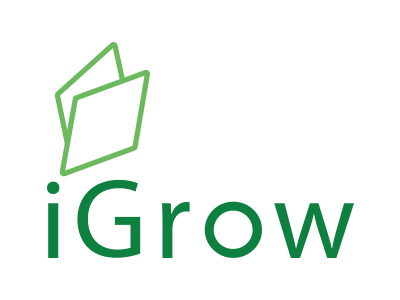
Welcome to iGrow News, Your Source for the World of Indoor Vertical Farming
USA: Vertical Field Signs Agreement To Provide Vertical Farms of Fresh Vegetables To Senior Living Homes In California
Vertical Field has developed and commercialized unique soil-based, vertical farms that operate in 20 and 40-foot containers that produce freshly harvested and pesticide-free produce
Company To Deliver Unparalleled Produce Quality Via
Freshly-Harvested On-site Vertical Farms in 8 Calson
Management Nursing Homes Across The State
News & Photos by: Vertical Field
May 26, 2021
RA'AANA, Israel, May 26, 2021 /PRNewswire/ -- Vertical Field - ("VF" or the "Company"), a global ag-tech company that develops vertical farming systems, has signed an agreement with Calson Management to supply assisted living homes with on-site vertical farming units. According to the agreement, Vertical Field will provide a demo unit to the Glen Cove senior living lodge in Vallejo, California, and after a successful pilot will expand to seven other centers.
Vertical Field has developed and commercialized unique soil-based, vertical farms that operate in 20 and 40-foot containers that produce freshly harvested and pesticide-free produce. The VF indoor farms are capable of growing a variety of fresh greens and other crops year-round with no seasonality barriers while minimizing supply chain logistics and storage, eliminating the need for transportation, and minimizing inventory losses.
Vertical Field's urban farms use 90% less water and 30 times less land than conventional farming methods. Each portable unit is made up recycled shipping containers that grow produce in controlled conditions. Advanced sensors and monitors, climate control technology, and state-of-the-art lighting create the optimum conditions for crops to grow quickly and efficiently year-round, regardless of the weather.
The Company provides vertical farming for supermarkets, restaurants and multi-site facilities in the United States, Ukraine, United Arab Emirates, Israel, Russia, and others.
"We are very excited to launch our first partnership with an assisted living center, providing senior citizens freshly harvested, high-quality produce grown right outside their residence" says Guy Elitzur, Vertical Field's CEO. "This partnership supports our values of ensuring that nutritious produce reaches the homes of all people- no matter where they live. We look forward to continuing to expand to many other assisted living centers, and to making delicious and quality food accessible to senior citizens and other marginalized communities throughout the world."
About Vertical Field: Vertical Field is an ag-tech company that develops innovative and proprietary vertical growing systems for the urban environment. Our urban farms make efficient use of city space by growing crops vertically and on-site, bringing healthy, fresh, and local produce all the way to the consumer.
About Calson Management:
Calson Management provides a full suite of services and solutions for every aspect of a Senior Living project, and is committed to excellence in providing personal services in a warm, loving, and supportive environment. The Reyes family (partners and managers) have been involved in Senior Living for more than 30 years, and is dedicated to creating unique, specialized communities for seniors throughout California. Our family and our team members work to provide safe, engaging, and comfortable communities.
"Enhancing the health and wellbeing of our seniors is a priority at Calson Management, which is why partnering with Vertical Field to supply senior living homes with fresh, nutritious, and on-site produce was a natural decision. By bringing the farm all the way to our residents, seniors can see where the food grows and enjoy high-quality produce, furthering a living home's ability to create a happy, safe, and comfortable community." – Jason Reyes, Principal, Calson Management
For further information https://www.verticalfield.com
News & Photo Source: Vertical Field
USA - FLORIDA: St. Pete’s Brick Street Farms Gets Multi-Million-Dollar Investment From Lykes Bros
Lykes Bros., one of the oldest and largest agribusinesses in Florida, is putting a big bet on the future of farming as it invests in Brick Street Farms, an urban farm, and market in St. Petersburg
May 20, 2021
Photo credit: Brick Street Farms
Lykes Bros., one of the oldest and largest agribusinesses in Florida, is putting a big bet on the future of farming as it invests in Brick Street Farms, an urban farm and market in St. Petersburg.
Lykes is making a “significant” investment in Brick Street Farms, the two companies announced at a news conference Thursday. The amount of investment was not disclosed, but a news release described it as “multi-million dollar” investment. Lykes will take a 20 percent ownership stake in Brick Street Farms because of the deal, Mallory Dimmitt, vice president of strategic partnerships at Lykes, told the St. Pete Catalyst.
Brick Street Farms will use the investment to accelerate the expansion of Brick Street Farms hubs, an all-inclusive onsite farming and retail shopping experience in urban cores, said Shannon O’Malley, founder and CEO. The company has self-contained, environmentally sustainable THRIVE containers that will be placed in each hub. Each hub will grow between 16 to 20 acres of farmland on one-third acre lots.
Mallory Dimmitt, vice president at Lykes Bros., announces investment in Brick Street Farms while Nikki Fried, Florida Ag Commissioner, looks on.
The first new hub will open in St. Petersburg’s Warehouse Arts District in late 2021, with an expansion to Tampa in early 2022 followed by more hubs on the east coast, O’Malley said.
“We are the future of farming, and our new investors have the perfect expertise to help us take our successful business model in sustainable farming to feed more people healthy food,” O’Malley said.
The two companies first connected in November at the Florida-Israel Agriculture Innovation Summit, hosted by the Florida Department of Agriculture and Consumer Services, said Nikki Fried, Florida Department of Agriculture Commissioner.
The collaboration meets several goals, including feeding people in urban locations, fighting urban food deserts and food insecurity, bringing farm-to-fork produce closer to people and bringing cutting edge agriculture technology to everyone.
From left, Tampa Mayor Jane Castor, St. Petersburg Mayor Rick Kriseman and Shannon O’Malley, founder and CEO, Brick Street Farms
Brick Street Farms is a hub of innovation and creativity and is the only female-founded and led company in the vertical farming industry, said St. Petersburg Mayor Rick Kriseman. He also highlighted the work of the company’s non-profit Desert Farms Foundation.
“Not only is Brick Street Farms working to make us healthier by providing us some of the best and freshest food around, but through its 501c3, Brick Street Farms is working to end food deserts through the Tampa Bay area,” Kriseman said.
Every urban environment struggles with food deserts, said Tampa Mayor Jane Castor.
“The problems that occur from those food deserts are often times for many communities insurmountable. This is a solution to so many problems,” Castor said.
She also praised the company’s business model. It is financially successful by providing produce to a number of restaurants, Castor said.
While an urban focus might seem like an unusual fit for company like Lykes, which owns hundreds of thousands of rural acres throughout the state, “We know from our experience that innovation is what moves the agriculture industry forward,” said Dimmitt, who will join the Brick Street Farms board of directors.
“In addition to innovations in sustainable production and the technology it uses, the job opportunities and related job training and skills are key to Florida’s future and to our health and wellness,” Dimmitt said. “What could be better medicine than high-quality nutrient-dense greens grown close to the consumer where they have direct access, all while creating community.”
Brick Street Farms, at 2233 3rd Ave. S. was founded in 2016 by O’Malley and her husband, Brad Doyle. Read more about O’Malley in St. Pete Catalyst‘s Hustle profile.
This Weeks Episode - Season 3 Episode 34
Join Harry Duran, host of Vertical Farming Podcast, as he welcomes to the show, Chief Executive Officer and co-founder of LettUs Grow, Charlie Guy. LettUs Grow brings affordable food growing to the modern city through their patent-pending aeroponics technology
Join Harry Duran, host of Vertical Farming Podcast, as he welcomes to the show, Chief Executive Officer and co-founder of LettUs Grow, Charlie Guy. LettUs Grow brings affordable food growing to the modern city through their patent-pending aeroponics technology.
With a background in renewable energy consultancy and engineering design, Charlie is a proponent of tech for good and is passionate about all manners of sustainability.
In this episode, Harry and Charlie discuss the work Charlie is doing at LettUs Grow to connect greenhouses with vertical farms. They talk about some of the benefits of aeroponics and technological advances that have been made in recent years.
Finally, Charlie speaks to the connection between our food systems and our energy grids and shares what he’s most excited about for the future of LettUs Grow and the overall AgTech industry.
Listen & Subscribe
Indoor Vertical Farming Grows Up
Bryan Walsh, author of Future
Indoor vertical farming, where crops are raised in automated stacks, often in or near cities, offers a way to sustainably meet the growing demand for food — if its energy demand can be reduced.
Why it matters: With the global population still rising — albeit more slowly — and more people moving to urban areas, the world needs ways to produce more food without clearing land for conventional farms.
Driving the news: New York-based vertical farming startup Bowery Farming on Tuesday announced a new $300 million funding round — the largest in the industry's history — that values the company at $2.3 billion.
The deal accelerates the momentum in venture capital funding for vertical farming companies, which hit nearly $1.9 billion globally in 2020, almost tripling investment from the year before.
"We're going to need 50–70% more food over the next 30 years, according to the UN," says Irving Fain, the CEO, and founder of Bowery Farming, which has two commercial vertical farms in New Jersey and Maryland and sells its leafy greens to 850 grocery stores. "Indoor farming is not the only answer to that challenge, but it's part of the solution."
How it works: Food has been grown indoors in greenhouses for decades, and it's industrialized to the point that the Netherlands has become the second-largest vegetable exporter in the world chiefly through greenhouses.
Vertical farming takes greenhouses to the next level —literally — with crops grown in tower-like walls of plant-holding cells that require no soil. Like an apartment tower versus a suburban tract, that means more food can be grown on a smaller footprint, which is ideal for cities.
Water and nutrients are delivered to crops either aeroponically — via the air through misting — or hydroponically, in which the plants are grown in nutrient-rich water. "You get high density and high output, while using 90% less water" than conventional farming, says Micki Seibel, VP of product at the vertical farming startup Unfold.
Growing light is delivered via LED lamps. While more expensive than sunlight — which currently remains free — the LED lamps aren't weather-dependent, and like water, nutrients and temperature in the vertical farms, the light can be controlled precisely, vastly enhancing yield and reducing grow times.
Because vertical farming uses so little space, "we can move the farm to the people rather than the food," says James Woolard, chief marketing officer at Freight Farms, which develops mobile hydroponic freight containers modified for indoor farming.
By the numbers: There are more than 2,000 vertical farms in the U.S. Most are run by small growers with a few bigger players, including Bowery Farming, Newark-based AeroFarms, and Wyoming-based Plenty.
Internationally, says Seibel, "Japan has looked at vertical farming as a way to increase food security and reclaim production lost during the tsunami, while Singapore — which imports 90% of its food — is making significant investments in the sector to increase its own food security."
A recent report pegs the size of the vertical farming market at $240 million in 2019 and projects it will grow to over $1 billion by 2027.
The catch: Even with that growth, vertical farming will likely still remain a niche player — the output of U.S. farms alone was worth $136 billion in 2019.
In part because of the price of supplying artificial light, vertical farms have struggled to break even in the past, and they chiefly produce comparatively priced leafy greens rather than the commodity crops that make up the backbone of the food system.
What's next: Second-generation vertical farms are taking advantage of efficiency advances in LED technology, as well as automation and sensors that can reduce labor and setup costs and enhance yield.
The ability of vertical farms to maintain the ideal environment for high-quality crops like tomatoes or lettuce anywhere in the world at any time of the year is turning agriculture into a high-tech industry.
"All the externalities that have been uncontrollable [in farming] historically are now very much controllable," says Bowery's Fain.
What to watch: The development of AeroFarms's 136,000-square-foot Model 5 facility in Virginia, which is set to be the largest and most technologically advanced vertical aeroponic farm when it is scheduled to be completed in mid-2022.
The bottom line: Agriculture made cities possible. Now vertical farming holds out the possibility that cities could become farms themselves
Lead Illustration: Shoshana Gordon/Axios
Top 4 Vertical Farming Stocks
As the world’s population grows, there are more mouths to feed. This has presented some big challenges in agriculture. Although, we’ve continued to innovate and overcome. There have been some great investing opportunities and vertical farming stocks are up next
By Rob Otman
Originally posted May 26, 2021
As the world’s population grows, there are more mouths to feed. This has presented some big challenges in agriculture. Although, we’ve continued to innovate and overcome. There have been some great investing opportunities and vertical farming stocks are up next.
In general, farmland has been a great area to invest. To help explain why this is the case, here’s a quote from Mark Twain…
Buy land, they’re not making it anymore.
That’s been a good rule for investors to live by. Although, we’re now managing land in much different ways. New forms of precision farming are taking root and crop yields are increasing. On top of that, we now have the technology to grow produce more efficiently indoors.
To benefit from these big trends, you can check out this list of the top agriculture stocks. And there’s a little overlap with the list of vertical farming stocks below. The companies on this list are delivering some unique farming products and solutions…
Top Vertical Farming Stocks
AppHarvest (Nasdaq: APPH)
Scotts Miracle-Gro (NYSE: SMG)
CubicFarm Systems (OTC: CUBXF)
AeroFarms (Nasdaq: ARFM)
AppHarvest
AppHarvest has a few of the largest indoor farms in the U.S. There are two 60-acre indoor farms. One is outside Richmond, Kentucky and the other is in Morehead, Kentucky. On top of that, the company has another 15 acre indoor farm in Berea, Kentucky.
With these farms, AppHarvest is working to cultivate fresh fruits, veggies, and leafy greens. It’s still early stages but the potential is huge. The company is using conventional agricultural techniques, along with cutting-edge technology. Without that, it wouldn’t be possible.
One big benefit to this vertical farming stock is sustainability. The indoor growing makes it climate-resilient and there’s no agricultural runoff. It also uses up to 80% less water than traditional agriculture.
Scotts Miracle-Gro
As far as vertical farming stocks go, Scotts Miracle-Gro isn’t a direct play. It has a wide range of products and services. Although, it has made some big strides into precision gardening and hydroponics. Both are vital for growing plants vertically indoors.
In 2018, Scotts Miracle-Gro announced the acquisition of Sunlight Supply Inc. It’s a hydroponics supplier and the deal came in at $450 million in cash and stock. In 2020, Scotts also acquired AeroGrow International, a hydroponics maker.
Scotts Miracle-Gro has many reputable brands but it’s not resting on its laurels. The company is beefing up its indoor farming products. It has more than 100 on-staff research scientists, specialists, and engineers, as well as partnerships with leading academic institutions.
This helps make Scotts Miracle-Gro one of the top vertical farming companies. It’s well-positioned to grow and caters to both small and large growers.
CubicFarm Systems
CubicFarm Systems points out that 1.3 billion tons of produce rots in transport every year. We’re shipping food great lengths but with modern technology, that’s not necessary. CubicFarm is building and selling automated growing machines. They’re used for fresh produce, nutritious livestock feed, and plant propagation.
CubicFarm also uses hydroponic technology. It provides complete indoor agricultural systems. The company also has vertical farm consultants. They help provide research and solutions for clients. On top of that, CubicFarm has an experienced leadership team.
If you decide to invest in CubicFarm stock, it’s a smaller Canadian company. It’s headquartered in British Columbia and its stock trades on the Toronto Stock Exchange (TSX). Although, you can buy shares in the U.S. over-the-counter (OTC) markets.
AeroFarms
There’s not much of a track record with AeroFarms, at least when it comes to trading publicly. This company is soon going public via a SPAC. To learn more about that process, feel free to click on that link.
Until this SPAC transaction closes, investors can buy into Spring Valley Acquisition Corp. (Nasdaq: SV). Once it closes, those shares will convert to AeroFarms with the ticker ARFM. This creates a unique opportunity to buy one of the best vertical farming stocks…
AeroFarms was founded in 2004 and is a world leader in vertical farming. It’s helping to solve issues from population growth, water scarcity, arable land loss, and supply chain risks. AeroFarms also achieves up to 390 times greater productivity per square foot versus traditional farming.
To accomplish this, AeroFarms takes a data-driven approach. Its plant scientists monitor millions of data points every harvest. The company has also gained some protection with patents.
Buying Vertical Farming Stocks and New Opportunities
The companies above give great exposure to innovative farming. Indoor growing will continue to expand, along with the world’s population. The push for green stocks and sustainability is helping as well.
Advancing technology is making this a reality. Some costs are dropping and output for produce is increasing. On top of that, quality control is becoming more fine-tuned. Indoor growing is also helping reduce food supply chain issues.
As a result, the vertical farming stocks above might see some high returns ahead. And whether you invest or not, you’ll likely benefit from these companies.
If you’re looking for even better investing opportunities, consider signing up for Manward Financial Digest. It’s a free e-letter that’s packed with investing insight. The founder and expert behind it, Andy Snyder, delivers big ideas that are easy to digest.
Bowery Farming Secures $300 Million To Continue US Expansion
The company has secured more than $472 million in funding to date, bringing its valuation to $2.3 billion
Bowery Farming has secured $300 million to continue the expansion of its network of indoor farms across the United States. The company has secured more than $472 million in funding to date, bringing its valuation to $2.3 billion.
The funding will provide resources to accelerate advancements in farm design and the BoweryOS, enabling more and more communities access to a reliable supply of locally-grown produce, year-round.
Accelerating technologies
“This infusion of new capital from Fidelity, other new investors, and the additional support of our long-term investor partners is an acknowledgment of the critical need for new solutions to our current agricultural system," said Irving Fain, CEO and Founder of Bowery Farming.
"Next to that, it's the enormous economic opportunity that comes with supporting our mission. This funding not only fuels our continued expansion but the ongoing development of our proprietary technology, which sits at the core of our business and our ability to rapidly and efficiently scale towards an increasingly important opportunity in front of us.”
“Bowery’s approach to indoor farming represents a meaningful disruption to the traditional produce supply chain, and its systems-based approach to engineering and farm design is unparalleled,” said Andy Wheeler, General Partner at GV. “I look forward to continuing to partner with the Bowery team as they build and scale the largest indoor farming network in the U.S. and bring more sustainable produce to consumers.”
Rapid growth
Now in over 850 grocery stores, Bowery has experienced more than 750% growth since January 2020 at brick-and-mortar retailers like Albertsons Companies, Giant Food, Walmart and Whole Foods Market, and more than quadrupled e-commerce sales through e-commerce platforms, including Amazon Fresh.
In January 2021, Injong Rhee (formerly VP at Google and CTO of Samsung Mobile) joined Bowery as Chief Technology Officer to oversee the seamless integration and ongoing development of technology across the growing network.
The Company is currently transforming an industrial site in Bethlehem, PA into its largest, most technologically advanced and sustainable farm yet, expanding its reach further into the Northeast and Pennsylvania region. Bowery will be breaking ground on additional large-scale commercial farms this year, and is actively engaged in identifying new farm locations in the United States with an eye towards global expansion.
25 May 2021
USA: Big Ideas Grow In Wisconsin
Fork Farms has created a unique hydroponic growing system, called the Flex Farm, that allows consumers to grow up to 394 pounds of fresh food a year in just nine square feet of space
May 25, 2021
WEDC
Wisconsin Economic Development Corporation (WEDC) Secretary and CEO Missy Hughes visited Green Bay’s Fork Farms with a simple message: Wisconsin can help businesses and entrepreneurs bring big ideas to life.
“With our state’s talent, workforce and top-ranked university system, Wisconsin businesses are creating solutions for today’s problems and opportunities for tomorrow,” Hughes said. “Innovation is one of the keys to recovering from the COVID-19 pandemic and building a more prosperous economy for everyone.”
In April, Fork Farms was certified as a Qualified New Business Venture by WEDC. That certification allows investors in the company to receive tax credits up to 25% of the value of the investment made.
Fork Farms has created a unique hydroponic growing system, called the Flex Farm, that allows consumers to grow up to 394 pounds of fresh food a year in just nine square feet of space. CEO and co-founder Alex Tyink, who at the time was an opera singer in New York City, was inspired to start the company after working at a Brooklyn rooftop garden and discovering the physical and mental health benefits to eating and growing one’s own food.
“WEDC’s QNBV designation will provide Fork Farms significant lift to our organization's mission,” Tyink said. “It will aid us in growing our business and focusing on ways that we can create transformative social benefit. Overall, we believe their support of the local startup community is critical to building a vibrant Wisconsin state economy."
The company, which is headquartered at Green Bay’s TitletownTech, continues to spread its message of fresh food and environmental sustainability by partnering with nonprofit groups such as community centers and schools to inspire a new generation of growers and creators.
Polygreens Podcast Episode 28 Jake Emling
Beginning in July 2018 he joined CropKing, Inc. based out of Lodi, Ohio. His experience with hydroponics, aquaculture, and aquaponics was instrumental to his desire to start Root 42 Harvests with his wife Katie
Jake attended Michigan State University where he earned both undergraduate and graduate degrees in horticulture. He has nine years of experience across a variety of specialties including agriculture, agronomy, entomology, and viticulture.
During his early career in Michigan, he worked for Michigan State University, AgroLiquid, and the U.S. Department of Agriculture.
Beginning in July 2018 he joined CropKing, Inc. based out of Lodi, Ohio. His experience with hydroponics, aquaculture, and aquaponics was instrumental to his desire to start Root 42 Harvests with his wife Katie.
Latest Episode
3 Challenges of Vertical Farming And Their Solutions
The world is continuing to grow. By the year 2050, researchers estimate that there will be nearly 10 billion people on the planet. As the population increases, the demand for food and food security also increases
Source: Shannon Flynn, ReHack
05/26/21
The world is continuing to grow. By the year 2050, researchers estimate that there will be nearly 10 billion people on the planet. As the population increases, the demand for food and food security also increases.
Traditional farming methods won’t be able to sustainably keep up with the necessary food production to feed the population. That’s why farmers and researchers have been developing new means of feeding people, especially in urban areas.
The advent of vertical farming has taken the agricultural industry by storm. Although it has proven to be beneficial to farmers and the environment alike, there are some challenges that vertical farmers face. Below are three challenges of vertical farming and their solutions. As long as the solutions are available, vertical farming can still be a reliable way to feed the population.
Vertical Farming Basics
Vertical farming takes traditional farming to new levels — literally. Instead of conventional horizontal, soil-based farming, vertical farming implements hydroponics into vertical buildings. Crops grow upwards instead of outwards.
The buildings use a combination of climate and light-controlled areas to grow the plants. It creates a perfect environment for plants to thrive. This type of farming is optimal in urban areas because it takes up much less space than a traditional farm.
Therefore, populations in cities and urban communities have the opportunity to get fresh produce a few blocks away from their homes. Since most of the world’s population will reside in urban areas, this provides greater food security for them.
Vertical farming has evolved over the years to include more than just fruits and vegetables. Seafood producers wanted a more sustainable approach to seafood production, so they have also implemented vertical farming techniques. Seafoods like mussels, scallops, and seaweed grow vertically on ropes, which creates a more biodiverse and resilient seafood system.
Challenges of Vertical Farming and Their Solutions
Unfortunately, there are challenges that vertical farmers face that they must solve to meet those future food needs and to remain sustainable. Here are some of the challenges, along with potential solutions, of vertical farming.
Location
Although vertical farms can go almost anywhere, farmers have to choose the correct location. If it’s too far from potential consumers, then it won’t be a lucrative business. One could have the best place, but if there isn’t a demand for food there, then they won’t be able to sell the produce.
Plus, land in cities can be a bit more expensive. Smaller vertical farms have a more difficult time finding land they can afford, along with permits and insurance.
The solution is to research the considered location for a vertical farm. What kinds of food are the people there looking for? Can a vertical farm provide that for them? Will they be a loyal customer to the farm? Without a good location, a vertical farm won’t get far. Fundraising, loans, and grants are great options for farmers who may not have the funds for a location, too.
Temperature and Humidity Control
The next challenge is temperature and humidity control. These two need to be spot on to produce vegetables and fruits. Managing them can take a while to overcome. Farmers often have to try various recipes of cooling, dehumidification and heating. Vertical farms are usually well-insulated, so when the weather gets warmer, the farmer must cool it and remove humidity.
Before installing an HVAC system, it’s wise to ask for professional help to know how large of a system will be needed for the building. This is the best solution to this challenge, and it will save a lot of headaches in the future.
Multitasking
Another challenge is ensuring proper management of the entire vertical farm. Many farmers who set out to start their industry in vertical farming rely on themselves and possibly a couple of other people to get all of the work done. Vertical farms attempt to do too many things simultaneously, like growing food and selling technology, and managing day-to-day tasks.
New vertical farmers should focus on one thing, like growing food and selling it. This helps build a solid customer base. Choosing either growing and selling or developing technology so allows the farmer to put their best effort into it.
Farming of the Future
Vertical farming has become a popular solution to the growing problem of food security. However, there are challenges within the industry that must first be addressed and overcome to remain a sustainable business. These challenges and solutions are excellent learning tools to grow a thriving vertical farm.
Tags: Indoor & Vertical Farming, Processing & Supply Chain | Business Development, vertical farming
Aquaponics Is Complex: ‘It’s Everything, Anything You Can Really Think Of’
The needs of the fish, bacteria, and plants must be addressed to get and maintain conditions for success
The needs of the fish, bacteria, and plants must be addressed to get and maintain conditions for success.
May 16, 2021
Unlike other agricultural techniques that focus on a single product, aquaponics growers must consider both the fish and the plants when altering the conditions of the system.
Aquaponic systems are often described as their own ecosystems. Everything from the types of organisms in the system to the bacteria breaking down waste impact the productivity and success of the system.
Fish meal is the major source of nutrients in the entire system. What the fish are fed, and how much, plays a role in determining which nutrients will be available for the plants further down the line.
“(The fish meal) will break down into the fundamental components of the fertilizer, which will then be broken down further by beneficial bacteria in the system,” says Trevor Kenkel, owner of Springworks aquaponics farm in Lisbon. “It will go on to then generate the major macronutrients for the plants, but also the micronutrients as well.”
Kenkel said they also monitor the amount of food they feed the fish to prevent excess nutrients in the system.
“The amount of nutrients that are thrown off out of a system is really significant, and it’s so concentrated,” he said. “If we weren’t running a system to capture this afterward, you would either be dumping those into a local ecosystem, or you’d have to find some other way to treat them, which can be very expensive.”
Managing the greenhouse environment can also be difficult, particularly in Maine. Growing produce in the summer and winter is very different, Kenkel said.
Springworks’ greenhouses have lights that supplement the sun on cloudy, gray days. Additionally, a system helps control the temperature within the greenhouses.
Paul Brown, a professor at Purdue University who studies aquaponics, said many factors are involved. For instance, different types of fish provide different kinds of nutrients, and different plants require more of some nutrients than others.
Even the kinds of microorganisms breaking waste down into fertilizer play a part in this complex system. At times, Brown said, it can become necessary to add additional nutrients to make up for deficiencies in the system. The acidity and salinity of the water can also be major factors.
Springworks has plants growing to maturity constantly, allowing Kenkel and his team to measure different qualities and environmental factors: the location in the greenhouse the plant grew in, the density of the leaves, and the effects of different temperatures, for example.
“It’s everything, anything you can really think of,” said Kenkel, who studied plant physiology at Bowdoin College.
Jungle Aims To Supply 2000 Supermarkets In The EU By 2025
Jungle is a vertical farming company that first began in a 15-square meter container installed near a supermarket in Lisbon, Portugal
Expanding Throughout France,
With Another Two Farms
In The Pipeline
“In France, associating technology to food production can be challenging since the country has a really strong agricultural culture. We figured that if we manage to succeed in France, then we can do it anywhere,” says Gilles Dreyfus, President & co-founder at Jungle.
Jungle is a vertical farming company that first began in a 15-square meter container installed near a supermarket in Lisbon, Portugal. However, founders Gilles Dreyfus and Nicholas Séguy both dreamed of establishing the company in France due in part to the challenges posed by the French agri-food sector.
In March 2021, Jungle announced that it had raised €42 million to expand across the United Kingdom and Europe, with plans to supply more than 2,000 points of sale by 2024.
Gilles Dreyfus
Expanding throughout France
By Q2 of 2022, Jungle plans to have an even larger production facility in southern France, in close proximity to the food distribution and logistics centers. Next to that, the company has another farm in the pipeline at an unknown location. “We’ll be delivering our products to the supermarkets’ logistics centers and they will deliver it to their stores. We won’t be delivering store-to-store, which further reduces our carbon footprint,” says Gilles.
After spending 2.5 years researching the optimal growing recipes, Jungle partnered with a French retailer in Lisbon and built its team in Lisbon over the course of three years. In Portugal, Jungle expanded from being available in one store to ten stores. Despite the obvious market opportunities in Lisbon, Gilles explains that a primary inconvenience of establishing a vertical farm in Lisbon is the distance from consumers, with the country’s 10 million people being dispersed across the country which makes it more difficult to tackle a large consumer base. In contrast, Paris’s metropolitan area has roughly 14 million people.
First Lisbon, then France
Jungle’s productivity in Lisbon paid off, as the company soon attracted the interest of major French retail chain Monoprix in mid-2019. In response, Gilles and Nicholas created Jungle France in August 2019 and began with a small unit as a pilot project in January 2020. After demonstrating impressive KPIs over a few months, Jungle signed an agreement with Monoprix in October 2020 to supply 120 stores.
Jungle France has secured its first farm location in Château-Thierry in September 2019. roughly 80 km from Paris. The Château-Thierry farm has a total footprint of 3,800 m2, of which half is dedicated to growing while the other half is used for germination, equipment washing, packaging, delivery and administration. The floor area for cultivation is thus roughly 1,800 m2 and the room is 10 m tall, bringing the net production area to 5,500 m2, according to Gilles.
Bringing vertical farming to France
As Gilles mentions, establishing a vertical farm in France can be challenging due to the strong agricultural culture in the country, which has somewhat disfavored hydroponics and alternative forms of agriculture. This has not made marketing impossible for Jungle; rather, the company has simply taken different approaches to ensure that their products are understood and accepted. One of the key elements of Jungle’s approach has been to remain humble and not attempt to completely revolutionize the agricultural sector.
“Our branding doesn’t focus on the fact that our products have been grown vertically; we’re not trying to hide anything, but our market research has shown that highlighting technology isn’t always appealing to the customers,” says Gilles.
He compares it to the introduction of organic agriculture in the 1980s, which was poorly received and took several decades to be widely accepted as environmentally superior to conventional agriculture.
Jungle's products
“Nowadays, information travels much faster so the time taken to educate the population about vertical farming is much shorter, maybe 4-5 years. But Jungle’s position is not to educate people; it is to produce healthy plants on an industrial level and at reasonable prices for the masses. So for marketing and branding, we have taken a simple route,” explains Gilles.
In supermarkets, Jungle products are sold in company-provided displays. So far, the reception has been good as people are beginning to understand the benefits of vertical farming with respect to efficient energy and water use, lack of pesticides, and overall environmental sustainability. According to Gilles, it also helps that Jungle products are roughly 20% less expensive than their organic counterparts.
More partnerships and avenues ahead in 2021
While Jungle currently produces herbs, salads, microgreens, and flowers, the company is planning to expand its portfolio and its consistent research on different vine crops. Jungle is also excited about impending partnerships that will be announced in the coming months, which will allow the company to further expand its client base and possibly access cosmetic industries.
For more information:
Gilles Dreyfus, Co-Founder
Jungle
gdreyfus@jungle.bio
www.jungle.bio/old-home
Publication date: Tue 25 May 2021
Author: Rebekka Boekhout
© VerticalFarmDaily.com
USA: Vertical Harvest Maine And Sodexo
In a partnership announced last week, Sodexo, also one of Maine's largest employers, committed to serving our produce on collegiate campuses from Canadian border-hugging Fort Kent to South Portland
Vertical Harvest Farms is thrilled to announce a partnership with Sodexo, a global food service provider, to source as much as 80-percent of its lettuce products from our new Westbrook, Maine farm. The 70,000-square-foot farm, scheduled to break ground later this summer, will grow over 1-million pounds of greens.
In a partnership announced last week, Sodexo, also one of Maine's largest employers, committed to serving our produce on collegiate campuses from Canadian border-hugging Fort Kent to South Portland. "The partnership with Vertical Harvest will be a game-changer for Sodexo’s ability to buy fresh produce twelve months per year,” says Varun Avasthi, Director of Strategic Partnerships, Sodexo.
Read the story on our blog by clicking the button below.
Read Now
CANADA - MONTREAL: Indoor Farming Technology Seeks To Localize Agriculture
“The goal is to have the first crops in the system in August of this year,” Zeman said. “It’s going to take a pretty serious pull from everyone involved to get us there.” Whereas traditional agriculture grows in outdoor fields or gardens, Interius Farms uses hydroponics and vertical farming to grow plants indoors, offering a climate-controlled environment and artificial lighting in place of sunlight.
A Canadian company is pioneering new technology for growing produce indoors, utilizing hydroponics to provide year-round, cost-effective food production. Interius Farms, based in Montreal, developed the innovative system as a means to localize agriculture in a country where fresh produce is imported at least seven months a year from other parts of the U.S. and North America.
Founded in 2018 by longtime friends Jonnie Lawson and Tristan Zeman, the company is taking vertical farming to the next level with its 8-foot rotating rack design—exposing plants to a single light fixture saving on both space and energy demand.
More efficiency
While the project is currently in its beta stage, Interius Farms is ambitiously ramping up to commercial scale, moving into a 14,000-square-foot facility to grow leafy greens, including lettuce, kale, cilantro, parsley, and basil.
The rotating rack eliminates the need for additional lighting systems, maximizing energy efficiency. Zeman said the system requires 40-80% less lighting and 92% less land than traditional agriculture. The original proof of concept was done in the corner of Zeman’s Chicago apartment. Now, he said they are zeroing in on a commercial facility where Interius Farms can grow a significant amount of food. “5,000 square feet of growing space produces over a million heads of lettuce,” he said.
Growing with hydroponics is inherently more expensive, Zeman said, with higher costs of inputs. He knows they cannot compete on direct cost with field lettuce. However, where the technology proves especially valuable is how it insulates against seasonal price fluctuations of produce and other shocks in the supply chain, such as disease outbreaks and natural disasters in other parts of the world.
Collaboration
Interius Farms is also working with urban-gro, a Colorado-based company that focuses on engineering efficient and profitable controlled environment agriculture facilities. Though urban-gro is traditionally rooted in cannabis, the business is expanding its expertise to work with innovators in other areas of farming. “We are excited to be working with Interius Farms and their innovative and patented approach to growing fresh and sustainable foods for the Canadian market,” said Jim Dennedy, urban-gro’s president and chief operating officer.
The mission of Interius Farms, according to Zeman, is to localize Canadian agriculture through its platform. Buyers will have access to locally grown food even in harsh winter months while at the same time giving themselves an “insurance policy” against volatile prices caused by supply chain disruptions.
“We offer a fresher and more sustainable product, and we introduce price and business sustainability into the Canadian food market, especially in those import months,” Zeman said.
Seasonal fluctuations can increase the price of field lettuce by as much as 85% during the non-growing months, Zeman said. “When the vast majority of the Canadian supply chain in the winter is coming from the American Southwest, you’re very exposed, and you’re not getting very high-quality produce by the time it’s been shipped up here,” Zeman added.
The fresh produce
More control
Looking ahead, Zeman said he has heard from some consumers who question whether indoor agriculture produces healthy, natural food. That is a perception the company will battle, he said, though he points out Interius Farms can offer enhanced traceability with its design. “Everyone wants to know exactly where their food came from,” he said. “And we can tell you, from the seed, exactly what nutrients it has received. For every second of the plant’s life, we can tell you exactly what the plant has received, whereas if you’re in the field, many factors are out of your control.”
Over the next six months, Zeman said Interius Farms and urban-gro will be joined at the hip, testing their commercial facility’s design, vendors, lighting fixtures and other options. “Through our engagement with urban-gro, we gain the advantage of supplementing our internal expertise with the urban-gro team that has spent decades working with complex systems. We can rely on urban-gro to guide us in developing the right solutions for our unique application. The ultimate goal is to be in that facility, to have that anchor customer—which we feel like we’re very close to having in place—and growing very soon in our first facility,” Zeman said.
Lead photo: From the left: Brady Deslippe (Chief Technology Officer) and Tristan Zeman (Founder/President)
For more information:
Publication date: Thu 27 May 2021
Author: Andrea Di Pastena
© HortiDaily.com
Noor III is The Newest Stage of The Ouarzazate Solar Power Station in Ouarzazate, Morocco
The Noor III CSP tower can produce and then store enough energy to provide continuous power to the surrounding area for ten days
Noor III is the newest stage of the Ouarzazate Solar Power Station in Ouarzazate, Morocco. This site utilizes a concentrated solar power (CSP) tower design with 7,400 heliostat mirrors that focus the sun’s thermal energy toward the top of an 820-foot-high (250 meters) tower at its center.
At the top of the tower, there is molten salt, which is used in this process due to its ability to get very hot (500–1022°F / 260–550°C). The molten salt then circulates from the tower to a storage tank, where it is used to produce steam and generate electricity.
The Noor III CSP tower can produce and then store enough energy to provide continuous power to the surrounding area for ten days.
–
31.059494°, -6.870344°
Indoor Ag Science Cafe’s Latest Video Checks Out How To Turn A Smart Phone Into A Sensor
Dr. Krishna Nemali, Assistant Professor and Extension Specialist at Purdue University, has developed an easy-to-use, affordable smart sensor that’s proving valuable to indoor farmers for improving farm productivity and crop quality
Purdue University professor turns smartphones into smart sensors
Dr. Krishna Nemali, Assistant Professor and Extension Specialist at Purdue University, has developed an easy-to-use, affordable smart sensor that’s proving valuable to indoor farmers for improving farm productivity and crop quality.
Using only a smartphone and a connection to Dr. Nemali’s apps, users can quickly and precisely monitor/measure a wide variety of production and growth parameters including light efficiency, germination rate, plant size (area, height, weight), color (intensity, progression), damage (nutrient deficiency, insect), biochemistry (chlorophyll, nitrogen and other micronutrients), and stress index.
Dr. Nemali plans to make his smart sensor tool available in January 2022 for a nominal annual fee, which will support the development of future applications.
For more information: http://scri-optimia.org/showcafe.php?ID=111113
Indoor Ag Science Café is an outreach program of the OptimIA project, funded by the USDA SCRI grant program.
Interested parties can join the free café forums, live or recorded (http://www.scri-optimia.org).
The café forum is designed to serve as a communication platform among scientists and indoor farming professionals.
Indoor Vertical Farming Startup Bowery Farming Raises $300 Million
Vertical farming grows its produce in stacked arrangements in technologically controlled environments, reducing the need for vast expanses of land and bringing mass production right in to urban areas
MAY 25, 202
(Reuters) - New York-based indoor vertical farming startup Bowery Farming said on Tuesday it raised $300 million in its latest funding round, valuing the company at $2.3 billion as the pandemic shed light on the importance of securing the local food supply.
Vertical farming grows its produce in stacked arrangements in technologically controlled environments, reducing the need for vast expanses of land and bringing mass production right in to urban areas.
While the new industry has struggled to break even in the past, the drop in technology costs, such as LED lights, is changing the economics and fueling investor interest.
According to PitchBook data, nearly $1.9 billion of global venture capital was invested in indoor farming in 2020, nearly tripling investment in 2019. (Graphic: Global VC Funding in Indoor Farming, )
Bowery’s latest funding round, led by Fidelity Management & Research Company LLC, would be the largest vertical farming deal on record, based on previous such deals listed by PitchBook.
The company’s leafy greens are sold in over 800 grocery stores and it has two commercial farms in New York and Maryland, and a third coming online this year in Pennsylvania, said Irving Fain, Bowery’s CEO and Founder. Fain said the products are the same or lower in price than their organic rivals, but declined to say whether Bowery was selling them at a profit.
“The real benefit of what we’re growing at Bowery is, first of all, it’s completely pesticide-free,” said Fain, adding that a large part of the power used for the farms is renewable with an aim to eventually make it fully renewable.
He said the new funds will be used to expand farms across the United States, looking for global expansion opportunities, and developing new crops and technology to grow things like strawberries, tomatoes, and carrots indoors and near consumers as well.
Bowery’s investors include GV, formerly known as Google Ventures, General Catalyst, GGV Capital, and Temasek.
Reporting By Jane Lanhee Lee; Editing by Sam Holmes
Image Credits: Bowery Farming
Our Standards: The Thomson Reuters Trust Principles.
RSVP - Indoor Ag Science Cafe June 1st
Indoor Ag Science Cafe is an open discussion forum, planned and organized by OptimIA project team supported by USDA SCRI grants
June Indoor Ag Science Cafe
June 1st Tuesday 11:00 AM Eastern
Please sign up, thank you!
"All Season Oishii Berry:
America's first vertical strawberry farm"
by Hiroki Koga
Oishii
Please register to receive your Zoom link.
The recording will not be available for this cafe.
Indoor Ag Science Cafe is an open discussion forum, planned and organized by OptimIA
project team supported by USDA SCRI grants.
Register here
Purpose At Work: How Square Roots Is Growing A Sustainable Food Movement
How can we reduce the climate impacts of our food system? How can we get the freshest produce to people in urban areas? How can we offer fulfilling jobs to today’s youth? These are all issues that Square Roots is working to address
May 24, 2021
Purpose At Work: How Square Roots Is Growing A Sustainable Food Movement
PHOTO PROVIDED BY SQUARE ROOTS
How can we reduce the climate impacts of our food system? How can we get the freshest produce to people in urban areas? How can we offer fulfilling jobs to today’s youth? These are all issues that Square Roots is working to address.
“The mission of the company is to bring locally grown food to people in cities, all across the world while empowering the next generation of leaders in urban agriculture,” Tobias Peggs, Co-founder, and CEO of Square Roots, tells We First.
The agriculture startup’s modular and technology-first design is transforming how food is grown and distributed in amazing ways. The scalability and data-driven approach make Square Roots an excellent example of a company demonstrating how to scale business growth and impact.
Founding story
Before Square Roots, Tobias received a Ph.D. in machine learning and had worked for a number of successful startups, one of which was acquired by Walmart. “I worked as a data scientist there for a year. One of the projects they had me do was study global grocery buying behaviors.” With around 300 million customers, Tobias had a massive amount of data to pull insights from.
“That's a lot of bananas flying all over the world,” he says. “You begin to think about the impact of transportation on the planet. “As food is traveling, nutrients are breaking down and maybe the quality of food isn't as good at the end of long supply chains as it would be for local food. Customers don't have any idea of where that food comes from. The sense of community around food was just lost.”
MORE FOR YOU
Vertical Indoor Farms Make Sense
The insights Peggs was having lit a spark in his entrepreneurial engine. “People want food from all over the world. That's not going to change,” he says. “Instead of shipping food, how about we ship environmental data from one part of the world to the other?” By collecting data on the best growing conditions, Tobias could hypothetically grow anything at any time of year in a controlled indoor environment made from repurposed shipping containers and deliver that to a nearby retail store on the day it’s picked. “It looks and smells amazing, which also means all the nutrients are intact,” he says. “That was the idea behind Square Roots.”
Peggs cofounded the company with Kimbal Musk, “He would say, ‘Can it feed the world? And are we going to make a massive positive impact? If so, let's figure out how to get this done,’” Peggs recalls. The two innovators began by working together in a WeWork office. “With the experience of being involved in a number of startup companies before—some successful, some failure—I know for sure that if you don't get started, you're going to fail.”
In the two-man brainstorming sessions, Peggs and Musk would visualize the business at scale. “We saw these modular farms in every city across the world. That is the way that we're able to think about feeding every consumer on the planet with locally-grown food,” Peggs says. “There was a missing piece of the puzzle. There wouldn't be enough farmers to hire to staff all of those farms.” That realization was the foundation of the second pillar of Square Roots’ purpose, “To provide pathways for young people to come into the farming industry and become the future leaders,” he shares.
Leading with purpose
Purpose At Work: How Square Roots Is Growing A Sustainable Food Movement
PHOTO PROVIDED BY SQUARE ROOTS
Square Roots’ core business was structured to address some of the world’s biggest challenges. Food is interconnected with climate, which also poses risks on outdoor crops. It is also fundamental to public health and prosperity. As the global population rises, our planet’s carrying capacity will be tested. We need to innovate to meet that rising global demand for food.
The model relies on able-bodied young people to tend to the crops. The talent pool of skilled farmers in the U.S. is aging. The average farmer is 58 years old. “Who the hell is going to grow all the food when our current farmers retire in five or 10 years’ time? ” Tobias proposes. “We had to figure out a way to bring young people into the industry and train them quickly so they could be not just productive farmers, but feel infused about a career in a completely new industry.”
To overcome the hurdle, the founders developed hardware, software and teaching methods. “We had an investment banker who was bored sitting behind a spreadsheet all day. He quit his job to join Square Roots because he wanted to make an impact on the world. He was growing the most delicious kale, you've ever tasted in your life,” Peggs says. “That was six months after making the transition, it was magic to see that.” Within a year they trained 10 people, many with no previous farming experience.
In addition to creating purpose-driven employment opportunities, Square Roots is addressing climate through transportation and waste. “Forty percent of food from industrial systems is wasted. We waste around 3%,” Tobias says. A significant portion of wasted food is discarded before it even hits the shelf, due to damages during shipping or spoiling quickly. “Because we're indoor, there's a lot of precision, a lot of control. We can grow food for demand.”
Modular design
Square Roots’ structure allows it to be replicated and optimized from a systems approach. It's a distributed model. “We deploy clusters of these modular farms together so there's some operational scale and the business economics work,” Peggs explains. “Each farm serves its local market and runs its own independent business entity, set on top of a standard technology platform.” Every compound grows, harvests packages and delivers produce to local retailers. “We look after everything from seed to shelf.”
The growing startup has set up operations in Brooklyn, New York, and Grand Rapids, Michigan with plans for expansion across the Midwest, the North East in cities around the world where demand is large enough. People can see inside the shipping containers and when Covid-19 is under control, you can schedule a farm tour. “While its a very scalable platform, the consumer experience is a hyper-local one.”
Leveraging data & technology
When it comes to deciding what to grow, Square Roots focuses on crops that require the least amount of energy. “Walk into a supermarket. Lineup every single fruit and vegetable from the lightest to the heaviest. And that's essentially our product roadmap for the next 20 years,” Peggs says.
They also choose crops based on economic yields based on competitive market prices. “This is where data science and technology marry,” Tobias says. “Outdoor farmers can’t suddenly look at the sun, make it twice as efficient and reduce costs or double their yield. Indoor farmers can.”
Integration of AI machine learning empowers Square Roots to optimize at scale. “We're building a network of cloud-connected modular farms,” Tobias says. The company monitors and collects data from each of those farms every second. “We’re looking at temperature, humidity, nutrients, yield, taste and texture,” Peggs says. “ If in one particular box, a farmer did something or we changed an environmental parameter that increased yield or improves efficiency, we can spot that information from the data and push that new instruction out across the whole network. The whole network is learning how to farm better as we go about building the business.”
Building community
Food has the potential to unite people. While Square Roots farms are indoors, they connect and share knowledge with outdoor farmers. “ I'll give you an example,” Tobias says. “A good technique in organic farming is known as integrated pest management, where a farmer might release beneficial insects onto the crop, essentially ridding the nasty insects that we don't want. We use that technique inside the farm.”
“The farmers that we work with are very much on the same mission, which is how do we get people more connected with where their food comes from? How do we build that sense of community around food? And I think the common enemy is the industrial food system,” Peggs says. That common enemy also resonates with employees, consumers and other key stakeholders who join together around a set of core values.
“I know pretty much every founder or CEO of every indoor farming company. There's remarkable alignment around that mission,” Tobias says. “Everybody understands that we've got to change the food system and if we're helping each other out, it's better for all of us,” Tobias mentions companies like Gotham Greens and Oishii that are also innovating in the indoor farming space.
Purpose also informs Square Roots’ investor strategy. “We’re a venture-backed company. When we're talking with investors, we want to make sure that they're mission aligned. I can’t tell you how many investors have talked to me about considering cannabis. It’s not aligned with our mission.” A lot of people don't realize that the power of purpose is just as compelling in terms of what you don't do, as opposed to what you do.
The takeaway here is that building your community around shared purpose fosters goodwill amongst team members and customers. It also presents collaborative opportunities with other brands and organizations working towards the same goal.
Challenges and opportunities
With the opaque information in the industrial food system and increased health consciousness, consumers are looking for transparency. In addition to its open invitation to check out the farms, the company includes a QR code on each product. You can scan the code and learn all about where it's made and the value chain.
Purpose At Work: How Square Roots Is Growing A Sustainable Food Movement
PHOTO PROVIDED BY SQUARE ROOTS
Covid-19 has also presented challenges for businesses across sectors and Square Roots is no exception. Before the pandemic, they trained new hires to be farmers in classrooms. “If we didn't have our mission, it would have been easy to say, ‘We got to keep growing, forget this farmer training stuff. We're just going to go hire experienced people.’ Or we could have developed a robot to do part of the job of a farmer,” Tobias says.
“The mission allowed us to focus on solving issues with our current business model,” he continues. “It was already misaligned. Everyone was able to get behind it very quickly. And we were actually able to solve problems and put in place new programs and new policies ridiculously quickly. Never waste a good crisis.”
Despite adversity, the startup has started true to its mission and transitioned to digital and socially distanced training, and built a more robust system than before.
The future of food
Technology and data are a critical aspect of emerging agriculture trends. “Food is a $12 trillion industry,” Peggs states. “There's about 20 companies that have raised a bunch of money and are doing this stuff in America.”
“Indoor farming actually reminds me of the internet in the early '90s,” he says. “We know this thing is inevitable, but no one can quite yet tell you what shape it's going to take in the future. Indoor farming is like that. We're all helping each other figure out how this eventually feeds every consumer in the world.”
While innovation is budding, “The food system has to become a lot more responsible and sustainable,” Peggs says. “The current food system cannot feed the new future world, which has 10 billion people, 70% living in urban areas that are not near these industrial farms.”
We’ve seen changes over the last two decades with the organic food movement, which now grosses $25 to $30 billion annually, Tobias says. He thinks that Covid-19 will accelerate the shift towards healthy and sustainable food. “People were forced to stay at home and cook. You get more curious about the food that you're buying, and you observe how long it lasts in your refrigerator. You get more educated,” Tobias says. “We are in the first inning of indoor farming. We're just getting started.”
Lessons for entrepreneurs
With his experience from Square Roots and beyond, Tobias Peggs’ insights offer valuable lessons for entrepreneurs looking to Lead With We. Here are three teachings from Peggs on how to build a successful startup.
“Be prepared to be told, "No, we're not interested."
“You have to be a bit of a missionary and sign up for having a lot of stamina. Just be consistent with the drumbeat that this idea—no matter how crazy it might seem—you can do it.”
“There are going to be bumps in the road, there are going to be things that don't go quite right. If there's a shared purpose articulation of what the mission is, you move through those things and you make it happen. Purpose is a very powerful multiplier.”
Simon Mainwaring is the founder and CEO of We First, a strategic consultancy that accelerates growth and impact for purpose-driven brands by putting 'We' first. I specialize in brand strategy, culture building and impact storytelling for startups, high-growth companies, and Fortune 500 corporations. My national podcast is LeadWithWe.com on Spotify, Google and Apple. My book, We First: How brands and consumers use social media to build a better world is a New York Times, Wall Street Journal, and Amazon bestseller, and strategy+business named it the Best Business Marketing Book of the Year. I deliver keynotes, training, and workshops that help brands define, integrate and activate their purpose to drive growth and scale impact.
Visit SimonMainwaring.com for speaking and WeFirstBranding.com for consulting
A Lot of Promise’: Vertical Farming Takes Root In Virginia
Since its inception at the turn of the millennium, vertical farming — which in its simplest form is any system where plants are grown in vertical stacks — has promised to revolutionize yields by allowing producers to multiply their crop outputs by six to eight or even more times without expanding their footprint
May 24, 2021
Imagine a field of lettuce.
Say the lettuces are all buttercrunch, and they dot the field like crisp rosettes. Each has been seeded by a farmer, kept free of pests, watered for weeks, and finally cut at the base before being rinsed and packed for transport. Each is destined for a different meal: a lazy evening salad on the porch, an artfully arranged plate at a restaurant two-top, the vegetarian alternative at grandma’s 80th.
Now imagine six of these fields, all stacked on top of one another.
The idea isn’t far-fetched. In fact, it’s already a reality in Virginia, where a new, more technologically oriented form of agriculture known as vertical farming is quietly taking root.
“There’s a lot of promise,” said Tony Banks, senior assistant director of agriculture, development, and innovation for the Virginia Farm Bureau Federation. “As we continue to watch urban encroachment and we have this demand to have food produced closer to where people actually live, we’re going to see more and more of it.”
Since its inception at the turn of the millennium, vertical farming — which in its simplest form is any system where plants are grown in vertical stacks — has promised to revolutionize yields by allowing producers to multiply their crop outputs by six to eight or even more times without expanding their footprint.
“You’re trying to use an area more intensively. Because you’re limited by horizontal space, you want to maximize vertical space,” said Leonard Githinji, a professor of sustainable and urban agriculture at Virginia State University who also works with Virginia Cooperative Extension.
The concept is flexible and scalable. The stacks can be small, nothing more than a narrow shelf installed at a restaurant or in a convenience store to grow produce within a customer’s reach. Or they can fill a warehouse, bringing an industrial dimension to agriculture.
“There’s a wide range. On one end, it’s almost you have a greenhouse that’s highly automated,” said Banks. “On the other end, you could be in a warehouse and everything is grown on huge assemblies of racks and you have complete artificial lighting and hydroponics.”
The latter type of vertical farming is “high-tech manufacturing, essentially,” said Scott Lowman, director of the Controlled Environment Agriculture Innovation Center at the Institute for Advanced Learning and Research in Danville, where scientists and other experts are exploring the promise of various types of indoor agriculture can hold for Virginia.
Hopes are high, particularly in the historic tobacco region of Southside, where state officials have been working for several decades to encourage farmers who once depended on the golden leaf to diversify their enterprises. It’s no accident that the Controlled Environment Agriculture Innovation Center was sited in a region with a rich agricultural history and an abundance of old warehouses once devoted to tobacco and now empty.
Nor was it an accident that in 2019, Gov. Ralph Northam’s office announced that vertical farming company AeroFarms had decided to build a $42 million facility in an industrial park jointly operated by Danville and Pittsylvania County. Virginia aggressively courted the project with some $1.5 million in state grant funds and incentives. In exchange, AeroFarms promised to build the facility, employ 92 people and purchase roughly $20 million of Virginia agricultural or forest products.
But while AeroFarms’ Virginia location will be the largest vertical farm in the state once built, it won’t be the only one. Over the past few years, other operations have quietly been putting down roots. Shenandoah Farms in Rockingham operates a large-scale facility that grows herbs and lettuces. In Lorton, Beanstalk grows a range of greens. Fresh Impact Farms in Arlington, which grows herbs, greens, and edible flowers, announced an expansion this spring in conjunction with the governor’s office. Babylon Micro-Farms in Richmond is developing sophisticated technology to spread small-scale vertical farms around the country. Other efforts are underway.
“We’re in a great position on the East Coast in terms of population centers,” said Lowman. “And it’s a friendly environment for business, and we have a legacy of hard-working labor.”
Controlled environment agriculture
While vertical farming is relatively new, its lineage is much longer, nesting within the family tree of controlled environment agriculture, which encompasses any type of production that takes place within a structure.
From Roman orangeries to modern-day greenhouses, controlled environment agriculture offers the advantage embedded in its first descriptor: control.
Outdoors, farmers are at the whim of the weather, plagued by pests and disease, and caught in a never-ending struggle to keep water and fertilizer confined to their fields.
Indoors, the equation changes. Because of the precision-engineered systems, controlled environment agriculture tends to require less water, less fertilizer, and few or no pesticides compared to conventional agriculture. And, depending on a particular system’s design, it can allow producers to grow crops 24/7, 365 days a year. AeroFarms has said that its technology allows it to produce leafy greens “at a rate 390 times more productive than field-grown plants.”
A vertical micro-farm known as a cropbox. (Virginia State University)
“I can now schedule my crops,” said Michael Evans, director of Virginia Tech’s School of Plant and Environmental Sciences. “I can basically optimize the environment for that crop.”
There are, of course, drawbacks. Everything nature once provided to a plant must now be provided by a human — or a machine.
“With a greenhouse, you’re taking advantage of natural sunlight. You’re not paying for that,” said Evans. “But you’re paying quite a bit for heating and cooling. When you flip to an indoor vertical system, the disadvantage is that now you have to supply the light.” Other costs diminish at the same time: without the translucent walls of a greenhouse, “your heating and cooling can go down because it’s better insulated.”
For years, prohibitively high energy costs boxed out vertical farming as a viable option for producers working in controlled environment agriculture. What would change the playing field was a technological innovation: the high-powered and highly efficient LED.
“The thing that really changed that made indoor vertical farming work and become an economic possibility was really the development of LED lighting, because that changes the energy equation a lot,” said Evans. “It makes providing the light the crops need much economically viable.”
A new generation of farmers
Despite its promise, vertical farming won’t replace conventional agriculture, experts say. Many of Virginia’s biggest commodity crops — soybeans, corn, hay — are grown at such a large scale that trying to transport them indoors would be an exercise in absurdity.
Where controlled environment agriculture has found a growing niche is in the produce most familiar to the average Virginian: lettuces, herbs, tomatoes, cucumbers, peppers, herbs, microgreens, and more. Experiments in growing strawberries indoors are also underway, and Evans pointed out that once legalized, marijuana may not be far behind, although the federal government’s continued classification of the plant as illegal will keep institutions like Virginia Tech from working with it.
For consumers of these products, the idea of local food grown only a short distance away is increasingly appealing. That can be an argument in favor of controlled environment agriculture and vertical farming, said Banks.
“When we import food into this country, what we import is fruits and vegetables that require a lot of hand labor,” he said. “So there’s opportunity there to offset some of those imports and reduce our reliance on food produced overseas.”
Both Banks and Evans also noted an unusual aspect of vertical farming: its allure for younger and often more urban Virginians.
“It’s getting a whole new generation of folks interested in agriculture. It’s a different type of agriculture, but it’s getting a lot of students,” said Evans. At Virginia Tech’s School of Plant and Environmental Sciences, he added, “we have to change our curriculum for what we’re teaching to prepare students interested in controlled environment agriculture.”
For a younger generation increasingly concerned with social and political justice, the opportunity offered by controlled environment agriculture and vertical farming to fill food deserts and involve local workers in local food systems is an attractive prospect. Many students are eager to look beyond the existing agricultural structures, said Githinji, who recently received a $600,000 grant from the U.S. National Institute of Food and Agriculture to explore the use of “micro-farms,” which incorporate vertical farming systems, as a way to address food deserts in urban neighborhoods.
It’s not unusual for extension agents to get calls in which people are saying, “‘As much as I want to grow more food, I can’t afford to buy even another quarter acre,” he said. “So you get people asking what they can do with what they have.”
The other draw is the technology. While vertical farming can be small- or large-scale, its larger applications rely on evolving and increasingly sophisticated technology that has piqued interest among the startup community.
“This is a really exciting industry that’s rapidly entering the mainstream,” said Alexander Olesen, CEO, and co-founder of Babylon Micro-Farms, a Richmond-based startup that develops indoor growing systems for institutional food service settings, such as hospitals, schools, and universities. Babylon, which in 2020 was the recipient of a $75,000 grant from the Commonwealth Research Commercialization Fund that aims to support small businesses in emerging research and technology sectors, builds small-scale vertical farms “as a sustainable amenity for these locations.”
The field’s growing popularity is also driving a need for more workers, more expertise, and more training, said many of the people interviewed for this story. The Controlled Environment Agriculture Innovation Center in Danville, itself a recipient of $365,000 in state grant funds in 2020, is key to that effort. So too are plans announced by the governor’s office last month that will see hydroponic greenhouse startup Sunny Farms build a 1.2 million square foot greenhouse in Virginia Beach — one of the largest on the East Coast — and work with Virginia Tech and the Virginia community college system to develop educational training in controlled environment agriculture.
“Our goal is really to support the controlled environment agriculture industry in Virginia, but we’re also working on creating an innovative controlled environment agriculture ecosystem in Virginia,” said Evans.
These enterprises may be only the beginning.
“Once people see that it’s working, we’re going to see them flourishing all across the commonwealth,” said Githinji.
Lead photo: Controlled digital lights help produce high-density feed grass in a Grov Olympus vertical farming machine in Utah. The Olympus Tower Farm uses a controlled environment to grow sprouted wheat and barley grass in 857 square feet of space and uses 95 percent less water to produce 5,000 to 6,000 pounds of grass per day, replacing 35-50 acres of land. (Photo by George Frey/Getty Images)
Sarah covers environment and energy for the Mercury. Originally from McLean, she has spent over a decade in journalism and academic publishing. Most recently she covered environmental issues in Central Virginia for Chesapeake Bay Journal, and she has also written for the Progress-Index, the Caroline Progress, and multiple regional publications. In 2017, she was honored as one of Gatehouse’s Feature Writers of the Year, and she has been the recipient of numerous awards from the Virginia Press Association. She is a graduate of the College of William & Mary. Contact her at svogelsong@virginiamercury.com
Blue Radix & Ecoation Join Forces With The World's 1st Autonomous Find & Fix Solution
May 19, 2021, Rotterdam, Netherlands and North Vancouver, Canada
Blue Radix, an independent Dutch AI-tech specialist for the international greenhouse industry, and Ecoation Innovative Solutions Inc. (ecoation), a Canadian developer of automated greenhouse management and crop health monitoring technologies, have signed an agreement.
The collaboration aims to identify new ways to automate decision-making and action in the greenhouse, using vision technology and algorithms. ecoation and Blue Radix are using the data collected by ecoation’s OKO and platform to enhance the impact of Blue Radix’ algorithms for autonomous growing. By combining data sets, algorithms, and analytical efforts the companies are able to create new insights and applications that help growers worldwide to improve their crop strategy, quality and yield.
Blue Radix and ecoation look forward to ongoing collaborative efforts where the duo explores the multitude of innovation opportunities that become available when you combine ecoation’s OKO and platform with Blue Radix’ Crop Controller. Collaborating across data and algorithms has the potential to create value across many avenues, including optimizing crop strategy, autonomous steering, IPM enhancement, and understanding spatial climate distribution.
The World’s 1st Autonomous Find & Fix Solution
The first project the duo is working on is enhanced autonomous growing with crop data visualization. ecoation’s OKO collects sensory data and information about climate, integrated pest management, and crop work at every row and post to an SqM granularity. These insights greatly contribute to a complete and accurate view on the state of the crop. The broad range of data points, including fruit count, fruit colouring, and stem density, will be combined with the smart steering algorithms of Blue Radix’ Crop Controller. Crop Controller will actively, continuously and autonomously control the greenhouse conditions with the grower’s crop strategy as its starting point and the optimal crop status as its goal. E.g. by optimizing the plant load, plant stress is reduced avoiding weak plants that are vulnerable to pests and diseases. In this way ecoation and Blue Radix find and fix imperfections before they impact yield or crop quality.
Support growers
“Collaborating with Blue Radix means pioneering the future of ag more effectively, at a pace that would be difficult to reach if we carried on separately,” shared ecoation CEO Dr. Saber Miresmailli. “Both teams are committed to the same goal: to support growers in making the best possible decisions. Working together means unlocking new ways to get the most from the data and providing better insights to our customers that inform their decisions.”
“Ecoation offers solutions which are important components in a fully autonomous greenhouse. Optimization and steering with algorithms depends on high quality data and a robust crop strategy. Vision technology and enhanced analytics from ecoation provides this data and the necessary input to improve the grower’s crop strategy even further,” emphasizes Blue Radix CEO Ronald Hoek. “We strive for open collaboration and partnerships. Growers should always be able to choose freely what they want to do with their data and benefit from the best combination of services & products for their greenhouse.”
The duo will only work with greenhouse data retrieved from the customers of ecoation and Blue Radix who provide full consent. Transparency and data security is paramount, and this collaboration will rely on growers who are looking to optimize their greenhouse operations with autonomous processes and are interested in contributing to the future of ag with their facility data and insights.
About Blue Radix
Blue Radix is an independent Dutch AI-tech specialist for the international greenhouse industry. Blue Radix creates solutions with artificial intelligence for daily decisions and actions in greenhouses. Greenhouses offer an efficient way to produce food and flowers in a sustainable manner. But the number of skilled people with expertise of growing crops in greenhouses is declining every year. This has a direct and negative impact on yield, costs, continuity, and product quality. Blue Radix offers solutions for these challenges: smart algorithms which optimize and steer climate, irrigation, and energy continuously and autonomously, supported by off-site
Autonomous Greenhouse Managers. Blue Radix offers growers a digital brain for their greenhouse. More information at blue-radix.com. Find Blue Radix on LinkedIn, Twitter, and Instagram.
About ecoation
ecoation is an award-winning grower-centric platform that combines Human knowledge and experience with Machine precision and automation to increase operational visibility, assist growers, and enhance their decisions. Commercially available since September 2019, ecoation products can be found in greenhouses across the United States, Canada, Mexico, and Europe. With an experienced team of 60+ growers, scientists, engineers, and business professionals from all over the globe, ecoation is passionate about enabling a cleaner future and supporting growers in making the best possible decisions. At ecoation, we are on a mission to empower growers because we believe in doing so, we win together.
More information at ecoation.com. Find ecoation on LinkedIn, Twitter, and Instagram.
For media inquiries, please contact:
Blue Radix
Marijke van Rongen
Manager Global Marketing & Communications
marijke.vanrongen@blue-radix.com
+31 6 53 43 38 39
ecoation
Marketing and Media Contact
Cameron Lust