as snow and ice accumulation.
Takeaways on vertical farming
The approach of the farmers should change, and the status quo should be disrupted. Sarab explained that Indian farmers are treated as the bottom of the supply chain. If they could be provided with the proper tools and means to grow, market, and distribute food efficiently, she believes it could make them the leaders of the supply chain. The main issue Sarab stressed is to make sure you have enough customers for those high yields.
“The best part, since all labor-intensive tasks of conventional farming have been stripped out, it could be done by anybody”, Sarab proudly said. Adding some fun, fashion, and style to the business concept is also part of her branding.
I genuinely enjoy working at my farm and the message I want to spread is: this is cool! I can be fashionable and still be a farmer. -Sarab
Do you have an inspiring urban agriculture story to tell or innovative ideas to share? Contact us or leave a comment below!
SINGAPORE: New Vertical Farm To Produce 500,000 kg of Greens Annually
&ever has been awarded funding under SFA’s ‘30x30 Express’ grant to ramp up local food production over the next six to 24 months
&ever Singapore Pte Ltd (previously Farmers Cut Pte Ltd), a fully-owned subsidiary of &ever GmbH from Germany, will grow and deliver leafy greens to consumers in Singapore with its first indoor farm in the region.
Amid the global food supply challenges posed by the COVID-19 pandemic, the Singapore Food Agency (SFA) launched a ‘30x30 Express’ Grant earlier this year. The grant will support the country’s agri-food industry and accelerate the ramp-up of local production, with the aim of meeting 30 percent of Singapore’s nutritional needs with food produced locally by 2030.
&ever has been awarded funding under SFA’s ‘30x30 Express’ grant to ramp up local food production over the next six to 24 months. The grant is awarded to companies who make use of highly productive farming systems that can be constructed and implemented quickly to achieve high production levels.
&ever will produce annually up to 500,000 kg of leafy greens for consumers in Singapore using their Dryponics method. Dryponics keeps the plants alive, with the roots intact, until they reach the consumer. Consumers will be able to harvest the plants only seconds before consumption, resulting in higher nutritional value and better-tasting greens.
&ever’s fully automated technology allows for everything inside the farms to be controlled digitally- from the seeding to harvesting, CO2 levels, temperature, and airflow. IoT sensors and edge computing are collecting data throughout the farmhouses to produce and maintain the healthiest plants.
“To accelerate the ramp-up in local food production and meet our '30 by 30' goal, we will need to leverage productive farming technology. Technology can help farms achieve higher production levels, and be more resilient against the impacts of climate change. We are pleased to see our agri-food players, such as &ever Singapore adopting productive and innovative farming systems, and will continue to work with them to strengthen our food production capabilities. This in turn will enhance Singapore’s food security, and create good jobs for our people,” said Mr. Melvin Chow, Senior Director of SFA’s Food Supply Resilience division.
&ever has been present in the hyper-local agri-food scene since early 2019. With the successful launch of their first indoor farm in Kuwait earlier this year, they aim to bring their sustainable farming solution to other parts of the world with challenging climate conditions.
Dr. Henner Schwarz, CEO of &ever, said: “We are excited to continue our global roll-out and bring better tasting, highly nutritious salad to the people of Singapore.”
“At the same time we make a strong contribution to one of the world’s most exciting eco-systems for indoor vertical farming," added Mark Korzilius, founder and CISO of &ever.
For more information:
&ever
and-ever.com
27 Oct 2020
Biggest Swiss Fruit And Vegetables Cooperative Invests In Vertical Farming
A major Swiss domestic supplier, fenaco Landesprodukte, is working on a pilot facility for vertical farming. They're investing in YASAI, a spin-off of public university ETH Zurich. With an investment of CHF 500,000 in YASAI AG, the fenaco cooperative is participating in the construction of the pilot facility in Zurich
Fenaco Collaborates With YASAI
A major Swiss domestic supplier, fenaco Landesprodukte, is working on a pilot facility for vertical farming. They're investing in YASAI, a spin-off of public university ETH Zurich. With an investment of CHF 500,000 in YASAI AG, the fenaco cooperative is participating in the construction of the pilot facility in Zurich.
"Consumer demands for healthy, safe and sustainably produced food require innovative solutions from the agricultural and food industry. By participating in a pilot facility for the novel Vertical Farming production method, fenaco Landesprodukte wants to verify the advantages of this cultivation method", the company explains. "Thanks to its stacked installation, it increases productivity by a factor of 10 to 15 per square meter. Water consumption can be reduced by 90%."
"In the future, we do not want to produce ourselves, but rather use our experience in the field of vertical farming to open up a new, profitable business segment for growers," says Daniel Schwab, Head of the Vegetable Category at fenaco Landesprodukte. To this end, a sounding board was set up with vegetable producers from the Seeland region.
No chemical crop protection is used, or very small amounts only. In addition, year-round indoor production allows growth 24 hours a day, 365 days a year and it is possible to increase the proportion of Swiss vegetables and herbs. "The aim is also to demonstrate the economic efficiency for various product categories and to reduce energy consumption by exploiting synergies", they explain.
A strong signal for innovation in the agricultural and food industry
fenaco entering the field of vertical farming is a strong signal for innovation in the Swiss agricultural and food industry. The partnership with the ETH spin-off enables fenaco to better understand the potential for vertical farming and, if positive, to exploit economies of scale with larger plants. On the one hand, the product portfolio will be tested in cultivation and marketing and on the other hand, central agronomic questions will be addressed in a research project in cooperation with Agroscope.
"We are working on the farm of the future and regard this investment as a preliminary work and a basis for decision-making for future investments of our producers", says Markus Hämmerli, Head of fenaco products and research cooperations. This means the commitment is based on the goals of the fenaco cooperative: to support Swiss growers in the economic development of their companies.
Industry and technology know-how go hand in hand
The ETH spin-off YASAI under the leadership of CEO Mark Essam Zahran is the ideal partner for fenaco. The four founders and majority shareholders have excellent know-how in the field of software and hardware as well as a large international network. After several successful financing rounds, fenaco's financial commitment and the associated construction of the first pilot plant in Switzerland is an important milestone for the still young company.
"Thanks to the cooperation with fenaco, we now have a strong industrial partner with a lot of market and customer knowledge from the agricultural sector on our side. This is extremely valuable when scaling up the technology and entering the Swiss market," says Mark Zahran of YASAI. The partnership with fenaco also enables YASAI to distribute the vegetables and herbs it produces nationally in the retail trade and in the catering trade.
For more information:
www.fenaco.com
www.yasai.ch
29 Oct 2020
The Role of Silicon As a Nutrient In Hydroponic Recipes
Research has demonstrated that silicon is one of the most beneficial micro-elements for several plants. However, its role has not been considered as essential in plant nutrition
By Karla Garcia
Silicon (also known as silica, Si) is found in high quantities in open field production but is absent in hydroponic nutritional recipes. The lack of knowledge about the role of silicon (Si) in horticultural crops became apparent when using soilless/hydroponic systems.
Research has demonstrated that silicon is one of the most beneficial micro-elements for several plants. However, its role has not been considered as essential in plant nutrition. For this reason Si is not used as a common ingredient in hydroponic recipes. It is the aim of the present article to share the knowledge generated around the role of Si in plant nutrition in order to discuss its possible important function in nutrient recipes.
Despite not being a common ingredient in hydroponic recipes, several beneficial effects of silica have been demonstrated in hydroponic systems (Guntzer et al. 2012; Miyake and Takahashi 1983; Voogt and Sonneveld 2001). The use of Si as a nutrient in plants has shown a positive effect in mitigating environmental and pathogenic stresses. Some authors mention its function as an alternative way to control diseases. However, most of the results support its role as a good complement for disease treatment and prevention.
Van Bockhaven et al. 2013, demonstrated the induction of a broad-spectrum plant disease resistance by implementing Si as part of the fertilizer in plants. Other studies also showed (Hammerschmidt, 2005) Si as an ingredient with the potential to reduce rates and number of fungicide applications, specifically in control of powdery mildew. This same result has been supported by other studies done by Miyake and Takahashi, 1983 and Vercelli et al., 2017.
Silicon is deposited in plant cell walls helping to avoid pest incidence and damage by fungi. Also, the presence of silicon in cell walls can help to improve resistance to heat and drought contributing in the development of strong and healthy plants. This being the reason why many authors present data supporting its role as a nutrient with the potential to increase yields.
One particular issue in the use of Si in hydroponic recipes is pH. Si has a high pH that can affect some nutrient recipes. Also is difficult to maintain soluble in concentrated nutrient solutions. However, as we know, pH can be controlled. Si can be added as a separate ingredient in a different tank and recommendations indicate to reduce pH in the tank containing Si and water directly.
How much silicon should I use?
Now that we know the positive effects of Si in plants. How can we know which form or quantity of Si can be used in hydroponic systems? The requirements of Si by plants in order to get the beneficial effect of this nutrient can be crop-specific. Si can be added in nutrient recipes as silicon dioxide and common ranges used are from 50 to 150 ppm. Being 100 ppm is the most common level. It is important to always start with recommended low levels of Si because too much of this nutrient can affect the uptake of other elements.
It is important to mention that the use of Si complies with current sustainable agriculture EU regulations and is not toxic for humans. Plants can live without silicon, therefore it is not an essential nutrient. However, the more this nutrient is studied the more we know about its role in improving plant health and growth.
Superior Fresh Announces New Salad Variety: Citrus Splash
“We have created a balanced organic ecosystem by raising the cleanest, healthiest Atlantic salmon using organic practices and principles and applying our proprietary organic farming methods to grow the best tasting organic salads and greens you have ever eaten
Superior Fresh is proud to unveil its newest salad blend: Citrus Splash. Filled with bright sunny citrus notes, this blend offers consumers a unique opportunity to expand their culinary experience. Citrus Splash brings more than exceptional flavor to the salad bowl. Paired with our non-GMO, organically fed Superior Fresh Atlantic salmon, the possibilities are endless.
“We have always been about doing things a little differently,” says Todd Linsky of Superior Fresh. “We have created a balanced organic ecosystem by raising the cleanest, healthiest Atlantic salmon using organic practices and principles and applying our proprietary organic farming methods to grow the best tasting organic salads and greens you have ever eaten. We do this while raising the bar on sustainability with practices that give us the ability to grow lettuce using less than one gallon of water. And what’s really impactful is we actually reuse 99% of all water.”
Todd goes on to say, “You do not choose organic aquaponics as a growing method by sticking to what is established. You do not commit to 800 acres of soil regeneration if you are doing it like everyone else. We are taking the responsibility of being one of the largest USDA certified organic salad operations very seriously. Our customers expect us to bring our best using thoughtful innovation – every time – whether that be in the way that we farm or with what we grow.”
Citrus Splash is sure to make a splash in the produce pool. Look for it on the shelves of your local grocery store and inquire directly for wholesale, retail, and food service options.
Mon 19 Oct 2020
Indoor Farming Start-Up BrightFarms Raises $100m In Funding
The start-up has raised over $200 million in funding to date, and BrightFarms claims that it will use these latest funds to invest in its current farms and retail programs and expand its network of regional indoor farms across the US
By Martin White
21 October 2020
Indoor hydroponic farming start-up BrightFarms has secured $100 million in a Series E funding round led by Cox Enterprises, which now owns a majority stake in the company, and a further investment from Catalyst Investors.
BrightFarms builds and operates indoor farms near major metropolitan areas in the US, providing supermarkets and retailers with a consistent supply of locally grown produce. It currently operates indoor farms in Illinois, Ohio, Pennsylvania, and Virginia, with three new farms currently under development in North Carolina, Massachusetts, and Texas.
The start-up has raised over $200 million in funding to date, and BrightFarms claims that it will use these latest funds to invest in its current farms and retail programs and expand its network of regional indoor farms across the US.
BrightFarms claims that its growing methods “use 80% less water, 90% less land and 95% less shipping fuel than traditional agriculture”. The company claims that its indoor growing methods can provide pesticide-free packaged greens to supermarkets in as little as 24 hours after harvest.
The start-up has formed partnerships with major retailers including Ahold Delhaize, Kroger, and Walmart, distributing produce to over 2,000 stores in the US. The firm anticipates that it will expand its distribution to more than 15,000 stores by 2025.
Steve Platt, CEO of BrightFarms, said: “Our goal over the next five years is to make quality, locally-grown greens a staple on grocery shelves and in refrigerators nationwide.
“We are thrilled to have the strong financial backing of Cox Enterprises, an organization that closely aligns with our mission to build a healthier and more sustainable future and to have the additional support of our long-term partners at Catalyst Investors. Together we are ready to scale our model for local indoor farming in every major market in the US”
October Indoor Science Cafe - Recording Is Now Available!
Learning Critical Control Point For Hydroponic Food Safety "Hydroponic Crops -- How Can You Produce Safe Vegetables?"
Indoor Ag Science Cafe October Recording
Learning Critical Control Point
For Hydroponic Food Safety
"Hydroponic Crops --
How Can You Produce Safe Vegetables?"
by
Dr. Sanja Ilic (The Ohio State University)
This presentation 'Hydroponic Crops: How Can You Produce Safe Vegetables?' was given by Dr. Sanja Ilic (The Ohio State University) during our 23rd cafe forum on October 20th, 2020.
US - WISCONSIN - VIDEO - Appleton International Airport Starts Growing Its Own Greens In Hydroponic Garden
According to Pat Tracey with Appleton International Airport, “We want to provide travelers with a safe and healthy traveling experience and we’re just always looking for how can we make the airport a safer and healthier place.”
Oct. 23, 2020
GREENVILLE, Wis. (WBAY) - As part of renovations in the terminal, Appleton International Airport teamed up with ThedaCare to promote healthier travel. Even before the pandemic, the airport added hand sanitizing stations, healthier food options for on-the-go-travelers, as well as other upgrades. Now, some of the airport’s food will now be fresher than fresh.
Whether travelers are coming or going, at Appleton International Airport, they’re all greeted by a live plant wall. It’s not only aesthetically pleasing, but it also adds fresh air to the building. The restaurant menu has been upgraded to include more nutritious meals as well. It’s all part of ATW’s “Healthy Connection” partnership with ThedaCare.
According to Pat Tracey with Appleton International Airport, “We want to provide travelers with a safe and healthy traveling experience and we’re just always looking for how can we make the airport a safer and healthier place.”
It doesn’t get much healthier than farm to table.
“People are so sick and tired of getting food that’s traveled over 1500 miles, that only has a day or two of shelf life if any, and has lost a bunch of nutritional quality along the way. On top of all of the salmonella outbreaks with Romaine lettuces and things like that. We’re really getting tired of not having really fresh, high quality, affordable stuff,” says Alex Tyink with Fork Farms.
A recently-installed hydroponic garden, from Green Bay based Fork Farms, sits only about 15 feet away from the restaurant inside the airport terminal. The garden will produce 300 hundred pounds of fresh greens a year, food that will be harvested here and simply walked to the restaurant by its staff and incorporated in what they serve.
Tyink says, “These plants are only about a week old, just from planting the seed and so they have another two to three weeks left to go until they’ll be a nice big full head of lettuce and the staff here is going to put them into the sandwiches.”
While the hydroponics farm will produce enough leafy greens for sandwiches and burgers, the airport does hope to eventually expand the program,
Pat Tracey adds, “For business travelers who travel a lot on the road, the hardest thing is to eat healthy and so we’re trying to do our part and give people a good healthy option when they’re here in Appleton.”
How Hydroponics & Vertical Farming Can Improve Food Safety
Viraj Puri, co-founder, and CEO of a hydroponic vertical farm told Food Safety News that the hydroponic vegetable industry has a built-in food safety advantage over open-field farming. He believes that this advantage comes from its “physical infrastructure and higher levels of environmental controls.”
Our greenhouse team member utilizing food safety best practices at our R&D facility.
The United States Department of Agriculture sometimes refers to vertical farming as “controlled-environment agriculture” and there’s a good reason for this moniker.
Viraj Puri, co-founder, and CEO of a hydroponic vertical farm told Food Safety News that the hydroponic vegetable industry has a built-in food safety advantage over open-field farming. He believes that this advantage comes from its “physical infrastructure and higher levels of environmental controls.”
In recent years, the safety of our food supply has been called into question. Numerous food recalls are a regular part of news broadcasts across the country. Recently, it was found that fruit and vegetables failed import safety checks at a rate of 12.5%. At the same time, other categories such as meat, fish, and eggs, achieved compliance rates over 95%.
National producers of fruit and vegetables have also had problems. The recent outbreak related to contaminated romaine lettuce originated in California. This year’s recalls of onions and peaches also originated domestically.
Vertical farms using hydroponic technologies could usher in a revolution in food safety. Hydroponic growing has a plethora of food safety benefits. Year after year, pathogens are found in traditionally-grown (or soil-grown) crops. This is because the soil itself contains naturally-occurring pathogens, and traditional farms are open to contamination from outside sources such as animal droppings and tainted run-off. Hydroponic farming has the potential to drastically reduce the number of people who get sick via foodborne illness every year by eliminating these pathogens from the growing process.
Foodborne illnesses have originated from traditionally grown crops over and over, and the problem is growing. It’s important to understand the dangers of these foodborne illnesses, as well as what “food safety” is and how every individual along the food supply chain has a role to play. Fortunately, recent food safety news gives us hope that hydroponics can improve food safety.
Why We Need A Culture of Food Safety: The Dangers of Foodborne Illnesses
The Centers for Disease Control and Prevention estimates that 48 million people get sick (1 in 6), 128,000 are hospitalized, and 3,000 die from foodborne illnesses each year in the U.S. Food can be contaminated by many different disease-causing germs. There are many different types of foodborne illnesses (sometimes described as food poisoning or foodborne disease). Over 250 types of foodborne illnesses have so far been identified. The majority are infections caused by bacteria, parasites, and viruses. Food can also be contaminated with harmful toxins and chemicals.
Food may become contaminated during any stage of the food supply chain; from production, distribution, processing, preparation, to storage. Germs can spread to food from unclean utensils, surfaces, or equipment. And it’s not uncommon for these contaminated foods to make it to market and into kitchens and restaurants before anyone knows there is a problem.
What is Food Safety?
“Food safety” describes all operations and practices that are utilized to keep food safe. Keeping food safe is a joint effort involving everyone in the food supply chain. All along the food supply chain—from producers and farmers to wholesalers and retailers— there are standardized regulations and controls in place to reduce the risk of food contamination.
Part of food safety practices involves growing, handling, preparing, packaging, and storing food in a way that best reduces the risk of people getting ill from foodborne diseases. Food safety is a concern all over the world and one that we should take great care to address.
The fundamental principles of food safety focus on preventing food from becoming contaminated and causing food poisoning. This is achieved through several different methods, some of which include:
Understanding food allergies, food intolerance, and food poisoning
Keeping up high standards of personal hygiene (i.e hand-washing) when handling food at any step in the food supply chain
Storing, heating, and cooling food properly with regard to temperature, environment, and equipment
Using effective and adequate pest control measures
Cleaning and sanitizing all surfaces, utensils, and equipment
How Hydroponics Can Improve Food Safety
Unlike in traditional farming, wildlife and livestock can’t contaminate produce grown in a vertical farm’s greenhouses. It’s almost impossible to prevent such contamination in traditional agriculture where wide open fields are susceptible to bird droppings and animal encroachment.
Although there aren’t industry-wide food safety standards for hydroponic growers, the vast majority of companies have rigorous processes in place. Joel Cuello, Vice-Chair at the Association for Vertical Farming, said “vertical farms are, in fact, generally and significantly safer than conventional agriculture”. He believes that the reason many vertical farms don’t have internationally recognized food safety certifications is because their stellar food safety reputation is proof enough.
Since vertical farms use a hydroponic system for watering, there’s very little chance that contamination from water will infect the produce. Hydroponic systems add nutrients to tested or purified water and then apply that water directly to the plants’ roots. The system completely bypasses the use of soil, which is a possible contaminant with a lengthy history of getting people very sick. Hydroponic technology also avoids the problem of runoff from nearby sources of toxic chemicals or biological waste.
Food Safety News: Soil and E. coli
In recent food safety news, the major E. coli outbreak that started in September of 2019 and related to romaine lettuce seems to be over. Epidemiologic, laboratory, and traceback evidence conclusively showed where the contaminated romaine lettuce came from. The produce that made people sick in September of last year is no longer available for sale. However, it was grown in soil and harvested in the Salinas Valley growing region.
A total of 167 individuals from across 27 states were infected with the outbreak strain of E. coli O157:H7. Eighty-five people were hospitalized due to this outbreak, including 15 who developed hemolytic uremic syndrome—a kind of kidney failure. Luckily, no deaths were reported.
Some think E. coli results in little more than an upset stomach, but outbreaks can be very serious affairs and in some cases have caused death. At best, it causes vomiting, diarrhea, and stomach cramps; let alone an long-term aversion to lettuce after getting sick.
Hydroponic Greenhouses Are Safer Than Soil-Based Farming
The Centers for Disease Control, the Food and Drug Administration, and public health officials investigated the most recent E. coli outbreak in the United States. Their recommendation said that hydroponic-grown lettuce was not related to the current outbreak. In their words, “there is no recommendation for consumers to avoid using romaine harvested from these other sources.”
Hydroponic Growing Offers Many Food Safety Benefits
Hydroponic growing does not require high levels of pesticides and uses less water, land, and fertilizers than conventional farming.
Vertical farms also use a soilless medium for growing their plants. This means that food products are not infected by pathogens that can sometimes contaminate soil and be passed to traditionally grown crops.
Greenhouse vertical farms are highly controlled environments in which the light intensity, temperature, and humidity are closely monitored and controlled and the growing solution is strictly regulated. With so many levels of checks and controls, it is far less likely that pathogens and toxins could be introduced into these closed environments.
Eden Green Technology offers hydroponic systems that can help create a healthier food supply. Learn more about how to safely grow delicious produce here.
CANADA: Automated Guelph Vertical Farm Supplies Retailers With Local, Leafy Greens
An automated vertical farm in south Guelph is now fully operational. GoodLeaf Farms has the capacity to produce 800,000 units of locally grown leafy greens for Ontario retailers — including Loblaw banners, Longo’s, and Whole Foods — 12 months of the year
By Lilian Schaer
October 14, 2020
The Newly Opened Farm Grows Crops
40 to 50 Percent Faster Than Traditional Crops
There are 50 workers employed at the GoodLeaf Farms facility in Guelph. Photo: Lilian Schaer
An automated vertical farm in south Guelph is now fully operational. GoodLeaf Farms has the capacity to produce 800,000 units of locally grown leafy greens for Ontario retailers — including Loblaw banners, Longo’s, and Whole Foods — 12 months of the year.
“It’s really unique for Canada that we can grow 365 days of the year, and we can fill a gap in the market without going up against traditional farming,” said account manager Jacquie Needham during a tour of the facility on Sept. 15.
Why it matters:
The pandemic has heightened demand for locally grown foods less dependent on sometimes fragile global supply chains.
GoodLeaf’s crops include baby arugula and baby kale, along with four types of microgreens: pea shoots, Asian blend, spicy mustard medley, and arugula. While consumers are familiar with “baby” leafy greens, they’re less comfortable with what to do with microgreens, admits Needham.
“Micros are a learning curve for consumers, but they can be used to add nutritional elements to meals as garnishes, in salads or sandwiches, or as something you add to a smoothie,” she said.
“People are cooking more at home right now and experimenting more.”Vertical farming is an innovative process that naturally grows plants with hydroponics under specialized LED lights designed to maximize photosynthesis. In the GoodLeaf facility, carbon dioxide, water, nutrition, and light are carefully programmed and monitored for each specific crop.
Jacquie Needham, of GoodLeaf Farms, talked about the company’s products during a recent tour at the facility.’ photo: Lilian Schaer
According to Needham, that makes their growth cycles an estimated 40 to 50 percent shorter than traditional crops. From seed to store takes about 12 days for the microgreens and about 22 days for the baby leafy greens. That includes testing every crop for contaminants before shipping to ensure they’re safe — important at a time when North American produce recalls make headlines and can have far-reaching economic and health consequences.
Needham also pointed to the sustainability of vertical farming production. The GoodLeaf facility uses 95 percent less water than a traditional farm, doesn’t use pesticides, herbicides, or fungicides, and has no run-off issues that could impact local water supplies. The production is not organic, however.
“We are not certified organic because our production does not use soil, but we feel we have a cleaner product than organic because, in addition to being pesticide-free, it’s not exposed to wind or rain, for example,” she said. “It’s an education piece for consumers.”
GoodLeaf Farms was founded in 2011 in Nova Scotia by Gregg Curwin. That original Nova Scotia farm has now been converted into a research and development centre for the company.
The new Guelph facility employs about 50 people who work seven days a week and it’s the city’s research expertise and proximity to the Greater Toronto Area that brought GoodLeaf to the region.
The GoodLeaf building is located in an industrial area in south Guelph. photo: Lilian Schaer
“Ontario is a big hub for consumers, retail and foodservice, so we were looking for a place close to the market so we can get product to people as quickly as possible,” said Executive Director of Operations Juanita Moore. “And the University of Guelph has been a great help with research.”
Research conducted in controlled environments
GoodLeaf is working with university researchers on a number of horticulture and food safety projects, including studies on controlled environments and light spectrums. The company received $4.4 million in start-up innovation funding from Agriculture and Agri-Food Canada’s AgriInnovation Program.
“I’ve been the mayor (of Guelph) for six years now and this is one of my “wow” moments,” said Guelph Mayor Cam Guthrie following the tour. “Guelph is embracing the circular food economy and we are seeing it in action here. It’s a testament to what Guelph has to offer.”
Guelph MP Lloyd Longfield, who was also on the tour, pointed to vertical farming’s potential to help address climate change and food security issues in both urban and northern or Indigenous communities.
“This type of agriculture is consistent and gives predictability to the producers and it would be interesting to see if it could be used more widely,” he said.