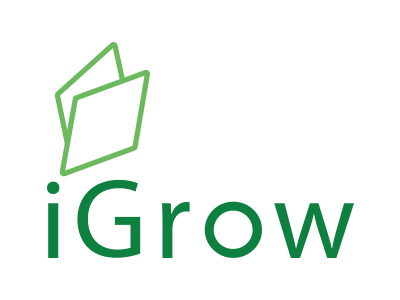
Welcome to iGrow News, Your Source for the World of Indoor Vertical Farming
2020 GLASE Summit - CANCELLED
GLASE will host its annual Summit in Leamington, Ont. Canada. Participants will discuss the latest GLASE research innovations, the CEA market trends and connect with Canadian greenhouse growers
2020 GLASE Summit
Leamington, Ont. Canada
Best Western Plus Conference Center
March 26 - 27, 2020
GLASE will host its annual Summit in Leamington, Ont. Canada. Participants will discuss the latest GLASE research innovations, the CEA market trends and connect with Canadian greenhouse growers.
Over 60% of Ontario's greenhouses can be found in Leamington/Kingsville area. With the largest concentration of greenhouses in North America (nearly 2,000 acres under cover) Leamington host some of the largest CEA facilities in Canada and US.
To learn more about it please contact GLASE director Erico Mattos at em796@cornell.edu
Stop Basil Downy Mildew With These Simple LED Strategies
Every basil grower’s worst nightmare is Basil Downy Mildew. You walk down the aisles, peer across the canopy, and then “Oh No!”. You see leaf yellowing and fuzzy purple growth. The once sweet smell of herbaceous goodness no longer smells so sweet knowing you have hours not days to react
"Every very basil grower’s worst nightmare is Basil Downy Mildew. You walk down the aisles, peer across the canopy, and then “Oh No!”. You see leaf yellowing and fuzzy purple growth. The once sweet smell of herbaceous goodness no longer smells so sweet knowing you have hours not days to react.
Image source: Cornell University
This awful gut feeling can be felt by any plant grower, and most know it too well. In cucumbers, it’s all about powdery mildew. In cannabis, white powdery mildew.
Traditional techniques call for using fungicides and adjusting your environment. These are still important methods given the severity of the situation, but there’s now a new promise of prevention strategies using light.
First, what is Basil Downy Mildew?
Basil that’s become infected with downy mildew will begin to turn yellow and may be mistaken for a problem with nutrition. This yellowing may be followed by dark brown or purple fuzz as sporulation continues to develop. Peronospora belbahrii is the Latin name for basil downy mildew.
The promise of using light to stop downy mildew in basil
Light has many effects on plants and other organisms’ physiology. In the case of downy mildew, disrupting the dark period with red light while managing temperature and humidity has been shown to prevent the production of spores in sweet basil.
Image source: Cohen Y, Vaknin M, Ben-Naim Y, Rubin AE (2013) Light Suppresses Sporulation and Epidemics of Peronospora belbahrii. PLoS ONE 8(11): e81282. https://doi.org/10.1371/journal.pone.0081282
Researchers at Bar-IIan University in Israel found that low-intensity red light inhibited sporulation of Peronospora belbahrii on sweet basil when applied during the dark period while maintaining moderate temperatures and low humidity.
Infected basil leaves were exposed to 5 or 10 micromoles of blue, green, red, or incandescent light. They were incubated at 20°C in moist conditions for 20 hours in a growth chamber.
Results showed that red light (at a peak of 625 nanometers) inhibited 99.7% sporulation regardless of the leaf surface exposed to light! Light strongly inhibited sporulation on leaves incubated at 15-27°C, but not on leaves incubated at 10°C.
What to do about powdery mildew in cucumbers
In the case of powdery mildew cucumber diseases, blue light has been shown to prevent the spread of disease by preventing the release of fungal spores.
Researchers at the Department of Chemical Biological Sciences in the Women’s University of Tokyo found that blue light can prevent the release of powdery mildew spores from developed fungal bodies and prevent the spread of disease melons.
Melon plants, inoculated with Podosphaera xanthii were grown in growth chambers under purple, blue, green, orange, red and broad-spectrum light, as well as in complete darkness and in a greenhouse under solar light. Light treatments were used on the powdery mildew for 14 days under continuous illumination of 59.5 micromoles of light.
Results showed that, while conidium fungal spores were still produced under all light treatments, spores were not released from conidiospores (or reproductive fungal spores) under blue light in the growth chamber. This research proves promising for preventing the spread of mildew in cucumbers, melons, and other cucurbits.
What this means for the future of Basil Downy and Powdery Mildew
These researchers have shown that light quality has the potential to stop the spread of fungal pathogens. It’s possible that in many cases, light spectrum must be readily controlled to inhibit the spread of mildew and other disease types.
In the case of fungal pathogens, light has been shown to suppress disease by disrupting the pathogen’s reproductive cycle and by exploiting natural adaptations in its circadian rhythm.
Depending on the fungi and plant species in question, this disruption can be a response to specific light wavelengths, the duration of the light period, duration of the dark period, total light intensity or a combination of these factors.
Light can also suppress disease by increasing the plant’s secondary metabolite production, which enhances the plant’s ability to defend against attack.
Using light to suppress disease in your operation
Research on light’s ability to suppress plant disease is in its early stages, but there are some important findings that can help guide growers when trialing light treatments for disease suppression.
Light treatments are plant and pathogen-specific, so it’s important to seek out information for light treatments specific to your particular crop and pathogen.
Depending on whether a disease is suppressed by enhancing the plant’s defense system or disrupting the pathogen’s physiological processes, light treatments may need to be applied throughout the plant’s entire growth cycle, limited to a short exposure or applied during a specific growth period in order to be effective.
Like all crop production processes, light treatment is only one part of the integrated strategy. Environmental factors like temperature and humidity, as well as production processes like irrigation and crop management, should be considered as part of an integrated pest management plan.
For more information:
LumiGrow
800-514-0487
info@lumigrow.com
www.lumigrow.com
Publication date: Mon 9 Mar 2020
Signify Expands Collaboration With Planet Farms
Thanks to the latest agreement, Europe’s largest vertical farm will boost the quality and yield of the crops using the Philips GreenPower LED production module managed by the Philips GrowWise Control System
Signify is expanding its collaboration with Planet Farms, a European operator of vertical farms based in Italy. Thanks to the latest agreement, Europe’s largest vertical farm will boost the quality and yield of the crops using the Philips GreenPower LED production module managed by the Philips GrowWise Control System.
Signify has also reached an agreement to provide horticultural LED grow lights to an additional five vertical farms that Planet Farms is planning to build in different European countries in the coming years, including Switzerland and the UK.
The Philips Greenpower LED production module, Signify’s latest horticultural LED innovation for vertical farming, helps growers optimize multilayer crop cultivation. By managing the lights with Philips GrowWise Control System, growers can easily create and run custom light recipes on dimmable and color-controllable modules to meet the needs of different crops and growth phases. This gives growers the ability and flexibility to create and control their own time-based light recipes and improve crop results and operational efficiency in closed, climate-controlled cultivation facilities.
“We started working with Signify five years ago because of the company’s knowledge and expertise of horticultural LEDs and light recipes,” said Luca Travaglini, co-founder and co-CEO of Planet Farms. “Thanks to the collaboration we’re able to grow high-quality crops all year round and that’s why we’re now expanding our collaboration. The GrowWise Contol System helps us easily adjust light recipes and continuously enhance the taste of our crops, which is crucial for us.”
This year, Planet Farms will finish construction of Europe’s largest vertical farm in Cavenago, just north of Milan. The vertical farm will cover more than 9,000 m2, which is the equivalent size of 45 tennis courts. Planet Farms operates an innovative integrated growth process that starts with the seeds and ends with packaged products. The production process is entirely automated meaning that consumers are the first to touch the crops.
“We’re proud to provide Europe’s largest vertical farm with our innovative lighting products and knowledge and expertise of light recipes. This next step in our collaboration shows that we can really help vertical farmers around the globe to improve the quality, yield and taste of their produce,” said Udo van Slooten, Business Leader Horticulture lighting at Signify. “The plans to build another five farms across Europe shows that vertical farming is rapidly growing and evolving. It’s a thrilling time to be involved in vertical farming, and we’re excited to help shape its future.”
Signify and Planet Farms formalized their collaboration in 2018 when Planet Farms announced the construction of Italy’s first vertical farm research lab in Milan. This lab opened in 2019. Signify supported Planet Farms with its lighting expertise for vertical farming and by providing its Philips GreenPower LED production module Dynamic grow lights.
For more information:
Signify: www.philips.com/horti
Texas A&M AgriLife Expands Urban Agriculture Research
Niu’s research is in urban horticulture specifically. This can conjure images of community and backyard gardens, or rooftop and balcony plant installations, but her focus is producing quality food in controlled environments
A living, vertical salad bar in the employee break room is more than just a novelty at the Texas A&M AgriLife Center at Dallas. It is a small, and delicious, sign of the comprehensive urban agriculture research ramping up at the center in 2020.
Genhua Niu, Ph.D. Texas A&M AgriLife Research professor of controlled environment agriculture, with an indoor vertical garden system at the Texas A&M AgriLife Center at Dallas (Texas A&M AgriLife photo by Patricia Moran)
The purple-glowing installation arrived at Dallas with Genhua Niu, Ph.D., and Texas A&M AgriLife Research professor of controlled environment agriculture. Her research team represents one component of an overarching push by Texas A&M AgriLife to realize sustainable production of nutritious food within cities — the next frontier in commercial agriculture.
Niu’s research is in urban horticulture specifically. This can conjure images of community and backyard gardens, or rooftop and balcony plant installations, but her focus is producing quality food in controlled environments. Her studies are especially relevant in Dallas — of which certain communities are urban food deserts — and they carry promising implications for agriculture industries across rural Texas, too.
“AgriLife’s substantial investments in urban agriculture innovation reflect our commitment to better human nutrition and health at every interval along the food supply chain,” said Patrick Stover, Ph.D., vice chancellor and dean of Texas A&M’s College of Agriculture and Life Sciences and director of AgriLife Research. “In addressing these obstacles, we can bring to bear the considerable research and extension resources of the Texas A&M University System.”
Bringing urban horticulture to Dallas
Niu comes to Dallas from the AgriLife Center at El Paso, where her work since 2004 hinged on research conducted in varying greenhouse settings. Now, controlled environments at the renovated urban center at Dallas allow her to direct innovation toward vertical farming systems housed fully indoors.
Niu earned her doctorate in horticultural engineering at Chiba University in Japan as controlled environment agriculture there gained momentum in the 1980s. The research area has seen rapid growth in recent years on the heels of climate change concern and increasing limitations of global open-field production.
Greenhouses, the focus of much of Niu’s research to date, also pose obstacles to agricultural economics and environmental sustainability.
Niu said plants utilize about 43% of sunlight to grow; the surplus becomes heat. And glass and clear plastics — typical greenhouse covers — can make temperature control difficult during harsher outdoor conditions. Consequently, these systems require energy-intensive heating and cooling in winter and summer.
“There are still problems to economic feasibility, like very high upfront investment and operational expenditures,” Niu said.
But opportunity for controlled environment agriculture, or CEA development, is ripe across Texas.
Niu peers into vertical grow rack. (Texas A&M AgriLife photo by Patricia Moran)
On the horizon: Seedlings
For example, she said, many open-field crop producers — who comprise the majority of Texas farmers — acquire transplant seedlings from out-of-state sellers who grow them in controlled environments. Valuable Texas examples include tomato and pepper transplants produced in winter. Dollars for out-of-state seedlings might be kept in Texas down the line by bolstering the state’s own urban production capacity, and by delivering emerging knowledge to farmers and urban upstarts via the Texas A&M AgriLife Extension Service.
On the practical side of implementation, Niu said, “In my opinion, it would be easier to do in Texas because we have high temperatures, which means lower heating costs in winter than northern states.”
Better technology: Controlled environment agriculture
She also seeks opportunities for improving controlled environmental agriculture technology.
“How can we design lighting systems in a way that the plants use most efficiently?” she asked. “How do we use less energy and produce more lumens? Can we reduce labor costs through automation? Do we need to heat the whole greenhouse or just the nutrient solution? How do we control temperature efficiently while improving quality and productivity?”
These are the questions her team works to answer in Dallas. At the same time, the second edition of Niu’s co-edited and co-authored textbook, Plant Factory: An Indoor Vertical Farming System for Efficient Quality Food Production, is available following its publication in late 2019.
LED light fixtures in a vertical grow rack at Dallas (Texas A&M AgriLife photo by Patricia Moran)
The 33-chapter text is a collaboration with Niu’s Chiba University mentor Toyoki Kozai, Michiko Takagaki and other contributors to the CEA field. It covers the latest information on each area of controlled environment horticulture: plant-light responses, advances in LED technology, environmental effects on plants as well as production for pharmaceuticals and transplant production among a range of other CEA topics.
Niu’s research in Dallas over the next year aims to expand emerging knowledge in these areas. Her laboratories now house controlled environment studies of leafy greens, and she will pursue future research on specialty greens, pharmaceutical-grade plant production and a range of other controlled environment agriculture systems.
“It is a field of innumerable possibilities,” Niu said.
Find urban horticulture program information, a curriculum vitae and listing of Niu’s publications at dallas.tamu.edu/urbanhort.
Source: AgriLife Today (Gabe Saldana)
Publication date: Wed 19 Feb 2020
The Influence of Temperature And Daily Light Integral on Culinary Herb Production
Greenhouse average daily temperature (ADT) and daily light integral (DLI) can be adjusted to improve crop timing, maximize biomass production, and increase crop quality
Date: March 12, 2020
Time: 2 p.m. - 3 p.m. EST
Presented by: Roberto Lopez and Kellie Walters
Register here
Greenhouse average daily temperature (ADT) and daily light integral (DLI) can be adjusted to improve crop timing, maximize biomass production, and increase crop quality. In this webinar, Michigan State University researchers will discuss how the growth, development, and color of culinary herbs is influenced by ADT and DLI. They will share research on crops including sweet basil, purple basil, sage, and spearmint, giving research-backed tips on how to use these environmental parameters to improve crop yield and quality.
Join today
If you have any questions or would like to know more about GLASE, please contact its executive director Erico Mattos at em796@cornell.edu
Special thanks to our Industry partners
What Are The Challenges To Running A Successful Indoor Farm?
The amount of investments made in the vertical farming and controlled environment agriculture industries has been well documented. Those companies that successfully raise capital are seen as industry heroes and it’s quickly assumed that they must have all the answers. But, the big question is…do they?
October 3, 2019
(I had the opportunity to host the Great Lakes Ag-Tech Summit in Cleveland on Sept. 23, 2019.)
The amount of investments made in the vertical farming and controlled environment agriculture industries has been well documented. Those companies that successfully raise capital are seen as industry heroes and it’s quickly assumed that they must have all the answers. But, the big question is…do they?
In order to answer that question, it is important to be specific about the questions we are asking, the assumptions we are making and to understand that the answers will come from a wide variety of different perspectives.
List of questions
Examples of questions I am receiving and ones that we might want to ask include:
Can a farm using controlled environment agriculture techniques be profitable?
What crops have proven to be profitable in a greenhouse?
What crops have proven to be profitable in a warehouse?
What crops have proven to be profitable in a shipping container?
What segment of the produce industry are these farms capable of serving?
What defines a vertical farm?
What is the difference between a greenhouse and an indoor ag facility?
What makes controlled environment agriculture techniques and innovations unique?
Does geographic location play a role in designing a controlled environment agriculture facility?
Why invest in controlled environment agriculture?
What problems are we solving?
Is controlled environment agriculture environmentally sustainable?
The answers to all these questions are extremely important. The answers provide important insight on whether there are existing examples of multiple successful projects in a given region for a given set of crops to be produced in a controlled environment agriculture facility.
An example of how this plays out can be seen when looking at the greenhouse-grown vegetable industry. There are a number of Dutch greenhouse experts for those climates and crops that companies have proven successful over the past decades. But this does not mean that their expertise necessarily transfers to every situation. Any time ag technology and “experience” are taken to a new climate and introduced to a new market and crop there will be problems, mistakes, and failures. This has been proven time and time again.
Successful business models
It is also important to realize that it is highly likely that there are many different business models that can be successful as we look at innovation to solve growing problems within horticulture and agriculture. This can easily be seen in existing greenhouse industries.
For those of us close to the industry, we can acknowledge the fact that there are low-, medium- and high-tech greenhouse facilities that are capable of producing good quality crops consistently and profitably. The reason for this is that depending on where the greenhouse is built and the crops that are grown, the greenhouse and the technology within it are designed to serve different purposes based on labor and access to natural resources. It is likely that as the indoor ag industry matures, we will find similar models.
Hurdles to overcome
So, what are the hurdles the indoor ag industry needs to overcome in order to be successful? And how are we as an industry going to achieve this success?
Based on my conversations with many industry leaders, these are the top 11 topics we need to address:
Finally, how are we as an industry going to provide solutions to these challenges or other larger problems?
First, we need to agree on which challenges we should address first and which ones we have the best chance of overcoming. Second, we need to be self-critical. We need to determine if these challenges are caused by problems we created and determine if they really need to be solved?
We then need to learn from other industries that have come before us. This means we need some level of open collaboration. We will need some form of standardization. We will need to focus on education. And finally, we will need some luck.
“Alone we can do so little, together we can do so much.” – Helen Keller
If you are interested in taking this conversation to the next level, I encourage you to join me on social media, at one of the many upcoming events I will be participating in or through collaboration.
Written by Chris Higgins – Urban Ag News and Hort Americas.
Wasabi Japonica Grown Under GE LED Grow Lights
Contact Hort Americas if you are looking to learn more about using the Current LED grow lights to produce crops grown in tissue culture and micropropagation facilities
The “Hardest to Grow” Plant in the World
The Opportunity
Wasabi Japonica is widely accredited as the “hardest to grow” plant in the world. The plants are native to Japan and require a very specific set of environmental conditions to successfully produce healthy plants.
Wasabi is most commonly associated with Japanese food, where it is used as a unique spice and as a condiment on sushi, but many are now learning of its secondary metabolites that possess distinct health benefits including significant anti-cancer and antimicrobial properties. Unfortunately, few growers outside of Japan have successfully grown Wasabi Japonica commercially. This has led not only to a high global demand for fresh grown product, but also to an increasing amount of interest from commercial growers trying to tap into a market that now pays an estimated $325/£250 per kilo of rhizome.
The Possibilities and the Challenges
Successful field cultivation is difficult because of the specific parameters required for growth over a relatively long harvest period of up to 2 years. Wasabi is also highly susceptible to pests and disease. Although resistant strains are available in Asia, the West is restricted to two main varieties: Mazuma and Daruma. Vegetative propagation can be successful for F1 generations, but thereafter, endogenous fungal infection leads to poor yields and major crop loss. Therefore, it is important to grow from clean stock produced under controlled environmental conditions.
A small startup in Scotland called The Functional Plant Company is currently working with LED grow lights from GE Current, a Daintree company to grow wasabi. The Functional Plant Company is using a variety of hydroponic and micropropagation techniques to produce plantlets from tissue culture through to acclimation and eventually full maturity. They are proving that light intensity and spectrum are equally important factors in establishing new cuticle and stomatal development. Their aim to prove this can become more efficient and faster by using GE LED battens as compared to natural daylight.
Finding Success with LED Grow Lights
Trials show the plants have established good root production using the Arize Lynk LED Grow Lights at 60umols/m2/s, although they noted the leaf canopy growth is slower and darker than when using TLEDs at equal intensity. The Functional Plant Company added that interesting results also arose when trying other spectrums of the Arize LED grow lights. They have noted a darker callus at higher light levels with high percentage of red light, while lower intensity prevents leaf burn and dehydration during early acclimation.
They concluded by noting that the Arize LED grow lights are very energy efficient, generating little heat—which is perfect for Wasabi as even a small temperature increase can cause wilt and plant loss.
Contact Hort Americas if you are looking to learn more about using the Current LED grow lights to produce crops grown in tissue culture and micropropagation facilities.
GERMANY: February 12-14, Wageningen Lighting In Greenhouses And Vertical Farms 2020
Do you want to improve the use of LED lighting in greenhouse production or vertical farming?
Do you want to improve the use of LED lighting in greenhouse production or vertical farming? Would you like to know how to reduce energy use and carbon foot print, how to improve production, or how to improve quality? Do you want to understand the different characteristics of light and how they affect physiological plant processes? Then this course might be valuable for you.
In this course on lighting in greenhouses and vertical farms Wageningen UR scientists will share their unique knowledge with international students, researchers, and horticultural and light experts.
For whom?
This intensive course is meant for professionals in lighting, greenhouse production and vertical farms as well as MSc and PhD students, post-docs and junior scientists from all over the world.
Course objectives
The aim of this course is to learn the basic principles behind the effects of LED lighting on plant growth, yield, product quality, and energy use efficiency. It aims that participants also understand how to apply this information in their daily practice by developing strategies to optimize the use of lighting in relation to the whole production system.
Learning outcomes
This course gives participants an in-depth view on:
Perception of light by plants
Major plant physiological and morphological processes affected by light
How lighting can be used effectively in greenhouses and vertical farms
The different characteristics of light and how to measure.
Click here for more information and to register.
Publication date: Fri 20 Dec 2019
Can Far-Red Light Improve Plant Growth
When it comes to using artificial light, especially with LEDs, in controlled environment production, growers are primarily using a combination of red and blue light or white light
CAN FAR-RED LIGHT IMPROVE PLANT GROWTH?
While the focus for using artificial light in controlled environment agriculture has been primarily on red and blue light, growers may be missing out on the benefits that far-red light has to offer.
By David Kuack
When it comes to using artificial light, especially with LEDs, in controlled environment production, growers are primarily using a combination of red and blue light or white light.
“Plants under red and blue light have a decent photosynthetic rate,” said Dr. Shuyang Zhen, who is a postdoctoral fellow in the Plants, Soil and Climate Department at Utah State University. “Adding far-red light, which are photons with wavelengths from 700-750 nanometers (nm), can increase the photosynthetic rate as plants now utilize light more efficiently to produce carbohydrates.
“However, with most LEDs, there is no far-red light at all. If growers are using a broader spectrum white LED like cool white or warm white, they have a small fraction of far-red light, but it is not enough. We tested white LEDs that contain 2-8 percent far-red light and found there was an increase in the photosynthetic rate and efficiency compared to red/blue LEDs, which do not contain any far-red. But the amount of far-red light in white LEDs is not enough to maximize the photosynthetic rate and efficiency. These LEDs can be made more efficient by including additional far-red light.”
Dr. Shuyang Zhen, a postdoctoral fellow at Utah State University, has found that combining far-red light with red and blue light boosts the photosynthetic rate of greenhouse and field crops.
Photos courtesy of Dr. Shuyang Zhen, Utah St. Univ.
Impact of far-red light on photosynthesis
Zhen said many growers are familiar with how far-red light can affect plant morphology.
“Far-red light can cause stems to elongate and leaves to expand,” she said. “Far-red light also has some effect on flower regulation.”
Zhen has focused her research on the effects of far-red light on photosynthesis.
“We have looked in detail at how photosynthesis works,” she said. “There are two photosystems that are connected to carry out the light reaction of photosynthesis. Far-red light only stimulates one of those photosystems. The other photosystem is not really stimulated.
“Overall, there really isn’t much photosynthetic activity occurring by far-red light alone. There is a big decrease in photosynthetic activity when the light goes above 700 nanometers, which is the far-red light region. That is the reason that those light wavelengths have been ignored. But the photosynthetic rate is boosted when red, blue and far-red light are combined. Far-red, blue and red light have a synergistic effect.”
Impact of far-red light on plant growth
Zhen and her colleagues trialed the impact of far-red light on canopy photosynthesis of over a dozen plant species, including greenhouse leafy greens, cucumbers and tomatoes and field crops, including potatoes, rice, wheat, and corn. Sunlight has almost 20 percent far-red light.
“When plants are exposed to a cool white LED, which contains about 2 percent far-red, by adding up to 40 percent far-red light the photosynthetic rate is increased,” she said. “All of the species we trialed benefited from the addition of far-red light in terms of increasing photosynthesis.”
Zhen said the effects of far-red light during long-term plant cultivation varied depending on the plant species.
“Photosynthesis for all of the species benefitted from far-red light, but there were differences in the morphological responses of the plants,” she said. “Lettuce exposed to far-red light had expanded leaves and an increased leaf area. This is a good thing because lettuce can capture radiation more efficiently so they capture more light and grow faster.”
Zhen grew green-leaf lettuce varieties with red and blue LEDs and cool white LEDs, which are commonly used by commercial growers.
“We designed the experiment so the total number of photons (400-750 nm) for all of the light treatments was the same,” she said. “The plants were placed under LEDs with and without far-red light.
“The morphological response for lettuce grown under far-red light was leaves that expanded faster resulting in better radiation capture. Plants produced 30 percent more biomass. Long term there is this benefit with lettuce.”
The study with lettuce was stopped before the plants were ready to harvest. However, based on the results, Zhen said it could be concluded that lettuce grown with far-red light could shorten the production time.
“During the four weeks that the plants were exposed to far-red light they grew bigger and faster,” she said. “It is reasonable to say that the plants could have reached salable size sooner compared to the treatments with no far-red light. For the production of green lettuce, I would recommend incorporating far-red light.
Green-leaf lettuce varieties were grown under red and blue LEDs and cool white LEDs with and without far-red light. Lettuce grown with far-red light produced leaves that expanded faster resulting in better radiation capture. From left: red/blue, red/blue + far-red, white, white + far-red.
“For other species, far-red light may not be as beneficial. The increase in biomass might be in the stem and cause the plants to stretch. Cucumber was one of the species that adding far-red light long term doesn’t have much benefit.”
Based on the results of her trials Zhen said there is compelling evidence that increasing the amount of far-red light increases the photosynthetic rate.
“Further research needs to be done to determine the effects of far-red light on long term crops like cucumber and tomato,” she said. “Does exposure to far-red light and the accumulation of biomass speed up flowering? That part is not as well characterized. I haven’t done much in that area of research. There is research going on at other universities that characterize the long term effects of far-red light.”
The effects of UV light
Zhen is also interested in studying the effects of ultraviolet light on the photosynthetic rate.
“UV-B light wavelengths from 280 to 320 nm tend to trigger secondary metabolite production like the flavoring compounds in plants,” she said. “An example is field-grown tomatoes vs. greenhouse-grown tomatoes. Greenhouse glazing blocks UV light so plants often don’t produce as much of the flavoring compounds. These compounds are important for crops like herbs including basil. UV light may also trigger some stress responses causing plant damage.
Both greenhouse and field crops, including potato, experienced an increase in photosynthetic rate when exposed to far-red light.
“I am interested in UVA wavelengths from 320-400 nm. We started with violet photons that peak around 400-408 nm. These wavelengths are different from UV light. We are looking at the photosynthetic efficiency of these violet wavelengths, which have the potential to be utilized by growers. A typical white LED doesn’t contain any wavelengths below 400 nm.”
Zhen is using violet LEDs to study the impact on photosynthesis and the long term growth of cucumber and lettuce.
“For both of these species, violet wavelengths were as efficient for photosynthesis as commonly used blue LED wavelengths,” she said. “There wasn’t much difference in the photosynthetic rate at plant canopy level. But for cucumber, there was 15 percent more biomass production under violet wavelengths than under blue wavelengths, mainly due to leaf expansion. In the case of lettuce, violet light actually caused bleaching or yellowing of the leaves. We are trying to determine the effects of violet light on photosynthesis and plant growth before looking at the effects of shorter-wavelength UV photons.
“LED technology is moving so fast. Growers have the ability to change the colors and the intensity, but they can’t really take full advantage of that amazing capability because we still don’t fully understand how a particular color and intensity impact short- and long-term plant growth and development. We also need to learn more about how species and cultivars respond to the wavelengths. An increase in the short-term photosynthetic rate may not correlate with a long-term response or an increase in growth.”
For more: Shuyang Zhen, Utah State University, Plants, Soil and Climate Department, Logan, UT 84322; shuyang.zhen@usu.edu.
David Kuack is a freelance technical writer in Fort Worth, Texas; dkuack@gmail.com.
Why ‘Vertical’ Farming Is Growing In The UK
Vertical farming – sometimes called indoor farming – is the practice of growing plants under fully controlled conditions in buildings in many stacked layers, without solar light. Unlike glasshouse production, which relies on sunlight, it makes use of LED lighting to provide different wavelengths of light, according to crop and growth stage need
18 December 2019
Louise Impey
© Wu Kailiang/Alamy Stock Photo
Being able to produce crops 365 days a year, without the need for pesticides or much human intervention, while being unaffected by the weather, will appeal to many growers after such prolonged, wet autumn.
Vertical farming – sometimes called indoor farming – is the practice of growing plants under fully controlled conditions in buildings in many stacked layers, without solar light.
Unlike glasshouse production, which relies on sunlight, it makes use of LED lighting to provide different wavelengths of light, according to crop and growth stage need.
Together with soil-less growing techniques and environmental control systems, vertical farming is a specialist business.
Vertical farming – what is it?
The practice of growing crops in stacked layers, vertical farming often incorporates controlled environment agriculture and can be housed in buildings, shipping containers, underground tunnels and even abandoned mine shafts.
Vertical farms use soil-free growing techniques and stack crops in specially designed beds and trays, making use of artificial lighting and climate control to get the desired results.
During the growing process, four elements are controlled – lighting, irrigation, fertigation and climate.
Global and fast-growing
And it’s a fast-growing sector. Worldwide, it was worth £1.72bn in 2018, with experts predicting that will rise to £9.84bn by 2026. Japan and the US are leading the way, but other countries are catching on.
Enthusiasts say that vertical farming offers a means of guaranteeing yields and reducing the industry’s environmental impact, while improving the supply of safe, healthy and nutritious food and minimising the miles involved in its distribution.
Their vision – locally grown, quick-to-market fruit and vegetables, produced in the neighbourhood where it is consumed, with the traceability and integrity that food supply chains demand – is already being delivered by various facilities worldwide.
Solutions to challenges
These high-tech units are presented as the solution to many of the challenges facing traditional production methods, such as pollution and water use – even if they are currently limited to higher- or added-value crops in order to be profitable.
As they spring up around the world, they are also seen as a means of reducing reliance on food imports.
The use of automation and robotics to keep human intervention and labour costs to a minimum is attracting interest, while less food waste and making better use of limited land space are bonus features too.
Trends driving vertical farming
Environmental impact of food production
Demand for healthy, safe food
Legislation
Urbanisation
Growing world population
Scarcity of natural resources
Changing eating habits
UK projects
In the UK, there have been several big projects announced in the last 12 months. Edinburgh-based Shockingly Fresh has ambitions to develop 40 sites and already has five on the go – one in Scotland and four in England.
Ocado is involved too, having invested £17m in the sector during 2019. That has seen it enter a joint venture with 32ha, a US firm, and Priva Holdings in the Netherlands, known as Infinite Acres.
It has also taken a 58% stake in Jones Food Company, a Lincolnshire-based business producing 420t of leafy greens each year at a facility of 5,120sq m – equivalent in size to 26 tennis courts.
In London, there is Growing Underground, which produces micro greens and salad leaves below the busy streets of Clapham, while in Bristol there is LettUs Grow, which provides the cutting edge technology required.
Technological advances
According to Leo Marcelis of Wageningen University, the vertical farming industry received a kick start from advances in the performance of LED lighting, which can be used to provide the type of light that different plant species need at a much better price than the previously used high-pressure sodium lamps.
“This is the most interesting bit,” he says. “LED lights, which are essential for replicating natural daylight, can be used to change the way plants grow, when they flower and how they taste. It’s all about varying the spectrum used at different growth stages.”
LED lights have other advantages, he notes. “They can be positioned between plants and layers, produce hardly any heat radiation and are more energy efficient.”
Asked whether vertical farming is sustainable, Prof Marcelis says that the current bottleneck is energy use.
“It meets so many requirements, such as much lower water and nutrient use, but it is energy-intensive. Of course, that is improving all the time, especially with lower-cost LED lighting and other technical developments.”
Vertical farming is capital intensive too. Plenty of start-up funding is required, with pay-back times depending on the unit’s operational efficiency and chosen retail route. While some have failed, others are finally starting to make small profits.
Case Study: LettUs Grow
© Jack Wiseall Photography
Extreme weather events and consumer demand for freshness are the two reasons LettUs Grow’s co-founder Charlie Guy (pictured) cites as being behind the current interest in vertical farming.
In addition, being able to get consistent yields and produce quality for 12 months of the year, with the traceability and integrity that supply chains require, is opening up market opportunities for both existing growers and entrepreneurs, he says.
“Whether it’s a very cold spell, such as the Beast from the East, or a lengthy summer drought bringing water shortages, the frequency of extreme weather events is increasing. This has a cost to both growers and consumers.”
Diversification
His Bristol-based company designs the hardware and software needs for indoor growing facilities and is seeing interest from traditional producers, who are looking at an indoor system as a diversification project.
“For existing growers, they can add a valuable revenue stream,” he says. “They are predictable and scaleable, offer year-round production and tend to fit in well with existing projects such as renewable energy and anaerobic digesters.”
Technology
The LettUs Grow concept is based on aeroponics and a technology platform known as Ostara. Aeroponics give better growth rates than hydroponics, he claims, while using up to 95% less water than conventional agriculture.
“Aeroponics puts more oxygen in the root zone, which is why the plants perform better.”
Ostara – its cloud-hosted software – offers closed-loop control.
Mr. Guy explains it that does the data capture and automated control of the growing environment, bringing the food safety and traceability that’s needed, but also offering the potential to use sensors and robotic technology.
“That’s important because energy and labour should be the two key areas of focus with any vertical farming project,” he says. “They have the final say on profitability.”
Vertical farming is not just about lettuce, he stresses. “Although the focus has been on high-value herbs and pea shoots, there are around 60 different crops that can be grown in this way.
“The key to choosing what’s right for you is to look at what access you have to various markets, rather than opting for the fashionable crops.”
Hydroponics or aeroponics?
Both hydroponics and aeroponics deal with plants without the traditional growing medium of soil.
How the plants’ roots are situated in the systems determines the way in which they receive nutrients.
In hydroponic systems, the roots are submerged in water and nutrients are delivered in the water.
In aeroponics, the roots are exposed and sprayed with a mist containing water and nutrients, resulting in a humid, fog-like environment
How IGS Reduces Vertical Farming Costs
While vertical farming is not the ultimate solution to the world’s farming challenges, it does give control over many variables or, perhaps more accurately, the weather
December 11, 2019
Editor’s Note: Intelligent Growth Solutions (IGS) is a portfolio company of AgFunder’s and recently attracted investment from leading agtech investor Ospraie. IGS offers plug and play vertical farming technology to vertical farm operators, which they say can increase efficiencies and substantially reduce costs compared to other vertical farming operations. It can be hard to explain exactly how the technology does this, so we caught up with Niall Skinner, lead mechanical engineer at IGS to get an in-depth explanation of how the tech works.
What core challenges facing the vertical farming market does the IGS technology address, and how?
While vertical farming is not the ultimate solution to the world’s farming challenges, it does give control over many variables or, perhaps more accurately, the weather. At IGS we have gone back to basics in our technological approach to make weather control a reality, building four families of patents and patents pending along the way.
We recognised that running a vertical farm needs to be simple, even if the technology behind it is not! By its very design, a vertical farm is often a far more technical and complex environment than a traditional farm or even a glasshouse environment would be. An overly technical system can, however, be off-putting, so we have turned the thinking on its head: there are no computers, cables or capacitors in our systems.
We thought outside the box (quite literally) to work out how to bring weather from the outside in, and allow it to be controlled through a mobile phone app. Our ‘plug and play’ modular systems address the challenges of power and labour costs and offer opportunity to pre-programme ‘weather recipes’ to ensure maximum productivity across yield, consistency and quality. Core to our R&D efforts was to ensure greater commercial viability for operators and the focus on power reducing technology and automation has been paramount. Our approach has enabled us to demonstrate clearly reductions of up to 50% power usage and 80% labour costs.
In addition to our power management capabilities, we are particularly excited about our patents that address the serious challenge of ventilation in a closed space. Keeping crops at an even temperature under hot lights while balancing the CO2 they inhale and the oxygen the exhale is very tricky, but our patent-pending (in this case) technology provides a solution that delivers the required balance, even as it captures, condenses and reuses the water vapour the plants emit.
Can you explain in more detail how your technology can reduce power consumption in a vertical farm
We have developed a power-management platform that flexes with the grid in real-time, allowing it to respond to external impacts such as grid stability and power availability. This means that power can be pulled when it is cheaper or pushed back when it is more expensive and in-demand: in effect, it imitates the role of a large battery where the excess energy is converted into grown produce. The use of industrial Omron SYSMAC programmable logic controllers (PLCs) to automate our system allows automatic recovery from power loss events and means that individual towers and sites get the power they need. As a result, none of the systems need to be reset, reprogrammed or manually repositioned.
Our system has a baseline power consumption of 60 kilowatts (kW), which can be rapidly increased to 105 kW or reduced to 30 kW for short periods to optimise grid stability. Other drains on power include heating and air conditioning, but all our systems including watering are on closed loop systems to minimise power consumption. Our design reduces the need for HEPA (high-efficiency particulate air) filtration to clean large volumes of incoming air, and the heating and/or cooling of this air depending on location and season – all of which are a drain on power. In combination these efficiencies contribute to a power-saving of 50%.
With over 1000 LEDs per tray, lighting forms over two-thirds of the system’s power requirements. We were determined to develop a more efficient system to drive the LEDs, and this is where the three-phase power supply design was born. This system is more commonly used to power machinery in an industrial environment but works by transferring the power supply to a safe voltage level and transmitting it to each individual tray within the tower using aluminium tubes rather than cables. By using tubes rather than cables, we can improve transmission efficiency. Aluminium tubes are also much cheaper and lighter than comparable copper cables. By using three-phase power at a tray level, we can also further reduce losses of power and provide inherent phase balancing. This eliminates the need for costly and inefficient filtering and power factor correction, as well as the use of capacitors for single-phase conversion. These measures contribute to an increase of between 5% and 10% in driver efficiency,
Your approach to the technology replicates a more industrialised environment – why is that?
Initially, when the founding team of engineers came together at IGS, the background was more heavily based in industrial operations. This has actually been a considerable advantage in helping us look differently at the vertical farming environment; it is our industrial environment approach this is key to this. We operate our farms in large steel frame warehouses with insulated cladding walls to provide isolation from the external environment. For example, the standard buildings are 10 metres in height, which allows up to 26 trays to be stacked in towers up to 9 metres high, but we do offer a range of options in addition to this. It really is closer in style to an industrial unit than a more traditional agricultural setting; handling the trays in this environment requires no human involvement whatsoever. It is here we generate savings of as much as 80% in the area of labour.
Within each tower, we have established standalone ventilation and irrigation closed-loop systems, which automatically sterilise and recycle air and water so that the only regular inputs the system needs are power, seed, nutrients, carbon dioxide and harvested rainwater. The air is sterilised by UV filtration technology – similar to that used in clean rooms. Standard industrial chillers and cooling coils cool and dehumidify the air which is then heated as needed, also drawing on waste heat from multiple areas in the facility. Carbon dioxide can be added to this loop when required too. This optimised management right across the components of our system when compared with conventional and glasshouse environments contribute to an overall reduction of power consumption of between 40 and 50%.
All the important factors – light, heat, humidity, water, nutrients, and crop movement – are controlled by industrial programmable logic controllers (PLCs), that run on an architecture that does not need unpredictable updates. The Omron SYSMAC PLCs use feedback from sensors distributed throughout the tower and systems that is transferred to a cloud-based control system. This removes the need for computers and wiring. It makes the whole system much more simple to operate, maintain and control.
With greater control over your LED systems than many (if not all) competitors, how and why have you focused your innovation on this area? What benefits does it bring?
Lighting was always going to be a key area when we were developing our systems as this is where the greatest power consumption comes from. We have focused on light intensity and dimming particularly so we can control each individual colour in the spectrum. Our LEDs are fitted in clusters, with each cluster containing all types of LED. Our system can vary the spectrum or pulse width modulation (PWM) and intensity to simulate solar radiation. We believe this is a unique feature of our system.
Each wavelength can be turned on or off or dimmed via PWM, linear dimming or a combination of both. However, we are still at the early stages of understanding how the optimal mix of light for each crop and stage of growth can impact on different ranges of crops. This is where we use AI to measure and understand the crops’ progress in order to enhance our learning in this area. We are already making some very interesting observations across a range of crops and are showing yield improvements of up to 2-3 times increase.
Our system can also vary intensity through linear dimming or PWM. We can vary PWM infinitely in 0.01% increments over all wavelengths simultaneously and maintain 90% electrical efficiency from grid to LEDs. This means that we can really assess how the delivery of the light is impacting on how well the crops grow.
How important are AI and data aggregation in the future of vertical farming?
It is going to be absolutely pivotal, a real game-changer. It allows control, predictability and the ability to absolutely guarantee the quality, consistency, and yield of produce every single time. We have inbuilt AI and data collection capabilities in all of our systems and that makes day-to-day management considerably easier. It also allows for historic patterns to be tracked which enables us to predict future growing methods and deliver optimum data for the best growing results to our customers in the future.
Netled’s Niko Kurumaa On The Potential of Indoor Agriculture In North America
He told Contain, “most leafy greens are grown with pesticides in California and Mexico and then are shipped thousands of miles all over North America. People are starting to see that this isn’t an ethical way to produce food.”
Nov 29, 2019
When we dialed Niko Kurumaa, sales manager at Netled, he took Contain’s call from the rooftop of a hotel in Los Angeles. When asked how his day was going, the tone of his voice was as bright and cheery as the California sun, “Well, it’s nice here so you could say that I’m doing pretty well,” he said.
But Kurumaa was pretty far away from his home-base in Finland. So, what brought him all the way from the cold of Finland to the American west coast?
He was there for one reason: the promise of indoor agriculture in North America.
Kurumaa is the sales manager at Netled, a Finnish company that sells indoor agricultural tech like LED lights for indoor growing and fully integrated vertical farms. And now he’s in the United States to lead sales at the company as it enters the North American indoor agricultural market.
“We at Netled think that there is a huge potential for our products in North America.” He continued, “We have always been a global company, but now we see that North America has the need and the market for indoor growing technology.”
Photo courtesy of Shutterstock
Netled is new to the indoor agriculture market — Kurumaa has been working in the United States for around five months now and has one LED lighting project in the United States so far. Although their experience working in the United States may be limited, this is just the beginning, and they see the potential for future business.
Growing North American indoor agriculture
When Kurumaa talks about Netled’s reasoning behind entering the United States, it all comes down to the economics of indoor farming and the quality of greens grown by their indoor farms.
“Our [vertical farming] system doesn’t just grow better quality greens; it’s economically feasible when you compare it to the traditional ways of growing greens and herbs” Kurumaa explained.
But the Company has seen some challenges to entering the U.S. market, like communicating its feasibility to possible customers.
“There are times when we need to explain the process of indoor agriculture when we meet potential growers. Some people don’t even believe that this technology exists, because people know less about it.”
This makes selling their technologies a challenge, but they find ways to overcome misunderstandings.
“We have two reference farms. One in the UK to go with our customers and a larger one in Finland that has around 47,000 square feet of growing space,” he told Contain.
The company can take growers there so that they can see first hand how vertical farming works. In addition to the farms, Netled has even set up their office as an indoor farm just so that visitors can see their technology in action when they come in for meetings.
Proving the value of indoor agriculture may be a challenge, but to Kurumaa, the promises dwarf any barriers they face to entering the market.
“South California has a long drought season and forest fires are raging. We need to think about how we use land and water. Systems like ours use about 99 percent less than conventional farms,” he said.
He told Contain, “most leafy greens are grown with pesticides in California and Mexico and then are shipped thousands of miles all over North America. People are starting to see that this isn’t an ethical way to produce food.”
He paused and then said, “Now we can produce much better lettuce in urban areas right next to the consumer. There is no reason to ship lettuce the long distances.”
It just goes to show that for this company, the call for indoor agriculture isn’t just about economic feasibility. It is about providing a brighter future for the regions of the United States like the American west. As Netled expands the business to the United States, they bring an economic rational, and an ethical imperative to live more sustainably.
WRITTEN BY
Nicola Kerslake
We’re Contain Inc. We use data to improve access to capital for indoor growers, those farming in warehouses, containers & greenhouses. https://www.contain.ag/
China's First Intelligent LED Plant Factory in Beijing
the experts of the Chinese Academy of Agricultural Sciences and the factories responsible for researching this technology are very confident. They believe that in the future smart agriculture will become the norm, and the LED smart factory is a business card for Chinese agriculture to go international
This farm at the third ring road in Beijing is the first intelligent LED plant factory in China. The factory is highly modernized and managed by the protected agricultural IoT control system.
In more detail, there are dozens of sensors in the factory to jointly manage various parameters of the plant during its growth. Sensors and artificial intelligence cameras are also monitored throughout the process to adjust various parameters in real-time. Through the sensor and the visual analysis system equipped with artificial intelligence cameras, the parameters such as temperature, light, water and gas fertilizer are continuously optimized, and the changes of plant growth phenotypic parameters are collected and learned and calculated.
The data model of crop growth optimization is obtained, and the “plant dialogue” is implemented. The goal is to achieve maximum yield and quality with the least amount of resources.
In this “farm” built of steel the “farmland” is a row of five-layer double-row seedling racks in the house.
The person in charge of the farm said that the seedling efficiency per unit area of this seedling rack is more than 40 times that of conventional seedlings, and the seedling cycle can be shortened by 40%. Take an example of the cultivation of lettuce. From planting to harvesting, the plant factory only takes 20 days by using the so-called "Deep Flow Technique (DFT)". Besides, the output per unit area is more than 25 times that of open field cultivation, while the produce is still of high quality.
Going against tradition
In fact, this highly efficient method of cultivating vegetables is not a rare thing. As early as 1903, countries began to plant vegetables in a vertical way. But when the LED light source solved the sunshine problem in plant growth, and new technologies allowed for better control, vertical farming really started to take off.
In 2005, Yang Qichang, chief of the "Facilities Plant Environmental Engineering Team" of the Institute of Agricultural Environment and Sustainable Development of the Chinese Academy of Agricultural Sciences, found that the red and blue light combination of LED can provide an ideal spectrum for plant photosynthesis; he immediately imagined that using LEDs in plant factories instead of fluorescent lamps at that time would be a new development direction.
Since the spectral components of civil-used and plant-used LEDs were very different at that time, the team had contacted many domestic research institutes such as the Institute of Semiconductors of the Chinese Academy of Sciences and spent several times the price of civil-used LEDs to jointly develop 4 sets of LED plant light source panel systems. Since then, they have carried out many experimental pieces of researches on plant seedling, leaf vegetable cultivation, medicinal plant cultivation, and plant tissue culture, and obtained a large number of plant light formula parameters.
Afterwards, under the support of the national “863” project “Intelligent Plant Factory Production Technology Research”, the Innovation Project of the Chinese Academy of Agricultural Sciences, and 15 research units jointly tackled the problem and finally obtained a series of innovative breakthroughs: first proposed multiple light formulas for plants, and created LED energy-saving light source based on light formulas and its light environment control technology equipment; first proposed light-temperature coupled energy-saving environment control method, and created the energy-saving environmental regulation technology equipment of the plant factory; first proposed a light-nutrition regulation method for vegetable quality, and created a short-term continuous illumination to improve quality technology and technical equipment before mining; first proposed an intelligent management and control method for plant factory efficacy, energy efficiency and nutritional quality improvement, and created an intelligent management and control system based on the IoT.
Indeed, LED plant factory technology is time-consuming and labor-intensive, but this technology can help the growth of vegetables which means they can be moved indoors, completely freeing the restrictions of land, sunlight, and water. It also has the advantage of “efficient production”. Yang Qichang explained that the unit area yield can reach dozens or even hundreds of times of natural cultivation in the open field, and the water consumption is less than 5%.
However, only 10 years ago, only a few developed countries such as Japan, the United States, and the Netherlands mastered this technology. Today, as environmental and health issues are increasingly mentioned, this technology is used in all areas of agricultural production in various countries.
A long way to go
For China, although the development of this technology has good achievements, it still has obstacles on the way forward. There is a lack of professionals in this technology, and a lot of research and development funds are needed.
However, the experts of the Chinese Academy of Agricultural Sciences and the factories responsible for researching this technology are very confident. They believe that in the future smart agriculture will become the norm, and the LED smart factory is a business card for Chinese agriculture to go international.
Source: chinadaily.com.cn; sheshiyuanyi.com
Publication date: Mon 25 Nov 2019
Violet Defense Group Raises $2 Million For Expansion of It's Germ-Killing And Ag Light Businesses
“This infusion of additional capital will enable us to take both companies to their next level of growth, including further build-out of our management team and the product inventory necessary to accelerate the rich pipeline of opportunities that are developing for our products,” added Terrance Berland, CEO of Violet Defense Group
ORLANDO, Fla. – November 5, 2019 - Violet Defense Group announced today that it has raised an additional $2 million in funding for its germ-killing business, Violet Defense and its agricultural lighting business, Violet Gro. This round of capital was led by Kirenaga Partners, an early-stage venture capital firm with offices in New York and Orlando, Florida.
“This infusion of additional capital will enable us to take both companies to their next level of growth, including further build-out of our management team and the product inventory necessary to accelerate the rich pipeline of opportunities that are developing for our products,” added Terrance Berland, CEO of Violet Defense Group.
Violet Defense introduced the first known pulsed Xenon UV disinfection system that could be installed in the ceiling and work automatically to kill up to 99.9% of key pathogens of concern in both healthcare and other commercial spaces, such as athletic facilities, office buildings, food production facilities, hotels, schools, and more. Violet Defense has established an exclusive partnership with Puro Lighting for commercialization of the Violet Defense technology throughout the United States and Canada. Puro Lighting is a Denver-based company dedicated to protecting people’s health and promoting wellness with specialized lighting technologies, which markets its products directly and also through an extensive network of medical and lighting agencies and distributors.
Violet Gro combines cutting-edge design with patented technology to produce LED grow lights that are highly energy-efficient and produce very little heat, thereby lending themselves to substantial cost savings of up to 70% when compared against traditional lighting solutions.
“We have a unique ability with our technology to solve critical issues in the indoor agriculture space from energy savings to improved conditions for growing healthy, vibrant plants,” said Kurt Kucera, President of Violet Gro.
A key commercialization opportunity for Violet Gro is its partnership with Hyperponic, which selected Violet Gro as its primary lighting supplier for its CropTower TM in June of this year. The Hyperponic CropTowerTM is a technologically advanced and fully integrated growing system that provides a complete computer-controlled environment and nutrition management system to facilitate increased quality and consistency, faster production, reduced space requirement and better yields at lower costs.
The Violet Gro team will be showcasing its latest technology, including its next-generation grow light, its UV light prototype and a version of the CropTowerTM at MJBizCon, the preeminent Marijuana Business Conference in Las Vegas, December 11-13, 2019.
###
About Violet Defense Group
Violet Defense Group is an advanced photonics company based in Celebration, Florida helping to leverage its patented technology for solutions that lead to a healthier world. As the parent company to Violet Defense, the germ-killing technology company, and Violet Gro, the agricultural lighting company, Violet Defense Group is committed to harnessing the power of the sun to bring its benefits to indoor environments.
About Violet Defense
Violet Defense uses UV disinfection to protect everyday spaces from harmful pathogens by killing up to 99.9% of bacteria and viruses, including E. coli, Salmonella, MRSA, C. diff., Norovirus, and C. auris. Violet Defense’s technology is the only known Pulsed Xenon solution that can be installed into a room full-time, creating a continuous way to address disinfection needs of all types of settings. For more information, visit www.violetdefense.com or follow us on Facebook (@violetdefense).
About Violet Gro
Violet Gro’s LED grow lights combine cutting-edge design with the patented technology to create cost-effective, long-term solutions to indoor growing, providing plants more light with less heat, leading to substantial energy savings. Violet Gro is uniquely capable of incorporating UV light into grow environments to protect against harmful mold, mildew, and pests, as well as drive increases in medical substances produced by plants. For more information, visit www.violetgro.com or follow us on Facebook (@violetgro) or Instagram (@violet_gro).
Media Contact for Violet Defense Group:
Jessica Jones, Vice President of Marketing
407.433.1104, x1002
Indoor Farming Technology Leader SANANBIO (R) Debuts UPLIFT (TM) Vertical Farming System
SANANBIO firmly believes that agriculture technology should be based on science paired with input from farmers
10/02/19
SANANBIO®, a leading provider in LED horticulture lighting and vertical farm technology, announces the commercial release of its fully automated vertical farming system: UPLIFT™ (Unmanned Platform of Lean and Intelligent Farming Technology). Decades of manufacturing and automation experience, combined with successful multi-year vertical farm operations through parent company Sanan Optoelectronics, have given SANANBIO the expertise necessary to design and prove the concept of UPLIFT.
SANANBIO firmly believes that agriculture technology should be based on science paired with input from farmers. Michael Yates, Sananbio VP of Sales, said, "With over one million square feet of commercial vertical farms currently using RADIX, farmers and investors in more than 10 countries believe in our company's highly engineered grow technology. The proof is in the plants as our customers like to say."
Sananbio UPLIFT
Fully automated vertical farming system
UPLIFT is based on RADIX™, SANANBIO's highly successful manual vertical grow system being used in farms today. "Farmers and investors in more than 10 countries and a combined one million square feet of commercial space believe in our company's highly engineered grow technology. The proof is in the plants as our customers like to say," said Yates.
UPLIFT offers a full suite of automation for growing vertically. From seeding and germination to transplanting and harvesting, the high-stack, high-cube configuration offers the latest advancements in vertical farming solutions that reduce labor while achieving higher yields. The UPLIFT farming platform also benefits from an industry-standard production and inventory management system facilitating crop management, farm production planning, and crop traceability.
"Labor costs continue to be a major challenge for vertical farm operators while also maintaining profitability," stated Dr. Charlie Wang, Sananbio U.S. CEO. "The UPLIFT system will help operators significantly reduce labor costs so they can sell more fresh and healthy produce and, therefore, receive better returns on their investment. The system also provides an open platform to integrate technology that enables farms with more intelligence and controls, allowing for maximized yields and profitability."
SANANBIO's is prepared to work with leading farmers and investors in the industry who share the same passion to build ground-breaking projects in controlled environment agriculture using this cutting-edge technology.
ABOUT SANANBIO®
SANANBIO^® is a trademark carried and backed by Sanan Sino-science Photobiotech, a company invested in by Sanan Optoelectronics, one of the world's largest LED chip manufacturers. Supported by an elite R&D team comprised of plant scientists, researchers, and engineers, SANANBIO utilizes state-of-the-art technology that enables growers in the horticulture industry to increase the quality and quantity of their yields. Years of extensive research and real-world deployment and operations allow SANANBIO to offer its customers proven, scalable, efficient and cost-effective solutions in LED horticulture lighting and Controlled Environment Agriculture (CEA) vertical farming grow systems. SANANBIO empowers growers with the technology and knowledge to achieve unprecedented results in farming operations. Learn more at https://sananbious.com/.
Lighting Research Consortium Brings CEA Community Industry-Ready Technologies
The goal of the consortium, an initiative between NYSERDA, Cornell University and Rensselaer Polytechnic Institute, with Rutgers University participating as a collaborator, is to reduce carbon emissions, Erico explains
Without light, plants can't grow. The continued advance of controlled environment agriculture means that sunlight is often supplemented and in some cases completely replaced by artificial lighting. It works well, but there's one caveat: artificial lighting can take a lot of energy. Reason enough for the New York State Energy Research and Development Authority (NYSERDA) to kickstart the Greenhouse Lighting and Systems Engineering (GLASE) consortium with $5 million in funding. That was in June 2017. What's happened since then? Erico Mattos, the consortium's Executive Director, tells us more.
The goal of the consortium, an initiative between NYSERDA, Cornell University and Rensselaer Polytechnic Institute, with Rutgers University participating as a collaborator, is to reduce carbon emissions, Erico explains. "NYSERDA saw the growth of the CEA industry, indoor farms and greenhouses, and with technologies evolving really fast, especially on greenhouse systems like lighting controls and LEDs, they realized that there's a lot of room for technology development that can help reduce the energy consumption of lighting and integrated systems in greenhouses. So NYSERDA sponsored this program with the objective to reduce the carbon emissions coming from greenhouses' electricity use by 70% from the levels of 2017."
Cornell University Greenhouse
To achieve this ambitious goal, a combination of engineering and plant physiology is used. “At Rensselaer Polytechnic Institute we work with the center for Lighting Enabled Systems & Applications (LESA). Led by Dr. Elsebeth Kolmos, LESA engineers are developing new LED research modules, new driver technologies, and spectroanalysis to optimize plant growth under LED lights. At Cornell University, a team of researchers led by Dr. Neil Mattson is developing integrated lighting control systems based on plant physiology responses to optimize crop production yield and reduce operational costs in commercial greenhouses".
Focus on food, but everyone benefits
The consortium focuses their research on food crops - they work with the following crop models:
Lettuce
Strawberry
Tomatoes
"Those are the crops we use to do research. But the outcomes of this research," Erico points out, "can be applied to any of the industries. And our outreach activities, which are not sponsored by the NYSERDA funds but paid for by membership fees, are open to the entire CEA industry. They're pretty much crop agnostic." That means cannabis or ornamental growers, for instance, can also benefit from the consortium's efforts.
And while the consortium was started in New York, that doesn't mean it's geographically limited. "We started in New York because all the founding members are here, but at this time we have members all across the US, we have 22 industry members today, including an international body of farms, in the Middle East. For now, we're establishing a base in the US, the next step is going international."
Diagram of GLASE work frame
Sharing knowledge and technology
The consortium focuses on the following types of industry members:
CEA growers
Lighting, sensing and control manufacturers
Basic manufacturers (companies that make the LEDs, drivers, etc. that go into lighting, sensing and control)
Retailers
Service providers
So what do those members actually get out of it? "Growers get all this knowledge that we are generating. With the GLASE consortium, we have more than 300 technical milestones, from the development of new LEDs to implemented systems in greenhouses."
For growers, GLASE offers knowledge and technology transfer. "The knowledge transfer happens through our outreach activities, like webinars, industry talks, industry advisory board meetings where growers come together with manufacturers and we discuss all the research that we're doing." In addition, grower members have access to the GLASE researchers at Cornell, RPI and Rutgers University.
When it comes to the technology transfer, members of the consortium have first-hand access to technology that's developed by those researchers. "If there's any IP, for example, it's disclosed to members first - they have the right of first refusal.”
GLASE Commercial pilot: SAF Produce, Berlin, NY
Practical results
According to Erico, these are exciting times for the consortium. After the start-up phase, now the time has come to start harvesting. For instance, the consortium has developed their own LED module for lighting research. They use these to research how growers can best use lighting in their cultivation. But there's also something in it for the manufacturers: "Everything we do in these research fixtures, they can take that information and use this to guide product development.”
This research is conducted in the context of the milestones set by NYSERDA, but the GLASE researchers do get feedback from industry members during quarterly meetings (two of them by phone, two of them in-person meetings) on how this knowledge can be applied practically. "For example," Erico says, "they can make recommendations on what to research next, or on how to better implement the technology we're developing into commercial facilities." Using this feedback, the researchers tweak or adjust their research to end up with a practically implementable solution. “We are working to de-risk the technology development process by validating new technics in the lab and in commercial pilot greenhouses to provide the CEA community industry ready technologies.”
GLASE Commercial pilot: Wheatfield Gardens, Buffalo, NY
For the practical implementation, GLASE is working with two commercial lettuce greenhouses in New York State: SAF Produce in Berlin, and Wheatfield Gardens in Buffalo. Both greenhouses were retrofitted with LEDs. "It is our goal to implement all the technologies that were developed by GLASE in each of those greenhouses, establishing a baseline on the energy consumption and then compare the results before and after." This is an ongoing process, and GLASE will publish the results at a later stage.
For more information:
Greenhouse Lighting and Systems Engineering
glase.org
Publication date: 9/18/2019
Author: Jan Jacob Mekes
© HortiDaily.com
Illumitex Launches NeoPAR-XO LED for Vertical Farming With 1820 PPF Output And FarmVision AI
Illumitex, a leader in LED Grow Lights and Digital Ag, announces NeoPARTM XO, a major upgrade to their grow proven NeoPAR LED lighting system designed for vertical agricultural systems.
Illumitex upgrades it’s popular grow-proven NeoPAR LED lighting system for vertical-farming to record performance levels and adds FarmVisionAITM to see every plant, from anywhere, at anytime
[Austin, Texas, Oct. 7, 2019] Illumitex, a leader in LED Grow Lights and Digital Ag, announces NeoPARTM XO, a major upgrade to their grow proven NeoPAR LED lighting system designed for vertical agricultural systems. The new NeoPAR XO is a major leap forward in lighting performance and brings the benefits of Illumitex’s horticulturist-curated artificial-intelligent machine-learning FarmVisionAI to the difficult task of vertical farming.
NeoPAR XO takes Illumitex’s proven LED platform to the highest output commercially available at 1820 mol/sec with an efficiency of 2.6 mol/J. The system comes available with a wide range of features, highlighted below, that enable easy, worry-free vertical farming at the largest, densest scales. The high efficiency and low maintenance deliver the dream of profitable and sustainable urban farming ecosystems.
The new NeoPAR XO LED platform goes a step further in performance and capabilities with a native FarmVisionAI integration option. FarmVisionAI gives farmers “peace of mind” with integrated cameras and cloud-based AI that allows them to see any plant, at any level, from anywhere, at any time. FarmWatchTM is the visualization platform allowing you to see every plant on your farm at scale. Digital ScoutTM is the artificial intelligence that is trained to detect nutrition deficiencies, canopy density, and flower counts. “FarmVisionAI for vertical growing is absolutely essential in managing the added complexity of vertical systems,” says Dennis Riling VP of Business Development at Illumitex. “Our
DigitalScout can detect biotic and/or abiotic anomalies early in the grow cycle to prevent loss and help improve quality.”
To learn more come see Illumitex at the Canadian greenhouse conference on October 9 & 10 in Niagara Falls ON, Canada. If you can’t make the show look us up at www.illumitex.ca to learn more about LED lighting for horticulture and digital transformation of agriculture.
About Illumitex, Inc.: Illumitex is breaking the boundaries of traditional lighting by combining LED light fixtures with hi-res cameras and cloud-based horticulturist-curated artificial intelligence to deliver radically new value to growers and farmers. With more than a decade of experience in both LED lighting and horticultural science, an absolute dedication to quality and performance, and knowledgeable support for the success of every customer, grow and crop – Illumitex, Inc. is the optimum partner for your greenhouse, vertical farm or any indoor grow initiative.
###
Lighting Control Platform Enables Dimming on Demand
Based on research conducted at the University of Georgia, Candidus has developed an adaptive lighting control system that assures that supplemental light is provided when the crop can best use that light and only in the amount that can be effectively used by the crop
Candidus is a startup company in Athens, GA, USA, that focuses on smart lighting control systems for the greenhouse industry. Their mission is to reduce the cost of supplemental lighting for greenhouse growers by implementing an adaptive lighting control system.
Candidus was co-founded by Drs. Erico Mattos and Marc van Iersel in 2017. Dr. Mattos studied photosynthesis optimization using LED lighting at the University of Georgia and previously founded a LED lighting company. Dr. van Iersel is a professor of horticulture at the University of Georgia, with a background in plant physiology and environmental measurement and control. His research focus is the optimization of the cost-effectiveness of LED lighting in horticulture.
Integration with third-party lighting
Candidus was awarded a US Department of Agriculture grant to develop an innovative adaptive lighting control system. Based on research conducted at the University of Georgia, Candidus has developed an adaptive lighting control system that assures that supplemental light is provided when the crop can best use that light and only in the amount that can be effectively used by the crop. The system will not change the basic lighting settings. "Because growers, not us, should decide how to grow their crop", Marc van Iersel clarifies. "But growers can very easily change the photoperiod and daily light integral, after which the controller will implement it."
Using instantaneous light measurements and a proprietary algorithm, Candidus’ control system determines exactly how much supplemental light to provide and when. Using an industrial microcomputer, the control system monitors the ambient sunlight and sends a dimming signal to third-party lights. Candidus’ supplemental lighting control system technology is particularly well-suited for use with dimmable LED fixtures, but can also be used with non-dimmable LED or HPS lights.
The Candidus controller
Candidus does not make light fixtures. Instead, the focus is on the development of optimal control systems for third party lights. The company is already working with several light manufacturers. "So far we have worked with Fluence BioEngineering and our first round of grower trials used their VYPRx Plus lights. We are also working with Illumitex and Osram", Marc says. "Most dimmable LED fixtures take a 0 – 10 VDC signal to control light output and our technology is fully compatible with such lights, regardless of brand. Osram uses a proprietary protocol for dimming, so that requires coordination between Osram and Candidus. But our hardware is fully capable of dimming those lights as well."
"Adjusting the lighting is simple and there really are no big challenges on that end of things as long as lighting manufacturers use dimmable drivers", Marc continues. "Some companies, like Signify, use non-dimmable drivers and those lights can only be turned on and off. The bigger challenge is with lighting systems that may not be designed in a way that allows growers to actually achieve their goals. For example, the overall lighting capacity may not be enough to allow growers to actually achieve the daily light integral when needed."
Web-based interface
Greenhouse growers use the control system through a web-based interface, entering only a few simple settings: the daily light integral target value, the time the lights should come on, and when the light should go off. If needed, growers can also program in low-intensity night interruption lighting for control of flowering of photoperiodic crops.
A sample of the monthly report growers get. Click here for a bigger version.
While the crop growth isn't monitored directly, Marc says they can make recommendations for a wide range of crops. "If growers are willing to share information on crop growth, we can make refinements in the lighting strategy."
At the moment, the Candidus platform doesn't tie in with existing cultivation software, but the company is interested in doing this in the future. "Hopefully, our software can be an integral component of control systems made by companies like Priva and Hoogendoorn", Marc says.
For more information
Candidus
info@candidus.us
www.candidus.us
Publication date: 9/16/2019
Author: Jan Jacob Mekes
© HortiDaily.com
UK: Heliospectra To Supply New Technology For John Innes Centre
This order of Heliospectra’s fully controllable Elixia LED lights complements the previous orders made by the customer and will be part of a project retrofitting glasshouses automated by Heliospectra’s helioCORE light control software
Heliospectra, an intelligent lighting technology provider for greenhouse and controlled plant growth environments, announces a new order from the John Innes Centre in the United Kingdom. This order of Heliospectra’s fully controllable Elixia LED lights complements the previous orders made by the customer and will be part of a project retrofitting glasshouses automated by Heliospectra’s helioCORE light control software. The order value is SEK 2.4 million (£ 200,000).
The John Innes Centre is an independent, international research center of excellence in plant science, genetics and microbiology. To meet the challenge of feeding a growing population, plant breeders and scientists are continuously looking for ways to increase genetic gain in crop production. As a result, the John Innes Centre has become one of the world’s leading research centers on speed breeding which is a cultivation technique allowing researchers to shorten the breeding cycle and accelerate research studies through rapid generation of crops.
“A growing human population and changing environment have increased the concern regarding food security. We desperately need crops better suited to today’s climate. At the John Innes Centre, we are well-known for our speed breeding research and are conducting ongoing crop research on a range of different crops. For that, we need a solution that allows for complete control of all environmental parameters, such as light, temperature, and humidity,” said John Lord, Horticulture Manager at John Innes Centre. “Heliospectra’s ELIXIA lights enable us to upgrade our lighting environment to market-leading lighting standards with spectrum-based control. We have the capability to program each individual wavelength to adapt to individual crop needs.”
”The John Innes Centre is one of Europe’s leading research institutions with critical speed breeding expertise as the world is accelerating food production to support an additional two billion people by 2050. Heliospectra continues to work with the John Innes team to expand their large-scale helioCORE installation. We look forward to supporting their work and significant advancements in crop performance with our pioneering horticulture lighting, automation, and light control solutions,” said Peter Nyberg, Head of Technology and Development at Heliospectra.
Heliospectra's ELIXIA light creates clear business benefits for cultivation teams and researchers around the world. The fully adjustable LED lighting solution is compatible with Heliospectra's helioCORE light control software, enabling growers to improve the quality of plants and accelerate harvest and production cycles while providing consistent and standardized returns 365 days a year.
The order will be delivered in Q3 and visible in the accounts for Q4 2019.
For more information:
Heliospectra
Box 5401 SE-402 29 Göteborg Sweden
Phone: +46 31 40 67 10
Fax: +46 31 83 37 82
info@heliospectra.com
www.heliospectra.com
Publication date: 9/19/2019
Nurturing The Seeds of Vertical Farming
Vertical farming involves building indoor farms with LED lights to replace the sun and control every single variable in that farm to optimize plant growth
09.10.2019
By Dan Malovany
Vertical farming today is moving from a conceptual phase to the mainstream as a greater abundance of food is profitably grown in urban areas and new crops come under development, said Henry Gordon-Smith, founder, Agritecture Consulting Services during his Fresh Take Talk at the International Baking Industry Exposition on this cutting-edge movement on Sept. 8.
Vertical farming involves building indoor farms with LED lights to replace the sun and control every single variable in that farm to optimize plant growth. Despite the fact the first U.S. vertical farms are less than a decade old, the sustainable industry has blossomed with the flourishing demand for local, safe produce and farm-fresh ingredients as well as the need of city dwellers concerned about climate change to reconnect with food systems in their local communities.
Such farms allow craft bakers, high-end retailers and fine restaurants to fill a void and offer fresh-grown food harvested year-round.
“Retailers should think about value-added products through vertical farming through enhancing the retail experience or through growing something that could be used in their bakery products,” Mr. Gordon-Smith said.
He added they create the opportunity to cultivate customer loyalty through marketing value-added baked foods with herbs, vegetables and other free-from-pesticides ingredients harvested in their store or at a nearly indoor farm. These herbs and vegetables also can be sown in larger vertical farms that offer fresh seasonal food or in a smaller unit inside a store that also promotes a theater of community that grounds city dwellers with the food they consume.
The multi-level farms range from 250 square feet for a small retail shop to 3,000 to 10,000 square feet for a medium-sized operation that supplies the nearby neighborhood. The world’s largest one is about 60,000 square feet. Mr. Gordon-Smith said vertical farming is prospering globally, especially in colder climates and congested urban areas where farm-fresh food isn’t readily available.
Typically, wheat isn’t the best crop for vertical farms, mainly because it takes so much space to grow the volume needed to produce baked foods. Mr. Gordon-Smith added that wheat requires a soil structure that hydroponic soil cannot provide, although there may be opportunities to foster the growth of heirloom and specialty wheat as the trend expands. However, rosemary and other key minor fresh components in baked goods are more practical today.
“You’re essentially driving the value of a fresh product, and fresh wheat isn’t a huge value proposition because it’s stored and transports very well,” Mr. Gordon-Smith said. “Fresh lettuce doesn’t, so you can see why fresh lettuce and other products would be grown in a vertical farm and not wheat.”
Mr. Gordon-Smith expected vertical farming research of wheat, cocoa and other value-added commodities could become more widely available in five years. In recent years, he added, the quality of wheat has deteriorated due to myriad variables. The urban farms provide the possibility of naturally raising the quality of wheat by controlling all of the variables involved in growing the crop.
“We’re going to see more and more research on how to grow wheat indoors and how to develop indoor systems to grow wheat,” he said.
Lead photo: Source: Adobe Stock