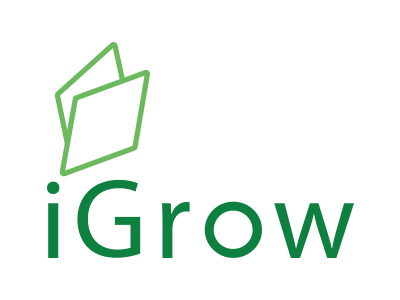
Welcome to iGrow News, Your Source for the World of Indoor Vertical Farming
A Couple of Showrooms In Europe Need To Get The Ball Rolling For Verde Compacto - Shipping Container Farm
"People Are Immediately Enthusiastic When They See It"
"People Are Immediately Enthusiastic When They See It"
He, partly joking, calls himself ‘a born and raised’ city dweller from the heart of Amsterdam: Olivier Kappetein. As a representative of Mexican vertical farming company Verde Compacto in Europe, this is not ideal; will people be willing to listen to him given his background and his not yet widely undisputed product?
"Unfortunately not always, but that is why I’m looking for partners to start showrooms within Europe where we can display our cultivation systems. If people could actually see what we do, they would also see the potential in it. Of this, I’m sure. And yes, I know very well that vertical farming is not the solution to the global food problem, but I do believe there are many situations in which our systems would come in handy.”
The team of Verde Compacto that develops the container farm Huvster and the smaller Veggiebox cultivation variety
Advancing a Mexican family-run company
Before going further into the systems (such as the cultivation containers), we need to go back to where it all began. How does a young man from Amsterdam end up at a Mexican company active in vertical farming? “I was introduced to a Mexican through my dad a few years ago. It turns out he worked at Verde Compacto where he developed fertilizers. Through those fertilizers, they came into contact with vertical farming and decided to continue in that field.
I went to Mexico myself and got to know the family-run business better. They are ambitious and want to expand their brand in Europe and were looking for someone who could help them with that. With my degree in Business Administration, I can take on that role, and after doing my research to understand the relatively young market better, I now want to take some real steps forward.”
Opportunities, among others for apocalyptic bunkers
In the beginning, Olivier planned to aim all of his efforts in the Netherlands at first, but due to, among other things, the coronavirus, getting to know the market better, and the reservations against vertical farming in the Netherlands, he had to look in other places as well. “I want to build a couple of showrooms where people can see our products both in the Netherlands and in other European countries. We make cultivation systems in various sizes, from container to fridge-sized systems, always according to the vertical farming principle with a high productivity per square meter of 253 kilograms. I see a potential for these systems in, for example, Scandinavia, Germany, and the United Kingdom, countries with large urban areas or difficult growing climates. The younger generations in those places have a demand for sustainable, local products.”
But Olivier also has his eyes set outside of Europe, like in the Middle East. He is also looking into bunkers. Actual bunkers. “It is currently trendy for rich people worldwide to build apocalypse bunkers out of fear for the end of the world. Those people want to be self-sufficient in those bunkers, which is where our systems come into play. A great niche market with requests from the United States, Australia, and New Zealand, to name a few.”
Realistic due to size
In any case, Olivier is a realist: replacing large, traditional cultivation companies with vertical farms in whatever way can not be justified anywhere. “To give you an indication of our system size: recently, we started working together with The Goat Project, an Italian vertical farming project. Up to an investment amount of 30 million euros, we will be delivering together, but after that, they take on everything up to an investment amount of 3 billion euros.”
That is why Olivier aims first and foremost on restaurants and supermarkets, where the consumer can choose how the product they will eat is grown. But, the systems can just as well be used for ornamental cultivation or cannabis cultivation, both medical and recreational. “For that latter type of cultivation, we developed a specialized system which could also be used to cultivate tomatoes, though on such a small scale that would not be very profitable.”
Strawberry yogurt
However, it would be profitable for an Icelandic producer of strawberry yogurt. Importing fresh strawberries to the island is more expensive than growing them yourself in a vertical farm. “The energy comes from the earth in Iceland due to the geysers, but there are many more situations in which, with a bit of thinking and using the local circumstances, a generally more expensive system works. The ROI of our systems is about one to three years, with a very high productivity per square meter (5700 plants in a 12-meter container named Huvster), the second-highest for container cultivation on the market.”
Rotating LED lighting increases energy efficiency
Critics often point out the high energy input of vertical farming. Olivier recognizes that, but refers to the clever use of local circumstances, and the technological innovations developed by Verde Compacto meant to increase efficiency. Rotating lights, for instance, a unique system compared to many other vertical farming systems. “Instead of cultivating in layers, we work with cultivating in standing tubes with LED strips rotating around them so that every plant gets the light it needs, but the energy input in kilowatt-hours is 50% lower per square meter and the production per square meter higher.”
Make them enthusiastic
Back to the restaurants, which is what Olivier focuses on in Europe first. He imagines one of the cultivation containers walls being see-through so that the consumers can take a peek at the cultivation facility. “Especially large groups of young consumers who want to, for instance, eat vegetarian or vegan, I expect will be very enthusiastic, and so will the investors. It is also easier to talk about something if it is physically there and allows fresh and healthy foods to be sourced closer to home.”
However, Olivier is aware of the disadvantage that European supermarkets are not yet able to sell products grown in vertical farms under an organic quality mark. According to him, that hampers the growth of vertical farming. “At the moment, they lose their organic quality mark as soon as they cultivate on water because the standards are pretty outdated when compared to the technological cultivation developments.”
Win-win situation
But it is not an insurmountable problem, especially given the worldwide increase in demand for local products during the pandemic. But is this true given the fact that Verde Compacto is Mexican, and in the Netherlands, many well-known players are active in offering cultivation solutions? “I don’t think that matters all too much these days. Price-wise we don’t differ much from European or North American systems. Every system has its pros and cons. I am very open about that. A well-thought-out calculation is always required, but both parties can create a win-win situation when it happens. Of this, I, and hopefully my future partners as well, am sure. I'm looking forward to discussing it with them.”
For more information:
Verde Compacto
www.verdecompacto.com
Olivier Kappetein
olivier.kappetein@verdecompacto.com
+316 14 62 13 10
41 Million Dollar Investment To Boost Abu Dhabi's Agriculture Technology
The Abu Dhabi Investment Office, ADIO, announced today individual partnerships with Pure Harvest Smart Farms, Pure Harvest, FreshToHome, and Nanoracks that will see the companies receive financial and non-financial incentives totaling AED 152 million (USD 41 million)
Three innovative agriculture companies will develop cutting-edge projects in Abu Dhabi to boost the emirate’s agriculture technology, AgTech, capabilities across land, sea, and space.
The Abu Dhabi Investment Office, ADIO, announced today individual partnerships with Pure Harvest Smart Farms, Pure Harvest, FreshToHome, and Nanoracks that will see the companies receive financial and non-financial incentives totaling AED 152 million (USD 41 million). The research and technologies developed by these companies will expand existing capabilities in Abu Dhabi’s AgTech ecosystem and promote innovation in the sector to address global food security challenges.
New partnerships
The new partnerships are a continuation of ADIO’s efforts to accelerate the growth of Abu Dhabi’s AgTech ecosystem through the AgTech Incentive Programme, which was established under Ghadan 21, Abu Dhabi’s accelerator program. The Programme is open to both local and international AgTech companies. The partnerships follow ADIO’s AED 367 million (USD 100 million) investment earlier this year to bring four AgTech pioneers – AeroFarms, Madar Farms, RNZ, and Responsive Drip Irrigation, RDI, – to the emirate to develop next-generation agriculture solutions in arid and desert climates.
Dr. Tariq Bin Hendi, Director General of ADIO, said: "Abu Dhabi is pressing ahead at full steam with our mission to ‘turn the desert green’ and solve long-term global food security issues. We have created an environment where innovative ideas can flourish and this has enabled the rapid expansion of our AgTech sector. Innovations from the companies we partnered with earlier this year are already propelling the growth of Abu Dhabi’s 24,000 farms. Partnering with Pure Harvest, FreshToHome and Nanoracks adds a realm of new capabilities to the ecosystem across land, sea, and space."
Bin Hendi continued: "We are driving innovation across the entire agriculture value chain and this is producing a compounding effect that is benefiting farmers, innovators, and companies in our region and beyond."
Pure Harvest, FreshToHome, and Nanoracks have been awarded financial and non-financial incentives to expand operations in Abu Dhabi. The competitive incentive packages include rebates on innovation-linked high-skilled payroll, high-tech CAPEX, as well as land, utility, and intellectual property support.
Since the beginning of 2020, ADIO has attracted seven AgTech companies to Abu Dhabi, each bringing a complementary skill to expand the ecosystem. ADIO’s new partnerships with Pure Harvest, FreshToHome, and Nanoracks will build on the achievements made by AeroFarms, Madar Farms, RNZ and RDI, the AgTech pioneers ADIO partnered with earlier this year to establish R&D and production facilities in Abu Dhabi.
Pure Harvest is a home-grown, tech-enabled farming venture that uses cutting-edge food production systems to grow fresh fruits and vegetables in a climate-controlled environment, enabling year-round production anywhere, while using seven times less water compared to traditional farming methods.
Pure Harvest will invest in smart farming and infrastructure technologies at its new farms in Al Ain, Abu Dhabi, to optimize growing conditions through hardware design innovations, artificial intelligence, autonomous growing and robotics, plant science research, and desert-optimized machines. The company will also progress R&D and deployment of a commercial-scale algae bioreactor production facility that will grow higher quality, healthier Omega-3 fatty acids without the limitations and challenges of traditional animal sources.
Sky Kurtz, Co-Founder, and CEO of Pure Harvest, said: "We are delighted to have received the support of ADIO to further invest in our home-grown, innovative growing solutions. It also serves as a powerful endorsement of our business case and mission as we pursue innovation to address food security locally and internationally. As one of the pioneering champions in the region’s emerging AgTech sector, this commitment will give us the resources we need to drive and expand our R&D capabilities and will position us for international expansion from our strategic base in Abu Dhabi. This partnership further demonstrates how committed the government is in supporting and enabling innovative technology companies, providing them with the tools, resources, and support to thrive and make a large-scale impact in the region."
FreshToHome is an e-grocery platform for fresh, chemical-free produce. The company maintains complete control over its supply chain, inventory, and logistics by obtaining produce directly from the source through an AI-powered auction process. ADIO’s partnership will aid the expansion of FreshToHome’s land and sea operational and processing capabilities in the UAE, bringing expertise in aquaculture, contract farming for marine and freshwater fish species, and precision agriculture to Abu Dhabi. It will also invest in innovative fish farming technologies and cold chain.
Shan Kadavil, CEO and Co-Founder of FreshToHome, said: "At FreshToHome we use cutting-edge research in AI and precision aquaculture for furthering food security in a sustainable manner while also giving better value to consumers, fishermen, and farmers. To this end, we intend to bring our US patent pending AI-powered Virtual Commodities Exchange technology, our e-grocery platform, and our nano farm aquaculture technology to Abu Dhabi, enhancing food production and distribution for the region. ADIO has been a terrific partner to us and we are thankful for their support in helping us be part of the vision."
US-based Nanoracks is the single largest commercial user of the International Space Station and is building the first-ever commercial AgTech space research program. Nanoracks’ ‘StarLab Space Farming Center’ in Abu Dhabi will be a commercial space research facility focused on advancing knowledge and technology for organisms and food produced in space and in equally extreme climates on Earth. The space-based technology will be applied to desert agriculture to address pressing environmental and food security challenges and to benefit long-term human space exploration.
Allen Herbert, SVP of Business Development and Strategy, and Head of Nanoracks, UAE, said: "Much of today’s technology used for vertical, urban and closed environment agriculture initially came from space research from 30 years ago, and Nanoracks is ready to synergize these technologies back to in-space exploration. We firmly believe that space research holds the keys to solving major challenges on Earth from climate change to food security. And our StarLab Space Farming Center in Abu Dhabi is just the beginning.
We’re building a global research and development team that will produce and commercialize organisms, technology, and innovative products that will not only revolutionize farming in Earth’s deserts and harsh environments but also change the way humans are able to explore deeper into our universe."
For more information:
www.wam.ae
11 Nov 2020
Aponix Upgrades 3D-NFT Vertical Barrels Components To ‘Version 3'
The Aponix vertical barrel system is an alternative vertical NFT solution from Germany that can be used instead of rack systems to use vertical space more efficiently in hydroponic setups and at the same time use natural sunlight better
The Aponix vertical barrel system is an alternative vertical NFT solution from Germany that can be used instead of rack systems to use vertical space more efficiently in hydroponic setups and at the same time use natural sunlight better. The system aims to maximize the number of possible grow spaces per level arranged in a given 3D room by increasing the diameter from a ‘Tower’ to a ‘Barrel’.
The whole system is based on lego-like ring segment pieces that serve either as spacers or provide differently organized inserts for standard 2-inch netpots. Assembling multiple of these ring segment pieces will result in stackable ring segments or barrel levels to assemble one or multiple such vertical cylinders. With more ring segments stacked, the height and the number of grow spaces are increased.
By the end of 2020, Aponix will have developed the new ‘Version 3’ that will incorporate all collected improvements from the existing global user based from the last 3 years and adding a few more features:
Liquid will be guided more precisely inside. It will also have a new more robust and tight connection mechanism and air traps to keep liquid inside also on high flow rates.
There will be a backwards-compatible and reusable grow plug insert, that is supposed to replace 2-inch one-time use plastic netpots also in other systems. It will also have an optional plant trellis insert to grow larger flowers and fruiting dwarf varieties.
There will be a new lid-base that speeds up setup of lines of vertical barrels and enable rotation of the units if needed.
There will also be a dedicated sprinkler dome lid enabling different sprinkler options including own solutions and also the own existing pressure-less irrigation option using the water buffer.
Vertical barrels will be more stable and can be built higher using the new V3 part.
There will only be a single ring segment piece in ‘Version 3’ with 2 grow pod inserts that only allow 2 stacking positions instead of 4 in V2. If spaces are unused they can be capped with a nice green cover plug.
As of 2020. Aponix also changed their market strategy from looking for distributors to starting to work only with product partners who bring in own engineering and create more specific and distinguishable solutions based on aponix components. Aponix parts are now defined as being mere infrastructure parts that always need to be integrated into a greater individual context involving more or less horticulture engineering depending on the application. Which means product partners create their own unique solutions based on aponix components adding other external even competitive pieces, logic and/or service and market them independently under their own brand and own product name.
For more information:
Aponix
hello@aponix.eu
www.aponix.eu
Mon 9 Nov 2020
An Urban's Rural View - Vertical Farming Is Looking Up
It looks like some of the big boys in agriculture are finally taking vertical farming seriously
11/2/2020
By Urban C Lehner , Editor Emeritus
Connect with Urban: @urbanize
It looks like some of the big boys in agriculture are finally taking vertical farming seriously.
Last month one of the biggest, the berry behemoth Driscoll's, became an investor in and joint venture partner of Plenty Unlimited, an indoor vertical-farming startup. (https://www.businesswire.com/…) (https://agfundernews.com/…) From Driscoll's and Japanese tech investor SoftBank, Plenty is getting $140 million, bringing its total funding to $500 million. More importantly, it's getting to work with Driscoll's on growing strawberries indoors.
Entrepreneurs have been trying to make a go of indoor vertical farming since 1999 when Columbia University professor Dickson Despommier and his students developed the concept. It seemed like a no-brainer to grow food close to where it would be consumed, with high yields on minimal acreage, with less water and fewer if any chemicals, without soil in some iterations, and without fear of droughts, fires, floods, frost or high winds.
The disadvantages were less obvious -- but debilitating. For conventional farms, the sun provides free photosynthesis. For farms inside buildings, the cost of artificial lighting is horrific, and the cost of climate control makes matters worse. An Irish researcher contends that in the United Kingdom, indoor farms require more than ten times the energy of heated greenhouses. He recommends rooftops for those who want to grow food in cities. (https://theconversation.com/…)
Other disadvantages include high costs for labor, rent, and capital-equipment depreciation. "Despite the advances that have been made in controlled environment agriculture, it isn't quite ready for prime time and many opportunities for innovation remain," a Cambridge Consultants paper concluded. (https://www.cambridgeconsultants.com/…)
Vertical farmers, venture capitalists, consultants, academics, and others are doing cartwheels trying to solve these problems. Plenty Unlimited uses wind power and solar cells to generate its electricity and has developed special forms of plastic LED lights. A University of Florida researcher is working on pulsing light -- five seconds on, 10 or 20 seconds off -- and seeing signs that it cuts lighting costs substantially without hindering plant growth. (https://theconversation.com/…)
While depreciation costs are high, capital is available; fearless investors are hurling money at the sector. Rent costs could start coming down, too. With the pandemic encouraging more work from home, there will be surplus space in office buildings. (On the other hand, some vertical farms sell directly to restaurants, which the pandemic has been hard on.)
Though making progress, vertical farming remains a tiny corner of the multi-trillion-dollar agriculture and food business. A market research firm estimated it at $212 million in 2019 and predicted it would hit $1.4 billion by 2027. (https://www.prnewswire.com/…) When I last covered this subject in 2015, many vertical farms were still losing money. It's likely many lose money today. (https://www.dtnpf.com/…)
All that said, vertical farming has come a long way in the last few years. Hundreds of operations have germinated and sprouted in countries around the world. There have been innovations in lighting and climate control.
After years of growing mostly leafy greens and herbs, vertical farms are preparing to add crops like potatoes, tomatoes, and blueberries. As vertical-farm pioneer Despommier wrote in the Wall Street Journal recently, "Vertical farms are no longer some futuristic fantasy." (https://www.wsj.com/…)
As an example, Despommier cited Infarm, a company that was started in Israel, is now headquartered in Berlin and employs 400 people in 40 countries, mostly European. According to Despommier, who serves as an unpaid adviser to Infarm, the company provides grocery stores with automated, hydroponic systems that allow them to grow food in their produce aisles.
"Each store selects its own mix of greens and herbs, and consumers are encouraged to choose, taste and harvest from a menu growing right in front of them," he wrote. You can't cut transportation costs much more or provide much greater freshness.
And now, to move the sector further forward, comes Driscoll's and Plenty.
You can see the benefits to Plenty in this deal. They go beyond the $140 million and the expansion into a new and promising product, strawberries. They're hitching their wagon to a company that controls about a third of the $6 billion U.S. berry market. It has proprietary genetics and a team of geneticists developing new products. It has a recognized brand name and marketing muscle; the "clamshell" berry package was its idea. (https://www.newyorker.com/…)
What does Driscoll's get out of the arrangement? Plenty, too, has plenty to offer a partner. It says its Laramie, Wyoming, farm -- where Driscoll's berries will be grown -- is "the largest privately-owned vertical farm research and development center in the world." Plenty says it's "currently building the world's highest-output, vertical, indoor farm in Compton, California." https://www.businesswire.com/…)
But why vertical farming in the first place? Bloomberg emphasized Driscoll's desire to learn robotics from Plenty, whose farms are highly automated. Labor is a big part of Driscoll's cost structure and immigrant labor is becoming scarcer in the U.S. (https://www.bloomberg.com/…)
The Financial Times pointed to the fires in Driscoll's home state of California. A Driscoll's executive told the FT that instead of moving a whole farm farther up the mountain to get away from them, it can move to vertical farms. (https://www.ft.com/…)
The FT also mentioned "deglobalization," by which it apparently meant that in the future there may be less cross-border trade in food. That would encourage big players like Driscoll's to produce locally. The FT noted that two of Driscoll's biggest markets are in Hong Kong and the Arab world. It won't grow berries outside in either place but could grow them vertically indoors.
Whatever the reasons, what Driscoll's has done is big. Of all the progress vertical farming has made over the last several years, getting the big boys in ag to take it seriously is arguably the most important.
Urban Lehner can be reached at urbanize@gmail.com
Vertical Farming Made Easy With Sarab From Ecotwigs
Sarab lives in Mumbai, India. In 2017, she completed an internship in Canada at the In.Genius Farms, a small-scale vertical farm in Laval, Quebec. Mentored by Khaled Majouji, aka The Plant Charmer, she learned about the potential of vertical farming. Once back home, she decided to be the change she wanted to see in her country
August 5, 2020
Sarab lives in Mumbai, India. In 2017, she completed an internship in Canada at the In.Genius Farms, a small-scale vertical farm in Laval, Quebec. Mentored by Khaled Majouji, aka The Plant Charmer, she learned about the potential of vertical farming. Once back home, she decided to be the change she wanted to see in her country.
Inspired by her experience in Canada, Sarab started her own startup: Ecotwigs. With the help of her father, Gurmukh Singh, an entrepreneur in computer numerical control (CNC) machinery, they designed and developed a ready-to-assemble vertical farming system.
It can be produced on an industrial scale, delivered wherever it is needed, and easily deployed upon reception.
Sarab at her vertical farm near Mumbai
As in many countries, the COVID-19 pandemic has disrupted the mobility of agricultural workers in India, adding pressure to food supply chains and compromising the food security of the most vulnerable populations. The situation raised awareness on the importance of local farming and shorter supply chains.
Sarab vertical farming solution comes at the right time. It aims to solve a few problems at once:
requires less land;
reduces the workload and dependence on seasonal foreign workers;
increases yields per square-foot;
improves food salubrity;
simplifies traceability;
and fosters profitability.
Given the current pandemic, such a farming system, which also requires limited interactions and manipulations while operated, would be more than handy.
How it all started
Sarab studied sciences in Junior college. “It was the rational choice”, she said. However, her real dream was to become a pastry chef. She had always been fascinated by big wedding cakes, but convincing her dad about this career choice was challenging.
Nonetheless, while in college she started a side gig as a freelance pastry chef. She liked it so much that after college, she did a bachelor’s degree in Hotel and Hospitality Administration. While studying, she spent a semester working as an intern at the Danat Jebel Dhanna Resort on the outskirts of Abu Dhabi in Ruwais city.
Before completing her bachelor’s degree, a research topic on lifestyle diseases based on our diets shed a different light on her passion. “I realized that what I was loving [baking cakes] was making people diabetic”, she said. “I thought I was giving people joy, but I was giving them diabetes”, she added.
Sarab explained that although she still enjoys baking and has nothing against eating pastries, it may not be the purpose she wanted in life. When she graduated, suddenly she felt like she didn’t want to follow this path anymore.
One day, while waiting for a friend near a market, she was watching how the food was handled. Among other things, she noticed bunches of cilantro unloaded directly on the dirty pavement of a street in Mumbai. Given that cilantro is a garnish in almost every Indian dish, she thought that she could do better. She started to crawl Youtube and looked at hours of videos on how to grow food. The first thing she tried was to grow kiwis from seeds. “I never stopped after that”, she said.
She made a rooftop garden, but without any background in agriculture, she admitted her results were suboptimal. Nevertheless, she was determined to pursue this new path. In 2017, she was following Khaled, aka The Plant Charmer, on Instagram. When she saw a post about an internship opportunity at his new vertical farm, she jumped on it.
The Instagram post that caught Sarab’s attention
Although it sounded like a crazy idea to her parents, generating some fuss in her family, they ended up being supportive of her choice. “Going to Khaled’s farm was the best decision in my life”, she said.
When I was at Khaled’s farm it struck me: this is the future of farming. – Sarab
Sarab wanted to see the full cycle, from seedling to harvesting, including everything in between. “I was supposed to do a one-month internship only”, she explained. “But I was so fascinated on how the system works, I asked to stay longer”, she added.
Sarab at the In.Genius Farm in Laval, QC, Canada
At the end of her internship, another big decision was awaiting Sarab. She had to decide whether to stay in Canada and apply for permanent residence, or to return to India. “The greatest accomplishment in our country is to leave”, Sarab said. “With everything I learned, I felt like the right thing to do was to bring back this knowledge and do something for my country”, she added.
When she returned home, she faced a few challenges. The same as any small-scale urban farming entrepreneurs would encounter in India and elsewhere: access to land, in or near the city, is difficult.
The real estate in Mumbai and other major Indian cities is as expensive as any major city in North America or Europe. It makes farming possible only in remote and often deficiently developed regions. Moreover, a lot of lands in or near the cities and suburbs are highly contaminated, making agriculture beyond gardening nearly impossible. Luckily, Sarab’s uncle provided her with the opportunity to develop her project on an 18,000 sq.-ft plot of land he owns, only 20 minutes away from Mumbai’s suburbs.
Why vertical farming
A new climate report from the United Nations has warned that the world might face a food crisis due to climate change and overexploitation of land and water resources. The vertical farming infrastructure proposed by Sarab aims to enable growing food wherever there is place while reducing pressure on farmlands and fostering soil regeneration.
Without farming the land itself, the annual yields are still calculated in metric tons on less than an acre. By growing above the ground, pest damage and diseases are drastically reduced without the need for any pesticides or harmful chemicals.
For Sarab, vertical farming as she learned it at the In.Genius Farms makes organic farming way easier. “It reduces operational costs, requires fewer resources [human and natural], while increasing yields and margins”, she explained.
“Vertical farming with my infrastructure can be done by anybody because the hard work factors of conventional farming were removed”, she said. “There’s no kneeling, no bending, and no weeding”, she added. From her experience at In.Genius farms, Sarab thinks that 1 worker for every 100 units is more than enough (100 units cover about 10,000 sq.-ft.).
Business model
Once back from her internship at In.Genius Farms, Sarab realized something: she didn’t want to start a farm, she wanted to become the vertical farming infrastructure provider.
I want to be the person who set [up] vertical farms for others because that’s the future. – Sarab
Sarab explains that going through the process of figuring out vertical farming by yourself can be daunting. “Of course some could do it by themselves, but it would turn out to be expensive and time-consuming”, she said. “I want to make things simple and affordable to those wishing to start a vertical farm”, she added.
Her business model is to provide customers with a turnkey vertical agricultural infrastructure and technical assistance to ensure they reach the full yield potential. Therefore, land use and the time, effort, and money spent would be optimized.
As what IKEA does to home furniture, Ecotwigs does to farms by designing and selling ready-to-assemble vertical farms. – Sarab
Sarab’s main market for her vertical farming infrastructure will be existing farmers, but also a new generation of food entrepreneurs who own small plots of land and wish to start small-scale farming businesses. For Sarab, too many farmers in India (and elsewhere) are not treating their farm as a business, and when they do, it is often not managed efficiently. Thus, she wants to provide them with proper customer support to create lasting prosperity.
Vertical Farming Systems
As Sarab’s father noticed her enthusiasm for vertical farming, he decided to help her in her venture. He helped her design and engineer a new system following her experience in Canada.
This A-frame is made of inert material. Suitable for outdoor and indoor farming, it is lighter than wood and easier to assemble (or disassemble if needed). Moreover, it is made to last a minimum of 10 years.
A 100 units farm can be assembled within a week by 2 people. – Sarab
One unit can be assembled by 2 people in 30 minutes. Each A-frame unit includes 10 rammers that are 12 feet long (or 3.90 meters). There are 5 rammers on each side. Working 7.5 hours per day, it would take two people about 7 days to set up a 100 unit vertical farm on 10,000 sq.-ft.
Depending on the crop and location, each unit can generate from $400 to over $1000 in revenue per season. The price to buy a unit is not yet settled. Nevertheless, the price range will be established to allow clients to get a great return on investment (ROI).
Our challenge was to design the most profitable, eco-friendly, food-safe, sturdy, and long-lasting farming system. – Sarab
The rain gutters, as used on the In.Genius Farms’ A-frame, are replaced by a custom made rammers. For marketing purposes, Sarab and her father decided to change the name of this component, which is the channel used to grow food. “In India, when you say gutters, it is associated to a filthy place”, she explained. “It is not the place where people would want their food to grow”, she added.
The rammers’ length, width, and depth were increased to allow higher yields per unit and the growth of a wider variety of crops. The angle of the rammers was set to get a maximum sun or LED light exposure. The system can be deployed either as a few units in a backyard, on rooftops, or at scale on acres.
The next steps
Sarab currently operates a 30 unit vertical farm. It serves as a research and development lab. “That is where data are validated”, she said. Sarab is growing varieties of lettuce and spinach, arugula, peanuts, sweet bell peppers, edible flowers, and eggplants. She will also experiment with growing strawberries, which is unusual for Mumbai’s climate.
As the rammers are longer, deeper, and wider than the model she experienced at the In.Genius farms, bigger crops like cauliflower, celery, and zucchinis will be tested as well. The food harvested at her farm will be for friends and family. With 30 vertical farming units, Sarab already knows that she will not have the volume necessary to consistently supply clients like chefs or grocery stores.
Her focus is on supplying the infrastructure and acting as a vertical farming consultant to her clients. Thus, operating the farm to gather data is the priority. The system will be continuously tested to make sure it can perform well, and that yield expectations are accurate.
Sarab explained that “when a client is looking to invest in infrastructure like this, we need to give them the proper numbers. And I know that at one point, the numbers will speak for themselves”.
Sarab is well aware of the Canadian winter. “Made of inert material, these A-frames do not react much to temperature fluctuations”, she explained. She also knows how robust the system needs to be to endure the cold temperature of northern countries, as well as snow and ice accumulation.
Takeaways on vertical farming
The approach of the farmers should change, and the status quo should be disrupted. Sarab explained that Indian farmers are treated as the bottom of the supply chain. If they could be provided with the proper tools and means to grow, market, and distribute food efficiently, she believes it could make them the leaders of the supply chain. The main issue Sarab stressed is to make sure you have enough customers for those high yields.
“The best part, since all labor-intensive tasks of conventional farming have been stripped out, it could be done by anybody”, Sarab proudly said. Adding some fun, fashion, and style to the business concept is also part of her branding.
I genuinely enjoy working at my farm and the message I want to spread is: this is cool! I can be fashionable and still be a farmer. -Sarab
Do you have an inspiring urban agriculture story to tell or innovative ideas to share? Contact us or leave a comment below!
NEW ZEALAND: Southland Lawyer-Turned Lettuce Farmer Expanding Hydroponics Business
Aviation lawyer Angela Beazer, who has been working for the Civil Aviation Authority part-time, was a recent recipient of a $2.5 million Provincial Growth Fund loan
1 November 2020
Otago Daily Times
By: Mary-Jo Tohill
A Southland lawyer-turned lettuce farmer is looking forward to devoting all her time to expanding her hydroponics business.
Aviation lawyer Angela Beazer, who has been working for the Civil Aviation Authority part-time, was a recent recipient of a $2.5 million Provincial Growth Fund loan.
While flying high, the 45-year-old has her feet firmly on the ground. With plans afoot to triple the lettuce farm's production, it had become clear to her she could no longer do both jobs and would have to quit one.
"But now I'm ready for change. I've been trying to juggle both, but they're not complimentary.
"I have a life many people would envy. I can work on my own schedule. I can be there to pick up my daughter from school, but as I say, they (lawyer/lettuce growing) are not complementary. I could not give 100 percent to both. If I do something I like to do it properly.
"I'm quite looking forward to focusing just on the lettuces."
If someone had told the former career professional eight years ago that she was destined to become a lettuce farmer, she would have laughed.
"I pictured lettuces sown out in the middle of the muddy paddock. Not my cup of tea at all."
She and her partner, Craig Macalister, had already taken a big leap of faith when they moved from Wellington to Invercargill so that he could take up a new position with financial advisory and accountancy firm Findex.
However, it was their frustration at not being able to find a suitable rural lifestyle block that led them to a property in Myross Bush.
Shoulder-tapped by a real estate agent, they went out and looked at a place that happened to have a hydroponics setup — Drysdale Hydroponics.
"I knew nothing about growing lettuces. We'd been down here about a year. I had a plot where I grew some veggies — a bit of broccoli, some cauliflower, a few potatoes. Actually, the potatoes were already there. That was about the extent of my horticultural experience."
Fast forward eight years and now she grows lettuce by the hundreds at her farm Southern Hydroponics, still trading as Drysdale Hydroponics, near Invercargill.
And with the expansion that will employ another 30 people, she's set to grow more, and other vegetable crops, including capsicums and tomatoes.
"We're been producing a fairly fixed amount of product. The business does need to expand because there's more competition. The minimum wage's gone up, so you either shut down or you expand and make it worthwhile."
Increasing production and lowering costs made for better economies of scale. Beazer liked the concept of hydroponics as an efficient way of growing food on a large scale.
However, while it had been a great move, it was also a huge lifestyle change,
"I think sometimes, 'why am I doing it?' But you're working at waist height — you're not having to bend and I quite like working undercover, but still feeling like you're working outdoors.
"On the other hand, this is a 24/7, 365-day operation. Someone has to be here watching all the time. There's a lot that goes on behind the scenes."
It was sometimes hard to close the greenhouse door and walk away when you had to be constantly checking things like nutrients and temperature, she said.
"One thing I'm really looking forward to is being able to move to a heat pump from the boiler, with the expansion."
There might also be time to take up some interests again — like Zumba.
"I was doing it, but since lockdown and everything I haven't got back into it and I've been a bit of a lazy bum and not been doing it."
Lead photo: Angela Beazer surveys her hydroponic lettuces. Photo / Supplied
Unleashing The Potential of Indoor Sole-Source LEDs on Tomato Production
Enlightening collaboration between Heliospectra and the University of Tokyo
Enlightening Collaboration Between Heliospectra And The University of Tokyo
Heliospectra announced a collaboration with the Institute for Sustainable Agro-ecosystem Services (ISAS), the University of Tokyo. In an effort to redefine and unleash the potential of indoor tomato production, this will be a joint research project with the University’s Institute for Sustainable Agro-ecosystem Services (ISAS), in collaboration with Associate Professor Wataru Yamori at the Agricultural Biology and Biogeochemistry Group, and Heliospectra Japan.
With the average age of Japanese farmers reaching 67 years old and younger generations migrating to cities, traditional farming is facing a crisis. This is forcing the country to investigate new ways to produce food. Plant factories are scaling to meet consumer food demand, mainly in vegetable cultivation in both solar and artificial light environments, and the industry is growing. Japan already has approximately 200 lettuce factories using artificial light, and that number is expected to double by 2025. However, to-date, plant factories have been unsuccessful in cultivating light-hungry vine crops such as tomatoes in indoor artificial light. Heliospectra and the University of Tokyo want to challenge this.
Working together, they are looking to build a business model for Japan’s plant factories and PFAL (Plant Factory with Artificial Lighting) organizations for indoor tomato cultivation. In the University lab, the Professor and his students will be using Heliospectra’s MITRA linear, the horticulture market’s first truly modular LED light. Designed by growers for growers, MITRA is a solution for high-light crops, with high-intensity light output and electrical efficacy of up to 2.8 µmol/J.
“We are very excited to be a part of this research together with Dr. Yamori and the ISAS at the University of Tokyo. Over the years, Heliospectra has conducted research on light’s effect on tomatoes in indoor facilities with great results,” comments Yasuhiro Suzuki, General Manager of Heliospectra Japan. “We now look forward to further expanding our knowledge and developing more effective indoor cultivation of tomatoes for commercial use. We look forward to collaborating with the university and sharing with the world our knowledge of growing tomatoes indoors.”
For more information:
Heliospectra
info@heliospectra.com
www.heliospectra.com
Publication date: Thu 29 Oct 2020
Singapore’s Farms Face An Even Greater Challenge In A Post-COVID-19 World
A question now arises as to whether the '30 by 30' food supply vision will suffice for the country. The programme For Food’s Sake! finds out what changes are needed in the growing agri-tech sector
A question now arises as to whether the '30 by 30' food supply vision will suffice for the country. The program For Food’s Sake! finds out what changes are needed in the growing agri-tech sector.
Figuring out new ways to increase productivity on farms is one of the challenges.
01 Nov 2020
SINGAPORE: It is a vision that predates COVID-19. Spurred by threats like climate change, Singapore set about having 30 percent of its food produced locally by 2030, to improve its food security.
But food security expert Paul Teng thinks the country is not going far enough with its “30 by 30” goal set last year.
“Even if we achieve that in 10 years’ time, we’re still dependent on the rest of the world for the remaining 70 percent. If all things are normal, then it should be enough … to create a buffer,” he says.
“But if indeed all the worst-case climate change scenarios come true, and there are many other black swan events, then we may need more than two or three months’ worth.”
Professor Paul Teng.
The professor, an adjunct senior fellow at Nanyang Technological University’s S. Rajaratnam School of International Studies, sees COVID-19 as a “wake-up call” to do more.
“I don’t imagine that the COVID-19 pandemic will be the last time that we’ll be disrupted in terms of food supplies … If you look around Asia at the moment, you’ve got a whole host of issues affecting us,” he notes.
“The armyworm is just one example. But there are many other pest problems, disease problems … Anything could flare up and affect our supply chain. Then there’s also politics.”
There are 220 farms in Singapore as of last year, producing mainly leafy vegetables, fish and eggs.
Millions of dollars are being poured into this growing agri-food industry. But it still produces less than 10 percent of the country’s food, and the rest is imported from more than 170 countries and regions.
Local farms contributed 14 percent of Singapore's consumption of leafy vegetables last year.
Most of the farms are “not what I’d call modern farms”, says Teng, urging improvements in productivity. Not only that, other changes are also needed more than ever, the programme For Food’s Sake! finds out.
THE ISSUE OF LAND
One of Singapore’s largest producers of Asian leafy vegetables is Farm 85, which lies on 12 hectares of land in Lim Chu Kang — roughly the size of 17 football fields.
But its owner, Tan Koon Hua, who started the farm in 1991, does not think it is easy to increase production further.
“The most we can do is to find ways to prevent disruptions,” says the 52-year-old, citing the example of greenhouses, which he has built to protect his crops against changes in weather.
For Food’s Sake! host Ming Tan (left) with Tan Koon Hua.
The other solution, he believes, is a bigger land area. One of the reasons the work on the farm is laborious is its current size, agrees his son Zach, who works there.
For example, while large farms overseas “can invest in a big tractor” to aerate the soil, Farm 85 uses hand-operated soil tiller machines, cites the 26-year-old.
Less than one per cent of Singapore’s land is used for agriculture. In recent years, new plots have been released for farming, but in smaller parcel sizes ranging from about 0.6 to two hectares.
The largest plots awarded have been about six hectares, which means farmers still need to reduce their reliance on land.
Short leases have been another disincentive to making long-term investments in better equipment or infrastructure. It is one of the reasons, along with lack of technical know-how, that farmers are not as productive they could be, according to Teng.
Farm 85.
Today, the new plots have longer lease terms of up to 20 years, compared with previous ad-hoc lease extensions that were as short as three years.
PRODUCTIVITY PLATFORMS AND PITFALLS
To further help with productivity, the government has made several grants available since 2014. At least three are targeted specifically at the agriculture industry.
One is the Singapore Food Agency’s (SFA’s) S$63-million Agriculture Productivity Fund. It is meant for farmers to invest in more innovative systems that can boost their yield, for example under a scheme — capped at S$50,000 — for the purchase of equipment.
There is also a scheme for farmers to convert their farm into a more high-tech farming system.
There are funding schemes for farmers to transform the work done on their farms.
To apply, the proposal they submit must include: The project’s objectives; a comprehensive description of the farming system, with the layout; brochures of the equipment; a full business plan; and a track record of the project team’s area of expertise.
For Food’s Sake! host Ming Tan was uncertain, however, whether farmers are able to “suddenly just provide this information”. “If they already knew how to do these (high-tech) things, don’t you think they’d have done them?” he questioned.
So a new type of farmer has sprung up in recent years. Ex-engineers and venture capitalists are among those who have set up tech-focused farms that do not rely on large fields.
Between 2015 and 2019, the number of vegetable farms increased from 54 to 83. Despite this increase of 54 percent, the production of leafy vegetables rose only by 11 percent, from 11,400 to 12,700 tonnes.
Up to 14 types of local vegetables are grown on Farm 85.
There are “still a lot of challenges on the ground”, an industry insider tells Ming. “There aren’t that many dedicated contractors who can build farms … Almost always the infrastructure cost starts ballooning,” he says.
Plus … you need to spend time, effort and money training everyone from scratch literally. We don’t have a ready pool of skilled indoor farmers.
In this high-tech farming space, proprietary technologies have been brought in from different parts of the world, but “these are also varied in terms of how (they’re) translated on the ground in Singapore, in the context of a tropical environment”.
“There’s a lot of clamor, sound … and hype coming,” he adds. “Still … they all need to translate into a viable business.”
IT’S EARLY DAYS YET
According to the SFA, the outlook for high-tech farms is not bleak.
A high-tech farm with lighting, climate control and plant racks extending to the ceiling.
“It’s a really nascent technology and sector. And as with any other new industry, it would take time for commercial models to sort of become viable,” says SFA deputy director (Food Supply Resilience) Sim Wi Min.
“There’s almost a five-year period where they have to do construction and fine-tune their operations. So while you don’t see that corresponding amount of production, I assure you we’ll see more production in years to come.”
She acknowledges that there are “inherent risks” involved, as “technology doesn’t come cheap”. Some farms that were grant recipients, for example, have wound down earlier than expected.
“Some of them don’t make it. Sometimes it’s not because the technologies don’t work. It could be that partnerships fall through,” she adds. “But cases that are successful outweigh those who exit the industry.”
Sim Wi Min.
One of the success stories is ComCrop, which was one of the first to attempt rooftop farming in Singapore eight years ago. Located in a Woodlands industrial estate, its crops are grown using hydroponics instead of traditional soil-based methods.
Chief executive officer Peter Barber thinks of it as a hybrid farm, using sunlight and a greenhouse designed for constant airflow, unlike high-tech indoor farms that use artificial lights and air conditioning. And he can see why the latter might struggle.
“These two worlds (high-tech and traditional farming) have operated in isolation,” he says. “(The traditional farmers) know what they need to do to grow vegetables, but they may not be so adept on the technological side.
“Then you’ve got the tech guys who have all their artificial intelligence and their robots … The problem is, the new guys don’t have the growing experience, and I think that’s why they’re falling down on the volume side.”
Peter Barber shows Ming around ComCrop's rooftop farm in Woodlands.
To create a flourishing industry, he says “we have to build an ecosystem”.
“Then we need the support of the food agency to make sure that Singaporean consumers see the quality, the safety and the nutritional value of what’s grown here in Singapore … and say, ‘That’s a gold standard,’” he adds.
“We still haven’t seen the full repercussions of the food supply problems that’ve been created by COVID. If we don’t change how much we’re growing here, we’re going to be paying more for food no matter which way we look at it.”
BRIDGING THE NUTRITION GAP
In the supermarket, however, some consumers have a preference for one type of vegetable over the other. Demand for vegetables from soil-based farms is higher than for those from high-tech farms, according to NTUC FairPrice, Singapore’s largest supermarket chain.
WATCH: Why aren’t Singaporeans buying more locally farmed produce? (5:26)
As a chef, Ming expected this to have something to do with taste. But in a blind taste test of bok choy (Chinese cabbage), the results were split evenly among customers at a tze char restaurant.
It turns out, however, that some people think soil-grown vegetables are more nutritious, as Ming found out when he asked on Instagram why people preferred to buy these vegetables.
Plant scientist Mandar Godge, who specializes in the study of Asian leafy vegetables, knows what is behind this partiality.
“There was a stark difference between the hydroponics-grown leafy vegetables and soil-grown (ones) five years ago, or even three years ago, in terms of the nutritional density,” says the Temasek Polytechnic researcher and lecturer.
“Now, the gap is bridged. We’re looking at very improved hydroponics techniques coming in and (producing) a similar nutritional density (to that) which we get in soil-based farming.”
Dr. Mandar Godge.
Over the past decade, scientists like him have been trying to supercharge hydroponics produce by, for example, customising them “based on what kinds of properties you need”, like high levels of vitamins and minerals.
Things like enzymes added to the water can “boost” the nutritional value of the leafy vegetables. Different light intensities can also make a difference in terms of the taste.
The nutritional density of the leafy vegetables in his laboratory, he says, “is much higher compared to what’s available”. And for more farms to adopt these technologies, he suggests that a “technology showcase has to be done Singapore-wide”.
THE DUTCH EXAMPLE
One country that has successfully mass-adopted technology in its farming systems, including urban farming, is the Netherlands. Despite its size, it has become the world’s second-largest food exporter by value.
The Netherlands.
Pepper farmer Ron Jansen, for example, has transformed his grandfather’s farm, Jansen Paprika — located one hour north of Amsterdam — into one of Holland’s most modern farms.
His farm, the size of eight football fields, produces more than 2,000 tonnes of peppers each year, which is 15 times more than what his grandfather grew.
To ensure optimum conditions for his plants, he uses temperature and humidity sensors, which he can track from his office. Machines do the heavy lifting. And he is looking to adopt more cutting-edge technology.
“There are tests to grow plants autonomously — so not by hand. You put your set-up in your computer, and the computer will think for you,” he cites.
Ron Jansen.
Universities play an important part in Holland’s agricultural sector, whose exports last year were worth 95 billion euros (S$152 billion).
“One of the missions of the university is to set up research and demonstration centres to show the possibilities of technology … and transfer the knowledge,” says plant researcher Sjaak Bakker from Wageningen University and Research.
To facilitate this, a central organisation groups farmers according to the crops they grow, where they present their problems to researchers and government agencies, and collectively brainstorm solutions.
“Farmers can’t survive on their own. They need a certain scale in doing research and … innovation,” Bakker adds. “This is why the ecosystem in the Netherlands has come this far and is such a successful sector.”
Dr Sjaak Bakker.
THE NEED TO CHANGE PERCEPTIONS
There are more than 20 agricultural universities in Holland that prime people for the industry. In contrast, there are no universities or polytechnics in Singapore offering agriculture as a full-time course. Most farmhands here are foreign workers.
“Not a lot of Singaporeans want to come to a farm and work. It’s hard work, it’s all day … and you have to be here, rain or shine,” says Zach.
Although he is an anomaly, he has helped out on his father’s farm since he was in school. Bjorn Low is even more of an outlier. Eight years ago, he quit the advertising industry to become an urban farmer.
The co-founder of Edible Garden City now has a team of 40 people, with an average age of 25. He thinks it is important to change the perception of farming and to have more young people see it as a career.
WATCH: The full episode — Growing more of our own food: Can Singapore get there? (47:24)
“This is a national security issue. And so, urban farmers or agriculturalists coming up should be seen as an important part of the economy for the future,” says the 39-year-old.
"We need new ideas in this space and to encourage young people to experiment in this space and then drive other initiatives in the local agricultural industry."
He also wants consumers to “step up” for the sake of their food security in future. “Buy local food,” he urges.
“Sometimes the price points … may be five per cent, two per cent higher than things that are produced in Malaysia or Indonesia or Thailand. And consumers are not willing to fork out that additional 20 cents.”
Bjorn Low.
To this end, Restaurant Labyrinth chef and owner Han Li Guang makes a point of sourcing 80 per cent of his produce — including mussels and herbs — from local farms.
The 35-year-old believes restaurants have a part to play, and can even lead the charge, in getting people to buy more local produce.
“We’re like a showroom for Singapore’s agricultural produce … If we can convince people to ‘use local’, no matter how many percent, it’s a good start,” he says.
“My hope for the future is … we’ll see consumption of local produce as a norm.”
Han Li Guang plates up a locally grown dish for Ming.
US: MAINE - Planning Board Signals Support For Vertical Greenhouse/Parking Garage In Downtown Westbrook
The $60 million project is a collaboration between the city and developers that would see the Mechanic Street parking lot downtown turned into a free parking garage, topped with over 50 apartments and a Vertical Harvest farm along the structure’s side
The Vertical Harvest Project Will Go
To The Planning Board For Approval In November
AMERICAN JOURNAL
BY CHANCE VILES
The Westbrook Planning Board will vote Nov. 3 on a proposed $60 million combination greenhouse, apartment complex and parking garage. Courtesy
WESTBROOK— Planning Board members spoke in favor of a multi-use parking garage and vertical greenhouse at a public hearing Oct. 20.
The $60 million project is a collaboration between the city and developers that would see the Mechanic Street parking lot downtown turned into a free parking garage, topped with over 50 apartments and a Vertical Harvest farm along the structure’s side.
A rendering of what the view would be looking southwest from Main Street. Courtesy
“I love this project,” Ward 2 member Jason Frazier said. “It has jobs, parking, housing. It’s the perfect project.”
RELATED
Read more about the Vertical Harvest
The greenhouse would produce about 1 million pounds of food per year and bring in 56 full-time jobs with a focus on providing careers for people with disabilities.
“This is the equivalent of 40 acres worth of food, using 90% less land and water,” developer Nona Yehia said. “We recirculate all of the water we use in the greenhouse. … We aim for our food to be sold and consumed within the state of Maine and from farm-to-fork in less than 24 hours.”
The Planning Board members, on the right, look at the first-floor ground plan at their public hearing Oct. 20. Courtesy photo
The garage will be maintained by the developers, while city residents will still have access to over 400 free parking spaces.
Advertisement
According to Economic Development Director Dan Stevenson, they are confident the greenhouse will be successful, though developers did say that if need be, it could be turned into some other workspace.
“In my career, this is one of the strongest business models I have seen,” Economic Development Director Daniel Stevenson said.
RELATED
Read more about the whole project
“I am thrilled,” Ward 4 member Robin Tannenbaum said. “We are touching a lot of exciting areas and contributing to densification. To set the bar high, where there is still room, I’d like to see more development of the design to let the building sing.”
“Coming from the other side of the river into Main Street and into the downtown, that building is going to tower over all of these other, so why not?” Board Chairperson Rene Daniels said. “It would make it pop, it would be outstanding,”
The city will be paying $15 million for the parking garage through an agreement using tax revenue generated from the project, Stevenson said, meaning there will be no direct impact on taxpayers. Developers will take on $40 million of the cost.
“It’s been a goal of ours for a while to start expanding vertically downtown, and this meets that,” Ward 5 member Ed Reidman said.
The Planning Board will vote on the project Nov. 3.
A rendering of the building. Some Board members called for a more lively facade for the apartments on the top floor. Courtesy
Developers say there will be space outdoors with vegetation for some outdoor opportunities, as well as common spaces within the building for residents. Courtesy
Real Leaf Farm Receives Significant Endorsement By Just Transition Commission Through The Award of €1 million In Grants.
The JFT awarded projects that represented innovative and inspiring plans for the Midlands and who are committed to creating a green and sustainable economy for the region
Real Leaf Farm receives significant endorsement by Just Transition Commission through the award of €1 million in grants. This recognizes Real Leaf Farm’s role in creating a green and sustainable economy for the Midlands.
Real Leaf Farm (RLF) is delighted to be been selected as one of the key projects in the Midlands under the Just Transition Fund (JFT). The JFT awarded projects that represented innovative and inspiring plans for the Midlands and who are committed to creating a green and sustainable economy for the region.
Real Leaf Farm’s mission is to grow fresh, nutritious leafy greens for the local food market using sustainable farming methods that have low environmental impact. The elimination of herbicides and pesticides not only makes RLF a provider of clean, natural, food products but is better for the environmental, leaving no residues behind.
Speaking at the launch, Real Leaf Farm CEO, Karen Hennessy said “RLF is developing a scalable sustainable business - generating income, creating jobs, providing innovative solutions to food production and supporting Midland communities while aligning to the region’s natural strengths in horticulture. The award today of €1 million is a significant endorsement by the government of these plans and I would like to sincerely thank the Just Transition Commission and the Department of the Environment, Climate and Communication”.
Commenting on the grant award, Eddie Kilbane, Founder of Real Leaf Farm said “the development of Sustainable Smart Hydroponic Farming, in Ireland as a whole, will play an important role in social well-being and strengthen self-sufficiency, by diminishing risks connected to the reliance on the global food production system, and long delivery chains; thus creating more resilient communities”.
The first site is planned for the Midlands partnering with Bord na Móna. RLF will repurpose underutilized buildings and to build a new, state of the art, glasshouse thereby reusing and conserving old buildings and bringing jobs back into the peatlands community.
For further information on Real Leaf Farm please visit www.realleaffarm.com
-ENDS-
For further press information, please contact:
Karen Hennessy at khennessy@realleaffarm.com
About Real Leaf Farm
RLF is a new agri-tech company leading the development of sustainable hydroponic farming across Ireland and the UK. It is a pioneering and disruptive business which will be Ireland’s first 100% Hydroponic farm, growing delicious pesticide-free, herbicide-free, salad vegetable produce, 365 days a year. This is smart farming for a sustainable planet in the 21st century.
Through its unique Agri-Tech Solution, RLF has total control over variables like climate and light and uses significantly less land and water compared to conventional outdoor farming. By combining cutting edge technology and design with optimal agriculture methods, RLF is making fresh, nutrient-rich, and tasty food accessible locally, throughout the year, whilst minimizing wastage, excessive transport and ensuring food security.
There is a unique opportunity to be first to market, in a growing sector, through import substitution and the development of a more efficient and sustainable farming model. This project will deliver direct and indirect employment for transition impacted communities, providing sustainable, safe and secure food for local supply. It is also a Brexit solution provider as most of our imports are currently traveling through the UK land bridge.
About Just Transition Fund
The Just Transition Fund is a key pillar of the government’s just transition plan for the Midlands region. A 2020 fund will be available for projects focusing on retraining workers and proposals to generate sustainable employment in the green enterprise in the region, and supporting communities to transition to a low carbon economy.
The objective of the Just Transition Fund 2020 call is to fund innovative projects that contribute to the economic, social, and environmental sustainability of the Wider Midlands region and which have employment and enterprise potential. It will support projects that take a whole-of-Midlands strategic approach and complement other sources of public funding.
Provisional offers of funding, totaling €27.8 million, have been made to 47 projects in the Midlands under the Just Transition Fund. The projects represent innovative and inspiring plans from businesses, local authorities, and communities in the Midlands who are committed to creating a green and sustainable economy for the region. This dedication from the community and targeted support will make the region an attractive and sustainable place to live and work. It will fund training and reskilling so local businesses and communities can adjust to a low-carbon transition.
US: Growing Up: Vertical Farming Makes the Most of Limited Space
To increase agricultural yields, a CALS horticultural scientist and his students are literally looking up. They want to know if growing plants indoors in vertically stacked layers could be part of the solution to feeding a fast-growing world population as farmland becomes scarcer
Horticultural scientist Ricardo Hernandez and Mark Watson work with lettuce plants inside the vertical farm near the JC Raulston Arboretum. (2019)
October 26, 2020 | Dee Shore
To increase agricultural yields, a CALS horticultural scientist and his students are literally looking up. They want to know if growing plants indoors in vertically stacked layers could be part of the solution to feeding a fast-growing world population as farmland becomes scarcer.
Ricardo Hernandez, a leading expert on growing plants in controlled environments, is exploring ways to make vertical farming profitable and sustainable. He and his students have modified a donated shipping container to grow produce and herbs on campus.
Mark Watson, who graduated in May, says that indoor vertical farming has several advantages. It allows for year-round production, and it’s less susceptible to weather extremes. It can also be used in urban settings, potentially reducing food losses that occur in getting crops from rural farms to tables.
Still, substantial challenges remain. Indoor production requires significant energy, which pushes farmers’ costs up.
Watson hadn’t heard of vertical farming before he took Hernandez’s controlled-environment horticulture class in 2019. He went on to win a national award for independent research on the best temperature and humidity to allow tomato plants to heal indoors after being grafted onto the rootstocks of other plants.
He also served as president of NC State’s Vertical Farms Club, which is testing leafy greens and other food crops in the shipping container and exploring marketing opportunities. The club includes students in horticulture, plant and microbial biology, crop and soil sciences, electrical and computer engineering, and mechanical and aerospace engineering.
Hernandez sees possibilities for farmers to raise high-value seedlings in vertical farms. As he explains, “Using a controlled environment can be key, because we can grow plants in high density and manipulate the environment—the lighting, the temperature, air movements and carbon dioxide concentrations—to produce the best seedlings possible.”
SINGAPORE: Port CEO Wants To Stop Food Rotting On Ships
The food industry accounts for almost a quarter of global carbon emissions. Yet 30% of production is wasted because it doesn’t arrive in an edible form — caused by “logistical failures” that can be addressed using information technology, said Tan Chong Meng, the chief executive officer of PSA International Group in Singapore
Port CEO Wants To Stop Food Rotting On Ships
October 28, 2020
One of the largest container port operators is calling on the shipping industry to tackle a growing yet often overlooked major environmental problem: spoiled food from hauling produce around the world.
The food industry accounts for almost a quarter of global carbon emissions. Yet 30% of production is wasted because it doesn’t arrive in an edible form — caused by “logistical failures” that can be addressed using information technology, said Tan Chong Meng, the chief executive officer of PSA International Group in Singapore.
Reducing that wastage through “digitalization” to move food more efficiently is “a huge opportunity” for the freight industry, which emits about 800 million tons of carbon dioxide, Tan told the Singapore International Energy Week conference.
The shipping companies that move 90% of the world’s goods including food have pledged to decarbonize in the next 30 years by curbing fossil-fuel emissions. That commitment focuses on the pollution caused by fuel, but doesn’t include the indirect emissions from food waste. About 1.3 billion tons of global food production is lost before reaching consumers’ plates every year, according to the Food and Agriculture Organization of the United Nations.
Supply disruptions caused by the coronavirus pandemic have put the spotlight on food security, prompting calls for reduced wastage to boost self-sufficiency. In August, China’s President Xi Jinping introduced a “Clean Plates Campaign” to tackle the “shocking and distressing” problem of food waste.
In Singapore, which relies on imports for more than 90% of its food and increased wastage by 20% over the past decade, President Halimah Yacob urged citizens to help overcome the problem.
Some 10% of developed nations’ greenhouse gas emissions are created by producing food that’s never eaten, according to the UN Environment Programme. About 14% of the world’s food is lost after harvesting and before reaching the retail level, and good infrastructure and efficient trade logistics are key to preventing food losses, according to the UN Food and Agriculture Organization.
Lead photo: Photo: Bloomberg
GP Solutions, Inc. Enters Into Distribution Agreement With Advanced Container Technologies, Inc.
A key component of the agreement is ACT's exclusivity to market GP Solutions "Grow Pods." GP Solutions "Grow Pods" has become a popular and trusted technology in the agriculture industry. Subsequently, ACT completed a share exchange on October 9th, 2020, with Medtainer, Inc., (MDTRD). Medtainer, Inc. is a California based company that specializes in manufacturing, branding, sales and marketing consultation
NEWS PROVIDED BY
Oct 27, 2020
CORONA, Calif., Oct. 27, 2020,/PRNewswire/ -- On August 6th, 2020, GP Solutions, Inc. (GWPD) finalized a distribution agreement with California-based Advanced Container Technologies, Inc., (ACT). The agreement states ACT has the exclusive right to market, sell, and distribute GP's products in the United States and its territories. This agreement has an initial term that expires on December 31, 2025, and is renewable indefinitely as long as ACT meets prescribed sales targets. GP manufactures fully insulated, food-grade shipping containers that are specifically modified to provide an optimally controlled environment for growing a wide range of horticultural and agricultural products in all environments and climates.
A key component of the agreement is ACT's exclusivity to market GP Solutions "Grow Pods." GP Solutions "Grow Pods" have become a popular and trusted technology in the agriculture industry. Subsequently, ACT completed a share exchange on October 9th, 2020, with Medtainer, Inc., (MDTRD). Medtainer, Inc. is a California based company that specializes in manufacturing, branding, sales, and marketing consultation.
GP Solutions, Inc. President, George Natzic, stated, "We are very excited about the prospects of this agreement allowing ACT to use its expertise to market and sell GP Solutions' Grow Pods." Also stating, "This also allows GP Solutions to focus on manufacturing new products and executing our business model into new industries and territories."
GrowPods are controlled environment micro-farms with a sealed eco-system, utilizing filtered air and water while maintaining a pest-free environment to eliminate pathogens. Grow Pods offers farmers a high-margin niche to expand into and gives consumers access to safe, tested, and nutritious "Super Foods."
For more information, call: (855) 247-8054 or visit: www.growpodsolutions.com.
Connect:
Website: www.growpodsolutions.com
Facebook: facebook.com/GrowPodTechnology
Twitter: @GrowPodSolution
Forward-Looking Statements
This release includes predictions or information that might be considered "forward-looking" within securities laws. These statements represent Company's current judgments, but are subject to uncertainties that could cause results to differ. Readers are cautioned to not place undue reliance on these statements, which reflect management's opinions only as of the date of this release. The Company is not obligated to revise any statements in light of new information or events.
SOURCE GP Solutions
Related Links
https://www.growpodsolutions.com
Also from this source
Vertical Farm Market Projected to Reach $7.3 Billion...
Test Results Show Lettuce Grown in GrowPods to be Pathogen Free...
"I Can See Hydroponics Becoming Bigger, From Commercial Use To Homes"
A University of British Columbia student design team is developing a fully autonomous agricultural robot, driven by their belief that Canada can lead the world in sustainable farming.
A University of British Columbia student design team is developing a fully autonomous agricultural robot, driven by their belief that Canada can lead the world in sustainable farming.
The UBC AgroBot aims to precisely exterminate weeds and fertilize crops as well as record data from a farmer’s operation. The team has grown from four to 40 plus students with backgrounds in various engineering disciplines and many with no prior exposure to agriculture.
The AgroBot project involves four teams of students. The chassis team designs the mechanical body, structure and driving system. The extermination team works on the mechanics and chemical design to target weeds. The navigation team develops the autonomous software to navigate crop rows and the image recognition team uses machine learning technology to allow the robot to identify crops and weeds.
“To sustainably produce enough food for the world, there is an urgent need for innovation in the field of agriculture,” says Wendie Wu, AgroBot team member. “Engineering students are drawn by the technologies we see working in other industries and they’re eager to apply them in agriculture and help operations be as sustainable as possible.”
The UBC team was the only Canadian university design team planning to attend the AgGrowBot Challenge hosted by Indiana’s Purdue University last May, however the COVID-19 pandemic prevented the AgroBot team from attending. Still, their success has been noticed at UBC where they were granted official engineering design team status and have received financial support from various organizations, including Farm Credit Canada (FCC).
“Agriculture continues to be one of the most innovative and agile industries in Canada, says FCC marketing vice president Fred Wall. “In order to feed a growing world population, we need to focus on sustainability and technology. FCC applauds the UBC AgroBot students for seeing the opportunity to apply their skills in agriculture and make a real difference for the food sector.”
The interest and success of the AgroBot project has UBC supporting an aquaponics project as well, dubbed AgroPonics. It involves applying similar machine learning, image recognition and automation technologies to building an autonomous indoor garden system that is functional without soil.
Team member Seline Choe is motivated about what agritech can do for agriculture and food in Canada. “The agritech industry is growing fast. I see the opportunity to use more image recognition and data collection for the benefit of everyone. There are a lot of companies in the research phase and we can be a part of the talent pipeline that will evolve those technologies,” Seline adds. “I can see hydroponics becoming bigger, from commercial use to homes, it can be a more efficient way to grow food by optimizing growing conditions. We need to come up with new ways to support the world’s population with the food it needs.”
The UBC students are continuing to work on both the AgroBot and AgroPonics projects. They hope to implement their products on local farms and on the university campus in the near future.
For more information:
Farm Credit Canada
www.fcc-fac.ca
28 Oct 2020
VIDEOS: Vertical Farming Goes High-Tech And Underground
Vertical Farms Are Evolving Into A Major
Food Industry Powered by Sophisticated
Technologies And Production Methods
Growing fresh produce in underground areas
Transforming a tunnel into a vertical farming operation
Infarm allows customers to pick the produce themselves
Vertical farming companies are facing an array of challenges
Technology and lower costs are critical for the industry’s sustainability
Innovation is vital to solving the world’s greatest challenges
Farmers around the world are heading towards an uncertain future. Apart from the prospect of feeding the global population that’s set to reach around 10.9 billion by 2100, they are also facing climate change-induced floods, droughts, and heatwaves. Fertile land is in ever shorter supply as soil erosion intensifies. Farming is also to blame for some of these problems as the CO2 footprint of food accounts for 17 percent of total global emissions. And by the time plants get transported to supermarkets, they lose 45 percent of their nutrients. As it becomes increasingly apparent that traditional agriculture is unsustainable, growing food in an artificial environment is emerging as a potentially better way forward.
Instead of plowing fields, farmers would produce food in vertically stacked trays. Soil would be replaced by nutrient-rich water, while LED lights would act as the sun to ensure plants photosynthesize. This practice, known as vertical farming, offers many benefits. The indoor environment protects crops from extreme weather events and pests, which means that food grows fast and there’s no need for pesticides. Also, food is grown close to cities, which not only reduces food miles and the related carbon footprint but also provides consumers with fresh and tasty crops.
However, vertical farming faces certain challenges as well. Companies have to constantly innovate to cut production costs and turn a profit, which is vital for the survival of this industry. But entrepreneurs remain optimistic. The global vertical farming market is forecasted to reach $12.77 billion by 2026 and people are becoming increasingly aware that there’s a better way to feed the populGrowing fresh produce in underground areas
High rents and the lack of space have prompted some modern urban farmers to go underground. In London, for instance, a farm called Growing Underground operates from a World War II bomb shelter located 33 metres below Clapham High Street. Owned by Stephen Dring and Richard Ballard, the vertical farming facility produces an array of herb and salad mixes, including parsley, red mustard, coriander, and pea shoots. Fresh produce is then sold through Marks & Spencer, Waitrose, Ocado, and several other retailers. Some restaurants have also expressed interest in buying fresh produce, says Ballard.
He also points to many advantages of vertical farming. For instance, his farm delivers 60 harvests a year, compared with around seven that can be achieved in traditional agriculture. Furthermore, Growing Underground is carbon neutral and uses 70 percent less water than typical farms. The only major cost he’s trying to reduce is the electricity that powers the lights. And his ambitions are global. “The UK is the hardest market for growing salad. We’ve got very low prices in the supermarket, so if we can make it work here we can make it work anywhere,” says Ballard.
Underground vertical farming is thriving in other British cities as well. The Liverpool-based social enterprise Farm Urban, for example, provides customers with a weekly box of living salad leaves, edible flowers, and fragrant herbs. Jens Thomas, the company’s technical director, says that the product is pesticide-free and “it’s grown using 90% less water than if it was grown in a field; it’s zero-waste; and it’s hyper-local.” Farm Urban is trying to promote healthy and sustainable living. For each box of greens customers buy, the company delivers a box of greens to a local school. This activity is part of the Greens for Good campaign that aims to reconnect people with locally-grown food.
In New York, the vertical farming business Farm. One is also growing. Its underground farms produce over 500 different herbs, edible flowers, and microgreens year-round, using specialized software to manage multiple operations, such as seed, harvest, and flavor optimization. Founded by Rob Laing, the company supplies fresh produce to various New York-based restaurants, including Atera, Ai Fiori, Benno, and Flora Bar. All deliveries are made by bike and subway. Also, visitors can book a tour of the farm or take a class in hydroponics to learn how to grow vegetables in a soil-free environment.
Transforming a tunnel into a vertical farming operation
Successful vertical farming businesses can also be launched outside of cities. NEXTON, a South Korea-based startup, has built vertical farms in a former highway tunnel, located 190 kilometres south of the capital city of Seoul. Growing salads, leafy greens, and strawberries beneath mountains has many advantages. For one, the 6,500-square-metre facility naturally maintains a temperature that ranges between 10 to 20 degrees Celsius, which translates into lower energy spend for cooling or heating. Furthermore, labor costs are reduced by automating various operations. And as farming is done without pesticide or herbicide, with sensors monitoring humidity and CO2 concentrations, customers receive both healthy and affordable products.
Choi Jae-bin, the CEO of NextOn, also uses non-tech tactics to boost production. For instance, the music of Beethoven and Schubert is played in the 600-metre-long tunnel as Jae-bin believes it will help plants to grow faster. And his plan is to build more farms in urban areas. “Plants easily grow at home, at nearby stores, at hamburger restaurants, or even at metro stations. I think the system to grow crops far away from a city and transporting it will disappear,” he says.
Infarm allows customers to pick produce themselves
Infarm, a Berlin-based startup, has already achieved in several European countries what Jae-bin plans to do in South Korea. The German company builds modular farms that are placed in customer-facing locations, such as schools, grocery stores, restaurants, and shopping malls, enabling customers to pick the produce themselves. Clients can also add more modules if they want to increase the farming output, while the production is monitored and controlled through a cloud-based platform. Essentially, the whole thing functions as a ‘farming as a service’ operation that combines the IoT, Big Data, and cloud analytics.
The company is working with 25 major food retailers in Germany, France, and Switzerland, including Migros, Casino, Intermarche, Auchan, Selgros, and AmazonFresh. Furthermore, it has installed more than 200 in-store farms, as well as 150 farms in distribution centres. And in 2019, Infarm raised $100 million in Series B investment round. The funding will be used to expand research and development, sales, and operation teams. Also, the startup plans to increase its presence in the UK and negotiate partnerships with retailers in the US and Japan.
Vertical farming companies are facing an array of challenges
While the rise of vertical farming companies has been impressive, the industry is facing many challenges and its survival depends on reducing costs and increasing productivity. Take, for example, the fact that deploying even a small, low-tech vertical farm with the 1st generation technology costs around $280,000. On the other hand, the cost of setting up more complex farms with advanced tech can go over $15 million. There are also operating expenses such as lighting and labour that can further pressure companies’ bottom line, making it hard to compete with organic and traditional producers.
So it comes as no surprise that return on investment (ROI) in vertical farming projects is mediocre at best. The current market prices don’t make the situation any easier either. A kilogram of vertically-grown leafy greens is around $33, while organic produce costs $23. To gain a competitive edge, vertical farming startups need to take several measures.
Technology and lower costs are critical for the industry’s sustainability
The first step in ensuring the long-term profitability of vertical farms is transitioning to 2nd generation technology. This means that in addition to automatic control of irrigation, humidity, lighting, CO2, and other relevant parameters, farms should also be capable of autonomously collecting data and optimizing growing processes. They also need to implement cutting-edge machines that will autonomously run planting and weeding operations in the facility, and harvest sort and package produce for shipping. These improvements can enable the second generation of vertical farms to yield 55 times more produce than conventional farms.
Increased automation will also cut labour expenses. Intelligent Growth Solutions, a UK-based agritech business, has reportedly developed an automated farming system that uses modular structures to reduce labour needs by up to 80 percent. Furthermore, LED lighting efficiency is likely to improve by an additional 70 percent by 2030, reducing the energy spend. Boaz Toledano, a business consultant specializing in vertical farming, says that “lighting improvements should reduce OPEX [operating expenses] by 12%, and automation should cut OPEX by a further 20%+”.
Companies can also reduce costs by setting up farming operations underground. This would not only help them avoid the high cost of renting in urban centres but also enable them to enjoy the benefits of having a steady temperature. Underground facilities also offer better protection against natural disasters and can be more easily adapted to producers’ needs.
Innovation is vital to solving the world’s greatest challenges
New technologies are moving the food industry forward. Vertical farming, though still gaining traction, could help solve some of the world’s greatest challenges, such as food shortage. Tasked with feeding the growing global population, today’s agriculture producers still primarily rely on farming practices that hurt the environment. As it becomes clear that traditional farming is unsustainable, innovative entrepreneurs and scientists have come up with a potential solution. Vertical farming is increasingly hailed as an alternative food production method that can provide people with healthy and fresh produce. Thriving in undergrounds, stores, and restaurants around the world, vertical farms are becoming a major industry. But their survival depends on the ability of businesses to lower food production costs and increase productivity.
This article is written by Richard van Hooijdonk
Trendwatcher, futurist, and international keynote speaker Richard van Hooijdonk takes you to an inspiring future that will dramatically change the way we live, work, and do business. All lectures
How The Pandemic Has Accelerated The Next Generation of Farming
Vertical farming, or the practice of cultivating crops in vertically stacked shelves and often in a controlled indoor environment, allows produce to be shipped to grocery stores, restaurants and other dining services in a matter of minutes
Vertical farming has provided an innovative
way to serve customers and ensure clean food
Coronavirus puts farmers in 'dire need' of help from government: Farm Bureau president
Farm Bureau President Zippy Duvall discusses how coronavirus is challenging farmers, trade with China, and reopening the economy.
The foodservice industry is betting big on vertical farming as the pandemic ushers in a heightened awareness of food safety and cleanliness.
Vertical farming, or the practice of cultivating crops in vertically stacked shelves and often in a controlled indoor environment, allows produce to be shipped to grocery stores, restaurants and other dining services in a matter of minutes.
EVEN WITH A STRONG CROP THIS YEAR, US FARMERS ARE SUFFERING
A new report by Allied Market Research shows that the global market for vertical farming crops is projected to reach $1.38 billion by 2027 with a compounded annual growth rate of 26.2% from 2021 to 2027. Last year alone, the industry was estimated to be around $212.4 million.
Amid the trajectory for growth, the coronavirus outbreak has accelerated the demand for fresh and locally grown produce. And as restaurants reopen, vertical farming has provided an innovative way to serve customers and ensure clean food.
“The pandemic has certainly shed light on the fact that everybody is very aware of cleanliness and safety, and food is no exception,” CEO of Kalera Daniel Malechuk told FOX Business. “What vertical farming can offer is something that is local, something that hasn’t been in a journey to get to the end or touched by a significant number of people and something that is grown in a clean room where the product is not subject to harmful elements or exposure.”
TRUMP ANNOUNCES $13B WORTH OF NEW RELIEF FUNDING FOR US FARMERS
Kalera, an indoor vertical farming company with hydroponic technology, is on track for rapid growth, particularly in high dense urban markets. After opening the largest vertical farming facility in Texas, the ag-tech company has plans to expand to Atlanta where it will be the highest production volume vertical farm in the Southeast, as well as Denver by 2021. Aside from its typical operations providing lettuce and microgreens to theme parks and restaurants, Kalera has also entered the grocery space marked by a deal with Publix that went into effect in April.
(Credit: Kalera)
“We love supporting our local growers—whether they are growing in a field or on top of a hotel,” Business Development Director Produce and Floral of Publix Super Markets Curt Epperson told FOX Business. “Our customers really appreciate hydroponically grown leafy greens, not only because they are flavorful but because they are sustainable. We’re excited to see where vertical farming goes in the future. Wherever that is, you can be sure that we’ll be keeping in touch with our local hydroponic farmers, finding out what they’re doing, and talking about how we can work together.”
Hydroponically grown greens emerged in grocery stores prior to COVID-19, but the global health crisis has only accentuated the need to know where food comes from and how it is grown.
(Credit: Kalera)
With technology that doesn't require soil to grow plants and consumes up to 10 times less water compared to traditional soil-based growth, hydroponic systems are not only sustainable but also can be controlled to minimize pesticides and other dangerous chemicals.
Additionally, the minimal transport involved allows produce to reach store shelves without traveling thousands of miles and being exposed to more touchpoints.
Global supply chain disruption has also forced retail chains like Publix to secure produce that does not conflict with restrictions on transportation, which particularly came to light during the first phase of lockdown and with varying state travel mandates.
US FARMERS SCRAMBLE FOR HELP AS COVID-19 SCUTTLES IMMIGRANT WORKFORCE
On top of that, more customers are turning to vertical farming solutions like Kalera for lettuce due to the shortage caused by the California wildfires, where the ash in the fields have affected the growth and safety of the traditional product.
And as vertical farming becomes more attractive in light of the pandemic, more cities will tap into these alternative methods, according to Kalera’s Daniel Malechuk.
“What Kalera is able to do is to offer and shed new light on farming is the backbone of American society and one of our strengths as a nation,” Malechuk said. And leading the wave of the ag-tech revolution is what vertical farming companies like Kalera are doing.”
Korean Smart Farm Company Farm8 Eyes IPO In 2022
The firm has been seeing robust growth despite the coronavirus slump, gaining recognition for its eco-friendly agricultural cultivation and processing technologies. It is the country’s leading smart farm factory, incorporating the latest technologies including artificial intelligence and internet of things to optimize and automate the cultivation process
2020.10.23
Photo provided by Farm8
Farm8, a South Korean agricultural firm with advanced technologies in indoor farming, is seeking to go public on the main Kospi in 2022 after gaining confidence from capital investment.
Farm8’s biggest backer IMM Investment is expected to play a pivotal role in the initial public offering and likely to remain as its No. 1 shareholder to drive the company’s global expansion.
The Seoul-based alternative asset investment firm first linked up with Farm8 in 2014 by investing 16 billion won ($14.1 million) and has since been an ardent supporter of the company, backing its financing, benchmarking and promotion efforts.
In March this year, it helped pulled 10 billion in outside capital, including 5 billion won from state-run Korea Development Bank.
Farm8’s valuation is estimated at 80 billion won after its rights issue.
Farm8 posted 47.2 billion won in revenue last year, up 7.5 percent from 2018. Sales this year are estimated to jump 25 percent to 58 billion won, according to the company.
The firm has been seeing robust growth despite the coronavirus slump, gaining recognition for its eco-friendly agricultural cultivation and processing technologies. It is the country’s leading smart farm factory, incorporating the latest technologies including artificial intelligence and internet of things to optimize and automate the cultivation process.
Farm8 has installed Metro Farms in five subway stations in Seoul and is planning to build a container smart farm in South Korea’s Antarctic research station by the end of this year. It aims to triple its smart farm capacity to 9,910 square meters next year.
The firm also plans to add more value-added crops such as ginseng and strawberries and is exploring options of using these ingredients for cosmetic and medical purposes.
Korea’s smart farm market is estimated to be worth 2.6 trillion won this year, with potential to grow even further amid pledges of government support.
Farm8 is also intent on taking its business global. It said it aims to build its presence in Asian markets including Mongolia, Singapore and Japan, and eventually break into North America and Europe.
By Park Chang-young and Kim Hyo-jin
US - INDIANIA - Vertical Farm Is On The Way Up In Nappanee
No matter what the weather is outside, the inside of Micro Farms' futuristic, squared-off, Venlo Dutch greenhouse is as balmy as a pleasant summer evening. The facility covers just one-quarter of an acre of land, but the output of produce sustains the cash-and-carry business managed by Dion Graber
by Steve Grinczel
October 23, 2020
It's harvest time throughout Michiana.
Then again, it's always harvest time at Micro Farms LLC in Nappanee, where growing season for tomatoes, lettuce, cucumbers and peppers includes every day from Jan. 1 to Dec. 31.
No matter what the weather is outside, the inside of Micro Farms' futuristic, squared-off, Venlo Dutch greenhouse is as balmy as a pleasant summer evening. The facility covers just one-quarter of an acre of land, but the output of produce sustains the cash-and-carry business managed by Dion Graber.
"We have the best of all seasons in Indiana here inside, so that's what's really nice," he said.
Cucumbers and lettuce are harvested on a daily basis and tomatoes and peppers are picked three times a week.
"With most of your outdoor stuff, some things harvest earlier in the season, but basically, you have four months of harvest, so they're all done now. We have 12, and that's what really sets us apart," Graber said. "It is really hard to grow in winter, with a lot less lighting and stuff, so your production is down, but we're still able to produce fresh produce when it's snowing outside."
Evidence of greenhouse-like structures dates back to the 1400s, but Graber's facility—known as a vertical farm—has more in common with science fiction than archeology.
Micro Farms' hundreds of plants are grown in a high-tech, aeroponic-hydroponic system, which means their roots never touch a speck of dirt.
Seeds are germinated in foam cubes and eventually moved to the main growing area where they reach up to the underside of the pitched roof. Four varieties of lettuce grow in patented plastic cups, developed by Micro Farms, that fit into wide PVC tubes.
"Nothing is sitting in water," Graber said. "Our tubes are a combination of aeroponics and hydroponics. There's a nozzle that comes down the middle of each tube and sprays out. The cups hold the cube of lettuce, and then the water just drips down through and the roots grow into the middle of the tube."
Tomatoes, cucumbers and peppers are rooted in rows of large, rockwool growing medium cubes set on the floor.
"With that, you have fewer chances for diseases," Graber said.
Non-stinging bumblebees are brought in to pollinate the plants and other natural means are used to control pests. No chemical growth or pesticide inputs are used, Graber said.
Tomato vines produce optimally for six to eight months and average about 45 to 55 feet in length. Cucumber plants average about 3 inches of growth per day and plants eventually stand 18 feet tall. Pepper plants get up to 15 feet.
While water is obviously key component of a hydroponic operation, greenhouses typically use far less water to grow the same plant cultivated outdoors.
"We also collect rain water off of this roof and the building next door to feed our plants," Graber said. "Close to 80 percent of our water is rain water. We have about 35,000 gallons worth of storage."
The watering system, located in the basement, is tailored to the needs of each crop with nutrients Graber compared to over-the-counter, human health supplements.
Graber grew up on his family's nearby farm that transitioned from dairy to spe-cialty beef cattle when he was a youngster. His father, Loren, became interested in hydroponics after reading an article about the Epcot theme park at Walt Disney World in Orlando, Fla., where they have been growing and abundance of vegetables indoors without soil or "fairy dust," according to FarmFlavor.com, since 1982.
"That really intrigued him so he kind of just stayed with it, and 25 years later he and his agronomist, Steve Kiefer, decided to go into the greenhouse business, and here we are, six years in now," Graber said. "I was working on the farm with the cows and doing custom hay, and helped build the greenhouse.
"I wasn't planning on working here, but then it just all came together and decided to give it a shot."
In addi-tion to being self-taught, Graber crammed his way through Arizona State University remote classes on growing tomatoes and peppers indoors.
As arable farmland continues to dwindle and populations grow, hydroponic agriculture has long been studied as a potential solution to increased demand on the world's food supply. Hydroponic plants are generally considered three to 10 times more productive than outdoor soil-based plants. According to Neil Mattson, of Cornell University's School of Integrative Plant Science, 20 to 50 times more lettuce per acre can be produced in a greenhouse than in a field.
In a recent LAist.com story, Plenty farms, a San Francisco-based startup, claimed its state-of-the-art vertical system can grow 350 times more produce per square foot than a conventional farm can.
In 2006, Epcot set a world record with 32,000 tomatoes produced by a single plant over a 16-month period.
"We're looking at how to grow things indoors and what works best in this area," Graber said. "This is basically a university for growing. I've tried close to 60-some different kinds of lettuce, four different kinds of tomatoes, six different kinds of peppers and four different kinds of cucumbers just to see what works best in this environment."
Graber makes due with whatever sunshine Mother Nature will provide, while supplementing minimally with artificial light.
"You actually have a little more wattage of sunlight in winter than you think with all the reflection," he said. "That's why everything inside of this greenhouse is powder-coated white because 1 percent more reflection creates 1 percent more yield, and you've got rays bouncing all over the place in here.
"It's definitely big for us to be able to grow fresh produce all year-round."
Graber's mature produce looks uniform and flawless, and he said it compares favorably with similar products grown outdoors.
"We feel we're pretty close to garden-taste," he said. "Some people prefer different flavors, and our lettuce definitely sets us apart just because of how fresh it is. It's harvested less than eight hours before you get it."
Graber sells his produce on-site on Wednesday and Friday afternoons with an order-and-drive-through set-up patterned after the one the Chick-fil-A fast-food chain has been employing during the pandemic.
"Even in the dead of winter, you never have to get out of your vehicle," Graber said. "We also supply some mom-and-pop grocery stores, a couple of restaurants and a bakery."
Micro Farms is also part of a start-up, online delivery service called Local Farms Direct (localfarms direct.com) that is designed to deliver fresh produce and a wide variety of fresh baked goods from Amish bakers and other private bakeries to work environments, such as office complexes.
"One of the best things about this job is you see new growth and progress every day with your plants, along with just being able to get your customers some healthy food throughout the year," Graber said. "We have a very loyal base of customers."
With advancements in LED lighting, hydroponic producers are able to grow produce in almost any enclosed space, including abandoned buildings, warehouses and even caves. Futurists have long envisioned the day when urban crops for big cities will be grown indoors in tall buildings occupying a real estate footprint that's a fraction of a farm field.
Indoor farming was a $23.75 billion industry in 2016 and expected to grow to $40.25 billion in 2020, according to MarketsandMarkets.com study.
"This is definitely just the beginning," Graber said. "I would have said, when this first was built, we were one of the most advanced facilities in Indiana if not the U.S. We've probably been way surpassed by now because this industry is growing very fast.
"It's food and people have to have food to live."
Purdue Study Addresses Environmental, Economic Impacts of Hydroponic, Aquaponics Systems
Hydroponics and aquaponics offer promise for growing produce and raising fish. But some may be wary of entering the industries because of perceptions about high capital and operational costs and environmental impacts
October 22, 2020
Story by Brian Wallheimer
Hydroponics and aquaponics offer promise for growing produce and raising fish. But some may be wary of entering the industries because of perceptions about high capital and operational costs and environmental impacts.
Purdue University scientists compared the environmental performances of both systems and calculated their economic efficiencies in Indiana. Their findings, published in the Journal of Cleaner Production, inform those interested in entering hydroponic or aquaponic industries on how to get the most for their investment with the least environmental footprint.
Hydroponics and aquaponics are soilless systems. Hydroponic plants are grown in water containing chemical fertilizers as nutrients. Aquaponics adds the raising of fish and uses fish waste to replace chemical fertilizers. These indoor operations come with upfront capital costs and require use of significant amounts of energy for lighting, heating and water pumping, as well as fish feed and fertilizers.
For one month, graduate students Peng Chen and Gaotian Zhu raised six vegetables in a hydroponic system and those same vegetables with tilapia in an aquaponic system. Experiments were conducted in the lab of Hye-Ji Kim, a Purdue assistant professor of horticulture and landscape architecture, and in collaboration with Paul Brown, a Purdue professor of forestry and natural resources. Jen-Yi Huang, a Purdue assistant professor of food science and the leader of the project, worked with the students to conduct a life cycle assessment using the data they collected.
Purdue University researchers conducted a life cycle assessment of hydroponic and aquaponic growing systems in Indiana to measure their environmental and economic impacts. (Photo provided by Peng Chen)
The researchers found that the aquaponic system led to 45 percent less environmental impact when considering fossil fuel use, global warming, water acidification and eutrophication created by resources used as well as waste and emissions released. Twice as much food is grown in the aquaponic systems with little added environmental cost.
“The aquaponic system is more environmentally friendly when you look at the total environmental footprint per US dollar of economic value of the products,” Huang said. “But that is based on using Indiana’s current energy mix. If we consider using more renewable energy sources, things start to change.”
Indiana currently gets almost 60 percent of its energy from coal-fired power plants, according to the U.S. Energy Information Administration, with about one-third coming from natural gas. The less electricity hydroponic and aquaponic growers source from fossil fuels, the more environmentally friendly their operations become.
Chen said that changing the mix and getting one-third of power from coal, natural gas and wind would reduce the environmental impacts of hydroponics by up to 48 percent. If an operation sourced its electricity solely from wind energy, hydroponic operations would be considered slightly more environmentally friendly than aquaponics.
“By using wind energy, which is largely produced in Indiana, farmers can reduce their environmental footprint enough to make these two systems essentially equal in terms of the economic output gained for the environmental cost,” Chen said. “By choosing more plant-based fish feed, the environmental impacts can be further reduced in aquaponic systems.”
INDIA: Aquaponics Unit Gets Off The Ground In Ludhiana Vet Varsity
The system was established by Centre for Development of Advanced Computing (C-DAC), Mohali, under the collaborative project funded by the ministry of electronics and information technology (MEITY), GOI
Was Inaugurated by Sanjay Dhotre,
Union Minister of State For Education,
Communication And Electronics And IT
CHANDIGARH
Oct 14, 2020, HT Correspondent
Hindustan Times, Ludhiana
The aquaponics unit in Ludhiana. (HT photo)
Sanjay Dhotre Union minister of state for education, communication and electronics and IT, on Wednesday virtually inaugurated an ‘Aquaponics vertical farming system’ developed at Guru Angad Dev Veterinary and Animal Sciences University (GADVASU).
The system was established by Centre for Development of Advanced Computing (C-DAC), Mohali, under the collaborative project funded by the ministry of electronics and information technology (MEITY), GOI.
Dhotre emphasized on the need to modernize food production sectors to double farmers’ income and enhance climate change resilience among the farming community.
He said that aquaponics is a promising technology for organic farming and there is a need to publicize such technologies for the wellbeing of the environment and humans.
Inderjeet Singh, the vice-chancellor of GADVASU, said that aquaponics involves a synergistic combination of aquaculture and hydroponics to promote vertical farming with enhanced nutrient utilization efficiency through recycling of water between the two components to produce fish and vegetables together.
He added that it offers potential future solutions to global warming, with only 10-12% water and land requirement compared to traditional fish and vegetable farming systems, fulfilling the concept of ‘More crop per drop’.The V-C said that the facility will help GADVASU take up required R&D for its optimized utilization under climatic conditions of the state, especially for stakeholders with small landholdings.
In the keynote address, Hemant Darbari, DG, C-DAC, said that the automated aquaponics system will serve as an excellent R&D and demonstration provision for skill development in aspiring stakeholders of the region to produce more food from less land.
Jyoti Arora, special secretary, MEITY, spoke on making the facility sustainable through innovative techniques to attract more youth into the technology-driven agriculture sector.
The project in charge, Jaspal Singh, joint director, C-DAC, and his team implemented the project at GADVASU with Meera D Ansal, dean, college of fisheries, and Kulbir Singh, principle olericulturist, PAU, under the leadership of JPS Gill, director research, GADVASU.