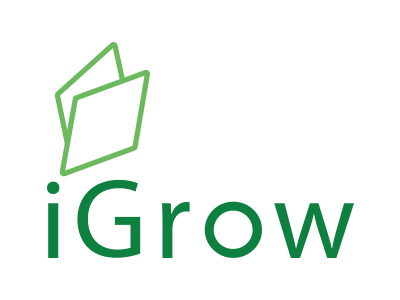
Welcome to iGrow News, Your Source for the World of Indoor Vertical Farming
SINGAPORE: High-Tech Vertical Farms To Begin Operations Next Year And Bring Fresher Leafy Greens To S’poreans’ Plates
From next year, Singaporeans can expect more of their favorite Asian vegetables to reach their plates quicker and fresher, thanks to a slew of high-tech urban farms that are set to begin operations
By LOW YOUJIN
NOVEMBER 15, 2020
&ever's dryponics cultivation technique will allow customers to harvest their vegetables just before they decide to use it.
&ever, Indoor Farm Factory Innovation and Genesis One Tech Farm are part of eight companies that have accepted SFA’s 30X30 Express Grant
The grant will help these companies accelerate Singapore’s efforts to meet 30 percent of its nutritional needs locally by 2030
The benefits of indoor farming are that it requires less space to grow crops, and optimal growing conditions can be replicated
Representatives from the three companies said prices will be competitive, and they will offer Singaporeans fresher and higher quality produce
SINGAPORE — From next year, Singaporeans can expect more of their favorite Asian vegetables to reach their plates quicker and fresher, thanks to a slew of high-tech urban farms that are set to begin operations.
For vertical farming company &ever, it can even sell its vegetables “while they are still living”, said the firm’s chief executive officer Henner Schwarz.“You don't need to refrigerate it down to 4°C (to keep it fresh),” he said. “You can actually have it at room temperature when you buy it at the supermarket, and it continues to grow at home. It stays fresh for at least a week.”&ever currently has a fully operational indoor farm using the same technology in Kuwait that produces about half a tonne of vegetables each day.
Its Singapore outfit, which will be located within the Changi vicinity and will be operating from around October next year, will be larger and produce more than double that amount — about 1.25 tonnes a day — said Dr. Schwarz.
The Hamburg-based company is just one of eight companies — an egg farm and seven vegetable farms — to have accepted the Singapore Food Agency’s (SFA) 30x30 Express Grant to ramp up local food production.
The SFA said the grant will accelerate Singapore’s efforts to meet its 30 by 30 goal, which is to secure 30 percent of the country’s nutritional needs with food produced locally by 2030.
It will also help to minimize disruptions to Singapore’s food security, due to events such as the Covid-19 pandemic.
Part of the grant requirements, said some recipients who are growing vegetables, is to ensure at least 50 percent of the crops grown are Asian greens like xiao bai cai or kangkong.
THE SINGAPORE FIRMS
Two Singaporean companies that have accepted the grant have similarly shared some of the innovative technologies that they will be using.
Over at the south-western end of the island, Indoor Farm Factory Innovation (IFFI) intends to leverage on its parent company Tranzplus’ knowledge of automation to make its work processes more efficient.
Mr. Alfred Tham, IFFI’s chief executive officer, said robotics will also help reduce operational costs at its 38,000 square foot facility at JTC Space @ Tuas when it is ready for operation in the second half of next year.
Beyond that, Mr. Tham said their machines will have the ability to analyze the condition of the plants, such as when they will be ready for harvest.
All this, he said, will not only help to reduce manpower needs but also scale up production to meet SFA’s minimum requirement of 200 tonnes of produce annually.
Mr. Tham said IFFI will be using an indoor farming methodology of soil-based cultivation, which allows them to have greater flexibility in the variety of crops that they can grow.
What this means is that the plants can be grown in separate containers, which enables them to customize the growing conditions as needed.
Moreover, it reduces the risk of cross-contamination between plants, said Mr. Tham. Still, Mr. Tham said they will be utilizing a special water treatment system to reduce bacteria.
Mr. Alfred Tham, CEO of IFFI, beside a robotic arm that will be featured in his firm's vertical farm facility in Tuas. Photo: Low Youjin/TODAY
Meanwhile, Genesis One Tech Farm intends to take its operations closer to the heartlands and will have a 10,000sq ft facility situated in Eunos that is about a three-minute walk from the Singpost Centre.
The farm’s director, Mr. Shawn Ow, expects operations to begin within the first quarter of next year.
One of the key technical features of the subsidiary of the investment holding and managing company, TSL Group, is the use of a custom-designed hybrid Nutrient Film Technology system, coupled with 5G energy-saving LED lighting in order to maximize growth cycle efficiency.
Mr. Ow said the system enables the firm to recycle the water used, thus using a fraction of the water requirements generally associated with a hydroponic system and minimizing the environmental waste impact.
But more importantly, said Mr. Ow, is that his company hopes to provide jobs for Singaporeans. It is exploring hiring residents living around the area on a part-time basis and is also in discussions with an institution supporting the rehabilitation of ex-offenders.
And as the firm is located within the heartlands, it is also not ruling out the possibility of allowing potential customers to buy directly from its facility.
Mr. Shawn Ow, director of Genesis One Tech Farm, at his company's test lab. Photo: Nuria Ling/TODAY
‘BUY LOCAL’
For Mr. Tham, he plans to start a cafe in Bukit Panjang which will not only feature its produce on the menu but a cultivation showroom to raise awareness about indoor farming.“When we talk about indoor farms, not many have seen it,” he said.
The Big Read: Singapore has been buttressing its food security for decades. Now, people realize why
Aside from taking up far less space compared to a traditional open-air farm, vertical indoor farms are also not at the mercy of the weather, said the representatives from the three companies.
Moreover, growing conditions such as temperature, humidity, and lighting conditions can be replicated so that plants that do not normally thrive in the tropics can be grown indoors instead.
Price-wise, the representatives said it will be competitive.
The prices may not be cheaper than the vegetables imported from Malaysia, but Mr. Tham said they will definitely be fresher and of higher quality. It also offers a better alternative compared to imports from further away.“If you are choosing between imports from Japan or local produce, buy local,” he said. “The reason is very simple — it reduces the carbon footprint.”
TOPICS
SINGAPORE FOOD AGENCY FOOD FARMING AGRICULTURE FOOD SECURITY
Breakthrough Biological Innovation – The Key To Profitable And Sustainable Vertical Farming
Vertical farming, first conceptualized in the late ’90s, is premised on the idea of “a farm within a skyscraper” where environmental conditions, nutrition, and lighting can be optimized
Algae-Based Biostimulants Improve Growth Velocity, Yield, And Quality
In Hydroponic And Aeroponic Indoor Farming
The rapid growth of urban agglomerations across the planet presents serious food security challenges. The US Census Bureau estimated that 80% of Americans lived in cities in 2015. Vertical farming is generally regarded as the most promising approach to supplying cities with fresh leafy greens, vegetables, and small fruits, but skeptics point out that we still have a long way to go before indoor “plant factories” can reach the scale and efficiencies that would make them a truly sustainable source of nutrition for millions of people.
Vertical farming, first conceptualized in the late ’90s, is premised on the idea of “a farm within a skyscraper” where environmental conditions, nutrition, and lighting can be optimized. Growing crops in layers instead of rows, usually employing hydroponics, is a concept that has seduced investors globally. We all see the advantages of growing our food locally - in shipping containers, in warehouses and maybe even in skyscrapers to reduce the need for trans-continental shipping, to generate employment and limit pesticide and chemical-input intensive outdoor farming.
The major barrier to the upscale of vertical farming is economic sustainability and this is mainly related to the energy costs associated with artificial lighting. Can local, vertically grown produce be sold affordably? Despite remarkable technological advances in lighting technology and automation and the availability of renewable energy, there is still an urgent need to develop innovative solutions to get vertical farming over the “tipping point” from a promising food security approach and into a real, long- term and indispensable part of urban food systems.
Doing More with Less
How can vertical farms use less energy and produce more and better? In Chicago, Back of the Yards Algae Sciences, a sustainable industrial biotechnology company, has been working on a simple but elegant solution; grow in less time. After almost 2 years of intensive research, they just published a paper demonstrating that an algae-derived biostimulant (a formulated biological material for improving plant growth) shortened the time between planting and harvesting hydroponically grown red leaf and green leaf lettuce by six days. Since traditionally farmed, outdoor-gown lettuce is currently three-to-five times less expensive to grow than vertically farmed lettuce, a shortened growing period may have significant implications for the economic sustainability of vertical farming as it reduces energy inputs and labor costs.
This breakthrough research was based on the concept of trying to translate the amazing interaction between plants and their soil environments into hydroponic and aeroponic systems. The team was already developing a proprietary Spirulina (blue-green algae) extract for the food and alternative protein markets and began to explore whether phycocyanin, a protein-pigment complex that acts as a key regulator of photosynthesis in blue-green algae, could play a similar role in plants growth.
A series of experiments produced evidence that a phycocyanin-rich Spirulina extract worked as a biostimulant in hydroponics, improving growth, yield, and quality of lettuce while cutting maturation time by 6 days-or 21%-compared to control groups. The faster-growing treatment groups also produced 12.5% more lettuce and were 22% better at photosynthesis than control groups. The treated lettuce was more robust; a mean increase of 2.6cm in leaf length and 2.2cm in basal stem diameter compared to the untreated lettuce was observed and. In the shelf-life test, wilting was seen 2-3 days after it was observed in control groups.
Treatment groups were brighter green (specifically 17% brighter and 75% greener) and better tasting. They had firmer texture, a stronger aroma, and more intense flavor than the untreated group, according to an independent certification company. Using analytical chemistry techniques, the team also examined nutrient content by comparing flavonoid-antioxidant levels in control and experimental groups. Their findings suggested experimental groups were more nutrient-rich, where one flavonoid, Quercetin, had a mean increase of 30% in the treated lettuce.
What it Means
Back of the Yards Algae Sciences was working to cut growing time in hydroponically grown lettuce using a biostimulant to give vertical farmers a new avenue for reducing energy inputs. They were successful and also happened to find that Spirulina extract biostimulants improved color, vigor, nutrient content, and preservation. These product quality findings will support vertical farming in improving profitability by ensuring better selling prices. But perhaps the most exciting aspect of developing natural biostimulants specifically for vertical farming is the possibility to extend the indoor farming sector into row crops as food staples (wheat, soy, corn), ensuring not only better and more secure food supplies for urban populations, but also protecting the environment.
This research is available at: https://www.preprints.org/manuscript/202011.0354/v1
For further information – www.algaesciences.com
Autogrow Challenges Other Industry Players To Publish APIs
“To date, large industry players have not publicly published APIs’, but our argument is that it’s your data - you should be able to do what you want with it,” says Chief Technology Officer Jonathan Morgan
Autogrow is calling for more public APIs (Application Programming Interface), giving increased access for growers to their own data, and fostering faster innovation in the Controlled Environment Agriculture industry.
“To date, large industry players have not publicly published APIs’, but our argument is that it’s your data - you should be able to do what you want with it,” says Chief Technology Officer Jonathan Morgan.
“There can be a protectionist approach to development to dissuade people from building their own versions or integrating other products. But you will never keep up with all the customer requests or in the same timeframe as the 15 other companies working on the same improvements in the market. Access equals innovation - simple as that.”
Autogrow's FarmRoad has launched their public API on a new Developer Portal which is product agnostic and welcomes all industry players. This will allow growers to use the platform to build a ‘best of breed’ solution for their operation, no matter what their current technology providers are.
“You don’t have to rip and replace your existing technology. You just need to use an API to connect it to FarmRoad and then see all your information in one place. You can also give third parties secure access to specific areas of your information – keeping control of what you want them to see.”
“As innovation accelerates it creates a unique challenge of being able to centralize all of your data in one place – regardless of the source. We’ve been offering public APIs for over three years and are certainly the leaders when it comes to cloud technology,” notes Mr. Morgan.
Initially, the FarmRoad Developer Portal will give access to:
Measurements: Over 39 different measurement data types related to the environment and crop registration.
Events: Capturing key events or notes for example pest detection or spray regimes.
Farms/compartments/sectors: Get the full picture from different areas of the farm. Giving comparative studies, trends or with permission-based access.
“This is just the beginning for what FarmRoad will be able to offer. With API availability, growers will be able to create their own custom applications alongside the work we are doing. It’s a great developer community which can evolve and scale as businesses and the industry changes.”
For more information on the FarmRoad Developer Portal - https://farmroad.io/developer
For more information on the API documentation - https://developer.farmroad.io/
For more information on Yield Prediction by FarmRoad - https://www.farmroad.io/
11 Nov 2020
CombaGroup SA Reveals Rebrand With New Name, Logo, and Products
The new name, CleanGreens, is synonymous with powering clean, sustainable solutions in the agrotech space. It also reflects the company's mission to represent more directly what they are bringing to the table: fresh, healthy, premium quality yields of their customers’ favorite crops
Molondin, Switzerland – 5 November 2020: On the 21st October 2020, CombaGroup SA has announced the company's complete rebranding and launch of its new website.
Last year, the company realized it was time to leverage its unique position in the field of mobile aeroponic growing solutions. This year, they've rebranded to solidify their stance, offering, and direction within the industry.
The new name, CleanGreens, is synonymous with powering clean, sustainable solutions in the agrotech space. It also reflects the company's mission to represent more directly what they are bringing to the table: fresh, healthy, premium quality yields of their customers’ favorite crops.
The rebranding is a response to accelerated company growth and a renewal of its corporate vision, subtly captured by its new
With six years of R&D and technology breakthroughs in mobile irrigation and agronomy expertise, CleanGreens is proud to offer CleanGreens Pro, a system designed to be as simple as A-B-C, with immediate support and maintenance as well as a technical hotline available in addition to the built-in resources.
As a platform, CleanGreens is expanding to welcome new communities of users and has gone even further in solidifying its global position going forward. It has released new product packages and features that allow its clients to build, manage, and deploy custom applications quickly with its own intuitive, integrated, cloud-based operating application, GURU by CleanGreens. The platform gives clients the ability to grow exactly what they want with the support they require whenever they need it.
Based on the experiences and feedback from CleanGreens’ agronomist team and customers, this new app assists in key tasks like sowing, harvesting, and preventive maintenance and also features built-in reminders, alerts, and real-time records. It’s like having your own personal CleanGreens agro-expert assistant at your fingertips.
Currently, there are seven cultivation lines in operation in three locations: Molondin and Geneva in Switzerland, and Châteauneuf-sur-Loire in France. More are in the pipeline for the future. The new improvements have allowed CleanGreens to meet elevated customer demands for more of its innovative products and technologies.
"Our complete solution is different from any system in the market and our re-branding is largely driven by our effort to reflect this for our products, mission, vision, and of course, our customers and consumers,” says Serge Gander, CEO.
He adds: ”We've taken a clean, modern approach to the name, the website's design and the user experience in our new look and rebrand. We purposefully set out to challenge the status quo in all aspects of our business and this redesign reflects that." logo with the notion of interaction and connectedness. These are core to the capabilities of scalable mobile aeroponic technology platforms that are a priority for both CleanGreens and its clients and partners.
Please visit the revamped website www.cleangreens.ch to explore the new website and learn more about the products and services offered.
About CleanGreens
CleanGreens is a Swiss agro-technology company that provides farmers and industrialists with innovative mobile aeroponic farming solutions for growing fresh, environmentally-friendly, nutrient-rich vegetables. A certified B Corp company CleanGreens’ patented technology significantly reduces water consumption and contamination risks while offering maximum productivity per square meter and minimizing environmental impact. Automated irrigation and mechanized spacing system produce clean, quality, pesticide-free salads, aromatic herbs, and medicinal plants all year round, thus providing consumers with healthy, responsible products.
For more information
info@cleangreens.ch +41 21 545 99 25 www.cleangreens.ch
Media information online
Media information and images can be downloaded directly from cleangreens.ch Journalists can subscribe to our media mailings to receive information on CleanGreens’ aeroponic solutions and technology.
For the latest updates on CleanGreens, visit www.cleangreens.ch, or follow on Instagram, Twitter @SmartLettuce, Pinterest, and LinkedIn.
VIDEOS: Vertical Farming Goes High-Tech And Underground
Vertical Farms Are Evolving Into A Major
Food Industry Powered by Sophisticated
Technologies And Production Methods
Growing fresh produce in underground areas
Transforming a tunnel into a vertical farming operation
Infarm allows customers to pick the produce themselves
Vertical farming companies are facing an array of challenges
Technology and lower costs are critical for the industry’s sustainability
Innovation is vital to solving the world’s greatest challenges
Farmers around the world are heading towards an uncertain future. Apart from the prospect of feeding the global population that’s set to reach around 10.9 billion by 2100, they are also facing climate change-induced floods, droughts, and heatwaves. Fertile land is in ever shorter supply as soil erosion intensifies. Farming is also to blame for some of these problems as the CO2 footprint of food accounts for 17 percent of total global emissions. And by the time plants get transported to supermarkets, they lose 45 percent of their nutrients. As it becomes increasingly apparent that traditional agriculture is unsustainable, growing food in an artificial environment is emerging as a potentially better way forward.
Instead of plowing fields, farmers would produce food in vertically stacked trays. Soil would be replaced by nutrient-rich water, while LED lights would act as the sun to ensure plants photosynthesize. This practice, known as vertical farming, offers many benefits. The indoor environment protects crops from extreme weather events and pests, which means that food grows fast and there’s no need for pesticides. Also, food is grown close to cities, which not only reduces food miles and the related carbon footprint but also provides consumers with fresh and tasty crops.
However, vertical farming faces certain challenges as well. Companies have to constantly innovate to cut production costs and turn a profit, which is vital for the survival of this industry. But entrepreneurs remain optimistic. The global vertical farming market is forecasted to reach $12.77 billion by 2026 and people are becoming increasingly aware that there’s a better way to feed the populGrowing fresh produce in underground areas
High rents and the lack of space have prompted some modern urban farmers to go underground. In London, for instance, a farm called Growing Underground operates from a World War II bomb shelter located 33 metres below Clapham High Street. Owned by Stephen Dring and Richard Ballard, the vertical farming facility produces an array of herb and salad mixes, including parsley, red mustard, coriander, and pea shoots. Fresh produce is then sold through Marks & Spencer, Waitrose, Ocado, and several other retailers. Some restaurants have also expressed interest in buying fresh produce, says Ballard.
He also points to many advantages of vertical farming. For instance, his farm delivers 60 harvests a year, compared with around seven that can be achieved in traditional agriculture. Furthermore, Growing Underground is carbon neutral and uses 70 percent less water than typical farms. The only major cost he’s trying to reduce is the electricity that powers the lights. And his ambitions are global. “The UK is the hardest market for growing salad. We’ve got very low prices in the supermarket, so if we can make it work here we can make it work anywhere,” says Ballard.
Underground vertical farming is thriving in other British cities as well. The Liverpool-based social enterprise Farm Urban, for example, provides customers with a weekly box of living salad leaves, edible flowers, and fragrant herbs. Jens Thomas, the company’s technical director, says that the product is pesticide-free and “it’s grown using 90% less water than if it was grown in a field; it’s zero-waste; and it’s hyper-local.” Farm Urban is trying to promote healthy and sustainable living. For each box of greens customers buy, the company delivers a box of greens to a local school. This activity is part of the Greens for Good campaign that aims to reconnect people with locally-grown food.
In New York, the vertical farming business Farm. One is also growing. Its underground farms produce over 500 different herbs, edible flowers, and microgreens year-round, using specialized software to manage multiple operations, such as seed, harvest, and flavor optimization. Founded by Rob Laing, the company supplies fresh produce to various New York-based restaurants, including Atera, Ai Fiori, Benno, and Flora Bar. All deliveries are made by bike and subway. Also, visitors can book a tour of the farm or take a class in hydroponics to learn how to grow vegetables in a soil-free environment.
Transforming a tunnel into a vertical farming operation
Successful vertical farming businesses can also be launched outside of cities. NEXTON, a South Korea-based startup, has built vertical farms in a former highway tunnel, located 190 kilometres south of the capital city of Seoul. Growing salads, leafy greens, and strawberries beneath mountains has many advantages. For one, the 6,500-square-metre facility naturally maintains a temperature that ranges between 10 to 20 degrees Celsius, which translates into lower energy spend for cooling or heating. Furthermore, labor costs are reduced by automating various operations. And as farming is done without pesticide or herbicide, with sensors monitoring humidity and CO2 concentrations, customers receive both healthy and affordable products.
Choi Jae-bin, the CEO of NextOn, also uses non-tech tactics to boost production. For instance, the music of Beethoven and Schubert is played in the 600-metre-long tunnel as Jae-bin believes it will help plants to grow faster. And his plan is to build more farms in urban areas. “Plants easily grow at home, at nearby stores, at hamburger restaurants, or even at metro stations. I think the system to grow crops far away from a city and transporting it will disappear,” he says.
Infarm allows customers to pick produce themselves
Infarm, a Berlin-based startup, has already achieved in several European countries what Jae-bin plans to do in South Korea. The German company builds modular farms that are placed in customer-facing locations, such as schools, grocery stores, restaurants, and shopping malls, enabling customers to pick the produce themselves. Clients can also add more modules if they want to increase the farming output, while the production is monitored and controlled through a cloud-based platform. Essentially, the whole thing functions as a ‘farming as a service’ operation that combines the IoT, Big Data, and cloud analytics.
The company is working with 25 major food retailers in Germany, France, and Switzerland, including Migros, Casino, Intermarche, Auchan, Selgros, and AmazonFresh. Furthermore, it has installed more than 200 in-store farms, as well as 150 farms in distribution centres. And in 2019, Infarm raised $100 million in Series B investment round. The funding will be used to expand research and development, sales, and operation teams. Also, the startup plans to increase its presence in the UK and negotiate partnerships with retailers in the US and Japan.
Vertical farming companies are facing an array of challenges
While the rise of vertical farming companies has been impressive, the industry is facing many challenges and its survival depends on reducing costs and increasing productivity. Take, for example, the fact that deploying even a small, low-tech vertical farm with the 1st generation technology costs around $280,000. On the other hand, the cost of setting up more complex farms with advanced tech can go over $15 million. There are also operating expenses such as lighting and labour that can further pressure companies’ bottom line, making it hard to compete with organic and traditional producers.
So it comes as no surprise that return on investment (ROI) in vertical farming projects is mediocre at best. The current market prices don’t make the situation any easier either. A kilogram of vertically-grown leafy greens is around $33, while organic produce costs $23. To gain a competitive edge, vertical farming startups need to take several measures.
Technology and lower costs are critical for the industry’s sustainability
The first step in ensuring the long-term profitability of vertical farms is transitioning to 2nd generation technology. This means that in addition to automatic control of irrigation, humidity, lighting, CO2, and other relevant parameters, farms should also be capable of autonomously collecting data and optimizing growing processes. They also need to implement cutting-edge machines that will autonomously run planting and weeding operations in the facility, and harvest sort and package produce for shipping. These improvements can enable the second generation of vertical farms to yield 55 times more produce than conventional farms.
Increased automation will also cut labour expenses. Intelligent Growth Solutions, a UK-based agritech business, has reportedly developed an automated farming system that uses modular structures to reduce labour needs by up to 80 percent. Furthermore, LED lighting efficiency is likely to improve by an additional 70 percent by 2030, reducing the energy spend. Boaz Toledano, a business consultant specializing in vertical farming, says that “lighting improvements should reduce OPEX [operating expenses] by 12%, and automation should cut OPEX by a further 20%+”.
Companies can also reduce costs by setting up farming operations underground. This would not only help them avoid the high cost of renting in urban centres but also enable them to enjoy the benefits of having a steady temperature. Underground facilities also offer better protection against natural disasters and can be more easily adapted to producers’ needs.
Innovation is vital to solving the world’s greatest challenges
New technologies are moving the food industry forward. Vertical farming, though still gaining traction, could help solve some of the world’s greatest challenges, such as food shortage. Tasked with feeding the growing global population, today’s agriculture producers still primarily rely on farming practices that hurt the environment. As it becomes clear that traditional farming is unsustainable, innovative entrepreneurs and scientists have come up with a potential solution. Vertical farming is increasingly hailed as an alternative food production method that can provide people with healthy and fresh produce. Thriving in undergrounds, stores, and restaurants around the world, vertical farms are becoming a major industry. But their survival depends on the ability of businesses to lower food production costs and increase productivity.
This article is written by Richard van Hooijdonk
Trendwatcher, futurist, and international keynote speaker Richard van Hooijdonk takes you to an inspiring future that will dramatically change the way we live, work, and do business. All lectures
Tech-Magnate Jack Ma Visits Dezhou Greenhouse
Jack Ma congratulated China on its achievements in the development of smart agriculture and said: At present, the modern agricultural industry, is similar to the Internet at the beginning of the 21st century, is undergoing tremendous changes, and there is still much room for future development
The Chinese horticultural industry might get ready to rumble as two major business magnates found their way into the greenhouse. Last week Jack Ma (Ma Yun), founder and CEO of Alibaba, and Sun Hongbin, CEO of Sunac, visited the Kaisheng Haofeng Facility. This is the largest greenhouse in the Shandong Province in the Lingcheng District, Dezhou City. They were joined by representatives of the Dezhou Financial Investment Group, Qingdao Haofeng Food Group, and Kaisheng Haofeng (Dezhou) Intelligent Agriculture.
Photograph source: Kaisheng Haofeng (Dezhou) Intelligent Agriculture Co., Ltd.
Technology in the greenhouse
With Alibaba Jack Ma has created one of the biggest technology multinationals in the world, specializing in e-commerce, retail, internet, and technology. Now he took a peek at the "high-quality" scientific and technological content behind a small tomato.
The committee members of the Dezhou Financial Investment Group and vice-CEO Yu Ruihua introduced the modern greenhouse, in what the control over temperature, light, water, carbon dioxide, and fertilizer is integrated via the automatic environmental-control system. The process, including seed selection, seedling raising, planting, pest control, irrigation, picking, packaging, etc., is designed based on the growth requirements of the tomato plants. Besides, standardized management is strictly implemented. The greenhouse uses an automatic screening line with the spectral system, the automatic weighting and screening can be carried out according to the color, weight, and defect degree of tomatoes, ensuring uniform product quality and uniform gram weight.
"The tomatoes planted in this way are not only high in value but also good in taste full of seeds, juice, and rich vitamins", the team explained. After that, the technical operation team reported in detail the variety selection, research, development, plant model construction, digital management, and standardization system of the smart greenhouse.
Second season
The smart greenhouse's second planting season has just finished. The intelligent farm is buzzing with energy and the plants flourish. Jack Ma paid close attention to the growing conditions of the tomato plants, including the coconut coir growth medium, drip irrigation, liquid fertilizer, and other innovative plantation technologies. The bumblebee pollination attracted particular attention. During the period when the tomato plants blossom, the farmers use bumblebees to pollinate the flowers. They do not add hormones, but improve fruit ratio naturally. The tomatoes are juicy and plump, and the flavor is excellent.
Photograph source: Kaisheng Haofeng (Dezhou) Intelligent Agriculture Co., Ltd.
The inspection tour was followed by a conference where the technical operation team provided a detailed report on the development and selection of product varieties in the smart greenhouse, plantation installations, digital management, and standardized systems.
Jack Ma congratulated China on its achievements in the development of smart agriculture and said: At present, the modern agricultural industry, is similar to the Internet at the beginning of the 21st century, is undergoing tremendous changes, and there is still much room for future development. The development of agriculture should pay attention to the input of talents and technology. He hopes to discuss more development possibilities about agriculture with everyone and jointly promote the progress of farmers, industries, and the whole society.
19 Oct 2020
Plenty Bags $140m In Funding For Its Indoor Farming Tech
The Series D round was led by existing investor, SoftBank Vision Fund 1, with participation from new investor Driscoll’s, a California-based agriculture business that claims to control around one-third of the $6bn berry market in the US
10/14/20
Image: Plenty
Californian Indoor Agriculture Business Plenty
Has Raised $140m In Its Latest Funding Round,
Bringing The Total Raised By The Start-Up To $500m
On Wednesday (14 October), San Francisco vertical farming business Plenty announced that it has raised $140m in Series D funding.
The Series D round was led by existing investor, SoftBank Vision Fund 1, with participation from new investor Driscoll’s, a California-based agriculture business that claims to control around one-third of the $6bn berry market in the US.
Plenty, which was previously listed as an urban agriculture start-up to watch on Siliconrepublic.com, plans to use the latest round of funding to fuel growth and execute new commercial collaborations with Driscoll’s and US grocery business Albertsons.
Plenty’s technology
Plenty was co-founded by Matt Barnard, Jack Oslan, Nate Mazonson, and Nate Storey in 2014. The company’s vertical farming technology can grow produce all year round, and Plenty claims that it uses 99pc less land and 95pc less water to grow crops than traditional methods.
Plenty’s San Francisco farm uses 100pc renewable energy and according to the company, the firm can grow 1,500 acres of produce in a building the size of a big-box grocery store.
To date, Plenty has raised more than $500m from investors including Bezos Expeditions, Innovation Endeavors, and DCM Ventures. Plenty is currently developing a new indoor farm in Compton, California, which the start-up believes could become the world’s highest-output vertical farm.
Jeff Housenbold, managing partner at SoftBank Investment Advisers, said: “In just 30 years’ time, the world will need 70pc more food than we currently produce, requiring more efficient use of land and water. Without innovation in agriculture, this demand will be impossible to meet.
“We believe Plenty is transforming the way food is made and are pleased to continue supporting their mission to build sustainable, intelligent farms that deliver healthy, safe produce with a focus on premium flavour.”
Plenty’s agriculture platform uses data analytics, machine learning, and customized lighting to iterate at high speeds, using 200 years’ worth of growing data. The company said that it has seen a 700pc yield improvement in leafy greens over the last 24 months by using this data.
Barnard, who serves as chief executive of Plenty, said: “The recent disruptions in the global supply chain caused by the west coast wildfires and Covid-19 have highlighted how quickly our access to quality produce can be thwarted.
“Plenty’s controlled and resilient farms and local distribution made it easy for us to scale quickly, even during the pandemic, demonstrating that our indoor, vertical farm flourishes under environmental pressures and delivers delicious greens along with the sales that come with it.”
Kelly Earley is a journalist with Siliconrepublic.com
RELATED: ANALYTICS, FOOD, AGRITECH, FUNDING AND INVESTMENT, SAN FRANCISCO, AGRICULTURE
UK: £5m Funding Award For John Innes Centre To Modernize Horticultural Facilities
A little over £3m of the investment will provide new Controlled Environment Rooms (CERs) for plant and microbial experiments. CER’s offer scientists precise control of environmental factors such as light, temperature, and humidity
A multi-million-pound project to modernize the horticultural facilities at John Innes Centre has been approved.
The £5.1m upgrade is funded by UKRI-BBSRC. Work will begin in Autumn 2020, and the project set to be completed by March 2021.
The company's Horticultural Services support the world-renowned science of the John Innes Centre and The Sainsbury Laboratory and occupies a large site on the Norwich Research Park.
A little over £3m of the investment will provide new Controlled Environment Rooms (CERs) for plant and microbial experiments. CER’s offer scientists precise control of environmental factors such as light, temperature, and humidity. The upgrade will also improve the containment measures required for experiments that investigate plant pathogens, or for growing genetically modified plants.
The new infrastructure offers energy efficiency and sustainability gains due to LED lighting, wastewater treatment, and rainwater harvesting. The reduction in utility costs from installing these technologies is estimated to be £116,000 per year.
Further savings will be achieved by more efficient use of glasshouse space (£200,000 per year) and reduced reliance on off-site horticultural facilities (£240,000) per year.
The current glasshouses (which cover an area of 5,775m2) is mostly single-span structures designed and built several decades ago. This investment is the start of a long-term move away from using glasshouses and towards controlled environments which better enable consistency of inputs and experimental results.
Head of Horticultural Services at the John Innes Centre, John Lord said: “World-class science needs world–class, market-leading technology. This investment is timely because there is a desperate need for our scientists to work on solutions to the challenges that face us. From understanding pathogens that cause plant diseases, to creating climate-resilient, nutritious crops that feed the world.
“This investment will bring a much-needed upgrade, providing facilities that are relevant and appropriate for the world-leading plant and microbial science that takes place on the Norwich Research Park. It also future proofs the site to fit with longer-term ambitions to redevelop the infrastructure here.”
Features of the new modernization include 30m2 of large walk-in growth space which offers LED lighting, nutrient enrichment, climate control, and state-of-the-art irrigation systems. The spaces will be configurable, it can be divided into multiple layers or used as a large open space, offering the next step towards bigger trials for crops.
The new facility will also benefit from a sustainable water supply, as it will harvest rainwater. The rainwater will be monitored and treated onsite to ensure it is free from phytopathogens, and that it has the correct pH. This soft, nutrient-rich harvested rainwater means that scientists will be able to minimize the use of fertilizers, and the consistent, monitored water supply will ensure that scientific experiments are reliable and repeatable.
“This is the start of a wider, long term project to update horticultural services at the John Innes Centre to ensure that it continues to meet the needs of science of today while being flexible enough to meet the needs of tomorrow as problems and new technologies arise,” said John.
For more information:
John Innes Centre
www.jic.ac.uk
Publication date: Thu 8 Oct 2020
Groundless Myths
Since Aristotle, people believed that plants exclusively feed on organic matter. Only in the 18th century did these ideas begin to be questioned
05-10-2020 | iFarm
Since Aristotle, people believed that plants exclusively feed on organic matter. Only in the 18th century did these ideas begin to be questioned. Scientists discovered that in fact plants’ primary source of nutrition is inorganic in nature. Similar myths exist today. One of them is that soilless cultivation is an artificial process, during which tasteless vegetables, berries and greens grow rapidly almost on "steroids". We compared hydroponics — one of the most common and sustainable soilless crop cultivation technologies, with traditional farming to identify their key differences and similarities.
A bit of history
The concept of "hydroponics" was introduced in the 1930s by the American biologist William Gericke.
During the Second World War, the first hydroponic plantations were launched using this technology. Since the 1970s, hydroponic systems of various modifications have begun to appear in different parts of the world. Today NASA is working on an inflatable expandable greenhouse where hydroponics will be used. It is planned to be installed on Mars so that the first settlers can provide themselves with fresh vegetables, berries and herbs like on the Earth.
Hydroponics combines several methods of plant cultivation in artificial environments: wick and drip irrigation systems, flooding irrigation, nutrient layer method, etc. On iFarm vertical farms, we use the flow hydroponics method: seeds are sown in one of the types of substrate (peat or mineral wool), and nutrient solution is served into the pots from below.
A huge advantage of hydroponics is its controllability. The technology makes it possible to create ideal conditions for plants in terms of nutrition, lighting, temperature, and environment. In an optimal microclimate, they reveal their maximum potential, useful properties, have a prominent taste and aroma.
Nutrient intake
All elements of root nutrition are absorbed by plants either from the soil or a mixture of water-soluble fertilizers only in the form of ions.
Growing in soil
The content and availability of macro and microelements (nitrogen, potassium, phosphorus, magnesium, iron, etc.) in the soil is influenced by the temperature of air and soil, the amount of solar energy and moisture, the pH of the environment. Natural conditions are very unstable: air temperature and pressure fluctuate during the day, the sun is often covered with clouds, there may or may not be any rain for several days. All this affects the availability of nutrients for plants, causing a deficit of one or more of them, which in turn reduces yields and product quality. To accelerate plant growth and ensure yields, people began to use mineral or organic fertilizers.
Hydroponics
The microclimate inside a vertical farm is stable and the plants get nutrition in the amount they require. "We do not accelerate the growth of plants, but create conditions in which they can fully develop, without experiencing a lack or excess of nutrients and stress from changes in the environment. All this allows you to get tastier and earlier harvests," said Natalia Smirnova, a plant nutrition specialist at iFarm. iFarm labs select balanced nutrition for all crops grown on vertical farms. In fact, macro- and microelements are the same, but the delivery methods to the root systems may differ.
iFarm agrochemists select a balanced diet not only for each crop, but also for a specific phase of its development (the amount and ratio of consumed macro- and microelements depends on it). They can adjust the supply of nutrients to plants to get fruits not only with specified taste characteristics but also with a specific concentration of iron, silicon, vitamins, carotene, and other components important for human health.
The quality of vegetables, berries, or herbs does not depend on the method of their cultivation, but on the conditions the plants grew in, regardless of the environment being natural or artificial. Products that taste like "plastic" are often obtained using a large number of fertilizers, growth stimulants and pesticides, helping fruits to gain weight faster and increasing their shelf life. They are usually harvested without being given time for natural ripening or accumulation of nutrients (although two or three times per season).
Natalia Smirnova
Candidate of Biological Sciences,
iFarm plant nutrition specialist
Protecting from pests and diseases
In the closed ecosystems of vertical farms pests cannot infect the plantings (there is no need to fight them, that is why production is pesticide-free unlike traditional field farming or greenhouses). You can lose crops only due to disturbances in plant nutrition.
Growing in soil
10 billion microorganisms live in 1 g of black soil. Some of them are pathogens (fungi, viruses, and bacteria) that cause various diseases in plants. In order to protect crops and keep harvests, agricultural producers are forced to use chemical agents (pesticides: herbicides, fungicides, insecticides) in the fields while growing. In addition, ripe fruits are also processed for safety during transportation. Pesticides remain on products even after washing in water and, once they enter the human body, can cause diseases of the gastrointestinal tract, oncology, reproductive and endocrine disorders, etc.
Hydroponics
Vertical farms using iFarm technologies have a closed microclimate. An energy-efficient air purification and disinfection system ensures complete absence of outside air, any pollution, pests or diseases. The substrate that holds the roots of plants is purchased from leading international manufacturers. iFarm agronomists always check suppliers' quality certificates and test substrates in laboratories. For the nutrient solutions, we use treated water, purified in a special system that eliminates any impurities letting in only oxygen and water molecules through a membrane. There is simply no need to use pesticides.
Soilless cultivation also allows to carry out an early analysis of the root systems, giving a chance to evaluate every single plant’s condition. On vertical farms, root access is always open.
Water consumption
Vertical farms use 90% less water than greenhouses. Special engineering solutions can help to further improve this number to save even more water, allowing the plants to receive precisely required amount of moisture.
Growing in soil
Producers annually calculate the irrigation norm rate — the amount of water plants require to fully grow. It depends on the climate, soil properties, crop characteristics, cultivation technology. However, it is difficult to calculate accurately due to the unreliability of weather forecasts. As a result, plants may receive too little or too much water. Failure to comply with irrigation norms washes away the upper layers of the soil: irrigation erosion annually carries away 100−150 t/ha of soil, 0.8−1 t of humus, 100−120 kg of nitrogen, and 110−165 kg of phosphorus. On such soils, crops grow unevenly, and yields decrease.
Hydroponics
Thanks to the automated microclimate, the amount of water required by plants to fully develop is determined with an accuracy of a milliliter. iFarm engineers have also developed a dehumidification system to collect moisture evaporated by plants, filter, decontaminate and reuse it to water crops. This will help save even more water, which is incredibly useful in regions where water resources are limited (when grown in soil, moisture released by plants simply evaporates).
www.nutrienhorticulture.com.au
The advantages of hydroponics (climate controllability, pesticide-free production, preservation of the environment) stimulate the growth of the global vertical farming market. According to Research and Markets, in 2017 it was about $ 2.3 billion, and by 2023 it will grow to almost $ 7.5 billion, adding more than 20% annually.
Source and Photo Courtesy of iFarm
Autogrow Expands Into Europe With New Role And New Farm Solutions
CEO Darryn Keiller says, “this expansion into Europe is counter-intuitive during a pandemic however innovation and crop production doesn’t slow down, and the challenges growers face haven’t disappeared because of COVID-19
29 September 2020: Autogrow has ramped up their activity in the Northern Hemisphere by establishing a new Sales Director Europe and U.K. role based in the Netherlands supporting their expanding customer base for new digital farming solutions FarmRoad® and Folium®.
CEO Darryn Keiller says, “this expansion into Europe is counter-intuitive during a pandemic however innovation and crop production doesn’t slow down, and the challenges growers face haven’t disappeared because of COVID-19. In fact, they have been exacerbated by the pandemic. We think now is the perfect time to introduce solutions that will help growers with productivity, gain greater economic benefits, and transform the market. Added to which, with cross-border restrictions and travel limitations likely to remain in place in the foreseeable future, establishing a local presence is the right move.”
“The Netherlands has been recognized by the World Economic Forum as a leader in efficient and sustainable agriculture and, after the United States, is the second-largest exporter of agriculture in the world. By establishing a role in the region, we create strong ties with growers and, like our partnerships in the United States, introduce our new digital farming solutions FarmRoad and Folium.”
Autogrow has been working closely over the past few months with customers and distributors in the region including some of the largest tomato producers. They are delighted to be working alongside Van der Voort, a member of the Prominent farming cooperative, who share Autogrow's focus on sustainable farming practices.
“We have been growing tomatoes for over 50 years and technology has always played a pivotal role in our success. With multiple farms and increasing production, we look for solutions that are leading the AgTech market. The work the Autogrow team are doing with sensor technology and farm management solutions is cutting edge and we are excited to be working together,” says Van der Voort Co-Owner, Joost Van der Voort.
Although Autogrow’s headquarters is based in New Zealand, large geographical distances have never hindered the organization from successfully operating on the global stage. Their endeavors also have the support of the New Zealand Government.
“It’s exciting to see AgTech innovation developed in New Zealand supporting growers here,” says Ariane Gonzalez, New Zealand Trade Commissioner to the Netherlands.
“New Zealand is recognized on the global stage for producing efficient and effective agricultural solutions that work in a range of climates, and this is another great example of that in action,” says Ms Gonzalez.
In addition, Autogrow has assistance from InnovationQuarter, the regional economic development agency for the Province of Zuid-Holland.
"The Netherlands, and Rotterdam - The Hague area specifically, is the worldwide center of horticulture. We are eager to attract and facilitate innovators with exciting solutions as Autogrow. They are a great addition to our region and the sector and support our regional economy. Next to that they benefit and contribute to strengthening our ecosystem of innovative companies in horticulture, impacting the societal challenge for feeding and greening the mega-cities of the future,” explains Chris van Voorden, Head of Internationalization at InnovationQuarter.
Autogrow is currently recruiting for the new role with the expectation to have someone in place over the next few months.
To see the advertised role - https://www.ceresrecruitment.nl/en/vacancy/sales-director-uk-europe/CEBI03123-en
For more information on Folium Network Sensor - https://autogrow.com/products/folium
For more information on Yield Prediction by FarmRoad - https://www.farmroad.io/
MEDIA QUERIES
Kylie Horomia, Head of Brand & Communications
(e) Kylie.horomia@autogrow.com
(m) +6421 733 025
(w) www.autogrow.com www.farmroad.io
Sales queries – sales@autogrow.com
About Autogrow
Autogrow leverages the power of technology, data science, and plant biology to provide indoor growers affordable, accessible, and easy-to-use innovation – 24/7, anywhere in the world.
Our hardware, software, and data solutions support growers and resellers in over 40 countries producing over 100 different crop types.
We are the experts in Controlled Environment Agriculture (CEA) and continue to stay ahead of a rapidly evolving landscape.
How Space-Saving Retailers Can Bring Fresh Farming Indoors
Farm.One’s latest “mini-farm” in a Manhattan Whole Foods sets a precedent for other stores
SEP 23, 2020
Melissa Kvidahl Reilly | Sep 28, 2020
Retailers who pride themselves on using their own homegrown ingredients in foodservice operations previously looked to a rooftop or back lot for garden space. But New York’s Farm.One is changing the game, making it possible for even the most urban locations to optimize space and offer open, transparent, and clean food production.
Previously known for its restaurant partnerships, the brand recently opened a “mini-farm” at the new Whole Foods Market Manhattan West location. The custom-designed, 32-square-foot structure holds 150 plant sites on three growing levels. These plant sites provide the store’s food and beverage preparers with freshly grown and harvested blue spice basil. This type of structure will be a big part of Farm.One’s strategy going forward, and it’s currently on the hunt for new retail partners.
Farm.OneMini-farms can offer as many as 700 varieties of hydroponic-grown crops. “A display farm can have multiple crops, or just one as is the case in the Whole Foods Manhattan West farm,” says Michael Chin, the company’s vice president of corporate development. And, Farm.One can build, install, and train stores on using farms anywhere in the world.
The bottom line? This isn’t the indoor farming of decades past. “Indoor farming has come a long way, especially in the last few years,” says Chin. “We can now produce fresh, clean and healthy food and ingredients profitably, and in an environmentally responsible way. Developments in technology and new techniques will continue to help make onsite production even more accessible to retailers and other businesses in the years to come.”
TAGS: RETAILER AND DISTRIBUTOR
Indoor Ag Gets Social With New Farmbook Networking & Data Collection Initiative
“You don’t see a forum where people can get together who have small and medium-sized operations or who are thinking about investing in it. I get lots of calls from people asking for an hour of my time because they want to talk about the industry,” Farmbook’s Boston-based co-creator Peter Tasgal told AFN
September 28, 2020
Controlled environment agriculture (CEA) has seen a renewed bout of interest recently, but there are plenty of pain points still plaguing the growing industry. A new non-profit initiative called The Farmbook Project is hoping to resolve some of those issues by providing indoor growers with more opportunities to connect while aggregating data to establish benchmarks.
“You don’t see a forum where people can get together who have small and medium-sized operations or who are thinking about investing in it. I get lots of calls from people asking for an hour of my time because they want to talk about the industry,” Farmbook’s Boston-based co-creator Peter Tasgal told AFN. His fellow co-creator is Albuquerque-based Xander Yang, who has been working in the vertical farming industry for the last five years.
What Tasgal noticed was, when he got these requests, people were always asking him the same questions. He realized that growers in the space were mostly isolated and likely hungering for a chance to connect with their CEA colleagues. Growers in the space have a long history of keeping information to themselves, according to Farmbook. And while there may be a few good reasons for holding this info close to the chest, a bit more sharing could help move the industry forward as a whole.
Aggregating data confidentially through the Farmbook platform can also help with tackling another problem many CEA operators face: a lack of business planning and coaching. Having a cohesive business plan can help attract more investors, according to the Farmbook team. Investors cannot predict whether they will meet their ROI needs if an operation doesn’t have a business plan addressing how it plans to succeed.
In the CEA space, startups have chosen a wide variety of routes to market, including direct sales through grocers, selling to restaurants, and wholesaling. Others sell equipment in the form of turnkey container farms.
Invest with Impact. Click here.
Considering that 75% of all retail tomato sales in the US come from greenhouse production, by Farmbook’s estimate, there should be plenty of data to sift through.
“We’ll certainly have to look at the data because […] we don’t want all the data to come from successful operators. That won’t be helpful,” Tasgal said. “We are looking to get information from a wide range of operators.”
Perhaps Farmbook’s biggest objective is to standardize some of the metrics used in CEA production, such as pounds of production per plant hole per annum. The initiative thinks the use of such standards would be valuable not only for existing producers, but also for prospective farmers trying to determine how to start their own operations. Investors assessing revenue forecasts and retail purchasing managers who need to know a potential supplier’s capacity could also benefit from standardized metrics.
“In the retail industry or in the car industry there is always lots of information available that people use to benchmark themselves or to figure out how to set up. Performance indicators,” Tasgal said. “I think people know that information in this space [but aren’t sharing it] and I think that’s hindering growth.”
Farmbook is still testing its platform, but the website is live and project members are working to grow the team to capture a wide range of industry views.
As indoor ag continues to grow and evolve, it’s finding ways to fit in with, or compete against, the existing food chain. There is a variety of opinions regarding the ultimate role that CEA will have to play in our future food system.
“I think it will never be a pure commodity. Just the cost structure of indoor farms necessarily requires that it has to be somewhat of a specialized product,” Tasgal said. “That’s not to mean small – just that you won’t ever be growing wheat, cotton, or large commodity grains indoors. But when 75% of eating tomatoes are grown indoors that is pretty amazing. It tells me that the tomato business is becoming a purely indoor market.”
Do you think the CEA industry needs more benchmarks? Let me know at lauren@agfunder.com
Crops Can Now 'Tell' Growers When They Are Stressed
All plants use internal electrical, mechanical, and chemical signaling networks to coordinate growth, reproduction, and defense – and Vivent is the first company in the world to launch a commercial crop health diagnostic system based on plant electrophysiology
Vivent, the Swiss biosignals analysis specialist, has closed a multi-million Euro Series A funding round. This first external investment from Astanor Ventures, will be used to expand sales of a unique plant electrophysiology system that diagnoses crop stress in real-time.
All plants use internal electrical, mechanical, and chemical signaling networks to coordinate growth, reproduction, and defense – and Vivent is the first company in the world to launch a commercial crop health diagnostic system based on plant electrophysiology.
Electrical signals are some of the fastest to transmit information throughout a plant – from roots to shoots. Vivent’s crop diagnostics system, called ‘PhytlSigns’, uses AI to interpret signals linked to plant stress and diagnoses pathogens and pests prior to the appearance of any visible symptoms. Early diagnosis increases yields, improves crop protection effectiveness, and encourages the adoption of environmentally preferable protection solutions.
“Growers are using PhytlSigns to monitor their crops in real-time. This additional information is improving their decision-making on climate control, irrigation, and crop protection,” explains Carrol Plummer, founder, and CEO.
“Thanks to low-cost powerful machine learning, we can give growers real-time information that results in safer, higher-quality, and tastier food with less reliance on preventive spraying and more focus on environmentally preferable crop protection. We are very excited to be working with Astanor, a top deep-tech venture fund, with ambitions to enhance food quality, security, and sustainability.”
Christina Ulardic, Partner at Astanor Ventures and new Vivent board member, explains that “Vivent is pioneering a new relationship with the crops we grow. It is remarkable to be able to see precisely how plants are responding to stressors in the environment and to learn how we can use these signals to provide treatments which improve plant husbandry.”
Vivent is already working with top global crop protection companies and growers in several countries to improve yields and product quality. Customers value early diagnosis of plant diseases, particularly those in roots, which are hard to identify using other methods.
For more information:
Vivent
www.phytlsigns.com
Publication date: Mon 28 Sep 2020
ABU DHABI: US Educator Outlines Urban Farming Vision in ADIBF Virtual Session
American educator, urban farmer, and innovator Stephen Ritz revealed how his tower garden-growing technology is flourishing in the UAE during the latest Abu Dhabi International Book Fair, ADIBF, Virtual Session
ABU DHABI, 2nd June 2020 (WAM)
American educator, urban farmer, and innovator Stephen Ritz revealed how his tower garden-growing technology is flourishing in the UAE during the latest Abu Dhabi International Book Fair, ADIBF, Virtual Session.
The talk, titled ‘Changing the World with the Power of a Plant’, on Thursday covered Ritz’s rise to fame through his innovative teaching methods in some of the USA’s poorest communities, his ongoing projects in the UAE, and the numerous books he has published.
As the 30th edition of ADIBF has been postponed until next year, the Department of Culture and Tourism – Abu Dhabi, has instead organized the virtual sessions for scheduled guests to present their talks online, so viewers can watch safely in their homes.
Ritz, who has become known as ‘America’s Favourite Teacher’, has spawned a green movement through the changes he brought to the school where he taught in the South Bronx, New York. Utilizing hydroponics and aquaponics, he began to grow plants in the classroom, which in turn encouraged his students to follow sustainable and healthy lifestyles.
He first came to the UAE in 2015 as one of the ten finalists in the Global Teacher Prize. While he didn’t win, he used his runner-up prize money to create the Green Bronx Machine, a curriculum for a green classroom, which is now being taught around the world.
His work caught the attention of Dr. Abdulla Al Karam, Chairman of the Board of Directors and Director-General of the Knowledge and Human Development Authority, KHDA, in Dubai, who invited Ritz back to the UAE. Soon Ritz was visiting schools, universities, and businesses here to explain his methods. He also began working alongside Sheikh Dr. Abdul Aziz bin Ali Al Nuaimi, the Environmental Advisor to the Government of Ajman, who is also known as the ‘Green Sheikh’ for his environmental work. The pair are currently authoring a book called Bringing the Farm to the Desert to be released in 2021.
Ritz also works with Esol Education, the international network of private schools that operates many schools across the UAE, and has been appointed as its Director of Health, Wellness and Innovation. He is now based at Fairgreen International School in The Sustainable City, Dubai, hence he says he now thinks of the UAE as his "second home".
Ritz said he enjoys nothing more than meeting children, inspiring teachers, inspiring healthy living, and inspiring healthy learning for everyone across the UAE through his passion, purpose, and hope.
With the 30th edition of the ADIBF postponed until next year, the DCT Abu Dhabi has launched a series of live virtual broadcasts to showcase artists and authors and open up new creative conversations with readers.
The virtual sessions will run until Monday, 15th June 2020, and feature ten speakers from around the world, to discuss a wide variety of themes – from history and education to entertainment and science – designed to appeal a wide audience of different age groups and tastes.
Other ADIBF Virtual Sessions have featured the Swedish behavioral expert Thomas Erikson, military survival specialist John Hudson; Lemn Sissay, the award-winning British-Ethiopian poet; and Annabel Karmel, the children’s cookbook author.
WAM/Tariq alfaham/Nour Salman
Tech-Driven Vertical Farming Company Kalera Announces New CIO, VP of Sales
Today, technology-driven vertical farming company Kalera announced that it has hired two new executives to fill the positions of CIO and VP of Sales. New Chief Information Officer Jeremy Johnston brings over 15 years of experience in a broad range of fields, including technology, manufacturing, and retail
The appointment of these executives coincides with Kalera’s recent expansion into new markets
ORLANDO, Fla., June 02, 2020 (GLOBE NEWSWIRE) | Source: Kalera
Today, technology-driven vertical farming company Kalera announced that it has hired two new executives to fill the positions of CIO and VP of Sales. New Chief Information Officer Jeremy Johnston brings over 15 years of experience in a broad range of fields, including technology, manufacturing, and retail. The newly appointed VP of Sales Jeff Larsen brings with him 23 years of sales experience from a diverse set of industries with Fortune 100 companies.
With over 15 years of experience, Jeremy Johnston has spent his career leading information technology for the world’s largest companies including Deloitte, Amazon, and National Oilwell Varco. Most recently, Johnston worked in technology as the CTO of Qoreboard and PH6 Labs. He has also worked with global technology at Deloitte, where he managed several massive technology transformations in the oil & gas and healthcare verticals.
New Chief Information Officer Jeremy Johnston brings over 15 years of experience in a broad range of fields, including technology, manufacturing, and retail.
At Amazon, Johnston led the design and implementation of Amazon’s internal HRIS system responsible for the timekeeping and payroll for over 250,000 employees across nine countries. Johnston spent eight years at National Oilwell Varco early in his career where he oversaw custom application development, data warehousing, and ERP implementation for over 40,000 employees in 21 countries. Johnston will manage Kalera’s Information Technology policies, procedures, strategies, standards, and roadmap. At Kalera, being a data-driven company, advanced automation and data collection with IoT, Big Data Analytics and AI capabilities are essential.
“I am thrilled to be joining a company as forward-thinking and exciting as Kalera. I believe my global experience with diverse, complex companies will inform and accelerate Kalera’s rapid growth plans as we change the way produce is grown around the world,” said Jeremy Johnston, Kalera’s new Chief Information Officer.
Kalera has also named Jeff Larsen the Vice President of Sales. A multi-faceted and seasoned sales professional, Larsen has achieved many awards and accolades across a diverse range of industries. Larsen has over 20 years of experience in sales across various industries with Fortune 100 companies. Larsen has excelled at both regional and national levels in large scale distribution, business development, and account management.
The newly appointed VP of Sales Jeff Larsen brings with him 23 years of sales experience from a diverse set of industries with Fortune 100 companies.
“From foodservice and hospitality to grocery, I am excited to be supporting this groundbreaking business with my years of sales expertise,” noted Jeff Larsen, Kalera’s new Vice President of Sales. “People need safe, delicious and affordable produce now more than ever. Kalera is leading the charge in supplying the public with the freshest, most delicious lettuce on the market.”
"As Kalera continues to focus on our rapid national and international expansion, building a world-class executive team has been among our top priorities, and we are beyond excited to welcome Jeremy and Jeff to the Kalera family,” noted Kalera CEO Daniel Malechuk.
Kalera has experienced significant growth in recent months, with plans of its new growing facility in Atlanta being announced only months after the opening of its facility in Orlando. Its Orlando facility is currently the single largest indoor vertical farm in the Southeastern United States, and the Atlanta facility will be even larger. Kalera also made headlines after pivoting their business strategy amidst the COVID-19 crisis, shifting from a foodservice-focus to land their produce in the aisles of Publix. During this time, Kalera also organized giveaways for the Orlando community, giving away tens of thousands of heads of lettuce to provide access to fresh, local, produce to residents.
Central to Kalera’s business is good science. The company is planting non-GMO seed, and over the past several years has perfected plant and data science-driven methods to naturally optimize the factors that make plants thrive. Kalera manages these natural factors in a way that makes plants reach their maximum potential, resulting in the highest quality produce, grown locally with consistent high yields year-round.
By using a closed-loop irrigation system, Kalera’s plants grow while consuming 95% less water compared to field farming. While a head of lettuce grown in a field may use as much as 60 gallons of water, Kalera’s systems result in a healthier plant with less than five gallons.
The company utilizes cleanroom technology and processes to eliminate the use of chemicals and remove exposure to pathogens. With indoor facilities situated right where the demand is, Kalera is able to supply an abundance of produce locally, eliminating the need to travel long distances when shipping perishable products and ensuring the highest quality and freshness.
About Kalera
Kalera is a technology-driven vertical farming company with unique growing methods combining optimized nutrients and light recipes, precise environmental controls, and cleanroom standards to produce safe, highly nutritious, pesticide-free, non-GMO vegetables with consistent high quality and longer shelf life year-round. The company’s high-yield, automated, data-driven hydroponic production facilities have been designed for rapid rollout with industry-leading payback times to grow vegetables faster, cleaner, at a lower cost, and with less environmental impact.
Elka Karl
Phone: 510-508-7328
Email: elka@dadascope.com
Valoya Announces Its Spectrum Technology Licensing Program
Valoya’s extensive patent portfolio in the field of horticultural LED lighting is a result of significant innovation and investments into R&D over the past 11 years
Valoya, the research-driven LED grow light manufacturer has today announced a licensing program making their patented technology available to LED manufacturers and horticultural LED fixture providers.
Valoya’s extensive patent portfolio in the field of horticultural LED lighting is a result of significant innovation and investments into R&D over the past 11 years. The patents are in the field of light spectra for plant cultivation and lighting applications. At the moment, the portfolio consists of over 100 patents, all of which can be reviewed at valoya.com/patents.
'We have always been curious about the possibilities of light and how its potential could be pushed further to make cultivation of crops we use for food or medicine production more efficient. When we started in 2009, LED meant piercing purple light produced by red and blue chips. We were the first to apply wide spectrum LED light to plants in our experiments and to introduce wide spectrum light to the market. We are now in a business phase where we can extend this intellectual property and know-how to other companies wishing to produce premium quality horticultural LED luminaires through our licensing program' comments Lars Aikala, the CEO and Co-Founder of Valoya.
The research and development at Valoya does not stop. ‘After having conducted over 600 plant trials on over 300 plant varieties/species, we have an understanding of plant response to light, unmatched by other LED companies in the market. The focus remains on advancing horticulture through developing even better spectra and helping our customers grow. We are happy we get to share this expertise with other companies now’, comments Nemanja Rodic, Marketing Director of Valoya.
To learn more about Valoya's patent licensing program,
please click here.
About Valoya
Valoya is a provider of high end, energy-efficient LED grow lights for use in crop science, vertical farming, and medicinal plants cultivation. Valoya LED grow lights have been developed using Valoya's proprietary LED technology and extensive plant photobiology research. Valoya's customer base includes numerous vertical farms, greenhouses, and research institutions all over the world (including 8 out of 10 world’s largest agricultural companies).
Additional information:f
Valoya Oy, Finland
Tel: +358 10 2350300
Email: sales@valoya.com
Web: www.valoya.com
Facebook: https://www.facebook.com/valoyafi/
Twitter: https://twitter.com/valoya
Aquaponics AI, A US-Based Aquaponic Technology Research Company, Just Unleashed Their Software Into The Wild
In addition to being the forerunner in Aquaponic technology, they also have invaluable libraries for fish, plants, and diseases, as well as calculators for managing your system
Aquaponics AI, a US-based aquaponic technology research company, just unleashed its software into the wild. It’s the system every aquaponic grower has been waiting for. It has traditionally been difficult to get started in Aquaponics because of the steep learning curve but they are making it easy to get started and maintain a system with features like a project template that gets your system running with recommended maintenance schedules by big players in Aquaponics.
They’re bringing innovative usage of artificial intelligence and big data to Aquaponics for the betterment of the global aquaponics community. Their vision is to unleash your Aquaponic growing powers. You’re the beneficiary of high-quality produce and revenue streams created from your system.
In addition to being the forerunner in Aquaponic technology, they also have invaluable libraries for fish, plants, and diseases, as well as calculators for managing your system.
“We’re about empowering people to be the best aquaponic growers possible. Tech is what gives people the tools to do awesome things.” - Jonathan Reyes, CEO, and Co-founder of Aquaponics AI
You can see the latest developments on their website https://aquaponics.ai alongside invaluable resources and calculators that are available for free.
Tags: Aquaponics, Dashboard, IoT, Sensors, Cloud
We Want To Grow Every Lettuce Variety Without Having To Think About The Light Recipe
The construction of the greenhouse for lettuce growers From Boer in the Dutch town of Dinteloord is in full swing, while this is happening they are already thinking about equipping the greenhouse with the latest technology
The construction of the greenhouse for lettuce growers From Boer in the Dutch town of Dinteloord is in full swing, while this is happening they are already thinking about equipping the greenhouse with the latest technology. For instance, regarding the perfect light needed during cultivation. To figure these things out, Rofianda Lighting Solutions and Form Boer had a meeting. The plans changed a hand full of times, but they have now devised a complete plan.
'Without' thinking
Rofianda and From Boer met in the spring of 2019. Due to modernization, the re-locating, and the current technological developments, the lettuce growers are looking into the questions regarding lighting. The researches’ most important goal is to find a way to cultivate every variety of lettuce without having to think about strict lighting recipes.
“To achieve this goal, Rofianda Lighting Solutions full-spectrum sunlight lighting is perfect”, says Arjan Boer. “You only need to decide on the lighting level, and the plant will take care of the rest.”
'Sunlight lamps’ versus red and blue LEDs
In a testing greenhouse, the results for lighting lettuce under sunlight lamps were compared to the results of those same varieties under red and blue LEDs. The results for lighting under Rofianda Lighting Solution lamps were very noticeable. “The overall growth is close to how it is in nature, and the root forming is much better than when using the LEDs.”
Micromol discussion
Because Arjan and Leonard want to equip their new greenhouse with the latest technology, cultivation will happen in a most modern way. Ronald Gronsveld, owner of Rofianda Lighting Solutions, and the brothers Boer have invested a considerable amount of time in creating just the right lighting plan for the automated cultivation department.
“These types of challenges form the cornerstone of our existence”, says Ronald. “We don’t just supply a few lamps, but think along with the growers when it comes to questions regarding design, installation, costs, lighting levels, the impact of lighting on the cultivation as a whole and payback period. More is not always better, especially in the current discussion regarding micromole. The quality of the light is much more important than the quantity”, in Ronald’s opinion.
The right choices
Arjan confirms that the plans have changed a few times and that they eventually reached a complete plan. “The contact was abundant, and we managed to make the right choices together”, says Arjan.
In the middle of March, the signatures were placed, and the entire cultivation will be equipped with lighting technology that was designed in the Netherlands.
For more information:
From Boer
www.fromboer.nl
Rofianda
info@rofianda.nl
www.rofianda.nl
By Horti Daily | May 4, 2020
Autogrow Cracks The Yield Prediction Code With FarmRoad
After three years of research, development, lab and farm trials; Autogrow’s FarmRoad solution has set the global benchmark for crop yield prediction with an initial 90 percent accuracy rate
After three years of research, development, lab and farm trials; Autogrow’s FarmRoad solution has set the global benchmark for crop yield prediction with an initial 90 percent accuracy rate.
“Accurately predicting harvest time and yield is the holy grail of agriculture. It allows clarity of availability to the entire food chain from the grower to the marketer and on to the consumer. Getting 90 percent accuracy rate up to six weeks out in our first three farms has been exceptional,” says CEO Darryn Keiller.
“Under-production and over-production can financially impact a farm. Under supply brings both less revenue, potential financial penalties from purchasers e.g. supermarket chains and the need to buy off a competitor to meet contractual requirements. Over production creates a surplus, which is then sold on the open market, usually at a price less than market value. It’s an unpalatable and expensive roller coaster ride.”
“When you consider the numbers, the ROI (return on investment) of increasing yield prediction of tomatoes by 10 percent - from 80 to 90 percent - based on a 30ha grower producing 60kg/sqm could be up to USD $1.3million. Savings can also be made with regards to labor by automating manual forecasting and through increased efficiency of farming practices.”
FarmRoad’s Yield Prediction model has initially been created to service large scale greenhouse tomato producers combining the biophysical understanding of crop varieties, with crop and environmental data and proprietary A.I. based models and engines. The service is built and hosted on AWS cloud, and can be delivered to any enterprise farm operator, anywhere in the world.
“Not only do we have on average 90 percent accuracy but we are achieving that working with three different growers in Canada, Australia, and New Zealand, using a mix of hydroponic substrate and soil and utilizing three different tomato cultivars - Marnax by Axia Seeds, Maxeza by Enza Zaden and Merlice by De Ruiter Seeds; showing the flexibility of our AI-based prediction,” says Mr. Keiller.
Accurate yield prediction is dependent on available data and variables include weather, pest and pathogen events and management practices. The industry baseline for large scale greenhouse production ranges from no prediction to 80 percent certainty up to two weeks in advance for the more experienced growers. FarmRoad is 90 percent accurate from one to six weeks in advance and anticipates achieving 95 percent accuracy within six months.
“Tomatoes are one of the most complex plants to apply yield prediction, but there is also a substantial amount of data available due to the crop registration techniques growers utilize. The key to prediction is the availability of data and we have been incredibly lucky to work with some fantastic growers with over 40+ years of experience who have shared their knowledge and data,” says Chief Technology Officer Jonathan Morgan.
“The first step is getting the data, but the biggest challenge has been turning the data into a form that works. When you look at environmental data, it is great for controlling systems but it’s not easy to go from the real-time data to a prediction of how plants are going to grow. When you also add in unexpected variables like a grower changing from loose pick to truss tomatoes half-way through the growing cycle, then your accuracy rate can decrease.”
With yield prediction achieved, Autogrow is currently developing crop registration and crop planning services.
“Yield Prediction by FarmRoad, is one of our many industry-leading services designed to enhance crop productivity and make farm operators more profitable. With their personalized yield model, growers can utilize their prediction and trends to materially improve farm profitability. The future is A.I. and digital farming, and we look forward to working with large scale growers who are looking to utilize their own data and gain a competitive and financial edge,” says Mr. Keiller.
For more information www.farmroad.io or email info@farmroad.io
MEDIA QUERIES
Kylie Horomia, Head of Communications
(e) Kylie.horomia@autogrow.com
(m) +6421 733 025
(w) www.autogrow.com www.farmroad.io www.cropsonmars.com
Sales queries – info@farmroad.io
About Autogrow
Autogrow leverages the power of technology, data science, and plant biology to provide indoor growers affordable, accessible, and easy-to-use innovation – 24/7, anywhere in the world.
Our hardware, software, and data solutions support growers and resellers in over 40 countries producing over 100 different crop types.
We are the experts in Controlled Environment Agriculture (CEA) and continue to stay ahead of a rapidly evolving landscape.
Autogrow, Level 1, Building 3, 61 Constellation Drive, Mairangi Bay, Auckland 0632, New Zealand
Researchers Aim To Cut The Energy Footprint Of Indoor Farms
Indoor farms can grow vegetables close to cities, where there are lots of people to feed. Farming indoors can also extend the growing season in cold climates and protect crops from damage during extreme weather.
But growing food indoors is energy intensive, so it can produce a lot of carbon pollution.
“Lighting is a big factor,” says Erico Mattos of the Greenhouse Lighting and Systems Engineering Consortium. “You have the heating and cooling systems, ventilation systems, all the systems that you have to control. So it’s really important for us to reduce this energy demand.”
Mattos’s group is working to reduce the energy used in indoor farms and greenhouses.
“The challenge is, how can we still provide all these inputs that the plants require, the crops require to grow, but using energy with the most efficient way as possible?” he says.
Researchers are tackling the problem from multiple angles. For example, they’re designing high-efficiency LED lights and they’re experimenting with ways to optimize specific crops’ growth with customized lighting, ventilation, and humidity controls.
Mattos says these technologies and systems will help make greenhouses and indoor farms more cost-effective and better for the climate.
Lead Photo Credit: Terry Rice